淬火裂纹
45钢淬火开裂解决方案

45钢淬火开裂解决方案1. 引言钢材是广泛应用于机械制造和工业领域的材料之一,而淬火是对钢材进行热处理的一种常用方法。
然而,淬火过程中可能会出现开裂问题,这给钢材的性能和可靠性带来了威胁。
因此,针对淬火开裂问题,需要制定解决方案,以确保钢材质量和使用寿命。
2. 开裂原因分析钢材淬火开裂的原因很多,主要包括以下几个方面:2.1 内应力过大在淬火过程中,钢材的表面和内部会迅速冷却,造成急剧的温度和应力变化。
当冷却速度过快或不均匀时,钢材产生内部应力过大,容易导致开裂。
2.2 压缩应力不足淬火后,钢材表面会形成一层脆性的马氏体,而内部保留了一定的奥氏体组织。
如果钢材内部奥氏体的体积增大,而表面的马氏体受到压缩不足,也容易导致开裂。
2.3 杂质和夹杂物钢材中的杂质和夹杂物也是导致开裂的重要原因之一。
杂质会降低钢材的韧性和延展性,夹杂物则成为开裂的起始点。
2.4 硬度不均匀淬火后,钢材的硬度分布不均匀也会导致开裂。
硬度过高或过低的区域容易发生应力集中,从而引发开裂。
3. 解决方案针对淬火开裂问题,我们提出以下解决方案:3.1 优化淬火工艺参数通过优化淬火工艺参数,可以控制钢材的冷却速度和温度梯度,从而减小内应力和压缩不足的问题。
合理选择淬火介质和温度,以避免过快或不均匀的冷却。
3.2 降低表面应力在淬火过程中,采取一些措施来降低钢材表面应力。
例如,可对钢材进行预处理,如表面机械处理、脱碳退火等,以减少开裂的风险。
3.3 优化钢材的化学成分合理控制钢材的化学成分,降低杂质和夹杂物的含量。
采用纯净的原材料和改进冶炼工艺,可以有效减少开裂的概率。
3.4 加强表面处理在淬火前对钢材进行表面处理,如酸洗、喷丸、抛光等,可以去除一些表面缺陷和杂质,减少开裂的可能性。
同时,还可以增加表面硬度分布的均匀性。
3.5 适当回火处理淬火后,适当进行回火处理,有助于减轻内应力,改善钢材的韧性。
选择合适的回火温度和时间,以平衡硬度和韧性的要求,避免开裂的发生。
铸件淬火开裂的原因
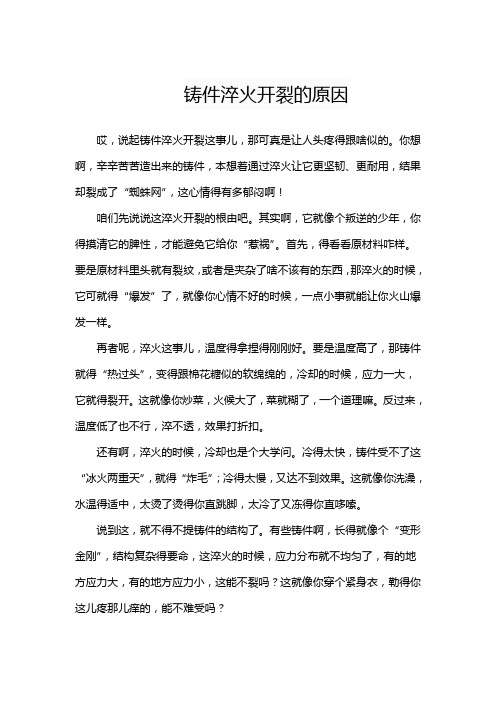
铸件淬火开裂的原因哎,说起铸件淬火开裂这事儿,那可真是让人头疼得跟啥似的。
你想啊,辛辛苦苦造出来的铸件,本想着通过淬火让它更坚韧、更耐用,结果却裂成了“蜘蛛网”,这心情得有多郁闷啊!咱们先说说这淬火开裂的根由吧。
其实啊,它就像个叛逆的少年,你得摸清它的脾性,才能避免它给你“惹祸”。
首先,得看看原材料咋样。
要是原材料里头就有裂纹,或者是夹杂了啥不该有的东西,那淬火的时候,它可就得“爆发”了,就像你心情不好的时候,一点小事就能让你火山爆发一样。
再者呢,淬火这事儿,温度得拿捏得刚刚好。
要是温度高了,那铸件就得“热过头”,变得跟棉花糖似的软绵绵的,冷却的时候,应力一大,它就得裂开。
这就像你炒菜,火候大了,菜就糊了,一个道理嘛。
反过来,温度低了也不行,淬不透,效果打折扣。
还有啊,淬火的时候,冷却也是个大学问。
冷得太快,铸件受不了这“冰火两重天”,就得“炸毛”;冷得太慢,又达不到效果。
这就像你洗澡,水温得适中,太烫了烫得你直跳脚,太冷了又冻得你直哆嗦。
说到这,就不得不提铸件的结构了。
有些铸件啊,长得就像个“变形金刚”,结构复杂得要命,这淬火的时候,应力分布就不均匀了,有的地方应力大,有的地方应力小,这能不裂吗?这就像你穿个紧身衣,勒得你这儿疼那儿痒的,能不难受吗?再来说说工艺吧。
淬火这活儿,得是个精细活儿,每个步骤都得小心翼翼。
要是装炉方式不对,或者淬火介质没选对,那铸件就得遭殃了。
这就像你做饭,食材得新鲜,调料得适量,火候得掌握得好,才能做出美味佳肴来。
当然了,除了这些“硬件”因素外,还有一些“软件”因素也得注意。
比如铸造过程中的挤压、脱模等步骤,都得小心翼翼,稍有不慎,铸件就得“受伤”。
这就像你带孩子,得时刻关注他的安全,一不小心磕了碰了,那可就是心疼得要命啊!所以啊,要想避免铸件淬火开裂,就得从多方面下手。
原材料得选好,温度得控制好,冷却得得当,工艺得精细,还得时刻关注铸件的安全。
这就像你养花一样,得用心呵护,才能让它茁壮成长,绽放出美丽的花朵来。
淬火裂纹

如水-油、水-空、盐水-油、油-空
气、碱-空气。
▪ ②、三介质淬火:适用于形状复杂 、变形要求严格的零件如碳素钢零件。
▪ (3)、分级淬火:快冷至Ms点上保温 后空冷。如截面大、易变形开裂的高 碳、高速钢等,应采用2次或3次的逐 级分级淬火。
▪ (4)、马氏体等温淬火:冷却至Ms点 下50-100度等温保持。一般用油淬。
▪ (2)、大截面零件(直径或厚度>50) 的高碳钢:淬火前正火。小截面高碳钢件 淬火前应球化退火。
▪ (3)、淬火前应消除亚共析钢的魏氏组 织。
▪ (4)、高铬钢、轴承钢和高速钢:避免 偏析,严重时应降低淬火温度。
C、加热参数合理:
▪ (1)、介质:真空、保护气氛、电 阻、盐浴、火焰炉淬裂倾向逐渐增大。
淬火产生的淬火裂纹
疲劳裂纹起源于淬火裂纹
二、宏观形态
▪ 1、纵向裂纹多半产生在淬透的钢件上,表层的切向拉应力 大于轴向拉应力时才能出现。这种裂纹沿轴向分布,由表 面裂向心部
▪ 2、横向裂纹它是在工件未淬透的情况下,产生于淬透层与 未淬透的心部之间的过渡区。内应力特征是表面受压,距 离表面一定距离处压应力变为拉应力,轴向拉应力最大, 产生的是横向裂纹
▪ 防止淬裂措施:M等温淬火、分级淬火、 水-油淬火、水-空气双液淬火。
四、预防淬火裂纹的方法
▪ A、正确设计产品。 ▪ (1)、技术性和经济性。 ▪ (2)、结构设计:
①、截面尺寸均匀; ▪ ②、圆角过渡; ▪ ③、形状:球形冷却快于板料。 ▪ (3)、热处理条件
B、合理安排工艺路线
▪ (1)、形状复杂精度高的零件,粗精加 工之间的淬火前应安排去应力退火。
淬火裂纹
▪ 1、淬火目的:强化钢件,获得M。
淬火裂纹产生的原因是什么,常见淬火裂纹有哪几种

淬火裂纹产生的原因是什么,常见淬火裂纹有哪几种
一、淬火裂纹产生原因
1、钢制工件常由于结构设计不合理、钢材选择不当、淬火温度控制不正确、淬火冷却速度不合适等,而产生淬火裂纹。
2、增大淬火内应力,会使已形成的淬火显微裂纹扩展,形成淬火裂纹。
3、由于增大了显微裂纹的形成敏感度,增加了显微裂纹的数量,从而增大淬火裂纹的形成。
二、常见淬火裂纹类型
淬火裂纹一般来讲通常分为纵向裂纹、横向裂纹、网状裂纹、剥离裂纹四种。
1、纵向裂纹(又称轴向裂纹)
这类裂纹特征是沿轴向分布,由工件表面裂向心部,深度不等,一般深而长,在钢件上常用一条或数条。
2、横向裂纹(弧形裂纹)
横向裂纹的断口分析表明,断口与工件轴线垂直,断裂的产生不是源于表面,而是在内部。
裂纹在内部产生,以放射状向周围扩展。
工件的凹槽、棱角、截面突变处常发生弧形裂纹。
淬火工件有软点时,软点周围也存在一个过渡区,该处存在着很大的拉应力,从而引起弧形裂纹。
带槽、中心孔或销孔的零件淬火时,这些部位冷却较慢,相应的淬硬层较薄,故在过渡区由于拉应力作用易形成弧形裂纹。
3、网状裂纹
这种裂纹是一种表面裂纹,其深度较浅,一般在0.01~1.5mm左右。
裂纹走向具有任意方向性,与工件的外形无关,许多裂纹相互连接构成网状。
当裂纹变深时,网状逐渐消失;当达到1mm以上时,就变成任意走向的或纵向分布的少数条纹了。
4、剥离裂纹
这种裂纹多发生在表面淬火,或表面渗碳,渗氮和渗硼等化学热处理的工件中。
裂纹的位置多在硬化层和心部交界处,即多产生在过渡区中。
淬火开裂原因范文
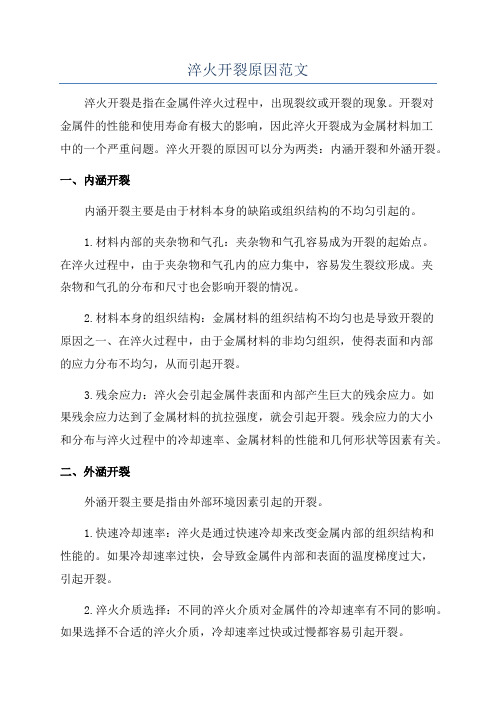
淬火开裂原因范文淬火开裂是指在金属件淬火过程中,出现裂纹或开裂的现象。
开裂对金属件的性能和使用寿命有极大的影响,因此淬火开裂成为金属材料加工中的一个严重问题。
淬火开裂的原因可以分为两类:内涵开裂和外涵开裂。
一、内涵开裂内涵开裂主要是由于材料本身的缺陷或组织结构的不均匀引起的。
1.材料内部的夹杂物和气孔:夹杂物和气孔容易成为开裂的起始点。
在淬火过程中,由于夹杂物和气孔内的应力集中,容易发生裂纹形成。
夹杂物和气孔的分布和尺寸也会影响开裂的情况。
2.材料本身的组织结构:金属材料的组织结构不均匀也是导致开裂的原因之一、在淬火过程中,由于金属材料的非均匀组织,使得表面和内部的应力分布不均匀,从而引起开裂。
3.残余应力:淬火会引起金属件表面和内部产生巨大的残余应力。
如果残余应力达到了金属材料的抗拉强度,就会引起开裂。
残余应力的大小和分布与淬火过程中的冷却速率、金属材料的性能和几何形状等因素有关。
二、外涵开裂外涵开裂主要是指由外部环境因素引起的开裂。
1.快速冷却速率:淬火是通过快速冷却来改变金属内部的组织结构和性能的。
如果冷却速率过快,会导致金属件内部和表面的温度梯度过大,引起开裂。
2.淬火介质选择:不同的淬火介质对金属件的冷却速率有不同的影响。
如果选择不合适的淬火介质,冷却速率过快或过慢都容易引起开裂。
3.加工缺陷:在金属件的加工过程中,如果存在一些加工缺陷,如划痕、凹陷、磨损等,淬火时会加深这些缺陷,导致开裂。
4.过度淬火:过度淬火是指冷却速率过快,温度过低,或者淬火时间过长等情况。
这会导致金属内部和表面的应力过大,造成开裂。
5.不合理的加工工艺:金属材料的淬火工艺需要根据具体材料的性能和要求来确定。
如果加工工艺不合理,如选择不适合的加热温度、加热时间过长等,都会引起开裂的问题。
综上所述,淬火开裂是由于材料的缺陷、组织结构不均匀,以及外部环境因素的影响而引起的。
为了避免开裂问题的发生,需要通过控制材料的质量、改善组织结构、合理选择加工工艺和淬火条件等方面的措施来减少或消除开裂情况的发生。
淬火处理常见裂纹类型及预防措施
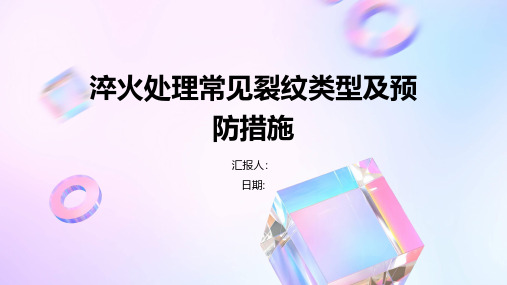
淬火处理常见裂纹类型及预防措施汇报人:日期:•淬火处理概述•淬火处理常见裂纹类型•淬火处理裂纹的预防措施目录•淬火处理的质量控制•淬火处理技术的发展趋势01淬火处理概述0102淬火处理的目的和原理淬火处理的原理是将金属材料加热到一定温度后迅速冷却,通过快速冷却使金属内部结构发生改变,从而实现性能的提升。
淬火处理的目的是提高金属材料的强度、硬度、耐磨性和韧性等性能。
将金属材料加热到一定温度。
保温一定时间,使金属内部结构调整均匀。
迅速冷却,使金属内部结构发生改变。
回火处理,进一步稳定金属内部结构,提高性能。
01020304淬火处理的基本步骤02淬火处理常见裂纹类型应力裂纹是在淬火过程中,由于工件内部温度不均匀,导致局部区域产生拉应力而产生的裂纹。
定义淬火过程中,工件内部温度变化大,导致内应力集中,尤其是在工件形状复杂或截面尺寸变化剧烈时,更容易产生应力裂纹。
原因采用缓慢淬火工艺,减小工件内外温差,降低淬火应力;合理设计工件结构,避免截面尺寸变化剧烈。
预防措施原因淬火后,工件内部仍存在一定的残余应力,当这些应力超过材料的屈服强度时,就会产生延迟裂纹。
定义延迟裂纹是淬火后,在工件冷却过程中,由于工件内部存在淬火应力,随着时间的推移,应力逐渐释放而产生的裂纹。
预防措施优化淬火工艺,降低淬火应力;淬火后进行回火处理,进一步释放内应力;采用喷丸、碾压等表面强化处理工艺,提高工件表面强度和抗疲劳性能。
淬火裂纹是由于淬火过程中,工件内部或表面局部区域温度过高或过低,导致相变不均匀,产生裂纹或开裂现象。
定义淬火过程中,工件内部或表面局部温度过高或过低,导致相变不均匀,产生淬火裂纹;淬火介质选择不当或冷却条件不良,也会引起淬火裂纹。
原因合理选择淬火介质和冷却条件;采用预冷、分级淬火等工艺措施,减小温度变化梯度;优化淬火工艺参数,避免出现过热、过冷现象。
预防措施淬火裂纹03淬火处理裂纹的预防措施预冷处理在淬火前进行预冷处理,可以减少工件在淬火过程中的温度变化,从而降低热应力。
模具钢淬火中的裂纹分析及解决方案
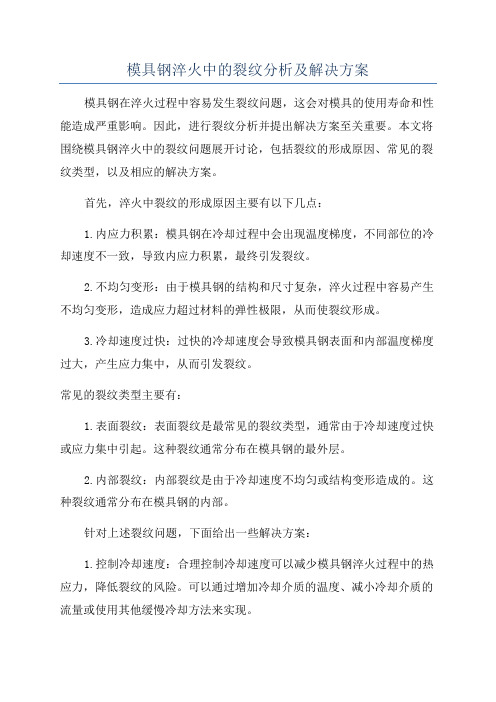
模具钢淬火中的裂纹分析及解决方案模具钢在淬火过程中容易发生裂纹问题,这会对模具的使用寿命和性能造成严重影响。
因此,进行裂纹分析并提出解决方案至关重要。
本文将围绕模具钢淬火中的裂纹问题展开讨论,包括裂纹的形成原因、常见的裂纹类型,以及相应的解决方案。
首先,淬火中裂纹的形成原因主要有以下几点:1.内应力积累:模具钢在冷却过程中会出现温度梯度,不同部位的冷却速度不一致,导致内应力积累,最终引发裂纹。
2.不均匀变形:由于模具钢的结构和尺寸复杂,淬火过程中容易产生不均匀变形,造成应力超过材料的弹性极限,从而使裂纹形成。
3.冷却速度过快:过快的冷却速度会导致模具钢表面和内部温度梯度过大,产生应力集中,从而引发裂纹。
常见的裂纹类型主要有:1.表面裂纹:表面裂纹是最常见的裂纹类型,通常由于冷却速度过快或应力集中引起。
这种裂纹通常分布在模具钢的最外层。
2.内部裂纹:内部裂纹是由于冷却速度不均匀或结构变形造成的。
这种裂纹通常分布在模具钢的内部。
针对上述裂纹问题,下面给出一些解决方案:1.控制冷却速度:合理控制冷却速度可以减少模具钢淬火过程中的热应力,降低裂纹的风险。
可以通过增加冷却介质的温度、减小冷却介质的流量或使用其他缓慢冷却方法来实现。
2.合理设计模具结构:模具的设计结构应该避免尖角和过于薄壁的部位,以减少应力集中导致的裂纹。
在可能的情况下,可以添加过渡圆角和半径,有助于减少裂纹的风险。
3.适当的预处理:通过适当的热处理工艺可以改善模具钢的力学性能和织构,减少应力集中和变形,降低裂纹的发生。
这包括应用回火、退火和正火等热处理方法。
4.使用有效的质量控制措施:在制造模具钢过程中,需要严格控制原材料的质量,以确保材料的均匀性和稳定性。
此外,必须严格控制加工中的工艺参数,以确保产品的质量。
总结起来,模具钢淬火中的裂纹问题对模具的使用寿命和性能都有很大的影响。
针对裂纹的形成原因和类型,我们可以通过控制冷却速度、合理设计模具结构、适当的预处理和使用有效的质量控制措施等方面来解决这一问题。
淬火裂纹的特征

淬火裂纹的特征
淬火裂纹是在金属材料淬火过程中产生的一种缺陷,通常是由于金属在快速冷却的过程中发生的热应力引起的。
以下是淬火裂纹的一些特征:
1.形状和方向:淬火裂纹通常呈现为细长的裂缝,其方向与金属的冷却方向有关。
这些裂纹可能是沿晶体结构的方向延伸,也可能是穿过晶界。
2.位置:裂纹通常出现在零件的表面或近表面区域。
这是因为表面区域冷却更快,产生的热应力更大,容易导致裂纹的形成。
3.细小裂纹:淬火裂纹可以非常细小,有时候肉眼难以察觉,需要借助显微镜或其他检测工具。
4.交叉裂纹:裂纹可能沿着不同的方向交叉,形成复杂的网络状结构。
5.裂纹的密度:淬火裂纹的密度取决于材料的性质、淬火过程的参数以及材料的初始结构。
高碳钢等易于淬火裂纹的材料通常表现出较高的裂纹密度。
6.表面硬度的改变:淬火裂纹可能导致局部硬度的显著变化。
裂纹处的硬度通常较高。
7.形成条件:淬火裂纹主要由于淬火过程中产生的热应力引起。
这种应力是由于材料表面和内部的温度梯度导致的。
因此,淬火温度、冷却速率以及材料的成分和结构都是影响淬火裂纹形成的重要因素。
为了防止淬火裂纹的产生,可以采取一些措施,如适当控制淬火工艺参数、降低材料的碳含量、进行预热等。
此外,对于一些关键部件,还可以采用热处理后的再回火工艺,以减轻淬火裂纹的影响。
热处理淬火裂纹和磨削裂纹
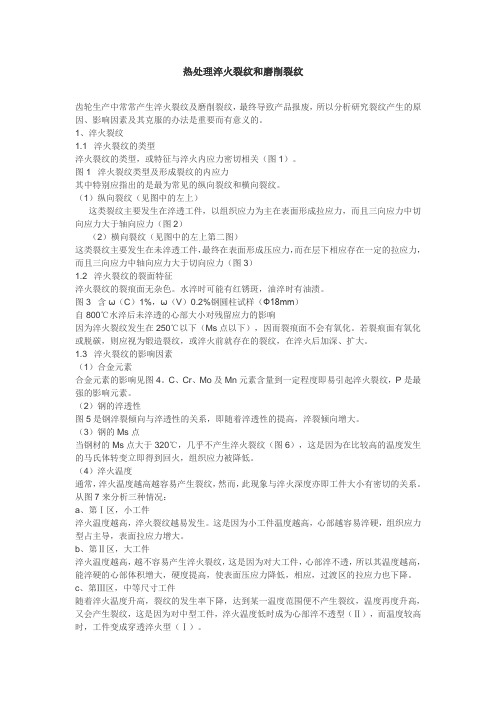
热处理淬火裂纹和磨削裂纹齿轮生产中常常产生淬火裂纹及磨削裂纹,最终导致产品报废,所以分析研究裂纹产生的原因、影响因素及其克服的办法是重要而有意义的。
1、淬火裂纹1.1 淬火裂纹的类型淬火裂纹的类型,或特征与淬火内应力密切相关(图1)。
图1 淬火裂纹类型及形成裂纹的内应力其中特别应指出的是最为常见的纵向裂纹和横向裂纹。
(1)纵向裂纹(见图中的左上)这类裂纹主要发生在淬透工件,以组织应力为主在表面形成拉应力,而且三向应力中切向应力大于轴向应力(图2)(2)横向裂纹(见图中的左上第二图)这类裂纹主要发生在未淬透工件,最终在表面形成压应力,而在层下相应存在一定的拉应力,而且三向应力中轴向应力大于切向应力(图3)1.2 淬火裂纹的裂面特征淬火裂纹的裂痕面无杂色。
水淬时可能有红锈斑,油淬时有油渍。
图3 含ω(C)1%,ω(V)0.2%钢圆柱试样(Ф18mm)自800℃水淬后未淬透的心部大小对残留应力的影响因为淬火裂纹发生在250℃以下(Ms点以下),因而裂痕面不会有氧化。
若裂痕面有氧化或脱碳,则应视为锻造裂纹,或淬火前就存在的裂纹,在淬火后加深、扩大。
1.3 淬火裂纹的影响因素(1)合金元素合金元素的影响见图4。
C、Cr、Mo及Mn元素含量到一定程度即易引起淬火裂纹,P是最强的影响元素。
(2)钢的淬透性图5是钢淬裂倾向与淬透性的关系,即随着淬透性的提高,淬裂倾向增大。
(3)钢的Ms点当钢材的Ms点大于320℃,几乎不产生淬火裂纹(图6),这是因为在比较高的温度发生的马氏体转变立即得到回火,组织应力被降低。
(4)淬火温度通常,淬火温度越高越容易产生裂纹,然而,此现象与淬火深度亦即工件大小有密切的关系。
从图7来分析三种情况:a、第Ⅰ区,小工件淬火温度越高,淬火裂纹越易发生。
这是因为小工件温度越高,心部越容易淬硬,组织应力型占主导,表面拉应力增大。
b、第Ⅱ区,大工件淬火温度越高,越不容易产生淬火裂纹,这是因为对大工件,心部淬不透,所以其温度越高,能淬硬的心部体积增大,硬度提高,使表面压应力降低,相应,过渡区的拉应力也下降。
淬火时出现裂纹的原因及解决方法
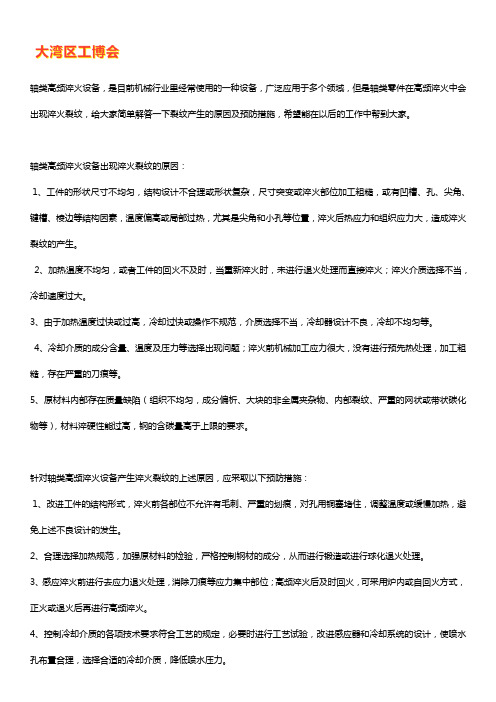
轴类高频淬火设备,是目前机械行业里经常使用的一种设备,广泛应用于多个领域,但是轴类零件在高频淬火中会出现淬火裂纹,给大家简单解答一下裂纹产生的原因及预防措施,希望能在以后的工作中帮到大家。
轴类高频淬火设备出现淬火裂纹的原因:1、工件的形状尺寸不均匀,结构设计不合理或形状复杂,尺寸突变或淬火部位加工粗糙,或有凹槽、孔、尖角、键槽、棱边等结构因素,温度偏高或局部过热,尤其是尖角和小孔等位置,淬火后热应力和组织应力大,造成淬火裂纹的产生。
2、加热温度不均匀,或者工件的回火不及时,当重新淬火时,未进行退火处理而直接淬火;淬火介质选择不当,冷却速度过大。
3、由于加热温度过快或过高,冷却过快或操作不规范,介质选择不当,冷却器设计不良,冷却不均匀等。
4、冷却介质的成分含量、温度及压力等选择出现问题;淬火前机械加工应力很大,没有进行预先热处理,加工粗糙,存在严重的刀痕等。
5、原材料内部存在质量缺陷(组织不均匀,成分偏析、大块的非金属夹杂物、内部裂纹、严重的网状或带状碳化物等),材料淬硬性能过高,钢的含碳量高于上限的要求。
针对轴类高频淬火设备产生淬火裂纹的上述原因,应采取以下预防措施:1、改进工件的结构形式,淬火前各部位不允许有毛刺、严重的划痕,对孔用铜塞堵住,调整温度或缓慢加热,避免上述不良设计的发生。
2、合理选择加热规范,加强原材料的检验,严格控制钢材的成分,从而进行锻造或进行球化退火处理。
3、感应淬火前进行去应力退火处理,消除刀痕等应力集中部位;高频淬火后及时回火,可采用炉内或自回火方式,正火或退火后再进行高频淬火。
4、控制冷却介质的各项技术要求符合工艺的规定,必要时进行工艺试验,改进感应器和冷却系统的设计,使喷水孔布置合理,选择合适的冷却介质,降低喷水压力。
热处理缺陷
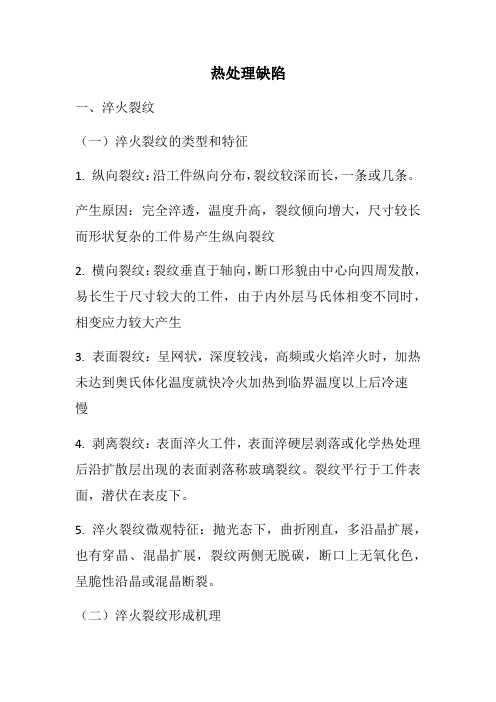
热处理缺陷一、淬火裂纹(一)淬火裂纹的类型和特征1. 纵向裂纹:沿工件纵向分布,裂纹较深而长,一条或几条。
产生原因:完全淬透,温度升高,裂纹倾向增大,尺寸较长而形状复杂的工件易产生纵向裂纹2. 横向裂纹:裂纹垂直于轴向,断口形貌由中心向四周发散,易长生于尺寸较大的工件,由于内外层马氏体相变不同时,相变应力较大产生3. 表面裂纹:呈网状,深度较浅,高频或火焰淬火时,加热未达到奥氏体化温度就快冷火加热到临界温度以上后冷速慢4. 剥离裂纹:表面淬火工件,表面淬硬层剥落或化学热处理后沿扩散层出现的表面剥落称玻璃裂纹。
裂纹平行于工件表面,潜伏在表皮下。
5. 淬火裂纹微观特征:抛光态下,曲折刚直,多沿晶扩展,也有穿晶、混晶扩展,裂纹两侧无脱碳,断口上无氧化色,呈脆性沿晶或混晶断裂。
(二)淬火裂纹形成机理钢中奥氏体向马氏体转变时体积增大所产生的应力导致淬火裂纹。
当钢淬火冷却时,在首先达到M s点温度的工件外层率先形成马氏体,发生体积膨胀,产生应力,外表面的马氏体膨胀几乎不受限制。
继续冷却当靠近中心部位的材料到达M s点温度时,新生的马氏体膨胀收到早已形成的外层马氏体的限制,产生使表面张开的内应力。
当马氏体大量形成所产生的内应力大于零件外层淬火状态的马氏体强度时,便出现开裂。
(三)影响淬火裂纹的因素1. 钢的化学成分:含碳、铬、钼、磷高易引起裂纹2. 材料缺陷:发纹、气泡、碳化物偏析、非金属夹杂、过热、折叠、微裂纹等3. 钢件形状结构:截面急剧变化的工件,有尖角、缺口、孔洞、槽口、冲压标记、刻痕、加工刀痕等应力集中部位易发生。
4. 淬火前原始组织:球状珠光体比片状珠光体不易产生淬火裂纹,因球状珠光体淬成马氏体时其比容变化小、应力小5. 淬火温度淬火温度高易产生裂纹,奥氏体晶粒粗大,淬透性提高,淬裂倾向大。
淬火温度与淬火裂纹发生率之间有三种情况:1)对于小型零件,淬火温度高,淬火裂纹发生率高2)对于大型零件,淬火温度高,淬火裂纹发生率低3)对于中型零件,裂纹发生有个转变温度6. 冷却速度冷速快,使表面产生压应力,内层为张应力,这种应力不易产生裂纹,但冷到马氏体转变点以下时产生相变应力,表面为张应力,易产生淬火裂纹。
淬火易出现的问题及解决方法

淬火易出现的问题及解决方法
淬火是一种金属材料的热处理方法,可以提高材料的硬度和强度。
在淬火过程中可能出现以下问题:
1. 非均匀淬火:由于材料的形状、组织结构和尺寸的不同,淬火后的硬度和强度可能会出现不均匀分布。
解决方法可以采用多次淬火、适当改变淬火介质的工艺参数以及合理的加热和冷却速度控制。
2. 出现裂纹:材料在淬火过程中由于温度梯度影响,可能出现内部或表面的裂纹。
解决方法可以通过加强材料的均匀加热和冷却过程,避免急冷和过热,适当地进行回火处理,消除内部应力。
3. 变形或翘曲:一些材料在淬火过程中由于温度变化引起的体积变化可能会导致材料的变形或翘曲。
解决方法可以采用预热处理,减小温度梯度;在淬火后进行回火处理,减小材料的内应力。
4. 高温氧化:在高温环境下,金属材料可能会与空气中的氧气发生反应,产生氧化层。
解决方法可以采用保护气氛或真空条件下的淬火,减少材料与氧气接触;在淬火后进行酸洗或电解去氧化。
5. 淬火介质的选择:不同的金属材料需要选择合适的淬火介质。
解决方法可以根据材料的成分和要求,选用适当的淬火介质,如水、油或盐。
总的来说,淬火过程中出现的问题需要合理设置工艺参数,选择适当的淬火介质,进行必要的热处理工艺控制,以获得理想的材料性能。
【doc】淬火裂纹的特征及鉴别

淬火裂纹的特征及鉴别淬火裂纹的特征及鉴别杭州市机械科学研究所杨廷质钢在热处理过程中所形成的裂纹,总称为处理裂纹.产生热处理裂纹的因素是多方面的,有原材料的缺陷,有淬火加热温度过高,有冷却方法不当,有零件几何形状设计不合理等等.下面,本人据多年金相检验的体会,分别按上述诸因素对淬火裂纹的特征及鉴别法作一简单的叙述一,原材料缺陷引起淬火开裂1.夹杂物引起淬火裂纹存在于金属中的氧化物,硅酸盐和硫化物等均属夹杂物它们在冷热加工过程中,会沿着加工方向伸长扩展成条片状,或碎裂成更小的颗粒而以断续的链状分布,作为独立相存在钢中(图1,图2).图l塑性夹杂物100×一部嚣圈2脆性夹杂袖100×象这类夹杂物,直接破坏了钢中基体组织的连续性,使组缨不均习增加.钢锭中有些非16金属夹杂物具有较母相金属为低的熔点,当热加工时,由于非金属夹杂物的熔融或软化,从而降低了钢在热态下的强度.并在该处起着局部缺口的作用,导致应力集中,往往成为淬火裂纹的起源.由于非金属夹杂物引起淬火开裂,必然与这些献路保持着一定联系.因此,在作金相分析时,在裂纹附近常能看到伴有夹杂物分布的特征(圈3).图3裂纹附近夹杂枷5OX有时也能看到在受侵蚀的金相磨面上有细短微裂纹.这种细短微裂纹在侵蚀前用显微镜观察是非金属夹杂物,象这种微细裂纹称为发纹,不是淬火裂纹.在作淬火裂纹分析时,有时也会误判不是由原材料夹杂物引起的淬火裂纹,却认为是原材料夹杂物引起淬火裂纹.如45号钢机6mm螺栓,诩质后在粗加工时发现表面开裂(图4),经金相观察,裂纹处有夹杂物存在(图5,圈0).而裂纹边缘未发现脱碳(图7).这说明该裂纹是淬火裂纹.是否可以说该淬火裂纹是由于原材料夹杂物所引起呢?不是从幽6可以观察到,该夹杂物是沿纵向成60.角方向延伸(也是治裂纹方向延伸).经金相鉴别,该夹杂物是氧化物,是由于螺栓毛坯在高温回火时所引起氧化的结图4~16mm螺拴表面洋火裂纹果.并非是原材料所存在的夹杂物.而造成淬火裂纹其主要原因是淬火加热温度过高所gI起淬火开裂.沿纵向延伸夹杂物100×图7裂纹边缘未发现脱碳4002.碳化物偏析引起淬火开裂这种情况多见于台金工具钢和高速钢一类,因这些钢存在碳化物不均匀,且在压力加工中又未能破碎,就会星网状分布或呈严重带状偏析(图8,9).图8W8Cr4V铜碳化物呈难状分布100×图6沿纵向成60.角廷伸夹杂物100×图9WIsCr,V钢碳化物呈带状分布100x这种碳化物形状会使钢的机械性能呈各向异性,降低钢材热处理后的强度和韧性,表1为碳化物不均匀度对Wr'V高速钢机械性能的影响而在碳化物偏析处,碳及合金元素含量较高,在该处过热敏感性较大,在正常淬火温度也易获得较粗大的淬火马氏体组织(图10).在碳化物发生严重偏析处,因淬火时有高的局部应力,就会沿着碳化物偏析处产生淬火裂纹(图11).表一1碳化物不均匀度对Wl.Cr,V铜的机械性能的影响不均匀性HR口红硬性HRo袅别:N/mmN-mlcm'硬度600℃e25℃650℃358922.665.261.359.051.13421.664.561.059.050.6310816.76559.058.0.50.117-一翟固lOWl8Cr.V铜碳化物偏折处固13淬火前裂纹1O0X 粗大针状马氏体500×图IIWsCr4V钢沿碳化物偏折处开裂l00X3.原材料裂纹在淬火时的扩展当原材料裂纹暴露在工作表面时,固裂纹细小,有时不易被发现,在热处理淬火时,由于内应力的作用,使工作在原有的裂纹处进一步扩大,成为淬犬裂纹(图12).鉴图1245号钢在原有裂垃上扩展l00X别裂纹是热处理裂纹还是热处理前存在的裂纹,可借助子金相显徽镜来鉴别.如果裂纹在热处理之前即已存在,工件经淬火加热之后,其裂纹一般较为宽阔,裂纹两侧将会发生氧化脱碳现象(图i3).这是由于在淬火加热时,空气沿着裂缝渗入,使裂纹两侧发生严重脱碳.如果裂纹隐藏在工件内部,淬火加热时,裂纹不可能和空气接触,裂纹周围就无脱碳现象.由此可见裂纹两侧有氧化脱碳现象多系发生在淬火之前j反之,不能说裂纹两侧没有脱碳均是淬火裂纹.18二,淬火加热温度过高引起开裂荆在过高的温度下加热时,会使奥氏体晶粒粗大,加热温度愈高或高温停留时间过长,则奥氏体晶粒将会愈粗大.这种粗大奥氏体晶粒会使锶的力学性能变坏,如冲击性能下降.由于加热温度过高,在同样的淬火冷却条件下,淬裂的倾向比在正常加热温度况下来得大.当工件几何形状愈复杂,冷却愈剧烈,产生裂纹的可能性也就越大.淬火加热温度过高形成的裂纹多具有一个共同的特点:奥氏体晶粒粗大,裂纹一般是沿着奥氏体晶界分布.在显微组织中可以看到粗大针状马氏体(图14).图1445号钢粗大针状马氏体裂纹浩奥氏体晶界分布400X淬火加热温度过高而引起开裂在工具钢中尤为常见.因为工具钢过热后,不仅晶粒易粗大,而且还有较多的碳化物溶入奥氏体中,使高碳马氏体的数量增加,显微裂纹增多,脆性增加,强度降低,易造成工件在津火时开裂.图15为9CrSi钢和T10钢在水中淬火出现裂纹的试祥数量与淬火温度的关系.随着淬火温度的提高,试样产生裂纹的数量四呷曩呈直线上升.,鬃挫裂技{;;符硝百j仳c图159CrSi钢和Tl0钢在水淬火产生裂纹试样的数量与加热温度的关系W.Cr.V高速钢,对热硬性影响最大的两个元素钨和钒,溶入奥氏体的数量随温度的升高而增加.为了使刀具在淬火回火后获得最佳的切削性能,一般都采用126o.~1280'C淬火,该温度已接近高速锕开始熔化温度.因此,在高速钢淬火时温度控制稍有不慎就会gl起过热和过烧.图l6为高速钢过热的组织,一次破化物形状发生改变,晶粒边界部分碳化物熔化.冷却时析出半网状和阿状碳化物.图17为淬火加热时过烧金相组织,以致晶界发生熔化,出现祖大莱氏体共晶组织.图l8为淬火加热时温度过高而Be起开裂.由图l8可见,这类裂纹往往发生在网状碱化物区域,产生裂纹的原因是高速钢过热形成的共晶碳化物治晶界呈网状分布,使刀具产生很大脆性.在淬火时,由于粗大晶粒引起的巨大的淬火应力,常导致沿晶界开裂.图l6W,BCr.V钢过热,一班碳化物形状发生改童500x图l7W.sCrIv钢过烧,晶界发生熔亿500x固18W1日Cr'v钢淬火加热温度过高l起淬火开裂500×三,淬火冷却方法不当号I起开裂由热处理所引起的缺陷,淬裂是最严重的一种.—旦淬裂,工件就会报废,在经济上损失是很大的.淬裂出现在淬火冷却末期或者说裂纹是发生在钢的马氏体转变点Ms~Mz区间.为了获得马氏体组织和足够的淬硬层深度,就必须采用一定速度冷却.工件在急冷时必然会使表面与心部,厚的部分与薄的部分形成很大的温差,从而使工件在各部分发生体积的热胀冷缩不一致,组织转变不协调(转变时间和转变量不一致).因此,在淬火过程中必然会产生内应力,当瞬时内应力超过工件在该温度下的弹性极限就会使工件变形.超过该工件的断裂强度时,就会导致工件开裂.如某柴油机厂一零件是由40Mn钢制造,由于使用淬火介质不当,出现大批工件开裂.因40Mnz钢是中碳合金钢,其淬火介质适宜用油,该厂淬火介质采用水,以致冷却速度过快,增加了工件的内应力,引超大量开裂. (下转第24页)l拿?千赫,相移很小,忽略不计.叉因为交变主磁通与电磁澈振力变化同相,所以巾.F:0,cw÷0则中=巾=97l+札.+中:.lo(3)实测表明,功率放大器输出电流最大失真度小于l%,一般在0.5左右,应该说是比较好的.电磁激振器上的直流信号和交流信号共同作用下的铁心线圈是个非线性元件,即使流经交流线圈中的功放输出电压是正弦波,而电流常是非正弦波.又如果非正弦波的电流与正弦波的差q不大,可用等效的正弦波来代替非正弦波(电流).此时,等效正弦波的有效值要等于被替代非正弦波的有效值. 引入这个概念,可画向量图(图2).等值正弦电流i等可分解为两个分量.由铁心损失引起的ix及产生主磁通的分量i.(和同相),口就是I.,上面推导过程中l?已经E图2向量图消掉了,故无需求得.至手机.r就是毒与之间的角,根据它的定义知饥.:90.表l额率cHzlz..的电压放大嚣的相善度2O】l8'●O~56I18260~226l181227~600l180剩下,我们实测了BK2010的电压放大器系统的相移至此:m4-90+o<4)若(4)式中是正值的话即表示振动响应超前于力,如正的角度数大于360.则应化成正的角度数减去360.的角度,例如4-365.等于4-5.这耐,若振动响应滞后于力的话,即为负值,那么=一E360'一(lI7l4-90.+巾i?l.)]如超前315.,即为蒲后45.考虑进一步提高相位测试精度的措施有=个方面li.从CW6仪到相位差计中问加一跟踪滤波器.2.在实测2010的电压放大器相移时在其输入端并接积分器GZ-1,这样相移数更符合实际.(上接第l9页)四,工件几何形状设计不合理引起淬火开裂零件设计应考虑到其形状有利于在以后的加工及热处理中减少变形和开裂等因素. 在尽可能满足使用要求的条件下,应尽量减少工件截面厚薄的悬殊及形状不对称.要避免薄边和尖角,做到工件厚薄交界处尽可能24-平滑过凄,不对称工件可采用工艺孔,来改善冷却条件.对于形状复杂较大的模具,可采用组合结构,变繁为简,变大为小.在淬火时有效地减少变形和开裂,这样才能提高产品的合格率.}I起淬火裂纹的因素还有很多,它往往不是只由一个因素来决定,而是由多种因素叠加在一起而发生,故而要进行综合分析, 才能找出其开裂的真正原因.参考资料(略)。
淬火裂纹

淬火裂纹是指在淬火过程中或在淬火后的室温放置过程中产生的裂纹。
后者又叫时效裂纹。
造成淬火开裂的原因很多,在分析淬火裂纹时,应根据裂纹特征加以区分。
一、淬火裂纹的特征在淬火过程中,当淬火产生的巨大应力大于材料本身的强度时,便会导致裂纹产生。
淬火裂纹往往是在马氏体转变开始进行后不久产生的,裂纹的分布则没有一定的规律,但一般容易在工件的棱角槽口、截面突变处形成。
在显微镜下观察到的淬火开裂,可能是沿晶开裂,也可能是穿晶开裂;有的呈放射状,也有的呈单独线条状或呈网状。
因在马氏体转变区的冷却过快而引起的淬火裂纹,往往是穿晶分布,而且裂纹较直,周围没有分枝的小裂纹。
因淬火加热温度过高而引起的淬火裂纹,都是沿晶分布,裂纹尾端尖细,并呈现过热特征:结构钢中可观察到粗针状马氏体;工具钢中可观察到共晶或角状碳化物。
表面脱碳的高碳钢工件,淬火后容易形成网状裂纹。
这是因为,表面脱碳层在淬火冷却时的体积胀大比未脱碳的心部小,表面材料受心部膨胀的作用而被拉裂呈网状。
二、非淬火裂纹的特征淬火后发生的裂纹,不一定都是淬火所造成的,一般可根据下面的特征来区分。
淬火后发现的裂纹,如果裂纹两侧有氧化脱碳现象,则可以肯定裂纹在淬火之前就已经存在。
淬火冷却过程中,只有当马氏体转变量达到一定数量时,裂纹才有可能形成。
与此相对应的温度,大约在250℃以下。
在这样的低温下,即使产生了裂纹,裂纹两侧也不会发生脱碳和出现明显氧化。
所以,有氧化脱碳现象的裂纹是非淬火裂纹。
如果裂纹在淬火前已经存在,又不与表面相通,这样的内部裂纹虽不会产生氧化脱碳,但裂纹的线条显得柔软,尾端圆秃,也容易与淬火裂纹的线条刚健有力,尾端尖细的特征区别开来。
三、实例分析实例一:40Cr钢制成的转子轴,经锻造、淬火后发现裂纹。
裂纹两侧有氧化迹象,经金相检验,裂纹两侧存在脱碳层,而且裂纹两侧的铁素体呈较大的柱状晶粒,其晶界与裂纹大致垂直。
结论:裂纹是在锻造时形成的非淬火裂纹。
当工件在锻造过程中形成裂纹时,淬火加热即引起裂纹两侧氧化脱碳。
热处理淬火十种裂纹分析与措施(参考资料)
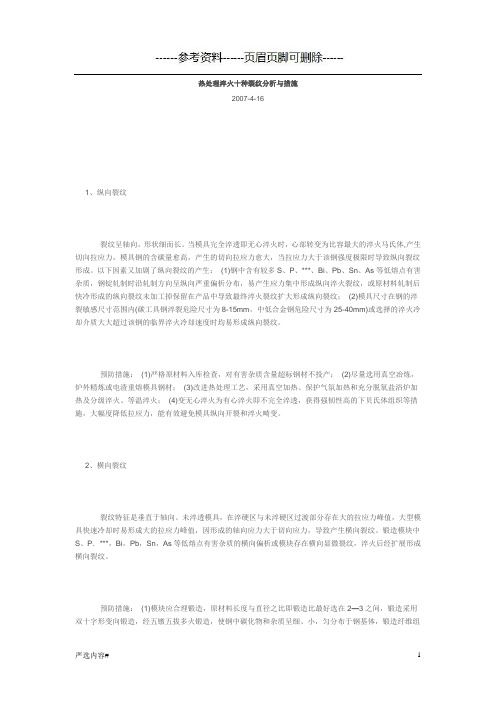
热处理淬火十种裂纹分析与措施2007-4-161、纵向裂纹裂纹呈轴向,形状细而长。
当模具完全淬透即无心淬火时,心部转变为比容最大的淬火马氏体,产生切向拉应力,模具钢的含碳量愈高,产生的切向拉应力愈大,当拉应力大于该钢强度极限时导致纵向裂纹形成。
以下因素又加剧了纵向裂纹的产生:(1)钢中含有较多S、P、***、Bi、Pb、Sn、As等低熔点有害杂质,钢锭轧制时沿轧制方向呈纵向严重偏析分布,易产生应力集中形成纵向淬火裂纹,或原材料轧制后快冷形成的纵向裂纹未加工掉保留在产品中导致最终淬火裂纹扩大形成纵向裂纹;(2)模具尺寸在钢的淬裂敏感尺寸范围内(碳工具钢淬裂危险尺寸为8-15mm,中低合金钢危险尺寸为25-40mm)或选择的淬火冷却介质大大超过该钢的临界淬火冷却速度时均易形成纵向裂纹。
预防措施:(1)严格原材料入库检查,对有害杂质含量超标钢材不投产;(2)尽量选用真空冶炼,炉外精炼或电渣重熔模具钢材;(3)改进热处理工艺,采用真空加热、保护气氛加热和充分脱氧盐浴炉加热及分级淬火、等温淬火;(4)变无心淬火为有心淬火即不完全淬透,获得强韧性高的下贝氏体组织等措施,大幅度降低拉应力,能有效避免模具纵向开裂和淬火畸变。
2、横向裂纹裂纹特征是垂直于轴向。
未淬透模具,在淬硬区与未淬硬区过渡部分存在大的拉应力峰值,大型模具快速冷却时易形成大的拉应力峰值,因形成的轴向应力大于切向应力,导致产生横向裂纹。
锻造模块中S、P.***,Bi,Pb,Sn,As等低熔点有害杂质的横向偏析或模块存在横向显微裂纹,淬火后经扩展形成横向裂纹。
预防措施:(1)模块应合理锻造,原材料长度与直径之比即锻造比最好选在2—3之间,锻造采用双十字形变向锻造,经五镦五拔多火锻造,使钢中碳化物和杂质呈细、小,匀分布于钢基体,锻造纤维组织围绕型腔无定向分布,大幅度提高模块横向力学性能,减少和消除应力源;(2)选择理想的冷却速度和冷却介质:在钢的Ms点以上快冷,大于该钢临界淬火冷却速度,钢中过冷奥氏体产生的应力为热应力,表层为压应力,内层为张应力,相互抵消,有效防止热应力裂纹形成,在钢的Ms—Mf之间缓冷,大幅度降低形成淬火马氏体时的组织应力。
分析钢材的淬火裂纹原理
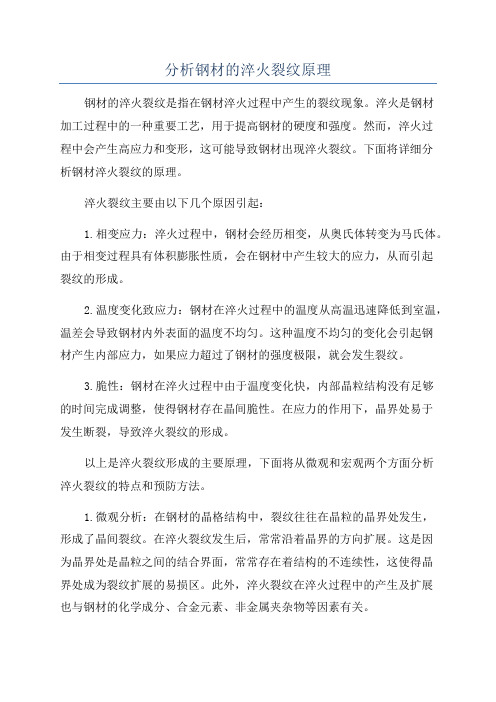
分析钢材的淬火裂纹原理钢材的淬火裂纹是指在钢材淬火过程中产生的裂纹现象。
淬火是钢材加工过程中的一种重要工艺,用于提高钢材的硬度和强度。
然而,淬火过程中会产生高应力和变形,这可能导致钢材出现淬火裂纹。
下面将详细分析钢材淬火裂纹的原理。
淬火裂纹主要由以下几个原因引起:1.相变应力:淬火过程中,钢材会经历相变,从奥氏体转变为马氏体。
由于相变过程具有体积膨胀性质,会在钢材中产生较大的应力,从而引起裂纹的形成。
2.温度变化致应力:钢材在淬火过程中的温度从高温迅速降低到室温,温差会导致钢材内外表面的温度不均匀。
这种温度不均匀的变化会引起钢材产生内部应力,如果应力超过了钢材的强度极限,就会发生裂纹。
3.脆性:钢材在淬火过程中由于温度变化快,内部晶粒结构没有足够的时间完成调整,使得钢材存在晶间脆性。
在应力的作用下,晶界处易于发生断裂,导致淬火裂纹的形成。
以上是淬火裂纹形成的主要原理,下面将从微观和宏观两个方面分析淬火裂纹的特点和预防方法。
1.微观分析:在钢材的晶格结构中,裂纹往往在晶粒的晶界处发生,形成了晶间裂纹。
在淬火裂纹发生后,常常沿着晶界的方向扩展。
这是因为晶界处是晶粒之间的结合界面,常常存在着结构的不连续性,这使得晶界处成为裂纹扩展的易损区。
此外,淬火裂纹在淬火过程中的产生及扩展也与钢材的化学成分、合金元素、非金属夹杂物等因素有关。
2.宏观分析:通常情况下,淬火裂纹可分为两种类型:表面淬火裂纹和内部淬火裂纹。
表面淬火裂纹主要位于钢材的表面,其形成原因通常是在淬火过程中,钢材的表面和内部温度变化不均匀,导致表面产生应力过大而产生裂纹。
内部淬火裂纹则主要存在于钢材的内部,通常由于钢材内部组织的不均匀性或者淬火工艺参数不当而引起。
为了预防和控制钢材的淬火裂纹,可以采取以下一些措施:1.选择合适的合金元素:适当添加合适的合金元素,如铬、钼、镍等,可以改善钢材的组织结构,减少淬火裂纹的产生。
2.控制淬火冷却速度:合理控制淬火冷却速度,避免温度变化过快,以减少温度差引起的应力。
淬火裂纹实例分析报告
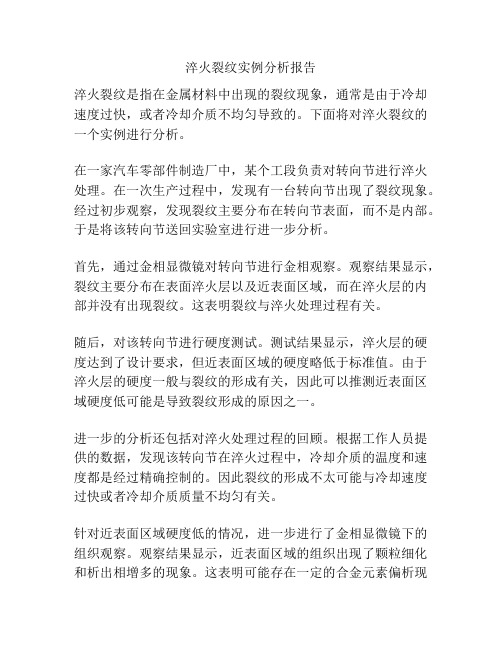
淬火裂纹实例分析报告淬火裂纹是指在金属材料中出现的裂纹现象,通常是由于冷却速度过快,或者冷却介质不均匀导致的。
下面将对淬火裂纹的一个实例进行分析。
在一家汽车零部件制造厂中,某个工段负责对转向节进行淬火处理。
在一次生产过程中,发现有一台转向节出现了裂纹现象。
经过初步观察,发现裂纹主要分布在转向节表面,而不是内部。
于是将该转向节送回实验室进行进一步分析。
首先,通过金相显微镜对转向节进行金相观察。
观察结果显示,裂纹主要分布在表面淬火层以及近表面区域,而在淬火层的内部并没有出现裂纹。
这表明裂纹与淬火处理过程有关。
随后,对该转向节进行硬度测试。
测试结果显示,淬火层的硬度达到了设计要求,但近表面区域的硬度略低于标准值。
由于淬火层的硬度一般与裂纹的形成有关,因此可以推测近表面区域硬度低可能是导致裂纹形成的原因之一。
进一步的分析还包括对淬火处理过程的回顾。
根据工作人员提供的数据,发现该转向节在淬火过程中,冷却介质的温度和速度都是经过精确控制的。
因此裂纹的形成不太可能与冷却速度过快或者冷却介质质量不均匀有关。
针对近表面区域硬度低的情况,进一步进行了金相显微镜下的组织观察。
观察结果显示,近表面区域的组织出现了颗粒细化和析出相增多的现象。
这表明可能存在一定的合金元素偏析现象,导致近表面区域的化学组成和机械性能有所不同。
进一步的化学成分分析也证实了这一点。
综合以上分析结果,可以初步得出结论:该转向节出现淬火裂纹的原因是由于近表面区域的合金元素偏析所导致的。
该裂纹一般不会对转向节的强度和使用寿命产生明显影响,但是对于外观造型和质量要求较高的产品而言,仍需要进一步改进淬火工艺,以避免类似问题的再次发生。
最后,需要指出的是,以上分析结果仅针对该实例进行分析,对于其他情况可能不具有普遍适用性。
因此,在实际生产中,对于淬火裂纹的预防和处理,还需要结合具体材料和工艺特点,采取相应的措施和改进方案。
淬火裂纹的主要特征_理论说明以及概述
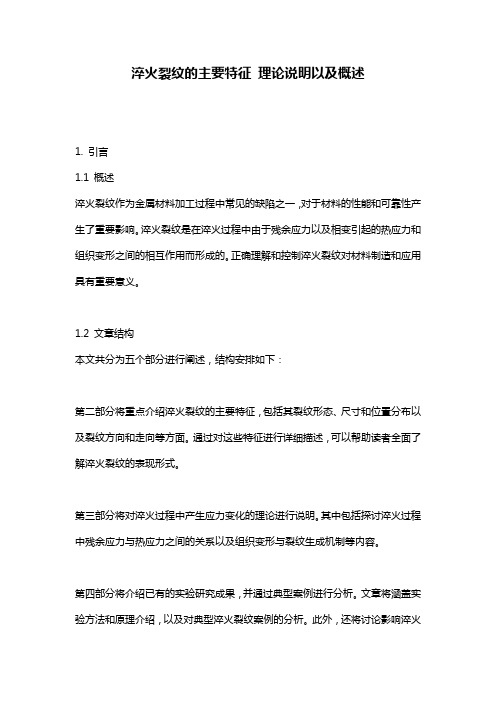
淬火裂纹的主要特征理论说明以及概述1. 引言1.1 概述淬火裂纹作为金属材料加工过程中常见的缺陷之一,对于材料的性能和可靠性产生了重要影响。
淬火裂纹是在淬火过程中由于残余应力以及相变引起的热应力和组织变形之间的相互作用而形成的。
正确理解和控制淬火裂纹对材料制造和应用具有重要意义。
1.2 文章结构本文共分为五个部分进行阐述,结构安排如下:第二部分将重点介绍淬火裂纹的主要特征,包括其裂纹形态、尺寸和位置分布以及裂纹方向和走向等方面。
通过对这些特征进行详细描述,可以帮助读者全面了解淬火裂纹的表现形式。
第三部分将对淬火过程中产生应力变化的理论进行说明。
其中包括探讨淬火过程中残余应力与热应力之间的关系以及组织变形与裂纹生成机制等内容。
第四部分将介绍已有的实验研究成果,并通过典型案例进行分析。
文章将涵盖实验方法和原理介绍,以及对典型淬火裂纹案例的分析。
此外,还将讨论影响淬火裂纹形成的因素以及相应的控制策略。
最后一部分为总结与展望,在总结中将对本文进行概括性陈述,并概述已有研究存在的不足之处。
同时,还将提出改进建议,并展望未来在淬火裂纹领域中可开展的研究方向。
1.3 目的本文旨在全面阐述淬火裂纹的主要特征、理论说明以及实验研究,并探讨其应变机制和析出物与裂纹形成关系。
通过对淬火裂纹相关理论和实践研究情况的综合分析,旨在提供对淬火过程中可能产生的问题有更加准确的认识,同时为其他研究者和工程师提供相关知识和指导,以进一步改进材料制造工艺并降低淬火裂纹风险。
2. 淬火裂纹的主要特征:2.1 裂纹形态:淬火裂纹通常呈现为沿材料表面或内部延伸的细小裂隙。
这些裂纹可以是直线状、分叉状或环形等不同形态。
在金属材料中,淬火裂纹往往呈现出透明的外观,观察时需要使用显微镜或增大镜进行辨识。
2.2 裂纹尺寸和位置分布:淬火裂纹的尺寸通常范围在几微米到数百微米之间。
它们可以在材料表面或内部发生,但更常见的是沿着晶界、晶粒边界或孪生界面形成。
- 1、下载文档前请自行甄别文档内容的完整性,平台不提供额外的编辑、内容补充、找答案等附加服务。
- 2、"仅部分预览"的文档,不可在线预览部分如存在完整性等问题,可反馈申请退款(可完整预览的文档不适用该条件!)。
- 3、如文档侵犯您的权益,请联系客服反馈,我们会尽快为您处理(人工客服工作时间:9:00-18:30)。
淬火裂纹淬火裂纹是指在淬火过程中或在淬火后的室温放置过程中产生的裂纹。
后者又叫时效裂纹。
造成淬火开裂的原因很多,在分析淬火裂纹时,应根据裂纹特征加以区分。
淬火裂纹的特征在淬火过程中,当淬火产生的巨大应力大于材料本身的强度并超过塑性变形极限时,便会导致裂纹产生。
淬火裂纹往往是在马氏体转变开始进行后不久产生的,裂纹的分布则没有一定的规律,但一般容易在工件的尖角、截面突变处形成。
在显微镜下观察到的淬火开裂,可能是沿晶开裂,也可能是穿晶开裂;有的呈放射状,也有的呈单独线条状或呈网状。
因在马氏体转变区的冷却过快而引起的淬火裂纹,往往是穿晶分布,而且裂纹较直,周围没有分枝的小裂纹。
因淬火加热温度过高而引起的淬火裂纹,都是沿晶分布,裂纹尾端尖细,并呈现过热特征:结构钢中可观察到粗针状马氏体;工具钢中可观察到共晶或角状碳化物。
表面脱碳的高碳钢工件,淬火后容易形成网状裂纹。
这是因为,表面脱碳层在淬火冷却时的体积胀比未脱碳的心部小,表面材料受心部膨胀的作用而被拉裂呈网状。
非淬火裂纹的特征淬火后发生的裂纹,不一定都是淬火所造成的,可根据下面特征来区分:淬火后发现的裂纹,如果裂纹两侧有氧化脱碳现象,则可以肯定裂纹在淬火之前就已经存在。
淬火冷却过程中,只有当马氏体转变量达到一定数量时,裂纹才有可能形成。
与此相对应的温度,大约在250℃以下。
在这样的低温下,即使产生了裂纹,裂纹两侧也不会发生脱碳和出现明显氧化。
所以,有氧化脱碳现象的裂纹是非淬火裂纹。
如果裂纹在淬火前已经存在,又不与表面相通,这样的内部裂纹虽不会产生氧化脱碳,但裂纹的线条显得柔软,尾端圆秃,也容易与淬火裂纹的线条刚健有力,尾端尖细的特征区别开来。
实例探讨1、轴,40Cr,经锻造、淬火后发现裂纹。
裂纹两侧有氧化迹象,金相检验,裂纹两侧存在脱碳层,而且裂纹两侧的铁素体呈较大的柱状晶粒,其晶界与裂纹大致垂直。
结论:裂纹是在锻造时形成的非淬火裂纹。
当工件在锻造过程中形成裂纹时,淬火加热即引起裂纹两侧氧化脱碳。
随着脱碳过程的进行,裂纹两侧的碳含量降低,铁索体晶粒开始生核。
当沿裂纹两侧生核的铁素体晶粒长大到彼此接触后,便向离裂纹两侧较远的基体方向生长。
由于裂纹两侧在脱碳过程中碳浓度的下降,也是由裂纹的开口部位向内部发展,因而为铁素体晶粒的不断长大提供了条件,故最终长大为晶界与裂纹相垂直的柱状晶体。
2、半轴套座,40Cr,淬火后出现开裂。
金相检验,裂纹两侧有全脱碳层,其中的铁素体呈粗大柱状晶粒,并与裂纹垂直。
全脱碳层内侧的组织为板条马氏体加少量托氏体,这种组织是正常淬火组织。
结论:在加工过程中未经锻造,因此属原材料带来的非淬火裂纹。
3、齿轮铣刀,高速钢,淬火后在内孔壁上出现裂纹。
金相检验,发现裂纹附近的碳化物呈不均匀的带状分布。
结论:这是由于组织不均匀所造成的淬火裂纹。
当钢的显微组织中存在碳化物聚集时,这些地方碳和合金元素的含量比较高,造成临界温度降低。
因此,即使是在正常的温度下进行淬火加热,对于碳化物聚集处来讲,加热温度已显得过高了。
其结果是这些地方出现过热组织,降低了钢的强度,淬火冷却时,在应力作用下产生开裂。
高速钢的碳化物不均匀性是这种钢的重要质量指标之一。
为减少或预防这类缺陷发生,冶金厂和使用厂都在不断采取措施,如使用厂用改锻工艺来均匀组织。
当碳化物不均匀性的改善程度受到限制时,可在保证硬度的前提下采用较低淬火加热温度来避免过热组织产生。
4、W18Cr4V钢制模具,高温盐浴中加热后油冷,发现开裂。
从裂纹特征上看是冷却过快所致。
因工件截面较大,冷却时内外温差也大,当表面转变为马氏体时,内部仍处于奥氏体状态,以后的冷却过程中才逐步转变为马氏体,致使表层受内部体积胀大的作用承受很大的拉应力而开裂。
因此,可以判断为淬火裂纹。
机床零件淬火裂纹分析淬火是目前用来提高钢件机械性能的一种行之有效的方法。
通过淬火及回火,可以大幅度提高钢的强度、韧性及疲劳强度,并可获得他们之间的各种配合,以满足不同的需要。
钢件淬火时伴随着一种组织转变---马氏体转变,马氏体是一种脆性相,在宏观淬火内应力的作用下容易使钢件产生淬火裂纹。
在机床零件加工的过程中淬火裂纹是零件较严重的热处理缺陷之一,导致零件报废,既浪费了材料与加工费用,又影响了生产,造成了一定的经济损失。
因此,分析钢件产生淬火裂纹的原因,找出其规律,采取预防措施是很必要的。
一.综述淬火裂纹是由许多因素造成的,有其内部的原因,也有其外部的原因。
总的来说,马氏体的本质脆性是淬火裂纹的内因,而马氏体的晶体结构、亚结构、化学成分、冶金缺陷等是马氏体本质脆性的影响因素;钢件的宏观淬火内应力来源于加热和冷却过程中的热应力和组织应力是造成淬火开裂的外因。
下面将从微观到宏观,从内部到外部对钢件的淬火裂纹进行分析,并采取措施防止裂纹的发生。
二、马氏体本质脆性—钢件淬火裂纹的内因众所周知,中高碳钢淬火后,其韧性低,脆性大,易产生显微裂纹和宏观开裂。
这主要是由马氏体的本质脆性决定的。
而马氏体的本质脆性又决定于马氏体的碳固容量、亚结构、显微应力及显微裂纹。
2.1.马氏体中的碳固容量马氏体是碳在α-Fe中的溶解度极小(《0.02%》α-Fe中容纳过量碳的结果,必将使其晶格发生畸变,晶格中过饱和的碳原子强烈地消弱了铁原子间的结合力。
因此,随着马氏体中碳固容量的增加,钢件脆性倾向增大。
2.2马氏体的亚结构板条马氏体是由高密度的位错组成的,板条马氏体中的位错易于滑动,其可动性比孪晶大,位错的运动能缓和局部区域的应力集中,延迟裂纹形核,其韧性好、脆性小。
片状马氏体中的大量细小孪晶使华亿变形不易进行,降低了其塑性和韧性,易于诱发裂纹,脆性较大。
2.3马氏体中的显微裂纹马氏体形成时容易产生显微裂纹,这是指在中高碳钢中,而低碳钢的马氏体组织中难以形成显微裂纹。
这是因为低碳马氏体为平行的板条,相互碰撞的机会少,且本身的塑性高,可以通过变形而使应力松弛,不易产生显微裂纹。
而高碳马氏体内由于马氏体片相互碰撞,片状马氏体又不能作相应的形变来消除应力,造成碰遇处得应力场,当应力足够大时就形成显微裂纹。
这种先天的缺陷使高碳马氏体进一步增加了脆性,在其它应力的作用下,显微裂纹可能发展为宏观开裂。
影响形成显微裂纹的因素很多,如淬火介质的温度,马氏体的形成量,奥氏体的原始晶粒大小,马氏体的长度和厚度等。
当淬火介质的温度由40℃降到负50℃的时候,显微裂纹剧烈增多,在此温度范围内,马氏体数量也增加较快。
马氏体片愈粗大,则形成显微裂纹的敏感度愈大,奥氏体晶粒越粗大,马氏体往往愈大,先形成的马氏体片为其它马氏体碰撞的几率越大,或碰撞遇到晶界的几率也愈大,形成显微裂纹的敏感度愈大。
在实际生产中,对高碳钢可采用较低的淬火温度,缩短保温时间,采用等温淬火活淬火后及时回火,可降低或避免高碳马氏体中显微裂纹的产生。
以上讨论了马氏体的本质脆性和马氏体的显微裂纹。
马氏体的显微裂纹是由于马氏体片互相碰撞,在碰遇处产生应力及应力集中造成的。
但是这类应力不足以使钢件产生宏观开裂,只有在淬火宏观应力及其它外力的作用下才能引起工件的宏观开裂。
三.淬火宏观内应力—钢件淬火裂纹的外因钢件淬火过程中经过加热、保温、冷却的过程。
钢件在加热和冷却的过程中,由于热胀冷缩发生体积变化,同事还发生相变,金属相变都伴有比容的变化,比如淬火冷却时,由奥氏体转化为马氏体,马氏体的比容大于奥氏体,产生了体积膨胀,工件的体积变化使工件各个部分之间受到牵制便形成了内应力。
由热胀冷缩引起的内应力为热应力,由于相变产生的内应力为组织应力。
钢件内应力随着热处理过程的进行,其大小、方向、分布随时都在发生着变化,热处理后在工件中尚未松弛而残留下来的内应力为残余内应力,热处理后的内应力是热应力和组织应力的叠加。
钢件淬火时,在冷却初期,未产生相变,表层的温度梯度比内部大,只有热应力,随着冷却过程的进行,表层和内层的温差减小,热应力影响小,这时以组织应力为主,表层首先冷却到Ms点生成马氏体组织而膨胀,这时给尚处于奥氏体状态的心部以拉应力,表现为心部受拉应力,表层受压力。
由于奥氏体所行很好,此应力可通过奥氏体的塑性变形而松弛。
当心部也转变为马氏体时,由于表层已形成的马氏体硬度高、脆性大、塑性极小,心部对表层产生拉应力,心部产生压应力,并被作为残余应力保存下来。
图1为Fe11.7Ni合金900℃水淬后的残余应力分布。
由图1可以看出,钢件表面的切向拉应力很大,如果超过钢的抗拉强度,那么工件将开裂,产生纵向裂纹。
中心未淬硬时,表层受压应力,心部受拉应力。
如图 2.心部由于珠光体的塑性好而不会被拉裂,与中心被淬硬的相比,较难淬裂。
零件渗碳淬火后,对45、20Cr、18CrMnTi钢来说表层受压应力,心部为拉应力,一般不易淬裂。
对于渗碳铬镍钢则不同,表层为拉应力。
图3为20Cr2Ni4A钢应力沿硬化层的分布,渗碳铬镍钢渗碳后,渗层中的含碳量远远高于心部的含碳量,渗碳层内碳浓度由表面向内部逐渐降低,因而渗层内不同区域奥氏体稳定性和转变机构不一致,造成了沿渗碳层厚度的组织不均匀,渗碳淬火后产生了内应力,在一定冷却速度下,渗碳层表面过共析层先冷却收缩转变为屈氏体加渗碳体,随着冷却进行,内层较稳定的奥氏体转变为马氏体,过渡层为索氏体或屈氏体,从而表层受到了很大拉应力作用,若表层屈氏体较薄时,则该区域的拉应力增大。
由于马氏体比容最大,膨胀产生压应力,使屈氏体表层产生无规则的裂纹。
如果马氏体受到很大压应力作用,可以形成剥离裂纹。
钢件感应加热淬火时,使表层局部区域发生组织结构的变化。
由于表层硬化层和心部组之间较大的差异,以及快速加热、急冷引起热应力和组织应力的综合叠加,在冷却初期,表层和内层由于温差很大引起热应力,使表层受拉、心部受压。
随冷却进一步进行,表层压应力和内部拉应力继续增大,最后,残余应力为表层呈压应力,心部为拉应力。
图4为球墨铸铁无心圆柱,以旋转移动法进行外表面的高频淬火,改变移动速度得到不同的淬硬深度形成的残余应力分布图。
由图可以看出,随着硬化层深度的增加将使切向应力比轴向应力大转变为轴向应力比切向应力大。
心部拉应力增加而硬化层的压应力变小。
当硬化层极薄时,其表面压应力太小,且拉应力极大值接近表面,这时将以硬化层稍下为起点发生破坏。
硬化层极厚时,表层拉应力将增加当超过了钢的断裂强度时,工件表面将出现裂纹,当然为纵向裂纹。
钢件淬火后零件各部分的应力是复杂的,而且是不均匀的。
这些都增加了钢的脆性。
淬火裂纹是淬火钢的脆性断裂。
压应力作用不可能断裂,只有拉应力作用才能导致钢件断裂。
如圆筒类零件。
淬透时在孔的内侧产生淬火裂纹,这是因为外侧冷却快,孔内侧冷却慢,组织应力引起主导作用,在内侧呈拉应力,造成淬火裂纹。
如果加大内孔的冷却速度,以增加压应力的成分,削弱拉应力,就可避免淬火裂纹。