11-05-0380-00-000n-tgn-sync-proposal-update-to-tgn-may-2005
柔性检查作用域套件-USB 产品说明书
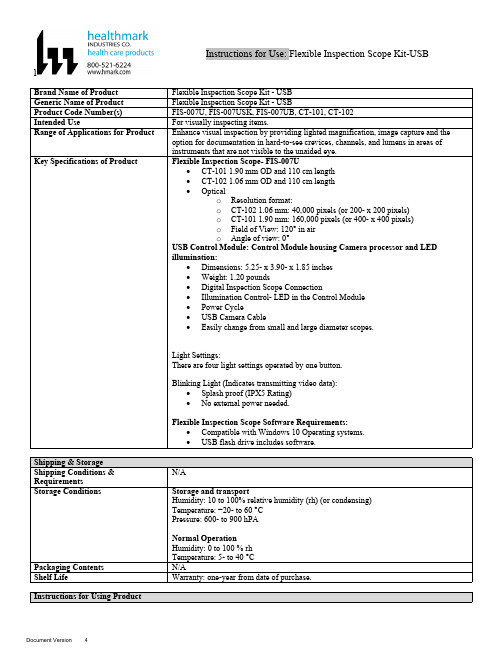
lInstructions for Use: Flexible Inspection Scope Kit-USB Brand Name of ProductFlexible Inspection Scope Kit - USB Generic Name of ProductFlexible Inspection Scope Kit - USB Product Code Number(s)FIS-007U, FIS-007USK, FIS-007UB, CT-101, CT-102Intended UseFor visually inspecting items.Range of Applications for ProductEnhance visual inspection by providing lighted magnification, image capture and the option for documentation in hard-to-see crevices, channels, and lumens in areas of instruments that are not visible to the unaided eye.Key Specifications of Product Flexible Inspection Scope- FIS-007U∙CT-101 1.90 mm OD and 110 cm length∙CT-102 1.06 mm OD and 110 cm length∙Opticalo Resolution format:o CT-102 1.06 mm: 40,000 pixels (or 200- x 200 pixels)o CT-101 1.90 mm: 160,000 pixels (or 400- x 400 pixels)o Field of View: 120° in airo Angle of view: 0°USB Control Module: Control Module housing Camera processor and LEDillumination:∙Dimensions: 5.25- x 3.90- x 1.85 inches∙Weight: 1.20 pounds ∙Digital Inspection Scope Connection∙Illumination Control- LED in the Control Module∙Power Cycle∙USB Camera Cable∙Easily change from small and large diameter scopes.Light Settings:There are four light settings operated by one button.Blinking Light (Indicates transmitting video data):∙Splash proof (IPX5 Rating)∙No external power needed.Flexible Inspection Scope Software Requirements:∙Compatible with Windows 10 Operating systems.∙USB flash drive includes software.Unpacking Flexible Inspection Scope:Carefully inspect for shipping damage. If there is any damage contact the shipping carrier and Heatlhmarkcustomer service 800-521-6224 immediately.USB Control Module: (Fig. 1).1.Digital Inspection Scope Connection 2.Illumination Control 3.Power Cycle B (Type C) on the right side of the boxFigure 1Flexible Inspection Scope™: (Fig. 2).∙CT-101 1.90 mm O.D. and 110 cm length ∙CT-102 1.06 mm O.D. and 110 cm lengthLarge1.90 mmSmall 1.06 mmFigure 2Flexible Inspection Scope™ Features3214Light/Illumination Settings: (Fig. 3).∙Five (5) light settingso Light on control indicats setting levelo Fifth setting is OFF∙Press light button to advance to next setting.∙Fifth setting turns the light OFF.Figure 3Power Cycle ButtonPress button to RESET camera (Fig. 4).Figure 41.Flexible Inspection Scope™ Plug (Fig. 5).Contains camera video connection as well as LED Light for illumination.1Figure 52.Flexible Working Length (Fig. 6).The portion of the Flexible Inspection Scope™ that is inserted into an item during visual inspection.The measuring scale markings on the Flexible Working Length are in centimeters (accuracy = ± 0.5 cm)2Figure 63.Distal Camera (Fig. 7).Distal portion of Flexible Inspection Scope™ that contains the camera lens3Figure 7SOFTWARE INSTALLATION:Note: This section is done only once when connecting the scope to the computer for the first time.∙System Requirements: MS Windows 10∙Install the Flexible Inspection Scope™ Software from the USB flash drive on a computer.Note: If you have any IT policies that may block this installation, please contact your IT team to give access to Healthmark scope viewer to install.1. Insert the USB Flash drive into your computer, and double click on the Healthmark Scope Viewer installer package to begin installation.2. The “Welcome to the Healthmark Scope Viewer Setup Wizard” screen pops up. Click on Next.3. Select the first tab Typical or setup type of your choice, click Next.4. Click Install and wait for installation to complete.5. Click Finish.STARTING SOFTWARE & CONNECTING SCOPE TO PC:(Fig 8).1.Open the Windows PC viewer software.2.Connect the Control Module to PC using USB Cable.3.Plug the Flexible Inspection Scope into the Control Module.4.In the viewer software, click Settings and Select USB Video Device, click on the desiredresolution, select the preferred Video Output Format, and then Click OK.5.Press the Power Cycle Button.Figure 86.Now you can start using the scope.Verifing OperationFollowing the steps listed below will ensure the proper use and performance of the Flexible Inspection Scope™. The Flexile Inspection Scope™ can be checked for normal operation by connecting it as described in the Startup section of this IFU.Normal operation includes:∙An image appearing on your computer monitor or HDMI Monitor.∙ A blinking light on Control Module near the Power Cycle button that indicates the image feed is transmitting.∙White light emitting from the distal end of the Digital Inspection Scope.∙An LED light on the control module top panel that indicates the light intensity of the device. Using SoftwareHealthmark Scope Viewer Software (Fig. 9).1.Capture button: Captures a Reference Image and saves it to the Reference Image folder.2.Main Image Window: Displays the image from the camera.3.Reference Image Window: Displays a reference image.4.Clear Button: Removes the image from the Reference image window.5.Open Reference Image button: Allows selection of a reference image from the Reference Imagefolder.6.Settings Button: Click to select the video camera and resolution settings.7.File Location Button: Click to change location where captured images are being saved.8.File Location Window: Shows the file path where captured images are being saved currently.9.Capture Image Button: Captures images and adds them to the File Location selected by the user(as shown in the File Location Window).10.Capture Video button: Click to record video. Click again to stop recording video.11.File Prefix: Type in text that you would like included in the file name of Captured Images.Figure 9Selecting Video Device or CameraFollow the directions below to select the video device or camera used to capture images using the Flexible Inspection Scope™ Viewer Software. (Fig. 10).1.Click Settings button in the lower left of the Scope Viewer software to display a list of videodevices or cameras being detected by your computer2.Select a device for capturing images using the Scope Viewera.The example below shows a webcam and USB Video Device in the Settings box. Select theUSB Video Device for the Flexible Inspection Scope™.b.You can also select your preferred Video Output Format from the dropdown box3.Click OK to view the selected Video Device.231Figure 10Capturing Still PicturesFollow the instructions for capturing still pictures from the Main Image Window.Select the Capture Image button. (Fig. 11).Figure 11Note: When an image is captured, “Image Captured” in red text will flash on the lower portion of the screen and a new file will appear in the Files Location.Capturing Video ImagesFollow the instructions below for capturing video from the Main Image Window.1.Select the Capture Video Button (Fig. 12).Figure 122.When the video is recording “Recording…” in red text will appear toward the bottom of thesoftware window.3.To stop recording, click Stop Capture. (Fig. 13).Figure 13Setting File PrefixFollowing the steps below allows you to create a file prefix that will appear after the underscore of image file names save to the File Location specified by the user.1.Click in the field next to File Prefix.2.Enter the characters that you would like to be included in the file name. (Fig 14).Figure 14Setting Location for Saved FilesFollowing the steps below allows you to set the file location of saved images using the Scope Viewer software.1.Click the File Location button.2.Select the file location you want to save captured images. (Fig 15).Figure 15Displaying Reference ImageThere are two ways to display a still image in the Reference Image Window on the Scope Viewer software.1.To display an image currently being displayed in the Main Image Window, click the Capture button. Note: The images will be saved in a file folder titled Reference Images in the designated File Location that the user specified in the File Location field. (Fig. 16).Figure 162.To display a saved image in the Reference Image Window from your File Location:a.Click the Open Reference Image button (Fig. 16 above).b.Select the file you want to display (Fig. 17 below).c.Click the OK Button, to display the image in the Reference Image Window. (Fig. 17).Figure 17Switching to a Different Flexible Inspection Scope™ on the Control Module:1.Press the Power button on the Control Module once.2.Disconnect the current Flexible Inspection Scope from the Control Module.3.Repeat the steps in the “STARTING SOFTWARE & CONNECTING SCOPE TO PC” procedure.Inserting Scope in ItemFigure 1Rotating Device to Avoid ObstacleFigure 2 Performing InspectionWipe down the Flexible Inspection Scope™ with a compatible wipe. Follow the manufacturer’s (Mfr.’s)Instructions for Use (IFU) for appropriate wipe usage. Click here to see the Chemical Compatibility Chart(PDF) for approved cleaning.The Flexible Inspection Scope™ is made of the same material as other common endoscopes. Any wipe,solution, or low temperature (≤ 60 °C [140 °F]) method intended for the reprocessing of endoscopes is likelycompatible with the Generation II Flexible Inspection Scope™ Catheters if used according to the productlabeling.Solutions Containing (Flexible Inspection Scope Only)Alcohol Ethoxylates Neutral or Near-Neutral pH DetergentsEnzymatic Cleaning Solutions Enzymatic DetergentsSodium Borated, Decahydrate Tetrapotassium PyrophosphateFlexible Inspection Scope™ has a fluid ingress protection rating of IPX7 (Waterproof) and can withstandimmersion in fluid up to one (1)-meter in depth for up to 30 minutes.Control Module USB has a fluid ingress protection rating of IPX5 (Water resistant) and can withstand asustained, low pressure water jet spray for up to three minutes.For Thorough Cleaning: CablesFollow the cleaning agent Mfr.’s IFU.1.Unplug and disconnect all components from the Control box prior to cleaning.2.Do not submerge or soak the cable for disinfection (cable is not waterproof).3.Wipe thoroughly with non-linting wipe moistened with facility approved neutral detergent. Use theappropriate brushes with detergent solution to remove any residues from areas that cannot bereached with the wipes.For Thorough Cleaning: Control Module1.Unplug and disconnect all components from the Control box prior to cleaning.2.Do not submerge or soak the cable for disinfection (Control Box is not waterproof).3.Wipe thoroughly with non-linting wipe moistened with facility approved neutral detergent. Use theappropriate brushes with detergent solution to remove any residues from areas that cannot bereached with the wipes.Note: Do NOT soak. Control Module and cables are not waterproof and should not be immersed.N/ACleaning –AutomatedDisinfection Control Module and CablesThese may be cleaned with alcohol based disinfectant wipes.Compatible agents (wipes and solutions) for disinfecting Flexible Inspection Scope™ and ControlModule:∙Hydrogen peroxide∙Isopropyl alcohol (IPA)∙Sodium hypochlorite (Bleach)∙Ortho-phenylphenol∙Quaternary ammonium.High-Level Disinfection (Flexible Inspection Scope™ Only)∙Select only disinfecting solutions listed in the compatible disinfecting methods.∙Follow all recommendations regarding health-hazards, dispensing, measuring, and storage from the Mfr. of cleaning and disinfecting agents.∙Soak the Flexible Inspection Scope™ in selected disinfecting solution per Mfr.’s IFU.∙Rinse the Flexible Inspection Scope™ with critical (sterile) water, again, following the disinfecting solutions Mfr.’s instructions.Reprocessing Chemical Compatibility Chart (PDF): Click here.。
ATE Corporation AS-05 Antenna Set 30 MHz to 18 GHz
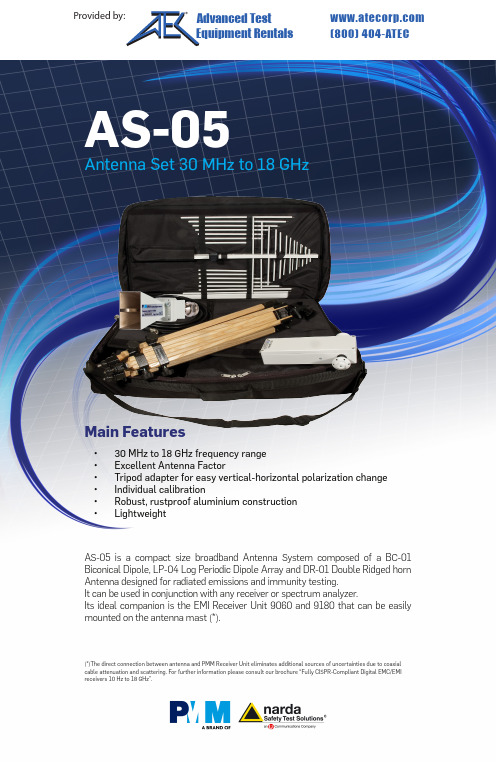
Main Features•30 MHz to 18 GHz frequency range •Excellent Antenna Factor•Tripod adapter for easy vertical-horizontal polarization change •Individual calibration•Robust, rustproof aluminium construction •LightweightAS-05 is a compact size broadband Antenna System composed of a BC-01 Biconical Dipole, LP-04 Log Periodic Dipole Array and DR-01 Double Ridged horn Antenna designed for radiated emissions and immunity testing. It can be used in conjunction with any receiver or spectrum analyzer.Its ideal companion is the EMI Receiver Unit 9060 and 9180 that can be easily mounted on the antenna mast (*).(*)The direct connection between antenna and PMM Receiver Unit eliminates additional sources of uncertainties due to coaxial cable attenuation and scattering. For further information please consult our brochure “Fully CISPR-Compliant Digital EMC/EMI receivers 10 Hz to 18 GHz”.Antenna Set 30 MHz to 18 GHzProvided by: (800)404-ATECAdvanced Test Equipment Rentals®Ordering Information:AS-05 antenna set 30 MHz to 18 GHz with individual calibration reports.AS-05/TC antenna set 30 MHz to 18 GHz with typical calibration reports.Includes: BC-01 biconical antenna; LP-04 Log-periodic antenna; DR-01Double-rideged antenna; TR-01 wooden tripod; RF cable, 6 GHz, N(m)-N(m), 5 m; Soft carrying case; Rigid carrying case (for DR-01), Operating manual; Calibration reports*.* Individual calibration reports are provided with AS-05.AS-05/TC does not include individual calibration but typical antenna factor.Optional accessories:Additional TR-01 Wooden tripod extensible 60 - 180 cm with antenna mounting adapter for fast horizontal to vertical polaritazion changing. Additional RF cable, 3 GHz, N(m)-N(m), 5 m.Sales Office:Via Leonardo da Vinci, 21/2320090 Segrate (Milano) - ITALY Phone: +39 02 2699871Fax: +39 02 26998700Headquarter:Via Benessea, 29/B17035 Cisano sul Neva (SV) - ITALY Phone: +39 0182 58641Fax: +39 0182 586400E-Mail:**************************Internet: www.narda-sts.itRelated ProductsReceiversAntennasCalibrations service• 7010/00: EMI receiver 150 kHz to 1 GHz • 7010/01: EMI receiver 9 kHz to 1 GHz • 7010/03: EMI receiver 9 kHz to 3 GHz • 9010: EMI receiver 10 Hz to 30 MHz • 9010F: EMI receiver 10 Hz to 30 MHz• 9010/03P: EMI receiver 10 Hz to 300 MHz • 9010/30P: EMI receiver 10 Hz to 3 GHz • 9010/60P: EMI receiver 10 Hz to 6 GHz • 9030: EMI Receiver 30 MHz to 3 GHz • 9060: EMI Receiver 30 MHz to 6 GHz •FR-4003: Field Receiver 9 kHz to 30 MHz• LP-02: Log Periodic Antenna 200 MHz to 3 GHz • LP-03: Log Periodic Antenna 800 MHz to 6 GHz • TR-01: Antenna Tripod• VDH-01: Van der Hoofden test-head 20 kHz to 10 MHz • Antenna Set AS-02 (BC01+LP02+TR01)• Antenna Set AS-03 (BC01+LP02+LP03+TR01) • Antenna Set AS-04 (BC01+LP04+TR01)• RA01: Rod Antenna 9 kHz to 30 MHz• RA01-HV: Rod Antenna 150 kHz to 30 MHz •RA01-MIL: Rod Antenna 9 kHz to 30 MHz• Ansi 63,5 Antenna Factor • SAE ARP 958-D• Free-Space Antenna FactorSPECIFICATIONSFrequency range GainAntenna factor Max input power Connector Dimensions (L x H x W)Weight Colour Impedance ConstructionBC-0130 to 200 MHz -15 +2 dBi typical 8 to 14 dB/m typical 100 W N-female 65 x 65 x 137 cm1,8 kg RAL 703550 Ω nominal AluminiumA S 05-F E N -60801 - S p e c i fi c a t i o n s s u b j e c t t o c h a n g e s w i t h o u t p r i o r n o t i c eAS-05Antenna set 30 MHz to 18 GHzLP-04200 MHz to 6 GHz 6 dBi typical 12 to 40 dB/m typical100 W N-female 78 x 10 x 75 cm 1,1 kg RAL 703550 Ω nominal AluminiumDR-016 to 18 GHz 9 to 16 dBi typical 36 to 41 dB/m typical 150 W N-female 55 x 44 x 177 mm 0,25 kg RAL 703550 Ω nominal AluminiumBC-01 - Antenna Factor 106141822A F (d B /m )3090150210MHz MHz MHz MHz LP-04 - Antenna Factor 155253545A F (d B /m )1356GHzGHz GHz GHz DR-01 - Antenna Factor3634384042A F (d B /m )6101418GHzGHz GHz GHz。
北大西洋工业集团Model 8500角度位置指示器说明书
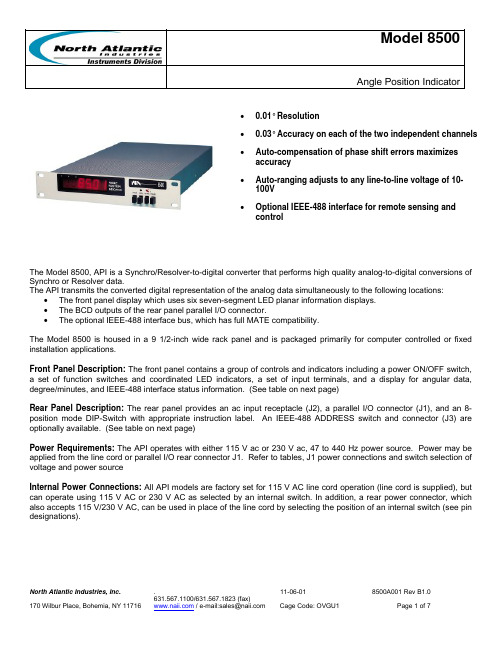
Model 8500Angle Position Indicator• 0.01° Resolution• 0.03° Accuracy on each of the two independent channels • Auto-compensation of phase shift errors maximizes accuracy• Auto-ranging adjusts to any line-to-line voltage of 10-100V•Optional IEEE-488 interface for remote sensing and controlThe Model 8500, API is a Synchro/Resolver-to-digital converter that performs high quality analog-to-digital conversions of Synchro or Resolver data.The API transmits the converted digital representation of the analog data simultaneously to the following locations:• The front panel display which uses six seven-segment LED planar information displays. • The BCD outputs of the rear panel parallel I/O connector.• The optional IEEE-488 interface bus, which has full MATE compatibility.The Model 8500 is housed in a 9 1/2-inch wide rack panel and is packaged primarily for computer controlled or fixed installation applications.Front Panel Description: The front panel contains a group of controls and indicators including a power ON/OFF switch, a set of function switches and coordinated LED indicators, a set of input terminals, and a display for angular data, degree/minutes, and IEEE-488 interface status information. (See table on next page)Rear Panel Description: The rear panel provides an ac input receptacle (J2), a parallel I/O connector (J1), and an 8-position mode DIP-Switch with appropriate instruction label. An IEEE-488 ADDRESS switch and connector (J3) are optionally available. (See table on next page)Power Requirements: The API operates with either 115 V ac or 230 V ac, 47 to 440 Hz power source. Power may be applied from the line cord or parallel I/O rear connector J1. Refer to tables, J1 power connections and switch selection of voltage and power sourceInternal Power Connections: All API models are factory set for 115 V AC line cord operation (line cord is supplied), but can operate using 115 V AC or 230 V AC as selected by an internal switch. In addition, a rear power connector, which also accepts 115 V/230 V AC, can be used in place of the line cord by selecting the position of an internal switch (see pin designations).SpecificationsItem Specification Input SpecificationsInputchannels Signalinputs 2 (selectable)Automatic line-to-line tracking, Synchro orResolver.10 to 100 V L-L, 47-440 Hz (F2, option 2) or 360 to 1200 Hz (F2, option 4).Signal input impedance Reference levels 250 k ohms (minimum)1 to 115 V rms, all frequency ranges.(All Synchro or Resolver data must be derived from this reference.)Reference input impedance Power requirements 100 k ohms (minimum) 115/230 V rms_+ 10% 47 to 440 Hz, 20 VAData Freeze DF DFFreeze Track+5 V 0 V or open0 V +5 V or open(Display and output frozen; internalcircuitry continues to track signal.)Channel Remote Program 0 V or GND=CH1, +5 V or OPEN=CH2 Output SpecificationsDisplayReadoutresolution Digital output dataDigital output levelLogic1LogicConverterBusy 5 decimal digits, 0.56-inch high LED indicators for channel and remote0.01 degree or 1 minute (F2, option 2 or 4) 5 decades of BCD digits (1,2,4,8 code)+3.9 V minimum, 4 standard LS TTL loads 0.1 V maximumTTL compatible (pulses are present when converter is busy)Performance SpecificationsAngular Accuracy 0.03 degreesNorth Atlantic Industries, Inc. . 11-06-01SpecificationsItem SpecificationAngular Resolution 0.01 degreesAngular Range 0 to 359.99 degrees or 0 to 359 degrees 59minutes; or, -179.99 to +180 degrees or -179 degrees 59minutes to +180 degrees 00 minutes (F2=2 or 4) Auto phase correction Automatically corrects for signal phase shift up to_+ 80degrees.Trackingspeed Selectable:Lo speed = 180 degrees/sec with no tracking error, 47-440 Hz (F2, option 2)Hi speed = 1800 degrees/sec with no tracking error, 360-1200 Hz (F2, option 4)Settling time Dependent on tracking speed selected and frequency range:Less than 1.5 seconds for 180 degrees step change, Lotracking speed and 47-440 Hz (F2, option 2).Less than 1.0 seconds for 180 degrees step change, Hitracking speed and 360-1200 Hz (F2, option 4). Velocity output:HI Tracking rate 2.85 mV dc/degree/second (nominal)LO Tracking rate 28.5 mV dc/degree/second (nominal)Operating modeFaultindications Lamptest Track onlyNo reference present: all 8s displayedNo Synchro or Resolver connected or input line-to-line voltage is too low: display is blanked.Over velocity: "o" displayed to left of angle displayOptional IEEE-488 MATE relay closureDisconnect reference to display all 8s or apply logic "0" to J1-38.Mechanical Specifications Front Panel Color (See figure 2-1 Outline and Dimension Drawing, API Model 8500)Semi-gloss gray, 26440 per Fed-Std-595 window area black #27038 per Fed-Std-595Markings Semi-gloss black enamel 27038 per Fed-Std-595; PantoneWarm Red U (warnings and logo only); White #27875 perFed-Std-595Size 9.5" W x 1.75" H x 12" DWeight 4 lbs. (maximum)Operating Temperature 0-50o CNorth Atlantic Industries, Inc. . 11-06-01ORDERING INFORMATIONFeatures and Options:To identify the Model 8500 options, a three-digit number is assigned in accordance with table below.For example, the Standard Model 8500 with half rack mounting (1), 47 Hz to 440 Hz frequency selectable display (2), and parallel interface (1) would have an option number of F121.8500-F 1 2 1F1F2F3No. Feature OptionsF1 Configuration Options 1. Panel mount, half rack2. Bench use (includes front terminals and stand)3. Panel mount, full rackF2 Frequency and Display 2. 47-440 Hz, selectable display4. 360 Hz to 1200 Hz, selectable displayF3 Interface 1.Parallelonly2. Parallel and IEEEAccessories:The API can be ordered with mounting adapters for mounting either one or two units in a standard 19-inch equipment rack. The table below describes full rack and tandem full rack mounting accessories:Type of Mount Description NAI P/N Full Rack Mounting Mounts one unit in 19-inch rack 300697Tandem Full Rack Mounting Mounts two units side by side in 19-inchrack300698The parallel I/O 50-pin mating connector, J1 is supplied by North Atlantic Industries (NAI P/N 783718) but operator must make cable assembly. It consists of the following parts:Description AMP P/N QtyShellClamp Retainer Pins 205211-1205732-1205980-166569-311250North Atlantic Industries, Inc. . 11-06-01Front Panel Controls and IndicatorsControl/Indicator FunctionPWR push button Alternate Acting Switch. Turns power on and off (push button in: power on;push button out: power off).REM push button Alternate Acting Switch. Selects remote operation of the API (push buttonin: Remote; push button out: local).CHAN push button Alternate Acting Switch. Selects input channel (push button in: CH 1; pushbutton out: CH 2).HOLD push button Momentary Switch. Push in to freeze display and output data.REM LED When ON, indicates the API is in remote operation.CHAN LED When on, indicates Channel 1 is selected.When off, indicates Channel 2 is selected.CAUTIONTerminals S1, S2, S3, S4, and REF HI and LO are directlyconnected to the transformer inputs and must not be used ifJ1 inputs are used. Refer to table 2-1, J1 pin connections.S1,S2,S3,S4Accepts Synchro or Resolver input signals (bench units only).TerminalsAccepts reference input signal (bench units only).REF HI and LOTerminalsRear Panel DescriptionControl/Indicator FunctionInput Power Receptacle Power cable connector (J2) for 115 V ac or 230 V ac input.ADDRESS Switches ADDRESS DIP switches set unit address for IEEE bus.Parallel I/O Connector Provides API interconnection with external systems, powersources, etc. Refer to table 2-1.MODES Switch 8-position DIP switch which controls selectable modes. Referto paragraph 3-3.3.IEEE-488 Connector (optional) Connects IEEE-488 standard I/O bus to unit.North Atlantic Industries, Inc. . 11-06-01Mode Switch SW2Switch NumberSwitchSignal NameSwitch Position1 01 CH1 SYN Channel 1 in Resolver mode or forremote control of Channel 1.Channel 1 in Synchro mode.2 CH2 SYN Channel 2 in Resolver mode or forremote control of Channel 2.Channel 2 in Synchro mode.3 INT/EXTREF Selects auto phase correctedinternal reference.Selects external reference.4 Bandwidth(H/L) Selects low bandwidth (trackingspeed) or remote control of trackingspeed.Selects high bandwidth (trackingspeed).5 Deg/Min Selects 2 LSDs of display in minutesof arc. Selects 2 LSDs of display in hundredths of degrees.6 Display(U/B) Unipolar display.(0o to 359.99o) or remote control ofdisplay.Bipolar display_+ 180o.7 Sign Sign bit equals plus sign (+) in F2=2or 4 units. Sign bit equals minus sign (-) in F2=2 or 4 units.8 P/I Selects IEEE-488 interface forremote control Selects parallel interface for remote control.North Atlantic Industries, Inc. . 11-06-01J1 Pin DesignationsPin Function1 Power input Hi (internal switch enables pins 1 & 2; disables IEC power connector2 Power input loground3 Chassisground4 Digital(Channel 1)5 S16 S2 “ “7 S3 “ “8 S4 “ “9 R1 “ “10 R2 “ “Busy11 Converter12 .04° or 4’13 .01° or 1’14 .8° or not used15 .2° or 20’16 4°17 1°18 Channel 2 Synchro jumper (connect to pin 35 for channel 2 Synchro operation)19 NC20 Tracking HI/LO input21 S1 (Channel 2)22 S2 “ “23 S3 “ “24 S4 “ “25 R1 “ “26 R2 “ “27 Data freeze (DF)28 .02° or 2’29 .08° or 8’30 .1° or 10’31 .4° or 40’32 2°33 8°34 Channel 1 Synchro jumper (connect to pin 35 for channel 1 Synchro operation)35 Synchro jumper common36 Fault 1 (not used)37 Fault 2 (not used)38 Lamp Test39 Unipolar/Bipolar for F2=2 or 4(Built in Test Equipment)output40 BITE(analog)output41 VelocityFreeze(DF)42 Data(0=CH1, 1=CH2)Program43 Remotespare44 NC45 20°BCD Outputs46 40° “ “47 80° “ “48 10° “ “49 100° “ “50 200° or sign bit in bipolar “ “North Atlantic Industries, Inc. . 11-06-01。
AlphaScreen SureFire STAT3 (p-Tyr705) Assay Kits产品
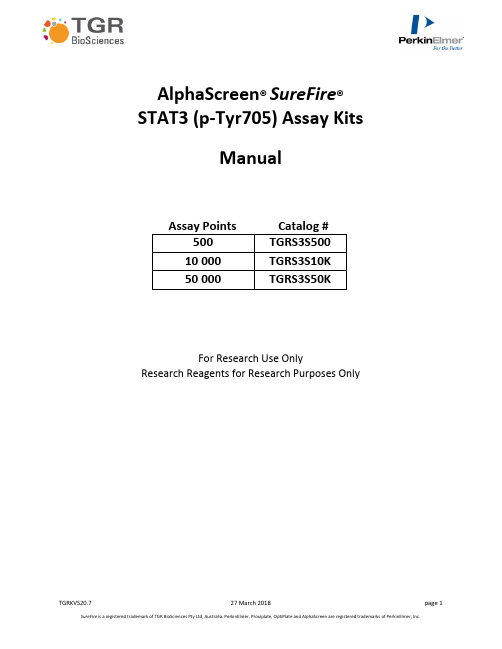
AlphaScreen®SureFire®STAT3 (p-Tyr705) Assay KitsManualAssay Points Catalog #500TGRS3S50010 000TGRS3S10K50 000TGRS3S50KFor Research Use OnlyResearch Reagents for Research Purposes OnlyGeneral Information on the AlphaScreen® SureFire® p-STAT3 assayThe AlphaScreen® SureFire® p-STAT3 assay is used to measure the phosphorylation of endogenous STAT3αand STAT3βin cellular lysates. The assay is an ideal system for the screening of both modulators of receptor activation (e.g. agonists and antagonists) as well as agents acting intracellularly, such as small molecule inhibitors of upstream events. The assay will measure STAT3 phosphorylation by either cloned or endogenous receptors, and can be applied to primary cells.This assay eliminates the need for laborious techniques, such as Western blotting or conventional ELISA. It is a homogeneous assay, in that no sample washing steps are required, which allows for minimal handling, short assay times, and robotic operation if desired. The assay utilizes the bead-based Alpha Technology, and requires an Alpha Technology-compatible plate reader.Alpha Technology AlphaScreen® SureFire® Assay PrincipleAlphaScreen® SureFire® technology allows the detection of phosphorylated proteins in cellular lysates in a highly sensitive, quantitative and user friendly assay. In these assays, sandwich antibody complexes, which are only formed in the presence of analyte, are captured by AlphaScreen donor and acceptor beads, bringing them into close proximity. The excitation of the donor bead provokes the release of singlet oxygen molecules that triggers a cascade of energy transfer in the Acceptor beads, resulting in the emission of light at 520-620nm.Kit-Specificity informationThis assay kit contains antibodies which recognize the phospho-Tyr705-epitope, and a distal epitope on STAT3αand STAT3β. The proteins detected by this kit correspond to GenBank Accessions NP_644805 and NP_998827.These antibodies recognize STAT3 of human, mouse and rat origin. Other species should be tested on a case-by-case basis.Kit ContentsKit Size500 points10,000 points50,000 pointsLysis buffer (5X) 1 x 10 mL 4 x 60 mL 3 x 400 mL Activation buffer 1 x 2 mL 1 x 60 mL 1 x 300 mL Reaction buffer 1 x 2.6 mL 1 x 45 mL 1 x 225 mL Dilution buffer 1 x 1.5 mL1 x 25 mL2 x 60 mLPositive Control Lysate 1 tube to be re-dissolved in 250 µL H 2O Negative Control Lysate1 tube to be re-dissolved in 250 µL H 2OStorage conditions upon receiptThe kit buffers e.g. 5X Lysis buffer, Activation buffer and Reaction buffer should be stored at 4°C. DO NOT freeze the kit buffers – the Reaction buffer contains antibodies and freeze/thaw cycles can lead to a loss of activity.Materials Required But Not ProvidedThe AlphaScreen SureFire assay kits are optimized to work with AlphaScreen Protein A general IgG detection beads. These are available separately from PerkinElmer. The AlphaScreen Protein A general IgG detection kits contain a biotinylated rabbit IgG control, which can be used to test the instrument settings and bead performance.ItemSuggested source Catalog # Size Protein A general IgG detection kit(contains the Acceptor and Donor Beads) PerkinElmer Inc. 6760617C 6760617M 6760617R 500 pt 10,000 pt 50,000 pt Proxiplate™-384 Plus, white, shallow well assay platePerkinElmer Inc. 6008280 6008289 50/box 200/box Optiplate™-384 Plus, white, assay plate PerkinElmer Inc. 6007290 6007299 50/box 200/box TopSeal-A 384, clear adhesive sealing film PerkinElmer Inc. 6050185100/boxEnvision® or Enspire® Alpha-readerPerkinElmer Inc.--Buffer preparation and subsequent storage conditions5X Lysis bufferStore 5X Lysis buffer at 4°C. For assay, dilute 5-fold in water immediately prior to use. Discard unused buffer. Activation bufferPrecipitation will occur during storage 4°C. To re-dissolve, warm to 37°C and mix. Alternatively, Activation buffer can be stored at room temperature with no loss in activity.Reaction buffer*Keep on ice while in use. Do not freeze.Once diluted discard unused reaction buffer. AlphaScreen ® Protein A IgG KitStore at 4°C in the dark.Acceptor Mix(Reaction buffer + Activation buffer +AlphaScreen ® Acceptor beads)Immediately prior to use, dilute Activation buffer B 5-fold in Reaction buffer (e.g. take 98 μL Activation buffer and dilute in 392 μL Reaction buffer).Dilute Acceptor beads 50-fold in Acceptor mix (e.g. add10 μL Acceptor beads to 490 μL of premixed Reactionbuffer + Activation buffer).The Acceptor mix should be used immediately for best results. Excess mix should be discarded.Donor Mix**(Dilution buffer + AlphaScreen ®Donor beads)Immediately prior to use, dilute Donor beads 20-fold in Dilution buffer (e.g. add 10 μL Don or beads to 190 μLDilution buffer).The Donor mix should be used immediately for best results. Excess mix should be discarded.Assay Control lysateAfter reconstitution in 250 μL water, lysates should be frozen at -20°C in single use aliquots and used within 1 month.* Do not vortex the Reaction buffer, as vigorous mixing can damage some antibodies. ** Prepare and use Donor Mix under low-light conditions.Control Lysate informationControl lysates are prepared from A431 cells (ATCC #CRL-1555) at a concentration of approximately 1 mg/mL. The controls are supplied lyophilized, and should be reconstituted in either dd H 2O or MilliQ® H 2O. Once reconstituted, lysates should be stored frozen in single use aliquots.Negative Lysate: Prepared from A431 cells treated with EGF receptor inhibitor (2 μM AG1478)for 2 hours prior to lysis.Positive Lysate: Prepared from A431 cells treated with 200 ng/mL EGF for 10 minutes.p-STAT3 AlphaScreen® SureFire® Assay ProtocolsA. 2-Plate Assay - assay protocol for adherent cellsCell Seeding1. Seed cell s (200 μL of cells for 96 well plates, 50 μL for 384 well plates) in tissue culture plates. Incubate at 37°C overnight in serum-containing media.Cell Treatment2. Remove culture media, and stimulate the cells with 50 μL agonists prepared in serum-free media (25 µL for 384-well plates). (If testing antagonists, prior to stimulation remove culture medium and replace with 50 μL serum-free media containing antagonists (25 µL for 384-well plates)). Return cells to 37°C incubator for desired time. 1 hour is often sufficient for signal transduction inhibitors, and 5 minutes for receptor agonists.Note: Peptidic agonists and antagonists can often stick to plastic surfaces. To minimize this effect, dilute in serum-free media containing a suitable carrier protein (e.g. 0.1% IgG free BSA - Jackson Immunoresearch Cat #001-000-161).Lysate Preparation5. To lyse cells, remove medium from wells, and add freshly prepared 1X Lysis Buffer(50-100 μL fora 96 well plate, 25 μL for a 384 well plate). Agitate on a plate shaker (~350 rpm) for 10 minutes at room temperature.6. Take 4 μL of the lysate and transfer to a 384-well Proxiplate™ for assay. (Add 4 μL Control lysates to separate wells if required).SureFire Assay7. Add 5 μL of Acceptor Mix to wells. Seal plate with Topseal-A adhesive film, and incubate for 2 hours at room temperature.8. Add 2 μL of Donor Mix to wells under subdued light. Seal plate with Topseal-A adhesive film, and cover plate with foil. Incubate for 2 hours at room temperature.Note: Longer incubation may give greater sensitivity. Plates can be incubated overnight if required.9. Read plate on an Alpha Technology-compatible plate reader, using standard AlphaScreen settings.B. 1 Plate Assay - assay protocol for non-adherent cells, and for high-throughput applications. Note: the larger volumes required using this assay will result in achieving less assay points per kit. Cell Seeding1. Harvest cells by centrifugation, and re-suspend cells in HBSS at a suitable cell density. We recommend 107cells/mL as a starting point. Seed 4 μL of cells/well into a 384-well culture plate.2. If using test agents/inhibitors, add 2 μL/well of 4X inhibitors prepared in HBSS.Note: Peptidic agonists and antagonists can often stick to plastic surfaces. To minimize this effect, dilute in serum-free media containing a suitable carrier protein (e.g. 0.1% IgG free BSA - Jackson Immunoresearch Cat #001-000-161).3. Return cells to incubator at 37°C for 1-2 hours.Cell Treatment4. Stimulate cells with agonists by addition of 2 μL/well of 4X agonist stock in HBSS containing 0.1% BSA. The final volume in the wells should be 8 μL. (if no antagonists were used in step 2, stimulate the cells with 4 μL/well of 2X agonist, to give a final volume in the wells of 8 μL.)Lysate Preparation5. To lyse the cells, add 2 μL/well 5X Lysis buffer.(Add 10 μL control lysates to separate wells if required)SureFire Assay6. Add 8 μL of Acceptor Mix to wells. Seal plate with Topseal-A adhesive film, and incubate for 2 hours at room temperature.7. Add 3 μL of Donor Mix to wells under subdued light. Seal plate with Topseal-A adhesive film, and cover plate with foil. Incubate for 2 hours at room temperature.Note: Longer incubation may give greater sensitivity. Plates can be incubated overnight if required.8. Read plate on an Alpha Technology-compatible plate reader, using standard AlphaScreen settings.Representative DataWestern blot analysis (35 μg protein/lane) of phospho-STAT3 in lysates generated from either unstimulated (-) or IL6-stimulated (+) THP-1 cells, or the AlphaScreen SureFire assay (3.5 μg protein/well), using the standard 2-plate protocol.THP-1 cells (ATCC Cat# TIB-202) were harvested from growing flasks, resuspended in HBSS, and seeded at 25K cells/well in 384-well microplates. Cells were incubated for 2 hours at 37°C, and stimulated with IL-6 for 10 minutes at room temperature (left) or pre-treated with JAK inhibitor I for 2 hours at 37°C, then stimulated with IL-6 (right). Cells were lysed with 5X Lysis buffer with shaking at RT for 10 minutes, and analyzed for phospho-STAT3 using the standard 1-plate protocol.Frequently Asked Questions & TroubleshootingFor comprehensive information on assay optimization and troubleshooting, please refer to the following resources:▪ Guide to AlphaScreen® SureFire ® assay optimization ▪ AlphaScreen® SureFire ® user guideTo download these resources, and other related technical information, visit /category/alpha-surefire-kitsFor general information on AlphaScreen® SureFire ® assays, visit - +Customer CareTo contact the customer care team, please visit /ServiceCallFor more information regarding related AlphaScreen® SureFire® products andprotocols refer to:PerkinElmer web site: TGR BioSciences website: FOR RESEARCH USE ONLY. NOT FOR USE IN DIAGNOSTIC PROCEDURES.This product is not for resale or distribution except by authorized distributors.LIMITED WARRANTY: PerkinElmer, Inc. warrants that, at the time of shipment, the products sold by it are free from defects in material and workmanship and conform to specifications which accompany the product. PerkinElmer Inc. makes no other warranty, express or implied with respect to the products, including any warranty of merchantability or fitness for any particular purpose. Notification of any breach of warranty must be made within 60 days of receipt unless provided in writing by PerkinElmer Inc. No claim shall be honored if the customer fails to notify PerkinElmer Inc. within the period specified. The sole and exclusive remedy of the customer for any liability of PerkinElmer Inc. of any kind including liability based upon warranty (express or implied whether contained herein or elsewhere), strict liability contract or otherwise is limited to the replacement of the goods or the refunds of the invoice price of goods. PerkinElmer Inc. shall not in any case be liable for special, incidental or consequential damages of any kind.。
DrayTek VigorAP 960C 802.11ax Ceiling-mount Access
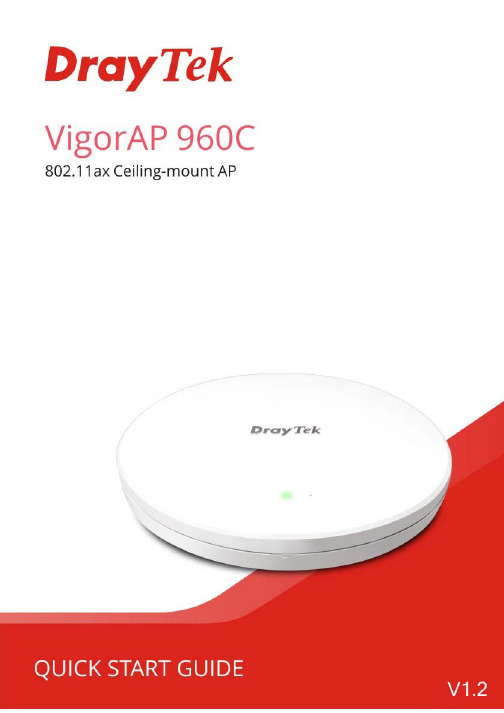
VigorAP 960C802.11ax Ceiling-mount AccessPointQuick Start GuideVersion: 1.2Firmware Version: V1.4.5(For future update, please visit DrayTek web site)Date: Dec. 21, 2022Intellectual Property Rights (IPR) InformationCopyrights © All rights reserved. This publication contains information that is protected by copyright. No part may be reproduced, transmitted, transcribed, stored ina retrieval system, or translated into any language without written permissionfrom the copyright holders.Trademarks The following trademarks are used in this document:●Microsoft is a registered trademark of Microsoft Corp.●Windows, Windows 8, 10, 11 and Explorer are trademarks of MicrosoftCorp.●Apple and Mac OS are registered trademarks of Apple Inc.●Other products may be trademarks or registered trademarks of theirrespective manufacturers.Safety Instructions and ApprovalSafety Instructions ●Read the installation guide thoroughly before you set up the device.●The device is a complicated electronic unit that may be repaired only beauthorized and qualified personnel. Do not try to open or repair thedevice yourself.●Do not place the device in a damp or humid place, e.g. a bathroom.●Do not stack the devices.●The device should be used in a sheltered area, within a temperaturerange of 0 to +40 Celsius.●Do not expose the device to direct sunlight or other heat sources. Thehousing and electronic components may be damaged by direct sunlight or heat sources.●Do not deploy the cable for LAN connection outdoor to preventelectronic shock hazards.●Keep the package out of reach of children.●When you want to dispose of the device, please follow local regulationson conservation of the environment.Warranty We warrant to the original end user (purchaser) that the device will be free from any defects in workmanship or materials for a period of two (2) yearsfrom the date of purchase from the dealer. Please keep your purchase receiptin a safe place as it serves as proof of date of purchase. During the warrantyperiod, and upon proof of purchase, should the product have indications offailure due to faulty workmanship and/or materials, we will, at our discretion,repair or replace the defective products or components, without charge foreither parts or labor, to whatever extent we deem necessary tore-store theproduct to proper operating condition. Any replacement will consist of a newor re-manufactured functionally equivalent product of equal value, and willbe offered solely at our discretion. This warranty will not apply if the productis modified, misused, tampered with, damaged by an act of God, or subjectedto abnormal working conditions. The warranty does not cover the bundled orlicensed software of other vendors. Defects which do not significantly affectthe usability of the product will not be covered by the warranty. We reservethe right to revise the manual and online documentation and to make changesfrom time to time in the contents hereof without obligation to notify anyperson of such revision or changes.Declaration of ConformityHereby, DrayTek Corporation declares that the radio equipment type VigorAP 960C is in compliance with Directive 2014/53/EU.The full text of the EU declaration of conformity is available at the following internet address: https:///VigorAP 960C/Document/CE/Manufacturer: DrayTek Corp.Address: No.26, Fushing Rd., Hukou, Hsinchu Industrial Park, Hsinchu 303, Taiwan Product: VigorAP 960CFrequency Information for Europe area:2.4GHz WLAN 2400MHz - 2483MHz, max. TX power: 19.95dBm5GHz WLAN 5150MHz - 5350MHz, max. TX power: 22.84dBm5470MHz - 5725MHz, max. TX power: 28.14dBmRequirements in AT/BE/BG/CZ/DZ/DK/EE/FR/DE/IS/IE/IT/EL/ES/CY/LV/LI/LT/ LU/HU/MT/NL/NO/PL/PT/RO/SI/SK/TR/FI/SE/CH/HR.5150MHz~5350MHz is for indoor use only.This product is designed for 2.4GHz and 5GHz WLAN network throughout the EC region.Declaration of ConformityHereby, DrayTek Corporation declares that the radio equipment type VigorAP 960C is in compliance with Regulation SI 2017 No. 1206.Manufacturer: DrayTek Corp.Address: No.26, Fushing Rd., Hukou, Hsinchu Industrial Park, Hsinchu 303, Taiwan Product: VigorAP 960CImporter: CMS Distribution Ltd: Bohola Road, Kiltimagh, Co Mayo, IrelandFrequency Information for UK area:2.4GHz WLAN 2400MHz - 2483MHz, max. TX power: 19.95dBm5GHz WLAN 5150MHz - 5350MHz, max. TX power: 22.84dBm5470MHz - 5725MHz, max. TX power: 28.14dBmRequirements in UK. 5150MHz~5350MHz is for indoor use only.This product is designed 2.4GHz and 5GHz WLAN network use in the UK & Ireland.Regulatory InformationFederal Communication Commission Interference StatementThis equipment has been tested and found to comply with the limits for a Class B digital device, pursuant to Part 15 of the FCC Rules. These limits are designed to provide reasonable protection against harmful interference in a residential installation. This equipment generates, uses and can radiate radio frequency energy and, if not installed and used in accordance with the instructions, may cause harmful interference to radio communications. However, there is no guarantee that interference will not occur in a particular installation. If this equipment does cause harmfulinterference to radio or television reception, which can be determined by turning the equipment off and on, the user is encouraged to try to correct the interference by one of the following measures:● Reorient or relocate the receiving antenna.● Increase the separation between the equipment and receiver.● Connect the equipment into an outlet on a circuit different from that to which the receiver is connected.●Consult the dealer or an experienced radio/TV technician for help.This device complies with Part 15 of the FCC Rules. Operation is subject to the following two conditions:(1) This device may not cause harmful interference, and(2) This device may accept any interference received, including interference that may cause undesired operation.Company nameABP International Inc.Address 13988 Diplomat Drive Suite 180 Dallas TX 75234 ZIP Code 75234E-mail*******************USA Local Representative Contact PersonMr. Robert MesserTel. 19728311600Caution ● Any changes or modifications not expressly approved by the grantee of this device could void the user's authority to operate the equipment.● Any changes or modifications not expressly approved by the party responsible for compliance could void the user's authority to operate this equipment.● This transmitter must not be co-located or operating in conjunction with any other antenna or transmitter.●Radiation Exposure Statement: This equipment complies with FCC radiation exposure limits set forth for an uncontrolled environment. This equipment should be installed and operated with minimum distance 20cm between the radiator & your body.External Power Supply ErP Information1 2A Manufacturer DVE DVEB Address No.5, Baogao Rd, XindianDist, New Taipei City(23144), TaiwanNo.5, Baogao Rd, XindianDist, New Taipei City(23144), Taiwan DSA-12PF09-12 FUK DSA-18PFR-12 FUKC Model identifierDSA-12PF09-12 FEU DSA-18PFR-12 FEU D Input voltage 100~240V 100~240VInput AC frequency 50/60Hz 50/60HzEOutput voltage DC 12.0V 12.0VF Output current 1.0A 1.5AG Output power 12.0W 18.0WH Average active efficiency 83.3% 85.5%I Efficiency at low load 10% 80.8% 83.7%J No-load power consumption 0.06W 0.07W*The external power supply used for each product will be model dependent.For more update, please visit .T a b l e o f C o n t e n t s1. Package Content (1)2. Panel Explanation (2)3. Installation (3)3.1 Ceiling-mount Installation (Wooden Ceiling) (3)3.2 Ceiling-mount Installation (Plasterboard Ceiling) (4)3.3 Suspended Ceiling (Lightweight Steel Frame) Installation (5)3.4 Wall-Mounted Installation (7)4. Connection and Configuration (8)4.1 Notifications for Hardware Connection (8)4.2 Connect to a Vigor Router using AP Management (9)4.3 Web Configurations (10)5. Customer Service (14)Be a Registered Owner (14)Firmware & Tools Updates (14)1.P a c k a g e C o n t e n tTake a look at the package content. If there is anything missed or damaged, please contact DrayTek or dealer immediately.VigorAP 960C Main Unit Ceiling mount bracket & Quick StartGuideT-Rail Mounting Kits(Used for suspended ceiling)Fixings and Screws(for ceiling mounting) RJ-45 Cable (Ethernet)Screw set (for wall mounting) The type of the power adapter depends on the country that the AP will be installed:UK-type Power Adapter EU-type Power AdapterUSA/Taiwan-type Power Adapter AU/NZ-type Power AdapterThe maximum power consumption is 11 Watt.2. P a n e l E x p l a n a t i o nLED Status ExplanationOn The system is in boot-loader mode. OffThe system is not ready or fails.Blue LEDBlinking The system is in AP mode and work normally.Green LED BlinkingThe system is in Mesh mode or Range Extender modeand works normally.Orange LED Blinking The system is in TFTP mode. Off Off VigorAP is turned off or not functioning. Interface Explanation Ethernet Port Connects to LAN or router.Supports PoE power & Gigabit (1000BaseT).Power Jack (DC IN) Connecter for a power adapter. Hole Explanation Factory Reset Restores the unit back to factory default settings.To use, insert a small item such as an unbent paperclip into the hole. You will feel the button inside depress gently. Hold it for 5 seconds. The VigorAP will restart with the factory default configuration and the LED will blink blue.Note● For the sake of security, make the accessory kit away fromchildren.● Remove the protective film from the access point before useto ensure ventilation.LEDFactory ResetEthernet PortPower Jack (DC IN)3. I n s t a l l a t i o nVigorAP can be installed under certain locations: wooden ceiling, plasterboard ceilings, light-weighted steel frame and wall.3.1 C e i l i n g -m o u n t I n s t a l l a t i o n (W o o d e n C e i l i n g )1. Place the bracket under the wooden ceiling and fasten two screws firmly (asshown in Figure below, Step 1). 2. When the bracket is in place, fasten two screws firmly (as shown in Figurebelow, Step 2) on the bottom of VigorAP. 3. Make the device just below the bracket. Put the screws installed in Step 2 onthe holes of the bracket (as shown in Figure below, Step 3). 4. Gently rotate the device to make screws slide into the notches of thebracket and move forward till it is firmly fixed.Step 1Step 2BracketStep 33.2 C e i l i n g -m o u n t I n s t a l l a t i o n (P l a s t e r b o a r d C e i l i n g )1. Place the bracket under the plasterboard ceiling and fasten two turnbuckles firmly (as shown in Figure below, Step 1).2. Make the screws pass through the bracket and insert into the turnbuckles (asshown in Figure below, Step 2). Fasten them to offer more powerful supporting force.3. When the bracket is in place, fasten two screws firmly (as shown in Figurebelow, Step 3) on the bottom of VigorAP.4. Make the device just below the bracket. Put the screws installed in Step 3 onthe screw holes of the bracket (as shown in Figure below, Step 4).5. Gently rotate the device to make screws slide into the notches of thebracket and move forward till it is firmly fixed.BracketStep 1Step 2Step 3Step 43.3 S u s p e n d e d C e i l i n g (L i g h t w e i g h t S t e e l F r a m e )I n s t a l l a t i o nYou cannot screw into ceiling tiles as they are weak and not suitable for bearing loads. Your VigorAP is supplied with mounts (T-Rail brackets) which attach directly to the metal grid (‘T-Rail’) of your suspended ceiling.1. Choose one set of T-Rail mounting kits from the bundled package.2. Put the T-Rail brackets on the holes of the bottom side of the device. Fastenthem with suitable screws.3. If a larger gap is required between the ceiling and the VigorAP, use theextension pieces to extend the height of the brackets.T-Rail BracketExtension PieceT-Rail BracketExtension Piece4.Attach the T-Rail brackets to the ceiling frame.NoteWarning: The screw set shown below is for wall mounting only. Do not use such set for ceiling mounting due to the danger offalling.3.4 W a l l -M o u n t e d I n s t a l l a t i o nFor wall-mounting, the VigorAP has keyhole type mounting slots on the underside. You can fit the AP at any axis (i.e. 12, 3, 6 or 9 O’Clock) to allow for cable entry from the most convenient location if you are using side entry – note the position of the side entry cable cutout.1. A template is provided on the VigorAP’s packaging box to enable you tospace the screws correctly on the wall.2. Place the template on the wall and drill the holes according to therecommended instruction.3. Fit screws into the wall using the appropriate type of wall plug (as shown inthe ceiling section) but do not use the ceiling bracket – the VigorAP hangs directly onto the screws.Wall (wooden, concrete, plasterboard or others)4.C o n n e c t i o n a n d C o n f i g u r a t i o n4.1N o t i f i c a t i o n s f o r H a r d w a r e C o n n e c t i o n●If required, remove the protective cap of VigorAP to create extra spacefor the cables to pass through.●Connect VigorAP to Vigor router (via LAN port) with Ethernet cable.●Connect VigorAP to PoE switch (via LAN port) with Ethernet cable. Forconnecting with PoE switch, do not connect the power adapter. VigorAPwill get the power from the switch directly.4.2C o n n e c t t o a V i g o r R o u t e r u s i n g A P M a n a g e m e n tYour VigorAP can be used with Vigor routers which support AP management (such as the Vigor2865 or Vigor2927 series). AP Management enables you to monitor and manage multiple DrayTek APs from a single interface.1.Connect one end of the power adapter to power port of VigorAP, and theother side into a wall outlet.2.Access into the web user interface of Vigor router. Here we take Vigor2865as an example. Open Central Management>>AP>>Status.3.Locate VigorAP 960C. Click the IP address assigned by Vigor router to accessinto web user interface of VigorAP 960C.4.After typing username and password (admin/admin), the main screen will bedisplayed.4.3W e b C o n f i g u r a t i o n sThis section will guide you to install the AP and make configuration for VigorAP.C o n n e c t e d A s a M e s h N o d e(i n M e s h N e t w o r k)❶Install VigorAP on to the ceiling.❷As a mesh node, settings related to VigorAP 960C must be configured by a remote Mesh Root (e.g., VigorAP 903) within the mesh network.The user must detect VigorAP 960C via a Mesh Root to add it as a meshnode.C o n n e c t e d A s a n A c c e s s P o i n tAs an access point, VigorAP 960C must be connected to a router and configured in AP (Access Point) / Range Extender mode.❶Install VigorAP on to the ceiling.❷Use a twisted-pair cable with RJ-45 plugs at both ends, and plug into Ethernet device (e.g., Vigor router) and Ethernet port of VigorAP.❸ There are two methods to configure VigorAP.Method 1:(a) First, open a web browser on your PC and type https://192.168.1.2. Apop-up window will open to ask for username and password.Note You may either simply set up your computer to get IPdynamically from the router or set up the IP address of thecomputer to be in the same subnet as the IP address ofVigorAP 960C.● If there is no DHCP server on the network, then VigorAP960C will have an IP address of 192.168.1.2.● If there is DHCP available on the network, then VigorAP960C will receive its IP address via the DHCP server.● If you connect to VigorAP by wireless LAN, you could tryto access the web user interface through .(b) After clicking Login, Quick Start Wizard for configuring wirelesssettings will appear as follows.(c)Follow the on-screen steps to finish the network connection.Method 2:(a)Use a mobile phone to scan the QR code named with DrayTek WirelessApp to download DrayTek Wireless APP.(b)After downloading, run the APP.(c)From the home page, click the Connect icon to access the Connectpage. Next, press the QR code icon next to Scan QR Code on yourphone screen to open the camera.Scan the QR code named with Connect SSID to access the web user interface (configuration wizard) of VigorAP 960C. (For iOS users, the SSID and the password will be shown first. Simply click the Connect button to access the web user interface of VigorAP.)5.C u s t o m e r S e r v i c eIf the device cannot work correctly after trying many efforts, please contact your dealer/DrayTek for further help right away. For any questions, please feel freetosende-mailto“*******************”.B e a R e g i s t e r e d O w n e rWeb registration is preferred. You can register your Vigor router viahttps://..F i r m w a r e&T o o l s U p d a t e sDue to the continuous evolution of DrayTek technology, all routers will beregularly upgraded. Please consult the DrayTek web site for more information on newest firmware, tools and documents.https://GPL Notice This DrayTek product uses software partially or completely licensedunder the terms of the GNU GENERAL PUBLIC LICENSE. The author ofthe software does not provide any warranty. A Limited Warranty isoffered on DrayTek products. This Limited Warranty does not coverany software applications or programs.To download source codes please visit:GNU GENERAL PUBLIC LICENSE:https:///licenses/gpl-2.0Version 2, June 1991For any question, please feel free to contact DrayTek technical*************************************************.14。
海尔商业空调中央控制器系统说明书
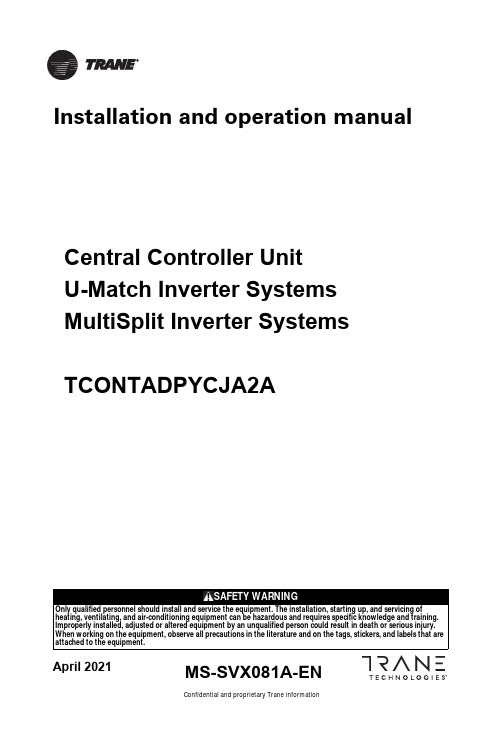
Central Controller U nit UMatch Inverter Systems MultiSplit Inverter SystemsTCONTADPYCJA2AConfidential and proprietary Trane informationA pril 2021Installation and operation manualMS-SVX081A-ENUser manuals and installation manuals for remote control detector TCONTADPYCJA2AFunctions IntroductionRemote control detector(short form:Detector)is essential equipment of remote monitor system of Haier commercial A/C.By connecting the interface in indoot units or outdoor units,this detector can reach functions of remote an central control◆Communication function1.with air conditioning communication:①. YCJ-A002 can at most connect two same model units by six-pin fixed screw. It canrealize double switching function. It can control air conditioning to work in different ways according to the requirement of detector, at the same time query the airconditioner's operation information and fault information.munication with RS-485:①. Communication with the central controllerBM1 dip switch as (1: OFF, 2: OFF)Communicate with the central controller via RS-485 interface bus (A, B). It receives commands from central controller according to the units address what is set by detector dip switch. And to realize internal control or query request, and answer the reception status and air conditioning operation information and fault information.②Communication with the central controllerBM1 dip switch as (1: ON, 2: OFF)Communicate with the central controller by RS-485 bus port. According to the detector within the dip switch setting address, Receive commands from the central controller. Have internal control or query request, and answer the reception status and air conditioning operation informationand fault information.③Communicate with remote devices. Detector has RS-485 port, and the protocol is Modbus RTU, users can use the private network and open protocol to create remote control program, no need other accessories.The BM1 dip switch as (1: OFF, 2: ON).④communication with the central control systemD ip switch BM1 (1: ON,2: ON)Communicate with the central control system by RS-485 bus port(A, B). it receives12commands from central controller according to the units address what is set by detector dip switch. And to realize internal control or query request, and answer the reception status and air conditioning operation information and fault information.In order to improve the reliability of air conditioning, the detector has double switching function, set SW1 to single unit mode, detector controls the A unit according to the command from the host equipment. Set SW1 to double switching mode, it can realize double switching function.Double switching function realization: under normal condition, the detector control one unit ON and another unit OFF, when reach the switch time, detector wake up the OFF state unit and the ON state unit will still work half an hour and then OFF.If any air conditioner has failure, switch time will stop, the detector automatically wake up another unit, and let the failure unit OFF, then upload the failure information. After the failure restore, automatically change to the double switching function; if air-conditioner operate for some time and cannot reach setting temperature, switch time will stop, the detector automatically wake up another air conditioner, double units operate until reaching the setting temperature, then automatically turn off that air conditioner, and automatically restore the double switching function. Factory default switch time is 12 hoursDetector has three lights, yellow light is for RS-485 communication , red and green lights are for the air conditioner communication, When the communication is normal, lights in accordance with the frequency of 0.5s flashing, when have failure, lights in according with the frequency of 1s flashing, stop 2s flashingThrough the RS-485 bus to build a central control network, In order to reduce the impact of unified operation of air conditioning on the power grid, the detector set the delay start function, the delay time is automatically generated by the detector【1】【2】BM10:OFF 1:ON numbe485communication mode details00①TCONTCCMYCZG1/TCONTCCMYCZ256 single unit10②/01③Modbus rtu standard protocol 11④BMS system◆Dual switch function◆Address setting function◆Operation status displasy function◆Delay control functionThe detector with 8-bit dip switch (SW1), the highest bit D8 bit, for setting the single mode or double-switch mode,(D7, D6, D5, D4, D3, D2, D1) is used to set the number (central control network or double switch time when select the dual switch mode)◆Double switching function instructions◆use central controller for central control functionSystem OverviewDetector connects with the two same model units through six-pin fixed screw. Set the dip switch to double switching model. Only use the double switching function, the system does not need connect the other components; double switching time can be chosen 8,10,12,14 hours by dip switch setting.the specific settings and the corresponding time see dip switch list12V 、COM 、GND ports of detector connect with air conditioner. Dip switch set to singlemode, the specific settings and the corresponding address see dip switch list, The system also needs to connect withcentral controller, Each detector connect with central Controller by 2-pin fix screw(A,B).DetectorsIndoor Unit Indoor UnitOutdoor Unit Outdoor Unit4◆Status check◆When servicing, be sure to power off the power supplyMaintenanceDimension drawing•When select the single unit mode and control A unit, when A unit failure occurs, the detector will query fault information and upload it, when select double switch mode,detectorcontrolA unit and B unit, if one of air conditioner is faulty, the detector will query the fault information and upload it•Detector operating status and running lamp display: When operation properly, running lamp for 0.5 seconds off 0.5 secondsfor a cycle to indicate,When have the fault to flash 1 second, stop 2 seconds to cycle to indicate, yellow lamp for the central control of communication status indication, red light for the air conditioner A unit communication Status indication, green lamp for air conditioning B unit communication status indication•Wipe clean with a soft cloth and be careful not to touch the electrical parts.•Do not use gasoline, thinner, decontamination powder, chemical wipes, etc. to avoid damage to electrical parts.•Check whether the wiring with the central control and air conditioning is normal, there is no broken wire or the existence of loosening of the connection.Interface Description:1-air conditioning A communication port,three-core shielded communication wire connection, wire length is not more than 10meter2-air conditioning B communication port,three-core shielded communication wire connection, wire length is not more than 10meter3 - dial switch is used for centralized control interface of detector detector Communication Associationand dual switching functionIOS device to achieve remote control.Installation and commissioning◆installation and wiring of the basic requirements:Use a screw driver to install detector, screw spacing see the right figure.Keep the detector on a wall or other reliable location to ensure that there is no water and other creatures that may cause failure to enter.1.Central control network design planning principles:(1) Detector, in order to maintain the appropriate response speed and communication reliability, the number of detectors in one central system should not exceed 64 pieces (2)A/C should be ready for network ,bu sure to be installed and us according to instructions(3) Detector installation position does not leave the air conditioner too far; do not exceed the wiring length(4) Detector address number in strict accordance with the order from small to large allocation(5) Detector power from the indoor unit, 12V, need have distance with the high voltage cable .and the shieldlayer needs earth one side(6) Central control bus wire length limit less than 1000 meters(7) both ends of the bus in the A bus and B bus were connected between the 100 ohm metal film precision resistance (depending on the scene to match)(8) bus shielded wire single point grounding, the proposed layout in the middle of the communication bus location, and centralized controller similar(9) Central controller installation location in principle arranged in the middle of the communication bus position, and the communication bus shield ground similar2.Detector and air conditioning connection: Detector through the air conditioning interface six screws fixed terminal (12V、COM1、GND、12V、COM2、GND) ,andup to two air-conditioning (A, B) for wired communication; detector and air conditioning connection with the uniform wiring, one end of the wiring terminal with plug connect to air conditioning indoor PCB remote control terminal. If the detector does not operation properly during commissioning, it can be check by change the wiring polarity + - . Also can be based on the running lamp show the operation status of the air conditioning and communication interface to determine whether the normal.3.After the communication bus wiring is completed, connect the detector and the communication bus: the connection method of hand by hand type, all A ports in the same Bus, all B ports on another bus, the communication bus shielding line in the communication bus in a single point of grounding, communication bus total length Limited to less than 1000 meters.◆According to the host equipment to select RS-485 interface protocol by dip switch BM1:Detector built a variety of different protocols to correspond to different host equipment, the use of four different protocols corresponding to four different conditions:1.The host equipment is a centralcontroller, central controller can choose to select the device type for single unit, in order to be able to deal with different system structure, the detector has two built-in protocols that communicate with the central controller.5①central controller, select the communication mode for the single unit, then dip switch: BM1: 1: OFF; 2: OFF.The system diagram is as follows:67②the host equipment for the third party communication equipment, the detector provides the standard Modbusrtu protocol, BM1 dip switch: 1: ON; 2: OFF, The communication between the detector and the air conditioner is consistent with the other 3. When the detector is used as a third-party protocol converter, it should be specificAccess to the requirements of third-party host device connection; the basic functions are as follows:The address of the address set by SW1 changes to the slave address in the Modbus RTU communicationSerial port9600,8,n ,1130B modbusrtu query01 control 05/15WORD name Unit Range Remarks 01 function code 0Indoor units on/off Read operation to obtain the current switchunit status 0: off 1: onWrite operation to change the switch state 0: off 1: on03 function code query 03 control 06/16 0I n t e r n a l s e t t i n g temperature ℃16-30Read operation Get current setting temperature, write operationChange set temperature1within the machine running mode 1--5Read operation to obtain the current operating mode: 1 - cooling 2 - heating 3 - dehumidification4 – Fan only5 - automatic Write operation to change the operating mode: 1 - cooling 2 - heating 3 - dehumidification 4 – Fan only 5 - automatic2Fan speed 1--4Read operation to obtain the current fan speed: 1 - low speed 2 – middle speed 3 - high speed4 – Automatic speedWrite operation to change the fan speed: 1 - low speed 2 – middle speed 3 - high speed 4 -Automatic speed3i n d o o r c o n t r o lmode1--4 1 is not locked; 2 empty - query back to 1, issued to write 1; 3 query back to 1,Issued to write 1; 4 - lock 04 function code read only 0indoortemp ℃301℃1Fault code 0-256within the indoor fault code 0-256 value of 0 that no error ,2machine numberThe number of internal indoor This address exists , query back 08◆Power test :◆RS485 interface dip switch instructions1.Power test: After the equipment is connected, the power test①first verify the detector and air conditioner communication status, the red lightshould be light 0.5 seconds off 0.5 seconds as a cycle to indicate, If the indicator does not light or flashes for 1 second and stops for 2 seconds, it should check whether the communication wire of the air conditioner and detector are the connection is correct and the air conditioner is powered up until the indicator flashes normally.②check 485 communication indicator (yellow lamp), should be light 0.5 seconds off 0.5seconds as a cycle to indicate, if the instructions If the lamp does not light or flashes for 1 second and stops for 2 seconds, it should check whether the BM1 protocol is correct; the communication wire is connectedWhether it is correct; whether there is a device with a repeated address, etc., until the indicator flashes normally2.The detector and the host equipment communication, if the host equipment to normal monitoring and control of air conditioners, the completion of debugging.Performance parameters and accessoriesDetector built a variety of different protocols to correspond to different equipment, the use of four different protocols corresponding to four different conditions:1.The host equipment is a centralcontroller, central controller can choose to select the device type for single unit , in order to be able to deal with different the system structure, the detector has two built-in protocols that communicate with the central controller.①central controller, select the communication mode for the unit, then dip switch BM1:1: OFF; 2: OFF.performance parameter DC12VPower consumption Power consumption is less than 3W Detector code number 0151800130BAccessoriesair conditioning communication 3 core shielded wire, special number 0010452854, color white, yellow, and redPerformance parameter9S W 1(1m e a n O N ,0 m e a n O F F )B M 1c o d e1:O F F ;2:O F F1:O N ;2:O F F 1:O F F ;2:O N 1:0N ;2:O N[1][2][3][4][5][6][7][8]D e fi n i t i o n : u n i t a r y a i r c o n d i t i o n e D e fi n i t i o n :V R F D e fi n i t i o n :M o d b u s R T U D e fi n i t i o n :B M S G a t e a d d r U n i t a d d r 1---0000D u a l m o d e a d d r =1D u a l m o d e a d d r =1-1D u a l m o d e s l a v e I D =1D u a l m o d e 3101---0001D u a l m o d e a d d r =2D u a l m o d e a d d r =2-2D u a l m o d e s l a v e I D =2D u a l m o d e 311—— —— —— —— —— —— 1---1110D u a l m o d e a d d r =15D u a l m o d e a d d r =15-15D u a l m o d e s l a v e I D =15D u a l m o d e 31141---1111D u a l m o d e a d d r =16D u a l m o d e a d d r =16-16D u a l m o d e s l a v e I D =16D u a l m o d e 3115-0000000S i n g l e m o d e a d d r =1S i n g l e m o d e a d d r =1-1S i n g l e m o d e s l a v e I D =1S i n g l e m o d e 310-0000001S i n g l e m o d e a d d r =2S i n g l e m o d e a d d r =2-2S i n g l e m o d e s l a v e I D =2S i n g l e m o d e 311—— —— —— —— —— —— -0100110S i n g l e m o d e a d d r =39S i n g l e m o d e a d d r =39-39S i n g l e m o d e s l a v e I D =39S i n g l e m o d e 3138-0100111S i n g l e m o d e a d d r =40S i n g l e m o d e a d d r =40-40S i n g l e m o d e s l a v e I D =40S i n g l e m o d e 3139-0101000S i n g l e m o d e a d d r =41S i n g l e m o d e a d d r =41-41S i n g l e m o d e s l a v e I D =41S i n g l e m o d e 300-0101001S i n g l e m o d e a d d r =42S i n g l e m o d e a d d r =42-42S i n g l e m o d e s l a v e I D =42S i n g l e m o d e 301—— —— —— —— —— —— -1001110S i n g l e m o d e a d d r =79S i n g l e m o d e a d d r =79-79S i n g l e m o d e s l a v e I D =79S i n g l e m o d e 3038-1001111S i n g l e m o d e a d d r =80S i n g l e m o d e a d d r =80-80S i n g l e m o d e s l a v e I D =80S i n g l e m o d e 3039-1010000S i n g l e m o d e a d d r =81S i n g l e m o d e a d d r =81-81S i n g l e m o d e s l a v e I D =81S i n g l e m o d e 290-1010001S i n g l e m o d e a d d r =82S i n g l e m o d e a d d r =82-82S i n g l e m o d e s l a v e I D =82S i n g l e m o d e 291—— —— —— —— —— —— -1110110S i n g l e m o d e a d d r =119S i n g l e m o d e a d d r =119-119S i n g l e m o d e s l a v e I D =119S i n g l e m o d e 2938-1110111S i n g l e m o d e a d d r =120S i n g l e m o d e a d d r =120-120S i n g l e m o d e s l a v e I D =120S i n g l e m o d e 2939-1111000S i n g l e m o d e a d d r =121S i n g l e m o d e a d d r =121-121S i n g l e m o d e s l a v e I D =121S i n g l e m o d e 280-1111001S i n g l e m o d e a d d r =122S i n g l e m o d e a d d r =122-122S i n g l e m o d e s l a v e I D =122S i n g l e m o d e 281—— —— —— —— —— —— -1111110S i n g l e m o d e a d d r =127S i n g l e m o d e a d d r =127-127S i n g l e m o d e s l a v e I D =127S i n g l e m o d e 286-1111111S i n g l e m o d e a d d r =128S i n g l e m o d e a d d r =128-128S i n g l e m o d e s l a v e I D =128S i n g l e m o d e 287◆ Address setting functionSW01Definition[1][2][3][4][5][6][7][8]0———————Single mode 1———————Double Switch mode —00—————Double Switch time 8 hours —01—————Double Switch time 10 hours —10—————Double Switch time 12 hours —11—————Double Switch time 24 hours———0————Dual operation at ambient temperature of 34℃———1————Dual operation at ambient temperature of 32℃1———0000Double Switch mode and ad-dress=11———0001Double Switch mode and ad-dress=2———1———1110Double Switch mode and ad-dress=151———1111Double Switch mode and ad-dress=1600000000Single mode and address=100000001Single mode and address=2———01111110Single mode and address=12701111110Single mode and address=12810Trane - by Trane Technologies (NYSE: TT), a global climate innovator - creates comfortable, energy efficient indoor environments for commercial and residential applications. For more information, please visit or .Trane has a policy of continuous product and product data improvement and reserves the right to change design and specifications without notice. We are committed to using environmentally conscious print practices.©2020 TraneConfidential and proprietary Trane information。
Futronic MKII MANAGER User Manual

Futronic MKII MANAGER(PC SOFTWARE)User ManualVersion 01 March 2019Klokkestoebervej 4. DK-9490 Pandrup. DenmarkTel: +45 96 44 44 44, Fax: +45 96 44 44 45E-mail:*********************,TABLE OF CONTENTTABLE OF CONTENT (2)INTRODUCTION (3)How to download and install (3)TEST RESULTS (4)DSC COMPOSER (5)AIS COMPOSER (6)SETTINGS (7)EPIRB TEST REPORT GENERATOR (8)1. Generating reports out of stored test results (8)2. PC-controlled EPIRB tests (10)NATIONAL MARINE ELECTRONIC ASSOCIATION (NMEA) (11)VHF SENSITIVITY TEST (13)UPGRADE (14)INTRODUCTIONFutronic MKll manager allows you to:-View all test results and save them to a PC-Compose custom-made DSC messages-Compose custom-made AIS messages-Perform test box settings that cannot all be done on the test box itself-Perform PC-controlled EPIRB testsand generate complete finished EPIRB Test Reports-Monitor NMEA messages to detect suspected errors on the NMEA 0183 version 2.-Determine the VHF channels to be tested for sensitivity-Upgrade your test box with new facilities purchased from DanphoneHow to download and install1) Download Futronic MKll manager from Danphones’ website:/futronic-gmdss-testers/futronic-mkii/2) Open the zipped file.3) Double click on the file Installation guide and follow the instructions.USB Cable4) Once installed, the PC program will open a 6-tabbed dialogue box on your PC screen: Test Results - DSC Composer - AIS Composer - Settings - EPIRB- NMEA –Sensitivity -UpgradeThe tabs are explained on the following pages.TEST RESULTSThe Test Results tab provides access to all the tests and test results stored in the test box. Tests are organized with a header in the Index window to the left, under which the individualtest results are displayed in the window at the right hand side.Headers are indexed in time order with the latest test on top.Please note: In order to view a test result, you must select its header first.Press Save to PC in order to save the test results on your PC and to bring them into your own test report format, if so wished.Press Update to update the Index list with new tests performed after you opened the PC program.Press Delete to delete a test from the Index list.Press Disconnect to disconnect the test box from your PC.DSC COMPOSERUnder the DSC Composer tab you can compose your own custom-made DSC messages and transfer them to the test box accordingly.Please refer to ITU-R M.493 for composing of DSC messages.The test box can contain one DSC message for VHF, TFC and MF/HF respectively.Custom-made DSC messages can also be saved on your PC for later use.AIS COMPOSERUnder the AIS Composer tab you can compose and save your own custom-made AIS messages.When transferred to the test box, the AIS message will be transmitted on both AIS channels, AIS1 and AIS2.SETTINGSThe Settings tab allows you to change the test box settings.Test box MMSI: Write and set new MMSI number for the test box here.Target MMSI: Write and set MMSI number of the device to be tested here.LCD backlight time out: Write and set backlight time out between 0 and 200 seconds here. LCD contrast: Write and set contrast between 0 and 100% here.OCXD time out: Write and set OCXO time out between 0 and 99 minutes here.Show raw DSC on LCD: Click here to have raw DSC data presented in the display along with clear text.Sync Test Box Time with PC: Click here to synchronize the current date and time in the test box with the date and time in your PC.EPIRB TEST REPORT GENERATORThe EPIRB tab offers two options:1. Generation of complete EPIRB test reports out of test results from the test box,2. PC-controlled EPIRB testing and simultaneous generation of test reports.1. Generating reports out of stored test resultsThis feature allows you to generate complete EPIRB test reports out of the test results stored in the test box.1) Select the EPIRB test from the list at the right hand side. If there is no list,go to the “Test results” ta b and select from the Index a header that contains the relevant EPIRB test. Then return to the “EPIRB” tab.2) Fill in the beacon information form in the EPIRB dialogue box at the left hand side.3) Press “Generate Report” to cr eate the EPIRB Test Report (HTML format).See example of an EPIRB Test report on the next page.During the installation of the Futronic MKll manager, a default report template has been placed in C:\EPIRB\ on your PC. Feel free to use this HTML document as the basis for creating your own layout or design, if so wished. Then, press “Get template” and select the new one from your file system instead of the default template.Please note: Default limits of the frequency tolerance and minimum signal level are +/- 5 kHz and 190 respectively. Other limits may be inserted in accordance with specifications. Should the limits be exceeded during test, the report will write “Failed” in the status line.Example of Test Report based on the default HTML design:2. PC-controlled EPIRB testsIn addition to generating test reports from EPIRB tests stored in the memory, the EPIRB tab also enables you to perform PC-controlled EPIRB tests generating test reports automatically. With this, the system will not transfer the test results to the test box, but still generate finished test reports that can be stored in your PC.1) Turn the test box on. No need to select EPIRB tests, your PC will take control.2) Deselect all tests from the header list at the right-hand side, if any.3) Select frequency in the EPIRB dialogue box at the left-hand sideand fill in the beacon information form.4) Press “Start PC-controlled Test” and then activate the EPIRB.5) Wait for the EPIRB Test Report to be automatically generated (HTML format).See example of an EPIRB Test report on the previous page.NATIONAL MARINE ELECTRONIC ASSOCIATION (NMEA)The NMEA tab enables monitoring of NMEA 0183 version 2 messages.This feature enables monitoring of NMEA supporting units by retrieving NMEA messages via the pilot plug. Connect the NMEA bus to the pilot plug on the Futronic test box and press “Get NME A”. The test box automatically transfer the requested messages to the PC. All messages can be saved as text files.Activate filter to restrain the messages to one type.VHF SENSITIVITY TESTThe Sensitivity tab enables determination of the VHF channels to be tested for sensitivity. Futronic MKll manager allows you to configure the Futronic test box on 6 selected VHF channels. Set the VHF channel between 01 – 28 or 60 – 88, 2006, 2019, 2020, 2024 – 2028, 2078, 2079, 2084, 2085 and press “Save”.The channel is hereby visible on the test box and ready for testing.Press ↑ and ↓ on the test box to choose between the predefined channels.UPGRADEThe Upgrade tab is for upgrading the Futronic test box model.If your test box is a GMDSS-only model and you have purchased the additional AIS test facility from Danphone, you will be given an access key to be entered, and the new facility will work immediately.。
Mimo Vue 10.1” HD Display HDMI Capture User’s Manu
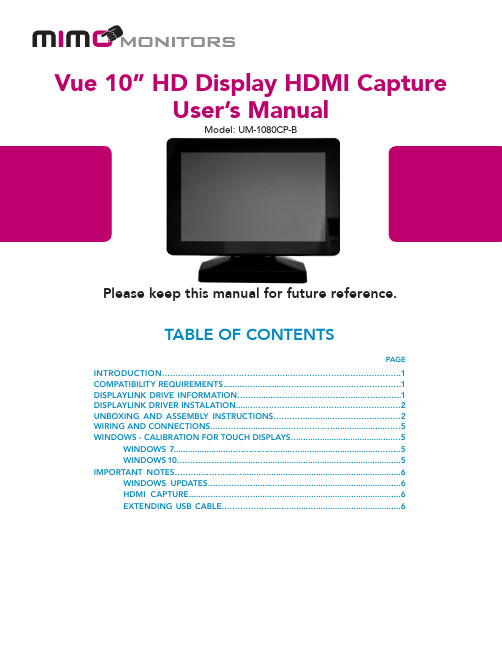
Model: UM-1080CP-BPlease keep this manual for future reference.TABLE OF CONTENTSPAGE INTRODUCTION........................................................................................1COMPATIBILITY REQUIREMENTS......................................................................1DISPLAYLINK DRIVE INFORMATION................................................................1DISPLAYLINK DRIVER INSTALATION...............................................................2UNBOXING AND ASSEMBLY INSTRUCTIONS.................................................2WIRING AND CONNECTIONS.............................................................................5WINDOWS - CALIBRATION FOR TOUCH DISPLAYS..............................................5 WINDOWS 7.............................................................................................5 WINDOWS 10............................................................................................5IMPORTANT NOTES.............................................................................................6 WINDOWS UPDATES...............................................................................6 HDMI CAPTURE.......................................................................................6 EXTENDING USB CABLE. (6)Vue 10” HD Display HDMI Capture User’s ManualIntroductionDesigned to be a perfect conference room control interface, the Mimo Vue HD with HDMI capture UM-1080CP-B is the second generation of Mimo Monitors 10.1” monitor line. It features a modern zero bezel design, nearly 180-degree viewing angle from its bright, high contrast, IPS screen, and a resolution of 1280x800. The Mimo Vue HD includes a 10-point projected capacitive touch panel for developing an intuitive human interface.This capture device allows your USB 3.0 connected computer to stream high-quality HDMI® video, up to 1080p video at 60 frames per second. The capture device converts video and audio from your HDMI source device into standard UVC (USB Video Class) and UAC (USB Audio Class). The HDMI capture interface is integrated into the display and shares the USB connection to the host computer. This video data stream can be presented to other displays with video processing, sent over the internet to other online meeting participants, or many other options.Compatibility requirements:•Android - Requires DisplayLink Presenter application installed on Android device and a connection to a DisplayLink Universal Hub. Please review the information provided atDisplayLink for Android.•Mac - Requires DisplayLink driver. Please review the information provided at this page: DisplayLink for MacOS.•Windows - Requires DisplayLink driver. Please review the information provided at DisplayLink for Windows.•Ubuntu - Requires Intel-based x86 32 or 64-bit system running Ubuntu version 14 or later. Please review the information provided at DisplayLink - Ubuntu Driver Download.•Chromebox - No additional requirements. Please contact us if you experience issues during set up. Please review the information provided at DisplayLink - Native Chrome OS Support.DisplayLink Driver InformationIf noted above, DisplayLink driver must be installed on the computer. If you have Windows 10 or newer, the DisplayLink driver should be pre-installed on the computer. If Windows does not locate the driver locally, and if the computer is connected to the internet, Windows should automatically search online, download, and install the appropriate drivers. If necessary, please follow the instructions below to manually install the DisplayLink drivers.Please visit DisplayLink Support for important information such as: how to identify whether your operating is supported; how to identify operating system version, build, and system type; known issues and troubleshooting steps.DisplayLink Driver InstallationGo to . At the top left of the screen, you will find a button labeled DOWNLOAD DRIVERS, click on that button to download the necessary driver(s). The website will then prompt you to select the correct Supported Operating System. The website will then prompt you to select the correct version of the operating system you are running on the computer being set up.Note that while DisplayLink offers BETA versions for download, we recommend downloading the latest non-BETA released version.Unboxing and Assembly InstructionsUnbox the various components and ensure that nothing is missing. The following items should be included. See Figure 3 for component pictures and plankton assembly instructions.1. Mimo Vue HD Display (screen)2. Stand3. Hinge Cover4. Cable Cover5. HDMI Cable, green connectors6. USB 3.0 Cable, blue connectors, dual to single7. Power Cable, red connectors8. Stand9. Hinge Cover10. Cable Cover11. DC Power adapter with USB power output port12. Stand screws13. Cable cover screwsFigure 1: Components and Plankton Assembly InstructionsFigure 3: Wiring DiagramWiring and ConnectionsAs shown in Figure 4, all connectors are color-coded as are the connections on the back of the Mimo Vue. Simply match the connector style and color and insert. The red connector is for power and should be connected to the power adapter USB port and the display. The blue connector should be connected to the PC/NUC and the Mimo Vue. This cable is 3.0M long but can be extended using active cabling. See the Important Notes section on page 8 for details. The green connector is for HDMI capture, requires USB 3.0 capability, and should be connected to the Mimo Vue and any device that is trying to share its display.Windows - Calibration for Touch DisplaysWindows 7: If you are running Windows 7 the following steps for calibration still apply, however, you will need to install additional Mimo drivers. Please either call Mimo Monitors at 855-937-6466 or you may send an email request to *********************.Windows 10:Once all the components are properly connected and powered on, it is necessary to let the operating system know which of the displays in your configuration has touch capability. For example, if you’re using Windows 10, t ap the Windows Start button and select Settings. In the “Find a setting” box, at the top center of the screen, type “calibrate the screen for pen or touch input” and tap the Enter key. The Tablet PC Settings dialog window will pop up. Tap the Setup button as shown in Figure 2 below.Figure 1: Touch Screen SettingsOnce Setup is selected, all the connected screens will go white and one of the screens will display “Touch this screen to identify it as the touchscreen” and “If this is not the Tablet PC screen, press Enter to move to the next screen. To close the tool press Esc.” to move to the next display. So, if the screen with the above message is displayed, either tap the screen or tap the Enter key until the correct display is selected. Once selected click on Calibrate to be guided through the calibration process and complete the setup.Figure 2: Touch Screen SelectionAt this point, your system should be working and setup is complete.Important Notes1. Windows updates: Before updating Windows, uninstall any DisplayLink drivers thatmight already be installed. The latest DisplayLink drivers will be loaded by Windows. If you experience problems after updating Windows, you may need to manually install the drivers. Please refer to page 3 (above) for instructions and a link to DisplayLink drivers and resources.2. HDMI Capture: There must be an active HDMI signal for this feature to work. Pleasemake sure that the HMDI cable is connected to the PC.3. Extending USB Cable (Blue): If necessary, the USB cable can be extended usingactive cabling. Please read this related article on our website: USB extension and the UM-1080CP-B.。
常见响应状态码
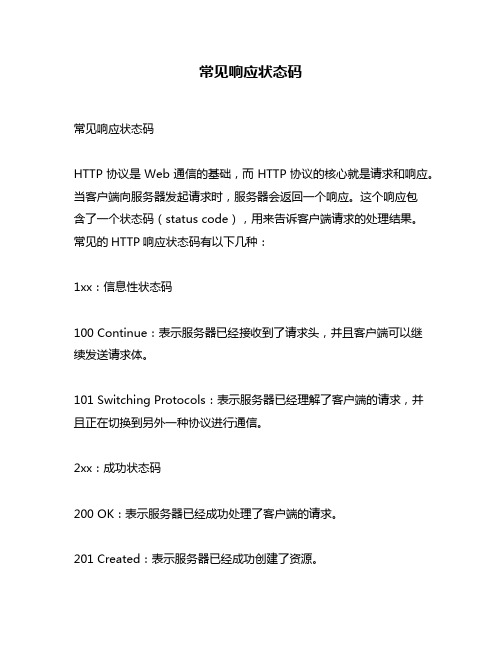
常见响应状态码常见响应状态码HTTP协议是Web通信的基础,而HTTP协议的核心就是请求和响应。
当客户端向服务器发起请求时,服务器会返回一个响应。
这个响应包含了一个状态码(status code),用来告诉客户端请求的处理结果。
常见的HTTP响应状态码有以下几种:1xx:信息性状态码100 Continue:表示服务器已经接收到了请求头,并且客户端可以继续发送请求体。
101 Switching Protocols:表示服务器已经理解了客户端的请求,并且正在切换到另外一种协议进行通信。
2xx:成功状态码200 OK:表示服务器已经成功处理了客户端的请求。
201 Created:表示服务器已经成功创建了资源。
202 Accepted:表示服务器已经接受了客户端的请求,但是还没有处理完成。
204 No Content:表示服务器已经成功处理了客户端的请求,但是没有返回任何内容。
206 Partial Content:表示服务器已经成功处理了部分GET请求,返回部分内容。
3xx:重定向状态码301 Moved Permanently:永久性重定向。
表示被请求资源被永久移动到新位置,并且将来所有对此资源的访问都要使用新地址替代旧地址。
302 Found / 303 See Other / 307 Temporary Redirect :临时性重定向。
这些状态码都表明被请求资源暂时被移动到新位置,但是将来还会返回原来的位置。
304 Not Modified:表示客户端缓存的资源没有发生变化,可以直接使用缓存中的资源。
4xx:客户端错误状态码400 Bad Request:表示客户端发送了一个错误的请求。
401 Unauthorized:表示需要进行身份验证才能访问被请求资源。
403 Forbidden:表示服务器拒绝了客户端的请求。
通常是因为客户端没有权限访问被请求资源。
404 Not Found:表示服务器无法找到被请求的资源。
网络安全错误错误代码
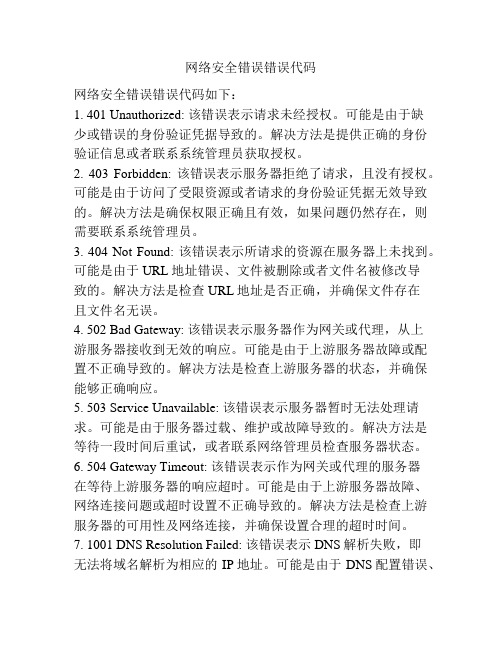
网络安全错误错误代码网络安全错误错误代码如下:1. 401 Unauthorized: 该错误表示请求未经授权。
可能是由于缺少或错误的身份验证凭据导致的。
解决方法是提供正确的身份验证信息或者联系系统管理员获取授权。
2. 403 Forbidden: 该错误表示服务器拒绝了请求,且没有授权。
可能是由于访问了受限资源或者请求的身份验证凭据无效导致的。
解决方法是确保权限正确且有效,如果问题仍然存在,则需要联系系统管理员。
3. 404 Not Found: 该错误表示所请求的资源在服务器上未找到。
可能是由于URL地址错误、文件被删除或者文件名被修改导致的。
解决方法是检查URL地址是否正确,并确保文件存在且文件名无误。
4. 502 Bad Gateway: 该错误表示服务器作为网关或代理,从上游服务器接收到无效的响应。
可能是由于上游服务器故障或配置不正确导致的。
解决方法是检查上游服务器的状态,并确保能够正确响应。
5. 503 Service Unavailable: 该错误表示服务器暂时无法处理请求。
可能是由于服务器过载、维护或故障导致的。
解决方法是等待一段时间后重试,或者联系网络管理员检查服务器状态。
6. 504 Gateway Timeout: 该错误表示作为网关或代理的服务器在等待上游服务器的响应超时。
可能是由于上游服务器故障、网络连接问题或超时设置不正确导致的。
解决方法是检查上游服务器的可用性及网络连接,并确保设置合理的超时时间。
7. 1001 DNS Resolution Failed: 该错误表示DNS解析失败,即无法将域名解析为相应的IP地址。
可能是由于DNS配置错误、网络连接问题或者域名不存在导致的。
解决方法是检查DNS 配置,确保网络连接正常,并确认域名正确存在。
8. 1002 Connection Timed Out: 该错误表示连接超时,即无法在一定时间内建立服务器连接。
可能是由于网络连接问题、服务器故障或防火墙限制导致的。
Unicore UM4B0 Installation and Operation User Manu

U ni c o r e C o n f i dINSTALLATION AND OPERATIONUSER MANUALData subject to change without notice.Communications, Inc.Copyright© 2009-2021, Unicore RTK Positioning ModuleAll-constellation All-frequency GPS/BDS/GLONASS/Galileo U M 4B0DisclaimerInformation in this document is subject to change without notice and does not represent a commitment on the part of Unicore Communications, Inc. No part of this manual may be reproduced or transmitted in any form or by any means, electronic or mechanical, including photocopying and recording, for any purpose without the express written permission of a duly authorized representative of Unicore Communications, Inc. The information contained within this manual is believed to be true and correct at the time of publication.© Copyright 2009-2021 Unicore Communications, Inc. All rights RSV.UM4B0 User Manual ForewordThis <User Manual> offers you information in the features of the hardware, the installation, specification and use of UNICORECOMM UM4B0 product.This manual is a generic version. Please refer to the appropriate part of the manual according to your purchased product configuration, concerning CORS, RTK and Heading.Readers it applies toThis <User Manual> is applied to the technicists who know GNSS Receiver to some extent but not to the general readers.Contents1INTRODUCTION (1)1.1O VERVIEW (1)1.2K EY F EATURES (1)1.3T ECHNICAL S PECIFICATIONS (2)1.4I NTERFACES (2)2HARDWARE (3)2.1D IMENSIONS (3)2.2P IN D EFINITION (T OP V IEW) (4)2.3E LECTRICAL S PECIFICATIONS (6)2.4O PERATIONAL C ONDITIONS (7)2.5P HYSICAL S PECIFICATIONS (7)3HARDWARE DESIGN (8)3.1D ESIGN IN C ONSIDERATIONS (8)3.2UM4B0R EFERENCE D ESIGN (9)3.3P INS (10)3.4PCB P ACKAGING (11)3.5R ESET S IGNAL (12)3.6A NTENNA (12)3.7E XTERNAL A NTENNA F EED D ESIGN (12)4INSTALLATION AND CONFIGURATION (14)4.1ESD H ANDLING P RECAUTIONS (14)4.2H ARDWARE I NSTALLATION (14)4.3S TART U P (17)4.4C ONFIGURATION AND O UTPUT (17)4.4.1Operation Procedures (18)5CONFIGURATION COMMANDS (19)5.1RTK R EFERENCE S TATION C ONFIGURATION (20)5.2RTK R OVER C ONFIGURATION (21)5.3M OVING B ASE C ONFIGURATIONS (21)5.4H EADING C ONFIGURATION (21)6ANTENNA DETECTION (22)7FIRMWARE UPGRADE (22)8PRODUCTION REQUIREMENT (24)9PACKAGING (25)1Introduction1.1OverviewUM4B0 is a high precision positioning and heading RTK module developed by Unicore Communications, targeting light robots, UAVs, intelligent vehicles, GIS information collection, etc.By employing a single UC4C0 (432 channel tracking) baseband chip and a single RF chip, using single-sided SMD packaging, UM4B0 has achieved the smallest size(30x40mm) in this industry with high accuracy heading and positioning output. It can simultaneously track BDS B1I/B2I/B3I/B1C/B2a + GPS L1/L2/L5 + GLONASSL1/L2+Galileo E1/E5a/E5b.Figure 1-1 UM4B0 Module1.2Key Features•30*40mm, the smallest multi-system multi-frequency high precision module •Support GPS L1/L2/L5+GLONASS L1/L2+BDS B1I/B2I/B3I/B1C/B2a+Galileo E1/E5a/E5b•Based on 432 channel NebulasII GNSS SoC•20Hz update rate•Instant RTK initialization and long-distance RTK•Enhanced multi-system multi-frequency RTK technology, JamShield adaptive narrow-band anti-interference and U-AutoAlign multi-path mitigation •Support odometer input and external high-performance IMU interface* •SMD packagingUM4B0 User Manual 1.3Technical SpecificationsTable 1-1 Performance SpecificationsTable 1-2 Functional Ports1.4InterfacesFigure 1-2 Block Diagram1.RF PartThe receiver gets filtered and enhanced GNSS signal from the antenna via a coaxial cable. The RF part converts the RF input signals into the IF signal, and converts IF analog signal into digital signals required for NebulasII (UC4C0) digital processing.2.NebulasII SoC (UC4C0)The UM4B0 incorporates the processing from the NebulasII (UC4C0), UNICORECOMM’s new generation high precision GNSS SoC with 55nm low power design, which supports up to 12 digital intermediate frequency or 8 analog intermediate frequency signals and can track 12 navigation signals with 432 channels.3.1PPSUM4B0 outputs 1 PPS with adjustable pulse width and polarity.4.EventUM4B0 provides 1 Event Mark Input with adjustable pulse width and polarity.2Hardware2.1DimensionsUM4B0 User ManualFigure 2-1 Mechanical Dimensions2.2Pin Definition (Top View)Figure 2-2 UM4B0 Pin DiagramTable 2-2 Pin DefinitionUM4B0 User Manual2.3Electrical SpecificationsTable 2-3 Absolute Maximum Ratings2.4Operational ConditionsTable 2-4 Operational ConditionsNOTE: Since the product contains capacitors at the input, inrush current will occur during power-on. Evaluate in the actual environment in order to check the effect of the supply voltage drop due to the inrush current.2.5Physical SpecificationsTable 2-5 Physical Specifications3Hardware Design3.1Design in ConsiderationsTo make UM4B0 work properly, you need to properly connect the following:The module VCC power-on behavior is repeatable, the initial level is lower than0.4V, and the undershoot and ringing should be guaranteed to be within 5% VCC Provide stable power to the VCC pinConnect all the GND pins to groundConnect VBAT pin to a 3.0V power supplyConnect ANT_IN signal to the antenna, and ensure the 50-ohm impedance matchingConnect ANT_PWR to +3.3~5.5 V voltage, then supply +3.3~5.5 V feed to the antenna through ANT_INEnsure COM1 is connected to a PC or an external processor, and users can use this serial port to receive position data. COM1 is also necessary for firmwareupgradesProperly connect the module’s reset pin FRESET_N to ensure complete reset of the module. It will restore the module to the manufacturing configuration.When ANT_NLOD, ANT_FFLG and antenna detection indication signal are connected, the IO without any pull-up/down of the client MCU terminal isrequired at the input.In order to obtain proper performance, special concerns should be paid during the design:Power supply: A table and low ripple power supply is necessary for good performance. Make sure the peak-to-peak voltage ripple does not exceed50mVpp. It is recommended to use a power chip with current output capacity greater than 2A to power the board.-Use LDO to ensure the purity of power supply-Try to place LDO close to the module in layout-Widen the tracks of power circuit or use copper pour surface to transmit current-Avoid walking through any high-power or high inductance devices such as a magnetic coilInterfaces: Ensure that the signals and baud rate of the main equipment match those of the UM4B0 moduleAntenna interface: Make sure the antenna impedance matches, and the cable is short without any kinks, try to avoid all acute anglesTry to avoid designing in any circuits underneath UM4B0This module is a temperature sensitive device, so dramatic changes in temperature will result in reduced performance. Keep it away as far as possible from any high-power high-temperature air and heating devices3.2UM4B0 Reference DesignFigure 3-1 Minimum Reference DesignFigure 3-2 UM4B0 Reference Design 3.3PinsTable 3-1 Pin Notes3.4 PCB PackagingFigure 3-3 UM4B0 recommended PCB Packaging (unit: mil, in brackets: mm)3.5Reset SignalUM4B0 module can’t work properly unless it is correctly reset after power on. To ensure effective reset, the reset pin (RST) and power supply pin (VCC) must meet the following time sequence requirement. To reset UM4B0 during normal operation, please pull RST pin to low level for more than 5ms.Figure 3-4 UM4B0 RST3.6AntennaThe module has the antenna input pin ANT_IN, which provides a +3.3V antenna feed. When an active antenna of +3.3~5V is adopted, please make sure the 50 Ω antenna impedance is matched.Figure 3-5 UM4B0 Active Antenna Connection3.7External Antenna Feed DesignUM4B0 feeds the antenna signals to the required circuits internally, but in order to effectively prevent damage from lightning and surges, circuit protection should be installed externally to protect the module.High voltage and high-power protection chips should be used to feed the antenna from the outside of the module. A gas discharge tube, varistor, TVS tube and other high-power protective devices may also be used in the antenna circuit to effectively improve the prevention against lightning stroke and surge.ANTFigure 3-6 UM4B0 External Antenna Feed Reference CircuitRemarks:a)L1, feed inductor, 68nH RF inductor in 0603 package is recommended;b)C1, decoupling capacitor, it is recommended to connect two capacitors of 100nF/100pFin parallel;c)C2, DC blocking capacitor, recommended 100pF capacitor.4Installation and Configuration4.1ESD Handling PrecautionsUM4B0 Module is an Electrostatic Sensitive Device (ESD) and special precautions when handling are required.Electrostatic discharge may cause damages to the device. All operations mentioned in this chapter should be carried out on an antistatic workbench, wearing an antistatic wrist strap and using a conductive foam pad. If anantistatic workbench is not available, wear an antistatic wrist strap and connect the other end to a metal frame to avoid the effects of static electricity.Hold the edge of the module, not in direct contact with the componentsPlease check carefully whether the module has obviously loose or damaged components.Figure 4-1 Typical Installation of UM4B0Please check the contents of the package carefully after receiving the package of UM4B0.UM4B0 EVK suite (or evaluation board)User manualUPrecise softwareQualified antennaMMCX antenna cablePC or Laptop with serial ports (Win7 or above), with UPrecise installed4.2Hardware InstallationAfter the above preparation, please follow the steps below to install:Step 1: Make sure to take all the anti-static measures, such as wearing an anti-static wrist strap, grounding the workbench;Step 2: Align UM4B0 transfer board positioning holes and pins with EVK, and fix it in the EVK. EVK provides power supply and standard communication interface for the module to communicate with peripheral devices;NOTE: The RF connector of the board is MMCX, and the suitable connecting wire should be selected according to the package. The input signal gain at the antenna interface is optimal between 20 and 36 dB. Please select the appropriate antenna, antenna cable and online LNA accordingly.Figure 4-2 Installation InstructionStep 3: Select the GNSS antenna with appropriate gain, and fix it in a stable, non-block area, using the coaxial radio frequency cable to connect the antenna to UM4B0 EVK;Step 4: Connect the PC to the EVK serial port through direct serial cable;Figure 4-3 Connect the Serial PortStep 5: Connect a 12V adapter to the EVK power input, and switch on to powerthe device;Figure 4-4 Connect the AntennaStep 6: Open the UPrecise software on the PC;Step 7: Control the receiver through UPrecise to send commands or to log data.4.3Start UpThe power supply for UM4B0 is 3.3VDC. Before powering on the device, please connect UM4B0 serial port to the GNSS antenna. The receiver is started and the communication is connected after powering up. Testing tools are provided for module testing.4.4Configuration and OutputUNICORECOMM UPrecise software provides a user-friendly graphical interface to control and display the operation of your receiver. The features of Uprecise include: Logging Control View: Graphic interface for data loggingConsole window for sending command to the receiver (Console View)Displaying the receiver’s output in ASCII-format (ASCII View)Graphic window for displaying Position of satellite, PRN, and Signal/Noise Ratio (Constellation View)Historical and present Trajectory of the receiver (Trajectory View)Position/Velocity/Time of the receiver (PVT View)Apart from the basic functions above, UPrecise offers advanced functions as follows: Selecting and recording the logSending commands to the receiverOperating and configuration of the ASCII viewThe trajectory view for displaying the present point and the past point of the receiverSwitching Views over the tracking windowSwitching between Constellation ViewsResetting the receiverReplaying the GGA logFigure 4-5 UPrecise SoftwareUM4B0 User Manual 4.4.1Operation ProceduresStep 1. Follow 4.2 Installation Guide to connect the power source, antenna to the board, and turn on the EVK switchStep 2. Click file - > connect the serial port, and set the baud rate; the default baud rate of UB4B0M is 115200bpsFigure 4-6 Connect the Serial PortStep 3. Click the receiver settings button to configure the NMEA message output. Itis recommended to configure GPGGA, GPGSV, and other messages.Figure 4-7 NMEA Data OutputStep 4. Click the receiver settings button to configure the NMEA message output, then click send. It is recommended to configure GPGGA, GPGSV, and other messages. Step 5.In the data session window, click “Send all Message” to complete all the NMEA message output (update rate 1Hz). Right click in the data session window to adjust: output log font size, stop / resume log output, or clear log content, etc.Step 6. Use various views of UPrecise to configure or input commands as required.5Configuration CommandsUM4B0 supports abbreviated ASCII format. Simplified ASCII format without check bit is more accessible to user commands. All commands are composed of a log heading and configuration parameters (If parameters are null, there will be only one heading in the command). Header field contains the command name or message headers. UM4B0 is simple to use, and common instructions are shown in the following table:UM4B0 User Manual5.1RTK Reference Station ConfigurationIf the precise coordinates are known, the precise coordinates could be set as in this example:Mode base 40.07898324818 116.23660197714 60.4265 // set lat lon heightrtcm1033 com2 10 // RTCM1033 input from com2rtcm1006 com2 10rtcm1074 com2 1rtcm1084 com2 1rtcm1094 com2 1rtcm1124 com2 1saveconfigIf precise coordinates are unknown:Mode base time 60 1.5 2.0 // 60 seconds position averagertcm1033 com2 10rtcm1006 com2 10rtcm1074 com2 1rtcm1084 com2 1rtcm1094 com2 1rtcm1124 com2 1saveconfig5.2RTK Rover ConfigurationRTK Rover stations (rover station) receive differential correction data sent from reference stations and receive satellite signals to provide an RTK positioning solution and realize RTK high-precision positioning with cm or mm-level accuracy. Common instructions for configuring RTK rover are as follows:gngga 1saveconfig5.3Moving Base ConfigurationsRTK reference station provides precisely known coordinates of a fixed station. Unlike the RTK reference station, moving base station is in motion, at the same time receives the satellite information, and sends it to the rover station receiver (to be determined) directly or after processing. The rover station receiver receives satellite observations as well as information from the moving base station, to make relative positioning and determine the position of the rover station. Commonly used instructions to set the moving base station are as follows:Mode movingbasertcm1006 com2 1rtcm1074 com2 1rtcm1084 com2 1rtcm1094 com2 1rtcm1124 com2 1saveconfig5.4Heading ConfigurationGNSS heading refers to the clockwise angle between true North and the baseline vector constituted by the two GNSS antennas. Commonly used instructions are as follows:Mode headinggphdt com1 1saveconfigUM4B0 User Manual6Antenna Detection1The UM4B0 module offers antenna open/short detection. The corresponding pins are ANT_NLOAD and ANT_FFLG.•The current monitoring chip outputs 2 bit high and low voltage; the software portion sets 2 bit IO of corresponding NII as input pull-up, and then queries the status of 2 bit IO to check the antenna state.•If ANT_PWR malfunctions, the query result is invalid.•If the antenna is not fed by ANT_PWR but by other means, the query result is invalid.7Firmware UpgradeUprecise software is used for the remote update of UM4B0. Please follow the steps below to upgrade the device:Figure 7-1 Update InterfaceClick “…” to browse the firmware update package, and click“Start” to start the firmware upgrading process (uncheck software reset):1 Optional by FirmwareFigure 7-2 Update StepsWaiting for the process to complete 100% (the upgrade time is normally within 5min):Figure 7-3 Update StepsPlease use COM1 only to update firmware.UM4B0 User Manual8Production RequirementRecommended thermal cycle curve is as follows:Figure 8-1 Soldering TemperatureTemperature rising stage∙Rising slope: Max. 3℃/s∙Rising temperature range:50℃-150℃Preheating stage∙Preheating time: 60 – 120 s∙Preheating temperature range: 150 - 180℃Reflux Stage∙Over melting temperature (217℃) time: 40 – 60 s∙Peak temperature: no higher than 245℃Cooling Stage∙Cooling slope: Max. 4℃ / sNotes:In order to prevent fall off during soldering of the modules, please avoid soldering the module in the back of the Board during design, that is, better not to go through soldering cycle twice.The setting of temperature depends on many factors, such as type of Board, solder paste type, solder paste thickness, etc. Please also refer to the relevant IPC standards and indicators for solder paste.Since the lead soldering temperatures are relatively low, if using this soldering method, please give priority to other components on the Board.9PackagingUM4B0 modules are delivered in trays, which is suitable for mainstream SMT equipment. Each box contains 5 trays, so there are 150 UM4B0 modules in the box. Table 9-1 Package Informationw 。
企业常见英语
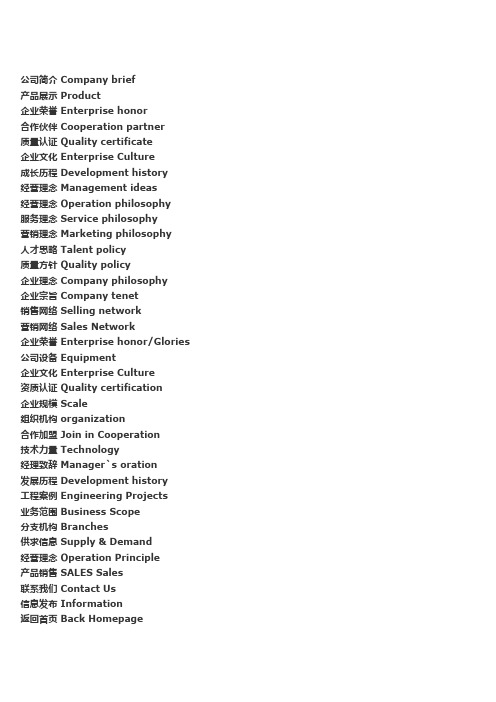
网站地图 Site Map 服务和支持 Service & Support 如何购买 How To Buy 服务和维护合同 工程实例 Engineering Projects 实例 Projects User Profile 用户信息 User register 用户注册 Username: * Must between 2 to 24 chars 用户名 必须 是2到24个字节 Password: * Must between 6 to 16 chars 密码 Confirm Password 重复密码 *Must match the password above Congratulations, you can now access your p祝e贺rs,你on现a在liz可e以d 从pa任g何e 一fr页om进入an你y的c个om人p电u脑te使r用us的in电g子y邮ou件r地 址和你的密码. 已发送电子邮件给你了,你的资料.
性别 Gender 不知道 Unkown 男的 Male 女的 Female 电子邮件(隐藏我的邮箱地址) Email(Hide my Email address ) 验证码 Security Code: 收缩所有 Collapse all 展开所有 Expand all 登入 Sign in 我的密码丢失了 I lost my password 已经存在的用于(已经注册的用的登录)Existing User 现在就注册 Sign up now 正在检验 checking... 保存我的信息 Save my information
VPN错误代码列表大全
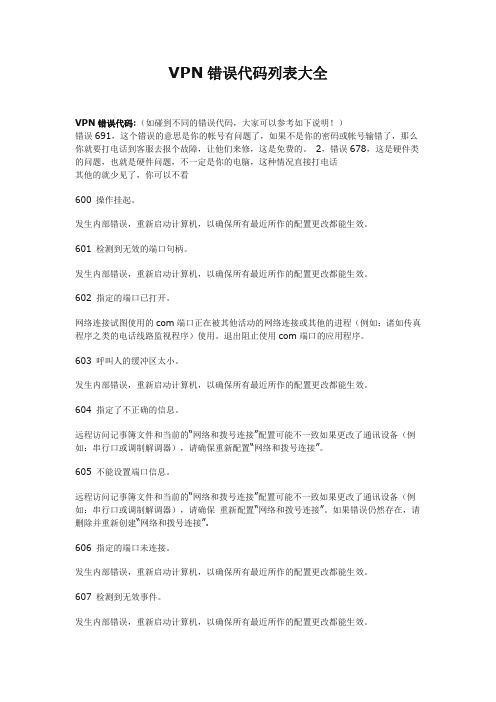
VPN错误代码列表大全VPN错误代码:(如碰到不同的错误代码,大家可以参考如下说明!)错误691,这个错误的意思是你的帐号有问题了,如果不是你的密码或帐号输错了,那么你就要打电话到客服去报个故障,让他们来修,这是免费的。
2,错误678,这是硬件类的问题,也就是硬件问题,不一定是你的电脑,这种情况直接打电话其他的就少见了,你可以不看600 操作挂起。
发生内部错误,重新启动计算机,以确保所有最近所作的配置更改都能生效。
601 检测到无效的端口句柄。
发生内部错误,重新启动计算机,以确保所有最近所作的配置更改都能生效。
602 指定的端口已打开。
网络连接试图使用的com端口正在被其他活动的网络连接或其他的进程(例如:诸如传真程序之类的电话线路监视程序)使用。
退出阻止使用com端口的应用程序。
603 呼叫人的缓冲区太小。
发生内部错误,重新启动计算机,以确保所有最近所作的配置更改都能生效。
604 指定了不正确的信息。
远程访问记事簿文件和当前的“网络和拨号连接”配置可能不一致如果更改了通讯设备(例如:串行口或调制解调器),请确保重新配置“网络和拨号连接”。
605 不能设置端口信息。
远程访问记事簿文件和当前的“网络和拨号连接”配置可能不一致如果更改了通讯设备(例如:串行口或调制解调器),请确保重新配置“网络和拨号连接”。
如果错误仍然存在,请删除并重新创建“网络和拨号连接”.606 指定的端口未连接。
发生内部错误,重新启动计算机,以确保所有最近所作的配置更改都能生效。
607 检测到无效事件。
发生内部错误,重新启动计算机,以确保所有最近所作的配置更改都能生效。
608 指定的设备不存在。
远程访问记事簿文件和当前的“网络和拨号连接”配置可能不一致如果更改了通讯设备(例如:串行口或调制解调器),请确保重新配置“网络和拨号连接”。
如果错误仍然存在,请删除并重新创建“网络和拨号连接”.609 指定的设备类型不存在。
远程访问记事簿文件和当前的“网络和拨号连接”配置可能不一致如果更改了通讯设备(例如:串行口或调制解调器),请确保重新配置“网络和拨号连接”。
Soyal 701 Client Software User Manual
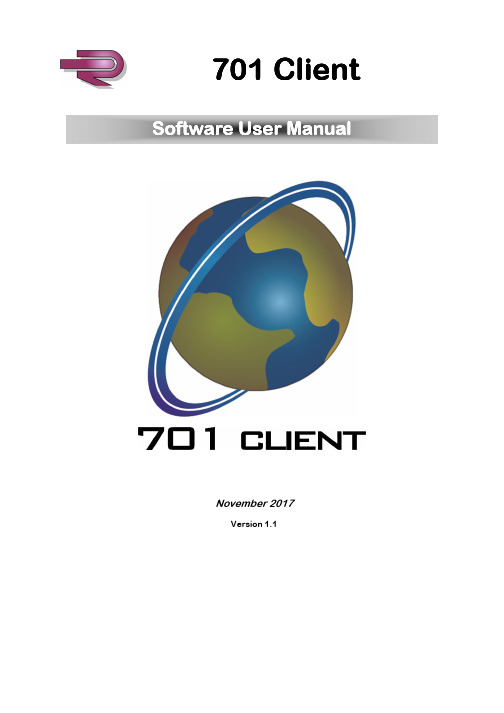
November 2017Version 1.1701 Client 701 Client000084879500012, 62362The site code is the first 5 digits, the card code is the next 5 digits. The site code and card code will not show any leading zeros when entered into the User Card Edit screen for example site code 00012, card code 00102 will display as site code 12, card code 102 in the User Card Edit screen.The initial screen will usually show live current transaction records (similar to the example below) , if there are no transaction records showing refer to Page 15.Tick the “Lock” box, this locks the screen on a live system to enable adding, editing or deleting of tokens. If the screen is unlocked, it will jump to the user number of every valid token presented to a reader.Select the relevant User Number with the up and down arrows (see page 2&3)Input the token number in the two boxes, the token number is made up of a Site Code and a Card Code. The Site Code goes in the left hand box and the Card Code goes in the right hand box (see page 3)Select Card Only with the drop down arrow.Select relevant Time Zone if set, if not required leave as default which is “ALL”Select relevant Door Group if set, if not required leave as default which is “ALL” Enter Name of User if required. Enter Department names if required. To edit the department names, highlight the text showing “ Dep_00” and “Dep2_00” and type in the required name.Click Save.If multiple cards/tokens are to be installed refer to Page 7 Otherwise when all card/token modifications are complete and saved click exit then proceed to download the revised data to the controller(s) See page 122 Click button 8 “Users”, the User Card Edit window will open.1 111 3 45 6 7810 111Click on the “Tools” button with the User Card Edit window open.Select “Card Copy” from the drop down menu, the following window will open.3Adding 50 cards/tokens, alldata copied except UserName. Cardcode willIncrement automatically.45Enter the Start and End Addresses. The Start Address is the User Number of the Token to be copied, the End Address is the User Number of the final Token to be added.For example, If the Token to be copied is entered as User Number 14, and 20 Tokens need to be programmed, the Start Address is 14 and the End Address is 33.Click button 8 “Users”, the User Card Edit window will open.Tick the “Lock” box, this locks the screen on a live system to enable adding, editing or deleting of tokens. If the screen is unlocked, it will jump to the user number of every valid token presented to a reader.Select the relevant User Number with the up and down arrows.If the User Number is unknown, enter the User Name or Card Code of the token to be deleted in the search box and click the “Search “ button.The search results will be shown in this section. To select the Token to be deleted, double click on the line containing the user data.Click the “Clear Data Field” button, the following window will open.7Click the “Yes” button, the details for the current user card will be deleted. Repeat for 123 456Enter the Start and End Addresses. The Start Address is the User Number of the Token to be copied, the End Address is the User Number of the final blank Token to be cleared. For example, If the Token to be cleared is entered as User Number 14, and 20 Tokens needto be cleared, the Start Address is 14 and the End Address is 33.Select all parameters as shown.Click “YES”, the blank Tokens will be copied into the database and the window will When the “Card Copy” window closes the “User Card Edit” window will remain open. Either continue editing user card data or Save and Exit .Click on the “Tools” button within the User Card Edit window.Select “Card Copy” from the drop down menu, the following window will open.4351Deleting 50 cards/tokens, alldata copied. Card code willIncrement automatically.The first card/token in thesequence must have had allof its data deleted by usingthe delete tokeninformation on page 8.3 2To check available Door Groups Click button 9 “Door Group Edit”, the Door Group Edit window will open as shown below:11112 1To check available Time Zones click button B “Time Zone Edit” The “Time Zone Edit” window will open as shown below:Select the controllers to be updated (If it is all controllers click “All On-line” )Click “All Items” button.The green progress bars and percentage indicator will slowly increase.When the download has finished the window will close.If you do not wish to download data click Exit.1 2 3 4 123 456Click button F “Download Data”, the Download To Controller window will open.1To back up the 701Client Data to an external source: 1Click on the button marked File Path.The window below will then show the File Path i.e. C:\Users\m.fall\Desktop\701 Client Backup 040417\The backup folder in this case has been named “701 Client Backup 040417”Check the file path is correct. Left click “Backup” to backup the data. Once the backup is complete Left Click the Exit Button1122If the transaction record is not displayed or you wish to view transaction records for other days select Icon 3 Daily Transaction Records as identified above. This will open the window below.The records are stored in thefollowing format: 20170406This is a year/month/dayFormat.As each daily record is openedthe windows will be tiled onthe main screen.To open the current daily event log select the folder that has the required year/month/ day reference.The controllers in the above example are as follows:Node ID=1 AR-727HB-RAY H Series 2 Door Controller - Controller 1, Doors 1 and 2 Node ID=2 AR-331EF E series Controller - Controller 2, Door 3Node ID=3 AR-727H H Series Controller - Controller 3, Door 4System Parameters (see Page 21) have been set for : Huge Door Group Mode and Show Detail Node Address. The transactions highlighted above show a valid User Token being701 Client Message ID’s M01 Invalid PINM02 Keypad LockedM03 Invalid Card (Card Code in event detail) M04 Time Zone Error M05 Door Group ErrorM06 User Card—Date expired M08 Incorrect PINM09 Duress Code Used M11 Normal Access M14 Arming M15 Disarming M16 Egress (RTE)M17 Alarming (description in event detail ) L20 Server or Client Login L21 Server or Client LogoutL22 Controller OFF line (controller ID etc ) L23 Controller ON line (controller ID etc ) M24 (Device type ) Power ON M28 Access by PinM30 Anti-pass back errorM31 Reader disconnected at controller M32 Reader reconnected at controller M33 User changed PIN codeM34 User changed PIN code errorM35 Controller entered Auto Open procedure M36 Controller exited Auto Open procedure M37 Disarmed by auto time procedure M38 Armed by auto time procedure M39 Access by Finger/Vein M56 Fingerprint Access FailedL is software generated, M is controller generated.701 CLIENT EVENT LOG 701 CLIENT EVENT LOG MESSAGE DESCRIPTIONS MESSAGE DESCRIPTIONSTABLE OF USERSTABLE OF USERSName of On-Site Programmer(s):W e r e c o m m e n d t h i s p a g e s h o u l d b e f i l l e d i n a n d r e g u l a r l y u p d a t e d a n d k e p t i n a s a f e a n d s e c u r e l o c a t i o n b y t h e p e r s o n r e s p o n s i b l e f o r t h e u p k e e p o f t h e s y s t e m.。
英文版邀请招标文件
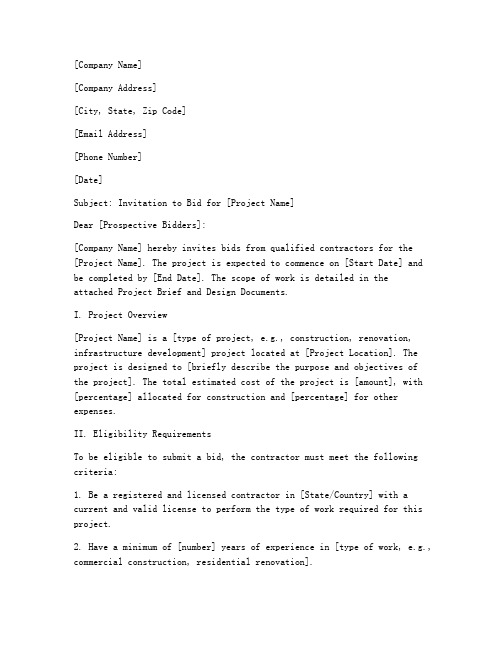
[Company Name][Company Address][City, State, Zip Code][Email Address][Phone Number][Date]Subject: Invitation to Bid for [Project Name]Dear [Prospective Bidders]:[Company Name] hereby invites bids from qualified contractors for the [Project Name]. The project is expected to commence on [Start Date] and be completed by [End Date]. The scope of work is detailed in theattached Project Brief and Design Documents.I. Project Overview[Project Name] is a [type of project, e.g., construction, renovation, infrastructure development] project located at [Project Location]. The project is designed to [briefly describe the purpose and objectives of the project]. The total estimated cost of the project is [amount], with [percentage] allocated for construction and [percentage] for other expenses.II. Eligibility RequirementsTo be eligible to submit a bid, the contractor must meet the following criteria:1. Be a registered and licensed contractor in [State/Country] with a current and valid license to perform the type of work required for this project.2. Have a minimum of [number] years of experience in [type of work, e.g., commercial construction, residential renovation].3. Provide evidence of current general liability insurance with a minimum coverage limit of [amount].4. Provide a list of at least [number] completed projects similar to [Project Name] within the past [number] years.5. Submit a financial statement or letters of credit from a financial institution demonstrating the ability to finance the project.6. Have no unresolved complaints or violations against the contractor with any governmental agency or bonding authority.III. Bid Submission RequirementsBids must be submitted in a sealed envelope marked “Invitation to Bid for [Project Name]” and deliver ed to [Company Name] at the address listed above by [Bid Submission Deadline]. Late submissions will not be considered.The bid must include the following:1. Bidder Information: Name, address, phone number, email address, and contact person for the bidder.2. Technical Proposal: Detailed description of the proposed work, including methods, materials, and equipment to be used.3. Schedule: Project schedule with milestones and completion dates.4. Cost Proposal: Itemized breakdown of all costs associated with the project, including labor, materials, equipment, and any other expenses.5. Bonding and Insurance: Proof of required bonding and insurance coverage.6. Additional Documents: Any other documents required by [Company Name] or as specified in the Project Brief.IV. Evaluation CriteriaBids will be evaluated based on the following criteria:1. Technical Proposal: The completeness, feasibility, and innovation of the proposed technical approach.2. Schedule: The reasonableness and practicality of the proposed project schedule.3. Cost: The total cost of the project, considering both the initial bid and any potential changes or additional costs.4. Experience and Qualifications: The contractor’s relevant experience, qualifications, and past performance.5. Financial Stability: The financial stability and ability of the contractor to complete the project.V. Award Process[Company Name] reserves the right to reject any or all bids. The award will be made to the bidder whose bid is determined to be the most advantageous to [Company Name], considering the evaluation criteria listed above.VI. Questions and ClarificationsAny questions or clarifications regarding the bid invitation should be submitted in writing to [Company Name] at the address listed above by [Question Clarification Deadline]. Responses will be provided in writing to all bidders.VII. Bid SecurityBidders are required to submit a bid security in the amount of [amount] to ensure the bid is submitted in good faith. The bid security will be returned to the bidder upon the opening of bids, provided the bid is not withdrawn.VIII. ConfidentialityAll information provided by bidders and any discussions held during the bid process will be kept confidential and will not be disclosed to any third party without the consent of the bidder.IX. Miscellaneous1. All bids are subject to acceptance by [Company Name] and may be withdrawn at any time prior to award.2. [Company Name] reserves the right to negotiate with any bidder and to make changes to the project specifications or requirements at any time prior to award.3. The bidder acknowledges that any failure to comply with the terms and conditions of this invitation to bid may result in disqualification.X. Contact InformationFor any further information or inquiries, please contact:[Name][Title][Company Name][Email Address][Phone Number]Thank you for your interest in [Project Name]. We look forward to receiving your bid and hope to have the opportunity to work with you on this exciting project.Sincerely,[Your Name][Your Title][Company Name]Enclosures:1. Project Brief2. Design Documents3. Bid Submission Form ---[Company Name] [Company Address] [City, State, Zip Code] [Email Address] [Phone Number]。
http状态响应码对照表
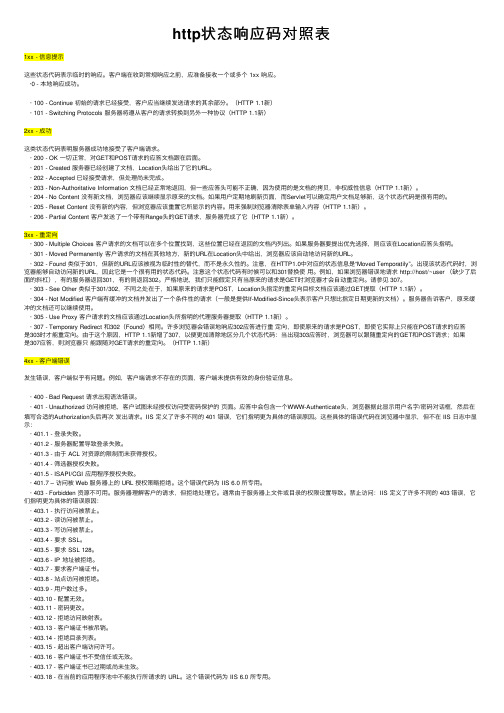
http状态响应码对照表1xx - 信息提⽰这些状态代码表⽰临时的响应。
客户端在收到常规响应之前,应准备接收⼀个或多个 1xx 响应。
·0- 本地响应成功。
· 100- Continue 初始的请求已经接受,客户应当继续发送请求的其余部分。
(HTTP 1.1新) · 101- Switching Protocols 服务器将遵从客户的请求转换到另外⼀种协议(HTTP 1.1新)2xx - 成功这类状态代码表明服务器成功地接受了客户端请求。
· 200- OK ⼀切正常,对GET和POST请求的应答⽂档跟在后⾯。
· 201- Created 服务器已经创建了⽂档,Location头给出了它的URL。
· 202- Accepted 已经接受请求,但处理尚未完成。
· 203- Non-Authoritative Information ⽂档已经正常地返回,但⼀些应答头可能不正确,因为使⽤的是⽂档的拷贝,⾮权威性信息(HTTP 1.1新)。
· 204- No Content 没有新⽂档,浏览器应该继续显⽰原来的⽂档。
如果⽤户定期地刷新页⾯,⽽Servlet可以确定⽤户⽂档⾜够新,这个状态代码是很有⽤的。
· 205- Reset Content 没有新的内容,但浏览器应该重置它所显⽰的内容。
⽤来强制浏览器清除表单输⼊内容(HTTP 1.1新)。
· 206- Partial Content 客户发送了⼀个带有Range头的GET请求,服务器完成了它(HTTP 1.1新)。
3xx - 重定向 · 300- Multiple Choices 客户请求的⽂档可以在多个位置找到,这些位置已经在返回的⽂档内列出。
如果服务器要提出优先选择,则应该在Location应答头指明。
· 301- Moved Permanently 客户请求的⽂档在其他地⽅,新的URL在Location头中给出,浏览器应该⾃动地访问新的URL。
- 1、下载文档前请自行甄别文档内容的完整性,平台不提供额外的编辑、内容补充、找答案等附加服务。
- 2、"仅部分预览"的文档,不可在线预览部分如存在完整性等问题,可反馈申请退款(可完整预览的文档不适用该条件!)。
- 3、如文档侵犯您的权益,请联系客服反馈,我们会尽快为您处理(人工客服工作时间:9:00-18:30)。
doc.: IEEE 802.11-05/380r0
Mitsubishi Electric Corporation Royal Philips Electronics Intel Corporation Qualcomm Incorporated Intel Corporation Samsung Electronics Co Ltd Royal Philips Electronics InterDigital Communications Corporation Panasonic Institute for Infocomm Research Cisco Systems Agere Systems Toshiba Corporation Royal Philips Electronics Sharp Nortel Networks Sony Electronics Royal Philips Electronics Marvell Semiconductor Royal Phiips Electronics Qualcomm Incorporated Sanyo Electric Co Ltd Atheros Communications Intel Corporation Qualcomm Incorporated InterDigital Communications Corporation
this document is subject to change in form and content after further study. The contributor(s) reserve(s) the right to add, amend or withdraw material contained herein.
Phone
+1 610 712 6616
mujtaba@
Notice: This document has been prepared to assist IEEE 802.11. It is offered as a basis for discussion and is not binding on the contributing individual(s) or organization(s). The material in
Release: The contributor grants a free, irrevocable license to the IEEE to incorporate material contained in this contribution, and any modifications thereof, in the creation of an IEEE
May 2005
doc.: IEEE 802.11-05/380r0
TGn Sync Proposal Update to TGn May 2005
Date: 2005-05-16
Author Name
Syed Aon Mujtaba
Company
Agere Systems
Address
555 Union Blvd., Allentown, PA 18109, USA
Patent Policy and Procedures: The contributor is familiar with the IEEE 802 Patent Policy and Procedures <http:// /guides/bylaws/sb-bylaws.pdf>, including the statement
Slide 3
jzhang@ job.oostveen@ joe.pitarresi@ Johnk@ john.sadowsky@ jon.rosdahl@ joerg.habetha@ joseph.levy@ kobayashi.kiyotaka@ liyuan@.sg lchia@ mecramer@ masahiro3.takagi@toshiba.co.jp monisha.ghosh@ miki@slab.tnr.sharp.co.jp osama@ paul.feinberg@ pen.li@ ploc@ ronald.rietman@ snanda@ snakao@gf.hm.rd.sanyo.co.jp sheung@ stephen.j.shellhammer@ subrad@ sudheer.grandhi@
Syed Aon Mujtaba, Agere Systems, et. al.
May 2005
Jin Zhang Job Oostveen Joe Pitarresi John Ketchum John Sadowsky Jon Rosdahl Jorg Habetha Joseph Levy Kiyotaka Kobayashi Li Yuan Luke Qian Mary Cramer Masahiro Takagi Monisha Gosh Morgan Miki Osama Aboul-Magd Paul Feinberg Pen Li Peter Loc Ronald Rietman Sanjiv Nanda Seigo Nakao Sheung Li Stephen Shellhammer Subra Dravida Sudheer Grandhi
Su1-05/380r0
Company Intel Corporation Nortel Networks C-cation, Inc Cisco Systems Mitsubishi Electric Corporation Cisco Systems Nortel Networks Samsung Electronics Co Ltd Toshiba Corporation Mitsubishi Electric Corporation Toshiba Corporation Calypso Consulting Samsung Electronic Co Ltd Cisco Systems InterDigital Communications Corporation InterDigital Communications Corporation Tohoku University Tohoku University Atheros Communications Marvell Semiconductor Panasonic Intel Corporation Marvell Semiconductor Atheros Communications
Submission
Slide 1
Syed Aon Mujtaba, Agere Systems, et. al.
May 2005
Additional Authors: Name Adrian P. Stephens Alek Purkovic Alexander L. Cheng Andrew Myles Andy Molisch Brian Hart Brian Johnson Chiu Ngo Daisuke Takeda Daqing Gu Darren McNamara David Bagby Dongjun (DJ) Lee Eldad Perahia Eldad Zeira Fatih Ozluturk Hiroshi Oguma Hiroyuki Nakase Huanchun Ye Hui-Ling Lou Isaac Lim Wei Lih J. Mike Wilson James Chen Jeff Gilbert
Slide 2
email Adrian.p.stephens@ apurkovi@ AlexCheng@ amyles@ molisch@ brianh@ brjohnso@ chiu.ngo@ daisuke.takeda@toshiba.co.jp dgu@ Darren.McNamara@ david.bagby@ djthekid.lee@ eperahia@ eldad.zeira@ fatih.ozluturk@ oguma@wit.riec.tohoku.ac.jp nakase@riec.tohoku.ac.jp hcye@ hlou@ wllim@.sg james.mike.wilson@ jamesc@ gilbertj@
Standards publication; to copyright in the IEEE’s name any IEEE Standards publication even though it may include portions of this contribution; and at the IEEE’s sole discretion to permit others to reproduce in whole or in part the resulting IEEE Standards publication. The contributor also acknowledges and accepts that this contribution may be made public by IEEE 802.11.
"IEEE standards may include the known use of patent(s), including patent applications, provided the IEEE receives assurance from the patent holder or applicant with respect to patents essential for compliance with both mandatory and optional portions of the standard." Early disclosure to the Working Group of patent information that might be relevant to the standard is essential to reduce the possibility for delays in the development process and increase the likelihood that the draft publication will be approved for publication. Please notify the Chair <stuart.kerry@> as early as possible, in written or electronic form, if patented technology (or technology under patent application) might be incorporated into a draft standard being developed within the IEEE 802.11 Working Group. If you have questions, contact the IEEE Patent Committee Administrator at <patcom@>.