挤出管材的模具设计及加工工艺共108页文档
挤出管材的模具设计及加工工艺

挤出管材的模具设计及加工工艺挤出管材是一种常见的金属加工工艺,通过在高温下将金属材料挤出成为管状,广泛应用于建筑、航空航天、汽车等行业。
挤出管材的模具设计及加工工艺对最终产品的质量和性能具有重要影响。
下面将详细介绍挤出管材的模具设计及加工工艺。
一、模具设计:1.材料选择:挤出管材的模具通常由高温耐磨的材料制成,如合金钢、硬质合金等。
模具的选择要根据生产管材的材料种类和工艺要求来确定。
2.模具结构设计:挤出管材的模具可分为双孔型和多孔型。
双孔型模具适用于直径较小的管材生产,而多孔型模具适用于直径较大的管材生产。
模具的结构设计应考虑到挤出管材的形状和尺寸要求,确保良好的挤出效果和生产效率。
3.流道设计:模具的流道设计直接影响到挤出管材的形状和尺寸精度。
流道的设计应考虑到金属材料的流动性和冷却效果,并采用适当的形状和尺寸,以确保挤出管材的质量和性能。
4.冷却系统设计:模具的冷却系统设计对挤出管材的质量和生产效率有重要影响。
冷却系统应考虑到金属材料的冷却速度和温度控制,以确保挤出管材的内外壁均匀冷却,减少挤出过程中的热变形和内应力。
二、加工工艺:1.材料准备:将选定的金属材料加热至合适的温度,使其具有适当的塑性和流动性。
同时,对金属材料进行预处理,去除表面氧化物和杂质,以提高挤出管材的质量。
2.模具装载:将加热好的金属材料注入到模具的进料口,并通过挤出机推动金属材料进入到模具的流道和挤出口,实现金属材料的挤出成型。
3.冷却固化:经过流道和挤出口的挤出管材进入冷却系统,通过水冷却或自然冷却的方式,使管材迅速冷却固化,提高管材的机械性能和尺寸精度。
4.后续处理:挤出管材经过冷却固化后,需要进行切割、去毛刺、修磨等后续处理工艺,以得到满足要求的管材产品。
挤出管材的模具设计及加工工艺,需要综合考虑金属材料的特性、挤出管材的形状和尺寸要求等因素,并采用合适的材料和工艺参数,以确保挤出管材的质量和性能。
同时,定期对模具进行维护和保养,以延长模具寿命和提高生产效率。
最新塑料管材挤出模具设计
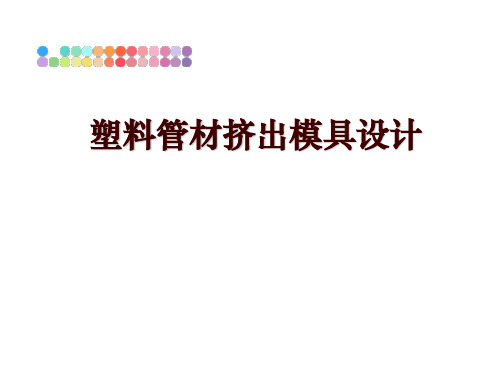
离模膨胀
拉伸比
(4)结构紧凑 在满足强度条件下,机头结构应紧凑,其形状 应尽量做得规则而对称,使传热均匀,装卸方便 和不漏料。
(5)选材要合理 由于机头磨损较大,有的塑料又有较强的腐蚀
性,所以机头材料应选择耐磨、硬度较高的碳钢 或合金钢,有的甚至要镀铬,以提高机头耐腐蚀 性。
此外,机头的结构尺寸还和制品的形状、加热 方法、螺杆形状、挤出速度等因素有关。设计者 应根据具体情况灵活应用上述原则。
8.2典型挤出机头及设计 常见的挤出机头有:
7.堵塞 防止压缩空气泄漏,保证管内一定的压力
8.1.2挤出成型机头分类及其设计原则 1.分类 由于挤出制品的形状和要求不同,因此要有相 应的机头满足制品的要求,机头种类很多,大致 可按以下三种特征来进行分类:
(l)按机头用头 吹管机头
挤板机头
如图所示,多孔板的作用是 将物料由螺螺旋运动变为直 线运动,同时还能阻止未塑 化的塑料和机械杂质进入机 头口此外,多孔板还能形成 一定的机头压力,使制品更 加密实。
3.分流器和分流器支架
分流器又叫鱼雷头。塑料 通过分流器变成薄环状, 便于进一步加热和塑化。 大型挤出机的分流器内部 还装有加热装置。
(2)弯管式机头 右图为弯管式机头,
其结构特点是内部不 设分流器支架,熔体 在机头中包围芯棒流 动成型,因此只产生 一条分流痕迹。这种 机头最突出的优点是: 挤出机机筒容
易接近芯棒上端,芯棒容易被加热;与它配合的冷 却装置可以同时对管材的内外径进行冷却定型,所 以定型精度较高:流动阻力较小,料流稳定,出料 均匀,生产率高,产品质量好。但结构复杂,制造 困难,生产占地面积较大。 PP PE
挤出管材的模具设计及加工工艺
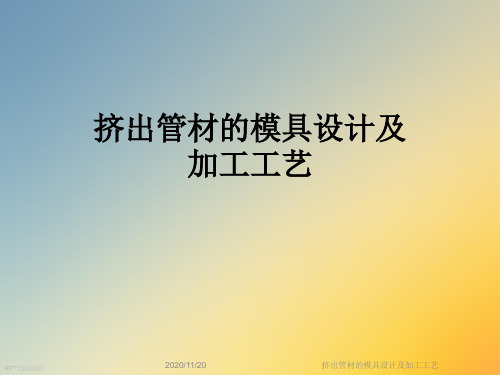
PPT文档演模板
挤出管材的模具设计及加工工艺
管机头
PPT文档演模板
挤出管材的模具设计及加工工艺
•芯棒直径d
•经验公式:
• 壁厚调节
•目的:管材壁厚均匀 •调节螺钉数量: •S=4~8
PPT文档演模板
挤出管材的模具设计及加工工艺
•三、特点
•1.优点 •⑴ 结构简单,成本低; •⑵ 中心进料,易于物料均匀分配; •⑶ 应用广泛。
•2.缺点 •⑴ 体积大,重量大; •⑵分流筋多,熔接线多。
PPT文档演模板
•5、调节螺栓 •7、芯棒支架
•1、橡皮片堵 头
•2、定径套
•3、口模 •4、芯棒
•6、分流锥
•8、模体
PPT文档演模板
•9、过滤 板
挤出管材的模具设计及加工工艺
•二、设计要点
•1. 压缩比 ε
PPT文档演模板
•压缩比——分流器支架出口处截面积与芯棒口模间的
•
截面积之比
•ε=3~ 10
•低粘度物料:4~10
PPT文档演模板
挤出管材的模具设计及加工工艺
PPT文档演模板
挤出管材的模具设计及加工工艺
多孔板(筛板)式分流板的实物图和挤 出物流痕的照片。
PPT文档演模板
挤出管材的模具设计及加工工艺
•蓝式管机头
•1.结构 • 2.工作原理
PPT文档演模板
挤出管材的模具设计及加工工艺
简单蓝式机头
PPT文档演模板
高粘度物料:3~6
•另一种方法:取分流器支架直径与口模直径之比
•UPVC:D/d=1.4~1.6 •PE:D/d=1.4~2
•大管取小值;小管取大值
挤出管材的模具设计及加工工艺
塑料管材挤出模具设计
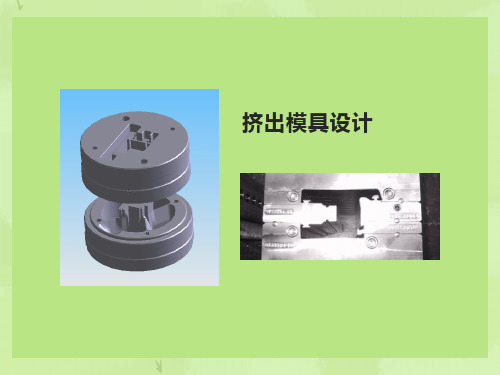
(直径<80mm)硬管挤出模具
下图所示是成型管材直径小于80mm用成型模具结构。采用内压法定径,定径套外腔是带有能通冷却循环水的环形套,冷却管坯;生产时,通过分流锥支架肋上的小孔,把压缩空气输入管坯内,管坯前端装有气堵,防止管内压缩空气逸出。分流锥、支架和芯轴也是用螺纹连接成一体,依靠分流锥支架外圆与模具体内圆紧密配合定位。保证分流锥、支架和芯轴与模具体装配后的同心精度。
PP
1.0.~1.2
HDPE
1.1~1.2
LDPE
1.2~1.5
口模定型段长度L1,与塑料性质、管材的形状、壁厚、直径大小及牵引速度有关。其值可按管材外径或管材壁厚来确定:
单击此处添加小标题
1
口模结构尺寸从图中可 以看到,主要是平直段 长度、内径和压缩角。 平直段(也叫定型段) 长度L1=(0.5~3)D 内径 d1= D/k 式中D —管材外径( mm) k—系数,k=1. 01~1.06。 压缩角α取14 °~50 °之间。
(4)结构紧凑
(5)选材要合理
02
01
03
04
05
常见的挤出机头有:
2典型挤出机头及设计
管材挤出机头、
异型材挤出机头
电线电缆包覆机头
1.管材挤出机头的结构形式
常见的管材挤出机头结构形式有以下三种: 直管式机头 图示为直管式机头。其结构 简单,具有分流器支架,芯模加热困难,定型长度较长:适用于PVC、PA、PC、PE、PP等塑 料的薄壁小口径的管材挤出。是挤出成型塑料 管材应用最广泛的一种模具结构
口模内径不等于塑料管材外
挤出成型工艺及模具设计

2020/3/31
2020/3/31
三、管材挤出机机头的设计
常用的挤管机头有:直通式、直角式和旁侧式
直通式挤管机头
1-芯棒 2-口模 3-调节螺钉 4-分流器支架 5-分流器 6-加热器 7机头体
2020/3/31
2020/3/31
2020/3/31
挤出机头结构
1-管材 2-定型模 3-口 模 4-芯棒 5-调节螺钉 6-分流器 7-分流器支架 8-机头体 9-过滤网 10电加热圈
④ 压缩角 低粘度塑料45~ 60° ,高粘度塑料30 ~ 50° 。
2020/3/31
(3) 分流器和分流器支架 ① 分流器设计需确定的尺寸
❖分流器的角度α
低粘度塑料30°~80°, 高粘度塑料取30°~60°。
❖分流锥长度L3
L3 =(1~1.5) D0
❖分流器头部圆角半径r
取0.5~2mm
2020/3/31
② 分流器支架
① 支承分流器及芯棒,另外起搅拌物料的作用。 ② 小型机头,分流器和分流器支架可以做成一个整体。 ③ 为了消除塑料通过分流器后形成的接合线,分流器支架
上的分流肋应做成流线型,一般3~8根。 ④ 分流器支架设有进气孔和导线孔,用以通入压缩空气和
内装置电热器时导入导线。
2020/3/31
2020/3/31
④机头内设有调节装置
调节熔体流量、口模和芯棒侧隙、挤出压力、成型温度、 挤出速度等。
⑤合理选择材料
机头的零件要承受熔体的压力作用,所以要有足够的强度 。必要时对连接零件进行强度校核。
与熔体接触的零件要有足够的耐磨性和耐腐蚀性,必要时 表面要镀铬处理。主要零件进行调质处理,硬度45~ 50HRC。
挤出成型—管材挤出工艺实例(高分子成型课件)

空
内通冷却水降温。
定 £ 尺寸准确,光滑度高,但内壁可能
径
较为粗糙。
法
七、挤出工艺实例(管材)
(一)工艺设备 4 冷却装置
可用的装置有冷却水槽和喷淋水箱两种。
为防止管材冷却过程中发生弯曲变形,采用沿管材圆周上均匀布置 喷水头对管材进行喷淋冷却。
七、挤出工艺实例(管材)
(一)工艺设备 5 牵引装置
②外径定型:外径定型:结构简单、操作方便,为我国普遍采用。
£ 在管子内部通入一定压力压缩空气 (0.03~0.28Mpa)。
内 £ 为保证管内压力,可用塞子堵住,
压
防止漏气,使压力稳定。
£ 压缩空气最好经过预热,因为冷空
法
气会使芯棒温度降低,造成管子内
壁不光。
£ 实质一个金属圆筒,管子靠真空孔
真
抽真空吸附在管壁上,圆筒定型套
七、挤出工艺实例(管材)
加料 堆放
挤出 切割
口模 牵引
定型 冷却
七、挤出工艺实例(管材)
(一)工艺设备
1 挤出机 (1)单螺杆挤出机
£ 据管材的截面积与挤出机螺杆的截面积之比选用合适的挤出机型号。 £ 流动性好的塑料熔体(PP,SPVC),取0.35-0.40;流动性差的塑料
熔体(RPVC)0.25-0.30。
6 切割装置——硬质管材 ①圆锯切割机:小口径管材 ②行星式自动切割机:大口径管材 注意 切割装置应该在切割时能够随管材一起移动,切割完成 后应能返回原位
七、挤出工艺实例(管材)
(一)工艺设备
7 扩口装置
七、挤出工艺实例(管材)
(二)操作规程及工艺参数设置 1 操作规程
1 开机预热:料筒、机头和口模温度一般应比正常操作温度高10~20℃,口 模处温度应略低,以防至管材由于自重而下垂,利于消除管材中的气泡。 2 调整螺杆转速:螺杆转速应由零缓慢增加至预定挤出量。 3 校验同心度:调整管材、定径套、冷却器之间的同心度。 4 挤出进入牵引机:引管或靠人工将管坯引入牵引机,牵引速度也应由慢到 快,直至达到规定的速度。 5 工艺参数(螺杆温度,冷却水温度等)调节 6 初步检验:依据国家标准或客户标准对产品进行检测 7 生产过程中注意的问题:对易产生内应力的管材应保持冷却水一定的水温
挤出管材的模具设计及加工工艺培训课件

直通式管机头
第二十五页,共106页。
直通式管机头
一、基本结构和工作(gōng1z.u基ò)本(jīběn2).工作原理
原理
结构
口模、芯棒、分流器、分流器支架、机 头体、调节(tiáojié)螺钉、连接螺钉等
第二十六页,共106页。
直通机头
第二十七页,共106页。
大口径(kǒujìng)管材挤出机头示 意图
按用途分: 硬管、软管、波纹管、复合管等
第二页,共106页。
塑料(sùliào)挤出成型设备
• 挤管成型(chéngxíng)设备
第三页,共106页。
管材(ɡuǎn cái)生产线
第四页,共106页。
管材生产(shēngchǎn)工艺流程 图
第五页,共106页。
一般管材(ɡuǎn cái)生产线工艺 过程
L1≈3D 国外资料: L1=(10~30)h
国内资料: L1=(30~40)h
D ——管材外径 h ——管材壁厚
UPVC:(18~33)h PE: (14~22)h PA: (13~23)h
PPVC:(15~25)h PP: (14~22)h
第三十五页,共106页。
口模直径 (z影h响íjì(nyǐgn)gDxiǎng)口模直径的因素:
• 原料→真空(zhēnkōng)上料→原料干燥 → 单螺杆挤出机→机头模具→定径套→喷淋 真空(zhēnkōng)定型箱→喷淋冷却水箱→ 喷码机→履带牵引机→成品检测包装
第六页,共106页。
带有标记(biāojì)管材生产线工艺 过程
• 原料+色母料→混合→真空上料→原料干燥
• →单螺杆挤出机→色线挤出机→机头模具
第四十四页,共106页。
挤出 管材 工艺

1 外径定径 外径定径适用于对管材外径尺寸精度要求高、 外表面粗糙度低的情况。 按照压力产生方式不同,外径定径又分为内压法 和真空法。
(1) 内压法外定径 定型套内径径向尺寸应考虑管材定型后收缩因素、 膨胀效应及牵引等对管材尺寸的影响。定型长度仍 应依据管材壁厚、牵引速度而定。
1) 当管材直径Ds>35mm,定径套长度L<10Ds,定 径套内径d>(0.8%~1.2%)Ds 2) 当管材直径Ds>100mm,定径套长度L=(3~5)Ds, 定径套内径尺寸不小于口模内径
挤出材料 聚烯烃 聚氯乙烯
定型套内径 (1.02-1.04)DS (1.00-1.02)DS
定型套长度 10DS 10DS
(2) 真空法外定径 真空定型套与机头口模不能联接在一起,应有 20~100mm距离。
1) 定径套内的真空度一般要求53~66kPa,真空孔径在 0.6~1.2mm范围内,与塑料熔体粘度和管壁厚有关,粘度大 或管壁厚度大时,孔径取大值,反之取小值 2) 真空定径套内径见表3-6 3) 真空定径套的长度一般应大于其他类型定径套长度
L1=(棒外径、型棒成型段长度、 压缩段长度,压缩角
(1) 芯棒的外径
d D 2 (0.83 ~ 0.94)t
L1‘≥L1
(2) 芯棒成型段长度L1‘ (3) 芯棒压缩段段长度L2
L2=(1.5~2.5)D0 (4) 压缩角β 低粘度塑料,β=45~60°
1 口模
确定口模内径和定型段长度
(1) 口模的内径D 由于管材离开口模后压力降低,体积膨胀;同冷 却和牵引收缩等原因使塑件外径不等于口模内径 d
s
确定口模的内径D方法:
D=k
(2) 定型段长度L1
口模与型棒的平直部分的长度成为定型段 定型段长度过长会使料流阻力过大,过短起不到定型作用 A 按管材外径确定L1 B 按管材壁厚确定L1 L1=nt
挤管式模具的设计资料
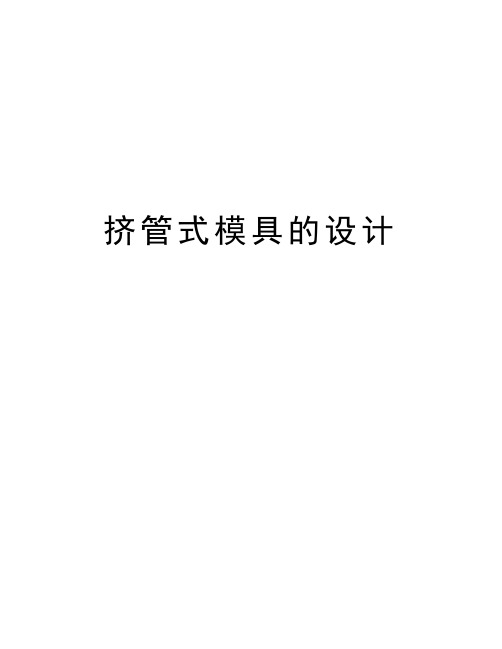
挤管式模具的设计电缆绝缘挤管式模具的设计挤塑模具是塑料挤出过程中最后的定型装置,其几何形状、结构形式和尺寸、温度高低、压力大小等直接决定电缆加工的成败。
电线电缆生产中使用的挤塑模具(模芯和模套)主要有三种形式:挤压式、半挤压式和挤管式。
近期我们对挤管式模具重新进行了研究和设计,以便提高生产效率及产品性能和质量,优化加工工艺。
下面就具体设计理念做个介绍。
1 挤管式模芯1.1 材料的选用挤管式模芯的结构特点是它的定径区是一个薄壁圆管,一般不能进行热处理。
因此,所用材料的耐磨性必须予以充分考虑,所以多用耐磨的合金刚制成,如38CrMoAl,加工成毛坯并留有一定裕量,经调质处理后再精加工,必须确保零件加工的同心度。
1.2 相关几何尺寸的设计及符号的说明现以φ90mm挤出机,挤制导体截面为120mm2的绝缘为例,其挤管式模芯结构见图1图中,D为模芯外锥最大直径;D1为模芯与机头结合锥体的最小端直径;D}为模芯内锥最大内径;α为模芯外锥角;d为模芯定径区内径;dノ为模芯定径区外圆直径;ι1为模芯定径区外圆柱长度;ι1为模芯定径区内圆柱长度;Lˊ为模芯与机头结合锥体长度;L为模芯总长度;αˊ为模芯与机头结合锥体角度;δ为模芯定径区壁厚。
其中,D、D1、Lˊ、D}均根据机头尺寸而定。
图1 挤管式模芯结构(1)模芯外锥角α。
该角度是根据机头结构和塑料流动特性设计的,α角越小,流道越平滑,突变小,对绝缘层结构有利。
(2)模芯外锥最大直径D、锥体最小端直径D1以及α1角和模芯中长度L。
这些尺寸是由机头模芯座的尺寸所决定的,而且与机头模芯座尺寸必须严格吻合,加工精度要高,表面须抛光。
(3)内锥最大直径D1。
该尺寸主要决定于加工条件,在保证壁厚的前提下越大越好,越小越难加工。
在φ90mm以下的挤塑机,模芯与机头的联接时采用螺纹,在这种情况下必须保证螺柱的壁厚。
在特殊情况下,如内加工困难,可加工成台阶式内孔。
(4)模芯定径区内径d。