art3A10.10072FPL00003956
ARTISAN技术集团的预览目录:IC200UEX636-C及GFK-1645H 11-1数字扩展单
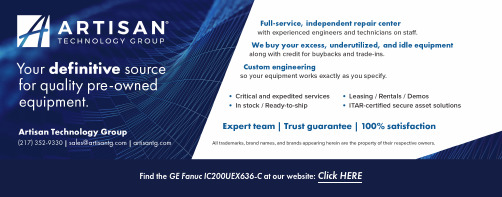
GFK-1645H 11-1Analog Expansion UnitsThis chapter describes the following VersaMax Micro PLC Analog Expansion Units:▪ IC200UEX616 6 Point Analog Expansion Unit, (4) Analog In and(2) Analog Out, 12 VDC Power Supply▪ IC200UEX624 4 Point Analog Expansion Unit, (4) Analog In, 24 VDC Power Supply▪ IC200UEX6266 Point Analog Expansion Unit, (4) Analog In and(2) Analog Out, 24 VDC Power Supply▪ IC200UEX6366 Point Analog Expansion Unit, (4) Analog In and(2) Analog Out, 100/240 VAC Power SupplyGE FANUC SparesFeatures of Analog Expansion UnitsAnalog, Expansion Units have the features shown below. Expansion Units can belocated up to 2 meters from the Micro PLC.Removable Terminal StripsThe removable terminal assemblies are protected by hinged covers. After turningoff power to the Expansion Unit, a terminal assembly and attached field wiring canbe separated from the Expansion Unit by removing two screws.Expansion ConnectorThe connector on the left side of the Expansion Unit is used to connect to theMicro PLC or to the outgoing connector on the previous Expansion Unit. Theconnector on the right side of the Expansion Unit can be used to attach to the nextExpansion Unit.Status LEDsLEDs on the Expansion Unit provide quick visual verification of operating status.Expansion Unit LEDs indicate local Power and OK mode.CablesA 0.1 meter ribbon cable (IC200CBL501) is provided with each Expansion Unit.Cables are also available in 0.5 meter (IC200CBL505) and 1 meter(IC200CBL510) lengths.11-2 VersaMax® Micro PLCs and Nano PLCs User’s Manual – June 2008 GFK-1645HGFK-1645HChapter 11 Analog Expansion Units 11-3Analog Expansion Unit SpecificationsModule Dimensions Height: 90mm (3.6 inches), Depth: 76mm (3.0 inches) Width: 150mm (6.0 inches) Inputs 4 analog inputsOutputs2 analog outputs (all models except UEX624)Power Specifications for Analog Expansion UnitsIC200UEX616 IC200UEX624, UEX626IC200UEX636Power voltage 12VDC 24VDC 100/110/120/200/210/220V (50/60Hz) VACRange 9.6VDC - 15VDC 19.2VDC to 30VDC 85 to 264VAC Hold-up 10.1ms at 9.6V 24.5ms at 19.2V 223ms at 85V Inrush Current/Time 0.9A / 1ms at 15V 2.5V / 1ms at 30V 4A / 5ms at 264V Input Current 0.15A at 15V 0.1A at 30V 0.06A at 264V Input Power Supply Rating 2.25W 3W 15VA The DC power source must have enough transient current capability to support the inrush current of the power supply and to maintain the nominal voltage level.Input and Output SpecificationsAnalog Input Channels (IC200UEX6**) 4, differentialInput ranges0 to 10V (10.23V maximum)-10V to +10V ( -10.23V min. and +10.23V max.) 0 to 20mA (20.47mA maximum) 4 to 20mA (20.47mA maximum) Resolution 12 bitsAccuracy ±1% of full scale over full operating temperature range Linearity ±3 LSB maximum Isolationnon-isolated Common mode voltage ±40 V maximum Current input impedance 249 Ohms Voltage input impedance 200 kOhmsInput filter time20ms to reach 1% error for step input Analog Output Channels 2, single-ended, non isolated Output ranges0 to 10V (10.23V maximum) 0 to 20mA (20.47mA maximum) 4 to 20mA (20.47mA maximum) Resolution 12 bitsAccuracy±1% of full scale over operating temperature range Current: maximum terminal voltage user load range output load capacitance output load inductance 10V (at 20mA output) 10 to 500 ohms 2000 pF maximum 1 Henry maximumVoltage: output loading output load capacitance10 kOhm minimum at 10 volts 1 µF maximumGE FANUC Spares11-4 VersaMax® Micro PLCs and Nano PLCs User’s Manual – June 2008GFK-1645HAnalog OperationThis section explains how a VersaMax Micro PLC Expansion Unit with analog channels processes analog data. Unlike discrete expansion units, if one analog unit fails all subsequent analog expansion units will stop communicating.However, expansion units before the failed unit continue to be available. If an analog expansion fails at power up, no expansion units (discrete or analog) will be functional.Analog I/O ParametersEach analog channel can be configured to operate in either voltage or current mode. If current mode operation is selected, the range can then be configured as either 4-20mA or 0-20mA. If voltage mode operation is selected (inputs only), the range can then be configured as either 0-10V or –10V to +10V.Parameter Choices Default ValueVoltage or current mode Voltage, Current Voltage Current range selection4–20mA, 0–20mA 4–20mA Voltage range selection (Inputs Only)0-10V, -10-+10V0-10VInput/Output Values Compared to Process DataThe Expansion Unit processes analog channels using fixed conversion values for both current and voltage mode operation. The table below shows the relationship between the analog input and output values used by the application program, and the actual analog input or output for each mode. These values include the automatic adjustments for gain.In this ConfiguredMode: This is the Analog Signal Range This is the Equivalent Process Data %AI or %AQRangeFor the Default Calibration, theValue in the%AI or %AQ Reference Equals:Voltage 0 to +10V 0 to 10,000mV 0 to 32000 3.2 x mV Voltage –10 to +10V (Inputs Only) -10,000mv to +10,0000mV -32000 to 32000 3.2 x mV Current 0 to 20mA 0 to 20,000µA 0 to 32000 1.6 x µA Current 4 to 20mA4,000 to 20,000µA0 to 320002 x µA –8000GFK-1645HChapter 11 Analog Expansion Units 11-5Count Resolution for Analog Expansion UnitsFor analog expansion units, count resolution is controlled by a dip switch setting on the module. Switch 6 should be set to ON by default. If unexpected results are observed, check the position of switch 6. If switch 6 is not ON, power down the system and set switch 6 to ON. Do NOT change any of the other switches.LED IndicationsThe module’s LEDs indicate the status of the module and of the analog inputs.IN 1 IN2 IN3 IN4POW OKIf an initialization error occurs, the OK LED blinks rapidly. During normal operation, the analog input LEDs should be off.GE FANUC Spares11-6 VersaMax® Micro PLCs and Nano PLCs User’s Manual – June 2008GFK-1645HAnalog Input ProcessingThe Expansion Unit processes analog input channels with a 12-bit successive-approximation A/D converter. It converts the analog value into a digital count, calculates the %AI value as described below, then places the result into theappropriate %AI input reference (these references are described in chapter 21).Automatic Conversion of Analog Voltage or Current to CountsIn voltage mode, the Expansion Unit first converts the 0 to 10,000mV input signal to a count in the range of 0 to 4,000 (or –10,000mV to 10,000mV signal to a range of –4,000 to 4,000). The fixed multiplier for this conversion is 2.5.In current mode, the Expansion Unit first converts the 0 to 20,000µA input signal to a count value in the range of 0 to 4,000. The fixed multiplier for this conversion is 5. The conversion for both current modes (0-20mA and 4-20mA) is the same.Automatic Gain and Offset Adjustment for Analog InputsThe Expansion Unit then converts the A/D converter's input count value from the range of 0 to 4000 to a final %AI input value in the range of 0 to 32,000. Itmultiplies the count value by 8 (32000 / 4000) to get the final analog input ($AI):(input count X 8) = %AI valueAny calculated value above 32,767 is clamped at that maximum value. Any calculated value less than 0 is clamped at 0.Analog Input Conversion SummaryThe table below summarizes the conversion of voltage or current inputs to counts and then to %AI values.Input SignalConversion Factor A/D ConverterVAlueGain Factor %AI Range Voltage Mode (0 to 10,000mV) 2.50–4000 counts8 0–32,000 Voltage Mode (-10,000 to 10,000mV)2.5 -4000 to 4000counts8-32,000 to 32,000 Current Mode (0–20mA) or (4–20mA)5 0–4000 counts 80–32,000GFK-1645HChapter 11 Analog Expansion Units 11-7Analog Output ProcessingTo generate the analog output signal, the Expansion Unit converts the value in the %AQ output reference into a count value for the 12-bit D/A converter, which then drives the analog output.Automatic Gain and Offset Adjustment for Analog OutputsThe application's %AQ output range of 0 to 32000 corresponds to the D/Aconverter's output count range of 0 to 4000. The Expansion Unit first multiplies the %AQ value from the program by .125 (4000 / 32000) to produce the count value for the D/A converter:(%AQ X .125) = D/A countAny calculated value that exceeds 4095 (212-1) is clamped at that maximum value. Any calculated value less than 0 is clamped at 0. The range 0 to 4095 corresponds to %AQ values between 0 and 32,767.Automatic Conversion of Counts to Analog Voltage or CurrentIn voltage mode, the D/A converter then converts the count value in the range of 0 to 4,000 counts to an analog signal from 0 to 10,000mV. The output voltage gain (ratio) for this conversion is 2.5.In current mode, the D/A converter converts the count value to an analog signal from 0 to 20,000µA. The output current gain for this conversion is 5. The conversion for both current modes (0-20mA and 4-20mA) is the same.Analog Output Data Conversion SummaryThe table below summarizes the conversion of %AQ values to counts and then to voltage or current levels.%AQ Range Gain, Factor D/A Converter Range Conversion Factor Output Signal0– 32,000 0.125 0–4,000 counts 2.5 Voltage Mode (0–10,000mV) 0–32,0000.1250–4,000 counts5Current Mode (0–20mA)or (4–20mA)GE FANUC Spares11-8 VersaMax® Micro PLCs and Nano PLCs User’s Manual – June 2008GFK-1645HWiring DiagramPower Supply:UEX616: 12VDC UEX624: 24VDC UEX626: 24VDC UEX636: 100/240VACConnect jumpers in current mode2 Voltage or Current Analog OutputsOn modules IC200UEX616, UEX626 and UEX 636, voltage and current outputs are present on their respective output terminals at the same time. For proper module operation, only the output terminals that correspond to the voltage / current output configuration should be connected.。
Parker Hannifin 微型空气过滤器 PF504 产品选择手册说明书

Ordering InformationBOLD ITEMS ARE MOST POPULAR.AutomaticDrainManualDrainPF504 Series1/4 Inch PortsCatalog 0700P-EMiniature PF504 SeriesPF504 FilterDimensionsA1.56(40)C0.31(8)D3.69(94)E4.00(102)F1.58(40)inches(mm)Standard part numbers shown bold.For other models refer to ordering information below.SCFM = Standard cubic feet per minute at 90 PSIG inlet and 5 PSIGpressure drop.PortSizeNPT BSPPManual Twist Drain Manual Twist Drain1/4"PF504-02DHSS PF504G02DHSSFeatures• Stainless steel construction handlesmost corrosive environments.• Fluorocarbon seals standard.• Meets NACE specificationsMR-01-75/ISO 15156.• 1/8" female threaded drain.• High Flow: 1/4" - 23 SCFM§Port Type- NPTG BSPPPort Size02 1/4 InchBowlD Metal BowlwithoutSight GaugeElementH 20 MicronG 5 MicronMaterialSS Stainless SteelPF504 - 02 D H SSOptionsBlank ManualTwist DrainR AutomaticPulse DrainFlow - dm /sP r e s s u r e D r o p - b a r3nPrimary Pressure - PSIG1.7 bar3.4 bar 5.2 bar 6.9 bar Primary Pressure - barPF504 Series Air Line FiltersCatalog 0700P-E Technical Specifications – PF504PF504 Filter Kits & AccessoriesDrain Kits –Automatic Pulse Drain ................................................RK504SY -SS Manual Twist Drain–Small (Old) ..........................................................SA600Y7-1SS Large (New) ...............................................................SAP05481Filter Element Kits –Particulate (5 Micron) .......................................................EK504VY Particulate (20 Micron) .......................................................EK504Y Pipe Nipple –1/4" 316 Stainless Steel ................................................616Y28-SSSpecificationsBowl Capacity ..................................................................1.0 Ounces Filter Rating ........................................................................20 Micron Sump Capacity ..................................................................0.4 Ounce Port Threads ..........................................................................1/4 InchPressure & Temperature Ratings –Manual T wist Drain ............................0 to 300 PSIG (0 to 20.7 bar) 0°F to 180°F (-18°C to 82°C) Auto Pulse Drain ..................................10 to 175 PSIG (0 to 12 bar) 32°F to 150°F (0°C to 66°C)Note: Air must be dry enough to avoid ice formation attemperatures below 32°F (0°C)Weight........................................................................0.6 lb. (0.27 kg)Materials of ConstructionBody .....................................................................316 Stainless Steel Bowls ...................................................................316 Stainless Steel Deflector ..................................................................................Acetal Drain ....................................................................316 Stainless Steel Element Holder .......................................................................Acetal Filter Element ................................................................Polyethylene Seals .............................................................................FluorocarbonOperationFirst Stage Filtration:Air enters at inlet port and flows through deflector plate (A) which causes a swirling action. Liquids and coarse particles are forced to the bowl interior wall (B) by the centrifugalaction of the swirling air. They are then carried down the bowl wall by the force of gravity. The baffle (D) separates the lower portion of the bowl into a “quiet zone” (E) where the removed liquid and particles collect, unaffected by the swirling air, and are therefore not reentrained into the flowing air.Second Stage Filtration:After liquids and large particles are removed in the first stages of filtration, the air flows through element (C) where smaller particles are filtered out. The filtered air then passes downstream. Collected liquids and particles in the “quiet zone” (E) should be drained before their level reaches a height where they would be reentrained in the flowing air. This can be accomplished by unscrewing the drain valve (F) slightly until the liquid begins to drain.Technical InformationE F(Revised 11-21-12)。
ARTISAN TECHNOLOGY GROUP 设备购买、贮备、租赁和维修服务说明说明书

RACAL INSTRUMENTS™1261B/BLVXI MAINFRAMEPublication No. 980800 Rev. AAstronics Test Systems Inc.4 Goodyear, Irvine, CA 92618Tel: (800) 722-2528, (949) 859-8999; Fax: (949) 859-7139*****************************@*****************************://Copyright 1998 by Astronics Test Systems Inc. Printed in the United States of America. All rights reserved. This book or parts thereof may not be reproduced in any form without written permission of the publisher.THANK YOU FOR PURCHASING THISFor this product, or any other Astronics Test Systems product that incorporates software drivers, you may access our web site to verify and/or download the latest driver versions. The web address for driver downloads is:/support/downloadsIf you have any questions about software driver downloads or our privacy policy, please contact us at:*********************All Astronics Test Systems products are designed to exacting standards and manufactured in full compliance to our AS9100 Quality Management System processes.This warranty does not apply to defects resulting from any modification(s) of any product or part without Astronics Test Systems express written consent, or misuse of any product or part. The warranty also does not apply to fuses, software, non-rechargeable batteries, damage from battery leakage, or problems arising from normal wear, such as mechanical relay life, or failure to follow instructions.This warranty is in lieu of all other warranties, expressed or implied, including any implied warranty of merchantability or fitness for a particular use. The remedies provided herein are buyer’s sole and exclusive remedies.For the specific terms of your standard warranty, contact Customer Support. Please have the following information available to facilitate service.1. Product serial number2. Product model number3. Your company and contact informationYou may contact Customer Support by:E-Mail: *************************Telephone: +1 800 722 3262 (USA)Fax: +1 949 859 7139 (USA)Authorization is required from Astronics Test Systems before you send us your product or sub-assembly for service or calibration. Call or contact Customer Support at 1-800-722-3262 or 1-949-859-8999 or via fax at 1-949-859-7139. We can also be reached at: *************************.If the original packing material is unavailable, ship the product or sub-assembly in an ESD shielding bag and use appropriate packing materials to surround and protect the product.This document and the technical data herein disclosed, are proprietary to Astronics Test Systems, and shall not, without express written permission of Astronics Test Systems, be used in whole or in part to solicit quotations from a competitive source or used for manufacture by anyone other than Astronics Test Systems. The information herein has been developed at private expense, and may only be used for operation and maintenance reference purposes or for purposes of engineering evaluation and incorporation into technical specifications and other documents which specify procurement of products from Astronics Test Systems.TRADEMARKS AND SERVICE MARKSAll trademarks and service marks used in this document are the property of their respective owners.•Racal Instruments, Talon Instruments, Trig-Tek, ActivATE, Adapt-A-Switch, N-GEN, and PAWS are trademarks of Astronics Test Systems in the United States.DISCLAIMERBuyer acknowledges and agrees that it is responsible for the operation of the goods purchased and should ensure that they are used properly and in accordance with this document and any other instructions provided by Seller. Astronics Test Systems products are not specifically designed, manufactured or intended to be used as parts, assemblies or components in planning, construction, maintenance or operation of a nuclear facility, or in life support or safety critical applications in which the failure of the Astronics Test Systems product could create a situation where personal injury or death could occur. Should Buyer purchase Astronics Test Systems product for such unintended application, Buyer shall indemnify and hold Astronics Test Systems, its officers, employees, subsidiaries, affiliates and distributors harmless against all claims arising out of a claim for personal injury or death associated with such unintended use.FOR YOUR SAFETYBefore undertaking any troubleshooting, maintenance or exploratory procedure, read carefully theWARNINGS and CAUTION notices.This equipment contains voltage hazardous tohuman life and safety, and is capable of inflictingpersonal injury. If this instrument is to be powered from the AC line (mains) through an autotransformer, ensure the common connector is connected to the neutral (earth pole) of the powersupply.Before operating the unit, ensure the conductor (green wire) is connected to the ground(earth) conductor of the power outlet. Do not use a two-conductor extension cord or athree-prong/two-prong adapter. This will defeat the protective feature of the thirdconductor in the power cord.Maintenance and calibration procedures sometimes call for operation of the unit withpower applied and protective covers removed. Read the procedures and heed warningsto avoid “live” circuit points.Before operating this instrument:1. Ensure the proper fuse is in place for the power source to operate.2. Ensure all other devices connected to or in proximity to this instrument are properly grounded orconnected to the protective third-wire earth ground.If the instrument:- fails to operate satisfactorily- shows visible damage- has been stored under unfavorable conditions - has sustained stressDo not operate until performance is checked by qualified personnel.This page was left intentionally blank.Publication No. 980800 Rev. A 1261B/BL User Manual Astronics Test Systems vDOCUMENT CHANGE HISTORY Revision Date Description of ChangeA 10/07/10 Revised per EO 30291UL Regulations require UL data removal on pageA-5.Revised and replaced first 4 pages. Manual nowrev. letter controlled. Added document changehistory page v in front of chapter 1.Removed Chap 6 and 7 the information needed isincluded in the first 4 pages starting at the cover.1261B/BL User Manual Publication No. 980800 Rev. AThis page was left intentionally blank.vi Astronics Test Systems。
ARTISAN技术集团设备购买与售卖说明书
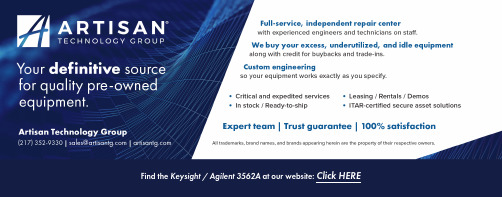
ErrataTitle & Document Type:Manual Part Number:Revision Date:HP References in this ManualThis manual may contain references to HP or Hewlett-Packard. Please note that Hewlett-Packard's former test and measurement, semiconductor products an d chemical analysisbusinesses are now part of Agilent Technologies. We have made no changes to thismanual copy. The HP XXXX referred to in this document is now the Agilent XXXX.For example, model number HP8648A is now model number Agilent 8648A.About this ManualWe’ve added this manual to the Agilent website in an effort to help you support yourproduct. This manual provides the best information we could find. It may be incomplete or contain dated information, and the scan quality may not be ideal. If we find a bettercopy in the future, we will add it to the Agilent website.Support for Your ProductAgilent no longer sells or supports this product. You will find any other availableproduct information on the Agilent Test & Measurement website:Search for the model number of this product, and the resulting product page will guideyou to any available information. Our service centers may be able to perform calibrationif no repair parts are needed, but no other support from Agilent is available.3562A Programming Manual03562-90031October 1985Artisan Technology Group - Quality Instrumentation ... Guaranteed | (888) 88-SOURCE | Artisan Technology Group - Quality Instrumentation ... Guaranteed | (888) 88-SOURCE | Artisan Technology Group - Quality Instrumentation ... Guaranteed | (888) 88-SOURCE | Artisan Technology Group - Quality Instrumentation ... Guaranteed | (888) 88-SOURCE | Artisan Technology Group - Quality Instrumentation ... Guaranteed | (888) 88-SOURCE | Artisan Technology Group - Quality Instrumentation ... Guaranteed | (888) 88-SOURCE | Artisan Technology Group - Quality Instrumentation ... Guaranteed | (888) 88-SOURCE | Artisan Technology Group - Quality Instrumentation ... Guaranteed | (888) 88-SOURCE | Artisan Technology Group - Quality Instrumentation ... Guaranteed | (888) 88-SOURCE | 。
佳能绘图仪错误代码

佳能绘图仪错误代码适用于iPF5000、iPF500、iPF600、iPF700、iPF8000、iPF9000 01810104-1000 1000 Bk墨盒基本为空警报01810101-1001 1001 Y墨盒基本为空警报01810102-1002 1002 M墨盒基本为空警报01810103-1003 1003 C墨盒基本为空警报01810112-1004 1004 PM墨盒基本为空警报01810113-1005 1005 PC墨盒基本为空警报01810106-1006 1006 MBk墨盒基本为空警报01810107-1007 1007 MBk2墨盒基本为空警报01810105-1008 1008 Gy墨盒基本为空警报01810107-1009 1009 PGy墨盒基本为空警报01810107-100A 100A R墨盒基本为空警报01810109-100B 100B B墨盒基本为空警报01810108-100C 100C G墨盒基本为空警报00000000-100F 100F 强制供应界线警报0180050-1010 1010 不吐墨喷嘴数警报级别警报01800500-1012 1012 不吐墨检测中打印头(R)的不吐墨喷嘴过多警报01800500-1013 1013 不吐墨检测中打印头L的不吐墨喷嘴过多警报01341221-1100 1100 维护暗箱将满警报01341222-1101 1101 喷雾台将满警报01341223-1221 1221 GARO未支持说明警报01341225-1222 1222 GARO参数个数不正确(没有参数)警报01341231-1223 1223 GARO 省略了不能省略项目警报01341232-1225 1225 GARO 其它警告警报01341233-1231 1231 GARO 未支持说明警报01341234-1232 1232 GARO 参数个数不正确警报01341235-1233 1233 GARO 省略了不能省略项目警报01341236-1234 1234 GARO 数据超出范围警报01341237-1235 1235 GARO 其它警告警报03010000-200A 200A 不能检测到纸宽错误03010000-200B 200B 台板上的位置不正确错误03010000-200C 200C 不能检测到纸张前端错误03010000-200D 200D 不能检测到切纸的后端错误03010000-200E 200E 纸张小于打印机可以运送的最小尺寸错误03010000-200F 200F 纸张大于打印机可以运送的最大尺寸错误03016000-2010 2010 斜行错误03870001-2015 2015 剪切失败错误03010000-2016 2016 供纸中的纸张脱离错误03010000-2017 2017 纸张(右)侧检测错误错误03010000-2018 2018 纸张(左)侧检测错误错误03060200-201E 201E 介质配置工具中的纸盒供纸设置为[否]时,接收到指定纸盒命令错误03861001-2405 2405 无边距打印时,纸张位置不正确错误03861001-2406 2406 数据不适合无边距打印错误03810104-2500 2500 Bk 墨盒为空错误03810101-2501 2501 Y 墨盒为空错误03810102-2502 2502 M 墨盒为空错误03810103-2503 2503 C 墨盒为空错误03810103-2504 2504 PM 墨盒为空错误03810112-2504 2504 PM 墨盒为空错误03810103-2505 2505 PC 墨盒为空错误03810113-2505 2505 PC 墨盒为空错误03810106-2506 2506 MBk 墨盒为空错误03810106-2507 2507 MBk2 墨盒为空错误03810105-2508 2508 Gy 墨盒为空错误03810115-2509 2509 PGy 墨盒为空错误03810107-250A 250A R 墨盒为空错误03810109-250B 250B B 墨盒为空错误03810108-250C 250C G 墨盒为空错误03830104-2520 2520 Bk 未安装墨盒错误03830101-2521 2521 Y 未安装墨盒错误03830102-2522 2522 M 未安装墨盒错误03830103-2523 2523 C 未安装墨盒错误03830112-2524 2524 PM 未安装墨盒错误03830113-2525 2525 PC 未安装墨盒错误03830106-2526 2526 MBk 未安装墨盒错误03830106-2527 2527 MBk2 未安装墨盒错误03830105-2528 2528 Gy 未安装墨盒错误03830115-2529 2529 PGy 未安装墨盒错误03830107-252A 252A R 未安装墨盒错误03830109-252B 252B B 未安装墨盒错误03830108-252C 252C G 未安装墨盒错误03830204-2540 2540 Bk 墨盒ID 错误错误03830201-2541 2541 Y 墨盒ID 错误错误03830202-2542 2542 M 墨盒ID 错误错误03830203-2543 2543 C 墨盒ID 错误错误03830212-2544 2544 PM 墨盒ID 错误错误03830213-2545 2545 PC 墨盒ID 错误错误03830206-2546 2546 MBk 墨盒ID 错误错误03830206-2547 2547 MBk2 墨盒ID 错误错误03830215-2549 2549 PGy 墨盒ID 错误错误03830207-254A 254A R 墨盒ID 错误错误03830209-254B 254B B 墨盒ID 错误错误03830208-254C 254C G 墨盒ID 错误错误03830304-2560 2560 Bk 墨盒EEPROM 异常错误03830205-2548 2548 Gy 墨盒ID 错误错误03830301-2561 2561 Y 墨盒EEPROM 异常错误03830302-2562 2562 M 墨盒EEPROM 异常错误03830303-2563 2563 C 墨盒EEPROM 异常错误03830312-2564 2564 PM 墨盒EEPROM 异常错误03830313-2565 2565 PC 墨盒EEPROM 异常错误03830306-2566 2566 MBk 墨盒EEPROM 异常错误03830306-2567 2567 MBk2 墨盒EEPROM 异常错误03830305-2568 2568 Gy 墨盒EEPROM 异常错误03830315-2569 2569 PGy 墨盒EEPROM 异常错误03830307-256A 256A R 墨盒EEPROM 异常错误03830309-256B 256B B 墨盒EEPROM 异常错误03830308-256C 256C G 墨盒EEPROM 异常错误03830304-2570 2570 Bk 墨盒中墨水不足错误03830312-2571 2571 Y 墨盒中墨水不足错误03830303-2572 2572 M 墨盒中墨水不足错误03830313-2573 2573 C 墨盒中墨水不足错误03830301-2574 2574 PM 墨盒中墨水不足错误03810213-2575 2575 PC 墨盒中墨水不足错误03830306-2576 2576 MBk 墨盒中墨水不足错误03830306-2577 2577 MBk2 墨盒中墨水不足错误03830305-2578 2578 Gy 墨盒中墨水不足错误03830315-2579 2579 PGy 墨盒中墨水不足错误03830307-257A 257A R 墨盒中墨水不足错误03830309-257B 257B B 墨盒中墨水不足错误03830308-257C 257C G 墨盒中墨水不足错误03810204-2580 2580 Bk 墨盒余量不足错误03810201-2581 2581 Y 墨盒余量不足错误03810202-2582 2582 M 墨盒余量不足错误03810203-2583 2583 C 墨盒余量不足错误03810212-2584 2584 PM 墨盒余量不足错误03810213-2585 2585 PC 墨盒余量不足错误03810206-2586 2586 MBk 墨盒余量不足错误03810206-2587 2587 MBk2 墨盒余量不足错误03810205-2588 2588 Gy 墨盒余量不足错误03810215-2589 2589 PGy 墨盒余量不足错误03810207-258A 258A R 墨盒余量不足错误03810209-258B 258B B 墨盒余量不足错误03810208-258C 258C G 墨盒余量不足错误03810204-2590 2590 Bk 墨盒余量不足错误03810201-2591 2591 Y 墨盒余量不足错误03810202-2592 2592 M 墨盒余量不足错误03810203-2593 2593 C 墨盒余量不足错误03810212-2594 2594 PM 墨盒余量不足错误03810213-2595 2595 PC 墨盒余量不足错误03810206-2596 2596 MBk 墨盒余量不足错误03810206-2597 2597 MBk2 墨盒余量不足错误03810205-2598 2598 Gy 墨盒余量不足错误03810215-2599 2599 PGy 墨盒余量不足错误03810207-259A 259A R 墨盒余量不足错误03810209-259B 259B B 墨盒余量不足错误03810208-259C 259C G 墨盒余量不足错误03130031-260E 260E 盖帽检测异常错误03130031-260F 260F 盖帽基准面错误错误03130031-2618 2618 VH 电压异常错误错误03800100-2800 2800 电压异常错误错误03800101-2800 2800 没有安装打印头(R)错误03800300-2801 2801 打印头(R) DI 纠正失败错误03800301-2801 2801 打印头(R) DI 纠正失败错误03800200-2802 2802 安装了不正确打印头(R)错误03800201-2802 2802 安装了不正确打印头(R)错误03800400-2803 2803 安装了不正确打印头(R)错误03800401-2803 2803 打印头(R)的EEPROM异常错误03800200-2804 2804 打印头R 被左右相反的安装错误03800201-2804 2804 打印头R 被左右相反的安装错误03800202-2807 2807 打印头R 被左右相反的安装错误03800101-2808 2808 打印头L不存在错误03800102-2808 2808 没有安装打印头L 错误03800301-2809 2809 打印头L 的DI纠正失败错误03800302-2809 2809 打印头L 的DI纠正失败错误03800201-280A 280A 安装了不正确的打印头L 错误03800202-280A 280A 安装了不正确的打印头L 错误03800401-280B 280B 打印头L 的EEPROM 异常错误03800402-280B 280B 打印头L 的EEPROM 异常错误03800500-280C 280C 不吐墨检测中不吐墨喷嘴过多警报03800501-280D 280D 不吐墨检测中打印头(R)的不吐墨喷嘴过多警报03800502-280E 280E 不吐墨检测中打印头L的不吐墨喷嘴过多警报03800200-2811 2811 打印头版本不同错误03800201-2812 2812 打印头(R)版本不同错误03800202-2813 2813 打印头L版本不同错误03841201-2816 2816 维护暗箱EEPROM 异常错误03841201-2817 2817 维护暗箱ID错误错误03841101-2818 2818 无维护暗箱错误03841001-2819 2819 维护暗箱已满错误01841001-281A 281A 维护暗箱的剩余容量不够执行清洗任务错误03841001-281B 281B 维护暗箱的剩余容量不够执行完成各个清洗任务错误03010000-2820 2820 打印头定位不能调整错误03010000-2821 2821 不能进行LF调整错误03010000-2822 2822 不能进行偏芯修正错误03010000-2823 2823 打印头检查错误错误03010000-2824 2824 不能进行光轴调整错误01861003-2902 2902 硬盘的无剩余空间,不能进行复印、打印和错误恢复动作的状态错误011A1001-2905 2905 在HDD 的永久保存领域无剩余空间时,执行了任务保存错误011A1006-2906 2906 HDD 的永久保存领域中已经保存了100个任务,之后又执行了新的任务保存错误031A1001-2908 2908 HDD 格式异常错误031A1006-2909 2909 HDD 文件异常错误03130031-291B 291B 推动移动超时错误03130031-291D 291D 加速传感器检测失败错误03890000-2920 2920 不能卷纸错误错误03890000-2921 2921 卷纸不停止错误错误03060A00-2E00 2E00 接收了滚纸指定的数据,但是放置没有滚纸错误03060A00-2E01 2E01 打印测试开始时没有滚纸错误03860002-2E02 2E02 接收了指定切纸的数据,但是切纸没有被放置错误03060200-2E03 2E03 接收了指定纸盒的数据,但是纸盒中没有被放置切纸错误03862000-2E09 2E09 滚纸余量检测到滚纸不足错误03860002-2E0A 2E0A 切纸安装完成时,接收到指定滚纸的数据错误03060200-2E0B 2E0B 手动切纸安装完成时,接收到指定纸盒的数据错误03860002-2E0C 2E0C 滚纸安装完成时,接收到指定切纸的数据错误03060A00-2E0E 2E0E 滚纸单元没有安装错误03031000-2E0F 2E0F 上盖异常打开错误03031000-2E11 2E11 输送筒盖子异常打开错误03031000-2E12 2E12 释放杆异常错误03060000-2E14 2E14 接收数据的宽度和纸张宽度不一致错误03061000-2E15 2E15 数据的纸张种类不一致错误03060000-2E16 2E16 数据的纸张种类和尺寸不一致(只有纸盒的情况)错误03180101-2E17 2E17 未安装纸盒错误03060A00-2E1B 2E1B 滚纸用完错误03010000-2E1C 2E1C 不能排纸错误03010000-2E1F 2E1F 调整方式打印时,纸张太小错误03030000-2E21 2E21 IEEE1394 界面异常错误03180003-2E22 2E22 介质配置工具中的纸盒供纸设置为[否]时,接收到了指定纸盒的任务错误03130031-2E23 2E23 切割单元故障错误03010000-2E25 2E25 供纸错误错误03010000-2E27 2E27 打印中纸张脱离/供纸、打印、排纸过程中发生了LF脱离(JAM1)错误03130031-2F13 2F13 A/D 转换器外部触发器输出停止错误03130031-2F14 2F14 ASIC 记录器不能写入错误03130031-2F16 2F16 喷雾风扇错误错误03130031-2F17 2F17 台板风扇错误错误03130031-2F1F 2F1F 清洗马达原位置检测错误错误03130031-2F20 2F20 盖帽马达凸轮位置异常错误错误03130031-2F22 2F22 抽墨移动超时错误03130031-2F23 2F23 清洁马达错误错误03130031-2F24 2F24 切割器移动超时错误03130031-2F25 2F25 不能检测到输送马达原位置错误03130031-2F26 2F26 搬运错误错误03130031-2F27 2F27 搬运超时错误03130031-2F28 2F28 清洁传感器错误错误03010000-2F29 2F29 LF 运送超时错误错误03130031-2F2A 2F2A 不能检测到LF 原位置错误03130031-2F2B 2F2B LF 动作不能进行错误03130031-2F2D 2F2D 纸盒动作不能进行错误03130031-2F2E 2F2E 滚纸移动超时错误03800500-2F2F 2F2F 不吐墨检测错误错误03800500-2F30 2F30 不吐墨检测位置调整错误错误03130031-2F32 2F32 多功能传感器异常错误03010000-2F33 2F33 因为是不能调整的媒体所以不能进行调整错误03010000-2F34 2F34 传感器校准错误错误03130031-2F3A 2F3A 墨水供给阀马达错误错误E146-4001 4001 无边距/流动预备吐墨/喷雾回收台整体维修呼叫E602-401A 401A HDD 错误(故障)维修呼叫E602-401B 401B HDD 接触不良维修呼叫E198-401C 401C RTC 错误维修呼叫E198-401D 401D RTC 电池不足维修呼叫E198-401E 401E RTC 时钟停止维修呼叫03130031-4027 4027 推动移动超时错误E194-4034 4034 传感器校准错误(用户模式下不会发生)错误E161-403E 403E 打印头R 异常升温维修呼叫E161-403F 403F 打印头L 异常升温维修呼叫E196-4040 4040 校验和错误维修呼叫E196-4041 4041 FLASH ROM 取出失败维修呼叫03900001-4042 4042 介质配置工具数据传送失败错误E196-4042 4042 介质配置工具数据传送失败维修呼叫E196-4043 4043 介质配置工具数据传送失败维修呼叫E196-4044 4044 EEPROM 尺寸错误维修呼叫E196-4045 4045 EEPROM 尺寸错误维修呼叫E141-4046 4046 恢复的回转次数已经达到5万次以上维修呼叫E144-4047 4047 供给相关的计数错误维修呼叫03900001-4049 4049 转送ROM 数据机型不同错误E196-4049 4049 转送ROM 数据机型不同维修呼叫E194-404A 404A 不吐墨检测计数错误维修呼叫才哥2012.10.01。
ARTISAN TECHNOLOGY GROUP 设备购买、维修与售卖说明书

Agilent 81689A / 81689B / 81649A Compact Tunable Laser Modules Technical SpecificationsFebruary 2002The 81689A, 81689B, 81649A compact tunable lasermodules offer superior performance now also in the compactmodule class. As they are tunable with continuous outputpower, they are the most flexible stimulus for the test ofoptical amplifiers, DWDM components as well as for the testof complete DWDM systems.Compact tunable lasers for C-and L-bandThe Agilent 81689A and 81689B modules operate in the C-band from 1525 nm to 1575 nm, whereas the Agilent 81649A covers the L-band from 1570 nm to 1620 nm.Test of optical amplifiersA variable amount of the compact, yet fully remote controlled Agilent 81689A, 81689B and 81649A tunable laser modules, in combination with the 81682A and 81642A high power Tunable Laser, is the ideal solution to characterize optical amplifiers for use in DWDM applications. The 81689A, 81689B and 81649A compact tunable laser modules provide the high stimulus power needed to test today's optical amplifiers. Together with the 81651A optical attenuator module, an output power dynamic range of more than60 dB can be achieved. Even without the attenuator module the power can be attenuated by 9dB (10dB for 81689B) e.g. to equalize power levels of several sources. Polarization Maintaining Fiber for the test of integrated optical devicesThe 81689A, 81689B and 81649A modules are ideally constructed to characterize integrated optical devices. Their optional Panda PMF output ports provide a well defined state of polarization to ensure constant measurement conditions on waveguidedevices. A PMF cable easily connectsan external optical modulator.The 81689A, 81689B and 81649A isavailable with both, standard single-mode fiber and Panda type PMF.Compact module for DWDMmulti-channel testThe 81689A, 81689B and 81489Aallow a realistic multi-channel test bedfor DWDM transmission systems to beset up.Their flexibility make them thepreferred choice for tests of DWDMtransmission system during installationand maintenance phases.Compact spare for DFBmodules in ITU gridsThe 81689B for the first time solvesthe sparing nightmare for users ofDWDM combs. In combination with acomb of 81662A DFB lasers the81689B can replace any DFB between1525nm and 1575nm without powerpenalty.Remote control & PnPsoftware drivers for easyprocess automationIts continuous, mode-hop free tuningmakes it quick and easy to set even themost complex configurations to thetarget wavelengths and power levels,just by dialing or using the vernier keys.A 8163B mainframe can host2 compact tunable laser modules. Thisallows for the most compact C- and L-band stimulus solution available today.Each 8164B mainframe can host up tofour units of the 81689A, 81689B or81649A in its upper slots.The 8166B is most interesting for highchannel count solutions. Up to17 compact tunable laser modules canbe hosted here.The 81649A, 81689A and 81689B areproduced to ISO 9001 internationalquality system standard as part ofAgilent's commitment to continuallyincreasing customer satisfactionthrough improved quality control.Specifications describe theinstrument's warranted performance.They are verified at the end of a 2 mlong patchcord and are valid afterwarm-up and for the stated outputpower and wavelength ranges.Each specification is assured bythoroughly analyzing all measurementuncertainties. Supplementaryperformance characteristics describethe instrument’s non-warranted typicalperformance.Every instrument is delivered with acommercial certificate of calibrationand a detailed test report.For further details on specifications,see the Definition of Terms in AppendixC of the Compact Tunable Laser User'sGuide.81689A, 81689B, 81649A Compact Tunable Laser for Multi-channel test applicationsAgilent 81689A Agilent 81689B Agilent 81649A Wavelength range1525 nm to 1575 nm1525 nm to 1575 nm1570 nm to 1620 nm Wavelength resolution0.01 nm, 1.25 GHz at 1550 nm0.01 nm, 1.25 GHz at 1550 nm0.01 nm, 1.17 GHz at 1595 nm Absolute wavelength accuracy (typ.) [1]±0.3 nm±0.3 nm±0.3 nmRelative wavelength accuracy [1]±0.3 nm±0.15 nm±0.15 nmWavelength repeatability [1]±0.05 nm±0.05 nm±0.05 nmWavelength stability(typ., over 24 h at constant temperature)[1] (typ., over 1 h at constant temperature)[1]±0.02 nm±0.01 nm±0.005 nm±0.01 nm±0.005 nmTuning speed (typ.)<10 sec/ 50 nm<10 sec/ 50 nm<10 sec/ 50 nmLinewidth (typ.) [2]with Coherence Control ON (typ.) [2]20 MHz---< 20MHz>100MHz< 20MHz>100MHzOutput power (continuous power on duringtuning)≥ 6 dBm (1525 –1575nm)≥ 10 dBm (1525 –1575nm)≥ 6 dBm (1570 –1620nm) Minimum output power–3 dBm0 dBm–3 dBmPower stability (at constant temperature) [3]±0.03 dB over 1 hour,typ. ±0.06 dB over 24 hours ±0.015 dB over 1 hour,typ. ±0.0075 dB over 1 hour,typ. ±0.05 dB over 24 hours±0.015 dB over 1 hour,typ. ±0.0075 dB over 1 hour,typ. ±0.05 dB over 24 hoursPower repeatability (typ.) [3]±0.02 dB±0.02 dB±0.02 dB Power linearity±0.1dB±0.1dB±0.1dB Power flatness versus wavelength±0.3 dB±0.2 dB±0.2 dBSide-mode suppression ratio (typ.) [2]> 40 dB(1525 – 1575 nm at 0 dBm)> 45 dB(1525 – 1575 nm at ≥ 3 dBm)> 45 dB(1570 – 1620 nm at ≥ 0 dBm)Signal to source spontaneous emission ratio (typ.) [4]≥ 39 dB/ nm(1525 –1575 nm at 6 dBm)≥ 44 dB/ nm(1525 –1575 nm at 10 dBm)≥ 42 dB/ nm(1570 – 1620 nm at 6 dBm)Relative intensity noise (RIN, typ.)< -137 dB/Hz(100 MHz – 2.5 GHz, at +3 dBm)< -137 dB/Hz(100 MHz – 2.5 GHz, at +7 dBm)< -137 dB/Hz(100 MHz – 2.5 GHz, at +3 dBm)Dimensions75 mm H, 32 mm W, 335 mm D(2.8" x 1.3" x 13.2")75 mm H, 32 mm W, 335 mm D(2.8" x 1.3" x 13.2")75 mm H, 32 mm W, 335 mm D(2.8" x 1.3" x 13.2")Weight 1 kg 1 kg 1 kg[1]At CW operation. Measured with wavelength meter based on wavelength in vacuum.[2]Measured by heterodyning method.[3]500 ms after changing power.[4]Measured with optical spectrum analyzer at 1 nm resolution bandwidth.Listed optionsOption 021: standard single mode fiber,straight contact output connectorOption 022: standard single mode fiber,angled contact output connectorOption 071: polarization maintainingfiber, straight contact output connectorOption 072: polarization maintainingfiber, angled contact output connectorSupplementary performance characteristics ModulationInternal digital modulation50% duty cycle, 200 Hz to 300 kHz.>45% duty cycle, 300 kHz to 1 MHz. Modulation output (via Mainframe): TTL reference signal.External digital modulation> 45% duty cycle, fall time< 300 ns, 200 Hz to 1 MHz. Modulation input (via Mainframe):TTL signal.External analog modulation≥ ±15% modulation depth,5 kHz to 1 MHz.Modulation input: 5 Vp-p Coherence control(81649A/81689B)For measurements on components with 2 m long patchcords and connectors with 14 dB return loss, the effective linewidth results in a typical power stability of< ±0.025 dB over1 minute by reducing interference effects in the test setup.GeneralOutput isolation (typ.):38 dBReturn loss (typ.):55 dB (options 022, 072)40 dB (options 021, 071)Polarization maintaining fiber (Options071, 072)Fiber type: Panda.Orientation: TE mode in slow axis,in line with connector key.Extinction ratio: 16 dB typ.Laser class:Class IIIb according to FDA 21 CFR1040.10, Class 3A according to IEC 825- 1; 1993.Recommended re-calibration period:2 years.Warm-up time:< 40 min,immediate operation after boot-up.EnvironmentalStorage temperature:–20 °C to +70 °C (81689A)–40 °C to +70 °C (81689B, 81649A)Operating temperature:15 °C to 35 °CHumidity:< 80 % R.H. at 15 °C to 35 °CSpecifications are valid in non-condensingconditions.Laser Safety InformationAll laser sources specified by this datasheet are classified as Class 1Maccording to IEC 60825-1 (2001).All laser sources comply with 21 CFR1040.10 except for deviations pursuantto Laser Notice No. 50, dated 2001-July-26This page intentially left blankAgilent Technologies’Test and Measurement Support,Services, and AssistanceAgilent Technologies aims to maximize the value you receive, while minimizing your risk and problems. We strive to ensure that you get the test and measurement capabilities you paid for and obtain the support you need. Our extensive support resources and services can help you choose the right Agilent products for your applications and apply them successfully. Every instrument and system we sell has a global warranty. Support is available for at least five years beyond the production life of the product. Two concepts underlie Agilent's overall support policy: "Our Promise" and "Your Advantage."Our PromiseOur Promise means your Agilent test and measurement equipment will meet its advertised performance and functionality. When you are choosing new equipment, we will help you with product information, including realistic performance specifications and practical recommendations from experienced test engineers. When you use Agilent equipment, we can verify that it works properly, help with product operation, and provide basic measurement assistance for the use of specified capabilities, at no extra cost upon request. Many self-help tools are available.Your AdvantageYour Advantage means that Agilent offers a wide range of additional expert test and measurement services, which you can purchase according to your unique technical and business needs. Solve problems efficiently and gain a competitive edge by contracting with us for calibration, extra-cost upgrades, out-of-warranty repairs, and on-site education and training, as well as design, system integration, project management, and other professional engineering services. Experienced Agilent engineers and technicians worldwide can help you maximize your productivity, optimize the return on investment of your Agilent instruments and systems, and obtain dependable measurement accuracy for the life of those products.By internet, phone, or fax, get assistance with all your test & measurement needsOnline assistance:Related Agilent Literature:/coms/lightwaveAgilent 8163A Lightwave MultimeterPhone or Fax Agilent 8164A Lightwave Measurement SystemUnited States:Agilent 8166A Lightwave Multichannel System(tel)180****4844Technical Specificationsp/n 5988-1568ENCanada:(tel)187****4414Agilent 81662A DFB Laser(fax) (905) 206 4120Agilent 81663A DFB LaserAgilent Fabry Perot LaserTechnical SpecificationsEurope:p/n 5988-1570EN(tel) (31 20) 547 2323(fax) (31 20) 547 2390Agilent Power Sensor ModulesJapan:Agilent Optical Heads(tel) (81) 426 56 7832Agilent Return Loss Modules(fax) (81) 426 56 7840Technical Specificationsp/n 5988-1569ENLatin America:(tel) (305) 269 7500(fax) (305) 269 7599Agilent 8163A/B Lightwave MultimeterAgilent 8164A/B Lightwave Measurement SystemAustralia:Agilent 8166A/B Lightwave Multichannel System(tel) 1 800 629 485 Configuration Guide(fax) (61 3) 9210 5947p/n 5988-1571ENNew Zealand:Agilent 8163B Lightwave Multimeter(tel) 0 800 738 378Agilent 8164B Lightwave Measurement System(fax) 64 4 495 8950Agilent 8166B Lightwave Multichannel SystemTechnical SpecificationsAsia Pacific:p/n 5988-3924EN(tel) (852) 3197 7777(fax) (852) 2506 9284Product specifications and descriptions in this document subject to change without notice.Copyright © 2001 Agilent TechnologiesFebruary 12 20025988-3675EN。
ARTISAN技术集团-OHP4000系列数字保持音频系统用户手册说明书

User ManualOn-Hold Plus 4000/4500 Digital On-Hold Audio SystemBefore using this unit, please read these operating instructions carefully.Afterwards, keep them handy for future reference.OHP 4000 Series User ManualMessageStudio Software - allows user to create fully customized on-hold audiocontent on a PC and record directly into OHP 4000's digital memory.Digital flash memory - design retains music/message content even during powerloss...unit ships with preloaded audio.LCD Control Panel - displays program length, time remaining in unit's memory, andunit's status.Trigger switch - unit can be triggered to start program content from the beginningwith an external trigger switch.Analog Phone Adapter Module (OHP4500 Only) - adds music-on-hold capabilityto most standard analog and KSU-less telephones with up to 4 lines and 50 stationsets.External Recording Capability - audio input allows user to record from anyexternal audio source.Built-In Monitor Speaker - allows user to monitor sound with the flip of a switch.Wall Mountable - unit can play and recorde while mounted in a vertical position.3-Year WarrantyOHP 4000 Series User ManualSet-up (OHP 4000)Plug AC adapter into wall outlet.Plug AC adapter cable into jack marked "DC12V".Plug "Connector Cable A" to "AUDIO OUT" jack.Plug other end of "Connector Cable A" into phone system's music-on-hold (moh) input jack. NOTE: If the jack cannot be located, contact your phone vendor for assistance.1234Connection to PBX or KEY phone systemsPlug the supplied "T adapter" into any modular phone jack which services line 1 and 2. (This will allow you to share the phone jack with any phone extension which you have plugged in to the wall jack.)Plug the provided phone cord into the jack marked "Line 1/2" on the adapter module.Plug the other end of the phone cord into the "T" adapter which is servicing line 1 and 2.REPEAT IF LINE 3 and/or 4 ARE PRESENT123Phone ExtensionsLine 1Line 2Line 3Line 4OHP 4000 Series User ManualOHP 4000 Series User Manualused to initiate manual RECORD SPEAKER displayed when audio is Record Mode Indicator displayed when unit Playback Indicator Recording ConnectionPlayer Controls & LCD DisplayControls & FunctionsPlug "Connector Cable B" into "speaker out" or "audio out" jack of your computer's sound card or connect to the "headphone" jack of your PC's speakers (if available).NOTE: If using CD or tape player for recording audio content,, connect to the headphone jackof the tape or CD player.Plug other end of "Connector Cable B" to "AUDIO IN" jack on the unit.12OHP 4000 Series User ManualOperationPlaybackPlaying Audio Stored in MemoryBy default, the unit is always in "playback" mode. When unit is playing,the LCD will display a running time and the segments on the speaker iconwill move.Playback After Power LossIf power to the unit is lost, the unit will resume playback as soon as poweris reapplied. The unit retains its recorded content after power loss.RecordingAuto RecordingA special software program called MessageStudio has been included whichallows you to make your own on-hold message productions. Eachproduction made with MessageStudio will include specially encoded synctones which will automatically start and stop the recording process on theOHP 4000. These tones will not be recorded. To record from other CDs ormusic sources, see "Manual-Recording" section on the following page.Beginning Auto RecordingTo begin recording using MessageStudio software, simply press "Play Mix"button on the MessageStudio Player software screen. A start tone will beheard and the unit will begin recording automatically. When finished, ashort series of tones will signal the unit to stop recording. After recording,the unit automatically returns to active play mode.NOTE: During recording, the LCD will display a moving arrow from the CDicon to the memory chip icon. You will hear what is being recordedthrough the built-in preview speaker. When recording is finished, thecounter on the LCD will display a running playback time.IMPORTANT: To avoid inadvertent erasure of stored audio program,remove "Connector Cable B" from the OHP 4000's "AUDIO IN" jack whenrecording is finished.OHP 4000 Series User ManualImpedance SwitchLocation -- right side of unitOperation -- Most telephone systems prefer an 8 ohm output. Ifyou are working with an older phone system, the 600 ohm settingmay be preferable.Speaker ButtonLocation -- left top, located below the "REC" buttonOperation -- Push "SPEAKER" button to listen to program playing fromdigital memory. Push "SPEAKER" button again to turn off speaker.Audio being recorded plays through speaker, regardless of speaker switchposition. Speaker switch position has no effect on "AUDIO OUT" playback.Volume ControlLocation -- rear panelOperation -- controls output level of "AUDIO OUT" jack. To adjust, turncontrol knob clockwise to increase volume. Set proper volume level bycalling in from a phone close to the unit (or cell phone) and having yourcall placed on hold.Power SwitchLocation -- rear panelOperation -- turns power on or off. When power is on, LCD is illuminated.OHP 4000 Series User ManualOther FunctionsRemote TriggerLocation -- rear panelConnection -- 2.5 mm mini jackOperation -- By connecting a momentary switch to this jack, theunit will play audio content from memory when triggered.Content will play through once and then reset, ready for nexttrigger sequence.Audio InLocation -- rear panel next to "TRIGGER" jackConnection -- 3.5 mm mini jackOperation -- Connect audio cable from the "LINE OUT" or"headphone out" jack of any external audio source to the "AUDIOIN" jack.Adding Additional MemoryConfigurationThe OHP 4000 comes standard with 8 minutes of flash memory.Memory can be expanded to 16, 24 or 32 minutes by addingmemory modules in 8-minute increments. Memory modules can beplaced into 3 available memory expansion slots located on thecircuit board. The memory slots can be accessed by removing thethe 5 screws on the bottom of the unit and then lifting awaybottom portion of the housing.Installation1. Turn power switch to OFF position and disconnect all cords andcables from the unit.2. Remove five screws in bottom of unit.3. Remove lower portion of the case housing.4. Carefully insert the 24-pin memory module chip in the openexpansion slot (next to the existing chip).5. Reconnect cords and cables.6. Turn power switch to ON position.OHP 4000 Series User ManualMessageStudio TMPlayer Softwarefiles from the MessageStudio CD-ROM(choose from 20 music selections)message files from the MessageStudio CD-ROM or...add a custom message about your company!Choose the time interval between messagesView the length of your final productionRecord a message in your own voiceLaunch the MessageStudio Writer SoftwareMessageStudio Player Main WindowUsing MessageStudio software, creating professional sounding custom on-hold audio is simple, quick and easy. PC with a 486 or better processor and a 16-bit sound card.new on-hold message productions any time you wish. You may record new messages in your own voice (using a mic hooked up to your PC sound card) or have messages professionally produced by On-Hold Plus or any other professional voice talent (see MessageStudio Writer on the following page). When your production is finished, you will record it into the digital flash memory in your OHP 4000. For details on recording into the OHP 4000, see the "Auto Recording" section in this manual.MessageStudio works with any .WAV or .MP3 audio files. There are 20 different music files as well as a choice of professionally voiced "thanks for holding..." messages included with the MessageStudio software.Recording Messages in Your Own VoiceUsing the MessageStudio Player Software and a mic hooked up to your PC's sound card, you can record professional sounding messages in your own voice. To record, click the "RECORD MSG" button in the MessageStudio Player window.NOTE: Confirm that your "MICROPHONE" is selected as a recording input in your sound card controls and that the volume is turned up.Creating Custom On-Hold AudioOHP 4000 Series User ManualCreating an On-Hold Audio ScriptTo assist you in writing your on-hold audio script, the MessageStudiosoftware includes a fun and easy scriptwriting utility called MessageStudioWriter. This utility may be accessed from the main screen of the software byclicking on the "Write Msg." button (located at the bottom right of thescreen). Even if you’re not a Madison Avenue copywriter, you’ll find theprocess quick, easy and fun. Just by asking a few questions, the intuitivesoftware will create several choices of beginning and ending sentences foryou. Simply click on your choices, add a sentence or two of your own, andyou’re done...it’s that easy.Your finished script can either be read by you or submitted to On-HoldPlus for professional voice-over of your custom messages.MessageStudio Writer Main WindowProfessional Production Services from On-Hold PlusOn-Hold Plus offers complete, professional production services featuring"national broadcast quality voice talent". Your finished on-hold messages(four 30-second message segments) can be e-mailed or sent to you on a CD-ROM. Your messages will be sent to you within 3 to 5 working days (e-maildelivery) or 10 to 15 days (CD-ROM delivery) from receipt of your script.Using the MessageStudio Player, you will add these professionally voicedmessage files to the program for playback with your choice of backgroundmusic.To submit your production to On-Hold Plus for professional production, justfollow the step-by-step instructions in the MessageStudio Writer software.OHP 4000 Series User ManualWarrantyLimited WarrantyOn-Hold Plus warrants this product to be free from manufacturing defects in materialand workmanship under normal use and conditions for a period of 3 years from date oforiginal purchase in the United States.Should service be necessary under this warranty for any reason due to manufacturingdefect during this 3-year period from date of original purchase, On-Hold Plus will eitherrepair the unit or replace it with a reconditioned unit at no charge.You may return the unit to On-Hold Plus at the address listed below.• Pack the unit in a well-padded, heavy, corrugated box.• Enclose proof of purchase.• Enclose your check or money order payable to On-Hold Plus in the amount of $10.00to cover shipping and handling costs.• Ship the unit prepaid via UPS or parcel post (insured).Note: This warranty is void if the product is:(a) Damaged through negligence, misuse, abuse, or accident.(b) Modified in any way.(c) Damaged because it is improperly connected to the equipment of othermanufacturers.This warranty does not cover:(a) Damage to equipment not properly connected to the product.(b) Costs incurred in the shipping of the product to On-Hold Plus.(c) Damage or improper operation of unit caused by customer abuse, misuse, negligence,or failure to follow operating instructions provided with the product.(d) Ordinary adjustments to the product which can be performed by customer asoutlined in the owner's manual.(e) Damage to compact discs.THIS WARRANTY IS NON-TRANSFERABLE AND APPLIES ONLY TO THE ORIGINALPURCHASER AND DOES NOT EXTEND TO SUBSEQUENT OWNERS OF THE PRODUCT. ANYAPPLICABLE IMPLIED WARRANTIES, INCLUDING THE WARRANTY OF MERCHANTABILITYARE LIMITED IN DURATION TO A PERIOD OF THE EXPRESS WARRANTY AS PROVIDEDHEREIN BEGINNING WITH THE DATE OF ORIGINAL PURCHASE AT RETAIL AND NOWARRANTIES, WHETHER EXPRESS OR IMPLIED, SHALL APPLY TO THIS PRODUCTTHEREAFTER. On-Hold Plus MAKES NO WARRANTY AS TO THE FITNESS OF THE PRODUCTFOR ANY PARTICULAR PURPOSE OR USE.UNDER NO CIRCUMSTANCES SHALL On-Hold Plus BE LIABLE FOR ANY LOSS, DIRECT,INDIRECT, INCIDENTAL, SPECIAL, OR CONSEQUENTIAL DAMAGE ARISING OUT OF OR INCONNECTION WITH THE USE OF THIS PRODUCT.THIS WARRANTY IS VALID ONLY IN THE UNITED STATES OF AMERICA. THIS WARRANTYGIVES YOU SPECIFIC LEGAL RIGHTS. HOWEVER, YOU MAY HAVE OTHER RIGHTS WHICHMAY VARY FROM STATE TO STATE. SOME STATES DO NOT ALLOW LIMITATION ONIMPLIED WARRANTIES OR EXCLUSION OF CONSEQUENTIAL DAMAGE. THEREFORE THESERESTRICTIONS MAY NOT APPLY TO YOU.On-Hold Plus and MessageStudio are registered trademarks of IntelliTouch Communications. © IntelliTouch Communications. All rights reserved.No part of this document may be photocopied, reproduced, or translated into another language without the prior written consent of IntelliTouch Communications. FCC Information This equipment has been tested and found to comply with the limits for a Class B digital device, pursuant to Part 15 of the FCC Rules. These limits are designed to provide reasonable protection against harmful interference in a residential installation. This equipment generates, uses, and can radiate radio frequency energy and, if not installed and used in accordance with the instructions, may cause harmful interference to radio communications. However, there is no guarantee that interference will not occur in a particular installation. If this equipment does cause harmful interference to radio or television reception, which can be determined by turning the equipment off and on, the user is encouraged to try to correct the interference by one or more of the following measures:- Reorient or relocate the receiving antenna.- Increase the separation between the equipment and receiver.- Connect the equipment into an outlet on a circuit different from that to which the receiver is connected.- Consult the dealer or an experienced radio/TV technician for help.You are cautioned that any changes or modifications not expressly approved in this manual could void your authority to operate this equipment.PrecautionsInstallationNever install the unit where it would be subjected to:- heat sources such as radiators or air ducts.- direct sunlight.- excessive dust.- moisture or rain.- mechanical vibration or shock.- unleveled surface.• When the unit is used with an AC power adapter, do not wrap the unit in a cloth, blanket, etc. If you do so,the temperature inside and outside the unit may rise considerably, resulting in malfunctioning of the unitor serious accidents.• If the unit is brought directly from a cold to a warm location, or is placed in a very damp room, moisture maycondense on the lens inside the unit. Should this occur, the unit will not operate. In this case, remove thedisc and leave the unit in a warm place for several hours until the moisture evaporates.• For the unit to operate at its best, it should not be subjected to temperatures below 5˚C (41˚F) or above 35˚C(95˚F).Warnings • Before operating the unit, please read this manual thoroughly and retain it for future reference.• To prevent fire or shock ha zard, do not expose the unit to rain or moisture. To avoid electrical shock, do notopen the cabinet. Refer servicing to qualified personnel only.• The use of optical instruments with this product will increase eye hazard.Care & MaintenanceCleaning -- Do not use volatile chemicals on this unit. Clean by lightly wiping with a soft cloth.Customer SupportToll-free customer support is available from 8AM to 5PM (PST) Monday thru Friday by calling 800-839-7277Information。
ARTISAN技术组合购买指南说明书

INSTALLATION GUIDENI PXI-8186/8187This document contains information about installing yourNI PXI-8186/8187 controller in a PXI chassis.For complete configuration and troubleshooting information (includinginformation about BIOS setup, adding RAM, and so on), refer to theNI PXI-8186/8187 User Manual. The manual is in PDF format on therecovery CD included with your controller and on the National InstrumentsWeb site, .Installing the NI PXI-8186/8187This section contains general installation instructions for theNI PXI-8186/8187. Consult your PXI chassis user manual for specificinstructions and warnings.1.Plug in your chassis before installing the NI PXI-8186/8187. Thepower cord grounds the chassis and protects it from electrical damagewhile you install the module. (Make sure the power switch isturned off.)Caution To protect both yourself and the chassis from electrical hazards, leave the chassispowered off until you finish installing the NI PXI-8186/8187 module.2.Remove any filler panels blocking access to the system controller slot(Slot 1) in the chassis.3.Touch the metal part of the case to discharge any static electricity thatmight be on your clothes or body.4.Remove the protective plastic covers from the four bracket-retainingscrews as shown in Figure1.NI PXI-8186/8187 Installation Guide Figure 1. Removing Protective Screw Caps5.Make sure the injector/ejector handle is in its downward position.Align the NI PXI-8186/8187 with the card guides on the top andbottom of the system controller slot.CautionDo not raise the injector/ejector handle as you insert the NI PXI-8186/8187. Themodule will not insert properly unless the handle is in its downward position so that it doesnot interfere with the injector rail on the chassis.6.Hold the handle as you slowly slide the module into the chassis until the handle catches on the injector/ejector rail.7.Raise the injector/ejector handle until the module firmly seatsinto the backplane receptacle connectors. The front panel of theNI PXI-8186/8187 should be even with the front panel of the chassis.8.Tighten the four bracket-retaining screws on the top and bottom of thefront panel to secure the NI PXI-8186/8187 to the chassis.9.Check the installation.10.Connect the keyboard and mouse to the appropriate connectors. If youare using a PS/2 keyboard and a PS/2 mouse, use the Y-splitter adapterincluded with your controller to connect both to the PS/2 connector.11.Connect the VGA monitor video cable to the VGA connector.12.Connect devices to ports as required by your system configuration.13.Power on the chassis.14.Verify that the controller boots. If the controller does not boot, refer tothe What If the NI PXI-8186/8187 Does Not Boot? section.Figure2 shows an NI PXI-8186 installed in the system controller slot of aNational Instruments PXI-1042 chassis. You can place PXI devices in anyother slot.1PXI-1042 Chassis2NI PXI-8186 Controller3Injector/Ejector RailFigure 2. NI PXI-8186 Controller Installed in a PXI ChassisHow to Remove the Controller from the PXI ChassisThe NI PXI-8186/8187 controller is designed for easy handling. Completethe following steps to remove the unit from the PXI chassis:1.Power off the chassis.2.Remove the bracket-retaining screws in the front panel.3.Press the injector/ejector handle down.4.Slide the unit out of the chassis.© National Instruments Corporation3NI PXI-8186/8187 Installation GuideNational Instruments™, NI™, and ™ are trademarks of National Instruments Corporation. Product and company names mentioned herein are trademarks or trade names of their respective companies. For patents covering National Instruments products, refer to the appropriate location:Help»Patents in your software, the patents.txt file on your CD, or /patents.© 2003–2004 National Instruments Corp. All rights reserved.323683B-01Jun04 *323683B-01*What If the NI PXI-8186/8187 Does Not Boot?Several problems can cause a controller not to boot. Here are some thingsto look for and possible solutions.Things to Notice:•Which LEDs come on? The Power OK LED should stay lit.The Drive LED should blink during boot as the disk is accessed.•What appears on the display? Does it hang at some particular point(BIOS, Operating System, and so on)? If nothing appears on thescreen, try a different monitor. Does your monitor work with adifferent PC? If it hangs, note the last screen output that you saw forreference when consulting National Instruments technical support.•What has changed about the system? Did you recently move thesystem? Was there electrical storm activity? Did you recently adda new module, memory chip, or piece of software?Things to Try:•Make sure the chassis is plugged in to a working power source.•Check any fuses or circuit breakers in the chassis or other powersupply (possibly a UPS).•Make sure the controller module is firmly seated in the chassis.•Remove all other modules from the chassis.•Remove any nonessential cables or devices.•Try the controller in a different chassis.•Try a similar controller in this same chassis.•Recover the hard drive on the controller.•Clear the CMOS.。
派克核电门户网站产品说明书
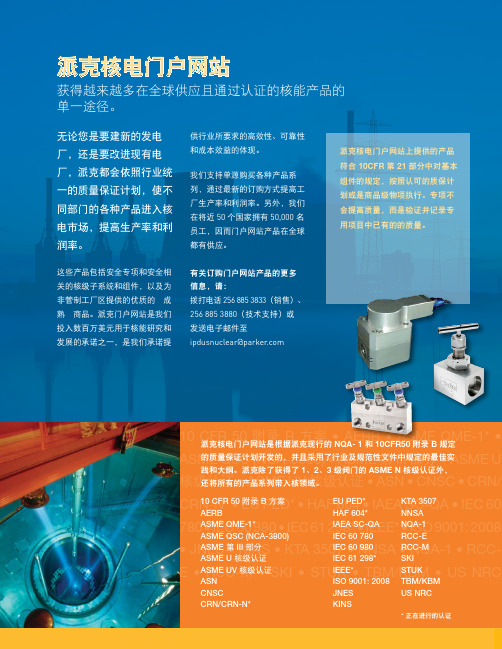
10 CFR 50 • AERB • ASME QME-1* • ASME QSC (NCA-3800) • ASME 第 III 部分 • ASME U核级认证核级认证 • ASN • CNSC CRN-N* HAF 604 • IAEA SC-QA 780 298* • IEEE* • ISO 9001: •E 派克核电门户网站无论您是要建新的发电厂,还是要改进现有电厂,派克都会依照行业统一的质量保证计划,使不同部门的各种产品进入核电市场,提高生产率和利润率。
这些产品包括安全专项和安全相关的核级子系统和组件,以及为非管制工厂区提供的优质的“成熟”商品。
派克门户网站是我们投入数百万美元用于核能研究和发展的承诺之一,是我们承诺提获得越来越多在全球供应且通过认证的核能产品的单一途径。
供行业所要求的高效性、可靠性和成本效益的体现。
我们支持单源购买各种产品系列,通过最新的订购方式提高工厂生产率和利润率。
另外,我们在将近 50 个国家拥有 50,000 名员工,因而门户网站产品在全球都有供应。
有关订购门户网站产品的更多信息,请:拨打电话 256 885 3833(销售)、256 885 3880(技术支持)或 发送电子邮件至 ipdusnuclear@parker .com派克核电门户网站是根据派克现行的 NQA- 1 和 10CFR50 附录 B 规定的质量保证计划开发的,并且采用了行业及规范性文件中规定的最佳实3 级阀门的 ASME N 核级认证外,派克核电门户网站上提供的产品符合 10CFR 第 21 部分中对基本组件的规定,按照认可的质保计划或是商品级物项执行。
专项不会提高质量,而是验证并记录专用项目中已有的的质量。
EU PED*HAF 604*IAEA SC-QA KTA 3507NNSANQA-1Parker Hannifin Ltd.Tachbrook Park DriveTachbrook Park,Warwick, CV34 6TU英国电话:+44 (0) 1926 317 878传真:+44 (0) 1926 317 855********************欧洲、中东和非洲AE – 阿联酋,迪拜电话:+971 4 8127100********************AT – 奥地利,维也纳新城电话:+43 (0)2622 23501-0*************************AT – 东欧,维也纳新城电话:+43 (0)2622 23501 900****************************AZ – 阿塞拜疆,巴库电话:+994 50 2233 458****************************BE/LU – 比利时,尼韦尔电话:+32 (0)67 280 900*************************BY – 白俄罗斯,明斯克电话:+375 17 209 9399*************************CH – 瑞士,埃托瓦电话:+41 (0)21 821 87 00*****************************CZ – 捷克共和国,Klecany电话:+420 284 083 111*******************************DE – 德国,卡尔斯特电话:+49 (0)2131 4016 0*************************DK – 丹麦,巴勒鲁普电话:+45 43 56 04 00*************************ES – 西班牙,马德里电话:+34 902 330 001***********************FI – 芬兰,万塔河电话:+358 (0)20 753 2500parker. ****************FR – 法国,Contamine s/Arve电话:+33 (0)4 50 25 80 25************************GR – 希腊,雅典电话:+30 210 933 6450************************HU – 匈牙利,布达佩斯电话:+36 23 885 470*************************IE – 爱尔兰,都柏林电话:+353 (0)1 466 6370*************************IT – 意大利,Corsico (MI)电话:+39 02 45 19 21***********************KZ – 哈萨克斯坦,阿拉木图电话:+7 7273 561 000****************************NL – 荷兰,奥尔登扎尔电话:+31 (0)541 585 000********************NO – 挪威,阿斯克尔电话:+47 66 75 34 00************************PL – 波兰,华沙电话:+48 (0)22 573 24 00************************PT – 葡萄牙,莱萨·达·帕尔梅拉电话:351 22 999 7360**************************RO – 罗马尼亚,布加勒斯特电话:+40 21 252 1382*************************RU – 俄罗斯,莫斯科电话:+7 495 645-2156************************SE – 瑞典,Spånga电话:+46 (0)8 59 79 50 00************************SK – 斯洛伐克,班斯卡·比斯特里察电话:+421 484 162 252**************************SL – 斯洛文尼亚,新梅斯托电话:+386 7 337 6650**************************TR – 土耳其,伊斯坦布尔电话:+90 216 4997081************************UA – 乌克兰,基辅电话:+380 44 494 2731*************************UK – 英国,沃里克电话:+44 (0)1926 317 878********************ZA – 南非,坎普顿公园电话:+27 (0)11 961 0700*****************************北美地区CA – 加拿大,安大略省米尔顿电话:+1 905 693 3000US – 美国,克利夫兰电话:+1 216 896 3000亚太地区AU – 澳大利亚,城堡山电话:+61 (0)2-9634 7777CN – 中国,上海电话:+86 21 2899 5000HK – 香港电话:+852 2428 8008IN – 印度,孟买电话:+91 22 6513 7081-85JP – 日本,东京电话:+81 (0)3 6408 3901KR – 韩国,首尔电话:+82 2 559 0400MY – 马来西亚,莎阿南电话:+60 3 7849 0800NZ – 新西兰,惠灵顿电话:+64 9 574 1744SG – 新加坡电话:+65 6887 6300TH – 泰国,曼谷电话:+662 186 7000-99TW – 台湾,台北电话:+886 2 2298 8987南美AR – 阿根廷,布宜诺斯艾利斯电话:+54 3327 44 4129BR – 巴西,圣若泽杜斯坎普电话:+55 800 727 5374CL – 智利,圣地亚哥电话:+56 2 623 1216MX – 墨西哥,阿波达卡电话:+52 81 8156 6000核电门户网站手册 M&K 12/10 1M派克授权的本地经销商© 2010 派克汉尼汾公司派克全球办事处联系信息欧洲产品信息中心免费电话:00 800 27 27 5374(AT, BE, CH, CZ, DE, DK, EE, ES, FI, FR, IE,IL, IS, IT, LU, MT, NL, NO, PL, PT, RU, SE,SK, UK, ZA)– 一点的方式。
ARTISAN技术组合购物指南说明书

User's Guidee-mail: ************** GPIB HARDWARE MANUAL FOR USE WITHPCI-GPIB, ISA-GPIB142.6 CPCI-GPIB (12)2.5 PC104-GPIB (11)2.4.2 Windows 3.1 (11)2.4.1 Windows 95 (10)2.4 PCM-GPIB (8)2.3 ISA-GPIB/LC (6)2.2 ISA-GPIB (5)2.1 PCI-GPIB (5)CHAPTER TWO: INSTALLATION ...................31.2.3 Connection Configurations . (2)1.2.2 GPIB Electrical Signal Configuration (1)1.2.1 Talkers, Listeners, and Controllers (1)1.2 GPIB SYSTEM DESCRIPTION (1)1.1 HISTORY (1)CHAPTER ONE: INTRODUCTION ......................Chapter One: INTRODUCTION1.1 HISTORYThe GPIB (General Purpose Interface Bus) has become the worldwide standard for connecting instruments to computers. Invented in the 1960s by Hewlett Packard and originally designated as HPIB, the bus specification was eventually adopted by a wide variety of both instrument and computer manufacturers. The original specification was documented and sanctioned by the Institute of Electrical and Electronic Engineers as IEEE-488.The advent of the inexpensive and powerful personal computer has driven the GPIB market through explosive growth. As GPIB bus usage expanded, there arose the need for some additional capability and standardization, so in 1987, IEEE-488.2 was adopted. IEEE-488.2 was revised/ammended in 1992 and represents the current GPIB specification. The new specification provides some standardization among compliant instruments. These standardization greatly simplifies the job of the GPIB system designer since 488.2 compliant instruments share common programming conventions.1.2 GPIB SYSTEM DESCRIPTION1.2.1 Talker s, Listeners, and ControllersA GPIB device can be a Talker, Listener, and/or Controller. As the name implies a Talker sends data to one or more Listeners, A Listener accepts data from a Talker and a Controller manages the flow of information over the bus. A GPIB Digital Voltmeter is acting as a Listener as its input configurations and ranges are set, and then as a Talker when it actually sends its readings to the computer.The Controller is in charge of all communications over the bus. The Controller’s job is to make sure only one device tries to talk at a time, and make sure the correct Lis-teners are paying attention when the Talker talks. Each GPIB system has a single sys-tem controller. The system controller is ultimately in charge of the bus, and is in control as the bus is powered up. There can be more than one Controller on the bus and the System Controller can pass active control to another controller capable device, though only one can be Controller In Charge at a given time. TheGPIB board is usually designated as the System Controller.1.2.2 GPIB Electrical Signal Configuration1The GPIB is an 8-bit parallel data transfer bus. In addition to the 8 data bits, the bus carries three handshaking lines and five GPIB specific management and control lines. The remainder of the standard 24 pin GPIB cable is used for the cable shield, signal grounds and returns. The GPIB connector pin-out is shown in the diagram below:Standard GPIB Cable/ConnectorDATA LINESDIO1 through DIO8 are the data transfer bits. Most GPIB systems send 7-bit data and use the eight bit as a parity or disregard it entirely2HANDSHAKING LINESThere are three handshaking lines that control the data transfer between devices.NRFD (Not Ready For Data): this bit is used to indicate the readiness (or lack thereof) of a device to accept dataDAV (Data Valid): bit is used to indicate to receiving devices that data has been placed on the bus and is available to read.NDAC (Not Data Accepted): is asserted by the receiving device to indicate that data has been read and may now be removed from the bus.SYSTEM MANAGEMENT LINESATN (Attention): is used by the controller to specify how data on the DIO lines is interpreted and which devices must respond to the dataIFC (Interface Clear): is used by the system controller to place the entire system in a known quiescent (Cleared) state and to assert itself as Controller In Charge (CIC).SRQ (Service Request): is used by a device on the bus to indicate the need for atten-tion and requests an interrupt of the current event sequence.REN (Remote Enable): is used by the controller in conjunction with other messages to place a device on the bus into either remote or local modeEOI (End or Identify): Is used by Talkers to indicate the end of a message string, or is used by the Controller to command a polling sequence.1.2.3 Connection ConfigurationsThe GPIB specification is quite definitive regarding the number of devices and cable lengths allowed in a GPIB system. There can be no more than 15 devices on a single contiguous GPIB bus. Larger systems are possible by installing additional GPIB inter-face boards in your computerThe maximum, total length of all cables on a single GPIB system is 20 meters. In addition, cable length between consecutive devices may be no greater than 4 meters, and average cable length must be 2 meters or less. Stated another way, the total cable length (in meters) in the system may not be longer than 2 times the number of devices (up to 20 meters). Longer length systems are possible, but only with the use of a GPIB extender card.In addition to the above rules, at least two thirds of all devices on the bus should be powered on for proper operation.3Keeping the above constraints in mind, there is no limitation on the actual connection scheme used to connect the GPIB devices together. Star, Linear or any combination of both may be used. These are shown in the following diagrams.4,QVWUXPHQW &,QVWUXPHQW ',QVWUXPHQW $,QVWUXPHQW %Linear C onnectionC onfiguration ,QVWUXPHQW ',QVWUXPHQW &,QVWUXPHQW (,QVWUXPHQW $,QVWUXPHQW %S tar C onnectionC onfigurationChapter Two: INSTALLATION The following sections describe the hardware installation procedure for GPIB boards. After hardware installation, please refer to your GPIB software installation guide for additional setup and operation details.2.1 PCI-GPIBThe PCI-GPIB board is completely plug and play. To install this board into your sys-tem follow the simple steps shown below.1. Turn your computer off2. Open your computer case3. Insert the PCI-GPIB into any available PCI slot4. Put your computer’s case back on.5. Turn your computer back on, and follow the instructionsin the GPIB software manual you received with your board.52.2 ISA-GPIBThe only hardware configuration required prior to installing the ISA-GPIB/LC is set-ting the board’s Base Address switch. The location of the Base Address switch is shown in the photograph above, while the switch itself is shown in the diagram on the following page.Most computers will have Base Address 300 Hex (768 decimal) free and the default setting of the board is 300 Hex. If there is already a board in your system using address 300 HEX (768 Decimal), you will have to change the board’s base address prior to installing it in your computer. Other typically free addresses include 310 Hex and 330 Hex.6The following diagram shows the base address in its default 300 Hex setting.987 6 5 4S V65LThe address values corresponding to each of the switches are shown in the following table.Hex Dec.Switch Value Value Default9 200 512 up (200 Hex)8 100 256 up (100 Hex)7 80 128 down (0 Hex)6 40 64 down (0 Hex)5 20 32 down (0 Hex)4 10 16 down (0 Hex)-----------------total 300 HexNote: On this base address switch, Up is on, Down is off. This con-figuration is the opposite of most ISA baseddata acquisition boards.72.3 ISA-GPIB/LCThe following diagram shows the base address in its default 300 Hex setting.987654S V65LThe address values corresponding to each of the switches are shown in the following table.Hex Dec.Switch Value Value Default9200512up (200 Hex)8100256up (100 Hex)7 80128down (0 Hex)6 40 64down (0 Hex)5 20 32down (0 Hex)4 10 16down (0 Hex)-----------------total300 HexNote: On this base address switch, Up is on, Down is off. This con-figuration is the opposite of most ISA based data acquisitionboards.92.4 PCM-GPIBThe installation procedure is different for Windows 95 and DOS/Windows 3.1. These procedures are described below:10:LQGRZVThe PCM-GPIB board is completely plug and play. There are no switches or jumpers to set prior to installation in your computer. Simply follow the steps shown below to install you PCM-GPIB hardware. Once your hardware is installed, please refer to the GPIB-488.2 software manual.1. Start Windows 952. Insert the card into a free PC Card/PCMCIA slot. You do not have toturn the computer off. The system is designed for power on installation.3. Windows 95 will automatically detect the card and depending on theversion of Windows 95 you have, you will either see a New HardwareFound dialog box or a Update Device Driver Wizard box.4. Insert PCM-GPIB Disk 1 into your A drive and follow the instructionsprovided by the dialog box/wizard..If no New Hardware Found dialog box appears, check that you computer’s 32-bit PCMCIA drivers are enabled. This can be checked using the following Windows 95 sequence. Start>Settings>Control Panel>System and look in Performance section. It should read 32-bit. If not, enable 32-bit, shut down your computer and try the above procedure again.:LQGRZVMost users are now installing boards on systems with at least Windows 95 operating systems. However, if you wish to install the PCM-GPIB board in a machine running Windows 3.1 and/or DOS, you will need to use the DOS based Card & Socket serv-ices routine. This is included with most newer computers. However, if you need to purchase these routines, they are available as part number PCM-C&SS from Com-puterBoards for a nominal price. To run the C&SS installation routines, place the PCM-C&SS disk in drive a:, from your boot drive (usually C:) type A:Install and hit enter. Then simply follow the instructions on your screen.The PCM-GPIB hardware is completely plug and play. There are no switches or jumpers to set prior to installation in your computer. Once your hardware is installed, please refer to the GPIB-488.2 software manual.112.5 PC104-GPIBThe only hardware configuration required prior to installing the ISA-GPIB/LC is set-ting the board’s Base Address switch. The location of the Base Address switch is shown in the photograph above, while the switch itself is shown in the diagram on the following page.Most computers will have Base Address 300 Hex (768 decimal) free and the default setting of the board is 300 Hex. If there is already a board in your system using address 300 HEX (768 Decimal), you will have to change the board’s base address prior to installing it in your computer. Other typically free addresses include 310 Hex and 330 Hex.12The following diagram shows the base address in its default 300 Hex setting.987654S V65LThe address values corresponding to each of the switches are shown in the following table.Hex Dec.Switch Value Value Default9200512up (200 Hex)8100256up (100 Hex)7 80128down (0 Hex)6 40 64down (0 Hex)5 20 32down (0 Hex)4 10 16down (0 Hex)-----------------total300 HexNote: On this base address switch, Up is on, Down is off. This con-figuration is the opposite of most PC104 based data acquisitionboards.132.6 CPCI-GPIBThe CPCI-GPIB board is completely plug and play. To install this board install this board into you system follow the simple steps shown below.1. Turn your computer off2. Open your computer front panel (if enclosed)3. Insert the CPCI-GPIB into any available 3U CPCI slot4. Put your computer’s case back on (optional).5. Turn your computer back on, and follow the instructionsin the GPIB software manual you received with your board.14EC Declaration of ConformityDescriptionPart Number Computer to GPIB interface Computer to GPIB interface Computer to GPIB interface Computer to GPIB interface Computer to GPIB interface Computer to GPIB interface ISA-GPIBISA-GPIB/LCPCI-GPIBPC104-GPIBPCM-GPIB CPCI-GPIBto which this declaration relates, meets the essential requirements, is in conformitywith, and CE marking has been applied according to the relevant EC Directives listedbelow using the relevant section of the following EC standards and other normativedocuments:EU EMC Directive 89/336/EEC : Essential requirements relating to electromagneticcompatibility.EU 55022 Class B : Limits and methods of measurements of radio interferencecharacteristics of information technology equipment.EN 50082-1: EC generic immunity requirements.IEC 801-2: Electrostatic discharge requirements for industrial process measurementand control equipment.IEC 801-3: Radiated electromagnetic field requirements for industrial processmeasurements and control equipment.IEC 801-4: Electrically fast transients for industrial process measurement and controlequipment.Carl Haapaoja, Director of Quality Assurance。
赛默飞离子色谱配件编号

赛默飞离子色谱配件编号
3. 柱温箱:柱温箱是用来控制色谱柱温度的设备,其配件也会有编号,例如Part Number 345678。
4. 检测器:离子色谱仪的检测器也会有相应的编号,例如Part Number 901234。
请注意,这些编号仅为示例,具体的赛默飞离子色谱仪配件编号可能会因型号和配置而有 所不同。如果您需要了解特定型号的赛默飞离子色谱仪配件的编号,建议您参考赛默飞的官 方网站、产品手册或联系赛默飞的客户支持部门以获取准的信息。
赛默飞离子色谱配件编号
赛默飞离子色谱仪的配件编号可以根据具体的型号和需要而有所不同。以下是一些常见的 赛默飞离子色谱仪配件的编号示例:
1. 色谱柱:赛默飞的色谱柱通常以Part Number(编号)的形式标识,例如Part Number 123456。
2. 注射器:赛默飞的离子色谱仪常用的注射器也会有相应的编号,例如Part Number 789012。
Artisan Technology Group 产品说明书

Agilent Technologies355C, D, E, FVHF AttenuatorsOperating and ServiceManualAgilent Part Number: 00355-90051Printed in USAApril 2002Supersedes: November 2001NoticeThe information contained in this document is subject to change without notice.Agilent Technologies makes no warranty of any kind with regard to this material, including, but not limited to, the implied warranties of merchantability and fitness for a particular purpose. Agilent Technologies shall not be liable for errors contained herein or for incidental or consequential damages in connection with the furnishing, performance, or use of this material.Agilent Technologies assumes no responsibility for the use or reliability of its software on equipment that is not furnished by Agilent Technologies. This document contains proprietary information which is protected by copyright. All rights are reserved. No part of this document may be photocopied, reproduced, or translated to another language without prior written consent of Agilent Technologies.Restricted Rights LegendUse, duplication, or disclosure by the U.S. Government is subject to restrictions as set forth in subparagraph (c)(1)(ii) of the Rights in Technical Data and Computer Software clause at DFARS 252.227-7013 for DOD agencies, and subparagraphs (c)(1) and (c)(2) of the Commercial Computer Software Restricted Rights clause at FAR 52.227-19 for other agencies. Serial Number PrefixThe specifications in this manual apply to the instruments with the following serial numbers or greater:Model Serial Numbers (min.)355C2524A44630355D2522A46649355E1205A38159355F1203A03244© Copyright 1997, 2001, 2002Agilent Technologies, Incii VHF Attenuators Operating and Service ManualWhat You’ll Find in This Manual…This operating and service manual contains the following:•Instrument Description and Specifications•Replaceable Parts and Accessories•Installation Instructions•Operating Instructions•Schematics and DiagramsWarrantyCustom systems are warranted by contractual agreement between AgilentTechnologies and the Customer.Certification Agilent Technologies certifies that this product met its published specifications at the time ofshipment from the factory.Documentation Warranty THE MATERIAL CONTAINED IN THIS DOCUMENT IS PROVIDED "AS IS," AND IS SUBJECT TO BEING CHANGED, WITHOUT NOTICE, IN FUTURE EDITIONS. FURTHER, TO THE MAXIMUM EXTENT PERMITTED BY APPLICABLE LAW, AGILENT DISCLAIMS ALL WARRANTIES,EITHER EXPRESS OR IMPLIED WITH REGARD TO THIS MANUAL AND ANY INFORMATION CONTAINED HEREIN,INCLUDING BUT NOT LIMITED TO THE IMPLIED WARRANTIES OF MERCHANTABILITY AND FITNESS FOR A PARTICULAR PURPOSE. AGILENT SHALL NOT BE LIABLE FOR ERRORS OR FOR INCIDENTAL OR CONSEQUENTIAL DAMAGES IN CONNECTION WITH THE FURNISHING, USE, OR PERFORMANCE OF THIS DOCUMENT OR ANY INFORMATION CONTAINED HEREIN. SHOULD AGILENT AND THE USER HAVE A SEPARATE WRITTEN AGREEMENT WITH WARRANTY TERMS COVERING THE MATERIAL IN THIS DOCUMENT THAT CONFLICT WITH THESE TERMS, THE WARRANTY TERMS IN THE SEPARATE AGREEMENT WILL CONTROL.VHF Attenuators Operating and Service Manual iiiAssistance Product maintenance agreements and other customer assistance agreementsare available for Agilent Technologies products.For assistance,call your local Agilent Technologies Sales and Service Office(refer to“Support and Service”).Support and ServiceAny adjustment, maintenance, or repair of this product must be performedby qualified personnel. contact your local Agilent Technologies sales andservice office.Online assistance:/find/assistUnited States (tel)180****4844Latin America(tel) (305) 269 7500(fax) (305) 269 7599Canada(tel)187****4414(fax) (905) 282-6495New Zealand (tel) 0 800 738 378 (fax) (+64) 4 495 8950Japan(tel) (+81) 426 56 7832(fax) (+81) 426 56 7840Australia(tel) 1 800 629 485(fax) (+61) 3 9210 5947Malaysia(tel) 1 800 828 848 (fax) 1 800 801 664Philippines(tel) (632) 8426802(tel) (PLDT subscriber only):1 800 16510170(fax) (632) 8426809(fax) (PLDT subscriber only):1 800 16510288Thailand(tel) outside Bangkok:(088) 226 008(tel) within Bangkok:(662) 661 3999(fax) (66) 1 661 3714Taiwan(tel) 0800-047-866 (fax) (886) 2 25456723People’s Republic of China(tel) (preferred): 800-810-0189(tel) (alternate):10800-650-0021(fax) 10800-650-0121India(tel) 1-600-11-2929(fax) 000-800-650-1101iv VHF Attenuators Operating and Service ManualVHF Attenuators Operating and Service Manual vSafety and Regulatory InformationReview this product and related documentation to familiarize yourself withsafety markings and instructions before you operate the instrument Thisproduct has been designed and tested in accordance with international standards.WARNING The WARNING notice denotes a hazard. It calls attention to a procedure,practice,or the like,that,if not correctly performed or adhered to,could result in personal injury. Do not proceed beyond a WARNING notice until the indicated conditions are fully understood and met.CAUTION The CAUTION notice denotes a hazard. It calls attention to an operatingprocedure,practice,or the like,which,if not correctly performed or adheredto, could result in damage to the product or loss of important data. Do notproceed beyond a CAUTION notice until the indicated conditions are fullyunderstood and met.Instrument MarkingsWhen you see this symbol on your instrument, you should refer to the instrument’s instruction manual for important information.This symbol indicates hazardous voltages.The laser radiation symbol is marked on products that have a laser output.This symbol indicates that the instrument requires alternating current (ac) input.The CE mark is a registered trademark of the European Community. If it isaccompanied by a year, it indicates the year the design was proven.The CSA mark is a registered trademark of the Canadian Standards Association.1SM1-A This text indicates that the instruments an Industrial Scientific and Medical Group 1Class A product (CISPER 11, Clause 4).This ISM device complies with Canadian ICES-001.Cet appareil ISM est conforme a la norme NMB du Canada.This symbol indicates that the power line switch is ON.This symbol indicates that the power line switch is OFF or in STANDBY position.!Safety Earth Ground This is a Safety Class I product (provided with a protective earthing terminal).An uninterruptible safety earth ground must be provided from the main power source to the product input wiring terminals, power cord, or supplied power cord set. Whenever it is likely that the protection has been impaired, the product must be made inoperative and secured against any unintended operation.Before Applying Power Verify that the product is configured to match the available main powersource as described in the input power configuration instructions in thismanual. If this product is to be powered by autotransformer, make sure thecommon terminal is connected to the neutral(grounded)side of the ac powersupply.vi VHF Attenuators Operating and Service ManualTypeface ConventionsItalics•Used to emphasize important information:Use this software only with the xxxxxX system.•Used for the title of a publication:Refer to the xxxxxX System-Level User’s Guide.•Used to indicate a variable:Type LOAD BIN filename.Instrument Display•Used to show on-screen prompts and messages that you will see on thedisplay of an instrument:The xxxxxX will display the message CAL1 SAVED.[Keycap]•Used for labeled keys on the front panel of an instrument or on acomputer keyboard:Press[Return].{Softkey}•Used for simulated keys that appear on an instrument display:Press{Prior Menu}.User Entry•Used to indicate text that you will enter using the computer keyboard;text shown in this typeface must be typed exactly as printed:Type LOAD PARMFILE•Used for examples of programming code:#endif // ifndef NO_CLASSPath Name•Used for a subdirectory name or file path:Edit the file usr/local/bin/sample.txtComputer Display•Used to show messages, prompts, and window labels that appear on acomputer monitor:The Edit Parameters window will appear on the screen.•Used for menus, lists, dialog boxes, and button boxes on a computermonitor from which you make selections using the mouse or keyboard:Double-click EXIT to quit the program.VHF Attenuators Operating and Service Manual viiTypeface Conventionsviii VHF Attenuators Operating and Service ManualGeneral InformationGeneral InformationThis manual contains operating instructions for 355C, 355D, 355E, and355F VHF Attenuators. Included in the manual is the information requiredto install and test these attenuators.Description The Agilent Technologies Model 355C, 355D, 355E, and 355F attenuatorsare50-ohm,coaxial step attenuators usable from dc to1GHz.Models355Cand 355E provide 0 to 12 dB of attenuation in 1 dB steps.Models 355D and 355F provide 0 to 120 dB of attenuation in 10 dB steps.The 355C and 355D are manual attenuators. The 355E and 355F areprogrammable. The schematic for the Model 355C/D is shown in Figure1,and that of the Model 355E/F in Figure2.The attenuator sections consist of resistor pi networks which are switched inor bypassed by microswitches. In the 355C and 355D, the microswitchesare actuated by cams (see Figure1). In the 355E and 355F, themicroswitches are actuated by solenoids (see Figure2). The standard RFconnectors are BNC type.In the355E and355F,power must be continuously applied to the solenoid toactuate the microswitch(i.e.,to insert an attenuator section).Each solenoiddraws approximately at 15 Vdc.Dimensions for the individual instruments are provided in Table1,“Dimensions,” on page2.VHF Attenuators Operating and Service Manual1General InformationNOTE Dimensions are for general information only. If accurate dimensions arerequired for building special enclosures, contact your nearest AgilentTechnologies office.Table 1Dimensions355C, D355E, FLength152 mm (5.98 in)137 mm (5.39 in)Height69 mm (2.72 in)72 mm (2.83 in)Width (without RF connectors)45 mm (1.77 in)45 mm (1.77 in)Width (with connectors):Standard (BNC) Option 001 (Type-N) Option 005 (TNC)73 mm (2.88 in)94 mm (3.70 in)69 mm (2.72 in)73 mm (2.88 in)121 mm (4.76 in)24 mm (0.94 in)Protrusion of connectors:BNC Type-N TNC 14.06 mm (0.55 in)24.5 mm (1.00 in)12 mm (0.47 in)14.06 mm (0.55 in)24.5 mm (1.00 in)12 mm (0.47 in)General InformationFigure 1355C and 355D Schematic DiagramGeneral InformationFigure 2355E and 355F Schematic DiagramGeneral Information Specifications Instrument specifications are listed in Table2. These specifications are theperformance standards or limits against which the instruments may betested.Table 2SpecificationsMODELS 355C and 355EAttenuation Range0 to 12 dBAttenuation Steps 1 dBOverall Accuracy:at 1000 Hzdc to 500 MHz dc to 1000 MHz 0.1 dB 0.25 dB 0.35 dBMODELS 355D and 355FAttenuation Range0 to 120 dB Attenuation Steps10 dB Overall Accuracy:at 1000 Hz below 1000 MHz 0 to 120 dB 0.3 dB 0 to 90 dB 1.5 dB 90 to 120 dB 3 dBMODELS 355E and 355FSwitching Speed65 msRequired Solenoid Power+15 to +18 Vdc, 1/8 A MODELS 355C/E and 355D/FFrequency Range dc to 1000 MHz Impedance50 ohms (nominal) Maximum SWR (input and output):below 250 MHz below 500 MHz below 1000 MHz 1.2 1.3 1.5Maximum residual attenuation(insertion loss at 0 dB)0.20 dB + 2.30 dB/GHz Maximum power dissipation0.5W (average) Maximum pulse voltage350 Vpk 200sec ConnectorsStandard Option 001 Option 005BNC (female) Type-N (female) TNC (female)11. Available on the 355C only.General InformationPower RatingCAUTION Do not exceed the RF power rating of0.5W average,or2450W peak with amaximum pulse width of 200 s. Do not connect an attenuator RF input oroutput connector to greater than 5 Vdc. If the attenuator must be connectedto a device with a potential greater than 5 Vdc, use a blocking capacitor. Accessories Supplied The 355E and 355F programmable attenuators are supplied with a 7-pin,male connector (1251-1037) for the solenoid drive input.Attenuator Options Figure3on page7shows solenoid and connector wiring diagrams availableunder Option 007 for 355E and 355F.General Information Attenuator OptionsFigure 3355E and 355F Solenoid and Connector Wiring DiagramsInstallationInstallationInitial Inspection Inspect the shipping container for damage. If the shipping container orcushioning material is damaged, it should be kept until the contents of theshipment have been checked mechanically and electrically.A procedure forchecking electrical performance is given under“Operator’s Check” onpage9 (also see“Performance Tests” on page12). If the contents of theshipment are incomplete, if there is mechanical damage or defect, or if theinstrument does not pass the electrical performance test, notify the nearestAgilent Technologies office. Keep the shipping materials for the carrier'sinspection.Mating Connectors Mating RF input and output connectors used with the attenuators should be:•Standard . . . . . . . . . . . . . . . . . . . . . . . . . . . . . . . . . . . . . . . . . .Type BNC•Option 001 . . . . . . . . . . . . . . . . . . . . . . . . . . . . . . . . . . . . . . . . . .Type-N•Option 005 . . . . . . . . . . . . . . . . . . . . . . . . . . . . . . . . . . . . . . . .Type TNCFor the 355E and 355F, the solenoid drive connector plug is 7-pin maleconnector (1251-1037).Operating Environment The operating environment of the instrument should be within the following limitations:•Temperature . . . . . . . . . . . . . . . . . . . . . . . . . . . . . . . . . . . . .0˚ to +55 ˚C •Humidity . . . . . . . . . . . . . . . . . . . . . . . . . . . . . . . . . . . . . .<95% relative •Altitude. . . . . . . . . . . . . . . . . . . . . . . . . . . . . . . . . .<4,570 m (15,000 ft)Storage and Shipment EnvironmentThe instrument should be stored in a clean,dry environment.The followingenvironmental limitations apply to both storage and shipment:•Temperature. . . . . . . . . . . . . . . . . . . . . . . . . . . . . . . . . . . . . . . . .−40˚ C to +75 ˚C•Humidity . . . . . . . . . . . . . . . . . . . . . . . . . . . . . . . . . . . . .< 95% relative•Altitude. . . . . . . . . . . . . . . . . . . . . . . . . . . . . . . . . .< 7,620 m (25,000 ft)Original PackagingContainers and materials identical to original packaging are available fromAgilent Technologies. If the instrument is being returned to AgilentTechnologies, attach a tag indicating the type of service required, returnaddress, model number, and serial number. Also, mark the containerFRAGILE to assure careful handling. In any correspondence, refer to theinstrument by model number and full serial number.Operating InstructionsOperating InstructionsCAUTION Do not apply RF power greater than 0.5W average, or 2450W peak with amaximum pulse width of 200 s. If these limits are e xceeded, the attenuatormay be damaged.Either RF connector may be used as the input or output connector,except inthe case of the355D/F driven from a low impedance source.This is becausethe leaf switch (Figures 1 and 2) may be closed before the microswitchopens when the dial is switched from 50 dB to 60 dB. Should this occur, amomentary short is placed across the connector, inviting damage to eitherthe microswitch or the signal source. Therefore, if the signal source issubject to damage by a short,use the rear most connector for the input.(Thedial or solenoid connector is at the front of the attenuator.) This pads themomentary short with 50 dB of isolation. For the 355E and 355F, wire thesolenoid drive plug supplied using Figure 3 as a wiring guide. Anun-energized attenuator solenoid section is 0 dB. Apply +1 5 to +18 Vdc(with respect to pin H) to energize an attenuator solenoid. A programmingtable is also given in Figure 3.Operator’s Check This section describes the procedures for the operator to make a quick checkof the attenuator prior to use or if a failure is suspected.NOTE Troubleshooting consists of performing the following Operator's Check. Ifthe instrument does not perform within limits, return the instrument to thenearest Agilent Technologies office.DescriptionThe attenuator is driven from a 50-ohm signal source at 1 kHz. The outputlevel from the attenuator is detected by a narrow-bandwidth voltmeter (thatis,the SWR meter).The attenuator and detector range switches are steppedtogether and the variations in level noted. This verifies that each attenuatorsection is being properly switched and checks the low frequency accuracy ofthe attenuator.NOTE The SWR Meter used in this check is calibrated for a square-law detectorand therefore the range changes and errors (read in dB) are twice thatindicated by the meter.Operating InstructionsQuick-Check Procedures1.Connect equipment as shown in Figure4,with the Attenuator set to0dBattenuation.2.Set Test Oscillator to 0.3 Vrms at 1 kHz.3.Set the SWR Meter input to XTAL IMPED LOW and the range to 2 dB(expanded) for 355D or 355F or to 10 dB (with 0 dB expand) for 355C or 355E. Adjust its bandwidth to the center of the adjustment range.Fine tune oscillator frequency to obtain the maximum meter indication.4.Set attenuator and SWR meter range switch as listed in Figure 3, andverify that the SWR meter indicates within the limits shown.Figure 4 Operator’s Check SchematicOperating Instructions Table 3Operator’s ChecksOperating InstructionsPerformance Tests The attenuator can be tested to the accuracy of the specifications in Table1with an Automatic Network Analyzer or equivalent equipment of suitableaccuracy.If an Automatic Network Analyzer is available,test the attenuatorusing the procedures in the analyzer's operating manual. The 355E and355F attenuators must be programmed by a suitable circuit to provide thevarious values of attenuation (see Figure 3).AdjustmentsThe attenuators have no internal adjustments and should not be opened. Ifdefective, the attenuator should be returned to the nearest AgilentTechnologies office for repair.CAUTION The solenoids in the 355E and 355F have been precisely adjusted at thefactory. No attempt should be made to replace them except by factoryapproved service representatives. The operation of the attenuators will beunreliable if plungers are not kept with their proper solenoids. Do notinterchange or "swap" them.12VHF Attenuators Operating and Service ManualReplaceable PartsReplaceable PartsTable4 lists the replaceable parts which are the only parts that can bereplaced without access to the interior of the attenuator. For any partsneeding replacement that are not listed in Table4, return the instrument toAgilent Technologies.CAUTION Due to special fixtures necessary for assembly, do NOT attempt to replaceany parts not listed in Table4. If the instrument is opened, the warranty isvoid.Table 4Replaceable PartsDescription Part Number Quantity355CGlide (feet)0403-00264Dial Assembly0370-30701Dial Assembly (Option 003)00355-000011355DGlide (feet)0403-00264Dial Assembly0370-30711Dial Assembly (Option 003)00355-000021355E and FGlide (feet)0403-00264Connector (7-pin, male)1251-10371VHF Attenuators Operating and Service Manual13。
ARTISTAN技术集团产品说明说明书

Agilent 34980AMultifunction Switch/Measure Unit Data Sheet• 8-slot mainframe with 21 mix-and-match plug-in modules so you can create your own custom configuration • High-performance switching:Up to 560 2-wire multiplexer channels or 4096 matrix cross-points inone mainframe• Optional built-in 6 12-digit DMMlets you make 11 measurements with over 3000 readings/sec • Easy to integrate: Built-in Ethernet, USB 2.0, and GPIB connectivity, standard connectors and software drivers for most common programming environments• Includes FREE BenchLink Data Logger SoftwareC O N F I G U R E,C O N N E C T,G OIf you use automated test equipmentfor design validation or manufacturing, you now have a cost-effectivealternative to PXI and VXI test-system platforms. The 34980A multifunction switch/measure unit provides compa-rable functionality that is much easier to use than PXI and VXI and costsless. The 34980A helps you lower your cost of test and accelerate your test-system integration and development.The 34980A handles system switch-ing up to 26.5 GHz and provides basic measurements and system control. It also offers DMM measurements, coun-ter/ totalizer functionality, digital I/O with pattern capabilities, and analog outputs with basic waveforms— all in one low-cost, compact box. And with its standard connectors and software drivers, computer-standard I/O, and Web browser interface, the 34980A easily integrates into electronic functional test and data acquisition systems.Flexible switching, measure-ments, and system controlThe 34980A accommodates up to 8 plug-in modules to give you the flexibility you need. Choose from 21 different modules to define your own configuration. You can buy what you need now and add to it or recon-figure it as your requirements change.Whether you are measuring tempera-ture, AC or DC voltage, resistance, frequency, current, or custom mea-surements, the 34980A offers thefunctionality you need in a single box. Switch in different measurements with high-performance signal switching up to 300V with no external signal conditioning required. Choose between different switch types and topologies with frequency ranges from DC to 26.5 GHz. The 34980A offers high-density multiplexers for scanning multiple channels, matrices for connecting multiple points at one time, and general purpose switches for simple control and high power needs.Use the 34980A to route individual signals or monitor multiple signals over a specified period of time—monitor a single channel or multiple channels, set alarms, and identify irregularities.The 34980A offers flexible choices for system control. You can control external devices such as microwave switches, attenuators, solenoids, and power relays. Or use the digital inputs to sense limit-switch and digital-bus status.Optimized for test systemsThe 34980A has the performance you need for medium- to high-density switching/measurement applications such as design verification, functional test and data acquisition. Your signals are switched to the right measurement device without compromising signal integrity. Switch your signals to the optional internal DMM and achieve optimal throughput on switch closure time. Or, if you prefer, you can easily connect to external instruments such as DMMs, scopes, power supplies, and more. What’s more, with the built-in Ethernet interface, you can control the 34980A and collect data from anywhere on the network.The rugged instrument comes with a variety of system-ready features:• Web browser interface shows settings at a glance and provides remote access and control• Self-guiding front panel to configure, troubleshoot or view data • Low EMI and efficient system cooling• Heavy-duty cabling and connection options• Flexible rack mounting options • Relay counters help predict end-of-life• In-rack calibration for reduced maintenance time• DMM measurement accuracies include the switch for simple calculationsMake system connections easily and quickly with simple, reliable connection options:• Built-in Ethernet, USB 2.0, and GPIB connectivity• Low-cost, standard 50- or 78-pin Dsub connectors and cables • Detachable terminal blocks with strain relief• Mass interconnect solutions In addition, the 34980A comes with Agilent IO Libraries Suite. Quickly establish an error-free connection between your PC and instruments—regardless of vendor. The IO Libraries provide robust instrument control and work with the software development environment you choose.2High-performance unit provides low-cost alternative to PXI and VXI switch and measurement platformsEasier signal routingwith four2-wire internal analog buses. You can route your measurements directly to the internal DMM, or you can connect to external instruments through the analog bus connector on the rear of the mainframe. And since you have four 2-wire buses, you can dedicate one bus for use with the internal DMM and use the other three buses for module extensions or additional signal routing between modules, reducing your wiring needs. You can define up to 500 switch sequences to control complex signal routing and the order ofswitch closures. Assign a sequence, give it a name and then execute it with the name you created. Switch sequences are downloaded and stored in the instrument for ease of programming and increased throughput.External trigger capabilities make it easy for you to time and synchronize measurements and other events. This can help you determine when to begin or end an acquisition.Measurements you can trustGet proven performance from Agilent instruments, with the resolution, repeatability, speed, and accuracy you’ve come to expect.The 34980A offers built-in signal conditioning and modular flexibility. When you use it with the internalDMM, you can configure each channel independently for the measurements you choose. It includes a variety of features that give you confidence in your measurements:• 61⁄2 digits of resolution with .004% of accuracy with DC voltage measurements• Alarms per channel—high limit, low limit, or both• Math functions—use Mx+B for custom linear conversions and converting raw inputs• Built-in thermocouple reference for temperature measurements (34921T)• Time-stamped readings• Add more formulas with BenchLink Data Logger SoftwareThe integrated DMM is mounted inside the mainframe and does not consume any of the eight user-available slots. You can access the DMM through any switch module that connects to the analog bus, or directly from the analog bus connector on the rear of the mainframe. The internal DMM gives you the flexibility to measure 11 types of inputs:• Temperature with thermocouples, RTDs, or thermistors (with 34921A)• DC and AC voltage • 2- and 4-wire resistance • Frequency and period • DC and AC currentYou can control the DMM directly, or configure it to work in conjunction with the switches. Each switch chan-nel can be configured independently for measurement functions, scale factors and alarm limits. Advanced measurement features such as offset compensation, variable integration time, and delay are also selectable on a per-channel basis.The DMM inputs are shielded and optically isolated from the 34980A’s earth-referenced circuitry andcomputer interface, and as a result, you get up to 300 V of input isola-tion. This is important for reducing ground-loops and common-mode voltage errors associated with long wiring runs and floating sources.Simple DMM calibration isaccomplished with just the analog bus connection on the rear panel of the mainframe. You don’t need to remove the mainframe from the rack or dedicate a channel for calibration.Modules provide flexible system stimulus and controlSystem control —with analog outputs, open-collector digital outputs, clock generation, and isolated Form-Crelays for controlling external devices. Additionally, with the microwave switch/attenuator driver, high-frequency switches and attenuators can be efficiently controlled external to the 34980A mainframe.Analog sources —output eithervoltage or current. You can configure the 4-channel isolated D/A converter as a point-to-point arbitrary wave-form generator that lets you define up to 500,000 points per waveform.Digital patterns —send or receive digital data from your device under test. With on-board memory you can output communication protocols and bit streams or monitor digital input patterns and interrupt when a user-defined pattern is detected.35Free BenchLink Data Logger Software to Simplify data loggingThe BenchLink Data Logger software for the 34980A provides a convenient way to collect and analyze your data. This is a Windows® based application that uses a familiar spreadsheet envi-ronment to define measurement data to be collected. The tab-based format makes it easy to set up and initiate scans. Simply identify the measure-ments you want to acquire, initiate the process and see the data displayed real-time. The rich set of colorful graphics provides many options for analyzing and displaying your data. You can specify multiple channels per graph, or send collected data to multiple graphs. Use strip charts with markers and alarm indication, or his-tograms with statistics. And of course you can use BenchLink Data Logger to easily move data to other applications for further analysis, or for inclusion in your presentations and reports.34832A BenchLink Data Logger Pro adds limit checking and decision making Figure 2 34826A BenchLink Data Logger Software for high speed data logging with no programming.Figure 334832A BenchLink Data Logger Pro adds limit checking and decision makingEvent • Control Instruments • Send Notification(s)• Stop Scan• Control Instruments • Send Notification(s)• Stop Scan• Control Instruments • Send Notification(s)• Stop ScanEventE v en t s E v e n t sE v e n t sScan List A (Base)Scan List BScan List CEventStartAlso AvailableThe BenchLink Data LoggerPro Software adds limit checking and decision making for more complex applications. Simply identify the measurements you want to acquire, define limits and actions to be preformed, and then initiate the process. Your data is then collocated, evaluated and acted on real-time.6Intuitive front panel with self-guiding menusSet up scan listsSee results on bright, multiline displayScan multiple channels,close specified channel list,or monitor results on a single channel Use keypad to enter channel number or knob to scrollStore up to 500,000 readings with timestamp61⁄2digit DMM measurementswith 11 functionsSet I/O O ,date an n d other s s ystem feature e sStore a a nd recall instrum m ent setups s Access to four 2-wi wire analog busesExternal trigger to synchronize events 8-slots connect to optional internal DMM Built-in Ethernet,USB 2.0,and GPIB interfacesOptional terminal blocksIndustry standard DSub cables21 plug-in modules les to choose fromStandard DSub connector kitsConfigure measurements, manage sequences, view errors and alarmsPower and flexibility to get your job done8910111214151634945A moduleY1150A-Y1155Adistribution boardsrequired to controlswitches (ordered separate)34945EXT extender holds4 distribution boar34980A system control modules20212728Rack kitScrew Terminal Block2934934A High Density Configuration BlockStandard Dsub CableConnector kit30GPIB, providing faster, more efficient connectivity. Agilent is a founding member of the LXI For more information on Agilent Technologies’products, applications or services, pleasecontact your local Agilent office. The completelist is available at:/find/contactusAmericasCanada (877) 894-4414Latin America 305 269 7500United States (800) 829-4444Asia PacificAustralia 1 800 629 485China 800 810 0189Hong Kong 800 938 693India 1 800 112 929Japan 81 426 56 7832Korea 080 769 0800Malaysia 1 800 888 848 Singapore 180****8100Taiwan 0800 047 866Thailand 1 800 226 008EuropeAustria 0820 87 44 11Belgium 32 (0) 2 404 93 40 Denmark 45 70 13 15 15Finland 358 (0) 10 855 2100 France 0825 010 700Germany 01805 24 6333**0.14/minuteIreland 1890 924 204Italy 39 02 92 60 8484 Netherlands 31 (0) 20 547 2111Spain 34 (91) 631 3300Sweden 0200-88 22 55 Switzerland (French) 41 (21) 8113811(Opt 2) Switzerland (German) 0800 80 53 53 (Opt 1) United Kingdom 44 (0) 118 9276201Other European Countries:/find/contactusRevised: May 7, 2007Product specifications and descriptionsin this document subject to changewithout notice.© Agilent Technologies, Inc. 2008Printed in USA, June 13, 20085989-1437EN。
ARTISAN技术集团预览说明书

Integrated 3-Axis Motion Controller/DriverController GUI ManualV2.0.xESP301 Controller GUI Manual EDH0282En1030 — 01/17iiESP301 Controller GUI Manual Table of Contents1.0Introduction (1)1.1Purpose (1)1.2Overview (1)2.0Installation (2)2.1Install ESP301 Graphical User Interface (2)2.2Launch GUI (2)3.0User Interface (3)3.1Configuration (3)3.2Axis (4)3.3Main (5)3.4Jog (7)3.5Parameters (8)3.6Diagnostics (9)3.7About (10)Service Form (11)EDH0282En1030 — 01/17iiiESP301 Controller GUI Manual EDH0282En1030 — 01/17ivESP301 Controller GUI ManualESP301Integrated 3-AxisMotion Controller/Driver1.0Introduction1.1PurposeThe purpose of this document is to provide instructions on how to use the ESP301graphical user interface (GUI).1.2OverviewThe ESP301 GUI is a graphical user interface, that allows the user to control Newportstages with the ESP301 controller (execute motion, configure stages, etc.).EDH0282En1030 — 01/171ESP301 Controller GUI Manual 2.0Installation2.1Install ESP301 Graphical User InterfaceFollowing are steps to install the ESP301 GUI:•For 32 bit, Select and launch “ESP301 Utility Installer Win32.exe”. For 64 bit,Select and launch “ESP301 Utility Installer Win64.exe”.• A window opens up showing Install welcome page.•Click on “Next”.• A window opens up allowing destination folder selection. By default it is showingC:\.•Click on “Next”.•Ready to install window opens up. Click “Install”.•Then installation starts, wait for completion. Click on “Finish” to finalize theinstallation.32 bit installer will install “mandInterface.dll” in GAC_32 folderand 64 bit installer will install the dll in GAC_64 folder.NOTELabVIEW users can add a reference of the command interface dll from GACduring VI creation.2.2Launch GUIFrom Windows “START” menu, select “All Programs\Newport\MotionControl\ESP301\ESP301 Utility”.EDH0282En1030 — 01/17 2ESP301 Controller GUI Manual 3.0User Interface3.1ConfigurationThe Configuration tab allows the user to view and / or change information related to thelogging configuration and the instrument settings. Read only values are displayed forthe log file name and the log file path.The logging level may be changed to any of the settings in the drop-down list on theright hand side. Trace is the most detailed of the settings and when this setting isselected, the GUI logs everything. Critical Error is the least detailed of the settings andwhen selected, the GUI will only log errors that are defined to be critical.The polling interval defines the number of milliseconds between each time the GUIpolls the ESP301 for the latest information. The user may change the polling intervalby entering a value.The Save button saves the current settings to the configuration file.EDH0282En1030 — 01/173ESP301 Controller GUI ManualConfigurable settingsThe following table describes all the settings that can be changed by the user.3.2AxisThe combo box at the top of the window allows the selection of axes (1 to 3).EDH0282En1030 — 01/17 4ESP301 Controller GUI Manual3.3MainThe Main tab displays the main controls in the GUI like a virtual front panel. It isupdated each time the polling interval timer expires.“Initialization and Configuration”In the “Initialization and Configuration” area, the first button switches between theLocal and Remote states. The second button turns the motor: ON or OFF and StopMotion. The Home button commands the stage to go to the home position. The lastbutton “Save Pos.” memorizes the current positions in the combo box. As soon as a newposition is memorized, this is displayed in the trace.“Current Position”In the “Current Position” area, the current position is displayed in a text box andvisualized in a slider. The slider limits are defined with the ends of run. An LED showsthe current controller state. When you move the mouse over the LED, the controllerstate is displayed in an information balloon.“Incremental Motion / PR-Move Relative”In the “Incremental Motion / PR-Move Relative” area, two steps can be defined. Foreach step, a relative move is made in the negative direction or a positive direction.EDH0282En1030 — 01/175“Cyclic Motion” and “Target position / PA-Move Absolute”In the “Cyclic Motion” area, a motion cycle is configured with a number of cycles (Cycle) and a specified time in milliseconds (dwell). The motion cycle gets the defined target positions from the “Target position / PA-Move Absolute’ area to perform the cycle.In the “Target position / PA-Move Absolute” area, two target positions can be defined. The “Go to” button executes the absolute move to go to the specified target position.“Motion Configuration Values”In the “Motion Configuration Values”, the current ends of run and the velocity are displayed in a disabled text box: “Minimum end of run”, “Maximum end of run” and “Velocity”. These ends of run and the velocity can be modified and saved with the “Set” button.Memorized positionsThe combo box memorizes the positions using the “Save Pos.” button. Each of these positions can be renamed or deleted. To execute an absolute move to go to one of these memorized positions, select one item of the combo box and click on “Go to” button. When the mouse moves over to the combo box, the positions of the selected memorized position are showed in an information balloon.Rename a memorized position: Select an item from the combo box, edit the position name to change it and click on the “Rename” button to save the new position name. Delete a memorized position: Select an item from the combo box, right-click on the mouse and select the “Delete” menu to delete the selected memorized position.3.4JogThe Jog tab allows entry of the position value in the Jog mode.“Initialization and Configuration”In the “Initialization and Configuration” area, the first button switches between theLocal and Remote states. The second button “Save Pos.” allows memorizes the currentpositions in the combo box. As soon as a new position is memorized, this is displayed inthe trace.“Current Position”In the “Current Position” area, the current position is displayed in a text box andvisualized in the slider. The slider limits are defined with the ends of run. An LEDshows the current controller state. When you move the mouse over the LED, thecontroller state is displayed in an information balloon.“Jog Motion”In the “Jog Motion” area, an indefinite move (MV) can be performed in either thenegative direction or a positive direction. Motion starts when a button is held down andstops when the button is released.“Jog Velocity”In the “Jog Velocity” area, the jog velocity can be defined. Keep in mind that theslider’s scale is logarithmic.Memorized positions (defined by axis)The combo box memorizes the positions using the “Save Pos.” button. Each of thesepositions can be renamed or deleted. To execute an absolute move to go to one of thesememorized positions, select one item of the combo box and click on “Go to” button.When the mouse moves over to the combo box, the positions of the selected memorizedposition are showed in an information balloon.Rename a memorized position: Select an item from the combo box, edit the positionname to change it and click on the “Rename” button to save the new position name.Delete a memorized position: Select an item from the combo box, right-click on themouse and select the “Delete” menu to delete the selected memorized position.3.5ParametersThe Parameters tab display and allows changes tothe parameters of the instrument.3.6DiagnosticsThe Diagnostics tab allows the user to enter instrument commands and to view thehistory of commands sent and the responses received. This list of commands and thesyntax of each command can be found in the user’s manual for the instrument.A file of commands can be sent line by line to the instrument with the “SendCommand file” button.3.7AboutThe About tab displays information about the GUI and the connected instrument. Itdisplays the GUI name, version, and copyright information. It also displays theinstrument model and instrument key (serial number).Service FormYour Local RepresentativeTel.: __________________Fax: ___________________Name: _________________________________________________ Return authorization #: ____________________________________ Company:_______________________________________________ (Please obtain prior to return of item)Address: ________________________________________________ Date: __________________________________________________ Country: ________________________________________________ Phone Number: __________________________________________ P.O. Number: ____________________________________________ Fax Number: ____________________________________________ Item(s) Being Returned: ____________________________________Model#: ________________________________________________ Serial #: ________________________________________________Description: ________________________________________________________________________________________________________ Reasons of return of goods (please list any specific problems): ________________________________________________________________ __________________________________________________________________________________________________________________ __________________________________________________________________________________________________________________ __________________________________________________________________________________________________________________ __________________________________________________________________________________________________________________ __________________________________________________________________________________________________________________ __________________________________________________________________________________________________________________ __________________________________________________________________________________________________________________ __________________________________________________________________________________________________________________ __________________________________________________________________________________________________________________ __________________________________________________________________________________________________________________ __________________________________________________________________________________________________________________ __________________________________________________________________________________________________________________ __________________________________________________________________________________________________________________ __________________________________________________________________________________________________________________ __________________________________________________________________________________________________________________ __________________________________________________________________________________________________________________ __________________________________________________________________________________________________________________ __________________________________________________________________________________________________________________ __________________________________________________________________________________________________________________ __________________________________________________________________________________________________________________ __________________________________________________________________________________________________________________ __________________________________________________________________________________________________________________ __________________________________________________________________________________________________________________ __________________________________________________________________________________________________________________ __________________________________________________________________________________________________________________ __________________________________________________________________________________________________________________North America & Asia Newport Corporation 1791 Deere Ave.Irvine, CA 92606, USA SalesTel.: (800) 222-6440e-mail:*****************Technical Support Tel.: (800) 222-6440e-mail:****************Service, RMAs & Returns Tel.: (800) 222-6440e-mail:*******************EuropeMICRO-CONTROLE Spectra-Physics S.A.S 9, rue du Bois Sauvage 91055 Évry CEDEX FranceSalesTel.: +33 (0)1.60.91.68.68 e-mail:******************Technical Supporte-mail:***********************Service & ReturnsTel.: +33 (0)2.38.40.51.55Visit Newport Online at: 。
ARTISAN技术集团产品参数手册说明书

Agilent 16048D Test LeadsOperation and Service ManualFourth EditionAgilent Technologies Japan, Ltd.Agilent PN 16048-90031May 2000Printed in JapanArtisan Technology Group - Quality Instrumentation ... Guaranteed | (888) 88-SOURCE | 2NoticesThe information contained in this document is subject to change without notice.This document contains proprietary information that is protected by copyright.All rights are reserved. No part of this document may be photocopied, reproduced, or translated to another language without the prior written consent of the Agilent Technologies.Agilent Technologies Japan, LTD.Component Test PGU-Kobe1-3-2, Murotani, Nishi-Ku, Kobe-shi, Hyogo, 651-2241 Japan © Copyright 1990, 1998, 1999, 2000 Agilent Technologies Japan, LTD.Manual Printing HistoryThe manual’s printing date and part number indicate its current edition. The printing date changes when a new edition is printed. (Minor corrections and updates that are incorporated at reprint do not cause the date to change.) The manual part number changes when extensive technical changes are incorporated.1990 First EditionNovember 1998 Second EditionAugust 1999Third Edition (part number : 16048-90031)May 2000 Fourth Edition (part number : 16048-90031)Safety SummaryThe following general safety precautions must be observed during all phases of operation, service, and repair of this instrument. Failure to comply with these precautions or with specific WARNINGS elsewhere in this manual may impair the protection provided by the equipment. In addition it violates safety standards of design, manufacture, and intended use of the instrument.The Agilent Technologies assumes no liability for the customer’s failure to comply with these requirements.NOTE 16048D comply with INSTALLATION CATEGORY I and POLLUTIONDEGREE 2 in IEC61010-1. 16048D are INDOOR USE product.Artisan Technology Group - Quality Instrumentation ... Guaranteed | (888) 88-SOURCE | •Ground The InstrumentTo avoid electric shock hazard, the instrument chassis and cabinet must beconnected to a safety earth ground by the supplied power cable with earthblade.•DO NOT Operate In An Explosive AtmosphereDo not operate the instrument in the presence of flammable gasses or fumes.Operation of any electrical instrument in such an environment constitutes adefinite safety hazard.•Keep Away From Live CircuitsOperating personnel must not remove instrument covers. Componentreplacement and internal adjustments must be made by qualified maintenancepersonnel. Do not replace components with the power cable connected. Undercertain conditions, dangerous voltages may exist even with the power cableremoved. To avoid injuries, always disconnect power and discharge circuitsbefore touching them.•DO NOT Service Or Adjust AloneDo not attempt internal service or adjustment unless another person, capable ofrendering first aid and resuscitation, is present.•DO NOT Substitute Parts Or Modify InstrumentBecause of the danger of introducing additional hazards, do not installsubstitute parts or perform unauthorized modifications to the instrument.Return the instrument to a Agilent Technologies Sales and Service Office forservice and repair to ensure that safety features are maintained.•Dangerous Procedure WarningsWarnings, such as the example below, precede potentially dangerousprocedures throughout this manual. Instructions contained in the warningsmust be followed.WARNING Dangerous voltages, capable of causing death, are presenting this instrument.Use extreme caution when handling, testing, and adjusting this instrument.CertificationAgilent Technologies certifies that this product met its published specifications atthe time of shipment from the factory. Agilent Technologies further certifies thatits calibration measurements are traceable to the United States National Institute ofStandards and Technology, to the extent allowed by the Institution’s calibrationfacility, or to the calibration facilities of other International Standards Organizationmembers.3 Artisan Technology Group - Quality Instrumentation ... Guaranteed | (888) 88-SOURCE | WarrantyThis Agilent Technologies instrument product is warranted against defects inmaterial and workmanship for a period corresponding to the individual warrantyperiods of its component products. Instruments are warranted for a period of oneyear. Fixtures and adapters are warranted for a period of 90 days. During thewarranty period, Agilent Technologies will, at its option, either repair or replaceproducts that prove to be defective.For warranty service or repair, this product must be returned to a service facilitydesignated by Agilent Technologies. Buyer shall prepay shipping charges toAgilent Technologies and Agilent Technologies shall pay shipping charges toreturn the product to Buyer. However, Buyer shall pay all shipping charges, duties,and taxes for products returned to Agilent Technologies from another country.Agilent Technologies warrants that its software and firmware designated byAgilent Technologies for use with an instrument will execute its programminginstruction when property installed on that instrument. Agilent Technologies doesnot warrant that the operation of the instrument, or software, or firmware will beuninterrupted or error free.Limitation Of WarrantyThe foregoing warranty shall not apply to defects resulting from improper orinadequate maintenance by Buyer, Buyer-supplied software or interfacing,unauthorized modification or misuse, operation outside the environmentalspecifications for the product, or improper site preparation or maintenance. IMPORTANT No other warranty is expressed or implied. Agilent Technologies specificallydisclaims the implied warranties of merchantability and fitness for a particularpurpose.Exclusive RemediesThe remedies provided herein are buyer’s sole and exclusive remedies. AgilentTechnologies shall not be liable for any direct, indirect, special, incidental, orconsequential damages, whether based on contract, tort, or any other legal theory.4Artisan Technology Group - Quality Instrumentation ... Guaranteed | (888) 88-SOURCE | 5AssistanceProduct maintenance agreements and other customer assistance agreements are available for Agilent Technologies products.For any assistance, contact your nearest Agilent Technologies Sales and Service Office. Addresses are provided at the back of this manual.Safety SymbolGeneral definitions of safety symbols used on the instrument or in manuals are listed below.Instruction Manual symbol: the product is marked with this symbol when it is necessary for the user to refer to the instrument manual.WARNING This warning sign denotes a hazard. It calls attention to a procedure, practice, condition or the like, which, if not correctly performed or adhered to, could result in injury or death to personnel.CAUTION This Caution sign denotes a hazard. It calls attention to a procedure, practice, condition or the like, which, if not correctly performed or adhered to, could result in damage to or destruction of part or all of the product.NOTE Note denotes important information. It calls attention to a procedure, practice, condition or the like, which is essential to highlight.!Artisan Technology Group - Quality Instrumentation ... Guaranteed | (888) 88-SOURCE | 6Artisan Technology Group - Quality Instrumentation ... Guaranteed | (888) 88-SOURCE | 1.OperationProduct Description . . . . . . . . . . . . . . . . . . . . . . . . . . . . . . . . . . . . . . . . . . . . . . . 10Specifications. . . . . . . . . . . . . . . . . . . . . . . . . . . . . . . . . . . . . . . . . . . . . . . . . . . . 11Compensation for Fixture Residual Impedance Error . . . . . . . . . . . . . . . . . . . . . 12Operation . . . . . . . . . . . . . . . . . . . . . . . . . . . . . . . . . . . . . . . . . . . . . . . . . . . . . . . 132.ServiceMaintenance. . . . . . . . . . . . . . . . . . . . . . . . . . . . . . . . . . . . . . . . . . . . . . . . . . . . . 167 Artisan Technology Group - Quality Instrumentation ... Guaranteed | (888) 88-SOURCE | 8Artisan Technology Group - Quality Instrumentation ... Guaranteed | (888) 88-SOURCE | 1OperationThis operating note provides complete information on the 16048D Test Leads. The16048D is shown pictorially in Figure 1-1, its physical dimensions are given inTable 1-1. To order additional copies of this operating note, use the part numberlisted on the rear cover.9 Artisan Technology Group - Quality Instrumentation ... Guaranteed | (888) 88-SOURCE | 10Chapter 1OperationProduct DescriptionProduct DescriptionThe 16048D consists of a direct attachment, 4-terminal pair type fixture which is equipped with four BNC (m) terminated-coaxial test leads. These test leads areused to attach user-fabricated test fixtures. DC bias levels of up to ±40V can be applied to the 16048D. Cable length is 2 meter. The 16048D is shown in Figure 1-1.Figure 1-1Product OverviewOperationSpecificationsSpecificationsTable 1-1Specifications of the 16048DFunction:4-terminal pair type fixture which is equippedwith four BNC (m) terminated-coaxial test leads.Connector Type:BNC maleMaximum Voltage:± 40 V peak max. (AC+DC)Cable Length:2mWeight:460 gSafety Standards:EN61010-1:1993 +A2:1995IEC61010-1:1990 +A1:1992 +A2:1995CSA C22.2 No.1010.1:1992INSTALLATION CATEGORY IPOLLUTION DEGREE 2INDOOR USEChapter 111OperationCompensation for Fixture Residual Impedance ErrorCompensation for Fixture Residual Impedance ErrorThe 16048D has inherent stray capacitance, residual inductance, and residual resistance that affect the accuracy of measured values. To compensate for, or negate, these residuals to minimize measurement error, the instrument’sOpen/Short compensation procedure should be performed. The procedure is given in the instrument’s operating manual.12Chapter 1OperationOperationOperationSetup and measurement procedure is as follows:1.Connect the 16048D directly to the UNKNOWN terminals of the instrument.2.Connect the user-fabricated test fixture to the test leads.3.Perform Open/Short compensation as described in the instrument’s operationmanual.4.Connect the DUT to the test fixture.NOTE Connect the green lead to the chassis or grounded part on the test fixture to reduce the effects of stray capacitance between the DUT and the test fixture.Chapter 113OperationOperation14Chapter 12Service15ServiceMaintenanceMaintenanceAn exploded view of the 16048D (for parts identification) is shown in Figure 2-1. Do not disassemble any further than shown. Maintenance consists principally of cleaning contacts and replacing worn or damaged parts. Take special care when cleaning contacts. To order parts, use the Agilent Technologies part numbers listed in Table 2-1. If a faulty part is located in an assembly that cannot be disassembled, order the next higher assembly or return the whole device to the nearest Agilent Technologies Sales/Service Office for repair or replacement.16Chapter 2Chapter 217Service MaintenanceFigure 2-1Parts IdentificationServiceMaintenance Table 2-1Parts IdentificationReference Agilent PartNo.Qty.Description1*4SLEEVE-METAL2*4NUT3*4NUT-HEX4*4WASHER-FL MTLC5*4WASHER-FL NM60400-02031GROMMET-RND716048-616121WIRE ASSEMBLY8*1BOTTOM COVER9*4INSULATOR10*2CONNECTOR-BNC11*2BNC-ASSEMBLY122200-01031SCREW-MACH 4-40132190-02061WASHER-FL MTLC1416047-400001STOPPER1516048-040111TOP COVER162360-01923SCREW-MACH 6-32171400-07192CABLE TIE18*3GROMMET-RND19*1CABLE SHIELDED201400-04931CABLE TIE2116048-040131TOP COVER2216048-040141BOTTOM COVER2316048-616111CABLE ASSEMBLY24*4BNC-BOOT25*4SLEEVE26*4SLEEVE-FLEX .081ID27*4INSULATOR281250-00894CONTACT RF CONN291250-00524CONNECTOR-RF BNC18Chapter 2Chapter 219Service Maintenance*: Not separately replaceable.16048-60020a1TEST LEAD (1 thru 29)301250-01184CONNECTOR-RF BNC 312360-01152SCREW-MACH 6-323216032-100211PLATE332190-00164WASHER-LK INTL T 342950-00014NUT-HEX 3516032-100221PLATE SHIELD3616032-600011BNC BRACKET (30 thru 35)a.Agilent internal-only part number.ReferenceAgilent PartNo.Qty.DescriptionREGIONAL SALES AND SUPPORT OFFICESFor more information about Agilent Technologies test and measurement products, applications, services, and for a current sales office listing, visit our web site: /find/tmdir. You can also contact one of the following centers and ask for a test and measurement sales representative. 11/29/99United States:Agilent TechnologiesTest and Measurement Call Center P.O.Box 4026Englewood, CO 80155-4026(tel)180****4844Canada:Agilent Technologies Canada Inc. 5150 Spectrum Way Mississauga, OntarioL4W 5G1(tel)187****4414Europe:Agilent TechnologiesTest & MeasurementEuropean Marketing OrganizationP.O.Box 9991180 AZ AmstelveenThe Netherlands(tel) (31 20) 547 9999Japan:Agilent Technologies Japan Ltd.Call Center9-1, Takakura-Cho, Hachioji-Shi, Tokyo 192-8510, Japan(tel) (81) 426 56 7832(fax) (81) 426 56 7840Latin America:Agilent TechnologiesLatin American Region Headquarters 5200 Blue Lagoon Drive, Suite #950 Miami, Florida 33126U.S.A.(tel) (305) 267 4245(fax) (305) 267 4286Australia/New Zealand:Agilent Technologies Australia Pty Ltd 347 Burwood HighwayForest Hill, Victoria 3131(tel) 1-800 629 485 (Australia)(fax) (61 3) 9272 0749(tel) 0 800 738 378 (New Zealand) (fax) (64 4) 802 6881Asia Pacific:Agilent Technologies24/F, Cityplaza One, 1111 King’s Road, Taikoo Shing, Hong Kong(tel) (852)-3197-7777(fax) (852)-2506-9284。
Agilent 10702A和10766A线性光干散射仪及10703A和10767A反射仪说明书

7AAgilent10702A and 10766A Linear Interferometers, and Agilent10703A and 10767A RetroreflectorsChapter 7A Agilent10702A and 10766A Linear Interferometers, and Agilent10703A and 10767A RetroreflectorsIntroductionIntroductionThis subchapter describes:•the Agilent10702A Linear Interferometer, including the Agilent10702A-001 Linear Interferometer with Windows•the Agilent10703A Retroreflector•the Agilent10766A Linear Interferometer•the Agilent10767A Retroreflector•the Agilent10722A Plane Mirror Converter•the Agilent10722B High Stability Plane Mirror Interferometer7A-2User’s ManualChapter 7A Agilent10702A and 10766A Linear Interferometers, and Agilent10703A and 10767A RetroreflectorsDescriptionDescriptionThe Agilent10702A Linear Interferometer (see Figure 7A-1) and the Agilent10766A Linear Interferometer are intended forgeneral-purpose applications. Designed for use with a separate cube corner reflector, these products are paired with the Agilent10703A Retroreflector (see Figure 7A-1) or the Agilent10767A RetroreflectorFigure7A-1. Agilent 10702A Linear InterferometerAgilent10702A-001 Linear Interferometer with WindowsThe Agilent10702A Linear Interferometer, being the simplest interferometer, should be used whenever possible. The measurement retroreflector for this interferometer is the Agilent10703A Retroreflector. Displacement is measured between the interferometer and the retroreflector (cube corner). Either one or both can move. If the linear interferometer must move, the Agilent10702A-001 Linear Interferometer with Windows must be used (see Figure 7A-2). Normally, one optic is mounted on a moving part and the other is mounted on a fixed part and the displacement between the two is measured. A diagram of this is shown in Figure 7A-3. Note that for multi-axis installations each axis must be mechanically independent of the other. In other words, motion in the Y-axis should have no effect on the alignment of the X-axis optics.User’s Manual7A-3Chapter 7A Agilent10702A and 10766A Linear Interferometers, and Agilent10703A and 10767A RetroreflectorsDescriptionThe Agilent 10766A Linear Interferometer (see Figure 7A-4) is optically identical to the Agilent 10702A-001 Linear Interferometer with Windows. However, in order to withstand the handling and repeated installations of calibrator-type applications, the Agilent 10766A interferometer has a more-robust housing than the Agilent 10702A Option 001 interferometer (which is intended for laser transducer measurement system applications). Also, the Agilent 10766A interferometer has metric dimensions and metric threads, whereas the Agilent 10702A interferometer does not.Similarly, the Agilent 10767A Linear Retroreflector (see Figure 7A-4) is optically identical to the Agilent 10703A Retroreflector. However, in order to withstand the handling and repeated installations of calibrator-type applications, the Agilent 10767A retroreflector has a more-robust housing than the Agilent 10703A retroreflector (which is intended for laser transducer measurement system applications). Also, the Agilent 10767A interferometer has metric dimensions and metric threads, whereas the Agilent 10703A interferometer does not.The Agilent 10722A Plane Mirror Converter (see Figure 7A-5) is a quarter-wave plate accessory for the Agilent 10702A interferometer. With the Agilent 10722A converter and an additional Agilent10703A Retroreflector, the Agilent 10702A interferometer can be converted to an Agilent10706A Plane Mirror Interferometer. This configuration allows measurements of axial displacement of a plane mirror.With the Agilent 10722A Plane Mirror Converter and the Agilent 10723A High Stability Adapter, the Agilent 10702A Linear Interferometer can be converted to an Agilent 10706B High Stability Plane Mirror Interferometer. This configuration also allows measurements of axial displacement of a plane mirror. The Agilent 10723A adapter is discussed in the subchapter7C, “Agilent10706A Plane Mirror Interferometer,” of this manual. The High-stability Plane Mirror Interferometer is described in subchapter7D of this manual.7A-4User’s ManualChapter 7A Agilent10702A and 10766A Linear Interferometers, and Agilent10703A and 10767A RetroreflectorsDescriptionIf the Agilent10702A Linear Interferometer is placed in a beam which has been aligned parallel to the motion of travel, the outgoing beam can be deflected by as much as 30arc-minutes (θ) due to the incoming-outgoing beam parallelism specifications of the Agilent10702A interferometer. This could cause not only cosine error but also possible loss of signal during movement of the Agilent10703A Retroreflector.To compensate for this, alignment is performed with the Agilent10702A Linear Interferometer in place. This allows the laser beam to be aligned parallel to the motion of travel to minimize cosine error and maximize signal. Since the incoming beam is now not parallel to the motion of travel, the Agilent10702A Linear Interferometer must remain stationay. (See below).If the Agilent10702A Linear Interferometer, instead of the Agilent10703A Retroreflector, is moved during the measurement, the beam in the measurement path will remain parallel, but will be displaced. This displacement δ will occur at theIf motion of the linear interferometer is required, the Agilent10702A-001 Linear Interferometer withWindows should be used. This provides special wedge windows which makes the outgoing beam parallel to the incoming beam. This allows motion by either the Agilent10703A Retroreflector or the Agilent10702A-001 Linear Interferometer.Figure7A-2. Agilent 10702A-001 Linear Interferometer with Windows User’s Manual7A-5Chapter 7A Agilent10702A and 10766A Linear Interferometers, and Agilent10703A and 10767A RetroreflectorsDescriptionFigure7A-3. Three-axis machine tool Installation7A-6User’s ManualChapter 7A Agilent10702A and 10766A Linear Interferometers, and Agilent10703A and 10767A RetroreflectorsFigure7A-4. Agilent 10766A Linear Interferometer and Agilent 10767A Linear RetroreflectorFigure7A-5. Agilent 10722A Plane Mirror ConverterUser’s Manual7A-7Chapter 7A Agilent10702A and 10766A Linear Interferometers, and Agilent10703A and 10767A RetroreflectorsLaser Beam PathLaser Beam PathThe beam from the laser head is split at the surface of a polarizing beam-splitter.One frequency, f B, is reflected to the reference cube corner mounted on the housing (Figure7A-6). See “Measurement Direction Sense” section in Chapter7, “Measurement Optics,” for explanation of f A and f B beam paths.The second frequency, f A, is sent to the Agilent10703A Retroreflector and returned parallel to, but displaced from, the outgoing beam.Both frequencies then recombine with the polarizing beam splitter and travel back along a common axis to the photodetector in the receiver. One frequency includes a Doppler frequency shift whenever there is a relative motion between the Agilent10703A Retroreflector and the Agilent10702A Linear Interferometer. Rotating the interferometer 90°about the axis of the input beam switches which optical frequency is in the measurement path, thus changing the direction sense.Figure7A-6. Linear interferometer laser beam path7A-8User’s ManualChapter 7A Agilent10702A and 10766A Linear Interferometers, and Agilent10703A and 10767A RetroreflectorsLaser Beam PathDifferential measurementsA differential measurement is one in which both the reference beam and the measurement beam travel to external reflectors (either cube corners or mirrors) outside the interferometer housing. This allows measurement of the relative positions of the two external mirrors, either or both of which may be moving. Viewed another way, this allows measuring the motion of one reflector relative to a reference datum elsewhere in the machine, external to the interferometer itself. This is unlike the typical interferometer configuration because usually the reference beam path length does not change; in differential configurations, it can.Take care during design and layout of a differential measurement to avoid introduction of alignment errors, thermal or mechanical instabilities, and potential deadpath problems. Both reflectors (reference and measurement) should be of the same type (cube corner or plane mirror); this minimizes thermal drift problems with ambient temperature changes.To use an Agilent10702A or Agilent10766A interferometer in a differential measurement configuration, the reference cube corner can simply be detached from the interferometer housing and attached to the reference surface of interest. This is shown in Figure7A-7. Be aware that all installation and alignment requirements for the measurement reflector now apply also to the reference reflector.Figure7A-7. Differential measurements with the Agilent 10702A User’s Manual7A-9Chapter 7A Agilent10702A and 10766A Linear Interferometers, andAgilent10703A and 10767A RetroreflectorsSpecial ConsiderationsSpecial ConsiderationsEffect of optics on measurement direction senseThe orientation and configuration of the interferometers affects themeasurement direction sense. The direction sense depends on whichfrequency is in the measurement path of the interferometer. Forexample, if f1 (lower frequency) is in the reference path and the opticsare moving away from each other, the fringe counts will beINCREASING. This corresponds to using an Agilent5517A,Agilent5517B, or Agilent5517C Laser Head (mounting feet inhorizontal plane) with an Agilent10702A Linear Interferometermounted with labels facing up and down (see Figure7A-6).Interchanging f1 and f2 (perhaps by rotating the interferometer 90°) inthis example will result in the fringe counts DECREASING.The optical schematic for the interferometers, in Figure7A-6, showsthe reference and measurement laser beam paths for theseinterferometers.As with the laser heads, when the interferometers are rotated 90°, themeasurement direction sense will change. This rotation causesswitching of frequencies in the measurement path.Configuration effectsMany of the distance-measuring interferometers can be configured toturn the beam at right angles. When configuring the linear,single-beam, and plane mirror interferometers to turn the beam, themeasurement direction sense will be changed. This is because themeasurement reference paths are switched on the interferometers,therefore changing the direction sense.Moving interferometer instead of reflectorWhen moving the interferometer instead of the measurement reflectoris required, the Agilent10702A-001 (or Agilent 10766A) interferometershould be used. In practice, for alignment reasons, these are two of thefew interferometers that can be moved while making measurements.For a detailed explanation of the beam alignment problems involvedwith a moving-interferometer setup, see Figure7A-2.NOTE If a right-angle beam bend is made through the Agilent10702Ainterferometer, it must be the fixed component.7A-10User’s ManualMountingMountingVibration considerationsTo achieve the highest possible measurement accuracy, be sure your measurement system design and installation provide sufficient and appropriate isolation of the optical components from the effects of vibration. See Chapter3, “System Design Considerations,” and Chapter4, “System Installation and Alignment,” in this manual for more information.Adjustable mountsThe optical elements inside these Agilent laser measurement system optics are not precisely referenced to their housings. In most applications involving these optics, a few simple alignments during system installation can usually provide equal or better alignment than referencing the optics to their housings. Therefore, slight positioning adjustments of the unreferenced interferometers, beam splitters, and beam benders are needed for proper system alignment.Positioning adjustments for the Agilent10702A interferometer can be provided by using an Agilent10711A Adjustable Mount.Positioning adjustments for the Agilent10766A interferometer can be provided by using an Agilent 10785A Height Adjuster and Post (a base plate accessory, Agilent10784A, for the post is available), where appropriate. These mounting arrangements allow adjustment of pitch and yaw of any attached optic. (Roll adjustment is typically not required, and can usually be avoided by careful optical system layout.) FastenersThe Agilent10702A interferometer is supplied with mounting screws to mount it on the Agilent10711A Adjustable Mount.The Agilent10785A Height Adjuster and Post, and the Agilent10767A Linear Retroreflector, include captive hardware necessary for mounting and aligning the Agilent10766A Laser Interferometer. User’s Manual7A-11Installation7A-12User ’s ManualInstallationPre-installation checklistIn addition to reading chapters 2 through 4, and Chapter 15, “Accuracyand Repeatability,” complete the following items before installing alaser positioning system into any application.Complete Beam Path Loss Calculation (see “Calculation of signalloss ” in Chapter 3, “System Design Considerations,“ of this manual).Determine the direction sense for each axis, based on theorientation of the laser head, beam-directing optic, andinterferometer. Enter the direction sense for each axis into themeasurement system electronics. (See Chapter 5, “Laser Heads,”Chapter 14, “Principles of Operation,” and Chapter 15, “Accuracyand Repeatability,” in this manual.Provide for aligning the optics, laser head, and receiver(s) on themachine. (Ideally, you want to be able to translate beam in twodirections and rotate beam in two directions for each interferometerinput. This typically takes two adjustment optics with properorientations.)Be sure to allow for transmitted beam offset of beam splitters(Agilent 10700A and Agilent 10701A) in your design. (See the offsetspecifications under the “Specifications ” heading at the end of thissubchapter.)Refer to Chapter 4, “System Installation and Alignment,” in thismanual for installation instructions.Specifications and CharacteristicsUser ’s Manual 7A-13AlignmentAlignment aidsAlignment aids for these interferometers are listed in Chapter 4,“System Installation and Alignment ” and Chapter 9, “Accessories,” ofthis manual.ProcedureRefer to Chapter 4, “System Installation and Alignment ” in this manual for alignment instructions.Specifications and CharacteristicsSpecifications describe the device ’s warranted performance.Supplemental characteristics (indicated by TYPICAL or NOMINAL)are intended to provide non-warranted performance information usefulin applying the device.The basic optical resolution using a linear interferometer is one halfwavelength (0.316micron, 12.26microinches).Using electronic resolution extension, the system resolution isincreased significantly. Depending on the system, an additionalresolution extension factor of 32 (for Agilent 10885A and 10895A) or256 (for Agilent 10897B and 10898A) is usually available..NOTE The system resolution 1 is based on using 32X electronic resolutionextension. This is available with the Agilent 10885A andAgilent 10895A electronics.The system resolution 2 is based on using 256X electronic resolutionextension. This is available with the Agilent 10897B andAgilent 10898A electronics.Interferometer Fundamental OpticalResolutionSystem Resolution 1(see NOTE)System Resolution 2(see NOTE)Agilent 10702A λ/2 (316.5nm, 12.5µin)λ/64 (10.0nm, 0.4µin)λ/512 (1.2nm, 0.047µin)Agilent 10766Aλ/2 (316.5nm, 12.5µin)λ/64 (10.0nm, 0.4µin)λ/512 (1.2nm, 0.047µin)Specifications and CharacteristicsAgilent 10702A Linear Interferometer Specifications Dimensions: see figure belowWeight: 232grams (8.2ounces)Materials Used:Housing: Stainless Steel (416)Apertures: Plastic (Nylon)Optics: Optical Grade GlassAdhesives: Low Volatility (Vacuum Grade)Maximum Transmitted Beam Deviation: ± 30 arc-minutesOptical Efficiency (including Agilent10703A Reflector):Typical: 75%Worst Case: 71%Fundamental Optical Resolution: λ/2Non-linearity Error: <4.2nm (0.17µin)Figure7A-8. Agilent 10702A Linear Interferometer — dimensions7A-14User’s ManualSpecifications and CharacteristicsAgilent 10702A-001 Linear Interferometer with Windows SpecificationsDimensions: see figure belowWeight: 246grams (8.7ounces)Materials Used:Housing: Stainless Steel (416)Apertures: Plastic (Nylon)Optics: Optical Grade GlassAdhesives: Low Volatility (Vacuum Grade)Maximum Transmitted Beam Deviation: ± 30 arc-minutesOptical Efficiency (including Agilent10703A Reflector):Typical: 73%Worst Case: 69%Fundamental Optical Resolution: λ/2Non-linearity Error: <4.2nm (0.17µin)Figure7A-9. Agilent 10702A-001 Linear Interferometer with Windows — dimensionsUser’s Manual7A-15Specifications and Characteristics7A-16User ’s ManualAgilent 10703A Retroreflector SpecificationsFigure 7A-10. Agilent 10703A Retroreflector — dimensionsAgilent 10713B 1-Inch Cube Corner SpecificationsFigure 7A-11. Agilent 10713B 1-Inch Cube Corner, no housing — dimensionsDimensions: see figure belowWeight: 41.5grams (1.5ounces)Materials Used:Housing: Stainless Steel (416)Optics: Optical Grade GlassAdhesives: Low Volatility (Vacuum Grade)Dimensions: See drawings below.Weight: 11.4grams (0.4ounces)Nodal Point Depth: 12.57 mm (0.495 inch)3.0 mm(0.12)37.6 mm(1.48 D i a )23.9 mm (0.94)28.4 mm (1.12 D i a )33.3 mm(1.31)B ol tC i r c l e 20.3 mm A p e r t u r e(0.80 D i a )2.5 mm (0.10)(1.000 D i a )+ .000- .010+ .000- .030(0.900 Dia min.Clear Aperture)25.40 mm + 0.00- 0.25+ 0.00- 0.76 (.75022.86 mm)19.1 mmSpecifications and CharacteristicsAgilent 10766A Linear Interferometer Specifications Dimensions: see figure belowWeight: 312grams (11ounces)Materials Used:Housing: Stainless Steel (416)Apertures: Plastic (Nylon)Optics: Optical Grade GlassAdhesives: Low Volatility (Vacuum Grade)Optical Efficiency (interferometer combination plusremote Agilent10767A Retroreflector):Typical: 73%Worst Case: 69%A65.0mmFigure7A-12. Agilent 10766A Linear Interferometer — dimensions User’s Manual7A-17Specifications and CharacteristicsAgilent 10767A Retroreflector Specifications Dimensions: see figure belowWeight: 224grams (7.9ounces)Materials Used:Housing: Stainless Steel (416)Apertures: Plastic (Nylon)Optics: Optical Grade GlassAdhesives: Low Volatility (Vacuum Grade)Figure7A-13. Agilent 10767A Linear Retroreflector — dimensionsProduct specifications and descriptions in thisdocument subject to change without notice.Copyright (C) 2002 Agilent TechnologiesPrinted in U.S.A. 07/02This is a chapter from the manual titled:Laser and Optics User's ManualFor complete manual, order:Paper version: p/n 05517-90045CD version: p/n 05517-90063This chapter is p/n 05517-901087A-18User’s Manual。
ASUS ProArt Monitor 商品说明书

Key Features4 times the resolution of full HD 1080p with HDR for stunning details and image quality 1152 zones with 1600 nitspeak brightness anddeeper darkness to deliverthe best contrast andaccurate reproduction ofHDR contentsUp to 120 Hz Variable RefreshRate with FreeSync PremiumPro to optimize fast-rendering scenarioCombined with an IPS display, provides brighter imagery and supports the cinema-standard 98% DCI-P3 color gamut Over a billion onscreencolors to give you smoothergradations and a morenatural transition betweenhuesFactory pre-calibrated withASUS advanced gray-scaletracking technology toguarantee the △E colordifference value is less than 1ASUS ProArt™Calibration Technology to ensure color accuracy during different using scenarios Dolby Vision™HDRtransforms yourentertainment experiencewith ultravivid imaging thatbrings entertainment to life.Thunderbolt™3 technologyalong with 40Gbps datatransfer speeds, supports60W power delivery and dual4K UHD external displays MiniLEDHigh Refresh RateDisplay Panel Size : 32-inch (81.28cm) Wide Screen (16:9) Display Viewing Area(HxV) : 708.48 x 398.52 mm Panel Backlight/ Type : Mini LED / IPS True Resolution : 3840 x 2160Pixel Pitch : 0.1845 mm Display Colors : 1073.7M (10 bit)Color Saturation : 85% Rec.2020, 99.5% Adobe RGB, 98% DCI-P3 and 100% sRGB/Rec. 709Brightness : Peak: 1600 cd/m², Sustain 1000 cd/m²Contrast Ratio: 1000:1 (typical), 1000000:1 (HDR)Viewing Angle (CR ≧10) : 178°(H)/178°(V)Response Time : 5ms (GTG)Flicker-free : Yes HDR support : Yes, HDR-10, HLG, Dolby Vision Dynamically Local Dimming : 1152 zones Off-axis contrast optimization technology : Yes Refresh Rate (Max): 120 HzVideo Feature Trace Free Technology : Yes ProArt Preset : 14 modes (Standard / sRGB / Adobe RGB / DCI-P3 / Rec. 2020 / DICOM / Rec. 709 / HDR_PQ DCI / HDR_PQ Rec2020 / HDR_HLG_BT2100 /HDR_HLG_DCI / Dolby Vision / User mode1 / User mode2)Color Accuracy : △E < 1Gamma Adjustment : Yes (Support Gamma 2.6, 2.4, 2.2, 2.0, and 1.8) Color Adjustment : 6-axis (R, G, B, C, M, Y) Color Temperature Selection : 5 modes QuickFit : Yes (Paper / Alignment Grid / Ruler / Customization Modes)Picture-by-Picture : Yes (PBP x 4 with 2 Color Gamut Selection)HDCP support : Yes. 2.2ASUS Smart HDR Technology : Yes Adaptive-Sync/FreeSync ™Premium Pro support: Yes, 48-120Hz Motion Sync : Yes HDR Preview : YesAudio Feature 3W x 2 stereo, RMSIO ports Signal Input :DisplayPort1.4 x 1HDMI(v2.1) x 1HDMI(v2.0) x 2Thunderbolt ™3 USB-C ™x 2 (in x 1 + out x 1)Thunderbolt ™3 Power Delivery : 60WEarphone Jack : Yes (3.5mm Mini-jack)USB Hub:3x USB 3.2 Gen 2 Type-A Signal FrequencyDigital Signal Frequency : HDMI(v2.1), DisplayPort, Thunderbolt™3:180~264 KHz (H) / 48~120Hz (V)HDMI(v2.0) : 180~264 KHz (H) / 48~60Hz(V)Power Consumption Power On (Typical): < 55W Power Saving Mode : < 0.5W ; Power Off Mode : 0W (Hard Switch)100-240V, 50/60HzMechanical DesignChassis Colors : Black Tilt : +23°~ -5°Swivel : +60°~ -60°Ambient Light Sensor : Yes Pivot : 90°(Clockwise& Anticlockwise)Height Adjustment : 0 ~ 130 mm VESA Wall Mounting : 100 x 100 mm DimensionsPhys. Dimension with Stand (WxHxD) : 727 x (470 ~ 600) x 240 mm Phys. Dimension without Stand (WxHxD) : 727 x 426 x 93 mm Box Dimension (WxHxD) : 923 x 525x 386 mm WeightNet Weight (Esti.) : 14.64 Kg (WW) /18.3Kg (EU), Without Stand: 9.7 Kg, Gross Weight (Esti.) : 19.8 Kg (WW) /23.3Kg (EU)AccessoriesPower cord, Thunderbolt ™3 cable, DisplayPort cable, Ultra High-speed HDMI cable, USB-C to USB-A cable, Calibration Report, Quick Start Guide, Warranty Card, Monitor Hood, X-rite i1 Display Pro Compliance Standard UL/cUL, CB, CE, FCC, CCC, BSMI, CU, VCCI, J-MOSS, RoHS, WEEE, PSE, KCC, ICES-3, ErP, CEL, ISO 9241-307, UkrSEPRO, RCM, MEPS, PC Recycle, KC, e-Standby, TÜV Flicker Free, TÜV Low Blue Light, Windows 7 and 10 WHQL, Mac Compliance (Mac OS 10.10.x, 10.11.x, 10.12.x), VESA DisplayHDR 1400* Measuring a screen brightness of 200 nits without audio / USB / Card reader connection *Delta E < 1 is average value under sRGB and Adobe RGB color gamut *All specifications are subject to change without notice Display PA32UCG-KSpec SheetDisplayPort1.4Thunderbolt ™3 USB-CUSB-A Earphone Jack HDMI(v2.0) x 2HDMI(v2.1) x 1。
ARTISAN TECHNOLOGY GROUP 产品说明书.pdf_1703319272.7649

PCI-DIO2424-bit, Logic-level Digital I/OUser's GuideDocument Revision 3, May, 2009© Copyright 2009, Measurement Computing CorporationYour new Measurement Computing product comes with a fantastic extra —Management committed to your satisfaction!Thank you for choosing a Measurement Computing product—and congratulations! You own the finest, and you can now enjoy the protection of the most comprehensive warranties and unmatched phone tech support. It’s the embodiment of our mission: To provide PC-based data acquisition hardware and software that will save time and save money.Simple installations minimize the time between setting up your system and actually making measurements. We offer quick and simple access to outstanding live FREE technical support to help integrate MCC products into a DAQ system.Limited Lifetime Warranty: Most MCC products are covered by a limited lifetime warranty against defects in materials or workmanship for the life of the product, to the original purchaser, unless otherwise noted. Any products found to be defective in material or workmanship will be repaired, replaced with same or similar device, or refunded at MCC’s discretion. For specific information, please refer to the terms and conditions of sale.Harsh Environment Program: Any Measurement Computing product that is damaged due to misuse, or any reason, may be eligible for replacement with the same or similar device for 50% of the current list price. I/O boards face some harsh environments, some harsher than the boards are designed to withstand. Contact MCC to dete rmine your product’s eligibility for this program.30 Day Money-Back Guarantee: Any Measurement Computing Corporation product may be returned within 30 days of purchase for a full refund of the price paid for the product being returned. If you are not satisfied, or chose the wrong product by mistake, you do not have to keep it.These warranties are in lieu of all other warranties, expressed or implied, including any implied warranty of merchantability or fitness for a particular application. The remedies pr ovided herein are the buyer’s sole and exclusive remedies. Neither Measurement Computing Corporation, nor its employees shall be liable for any direct or indirect, special, incidental or consequential damage arising from the use of its products, even if Measurement Computing Corporation has been notified in advance of the possibility of such damages.Trademark and Copyright InformationTracerDAQ, Universal Library, Measurement Computing Corporation, and the Measurement Computing logo are either trademarks or registered trademarks of Measurement Computing Corporation.Windows, Microsoft, and Visual Studio are either trademarks or registered trademarks of Microsoft CorporationLabVIEW is a trademark of National Instruments.CompactFlash is a registered trademark of SanDisk Corporation.XBee and XBee-PRO are trademarks of MaxStream, Inc.All other trademarks are the property of their respective owners.Information furnished by Measurement Computing Corporation is believed to be accurate and reliable. However, no responsibility is assumed by Measurement Computing Corporation neither for its use; nor for any infringements of patents or other rights of third parties, which may result from its use. No license is granted by implication or otherwise under any patent or copyrights of Measurement Computing Corporation.All rights reserved. No part of this publication may be reproduced, stored in a retrieval system, or transmitted, in any form by any means, electronic, mechanical, by photocopying, recording, or otherwise without the prior written permission of Measurement Computing Corporation.Table of ContentsPrefaceAbout this User's Guide (6)What you will learn from this user's guide (6)Conventions in this user's guide (6)Where to find more information (6)Chapter 1Introducing the PCI-DIO24 (7)Software features (7)Chapter 2Installing the PCI-DIO24 (8)What comes with your PCI-DIO24 shipment? (8)Hardware (8)Additional documentation (8)Optional components (8)Unpacking the PCI-DIO24 (9)Installing the software (9)Installing the hardware (9)Configuring the hardware (9)Connecting the board for I/O operations (10)Connectors, cables – main I/O connector (10)Pin out – main I/O connector (10)Cabling (11)Field wiring and signal termination (11)Chapter 3Functional Details (12)PCI-DIO24 block diagram (12)DIO signals (12)Signal level control (13)Chapter 4Specifications (15)Power consumption (15)Digital input / output (15)Environmental (15)Main connector and pin out (16)Declaration of Conformity (17)Preface About this User's GuideWhat you will learn from this user's guideThis user's guide explains how to install, configure, and use the PCI-DIO24 so that you get the most out of the digital I/O features.This user's guide also refers you to related documents available on our web site, and to technical supportresources.Conventions in this user's guideCaution!Shaded caution statements present information to help you avoid injuring yourself and others, damaging your hardware, or losing your data.<:> Angle brackets that enclose numbers separated by a colon signify a range of numbers, such as those assigned to registers, bit settings, etc.bold text Bold text is used for the names of objects on the screen, such as buttons, text boxes, and check boxes. For example:1. Insert the disk or CD and click the OK button.italic text Italic text is used for the names of manuals and help topic titles, and to emphasize a word or phrase. For example:The Insta Cal® installation procedure is explained in the Quick Start Guide.Never touch the exposed pins or circuit connections on the board.Where to find more informationFor additional information relevant to the operation of your hardware, refer to the Documents subdirectory where you installed the MCC DAQ software (C:\Program Files\Measurement Computing\DAQ by default), or search for your device on our website at .If you need to program at the register level in your application, refer to the Register Map for the PCI-DIO24, PCI-DIO24H, PCI-DIO24/S, and PCI-DIO24/LP. This document is available on our website at/registermaps/RegMapPCI-DIO24X.pdf.Chapter 1 Introducing the PCI-DIO24This manual explains how to install, configure and use the PCI-DIO24 digital I/O board.The PCI-DIO24 provides 24 lines of digital I/O. An on-board, industry standard 82C55 programmableperipheral interface chip provides the 24 digital I/O lines in three eight-bit ports (Port A, Port B, and Port C).Port C can be further divided into two four-bit ports (Port C-HI and Port C-LO). You can configure each port independently for either input or output. All 24 I/O lines are accessible through the board's 37-pin connector.The I/O pins of an 82C55 are bi-directional CMOS TTL level.Software featuresFor information on the features of Insta Cal and the other software included with your PCI-DIO24, refer to the Quick Start Guide that shipped with your device. The Quick Start Guide is also available in PDF at/PDFmanuals/DAQ-Software-Quick-Start.pdf.Check /download.htm for the latest software version or versions of the software supported under less commonly used operating systems.Chapter 2 Installing the PCI-DIO24What comes with your PCI-DIO24 shipment?The following items are shipped with the PCI-DIO24.Hardware▪PCI-DIO24Additional documentationIn addition to this hardware user's guide, you should also receive the Quick Start Guide (available in PDF at /PDFmanuals/DAQ-Software-Quick-Start.pdf). This booklet supplies a brief description of the software you received with your PCI-DIO24 and information regarding installation of that software. Please read this booklet completely before installing any software or hardware.Optional componentsIf you ordered any of the following products with your board, they should be included with your shipment.▪CablesC37FF-x C37FFS-xPCI-DIO24 User's Guide Installing the PCI-DIO24▪Signal termination and conditioning accessoriesMCC provides signal termination products for use with the PCI-DIO24. Refer to the "Field wiring andsignal termination" section on page 11 for a complete list of compatible accessory products. Unpacking the PCI-DIO24As with any electronic device, you should take care while handling to avoid damage from staticelectricity. Before removing the PCI-DIO24 from its packaging, ground yourself using a wrist strap or by simply touching the computer chassis or other grounded object to eliminate any stored static charge.If any components are missing or damaged, notify Measurement Computing Corporation immediately by phone, fax, or e-mail:▪Phone: 508-946-5100 and follow the instructions for reaching Tech Support.▪Fax: 508-946-9500 to the attention of Tech Support▪Email: **********************Installing the softwareRefer to the Quick Start Guide for instructions on installing the software on the Measurement Computing Data Acquisition Software CD. This booklet is available in PDF at /PDFmanuals/DAQ-Software-Quick-Start.pdf.Installing the hardwareThe PCI-DIO24 board is completely plug-and-play, with no switches or jumpers to set. Configuration iscontrolled by your system's BIOS. To install your board, follow the steps below.1.Turn your computer off, open it up, and insert your board into an available PCI slot.2.Close your computer and turn it on.If you are using an operating system with support for plug-and-play (such as Windows 2000 or Windows XP), a dialog box pops up as the system loads indicating that new hardware has been detected. If theinformation file for this board is not already loaded onto your PC, you will be prompted for the diskcontaining this file. The MCC DAQ software contains this file. If required, insert the MeasurementComputing Data Acquisition Software CD and click OK.3.To test your installation and configure your board, run the Insta Cal utility installed in the previous section.Refer to the Quick Start Guide that came with your board for information on how to initially set up andload Insta Cal.Configuring the hardwareAll hardware configuration options on the PCI-DIO24 are software controlled.Connecting the board for I/O operationsConnectors, cables – main I/O connectorThe table below lists the board connector type, applicable cables, and compatible accessory products for the PCI-DIO24.Board connectors, cables, and accessory equipmentPin out – main I/O connectorThe I/O connector is a 37-pin, male D-type connector accessible from the rear of the computer through the expansion backplate. The signals available are direct connections to the digital I/O chips as well as the computer's internal power supplies. The pin out is identical to the CIO-DIO24, except that –5 VDC is not brought out. The PCI-DIO24 board's I/O connector is shown in Figure 1.Figure 1. PCI-DIO24 board connector pin outCabling20 137 192013719The red stripeidentifies pin # 1Figure 2. C37FF-x cableFigure 3. C37FFS-x cableField wiring and signal terminationYou can connect the PCI-DIO24 to the following termination boards using the C37FF-x or C37FFS-x cable:▪SCB-37 — 37-conductor, shielded signal connection/screw terminal box that provides two independent 37-pin connections.▪CIO-MINI37 — 4 x 4, 37-pin screw terminal board.▪CIO-MINI37-VERT— 37-pin screw terminal accessory with vertical 37-pin male D connector.▪CIO-SPADE50— 16" X 4" termination panel which mates with both 37-pin and 50-pin connectors. Details on these products are available on our web site at/products/screw_terminal_bnc.aspx.The following relay racks and accessory boards can be used with the PCI-DIO24:▪SSR-RACK24 — 24-position solid state relay rack..▪SSR-RACK08 — Eight-channel solid state relay rack.▪CIO-ERB08 — Eight-channel electromechanical relay accessory for digital I/O boards.▪CIO-SERB08 — Eight Form C and ten socketed relay accessory for digital I/O boards.▪CIO-ERB24 — 24-channel electromechanical relay accessory for digital I/O boards.Details on these products are available on our web site at /products/signal_conditioning.aspx.Chapter 3 Functional DetailsPCI-DIO24 block diagramPCI-DIO24 functions are illustrated in the block diagram shown here.Figure 4. Functional block diagramDIO signalsAll digital outputs and inputs on the PCI-DIO24 are CMOS TTL. Voltages and currents associated withexternal devices are usually far greater than can be supplied from a PCI-DIO24.Caution!Direct connections to high-current/high voltage devices will damage the board.The 82C55 digital I/O chip initializes all ports as inputs on power-up and reset. The state of the digital I/O lines is not defined as either logic high or logic low when in input mode. Input devices connected to the PCI-DIO24 board may detect either a high or a low, and therefore may be turned off or on at power-up.Signal level controlAll I/O bits are set to a high impedance input mode on power up and reset. To prevent unwanted signal levels, and to drive all inputs on the device you are controlling to a known state after power up or reset, install pull-up or pull-down resistors.A pull-up resistor pulls all digital pins up to +5 V (high logic level). A pull-down resistor pulls all digital pins down to 0 V (low logic level).The PCI-DIO24 has open locations where you can install a 2.2 K , eight-resistor single inline package (SIP) resistor network for each port. The SIP is made up of eight 2.2 K resistors. One side of each resistor isconnected to a single common point and brought out to a pin. The common line is marked with a dot or line at one end of the SIP. The remaining resistor ends are brought out to the other eight pins (see Figure 5).2.2K Ohm S IP(L I/O L inesFigure 5. Eight-resistor SIP schematicInstall the SIP on the PCI-DIO24 board at the locations labeled PORT A, PORT B and PORT C (adjacent tothe 37-pin connector). Figure 6 shows a schematic of an SIP installed in both the pull-up and pull-down positions.2.2 K SIP installed for pull-up2.2 K SIP installed for pull-downFigure 6. Pull-up and pull-down resistor SIP schematicWhen installed, the SIP establishes either a high or low logic level at each of the eight I/O lines on the port. At each board location, A, B, and C, there are 10 holes in a line. The hole on one end is marked "HI" and is connected to +5V. The other end is marked "LO" and is connected to GND. The eight holes in the middle connect to eight lines of the port, A, B or C.To pull-up lines, orient the SIP with the common pin (dot) toward the HI end; to pull-down, install the resistor with the common pin in the LO hole.SIPs (MCC part number SP-K2.29C). Use a different value only if necessary.Chapter 4 SpecificationsTypical for 25 °C unless otherwise specified.Specifications in italic text are guaranteed by design.Power consumptionTable 1. Power consumption specificationsDigital input / outputTable 2. Digital input / output specificationsEnvironmentalTable 3. Environmental specificationsPCI-DIO24 User's Guide SpecificationsMain connector and pin outTable 4. Board connector, cables, and accessory equipmentTable 5. Connector pin outCarl Haapaoja, Director of Quality AssuranceMeasurement Computing Corporation10 Commerce WaySuite 1008 Norton, Massachusetts 02766(508) 946-5100Fax: (508) 946-9500E-mail: ***************。
学印宝测试代码及故障代码

学印宝测试代码及故障代码面板信息第1 5章: 面板信息目录1. 故障类型& 故障号码 (1)52. 故障显示方法 (1)53. 故障类型 (1)54. 故障号码 (1)55. 卡纸故障显示 (1)56. 面板信息详细列表 (1)51) 叫修故障(Pxx) (1)52) 卡纸故障(Axx) (1)53) 耗材故障(Cxx) (1)54) 设置检查故障(Dxx) (1)55) 警告故障(Exx :叫修故障) (1)56) 警告故障(Fxx : 其它) (1)57) 参数故障(Hx) (1)58) 保存在内存中的故障 (1)5面板信息[15-1]面板信息1. 故障类型& 故障号码故障类型: 显示发生了什么类型的故障故障号码: 显示在哪里发生了故障例如: P01-520(主故障故障P01-520面板信息2.故障显示方法区域递滚卸版扫卸制分进出纸提示哪里发生了故障设置/ 故障LED指示灯(闪烁)设置/ 故障LED指示灯(闪烁或亮)注意:对于油墨和版纸剩余量闪烁:余量少于10%一直亮:空当按*键时,故障类型和故障号码以一秒的间隔切换。
一直亮闪烁面板信息3. 故障类型[信息描述P-xx 叫修故障需要维修人员进行修理,排除故障。
.A-xx 卡纸故障操作者可以按照用户手册中所给出的故障排除步骤进行排除。
b-xx 选配件故障检查连接,重新打开电源或按RESET键,可能排除故障。
c-xx耗材故障版纸卷空了耗材故障废版盒满了耗材故障墨瓶空耗材故障进纸台没有纸张d-xx 设置故障一个或多个开关或传感器为激活E-xx 警告另一种叫修故障。
如机器在此状态继续使用,可能导致问题F-xx 警告机器未处于可以工作的状态Hxxx输入合适的参数Jxx卡纸故障JXX显示取代了A-07、A-08、A-09和A-10卡纸故障显示。
当有JXX显示时,可能是四种A-XX故障之一或其组合。
.面板信息4. 故障号码故障类型后面跟有故障号码。
- 1、下载文档前请自行甄别文档内容的完整性,平台不提供额外的编辑、内容补充、找答案等附加服务。
- 2、"仅部分预览"的文档,不可在线预览部分如存在完整性等问题,可反馈申请退款(可完整预览的文档不适用该条件!)。
- 3、如文档侵犯您的权益,请联系客服反馈,我们会尽快为您处理(人工客服工作时间:9:00-18:30)。
Int J Adv Manuf Technol(2001)18:884–891 2001Springer-Verlag LondonLimitedOn-line Estimation of Workpiece Height by Using Neural Networks and Hierarchical Adaptive Control of WEDMM.T.Yan1,Y.S.Liao2,C.C.Chang21Department of Mechanical Engineering,Huafan University,Taipei Hsien,Taiwan;and2Department of Mechanical Engineering, National Taiwan University,TaiwanWire breakage and unstable machining drastically reduce the machining efficiency and accuracy in wire electrical discharge machining(WEDM).When a stair-shaped workpiece is machined,poor electrolyteflow around the steps leads to wire rupture or unstable machining.This paper presents a WEDM adaptive control system that maintains optimal machining and improves the stability of machining at the stair section where workpiece thickness changes.A three-layer back propagation neural network is used to estimate the thickness of a workpiece. The developed adaptive control system is executed in the hierarchical structure of three control loops,using fuzzy control strategy.In thefirst control loop,the total sparking frequency is controlled within a safe level for wire rupture suppression. In the second control loop,the proportion of abnormal sparks is maintained at a pre-determined level for process control purposes.Based on the estimated thickness of a workpiece, adaptive parameter optimisation is carried out to determine the optimal machining settings and to provide the reference targets for the other two control loops.Experimental results demonstrate that the workpiece height can be estimated by using a feed-forward neural network.The developed adaptive control system results in faster machining and better machining stability than does the commonly used gap voltage control system.Keywords:Adaptive control;Fuzzy control strategy;Neural networks;WEDM1.IntroductionWire breakage and unstable machining drastically reduce the machining efficiency and accuracy in wire electrical discharge machining(WEDM).When a stair-shaped workpiece is machined,poor electrolyteflow around the steps and workpiece Correspondence and offprint requests to:M.T.Yan,Department of Mechanical Engineering,Huafan University,No.1,Huafan Road, Shihtin Hsiang,223Taipei Hsien,Taiwan,R.O.C.E-mail:mtyan@ .tw edges leads to wire rupture or unstable machining.In order to carry out the processing of such a workpiece,a conservative machining setting is commonly used,but,the machining speed is greatly reduced.Many on-line monitoring and control sys-tems have been developed for the improvement of WEDM performance that includes wire rupture prevention,machining efficiency,and stability.Some adaptive control systems employed short sparks and sparking frequency as sensing para-meters to monitor and control wire rupture suppression[1–3]. Higher-power density along the wire electrode resulting from a great number of short sparks or the sudden increase of sparking frequency,contributes to wire rupture.Based on the detection of spark locations on-line,an adaptive control system has been developed to reduce the concentration of discharges at any point and thus to reduce wire breakage[4].A control system has been developed to reduce the risk of wire rupture based on a thermal model.The model is used to perform an on-line calculation of the temperature distribution over the wire electrode[5].Wire breakage can be avoided by these control systems,but they do not guarantee optimal and high-speed machining.An expert system for control of the WEDM process has been developed[6].However,a large amount of compu-tation is required because of the slow learning speed,so it does not work satisfactorily for on-line control purposes.An adaptive control system has therefore been developed to optim-ise the on-line sparking frequency by estimating the workpiece height with a multi-input model[7,8].Since the parameters of the proposed model rely heavily on machining conditions,a great number of experiments and statistical techniques are required to derive the explicit mathematical model.The WEDM metal removal process is characterised by non-linear,stochastic and time-varying characteristics.Moreover, the process features change drastically with machining para-meters.A precise mathematical model describing the WEDM process is difficult to obtain.Hence,classical control strategy and modern control technology based on a well-defined math-ematical model are not applicable for a wide variety of machin-ing conditions.Since a fuzzy control strategy does not need a mathematical model and its control structure is insensitive to variations of process dynamics and noise disturbance,this control strategy has proved to be successful in various complexOn-line Estimation of Workpiece Height885 processes where mathematical models are unknown or ill-defined[9].Fuzzy control strategy has been applied to theadaptive control of the WEDM process in our previous studies[10,11].However,lack of on-line estimation of the workpieceheight may cause the system not to run properly when a stair-shaped workpiece is machined.Artificial neural networks havebeen implemented in various manufacturingfields such as toolbreakage monitoring,inverse modelling of the cutting processand monitoring machining processes[12].The neural networkapproach has also been applied to modelling and on-linemonitoring of the EDM process[13,14].This paper presentsa WEDM adaptive control system that maintains optimal mach-ining conditions and improves the stability of machining atstair sections where the workpiece thickness changes.A three-layer back-propagation neural network is used to estimate thethickness of the workpiece.The developed adaptive controlsystem is executed in a hierarchical structure of three controlloops by using a fuzzy control strategy.In thefirst controlloop,the total sparking frequency is monitored and controlledwithin a safe level for wire rupture suppression.The proportionof abnormal sparks is maintained at a pre-determined level forprocess control purposes in the second control loop.In thethird control loop,adaptive parameter optimisation is carriedout to determine the optimal machining settings and to providethe reference targets for the other two control loops.Experi-ments demonstrate that the proposed adaptive control systemcan achieve better machining results than the commonly usedgap voltage control system.2.Hardware Set-up of the WEDMAdaptive Control SystemFigure1shows the hardware set-up of the WEDM adaptivecontrol system[3,11].The control system consists of aflushing-type WEDM machine,a WEDM sparking frequency monitor(composed of a photocouple circuit and an AX5216countercard),a PC,and an interface for communication between thePC and the CNC unit of the machine.The WEDM machineis a5-axis CNC machine with a transistor-controlled powergenerator.The power generator(composed of a lower-powercircuit,a high-power circuit,and a pulse generator)is an iso-energy power supply system.Normal sparks and arc sparkscan be discriminated by the pulse generator according to theignition delay time and the voltage level of each spark.Basedon the discrimination of gap status,the discharge durations ofnormal sparks and arc sparks are controlled and specifiedbyFig.1.Hardware set-up of the WEDM adaptive control system.means of on-time and arc on-time settings,respectively.Simi-larly,the pulse intervals of normal sparks and arc sparks are controlled by off-time and arc off-time settings,respectively. The discharge current of this power supply system has a triangular waveform with a current rise of400AsϪ1.Flush-ing pressure can be tuned by a hand valve.The adjustable parameters of this machine include on-time,off-time,arc on-time,arc off-time,servo reference voltage,feedrate override, wire speed,and wire tension,and their working ranges are given in Table1.Servo reference voltage and feedrate override represent the reference value and the servo gain,respectively, for the gap voltage control system with which this machine is equipped.It is clear that a higher value of servo gain may result in a fast transient response and unstable conditions in the steady state.By using the sparking frequency monitor,total sparks(Nt),normal sparks(Nn)and abnormal sparks(Na) (composed of arc discharge and short circuit)in a specific time interval(⌬t)are detected and counted.A PC/AT-586is used for calculation and implementation of the control algor-ithm.The sampling interval is adjustable within the range of 2–65535ms.Thus,the total sparking frequency(Ft)and the proportion of abnormal sparks(n a,referred as the abnormal ratio)can be computed as Nt/⌬t and Na/Nt,respectively.An RS485interface card is employed to handle the I/O (input/output)data and to communicate with the CNC unit through an RS232port.Through the interface,all machining parameters including power settings and servo reference voltage can be updated,and machining results including average gap voltage and machining feedrate can be accessed in real-time.3.On-line Estimation of Workpiece Height by Using Neural NetworkBecause of the stochastic nature of the discharge mechanism, it is still not easy to describe the WEDM process by an explicit mathematical model.In order to reduce the complexity and difficulty in deriving the workpiece height based on a mathematical model,a feedforward neural network is adopted here to estimate the workpiece height.The feedforward neural network is composed of many interconnected processing elements,called neurons or nodes,which operate in parallel, and can be grouped into input,hidden,and output layers.The outputs of nodes in one layer are transmitted to nodes in another layer through connections that amplify or attenuate the outputs through weight factors.An artificial neuron is divided Table1.Adjustable parameter of the WEDM machine.Items RangeOn-time0.1–0.9s(9steps)Off-time8–50s(43steps)Arc on-time0.1–0.5s(5steps)Arc off-time9–50s(42steps)Servo reference voltage30–70VFeedrate override0–310%Wire speed1–15mm minϪ1(15steps)Wire tension500–2500gf(15steps)886M.T.Yan et al.into two parts:a summation function and an activation function.The summation function for all of the inputs is calculated by net n jϭi W ji O nϪ1iϪn j(1) where net n j is the summation function of the j th neuron in the n th layer,W ji is the weight from the i th neuron in the(nϪ1)thlayer.O nϪ1iis the output of the i th neuron in the(nϪ1)th layer.n j is the threshold value of the j th neuron in the n th layer.The neuron performs nonlinear mapping of the result of the summation function through its activation function and then determines the output.The output of the neuron is then transmitted along the outgoing connections to serve as an input to subsequent neurons.In the present study,a sigmoid function is used as the activation function.The output of the j th neuron for the n th layer can be expressed asO n jϭf(net n j)ϭ11ϩnet n j(2)The connection weights are adapted properly using the back-propagation learning algorithm[15],which uses a gradient-descent technique to minimise the summation of the squared error between the calculated output of the network and the desired output.Thus,the weights in the n th layer are modified by an amount⌬W n ji,given by⌬W n ji(k)ϭϪѨEѨW n jiϩ␣⌬W k ji(kϪ1)(3)where E represents the squared error,is the learning rate,␣is the momentum coefficient,and k is the number of the current iteration.In a multilayer neural network,the weights of the nodal connection are randomly set and modified.A large number of iterations are required to back-propagate the error until an acceptable error tolerance level is achieved through the training process.The training of the network is carried out off-line.In this study,total sparking frequency,normal sparking frequency,arc sparking frequency,abnormal ratio,average gap voltage,real feedrate,variation of average gap voltage,and variation of feedrate are employed as input signals for the input layer of the neurons.The variation of gap voltage is specified as the difference between the mean value of ten successive sampling gap voltages and the current sampling gap voltage.Similarly,the variation of feedrate is specified as the difference between the mean value of ten successive sampling feedrates and the current sampling feedrate.Average gap volt-age and feedrate change drastically when the machining plate thickness is varied.Thus,change of average gap voltage and change of feedrate can be used as input signals to the neuron to distinguish a stable machining status from a transient machining status.Hence,the output layer of the neural network has two nodes,which represent the workpiece height and the machining status,respectively.The output value of the machining status ranges between zero and one.Stable machining status and transient machining status are specified as zero and one, respectively,during the training of the neural networks.In our case,a feedforward neural network of the8-9-2type with back-propagation learning is used here to estimate the work-piece height and distinguish the machining status.Thesampling Fig.2.Schematic diagram of the neural network for the estimation of the workpiece height.interval for data acquisition is200ms.Figure2shows a net schematic diagram of the neural work for the estimation of the workpiece height.4.Hierarchical Adaptive Control of WEDM Figure3shows a schematic diagram of the hierarchical adapt-ive control system.The developed adaptive control system is executed in a hierarchical structure of three control loops by using fuzzy control strategy.In thefirst control loop,the total sparking frequency is controlled within a safe level for wire rupture suppression.In the second control loop,theproportionFig.3.Schematic diagram of the hierarchical adaptive control system. to,pulse interval time;te,discharge duration;f,feedrate;Vs,servo reference voltage;Vg,average gap voltage;Ft,total sparking fre-quency;Fn,normal sparking frequency;Fa,arc sparking frequency; Yr,reference frequency;n r,reference ratio;H,estimated workpiece height;Ms,machining status.On-line Estimation of Workpiece Height887of abnormal sparks is maintained at a pre-determined level by regulating the servo reference voltage for process control pur-poses.Based on the estimated thickness of the workpiece through the feedforward neural network,adaptive parameter optimisation is implemented for the third loop by determining the optimal machining settings and providing the reference targets for the other two control loops during machining.A fuzzy controller uses a set of linguistic control rules related by the dual concepts of fuzzy implication and the composition rule of inference.In essence,the fuzzy controller provides a useful tool for converting heuristic control rules based on an expert’s knowledge or an operator’s experience into an auto-matic control strategy.The rule-based control strategy is often designed to simulate human experience and human intelligence.A typical fuzzy logic controller consists of four major parts: a fuzzifiation interface,a knowledge base,decision-making logic,and a defuzzification interface.A detailed discussion on the design of fuzzy controllers for adaptive control of the WEDM process is presented in the following subsections. 4.1Adaptive Control for Wire Rupture SuppressionWhen a stair-shaped workpiece is machined,poor electrolyte flow around step shapes leads to a sudden rise of sparking frequency,which causes wire rupture or unstable machining. Therefore,the sparking frequency should be controlled within a safe level in order to suppress wire breaking and unstable machining[3].In response to the sudden rise of sparking frequency,a fuzzy controller is provided by adjusting the pulse interval time(to)and discharge duration(te).Once the sparking frequency is controlled within a safe level,the control para-meters are restored to their initial values to maintain an optimal machining speed.Error and change of error are two variables commonly adopted for the input of a fuzzy logic controller.A scale mapping is carried out beforehand that transfers the range of values of the input variables into the corresponding universe of discourse.The linguistic variables to be used in the premise of control rules are defined as follows:e1ϵsparking frequency errorϭ(reference frequencyϪsparking frequency)ϫGE1 andce1ϵchange of sparking frequency errorϭ(current frequency errorϪprevious frequency error)ϫGCE1where GE1and GCE1are scaling factors and their values are found to be15and10,respectively.Five linguistic sets for the domains of definition denoted by NB,NS,ZO,PS and PB are specified,where P,B,S,N and ZO correspond,respect-ively,to positive,big,small,negative and zero.An isosceles triangle-shaped function is chosen as the membership function of each linguistic set for the input and output of the controller. Twenty-five control rules are formulated,as shown in Table 2.The max–min inference method and the mean of maximum method are used to perform fuzzy reasoning and defuzz-Table2.Rule base of the fuzzy controller for wire rupture prevention.⌬u1e1/ce1PB PS ZO NS NBPB PB PB PS ZO NSPS PS PS PS NS NSZO PS NS ZO NS NBNS NS NS NB NB NBNB NB NB NB NB NB⌬u2PB ZO ZO ZO ZO ZOPS ZO ZO ZO ZO ZOZO ZO ZO ZO ZO ZONS NS NS NS NS NSNB NB NB NB NB NBification,respectively[16].The real control parameters applied to the pulse generator are calculated from,u to(k)ϭu to(kϪ1)ϩ⌬u1(k)(4) u te(k)ϭu iϩ⌬u2(k)(5) where u to(k)represents the control signal at the k th sampling instance,and it is defined as the reciprocal of pulse interval time(to),i.e.toϭ1/u off,u te(k)represents the discharge duration (te)at the k th sampling instance,u i stands for the initial value of discharge duration,⌬u1and⌬u2are the output of the fuzzy controller.4.2Adaptive Process ControlThe objective of adaptive process control of WEDM is to maintain a high metal removal rate during roughing,and optimal and stable machining duringfinishing.A fuzzy control-ler is designed for adaptive process control by means of controlling the proportion of abnormal sparks at an optimal level.The optimal value of the abnormal ratio is40%–60%, as shown in our previous study[10].The linguistic variables used in the premise of the fuzzy controller are abnormal ratio error(e2)and change of the abnormal ratio error(ce2).The functional relationship represented by such a fuzzy controller can be described as⌬u sϭF(e2,ce2)(6) where⌬u s represents the output of the controller,and F(·) stands for the nonlinear relationship of the fuzzy controller. The domain of the input variables and the output variable are divided into seven fuzzy subsets,“Negative big”,“Negative medium”,“Negative small”,“Zero”,“Positive small”,“Positive medium”,“Positive big”and their domain ranges fromϪ3to 3.An isosceles triangle-shaped function is also chosen as the membership function of each linguistic set.Forty-nine fuzzy rules are designed according to the following concept.If the abnormal ratio is larger than the reference value,the servo reference voltage should be increased to improve the poor gap condition.If the abnormal ratio is lower than the pre-determ-ined level,the servo reference voltage should be decreased to maintain an optimal machining speed.The fuzzy control rules888M.T.Yan et al.Table3.Rule base of the fuzzy controller for adaptive process control.⌬u se2/ce2PB PM PS ZO NS NM NBPB NB NB NB NB NM NM NMPM NB NB NM NM NM NM NMPS NM NM NM NS NS NS NSZO NM NS NS ZO NS PS PSNS PS PS PS PS PS PS PSNM PM PM PM PM PM PM PMNB PB PB PB PB PB PB PBare given in Table3.The max–min inference method and the mean of maximum method are also used to carry out fuzzy reasoning and defuzzification,respectively.The servo reference voltage applied to the gap voltage control system is calcu-lated byus(k)ϭu s(kϪ1)ϩ⌬u s(k)(7) where u s(k)represents the servo reference voltage setting at the k th sampling instance,and⌬u s is the output of the fuzzy controller.4.3Adaptive Parameter OptimisationThe control loop for adaptive parameter optimisation aims to select the machining setting and to adjust the reference values for the other two control loops.The decision to carry out the control loop of parameter optimisation or not depends on the stability of machining conditions and the machining status from the neural network.A stability percentage(SP)is defined as the performance index to evaluate the machining condition, and it is expressed asSPϭͩ1Ϫn a(k)Ϫn a(kϪ1)n rͪϫ100%(8) where n a(k)represents the proportion of abnormal sparks at the k th sampling instance,and n r stands for the abnormal ratio reference.The machining condition is referred to as stable machining if the stability percentage is greater than95%,and vice versa.If stable machining is maintained for150sampling intervals(200ms)and the machining status is less than0.2,a rule-based control strategy is carried out to control the machin-ing parameters at the optimal setting.As shown in Table4,a specific rule is selected according to the on-line estimatedTable4.Rule base for the control loop of adaptive parameter optimis-ation.Workpiece Machining Reference Reference height setting ratio frequency0–H1S1R1F1H1–H2S2R2F2H2–H3S3R3F3%%%%H nϪ1–H n S n R n F n workpiece height.For example,if the estimated workpiece height ranges from H nϪ1to H n,the machining parameters,the abnormal ratio reference and the reference sparking frequency are set to S n,R n,and F n,respectively.5.Experimental ResultsThe developed neural networks and adaptive control strategies are implemented in a PC/AT using the C language.The sampling intervals for adaptive control for wire rupture sup-pression,adaptive process control and adaptive parameter optimisation are200ms,2s,and30s,respectively.Some experiments are conducted under the conditions of machining a workpiece with a sudden increase in height,a sudden decrease in height,or with a constant slope,to verify the applicability of the proposed adaptive control system.Machining settings and reference values used in the experiments is given in Table 5.The experimental results are presented compared with those of a gap voltage control system commonly used in commercial-ised WEDMmachines.Fig.4.(a)Estimated workpiece height and real feedrate,(b)sparking frequency and pulse interval time,and(c)abnormal ratio and servo reference voltage with adaptive control system when a workpiece with a sudden decrease in height is machined.On-line Estimation of Workpiece Height889 Table5.Machining setting and reference values used in the experimentsWorkpiece:SKD11tool steelWire electrode:Brass0.25mm diameterWire feed:7m minϪ1;Wire tension:1000gfUpper water pressure:6.5bar;Lower water pressure:11barWorkpiece On Off Arc on Arc off Reference Referenceheight time time time time ratio frequency(mm)(s)(s)(s)(s)(%)(kHz)28–330.9120.418483633–380.9120.418503838–430.9120.518524043–480.9120.518534248–530.9120.5185445Figure4shows the machining results with an adaptivecontrol system when a workpiece with a sudden decrease inheight is machined.As shown in Fig.4(a),the estimatedworkpiece height can follow the real workpiece thicknessduring machining.Figure4(b)demonstrates that the adaptivecontrol system can control the sparking frequency within areference level by adjusting the pulse interval time.Figure4(c)demonstrates that the abnormal ratio can be controlled toaFig.5.(a)Real feedrate,(b)sparking frequency,and(c)average gap voltage with gap voltage control system when a workpiece with a sudden decrease in height is machined.pre-determined level by adjusting the servo reference voltage. Figure5shows the machining results with the gap voltage control system under the same conditions as Fig.4.As illus-trated in Fig.5,poorflushing conditions lead to unstable machining at the stair section where the workpiece thickness changes.The adaptive control system enables the stability of machining conditions and the machining speed to improveby Fig.6.(a)Estimated workpiece height and real feedrate,(b)sparkingfrequency and pulse interval time,and(c)abnormal ratio and servo reference voltage with adaptive control system when a workpiece with a sudden increase in height machined.890M.T.Yan et al.15%compared with the commonly used gap voltage control system.Figure 6shows the machining results using an adaptive control system when a workpiece with a sudden increase in height is machined.For comparison purposes,the same test with gap voltage control system is conducted and the recorded data is shown in Fig.7.By comparing Figs 6and 7,it can be seen that the adaptive control system is capable of improving the machining speed and properly estimating the workpiece height within an acceptable accuracy of 1.6mm.Figure 8shows the experimental results of the adaptive control system when a workpiece with a constant slope height is machined.This figure indicates that the estimated workpiece height is similar to the real workpiece pro file.The developed adaptive control system can adapt suitable machining parameters to the gradual decrease in workpiece height.6.DiscussionHaving described the experiments on the hierarchical adaptive control system for the WEDM process,some issues when applying the neural network to the developed adapative control system for wire rupture prevention are addressed in thefollow-Fig.7.(a )Real feedrate,(b )sparking frequency,and (c )average gap voltage with gap voltage control system when a workpiece with a sudden increase in height is machined.ing discussion.In order to enhance the potential of a practical application,two approaches to applying the neural networks to the WEDM process are considered.For the first approach,the neural networks are trained under constant power settings and the corresponding weighting factors are recorded and stored in a memory space.Thus,networks can be applied to different machining conditions using the memory-based weighting fac-tors.For the second approach,the networks have power con-dition information by incorporating power settings as input signals.Since the process parameters are incorporated into the learning process,the networks are expected to operate well for a wide variety of machining conditions.Two types of wire-breaking phenomenon have been found and identi fied from our previous investigation [3,17].The first type is a sudden rise of total sparking frequency,and the duration of deterioration ranges from 50ms to 2s.This type of wire rupture often occurs when the machining conditions,particularly the discharge duration or the flushing pressure,are changed during the machining process.In the second type of wire breaking,the sparking frequency increases slightly and the duration of the premonitory symptoms lasts for 10s or more.This kind of wire breaking often takes place whenaFig.8.(a )Estimated workpiece height and real feedrate,(b )sparking frequency and pulse interval time,and (c )abnormal ratio and servo reference voltage with adaptive control system when a workpiece with a constant slope height is machined.On-line Estimation of Workpiece Height891stair-shaped workpiece is machined or a workpiece is machined under poorflushing conditions.Some workers have also shown that wire rupture may happen in a short time(5–40ms)[1,2]. Thus,the developed adaptive control system may not respond promptly and properly to some poor machining conditions in a short time(5ms)because of the bottleneck caused by communication delays and real-time control in a PC.Neverthe-less,the developed system can reduce the possibility of wire rupture and improve the stability of machining at some difficult machining conditions that include some of thefirst and second types of wire breaking processes.To enhance the potential of avoiding wire rupture in all machining conditions,the developed adaptive control system should be implemented using a DSP-based control card or a hardware control module which is directly linked to the power supply system of a WEDM machine.Such an adaptive control system will increase the hardware cost.Development of a DSP-based machining process monitoring and control system is under way.7.ConclusionA feedforward neural network is presented using a back-propagation learning algorithm for the estimation of the work-piece height in WEDM.The average error of workpiece height estimation is1.6mm,and the transient response to change in workpiece height is reasonably satisfactory.The developed adaptive control system is carried out in three hierarchical levels using a fuzzy control strategy.The sparking frequency is controlled within a safe level for wire rupture suppression, and the abnormal ratio is also controlled at the optimal level when a workpiece with variable height is machined.Experi-mental results also show that the neural network approach and fuzzy control strategy are suitable for such an uncertain and complicated process.The developed hierarchical adaptive control system enables the machining stability and the machin-ing speed to be improved by15%compared with a commonly used gap voltage control system.References1.N.Kinoshita,M.Fukui and G.Gamo,“Control of wire-EDMpreventing electrode from breaking”,Annals CIRP,31(1),pp.111–114,1982.2.K.P.Rajurkar and W.M.Wang“On-line monitor and controlfor wire breakage in WEDM”,Annals CIRP,40(1),pp.219–222,1991.3.M.T.Yan and Y.S.Liao,“Monitoring and self-learning fuzzycontrol for wire rupture prevention in wire electrical discharge machining”,International Journal of Machine Tools and Manufac-ture,36(3),pp.339–353,1996.4.K.Shoda,Y.Kaneko,H.Nishimura,M.Kunieda and M.X.Fan,“Adaptive control of WEDM with on-line detection of spark locations”,Proceeding of10th International Symposium for Elec-tro-Machining(ISEM-10),pp.410–416,1992.uwers,J.P.Kruth,Ph.Bleys,B.Van Coppenolle,L.Stevensand R.Derighetti,“Wire rupture using on-line pulse localization in WEDMB”,Proceeding of12th International Symposium for Electro-Machining(ISEM-12),pp.203–213,1998.6.W.Dekeyser,R.Snoeys and M.Jennes,“Expert system for wirecutting EDM,based on pulse classification and thermal modeling”, Robotics and Computer-Integrated Manufacturing,4(1/2),pp.219–224,1988.7.K.P.Rajurkar,W.M.Wang and J. A.McGeugh,“WEDMidentification and adaptive control for variable height components”, Annals CIRP,43(1),pp.199–202,1994.8.K.P.Rajurkar,W.M.Wang and W.S.Zhao,“WEDM-adaptivecontrol with a multiple input model for identification of workpiece height”,Annals CIRP,46(1),pp.147–150,1997.9.M.Sugeno,Industrial Application of Fuzzy Control,North-HollandAmsterdam,1985.10.M.T.Yan and Y.S.Liao,“Adaptive control of WEDM processusing the fuzzy control strategy”,Journal of Manufacturing Sys-tems,17(4),pp.263–274,1998.11.Y.S.Liao and J.C.Woo,“A new fuzzy control system for theadaptive control of WEDM process”,Proceeding of12th Inter-national Symposium for Electro-Machining(ISEM-12),pp.193–202,1998.12.J.Prohaszka,“A step toward intelligent manufacturing:modelingand monitoring of manufacturing processes through artificial neural networks”,Annals CIRP,42(1),pp.485–488,1993.13.T.A.Spedding and Z.Q.Wang,“Study on modeling of wireEDM process”,Journal of Materials Processing Technology,69, pp.18–28,1997.14.J.Y.Kao and Y.S.Tarng,“A neural-network approach for theon-line monitoring of the electrical discharge machining process”, Journal of Materials Processing Technology,69,pp.112–119, 1997.15.J.M.Zurada,Introduction to Artificial Neural Systems,West,1992.16.C.C.Lee,“Fuzzy logic in control systems:fuzzy logic controller–Part I and Part II,”IEEE Transactions on Systems,Man,and Cybernetics,20(2),pp.404–435,1990.17.Y.S.Liao,Y.Y.Chu and M.T.Yan,“Study of wire breakingprocess and monitoring of WEDM”,International Journal of Machine Tools and Manufacture,37(4),pp.555–567,1997.。