3871735_SHIELDED_HIGH_VOLTAGE_CONNECTOR
NORMA 4000 5000 Power Analyzer 用户说明手册说明书
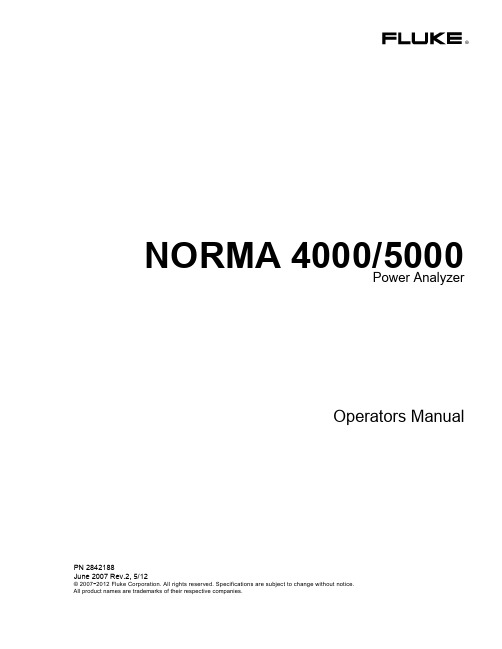
Since some countries or states do not allow limitation of the term of an implied warranty, or exclusion or limitation of incidental or consequential damages, the limitations and exclusions of this warranty may not apply to every buyer. If any provision of this Warranty is held invalid or unenforceable by a court or other decision-maker of competent jurisdiction, such holding will not affect the validity or enforceability of any other provision.
BEGRENZTE GEWÄHRLEISTUNG UND HAFTUNGSBESCHRÄNKUNG
Fluke gewährleistet, daß jedes Fluke-Produkt unter normalem Gebrauch und Service frei von Material- und Fertigungsdefekten ist. Die Garantiedauer beträgt 2 Jahre ab Versanddatum. Die Garantiedauer für Teile, Produktreparaturen und Service beträgt 90 Tage. Diese Garantie wird ausschließlich dem Erster
Atlas电枪错误代码

Atlas电枪错误代码?E001-E0090拧紧操作失败E100-E1991事件相关错误E200-E2992用户输入事件E300-E3993统计事件E400-E4994通信事件E500-E5995硬件事件(工具)E600-E6996硬件事件(DC3000/MC3000)E700-E7997硬件事件E800-E8998软件事件E900-E9999事件MMI3000事件代码E003扭矩测量值可能无效编程错误。
请检查程序并保证在第二操作阶段套筒转动过。
E102由于参数lock on reject,拧紧操作被禁止当参数lock on reject[C130]设置为禁止拧紧操作,则欲进行一个拧紧操作时会显示此事件代码.E103通过数字输入锁定工具工具通过数字输入被锁定。
E107由于采用线体控制而未打开批处理功能,拧紧操作被禁止若选择使用生产线控制一个工作,则当收到一个行控制起动信号时,工作才启动。
E112重复拧紧重复拧紧一个已经拧紧过的螺拴E113电流达到极限,退出拧紧操作当电流超过极限时,驱动器被禁止使用。
E117工具锁定-不能访问RBU Power Focus不能与RBB之间进行通信,且必须重启保护数据。
E120电机调整失败电机调整失败。
可能是在电机调整完成以前释放了扳机或工具产生故障。
E121开口调整失败此事件表明开口调整命令未能成功地执行。
E125超时警报或扭矩丢失警报当在Pset中启动超时报警功能,此事件代码表明由于超时拧紧操作退出。
此警报启动表明引起拧紧操作退出的基本原因是超时。
E126多步拧紧操作退出此事件表明当前运行的多步拧紧未完全执行(在拧紧操作完成前驱动器被关闭或工具扳机被释放)。
E127PVT关闭此事件表明在自攻中或拧紧操作的现行阶段驱动被关闭E128扳机过早释放当在Pset中启动扳机释放功能时,此事件表明工具扳机在拧紧操作达到最终目标以前被释放E129扭矩低于目标值当在Pset中启动“扭矩低于目标值”功能时,此事件表明扭矩结果值低于最终目标值,即使扭矩结果值大于最终扭矩最小值,扭矩状态也是NOK。
Gavita Pro 1000e DE US 208-240 SL安装和使用说明书
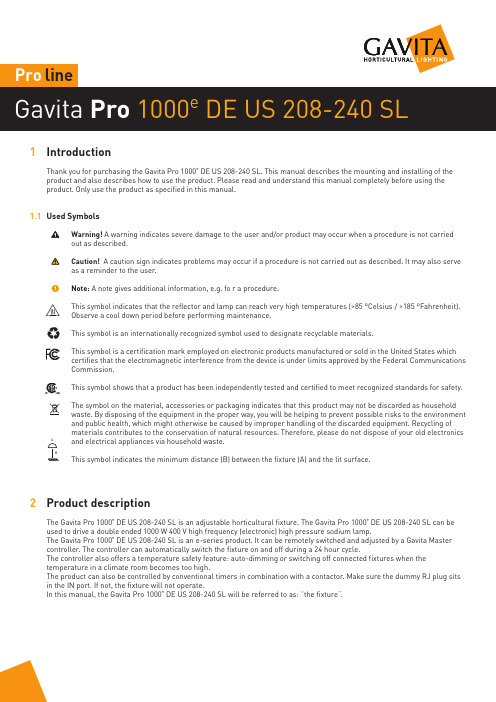
line1 IntroductionThank you for purchasing the Gavita Pro 1000e DE US 208-240 SL. This manual describes the mounting and installing of the product and also describes how to use the product. Please read and understand this manual completely before using the product. Only use the product as specified in this manual.1.1 Used SymbolsWarning! A warning indicates severe damage to the user and/or product may occur when a procedure is not carried out as described.Caution! A caution sign indicates problems may occur if a procedure is not carried out as described. It may also serve as a reminder to the user.N ote: A note gives additional information, e.g. fo r a procedure.This symbol indicates that the reflector and lamp can reach very high temperatures (>85 °Celsius / >185 °Fahrenheit). Observe a cool down period before performing maintenance.This symbol is an internationally recognized symbol used to designate recyclable materials.This symbol is a certification mark employed on electronic products manufactured or sold in the United States which certifies that the electromagnetic interference from the device is under limits approved by the Federal Communications Commission.This symbol shows that a product has been independently tested and certified to meet recognized standards for safety. The symbol on the material, accessories or packaging indicates that this product may not be discarded as household waste. By disposing of the equipment in the proper way, you will be helping to prevent possible risks to the environment and public health, which might otherwise be caused by improper handling of the discarded equipment. Recycling of materials contributes to the conservation of natural resources. Therefore, please do not dispose of your old electronics and electrical appliances via household waste.T his symbol indicates the minimum distance (B) between the fixture (A) and the lit surface. 2 Product descriptionThe Gavita Pro 1000e DE US 208-240 SL is an adjustable horticultural fixture. The Gavita Pro 1000e DE US 208-240 SL can beused to drive a double ended 1000 W 400 V high frequency (electronic) high pressure sodium lamp.The Gavita Pro 1000e DE US 208-240 SL is an e-series product. It can be remotely switched and adjusted by a Gavita Master controller. The controller can automatically switch the fixture on and off during a 24 hour cycle.The controller also offers a temperature safety feature: auto-dimming or switching off connected fixtures when the temperature in a climate room becomes too high.The product can also be controlled by conventional timers in combination with a contactor. Make sure the dummy RJ plug sits in the IN port. If not, the fixture will not operate.In this manual, the Gavita Pro 1000eDE US 208-240 SL will be referred to as: “the fixture”.1000eDE US 208-240 SL3 Product information and specifications3.1 General product informationProduct name Pro 1000e DE US 208-240 SLManufacturer Gavita International bvEAN Code8718403054422Part number18.30.14.24.20Plug type Nema 6-153.2 Technical specificationsProduct weight8.4 lbs (3.8 kg)Dimensions (L*W*H)22.2”x9.7”x7.8” (56,5x24.5x19.5cm) (height excl. mounting hooks)Temperature case< 70 °Celsius / 158 °FahrenheitTemperature ambient0 ~ 35 °Celsius / 32 ~ 95 °FahrenheitInput voltage +/-10%208 V AC240 V ACInput current at 100% 5.2 A 4.5 AInput current at 115% 5.9 A 5.1 AMax current 6.8 AInput power at 100%1000 WInput power at 115%1236 WApparent power +/- 3%1082 VAPower factor0.97 - 0.99Relative humidity< 70% (not condensating)Total Harmonic Distortion< 10%Frequency50 - 60 HzCertification c CSA usInsulation Class 1 - requires an earth connectionPower inlet IEC C14Power output settings50 - 115%External control signal:RJ connector built in (6P6C)Ignition voltage: 5 kV / 600 msInrush current:≤ 40 AmpsInrush duration:1,6msEarth leakage current:≤ 1 mA3.3 Compatible products and accessoriesProduct name Gavita part numberCompatible controllers Gavita EL1 Master controller41.00.12.20 Gavita EL2 Master controller 41.00.13.20Replacement reflector Gavita HR96 DE30.46.13.00 Gavita MD 135 DE HC30.07.13.00 Gavita W 150 DE31.26.13.00Compatible lamps Gavita Pro Plus 1000 W EL DE HPS26.10.16.12 Compatible power cord Power cord US 240 V, 2.5 meter / 8.2 ft44.30.41.10 Compatible interconnect cable Interconnect cable RJ43.50.00.17Repeater bus connection kit43.50.10.003.4 EnvironmentThe product is intended to be used in greenhouses and climate rooms. The product can be used in damp environments. The product may not be used in wet environments or outdoors. The lamps function optimally when the ambient temperature is between 20 ~ 30°C / 68 ~ 86° Fahrenheit.3.5 LegalThis device complies with Part 18 of the FCC Rules.CSA approved.4 Safety recommendations and warningsWarning! Carefully read the warnings below before using or working with the product!• Always adhere to the local rules and regulations when installing or using the fixture.• Do not open or disassemble the fixture, it contains no servicable parts inside. Opening the fixture can be dangerous and will void the warranty.• This product may cause interference to radio equipment and should not be installed near maritime safety communications equipment or other critical navigation or communication equipment operating between 0.45 - 30 MHz.• Do not use the fixture when either its lamp or its power cord are damaged. Replace the power cord only with originalcertified cords. Replace the lamp only with lamps specified by Gavita (see paragraph 3.3).• The use of other lamps may damage the product and lamp and will void the warranty.• Modifications to the cords can lead to unwanted electromagnetic effects, which makes the product not comply with legal requirements.• Do not expose the fixture to:-condensing humidity, heavy mist, fog or direct spray;-(ambient) temperatures outside the specified range;-dust and contamination;-direct sunlight during use or HID light that could heat up the ballast.• Always disconnect the fixture from mains before performing any maintenance.• Always allow for a cool down period of at least 30 minutes before touching the lamp or reflector. Touching the lamp or the reflector when the lamp is lit or immediately afterwards will result in severe burns!• Never touch the lamp with bare hands as this will cause damage to the lamp.• Do not use the fixture near flammable, explosive or reactive substances. The lamp and the reflector of the fixture reach temperatures of >85 °Celsius / 185 °Fahrenheit.• Do not use sulfur vaporizers or water misters. Sulfur and calcium deposits on your reflector will decrease its efficiency.• The installation and use of the fixture is the responsibility of the end user. Incorrect use or installation can lead to failure and damage to the fixture. Damage to the fixture and electronic circuitry as a result of incorrect installation and use revokes the warranty.5 Contents (1)A. Pro 1000e DE US 208-240 SL fixture1. Electronic ballast2. Pro-line bracket3. Lever to unlatch reflector4. Lamp sockets5. Reflector Gavita HR96 DE*6. Mounting points*The reflector is delivery dependent,it may differ from the imageB. Gavita Pro 1000 W EL 400 V lampC. Interconnect cable (RJ/RJ )Cable length: 2.5 m / 8 ftD. Power cord with NEMA 6-15 plugE. Dummy6 Controls, connections andindications (2)A. IEC C14 connectionB. Gavita 2xRJ connector1. RJ IN2. RJ OUTC. Status LED7 InstallationW arning! Avoid coiled cords. Coiled cords may lead to electromagnetic interference.W arning! Always install the lamp before connecting the fixture to the mains.W arning! When connecting the fixture to the controller it may ignite. Make sure either power is disconnected or the controller is switched off.W arning! Ensure the local cabling can support the voltage and current requirements of the fixture.7.1 Preparing the fixture for use• Switch off mains power.• Install the lamp in the fixture (see paragraph 10.1).• Hang the lamp by its two mounting points (3). The mountingspoint are spaced 407 mm / 16 inches apart.1.2. Gavita 2xRJ NEMA6-157.2 Repeater bus connection kit (optional)The repeater bus connection kit contains the following items:1. 2 x EMC ferrite snap-on black bag (13x12x5x25.5x2.4)2. 4 x Gavita splitter 1 to 2 6P6C grey RJ25 (in bag)3. 8 x grey modular jack interconnect cable 6P6C RJ25 (in bag)4. 8 x SNAP-ON ferrite grey (in bag)5. Interconnect cable 6p 82 ft (25mtr) grey (in bag)7.3 Preparation for use with a controllerUsing a daisy chain setup, a maximum of 100 fixtures can be connected to one controller. Up to 500 fixtures per daisy chain can be connected when using splitters. See section 7.4 and 7.5 of this manual and the manual of the controller.• Take the unstripped black interconnect cable.• Cut the cable (supplied with controller) to the desired length and strip both ends using a crimp tool (5).• Insert the cable end in the RJ14 connectors (6) and use the crimp tool to finish the assembly.7.5 Connecting up to 500 or 1000 fixturesUsing a setup with daisy chained splitters, up to 500 fixtures on EL1 and 1000 fixtures on EL2 (over two channels) can be connected as shown in fig. 10.• Use the black controller cable (item comes with the controller) to connect the primary channel of the controller to the input port of the first splitter (10A).• Remove the dummy from the input port of the fixtures (8).N ote: Keep the dummy in a safe place! The dummy is necessary to operate the fixture in standalone mode.• Use a grey 6PC6 modular jack interconnect cable (item 3.) to connect the output port of the splitter to the input port of the first fixture (10C).• Use a grey 6PC6 modular jack interconnect cable (item 3.) to connect the output port of the first fixture to the input port of the second (10D).• Repeat these steps to connect up to 100 fixtures per splitter output port (10E). Up to 500 fixtures can be connected to the primary channel.• Snap-on two grey ferrite cores (item 4.) on the grey interconnect cable (item 3.) close to the 6P6C plugs.• Use the grey 6PC6 modular jack interconnect cables (item 3.) to connect the outport of a splitter to the inport of the next (10B).• Use the black secondary channel (item comes with controller) (10G) to connect another 500 fixtures, in the same way the fixtures are connected to the primary channel.Warning! Ensure the power cord and the controller cables do not touch any of the reflectors.Warning! Distribute number of fixtures evenly over daisy chains.Warning! Ensure the repeater bus connections are integrated in a correctly set up installation for best results.Warning! Boosters should never be used to expand.Warning! The maximum cable length per splitter is 250m (100 interconnect cables).7.6 Connecting the fixture to the mainsWarning! Ensure the cord is not coiled and does not touch any hot surfaces.W arning! If external switching gear is used to switch the fixture, ensure it can cope with the inrush current of the fixture (see paragraph 3.2). Always use a double pole contactor suitable of switching a capacitive load. Never use householdtimers to switch the fixture!• If a controller is used, ensure the controller is connected to the fixture.• Plug the power cord into the mains.• Switch on mains power.8 Product useWarning! Never use the fixture without a lamp or reflector!C aution! Before you dim or boost your HPS lamp, make sure that you run it at nominal value (100%) for at least 100 hoursto stabilize the lamp. Failing to do so may lead to sub-optimal light levels and premature end of life failure of your lamp.8.1 Using the controller to adjust the output of the lampThe output of the lamp is steplessly variable from 50-115% when connected to a controller. Consult the controller manual for more information on controlling the output of the lamp.9 Troubleshooting using the status LEDThe multi colour status LED provides information on the condition of the controller and the lamp. Consult table 1 and 2 to interpret the status LED. LED signals are represented by colored dots.- All operating modes include GREEN;- All warning codes include RED;- All history codes (except the ignition code) include ORANGE;- WARNINGS and history codes overrule operating mode display.9.1 Status indicationsStatus LED message Status fixture Description Action / SolutionNo power / off The fixture is not connected to themains or the power is off Check powerBallast stand-by Fixture is connected to the mains and to a controller. Output of ballast is offBallast on Fixture is connected to the mains and to a controller. Output of ballast is onFixture is ignitingthe lamp Fixture is trying to restart the lamp No action required. When lamp doesn’t start: Lamp too hot, defect or not properly connected (remote). Disconnect, check power cord and connections9.2 Error or warning indicationsStatus LED message Status fixture Description Action / Solution Too low voltage Input voltage is too low Check mains voltageToo low voltageoccured in past See above, resetToo high voltage Input voltage is too high Check input voltage, check wiring and connection, check neutral in 3 phase systemsToo high voltageoccured in past See above, resetToo hightemperatureElectronics temperature is too high(max. 115 °Celsius / 239 °Fahrenheit)Disconnect from mains. Checkinstallation, clean ballast, checkenvironment temperature(max 35 °Celsius / 95 °Fahrenheit). Makesure fixture is not heated by HPS lamplight. Wait untill the lamp is cooled down,then reconnect to mainsToo hightemperatureoccured in pastSee above, resetNo signal fromcontrollerFixture is connected to the mains andset to EXT but there is no signal on thecontrol input.If a controller is connected, search forloose connections, defect contacts orshort-circuits.Table 1 Table 210 Inspection, maintenance and repairW arning! Disconnect the product from mains before performing anymaintenance or repairs.W arning! Do not open or disassemble the fixture, it contains no servicable partsinside. Opening the fixture can be dangerous and will void the warranty.W arning! Always allow for a cool down period of at least 30 minutes beforetouching the lamp or reflector.C aution! Do not clean the fixture with detergents, abrasives or other agressivesubstances.C aution! Do not touch the inside of the reflector during installation and do notuse water, abrasives or detergents to clean it. This will damage the reflectivesurface.•Contamination may couse overheating and decreased performance.-Clean the inside of the reflector only with a soft, dry cloth;-cloth.•damaged lamp.N ote:when the lamp runs on full power. If not, replace the lamp.• Regularly check the wiring of the product to ensure it is undamaged.10.1 P lacement and replacement of the lampWtouching the lamp or reflector.CAlways use a fabric glove to handle the lamp.C aution! Only use lamps specified by Gavita (see paragraph 3.3).N ote:whichever one comes first.• Switch off mains power.•if the lamp is damaged.• Open the lamp holders by sliding them outwards (11).• Carefully take the lamp out of the fixture (12).••springs hold the lamp (13).• Close the lamp holders by sliding them inwards (14).• Switch on mains power.10.2 P lacement and replacement of the reflectorW arning! Always allow for a cool down period of at least 30 minutes beforetouching the lamp or reflector.N ote: Gavita recommends replacing the reflector* after 5000 lighting hours.Depending on the environment and contamination levels the reflector will degrade.The Vega/Miro™ aluminum can not be cleaned without damage. Therefore werecommend to change the reflector once every year. Also replace the lamp whenreplacing the reflector.* The reflector is delivery dependent, it may differ from the image.• Switch off mains power.• Remove the lamp from the fixture (see paragraph 10.1).• Support the reflector on the side of the reflector lever to prevent it from falling(15).• Move the reflector lever up to retract the two pins holding the reflector in place(16).• Remove the reflector (17).• Place the new reflector. Ensure the reflector lever is in the opened position toallow the reflector to pass.• Ensure the holes in the reflector are aligned with the pins in the fixture (18).• Release the reflector lever so its two pins hold the reflector in place.• Insert the lamp in the lamp holder (see paragraph 10.1).• Switch on mains power.11 Storage and disposal• Store the fixture in a dry and clean environment, with an ambient temperature of-20 ~ 85 °Celsius / -4 ~ 185 °Fahrenheit.• The product must not be discarded as unsorted municipal waste, but must becollected separately for the purpose of treatment, recovery and environmentallysound disposal.C aution! The lamps are chemical hazardous waste and must be delivered to thedesignated authorities.C aution! The lamp contains mercury.12 WarrantyGavita International bv warrants the mechanical and electronic components oftheir product to be free of defects in material and workmanship if used undernormal operating conditions for a period of three (3) years from the original date of purchase. If the product shows any defects within this period and that defect is not due to user error or improper use Gavita International bv shall, at its discretion,either replace or repair the product using suitable new or reconditioned products or parts. For HPS lamps the warranty period is one (1) year from the original date of purchase. In case Gavita International bv decides to replace the entire product, this limited warranty shall apply to the replacement product for the remaining initial warranty period, i.e. three (3) years from the date of purchase of the original product.For service return the fixture to your shop with the original sales receipt.GAVITA International bv Oosteinderweg 127 1432 AH Aalsmeer The Netherlands Tel : +31(0)297-380 450 Fax : +31(0)297-380 451 E :*************** W : Manual: Gavita Pro 1000e DE US 208-240 SL Changes reserved - Version 17/46。
NEMA TS2

TS 2-2003 v02.06 Page i
CONTENTS
................................................................................................................................................xv Scope ..........................................................................................................................................................xvi History .........................................................................................................................................................xix TS 2-1998 Update.......................................................................................................................................xxi TS 2-2003 Update........................................................................................................................
国际电子(National Instruments)USB-7845R OEM 多功能数字实时接口设

SPECIFICATIONSNI USB-7845R OEMR Series for USB Multifunction RIO with Kintex-7 70T FPGA Français Deutsch日本語한국어简体中文/manualsThis document contains the specifications for the National InstrumentsUSB-7845R OEM device. Specifications are typical at 25 °C unless otherwise noted.Caution Using the NI USB-7845R OEM device in a manner not described in thisdocument may impair the protection the NI USB-7845R OEM device provides. Analog InputNumber of channels8 ............................................................................Input modes DIFF, NRSE, RSE (software-selectable; ............................................................................selection applies to all channels)Type of ADC Successive approximation register (SAR) ............................................................................Resolution16 bits ............................................................................Conversion time 2 µs ............................................................................Maximum sampling rate500 kS/s (per channel) ............................................................................Input impedancePowered on 1.25 GΩ ║ 2 pF....................................................................Powered off/overload 4.0 kΩ min....................................................................Input signal range±1 V, ±2 V, ±5 V, ±10 V (software-selectable) ............................................................................Input bias current±5 nA ............................................................................ ............................................................................Input offset current±5 nAInput coupling DC ............................................................................Overvoltage protection....................................................................Powered on±42 V maxPowered off±35 V max....................................................................Table 1. AI Operating Voltage Ranges Over TemperatureAI Absolute AccuracyAbsolute accuracy at full scale numbers is valid immediately following internal calibration and assumes the device is operating within 10 °C of the last external calibration. Accuracies listed are valid for up to one year from the device external calibration.Absolute accuracy at full scale on the analog input channels is determined using the following assumptions:•TempChangeFromLastExternalCal = 10 °C •TempChangeFromLastInternalCal = 1 °C•number_of_readings = 10,000•CoverageFactor = 3 σ1The minimum measurement voltage range is the largest voltage the NI USB-7845R OEM device is guaranteed to accurately measure.2| | NI USB-7845R OEM SpecificationsTable 2. AI Absolute Accuracy (Calibrated) (Continued)Table 3. AI Absolute Accuracy (Uncalibrated)Calculating Absolute AccuracyAbsoluteAccuracy=Reading⋅(GainError)+Range*(OffsetError)+NoiseUncertaintyGainError=ResidualGainError+GainTempco*(TempChangeFromLastInternalCal)+ReferenceTempco*(TempChangeFromLastExternalCal)OffsetError=ResidualOffsetError+OffsetTempco*(TempChangeFromLastInternalCal)+INL_ErrorNoiseUncertainty=Refer to the following equation for an example of calculating absolute accuracy.NI USB-7845R OEM Specifications| © National Instruments| 3Absolute accuracy at full scale on the analog input channels is determined using the following assumptions:•TempChangeFromLastExternalCal = 10 °C •TempChangeFromLastInternalCal = 1 °C•number_of_readings = 10,000•CoverageFactor = 3 σGainError=104.4ppm+20ppm*1+4ppm*10GainError=164.4ppmOffsetError=16.4ppm+4.18ppm*1+42.52ppmOffsetError=63.1ppmNoiseUncetainty=NoiseUncertainty=7.89µVAbsoluteAccuracy=10V*(GainError)+10V*(OffsetError)+NoiseUncertaintyAbsoluteAccuracy=2,283µVDC Transfer Characteristics ............................................................................INL Refer to the AI Accuracy TableDNL±0.4 LSB typ, ±0.9 LSB max ............................................................................No missing codes16 bits guaranteed ............................................................................CMRR, DC to 60 Hz-100 dB ............................................................................Dynamic CharacteristicsBandwidthSmall signal 1 MHz........................................................................................................................................Large signal500 kHz4| | NI USB-7845R OEM Specifications............................................................................Crosstalk-80 dB, DC to 100 kHzAnalog Output ............................................................................Output type Single-ended, voltage output ............................................................................Number of channels8 ............................................................................Resolution16 bits ............................................................................Update time 1.0 µs ............................................................................Maximum update rate 1 MS/sType of DAC Enhanced R-2R ............................................................................ ............................................................................Range±10 V ............................................................................Output coupling DCOutput impedance0.5 Ω............................................................................NI USB-7845R OEM Specifications| © National Instruments| 5............................................................................Minimum current drive±2.5 mAProtection Short circuit to ground ............................................................................Overvoltage protectionPowered on±15 V max....................................................................Powered off±10 V max....................................................................Power-on state User-configurable ............................................................................Power-on glitch-1 V for 1 µs ............................................................................Table 4. AO Operating Voltage Ranges for Over TemperatureAO Absolute AccuracyAbsolute accuracy at full scale numbers is valid immediately following internal calibration and assumes the device is operating within 10 °C of the last external calibration. Accuracies listed are valid for up to one year from the device external calibration.Absolute accuracy at full scale on the analog output channels is determined using the following assumptions:•TempChangeFromLastExternalCal = 10 °C •TempChangeFromLastInternalCal = 1 °C2The minimum measurement voltage range is the largest voltage the NI USB-7845R OEM device is guaranteed to accurately measure.6| | NI USB-7845R OEM SpecificationsTable 5. AO Absolute Accuracy (Calibrated) (Continued)Calculating Absolute AccuracyAbsoluteAccuracy=OutputValue*(GainError)+Range*(OffsetError)GainError=ResidualGainError+GainTempco*(TempChangeFromLastInternalCal)+ReferenceTempco*(TempChangeFromLastExternalCal)OffsetError=ResidualOffsetError+AOOffsetTempco*(TempChangeFromLastInternalCal)+INL_Error Refer to the following equation for an example of calculating absolute accuracy.Absolute accuracy at full scale on the analog output channels is determined using thefollowing assumptions:•TempChangeFromLastExternalCal = 10 °C•TempChangeFromLastInternalCal = 1 °CGainError=87.3ppm+12.6ppm*1+4ppm*10GainError=139.9ppmNI USB-7845R OEM Specifications| © National Instruments| 7OffsetError=41.1ppm+7.8ppm*1+61ppmOffsetError=109.9ppmAbsoluteAccuracy=10V*(GainError)+10V*(OffsetError)AbsoluteAccuracy=2,498µVDC Transfer CharacteristicsINL Refer to the AO Accuracy Table ............................................................................DNL±0.5 LSB typ, ±1 LSB max ............................................................................Monotonicity16 bits, guaranteed ............................................................................Dynamic CharacteristicsSlew rate-10 V/µs ............................................................................Noise250 µV rms, DC to 1 MHz ............................................................................Glitch energy at midscale transition±10 mV for 3 µs ............................................................................5V OutputOutput voltage 4.75 V to 5.1 V ............................................................................Output current0.5 A max ............................................................................Overvoltage protection±30 V ............................................................................ ............................................................................Overcurrent protection650 mA8| | NI USB-7845R OEM SpecificationsDigital I/OCompatibility LVTTL ............................................................................Logic family User-selectable ............................................................................Default software setting 3.3 V ............................................................................Maximum input 3.6 V ............................................................................NI USB-7845R OEM Specifications| © National Instruments| 9Table 10. Digital Output Logic Levels (Continued)Output currentSource 4.0 mA....................................................................Sink 4.0 mA....................................................................Input leakage current±15 µA max ............................................................................Input impedance50 kΩ typ, pull-down ............................................................................Power-on state Programmable, by line ............................................................................Protection±20 V, single line ............................................................................Digital I/O voltage switching time 2 ms max ............................................................................Note Refer to NI RIO Software Help for more information about switching times.Reconfigurable FPGAFPGA type Kintex-7 70T ............................................................................Number of flip-flops82,000 ............................................................................Number of LUTs41,000 ............................................................................Embedded block RAM4,860 kbits ............................................................................Number of DSP48 slices240 ............................................................................Timebase40, 80, 120, 160, or 200 MHz ............................................................................Timebase accuracy, onboard clock±100 ppm ............................................................................Calibration ............................................................................Recommended warm-up time15 minutesCalibration interval 1 year ............................................................................10| | NI USB-7845R OEM SpecificationsOnboard calibration referenceDC level3 5.000 V (±2 mV)....................................................................Temperature coefficient±4 ppm/°C max....................................................................Long-term stability±25 ppm/1,000 h....................................................................Note Refer to Calibration Certifications at /calibration to generate acalibration certificate for the NI USB-7845R OEM deviceBus Interface ............................................................................USB compatibility USB 2.0 Hi-Speed or Full-Speed4Data transfers DMA, interrupts, programmed I/O ............................................................................Number of DMA channels3 ............................................................................Power RequirementInput voltage9 V to 30 V ............................................................................Max power20 W ............................................................................ ............................................................................Overvoltage protection40 VNote You must use a UL Listed ITE power supply marked LPS with theNI USB-7845R OEM device.PhysicalNote If you need to clean the device, wipe it with a dry, clean towel.Dimensions (PCB)17.5 cm × 16.3 cm (6.9 in. × 6.4 in.) ............................................................................Weight183 g (6.45 oz) ............................................................................I/O connectors Analog- 1 × 50 pin box header, ............................................................................Digital- 3 × 34 pin box header3Actual value stored in Flash memory4Operating on a full-speed bus will result in lower performance and you might not be able to achieve maximum sampling/update rates.NI USB-7845R OEM Specifications| © National Instruments| 11Maximum Working VoltageMaximum working voltage refers to the signal voltage plus the common-mode voltage. Channel-to-earth±12 V, Measurement Category I ............................................................................Channel-to-channel±24 V, Measurement Category I ............................................................................Measurement Category I is for measurements performed on circuits not directly connected to the electrical distribution system referred to as MAINS voltage. MAINS is a hazardous live electrical supply system that powers equipment. This category is for measurements of voltages from specially protected secondary circuits. Such voltage measurements include signal levels, special equipment, limited-energy parts of equipment, circuits powered by regulated low-voltage sources, and electronics.Caution Do not use the NI USB-7845R OEM device for connection to signals inMeasurement Categories II, III, or IV.Note Measurement Categories CAT I and CAT O (Other) are equivalent. Thesetest and measurement circuits are not intended for direct connection to the MAINSbuilding installations of Measurement Categories CAT II, CAT III, or CAT IV. Environmental-40 °C to 70 °COperating temperature ............................................................................(IEC 60068-2-1, IEC 60068-2-2)Storage temperature-40 °C to 85 °C ............................................................................(IEC 60068-2-1, IEC 60068-2-2)10% to 90% RH, noncondensingOperating humidity ............................................................................(IEC 60068-2-56)Storage humidity (IEC 60068-2-56)5% to 95% RH, noncondensing ............................................................................ ............................................................................Pollution Degree2Maximum altitude2,000 m ............................................................................Indoor use only.Online Product CertificationTo obtain product certifications and the DoC for this product, visit /certification, search by model number or product line, and click the appropriate link in the Certification column.12| | NI USB-7845R OEM SpecificationsEnvironmental ManagementNI is committed to designing and manufacturing products in an environmentally responsible manner. NI recognizes that eliminating certain hazardous substances from our products is beneficial to the environment and to NI customers.For additional environmental information, refer to the Minimize Our Environmental Impact web page at /environment. This page contains the environmental regulations and directives with which NI complies, as well as other environmental information not included in this document.Waste Electrical and Electronic Equipment (WEEE)EU Customers At the end of the product life cycle, all products must be sent to aWEEE recycling center. For more information about WEEE recycling centers,National Instruments WEEE initiatives, and compliance withWEEE Directive 2002/96/EC on Waste Electrical and Electronic Equipment, visit/environment/weee.电子信息产品污染控制管理办法(中国RoHS)中国客户National Instruments符合中国电子信息产品中限制使用某些有害物质指令(RoHS)。
Indradrive 系列 故障代码
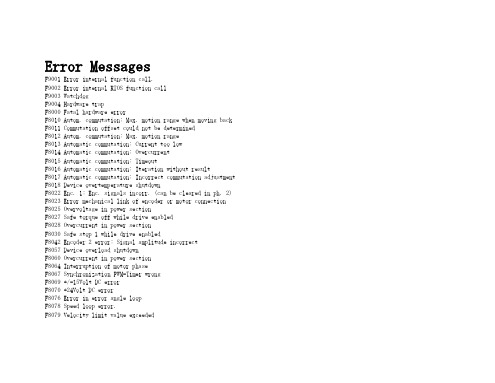
Error MessagesF9001 Error internal function call.F9002 Error internal RTOS function callF9003 WatchdogF9004 Hardware trapF8000 Fatal hardware errorF8010 Autom. commutation: Max. motion range when moving back F8011 Commutation offset could not be determinedF8012 Autom. commutation: Max. motion rangeF8013 Automatic commutation: Current too lowF8014 Automatic commutation: OvercurrentF8015 Automatic commutation: TimeoutF8016 Automatic commutation: Iteration without resultF8017 Automatic commutation: Incorrect commutation adjustment F8018 Device overtemperature shutdownF8022 Enc. 1: Enc. signals incorr. (can be cleared in ph. 2) F8023 Error mechanical link of encoder or motor connectionF8025 Overvoltage in power sectionF8027 Safe torque off while drive enabledF8028 Overcurrent in power sectionF8030 Safe stop 1 while drive enabledF8042 Encoder 2 error: Signal amplitude incorrectF8057 Device overload shutdownF8060 Overcurrent in power sectionF8064 Interruption of motor phaseF8067 Synchronization PWM-Timer wrongF8069 +/-15Volt DC errorF8070 +24Volt DC errorF8076 Error in error angle loopF8078 Speed loop error.F8079 Velocity limit value exceededF8091 Power section defectiveF8100 Error when initializing the parameter handlingF8102 Error when initializing power sectionF8118 Invalid power section/firmware combinationF8120 Invalid control section/firmware combinationF8122 Control section defectiveF8129 Incorrect optional module firmwareF8130 Firmware of option 2 of safety technology defectiveF8133 Error when checking interrupting circuitsF8134 SBS: Fatal errorF8135 SMD: Velocity exceededF8140 Fatal CCD error.F8201 Safety command for basic initialization incorrectF8203 Safety technology configuration parameter invalidF8813 Connection error mains chokeF8830 Power section errorF8838 Overcurrent external braking resistorF7010 Safely-limited increment exceededF7011 Safely-monitored position, exceeded in pos. DirectionF7012 Safely-monitored position, exceeded in neg. DirectionF7013 Safely-limited speed exceededF7020 Safe maximum speed exceededF7021 Safely-limited position exceededF7030 Position window Safe stop 2 exceededF7031 Incorrect direction of motionF7040 Validation error parameterized - effective thresholdF7041 Actual position value validation errorF7042 Validation error of safe operation modeF7043 Error of output stage interlockF7050 Time for stopping process exceeded8.3.15 F7051 Safely-monitored deceleration exceeded (159)8.4 Travel Range Errors (F6xxx) (161)8.4.1 Behavior in the Case of Travel Range Errors (161)8.4.2 F6010 PLC Runtime Error (162)8.4.3 F6024 Maximum braking time exceeded (163)8.4.4 F6028 Position limit value exceeded (overflow) (164)8.4.5 F6029 Positive position limit exceeded (164)8.4.6 F6030 Negative position limit exceeded (165)8.4.7 F6034 Emergency-Stop (166)8.4.8 F6042 Both travel range limit switches activated (167)8.4.9 F6043 Positive travel range limit switch activated (167)8.4.10 F6044 Negative travel range limit switch activated (168)8.4.11 F6140 CCD slave error (emergency halt) (169)8.5 Interface Errors (F4xxx) (169)8.5.1 Behavior in the Case of Interface Errors (169)8.5.2 F4001 Sync telegram failure (170)8.5.3 F4002 RTD telegram failure (171)8.5.4 F4003 Invalid communication phase shutdown (172)8.5.5 F4004 Error during phase progression (172)8.5.6 F4005 Error during phase regression (173)8.5.7 F4006 Phase switching without ready signal (173)8.5.8 F4009 Bus failure (173)8.5.9 F4012 Incorrect I/O length (175)8.5.10 F4016 PLC double real-time channel failure (176)8.5.11 F4017 S-III: Incorrect sequence during phase switch (176)8.5.12 F4034 Emergency-Stop (177)8.5.13 F4140 CCD communication error (178)8.6 Non-Fatal Safety Technology Errors (F3xxx) (178)8.6.1 Behavior in the Case of Non-Fatal Safety Technology Errors (178)8.6.2 F3111 Refer. missing when selecting safety related end pos (179)8.6.3 F3112 Safe reference missing (179)8.6.4 F3115 Brake check time interval exceeded (181)Troubleshooting Guide | Rexroth IndraDrive Electric Drivesand ControlsI Bosch Rexroth AG VII/XXIITable of ContentsPage8.6.5 F3116 Nominal load torque of holding system exceeded (182)8.6.6 F3117 Actual position values validation error (182)8.6.7 F3122 SBS: System error (183)8.6.8 F3123 SBS: Brake check missing (184)8.6.9 F3130 Error when checking input signals (185)8.6.10 F3131 Error when checking acknowledgment signal (185)8.6.11 F3132 Error when checking diagnostic output signal (186)8.6.12 F3133 Error when checking interrupting circuits (187)8.6.13 F3134 Dynamization time interval incorrect (188)8.6.14 F3135 Dynamization pulse width incorrect (189)8.6.15 F3140 Safety parameters validation error (192)8.6.16 F3141 Selection validation error (192)8.6.17 F3142 Activation time of enabling control exceeded (193)8.6.18 F3143 Safety command for clearing errors incorrect (194)8.6.19 F3144 Incorrect safety configuration (195)8.6.20 F3145 Error when unlocking the safety door (196)8.6.21 F3146 System error channel 2 (197)8.6.22 F3147 System error channel 1 (198)8.6.23 F3150 Safety command for system start incorrect (199)8.6.24 F3151 Safety command for system halt incorrect (200)8.6.25 F3152 Incorrect backup of safety technology data (201)8.6.26 F3160 Communication error of safe communication (202)8.7 Non-Fatal Errors (F2xxx) (202)8.7.1 Behavior in the Case of Non-Fatal Errors (202)8.7.2 F2002 Encoder assignment not allowed for synchronization (203)8.7.3 F2003 Motion step skipped (203)8.7.4 F2004 Error in MotionProfile (204)8.7.5 F2005 Cam table invalid (205)8.7.6 F2006 MMC was removed (206)8.7.7 F2007 Switching to non-initialized operation mode (206)8.7.8 F2008 RL The motor type has changed (207)8.7.9 F2009 PL Load parameter default values (208)8.7.10 F2010 Error when initializing digital I/O (-> S-0-0423) (209)8.7.11 F2011 PLC - Error no. 1 (210)8.7.12 F2012 PLC - Error no. 2 (210)8.7.13 F2013 PLC - Error no. 3 (211)8.7.14 F2014 PLC - Error no. 4 (211)8.7.15 F2018 Device overtemperature shutdown (211)8.7.16 F2019 Motor overtemperature shutdown (212)8.7.17 F2021 Motor temperature monitor defective (213)8.7.18 F2022 Device temperature monitor defective (214)8.7.19 F2025 Drive not ready for control (214)8.7.20 F2026 Undervoltage in power section (215)8.7.21 F2027 Excessive oscillation in DC bus (216)8.7.22 F2028 Excessive deviation (216)8.7.23 F2031 Encoder 1 error: Signal amplitude incorrect (217)VIII/XXII Bosch Rexroth AG | Electric Drivesand ControlsRexroth IndraDrive | Troubleshooting GuideTable of ContentsPage8.7.24 F2032 Validation error during commutation fine adjustment (217)8.7.25 F2033 External power supply X10 error (218)8.7.26 F2036 Excessive position feedback difference (219)8.7.27 F2037 Excessive position command difference (220)8.7.28 F2039 Maximum acceleration exceeded (220)8.7.29 F2040 Device overtemperature 2 shutdown (221)8.7.30 F2042 Encoder 2: Encoder signals incorrect (222)8.7.31 F2043 Measuring encoder: Encoder signals incorrect (222)8.7.32 F2044 External power supply X15 error (223)8.7.33 F2048 Low battery voltage (224)8.7.34 F2050 Overflow of target position preset memory (225)8.7.35 F2051 No sequential block in target position preset memory (225)8.7.36 F2053 Incr. encoder emulator: Pulse frequency too high (226)8.7.37 F2054 Incr. encoder emulator: Hardware error (226)8.7.38 F2055 External power supply dig. I/O error (227)8.7.39 F2057 Target position out of travel range (227)8.7.40 F2058 Internal overflow by positioning input (228)8.7.41 F2059 Incorrect command value direction when positioning (229)8.7.42 F2063 Internal overflow master axis generator (230)8.7.43 F2064 Incorrect cmd value direction master axis generator (230)8.7.44 F2067 Synchronization to master communication incorrect (231)8.7.45 F2068 Brake error (231)8.7.46 F2069 Error when releasing the motor holding brake (232)8.7.47 F2074 Actual pos. value 1 outside absolute encoder window (232)8.7.48 F2075 Actual pos. value 2 outside absolute encoder window (233)8.7.49 F2076 Actual pos. value 3 outside absolute encoder window (234)8.7.50 F2077 Current measurement trim wrong (235)8.7.51 F2086 Error supply module (236)8.7.52 F2087 Module group communication error (236)8.7.53 F2100 Incorrect access to command value memory (237)8.7.54 F2101 It was impossible to address MMC (237)8.7.55 F2102 It was impossible to address I2C memory (238)8.7.56 F2103 It was impossible to address EnDat memory (238)8.7.57 F2104 Commutation offset invalid (239)8.7.58 F2105 It was impossible to address Hiperface memory (239)8.7.59 F2110 Error in non-cyclical data communic. of power section (240)8.7.60 F2120 MMC: Defective or missing, replace (240)8.7.61 F2121 MMC: Incorrect data or file, create correctly (241)8.7.62 F2122 MMC: Incorrect IBF file, correct it (241)8.7.63 F2123 Retain data backup impossible (242)8.7.64 F2124 MMC: Saving too slowly, replace (243)8.7.65 F2130 Error comfort control panel (243)8.7.66 F2140 CCD slave error (243)8.7.67 F2150 MLD motion function block error (244)8.7.68 F2174 Loss of motor encoder reference (244)8.7.69 F2175 Loss of optional encoder reference (245)Troubleshooting Guide | Rexroth IndraDrive Electric Drivesand Controls| Bosch Rexroth AG IX/XXIITable of ContentsPage8.7.70 F2176 Loss of measuring encoder reference (246)8.7.71 F2177 Modulo limitation error of motor encoder (246)8.7.72 F2178 Modulo limitation error of optional encoder (247)8.7.73 F2179 Modulo limitation error of measuring encoder (247)8.7.74 F2190 Incorrect Ethernet configuration (248)8.7.75 F2260 Command current limit shutoff (249)8.7.76 F2270 Analog input 1 or 2, wire break (249)8.7.77 F2802 PLL is not synchronized (250)8.7.78 F2814 Undervoltage in mains (250)8.7.79 F2815 Overvoltage in mains (251)8.7.80 F2816 Softstart fault power supply unit (251)8.7.81 F2817 Overvoltage in power section (251)8.7.82 F2818 Phase failure (252)8.7.83 F2819 Mains failure (253)8.7.84 F2820 Braking resistor overload (253)8.7.85 F2821 Error in control of braking resistor (254)8.7.86 F2825 Switch-on threshold braking resistor too low (255)8.7.87 F2833 Ground fault in motor line (255)8.7.88 F2834 Contactor control error (256)8.7.89 F2835 Mains contactor wiring error (256)8.7.90 F2836 DC bus balancing monitor error (257)8.7.91 F2837 Contactor monitoring error (257)8.7.92 F2840 Error supply shutdown (257)8.7.93 F2860 Overcurrent in mains-side power section (258)8.7.94 F2890 Invalid device code (259)8.7.95 F2891 Incorrect interrupt timing (259)8.7.96 F2892 Hardware variant not supported (259)8.8 SERCOS Error Codes / Error Messages of Serial Communication (259)9 Warnings (Exxxx) (263)9.1 Fatal Warnings (E8xxx) (263)9.1.1 Behavior in the Case of Fatal Warnings (263)9.1.2 E8025 Overvoltage in power section (263)9.1.3 E8026 Undervoltage in power section (264)9.1.4 E8027 Safe torque off while drive enabled (265)9.1.5 E8028 Overcurrent in power section (265)9.1.6 E8029 Positive position limit exceeded (266)9.1.7 E8030 Negative position limit exceeded (267)9.1.8 E8034 Emergency-Stop (268)9.1.9 E8040 Torque/force actual value limit active (268)9.1.10 E8041 Current limit active (269)9.1.11 E8042 Both travel range limit switches activated (269)9.1.12 E8043 Positive travel range limit switch activated (270)9.1.13 E8044 Negative travel range limit switch activated (271)9.1.14 E8055 Motor overload, current limit active (271)9.1.15 E8057 Device overload, current limit active (272)X/XXII Bosch Rexroth AG | Electric Drivesand ControlsRexroth IndraDrive | Troubleshooting GuideTable of ContentsPage9.1.16 E8058 Drive system not ready for operation (273)9.1.17 E8260 Torque/force command value limit active (273)9.1.18 E8802 PLL is not synchronized (274)9.1.19 E8814 Undervoltage in mains (275)9.1.20 E8815 Overvoltage in mains (275)9.1.21 E8818 Phase failure (276)9.1.22 E8819 Mains failure (276)9.2 Warnings of Category E4xxx (277)9.2.1 E4001 Double MST failure shutdown (277)9.2.2 E4002 Double MDT failure shutdown (278)9.2.3 E4005 No command value input via master communication (279)9.2.4 E4007 SERCOS III: Consumer connection failed (280)9.2.5 E4008 Invalid addressing command value data container A (280)9.2.6 E4009 Invalid addressing actual value data container A (281)9.2.7 E4010 Slave not scanned or address 0 (281)9.2.8 E4012 Maximum number of CCD slaves exceeded (282)9.2.9 E4013 Incorrect CCD addressing (282)9.2.10 E4014 Incorrect phase switch of CCD slaves (283)9.3 Possible Warnings When Operating Safety Technology (E3xxx) (283)9.3.1 Behavior in Case a Safety Technology Warning Occurs (283)9.3.2 E3100 Error when checking input signals (284)9.3.3 E3101 Error when checking acknowledgment signal (284)9.3.4 E3102 Actual position values validation error (285)9.3.5 E3103 Dynamization failed (285)9.3.6 E3104 Safety parameters validation error (286)9.3.7 E3105 Validation error of safe operation mode (286)9.3.8 E3106 System error safety technology (287)9.3.9 E3107 Safe reference missing (287)9.3.10 E3108 Safely-monitored deceleration exceeded (288)9.3.11 E3110 Time interval of forced dynamization exceeded (289)9.3.12 E3115 Prewarning, end of brake check time interval (289)9.3.13 E3116 Nominal load torque of holding system reached (290)9.4 Non-Fatal Warnings (E2xxx) (290)9.4.1 Behavior in Case a Non-Fatal Warning Occurs (290)9.4.2 E2010 Position control with encoder 2 not possible (291)9.4.3 E2011 PLC - Warning no. 1 (291)9.4.4 E2012 PLC - Warning no. 2 (291)9.4.5 E2013 PLC - Warning no. 3 (292)9.4.6 E2014 PLC - Warning no. 4 (292)9.4.7 E2021 Motor temperature outside of measuring range (292)9.4.8 E2026 Undervoltage in power section (293)9.4.9 E2040 Device overtemperature 2 prewarning (294)9.4.10 E2047 Interpolation velocity = 0 (294)9.4.11 E2048 Interpolation acceleration = 0 (295)9.4.12 E2049 Positioning velocity >= limit value (296)9.4.13 E2050 Device overtemp. Prewarning (297)Troubleshooting Guide | Rexroth IndraDrive Electric Drivesand Controls| Bosch Rexroth AG XI/XXIITable of ContentsPage9.4.14 E2051 Motor overtemp. prewarning (298)9.4.15 E2053 Target position out of travel range (298)9.4.16 E2054 Not homed (300)9.4.17 E2055 Feedrate override S-0-0108 = 0 (300)9.4.18 E2056 Torque limit = 0 (301)9.4.19 E2058 Selected positioning block has not been programmed (302)9.4.20 E2059 Velocity command value limit active (302)9.4.21 E2061 Device overload prewarning (303)9.4.22 E2063 Velocity command value > limit value (304)9.4.23 E2064 Target position out of num. range (304)9.4.24 E2069 Holding brake torque too low (305)9.4.25 E2070 Acceleration limit active (306)9.4.26 E2074 Encoder 1: Encoder signals disturbed (306)9.4.27 E2075 Encoder 2: Encoder signals disturbed (307)9.4.28 E2076 Measuring encoder: Encoder signals disturbed (308)9.4.29 E2077 Absolute encoder monitoring, motor encoder (encoder alarm) (308)9.4.30 E2078 Absolute encoder monitoring, opt. encoder (encoder alarm) (309)9.4.31 E2079 Absolute enc. monitoring, measuring encoder (encoder alarm) (309)9.4.32 E2086 Prewarning supply module overload (310)9.4.33 E2092 Internal synchronization defective (310)9.4.34 E2100 Positioning velocity of master axis generator too high (311)9.4.35 E2101 Acceleration of master axis generator is zero (312)9.4.36 E2140 CCD error at node (312)9.4.37 E2270 Analog input 1 or 2, wire break (312)9.4.38 E2802 HW control of braking resistor (313)9.4.39 E2810 Drive system not ready for operation (314)9.4.40 E2814 Undervoltage in mains (314)9.4.41 E2816 Undervoltage in power section (314)9.4.42 E2818 Phase failure (315)9.4.43 E2819 Mains failure (315)9.4.44 E2820 Braking resistor overload prewarning (316)9.4.45 E2829 Not ready for power on (316)。
wm8978数据手册_引脚图_参数
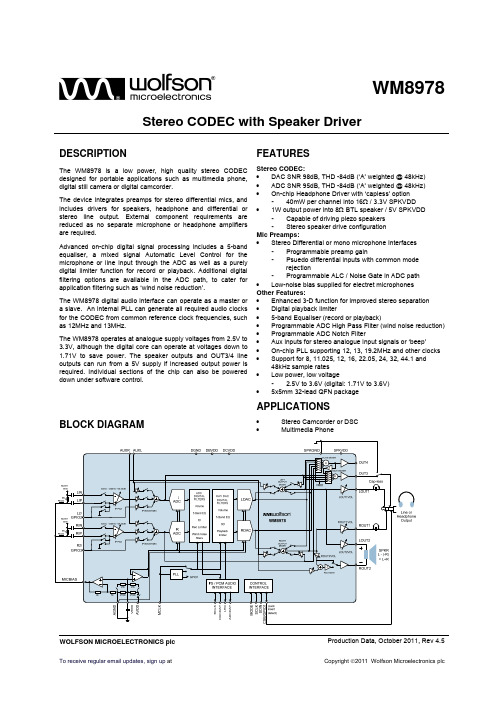
The device integrates preamps for stereo differential mics, and includes drivers for speakers, headphone and differential or stereo line output. External component requirements are reduced as no separate microphone or headphone amplifiers are required.
BLOCK DIAGRAM ................................................................................................ 1
FEATURES ............................................................................................................ 1
ZXGD3101EV2 EVALUATION BOARD USER GUIDE

ZXGD3101EV2 EVALUATION BOARD USER GUIDE DescriptionThis document describes how to connect and evaluate the ZXGD3101EV2 evaluation board, Figure 1. The purpose of this board is to demonstrate synchronous rectification and driving of a MOSFET as a Schottky/ultra-fast recovery diode replacement in Flyback converters. When the board is used to drive a synchronous MOSFET, it will yield efficiency improvement, whilst maintaining design simplicity and incurring minimal component count. The ZXGD3101 senses the voltage across the MOSFET and generates the gate drive voltage when a negative voltage is detected across the drain-source pin. This evaluation guide also includes useful guidelines on conditioning of Flyback converters, as well as a design tip to overcome premature driver turn-off and maximize the effectiveness of synchronous rectification.Note: The evaluation board is not recommended to be used with Flyback converters above 100kHz switching frequency.Figure 1 Evaluation board layout and connection diagramReference designThe ZXGD3101EV2 is configured to the reference design in Figure 2. The target application for the device is external adapters where the typical output voltage ranges from 12V to 20V. However, the evaluation board will work with output voltages up to 40V.Power, which could be sourced directly from the output of the power supply, is applied to the terminal block P1. At the other end of the board is a location for a three way header, P2. This is not fitted, so as to allow flexibility of mounting (forward or reverse). The purpose of the header is to allow the board to be soldered directly across a TO220 packaged synchronous MOSFET.R4, Q2, D1 and C1 are configured as a simple series regulator to maintain a stable Vcc. The values of Rref and Rbias in Figure 2 are based on a 10.3V Vcc. For supply voltages below this, these resistor values need to be reduced proportionally to maintain 5.3mA and 3.2mA into the ‘REF’ and ‘BIAS’ pins respectively. Refer to the datasheet for further information on selection of the resistor value.A fixed-bias-point constant current source (Q1, R2, R1//R5 and R3) is included on the board. The current source is not active in the original board setting and is only intended for elimination of premature turn-off problem on the controller (refer to the section ‘Overcoming premature turn-off’ for details).Figure 2: Evaluation board schematic diagram and connectionPlease note that the component part numbers are given as a guide only. Due to continual component development, all parts quoted should be checked for suitability and availability with their respective manufacturers.Table 1: Evaluation board component details (BOM)Ref. Value Package Part number Manufacturer NotesU1ZXGD3101SO8ZXGD3101N8Diodes ZetexQ1 FMMTA92 SOT23 FMMTA92 Diodes ZetexQ2 FMMT491A SOT23 FMMT491A Diodes Zetex500mWD1 11V Zener SOT23 BZX84C11 Diodes Inc. 300mWC1 1uF 50V 1206 C1206X105K5RAC Kemet X7R 10%R1 8.2kΩ0805 Generic 125mW, 1%, 200ppm/ºCR2 1KΩ0805 Generic 125mW, 1%, 200ppm/ºCR3 100Ω0805 Generic 125mW, 1%, 200ppm/ºCR4 10kΩ0805 Generic 125mW, 1%, 200ppm/ºC Rbias 1.8kΩ1206 Generic 125mW, 5%, 200ppm/ºC Rgate 0R 1206 Generic 125mW, 5%, 200ppm/ºCRref 3KΩ1206 Generic 125mW, 5%, 200ppm/ºCP1 2-way terminal GenericP2 3-way header GenericEvaluation procedure and operationTo perform a quick functional test of the ZXGD3101, the evaluation board can be used to drive a MOSFET as a diode replacement in high-side-rectification (see Fig. 3a), as the board can float to any potential. In practice, the supply voltage could be derived from an auxiliary supply winding across the transformer secondary. If the board is used for comparison against an existing synchronous rectification solution, the existing controller must disabled before proceed with the testing.The recommended device implementation is low side synchronous rectification (Fig. 3b), due to the ease of acquiring the required supply voltage directly, either from the power supply output post bleeder resistor, or from the emitter-follower-configured transistor. Before doing this test, it is important that the existing diode has been removed and/or a short has been applied across its cathode and anode terminals. The track linking the negative terminal of the converter’s output capacitor to the transformer secondary-side output should then be cut, and a MOSFET should be inserted. In general, the MOSFET should be selected to drop between 50 to 150mV at the peak of the secondary-side current to ensure MOSFET enhancement. The breakdown voltage of the MOSFET must be higher than the maximum drain-source voltage stress, plus some margin. Designers interested in squeezing the last percent of efficiency out of the module can place an additional Schottky or Ultra-fast-recovery diode in parallel with MOSET. The diode prevents body-diode conduction, so the trace inductance between it and the MOSFET should be kept small to create an efficient circulating energy flow path.Figure 3 Test options for ZXGD3101EV1 a) high side and b) low side(a)(b)Figure 3: Test options for ZXGD3101EV2 a) high side and b) low sideTo check for functionality, the circuit waveforms should be probed using an oscilloscope probe with a minimal length for the ground pin, and the probe should be connected directly to the pins of the device. If a current probe or transformer is used to measure reverse current flow, excessive wire-loop- inductance and injection of noise, which could disturb normal functioning of the controller, should be avoided.At synchronous MOSFET turn-on, current starts to flow through the body-diode after the primary switch turn-off (see Fig. 4). When this occurs, the drain of the MOSFET will be around -1.25V with respect to ground, due to body-diode conduction. The detector stage within the ZXGD3101 determines when the MOSFET needs to turn on by measuring the change in polarity of the V SD differential voltage, which, in turn, determines when the current is flowing through the secondary side. The turn-off phase of the ZXGD3101 happens differently depending on the mode of operation. It should be noted that the device is most suited to discontinuous and critical conduction mode, howeverit can also be used in continuous conduction mode. In discontinuous and critical conduction mode, the MOSFET current decays linearly and the controller proportionately backs off its gate-drive output when the on-resistance-induced conduction voltage drop is less than -50mV. Upon the conduction voltage crossing the turning off threshold, the gate drive is turned off quickly to eliminate any reverse current flow (see Figure 4a). If the board is evaluated with a converter in continuous conduction mode, the secondary side circulating current does not decay to zero prior to primary MOSFET turn-on. The controller then turns off the MOSFET quickly when the primary MOSFET current starts rising in less than 50ns delay time, as shown in Fig. 4b, so the possibility of cross conduction is minimized. This is critical because cross conduction due to the primary side MOSFET and secondary rectification MOSFET conducting simultaneously will degrade efficiency due to the nature of the fast transition.(a)(b)Figure 4: Synchronous rectification operating waveforms (a) Critical conduction mode and (b)Continuous conduction modeConditioning the power supply to maximize efficiency of ZXGD3101The ZXGD3101 can be susceptible to noise if a proper snubbing circuit on the primary side is not devised. Any high-frequency-resonance-ringing on the drain of the primary MOSFET will be reflected across the transformer as multiple synchronous MOSFET V SD transitions, which will cause spurious turn-on to occur. The controller is then not able to fully enhance the MOSFET until the oscillation is stabilized. To prevent this problem, the user is advised to strengthen the primary switch snubber circuit through either a damping resistor R d (see Fig. 5) or alternatively an additional snubbing R-C network. These have the effect of eliminating the oscillation by limiting the peak D clamp reverse recovery current and soften its reverse recovery characteristic. The improvement on the rising edge of the gate drive can be observed as in Figure 6.Figure 5: Recommended design for a synchronous rectified Flyback converter Another snubber network comprising of R snub and C snub should be fitted across the synchronous MOSFET to dampen out high frequency oscillations at the MOSFET’s fast turn-off edge. If the amplitude of oscillations is high, then the drain voltage could ring below the turn-on threshold. The controller could then be falsely triggered and provide an output high to drive the MOSFET gate. Apart from preventing premature turn-on of the controller, this also has the added benefit of reducing conducted EMI generation and device voltage stress.Furthermore, any parasitic inductance due to a combination of printed circuit board traces and component leads can also cause the voltage at the drain input of the ZXGD3101 to ring about ground. Proper layout attention must be paid to ensure the integrity of the V SD differential voltage. To mitigate noise induced malfunction, it is important to keep the drain input on the controller as close as possible to the synchronous MOSFET, preferably within 10mm. A minimal gate drive loop will also negate the effect of loop inductance inducing oscillation to the controller’s output gate drive voltage, reducing the requirement for series gate resistor damping.(a)(b)Figure 6: Oscillation-induced spurious turn on reduces efficiency of synchronous rectification(a) Oscillation due to clamp diode recovery (b) Improved clamp circuit Overcoming premature turn-offThe high current di/dt coupled with low R DS(on) voltage drop causes V SD to rise rapidly toward zero, which could make the controller more susceptible to closed-loop instability-induced malfunction under this circumstance. One phenomenon that could occur particularly with a sub-10mΩMOSFET is a sudden fall of the ZXGD3101’s internal bias transistor voltage gain, which causes the gate drive voltage to back off, even though the MOSFET is still conducting substantial current. When this happens it leads to premature fall-off of the controller gate drive voltage (refer to Fig. 7a) which causes inadequate enhancement of the MOSFET and reduces the effectiveness of synchronous rectification. To make matters worse, the subsequent ringing incurs additional gate charge loss and further deteriorates the efficiency.If the above mentioned problem is observed, the on-board constant bias current source should be used instead. This could be easily implemented using Q1 alongside R1, R2 and R3 (refer to Fig. 2).Although the board is originally tracked for Rbias biasing, the set up can be altered by using the solder links SL2 and SL3.To use the constant bias current source on the evaluation board,1. Ensure that SL2 is shorted and SL3 is open.2. Use a multimeter to check that the voltage across test points TP1 and TP2 is approximately500mV, to ensure that 5mA is sourced into the bias pin. To use the constant current source when VIN is less than 10V,1. Adjust the value of R1 and R2 accordingly to give 500mV across R32. Select new value for Rref according to the formula in the datasheet to source approximately3mA into the Ref pin. The set up has the positive effect of sustaining the gate voltage for a longer period within the conduction cycle and thus improving efficiency. The gate drive voltage also has slightamplitude increaseyielding better enhancing of the MOSFET. Most importantly, the back-end oscillations observed previously have also been eliminated as shown in Fig. 7b.Figure 7 DCM gate drive voltage a) showing premature turn off and b) premature turn-off andoscillations eliminated using a constant bias current source (b)(a)Sales officesThe Americas 3050 E. Hillcrest Drive Westlake Village,CA 91362-3154Tel: (+1) 805 446 4800 Fax: (+1) 805 446 4850EuropeKustermannparkBalanstraße 59,D-81541 MünchenGermanyTel: (+49) 894 549 490Fax: (+49) 894 549 4949Taiwan7F, No. 50,Min Chuan RoadHsin-TienTaipei, TaiwanTel: (+886) 289 146 000Fax: (+886) 289 146 639ShanghaiRm. 606, No.1158Changning RoadShanghai, ChinaTel: (+86) 215 241 4882Fax (+86) 215 241 4891ShenzhenRoom A1103-04,ANLIAN Plaza, #4018Jintian RoadFutian CBD,Shenzhen, ChinaTel: (+86) 755 882 849 88Fax: (+86) 755 882 849 99Korea6 Floor, Changhwa B/D,1005-5 Yeongtong-dong,Yeongtong-gu, Suwon-si,Gyeonggi-do, Korea 443-813Tel: (+82) 312 731 884Fax: (+82) 312 731 885IMPORTANT NOTICEDIODES INCORPORATED MAKES NO WARRANTY OF ANY KIND, EXPRESS OR IMPLIED, WITH REGARD TO THIS DOCUMENT, INCLUDING, BUT NOT LIMITED TO, THE IMPLIED WARRANTIES OF MERCHANTABILITY AND FITNESS FOR A PARTICULAR PURPOSE (AND THEIR EQUIVALENTS UNDER THE LAWS OF ANY JURISDICTION).Diodes Incorporated and its subsidiaries reserve the right to make modifications, enhancements, improvements, corrections or other changes without further notice to this document and any product described herein. Diodes Incorporated does not assume any liability arising out of the application or use of this document or any product described herein; neither does Diodes Incorporated convey any license under its patent or trademark rights, nor the rights of others. Any Customer or user of this document or products described herein in such applications shall assume all risks of such use and will agree to hold Diodes Incorporated and all the companies whose products are represented on Diodes Incorporated website, harmless against all damages.Diodes Incorporated does not warrant or accept any liability whatsoever in respect of any products purchased through unauthorized sales channels.Should Customers purchase or use Diodes Incorporated products for any unintended or unauthorized application, Customers shall indemnify and hold Diodes Incorporated and its representatives harmless against all claims, damages, expenses, and attorney fees arising out of, directly or indirectly, any claim of personal injury or death associated with such unintended or unauthorized application.Products described herein may be covered by one or more United States, international or foreign patents pending. Product names and markings noted herein may also be covered by one or more United States, international or foreign trademarks.LIFE SUPPORTDiodes Incorporated products are specifically not authorized for use as critical components in life support devices or systems without the express written approval of the Chief Executive Officer of Diodes Incorporated. As used herein:A. Life support devices or systems are devices or systems which:1. are intended to implant into the body, or2. support or sustain life and whose failure to perform when properly used in accordance with instructions for useprovided in the labeling can be reasonably expected to result in significant injury to the user.B. A critical component is any component in a life support device or system whose failure to perform can be reasonablybe expected to cause the failure of the life support device or to affect its safety or effectiveness.Customers represent that they have all necessary expertise in the safety and regulatory ramifications of their life support devices or systems, and acknowledge and agree that they are solely responsible for all legal, regulatory and safety-related requirements concerning their products and any use of Diodes Incorporated products in such safety-critical, life support devices or systems, notwithstanding any devices- or systems-related information or support that may be provided by Diodes Incorporated. Further, Customers must fully indemnify Diodes Incorporated and its representatives against any damages arising out of the use of Diodes Incorporated products in such safety-critical, life support devices or systems.Copyright © 2009, Diodes Incorporated。
FlexRay通信系统电气物理层规范V2.1修订本B

FlexRay Communications System Electrical Physical Layer SpecificationVersion 2.1Revision BFlexRay Electrical Physical Layer Specification Disclaimer DISCLAIMERThis specification as released by the FlexRay Consortium is intended for the purpose of information only. The use of material contained in this specification requires membership within the FlexRay Consortium or an agreement with the FlexRay Consortium. The FlexRay Consortium will not be liable for any unauthorized use of this Specification.Following the completion of the development of the FlexRay Communications System Specifications commercial exploitation licenses will be made available to End Users by way of an End User's License Agreement. Such licenses shall be contingent upon End Users granting reciprocal licenses to all Core Partners and non-assertions in favor of all Premium Associate Members and Associate Members.All details and mechanisms concerning the bus guardian concept are defined in the FlexRay Bus Guardian Specifications.The FlexRay Communications System is currently specified for a baud rate of 10 Mbit/s. It may be extended to additional baud rates.No part of this publication may be reproduced or utilized in any form or by any means, electronic or mechanical, including photocopying and microfilm, without permission in writing from the publisher.The word FlexRay and the FlexRay logo are registered trademarks.Copyright © 2004-2006 FlexRay Consortium. All rights reserved.The Core Partners of the FlexRay Consortium are BMW AG, DaimlerChrysler AG, Freescale Halbleiter Deutschland GmbH, General Motors Corporation, Philips GmbH, Robert Bosch GmbH and Volkswagen AG.Table of contentsCHAPTER 1 INTRODUCTION (7)1.1 Objective (7)1.2 Overview (7)1.3 References (7)1.4 Terms and definitions (8)1.5 List of abbreviations (8)1.6 Notational conventions (9)1.6.1 Parameter prefix conventions (9)1.7 Important preliminary notes (10)1.7.1 Bus speed (10)1.7.2 Functional classes (10)1.7.3 System and conformance tests (10)1.8 Revision history (11)1.8.1 Changes applied to “E-PL spec v2.1 Revision A” (11)1.9 Open issues (11)CHAPTER 2 COMMUNICATION CHANNEL BASICS (12)2.1 Objective (12)2.2 Propagation delay (12)2.2.1 Asymmetric delay (13)2.3 Truncation (14)2.4 Symbol length change (15)2.5 Collisions (15)2.6 EMC jitter (16)2.6.1 EMC jitter on signal edges (16)2.6.2 EMC jitter on TSS-truncation (16)2.6.3 EMC jitter on Symbol length change (16)2.7 Wake-up patterns (17)2.7.1 Overview (17)2.7.2 Valid wake-up pattern (17)2.7.3 Non valid wake-up patterns (18)CHAPTER 3 PRINCIPLE OF FLEXRAY NETWORKING (19)3.1 Objective (19)3.2 Interconnection of nodes (19)CHAPTER 4 NETWORK COMPONENTS (21)4.1 Objective (21)4.2 Cables (21)4.3 Connectors (21)4.4.1 Terminated cable end (22)4.4.2 Un-terminated cable end (23)4.5 Termination concept (23)4.6 Common mode chokes (24)4.7 DC bus load (24)CHAPTER 5 NETWORK TOPOLOGY (26)5.1 Objective (26)5.2 Point-to-point connection (26)5.3 Passive star (27)5.4 Linear passive bus (28)5.5 Active star network (29)5.6 Cascaded active stars (30)5.7 Hybrid topologies (31)5.8 Dual channel topologies (31)CHAPTER 6 ELECTRICAL SIGNALING (32)6.1 Objective (32)6.2 Overview (32)6.3 Bus state: Idle_LP (32)6.4 Bus state: Idle (32)6.5 Bus state: Data_1 (33)6.6 Bus state: Data_0 (33)CHAPTER 7 SIGNAL INTEGRITY (34)7.1 Objective (34)7.2 Definition of test planes (34)7.3 Eye-diagram at TP1 (35)7.4 Eye-diagram at TP4 (only valid for point-to-point connections) (36)CHAPTER 8 ELECTRICAL BUS DRIVER (37)8.1 Overview (37)8.2 Operation modes (38)8.2.1 BD_Normal mode (38)8.2.2 BD_Standby mode (38)8.2.3 BD_Sleep mode (optional) (38)8.2.4 BD_ReceiveOnly mode (optional) (38)8.3 Operation mode transitions (39)8.4 Bus Driver – Communication Controller interface (40)8.4.1 TxD/TxEN behavior in case a Bus Driver - Bus Guardian interface is implemented (40)8.4.2 TxD/TxEN - behavior in case a Bus Driver - Bus Guardian interface is not implemented (41)8.4.3 RxD - behavior (41)8.5 Bus Driver – Bus Guardian interface (optional) (42)8.6.1 Overview (43)8.6.2 Hard wired signals (Option A) (43)8.6.3 Serial Peripheral Interface (SPI) (Option B) (46)8.7 Bus Driver – Power supply interface (46)8.7.1 V CC supply voltage monitoring (47)8.7.2 V BAT supply voltage monitoring (47)8.7.3 Inhibit output (optional) (48)8.8 Bus Driver - Level shift interface (optional) (48)8.8.1 V IO voltage monitoring (48)8.9 Bus Driver - Bus interface (49)8.9.1 Receiver characteristics (49)8.9.2 Receiver behavior (50)8.9.3 Receiver timing characteristics (52)8.9.4 Receiver behavior at transition from idle to active and vice versa (54)8.9.5 Transmitter characteristics (56)8.9.6 Transmitter behavior at transition from idle to active and vice versa (58)8.9.7 Bus Driver - bus interface behavior, when not powered (59)8.9.8 Bus Driver - bus interface behavior under short-circuit conditions (59)8.10 Bus Driver – Wake-up interface (optional) (60)8.10.1 Local Wake-up operating requirements (60)8.11 Remote Wake-up event detector (optional) (60)8.11.1 Remote Wake-up operating requirements (60)8.12 Bus Driver behavior under fault conditions (61)8.12.1 Environmental errors (61)8.12.2 Behavior of unconnected digital input signals (62)8.12.3 Dynamic low battery voltage (63)8.12.4 Bus failure detection (64)8.12.5 Over-temperature protection (64)8.13 Bus Driver functional classes (65)8.13.1 Functional class “Bus Driver voltage regulator control” (65)8.13.2 Functional class “Bus Driver - Bus Guardian interface” (65)8.13.3 Functional class “Bus Driver internal voltage regulator” (65)8.13.4 Functional class “Bus Driver logic level adaptation” (65)8.14 Bus Driver signal summary (66)CHAPTER 9 ACTIVE STAR (68)9.1 Overview (68)9.2 Hardware realization (68)9.2.1 Active star - Communication Controller interface (optional) (69)9.2.2 Active star - Bus Guardian interface (optional) (69)9.2.3 Active star - Power supply interface (69)9.2.4 Active star - Bus interface (69)9.3 Basic functionality (69)9.4 Enhanced functionality (70)9.4.1 Functional class: “Active Star - Communication Controller interface” (70)9.4.2 Functional class: “Active Star - Bus Guardian interface” (71)9.4.3 Functional class "Active Star - Voltage regulator control" (71)9.4.4 Functional class "Active Star - Internal voltage regulator" (71)9.5 Active Star timing characteristics (71)9.6 Active Star operation modes (72)9.6.1 AS_Sleep (72)9.6.3 AS_Standby (72)9.7 Active Star operation mode transitions (73)9.7.1 Active Star behavior after wake-up (74)9.8 Operating states of branches (74)9.8.1 Branch_Idle (74)9.8.2 Branch_Active (74)9.8.3 Branch_FailSilent (74)9.9 Branch operating state transitions (75)9.10 Collisions (76)9.10.1 Collisions on busses (76)9.10.2 Collision of bus activity and TxEN (76)9.11 Active Star behavior under fault conditions (78)9.12 Behavior of unconnected digital input signals (79)CHAPTER 10 BUS GUARDIAN (80)CHAPTER 11 GENERAL FEATURES FOR FLEXRAY PARTS (81)11.1 Objective (81)11.2 Input voltage thresholds for digital signals (81)11.3 Voltage limits for digital output signals (81)11.4 ESD protection on chip level (82)11.5 ESD protection on ECU level (82)11.6 Operating temperature (82)11.7 Serial peripheral interface (SPI) (83)11.7.1 Behavior of unconnected digital input pins (83)CHAPTER 12 SYSTEM TIMING CONSTRAINTS (84)12.1 Objective (84)12.2 Overview of timing parameters (84)12.3 Requirements of the decoding process according to [PS05] (84)12.4 FlexRay topologies (85)12.4.1 Signal chain (87)12.4.2 Example of a signal chain (88)12.5 Description of asymmetry portions (89)12.5.1 Communication Controller (89)12.5.2 Contribution of the Bus Driver (90)12.5.3 Interface between the Bus Driver and Communication Controller (91)12.5.4 Passive networks (91)12.5.5 ECU (92)12.6 Requirements for Communication Controller (92)12.7 Overview of the network integrity (93)Chapter 1Introduction1.1 ObjectiveThis specification describes the electrical physical layer for FlexRay communications systems.1.2 OverviewThe electrical physical layer for FlexRay is designed to network automotive electronic control units (ECUs). The medium that is used is dual wires. Signaling on the bus is accomplished by asserting a differential voltage between those wires. Topology variations range from linear passive busses up to active star topologies. Furthermore the physical layer optionally incorporates a so called bus guardian as an instance, which may watch over the bus access and has the power to disable the bus access of a node module to a channel in case of mismatches in the time schedule.This specification includes the definition of electrical characteristics of the transmission itself and also documentation of basic functionality for bus driver (BD), bus guardian (BG) and active star (AS) devices.1.3 References[PS05] FlexRay Communications System - Protocol Specification, v2.1 Revision A,FlexRay Consortium, December 2005[EMC05] FlexRay Communications System - Physical Layer EMC Measurement Specification, v2.1, FlexRay Consortium, December 2005[EPLAN06] FlexRay Communications System - Electrical Physical Layer Application Notes, v2.1 Revision B, FlexRay Consortium, November 20061.4 Terms and definitionsFlexRay specific terms and definitions are listed in [PS05].1.5 List of abbreviationsAS: active starBD: bus driverBG: bus guardianBSS: byte start sequenceCC: communication controllerECU: electronic control unitSPI: serial peripheral interfaceTSS: transmission start sequenceuV BAT: means a voltage applied at the V BAT pin relative to ground of the semiconductor device uV ECU: means a voltage applied at the battery connector of an ECU relative to groundX: don’t carex: placeholder for a figure [2, 3, 4, …]1.6 Notational conventions1.6.1 Parameter prefix conventions<variable> ::= <prefix_1> [<prefix_2>] Name <prefix_1> ::= a | c | v | g | p<prefix_2> ::= d | l | n | ua AuxiliaryParameter Auxiliary parameter used in the definition or derivation of other parameters or in the derivation of constraints.c Protocol Constant Values used to define characteristics or limits of the protocol.These values are fixed for the protocol and cannot be changed.v Node Variable Values which will be changed depending on time, events, etc.g Cluster Parameter Parameter that must have the same value in all nodes in a cluster.p Node Parameter Parameter that may have different values in different nodes in thecluster.- Prefix 1 can be omittedThis table is mirrored from [PS05], where the binding definitions are made!Table 1-1: Prefix 1.d Time Duration Value (variable, parameter, etc.) describing a time duration, thetime between two points in timel Length Physical length of e.g. a cablen Amount Number of e.g. stubsu Voltage Differential voltage between two conducting materials (e.g. copperwires)The prefixes “l”, “n” and “u” are defined binding here. For all other prefixes refer to [PS05]Table 1-2: Prefix 2.1.7 Important preliminary notes1.7.1 Bus speedThe FlexRay communication system currently specifies for a data rate of 10MBit/s only.Thus the nominal time of one bit (gdBit) is 100ns.1.7.2 Functional classesIn chapters 8, 9 and 10, the physical layer devices BD, AS and the electrical interfaces of the BG are specified. This specification comprises the minimum functional features in order to ensure interoperability of FlexRay devices and compliance to constraints given by the FlexRay protocol. In addition to this, some ‘functional classes’ are introduced. Each functional class combines a set of specified options, which have to coexist when implemented. These functional classes may be implemented in order to enhance the set of functional features of FlexRay physical layer devices and make them more valuable for building automotive ECUs.1.7.3 System and conformance testsTests for system behavior and FlexRay conformance are currently under development. Some basic information and prerequisites can be found in this specification. Potentially, this kind of content is to be moved when appropriate test specification documents are available.1.8 Revision history1.8.1 Changes applied to “E-PL spec v2.1 Revision A”- Changes as listed in “Errata Sheet to E-PL v2.1 Rev. A”- Complete reworked chapter 121.9 Open issues- Chapter 10 to be updated – according to most recent BG conceptsChapter 2Communication Channel Basics2.1 ObjectiveThe electrical physical layer provides among other things an implementation of a FlexRay communication channel. In this section an abstract definition of the physical properties of this communication channel is given. Any physical layer that behaves according to these basics provides a valid FlexRay communication channel.2.2 Propagation delayBinary data streams transmitted from node module M are received at node module N with the propagation delay dPropagationDelay M,N. The propagation delay shall be measured from the falling edge in the Byte Start Sequence (BSS; see [PS05]) in the transmit (TxD) signal of node module M to the corresponding falling edge in the receive (RxD) signal at node module N.Node module MM,NNode module NFigure 2-1: Propagation delay.The actual propagation delay that occurs between node module M to node module N depends mainly on the topology of the path. The following equation must be true in order to meet the constraints given by the FlexRay protocol:dPropagationDelay M,N≤cPropagationDelayMaxIn [PS05] the parameter cPropagationDelayMax is limited to 2500ns. Consequently it is:Name Description Min Max Unit dPropagationDelay M,N Propagation delay from node module M to2500 nsnode module NTable 2-1: Propagation delay.See also section “Application hint: Propagation delay” in [EPLAN06].2.2.1 Asymmetric delayAs defined above the propagation delay is defined with help of the first negative edge after the TSS in the binary data stream.Due to the limitations of the FlexRay decoder module the channel plus the sending and receiving bus driver shall not introduce a static asymmetric delay that exceeds a certain level.For further consideration see chapter 12.Node module MM,NNode module NdAsymmetricDelayM,NFigure 2-2: Asymmetric propagation delay.2.3 TruncationThe channel may truncate the TSS (see [PS05]). The interval by which the TSS is truncated from a transmitting node module M to a receiving node module N is denoted as dFrameTSSTruncation M,N. The effect of truncation of the TSS of a frame is shown in figure 2-3.Node module MNode module NNFigure 2-3: Frame TSS Truncation.The truncation time is calculated as the difference of the duration of TSS at sender and duration of TSS at receiver: dFrameTSSTruncation M,N = dTSS M - dTSS N .The value of dFrameTSSTruncation M,N needs to be less than the maximum configurable value of the protocol parameter gdTSSTransmitter. The effect of truncation sums up of different portions, which are contributed by active stars and the activity detection in the receiving BDs.Name Description Min Max UnitdFrameTSSTruncation M,N Truncation on path from node module M to100 1350 nsnode module NTable 2-2: TSS Truncation.The truncation depends on the number of active stars in the path from node M to node N. More detailed information is given in [EPLAN06]2.4 Symbol length changeQuite similar to the truncation of the TSS the length of symbols is changed while traveling through the physical layer. Besides the truncation at the beginning by the activity detection time a lengthening at the end by the idle detection time occurs. These effects are described in detail in section 8.9.4.Name Description Min Max Unit dSymbolLengthChange M,N Change of length of a symbol on path from-1200 900 nsnode module M to node module NA negative value means that the symbol is shortened, a positive value means the symbol is elongated.Table 2-3: Symbol length change.2.5 CollisionsFlexRay is designed to perform communication without collisions. I.e. the nodes do not arbitrate on the channel and collisions do not happen during normal operation. However, during the startup phase of the protocol, collisions on the channel may happen. The electrical physical layer does not provide a means to resolve those collisions.In case of collisions of communication elements on the bus (at least two nodes are transmitting simultaneously) it cannot be predicted what signal the nodes will receive. At least some activity (noise) on the channel will be detected.Data_0 Data_0Data_0Data_0 Data_1Data_0 or Data_1Data_1 Data_0Data_1 or Data_0Data_1 Data_1Data_1For definition of Data_0 and Data_1 see chapter 6.Table 2-4: Data signal collision on the bus.2.6 EMC jitter2.6.1 EMC jitter on signal edgesJitter on signal edges, i.e. those edges that are different from first transition from HIGH to LOW at start of frame and the last transition from LOW to HIGH at the end of a frame, shall be considered in the course of system evaluation.2.6.2 EMC jitter on TSS-truncationJitter on the TSS-truncation, which means jitter on the first falling edge in a frame, might shorten the TSS additionally to the truncation as described in section 2.3.2.6.3 EMC jitter on Symbol length changeJitter on the two edges of symbols might lead to deviations of the symbol length change as described in section 2.4.2.7 Wake-up patterns2.7.1 OverviewIndependent from the data rate wake-up patterns can be sent to remotely wake nodes that are in Sleep mode.2.7.2 Valid wake-up patternA valid remote wake-up event is the reception of at least two consecutive wake-up symbols via the bus.The wake-up detector for such events shall be active when the BD is in a low power mode (e.g. BD_Standby or BD_Sleep (if implemented)).For remote wake-up in FlexRay systems, a wake-up pattern is sent via the bus as described in [PS05]. The FlexRay wake-up pattern consists of several repetitions of FlexRay wake-up symbols. The wake-up symbol is defined as a phase of Data_0 followed by a phase of Idle.A remote wake-up event occurs from BD's perspective when any sequence of { Data_0, Idle, Data_0, Idle } that starts after Idle and has a timing according to figure 2-4 and table 2-5 is received. The definition of the pattern [PS05] guarantees at the receiver: dWU01 > 4µs, dWU Idle1 > 4µs, dWU02 > 4µs, dWU Idle2 > 4µs and dWU < 48µs.tFigure 2-4: Valid signal for wake-up pattern recognition at receiver.Name Description Min Max Unit dWU0Detect Acceptance timeout for detection of a1 4 µsData_0 phase in wake-up patterndWU IdleDetect Acceptance timeout for detection of a Idle1 4 µsphase in wake-up patterndWU Timeout Acceptance timeout for wake-up pattern48 140 µsrecognitionTable 2-5: Wake-up pattern detection timing at receiver.Short discontinuities (e.g. due to external disturbances like injection of RF fields) in Data_0 or Idle phases shall not harm the recognition of a remote wake-up, therefore uBus shall be evaluated after integrative filtering in order to achieve a sufficient robustness against such disturbances. The acceptable discontinuities depend on implementation and need to be specified on BD product level.Moreover, the wake-up detector is allowed to judge Data_1 as Idle and the behavior needs to be specified on BD product level. Thus, the BD might also wake-up upon receiving other patterns, e.g. FlexRay frames.Mind that idle and activity detection is the process how the wake-up pattern is received, see section 8.9.2 Receiver behavior and especially table 8-16.2.7.3 Non valid wake-up patternsThe BD shall not wake-up, whena) the first idle phase is shorter than 1µs, while the Data_0 phases are 6µsb) the second Data_0 phase is shorter than 1µs, while the first Data_0 phaseand the first idle phase are 6µsc) the first idle phase is longer than 140µs, while the Data_0 phases are 6µsChapter 3Principle of FlexRay Networking3.1 ObjectiveThis chapter shows the basic operation principle of FlexRay networks.3.2 Interconnection of nodesThe FlexRay electrical physical layer provides a differential voltage link (= bus) between a transmitting and oneor more receiving communication modules. The differential voltage is measured between two signal lines, denoted BP (Bus Plus) and BM (Bus Minus). The fundamental mechanism of the bidirectional differential voltage link is shown below. The bidirectional link between any two nodes modules requires a transmitter and receiver circuit which are integrated in so called bus drivers.Bus driver Bus driverFigure 3-1: Principle of a differential voltage link.This structure can be extended with further bus drivers that are connected to the differential voltage link as depicted in the following figure. The differential voltage link is implemented by a dual wire cable. With each communication module one bus driver is added to the system.Bus driver Bus driverFigure 3-2: Principle of a linear passive bus.Limitations to the number of bus drivers (ECUs) and cable extents are documented in chapter 5. Furthermore, the bus can also comprise active stars, which are working in principle as bidirectional repeaters. The functionality of active stars is specified in chapter 9.Bus driverFigure 3-3: Principle of an active star network.Chapter 4Network Components4.1 ObjectiveThis chapter introduces some basic network components that are used to build up FlexRay networks.4.2 CablesThe objective of this subsection is to specify the required cable characteristics, but not to define a selection of cable types. The medium in use for FlexRay busses may be unshielded as well as shielded cables, as long as they provide the following characteristics:Name Description Min Max UnitZ0Differential mode impedance @ 10 MHz (*) 80 110 ΩT’0Specific line delay 10 ns / mα5MHz Cable attenuation @ 5 MHz (sine wave) 82 dB / km(*) see [EPLAN06]Table 4-1: Cable characteristics.4.3 ConnectorsThis specification does not prescribe certain connectors for FlexRay systems. However, any electrical connector used in FlexRay busses shall meet the following constraints:Name Description Min Max UnitR DCContact Contact resistance (including crimps) 50 mΩZ Connector Impedance of connector 70 200 Ωl Coupling Length coupling connection (*) 150 mmdContactInterruption (**)Contact resistance R> 1Ω100 nsDCContact(*) this parameter defines the length of the connectors including the termination areas of the cables(**) this requirement is to be generally understood as an quality issue and has no direct link with the timing performance of FlexRay.Table 4-2: Connector parameters.See further recommendations about connectors in [EPLAN06].4.4 Cable termination4.4.1 Terminated cable endThe simplest way to terminate the cable at an ECU consists of a single termination resistor between the bus wires BP and BM. Other termination possibilities are shown in [EPLAN06].Figure 4-1: Terminated cable end.In following sections, ECUs that have this kind of termination are symbolized with the following icon.Figure 4-2: Symbol: Terminated cable end.4.4.2 Un-terminated cable endAt an un-terminated cable end, no resistive element is connected between the bus wires.Figure 4-3: Un-terminated cable end.In following sections, ECUs that have this kind of termination are symbolized with the following icon.Figure 4-4: Symbol: Un-terminated cable end.4.5 Termination conceptThis specification does not prescribe a certain termination concept. Application specific solutions have to be found. Find some more general recommendations about termination in [EPLAN06].4.6 Common mode chokesThis specification does not prescribe a certain common mode choke for FlexRay systems. However, anycommon mode choke used in FlexRay systems shall meet the following constraints over the entire temperature range as specified in section 11.5:Name DescriptionMinMaxUnit R CMCResistance (per line)2 ΩTable 4-3: Common mode choke parameters.See further recommendations about common mode chokes in [EPLAN06].4.7 DC bus loadThe DC load a BD sees between the bus wires is R DCLoad . A network equivalent DC circuit is as follows:R DCLoad Figure 4-5: DC bus load.The schematic does not include parasitic resistances from common mode chokes (R CMC ), connectors (R Connector ) and the series resistance of the wiring (R Wire ), since those shall be neglected in the following calculation: The formula to calculate the overall DC bus load is:R DCLoad = (Σm (R Tm )-1)-1Equation 4-1: DC bus load.Name Description Min Max Unit R DCLoad DC bus load 40 55 ΩTable 4-4: DC bus load limitation.Mind that the termination resistance R Tm is usually a termination resistor in parallel to the BD’s receiver common mode input resistance (see section 8.9.1). The termination resistor might also be applied outside the ECU, e.g. at a network splice. In case of an un-terminated cable end according to section 4.3.2. the resistance R Tm represents only the BD’s receiver common mode input resistance.Some exemplary termination concepts for different bus structures are described in [EPLAN06]. All termination concepts have to consider the DC bus load limitation as defined here.Chapter 5Network Topology5.1 ObjectiveThis chapter introduces possible bus structures, their names and parameters. The layout of busses has to follow the constraints that are explained in this chapter. Application examples and recommendations are given in [EPLAN06].Dual channel applications, a main feature of FlexRay, are discussed at the end of this chapter.All FlexRay topologies are 'linear', which means that they are free from rings or closed loops respectively.A termination concept has to be found for each topology implementation individually. General hints can be found in [EPLAN06]. Whether a topology/termination combination composes a valid FlexRay network has to be judged according the signal integrity requirements as given in chapter 7.5.2 Point-to-point connectionThe point-to-point configuration is shown in figure 5-1. It represents the simplest bus and can be regarded as the basic element for the construction of more complex busses. For simplicity, the two-wire bus is shown as one thick line in the figures of this document.Figure 5-1: Point to point connection.5.3 Passive starFor connecting more than two ECUs a passive star structure can be used, which is a special case of a linear passive bus that is described in the following section. At a passive star all ECUs are connected to a single splice. The principle of a passive star network is shown in figure 5-2.Figure 5-2: Example of a passive star.Name Description Min Max Unit nSplice Number of splices (*) 1 1(*) if nSplice is 0, then refer to section 5.1, if nSplice is greater than 1, then refer to section 5.4Table 5-1: Parameters of a passive star.Practical limitations for nStub and lStub N depend on each other and depend also on other factors like cable type and termination concept; i.e. a passive star with nStub = 22 and each lStub = 12m for each stub is likely not to be operable.Examples of practical values are given in [EPLAN06], where also consideration about EMC robustness can be found in a separate section.。
NI ELVIS II系列产品规格说明说明书
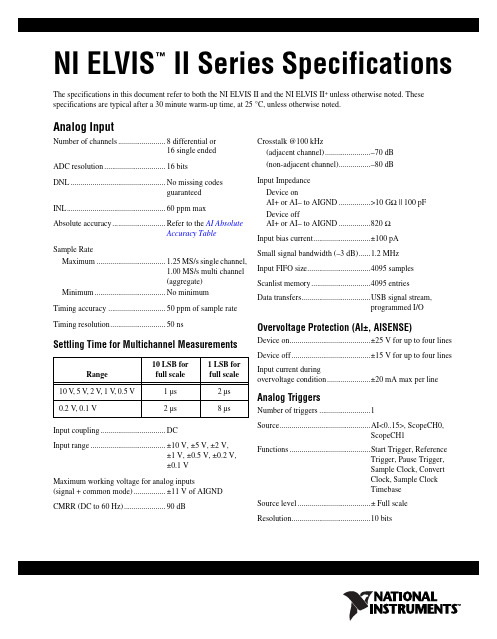
Arbitrary Waveform Generator/Analog Output
Number of channels.........................2
DAC resolution................................16 bits
DNL.................................................±1 LSB
Maximum working voltage for analog inputs (signal + common mode) ................ ±11 V of AIGND
CMRR (DC to 60 Hz) ..................... 90 dB
Source..............................................AI<0..15>, ScopeCH0, ScopeCH1
Small signal bandwidth (–3 dB)......1.2 MHz
Input FIFO size................................4095 samples
Scanlist memory ..............................4095 entries
Data B signal stream, programmed I/O
AD9273BSVZ-50;AD9273BSVZ-25;AD9273BBCZ-25;AD9273BSVZ-40;AD9273BBCZ-40;中文规格书,Datasheet资料

/
CLK+ CLK–
AD9273 TABLE OF CONTENTS
Features .............................................................................................. 1 Applications ....................................................................................... 1 General Description ......................................................................... 1 Functional Block Diagram .............................................................. 1 Revision History ............................................................................... 2 Product Highlights ........................................................................... 3 Specifications..................................................................................... 4 AC Specifications.......................................................................... 4 Digital Specifications ................................................................... 8 Switching Specifications .............................................................. 9 ADC Timing Diagrams ................................................................. 10 Absolute Maximum Ratings.......................................................... 11 Thermal Impedance ................................................................... 11 ESD Caution ................................................................................ 11 Pin Configuration and Function Descriptions ........................... 12 Typical Performance Characteristics ........................................... 15 Equivalent Circuits ......................................................................... 19 Theory of Operation ...................................................................... 21 Ultrasound .................................................................................. 21 Channel Overview ..................................................................... 22 Input Overdrive .......................................................................... 25 CW Doppler Operation............................................................. 25 TGC Operation ........................................................................... 27 ADC ............................................................................................. 31 Clock Input Considerations ...................................................... 31 Serial Port Interface (SPI) .............................................................. 38 Hardware Interface..................................................................... 38 Memory Map .................................................................................. 40 Reading the Memory Map Table .............................................. 40 Reserved Locations .................................................................... 40 Default Values ............................................................................. 40 Logic Levels ................................................................................. 40 Outline Dimensions ....................................................................... 44 Ordering Guide .......................................................................... 45
深圳科士达 EPower 100-120-160KVA 说明书

用 60KVA
100-120- 160 kVA 三相 双转换技术(VFI)含隔离变压器
深圳科士达科技发展有限公司
简体中文
索引
安全规范 .................................................................................................................................................................. 3 电磁干扰要求 .......................................................................................................................................................... 4 储存 .......................................................................................................................................................................... 5 安装环境 .................................................................................................................................................................. 5 前置作业 ............................
1757-ABRIO过程远程I O通信接口模块安装说明说明书
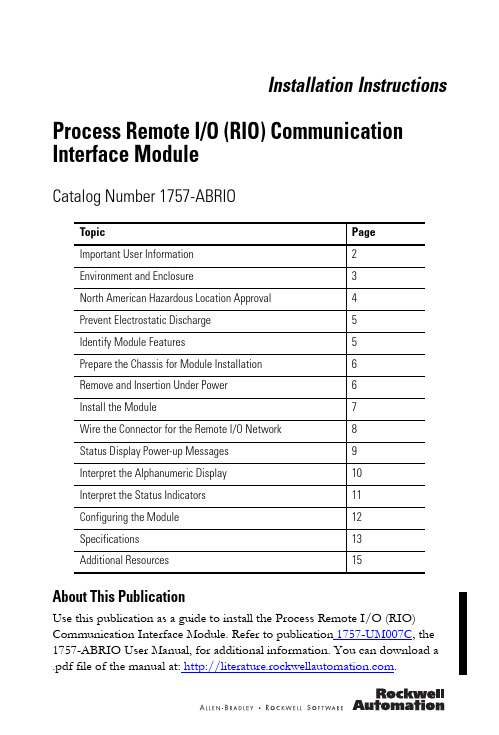
Installation InstructionsProcess Remote I/O (RIO) Communication Interface ModuleCatalog Number 1757-ABRIOAbout This PublicationUse this publication as a guide to install the Process Remote I/O (RIO) Communication Interface Module. Refer to publication 1757-UM007C , the 1757-ABRIO User Manual, for additional information. You can download a .pdf file of the manual at: .Topic PageImportant User Information 2Environment and Enclosure 3North American Hazardous Location Approval 4Prevent Electrostatic Discharge 5Identify Module Features 5Prepare the Chassis for Module Installation 6Remove and Insertion Under Power 6Install the Module 7Wire the Connector for the Remote I/O Network 8Status Display Power-up Messages 9Interpret the Alphanumeric Display 10Interpret the Status Indicators 11Configuring the Module 12Specifications 13Additional Resources 152 Process Remote I/O (RIO) Communication Interface ModuleImportant User InformationSolid state equipment has operational characteristics differing from those of electromechanical equipment. Safety Guidelines for the Application, Installation and Maintenance of Solid State Controls (publication SGI-1.1 available from your local Rockwell Automation sales office or online at) describes some important differences between solid state equipment and hard-wired electromechanical devices. Because of this difference, and also because of the wide variety of uses for solid state equipment, all persons responsible for applying this equipment must satisfy themselves that each intended application of this equipment is acceptable.In no event will Rockwell Automation, Inc. be responsible or liable for indirect or consequential damages resulting from the use or application of this equipment.The examples and diagrams in this manual are included solely for illustrative purposes. Because of the many variables and requirements associated with any particular installation, Rockwell Automation, Inc. cannot assume responsibility or liability for actual use based on the examples and diagrams.No patent liability is assumed by Rockwell Automation, Inc. with respect to use of information, circuits, equipment, or software described in this manual.Reproduction of the contents of this manual, in whole or in part, without written permission of Rockwell Automation, Inc., is prohibited.Throughout this manual, when necessary, we use notes to make you aware of safety considerations.Process Remote I/O (RIO) Communication Interface Module 3 Environment and EnclosureThis equipment is intended for use in a Pollution Degree 2 industrialenvironment, in overvoltage Category II applications (as defined in IECpublication 60664-1), at altitudes up to 2000 m (6561 ft) withoutderating.This equipment is considered Group 1, Class A industrial equipmentaccording to IEC/CISPR Publication 11. Without appropriateprecautions, there may be potential difficulties ensuringelectromagnetic compatibility in other environments due toconducted as well as radiated disturbance.This equipment is supplied as open-type equipment. It must bemounted within an enclosure that is suitably designed for thosespecific environmental conditions that will be present andappropriately designed to prevent personal injury resulting fromaccessibility to live parts. The enclosure must have suitableflame-retardant properties to prevent or minimize the spread of flame,complying with a flame spread rating of 5VA, V2, V1, V0 (orequivalent) if non-metallic. The interior of the enclosure must beaccessible only by the use of a tool. Subsequent sections of thispublication may contain additional information regarding specificenclosure type ratings that are required to comply with certainproduct safety certifications.In addition to this publication, see:•Industrial Automation Wiring and Grounding Guidelines, for additionalinstallation requirements, Allen-Bradley publication 1770-4.1.•NEMA Standards publication 250 and IEC publication 60529, asapplicable, for explanations of the degrees of protection provided bydifferent types of enclosure.4 Process Remote I/O (RIO) Communication Interface Module North American Hazardous Location ApprovalThe following information applies when operating this equipment in hazardous rmations sur l'utilisation de cet équipement en environnements dangereux.Products marked “CL I, DIV 2, GP A, B, C, D” are suitable for use in Class I Division 2 Groups A, B, C, D, Hazardous Locations and nonhazardous locations only. Each product is supplied with markings on the rating nameplate indicating the hazardous location temperature code. When combining products within a system, the most adverse temperature code (lowest “T” number) may be used to help determine the overall temperature code of the system. Combinations of equipment in your system are subject to investigation by the local Authority Having Jurisdiction at the time of installation.Les produits marqués “CL I, DIV 2, GP A, B, C, D” ne conviennent qu'à une utilisation en environnements de Classe I Division 2 Groupes A, B, C, D dangereux et non dangereux. Chaque produit est livré avec des marquages sur sa plaque d'identification qui indiquent le code de température pour les environnements dangereux. Lorsque plusieurs produits sont combinés dans un système, le code de température le plus défavorable (code detempérature le plus faible) peut être utilisé pourdéterminer le code de température global dusystème. Les combinaisons d'équipements dans le système sont sujettes à inspection par les autorités locales qualifiées au moment de l'installation.EXPLOSION HAZARDDo not disconnect equipment unless power has been removed or the area is known to be nonhazardous.Do not disconnect connections to this equipment unless power has been removed or the area is known to be nonhazardous. Secure any external connections that mate to this equipment by using screws, sliding latches, threaded connectors, or other means provided with this product. Substitution of components may impair suitability for Class I, Division 2.If this product contains batteries, they must only be changed in an area known to be nonhazardous.RISQUE D'EXPLOSION Couper le courant ou s'assurer que l'environnement est classé non dangereux avant dedébrancher l'équipement. Couper le courant ou s'assurer que l'environnement est classé non dangereux avant dedébrancher les connecteurs. Fixer tous les connecteurs externes reliés à cetéquipement à l'aide de vis, loquets coulissants, connecteurs filetés ou autres moyens fournis avec ce produit. La substitution de composants peut rendre cet équipement inadapté à une utilisation en environnement de Classe I, Division 2.S'assurer que l'environnement est classé non dangereux avant de changer les piles.Process Remote I/O (RIO) Communication Interface Module 5Prevent Electrostatic Discharge Identify Module Features This equipment is sensitive to electrostatic discharge, which cancause internal damage and affect normal operation. Follow theseguidelines when you handle this equipment:•Touch a grounded object to discharge potential static.•Wear an approved grounding wriststrap.•Do not touch connectors or pins on component boards.•Do not touch circuit components inside the equipment.•Use a static-safe workstation, if available.•Store the equipment in appropriate static-safe packaging whennot in use.6 Process Remote I/O (RIO) Communication Interface ModulePrepare the Chassis for Module InstallationBefore you install the 1757-ABRIO module, you must install and connect a ProcessLogix or ControlLogix chassis and power supply.Determine Module Slot LocationChassis slots are numbered starting from the left, starting at 0. Slot 0 is the first slot to the right of the power supply.You can:•use any size chassis.•install the module in any available slot.•install multiple 1757-ABRIO modules in the same chassis, dependingon how your power supply is rated.Remove and Insertion Under PowerYou can install or remove the module while the chassis is powered if you observe these precautions.When you insert or remove the module while backplane power is on,an electrical arc can occur. If you connect or disconnect thecommunications cable with power applied to this module or anydevice on the network, an electrical arc can occur. This could causean explosion in hazardous location installations.Be sure that power is removed or the area is nonhazardous beforeproceeding.Repeated electrical arcing causes excessive wear to contacts onboth the module and its mating connector. Worn contacts may createelectrical resistance that can affect module operation.Process Remote I/O (RIO) Communication Interface Module 7 Install the ModuleDo not force the module into the backplane connector. If you cannotseat the module with firm pressure, check the alignment. Forcing themodule into the chassis can damage the backplane connector or themodule.To install the module, follow these steps.1.Align the module circuit board with the top and bottom guides in thechassis.2.Slide the module into the chassis in the appropriate slot.Make sure the module properly connects to the chassis backplane.The module is fully installed when it is flush with the other installedmodules, and the module locking clips click into place.3.To remove the module, push down on the locking clips at the top andbottom of each module.4.Slide the module out of the chassis.8 Process Remote I/O (RIO) Communication Interface ModuleWire the Connector for the Remote I/O NetworkFollow these steps to wire the connector.1.Connect Line 1 of the remote I/O cable to the upper pin.2.Connect the shield to the middle pin.3.Connect Line 2 to the lower pin on the 1757-ABRIO.4.Terminate both ends of a remote I/O network by using externalresistors attached to the physical ends of the network.There should be two and terminators on the network.Select Proper ResistorUse 82 ohm resistors if the network operates at 230.4 kbps or if the network operates at 57.6 kbps or 115.2 kbps and none of the devices in the table below are present. The maximum number of devices on the network is 32.Use 150 ohm resistors if the network contains any of the devices in the table below, or if the network operates at 57.6 kbps or 115.2 kbps and you do not require the network to support more than 16 devices.Device Type Catalog Number SeriesAdapters1771-AS All1771-ASB1771-DCMMiscellaneous1771-AFProcess Remote I/O (RIO) Communication Interface Module 9Removing or Replacing the ModuleIf you are replacing an existing module with an identical one, and you want to resume identical system operation, you must:•install the new module in the same slot.•run the configuration program and download the appropriateconfiguration to the module.Apply Chassis PowerTurn the rack power supply on.Check Power Supply and Module StatusThe rack power supply indicator should be green. The module OK status indicator should be solid red immediately after you turn on the rack power supply and then it turns solid green. Refer to the installation instructions for your particular 1756 rack power supply for recommended actions for checking your power supply.Status Display Power-up MessagesThe alphanumeric display shows the following messages at power-up.B#nn Stages in the start-up processes, nn is a hexadecimal number Boot Next stage in power-up sequence57ABRIO Ver x.xx.xx Module firmware versionIf the indicator on the 1757-ABRIO module does not cycle through these messages on powerup, refer to the Troubleshooting section of publication 1757-UM007C, the 1757-ABRIO User Manual.10 Process Remote I/O (RIO) Communication Interface ModulePower Supply IndicatorInterpret the Alphanumeric DisplayThe Process Remote I/O (RIO) Communication Interface Module displays alphanumeric messages that provide diagnostic information about your module. The warning messages display twice, then the normal display resumes. The following table summarizes the messages.Alphanumeric Display Message Descriptions POWER IndicatorPower Supply Status Recommended Action Off Not operating •Turn power switch ON.•Check power wiring connections.•Check fuse.On OperatingNone, normal operation.MessageDescription 57ABRIOVersion x.xx.xxThe module’s firmware version, displayed at powerup. The three parts of the version number are the major revision, the minor revision and the build number.ConfigThe module is being configured from the configuration program.InactiveThe module is not receiving any messages that read or write tags. It is scanning discrete I/O in program mode. Block transfers are not updating.ActiveThe module is receiving messages that read or write tags. It is scanning discrete I/O in run mode. Block transfers are updating.Forced ActiveThe module has been put into active mode by the configuration program.RIO Flash Config Invalid The configuration stored in Flash memory on the module is invalid due to the following possible reasons.•The module has never been configured.•The module firmware has been updated and the configurationformat has changed.• A fatal error has been captured.To clear the invalid state, download the I/O configuration.Process Remote I/O (RIO) Communication Interface Module 11Interpret the Status IndicatorsThe three status indicators on the module provide information about your module and the status of communication with a host processor and with the remote I/O network. The following tables outline the indicator condition and the corresponding status for each indicator.RIO Status Indicator – Remote Devices StatusThe RIO indicator displays the status of the remote I/O network connection.Error: Heard Another RIO MasterAnother master has been detected on the network because of the following possible reasons.•The module is connected to a network with another RIO master.•The module is connected to a Data Highway Plus network.RIO Master Config ScanAt startup, the module scans the RIO network to see what racks are connected.Rack xx I/O Grp yy Size MismatchThe rack size in the stored configuration on the module for the rack at rack number xx octal, starting I/O group yy, does not match the rack size on the network.Rack xx I/O Grp yy OfflineThe rack at rack number xx octal, starting I/O group yy, is not responding.Firmware Update The firmware on the module is being updated.IndicatorStatus GreenSuccessful communication with all configured racks.YellowIdle, no racks are configured.Red One or more configured racks is not responding or aprotocol error has occurred within the last second.MessageDescription12 Process Remote I/O (RIO) Communication Interface ModuleSYS Status Indicator – ControlBus StatusThe SYS indicator displays the status of communication with the processor.Indicator StatusGreen The module has successfully processed a request from the ControlBus backplane within the last five seconds.Yellow Idle, no requests received from the backplane in the last five seconds.Red The module has returned an error to a request from the backplanewithin the last second.OK Status Indicator – Module HealthIndicator StatusGreen Indicates that module has passed all power-up diagnostics and isfunctioning normally.Red Indicates that module startup diagnostics have failed or a major module fault such as watchdog time-out or jabber inhibit has occurred.If all three status indicators are solid red and the 4-characterdisplay shows the #xx, (where xx is the error number) this iswhere the fatal area occurs. Refer to publication1757-UM007C, the 1757-ABRIO User Manual for information onclearing fatal errors. Be sure to make a note of the error codenumbers to give Tech Support, if you need to call for help.Configuring the ModuleNow that you have installed your 1757-ABRIO module, you must configure it. Refer to publication 1757-UM007C, the 1757-ABRIO User Manual, for information on module configuration.Process Remote I/O (RIO) Communication Interface Module 13SpecificationsProcess Remote I/O (RIO) Communication Interface Module - 1757-ABRIO AttributeValue Module LocationProcessLogix or ControlLogix chassis Backplane Current675 mA @ +5.1V dc 5 mA @ 24 V dc Power dissipation, max 4 W Isolation Voltage 30V, continuous, basic insulation type Screw Terminal Torque 0.5...0.6 Nm (5...7 lb-in)Wiring Category (1)(1)Use this Conductor Category information for planning conductor routing. Refer to Industrial Automation Wiring and Grounding Guidelines, publication 1770-4.1.2 - on communications ports Wire Size20 AWG, 0.519mm 2Wire TypeBelden 9463 Twinaxial Environmental SpecificationsAttributeValue Temperature, operating 0…60 °C (32…140 °F)IEC 60068-2-1 (Test Ad, Operating Cold),IEC 60068-2-2 (Test Bd, Operating Dry Heat),IEC 60068-2-14 (Test Nb, Operating Thermal Shock)Temperature, nonoperating –40…85 °C (–40…185 °F)IEC 60068-2-1 (Test Ab, Un-packaged Nonoperating Cold),IEC 60068-2-2 (Test Bb, Un-packaged Nonoperating Dry Heat),IEC 60068-2-14 (Test Na, Un-packaged Nonoperating ThermalRelative Humidity 5…95% noncondensing IEC 60068-2-30 (Test Db, Un-packaged Nonoperating Damp Heat)Shock, operating IEC60068-2-27 (Test Ea, Unpackaged shock), 30gShock, nonoperating IEC60068-2-27 (Test Ea, Unpackaged shock), 50gVibrationIEC60068-2-6 (Test Fc, Operating): 2 g @ 10…500 Hz14 Process Remote I/O (RIO) Communication Interface ModuleEmissionsCISPR 11: Group 1, Class A ESD immunity IEC 61000-4-2:6 kV contact discharges 8 kV air discharges Radiated RF immunity IEC 61000-4-310V/m with 1 kHz sine-wave 80%AM from 80 MHz to 2000 MHz 10V/m with 200 Hz 50% Pulse 100%AM at 900 MhzEFT/B immunity IEC 61000-4-4:±2 kV at 5 kHz on communication portsSurge Transient Immunity IEC 61000-4-5:±2 kV line-earth (CM) on communication portsConducted RF Immunity IEC 61000-4-6:10V rms with 1 kHz sine-wave 80%AM from 150 kHz to 80 MHzEnclosure Type Rating None (open-style)North Americantemperature codeT4A CertificationsCertification ValueCertifications (when product is marked)(1)c-UL-us UL Listed Industrial Control Equipment, certified for US and Canada. See UL File E219376. UL Listed for Class I, Division 2 Group A,B,C,D HazardousLocations, certified for U.S. and Canada.See UL File E314476.CE European Union 2004/108/EC EMC Directive, compliant with:EN 61326; Meas./Control/Lab., Industrial RequirementsEN 61000-6-2; Industrial ImmunityEN 61000-6-4; Industrial EmissionsEN 61131-2; Programmable Controllers (Clause 8, Zone A & B)(1)See the Product Certification link at for Declarations of Conformity, Certificates, and other certification details.Environmental SpecificationsAttributeValueProcess Remote I/O (RIO) Communication Interface Module 15Additional ResourcesThese documents contain additional information concerning related Rockwell Automation products.You can view or download publications at . To order paper copies of technical documentation, contact your local Rockwell Automation distributor or sales representative.Resource Description Refer to publication 1757-UM007C , the1757-ABRIO User Manual for information onmodule configuration.Provides details about how to configure, access data, monitor and troubleshoot the module.Industrial Automation Wiring and GroundingGuidelines, publication 1770-4.1Provides general guidelines for installing a Rockwell Automation industrial system.Product Certifications website, Provides declarations of conformity, certificates, and other certification details.Rockwell Automation SupportRockwell Automation provides technical information on the Web to assist you in using its products. At , you can find technical manuals, a knowledge base of FAQs, technical and application notes, sample code and links to software service packs, and a MySupport feature that you can customize to make the best use of these tools.For an additional level of technical phone support for installation,configuration, and troubleshooting, we offer TechConnect support programs. For more information, contact your local distributor or Rockwell Automation representative, or visit .Installation AssistanceIf you experience a problem within the first 24 hours of installation, please review the information that's contained in this manual. You can also contact a special Customer Support number for initial help in getting your product up and running.New Product Satisfaction ReturnRockwell Automation tests all of its products to ensure that they are fully operational when shipped from the manufacturing facility. However, if your product is not functioning and needs to be returned, follow these procedures.Allen-Bradley, ProcessLogix, and ControlLogix, RSLinx, RSLinx OEM, RSNetWorx, and TechConnect aretrademarks of Rockwell Automation, Inc. Trademarks not belonging to Rockwell Automation are property of their respective companies.United States1.440.646.3434 Monday – Friday, 8 a.m. – 5 p.m. EST Outside United States Please contact your local Rockwell Automation representative for any technical support issues.United States Contact your distributor. You must provide a Customer Support case number (call the phone number above to obtain one) to your distributor in order to complete the return process.Outside United States Please contact your local Rockwell Automation representative for the return procedure.Publication 1757-IN916C-EN-P - March 2008PN 21307Supersedes Publication 1757-IN916B-EN-P - February 2004Copyright © 2008 Rockwell Automation, Inc. All rights reserved. Printed in the U.S.A.。
夜翼SX10 Professional Gaming 10-Gigabit 多Gigabit开关(G
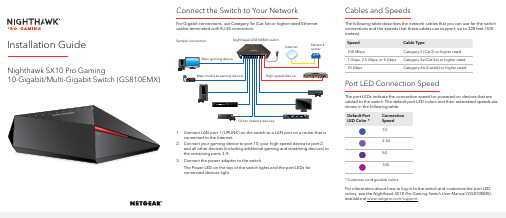
Installation GuideNighthawk SX10 Pro GamingConnect the Switch to Your NetworkFor Gigabit connections, use Category 5e (Cat 5e) or higher-rated Ethernet cables terminated with RJ-45 connectors.1. Connect LAN port 1 (UPLINK) on the switch to a LAN port on a router that isconnected to the Internet.2. Connect your gaming device to port 10, your high-speed device to port 2,and all other devices (including additional gaming and streaming devices) to the remaining ports 3–9.3. Connect the power adapter to the switch.The Power LED on the top of the switch lights and the port LEDs for connected devices light.Sample connection Cables and SpeedsThe following table describes the network cables that you can use for the switch connections and the speeds that these cables can support, up to 328 feet (100 meters).SpeedCable Type100 MbpsCategory 5 (Cat 5) or higher rated 1 Gbps, 2.5 Gbps, or 5 Gbps Category 5e (Cat 5e) or higher rated 10 GbpsCategory 6A (Cat 6A) or higher ratedPort LED Connection SpeedThe port LEDs indicate the connection speed for powered-on devices that are cabled to the switch. The default port LED colors and their associated speeds are shown in the following table.Default Port LED Color *Connection Speed1G 2.5G 5G 10G* Customer configurable colorsFor information about how to log in to the switch and customize the port LED colors, see the Nighthawk SX10 Pro Gaming Switch User Manual (GS810EMX), available at /support .Nighthawk GS810EMX switchNetwork routerMain media streaming deviceInternetOther network devicesNETGEAR, Inc.350 East Plumeria DriveSan Jose, CA 95134, USA NETGEAR INTL LTDBuilding 3, University Technology Centre Curraheen Road, Cork, Ireland© NETGEAR, Inc., NETGEAR and the NETGEAR Logo are trademarks of NETGEAR, Inc. Any non‑NETGEAR trademarks are used for reference purposes only.SupportThank you for purchasing this NETGEAR product. You can visit/support to register your product, get help, access the latest downloads and user manuals, and join our community. We recommend that you use only official NETGEAR support resources.Si ce produit est vendu au Canada, vous pouvez accéder à ce document en français canadien à /other/.(If this product is sold in Canada, you can access this document in Canadian French at /other/.)For the current EU Declaration of Conformity, visit/11621.For regulatory compliance information, visit/about/regulatory/.Do not use this device outdoors. If you connect cables or devices that are outdoors to this device, see /000057103 for safety and warranty information.See the regulatory compliance document before connecting the power supply.Access the SwitchWhen you access the switch, make sure that you are running the latest firmwareversion on your device. To find documentation, firmware, software, or other files,visit /support.Access the Switch From a Windows-Based Computer1. Open Windows Explorer.2. Click the Network link.3. If prompted, enable the Network Discovery feature.4. Under Network Infrastructure, locate the switch.5. Double-click Nighthawk SX10 (xx:xx:xx:xx:xx:xx) (where xx:xx:xx:xx:xx:xxis the MAC address of the switch).The login page of the web management interface opens.6. Enter the default switch password, which is password.The Home page displays the IP address of the switch.Access the Switch From the NETGEAR Discovery ToolThe NETGEAR Switch Discovery Tool lets you discover the switch in your networkand access the local browser interface of the switch from a Mac or a 64-bitWindows-based computer. Download the Switch Discovery Tool by visiting/support/product/netgear-switch-discovery-tool.aspx.Note: If you encounter an installation problem or cannot discover the switch,you may need to temporarily disable the firewall, Internet security, or antivirusprograms. Make sure to reenable the security services on your computer afterinstalling and discovering the switch.For information about how to access the switch by using the NETGEAR DiscoveryTool, see the GS810EMX switch user manual.May 2018Access the Switch From the NETGEAR Insight Mobile AppDuring initial setup, you must connect the switch to a WiFi network so that youcan access the switch from your mobile device with a local WiFi connection.1. On your iOS or Android mobile device, visit the app store, search forNETGEAR Insight, and download the app.2. Connect your mobile device to the WiFi network of the access point that isconnected to the switch.3. Open the NETGEAR Insight app on your mobile device.4. If you do not have a NETGEAR account, tap CREATE MYNETGEARACCOUNT and follow the onscreen instructions.5. To log in to your NETGEAR account, tap LOG IN and enter your credentials.6. Name your network and specify a device admin password that applies to alldevices that you add to this network.7. Tap the NEXT button.8. Add the switch with one of the following options:• Enter the serial number• Scan the barcode• Scan your networkNote: You might be prompted to connect the switch to power and toan uplink. Since you already did this (see Connect the Switch to YourNetwork), tap the NEXT button.The NETGEAR Insight app discovers the switch and registers it on thenetwork that you named in Step 6. If the app does not discover the switch,make sure that your mobile device and the switch are connected to the sameWiFi network.Insight9. In the NETGEAR Insight app, select the switch and tap the Visit WebInterface link.The login page of the local browser interface opens.10. Enter the switch password.The default password is password. The password is case-sensitive.The HOME page displays.。