外观检测缺陷
成品检验外观缺陷定义和判定基准(20080708)

● A≥2cm2 ● A≤2cm2
●
●
修 版次 订 1 A0 记 录
修订事项 初版发行
修订时间 2008-7-8
编写
确认
承认
受控印章
生效日期
2008-8-1
版次 A0 页次 1/4
成品缺陷描述和判定基准
文件类别 管理编号
成品检验基准书 OQC-STD-1-002
大分 类类
子类
序次
缺陷描述
商标 内 贴纸 箱
101 音质不良、能明显听出
音量 性
能
102 音质不良、不能明显听出 103 杂音、能明显听出 104 杂音、不能明显听出
105 音量小于规格值3%以上
106 不发光
光量 107 发光不稳定
108 光量小于规格值5%以上
音频 频
率 光频
109 大于或小于规格值5%以上 110 大于或小于规格值5%以上 111 不安定
成品缺陷描述和判定基准
文件类别 管理编号
成品检验基准书 OQC-STD-1-002
大分 类类
子类
序次
缺陷描述
94 大于规格值5%以上 始动电压
95 小于规格值5%以上
96 短路或无电流
97 电流大于规格值5%以上 定格电流
98 电流小于规格值5%以上
99 电流不安定、晃动超出规定范围5%以上
100 无音
4.缺陷描述和判定基准
大分 类类
子类
序次
缺陷描述
纸箱
外
箱 胶带
包 装
封存 箱钉
商标 贴纸
盖印
内 箱
纸箱
1 型号或规格错误 2 表面破损或折皱1×10cm以上 3 表面破损或折皱1×10cm以下 4 破裂引将起产品防护不良 5 破裂使产品得不到有效保护 6 表面污渍面积超过5×5cm以上 7 表面污渍面积超过5×5cm以下 8 灰尘或杂物附着严重、包装状态明显不良 9 无印刷或印刷错误 10 尺寸错误,导致无法装箱 11 未封、漏封 12 颜色错误、位置错误 13 未封牢、封歪斜10°以上 14 漏打造成产品防护不良 15 封钉不牢、位置不符 16 封钉划破内箱 17 漏贴商标、贴纸 18 商标、贴纸用错、 19 位置错、贴歪10°以上、贴皱 20 漏盖印、盖错印、印字模糊不清 21 盖印颜色不符、字体大小不符 22 型号及尺寸错误 23 表面破损或折皱1×2cm以上 24 表面破损或折皱1×2cm以下 25 破裂1×2cm以上 26 破裂1×2cm以下 27 表面污渍面积超过1×2cm以上 28 表面污渍面积超过1×2cm以下 29 灰尘或杂物附着严重 30 折叠不良、装入困难或包装状态不良
产品表面外观缺陷的限定标准

苏州荣科精密机械有限公司产品表面外观缺陷的限定标准1 范围本规范规定了产品中结构件的表面等级划分及其外观质量要求。
本规范适用于本公司及子公司结构产品表面外观的标准判定,产品的装配生产及结构验收;也可用于指导设计。
本规范同样适用于外购件的验收,当外购个别件不属于本公司专用型号时,也可按供应商的质量标准对其进行验收,具体要求应参照相应外购件的技术说明书等文件。
2 术语2.1 产品:指本公司确定的、处于向本公司客户发货状态下的物品,如整机、模块、散件。
2.2 A级表面:重要外观表面,体现产品外观形象,具有装饰性,可以直接正视到的主要外观表面。
2.3 B级表面:主要外表面,半装饰性的经常可见的外观表面。
2.4 C级表面:次要外表面和内表面,不是以装饰为目的,表面质量要求不高的结构表面。
除A、B级表面外的表面均为C级表面。
2.5 正视:指检查者站立于被检查表面的正面、视线与被检表面呈45-90度而进行观察。
2.6 金属表面:包括电镀、氧化、钝化、以及金属压铸面、金属机械加工面等表面为金属质感的表面,非喷涂面。
2.7 拉丝:是一种砂带磨削加工,通过砂带对金属表面进行磨削加工,去除金属表面缺陷,并形成具有一定粗糙度、纹路均匀的装饰表面。
2.8 喷涂保护面:零件在喷涂过程中,依据图纸要求,对不要求喷涂的表面进行了保护处理的表面。
3 缺陷定义3.1 金属表面3.1.1 模具痕:折弯等模具成型过程中在结构件表面产生的压痕、轻微凹坑等。
3.1.2 磨擦痕:加工过程中板材在机床台面运动过程中产生的轻微划痕,无凹入感。
3.1.3 运动部件摩擦痕:样本架等在运送过程中和基体产生的痕迹。
3.1.4 焊渣:指电镀、氧化前,金属焊接时飞溅到焊缝位置以外区域的、牢固粘附在基材表面的金属点状颗粒。
3.1.5 烧伤:拉丝处理时因操作不当、造成零件表面过热而留下的烧蚀痕迹。
3.1.6 凹坑:由于基体材料缺陷、或在加工过程中操作不当等原因而在材料表面留下的小坑状痕迹。
混凝土外观缺陷及超声测缺作业指导书

混凝土构件缺陷一、适用范围本作业指导书适用于外观缺陷检测和超声法检测混凝土内部缺陷.混凝土构件内部缺陷检测包括裂缝深度检测、不密实区检测和混凝土结合面质量检测。
二、检测目的采用观察及尺量判断混凝土构件外观缺陷:采用带波形显示功能的超声波检测仪,测量超声脉冲波在混凝土中的传播速度(简称声速),首波幅度(简称波幅)和接收信号主频率(简称主频)等声学参数并根据这些参数及其相对变化,判断混凝土中内部缺陷情况。
三、检测依据《超声法检测混凝土缺陷技术规程》CECS21:2000;《建筑结构检测技术标准》GB/T 50344-2004《混凝土结构工程施工质量验收规范》GB50204-2015《人民防空工程质量验收与评价标准》RFJ01-2015。
四、检测设备盒尺、手持测距仪、吊线、超声波检测仪。
五、抽检数量5。
1外观缺陷检测:全数检查;5。
2内部缺陷检测:当遇下列情况之一时应进行相应构件的内部缺陷检测①委托方要求:②混凝土外观质量检测中,混凝土表面存在修补痕迹或严重质量缺陷:③人防工程口部、防护密闭段、采光井、水封井、防毒防爆井等有防护密闭要求的部位,未一次整体浇筑混凝土:④后浇带、施工缝不符合《人民防空工程施工及验收规范》GB50134的规定。
行。
六、检测前准备6.1收集资料了解工程概况,结构型式,成型工艺等情况,收集《施工组织设计》《施工日志》等相关工程资料.6。
2制定检测方案,确定设备七、检测方法7。
1外观缺陷检测检验方法:观察,检测技术处理方案现浇结构外观质量缺陷7。
2内部缺陷检测7.2.1裂缝深度检测(1)平面检测法当结构的裂缝部位只有一个可测表面,估计裂缝深度又不大于500mm时,可采用单面平测法。
平测时应在裂缝的被测部位,以不同的测距,按跨缝和不跨裂缝布置测点(布置测点时应避开钢筋的影响)进行检测,其检测步骤为:①不跨缝的声时测量:将T和R换能器置于裂缝附近同一侧,以两个换能器内边缘间距1'等于100、150、200、250mm……,分别读取声时值(ti),绘制“时——距”坐标图,或用回归分析的方法求出声时与测距之间的回归直线方程:l i =a+bti每测点超声波实际传播距离li=1’+|a|式中:li—第i点的超声波实际传播距离(mm);1’—第i点的R、T换能器的内边缘间距(mm);a —“时-—距”图中1’轴的截距或回归直线方程的常数项(mm). 不跨缝平测的混凝土声速值为:V=(1n ’—11’)/(tn—t1) (km/s) (1)或V=b(km/s) (2)1n ’、 11’-—第n 点和第1点的测距(mm); tn 、t 1—-第n 点和第1点读取的声时值(us) b -—回归系数 ②跨缝的声时测量将T 、R 换能器分别置于以裂缝为对称的两侧,1'取100、150、200mm ……分别读取声时值t i 0,同时观察首波相位的变化。
缺陷种类及产生原因

焊接缺陷及其特征
(2)影响热裂纹(结晶裂纹)的因素
a.合金元素和杂质的影响。碳元素以及硫、磷等杂质
元素的增加,会扩大敏感温度区,使结晶裂纹的产生机 会增多。 b.冷却速度的影响。冷却速度增大,一是使结晶偏析 加重,二是使结晶温度区间增大,两者都会增大结晶裂
纹的出线机会。
c.结晶应力与拘束应力的影响。在脆性温度区内,金 属的强度极低,焊接应力又使这部分金属受拉,当拉应 力达到一定程度时,就会出现结晶裂纹。
c)再热裂纹:接头冷却后在加热至550~650℃时产生的裂
纹。再热裂纹产生于沉淀强化材料(如含Cr、Mo、V、Ti、
Nb元素的金属材料)的焊接热影响区内的粗晶区发展,呈
晶间开裂特征。
焊接缺陷及其特征
e)层状撕裂:在具有丁字接头或角接头的厚大构件中, 沿钢板的轧制方向分层出现的阶梯状裂纹。层状撕裂实质
焊接缺陷及其特征
3)防止结晶裂纹的措施
a.降低钢材和焊材的碳含量,减少硫、磷等有害元素的 含量。 b.加入一定的合金元素,减少柱状晶和偏析。如加入钼、 钒、钛、铌等细化晶粒。 c.采用熔深较浅的焊缝,改善散热条件使低熔点物质上 浮在焊缝表面二不存在于焊缝中。
d.合理选用焊接规范,采用预热和后热,减小冷却速度。
2,气 孔 气孔是指焊接时,熔池中的气泡在凝固时未能逸 出,而残留下来所形成的空穴。 气孔分类:可分为条虫状气孔、针孔、柱孔,按分 布可分为密集气孔,链孔等。 产生原因:母材或填充金属表面有锈,油污等,焊 条及焊剂未烘干,焊接线能量过小,熔池冷却速度 大等 气孔危害:减少截面积,降低强度、塑性、泄漏。
焊接缺陷及其特征
防止冷裂纹的措施 a.采用低氢型碱性焊条,严格烘干,在100~150℃下保存, 随取随用。 b.提高预热温度,采用后热措施,并保证层间温度不小
轴承出厂检测 外观缺陷检查标准(附检测样本图)

⚫CRB 外圈滚道超精一侧挡边被油石磨成白色one side rib become white by honing Stone in honing process
⚫内倒角磕碰伤/ Insider Corner dent
⚫套圈外径支撑划伤(有深度)/ Trace in the outer side surface(Depth) ⚫滚道中挡边支撑划伤(有深度)/ Scratch in middle rib (Depth)
⚫外圈外径表面有磨削烧伤及裂纹/ Grinding crack and burning in OD surface
⚫外圈外径面生锈/ Rust on the outer surface
⚫内圈滚道表面长划伤/ Long scratch on the raceway
⚫外圈外径表面有深磕伤/ Deep dent on the outer diameter
⚫内圈滚道有磕伤/ CRB Raceway dent
⚫外圈滚道有长划伤/ Long scratch on the raceway ⚫内圈滚道有长划伤/ Long scratch on the raceway
☺
⚫多处测量痕迹(有深度,能感觉) / Too many measuring marks(Depth, can feeling)
☺☺☺
☺⚫外径分段支撑座痕迹Subsection shoe marks on the OD
☺
⚫TRB内圈挡边有圆周划伤/ Circle scratch on the rib side face
⚫内圈滚道超精圆周划伤(有深度,能感觉)/ Circle scratch for honing raceway (Depth, can feeling)。
钢结构常见外观缺陷
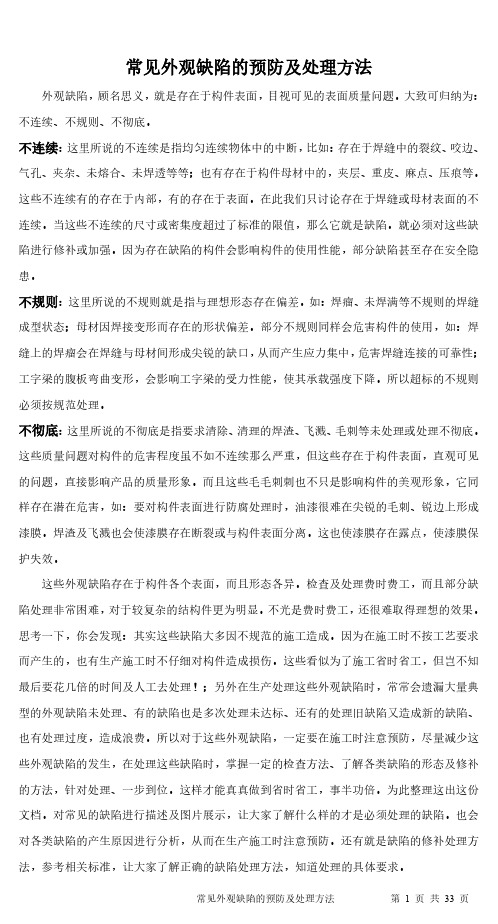
常见外观缺陷的预防及处理方法外观缺陷,顾名思义,就是存在于构件表面,目视可见的表面质量问题。
大致可归纳为:不连续、不规则、不彻底。
不连续:这里所说的不连续是指均匀连续物体中的中断,比如:存在于焊缝中的裂纹、咬边、气孔、夹杂、未熔合、未焊透等等;也有存在于构件母材中的,夹层、重皮、麻点、压痕等。
这些不连续有的存在于内部,有的存在于表面。
在此我们只讨论存在于焊缝或母材表面的不连续。
当这些不连续的尺寸或密集度超过了标准的限值,那么它就是缺陷。
就必须对这些缺陷进行修补或加强。
因为存在缺陷的构件会影响构件的使用性能,部分缺陷甚至存在安全隐患。
不规则:这里所说的不规则就是指与理想形态存在偏差。
如:焊瘤、未焊满等不规则的焊缝成型状态;母材因焊接变形而存在的形状偏差。
部分不规则同样会危害构件的使用,如:焊缝上的焊瘤会在焊缝与母材间形成尖锐的缺口,从而产生应力集中,危害焊缝连接的可靠性;工字梁的腹板弯曲变形,会影响工字梁的受力性能,使其承载强度下降。
所以超标的不规则必须按规范处理。
不彻底:这里所说的不彻底是指要求清除、清理的焊渣、飞溅、毛刺等未处理或处理不彻底。
这些质量问题对构件的危害程度虽不如不连续那么严重,但这些存在于构件表面,直观可见的问题,直接影响产品的质量形象。
而且这些毛毛刺刺也不只是影响构件的美观形象,它同样存在潜在危害,如:要对构件表面进行防腐处理时,油漆很难在尖锐的毛刺、锐边上形成漆膜。
焊渣及飞溅也会使漆膜存在断裂或与构件表面分离。
这也使漆膜存在露点,使漆膜保护失效。
这些外观缺陷存在于构件各个表面,而且形态各异。
检查及处理费时费工,而且部分缺陷处理非常困难,对于较复杂的结构件更为明显。
不光是费时费工,还很难取得理想的效果。
思考一下,你会发现:其实这些缺陷大多因不规范的施工造成。
因为在施工时不按工艺要求而产生的,也有生产施工时不仔细对构件造成损伤。
这些看似为了施工省时省工,但岂不知最后要花几倍的时间及人工去处理!;另外在生产处理这些外观缺陷时,常常会遗漏大量典型的外观缺陷未处理、有的缺陷也是多次处理未达标、还有的处理旧缺陷又造成新的缺陷、也有处理过度,造成浪费。
偏光片外观缺陷检测技术分析
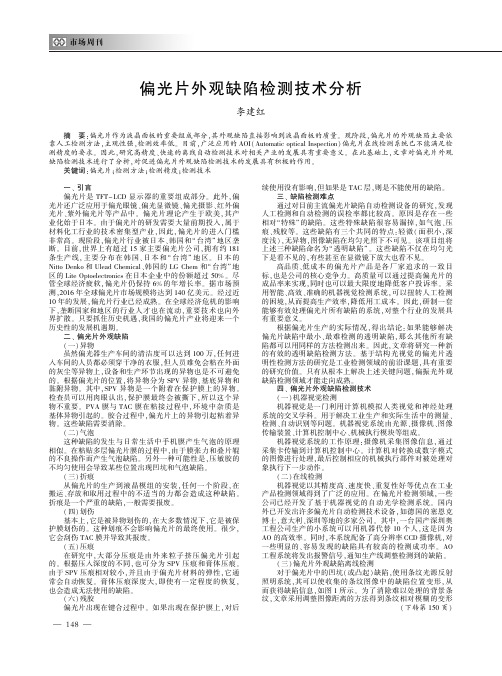
偏光片外观缺陷检测技术分析李建红摘㊀要:偏光片作为液晶面板的重要组成部分,其外观缺陷直接影响到液晶面板的质量㊂现阶段,偏光片的外观缺陷主要依靠人工检测方法,主观性强,检测效率低㊂目前,广泛应用的AOI(AutomaticopticalInspection)偏光片在线检测系统已不能满足检测精度的要求㊂因此,研究高精度㊁快速的离线自动检测技术对相关产业的发展具有重要意义㊂在此基础上,文章对偏光片外观缺陷检测技术进行了分析,对促进偏光片外观缺陷检测技术的发展具有积极的作用㊂关键词:偏光片;检测方法;检测精度;检测技术一㊁引言偏光片是TFT-LCD显示器的重要组成部分㊂此外,偏光片还广泛应用于偏光眼镜㊁偏光显微镜㊁偏光摄影㊁红外偏光片㊁紫外偏光片等产品中㊂偏光片理论产生于欧美,其产业化始于日本㊂由于偏光片的研发需要大量前期投入,属于材料化工行业的技术密集型产业,因此,偏光片的进入门槛非常高㊂现阶段,偏光片行业被日本㊁韩国和 台湾 地区垄断㊂目前,世界上有超过15家主要偏光片公司,拥有约181条生产线,主要分布在韩国㊁日本和 台湾 地区㊂日本的NittoDenko和UleadChemical㊁韩国的LGChem和 台湾 地区的LiteOptoelectronics在日本企业中的份额超过50%㊂尽管全球经济疲软,偏光片仍保持6%的年增长率㊂据市场预测,2016年全球偏光片市场规模将达到140亿美元㊂经过近10年的发展,偏光片行业已经成熟㊂在全球经济危机的影响下,垄断国家和地区的行业人才也在流动,重要技术也向外界扩散㊂只要抓住历史机遇,我国的偏光片产业将迎来一个历史性的发展机遇期㊂二㊁偏光片外观缺陷(一)异物虽然偏光器生产车间的清洁度可以达到100万,任何进入车间的人员都必须穿干净的衣服,但人员难免会粘在外面的灰尘等异物上,设备和生产环节出现的异物也是不可避免的㊂根据偏光片的位置,将异物分为SPV异物㊁基底异物和黏附异物㊂其中,SPV异物是一个附着在保护膜上的异物㊂检查员可以用肉眼认出,保护膜最终会被撕下,所以这个异物不重要㊂PVA膜与TAC膜在粘接过程中,环境中杂质是基体异物引起的㊂胶合过程中,偏光片上的异物引起粘着异物㊂这些缺陷需要消除㊂(二)气泡这种缺陷的发生与日常生活中手机膜产生气泡的原理相似㊂在粘贴多层偏光片膜的过程中,由于膜张力和叠片辊的不良操作而产生气泡缺陷㊂另外一种可能性是,压敏胶的不均匀使用会导致某些位置出现凹坑和气泡缺陷㊂(三)折痕从偏光片的生产到液晶模组的安装,任何一个阶段,在搬运㊁存放和取用过程中的不适当的力都会造成这种缺陷㊂折痕是一个严重的缺陷,一般需要报废㊂(四)划伤基本上,它是被异物划伤的,在大多数情况下,它是被保护膜划伤的㊂这种划痕不会影响偏光片的最终使用㊂很少,它会刮伤TAC膜并导致其报废㊂(五)压痕在研究中,大部分压痕是由外来粒子挤压偏光片引起的㊂根据压入深度的不同,也可分为SPV压痕和膏体压痕㊂由于SPV压痕相对较小,并且由于偏光片材料的弹性,它通常会自动恢复㊂膏体压痕深度大,即使有一定程度的恢复,也会造成无法使用的缺陷㊂(六)残胶偏光片出现在键合过程中㊂如果出现在保护膜上,对后续使用没有影响,但如果是TAC层,则是不能使用的缺陷㊂三㊁缺陷检测难点通过对目前主流偏光片缺陷自动检测设备的研究,发现人工检测和自动检测的误检率都比较高㊂原因是存在一些相对 特殊 的缺陷㊂这些特殊缺陷很容易漏掉,如气泡㊁压痕㊁残胶等㊂这些缺陷有三个共同的特点:轻微(面积小,深度浅),无异物,图像缺陷在均匀光照下不可见㊂该项目组将上述三种缺陷命名为 透明缺陷 ㊂这些缺陷不仅在均匀光下是看不见的,有些甚至在显微镜下放大也看不见㊂高品质㊁低成本的偏光片产品是各厂家追求的一致目标,也是公司的核心竞争力㊂高质量可以通过提高偏光片的成品率来实现,同时也可以最大限度地降低客户投诉率㊂采用智能㊁高效㊁准确的机器视觉检测系统,可以扭转人工检测的困境,从而提高生产效率,降低用工成本㊂因此,研制一套能够有效处理偏光片所有缺陷的系统,对整个行业的发展具有重要意义㊂根据偏光片生产的实际情况,得出结论:如果能够解决偏光片缺陷中最小㊁最难检测的透明缺陷,那么其他所有缺陷都可以用同样的方法检测出来㊂因此,文章将研究一种新的有效的透明缺陷检测方法㊂基于结构光视觉的偏光片透明性检测方法的研究是工业检测领域的前沿课题,具有重要的研究价值㊂只有从根本上解决上述关键问题,偏振光外观缺陷检测领域才能走向成熟㊂四㊁偏光片外观缺陷检测技术(一)机器视觉检测机器视觉是一门利用计算机模拟人类视觉和神经处理系统的交叉学科㊂用于解决工业生产和实际生活中的测量㊁检测㊁自动识别等问题㊂机器视觉系统由光源㊁摄像机㊁图像传输装置㊁计算机控制中心㊁机械执行模块等组成㊂机器视觉系统的工作原理:摄像机采集图像信息,通过采集卡传输到计算机控制中心㊂计算机对转换成数字模式的图像进行处理,最后控制相应的机械执行部件对被处理对象执行下一步动作㊂(二)在线检测机器视觉以其精度高㊁速度快㊁重复性好等优点在工业产品检测领域得到了广泛的应用㊂在偏光片检测领域,一些公司已经开发了基于机器视觉的自动光学检测系统㊂国内外已开发出许多偏光片自动检测技术设备,如德国的塞恩克博士,意大利㊁深圳等地的多家公司㊂其中,一台国产深圳奥工程公司生产的小系统可以用机器代替10个人,这是因为AO的高效率㊂同时,本系统配备了高分辨率CCD摄像机,对一些明显的㊁容易发现的缺陷具有较高的检测成功率㊂AO工程系统将发出报警信号,通知生产线调整检测到的缺陷㊂(三)偏光片外观缺陷离线检测对于偏光片中的凹坑(或凸起)缺陷,使用条纹光源反射照明系统,其可以使收集的条纹图像中的缺陷位置变形,从而获得缺陷信息,如图1所示㊂为了消除难以处理的背景条纹,文章采用调整图像距离的方法得到条纹相对模糊的变形㊀㊀㊀(下转第150页)(二)加强对会计核算的监督加强企业会计内部控制,是推动企业长远发展的必要手段㊂通过完善会计内部控制体系,有利于强化企业对财务会计工作的重视程度,节约企业的经营成本,提高企业的资金利用率㊂可协调企业的生产活动,使其高速运行,获得更多的经济效益,从而提高会计核算水平,保障会计信息质量㊂所以,在进行企业会计核算内部监督的同时,也应当充分发挥外部监督的作用㊂企业会计核算也应当在政府相关部门的监督下进行㊂通过这样的方式可以从内部以及外部方面对企业会计核算进行全面的监督,保障该项工作在科学的基础上能够顺利进行㊂(三)加强对企业会计内部控制人员专业素养的提升对企业会计内部控制人员的专业素养进行提升是极为必要的㊂企业应当积极组织对员工进行培训,进而使员工实现职业素养的提升㊂进入21世纪以来,人类进入了信息化时代,信息技术已经融入了人们生活的方方面面,企业内部会计控制的发展也势必离不开信息技术㊂故而企业应当在员工职业素养的培训过程中加强对员工信息技能的培养㊂通过这样的方式,员工能够更加迅速适应时代发展的变化,更好地满足时代对其提出的要求,进而推动企业的向前发展㊂五㊁结语企业为了在激烈的市场竞争中保持足够的竞争力,正在紧随时代的发展潮流积极进行改革,企业会计内部控制的改革就是其中的一项重要内容㊂我国的企业会计内部控制建设已经取得了一定的成效,但也仍旧存在一些问题,故而在日后的工作推进过程中应当不断加强对企业会计内部控制的重视程度㊂应当日益完善企业会计内部控制体系,加强对会计核算的监督,同时,还应当加强对员工职业素养的提升㊂只有这样,企业才能够保持长久的竞争力,不断提升经济效益,进而实现企业战略目标㊂参考文献:[1]杨健.探讨会计电算化对内部控制的影响[J].会计师,2018(15).[2]王贺.会计电算化条件下加强内部控制探讨[J].中国农业会计,2011(5).[3]王玲霞,王怡.高校会计电算化管理的内部控制[J].审计与理财,2011(6).[4]孙雪艳.会计电算化内部控制存在的问题及对策探讨[J].中国乡镇企业会计,2011(8).[5]廖毅珍.内部控制视角下企业会计工作存在的问题及措施分析[J].财讯,2019,33(23):33-34.[6]彭叶.浅谈中小企业会计内部控制的问题及其措施分析[J].当代会计,2020,28(4):115-116.作者简介:刘秀玲,呼和浩特惠则恒投资(集团)有限责任公司㊂(上接第148页)图像,然后采用固定阈值的方法对图像进行二值化,采用形态学处理得到缺陷㊂在处理凹坑(凸点)缺陷时,文章采用有针对性的反射光源照明方法获得理想的缺陷图像,处理算法简单快速㊂图1㊀条纹反射光照明(四)结构光检测结构光缺陷检测是在结构光测量的基础上发展起来的㊂利用机器视觉理解三维物体的计算领域,他认为所有空间物体都是由点㊁线㊁面组成的,三维图像的坐标可以通过二维图像获得㊂解决了三维曲面物体的重建和描述问题,文中所用的结构光测量系统基本保留至今㊂结构光测量原理如图2所示㊂图2㊀结构光测量原理根据光源投影的类型,结构光分为:点结构光㊁线结构光和面结构光㊂这三种光源在物体表面缺陷检测中也得到了广泛的应用㊂线结构光用于检测焊缝㊂在在线光源的照射下可以检测到异常部位,采集到的图片会发生严重变形㊂然后利用简单的图像处理算法对缺陷进行分析㊂与线结构光的单一线性光源不同,表面结构光源可分为重复图案传输法和编码图像传输法㊂虽然它存在计算复杂和结构光图像匹配的问题,但由于表面光源不需要像线结构光那样进行扫描,因此测量速度比线结构光大大加快㊂因此,表面结构光检测得到了广泛的应用㊂五㊁结语文章通过偏光片外观缺陷进行了概括性的分析,通过其中的缺陷检测难点归总,在此分析了偏光片外观缺陷检测技术,展示出各个检测技术的优缺点以及工作原理,希望能给偏光片外观缺陷检测技术一定的补充作用㊂参考文献:[1]黄广俊,邓元龙.融合改进LBP和SVM的偏光片外观缺陷检测与分类[J].计算机工程与应用,2019,v.56;No.965(22):257-261.[2]石鹏飞.基于深度学习的偏光片检测技术研究[J].机械管理开发,2019,v.34;No.193(5):168-169,178.作者简介:李建红,南京汉旗新材料股份有限公司㊂。
外观检验标准
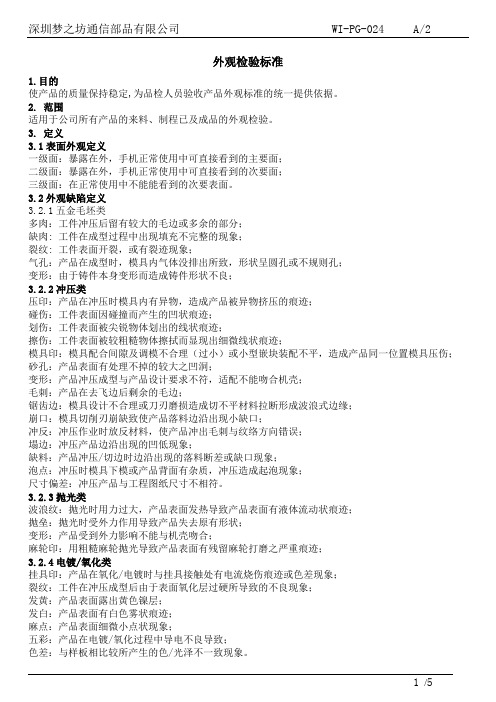
外观检验标准1.目的使产品的质量保持稳定,为品检人员验收产品外观标准的统一提供依据。
2. 范围适用于公司所有产品的来料、制程已及成品的外观检验。
3. 定义3.1表面外观定义一级面:暴露在外,手机正常使用中可直接看到的主要面;二级面:暴露在外,手机正常使用中可直接看到的次要面;三级面:在正常使用中不能能看到的次要表面。
3.2外观缺陷定义3.2.1五金毛坯类多肉:工件冲压后留有较大的毛边或多余的部分;缺肉: 工件在成型过程中出现填充不完整的现象;裂纹: 工件表面开裂,或有裂迹现象;气孔:产品在成型时,模具内气体没排出所致,形状呈圆孔或不规则孔;变形:由于铸件本身变形而造成铸件形状不良;3.2.2冲压类压印:产品在冲压时模具内有异物,造成产品被异物挤压的痕迹;碰伤:工件表面因碰撞而产生的凹状痕迹;划伤:工件表面被尖锐物体划出的线状痕迹;擦伤:工件表面被较粗糙物体擦拭而显现出细微线状痕迹;模具印:模具配合间隙及调模不合理(过小)或小型嵌块装配不平,造成产品同一位置模具压伤;砂孔:产品表面有处理不掉的较大之凹洞;变形:产品冲压成型与产品设计要求不符,适配不能吻合机壳;毛刺:产品在去飞边后剩余的毛边;锯齿边:模具设计不合理或刀刃磨损造成切不平材料拉断形成波浪式边缘;崩口:模具切削刃崩缺致使产品落料边沿出现小缺口;冲反:冲压作业时放反材料,使产品冲出毛刺与纹络方向错误;塌边:冲压产品边沿出现的凹低现象;缺料:产品冲压/切边时边沿出现的落料断差或缺口现象;泡点:冲压时模具下模或产品背面有杂质,冲压造成起泡现象;尺寸偏差:冲压产品与工程图纸尺寸不相符。
3.2.3抛光类波浪纹:抛光时用力过大,产品表面发热导致产品表面有液体流动状痕迹;抛垒:抛光时受外力作用导致产品失去原有形状;变形:产品受到外力影响不能与机壳吻合;麻轮印:用粗糙麻轮抛光导致产品表面有残留麻轮打磨之严重痕迹;3.2.4电镀/氧化类挂具印:产品在氧化/电镀时与挂具接触处有电流烧伤痕迹或色差现象;裂纹:工件在冲压成型后由于表面氧化层过硬所导致的不良现象;发黄:产品表面露出黄色镍层;发白:产品表面有白色雾状痕迹;麻点:产品表面细微小点状现象;五彩:产品在电镀/氧化过程中导电不良导致;色差:与样板相比较所产生的色/光泽不一致现象。
缺陷种类及产生原因分析

焊接缺陷及其特征 4.裂纹(焊接裂纹):
在焊接应力及其它致脆因素共同作用下,焊接接头中局部 地区的金属原子结合力遭到破坏而形成的新界面而产生缝隙, 称为焊接裂纹。 按其尺寸分为宏观、微观、超显微裂纹 按其方向可分为纵向裂纹、横向裂纹,辐射状(星状)裂纹 按发生的部位可分为根部裂纹、弧坑裂纹,熔合区裂纹、焊 趾裂纹及热响裂纹。 按产生的条件和时机可分为热裂纹(如结晶裂纹、液化裂纹 等)、冷裂纹(如氢致裂纹、层状撕裂等)以及再热裂纹。
焊接缺陷及其特征
3,夹渣:指焊后熔渣残留于焊缝中的现象。 夹渣又分金属夹渣和非金属夹渣两种。
焊接缺陷及其特征
产生原因: (1)坡口尺寸不合理。 (2)坡口有污物。 (3)焊接线能量过小。 (4)多层焊时,层间清渣不彻底。 (5)焊缝散热太快,液态金属凝固过快。 (6)药皮,焊剂化学成分不合理,熔点过高,冶金反应不完全 ,脱渣性不好等。 (7)钨极焊时电流过大,钨极融化脱落焊缝内。 (8)手工焊时焊条摆动不真确,熔渣不利于上浮。 夹渣危害:点状夹渣与气孔相同,带有尖端夹渣易形成应力集中 ,可能形成裂纹,危害比较大。
3.无坡口未焊透
焊接缺陷及其特征
焊接缺陷及其特征
焊接缺陷及其特征
焊接缺陷及其特征
二,铸件中常见缺陷 铸件是承压类特种设备中较少的工件,所以对常见 缺陷在这里只是简单介绍: 其常见缺陷有: 1. 气孔 2. 夹渣 3. 夹砂 4. 密集气孔 5. 冷隔 6. 缩孔和疏松 7. 裂纹。
焊接缺陷及其特征
第七章
缺陷种类及产生原因
缺陷种类及产生原因 无损检测最主要的用途是探测缺陷。了解材料 和焊逢中的缺陷种类和产生原因,有助于正确的 选择无损检测方法,正确判断和分析检测结果。
缺陷种类及产生原因
产品表面外观缺陷的限定标准

产品表面外观缺陷的限定标准公司内部编号:(GOOD-TMMT-MMUT-UUPTY-UUYY-DTTI-产品表面外观缺陷的限定标准正视:指检查者站立于被检查表面的正面、视线与被检表面呈 45-90°而进行的观察(如图1)。
图 1:“正视”位置示意图A级表面:从外部能直接看到、或日常维护时能被直接看到的表面。
A级表面分为A1、A2 两个表面。
(A1、A2表面划分见表下表)A1表面:在产品正常工作状态下、能直接正视到的产品正前外表面。
A2表面:在产品正常工作状态下、除A1表面以外的能直接正视到的外表面。
B级表面:除A级以外的所有表面。
金属表面:包括电镀、氧化、钝化、以及金属压铸面等非喷涂表面。
打磨:是一种砂带磨削加工,通过砂带对金属表面进行磨削加工,去除金属表面缺陷,并形成具有一定粗糙度、纹路均匀的装饰表面。
基材花斑:电镀或氧化前因基体材料腐蚀、或者材料中的杂质、或者材料微孔等原因所造成的、与周围材质表面不同光泽或粗糙度的斑块状花纹外观。
喷涂前划痕:指喷涂或氧化之前因操作不当、或对明显缺陷进行粗打磨等人为造成的基体材料上的一般呈细线型划伤或局部磨擦的痕迹。
浅划痕:膜层表面划伤,但未伤至底层(即底层未暴露);对其它无膜层表面则为:目测不明显、手指甲触摸无凹凸感、未伤及材料本体的伤痕。
深划痕:表面膜层划伤,且已伤至底层(即底层已暴露出来);对无膜层表面则为:目测明显、手指甲触摸有凹凸感、伤及材料本体的伤痕。
凹坑:由于基体材料缺陷、或在加工过程中操作不当等原因而在材料表面留下的小坑状痕迹。
凹凸痕:因基材受撞击或校形不良等而呈现出的明显变形、凹凸不平整的现象,手摸时有不平感觉。
打磨区:对基材上的腐蚀、划伤、焊接区、铆接区等部位进行机械打磨抛光后表现出的局部高光泽、光亮区域。
烧伤:拉丝处理时因操作不当、造成零件表面过热而留下的烧蚀痕迹。
水印:电镀或氧化后因清洗水未及时干燥或干燥不彻底所形成的斑纹、印迹。
电子产品外观检验标准(二)2024
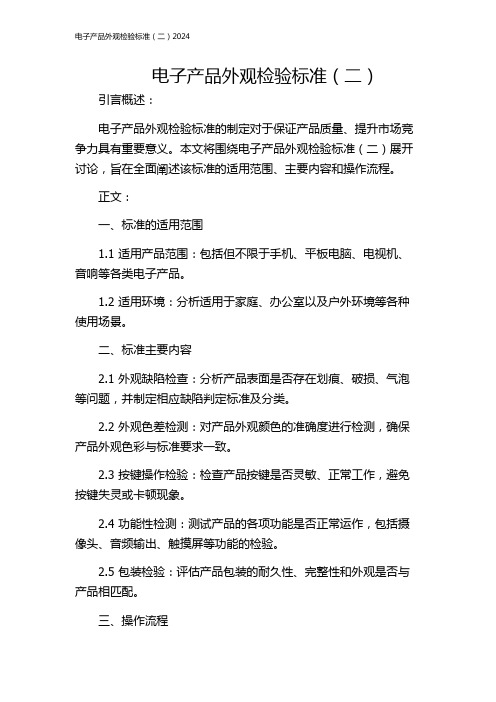
电子产品外观检验标准(二)引言概述:电子产品外观检验标准的制定对于保证产品质量、提升市场竞争力具有重要意义。
本文将围绕电子产品外观检验标准(二)展开讨论,旨在全面阐述该标准的适用范围、主要内容和操作流程。
正文:一、标准的适用范围1.1 适用产品范围:包括但不限于手机、平板电脑、电视机、音响等各类电子产品。
1.2 适用环境:分析适用于家庭、办公室以及户外环境等各种使用场景。
二、标准主要内容2.1 外观缺陷检查:分析产品表面是否存在划痕、破损、气泡等问题,并制定相应缺陷判定标准及分类。
2.2 外观色差检测:对产品外观颜色的准确度进行检测,确保产品外观色彩与标准要求一致。
2.3 按键操作检验:检查产品按键是否灵敏、正常工作,避免按键失灵或卡顿现象。
2.4 功能性检测:测试产品的各项功能是否正常运作,包括摄像头、音频输出、触摸屏等功能的检验。
2.5 包装检验:评估产品包装的耐久性、完整性和外观是否与产品相匹配。
三、操作流程3.1 制定外观检验计划:确定检验的具体内容、检验方法和检验设备的选择。
3.2 检验前准备:清理检验区域、准备检验工具并对检验设备进行校准和调试。
3.3 外观检验过程:按照标准要求进行逐项检验,记录检验结果并进行分类归档。
3.4 缺陷判定与处理:对检验结果中的缺陷进行判定,并制定具体的解决方案以保证产品质量。
3.5 报告撰写与总结:整理检验结果、撰写检验报告并总结本次检验的不足之处,为下次检验提供参考。
结论:电子产品外观检验标准的制定和执行对于确保产品质量、提高用户体验至关重要。
本文详细介绍了该标准的适用范围、主要内容和操作流程,旨在为电子产品制造商和检验机构提供指导,帮助其进行高效、准确的外观检验。
通过严格按照标准要求进行外观检验,能够保证产品质量稳定性,提高品牌形象,满足市场需求。
产品表面外观缺陷的限定标准
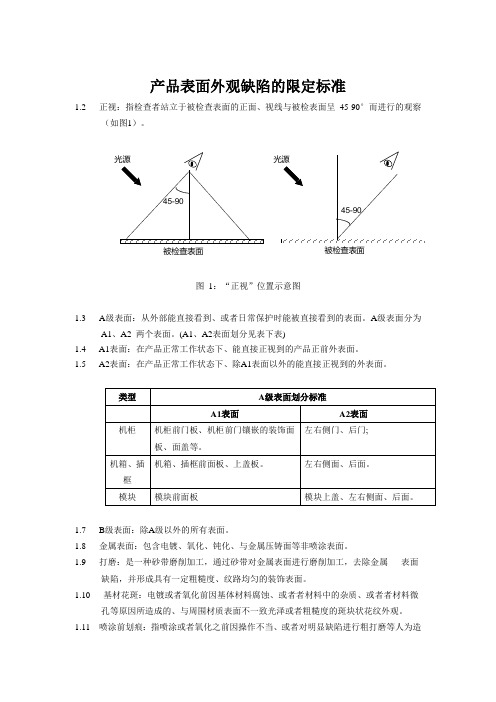
产品表面外观缺陷的限定标准1.2 正视:指检查者站立于被检查表面的正面、视线与被检表面呈45-90°而进行的观察(如图1)。
被检查表面被检查表面图1:“正视”位置示意图1.3 A级表面:从外部能直接看到、或者日常保护时能被直接看到的表面。
A级表面分为A1、A2 两个表面。
(A1、A2表面划分见表下表)1.4 A1表面:在产品正常工作状态下、能直接正视到的产品正前外表面。
1.5 A2表面:在产品正常工作状态下、除A1表面以外的能直接正视到的外表面。
1.7B级表面:除A级以外的所有表面。
1.8 金属表面:包含电镀、氧化、钝化、与金属压铸面等非喷涂表面。
1.9 打磨:是一种砂带磨削加工,通过砂带对金属表面进行磨削加工,去除金属表面缺陷,并形成具有一定粗糙度、纹路均匀的装饰表面。
1.10 基材花斑:电镀或者氧化前因基体材料腐蚀、或者者材料中的杂质、或者者材料微孔等原因所造成的、与周围材质表面不一致光泽或者粗糙度的斑块状花纹外观。
1.11 喷涂前划痕:指喷涂或者氧化之前因操作不当、或者对明显缺陷进行粗打磨等人为造成的基体材料上的通常呈细线型划伤或者局部磨擦的痕迹。
1.12 浅划痕:膜层表面划伤,但未伤至底层(即底层未暴露);对其它无膜层表面则为:目测不明显、手指甲触摸无凹凸感、未伤及材料本体的伤痕。
1.13 深划痕:表面膜层划伤,且已伤至底层(即底层已暴露出来);对无膜层表面则为:目测明显、手指甲触摸有凹凸感、伤及材料本体的伤痕。
1.14 凹坑:由于基体材料缺陷、或者在加工过程中操作不当等原因而在材料表面留下的小坑状痕迹。
1.15 凹凸痕:因基材受撞击或者校形不良等而呈现出的明显变形、凹凸不平整的现象,手摸时有不平感受。
1.16 打磨区:对基材上的腐蚀、划伤、焊接区、铆接区等部位进行机械打磨抛光后表现出的局部高光泽、光亮区域。
1.17 烧伤:拉丝处理时因操作不当、造成零件表面过热而留下的烧蚀痕迹。
品检中的典型缺陷识别技巧

品检中的典型缺陷识别技巧在品质检测过程中,准确识别产品缺陷是确保产品质量的关键一步。
而对于品检中的典型缺陷识别技巧,以下将介绍一些常见的方法和策略,以帮助品检人员更好地识别产品缺陷。
1. 合格标准的了解品检人员需要深入了解相关产品的合格标准。
合格标准通常包括产品的外观要求、物理性能、化学成分等方面的指标。
通过熟悉合格标准,品检人员可以知道产品应具备的品质特征,进而判断出可能存在的缺陷。
2. 视觉检查视觉检查是品检中最常用的一种方法。
通过仔细观察产品的外观特征,品检人员可以寻找产品上的明显缺陷,如划痕、破损、变形等。
还需要注意产品的颜色、纹理、光泽等方面,确保其与合格标准一致。
3. 使用辅助工具在一些细微缺陷的检测中,使用辅助工具可以提高识别的准确性。
例如,使用放大镜、显微镜等工具可以帮助品检人员观察到小尺寸、微小变化的缺陷。
还可以利用光源、照明设备等来提供适当的照明条件,以便更好地识别缺陷。
4. 对比检查对比检查是一种将产品与合格标准或参考样品进行对比的方法。
通过对比,品检人员可以更容易地发现产品中的差异。
对比可以在色彩、尺寸、形状等方面进行。
同时,品检人员还可以通过对比来判断产品表面的平整度、光洁度、粗糙度等特征是否符合要求。
5. 功能性测试除了外观缺陷,功能性缺陷也是需要重点关注的。
通过对产品进行功能性测试,品检人员可以了解产品能否正常工作、达到预期的性能指标。
功能性测试可以通过物理测试设备、实验室仪器等进行,以确保产品在使用过程中没有问题。
6. 定期培训与学习品检人员需要不断更新自己的知识和技术。
定期参加培训课程、学习相关的理论知识和经验,可以帮助品检人员更好地了解缺陷识别技巧的最新发展,并且提高自己的专业水平。
同时,了解行业中的新技术、新方法也有助于品检人员更加准确地识别产品缺陷。
在品检中,准确识别产品缺陷直接关系到产品质量和消费者满意度。
通过掌握合格标准、视觉检查、使用辅助工具、对比检查、功能性测试等缺陷识别技巧,品检人员可以更加准确地判断产品是否合格,及时发现并解决缺陷问题,确保产品质量。
光伏组件到货检测内容

光伏组件到货检测内容一、引言光伏组件作为光伏发电系统的关键组成部分,其质量直接影响到系统的发电效率和持续稳定运行。
因此,在光伏组件到货之后,对其进行严格的检测是非常重要的。
光伏组件到货检测内容主要包括外观检测、电性能检测和可靠性测试。
本文将详细介绍光伏组件到货检测的内容及其重要性。
二、外观检测1.外观缺陷检测外观缺陷检测主要包括对光伏组件表面的玻璃、背板、边框等部分进行检查。
主要目的是检测组件表面是否有明显的划痕、凹陷、污渍等缺陷,这些缺陷可能会影响组件的外观质量和光电转换效率。
应该在合适的光照条件下进行检测,以便更好地发现表面缺陷。
2.尺寸偏差检测光伏组件的尺寸偏差主要包括长度、宽度和厚度的偏差。
尺寸偏差会直接影响到组件的安装和使用,因此需要对组件的尺寸进行精确测量,确保其符合要求的尺寸标准。
3.标识符号检测光伏组件上通常会有很多标识符号,如产品型号、生产日期、生产厂家等。
这些标识符号的准确性和完整性对于组件的追溯和售后服务是非常重要的,因此需要对其进行认真检测。
三、电性能检测1.光电特性检测光伏组件的光电特性是评价其性能的重要指标之一。
光电特性检测主要包括进行光电转换效率、填充因子、开路电压和短路电流的测试。
这些参数直接影响组件的发电效率和性能表现,因此需要对其进行精确测量并与设计要求进行比较。
2.电学性能检测电学性能检测主要包括对组件的绝缘电阻、绝缘耐压、击穿电压和导通电阻等参数进行测试。
这些参数可以直接反映组件的电气性能和安全性能,确保组件在运行中不会出现电气故障。
四、可靠性测试1.环境适应性测试光伏组件安装在户外环境中,需要能够耐受各种恶劣的天气条件,如高温、低温、高湿度、辐射等。
因此,需要对组件的环境适应性进行测试,确保其能够在不同环境条件下稳定运行。
2.机械强度测试机械强度测试主要包括对组件的抗压、抗拉、抗冲击等力学性能进行测试。
这些参数直接反映了组件在安装和运行过程中的机械稳定性和安全性,确保其不会因为受力而发生破损或者变形。
探针不良判定标准
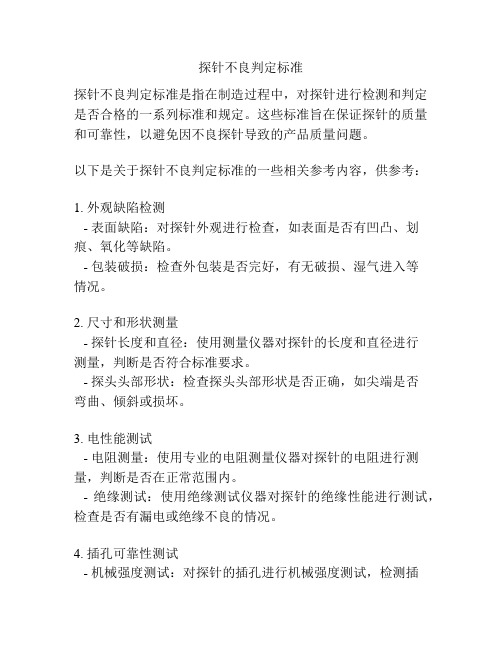
探针不良判定标准探针不良判定标准是指在制造过程中,对探针进行检测和判定是否合格的一系列标准和规定。
这些标准旨在保证探针的质量和可靠性,以避免因不良探针导致的产品质量问题。
以下是关于探针不良判定标准的一些相关参考内容,供参考:1. 外观缺陷检测- 表面缺陷:对探针外观进行检查,如表面是否有凹凸、划痕、氧化等缺陷。
- 包装破损:检查外包装是否完好,有无破损、湿气进入等情况。
2. 尺寸和形状测量- 探针长度和直径:使用测量仪器对探针的长度和直径进行测量,判断是否符合标准要求。
- 探头头部形状:检查探头头部形状是否正确,如尖端是否弯曲、倾斜或损坏。
3. 电性能测试- 电阻测量:使用专业的电阻测量仪器对探针的电阻进行测量,判断是否在正常范围内。
- 绝缘测试:使用绝缘测试仪器对探针的绝缘性能进行测试,检查是否有漏电或绝缘不良的情况。
4. 插孔可靠性测试- 机械强度测试:对探针的插孔进行机械强度测试,检测插孔的耐用性和抗压能力。
- 插拔测试:对探针的插孔进行多次插拔测试,检查插孔的可靠性和连接稳定性。
5. 焊接质量测试- 焊盘质量:检查探针的焊盘质量,包括焊盘外观是否光滑、无锡、无裂纹等。
- 焊点可靠性测试:对探针的焊点进行可靠性测试,包括剪切测试、拉力测试等,判断焊点是否牢固。
6. 灵敏度测试- 探针的灵敏度测试:对探针的灵敏度进行测试,包括灵敏度范围、灵敏度变化等指标的测量。
以上是对探针不良判定标准的一些相关参考内容,仅供参考。
实际应用中,具体的不良判定标准可能会根据不同产品、不同生产线和不同要求而有所不同,需要依据实际情况进行调整和制定。
在制定不良判定标准时,应充分考虑产品功能要求、质量标准和客户需求等因素,确保探针的质量符合要求。
产品表面外观缺陷的限定标准

本规范规定了华为技术有限公司结构件的表面等级划分及外观质量要求。
本规范适用于华为技术有限公司产品的结构件来料验收和生产、发货检验,也可用于指导设计。
简介Brief introduction:
本文件根据华为技术有限公司产品要求及生产技术水平而制定,同时兼顾已形成惯例的一些共识,并参考已在执行中的部分检验标准。
序号No.
文件编号Doc No.
文件名称Doc Title
DKBA0.400.0109
压铸件质量要求
DKBA0.400.0111
预镀钢板切口边防护质量要求
Q/DKBA3250
整机装配质量标准
DKBA0.400.0070
结构件印刷图文质量要求
DKBA0.450.0040
钣金冲压件通用技术要求
术语和定义Term&Definition:
L≤40,P≤3
可接受
中
L≤40,P≤3
L≤50,P≤4
大
L≤50,P≤4
L≤60,P≤5
超大
L≤60,P≤5
L≤100,P≤6
镀后划痕(注3)
小
各种
不允许
L≤20,P≤2
可接受
中
L≤40,P≤3
大
L≤50,P≤4
超大
L≤60,P≤5
基材花斑
不限
各种
不允许
缺陷面积总和≤被测面积的5%
缺陷面积总和≤被测面积的10%
镀层起泡
不限
各种
不允许
不允许
S≤2,P≤4
露白
黑点
小
镀锌彩
不允许
S≤2,P≤3
S≤3,P≤4
中
外观缺陷

7. 客户辨
由判定人员或市场服务人员直接访问 客户,征询他们的意见,获得第一手资料.有的 公司安排品保人员定期在销售柜台工作一 段时间,目的之一就是如此.
总之,对于产品的外观缺陷的判定也需 要经常调节,这样才能减少“错杀率”,因为 如果遭到错杀,所耗费的成本正是企业自己 需要支付的.
对于我们暂时难以判定的有外观缺陷的产品,可 记录下场站的内容、出厂号码等信息,并让其流入市 场.如果无客户投诉返回,则说明该缺陷程度客户可能 接受,甚至还能再放松些.这些有缺陷的产品数量尽可 能不要集中在同一批货里,要适当地分散开来.
试“放水”之后,无论是否有客户投诉,都需要对 产品外观缺陷进行调整,要么将标准放松,要么提高标 准.
可通过客户需求、理想标准、实际控 制这三个方面的相互关系,来描述对外观缺 陷的判定.
制作工程内虚拟的一个判定标准, 该判定标准略高于客户需求, 不会引发客户投诉.
理想标准
实际控制
判定人员(管理人员) 对产品的缺陷实际进 行的判定或调整,其如 果事分OK(良)或NG(
不良)两种.
客户需求
每一个客户对缺陷的可 接受程度.但需要注意 的是,每一个客户对外观 缺陷可接受的程度是不
外观缺陷的特点
3.变化性 随着时间的向后推移,事物发生了某种量变或质变. 对外观缺陷而言,包含了两种含义.
A.一般一样产品在供不应求时,可能人们对于 外观缺陷的存在不会太介意;但是如果供大于求时, 则消费者对于外观缺陷的要求要严格.
B.随着产品保管环境的变化,有的产品的外观 缺陷本身的量和质都发生的变化,如生锈严重、油 污扩大、颜色减淡、裂纹加深等等.
外观缺陷

实际控制
客户需求
判定人员(管理人员) 对产品的缺陷实际进 行的判定或调整,其如 果事分OK(良)或NG( 不良பைடு நூலகம்两种.
每一个客户对缺陷的可 接受程度.但需要注意 的是,每一个客户对外观 缺陷可接受的程度是不
完全一样的.
如何防止外观缺陷的出现?
1.事先防
(1) 防范作业人员在作业、检查过程中造成 缺陷.如要求接触产品外观的人员要戴手套、 指套,不得佩带戒指、留长指甲等.
外观缺陷的定义 及特点
外观缺陷的定义:
主要是指产品的外观材料上不影响到 产品的功能及性能的缺陷,通常包括产品 的伤痕、毛边、脏污、浇口、凹坑、色差 等小缺点.
.
外观缺陷的特点
1.非量化 很多企业对于外观规格的要求和定义较 为模糊. 比如,有的企业定义是: 距离30cm以上,普通照明条件下,连续看 5sec,不显眼即可….. 这些表述基本完全无法量化,很难让人 理解,而且也无法真正执行.事实上在这种情 况下,产品的质量行与不行,全在于人的感觉.
外观缺陷判定及如何防止出现这一现象
由于外观缺陷的特殊性,因此对于缺陷 的判定有时候是十分困难的,如何进行外观 缺陷的判定呢? 可通过客户需求、理想标准、实际控 制这三个方面的相互关系,来描述对外观缺 陷的判定.
制作工程内虚拟的一个判定标准, 该判定标准略高于客户需求, 不会引发客户投诉.
理想标准
6. 外行辨
有人可能会奇怪,外行怎么能够懂得选别和判定呢? 其实产品的外观缺陷与性能、功能等的判定是不同 的,就好像一个电视剧,人人都看,就算是不懂应该怎么 编剧的人,也还是会判断这个片子到底好不好看的.因 此,对于产品的外观缺陷的判断面言,可能外行的标准 其实才是最接近客户的要求的.因为我们的检验人员 们成天地面对着外观缺陷,会意识地对缺陷越检越严 格,时间一久,往往就可能远远地高于原先所设定的标 准. 因此,当产品的外观缺陷难以判定时,不妨找一些 不相干的外行来参与一下,听听他们的意见也不失为 一个好方法.