国外提高炼厂综合效益的技术研究进展
全球炼油技术研究与应用新进展(付兴国)

前言
石油炼化工业是国民经济的基础工业之一,不仅为国防、交通 和各个工业部门提供交通运输燃料和动力,而且生产大量石化产品, 与国民经济和人民生活息息相关。 炼油化工业务是中国石油的主营业务之一,在公司业务链中是 提升原油价值的核心环节,在整个产业链中起着承上启下的关键性 作用。当前和今后一段时间,炼油化工业务将有大的发展。预计到 2015年炼油能力将达到2.4亿吨/年,乙烯产能将达到711万吨/年。 从全球视野和战略角度跟踪、分析国际炼化行业发展形势和技术 趋势,对全面提升公司炼化业务和科技发展水平具有重要的参考和 指导意义。
316万吨/年
埃克森美孚公司博蒙特炼油厂
400万吨/年 675万吨/年
中海油惠州炼厂 印度信诚工业公司贾姆纳加尔炼厂
132万吨/年
JAM石化公司
45万吨/年
加拿大诺瓦化学公司
50万吨/年
沙特Sabic公司
石油化工研究院
Petrochemical Research Institute
炼化装置继续规模化大型化,产业集中度进一步提高
2000-2008年美国、西欧和新加坡炼油毛利
14
13.17
12
10.6 10.74
10
9.14
8 6.32
6
4.19 4.11
4.47
4
3.15
2
美国 西欧 新加坡
0 2000 2001 2002 2003 2004 2005 2006 2007 2008
数据来源:CERA
2000-2008年北美、西欧和亚太地区炼油装置负荷率 94
92 90 89.8
89.6 90.1
90
88.1
88
88
03国外炼油厂节能技术与先进经验(推荐文档)

二、炼油厂节能技术的发展
-4-
2. 热电联产 炼油厂能效的高低与其电能的供应方式关系很大。炼油厂特别适合热电联产。循 环发电需要一种受热体来吸收热力学上不能转化为电能的过剩热量。而炼油厂可以提 供这种受热体(即蒸汽),蒸汽吸热后可用于炼油厂工艺。这使得整个系统潜在效率很 高。在一种组合燃气轮机、高压锅炉和背压蒸汽轮机的发电方案中,发出满足全厂所 需电能的效率可达约80%。 在1973年第一次石油危机之前,炼油厂毛利高,能量成本低,电力价格所占绝对 份额相对较低。当时可以用于热电联产的唯一技术是蒸汽轮机,而其潜力有限(背压 发电数量有限,凝气轮机发电效率低)。20世纪60年代,燃气轮机首次进入发电市场, 但其成本很高。在第一次石油危机期间,尽管燃料和电力价格都在上涨,但电力成本 上涨速度慢于燃料,电力成本相对降低。许多炼油厂采取了改造预热流程和热量回收 流程、升级加热炉和节省蒸汽等措施,而投资高成本热电联产流程的炼油厂并不多。
中国石化集团公司经济技术研究院(EDRI)
二、炼油厂节能技术的发展
-6-
100% 80% 60% 40% 20% 0%
电力 被利用的热量 废热
20%
48%
67%
28%
33% 简单循环
52% 联合循环
52% 热电联产
三种发电模式的能量利用效率
中国石化集团公司经济技术研究院(EDRI)
二、炼油厂节能技术的发展
-7-
2. 热电联产 自1973年以来,埃克森美孚公司全球的炼油厂和化工厂能效提高了35%,相当于 节省了约18亿桶石油,大致相当于欧洲两年的车用燃料消费量。其中大部分来自热电 联产。目前,热电联产发电量占其发电总量的90%以上。该公司热电联产能力1980年 约为600 MW,1990年达到1500 MW,而2002年则达到了2900 MW。据称,与传统的发电 厂相比,每年可减少温室气体排放700万吨。
概述国外油田提高采收率发展现状
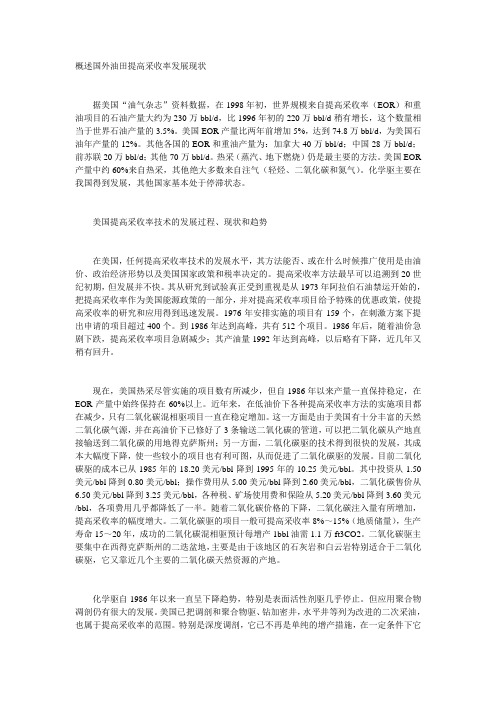
概述国外油田提高采收率发展现状据美国“油气杂志”资料数据,在1998年初,世界规模来自提高采收率(EOR)和重油项目的石油产量大约为230万bbl/d,比1996年初的220万bbl/d稍有增长,这个数量相当于世界石油产量的3.5%。
美国EOR产量比两年前增加5%,达到74.8万bbl/d,为美国石油年产量的12%。
其他各国的EOR和重油产量为:加拿大40万bbl/d;中国28万bbl/d;前苏联20万bbl/d;其他70万bbl/d。
热采(蒸汽、地下燃烧)仍是最主要的方法。
美国EOR 产量中约60%来自热采,其他绝大多数来自注气(轻烃、二氧化碳和氮气)。
化学驱主要在我国得到发展,其他国家基本处于停滞状态。
美国提高采收率技术的发展过程、现状和趋势在美国,任何提高采收率技术的发展水平,其方法能否、或在什么时候推广使用是由油价、政治经济形势以及美国国家政策和税率决定的。
提高采收率方法最早可以追溯到20世纪初期,但发展并不快。
其从研究到试验真正受到重视是从1973年阿拉伯石油禁运开始的,把提高采收率作为美国能源政策的一部分,并对提高采收率项目给予特殊的优惠政策,使提高采收率的研究和应用得到迅速发展。
1976年安排实施的项目有159个,在刺激方案下提出申请的项目超过400个。
到1986年达到高峰,共有512个项目。
1986年后,随着油价急剧下跌,提高采收率项目急剧减少;其产油量1992年达到高峰,以后略有下降,近几年又稍有回升。
现在,美国热采尽管实施的项目数有所减少,但自1986年以来产量一直保持稳定,在EOR产量中始终保持在60%以上。
近年来,在低油价下各种提高采收率方法的实施项目都在减少,只有二氧化碳混相驱项目一直在稳定增加。
这一方面是由于美国有十分丰富的天然二氧化碳气源,并在高油价下已修好了3条输送二氧化碳的管道,可以把二氧化碳从产地直接输送到二氧化碳的用地得克萨斯州;另一方面,二氧化碳驱的技术得到很快的发展,其成本大幅度下降,使一些较小的项目也有利可图,从而促进了二氧化碳驱的发展。
国内外油田提高采收率技术进展与展望

国内外油田提高采收率技术进展与展望目前,改善水驅、稠油热采、化学驱和气驱4类技术已进入矿场规模化应用,热采和气驱技术应用规模不断扩大,化学驱技术主要应用在中国,而微生物采油和物理法采油技术尚处于探索、试验阶段。
综合国外经验和我国具体情况,指出目前提高采收率技术的攻关方向和发展趋势。
研究认为,改善水驱技术通过层系细分重组和井网井型立体优化气驱技术应用规模有不断扩大的趋势,随着温室气体减排的要求,CO2驱油埋存项目不断增加。
化学驱技术向高温高盐油藏、大孔道油藏和聚合物驱后油藏发展。
标签:改善水驱;化学驱;提高采收率;油藏提高采收率技术,即国外通常指的强化和改善采收率技术,可概括为改善水驱、化学驱、稠油热采、气驱、微生物采油和物理法采油等六个方面。
目前,进入矿场规模化应用的提高采收率技术集中在热采、气驱和化学驱三大类。
改善水驱技术在我国已提到了战略高度。
微生物采油和物理法采油技术尚处于探索阶段。
通过对改善水驱、化学驱、热采和注气等技术的总结和展望,希望对我国尤其是中石化提高采收率战略决策有所启示和借鉴。
1 改善水驱技术水驱是应用规模最大,开采期限最长,调整工作量最多,开发成本最低的一种开发方式。
改善水驱技术按中、高渗透高含水油藏和低渗透油藏两个方面进行概括。
高含水油田储层以中、高渗透为主体,所占储量规模最大。
随着开发程度的越来越高,剩余油分布越来越复杂、高含水、地面设施老化和套管损坏等问题日益严重,给进一步提高采收率带来了严峻的技术与经济挑战。
开发调整的做法可以概括为如下几个方面。
随着多层砂岩油藏不断的层系细分和井网加密,注采系统不断完善与强化。
一方面,水油井数比逐渐增加,井距逐渐减小。
核心是增大驱替压力梯度,提高水驱控制程度。
另一方面,在油田开发后期,实施强化采液的同时,应采取各种措施降低无效注水量和产水量,通过提降结合,优化注采结构。
调堵调驱技术以扩大波及体积为核心。
调堵调驱技术除机械方法的井筒控制外,化学方法得到高度重视。
世界炼油前沿技术发展现状与展望

世界炼油前沿技术发展现状与展望一、行业发展趋势1.世界石油需求增幅变缓,发达国家炼厂开工率低位徘徊。
2.部分国际大石油公司剥离与削减下游投资。
3.原油质量与装置结构不匹配现象日益严重。
美国重点投资重油加工,但以页岩油和天然气凝析液的轻质原料却在大幅增加。
欧洲炼油商投资轻质原油加工,而加工的重质和含硫原油产量增加,过去几年利比亚、尼日利亚和和北海原油变得越来越重(API 30~40),欧洲炼油商却没有足够的能力来加工这类原油,使得许多原油被出售或者关停了一些炼油能力。
4.北美页岩气与页岩油对炼油业的影响逐渐增大。
来自页岩气的天然气凝析液又抢占了来自炼厂裂解原料的市场份额。
乙烷原料优势又使美国乙烯产业链整体利润上升,乙烷占乙烯原料结构的64%,石脑油只占13%。
二、未来发展展望重质油加工仍是重要方向。
三、行业挑战原油重质化与劣质化,环保要求更加苛刻,油价居高不下,非常规重质液体原料比例增加。
四、技术展望石油焦制氢技术将进入炼厂视野,深度炼化一体化技术将大幅提高经济效益,节能减排技术将成为关注的热点,替代燃料技术将逐渐成熟。
五、清洁燃料技术是发展主流传统的加氢技术将进一步改进,催化裂化脱硫技术将有新的发展。
六、重质油加工仍是重要方向超临界溶剂脱沥青组合工艺将取得重大突破,渣油加氢与焦化技术仍是并重的渣油加工手段。
七、重点领域发展动向1.催化裂化催化裂化的地位举足轻重,是重油转化、清洁油品生产、炼化一体化的主要途径之一。
提高催化裂化灵活性技术,如UOP的RxCat.技术,不受装置传统热平衡的限制,可增大剂油比、改进转化率、产品选择性和排放控制,从而降低操作成本。
开发多段提升管、多反应系统耦合FCC技术,实现提高柴汽比、直接生产高标号清洁汽油的目标,如中国石油的TSRFCC (两段提升管催化裂化)工艺。
开发用劣质原料生产高附加值轻烯烃的工艺和催化剂,如中国石油的TMP、KBR的ACO、Axens/Shaw的PetroRiser、中国石化DCC、UOP的PetroFCC等技术,其中TMP技术的丙烯产率>21%。
国内外电炉炼钢技术现状与发展趋势
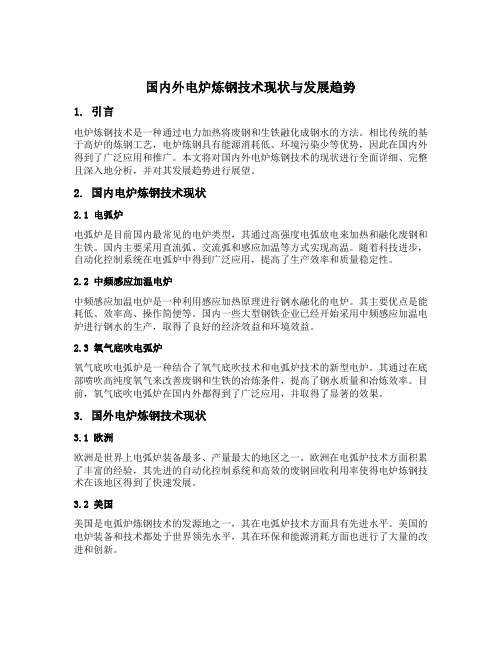
国内外电炉炼钢技术现状与发展趋势1. 引言电炉炼钢技术是一种通过电力加热将废钢和生铁融化成钢水的方法。
相比传统的基于高炉的炼钢工艺,电炉炼钢具有能源消耗低、环境污染少等优势,因此在国内外得到了广泛应用和推广。
本文将对国内外电炉炼钢技术的现状进行全面详细、完整且深入地分析,并对其发展趋势进行展望。
2. 国内电炉炼钢技术现状2.1 电弧炉电弧炉是目前国内最常见的电炉类型,其通过高强度电弧放电来加热和融化废钢和生铁。
国内主要采用直流弧、交流弧和感应加温等方式实现高温。
随着科技进步,自动化控制系统在电弧炉中得到广泛应用,提高了生产效率和质量稳定性。
2.2 中频感应加温电炉中频感应加温电炉是一种利用感应加热原理进行钢水融化的电炉。
其主要优点是能耗低、效率高、操作简便等。
国内一些大型钢铁企业已经开始采用中频感应加温电炉进行钢水的生产,取得了良好的经济效益和环境效益。
2.3 氧气底吹电弧炉氧气底吹电弧炉是一种结合了氧气底吹技术和电弧炉技术的新型电炉。
其通过在底部喷吹高纯度氧气来改善废钢和生铁的冶炼条件,提高了钢水质量和冶炼效率。
目前,氧气底吹电弧炉在国内外都得到了广泛应用,并取得了显著的效果。
3. 国外电炉炼钢技术现状3.1 欧洲欧洲是世界上电弧炉装备最多、产量最大的地区之一。
欧洲在电弧炉技术方面积累了丰富的经验,其先进的自动化控制系统和高效的废钢回收利用率使得电炉炼钢技术在该地区得到了快速发展。
3.2 美国美国是电弧炉炼钢技术的发源地之一,其在电弧炉技术方面具有先进水平。
美国的电炉装备和技术都处于世界领先水平,其在环保和能源消耗方面也进行了大量的改进和创新。
3.3 日本日本是世界上电弧炉装备密度最高的国家之一。
日本在电弧炉技术方面注重节能减排,通过采用高效的冷却系统、优化的气体循环等手段降低能耗和环境污染。
同时,日本还致力于提高钢水质量和冶炼效率,不断推动电炉炼钢技术向更高水平发展。
4. 电炉炼钢技术发展趋势4.1 自动化控制系统随着科技进步和人工智能技术的发展,自动化控制系统在电炉炼钢中将发挥越来越重要的作用。
第二部分国外石油炼制技术新进展2010..

13
国外炼油技术新进展
UOP最近推出一种还处于发展阶段的汽油吸附脱硫过程。该过程 使用的吸附剂为分子筛等固体物质,不仅能从汽油中脱硫,还可以脱 出氧和氮化物,脱除的硫化物包括有机硫、硫醇和噻吩。过程中汽油 收率略有损失,辛烷值变化不大。如果吸附剂寿命达到1 年的话,其投
资和操作费用仅为重馏分加氢脱硫操作费用的一半。
19
国外炼油技术新进展
从表5看出,在119种渣油中,能够直接作为RFCC原料的常压渣油 有25 %,多数渣油可用作固定床加氢处理过程原料。
20
国外炼油技术新进展
渣油处理过程的几种类型。表 6是已公布的渣油加氢专利技术和操 作条件。表 7是几种渣油加氢裂化过程的操作条件和氢耗。表 8是无催 化剂加氢过程的操作条件和氢耗。表 9是几种非加氢过程的操作条件。
炼油工艺新技术
第二部分 国外炼油技术进展
主讲人 沈健教授
1
国外炼油技术新进展
现代石油炼制技术的进步主要集中在两方面:
一是老过程的改进和新过程的开发。 二是新型催化剂的研制。
美国、日本和西欧是石油炼制工业发达地区,数十年来基本上 主宰了世界石油炼制工业的总发展趋势。
世界石油炼制技术最先进的美国,近十年来总原油加工能力变化 大约不大于7亿 ,渣油加工能力略有增加。正在运行的炼油厂数量减 少,由189个减少到169,仅1991年到1996年6年间就关掉6了座炼油厂。 加工的原油API下降,硫 、氮重金属含量增加 。有关环保法规越来越 严厉,市场对产品质量和技术含量要求越来越高。替代能源 ,如天然 气 、煤 、电、燃料 电池 、甲醇和乙醇,给石油炼制工业越来越大 的冲击 。
9
国外炼油技术新进展
重整过程是主要汽油生产过程。新一代催化剂为Pt-Ir/ Al2O3、PtRe/ Al2O3、Pt-Re/ Al2O3加分子筛、Pt/Al2O3,其作用是低压操作,减 少焦炭量,提高辛烷值,改善催化剂稳定性,连续操作。由于汽油对 芳烃和苯的限制越来越严厉,该过程作为主要汽油调合组分生产装置 的作用将降低,将主要用于生产BTX和氢气。为了改进操作效果,催 化重整原料可预分离,得到的C5/ C6去异构化,T90+馏分调入煤油或去 加氢裂化,中间馏分进重整。为了进一步提高重整油的作用,分出的 轻馏分可送苯饱和装置生产低苯汽油,重馏分进芳烃饱和装置生产低 芳烃煤油。 根据美国的经验,为生产新配方汽油,炼油厂应增加的投资为212美分/加仑。其高低取决于市场对汽油规格的要求;新配方汽油占炼 油厂汽油总量的比例;加工原油的类型;含氧汽油的产量。
延迟焦化在炼油工业中的技术优势及进展

延迟焦化在炼油工业中的技术优势及进展
延迟焦化是一种高级的炼油技术,利用该技术可以提高石油炼制产品的质量和产量。
目前,延迟焦化已成为国际炼油行业中最先进、最广泛应用的技术之一。
延迟焦化的技术优势主要包括以下几个方面:
1.提高产量:延迟焦化可以使原油的热值得到充分利用,提高产油率。
同时,使用高
效的预热技术可以降低原油粘度,使得炼油产量得到显著提高。
2.改善产品质量:延迟焦化能够提高炼油产品的质量,并消除其中许多有害成分。
其中,利用高温裂解技术可以减少硫、氮和金属等杂质的含量,并使得汽油和柴油的辛烷值、润滑油的黏度以及沥青的温度特性等都得到明显改善。
3.提高安全性:延迟焦化设备内部都有高度密封的装置,可以防止原油泄漏和空气污
染等安全问题的发生。
4.节约成本:由于延迟焦化可以使得产量得到提升,因此可以降低炼油生产成本,并
能够提高装置的经济效益。
随着科技的不断进步,延迟焦化技术也不断发展。
目前,国际上已经应用了各种新技
术和新材料,例如使用陶瓷材料制造高温反应器等等。
这些技术和材料的应用,不仅能够
提高设备的耐磨性,而且还能提高其安全性和使用寿命。
此外,近年来延迟焦化在能源领域得到大规模应用。
利用燃烧延迟焦化的残余物可以
进行再加工,以生成更多的燃料和化学品。
这种方法可以大幅提高延迟焦化的经济效益,
并使得能源及化工生产更加环保,减少对环境的污染。
总的来说,延迟焦化技术优势显著,通过不断的技术升级和改进应用,它正在成为炼
油工业中的不可或缺的一部分。
世界炼油技术的新进展

脱蜡 、 高辛烷值汽油 生产 、 汽油和柴油脱砘、 节能技术 等领域 的新进展情况。
关键词 : 界 世 炼 油 工 业 技 术 新 进 展
前 言
Mta 5 7 / 、. 1Mta 6 4 / , 国 、 / 、 . 2Mta 6 1 / 和 . 3Mta 美
20 0 5年全 球 原 油加 工 能 力 达 4 . ×1 。 , 2 5 0 t 比 西 欧 、 日本 、 东 、 加 坡 、 国 、 国 台 湾 等 地 的 中 新 韩 中
每 d的总 产 量 2 M 桶 中 , 硫 原 油仅 约 5 k桶 。 0 低 0
现在 全球 低硫 原 油 占产量 的 1 3 但仅 约 占全 球石 /,
油储 量 的 1 5 由 1 9 /。 9 4年 ~ 2 0 0 4年 世 界 原 油 生
产 的质量 分 布可 见 , 此期 间重 质 、 中硫原 油 产 量增 长 了 1 8 5 。其 次 , 界 级大 炼油公 司炼 油能 力 2 . 世
有 明显 变 化 。 如 中 国 石 化 、 国 石 油 、 国 瓦 莱 中 美
度 ( 温 )短接 触时 间 、 剂 / 比下操 作 , 用 特 高 、 高 油 采
种催 化剂 和 择形 添 加 剂 以及 下 流式 反 应 器 , 成 完
了每 d3 0桶 示 范装置 运行 验证 。在 HS C —F C中
江
西
石
油
化
工
20 0 6年
系列适 用 于 RF C装 置加工 高金 属含 量 的渣 油原 由于 采用 了戴 维 逊 的铝 溶 胶 专 利 技 术 , 催 化 体 C 该 料 , 化剂 内的分子 筛 具有 极佳 的抗 金属 性 能 , 催 当 系还 表现 出 优异 的耐 磨 损 性 能 , 装 置 能 保 持 良 使 催化 剂上 钒 含 量 很 高 时 , 化 剂 仍 然 保 持 很 好 的 好运 行 。 催 活 性与选 择 性 , 在世 界 3 5套炼 厂 催 化裂 化 装 置上
世界炼化技术进展和我国炼化科技发展建议
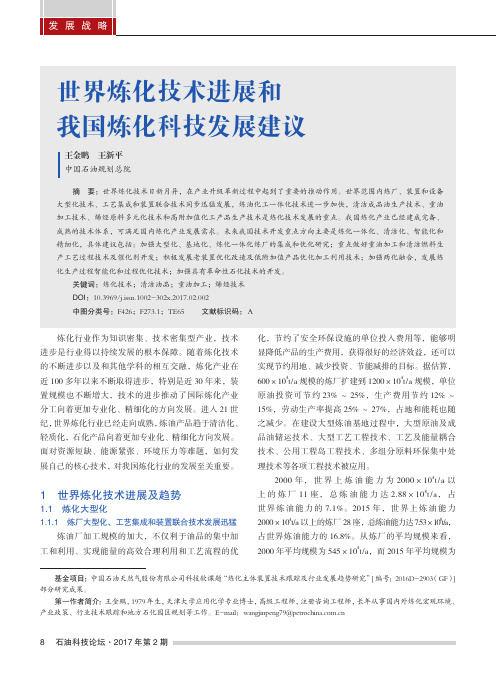
8
石油科技论坛·2017 年第 2 期
王金鹏 等:世界炼化技术进展和我国炼化科技发展建议
712×104t/a[1](表 1)。 表 1 世界炼厂装置平均规模
(单位:104t/ 座) 地区 亚太 西欧 东欧和前苏联 中东 非洲 北美 南美 世界 2000 年 492 689 5 2010 年 754 724 583 823 358 701 499 666 2015 年 878 750 615 836 373 752 441 712
化,节约了安全环保设施的单位投入费用等,能够明 显降低产品的生产费用,获得很好的经济效益,还可以 实现节约用地、减少投资、节能减排的目标。据估算, 600×104t/a 规模的炼厂扩建到 1200×104t/a 规模,单位 原油投资可节约 23% ~ 25%,生产费用节约 12% ~ 15%,劳动生产率提高 25% ~ 27%,占地和能耗也随 之减少。在建设大型炼油基地过程中,大型原油及成 品油储运技术、大型工艺工程技术、工艺及能量耦合 技术、公用工程岛工程技术、多组分原料环保集中处 理技术等各项工程技术被应用。 2000 年, 世 界 上 炼 油 能 力 为 2000×10 4t / a 以 上 的 炼 厂 11 座, 总 炼 油 能 力 达 2.88×10 8t / a, 占 世 界 炼 油 能 力 的 7.1%。2015 年, 世 界 上 炼 油 能 力 2000×104t/a 以上的炼厂 28 座,总炼油能力达 7.53×108t/a, 占世界炼油能力的 16.8%。从炼厂的平均规模来看, 2000 年平均规模为 545×104t/a,而 2015 年平均规模为
1 世界炼化技术进展及趋势
1.1 炼化大型化
1.1.1 炼厂大型化、工艺集成和装置联合技术发展迅猛 炼油厂加工规模的加大,不仅利于油品的集中加 工和利用、实现能量的高效合理利用和工艺流程的优
提质增效国外研究情况汇报

提质增效国外研究情况汇报在当前全球化的背景下,提高生产效率、优化资源配置、提升产品质量已成为各国企业和政府部门的共同追求。
为了更好地了解国外在提质增效方面的研究情况,本文将对国外相关研究进行汇报和总结,以期为我国相关领域的发展提供借鉴和启示。
首先,从美国的研究情况来看,美国一直以来都是全球科技创新的领先者。
在提质增效方面,美国企业和研究机构在生产自动化、智能制造、大数据分析等方面取得了许多成果。
例如,美国工程师们利用先进的机器人技术,实现了生产线的智能化和自动化,大大提高了生产效率和产品质量。
此外,美国的一些企业还通过大数据分析,优化了生产流程和产品设计,进一步提高了企业的竞争力。
其次,从欧洲的研究情况来看,欧洲在提质增效方面也有着不俗的表现。
欧洲一些国家在制定政策和推动产业升级方面做得较为出色。
比如,德国在制造业方面一直处于世界领先地位,其工匠精神和严格的质量管理体系为德国制造业的发展提供了有力支撑。
另外,欧洲一些国家还注重推动绿色制造和可持续发展,通过采用环保材料和清洁生产技术,提高了产品的质量和市场竞争力。
此外,亚洲国家也在提质增效方面取得了一些进展。
日本作为世界制造业强国,一直以来注重产品质量和生产效率。
日本企业在精益生产和精益管理方面有着丰富的经验,通过不断改进和创新,提高了生产效率和产品质量。
另外,中国作为世界工厂,也在近年来加大了对制造业的技术升级和质量提升力度,通过引进先进技术和管理经验,不断提高了产品质量和市场竞争力。
综上所述,国外在提质增效方面的研究情况丰富多彩,各国在这一领域都有着不同的经验和做法。
我国在借鉴国外经验的同时,也应结合自身国情,加大对制造业的技术创新和质量管理力度,不断提高产品质量和生产效率,为实现经济转型升级和可持续发展做出更大贡献。
国外采油工程方案进展

国外采油工程方案进展引言随着全球石油需求的不断增加,国外的油田开发工程变得愈发重要。
采油工程方案的进展对于国外的石油开发和生产至关重要。
本文将着重探讨国外采油工程方案的进展及其对全球能源需求的影响。
一、国外采油工程方案的背景国外的采油工程方案面临着许多挑战,包括技术、环境、政府政策等方面的制约。
然而,由于全球石油需求不断增加,国外采油工程方案仍然具有巨大的潜力。
各国的石油公司和政府部门纷纷加大对国外油田的开发投入,希望通过创新技术和合作方式来满足全球石油需求。
二、国外采油工程方案的技术进展国外的采油工程方案在技术上实现了许多突破,在提高采油效率、降低成本、保护环境等方面取得了显著成果。
例如,水平井、多级水平压裂、聚合物驱油技术等技术的应用使油田的开发效率大大提高。
此外,先进的采油设备和自动化控制系统的引入使得采油过程更加安全高效。
三、国外采油工程方案的环境保护进展随着对环境保护意识的提高,国外的采油工程方案在环境保护方面也取得了显著进展。
例如,在油田开发过程中,对地下水资源的保护和利用越来越受到重视。
采用生物地质技术和地下水循环利用技术可以减少对地下水资源的影响。
此外,各国政府和石油公司也加大了对环境保护的投入,采取了一系列举措来减少采油活动对环境的影响。
四、国外采油工程方案的政策支持进展为了促进国外油田的开发和生产,许多国家加大了对石油行业的政策支持力度。
例如,降低税收、简化审批手续、提供资金支持等举措都成为各国政府的重点政策。
这些政策支持为国外采油工程方案的进展提供了良好的政策环境。
五、国外采油工程方案的全球影响国外的采油工程方案对全球能源需求的影响不言而喻。
随着全球石油市场的不断变化,各国的石油需求也在不断增加。
国外采油工程方案的进展将对全球石油市场产生深远的影响,为全球能源供给做出重要贡献。
结论国外采油工程方案的进展对全球能源供给具有重要意义。
随着技术的不断进步、环境保护意识的提高和政策支持力度的增加,国外的采油工程方案将为全球能源供给做出更大的贡献。
国际环境下的生产效益提升
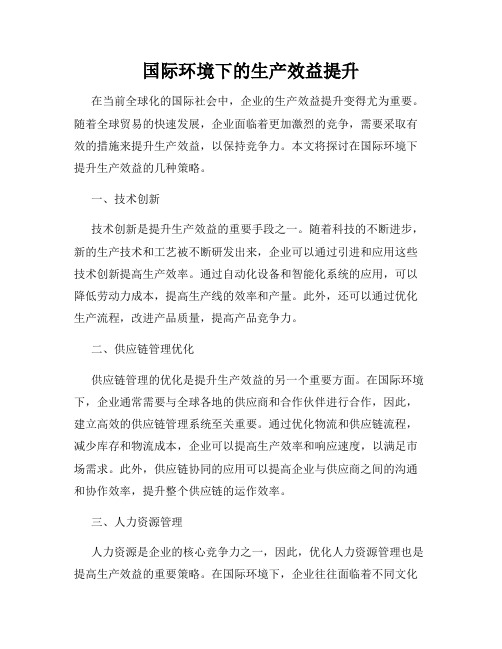
国际环境下的生产效益提升在当前全球化的国际社会中,企业的生产效益提升变得尤为重要。
随着全球贸易的快速发展,企业面临着更加激烈的竞争,需要采取有效的措施来提升生产效益,以保持竞争力。
本文将探讨在国际环境下提升生产效益的几种策略。
一、技术创新技术创新是提升生产效益的重要手段之一。
随着科技的不断进步,新的生产技术和工艺被不断研发出来,企业可以通过引进和应用这些技术创新提高生产效率。
通过自动化设备和智能化系统的应用,可以降低劳动力成本,提高生产线的效率和产量。
此外,还可以通过优化生产流程,改进产品质量,提高产品竞争力。
二、供应链管理优化供应链管理的优化是提升生产效益的另一个重要方面。
在国际环境下,企业通常需要与全球各地的供应商和合作伙伴进行合作,因此,建立高效的供应链管理系统至关重要。
通过优化物流和供应链流程,减少库存和物流成本,企业可以提高生产效率和响应速度,以满足市场需求。
此外,供应链协同的应用可以提高企业与供应商之间的沟通和协作效率,提升整个供应链的运作效率。
三、人力资源管理人力资源是企业的核心竞争力之一,因此,优化人力资源管理也是提高生产效益的重要策略。
在国际环境下,企业往往面临着不同文化背景和不同国家法律法规的挑战,因此,建立有效的人力资源管理体系尤为重要。
企业可以通过招聘和培训优秀人才,提高员工的工作效率和技能水平。
此外,激励机制的合理设计可以调动员工的积极性和创造力,提高工作效率和生产质量。
四、市场营销策略市场营销策略也是提升生产效益的关键因素之一。
在国际市场上,企业需要制定适应不同国家和地区的市场营销策略,以满足消费者需求并提高产品销量。
企业可以通过市场调研和市场定位来了解消费者需求,从而开发符合市场需求的新产品。
此外,有效的品牌推广和营销活动可以提高产品的知名度和美誉度,增加市场份额,从而提高生产效益。
五、合作伙伴关系建立在国际环境下,与合作伙伴的关系建立和合作是提升生产效益的有效手段。
国外:混炼技术的进步与发展

Mixing And Mix Design – Advances In MixingTechnologyAugust 10, 2015 by Prasanth Warrier14 Comments1.to secure properties in the finished product to satisfy service.2.to attain processing characteristics for efficient utilisation of availableequipment.3.to achieve the desirable properties and processibility at the lowest possiblecost.REQUIREMENTS FOR THE SUCCESS IN COMPOUNDING:THE INGREDIENTS AND FORMULATION OF A MIX:Today, a technical vulcanisate is made up of the following constituents :1.Base polymer or blend of polymers2.Crosslinking agents3.Accelerators4.Accelerator modifiers (Activators / retarders )5.Antidegradents6.Reinforcing fillers7.Processing aids8.Diluents9.Colouring materials10.Special AdditivesIn addition to the above, reclaimed rubber or vulcanised rubber crumb may be included and according to the manner of their use, function under groups 1, 7 or 8. SELECTION OF POLYMER AND COMPOUNDING INGREDIENTS: POLYMERRubbers are viscoelastic materials of low rigidity exhibiting large strain elasticity. The deformation imposed on rubber components are far larger than those encountered for most other materials, and the stress-strain relationships are correspondingly more complex.The ability of rubber to store elastic energy depends largely on the type of polymer used. In general, polymers having relatively high glass transition temperatures exhibit the highest energy losses during deformation. These energy losses are exploited in components intended to damp motion, but generally the higher the damping obtained the more sensitive are the modules and damping to frequency and temperature.The tensile strength of a rubber is low compared with other materials but the energy storage capacity at break can be greater than that of an equivalent mass of steel. Failure of rubber components rarely occurs by simple tensile failure: tearing or fatigue crack growth is more likely.A major factor determining the strength of rubber is an ability to crystallise under the influence of an applied strain. Rubbers possessing this ability (e.g., NR and CR) are intrinsically strong while those that do not crystallise rely on the incorporation of reinforcing fillers to impart adequate strength.A limitation on the use of rubbers in some applications is the effect of certain fluids. The extent of swelling or property change in a given fluid is critically dependent on both the rubber and the fluid. Selection of a rubber for a given application should take into account its resistance to any fluid it is likely to be in contact with in service.A similar consideration applies to the effects of temperature and the climate in which a product is to be used.Relative ratings of different polymer vulcanisates are as shown below:TEMPERATURE RANGE OF MOST COMMON ELASTOMERSElastomer Base Temp Range (°C)CR 40 – 100IIR 40 – 120NBR 40 – 100NR 55 – 90SBR 50 – 100CSM 20 – 120EPDM 50 – 1501.Optimum resistance to compression set is developed as cure continuesbeyond the level normally considered adequate to obtain a good general level of properties.2.Thiurmas in conventional systems give lower compression set than dothiazoles and sulphonamides alone.3.Partial replacement of sulphonamide with thiuram gives compression setresistance approaching that of thiuram used alone. These systems give good compromise between cost and technical performance.4.Semi EV system are superior to conventional system.Tension Set : The tensile analogue of compression set is termed tension set and is defined a residual tensile strain in a rubber after it has been stretched either to a given tensile strain and released.Resistance to liquids : By proper selection of the rubber type and other compounding ingredients, products can be designed for satisfactory use withwide range of liquids. Contact with an aggressive liquid can have two effects on rubber. The more obvious is change of dimension due to swelling which may be positive because of absorption of liquid or negative because of extraction of soluble compounding ingredients, e.g. Ester plasticizers by fuels. Swelling is diffusion controlled process. The rate of penetration depends more on the viscosity of the fluid rather than its exact chemical nature.Ageing resistance : It is known that many factors such as oxygen, ozone, sunlight, metal irons, heat and mechanical conditions may markedly contribute to the deterioration of rubber with the passage of time. Although complete prevention of degradation is impossible inhibitions can be done by use of antioxidants to minimise oxidation and carbon black to reduce sunlight effects.Heat resistance : In general, resistance to high temperature is a function of polymer structure and Crosslinking systems.Low temperature resistance : As the temperature falls there is an increase in stiffness the rubber passing through an intermediate transition state until it becomes brittle solid (glass hardening). The use of plasticizer may improve the low temperature flexibility. An additional factor in low temperature behaviour is crystallisation which may occur with certain rubbers particularly with NR and CR. PRINCIPLES OF MIXINGVulcanizable polymers cannot be used without compounding. Various additives like curative system, protective system, reinforcing agents, cheapeners and other process aids have to be mixed to the polymer or polymer blend “to make a coherent homogenous mass of all these ingredients, which will process satisfactory and on Vulcanisation will give the product capable of giving the desired performance, all with the minimum expenditure of machine time and energy.”Due to the partly elastic nature and very high viscosity of rubber, power intensive sturdy machinery like mixing mills or internal mixers is necessary to achieve the mixing of additives into the polymer. The ingredients are in form of liquids, solid powders or solid agglomerates.Phases during mixing of rubberThe mixing of solid ingredients into the solid polymer occurs in phases. During subdivision large lumps or agglomerates are broken down into smaller aggregates suitable for incorporation into the rubber.For instance carbon black pellets which have dimension of the order of 250-2000 µm get broken down into aggregates with dimensions of the order of 100 µm. Then these aggregates are absorbed or incorporated into the rubber to form a coherent mass.During mixing, shearing of the rubber generates shearing stress in rubber mass which imposes in turn shear stress on these aggregates and breaks these into their ultimate fine size which in case of carbon blacks is of the order of about1µm. in size. This phase is also known as intensive mixing or homogenization in micromolecular level.Distribution or homogenization in micromolecular level or extensive mixing is “the moving of the agglomerates / particles from one point to another, without changing the shape of the particle to increase the randomness of the mixture”. The ingredients incorporation is a very slow process.Another method of reducing incorporation time is to use powdered rubbers. In a simple ribbon blender the powdered rubbers can be mixed with the other compounding ingredients.The powdery mass is compacted in another machine and then fed to the internal mixer. Because of the large surface area of the powdered rubbers, the incorporation into polymer is very fast and only a very short mixing cycle in the internal mixer is adequate to achieve the mixing.Even after all ingredient is incorporated, dispersion/distribution of the ingredient is not complete. Good distribution is comparatively easy to achieve by paying proper attention to cutting and folding operations on a mixing mill or by just prolonging the mixing cycle in an internal mixer.Rebuild Farrel F270 Mixer From Pelmar Engineering LtdDispersion however is dependent on the shear stresses generated within the polymer and hence good dispersion may not be achieved by prolonged mixing . Careful consideration is necessary not only as regards the time of the mixing cycle but also for the order of addition of ingredients to the rubber.Viscosity break down occurs during mixing and is essential for smooth processing of the stock.Degree of dispersion of carbon black has profound influence on the physical properties of the vulcanisate. Undispersed carbon black (normally taken as carbon black agglomerates bigger in size than 9µm) act as gritty particles. Under tension, cracks develop at these spots.Failure properties like tensile strength, tear strength and consequently abrasion resistance come down as the degree of dispersion comes down. CONDITIONS FOR GOOD DISPERSION OF CARBON BLACKTo achieve dispersion of the carbon black, the polymer mass itself has to exert considerable shear stress on the carbon black agglomerate incorporated inside the polymer. This is achieved by passing the polymer carbon black batch through a narrow nip either between two rolls of a mixing mill moving at frictional speed or that in between rotor tip and chamber wall of an internal mixer.In internal mixer two additional conditions have to be fulfilled. Chamber loading must correct & Ram pressures must be adequate to hold the stock within the chamber.CONDITIONS FOR GOOD DISPERSION IN INTERNAL MIXER▪Narrow Clearance between Rotor▪Tip and Chamber wall (High Rate of Shear)▪Correct Volume Loading▪Adequate Ram Pressure▪High Viscosity of Polymer▪Low Polymer Temperature▪(High Viscosity and More Prominent Elastic Characteristics of Raw polymer)Kobelco Make MixersFor higher shear stress generation inside the polymer mass, polymer should have high viscosity. The temperature should be low so that thermoplasticity does not lead to lowering of polymer viscosity.Any sweeping of carbon black at the end of mixing cycle is to be avoided in regular production.The Master Batch (MB) is aged. Cooled MB goes to the cracker. Mechanical working of the cooled MB improves the degree of dispersion further. Then the MB is worked on Cracker mill, warming mills, feed mill and then to the extruder.It is possible to follow the mixing process in the internal mixer with the help of power / time curve (or amperage of drive motor / time curve). When carbon black is added the torque does not rise immediately. The carbon black added as palletised black is about 30% higher than the total chamber volume. As the carbon black is slowly absorbed into the rubber the torque increases. As more and more carbon black gets absorbed, stock volume becomes lower and the power curve comes down.Based on the power curve data on experimental batches, criteria like constant time or constant temperature are selected as dumping criteria. With constant time or constant temperature as the dump criteria, there will be variation in quality of the compound produced.The better criterion is the constant energy criterion. This is very versatile, and will automatically take care of any minor variation in operating conditions as well as of even major ones to give a consistent quality output. It can also be kept constant even when rotor rpm is changed or ram pressure is increased, while the time or temperature criteria will have to be re-established after a series of experiments.BLENDING OF POLYMERSIn compounds, sometimes polymer blends are used in order to cover deficiencies of one polymer by partial use of the other. However a homogenous dispersion of two different polymers on molecular scale is not possible.Most important condition for achieving good blending of polymers is that both polymers should have as near viscosities as possible during blending.HF Mixing Room ImageFUTURE DEVELOPMENTIn order to mix uniform, high quality, low-cost rubber in an environmentally clean area, the mixing systems in future must provide the following:-▪Accurate, automatic, clean and flexible weighing of all materials used in the mixed compound.▪Mixers that use :▪Either tangential or intermeshing 4-wing variable speed rotors depending on the product.▪Variable ram pressure and position during the mix cycle.▪Mix time based on feedback from instrumentation sensors that monitor and control in “Real Time “ temperature, viscosity, dispersion and energy.▪Greatly improved dust stops, rotor and chamber metal surfacing as well as mechanical and electrical components that will increase up-time and reduce overall maintenance cost.▪The down-stream equipment will be similar to what is used today but automation will either eliminate or minimise a need for the operator at themill, former or batch-off unit.▪Online automatic sampling and testing of each individual batch will be performed after the mill or forming machine and this data will be used tomake minor adjustments to the formula of the remaining batches as well asfurther processing down-stream.▪Controls will be more sophisticated with feedback loops to make sure each batch and formula will be compounded properly. They will automaticallyrecord and control the conditions of the mixer to provide a more consistentuniform mix.ZONE ANALYSIS OF UPSIDE DOWN POWER PROFILES :Power Curve Of Typical Banbury MixZONE – ILoading + wetting stage – Formation of a Single Mass of filler and rubber –penetration of Polymer in to filler voids – As the C-black is slowly absorbed into the rubber the torque increases. When the volume of rubber + C-black becomes equal to the chamber Vol., the raw comes to the lowest position, the raw hydraulic pressure on the stock disappears. The power shows first peak. More and more C-black gets absorbed, Stock volume becomes lower & the power curve comes down.ZONE – IIMost of the real dispersion work takes place. The filler agglomerates are gradually distributed through the polymer and then broken down ttotheir ultimate size. The power curve also starts rising till the whole stock with oil & C-black has consolidated. At this juncture the second power peak occur . ZONE – IIIPlasticization takes place.The power curve decrease beyond the second power peak has been found to obey first-order kinetic law,Log [(Po – Pt)/(Pt –Px)] = KtThe mixing should continue till dispersion half time. (i.e. (Po-Pt)/(Pt-Px) =0.5) after 2nd power Peak.TOTAL MIXING TIME = Black incorporation time + Dispersion half-time.To handle variety of rubber compounds on the same mill required that mill to have.▪Independent speed control on both rolls▪Widely variable speed on both rolls▪Independent temperature control on speed, friction ratio and temp. to be adapted to each individual .▪Hydraulically operated nip adjustmentTwo-Roll Mixing MillRECENT DEVELOPMENT FOR IMPROVING MIXING EFFICIENCY :1.Increased rotor speed2.Higher Ram Pressure3.Improved Rotor Design4.Improved Cooling System5.Continuous Mixing ProcessMAJOR CHANGES IN RUBBER & PLASTICS MIXINGOLD INTERMEDIATE NEWi) 2 Speed Rotor (20 –40 RPM) Variable (0 – 90 RPM)Type Pressure RamPressure(Psi)EffectivePressure(Psi)MixTime(%)OutputRatingNormal 90 25 100 100Intermediate 135 35 84 120High 280 70 70 143 IMPROVED COOLING SYSTEMTempered water / controlled water temperatures are selected relative to the coefficient of friction of the Sp. Polymer being mixed. Lowest possible Temp. at which the polymer gripping the metal surface enabling shear and turbulent flow of the polymer to take place rather than slippage.Polymer Tempered Water Temp. (max.) (°C)Highly Cryst. EPDM 60 – 70Natural Rubber 40 – 60SBR 50 – 60Low Cryst. EPDM 30 – 35Hypalon (CSPE) 30 – 35NBR (Nitrile) 20 – 25IIR (Butyl ) 20CR (Choloroprene) 151.Total Power consumption is reduced because More time is spent mixingrather than flopping around.2.Greater fill factor is obtained because the mix is hugging the metal duringthe whole time it is in the mixer.3.Batch to Batch consistency is improved because the temperature of themetal fluctuates in a very narrow range and each batch is exposed toessentially the same metal conditions at each step of the loading and mixing cycle.4.Improved dispersion due to absence of unbroken down polymer lumps.。
全球炼油加氢技术进展

全球炼油加氢技术进展全球炼油加氢技术进展炼油技术发展的动⼒源于新建企业的需求和现有企业在⽤技术的更新换代。
据有关机构完成的“全球炼⼚建设展望”(WRCO)报告统计分析,全球已公布的新建炼⼚和炼⼚扩能项⽬共计223个,预计到2021年将有106个项⽬。
其中,仅有19个是新建炼⼚,其余为现有炼⼚的扩能或改造项⽬,即对当今炼油业来说,对现有技术的更新换代更为迫切。
近年来炼油技术的主要发展趋势依然集中在以下5个⽅⾯:⼀是汽柴油质量升级;⼆是产品结构调整;三是炼油化⼯⼀体化;四是清洁⽣产技术;五是资源最⼤化利⽤技术。
在炼油技术已经⾮常成熟的今天,技术发展最突出的表现就是炼油催化剂的更新换代。
据美国催化剂集团(TCG)公司/美国催化剂集团资源(TCGR)公司报道,2015年全球炼油催化剂的消耗价值69亿美元,最主要的催化剂品种是加氢处理和催化裂化催化剂,按市场价值计各占40%,预计2021年炼油催化剂市值达到84亿美元。
在过去20年间,由于油品质量升级的关系,在所有炼油催化剂中加氢处理催化剂技术的发展最为显著,主要原因有以下3点:⼀是西欧、北美等先进发达国家炼⼚开始转向⽣产超低硫燃料;⼆是催化原料油加氢预处理需求增加;三是加氢裂化预处理提⾼中馏分油收率的需求增加。
由于环保法规对交通运输燃料中硫含量的要求不断趋严,全球脱硫能⼒出现快速增长,这种趋势将延续⾄2040年。
据欧佩克2016年世界⽯油展望报告预计,2016年新增脱硫能⼒的市场结构为:馏分油脱硫能⼒1650万桶/d,约占新增脱硫能⼒的71%;汽油脱硫能⼒420万桶/d,约占新增脱硫能⼒的18%;减压⽡斯油/残渣油处理能⼒250万桶/d,约占新增脱硫产能的11%。
到2021年新增脱硫能⼒约2亿t,2030年新增6.85亿t,2030—2040年新增2.8亿t,2040年新增11.5亿t,这些新增能⼒⼤部分来⾃亚太和中东地区,主要是满⾜欧Ⅳ和欧Ⅴ标准的燃料。
国内外炼油生产概况和炼油技术进展
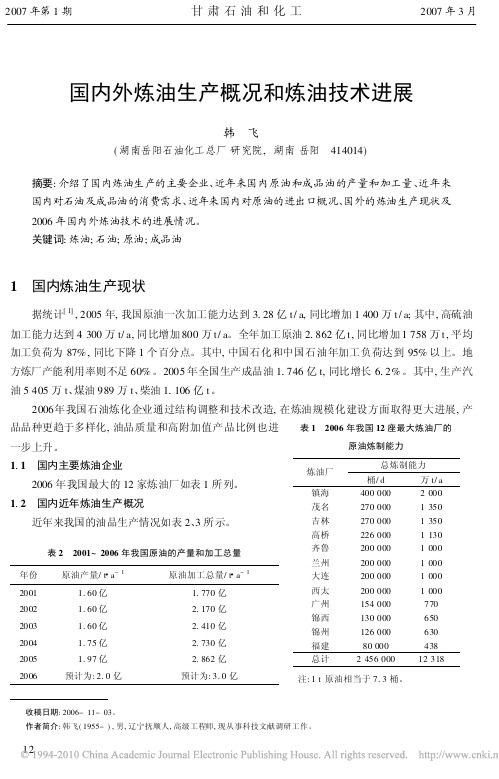
1
表 1 2006 年我国 12 座最大炼油厂的 原油炼制能力 炼油厂 镇海 茂名 吉林 高桥 齐鲁 总炼制能力 桶/ d 400 000 270 000 270 000 226 000 200 000 200 000 200 000 200 000 154 000 130 000 126 000 80 000 2 456 000 万 t/ a 2 000 1 350 1 350 1 130 1 000 1 000 1 000 1 000 770 650 630 438 12 318
2007 年第 1 期
甘肃石油和化工
2007 年 3 月
国内外炼油生产概况和炼油技术进展
韩 飞
414014) ( 湖南岳阳石油化工总厂 研究院 , 湖南 岳阳
摘要 : 介绍了国内炼油生产的主要企业、 近年来国内原油和成品油的产量和加工量 、 近年来 国内对石油及成品油的消费需求、 近年来国内对原油的进出口概况、 国外的炼油生产现状及 2006 年国内外炼油技术的进展情况。 关键词: 炼油; 石油; 原油 ; 成品油
表 4 2004 年 ~ 2006 年国内对石油和 成品油的消费需求 年份 2004 2005 2006 2004 2005 2006 名称 石油 石油 石油 成品油( 常规 ) 成品油( 常规 ) 成品油( 常规 ) 需求量 / 亿 t 3. 00 3. 15 3. 28 1. 570 1. 682 1. 770 布。 年份 2001 2002 2003 2004 2005 2006 表5 近年来我国原油的进出口总量 原油出口 总量/ 亿 t 0. 076 0. 072 0. 079 0. 071 0. 250 ( 石油出口量 , 包括原油 ) 预计 : 0. 260 ( 石油出口量 , 包括原油 )
欧洲炼焦技术现状和发展趋势简介
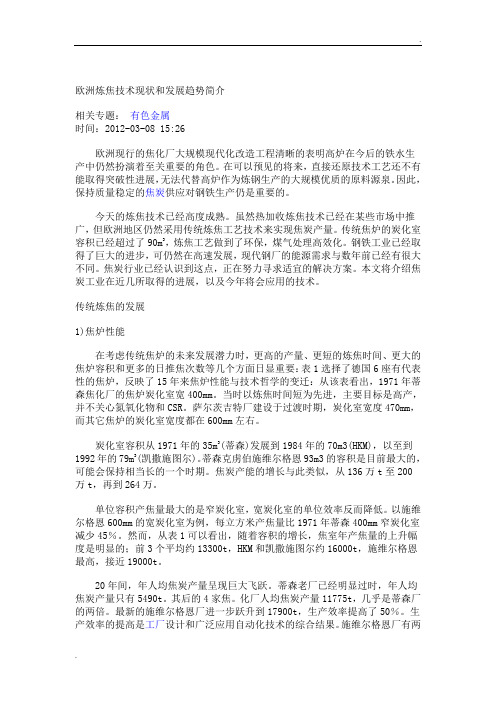
欧洲炼焦技术现状和发展趋势简介相关专题:有色金属时间:2012-03-08 15:26欧洲现行的焦化厂大规模现代化改造工程清晰的表明高炉在今后的铁水生产中仍然扮演着至关重要的角色。
在可以预见的将来,直接还原技术工艺还不有能取得突破性进展,无法代替高炉作为炼钢生产的大规模优质的原料源泉。
因此,保持质量稳定的焦炭供应对钢铁生产仍是重要的。
今天的炼焦技术已经高度成熟。
虽然热加收炼焦技术已经在某些市场中推广,但欧洲地区仍然采用传统炼焦工艺技术来实现焦炭产量。
传统焦炉的炭化室容积已经超过了90m3,炼焦工艺做到了环保,煤气处理高效化。
钢铁工业已经取得了巨大的进步,可仍然在高速发展,现代钢厂的能源需求与数年前已经有很大不同。
焦炭行业已经认识到这点,正在努力寻求适宜的解决方案。
本文将介绍焦炭工业在近几所取得的进展,以及今年将会应用的技术。
传统炼焦的发展1)焦炉性能在考虑传统焦炉的未来发展潜力时,更高的产量、更短的炼焦时间、更大的焦炉容积和更多的日推焦次数等几个方面日显重要:表1选择了德国6座有代表性的焦炉,反映了15年来焦炉性能与技术哲学的变迁:从该表看出,1971年蒂森焦化厂的焦炉炭化室宽400mm。
当时以炼焦时间短为先进,主要目标是高产,并不关心氮氧化物和CSR。
萨尔茨吉特厂建设于过渡时期,炭化室宽度470mm,而其它焦炉的炭化室宽度都在600mm左右。
炭化室容积从1971年的35m3(蒂森)发展到1984年的70m3(HKM),以至到1992年的79m3(凯撒施图尔)。
蒂森克虏伯施维尔格恩93m3的容积是目前最大的,可能会保持相当长的一个时期。
焦炭产能的增长与此类似,从136万t至200万t,再到264万。
单位容积产焦量最大的是窄炭化室,宽炭化室的单位效率反而降低。
以施维尔格恩600mm的宽炭化室为例,每立方米产焦量比1971年蒂森400mm窄炭化室减少45%。
然而,从表1可以看出,随着容积的增长,焦室年产焦量的上升幅度是明显的;前3个平均约13300t,HKM和凯撒施图尔约16000t,施维尔格恩最高,接近19000t。
- 1、下载文档前请自行甄别文档内容的完整性,平台不提供额外的编辑、内容补充、找答案等附加服务。
- 2、"仅部分预览"的文档,不可在线预览部分如存在完整性等问题,可反馈申请退款(可完整预览的文档不适用该条件!)。
- 3、如文档侵犯您的权益,请联系客服反馈,我们会尽快为您处理(人工客服工作时间:9:00-18:30)。
国外提高炼厂综合效益的技术研究进展
1 加氢裂化装臵处理重质原料
众所周知,传统加氢裂化技术根据生产目标,可以把瓦斯油(VGO)馏分的原油转化成柴油、喷气燃料油和石脑油等交通燃料。
虽然加氢裂化装臵处理VGO和更轻的进料油有很好的效果,但处理比VGO更重的原料油效率较低。
因此,沙特阿美石油公司(Saudi Aramco)一直致力于使利雅得炼厂有能力处理脱金属油(DMO),并且在过去几年已经做了大量工作,通过工艺和催化剂改进来加强这方面能力。
催化剂是基于Y分子筛改性以提高其催化活性。
预处理方法主要包括脱铝作用增加孔密度和沸石中嵌入Ti、Zr等过渡金属以及增强沸石酸性来提高馏分的选择性。
加氢裂化催化剂通过传统方法制备。
改性的USY沸石和联合剂混合然后依次经过挤压、干燥和煅烧,再通过浸渍法负载活性金属组分,通过干燥和煅烧即可制得催化剂。
进而研究了一系列因素变化所带来的影响,包括USY沸石、二氧化硅/氧化铝比例、金属类型、金属组分的含量、处理方式、粘合剂类型。
经过一系列研发工作,设计出85种催化剂,并测试长达2076天,挑选出合适催化剂进行放大和工业化。
每种催化剂测试15天来确定其活性和选择性。
挑选出的8种催化剂测试60天来确定产物收率、氢耗和长周期活性。
寿命测试180天来确定催化剂长周期稳定性。
催化剂的测试包括压力、温度、空速和氢油比对反应的影响。
进料是DMO和VGO的混合油来模拟阿拉伯轻原油。
催化剂的活性和选择性通过大于375℃的馏分油进行计算。
该研发项目自2007年开始,并于2010年完成,挑出四种催化剂进行放大和商业化。
催化剂工业化生产在2012年
完成,并在2013年在UOP炼厂完成了催化剂认证测试。
完成认证测试后,催化剂准备进行商业化发展。
工业化研究已经在利雅得炼厂完成了催化剂的测试。
2014年5月在利雅得炼厂装填了催化剂,并取得出人意料的效果。
该技术与常规加氢裂化技术在于加氢裂化预处理反应器级配装填多的加氢保护剂和加氢脱金属催化剂。
2 印度石油公司均相催化法减少焦化塔底油的再加工工艺
减粘裂化工艺是石油炼制过程中良好的热裂化方法,该工艺以减压塔底油为原料生产如天然气、石脑油、柴油高附加值产品。
由于减压塔底油的不稳定性(如减渣的粘度),限制了该工艺的高附加值的产品量。
目前减粘裂化装臵的质量转化率为15-20%,未转化的产品作为燃料油使用。
由于该法转化率较低,增大高附加值产品的收率需提高原料的停留时间至1小时,因此该法正逐渐被淘汰。
为解决该问题,相比加氢裂化法,均相催化裂化法具有催化剂制备简单、设备改造要求低、投资较少等优点,在众多的解决方案中该工艺是一种优良的解决方法。
在均相催化裂化工艺中,液相中水的质量百分比需高于5%,因此在减粘裂化过程中的加热单元,额外增加水的分离单元设备可以降低其在裂化塔中的停留时间,也可以降低塔的热负荷。
该工艺有众多优势,因此为该工艺研究了多类型的均相催化条件,以不同配比浓度的均相催化剂与减压渣油进行实验。
实验以75% MgSO4, 25% FeSO4(7H2O)制备的溶液与可溶于水并具有纳米尺寸粒径的MoS2在室温条件下混合,以
3:1wt%的配比制备了VisCat-07均相催化剂,溶解于减粘裂化油料中,进行油料的均相催化评价实验,并将试验进行工业放大,应用于17000桶/天生产能力的裂化装臵中,评价结果表明减压塔中焦油的质量转化率提高了4.5%,因此每套减粘裂化装臵可以提高近200万美元的经济效益。
3 用添加剂降低延迟焦化焦炭产率的实验研究
印度石油公司提出了采用添加剂方法降低焦化焦炭产率的方法研究。
延迟焦化是炼油厂应用最广泛的技术,它不需要任何催化剂就可以通过热裂解来提高重油的转化率。
装臵焦炭产率过高是技术的主要瓶颈问题,因此迫切需要开发降低延迟焦化装臵焦炭收率的技术。
到目前为止,降低焦炭产量主要集中在调整工艺参数上,如调整循环比、焦炭塔压力和最高炉出口温度等。
通过优化工艺参数,在不影响设备和生产进度的情况下,通过添加剂的使用,开发了延迟焦化过程中降低焦炭收率的技术,并在温度495℃,压力1.05kg/cm2,停留时间240分钟的条件下考察了4种添加剂的效果,其中一种添加剂可以使焦炭产率降低4%,同时液体馏分油收率相应提高3%,气体收率增加2%。
该技术目前仍处于实验室开发阶段。
4 日本Chiyoda公司混合二氧化钛加氢脱硫催化剂的工业应用
为了保护环境,许多国家的柴油含硫量指标都限制在10至15ppm以下的无硫水平。
此外,大量催化裂化装臵生产的催化轻循环油脱硫难度也较大。
为了解决这些问题,需要加氢脱硫活性较高的加氢脱硫(HDS)催化剂。
传统柴油加氢脱硫催化剂均采用氧化铝负载Co-Mo或Ni-Mo。
二氧化钛载体制备催化剂HDS活性更高,但因其比表面积极低而限制了其商业应用。
千代田公司通过对氧化铝颗粒表面层涂层二氧化钛的方法,开发了一种具有高的比表面积,等效的氧化铝的混合二氧化钛载体。
并进一步开发了(CT-HBT)的特性催化剂,活性较传统氧化铝催化剂提高1.5倍,活性对比见图1-2,可以高比例掺炼加工催化轻循环油生产低硫柴油。
该催化剂于2014年1月在日本西武石油有限公司的一个加氢脱硫装臵工业应用,装臵掺炼30%的催化轻循环油,已稳定运行31个月以上,显示了高的催化活性和稳定性。
最大的柴油加氢为30%无硫柴油的装臵。
图1:CT-HBT与传统氧化铝催化剂活性对比
5 用最小资本支出最大限度地提高柴油和氢的产率
印度石油公司通过技术革新,优化装臵进料并充分利用闲臵装臵,实现了最大限度地提高柴油和氢的产率。
就全球范围来说,对柴油的需求日益增加,加氢处理过。