SM2250 Product Brief
Moxa NPort W2150A W2250A Series 说明书

P/N: 1802021503014 *1802021503014*NPort W2150A/W2250A SeriesQuick Installation GuideEdition 6.1, September 2017Technical Support Contact Information/supportMoxa Americas:Toll-free: 1-888-669-2872 Tel: 1-714-528-6777 Fax: 1-714-528-6778 Moxa China (Shanghai office): Toll-free: 800-820-5036 Tel: +86-21-5258-9955 Fax: +86-21-5258-5505 Moxa Europe:Tel: +49-89-3 70 03 99-0 Fax: +49-89-3 70 03 99-99 Moxa Asia-Pacific:Tel: +886-2-8919-1230 Fax: +886-2-8919-1231 Moxa India:Tel: +91-80-4172-9088 Fax: +91-80-4132-10452017 Moxa Inc. All rights reserved.OverviewThe NPort W2150A/W2250A wireless device servers are an ideal choice for connecting serial devices or Ethernet devices, including PLCs, meters, and sensors, to an IP-based wireless LAN or Ethernet LAN. Features•Link any serial device to an IEEE 802.11a/b/g/n network• 1 and 2-port RS-232/422/485 models, up to 921.6 kbps•Web-based configuration over Ethernet or wireless LAN •Enhanced security for remote configuration with HTTPS, SSH •Secure data access with WEP, WPA, WPA2•Fast roaming when signal strength is weak•Wireless Client: data can be seamlessly transferred between serial line, LAN, and WLAN•Per-port offline port buffering and serial data log•Dual power inputs via a power jack and terminal block Package ChecklistBefore installing the NPort W2150A/W2250A device server, verify that the package contains the following items:• 1 NPort W2150A or NPort W2250A wireless device server• 1 antenna 2.4/5GHz: ANT-WDB-ARM-02•100 to 240 VAC power adapter (excluding T models)*• 1 Ethernet cable: CBL-RJ458P-100•Documentation and software CD•Quick installation guide (printed)•Warranty cardNOTE The power adapter is suitable for your region.Optional Accessories•DK-35A (35 mm DIN-rail mounting kit)•CBL-PJ21NOPEN-BK-30: Locking barrel plug to bare-wires cable •Mini DB9F-to-TB: DB9-female-to-terminal-block adapter for RS-422/485 applicationsNOTE Notify your sales representative if any of the above items are missing or damaged.Hardware IntroductionThe NPort W2150A models have one serial port; the NPort W2250A models have two serial ports. Both models support RS-232/422/485 operation with DB9 connectors and include one 10/100M Ethernet port.NPort W2150A/W2150A-TNPort W2250A/W2250A-TReset Button : The reset button is used to load the factory default settings. Use a pointed object to hold the reset button down for five seconds to load the factory defaults.NameColor FunctionEnd Panel LED IndicatorsEthernet Orange 10 Mbps Ethernet connectionGreen 100 Mbps Ethernet connectionOff Ethernet cable is disconnectedTop Panel LED IndicatorsReady Red Steady on:Power is on and the NPort is booting upBlinking: An IP conflict exists or the DHCP/BOOTPserver did not respond properlyGreen Steady on: The NPort is functioning normallyBlinking: The NPort is responding to LocatefunctionOff Power is off or a power error condition existsName Color FunctionWLAN GreenSteady on: Wireless enabledBlinking: The NPort can’t establish a WLANconnection with AP (Infrastructure) orstation (Ad-Hoc)Off Wireless not enabledSerial 1 Orange The serial port is receiving dataName Color FunctionSerial 2Green The serial port is transmitting data Off No data is flowing to or from the serial portSignal StrengthRed1 Red -The signal strength (RSSI) is lower than -94 dBm2 Red - The signal strength (RSSI) is between-94 to -87 dBmGreen3 Green - The signal strength (RSSI) is between-87 to -79 dBm4 Green - The signal strength (RSSI) is between-79 to -68 dBm5 Green - the signal strength (RSSI) is between-68 to -46 dBmPull-High/Low Resistors and Terminal Resistor for RS-422/485You may need to set the pull-high/low resistors whentermination resistors are used in certain RS-422 or RS-485 environments.S2(Serial 1) S3(Serial 2) DIP 1 DIP 2 DIP 3DIP 4 Pull-high Resistor Pull-low Resistor Terminal Resistor ReservedON1 kΩ 1 kΩ 120 Ω – OFF (Default)150 kΩ150 kΩN/A–S3 is for the NPort W2250A only.NOTE Do not use the 1 kΩ setting while in RS -232 mode. Doing so will degrade the RS-232 signals and reduce the effective communication distance.First-Time Hardware InstallationSTEP 1: After removing the NPort W2150A/W2250A from the box, usea crossover Ethernet cable to connect the NPort’s RJ45Ethernet port directly to your computer’s Ethernet port. STEP 2: Attach the power adapter to the NPort and then plug the adapter into an electrical outlet.STEP 3: Configure the NPort W2150A/W2250A through the Ethernet port. See the next section on how to install software. NOTE You must connect the Ethernet cable first before powering up your NPortSoftware Installation InformationInsert the Documentation and software CD into your PC. A window should open with several options displayed:•Click [Install COM Driver] and follow the on-screen instructions to install the COM drivers.•Click [Documents] and select NPort W2150A/W2250A Series User’s Manual to view the user’s manual.•Click [Install UTILITY] and follow the on-screen instructions to install the NPort Search Utility. This utility can be used to search for NPort W2150A/W2250A units on the network.Setting the IP AddressThe factory default IP settings are assigned as follows:LAN: Static; IP = 192.168.126.254; netmask = 255.255.255.0 WLAN: Static; IP = 192.168.127.254; netmask = 255.255.255.0If the NPort is configured for DHCP, but the DHCP server cannot be found, then the NPort will use the factory default IP settings.NOTE If you have forgotten the NPort’s IP address, use the NPort Search Utility from your PC to locate the NPort. After searchingthe LAN for NPort units, the NPort Search Utility will display the IPaddress of each unit.NOTE Ethernet Bridge Disabled (default): Only one network interface can be active at a time. If the Ethernet link is active, theWLAN will be inactive. If the WLAN is active, the Ethernet link willbe inactive.Ethernet Bridge Enabled: The LAN and WLAN will both beactive. Go to the web console, find the network settings page,and set Ethernet Bridge to Enabled.Open the web console to make configuration changes as follows: STEP 1: Open your web browser.STEP 2: In the address bar, enter 192.168.126.254 (the default IPaddress).STEP 3: The server will ask for the username and password before you log in. To configure the device server, you may use the defaultuser/default password "admin"/"moxa" to log in the webconsole.STEP 4: For first-time use, click the Wizard in the left navigation panel.The wizard will prompt you to configure the IP address, SSID,and security mode. For other settings, use the factory defaultsor modify the settings for your application.Pin Assignments and Cable WiringPin RS-232RS-422,4w RS-4852w RS-4851 DCD TxD-(A) –2 RXD TxD+(B) –3 TXD RxD+(B) Data+(B)4 DTR RxD-(A) Data-(A)5 GND GND GND6 DSR – –7 RTS – –8 CTS – –9 – ––SpecificationsPower RequirementsPower Input 12 to 48 VDCPower Consumption NPort W2150A: 179 mA @ 12 VDCNPort W2250A: 200 mA @ 12 VDCPower Connector Screw-type power jack and terminal block Physical CharacteristicsMaterial Aluminum sheet metal (1 mm) Dimensions 77 × 111 × 26 mm (no ears, no antenna)100 × 111 × 26 mm (with ears, no antenna) Antenna Length 109 mmMagnetic Isolation 1.5 kV magnetic isolation built in Environmental LimitsOperating TemperatureStandard Models: Wide Temp. Models: 0 to 55°C (32 to 131°F), 5 to 95%RH-40 to 75°C (-40 to 167°F), 5 to 95%RHStorage Temperature -40 to 85°C (-40 to 185°F), 5 to 95%RH Regulatory ApprovalsEMC CE: EN 55032 Class A/EN 55024ETSI EN 301 489-17,ETSI EN 301 489-1FCC: FCC Part 17 Subpart B, Class AFCC Part 15 Subpart B, Class A Safety UL: UL 60950-1LVD: EN 60950-1DSPR: ARIB-STD 33, ARIB-STD 66。
智能保电器:三利特斯普SMX2200XLRT2U说明书
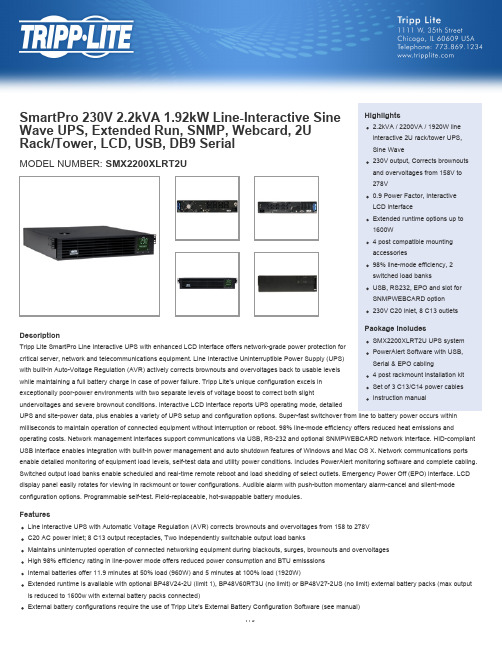
SmartPro 230V 2.2kVA 1.92kW Line-Interactive Sine Wave UPS, Extended Run, SNMP, Webcard, 2U Rack/Tower, LCD, USB, DB9 Serial Highlights2.2kVA / 2200VA / 1920W lineinteractive 2U rack/tower UPS, Sine WaveHot-swappable, user-replaceable internal batteries and external battery packs can be replaced with no disruption to connected equipmentFront panel LCD monitoring screen with MODE and ENTER buttons reports operating mode with 5-bar battery charge graphic, plus 7 selectable screens of detailed UPS and site power informationLCD interface also supports a number of advanced user setup and operating preferencesShips with 4 post rackmount installation hardware; Optional 2POSTRMKITWM enables 2 post rackmount/wallmount installation; Optional 2-9USTAND enables tower placementBuilt-in USB, RS-232 and optional SNMPWEBCARD accessory monitoring optionsHID-compliant USB interface enables integration with built-in power management and auto shutdown features of Windows and Mac OS XIncluded PowerAlert UPS monitoring software; Built-in Emergency Power Off (EPO) interface with cableOptional PDUBHV20 bypass PDU enables hot-swappable UPS replacement with no disruption to connected equipment SpecificationsOUTPUTOutput Volt Amp Capacity (VA)2200Output kVA Capacity (kVA) 2.2Output Watt Capacity (Watts)1920Output kW Capacity (kW) 1.92Nominal Output Voltage(s)220V; 230V; 240VSupportedNominal Voltage Details230V inverter output in battery modeFrequency Compatibility50 / 60 HzOutput Voltage Regulation (Line-15%, +6%Mode)Output Voltage Regulation (Battery+/- 5%Mode)Output Receptacles(8) C13Included Output Power Cables Includes 3 C13 to C14 output power cablesLoad Management Receptacles Two switchable single-outlet C13 load banksHot-Swap PDU options PDUBHV20 (2U / 6 C13, 2 C19 outlets)Output AC Waveform (AC Mode)Sine waveOutput AC Waveform (Battery Mode)Pure Sine waveINPUTRated input current (Maximum Load)10.7ANominal Input Voltage(s) Supported230V ACUPS Input Connection Type C20 inletUPS Input Connection Description IEC320-C20 input connection accepts a variety of detachable cordsets to match country or site-specific wallreceptaclesInput Circuit Breakers15AInput Phase Single-PhaseBATTERYFull Load Runtime (min.) 5 min. (1920w)Half Load Runtime (min.)11.9 min. (960w)Expandable Battery Runtime Extended runtime supported via optional external battery packsExternal Battery Pack Compatibility BP48V24-2U (limit 1); BP48V60RT-3U (multi-pack compatible); BP48V27-2US (multi-pack compatible)DC System Voltage (VDC)48Battery Recharge Rate (IncludedBatteries)Less than 4.5 hours from 10% to 90% (typical, full load discharge)Internal UPS Replacement BatteryCartridgeRBC94-2UBattery Access Front panel battery access doorBattery Replacement Description Hot-swappable, user replaceable batteriesVOLTAGE REGULATIONVoltage Regulation Description Automatic voltage regulation (AVR) maintains line power operation with an input voltage range of 158 to 278 Overvoltage Correction Voltage reduction of 12% applies when input is between 244-278VUndervoltage Correction Voltage boost of 12% applies when input voltage is between 183-206VSevere Undervoltage Correction Voltage boost of 24% applies when input voltage is between 158-182VLEDS ALARMS & SWITCHESFront Panel LCD Display Front panel LCD information and configuration screen offers detailed UPS and site power status and operating data, plus configuration of voltage, operating mode, alarm function and a variety of additional options (see manual for detailed LCD configuration and monitoring options)Audible Alarm Audible alarm indicates UPS startup, power-failure, low-battery, overload, UPS fault and remote shutdown conditionsAlarm Cancel Operation Power-fail alarm can be temporarily silenced using alarm-cancel switch; silent mode alarm configuration optionavailableSwitches 3 pushbutton switches control OFF / ON power status, MODE selection and MUTE / ENTER control functions SURGE / NOISE SUPPRESSIONUPS AC Suppression Joule Rating350UPS AC Suppression ResponseTimeInstantaneousEMI / RFI AC Noise Suppression YesPHYSICALIncluded Mounting AccessoryDescription4 post rackmount installation accessories includedInstallation Form Factors Supported2 post rackmount (2POSTRMKITWM); Wallmount (2POSTRMKITWM); Tower (2-9USTAND) with Optional AccessoriesPrimary Form Factor RackmountUPS Power Module Dimensions3.5 x 17.5 x 19.5(hwd, in.)UPS Power Module Dimensions8.9 x 44.4 x 49.5(hwd, cm)Rack Height (U Spaces)2UPS Power Module Weight (lbs.)68.75UPS Power Module Weight (kg)31.2UPS Shipping Dimensions (hwd / in.)9.25 x 24.75 x 22.5UPS Shipping Dimensions (hwd /23.5 x 62.9 x 57.2cm)Shipping Weight (lbs.)82.3Shipping Weight (kg)37.3Cooling Method FanUPS Housing Material SteelENVIRONMENTALOperating Temperature Range+32 to +104 degrees Fahrenheit / 0 to +40 degrees CelsiusStorage Temperature Range+5 to +122 degrees Fahrenheit / -15 to +50 degrees CelsiusRelative Humidity0 to 95%, non-condensingAC Mode BTU / Hr. (Full Load)161AC Mode Efficiency Rating (100%98%Load)COMMUNICATIONSCommunications Interface USB (HID enabled); DB9 Serial; EPO (emergency power off); Slot for SNMP/Web interfaceNetwork Monitoring Port Description Supports detailed monitoring of UPS and site power conditionsPowerAlert Software IncludedCommunications Cable USB, DB9 and EPO cabling includedWatchDog Compatibility Supports Watchdog application, OS and hard-reboot restart options for remote applications LINE / BATTERY TRANSFERTransfer Time 6 ms. (AC to DC) / 1 ms. (DC to AC)Low Voltage Transfer to Battery158VPower (Setpoint)High Voltage Transfer to Battery278VPower (Setpoint)SPECIAL FEATURESGrounding Lug Back panel grounding lugCold Start (Startup in Battery ModeCold-start operation supportedDuring a Power Failure)High Availability UPS Features Hot swappable batteriesGreen Energy-Saving Features Greater than 95% efficiency - GREEN UPS; Individually controllable load banksCERTIFICATIONSUPS Certifications CEUPS Certification Details IEC 62040-1, IEC 62040-2 Class A EMI, GOSTWARRANTYProduct Warranty Period2-year limited warranty(International)Product Warranty Period (Mexico)2-year limited warrantyProduct Warranty Period (Puerto2-year limited warrantyRico)© 2015 Tripp Lite. All rights reserved. All trademarks are the sole property of their respective owners. Tripp Lite has a policy of continuous improvement. Specifications are subject to change without notice. Photos may differ slightly from final products.。
微斯米微波式芯片公司2014年产品说明书
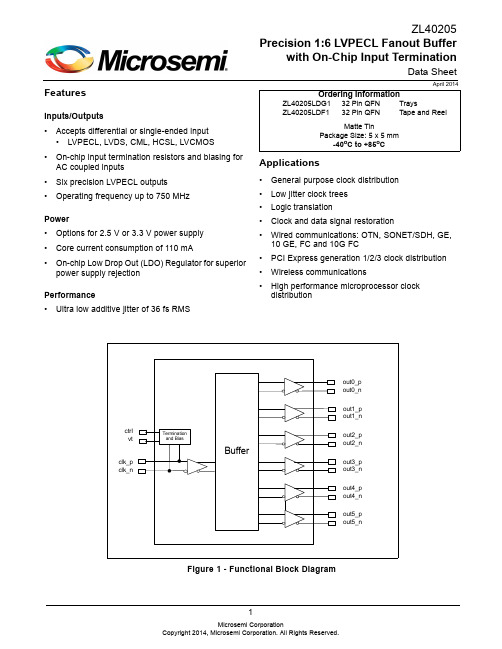
1FeaturesInputs/Outputs •Accepts differential or single-ended input •LVPECL, LVDS, CML, HCSL, LVCMOS •On-chip input termination resistors and biasing for AC coupled inputs•Six precision LVPECL outputs •Operating frequency up to 750 MHzPower •Options for 2.5 V or 3.3 V power supply •Core current consumption of 110 mA•On-chip Low Drop Out (LDO) Regulator for superior power supply rejectionPerformance •Ultra low additive jitter of 36 fs RMSApplications•General purpose clock distribution •Low jitter clock trees •Logic translation•Clock and data signal restoration•Wired communications: OTN, SONET/SDH, GE,10 GE, FC and 10G FC•PCI Express generation 1/2/3 clock distribution •Wireless communications•High performance microprocessor clock distributionApril 2014Figure 1 - Functional Block DiagramZL40205Precision 1:6 LVPECL Fanout Bufferwith On-Chip Input TerminationData SheetOrdering InformationZL40205LDG1 32 Pin QFN TraysZL40205LDF132 Pin QFNTape and ReelMatte TinPackage Size: 5 x 5 mm-40o C to +85o CTable of ContentsFeatures . . . . . . . . . . . . . . . . . . . . . . . . . . . . . . . . . . . . . . . . . . . . . . . . . . . . . . . . . . . . . . . . . . . . . . . . . . . . . . . . . 1 Inputs/Outputs . . . . . . . . . . . . . . . . . . . . . . . . . . . . . . . . . . . . . . . . . . . . . . . . . . . . . . . . . . . . . . . . . . . . . . . . .1 Power . . . . . . . . . . . . . . . . . . . . . . . . . . . . . . . . . . . . . . . . . . . . . . . . . . . . . . . . . . . . . . . . . . . . . . . . . . . . . . . .1 Performance . . . . . . . . . . . . . . . . . . . . . . . . . . . . . . . . . . . . . . . . . . . . . . . . . . . . . . . . . . . . . . . . . . . . . . . . . . .1 Applications . . . . . . . . . . . . . . . . . . . . . . . . . . . . . . . . . . . . . . . . . . . . . . . . . . . . . . . . . . . . . . . . . . . . . . . . . . . . . 1 Change Summary . . . . . . . . . . . . . . . . . . . . . . . . . . . . . . . . . . . . . . . . . . . . . . . . . . . . . . . . . . . . . . . . . . . . . . . . . 41.0 Package Description . . . . . . . . . . . . . . . . . . . . . . . . . . . . . . . . . . . . . . . . . . . . . . . . . . . . . . . . . . . . . . . . . . . .52.0 Pin Description. . . . . . . . . . . . . . . . . . . . . . . . . . . . . . . . . . . . . . . . . . . . . . . . . . . . . . . . . . . . . . . . . . . . . . . . .63.0 Functional Description . . . . . . . . . . . . . . . . . . . . . . . . . . . . . . . . . . . . . . . . . . . . . . . . . . . . . . . . . . . . . . . . . .73.1 Clock Inputs. . . . . . . . . . . . . . . . . . . . . . . . . . . . . . . . . . . . . . . . . . . . . . . . . . . . . . . . . . . . . . . . . . . . . . . . .73.2 Clock Outputs . . . . . . . . . . . . . . . . . . . . . . . . . . . . . . . . . . . . . . . . . . . . . . . . . . . . . . . . . . . . . . . . . . . . . .123.3 Device Additive Jitter. . . . . . . . . . . . . . . . . . . . . . . . . . . . . . . . . . . . . . . . . . . . . . . . . . . . . . . . . . . . . . . . .153.4 Power Supply . . . . . . . . . . . . . . . . . . . . . . . . . . . . . . . . . . . . . . . . . . . . . . . . . . . . . . . . . . . . . . . . . . . . . .163.4.1 Sensitivity to power supply noise. . . . . . . . . . . . . . . . . . . . . . . . . . . . . . . . . . . . . . . . . . . . . . . . . . .163.4.2 Power supply filtering. . . . . . . . . . . . . . . . . . . . . . . . . . . . . . . . . . . . . . . . . . . . . . . . . . . . . . . . . . . .163.4.3 PCB layout considerations. . . . . . . . . . . . . . . . . . . . . . . . . . . . . . . . . . . . . . . . . . . . . . . . . . . . . . . .164.0 AC and DC Electrical Characteristics . . . . . . . . . . . . . . . . . . . . . . . . . . . . . . . . . . . . . . . . . . . . . . . . . . . . .175.0 Performance Characterization . . . . . . . . . . . . . . . . . . . . . . . . . . . . . . . . . . . . . . . . . . . . . . . . . . . . . . . . . . .206.0 Typical Behavior . . . . . . . . . . . . . . . . . . . . . . . . . . . . . . . . . . . . . . . . . . . . . . . . . . . . . . . . . . . . . . . . . . . . . .217.0 Package Characteristics . . . . . . . . . . . . . . . . . . . . . . . . . . . . . . . . . . . . . . . . . . . . . . . . . . . . . . . . . . . . . . .238.0 Mechanical Drawing . . . . . . . . . . . . . . . . . . . . . . . . . . . . . . . . . . . . . . . . . . . . . . . . . . . . . . . . . . . . . . . . . . .24List of FiguresFigure 1 - Functional Block Diagram . . . . . . . . . . . . . . . . . . . . . . . . . . . . . . . . . . . . . . . . . . . . . . . . . . . . . . . . . . . . 1 Figure 2 - Pin Connections . . . . . . . . . . . . . . . . . . . . . . . . . . . . . . . . . . . . . . . . . . . . . . . . . . . . . . . . . . . . . . . . . . . 5 Figure 3 - Simplified Diagram of Input Stage. . . . . . . . . . . . . . . . . . . . . . . . . . . . . . . . . . . . . . . . . . . . . . . . . . . . . . 7 Figure 4 - Clock Input - LVPECL - DC Coupled. . . . . . . . . . . . . . . . . . . . . . . . . . . . . . . . . . . . . . . . . . . . . . . . . . . . 8 Figure 5 - Clock Input - LVPECL - AC Coupled. . . . . . . . . . . . . . . . . . . . . . . . . . . . . . . . . . . . . . . . . . . . . . . . . . . . 8 Figure 6 - Clock Input - LVDS - DC Coupled . . . . . . . . . . . . . . . . . . . . . . . . . . . . . . . . . . . . . . . . . . . . . . . . . . . . . . 9 Figure 7 - Clock Input - LVDS - AC Coupled . . . . . . . . . . . . . . . . . . . . . . . . . . . . . . . . . . . . . . . . . . . . . . . . . . . . . . 9 Figure 8 - Clock Input - CML- AC Coupled . . . . . . . . . . . . . . . . . . . . . . . . . . . . . . . . . . . . . . . . . . . . . . . . . . . . . . 10 Figure 9 - Clock Input - HCSL- AC Coupled . . . . . . . . . . . . . . . . . . . . . . . . . . . . . . . . . . . . . . . . . . . . . . . . . . . . . 10 Figure 10 - Clock Input - AC-coupled Single-Ended . . . . . . . . . . . . . . . . . . . . . . . . . . . . . . . . . . . . . . . . . . . . . . . 11 Figure 11 - Clock Input - DC-coupled 3.3V CMOS. . . . . . . . . . . . . . . . . . . . . . . . . . . . . . . . . . . . . . . . . . . . . . . . . 11 Figure 12 - Simplified Output Driver. . . . . . . . . . . . . . . . . . . . . . . . . . . . . . . . . . . . . . . . . . . . . . . . . . . . . . . . . . . . 12 Figure 13 - LVPECL Basic Output Termination . . . . . . . . . . . . . . . . . . . . . . . . . . . . . . . . . . . . . . . . . . . . . . . . . . . 12 Figure 14 - LVPECL Parallel Output Termination. . . . . . . . . . . . . . . . . . . . . . . . . . . . . . . . . . . . . . . . . . . . . . . . . . 13 Figure 15 - LVPECL Parallel Thevenin-Equivalent Output Termination. . . . . . . . . . . . . . . . . . . . . . . . . . . . . . . . . 13 Figure 16 - LVPECL AC Output Termination . . . . . . . . . . . . . . . . . . . . . . . . . . . . . . . . . . . . . . . . . . . . . . . . . . . . . 14 Figure 17 - LVPECL AC Output Termination for CML Inputs. . . . . . . . . . . . . . . . . . . . . . . . . . . . . . . . . . . . . . . . . 14 Figure 18 - Additive Jitter. . . . . . . . . . . . . . . . . . . . . . . . . . . . . . . . . . . . . . . . . . . . . . . . . . . . . . . . . . . . . . . . . . . . 15 Figure 19 - Decoupling Connections for Power Pins. . . . . . . . . . . . . . . . . . . . . . . . . . . . . . . . . . . . . . . . . . . . . . . 16 Figure 20 - Differential and Single-Ended Output Voltages Parameter Definitions . . . . . . . . . . . . . . . . . . . . . . . . 18 Figure 21 - Input To Output Timing . . . . . . . . . . . . . . . . . . . . . . . . . . . . . . . . . . . . . . . . . . . . . . . . . . . . . . . . . . . . 19Change SummaryPage Item Change1Applications Added PCI Express clock distribution.6Pin Description Added exposed pad to Pin Description.8Figure 4 and Figure 5Removed 22 ohm series resistors from Figure 4 and 5. These resistor are not required; however there is no impact to performance if the resistors are included.16Power supply filtering 18Figure 20Clarification of V ID and V OD .Below are the changes from the February 2013 issue to the April 2014 issue:Page Item Change8Figure 4Changed text to indicate the circuit is not recommended for VDD_driver=2.5V.Below are the changes from the November 2012 issue to the February 2013 issue:Corrected typo of 0.3 Ohm to 0.15 Ohm.1.0 Package DescriptionThe device is packaged in a 32 pin QFNFigure 2 - Pin Connections2.0 Pin DescriptionPin # Name Description3, 6clk_p, clk_n,Differential Input (Analog Input). Differential (or single ended) input signals.For all input configurations see “Clock Inputs” on page 728, 27, 26, 25, 24, 23, 18, 17, 16, 15, 14, 13out0_p, out0_nout1_p, out1_nout2_p, out2_nout3_p, out3_nout4_p, out4_nout5_p, out5_nDifferential Output (Analog Output). Differential outputs.9, 19,22, 32vdd Positive Supply Voltage. 2.5 V DC or 3.3 V DC nominal.1, 8vdd_core Positive Supply Voltage. 2.5 V DC or 3.3 V DC nominal.2, 7,20, 21gnd Ground. 0 V.4vt On-Chip Input Termination Node (Analog). Center tap between internal 50 Ohmtermination resistors.The use of this pin is detailed in section 3.1, “Clock Inputs“, for various input signal types.5ctrl Digital Control for On-Chip Input Termination (Input). Selects differential input mode;0: DC coupled LVPECL or LVDS modes1: AC coupled differential modesThis pin are internally pulled down to GND. The use of this pin is detailed in section 3.1,“Clock Inputs“, for various input signal types.10, 11,12, 29,30, 31NC No Connection. Leave unconnected.Exposed Pad Device GND.3.0 Functional DescriptionThe ZL40205 is an LVPECL clock fan out buffer with six output clock drivers capable of operating at frequencies up to 750MHz.The ZL40205 provides an internal input termination network for DC and AC coupled inputs; optional input biasing for AC coupled inputs is also provided. The ZL40205 can accept DC or AC coupled LVPECL and LVDS input signals, AC coupled CML or HCSL input signals, and single ended signals. A pin compatible device with external termination is also available.The ZL40205 is designed to fan out low-jitter reference clocks for wired or optical communications applications while adding minimal jitter to the clock signal. An internal linear power supply regulator and bulk capacitors minimize additive jitter due to power supply noise. The device operates from 2.5V+/-5% or 3.3V+/-5% supply. Its operation is guaranteed over the industrial temperature range -40°C to +85°C.The device block diagram is shown in Figure 1; its operation is described in the following sections.3.1 Clock InputsThe device has a differential input equipped with two on-chip 50 Ohm termination resistors arranged in series with a center tap. The input can accept many differential and single-ended signals with AC or DC coupling as appropriate. A control pin is available to enable internal biasing for AC coupled inputs. A block diagram of the input stage is in Figure 3.Receiverclk_n 50clk_pVt 50BiasctrlFigure 3 - Simplified Diagram of Input StageThis following figures give the components values and configuration for the various circuits compatible with the input stage and the use of the Vt and ctrl pins in each case.In the following diagrams where the ctrl pin is logically one and the Vt pin is not connected, the Vt pin can be instead connected to VDD with a capacitor. A capacitor can also help in Figure 4 between Vt and VDD. This capacitor will minimize the noise at the point between the two internal termination resistors and improve the overall performance of the device.Figure 4 - Clock Input - LVPECL - DC CoupledFigure 5 - Clock Input - LVPECL - AC CoupledFigure 6 - Clock Input - LVDS - DC CoupledFigure 7 - Clock Input - LVDS - AC CoupledFigure 8 - Clock Input - CML- AC CoupledFigure 9 - Clock Input - HCSL- AC CoupledFigure 10 - Clock Input - AC-coupled Single-EndedFigure 11 - Clock Input - DC-coupled 3.3V CMOS3.2 Clock OutputsLVPECL has a very low output impedance and a differential signal swing between 1V and 1.6 V. A simplified diagram for the output stage is shown in Figure 12.The LVPECL to LVDS output termination is not shown since there is a different device with the same inputs and LVDS outputs.out_pout_nFigure 12 - Simplified Output DriverThe methods to terminate the ZL40205 LVPECL drivers are shown in the following figures.Figure 15 - LVPECL Parallel Thevenin-Equivalent Output TerminationFigure 16 - LVPECL AC Output TerminationFigure 17 - LVPECL AC Output Termination for CML Inputs3.3 Device Additive JitterThe ZL40205 clock fanout buffer is not intended to filter clock jitter. The jitter performance of this type of device is characterized by its additive jitter. Additive jitter is the jitter the device would add to a hypothetical jitter-free clock as it passes through the device. The additive jitter of the ZL40205 is random and as such it is not correlated to the jitter of the input clock signal.The square of the resultant random RMS jitter at the output of the ZL40205 is equal to the sum of the squares of the various random RMS jitter sources including: input clock jitter; additive jitter of the buffer; and additive random jitter due to power supply noise. There may be additional deterministic jitter sources, but they are not shown in Figure 18.Figure 18 - Additive Jitter3.4 Power SupplyThis device operates employing either a 2.5V supply or 3.3V supply.3.4.1 Sensitivity to power supply noisePower supply noise from sources such as switching power supplies and high-power digital components such as FPGAs can induce additive jitter on clock buffer outputs. The ZL40205 is equipped with a low drop out (LDO) regulator and on-chip bulk capacitors to minimize additive jitter due to power supply noise. The on-chip regulation, recommended power supply filtering, and good PCB layout all work together to minimize the additive jitter from power supply noise.3.4.2 Power supply filteringJitter levels may increase when noise is present on the power pins. For optimal jitter performance, the device should be isolated from the power planes connected to its power supply pins as shown in Figure 19. •10 µF capacitors should be size 0603 or size 0805 X5R or X7R ceramic, 6.3 V minimum rating •0.1 µF capacitors should be size 0402 X5R ceramic, 6.3 V minimum rating •Capacitors should be placed next to the connected device power pins •A 0.15 Ohm resistor is recommended3.4.3 PCB layout considerationsThe power nets in Figure 19 can be implemented either as a plane island or routed power topology without changing the overall jitter performance of the device.ZL402051891922320.1 µF 0.1 µFvdd_core10 µF 0.1 µF0.15 Ωvdd0.1 µF 10 µFFigure 19 - Decoupling Connections for Power PinsAbsolute Maximum Ratings*Parameter Sym.Min.Max.Units 1Supply voltage V DD_R-0.5 4.6V 2Voltage on any digital pin V PIN-0.5VDD V 4LVPECL output current I out30mA 5Soldering temperature T260 °C 6Storage temperature T ST-55125 °C 7Junction temperature T j125 °C 8Voltage on input pin V input VDD V 9Input capacitance each pin C p500fF 4.0 AC and DC Electrical Characteristics* Exceeding these values may cause permanent damage. Functional operation under these conditions is not implied.* Voltages are with respect to ground (GND) unless otherwise statedRecommended Operating Conditions*Characteristics Sym.Min.Typ.Max.Units1Supply voltage 2.5 V mode V DD25 2.375 2.5 2.625V2Supply voltage 3.3 V mode V DD33 3.135 3.3 3.465V3Operating temperature T A-402585°C* Voltages are with respect to ground (GND) unless otherwise statedDC Electrical Characteristics - Current ConsumptionCharacteristics Sym.Min.Typ.Max.Units Notes 1Supply current LVPECL drivers -unloadedI dd_unload110mA Unloaded2Supply current LVPECL drivers - loaded (all outputs are active)I dd_load209mA Including powerto R L = 50DC Electrical Characteristics - Inputs and Outputs - for 3.3 V SupplyCharacteristics Sym.Min.Typ.Max.Units Notes1CMOS control logic high-level inputvoltageV CIH0.7*V DD V2CMOS control logic low-level inputvoltageV CIL0.3*V DD V3CMOS control logic Input leakagecurrentI IL1µA V I = V DD or 0 V4Differential input common modevoltageV CM 1.1 2.0V5Differential input voltage difference V ID0.251V6Differential input resistance V IR80100120ohm* This parameter was measured from 125 MHz to 750 MHz.* This parameter was measured from 125 MHz to 750 MHz.Figure 20 - Differential and Single-Ended Output Voltages Parameter Definitions7LVPECL output high voltage V OH V DD -1.40V 8LVPECL output low voltage V OL V DD - 1.62V 9LVPECL output differential voltage*V OD0.50.9VDC Electrical Characteristics - Inputs and Outputs - for 2.5 V SupplyCharacteristicsSym.Min.Typ.Max.Units Notes1Differential input common mode voltageV CM 1.1 1.6V 2Differential input voltage difference V ID 0.251V 3Differential input resistance V IR 80100120ohm 4LVPECL output high voltage V OH V DD -1.40V 5LVPECL output low voltage V OL V DD - 1.62V 6LVPECL output differential voltage*V OD0.40.9VDC Electrical Characteristics - Inputs and Outputs - for 3.3 V SupplyCharacteristicsSym.Min.Typ.Max.Units NotesAC Electrical Characteristics* - Inputs and Outputs (see Figure 21) - for 2.5/3.3 V supply.Characteristics Sym.Min.Typ.Max.Units Notes 1Maximum Operating Frequency1/t p750MHz2Input to output clock propagation delay t pd012ns3Output to output skew t out2out50100ps4Part to part output skew t part2part80300ps5Output clock Duty Cycle degradation t PWH/ t PWL-202Percent6LVPECL Output clock slew rate r SL0.75 1.2V/ns* Supply voltage and operating temperature are as per Recommended Operating ConditionsInputt Pt PWL t pdt PWHOutputFigure 21 - Input To Output TimingAdditive Jitter at 2.5 V*Output Frequency (MHz)Jitter MeasurementFilterTypical RMS (fs)Notes112512 kHz - 20 MHz 1392212.512 kHz - 20 MHz 1093311.0412 kHz - 20 MHz 85442512 kHz - 20 MHz 57550012 kHz - 20 MHz 506622.0812 kHz - 20 MHz 40775012 kHz - 20 MHz36Additive Jitter at 3.3 V*Output Frequency (MHz)Jitter MeasurementFilterTypical RMS (fs)Notes112512 kHz - 20 MHz 1152212.512 kHz - 20 MHz 853311.0412 kHz - 20 MHz 72442512 kHz - 20 MHz 55550012 kHz - 20 MHz 486622.0812 kHz - 20 MHz 41775012 kHz - 20 MHz395.0 Performance Characterization*The values in this table were taken with an approximate slew rate of 0.8 V/ns.*The values in this table were taken with an approximate slew rate of 0.8 V/ns.Additive Jitter from a Power Supply Tone*Carrier frequencyParameterTypicalUnitsNotes125MHz 25 mV at 100 kHz 115fs RMS 750MHz25 mV at 100 kHz59fs RMS* The values in this table are the additive periodic jitter caused by an interfering tone typically caused by a switching power supply. For this test, measurements were taken over the full temperature and voltage range for V DD = 2.5 V. The magnitude of the interfering tone is measured at the DUT.6.0 Typical BehaviorTypical Phase Noise at 622.08 MHzTypical Waveformat 155.52 MHzV OD versus FrequencyPropagation Delay versus TemperatureNote:This is for a single device. For more details see thePower Supply Tone Frequency (at 25 mV) versus PSRR at 125 MHz Power Supply Tone Frequency (at 25 mV) versus Additive Jitter at 125 MHzPower Supply Tone Magnitude (at 100 kHz) versus PSRR at 125 MHz Power Supply Tone Magnitude (at 100 kHz) versus Additive Jitter at 125 MHz7.0 Package CharacteristicsThermal DataParameter Symbol Test Condition Value UnitJunction to Ambient Thermal Resistance ΘJA Still Air1 m/s2 m/s 37.433.131.5o C/WJunction to Case Thermal Resistance ΘJC24.4o C/W Junction to Board Thermal Resistance ΘJB19.5o C/W Maximum Junction Temperature*T jmax125o C Maximum Ambient Temperature T A85o C© 2014 Microsemi Corporation. All rights reserved. Microsemi and the Microsemi logo are trademarks of Microsemi Corporation. All other trademarks and service marks are the property of their respective owners.Microsemi Corporation (NASDAQ: MSCC) offers a comprehensive portfolio of semiconductor and system solutions for communications, defense and security, aerospace and industrial markets. Products include high-performance and radiation-hardened analog mixed-signal integrated circuits, FPGAs, SoCs and ASICs; power management products; timing and synchronization devices and precise time solutions, setting the world’s standard for time; voice processing devices; RF solutions; discrete components; security technologies and scalable anti-tamper products; Power-over-Ethernet ICs and midspans; as well as custom design capabilities and services. Microsemi is headquartered in Aliso Viejo, Calif. and has approximately 3,400 employees globally. Learn more at .Microsemi Corporate Headquarters One One Enterprise, Aliso Viejo CA 92656 USA Within the USA: +1 (800) 713-4113Outside the USA: +1 (949) 380-6100Sales: +1 (949) 380-6136Fax: +1 (949) 215-4996E-mail: ***************************Information relating to products and services furnished herein by Microsemi Corporation or its subsidiaries (collectively “Microsemi”) is believed to be reliable. However, Microsemi assumes no liability for errors that may appear in this publication, or for liability otherwise arising from the application or use of any such information, product or service or for any infringement of patents or other intellectual property rights owned by third parties which may result from such application or use. Neither the supply of such information or purchase of product or service conveys any license, either express or implied, under patents or other intellectual property rights owned by Microsemi or licensed from third parties by Microsemi, whatsoever. Purchasers of products are also hereby notified that the use of product in certain ways or in combination with Microsemi, or non-Microsemi furnished goods or services may infringe patents or other intellectual property rights owned by Microsemi.This publication is issued to provide information only and (unless agreed by Microsemi in writing) may not be used, applied or reproduced for any purpose nor form part of any order or contract nor to be regarded as a representation relating to the products or services concerned. The products, their specifications, services and other information appearing in this publication are subject to change by Microsemi without notice. No warranty or guarantee express or implied is made regarding the capability, performance or suitability of any product or service. Information concerning possible methods of use is provided as a guide only and does not constitute any guarantee that such methods of use will be satisfactory in a specific piece of equipment. It is the user’s responsibility to fully determine the performance and suitability of any equipment using such information and to ensure that any publication or data used is up to date and has not been superseded. Manufacturing does not necessarily include testing of all functions or parameters. These products are not suitable for use in any medical and other products whose failure to perform may result in significant injury or death to the user. All products and materials are sold and services provided subject to Microsemi’s conditions of sale which are available on request.For more information about all Microsemi productsvisit our website at TECHNICAL DOCUMENTATION – NOT FOR RESALE。
ADUM2250中文资料

APPLICATIONS
Isolated I2C, SMBus, or PMBus Interfaces Multilevel I2C interfaces Power supplies Networking Power-over-Ethernet
GENERAL DESCRIPTION
The ADuM2250/ADuM22511 are hot-swappable digital isolators with nonlatching bidirectional communication channels that are compatible with I2C® interfaces. This eliminates the need for splitting I2C signals into separate transmit and receive signals for use with standalone optocouplers.
NRLMW223M250V25X50F中文资料
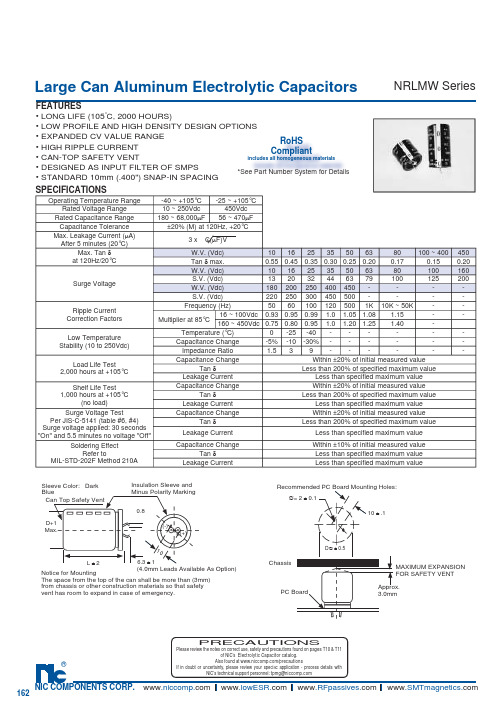
Large Can Aluminum Electrolytic CapacitorsFEATURES• LONG LIFE (105°C, 2000 HOURS)• LOW PROFILE AND HIGH DENSITY DESIGN OPTIONS • EXPANDED CV VALUE RANGE• HIGH RIPPLE CURRENT• CAN-TOP SAFETY VENT • DESIGNED AS INPUT FILTER OF SMPS• STANDARD 10mm (.400") SNAP-IN SPACING NRLMW SeriesSPECIFICATIONSNotice for MountingThe space from the top of the can shall be more than (3mm) from chassis or other construction materials so that safety vent has room to expand in case of emer g en c y.Sleeve Color: Dark BlueCan Top Safety VentInsulation Sleeve and Minus Polarity Marking(4.0mm Leads Available As Option)D+1Max.L ± 26.3 ± 10.810(-)(+)MAXIMUM EX P AN S IONFOR SAFETY VENT Approx. 3.0mmRecommended PC Board Mounting Holes:10 ± .1∅= 2 ± 0.1D ∅ ± 0.5ChassisPC BoardPRECAUTIONSPlease review the notes on correct use, safety and precautions found on pages T10 & T11of NIC’s Electrolytic Capacitor catalog . Operating Temperature Range-40 ~ +105°C -25 ~ +105°C Rated Voltage Range 10 ~ 250Vdc 450Vdc Rated Capacitance Range 180 ~ 68,000µF 56 ~ 470µF Capacitance Tolerance ±20% (M) at 120Hz, +20°CMax. Leakage Current (µA)After 5 minutes (20°C)3 x C(µF)VMax. Tan δat 120Hz/20°CW.V. (Vdc)10162535506380100 ~ 400450Tan δ max.0.550.450.350.300.250.200.170.150.20Surge VoltageW.V. (Vdc)10162535506380100160S.V. (Vdc)132032446379100125200W.V. (Vdc)180200250400450----S.V. (Vdc)220250300450500----Ripple Current Correction Factors Frequency (Hz)50601001205001K 10K ~ 50K --Multiplier at 85°C16 ~ 100Vdc0.930.950.99 1.0 1.05 1.08 1.15--160 ~ 450Vdc0.750.800.95 1.0 1.20 1.25 1.40-Low Temperature Stability (10 to 250Vdc)Temperature (°C)0-25-40------Capacitance Change -5%-10-30%------Impedance Ratio 1.539------Load Life Test 2,000 hours at +105°C Capacitance ChangeWithin ±20% of initial measured valueTan δLess than 200% of specifi ed maximum valueLeakage Current Less than specifi ed maximum value Shelf Life Test 1,000 hours at +105°C(no load)Capacitance ChangeWithin ±20% of initial measured value Tan δLess than 200% of specifi ed maximum valueLeakage Current Less than specifi ed maximum value Surge Voltage TestPer JIS-C-5141 (table #6, #4)Surge voltage applied: 30 seconds "On" and 5.5 minutes no voltage "Off"Capacitance ChangeWithin ±20% of initial measured value Tan δLess than 200% of specifi ed maximum valueLeakage Current Less than specifi ed maximum value Soldering EffectRefer toMIL-STD-202F Method 210ACapacitance ChangeWithin ±10% of initial measured valueTan δLess than specifi ed maximum value Leakage CurrentLess than specifi ed maximum valueRoHSCompliantincludes all homogeneous materials *See Part Number System for DetailsLarge Can Aluminum Electrolytic Capacitors NRLMW SeriesLarge Can Aluminum Electrolytic CapacitorsNRLMW SeriesNRLMW 471 M 250V 30X35 FRoHS compliant Case Size (mm) Voltage Rating Tolerance Code Capacitance Code SeriesPART NUMBER SYSTEM。
Measuring Amplifier Type 2525 产品说明书
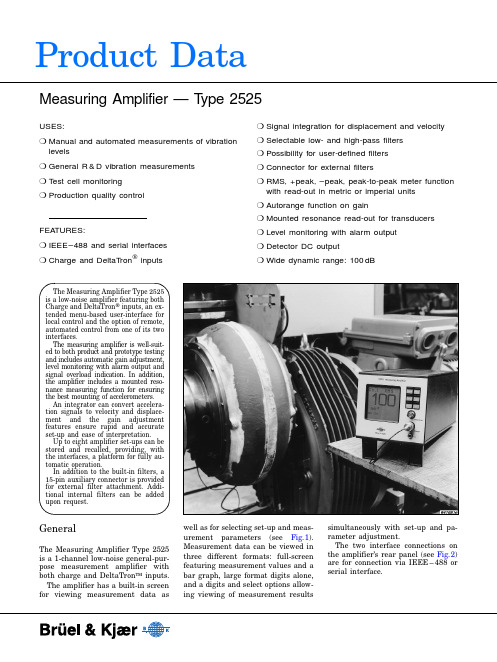
Product DataThe Measuring Amplifier Type 2525is a low-noise amplifier featuring both Charge and DeltaTron ® inputs, an ex-tended menu-based user-interface for local control and the option of remote,automated control from one of its two interfaces.The measuring amplifier is well-suit-ed to both product and prototype testing and includes automatic gain adjustment,level monitoring with alarm output and signal overload indication. In addition,the amplifier includes a mounted reso-nance measuring function for ensuring the best mounting of accelerometers.An integrator can convert accelera-tion signals to velocity and displace-ment and the gain adjustment features ensure rapid and accurate set-up and ease of interpretation.Up to eight amplifier set-ups can be stored and recalled, providing, with the interfaces, a platform for fully au-tomatic operation.In addition to the built-in filters, a 15-pin auxiliary connector is provided for external filter attachment. Addi-tional internal filters can be added upon request.Measuring Amplifier — Type 2525USES:r Manual and automated measurements of vibration levels r General R &D vibration measurements r T est cell monitoring r Production quality controlFEA TURES:r IEEE–488 and serial interfaces r Charge and DeltaT ron ® inputsr Signal integration for displacement and velocity r Selectable low- and high-pass filters r Possibility for user-defined filters r Connector for external filtersr RMS, +peak, –peak, peak-to-peak meter function with read-out in metric or imperial units r Autorange function on gainr Mounted resonance read-out for transducersr Level monitoring with alarm output r Detector DC outputr Wide dynamic range: 100dBGeneralThe Measuring Amplifier Type 2525is a 1-channel low-noise general-pur-pose measurement amplifier with both charge and DeltaTron ™ inputs.The amplifier has a built-in screen for viewing measurement data as well as for selecting set-up and meas-urement parameters (see Fig.1).Measurement data can be viewed in three different formats: full-screen featuring measurement values and a bar graph, large format digits alone,and a digits and select options allow-ing viewing of measurement resultssimultaneously with set-up and pa-rameter adjustment.The two interface connections on the amplifier’s rear panel (see Fig.2)are for connection via IEEE –488 or serial interface.Main FeaturesThe Measuring Amplifier Type 2525 includes a number of features which allow sophisticated and automatic measurement configuration as well as display set-up options which can be selected to best reflect the current application.Measurement Set-upThe measurement set-up consists of twelve menus which carry out (or lead to sub-menus which carry out) the following functions:r Measurement mode selection: ac-celeration, velocity displacement or forcer Transducer sensitivityr Input type: DeltaTron® or Charge (floating or grounded)r Input, output and fine gain select r Upper frequency limitr Lower frequency limitr Additional filter: internal or exter-nalr RMS averaging: exponential or lin-ear plus selectable averaging time r Peak hold timer Autorange (automatic gain adjust-ment)r Alarm On/Off, detector (RMS or peak), level, hold time and level exceed timer Detector DC outputDisplay Set-upMeasurement results can be dis-played in terms of RMS, positive or negative peak values, or peak-to-peak.Read-out value scales are selecta-ble as either absolute (with physical units shown) or dB. Bar graphs are shown with absolute values on a log-arithmic axis. Units can be specified as metric or imperial. Measurement values can be read-out in scientific notation (floating) or as fixed-point values (attenuator de-pendent).The Set-up Mode menu allows you to specify a full screen display which includes a bar graph of the current measurement as well as the instanta-neous measurement value, or the val-ues only. It is possible to make changes to the set-up while viewing their effect on the measurement values.General Set-up FeaturesIn addition to the measurement and display set-up features, a number of general options can be selected:r Select impulse frequency andread-out mounted resonance fre-quencyr Sine reference for sensitivity checkr Recall or store user-defined set-up,or recall factory set-upr Interface set-up: IEEE–488 ad-dress, serial baud rate, handshake,hardwired, modemr Back-lighting On/OffInterface ControlUnder the control of an external com-puting device via one of its two inter-faces, the amplifier’s extensivemeasurement and display featurescan be automated, allowing full inte-gration in a production line and au-tomated test environment.All features provided by the menusunder manual control (except thespecification of the interfaces them-selves) are also available via interface.In addition, interface control pro-vides some extra features with re-spect to resetting entire set-ups orindividual components, error hand-ling, and measurement and operationmonitoring and control.Fig.1 Measuring Amplifier Type 2525 front panel. The axes are not labelled as the displayis intended as a visual monitor onlyFig.2 Measuring Amplifier Type 2525 rear panel2Product and Prototype TestingAside from its sophisticated function-ality and possibilities for automated control, the Measuring Amplifier Type 2525 offers two main features which make it a must in the meas-urement chain of any automatedproduct test procedure:r Autorange (autogain)r Alarm monitoring functionThe autorange function makes set-ting up the amplifier easy in caseswhere you have little information re-garding the vibration levels themeasurement source can achieve.The alarm monitoring functionmakes it possible to select a monitor-ing level using RMS, positive or neg-ative peak values or peak-to-peak. Byspecifying a level exceed time, an ac-ceptable margin (e.g. noise margin)can be defined. The alarm hold timeensures that levels are held longenough to be discovered.CHARGE INPUT:Floating or grounded via TNC socket on front Max. Input 0 to 100kHz: 50nC peakMax. Common Mode Voltage on Floating Input: 5V peak at charge input level max. 10nC peak Common Mode Rejection Ratio (CMRR): With input gain +20 to +60dB:100Hz CMRR >60dB10kHz CMRR >45dBWith input gain –20 to +10dB:100Hz CMRR >50dB10kHz CMRR >40dBTotal Sensitivity:0.1pC to 10nC in steps of 10dB for 1V on AC output0.03pC to 10nC in steps of 0.01dB step for 1V on AC output, with reduced frequency rangeGain:Input Gain (before filtering and integration): Selectable from –20dB to +60dB in steps of 10dBVariable Gain (before filtering and integration): Selectable from 0dB to 11dB in steps of 0.01dB Output Gain (after filtering and integration): Selectable 0dB, 10dB and 20dBInherent Noise 2Hz to 22kHzSingle-ended: <5fC (<7fC @ 90% RH) Floating: <10fCon AC output, referred to input with maximum sensitivity, Lower Frequency Limit = 1Hz, and 1nF transducer capacitanceGain Accuracy (from input to AC output at 1kHz):Acceleration and force: Better than 2% Velocity: Better than 2.5%Displacement: Better than 3.0% @ 100Hz DeltaTron® INPUT:Via BNC socket on frontSensitivity:100µV to 10V in steps of 10dB for 1V on AC output30µV to 10V in steps of 0.01dB for 1V on AC output, with reduced frequency range Gain:Input Gain (before filtering and integration): Selectable from –20dB to +60dB in steps of 10dBVariable Gain (before filtering and integration): Selectable from 0dB to 11dB in steps of 0.01dBOutput Gain (after filtering and integration): Selectable 0dB, 10dB, 20dBGain Accuracy:Acceleration and force: Better than 2% Velocity: Better than 2.5%Displacement: Better than 3.0%Inherent Noise 2Hz to 22kHz:<20µV referred to input with maximum sensi-tivity and transducer output impedance <1kΩInput Impedance: >100kΩPower Supply for DeltaTron® Accelerometer: Constant Current: 4mA.Max Voltage on DeltaTron® input: 27V Out-of-range detection on DeltaTron® supply voltage (<3V or >21V)PREAMP OUTPUT:BNC socket on rearAcceleration signal after 1st order high-pass fil-ter, input gain and variable gain Max. Output: 5V peak (5mA peak)Output Impedance: 50ΩDC Offset: –50 <offset <+50mVAC OUTPUT:Via BNC socket on rearFully conditioned signalMax. Output: 5V peak (5mA peak)Output Impedance: 50ΩDC Offset: –10 <offset <+10mVFREQUENCY RANGE:Acceleration & Force:0.2Hz (better than –10% limit) to 100kHz (betterthan –20% limit)With variable gain selected: 0.2Hz to 40kHz(better than –10% limit)Velocity:1Hz to 10kHz (better than ±10% limits)Displacement:1Hz to 1kHz (better than ±10% limits)LOW–PASS FILTERS:2-pole Butterworth (maximally flat)Selectable –3dB limits of 1, 3, 10, 30kHz and OFFFilter Slope: 40dB/decadeAccuracy on –3dB Limit Freq.: ±5%, re 1kHzwithout filterHIGH-PASS FILTERS:3-pole Butterworth (maximally flat)Selectable –3dB limits of 0.1, 0.3, 1, 3, 10, 30Hzand OFFFilter Slope: 60dB/decadeAccuracy on –3dB Limit Freq.: ±10% (3, 10,30Hz), +10/−15% (0.1, 0.3, 1Hz), re 1kHz with-out filterADDITIONAL FILTERS:External filter connection via 15-pole D-sub-con-nector on rear.Optional custom internal filtering available on re-quest.External filter serially connected to standard fil-tersDISTORTION:<0.12% to 10kHz, <1% to 100kHzTEST OSCILLATOR:159.2Hz (=1000 rad/s), 100pC sinusoidal, ±1%SIGNAL RMS DECTECTOR:3 digits read out on LCDAccuracy for crest factor <3:Averaging Time:Exponential: 125ms, 1s, 10sLinear: 1s or 60s based on 125ms exp. val-uesSIGNAL PEAK DETECTOR:3 digits read out on LCD+Peak, –Peak:Settling time for a level shift from 0 to 3V onAC output:56µs (to –10% of value)72µs (to –5% of value)94µs (to –2% of value)Read-out (at AC output) value for a 3V peakof a period of one half sine with a (full period)frequency as listed:Max Peak Hold Time:0.5s to 60s in steps of 0.5s or infiniteMax peak reset functionDynamic range:+30mV to 3V on AC output (40dB)Peak-to-Peak:The numerical sum of +peak and –peak withextra hold time as described aboveOVERLOADS:Signal Overload:Peak overloading internal circuitsUpper 20dB:Indicates that at least one internal circuit is op-erating less than 20dB from overloadCM Overload:Common mode peak voltage >5V at floatingcharge inputDeltaTron® Overload:DeltaTron® supply voltage <3.0V or >21.0VGAIN AUTORANGE:None (manual gain setting)On output gain onlyOn input and output gainOVERLOAD RECOVERY TIME: <200µsTime for output to recover to within 250mV ofthe original value after termination of a half sinepulse of 50µs duration at the baseline. Pulseamplitude is 4 times the full scale input, peakACCELEROMETER MOUNTED RESONANCEMEASURING (EP patent 715.722, US patent5,753,793):Done via pulse method measuring. Excitingpulse ±15V, 3kHz to 60kHzCan be used with a number of Brüel&KjærCharge AccelerometersEXTERNAL FILTER:Connected between the internal filters and theoutput gainALARM FUNCTION:Level monitoring with alarm outputAlarm Output:In the 15-pole D-Sub socket on rear of amplifier Freq. RangeDynamic rangereferred to 1Von AC outputAccuracyreferredto input**1Hz to 10kHz+10dB to –30dB*±5%1Hz to 30kHz+10dB to –30dB*±10%1Hz to 100kHz+10dB to –20dB+10%–25%1Hz to 100kHz+10dB to –10dB+5%–20%For 60s linear averaging:*the dynamic range is +10 to −20dB**10% must be subtracted from the negativeaccuracy value (e.g. +5%, −15%, etc.)Sine FrequencyRead-out(% of FS peak value)1.0kHz–2%2.5kHz–8%5.0kHz–20%10.0kHz–40%Specifications 25253BP 1483–1499/06HEADQUARTERS: DK-2850Nærum·Denmark·Telephone:+4545800500·Fax:+4545801405·http://www.bk.dk·e-mail:**********Australia (02)9450-2066 · Austria 0043-1-8657400 · Brazil (011)5182-8166 · Canada (514)695-8225 · China (86)1068029906Czech Republic 02-67021100 · Finland (0)9-755 950 · France (01)69906900 · Germany 06103/908-5 6 · Hong Kong 25487486 · Hungary (1)2158305Ireland (01)4504922 · Italy (02)57604141 · Japan 03-3779-8671 · Republic of Korea (02)3473-0605 · Netherlands (0)30 6039994 · Norway 66771155Poland (22)8409392 · Portugal (1)4711453 · Singapore (65) 377-4512 · Slovak Republic 421754430701 · Spain (91)3681000 · Sweden (08)4498600 Switzerland 01/9436070 · Taiwan (02)7139303 · United Kingdom (0181)954-2366 · USA 180******** Local representatives and service organisations worldwideBrüel&Kjær reserves the right to change specifications and accessories without noticeOrdering InformationType 2525Measuring Amplifier Includes the following accessories:JP 0162:TNC to Microdot Adaptor AN 0010:Mains Cable VF 0032:T 630mA Fuse VF 0042:T 315mA Fuse LK 0014:Ferrite Cable Clamp VP 7758:Type 2525 Communication DemoProgramOptional AccessoriesAO 1382: 1.2m Microdot Accelerometer Cable, double screened for extra EMC protectionJP 1501:15-pole Sub-D Connector DH 0647:Housing for JP 1501JP 0145:BNC to Microdot Adaptor JP 0226:TNC to BNC AdaptorAO 0265:IEEE Interface Cables KK 0047:Frame for 19″ rackWH 3103:ISO 5349 Hand-arm filterWH 3267:900Hz to 1100Hz band pass filter WH 3112:A-weighting filterWH 3172:Whole body vibration z-filterRelay: SPDT, Max. 48V, 0.5A Alarm On/Off:Selectable via LCD and Interface bus Level:Selectable over the entire dynamic range. Mon-itoring will de-select while the autorange is changing gain (missing time periods after gain shifts)Level Exceed Time:Adjustable from 0 to 60s in steps of 1s Alarm Hold Time:Adjustable from 1 to 60s or infinite Alarm Reset Function Detector Type:Selectable RMS, +Peak, –Peak, Peak-to-Peak.Averaging/Hold time is transferred from detector set-up. Detectors are sampled at 125ms inter-vals (same interval as LCD meter digit updating)DETECTOR DC OUTPUT:In 15-pole D-Sub socket on rear V/unit: equal to V/unit for AC output Max Output: 3.5V (5mA peak)Output Impedance: 50ΩDC Offset: <±5mV Detector Type:Selectable RMS, +Peak, –Peak, Peak-to-Peak.Averaging/Hold time is transferred from detector set-upSampling Frequency:Output is updated at 125ms intervals (same in-terval as LCD meter digit updating). No curve fitting on outputIEEE –488 INTERFACE:The functions implemented conform to IEEE –488.1 and IEC 625–1 standards. Any function shown on display can be transmitted to and from the apparatus Functions Implemented:Source Handshake SH1Acceptor Handshake AH1Talker T6Listener L4Device Clear DC1Remote Local RL1SERIAL INTERFACE:Conforms to EIA/TIA–574 (“RS–232”)Baud Rate: 2400, 4800, 9600Parity: None Data Bits: 8Stop Bits: 1Handshake:X-On/X-Off, hardwired RTS/CTS, Modem DCDPower SupplyMains: 90V–127V or 200V–240V; 24VADimensions and WeightHeight : 132.5mm (5.22″)Width : 139.5mm (5.49″)Depth : 320mm (12.6″)Weight: 3.6kg (5.8lb.)Note: All values are typical unless measurement uncertainty or tolerance field is specified.Specifications 2525 (cont.)COMPLIANCE WITH STANDARDS:CE-mark indicates compliance with: EMC Directive and Low Voltage Directive.SafetyEN 61010–1 and IEC 1010–1: Safety requirements for electrical equipment for measurement, control and laboratory use.EMC EmissionEN 50081–1: Generic emission standard. Part 1: Residential, commercial and light industry.EN 50081–2: Generic emission standard. Part 2: Industrial environment.CISPR 22: Radio disturbance characteristics of information technology equipment. Class B Limits.FCC Rules, Part 15: Complies with the limits for a Class B digital device.EMC ImmunityEN 50082–1: Generic immunity standard. Part 1: Residential, commercial and light industry.EN 50082–2: Generic immunity standard. Part 2: Industrial environment. Note 1: The above is guaranteed using accessories listed in this Product Data sheet only.Note 2: See “EMC”TemperatureIEC 68–2–1 & IEC 68–2–2: Environmental Testing. Cold and Dry Heat.Operating Temperature: 5 to 40°C (41 to 104°F)Storage Temperature: –25 to +70°C (–13 to +158°F)Humidity IEC 68–2–3: Damp Heat: 90% RH (non-condensing at 40°C (104°F))MechanicalNon-operating:IEC 68–2–6: Vibration: 0.3mm, 20m/s 2, 10–500Hz IEC 68–2–27: Shock: 1000m/s 2IEC 68–2–29: Bump: 1000 bumps at 250m/s 2EnclosureIEC 529: Protection provided by enclosures: IP 20EMCSUSCEPTIBILITY TO DISTURBANCES SPECIFIED IN EN 50082–2:Measured using Accelerometer Cable AO 1382.Charge floating measurements according to User Manual with Ferrite Cable Clamp LK 0014mounted on accelerometer cable.At magnetic field 80A/m charge input noise can increase to 25fCRADIATED RF: (3 to 10V/m, 80% AM, 1kHz)CONDUCTED RF: (3 to 10V, 80% AM, 1kHz)1Measured with max. gain and 50Ω AC termination 2Measured with max. gain and 1nF terminationInput Radiated Conducted DeltaTron ®1<0.6mV<20µV Charge, single ended 2<0.3pC <0.02pC Charge, floating2<0.3pC<6pC。
Ericsson DS-2250 Vertical Turbo Card 维护手册说明书
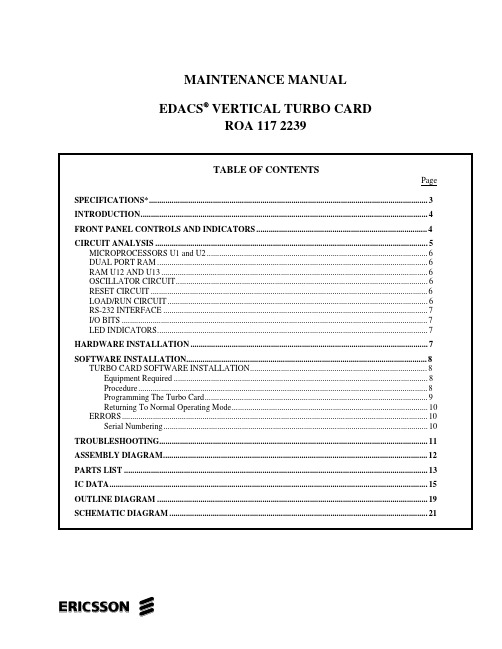
MAINTENANCE MANUALEDACS® VERTICAL TURBO CARDROA 117 2239ericssonzCopyright © Sepotember 1996,Ericsson Inc.SPECIFICATIONS*ITEM SPECIFICATION CURRENT DRAIN80 to 120 mAPOWER REQUIREMENTS+5 Vdc ±5%, 120 mA (maximum).+12 Vdc ±5%, 5 mA (maximum).-12 Vdc ±5%, 5 mA (maximum).MEMORY:VolatileNon-Volatile Inter-processor 64K bytes128K bytes in the DS-2250 microprocessors (battery powered) 8K bytes Dual PortCONNECTIONS RS-232 Serial Ports I/O Lines:InputsOutputs 96 pin DIN connector (P1) mating to VME backplane interface.Two (2), six pin modular RJ-12 connectors (J2 and J3)Two (2) Schmitt trigger lines with 100K ohm pull up to Vcc. Two (2) transistor buffered, open-collector lines with 100k ohm pull up to Vcc.All four (4) I/O lines diode clamped to within +0.5 Vdc above Vcc and -0.5 Vdc below ground.OSCILLATOR FREQUENCY11.0592 MHzINDICATORS (Operating Status)One red LED per DS-2250 microprocessorDIMENSIONS100 mm (high) x 220 mm )long)* These specifications are intended for use during servicing. Refer to appropriate Specification Sheet for the complete specification.INTRODUCTIONThe Vertical Turbo Card (ROA 117 2239) provides additional processing power and memory for the Ericsson Control Point Trunking Card (ROA 117 2240/3).The Turbo Card is manufactured using surface mount components. The card plugs into a Trunking Shelf along with the Control Point Trunking Card and the Simulcast Interface Card. Electrical connections are made by plugging the Turbo Card into the proper card slot which connects P1 into the shelf’s backplane.FRONT PANEL CONTROLS ANDINDICATORSThe Vertical Turbo Card’s front panel is shown in Figure 1 and described in the accompanying text.Figure 1 - Vertical Turbo Card Front PanelTable 1 - Connector ChartCIRCUIT ANALYSISThe Turbo Card consists of two independent microprocessor sections (See Figure 2). The heart of each section is a DS-2250 microprocessor, U1 or U2. In addition to its internal memory, each microprocessor has a 32K byte external RAM, U12 or U13. Each section also contains a 4K byte Dual Port RAM (DPRAM), U3 or U4, which provides the interface to the Trunking Card. A single oscillator, consisting of U14 and B1, provides the clock for both processors. Each processor uses one half of U8 to interface between its TTL I/O and its RS-232 serial port. When one of the processors triggers U9, it turns on either LED D1 or D2. A single input bit and a single output bit is available on each processor for I/O. The module has a single RESET button which resets both processors. LOAD/RUN circuits on each processor set the operating mode. Port 1 and INT 0 of both processors are tied together to provide a high speed parallel communication link between the two processors.Figure 2 - Turbo Card Block DiagramMICROPROCESSORS U1 and U2Microprocessors U1 and U2 are Dallas Semiconductor DS-2250 single-in-line package (SIP) modules. The DS-2250 is a special proprietary derivative of the Intel 8031 microprocessor containing the basic 8031 structure, a bootstrap loader, terminal interface, and internal control of 64K bytes of battery backed-up RAM. The RAM can be partitioned into two separate code and data areas, The code area can be write protected after it is initially loaded. An internal bit, ECE2, under program control alters the memory map allowing access to all available memory (see Figure 3). DUAL PORT RAMDual-port RAM (DPRAM) chips U3 and U4 interface with the Trunking Card's 8032 microprocessor (U1). One DPRAM port is connected to the Trunking Card and the other port is connected to either U1 or U2. To the Trunking Card, U3 and U4 appear as a single 8k byte memory block between addresses 0 and 1FFFH. To the Turbo Card microprocessor U1, U3 appears as a 4k byte RAM addressed from 0 to 0FFFH and likewise, U2 sees U4 as a 4k byte RAM addressed from 0 to 0FFFH. Thus, each microprocessor shares 4K bytes of memory with the Trunking Card processor. This permits the efficient exchange of data between the Trunking Card and the Turbo Card. Integrated circuits U11-D and U10-D drive the output enable (read) input (RAM CS) from the Trunking Card, while U10-A, B, and C along with U11-A and B drive DPRAM chip enables origninating from the Trunking Card write command (WRBAR).RAM U12 AND U13As shown in Figure 3, when ECE2 is 0, each processor accesses a 32K RAM at addresses 8000H to FFFFH. These RAM's are on the Turbo Card, not in the DS-2250, thus they are not powered by the DS-2250 battery. This volatile memory space is used as a temporary scratch pad by the processors. U10-E and U10-F drive the RAM CE (chip enable), pins of U12 and U13 respectively, from bit 15 of the address bus. A low enables the RAM. OSCILLATOR CIRCUITU14 is an unbuffered CMOS inverter (74HCU04). In this application, U14-A functions as a linear gain stage with crystal B1 in its feedback path, forming an oscillator at 11.0592 MHz. U14-B buffers the clock and drives both processors' clock input pins.RESET CIRCUITSwitch S1 resets the Turbo Card and the Trunking Card's S4 resets the Trunking Card. The software will usually start properly with only an S4 Trunking Card reset; however, both boards may be resetDepressing the Turbo Card's S1 grounds R21, R22, and the positive side of C21. This turns on PNP transistors Q4 and Q7 pulling the RESET input of each processor high. In this logic state, the microprocessors are reset and not operating. When S1 is released, the voltage on C21's positive terminal and the bases of Q4 and Q7 slowly rises as C21 charges through R8, R15, R21, and R22. Eventually, this voltage rises high enough to turn Q4 and Q7 off allowing the processor RESET inputs to fall low. RESET is kept low at this point by R7 and R14. R8 and R15 hold Q4 and Q7 in the off condition.LOAD/RUN CIRCUITDuring normal operation (RUN mode), the processors' RESET inputs are held low and the PSEN output controls external memory. Each DS-2250 is put into the LOAD mode by holding its RESET pin high and pulling its PSENFigure 3 - Memory Map For Each DS-2250pin low.Switch S2 selects RUN/LOAD mode for processor U1. Moving S2 down shorts pins 2 and 3, placing U1 in the LOAD mode. This applies Vcc (5V) to R10 and R12. Vcc on R10 turns on Q8 which turns on Q7 through R9 pulling U1's RESET high. Vcc on R12 turns on Q6 which holds PSEN low. When S2 is up (shorting pins 1 and 2) the processor is in the RUN mode. Vcc is not applied to R10 and R12. Q8 is held off by R11 and Q7 is held off by R8 so RESET is pulled low by R7. Q6 is held off by R13 so PSEN is not held low and may become an output of U1.Switch S3 selects RUN/LOAD mode for processor U2. Moving S3 down shorts pins 2 and 3, placing U2 in the LOAD mode. This applies Vcc (5V) to R17 and R19. Vcc on R17 turns on Q5 which turns on Q4 through R16 pulling U2's RESET high. Vcc on R19 turns on Q3 which holds PSEN low. When S3 is up (shorting pins 1 and 2) the processor is in the RUN mode. Vcc is not applied to R17 and R19. Q5 is held off by R18 and Q4 is held off by R15 so RESET is pulled low by R4. Q3 is held off by R20 so PSEN is not held low and may become an output of U2. RS-232 INTERFACEThe RS-232 interfaces are used to program the DS-2250 modules and to interface to other serial devices in future applications (refer to the Programming Instructions). An Intel hex format file from a PC can be loaded into memory via the serial ports. This manual and the Software Release Notes (SRN) provide complete instructions for loading software in the field.U8 is a dual TTL-to-RS-232 duplex serial interface. Capacitors C1, C2, C3, and C4 are used by U8 to convert 5V signals to RS-232 levels. Section 1 converts U1's serial port to RS-232 and section 2 converts U2's serial port to RS-232. The serial output for U1 is at J2-2 and the input is at J2-1. The serial output for U2 is at J3-2 and the input is at J3-1.I/O BITSOne output bit from U1 is available. It is buffered by Q9 and drives out on P1-B21. Weak pull-up R30 holds P1-B21 high when Q9 is turned off by U1. One input bit to U1is available. It is buffered from P1-B20 by U15-A and protected from static and overdrive by D3 and R27. Weak pull-up R35 holds the input high when not in use.One output bit from U2 is available. It is buffered by Q10 and drives out on P1-B23. Weak pull-up R32 holds J P1-B23 high when Q10 is turned off by U2. One input bit to U2 is available. It is buffered from P1-B22 by U15-B and protected from static and overdrive by D4 and R31. Weak pull-up R36 holds the input high when not in use.LED INDICATORSLED D1 is controlled by processor U1. The processor must apply pulses to retriggerable one-shot (monostable multivibrator) U9 pin 4 about every half second or faster to keep the LED on. This provides a visual indication that the microprocessor is running. The pulse on U9-4 retriggers the output on U9-6 keeping Q1 on and LED D1 on. If the pulses don't appear before the one-shot times out, U9-6 will fall low turning Q1 and D1 off. R1 and C17 determine the drop-out time.LED D2 is controlled by processor U2. The processor must apply pulses to retriggerable one-shot (monostable multivibrator) U9 pin 12 about every half second or faster to keep the LED on. This provides a visual indication that the microprocessor is running. The pulse on U9-12 retriggers the output on U9-10 keeping Q2 on and LED D2 on. If the pulses don't appear before the one-shot times out, U9-10 will fall low turning Q2 and D2 off. R4 and C18 determine the drop-out time.HARDWARE INSTALLATIONInstallation or removal of the Turbo Card involves sliding the assembly into or out of the VME Shelf. This may be accomplished with power applied without damaging the assembly.When installing the Turbo Card, ensure the card is installed in the designated slot. Refer to the specific application drawings.SOFTWARE INSTALLATIONThe following procedures provide instructions for programming the Turbo Card using software provided with the software media kit, an IBM compatible personal computer (PC), and programming cable 19B804346P111.TURBO CARD SOFTWARE INSTALLATIONThis procedure provides instructions for downloading the Turbo software to an IBM PC or compatible personal computer.The Turbo software is distributed in the Turbo Media Kit diskette as multiple files. These files must be loaded into the PC such that they are co-located with the Trunking Card PC Programmer. Once loaded the new software becomes available for selection.Equipment Required• IBM PC/XT/AT or compatible with at least 640Kmemory, monitor and keyboard running MS-DOS version 3.3 or higher.• Two Disk Drives, a single 3-1/2 inch HD floppy and fixed (hard) drive.• Serial Port configured as either COM1 or COM2.• Parallel port for connection to a printer (optional,but recommended).• CPTC Software Media Kit AE/LZY 213 767/2.• Programming Cable, 19B804346P111 (DB-9 toRJ-12).• TQ-3357 V4.03 (or later) PC Programmer Procedure1. Run the Trunking Card PC Programmer (TQ-3357).2. Load the Turbo Distribution diskette in the disk drive.3. From the Current Personalities Screen, access theLOAD utility by selecting the F8 Utils , F8 Files and then the F1 Load . The “New File Loader” dialog box will appear.4. Enter the path to the Turbo Distribution diskette files.Figure 4 - Trunking Card PC Programmer Load File Menu5. The programmer will load all files , including the FieldMacros into the PC Programmer’s working directories.6. It is now possible to program the Turbo Card.Programming The Turbo CardThis procedure downloads the Turbo software to the microprocessors U1 and U2 on the Turbo board.1. Refer to TQ-3357 Chapter 4 - Upgrading Firmwarewith the Load1E Utility for complete instructions on downloading the Turbo software .2. Connect the Programming Cable, 19B804346P111,from the PC's serial port connector to the Turbo card input port connector U1 COM (see Figure 5).3. With power ON, move the Turbo Card RN/PG switchesto the PG position (toward the right). This places the processors U1 and U2 into the programming mode. If either switch is already in the PG position, move the switch to the RN position and then back to the PG position.4. The Turbo Card LEDs U1 (D1) and U2 (D2) shouldturn OFF indicating that the Turbo Card is in the programming mode.5. Execute the "load1e.exe " program on the PC andfollow the on screen instructions.6. The "load1e.exe " program loads the file "1etop.hex "Figure 5 - Turbo Card Programminginto the Turbo Card's upper half of memory for use by the processor U1.7. Monitor the PC's on screen instructions and prompts.8. When directed, move the programming cable from theU1 COM connector to U2 COM.9. After the cable is moved to U2 COM, the PC willindicate it is loading the "1ebot.hex" file into the Turbo Card's lower half of memory for use by the processor U2.10. Disconnect the programming cable upon successfulcompletion of the programming procedure and return the Turbo Card to the Normal operating mode. Returning To Normal Operating ModeUpon successful completion of the programming, the PC displays a "FINISHED - SWITCH S2 AND S3 TO THE REAR" message.1. Move the Turbo Card RN/PG switches to the RNposition (toward the left). This places the processors U1 and U2 into the run mode.2. Press S1 to reset the Turbo Card.3. The Turbo Card LEDs, U1 (D1) and U2 (D2), will lightindicating the code is executing.4. This completes the Turbo Card programming. If anyproblems were encountered or if any error messages were received, refer to the Error section below or Trouble Shooting section of this manual.ERRORSThe transfer process uses the file 1ECRC.HEX for error checking and verification. Any error during this procedure generally indicates a defective communication link between the PC and Turbo Card. If errors occur, check connectors and cables. Cycle the RN/PG switch from the PG to RN and back to PG. Repeat the programming sequence.Errors usually generate one or more of the following:• Error 1Did not receive sign-on banner fromDS-2250.• Error 2Did not receive CR-LF from DS-2250.• Error 3Did not receive prompt from DS-2250.• Error 4Did not receive CRC value from DS-2250.• Error 5Did not receive serial number fromDS-2250."Cannot open COM Port" - The PC's COM Port is non-existent or in use by other software or hardware. A PC re-configuration is required."Cannot open 'filename' " - Be sure file exists in the appropriate directory."Bad CRC" - A CRC error means that after loading, memory contents are incorrect or the wrong "1ecrc.Hex" file was used. If the "1ecrc.Hex" file is the same shipped with the software, a Turbo Card hardware problem is indicated."Wrong serial number-check cables" - If cabling is correct, DS-2250 microprocessors may have been swapped. The four byte serial number is printed to the screen to help in restoring DS-2250's to their proper locations. The serial numbers will be the same, except for least significant bit, for both DS-2250's The least significant bit must be logic 1 for the top DS-2250 (U1) and logic 0 for the bottom DS-2250 (U2)."Illegal serial number" - Serial number is either invalid, was never programmed, or has been erased.Serial NumberingAn error will occur when U1 and U2 are swapped. Each processor has a unique serial number with U1 having an odd serial number and U2 having a serial number one digit less than U1’s serial number. The PC’s on screen information displays the processors’ serial numbers for verification. The most significant digits of U1 and U2’s serial numbers must match.Do not swap U1 and U2 DS2250 microprocessors or take one DS-2250 from one Turbo Card and put it in another Turbo Card. However, it is permissible to swap DS-2250's as pairs if the U1 and U2 positions are maintained.TROUBLESHOOTINGIf a problem is traced to the Turbo Card, perform the following checks and inspections:• If an error message is received while loading the Turbo Card software, review ProgrammingInstructions - Errors section for possible correctiveaction.• Visually check for damaged parts, unsoldered pins or parts, broken cable or pins (P1), or unseated DS-2250 modules.• Look for trash in the SIP sockets. A magnifying glass or low power microscope is helpful.• Verify the RN/PG switch is in the RN position in the RUN condition.• Check +5, +12 and -12 volt lines.• With a high speed, high impedance scope, check for oscillations at U14-4. A somewhat flattenedsine wave of about 4V amplitude at 11.0592 MHzshould be seen.If the problem persists, substitute the Turbo Card with a known good Turbo Card. Ensure the substitute card has the correct software loaded.If the DS-2250 modules are suspect, substitute the modules with modules from a known good board. Be sure to put U1 from the good Turbo Card into XU1 of the suspect Turbo Card and likewise for U2. Remember to swap DS-2250's as pairs and reprogram the Turbo card if necessary.VERTICAL TURBO CARD ROA 117 2239(1/1078 ROA 117 2239, Sh. 1, Rev. A)Revision: DPRODUCTION CHANGESChanges in the equipment to improve performance or simplify circuits are identified by a "Revision Letter," which is stamped after the model number of the unit. The revision stamped on the unit includes all previous revisions. Refer to the parts list for the descriptions of the parts affected by these revisions.R1A ROA 117 2239 - Initial production using 131-32 ROA 117 2239 Rev. C Parts List.R1B ROA 117 2239 - Changed part number for J2 and J3 from RNV 256 103 to RNV 403 19/06.U1, U2 - MICROCONTROLLER RYT 919 6004/1 (DS2250)U3, U4 - DUAL PORT RAM RYT 119 6100/1 (IDT7134SA70J)U5, U6 - 8X1 D LATCH RYT 306 6011/C (74HC573)CAUTION OBSERVE PRECAUTIONS FOR HANDLINGELECTROSTATICSENSITIVEDEVICESU9 - 2 X CMOS MONOSTABLE MULTI-VIBRATOR RYT 306 2024/C (74HC438)FUNCTION TABLEX = H or L = from L to H Vcc R RESET ATr A+Tr A-QA QA GNDA C A R RESETB Tr B+Tr B-QB QBB C B= from H to LU11 - 4X2 NAND GATE RYT 318 0000/C (74AC00)U14- 6 X INVERTER, SCHMITT TRIGGERRYT 306 6045/C (74HCU04)1234567(GND)141312111098(Vcc)TRUTH TABLEINPUTSOUTPUTS A1 (A2,A3,A4)B1 (B2,B3,B4)O1 (O2,O3,O4)L L H L H H H L H HHLGND6Y 5A 5Y 4A 4Y6A 1Y2A 2Y 3A 3Y 1A VccU12, U13 - 32K X 8 STATIC RAM RYT 119 6005/4C (EC155257AFL)A14A12A7A6A5A4A3A2A1A0I/01I/02I/03GNDV DD R/W A13A8A9A11A10I/08I/07I/06I/05I/04OUTLINE DIAGRAM AE/LZB 119 1887 R1AVERTICAL TURBO CARD(1078-ROA 117 2239, Sh. 1, Rev. A)This page intentionally left blankAE/LZB 119 1887 R1A SCHEMATIC DIAGRAMVERTICAL TURBO CARDROA 117 2239(1911-ROA 117 2239, Sh. 1, Rev. A)21VERTICAL TURBO CARD ROA 117 2239(1911-ROA 117 2239, Sh. 2, Rev. A)Ericsson Inc.Private Radio SystemsMountain View RoadLynchburg, Virginia 24502AE/LZB 119 1887R1A 1-800-528-7711 (Outside USA, 804-528-7711)Printed in U.S.A.AE/LZB 119 1887 R1A。
封口机URS用户需求

医用封口机(2台);工业热封机(3台);工业热封机(1台);超静音滚轴工作台(2台) 1.2目的:1.2.1 通过此项设备采购,满足车间呼吸袋、纸塑袋等封口包装要求。
1.2.2保证本生产线的文件资料齐全,并且符合GMP要求。
1.2.3本设备的安装符合生产工艺要求。
1.2.4本设备在需求范围内能够稳定运行。
1.2.5 本URS将对本次采购的封口机提出用户需求,以文件形式归档保存,为设计、购买及认证提供依据。
1.2.6 本次采采购的设备,需要在满足使用工艺要求的前提下,满足计算化系统管理要求。
1.2.7 该用户需求文件以文件形式总括了用户对计算机化系统的质量要求,也描述了用户对封口机的工作过程及功能期望,包括热封能力、功能、材料、外观、文件等方面,是合同等商业行为和SAT/FAT/DQ/IQ/OQ等后续技术、质量体系工作的基础,从而保证制造商所提供的产品符合我公司的所有要求。
该URS在移交给供应商之后,意味着所有对项目指定的要求被涵盖在供应商的供应范围之内。
本URS为改造项目的基本要求,但不限于此要求(制造商可提供高于URS要求的方案)。
制造商应在规定的时间内完成并达到本用户需求的设计目标和可接受的质量标准1.3规范:1.3.1该URS文件范围:1.3.2供货/施工范围1.4用户需求编制职责:1.5 依据标准:2.内容URS01: 该系统/设备涉及产品特性要求URS03:安全要求URS04:安装区域及位置要求URS05:安装环境要求URS06:电力要求URS07:设施/公用系统要求URS08:外观要求URS11:控制系统要求URS13:清洁要求URS14:文件要求URS15:设备转运要求URS16:验证/确认要求备注:标注*项为供应商必须响应项。
三星SIRIUS软启动器3RW5525-1HA14商品说明书
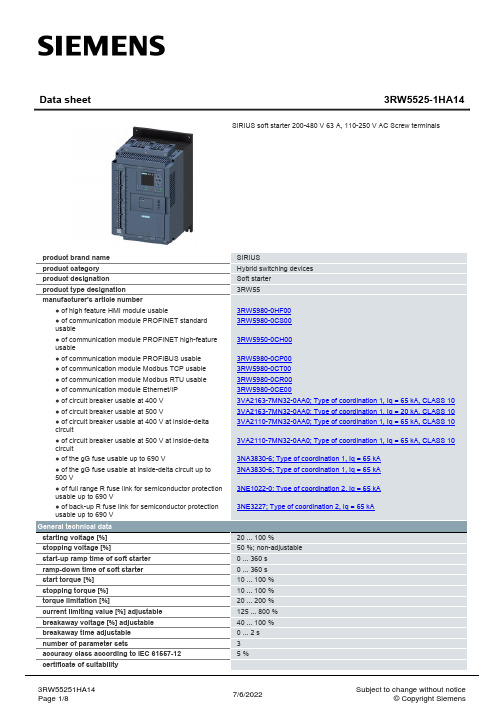
General technical data
starting voltage [%] stopping voltage [%] start-up ramp time of soft starter ramp-down time of soft starter start torque [%] stopping torque [%] torque limitation [%] current limiting value [%] adjustable breakaway voltage [%] adjustable breakaway time adjustable number of parameter sets accuracy class according to IEC 61557-12 certificate of suitability
Sun Fire X2250 服务器入门指南说明书
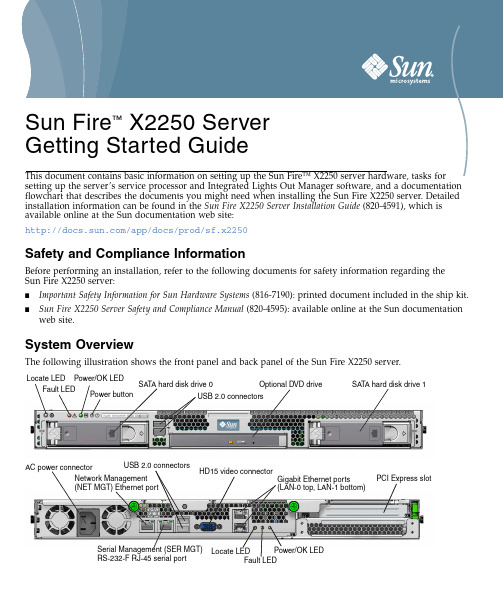
Sun Fire ™ X2250 Server Getting Started GuideThis document contains basic information on setting up the Sun Fire™X2250server hardware,tasks for setting up the server’s service processor and Integrated Lights Out Manager software,and a documentation flowchart that describes the documents you might need when installing the Sun Fire X2250server.Detailed installation information can be found in the Sun Fire X2250Server Installation Guide (820-4591),which is available online at the Sun documentation web site:/app/docs/prod/sf.x2250Safety and Compliance InformationBefore performing an installation,refer to the following documents for safety information regarding the Sun Fire X2250server:■Important Safety Information for Sun Hardware Systems (816-7190):printed document included in the ship kit.■Sun Fire X2250Server Safety and Compliance Manual (820-4595):available online at the Sun documentation web site.System OverviewThe following illustration shows the front panel and back panel of the Sun Fire X2250server.SA TA hard disk drive 1Optional DVD drive USB 2.0 connectors SA TA hard disk drive 0Locate LED Fault LED Power/OK LED Power button Locate LEDFault LEDPower/OK LED PCI Express slotGigabit Ethernet portsHD15 video connector (LAN-0 top, LAN-1 bottom)AC power connectorNetwork Management(NET MGT) Ethernet port USB 2.0 connectors Serial Management (SER MGT)RS-232-F RJ-45 serial portUnpacking the Sun Fire X2250ServerCarefully unpack all server components from the packing cartons:■Sun Fire X2250server■Optional Sun Fire X2250server accessory kit,including the following:■Sun Fire X2250Server Installation Guide(820-4591)■Additional license,safety,and registration documentation■Sun Fire X2250Server Tools&Drivers CD(includes drivers and additional software)■Optional rackmount kit containing rack rails and installation instructionsMounting the Server in a RackThe service label on the top cover of the Sun Fire X2250server contains instructions for installing your server into a four-post rack using the orderable slide-rail and cable management arm options.Detailed instructions can also be found online in the Sun Fire X2250Server Service Manual(820-4593)at the following URL:Connecting the CablesSee“System Overview”for the locations of the connectors.Connect the server and external devices as follows:1.Connect a serial null modem cable to the serial port.2.Connect Ethernet cables to the RJ-45LAN Gigabit Ethernet connectors as needed.Note the following guidelines regarding the Ethernet(LAN)ports.■The Network Management(NET MGT)Ethernet port or the Serial Management(SER MGT)RJ-45serial port can be used for server management and network access.See the Sun Fire X2250Server Installation Guide(820-4591)for detailed information about setting up the service processor for remote systemmanagement.■The two Gigabit Ethernet ports(LAN-0and LAN-1)are the primary network interface controllers (NICs)and should be used for network installation of the operating system and drivers.Powering On and Off the ServerYou only need to apply standby power to the server at this point so that you can perform initial configuration of the service processor.Procedures for powering on to main power mode and for shutting down from main power mode are also included in this section,for your reference.▼To Apply Standby Power for Initial Service Processor Configuration Use this procedure to apply standby power to the service processor(SP)before initial configuration.Caution–Do not operate the server without all fans,component heatsinks,air baffles,and the coverinstalled.Severe damage to server components can occur if operated without adequate coolingmechanisms.1.Connect a grounded AC power cord to the AC power connector on the back panel of the server and to agrounded AC power outlet.At this point,standby power is supplied only to the service processor and power supply fans.Do not apply main power to the rest of the server until you are ready to install a platform operating system.2.Continue with initial software setup tasks,as described in“Setting Up the Sun Fire X2250ServerSoftware”.▼To Power On Main Power Mode1.Verify that the power cord has been connected and that standby power is on.In standby power mode,the Power/OK LED on the front panel flashes.e a non-metallic stylus to press and release the recessed Power button on the server front panel.When main power is applied to the full server,the Power/OK LED next to the Power button lights and remains lit.Note–The first time the server powers on,the power-on self-test(POST)can take up to a minute to complete.▼To Power Off the Main Power ModeTo power off the server from main power mode,use one of the following two methods:■Graceful shutdown:Use a non-metallic stylus to press and release the Power button on the front panel.This causes Advanced Configuration and Power Interface(ACPI)enabled operating systems to perform an orderly shutdown of the operating system.■Emergency shutdown:Press and hold the Power button for four seconds to force main power off and enter standby power mode.When the main power is off,the Power/OK LED on the front panel will begin flashing,indicating that the server is in standby power mode.Caution–To completely power off the server,you must disconnect the AC power cords from theback panel of the server.Setting Up the Sun Fire X2250Server SoftwareThis section describes the tasks for initial setup of the server’s service processor and Integrated Lights Out Manager(ILOM)software.Refer to the Sun Fire X2250Server Installation Guide(820-4591)and the Sun Integrated Lights Out Manager2.0User’s Guide(820-1188)for detailed instructions on using ILOM to configure and manage the Sun Fire X2250server.Connecting to the ILOM Service ProcessorThere are three methods for connecting to the ILOM SP to perform initial setup and e the procedure that you prefer:■“Connect to ILOM Using a Serial Connection”■“Connect to ILOM Using an Ethernet Connection(DHCP)”■“Connect to ILOM Using an Ethernet Connection(Static IP Address)”Connect to ILOM Using a Serial ConnectionFollow these instructions to establish a serial connection to the ILOM SP so that you can perform initial configuration of ILOM.Note–This procedure assumes that you have already completed the hardware setup and have applied standby power to your server,as described in“Powering On and Off the Server”.▼To Connect to ILOM Using a Serial Connection1.Verify that your terminal,laptop,or terminal server is operational.2.Configure the terminal device or the terminal emulation software running on a laptop or PC to thefollowing settings:■8N1:eight data bits,no parity,one stop bit■9600baud■Disable hardware flow control(CTS/RTS)■Disable software flow control(XON/XOFF)3.Connect a serial cable from the RJ-45SER MGT port on the server’s back panel to a terminal device.4.Press Enter on the terminal device to establish a connection between the terminal device and theILOM SP.5.Log in to ILOM.The default user name is root;the default password is changeme.6.Configure your network settings using CLI.For instructions,see“Connect to ILOM Using an Ethernet Connection(Static IP Address)”.7.After configuring the server,continue with“Setting Up Platform Operating System and Driver Software”. Connect to ILOM Using an Ethernet Connection(DHCP)Follow these instructions to establish an Ethernet connection to the ILOM SP so that you can perform initial configuration of ILOM.Note–This procedure assumes that you have already completed the hardware setup and have applied standby power to your server,as described in“Powering On and Off the Server”.▼To Connect to ILOM Using an Ethernet Connection(DHCP)1.Verify that your DHCP server is configured to accept new media access control(MAC)addresses bychecking with your system administrator.2.Connect an Ethernet cable to the server’s RJ-45NET MGT Ethernet port.3.Obtain the ILOM SP IP address from one of the following locations.Record the IP address for futurereference.■CLI commands.The SP has a serial port to which you can attach a terminal device.If you log in to the SP and type the CLI command show/SP/network,the SP displays the current IP address.■Customer Information Sheet.This document is shipped with your server.■System BIOS Setup screen.Press F2during power-on,then choose Advanced→IPMI 2.0 Configuration→LAN Configuration→IP address.4.Open a session to the ILOM SP using the IP address that you obtained in Step3.You can use the CLI or the web interface.■To establish an SSH connection,type the DHCP-assigned IP address in the SSH application.For example: #ssh-1root129.144.82.20The default user name is root,which was included in the ssh command.The default password for the SP is changeme.■To establish a connection to the ILOM SP web interface,type the IP address of the ILOM SP in the browser locator box and press Enter.When prompted,type the default user name and password.5.After you have entered the user name and password in either the CLI or web interface,you can use theinterface to configure your ILOM SP.6.After configuring the server,continue with“Setting Up Platform Operating System and Driver Software”. Connect to ILOM Using an Ethernet Connection(Static IP Address)As an alternative to having your DHCP server assign an IP address to your ILOM SP,you can also assign a static IP address to it.You can do this by using the CLI over the network or serial port,by using the web interface,or by using the server’s BIOS Setup e the procedure you prefer.▼To Configure a Static IP Address Using the CLI1.Log in to the CLI using SSH or by connecting to the serial port.To establish an SSH connection to the ILOM CLI,type the DHCP-assigned IP address in the SSHapplication.For example:#ssh-1root129.144.82.20The default user name is root,which was included in the ssh command.The default password for the SP is changeme.2.Type the following commands,using your own addresses in place of the examples below:cd/SP/networkset pendingipaddress=129.144.82.26set pendingipnetmask=255.255.255.0set pendingipgateway=129.144.82.254set pendingipdiscovery=staticset commitpending=true▼To Configure a Static IP Address Using the Web Interface1.Determine the current IP address of the ILOM SP from one of the following locations:■CLI commands.The SP has a serial port to which you can attach a terminal device.If you log in to the SP and type the CLI command show/SP/network,the SP displays the current IP address.■System BIOS Setup screen.Press F2during power-on,then choose Advanced→IPMI 2.0 Configuration→LAN Configuration→IP Address.2.Connect to the ILOM SP through a web browser running on a remote system.To establish a connection to the ILOM SP,type the IP address in the browser locator box.The ILOM web interface Login screen appears.3.Log in to the web interface using the default user name,root,and the default password,changeme.4.Choose the Configuration tab and its Network tab to display information about the current networkconfiguration of your ILOM SP.5.Select the Use the Following IP Address option and type your static IP address information.▼To Configure a Static IP Address Using the BIOS Setup Utility1.Enter the BIOS Setup utility by pressing the F2key while the system is powering on and performingthe power-on self-test(POST).2.When the BIOS Main menu screen is displayed,select Advanced→IPMI 2.0Configuration→LANConfiguration→IP Address.3.On the IP Address Mode screen,select Static.4.Type the static IP address in the IP Address field.Click ESC to go back and enter the subnet mask and default gateway settings in their respective fields.5.Select Commit and press Enter to commit the changes.6.Select Refresh and press Enter to see your new static IP settings displayed in the Current IPaddress in BMC field.7.Press and release the right arrow key until the Exit menu screen is displayed.8.Follow the instructions on the Exit menu screen to save your changes and exit the BIOS Setup utility. Setting Up Platform Operating System and Driver SoftwareAfter configuring the ILOM SP with network settings,you can configure a preinstalled operating system or install a supported Solaris,Linux,or Windows platform operating system and drivers.For more information and instructions,see the following documents.■If your server contains the preinstalled Solaris10Operating System,refer to the Sun Fire X2250Server Installation Guide(820-4591)for instructions on configuring the Solaris OS on your server.■For details about installing a supported Solaris,Windows,or Linux OS and the required drivers,refer to the Sun Fire X2250Server Operating System Installation Guide(820-4592),or the Sun Installation Assistant for Windows and Linux User’s Guide(820-3357).Accessing Sun Fire X2250Server DocumentationThe flowchart below lists the documentation in the approximate order of the tasks that you might perform when installing a new system.Review the tasks on the left,then refer to the corresponding documents on the right.You can find the most up-to-date versions of all the documents at the Sun documentation web site:/app/docs/prod/sf.x2250Note –Documents that are designated as orderable printed options are not automatically included with the system.These documents must be specified as options when ordering the system.This documentation is also available on the product documentation web site.Sun OnlineViewing Current DocumentationTo see the most current version of a document,search for the Sun Fire X2250server on the Sun documentation web site:/The product documentation web site contains the most recent information.For critical updates to product information,see the product notes or release notes.To verify whether a document is more recent than the document that you have,refer to the final two digits of the part number for that document.(For example,XXX-XXXX-12is newer than XXX-XXXX-10.)Review safety information.Cable and power on server.Connect to the service processor, determine network settings.Configure the preinstalled Solaris operating system.Install supported operating systems and configure Review known issues and workarounds.Manage server accounts, monitor alerts, set remote accessand redirection, and view component status and event logs.Customize BIOS settings and RAID settings.Remove and replace hardware components.Important Safety Information for Sun Hardware Systems 816-7190 (printed)For this task...Refer to this documentProduct Notes 820-4594 (online)Operating System Installation Guide 820-4592 (online)ILOM Supplement for Sun Fire X2250 Server 820-4596 (online)Service Manual 820-4593 (online)T roubleshoot and isolate server problems.Installation Guide 820-4591 (orderable printed option and online)Safety and Compliance Manual 820-4595 (online)system utilities.Review system specifications.Sun Integrated Lights Out Manager 2.0 User’s Guide 820-1188 (online)Sun Installation Assistant 820-3357 (online)Part No. 820-4590-10, Rev. A May 2008Sun Microsystems, Inc.Translated versions of some documents are available at:Select a language from the drop-down list and navigate to the Sun Fire X2250server document collection.Available translations for the Sun Fire X2250server documentation include Simplified Chinese,Traditional Chinese,French,Japanese,and Korean.English documentation is revised more frequently and might be more up-to-date than the translated documentation.Downloading Sun Fire X2250Server Product UpdatesFor product updates,go to the following URL and navigate to the page for this product:/servers/index.jspContacting Sun Technical SupportIf you have technical questions about this product that are not answered in this document,go to:/service/contactingSun Welcomes Your CommentsSun is interested in improving its documentation and welcomes your comments and suggestions.You can submit your comments by going to:/hwdocs/feedback/Please include the title and part number of your document with your feedback:Sun Fire X2250Server Getting Started Guide ,part number 820-4590-10Copyright 2008Sun Microsystems,Inc.All rights e is subject to license terms.Third-party software,including font technology,is copyrighted and licensed from Sun suppliers.Portions may be derived from Berkeley BSD systems,licensed from U.of CA.Sun,Sun Microsystems,the Sun logo,Java,Sun Blade,and Solaris are trademarks or registered trademarks of Sun Microsystems,Inc.in the U.S.and in other countries.All SPARC trademarks are used under license and are trademarks or registered trademarks of SPARC International,Inc.in the U.S.and in other ernment Rights—Commercial ernment users are subject to the Sun Microsystems,Inc.standard license agreement and applicable provisions of the FAR and its supplements.Copyright 2008Sun Microsystems,Inc.Tous droits réservés.Distribuépar des licences qui en restreignent l’utilisation.Tout logiciel tiers,sa technologie relative aux polices de caractères comprise,est protégépar un copyright et licenciépar des fournisseurs de Sun.Des parties de ce produit peuvent dériver des systèmes Berkeley BSD licenciés par l’Universitéde Californie.Sun,Sun Microsystems,le logo Sun,Java,Sun Blade,et Solaris sont des marques de fabrique ou des marques déposées de Sun Microsystems,Inc.aux États-Unis et dans d’autres pays.Toutes les marques SPARC sont utilisées sous licence et sont des marques de fabrique ou des marques déposées de SPARC International,Inc.aux États-Unis et dans d’autres pays.。
信息化分保项目需求清单
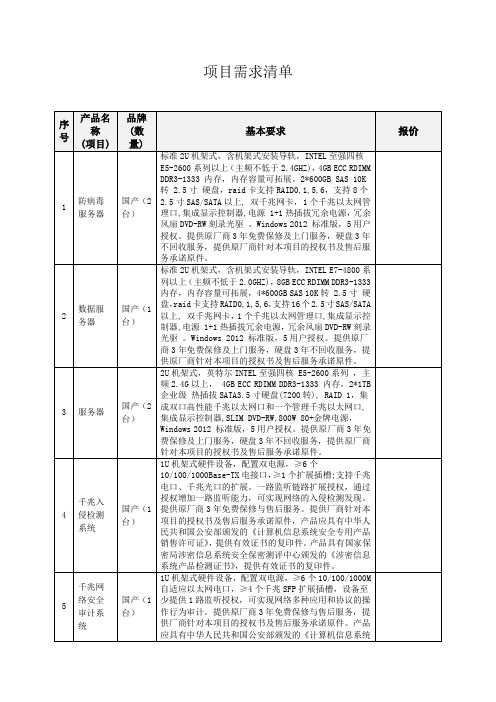
红黑隔离电源
国产
(5只)
隔离度:≧50Db(1500khz——30MHz)
电压:220V
电流:10A
负载:<2000W
支持滤波和屏蔽技术
防止电磁泄漏
抑制所有连接信息设备电源线传导泄漏发射。
符合相应的信息设备安全保密使用标准,具有国家保密局颁发的《电磁泄露发射防护产品检测证书》
11
屏蔽机柜
国产
(3台)
干扰方式: 相关干扰、空间乱数加密多重干扰
干扰带宽:10KHz-1.3GHz
保护方向:全向
干扰强度:<85dBμV/m
故障指示:声光报警
工作电压:220V±10% / 50Hz
功耗:<15W
产品符合国家保密标准BMB4-2000《电磁干扰器技术要求和测试方法》一级要求,产品具有国家保密局颁发的《电磁泄露发射防护产品检测证书》
3.网络系统达到百兆网标准,主干线路应有冗余。
4.布线系统中所有的电缆、光缆、信息模块、接插件、配线架、机柜等在其被安装的场所均应易识别,线缆布设应整齐,布线中的每根电缆、光缆、信息模块、配线架和端点应指定统一的标识符,电缆在两端应有标注;保证维护方便、操作灵活。
5.内网信息点数84个,机房布外网信息点1个。
3.供电系统:信息系统设备用电与动力、照明系统分开。不间断电源系统主机电源实际输出功率宜大于后端负载1.5倍,实际输出功率最小不得小于2KVA;满负荷运转时间不得小于120分钟。
4.空调系统:按照机房专用空调运行要求,实现24小时运行,并建立独立的新风系统。温度:夏季23±2℃,冬季20±2℃;相对湿度35~65 %;温度变化率<5℃/h,并不得凝露;机房地板下应敷设保温层,防止凝露。空调排水要合理规划,确保防漏防潮,关键部位安装漏水检测报警系统。
MOXA NPort W2150A W2250A产品说明书
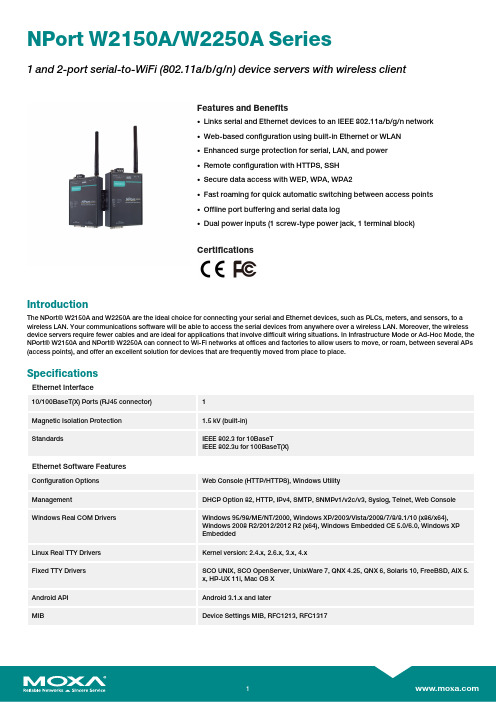
NPort W2150A/W2250A Series1and2-port serial-to-WiFi(802.11a/b/g/n)device servers with wireless clientFeatures and Benefits•Links serial and Ethernet devices to an IEEE802.11a/b/g/n network•Web-based configuration using built-in Ethernet or WLAN•Enhanced surge protection for serial,LAN,and power•Remote configuration with HTTPS,SSH•Secure data access with WEP,WPA,WPA2•Fast roaming for quick automatic switching between access points•Offline port buffering and serial data log•Dual power inputs(1screw-type power jack,1terminal block)CertificationsIntroductionThe NPort®W2150A and W2250A are the ideal choice for connecting your serial and Ethernet devices,such as PLCs,meters,and sensors,to a wireless LAN.Your communications software will be able to access the serial devices from anywhere over a wireless LAN.Moreover,the wireless device servers require fewer cables and are ideal for applications that involve difficult wiring situations.In Infrastructure Mode or Ad-Hoc Mode,the NPort®W2150A and NPort®W2250A can connect to Wi-Fi networks at offices and factories to allow users to move,or roam,between several APs (access points),and offer an excellent solution for devices that are frequently moved from place to place.SpecificationsEthernet Interface10/100BaseT(X)Ports(RJ45connector)1Magnetic Isolation Protection 1.5kV(built-in)Standards IEEE802.3for10BaseTIEEE802.3u for100BaseT(X)Ethernet Software FeaturesConfiguration Options Web Console(HTTP/HTTPS),Windows UtilityManagement DHCP Option82,HTTP,IPv4,SMTP,SNMPv1/v2c/v3,Syslog,Telnet,Web Console Windows Real COM Drivers Windows95/98/ME/NT/2000,Windows XP/2003/Vista/2008/7/8/8.1/10(x86/x64),Windows2008R2/2012/2012R2(x64),Windows Embedded CE5.0/6.0,Windows XPEmbeddedLinux Real TTY Drivers Kernel version:2.4.x,2.6.x,3.x,4.xFixed TTY Drivers SCO UNIX,SCO OpenServer,UnixWare7,QNX4.25,QNX6,Solaris10,FreeBSD,AIX5.x,HP-UX11i,Mac OS XAndroid API Android3.1.x and laterMIB Device Settings MIB,RFC1213,RFC1317Security HTTPS/SSL,Local Account Accessibility,TACACS+,SSHTime Management NTP Client,SNTP ClientWLAN InterfaceWLAN Standards802.11a/b/g/nReceiver Sensitivity for802.11a-91dBm@6Mbps-74dBm@54MbpsReceiver Sensitivity for802.11b-92dBm@1Mbps-84dBm@11MbpsReceiver Sensitivity for802.11g-91dBm@6Mbps-73dBm@54MbpsReceiver Sensitivity for802.11n(2.4GHz)-89dBm@6.5Mbps(20MHz)-71dBm@72.2Mbps(20MHz)Receiver Sensitivity for802.11n(5GHz)-89dBm@6.5Mbps(20MHz)-71dBm@72.2Mbps(20MHz)-85dBm@13.5Mbps(40MHz)-67dBm@150Mbps(40MHz)Modulation Type DSSSOFDMTransmission Distance Up to100meters(in open areas)Transmission Rate802.11a/g:54Mbps802.11b:11Mbps802.11n:6.5to150MbpsTransmitter Power for802.11b16±1.5dBm@1Mbps16±1.5dBm@11MbpsTransmitter Power for802.11g16±1.5dBm@6Mbps14±1.5dBm@54MbpsTransmitter Power for802.11a15±1.5dBm@6Mbps14±1.5dBm@54MbpsTransmitter Power for802.11n(2.4GHz)16dBm@1.5Mbps(6.5MHz)12dBm@1.5Mbps(72.2MHz)Transmitter Power for802.11n(5GHz)15dBm@1.5Mbps(6.5MHz)12dBm@1.5Mbps(150MHz)Wireless Security WEP encryption(64-bit and128-bit)WPA/WPA2-Enterprise(IEEE802.1X/RADIUS,TKIP,AES)WPA/WPA2-PersonalWLAN Modes Ad-hoc Mode,Infrastructure modeSerial InterfaceConnector DB9maleNo.of Ports NPort W2150A/W2150A-T:1NPort W2250A/W2250A-T:2Serial Standards RS-232,RS-422,RS-485Operation Modes Real COM mode,TCP Server mode,TCP Client mode,UDP mode,RFC2217mode,PairConnection mode,Ethernet Modem mode,DisabledBaudrate50bps to921.6kbpsData Bits5,6,7,8Stop Bits1,1.5,2Parity None,Even,Odd,Space,MarkFlow Control None,RTS/CTS,XON/XOFFRS-485Data Direction Control ADDC®(automatic data direction control)Pull High/Low Resistor for RS-4851kilo-ohm,150kilo-ohmsTerminator for RS-485120ohmsSurge1kVPhysical CharacteristicsHousing MetalInstallation Desktop,DIN-rail mounting(with optional kit),Wall mountingDimensions(with ears,without antenna)77x111x26mm(3.03x4.37x1.02in)Dimensions(without ears or antenna)100x111x26mm(3.94x4.37x1.02in)Weight NPort W2150A/W2150A-T:547g(1.21lb)NPort W2250A/W2250A-T:557g(1.23lb)Antenna Length109.79mm(4.32in)Environmental LimitsOperating Temperature Standard Models:0to55°C(32to131°F)Wide Temp.Models:-40to75°C(-40to167°F)Storage Temperature(package included)-40to75°C(-40to167°F)Ambient Relative Humidity5to95%(non-condensing)Power ParametersInput Current NPort W2150A/W2150A-T:179mA@12VDCNPort W2250A/W2250A-T:200mA@12VDCInput Voltage12to48VDCStandards and CertificationsEMC EN55032/24EMI CISPR32,FCC Part15B Class AEMS IEC61000-4-2ESD:Contact:4kV;Air:8kVIEC61000-4-3RS:80MHz to1GHz:3V/mIEC61000-4-4EFT:Power:2kV;Signal:2kVIEC61000-4-5Surge:Power:2kV;Signal:1kVIEC61000-4-6CS:150kHz to80MHz:3V/m;Signal:3V/mIEC61000-4-8PFMFIEC61000-4-11DIPsRadio Frequency CE(ETSI EN301893,ETSI EN300328,ETSI EN301489-17,ETSI EN301489-1),ARIBRCR STD-33,ARIB STD-66ReliabilityAlert Tools RTC(real-time clock)Automatic Reboot Trigger Built-in WDTMTBFTime NPort W2150A/W2150A-T:383,187hrsNPort W2250A/W2250A-T:363,327hrsStandardsTelcordia (Bellcore)Standard TR/SR WarrantyWarranty Period5years Details See /warrantyPackage ContentsDevice1x NPort W2150A/W2250A Series device server Power Supply1x power adapter,suitable for your region (standard temp.models only)Antenna1x 2.4/5GHz antenna Documentation 1x quick installation guide1x warranty card DimensionsOrdering InformationModel NameNo.of serial ports Serial Standards Baudrate Operating Temp.Input Current Input Voltage NPort W2150A 1RS-232/422/48550bps to 921.6kbps0to 55°C 179mA @12VDC 12-48VDC NPort W2250A 2RS-232/422/48550bps to 921.6kbps0to 55°C 200mA @12VDC 12-48VDC NPort W2150A-T 1RS-232/422/48550bps to 921.6kbps-40to 75°C 179mA @12VDC 12-48VDC NPort W2250A-T 2RS-232/422/48550bps to 921.6kbps -40to 75°C 200mA @12VDC 12-48VDCAccessories(sold separately)CablesCBL-F9M9-150DB9female to DB9male serial cable,1.5mCBL-F9M9-20DB9female to DB9male serial cable,20cmConnectorsADP-RJ458P-DB9F DB9female to RJ45connectorMini DB9F-to-TB DB9female to terminal block connectorDIN-Rail Mounting KitsDK35A DIN-rail mounting kit,35mmPower CordsCBL-PJ21NOPEN-BK-30Locking barrel plug to bare-wire cablePower AdaptersPWR-12050-WPAU-S1Locking barrel plug,12VDC,0.5A,100-240VAC,Australia(AU)plug,0to40°C operating temperature PWR-12050-WPCN-S1Locking barrel plug,12VDC,0.5A,100-240VAC,China(CN)plug,0to40°C operating temperature PWR-12050-WPEU-S1Locking barrel plug,12VDC,0.5A,100-240VAC,Continental Europe(EU)plug,0to40°C operatingtemperaturePWR-12050-WPUK-S1Locking barrel plug,12VDC,0.5A,100-240VAC,United Kingdom(UK)plug,0to40°C operatingtemperaturePWR-12050-WPUSJP-S1Locking barrel plug,12VDC,0.5A,100-240VAC,United States/Japan(US/JP)plug,0to40°Coperating temperaturePWR-12150-AU-SA-T Locking barrel plug,12VDC,1.5A,100-240VAC,Australia(AU)plug,-40to75°C operatingtemperatureApplicable Models:NPort W2150A-TNPort W2250A-TPWR-12150-CN-SA-T Locking barrel plug,12VDC,1.5A,100-240VAC,China(CN)plug,-40to75°C operating temperatureApplicable Models:NPort W2150A-TNPort W2250A-TPWR-12150-EU-SA-T Locking barrel plug,12VDC,1.5A,100-240VAC,Continental Europe(EU)plug,-40to75°C operatingtemperatureApplicable Models:NPort W2150A-TNPort W2250A-TPWR-12150-UK-SA-T Locking barrel plug,12VDC,1.5A,100-240VAC,United Kingdom(UK)plug,-40to75°C operatingtemperatureApplicable Models:NPort W2150A-TNPort W2250A-TPWR-12150-USJP-SA-T Locking barrel plug,12VDC1.5A,100-240VAC,United States/Japan(US/JP)plug,-40to75°Coperating temperatureApplicable Models:NPort W2150A-TNPort W2250A-TAntennasANT-WDB-ARM-02 2.4/5GHz,omni-directional rubber duck antenna,2dBi,RP-SMA(male)©Moxa Inc.All rights reserved.Updated Apr17,2019.This document and any portion thereof may not be reproduced or used in any manner whatsoever without the express written permission of Moxa Inc.Product specifications subject to change without notice.Visit our website for the most up-to-date product information.。
MIC2250 评估板说明书
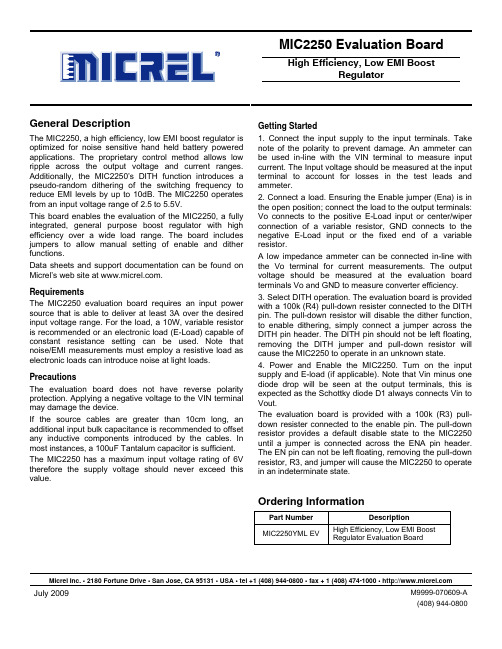
MIC2250 Evaluation BoardHigh Efficiency, Low EMI BoostRegulatorMicrel Inc. • 2180 Fortune Drive • San Jose, CA 95131 • USA • tel +1 (408) 944-0800 • fax + 1 (408) 474-1000 • General DescriptionThe MIC2250, a high efficiency, low EMI boost regulator is optimized for noise sensitive hand held battery powered applications. The proprietary control method allows low ripple across the output voltage and current ranges. Additionally, the MIC2250’s DITH function introduces a pseudo-random dithering of the switching frequency to reduce EMI levels by up to 10dB. The MIC2250 operates from an input voltage range of 2.5 to 5.5V. This board enables the evaluation of the MIC2250, a fully integrated, general purpose boost regulator with high efficiency over a wide load range. The board includes jumpers to allow manual setting of enable and dither functions. Data sheets and support documentation can be found on Micrel’s web site at . RequirementsThe MIC2250 evaluation board requires an input power source that is able to deliver at least 3A over the desired input voltage range. For the load, a 10W, variable resistor is recommended or an electronic load (E-Load) capable of constant resistance setting can be used. Note that noise/EMI measurements must employ a resistive load as electronic loads can introduce noise at light loads.PrecautionsThe evaluation board does not have reverse polarityprotection. Applying a negative voltage to the VIN terminalmay damage the device.If the source cables are greater than 10cm long, anadditional input bulk capacitance is recommended to offsetany inductive components introduced by the cables. Inmost instances, a 100uF Tantalum capacitor is sufficient.The MIC2250 has a maximum input voltage rating of 6V therefore the supply voltage should never exceed this value.Getting Started1. Connect the input supply to the input terminals. Take note of the polarity to prevent damage. An ammeter can be used in-line with the VIN terminal to measure input current. The Input voltage should be measured at the input terminal to account for losses in the test leads and ammeter.2. Connect a load. Ensuring the Enable jumper (Ena) is in the open position; connect the load to the output terminals: Vo connects to the positive E-Load input or center/wiper connection of a variable resistor, GND connects to the negative E-Load input or the fixed end of a variable resistor. A low impedance ammeter can be connected in-line with the Vo terminal for current measurements. The output voltage should be measured at the evaluation boardterminals Vo and GND to measure converter efficiency.3. Select DITH operation. The evaluation board is providedwith a 100k (R4) pull-down resister connected to the DITH pin. The pull-down resistor will disable the dither function, to enable dithering, simply connect a jumper across the DITH pin header. The DITH pin should not be left floating, removing the DITH jumper and pull-down resistor will cause the MIC2250 to operate in an unknown state. 4. Power and Enable the MIC2250. Turn on the input supply and E-load (if applicable). Note that Vin minus one diode drop will be seen at the output terminals, this isexpected as the Schottky diode D1 always connects Vin toVout.The evaluation board is provided with a 100k (R3) pull-down resister connected to the enable pin. The pull-downresistor provides a default disable state to the MIC2250until a jumper is connected across the ENA pin header.The EN pin can not be left floating, removing the pull-downresistor, R3, and jumper will cause the MIC2250 to operate in an indeterminate state.Ordering InformationPart NumberDescriptionMIC2250YML EVHigh Efficiency, Low EMI Boost Regulator Evaluation BoardEvaluation Board DescriptionBy default, the board includes feedback resistors set to give a nominal voltage of 15V at up to 300mA. The output voltage can be set between the limits of VIN and 32V. A list of common voltages and suitable components are shown below.V OUT R1 R2 5V 90.9k 30.1k 9V 102k 16.2k 12V 243k 28k15V 910k 82k 18V 1.07M 78.7k 24V 1.37M 75k 30 1.47M 63.4kThe equation for calculating R2 given a particular value of R1 and desired output voltage is:124.1112−×=VVOUTR RThe suggested values for R1 are shown below. In situations where the input voltage is less than 5V, afeedforward capacitor may be added to improve transient performance.Diode selectionFor most applications with output voltages under 12V, a Schottky diode is recommended. However, at higher output voltages, a standard diode may deliver greater efficiency. This is due to the higher reverse leakage current of a Schottky diode becoming significant at higher voltages and especially at high operating temperatures.V OUT Suggested max.R1C FF 5V < VOUT < 10V ~100k Ω 4.7nF 10V < VOUT < 15V ~240k Ω 2.2nF 15V < VOUT < 32V~1.5M Ω470pFEvaluation Board PerformanceEvaluation Board SchematicL1EnaDithBill of MaterialsItem Part number Manufacturer Description Quantity GRM21BR60J106M Murata(1)C2012X5R0J106K TDK(2)Capacitor, 10uF, 6.3V, X5R, size 0805 1 C108056D106KAT AVX(3)VJ0805G106KXYAT Vishay(4)C2 Optional GRM21BR61E225KA12L Murata(1)Capacitor, 2.2uF, 25V, X5R, size 0805 1 C308053C225MAT AVX(3)C2012X5R1E225K TDK(2)D1 SL04 Vishay(4)Schottky diode, 40V, 1A, size SMF 1 VLF5014AT-100MR92 TDK(2)Inductor, 10uH, 1.1A, 4.5x4.5x1.4mm1 L1LPS4018-103MLB Coilcraft(5)Inductor, 10uH, 1.3A, 3.9x3.9x1.7mmCDRH4D28C-100NC Sumida(6)Inductor, 10uH, 1.25A, 5.1x5.1x3mm R1 CRCW0603910KFKEYE3 Vishay Dale(4)Resistor, 910K, 1%, 1/16W, size 0603 1 R2 CRCW060382K0FKEYE3 Vishay Dale(4)Resistor, 82K, 1%, 1/16W, size 0603 1 R3,R4 CRCW06031003FKEYE3 Vishay Dale(4)Resistor, 100K, 1%, 1/16W, size 0603 2 U1 MIC2250YML Micrel, Inc(7)High Efficiency, Low EMI boost regulator 1 Notes:1. Murata: 2. TDK: 3. AVX: 4. Vishay: 5. Coilcraft: 6. Sumida: 7. Micrel, Inc.: PCB LayoutTop SilkscreenTop LayerBottom SilkscreenBottom Layer。
SignalCraft Technologies 2250谐振测量单元说明书

Getting Started GuideSC2250 – Harmonic Measurement UnitNumber: SCT-UM09D1VCDate: 2019-07-246815 – 8 Street NE, Suite 295Calgary, AB T2E7H7 CanadaThis document contains proprietary information and shall not be disclosed, in whole or in part, to any party without the expressed and written consent of an authorized representative of SignalCraft Technologies Inc. ©2013Revision HistoryTable of ContentsRevision History (2)Table of Contents (3)1.Purpose (4)2.Electromagnetic Compatibility (4)3.Unpacking and Installation (4)3.1Other Equipment (4)3.2Installing the SC2250 Instrument Driver (5)3.3Installing the SC2250 Hardware (5)4.Front Panel Connections (7)4.1Direct Connections to the SC2250 (7)4.2SC2250 Front Panel (8)5.Programming the SC2250 (10)5.1Configure in MAX (10)5.2Instrument Driver (10)1. PurposeThis document explains how to install, configure, and test the SCT SC2250. The SC2250 is a configurable 18.6 GHz up/down converter optimized for making harmonic measurements, in a single-slot PXI module. The SC2250 instrument driver, which is used to program the device, is available at /support .2. Electromagnetic CompatibilityThis product was tested and complies with the regulatory requirements and limits for electromagnetic compatibility (EMC) stated in the product specifications. These requirements and limits provide reasonable protection against harmful interference when the product is operated in the intended operational electromagnetic environment.This product is intended for use in industrial locations and environments. However, harmful interference may occur in some installations, when the product is connected to a peripheral or test device, or if the product is used in residential or commercial areas. To minimize interference with radio and television reception and prevent unacceptable performance degradation, install and use this product in strict accordance with the instructions in the product documentation.Furthermore, any changes or modifications to the product not expressly approved by SCT. could void your authority to operate it under your local regulatory rules.CAUTION: To ensure the specified EMC performance, operate this product only with shielded cables and accessories.CAUTION: To ensure the specified EMC performance, the length of all I/O cables except for that connected to the GPS antenna input must be no longer than 3 m (10 ft).3. Unpacking and InstallationCAUTION: To prevent electrostatic discharge from damaging the device, ground yourself using a grounding strap or by holding a grounded object, such as a computer chassis.• Touch the antistatic package to a metal part of a computer or PXIe chassis.•Remove the device from the package and inspect the device for loose components or any other sign of damage. Notify your reseller if the device appears damaged in any way. Do not attempt to install a damaged device.CAUTION: Never touch the exposed pins of any connectors. • Store the device in the antistatic package when the device is not in use.3.1Other EquipmentThere are several required items not included in your device kit that are needed to install and operate the SC2250.• A PXI Express chassis•A PXI Express embedded controller or MXI controller systemAdditional items will also be useful for most applications:• PXI Chassis Slot Blocker kit • SMA (m)-to-SMA (m) cables • SMA (m)-to-MMPX (m) cables •MMPX (m)-to-MMPX (m) cables3.2 Installing the SC2250 Instrument Driver•Download and install the latest version of National Instruments NI-RFSA software available at NI-RFSA NOTE: NI-RFSA v17.0 or later is required.• Download the latest version of the SC2250 instrument driver available at /support . • Unzip the downloaded instrument driver to a convenient location on your computer and run either the 32-bit (x86) or 64-bit (x64) installer depending upon the version of Windows that is installed. •Follow the instructions provided by the installation prompts.NOTE: Access and security messages will appear during installation. Accept the prompts to complete the installation.•When the installer completes, select Yes in the dialog box that prompts you to restart.3.3 Installing the SC2250 HardwareCAUTION: To prevent damage to the module caused by ESD or contamination, handle the device using the edges or the metal face plate.CAUTION: Ground yourself with a resistor-isolated wrist strap before installing the module, before touching the center pin of any connector, and before removing or adjusting any connections to the module.• Ensure that the environment you are using the SC2250 in meets the specifications outlined in the SC2250 Product Specification available at https:///support .• Ensure the AC power source is connected to the PXIe chassis before installing the module. The AC power cord grounds the chassis and protects it from electrical damage while you install the module. •Ensure that the PXIe chassis is powered off.• Inspect the slot pins on the chassis backplane for any bends or damage prior to installation. Do not install a device if the backplane is damaged.•Remove the black plastic caps from all the captive screws on the module front panel.•Identify a supported slot in the PXI chassis. SC2250 modules can only be installed in PXI Express peripheral slots. The following figure shows the symbols that indicate the slot types.1. PXI Express System Controller Slot2. PXI Peripheral Slot3. PXI Express Hybrid Peripheral Slot4. PXI Express System Timing Slot5. PXI Express Peripheral SlotFigure 1 - PXI Chassis Compatibility Symbols• Touch any metal part of the chassis to discharge static electricity. • Ensure that the ejector handle is in the unlatched (downward) position.•Place the module edges into the module guides at the top and bottom of the chassis. Slide the module into the slot until it is fully inserted.1. PXI Express Chassis2. Hardware Module3. Ejector Handle in Down (Unlatched Position)Figure 2 - Module Installation• Latch the module in place by pulling up on the ejector handle.• Secure the device front panel to the chassis using the front-panel mounting screws, which are found at the top and bottom of the module, under the ejector handle.•Cover all empty slots using filler panels or slot blockers to maximize cooling air flow.•Power on the chassis.4. Front Panel Connections4.1 Direct Connections to the SC2250The SC2250 is a precision RF instrument that is sensitive to ESD and transients. Ensure you are making proper direct connections to the SC2250 to avoid damaging the device.CAUTION: Apply external signals only while the SC2250 is powered on. Applying external signals while the device is powered off may cause damage.To prevent possible damage to the device, use caution when connecting signal sources directly to the connectors of the SC2250. Users should ensure they are properly grounded whenmanipulating cables or antennas connected to the SC2250 connectors. Ensure that there are no signal transients greater than the RF and DC specifications for the module that are being generated and sourced to the SC2250 connectors.4.2 SC2250 Front PanelFigure 3 - SC2250 Front PanelThe signal pins of this product's input/output ports can be damaged if subjected to ESD. To prevent damage, employ industry-standardESDprevention measures during installation, maintenance, and operation.Table 1 - SC2250 Front Panel Connector DescriptionTable 2 - SC2250 Front Panel LED Indicators5. Programming the SC22505.1 Configure in MAXUse National Instruments Measurement & Automation Explorer (MAX) to configure your SC2250 hardware. MAX informs other programs about which devices reside in the system and how they are configured. MAX is automatically installed with NI-RFSA• Launch MAX by navigating to Start»All Programs»National Instruments»NI MAX or by clicking the NI MAX desktop icon.• In the Configuration pane, expand Devices and Interfaces to see the list of installed devices. Installed devices appear under the name of their associated chassis.• Expand your Chassis tree item. MAX lists all devices installed in the chassis. SC2250 devices appear as “SCT SC2250” in the list. Your default device names may vary.•Record the device identifier , typically “PXI[m]Slot[n]” where [m] is the chassis number and [n] is the slot number MAX assigns to the hardware. Use this identifier when programming the SC2250.CAUTION: When you install, uninstall, or move a device in your system, resource identification of your devices may change. Whenever any of these changes occur, verify resource identification of all your devices in MAX, and, if necessary, make changes to your software and documentation.5.2 Instrument DriverThe instrument driver provided with the SC2250 is an IVI-C driver. You can use the SC2250 instrument driver to program the SC2250 in an ADE, which supports the use of C/C++ libraries, of your choice.To get started with the SC2250 instrument driver, see the SC2250 helpfile which can be found Start»All Programs»SCT»SC2250»SC2250 IVI Driver Documentation.。
argus DC2250 说明书
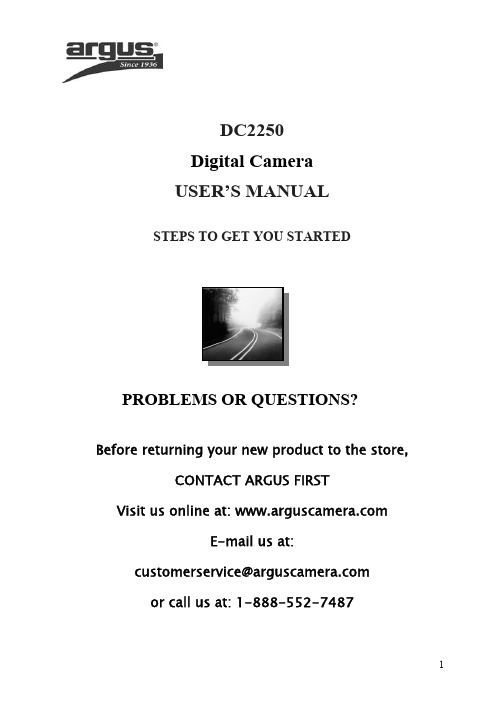
DC2250Digital CameraUSER’S MANUALSTEPS TO GET YOU STARTEDPROBLEMS OR QUESTIONS?Before returning your new product to the store, CONTACT ARGUS FIRSTVisit us online at:E-mail us at:customerservice@or call us at: 1-888-552-7487WelcomeThank you for choosing Argus Camera for your digital adventures. Whetheryou’re snapping memorable shots of yourfamily and friends or exploring the greatoutdoors, since 1936 Argus Camera has beenthere, sharpening your images with leadingedge technology. To get the utmost satisfaction from your DC2250 digital camera, please take a moment to read through this manual. Its information will send you on an educational journey into your camera’s multiple capabilities. Learn how fun and easy it is to take pictures digitally and then print them yourself without delay of film processing. Within minutes after snapping your pictures you may:•Transfer your pictures to your computer.•Enjoy multiple editing options.•Email your photos to friends and family anytime, anywhere!•Print your very own photos to enjoy for years to come.Thank you again to choosing Argus!TABLE OF CONTENTSCARING FOR YOUR CAMERA 4 FEATURES 5 BATTERY INSTALLATION 6 POWER (SLEEP MODE) 6 INSTALLING THE CF CARD 6 TAKING A PICTURE 7 SELF TIMER MODE 7 QUALTIY MODE 7 MOVIE MODE 8 TV SYSTEM SELECTION 8 DELETE MODE 8 INSTALLING DC2250 DRIVER 9 UNINSTALLING SOFTWARE 9 LIVE VIDEO MODE 9 DOWNLOADING PHOTOS USING PHOTO IMPRESSION 4.010 PHOTO AND SHARING MANAGEMENT USING10 PHOTOBASE 3.0VIDEO PLAYBACK USING VIDEOIMPRESSION 1.6 10 PLAYING MOVIE CLIPS USING QUICKTIME PLAYER 6 10Caring for Your CameraYour Argus camera is a precision instrument. Proper care will ensure years of quality performance.•Avoid exposing your camera to extreme temperatures. Prolonged exposure will adversely affect the camera’s internal components.•Keep camera dry.•To clean the lens surface, first blow away any dust or sand, then, if necessary, moisten a lens tissue or soft cloth with lens cleaning fluid and gently wipe the lens. DO NOT attempt to wipe away sand or dirt particles as this may scratch the lens’ surface.•Never touch the lens surface with your fingers.•Store your camera in a cool, dry, and well-ventilated area free of dust and chemicals.•When storing the camera for extended periods, remove the batteries.Features(1)Power (sleep-mode on/off button)(2)Mode button (scrolls through functions)(3)Select button (selects options within functions)(4)Flash Strobe (turns on and off the flash)(5)Shutter Release Button(6)USB Interface and TV Output connections(7)Battery compartment(8)View Finder(9)CF Card CoverBattery installationThis camera uses 4 AAA alkaline batteries. (Do not mix batteries of different types.)1.When replacing batteries, make sure the camera is turned off.2.Turn the camera upside down and slide the battery door toward the side of the camera to unlatch then swing it open.3.Install the batteries according to the polarity diagram on the inside panel of the battery compartment door.4.Close the battery door and slide it inward to lock in place. WARNING: Removing the batteries will erase the camera’s memory—any pictures left in the camera will be deleted.Power (sleep-mode on/off button)Pressing the button marked POWER located on the top of the camera will either wake up the camera or put it into sleep mode. The camera automatically defaults to sleep mode approx. 30 seconds after non-use. (When in sleep mode, the LCD has no display.)NOTE: To completely devoid the camera of power, and to preserve battery life, remove the batteries.Installing the CF cardThis camera accepts only CF type I cards.1.Make sure the camera is turned off.2.Open the card-slot door located on the bottom of the camera.3.Gently slide the CF card into the card slot terminal-end first with front of card facing front of camera. (CF card sold separately.)4.Close card slot door.5.To remove the CF card, open the card slot door and push the release button located beside the card slot.NOTE:•For best operation, use only high-quality CF cards such as SanDisc™ orKodak™.•When installed, the Argus DC2250 saves captured images and moviesdirectly to the CF card and bypasses its internal 6MB SDRAM memory. •Changing the batteries will not erase the CF card memory.Taking a Picture1)Look through the viewfinder and locate your subject.2)Press the shutter-release button. (The camera will beep, indicating that ithas recorded a picture.)Self-Timer Mode:Using the self-timer, the Argus DC2250 will automatically snap a picture ten seconds after pressing the shutter-release button.1)Preferably, mount the DC2250 onto a tripod or and otherwise solid surface.2)Aim the camera at the selected image.3)Press the SELECT button until the ( ) icon appears.4)Press the SHUTTER-RELEASE button.5)The camera will beep for ten seconds then automatically snap a picture. Quality Mode:The Argus DC2250 offers different qualities of image recording, fromFINE (high quality, uses most memory—stores less images) to ECONOMY (low quality, uses least memory—stores more images).To change image quality:1)Press the MODE button once—FEA appears on the LCD. (You havefive seconds to continue in this mode before the LCD defaultsback to main menu.)2)Press the SELECT button to change from FINE, to NORM, to ECON,to x2, to the movie icon, and back to FINE.3)Pause for approximately five seconds on the quality setting ofchoice. The LCD will default to main menu with your changedquality setting.Movie Mode:1)Press the MODE button once—FEA appears on the LCD. (You havefive seconds to continue in this mode before the LCD defaultsback to main menu.)2)Press the SELECT button to scroll to the movie icon.3)Pause for approximately five seconds on the movie icon. The LCDwill default to main menu with your changed quality setting.4)Press and hold the shutter-release button to record your movie.(During movie recording, the camera will emit a steady beep andthe movie icon will flash on the LCD screen.)5)To stop recording your movie, release the shutter-release button.(The movie may automatically stop recording under certainconditions—low battery, exhausted memory, etc.)TV System Selection:1)Use a TV cable to connect the camera to your TV.2)Press the Power button to turn on the camera.3)Press the Mode button until the NTSC or PAL icon appears on the LCDscreen.4)Press the Select button to set NTSC or PAL to match your TV system.5)The main menu will appear on your TV screen.NOTE:For USA and JAPAN, choose NTSC.For EUROPE, choose PAL.Delete Mode:1. Press the Mode button until the trash icon appears on the LCD screen.2. Press the Select button to delete all pictures.3. The trash icon blinks as the camera and/or CF card memory clears.4. The LCD screen will revert to the previous operating mode.Install DC2250 Camera Driver1)Insert installation CD into your computer's CD-ROM drive.2)Introduction screen will appear automatically.3)Click "DC2250 Camera Driver " .4)Follow on-screen instruction to install camera drivers.Installing Software for:Arcsoft™PhotoImpression 4.0Arcsoft™PhotoBase 3.0Arcsoft™VideoImpression 1.6QuictTime Player 61)Insert installation CD into your computer's CD-ROM drive.2)Introduction screen will appear automatically.3)Click on desired software from selection.4)Follow on-screen instructions.5)Restart your computer.Uninstalling Software:1)Search through: Start>Programs>desired software>Uninstall.2)Follow on-screen instructions to uninstall software.NOTE: For help, click "help" on the pull-down menu. For online help, click the "?" Icon.For Windows 98SE user, please go to Microsoft to update Windows for Mass Storage Function Support.As a USB Mass Storage Device, with the camera connected, itsmemory will simply appear as a disk drive to the host computer.Any files can be copied to and from the camera's memory, just likeany other file on any other disk drive.Mass Storage Mode (Manufacturer Default Setting)Live Video ModePress and hold "Mode" and "Shutter" buttons simultaneously for 5 seconds to switch between "SD-Mass Storage Mode" and "CD-Live Video Mode". (When running Photo Impression 4.0, please set to SD Mode.)Downloading Photos using PhotoImpression 4.01)Click "PhotoImpression 4.0" icon on desktop.2)Click "From Folder" button.3)Click "Browse ".4)Click "D:\ or G:\(Mass Storage Disk)SVI"; click OK.5)Use on-screen editing tools to modify images.Turn on the camera power before connecting the USB cable. Photo and Sharing Management Using PhotoBase 3.01)Click "PhotoBase 3.0" icon on desktop.2)Open Album menu bar.3)Select "Create New" and enter file name.4)Open Album menu bar and select " Add Image".5)Save the pictures to your computer.6)Share and manage your picturesVideo Playback using VideoImpression 1.61)Click "VideoImpression 1.6" icon on desktop.2)Click "New" button.3)Click "Capture".NOTE: Please set the camera to CD ModePlaying Movie Clips Using QuickTime Player 61)Change camera mode to SD2)Click "QuickTime Player" icon on desktop.3)Open "File" menu bar and select "Open Movie in New Player".4)Select "Desktop" and click "My Computer".5)Click "VOLUMELABE (F:)6)Click "SVI-0001"7)Movie will begin to play.SPECIFCATIONSImage Sensor CMOS 640x480 pixelsLens Specification F3.0, Sensor area 1/3". f=6.9mm,view angle 50, Glass LensO/S Microsoft® Windows®98/2000/ME/XP,Mac® OS 9/10Flash Strobe Yes (Auto, Flash off)White Balance AutoExposure Control AutoFrame Rate-Video Mode QVGA 320x240 pixels 10-13 fpsQQVGA 160x120 pixels 11-13 fpsStores Picture- Still Picture Mode (Based on 8 MB Compact Flash Card)VGA 640x480 pixels (Fine) up to 70 pictures VGA 640x480 pixels (Normal) up to 120 pictures QVGA 320x240 pixels (Economy) up to 480 picturesPC Interface USBStorage 8MB SDRAM Memory + CompactFlash Card (card not included;please purchase card separately) Compression JPEGDisplay Status LCDZoom 2x digital zoomMovie Clip QQVGA 160x120 pixels up to 40sec. @8fpsVideo Output NTSC or PALPower Source 4 x AAA 1.5V (not included) Dimensions 103mm x 70mm x 35mm11。
半导体传感器ADUM2250ARWZ中文规格书
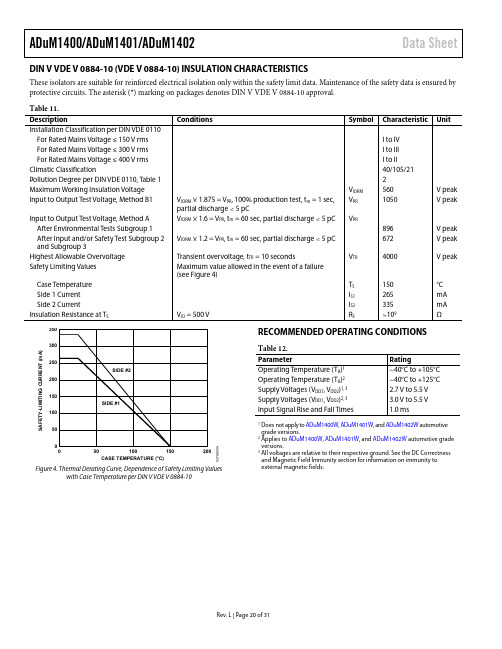
ADuM1400/ADuM1401/ADuM1402Data SheetRev. L | Page 20 of 31DIN V VDE V 0884-10 (VDE V 0884-10) INSULATION CHARACTERISTICSThese isolators are suitable for reinforced electrical isolation only within the safety limit data. Maintenance of the safety data is ensured by protective circuits. The asterisk (*) marking on packages denotes DIN V VDE V 0884-10 approval. Table 11.DescriptionConditions Symbol Characteristic Unit Installation Classification per DIN VDE 0110For Rated Mains Voltage ≤ 150 V rmsI to IV For Rated Mains Voltage ≤ 300 V rmsI to III For Rated Mains Voltage ≤ 400 V rmsI to II Climatic Classification40/105/21 Pollution Degree per DIN VDE 0110, Table 12 Maximum Working Insulation VoltageV IORM 560 V peak Input to Output Test Voltage, Method B1V IORM × 1.875 = V PR , 100% production test, t m = 1 sec, partial discharge < 5 pC V PR 1050 V peak Input to Output Test Voltage, Method AV IORM × 1.6 = V PR , t m = 60 sec, partial discharge < 5 pC V PR After Environmental Tests Subgroup 1896 V peak After Input and/or Safety Test Subgroup 2and Subgroup 3V IORM × 1.2 = V PR , t m = 60 sec, partial discharge < 5 pC 672 V peak Highest Allowable OvervoltageTransient overvoltage, t TR = 10 seconds V TR 4000 V peak Safety Limiting ValuesMaximum value allowed in the event of a failure (see Figure 4) Case TemperatureT S 150 °C Side 1 CurrentI S1 265 mA Side 2 CurrentI S2 335 mA Insulation Resistance at T SV IO = 500 V R S >109 Ω CASE TEMPERATURE (°C)S A F E T Y -L I M I T I N G C U R R E N T (m A )003503002502001501005050100150200SIDE #1SIDE #203786-004Figure 4. Thermal Derating Curve, Dependence of Safety Limiting Values with Case Temperature per DIN V VDE V 0884-10 RECOMMENDED OPERATING CONDITIONS Table 12.Parameter Rating Operating Temperature (T A )1 −40°C to +105°C Operating Temperature (T A )2 −40°C to +125°C Supply Voltages (V DD1, V DD2)1, 3 2.7 V to 5.5 V Supply Voltages (V DD1, V DD2)2, 3 3.0 V to 5.5 V Input Signal Rise and Fall Times 1.0 ms 1 Does not apply to ADuM1400W , ADuM1401W , and ADuM1402W automotive grade versions. 2 Applies to ADuM1400W , ADuM1401W , and ADuM1402W automotive grade versions. 3 All voltages are relative to their respective ground. See the DC Correctness and Magnetic Field Immunity section for information on immunity to external magnetic fields.Data SheetADuM1400/ADuM1401/ADuM1402 Rev. L | Page 21 of 31ABSOLUTE MAXIMUM RATINGSAmbient temperature = 25°C, unless otherwise noted. Table 13.ParameterRating Storage Temperature (T ST )−65°C to +150°C Ambient Operating Temperature (T A )1−40°C to +105°C Ambient Operating Temperature (T A )2−40°C to +125°C Supply Voltages (V DD1, V DD2)3−0.5 V to +7.0 V Input Voltage (V IA , V IB , V IC , V ID , V E1, V E2)3, 4−0.5 V to V DDI + 0.5 V Output Voltage (V OA , V OB , V OC , V OD )3, 4−0.5 V to V DDO + 0.5 V Average Output Current per Pin 5Side 1 (I O1)−18 mA to +18 mA Side 2 (I O2)−22 mA to +22 mA Common-Mode Transients 6−100 kV/µs to +100 kV/µs 1 Does not apply to ADuM1400W , ADuM1401W , and ADuM1402W automotive grade versions.2 Applies to ADuM1400W , ADuM1401W , and ADuM1402W automotive grade versions.3 All voltages are relative to their respective ground.4 V DDI and V DDO refer to the supply voltages on the input and output sides of a given channel, respectively. See the PC Board Layout section.5 See Figure 4 for maximum rated current values for various temperatures.6 This refers to common-mode transients across the insulation barrier. Common-mode transients exceeding the Absolute Maximum Ratings may cause latch-up or permanent damage.Stresses at or above those listed under Absolute Maximum Ratings may cause permanent damage to the product. This is a stress rating only; functional operation of the product at these or any other conditions above those indicated in the operational section of this specification is not implied. Operation beyond the maximum operating conditions for extended periods may affect product reliability. ESD CAUTION Table 14. Maximum Continuous Working Voltage 1ParameterMax Unit Constraint AC Voltage, Bipolar Waveform565 V peak 50-year minimum lifetime AC Voltage, Unipolar WaveformBasic Insulation1131 V peak Maximum approved working voltage per IEC 60950-1 Reinforced Insulation560 V peak Maximum approved working voltage per IEC 60950-1 and VDE V 0884-10 DC VoltageBasic Insulation1131 V peak Maximum approved working voltage per IEC 60950-1 Reinforced Insulation560 V peak Maximum approved working voltage per IEC 60950-1 and VDE V 0884-10 1 Refers to continuous voltage magnitude imposed across the isolation barrier. See the Insulation Lifetime section for more details. Table 15. Truth Table (Positive Logic)V Ix Input 1V Ex Input 1, 2 V DDI State 1 V DDO State 1 V Ox Output 1 Notes HH or NC Powered Powered H LH or NC Powered Powered L XL Powered Powered Z XH or NC Unpowered Powered H Outputs return to the input state within 1 µs of V DDI power restoration. XL Unpowered Powered Z X X Powered Unpowered Indeterminate Outputs return to the input state within 1 µs of V DDO power restoration if the V Ex state is H or NC. Outputs return to a high impedance statewithin 8 ns of V DDO power restoration if the V Ex state is L.1V Ix and V Ox refer to the input and output signals of a given channel (A, B, C, or D). V Ex refers to the output enable signal on the same side as the V Ox outputs. V DDI and V DDO refer to the supply voltages on the input and output sides of the given channel, respectively.2 In noisy environments, connecting V Ex to an external logic high or low is recommended.。
MEMORY存储芯片MX25R3235FZBIL0中文规格书
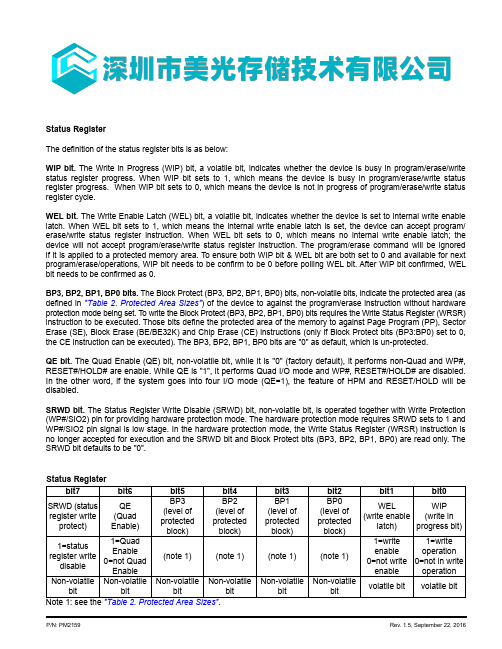
Status RegisterNote 1: see the "Table 2. Protected Area Sizes".bit7bit6bit5bit4bit3bit2bit1bit0SRWD (status register write protect)QE (Quad Enable)BP3 (level of protected block)BP2 (level of protected block)BP1 (level of protected block)BP0 (level ofprotected block)WEL (write enable latch)WIP (write inprogress bit)1=statusregister write disable1=QuadEnable0=not QuadEnable(note 1)(note 1)(note 1)(note 1)1=write enable 0=not write enable 1=write operation 0=not in write operation Non-volatile bit Non-volatile bit Non-volatile bit Non-volatile bit Non-volatile bit Non-volatilebit volatile bitvolatile bitStatus RegisterThe definition of the status register bits is as below:WIP bit. The Write in Progress (WIP) bit, a volatile bit, indicates whether the device is busy in program/erase/write status register progress. When WIP bit sets to 1, which means the device is busy in program/erase/write status register progress. When WIP bit sets to 0, which means the device is not in progress of program/erase/write status register cycle.WEL bit. The Write Enable Latch (WEL) bit, a volatile bit, indicates whether the device is set to internal write enable latch. When WEL bit sets to 1, which means the internal write enable latch is set, the device can accept program/erase/write status register instruction. When WEL bit sets to 0, which means no internal write enable latch; the device will not accept program/erase/write status register instruction. The program/erase command will be ignored if it is applied to a protected memory area. To ensure both WIP bit & WEL bit are both set to 0 and available for next program/erase/operations, WIP bit needs to be confirm to be 0 before polling WEL bit. After WIP bit confirmed, WEL bit needs to be confirmed as 0.BP3, BP2, BP1, BP0 bits. The Block Protect (BP3, BP2, BP1, BP0) bits, non-volatile bits, indicate the protected area (as defined in "Table 2. Protected Area Sizes") of the device to against the program/erase instruction without hardware protection mode being set. T o write the Block Protect (BP3, BP2, BP1, BP0) bits requires the Write Status Register (WRSR) instruction to be executed. Those bits define the protected area of the memory to against Page Program (PP), Sector Erase (SE), Block Erase (BE/BE32K) and Chip Erase (CE) instructions (only if Block Protect bits (BP3:BP0) set to 0, the CE instruction can be executed). The BP3, BP2, BP1, BP0 bits are "0" as default, which is un-protected.QE bit. The Quad Enable (QE) bit, non-volatile bit, while it is "0" (factory default), it performs non-Quad and WP#, RESET#/HOLD# are enable. While QE is "1", it performs Quad I/O mode and WP#, RESET#/HOLD# are disabled. In the other word, if the system goes into four I/O mode (QE=1), the feature of HPM and RESET/HOLD will be disabled.SRWD bit. The Status Register Write Disable (SRWD) bit, non-volatile bit, is operated together with Write Protection (WP#/SIO2) pin for providing hardware protection mode. The hardware protection mode requires SRWD sets to 1 and WP#/SIO2 pin signal is low stage. In the hardware protection mode, the Write Status Register (WRSR) instruction is no longer accepted for execution and the SRWD bit and Block Protect bits (BP3, BP2, BP1, BP0) are read only. The SRWD bit defaults to be "0".Configuration RegisterThe Configuration Register is able to change the default status of Flash memory. Flash memory will be configured after the CR bit is set.TB bitThe Top/Bottom (TB) bit is a non-volatile OTP bit. The Top/Bottom (TB) bit is used to configure the Block Protect area by BP bit (BP3, BP2, BP1, BP0), starting from TOP or Bottom of the memory array. The TB bit is defaulted as “0”, which means Top area protect. When it is set as “1”, the protect area will change to Bottom area of the memory device. To write the TB bit requires the Write Status Register (WRSR) instruction to be executed.L/H switch bitThe Low Power / High Performance bit is a volatile bit. User can change the value of L/H switch bit to keep Ultra Low Power mode or High Performance mode. Please check Ordering Information for the L/H Switch default support.Configuration Register - 1bit7bit6bit5bit4bit3bit2bit1bit0ReservedDC(DummyCycle)Reserved ReservedTB(top/bottomselected)Reserved Reserved Reservedx 2READ/4READDummyCyclex x0=Top areaprotect1=Bottomarea protect(Default=0)x x xx Volatile bit x x OTP x x x Configuration Register - 2bit7bit6bit5bit4bit3bit2bit1bit0 Reserved Reserved Reserved Reserved Reserved Reserved L/H Switch Reservedx x x x x x 0 = Ultra Low power mode1 = High performancemodexx x x x x x Volatile bit xDC Numbers of DummyCycles2READ 0 (default)4184READ 0 (default)6110Dummy Cycle Table10-9. Write Status Register (WRSR)The WRSR instruction is for changing the values of Status Register Bits and Configuration Register Bits. Before sending WRSR instruction, the Write Enable (WREN) instruction must be decoded and executed to set the Write Enable Latch (WEL) bit in advance. The WRSR instruction can change the value of Block Protect (BP3, BP2, BP1, BP0) bits to define the protected area of memory (as shown in "Table 2. Protected Area Sizes"). The WRSR also can set or reset the Quad enable (QE) bit and set or reset the Status Register Write Disable (SRWD) bit in accordance with Write Protection (WP#/SIO2) pin signal, but has no effect on bit1(WEL) and bit0 (WIP) of the status register. The WRSR instruction cannot be executed once the Hardware Protected Mode (HPM) is entered.The sequence of issuing WRSR instruction is: CS# goes low→ sending WRSR instruction code→ Status Register data on SI→CS# goes high.The CS# must go high exactly at the 8 bits, 16 bits or 24 bits data boundary; otherwise, the instruction will be rejected and not executed. The self-timed Write Status Register cycle time (tW) is initiated as soon as Chip Select (CS#) goes high. The Write in Progress (WIP) bit still can be checked during the Write Status Register cycle is in progress. The WIP sets 1 during the tW timing, and sets 0 when Write Status Register Cycle is completed, and the Write Enable Latch (WEL) bit is reset. Please note that there is another parameter, "Write Status Register cycle time for Mode Changing Switching (tWMS)", which is only for the self-timed of Mode Switching (changing L/H switch bit). For more detail please check "Table 17. AC Characteristics".Table 7. Protection ModesNote:1.As defined by the values in the Block Protect (BP3, BP2, BP1, BP0) bits of the Status Register, as shown in "Table2. Protected Area Sizes".ModeStatus register condition WP# and SRWD bit status Memory Software protectionmode (SPM)Status register can be written in (WEL bit is set to "1") andthe SRWD, BP0-BP3bits can be changed WP#=1 and SRWD bit=0, or WP#=0 and SRWD bit=0, or WP#=1 and SRWD=1The protected areacannotbe program or erase.Hardware protectionmode (HPM)The SRWD, BP0-BP3 of status register bits cannot bechangedWP#=0, SRWD bit=1The protected areacannotbe program or erase.Figure 15. WRSR flow。
- 1、下载文档前请自行甄别文档内容的完整性,平台不提供额外的编辑、内容补充、找答案等附加服务。
- 2、"仅部分预览"的文档,不可在线预览部分如存在完整性等问题,可反馈申请退款(可完整预览的文档不适用该条件!)。
- 3、如文档侵犯您的权益,请联系客服反馈,我们会尽快为您处理(人工客服工作时间:9:00-18:30)。
SATA II Solid State Disk Embedded Application High-Speed NAND Storage TFBGA 324-ball, 17x17 mm Lead-free and RoHS Compliant
Package
SATA Host
Zoom Family
Key Features
SATA Interface Compliant with Serial ATA Revision 2.6 specification 1.5 Gbps/ 3.0 Gbps interface rate Supports Native Command Queuing Supports TRIM command based on ATA-8 Supports 48-bit Logical Block Addressing (LBA) Supports partial and slumber mode Flash Interface Supports ONFI 2.1/2.2 Synchronous/Asynchronous Interface Supports Toggle Synchronous Interface 8 parallel channel flash interface 8 CE pins per channel to support 8/16 flash devices Global Wear Leveling Flash Memory Support Supports all 2x/3x nm MLC/SLC NAND Flash Supports 2KB, 4KB, and 8KB page size 2-plane Interleave structure Supports External DRAM DDR/DDR2/Mobile DDR Supports 16-bit data bus width only Supports DRAM with capacity of up to 2Gb Robust Data Protection Enhanced hardware BCH ECC engine Software/Hardware write protect option StaticDataRefresh technology ensures data integrity Early weak block retirement option Multiple data security zones Controller Core 32-bit RISC CPU Built-in 1.2V Power-On-Reset Built-in 2.5V and 2.3V voltage detectors for power fail protection Automatic sleep and wake-up mechanism to save power Upgradeable Firmware Supports firmware in system programming (ISP) function for firmware upgrade Operating Temperature Commercial version: 0°C ~ 70°C Industrial version: -40°C ~ 85°C
Mobile Storage SM2250
SATA Solid-State Drive Controller
With the powerful and configurable ECC engine and The SM2250 SATA SSD Controller is designed with outstanding performance and a high level of reliability for a wide range of applications: enterprise server, workstation system, online storage, notebook, and desktop. The SSD functions at much faster transfer speed by saving spin-up and seek time in traditional HDD and enables a shock-protected and quietoperating environment for mobile storage requirements without any moving mechanical parts. The SM2250 employees the 8 channel flash interface with advanced TRIM command, low write amplification factor, native command queuing, and global wear leveling to achieve the extremely high input/output per second (IOPS). From the moment of boot-up till the system powers off, Silicon Motion’s error correcting coding, bad block management and other proprietary technologies ensure the data correction and security. With all the featured designs in hardware and software, the SM2250 can fulfill a perfect storage system presenting higher performance and shorter response time for enterprise-class applications and high capacity consumer storage. Applications
U
Flash Controller
NAND Flash Die(s)
SRAM
DDR/ DDR2/ Mobile DDR
DRAM Controller
ROM
Power Saving Control
This publication, including all photographs, illustrations and software, is protected under international copyright laws, with all rights reserved. Neither this publication, nor any of the material contained herein, may be reproduced without written consent of the manufacturer. © Copyright 2011 Silicon Motion, Inc.