烧结余热发电工艺简介
烧结余热发电资料

1概论在钢铁生产过程中,烧结工序的能耗约占总能耗的10%,仅次于炼铁工序,位居第二。
在烧结工序总能耗中,有近50%的热能以烧结烟气和冷却机废气的显热形式排入大气。
由于烧结冷却机废气的温度不高,仅150~450℃,加上以前余热回收技术的局限,余热回收项目往往被忽略。
随着近几年来余热回收技术突飞猛进,钢铁行业的余热回收项目造价大幅度降低,同时余热回收效率大幅提高,特别是闪蒸发电技术和补汽凝汽式汽轮机在技术上获得突破,为钢铁行业余热回收创造了优越的条件。
时值目前国家能源紧缺、大力提倡生产过程节能降耗的关键时期,国家有关部门对企业节能指标提出了很高的要求。
在这样的形势和技术条件下,一些有远见的钢铁企业,迅速启动各种余热回收项目,不但完成了钢铁企业的节能降耗任务,同时也能为企业本身创造可观的经济效益。
烧结冷却机余热的回收,是通过回收烧结机尾落矿风箱及烧结冷却机密闭段的烟气加热余热锅炉来回收低品味余热能源,结合低温余热发电技术,用余热锅炉的过热蒸气来推动低参数的汽轮发电机组做功发电的最新成套技术;其与火力发电相比:1)不需要消耗一次能源。
2)不产生额外的废气、废渣、粉尘和其它有害气体。
具体来讲烧结冷却机余热回收的意义体现在如下几个方面:1)利用烧结环冷机烟气余热发电,部分代替来自电网的以化石燃料为能源的供电量,从而起到减少温室气体排放效果;2)降低烧结工序能耗,促进资源节约;降低产品单位价格,使企业更具竞争优势。
3)有利于企业可持续发展目标的实现,减少由常规火电厂带来的SO2、CO2、粉尘之类的大气污染物,有助于改善当地的能源结构,提高能源安全。
2 国家政策一国务院关于做好建设节约型社会近期重点工作的通知国发【2005】 21号文件中提出“在冶金、有色、煤炭、电力、化工、建材、造纸、酿造等重点行业组织开展循环经济试点”。
具体内容:1)钢铁工业。
要加快淘汰落后工艺和设备,提高新建、改扩建工程的能耗准入标准。
实现技术装备大型化、生产流程连续化、紧凑化、高效化,最大限度综合利用各种能源和资源。
烧结工艺及余热发电简介
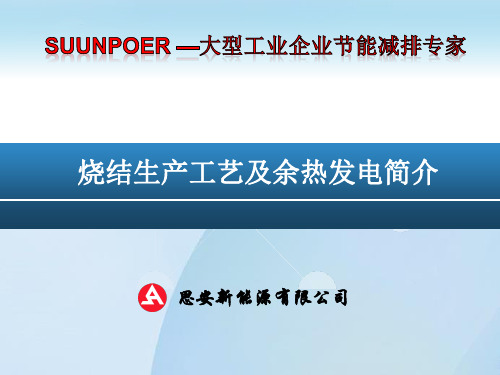
烧结余热回收段
序号
回收利用
1 用作点火、保温炉的助燃 空气
2 用于预热混合料
3 用于余热锅炉产蒸汽
4 用于余热发电
西安思安新能源有限公司
• 烧结中可广泛利用各种含铁粉尘和废料,扩大了矿石资 源,又改善了环境。因此自上世纪50年代以来,烧结生 产获得了迅速发展。
西安思安新能源有限公司源有限公司
2、 烧结反应过程
• 目前世界各国90%以上的烧结矿由抽风带式烧 结机生产,其他烧结方法有回转窑烧结,悬浮 烧结,抽风或鼓风盘式烧结和土法烧结等。
为使烧结的物料物性性质充分均匀,使烧结料内微粒物料造成 适宜的小球,在配料后设置混合工序。 一次混合的目的在于混匀,在沿混合机的长度方向均匀加水, 二次混合主要作用是造球,给水位置设在混合机的给料端。
西安思安新能源有限公司
2.4.5 设备(梭式布料机)
1、采用铺底料可以保护台车、 保证料层烧透、减少烧结烟气 含尘量。
烧结工艺过程及其设备
西安思安新能源有限公司
4、烧结工艺过程及其设备
1、烧结原、燃料及烧结矿 3、烧结 5、烧结矿冷却
2、配料 4、烧结饼破碎和筛分 6、烧结矿整粒和成品矿贮存
西安思安新能源有限公司
烧结前段工艺
烧结前段工艺流程
西安思安新能源有限公司
设备(料仓)
西安思安新能源有限公司
设备(混合机)
★烧结工艺设备环视
西安思安新能源有限公司
设备(烧结机)
西安思安新能源有限公司
余热发电的工艺流程、主要设备和工作原理简单介绍
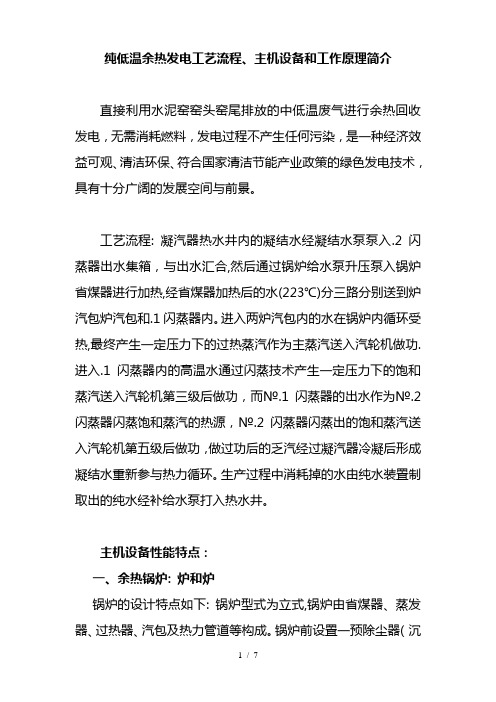
纯低温余热发电工艺流程、主机设备和工作原理简介直接利用水泥窑窑头窑尾排放的中低温废气进行余热回收发电,无需消耗燃料,发电过程不产生任何污染,是一种经济效益可观、清洁环保、符合国家清洁节能产业政策的绿色发电技术,具有十分广阔的发展空间与前景。
工艺流程: 凝汽器热水井内的凝结水经凝结水泵泵入.2闪蒸器出水集箱,与出水汇合,然后通过锅炉给水泵升压泵入锅炉省煤器进行加热,经省煤器加热后的水(223℃)分三路分别送到炉汽包炉汽包和.1闪蒸器内。
进入两炉汽包内的水在锅炉内循环受热,最终产生一定压力下的过热蒸汽作为主蒸汽送入汽轮机做功.进入.1闪蒸器内的高温水通过闪蒸技术产生一定压力下的饱和蒸汽送入汽轮机第三级后做功,而№.1闪蒸器的出水作为№.2闪蒸器闪蒸饱和蒸汽的热源,№.2闪蒸器闪蒸出的饱和蒸汽送入汽轮机第五级后做功,做过功后的乏汽经过凝汽器冷凝后形成凝结水重新参与热力循环。
生产过程中消耗掉的水由纯水装置制取出的纯水经补给水泵打入热水井。
主机设备性能特点:一、余热锅炉: 炉和炉锅炉的设计特点如下: 锅炉型式为立式,锅炉由省煤器、蒸发器、过热器、汽包及热力管道等构成。
锅炉前设置一预除尘器(沉降室),降低入炉粉尘。
废气流动方向为自上而下,换热管采用螺旋翅片管,以增大换热面积、减少粉尘磨损的作用。
锅炉内不易积灰,由烟气带走,故未设置除灰装置,工质循环方式为自然循环方式。
过热器作用:将饱和蒸汽变成过热蒸汽的加热设备,通过对蒸汽的再加热,提高其过热度(温度之差),提高其单位工质的做功能力。
蒸发器作用:通过与烟气的热交换,产生饱和蒸汽。
省煤器作用:设置这样一组受热面,对锅炉给水进行预热,提高给水温度,避免给水进入汽包,冷热温差过大,产生过大热应力对汽包安全形成威胁,同时也避免汽包水位波动过大,造成自动控制困难。
一方面最大限度地利用余热,降低排烟温度,另一方面,给水预热后形成高温高压水,作为闪蒸器产生饱和蒸汽的热源。
烧结机余热发电技术的详解
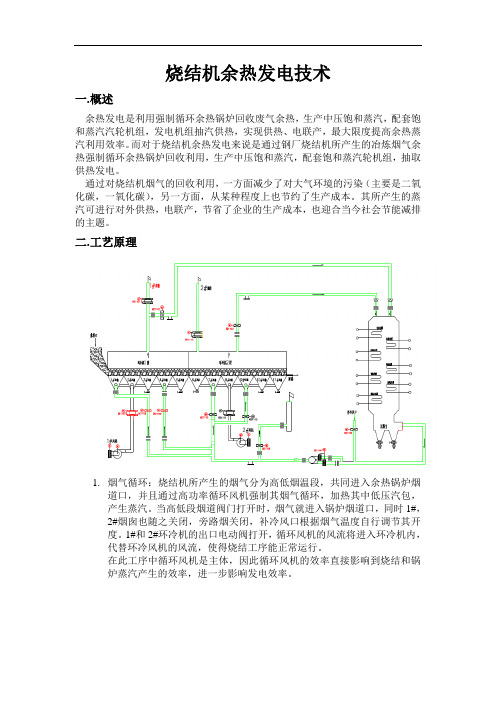
烧结机余热发电技术一.概述余热发电是利用强制循环余热锅炉回收废气余热,生产中压饱和蒸汽,配套饱和蒸汽汽轮机组,发电机组抽汽供热,实现供热、电联产,最大限度提高余热蒸汽利用效率。
而对于烧结机余热发电来说是通过钢厂烧结机所产生的冶炼烟气余热强制循环余热锅炉回收利用,生产中压饱和蒸汽,配套饱和蒸汽轮机组,抽取供热发电。
通过对烧结机烟气的回收利用,一方面减少了对大气环境的污染(主要是二氧化碳,一氧化碳),另一方面,从某种程度上也节约了生产成本。
其所产生的蒸汽可进行对外供热,电联产,节省了企业的生产成本,也迎合当今社会节能减排的主题。
二.工艺原理1.烟气循环:烧结机所产生的烟气分为高低烟温段,共同进入余热锅炉烟道口,并且通过高功率循环风机强制其烟气循环,加热其中低压汽包,产生蒸汽。
当高低段烟道阀门打开时,烟气就进入锅炉烟道口,同时1#,2#烟囱也随之关闭,旁路烟关闭,补冷风口根据烟气温度自行调节其开度。
1#和2#环冷机的出口电动阀打开,循环风机的风流将进入环冷机内,代替环冷风机的风流,使得烧结工序能正常运行。
在此工序中循环风机是主体,因此循环风机的效率直接影响到烧结和锅炉蒸汽产生的效率,进一步影响发电效率。
2.中压水循环:中压锅筒给水是来自汽机房凝结水经过低压除氧器处理后,由中压给水泵打入中压锅筒。
中压给水调节中最为重要的是给水三冲量调节,其调节方式是通过汽包水位,给水流量,主蒸汽流量。
给水三冲量调节中,给水流量的准确度直接影响到调节的准确和稳定度。
因此要进行三冲量的调节,给水流量和蒸汽流量以及水位的校验非常重要。
当主蒸汽温度达到一定值(主要由进入汽机的蒸汽温度决定)时,需要打开减温水调节阀来冷却中压减温汽,降低蒸汽温度,符合进入汽机蒸汽温度的要求。
3.低压水循环:低压汽包给水是来自汽机房凝结水经过除氧器处理后进入低压汽包。
对于低压汽包给水调节可以进行两冲量或单冲量调节,其具体调节方式可以根据现场情况而定。
钢铁企业烧结余热利用与发电技术

钢铁企业烧结余热利用与发电技术摘要:钢铁企业烧结工序的能耗仅次于炼铁工序,一般为钢铁企业总能耗的10%〜20%。
我国烧结工序的能耗与先进国家相比有较大差距,每吨烧结矿的平均能耗要高20kgce。
在烧结工序总能耗中,有近50%的热能以烧结机烟气和冷却机废气的显热形式排入大气,即浪费了热能又污染了环境。
据日本某钢铁厂热平衡测试数据表明,烧结机的热收入中烧结矿显热占28.2%、废气显热占31.8%。
可见,烧结厂余热回收的重点为烧结废(烟)气余热和烧结矿(产品)显热回收。
烧结余热也是目前我国低温余热资源应用的重点。
一、烧结余热利用方式与现状烧结余热主要利用方式有(1)在点火前对烧结料层进行预热;(2)送到点火器,进行热风点火;(3)实行热风烧结,回收烧结过程的热量和成品矿显热,降低烧结能耗;(4)利用余热锅炉回收烧结或冷却热废风,所产蒸汽用于预热烧结混合料或生活取暖等,或者进行蒸汽升值发电。
目前,我国大型烧结厂普遍采用了余热回收利用装置,但多数中、小烧结厂的余热仍未得到有效利用。
国内重点大中型企业,钢铁协会会员单位在2006年钢铁协会调研时,只有不到三分之一的烧结机配备了烧结余热利用设备,大部分是蒸汽回收并入全厂动力蒸汽管网,很少利用余热发电的。
近年来,随着低温烟气余热锅炉技术和低参数补汽式汽轮机技术的发展,使低温烟气余热发电成为可能。
二、烧结余热利用与发电技术目前我国烧结余热利用的重点和难点在于:由于存在漏风率高导致废气温度降低,又要保证进入除尘器前废气温度在露点以上等原因,回收利用烧结余热较困难。
因此,如何降低漏风率以提高烧结机烟气温度,以及在保证烧结废气除尘所需温度条件下,实现烧结机尾部高温段废气显热回收?烧结余热蒸汽发电核心技术的消化吸收和本土化,是烧结余热回收的重点。
如开发此技术将烧结矿余热充分利用,则钢铁行业年可节约能源约900万吨标准煤。
烧结余热发电是利用低温余热的一个有效途径,但目前来说应用很少,且存在一些问题,在运行过程中,由于烧结机和环冷机工况发生变化时,余热回收系统的工作参数也将随之变动,输出的蒸汽压力、温度、流量也将发生变化,从而影响发电机组的运行效率。
烧结厂余热利用技术简介
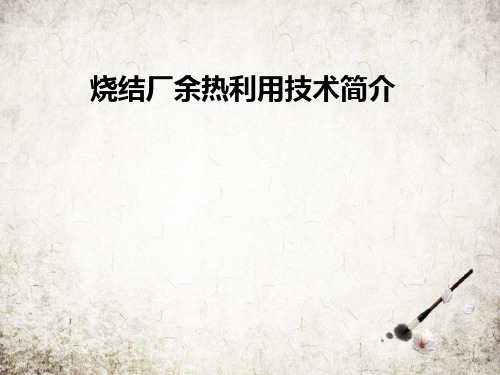
冷却机余热回收
冷却机余热回收的途径
烧结矿从烧结机尾经过热破碎后卸到冷却机上,卸出的烧结饼温度平均在 500∽800℃之间。热烧结矿经过冷却机冷却,使得从冷却机排出的烧结矿温度 在150 ℃以下。热烧结矿在冷却过程中其热能变为废气显热,废气温度随冷却 机部位的不同而不同,给矿部温度最高,在450 ℃以上,排矿部温度最低。余 热可以分为高、中、低三个温区分别利用。
火力发电
火力发电一般是指利用煤炭、石油和天然气等 燃料燃烧时产生的热能来加热水,使水变成高 温、高压水蒸气,然后再由水蒸气推动汽轮机 做功,进而带动发电机转动来发电的方式的总 称。我国的火电厂以燃煤为主。
目前火电在我国发电行业占据主导地位。
按照蒸汽的压力等级,火电厂可分为: 中低压(3.43MPa以下)、高压(8.83MPa) 、 超高压(12.75MPa)、亚临界(16.18MPa) 、 超临界(22.1MPa)、超超临界(30MPa)。
高温段余热利用
高温段余热废气能量品味比较高,动力回收形式效率也比较高,将热废气的热 能转换为能级较高的电能的回收方式为首选。通过余热锅炉将热废气余热转化 成蒸汽,再通过汽轮发电机组有效的转化为电能供烧结厂自用或并入企业电网 。
中温段余热利用
中温段温度低于300℃,采用余热锅炉进行回收热效率比较低,经济性比较差。采用直接 回收利用更为合理。该段废气为高含氧量的热空气,可以作为烧结点火助燃空气和热风烧 结。 热风助燃的优点:
国内余热利用情况
太钢一号烧结生产线余热利用系统为1998年日本政府实施“绿援计划 ”时在太钢援建的项目。通过设置2台强制循环余热锅炉,共用一个 汽包、锅炉给水系统和控制系统,产生1.0Mpa,193℃的饱和蒸汽, 送往生活蒸汽管网,对烧结环冷机余热进行回收。 马钢二炼 两套300m烧结机 装机17.5MW 05年9月投运 济钢二烧 一套320m烧结机 装机8.2MW 07年3月投运 山东宏达 两套132m烧结机 装机6MW 07年3月投运 红钢 两套90m烧结机 装机4.5MW 07年12月投运 安钢 360m2+400m2烧结机 装机25MW 08年9月23日并网发电
烧结余热发电工程设计方案
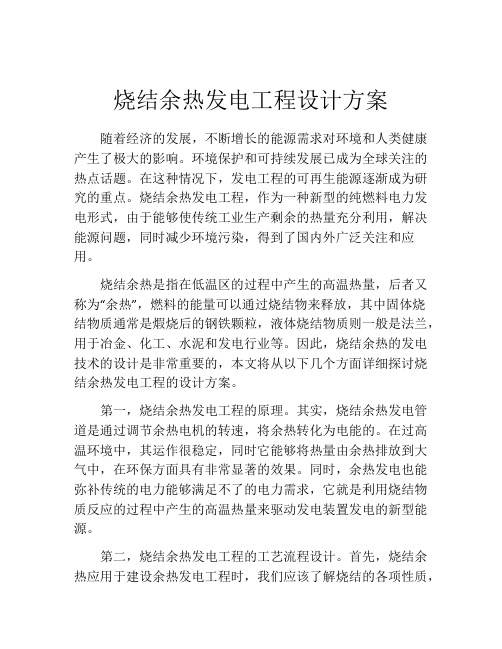
烧结余热发电工程设计方案随着经济的发展,不断增长的能源需求对环境和人类健康产生了极大的影响。
环境保护和可持续发展已成为全球关注的热点话题。
在这种情况下,发电工程的可再生能源逐渐成为研究的重点。
烧结余热发电工程,作为一种新型的纯燃料电力发电形式,由于能够使传统工业生产剩余的热量充分利用,解决能源问题,同时减少环境污染,得到了国内外广泛关注和应用。
烧结余热是指在低温区的过程中产生的高温热量,后者又称为“余热”,燃料的能量可以通过烧结物来释放,其中固体烧结物质通常是煆烧后的钢铁颗粒,液体烧结物质则一般是法兰,用于冶金、化工、水泥和发电行业等。
因此,烧结余热的发电技术的设计是非常重要的,本文将从以下几个方面详细探讨烧结余热发电工程的设计方案。
第一,烧结余热发电工程的原理。
其实,烧结余热发电管道是通过调节余热电机的转速,将余热转化为电能的。
在过高温环境中,其运作很稳定,同时它能够将热量由余热排放到大气中,在环保方面具有非常显著的效果。
同时,余热发电也能弥补传统的电力能够满足不了的电力需求,它就是利用烧结物质反应的过程中产生的高温热量来驱动发电装置发电的新型能源。
第二,烧结余热发电工程的工艺流程设计。
首先,烧结余热应用于建设余热发电工程时,我们应该了解烧结的各项性质,以确认如何正确的引导气流、实现物质的循环,以及烧结后产生的残留物,以便重新利用储热量。
其次,为了方便调控,烧结余热发电工程还需要适当的会加入水和气流调节措施,以保证稳定状态下的发电。
第三,烧结余热发电工程的重点设备设计。
重点设备设计方案包括余热锅炉和余热蒸汽发电机等。
在烧结物质反应的过程中,产生的高温余热需要通过余热锅炉进行回收,在回收过程中,余热蒸汽发电机也会在其中起到很大的作用,它可以将蒸汽转化为电力。
第四,烧结余热发电工程的经济性设计。
简单来说,可以通过成本和效益的比较来衡量烧结余热发电工程设计的合理性。
为了达到经济性设计的要求,可以采取多种策略来提高发电的能力和效率,如优化烧结工艺,提高机器运行的安全性和稳定性等。
烧结余热发电工程介绍

汇报结束,请各位领导专家指正! 谢谢!
中冶长天国际工程有限责任公司
130m2烧结环冷机采用过热器前置式余热锅炉(我公司专 有技术),能更多的吸收高温烟气的热量,保证过热蒸汽 的参数稳定并减少风管散热损失,从而稳定和提高汽轮发 电机组的发电量约1%。 高参数过热器布置在环冷机原有余热锅炉平台上,可降低 环冷机送往锅炉本体废气的温度,减小引风管道直径,节 省投资;同时还能降低风机压头约500Pa,降低循环风机 能耗约7%,减少自耗电率约2%。 与我公司承建的245m2烧结机改造工程同步设计和施工, 统一规划设计和协调施工。能提高两个工程间的设计一致 性,减少设计修改所带来的时间和投资上的浪费;同时还 能更加合理的安排施工场地、人员和物资的组织,保证工 程工期并节约施工费用。
中冶长天国际工程有限责任公司
4.3 烟风流程(见附图) 4.4 汽水流程(见附图) 4.5 装机方案
项 高压额定汽温 高压额定压力 低压额定蒸发量 低压额定汽温 低压额定汽压 1.6MPa 蒸汽 0.45MPa 蒸汽 设计发电功率 余热电站装机 目 高压额定蒸发量 130m2 烧结环冷机 18.5 360 1.6 4.0 190 0.45 电站装机 55 5.5 11.3 12.0 t/h t/h MW MW 245m2 烧结环冷机 36.5 360 1.6 6.5 190 0.45 单位 t/h ℃ MPa t/h ℃ MPa
用 心 铸 造 世 界
A partner of choice
方大特钢科技股份有限公司 烧结机改造工程余热发电投标汇报提纲
目
录
一. 项目背景 二.主要技术特点 三.余热资源 四.设计方案 五. 主要技术指标 六. 达标考核
中冶长天国际工程有限责任公司
烧结发电工艺

烧结、转炉余热发电的工艺与控制在烧结生产过程中,烧制好的成品即烧结矿温度在500—700℃,为了便于皮带输送,常常将其冷却至常温,在冷却的过程中产生大量的热空气(300---350℃)排放到大气中,此热空气流量很大,极具回收价值,是低温余热发电良好的余热资源。
在转炉炼钢的生产过程中,用于保护烟道的汽化冷却设备将产生大量的饱和蒸汽排向大气,此蒸汽的特点是量大、不稳定且湿度高,可回收此蒸汽直接驱动汽轮机发电。
一烧结余热发电1 原理与基本工艺1.1 原理经烧结机出来的高温烧结矿经过环冷机用鼓风机进行冷却,底部鼓入的冷风在穿过高温烧结矿时与其进行热交换,冷却后的低温烧结矿用皮带传输机输送至高炉炼铁,在高温烧结矿变成低温烧结矿的过程中会产生大量的高温废气,将这些高温废气通过引风机引入余热锅炉。
在余热锅炉中,高温烟气与除盐水进行热交换,除盐水汽化为一定压力和温度的饱和或过热蒸汽去驱动汽轮机转动带动发电机发电,作功后饱和水蒸汽变成凝结水送入锅炉,经余热锅炉后再次汽化为蒸汽;高温废气则变成低温废气经鼓风机送入环冷机与高温烧结矿热交换后再次产生高温废气。
这两个循环周而复始的进行,其原理图如图一所示:图1 申特钢铁烧结余热发电原理图1.2 基本工艺烧结余热发电由三部分组成:烟气回收再循环系统,锅炉热交换系统,汽轮机及发电机组系统。
锅炉采用双通道烟气进气系统,高温烟气经部分高压受热面换热,低温烟气经部分低压受热面换热,高温烟气烟温降至与低温烟气相当后,两股烟气混合再与其余的受热面换热,充分利用烟气的不同品质,实现烟气热能的梯级利用,提高能源回收效率。
其主要由烟囱、烟气管道、锅炉烟气进口电动门、环冷机进风电动门等组成,主要功能是利用锅炉引风机产生的负压将环冷机处的高温烟气引入锅炉。
具体流程为:烧结环冷机来约390℃的高温烟气,从锅炉顶部进入过热器,向下部流动;另一路烧结环冷机来约290℃的低温烟气进入高参数蒸发器上部,然后与过热器进入的高温烟气会合成一股,向下部流动,经高参数蒸发器1、高参数蒸发器2、高参数省煤器、低参数蒸发器、水预热器流出,通过引风机、循环风机机送入烧结环冷机循环,烟气流程如图二所示:图二烟气循环流程图锅炉系统主要由汽包、过热器、高温段蒸发器、低温段蒸发器、省煤器、水预热器和给水泵等组成,主要功能是吸收高温烟气的热量逐级将受热面内的水汽化为蒸汽。
烧结余热交流

五、影响烟气品质的主要因素
烧结冷却机产生的烟气温度和余热总量是评价余热 资源品质的重要指标,这与烧结矿的温度密切相关。冷却 机烟气温度受到烧结料层厚度、烧结终点控制、冷却风温、 冷却风速、冷却料层厚度、边缘效应及冷却机密封状况等 生产条件的影响。
六、系统的运行控制
余热发电系统依附于主体工艺,发电系统随烧 结机的运转率是评价发电系统运行和经济性的一个重 要指标。正常发电系统的运行控制技术已经非常成熟, 不存在任何问题,而余热发电系统的关键就在于使主 工艺和发电实现高度耦合。深入了解烧结工艺和发电 系统的运行特点,采取相应的运行控制技术显得非常 重要。现有大型烧结机的年作业率一般都在93%左右, 即年运行小时数约为8150h,检修时间一般分临时检 修、季(月)检修和年度检修。因此,处理好烧结余 热发电系统稳定运行的问题可以从以下几个方面着手:
结束语
1、烧结机的工艺和烧结矿的质量与余热发电要求的 矛盾有待进一步研究。 2、低温低压汽轮机的参数设计和运行参数的控制有 待进一步摸索。 3、发电运行人员的技术素质、烧结系统人员与余热 发电系统人员的积极性的高低对发电量有较大的影响展迅速,但尚未完善,当 前的研究中,最为关键的是对烧结矿在环冷机尚的冷 却过程的模型研究。如何在模型中定量的引入料层厚 度、机速、烧结矿终点温度、冷却风量等生产运行参 数对于废气流场分布的影响,是控制的关键。 (2)对于单炉单机项目,环冷机废气的稳定性问题 不容忽视,极易对项目的投运效果造成严重影响,对 烧结生产的综合管理水平和停机时间统计给予足够的 重视。 (3)对于烧结生产和余热发电之间的关联关系的认 识是余热电站运行中需要积累提高的关键内容,和发 电效益的提升关系紧密,行业内仍需加强运行经验的 要求。
二、烧结余热发电的基本工艺流程
烧结余热回收发电浅谈

烧结余热回收发电浅谈耿乃弟一、我国钢铁企业的能耗状况钢铁生产消耗大量的能源和载能工质, 其能耗占我国国民经济总能耗的10%左右。
成本中能源费用占有相当大的比重, 钢铁联合企业中这一比重已达到30%,甚至更高。
日本钢铁工业的吨钢能耗维持在0.65tce左右。
我国74家大中型钢铁企业的吨钢能耗为0.80tce,与日本相比差约0.15tce。
我国能耗最低的宝钢的吨钢能耗与日本相比也有约50kgce的差距。
我国能源消耗高的原因虽然很多, 企业规模小是一个很重要的原因。
我国重点大中型企业(进入统计范围内) 74 家钢产量占全国的90% ,而日本5大钢铁企业的钢产量占日本的70%以上。
由于装备小,一些节能效果显着,但投资大,投资回收期长的节能措施无法实施。
例如:日本干熄焦、高炉TRT、转炉煤气回收的普及率100%。
我国的干熄焦装置只有17套,年处理焦炭480万t,占我国机焦产量的4%。
TRT只在大高炉有少量装置。
二、钢铁企业余热余能资源情况钢铁企业余热余能的范围包括焦化、烧结/球团、炼铁、炼钢及轧钢等主要生产工序,各主要生产工序的余热余能参数大致如下:1、焦化工序的钢比系数为0.404t(焦)/(t钢);焦炉煤气产生量为410m3/(t 焦);红焦温度为1000℃,上升管焦炉煤气温度为700℃,焦炉烟气温度为200℃;2、烧结工序的钢比系数为1.44t(矿)/(t钢);机尾烧结矿温度为800℃,烧结烟气温度为300℃;球团工序的钢比系数为0.25t(矿)/(t钢),球团矿排出温度为500℃;3、炼铁工序的钢比系数为0.91t(铁)/(t钢);高炉渣产量为320t(渣)/(t 铁),液态高炉渣温度为1500℃;高炉煤气发生量为1650m3/t(铁),高炉煤气热值为3350kJ/m3,炉顶高炉煤气温度为200℃;高炉冷却水平均温度为40℃;热风炉排烟温度为500℃;4、炼钢工序转炉钢比系数为0.84t(钢)/(t钢),电炉钢比系数为0.16t(钢)/(t钢);连铸比为100%;连铸坯温度为900℃;钢渣温度为1550℃;转炉煤气产生量为115m3/(t钢),热值为8370kJ/m3,烟罩处转炉煤气温度为1600℃;电炉炉顶排放口烟气温度为1200℃;5、轧钢工序钢比系数为0.92t(材)/(t钢);加热炉炉尾或入蓄热式烧嘴烟气平均温度为900℃;加热炉汽化冷却蒸汽压力为1.5MPa,温度为200℃;基于以上参数,我国钢铁工业吨钢余热余能资源总量为0.455tce/(t钢),各工序所占比例见下图。
烧结余热发电工程

烧结余热发电工程烧结余热发电中冶集团北京冶金设备研究设计总院依托雄厚的人才优势,大力发展节能环保技术,为企业的节能减排服务。
采用当前余热利用的先进设计理念,结合钢铁行业烧结烟气余热的特点,设计了整套烧结冷却机余热发电系统。
该系统不需要消耗一次能源,不产生额外的废气、废渣、粉尘和其它有害气体;具有充分利用低温废气、变废为宝、净化环境的多重意义。
1. 降低烧结工序能耗,促进资源节约,降低单位产值的能耗,增加企业的效益;2. 有利于企业可持续发展目标的实现,减少由常规火电厂带来的CO2、SO2、NOX、粉尘之类的大气污染物,有助于改善当地的能源结构,提高能源安全。
在钢铁企业中,烧结工序能耗占总能耗的10一12%,仅次于炼铁而居第二位,我国烧结生产的能耗指标和先进国家相比,差距较大。
大体上而言,每吨烧结矿的平均能耗要高出20kg标煤。
国内先进企业烧结工序的燃气单耗一般为0.065GJ/t,而先进国家的指标则已达0.025-0.03 GJ/t。
烧结生产放散到大气中的气体显热为烧结总热耗的50%,其中冷却机废气带走的热量约占烧结总热量的30%左右,把这些气体的余热加以回收利用是烧结厂节能的重要途径。
此部分热量又在冷却机的冷却过程中大部分变为200-400℃左右的热废气,最终散失在大气中。
这部分低温余热数量大,是烧结工序节能和回收利用的重点。
在冷却机上布置有数个冷却风罩,过矿料层后的风温在第一风罩内一般可达250-400℃,第二风罩内风温一般为200℃左右。
本技术通过对冷却车罩子、落矿斗、冷却风机进行适当的改造,使废气温度可提高到360℃-420℃左右,余热锅炉将产生1.25-2.45Mpa、330℃的过热蒸汽,确保冷却机余热的充分利用。
烧结余热发电<<<<<==== 余热利用新方向通过余热回收系统,在得到蒸汽的同时,还可以获得电能,一举两得。
最重要的是电能要比蒸汽创造的价值更大,对降低烧结矿成本的贡献率更高。
烧结冷却机余热发电技术

烧结冷却机余热发电技术分析当前我国烧结环冷的烟气余热利用问题,根据我国现阶段建设节约型社会的迫切要求,余热利用和热电联产被作为重点节能工程提出,天津华能通过技术改造,成功解决烟气污染问题,利用余热生产饱和蒸汽,供生产生活使用,具有非常现实的意义。
标签:烟气;高温;翅片管蒸发器;蒸汽;过热器;布袋除尘器;热管蒸发器钢铁生产过程中,烧结工序的能耗约占总能耗的10%,仅次于炼铁工序,位居第二。
在烧结工序总能耗中,有近50%的热能以烧结烟气和冷却机废气的显热形式排入大氣。
烧结冷却机余热的回收,是通过回收烧结机尾落矿风箱及烧结冷却机密闭段的烟气加热余热锅炉来回收低品位余热能源,结合低温余热发电技术,用余热锅炉的过热蒸汽来推动低参数汽轮发电机组做功发电的最新成套节能技术。
由冷却机一段风箱排出烟气(300~450℃)拟进行余热发电,2段和3段排出烟气温度(100℃及以下)较低,经性价比计算,回收价值较低,同时考虑矿料的最终冷却效果,不考虑回收,只考虑利用一段风箱范围内的高温烟气进行余热回收。
配置一条循环风余热锅炉系统。
从简单的工艺流程图可以看出:在烧结环冷机一段风箱和二段风箱之间设置隔板,将两端烟气隔开。
在一段风箱原有烟囱顶部加装烟道碟阀并在烟囱上开孔,设置一个引出烟道,并加设烟气蝶阀,引出的高温烟气首先进入撞击式除尘器进行粗除尘,然后高温烟气进入余热锅炉,烟气降温到160℃进入新增加的循环风机。
同时在进入循环风机前的烟道上设计一个混风阀补冷风。
需要发电时,关闭烟囱顶部烟道阀,打开引出烟道蝶阀,开动引风机,烟气由上部进入余热回收系统的温度为300-450℃,烟气从余热回收系统上部进入,经换热器将温度降到160℃左右,经引风机鼓入原有冷却风系统,达到循环风利用的目的,同时余热锅炉产生的230℃的过热蒸汽去汽轮机发电。
主要设备及技术特点一、撞击式除尘器从烟道过来的含尘气体流过扩大的截面流速降低,并与撞击式除尘器内部挡板相撞,颗粒大的固体沉降下来,并通过撞击式除尘器下部的卸灰阀排走。
烧结余热发电工艺简介
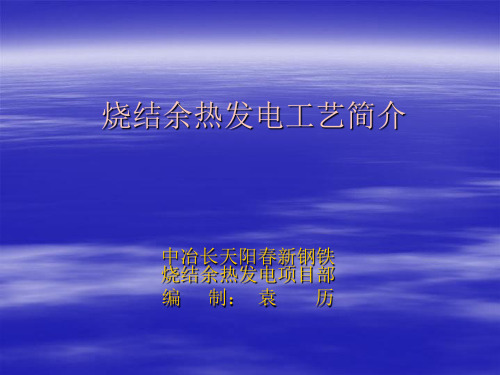
其中水是属于整个系统中可循环利用的能源介 质、烧结矿的热能是属于废能利用利于环保。
3、主要工艺系统构成 烧结余热发电工艺主要由锅炉烟风系统、锅炉汽
水系统、汽轮机汽水系统构成。
烧结余热发电工艺系统简图
锅炉烟风系统
1、主要设备:锅炉、循由中压蒸发器、低压过热器、 中压省煤器、低压蒸发器、水预热器,以及一个独立 中压过热器构成,其主要作用是烟风蕴含的热能转化 成水的内能形成高压过热蒸汽。
3、循环风机和引风机主要是从锅炉本体抽出经过锅炉 热交换后降温的烟风(该过程会使锅炉本体形成一个负压环境),转 移到环冷机上造成两个效果一、对环冷机上的烧结矿 进行风冷却、同时使得该烟风温度上升。二、在各取 风管道入口处形成高压环境
第二步、蒸汽在汽轮机中做完功在冷凝器中 冷凝成水由凝结水泵打往锅炉进一步循环使 用
知识回顾 Knowledge Review
aa11烧结余热发电工艺简介烧结余热发电工艺简介中冶长天阳春新钢铁中冶长天阳春新钢铁烧结余热发电项目部烧结余热发电项目部历历aa22一烧结余热发电基本概念烧结余热发电基本概念二锅炉烟风系统锅炉烟风系统三锅炉汽水系统锅炉汽水系统四汽轮机汽水系统汽轮机汽水系统aa33烧结余热发电基本概念烧结余热发电基本概念11能量角度分析能量角度分析第一步利用环冷机烧结矿冷却时释放的第一步利用环冷机烧结矿冷却时释放的热能转换成高压水蒸汽所蕴含的内能热能转换成高压水蒸汽所蕴含的内能主要是动能主要是动能和热能和热能第二步利用高压水蒸气的内能转化成汽第二步利用高压水蒸气的内能转化成汽轮机组的机械能轮机组的机械能第三步由汽轮机的机械能转化成发电机第三步由汽轮机的机械能转化成发电机的电能的电能22能源介质循环能源介质循环aa44第一步在环冷机上利用空气进行烧结矿的热能第一步在环冷机上利用空气进行烧结矿的热能交换交换第二步利用第一步之后的空气与锅炉里的水第二步利用第一步之后的空气与锅炉里的水进行能量交换进行能量交换这过程中水会变成高压的蒸汽这过程中水会变成高压的蒸汽第三步利用高压的蒸汽带动汽轮机旋转完成能第三步利用高压的蒸汽带动汽轮机旋转完成能量交换量交换第四步由旋转的汽轮机带动发电机发电产生电第四步由旋转的汽轮机带动发电机发电产生电其中水是属于整个系统中可循环利用的能源介其中水是属于整个系统中可循环利用的能源介质烧结矿的热能是属于废能利用利于环保质烧结矿的热能是属于废能利用利于环保
- 1、下载文档前请自行甄别文档内容的完整性,平台不提供额外的编辑、内容补充、找答案等附加服务。
- 2、"仅部分预览"的文档,不可在线预览部分如存在完整性等问题,可反馈申请退款(可完整预览的文档不适用该条件!)。
- 3、如文档侵犯您的权益,请联系客服反馈,我们会尽快为您处理(人工客服工作时间:9:00-18:30)。
中冶长天阳春新钢铁 烧结余热发电项目部 编 制: 袁 历
目
录
一、烧结余热发电基本概念 二、锅炉烟风系统 三、锅炉汽水系统 四、汽轮机汽水系统
烧结余热发电基本概念
1、能量角度分析 第一步、利用环冷机烧结矿冷却时释放的 热能转换成高压水蒸汽所蕴含的内能(主要是动能
和热能)
锅炉汽水系统
1、该子系统中主要设备由炉体、汽包、过热器、低参数过
热集箱、高参数过热集箱、给水泵够成。 2、该子系统主要是水在锅炉炉体中流动并吸收热能变成水 蒸气的过程。 3、该子系统主要工艺如下: 第一步、汽轮机的凝结水经过锅炉炉体的水预热器,带走炉 体的一部分热能后变成水汽混合物进入低压汽包 第二步、进入低压汽包的水在重力作用下进入两个低参数蒸 发器再进行热交换大部分变成蒸汽后上升回低压汽包 第三步、低压汽包的蒸汽进入低压过热器、低参数过热集箱 进一步加热升压后变成低压过热蒸汽送人汽轮机 第四步、低压汽包内的水由给水泵经过高参数省煤器进一步 热交换后的水汽混合物进入中压汽包 第五步、中压汽包的水在重力作用下进入三个高参数蒸发器 再进行热交换大部分变成蒸汽后上升回中压汽包 第六步、中压汽包的蒸汽进入过热器、高参数过热集箱后变 成高压过热蒸汽送统
1、主要设备:锅炉、循环风机、引风机 2 、锅炉内部从上至下由中压蒸发器、低压过热器、 中压省煤器、低压蒸发器、水预热器,以及一个独立 中压过热器构成,其主要作用是烟风蕴含的热能转化 成水的内能形成高压过热蒸汽。 3、循环风机和引风机主要是从锅炉本体抽出经过锅炉 热交换后降温的烟风(该过程会使锅炉本体形成一个负压环境),转 移到环冷机上造成两个效果一、对环冷机上的烧结矿 进行风冷却、同时使得该烟风温度上升。二、在各取 风管道入口处形成高压环境 4、在锅炉、环冷机、循环风机、引风机之间由烟风管 道链接形成一个近乎密闭的系统,并根据压差来实现 烟风的循环,完成烧结矿与锅炉水的热交换过程。
第二步、利用高压水蒸气的内能转化成汽 轮机组的机械能 第三步、由汽轮机的机械能转化成发电机 的电能 2、能源介质循环
第一步、在环冷机上利用空气进行烧结矿的热能 交换 第二步、利用第一步之后的空气与锅炉里的水 进行能量交换(这过程中水会变成高压的蒸汽) 第三步、利用高压的蒸汽带动汽轮机旋转完成能 量交换 第四步、由旋转的汽轮机带动发电机发电产生电 能 其中水是属于整个系统中可循环利用的能源介 质、烧结矿的热能是属于废能利用利于环保。 3、主要工艺系统构成 烧结余热发电工艺主要由锅炉烟风系统、锅炉汽 水系统、汽轮机汽水系统构成。
汽轮机汽水系统
1、该子系统主要设备由汽轮机、发电机、冷 凝器、凝结水泵、射水泵构成。 2、该子系统主要是过热蒸汽进人汽轮机中做 功凝结成水,汽轮机带动发电机发电的系统 3、该子系统主要工艺如下: 第一步、高参数过热蒸汽和低参数过热蒸汽 进入带动汽轮机旋转做功,汽轮机带动发电 机旋转发电 第二步、蒸汽在汽轮机中做完功在冷凝器中 冷凝成水由凝结水泵打往锅炉进一步循环使 用