Development of low temperature curing, 120°C, durable, corrosion protection powder coatings for tem
2023年中考英语热点时文阅读14 新发明与创造

2023年中考英语新热点时文阅读-新发明与创造01(2022·全国·九年级课时练习)In ancient times, the Four Great Inventions in China had a great influence on the whole world. In recent years, China once again has ____1____ its ability to change the world with its “four great new inventions”: high-speed railways, mobile payment, bike-sharing and online shopping.Do you know ____2____ the new inventions can appear in China? The “four great new inventions” are ____3____ related to China’s high-tech innovation (创新). For example, the operating mode of bike-sharing is based ____4____ the satellite navigation system (卫星导航系统), mobile payment, big data and other high technologies. This shows that China’s high-tech innovation has greatly ____5____ the quality of people’s lives.China has entered a new innovative era, thanks to the large amount of ____6____ that China has spent encouraging innovation. China is beginning to ____7____ in innovation in some ways.“The ‘four great new inventions’ have surely improved customer experience, and helped national and global(全球的) economy ____8____ at the same time,” said Charlie Dai, principal analyst (首席分析师) of an American market research company.As a whole, all the Chinese are ____9____ of their four new inventions. It is increasingly clear that China is innovating and no longer copying western ideas. More and more foreigners ____10____ to promote(促进) economic development in their countries by learning from China’s innovation.1.A.seemed B.appeared C.looked D.showed2.A.when B.what C.why D.where3.A.all B.both C.neither D.none4.A.in B.on C.to D.from5.A.improved B.finished C.invented D.wasted6.A.people B.water C.electricity D.money7.A.try B.lead C.win D.value8.A.develop B.warn C.mean D.live9.A.proud B.tired C.bored D.satisfied10.A.afford B.repeat C.hope D.wait02(2022·江西九江·二模)Sitting for longer than four hours a day increases a person’s chance of suffering (患)illness.Benoit Maltaone, a designer (设计者)from France, discovered that office workers spent about 70 percent of the day sitting down. To solve the problem caused by it in modern working life, he came up with a great idea— the two-legged chair, which is to encourage the user to move at his or her desk.The chair just has two legs and needs the user to balance (平衡)it. Although it looks dangerous, it can stop people from felling while using it. But the chair is a little uncomfortable, as the user has to keep it balanced. It is also good for other parts of the body, just like an exercise ball(姿势)._________ Most people don’t get much exercise during the day. People watch a lot of TV and work on computers. Many people suffer from spine (脊椎)problems. Companies are coming up with new products in our houses to make our lives easier. But trying to offer people an easier life causes lots of health problems.According to Benoit, the design is not about making money in the furniture (家具)market. It is to provide a product which tries to encourage people to move their whole body. The practice of this special chair can make people change their bad habits. It will encourage people to try to be more active. 11.What does the underlined word “it” refer to?A.The two-legged chair.B.Moving at his or her desk.C.Sitting for too long.D.The great idea.12.Choose the best sentence to fill in the blank “ ________” in Paragraph 4.A.Sitting long is so common now.B.Doing sports is so popular now.C.Working environment is so hard now.D.Keeping healthy is so cool now.13.What’s the purpose of this passage?A.To tell people how to keep away from sitting too long.B.To tell people how to stay away from health problems.C.To explain why people suffer from illness now.D.To show a two-legged chair designed to make people healthier.03(2022·浙江·松阳县教育局教研室一模)There are many TV cook shows where you wish you could reach through your screen and taste the delicious recipes yourself.Now, Japanese scientists have taken a huge step towards making that a reality, with the development of a lickable TV screen.The device is called Taste the TV (TTTV) and contains 10 taste cans that can spray taste samples onto the surface of the screen. The different tastes in the cans can then mix to create tastes similar to those being shown on screen, for example, coffee or pizza.It is an experimental technology, produced by Meiji University in Tokyo, Japan, with its developers expecting a commercial version to cost about £650.Japanese professor Miyashita and 30 students have developed all kinds of taste types. In his version the 10 taste cans spray a mixture of samples on to a roll of hygienic (卫生的) film that is placed over a flat TV-screen.“During the COVID-19, this kind of technology can improve the way people connect and communicate with the outside world,” said Miyashita.“The goal is to make it possible for people to have the experience of something like eating at a restauranton the other side of the world, even while at home,” he said.Miyashita has also been in talks with companies about using his spray technology for applications like a device that can apply a pizza or chocolate taste to a piece of toasted bread.14.The passage tells us the invention of _________.A.tasty cans B.TV cook showsC.a film technology D.a lickable TV screen15.Paragraph 3 talks about_________.A.what the device includes B.how the device worksC.what the device is called D.why the device is invented16.The writer uses what Miyashita says to express the _________ of the invention.A.ways B.purpose C.conditions D.importance17.From the passage, we know that the device is _________.A.widely used now B.popular with the JapaneseC.still in experiment D.liked by restaurant owners04(2022·湖北·武汉外国语学校(武汉实验外国语学校)模拟预测)Malaria (疟疾) has been a deadly problem for humans since ancient times. Usually, people get malaria when infected mosquitoes bite them. Countless people have died from it. Chinese scientist Tu Youyou found an effective drug called qinghaosu (青蒿素).This year marks the 50th anniversary of Tu’s discovery. In 1969, Tu became the director of a national project to develop a drug against malaria. Her team took a unique approach. They went back to books about classical Chinese medicine. After reading more than 2, 000 old remedies (药方), Tu and her team collected over 600 plants and listed almost 380 possible remedies for malaria.One remedy, which is 1, 600 years old, uses the sweet wormwood (青蒿) plant to treat malaria. Tu found it effective and tried to extract (提取) the qinghaosu from it in order to make drugs. The extraction failed at first, so Tu returned to the classical books again and finally found a way. She used a low-temperature method to extract the qinghaosu and succeeded in 1972.After her team showed that qinghaosu could treat malaria in mice and monkeys, Tu and two of her colleagues volunteered to test the drug on themselves before testing on human patients. It turned out thatqinghaosu was safe. All patients in the tests recovered. Gradually, qinghaosu became the first-line treatment for malaria recommended by the World Health Organization (WHO), saving millions of lives in China and other countries throughout the world.In 2015, when Tu was awarded with the Nobel Prize in physiology or medicine, she refused to take all of the credit (荣誉). Instead, she praised her colleagues and Chinese traditional medicine. She once proudly said, “Every scientist dreams of doing something that can help the world.”18.According to the passage, to find an effective drug called qinghaosu is ________.A.impossible B.uneasy C.unexpected D.complicated19.What do we know about the “qinghaosu”?A.It is extracted from the sweet wormwood plant at room-temperature.B.TuYouyou and her team spent three years finding it out.C.Tu and all her teammates volunteered to test it on themselves.D.It has saved millions of lives around the world.20.The underlined word “approach” in paragraph 2 probably means ________.A.idea B.way C.discussion D.drug21.We can find that Tu Youyou ________.A.took all the credit by herself B.did a lot and never gave upC.succeeded in curing malaria by accident D.won the Nobel Prize shortly after the success 22.We can infer that the writer’s writing purpose is to ________.A.praise traditional solution in China B.encourage young people to learn medicineC.show how the qinghaosu treats malaria D.make Chinese old remedies more popular05Liu Jichen, a student from Tsinghua University, has developed a WeChat mini-program called “Clear Plate”. ___23___ a meal, users can open the mini-program and take a photo of their ___24___ plates. Once the image is checked by the AI, users can collect points and use them to buy gifts or meals for children in poor ___25___ .“Technology is a good way to ___26___the problem of food waste,” Liu thought. He organised a team of twenty members to work on the project. In order to improve the mini-program, the team ___27___ half a year collecting over 100,000 photos in school dining halls and restaurants.In 2018, the mini-program wasput into use. Soon, it became one of ___28___ most popular mini-programs in universities across China.Meanwhile, Liu and his team, together ___29___ other organizations, started the “Clear Your Plate” campaign in November in the third year of his university. Almost 1.6 million college students were attracted and food waste was ___30___by 862 tons. “Through the campaign, we hope to encourage ___31___ to take action against food waste,” he said.Thanks to his great efforts, Liu stood out _____32_____ more than 7,600 people around the world and was rewarded one of the Young Leaders for the SDGs (可持续发展目标)by the UN.参考答案:1.D2.C3.A4.B5.A6.D7.B8.A9.A10.C【导语】本文主要讲述“新中国四大发明”:高铁,电子支付,共享单车和网上购物。
阳离子型延迟固化环氧胶粘剂的性能研究与应用

阳离子型延迟固化环氧月交粘剂的性研究与应用*付瑜李炳辉冷万里田湛秋(东莞新科技术研究开放有限公司广东523000)摘耍:采用柔韧性环氧树脂,增韧剂,柔性稀释剂,阳离子■引发剂和热致阳离子固化剂等制备了阳离子型延迟固化环氧胶粘剂(简称DCC Epoxy).利用FTIR表征了DCC Epoxy的结构特征,通过DSC研究了DCC Epoxy的热反应特性.将DCC Epoxy用于硬盘磁头粘接,研究了开放时间(Open-Time),固化条件,剪切强度,以及磁头热框变化情况.结果显示DCC Epoxy具有优异的柔韧性,剪切强度和磁头热框变化满足磁头性能要求.与目前传统的丙烯酸酯类胶粘剂比较,没有氧阻聚现象,固化温度低,固化程度高,挥发物含量低,收缩率低,具有明显的应用优势.关键词:阳离子型延迟固化;环氧胶粘剂;硬盘磁头粘接中BS分类号:TQ文献标识码:AStudy and Application of Delay Cure Cationic Epoxy AdhesiveFu Yu,Li Binghui,Leng Wanli,Tian Zhanqiu(Dongguan Xinke Technology Research and Development Co.s Ltd.,Guangdong,523000) Abstracts A delay cure cationic epoxy adhesive(DCC Epoxy)yvas prepared with flexible epoxy resin,toughening agent,flexible diluent, cationic initiator and thermally induced cationic cure agent.The structural characteristics of D CC E poxy were characterized by FTIR,and the thermal reaction characteristics of D CC Epoxy were studied by DSC.The open-time,curing conditions,adhesive strength and the head thermal crown change were studied while DCC Epoxy was used to HGA head.The results show that DCC Epoxy has an excellentflexible f eature,and the shearforce and head thermal crown change meet the requirements of H DD head p pared with the traditional acrylate adhesive,it has no oxygen inhibition phenomenon,low curing temperature,high curing degree,low volatile content and low shrinkage,which has obvious application advantages.Key words z cationic delayed curing;epoxy adhesive hard disk head bonding-U_—*—刖肯在数据存储硬盘中,读写磁头由胶粘剂粘接在不锈钢折片上形成磁头折片组合(Head Gimbal Assembly,HGA),并经其他装配工艺形成磁头臂组合(Head Stack Assembly, HSA)o胶粘剂的种类和固化特性对硬盘磁头的装配工艺和读写性能有着直接的影响。
骨组织低温保存技术的特点

中国组织工程研究与临床康复 第 12 卷 第 49 期 2008–12–02 出版Journal of Clinical Rehabilitative Tissue Engineering Research December 2, 2008 Vol.12, No.49综 述骨组织低温保存技术的特点**★邓琬子,刘宝林,林 萍,王 欣Technical characteristics of bone tissue cryopreservationDeng Wan-zi, Liu Bao-lin, Lin Ping, Wang Xin Abstract: The cryopreservation of engineered tissues and biological organs in vivo is the forefront topic in biomedical engineering. The structure of tissue is more complex than that of cell, and the heat and mass transfer of the tissue is more difficult to control. Adhesion of cells to materials plays an important role in the success of bone preservation. Vitrification method is an important method of successful cryopreservation of engineered tissue. Other favorable external factors, such as pressure and microwave, should be found actively. So far, the cryopreservation of organs has not achieved a major breakthrough. It is believed that with the development of scientific experiments and technology, the maturity of the studies on low temperature tolerance of various types of cells, tissues, organs and heat transfer law of biological materials, and the technology of decreasing the damage, the cryopreservation of organs will be achieved eventually.Deng WZ, Liu BL, Lin P, Wang X.Technical characteristics of bone tissue cryopreservation.Zhongguo Zuzhi Gongcheng Yanjiu yu Linchuang Kangfu 2008;12(49):9759-9761 [ ]Institute of Biothermal Sciences, School of Medical Instrument and Food Engineering, University of Shanghai for Science and Technology, Shanghai 200093, China Deng Wan-zi★, Studying for master’s degree, Institute of Biothermal Sciences, School of Medical Instrument and Food Engineering, University of Shanghai for Science and Technology, Shanghai 200093, China dengwanzi999@ Correspondence to: Liu Bao-lin, Professor, Institute of Biothermal Sciences, School of Medical Instrument and Food Engineering, University of Shanghai for Science and Technology, Shanghai 200093, China blliuk@ Supported by: the National Natural Science Foundation of China, No. 50576059, 50776060** Received: 2008-07-09 Accepted: 2008-11-22摘要:工程组织和生物活体器官的低温保存是当今生物医学工程最前沿的研究课题。
钻井液专业词汇(完整版)

薄弱地层@weak formation
泊松比@poisson’s ratio
剥离@peel off
补救@remediation
不分散泥浆@nondispersed mud
不干扰地质录井@play no role in geological logging
不均质储层@heterogeneous reservoir
醋酸@acetate
醋酸钠@sodium acetate
窜流@fluid channeling
脆裂@embrittlement crack
脆性@brittle/crisp ,fragility
催化剂@accelerant , catalyst
萃取剂@extracting agent
螯合@chelation
凹陷@sag
凹陷地层@subsidence formation
奥陶系@Ordovician system
API模拟法@API recommened method
B
多靶点@multiple target point
白沥青@white asphalt
白油@mineral oil
狄塞尔堵漏剂@diacel plugging agent
滴定@titration
底水丰富@basal water abundance
底水油藏井@bottom water reservoir well
第二界面@second contact surface
缔合物@associated matter
初始粘度@initial viscosity
初探@primary investigation
causes for ice ages托福阅读

Causes for Ice AgesIce ages are long periods of low global temperatures, characterized by the expansion of ice sheets and glaciers. These extreme cold periods are believed to have occurred multiple times throughout Earth’s history. Scientists have proposed various theories to explain the causes of ice ages. In this document, we will explore some of these theories.Orbital VariationsOne widely accepted theory suggests that variations in the Earth’s orbit around the sun, known as orbital variations, play a significant role in the onset of ice ages. These variations occur due to changes in the planet’s eccentricity, axial tilt, and precession. Eccentricity refers to the shape of Earth’s orbit, which can vary from a more circular shape to a more elongated one over a period of 100,000 years. Axial tilt refers to the tilt of Earth’s axis of rotation, which oscillates between approximately 22.1 and 24.5 degrees over a cycle of 41,000 years. Precession refers to the wobbling motion of Earth’s axis, which completes a full cycle in abou t 26,000 years.These orbital variations can affect the distribution of solar energy received by the Earth’s surface. For example, when the Earth’s orbit is more elongated (higher eccentricity), the amount of solar radiation reaching the planet’s surface d ecreases, leading to colder global temperatures. This decrease in solar radiation, in combination with other factors, can trigger the onset of an ice age.Solar OutputAnother proposed cause for ice ages is variations in solar output. The Sun is the primary source of heat for our planet, and its energy output is not constant. Over time, the Sun undergoes cyclic changes in activity, resulting in variations in the amount of radiation it emits. These variations in solar output are known as solar cycles or solar flares.During periods of lower solar activity, the amount of energy received by Earth decreases, leading to cooler temperatures. This decrease in solar output can potentially contribute to the onset of an ice age. However, it is important to note that while solar variations may play a role in ice age triggers, they are likely only one contributing factor among several.Atmospheric CompositionThe composition of the Earth’s atmosphere can also influence the onset of ice ages. Scientists believe that fluctuations in greenhouse gas concentrations, such as carbon dioxide (CO2) and methane (CH4), can impact global temperatures. Thesegases act as a “blanket” around the Earth, trapping heat and preventing it from escaping into space.During ice ages, the atmospheric concentration of greenhouse gases is thought to decrease. This reduction can lead to a cooling effect, as less heat is trapped in the atmosphere. The decrease in greenhouse gas concentration can be caused by various factors, including changes in volcanic activity, shifts in ocean circulation patterns, and the growth of ice sheets themselves, which can alter the exchange of gases between the atmosphere and the ocean.Geological ProcessesGeological processes, such as the movement of tectonic plates and the formation of mountain ranges, can also influence ice age occurrence. These processes can alter the circulation patterns of ocean currents, affecting the distribution of heat around the globe. Additionally, the growth of mountain ranges can impact atmospheric circulation patterns and create barriers that restrict the flow of air masses, leading to localized cooling.ConclusionIce ages are complex phenomena influenced by a combination of factors. Orbital variations, solar output fluctuations, atmospheric composition changes, and geological processes all contribute to the onset and duration of ice ages. Understanding these causes and their interactions can provide valuable insights into past ice ages and help predict future climatic changes on our planet.。
低温固化粉末涂料的研究进展

第51卷第3期 202丨年3月涂料工业PAINT &COAT1NGS INDUSTRYVol. 51 No. 3Mar. 2021低温固化粉末涂料的研究进展许伟坤1,王慧丽2,董亿政2,袁辉强2,范萍”(1.浙江工业大学材料科学与工程学院,杭州310014;2.浙江中法新材料有限公司,杭州310006)摘要:低温固化粉末涂料可节约能源、降低成本、并可将粉末涂料的应用领域拓展至热敏性底材,因此其研究与开发具有十分重要的意义。
然而低温固化粉末涂料自身存在着低温固化与其室温贮存稳定性及其制粉过程化学稳定性的矛盾。
针对低温固化粉末涂料现存的上述问题,着重从三个方面,即降低固化反应活化能、提高树脂基体低温流动性及防止制备过程中的预固化进行了分析,综 述了低温固化粉末涂料在配方设计、专用树脂设计的进展、固化促进剂微胶囊化以及超临界流体技术在低温固化粉末涂料中的应用情况。
并对今后低温固化粉末涂料的研发方向进行了展望。
关键词:粉末涂料;低温固化;反应活化能;低温流动性;预固化中图分类号:TQ637. 82 文献标识码:A文章编号:0253-4312(2021 )03-0076-07doi:10. 12020/j.issn.0253-4312. 2021. 3.76Research Progress in Low-Temperature Curing Powder CoatingsXu Weikun',Wang Huili:,Dong Yizheng2,Yuan Huiqiang2,Fan Ping1(1. Z h e jia n g U n iv e rs ity o f T e c h n o lo g y, C o lle g e o f M a te r ia ls S c ie n c e a n d E n g in e e r i n g, H a n g z h o u310014, C/iina;2.N e w S in o-F r e n c h P o ly m e r M a te r ia h C o., L td., H a n g z h o u310006.C h i n a)A bstract:Low-temperature curing powder coatings can not only save energy and reducecosts,but also expand the application of powder coatings to heat-sensitive substrates.Therefore,the research and development of it have great significance.However,the low- temperature curing powder coatings itself has the contradiction between the low-temperature curing,the storage stability at room temperature and the chemical stability during processing.Regarding to the above-mentioned problems existing in low-temperature curing powder coatings,three aspects were focused on for discussion in this paper,including reduction of the activation energy of the curing reaction,improvement of the fluidity of low-temperature of the resin matrix,and prevention of pre-curing during the process of powder preparation.The development of low-temperature curing powder coatings in design of foiTnulation and resin preparation,as well as the application of curing accelerator microencapsulation and supercritical fluid technology in low- temperature curing powder coatings were reviewed.Finally,the future development trend of low- temperature curing powder coatings was prospected.Key w ords:powder coatings;low-temperature curing;activation energy;fluidity at low- temperature;pre-curing **通信联系人许伟坤等:低温固化粉末涂料的研究进展粉末涂料是以树脂基料和固化剂为成膜物质,并辅以填料、颜料和功能性助剂的100%固体分的粉 末形态涂料。
耐热、耐寒测试 英语

耐热、耐寒测试英语Thermal Resilience: Pushing the Boundaries of Material EnduranceImagine a world where materials could withstand the harshest of environments, from the scorching heat of the desert to the bone-chilling cold of the Arctic. This is the realm of thermal resilience, a field of study that explores the remarkable ability of materials to maintain their structural integrity and functionality under extreme temperature conditions. As technology continues to push the boundaries of what's possible, the need for materials that can endure these extreme environments has become increasingly crucial.One of the primary applications of thermal resilience research is in the aerospace industry. As spacecraft and satellites venture deeper into the unknown, they must be equipped with components that can withstand the rigors of launch, the vacuum of space, and the dramatic temperature fluctuations encountered during orbit and re-entry. Engineers and materials scientists work tirelessly to develop alloys, ceramics, and composites that can withstand the intense heat and cold without compromising their performance.Consider the heat shield of a spacecraft, for example. During re-entry,the vehicle experiences temperatures that can reach thousands of degrees Celsius as it plunges through the Earth's atmosphere. The heat shield must be able to dissipate this energy and protect the delicate components and crew inside. Materials like ablative heat shields, which gradually erode to absorb the heat, or thermal protection systems made of high-temperature ceramics, are critical to ensuring the safety and success of these missions.But the need for thermal resilience extends far beyond the aerospace industry. In the automotive sector, materials that can withstand high temperatures are essential for components like engine blocks, turbochargers, and exhaust systems. These parts must be able to operate reliably in the harsh conditions of an internal combustion engine, where temperatures can reach hundreds of degrees Celsius.Similarly, in the energy industry, materials used in power generation equipment, such as turbines and nuclear reactors, must be able to withstand extreme temperatures and thermal cycling without compromising their structural integrity or performance. The development of advanced ceramics, superalloys, and composite materials has been instrumental in improving the efficiency and reliability of these critical systems.The challenge of thermal resilience is not limited to high-temperature environments. Materials that can withstand cryogenictemperatures, such as those encountered in liquid natural gas (LNG) storage and transportation, or in the superconducting magnets used in medical imaging equipment, are also in high demand. These materials must be able to maintain their strength, ductility, and insulating properties at temperatures as low as -200 degrees Celsius.Researchers and engineers have developed a range of techniques to assess the thermal resilience of materials, including thermal shock testing, thermal cycling, and high-temperature exposure experiments. These tests simulate the extreme conditions that materials may face in real-world applications, allowing for the evaluation of their performance and the development of new, more resilient materials.One such technique is the use of high-heat flux testing, where materials are exposed to intense, localized heat sources to simulate the extreme conditions encountered in applications like rocket nozzles or hypersonic vehicle leading edges. By understanding how materials respond to these intense thermal loads, engineers can design more robust and reliable systems.Another approach is the use of cryogenic testing, where materials are subjected to extreme cold temperatures to assess their low-temperature properties. This is particularly important for materials used in aerospace, energy, and medical applications, where the ability to maintain performance at cryogenic temperatures is critical.Beyond the development of new materials, the field of thermal resilience also encompasses the optimization of existing materials and the design of innovative thermal management systems. This can involve the use of advanced cooling technologies, insulation materials, and heat dissipation strategies to mitigate the effects of extreme temperatures and protect sensitive components.As the world continues to push the boundaries of what's possible, the importance of thermal resilience will only grow. From the exploration of distant planets to the development of next-generation energy systems, the ability of materials to withstand the harshest of environments will be a key driver of innovation and progress. By continuing to advance the science of thermal resilience, we can unlock new possibilities and push the limits of what we can achieve.。
泰约 PSR-4000 MP系列 液体光敏涂料 使用说明书

PSR-4000 MP SeriesUL Name: PSR-4000MP/CA-40MPLIQUID PHOTOIMAGEABLE SOLDER MASKScreen or Spray ApplicationGreen or Black Matte FinishDI version available for both Green and BlackDesigned specifically for the latest DI equipmentExcellent Solder Ball ResistanceResistance to No-Clean Flux ResidueWide Processing WindowWithstands ENIG & Immersion TinHard Surface FinishLow OdorPSR-4000 MP Series includes PSR-4000 MP and PSR-4000 MP Black as well as PSR-4000 MP DI and PSR-4000 MP Black DI. They are two-component, matte, alkaline developable LPI solder mask product for flood screen and spray application methods. This product has a very low odor, a wide process window and is capable of withstanding alternate metal finishes such as ENIG and immersion Tin. It has a matte finish and provides excellent solder ball resistance in no clean flux assembly applications. PSR-4000MP Series meets or exceeds the requirements of IPC SM-840E Class H and Class T, Bellcore GR-78- CORE Issue 1, and has a UL flammability rating of 94V-0.PSR-4000MP Series C OMPONENTS PSR-4000 MP Series / CA-40MPMixing Ratio 80 parts 20 partsColor Green or Black WhiteMixed PropertiesSolids 80%Viscosity 140 – 180 psSpecific Gravity 1.58M IXING PSR-4000 MP Series is supplied in pre-measured containerswith a mix ratio by weight of 80 grams PSR-4000 MP Series and20 grams CA-40 MP. PSR-4000 MP Series can be mixed byhand with a mixing spatula for 10 – 15 minutes. Mixing can bedone with a mechanical mixer at low speeds to minimize shearthinning for 10 –15 minutes.Pot life after mixing is 72 hours when stored in a dark place at ≤20°C (68°F).P RE-C LEANING Prior to solder mask application, the printed circuit boardsurface needs to be cleaned. Various cleaning methods includePumice, Aluminum Oxide, Mechanical Brush, and ChemicalClean. All of these methods will provide a clean surface for theapplication of PSR-4000 MP Series. Hold time after cleaning theprinted circuit board should be held to a minimum to reduce theoxidation of the copper surfaces.S CREEN P RINTING Method: Single Sided and Double Sided Screening•Screen Mesh: 86 – 110•Screen Mesh Angle: 22.5° Bias•Screen Tension: 20 - 28 Newtons•Squeegee: 60 – 80 durometer•Squeegee Angle: 27 – 35°•Printing Mode: Flood / Print / Print•Flood Pressure: 20 – 30 psi•Printing Speed: 2.0 – 9.9 inches/sec•Printing Pressure: 60 – 100 psiT ACK D RY C YCLE The Tack Dry step is required to remove solvent from thesolder mask film and produce a firm dry surface. The optimumdwell time and oven temperature will depend on oven type, ovenloading, air circulation, exhaust rate, and ramp times. Excessivetack dry times and temperature will result in difficulty developingsolder mask from through holes and a reduction in photo speed.Insufficient tack dry will result in artwork marking and/or sticking.Typical tack dry conditions for PSR-4000MP Series are asfollows:•Oven Temperature: 150 - 185°F (65 - 85°C)•For Single-Sided (Batch Oven)1st Side: Dwell Time: 10 - 20 minutes2nd Side: Dwell Time: 25 - 45 minutes•For Double-Sided (Conveyorized or Batch Oven)Dwell Time: 25 - 60 minutesE XPOSURE (Standard) PSR-4000 MP Series requires UV exposure to define soldermask dams and features. The spectral sensitivity of PSR-4000MP Series is in the area of 365 nm. Exposure times will vary bybulb type and age of the bulb. Below are guidelines forexposure.•Exposure Unit: 5 kW or higher•Stouffer Step 21: Clear 10 minimum (on metal / underphototool)•Energy: 400 mJ / cm2 minimum (under phototool)E XPOSURE (DI) PSR-4000MP Series uses UV-LED curing technology to definesolder mask dams and features. The spectral sensitivity is in thearea of 365 nm – 405nm. Exposure times will vary by power, lightsource, wavelength and age of the light source. Below areguidelines for exposing.Exposure Unit: Direct Imaging Exposure Unit•Stouffer Step 21: Clear 8 minimum (on metal)•Energy: 200 mJ / cm2 minimumD EVELOPMENT PSR-4000 MP Series is developed in an aqueous sodium orpotassium carbonate solution. Developing can be done in eithera horizontal or vertical machine.•Solution: 1% by wt. Sodium Carbonate or 1.2%Potassium Carbonate•pH: 10.6 or greater•Temperature: 85 - 105°F (29 - 41°C)•Spray Pressure: 25 - 45 psi•Dwell Time in developing chamber: 45 - 90 seconds•Water rinse is needed to remove developer solutionfollowed by drying of the boardF INAL C URE PSR-4000 MP Series needs to be thermally cured to insureoptimal final property performance. Thermal curing can be donein a batch oven or conveyorized oven.•Temperature: 275 – 300°F (135 – 149°C)•Time: 45 – 60 minutesUV C URE (O PTIONAL) PSR-4000 MP Series has good solder ball resistance. For evenbetter solder ball resistance a UV Bump can be done after FinalCure.•UV Energy: 2000 – 3000 mJ / cm2•Lamps: High Pressure Mercury LampsF INAL P ROPERTIES FOR PSR-4000 MP Series IPC-SM-840E, Class H & T, Solder Mask Vendor Testing RequirementsTESTSM-840PARAGRAPH REQUIREMENT RESULTVisual 3.4.8 Uniform in Appearance Pass Curing 3.4.5 Ref: 3.6.1.1, 3.7.1 and 3.7.2 Pass Non-Nutrient 3.4.6 Does not contribute to biological growth Pass Dimensional 3.4.10 No Solder Pickup and Withstand 500 VDC Pass Pencil Hardness 3.5.1 Minimum “F” Pass – 7H Adhesion 3.5.2 Rigid – Cu, Ni, FR-4 Pass Machinability 3.5.3 No Cracking or Tearing Pass Resistance to Solventsand Cleaning Agents 3.6.1.1 Table 3 Solvents PassHydrolytic Stability and Aging 3.6.2 No Change after 28 days of 95-99°Cand 90-98% RH PassSolderability 3.7.1 No Adverse Effect J-STD-003 Pass Resistance to Solder 3.7.2 No Solder Sticking Pass Dielectric Strength 3.8.1 500 VDC / mil Minimum 2900 VDC/mil Thermal Shock 3.9.3 No Blistering, Crazing or De-lamination Pass Specific Class “H” RequirementsTESTSM-840PARAGRAPH REQUIREMENT RESULTFlammability 3.6.3 UL 94V-0 Pass – File #E166421 Insulation Resistance 3.8.2Before Soldering 5 x 108 ohms minimum Pass (3.7 x 1012 ohms) After Soldering 5 x 108 ohms minimum Pass (3.1 x 1013 ohms) Moisture & Insulation Resistance 3.9.1Before Soldering–In Chamber 5 x 108 ohms minimum Pass (6.4 x 109 ohms) Before Soldering–Out of Chamber 5 x 108 ohms minimum Pass (1.2 x 1013 ohms) After Soldering-In 5 x 108 ohms minimum Pass (1.0 x 1010 ohms) After Soldering-Out of Chamber 5 x 108 ohms minimum Pass (1.0 x 1013 ohms) Electrochemical Migration 3.9.2 >2.0 x 106 ohms, nodendritic growthPass (1.25 x 1012 ohms) Specific Class “T” RequirementsTESTSM-840PARAGRAPH REQUIREMENT RESULTFlammability 3.6.3 Bellcore 02 Index – 28 minimum Pass – 75Insulation Resistance Before Soldering After Soldering 3.8.25 x 108 ohms minimum5 x 108 ohms minimumPass (4.3 x 1013 ohms) Pass(1.7 x 1012 ohms)F INAL P ROPERTIES FOR PSR-4000 MP Series Specific Class “T” RequirementsTESTSM-840PARAGRAPHREQUIREMENT RESULTMoisture & Insulation Resistance 3.9.1Before Soldering–In Chamber 5 x 108 ohms Pass (9.9 x 109 ohms) Before Soldering–Out of Chamber 5 x 108 ohms Pass (4.2 x 1011 ohms) After Soldering-In Chamber 5 x 108 ohms Pass (1.9 x 109 ohms)After Soldering-Out of Chamber 5 x 108 ohms Pass (2.2 x 1011 ohms) Electrochemical Migration 3.9.2 < 1 decade drop, nodendriticPass Additional Tests / ResultsTEST REQUIREMENT RESULT Electroless Nickel / Immersion Gold Resistance Nickel (85C/30min) Tape Test PassSolvent ResistanceAcetone:MEK: IPA: PMA: No attack – 24 hoursNo attack – 24 hoursNo attack – 24 hoursNo attack – 24 hoursPassPassPassPassAcid Resistance HCI – 10%: H2SO4 – 10%: No attack – 30 MinutesNo attack – 30 MinutesPassPassBase Resistance NaOH – 10%:Boiling Water No attack – 30 MinutesNo attack – 15 MinutesPassPassSolder / Flux Resistance (Alphametals)Alpha 857 water soluble:NR060 no-clean:3355-NB rosin-based:NR-3000A4 no-clean: Solder/Flux Resistance (Multicore) X32-10M no- clean:X32-06I no-clean: Solder/Flux Resistance-(Sanwa) SR-270 rosin-based: No attack – 1 x 10 sec float (260C)No attack – 1 x 10 sec float (260C)No attack – 1 x 10 sec float (260C)No attack – 1 x 10 sec float (260C)No attack – 1 x 10 sec float (260C)No attack – 1 x 10 sec float (260C)No attack – 1 x 10 sec float (260C)PassPassPassPassPassPassPassConformal Coating Adhesion: Humiseal 1 B31 acrylic:Humiseal 1A20 urethane:Dow Corning 3-1753 silicone: Crosscut (10/10) after tapeCrosscut (10/10) after tapeCrosscut (10/10) after tape100/100100/100100/100Glue Dot Adhesion – Loctite 3609 Adhesion to PSR-4000 MP Series ExcellentTg Internal Test 125° CCTE (TMA Method)Internal Test (α1 / α2)α1 = 57 ppm/α2 = 130 ppm Young’s Modulus (GPa) Internal Test 6.9 Taiyo America, Inc. (TAIYO) warrants its products to be free from defects in materials and workmanship for the specified warranty period (PSR-4000 MP Series / CA-40 MP Warranty period is 12 Months) provided the customer has, at all times, stored the ink at a temperature of 68o F or less. TAIYO accepts no responsibility or liability for damages, whether direct, indirect, or consequential, resulting from failure in the performance of its products. If a TAIYO product is found to be defective in material or workmanship, its liability is limited to the purchase price of the product found to be defective. TAIYO MAKES NO OTHER WARRANTY, EXPRESS OR IMPLIED, AND MAKES NO WARRANTY OF MERCHANTABILITY OR OF FITNESS FOR ANY PARTICULAR PURPOSE. TAIYO'S obligation under this warranty shall not include any transportation charges or costs of installation or any liability for direct, indirect, or consequential damages or delay. If requested by TAIYO, products for which a warranty claim is made are to be returned transportation prepaid to TAIYO'S factory. Any improper use or any alteration of TAIYO'S product by the customer, as in TAIYO'S judgment affects the product materially and adversely, shall void this limited warranty.。
聚氨酯封端低温固化阴极电泳涂料的研究进展_郭靖
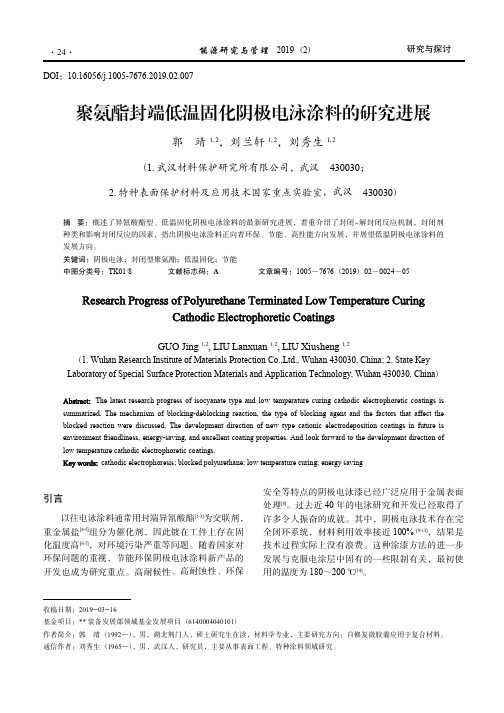
能源研究与管理2019(2)研究与探讨收稿日期:2019-03-16基金项目:**装备发展部领域基金发展项目(6140004040101)作者简介:郭靖(1992—),男,湖北荆门人,硕士研究生在读,材料学专业,主要研究方向:自修复微胶囊应用于复合材料。
通信作者:刘秀生(1965—),男,武汉人,研究员,主要从事表面工程、特种涂料领域研究。
摘要:概述了异氰酸酯型、低温固化阴极电泳涂料的最新研究进展,着重介绍了封闭-解封闭反应机制,封闭剂种类和影响封闭反应的因素,指出阴极电泳涂料正向着环保、节能、高性能方向发展,并展望低温阴极电泳涂料的发展方向。
关键词:阴极电泳;封闭型聚氨酯;低温固化;节能中图分类号:TK01+8文献标志码:A文章编号:1005-7676(2019)02-0024-05GUO Jing 1,2,LIU Lanxuan 1,2,LIU Xiusheng 1,2(1.Wuhan Research Institute of Materials Protection Co.,Ltd.,Wuhan 430030,China;2.State Key Laboratory of Special Surface Protection Materials and Application Technology,Wuhan 430030,China)The latest research progress of isocyanate type and low temperature curing cathodic electrophoretic coatings issummarized.The mechanism of blocking-deblocking reaction,the type of blocking agent and the factors that affect the blocked reaction were discussed.The development direction of new type cationic electrodeposition coatings in future is environment friendliness,energy-saving,and excellent coating properties.And look forward to the development direction of low temperature cathodic electrophoreticcoatings.cathodic electrophoresis;blocked polyurethane;low temperature curing;energy saving聚氨酯封端低温固化阴极电泳涂料的研究进展郭靖1,2,刘兰轩1,2,刘秀生1,2(1.武汉材料保护研究所有限公司,武汉430030;2.特种表面保护材料及应用技术国家重点实验室,武汉430030)引言以往电泳涂料通常用封端异氰酸酯[1-3]为交联剂,重金属盐[4-5]组分为催化剂,因此镀在工件上存在固化温度高[6-7],对环境污染严重等问题。
关于研究气候变化的英语作文
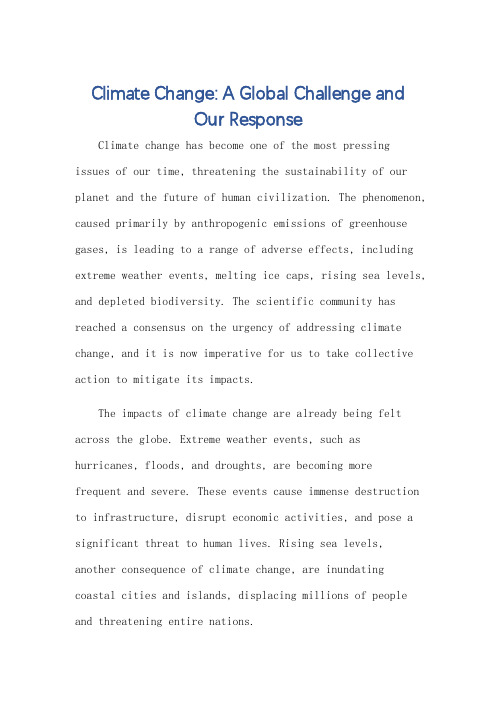
Climate Change: A Global Challenge andOur ResponseClimate change has become one of the most pressing issues of our time, threatening the sustainability of our planet and the future of human civilization. The phenomenon, caused primarily by anthropogenic emissions of greenhouse gases, is leading to a range of adverse effects, including extreme weather events, melting ice caps, rising sea levels, and depleted biodiversity. The scientific community has reached a consensus on the urgency of addressing climate change, and it is now imperative for us to take collective action to mitigate its impacts.The impacts of climate change are already being felt across the globe. Extreme weather events, such as hurricanes, floods, and droughts, are becoming morefrequent and severe. These events cause immense destruction to infrastructure, disrupt economic activities, and pose a significant threat to human lives. Rising sea levels, another consequence of climate change, are inundatingcoastal cities and islands, displacing millions of people and threatening entire nations.To address these challenges, it is crucial that we reduce our carbon emissions and transition to renewable sources of energy. We must invest in clean technologiessuch as solar, wind, and hydroelectric power, and phase out coal and other fossil fuels. Additionally, we need to adopt sustainable practices in agriculture, forestry, and urban planning to reduce our carbon footprint and protect our natural resources.Individual actions are also crucial in the fightagainst climate change. Simple measures such as reducing food waste, conserving water, and using publictransportation can significantly reduce our carbon emissions. Furthermore, we must raise awareness aboutclimate change and encourage others to adopt sustainable practices. Only through collective effort can we hope to mitigate the impacts of climate change and secure a sustainable future for ourselves and our planet.However, it is important to note that addressingclimate change is not just a matter of reducing carbon emissions. It also requires addressing the social and economic factors that drive climate change, such as poverty,inequality, and unsustainable development patterns. We must ensure that our efforts to mitigate climate change are inclusive and equitable, benefiting all people, regardlessof their geographical location or socio-economic status.In conclusion, climate change is a global challengethat requires urgent and concerted action from all of us.By adopting sustainable practices, investing in clean technologies, and raising awareness about climate change,we can mitigate its impacts and secure a sustainable future for ourselves and our planet. Let us come together and take responsibility for our actions, for the sake of our planet and future generations.**气候变化:全球性的挑战与我们的回应**气候变化已成为我们这个时代最紧迫的问题之一,它威胁着我们星球的可持续性,以及人类文明的未来。
不同模式超声波辅助低温腌制对牛肉品质的影响

基金项目:江苏省重点研发计划(现代农业重点项目)(编号:\2MW"()[()作者简介:吴梦迪,女,江苏大学在读硕士研究生。
通信作者:马海乐("'[)—),男,江苏大学教授,博士生导师,博士。
2J9<::JH:i Fc=%7;F%>D 收稿日期:2023 07 27 改回日期:2023 09 17犇犗犐:10.13652/犼.狊狆犼狓.1003.5788.2023.80720[文章编号]1003 5788(2023)09 0177 06不同模式超声波辅助低温腌制对牛肉品质的影响Effectsofdifferentmodesofultrasonicassistedlowtemperaturecuringonbeefquality吴梦迪犠犝犕犲狀犵犱犻 马海乐犕犃犎犪犻犾犲 刘会敏犔犐犝犎狌犻犿犻狀(江苏大学食品与生物工程学院,江苏镇江 212013)(犛犮犺狅狅犾狅犳犉狅狅犱犪狀犱犅犻狅犲狀犵犻狀犲犲狉犻狀犵,犑犻犪狀犵狊狌犝狀犻狏犲狉狊犻狋狔,犣犺犲狀犼犻犪狀犵,犑犻犪狀犵狊狌212013,犆犺犻狀犪)摘要:目的:探索适合家用冰箱冷藏室的绿色、快速的腌制方法。
方法:在低温条件下,采用不同频率组合的超声波辅助腌制牛肉,研究其对牛肉品质的影响。
结果:对比低温静腌,同步超声波22+40kHz(SIU22+40kHz)的腌制效果最好,其盐分含量(0.3274%)提高了74.15%(犘<0.05),蒸煮损失(34.933%)降低了11.45%(犘<0.05),硬度(293.545N)降低了18.39%(犘<0.05),回弹性(1.436N/mm2)降低了17.54%(犘<0.05),咀嚼性(2209.964N/mm)降低了20.12%(犘<0.05)。
结论:在2~6℃的低温条件下,超声波辅助低温腌制可以有效地提高牛肉的盐分含量,降低牛肉的蒸煮损失,改善牛肉的嫩度,同时较好地保持牛肉的色泽品质。
AgC-

银石墨2-5%的银石墨触头最主要的特性是抗熔焊高可靠性,低的接触电阻,温升小,作为滑动触头使用时有自润滑性能等,典型使用在低压断路等、电抗保护开关、线路保护开关、漏电保护开关和滑环转换器等采用烧结挤压工艺制造的银石墨触头材料,不仅致密化程度高,而且由于石墨质点呈纤维取向,更有利于在电弧作用下烧损率减少与Cu、AgNi配对使用。
途:作为弧触最大的应用领域是低压断路器,线路保护开关,故障电流保护开关,滑动电刷以及铁道信号继电,对许多应用场合,3%重量的石墨含量即可,在苛刻通断条件下,含量可到5%量比例.特性:导电性能好,接触电阻低,抗熔焊性高,在短路电流下也不会熔焊,滑动性能好,但电损蚀大,灭弧能力较差,在电弧的较长时间作用下,烧损剧烈,使灭弧罩积碳,脆弱和较难焊接.AgC触头材料性能特点及应用材料名称性能特点主要应用领域供货形式银石墨(AgC)用挤压法制造的AgC材料中C成纤维状分布。
由于C的脆性,使AgC成为所有触头材料中抗动熔焊性最好的材料。
而且AgC的接触电阻较低广泛应用于保护断路器中,通常与细晶银、银镍或铜非对称配对使用片材AgC触头产品机械物理性能工艺方法产品形状状态抗拉强度MPa延伸率%密度g/cm3电阻率μΩ·cm硬度(HV)AgC4/Ag-MSE-T 挤压片材退火/ / 8.95 2.09 43 - 50 AgC3/Ag-SS-T 模压片材退火/ / 9.40 2.32 46 - 56金相图片AgC4/Ag-MSE-T 200XAgC3/Ag-SS-T 100X 石墨粉镀银新工艺研究.E lectroless plating of silver on graphite powders and the study of its conductive adhesiveT ongxiang, Liang(Institute of Nuclear and New E nergy T echnology, T s inghua University); Wenli, Guo; Yinghui, Yan; Chunhe, T ang Source: International Journal of Adhesion and Adhesives, v 28, n 1-2, January, 2008, p 55-58ISSN: 0143-7496 CODEN: IJAA DKPublisher: Elsevier LtdAbstract: In this paper, silver plating graphite powders were developed by electroless plating method. The density of silver plating graphite powders was 2.61 g/cm3 and the ratio of silver for the powders was 25 wt%. After being mixed with epoxy resin and curing agent, silver plating graphite powders conductive adhesive was obtained, with the percolation concentration of 28 vol%. Compa red to pure Ag conductive adhesive, the new conductive adhesive has the advantage of low cost. Adhesives based on the graphite or Ag plating graphite powders exhibited higher tensile strength and larger failure elongations than pure Ag conductive adhesive. © 2007 Elsevier Ltd. All rights reserved. (7 refs.)Ei controlled terms: Silver plating- Adhesives- E lectroless plating- E poxy resins- Failure analysis- Graphite- T ensile strengthUncontrolled terms: Graphite pow ders- Conductive adhesiveClassification Code: 421Strength of Building Materials; Mechanical Properties - 482.2Minerals - 539.3Metal Plating - 539.3.2Electroless Plating - 547.1Precious Metals - 804.1Organic Compounds - 815.1.1Organic PolymersDatabase: CompendexDevelopment of new silver plated graphite powders used as conductive fillersmore optionsAuthor(s):Qu Zhan-minSource: Electroplating & Finishing Volume: 26 Issue: 9 Pages: 14-17 Published: September 2007Abstract: After oxidation treatment, the flake graphite powders were electrolessly copper plated followed by electroless silver plating. The process specifications were presented, the influential factors were analyzed and the deposit performances were tested. The results show that the silicone rubber with the addition of silver plated graphite powders has the volume resistivity of 2.0 * 10 -4Omega ldr cm and shielding effectiveness of 75 dB in the low-frequency region, and it is a kind of good conductive filler for electromagnetic shielding.Accession Number: 9793928Document Type: Journal PaperLanguage: ChineseTreatment: ExperimentalControlled Indexing: electroless deposition; electromagnetic shielding; electroplated coatings; graphite; oxidation; powders; silverUncontrolled Indexing:silver plated graphite powders; conductive fillers; oxidation treatment; flake graphite powders; electroless silver plating; silicone rubber; electromagnetic shielding; resistivity 0.0002 ohmcm; Ag-C; CClassification Codes: A6140G Structure of powders and porous materials; A8160 Corrosion, oxidation, etching, and other surface treatments; A8115L Deposition from liquid phases (melts and solutions)Numerical Data Indexing: resistivity 2.0E-06 ohmmChemical Indexing: AgC/ss Ag/ss C/ss AgC/bin Ag/bin C/bin; C/sur C/elAuthor Address: Qu Zhan-min; Meiwu Paper Ind. Co. Ltd., Xi'an, ChinaPublisher: Editorial Department of Electroplating and Finishing, ChinaNumber of References: 4CODEN: DYTUEMElectroless plating of silver on graphite powders and the study of its conductive adhesiveLiang Tongxiang, a, , Guo Wenli a, Yan Yinghui a and Tang Chunhe aa Institute of Nuclear and New Energy Technology, Tsinghua University, Beijing 100084, ChinaAccepted 14 March 2007.Available online 31 March 2007.AbstractIn this paper, silver plating graphite powders were developed by electroless plating method. The density of silver plating graphite powders was 2.61 g/cm3 and the ratio of silver for the powders was 25 wt%. After being mixed with epoxy resin and curing agent, silver plating graphite powders conductive adhesive was obtained, with the percolation concentration of 28 vol%. Compared to pure Ag conductive adhesive, the new conductive adhesive has the advantage of low cost. Adhesives based on the graphite or Ag plating graphite powders exhibited higher tensile strength and larger failure elongations than pure Ag conductive adhesive.Keywords: Silver plating; Graphite powders; Conductive adhesiveArticle Outline1. Introduction2. Experimental2.1. Sliver plating2.2. Conductive adhesives3. Results and discussion4. SummaryReferences1. IntroductionElectrically conductive adhesives offer a new prospective way to electrical connection of surface mount device components to printed circuit boards, because of their lower possible curing temperature, higher flexibility, fine pitch capability than thin-lead solders [1], [2] and [3]. Normally, high-performance conductive adhesives were designed by combining the thermosetting resin and the efficient electrically conductive fillers. Silver is used as the most popular electrically conductive filler due to its superior conductivity. The silver filler has one disadvantage of higher cost than that of copper and carbon black. Graphite or carbon powders can be used as conductive fillers, but the conductivity of this kind of adhesives is not satisfactory enough.Now, silver-coated flake copper, inorganic particles or polymer micro-spheres using as the filler for conductive adhesives have been studied [4], [5] and [6]. Considering various electrically conductive fillers, silver-coated inorganic particles or polymer micro-spheres are superior to graphite particles regarding the electrical conductivity of the adhesives, since the electrical conductivity of silver is much higher than that of inorganic particles. In addition to the high electrical conductivity of silver, the application of silver-plated particles leads also to the adhesives with low weight and low cost.In this paper, silver plating graphite powders were developed and a conductive adhesive was obtained using this silver plating graphite powders as the filler.2. Experimental2.1. Sliver platingFive gram natural graphite powders with the average size of 17 μm were used as raw materials. The graphite powders were degreased in oven at 600 °C for 20 min, and then were sensitized in 20% SnCl2 solution for 5 min. After being rinsed with distilled water, the powders were activated in 2% AgNO3 solution for 5 min.The treated graphite powders were immersed in the reducing agent solution of water, in which the polyglycol, ethanol and glucose (C6H12O6) were contained, and then stirred for 10 min.AgNO3 (99.8%) and aqueous ammonia (28–30%) were used for preparation of Ag solution. Transparent Ag solution was first prepared by dissolving the AgNO3 (3.3 g) in the water (180 ml) with addition of several drops of the aqueous ammonia, then NaOH (0.6 g) was added to the solution, finally several drops of aqueous ammonia were added until the Ag(NH3)+ solution became transparent again.The mixture of graphite powders and reducing agent solution were immersed in the Ag solution and stirred for 30 min at room temperature, the pH is about 11 during coating process. After washing and drying, the silver plating graphite powders were obtained.The surface morphology of the Ag plating graphite powders were observed by using a scanning electron microscope (Hitch S-3000N), and the structure was analyzed by XRD (D/MAX-III).2.2. Conductive adhesivesIn this study, three kinds of conductive adhesives were developed with different fillers in a similar average size, pure Ag particles, graphite powders and Ag plating graphite fillers. The conductive adhesives comprised of fillers, epoxy resin and hardeners. The epoxy resin used was a diglycidyl ether ofbisphenol-A, E51, from the Chenguang Research Institute of Chemical Industry (Sichuan, China). Hardeners for the epoxy were purchased from the Aldrich Chemical Company (Milwaukee, WI, USA) and were used without further purification. The electrically conductive adhesives were prepared by mixing three components of epoxy resins and hardeners with respective electrically conductive filler at room temperature for 30 min at the mixing speed of 20 rpm using a lab-scale mixer. The adhesive was cured at 145 °C for30 min and was then ready for characterization.The electrical resistivity of adhesives was measured by the four-point probe (Cascade Microtech, 54/5S, USA). The single overlapped adhesive joints were prepared after degreasing of the aluminum alloy slabs with toluene and subsequent bonding. The dimensions of the aluminum slabs were50×10×2 mm; the thickness of the adhesive layer was 0.1 mm. The bonded area of each adhesive joint was 1 cm2.The cylinder specimens (Φ5 mm×40 mm) of conductive adhesives for determination of stress–stain behavior were prepared by casting adhesives in steel forms.The strengths of adhesive joints and the stress–strain behavior were measured by tensile testing of aluminum single overlapped adhesive joints, using a universal testing device at a constant cross-head speed of 10 mm/min.3. Results and discussionFig. 1 shows the XRD patterns of Ag plating graphite powders. Ag coating exists as a FCC structure.Full-size image (15K)Fig. 1. XRD patterns of Ag plating graphite powders.Fig. 2 is the SEM imagines of as-received graphite powders and the Ag plating powders, Fig. 3 is the graph of Ag-graphite interface. It is indicated that there is an even Ag film coated on the surface of graphite powders.Full-size image (44K)Fig. 2. SEM imagines of graphite (a) and Ag plating graphite powders (b).Full-size image (55K)Fig. 3. SEM imagines of Ag–graphite interface.The density (in Hg) of as-received graphite powders is 2.12 g/cm3. After plating with silver, the powder density increased to 2.61 g/cm3. According to the following formula: M=D s(D m−D g)/(D m(D s−D g)),for the composite powders, the content of silver is about 25 wt%, and graphite is about 75 wt%. Where M is the content of silver, D s is the density of silver, D g is the density of graphite, and D m is the density of Ag plating graphite powders.The concentration of the filler, when internal conductive network of particles is formed within the polymeric matrix and the material becomeselectro-conductive is called percolation concentration (Φc). If the concentration of the filler is below Φc, the adhesive is insulate. The dependence of electrical resistivity (Ω cm) of the adhesives with three different fillers on the content of the fillers is shown in Fig. 4. In this paper three adhesives were produced by the same produce, and the data in Fig. 4 are the even value of five samples for each filler contents. It can be seen that around percolation concentration, the sharp decrease of electrical resistivity is observed in all cases. For pure Ag filler, Φc was found to be about 13 vol% (40 wt%), and the resistivity kept constant when the filler content is over 20 vol% (55 wt%). But for graphite and Ag plating graphite fillers, they have the same value, about 28 vol% (about20 wt%). Table 1 shows the resistivity of three kinds of conductive adhesives filled with suitable content of fillers, which indicted that when the Ag plating graphite powders were used, the conductive adhesive has a good electrical conductivity. Compared the weight percentage of fillers between pure Ag conductive adhesives and Ag plating graphite powders adhesives, Ag plating graphite powders conductive adhesives have much less fillers, in this point, the cost of conductive adhesive can be decreased.Full-size image (18K)Fig. 4. Log resistivity of conductive adhesives as a function of filler content.Table 1.Characters of conductive adhesivesfiller conductive adhesive. These differences can be mainly attributed to two reasons, specific surface of filler and shape of filler. Graphite and Ag plating graphite fillers increase the tensile strength of adhesive, probably due to its higher specific surface [7]. From Fig. 2 and Fig. 3 we can see that many graphite particles exhibit in spherical shape, the Ag fillers used here were Ag flake. Just like many composites, spherical fillers will increase the failure elongations of materials.Full-size image (21K)Fig. 5. Stress–strain behavior of as-produced conductive adhesives.4. SummarySilver plating graphite powders and its conductive adhesive were developed by electroless plating method. The density of silver plating graphite powders is 2.61 g/cm3 and the ratio of silver for the powders is 25 wt%.After mixed with epoxy resin and curing agent, silver plating graphite powders conductive adhesive was obtained, and the electrical resistance can reach 1.2×10−3Ω cm when suitable content of the fillers is added. Since the percolation concentration of Ag plating graphite conductive adhesive is about 20 wt%, which is much lower than that of Ag particle conductive adhesive, the new conductive adhesive has the advantage of low cost.| PDF (1463 K)| PDF (325 K)|| Corresponding author. Tel.: +86 10 8979 6090; fax: +86 10 6977 1464.。
巴斯夫光引发剂介绍 BR_Radiation_curing
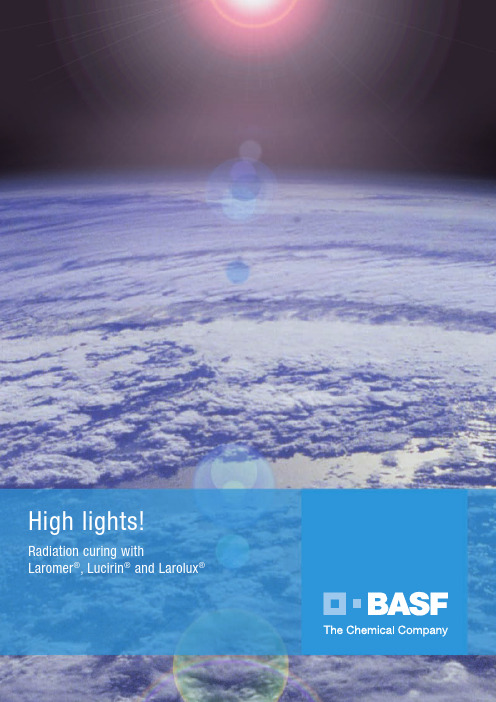
High lights! Radiation curing with Laromer®, Lucirin® and Larolux®Constancy of innovationsFor more than 30 years, BASF has constantly been setting standards in resource-saving, emission-free radiation curing products with its high-performance resins and photoinitiators. Fast drying, no VOC emission and energy efficiencies were and are the factors behind BASF`s success in this area. The goal to help our customers being more successful motivated us to develop not only resins, monomers and initiators but also curing technology like the Larolux® process to cure three-dimensional substrates.For the customer means with the customersPractical innovations and solutions are only possible if the practical world is brought into the laboratory. In BASF`s UV research centers, our scientists work out the standards for tomorrow`s radiation-curable products together with equipment manufacturers and customers. Quality needs a foundationBASF`s integrated system, known as “Verbund”, means a coordinated supply of raw materials from within the company itself and thus the highest level of delivery reliability and consistent product quality. In other words, regardless of when and where you need us, you can always count on BASF to the same extent.What do you expect?Simply expect more. The spectrum and possibilities for radiation curing are still far from being exploited to the fullest. We are put-ting all our efforts into continuing to offer you all the innovations and associated opportunities in a sure and reliable way. Our aim is to continue doing that as the leader in innovation.How to set standards day by day …Preserve the performance of your substrates Today and in the future, scratch resistance is an essential requirement for UV coating on parquet, furniture, plastic substrates and the next-generation automotive coatings. The new BASF product Laromer ® PO 9026, based on nano-technology, is designed to formulate radiation-curable coatings with outstanding scratch resistance.To combine the excellent scratch resistance with weather durability for any outdoor application, we have developed highly functional, aliphatic urethane acrylates. Depending on the way of applying the coating, you might choose Laromer ® UA 9050 as a solvent-based version for spray application or Laromer ® UA 9048 as a 100 % product diluted with Laromer ® DPGDA.Ambitious UV applications need specialized products One example is the success story of our photoinitiator Lucirin ® TPO, developed 25 years ago. With this initiator it became possible, for the first time, to cure pigmented varnishes without any yellowing. Since that time we have expanded the Lucirin ® TPO family to offer always an initiator that matches your requirements. The latest development is our Lucirin ® TPO-XL, a liquid phosphine oxide with improved efficiency and still remarkable low in yellowing.Principle features of BASF´s Lucirin ®photoinitiators• absorption in the longer-wave UV spectrum • formulation of very low-odor inks and coatings • most suitable for inert-atmosphere UV curing • good through-curing of thick films • negligible emissions and migration02 03environment [normalized]costs [normalized]low eco-efficiencyhigh eco-efficiencyDemand-based benefit:Coating of 1000 wooden doors with a semi-gloss, transparent appearance BASF target products:• U V roller coater based on Laromer ® PO 43 F and PO 77 F • applied coating amount approx. 60 g/m 2Alternative products:• N C coating (solid content 25 %) applied coating amount 240 g/m 2• a queous varnish (solid content 35 %) applied coating amount 200 g/m 2• 2C-PUR (solid content 48 %) applied coating amount 160 g/m 2Ecology and efficiency combinedHow eco-friendly is a product? How eco-friendly is its application? How eco-friendly is the final product? And how eco-friendly is the product by comparison with other products? These are questions that previously could never be answered accurately. That is why BASF developed the eco-efficiency analysis, where ecological factors and efficiency are combined so that different products and processes can be compared as a defined case study.The Eco-efficiency analysis:• a strategic tool developed by BASF to measure eco-efficiency • p rovide a quantitative measure of the economic and ecological benefits of a product or process as compared to other products or processes• i dentification of the most sustainable product or process for a defined customer benefit• e ach single study is based on solid facts with respect to the defined application onlyWhere ecology meets efficiencyThe result at a glance: Low cost and highly eco-efficient UV coatingsLaromer ® PO 43 FLaromer ® PO 77 FUV coatings applied by roller coaterSuccess factor:• i mmediately dry, allowing furtherprocessing• p referred technology for lowVOC emissionOur offer to our business partners:• e co-efficiency analysis for theirspecific products and processes04 05Product range of Laromer® gradesLaromer®Type of resin Type of thinner[content]FunctionalitycalculatedViscosity[Pa·s, 23°C]Hydroxyl value[mg KOH/g]DIN EN ISO 4629HardnessEpoxy acrylates LR 8765aliphatic epoxy acrylate- 2.00.6 -1.2approx. 330 LR 8986aromatic mod. epoxy acrylate- 2.4 3 - 6approx. 170LR 9019aromatic mod. epoxy acrylate- 2.415 - 25approx. 175LR 9023aromatic mod. epoxy acrylate DPGDA [15 %] 2.4 2 - 5approx. 150 Polyester acrylates PE 55 F - 3.125 - 45approx. 70 PE 56 F- 3.120 - 40approx. 70PE 46 T TPGDA [30 %] 2.8 1 - 3.5approx. 60LR 9004- 2.620 - 50approx. 60PE 9024 - 2.610 - 30 approx. 70PE 9045DPGDA [20 %] 2.5 2 - 7approx. 60PE 44 F- 3.0 2 - 5approx. 80LR 8800- 3.0 4 - 8approx. 80LR 8907DPGDA [25 %] 1.90.5 - 2approx. 120LR 8981- 3.0 4 -14approx. 80PE 9032modified polyester acrylate- 4.015 - 25approx. 50 Urethane acrylates UA 19 T aliphatic TPGDA [35 %] 2.016 - 30approx. 10 UA 9028 aliphatic butyl acetate [30 %] 2.00.8 - 1.6approx. 15UA 9030 aliphatic LR 8887 [30 %] 1.780 - 150approx. 12LR 8987aliphatic HDDA [30 %] 2.3 2 - 6approx. 11UA 9029 aliphatic butyl acetate [30 %] 2.40.5 - 1.2approx. 5UA 9033 aliphatic LR 8887 [30 %] 1.715 - 25approx. 6UA 9047aliphatic butyl acetate [30 %]> 6.0 2 - 7approx. 10UA 9048aliphatic DPGDA [25 %] 6.57 - 16approx. 10UA 9050aliphatic butyl acetate [20 %]8.0 1.5 - 5approx. 10 Polyether acrylates PO 33 F alkoxylated TMP-triacrylate- 3.00.07 - 0.13approx. 30 LR 8863ethoxylated TMP-triacrylate- 3.00.07 - 0.11approx. 10PO 43 F - 2.40.2 - 0.4approx. 100LR 8967- 2.60.12 - 0.19approx. 50LR 8982 - 2.70.22 - 0.3approx. 70LR 9007- 4.00.8 - 1.5approx. 130Elasticity Reactivity ChemicalresistanceCharacteristics EuropeEINECSUSATSCACanadaDSLJapanENCSChinaIECSCKoreaECL partially water-soluble, flexible, highly reactivelow viscosity, free of diluents, resistant to chemicalshighly reactive, resistant to chemicals---diluted version of Laromer® LR 9019--well balanced properties, leads to a tough filmimproved compatibility with reactive diluents in comparison to PE 55 Flow viscous, diluted version of Laromer® PE 56 Ftough with good adhesion---compatible with nitro-cellulose ---low viscous, diluted version of Laromer® LR 9004---free of diluents, low viscosity, low odor, flexible--hard, chemical resistant, low odor-highly flexible, use in combination with hard, less flexible binders----highly reactive, flexible with good sanding properties---abrasion-resistant in parquet applications ("falling sand")----elastic, low yellowing, flexible at temperature below 0°C-highly elastic, low yellowing, low viscous, monomer-free-highly elastic, low yellowing, good adhesion--scratch- and weather-resistant, use for outdoor applications----monomer-free version of Laromer® LR 8987----highly elastic, reactive, good adhesion--physical drying, best performance when UV-cured at high temperatue-----excellent scratch and abrasion resistance-----lowest yellowing, excellent scratch resistance-----low yellowing, low odor diluent SNUR--lower in viscosity than Laromer® PO 33 Fresistant to chemicals, all-round resinlow viscous version of Laromer® PO 43 Fpartially water-soluble (spray viscosity adjustable)--lowest extractable compounds, good scratch resistance--SNUR = Significant new use rule0607Product range of Laromer® gradesLaromer®Type of resin Type of thinner[content]FunctionalitycalculatedViscosity[Pa·s, 23 °C]Hydroxyl value[mg KOH/g]DIN EN ISO 4629HardnessAmine-modified polyether acrylates PO 77 F modified polyether acrylate- 2.9 1 - 3approx. 120 PO 84 F - 3.50.4 - 0.7approx. 50 PO 94 F- 3.50.3 - 0.6approx. 55 LR 8997- 3.40.3 - 0.5approx. 55 PO 83 F- 2.80.09 - 0.13approx. 30 LR 8889- 2.60.09 - 0.14approx. 60 LR 8869- 2.80.06 - 0.11approx. 30 LR 8996- 2.90.05 - 0.09approx. 30Water-basedproductsPE 55 WN polyester acrylate water [50 %] 2.20.25 - 0.65-PE 22 WN polyester acrylate water [50 %] 2.20.15 - 0.5-LR 8949aliphatic urethane acrylate dispersion water [60 %] 1.70.04 - 0.1-LR 8983aromatic urethane acrylate dispersion water [60 %]0.70.05 - 0.3-LR 9005aromatic urethane acrylate dispersion water [60 %] 2.00.02 - 0.25-Special radiation-curable productsUP 35 D unsaturated polyester DPGDA [45 %] 3.5 3 - 6-LR 8985modified polyether acrylate- 3.055 - 85approx. 25LR 9013modified polyether acrylate- 3.045 - 70approx. 25PO 9026 nano-modified polyether acrylate- 1.50.5 - 3-PA 9039adhesion promoter- 1.50.3 - 0.6-Dual-cure products LR 9000aliphatic urethane- 2 + 2 NCO 1 - 1.4-Elasticity Reactivity ChemicalresistanceCharacteristics EuropeEINECSUSATSCACanadaDSLJapanENCSChinaIECSCKoreaECL reactive all-round resin, good sanding properties---higher reactive, good pigment wetting SNUR--higher reactivity than Laromer® PO 84 F-highly reactive, very low in color---resistant to chemicals, low viscosity SNUR---reactive, low viscosity, elastic---harder than Laromer® LR 8889---reactive, very low in color and viscosity---flexible, easy to matt, adhesion to PVC--hard, resistant to chemicals, good sanding properties--good grain enhancement, resistant to chemicals, weather-resistant---excellent physical drying properties, easy to formulate---highly scratch-resistant and resistant to chemicals-hard, resistant, good sanding properties--excellent pigment wetting properties, low in shrinkage SNUR--excellent pigment wetting properties, low in shrinkage-contains 50 % nano-particles, very scratch-resistant--leads to good adhesion on different substrates-contains NCO- and UV-reactive groups within one moleculfor additional information see page 16---SNUR = Significant new use rule08091000000 100000 100001000 100 10UA 9048UA 9050UA 9047PE 9045Viscosity – reactivityand hardness – elasticityViscosity – reactivity / all products were cured with 1 UV lamp 120 W/cm. Initiator: 4 % Irgacure®1 500Hardness – elasticity / all products were cured 5 x 5 m/min with 1 UV lamp 120 W/cm. Initiator: 4 % Irgacure®1 500Erichsen indentation [mm]PE 9045UA 9047UA 9048UA 90501011Product range of monomersProduct Structure CAS number Mol mass[g/mol] Laromer® TMPTAtrimethylolpropane triacrylate15625-89-5approx. 300Laromer® BDDAbutanediol diacrylate1070-70-8approx. 200Laromer® HDDAhexanediol diacrylate13048-33-4approx. 230Laromer® TPGDAtripropyleneglycol diacrylate42978-66-5approx. 300Laromer® DPGDAdipropyleneglycol diacrylate57472-68-1approx. 240Laromer® POEAphenoxyethyl acrylate48145-04-6approx. 190Laromer® LR 8887trimethylolpropaneformalmonoacrylate66492-51-1approx. 200Laromer® TBCH4-t-butylcyclohexyl acrylate 84100-23-2282-104-8approx. 210Laromer® LAlauryl acrylate 12142156-97-0approx. 250Laromer® EDGAethyldiglycol acrylate7328-17-8approx. 188Laromer® BDMAbutanediol monoacrylate2478-10-6approx. 144Laromer® DCPAdihydrodicyclopentadienyl acrylate12542-30-2approx. 204Density [g/cm3]Contentof stabilizer[Me HQ]Color[APHA DINISO 6271]Viscosity[Pa·s, 25 °C]EuropeEINECSUSATSCACanadaDSLJapanENCSChinaIECSCKoreaECL1.102 (25 °C)200 ± 50 ppm max. 150approx. 1301.049 (45 °C)200 ± 50 ppm max. 150approx. 51.015 (25 °C)200 ± 50 ppm max. 150approx. 61.036 (25 °C)350 ± 50 ppm max. 150approx. 111.046 (25 °C)350 ± 50 ppm max. 150approx. 81.100 (25 °C)200 ± 50 ppm max. 250approx. 81.094 (25 °C)1000 ± 100 ppm max. 500approx. 40--0.940 (25 °C)200 ± 50 ppm max. 100approx. 9--0.870 (25 °C)200 ± 50 ppm max. 150approx. 61.006 (25 °C)2000 ± 200 ppmstabilizer blendmax. 250approx. 51.039 (25 °C)300 ± 50 ppm max. 50approx. 111.070 (25 °C)300 ± 50 ppm max. 250approx. 11-1213mPa·s7000600050004000300020001000Viscosity – reactivity and hardness – elasticity of monomersMonomers: viscosity – reactivity / formulation: 70 parts Laromer ® PE 56 F, 30 parts monomer, 4 parts Irgacure ®1 500B D D AH D D AMonomers: hardness – elasticity / formulation: 70 parts Laromer ® PE 56 F, 30 parts monomer, 4 parts Irgacure ®1 50014 15The dual innovation Laromer ® LR 9000Laromer ® LR 9000 for ambitious formulationsDual-cure resins are products, which combine two different cross-linking mechanisms within a single molecule. These innovative products allow the user to overcome various limitations, which are present in todays´s mono-curing systems.Laromer ® LR 9000 combines the advantage of rapid, UV-light-initiated polymerization of acrylic ester groups with the UV-light-independent polyaddition of the isocyanate groups. Laromer ® LR 9000 can be used as a single resin or in combination with a polyol in a two-component system. When it is used together with an OH- resp. polyol component, you might use the following formula to compute the theoretical equivalent quantity of Laromer ® LR 9000 required for crosslinking 100 g of any OH/polyol component.Laromer ® LR 9000 characteristicsOOO ON C ONCOLaromer ® LR 9000 is an isocyanatoacrylate which has a low,user-friendly viscosity, yet being labeled as a polymer.Viscosity (23 °C) 1 - 1.4 [Pa·s](DIN EN ISO 3129)NCO content 14.5 - 15.5 %(DIN EN ISO 11909)UV-functionality 2Color value ≤ 2(DIN ISO 6271)0.075 * [OH value] * [non - volatile fraction of OH component] NCO content of Laromer ® LR 9000Due to the possibility of chemical covalent bonding Laromer ® LR 9000 provides• e xcellent adhesion on a wide range of substrates • e asy access to chemical modification by additive reactions even at room temperature• s ubstrate sealing by chemical bonding betweenLaromer ® LR 9000 and porous substrates such as MDF to minimize emissions• i mproved through-curing of pigmented coatings layers where the pigment particles allow limited UV transmission16 17Lucirin ® photoinitiatorsThe Lucirin ® family stands for photoinitiators used in UV-curable coatings and inks. This photoinitiators are preferredly used to cure thick films, pigmented and/or UV-stabilized coatings and inks. Based on this property profile, even sophisticated applications can be realized. BASF offers these low-odor, acylphosphine oxide photoinitiators in powder and liquid forms.Lucirin ® BAPO – Particularly suitable for pigmented UV coatings and printing inks. It allows very thick films to be cured. Since its solubility is limited, it should be incorporated well.Lucirin ® TPO – It is used in pigmented and clear coatings to produce low-odor films. Of particular importance is the low yellowing - especially required for white-pigmented coatings and inks.Lucirin ® TPO-L – Being a liquid, it is very easy to incorporate into coatings formulations. The low yellowing makes it a good choice for light-colored coatings.Lucirin ® TPO-XL – Combines the advantages of the Lucirin ® types described above. Especially easy incorporation into recipes because of its liquid form of supply; little yellowing and high effectiveness make it the first choice.3.02.52.01.51.00.50m a s s e x t i n c t i o n l /(g *c m )wavelength [nm]300 320 340 360 380 400 420 440Lucirin ® TPOLucirin ® TPO-LLucirin ® TPO-XLLucirin ® BAPOExtinction spectrum in ethanol Solubility [%]AppearrancePurityn-Butyl acetate Laromer ® HDDALaromer ® TPGDALucirin ® BAPOpowder ≥ 98 %555Lucirin ® TPOpowder ≥ 97 %252015Lucirin ® TPO-L liquid ≥ 95 % > 50 > 50 > 50Lucirin ® TPO-XL liquid ≥ 95 % > 50 > 50 > 50Lucirin ® characteristicsLucirin ®photoinitiatorsThe major advantages:• s olvent-free or low-solventUV coatings meet the VOCDirective for 2007• 3D substrates• small-scale runs• low-cost, ozone-free UV lamps • s imple, low-cost oxygendisplacementor in short: simpler, faster and better!UV curing has already revolutionized coating technology, but anything good can be improved further – and even simplified, thus opening up new applications. A principle that applies to radiation technology for 3D applications or for small-scale runs. The technology of UV curing in carbon dioxide* recently developed by us uses a very simple method to eliminate technical difficulties that are otherwise caused by atmospheric oxygen. Atmospheric oxygen interferes with the curing reaction of UV coatings.Carbon dioxide is heavier than air and can easily be f illed into a tank to form an inert gas blanket. Losses due to escaping gas can thus be reduced. When the oxygen content is low the UV dose can be decreased to such an extent that simpler and cheaper UV lamps can be used. 3D objects can be illuminated by simple reflectors. All these factors save time and money, enhance quality, increase flexibility and additionally save the environment.*Application for patent WO 01/39897 submitted by BASF AktiengesellschaftLarolux® – UV curing of coatings in carbon dioxide atmosphereDoes this all sound too simple? It‘s true though. Contact us or our partners in the coatings industry.12346518 191 Aluminum reflectors:Lining the tank with aluminum(e.g., with aluminum foil) issufficient and permits perfectillumination of 3D substrateswithout special reflectors.2 UV lamps:As the UV dose can be reducedsubstantially it is now possibleto use low-cost UV lamps. Thedistance between lamp andsubstrate is of minor importance.3 Space:for introducing carbon dioxide;both gas or dry ice are possible 4 Carbon dioxide:Carbon dioxide is heavier thanair and can easily be filled intoa tank to form an inert gasblanket. The gas requirement is low and oxygen is therefore nolonger a problem.5 Permeable aluminum base:The carbon dioxide is slowlyintroduced through this anddistributed. Strong gas eddiesare thus avoided.Here, too, aluminum ensuresperfect UV yield.6 Objects:3D or 2D objects are fullyilluminated. The UV coatingis fully cured.E V P 1607 eBASF Aktiengesellschaft Performance Chemicals forCoatings, Plastics and Specialties 67056 Ludwigshafen Germany/resinsContact worldwideA siaBASF Auxiliary Chemicals Co. Technical Center for Coating 300 Jiangxinsha Road, Pudong 200137, Shanghai ChinaTel.: +86 21 58611828-2362Fax: +86 21 58611828-2735EuropeBASF Aktiengesellschaft Performance Chemicals forCoatings, Plastics and Specialties E-EVP/RD – J 55067056 Ludwigshafen GermanyTel.: +49 621 60-49923Fax: +49 621 60-72869North America BASF Corporation 1609 Biddle Avenue Wyandotte, MI 48192USATel.: +1-734-324-5278Fax: +1-734-324-5185Eastern Europe, Africa, West Asia BASF AktiengesellschaftRegional Business Management Performance Chemicals EUM/SE – Benckiserplatz 167056 Ludwigshafen GermanyTel.: +49 621 60-76429Fax: +49 621 60-6676429South America BASF S.A.Av. Faria Lima 3600 – 10° andar Itaim Bibi – São Paulo – SP 04538-132 BrazilTel.: +55 11 3043-3637Fax: +55 11 3043-3110The data contained in this publication are based on our current knowledge and experience. In view of the many factors that may affect processing and application of our product, these data do not relieve processors from carrying out their own investigations and tests; neither do these data imply any guarantee of certain properties, nor the suitability of the product for a specific purpose. Any descrip-tions, drawings, photographs, data, proportions, weights etc. given herein may change without prior information and do not constitute the agreed contractual quality of the product. It is the responsibility of the recipient of our products to ensure that any proprietary rights and existing laws and legislation are observed. When handling these products, advice and information given in the safety data sheet must be complied with. Further, protective and workplace hygiene measures adequate for handling chemicals must be observed.® = registered trademark of BASF Aktiengesellschaft®1 = registered trademark of Ciba Specialty Chemicals Holding Ltd.。
低温快速固化酚醛树脂的研究进展

第35卷第2期V ol.35No.22021年3月March 2021木材科学与技术Chinese Journal of Wood Science and Technology低温快速固化酚醛树脂的研究进展孙丕智,潘晴,徐文彪,李翔宇,时君友(北华大学材料科学与工程学院,吉林吉林132013)摘要:传统酚醛树脂作为木材胶黏剂,在人造板工业生产中热压时所需温度较高、时间较长,影响生产效率和产品性能,研制低温快速固化的酚醛树脂胶黏剂具有现实意义。
综述国内外酚醛树脂低温固化的研究进展,主要从改性树脂制备和使用固化剂两方面入手,分析间苯二酚、金属离子和尿素等化学改性酚醛树脂,以及单组分和复合型固化剂的作用机理,并对未来的研究方向提出建议。
关键词:木材胶黏剂;酚醛树脂;低温快速固化;改性;固化剂中图分类号:TS653;TQ433.43文献标识码:A文章编号:2096-9694(2021)02-0012-06Research Status Review of Low-Temperature Fast-Curing PhenolFormaldehyde ResinSUN Pi-zhi ,PAN Qing ,XU Wen-biao ,LI Xiang-yu ,SHI Jun-you(School of Materials Science and Engineering ,Beihua University ,Jilin 132013,Jilin ,China )Abstract:Traditional phenol formaldehyde resin,as wood adhesive,needs high temperature and extended time to cure during hot pressing of the wood-based panel manufacturing.To improve the production efficiency and product performance,the low-temperature fast-curing phenol formaldehyde resin has been identified as an significant valuable process development.The research implemented domestically and internationally on the low-temperature curing phenol formaldehyde resin is reviewed.The review focus on the preparation of modification resin and the application of the curing agent.The mechanism of phenol formaldehyde resin modification by resorcinol,metal ions and urea were analyzed.The reaction process of single component and composite curing agent are also discussed respectively.Suggestions for future research are proposed.Key words:wood adhesives;phenol formaldehyde resin;low-temperature fast-curing;modification;curing agent酚醛树脂胶黏剂因具有优良的胶合性能、耐热性和耐候性,广泛应用于室外家具和木结构建筑中,与三聚氰胺甲醛树脂胶黏剂、脲醛树脂胶黏剂并称为木材工业中的“三醛”胶黏剂[1]。
我国气温网格预报检验及客观订正方法研究进展

10Advances in Meteorological Science and Technology 气象科技进展 13(6)- 2023收稿日期:2022年8月5日;修回日期:2023年1月10日第一作者:刘嘉慧敏(1989—),Email :***************资助信息: 陕西省自然科学基础研究计划(2022JQ-279);陕西省气象局秦岭和黄土高原生态环境气象重点实验室面上基金(2022Y-1);陕西省自然科学基础研究计划(2021JQ-964)我国气温网格预报检验及客观订正方法研究进展刘嘉慧敏1, 2 潘留杰1, 2 戴昌明1, 2 胡启元1, 2 何林3 燕若彤4(1 陕西省气象台,西安 710014;2 秦岭和黄土高原生态环境气象重点实验室,西安 710044;3 陕西省气象信息中心,西安 710014;4 成都信息工程大学大气科学学院,成都 610225)摘要:中国气象局自2014年启动无缝隙精细化网格天气预报业务,高分辨率的智能网格预报已成为天气预报目前的主推业务和未来的发展方向。
近年来,随着数值模式统计后处理技术的飞速发展,气温网格预报质量稳步提升。
本文在总结现有气温网格预报精细化检验评估方法的基础上,系统梳理了单模式订正、多模式集成释用和大数据人工智能等数值模式释用技术在气温网格预报客观订正领域的最新进展,阐明了不同方法在气温网格预报领域的优势和劣势。
在当前人工智能、大数据、云计算等新型信息技术快速发展的背景下,未来气温网格预报需要吸纳更加多源的前沿研究成果,充分挖掘数值模式内在预报信息,使得预报向更加智慧化方向迈进。
关键词:网格预报,数值模式,检验评估,客观订正DOI:10.3969/j.issn.2095-1973.2023.06.002Research Progress on Objective Verification and Correction Methods for Grid Temperature ForecastLiu Jiahuimin 1, 2, Pan Liujie 1, 2, Dai Changming 1, 2, Hu Qiyuan 1, 2, He Lin 3, Yan Ruotong 4(1 Shaanxi Meteorological Observatory, Xi’an 710014; 2 Key Laboratory of Eco-Environment and Meteorology for the Qinling Mountains and Loess Plateau, Xi’an 710044; 3 Shaanxi Meteorological Information Center, Xi’an 710014;4 College of Atmospheric Sciences, Chengdu University of Information Technology, Chengdu 610225)Abstract: High-resolution intelligent grid forecast has become the main operational work and the development direction of future weather forecast since China Meteorological Administration launched the seamless fine grid weather forecast service in 2014. To date, with the rapid development of numerical model statistical post-processing technology, the quality of grid temperature forecast has been steadily improved. On the basis of summarizing the existing fine-scale testing and evaluation methods for grid temperature forecast, this paper systematically sorts out the latest progress of numerical model interpretation techniques, such as single model correction, multi-model integrated interpretation and big data artificial intelligence, in the field of objective correction of grid temperature forecast. The advantages and disadvantages of different methods in the field of grid temperature forecast are elucidated. In the context of the current rapid development of new information technologies such as artificial intelligence, big data, and cloud computing, grid temperature forecast needs to harness more cutting-edge research results from multiple sources, and fully utilize the inherent forecast information of numerical models for a smarter forecast in the future.Keywords: gridded forecasting, numerical model, verification and evaluation, objective correction0 引言近年来极端气温事件频发而引起的高温热浪、霜冻、寒潮等灾害性天气对社会经济发展的影响和威胁正引起各国政府的关注。
泡沫模的熟化烘干流程详解
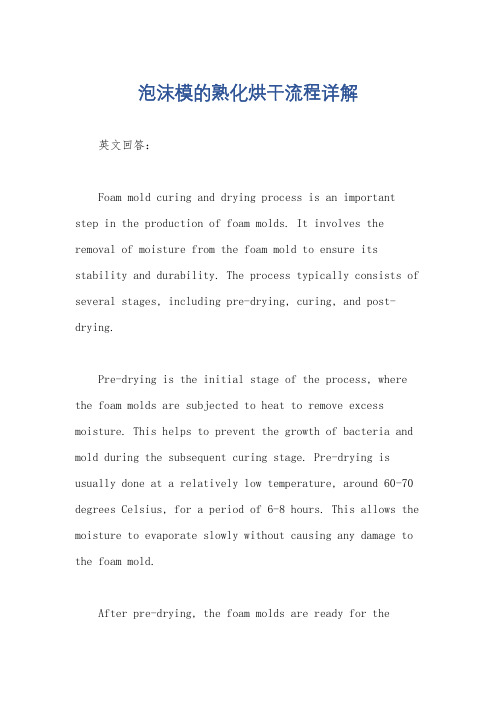
泡沫模的熟化烘干流程详解英文回答:Foam mold curing and drying process is an important step in the production of foam molds. It involves the removal of moisture from the foam mold to ensure its stability and durability. The process typically consists of several stages, including pre-drying, curing, and post-drying.Pre-drying is the initial stage of the process, where the foam molds are subjected to heat to remove excess moisture. This helps to prevent the growth of bacteria and mold during the subsequent curing stage. Pre-drying is usually done at a relatively low temperature, around 60-70 degrees Celsius, for a period of 6-8 hours. This allows the moisture to evaporate slowly without causing any damage to the foam mold.After pre-drying, the foam molds are ready for thecuring stage. Curing involves exposing the foam molds to higher temperatures to promote the cross-linking of the polymer chains and strengthen the structure of the foam. The temperature and duration of the curing stage vary depending on the specific type of foam and its intended application. For example, a polyurethane foam mold may be cured at a temperature of 100-120 degrees Celsius for 12-24 hours.Once the curing stage is complete, the foam molds are subjected to post-drying to remove any residual moisture. This is done at a lower temperature, typically around 40-50 degrees Celsius, for a period of 4-6 hours. Post-drying helps to ensure that the foam molds are completely dry and ready for further processing, such as trimming and finishing.It is important to note that the curing and drying process should be carefully controlled to avoid any damage to the foam molds. Excessive heat or prolonged exposure to high temperatures can cause deformation or shrinkage of the foam. On the other hand, insufficient curing and drying canresult in weak and unstable foam molds.中文回答:泡沫模的熟化烘干流程是泡沫模生产中的重要步骤。
导热灌封胶英语

导热灌封胶英语一、单词1. encapsulant [ɪnˈkæpsjələnt]- 释义:n. 密封剂;包封剂,在导热灌封胶语境下可表示灌封胶这种密封材料。
- 用法:This encapsulant is widely used in electronic device packaging.(这种灌封胶广泛用于电子设备封装。
)2. thermal [ˈθɜːml]- 释义:adj. 热的;热量的;由热造成的。
- 用法:Thermal conductivity is an important property of the encapsulant.(导热性是灌封胶的一个重要特性。
)3. conductive [kənˈdʌktɪv]- 释义:adj. 传导(性)的;能传导(热、电等)的。
- 用法:The conductive encapsulant can effectively dissipate heat.(这种导电灌封胶能有效地散热。
)4. adhesive [ədˈhiːsɪv]- 释义:n. 黏合剂;adj. 黏合的;有黏性的。
在导热灌封胶中也涉及到黏合的性能。
- 用法:The adhesive property of the encapsulant helps it to bond firmly.(灌封胶的黏合性有助于它牢固粘结。
)5. curing [ˈkjʊərɪŋ]- 释义:n. (使)固化;(使)变干;(使)硬化;v. cure的现在分词。
导热灌封胶需要经过固化过程。
- 用法:The curing time of the encapsulant is about 24 hours.(灌封胶的固化时间大约是24小时。
)二、短语1. thermal conductive encapsulant- 释义:导热灌封胶。
- 用法:We need to choose a suitable thermal conductive encapsulant for this project.(我们需要为这个项目选择一种合适的导热灌封胶。
银粉和触变剂对低温银浆挥发速率影响的研究

2.1 银粉振实密度对银浆干燥速率的影响 银粉是银浆的主体功能结构,影响银浆电阻、
密度和固化后膜层厚度。片状银粉搭接面积大,形
成有效导电通路多,被广泛应用于低温银浆中[11]。 通过不同球磨工艺、以不同粒径的不规则类球形银 粉为原料,制备振实密度 1.0~2.2 g/cm3 的片状银粉。 实验中银含量为 48%,载体中热塑性聚氨酯含量为 18%,实验数据如表 1 所列。
有机载体制备:溶剂为 DBE 和异佛尔酮,树脂 为热塑性聚氨酯。
触变剂预处理:触变剂加入 DBE 中,行星式重 力搅拌机高速分散。
按配方比例称取银粉、有机载体和预处理触变 剂,行星式重力搅拌机高速分散,三辊研磨机研磨 分散至细度小于 5 μm,得到导电银浆。 1.4 性能测试 1.4.1 溶剂挥发速率测定
为提高低温银浆的快速固化性能,本文利用触 变剂分散于银浆中形成微小颗粒及膨胀性的特点, 通过增加溶剂挥发通道,促进溶剂挥发;选用粘接 性好、无需固化剂的热塑性聚氨酯为粘接相,减少
收稿日期:2020-06-17 第一作者:幸七四,男,工程师,研究方向:贵金属电子浆料。E-mail:xqs@
g 有机膨润土(0.25%) 158
137 -15.33
h 改性聚脲(0.25%)
1%) 1320 1140 -15.79
银浆中加入触变剂后,相对于实验 d,实验 g 和 h 电阻值变化率降低,表明银浆中溶剂挥发速率 增快。触变剂加入银浆中能够增加溶剂挥发通道, 促进溶剂挥发,其机理为:触变剂吸附大量溶剂后 膨胀,浆料体积增大;触变剂以超细颗粒形式分散 于银浆中,形成微小骨架结构。实验 i 中加入气相 二氧化硅后,线路电阻升高。这是由于该型号气相 二氧化硅比表面积大(200 g/m2),加入后吸附大量溶 剂,浆料粘度明显升高,银粉分散性变差,导致线 路电阻升高[13]。
偏高岭土制备外墙保温材料试验
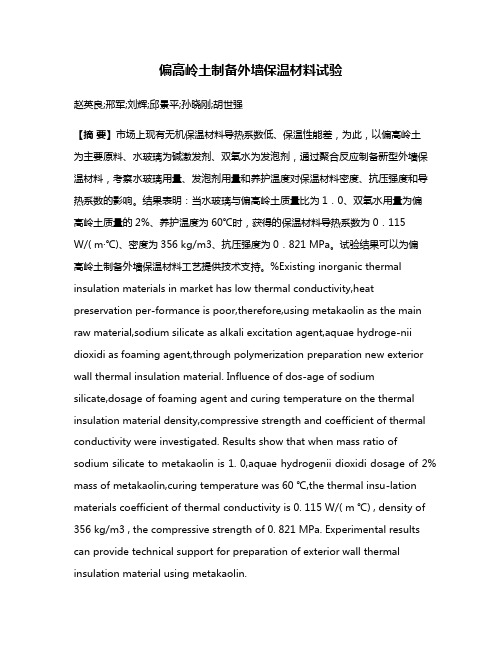
偏高岭土制备外墙保温材料试验赵英良;邢军;刘辉;邱景平;孙晓刚;胡世强【摘要】市场上现有无机保温材料导热系数低、保温性能差,为此,以偏高岭土为主要原料、水玻璃为碱激发剂、双氧水为发泡剂,通过聚合反应制备新型外墙保温材料,考察水玻璃用量、发泡剂用量和养护温度对保温材料密度、抗压强度和导热系数的影响。
结果表明:当水玻璃与偏高岭土质量比为1.0、双氧水用量为偏高岭土质量的2%、养护温度为60℃时,获得的保温材料导热系数为0.115W/( m·℃)、密度为356 kg/m3、抗压强度为0.821 MPa。
试验结果可以为偏高岭土制备外墙保温材料工艺提供技术支持。
%Existing inorganic thermal insulation materials in market has low thermal conductivity,heat preservation per-formance is poor,therefore,using metakaolin as the main raw material,sodium silicate as alkali excitation agent,aquae hydroge-nii dioxidi as foaming agent,through polymerization preparation new exterior wall thermal insulation material. Influence of dos-age of sodiumsilicate,dosage of foaming agent and curing temperature on the thermal insulation material density,compressive strength and coefficient of thermal conductivity were investigated. Results show that when mass ratio of sodium silicate to metakaolin is 1. 0,aquae hydrogenii dioxidi dosage of 2% mass of metakaolin,curing temperature was 60 ℃,the thermal insu-lation materials coefficient of thermal conductivity is 0. 115 W/( m ℃) , density of 356 kg/m3 , the compressive strength of 0. 821 MPa. Experimental results can provide technical support for preparation of exterior wall thermal insulation material using metakaolin.【期刊名称】《金属矿山》【年(卷),期】2016(000)010【总页数】4页(P193-196)【关键词】保温材料;偏高岭土;聚合反应【作者】赵英良;邢军;刘辉;邱景平;孙晓刚;胡世强【作者单位】东北大学资源与土木工程学院,辽宁沈阳110819;东北大学资源与土木工程学院,辽宁沈阳110819;招金矿业股份有限公司蚕庄金矿,山东招远265400;东北大学资源与土木工程学院,辽宁沈阳110819;东北大学资源与土木工程学院,辽宁沈阳110819;东北大学资源与土木工程学院,辽宁沈阳110819【正文语种】中文【中图分类】TD985近年来,随着我国城镇化和工业化建设步伐的加快,新增建筑面积逐年增加,当前我国建筑耗能约占到社会总能耗的30%左右,并且还将呈现递增的趋势[1]。
膜片开关银浆固化后变色失效分析
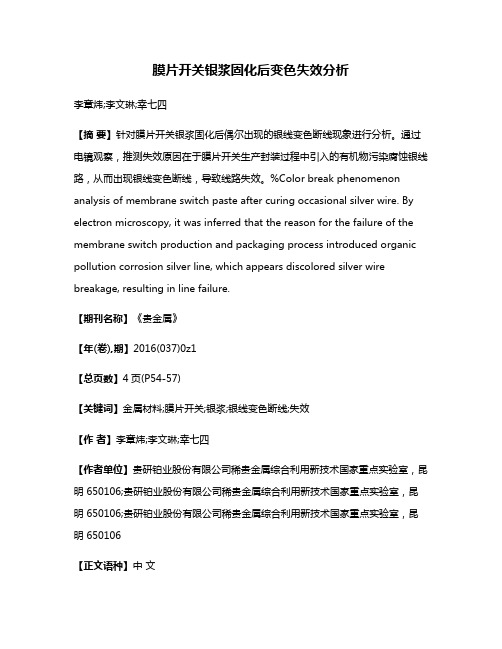
膜片开关银浆固化后变色失效分析李章炜;李文琳;幸七四【摘要】针对膜片开关银浆固化后偶尔出现的银线变色断线现象进行分析。
通过电镜观察,推测失效原因在于膜片开关生产封装过程中引入的有机物污染腐蚀银线路,从而出现银线变色断线,导致线路失效。
%Color break phenomenon analysis of membrane switch paste after curing occasional silver wire. By electron microscopy, it was inferred that the reason for the failure of the membrane switch production and packaging process introduced organic pollution corrosion silver line, which appears discolored silver wire breakage, resulting in line failure.【期刊名称】《贵金属》【年(卷),期】2016(037)0z1【总页数】4页(P54-57)【关键词】金属材料;膜片开关;银浆;银线变色断线;失效【作者】李章炜;李文琳;幸七四【作者单位】贵研铂业股份有限公司稀贵金属综合利用新技术国家重点实验室,昆明 650106;贵研铂业股份有限公司稀贵金属综合利用新技术国家重点实验室,昆明 650106;贵研铂业股份有限公司稀贵金属综合利用新技术国家重点实验室,昆明 650106【正文语种】中文【中图分类】TG146.3+3低温导电银浆因其优异的导电性、导热性和实用性,广泛应用于膜片开关、电容电极、触摸屏等方面[1-3]。
近期,使用膜片开关银浆的部分企业发现生产的少量产品局部出现线路变色问题,导致线路失效,但未能找出其发生的根本原因,也就无法寻找避免该类现象产生的措施来提升产品的成品率。
- 1、下载文档前请自行甄别文档内容的完整性,平台不提供额外的编辑、内容补充、找答案等附加服务。
- 2、"仅部分预览"的文档,不可在线预览部分如存在完整性等问题,可反馈申请退款(可完整预览的文档不适用该条件!)。
- 3、如文档侵犯您的权益,请联系客服反馈,我们会尽快为您处理(人工客服工作时间:9:00-18:30)。
Development of Low Temperature Curing, 120°C,Durable, Corrosion Protection Powder Coatings For Temperature Sensitive SubstratesGlen Merfeld,**** Steve Mordhorst, Rainer Koeniger, A. Ersin Acar, Chris Molaison, Joe Suriano, Pat Irwin, and Ron Singh Warner—GE Global Research*Ken Gray—Crosslink Powder Coatings, Inc.†Mark Smith—Honeywell-Department of Energy**Kevin Kovaleski and Greg Garrett—NavAir ‡Steve Finley and Debora Meredith—AFMC***Mike Spicer and Tom Naguy—AFRL †††Presented at the 31st Annual International Waterborne, High-Solids, and Powder Coatings Symposium, February 18-20, 2004, in New Orleans, LA.*One Research Cir., Building K1, Room 4B37, Niskayuna, NY.†Clearwater, FL.**Kansas City, MO.‡Patuxent River, MD.***WPAFB, OH.†††WPAFB, OH.****Author to whom correspondence should be addressed.Commercial low temperature cure powder coatings, including candidates representative of all the major coating chemistries, were evaluated. Nearly all failed to adequately react at a cure schedule of 120°C for 30 min, and none, even when prepared at their manufacturer’s lowest recommended cure conditions, met the stringent performance needs for temperature-sensitive military applications. Initial research is presented toward developing low temperature cure pow-der coatings that simultaneously meet all performance requirements at this target cure schedule. Using commercial resins, corrosion inhibitors, and catalysts, this research effort has closed gaps in low temperature cure coating perform-ance and has helped to identify critical deficiencies. This study establishes direction for future developments in new resin and catalyst technologies.Keywords: Differential scanning calorimetry, catalysis, corrosion, corrosion protection, powder, aluminum, low temper-ature cureJCT Research, Vol. 2, No. 8, October 2005Significant effort is expended and cost is incurred each year to procure, use, and dispose of toxic and haz-ardous materials associated with the use of solvent-borne corrosion protection coatings. Powder coatings have the potential to eliminate more than 95% of the volatile organic compounds and hazardous air pollutants released during the application of such coatings. Over the past years, powder coatings have increasingly gained pop-ularity as a result of their ecological advantages as well as their economical and performance benefits.1-7There are numerous military and civilian applications that require protective coatings, but they involve substrates that are made from materials such as low-tempered metal alloys,composites, plastic, or wood that would be structurally compromised by thermal treatments required to cure con-ventional powder coatings. The need for powder coatings that cure at ever lower temperatures has been presented extensively and much work on their development has been reported in the literature.8-28This article highlights research to develop a weather-able powder coating that cures at or below 120°C within 30 min. For specific military applications, this cure sched-ule is dictated by the temperature sensitive nature of 2024-grade aluminum alloy that is used in several types of aircraft parts, weapon systems, and support equipment.Due to the T3 heat treatment, prolonged exposure to tem-peratures above 120°C can compromise the structural in-tegrity of the alloy. I n addition to the low temperature cure target, the final coating must also meet functional re-quirements for corrosion and chemical resistance, adhe-sion, impact strength, and exterior durability. With the help of research and qualification partners representing several military and government agencies, a comprehen-sive list of coating performance specifications and tests was compiled from military specification reports and joint test protocols. An abbreviated summary of the perform-ance criteria is provided in Table1. Only surface quality lacks a quantified specification target at this time.This article presents the results from a benchmark evalu-ation of several state-of-the-art low temperature cure pow-der coatings. Additionally, progress from early efforts to de-velop powder coatings specifically for a 120°C/30 min cure schedule is evaluated against performance targets. EXPERIMENTALMaterials and Test SubstratesAll the materials used in this study, including finished powders and raw materials, were used as received from their manufacturers. In formulation studies, four grades of acid functional polyester resins, denoted A, B, C, and D with corresponding equivalent molecular weights of 1700, 1600, 1630, and 1650, were combined 93:7 with trigly-cidylisocyanurate (TG C) (Araldite PT 810, Huntsman Chemical). Three different catalysts were used in this work: choline chloride (Actiron CC6, Synthron Inc.), and two benzyltrimethylammonium halides (chloride and bromide salts, both from Aldrich Chemical). Two types of corrosion inhibitors were used: zinc phosphate (Halox, Rockwood Pigments), and barium metaborate (Butrol 23, Buckman Laboratories).Chromated aluminum, 2024T3, was the primary sub-strate for this research. For testing coating flexibility, a softer T0 annealed version of the same alloy was used with an anodized surface treatment; this substrate type is spec-ified in MIL-PRF-85285. All aluminum test substrates were obtained from Q-Panel Lab Products. For standardized im-pact testing, untreated 1008 steel panels (R-46, Q-Panel Lab Products) were used.Melt Compounding and Powder GrindingRaw materials were dry-blended by either hand shakingin a bag (one minute) or in a Henschel mechanical mixer(60 sec at 2000 rpm). Each formulation, 4.5 kg in size, wasthen melt-mixed on a 50-mm twin-screw extruder (labmodel Baker Perkins) at 500 rpm with a max barrel tem-perature of 88°C. Extrudate was passed through water-cooled pinch-rolls and collected onto a stainless steel belt;from exit of the extruder, approximately 60 sec was re-quired to reach ambient temperature. Powder grindingwas performed using an air classifying mill, ACM-5, fol-lowed by sieving through a 140 mesh screen. This processproduced powders with a mean size of 40–50 microns(95% < 105 microns) as measured using a Malvern Series2600 laser analyzer.Thermal AnalysisSamples, 15–20 mg in size, were analyzed using aPerkin Elmer DSC 7. The testing protocol utilized anisothermal hold at 120°C for 30 min followed by a rapidquench and then a temperature scan from 25–300°C at10°C/min. Heat of reaction and the corresponding curedpowder percent conversion curve were obtained from theisothermal portion of the test while the cured network Tg and residual heat of reaction were assessed from the fol-low-up scan. Both heats of reaction were used to calculateactual percent conversion at 120°C for 30 min. Coating PreparationPrior to coating, test substrates were cleaned with anMEK wipe. All powders were applied in an ETI Flexicoat®manual powder coating booth using a Nordson SureCoat®cup gun with an applied voltage of 70 kV, application pres-sure of 30 psi, and rinse rate setting of 20 psi. Curing wasperformed in a Blue-M convection oven. For each panel,mean coating thickness and standard deviation were mon-itored based on six measurements using an ElektroPhysikMinitest 4100. After curing, panels were held at ambientconditions for a minimum of 24 hr before testing.G. Merfeld et al.Table 1—Target Performance Specifications for 120°C/30 min Cure Powder CoatingsSpecification* Property Test Units LSL USL Thickness Gauge (eddy current, magnetic induction)mils 2.3 3.2 Adhesion Crosshatch ASTM D 3359-97ASTM scale4B—Flexibility Mandrel bend ASTM D 522-93failure dia. in.—0.25 Toughness Direct impact ASTM D 5420in.-lb150—Hardness Pencil hardness ASTM D 3363pencil #2H—Exterior Durability Xenon arc, 2000 hr ASTM G 26-96delta color—2 Chemical Resistance Skydrol fluid immersion, 7 days delta pencil #—2 MEK double rubs ASTM D 5402double rubs200—Color Match Colorimetry ASTM D 2244delta color—2 Gloss60° gloss ASTM D 523gloss units90—Surface Quality†DOI wavescan, calibrated to PCI standards standard #——Corrosion Resistance Salt fog, ASTM B 117hr to failure2000—SO2 500 hr, ASTM G 85scribe undercut rating7—Cyclic on scribed steel GM 954P cylces to failure80—Filiform ASTM 2803-93in.—0.25 *LSL=Lower Spec Limit; USL=Upper Spec Limit.†Specification not yet defined.Property EvaluationAdhesion testing was performed using a Gardner cross-hatch knife and Permacel®tape in accordance with ASTM D 3359. Flexibility testing followed ASTM D 522 and was performed with a Gardner mandrel bend tester. Direct im-pact strength was tested in accordance with ASTM D 5420 using a Gardner impact tester. Pencil hardness was as-sessed following ASTM D 3363. Solvent resistance was de-termined using the MEK double rub test, ASTM D 5402, with failure report at substrate read-through.SO2and salt fog corrosion tests were performed usingstandard ASTM test methods G 85 and B 117, respec-tively, on both steel and aluminum substrates. Forsalt fog testing, time to failure, assessed as greaterthan 1/8in. undercutting from edge of scribe on coating, up to the test duration of 2000 hr, was re-ported. For SO2testing, performance was reportedas creep after 500 hr of exposure rated on an ASTM scale. A failure rating of 6 corresponds to undercut-ting from edge of scribe by more than 1/16in.For accelerated weathering, an Atlas Ci35a Xenon Weather-Ometer®was used. To assess performance, color coordinates were measured as a function of ex-posure using a Macbeth Colorimeter (Color-Eye 7000A) following ASTM D 2244. The ΔE color change is reported after 2000 hr of exposure.Gloss was measured at 60° using a BYK Gardner Tri-Gloss Meter. Coating surface quality was deter-ness of image (DOI) instrument calibrated relative to the Powder Coatingquality standards. Results are reported in PCI units ranging from 1–10, with 10 corresponding to the best quality. In samples where gloss was inadequate to allow for use of the Wavescan, visual assessments were made by side-by-side comparison to the sur-face quality standards.RESULTS AND DISCUSSIONCommercial Low Temperature Cure PerformanceTo assess current state-of-the-art technology in low temperature cure powder coatings, product literature,websites, and technical support from many commercialmanufacturers were consulted. Several best-in-class lowtemperature curing powders were sampled from each ofthe major conventional chemistries including acrylate,epoxy, urethane, and polyester crosslinked using eithertriglycidylisocyanurate (TG C) or hydroxyalkylamide(HAA). For each of the five chemistry families, differential Corrosion Protection Powder Coatings for Temperature Sensitive SubstratesTable 2—Commercial Low Temperature Cure Powder Coating PerformanceProperty Test PE/TGIC PE/HAA Urethane Epoxy Acrylate Cure Schedule*—148°C154°C177°C121°C148°C20 min30 min20 min15 min15 min Adhesion Crosshatch5B4B–5B5B5B5B Flexibility Mandrel bend0.12510.1250.1250.125 Toughness Direct impact20201002020 Hardness Pencil hardness H HB HB HB H Chem. Resist.MEK double rub184806220067 Durability Xenon arc0.5 5.60.6 2.8—Surface Quality†PCI standard45448 Corrosion Resistance Salt fog (AL)>2000>2000>2000>2000>2000 Salt fog (Steel)<1576<1081<1576<2085<674SO2 (AL)88555SO2(Steel)910956*Manufacturer recommended lowest temperature cure schedule.Shaded responses indicate failure relative to performance requirements provided in Table1.†Specification not defined.Figure 1—Star plot showing property tradeoffs for selected powder coatings pre-pared at their manufacturer’s lowest recommended cure schedule. Responseshave been normalized from 0 to 1, with 1 corresponding to the best possibleperformance. Specification targets are included for reference.scanning calorimetry (DSC) scans at 10°C/min were used to down-select the fastest low temperature reaction kinet-ics based on onset and peak exotherm temperatures. The down-selected powders were then applied and cured as nominally 3-mil thick powder coatings according to their respective manufacturer’s lowest recommended cure schedule and evaluated.Key performance attributes for each coating are summa-rized in Table2. These were evaluated using the correspon-ding test methodologies indicated in Table1. The cure schedule used for each coating is also provided in Table2. Responses that fail to meet Table1 performance criteria have been shaded dark. Overall, there are tradeoffs among the chemistries, and clearly no solution meets all cure and performance expectations. When selected powders were prepared closer to their manufacturer’s standard cure con-ditions, coating performance improved, most notably chemical resistance. For example, the resistance to MEK double rubs increased to the test limit of 200 for the PE/TGIC and PE/HAA coatings, and to 175 for the acrylate. These results underscore the challenge of designing a pow-der coating that can effectively crosslink at 120°C within 30 min and simultaneously meet the performance goals of this research effort. This is further emphasized by the plot in Figure1, which simultaneously compares each of the five candidate coatings relative to select specification targets.Many low temperature curing limitations identified in Table2 can be linked to the nature of the crosslinking mech-anism or the base resin chemistry.29The acid/hydroxyl reac-tion is the least reactive mechanism represented. Its curing temperature is limited by the nature of the esterification re-action and the need to drive off water to obtain high con-versions. HAA crosslinkers rely on this scheme. Slightly lower temperatures can be used to cure hydroxyl functional resins with protected or dimerized isocyanates to yield ure-thane coatings. However, the deblocking temperatures ofthe protective group or the ring-opening kinetics of the uretidionelimit the minimum cure temperatureto approximately 140°C.30,31The other three coatings chem-istries, PE/TGI C, epoxy, and acry-late, are all based on epoxy type re-actions. These have the greatestpotential for low temperature cure.Epoxies can crosslink with a varietyof different chemical functionali-ties, such as acids, aromatic hydrox-yls, amines, or even through cat-alyzed homopolymerization.32Useof bisphenol-A (BPA) and novolac-modified epoxies is effectively restricted to interior appli-cations because of their poor weathering attributes. Poor exterior durability is evident in the epoxy coating in Table 3.29Cycloaliphatic epoxies do not suffer from the ultravi-olet light instability of the aromatics, but resins suitable for powder coatings are unavailable.For exterior applications, acrylate resins functionalized with epoxy moieties such as glycidyl methacrylate are in-creasingly finding use. They offer excellent exterior dura-bility and scratch resistance, but many times this comes at the price of poor chemical resistance and brittleness. Acid functional polyesters are often combined with multifunc-tional epoxy crosslinkers, most commonly TGIC, to deliver both low temperature cure kinetics and exterior durability. Despite concerns about the potential toxicity of TGI C, there are no commercial alternatives that offer similar per-formance. Of the commercially available resins, PE/TGI C chemistry offers the best opportunity to develop 120°C cure, exterior powder coatings with the properties outlined in Table1. The next section presents development efforts toward achieving the low temperature cure and coating performance goals building on PE/TGIC chemistries. Resin Screening StudyFour different commercial acid functional polyester resins were sampled from their manufacturers as candi-dates for low temperature curing powder coatings. These were incorporated into the general factorial screening study illustrated in Figure 2wherein each of the four resins, combined 93/7 with TGI C crosslinker, were formulated with two different corrosion inhibitors, either zinc phos-phate or barium metaborate, and a choline chloride cata-lyst at levels of 0, 0.3, or 0.5 percent of total formulation. Details on the powder formulations are given in Table3. Sample panels of each of the 24 powder coatings produced in this design were prepared by curing at 120°C for 30 min.For the sake of rapid screening, the complete perform-ance specification list was pared down to eight key per-formance attributes that include: adhesion, flexibility, toughness, hardness, chemical resistance, gloss, and sur-face quality. The corresponding tests for these are indi-cated in Table1 and the screening results are summarized in Table4. All test coatings met the 2.3–3.2 mil thickness specification.At a high level, the results in Table4 showed a signifi-cant effect of resin type on coating performance with resinG. Merfeld et al.Table 3—Powder Coating Formulations Used in Resin Screening ExperimentsFormulation NumberComponent123456 Acid polyester65.065.065.065.065.065.0 TGIC 4.9 4.9 4.9 4.9 4.9 4.9 Curing catalyst0.00.30.50.00.30.5 Flow promoter 1.5 1.5 1.5 1.5 1.5 1.5 Degassing agent0.50.50.50.50.50.5 Antioxiant 1.0 1.0 1.0 1.0 1.0 1.0 Zinc phosphate 5.0 4.7 4.50.00.00.0 Barium metaborate0.00.00.0 5.0 4.7 4.5 Filler & pigment22.122.122.122.122.122.1 Totals100100100100100100 Figure 2—Experimental design for resin screening study. Twenty-fourpowder coatings were developed and evaluated using commercial acidfunctional polyester resins.D systems, and in particular formulations D-2 and D-3,meeting the greatest number of the key performance pared to resin systems A and B, systems C and D of-fered simultaneous improvements in flexibility and chem-ical resistance, but, depending on corrosion inhibitor type,suffered slight to moderate reductions in gloss. Irrespective of resin system, use of barium metaborate appears to ad-versely affect gloss, especially at higher catalyst loadings.Within the resin D formulations, those with zinc phos-phate and added catalyst outperformed analogous formu-lations with barium metaborate, particularly in chemical resistance. Across all formulations investigated, including the best overall performers, the most severe deficiency was seen in direct impact toughness with values well below the 150 in.-lb goal. These results emphasize the strong effect of component interactions and the potential for competing tradeoffs between per-formance attributes.Many of the impor-tant factors that likely differentiate these four resins such as chemical structure, molecular weight, functionality,polydispersity, as well as type and level of pre-catalysis were not pro-vided by their manufac-turers. Without this information it is diffi-cult to draw correla-tions between chem-istry and performance.I t is possible, however,to compare the reaction kinetics of the four resin systems to learn more about their differ-ences and how these might affect coating performance.Figure 3 is a compila-tion of plots for DSC-measured heat evolu-tion as a function of time at 120°C for the four resin sys-tems. Without catalyst addition (formulations 1 and 4 in each resin series), both the reaction rate and total evolvedheat were strongly dependent on the base resin. This wasnot unexpected as manufacturers commonly precatalyze their resins. The results in Figure 3 suggest resins A and B were less precatalyzed than resins C and D. In fact, with-out additional catalyst, resin A did not show any apprecia-ble reaction at 120°C, whereas added catalyst had little ef-fect on the total heat of reaction for resins C and D with average values of approximately 22 and 15 J/g, respec-tively. The lesser precatalyzed resins, A and B, showed the greatest increase in reaction rate and total exotherm with catalyst addition. I n these same systems, corrosion in-hibitor selection had a notable effect on reaction kinetics;relative to formulations with zinc phosphate, use of bar-Corrosion Protection Powder Coatings for Temperature Sensitive SubstratesTable 4—Resin Screening SummaryResin AResin BResin CResin DNF = No FailureShaded responses indicate failure relative to performance requirements.Figure 3—Heat of reaction at 120°C versus reaction time for resin screening formulations. Legends indicate corre-sponding formulation numbers provided in Table 4. Note that formulations A-1 and A-4 show no heat of reaction.ium metaborate is associated with a faster reaction rate and higher total heat of reaction. This is consistent with the overall reduction in gloss observed with barium metaborate. Moreover, barium metaborate with the highly precatalyzed resin D may have over-accelerated the reaction producing network heterogeneity and caused a drop in chemical resistance.Using follow-up DSC scans, reaction conversion not re-alized after 30 min at 120°C was measured for each of the 24 resin screening formulations. It should be noted that the crosslinked coatings made in this work have glass transition temperatures between 50 and 60°C, and thus, at the 120°C cure condition vitrification should not limit reaction conversion. The recovered residual heat of reac-tion was added to the 120°C exotherm to calculate a total potential heat of reaction. Figure4 shows the results of this analysis. Inspection of the data shows that for resins A and B, only certain combinations of catalyst and corro-sion inhibitor yielded complete reaction conversion; whereas for resins C and D, complete reaction conversion was attained in all formulations. For the most part, the to-tal potential heat of reaction was unaffected by formula-tion changes. Exceptions of note occurred in resins B and D. Barium metaborate alone or the combination of zinc phosphate and choline chloride both acted to lower the total potential heat of reaction in resin B by about 35%.I n resin D, a choline chloride loading of 0.5% caused a 20% reduction in the total potential heat of reaction. This observation may be indicative of undesirable prereaction during processing that could have the effect of lowering the measurable exotherm.Increased CatalystHigher catalyst loadings of 0.6 and 0.75% were inves-tigated in resins C and D using only the zinc phosphate corrosion inhibitor. Adhesion and flexibility were unaf-fected by the increased catalyst levels while hardness, gloss, and surface quality showed slight formulation spe-cific changes. The lone exception was in resin D with 0.75% catalyst where both pencil hardness and gloss dropped significantly to values of F and 55, respectively.Combined with earlier results, direct impact and chem-ical resistance are plotted as a function of catalyst level in Figure5. Resin system C was relatively unaffected by cata-lyst loading, suggesting that this commercial resin was al-ready highly catalyzed. A more pronounced effect was ev-ident in resin D where chemical resistance was improved to the test limit of 200 double rubs with 0.3 and 0.5% cat-alyst but dropped off at 0.6%, while impact values simul-taneously increased to the test limit of 160 in.-lb. A trade-off in chemical resistance and impact is not unusual, butG. Merfeld et al.Figure 4—Heat evolved at 120°C in 30 min (white bars) and total potential heat of reaction (black bars) for resin screen-ing formulations. The total potential was estimated by adding the residual heat recovered in a second scan to the heatevolved at 120°C. The numbers below each set of bars correspond to Table4 formulations. Note that formulations A-1and A-4 show no heat of reaction at 120°C within 30 min.Figure 5—Direct impact (solid lines) and chemical resistance (dashedlines) versus catalyst loading in resin systems C (triangles) and D(squares) using zinc phospate corrosion inhibitor.Corrosion Protection Powder Coatings for Temperature Sensitive Substratesit is surprising that this occurred at higher catalyst load-ings. Normally, increasing crosslink density improves chemical resistance and penalizes impact resistance. Partial reaction during processing could lead to gel parti-cles and heterogeneous crosslinking of the coating film. This might explain the reduced solvent resistance and im-proved impact results at the highest catalyst loadings. Catalyst TypeTo this point, only choline chloride has been consid-ered as the added catalyst in coating formulations. Many other candidates exist for the acid/epoxy reaction and several of these have been screened in our laboratory specifically for rapid cure kinetics at 120°C, latency at 93°C melt processing, and minimal yellowing under 160°C over bake conditions.33In addition to the choline chloride, our work has identified promise in two ben-zyltrimethylammonium salts based on either bromide (BTMA-Br) or chloride (BTMA-Cl) counter ions.As an extension to the present study, BTMA-Br and BTMA-Cl, along with choline chloride, were screened in formulations based on resin D with either zinc phos-phate or barium metaborate corrosion inhibitors. Two catalyst levels were considered, 0.5 and 0.75%. These lev-els were chosen to capture the low and high extremes of the potential formulation space. In a first pass at the for-mulation design, a higher catalyst level of 1.0% was se-lected, but screening tests found gel formation during extrusion, so the level was lowered to 0.75%. The per-formance of coatings prepared in this study is summa-rized in Table5, with shading again used to denote below target performance.Relative to noncatalyzed controls (blends D-1 and D-4 in Table4), good flexibility and hardness were generally realized across the formulations summarized in Table5, and in several formulations considerable improvements in toughness were made. At the same time, gloss, surface quality, and chemical resistance were compromised; the effect was more significant in the most highly catalyzed formulations. The limited exceptions were the combina-tions of zinc phosphate and BTMA-Cl, which showed slightly enhanced chemical resistance. I n four of the six formulations, the higher catalyst level actually caused a reduction in DSC measured heat of reaction at 120°C in 30 min. Prereaction during melt compounding is the most probable cause.The Table5 formulations based on low-level (0.5%) choline chloride with either corrosion inhibitor represent formulation replicates of chemistries studied in the resin screening study, specifically formulations D-3 and D-6 in Table4. Similarly, an analogue to the high-level (0.75%) choline chloride with zinc phosphate formulation in Table 5 was previously examined in the increased catalyst study. Even though the noted formulations are the same, pro-cessing changes were made between the earlier and later studies. Specifically, hand mixing of components was used in the resin screening and increased catalyst work, whereas more intense machine (Henschel) mixing was used in the catalyst screening study. Comparing 0.5% ana-logue formulations, the more aggressively mixed versions showed significant improvements in impact resistance and simultaneous reductions in chemical resistance. This is similar to the effect observed in Figure4 with an increase in the catalyst loading to the highest levels. It is reason-able to suspect that improved reagent mixing increased reagent homogeneity and, thereby, catalyst efficiency. Further building in this direction, a comparison of 0.75% analogues reveals a precipitous drop in both toughness and chemical resistance in the more intensely mixed cat-alyst screening formulation. This suggests an upper limit where over-catalysis is systemically detrimental. Even be-low this limit, the lack of processing robustness of highly catalyzed formulations may challenge their viability. CONCLUSIONSAs a benchmark for this research, several commercial low temperature cure powder coatings, including candi-dates representative of all the major coating chemistries, were sampled and tested. The results highlight tradeoffsTable 5—Catalyst Screening Study(a)Catalysts: benzltrimethylammonium chloride (BMTA-Cl) and bromide (BTMA-Br), Choline Chloride Catalyst Levels: Low –0.5, High –0.75 pph.(b)NF = No Failure.Shaded responses indicate failure relative to performance requirements.。