位移控制器指南内容
位移仪表说明书

A系列单显位移仪表使用说明书一、主要特点:1、适用于直接配位移传感器对相应物理量的测量控制2、开放式仪表参数设定3、支持多机网络通讯(需订货时说明),配专用软件,可方便地实现仪表与上位机的联网测控管理。
4、设定参数密码锁定,断电后永久保存。
二、技术参数输入信号模拟量0~5KΩ/ 0~5V / 4~20mA测量范围-1999~9999 字测量精度0.2%FS ± 1 字或0.5% FS ± 1 字分辨率1、0.1、0.001 字显示方式.-1999~9999 测量值显示.-1999~9999 设定值显示.发光二极管工作状态显示输出信号馈电输出DC24V,负载能力≤30mA控制方式可选择1~4 限控制或1~4 组带差式控制,LED 指示。
控制方式为继电器ON/OFF 带回差/带差(用户可自由设定)控制精度± 1 字报警方式可选择1~4 限报警,LED 指示。
报警方式为继电器ON/OFF 带回差(用户自由设定)报警精度± 1 字参数设定面板轻触式按键数字设定参数设定值断电后永久保存参数设定值密码锁定保护方式继电器输出状态LED 指示输入超/欠量程指示电源欠压自动复位工作异常自动复位(Watch Dog)联机通讯通讯协议为二线制、三线制或四线制,也可由用户特殊要求,波特率300~9600bps 可由仪表内部参数自由设定。
接口和主机采用光电隔离,提高系统的可靠性及数据的安全。
通讯距离可达1 公里,配上位机采集各种信号与数据,构成能源管理和控制系统。
配用软件,可实现多台仪表与一台或多台微机进行联机通讯,系统采用主——从通讯方式,能方便的构成各种能源管理和控制系统。
整个控制回路只需一根二(三、四)芯电缆,既查实现与上位机通讯,上位微机可呼叫用户设定的设备号,随时调用各台仪表的现场数据,并可进行仪表内部参数设定。
使用环境环境温度0 ~ 50℃相对湿度≤85%RH 避免强腐蚀气体供电电压AC220V+10-15%(50Hz±2Hz)线性电源供电功耗≤5W结构标准卡入式重量420g项目功能按压然后抬起按下不放保持5秒SET参数设定选择键1)在显示测量值时则进入一级参数设定,显示参数CLK符号。
位移、计数、角度显示控制仪AW系列使用说明

P-1P-2 P-3 P-4版本号AWXAI位移、计数、角度显示控制仪AW 系列使用本产品前请认真阅读本说明书,在理解内容的基础上正确使用。
并妥善保存,以便需要时参考。
■ 安全须知◆请务必遵守下述各条及本说明书所记载的注意事项,如果不遵守注意事项进行使用,有导致重大伤害或事故的危险。
◆ 如果本产品的故障或异常可能导致系统重大事故的场合,请在外部设置适当的保护电路。
◆ 请勿在本产品所记载的规格范围之外使用。
否则可能导致触电、火灾、故障。
◆ 请勿使用在易燃、易爆气体的场所。
◆ 请勿触摸电源端子等高电压部位。
否则有触电的危险。
◆ 请勿拆卸以及改造本产品。
否则可能导致触电、火灾、故障。
◆ 请不要使用在原子能设备以及与生命相关的医疗器械等设备上。
◆ 本产品的所有输入输出信号线,为了防止浪涌发生,请设置适当的浪涌抑制电路。
◆ 本产品的安装形式为盘式安装,为了避免用户接近电源端子等高电压部分,请在最终产品上采取必要措施。
◆ 为了防止仪表损坏和防止机器故障,请在与本仪表接续的电源线或大电流容量的输入输出线上,安装适当容量的保险丝等安全断路器件保护仪表。
◆ 请不要将金属片或导线碎屑混入本产品中,否则可能导致触电、火灾、故障。
◆ 请确实地拧紧端子螺丝,如果不完全拧紧,可能导致触电、火灾。
◆ 请务必在切断电源后再进行清洁。
◆ 清洁时,请用干的软布擦去本产品的污垢。
请不要使用吸湿剂。
否则可能导致变形、变色。
◆ 请不要使用硬物擦蹭或敲打显示部分。
◆ 本产品的安装、调试、维护应由具备资质的工程技术人员进行。
◆ 为了长期安全地使用本产品,定期维修是必要的。
本产品的某些部件有的受寿命限制,有的因常年使用性能会发生变化。
◆ 本说明书如有变动,恕不通知,随时更新,查阅时请以最新版本为准。
如有疑问,请与本公司联系。
◆ 本公司不承担除产品本身以外的任何直接或间接损失。
为了防止触电和防止机器故障,请务必在关断电源后,再进行本机器的安装、拆卸。
位移控制实验报告结论(3篇)

第1篇一、实验背景位移控制实验是研究机械运动过程中,如何精确控制物体位移的一种实验。
本实验旨在通过搭建位移控制系统,验证位移控制原理,并对实验结果进行分析,为实际工程应用提供理论依据。
二、实验目的1. 理解位移控制的基本原理和实现方法;2. 掌握位移控制系统的搭建和调试技巧;3. 分析实验数据,验证位移控制效果;4. 为实际工程应用提供参考。
三、实验原理位移控制实验主要基于以下原理:1. PID控制原理:PID控制(比例-积分-微分)是一种常用的控制算法,通过调整比例、积分和微分三个参数,实现对系统输出的精确控制。
2. 步进电机控制原理:步进电机是一种将电脉冲信号转换为角位移的执行器,通过控制脉冲信号的频率和数量,实现精确的角位移控制。
3. 传感器反馈原理:通过传感器实时检测位移,并将反馈信号送回控制系统,实现闭环控制。
四、实验方法1. 搭建位移控制系统:本实验采用步进电机作为执行器,搭建了一个简单的位移控制系统。
系统主要由控制器、步进电机、驱动器和传感器组成。
2. 编程实现PID控制:利用C语言编写程序,实现对步进电机的精确控制。
程序中包含PID控制算法,通过调整PID参数,实现对位移的精确控制。
3. 实验数据采集:通过传感器实时采集位移数据,并记录实验过程中的位移变化。
五、实验结果与分析1. 实验结果:通过实验,验证了位移控制系统的稳定性和可靠性。
在给定的控制参数下,系统能够实现对位移的精确控制。
2. 结果分析:- PID参数优化:通过调整PID参数,实验结果表明,在合适的参数设置下,系统能够实现较好的控制效果。
- 传感器反馈对控制效果的影响:实验结果表明,传感器反馈对控制效果有显著影响。
当传感器反馈信号准确时,系统能够更好地跟踪目标位移。
- 步进电机性能对控制效果的影响:步进电机的性能对控制效果也有一定影响。
高性能的步进电机具有更高的精度和稳定性,有利于提高控制效果。
六、实验结论1. 位移控制实验验证了PID控制原理在位移控制系统中的应用,为实际工程应用提供了理论依据。
RDZW-2Na型智能轴向位移监视仪使用说明书

1.面板上的失效灯亮,说明传感器工作在非线性区段内或传感器系统有损坏;正常时灭。 2.显示跳动:前置器外壳、延长电缆高频接头、信号地线与机壳或大地连通,检查、排除短路点,使之绝缘。
八、仪表的质量保证
仪表出厂之日起一年内因厂方制造质量问题而引起不正常使用,本公司给予免费修理,如果用户自行拆装或保 管使用不当而造成损坏,则酌情收费修理。服务电话:0510-6296963-8008。
位键 5 次可将历史峰值清零。此时,按返回键,则返回测量状态;如果按功能键,则进入报警设置。 2 报警设置
在报警设置时,报警设置值不能超过仪表的量程,并且正报警、正停机值必须大于 0;负报警、负停机值必须 小于 0。 2.1 正停机设置:这时数码管显示“H1”,再按下功能键,数码管显示系统当前正停机值。其中有 1 位数字闪烁, 表示该位数值可以用加一键修改,每按一次加一键该位数值加 1,从 0~9 循环显示。用移位键可循环左移闪烁位; 修改完毕后,按下功能键存入,并进入正报警设置。 2.2 正报警设置:这时数码管显示“H2”,再按下功能键,数码管显示系统当前正报警值。修改方法同上,按下功 能键存入,进入负报警设置。
在报警延时设置状态下按 5 次移位键进入安装方向设置。 6.1 安装方向设置:这时数码管显示“P1”, 再按下功能键,数码管显示系统传感器当前的安装方向:0 正向远离, 1 正向接近,数字闪烁,用加一键修改,每按一次加一键,该位数值在 0 和 1 之间变化。修改完毕后,按下功能键 存入,并进入正向量程设置。 6.2 正向量程设置:这时数码管显示“P2”,再按下功能键,数码管显示正向量程设定值。其中有 1 位数字闪烁, 表示该位数值可以用加一键修改,每按一次加一键,该位数值加 1,从 0~9 循环显示。用移位键可循环左移闪烁位; 修改完毕后,按下功能键存入,并进入负量程设置。
轴向位移遮断器实验及汽动热网泵实验。作业指导

2#机轴向位移控制器试验作业指导书1、5#炉暖管至2#机电动隔离器门前。
2、检查2#机电动隔离汽门关闭,旁路门关闭。
3、打开2#机电动隔离汽门前疏水门4、检查汽轮油泵供汽门开启。
5、检查2#机汽轮油泵进汽门关闭6、打开2#机汽轮油泵疏水门7、起动汽轮油泵①电动隔离汽门前主汽压力达到l.8MPa表压,微开汽轮油泵进汽门,保持进汽门压力0.2 - 0.3MPa表压,疏水暖机3 -5分钟。
②逐渐开大汽轮油泵进汽门,保持进汽压力0.6 - 0.8MPa 表压,中速暖机5-10分钟。
③听、测汽轮油泵声音,确认工作正常后,逐渐提升转速,保持汽轮机油泵出口油压在0.8 - 0.9MPa表压,关汽轮油泵疏水门。
④在升压暖管过程中,应注意调整汽轮油泵进汽压力,防止超压超速,造成汽轮油泵飞车。
8、轴向位移控制器试验①将危机保安器及轴向位移控制器挂闸。
②全开启动阀手轮。
③旋转自动主汽门操纵座手轮,开启自动主汽门到1/3行程后,将轴向位移控制器捏手拉出使其动作,检查自动主汽门、调节汽阀、抽汽逆止门迅速关闭。
汽动热网泵启动试验作业指导书1、泵内及泵入口管道充水①检查三条线供回水阀门全部关闭。
②热网泵顶部放气门全部开启。
③开启热网直通门。
④开启南线热网泵旁路门。
⑤启动热网泵房补水泵(原南线补水泵),进行补水。
⑥热网泵顶部放气门有水流出后,停止补水。
2、汽动热网泵暖管①开启分汽缸至汽动热网泵供汽管道上所有疏水门②稍开分汽缸至汽动热网泵供汽门。
3、汽动热网泵启动前检查①检查向空排气门开启。
②检查汽轮机各部位疏水门全部开启。
③检查汽轮机排气门确已严密关闭。
④检查轴承室油位正常。
⑤将汽轮机挂闸,电动调节门在0位。
4、汽动热网泵启动①开机前确定管道温度200℃以上,压力0.8MP左右,开启汽动泵进汽调节门。
②逐渐开启主汽门冲转,将转速提升到400r/min暖机20min,同时检查机组振动情况。
③逐渐将转速提升到~800r/min暖机20min,同时检查机组振动情况。
YK14系列智能型四通道位移控制仪

YK-14系列智能型四通道位移控制仪操作说明书一、概述YK-14系列智能型四通道位移控制仪采用先进的微电脑技术及芯片,性能可靠,抗干扰能力强, 与位移传感器、变送器配合使用,可同时对四路位移参数进行显示测量、报警控制、变送输出、数据采集及通讯。
二、主要技术指标1.4路电位计信号与位移传感器2.分辨力:1/20000、14位A/D转换器3.测量精度:±0.2%FS,仪器自动对时漂、温漂进行校正,在整个使用温度范围(0~50℃)内长时间地保证测量精度。
4.显示方式:四路4位测量值同时显示。
5.断电保护:断电后参数不丢失,重新上电后无需重设。
6.采用先进的全自动数字式本机调校系统,无需电位计调整。
7.报警:上下限统一报警,并有接点输出,输出容量为AC220V/3A。
8.工作环境:-5~+50℃,湿度小于90%。
9.电源:AC85~265V,功耗小于5W。
10.外形尺寸: 160×80×125mm(横式) 80×160×125mm(竖式)三、端子接线四、操作说明(一)按键功能■—在设定过程中,按一下返回上一次设定操作,按下不动大于2秒钟则退出设定状态。
En—设定状态时,用于存贮参数的新设定值并进入下一个参数设置▲—在设定状态时,用于增加设定值。
▼—在设定状态时,用于减少设定值。
设定状态下,若按下▲或▼键不动,数值将快速增减,松手后停止。
(二)上电自检⑴按仪表的接线图连接好仪表的电源、输入、输出、报警等接线。
⑵仔细检查仪表的接线,正确无误后方可接通电源。
⑶上电后仪表显示HELO,PASS表示仪表自检通过,如果显示-HH-表示超量限或断偶及热阻开路,仪表采用人机对话形式来输入参数,用各种提示符来提示应输入的数据。
(三)参数设定(1)仪表在设定状态下,上排通道1数码管显示功能提示符,通道2显示设定值;工作状态下,四通道测量值同时显示。
(2)如果设定过程中12秒钟不改变参数,仪表自动返回运行。
简易单轴运动控制器使用说明书

简易单轴运动控制器使用说明书该款简易单轴运动控制器SAMC(Simple Axis Motion Controller)不需编程,提供多种运动方式:单向单次、往返单次、单向连续、往返连续,自动回原点等,参数设置合理简单,工作中实时显示位置状态,适用于单轴步进电机的各种场合控制应用,如自动送料、自动冲床、自动剪板机、器件编带、商标印刷、切标机、切带机、化妆品封尾等。
一、性能指标:1.输出脉冲频率:20KHz。
2.位置最大设置值999900脉冲。
3.速度最小设置值100Hz、加速度最小设置值100Hz/s。
二、电气特性:1.工作电源:DC24V。
2.输入检测口:5V开关信号(IO1\IO2\IO3\IO4,TTL电平)。
3.输出控制口:P+、P-、D+、D-、E+、E-都是差分输出,当用作单端时,可利用Vcc(+5V)与P+、D+、E+配合使用。
三、使用操作说明控制器底端有六个按键,分别是MODE、SET、SHIFT、UP、RUN、STOP分别表示模式、设定、移位、上加、运行、停止。
控制器通电(24V)以后,数码管全部显示零。
1.位移设定按下MODE键,则显示1,表示位移设定模式,如需进入该模式,则按下SET键,此时百位闪烁(位移、速度、加速度的设置值规定都是100的整数倍,所以位移、速度、加速度都是从百位开始设置),每按下一次UP键、数字显示增加1,百位设置完成后,按SHIFT 键,则千位开始闪烁,同样方法完成各位设置。
当位移值设定好以后,则再次按下SET键,此时设定的位移值成功被CPU读取。
位移初始默认值是40000。
2.最大速度设定再次按下MODE键,则显示2,表示最大速度设定模式,最大速度表示位移进给过程中最大进给速度,如需进入该模式,则按下SET键,此时百位闪烁,每按下一次UP键、数字显示增加1,百位设置完成后,按SHIFT键,则千位开始闪烁,同样方法完成各位设置。
当最大速度设定好以后,则再次按下SET键,此时设定的最大速度成功被CPU读取。
GT系列运动控制器用户手册(061230版)

固高科技(深圳)有限公司 地 址:深圳市高新技术产业园南区深港产学研基地西座二层W211室 电 话:0755-******** 26970819 26970824 传 真:0755-******** 电子邮件:support@ 网 址: 固高科技(香港)有限公司地 址:香港九龙清水湾香港科技大学新翼楼3639室电 话:(852) 2358-1033传 真:(852) 2358-4931电子邮件:info@网 址:/GT 系列运动控制器用户手册务必将此手册交给用户z 非常感谢您选购GT 系列运动控制器z 在您使用之前,请仔细阅读此手册,确保正确使用。
z 请将此手册妥善保存,以备随时查阅。
版权声明目录第一章概述------------------------------------------------------------------------------------------------------------------1-11.1简介..........................................................................................................................................................1-11.2 GT系列运动控制器型号及含义...........................................................................................................1-11.3 GT系列控制器功能列表.......................................................................................................................1-21.4 电机控制系统的基本组成.....................................................................................................................1-3第二章快速使用 ------------------------------------------------------------------------------------------------------------2-12.1 开箱检查...............................................................................................................................................2-12.2 GT系列运动控制卡的外形结构........................................................................................................2-12.3 安装步骤.................................................................................................................................................2-22.3.1 步骤1:在运动控制卡上设置跳线(仅对ISA卡).............................................................2-22.3.2 步骤2:将运动控制卡插入计算机.........................................................................................2-52.3.3 步骤3:安装控制器通讯驱动(Windows操作系统).........................................................2-52.3.4 步骤4:建立主机与运动控制器的通讯(Windows操作系统).........................................2-62.3.5 步骤5:连接电机和驱动器.....................................................................................................2-62.3.6 步骤6:连接控制卡和端子板.................................................................................................2-72.3.7 步骤7:连接驱动器、系统输入/输出和端子板....................................................................2-7第三章系统调试------------------------------------------------------------------------------------------------------------3-13.1 系统初始化.............................................................................................................................................3-13.2 设置控制输出,驱动使能(轴开启).................................................................................................3-33.3 PID参数调节.......................................................................................................................................3-43.4 以梯形曲线运动模式实现单轴运动.....................................................................................................3-4附录A 技术参数-----------------------------------------------------------------------------------------------------------A-1附录B 位置、速度、加速度设置---------------------------------------------------------------------------------------B-1B.1 位置设置...............................................................................................................................................B-1B.2 速度设置...............................................................................................................................................B-1B.3 加速度设置...........................................................................................................................................B-2附录C 典型接线-----------------------------------------------------------------------------------------------------------C-1C.1 控制器与Panasonic驱动器速度控制方式接线.................................................................................C-1C.2 控制器与Panasonic驱动器位置控制方式接线.................................................................................C-2C.3 控制器与SANYO DENKI PV1系列驱动器速度控制方式接线......................................................C-3C.4 控制器与SANYO DENKI PV1系列驱动器位置控制方式接线......................................................C-4C.5 控制器与SANYO DENKI PY0/PY2系列驱动器速度控制方式接线........................................................C-5C.6 控制器与SANYO DENKI PY0/PY2系列驱动器位置控制方式接线........................................................C-6C.7 控制器与SANYO DENKI PU系列驱动器速度控制方式接线.................................................................C-7C.8 控制器与Y ASKA W A SER VOP ACK系列驱动器速度/力矩控制方式接线...............................................................C-8C.9 控制器与Y ASKA W A SER VOP ACK系列驱动器位置控制方式接线........................................................C-9C.10 控制器与YASKAWA SGDE系列驱动器位置控制方式接线.......................................................C-10C.11 控制器与YASKAWA SGDM系列驱动器速度控制方式接线.......................................................C-11C.12 控制器与YASKAWA SGDM系列驱动器位置控制方式接线......................................................C-12C.13 控制器与三菱MEL SERVO-J2-SUPER系列驱动器速度控制方式接线.....................................C-13C.14 控制器与三菱MEL SERVO-J2-SUPER系列驱动器位置控制方式接线.....................................C-14C.15 控制器与FALDIC-W系列驱动器速度控制方式接线..................................................................C-15C.16 控制器与FALDIC-W系列驱动器位置控制方式接线..................................................................C-16 附录D 故障处理-----------------------------------------------------------------------------------------------------------D-1附录E GT Commander使用说明----------------------------------------------------------------------------------------E-1E.1 GTCommander窗口介绍及基本操作..................................................................................................E-1E.1.1 菜单和工具栏............................................................................................................................E-9E.1.2 系统状态显示............................................................................................................................E-9E.1.3 基于轴的控制............................................................................................................................E-9E.1.4 基于坐标系的控制....................................................................................................................E-9E.1.5 输入输出控制..........................................................................................................................E-10E.1.6 GT命令编辑和运行.................................................................................................................E-10E.1.7 基本参数设置窗口..................................................................................................................E-10E.1.8 选项设置窗口..........................................................................................................................E-10E.1.9 状态栏......................................................................................................................................E-10E.1.10 XY(Z)平台控制窗口..............................................................................................................E-10E.1.11 XY(Z)平台基本参数设置窗口................................................................................................E-11E.2 操作示例..............................................................................................................................................E-11E.3 异常情况解决.....................................................................................................................................E-13E.4 初始化文件GTCmd.ini和XY(Z)Table.ini.......................................................................................E-13E.5 GT Commander文件列表...................................................................................................................E-141.4 电机控制系统的基本组成1.运动控制器及其端子板;2a. 对于ISA总线卡,具有ISA插槽的IBM-PC或其兼容机;——或——2b. 对于PCI总线卡,具有PCI插槽的IBM-PC或其兼容机;3.具有增量式编码器的伺服电机或步进电机;4.驱动器;5.驱动器电源;6.+12V~+24V直流电源(用于接口板电源);7.原点开关、正/负限位开关(根据系统需要可选)。
基于PLC的XY轴位移控制系统设计说明
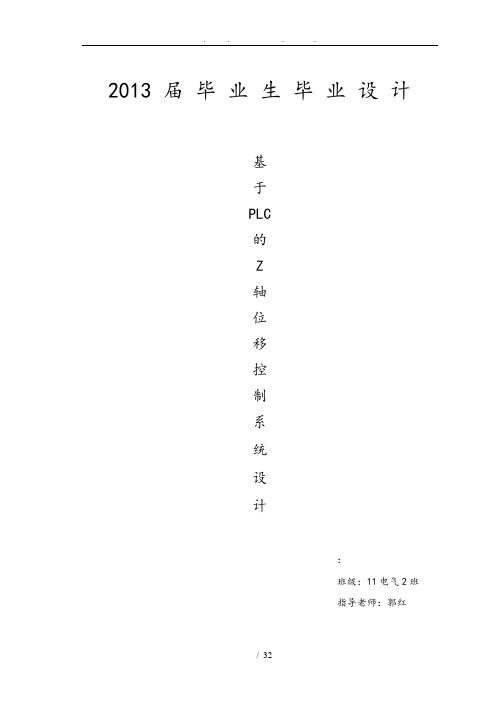
2013 届毕业生毕业设计基于PLC的Z轴位移控制系统设计:班级:11电气2班指导老师:郭红摘要随着电子信息产业的迅速发展,SMT技术已经成为电子组装技术中不可或缺的一部分。
SMT技术是指将表面贴装的电子组件,直接焊接于印刷电路底版的表面上,与传统插装工艺不同,SMT工艺的元件与焊点均在同一表面上。
并具有微型化、大规模化、自动化的优点。
当今绝大部分现代工业中的电器,电子产品都离不开SMT 技术的应用。
本设计是采用S7—200控制三相六拍的反应式步进电机,通过软件设计移位脉冲频率来控制步进电机的匀速前进。
移位寄存器指令MW0的低八位按照三相六拍的步进顺序进行赋值来控制步进动机的转动。
关键词贴片机、位移、S7-200PLC、步进电机目录第1章绪论11.1 设计背景11.2 系统设计的任务2第2章 Z轴位移控制系统工作原理V2.1 PLC控制步进电机V2.2 步进电机简介52.3 PLC的发展概述6第3章Z轴位移控制系统总体设计93.1步进电机的控制方式93.2 驱动电路93.3 PLC驱动步进电机10第4章控制系统硬件设计114.1西门子S7-200控制45BF00三相步进电动机114.2 S7—200的介绍124.3步进电机的选择134.4驱动器的选择144.5丝杆的选择154.6硬件配置 15第5章控制系统的软件设计165.1 STEP7概述165.2梯形图设计175.3程序设计说明18结论19参考文献20致21附录22第1章绪论1.1 设计背景随着电子信息产业的迅速发展,SMT技术已经成为电子组装技术中不可或缺的一部分。
SMT技术是指将表面贴装的电子组件,直接焊接于印刷电路底版的表面上,与传统插装工艺不同,SMT工艺的元件与焊点均在同一表面上。
并具有微型化、大规模化、自动化的优点。
当今绝大部分现代工业中的电器,电子产品都离不开SMT 技术的应用。
而贴装工艺更是SMT工序中不可或缺的一道。
贴片机的组主要作用是将表面组装元器件准确安装到PCB的固定位置上。
位移控制器
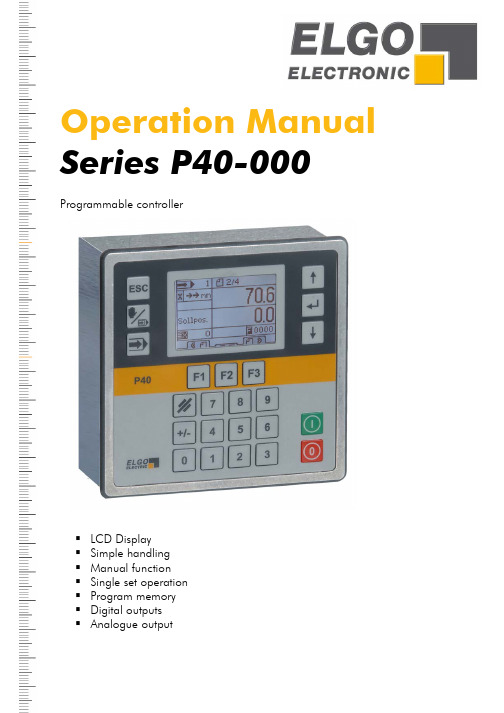
Operation Manual Series P40-000Programmable controllerLCD DisplaySimple handlingManual functionSingle set operationProgram memoryDigital outputsAnalogue output1 GENERAL INFORMATION (4)1.1 I NFORMATION O PERATION M ANUAL (4)1.2 E XPLANATION OF S YMBOLS (4)1.3 S TATEMENT OF W ARRANTIES (5)2 SAFETY (6)2.1 G ENERAL C AUSE OF R ISK (6)2.2 P ERSONAL P ROTECTIVE E QUIPMENT (6)2.3 C ONVENTIONAL U SE (7)3 TRANSPORT AND STORAGE (8)3.1 S AFETY I NSTRUCTIONS FOR T RANSPORT/U NPACKING AND L OADING (8)3.2 H ANDLING OF P ACKAGING M ATERIAL (8)3.3 C HECK OF T RANSPORT (8)3.4 S TORAGE (8)4 PRODUCT FEATURES (9)5 CONFIGURATION / FUNCTIONS (10)5.1 E LEMENTS (10)5.1.1 Control Elements (10)5.1.2 Display Elements (two‐axes‐version in the Program‐Mode is displayed here) (10)5.1.3 Function of Keys (11)6 INSTALLATION / INITIAL OPERATION (12)6.1 M ENU, S ECTIONS AND P ARAMETERS (12)6.1.1 Axis Menu / Distances (13)6.1.1.1 Distance / Longitudes Parameters (14)6.1.2 Axis menu / Times (18)6.1.2.1 Parameters of Time (19)6.1.3 Axis menu/analogue (20)6.1.3.1 Analogue Parameters (21)6.1.4 Axis menu/general parameters (23)6.1.4.1 System Parameters (24)6.1.5 Reference (29)6.1.5.1 Functioning of the reference drive (29)6.1.6 Menu / System (30)6.1.6.1 Menu / System Parameter (31)6.1.6.2 System‐Times (33)6.2 F UNCTIONING OF THE INPUTS/OUTPUTS (34)6.2.1 Functioning of the inputs (34)6.2.2 Functioning of the Outputs (35)6.3 C ONFIGURATION OF I NPUTS AND O UTPUTS (37)6.3.1 Linking the Inputs with Functions (37)6.3.2 Assigning the Logic to Inputs (37)6.3.3 Linking the Outputs with Functions (37)6.3.4 Assigning the Logic to Outputs (37)7 OPERATION (38)7.1 O PERATION M ODES (38)7.1.1 Manual Mode (38)7.1.2 Single Mode (38)7.1.3 Program Mode (38)7.1.3.1 Entering a Program (39)7.1.3.2 Processing a Program (39)8 DIAGNOSTICS / ERROR SEARCH (40)8.1 D IAGNOSTICS (40)8.2 E RROR M ESSAGE (40)9 INTERFERENCE (41)9.1 S ECURITY (41)9.2 E LECTRICAL I NTERFERENCE S UPPRESSION (42)9.3 R ESTART AFTER F AULT C LEARANCE (42)9.4 EMC I NFORMATION (43)10 MAINTENANCE (43)11 TECHNICAL DATA (44)11.1 D IMENSIONS (44)11.2 T ABLES OF PARAMETERS (45)11.2.1 Parameter of axes (45)11.2.2 System parameter (46)11.3 T ABLES OF I/O C ONFIGURATION (46)11.3.1 Mappings of the inputs (46)11.3.2 Assignment of the outputs (47)11.4 C ONNECTOR PIN ASSIGNMENT (48)11.4.1 Overview connector pin assignment (49)11.5 E XAMPLE WIRING DIAGRAM (51)12 TYPE DESIGNATION (52)13 ACCESSORIES (53)1General Information1.1Information Operation ManualThe manual contains important information regarding the handling of the controller.Precondition for safe operation is the compliance with the specified safety and handling instructions. Moreover, observe the existing local accident prevention regulation and general safety rules.Please read the operation manual carefully before starting to work. The manual is part of the product and should be kept accessible for the personnel near the device at anytime. The illustrations in the manual are for better representation of the facts; they are not necessarily to scale and can be slightly different to the actual construction.1.2Explanation of SymbolsWarning noticesWarning notices are characterized by symbols in the operation manual.The notes will be introduced through signal words to express the magnitude of the danger.Follow these advices in order to avoid accidents and injuries to persons and property.DANGER!This symbol in connection with the signal word …Danger“ indicates animmediate danger for the life and health of persons.Failure to heed these instructions can result in serious damage tohealth and even perilous injury.WARNING!This symbol in connection with the signal word …Warning“ indicates apossible danger to the life and health of persons.Failure to heed these instructions can result in serious damage tohealth and even fatal injury.ATTENTION!This symbol in connection with the signal word …Caution“ indicates apossibly dangerous situation.Failure to heed these instructions can lead to minor injury or propertydamage.Specific safety instructions:DANGER!This symbol in connection with the signal word “Danger” indicates animmediate danger for the life and health of persons through electricity.Failure to heed these instructions can result in perilous injuries ordeath. The operations have to be carried out only by an electrician.Tips and recommendations:1.3 Statement of WarrantiesThe warranty conditions are in a separate document in the sales documents.GuaranteeThe producer guarantees the functional capability of the process engineering and the selected parameter. The period of warranty is one year and begins with the date of delivery.Dismounting and disposalUnless agreements on redemption and disposal have been made, demount and dispose the device environmentally compatible taking into account the security instructions of this manual.Before dismountingDisconnect the power supply and secure against re-start, then disconnect supply lines physically and discharge remaining energy. Remove operating and auxiliary materials.DisposalRecycle the decomposed elements:Collect metal scrapElectronic components in electronic scrap Recycle plastic partsDispose the rest of the components according to their material consistenceATTENTION!Wrong disposal causes damage to the environment!Electronic waste, electronic components, lubricants and operating supplies are liable to treatment of hazardous waste and only approved specialized companies should perform disposal.Local authorities and waste management facilities provide information about environmentally suitable disposal.2Safety2.1General Cause of RiskThis chapter gives an overview about all important safety aspects to guarantee an optimal protection of employees as well as a safe and transference-free operation.Non-observance of the instructions mentioned in this operation manual can result in hazardous situations.2.2Personal Protective EquipmentEmployees should wear protective clothing during installation of the device to minimize the risk of accidents.Therefore:Change into protective clothing before beginning the work process. Also observe any labels in the operating area regarding protective clothing.For all works, generally wear:Safety working clothing... is close-fitting and tear-proof working clothingwith tight sleeves and without distant parts.It serves to protect against being gripped bymovable machinery parts. Also wear no rings,necklaces or other jewellery.Safety gloves... for protecting the hands against abrasion andcuts.2.3 Conventional UseThe controller P40 is for the limited purpose as described in this manual:CAUTION!Danger through non-conventional use!An ELGO position control of the series P40 is not a safe control inthe sense of the norm EN 61508. Safety-relevant shutdowns likeemergency stop cannot be realised with the controller.Non-intended use and non-observance of this operation manualcan lead to dangerous situations.Therefore:Use P40 only as describedStrictly follow this manualAvoid in particular the following uses, they are considered as non-conventional:Remodelling, refitting or changing of the devi ce or parts of it withthe intention to alter the functionality or the scope of the positioncontroller.Demand due to damage from non-intended use is excluded.The operator is liable for all damages during non-conventional use.Transport and Storage3Transport and Storage3.1Safety Instructions for Transport/Unpacking and LoadingATTENTION!Professional transport only.Do not throw, hit or fold the package.3.2Handling of Packaging MaterialAdverts for proper disposal refer to chapter General Information.3.3Check of TransportExamine delivery immediately after receiving for completeness and transport damages.In case of externally recognizable transport damages:Do not accept the delivery or do accept under reserveNote extent of damages on the transportation documents or on the delivery noteInitiate complaint immediatelyINFORMATION!Claim any damages you recognize as soon aspossible. The claims for damage can only beasserted in the lawful reclaim periods.3.4StorageStore device only under following conditions:Do not store outsideKeep dry and dust-freeDo not expose to aggressive mediaProtect from direct sun lightAvoid mechanical shocksStorage temperature: -20 to + 50 °CRelative humidity: max. 60%Inspect packages regularly if stored for an extensive period of time (> 3 months)Product Features4 Product FeaturesEssential features:Single or Two Axis-ControllerAnalogue or digital outputs for 1 - 3 speed operation16 free programmable digital in-/outputs (optional 8 digital in-/outputs)Program memory for up to 1000 setsGeneral: The single axis controller of P40 series is applicable to easy positioning tasks. An importantfeature is the easy structured function menu. It allows a quick and comfortable setting of the targetvalue, if necessary a specific quantity of desiredpieces.Target and actual value of the axes plus quantity will be displayed on the front panel. The keyboard is simple and user-friendly. With the keyboard the target and the actual value can be forced and thepositioning can be started.The P40 series has an internal program memory for up to 1000 lines. For the positioning two different kinds of output signals are available:Switch mode positioning and PID-analogue output. The P40 series can alternatively be supplied with 24VDC.Basic modes of operation:The P40 consists of three general operation modes:Manual: Inching operation moves the axes through operating the keypad.Single: A whole set can be processed.Program: In the program mode data sets can be strung together or programmed.This set of records is then processed sequentially. The program consists in this case ofseveral different data sets.Configuration / Functions5 Configuration / Functions5.1 Elements5.1.1 Control ElementsEscape Menu NavigationOperation Mode Function keys Start5.1.2 Display Elements (two-axes-version in the Program-Mode is displayed here)ADVICE! Display elements can vary depending on control mode and configuration.Input StopProgram Number Set NumberSymbol operating mode Actual ValuePage through the data setsAuxiliary FunctionTarget ValueAbsolute / Incremental PositionCounterProgram-CounterConfiguration / Functions5.1.3Function of KeysChange Operation mode between …Manual“ and …Single“Operation Mode “Program” (only at activated program mode)Activating (pressing 3 sec.) or exiting the Operation Mode or a Sub menu.Select or ConfirmCursor navigation …up“Cursor navigation …down“...Function keys (addicted to Menu or Operation mode)Clear or reset an inputChange of Sign...Enter Target Value or Parameter valueStart PositioningStop Positioning6Installation / Initial Operation6.1Menu, Sections and ParametersModeModeModeTimesAnalogue (only with Option PID )version)TimesAnalogue (only with Option PID )PasswordInputOutputKeyboardVersionINFORMATION!The service operation/parameter level can be reached byholding the “ESC” button for about 3 seconds.Most of the parameters, if not otherwise designated canonly be changed after entering the password/ PIN code.PIN CODE: 2505656.1.1 Axis Menu / DistancesRelevant distances for the axes can be set in this menu.6.1.1.1 Distance / Longitudes ParametersSlow forward/slow backward = middle speedThis parameter serves the input of the distance, at which the controller switches from high speed to slow speed before reaching the target position.Creep forward/creep backward = slow speedThis parameter serves the input of the distance, at which the controller switches from slow speed to creep speed before reaching the target position.Correction stop forward/correction stop backwardHere a constant overrun can be compensated.Example:The target position is overrun by 0.2 mm constantly. The data entry has to be 0.2mm.The stop command is then moved forward by 0.2 mm.When starting the operation the stop offset is set first to "0" in order to be able to calibrate the overrun accurately. For an exact positioning the stop offset should be as small as possible (0.0 to0.2 mm) i.e. the mechanical friction should be steady over the entire run distance and the slowspeed and/or creep speed must be adjusted accordingly small.INFORMATION!When positioning with PID, the correction stopserves as tolerance window.Example: Positioning with two speedsFor the adjustment of the parameters generally applies:Example: Positioning with three speedsHere for the adjustment of the parameters generally applies:Slow speed> Creep speed > Correction stopSlow speed = Creep speed > Correction stop100,0mmSlow speed: 10,0mm Creep speed: 10,0mmCorrection stop: 1,0mm99,0mm 90,0mm 100,0mm100,0mmSlow speed: 20,0mm Creep speed: 10,0mm Correction stop: 1,0mm99,0mm90,0mmFast80,0mm100,0mmTolerance windowIf the current actual position of the target position corresponds + / - to the value of "tolerance window", the corresponding output "tolerance zone" (see the main configuration) is set. ManipulationIt is possible to adjust the indicator of the actual value of the corresponding axis to the target value within the entered tolerance window. The entered range of tolerance is always active in the + and – range around the demand value. The real actual value is saved in the processor, i.e. no positioning errors add up.Example:Entered Value = 0,2mm (i.e. Tolerance Window +/- 0.2mm)Internal actual value 99.8mmDisplayed actual value 100.0mmTarget Value 100.0mmINFORMATION!The tolerance window should be set to zero before startingto operate.Spindle compensationIn order to adjust spindle or sprocket tolerances the target position must always be approached from the same direction, i.e. in one direction the target position will be overrun by the entered value. After expiration of the time that was entered in menu/times/backlash dwell the entered target position will be reached again.Forced loopIf the actual value is within the range target value +/- value of forced loop window during an absolute positioning a forced loop is moved.Reference valueA reference value and a reference position can be forced in this parameter.Retract lengthWhen activating the external retract input, the axis moves depending on the retract mode (see6.1.4.1 System parameters Æ Retract Mode) around this value or on this value.Software-end position minimum/maximumThese two values can be used if no mechanical switch end-positions are present or additionally for already existing mechanical switch end-positions.End position min.: This value should be between the smallest length/position that has to be proceeded and zero (respectively shortly before the mechanical switch end-position).End position max.: This value should be between the largest length/position that has to be proceeded and the maximum length (respectively shortly before the mechanical switch end-position). FactorThe factor for analysis of the pulses is set here.INFORMATION!As of the Software Version 1.64 the decimal point (number ofpositions after decimal point) is calculated automatically.The controller has 4-edge-triggering!Displacement (no PIN necessary)Here positive or negative dimensions are programmed, which are added to the actual value by activating an allocated input.Tool correction (Saw blade) (no PIN necessary)In the incremental measurement mode this correction value is automatically added, i.e. the positioning process continues working off to this value6.1.2Axis menu / TimesThe times relevant for the respective axis can be entered here.6.1.2.1Parameters of TimePosition reachedThe output signal is based on a variable time during input of a time value or statically/maintained(axis in position) if the value is set to 0.I t is set if the according axis has reached the target position.Spindle compensationIn the peak of the loop drive, the drive signals decline. The controller returns to the target valuewhen the parameterized time has expired (adjustment range 0.0 sec. … 99.9 sec.). If the value iszero, there is no waiting period at the peak.Manual changeHere the time in manual mode can be entered to set the speed from the low speed to the nexthigher speed.MonitoringHere a time (adjustment range 0.0 sec. ... 99.9 sec.) is set to monitor the measurement system. Ifthere are no signals from the measuring system during the programmed period of time, the drivesignals are switched off to stop the engine. If the value is zero the monitoring is deactivated.Delay control enableAfter the start command the output “control enable” is activated. After reaching the target positionand only after the expiration of the programmed time (adjustment range 0.0 sec. … 99.9 sec.) in the parameter “fall delay time control enable” the output is set back. If the parameter “delay controlenable” is at the value of zero, the output for the control enable is adjusted statically and remainsset until a change of operation modes respectively until activating the stop key.Start delayAt a starting command the start of the positioning is delayed for the entered time.Shutdown controlHere the time for shutdown after the position is reached is entered (adjustment range 0.0 sec. ...99.9 sec.).Retract timeThe dwell-time at the peak is entered here (adjustment range 0.0 sec. …99.9 sec.). After this timethe position control is set back from the retract peak to the target value. In addition this value is alsoused for a retraction on time.Reference timeIn the peak of the reference run, the drive signals decline. The controller will continue positioningwhen this time has expired (adjustment range 0.1 sec. ... 99.9 sec.).Quantity reachedHere the time is entered in 0.1 sec. for the signal “quantity reached”. If the value = 0, the output“quantity reached” is statically set.6.1.3 Axis menu/analogueThe axis relevant analogue parameters can be set in this menu.INFORMATION!The parameters for analogue mode are only of interest for devices with option PID.6.1.3.1 Analogue ParametersVelocityThe maximum speed is set in this parameter, in rpm. Should there be gearing between the motor and the measuring system, this has to be considered in the calculations (e.g. gear or spindle)Example!Demanded (below the maximum possible !) motor speed rpm = 3000 Gearing ratio i = 10V = rpm/i = 3000 rpm/10 = 300 rpmAccelerationThe acceleration during positioning is set in this parameter in revolutions per square second (][2s ][U ). Also here you have to consider possible gearing ratio.P-PortionProportional amplification: setting range 1 (99999)General:The P-controller exclusively consists of a proportional portion and has thereby its reinforcing characteristic. The P-term multiplies the input value with a constant coefficient.P40:At offset the difference between the target and actual value is multiplied with the entered value and shown as power-sharing. The bigger the proportional amplification the more sensitive the control loop will be (possibly even unstable).I-portion / I-LimitIntegral step: setting range 1 ... 99999 General:An I-controller (integrating controller) determines the control value through timed integration of the offset taking the reset time into account. A continuing offset leads to further increase of the analogue output. The reset time determines how big the temporal influence is. The maximum reset time is limited through I-limit. The step response of the I-portion is a linear increase. That means for a constant offset the integral will be increased and thus reinforces the I-portion.P40:At offset the analogue control voltage will continue to increase step by step until there is zero difference between the target and actual position and the entered I-limit in this parameter is reachedrespectively. The greater the I-portion, the slower is the response.D-portionDifferential voltage: setting 1 (1000)General:The D-controller (differential controller) determines the control value from the derivative with respect to time of the offset.P40:At offset a short voltage pulse proportional to the rate of change will be put out to compensate quickly without sacrificing the stability of the control loop permanently. The value of the voltage pulse is entered. (max + / - 10 V).Impulses encoder (rotary encoder resolution)The number of pulses per revolution of the engine is entered in this parameter. This enables amongst others the calculation of speed to be effected (max. 9999 pulses per revolution).Stop modeValue Mode0 the voltage of the analogue output is set to 0V1 the drive is set to shutdown through the highest possible acceleration2 the drive is set to shutdown through an acceleration according to the adjustedparameterManual fastHere the speed “fast” for moving the axis in manual mode can be defined.Manual slowHere the speed …slow“ for moving the axis in manual mode can be defined.v Reference mode 1Here the reference run speed of the stopping point until reaching the initiator is defined.v Reference mode 2Here the reference run speed of stopping point until reaching the index pulse is defined.6.1.4Axis menu/general parametersSystem relevant general parameters can be entered in this parameter.6.1.4.1 System ParametersAxis typeThe type of axis is defined.Digital + CPU (use with positioning through digital drive signals)Digital + PID (use with PID version)Button manual modeThe function of the keys in manual mode is defined in this parameter.off (The buttons F1, F3 on the control are deactivated for the according axis.This axis can only be moved via the correspondingly assigned inputs.)normalinvertedDrive signal configurationWith configuration of the drive signals different starting combinations for the corresponding speeds can be adjusted.Drive signals Æ Mode 13 speedsSpeed = output signals 1-3 ascending Output 4 sets direction reverseOutput signals 1234Creep forward XSlow forward X XFast forward X X XCreep backward X XSlow backward X X XFast backward X X X XDrive signals Æ Mode 22 speeds ((ELGO Standard) Independent outputs for forwards and reverseIndependent outputs for fast and slowOutput signals 1 2 3 4Creep forward X X Slow forward Fast forward X X Creep backward X X Slow backwardFast backward X XDrive signals Æ Mode 32 speedsspeed = output signals 2 + 3output 4 set direction reverseOutput signals 1 2 3 4Creep forward X XSlow forwardFast forward X XCreep backward X X XSlow backwardFast backward X XXDrive signals = Mode 42 speeds Independent outputs for direction and speedOutput signals 1 2 3 4Creep forward XSlow forwardFast forward XCreep backward XSlow backwardFast backward XDrive signals = Mode 53 speedsSpeed forward = output signals 1-3 ascendingSpeed backward = always fastoutput 4 sets direction reverseOutput signals 1 2 3 4Creep forward XSlow forward X XFast forward X X XCreep backward X X X XSlow backward X X X XFast backward X X X XDrive signals = Mode 6speeds3Binary codedoutput 1 = forwardoutput 4 = backwardoutputs 2+3 = speedOutput signals 1 2 3 4Creep forward X XSlow forward X XFast forward X X XCreep backward X XSlow backward X XFast backward X X XDrive signals = Mode 73speedseparatelyForward/backwardOutput signals 1 2 3 4forward XCreepSlow forward X XFast forward X X Xbackward XCreepSlow backward X XFast backward X X XReference mode7.1Operation Modes)(seeMode 1 Reference via parameter with “F2”- button *Mode 2 Reference via parameter & external input *Mode 3 Reference via Target value & “F2” buttonMode 4 Reference via Target value & external input **Mode 5 Reference drive pos. via parameter with “F2” button **Mode 6 Reference drive pos. via external input. **Mode 7 Reference drive neg. via “F2” button **Mode 8 Reference drive neg. via external input *** see axis parameters Æ axis Æ distances Æ reference value** see axis parameters Æ axis Æ time Æ reversion Ref. driveExtra on PID – positioning:Æ Axis Æ Analogue Æ v. Ref. drive part 1Axis-ParameterÆv. Ref. drive part 2Above the “F2”-button the reference symbol of the corresponding axis is displayedExternal input has to be allocated.Spindle compensation modeNo spindle compensationNegative spindle compensation -Positive spindle compensation +With forced loop -With forced loop +Software end-positionall end positions activeend position min deactivatedend position max deactivatedall end positions deactivatedHardware end-positionall end positions activeend position min (defined input) deactivatedend position max (defined input) deactivatedall end positions deactivatedRetract modeMode 1 Descent/retract to actual value + adjusted value*Mode 2 Descent/retract to adjusted value*Mode 3 Descent/retract positive to actual value for the adjusted time period**Mode 4 Descent/retract to actual value + adjusted value* without returnMode 5 Descent/retract to adjusted value* without returnMode 6 Descent/retract positive to actual value for the adjusted time period** without return Mode 7 Descent/retract to actual value – adjusted value*Mode 8 Descent/retract negative to actual value for the adjusted time period**Mode 9 Descent/retract to actual value – adjusted value* without returnMode10 Descent/retract negative to actual value for the adjusted time period** without return * see axis parameter Æ axis Æ distances Æ descent/retract distance** see axis parameter Æ axis Æ time Æ descentError compensationHere the activity of the error compensation is defined for incremental measurement positioning.offonCounterWith this parameter the counter mode will be set into the “single mode”.without counterauto decrement *auto decrement + Stop *auto increment *auto decrement/ increment *decrement **decrement + Stop **increment **decrement/ increment **。
位移控制器指南内容
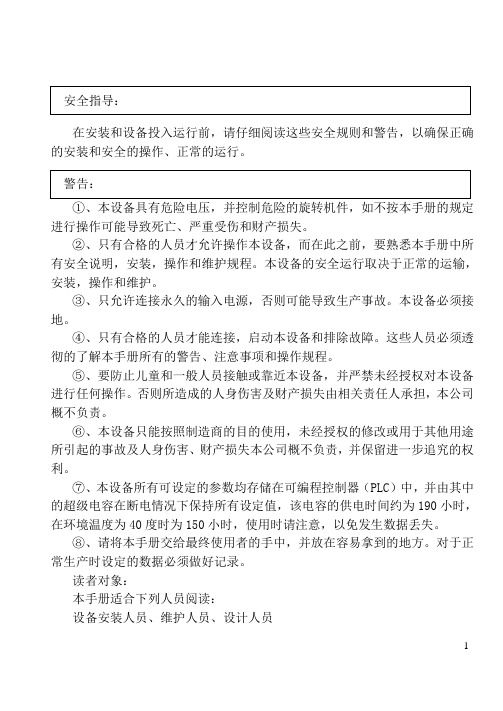
在安装和设备投入运行前,请仔细阅读这些安全规则和警告,以确保正确的安装和安全的操作、正常的运行。
①、本设备具有危险电压,并控制危险的旋转机件,如不按本手册的规定进行操作可能导致死亡、严重受伤和财产损失。
②、只有合格的人员才允许操作本设备,而在此之前,要熟悉本手册中所有安全说明,安装,操作和维护规程。
本设备的安全运行取决于正常的运输,安装,操作和维护。
③、只允许连接永久的输入电源,否则可能导致生产事故。
本设备必须接地。
④、只有合格的人员才能连接,启动本设备和排除故障。
这些人员必须透彻的了解本手册所有的警告、注意事项和操作规程。
⑤、要防止儿童和一般人员接触或靠近本设备,并严禁未经授权对本设备进行任何操作。
否则所造成的人身伤害及财产损失由相关责任人承担,本公司概不负责。
⑥、本设备只能按照制造商的目的使用,未经授权的修改或用于其他用途所引起的事故及人身伤害、财产损失本公司概不负责,并保留进一步追究的权利。
⑦、本设备所有可设定的参数均存储在可编程控制器(PLC)中,并由其中的超级电容在断电情况下保持所有设定值,该电容的供电时间约为190小时,在环境温度为40度时为150小时,使用时请注意,以免发生数据丢失。
⑧、请将本手册交给最终使用者的手中,并放在容易拿到的地方。
对于正常生产时设定的数据必须做好记录。
读者对象:本手册适合下列人员阅读:设备安装人员、维护人员、设计人员第一章设备描述1、概述WY21X系列位移控制器是我公司开发研制的一种新型位移控制器,基本结构如下图所示。
其控制的核心部分是可编程控制器,因此运行可靠;响应速度快,可达毫秒级;并具有远程通讯能力,可以直接和其它控制系统(如:PLC 系统、工业控制网络系统)相连接;并可提供标准模拟量输出信号(电压或电流,此项可选)和远程数字显示模块(此项可选)等优点。
系统结构图物体的位移通过绝对型编码器进行检测,因此分辨率高。
由受控设备通过现场变送单元的传动机构带动编码器一起旋转,编码器将位移转换为脉冲编码信号,送到PLC的输入端。
位移测量与控制系统

亮条: 暗条:
Δφ=2kπ, k=0,1,l,2,… 相长干涉
Δφ=2kπ, k=0,1,l,2,… 相消干涉
结构:
光 源
观察屏、 光电接收
固定 反射镜 半透半反镜
被测物体
实现要点:(1)单一光源
(2)被测物体
(3)光电接收
伺服电机
伺服电机 编码器
角编码器在机器人控制中的应用
利用编码器测量伺服电机 的转速、转角,并通过伺服 控制系统控制其各种运行参 数。
•转速测量 •转子磁极位置测量 •角位移测量
编码器在伺服电机中的应用
编码器在数控加工中心的刀 库选刀控制中的应用
角编码器与旋转刀库连接
刀具 旋转刀库 角编码器的输出为当前刀具号
被加工工件
光栅在机床上的安装位置(2个自由度)
光栅在机床上的安装位置(3个自由度)
数显表
2自由度光栅数显表
X位移显示 Z或Y位移显示
•2021/3/8
素材和资料部分来自 网络,如有帮助请下载!
•43
相邻两数只有一位不同每次只有一位变化转换放大足够电平驱动整形接近理想方波细分提高分辨率光学电路多位码同时动作同步误差错码读数直观不易电路处理直观易于后续电路和计算机处理角度位置二进制码十进制码002254506759001125135015751800202522502475270029253150337500000001001000110100010101100111100010011010101111001101111011111011121314150000000100110010011001110101010011001101111111101010101110011000位绝对码光电编码器码制每一个微小的角位移都有一个对应的编码常以二进制数据形式来表示
PLC移位控制

SRW LW0, 3
以第二条指令为例,指令执行情况如下表所示。
精品文档
13
知识3 基本逻辑指令
➢左移和右移指令:
精品文档
14
知识3 基本逻辑指令
➢左移和右移指令:
循环左移和循环右移根据所循环移位的数的长度分别又可 分为字节型、字型、双字型。 循环移位特点: 移位数据存储单元的移出端与另一端相连,同时又与SM1.1 (溢出)相连,所以最后被移出的位被移到另一端的同时, 也被放到SM1.1位存储单元。例如在循环右移时,移位数据 的最右端位移入最左端,同时又进入SM1.1。SM1.1始终存 放最后一次被移出的位。
培养学生安全操作规范操作文明生产的行为和团结协作的精神1舞台灯光控制的控制思想2绘制梯形图3正确接线4实验验证5故障排除1常用电工工具
项目四 舞台灯光控制
能力(技能)目标
1、能够在理解舞台灯光控制原理; 2、根据电气原理图编制梯形图; 3、能够正确接线; 4、能通过实验对项目进行验证; 5、会对所出现的故障进行排查与纠错。
精品文档
9
知识3 基本逻辑指令
➢移位指令:
1. 左移和右移 2. 循环左移、循环右移 3. 寄存器移位
精品文档
10
知识3 基本逻辑指令
➢左移和右移指令:
(1)字节左移和字节右移 SLB和SRB,字节左移和字节右移。使能输入
有效时,把字节型输入数据IN左移或右移N 位后,再将结果输出到OUT所指的字节存储 单元。最大实际可移位次数为8。
*AC、*LD。
• 指令格式: BIR IN1, OUT
• 例: BIR IB0, VB10
精品文档
dc5000d位移控制器说明书

dc5000d位移控制器说明书1. 概述本产品为dc5000d位移控制器,公司遵循国家行业执行标准:GB7000.13-1999,确属本公司产品质量问题,自购置之日起保修期为3个(非正常使用而致使产品损坏,烧坏的,不属保修之列。
)2. dc5000d位移控制器技术特性本产品额定容量高达900mAH。
超长寿命电池,高达500次以上循环使用。
采用节能,高功率,超长寿命的LED灯泡。
充电保护:充电状态显示红灯,充电满显示绿灯。
3. dc5000d位移控制器工作原理LED灯由电池提供电源而发光,此电池充电后可重复使用。
4. dc5000d位移控制器结构特性:(略)6. dc5000d位移控制器使用和操作充电时灯头应朝下,将手电筒交流插头完全推出,直接插入AC110V/220V电源插座上,此时红灯亮起,表示手电筒处于充电状态;当充电充满时,绿灯亮起,表示充电已充满。
dc5000d位移控制器使用时推动开关按键,前档为6个LED灯亮,中间档为3个LED灯亮,后档为关灯。
dc5000d位移控制器充满电,3个LED灯可连续使用约26个小时,6个LED灯可连续使用16个小时7.dc5000d位移控制器故障分析与排除①使用过程中若发现灯不亮或者光线很暗,则有可能是电池电量不足,如果充电后灯变亮则说明手电筒功能正常,如果充电后仍然不亮,则有可能是线路故障,可以到本公司自费维修。
②使用几年后若发现充电后灯不亮,则极有可能是电池寿命已到,应及时到本公司自费更换。
8. 维修和保养在使用过程中,如LED灯泡亮度变暗时,电池处于完全放电状态,为保护电池,应停止使用,并及时充电(不应在LED灯泡无光时才充电,否则电池极易损坏失效。
)手电筒应该经常充电使用,请勿长期搁置,如不经常使用,请在存放2个月内补充电一次,否则会降低电池寿命9.dc5000d位移控制器注意事项请选择优质插座,并保持安全规范充电操作。
产品充电时切勿使用,以免烧坏LED灯泡或电源内部充电部件。
振动、位移、转速设置方法
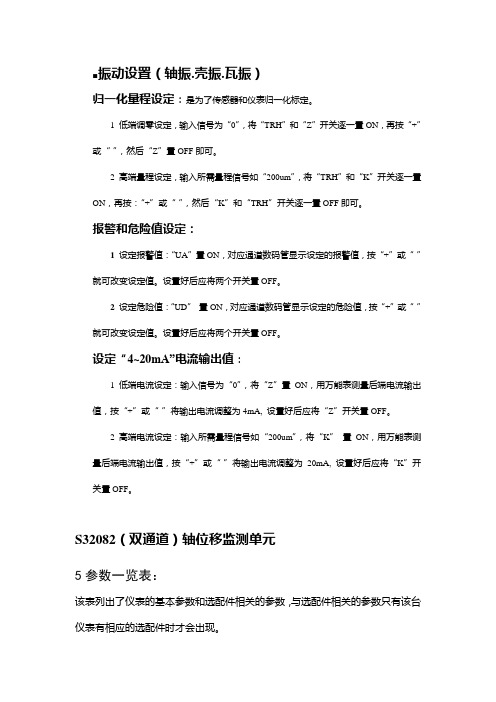
■振动设置(轴振.壳振.瓦振)归一化量程设定:是为了传感器和仪表归一化标定。
1 低端调零设定,输入信号为“0”,将“TRH”和“Z”开关逐一置ON,再按“+”或“-”,然后“Z”置OFF即可。
2 高端量程设定,输入所需量程信号如“200um”,将“TRH”和“K”开关逐一置ON,再按:“+”或“-”,然后“K”和“TRH”开关逐一置OFF即可。
报警和危险值设定:1设定报警值:“UA”置ON,对应通道数码管显示设定的报警值,按“+”或“-”就可改变设定值。
设置好后应将两个开关置OFF。
2设定危险值:“UD”置ON,对应通道数码管显示设定的危险值,按“+”或“-”就可改变设定值。
设置好后应将两个开关置OFF。
设定“4~20mA”电流输出值:1 低端电流设定:输入信号为“0”,将“Z”置ON,用万能表测量后端电流输出值,按“+”或“-”将输出电流调整为4mA, 设置好后应将“Z”开关置OFF。
2 高端电流设定:输入所需量程信号如“200um”,将“K”置ON,用万能表测量后端电流输出值,按“+”或“-”将输出电流调整为20mA, 设置好后应将“K”开关置OFF。
S32082(双通道)轴位移监测单元5参数一览表:该表列出了仪表的基本参数和选配件相关的参数,与选配件相关的参数只有该台仪表有相应的选配件时才会出现。
“说明”一栏是该参数在本说明书的章节“地址”一栏是计算机读或设置该参数时的地址。
无通信功能的仪表与此无关“取值范围”一栏是该参数的设置范围以及符号表示的参数内容与数值的关系。
无通信功能的仪表与此无关。
第一组参数:报警设定值符号名称内容地址取值范围说明A V 偏差报警方式的比较值00H -1999~9999 7.3 AH 第1报警点设定值01H -1999~9999 7.3AL 第2报警点设定值02H -1999~9999 7.3AHH 第3报警点设定值03H -1999~9999 7.3ALL 第4报警点设定值04H -1999~9999 7.3o_L 仪表正常灯电压下限05H 0~-20.0 7.2 o-H 仪表正常灯电压上限06H 0~-20.0 7.2 第2组参数:报警组态符号名称内容地址取值范围说明OA 密码10H 0~9999 6.4ALo1 第1报警点报警方式11H -1999~9999 7.3 ALo2 第2报警点报警方式12H -1999~9999 7.3 3ALo3 第3报警点报警方式13H -1999~9999 7.3 4ALo4 第4报警点报警方式14H -1999~9999 7.3 HYA1 第1报警点灵敏度19H 0~8000 7.3 HYA2 第2报警点灵敏度1AH 0~8000 7.33HYA3 第3报警点灵敏度1BH 0~8000 7.3 4HYA4 第4报警点灵敏度1CH 0~8000 7.3 CYT 报警延时1FH 0~20 7.3第3组参数:折线运算符号名称内容地址取值范围说明c1 第1折线点测量值20H -1999~9999 7.2b1 第1折线点标准值21H -1999~9999 7.2c2 第2折线点测量值22H -1999~9999 7.2b2 第2折线点标准值23H -1999~9999 7.23c3 第3折线点测量值24H -1999~9999 7.2 3b3 第3折线点标准值25H -1999~9999 7.2 4c4 第4折线点测量值26H -1999~9999 7.2 4b4 第4折线点标准值27H -1999~9999 7.2 5c5 第5折线点测量值28H -1999~9999 7.2 5b5 第5折线点标准值29H -1999~9999 7.2 6c6 第6折线点测量值2AH -1999~9999 7.2 6b6 第6折线点标准值2BH -1999~9999 7.2 7c7 第7折线点测量值2CH -1999~9999 7.2 7b7 第7折线点标准值2DH -1999~9999 7.28 c8 第8折线点测量值 2EH -1999~9999 7.2 8b8 第8折线点标准值 2FH -1999~9999 7.2第4组参数:测量及显示 符号 名称 内容 地址 取值范围 说明inch 输入信号选择 30H 0~147.1 In-d 显示小数点位置选择 31H 注27.1 u-r 量程下限 32H -1999~99997.1 f-r 量程上限 33H -1999~99997.1 in-A 零点修正值 34H -1999~99998 Fi 満度修正值 35H 0500~15008 c-d 折线功能选择 37H 注37.2 i-L 仪表输入电压下限 38H 0~-207.1 i-H 仪表输入电压上限 39H 0~-207.1clr 清零许可参数 3AH ON/OFF 设置为ON 时才有清零功能inch故障代用值3CH-1999~99997.1第5组参数:通信信号接口,变送输出等符号 名称 内容 地址 取值范围 说明Fbao 峰值保持方式 4CH 0~3 0和3可设,出厂设置为1 Op 输出信号选择 4DH 0~24~20MA bA-L 变送输出下限 4EH -1999~99997.1bA-H变送输出上限4FH-1999~99997.16操作6.1面板及按键说明名称说明1显示窗● 显示测量值● 在参数设定状态下显示参数值 ● 显示参数符号●在峰-谷值状态下显示峰-谷值 2警戒/危险指示灯 各报警点的报警状态显示3正常指示灯 传感器输入在正常范围内(-2V ~-18V )4设置键● 测量状态下,按住2秒钟以上不松开则进入设置状态 ● 在设置状态下,显示参数符号时,按住2秒钟以上不松开进入下一组参数或返回测量状态。
JMDL-21xxAT 智能数码通用位移计 使用手册说明书

JMDL-21xxAT 智能数码通用位移计长沙金码测控科技股份有限公司www 产品使用手册版本:V3.0修订日期:2023年4月版权声明 本文件所含信息归长沙金码测控科技股份有限公司所有,文件中所有信息、数据、设计以及所含图样均属长沙金码测控科技股份有限公司所有,未经书面许可,不得以任何形式(包括影印或其他方式)翻印或复制,间接或直接透露给外界个人或团体。
本仪器的安装、维护、操作需由专业技术人员进行,长沙金码测控科技股份有限公司对本产品拥有更改的权利。
长沙金码测控科技股份有限公司版权所有一. 产品概述二.特点三.主要性能指标四.连接仪表五.产品安装与使用六.拆卸七.产品维护与其它注意事项1111223目录欢迎使用长沙金码测控科技股份有限公司的产品!您拥有金码传感器及其检测设备的同时,就标志着您掌握了最先进的工程检测手段和享有本公司的优质服务,使用本产品之前请详细阅读本说明书或来电垂询,谢谢!JMDL-21xxAT系列智能数码位移传感广泛应用于建筑、铁路、水电、大坝等工程领域的结构相对位移变化和伸缩缝位移变化的精密测量。
一、产品概述1、采用电感调频原理设计制造,具有高灵敏度、高精度、高稳定性、温度影响小的优点,适用于长期观测。
2、位移计内置存贮芯片,具有智能记忆功能,出厂时已将传感器型号、编号、标定系数等参数永久存贮在传感器内,并可保存800次您所需要的测量结果,如测量时间、测点温度(温度型)、绝对位移值、相对位移值、零点值等。
3、采用全数字检测,信号长距离传输不失真,抗干扰能力强。
4、绝缘性能良好,防水耐用。
5、配备综合测试仪即可直接显示位移值,测量直观、简便、快捷。
6、配备自动化采集系统可实现无人职守测量或进行远程监控。
1、连线方法说明:A.直接连接:综合测试仪配备传感器连接插口(防水航空插头),对于配备插头的位移计可直接插入仪表测量。
注:位移计可焊接防水航空插头,连接方法为1红线,2黄线,3蓝线,4绿线。
SDW系列多点位移计使用说明书

S D W系列多点位移计使用说明书1 简述 ............................................................................................................................................. -2 -2 特性 ............................................................................................................................................. - 2 -3 技术指标...................................................................................................................................... - 2 -4 验收与保管.................................................................................................................................. - 2 -5 检验及安装埋设.......................................................................................................................... - 3 -6 测读方法...................................................................................................................................... -7 -7 结果计算...................................................................................................................................... - 8 -SDW系列多点位移计使用说明书1 简述SDW系列多点位移计由位移传感器,位移传递杆、保护管、锚头等组成的长距离位移监测仪器,除保护管和锚头外,均使用不锈钢材料制成。
- 1、下载文档前请自行甄别文档内容的完整性,平台不提供额外的编辑、内容补充、找答案等附加服务。
- 2、"仅部分预览"的文档,不可在线预览部分如存在完整性等问题,可反馈申请退款(可完整预览的文档不适用该条件!)。
- 3、如文档侵犯您的权益,请联系客服反馈,我们会尽快为您处理(人工客服工作时间:9:00-18:30)。
在安装和设备投入运行前,请仔细阅读这些安全规则和警告,以确保正确的安装和安全的操作、正常的运行。
①、本设备具有危险电压,并控制危险的旋转机件,如不按本手册的规定进行操作可能导致死亡、严重受伤和财产损失。
②、只有合格的人员才允许操作本设备,而在此之前,要熟悉本手册中所有安全说明,安装,操作和维护规程。
本设备的安全运行取决于正常的运输,安装,操作和维护。
③、只允许连接永久的输入电源,否则可能导致生产事故。
本设备必须接地。
④、只有合格的人员才能连接,启动本设备和排除故障。
这些人员必须透彻的了解本手册所有的警告、注意事项和操作规程。
⑤、要防止儿童和一般人员接触或靠近本设备,并严禁未经授权对本设备进行任何操作。
否则所造成的人身伤害及财产损失由相关责任人承担,本公司概不负责。
⑥、本设备只能按照制造商的目的使用,未经授权的修改或用于其他用途所引起的事故及人身伤害、财产损失本公司概不负责,并保留进一步追究的权利。
⑦、本设备所有可设定的参数均存储在可编程控制器(PLC)中,并由其中的超级电容在断电情况下保持所有设定值,该电容的供电时间约为190小时,在环境温度为40度时为150小时,使用时请注意,以免发生数据丢失。
⑧、请将本手册交给最终使用者的手中,并放在容易拿到的地方。
对于正常生产时设定的数据必须做好记录。
读者对象:本手册适合下列人员阅读:设备安装人员、维护人员、设计人员第一章设备描述1、概述WY21X系列位移控制器是我公司开发研制的一种新型位移控制器,基本结构如下图所示。
其控制的核心部分是可编程控制器,因此运行可靠;响应速度快,可达毫秒级;并具有远程通讯能力,可以直接和其它控制系统(如:PLC 系统、工业控制网络系统)相连接;并可提供标准模拟量输出信号(电压或电流,此项可选)和远程数字显示模块(此项可选)等优点。
系统结构图物体的位移通过绝对型编码器进行检测,因此分辨率高。
由受控设备通过现场变送单元的传动机构带动编码器一起旋转,编码器将位移转换为脉冲编码信号,送到PLC的输入端。
然后经PLC进行译码、累加运算后,将物体的位移转换为数字在操作面板上显示出来,同时与操作面板中可调的设定参数相比较,在合适的位置产生不同的控制信号和各种保护输出,从而达到了控制设备动作的目的。
该设备的调节不需要任何工具,只需对操作面板进行操作,可在几秒钟内轻松完成,减少劳动强度,节约时间。
所有参数均为数字显示,人机界面友好,调整方便迅速尤其是不用停车,可在机器设备运行过程中进行调整,并可根据用户要求提供多种保护功能例如过速保护和零速保护等优点。
该设备适用范围极广,可广泛用于对物体位移检测及定长控制的各种场合,尤其在炼铁炉卷扬和石灰竖炉卷扬的料车位移控制、炼钢炉氧枪位移控制,轮胎厂胎面切割,焦化厂料车位移控制和其它位移检测系统等自动化工业控制场合被广泛应用,国内已有几十家相关企业相继采用,有的甚至直接取代机械凸轮式主令控制器并取得了满意的使用效果和显著的经济效益。
该设备在运行中几乎做到了零故障, 而赢得了广大用户的青睐。
2、设备构成本控制器由控制箱、编码器箱组成。
编码器箱由机座、传动机构和八位绝对型旋转编码器组成。
编码器箱安装在现场,通过齿轮或链条与受控设备传动轴连接。
由旋转编码器和连接电缆将现场位置信号送至控制箱,控制箱由SIEMENS操作面板TD400、SIEMENS的S7-200PLC:CPU 22X、输出继电器(根据需要)等组成。
控制箱安装在现场墙上或支架上,也可以安装在控制室或操作室内,通过电缆与编码器箱相连接,共同组成位移控制器。
3、TD400 操作面板示意图:①信息显示窗口 ②信息选择键 ③F8-F16选择键④菜单/退出/放弃键 ⑤选行/确认键 ⑥上/下/左/右箭头键4、订货型号:第二章系统原理1、原点的描述:在实际应用中该控制器可以用在很多场合,本指南仅以典型的受控设备:高炉中的单斗上料料车为例,如果是双车可选其一为受控参考设备,其他应用场合均可参照此例。
在操作面板TD400中,可以显示很多信息,而信息显示窗口最多只能显示二条信息,在默认情况下F1-F8键的每个键都对应四条信息,按任何一个键就可以进行信息的显示切换,关于F1-F8键及其信息的对应关系可详见下表。
按下F1键,信息显示窗口会显示信息:“料车位置:***”,***是-32768—+32767之间的数据。
“料车位置”是指料车在斜桥上实际位置对应的编码数,它反映了料车当前所在斜桥上位置(码数),而此位置是以参考点“原点”为坐标的,具体反映了料车距参考点“原点”的实际位置。
可以将斜桥理解为一个斜方向的坐标轴,以“原点”为坐标0点,该坐标的最小值和最大值的分别是-32768到+32767。
而该坐标的原点可以是任一位置,即可以将料车在斜桥上的任一位置设为原点。
为方便起见通常将料车在斜桥底部的装料位置设为原点。
“料车位置”及其他的设定限位都以“原点”为参考点。
当“原点”所对应的实际物理位置变化时,“料车位置”及其它限位所反映的实际物理位置都会发生相应变化。
料车在斜桥上运行时,同步带动编码器旋转,反映到PLC的是一系列的编码,料车在斜桥上整个行程中任一位置都有一个相对于“原点”的编码,这些编码按十进制整数连续排列(-32767——+32767之间),这些编码都反映了料车料车位置置与原点之间的距离关系(码数),也就是用数字反应了料车在斜桥上的实际位置,通过精度(mm/点)可以计算出料车位置置距原点位置的米数。
如料车在“原点”位置时对应的编码是“0”,“料车位置”显示是0,相对“原点”的距离是0点;料车运行到斜桥中间时,对应的编码是“630”,也就是与原点“0”的距离是630个点。
料车在运行当中对应的编码连续变化,“料车位置”也随之不断变化。
当料车上升时,“料车位置”显示的数据是不断增加的,反之当料车下降时,“料车位置”显示的数据是不断减少的。
如果是双料车则参考料车上升时该数据是增加的,而另一料车上升时该数据是减少的。
2、精度与齿数比的计算如果料车在最底部(装料位置)时“料车位置”是0,到顶部是1000,料车整个行程是:1000个点。
如料车实际物理行程从底部(“原点”的对应位置)到顶部(“料车位置”为1000点对应的位置)是30米,则每个点的精度就是:30000mm/1000=30mm,也就是“料车位置”每增加或减少1个点,料车实际正向或反向运行约30mm;该控制器的精度就是30mm/点。
该精度可以通过传动机构的齿数比进行调整,一旦确定后就不可以修改。
齿数比的数值与控制器精度有关。
齿数比数值可用以下方法计算:首先,测量卷扬的滚筒直径D;确定控制器精度J。
D/J=S;S/256=C;C是滚筒旋转一周时编码器旋转的圈数。
所以,“1 :C”就是滚筒与传动机构的齿数比。
(齿轮模数视现场情况而定,一般采用2或3。
)3、控制信号“料车位置”编码在某一范围内时,该控制器输出一个控制信号(接通或断开),例如上减速、下减速、上限位、下限位等。
参与系统控制或连锁,起到限位的作用,这一范围用两个数字或一个数字表示。
如:PLC的输出点Q0.0功能为下限位且设定为10,则当“料车位置”编码显示的数字大于(或小于)该设定数字时,Q0.0输出信号。
至于是大于还是小于则根据实际情况而定。
PLC的输出点Q0.1功能为上加速且设为“50->750”(50到750为上升加速区间)时,则“料车位置”编码显示在50到750的区间范围内时(如:“料车位置”是51时),Q0.1输出接通,不在这一范围内时Q0.1断开。
注意:该区间必须是一个从小到大的一个数字区间。
设定为“1->100”,表示一个从“1”到“100”的一个数字区间。
设定要求必须遵循小数在前大数在后的原则,否则该信号将不会起到预定的作用!4、举例说明下例中以PLC的输出点Q0.0、Q0.1、 Q0.2、Q0.3分别作为系统中的常闭下超限位、下超限位、上限位、下限位、低速位、高速位使用。
该信号通过接线引入到控制回路中。
假设料车初始在炉底0位,此时上超限、下超限、上限位闭合,当料车上升时“料车位置”编码连续增加,当“料车位置”编码上升大于50以后“低速位”限位Q0.4输出接通,继续上升到80后,“高速位”Q0.5闭合,通过调速装置控制系统控制料车以高速运行,继续上升到大于800以后“低速位”点Q0.4断开,料车减速,继续上行到900后,“高速位”Q0.5断开,控制系统改变料车的速度以低速运行,上升到达大于1000时,上限位Q0.2断开,料车经抱闸制动停车。
料车下降过程中,“料车位置”编码连续减少,,当“料车位置”编码减少小于950以后“低速位”限位Q0.4输出接通,继下降到920后,“高速位”Q0.5闭合,通过调速装置控制系统控制料车以高速运行,继续下降到小于200以后“低速位”点Q0.4断开,料车减速,继续下行到100后,“高速位”Q0.5断开,控制系统改变料车的速度以低速运行,下降到达小于1000时,下限位Q0.3断开,料车经抱闸制动停车。
具体见下图指示料车行程示意图5、参数设定的基本步骤所有的参数设定直接通过操作面板TD200的按键进行设定,无需其它工具,方便快捷。
在几十秒内即可完成设定,极大的减少了操作人员的劳动强度,提高了劳动效率。
并且可以在料车运行过程中设定参数,不用停车。
具体的操作步骤如下:①、按F1-F8键中的某个按键,首先选定需要修改的信息。
②、用上/下箭头键,在信息显示窗口中选择要修改的信息的行,使光标在要修改信息行前第一个字符上闪烁。
③、按ENTER键确认,使光标移动到当前信息行中要修改的数字区域,如果该参数只有一个设定数字则光标在数字区数字的最后一个字符上闪烁;如果是一个数字区间即两个数字,则光标在数字区第一个数字的最后一个字符上闪烁。
如果此时想放弃修改请按ESC键,退出当前选择行,光标消失,设定的参数不会发生变化,进行第⑥步。
④、按上/下箭头键增加、减小数字。
⑤、按ENTER键使修改结果有效,即修改结果已进入PLC的存储器中。
如果设定参数为一个数字区间则光标会移动到第二个数字的最后一个字符上闪烁,再重复第④步的操作,修改完毕后按ENTER键当前行消失;如要放弃修改,请按ESC键使当前修改无效,光标消失。
⑥、按F1键,使窗口显示“料车位置”信息。
注意:如在信息显示窗口中不显示预先定义好的、与本系统有关的信息之一时,可连续按ESC键,直到信息显示窗口中显示预先定义好的、与本系统有关的信息之一,如果需要进行参数设定,可参照上述步骤进行,或按F1键显示“料车位置”信息。
第三章、调试步骤1、位移控制器调试的步骤该位移控制器的调试基本分为两步:离线调试和在线调试。
离线调试是在设备安装之前对该控制器进行检验和模拟运行调试,以检查设备是否正常和满足技术要求。