工业工程七大手法标准工时的计算方法
工业工程-标准工时的计算与方法

研析實施某一設定工作所需時間,以求衡定完成任一單位計件或成品之標準工作時間,再據以訂制作業員之”一日合理工作量”.
2.範圍:
本廠所有生產之產品.
3.名詞解釋:
正常速度(時間):操作速度不快亦不慢,經長時間操作對作業員之生理與心理方面無損害而言.此種狀況下所需時間稱為正常時間.
正常作業員:受過良好訓練的合格操作人員.
觀測時間:經實際操作測量出的時間.
評比系數:指調整至平均工人正常速度之基準,系數不可超過1.
寬放率:指因個人私務,疲勞與被迫,暫停工所給予之時間比例率,其範圍
值為8%-15%.
5.3.2.2標準工時數據:將所測之各站別所需時間以分門別類,制作標準工時數據.
5.3.2.3時間公式:凡變值站別甚多之非重復性工作,可選擇具有代表性之變值逐一研究,然後依所得資料予以整理,研析各變值站別之時間關系,歸納成一代數式,以迅速計列各種不同變值站別所需之時間,此代數式稱為時間公式.
6.標準工時的計算:
由定額人員,技術人員和有經驗的老工人組成估列小組,根據產品設計圖紙,工藝規程,工裝條件和設備狀態,以及生產組織形式,憑各自的實踐經驗來估計工時.
5.2經驗法:
根據過去經驗之累積記錄而設定.
5.3衡量法:根據事實而定.
5.3.1直接測定法
5.3.1.1碼表測時:直接用碼表測時,經評估比正常時間再加以寬放而成標準時間.
標準工作條件:標準工作方法與設備及標準工作環境.
寬放時間:因個人私務,疲勞與被迫,暫停工作所給予之時間.
4.定義:
即一個合格的工人(具有正常的體力和智力,在勞動技術方面受過良好訓練,並具有一定熟練程度的工人)在標準的作業方法和條件下,以正常的作業速度完成某一工作所需的時間.
工业工程七大手法和五项原则

工业工程七大手法和五项原则嘿,小伙伴们,今天我们聊聊工业工程那些既有趣又实用的秘密武器。
别看工业工程这名字一听就像是高大上的东西,其实它里边藏着一大堆让你眼前一亮的绝招。
那啥,七大手法和五项原则就像是给你的工作加了个“超级加倍”的魔法,让你干活儿更轻松,效果更棒。
好了,咱们一块儿来扒一扒这些工业工程的“黑科技”吧!1. 七大手法大公开1.1 流程图首先,来聊聊流程图。
这个家伙可以说是工业工程的“老大哥”了,啥事儿都得从它开始。
流程图就是把工作步骤像做菜谱一样,逐一列出来。
不管是生产线还是办公室,流程图就像是你人生的GPS,不迷路的关键就在于它。
你看,图里每一步都清清楚楚,一目了然。
没了它,你的工作就像是蒙着眼睛打拳,乱打一气,根本没办法击中目标。
1.2 作业分析然后是作业分析,这玩意儿也很重要。
它就像是对你工作的“体检报告”,告诉你哪里做得好,哪里需要改进。
通过作业分析,你可以发现哪些环节浪费时间,哪些动作重复无聊。
比方说,你在工作时一会儿找这个,一会儿找那个,搞得人心烦意乱。
作业分析帮你找出这些麻烦点,让你能一招制敌,不再被小问题绊脚。
1.3 时间研究再来看看时间研究。
这个就是工业工程界的“时钟专家”了。
它通过细致的观察和测量,告诉你每一步工作到底要多久。
简单说,就是帮你把时间花得更值,更高效。
时间研究就像是为你的工作设置了个闹钟,让你能按部就班地完成任务,而不会拖拖拉拉。
1.4 动作研究接着是动作研究。
这家伙的使命就是让你的动作更加“省力”,减少不必要的动作。
就像你在厨房里炒菜时,如果切菜的动作能更顺手,那炒出来的菜肯定更快。
动作研究就是帮你找出这些省力的“窍门”,让你干活时更加顺畅,减少那些无谓的弯路。
1.5 仓库管理说到仓库管理,它就是你工作的“守门员”。
仓库管理让你的物料存放更加有序,不会一堆乱七八糟的东西挤在一起。
像你家里整理衣柜一样,分类放置,方便取用。
一个整理得当的仓库能大大减少找东西的时间,提高整体的工作效率。
【IE知识】81个IE(工业工程)专业术语,基础掌握牢很重要!

【IE知识】81个IE(工业工程)专业术语,基础掌握牢很重要!展开全文1.标准工时/标准时间在适宜的操作条件下,用最合适的操作方法,以普通熟练工人的正常速度完成标准作业所需的劳动时间标准时间=正常时间*(1 宽放率)=(观测时间*评比系数)*(1 宽放率)2.工时定额对某种作业的工时规定一个额度,即使对同一作业,由于用途不同可能有不同量值的定额,如现行定额、计划定额、目标定额等3.标准时间与工时定额的关系标准时间是制定工作定额的依据、工时定额是标准时间的结果4.时间研究时间研究是一种作业测定技术,旨在决定一位合格、适当、训练有素的操作者,在标准状态下,对一特定的工作以正常速度操作所需要的时间5.时间研究的研究方法时间研究是用抽样调查技术来对操作者的作业进行观测,以决定作业的时间标准6.剔除异常值的方法三倍标准偏差法:正常值为x /-3 内的数据,超出者为异常值7.每一单元的平均操作时间平均操作时间=Σ(观测时间值)/ 观测次数8.正常时间正常时间=Σ(单元观测时间X单元评比百分率)/ 观测次数9.宽放时间的种类私事宽放\疲劳宽放\周期动作宽放时间\干扰宽放时间\临时宽放时间\政策宽放时间\程序宽放10.宽放率宽放率(%)=(宽放时间/正常时间) X100%11.宽放时间宽放时间=正常时间X宽放率12.标准时间标准时间=平均操作时间X评比宽放时间13.瓶颈生产线作业工时最长的工站的标准工时称之为瓶颈\产出的速度取决于时间最长的工站14.实测时间作业者完成操作的实际时间15.节拍根据生产计划所得的一个工程所需的时间16.平衡率生产线各工程工作分割的均衡度,用于衡量流程中各工站节拍符合度的一个综合比值=Σ(T1 T2 ...... Tk)/Tbottleneck*K17.不平衡率生产线各工程工作分割的不均衡度不平衡率=(最大值-最小值)/平均值*100%18.平衡损失平衡损失=瓶颈工站的实际时间×工站数×FG-正常时间19.操作损失生产中异常及不良造成的损失操作损失=(设定产能-实际产量)?单件标准时间-额外产出工时=不良品损失计划外停线(机)工时20.总损失总损失=稼动损失平衡损失操作损失21.快速切换通过各种手段,尽可能的缩短作业切换时间,以减少时间浪费,达成提高综合效益之目的22.作业切换时间是指前一品种加工结束到下一品种加工出良品的这段时间23.外部切换时间不必停机也能进行的切换作业时间24.内部切换时间必须停机才能进行的切换以及为保证质量进行的调整、检查等占用的切换时间25.JIT的基本思想只在需要的时候、按需要的量、生产所需的产品,故又被称为准时制生产、适时生产方式、广告牌生产方式26.JIT的核心零库存和快速应对市场变化27.劳动定额的时间构成劳动定额的时间构成=作业时间布置工作地时间休息与生理需要时间准备与结束时间/批量劳动定额的时间构成可供时间:上班时间内,为某产品生产而投入的所有时间可供工时=可供时间 *人数-借出工时投入工时=可供工时-计划停线工时稼动率=投入工时/可供工时 *100%计划停线工时=计划停线时间*人数计划停线时间=无计划时间换线时间判停时间设定产能(H) =3600(S)/瓶颈时间(S)设定产能(班)=投入时间/瓶颈时间(S)总工时=瓶颈时间*作业人数实际产量是可供时间内所产出的良品数人均产能=实际产量/投入时间/人数单机台产能=实际产量/投入时间/机台数平衡损失=(总工时-单件标准时间)*设定产能操作效率=实际产量/设定产能*100%整体工厂效率(OPE)=平衡率*稼动率*操作效率平衡损失=(瓶颈*作业人数-单件标准时间)*设定产能操作损失=(设定产能-实际产量)*单件标准时间-额外产出工时=不良品损失计划外停线(机)工时28.工费率平均每小时发生费用=单位时间内发生总费用/单位时间内投入工时29.单件成本平均每件分摊成本=某批产品花费总成本/该批产品总量30.成本下降率Σ[(上期单件成本-本期单件成本)*实际产量]/Σ(上期单件成本*实际产量)*100%31.机会成本机会成本=投资额*行业平均盈利率经营收益=收益-机会成本节省成本﹕=(改善前需求工时-改善后需求工时)*工费率交付周期=∑(CT*批量)32.所有机器效率=Total S.T*Output/(可利用时间*机台数)人工利用率 = 人工操作时间*目标产能/工作时间机器稼动率 = 机器作业时间*目标产能/工作时间MFG效率=实际产量/除非计划停机损失后可生产数量总生产效率=实际产量/可生产数量33.无效时间指花费在进行与生产不是有直接关系的活动之时间,如:开会,培训,消防演习,健康枪查,5S等.34.生产是一切社会组织将它的输入转化为输出的过程,是人们创造物质产品的有组织的活动35.时间序列模型以时间为独立变量,利用过去需求随时间变化的关系来预测未来的需求36.预测监控通过预测监控来检验过去起作用的预测模型是否仍然有效37.因果关系模型利用变量(包括时间,如广告投入vs销量)之间的相互关系,通过一种变量的变化来预测另一种变量的未来变化38.CYCLE TIME(C/T)周期时间每单位工序中1个循环的作业所需的时间单位工序C/T的和/ 测试次数39.(T/T)节拍时间制造一件物品时所需要的实际时间作业时间/ 需求数40.NECK TIME整个工序中1个循环作业时间最长的工序时间=最大的CYCLE TIME41.RATING作业按标准方法进行时作业速度的快或慢的程度用数字进行换算的时间很快︰125%;快︰100%;一般︰85%;慢︰60%42.净作业时间作业按标准方法进行时所需的最少时间CYCLE TIME*RATING(%)43.运转率产品所需的时间及实际生产中所用的时间之比NECK TIME /TACT × 100 %44.运转损失生产产品所需的时间和实际所用的时间之比(Tact Time-Neck Time)/ TACT TIME× 100 %45.平衡损失作业人员之间由于作业量的不公平导致的作业要素时间的不均衡程度的比(Neck Time-Cycle Time)/TACT TIME× 100 %46.效率损失按标准方法进行作业时需要的最少时间和与实际作业中所用的时间之差的比(Cycle Time-净作业时间)/ TACT TIME× 100 %47.综合损耗损耗的总合计运转损失+平衡损失+效率损失48.时间观测法用秒表观测分析作业人员的作业时间或设备运转的方法49.防呆法作业人员或设备上装上无需小心作业也绝不出错的防止出错装置50.生产率一般用产量对投入的比OUT PUT /IN PUT51.工时人或机器能做的或已做的量用时间来表示52.拥有工时拥有人员的工时拥有人员×正常作业时间53.考勤工时实际上没投入到作业的工时(缺勤、休假、出差、支持等)相关人员×相关时间54.出勤工时实际投入到作业的人员的工时拥有工时-考勤工时55.追加工时正常出勤工时以外追加作业的工时,即加班,特殊出勤、接受支持等相关人员×相关时间56.作业工时投入到作业中的总工时出勤工时+追加工时57.实际生产工时作业工时中去掉损失工时,实际投入到作业的工时作业工时-损失工时58.损失工时不属于作业人员责任范围的损耗工时(会议、教育、早会、待料、材料不良、机械故障、机型变更、不良返工等)相关人员×相关时间59.作业工时效率生产产品所需的时间(标准时间)和实际用的时间之比标准工时/作业工时× 100 %60.实际生产工时效率损失工时以外的纯作业时间和实际生产所用的时间之比标准工时/实动工时× 100 %61.实际生产率生产产品所需的时间和纯生产所需的时间之比标准工时/实动工时× 100 %62.效率管理为了减少生产要素的损耗,用一线监督人员的指导监督来达到适当地提升并维持作业人员对作业的态度的一种管理模式标准时间/实际时间63.PAC (Performance Analysis & Control)为了能做到只要作业努力就能提升及维持能力的效率管理模式的一种。
标准工时计算方法
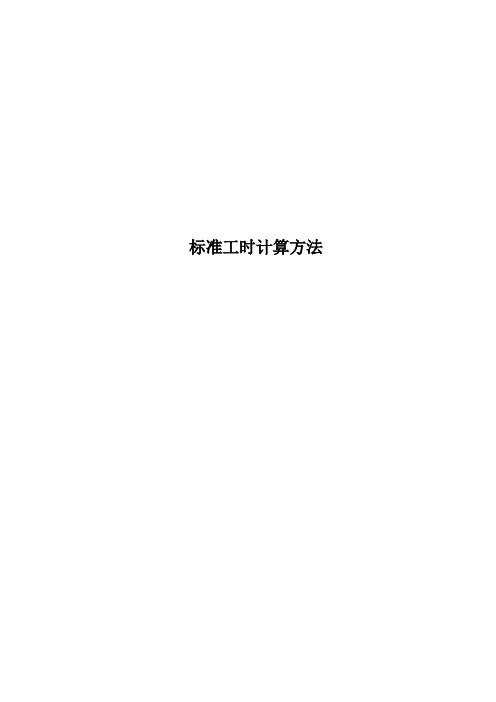
标准工时计算方法标准工时计算方法一、目的:规范标准工时制定与修改作业,使标准工时具有完整性,使ERP系统运行之排程合理和成本准确。
二、名词定义:2.1、标准工时:在特定的工作环境条件下,用规定的作业方法和设备,以普通熟练工作者的正常速度完成一定质量和数量的工作所必需的时间。
2.2、宽放时间:指作业员除正常工作时间之外必须的停顿及休息的时间。
包括操作者个人事情引起的延迟,疲劳或无法避免的作业延迟等时间。
对于没有规定发生时间、发生频率、所需时间的不规则要素作业,并不在正常时间范围之内,而属于宽放时间。
2.3、标准速度:没有过度体力和精神疲劳状态下,每天能连续工作,只要努力就容易达到标准作业成果的速度。
三、标准工时的构成:3.1、标准时间=正常时间+宽放时间=观测时间*(1+熟练修正数+努力修正数)+观测时间*宽放率3.2、正常时间:正常时间设定方法如下:直接观测法:秒表观测法;摄影分析法;work sampling法。
优点:比较简单;任何人都可以做。
缺点:难于跟标准速度相比较,需要评价标准速度;生产之前不能设定。
合成法:动作分析法、历史数据法。
优点:信赖程度和一贯性高;客观性和普遍性高;不需要评价标准速度;可在生产之前设定;容易消除不必要动作。
缺点:需要教育和训练。
3.3、宽放时间:作业宽放时间:补偿作业过程中发生不规则的要素作业。
如用处理不良品等。
注:宽放种类很多,但在实际计算标准工时时,不能将所有宽放都考虑在内,因宽放越多说明作业效率越低,一般宽放效率10%-20%之间均为正常尺度,根据本公司产品特点总宽放率设置为10%-20% 总宽放率=Σ+各宽放率=15%四、评比4.1定义:作业观测者(时间研究者)把头脑中的正规作业状态(速度、动作等) 和观测对象(操作者)的作业状态相比较,使之定量化。
4.2评比技术:标准作业状态(作业速度)并对之有感性化的认知。
评价结果定量化。
4.3平准化法(平准化法又称西屋法)a、准备秒表,笔和记录窗体《现场观测工时统计表》。
{IE工业工程}IE的定义工作范畴与七大手法
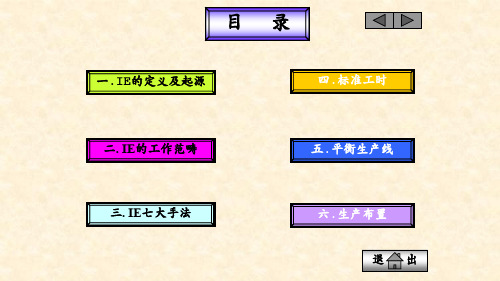
六.生产布置五.平衡生产线四.标准工时三. IE 七大手法二. IE 的工作范畴一.IE的定义及起源目录 一.IE 的定义及起源返回 目錄1.IE的定义:IE是英文Industrial(工业) Engineering(工程)的简称,直译为工业工程.它是對人員、物料、設備、能源和信息所組成的集成系統進行設計、改善和設置的一門學科.它綜合運用數學、物理學和社會科學方面的專門知識和技術,以及工程分析和設計的原理與方法,對該系統所取得的成果進行確定、預測和評價.2.IE的起源:工业工程之创立,要追溯到18世纪开始之工业革命.但一般人认为主要起源于1881年泰勒首创的时间研究,以及1885年吉尔布雷斯首创的动作研究.3.IE的工作目标:提高生产效率、降低产品成本、提高产品品质二.IE的工作范畴1.操作方法的设计和改善2.操作标准时间的设订3.制程、夹具与工具的设计改善4.產線設計5.流程與排線規劃6.成本的计算与分析7.产能计劃与分析8.工厂布置9.損耗分析10.工作评价与奖工制度的设立11.事务流程的改善12.系统或制度的设计談到IE 的工作范疇,其實很多很多,只是根據不同的企業,不同的管理者,其工作內容有所不同,但就工業工程學而言,其工作范疇大致可包括:三.IE七大手法1.動改法全稱为動作改善法,是指对人體動作进行改善,以減少疲勞,使工作更為舒適、更有效率,即以最少的勞力達到最大的工作效果.2.防錯法防錯法又稱防愚法,其義為防止愚笨的人做錯事.也就是說,連愚笨的人也不會做錯事的設計方法.3.五五法藉著質問的技巧來發掘出改善的構想,即5W(为什么WHY,何人WHO,何时WHEN,何地WHERE,何事WHAT)1H(如何HOW)法.4.雙手法全称为双手操作法,是研究人體雙手在工作時的過程(有无一手常处于闲置现象),藉以發掘出可改善之地方(可否左右手交替式作业).5.人機法全称为人机配合法,是研究探討操作人員與機器工作的過程(操作人之時間或機器之時間是否妥善),藉以發掘出可改善的地方(可否一人多机,或一机多人等).6.流程法研究探討牽涉到幾個不同工作站或地點之流動關係,藉以發掘出可改善的地方(驅除不必要的手續与流程).7.抽查法工作抽查法是指應用統計學上的抽樣原理來研究工作中人員與機器設備等之活動情形,以便迅速有效地了解問題的真象.2.標準工时的構成標準工时=正常工时*(1+宽放率)或标准工时=正常工时+宽放工时1.標準工時的定义即标准(Standard)时间(Time),是指在正常条件下(包含某些無法免除的因素),一個受过训练的熟练工作者,在不受外在不良影响的条件下,以规定的作业方法和用具,完成一定的质和量的工作所需的时间 。
工业工程(IE)七大手法(完整版)
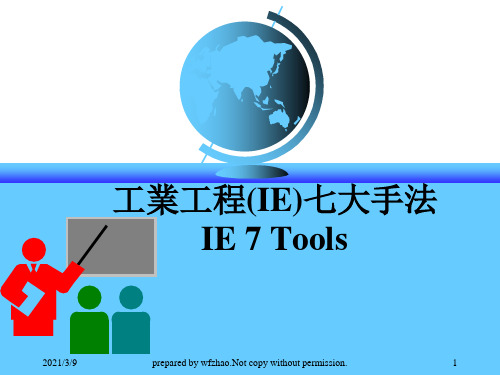
4.IE的主要範圍?
* 工程分析 * 價值分析(V.A) * 動作研究 * 工作標準
* 時間研究 * 時間標準
* 工廠布置 * 運搬設計
5.為甚麼要有改善(IE)七大手法?
* 以不教而戰,謂之殺.
* 徒然要求改善而不講求方法、技巧,於事無補.
* 給人一條魚吃,不如教他捕魚的技術.
* 要求捕更多的魚,首先必須講求捕魚技術的傳授與使用.
而所有企業的目的均系希望以最小的投入(INPUT)得到最大的 產出(OUTPUT),以致獨得最大的效益.那麼如何在品質保證的基礎 上,使企業獨得最大的效益呢?只有降低成本和提高企業的生產力, 把這些“投入”做最有效的組合,以達到品質穩定、效率高、交期 準、浪費少、成本低.這就是近代工業界工業工程(IE)所要做
工業工程(IE)七大手法 IE 7 Tools
2021/3/9
prepared by wfzhao.Not copy without permission.
1
前言
質量代表了一個國家的科學技術、生產水平、管理水平和文 化水平.
產品質量的提高,意味著經濟效益的提高.當今世界經濟的發 展正經歷著由數量型增長向質量型增長的轉變,市場竟爭也由人格 竟爭為主轉向質量竟爭為主.
出可資改善的地方.
4.五五法 藉著質問的技巧來發掘出改善的構想.
5.人機法 研究操作人員與機器工作的過程,藉以發掘出可資改善的地方.
6.雙手法 研究人體雙手在工作時的過程,藉以發掘出可資改善之地方.
7.抽查法 藉著抽樣觀察的方法能很迅速有效地了解問題的真象.
IE七大手法之一 — 防呆法
1.意義
防呆法(fool proof)又稱防愚法,其義為防止愚笨的人做錯事.也就是說, 連愚笨的人也不會做錯事的設計方法.
标准工时计算方法

标准工时计算方法标准工时计算方法目的:规范标准工时制定与修改作业,使标准工时具有完整性,使ERP系统运行之排程合理和成本准确。
名词定义:标准工时:在特定的工作环境条件下,用规定的作业方法和设备,以普通熟练工作者的正常速度完成一定质量和数量的工作所必需的时间。
宽放时间:指作业员除正常工作时间之外必须的停顿及休息的时间。
包括操作者个人事情引起的延迟,疲劳或无法避免的作业延迟等时间。
对于没有规定发生时间、发生频率、所需时间的不规则要素作业,并不在正常时间范围之内,而属于宽放时间。
标准速度:没有过度体力和精神疲劳状态下,每天能连续工作,只要努力就容易达到标准作业成果的速度。
标准工时的构成:标准时间=正常时间+宽放时间=观测时间*(1+熟练修正数+努力修正数)+观测时间*宽放率正常时间:主体作业时间:按照作业目的进行的作业。
指能创造价值的作业,如改变产品外形,改变产品性能等。
副作业时间:与主体作业同步发生,起附属作用。
如取放工具、检查等。
正常时间设定方法如下:直接观测法:秒表观测法;摄影分析法;work sampling 法。
优点:比较简单;任何人都可以做。
缺点:难于跟标准速度相比较,需要评价标准速度;生产之前不能设定。
合成法:动作分析法、历史数据法。
优点:信赖程度和一贯性高;客观性和普遍性高;不需要评价标准速度;可在生产之前设定;容易消除不必要动作。
缺点:需要教育和训练。
宽放时间:私事宽放时间:作业过程中,满足生理要求的宽放时间,如上厕所,喝水,擦汗。
疲劳宽放时间:为了补偿工作过程中体力和精神疲劳,采取的休息或操作速度减弱的宽放时间。
特殊宽放:研究宽放、机械干涉宽放、奖励宽放、工厂宽放、其它宽放。
作业宽放时间:补偿作业过程中发生不规则的要素作业。
如用处理不良品等。
集体宽放时间:集体作业时,对于个体差异产生损失的补偿。
如熟练度的差异,工位编排产生的损失等。
宽放系数表:NO12疲劳姿态宽放范围5%-7%宽放率5%2%-6%0%-7%3%1%1%-2%2%0%-5%0%-5%1%-3%2%1%1%3异常、宽放名称个人重量噪音倦怠自检、互检4567注: 宽放种类很多,但在实际计算标准工时时,不能将所有宽放都考虑在内。
工业工程七大手法标准工时的计算方法

工业工程七大手法标准工时的计算方法引言工业工程是一门关注如何改进和优化生产过程的学科。
而标准工时的计算方法在工业工程中起到了举足轻重的作用。
标准工时的准确计算可以帮助企业有效衡量生产效率和工时成本,进而优化生产过程,提高生产效率和产品质量。
本文将介绍工业工程中常用的七大手法以及它们在标准工时计算中的应用。
七大手法1.时间测量法:时间测量法是通过观察和记录工作任务的各个步骤所花费的时间来计算标准工时。
通过对多个工人进行观察和测量,可以计算出标准工时的平均值。
这种方法适用于任务比较简单和重复性高的工作。
2.工序分析法:工序分析法是通过将一个复杂的工作过程细分为多个工序,然后对每个工序进行分析和计算标准工时。
通过对每个工序的时间测量和工艺要求的评估,可以得出每个工序的标准工时,再进行累加得出整个工作过程的标准工时。
3.工作抽样法:工作抽样法通过随机选取一定数量的样本来观察工作任务的执行情况,然后根据观察结果计算标准工时。
这种方法适用于工作内容比较繁杂和复杂的情况,可以减少整个工作过程的测量时间。
4.分析比较法:分析比较法是通过对相似工作任务的时间数据进行比较和分析,来推测出新工作任务的标准工时。
这种方法适用于没有充分时间进行细致测量和分析的情况,可以快速估计出标准工时。
5.工时调查法:工时调查法是通过对工人进行访谈和调查来获取工作任务的工时数据,然后进行分析和计算标准工时。
这种方法适用于工作任务比较复杂,难以测量的情况,可以直接从工人口中获取关键数据。
6.工时测定法:工时测定法是通过实地观察和测量来获取工作任务的工时数据,然后进行分析和计算标准工时。
这种方法比较准确,但需要耗费较多的时间和资源。
7.标准时间法:标准时间法是通过统计和分析大量的历史工时数据,来估计新工作任务的标准工时。
这种方法适用于工作任务比较规范和重复性高的情况,可以通过历史数据的模型来进行标准工时的计算。
标准工时的计算方法在实际应用中,以上七大手法可以根据具体情况进行组合和调整,以得出准确的标准工时。
标准工时计算方法
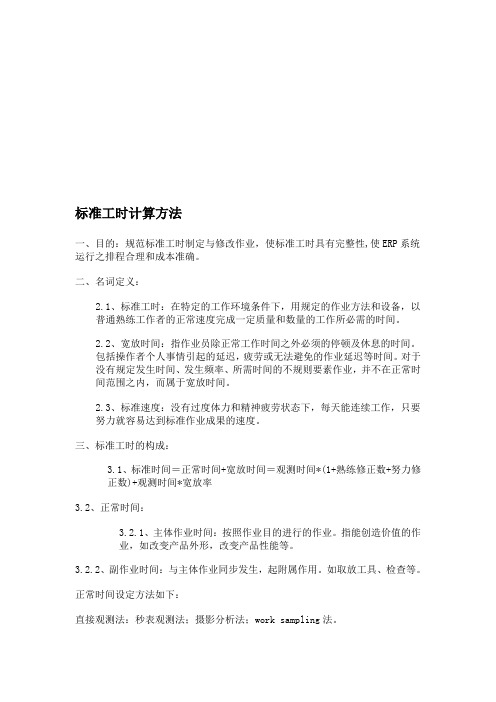
标准工时计算方法一、目的:规范标准工时制定与修改作业,使标准工时具有完整性,使ERP系统运行之排程合理和成本准确。
二、名词定义:2.1、标准工时:在特定的工作环境条件下,用规定的作业方法和设备,以普通熟练工作者的正常速度完成一定质量和数量的工作所必需的时间。
2.2、宽放时间:指作业员除正常工作时间之外必须的停顿及休息的时间。
包括操作者个人事情引起的延迟,疲劳或无法避免的作业延迟等时间。
对于没有规定发生时间、发生频率、所需时间的不规则要素作业,并不在正常时间范围之内,而属于宽放时间。
2.3、标准速度:没有过度体力和精神疲劳状态下,每天能连续工作,只要努力就容易达到标准作业成果的速度。
三、标准工时的构成:3.1、标准时间=正常时间+宽放时间=观测时间*(1+熟练修正数+努力修正数)+观测时间*宽放率3.2、正常时间:3.2.1、主体作业时间:按照作业目的进行的作业。
指能创造价值的作业,如改变产品外形,改变产品性能等。
3.2.2、副作业时间:与主体作业同步发生,起附属作用。
如取放工具、检查等。
正常时间设定方法如下:直接观测法:秒表观测法;摄影分析法;work sampling法。
优点:比较简单;任何人都可以做。
缺点:难于跟标准速度相比较,需要评价标准速度;生产之前不能设定。
合成法:动作分析法、历史数据法。
优点:信赖程度和一贯性高;客观性和普遍性高;不需要评价标准速度;可在生产之前设定;容易消除不必要动作。
缺点:需要教育和训练。
3.3、宽放时间:3.3.1、私事宽放时间:作业过程中,满足生理要求的宽放时间,如上厕所,喝水,擦汗。
3.3.2、疲劳宽放时间:为了补偿工作过程中体力和精神疲劳,采取的休息或操作速度减弱的宽放时间。
3.3.3、特殊宽放:学习宽放、机械干涉宽放、奖励宽放、工厂宽放、其它宽放.作业宽放时间:补偿作业过程中发生不规则的要素作业。
如用处理不良品等。
3.3.4、集体宽放时间:集体作业时,对于个体差异产生损失的补偿。
标准工时是在正常操作条件下,以标准的作业方法及合理的劳动强度和速度完成符合质量要求的所需的作业时间

标准工时是在正常操作条件下,以标准的作业方法及合理的劳动强度和速度完成符合质量要求的所需的作业时间标准工时是指操作者在中等劳动强度和熟练程度下连续完成一件产品所需要的时间。
标准工时=正常时间+宽放时间正常时间=观测时间X评定系数观测时间采用秒表测时法获得,或者直接用MTM、WF、MOD等方法计算标准时间,也可以用标准资料法来预测标准工时。
标准工时主要用于人员编制(人事)、工时成本计算(财务)、工厂的先期规划(规划)、以及计划排产(生产管理及计划)等,标准工时是一个企业的基础性数据,属于企业机密。
什么是标准工时制,哪些工种实行标准工时制?问:什么是标准工时制,哪些工种实行标准工时制?答:标准工时制是指职工实行每日工作8小时,平均每周工资40小时,星期六、星期日为周休息日的工作制度。
实行这一制度,应保证完成生产和工作任务,不增加人员编制和财政支出,不减少职工的收入。
我市各级国家机关、社会团体、企业事业单位以及其他组织的职工,一律实行没日工作8小时,平均每周工作40小时的标准工时制度。
什么是标准工时制度、综合计算工时工作制、不定时工作制和非全日什么是标准工时制度、综合计算工时工作制、不定时工作制和非全日制工作制?答:(1)我国现在实行的是每日工作不超过8小时、每周工作不超过40小时的工时制度,这是标准工作时间。
(2)综合计算工时工作制是针对因工作性质特殊,需连续作业或受季节及自然条件限制的企业部分职工,采用的以周、月、季、年等为周期的综合计算工作时间的一种工时制度。
在综合计算工作时间的周期内,具体某一天、某一周的工作时间可以超过8小时或40小时。
(3)不定时工作制是指每一工作日没有固定的上下班时间限制的工作时间制度。
经批准实行不定时工作制的职工,不受日延长工作时间标准和月延长工作时间标准的限制,但用人单位应采用弹性工作时间等适当的工作和休息方式,确保职工的休息休假权利和生产、工作任务的完成。
(4)非全日制工作制是指以小时计酬,劳动者在同一用人单位平均每日工作时间不超过4小时,同时为一个以上用人单位提供非全日制工作的,每周累计工作时间不得超过40小时的用工形式。
如何计算标准工时和产能?
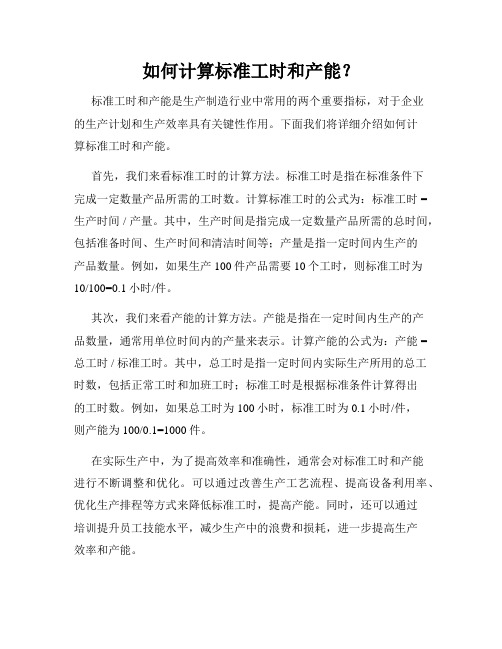
如何计算标准工时和产能?标准工时和产能是生产制造行业中常用的两个重要指标,对于企业的生产计划和生产效率具有关键性作用。
下面我们将详细介绍如何计算标准工时和产能。
首先,我们来看标准工时的计算方法。
标准工时是指在标准条件下完成一定数量产品所需的工时数。
计算标准工时的公式为:标准工时 = 生产时间 / 产量。
其中,生产时间是指完成一定数量产品所需的总时间,包括准备时间、生产时间和清洁时间等;产量是指一定时间内生产的产品数量。
例如,如果生产100件产品需要10个工时,则标准工时为10/100=0.1小时/件。
其次,我们来看产能的计算方法。
产能是指在一定时间内生产的产品数量,通常用单位时间内的产量来表示。
计算产能的公式为:产能 = 总工时 / 标准工时。
其中,总工时是指一定时间内实际生产所用的总工时数,包括正常工时和加班工时;标准工时是根据标准条件计算得出的工时数。
例如,如果总工时为100小时,标准工时为0.1小时/件,则产能为100/0.1=1000件。
在实际生产中,为了提高效率和准确性,通常会对标准工时和产能进行不断调整和优化。
可以通过改善生产工艺流程、提高设备利用率、优化生产排程等方式来降低标准工时,提高产能。
同时,还可以通过培训提升员工技能水平,减少生产中的浪费和损耗,进一步提高生产效率和产能。
总之,计算标准工时和产能是企业管理中至关重要的一环,它直接影响到生产效率和盈利能力。
只有通过科学合理地计算和分析标准工时和产能,企业才能更好地制定生产计划、合理安排生产资源,提高生产效率,降低成本,实现经济效益最大化。
希望以上内容对您有所帮助。
工业工程IE七大手法
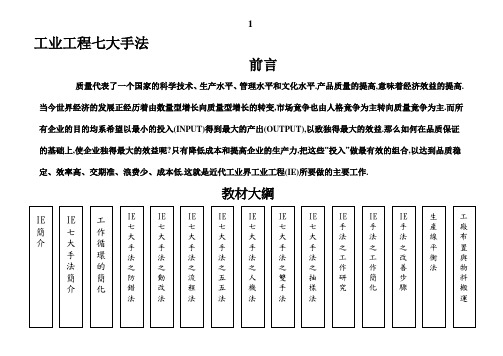
1工业工程七大手法前言质量代表了一个国家的科学技术、生产水平、管理水平和文化水平.产品质量的提高,意味着经济效益的提高.当今世界经济的发展正经历着由数量型增长向质量型增长的转变,市场竟争也由人格竟争为主转向质量竟争为主.而所有企业的目的均系希望以最小的投入(INPUT)得到最大的产出(OUTPUT),以致独得最大的效益.那么如何在品质保证的基础上,使企业独得最大的效益呢?只有降低成本和提高企业的生产力,把这些“投入”做最有效的组合,以达到品质稳定、效率高、交期准、浪费少、成本低.这就是近代工业界工业工程(IE)所要做的主要工作.教材大綱IE简介1.甚么是IE?IE就是指INDUSTRIAL(工业) ENGINEERING(工程).它由两字词之首字母组合而成.2.IE的起源?IE的基础也是最早的起源来自于『工作研究』,而『工作研究』的主要构成是来自泰勒(Frederick W.Taylor 1856~1915)的『工作研究』与吉尔布雷斯(Frank B Gilbreth 1868~1924)的『动作研究』二者所构成.3.IE的目的?应用科学及社会学的知识,以合理化、舒适化的途径来改善我们工作的品质及效率以达到提高生产力增进公司之利润进而使公司能长期的生存发展下去,个人的前途也有寄托之所在.因此,简单地说,IE的目的就是充分利用工厂的人力、设备、材料,以最经济有效的工作方法,使企业独得最大的效益.4.为甚么要有IE?*持续的进步是企业及个人长久生存的根基.*改善就是进步的原动力,没有改善就没有进步.*改善是永无止境的,必须长久持续去进行4.IE的主要范围?*工程分析*价值分析(V.A) *动作研究*工作标准*时间研究*时间标准*工厂布置*运搬设计5.为甚么要有改善(IE)七大手法?*以不教而战,谓之杀.*徒然要求改善而不讲求方法、技巧,于事无补.*给人一条鱼吃,不如教他捕鱼的技术.*要求捕更多的鱼,首先必须讲求捕鱼技术的传授与使用.*改善七大手法(IE 7 TOOLS)就是协助我们改善我们工作的技术IE七大手法简介改善(IE)七大手法有哪些?名称目的1.动改法改善人体动作,减少疲劳使工作更舒适、有效率,不要蛮干.2.防错法避免做错事,使工作第一次就做好的,精神能够具体实现.3.五五法借着质问的技巧来发掘出改善的构想.4.双手法研究人体双手在工作时的过程,以发掘出可资改善之地方.5.人机法研究操作员与机器工作的过程,以发掘出可资改善的地方.6.流程法研究探讨牵涉到几个不同工作站或地点之流动关系,藉以发掘出可资改善的地方.7.抽查法借着抽样观察的方法能很迅速有效地了解问题的真象.有效的實施「工作簡化」機構—增加生產 實際 降低成本 利益個人—工時縮短收益增加機構—提高工作 管理上 情緒收獲 個人—聰明才智有發展機會提高 工作效率IE 手法—工作简化的循环IE 七大手法之一 — 防错法1.意义防错法又称防愚法,其义为防止愚笨的人做错事.也就是说,连愚笨的人也不会做错事的设计方法.狭义: 如何设计一个东西(一套方法),使错误绝不会发生.广义: 如何设计一个东西(方法),使错误发生的机会减至最低的程度.因此,更具体的说”防错法”是:1. 具有即使有人为疏忽也不会发生错误的构造—不需要注意力.2. 具有外行人来做也不会做错的构造 —不需要经验与直觉.3. 具有不管谁或何时工作不出差错的构造—不需专门知识与高度技能.2.功用1>. 积极: 使任何的错误,绝不会发生. 2>. 消极: 使错误发生的机会减至最低程度.3.应用范围任何工作无论是在机械操作、产品使用上,以及文书处理等皆可应用到4.基本原则在进行”防错法”时,有以下四原则可供参考:1>. 使作业的动作轻松2>. 使作业不要技能与直觉3>. 使作业不会有危险4>. 使作业不依赖感官EXL:在连续几个测试站间加档板,防止未测品流至下一站.5.基本原理1>. 排除化: 剔除会造成错误的原因.2>. 替代化: 利用更确实的方法来代替.3>. 容易化: 使作业变得更容易、更合适、更独特,或共同性以减低失败.适合化、共同化、集中化、特殊/个别化.4>. 异常检出: 虽然已经有不良或错误现象,但在下一制程中,能将之检出,以减少或剔除其危害性.5>. 缓和影响: 作业失败的影响在其波及过程中,用方法使其缓和或吸收.6.应用原理1>. 断根原理: 会造成错误的原因从根本上排除掉,使绝不发生错误.2>. 保险原理: 采用二个以上的动作需共同或依序执行才能完成工作.3>. 自动原理: 以各种光学、电学、力学、机构学、化学等原理来限制某些动作的执行或不执行,以避免错误之发生.目前这些自动开关非常普遍,非常简易的“自动化”之应用4>. 相符原理: 藉用检核是否相符合的动作,来防止错误的发生.5>. 顺序原理: 避免工作之顺序或流程前后倒置,可依编号顺序排列,可以减少或避免错误的发生.6>. 隔离原理: 藉分隔不同区域的方式,来达到保护某些地区,使不能造成危险或错误的现象发生.隔离原理亦称保护原理.7>. 复制原理: 同一件工作,如需做二次以上,最好采用“复制”方式来达成,省时又不错误.8>. 层别原理: 为避免将不同工作做错,而设法加以区别出来.9>. 警告原理: 如有不正常的现象发生,能以声光或其它方式显示出各种“警告”的讯号,以避免错误即将发生.10>. 缓和原理: 以藉各种方法来减少错误发生后所造成的损害,虽不能完全排除错误的发生,但是可以降低其损害的程度. EXL: 1.鸡蛋之隔层装运盒减少搬运途中的损伤.(缓和原理)2.设立多层检查方法,考试后检查有没有犯错的地方.(保险原理)3.自动消防洒水系统,火灾发生了开始自动洒水灭火.(警告原理)4.汽车之安全带,骑机车戴安全帽.(保险原理)5.加保利龙或纸板以减少产品在搬运中之碰伤.(缓和原理)6.原子笔放在桌上老是给别人不经意中拿走,贴上姓名条或加条绳子固定在桌上.(隔离原理、警告原理、缓和原理IE七大手法之二—动改法1.手法名称又称动作改善法,简称为“动改法”,是:*省力动作原则*省时动作原则*动作舒适原则*动作简化原则此原则以最少的劳力达到最大的工作效果,其原为吉尔博斯(Gibreth)最先提出,后经研究整理增删.其中以巴恩斯(Ralph M.Barnes)将之补充完成.2.动作改善原则可分为三大类二十项.3.三大分类为:1>. 有关于人体动用方面之原则,共包含8项.2>. 有关于工作场所之布置与环境之原则,共包含6项.3>. 有关于工具和设备之设计原则.共包含6项.详细之20项原则将在后面详加介绍.4.有关人体动用原则(动作经济原则)原则1: 两手同时开始及完成动作原则2: 除休息时间外,两手不应同时空闲原则3: 两臂之动作应反射同时对称. 原则4: 尽可能以最低级动作工作说明:欲使动作迅速而轻易,唯有从动作距离之缩短,以及动作所耗体力减少上着手.欲达到此目的,其实际对策则为选取级次最低之动作,使动作范围缩小.原则5: 物体之”动量”尽可能利用;但如需用肌力制止时,则应将其减至最小度.原则6: 连续曲线运动较方向突变直线运动为佳.原则7: 弹道式运动较轻快. 原则8: 动作宜轻松有节奏.原则9: 眼睛的视点应尽少变动并尽量接近.原则10: 适当之照明;应有适当之照明设备,使视觉满意舒适. (所谓合适的照明,其意义应包括: 1>.必须有合适其工作的充足光度.2>.必须有合适颜色的光线,且应避免闪光. 3>.必须有合适的投射方向.)原则11: 工作抬椅高度适当舒适原则12: 尽量以足踏/夹具替代手之工作.IE七大手法之四—五五法1.手法名称:5 * 5W 1H法;又称5 * 5何法;又称质疑创意法;简称五五法.2.目的:学习本手法的目的是在:熟悉有系统的质问的技巧,以协助吾人发掘出问题的真正根源所在以及可能的创造改善途径.3.名词释义3.1 基本观念*头脑就像降落伞,○○○只有在开放的情况下才工作○○○.*工作改善最大的阻碍,并不在于技术不足,而是在于一个人的想法~当他觉得是以最好的方法在工作着,并且以为满足.*当您认为工作已无法改善了,那就代表您已落伍了,虽然您是专家,拥有高深的学识.*一个虽没有多大学识的人,只要他认为工作仍有改善的可能,那么他就比您更适合这工作.3.2 何处最需要改善※您的时间非常富贵,应妥善运用;挑最重要的事情优先做!瓶颈的地方是最值得改善的,顺利的地方留待以后有时间再去研究.耗时多的地方往往是改善的好机会.紧急情况由于材料、工具设备或公文制度造成时间及人力的浪费~是极需改善的地方.浪费须要改善的事物,往往不是显而易见的,除非您小心的观察,否则日过一日在浪费的情况下而不自觉~细心地找出材料、时间及人力的浪费.3.3 工作之构成: 每一工作均包含三部份:1.预备: 时间和劳力花在诸如调整机器,放置加工物等准备工作上.2.操作: 实际工作,附加价值于产品上.3.收拾: 时间和劳力花在诸如取下加工物,处置残余物屑,存放或清理等工作,无生产性的动作.最易显出改善成果的地方在于免除<操作>,因为它也自动地将<预备>和<收拾>的时间,劳力免除了.请记住<预备>及<收拾>只会增加产品的成本并不增加它的价值.3.4 改善之探讨方向每件工作都可依照下列4个主要的方向去探讨可能的方向.应持有「目前的方法绝非仅有且最好的,必然有更好的方法」的态度.剔除: 许多操作可能是不必的,只是规随习而不察剔除是最好的方向.合并: 将二种以上的动作尝试结合在一起是为合并.吾人应寻求合并的可能性,二个操作一起做可以省掉搬运、检验、存放等动作.如果二个操作不易合并时,应尽可能将搬运合并在操作中.变更/重组: 应改变次序、地点及人员的可能性,这些改变可能引出删除和合并的灵感.简化: 在删除、合并及变更操作等检讨后,研究「如何」来做以达到简化的目的.IE七大手法之四—五五法9IE七大手法之五—人机法IE七大手法之六—双手法1.手法名称:人机配合法(Man-Machine Chart);简称为“人机法”.2.目的:学习如何记录人与机器配合工作时之过程.1>. 发掘空闲与等待时间2>. 使工作平衡3>. 减少周程时间4>. 获得最大的机器利用率5>. 合适的指派人员与机器6>. 决定最合适的方法3.意义:以图表方式,记录操作员与一部或多部机器之操作关系,并藉此记录来做进一步之分析与改善.4.应用范围:1>. 1人操作1部机器或多部机器2>. 数人操作1部机器或多部机器.3>. 数人操作一共同之工作.5.功用:1>. 了解在现况下,操作人之时间或机器之时间是否妥善应用.2>. 依上述之记录加以质疑,寻求改善之地方3>. 用以比较改善前及改善后之差异情形. 1.手法名称:双手操作法,简称为“双手法”.2.目的:学习有系统的记录人体双手(足)动作的过程.有一个古老的故事说:”上帝造人为何要给一个嘴巴,二个眼睛,二个耳朵以及二双手呢?”那是因为上帝希望每一个人能少说,多看,多听,多做.这样的故事我们都非常清楚与了解.但是我们若进一步加以探讨,我们是否尽力发挥我们”双手万能”的功用.每一个人都会说”当然是”如果再问下,去您的双手在工作时,有一只手在”闲置”的状态下,所占之比率例有多少,相信有许多人不能够回答出来.“双手操作法”就是希望能帮助我们了解双手在操作时”闲置”的状况,并寻求改善的方法,以发挥双手的能力.3.意义:以图表的方式,来记录操作者双手(足)的动作过程,藉此记录来做进一步之分析及改善.4.应用范围1>. 适用于以人为主的工作,即研究的对象为人体的双手或双足.2>. 专注于某一「固定工作地点之研究」,即该工作固定在此点上实施.3>. 该件工作有「高度重复性」,即该件工作会再次大量生产.非重复性之工作,则因研究改善后无法再次应用于同一件工作内,而失去研究改善之目的.10 5.功用1>. 用以记载现行操作者双手(足)的动作过程.2>. 依(1>.)之记录,加以质疑,寻求改善之地方.3>. 用以比较改善前及改善后之差异情形.6.名词释义1>. 右手操作图:为双手操作图之另一称呼,盖左右手即是双手之义.2>. 操作者操作图:为双手操作图之另一称呼.盖其研究对象系以操作者之双手(足)之动作为主.3>.代表:”移动”,表示手由一地点移动到另一地点:代表”把持”,一手握住一个物体,另一手正在工作,此时握住东西之手,是为”把持”之状态.:代表”等待”,一手正在等待下一个动作.6>. :代表”作业”或”操作”,手正从事有生产性的动作,皆是. EXL:将物体结合在一起,分开、弯曲、转动、对准、拿起、放下、抓取等等.7>.正常工作范围:以在坐姿状态双手之正常活动可及之范围,是为正常工作范围,约在37~40公分之范围内.IE七大手法之七—工作抽查法1.定义工作抽查法系指应用统计学上的抽样原理来研究工作中人员与机器设备之活动情形,它是一个了解事实最有效的工具之一.它可在最短的时间和最低的成本之下获得有关人与设备之间的有用信息.2.常用的三种主要用途: 1>. 人与机器活动状况抽样: EXL:决定操作员每天工作占百分之几,空间占百分之几.2>. 绩效抽样: EXL:成型机待机之比率,操作员之工作绩效等.3>. 工作衡量: EXL:建立操作标准工时,尤其适用于文书性质的作业.3.工作抽查之好处:1>. 观测时间短,并可同时观测数部机器或操作人员之状况.2>. 调查时间较长,可去除因每日不同之各别所造成之差异现象,因此共结果较为客观可靠.3>. 所被观测的对象所产生的干扰次数及时间较短.总之,工作抽查不需使用马表的技巧,不需费大批专门人员连续时间的观测.更不需对个人的努力或成绩作主观的评判,而能比任何其它测试方法在较短的时间、较少的成本、较佳的客观情形之下,获得有关人员或机器的工作实在状况,作为管理上采取行动的根据.4.实施『工作抽查』的步骤:1>.宣传与训练2>.究订抽查的目的3>.详加观察,收集有关资料4>.决定抽查的工作项目5>.设计记录用表格6>.决定观测次数7>.决定观测时间8>.现场观测9>.观察结果的整理与检讨10>.决定时间标准11>.决定工作绩效IE手法—时间研究1.定义为一种应用技术,指在决定一合格人员在一定的标准下完成某一定工作所需的时间,其必须先建立标准方法,再建立标准时间.实施「方法改善」,机构方面增加生产降低成本,实施「时间研究」,工作者始可增加收益.2.作用1>. 决定工作时间标准,并用以控制人工成本.2>. 拟订标准时间作为奖金制度的依据.3>. 冯以决定工作日程及工作计划.4>. 决定标准成本,并作为准备预算的依据.5>. 在制造前先计算成本.此种数据决定制造成本及售价都很有价值.6>. 决定机器的使用效率,并用以帮助解决生产线的平衡.7>. 决定操作人员操作的安排,一个能操作若干台机器?或需若干人组成一组来操作机器.8>. 除可用以决定直接人工的工资外,并亦可用以间接人工的工资3.时间研究的目的1>. 作业改善: 透过时间的研究,运用工程分析、作业简化、动作研究、动作经济原则上列几种技法将隐藏现代方法内的无效时间予以清出以便设法去除.所谓无效时间包括:等待时间、间接时间、装卸时间.4.时间研究的准备1>. 工厂布置方法2>. 产品的制程分割状况3>. 各工序的作业方法4>. 材料、零件的供应品质是否稳定5>. 人员流动状况对以上5项先做了解,尤其管理制度不佳的工厂应针对问题进行改善,加上后面的工作准备,时间研究才易奏效.6>. 时间研究方法及用具的决定7>. 时间研究的观测方法8>. 作业要素的分清9>. 观测中的记录方法10>. 记录之整理11>. 改善项目提出之方法12>. 制订标准时间的方法5.实施「时间研究」的基本程序1>. 选择: 选择需要测时的工作,注意选择适合测时的工作及对象. 2>. 记录: 记录所有与工作环境、单元和方法及作業员等有关的资料.3>. 测时: 用测时的方法测计工作中每一单元的时间,至于所需测计的「周程」次数,须足以保证能获得具有代表性的实况为准. 4>. 检查: 严格检查已记录的各种数据及各单元的时间,确保非生产性单元或偶发性单元均已自生产性单元内分开.5>. 评比: 评比所记录各单元的时间,并决定每个单元的代表时间.6>. 宽放: 决定操作最合适的宽放时间,其中常包括私事、疲劳、程序、临时等宽放.7>. 标准时间: 应明白的公开宣布,有关操作中的各项动作的时间均已订定并规定此等时间为操作的标准时间.6.测时的方法一般做作业测定大致分成直接法与间接法:直接法有: 马表法、摄像机法等.间接法有: 预定动作时间标准法(Predetermined Motion Time Standard Approach-PTS) 、作业要素法(Work factor-W.F) 、方法时间度量法(Methods-Time Measurement-MTM)等等.最常用之测时法为马表测时法(stop watch time study):即使用马表到现场实地测工作时间,据以订定标准工时的方法.马表测时法常分为四种: 连续记录时法、飞回记时法、累积记时法、周程记时法.7.标准时间的构成标准时间= 实测时间+ 宽裕时间1>.宽裕时间分为作业宽裕、需要宽裕、疲劳宽裕.1. 作业宽裕主要是材料、零件、机器或工具等关系在连续作业过程中偶然可能产生非正规的作业要素时间. EXL:零件掉落地上要捡起、工作台偶尔要清理等.2. 需要宽裕指连续性的工作中,会因生理上的需要可能之中断时间.EXL:如上洗手间、喝水等.3. 疲劳宽裕指在作业中产生的工作疲劳,会降低工作速度,此疲劳宽裕为弥补其时间.IE手法—工作简化法1.概念工作简化为科学管理之工具.其目的即在利用科学的方法寻求最经济有效的工作方法.以求工作效率的增加,且使工作都轻松愉快,工作简化主要是消除浪费;而世界上最大的浪费,莫过于动作的浪费.改善动作,即可改善工作.所以欲求效率,必须养成「动作观念」(Motion Minded),即注意动作、分析动作、改善动作,这也就是「工作简化」中从开始就必须建立起来的观念.2.工作简化之优点节省动作减少工时提高效率降低成本增加利润提高工资3.工作简化之基本原则将现行工作内隐藏的无效工作量与无效时间,设法予以取消,或尽可能予以减小,以合使整个工作时间得以缩短,而提高效率,完成改善工作所希求的目标.4.工作简化的方法1>. 择出生产上或业务上或工作上拟改善的项目:*在生产上或业务上或工作上拟改善的项目.*占大量的时间或人工的工作*反复性的工作*消耗大量材料的工作*布置不当或搬运不可理的工作2.现状分析及检讨使用IE的分析手法如:*工程流程图*制品工程分析*作业者工程分析*工厂布置与搬运*动作分析3.动用5W2H法来发问*WHY? 为何如此做,有否必要?(为什么)*WHAT? 目的是甚么,这个工作(动作)可否考虑?(什么目标) *WHERE? 有无比这里做更好?(哪里)*WHEN? 时间的安排好不好?有无更好的安排方法?(何时) *WHO? 谁来做?几个人做?有否更适当的.(谁来执行)*HOW TO DO? 这样做法有没有更好的?(如何执行)*HOW MUCH? 这样做的成本?变更后的成本又如何?(成本如何) 4.动用IE手法剔(除) 、合(并) 、排(重排) 、简化来寻求新方法※剔除经过WHY、WHAT、HOW TO DO分析后认为没必要的,可试着剔除.※合并数人同一工作,数地同一工作或数次来回的做,可以考虑能否合并.※重排经试着剔除、合并后的工作,继续以WHEN、WHERE、WHO 加以研究,工作顺序可否重排.※简化经过上述剔、合、排后之工作是否最简单、最佳效果,是否可再简化.5.制订新的工作标准再好的方法也会受到抵制或排拆,当新的方法产生后,应制订成新的工作标准.6.效果跟催(Follow up)新的方法实施应加予跟催及控制、查看.1>.有无照新方法作业.2>.新方法实际效果与预期效果比较.3>.新方法实施过程中,产生之问题迅速排除.13IE改善步骤1.解决问题的步骤(QC事项)四大阶段:※计划(Plan) ※执行(Do) ※检查(Check) ※行动(Action) 八大步骤: 1>.选择主题(找出问题,缩小范围,主题的决定).2>.选择理由(整理选定的主题,目标明确化,活动计划).3>.现状掌握(正确的掌握现状,提出不满意的问题目标设定)4>.分析(臆设的提出,臆设的检查及证明,不良处的再现.)5>.对策(对策的提出及实施).6>.效果(有形、无形效果之掌握).7>.固定(标准化、彻底的了解、实施、完全的确认).8>.反省(活动的反省、今后计划、将缺失检讨用于下次活动).2.改善后的检查表(发现任务的检查表)※五大任务之检查要素: 1.品质(Quality) 2.成本(Cost)3.生产量(Output)4.士气(Morale)5.安全(Safety) 1.品质(Quality)问题点: 维持与提高品质活动的重点: 1>.减少不良的工作减少离散度2>.减少因疏忽而引起的不良品3>.减少初期的不良产品4>.减少品质的异常5>.减少赔价请求.6>.提高品质7>.提高品质能力活动的结果: 1>.使工程处于安定状态2>.防止抱怨的再度发生3>.确实的遵守作业指导书4>.使管理点明确5>.依照管理图进行管理工程6>.标准化7>.提高信赖性8>.使管理制度化2.成本(Cost)问题点: 降低成本活动的重点: 1>.削减经费2>.节约材料及零件支出3>.降低单价活动的结果: 1>.减少工数2>.减少修正的次数3>.裁减人员4>.提高材料的利用率5>.提高设备的转动率.3.生产量(Output)问题点: 量的确保,遵守交货期限活动的重点: 1>.增加生产量2>.遵守交货期3>.减少库存4>.加强存货管理5>.改善配置6>.提高效率活动的结果: 1>.提高生产力2>.缩短作业时间3>.加强管理4>.改善工具5>.提高设备的运转率4.士气(Morale)。
IE七大手法工业工程课件

IE七大手法工业工程课件
11
擋板
NG 點膠前和點膠後未清楚區別
OK
點膠前和點膠後清楚區別
IE七大手法工业工程课件
12
– 藉“不对称的形状”来达 成
IE七大手法工业工程课件
13
IE七大手法工业工程课件
14
• 2.保险原理:藉用二个以上的动作必需共同或依序执行才 能完成工作,藉“共同”动作必须同时执行来完成。
例:“先进先出”架用来以正确的测试顺序分派 产品。当一盒产品拿出使用时,另一盒产品滑下 ,保证正确的次序。
IE七大手法工业工程课件
40
防错十大原理
• 6.隔离原理:藉分隔不同区域的方式,来达到保 获某些地区,使其不能造成危险或错误的现象发 生。隔离原理亦称保获原理。
– 例:家庭中危险的物品放入专门之柜子中加锁并置于 高处,预防无知的小孩取用而造成危险。
IE七大手法工业工程课件
35
檢查PCB治具
PCB背面零件過多,背檢無法檢查完全, 套上套板可以避免漏檢查
IE七大手法工业工程课件
36
DPS-200PB-138 A
---- 出 貨 段
之前 量線 材
客戶反饋卡 鉤變形
之后 量線 材
卡鉤防止變
形并防呆
IE七大手法工业工程课件
37
防错十大原理
• 5.顺序原理:避免工作之顺序或流程前后倒置, 可依编号顺序排列,可以减少或避免错误的发生。
对某一产品所需的部件预先清点 出来交给工人。如果产品批装配 完成后仍有部件剩余或者是部件 不够,马上就知道有异常发生。 这种检查方法可防止产品在缺件 的情况下流入市场。
IE七大手法工业工程课件
33
IE七大手法工业工程课件
标准工时计算方法
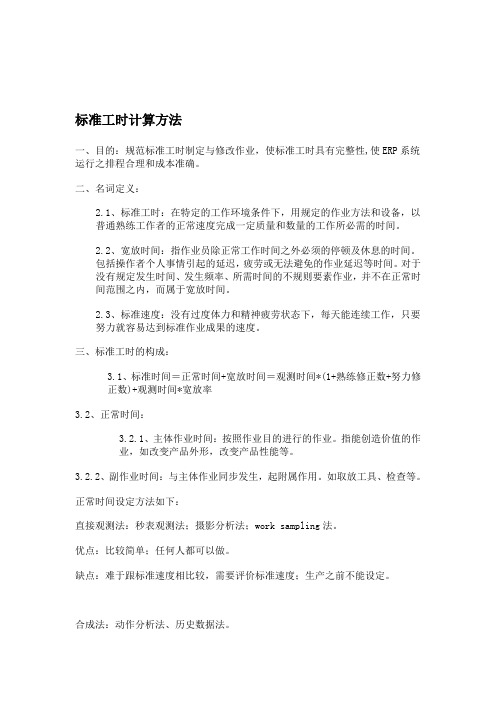
标准工时计算方法一、目的:规范标准工时制定与修改作业,使标准工时具有完整性,使ERP系统运行之排程合理和成本准确。
二、名词定义:2.1、标准工时:在特定的工作环境条件下,用规定的作业方法和设备,以普通熟练工作者的正常速度完成一定质量和数量的工作所必需的时间。
2.2、宽放时间:指作业员除正常工作时间之外必须的停顿及休息的时间。
包括操作者个人事情引起的延迟,疲劳或无法避免的作业延迟等时间。
对于没有规定发生时间、发生频率、所需时间的不规则要素作业,并不在正常时间范围之内,而属于宽放时间。
2.3、标准速度:没有过度体力和精神疲劳状态下,每天能连续工作,只要努力就容易达到标准作业成果的速度。
三、标准工时的构成:3.1、标准时间=正常时间+宽放时间=观测时间*(1+熟练修正数+努力修正数)+观测时间*宽放率3.2、正常时间:3.2.1、主体作业时间:按照作业目的进行的作业。
指能创造价值的作业,如改变产品外形,改变产品性能等。
3.2.2、副作业时间:与主体作业同步发生,起附属作用。
如取放工具、检查等。
正常时间设定方法如下:直接观测法:秒表观测法;摄影分析法;work sampling法。
优点:比较简单;任何人都可以做。
缺点:难于跟标准速度相比较,需要评价标准速度;生产之前不能设定。
合成法:动作分析法、历史数据法。
优点:信赖程度和一贯性高;客观性和普遍性高;不需要评价标准速度;可在生产之前设定;容易消除不必要动作。
缺点:需要教育和训练。
3.3、宽放时间:3.3.1、私事宽放时间:作业过程中,满足生理要求的宽放时间,如上厕所,喝水,擦汗。
3.3.2、疲劳宽放时间:为了补偿工作过程中体力和精神疲劳,采取的休息或操作速度减弱的宽放时间。
3.3.3、特殊宽放:学习宽放、机械干涉宽放、奖励宽放、工厂宽放、其它宽放.作业宽放时间:补偿作业过程中发生不规则的要素作业。
如用处理不良品等。
3.3.4、集体宽放时间:集体作业时,对于个体差异产生损失的补偿。
六西格玛管理与工业工程七大手法

1、六西格玛管理六西格玛是一种能够严格、集中和高效地改善企业流程管理质量的实施原则和技术。
它包含了众多管理前沿的先锋成果,以”零缺陷”的完美商业追求,带动质量成本的大幅度降低,最终实现财务成效的显著提升与企业竞争力的重大突破。
6西格玛管理包含两个方面的含义:其一、是对不合格的一种测量评价指标;其二:是驱动经营绩效改进的一种方法论和管理模式。
西格玛即希腊字σ的译音,是统计学家用语衡量工艺流程中的变化性而使用的代码。
企业也可以用西格玛的级别来衡量在商业流程管理方面的表现。
传统的公司一般品质要求已提升至3sigma.这就是说产品的合格率已达至99.73%的水平,只有0.27%为次货。
又或者解释为每一千货产品只有2.7件为次品。
很多人认为产品达至此水平已非常满意。
可是,根据专家研究结果证明,如果产品达到99.73%合格率的话,以下事件便会继续在现实中发生:每年有20,000次配错药事件;每年不超过15,000婴儿出生时会被抛落地上;每年平均有9小时没有水、电、暖气供应;每星期有500宗做错手术事件;每小时有2000封信邮寄错误。
由此可以看出,随着人们对产品质量要求的不断提高和现代生产管理流程的日益复杂化,企业越来越需要象六西格玛这样的高端流程质量管理标准,以保持在激烈的市场竞争中的优势地位。
事实上,日本已把”6 Sigma”作为他们品质要求的指标。
管理专家Ronald Snee先生将管理定义为:“寻求同时增加顾客满意和企业经济增长的经营战略途径。
”管理专家Tom Pyzdek:“6西格玛管理是一种全新的管理企业的方式。
6西格玛主要不是技术项目,而是管理项目。
”下面是韦尔奇先生在接受美国著名作家珍妮特·洛尔采访时谈到的6西格玛管理:“品质的含意从字面上来看,乃是要提供一个超越顶级的事物,而不仅是比大多数的事物更好而已。
”80年代初,当通用电器面临竞争者的威胁时,韦尔奇曾说道:摩托罗拉、惠普科技、德州仪器和施乐公司并没有足够的资本与我们抗衡,而他们的竞争力来自于他们的产品品质。
(IE工业工程)IE七大手法介绍

壹、IE七大手法介绍一、什么是IEIE就是指Industrial工业,Engineering工程,是由二个英文字母的前缀结合。
“IE”是应用科学及社会学的知识,以合理化、舒适化的途径来改善我们工作的品质及效率,以达到提高生产力,增进公司之利润,进而使公司能长期的生存发展,个人的前途也有寄托之所在。
因此,简单地说“IE”就是代表“合理化及改善”的意义,为了顾及记忆的方便,我们就以中文“改善”来代表“IE”的含义。
二、改善(IE)七大手法1. 手法名称简称(1)防止呆子法(Fool-Proof) 防呆法(2)动作改善法(动作经济原则) 动改法(3)流程程序法流程法(4)5X5WIH(5X5何法) 五五法(5)人机配合法(多动作法) 人机法(6)双手操作法双手法(7)工作抽查法抽查法三、七大手法的用途名称用途(1)防呆法如何避免做错事情,使工作第一次就做好的精神能够具体实现。
(2)动改法改善人体动作的方式,减少疲劳使工作更为舒适、更有效率,不要蛮干。
(3)流程法研究探讨牵涉到几个不同工作站或地点之流动关系,藉以发掘出可资改善的地方。
(4)五五法借着质问的技巧来发掘出改善的构想。
(5)人机法研究探讨操作人员与机器工作的过程,藉以掘出可资改善的地方。
(6)双手法研究人体双手在工作时的过程,藉以发掘出可资改善的地方。
(7)抽查法借着抽样观察的方法能很迅速有效地了解问题的真象。
四、改善(IE)七大手法与品管(QC)七大手法之差别“品管(QC)七手法”较着重于对问题的分析与重点的选择,但对如何加以改善则较少可应用。
“改善(IE)七手法”较着重于客观详尽了解问题之现象,以及改善方法的应用,以期达到改善的目标。
有了“改善(IE)七手法”正可弥补品管(QC)手法的缺陷而达到相辅相成之效果,使得改善的效果更为落实也更容易实现。
同时最重要的是改善(IE)七手法亦可单独使用,因其本身具有分析、发掘问题的技巧之故。
贰、防呆法(Fool-Proof)一、目的认识“防呆法”的意义,及学习如何应用“防呆法”的原理于我们的工作上,以避免工作错误的发生,进而达到“第一次就把工作做对”之境界。
工业工程七大手法

不自覺~細心地找出材料、時間及人力的浪費. 3.3 工作之構成
所謂合適的照明,其意義應包括:
1>.必須有合適其工作的充足光度.
2>.必須有合適顏色的光線,且應避免閃光.
3>.必須有合適的投射方向.
原則11: 工作抬椅高度適當舒適
原則12: 盡量以足踏/夾具替代手之工作.
工业工程七大手法
IE七大手法之二 — 動改法
14
原則13: 盡可能將二種工具合並. EXL: 將兩種功能不同的印章,修改成具有兩種功能的單獨印章. 原則14: 工具物料預放在工作位置. 原則15: 依手指負荷能力分配工作.
原則16: 手柄接觸面盡可能加大 原則17: 操作桿應盡可能少變更姿勢.
工业工程七大手法
IE七大手法之三 — 流程法
15
現場作業改善方法:
工业工程七大手法
IE七大手法之三 — 流程法
16
現場作業改善方法:(接上一頁)
工业工程七大手法
IE七大手法之四 — 五五法
17
1.手法名稱:
5 * 5W 1H法;又稱5 * 5何法;又稱質疑創意法;簡稱五五法.
的主要工作.
工业工程七大手法
教材大綱
2
工业工程七大手法
IE簡介
3
1.甚麼是IE?
IE就是指INDUSTRIAL(工業) ENGINEERING(工程).它由兩字詞之首字母組合而成.
标准工时测算方法

标准⼯时测算⽅法⼀、⽬的:规范标准⼯时制定与修改作业,使标准⼯时具有完整性,使ERP系统运⾏之排程合理和成本准确。
⼆、名词定义:2.1、标准⼯时:在特定的⼯作环境条件下,⽤规定的作业⽅法和设备,以普通熟练⼯作者的正常速度完成⼀定质量和数量的⼯作所必需的时间。
2.2、宽放时间:指作业员除正常⼯作时间之外必须的停顿及休息的时间。
包括操作者个⼈事情引起的延迟,疲劳或⽆法避免的作业延迟等时间。
对于没有规定发⽣时间、发⽣频率、所需时间的不规则要素作业,并不在正常时间范围之内,⽽属于宽放时间。
2.3、标准速度:没有过度体⼒和精神疲劳状态下,每天能连续⼯作,只要努⼒就容易达到标准作业成果的速度。
三、标准⼯时的构成:3.1、标准时间=正常时间+宽放时间=观测时间*(1+熟练修正数+努⼒修正数)+观测时间*宽放率3.2、正常时间:3.2.1、主体作业时间:按照作业⽬的进⾏的作业。
指能创造价值的作业,如改变产品外形,改变产品性能等。
3.2.2、副作业时间:与主体作业同步发⽣,起附属作⽤。
如取放⼯具、检查等。
正常时间设定⽅法如下:直接观测法:秒表观测法;摄影分析法;work sampling法。
优点:⽐较简单;任何⼈都可以做。
缺点:难于跟标准速度相⽐较,需要评价标准速度;⽣产之前不能设定。
合成法:动作分析法、历史数据法。
优点:信赖程度和⼀贯性⾼;客观性和普遍性⾼;不需要评价标准速度;可在⽣产之前设定;容易消除不必要动作。
缺点:需要教育和训练。
3.3、宽放时间:3.3.1、私事宽放时间:作业过程中,满⾜⽣理要求的宽放时间,如上厕所,喝⽔,擦汗。
3.3.2、疲劳宽放时间:为了补偿⼯作过程中体⼒和精神疲劳,采取的休息或操作速度减弱的宽放时间。
3.3.3、特殊宽放:学习宽放、机械⼲涉宽放、奖励宽放、⼯⼚宽放、其它宽放. 作业宽放时间:补偿作业过程中发⽣不规则的要素作业。
如⽤处理不良品等。
3.3.4、集体宽放时间:集体作业时,对于个体差异产⽣损失的补偿。
工业工程--标准工时
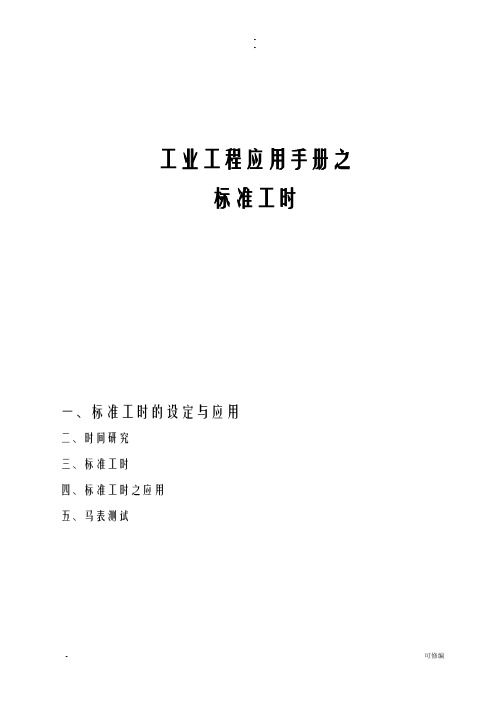
工业工程应用手册之标准工时一、标准工时的设定与应用二、时间研究三、标准工时四、标准工时之应用五、马表测试一,时间研究●泰勒1856-1915☉以马表测量为主。
进展工作研究及寻求改进式☉主:花费工作时间最少者即是最正确之工作法●吉尔柏思:☉研究操作者之动作,再去删除,合并,重组,简化等步骤。
使法最好。
☉主:能用最经济有效的法去完成工作,时间自然会减少。
二,标准工时1,定义;在一定标准条件下,以一定的作业法,由合格且受有良好训练的作业员,以正常的速度完成某项作业所需的时间。
2,标准工时围2.1工作条件:环境,设备,夹治具材料┈2.2作业法:加工式,操作次序,操作动作,操作布置,姿势┈2.3作业员:合格,受完全训练2.4速度:正常速度3,标准工时的维护3.1标准工时法的训练及查核3.2工作法,作业条件,设备,材料等改变时之报告制度设计。
3.3标准工时之诉怨回馈调查及改订。
3.4定期复查制度4.标准工时的构造正常工时=观测工时╳评比因素标准工时=正常工时╳〔1+放宽率〕=正常工时+宽放工时6.标准工时估算三.标准工时之应用1.能效管理:☉效率是对标准时间达成程度的指数,标准时间决定之后。
管理人员必须督导作业员在标准时间完成作业。
2.日程管理:制造部门依据标准时间计算出应生产的产品数量,安排人员设备的配置,日程方案,生产管理等工作,以达成要求的数量。
3.人员本钱计算:☉标准时间计算的根本数据。
4.工作绩效评估及奖金计算。
☉实施奖工制度必须籍由标准时间来衡量工作绩效,才能公平合理计算奖金。
5.设备能力:机器设备具有多少能力,必须依据标准工时来计算分析,以作为设备购置之依据,及来取适当之应变措施。
6.人员及负荷计算☉生产方案拟定后,可依据标准时间计算所需之人工小时及所需人员,而目前机器设备具有多少能力。
其负荷的情况都需依据标准工时来计算。
7.人机配合的计算☉依据标准时间,可适当安排人员及机器的配置以减少人力的浪费。
- 1、下载文档前请自行甄别文档内容的完整性,平台不提供额外的编辑、内容补充、找答案等附加服务。
- 2、"仅部分预览"的文档,不可在线预览部分如存在完整性等问题,可反馈申请退款(可完整预览的文档不适用该条件!)。
- 3、如文档侵犯您的权益,请联系客服反馈,我们会尽快为您处理(人工客服工作时间:9:00-18:30)。
路漫漫其悠远
路漫漫其悠远
路漫漫其悠远
路漫漫其悠远
路漫漫其悠远
路漫漫其悠远
路漫漫其悠远
路漫漫其悠远
路漫漫其悠远
路漫漫其悠远
路漫漫其悠远
路漫漫其悠远
路漫漫其悠远
路漫漫其悠远
路漫漫其悠远
路漫漫其悠远
路漫漫其悠远
路漫漫其悠远
路漫漫其悠远
路漫漫其悠远
路漫漫其悠远
路漫漫其悠远
路漫漫其悠远
路漫漫其悠远
路漫漫其悠远
路漫漫其悠远
路漫漫其悠远
标准工时的计算
• 标准工时 1, 定义;在一定标准条件下,以一定的作业方法,由合格且受有良好训练 的作业员,以正常的速度完成某项作业所需的时间。 2, 标准工时范围 2.1 工作条件:环境,设备,夹治具材料┈ 2.2 作业方法:加工方式,操作次序,操作动作,操作布置,姿势┈ 2.3 作业员:合格,受完全训练 2.4 速度:正常速度 3, 标准工时的维护 3.1标准工时方法的训练及查核 3.2工作方法,作业条件,设备,材料等改变时之报告制度设计。 3.3标准工时之诉怨回馈调查及改订。 3.4定期复查制度 4. 标准工时的结构 5. 标准工时公式 正常工时=观测工时╳评比因素 标准工时=正常工时╳(1+放宽率) =正常工时+宽放工时
路漫漫其悠远
路漫漫其悠远
工业工程七大手法标准 工时的计算方法
路漫漫其悠远 2020/3/24
路漫漫其悠远
路漫漫其悠远
路漫漫其悠远
路漫漫其悠远
路漫漫其悠远
路漫漫其悠远
路漫漫其悠远
路漫漫ቤተ መጻሕፍቲ ባይዱ悠远
路漫漫其悠远
路漫漫其悠远
路漫漫其悠远
路漫漫其悠远
路漫漫其悠远
路漫漫其悠远
路漫漫其悠远
路漫漫其悠远
路漫漫其悠远