数控铣床工装夹具的设计及其应用
浅谈数控铣床工装夹具的设计

106报 刊 荟 萃科技纵横kejizongheng随着数控机床的发展与普及,有效的提高了机械制造业的生产效率和加工质量。
其中,在数控铣床加工过程中,处在能够把机床、工件、刀具固定在正确的位置上的工装夹具有着很重要的作用,能够让数控铣床在加工过程中更为精准性,提高数控铣床加工的工作效率和加工潜力,有效的扩大了机床的使用范围。
对此,设计一些专用的工装夹具是具有很大的必要性的。
一、诠释数控铣床工装夹具在机械加工中,为完成需要的加工工序,装配工序及检验工序等,首要的就是要把加工工件进行固定,以用来保证加工工具能够处于正确的位置,这种用来固定、支撑、夹紧加工材料的工具叫做数控铣床的工装夹具。
工装夹具通常由定位元件(确定工件在夹具中的正确位置)、夹紧装置、对刀引导元件(确定刀具与工件的相对位置或导引刀具方向)、分度装置(使工件在一次安装中能完成数个工位的加工,有回转分度装置和直线移动分度装置两类)、连接元件以及夹具体(夹具底座)等组成。
通常数控铣床工装夹具的有塑料材质的,也有金属块的。
在数控机床上加工工件时,设计一套合理的数控铣床工装夹具可以充分发挥数控机床加工潜力,提供机械加工的效率,有效的降低生产成本,同时还可以扩大机床的使用范围,保证加工精度。
二、数控铣床工装夹具的设计研究(一)精选工装夹具的材质工装夹具是机械制造中最基本的工艺元素,从当前制造业的发展现状来看,存在专业性太强、管理较为混乱等现象,工装夹具从制作、管理、快速换产已成为制约企业发展的障碍之一。
实施工装夹具标准化、系列化能从根本上解决这一问题。
对此,我们在数控铣床工装夹具的设计首先要从材质选择出发,需要工装夹具具有刚性和较强的稳定性,这也才能突出机械加工防震功效,确保工装夹具的受力能够均衡,提高数控铣床的精准度,通常工装夹具的成本要占整个生产系统的10%-20%,足以看出工装夹具在整个数控铣床加工工具中的重要地位。
(二)根据加工材料,合理选择工装夹具的元件数控铣床工装夹具有螺栓、压板和凸轮等元件,根据加工材料的不通过,我们可以选择适当的数控铣床工装夹具的元件,用来固定加工材料。
数控铣床工装夹具设计与改进建议

数控铣床工装夹具设计与改进建议一、背景介绍数控铣床工装夹具是数控铣床加工过程中不可或缺的一部分,它的设计质量直接关系到产品加工的精度和效率。
随着数控技术的不断发展,工装夹具设计也在不断改进和完善。
本文将围绕数控铣床工装夹具的设计与改进建议展开讨论。
二、工装夹具设计要点1.稳固性稳固性是工装夹具设计的首要考虑因素,只有确保工件在加工过程中保持稳定性,才能保证加工精度。
在设计工装夹具时,必须考虑如何使工件牢固地固定在夹具上,并确保夹具本身在加工中不会出现松动或变形。
2.可靠性工装夹具必须具有良好的可靠性,能够在长时间加工过程中保持稳定性,不会出现故障或损坏。
在材料选择和加工工艺上,应尽量确保工装夹具的耐磨性和耐腐蚀性。
3.易操作性工装夹具的设计还应考虑操作人员的使用便利性,夹具应能够快速、简便地进行装夹和调整,提高工作效率。
4.适用性不同的加工工件需要不同的工装夹具,因此在设计工装夹具时,需要考虑其适用范围,设计出通用性较强的夹具,以适应不同类型工件的加工需求。
5.成本效益在工装夹具设计中,成本效益是一个重要考虑因素。
设计应尽量减少材料消耗和加工成本,降低生产成本的同时确保工装夹具的质量和性能。
三、工装夹具设计的改进建议1.采用高强度材料为了提高工装夹具的稳固性和可靠性,建议在材料选择上采用高强度、耐磨、耐腐蚀的材料,如合金钢、不锈钢等,以确保夹具在长时间加工中不会出现松动、变形或损坏的情况。
2.模块化设计采用模块化设计的工装夹具具有更好的适用性,可以根据不同工件的加工需求进行组合和调整,提高了工装夹具的通用性和灵活性,减少了成本。
3.优化结构工装夹具的结构设计应该简单而合理,减少不必要的零部件,提高夹具的稳定性和使用寿命。
同时在关键部位采用加强结构,提高了夹具的承载能力。
4.引入自动化元素随着自动化技术的发展,可以考虑在工装夹具设计中引入一些自动化元素,如传感器、执行机构等,实现夹具的自动调整和监测,提高工作效率和加工精度。
数控铣床工装夹具设计与改进建议
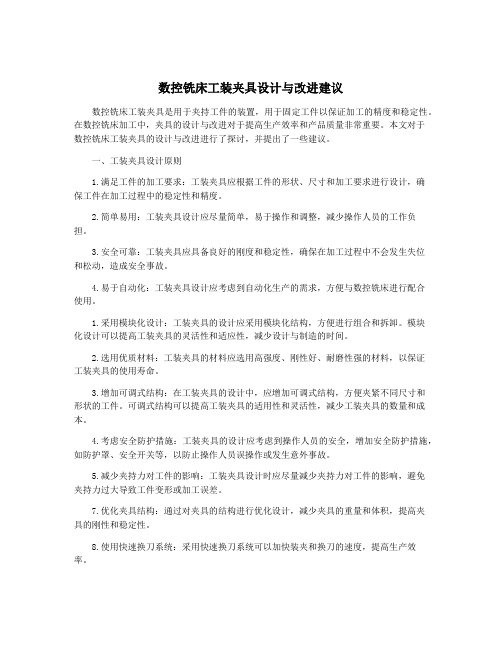
数控铣床工装夹具设计与改进建议数控铣床工装夹具是用于夹持工件的装置,用于固定工件以保证加工的精度和稳定性。
在数控铣床加工中,夹具的设计与改进对于提高生产效率和产品质量非常重要。
本文对于数控铣床工装夹具的设计与改进进行了探讨,并提出了一些建议。
一、工装夹具设计原则1.满足工件的加工要求:工装夹具应根据工件的形状、尺寸和加工要求进行设计,确保工件在加工过程中的稳定性和精度。
2.简单易用:工装夹具设计应尽量简单,易于操作和调整,减少操作人员的工作负担。
3.安全可靠:工装夹具应具备良好的刚度和稳定性,确保在加工过程中不会发生失位和松动,造成安全事故。
4.易于自动化:工装夹具设计应考虑到自动化生产的需求,方便与数控铣床进行配合使用。
1.采用模块化设计:工装夹具的设计应采用模块化结构,方便进行组合和拆卸。
模块化设计可以提高工装夹具的灵活性和适应性,减少设计与制造的时间。
2.选用优质材料:工装夹具的材料应选用高强度、刚性好、耐磨性强的材料,以保证工装夹具的使用寿命。
3.增加可调式结构:在工装夹具的设计中,应增加可调式结构,方便夹紧不同尺寸和形状的工件。
可调式结构可以提高工装夹具的适用性和灵活性,减少工装夹具的数量和成本。
4.考虑安全防护措施:工装夹具的设计应考虑到操作人员的安全,增加安全防护措施,如防护罩、安全开关等,以防止操作人员误操作或发生意外事故。
5.减少夹持力对工件的影响:工装夹具设计时应尽量减少夹持力对工件的影响,避免夹持力过大导致工件变形或加工误差。
7.优化夹具结构:通过对夹具的结构进行优化设计,减少夹具的重量和体积,提高夹具的刚性和稳定性。
8.使用快速换刀系统:采用快速换刀系统可以加快装夹和换刀的速度,提高生产效率。
9.加强对工装夹具的维护和保养:工装夹具应定期进行维护和保养,及时更换损坏的零部件,确保夹具的正常运行。
10.与使用者深入沟通:设计人员应与实际使用工装夹具的操作人员进行深入沟通,了解使用过程中的问题和需求,根据实际情况进行改进设计。
数控铣床工装夹具设计与改进建议

数控铣床工装夹具设计与改进建议随着现代机械加工技术的不断发展,数控铣床在工业生产中的应用越来越广泛。
作为数控铣床加工的重要辅助设备,工装夹具在工件定位、夹持、刀具安装等方面发挥着至关重要的作用。
合理设计和改进建工装夹具对提高数控铣床加工效率和质量具有重要意义。
本文将对数控铣床工装夹具的设计与改进建议进行探讨。
一、工装夹具设计原则1. 确定加工定位准确性工装夹具在数控铣床加工中起到定位和夹紧工件的作用,因此必须确保夹具的精度和定位准确度。
在设计工装夹具时,需要考虑工件的形状、尺寸和加工要求,以确保夹具与工件的匹配度和夹持稳定性。
2. 提高加工效率工装夹具的设计不仅要考虑加工定位的准确性,还应考虑加工效率。
合理的工装夹具设计可以减少工艺调试时间,提高生产效率。
采用模块化设计的工装夹具可以快速更换夹具部件,适应不同工件的加工需求,降低换夹时间和生产成本。
3. 考虑安全性和易用性工装夹具不仅需要满足加工要求,还要考虑操作安全性和使用便捷性。
设计时应避免锐角和突出部件,减少工人受伤风险。
还要考虑到操作人员的使用习惯和操作空间,设计夹具应尽量简化操作流程,减少操作难度,提高工作效率。
4. 考虑成本和材料选择在工装夹具设计中,要综合考虑使用成本和材料选择。
合理的设计可以降低制造成本,提高夹具的使用寿命。
选择适当的材料和加工工艺,可以提高夹具的强度和耐磨性,降低维护成本。
二、工装夹具改进建议1. 采用新型夹具设计随着材料科学和加工技术的不断发展,新型夹具设计方案不断涌现。
采用合成材料、3D打印技术等,可以设计出更轻便、更精确、更适应复杂形状工件加工的工装夹具。
在改进建议中,可以考虑采用新型材料和工艺,提高夹具的使用性能。
现代数控铣床智能化程度不断提高,自动化夹具设计可以提高生产效率和加工精度。
采用气动、液压或电动夹具设计,可以实现夹具的自动卸载和更换,减少人工干预,提高生产效率。
在改进建议中,可以考虑引入自动化夹具设计,提高生产线整体智能化水平。
数控铣床工装夹具设计与改进建议

数控铣床工装夹具设计与改进建议
数控铣床是现代制造业中非常重要的加工设备,其工装夹具设计的好坏直接影响加工质量和效率。
本文将针对数控铣床工装夹具的设计与改进建议进行探讨,并提出一些具体的建议。
一、工装夹具设计原则
1. 稳固性:工装夹具应该能够牢固地夹持工件,确保加工过程中工件不会发生移位或者晃动。
2. 精度:工装夹具的设计应考虑工件的加工精度要求,确保夹具的精度能够满足加工要求。
3. 高效性:工装夹具应尽可能地减少安装和调整时间,提高加工效率。
4. 多功能性:工装夹具设计应该考虑多样化的加工需求,确保一套夹具能够适用于多种工件的加工。
二、现有工装夹具存在的问题
1. 精度不足:部分工装夹具的精度无法满足高精度加工要求,导致加工出现偏差。
2. 调整繁琐:部分工装夹具的调整过程繁琐,需要耗费大量时间。
3. 单一性:部分工装夹具只能适用于特定类型的工件加工,多种工件需要不同的夹具,无法通用。
三、改进建议
1. 提高夹具精度:可以采用高精度的夹具材料,并在夹具的制造加工过程中采用精密的加工工艺,以提高夹具的精度。
2. 简化调整程序:可以设计一种可调节的夹具结构,使用螺旋或者快速夹紧机构,简化夹具的调整过程。
3. 多功能性设计:可以设计一种模块化的夹具结构,使其能够适用于不同类型的工件加工,降低夹具的成本,提高其适用范围。
五、结语
数控铣床的工装夹具设计对加工质量和效率有着重要的影响,因此需要不断改进建议来提高夹具的稳固性、精度、高效性和多功能性。
希望本文的建议对数控铣床工装夹具的设计与改进建议有所帮助。
数控铣床工装夹具的设计分析

数控铣床工装夹具的设计分析摘要随着我国工业发展,要加强对数控铣床技术的研究,在实际生产活动中可以发挥出有效作用。
在数控铣床运行中,要保证机床、工件、道具处于准确位置,为了实现这一目标,要对工装夹具进行合理设计。
文章先介绍数控铣床工装夹具设计的基本要求,再分析工装夹具设计应该注意的问题,最后提出实施策略,保证数控铣床的质量。
关键词数控铣床工装夹具设计一、引言目前数控铣床技术朝着高速、智能化方向发展,这对工装夹具设计提出了更高要求,因此要树立起创新意识,不断优化设计方案,确保满足更高要求。
提高对工装夹具设计的重视程度,进一步完善数控铣床性能,有利于提高生产水平。
窗体底端窗体底端二、数控铣床工装夹具设计需要注意的问题2.1保证工件加工的精度数控铣床工装夹具设计要保证加工的稳定性,减少不利因素影响,达到生产质量标准。
为了提升夹具的准确性,可以用专业仪器来进行检测,发现问题要及时调整,保证达到规定标准。
2.2提高加工效率采用通用化程度较高的工装夹具,可以有效提升夹具装配的调整效率,从而使得加工准备时间缩短。
提高加工效率促进液压装置的使用,还可以采用多工位夹具和可调换夹具等措施。
2.3注意防碰撞的校核在数控技术发展过程中,数控铣床加工过程中需要使用更多的刀具,由于数量比较多,所以加工过程中工具和夹具之间容易发生碰撞。
为了避免这种问题发生,在对工装夹具设计时要严格按照规定去执行,避免工具与刀具之间的干扰。
数控铣床夹具结构具有复杂性的特点,为了保证达到理想效果,设计人员先要建立一个仿真模型,对加工具体情况进行观察,便于更好做出调整。
三、数控铣床工装夹具的设计内容(一)固定方式设计工装夹具的固定方式设计首先必须要保证固定工件的稳定性,避免加工件在加工过程中出现位移,从而影响加工精度,所以一般会设计夹持构件,以保证工件是沿作用力方向进行固定的。
夹持构件能够使多个被加工工件在同一位置进行加工,从而保持加工件加工公差在合理的范围当中。
数控铣床工装夹具设计与改进建议

数控铣床工装夹具设计与改进建议随着工业智能化的不断推进,数控铣床的应用越来越广泛。
而工装夹具作为数控铣床的重要配套设备,扮演着关键的角色。
本文将围绕数控铣床工装夹具的设计与改进提出相关建议。
对于数控铣床工装夹具的设计,应注重以下几个方面:1. 材料选用:选用高强度、耐磨、耐高温、耐腐蚀的材料,以提高工装夹具的寿命和使用效果。
2. 结构设计:结构应简洁明了,便于安装和拆卸,减少操作的时间和难度。
应考虑夹具的刚性和稳定性,以保证加工精度和稳定性。
3. 夹具定位精度:精确的夹具定位是保证加工精度的关键。
应通过合理设计夹具定位结构,减小夹具的运动误差,提高夹具的定位精度。
4. 夹持力控制:夹具的夹持力也是影响加工质量的关键因素,应通过合理设计夹具夹持结构,保证夹持力的均匀分布和稳定控制。
应根据加工对象的材料特性和加工要求,确定夹持力的大小。
1. 自动化改进:将现有的手动夹具改进为自动夹具,减少人力操作,提高工作效率和质量。
可以借助传感器和控制系统实现夹具自动定位和夹持力的自动调节。
2. 模块化设计:将工装夹具设计为模块化结构,可以根据加工需求将不同功能的模块组合使用,提高工装夹具的灵活性和多功能性。
3. 抗振性改进:在夹具的设计中加入抗振性措施,减小振动对加工精度的影响。
可以采用减震材料、抗振支撑结构等方式来改善夹具的抗振性能。
4. 自适应调节:根据不同的加工对象和加工要求,夹具能够自适应地做出相应的调节,提高加工的适应性和灵活性。
最后需要强调的是,数控铣床工装夹具的设计与改进需要与实际加工需求相结合,充分考虑加工对象的特点和加工要求,合理选择夹具的类型和结构,以提高加工效率和加工质量。
还需不断关注新材料、新技术的发展,时刻保持创新思维,以推动工装夹具的设计与改进。
数控铣床工装夹具设计与改进建议

数控铣床工装夹具设计与改进建议随着制造业技术的不断提高,数控铣床作为现代加工制造的关键设备,其功能越来越强大,操作也越来越方便快捷。
然而,数控铣床在加工过程中,需要合适的工装夹具才能发挥其最高效率,因此,工装夹具的设计与改进也成为制造业的重要课题。
以下是本人在工作过程中总结的数控铣床工装夹具设计与改进建议:I. 设计工装夹具时考虑材料的选择工装夹具的材料选用必须符合工装的作用,干净和安全等要求,同时还需考虑成本的因素。
一般情况下,有一下几种选择:1.硬质合金硬质合金具有高硬度和耐磨损性,而且制造工艺比较简单,适合制作一些形状复杂,要求精度高的工装夹具。
2.钢材钢材成本低廉,加工过程容易,因此通常选用钢材制作简单的工装夹具,但是要考虑其厚度和强度,以确保夹具的稳定性和可靠性。
3.塑料塑料制作工装夹具可以减轻整个设备的重量,并且具有防锈蚀和易清洁等优点,但是也需要考虑其强度和耐用度来保证夹具的稳定性和安全性。
II. 考虑制造工艺工装夹具不仅需要具有合适的强度和刚度,还希望其制造工艺简单、易于加工。
因此,在设计工装夹具时,应尽量避免零部件的复杂形状,以便于加工和组装。
若夹具比较复杂,可以先用软件绘制一个三维图,通过虚拟构建,对夹具进行测试和验证,找出设计缺陷,最终得出优秀的零部件设计方案。
III. 提高工装夹具的精度在数控铣床的加工过程中,精度和稳定性是关键,因此夹具精度的要求也很高。
为了提高工装夹具的精度,应尽量减小夹具的变形和误差,并使用高精度的工具进行加工。
同时,在夹具的设计过程中要充分考虑安全性,确保操作人员的人身安全,防止夹具破裂或者错位等现象的发生。
工装夹具的设计不是单一的决策,而是根据实际加工情况不断完善和改进的过程,因此,对夹具进行定期检查和评估,对出现问题的夹具需要进行改进,以提高工装夹具的性能和工作效率。
同时,收集并分析工作现场的反馈信息,不断完善工装夹具的设计和加工方法。
总之,工装夹具是数控铣床的重要组成部分,其设计和改进是提高数控铣床生产效率和质量的关键环节。
数控铣床工装夹具设计与改进

数控铣床工装夹具设计与改进摘要:在数控技术操作中,铣床应用比较广泛,其可以用于平面、斜面和成型面加工。
工装夹具主要是根据工件加工过程的某道工序要求以及相关生产需要等进行具体设计的。
而夹具设计质量对工件质量、生产效率以及生产成本等影响较大。
夹具设计应简单实用,可制造性好,便于装配维修。
但实际生产过程中,工装夹具的质量和效率限制着数控铣床的大量应用,如何采用合理改进方法解决机床夹具设计中存在的问题意义重大。
关键词:数控铣床工装;夹具设计;改进前言:随着我国数控技术的不断发展,数控铣床在日常加工生产中发挥着越来越重要的作用。
夹具的设计直接决定了生产加工的质量。
目前,数控铣床正朝着复合化、精密化、智能化、高效化的方向发展,这必然要求对原有的夹具设计进行改进。
1、数控铣床夹具设计要点数控铣床的实际应用对夹具要求不高,只有夹具能起到很好的定位固定作用。
因此,在设计夹具时,应紧密符合数控铣床的应用要求。
一般来说,数控铣床的夹具设计需要满足以下几点:第一,夹具要有较大程度的开放性,因为在加工工件的过程中,需要在加工完成后完全暴露在机器外,同时保持一定的操作空间和安全距离。
因此,所需夹紧机构的部件相对较低,大的开放度可以避免轴套和刀具。
其次,夹具还应采用非定向方式安装,以满足机床零件安装定向所使用的数控机床应与编程坐标系一致的要求,这样可以灵活地转换零件定位面与数控机床之间的坐标;再次,设计夹具的刚度,提高其稳定性,以满足数控铣床的要求。
2.数控铣床夹具的设计步骤和内容首先对工件进行分析,确定加工工艺和流程。
要求工人充分了解工件的特点、材料性能和相应的技术要求。
同时对加工余量、精度、定位、表面状况进行分析,对工序的顺序和衔接进行认真分析,确定科学合理的加工路线。
刀具走刀次数的确定在夹具设计过程中尤为重要。
刀具走刀次数可以由刀具和机床的参数决定。
在加工过程中,尽可能加快装夹速度,保证一次装夹和加工成型,可以大大提高生产效率和加工精度。
数控铣床工装夹具设计及改进策略分析

管理及其他M anagement and other数控铣床工装夹具设计及改进策略分析苏家兵摘要:在我国经济迅猛发展的今天,科技事业也取得了长足进步。
数控技术作为一项关键的工业技术,在其中扮演着重要的角色。
利用数控铣床的优势,可以在一定程度上提高企业的生产效率,并为企业带来更多的经济效益。
因此,通过大量的调研和试验,对数控铣床工装夹具的设计要点进行了分析,以期对制造业起到积极的促进作用。
关键词:数控铣床;工装夹具;设计要素;改进策略;制造业随着我国经济社会和科学技术的不断发展,装备制造业的发展速度也在加快。
其中,数控铣床由于其高精度和快速生产的特点,在各个工业生产领域得到了广泛的应用。
在实际制造过程中,操作人员需要花费大量时间选择工件、刀具等,并对其进行调试,同时还需要对所制造的零部件进行检验。
为了提高数控铣床的加工技术,合理地使用数控机床的工装夹具是必要的。
这样可以有效地提高产品的精度,并减轻操作人员的劳动强度。
在数控铣削中,工装夹具技术起着至关重要的作用,它可以使工件在加工过程中保持有序的工作状态。
特别是在大规模生产中,采用工装夹具可以有效地降低各种资源的损耗,从而提高工作效率。
尽管夹具本身并不具备切削加工功能,但它能够将工件固定到特定位置,在实际生产中减少加工误差。
因此,机床工装夹具的设计和改进显得非常关键。
1 数控铣床工装夹具应用现状及设计要求1.1 数控铣床工装夹具应用现状夹具是用于精确支撑、定位和夹持一个或多个工件的装置,以便于加工、切削,或用于装配、检验、焊接等。
夹具在批量生产中起到减少工作时间浪费、提高生产效率、保持产品质量、降低产品不合格率的作用。
工装夹具虽然没有切割功能,但可以固定工件在一定位置,以承受切割时的力量。
根据工作性质、加工机械和工件尺寸的不同,工装夹具的结构也会有相应变化。
由于工厂的设备、工艺、生产成本等因素,导致相同产品的工装夹具设计存在较大差别。
数控铣床是一种多刀片工具,在切削时会产生较大的切削力,因此数控铣床上的工装夹具必须具有较高的夹紧和强度,才能承受产生的铣削力。
数控铣床工装夹具设计与改进建议

数控铣床工装夹具设计与改进建议随着现代制造技术的不断发展,数控铣床在工业生产中扮演着越来越重要的角色。
而工装夹具作为数控铣床加工的重要配套设备,对于产品加工的精度和效率有着至关重要的影响。
针对数控铣床工装夹具的设计与改进建议显得尤为重要。
一、设计原则1. 精准度和刚性工装夹具的设计应该以提高产品加工的精度和效率为首要目标,在设计过程中需要考虑到夹具的精准度和刚性,确保夹具在加工过程中不会产生变形和位移,从而保证加工的精度和稳定性。
2. 通用性和灵活性由于不同产品在加工过程中会有不同的需求,因此设计的工装夹具应该具有一定的通用性和灵活性,能够适应多种产品的加工需求,减少更换夹具的频率,提高生产的效率和灵活性。
3. 安全性和稳定性在工装夹具的设计中,应该考虑到操作人员的安全和夹具的稳定性,避免在加工过程中产生意外或者夹具失稳而导致产品质量的下降。
二、设计与改进建议1. 结构设计优化目前很多工装夹具的结构设计存在一定的问题,比如夹具重量过大、结构复杂等,这些问题会影响到夹具的精度、稳定性和操作灵活性。
需要对夹具的结构进行优化设计,减少夹具的重量,简化夹具的结构,提高夹具的刚性,从而提高加工的精度和效率。
2. 加工精度提升目前很多工装夹具在加工过程中存在精度不足的问题,这会导致产品加工出现偏差,影响产品的质量。
需要在夹具的设计和制造过程中加大对精度的控制,确保夹具可以在加工过程中保持稳定的精度,保证产品加工的质量。
3. 自动化改造随着智能制造技术的发展,工装夹具的自动化程度也需要不断提升。
在设计和改进建议中,可以考虑对工装夹具进行自动化改造,引入传感器、控制系统等智能设备,实现夹具的自动调整和监控,提高生产的智能化水平。
4. 材料选用优化夹具的材料选用直接影响到夹具的刚性、耐磨性和使用寿命。
在设计和改进建议中,应该对夹具的材料进行合理选择,选用高强度、耐磨性好的材料,以提高夹具的使用寿命和加工稳定性。
5. 标准化和模块化设计为了提高生产的效率和灵活性,工装夹具的设计应该考虑到标准化和模块化,通过设计标准化的夹具零部件,实现夹具的通用化和模块化,减少夹具更换的频率,提高生产的灵活性和效率。
数控铣床工装夹具设计与改进建议
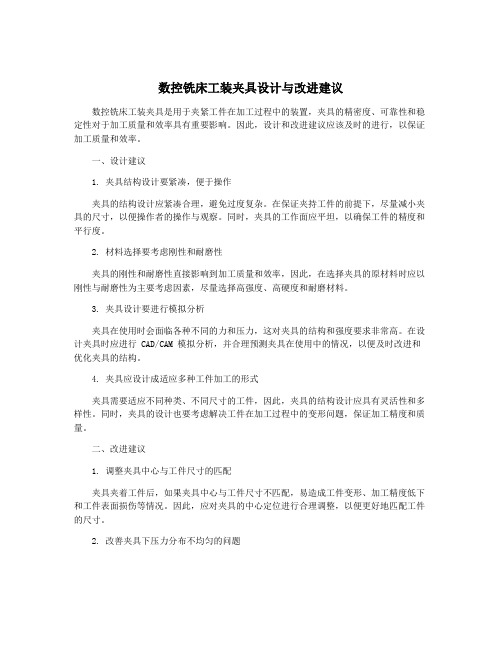
数控铣床工装夹具设计与改进建议数控铣床工装夹具是用于夹紧工件在加工过程中的装置,夹具的精密度、可靠性和稳定性对于加工质量和效率具有重要影响。
因此,设计和改进建议应该及时的进行,以保证加工质量和效率。
一、设计建议1. 夹具结构设计要紧凑,便于操作夹具的结构设计应紧凑合理,避免过度复杂。
在保证夹持工件的前提下,尽量减小夹具的尺寸,以便操作者的操作与观察。
同时,夹具的工作面应平坦,以确保工件的精度和平行度。
2. 材料选择要考虑刚性和耐磨性夹具的刚性和耐磨性直接影响到加工质量和效率,因此,在选择夹具的原材料时应以刚性与耐磨性为主要考虑因素,尽量选择高强度、高硬度和耐磨材料。
3. 夹具设计要进行模拟分析夹具在使用时会面临各种不同的力和压力,这对夹具的结构和强度要求非常高。
在设计夹具时应进行 CAD/CAM 模拟分析,并合理预测夹具在使用中的情况,以便及时改进和优化夹具的结构。
4. 夹具应设计成适应多种工件加工的形式夹具需要适应不同种类、不同尺寸的工件,因此,夹具的结构设计应具有灵活性和多样性。
同时,夹具的设计也要考虑解决工件在加工过程中的变形问题,保证加工精度和质量。
二、改进建议1. 调整夹具中心与工件尺寸的匹配夹具夹着工件后,如果夹具中心与工件尺寸不匹配,易造成工件变形、加工精度低下和工件表面损伤等情况。
因此,应对夹具的中心定位进行合理调整,以便更好地匹配工件的尺寸。
2. 改善夹具下压力分布不均匀的问题在夹紧工件的过程中,夹具下的压力分布不能均匀,将导致在加工过程中工件受力不均匀,从而影响加工质量。
因此,在夹具的结构设计和制造加工过程中,应注重夹具下压力的均匀分布,以保障加工质量和效率。
3. 采用专门的夹口设计夹口是夹具中具有特殊结构的部件,它的设计直接影响到夹持工件的牢度和精度。
因此,应该采用专门的夹口设计,以便在夹持工件时具有更优异的性能,使夹具在使用过程中具有更可靠的性能和更优异的加工精度。
4. 采用冷却系统在加工高硬度、高难度工件时,夹具的工作面与工件的摩擦热容易造成工件表面热处理而出现问题。
数控铣床工装夹具的设计及其理论探讨

DOI:10.16660/ki.1674-098X.2019.07.102数控铣床工装夹具的设计及其理论探讨①邹国楚(广东省城市建设技师学院 广东广州 510520)摘 要:在21世纪,我国的制造加工业的规模经历了前所未有的飞速发展,水平也大大提高,水平的提高离不开数控铣床的广泛应用。
夹具装置的使用对于保障机床、工件及道具的正确对位非常重要,其设计的科学性是决定应用质量的基础工作。
文章主要论述了数控铣床工装夹具的设计要点和设计内容以及设计方法应用的改进等,旨在通过理论层面的探讨,为实际设计应用提供有价值的参考。
关键词:数控铣床 工装夹具 设计 应用改进中图分类号:TG547 文献标识码:A 文章编号:1674-098X(2019)03(a)-0102-02随着“一带一路”的深入发展,中国已经成为世界制造业的主力军,互联网科技和人工智能的发展使得数控技术在制造业中的应用更加广泛和深入,数控技术在制造业中的应用水平直接关系到制造业的发展前景。
数控铣床工装夹具的设计水平决定了制造加工产品质量。
基于产品生产加工的多样化需求,工装夹具的设计也必须多样化,以满足实际应用的要求。
1 数控铣床工装夹具的设计要点和内容1.1 数控铣床工装夹具的设计要点在设计数控铣床工装夹具时,设计者必须依据对应的标准,从整体上把控数控铣床工装夹具的设计质量。
设计必须有准确的原始工艺文件,设计者在安装工装夹具设计时,要准确把握工序坐标及工艺文件等。
工序坐标图的重要性毋庸置疑,它是工件结构形状和加工部位的主要依据,程序原点和走刀路线的合理与否决定了产品加工的质量。
在设计数控铣床工装夹具时,要确保工件加工的精度,要注重工件定位精度以及加工的稳定性。
注重机床和夹具联系表面的耐磨性和形状精度的提高。
除此之外,在设计数控铣床工装夹具时,还要注重加工效率的提高,注重防碰撞校核方面的因素。
1.2 数控铣床工装夹具的设计内容在设计数控铣床工装夹具过程中,需要考虑的问题非常多,这就要求设计者在设计时综合考虑,注意各个方面因素对都设计质量的影响。
数控铣床工装夹具设计内容分析

数控铣床工装夹具设计内容分析随着先进制造业的迅猛发展,作为集高精密、高速度和复合化等特点于一身的数控铣床在生产中被广泛的推广和应用,并大大提高了产品的精度,降低了工作强度。
在数控铣床操作加工的过程中,材料的准备、程序的编制调试、工装夹具的准备以及工件检测等步骤占用了很多生产时间,影响了数控机床加工的效率。
因此,本文对数控铣床工装夹具内容的设计进行深入的分析,以便提高工作效率。
标签:数控铣床;工装夹具;设计内容1、数控铣床工装夹具设计的要求首先,为了使加工的部件截面在加工中尽可能的显露在能够加工的空间里,夹具要最大限度的开敞。
也就是部件加工面与夹具应该保持足够的宽度,不影响加工,夹具要尽可能的减少与部件的接触面积,以避免在机械操作中,铣床主轴套筒或者刀具与夹具发生碰撞;其次,为了确保铣床部件安装方位与机床的编程坐标系方向一致,工装夹具在机床上采取定向安装,使夹具与数控机床之间保持坐标一致;再次,夹具应该有较好的刚性、稳定性和精确性,避免在部件加工中对夹具重新进行设计与操作,如果在生产加工中,因夹紧的问题更换夹具时,要对夹具进行设计,不要因为夹具更换而导致加工部件的精确性出现问题。
此外,对工装夹具进行设计时,除了要考虑夹具的定位和精确度之外,还要考虑在数控铣床的加工过程中,应使加工过程更加的灵活、方便,减少加工的劳动强度,提高加工部件的质量。
2、数控铣床工装夹具的设计内容2.1数控铣床工装夹具的固定方式在数控铣床工装夹具的固定方式上,为了防止各个工件在实际加工时出现移动,工件的固定方向必须要与作用力的方向保持一致,这也叫做夹持构件的固定方式。
在使用工装夹具对工作物进行夹持时,不同时期所夹持的工作物应该保持在完全一致的位置,这样各个工件在完成加工之后,其参数才会保持在合适的公差范围以内。
工件的夹持利用的是力学中的机械原理,用相对较小的施力在特定环境下可以产生非常大的夹持力。
一般而言,夹持构件在设计时不应单独依靠一个元件进行设计,而应当将多个元件组合起来。
数控铣床工装夹具设计与改进建议

数控铣床工装夹具设计与改进建议随着数控铣床的广泛应用,工装夹具在生产加工中扮演着重要的角色。
一个合理设计的工装夹具能够提高工件的加工精度和生产效率。
本文将就数控铣床工装夹具的设计与改进建议进行探讨。
一、夹具设计时需考虑的因素1. 材料选择:选择具有一定机械强度和耐磨性的材料,以确保夹具的稳定性和耐用性。
2. 结构设计:夹具的结构设计应简洁合理,以降低制造成本和提高使用性能。
夹具的结构应考虑工具刀具的切削力和振动对夹持力的影响,以提高加工精度。
3. 夹具定位:夹具的定位准确度是影响加工精度的重要因素。
在设计夹具时,要考虑工件的定位特点,合理选择定位方式,并确保定位精度。
4. 夹具力的控制:夹具对工件的夹持力应适中。
夹具力过小会导致工件移位和变形,从而影响加工精度;夹具力过大会加剧工件与夹具的磨损,缩短夹具的使用寿命。
在设计过程中要合理控制夹具力。
5. 夹具安装与拆卸:夹具的安装与拆卸过程应简便快捷,以提高生产效率。
1. 使用模块化设计:采用模块化设计,可以实现夹具的组装、拆卸和更换。
模块化设计能够提高夹具的使用灵活性和适用范围,同时降低制造成本和维护成本。
2. 引入传感器技术:通过在夹具中加入传感器,可以实时感知工件的状态和夹持力的变化情况。
根据传感器反馈的信息,可以及时调整夹具的夹持力,保持加工精度,同时避免因夹具力过大而导致的工件变形和夹具磨损。
3. 引入自动化控制技术:结合数控系统,实现夹具的自动化控制,可以提高生产效率和加工精度。
通过编程控制夹具的夹持力、定位精度等参数,可以实现加工过程的自动化监控和调整。
4. 优化夹具结构:通过分析加工过程的特点和工具刀具的力学特性,优化夹具的结构设计。
合理安排夹具的刚度和阻尼特性,减少夹具在加工过程中的振动,提高加工精度。
5. 加强夹具维护与管理:定期对夹具进行维护和保养,及时更换磨损的零部件,保持夹具的正常使用状态。
要建立夹具管理制度,对夹具进行统一编号、分类和分类,加强夹具的使用和管理。
数控铣床工装夹具设计与改进建议
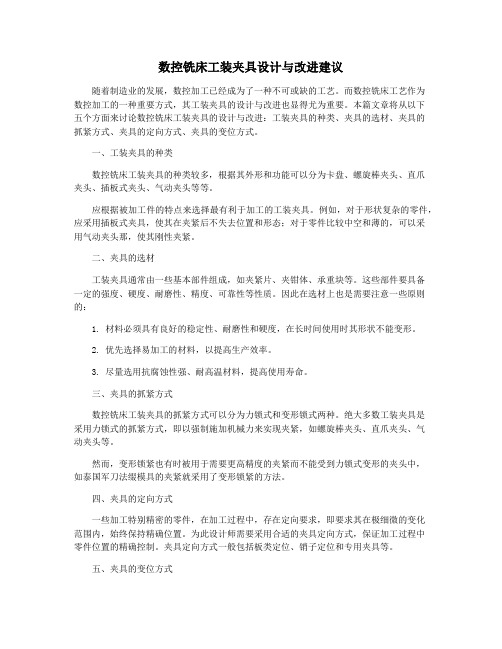
数控铣床工装夹具设计与改进建议随着制造业的发展,数控加工已经成为了一种不可或缺的工艺。
而数控铣床工艺作为数控加工的一种重要方式,其工装夹具的设计与改进也显得尤为重要。
本篇文章将从以下五个方面来讨论数控铣床工装夹具的设计与改进:工装夹具的种类、夹具的选材、夹具的抓紧方式、夹具的定向方式、夹具的变位方式。
一、工装夹具的种类数控铣床工装夹具的种类较多,根据其外形和功能可以分为卡盘、螺旋棒夹头、直爪夹头、插板式夹头、气动夹头等等。
应根据被加工件的特点来选择最有利于加工的工装夹具。
例如,对于形状复杂的零件,应采用插板式夹具,使其在夹紧后不失去位置和形态;对于零件比较中空和薄的,可以采用气动夹头那,使其刚性夹紧。
二、夹具的选材工装夹具通常由一些基本部件组成,如夹紧片、夹钳体、承重块等。
这些部件要具备一定的强度、硬度、耐磨性、精度、可靠性等性质。
因此在选材上也是需要注意一些原则的:1. 材料必须具有良好的稳定性、耐磨性和硬度,在长时间使用时其形状不能变形。
2. 优先选择易加工的材料,以提高生产效率。
3. 尽量选用抗腐蚀性强、耐高温材料,提高使用寿命。
三、夹具的抓紧方式数控铣床工装夹具的抓紧方式可以分为力锁式和变形锁式两种。
绝大多数工装夹具是采用力锁式的抓紧方式,即以强制施加机械力来实现夹紧,如螺旋棒夹头、直爪夹头、气动夹头等。
然而,变形锁紧也有时被用于需要更高精度的夹紧而不能受到力锁式变形的夹头中,如泰国军刀法缀模具的夹紧就采用了变形锁紧的方法。
四、夹具的定向方式一些加工特别精密的零件,在加工过程中,存在定向要求,即要求其在极细微的变化范围内,始终保持精确位置。
为此设计师需要采用合适的夹具定向方式,保证加工过程中零件位置的精确控制。
夹具定向方式一般包括板类定位、销子定位和专用夹具等。
五、夹具的变位方式在加工时,为了达到不同加工要求,需要进行夹具工作位置的更改。
根据夹具的变位方向,可以将夹具的变位方式分为三类,分别为平动、旋转、旋转与平动相结合的夹具变位方式。
数控铣床工装夹具设计与优化
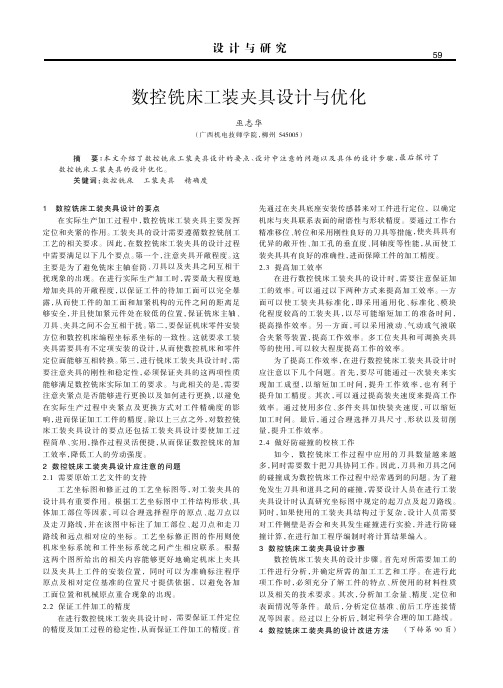
1数控铣床工装夹具设计的要点在实际生产加工过程中,数控铣床工装夹具主要发挥定位和夹紧的作用。
工装夹具的设计需要遵循数控铣削工工艺的相关要求。
因此,在数控铣床工装夹具的设计过程中需要满足以下几个要点。
第一个,注意夹具开敞程度。
这主要是为了避免铣床主轴套筒、刀具以及夹具之间互相干扰现象的出现。
在进行实际生产加工时,需要最大程度地增加夹具的开敞程度,以保证工件的待加工面可以完全暴露,从而使工件的加工面和加紧机构的元件之间的距离足够安全,并且使加紧元件处在较低的位置,保证铣床主轴、刀具、夹具之间不会互相干扰。
第二,要保证机床零件安装方位和数控机床编程坐标系坐标的一致性。
这就要求工装夹具需要具有不定项安装的设计,从而使数控机床和零件定位面能够互相转换。
第三,进行铣床工装夹具设计时,需要注意夹具的刚性和稳定性,必须保证夹具的这两项性质能够满足数控铣床实际加工的要求。
与此相关的是,需要注意夹紧点是否能够进行更换以及如何进行更换,以避免在实际生产过程中夹紧点及更换方式对工件精确度的影响,进而保证加工工件的精度。
除以上三点之外,对数控铣床工装夹具设计的要点还包括工装夹具设计要使加工过程简单、实用,操作过程灵活便捷,从而保证数控铣床的加工效率,降低工人的劳动强度。
2数控铣床工装夹具设计应注意的问题2.1需要原始工艺文件的支持工艺坐标图和修正过的工艺坐标图等,对工装夹具的设计具有重要作用。
根据工艺坐标图中工件结构形状、具体加工部位等因素,可以合理选择程序的原点、起刀点以及走刀路线,并在该图中标注了加工部位、起刀点和走刀路线和远点相对应的坐标。
工艺坐标修正图的作用则使机床坐标系统和工件坐标系统之间产生相应联系。
根据这两个图所给出的相关内容能够更好地确定机床上夹具以及夹具上工件的安装位置,同时可以为准确标注程序原点及相对定位基准的位置尺寸提供依据,以避免各加工面位置和机械原点重合现象的出现。
2.2保证工件加工的精度在进行数控铣床工装夹具设计时,需要保证工件定位的精度及加工过程的稳定性,从而保证工件加工的精度。
数控铣床工装夹具的设计分析
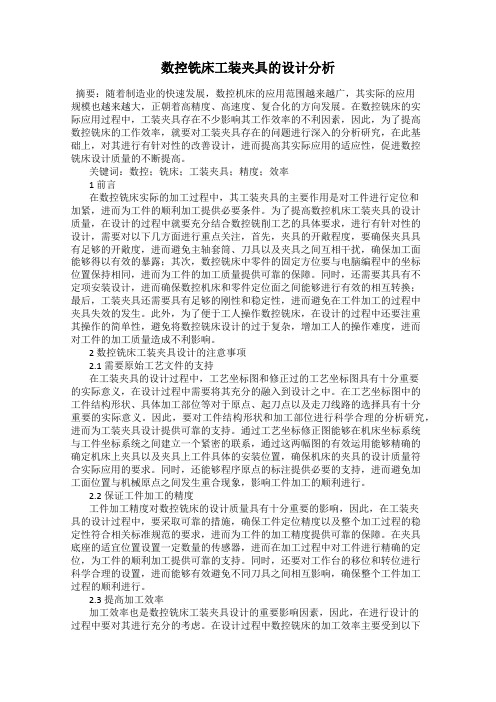
数控铣床工装夹具的设计分析摘要:随着制造业的快速发展,数控机床的应用范围越来越广,其实际的应用规模也越来越大,正朝着高精度、高速度、复合化的方向发展。
在数控铣床的实际应用过程中,工装夹具存在不少影响其工作效率的不利因素,因此,为了提高数控铣床的工作效率,就要对工装夹具存在的问题进行深入的分析研究,在此基础上,对其进行有针对性的改善设计,进而提高其实际应用的适应性,促进数控铣床设计质量的不断提高。
关键词:数控;铣床;工装夹具;精度;效率1 前言在数控铣床实际的加工过程中,其工装夹具的主要作用是对工件进行定位和加紧,进而为工件的顺利加工提供必要条件。
为了提高数控机床工装夹具的设计质量,在设计的过程中就要充分结合数控铣削工艺的具体要求,进行有针对性的设计,需要对以下几方面进行重点关注,首先,夹具的开敞程度,要确保夹具具有足够的开敞度,进而避免主轴套筒、刀具以及夹具之间互相干扰,确保加工面能够得以有效的暴露;其次,数控铣床中零件的固定方位要与电脑编程中的坐标位置保持相同,进而为工件的加工质量提供可靠的保障。
同时,还需要其具有不定项安装设计,进而确保数控机床和零件定位面之间能够进行有效的相互转换;最后,工装夹具还需要具有足够的刚性和稳定性,进而避免在工件加工的过程中夹具失效的发生。
此外,为了便于工人操作数控铣床,在设计的过程中还要注重其操作的简单性,避免将数控铣床设计的过于复杂,增加工人的操作难度,进而对工件的加工质量造成不利影响。
2 数控铣床工装夹具设计的注意事项2.1 需要原始工艺文件的支持在工装夹具的设计过程中,工艺坐标图和修正过的工艺坐标图具有十分重要的实际意义,在设计过程中需要将其充分的融入到设计之中。
在工艺坐标图中的工件结构形状、具体加工部位等对于原点、起刀点以及走刀线路的选择具有十分重要的实际意义。
因此,要对工件结构形状和加工部位进行科学合理的分析研究,进而为工装夹具设计提供可靠的支持。
通过工艺坐标修正图能够在机床坐标系统与工件坐标系统之间建立一个紧密的联系,通过这两幅图的有效运用能够精确的确定机床上夹具以及夹具上工件具体的安装位置,确保机床的夹具的设计质量符合实际应用的要求。
关于数控铣床工装夹具设计的探讨

关于数控铣床工装夹具设计的探讨摘要:数控铣床(CNC)的研发是在传统铣床设备中添设数字可控制系统,随着系统集成功能的实现,令终端设备可通过信息指令完成逻辑性操作。
在铣床智能化操控系统的支持下,可降低人力资源的投入,提高企业运营收益。
随着工业产业的高速发展,数控加工技术的多维度、高精度操控模式,可完成高难度复杂结构部件的加工,真正实现柔性加工与硬性加工的融合,提高金属构件的加工质量。
本文就关于数控铣床工装夹具设计进行探讨,仅供参考。
关键词:数控机床;铣床工装;夹具设计引言在数控铣床中,工装夹具因其自身特有的优势发挥了重要作用。
因此,可以这样说,“没有工装夹具,数控铣床作用便不能够得到有效发挥”。
同时,还可能会在一定程度上限制工件生产质量和效率的提升。
就目前我国经济发展形势来看,正处在转型关键阶段,在国家相关发展战略和规划影响下,制造业也得到了迅猛发展。
如果仍然采取传统夹具,将可能会限制企业长远发展,导致其无法在激烈市场竞争中取得优势。
为此,在今后工作中,制造企业相关工作人员必须要充分认识到夹具功能改进所产生的积极作用。
从整个行业发展规划角度出发,进行综合性考虑,从而为企业稳定发展奠定良好基础。
1数控铣床工装夹具设计的重点内容1.1管接头自动转位加工技术分析加工时,将被加工零件放置于自动转位夹具中间,自动转位夹具在机床液压系统控制下自动向机床主轴中心线方向收紧,实现自动夹紧、快速定位功能。
完成一侧管嘴的加工内容后,夹紧活塞在机床液压系统控制下,沿着夹具旋转轴线转动,驱动夹紧底座、夹口及自动转位夹具旋转,被加工零件随着自动转位夹具一同旋转,实现被加工零件自动转位功能,随即可进行另一侧管嘴的加工。
自动转位夹具旋转过程中,夹具与零件之间的位置关系未发生变化,因此无需再次对刀、测量等操作,重复定位精度由机床底座自身决定,加工质量稳定。
通过此技术即可实现管接头零件一次装夹,自动转位加工多侧管嘴,大幅提高零件加工效率,减小因多次装夹误差导致的管嘴轴线偏差。
数控铣床工装夹具的设计及其应用

数控铣床工装夹具的设计及其应用【摘要】本文依据数控铣床的加工特征,给出了数控铣床工装夹具的具体设计方法,并且给出了数控铣床工装夹具的实际应用,有利于充分发挥数控铣床的加工潜力。
【关键词】数控铣床工装夹具设计应用一般情况下,在机械加工过程中会使用到机床夹具,对于传统的机床夹具来说,其设计过程不仅具有详尽的资料而且具有成熟的经验作为人们的参考和借鉴。
随着我们国家数控铣床的不断发展与应用,传统意义上的机械加工向着高效率、高适应性以及高精度的方向发展。
然而,在实际应用中,有关于数控铣床工装夹具的设计内容非常少,本文依据数控铣床的加工特征,探讨数控铣床工装夹具的设计方法,有利于充分发挥数控铣床的加工潜力。
1 数控铣床工装夹具的设计数控铣床主要是以压缩空气作为自身的动力,实现松开与夹紧刀具操作,方便于进行手动换刀,通常我们利用加工中心实现数控铣床的自动换刀过程。
在加工过程中,通过换刀能够实现逐次加工各种表面的功能,但是,在每一次进行换刀的时候都需要耗费许多时间,尤其是在自动换刀的过程中,会发生一些故障。
因此,我们在符合加工要求之下,尽量减少换刀的次数,进而节省有用时间,提高数控铣床的可靠性。
下面我们通过比较合理的数控铣床工装夹具设计方法,科学地调整施工工艺,最大程度地降低换刀的次数。
如下图所示的工件,需要在立式的加工中心之上实现扩、铰a孔与b孔,原来的工装夹具的设计方法是每一次只装夹1个工件,该方法的加工工艺如下:换a孔扩孔刀、扩孔换b孔扩孔刀、扩孔换a孔铰刀、铰孔换b孔铰刀、铰b孔。
从上面的加工工艺上看,每次对1个工件进行加工,就需要更换4次刀。
我们现在依据工件所具有的外形的尺寸以及机床的行程,对工装夹具进行设计,将p工件面C或者面D,孔作为加工时用于定位的基准,具有重要的作用,对于工装夹具来说,通常使用一圆柱销和一菱形销进行工件的定位操作。
经过比较巧妙地设计,能够使得一套工装夹具在一个相同的工序里面实现工件加工操作,并且一次可以安装6个工件。
- 1、下载文档前请自行甄别文档内容的完整性,平台不提供额外的编辑、内容补充、找答案等附加服务。
- 2、"仅部分预览"的文档,不可在线预览部分如存在完整性等问题,可反馈申请退款(可完整预览的文档不适用该条件!)。
- 3、如文档侵犯您的权益,请联系客服反馈,我们会尽快为您处理(人工客服工作时间:9:00-18:30)。
数控铣床工装夹具的设计及其应用
作者:赵少君张亚平吴志清
来源:《商情》2011年第43期
【摘要】本文针对数控铣床工装夹具的设计要点与设计的步骤内容进行了探讨,并以实例对工装夹具的设计应用做了相应的说明。
并阐述了数控铣床的工装夹具设计中涉及到的各方面的问题。
【关键词】数控铣床;工装夹具;设计要点;步骤内容
铣床指主要加工平面、垂直面、斜面、各种沟槽或成型面,利用分度头也可以加工螺旋槽,凸轮、成型面等。
机床夹具是根据工件工艺规程的某道工序要求及生产批量等进行设计的,夹具设计的质量直接影响到工件的质量、生产率及生产成本。
所以机床夹具的设计和制造是非常重要的。
设计的夹具应尽量简单、容易制造、装配、检验、维修等,要操作方便、使用安全。
但是,在实际生产中,机床夹具的效率一直是制约机电产品生产快速发展的瓶颈,如何解决机床夹具设计中存在的问题。
以下就此问题做一些探讨。
一、数控铣床工装夹具设计的要点
1、夹具应避免损伤工件。
工件夹紧时,夹具的夹紧力不能过大,把工件夹变形,或过小而夹不稳工件。
而夹具的材料过硬则会划伤工件。
工件夹紧时,应使工件的各个受力点的受力均衡,以免造成工件的倾斜。
夹紧力也应在主支承点上,力求靠近切削部位及刚性好的部位。
因此,夹紧力的方向应尽量与切削力、工件重力等方向保持一致,以减少夹紧力,且垂直指向工件刚度最大的方向,以防止或减少工件变形。
2、设置恰当的程序原点、起刀点和走刀路线。
在设计夹具时,要在工艺图中标明加工部位、起刀点及走刀路线相对程序原点的坐标位置,作为建立工件坐标系统与机床坐标系统间的联系。
3、提高夹具制造效率。
制造夹具时应采用标准化、通用化程度高的组合夹具、模块化夹具以及成组夹具等,提高夹具件各部件的通用性,可以尽快的利用已有的组件组合生成新的夹具,缩短产品生产准备周期。
为使机动和辅助时间重合,应大量采用气动、液压夹紧以及联合夹紧等装置,与采用多件和多位的联动夹紧机构,并尽量采用可调换夹具。
4、进行夹具防碰撞检验。
在设计夹具时,应充分考虑到各个加工要求,避免刀具与夹具碰撞的情况发生。
所以夹具设计时应清楚加工的起刀点与走刀路线,以确保夹具不与刀具或机
床发生干涉。
设计者可以通过一些模型或者电脑的仿真软件来检验刀具是否与夹具发生干涉。
必要时应进行防碰撞计算,并将结果准确地编入加工程序。
二、数控铣床工装夹具的设计步骤与内容
1、分析工件,选择好加工工艺与工序。
首先了解工件的作用、特点、材料生产规模及技术要求。
分析工件加工中的加工余量、加工精度、加工表面、定位基准以及前后工序的联系等情况,确定出合理的加工路线。
设计夹具时,还要根据刀具、机床的参数,确定走刀次数,尽量使用一次装夹、多方位加工,一次加工成形。
可以提高生产效率、提高加工精度。
2、提高装夹速度。
在数控机床上加工工件时,定位机构的设计非常重要,好的定位机构可以对工件的装夹起到导向的作用,并对工件的加工精度起到决定性的作用。
工件的定位安装应力求使设计基准、工艺基准与编程计算的基准统一。
尽量在一次定位装夹后,加工出尽可能多的待加工表面,避免采用人工调整方式的加工方案。
以充分发挥数控机床的效能。
在成批生产中还可采用多位、多件夹具,以提高加工效率。
3、选好对刀点。
为了便于计算和程序简化,对刀点要选择与零件的定位基准容易换算的地方。
这样在机床上找正容易,加工中便于检查,减少加工误差,我们通常把对刀点选择在工件的基准上。
4、选择合适的刀具和切削用量。
在设计夹具时,必须充分考虑夹具、工件在铣床工作台上的位置。
根据机床的行程、各加工部位刀具的配置及刀具的长度、各工位上的加工轨迹,来选择合理的刀具类型及刀具长度,确定工件在工作台上的最佳位置。
否则,将会使机床超程、撞刀情况,影响提高生产效率和加工质量。
在选择数控机床的切削用量时,如果是粗加工,一般以提高生产率为主,切削量较大,切削力也大,这时要考虑工件装夹的稳定性,夹具是否能承受。
要是半精加工和精加工,应该注重工件装夹的精度。
5、机床夹具设计的标准化与通用化。
在进行夹具设计时要考虑夹具的标准化与通用化。
夹具设计的标准化是指夹具设计时,尽量使用统一标准,这样方便夹具各个零部件间的互换,提高夹具制造的精度与生产效率。
夹具的通用化,夹具设计时不以单一产品为生产对象,而是按若干产品的零部件结构和加工相似性来组织设计或生产。
在夹具设计的开始阶段首先按照零件的结构特征、规格尺寸有计划、有针对性的进行归类排序,进而在工装夹具的设计中提高夹具的通用性。
三、以例轴盖机加工的工装夹具为例
以下以轴盖机加工的工装夹具为例讲述铣床加工时的工装夹具的设计应用。
1、工件进行分析。
如图1和图2所示。
1.基准面
2.轴面
3.“O”型槽
4.油封孔
5.螺栓过孔
6.工艺搭台
图1、图2中所标出来的位置为需要加工的地方。
1处为装配基准面,要求与轴的垂直度为0,05,2处外轴面与油封孔同轴度为0,05,3处为零件密封位置,通过O型圈进行密封,密封槽的深度要求1.8±0.1mm。
2、加工方案的选定。
由于有上述的技术要求,一序加工内容:先加工装配基准面作为零件的基准,再以专用成型刀一次加工轴面及密封槽,通过反镗刀加工油封孔保证同轴度,再加工三个装配螺栓孔。
二序加工内容:加工5处得M6螺纹孔和铣掉两处的工艺搭台。
3、夹具设计方案
为了能保证零件的垂直度及同轴度,需要在同一工位,一次装夹加工保证。
考虑到零件生产的需要、机床的充分利用以及生产的稳定性,夹具采用液压夹紧和双工位加工方式。
一工位定位方式:以5处的预铸孔和油封孔外轴作为定位,由于零件的外型尺寸较小,加工装夹不方便,为了便于加工装夹,采用在零件上增加工艺搭台6处进行装夹;二工位定位方式:以一工位加工出来的A孔和轴端面作定位,夹紧产品的毛坯面固定产品。
根据上述的分析,设计出的夹具如图3所示。
4、夹具工作原理:如图3所示,一工位以定位销1和定位孔2把产品定位好,以三处支承10和压紧块4压紧固定产品;二工位以定位销6和定位孔7把产品定位好,以三处支承11和压紧块压紧固定产品。
通过夹具开关9控制液压油路控制压紧块动作夹紧工件进行加工。
加工时,工件先在一工位加工相应部分,然后移到二工位进行装夹,同时可在一工位装夹新毛坯后,与二工位工件一起进行加工,这样可以在一台机台上完成两个工序,提高了机床的利用率如图4所示。
5、本工装夹具的设计要点:
(1)本次夹具设计采用的是液压系统进行夹紧,使得加工时操作更加简单便捷,能够灵活的调整装夹的力度,避免夹伤工件。
(2)采用双工位装夹加工,可以利用一台机床加工两个工序,可以起到提高机床利用率的作用。
(3)在工件的精度要求下,采用一次装夹尽可能多的加工工件的加工面,避免多次装夹影响精度。
(4)工件的外形过少与形状不规则,需要增加工艺搭台进行夹紧。
四、总结。