反应条件对悬浮床加氢裂化过程的影响
重油悬浮床加氢裂化的工艺条件的确定
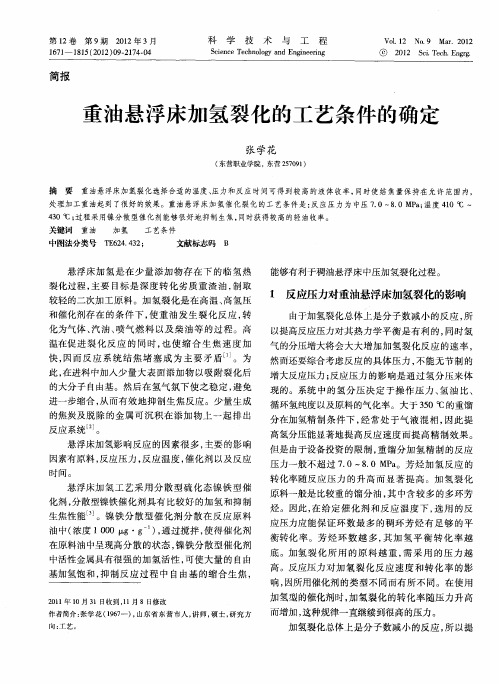
处 理加 工重油起到 了很好 的效果。重油悬浮床加 氢催 化裂化 的工艺条件是 : 应压力 为 中压 70~ . a 温度 40℃ 反 . 8 0MP ; 1
4 0℃ ; 3 过程采用镍分散 型催化剂能够很好地抑制生焦, 同时获得 较高 的轻油收率。 关键词 重油 加氢 工艺条件
中图法分类号
第1 2卷 第 9期
2 1 年 3月 02
科
学
技
术
与
工
程
Vo. 2 No 9 Ma .2 1 11 . r 02
17 — 1 1 (0 2 0 —14 0 6 1 85 2 1 ) 92 7 -4
S in e T c n l g n n i e r g c e c e h oo y a d E gn ei n
将很 大程 度上 加快 了反应 的进度 。
③ 较高 的初始 压 力下 , 能够 明显 的提 高 产物 的 收率 , 图中可 以看 出 , 相 同 的反应 温 度 下 , 高 从 在 较
化率 的提高可以通过液体产率来体现 , 关于压力对
加氢 裂化 的影 响可 以通过 图 1 来体 现 。
悬浮床加氢影响反应 的因素很多 , 主要 的影响
因素有原料 , 反应 压力 , 应 温度 , 化 剂 以及 反 应 反 催
时间。
悬浮床 加 氢 工 艺 采 用 分 散 型 硫 化 态 镍 铁 型 催 化剂, 分散 型镍铁 催 化 剂具 有 比较好 的加 氢 和抑 制 生焦 性 能 J 。镍 铁分 散 型催 化 剂 分 散 在 反 应 原 料 油中( 浓度 1 0 g・ ) 通过 搅 拌 , 0 0 g , 使得 催 化 剂 在 原料油 中呈 现高分 散 的状 态 , 镍铁 分 散 型催 化 剂 中活性金 属具有 很强 的加 氢 活性 , 可使 大量 的 自由
加氢裂化反应影响因素
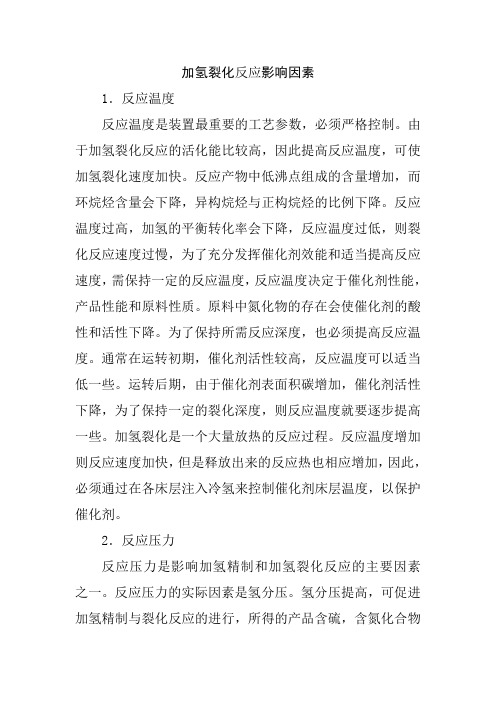
加氢裂化反应影响因素1.反应温度反应温度是装置最重要的工艺参数,必须严格控制。
由于加氢裂化反应的活化能比较高,因此提高反应温度,可使加氢裂化速度加快。
反应产物中低沸点组成的含量增加,而环烷烃含量会下降,异构烷烃与正构烷烃的比例下降。
反应温度过高,加氢的平衡转化率会下降,反应温度过低,则裂化反应速度过慢,为了充分发挥催化剂效能和适当提高反应速度,需保持一定的反应温度,反应温度决定于催化剂性能,产品性能和原料性质。
原料中氮化物的存在会使催化剂的酸性和活性下降。
为了保持所需反应深度,也必须提高反应温度。
通常在运转初期,催化剂活性较高,反应温度可以适当低一些。
运转后期,由于催化剂表面积碳增加,催化剂活性下降,为了保持一定的裂化深度,则反应温度就要逐步提高一些。
加氢裂化是一个大量放热的反应过程。
反应温度增加则反应速度加快,但是释放出来的反应热也相应增加,因此,必须通过在各床层注入冷氢来控制催化剂床层温度,以保护催化剂。
2.反应压力反应压力是影响加氢精制和加氢裂化反应的主要因素之一。
反应压力的实际因素是氢分压。
氢分压提高,可促进加氢精制与裂化反应的进行,所得的产品含硫,含氮化合物减少,更重要的是可减少结焦,保持催化剂活化,提高催化剂的稳定性。
反应器中的氢分压等于油汽加上循环氢的总压与氢气占全部气体分子数的乘积。
本装置补充氢纯度确定为99.9%。
从经济角度出发,不采用提高补充氢纯度的办法来提高氢分压。
3.氢油比氢油体积比有两种,其一是反应器入口的氢油比,其二是总冷氢油比。
反应器入口氢油比是每小时通过反应器内氢气(循环氢气+新氢)体积与每小时通过的原料油体积之比。
(单位为Nm3 /m3)。
总冷氢油体积比是每小时通入反应器的总冷氢气体积总和与每小时通过的原料油体积之比。
在加氢反应器中只有一部分氢气起反应。
大部分氢气仍以自由状态存在。
采用高氢油比,可提高氢分压,有利于传质和加氢反应的进行,在一定范围内防止油料在催化剂表面结焦。
悬浮床加氢裂化技术应用分析!

悬浮床加氢裂化技术应⽤分析!信息来源:超级⽯化主要内容:随着空⽓质量变差危害⼈类⽣活环境,急需研究开发出加⼯劣质原料油的有效⼿段,悬浮床加氢裂化技术便是其中之⼀。
⽂中针对此技术的现状及发展进⾏了系统综述,阐述了悬浮床反应器在煤—油共炼、煤焦油加氢⽅⾯的技术特点及优势,并概括了其⾯临的问题。
关键词:悬浮床加氢;煤—油共练;煤焦油加氢;延长⽯油20世纪80年代,悬浮床加氢裂化技术的研究⽐较活跃,包括国外德国的VCC技术、加拿⼤的CAN-MET技术、美国环球油品公司的VOP-Aurabon技术、意⼤利ENI公司开发的EST技术以及国内华东⽯油⼤学开发的新型悬浮床加氢技术等[1]。
1 悬浮床加氢裂化技术的现状悬浮床加氢裂化⼯艺,有煤—油共炼、重劣质油(煤焦油、渣油、FCC油浆)轻质化、煤直接液化3种加⼯模式,具有氢耗低、转化率⾼、馏分油收率⾼、投资少等优势[2]。
典型⼯艺条件对⽐见表1。
表1典型悬浮床加氢裂化⼯艺条件对⽐2 悬浮床加氢裂化技术及应⽤2.1 煤—油共炼2.1.1 ⼯艺流程煤—油共炼是将⼀定浓度的煤与重劣质油按⽐例混合,在15~22 MPa、450~470℃以及催化剂条件下,使油煤浆1次通过反应器,加氢裂解成轻、中质油和少量烃类⽓体的⼯艺技术[3]。
煤—油共炼结合了重质油加⼯和煤直接液化2项技术,使煤的直接液化更容易,同时提⾼了重油和渣油的有效利⽤率,是煤直接液化技术的改良版。
煤—油共炼中试装置⼯艺流程见图1。
悬浮床加氢裂化试验装置通过多次不同原料和不同浓度下的试验研究,试验结果表明,以西湾煤和榆炼FCC油浆为原料,在反应温度468℃、系统压⼒22 MPa、煤浓度45%的条件下,煤转化率最⾼达94%,沥青质转化率达90%,>525℃渣油转化率⾼于90%,总液体收率达70%以上。
图1煤—油共炼装置的基本流程在多次的试验研究下,对控制参数进⾏了优化调整,并根据总结出的经验,为煤—油共炼技术研究提供了数据⽀撑。
悬浮床加氢裂化反应特征分析

解效果较好 , 随着反应 的持续 , 反应 物转 化程度变大 , 大部分油 渣等 皆已经裂化转化 , 残余的部分转 化效率开始 降低 。因此实 际反应过程 中, 通过增加反应时间来达到 提高转化效 果 的作用 并不十分 明显 。
1 . 4胶 体 稳 定 性 影 响
胶质 、 沥青质是原油 中含有 的大 分子物 质 , 其 中沥青 质对 胶体稳定性影 响最大 。以往 的实践表 明 , 原油组 分越 不稳 定 , 其 中沥青质越容易聚结 。沥青质 中含有硫 、 氧、 氮等原子 , 这些 原子 的存在 , 为重油胶体提供形成 的基 础条件 。因此 在转化裂 化过程 , 此类硫、 氧、 氮等 原 子 含 量越 多 , 渣 油 的胶 体稳 定 性 越 好 。 2 加 氢 产 物 组 分 变 化 从某炼化厂选用 的工 艺设备 反应 温度 为 4 5 0  ̄ C, 催 化剂浓 度为 2 0 0  ̄ g / g 、 反应 时间为 2 h , 并设置不 同的加氢 压力 , 来分析 不 同加氢压力下 反应 物 的组 分含 量变 化 ( 表1 ) 。通 过实 验分 析反应 出, 随着 加氢压力 的增 加 , 反应后 产物 内饱 和组分 逐渐 增加 , 芳香 类组分逐渐 降低 , 胶质组分逐 渐增加 , 沥青质组分逐 渐降低 。 表 1不 劣质化和产品 清洁化趋 势加剧 , 渣油加氢裂化技术的重要性 日益提 高, 加 氢裂化工 艺技 术的要 求和 革新正稳步推进 , 就 目前几种加 氢裂化工艺技 术对比来看 , 悬浮床加 氢裂化技 术具有更多的优 势。通过讨论 悬浮床加 氢裂化 工艺 转化效果的影响 因素 , 主要 包括 温度 、 压 力、 反应 时间和胶体稳 定性。 同时也分析 了加氢裂化转化过程 在不 同工况下 , 各 目的 产品 组分含量的 变化情况 。根据生产 实践 , 优化 了更为合理 的工艺、 设备运行参数 , 为该工艺技术的推广应用提 供 了充分的 实践数据 。 关键词 : 悬浮床 ; 加氢裂化 ; 深度 裂化 ; 胶体稳定 中图分类号 : T E 6 2 4 文献识别码 : B
重油悬浮床加氢裂化的工艺条件的确定

重油悬浮床加氢裂化的工艺条件的确定张学花【摘要】重油悬浮床加氢裂化选择合适的温度、压力和反应时间可得到较高的液体收率,同时使结焦量保持在允许范围内,处理加工重油起到了很好的效果.重油悬浮床加氢催化裂化的工艺条件是:反应压力为中压7.0 ~8.0 MPa;温度410℃~430℃;过程采用镍分散型催化剂能够很好地抑制生焦,同时获得较高的轻油收率.%Sluny-bed hydrocracking of heavy oil to choose the right temperature, pressure and reaction time available to a higher liquid yield, while the amount of coke to keep within the allowable range, dealing with pro cessing of heavy oil has played a very good effect. Suspended bed hydrocracking of heavy oil catalytic cracking process conditions are; reaction pressure in the pressure 7.0 ~ 8.0 Mpa; temperature of 410 ℃ ~ 430 ℃ ; process using nickel - dispersed catalyst can good inhibition of coke, and get higher light oil yield.【期刊名称】《科学技术与工程》【年(卷),期】2012(012)009【总页数】4页(P2174-2177)【关键词】重油;加氢;工艺条件【作者】张学花【作者单位】东营职业学院,东营257091【正文语种】中文【中图分类】TE624.432悬浮床加氢是在少量添加物存在下的临氢热裂化过程,主要目标是深度转化劣质重渣油,制取较轻的二次加工原料。
加氢裂化装置反应岗位操作因素分析

加氢裂化装置反应岗位操作因素分析1.反应温度反应温度是控制脱硫脱氮率的重要手段。
对于1401-R-101,提高反应温度,提高了脱硫脱氮率,为裂化反应创造条件。
对于1401-R-102,提高反应温度可使裂解反应速度加快,原料的裂化程度加深,生成油中低沸点组分含量增加,气体产率增加。
提高反应温度对产品化学组成有明显影响,正构烷烃含量增加,异构烷烃含量降低,异构烷/正构烷的比值下降。
提高反应温度也可加快加氢速度。
故脱硫、脱氮率提高,烯烃的饱和深度亦提高,产品安定性好。
反应温度提高会使催化剂表面积炭结焦速度加快,影响其寿命。
所以,温度的选择一般受催化剂活性影响。
并且力争在催化剂活性允许的条件下,采用尽可能低的反应温度。
加氢裂化反应是一个高放热反应,反应器的温升取决于各种反应发生的程度。
在加氢裂化反应过程中,冷氢用于调节反应温度,使催化剂得到最有效的利用。
催化剂床层温度是加氢裂化工艺最重要的操作参数。
其它工艺参数对反应的影响,可用调整催化剂床层温度来补偿。
当正常运行尾油100%循环时,循环油量变化时由操作人员调整1401-R-102温度而控制。
当循环油量开始增加时,操作人员应稍稍增加1401-R-102反应器的温度;当循环油量减小时,略降低点温度。
根据不同裂化催化剂对氮含量的要求,由工艺指标确定。
催化剂活性下降时,所有反应器需要较高的温度。
在与设计进料率相应的同一条件下,当进料量减少时,为了避免过量转化,在这种条件下需要降低催化剂床层温度。
反应系统温度的限制:控制精制催化剂任一床层温升不超过30℃,裂化催化剂任一床层温升不超过12℃。
反应加热炉壁温≯520℃。
反应加热炉炉膛温度控制≯850℃。
床层最高温度控制≯440℃。
2.反应压力为了维持压力恒定,在循环氢压缩机入口分液罐1401-D-108顶装设压控调节阀。
在正常情况下该调节阀的给定值不得任意变动。
在正常运转过程中,由于催化剂床层的结焦,反应器压降增大,为保持1401-D-108的压力,反应器入口压力将逐渐提高。
悬浮床加氢裂化工艺分析研究
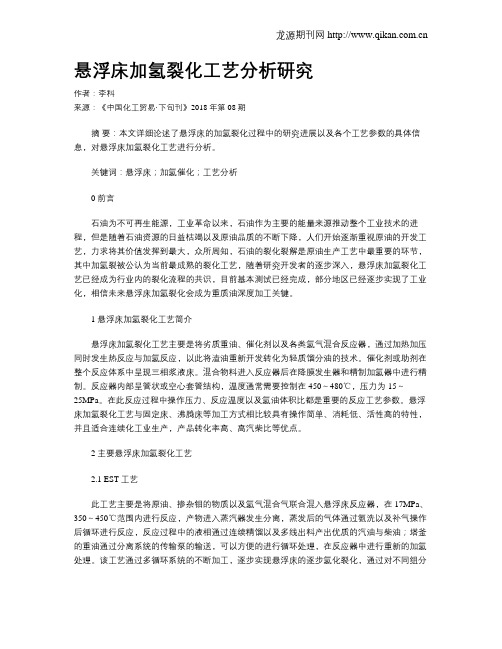
悬浮床加氢裂化工艺分析研究作者:李科来源:《中国化工贸易·下旬刊》2018年第08期摘要:本文详细论述了悬浮床的加氢裂化过程中的研究进展以及各个工艺参数的具体信息,对悬浮床加氢裂化工艺进行分析。
关键词:悬浮床;加氢催化;工艺分析0 前言石油为不可再生能源,工业革命以来,石油作为主要的能量来源推动整个工业技术的进程,但是随着石油资源的日益枯竭以及原油品质的不断下降,人们开始逐渐重视原油的开发工艺,力求将其价值发挥到最大,众所周知,石油的裂化裂解是原油生产工艺中最重要的环节,其中加氢裂被公认为当前最成熟的裂化工艺,随着研究开发者的逐步深入,悬浮床加氢裂化工艺已经成为行业内的裂化流程的共识,目前基本测试已经完成,部分地区已经逐步实现了工业化,相信未来悬浮床加氢裂化会成为重质油深度加工关键。
1 悬浮床加氢裂化工艺简介悬浮床加氢裂化工艺主要是将劣质重油、催化剂以及各类氢气混合反应器,通过加热加压同时发生热反应与加氢反应,以此将渣油重新开发转化为轻质馏分油的技术。
催化剂或助剂在整个反应体系中呈现三相浆液床。
混合物料进入反应器后在降膜发生器和精制加氢器中进行精制。
反应器内部呈管状或空心套管结构,温度通常需要控制在450~480℃,压力为15~25MPa。
在此反应过程中操作压力、反应温度以及氢油体积比都是重要的反应工艺参数。
悬浮床加氢裂化工艺与固定床、沸腾床等加工方式相比较具有操作简单、消耗低、活性高的特性,并且适合连续化工业生产,产品转化率高、高汽柴比等优点。
2 主要悬浮床加氢裂化工艺2.1 EST工艺此工艺主要是将原油、掺杂钼的物质以及氢气混合气联合混入悬浮床反应器,在17MPa、350~450℃范围内进行反应,产物进入蒸汽器发生分离,蒸发后的气体通过氨洗以及补气操作后循环进行反应,反应过程中的液相通过连续精馏以及多线出料产出优质的汽油与柴油;塔釜的重油通过分离系统的传输泵的输送,可以方便的进行循环处理,在反应器中进行重新的加氢处理。
催化剂对重油悬浮床中压加氢工艺的影响研究
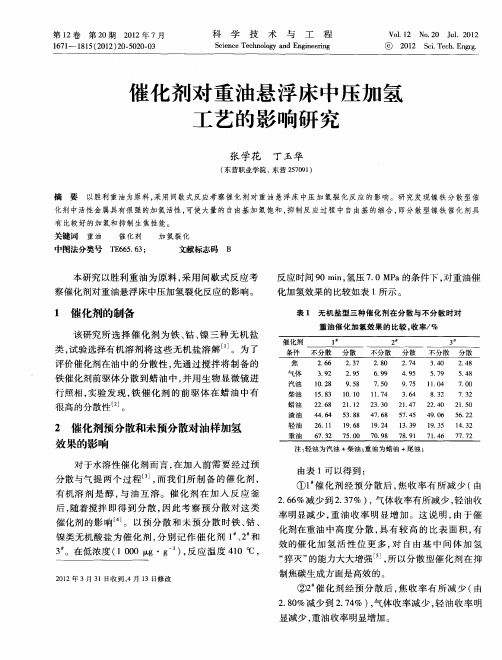
焦
3 不 同催化剂对油样催化加氢效果 的影响
以铁 、 、 三 种 无 机 盐 为 催 化 剂 , 低 浓 度 钴 镍 在 ( 0 g・ ) 反 应 温 度 为 4 0℃ , 1 0t g , 0 x 1 反应 时 间 为 9 n 氢 压为 6 0MP 0mi , . a的条 件下 , 对重 油催 化加 氢
率 减 少 , 收 率 略 有 减 少 (由 03 % 减 少 到 焦 .3 02 % ) 变化 不是 很 明显 。轻 油 收率 也 略 有减 少 , .6 ,
重 油 收率有所 增加 。
③新型催化剂在超重油 中, 过预硫化后 , 经 催
化 活性 有所增 强 , 但不 是很 明显 。
表 3 镍 催 化 剂 预 硫 化 对 超 重 表 4 铁 催 化 剂 预 硫化 对 油 催 化 加 氢 反应产物的影响
有机 溶 剂 是 醇 , 油 互 溶 。催 化 剂 在 加 入 反 应 釜 与
由表 1 以得到 : 可
①1催化剂经预分散后 , 焦收率有 所减少 ( 由
26 %减少 到 23 % ) 气 体 收率有所 减 少 , 油收 .6 .7 , 轻
率 明显减 少 , 油 收 率 明显 增 加 。这 说 明 , 重 由于 催 化 剂在 重油 中高 度 分 散 , 有 较 高 的 比表 面 积 , 具 有 效 的催 化 加 氢 活 性 位 更 多 , 自 由基 中 间 体 加 氢 对 “ 灭” 猝 的能力 大 大增强 J所 以分 散 型催 化 剂 在抑 , 制焦碳 生成 方 面是高效 的。
轻 油
3 2 .3
0 3 .3 1. 2 6 4 1. 2 7 4 2.2 6 1 3.8 6 4
3.4 3 8
加氢裂化反应原理及影响因素
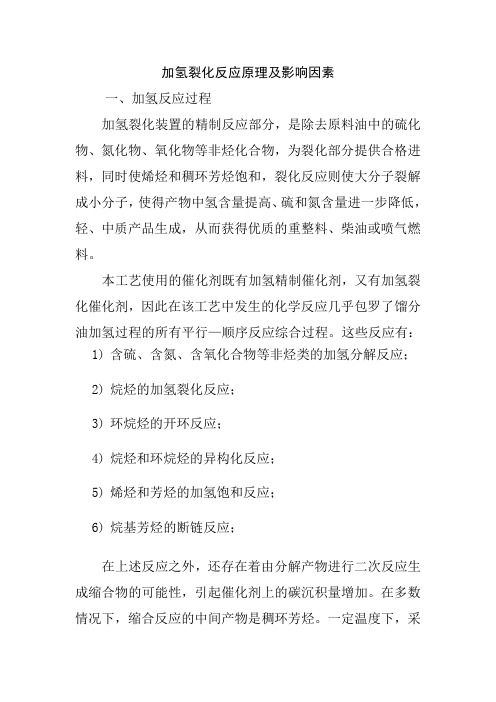
加氢裂化反应原理及影响因素一、加氢反应过程加氢裂化装置的精制反应部分,是除去原料油中的硫化物、氮化物、氧化物等非烃化合物,为裂化部分提供合格进料,同时使烯烃和稠环芳烃饱和,裂化反应则使大分子裂解成小分子,使得产物中氢含量提高、硫和氮含量进一步降低,轻、中质产品生成,从而获得优质的重整料、柴油或喷气燃料。
本工艺使用的催化剂既有加氢精制催化剂,又有加氢裂化催化剂,因此在该工艺中发生的化学反应几乎包罗了馏分油加氢过程的所有平行—顺序反应综合过程。
这些反应有:1)含硫、含氮、含氧化合物等非烃类的加氢分解反应;2)烷烃的加氢裂化反应;3)环烷烃的开环反应;4)烷烃和环烷烃的异构化反应;5)烯烃和芳烃的加氢饱和反应;6)烷基芳烃的断链反应;在上述反应之外,还存在着由分解产物进行二次反应生成缩合物的可能性,引起催化剂上的碳沉积量增加。
在多数情况下,缩合反应的中间产物是稠环芳烃。
一定温度下,采用较高的氢分压将会降低这类中间产物的浓度,从而减少催化剂上焦炭的生成。
温度的升高有利于生成中间产物,催化剂表面积炭增加。
原料油中的稠环分子浓度越高,焦炭的生成也就越多。
以上这些反应进行的深度和速度除与原料的化学组成有关外,还与催化剂的性能和反应条件有密切的关系。
二、加氢精制的原理1.加氢脱硫(HDS)反应原料油中的硫化物,在加氢精制条件下,可以转化为H2S 和相应的烃类,烃类留在产品中,而H2S从反应物中脱除,从而脱除掉硫。
主要的反应如下:硫醇加氢反应:RSH + H2 RH + H2S硫醚加氢反应:RSR`+ 2H2 RH + R`H + H2S二硫化物加氢反应:RSSR`+ 3H2 RH + R`H + 2H2S 杂环硫化物加氢反应:HC CHHC CH + 4H2 C4H10 + H2S S馏分油中的含硫化合物类型主要包括脂肪族类和非脂肪族(噻吩)类硫化物,非脂肪族类硫化物又可以按照分子中并含苯环的多少而分为噻吩类、苯并噻吩类、二苯并噻吩类等硫化物。
加氢裂化技术影响因素研究
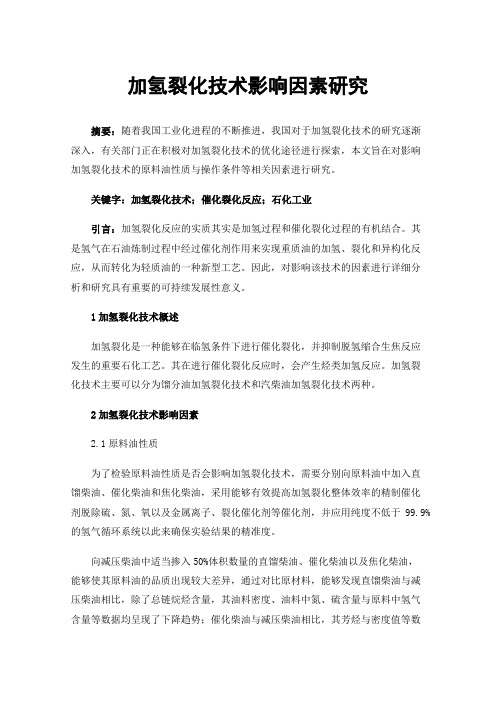
加氢裂化技术影响因素研究摘要:随着我国工业化进程的不断推进,我国对于加氢裂化技术的研究逐渐深入,有关部门正在积极对加氢裂化技术的优化途径进行探索,本文旨在对影响加氢裂化技术的原料油性质与操作条件等相关因素进行研究。
关键字:加氢裂化技术;催化裂化反应;石化工业引言:加氢裂化反应的实质其实是加氢过程和催化裂化过程的有机结合。
其是氢气在石油炼制过程中经过催化剂作用来实现重质油的加氢、裂化和异构化反应,从而转化为轻质油的一种新型工艺。
因此,对影响该技术的因素进行详细分析和研究具有重要的可持续发展性意义。
1加氢裂化技术概述加氢裂化是一种能够在临氢条件下进行催化裂化,并抑制脱氢缩合生焦反应发生的重要石化工艺。
其在进行催化裂化反应时,会产生烃类加氢反应。
加氢裂化技术主要可以分为馏分油加氢裂化技术和汽柴油加氢裂化技术两种。
2加氢裂化技术影响因素2.1原料油性质为了检验原料油性质是否会影响加氢裂化技术,需要分别向原料油中加入直馏柴油、催化柴油和焦化柴油,采用能够有效提高加氢裂化整体效率的精制催化剂脱除硫、氮、氧以及金属离子、裂化催化剂等催化剂,并应用纯度不低于99.9%的氢气循环系统以此来确保实验结果的精准度。
向减压柴油中适当掺入50%体积数量的直馏柴油、催化柴油以及焦化柴油,能够使其原料油的品质出现较大差异,通过对比原材料,能够发现直馏柴油与减压柴油相比,除了总链烷烃含量,其油料密度、油料中氮、硫含量与原料中氢气含量等数据均呈现了下降趋势;催化柴油与减压柴油相比,其芳烃与密度值等数据出现了显著的提升,其加氢裂化后的氮和硫含量也存在显著的变化;焦化柴油与减压柴油相比,其裂化后的硫含量明显上升,氮含量则呈现下降趋势。
由于向减压柴油中加入不同种类油料时,其加氢裂化后的产物中不同种类元素的含量会出现明显变化,因此,能够科学的得出原料油的性质会直接影响加氢裂化的工艺条件和产品质量这一结论。
只有根据实际情况严格的控制油料掺炼比例,才能够达到节能减排的目的[1]。
大港常压渣油悬浮床加氢裂化反应
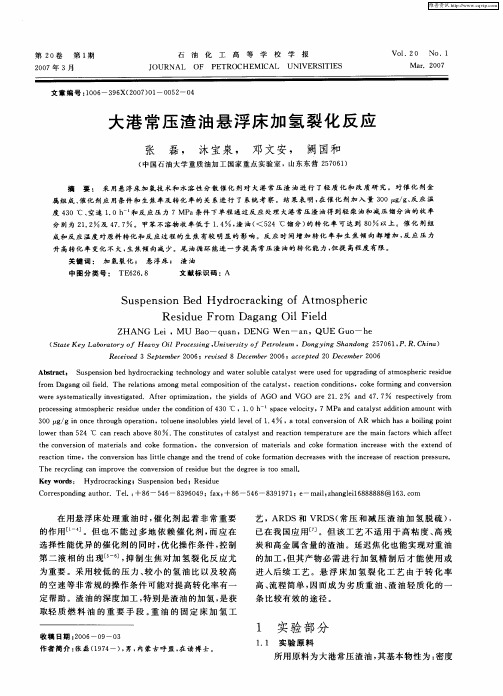
3 0b / n o c h o g p rt n o u n n ou lsyedlv l f1 4 ,attlc n eso fAR whc a ol g p it 0 t g i n et r u ho eai 。tle eis lb e il e e . g o o oa o v rino ih h sab ii on n
we e s tm atc ly i e tga e r yse ial nv s i t d. A fe ptm ia i t r o i z ton, t e y eds o GO nd V GO r .2 h il f A a a e 21 a .7 nd 47 r pe tv l r m es c ie y fo
关键 词 : 加 氢 裂 化 ; 悬 浮床 ; 渣 油
中 图 分 类 号 : TE6 6 8 2. 文 献 标 识 码 :A
Su pe in Be y r r c i fA t o ph rc s nso d H d 0c a k ng 0 m s e i Re i e Fr sdu om g ng Oi Fil Da a l ENG e — a W n n,QU E Gu — h o e
( tt y La o ao y o a y Oi o esn Un v riy o toe m ,Do g n a d n 5 0 1 P. Ch n ) S aeKe b r t r f He v lPrcsig, ie st f Per lu n yigSh n o g 2 7 6 , R. ia
l owe ha 4 ℃ c n r a h a ov 0 . r t n 52 a e c b e 8 The c ns iut sofc als nd r a to e p r t e a e t an f ct s whih a f c o tt e at y ta e c in t m e a ur r he m i a or c fe t
悬浮床重油加氢裂化技术进展 刘亮 师东

悬浮床重油加氢裂化技术进展刘亮师东摘要:悬浮床加氢技术是在催化剂和氢气存在下的高温高压的加氢裂化技术。
反应主要是热裂化,目的是将渣油转化成高附加值的轻馏分油。
催化剂的存在抑制生焦反应,得到更稳定的产品。
该技术在处理含大量金属、碳残留和沥青质的渣油有优势,且操作灵活。
关键词:渣油;重油;悬浮床;加氢裂化随着原油劣质化、重质化和产品清洁化趋势加剧,渣油加氢技术的重要性日益提高,其中悬浮床加氢裂化技术因具有原料适应性强、工艺简单、转化率高和轻油收率高等特点而引起了普遍关注,近年来研究开发日趋活跃。
一、重油悬浮床加氢技术对中国石油的意义我国每年生产2-3千万吨高金属、高残炭、高硫的稠油,随着石油的开采,劣质稠油的产量逐年增加。
然而,由于稠油质量太差,目前我国现有重油加工工艺(重油催化裂化、重油固定床加氢裂化等)很难加工这种劣质稠油,人们常将它称为“愁油”,因而迫切需要开发一种新工艺解决劣质稠油的加工问题。
目前我国自主开发的炼油加工工艺比较少。
而重油悬浮床加氢工艺是我国炼油工业自建国以来依靠自己力量,独立开发并拥有全套工艺自主知识产权的重大炼油技术创新项目之一。
中油集团公司将本项目定为公司核心技术项目,科技部列入“当前优先发展的高新技术产业化重点领域指南”,本工艺流程中的重要单元设备是目前世界上同类工艺未曾采用的,整套工艺已获得中国发明专利,并在美国申请了发明专利。
它为我国大量劣质稠油加工开辟一条新的技术路线,对我国能源安全战略具有重要意义。
二、主要渣油悬浮床加氢裂化技术进展1.意大利埃尼公司的EST技术,埃尼公司从20世纪90年代开始,在实验室和中型装置上进行了大量研发工作,开发了渣油几乎完全转化并改质的悬浮床加氢裂化工艺———EST技术,可将非常规原油(如加拿大油砂等)转化成馏分油,或改质为比重低的合成原油,该过程不产生残渣副产品(如石油焦或重燃料油)。
EST技术被视为渣油转化和非常规原油改质的一项重大技术创新。
悬浮床加氢工艺技术

悬浮床加氢工艺技术悬浮床加氢工艺技术是一种新型的炼油工艺,其主要原理是利用氢气对石油中的硫、氮等杂质进行加氢处理,提高原油的质量和产率。
悬浮床是一种特殊的反应器,在其内部的杂质去除效果更好。
悬浮床加氢工艺技术的核心在于悬浮床反应器的设计和运行。
悬浮床反应器是一种密封的金属容器,内部装有催化剂和原料油。
其设计独特的底部结构和排气系统,可以使原料油在反应器中形成悬浮状态。
在悬浮床反应器中,催化剂和原料油通过氢气的作用进行反应。
由于原料油处于悬浮状态,所以其与催化剂的接触面积更大,反应效果更好。
此外,悬浮床反应器具有较好的热传递性能,可以实现反应过程的均热,提高反应的效率。
悬浮床加氢工艺技术的关键在于优化催化剂的选择和调控。
催化剂是实现加氢反应的关键,具有良好的选择性和稳定性才能保证反应的效果。
目前,常用的催化剂有镍、钼、铜等金属。
在悬浮床加氢工艺技术中,还需要注意反应条件的控制。
温度、压力、流速等参数都会对反应的效果产生影响。
合理选择和控制这些参数,可以实现加氢反应的最佳效果。
悬浮床加氢工艺技术的应用非常广泛。
首先它可以用于石油炼制过程中的脱硫和脱氮。
硫化物和氮化物是石油中常见的杂质,会对环境和人体健康造成影响。
利用悬浮床加氢工艺技术可以将这些杂质去除,提高石油的质量。
其次,悬浮床加氢工艺技术也可以用于石油加工中的重整和裂化等过程。
重整和裂化是石油炼制中常用的工艺,可以提高石油的产率和降低成本。
总之,悬浮床加氢工艺技术是一种先进的炼油工艺,具有优异的处理效果和应用前景。
随着石油需求的增加和环境保护意识的提高,悬浮床加氢工艺技术将会在石油工业领域得到广泛应用。
悬浮床加氢裂化技术
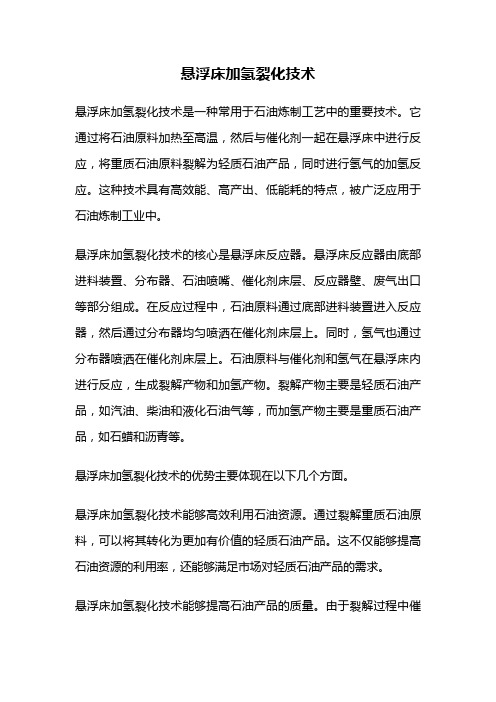
悬浮床加氢裂化技术悬浮床加氢裂化技术是一种常用于石油炼制工艺中的重要技术。
它通过将石油原料加热至高温,然后与催化剂一起在悬浮床中进行反应,将重质石油原料裂解为轻质石油产品,同时进行氢气的加氢反应。
这种技术具有高效能、高产出、低能耗的特点,被广泛应用于石油炼制工业中。
悬浮床加氢裂化技术的核心是悬浮床反应器。
悬浮床反应器由底部进料装置、分布器、石油喷嘴、催化剂床层、反应器壁、废气出口等部分组成。
在反应过程中,石油原料通过底部进料装置进入反应器,然后通过分布器均匀喷洒在催化剂床层上。
同时,氢气也通过分布器喷洒在催化剂床层上。
石油原料与催化剂和氢气在悬浮床内进行反应,生成裂解产物和加氢产物。
裂解产物主要是轻质石油产品,如汽油、柴油和液化石油气等,而加氢产物主要是重质石油产品,如石蜡和沥青等。
悬浮床加氢裂化技术的优势主要体现在以下几个方面。
悬浮床加氢裂化技术能够高效利用石油资源。
通过裂解重质石油原料,可以将其转化为更加有价值的轻质石油产品。
这不仅能够提高石油资源的利用率,还能够满足市场对轻质石油产品的需求。
悬浮床加氢裂化技术能够提高石油产品的质量。
由于裂解过程中催化剂的作用,可以使得裂解产物中的不饱和烃和硫化物含量较低,从而改善了石油产品的质量。
同时,加氢反应可以进一步降低产物中的硫含量,使得石油产品更加清洁。
悬浮床加氢裂化技术具有较高的产出和能耗效益。
由于悬浮床反应器的结构特点,反应器内的催化剂床层能够保持较好的流动性,从而提高了反应器的转化率和产出率。
同时,悬浮床加氢裂化技术还能够利用反应过程中产生的热量,进行废热回收,从而降低了能耗。
悬浮床加氢裂化技术具有较好的适应性和灵活性。
根据不同的石油原料和产品要求,可以调整催化剂的成分和反应条件,以获得理想的产物分布。
同时,悬浮床反应器的设计和操作也相对较为简单,具有较高的操作稳定性和可靠性。
悬浮床加氢裂化技术是一种高效能、高产出、低能耗的石油加工技术。
通过悬浮床反应器的设计和操作,能够将重质石油原料裂解为轻质石油产品,同时进行氢气的加氢反应。
从三聚环保说起,谈谈悬浮床加氢技术

从三聚环保说起,谈谈悬浮床加氢技术展开全文“大地”出品三聚环保:谈谈悬浮床加氢技术前言国内的悬浮床加氢技术发展到底如何呢?“大地”给大家看几则新闻。
1)神华集团2004年8月25日神华煤直接液化在内蒙古**鄂尔多斯市,伊金霍洛旗乌兰木伦镇举行了开工典礼。
2008年12月30日神华集团鄂尔多斯煤直接液化示范工程,第一条百万吨级生产线投煤试车;于2008年,12月31日,生产流程全部打通,顺利实现油渣成型,产出合格的柴油和石脑油。
2)、延长石化2012年4月18日全球首个煤油一体化的项目开始建设,采用的技术是KBR的悬浮床加氢技术,建设规模为45万吨/年,投资17.9亿元。
原料为榆林炼油厂的渣油与当地的低阶煤混炼后加氢,主要产品为石脑油、液化气、粗汽油及柴油。
2014年8月8日延长石油集团悬浮床加氢裂化中试评价装置(VCC)进料,进料油煤浆中煤粉浓度达到45%,反应温度468℃,转化率、液收均超过预期,实现了重油轻质化和油煤共炼的重大技术突破。
3)鹤壁华石联合能源科技有限公司2015年1月8日,鹤壁华石联合能源科技有限公司的煤焦油综合利用项目开始建设,项目采用的国内自主的悬浮床加氢技术,项目的总投资约200亿元。
2016年4月15日,我国首套自主研发的超级悬浮床(Mixed cracking treatment,简称MCT)工业示范装置一次开车成功。
上面说到了国内几个企业使用的几个悬浮床加氢技术:神华集团使用的是自主的沸腾床加氢T-Star工艺,应该是使用悬浮床反应器的沸腾床缓和加氢裂化工艺。
参考为国际的H-Oil工艺。
延长石化使用的是KBR公司的悬浮床加氢技术。
鹤壁华石联合能源科技有限公司使用的是三聚环保自主研发的悬浮床加氢技术。
一、国际悬浮床加氢技术悬浮床渣油加氢技术是一种劣质渣油的加氢裂化工艺过程,具有原料适应性强、工艺简单、操作灵活、转化率高等特点。
能够加工其它渣油加氢技术难以加工的原料,如油砂沥青等稠油原料,是一种非常有前景的渣油加氢转化技术。
加氢裂化操作因素变化的分析

操作参数对反应过程的影响主要讨论反应温度、压力、氢油比及空速等操作参数对加氢裂化转化深度、产品分布以及产品质量的影响。
讨论的前提:反应器物流近似于活塞流且径向温差很小(不存在沟流、返混)。
一.反应温度1.CAT、CAT1、CAT2、BAT11、BAT12、BAT13、BAT21、BAT22、BAT23、BAT24介绍CAT(Catalyzer Average Temperature)为一个反应器中催化剂的平均温度,其值等于该反应器中每一床层温度和该床层的催化剂在反应器总催化剂中所占体积百分数乘积之和(加权平均温度)。
BAT(Bed Average Temperature)为床层的平均温度,其值等于某一床层入口温度和出口温度的算术平均值。
温度分布是指每个反应器所有床层从上到下每个床层出入口温度所形成的曲线图。
一般要求在同一反应器中每个床层进出口温度是相同的,这样所形成的温度分布为“平坦的”。
相对于平坦的温度分布曲线,有上升的温度曲线和下降的温度曲线,两相比较,有相同的转化率下,平坦的温度分布曲线使催化剂有较均匀的工作条件使催化剂寿命延长。
反应温度对反应过程的影响机理简述。
反应器中的反应主要分加氢精制反应和加氢裂化反应。
精制反应器中以加氢精制反应为主,伴有加氢裂化反应,裂化反应器中以加氢裂化反应为主,伴有加氢精制反应。
前面花主任在讲《加氢裂化过程的化学反应》时对加氢裂化过程中涉及到的各类化学反应讲得比较详细。
从反应动力学和反应热力学两个角度综合分析,得出的结论是提高反应温度有利于精制反应和裂化反应的进行。
2.反应温度对转化率的影响转化率:加氢裂化是重质烃/非烃复杂混合物轻质化的过程,过程的裂化转化率理论上指的是通过反应生成进料中原来未含有的轻馏分产率。
但有两种情况需要说明:1)由于进料往往为很宽的馏分油,进料本身就含有一部分轻质产品组分,它并非由裂化产生;2)进料中最重的部分通过轻微裂化变成较小的分子,但其沸点范围仍在原料范围之中而未进入轻质产品,还是比我们需要的产品重。
加氢裂化反应影响因素
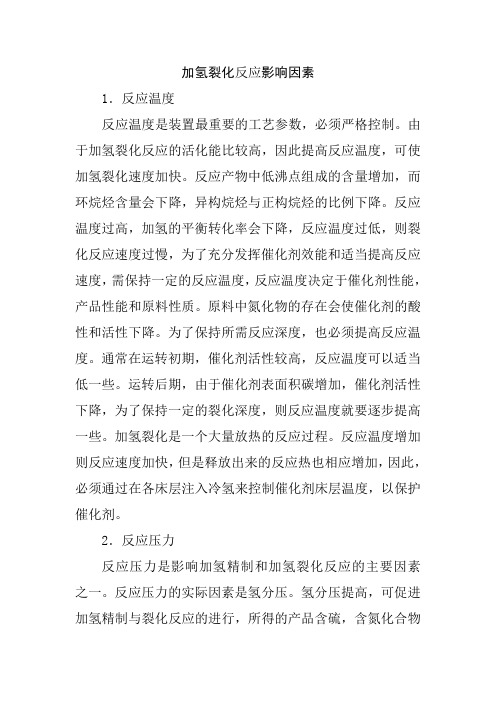
加氢裂化反应影响因素1.反应温度反应温度是装置最重要的工艺参数,必须严格控制。
由于加氢裂化反应的活化能比较高,因此提高反应温度,可使加氢裂化速度加快。
反应产物中低沸点组成的含量增加,而环烷烃含量会下降,异构烷烃与正构烷烃的比例下降。
反应温度过高,加氢的平衡转化率会下降,反应温度过低,则裂化反应速度过慢,为了充分发挥催化剂效能和适当提高反应速度,需保持一定的反应温度,反应温度决定于催化剂性能,产品性能和原料性质。
原料中氮化物的存在会使催化剂的酸性和活性下降。
为了保持所需反应深度,也必须提高反应温度。
通常在运转初期,催化剂活性较高,反应温度可以适当低一些。
运转后期,由于催化剂表面积碳增加,催化剂活性下降,为了保持一定的裂化深度,则反应温度就要逐步提高一些。
加氢裂化是一个大量放热的反应过程。
反应温度增加则反应速度加快,但是释放出来的反应热也相应增加,因此,必须通过在各床层注入冷氢来控制催化剂床层温度,以保护催化剂。
2.反应压力反应压力是影响加氢精制和加氢裂化反应的主要因素之一。
反应压力的实际因素是氢分压。
氢分压提高,可促进加氢精制与裂化反应的进行,所得的产品含硫,含氮化合物减少,更重要的是可减少结焦,保持催化剂活化,提高催化剂的稳定性。
反应器中的氢分压等于油汽加上循环氢的总压与氢气占全部气体分子数的乘积。
本装置补充氢纯度确定为99.9%。
从经济角度出发,不采用提高补充氢纯度的办法来提高氢分压。
3.氢油比氢油体积比有两种,其一是反应器入口的氢油比,其二是总冷氢油比。
反应器入口氢油比是每小时通过反应器内氢气(循环氢气+新氢)体积与每小时通过的原料油体积之比。
(单位为Nm3 /m3)。
总冷氢油体积比是每小时通入反应器的总冷氢气体积总和与每小时通过的原料油体积之比。
在加氢反应器中只有一部分氢气起反应。
大部分氢气仍以自由状态存在。
采用高氢油比,可提高氢分压,有利于传质和加氢反应的进行,在一定范围内防止油料在催化剂表面结焦。
加氢裂化反应影响因素
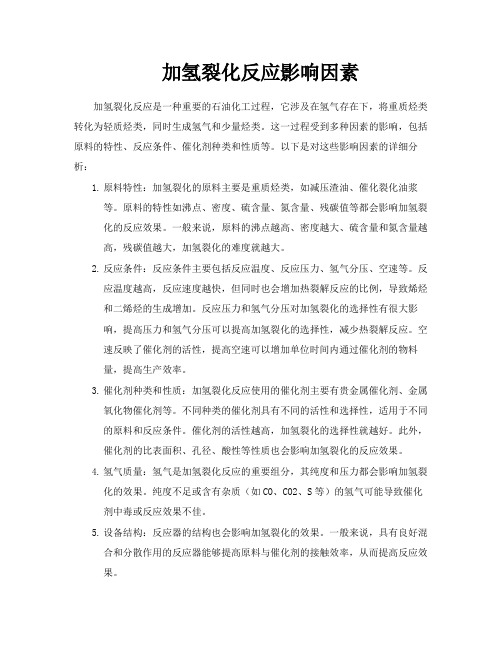
加氢裂化反应影响因素加氢裂化反应是一种重要的石油化工过程,它涉及在氢气存在下,将重质烃类转化为轻质烃类,同时生成氢气和少量烃类。
这一过程受到多种因素的影响,包括原料的特性、反应条件、催化剂种类和性质等。
以下是对这些影响因素的详细分析:1.原料特性:加氢裂化的原料主要是重质烃类,如减压渣油、催化裂化油浆等。
原料的特性如沸点、密度、硫含量、氮含量、残碳值等都会影响加氢裂化的反应效果。
一般来说,原料的沸点越高、密度越大、硫含量和氮含量越高,残碳值越大,加氢裂化的难度就越大。
2.反应条件:反应条件主要包括反应温度、反应压力、氢气分压、空速等。
反应温度越高,反应速度越快,但同时也会增加热裂解反应的比例,导致烯烃和二烯烃的生成增加。
反应压力和氢气分压对加氢裂化的选择性有很大影响,提高压力和氢气分压可以提高加氢裂化的选择性,减少热裂解反应。
空速反映了催化剂的活性,提高空速可以增加单位时间内通过催化剂的物料量,提高生产效率。
3.催化剂种类和性质:加氢裂化反应使用的催化剂主要有贵金属催化剂、金属氧化物催化剂等。
不同种类的催化剂具有不同的活性和选择性,适用于不同的原料和反应条件。
催化剂的活性越高,加氢裂化的选择性就越好。
此外,催化剂的比表面积、孔径、酸性等性质也会影响加氢裂化的反应效果。
4.氢气质量:氢气是加氢裂化反应的重要组分,其纯度和压力都会影响加氢裂化的效果。
纯度不足或含有杂质(如CO、CO2、S等)的氢气可能导致催化剂中毒或反应效果不佳。
5.设备结构:反应器的结构也会影响加氢裂化的效果。
一般来说,具有良好混合和分散作用的反应器能够提高原料与催化剂的接触效率,从而提高反应效果。
6.操作因素:操作因素包括原料的预处理、进料方式、反应温度控制等。
预处理可以改善原料的性质,提高加氢裂化的效果。
进料方式对原料与催化剂的接触效率和反应速度都有影响。
反应温度控制不当可能导致局部过热或反应不均匀,从而影响产品分布和产品质量。
- 1、下载文档前请自行甄别文档内容的完整性,平台不提供额外的编辑、内容补充、找答案等附加服务。
- 2、"仅部分预览"的文档,不可在线预览部分如存在完整性等问题,可反馈申请退款(可完整预览的文档不适用该条件!)。
- 3、如文档侵犯您的权益,请联系客服反馈,我们会尽快为您处理(人工客服工作时间:9:00-18:30)。
第3 4卷 第 3 期
20 06年 6月
燃
料
化
学
学
报
Vo . 4 NO. 13 3 Jn 0 6 u .2 O
J u n lo u l e sr n e h o o y o r a fF e Ch mity a d T c n l g
Ef e to e c i n o ii nso dr c a k n l su r e f c fr a to c nd to n hy O r c i g i l r y b d l
Z O J —h n QU oh H U i su , E Gu -e a
( ol eo hmir n hm cl n ier g hn nvri e oem ( a t hn ) Dog i 27 6 , hn ) C l g e fC e s ya dC e i gnei ,C i U i st o t lu E s C ia , nyn t aE n a e y fP r g 501 C i a
tle zn r x mi e ac eco .P esr a i ee t fe t e e dn n temoe ua t cue o yb n e e weee a n d i ab thra tr rsu eh sdf rn fcsd p n igo lc lrsr tr f n f e h u
r a t t .W i asn f p r a h d o e r s u ,me c a k n e c o f tr b t l e z n s p o t d e ca s n t me r ii g o a t y g n p e s r h i l r e r c g r a t n o et u yb n e e i r mp e i i . r
Ab ta t ]eefc f at l y r g np es r ti s r c :1h fe t r a d o e rsuewi n3№ op i h h ~2 8 o rc igo uyb n e ea dtr.u ncak n f tle z n n et . b b
文章 编 号 : 2 32 0 (0 6 0 -340 05 - 9 20 )30 2 -4 4
反应 条 件对 悬浮床 加 氢裂 化 过 程 的影 响
周 家顺 ,阙 国和
( 中国石 油大学 ( 华东 ) 化学 化工学 院 , 山东 东营 2 7 6 ) 5 0 1
摘
要: 在间歇 式反应釜 中, 考察了氢分压 3MP 一 8M a对叔丁基 苯和正 丁基 苯裂 化反应 的影响 。结 果表 明 , a 2 P 氢分 压变化
.
d e ss d e u swa t i u d.W i t er ii g o i a y o e r su e t er a t n fh d o mc n d t e f r t n o m as f n t h d g n p e s r h c o so y c k g a o ma o f h n i i l r e i r i n h i t l e e i s l b e f c o e p o td s l n o sy fe t o a t n t mp r t r d t l s i u s d o u n n o u l a t n a r mo e i t e u l .E f c s f e ci r i r mu a r o e e a u a me ae a o ds se e n i l c
对不 同分子结构 的反应 物有 不同的影响。叔丁基苯 的转 化率随 氢分压 的升高 而提 高 , 正丁基 苯的转 化率 随氢分压 的升高 而 降低 。氢分压的提高促进 了与芳香环 连接的碳键的断裂 , 与反 应物的分子结 构无关 。在 此基础上 , 考察 了初氢 压的变化对轮 古常压渣油 ( G R) L A 和克拉玛依常压渣油 ( M R) 浮床加 氢裂 化 的影 响, KA 悬 讨论 了温度 和反应 时间对 悬 浮床加 氢过程 的影 响, 初氢压的提高对渣油的转化和 甲苯不溶物 的生成 都有促进 作用 。 关键词 :反应条件 ; 丁基苯 ; 叔 正丁基苯 ;常压渣油 ; 悬浮床 ; 加氢 裂化 中图分类号 : E 2 . 3 T 644 2 文献标 识码 : A
.
wh l e c n e s n o u y b n e ei e t ce .I y c s .t eb e k o — C b n sb t e ea o t i g i t பைடு நூலகம் v ri f t le z n s s it d n a a e h r a fC eh o b r r n o d ewe n t ma crn h r i n o eb a h c an ae p o t d wi t n r a i g o at h d o e r su e a e n t b v a d te wh l r c h i l r mo e t e i c e sn fp r a y r g n p e s r B s d o e a o e r . h n h h i l h e s i,t e e e to ii y r g n p su e o lry b d h d o r c i g o u g d Ka a y amo p ei s u t h f c fi t h d o e r s n s r e y c a k n fL n u a r ma t s h r r i n a l e r u r n ce .