车刀角度选择
车刀种类和角度选择原则详解
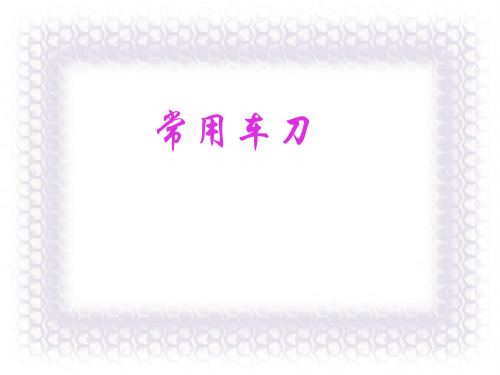
车刀不对准工件中心对角度的影响
五、车刀刃磨
无论硬质合金车刀(焊接)或高速钢 车刀,在使用之前都要根据切削条 件所选择的合理切削角度进行刃磨 ,一把用钝了的车刀,为恢复原有 的几何形状和角度,也必须重新刃 磨。
重 要 性
三分手艺、七分刀 徒弟的手、师傅的刀
1.磨刀步骤(图a~d)
⑴磨前刀面 把前角和刃倾角磨正确。 ⑵磨主后刀面 把主偏角和主后角磨正确。 ⑶磨副后刀面 把副偏角和副后角磨正确。 ⑷磨刀尖圆弧 圆弧半径约0.5~2mm左右。 ⑸研磨刀刃 车刀在砂轮上磨好以后,再用油石加些机油研磨车 刀的前面及后面,使刀刃锐利和光洁。这样可延长车刀的使用寿命。 车刀用钝程度不大时,也可用油石在刀架上修磨。硬质合金车刀可 用碳化硅油石修磨。
前角γo
——在主切削刃选定点的正交平面po内, 前刀面与基面之间的夹角
。
后角αo
——在正交平面po内,主后刀面与切削 平面之间的夹角。
主偏角κr
——主切削刃在基面上的投影与进给方 向的夹角。
刃倾角λs ——在切削平面ps内,主切削刃与 基面pr的夹角。
其他角度:
副前角γoˊ、 副后角αoˊ、 副偏角κrˊ、 刃倾角λsˊ
3.主偏角、副偏角的选择 (1)主偏角的选择 A、主偏角κr的增大或减小对切削加工有利的一 面 在背吃刀量ap与进给量f 不变时,主偏角κr减小 将使切削厚度hD减小,切削宽度bD增加,参加 切削的切削刃长度也相应增加,切削刃单位长度 上的受力减小,散热条件也得到改善。 主偏角κr减小时,刀尖角增大,刀尖强度提高, 刀尖散热体积增大。 所以,主偏角κr减小,能提高刀具耐用度。
(4)良好的工艺性和经济性
车刀的主要角度及其作用

车刀的主要角度及其作用车刀的主要角度有前角(γ0)、后角(α0)、主偏角(Kr)、副偏角(Kr’)和刃倾角(λs)。
为了确定车刀的角度,要建立三个坐标平面:切削平面、基面和主剖面。
对车削而言,如果不考虑车刀安装和切削运动的影响,切削平面可以认为是铅垂面;基面是水平面;当主切削刃水平时,垂直于主切削刃所作的剖面为主剖面。
(1)前角γ0在主剖面中测量,是前刀面与基面之间的夹角。
其作用是使刀刃锋利,便于切削。
但前角不能太大,否则会削弱刀刃的强度,容易磨损甚至崩坏。
加工塑性材料时,前角可选大些,如用硬质合金车刀切削钢件可取γ0=10~20,加工脆性材料,车刀的前角γ0应比粗加工大,以利于刀刃锋利,工件的粗糙度小。
(2)后角α0在主剖面中测量,是主后面与切削平面之间的夹角。
其作用是减小车削时主后面与工件的摩擦,一般取α0=6~12°,粗车时取小值,精车时取大值。
(3)主偏角Kr在基面中测量,它是主切削刃在基面的投影与进给方向的夹角。
其作用是:1)可改变主切削刃参加切削的长度,影响刀具寿命。
2)影响径向切削力的大小。
小的主偏角可增加主切削刃参加切削的长度,因而散热较好,对延长刀具使用寿命有利。
但在加工细长轴时,工件刚度不足,小的主偏角会使刀具作用在工件上的径向力增大,易产生弯曲和振动,因此,主偏角应选大些。
车刀常用的主偏角有45°、60°、75°、90°等几种,其中45°多。
(4)副偏角Kr’在基面中测量,是副切削刃在基面上的投影与进给反方向的夹角。
其主要作用是减小副切削刃与已加工表面之间的摩擦,以改善已加工表面的精糙度。
在切削深度ap、进给量f、主偏角Kr相等的条件下,减小副偏角Kr’,可减小车削后的残留面积,从而减小表面粗糙度,一般选取Kr′=5~15°。
(5)刃倾角入λs 在切削平面中测量,是主切削刃与基面的夹角。
其作用主要是控制切屑的流动方向。
如何合理的选取车刀的几何角度

如何合理的选取车刀的几何角度
1、前角γ0(在正交面的上测量的前刀面与基面之间的夹角)。
它表示前刀面的倾斜程度。
前角越大,刀刃越锋利,切削时就越省力。
但前角过大会削弱刀头强度,影响刀具的寿命。
前角的选取决定于工件材料、刀具材料和加工性质。
硬质合金车刀γ0通常取-5º~+25º。
2、后角α0。
在正交平面上测量的主后刀面与切削平面之间的夹角。
它表示主后刀面的倾斜程度。
后角的作用主要是减少刀具与加工表面之间的摩擦,后角越大,摩擦越小,但后角过大会削弱切削刃的强度及耐用度。
一般取α0为60~120。
3、主偏角k r。
主切削刃在基面上的投影与进给方向之间的夹角。
主偏角能影响主切削刃和刀头受力情况及散热情况。
加工强度、硬度较高的材料时,应选较小的主偏角,以提高刀具的耐用度。
加工细长工件时,应选较大的主偏角,以减少径向切削力引起工件的变形和振动。
一般取k r为300~900。
4、副偏角k r'。
副切削刃在基面上的投影与进给反方向之间的夹角。
副偏角的作用是减少副切削刃与工件已加工表面之间的摩擦。
副偏角越大,摩擦越小。
但k r过大,又会增大已加工表面的粗糙度。
一般取k r为50~150。
车刀的几何角度:。
90度外圆车刀角度参数
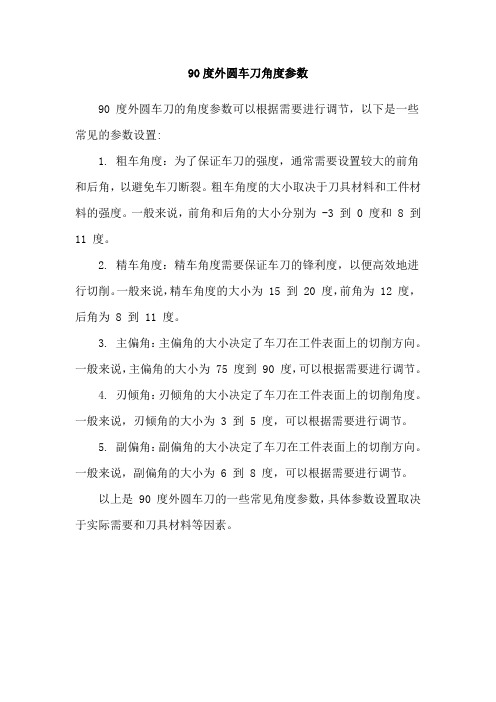
90度外圆车刀角度参数
90 度外圆车刀的角度参数可以根据需要进行调节,以下是一些常见的参数设置:
1. 粗车角度:为了保证车刀的强度,通常需要设置较大的前角和后角,以避免车刀断裂。
粗车角度的大小取决于刀具材料和工件材料的强度。
一般来说,前角和后角的大小分别为 -3 到 0 度和 8 到11 度。
2. 精车角度:精车角度需要保证车刀的锋利度,以便高效地进行切削。
一般来说,精车角度的大小为 15 到 20 度,前角为 12 度,后角为 8 到 11 度。
3. 主偏角:主偏角的大小决定了车刀在工件表面上的切削方向。
一般来说,主偏角的大小为 75 度到 90 度,可以根据需要进行调节。
4. 刃倾角:刃倾角的大小决定了车刀在工件表面上的切削角度。
一般来说,刃倾角的大小为 3 到 5 度,可以根据需要进行调节。
5. 副偏角:副偏角的大小决定了车刀在工件表面上的切削方向。
一般来说,副偏角的大小为 6 到 8 度,可以根据需要进行调节。
以上是 90 度外圆车刀的一些常见角度参数,具体参数设置取决于实际需要和刀具材料等因素。
刀主要角度
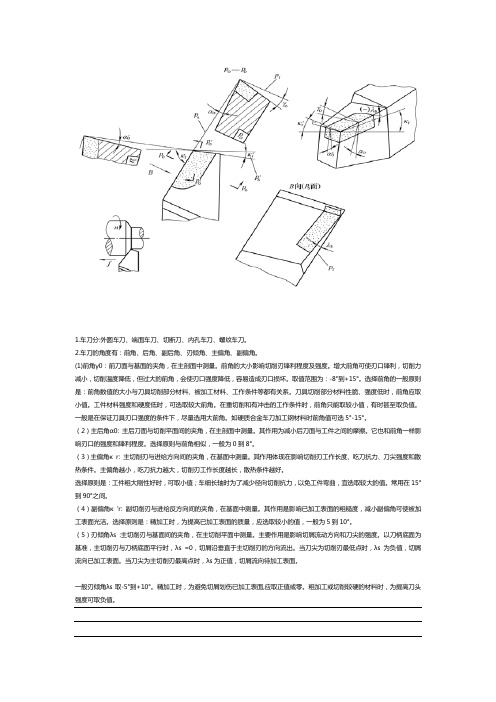
1.车刀分:外圆车刀、端面车刀、切断刀、内孔车刀、螺纹车刀。
2.车刀的角度有:前角、后角、副后角、刃倾角、主偏角、副偏角。
(1)前角γ0:前刀面与基面的夹角,在主剖面中测量。
前角的大小影响切削刃锋利程度及强度。
增大前角可使刃口锋利,切削力减小,切削温度降低,但过大的前角,会使刃口强度降低,容易造成刃口损坏。
取值范围为:-8°到+15°。
选择前角的一般原则是:前角数值的大小与刀具切削部分材料、被加工材料、工作条件等都有关系。
刀具切削部分材料性脆、强度低时,前角应取小值。
工件材料强度和硬度低时,可选取较大前角。
在重切削和有冲击的工作条件时,前角只能取较小值,有时甚至取负值。
一般是在保证刀具刃口强度的条件下,尽量选用大前角。
如硬质合金车刀加工钢材料时前角值可选5°-15°。
(2)主后角α0: 主后刀面与切削平面间的夹角,在主剖面中测量。
其作用为减小后刀面与工件之间的摩擦。
它也和前角一样影响刃口的强度和锋利程度。
选择原则与前角相似,一般为0到8°。
(3)主偏角κr: 主切削刃与进给方向间的夹角,在基面中测量。
其作用体现在影响切削刃工作长度、吃刀抗力、刀尖强度和散热条件。
主偏角越小,吃刀抗力越大,切削刃工作长度越长,散热条件越好。
选择原则是:工件粗大刚性好时,可取小值;车细长轴时为了减少径向切削抗力,以免工件弯曲,宜选取较大的值。
常用在15°到90°之间。
(4)副偏角κ'r: 副切削刃与进给反方向间的夹角,在基面中测量。
其作用是影响已加工表面的粗糙度,减小副偏角可使被加工表面光洁。
选择原则是:精加工时,为提高已加工表面的质量,应选取较小的值,一般为5到10°。
(5)刃倾角λs :主切削刃与基面间的夹角,在主切削平面中测量。
主要作用是影响切屑流动方向和刀尖的强度。
以刀柄底面为基准,主切削刃与刀柄底面平行时,λs =0,切屑沿垂直于主切削刃的方向流出。
解释车刀的主要几何角度,并说明对车削加工的影响

在车削加工中,车刀的主要几何角度对加工效果和加工质量有着重要的影响。
在本文中,我将从深度和广度上对车刀的几何角度进行全面评估,并探讨它们对车削加工的影响。
1. 切削角:切削角是指车刀切削刃上的主切削刃与前方切削方向的夹角。
切削角的大小直接影响着切屑的形成和流动。
当切削角较大时,切削力减小,但切削刃容易磨损;当切削角较小时,切削力增大,但切削刃磨损减小。
选择适当的切削角对于保证加工质量和提高加工效率至关重要。
2. 后角:后角是指车刀主切削刃与切削方向之间的夹角。
后角的大小影响着车刀的进给力和阻力。
当后角增大时,进给力增大,加工效率提高;但阻力也会增大,对车刀和工件的刚性要求也会增加。
合理选择后角是为了在保证加工效率的尽可能减小刀具和工件的损耗。
3. 主偏角:主偏角是指车刀主切削刃与工件表面的夹角。
主偏角的大小直接影响着工件的表面质量和加工精度。
一般来说,主偏角越小,加工表面的质量越好,但车刀的刚度和稳定性要求也越高。
在实际应用中需要根据工件的要求和加工条件选择合适的主偏角。
4. 副偏角:副偏角是指车刀副切削刃与工件表面的夹角。
副偏角的大小影响着切削刃与工件的接触面积和切削力的大小。
合理选择副偏角可以有效减小切削力,提高车削加工的效率和质量。
车刀的几何角度对车削加工有着重要的影响,其合理选择可以有效提高加工效率和加工质量。
在实际应用中,需要根据具体的加工要求和工件材料来选择合适的几何角度,以达到最佳的加工效果。
个人观点和理解:车刀的几何角度是车削加工中的关键参数,合理选择和调整这些角度对于提高加工质量和效率至关重要。
在实际应用中,需要综合考虑工件材料、加工条件和车刀性能等因素,进行合理的选择和调整,以达到最佳的加工效果。
以上是对“解释车刀的主要几何角度,并说明对车削加工的影响”的文章撰写,希望能帮助你更深入地理解这一主题。
在车削加工中,车刀的几何角度对加工效果和加工质量有着重要的影响。
除了切削角、后角、主偏角和副偏角外,还有其他几何角度也对车削加工起着重要作用,比如前角、刀尖半径等。
(完整版)刀具角度选择
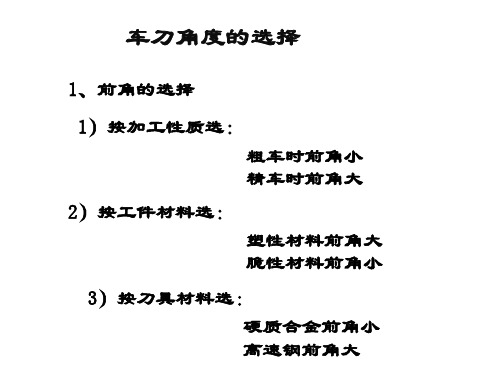
3、主偏角的选择
1)按工件形状选: 有直角台阶时主偏角大于等于90度;
2)按工件材料选: 材料硬(软)时选较小(大)主偏角;
3)按工件刚性选: 刚性好(差)时选较小(大)主偏角。
4、副偏角的选择 1)一般选60~80; 2)按工件表面粗糙度要求选: 要求高时选较小副偏角,但不 能太小,太小会加大与已加工 表面的摩擦,反而降低表面粗 糙度。
5、刃倾角的选择 粗车:选负值(可避免刀尖受冲击,保护刀尖); 精车:选正值(使切屑向待加工表面流出)。
车刀角度的选择
1、前角的选择
1)按加工性质选: 粗车时前角小 精车时前角大
2)按工件材料选: 塑性材料前角大 脆性材料前角小
3)按刀具材料选: 硬质合金前角小 高速钢前角大
2、后角的选择
1)按加工性质选: 粗车时后角小 精车时后角大
2)按工件材料选: 塑性材料后角大 脆性材角大。
车刀的几何角度及选择原则

车刀的几何角度及选择原则newmaker为了决定车刀刃口的锋利程度及其在空间的位置,必须建立一个坐标系,该坐标系由三个基准平面构成。
下面以外圆车刀为例,介绍车刀的几何角度。
如图所示。
基面:过主切削刃选定点的平面,此平面在主切削刃为水平时包含主刀刃并与车刀安装底面即水平面平行,此平面主要作为度量前刀面在空间位置的基准平面。
切削平面:过主切削刃选定点与主切削刃相切,并与基面相垂直的平面。
此平面主要作为度量主后刀面在空间位置的基准面。
主剖面:过主切削刃选定点并同时垂直于基面和主切削平面的平面。
(1)、前角γ0 前刀面与基面的夹角,在主剖面中测量。
前角的大小影响切削刃锋利程度及强度。
增大前角可使刃口锋利,切削力减小,切削温度降低,但过大的前角,会使刃口强度降低,容易造成刃口损坏。
取值范围为:-8°到+15°。
选择前角的一般原则是:前角数值的大小与刀具切削部分材料、被加工材料、工作条件等都有关系。
刀具切削部分材料性脆、强度低时,前角应取小值。
工件材料强度和硬度低时,可选取较大前角。
在重切削和有冲击的工作条件时,前角只能取较小值,有时甚至取负值。
一般是在保证刀具刃口强度的条件下,尽量选用大前角。
如硬质合金车刀加工钢材料时前角值可选5°-15°。
(2)、主后角α0 主后刀面与切削平面间的夹角,在主剖面中测量。
其作用为减小后刀面与工件之间的摩擦。
它也和前角一样影响刃口的强度和锋利程度。
选择原则与前角相似,一般为0到8°。
(3)、主偏角κ r 主切削刃与进给方向间的夹角,在基面中测量。
其作用体现在影响切削刃工作长度、吃刀抗力、刀尖强度和散热条件。
主偏角越小,吃刀抗力越大,切削刃工作长度越长,散热条件越好。
选择原则是:工件粗大刚性好时,可取小值;车细长轴时为了减少径向切削抗力,以免工件弯曲,宜选取较大的值。
常用在15°到90°之间。
(4)、副偏角κ 'r 副切削刃与进给反方向间的夹角,在基面中测量。
车刀角度的选择

车刀角度的选择一,车刀的安装位置对车刀角度的影响。
,车刀装得高于或低于中心时对车刀角度的影响。
1.当刀尖对准工件中心安装时前角与后角不变。
2.当刀尖装得高于工件中心时,前角增大,后角减小。
3.当刀尖装得低于工件中心时,前角减小,后角增大。
车内孔时,刀尖的三种安装位置,除当刀尖对准工件中心安装时车刀前角后角不变,其余两种情况,对车刀前角的影响,均与车外圆时相反。
,车刀装得歪斜对车刀角度的影响,车刀装的偏斜会使车刀的主偏角和副偏角发生变化经。
1.当刀杆装的与工件垂直时,主偏角与副偏角不改变。
2.当刀杆装的向右歪斜时,则主偏角增大,副偏角减小。
3.当刀杆装的向左歪斜时,则主偏角减小,副偏角增大。
车削圆锥时,刀杆装的与工件圆锥母线垂直,否则主偏角也会发生变化,影响加工质量。
螺纹车刀如果装得不正,就会引起螺纹牙型半角误差。
切断刀如果装得不正,就会使切断面凹凸不平,甚至断刀。
精车刀装得不正会影响工件的表面粗糙度。
,进给运动对车刀角度的影响,车削时除工件做旋转运动外,车刀还必须做直线运动,这两个运动合成螺旋运动。
在横向车削时,车刀按一定大小的走刀量进给,刀尖在工件的端面上的运动轨迹是阿基米德螺旋线,刀具愈近工件中心或走刀量愈大时,螺旋线愈倾斜,跟螺旋线始终相切的切削平面位置也随之变化,车刀工作时的实际后角减小,前角增大。
在纵向车削时,由于车刀刀尖在工件上的运动轨迹是一条螺旋线,跟螺旋线相切的切削平面位置也随之倾斜,所以也影响刀具的实际工件角度,因此车刀工件时的实际工件角度:Γ0i=τ0+ττ式中τ——螺旋角f——进给量,mm/rD——工件直径mm.一般车削时,走刀量较小,由于进给运动所引起的τ值可以忽略不计,但当车削大螺距螺纹时或多头螺纹时, τ值较大,在刃磨刀具时应考虑,它对工件角度的影响.二,刀具切削部分的几何参数的选择。
1,前角的选择1.前角的作用。
1,加大前角,刀具锋利,减少切屑变形,降低切削力,和切削热,但前角过大影响刀具的强度。
车刀角度的作用及选用原则
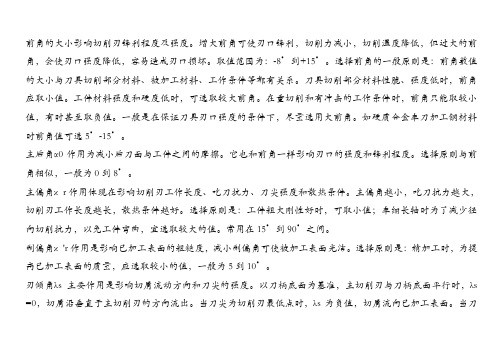
前角的大小影响切削刃锋利程度及强度。
增大前角可使刃口锋利,切削力减小,切削温度降低,但过大的前角,会使刃口强度降低,容易造成刃口损坏。
取值范围为:-8°到+15°。
选择前角的一般原则是:前角数值的大小与刀具切削部分材料、被加工材料、工作条件等都有关系。
刀具切削部分材料性脆、强度低时,前角应取小值。
工件材料强度和硬度低时,可选取较大前角。
在重切削和有冲击的工作条件时,前角只能取较小值,有时甚至取负值。
一般是在保证刀具刃口强度的条件下,尽量选用大前角。
如硬质合金车刀加工钢材料时前角值可选5°-15°。
主后角α0作用为减小后刀面与工件之间的摩擦。
它也和前角一样影响刃口的强度和锋利程度。
选择原则与前角相似,一般为0到8°。
主偏角κr作用体现在影响切削刃工作长度、吃刀抗力、刀尖强度和散热条件。
主偏角越小,吃刀抗力越大,切削刃工作长度越长,散热条件越好。
选择原则是:工件粗大刚性好时,可取小值;车细长轴时为了减少径向切削抗力,以免工件弯曲,宜选取较大的值。
常用在15°到90°之间。
副偏角κ'r作用是影响已加工表面的粗糙度,减小副偏角可使被加工表面光洁。
选择原则是:精加工时,为提高已加工表面的质量,应选取较小的值,一般为5到10°。
刃倾角λs主要作用是影响切屑流动方向和刀尖的强度。
以刀柄底面为基准,主切削刃与刀柄底面平行时,λs =0,切屑沿垂直于主切削刃的方向流出。
当刀尖为切削刃最低点时,λs为负值,切屑流向已加工表面。
当刀尖为主切削刃最高点时,λs为正值,切屑流向待加工表面。
一般刃倾角λs取-5°到+10°。
精加工时,为避免切屑划伤已加工表面,应取正值或零。
粗加工或切削较硬的材料时,为提高刀头强度可取负值。
车刀的主要角度及其作用来源:本站浏览次数:289车刀的主要角度有前角(γ0)、后角(α0)、主编角(Kr)、副偏角(Kr’)和刃倾角(λs)。
车刀的主要角度

二、车刀的角度
1、前角:前刀面与基面之间的夹角 2、后角:后刀面与切削平面之间的夹角 3、楔角:前刀面与后刀面之间的夹角 三个角之和为90度
二、车刀的角度
4、主偏角:主切削刃在基面内的投影与进给方向之间 的夹角
5、副偏角:主切削刃在基面内的投影与进给方 向之间的夹角 6、刀尖角:主切削与副切削刃在基面内的投影 之间的夹角
二、车刀几何角度的选择
(3)前角的选择:
选择原则:在刀具强度允许的条件下,尽量选较大的前角, 具体选择时根据工件的材料、刀具材料、加工性质等因素 选择。 ①加工脆性材料或硬度较高的材料时应选较小的前角, 反之,选较大的前角 ②高速钢车刀的前角一般应大于硬质合金车刀的前角。 ③精加工时选择较大的前角,反之选较小的前角。
三个角之和为180度
7、刃倾角:主切削刃与基面之间的夹角
二、车刀几何角度的选择
1、前角的选择: (1)前角的作用:
①影响车刀的锋利程序、切削力的大小与切削变形的大小。 ②影响车刀强度、受力情况和散热条件。
③影响加工表面质量。前角增大,刃口锋利,摩擦力小, 提高表面质量。 (2)前角正负的规定:我们要磨成正前角,刀尖高一点
2、后角的选择:
(1)后角的作用: ①减小后刀面与过渡表面之间的摩擦。 ②增大后角可使车刀刃口锋利。 (2)后角的正负的规定: 我们要磨成正后角,刀尖朝外面倾斜 (3)后角的选择: ①粗车时:选择较小的前角。
②精车时:选择较大的前角。
2、后角的选择:
③断续切削时或切削力较大时选取较大的前角。
3、主偏角与副偏角的选择:
(1)主偏角的作用:影响车刀的散热条件、断效果。
(2)主偏角的选择 ①刚性较差时选较大的主偏角。硬度高的工件选较小的 主偏角 ②刚性较差时选较大的主偏角。
螺纹车刀角度参数

螺纹车刀角度参数
以下是螺纹车刀的主要角度参数:
1. 刀尖角:此角度等于牙型角。
车削普通螺纹时,牙型角为60度。
英制螺纹时,牙型角为55度。
2. 前角:一般为0度至15度。
精车或精度要求高的螺纹,径向前角取得小些,约为0度至5度。
3. 后角:一般为5度至15度。
因受螺纹升角的影响,进刀方向一面的后角应磨得稍大些。
但大直径、小螺距的三角形螺纹,这种影响可忽略不计。
此外,在车削较大螺距以及硬度较高的螺纹时,应在车刀的两个切削刃上磨出宽度为4mm的倒棱,以防止崩刃并减少切削力。
以上信息仅供参考,如需了解更多信息,建议查阅专业书籍或咨询专业人士。
刀具角度的标注

1.75°内孔车刀几何角度:主偏角Kr二75。
,副偏角Kr'二15。
,前角丫0二10。
后角a 0二8,副后角a 0'二8,刃倾角入S二5°
答案:
2. 75°外圆车刀几何角度:主偏角K T二75°,副偏角KJ二15°,前角丫o二10.,后角a o二8,副后角a o二8,刃倾角入S二—5°
答案:
3.60°内孔车刀几何角度:主偏角Kr二60,副偏角Kr'二15°,前角丫0二10。
后角
a 0二8,副后角a 0'二8,刃倾角入s = — 5
答案:
4. 90°外圆车刀几何角度:主偏角Kr二90°,副偏角Kr - 15°,前角丫0二10。
后角a 0二8,副后角a 0'二8,刃倾角入s二5°
答案:
5. 45°内孔车刀几何角度: 主偏角Kr二45°,副偏角Kr1 - 15。
,
前角丫o二10°,后角日o二10°,副后角曰o二10°,刃倾角入S二-5°答案:
F O-P D
6. 45°端面车刀几何角度:主偏角Kr二45°,副偏角Kr'二45°,前角丫0二5后角
a 0二8,副后角a 0'二8,刃倾角入S二5°
答案:
5. 45°内孔车刀几何角度: 主偏角Kr二45°,副偏角Kr1 - 15。
,。
车刀的主要几何角度及选择

车刀的重要几何角度及选择1)前角(γ0 )选择的原则前角的大小重要解决刀头的坚固性与锋利性的冲突。
因此首先要依据加工材料的硬度来选择前角。
加工材料的硬度高,前角取小值,反之取大值。
其次要依据加工性质来考虑前角的大小,粗加工时前角要取小值,精加工时前角应取大值。
前角一般在—5°~25°选取。
通常,制作车刀时并没有预先制出前角(γ0),而是靠在车刀上刃磨出排屑槽来获得前角的。
排屑槽也叫断屑槽,它的作用是折断切屑,不产生缠绕;掌控切屑的流出方向,保持已加工表面的精度;降低切削抗力,延长刀具寿命。
2)后角(α0 )选择的原则首先考虑加工性质。
精加工时,后角取大值,粗加工时,后角取小值。
其次考虑加工材料的硬度,加工材料硬度高,主后角取小值,以加强刀头的坚固性;反之,后角应取小值。
后角不能为零度或负值,一般在6°~12°选取。
3)主偏角(Kr )的选用原则首先考虑车床、夹具和刀具构成的车削工艺系统的刚性,如系统刚性好,主偏角应取小值,这样有利于提高车刀使用寿命、改善散热条件及表面粗造度。
其次要考虑加工工件的几何形状,当加工台阶时,主偏角应取90°,加工中心切入的工件,主偏角一般取60 °。
主偏角一般在30°~90°,*常用的是45°、75 °、90 °。
4)副偏角(Kr)的选择原则首先考虑车刀、工件和夹具有充足的刚性,才能减小副偏角;反之,应取大值;其次,考虑加工性质,精加工时,副偏角可取10°~15°,粗加工时,副偏角可取5°左右。
5)刃倾角(λS)的选择原则重要看加工性质,粗加工时,工件对车刀冲击大,取λS≤ 0°,精加工时,工件对车刀冲击力小,取λS≥ 0°;通常取λS=0°。
刃倾角一般在—10°~5°选取。
车刀切削部分的四个基本角度
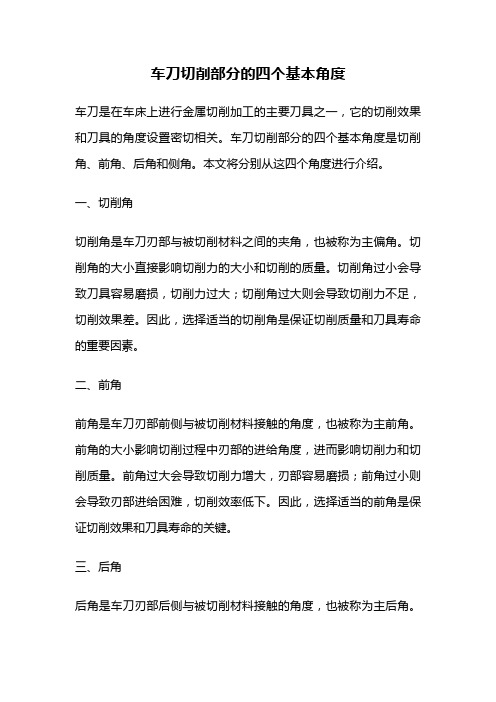
车刀切削部分的四个基本角度车刀是在车床上进行金属切削加工的主要刀具之一,它的切削效果和刀具的角度设置密切相关。
车刀切削部分的四个基本角度是切削角、前角、后角和侧角。
本文将分别从这四个角度进行介绍。
一、切削角切削角是车刀刃部与被切削材料之间的夹角,也被称为主偏角。
切削角的大小直接影响切削力的大小和切削的质量。
切削角过小会导致刀具容易磨损,切削力过大;切削角过大则会导致切削力不足,切削效果差。
因此,选择适当的切削角是保证切削质量和刀具寿命的重要因素。
二、前角前角是车刀刃部前侧与被切削材料接触的角度,也被称为主前角。
前角的大小影响切削过程中刃部的进给角度,进而影响切削力和切削质量。
前角过大会导致切削力增大,刃部容易磨损;前角过小则会导致刃部进给困难,切削效率低下。
因此,选择适当的前角是保证切削效果和刀具寿命的关键。
三、后角后角是车刀刃部后侧与被切削材料接触的角度,也被称为主后角。
后角的大小影响切削过程中刃部的切削深度,进而影响切削力和切削质量。
后角过大会导致切削力增大,刃部容易磨损;后角过小则会导致刃部切削深度不足,切削效果差。
因此,选择适当的后角是保证切削效果和刀具寿命的关键。
四、侧角侧角是车刀刃部侧面与被切削材料接触的角度,也被称为主侧角。
侧角的大小影响切削过程中的切削力和切削质量。
侧角过大会导致切削力增大,刀具容易破碎;侧角过小则会导致切削力不足,切削效率低下。
因此,选择适当的侧角是保证切削质量和刀具寿命的关键。
总结车刀切削部分的四个基本角度,即切削角、前角、后角和侧角,是影响车刀切削效果和刀具寿命的重要因素。
选择适当的角度可以保证切削质量和刀具寿命,同时减少切削力和提高切削效率。
因此,在进行车刀切削加工时,需要根据被切削材料的性质和切削要求来合理设置这四个角度,以获得最佳的切削效果。
车刀种类和刀刃角度选取原则

正交平面参考系
1.正交平面参考系时各参考面 :(右图)
——过切削刃选定点平行或垂直刀具安装面(或轴线)的平面。
——过切削刃选定点与 切削刃相切并垂直于基面的平面。
切削平面ps
正交平面po
基面pr
2. 刀具的标注角度
前角γo ——在主切削刃选定点的正交平面po内,前刀面与基面之间的夹角。 后角αo ——在正交平面po内,主后刀面与切削平面之间的夹角。
3.在一定切削条件下的基本选择方法 :
1)前角和前刀面形状的选择
5)刃倾角的选择
3)主偏角、副偏角的选择
2)后角及形状的选择
4)刀尖形状的选择
1.前角和前刀面形状的选择 (1) 前角的选择: 在选择刀具前角时首先应保证刀刃锋利,同时也要兼顾刀刃的强度与耐用度。 刀具前角的合理选择,主要由刀具材料和工件材料的种类与性质决定。
三分手艺、七分刀
徒弟的手、师傅的刀
重要性
1.磨刀步骤(图a~d)
(a) (b) (c) (d) 图a~d 刃磨外圆车刀的一般步骤 a)磨前刀面 b)磨主后刀面 c)磨副后刀面 d)磨刀尖圆弧
C、负前角平面型 (右图) 特点:切削刃强度较好, 但刀刃较钝,切削变形大。 主要用于硬脆刀具材料。加工高强度高硬度材料,如淬火钢。 图示类型负前角后部加有正前角,有利于切屑流出。
45度车刀角度参数
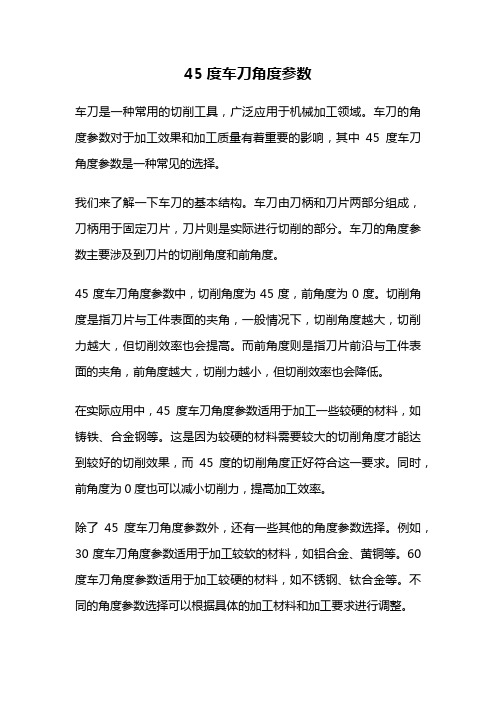
45度车刀角度参数
车刀是一种常用的切削工具,广泛应用于机械加工领域。
车刀的角度参数对于加工效果和加工质量有着重要的影响,其中45度车刀角度参数是一种常见的选择。
我们来了解一下车刀的基本结构。
车刀由刀柄和刀片两部分组成,刀柄用于固定刀片,刀片则是实际进行切削的部分。
车刀的角度参数主要涉及到刀片的切削角度和前角度。
45度车刀角度参数中,切削角度为45度,前角度为0度。
切削角度是指刀片与工件表面的夹角,一般情况下,切削角度越大,切削力越大,但切削效率也会提高。
而前角度则是指刀片前沿与工件表面的夹角,前角度越大,切削力越小,但切削效率也会降低。
在实际应用中,45度车刀角度参数适用于加工一些较硬的材料,如铸铁、合金钢等。
这是因为较硬的材料需要较大的切削角度才能达到较好的切削效果,而45度的切削角度正好符合这一要求。
同时,前角度为0度也可以减小切削力,提高加工效率。
除了45度车刀角度参数外,还有一些其他的角度参数选择。
例如,30度车刀角度参数适用于加工较软的材料,如铝合金、黄铜等。
60度车刀角度参数适用于加工较硬的材料,如不锈钢、钛合金等。
不同的角度参数选择可以根据具体的加工材料和加工要求进行调整。
车刀的角度参数对于加工效果和加工质量有着重要的影响。
在选择角度参数时,需要根据具体的加工材料和加工要求进行调整,以达到最佳的加工效果。
45度车刀角度参数是一种常见的选择,适用于加工一些较硬的材料。
刀具角度选择

1、前角的选择
1)按加工性质选: 粗车时前角小 精车时前角大
2)按工件材料选: 塑性材料前角大 脆性材料前角小
3)按刀具材料选: 硬质合金前角小 高速钢前角大
2、后角的选择
1)按加工性质选: 粗车时后角小 精车时后角大
2)按工件材料选: 塑性材料后角大 脆性材料后角小
3)选负值(可避免刀尖受冲击,保护刀尖); 精车:选正值(使切屑向待加工表面流出)。
3、主偏角的选择
1)按工件形状选: 有直角台阶时主偏角大于等于90度;
2)按工件材料选: 材料硬(软)时选较小(大)主偏角;
3)按工件刚性选: 刚性好(差)时选较小(大)主偏角。
4、副偏角的选择 1)一般选60~80; 2)按工件表面粗糙度要求选: 要求高时选较小副偏角,但不 能太小,太小会加大与已加工 表面的摩擦,反而降低表面粗 糙度。
- 1、下载文档前请自行甄别文档内容的完整性,平台不提供额外的编辑、内容补充、找答案等附加服务。
- 2、"仅部分预览"的文档,不可在线预览部分如存在完整性等问题,可反馈申请退款(可完整预览的文档不适用该条件!)。
- 3、如文档侵犯您的权益,请联系客服反馈,我们会尽快为您处理(人工客服工作时间:9:00-18:30)。
车刀(指整体车刀与焊接车刀)用钝后重新刃磨是在砂轮机上刃磨的。
磨高速钢车刀用氧化铝砂轮(白色),磨硬质合金刀头用碳化硅砂轮(绿色)。
砂轮的特性由磨料、粒度、硬度、结合剂和组织5个因素决定。
{1)磨料,常用的磨料有氧化物系、碳化物系和高硬磨料系3种。
船上和工厂常用的是氧化铝砂轮和碳化硅砂轮。
氧化铝砂轮磨粒硬度低(HV2000-HV2400)、韧性大,适用刃磨高速钢车刀,其中白色的叫做白刚玉,灰褐色的叫做棕刚玉。
7D*a&v&m!B-d
碳化硅砂轮的磨粒硬度比氧化铝砂轮的磨粒高(Hv2800以上) 。
性脆而锋利,并且具有良好的导热性和导电性,适用刃磨硬质合金。
其中常用的是黑色和绿色的碳化硅砂轮。
而绿色的碳化硅砂轮更适合刃磨硬质合金车刀。
1L9V4t;l0E
2)粒度:粒度表示磨粒大小的程度。
以磨粒能通过每英寸长度上多少个孔眼的数字作为表示符号。
例如60粒度是指磨粒刚可通过每英寸长度上有60个孔眼的筛网。
因此,数字越大则表示磨粒越细。
粗磨车刀应选磨粒号数小的砂轮,精磨车刀应选号数大( 即磨粒细) 的砂轮。
船上常用的粒度为46 号—台0 号的中软或中硬的砂轮。
3)硬度:砂轮的硬度是反映磨粒在磨削力作用下,从砂轮表面上脱落的难易程度。
砂轮硬,即表面磨粒难以脱落;砂轮软,表示磨粒容易脱落。
砂轮的软硬和磨粒的软硬是两个不同的概念,必须区分清楚。
刃磨高速钢车刀和硬质合金车刀时应选软或中软的砂轮.
另外,在选择砂轮时还应考虑砂轮的结合剂和组织。
船上和工厂一般选用陶瓷结合剂(代号A)和中等组织的砂轮。
综上所述,我们应根据刀具材料正确选用砂轮。
刃磨高速钢车刀时,应选用粒度为46号到60号的软或中软的氧化铝砂轮。
刃磨硬质合金车刀时,应选用粒度为60号到80号的软或中软的碳化硅砂轮,两者不能搞错。
2.车刀刃磨的步骤如下:
外圆车刀刃磨的步骤
磨主后刀面,同时磨出主偏角及主后角,
磨副后刀面,同时磨出副偏角及副后角,
磨前面,同时磨出前角,
修磨各刀面及刀尖,
3.刃磨车刀的姿势及方法是:
人站立在砂轮机的侧面,以防砂轮碎裂时,碎片飞出伤人;
(2)两手握刀的距离放开,两肘夹紧腰部,以减小磨刀时的抖动
(3)磨刀时,车刀要放在砂轮的水平中心,刀尖略向上翘约3°~8°,车刀接触砂轮后应作左右方向水平移动。
当车刀离开砂轮时,车刀需向上抬起,以防磨好的刀刃被砂轮碰伤;(4)磨后刀面时,刀杆尾部向左偏过一个主偏角的角度;磨副后刀面时,刀杆尾部向右偏过一个副偏角的角度;
(5)修磨刀尖圆弧时,通常以左手握车刀前端为支点,用右手转动车刀的尾部。
4.磨刀安全知识
1)刃磨刀具前,应首先检查砂轮有无裂纹,砂轮轴螺母是否拧紧,并经试转后使用,以免砂轮碎裂或飞出伤人。
2)刃磨刀具不能用力过大,否则会使手打滑而触及砂轮面,造成工伤事故。
3)磨刀时应戴防护眼镜,以免砂砾和铁屑飞入眼中。
4)磨刀时不要正对砂轮的旋转方向站立,以防意外。
5)磨小刀头时,必须把小刀头装入刀杆上。
6)砂轮支架与砂轮的间隙不得大于3mm,入发现过大,应调其间隙。
一、切槽
切槽时用切槽刀。
切槽刀前为主切削刃,两测为副切削刃。
安装切槽刀,其主切削刃应平行于工件轴线,主刀刃与工件轴线同一高度。
切窄槽,主切削刃宽度等于槽宽,横向走刀一次将槽切出。
切宽槽,主切削刃宽度小于槽宽,分几次横向走刀,切出槽宽;切出槽宽后,纵向走刀精车槽底,切完宽槽。
二、切断
切断车刀和切槽车刀基本相同,但其主切削刃较窄,刀头较长。
在切断过程中,散热条件差,刀具刚度低,因此须减小切削用量,以防止机床和工件的振动。
切断操作注意事项:切断刀装夹时,不易伸出过长同时切断刀的中心线必须装的跟工件中心线垂直以保证两个副偏角对称;车断实心工件时,切断刀的主切削刃必须装的与工件中心等高,否则不能车到中心,而且容易崩刀,甚至折断车刀;切断刀的底平面应平整,以保证两个副后角对称. 切断时,工件一般用卡盘夹持。
切断处应靠近卡盘,以免引起工件振动。
2.安装切断刀时,刀尖要对准工件中心,刀杆与工件轴线垂直,刀杆不能伸出过长,但必须保证切断时刀架不碰卡盘。
3.切断时应降低切削速度,并应尽可能减小主轴和刀架滑动部分的配合间隙。
4. 手动进给要均匀。
快切断时,应放慢进给速度,以免刀头折断。
5.切断钢时,需加切削液。