NCP1593-D
瓦房店光达轴承制造有限公司2-3月份轧机库存

1 3 8 2 0,5 2 2 5 6 8 9
(2018年2-3月份)轧机成 品 轴 承 库 存 明 细 瓦房店光达轴承制造有限公司
名称 轴承 轴承 轴承 轴承 轴承 轴承 轴承 轴承 轴承 轴承 轴承 轴承 轴承 轴承 轴承 轴承 轴承 轴承 轴承 轴承 轴承 轴承 轴承 轴承 轴承 轴承 轴承 轴承 轴承 轴承 轴承
轴承型号 FC202870外组带铆钉 LFC202870/02废品 FC2443126 FC2443126/02 FC2443126挡圈 RFC243692/02 FC263590 FC2842160/02 FC2838119 FCD3045112/02 FCD3045112 FC3042120 FC3045120 SFC3045120 FC3045120/02 FC3046156-313891A FC3046156外组 FC313823外组 FC3248124EY1外组 FC3248168/02 FC3248168F3P64
FC3652168铁保 SFC3652168铁保 FC3652168 FC3658192/02 FC3658192 FC3852168外组 FC3852168EY1外组 FC3854168外组内沟212 FC3854168/02 FC4056170外组 FC4056170 FC4056188内沟222 FC4056188/02内沟222 FC4058202 FC4058202外组 FC4058202/02 FC4058202M/P64 FC4054170外组 FC4054170 FC4054170/02 FC4056200 FC4056200/02 FC4058192 FC4260170外组 FC4260170 FC4460192 FC4460192/02 FC4462192外组 FC4462192/02间包 FCD4462192/02 FCDP4462192 FC4462225/02 SFCD4462225 FC4464210/02 FC4666206 FC4866220外组
NFD Composite Material (Jiangsu) Co., Ltd Hepla

Hepla® H1130GBMaterial Description:Hepla® H1130GB is a Acrylonitrile Butadiene Styrene (ABS) product filled with 30% glass bead.Characteristics include:Electrical Insulation.Material Status•Commercial: ActiveAvailability •Asia Pacific•North America •Europe•Latin America •Middle East•AfricaFiller/Reinforcement •Glass Bead, 30% Filler by WeightFeatures •Good Dimensional Stability•Electrical InsulationRoHS Compliance •RoHS CompliantProcessing Method•Injection MoldingTypical Value Unit Test Method Density/Specific Gravity 1.27g/cm3ASTM D792 Moisture Content0.1%Molding Shrinkage - Flow (3.20 mm)0.3 to 0.6%ASTM D955Typical Value Unit Test Method Tensile Modulus3580MPa ASTM D638 Tensile Strength32MPa ASTM D638 Tensile Elongation (Yield)> 10%ASTM D638 Flexural Modulus3250MPa ASTM D790 Flexural Strength60MPa ASTM D790Typical Value Unit Test Method Notched Izod Impact(3.2mm) 60J/m ASTM D256 Unnotched Izod Impact(3.2mm)320J/m ASTM D4812Typical Value Unit Test Method Flame Rating(1.5mm)HB UL 94Typical Value UnitInjection Pressure68.9 to 103MPaProcessing (Melt) Temp204 to 238℃Mold Temperature63 to 85℃Drying Temperature 82℃Drying Time2hrDew Point-18℃CAUTION/警告!Before using, read the Molding Guide, Material Safety Data Sheets, and Bulletins available from NFD Advanced Composites Sales offices and Distributors supplied to your company. Caution! During drying, purging and molding, small amounts of hazardous gases and/or particulate matter may be released. These may irritate eyes, nose and throat. Use adequate local exhaust ventilation during thermal processing. To prevent resin decomposition, do not contaminate the resin or exceed the recommended melt temperature or hold-up time. Avoid inhalation or skin and eyes contact. Sweep up and dispose of spilled resin to eliminate slipping hazard.在使用之前,请阅读NFD公司销售办事处和经销商提供给贵公司的材料成型指南、材料安全数据表和公告。
液晶电源管理芯片代换大全

MP2104 OCP2150-LTC3406/直接代换
AT1366/MP2104 直接代换
ACT6906-LTC3406/AT1366/直接代换
MP2104 OCP2160-LTC3407直接代换
ACT4065-ZA3020/MP1580 直接代换
1200AP40 1200AP60、1203P60
200D6、203D6 DAP8A 可互代
203D6/1203P6 DAP8A
2S0680 2S0880
3S0680 3S0880
5S0765 DP104、DP704
8S0765C DP704加24V的稳压二极管
ACT4060 ZA3020LV/MP1410/MP9141
电源IC(ZSTR-G5643D G5653D G8653D 直接代换
203D6/1203P6和DAP8A 直接代换 DM0465R。DM0565R用cm0565r代换成功 (取掉4脚的稳压二极管)
LD7575PS 可用203D6代(没试过,只是1脚的对地电阻不同,改了就可了)
LD7552可用SG6841代(不过要改4脚电阻,)
STR G5653直接用STR G8656代换 试验成功!
. FSCQ1565>1265>0765>0565
FS5Q1565>1265>0765>0565
5Q系列供电为20V,CQ系列供电为18V,5Q代换CQ系列时需拆除那个稳压二极管,短接10欧姆电阻!
STRG8656>8654>5653
OCP2160 LTC3407
OCP2576 LM2576
Motorola 3.5 kHz 产品说明书
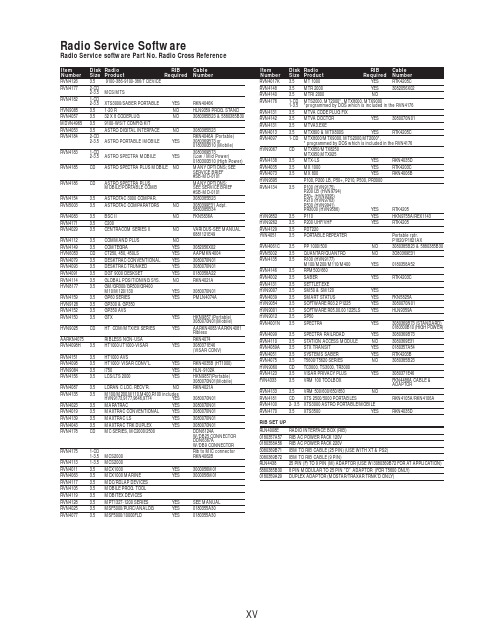
RVN4126 3.59100-386-9100-386/T DEVICERVN41772-CD2-3.5MCS/MTSRVN41821-CD2-3.5XTS3000/SABER PORTABLE YES RKN4046KHVN9085 3.51-20 R NO HLN9359 PROG. STAND RVN4057 3.532 X 8 CODEPLUG NO3080385B23 & 5880385B30 MDVN4965 3.59100-WS/T CONFIG KITRVN4053 3.5ASTRO DIGITAL INTERFACE NO3080385B23RVN41842-CD RKN4046A (Portable) 2-3.5ASTRO PORTABLE /MOBILE YES3080369B73 or0180300B10 (Mobile) RVN41831-CD3080369B732-3.5ASTRO SPECTRA MOBILE YES(Low / Mid Power)0180300B10 (High Power) RVN4185CD ASTRO SPECTRA PLUS MOBILE NO MANY OPTIONS; SEESERVICE BRIEF#SB-MO-0101RVN4186CD ASTRO SPECTRA PLUS MANY OPTIONS;MOBILE/PORTABLE COMB SEE SERVICE BRIEF#SB-MO-0101RVN4154 3.5ASTROTAC 3000 COMPAR.3080385B23RVN5003 3.5ASTROTAC COMPARATORS NO3080399E31 Adpt.5880385B34RVN4083 3.5BSC II NO FKN5836ARVN4171 3.5C200RVN4029 3.5CENTRACOM SERIES II NO VARIOUS-SEE MANUAL6881121E49RVN4112 3.5COMMAND PLUS NORVN4149 3.5COMTEGRA YES3082056X02HVN6053CD CT250, 450, 450LS YES AAPMKN4004RVN4079 3.5DESKTRAC CONVENTIONAL YES3080070N01RVN4093 3.5DESKTRAC TRUNKED YES3080070N01RVN4091 3.5DGT 9000 DESKSET YES0180358A22RVN4114 3.5GLOBAL POSITIONING SYS.NO RKN4021AHVN8177 3.5GM/GR300/GR500/GR400M10/M120/130YES3080070N01RVN4159 3.5GP60 SERIES YES PMLN4074AHVN9128 3.5GP300 & GP350RVN4152 3.5GP350 AVSRVN4150 3.5GTX YES HKN9857 (Portable)3080070N01(Mobile) HVN9025CD HT CDM/MTX/EX SERIES YES AARKN4083/AARKN4081RiblessAARKN4075RIBLESS NON-USA RKN4074RVN4098H 3.5HT1000/JT1000-VISAR YES3080371E46(VISAR CONV)RVN4151 3.5HT1000 AVSRVN4098 3.5HT1000/ VISAR CONV’L.YES RKN4035B (HT1000) HVN9084 3.5i750YES HLN-9102ARVN4156 3.5LCS/LTS 2000YES HKN9857(Portable)3080070N01(Mobile) RVN4087 3.5LORAN C LOC. RECV’R.NO RKN4021ARVN4135 3.5M100/M200,M110,M400,R100 includesHVN9173,9177,9646,9774YES3080070N01RVN4023 3.5MARATRAC YES3080070N01RVN4019 3.5MAXTRAC CONVENTIONAL YES3080070N01RVN4139 3.5MAXTRAC LS YES3080070N01RVN4043 3.5MAXTRAC TRK DUPLEX YES3080070N01RVN4178CD MC SERIES, MC2000/2500DDN6124AW/DB25 CONNECTORDDN6367AW/DB9 CONNECTOR RVN41751-CD Rib to MIC connector 1-3.5MCS2000 RKN4062BRVN41131-3.5MCS2000RVN4011 3.5MCX1000YES3000056M01RVN4063 3.5MCX1000 MARINE YES3000056M01RVN4117 3.5MDC/RDLAP DEVICESRVN4105 3.5MOBILE PROG. TOOLRVN4119 3.5MOBITEX DEVICESRVN4128 3.5MPT1327-1200 SERIES YES SEE MANUALRVN4025 3.5MSF5000/PURC/ANALOG YES0180355A30RVN4077 3.5MSF5000/10000FLD YES0180355A30RVN4017K 3.5MT 1000YES RTK4205CRVN4148 3.5MTR 2000YES3082056X02RVN4140 3.5MTRI 2000NORVN41761-CD MTS2000, MT2000*, MTX8000, MTX90001-3.5*programmed by DOS which is included in the RVN4176RVN4131 3.5MTVA CODE PLUG FIXRVN4142 3.5MTVA DOCTOR YES3080070N01RVN4131 3.5MTVA3.EXERVN4013 3.5MTX800 & MTX800S YES RTK4205CRVN4097 1-CD MTX8000/MTX9000,MTS2000,MT2000*,* programmed by DOS which is included in the RVN4176HVN9067CD MTX850/MTX8250MTX950,MTX925RVN4138 3.5MTX-LS YES RKN4035DRVN4035 3.5MX 1000YES RTK4203CRVN4073 3.5MX 800YES RKN4006BHVN9395 P100, P200 LB, P50+, P210, P500, PR3000RVN4134 3.5P100 (HVN9175)P200 LB (HVN9794)P50+ (HVN9395)P210 (HVN9763)P500 (HVN9941)PR3000 (HVN9586)YES RTK4205HVN9852 3.5P110YES HKN9755A/REX1143 HVN9262 3.5P200 UHF/VHF YES RTK4205RVN4129 3.5PDT220YVN4051 3.5PORTABLE REPEATER Portable rptr.P1820/P1821AXRVN4061C 3.5PP 1000/500NO3080385B23 & 5880385B30 RVN5002 3.5QUANTAR/QUANTRO NO3O80369E31RVN4135 3.5R100 (HVN9177)M100/M200/M110/M400YES0180358A52RVN4146 3.5RPM500/660RVN4002 3.5SABER YES RTK4203CRVN4131 3.5SETTLET.EXEHVN9007 3.5SM50 & SM120YESRVN4039 3.5SMART STATUS YES FKN5825AHVN9054 3.5SOFTWARE R03.2 P1225YES3080070N01HVN9001 3.5SOFTWARE R05.00.00 1225LS YES HLN9359AHVN9012 3.5SP50RVN4001N 3.5SPECTRA YES3080369B73 (STANDARD)0180300B10 (HIGH POWER) RVN4099 3.5SPECTRA RAILROAD YES3080369B73RVN4110 3.5STATION ACCESS MODULE NO3080369E31RVN4089A 3.5STX TRANSIT YES0180357A54RVN4051 3.5SYSTEMS SABER YES RTK4203BRVN4075 3.5T5600/T5620 SERIES NO3080385B23HVN9060CD TC3000, TS3000, TR3000RVN4123 3.5VISAR PRIVACY PLUS YES3080371E46FVN4333 3.5VRM 100 TOOLBOX FKN4486A CABLE &ADAPTORRVN4133 3.5VRM 500/600/650/850NORVN4181CD XTS 2500/5000 PORTABLES RKN4105A/RKN4106A RVN41002- 3.5XTS3000 ASTRO PORTABLE/MOBILERVN4170 3.5XTS3500YES RKN4035DRIB SET UPRLN4008E RADIO INTERFACE BOX (RIB)0180357A57RIB AC POWER PACK 120V0180358A56RIB AC POWER PACK 220V3080369B71IBM TO RIB CABLE (25 PIN) (USE WITH XT & PS2)3080369B72IBM TO RIB CABLE (9 PIN)RLN443825 PIN (F) TO 9 PIN (M) ADAPTOR (USE W/3080369B72 FOR AT APPLICATION) 5880385B308 PIN MODULAR TO 25 PIN ”D” ADAPTOR (FOR T5600 ONLY)0180359A29DUPLEX ADAPTOR (MOSTAR/TRAXAR TRNK’D ONLY)Item Disk Radio RIB Cable Number Size Product Required Number Item Disk Radio RIB Cable Number Size Product Required NumberUtilizing your personal computer, Radio Service Software (RSS)/Customer Programming Software (CPS)/CustomerConfiguration Software (CCS) enables you to add or reprogram features/parameters as your requirements change. RSS/CPS/CCS is compatible with IBM XT, AT, PS/2 models 30, 50, 60 and 80.Requires 640K RAM. DOS 3.1 or later. Consult the RSS users guide for the computer configuration and DOS requirements. (ForHT1000, MT/MTS2000, MTX838/8000/9000, Visar and some newer products —IBM model 386, 4 MEG RAM and DOS 5.0 or higher are recommended.) A Radio Interface Box (RIB) may be required as well as the appropriate cables. The RIB and cables must be ordered separately.Licensing:A license is required before a software (RVN) order is placed. The software license is site specific (customer number and ultimate destination tag). All sites/locations must purchase their own software.Be sure to place subsequent orders using the original customer number and ship-to-tag or other licensed sites; ordering software without a licensed customer number and ultimate tag may result in unnecessary delays. To obtain a no charge license agreement kit, order RPX4719. To place an order in the U.S. call 1-800-422-4210. Outside the U.S., FAX 847-576-3023.Subscription Program:The purchase of Radio ServiceSoftware/Customer Programming/Customer ConfigurationSoftware (RVN & HVN kits) entitles the buyer/subscriber to three years of free upgrades. At the end of these three years, the sub-scriber must purchase the same Radio Service Software kit to receive an additional three years of free upgrades. If the sub-scriber does not elect to purchase the same Radio Service Software kit, no upgrades will be sent. Annually a subscription status report is mailed to inform subscribers of the RSS/CPS/CCS items on our database and their expiration dates.Notes:1)A subscription service is offered on “RVN”-Radio Service Software/Customer Programming/Customer Configuration Software kits only.2)“RVN” software must only be procured through Radio Products and Services Division (RPSD). Software not procured through the RPSD will not be recorded on the subscription database; upgrades will not be mailed.3)Upgrades are mailed to the original buyer (customer number & ultimate tag).4)SP software is available through the radio product groups.The Motorola General Radio Service Software Agreement is now available on Motorola Online. If you need assistance please feel free to submit a “Contact Us” or call 800-422-4210.SMART RIB SET UPRLN1015D SMART RIB0180302E27 AC POWER PACK 120V 2580373E86 AC POWER PACK 220V3080390B49SMARTRIB CABLE (9 PIN (F) TO 9 PIN (M) (USE WITH AT)3080390B48SMARTRIB CABLE (25 PIN (F) TO 9 PIN (M) (USE WITH XT)RLN4488ASMART RIB BATTERY PACKWIRELESS DATA GROUP PRODUTS SOFTWARERVN4126 3.59100-386/9100T DEVICES MDVN4965 3.59100-WS/T CONFIG’TN RVN41173.5MDC/RDLAP DEVICESPAGING PRODUCTS MANUALS6881011B54 3.5ADVISOR6881029B90 3.5ADVISOR ELITE 6881023B20 3.5ADVISOR GOLD 6881020B35 3.5ADVISOR PRO FLX 6881032B30 3.5BR8506881032B30 3.5LS3506881032B30 3.5LS5506881032B30 3.5LS7506881033B10 3.5LS9506881035B20 3.5MINITOR III8262947A15 3.5PAGEWRITER 20008262947A15 3.5PAGEWRITER 2000X 6881028B10 3.5TALKABOUT T3406881029B35 3.5TIMEPORT P7308262947A15 3.5TIMEPORT P930NLN3548BUNIVERSAL INTERFACE KITItem Disk Radio NumberSize Product。
NCP1380ADR2G,NCP1380BDR2G,NCP1380CDR2G,NCP1380DDR2G,NCP1380DGEVB, 规格书,Datasheet 资料
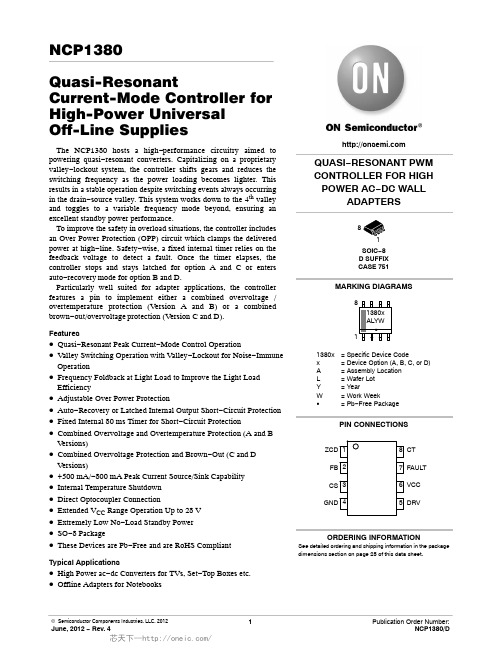
NCP1380Quasi-ResonantCurrent-Mode Controller for High-Power UniversalOff-Line SuppliesThe NCP1380 hosts a high−performance circuitry aimed to powering quasi−resonant converters. Capitalizing on a proprietary valley−lockout system, the controller shifts gears and reduces the switching frequency as the power loading becomes lighter. This results in a stable operation despite switching events always occurring in the drain−source valley. This system works down to the 4th valley and toggles to a variable frequency mode beyond, ensuring an excellent standby power performance.To improve the safety in overload situations, the controller includes an Over Power Protection (OPP) circuit which clamps the delivered power at high−line. Safety−wise, a fixed internal timer relies on the feedback voltage to detect a fault. Once the timer elapses, the controller stops and stays latched for option A and C or enters auto−recovery mode for option B and D.Particularly well suited for adapter applications, the controller features a pin to implement either a combined overvoltage / overtemperature protection (Version A and B) or a combined brown−out/overvoltage protection (Version C and D).Features•Quasi−Resonant Peak Current−Mode Control Operation •Valley Switching Operation with Valley−Lockout for Noise−Immune Operation•Frequency Foldback at Light Load to Improve the Light Load Efficiency•Adjustable Over Power Protection•Auto−Recovery or Latched Internal Output Short−Circuit Protection •Fixed Internal 80 ms Timer for Short−Circuit Protection •Combined Overvoltage and Overtemperature Protection (A and B Versions)•Combined Overvoltage Protection and Brown−Out (C and D Versions)•+500 mA/−800 mA Peak Current Source/Sink Capability •Internal Temperature Shutdown•Direct Optocoupler Connection•Extended V CC Range Operation Up to 28 V•Extremely Low No−Load Standby Power•SO−8 Package•These Devices are Pb−Free and are RoHS CompliantTypical Applications•High Power ac−dc Converters for TVs, Set−Top Boxes etc.•Offline Adapters for NotebooksSee detailed ordering and shipping information in the package dimensions section on page 25 of this data sheet.ORDERING INFORMATION81380x= Specific Device Codex= Device Option (A, B, C, or D)A= Assembly LocationL= Wafer LotY= YearW= Work WeekG= Pb−Free PackageMARKING DIAGRAMSSOIC−8D SUFFIXCASE 75112348765PIN CONNECTIONSZCDFBCSGNDCTFAULTVCCDRVQUASI−RESONANT PWMCONTROLLER FOR HIGHPOWER AC−DC WALLADAPTERSTYPICAL APPLICATION EXAMPLEFigure 1. Typical Application Schematic for A and B Versions VoutVoutPIN FUNCTION DESCRIPTIONPin N5Pin Name Function Pin Description1ZCD Zero Crossing DetectionAdjust the over power protection Connected to the auxiliary winding, this pin detects the core reset event.Also, injecting a negative voltage smaller than 0.3 V on this pin will perform over power protection.2FB Feedback pin Hooking an optocoupler collector to this pin will allowregulation.3CS Current sense This pin monitors the primary peak.4GND−The controller ground5DRV Driver output The driver’s output to an external MOSFET6V CC Supplies the controller This pin is connected to an external auxiliary voltage.7Fault Over voltage and Over temperatureprotection (A and B versions)Over−voltage and Brown−outprotection (C and D versions)Pulling this pin down with an NTC or up with a zener diode allows to latch the controller.This pin observes the HV rail and protects the circuit in case of low main conditions. It also offers a way to latch the circuit in case of over voltage event.8C T Timing capacitor A capacitor connected to this pin acts as the timingcapacitor in foldback mode.NCP1380 OPTIONSOTP OVP Brown−Out Auto−RecoveryOvercurrentProtectionLatchedOvercurrentProtectionNCP1380 / A Yes Yes Yes NCP1380 / B Yes Yes YesNCP1380 / C Yes Yes Yes NCP1380 / D Yes Yes YesINTERNAL CIRCUIT ARCHITECTUREFigure 3. Internal Circuit Architecture for Versions A and BFigure 4. Internal Circuit Architecture for Versions C and DMAXIMUM RATINGS TABLESymbol Rating Value UnitV CC(MAX) I CC(MAX)Maximum Power Supply voltage, V CC pin, continuous voltageMaximum current for V CC pin−0.3 to 28±30VmAV DRV(MAX) I DRV(MAX)Maximum driver pin voltage, DRV pin, continuous voltageMaximum current for DRV pin−0.3 to 20±1000VmAV MAX I MAX Maximum voltage on low power pins (except pins DRV and V CC)Current range for low power pins (except pins ZCD, DRV and V CC)−0.3 to 10±10VmAI ZCD(MAX)Maximum current for ZCD pin+3 / −2mAR q JA Thermal Resistance Junction−to−Air120°C/W T J(MAX)Maximum Junction Temperature150°C Operating Temperature Range−40 to +125°CStorage Temperature Range−60 to +150°CESD Capability, HBM Model (Note 1)4kVESD Capability, MM Model (Note 1)200VESD Capability, CDM Model (Note 1)2kV Stresses exceeding Maximum Ratings may damage the device. Maximum Ratings are stress ratings only. Functional operation above theRecommended Operating Conditions is not implied. Extended exposure to stresses above the Recommended Operating Conditions may affect device reliability.1.This device series contains ESD protection and exceeds the following tests:Human Body Model 4000 V per JEDEC Standard JESD22, Method A114EMachine Model 200 V per JEDEC Standard JESD22, Method A115ACharged Device Model 2000 V per JEDEC Standard JESD22−C101D.2.This device contains latchup protection and exceeds 100 mA per JEDEC Standard JESD78.ELECTRICAL CHARACTERISTICS (Unless otherwise noted: For typical values T J = 25°C, V CC = 12 V, V ZCD = 0 V, V FB = 3 V,V CS = 0 V, V fault = 1.5 V, C T = 680 pF) For min/max values T J = −40°C to +125°C, Max T J = 150°C, V CC = 12 V)Symbol Condition Min Typ Max Unit SUPPLY SECTION − STARTUP AND SUPPLY CIRCUITSV CC(on) V CC(off) V CC(HYS) V CC(latch) V CC(reset)Supply VoltageStartup ThresholdMinimum Operating VoltageHysteresis V CC(on)− V CC(off)Clamped V CC when latched−offInternal logic resetV CC increasingV CC decreasingV CC decreasing, I CC = 30 m A168.37.26.261798.07.27189.49.28.28Vt VCC(off) t VCC(reset)V CC(off) noise filterV CC(reset)noise filter−−520−−m sI CC(start)Startup current FB pin openV CC = V CC(on)− 0.5 V−1020m AI CC(disch)Current that discharges V CC when the controllergets latchedV CC = 12 V 3.0 4.0 5.0mAI CC(latch)Current into V CC that keeps the controller latched(Note 3)V CC = V CC(latch)30−−m AI CC1 I CC2 I CC3A I CC3B Supply CurrentDevice Disabled/Fault (Note 3) B, C, and D onlyDevice Enabled/No output load on pin 5Device Switching (F SW = 65 kHz)Device Switching VCO modeV CC > V CC(off)F sw = 10 kHzC DRV = 1 nF, F SW = 65 kHzC DRV = 1 nF, V FB = 1.25 V−−−−1.71.72.652.02.02.03.0−mACURRENT COMPARATOR − CURRENT SENSEV ILIM Current Sense Voltage Threshold V FB = 4 V, V CS increasing0.760.80.84V t LEB Leading Edge Blanking Duration for V ILIM Minimum on time minus t ILIM210275330ns3.Guaranteed by design.4.The peak current setpoint goes down as the load decreases. It is frozen below I peak(VCO)(I peak = cst)5.If negative voltage in excess to −300 mV is applied to ZCD pin, the current setpoint decrease is no longer guaranteed to be linear6.Minimum value for T J = 125°C7.NTC with R110 = 8.8 k W.Symbol UnitMaxTypMinConditionCURRENT COMPARATOR − CURRENT SENSEI bias Input Bias Current (Note 3)DRV high−2−2m At ILIM Propagation Delay V CS > V ILIM to DRV turn−off−125175ns I peak(VCO)Percentage of maximum peak current level atwhich VCO takes over (Note 4)V FB = 0.4 V, V CS increasing15.417.519.6%V OPP(MAX)Setpoint decrease for V ZCD = −300 mV (Note 5)V ZCD = −300 mV, V FB = 4 V,V CS increasing3537.540% V CS(stop)Threshold for immediate fault protection activation 1.125 1.200 1.275V t BCS Leading Edge Blanking Duration for V CS(stop)−120−ns DRIVE OUTPUT − GATE DRIVER SNK R SRC Drive ResistanceDRV SinkDRV SourceV DRV = 10 VV DRV = 2 V−−12.520−−WI SNK I SRC Drive current capabilityDRV SinkDRV SourceV DRV = 10 VV DRV = 2 V−−800500−−mAt r Rise Time (10% to 90%)C DRV = 1 nF, V DRV from 0 to12 V−4075nst f Fall Time (90% to 10%)C DRV = 1 nF, V DRV from 0 to12 V−2560nsV DRV(low)DRV Low Voltage V CC = V CC(off) + 0.2 VC DRV = 1 nF, R DRV = 33 k W8.49.1−VV DRV(high)DRV High Voltage (Note 6)V CC = V CC(MAX)C DRV = 1 nF10.513.015.5V DEMAGNETIZATION INPUT − ZERO VOLTAGE DETECTION CIRCUITV ZCD(TH)ZCD threshold voltage V ZCD decreasing355590mV V ZCD(HYS)ZCD hysteresis V ZCD increasing153555mVV CH V CL Input clamp voltageHigh stateLow stateI pin1 = 3.0 mAI pin1 = −2.0 mA8−0.910−0.712−0.3Vt DEM Propagation Delay V ZCD decreasing from 4 V to−0.3 V−150250ns C PAR Internal input capacitance−10−pF t BLANK Blanking delay after on−time 2.30 3.15 4.00m st outSS t out Timeout after last demag transition During soft−startAfter the end of soft−start285.0415.9546.7m sR ZCD(pdown)Pulldown resistor (Note 3)140320700k W TIMING CAPACITORV CT(MAX)Maximum voltage on C T pin V FB < V FB(TH) 5.15 5.40 5.65VI CT Source current V CT = 0 V182022m A V CT(MIN)Minimum voltage on C T pin, discharge switchactivated−−90mVC T Recommended timing capacitor value220pF3.Guaranteed by design.4.The peak current setpoint goes down as the load decreases. It is frozen below I peak(VCO)(I peak = cst)5.If negative voltage in excess to −300 mV is applied to ZCD pin, the current setpoint decrease is no longer guaranteed to be linear6.Minimum value for T J = 125°C7.NTC with R110 = 8.8 k W.Symbol UnitMaxTypMinConditionFEEDBACK SECTIONR FB(pullup)Internal pullup resistor151822k WI ratio Pin FB to current setpoint division ratio 3.8 4.0 4.2V FB(TH)FB pin threshold under which C T is clamped toV CT(MAX)0.260.30.34VV H2D V H3D V H4D V HVCOD V HVCOI V H4I V H3I V H2I Valley thresholdFB voltage where 1st valley ends and 2nd valleystartsFB voltage where 2nd valley ends and 3rd valleystartsFB voltage where 3rd valley ends and 4th valleystartsFB voltage where 4th valley ends and VCO startsFB voltage where VCO ends and 4th valley startsFB voltage where 4th valley ends and 3rd valleystartsFB voltage where 3rd valley ends and 2nd valleystartsFB voltage where 2nd valley ends and 1st valleystartsV FB decreasesV FB decreasesV FB decreasesV FB decreasesV FB increasesV FB increasesV FB increasesV FB increases1.3161.1280.8460.7321.3161.5041.6921.8801.41.20.90.81.41.61.82.01.4841.2720.9540.8281.4841.6961.9082.120VFAULT PROTECTION (ALL VERSIONS)T SHDN Thermal Shutdown Device switching (F SWaround 65 kHz)140−170°C T SHDN(HYS)Thermal Shutdown Hysteresis−40−°C t OVLD Overload Timer V FB = 4 V, V CS > V ILIM758595mst SSTART Soft−start duration V FB = 4 V, V CS ramping up,measured from 1st DRVpulse to V CS(peak) = 90% ofV ILIM2.83.84.8msR Fault(clamp)Clamp series resistor 1.3 1.55 1.8k W V OVP Fault detection level for OVP V Fault increasing 2.35 2.5 2.65V t latch(delay)Delay before latch confirmation22.53037.5m s FAULT PROTECTION A & B VERSIONSI OTP(REF)Reference current for direct connection of anNTC (Note 7)V Fault = V OTP + 0.2 V859197m A V OTP Fault detection level for OTP V Fault decreasing0.7440.80.856V V Fault(clamp)Clamped voltage (Fault pin left open)Fault pin open 1.13 1.35 1.57V FAULT PROTECTION C & D VERSIONSV BO Brown−Out level V Fault decreasing0.7440.80.856VI BO Sourced hysteresis current V Fault > V BO V Fault = V BO + 0.2 V91011m A t BO(delay)Delay before entering and exiting Brown−out22.53037.5m s V Fault(clamp)Clamped voltage (Fault pin left open)Fault pin open 1.0 1.2 1.4V3.Guaranteed by design.4.The peak current setpoint goes down as the load decreases. It is frozen below I peak(VCO)(I peak = cst)5.If negative voltage in excess to −300 mV is applied to ZCD pin, the current setpoint decrease is no longer guaranteed to be linear6.Minimum value for T J = 125°C7.NTC with R110 = 8.8 k W.17.0017.0517.1017.1517.2017.2517.30−40−20020406080100120Figure 5. V CC(on) vs. Junction TemperatureT J , JUNCTION TEMPERATURE (°C)V C C (o n ), (V )8.708.758.808.858.908.959.00−40−20020406080100120Figure 6. V CC(off) vs. Junction TemperatureT J , JUNCTION TEMPERATURE (°C)V C C (o f f ), (V )1.301.401.501.601.701.801.90−40−20020406080100120Figure 7. I CC2 vs. Junction TemperatureT J , JUNCTION TEMPERATURE (°C)I C C 2, (m A )2.202.302.402.502.602.702.80−40−20020406080100120T J , JUNCTION TEMPERATURE (°C)Figure 8. I CC3A vs. Junction TemperatureI C C 3A , (m A )1.601.701.801.902.002.102.202.302.40−40−2020406080100120Figure 9. I CC3B vs. Junction TemperatureT J , JUNCTION TEMPERATURE (°C)I C C 3B , (m A )6.06.57.07.58.08.59.09.510.0−40−20020406080100120I C C (s t a r t ), (m A )T J , JUNCTION TEMPERATURE (°C)Figure 10. I CC(start) vs. Junction Temperature780785790795800805810−40−20020406080100120T J , JUNCTION TEMPERATURE (°C)V I L I M , (m V )Figure 11. V ILIM vs. Junction Temperature 210230250270290310330−40−20020406080100120T L E B , (n s )T J , JUNCTION TEMPERATURE (°C)Figure 12. T LEB vs. Junction Temperature1.1251.1451.1651.1851.2051.2251.2451.265−40−2020406080100120Figure 13. V CS(stop) vs. Junction TemperatureT J , JUNCTION TEMPERATURE (°C)V C S (s t o p ), (V )36.036.537.037.538.038.539.0−40−20020406080100120Figure 14. V OPP(MAX) vs. Junction TemperatureV O P P (m a x ), (%)8.88.99.09.19.29.39.4−40−2020406080100120T J , JUNCTION TEMPERATURE (°C)V D R V (l o w ), (V )Figure 15. V DRV(low) vs. Junction Temperature10.511.011.512.012.513.013.514.014.5−40−20020406080100120V D R V (h i g h ), (V )T J , JUNCTION TEMPERATURE (°C)Figure 16. V DRV(high) vs. Junction Temperature354555657585−40−2020406080100120V Z C D (t h ), (V )T J , JUNCTION TEMPERATURE (°C)Figure 17. V ZCD(th) vs. Junction Temperature 152025303540455055−40−2020406080100120T J , JUNCTION TEMPERATURE (°C)Figure 18. V ZCD(hys) vs. Junction TemperatureV Z C D (h y s ), (V )2.903.03.103.203.303.403.50−40−2020406080100120T B L A N K , (m s )Figure 19. T BLANK vs. Junction TemperatureT J , JUNCTION TEMPERATURE (°C)35.037.039.041.043.045.047.049.0−40−2020406080100120T J , JUNCTION TEMPERATURE (°C)T o u t S S , (m s )Figure 20. T outSS vs. Junction Temperature5.05.25.45.65.86.06.26.46.6−40−20020406080100120Figure 21. T out vs. Junction Temperature T o u t , (m s )T J , JUNCTION TEMPERATURE (°C)780785790795800805810−40−20020406080100120T J , JUNCTION TEMPERATURE (°C)V O T P , (m V )Figure 22. V OTP vs. Junction Temperature86.087.088.089.090.091.092.0−40−20020406080100120I O T P , (m A )T J , JUNCTION TEMPERATURE (°C)Figure 23. I OTP vs. Junction Temperature 780785790795800805810−40−20020406080100120T J , JUNCTION TEMPERATURE (°C)V B O , (m V )Figure 24. V BO vs. Junction Temperature9.29.49.69.810.010.210.4−40−20020406080100120I B O , (m A )T J , JUNCTION TEMPERATURE (°C)Figure 25. I BO vs. Junction TemperatureAPPLICATION INFORMATIONThe NCP1380 implements a standard current−mode architecture operating in quasi−resonant mode. Due to a proprietary circuitry, the controller prevents valley−jumping instability and steadily locks out in selected valley as the power demand goes down. Once the fourth valley is reached, the controller continues to reduce the frequency further down, offering excellent efficiency over a wide operating range. Thanks to a fault timer combined to an OPP circuitry, the controller is able to efficiently limit the output power at high−line.•Quasi−Resonance Current−mode operation: implementing quasi−resonance operation in peak current−mode control, the NCP1380 optimizes the efficiency by switching in the valley of the MOSFET drain−source voltage. Thanks to a proprietary circuitry, the controller locks−out in a selected valley and remains locked until the output loading significantly changes. When the load becomes lighter, the controller jumps into the next valley. It can go down to the 4th valley if necessary. Beyond this point, the controller reduces its switching frequency by freezing the peak current setpoint. During quasi−resonance operation, in case of very damped valleys, a 5.5 m s timer emulates the missing valleys.•Frequency reduction in light−load conditions: when the 4th valley is left, the controller reduces the switching frequency which naturally improves the standby power by a reduction of all switching losses.•Overpower protection (OPP): When the voltage on ZCD pin swings in flyback polarity, a direct image if the input voltage is applied on ZCD pin. We can thus reduce the peak current depending of V ZCD during the on−time.•Internal soft−start: A soft−start precludes the main power switch from being stressed upon startup. Its duration is fixed and equal to 4 ms.•Fault input (A and B versions): By combining a dual threshold on the Fault pin, the controller allows the direct connection of an NTC to ground plus a zener diode to a monitored voltage. In case the pin is brought below the OTP threshold by the NTC or above the OVP threshold by the zener diode, the circuit permanently latches−off and V CC is clamped to 7.2 V.•Fault input (C and D versions): The C and D versions of NCP1380 include a brown−out circuit which safely stops the controller in case the input voltage is too low. Restart occurs via a complete startup sequence (latch reset and soft−start). During normal operation, the voltage on this pin is clamped to V clamp to give enough room for OVP detection. If the voltage on this pin increases above 2.5 V, the part latches−off.•Short−circuit protection: Short−circuit and especially over−load protections are difficult to implement when a strong leakage inductance between auxiliary and power windings affects the transformer (where the auxiliary winding level does not properly collapse in presence of an output short). Here, when the internal 0.8 V maximum peak current limit is activated, the timer starts counting up. If the fault disappears, the timer counts down. If the timer reaches completion while the error flag is still present, the controller stops the pulses. This protection is latched on A and C version (the user must unplug and re−plug the power supply to restart the controller) and auto−recovery on B and D versions (if the fault disappears, the SMPS automatically resumes operation). In addition, all versions feature a winding short−circuit protection, that senses the CS signal and stops the controller if V CS reaches 1.5 x V ILIM (after a reduced LEB of t BCS). This additional comparator is enabled only during the main LEB duration t LEB, for noise immunity reason.NCP1380 OPERATING MODESNCP1380 has two operating mode: quasi−resonant operation and VCO operation for the frequency foldback. The operating mode is fixed by the FB voltage as portrayed by Figure 26:•Quasi−resonant operation occurs for FB voltage higher than 0.8 V (FB decreasing) or higher than 1.4 V (FB increasing) which correspond to high output power and medium output power. The peak current is variable and is set by the FB voltage divided by 4.•Frequency foldback or VCO mode occurs for FB voltage lower than 0.8 V (FB decreasing) or lower than 1.4 V (FB increasing). This corresponds to low output power.During VCO mode, the peak current decreases down to 17.5% of its maximum value and is then frozen. The switching frequency is variable and decreases as the output load decreases.The switching frequency is set by the end of charge of the capacitor connected to the C T pin. This capacitor is charged with a constant current source and the capacitor voltage is compared to an internal threshold fixed by FB voltage. When this capacitor voltage reaches the threshold the capacitor is rapidly discharged down to 0 V and a new period start.Figure 26. Operating Valley According to FB VoltageVALLEY DETECTION AND SELECTIONThe valley detection is done by monitoring the voltage of the auxiliary winding of the transformer. A valley is detected when the voltage on pin 1 crosses down the 55 mV internalthreshold. When a valley is detected, an internal counter is incremented. The operating valley (1st , 2nd , 3rd or 4th ) is determined by the FB voltage as shown by Figure 26.VDDVDDAs the output load decreases (FB voltage decreases), the valleys are incremented from the first to the fourth. When the fourth valley is reached, if FB voltage further decreases below 0.8 V, the controller enters VCO mode.During VCO operation, the peak current continues to decrease until it reaches 17.5% of the maximum peak current: the switching frequency expands to deliver the necessary output power. This allows achieving very low standby power consumption.The Figure 28 shows a simulation case where the output current of a 19 V, 60 W adapter decreases from 2.8 A to 0.1 A. No instability is seen during the valley transitions (Figures 29, 30, 31 and 32)Figure 28. Output Load is Decreased from 2.8 A Down to 100 mA at 120 Vdc Input VoltageFigure 29. Zoom 1: 1st to 2nd Valley TransitionFigure 30. Zoom 2: 2nd to 3rd Valley TransitionFigure 31. Zoom 3: 3rd to 4thValley TransitionFigure 32. Zoom 4: 4th Valley to VCO Mode TransitionTime OutIn case of extremely damped free oscillations, the ZCD comparator can be unable to detect the valleys. To avoid such situation, NCP1380 integrates a Time Out function that acts as a substitute clock for the decimal counter inside the logic bloc. The controller thus continues its normal operation. To avoid having a too big step in frequency, the time out duration is set to 5.5 m s. Figures 34 and 35 detail the time out operation.The NCP1380 also features an extended time out during the soft −start.Indeed, at startup, the output voltage reflected on the auxiliary winding is low. Because of the voltage drop introduced by the Over Power Compensation diode (Figure 40), the voltage on the ZCD pin is very low and the ZCD comparator might be unable to detect the valleys. In this condition, setting the DRV Latch with the 5.5 m s time −out can lead to a continuous conduction mode operation (CCM) at the beginning of the soft −start. This CCM operation only last a few cycles until the voltage on ZCD pin becomes high enough to be detected by the ZCD comparator. To avoid this, the time −out duration is extended to 40 m s during the soft −start in order to ensure that the transformer is fully demagnetized before the MOSFET is turned −on.Figure 33. Time Out CircuitFigure 34. Time Out Case n 51: the 3rd Valley is MissingFigure 35. Time Out Case n 52: the 3rd and 4th Valley are MissingVCO MODE OR FREQUENCY FOLDBACKVCO operation occurs for FB voltage lower than 0.8 V (FB decreasing), or lower than 1.4 V (FB increasing). This corresponds to low output power.During VCO operation, the peak current is fixed to 17.5%of his maximum value and the frequency is variable and expands as the output power decreases.The frequency is set by the end of charge of the capacitor connected to the C T pin. This capacitor is charged with a constant current source and its voltage is compared to an internal threshold (V FBth ) fixed by FB voltage (seeFigure 27). When this capacitor voltage reaches the threshold, the capacitor is rapidly discharged down to 0 V and a new period start. The internal threshold is inversely proportional to FB voltage. The relationship between V FB and V FBth is given by Equation 1.V FBth +6.5*(10ń3)V FB(eq. 1)When V FB is lower than 0.3 V , V CT is clamped to V CT(MAX) which is typically 5.5 V . Figure 36 shows the VCO mode at works.Figure 36. In VCO Mode, as the Power Output Decreases, the Frequency ExpandsSHORT−CIRCUIT OR OVERLOAD MODE Figure 37 shows the implementation of the fault timer.Figure 37. Overload Detection SchematicWhen the current in the MOSFET is higher than V ILIM / R sense, “Max Ip” comparator trips and the digital timer starts counting: the timer count is incremented each 10 ms. When the current comes back within safe limits, “Max Ip”comparator becomes silent and the timer count down: the timer count is decremented each 10 ms. In normal overload conditions the timer reaches its completion when it has counted up 8 times 10 ms.On B and D version, when the timers reaches its completion, the circuit enter auto−recovery mode: the circuit stops all operations and V CC decreases via the circuit own consumption (I CC1). When V CC reaches V CC(off), the circuit goes in startup mode and restart switching. (see Figure 38) This ensures a low duty−cycle burst operation in fault mode.On A and C versions, when the timers finishes counting 80 ms, the circuit goes in latch mode (Figure 39): the DRV pulses stop and V CC is pulled down to V CC(latch) which is 7.2 V typically. The circuit un−latches when the current circulating in V CC pin drops below I CC(latch).In parallel to the cycle−by−cycle sensing of the CS pin, another comparator with a reduced LEB (t BCS) and a threshold of 1.2 V is able to sense winding short−circuit and immediately shut down the controller. Depending on the version, this additional protection is either latched or auto−recovery, according to the overload protection behavior.Figure 38. Auto−Recovery Short−Circuit Protection on B and D VersionsFigure 39. Latched Short−Circuit Protection on A and C VersionsOVER POWER COMPENSATIONThe over power compensation is achieved by monitoring the signal on ZCD pin (pin 1). Indeed, a negative voltage applied on this pin directly affects the internal voltage reference setting the maximum peak current (Figure 40). When the power MOSFET is turned−on, the auxiliary winding voltage becomes a negative voltage proportional to the input voltage. As the auxiliary winding is already connected to ZCD pin for the valley detection, by selecting the right values for R opu and R opl, we can easily perform over power compensation.AuRz cdDemagFigure 40. Over Power Compensation CircuitTo ensure optimal zero−crossing detection, a diode isneeded to bypass R opu during the off−time.If we apply the resistor divider law on the pin 1 during theon−time, we obtain the following relationship:R ZCD)R opuR opl +*N p,aux V in*V OPPV OPP(eq. 2)Where:N p,aux is the auxiliary to primary turn ration: N p,aux = N aux / N pV in is the DC input voltageV OPP is the negative OPP voltageBy selecting a value for R opl, we can easily deduce R opu using Equation 2. While selecting the value for R opl, we must be careful not choosing a too low value for this resistor in order to have enough voltage for zero−crossing detection during the off−time. We recommend having at least 8 V on ZCD pin, the maximum voltage being 10 V.During the off−time, ZCD pin voltage can be expressed as follows:V ZCD+R oplR ZCD)R oplǒV aux*VdǓ(eq. 3)We can thus deduce the relationship between R opl and R ZCD:R ZCD R opl +V aux*V d*V ZCDV ZCD(eq. 4)Design example:V aux = 18 VV d = 0.6 VN p,aux = 0.18If we want at least 8 V on ZCD pin, we have:R ZCDR opl+V aux*V d*V ZCDV ZCD(eq. 5)+18*0.6*88[1.2We can choose: R ZCD = 1 k W and R opl = 1 k W.For the over power compensation, we need to decrease thepeak current by 37.5% at high line (370 Vdc). Thecorresponding OPP voltage is:V OPP+0.375V ILIM+−300mV(eq. 6)Using Equation 2, we have:R ZCD)R opuR opt+*N p,aux V lin*V OPPV OPP(eq. 7)+−0.18370*(−0.3)(−0.3)+221Thus,R opu+221Ropl*R ZCD+2211k*1k+220k W(eq. 8)。
Datasheet MLX90614 中文 数据手册 rev008
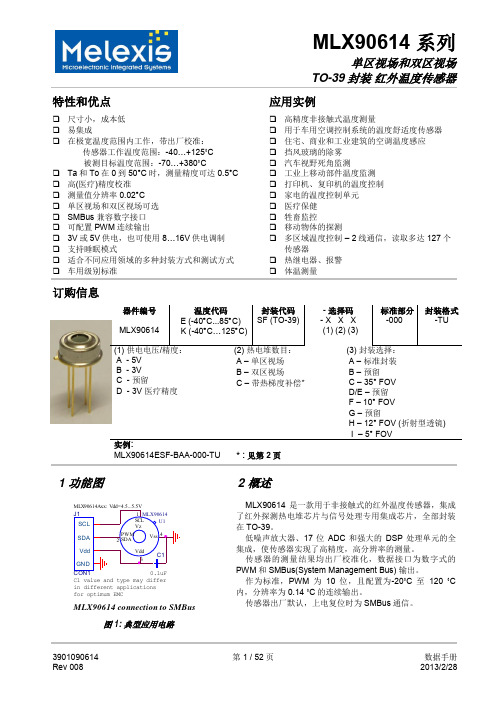
10-位 PWM 输出模式是连续输出所测物体温度的标准配置,测量物体的温度范围为-20…120 °C,分辨 率为 0.14 °C。PWM 通过修改 EEPROM 内 2 个单元的值,实际上可以根据需求调整至任何温度范围,而这对 出厂校准结果并无影响。
传感器的测量结果均出厂校准化,数据接口为数字式的 PWM 和 SMBus(System Management Bus) 输出。
作为标准,PWM 为 10 位,且配置为-20˚C 至 120 ˚C 内,分辨率为 0.14 ˚C 的连续输出。
传感器出厂默认,上电复位时为 SMBus 通信。
3901090614 Rev 008
PWM 引脚也可配置为热继电器(输入是 To),这样可以实现简单且性价比高的恒温控制器或温度报警(冰 点/沸点)应用,其中的温度临界值是用户可编程的。在 SMBus 系统里,这个功能可以作为处理器的中断信号, 以此触发读取主线上从动器的值,并确定精度条件。
传感器有两种供电电压选择:5V 或 3V(电池供电)。其中,5V 也可简便的从更高供电电压(例如 8 至 16V)上通过外接元件调制。(具体请参考“应用信息”)
MLX90614 connection to SMBus
图 1: 典型应用电路
2 概述
MLX90614 是一款用于非接触式的红外温度传感器,集成 了红外探测热电堆芯片与信号处理专用集成芯片,全部封装 在 TO-39。
低噪声放大器、17 位 ADC 和强大的 DSP 处理单元的全 集成,使传感器实现了高精度,高分辨率的测量。
Nipro 产品数据册:单用途翼型肾脏细胞注射器说明书

H O S P I T A L P R O D U C T WING CATHSTERILE, SINGLE-USE WINGED CATHETER WITH INJECTION PORT FOR IV INFUSIONPRODUCT DATA SHEET2PRODUCT COMPLIANCE• CE-marked, Class IIa Medical Devices, Rule 7, MDD 93/42/EEC, UMDNS 10727• Complies with the following norms, directives, and regulations: ―ISO 594-1: 1986 ―EN 980:2008 ―EN 1041:2008 ―EN 1707:1996 ―ISO 7864:2016―ISO 9626:2016 ―EN ISO 10555-1:2013 ―EN ISO 10993-1/4/5/7/11 ―ISO 10993-10:2010 ―EN ISO 11135-1:2014―EN ISO 11607-1:2009 /AMD 2014 ―EN ISO 13485:2016 ―EN ISO 14971: 2012• Labels contain 12 languagesMANUFACTURING DETAILSLegal manufacturer: Nipro Corporation Country of origin: ThailandSTERILIZATION AND SHELF LIFESterilizationSingle-use only Indicator stickerShelf lifeEtO (Ethylene oxide)Each outer box (or shipping carton) contains a chemical indicator that indicates sterility. This indicator comes in the form of a [blue] sticker that turns[red] when sterilized.5 yearsWING CATHSTERILE, SINGLE-USE WINGED CATHETER WITH INJECTION PORT FOR IV INFUSION• Ultra sharp three-beveled needle to minimize discomfort • Radiopaque• Injection port with universal luer fitting • Flexible wings for easy grip• Color-coded wings and hub to indicate gauge• Siliconization of needle minimizes penetration and gliding force• T ransparent ETFE catheter tube for quick visualization of blood in the flashback chamber to facilitate insertion • Flashback in hub means the needle is correctly in the vein • Flashback in catheter means the catheter is correctly in the vein • Latex-free, DEHP-free, PVC-free • Available in 16-18-20-22-24 G• IV infusion duration: hours to several days • For use by healthcare professionals onlyClass IIa Medical DevicesRule 7MDD 93/42/EEC UMDNS 1072701233MATERIALS USEDDEHP-free Latex-free PVC-free PRODUCT RANGE OVERVIEWPACKAGING DETAILSLanguages12 languages on inner and outer box:English (EN), French (FR), Dutch (NL), German (DE), Spanish (ES), Italian (IT), Portuguese (PT), Greek (EL), Swedish (SV), Danish (DA), Norwegian (NO), and Finnish (FI)GlueMaterial: Acrylic resinNeedle (cannula)Material:Stainless steel SUS-304Needle hub Material:Polycarbonate (PC)Catheter hubMaterial: Polypropylene (PP)Port capMaterial: Polyethylene (PE)Catheter tubeMaterial: Ethyltetrafluoroethylene (ETFE)Cutting angleThree-beveledLuer capMaterial: Polypropylene (PP)Cap connectorMaterial: Polypropylene (PP)Caulking pinMaterial: Stainless steel SUS-304One-way valveMaterial: Silicone tubeLubricantMaterial: Silicone PolydimethylsiloxaneMembrane filterMaterial: Random micro glass filterVent fittingMaterial: Polypropylene (PP)Catheter wingMaterial: Polypropylene (PP)Nipro Medical Europe : European Headquarters, Blokhuisstraat 42, 2800 Mechelen, Belgium T: +32 (0)15 263 500 | F: +32 (0)15 263 510 |***********************| D a t a s h e e t - W i n g _C a t h - T H A - 27.N o v 2019Label detailsTransport conditionsClosed and dryStorage conditions Open the packaging only immediately before use to guarantee sterility.。
NCP1595A中文资料
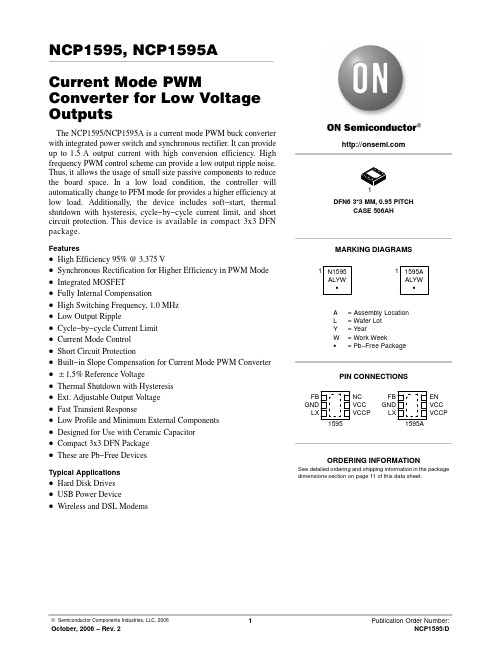
NCP1595, NCP1595A Current Mode PWM Converter for Low Voltage OutputsThe NCP1595/NCP1595A is a current mode PWM buck converter with integrated power switch and synchronous rectifier. It can provide up to 1.5 A output current with high conversion efficiency. High frequency PWM control scheme can provide a low output ripple noise. Thus, it allows the usage of small size passive components to reduce the board space. In a low load condition, the controller will automatically change to PFM mode for provides a higher efficiency at low load. Additionally, the device includes soft−start, thermal shutdown with hysteresis, cycle−by−cycle current limit, and short circuit protection. This device is available in compact 3x3 DFN package.Features•High Efficiency 95% @ 3.375 V•Synchronous Rectification for Higher Efficiency in PWM Mode •Integrated MOSFET•Fully Internal Compensation•High Switching Frequency, 1.0 MHz•Low Output Ripple•Cycle−by−cycle Current Limit•Current Mode Control•Short Circuit Protection•Built−in Slope Compensation for Current Mode PWM Converter •$1.5% Reference V oltage•Thermal Shutdown with Hysteresis•Ext. Adjustable Output V oltage•Fast Transient Response•Low Profile and Minimum External Components •Designed for Use with Ceramic Capacitor•Compact 3x3 DFN Package•These are Pb−Free DevicesTypical Applications•Hard Disk Drives•USB Power Device•Wireless and DSL ModemsSee detailed ordering and shipping information in the package dimensions section on page 11 of this data sheet.ORDERING INFORMATIONINV INFigure 1. Typical Operating CircuitABSOLUTE MAXIMUM RATINGSRating Symbol Value Unit Power Supply (Pin 4, 5)V IN7.0−0.3 (DC)−1.0 (100 ns)VInput / Output PinsPin 1,3,6V IO 6.5,−0.3 (DC)−1.0 (100 ns)VThermal Characteristics3x3 DFN Plastic PackageMaximum Power Dissipation @ T A = 25°CThermal Resistance Junction−to−AirP DR q JA145068.5mW°C/W Operating Junction Temperature Range (Note 4)T J−40 to + 150°C Operating Ambient Temperature Range T A−40 to + 85°C Storage Temperature Range T stg− 55 to +150°C Moisture Sensitivity Level (Note 3)1−Stresses exceeding Maximum Ratings may damage the device. Maximum Ratings are stress ratings only. Functional operation above the Recommended Operating Conditions is not implied. Extended exposure to stresses above the Recommended Operating Conditions may affect device reliability.NOTE:ESD data available upon request.1.This device series contains ESD protection and exceeds the following tests:Human Body Model (HBM) 2.0 kV per JEDEC standard: JESD22−A114.Machine Model (MM) 200 V per JEDEC standard: JESD22−A115.tchup Current Maximum Rating: 150 mA per JEDEC standard: JESD78.3.Moisture Sensitivity Level (MSL): 1 per IPC/JEDEC standard: J−STD−020A.4.The maximum package power dissipation limit must not be exceeded.PD+TJ(max)*T AR q JAELECTRICAL CHARACTERISTICS(V IN = 5.0 V, V OUT = 1.2 V, T A = 25°C for typical value, −40°C v T A v 85°C for min/max values unless otherwise noted)Characteristic Symbol Min Typ Max Unit Operating Voltage V IN 4.0− 5.5V Under Voltage Lockout Threshold V UVLO 3.2 3.5 3.8V Under Voltage Lockout hysteresis V UVLO_HYS180mVP FET Leakage Current (Pin 5, 4) T A = 25°CT A = −40°C to 85°C I LEAK−P1.01015m AN FET Leakage Current (Pin 3, 2) T A = 25°CT A = −40°C to 85°C I LEAK−N1.01015m AFEEDBACK VOLTAGEFB Input Threshold (T A = −40°C to 85°C)V FB0.7880.8000.812V FB Input Current I FB10100nA Overvoltage Protect Higher than FB Threshold (T A = 25°C)V OVP 2.0 5.010.0% THERMAL SHUTDOWNThermal Shutdown Threshold (Note 5)T SHDN TBD160−°C Hysteresis T SDHYS30°C PWM SMPS MODEMinimum ON−Time TON MIN100ns Switching Frequency (T A = −40°C to 85°C)F OSC0.8 1.0 1.2MHz Internal PFET ON−Resistance (I LX = 100 mA, V IN = 5.0 V, T A = 25°C)(Note 5)R DS(ON)_P−0.20.3WInternal NFET ON−Resistance (I LX = 100 mA, V IN = 5.0 V, T A = 25°C)(Note 5)R DS(ON)_N−0.150.22W Maximum Duty Cycle D MAX−−100% Soft−Start Time (V IN = 5.0 V, V o = 1.2 V, I LOAD = 0 mA, T A = 25°C) (Note 6)T SS− 1.0−ms Main PFET Switch Current Limit (Note 5)I LIM 2.0 2.5A ENABLE (NCP1595A)Enable Threshold High (NCP1595A Only)V EN_H 1.8V Enable Threshold Low V EN_L0.4V Enable bias current ( EN = 0 V)I EN500TBD nA Total DeviceQuiescent Current Into V CCP (V IN = 5 V, V FB = 1.0 V, T A = 25°C)I CCP10m A Quiescent Current Into V CC (V IN = 5 V, V FB = 1.0 V, T A = 25°C)I CC900m A Shutdown Quiescent Current into V CC and V CCP (NCP1595A Only)(EN = 0, V IN = 5 V, V FB = 1.0 V, T A = 25°C)I CC_SD 1.5 3.0m A5.Values are design guarantee.6.Design guarantee, value depends on voltage at V OUT.PIN FUNCTION DESCRIPTIONSPin #Symbol Pin DescriptionNCP15951FB Feedback pin. Part is internally compensated. Only necessary to place a voltage divider or connect the out-put directly to this pin.2GND Ground3LX Pin connected internally to power switch. Connect externally to inductor.4VCCP Power connection to the power switch.5VCC IC power connection.6NC No ConnectionNCP1595A1FB Feedback pin. Part is internally compensated. Only necessary to place a voltage divider or connect the out-put directly to this pin.2GND Ground3LX Pin connected internally to power switch. Connect externally to inductor.4VCCP Power connection to the power switch.5VCC IC power connection.6EN Device Enable pin. This pin has an internal current source pull up. No connect is enable the device. With this pin pulled down below 0.4 V, the device is disabled and enters the shutdown mode.V INV INFigure 2. Detail Block DiagramEXTERNAL COMPONENT REFERENCE DATADevice V OUT Inductor Model Inductor (L1)C IN (C1)C OUT (C2)R1R2NCP1595/ NCP1595A 3.3 V CDC5D23 3R3 (1 A)CDRH6D38 3R3 (1.5 A)3.3 m H22 m F22 m F x 222 m F22 m F x 231 k10 kNCP1595/ NCP1595A 2.5 V CDC5D23 3R3 (1 A)CDRH6D38 3R3 (1.5 A)3.3 m H22 m F22 m F x 222 m F22 m F x 221 k10 kNCP1595/ NCP1595A 1.5 V CDC5D23 3R3 (1 A)CDRH6D38 3R3 (1.5 A)3.3 m H22 m F22 m F x 222 m F22 m F x 28 k10 kNCP1595/ NCP1595A 1.2 V CDC5D23 3R3 (1 A)CDRH6D38 3R3 (1.5 A)3.3 m H22 m F22 m F x 222 m F22 m F x 25 k10 kTYPICAL OPERATING CHARACTERISTICSLOW SIDE AMBIENT TEMPERATURE, (T A /°C)0.000.050.100.150.200.250.30−4002585Figure 3. Switch ON Resistance vs.TemperatureL O W S I D E S W I T C H O N R E S I S T A N C E /WFigure 4. Feedback Input Threshold vs.Temperature0.7850.7900.7950.8000.8050.8100.815−4002585AMBIENT TEMPERATURE, (T A /°C)F B I N P U T T H R E S H O L D V F B /VFigure 5. Switching Frequency vs.Temperature0.70.80.91.01.11.21.3−4002585AMBIENT TEMPERATURE, (T A /°C)S W I T C H F R E Q U E N C Y , F O S C /M H ZFigure 6. Main P−FET Current Limit vs.Temperature1.51.82.02.32.52.83.0−4002585AMBIENT TEMPERATURE, (T A /°C)M A I N P −F E T C U R R E N T L I M I T , I L I M /V600700800900100011001200−402585AMBIENT TEMPERATURE, (T A /°C)Q U I E S C E N T C U R R E N T I N T O V C C , I C C /m A Figure 7. Quiescent Current Into V CC vs.Temperature0123456−4002585S H U T D O W N Q U I E S C E N T C U R R E N T , I C C _S D /m AAMBIENT TEMPERATURE, (T A /°C)Figure 8. Shutdown Quiescent Current vs.TemperatureFigure 9. Output Voltage Change vs. OutputCurrentFigure 10. Efficiency vs. Output CurrentFigure 11. Output Voltage Change vs.Output CurrentFigure 12. Efficiency vs. Output CurrentFigure 13. Efficiency vs. Output CurrentFigure 14. Output Voltage Change vs.Output Current−1.5−1.0−0.50.00.51.01.51010010001000010100100010000−1.5−1.0−0.50.00.51.01.51010010001000010100100010000−1.5−1.0−0.50.00.51.01.51010010001000010100100010000O U T P U T E F F I C I E N C Y , %O U T P U T E F F I C I E N C Y , %O U T P U T V O L T A G E C H A N G E , D V O U T /%O U T P U T V O L T A G E C H A N G E , D V O U T /%O U T P U T V O L T A G E C H A N G E , D V O U T /%(V IN = 5 V, I LOAD = 700 mA, L = 3.3 m H, C OUT = 20 m F)Upper Trace: L X Pin Switching Waveform, 2 V / div.Middle Trace: Output Ripple Voltage, 20 mV / div.Lower Trace: Inductor Current, 1 A / div.(V IN = 5 V, I LOAD = 100 mA, L = 3.3 m H, C OUT = 20 m F)Upper Trace: L X Pin Switching Waveform, 2 V / div.Middle Trace: Output Ripple Voltage, 20 mV / div.Lower Trace: Inductor Current, 1 A / div.Figure 15. DCM Switching Waveform forV OUT = 3.3 V Figure 16. CCM Switching Waveform forV OUT = 3.3 V(V IN = 5 V, I LOAD = 100 mA, L = 3.3 m H, C OUT = 20 m F)Upper Trace: L X Pin Switching Waveform, 2 V / div.Middle Trace: Output Ripple Voltage, 20 mV / div.Lower Trace: Inductor Current, 1 A / div.(V IN = 5 V, I LOAD = 700 mA, L = 3.3 m H, C OUT = 20 m F)Upper Trace: L X Pin Switching Waveform, 2 V / div.Middle Trace: Output Ripple Voltage, 20 mV / div.Lower Trace: Inductor Current, 1 A / div.Figure 17. DCM Switching Waveform forV OUT = 1.2 V Figure 18. CCM Switching Waveform forV OUT = 1.2 V(V IN = 5 V, I LOAD = 10 mA, L = 3.3 m H, C OUT = 20 m F x 2)Upper Trace: Input Voltage, 2 V/ div.Middle Trace: Output Voltage, 1 V/ div.Lower Trace: Input Current, 1 A / div.(V IN = 5 V, I LOAD= 10 mA, L = 3.3 m H, C OUT = 20 m F x 2)Upper Trace: Input Voltage, 2 V/ div.Middle Trace: Output Voltage, 1 V / div.Lower Trace: Input Current, 1 A / div.Figure 19. Soft−Start Waveforms for V OUT = 3.3 V Figure 20. Soft−Start Waveforms for V OUT = 1.2 V(V IN = 5 V, L = 3.3 m H, C OUT = 20 m F x 2)Upper Trace: Output Dynamic Voltage, 100 mV / div. Lower Trace: Output Current, 500 mA / div.(V IN = 5 V, L = 3.3 m H, C OUT = 20 m F x 2)Upper Trace: Output Dynamic Voltage, 100 mV / div.Lower Trace: Output Current, 500 mA / div.(V IN = 5 V, L = 3.3 H, C OUT = 20 m F x 2)Upper Trace: Output Dynamic Voltage, 100 mV / div.Lower Trace: Output Current, 500 mA / div.(V IN = 5 V, L = 3.3 H, C OUT = 20 m F x 2)Upper Trace: Output Dynamic Voltage, 100 mV / div.Lower Trace: Output Current, 500 mA / div.Figure 21. Load Regulation for V OUT = 3.3 V Figure 22. Load Regulation for V OUT = 3.3 V Figure 23. Load Regulation for V OUT = 1.2 V Figure 24. Load Regulation for V OUT = 1.2 VDETAILED OPERATING DESCRIPTIONIntroductionNCP1595 operates as a current mode buck converter with switching frequency at 1.0 MHz. The P−Channel main switch is set by the positive edge of the clock cycle going into the PWM latch. The main switch is reset by the PWM latch in the following three cases:1.PWM comparator output trips as the peak inductorcurrent signal reaches a threshold level establishedby the error amplifier.2.The inductor current has reached the current limit.3.Overvoltage at output occurs.After a minimum dead time, the N−Channel synchronized switch will turn on and the inductor current will ramp down. If the inductor current ramps down to zero before the initiation of next clock cycle, the regulator runs at discontinuous conduction mode (DCM). Otherwise the regulator is at continuous conduction mode (CCM). The N−Channel switch will turn off when the clock cycle starts. The duty cycle is given by the ratio of output voltage to input voltage. The duty cycle is allowed to go to 100% to increase transient load response when going from light load to heavy load.Error Amplifier and Slope CompensationA fully internal compensated error amplifier is provided inside NCP1595. No external circuitry is needed to stabilize the device. The error amplifier provides an error signal to the PWM comparator by comparing the feedback voltage (800 mV) with internal voltage reference of 1.2 V. Current mode converter can exhibit instability at duty cycles over 50%. A slope compensation circuit is provided inside NCP1595 to overcome the potential instability. Slope compensation consists of a ramp signal generated by the synchronization block and adding this to the inductor current signal. The summed signal is then applied to the PWM comparator.Soft−Start and Current LimitA soft start circuit is internally implemented to reduce the in−rush current during startup. This helps to reduce the output voltage overshoot.The current limit is set to allow peak switch current in excess of 2 A. The intended output current of the system is 1.5 A. The ripple current is calculated to be approximately 350 mA with a 3.3 m H inductor. Therefore, the peak current at 1.5 A output will be approximately 1.7 A. A 2 A set point will allow for transient currents during load step. The current limit circuit is implemented as a cycle−by−cycle current limit. Each on−cycle is treated as a separate situation. Current limiting is implemented by monitoring the P−Channel switch current buildup during conduction with a current limit comparator. The output of the current limit comparator resets the PWM latch, immediately terminating the current cycle.Over−Voltage ProtectionOvervoltage occurs when the feedback voltage exceeds 5% of its regulated voltage. In this case, the P−Channel main switch will be reset and the N−Channel synchronized switch is turn on to sink current from the output voltage which helps to drop its feedback voltage back to the regulated voltage. Thermal ShutdownInternal Thermal Shutdown circuitry is provided to protect the integrated circuit in the event when maximum junction temperature is exceeded. When activated, typically at 160°C, the shutdown signal will disable the P−Channel and N−Channel switch. The thermal shutdown circuit is designed with 30°C of hysteresis. This means that the switching will not start until the die temperature drops by this amount. This feature is provided to prevent catastrophic failures from accidental device overheating. It is not intended as a substitute for proper heat sinking. NCP1595 is contained in the thermally enhanced DFN package.11APPLICATION INFORMATIONOutput Voltage SelectionThe output voltage is programmed through an external resistor divider connect from V OUT to FB then to GND.For internal compensation and noise immunity, the resistor from FB to GND should be in 10 k to 20 k ranges.The relationship between the output voltage and feedback resistor is given by:V OUT +V FB ǒ1)R1R2Ǔ(eq. 1)V OUT : Output voltage V FB : Feedback V oltageR1: Feedback resistor from V OUT to FB.R2: Feedback resistor from FB to GND.Input Capacitor selectionIn the PWM buck converter, the input current is pulsating current with switching noise. Therefore, a bypass input capacitor must choose for reduce the peak current drawn from the power supply. For NCP1595, low ESR ceramic capacitor of 10 m F should be used for most of cases. Also,the input capacitor should be placed as close as possible to the V CCA pin for effective bypass the supply noise.Inductor selectionThe inductor parameters are including three items, which are DC resistance, inductor value and saturation current.Inductor DC resistance will effect the convector overall efficiency, low DC resistor value can provide a higher efficiency. Thus, inductor value are depend on the inductorripple current, input voltage, output voltage, output current and operation frequency, the inductor value is given by:D IL +V OUT L F SWǒ1*V OUT V INǓ(eq. 2)D IL : peak to peak inductor ripple current L: inductor valueFSW: switching frequencyAfter selected a suitable value of the inductor, it should be check out the inductor saturation current. The saturation current of the inductor should be higher than the maximum load plus the ripple current.D IL(MAX)+D IOUT(MAX))D IL 2(eq. 3)D IL(MAX): Maximum inductor current D IOUT(MAX): Maximum output currentOutput Capacitor selectionOutput capacitor value is based on the target output ripple voltage. For NCP1595, the output capacitor is required a ceramic capacitors with low ESR value. Assume buck converter duty cycle is 50%. The output ripple voltage in PWM mode is given by:D VOUT [D ILǒ14 FSWCOUT)ESR Ǔ(eq. 4)In general, value of ceramic capacitor using 20 m F should be a good choice.ORDERING INFORMATIONDevicePackage Shipping †NCP1595MNR2G DFN−6(Pb−Free)3000 / Tape & Reel NCP1595AMNR2GDFN−6(Pb−Free)3000 / Tape & Reel†For information on tape and reel specifications, including part orientation and tape sizes, please refer to our Tape and Reel Packaging Specifications Brochure, BRD8011/D.PACKAGE DIMENSIONSDFN6 3*3 MM, 0.95 PITCHCASE 506AH−01ǒmmǓ*For additional information on our Pb−Free strategy and solderingdetails, please download the ON Semiconductor Soldering andMounting Techniques Reference Manual, SOLDERRM/D.ON Semiconductor and are registered trademarks of Semiconductor Components Industries, LLC (SCILLC). SCILLC reserves the right to make changes without further notice to any products herein. SCILLC makes no warranty, representation or guarantee regarding the suitability of its products for any particular purpose, nor does SCILLC assume any liability arising out of the application or use of any product or circuit, and specifically disclaims any and all liability, including without limitation special, consequential or incidental damages.“Typical” parameters which may be provided in SCILLC data sheets and/or specifications can and do vary in different applications and actual performance may vary over time. All operating parameters, including “Typicals” must be validated for each customer application by customer’s technical experts. SCILLC does not convey any license under its patent rights nor the rights of others. SCILLC products are not designed, intended, or authorized for use as components in systems intended for surgical implant into the body, or other applications intended to support or sustain life, or for any other application in which the failure of the SCILLC product could create a situation where personal injury or death may occur. Should Buyer purchase or use SCILLC products for any such unintended or unauthorized application, Buyer shall indemnify and hold SCILLC and its officers, employees, subsidiaries, affiliates, and distributors harmless against all claims, costs, damages, and expenses, and reasonable attorney fees arising out of, directly or indirectly, any claim of personal injury or death associated with such unintended or unauthorized use, even if such claim alleges that SCILLC was negligent regarding the design or manufacture of the part. SCILLC is an Equal Opportunity/Affirmative Action Employer. This literature is subject to all applicable copyright laws and is not for resale in any manner.PUBLICATION ORDERING INFORMATION。
部分液晶电源管理芯片代换
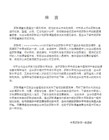
OCP2150 LTC3406/AT1366/MP2104
OCP2160 LTC3407
OCP2576 LM2576
OCP3601 MB3800
OCP5001 TL5001
OMC2596 LM2596/AP1501
DAP02ALSZ SG6841
DAP02ALSZ SG6841
DAP7A、DP8A 203D6、1203P6
DH321、DL321 Q100、DM0265R
DM0465R DM/CM0565R
DM0465R/DM0565R 用cm0565r代换(取掉4脚的稳压二极管)
DP104 5S0765
ACT4065 ZA3020/MP1580
ACT4070 ZA3030/MP1583/MP1591MP1593/MP1430
ACT6311 LT1937
ACT6906 LTC3406/AT1366/MP2104
AMC2576 LM2576
AMC2596 LM2596
AMC3100 LTC3406/AT1366/MP2104
OCP2160 LTC3407
OCP2576 LM2576
OCP3601 MB3800
OCP5001 TL5001
OMC2596 LM2596/AP1501
PT1301 RJ9266
PT4101 AJC1648/MP3202
PT4102 LT1937/AJC1896/AP1522/RJ9271/MP1540
AMC34063A AMC34063
AMC7660 AJC1564
LCDHome论坛_电源模块代换大全
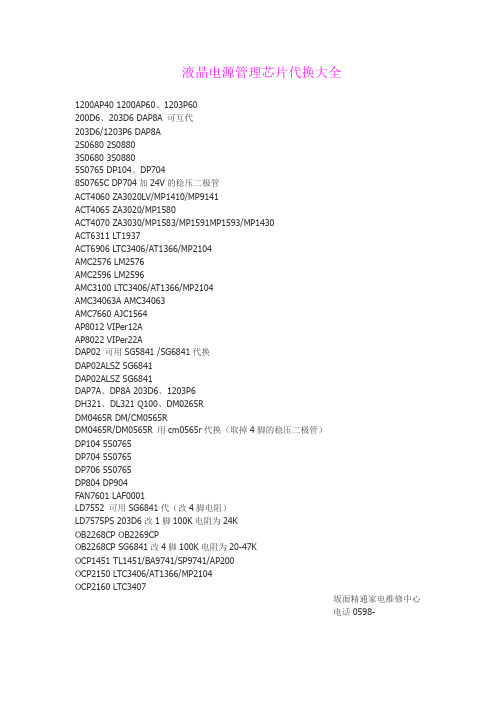
液晶电源管理芯片代换大全1200AP40 1200AP60、1203P60200D6、203D6 DAP8A 可互代203D6/1203P6 DAP8A2S0680 2S08803S0680 3S08805S0765 DP104、DP7048S0765C DP704加24V的稳压二极管ACT4060 ZA3020LV/MP1410/MP9141ACT4065 ZA3020/MP1580ACT4070 ZA3030/MP1583/MP1591MP1593/MP1430ACT6311 LT1937ACT6906 LTC3406/AT1366/MP2104AMC2576 LM2576AMC2596 LM2596AMC3100 LTC3406/AT1366/MP2104AMC34063A AMC34063AMC7660 AJC1564AP8012 VIPer12AAP8022 VIPer22ADAP02 可用SG5841 /SG6841代换DAP02ALSZ SG6841DAP02ALSZ SG6841DAP7A、DP8A 203D6、1203P6DH321、DL321 Q100、DM0265RDM0465R DM/CM0565RDM0465R/DM0565R 用cm0565r代换(取掉4脚的稳压二极管)DP104 5S0765DP704 5S0765DP706 5S0765DP804 DP904FAN7601 LAF0001LD7552 可用SG6841代(改4脚电阻)LD7575PS 203D6改1脚100K电阻为24KOB2268CP OB2269CPOB2268CP SG6841改4脚100K电阻为20-47KOCP1451 TL1451/BA9741/SP9741/AP200OCP2150 LTC3406/AT1366/MP2104OCP2160 LTC3407坂面精通家电维修中心电话0598-OCP2576 LM2576OCP3601 MB3800OCP5001 TL5001OMC2596 LM2596/AP1501PT1301 RJ9266PT4101 AJC1648/MP3202PT4102 LT1937/AJC1896/AP1522/RJ9271/MP1540SG5841SZ SG6841DZ/SG6841DSM9621 RJ9621/AJC1642SP1937 LT1937/AJC1896/AP1522/RJ9271/MP1540STR-G5643D STR-G5653D、STR-G8653DTEA1507 TEA1533TEA1530 TEA1532对应引脚功能接入THX202H TFC719THX203H TFC718STOP246Y TOP247YVA7910 MAX1674/75 L6920 AJC1610VIPer12A VIPer22A[audio01]ICE2A165(1A/650V.31W);ICE2A265(2A/650V.52W);ICE2B0565(0.5A/650V.23W):ICE2B165(1A/650V.31W);ICE2B265(2A/650V.52W);ICE2A180(1A/800V.29W);ICE2A280(2A/800.50W).KA5H0365R, KA5M0365R, KA5L0365R, KA5M0365RN# u) t! u1 W1 B) R, PKA5L0365RN, KA5H0380R, KA5M0380R, KA5L0380R1、KA5Q1265RF/RT(大小两种体积)、KA5Q0765、FSCQ1265RT、KACQ1265RF、FSCQ0765RT、FSCQ1565Q这是一类的,这些型号的引脚功能全都一样,只是输出功率不一样。
飞利浦电视维修通告一览表
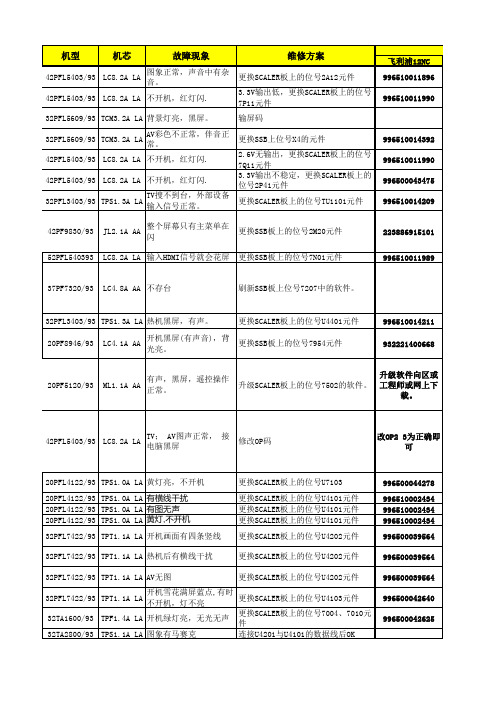
升级软件向区或 有声,黑屏,遥控操作 升级SCALER板上的位号7502的软件。 工程师或网上下 正常。 载。
42PFL5403/93 LC8.2A LA
TV; AV图声正常, 接 修改OP码 电脑黑屏
改OP2 3为正确 即可
20PFL4122/93 TPS1.0A LA 黄灯亮,不开机 20PFL4122/93 TPS1.0A LA 有横线干扰 20PFL4122/93 TPS1.0A LA 有图无声 20PFL4122/93 TPS1.0A LA 黄灯,不开机 32PFL7422/93 TPT1.1A LA 开机画面有四条竖线 32PFL7422/93 TPT1.1A LA 热机后有横线干扰 32PFL7422/93 TPT1.1A LA AV无图 32PFL7422/93 TPT1.1A LA
LC4.9AAB 有VA电压无VS电压 TPS1.1A TCM3.2
42PFL5609 42PFL5609
TCM3.2 TCM3.2
菜单正常但TV/AV/分量 换U4101 均无图像 同时更换F801 C807 Q803 R859 U805 不开机,电源板坏目测 D805。C807必须由原机330P/1KV更换 C807可见炸裂痕迹 成330P/2KV高压电容 开机保护,红灯闪3次电 更换R844,或清除R844和印板上红胶 源上的24V输出只有17V 再重装。 左右 测量C840两端电压只有310V左右,必 热机后会黑屏 须更换R815、R816、R813
此问题是由于机器进入了老化模式, 原因是:在PC模式下,本机按键:频 道(+)和音量(+)同时按住而引起 。 画面白屏,出现“AGING 1) 检查上述两个按键是否损坏而造 TPT1.2A LA xxPFL7422/93 ”字样问题的解决 成粘连,如果损坏,则更换之。 2)检查按键板上的SDM电容是否漏 电,如果漏电,更换之。 退出老化模式: 将电视机通过VGA连接到PC,当电视 42PFL7409/93 LC9.1ALA 47PFL5609/93 TCM3.2 47PFL5609/93 TCM3.2 42PFL5609/93 TCM3.2 42PFL5609/93 TCM3.2 图像正常,喇叭。耳机 换SSB板7701 声音很小。 开机炸保险丝 有声音黑屏 换电源板C812 C811 换电源板T904 932226831671 C812 C811 T904 R870 996510022583
MP1593中文资料

EV1593DN-00A (MP1593)4.75V to 28V Input, Up to 3A Output Step-Down DC/DC ConverterEVALUATION BOARD - INITIAL RELEASEMonolithic Power SystemsGENERAL DESCRIPTIONThe EV1593DN-00A is the Evaluation Board forMPS’ MP1593 Step-Down DC/DC Converter. It features a wide supply range of 4.75V to 28V and a continuous output current up to 3A. The output voltage is set to 3.3V, but can be easily adjusted to other levels from 1.22V. A 385KHz high switching frequency allows the use of small, low cost capacitors and inductors. Current mode control and an integrated power MOSFET minimize component count, board area, and solution cost. Fault condition protection includes cycle-by-cycle current limiting, thermal shutdown, and under-voltage lockout. Internal soft-start reduces the turn-on stress. The small but thermally enhanced 8-pin SOIC package minimizes board area and provides excellent thermal management.ELECTRICAL SPECIFICATIONParameter Symbol Value Units Supply Voltage V IN 4.75 – 28VOutput Voltage V OUT 3.3 V Output CurrentI OUT 0 – 3AFEATURES• Up to 3A Output Current• Wide 4.75 to 28V Operating Input Range • Monolithic Buck with 100m Ω Internal FET • Fixed 385KHz Frequency• All Ceramic Input and Output Capacitors • Programmable Soft-Start• Programmable Input Under-Voltage LockoutAPPLICATIONS• Distributed Power Systems • Battery Charger• Pre-Regulator for Linear Regulators, “MPS”, “Monolithic Power Systems”, and “The Future of Analog ICTechnology” are Registered Trademarks of Monolithic Power Systems, Inc.EV1593DN-00A EVALUATION BOARD(2.1”X x 1.3”Y x 0.4”Z)Board NumberMPS IC NumberEV1593DN-00A MP1593E F F I C I E N C Y (%)10095908580757065605550LOAD CURRENT (mA)EV1593_TAC _EC01Efficiency vsLoad Current500100015002000250030003500EV1593DN-00A – 4.75V-28V INPUT, UP TO 3A OUTPUT STEP-DOWN CONVERTEREVALUATION BOARD - INITIAL RELEASEEVALUATION BOARD SCHEMATICEV1593_S01SWGNDGNDVIN EN SSVOUTEV1593DN-00A BILL OF MATERIALSQty Ref DescriptionPackage Manufacturer Part Number 1 C1 Ceramic Capacitor, 22nF, 50V, X7R 0805 Any2 C2, C8 Ceramic Capacitor, 10µF, 50V, Y5V 1210 Murata GRM32DF51H106ZA01L 1 C3 Ceramic Capacitor, 8.2nF, 50V, X7R 0603 Any 0 C4, C7 Open2 C5, C9 Ceramic Capacitor, 22µF, 16V, X5R 1210 Taiyo Yuden EMK3Z5BJ226MM 1 C6 Ceramic Capacitor, 0.1µF, 50V, X7R 0805 Any 1 L1 Inductor, 10µH, 4A Sumida CDRH8D43-100NC 0 D1 Schottky Diode, 40V, 3A SMA Diodes Inc. B340A 1 U1 28V, 3A, Step Down Converter SOIC8 MPS MP1593DN 1 R1 Resistor, 16.9k Ω, 1% 0603 Any 1 R2 Resistor, 5.6k Ω, 5% 0603 Any 1 R3 Resistor, 10k Ω, 1% 0603 Any 0 R4 Open 0 R5 OpenEV1593DN-00A – 4.75V-28V INPUT, UP TO 3A OUTPUT STEP-DOWN CONVERTEREVALUATION BOARD - INITIAL RELEASETYPICAL PERFORMANCE CHARACTERISTICS10095908580757065605550E F F I C I E N C Y (%)500100015002000250030003500LOAD CURRENT (mA)EV1593_TPC05Efficiency vs Load CurrentLOAD CURRENT (mA)EV1593_TPC06Efficiency vs Load Current500100015002000250030003500V OUT 1V/Div.I L1A/Div.I L1A/Div.V OUT10mV/Div.V SW 10V/Div.V IN100mV/Div.EV1593-WF03Soft-StartWaveforms V OUT 1V/Div.I L1A/Div.4ms/Div.V IN = 12V, V OUT = 3.3V, 1A - 2A STEPEV1593-WF01Load Transient WaveformsEV1593-WF04Switching WaveformsEV1593-WF02Turn Off WaveformsEV1593DN-00A – 4.75V-28V INPUT, UP TO 3A OUTPUT STEP-DOWN CONVERTEREVALUATION BOARD - INITIAL RELEASE PRINTED CIRCUIT BOARD LAYOUTFigure 1—Top Silk Layer Figure 2—Top LayerFigure 3— Bottom LayerEV1593DN-00A – 4.75V-28V INPUT, UP TO 3A OUTPUT STEP-DOWN CONVERTEREVALUATION BOARD - INITIAL RELEASENOTICE: MPS believes the information in this document to be accurate and reliable. However, it is subject to change withoutnotice. Contact MPS for current specifications. MPS encourages users of its products to ensure that third party Intellectual Property rights are not infringed upon when integrating MPS products into any application. MPS cannot assume any legal responsibility for any said applications.EV1593DN-00A (MP1593) Rev. 1.0 Monolithic Power Systems, Inc. 5QUICK START GUIDE1. Connect the positive terminal of the load to VOUT pins, and the negative terminal of the load toGND pins 2. Preset the power supply output to 4.75V – 28V and turn off the power supply.3. Connect the positive terminal of the power supply output to the VIN pin and the negativeterminal of the power supply output to the GND pin 4. Turn the power supply on. The MP1593 will automatically startup.5. To use the Enable function, apply a digital input to EN pin. Drive EN higher than 2.5V to turn onthe regulator, drive EN less than 0.7V to turn it off. 6. An input under voltage lockout (UVLO) function can be implemented by the addition of a resistordivider R4 and R5.The EN threshold is 2.5V, so V IN UVLO threshold is V 5.25R 4R 1×⎟⎠⎞⎜⎝⎛+.RECOMMENDED COMPONENTS FOR STANDARD OUTPUT VOLTAGESThe output voltage of this board is set to 3.3V.This board is laid out to accommodate most commonly used inductors and output capacitors and to be programmed for most standard output voltages. The following table lists recommended components for some standard output voltages.Listed compensation components (R2, C3) values are based on the output capacitor installed on this board. For other capacitors, refer to the Application Information section in the MP1593 datasheet.Table 1—Recommended Components for Standard Output VoltagesVOUT R1 R2 C3 L1 1.8V 4.75k Ω 3k Ω 4.7nF 4.7µH 2.5V 10.5k Ω 3.9k Ω 5.6nF 4.7-6.8µH 3.3V 16.9k Ω 5.6k Ω 8.2nF 6.8-10µH 5V 30.9k Ω 7.5k Ω 10nF 10-15µH 12V 88.7k Ω 10k Ω 3.3nF 15-22µH。
硝苯地平缓释片(II)CTD资料

注册分类第1 页共126 页上海玉瑞生物科技(安阳)药业有限公司硝苯平缓释片(Ⅱ)申报生产资料 模块 --3.2.P.5 制剂质量控制CTD第 2 页 共 126页表 3.2.P.5.3.2-2 鉴别(二)保留时间统计表表 3.2.P.5.3.3.3.1-2 中国药典流动相(甲醇 - 水( 60:40))实验结果注:峰纯度合格标准:纯度角度<纯度阈值。
结论:中国药典流动相中酸破坏样品杂质Ⅰ峰、杂质Ⅱ峰纯度不合格,且杂质Ⅰ峰与前杂质峰分离度不合格。
碱破坏样品杂质Ⅰ峰纯度不合格表 3.2.P.5.3.3.3.1-3美国药典流动相(乙腈 - 甲醇 - 水( 50:25:25))实验结果上海玉瑞生物科技(安阳)药业有限公司硝苯平缓释片(Ⅱ)申报生产资料CTD 模块--3.2.P.5 制剂质量控制注:峰纯度合格标准:纯度角度<纯度阈值。
结论:美国药典流动相中光照破坏样品杂质Ⅰ峰纯度不合格,酸破坏样品杂质Ⅰ峰纯度不合格,且杂质Ⅰ峰与前杂质峰分离度不合格。
碱破坏样品杂质Ⅱ峰纯度不合格。
; 表3.2.P.5.3.3.3.1-4英国药典流动相(乙腈- 甲醇- 水(9:36:55))实验结果第3 页共126页上海玉瑞生物科技(安阳)药业有限公司硝苯平缓释片(Ⅱ)申报生产资料 模块 --3.2.P.5 制剂质量控制CTD第 4 页 共 126页注:峰纯度合格标准:纯度角度<纯度阈值。
结论:各破坏样品溶液中,主峰、杂质Ⅰ、Ⅱ与前后峰分离度均符合规定,峰纯度均符合要求,但主峰保留时间达到 时间可能过长。
45分钟, 后续可能杂质洗脱上海玉瑞生物科技(安阳)药业有限公司硝苯平缓释片(Ⅱ)申报生产资料 模块 --3.2.P.5 制剂质量控制第 5 页 共 126 页CTD① 中国药典流动相改进 总流速 :1.0ml/min 流动相:甲醇 - 水(45:55)表 3.2.P.5.3.3.3.2-2中国药典流动相改进(甲醇:水 -45 :55)注:峰纯度合格标准:纯度角度<纯度阈值。
液晶电源管理芯片型号与封装代换型号

液晶品牌与型号电源管理芯片型号与封装可代换型号xaslipyelBENQ 71G+1200AP40 直插1200AP10 1200AP60AOC 712SI EA1532A贴片xaslipyel三星940BW DM0565Rxaslipyel优派型号忘记 TOP245YNxaslipyelLG W1934S TOP246YNxaslipyel飞利浦170s6 dap02alsz 贴片xaslipyelLG型号忘记 LAF0001 可以用FAN7601代xaslipyel飞利浦170s6 dap02alsz=sg6841xaslipyelHP17驱动高压电源全一体 SG5841SZ贴片,可用SG6841DZ 代用。
xaslipyel联想后来出的像IBM的 17的,SG6841DZ 可用SG6841D代用xaslipyel三星型号忘记 DM0465R(我记得还有这么一款的)xaslipyel飞利浦170c7 EA1532A贴片xaslipyel200D6、203D6、DAP8A 三种可以代用xaslipyel优派VA1703WB ld7552bps 贴片xaslipyel其他我知道的常用型号有xaslipyelSG6841DZ 贴片很多机器上用到xaslipyelSG5841SZ 贴片用SG6841DZ可以代用,xaslipyel美格WB9 LD7575PS清华同方 XP911W LD7575PS联想LXM -WL19AH LXM-WL19BH LD7575PS(早期有的用:NCP1203D6)联想LXM-17CH: 1203D6方正17寸:1203D6与LD7575PS方正19寸:LD7575PSBenQ: FP94VW FP73G FP71G+S FP71G+G FP71GX等都是用:1200AP40 LG 22(南京同创):LAF001与STR W6252 。
LG 19寸:LAF001 联想L193(福建-捷联代工):NCP1203D6PHILIPS 170S5 (FAN7601)还有LD7575可用203D6代用,只是1脚的对地电阻不同,LD7575是100K,203D6是24.1K,LP7552可用SG6841代用希望大家都列下来,这样子备PWM IC的时候就有个数了,知道买什么样子的电源管理芯片备用着,有时候手上没有,知道是电源管理坏了在那里干着急,反正PWM IC便宜的,可以每样备个2个,以备不时之需介绍几个LCD液晶显示器电源IC的代换希望能帮上大家.DAP8A\DAP7A\LD7575\203D6可以直接代换DAP02\SG5841\SG6841可以直接代换1200AP40\1200AP60\1203P60可以直接代换DM0465R\CM0565R\DM0565R可以直接代换TOP246Y\TOP247Y可以直接代换常见显示器IC代换OCP5001-----------TL5001AMC3100----------LTC3406/AT1366/MP2104 OCP2150----------- LTC3406/AT1366/MP2104 ACT6906----------- LTC3406/AT1366/MP2104 OCP2160-----------LTC3407AMC34063A-----------AMC34063AMC7660------------AJC1564ACT4060--------------ZA3020LV/MP1410/MP9141ACT4065------------ZA3020/MP1580ACT4070----------ZA3030/MP1583/MP1591MP1593/MP1430 AMC2576-------LM2576AMC2596-------LM2596OCP2576--------LM2576OMC2596-------LM2596/AP1501VA7910---------MAX1674/75 L6920 AJC1610SM9621---------RJ9621/AJC1642PT1301----------RJ9266PT4101----------AJC1648/MP3202PT4102----------LT1937/AJC1896/AP1522/RJ9271/MP1540 ACT6311-------LT1937SP1937-----------LT1937/AJC1896/AP1522/RJ9271/MP1540 OCP3601---------MB3800OCP1451---------TL1451/BA9741/SP9741/AP200电源IC STR-G5643D G5653D G8653D 直接代换203D6和DAP8A 直接代换1200AP40和1200AP60直接代换5S0765和DP104、DP704直接代换DP804和DP904直接代换2S0680和2S0880直接代换TEA1507和TEA1533直接代换三星的DP104,704,804可以用5S0765代换,DP904不能用任何块代换行场振荡、场输出、视频ICTDA9109和SID2511、KB2511、STV7779直接代换TDA9103和STV7778直接代换TDA9112和TDA9113直接代换TDA9115和TDA9116、STV6888直接代换TDA9118和STV9118直接代换TDA8172和TDA9302、TDA8177直接代换TDA1675 和DBL2056直接代换TDA9210和STV9210直接代换LM1203和LM2203、DBL2054直接代换TDA9116用STV6888代换,TDA4856可以用TDA4841PS代换,TDA9112可以用TDA9113代换,S1D2511可以用TDA9109代换203D6200D6LD7575DAP8A203X6直接代换SG6841SG5841DAPO2直接代换DM0456 DM0565直接代换1200AP401200AP601203AP10直接代。
电源IC代换
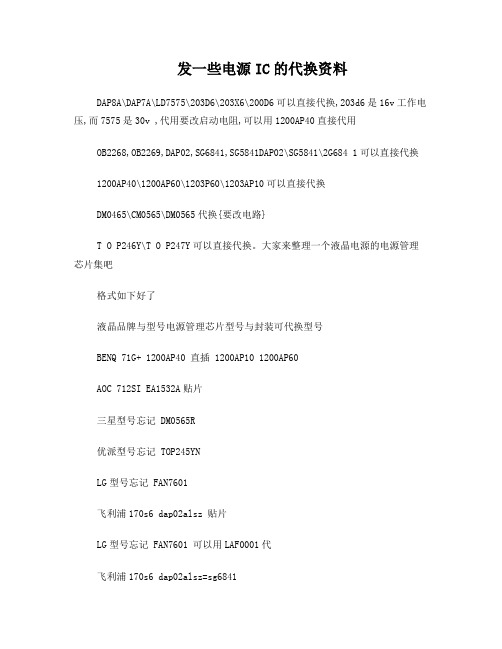
发一些电源IC的代换资料DAP8A\DAP7A\LD7575\203D6\203X6\200D6可以直接代换,203d6是16v工作电压,而7575是30v ,代用要改启动电阻,可以用1200AP40直接代用OB2268,OB2269,DAP02,SG6841,SG5841DAP02\SG5841\2G684 1可以直接代换1200AP40\1200AP60\1203P60\1203AP10可以直接代换DM0465\CM0565\DM0565代换{要改电路}T O P246Y\T O P247Y可以直接代换。
大家来整理一个液晶电源的电源管理芯片集吧格式如下好了液晶品牌与型号电源管理芯片型号与封装可代换型号BENQ 71G+ 1200AP40 直插 1200AP10 1200AP60AOC 712SI EA1532A贴片三星型号忘记 DM0565R优派型号忘记 TOP245YNLG型号忘记 FAN7601飞利浦170s6 dap02alsz 贴片LG型号忘记 FAN7601 可以用LAF0001代飞利浦170s6 dap02alsz=sg6841美格WB9D7575PS清华同方XP911WD7575PS联想LXM -WL19AH LXM-WL19BH D7575PS(早期有的用:NCP1203D6) 联想LXM-17CH:1203D6方正17寸:1203D6与LD7575PS方正19寸:LD7575PSBenQ: FP94VW FP73G FP71G+S FP71G+G FP71GX等都是用:1200AP40 LG 22(南京同创):LAF001与STR W6252 。
LG 19寸:LAF001联想L193(福建-捷联代工):NCP1203D6PHILIPS 170S5FAN7601)PHILIPS 15寸(老产品):(FAN7601)LG型号忘记 FAN7601 可以用LAF0001代其他我知道的常用型号有SG6841DZ 贴片很多机器上用到SG5841SZ 贴片用SG6841DZ可以代用,DAP8A与203D6可代用还有LD7575可用203D6代用,只是1脚的对地电阻不同,LD7575是100K,203D6是24.1K,LP7552可用SG6841代用203D6 NCP1203D60R2 NCP1203D60R2G和DAP8A直接代换DAP02ALSZ与SG6841S可以互换1200AP40和1200AP60直接代换5S0765和DP104、DP704直接代换DP804和DP904直接代换2S0680和2S0880直接代换TEA1507和TEA1533直接代换LD7535兼容SG6848 (6849) / SG5701 / SG5848 /LD7535 (7550) / OB2262 (2263) / OB2278 (2279)RS2051LD7575和NCP1203、NCP1200 OB2268 SG5841 LD7552 OB2269 OB2268 RS2042CR6860兼容ACT30,CR6853兼容OB2263,CR6201兼容THX201,TFC718;CR6202兼容THX202,TFC719;CR6203兼容THX203,TFC718S。
- 1、下载文档前请自行甄别文档内容的完整性,平台不提供额外的编辑、内容补充、找答案等附加服务。
- 2、"仅部分预览"的文档,不可在线预览部分如存在完整性等问题,可反馈申请退款(可完整预览的文档不适用该条件!)。
- 3、如文档侵犯您的权益,请联系客服反馈,我们会尽快为您处理(人工客服工作时间:9:00-18:30)。
NCP1593A, NCP1593B1 MHz, 3 A Synchronous Buck RegulatorThe NCP1593 is a fixed 1 MHz, high−output−current, synchronous PWM converter that integrates a low−resistance, high−side P−channel MOSFET and a low−side N−channel MOSFET. The NCP1593 utilizes internally compensated current mode control to provide good transient response, ease of implementation and excellent loop stability. It regulates input voltages from 4.0 V to 5.5 V down to an output voltage as low as 0.6 V and is able to supply up to 3 A of load current.The NCP1593 includes an internally fixed switching frequency (F SW), and an internal soft−start to limit inrush current. Other features include cycle−by−cycle current limiting, 100% duty cycle operation, short− circuit protection, power saving mode and thermal shutdown. Features•Wide Input V oltage Range: from 4.0 V to 5.5 V•Internal 90 m W High−Side P−Channel MOSFET and 60 m W Low−Side N−Channel MOSFET•Fixed 1 MHz Switching Frequency•Cycle−by−Cycle Current Limiting•Hiccup Mode Short−Circuit Protection•Overtemperature Protection•Internal Soft−Start•Start−up with Pre−Biased Output Load •Adjustable Output V oltage Down to 0.6 V •Diode Emulation During Light Load•100% Duty Cycle Operation to Extend the Battery Life •These are Pb−Free DevicesApplications•Set−T op Boxes•DVD Drives and HDD•LCD Monitors and TVs•Cable Modems•USB Modems•Telecom/Networking/Datacom EquipmentDevice Package Shipping†ORDERING INFORMATIONNCP1593AMNTWG DFN10(Pb−Free)3000 / Tape &ReelDFN10CASE 485CMARKINGDIAGRAMS†For information on tape and reel specifications, including part orientation and tape sizes, please refer to our T ape and Reel Packaging Specifications Brochure, BRD8011/D.VCCPVCCPVCCANCLXLX(Top View)PIN CONNECTIONSA= Assembly LocationL= Wafer LotY= YearW= Work WeekG= Pb−Free Package1593AALYW GG(Note: Microdot may be in either location)SSPGFBENNCP1593BMNTWGVCCPVCCPVCCALXLXLX(Top View)NCPGFBEN1593BALYW GGDFN10(Pb−Free)3000 / Tape &ReelBLOCK DIAGRAMFigure 1. Block DiagramVCCPLXPGNDVCCENFBPGLXSS PIN DESCRIPTIONSPin No Symbol Description1NC / LX No connect pin for NCP1593A. The user may ground this pin or leave it floating. / LX pin for NCP1593B 2, 3LX The drains of the internal MOSFETs. The output inductor should be connected to these pins.4PG Open drain output from the Power Good logic. When the FB voltage is within regulation, this is a high impedance pin. Otherwise it is pulled low.5EN Logic input to enable the part. Logic high to turn on the part and a logic low to shut off the part. An intern-al pullup forces the part into an enable state when no external bias is present on the pin.6FB Feedback input pin of the Error Amplifier. Connect a resistor divider from the converter’s output voltage to this pin to set the converter’s regulated voltage.7SS / NC An external capacitor on this pin sets the soft −start ramp time. Leaving this pin open sets the soft −start time at 500 m s. For NCP1593B this pin is a no connect and should be left floating.8V CC Input supply pin for internal bias circuitry. Connect a 0.1 m F ceramic bypass capacitor to this pin. Directly connect the V CC pin to the V CCP pin on the board.9, 10V CCP Input for the power stageEPGNDExposed pad of the package provides both electrical contact to the ground and good thermal contact to the PCB. This pad must be soldered to the PCB for proper operation.APPLICATION CIRCUITFigure 2. Recommended Application CircuitV inV outABSOLUTE MAXIMUM RATINGSRatingSymbol Value Unit Power Supply Pin (Pins 8, 9, 10) to GNDV in6.5−0.3 (DC)−1.0 (t < 100 ns)VLX to GND V in + 0.7V in + 1.0 (t < 20 ns)−0.7 (DC)−5.0 (t < 100 ns)VAll other pins 6.0−0.3 (DC)−1.0 (t < 100 ns)VOperating Ambient Temperature Range (Note 1)T A −40 to +85°C Operating Junction Temperature Range (Note 1)T J −40 to +125°C Maximum Junction Temperature T J(MAX)+150°C Storage Temperature RangeT S −55 to +150°C Thermal Resistance Junction −to −Air (Note 2)R q JA68°C/WStresses exceeding Maximum Ratings may damage the device. Maximum Ratings are stress ratings only. Functional operation above the Recommended Operating Conditions is not implied. Extended exposure to stresses above the Recommended Operating Conditions may affect device reliability.1.The maximum package power dissipation limit must not be exceeded.P D +T J(max)*T AR q JA2.R q JA measured on approximately 1x1 inch sq. of 1 oz. Copper FR −4 or G −10 board.ELECTRICAL CHARACTERISTICS (−40°C < T J < 125°C, V CC = 4.0 V − 5.5 V, for min/max values unless noted otherwise) Parameter Symbol Test Conditions Min Typ Max Unit Input Voltage Range V IN 4.0 5.5V V CC UVLO Threshold V UVLO 2.4 2.5 2.6V UVLO Hysteresis V UVLO_hys220mV V CC Quiescent Current I INVCC 1.0 1.5mA VCCP Quiescent Current I INVCCP2050m A Shutdown Supply Current I QSHDN 1.8 3.0m A FEEDBACK VOLTAGEReference Voltage V FB0.5910.60.609V Reference Voltage V FB T J = 25°C0.5940.60.606V Feedback Input Bias Current I FB10100nA Feedback Voltage Line Regulation (Note 3)V CC = 4.0 V to 5.5 V−65dB PWMMaximum Duty Cycle (Regulating) d.c.MAX95% Maximum Duty Cycle (LDO mode) d.c.LDO Vout > d.c.MAX* V IN100% Minimum Controllable On Time t ONmin35ns Current LimitCycle-by-cycle Current Limit (Note 3)I LIM V CC = 5.0 V, T J = 25°C 4.9A OscillatorSwitching Frequency f SW0.87 1.0 1.13MHz MOSFET’sHigh-Side MOSFET On Resistance R DSonH I DS = 100 mA, V IN = 5.0 V90190m W High-Side MOSFET Leakage I lkgH LX = 0 V10m A Low-Side MOSFET On Resistance R DSonL I DS = 100 mA, V IN = 5.0 V6090m W Low-Side MOSFET Leakage I lkgL LX = 5 V10m A POWER GOODPower Good Rising Threshold V PGH0.510.54V Power Good Falling Threshold V PHL0.480.51V Power Good Hysteresis (High-to-Low)V PGhys30mV Power Good Pulldown Voltage V RPG I PG = 2.5 mA130250mV ENABLEEnable High Threshold V ENHI 1.4V Enable Low Threshold V ENLO0.4V Enable Hysteresis V ENhys200mV Enable Pullup Current I EN 1.4 3.0m A Soft-StartDefault Soft-start Ramp Time t SS SS = open; f SW = 1MHz0.50.580.65ms Maximum Soft-start Ramp time t SS SS = max cap; f SW = 1MHz10ms Hiccup Timer 4 * t SS ms Soft-start Current I SS0.510.70.87m A Thermal ShutdownThermal Shutdown Threshold185°C Thermal Shutdown Hysteresis30°C 3.Guaranteed by Characterization.Figure 3. Efficiency vs. Output Current (3.3 V)Figure 4. Efficiency vs. Output Current (1.8 V)I OUT , OUTPUT CURRENT (A)I OUT , OUTPUT CURRENT (A)Figure 5. Efficiency vs. Output Current (1.05 V)Figure 6. Load Regulation (3.3 V)I OUT , OUTPUT CURRENT (A)I OUT , OUTPUT CURRENT (A)Figure 7. Load Regulation (1.8 V)Figure 8. Load Regulation (1.05 V)I OUT , OUTPUT CURRENT (A)I OUT , OUTPUT CURRENT (A)E F F I C I E N C Y (%)E F F I C I E N C Y (%)E F F I C I E N C Y (%)V O U T , O U T P U T V O L T A G E (V )V O U T , O U T P U T V O L T A G E (V )V O U T , O U T P U T V O L T A G E (V )Figure 9. Current Limit vs. TemperatureFigure 10. Current Limit vs. Input VoltageT J , JUNCTION TEMPERATURE (°C)INPUT VOLTAGE (V)5.505.255.004.754.504.254.003.503.754.004.254.755.005.255.50Figure 11. R DS(ON) vs. TemperatureFigure 12. Load Transient ResponseT J , JUNCTION TEMPERATURE (°C)Figure 13. Load Transient Response Figure 14. No Load Switching (1.05 V)P E A K C U R R E N T L I M I T (A )P E A K C U R R E N T L I M I T (A )R D S (O N ) (m W )4.50(VIN = 5 V, VOUT = 1.05 V, IOUT = 0.5 A to 3.0 A)Upper Trace: Output Voltage, 50 mV / div Lower Trace: Output Current, 2 A / divTime = 200 m s/div(VIN = 5 V, VOUT = 1.05 V, IOUT = 0.5 A to 3.0 A)Upper Trace: Output Voltage, 50 mV / div Lower Trace: Output Current, 2 A / divTime = 200 m s/div(VIN = 5 V, VOUT = 1.05 V, IOUT = 0 A)Upper Trace: LX Pin Switching Waveforms, 5 V / divMiddle Trace: Output Voltage, 20 mV / div Lower Trace: Inductor Current, 100 mA / divTime = 20 m s / divFigure 15. No Load Switching (1.8 V)Figure 16. No Load Switching (3.3 V)Figure 17. DCM Switching (1.05 V)Figure 18. DCM Switching (1.8 V)Figure 19. DCM Switching (3.3 V)Figure 20. CCM Switching (1.8 V)(VIN = 5 V, VOUT = 1.8 V, IOUT = 0 A)Upper Trace: LX Pin Switching Waveforms, 5 V / divMiddle Trace: Output Voltage, 20 mV / div Lower Trace: Inductor Current, 100 mA / divTime = 10 m s / div (VIN = 5 V, VOUT = 3.3 V, IOUT = 0 A)Upper Trace: LX Pin Switching Waveforms, 5 V / divMiddle Trace: Output Voltage, 20 mV / div Lower Trace: Inductor Current, 200 mA / divTime = 10 m s / div(VIN = 5 V, VOUT = 1.05 V, IOUT = 100 mA)Upper Trace: LX Pin Switching Waveforms, 5 V / divMiddle Trace: Output Voltage, 20 mV / div Lower Trace: Inductor Current, 200 mA / divTime = 500 ns / div (VIN = 5 V, VOUT = 1.8 V, IOUT = 150 A)Upper Trace: LX Pin Switching Waveforms, 5 V / divMiddle Trace: Output Voltage, 20 mV / div Lower Trace: Inductor Current, 200 mA / divTime = 500 ns / div(VIN = 5 V, VOUT = 3.3 V, IOUT = 100 mA)Upper Trace: LX Pin Switching Waveforms, 5 V / divMiddle Trace: Output Voltage, 20 mV / div Lower Trace: Inductor Current, 200 mA / divTime = 500 ns / div (VIN = 5 V, VOUT = 1.8 V, IOUT = 3 A)Upper Trace: LX Pin Switching Waveforms, 5 V / divMiddle Trace: Output Voltage, 20 mV / div Lower Trace: Inductor Current, 2 A / divTime = 500 ns / divFigure 21. Power On from Input VoltageFigure 22. Power Off from Input VoltageFigure 23. Power On from Enable Figure 24. Power On from Enable CSS = 4.7 nFigure 25. Power Off from Enable Figure 26. Short Circuit Operation(VIN = 5 V, VOUT = 1.8 V, IOUT = 3 A)Upper Trace: Input Voltage, 5 V / divSecond Trace: Power Good Pin Voltage, 5 V / divThird Trace: Output Voltage, 2 V / div Lower Trace: Inductor Current, 2 A / divTime = 1 ms / div(VIN = 5 V, VOUT = 1.8 V, IOUT = 3 A)Upper Trace: Input Voltage, 5 V / divSecond Trace: Power Good Pin Voltage, 5 V / divThird Trace: Output Voltage, 2 V / div Lower Trace: Inductor Current, 2 A / divTime = 200 m s / div(VIN = 5 V, VOUT = 1.8 V, IOUT = 3 A, no CSS)Upper Trace: Enable Pin Voltage, 5 V / div Second Trace: Power Good Pin Voltage, 5 V / divThird Trace: Output Voltage, 2 V / div Lower Trace: Inductor Current, 2 A / divTime = 2 ms / div (VIN = 5 V, VOUT = 1.8 V, IOUT = 3 A, CSS = 4.7 nF)Upper Trace: Enable Pin Voltage, 5 V / div Second Trace: Power Good Pin Voltage, 5 V / divThird Trace: Output Voltage, 2 V / div Lower Trace: Inductor Current, 2 A / divTime = 2 ms / div(VIN = 5 V, VOUT = 1.8 V, IOUT = 3 A)Upper Trace: Enable Pin Voltage, 5 V / div Second Trace: Power Good Pin Voltage, 5 V / divThird Trace: Output Voltage, 2 V / div Lower Trace: Inductor Current, 2 A / divTime = 200 m s / div(VIN = 5 V, VOUT = 1.8 V, IOUT = Current Limit, no CSS)Upper Trace: LX Pin Voltage, 5 V / div Middle Trace: Output Voltage, 2 V / div Lower Trace: Inductor Current, 2 A / divTime = 500 m s / divDETAILED DESCRIPTION OverviewThe NCP1593 is a synchronous PWM controller that incorporates all the control and protection circuitry necessary to satisfy a wide range of applications. The NCP1593 employs current mode control to provide fast transient response, simple compensation, and excellent stability. The features of the NCP1593 include a precision reference, fixed 1 MHz switching frequency, a transconductance error amplifier, an integrated high−side P−channel MOSFET and low−side N−Channel MOSFET, internal soft−start, and very low shutdown current. The protection features of the NCP1593 include internal soft−start, pulse−by−pulse current limit, and thermal shutdown.Reference VoltageThe NCP1593 incorporates an internal reference that allows output voltages as low as 0.6 V. The tolerance of the internal reference is guaranteed over the entire operating temperature range of the controller. The reference voltage is trimmed using a test configuration that accounts for error amplifier offset and bias currents.Oscillator FrequencyA fixed precision oscillator is provided. The oscillator frequency range is 1 MHz with $13% variation. Transconductance Error AmplifierThe transconductance error amplifier’s primary function is to regulate the converter’s output voltage using a resistor divider connected from the converter’s output to the FB pin of the controller, as shown in the applications schematic. If a Fault occurs, the amplifier’s output is immediately pulled to GND and PWM switching is inhibited.Soft−StartTo limit the startup inrush current, a soft−start circuit is used to ramp up the reference voltage from 0 V to its final value linearly. This soft−start time is internally set to a typical value of 500 m s, or it can be externally adjusted by adding a capacitor (C SS) from the SS pin to GND. The following formulas show how to set the externally adjustable soft-start time. The maximum allowable C SS is 10 nF.t SS+ǒCSSV FBǓI SS(eq. 1) Where:V FB: Reference voltage, typically 0.6 VI SS: Soft−start current, typically 0.7 m AOutput MOSFETsThe NCP1593 includes low R DS(on), both high−side P−channel and low−side N−channel MOSFETs capable of delivering up to 3.0 A of current. When the controller is disabled or during a Fault condition, the controller’s output stage is tri−stated by turning OFF both the upper and lower MOSFETs.Pulse Width ModulationA high−speed PWM comparator, capable of pulse widths as low as 35 ns, is included in the NCP1593. The inverting input of the comparator is connected to the output of the error amplifier. The non−inverting input is connected to the the current sense signal. At the beginning of each PWM cycle, the CLK signal sets the PWM flip−flop and the upper MOSFET is turned ON. When the current sense signal rises above the error amplifier’s voltage then the comparator will reset the PWM flip−flop and the upper MOSFET will be turned OFF.Current SenseThe NCP1593 monitors the current in the upper MOSFET. The current signal is required by the PWM comparator and the pulse−by−pulse current limiter.PROTECTIONSUndervoltage Lockout (UVLO)The under voltage lockout feature prevents the controller from switching when the input voltage is too low to power the internal power supplies and reference. Hysteresis is incorporated in the UVLO comparator to prevent resistive drops in the wiring or PCB traces from causing ON/OFF cycling of the controller during heavy loading at power up or power down.Overcurrent Protection (OCP)NCP1593 detects high side switch current and then compares to a voltage level representing the overcurrent threshold limit. If the current through the high side FET exceeds the overcurrent threshold limit for seven consecutive switching cycles, overcurrent protection is triggered.Once the overcurrent protection occurs, hiccup mode engages. First, hiccup mode, turns off both FETs and discharges the internal compensation network at the output of the OTA. Next, the IC waits typically 4 x t SS ms and then resets the overcurrent counter. After this reset, the circuit attempts another normal soft−start. Hiccup mode reduces input supply current and power dissipation during a short circuit. It also allows for much improved system up−time, allowing auto−restart upon removal of a temporary short−circuit.Pre−Bias StartupIn some applications the controller will be required to start switching when it’s output capacitors are charged anywhere from slightly above 0 V to just below the regulation voltage. This situation occurs for a number of reasons: the converter’s output capacitors may have residual charge on them or the converter’s output may be held up by a low current standby power supply. NCP1593 supports pre−bias start up by holding off switching off until the soft start ramp reaches the FB Pin voltage.Power GoodPower Good (PG) is an open-drain output that requires a pull−up resistor. It is actively held low in soft−start, standby, and shutdown. PG releases when the FB voltage and thus the output voltage rises above 90% of nominal regulation point. The PG goes low when the FB voltage falls below 85% of the regulation point.Thermal ShutdownThe NCP1593 protects itself from over heating with an internal thermal monitoring circuit. If the junction temperature exceeds the thermal shutdown threshold both the upper and lower MOSFETs will be shut OFF.APPLICATION INFORMATION Programming the Output VoltageThe output voltage is set using a resistive voltage dividerfrom the output voltage to FB pin (see Figure 27). So theoutput voltage is calculated according to Eq.1.V out+V FB@R1)R2R2(eq. 2)Figure 27. Output dividerInductor SelectionThe inductor is the key component in the switching regulator. The selection of inductor involves trade−offs among size, cost and efficiency. The inductor value is selected according to the equation 2.L+V outf@I ripple@ǒ1*V out V in(max)Ǔ(eq. 3)Where V out− the output voltage;f− switching frequency, 1.0 MHz;I ripple− Ripple current, usually it’s 20% − 30% of output current;V in(max)− maximum input voltage.Choose a standard value close to the calculated value to maintain a maximum ripple current within 30% of the maximum load current. If the ripple current exceeds this 30% limit, the next larger value should be selected.The inductor’s RMS current rating must be greater than the maximum load current and its saturation current should be about 30% higher. For robust operation in fault conditions (start−up or short circuit), the saturation current should be high enough. To keep the efficiency high, the series resistance (DCR) should be less than 0.1 W, and the core material should be intended for high frequency applications. Output Capacitor SelectionThe output capacitor acts to smooth the dc output voltage and also provides energy storage. So the major parameter necessary to define the output capacitor is the maximum allowed output voltage ripple of the converter. This ripple is related to capacitance and the ESR. The minimum capacitance required for a certain output ripple can be calculated by Equation 4.C OUT(min)+I ripple8@f@V ripple(eq. 4)Where V ripple is the allowed output voltage ripple.The required ESR for this amount of ripple can be calculated by equation 5.ESR+V rippleI ripple(eq. 5) Based on Equation 3 to choose capacitor and check its ESR according to Equation 4. If ESR exceeds the value from Eq.4, multiple capacitors should be used in parallel. Ceramic capacitor can be used in most of the applications. In addition, both surface mount tantalum and through−hole aluminum electrolytic capacitors can be used as well. Input Capacitor SelectionThe input capacitor can be calculated by Equation 6.C in(min)+I out(max)@D max@1f@V in(ripple)(eq. 6) Where V in(ripple) is the required input ripple voltage.D max+V outV in(min)is the maximum duty cycle.(eq. 7)Power DissipationThe NCP1593 is available in a thermally enhanced 10−pin, DFN package. When the die temperature reaches +185°C, the NCP1593 shuts down (see the Thermal−Overload Protection section). The power dissipated in the device is the sum of the power dissipated from supply current (PQ), power dissipated due to switching the internal power MOSFET (P SW), and the power dissipated due to the RMS current through the internal power MOSFET (PON). The total power dissipated in the package must be limited so the junction temperature does not exceed its absolute maximum rating of +150°C at maximum ambient temperature. Calculate the power lost in the NCP1593 using the following equations:1.High side MOSFETThe conduction loss in the top switch is:P HSON+I2RMS_HSFET R DS(on)HS(eq. 8) Where:I RMS_FET+ǒI out2)D I PP212ǓDǸ(eq. 9)D I PP is the peak−to−peak inductor current ripple.The power lost due to switching the internal power high side MOSFET is:P HSSW +V in @I out @ǒt r )t f Ǔ@f SW2(eq. 10)t r and t f are the rise and fall times of the internal power MOSFET measured at SW node. Typical rise times are 4 ns (rising) and 2 ns (falling).2.Low side MOSFETThe power dissipated in the top switch is:P LSON +I RMS_LSFET 2@R DS(on)LS(eq. 11)Where:I RMS_LSFET +ǒI out2)D I PP 212Ǔ@(1*D )Ǹ(eq. 12)D I PP is the peak −to −peak inductor current ripple.The switching loss for the low side MOSFET can be ignored.The power lost due to the quiescent current (I Q ) of the device is:P Q +V in @I Q(eq. 13)I Q is the switching quiescent current of the NCP1593.P TOTAL +P HSON )P HSSW )P LSON )P Q(eq. 14)Calculate the temperature rise of the die using the following equation:T J +T C )ǒP TOTAL @q JA Ǔ(eq. 15)q JC is the junction −to −case thermal resistance equal to 68°C/W. T A is the ambient temperature and TJ is the junction temperature, or die temperature. Solder the underside −exposed pad to a large copper GND plane. If thedie temperature reaches the thermal shutdown threshold the NCP1593 shut down and does not restart again until the die temperature cools by 30°C.Layout ConsiderationAs with all high frequency switchers, when considering layout, care must be taken in order to achieve optimal electrical, thermal and noise performance. For 1.0MHz switching frequency, switch rise and fall times are typically in few nanosecond range. To prevent noise both radiated and conducted the high speed switching current path must be kept as short as possible. Shortening the current path will also reduce the parasitic trace inductance of approximately 25 nH/inch. At switch off, this parasitic inductance produces a flyback spike across the NCP1593 switch. When operating at higher currents and input voltages, with poor layout, this spike can generate voltages across the NCP1593that may exceed its absolute maximum rating. A ground plane should always be used under the switcher circuitry to prevent interplane coupling and overall noise.The FB component should be kept as far away as possible from the switch node. The ground for these components should be separated from the switch current path. Failure to do so will result in poor stability or subharmonic like oscillation.Board layout also has a significant effect on thermal resistance. Reducing the thermal resistance from ground pin and exposed pad onto the board will reduce die temperature and increase the power capability of the NCP1593. This is achieved by providing as much copper area as possible around the exposed pad. Adding multiple thermal vias under and around this pad to an internal ground plane will also help. Similar treatment to the inductor pads will reduce any additional heating effects.PACKAGE DIMENSIONSDFN10 3x3, 0.5PCASE 485C−01ISSUE B ArrayDIMENSIONS: MILLIMETERS*For additional information on our Pb−Free strategy and solderingdetails, please download the ON Semiconductor Soldering andMounting Techniques Reference Manual, SOLDERRM/D.ON Semiconductor and are registered trademarks of Semiconductor Components Industries, LLC (SCILLC). SCILLC reserves the right to make changes without further notice to any products herein. SCILLC makes no warranty, representation or guarantee regarding the suitability of its products for any particular purpose, nor does SCILLC assume any liability arising out of the application or use of any product or circuit, and specifically disclaims any and all liability, including without limitation special, consequential or incidental damages.“Typical” parameters which may be provided in SCILLC data sheets and/or specifications can and do vary in different applications and actual performance may vary over time. All operating parameters, including “Typicals” must be validated for each customer application by customer’s technical experts. SCILLC does not convey any license under its patent rights nor the rights of others. SCILLC products are not designed, intended, or authorized for use as components in systems intended for surgical implant into the body, or other applications intended to support or sustain life, or for any other application in which the failure of the SCILLC product could create a situation where personal injury or death may occur. Should Buyer purchase or use SCILLC products for any such unintended or unauthorized application, Buyer shall indemnify and hold SCILLC and its officers, employees, subsidiaries, affiliates, and distributors harmless against all claims, costs, damages, and expenses, and reasonable attorney fees arising out of, directly or indirectly, any claim of personal injury or death associated with such unintended or unauthorized use, even if such claim alleges that SCILLC was negligent regarding the design or manufacture of the part. SCILLC is an Equal Opportunity/Affirmative Action Employer. This literature is subject to all applicable copyright laws and is not for resale in any manner.PUBLICATION ORDERING INFORMATION。