镀锌的方法
镀锌的工艺流程和步骤
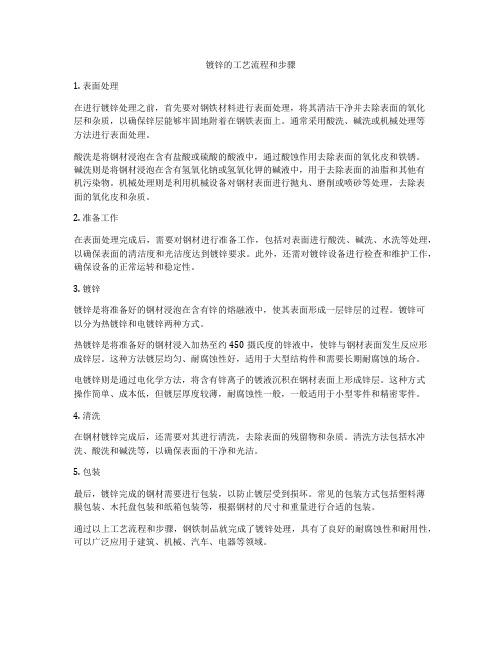
镀锌的工艺流程和步骤1. 表面处理在进行镀锌处理之前,首先要对钢铁材料进行表面处理,将其清洁干净并去除表面的氧化层和杂质,以确保锌层能够牢固地附着在钢铁表面上。
通常采用酸洗、碱洗或机械处理等方法进行表面处理。
酸洗是将钢材浸泡在含有盐酸或硫酸的酸液中,通过酸蚀作用去除表面的氧化皮和铁锈。
碱洗则是将钢材浸泡在含有氢氧化钠或氢氧化钾的碱液中,用于去除表面的油脂和其他有机污染物。
机械处理则是利用机械设备对钢材表面进行抛丸、磨削或喷砂等处理,去除表面的氧化皮和杂质。
2. 准备工作在表面处理完成后,需要对钢材进行准备工作,包括对表面进行酸洗、碱洗、水洗等处理,以确保表面的清洁度和光洁度达到镀锌要求。
此外,还需对镀锌设备进行检查和维护工作,确保设备的正常运转和稳定性。
3. 镀锌镀锌是将准备好的钢材浸泡在含有锌的熔融液中,使其表面形成一层锌层的过程。
镀锌可以分为热镀锌和电镀锌两种方式。
热镀锌是将准备好的钢材浸入加热至约450摄氏度的锌液中,使锌与钢材表面发生反应形成锌层。
这种方法镀层均匀、耐腐蚀性好,适用于大型结构件和需要长期耐腐蚀的场合。
电镀锌则是通过电化学方法,将含有锌离子的镀液沉积在钢材表面上形成锌层。
这种方式操作简单、成本低,但镀层厚度较薄,耐腐蚀性一般,一般适用于小型零件和精密零件。
4. 清洗在钢材镀锌完成后,还需要对其进行清洗,去除表面的残留物和杂质。
清洗方法包括水冲洗、酸洗和碱洗等,以确保表面的干净和光洁。
5. 包装最后,镀锌完成的钢材需要进行包装,以防止镀层受到损坏。
常见的包装方式包括塑料薄膜包装、木托盘包装和纸箱包装等,根据钢材的尺寸和重量进行合适的包装。
通过以上工艺流程和步骤,钢铁制品就完成了镀锌处理,具有了良好的耐腐蚀性和耐用性,可以广泛应用于建筑、机械、汽车、电器等领域。
热镀锌和冷镀锌施工方案

热镀锌和冷镀锌施工方案1. 引言热镀锌和冷镀锌是常见的金属表面处理方法,用于保护钢铁材料免受腐蚀和氧化的影响。
本文将介绍热镀锌和冷镀锌的施工方案,并对两种方法的优缺点进行比较。
2. 热镀锌施工方案热镀锌是将钢铁材料浸入高温的锌液中,使锌粒与钢铁表面形成合金层的过程。
以下是热镀锌的施工方案:2.1 准备工作在进行热镀锌之前,需要做好以下准备工作:•清洁钢铁表面:确保表面没有污垢、油脂等物质,可以使用溶剂或碱性清洗剂进行清洁。
•检测钢铁材料:对材料进行表面检测,确保没有明显的缺陷和损伤。
热镀锌的过程可以分为以下几个步骤:•酸洗:将钢铁材料浸泡在酸性溶液中,去除钢铁表面的氧化物和污垢。
•引入锌液槽:将经过酸洗的钢铁材料放入热镀锌设备中的锌液槽。
•高温浸泡:将钢铁材料在高温下浸泡在锌液中,使锌与钢铁表面发生反应并形成合金层。
•离开锌液槽:将镀锌钢材从锌液槽中取出,允许多余的锌液自流干。
•冷却:待镀锌钢材冷却后,进行下一步处理(如修剪、涂漆等)。
3. 冷镀锌施工方案冷镀锌是将锌粉喷涂在钢材表面的一种镀锌方法。
以下是冷镀锌的施工方案:3.1 准备工作在进行冷镀锌之前,需要做好以下准备工作:•清洁钢铁表面:与热镀锌相似,确保表面没有污垢、油脂等物质。
•检测钢铁材料:对材料进行表面检测,确保没有明显的缺陷和损伤。
冷镀锌的过程可以分为以下几个步骤:•喷涂底漆:首先,对钢铁表面进行喷涂底漆,用于增强附着力和防止腐蚀。
•喷涂锌粉:使用专用的喷涂设备,将锌粉均匀喷涂在钢铁表面上。
•固化:待喷涂的锌粉固化后,可以进行下一步处理(如修剪、涂漆等)。
4. 热镀锌和冷镀锌的比较热镀锌和冷镀锌都是常见的钢铁表面处理方法,但它们有不同的特点和适用场景。
以下是二者的比较:•成本:热镀锌的设备和工艺要求相对较高,导致其成本较高。
冷镀锌相对较便宜。
•镀层厚度:热镀锌的镀层厚度相对较厚,可以提供更好的耐腐蚀性能。
冷镀锌的镀层较薄,适用于一些低腐蚀环境。
镀锌的几种方法
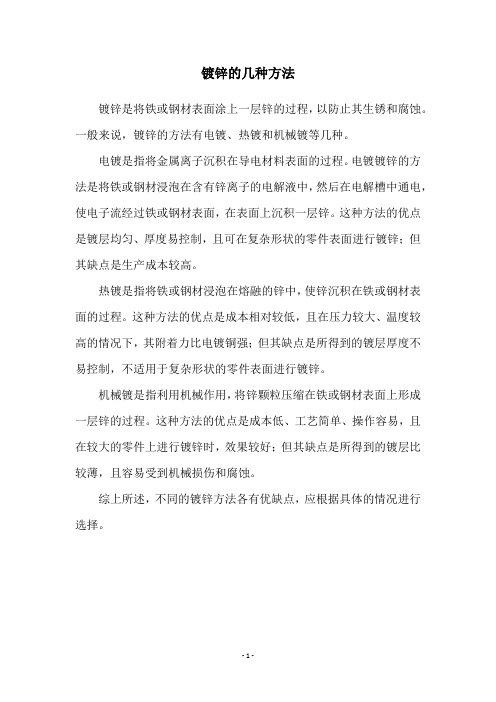
镀锌的几种方法
镀锌是将铁或钢材表面涂上一层锌的过程,以防止其生锈和腐蚀。
一般来说,镀锌的方法有电镀、热镀和机械镀等几种。
电镀是指将金属离子沉积在导电材料表面的过程。
电镀镀锌的方法是将铁或钢材浸泡在含有锌离子的电解液中,然后在电解槽中通电,使电子流经过铁或钢材表面,在表面上沉积一层锌。
这种方法的优点是镀层均匀、厚度易控制,且可在复杂形状的零件表面进行镀锌;但其缺点是生产成本较高。
热镀是指将铁或钢材浸泡在熔融的锌中,使锌沉积在铁或钢材表面的过程。
这种方法的优点是成本相对较低,且在压力较大、温度较高的情况下,其附着力比电镀铜强;但其缺点是所得到的镀层厚度不易控制,不适用于复杂形状的零件表面进行镀锌。
机械镀是指利用机械作用,将锌颗粒压缩在铁或钢材表面上形成一层锌的过程。
这种方法的优点是成本低、工艺简单、操作容易,且在较大的零件上进行镀锌时,效果较好;但其缺点是所得到的镀层比较薄,且容易受到机械损伤和腐蚀。
综上所述,不同的镀锌方法各有优缺点,应根据具体的情况进行选择。
- 1 -。
镀锌原理及方法
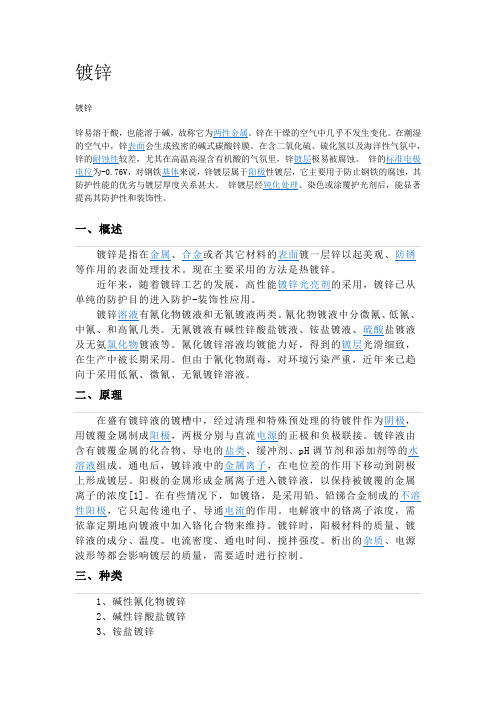
三、种类1、碱性氰化物镀锌2、碱性锌酸盐镀锌3、铵盐镀锌4、钾盐镀锌5、铵钾混合浴镀锌6、硫酸盐镀锌三、镀锌层的后处理1、去氢2、钝化3、着色热镀锌现在钢板的表面镀锌主要采用的方法是热镀锌。
热镀锌是由较古老的热镀方法发展而来的,自从1836年法国把热镀锌应用于工业以来,已经有一百七十年的历史了。
然而,热镀锌工业是近三十年来伴随冷轧带钢的飞速发展而得到了大规模发展。
热镀锌板的生产工序主要包括:原板准备→镀前处理→热浸镀→镀后处理→成品检验等。
按照习惯往往根据镀前处理方法的不同把热镀锌工艺分为线外退火和线内退火两大类,即湿法(单张钢板热镀锌法)、线外退火(单张钢板热镀锌法)、热镀锌惠林(Wheeling)法(带钢连续热镀锌法)、线内退火森吉米尔(Sendzimir)法(保护气体法)、改良森吉米尔法、美钢联法(同日本川崎法)、赛拉斯(Selas)法和莎伦(Sharon)法。
线外退火就是热轧或冷轧钢板进入热镀锌作业线之前,首先在抽底式退火炉或罩式退火炉中进行再结晶退火,这样,镀锌线就不存在退火工序了。
钢板在热镀锌之前必须保持一个无氧化物和其他脏物存在的洁净的纯铁活性表面。
这种方法是先由酸洗的方法把经退火的表面氧化铁皮清除,然后涂上一层由氯化锌或由氯化铵和氯化锌混合组成的溶剂进行保护,从而防止钢板再被氧化。
(1)湿法热镀锌钢板表面的溶剂不经烘干(即表面还是湿的)就进入起表面覆盖有熔融态溶剂的锌液进行热镀锌。
此方法的缺点是:a.只能在无铅状态下镀锌,镀层的合金层很厚且粘附性很坏。
b.生成的锌渣都积存在锌液和铅液的界面处而不能沉积锅底(因为锌渣的比重大于锌液而小于铅液),这样钢板因穿过锌层污染了表面。
因此,该方法已基本被淘汰。
(2)单张钢板这种方法一般是采用热轧叠轧板作为原料,首先把经过退火的钢板送入酸洗车间,用硫酸或盐酸清除钢板表面的氧热镀锌法化铁皮。
酸洗之后的钢板立即进入水箱中浸泡等待镀锌,这样可以防止钢板再氧化。
镀锌的几种方法
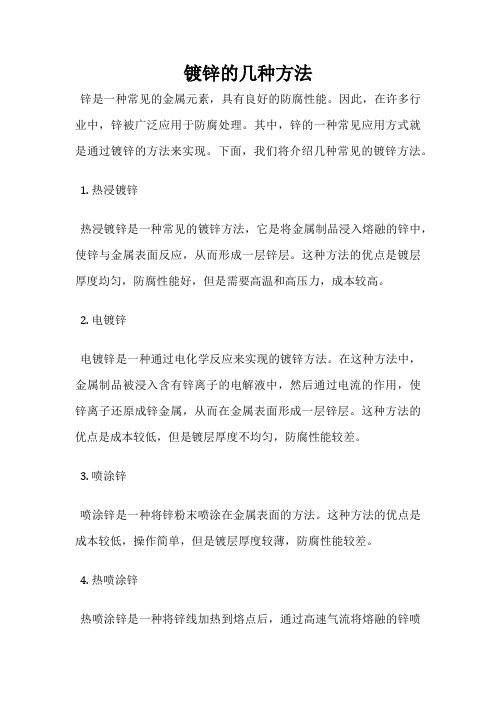
镀锌的几种方法
锌是一种常见的金属元素,具有良好的防腐性能。
因此,在许多行业中,锌被广泛应用于防腐处理。
其中,锌的一种常见应用方式就是通过镀锌的方法来实现。
下面,我们将介绍几种常见的镀锌方法。
1. 热浸镀锌
热浸镀锌是一种常见的镀锌方法,它是将金属制品浸入熔融的锌中,使锌与金属表面反应,从而形成一层锌层。
这种方法的优点是镀层厚度均匀,防腐性能好,但是需要高温和高压力,成本较高。
2. 电镀锌
电镀锌是一种通过电化学反应来实现的镀锌方法。
在这种方法中,金属制品被浸入含有锌离子的电解液中,然后通过电流的作用,使锌离子还原成锌金属,从而在金属表面形成一层锌层。
这种方法的优点是成本较低,但是镀层厚度不均匀,防腐性能较差。
3. 喷涂锌
喷涂锌是一种将锌粉末喷涂在金属表面的方法。
这种方法的优点是成本较低,操作简单,但是镀层厚度较薄,防腐性能较差。
4. 热喷涂锌
热喷涂锌是一种将锌线加热到熔点后,通过高速气流将熔融的锌喷
涂在金属表面的方法。
这种方法的优点是成本较低,操作简单,镀层厚度均匀,防腐性能好,但是需要专业设备和技术。
镀锌是一种常见的防腐处理方法,不同的镀锌方法有各自的优缺点,需要根据具体情况选择合适的方法。
镀锌工艺流程

镀锌工艺流程镀锌工艺流程是一种常用的金属防腐方法,通过在金属表面镀上一层锌来保护金属免受氧化和腐蚀的影响。
下面将从选材、预处理、镀锌、后处理四个方面介绍镀锌工艺流程。
首先是选材阶段。
常见的需要镀锌的金属材料有钢铁、铝和铜等。
在选材时,需要考虑材料的耐腐蚀性、强度和使用环境等因素。
一般来说,钢铁是最常见的镀锌材料,因为它具有较高的强度和耐腐蚀性。
接下来是预处理阶段。
在进行镀锌之前,需要对金属表面进行一系列的预处理,以确保镀层的质量和附着力。
预处理的步骤主要包括除油、除锈和表面活化。
除油是指将金属表面的油污和污垢清除干净,可以采用溶剂清洗或碱洗的方法。
除锈是指将金属表面的氧化铁皮和锈蚀物清除,可以采用机械除锈、酸洗或喷砂的方法。
表面活化是指通过酸洗或碱洗等方法,使金属表面形成一层活性物质,以提高镀锌层的附着力。
然后是镀锌阶段。
镀锌是将金属材料浸泡在熔融的锌液中,使锌与金属表面发生反应,形成一层锌铁合金的过程。
镀锌可以采用热镀锌和电镀锌两种方法。
热镀锌是将金属材料浸入温度约为450摄氏度的熔融锌液中,使锌与金属表面发生反应,形成一层锌铁合金层。
电镀锌是利用电解的原理,在金属表面电镀一层薄薄的锌层。
最后是后处理阶段。
镀锌完成后,需要对金属材料进行一些后处理工作,以提高镀层的质量和外观。
后处理的步骤主要包括冷却、清洗和干燥。
冷却是指将镀锌材料从熔融锌液中取出后,进行自然冷却,使镀锌层逐渐固化。
清洗是指将镀锌材料浸泡在酸溶液或碱溶液中,去除表面的氧化物和残留的锌液。
干燥是指将清洗后的镀锌材料进行干燥处理,以保证镀层的质量和外观。
镀锌工艺流程包括选材、预处理、镀锌和后处理四个阶段。
选材阶段需要考虑材料的耐腐蚀性和强度等因素;预处理阶段包括除油、除锈和表面活化等步骤;镀锌阶段可以采用热镀锌和电镀锌两种方法;后处理阶段需要进行冷却、清洗和干燥等处理。
通过这些步骤,可以保护金属材料免受氧化和腐蚀的影响,延长其使用寿命。
镀锌 无铬钝化
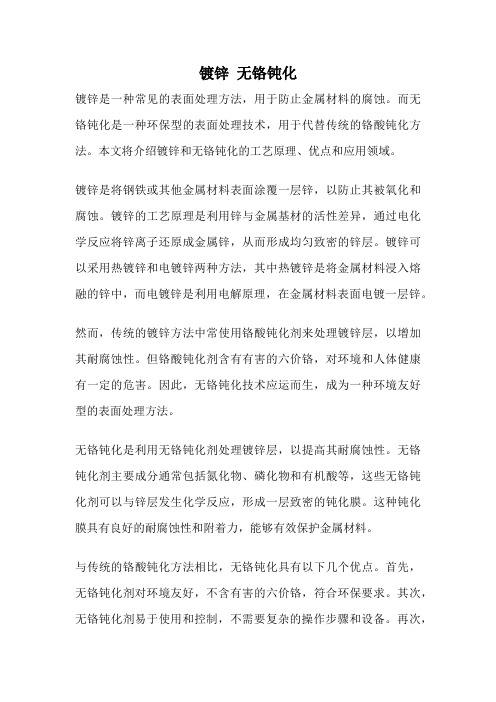
镀锌无铬钝化镀锌是一种常见的表面处理方法,用于防止金属材料的腐蚀。
而无铬钝化是一种环保型的表面处理技术,用于代替传统的铬酸钝化方法。
本文将介绍镀锌和无铬钝化的工艺原理、优点和应用领域。
镀锌是将钢铁或其他金属材料表面涂覆一层锌,以防止其被氧化和腐蚀。
镀锌的工艺原理是利用锌与金属基材的活性差异,通过电化学反应将锌离子还原成金属锌,从而形成均匀致密的锌层。
镀锌可以采用热镀锌和电镀锌两种方法,其中热镀锌是将金属材料浸入熔融的锌中,而电镀锌是利用电解原理,在金属材料表面电镀一层锌。
然而,传统的镀锌方法中常使用铬酸钝化剂来处理镀锌层,以增加其耐腐蚀性。
但铬酸钝化剂含有有害的六价铬,对环境和人体健康有一定的危害。
因此,无铬钝化技术应运而生,成为一种环境友好型的表面处理方法。
无铬钝化是利用无铬钝化剂处理镀锌层,以提高其耐腐蚀性。
无铬钝化剂主要成分通常包括氮化物、磷化物和有机酸等,这些无铬钝化剂可以与锌层发生化学反应,形成一层致密的钝化膜。
这种钝化膜具有良好的耐腐蚀性和附着力,能够有效保护金属材料。
与传统的铬酸钝化方法相比,无铬钝化具有以下几个优点。
首先,无铬钝化剂对环境友好,不含有害的六价铬,符合环保要求。
其次,无铬钝化剂易于使用和控制,不需要复杂的操作步骤和设备。
再次,无铬钝化膜的耐腐蚀性和附着力较好,可以提高镀锌层的使用寿命。
此外,无铬钝化技术还可以应用于不同种类的金属材料,具有广泛的适用性。
无铬钝化技术在许多领域都得到了广泛的应用。
在汽车工业中,无铬钝化技术可以用于镀锌钢板的表面处理,提高汽车车身的耐腐蚀性。
在电子行业中,无铬钝化技术可以用于镀锌接插件、电子元器件等的表面处理,提高其导电性和耐腐蚀性。
在建筑行业中,无铬钝化技术可以用于镀锌钢管、钢结构等的表面处理,延长其使用寿命。
镀锌和无铬钝化是两种常见的表面处理方法。
镀锌可以通过热镀锌和电镀锌两种方法实现,用于防止金属材料的腐蚀。
而无铬钝化是一种环保型的表面处理技术,通过使用无铬钝化剂处理镀锌层,提高其耐腐蚀性。
镀锌方法分类

镀锌方法分类镀锌是一种将铁、钢制品表面镀上锌层的防腐处理方法。
镀锌不仅可以提高产品的耐腐蚀性能,还可以美化产品表面,增加产品的使用寿命。
根据不同的镀锌方法,可以将其分为以下几种:1. 热浸镀锌热浸镀锌是将铁、钢制品浸泡在熔融的锌液中进行的一种镀锌方式。
在这种镀锌方式中,铁、钢制品会先进行酸洗处理,然后经过烘干后浸泡在熔融的锌液中,使其表面镀上一层锌,形成镀锌层。
这种镀锌方式具有镀层厚度均匀、耐腐蚀性能好、涂层附着力强等优点,广泛应用于建筑、汽车、机械制造等领域。
2. 电镀锌电镀锌是将铁、钢制品放入含锌离子的电解液中进行的一种镀锌方式。
在电镀锌过程中,铁、钢制品作为阴极,电解液中的锌离子在电流的作用下被还原成金属锌并附着在铁、钢制品表面,形成镀锌层。
电镀锌具有镀层厚度均匀、涂层附着力强、表面光洁度高等优点,广泛应用于电子、家电、汽车等领域。
3. 高温热浸镀锌高温热浸镀锌是将铁、钢制品在高温条件下浸泡在含锌的熔体中进行的一种镀锌方式。
在这种镀锌方式中,铁、钢制品经过预处理后,浸泡在高温的熔体中,锌在高温下与铁、钢制品表面反应,形成坚固、耐腐蚀性能好的镀锌层。
这种镀锌方式具有镀层均匀、耐腐蚀性能好、抗磨损性强等优点,广泛应用于建筑、电力、交通等领域。
4. 机械镀锌机械镀锌是利用机械力将锌粉附着在铁、钢制品表面形成镀锌层的一种镀锌方式。
在机械镀锌过程中,铁、钢制品经过酸洗、水洗、烘干等处理后,将锌粉通过机械力附着在铁、钢制品表面形成镀锌层。
这种镀锌方式具有成本低、操作简便、适用于大批量生产等优点,广泛应用于家具、五金制品等领域。
不同的镀锌方法适用于不同的领域,具有各自的优缺点。
在实际生产中,需要根据产品的具体情况选择合适的镀锌方式,以提高产品的质量和使用寿命。
手工镀锌工艺流程
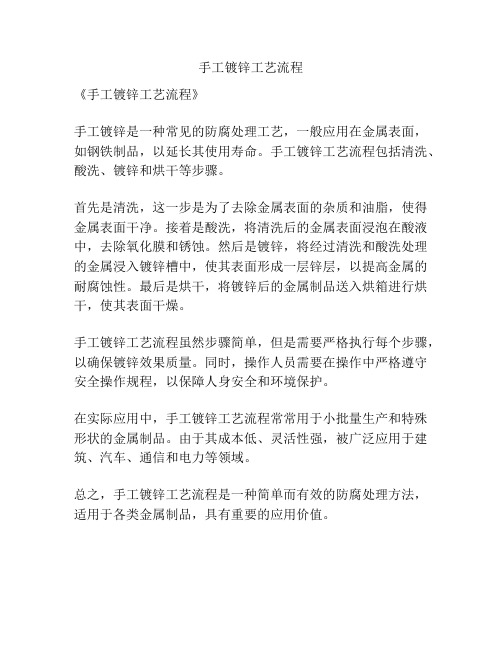
手工镀锌工艺流程
《手工镀锌工艺流程》
手工镀锌是一种常见的防腐处理工艺,一般应用在金属表面,如钢铁制品,以延长其使用寿命。
手工镀锌工艺流程包括清洗、酸洗、镀锌和烘干等步骤。
首先是清洗,这一步是为了去除金属表面的杂质和油脂,使得金属表面干净。
接着是酸洗,将清洗后的金属表面浸泡在酸液中,去除氧化膜和锈蚀。
然后是镀锌,将经过清洗和酸洗处理的金属浸入镀锌槽中,使其表面形成一层锌层,以提高金属的耐腐蚀性。
最后是烘干,将镀锌后的金属制品送入烘箱进行烘干,使其表面干燥。
手工镀锌工艺流程虽然步骤简单,但是需要严格执行每个步骤,以确保镀锌效果质量。
同时,操作人员需要在操作中严格遵守安全操作规程,以保障人身安全和环境保护。
在实际应用中,手工镀锌工艺流程常常用于小批量生产和特殊形状的金属制品。
由于其成本低、灵活性强,被广泛应用于建筑、汽车、通信和电力等领域。
总之,手工镀锌工艺流程是一种简单而有效的防腐处理方法,适用于各类金属制品,具有重要的应用价值。
镀锌方法分类
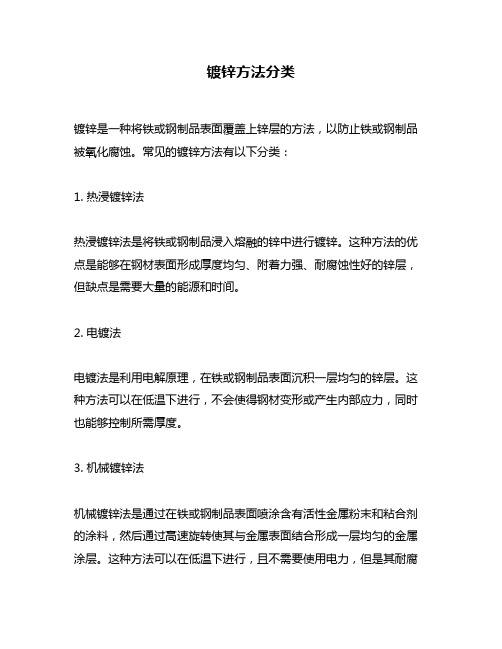
镀锌方法分类
镀锌是一种将铁或钢制品表面覆盖上锌层的方法,以防止铁或钢制品被氧化腐蚀。
常见的镀锌方法有以下分类:
1. 热浸镀锌法
热浸镀锌法是将铁或钢制品浸入熔融的锌中进行镀锌。
这种方法的优点是能够在钢材表面形成厚度均匀、附着力强、耐腐蚀性好的锌层,但缺点是需要大量的能源和时间。
2. 电镀法
电镀法是利用电解原理,在铁或钢制品表面沉积一层均匀的锌层。
这种方法可以在低温下进行,不会使得钢材变形或产生内部应力,同时也能够控制所需厚度。
3. 机械镀锌法
机械镀锌法是通过在铁或钢制品表面喷涂含有活性金属粉末和粘合剂的涂料,然后通过高速旋转使其与金属表面结合形成一层均匀的金属涂层。
这种方法可以在低温下进行,且不需要使用电力,但是其耐腐
蚀性较差。
4. 喷涂法
喷涂法是将含有锌粉末的涂料喷涂在铁或钢制品表面,然后通过烘干使其形成一层均匀的锌层。
这种方法可以在低温下进行,且具有较好的耐腐蚀性。
总之,以上四种方法各有优缺点,应根据不同的需要选择合适的方法进行镀锌处理。
最简单的镀锌方法
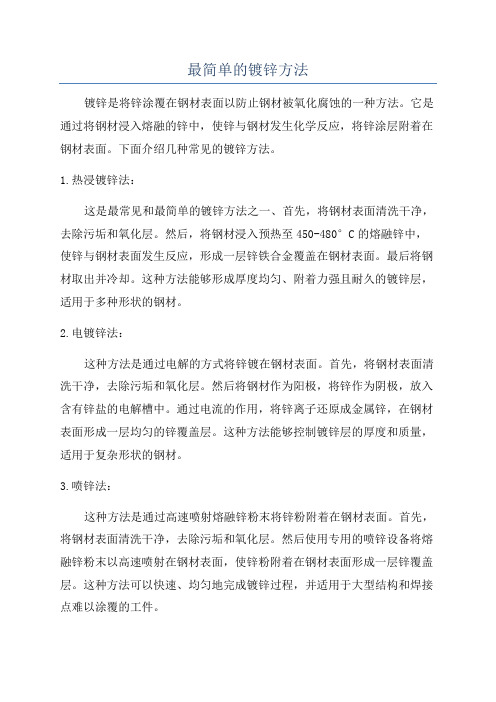
最简单的镀锌方法镀锌是将锌涂覆在钢材表面以防止钢材被氧化腐蚀的一种方法。
它是通过将钢材浸入熔融的锌中,使锌与钢材发生化学反应,将锌涂层附着在钢材表面。
下面介绍几种常见的镀锌方法。
1.热浸镀锌法:这是最常见和最简单的镀锌方法之一、首先,将钢材表面清洗干净,去除污垢和氧化层。
然后,将钢材浸入预热至450-480°C的熔融锌中,使锌与钢材表面发生反应,形成一层锌铁合金覆盖在钢材表面。
最后将钢材取出并冷却。
这种方法能够形成厚度均匀、附着力强且耐久的镀锌层,适用于多种形状的钢材。
2.电镀锌法:这种方法是通过电解的方式将锌镀在钢材表面。
首先,将钢材表面清洗干净,去除污垢和氧化层。
然后将钢材作为阳极,将锌作为阴极,放入含有锌盐的电解槽中。
通过电流的作用,将锌离子还原成金属锌,在钢材表面形成一层均匀的锌覆盖层。
这种方法能够控制镀锌层的厚度和质量,适用于复杂形状的钢材。
3.喷锌法:这种方法是通过高速喷射熔融锌粉末将锌粉附着在钢材表面。
首先,将钢材表面清洗干净,去除污垢和氧化层。
然后使用专用的喷锌设备将熔融锌粉末以高速喷射在钢材表面,使锌粉附着在钢材表面形成一层锌覆盖层。
这种方法可以快速、均匀地完成镀锌过程,并适用于大型结构和焊接点难以涂覆的工件。
4.热喷涂锌法:这种方法是通过热喷涂设备将熔融锌颗粒喷射在钢材表面。
首先,将钢材表面清洗干净,去除污垢和氧化层。
然后使用专用的喷涂设备将熔融锌颗粒通过喷嘴喷射在钢材表面,使锌颗粒附着在钢材表面形成一层锌覆盖层。
这种方法适用于大型结构和无法浸入液态锌中的工件。
总之,以上介绍了几种常见的镀锌方法,每种方法都有其适用的场景。
在选择时需要考虑工件的形状、尺寸和要求等因素。
无论采用哪种方法,镀锌工艺都应该精细控制,以保证锌层的均匀性、附着力和耐久性。
最简单的镀锌方法

最简单的镀锌方法
镀锌是将铁或钢表面覆盖一层锌金属的处理过程,以保护铁或钢不被氧化腐蚀。
锌金属在空气中可以形成一层致密的氧化锌保护层,使铁或钢表面不受腐蚀侵害,延长使用寿命。
最简单的镀锌方法是通过使用镀锌喷涂剂来实现,以下是详细的步骤:
1.准备工作:首先需要将待镀锌的材料表面清洁干净,去除油污和其他杂质。
2.涂抹喷涂剂:将镀锌喷涂剂倒入喷枪中,并将喷涂剂均匀地涂抹在材料表面上,注意要让涂层均匀,不要有漏涂的地方。
3.等待干燥:等待喷涂剂干燥,这个时间会根据不同的喷涂剂而有所不同,一般需要几个小时。
4.需要多次涂抹:建议进行多次涂抹,以确定涂层的厚度,达到更好的保护效果。
总结:使用镀锌喷涂剂是一种简单而便捷的镀锌方法,既能减缓铁或钢在空气中氧化的速度,又能让其继续保持美观的外观。
铜镀锌的方法

铜镀锌的方法嘿,朋友们!今天咱就来讲讲铜镀锌的方法。
你可别小看这铜镀锌,这就好比给铜穿上一件特别的“保护衣”呢!首先啊,得把要镀锌的铜物件好好地清理干净。
就像人要出门得先梳洗打扮整齐一样,铜物件也得干干净净的,不能有油污啊、锈迹啥的。
这一步可重要啦,要是没弄干净,那后面的镀锌效果可就大打折扣咯。
然后呢,就是准备镀锌溶液啦。
这就好像是给铜准备的一顿“大餐”。
这个溶液得调配得恰到好处,各种成分的比例可得掌握好。
不然的话,就像是做饭盐放多了或者放少了,味道就不对啦。
接下来,把清理好的铜物件小心翼翼地放进镀锌溶液里。
哎呀呀,这时候可得轻点儿,别把铜物件给磕着碰着了。
然后就等着镀锌慢慢进行。
想象一下,铜物件在溶液里,就像在泡一个特别的“温泉浴”,镀锌的过程就像是给它一点点地披上那层闪亮的“外衣”。
这个过程可不能着急,得让它慢慢地发生反应,这样镀出来的锌层才会牢固、均匀。
在这个过程中,还得时刻注意观察着。
就跟照顾小婴儿似的,得时刻留意着有没有啥异常情况。
要是发现有不对劲的地方,就得赶紧采取措施。
等镀锌完成后,把铜物件捞出来,哇哦,你就会看到它已经焕然一新啦!那层锌就像是给它穿上了一件银光闪闪的铠甲。
铜镀锌的方法其实并不复杂,但每一个步骤都得认真对待。
就像建房子一样,每一块砖都得砌好,房子才会牢固。
镀锌也是这样,每一个环节都做好了,才能得到一个完美的铜镀锌物件。
所以啊,朋友们,要是你们也想给铜物件镀锌,可别马虎哦。
认真做好每一步,就能让铜物件变得更加漂亮、耐用。
这不是很好嘛!大家都赶紧去试试吧!。
镀锌的正确操作方法
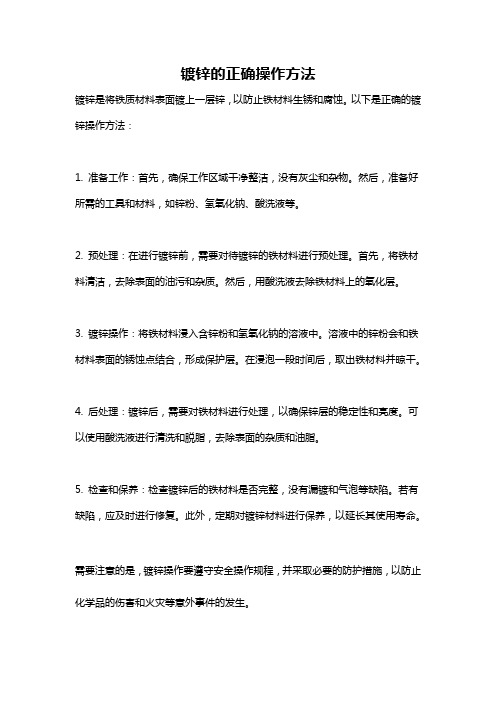
镀锌的正确操作方法
镀锌是将铁质材料表面镀上一层锌,以防止铁材料生锈和腐蚀。
以下是正确的镀锌操作方法:
1. 准备工作:首先,确保工作区域干净整洁,没有灰尘和杂物。
然后,准备好所需的工具和材料,如锌粉、氢氧化钠、酸洗液等。
2. 预处理:在进行镀锌前,需要对待镀锌的铁材料进行预处理。
首先,将铁材料清洁,去除表面的油污和杂质。
然后,用酸洗液去除铁材料上的氧化层。
3. 镀锌操作:将铁材料浸入含锌粉和氢氧化钠的溶液中。
溶液中的锌粉会和铁材料表面的锈蚀点结合,形成保护层。
在浸泡一段时间后,取出铁材料并晾干。
4. 后处理:镀锌后,需要对铁材料进行处理,以确保锌层的稳定性和亮度。
可以使用酸洗液进行清洗和脱脂,去除表面的杂质和油脂。
5. 检查和保养:检查镀锌后的铁材料是否完整,没有漏镀和气泡等缺陷。
若有缺陷,应及时进行修复。
此外,定期对镀锌材料进行保养,以延长其使用寿命。
需要注意的是,镀锌操作要遵守安全操作规程,并采取必要的防护措施,以防止化学品的伤害和火灾等意外事件的发生。
手工镀锌工艺流程

手工镀锌工艺流程手工镀锌工艺流程是指通过人工操作将金属制品表面覆盖上一层锌层的工作过程。
手工镀锌是一种传统而常用的防锈工艺,可以有效延长金属制品的使用寿命。
首先,准备好所需材料和工具。
手工镀锌需要的材料包括金属制品、锌碎、锌粉和中性酸盐酸洗液等。
工具包括刷子、刮刀、刷毛和喷枪等。
第二步,清洗金属制品表面。
首先使用刷子将金属制品的表面清洁干净,去除油污和杂质。
然后使用酸洗液进行酸洗处理,以去除金属表面的氧化层和锈蚀物,增加表面的粗糙度。
第三步,涂覆锌碎或锌粉。
将适量的锌碎或锌粉放入容器中,加入适量的中性酸盐酸洗液。
然后用刮刀将锌碎或锌粉均匀涂覆在金属制品的表面上,确保表面被完全覆盖。
第四步,刷洗金属制品表面。
使用刷子将涂有锌碎或锌粉的金属制品反复刷洗,以增加锌层的附着力和均匀度。
要注意刷洗的力度要适中,避免刷掉锌层或损坏金属制品的表面。
第五步,烘干金属制品。
将涂有锌碎或锌粉的金属制品放入烘干设备中进行烘干,以加快锌层的固化过程。
烘干温度和时间根据不同的材料和实际情况进行调整,一般在50-100摄氏度之间。
第六步,冷却金属制品。
将烘干后的金属制品取出,放置在通风良好的地方进行自然冷却,避免过快冷却导致锌层脱落或产生变形。
第七步,修整和检查。
将冷却后的金属制品进行修整和检查,修整表面不平整的地方,检查锌层的均匀性和质量,确保表面涂覆的锌层完整、紧密和均匀。
最后,包装和储存。
将镀锌完毕的金属制品进行包装,防止锌层受到潮湿和碰撞。
储存金属制品时要注意通风干燥,避免受潮和锌层受到损坏。
手工镀锌工艺流程需要仔细操作和较长的时间,但是能够制作出质量上乘的镀锌制品。
手工镀锌的优点是工艺简单、成本低廉,适用于小批量生产和个性化要求较高的金属制品。
同时,手工镀锌也存在一些缺点,如生产效率低、工艺难以控制等。
因此,在大规模生产和对质量要求较高的情况下,一般会选择机械化镀锌工艺。
电镀锌的操作方法

电镀锌的操作方法
电镀锌是一种常用的表面处理方法,可以有效地提高金属材料的耐腐蚀性能。
其操作方法如下:
1. 准备工作:首先需要准备好电镀槽、阳极和阴极,并确保它们的清洁度和完整性。
同时,还需要准备好合适的镀液和相应的控制设备。
2. 表面处理:将需要电镀的金属材料进行表面处理,包括去除表面的油污、氧化皮和其他杂质,使得表面光洁干净。
3. 阴极处理:将经过表面处理的金属材料作为阴极放入电镀槽中。
4. 阳极处理:将阳极也放入电镀槽中,并将镀液注入槽中。
5. 电镀过程:打开电源,使阴极和阳极之间形成电流流动,金属材料表面开始镀上一层锌。
6. 控制镀层厚度:通过控制电镀时间和电流密度来控制镀层的厚度,一般要求镀层的均匀性。
7. 清洗和干燥:将电镀后的金属材料进行清洗和干燥,以去除残留的镀液和水分。
8. 检验质量:对电镀后的金属材料进行外观和质量检验,确保镀层的均匀性和耐腐蚀性能。
以上就是电镀锌的操作方法,通过严格的操作控制和质量检验,可以得到高质量的电镀锌产品。
电镀锌的原理和工艺

电镀锌的原理和工艺电镀锌是一种将锌金属覆盖在其他金属表面的方法,以提高其耐腐蚀性能。
电镀锌的原理是利用电化学反应,在电解液中通过电流将锌离子还原到金属锌上,形成一层均匀的锌层。
下面将详细介绍电镀锌的工艺和原理。
电镀锌的工艺主要分为预处理、电解和后处理三个阶段。
预处理阶段:首先需要将要进行电镀的金属表面进行清洗。
清洗的目的是去除金属表面的油污、脱脂剂残留、铁锈等杂质,以保证电镀涂层的质量。
清洗方法可以使用化学方法或机械方法,例如酸洗、碱洗、化学溶剂清洗、机械擦洗等。
此外,还需要进行除锈处理,以确保金属表面的光洁度。
电解阶段:首先需要将预处理后的金属样品作为阴极,将电镀用的锌盐溶液作为阳极,置于容器中。
将阳极和阴极通过电源连接,施加电流。
在电解液中,锌盐会分解成锌离子和氯离子。
电流通过电解液,将金属离子还原到阴极上,锌离子被还原成金属锌,并将锌沉积在金属样品上,形成一层均匀的锌涂层。
电镀时间和电流密度的选择会影响锌涂层的厚度和形态。
后处理阶段:电镀完成后,需要对锌涂层进行处理,以增加其耐腐蚀性能和装饰效果。
常见的后处理方法包括清洗处理、封闭处理和覆盖处理。
清洗处理的目的是去除电镀过程中形成的氧化物和其他杂质。
封闭处理主要是通过浸泡在镀锌部件中的化学物质,形成一层防锈膜,以增加其耐腐蚀性能。
覆盖处理是在锌涂层上再涂一层有机涂料,以增加其装饰效果和耐腐蚀性。
电镀锌的原理是基于电化学原理。
在电解液中,电流通过电解液,将锌盐分解成锌离子和氯离子。
锌离子被还原成金属锌,沉积在金属样品的表面,形成一层锌涂层。
电镀过程中,阳极上的金属被溶解,作为离子进入电解液。
与之相对的阴极上的金属表面接收到足够的电子,将离子还原成金属,并沉积到阴极表面。
电镀锌的工艺在很多领域都有广泛应用。
电镀锌可以显著提高金属的耐腐蚀性,防止金属表面氧化和腐蚀。
此外,电镀锌还可以增加金属产品的装饰效果。
常见的电镀锌产品包括铁制品、钢制品、合金制品、铜制品等。
电镀锌的流程

电镀锌的流程
电镀锌是一种常见的防腐蚀处理方法,通过在金属表面镀一层锌,可以有效防止金属氧化和腐蚀。
电镀锌的流程一般包括表面处理、电镀和后处理等环节。
首先,进行表面处理。
表面处理是电镀锌过程中非常重要的一步,它可以影响到后续电镀层的质量和附着力。
表面处理一般包括
去油、酸洗、磷化等步骤。
去油是指将金属表面的油污和杂质清洗
干净,以保证电镀层的附着力。
酸洗则是利用酸性溶液去除金属表
面的氧化层和锈蚀,使金属表面变得光滑。
磷化是在金属表面形成
一层磷化物,增强金属表面与电镀层的结合力。
接下来是电镀过程。
电镀锌一般采用热镀锌和冷镀锌两种方法。
热镀锌是将金属浸入熔化的锌液中,通过化学反应形成一层锌层。
冷镀锌则是在金属表面通过电化学方法沉积一层锌层。
在电镀过程中,需要控制好电镀时间、温度和电流密度等参数,以确保电镀层
的均匀性和质量。
最后是后处理环节。
后处理是为了增强电镀层的耐腐蚀性能和
美观度。
一般来说,电镀锌后会进行烘干、光亮处理和封闭处理等
步骤。
烘干是将电镀后的金属材料进行烘干,去除表面的水分。
光亮处理则是通过化学方法或机械方法,使电镀层表面更加光滑和有光泽。
封闭处理是在电镀层表面形成一层保护膜,增强电镀层的耐腐蚀性能。
总的来说,电镀锌的流程包括表面处理、电镀和后处理三个主要环节。
通过这些环节的精心控制和操作,可以获得质量优良的电镀锌产品,提高金属材料的耐腐蚀性能和使用寿命。
- 1、下载文档前请自行甄别文档内容的完整性,平台不提供额外的编辑、内容补充、找答案等附加服务。
- 2、"仅部分预览"的文档,不可在线预览部分如存在完整性等问题,可反馈申请退款(可完整预览的文档不适用该条件!)。
- 3、如文档侵犯您的权益,请联系客服反馈,我们会尽快为您处理(人工客服工作时间:9:00-18:30)。
锌酸盐镀锌工艺的故障原因与处理方法:锌酸盐镀锌层起泡故障的分析与处理实例首先我们从零件的制备加工检查,没有发现出现起泡的可疑环节,所以重点考虑电镀各个工序的影响。
零件表面的油污,一般是经化学除油、电解除油清除干净。
但若操作不当或者除油液成分失调,可能会有少量油珠残留在零件表面,这就可能引起镀锌层的起泡。
零件若酸洗除锈时间过长,可能由于过腐蚀也会引起镀层的起泡。
此外,镀前活化不充分,没有活化,零件表面形成了一层薄氧化膜,也会导致镀层结合力变差而起泡。
因此,碱性锌酸盐镀锌前处理要严格控制。
前处理流程为:化学除油→热水洗→冷水洗→酸洗除锈→2次流动水洗→电解除油→热水洗→流水洗→镀前活化→2次流动水洗→镀锌。
除油液要定期加料;酸洗液、镀前活化液要定期更换,而且要严防铜杂质的危害。
(1)电镀工序中引起镀层起泡的可能因素。
挂具选择不当会引起锌镀层起泡,这一点往往易被人们忽略。
一般是用焊锡或铜将挂钩与杆子焊接在一起,再浸塑、浸漆,或用聚氯乙烯薄膜包扎。
若包扎破损,焊接处易受电解质腐蚀,腐蚀产物附着在零件表面、零件自上而下便产生带状密集小泡,因此,应经常检查挂具焊接处是否破损以防止挂具腐蚀而引起镀层起泡。
镀液操作或维护不当导致锌镀层起泡。
镀液中添加剂含量过高,易夹杂在镀层中使得内应力骤增,导致镀层起泡;镀液中重金属杂质,如铅、铜等含量过高,使锌层中夹杂过多的铅、铜等杂质,镀层与基体结合不良而起泡;光亮剂香草醛加入过多,镀层的光亮性虽好,但脆性增大,导致镀层起泡,此外,操作条件控制不当如温度太低,电流密度太大,也会导致镀层夹杂有机杂质,引起起泡。
镀后钝化工序的影响。
镀后出光、钝化操作不当,清洗不彻底,出光液、钝化液残留在镀层内,烘烤老化也容易引起镀锌层起泡。
(2)采取措施,严格控制镀锌工序消除起泡故障。
①生产厂首先把好了原材料关,选用性能优良的锌酸盐镀锌原料和添加剂,并且在添加剂加入镀槽前,先进行霍耳槽实验。
②加强镀锌槽液的维护,严格控制添加剂及光亮剂的补充量,以"少加勤加"为原则,或者根据霍耳槽试验计量补加。
③将掉入镀槽内的零件及时捞出,铜挂钩一律不能浸入镀液中。
④检查锌阳极的纯度,采用0号锌或1号锌,不用2号锌。
⑤严格按锌酸盐电镀锌工艺规程,控制电流密度和温度,冬季适当加温至15℃以上,并尽可能减少添加剂及光亮剂的用量。
⑥严格控制零件镀锌层厚度,尤其是零件边角的厚度太厚,特别容易发生镀层起泡。
⑦定期对镀液中有机物和重金属杂质进行大处理(加人lm L/L过氧化氢,搅拌30mi n,将镀液加温至60℃~70℃,再加入专用活性炭59/L~l09/L,锌粉19/L~29/L,充分搅拌30m i n~60mi n,静置4h,过滤,调整镀液成分,即可试镀),保证镀锌溶液处在一个好的工作状态。
⑧加强镀后处理工序,加强各道工序的漂洗,经常更换浸泡用热水,可大大减少因后处理不当而产生的起泡现象。
⑨严格控制老化温度,避免镀锌层与基体因热胀冷缩差异太大而起泡。
有些情况下,不一定是电镀工序过程出现了镀层起泡的现象,电镀生产的周围环境也可能引起电镀层的起泡。
如某厂碱性锌酸盐镀锌每年4月份~5月份总是发生镀锌层严重起泡的故障,而且开始找不出原因,只得每年停产一个多月。
后来通过观察分析发现,当镀液表面浮有一些微小的丝状物时,镀层起泡就严重,而当时的季节正是厂区周围梧桐树的开花期,其花瓣呈微小丝状的物质飘荡,或多或少落人的镀锌槽。
当采取措施阻挡了花瓣微小丝状物的影响后,这种镀锌层起泡的故障就消除了。
这说明出现电镀故障,有时候除了电镀工艺生产之外,还要从周围的环境可能的影响考虑。
锌酸盐镀锌工艺的故障原因与处理方法:低电流密度区出现黑色或灰色镀层1.原因分析铅离子污染:当镀锌液中铅离子的含量超过15m9/L时,镀液的分散能力下降,镀层经稀硝酸出光后会出现黑色或灰色条纹。
铅离子主要是由劣质锌阳极带人的,为防止铅的污染,锌阳极需用0#锌或l#锌。
铁离子污染:镀液中铁离子含量高达50m9/L,如铁离子含量进一步提高,镀液就会出现胶体絮状物,镀层钝化后会出现紫蓝色,而且镀层容易出现气泡。
铁离子主要是由劣质氢氧化钠或工件带人。
因此,要选用白色片碱,带赤色的氢氧化钠绝对不可用,工件进入镀槽前应彻底清洗。
为调解阴、阳极面积比例,应当使用镍板或镀镍铁板作为阳极。
铜离子污染:镀液中铜离子含量高达20m9/L时,得到的镀锌层粗糙,光亮度降低,且光亮电流密度范围随铜离子含量的增加而逐渐缩小。
铜离子主要是由挂勾和洗刷导电铜杠时带入的。
2.解决方法硫化钠处理:取0.19/L~0.59/L化学纯硫化钠,溶于20倍以上的冷水中,在剧烈搅拌下,缓慢加入到镀液中,加完后继续搅拌20m in,使之与镀液中的重金属离子充分反应,生成硫化物沉淀去除。
锌粉处理:取l9/L~39/L锌粉,在剧烈搅拌下缓慢加入镀液中,使之与重金属离子发生置换反应,加完后继续搅拌20mi n,静止2h后进行过滤,静置时间不宜过长,否则失去处理意义。
低电流电解处理:取镀镍铁板数块作阴极(面积宜大些),以0.1A/d m2~0.2A/dm2的电流密度进行电解处理,处理时间视试镀后情况而定。
使用过的镀镍铁板表面的黑色镀层必须在酸中退除,然后方可作阳极使用。
该方法的优点是:操作简便,不损耗镀液。
C K-778碱性镀锌溶液净化处理:取29/L~39/L C K-778碱性镀锌溶液净化剂,用与锌粉同样方法进行处理,但不必过滤。
净化剂加完后在继续搅拌和静置过程中镀液中会出现漂浮物,可边搅拌边用布网捞去,处理完后最好再用低电流电解处理,并添加1/3原配方量的镀锌添加剂和光亮剂。
锌酸盐镀锌工艺的故障原因与处理方法:镀锌层出现粗糙或粗糙发暗的原因及解决方法1.原因分析按正常情况下氧化锌与氢氧化钠的比例为l:(10~12),过高或过低即会出现上述故障。
即镀锌层粗糙是氧化锌比例偏低而氢氧化钠比例偏高造成的,这种比例失调还会出现电镀沉积速度缓慢、允许电流密度上限降低、工件表面析氢加重等故障。
反过来,氧化锌比例偏高而氢氧化钠比例偏低也会造成镀锌层的粗糙与发暗,这时还会出现工件边缘部位有气泡,沉积速度缓慢,分散能力和深镀能力降低,电流升不上去,镀层结合力差等问题。
2.解决方法调整上述两种情况的故障,一般在日常维护中既要控制好氧化锌与氢氧化钠的比例,又要考虑到氧化锌与氢氧化钠的实际含量,即使氧化锌的比例偏低,也不直接添加氧化锌,而是调节锌阳极的面积,暂停使用不溶性阳极,溶液中锌含量就会很快上去。
当氧化锌含量高了,可以以镀镍铁板代替锌阳极板,添加氢氧化钠至l209/L,这一故障即能很快获得解决。
锌酸盐镀锌工艺的故障原因与处理方法:镀层钝化膜质量故障(发花、变色、变暗等) 目前镀锌进行钝化处理的工艺主要低铬彩色钝化和三价铬钝化,在钝化后有时放置一夜或几天时间,钝化膜的表面就会出现雨点状白点,大小不一,钝化膜也变暗变淡,光亮度下降。
1.原因分析实际上发生这种故障的原因更复杂,可能有镀液的问题;前处理不良的问题;基材有麻点,镀后出光等清洗不良的问题;钝化液成分比例失调的问题;钝化膜老化时间不够的问题;环境的问题,空气中水蒸气、酸雾严重使得钝化膜色泽变化和腐蚀等。
2.解决方法针对上述可能的原因,逐条采取措施。
调整镀液成分到工艺规范,并且对镀液进行锌粉、硫化钠处理,再进行电解处理;加强除油、活化等前处理工序;加强镀后清洗和出光工序;严格控制钝化溶液成分和钝化工艺参数,控制好钝化膜的色彩;加强钝化后老化工艺的控制;改善工作环境,镀后零件尽快入库等。
尤其要注意的是钝化后的老化问题,因为热水槽老化温度过高(>70℃),就会使得钝化膜中的六价铬溶解,形成耐蚀性很差的多孔钝化膜。
就容易出现镀锌层钝化膜表面的雨点状白点,钝化膜变暗变淡,光亮度下降的故障。
严格控制钝化老化工序(60℃),这种故障就可以消除,生产恢复到正常。
其他环节也会出现钝化质量的故障的问题,如某厂采用D E碱性锌酸盐镀锌液,低铬钝化的滚镀锌工艺生产线,出现了钝化膜发花,表面有许多大块不规则灰黑色斑块的故障。
经分析是由于镀锌后的清洗槽中白色絮状沉淀较多,出光槽溶液呈黄棕色,p H值接近4,这些都可能带来电镀故障,由于清洗不干净和出光液p H高,造成电镀零件表面碱性镀液的清洗不够,出光液的出光作用下降,导致钝化膜发花等故障。
通过增加一道热水洗,将出光液pH调至l左右后,故障排除,生产恢复到正常。
锌酸盐镀锌工艺的故障原因与处理方法:锌酸盐镀锌中阳极板引起的故障实例在一个工厂的实际生产中,发现锌酸盐镀锌液中可能是镀液中杂质的影响,造成了镀锌层粗糙、灰暗、无光泽,甚至镀不上的故障。
但是在解决这个故障过程中,先是调整镀液中的氧化锌和氢氧化钠的比例,调整添加剂和光亮剂的含量,然后再电解处理几小时等措施。
但是镀锌层的质量仍然没有获得好转,在大电流密度下电镀,使得零件的边角烧焦,有镀层的部位也比较粗糙,镀液的分散能力和深镀能力极差,镀层经硝酸出光后,表面呈黑褐色。
怎么办?消除镀液中杂质最好的方法是对镀液进行去杂质处理:在镀液中加入锌粉29/L,活性炭29/L,经过搅拌、静置、过滤,然后进行镀液成分分析,调整成分到工艺规范范围,镀液恢复了正常,镀锌层的质量达到了要求。
但是,没过几天,没有补充其他成分,镀层又出现了上述故障,这种情况下分析杂质的来源可能是锌阳极所为,把锌阳极从镀液中取出,发现表面有异常发蓝现象,用水冲洗和用刷子刷洗后,锌阳极表面呈现出黑点,把这种黑点进行分析,发现是有机物的焦化和金属杂质,检查发现,这些物质是在浇铸锌阳极时造成的,问题找到了,更换了电镀槽内的锌阳极,彻底排除了这种电镀锌的故障。
锌阳极引起的电镀故障问题不只是一二例,某厂建成了32000L镀液的大型自动镀锌线,选用了AC F一Ⅱ碱性无氰镀锌工艺。
该工艺具有优良的分散和深镀能力,电流密度范围宽,镀层光亮度与钾盐镀锌相近,镀层与基体结合牢固,钝化膜附着力极好,彩色和深色钝化膜镀层耐腐蚀能力强等性能特点。
但是在新配镀液开始批量生产时,很快发现形状复杂的零件朝上的内腔和低电流区存在严重的镀层粗糙、发黑现象,而此现象在小试中均从未发现。
经过分析和试验,排除了这种镀锌液的成分失调、循环过滤差以及可能存在重金属杂质等情况,初步判定产生故障的根源在阳极的Zn板。
因为观察镀液中的Zn板发现,其表面有一层厚密的黑色细粉状物质,而同时悬挂的不溶性铁板则未见任何异常。
将Zn阳极板取出,进行酸洗、擦拭干净后重新放入镀槽中,继续电镀,零件内腔和低电流区的上述症状明显减轻。
但随着电镀时间的延长,Zn阳极表面的黑色细粉状物质逐渐增多,故障又重新出现,从而最终确定故障原因是,Z n板表面的黑色细粉状物质沉落于朝向上方的零件内腔和低电流区,再加上镀液的均镀能力好,零件内腔和低电流区镀层在细粉的不断沉落中快速沉积,故形成粗糙发黑的不合格镀层(零件外部和高电流区因极化较大和不易沉落黑色细粉物质,镀层属于正常沉积,所以镀层尚好)。