如何建立OEE管理体系ppt课件
合集下载
OEE(设备综合效率)分析与管理ppt课件

计划运行时间=12*60-10=710(min) 实际运行时间=710-30-40-20=620(min) 时间利用率=620/710*100%=87% 设备性能率=1200*0.5/620)*100%=97% 质量指数(QDI)=(1200-50)/1200*100%=96% OEE=时间利用率*设备性能率*质量指数 =87%*97%*96% =81% TEEP=710/720*81%*100% =79.8%
故障是冰山的一角
“如果我们问一问为什么会发生这样的情况——为什么、为什么、—— 我们通常能找出问题,以及解决问题的方法。
灰尘、污垢、原料粘附 磨损、偏斜、松动、泄露 腐蚀、变形、伤痕、裂纹 温度、震动、声音等异常
故障
灰尘、污垢、原料粘附 磨损、偏斜、松动、泄露 腐蚀、变形、伤痕、裂纹 温度、震动、声音等异常
OEE衡量的是礁石的大小,说明应该先从哪块暗礁着手处理。
8.OEE可带来的管理效益
1.企业规划: A、可以为企业规划提供客观科學的決策依据。 B、可以为企业提供很多的增值意見和建议。
2.生产管理: A、现场实时数据的收集,建立监控管理系统。 B、对OEE数据分析,规避潜在风险,降低设备六大损失,挖掘设备最大潜能。 C、为企业精益生产管理提供可视化的生产報告。
您是不是正在制造一个不合格产品
早晨机器的启动需要花去一定的时间
二、OEE的定义及开展目的
1.OEE是什么?
OEE代表整体设备效能; 这是一种严格的机器总体性能的衡量手段,揭示时间浪费存在于哪里,统计各种时间浪费,目的在于实现改进。
总时间损失
生产转换
故障停机
传统效率衡量方式只计算了部分时间损失
计划外停机
速度缓慢
设备损坏
故障是冰山的一角
“如果我们问一问为什么会发生这样的情况——为什么、为什么、—— 我们通常能找出问题,以及解决问题的方法。
灰尘、污垢、原料粘附 磨损、偏斜、松动、泄露 腐蚀、变形、伤痕、裂纹 温度、震动、声音等异常
故障
灰尘、污垢、原料粘附 磨损、偏斜、松动、泄露 腐蚀、变形、伤痕、裂纹 温度、震动、声音等异常
OEE衡量的是礁石的大小,说明应该先从哪块暗礁着手处理。
8.OEE可带来的管理效益
1.企业规划: A、可以为企业规划提供客观科學的決策依据。 B、可以为企业提供很多的增值意見和建议。
2.生产管理: A、现场实时数据的收集,建立监控管理系统。 B、对OEE数据分析,规避潜在风险,降低设备六大损失,挖掘设备最大潜能。 C、为企业精益生产管理提供可视化的生产報告。
您是不是正在制造一个不合格产品
早晨机器的启动需要花去一定的时间
二、OEE的定义及开展目的
1.OEE是什么?
OEE代表整体设备效能; 这是一种严格的机器总体性能的衡量手段,揭示时间浪费存在于哪里,统计各种时间浪费,目的在于实现改进。
总时间损失
生产转换
故障停机
传统效率衡量方式只计算了部分时间损失
计划外停机
速度缓慢
设备损坏
oee培训ppt课件
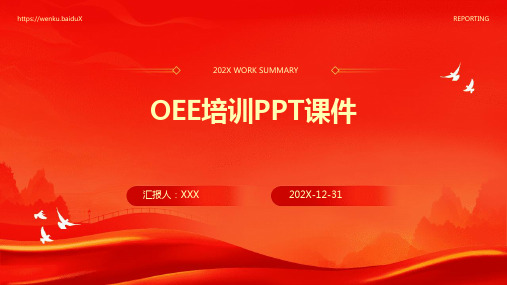
RY
OEE培训PPT课件
汇报人:XXX
202X-12-31
REPORTING
目录
• OEE基本概念 • OEE的重要性和影响 • 如何提高OEE • OEE的监控与改进 • OEE的未来人和时间节点,确保措施的 有效执行。
对改进措施进行风险评估和经 济效益分析,确保措施的公道 性和可行性。
跟踪改进效果
实施改进措施后,持 续监测OEE数据的变 化情况,评估改进效 果。
根据跟踪结果,及时 调整和优化改进措施 ,持续提高OEE水平 。
对改进效果进行统计 分析和可视化展示, 便于团队成员了解改 进成果。
下落生产成本
提高装备效率可以下落生产成本,因为装备效率的提高意味 着生产进程中所需的人力和物力资源更少,能源消耗更低, 从而下落了生产成本。
OEE培训可以帮助员工更好地掌握成本控制的方法和技能, 通过优化生产流程、减少浪费等措施,进一步下落生产成本 。
提升产品质量
01
装备效率的提高可以提升产品质 量,因为装备的稳定高效运行可 以减少产品缺陷和不良品率。
PART 04
OEE的监控与改进
OEE数据收集与整理
确定数据收集的指标
根据装备特点和生产要求,确定需要收集的OEE指标,如开机率 、故障率、准备时间等。
制定数据收集计划
确定数据收集的时间间隔、采集人员和采集方式,确保数据的准确 性和实时性。
数据整理与存储
对收集到的数据进行整理、分类和存储,便于后续的分析和查询。
备用装备
配备备用装备,在主装备故障时,能 够迅速切换到备用装备,保证生产连 续性。
提高操作员技能
培训教育
定期对操作员进行技能培训和安 全教育,提高操作员的专业素养
OEE培训PPT课件
汇报人:XXX
202X-12-31
REPORTING
目录
• OEE基本概念 • OEE的重要性和影响 • 如何提高OEE • OEE的监控与改进 • OEE的未来人和时间节点,确保措施的 有效执行。
对改进措施进行风险评估和经 济效益分析,确保措施的公道 性和可行性。
跟踪改进效果
实施改进措施后,持 续监测OEE数据的变 化情况,评估改进效 果。
根据跟踪结果,及时 调整和优化改进措施 ,持续提高OEE水平 。
对改进效果进行统计 分析和可视化展示, 便于团队成员了解改 进成果。
下落生产成本
提高装备效率可以下落生产成本,因为装备效率的提高意味 着生产进程中所需的人力和物力资源更少,能源消耗更低, 从而下落了生产成本。
OEE培训可以帮助员工更好地掌握成本控制的方法和技能, 通过优化生产流程、减少浪费等措施,进一步下落生产成本 。
提升产品质量
01
装备效率的提高可以提升产品质 量,因为装备的稳定高效运行可 以减少产品缺陷和不良品率。
PART 04
OEE的监控与改进
OEE数据收集与整理
确定数据收集的指标
根据装备特点和生产要求,确定需要收集的OEE指标,如开机率 、故障率、准备时间等。
制定数据收集计划
确定数据收集的时间间隔、采集人员和采集方式,确保数据的准确 性和实时性。
数据整理与存储
对收集到的数据进行整理、分类和存储,便于后续的分析和查询。
备用装备
配备备用装备,在主装备故障时,能 够迅速切换到备用装备,保证生产连 续性。
提高操作员技能
培训教育
定期对操作员进行技能培训和安 全教育,提高操作员的专业素养
OEE(设备整体效能)-ppt课件
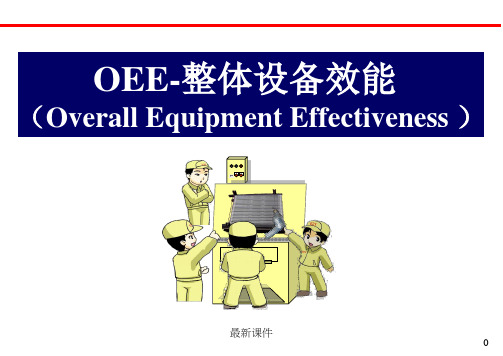
B1 非工作日 设备关闭的天数,或者用当月的天数减去成型车间运行的天数
B2 突发异常事件 工作的天数与工厂运营的时间差异。这个差异可能是由罢工,临时解雇,暂停工作,缺乏能源以及考虑的但没有工作的天数。 加班和额外的天数(在计划中没有预见的天数)需要减去。
C 设备不可用于生产 这部分指的是设备由于(试验,调试,升级,检修,移动)等原因不能用于正常生产的时间
产品生产 频繁故障
线换线时
启动废品 间长
空转小
产品质
运行缓慢
停机频
量低下
繁
库存水平
最新课件
OEE衡量的是礁石的大小,说 明应该先从哪块暗礁着手处理
30 58%
20
154 160
120 90%
80 48
40
0 textile bobbin ply bobbin
98%
10
21,2
0
Material change
T 周期时间-生产单位产品所需要的时间
7
D1. OEE 报表说明
A TOTAL TIME(总时间)
公式
定义
B1 DAYS NOT WORKED(非工作日)
B2 EXCEPTIONAL EVENTS(突发异常事件)
班
B LOSS FOR DAYS NOT WORKED(非工作日损失)
B=B1+B2 长
V=[(G-H)/G]
W PERFORMANCE EFFICIENCY(表现率) X QUALITY RATE(质量指数)
最新课件 W=T*(R+M)/I
H6 MATERIAL CHANGE(换料) H7 ABSENCE NOT PLANNED(非计划性停机 H NON AVAILABILITY LOSS(不可利用损失)
OEE培训教材(ppt44张)

时
间
5大人力损失
11 12 13 14
3大原材料与能源损失
成
15 16
本
我们的近邻联合利华世界500强在经过近10年的OE 的管理,2010年才从12大损失向16大损失迈进。
其中它是先做6大损失到9大损失到12大损失不断的摸索 才有今天的成绩。数据显示联合利华洗衣粉的产量从2004 日产260T/D到2010年日产近1000T/D。其中生产机器只增 了50%。在OEE的数据支撑下结合一些优良的管理方法再 加上公司员工的群策群力下设备的效率平均提高了48.6%
…
OEE 表格
原来 修改制作 在修改的
你会选择那种表?
中国员工的画像
海尔总裁张瑞敏关于人的品质有一段精彩的论述; “如果训练一个日本人,让他每天擦六遍桌子,他一定 会这样做;而一个中国人开始会擦六遍,慢慢觉得五遍 四遍也可以,最后索性不擦了”,“中国人坐事最大毛 是不认真,做事不到位,每天工作欠缺一点,天长地久 成为落后的顽症”。
OEE表的填写标准
上班第一时间填写OEE表上的日期、班次 、机器号、包装机、设定速度 开班清理、点检、润滑后填写开停车时间 开机至机器正常运行时填写试车时间 运行过程中出现如故障、小停机调整等填 写相应项,吃饭停机后要填写吃饭时间 不得提前填写或推迟填写
【OEE】要注意的问题
设备综合效率 = 时间利用率 * 设备性能率 * 产品合格率
1. 时间利用率 = (负荷时间 - 停机损失) / 负荷时间 * 100%
2. 设备性能率 = 生产产品数 / (利用时间 * 设计速度) * 100
3. 质量缺陷率 = (生产产品数 - 不合格品) / 生产产品数 * 1
TPM与PAMCO OEE的差别
OEE(设备综合效率)简介 PPT
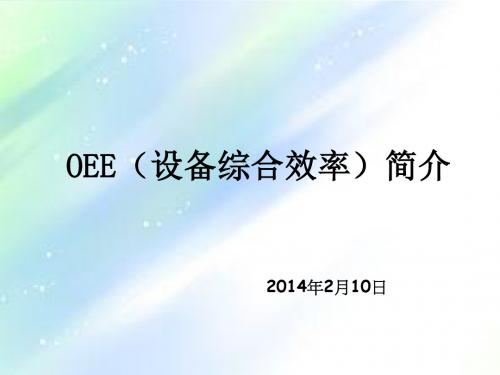
请问该设备的设备综合效率为多少?
A:实际作业时间 =480+30=510min C:负荷时间 510-50=460min E:利用时间 C-D =390min H:合格率 98% J:实际节拍1.1
B:计划停止时间 50min D:停机损失时间 70min G:生产量418件 I:理论节拍0.8
时间利用率= 设备性能率=
技能员技能的提升
RTC培训(制造、保全)
故障零化 严格执行点检表制度 提升保养人员的技能 对故障的彻底分析与对策 改进设计上的缺陷
提高品质 提高合格率 返修率的降减
减少短暂停线 三现主义的想法 PM分析 改善课题 小暂停管控
系统水准
消除
超出管制
OEE管制 保持
TPM改善
!
• OEE要作为一系列一体化的综合关键业绩指标中 的一部分来运用而不能孤立使用,否则将造成生
产批次规模加大或有质量缺陷的产品
!
• OEE必须与精益原则相符,要确保对OEE的计 算不会导致浪费合理化、制度化,例如,绝不要 允许给换线留出时间
20
注意: 0<OEE<100
设备超负荷运行
为什么有的企业 OEE>100?
完成停止时间+加班时间
加班时间
实际作业时间
负荷时间:为了完成生产计划、设备必须运转的时间
负荷时间 = 实际作业时间 - 计划停止时间
计划停止时间包含早晚例会、休息时间、始业点检、安全点检、
自主保全、体制展开、试作、计划停止时间等时间
负荷时间
利用时间= 负荷时间-停线时间
实际作业时间
停线时间:工具更换、调整、故障停止、上下流等待、
计划停 止时间
质量维持、确认、工件不良、操作失误、作业缓滞停止等时间
A:实际作业时间 =480+30=510min C:负荷时间 510-50=460min E:利用时间 C-D =390min H:合格率 98% J:实际节拍1.1
B:计划停止时间 50min D:停机损失时间 70min G:生产量418件 I:理论节拍0.8
时间利用率= 设备性能率=
技能员技能的提升
RTC培训(制造、保全)
故障零化 严格执行点检表制度 提升保养人员的技能 对故障的彻底分析与对策 改进设计上的缺陷
提高品质 提高合格率 返修率的降减
减少短暂停线 三现主义的想法 PM分析 改善课题 小暂停管控
系统水准
消除
超出管制
OEE管制 保持
TPM改善
!
• OEE要作为一系列一体化的综合关键业绩指标中 的一部分来运用而不能孤立使用,否则将造成生
产批次规模加大或有质量缺陷的产品
!
• OEE必须与精益原则相符,要确保对OEE的计 算不会导致浪费合理化、制度化,例如,绝不要 允许给换线留出时间
20
注意: 0<OEE<100
设备超负荷运行
为什么有的企业 OEE>100?
完成停止时间+加班时间
加班时间
实际作业时间
负荷时间:为了完成生产计划、设备必须运转的时间
负荷时间 = 实际作业时间 - 计划停止时间
计划停止时间包含早晚例会、休息时间、始业点检、安全点检、
自主保全、体制展开、试作、计划停止时间等时间
负荷时间
利用时间= 负荷时间-停线时间
实际作业时间
停线时间:工具更换、调整、故障停止、上下流等待、
计划停 止时间
质量维持、确认、工件不良、操作失误、作业缓滞停止等时间
OEE经典解析ppt课件
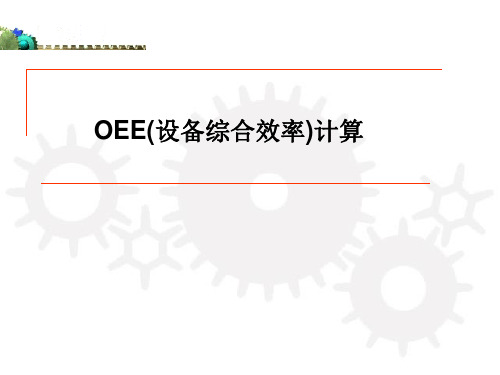
• 设某设备某天工作时间为8小时,班前计划停机10 分钟,故障停机30分钟,设备调整35分钟, 产品 的理论加工周期为1min/件,一天共加工产品400 件,有20件废品,求这台设备的OEE。
①OEE=时间稼动率*性能稼动率*合格率 =86%*98%*95% =80%
②OEE=380/(8*60-10) =80%
一、为什么要实施TPM
丰田等企业为什么会成功
追求精细化管理,维护管理工具
丰田公司数十年如一日的不断追求精细化管理,追求 零库存、零缺陷、低成本和零损耗等。丰田公司有效地运 用了各种各样的管理工具,如5S活动,TQC、TPM、IE、 JIT等,为企业的管理提升服务。这些管理工具在丰田都 能得到有效的坚持,这是它获得成功的必要条件之一。
=(F-T)/F =O / N =L / K =U x V x W
Process 1 Process 2 Process 3 Process 4 Process 5
Capacity analysis Y. Planned uptime (hours/day) Z. Planned uptime (days/week) AA. Planned rate of production (parts/minute) AB. Theoretical production capacity per day AC. Theoretical production capacity per week AD. Weekly Demand AE. Weekly Parts Available for Shipment AF. Daily Demand (DPV) AG. Daily Parts Available for Shipment AH. Percent above/below DPV
①OEE=时间稼动率*性能稼动率*合格率 =86%*98%*95% =80%
②OEE=380/(8*60-10) =80%
一、为什么要实施TPM
丰田等企业为什么会成功
追求精细化管理,维护管理工具
丰田公司数十年如一日的不断追求精细化管理,追求 零库存、零缺陷、低成本和零损耗等。丰田公司有效地运 用了各种各样的管理工具,如5S活动,TQC、TPM、IE、 JIT等,为企业的管理提升服务。这些管理工具在丰田都 能得到有效的坚持,这是它获得成功的必要条件之一。
=(F-T)/F =O / N =L / K =U x V x W
Process 1 Process 2 Process 3 Process 4 Process 5
Capacity analysis Y. Planned uptime (hours/day) Z. Planned uptime (days/week) AA. Planned rate of production (parts/minute) AB. Theoretical production capacity per day AC. Theoretical production capacity per week AD. Weekly Demand AE. Weekly Parts Available for Shipment AF. Daily Demand (DPV) AG. Daily Parts Available for Shipment AH. Percent above/below DPV
OEE培训PPT课件
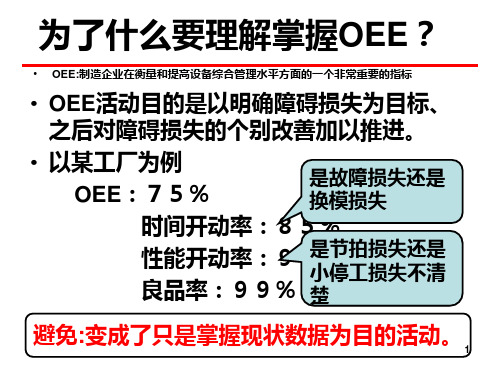
・・・ 23,000分
理论生产时间=∑(计划节拍×生产量)
8
为什么对以手工作业为主体的装配线 参考 应用OEE是不合适的呢?
手工作业为主体的装配线,比方说即使装配设备在 工序内存在,但装配线的频颈还是人的工作,工作的标 准时间成为了理论节拍。
在1个作业周期内,由于作业的次序和熟练度的不 同、作业速度的偏差,存在物品的取放、行走、搬运、 目测监视、修正调整、停工待料等的低附加值作业的损 失、以及由于各作业工序间的作业节拍不同,而产生的 生产线平衡损失(组成效率)等。
休息时间80min,设备故障、工艺调试停机30min。生产线
各工位周期如下表,本班生产了550个,报废2个,维修品数
4个。 OEE?
1
螺钉机
2
旋入机
0.95min 0.9min
3
布胶机
0.8min
4
配光机
0.76min
负荷时间-停止时间
*时间开动率=
负荷时间 =
630min-30min 630min
換)
首先来看看「作业分析」!
例)59厂 UX101自动线ンC9
动力头换模 1 工具准备 2 拆卸外套
拆卸装配螺栓 3 (寻找不够的工具) 4 拆卸动力头 5 清扫拆卸下的动力头
4’43” 34”
8’24” (2’17”)
2’05” 3’15”
有没有徒劳 无用的作业?
作业的顺序 合适吗?
标准化
6 清扫新的动力头
设备故障损失・准备调整损失・小 设备故障损失・准备调整损失・节
停工损失・速度低下损失・质量损 拍低下损失・作业充实度・质量损
失・・
失・・
OEE(设备综合效率)
OEE对人的 作业效率
理论生产时间=∑(计划节拍×生产量)
8
为什么对以手工作业为主体的装配线 参考 应用OEE是不合适的呢?
手工作业为主体的装配线,比方说即使装配设备在 工序内存在,但装配线的频颈还是人的工作,工作的标 准时间成为了理论节拍。
在1个作业周期内,由于作业的次序和熟练度的不 同、作业速度的偏差,存在物品的取放、行走、搬运、 目测监视、修正调整、停工待料等的低附加值作业的损 失、以及由于各作业工序间的作业节拍不同,而产生的 生产线平衡损失(组成效率)等。
休息时间80min,设备故障、工艺调试停机30min。生产线
各工位周期如下表,本班生产了550个,报废2个,维修品数
4个。 OEE?
1
螺钉机
2
旋入机
0.95min 0.9min
3
布胶机
0.8min
4
配光机
0.76min
负荷时间-停止时间
*时间开动率=
负荷时间 =
630min-30min 630min
換)
首先来看看「作业分析」!
例)59厂 UX101自动线ンC9
动力头换模 1 工具准备 2 拆卸外套
拆卸装配螺栓 3 (寻找不够的工具) 4 拆卸动力头 5 清扫拆卸下的动力头
4’43” 34”
8’24” (2’17”)
2’05” 3’15”
有没有徒劳 无用的作业?
作业的顺序 合适吗?
标准化
6 清扫新的动力头
设备故障损失・准备调整损失・小 设备故障损失・准备调整损失・节
停工损失・速度低下损失・质量损 拍低下损失・作业充实度・质量损
失・・
失・・
OEE(设备综合效率)
OEE对人的 作业效率
OEE设备综合效率分析与管理ppt
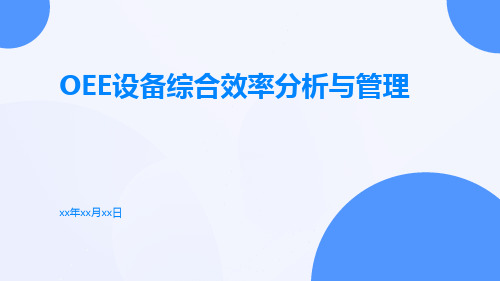
维护记录
详细的维护记录有助于发现和解决潜在问 题,预防性维护可以降低设备故障率,提 高OEE。
03
OEE设备综合效率改善方法
优化生产计划
均衡生产计划
合理安排生产任务,避免设备负 载波动过大,保证设备稳定、高 效运行。
优化生产排程
结合设备实际运行情况,合理调 整生产顺序和时间,降低设备空 转和等待时间。
OEE定义
OEE是设备综合效率的缩写,是指设备在生产过程中实际发 挥的生产效率与理论生产效率的比率。它涵盖了设备的时间 、性能和质量的综合指标,是衡量设备运行效率和生产效益 的重要参数。
OEE计算方法
OEE的计算方法是将设备的实际产量除以设备理论产量,再 乘以100%。
OEE的重要性及与企业生产效率的关系
OEE的重要性
OEE的高低直接反映了设备的运行状况和生产效率,对于企业而言,提高 OEE意味着提高设备的生产效率和产量,降低生产成本,增强市场竞争力。
OEE与企业生产效率的关系
OEE是企业生产效率的关键指标之一,它直接反映了企业的生产效率和运营状 况。OEE的高低将直接影响企业的生产成本、交货周期和客户满意度等方面。
分析现状和问题
针对现有的设备和生产状况,识别影响OEE的关键因素和问题,确定改善措施的优先级。
制定改善计划
根据现状和问题,制定详细的改善计划,包括设备维护、设备效率提升、操作人员培训等方面的具体措施。
实施OEE数据采集与统计
要点一
选择合适的OEE计算 方法
根据设备和生产特点,选择适合的 OEE计算方法,明确各项参数的测量 和计算方式。
OEE设备综合效率分析与管理
xx年xx月xx日Leabharlann contents目录
OEE培训材料ppt课件
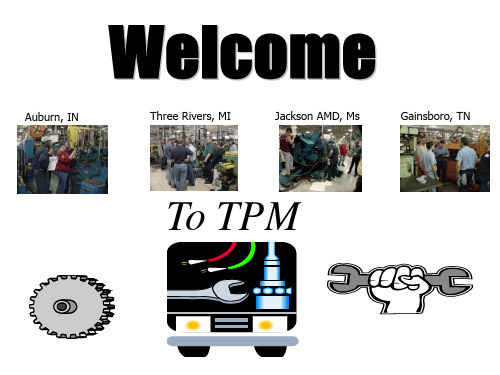
Auburn, IN
Three Rivers, MI
Jackson AMD, Ms
Gainsboro, TN
To TPM
六种损失对设备可生产时间的影响
8 小时
总机器可用时间
设备可用性角 度衡量
总可操作时间
6小时
停机损失
剩余操作时间
4.8小时
生产效率角度衡 量
速度损失
最终可操作时间 不良损失
3.2 小时
2. Observe proper "Lockout/Tagout" procedures when shutting down your equipment
for cleaning.
3. Systematically clean each part of the equipment using the checklist on the next
TPM Services
美国工厂 平均水平
30-45% OEE
55-70%
损失
隐藏的工厂
最大产
85% OEE 15%
损失
能
世界级
TPM Services
OEE
如何计算OEE
设备有效性 X 生产效率 X 质量结果
停机 换型 & 调整 其他
等待 & 微小停机 速度减缓
制程不良 开机或换型不良
提醒: OEE 衡量制造过程中的六种损失
page.
Note: An "abnormal condition" is defined as any condition within, or around the machine that affects the appearance and performance of the machine or production cell. a "normal condition" is defined as a condition in which the machine's appearance and performance is in "like new" condition and no waste is generated in time, resources, or materials. An abnormal condition can be a broken bolt, a leak, a worn or damaged part, it can also be a dirty part. As you document these conditions on your "Abnormality Summary Sheet" try and discover the reasons for them. Ask yourself the following questions:
Three Rivers, MI
Jackson AMD, Ms
Gainsboro, TN
To TPM
六种损失对设备可生产时间的影响
8 小时
总机器可用时间
设备可用性角 度衡量
总可操作时间
6小时
停机损失
剩余操作时间
4.8小时
生产效率角度衡 量
速度损失
最终可操作时间 不良损失
3.2 小时
2. Observe proper "Lockout/Tagout" procedures when shutting down your equipment
for cleaning.
3. Systematically clean each part of the equipment using the checklist on the next
TPM Services
美国工厂 平均水平
30-45% OEE
55-70%
损失
隐藏的工厂
最大产
85% OEE 15%
损失
能
世界级
TPM Services
OEE
如何计算OEE
设备有效性 X 生产效率 X 质量结果
停机 换型 & 调整 其他
等待 & 微小停机 速度减缓
制程不良 开机或换型不良
提醒: OEE 衡量制造过程中的六种损失
page.
Note: An "abnormal condition" is defined as any condition within, or around the machine that affects the appearance and performance of the machine or production cell. a "normal condition" is defined as a condition in which the machine's appearance and performance is in "like new" condition and no waste is generated in time, resources, or materials. An abnormal condition can be a broken bolt, a leak, a worn or damaged part, it can also be a dirty part. As you document these conditions on your "Abnormality Summary Sheet" try and discover the reasons for them. Ask yourself the following questions:
如何建立OEE管理体系PPT15页
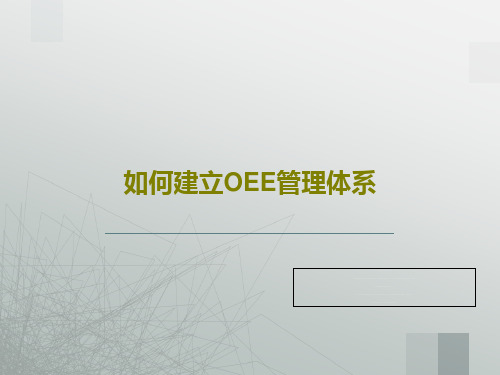
谢谢
11、越是没有本领的就越加自命不凡。——邓拓 12、越是无能的人,越喜欢挑剔别人的错儿。——爱尔兰 13、知人者智,自知者明。胜人者有力,自胜者强。——老子 14、意志坚强的人能把世界放在手中像泥块一样任意揉捏。——歌德 15、最具挑战性的挑战莫过于提升自我。——迈克尔·F·斯特利
如何建立OEE管理体系
31、别人笑我太疯癫,我笑他人看不 穿。(名 言网) 32、我不想听失意者的哭泣,抱怨者 的牢骚 ,这是 羊群中 的瘟疫 ,我不 能被它 传染。 我要尽 量避免 绝望, 辛勤耕 耘,忍 受苦楚 。我一 试再试 ,争取 每天的 成功, 避免以 失败收 常在别 人停滞 不前时 ,我继 续拼搏 。
33、如果惧怕前面跌宕的山岩,生命 就永远 只能是 死水一 潭。 34、当你眼泪忍不住要流出来的时候 ,睁大 眼睛, 千万别 眨眼!你会看到 世界由 清晰变 模糊的 全过程 ,心会 在你泪 水落下 的那一 刻变得 清澈明 晰。盐 。注定 要融化 的,也 许是用 眼泪的 方式。
35、不要以为自己成功一次就可以了 ,也不 要以为 过去的 光荣可 以被永 远肯定 。
Hale Waihona Puke
如何建立OEE管理体系ppt课件
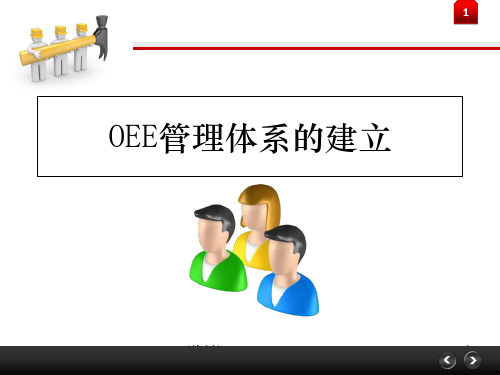
8、持续改进
持续改进才能不断地改善设备综合利用率(即OEE),这才是OEE 体系的本质。
ppt精选版
9
10
五、使用OEE的注意事项
1、OEE要应用在一台机器上,而不是整个生产线,这样才 有意义; 2、OEE应该是综合指标中一部分,而不应该被孤立应用; 3、OEE应该与精准原则相符,不应导致浪费合理化、制度 化。
ppt精选版
10
11
六、OEE用于考核时的局限性
OEE是一个基于设备模型的指标,有以下局限: 1、作业人员未纳入考核; 2、对于自动化程度低,或手工作业较多的作业方式,如单 纯以OEE作为主要衡量指标,由于设备因素的弱化,因而 OEE显得片面; 3、即使自动化程度较高,但在要投入较多人工作业的情况 下,OEE也会脱离作为衡量综合效率指标的有效性;
ppt精选版
4
5
四、如何建立OEE体系?
1、科学、规范的设备管理制度;
科学的管理制度是指导企业规范化管理的依据,必须符合生产现场的实 际情况,并和企业文化和企业核心目标相一致。
制定的目标应能实现,避免过高标准导致制度流于形式。 制度本身要求是闭式循环,能体现纠正和改进措施,指导参与者在某 一环节出现错误时,该如何去处理。
表现性=理想周期时间/(操作时间/总产量)=(总产量/操作时间)/生产速率 表现性考虑生产速度上的损失。包括任何导致生产不能以最大速度运行的
因素。 质量指数=良品/总产量 质量指数考虑质量的损失,它用来反映没有满足质量要求的产品(包括返工
的产品)。
ppt精选版
2
3
二、一般制造业设备的6大损失
所有生产时间 操作时间 负荷时间 有效利用时间
ppt精选版
7
8
持续改进才能不断地改善设备综合利用率(即OEE),这才是OEE 体系的本质。
ppt精选版
9
10
五、使用OEE的注意事项
1、OEE要应用在一台机器上,而不是整个生产线,这样才 有意义; 2、OEE应该是综合指标中一部分,而不应该被孤立应用; 3、OEE应该与精准原则相符,不应导致浪费合理化、制度 化。
ppt精选版
10
11
六、OEE用于考核时的局限性
OEE是一个基于设备模型的指标,有以下局限: 1、作业人员未纳入考核; 2、对于自动化程度低,或手工作业较多的作业方式,如单 纯以OEE作为主要衡量指标,由于设备因素的弱化,因而 OEE显得片面; 3、即使自动化程度较高,但在要投入较多人工作业的情况 下,OEE也会脱离作为衡量综合效率指标的有效性;
ppt精选版
4
5
四、如何建立OEE体系?
1、科学、规范的设备管理制度;
科学的管理制度是指导企业规范化管理的依据,必须符合生产现场的实 际情况,并和企业文化和企业核心目标相一致。
制定的目标应能实现,避免过高标准导致制度流于形式。 制度本身要求是闭式循环,能体现纠正和改进措施,指导参与者在某 一环节出现错误时,该如何去处理。
表现性=理想周期时间/(操作时间/总产量)=(总产量/操作时间)/生产速率 表现性考虑生产速度上的损失。包括任何导致生产不能以最大速度运行的
因素。 质量指数=良品/总产量 质量指数考虑质量的损失,它用来反映没有满足质量要求的产品(包括返工
的产品)。
ppt精选版
2
3
二、一般制造业设备的6大损失
所有生产时间 操作时间 负荷时间 有效利用时间
ppt精选版
7
8
OEE培训资料ppt课件
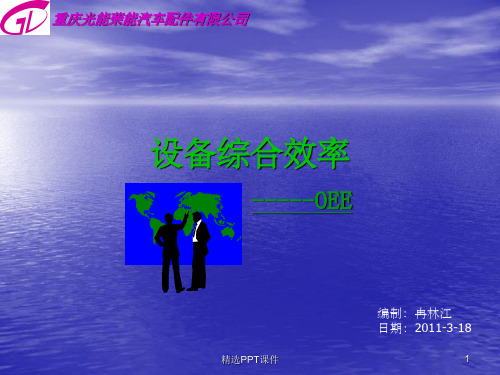
精选PPT课件
15
重庆光能荣能汽车配件有限公司
谢 谢 大 家!
精选PPT课件
16
1. 停工和故障的损失 设备失效需要执行维护操作。其原因有:
–机器过载 –螺钉和螺帽松开 –过渡磨损 –缺少润滑油 –污染物
4. 降低速度的损失
设备在低于其标准设计速度运行导致的 损失。其原因有:
–机器磨损 –人为干扰 –工具磨损 –机器过载
2. 换装和调试的损失
从一种产品到另一种产品换产的时间损 失,或运行时对设置的改动。其原因有:
2. 设备效率损失的分类
大分类 计划损失 停止损失 性能损失 不良损失
中分类 交班时间/就餐/休息/生产中断/预防维修 设备故障/动力事故/换产/流量不足 流量调节/资材短缺/品质问题
瞬间停止/速度降低/空转
不良/再作业
Hale Waihona Puke 公司认可的损失影响OEE 的损失
精选PPT课件
7
重庆光能荣能汽车配件有限公司
影响OEE的六大损失
重庆光能荣能汽车配件有限公司
设备综合效率
-----OEE
精选PPT课件
编制:冉林江 日期:2011-3-18
1
重庆光能荣能汽车配件有限公司
OEE(设备综合效率)
01.设备综合效率的定义 02. 设备效率损失的分类 03. 设备综合效率的计算
精选PPT课件
2
重庆光能荣能汽车配件有限公司
1.设备综合效率的定义
多数企业的OEE标准
世界级企业的OEE标准
废品/返工8%
准备时间10%
设备OEE 50%
停机13%
小中断19%
精选PPT课件
5%
OEE培训讲义PPT课件

花了30分钟,设备中途故障与修复总时间为15分钟。(B=A-30-15=460-3015=415) • 请计算这一班的Availability.(Availability=415/460=0.90)
第10页/共16页
的计算---Performance性能稼动率
第11页/共16页
Performance的计算练习C
OEE
第2页/共16页
1.设备关连损失
• Availability (时间) • Performance (性能) • Quality (品质)
• Availability: Downtime Losses – 停机损失 • Breakdowns – 故障 • Setup Time – 工程变换与调整 • Performance: Speed Losses – 速度损失 • Minor Stoppages – 小停止 • Reduced Operating Speed – 速度低下 • Quality: Defect Losses – 不良损失
• Scrap and Rework – 报第废3页与/共重1工6页
的定义
第4页/共16页
的组成及其计算
第5页/共16页
I.OEE 的组成
第6页/共16页
挂图
第7页/共16页
的损失结构图
第8页/共16页
的计算---Availability时间稼动率
第9页/共16页
Availability的计算练习
第14页/共16页
结束语:
谢谢大家
第15页/共16页
感谢您的观看!
第16页/共16页
• Availability = B / A • [练习] • 某公司每班上班总时间为540分钟,其中用餐时间与休息为60分钟,上班前的交
第10页/共16页
的计算---Performance性能稼动率
第11页/共16页
Performance的计算练习C
OEE
第2页/共16页
1.设备关连损失
• Availability (时间) • Performance (性能) • Quality (品质)
• Availability: Downtime Losses – 停机损失 • Breakdowns – 故障 • Setup Time – 工程变换与调整 • Performance: Speed Losses – 速度损失 • Minor Stoppages – 小停止 • Reduced Operating Speed – 速度低下 • Quality: Defect Losses – 不良损失
• Scrap and Rework – 报第废3页与/共重1工6页
的定义
第4页/共16页
的组成及其计算
第5页/共16页
I.OEE 的组成
第6页/共16页
挂图
第7页/共16页
的损失结构图
第8页/共16页
的计算---Availability时间稼动率
第9页/共16页
Availability的计算练习
第14页/共16页
结束语:
谢谢大家
第15页/共16页
感谢您的观看!
第16页/共16页
• Availability = B / A • [练习] • 某公司每班上班总时间为540分钟,其中用餐时间与休息为60分钟,上班前的交
相关主题
- 1、下载文档前请自行甄别文档内容的完整性,平台不提供额外的编辑、内容补充、找答案等附加服务。
- 2、"仅部分预览"的文档,不可在线预览部分如存在完整性等问题,可反馈申请退款(可完整预览的文档不适用该条件!)。
- 3、如文档侵犯您的权益,请联系客服反馈,我们会尽快为您处理(人工客服工作时间:9:00-18:30)。
表现性=理想周期时间/(操作时间/总产量)=(总产量/操作时间)/生产速率 表现性考虑生产速度上的损失。包括任何导致生产不能以最大速度运行的
因素。 质量指数=良品/总产量 质量指数考虑质量的损失,它用来反映没有满足质量要求的产品(包括返工
的产品)。
.
2
3
二、一般制造业设备的6大损失
所有生产时间 操作时间 负荷时间 有效利用时间
8、持续改进
持续改进才能不断地改善设备综合利用率(即OEE),这才是OEE 体系的本质。
.
9
10
五、使用OEE的注意事项
1、OEE要应用在一台机器上,而不是整个生产线,这样才 有意义; 2、OEE应该是综合指标中一部分,而不应该被孤立应用; 3、OEE应该与精准原则相符,不应导致浪费合理化、制度 化。
.
4
5
四、如何建立OEE体系?
1、科学、规范的设备管理制度;
科学的管理制度是指导企业规范化管理的依据,必须符合生产现场的实 际情况,并和企业文化和企业核心目标相一致。
制定的目标应能实现,避免过高标准导致制度流于形式。 制度本身要求是闭式循环,能体现纠正和改进措施,指导参与者在某 一环节出现错误时,该如何去处理。
.
10
11
六、OEE用于考核时的局限性
OEE是一个基于设备模型的指标,有以下局限: 1、作业人员未纳入考核; 2、对于自动化程度低,或手工作业较多的作业方式,如单 纯以OEE作为主要衡量指标,由于设备因素的弱化,因而 OEE显得片面; 3、即使自动化程度较高,但在要投入较多人工作业的情况 下,OEE也会脱离作为衡量综合效率指标的有效性;
停机损失:
1.故障 2.更换品种 / 清洁
/ 调节 3.启动 / 停机(故障、调 整)
可用率
性能损失:
4.小停机 / 空转 5.速度损失
表现性
净利用时间 创造价值时间
缺陷损失:
6.质量缺陷返工
质量指数
.
3
4
三、建立OEE的意义
实践证明OEE是一个极好的基准工具,通过OEE模型的各子项分析,它准确 清楚地告诉你设备效率如何,在生产的哪个环节有多少损失,以及你可以进行 那些改善工作。长期的使用OEE工具,企业可以轻松的找到影响生产效率的瓶 颈,并进行改进和跟踪。达到提高生产效率的目的,同时使公司避免不必要的 耗费。
.
7
8
6、消除损失
如何消除损失? 1)通过名称,特性等定义现场的损失 2)建立机制以测量损失
什么设备?什么损失?发生时间?发生地点?如何发生? 3)确定损失结构
确定瓶颈设备/生产线
4)损失重点 着重于最大损失并从其着手
5)寻求降低损失的有效途径
.
8
9
7、衡量改进成果
实践是检验真理的标准。在经过分析、消除损失后,通过生产来检 验改进的成果。
.
6
7
4、对原始数据进行整理、统计、计算
自动化采集的数据在进行整理、统计、计算时的优势尤其明显。因 为自动化采集的信息可以按需求生成相应的数据格式,便于统计和 计算。可以节约出大量的人力和物力,让专业技术人员专注于数据 的计算。
5、分析、量化损失
OEE计算结果将反应设备损失的节点,分析、量化后,以便于分清 损失程度的轻重缓急
2、合理、科学的管理组织结构;
合理科学的设备管理组织机构,是开展设备管理工作的基础,也是规范 化设备管理的组成实体。
组织结构应达到分工合理、责职分明、人人有事做、事事有人负责。
.
5
6
3、建立良好的OEE基础数据收集模式
数据收集模式主要有:人工采集和自动化采集。 人工采集需要员工极度的认真负责,且需要系统化培训,对员工的 要求较高。在实际的应用中,当与班次,员工,设备,产品等生产 要素联系在一起时,利用人工采集数据便变得十分麻烦费事,且可 能存在数据失真的风险。 自动化采集可以轻松地获取有关设备的生产信息,为OEE的计算提 供最有价值的数据,无人工采集的缺点。是比较理想的采集手段。
1
OEE管理体系的建立
.
1
2
一、什么是OEE?
OEE是Overall Equipment Effectiveness(全局设备效率)的缩写,它由可
用率,表现性以及质量指数三个关键要素组成 ,即: OEE=可用率X表现性X质量指数。
其中: 可用率=操作时间/计划工作时间 它是用来考虑停工所带来的损失,包括引起计划生产发生停工的任何事件。
.ቤተ መጻሕፍቲ ባይዱ
11
12
4、对设备利用率较低的生产作业,OEE的有效性也会削弱; 5、OEE指标不能有效衡量投资回报,可能在实践中忽视制 造技术进步的作用。
.
12
See you soon…
.
13
因素。 质量指数=良品/总产量 质量指数考虑质量的损失,它用来反映没有满足质量要求的产品(包括返工
的产品)。
.
2
3
二、一般制造业设备的6大损失
所有生产时间 操作时间 负荷时间 有效利用时间
8、持续改进
持续改进才能不断地改善设备综合利用率(即OEE),这才是OEE 体系的本质。
.
9
10
五、使用OEE的注意事项
1、OEE要应用在一台机器上,而不是整个生产线,这样才 有意义; 2、OEE应该是综合指标中一部分,而不应该被孤立应用; 3、OEE应该与精准原则相符,不应导致浪费合理化、制度 化。
.
4
5
四、如何建立OEE体系?
1、科学、规范的设备管理制度;
科学的管理制度是指导企业规范化管理的依据,必须符合生产现场的实 际情况,并和企业文化和企业核心目标相一致。
制定的目标应能实现,避免过高标准导致制度流于形式。 制度本身要求是闭式循环,能体现纠正和改进措施,指导参与者在某 一环节出现错误时,该如何去处理。
.
10
11
六、OEE用于考核时的局限性
OEE是一个基于设备模型的指标,有以下局限: 1、作业人员未纳入考核; 2、对于自动化程度低,或手工作业较多的作业方式,如单 纯以OEE作为主要衡量指标,由于设备因素的弱化,因而 OEE显得片面; 3、即使自动化程度较高,但在要投入较多人工作业的情况 下,OEE也会脱离作为衡量综合效率指标的有效性;
停机损失:
1.故障 2.更换品种 / 清洁
/ 调节 3.启动 / 停机(故障、调 整)
可用率
性能损失:
4.小停机 / 空转 5.速度损失
表现性
净利用时间 创造价值时间
缺陷损失:
6.质量缺陷返工
质量指数
.
3
4
三、建立OEE的意义
实践证明OEE是一个极好的基准工具,通过OEE模型的各子项分析,它准确 清楚地告诉你设备效率如何,在生产的哪个环节有多少损失,以及你可以进行 那些改善工作。长期的使用OEE工具,企业可以轻松的找到影响生产效率的瓶 颈,并进行改进和跟踪。达到提高生产效率的目的,同时使公司避免不必要的 耗费。
.
7
8
6、消除损失
如何消除损失? 1)通过名称,特性等定义现场的损失 2)建立机制以测量损失
什么设备?什么损失?发生时间?发生地点?如何发生? 3)确定损失结构
确定瓶颈设备/生产线
4)损失重点 着重于最大损失并从其着手
5)寻求降低损失的有效途径
.
8
9
7、衡量改进成果
实践是检验真理的标准。在经过分析、消除损失后,通过生产来检 验改进的成果。
.
6
7
4、对原始数据进行整理、统计、计算
自动化采集的数据在进行整理、统计、计算时的优势尤其明显。因 为自动化采集的信息可以按需求生成相应的数据格式,便于统计和 计算。可以节约出大量的人力和物力,让专业技术人员专注于数据 的计算。
5、分析、量化损失
OEE计算结果将反应设备损失的节点,分析、量化后,以便于分清 损失程度的轻重缓急
2、合理、科学的管理组织结构;
合理科学的设备管理组织机构,是开展设备管理工作的基础,也是规范 化设备管理的组成实体。
组织结构应达到分工合理、责职分明、人人有事做、事事有人负责。
.
5
6
3、建立良好的OEE基础数据收集模式
数据收集模式主要有:人工采集和自动化采集。 人工采集需要员工极度的认真负责,且需要系统化培训,对员工的 要求较高。在实际的应用中,当与班次,员工,设备,产品等生产 要素联系在一起时,利用人工采集数据便变得十分麻烦费事,且可 能存在数据失真的风险。 自动化采集可以轻松地获取有关设备的生产信息,为OEE的计算提 供最有价值的数据,无人工采集的缺点。是比较理想的采集手段。
1
OEE管理体系的建立
.
1
2
一、什么是OEE?
OEE是Overall Equipment Effectiveness(全局设备效率)的缩写,它由可
用率,表现性以及质量指数三个关键要素组成 ,即: OEE=可用率X表现性X质量指数。
其中: 可用率=操作时间/计划工作时间 它是用来考虑停工所带来的损失,包括引起计划生产发生停工的任何事件。
.ቤተ መጻሕፍቲ ባይዱ
11
12
4、对设备利用率较低的生产作业,OEE的有效性也会削弱; 5、OEE指标不能有效衡量投资回报,可能在实践中忽视制 造技术进步的作用。
.
12
See you soon…
.
13