水平直接电镀之导电膜配方工艺DMSE操作方法
线路导电膜工艺流程

线路导电膜工艺流程英文回答:The process of circuit conductive film manufacturing involves several steps. Here is a general outline of the process:1. Substrate Preparation: The first step is to prepare the substrate on which the conductive film will be applied. This can be done by cleaning the substrate to remove any dirt, dust, or grease that may interfere with the adhesion of the film.2. Coating Application: The conductive film is then applied to the substrate using a coating technique. There are several methods for applying the film, including spin coating, spray coating, and dip coating. The choice of method depends on factors such as the film thickness required and the desired uniformity of the coating.3. Drying: After the conductive film is applied, it needs to be dried to remove any solvents or water presentin the coating. This can be done using a drying oven or by exposing the film to air at room temperature. The drying process should be carefully controlled to ensure the film does not crack or peel.4. Annealing: Once the film is dry, it may undergo an annealing process to improve its electrical conductivityand stability. Annealing is typically done by heating the film to a specific temperature for a certain period of time. This step helps to remove any residual stress in the film and enhances its performance.5. Patterning: After the conductive film is annealed,it may be patterned to create the desired circuit layout. This can be done using techniques such as photolithography, where a patterned mask is used to selectively expose thefilm to light. The exposed areas can then be etched away to leave behind the desired circuit pattern.6. Post-treatment: Once the conductive film ispatterned, it may undergo additional post-treatment steps to enhance its properties. This can include treatments such as surface modification, coating with protective layers, or annealing at specific temperatures to further improve conductivity.7. Testing and Quality Control: Finally, the manufactured conductive film undergoes testing and quality control measures to ensure it meets the required specifications. This can include electrical conductivity testing, adhesion testing, and visual inspection to check for any defects or inconsistencies.中文回答:线路导电膜的制造工艺包括以下几个步骤:1. 基材准备,首先需要准备好导电膜将要涂覆的基材。
滚镀导电方案
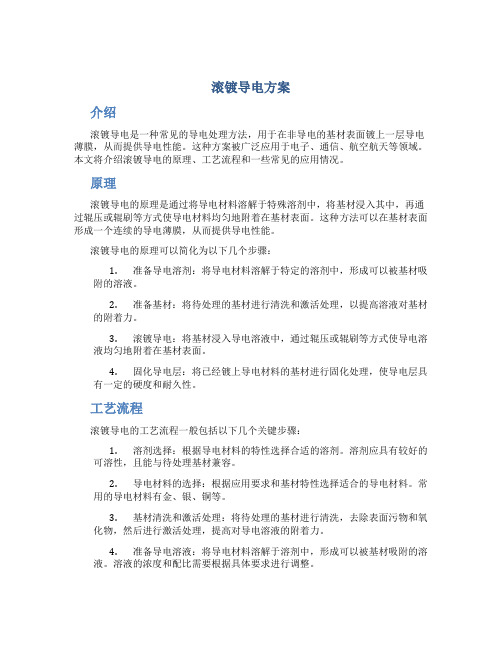
滚镀导电方案介绍滚镀导电是一种常见的导电处理方法,用于在非导电的基材表面镀上一层导电薄膜,从而提供导电性能。
这种方案被广泛应用于电子、通信、航空航天等领域。
本文将介绍滚镀导电的原理、工艺流程和一些常见的应用情况。
原理滚镀导电的原理是通过将导电材料溶解于特殊溶剂中,将基材浸入其中,再通过辊压或辊刷等方式使导电材料均匀地附着在基材表面。
这种方法可以在基材表面形成一个连续的导电薄膜,从而提供导电性能。
滚镀导电的原理可以简化为以下几个步骤:1.准备导电溶剂:将导电材料溶解于特定的溶剂中,形成可以被基材吸附的溶液。
2.准备基材:将待处理的基材进行清洗和激活处理,以提高溶液对基材的附着力。
3.滚镀导电:将基材浸入导电溶液中,通过辊压或辊刷等方式使导电溶液均匀地附着在基材表面。
4.固化导电层:将已经镀上导电材料的基材进行固化处理,使导电层具有一定的硬度和耐久性。
工艺流程滚镀导电的工艺流程一般包括以下几个关键步骤:1.溶剂选择:根据导电材料的特性选择合适的溶剂。
溶剂应具有较好的可溶性,且能与待处理基材兼容。
2.导电材料的选择:根据应用要求和基材特性选择适合的导电材料。
常用的导电材料有金、银、铜等。
3.基材清洗和激活处理:将待处理的基材进行清洗,去除表面污物和氧化物,然后进行激活处理,提高对导电溶液的附着力。
4.准备导电溶液:将导电材料溶解于溶剂中,形成可以被基材吸附的溶液。
溶液的浓度和配比需要根据具体要求进行调整。
5.滚镀导电:将基材浸入导电溶液中,通过辊压或辊刷等方式使导电溶液均匀地附着在基材表面。
滚镀的时间和压力需要根据导电溶液的性质和基材的特性进行控制。
6.固化导电层:将已经镀上导电材料的基材进行固化处理,一般通过加热、紫外线照射或化学反应等方式使导电层具有一定的硬度和耐久性。
7.表面处理:根据具体应用需求,对导电层进行表面处理,如抛光、喷漆、涂覆保护层等。
应用情况滚镀导电方案在多个领域中得到了广泛应用,以下是一些常见的应用情况:1.电子产品:滚镀导电常用于电子产品的印制电路板(PCB)制造,可以在非导电的基材上形成导电电路,实现电子元器件的连接和信号传输。
导电涂层喷涂工艺流程

导电涂层喷涂工艺流程
导电涂层喷涂工艺流程:
①表面预处理:清洁待喷涂物体的表面,去除油污、尘埃和其他杂质,必要时进行打磨或化学处理,以增强涂层的附着力。
②调配导电漆:按照产品说明书的比例将导电漆与稀释剂混合,充分搅拌至均匀,确保金属填充物分散良好,避免沉淀。
③喷涂设备调试:设置喷枪的气压、流量和喷幅,调整喷嘴大小和喷涂距离,以获得最佳的雾化效果和涂层厚度。
④试喷与调整:在非关键区域进行试喷,检查涂层的均匀性和覆盖度,必要时调整喷涂参数。
⑤正式喷涂:采用十字涂装法等技术,均匀地喷涂导电漆,控制涂层厚度在指定范围内,通常为10-14微米。
⑥间歇搅拌:在喷涂过程中,定期搅拌容器内的导电漆,防止金属填充物沉淀,影响导电性能。
⑦干燥固化:让喷涂后的物体自然干燥或在适宜的温度下加速固化,确保涂层完全硬化。
⑧质量检查:使用电阻测试仪等设备检测涂层的导电性能,检查是否有漏喷、涂层过薄或过厚的情况。
⑨修补与重涂:如果发现不合格区域,进行局部修补或重新喷涂,直到满足质量标准。
⑩最终检验:进行全面的质量检验,包括外观检查、导电性能测试和附着力测试,确保成品符合要求。
导电涂料的合成工艺技术路线
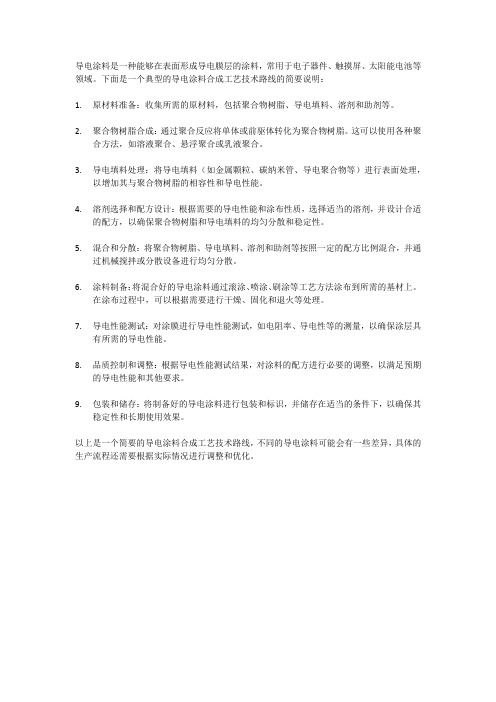
导电涂料是一种能够在表面形成导电膜层的涂料,常用于电子器件、触摸屏、太阳能电池等领域。
下面是一个典型的导电涂料合成工艺技术路线的简要说明:
1.原材料准备:收集所需的原材料,包括聚合物树脂、导电填料、溶剂和助剂等。
2.聚合物树脂合成:通过聚合反应将单体或前驱体转化为聚合物树脂。
这可以使用各种聚
合方法,如溶液聚合、悬浮聚合或乳液聚合。
3.导电填料处理:将导电填料(如金属颗粒、碳纳米管、导电聚合物等)进行表面处理,
以增加其与聚合物树脂的相容性和导电性能。
4.溶剂选择和配方设计:根据需要的导电性能和涂布性质,选择适当的溶剂,并设计合适
的配方,以确保聚合物树脂和导电填料的均匀分散和稳定性。
5.混合和分散:将聚合物树脂、导电填料、溶剂和助剂等按照一定的配方比例混合,并通
过机械搅拌或分散设备进行均匀分散。
6.涂料制备:将混合好的导电涂料通过滚涂、喷涂、刷涂等工艺方法涂布到所需的基材上。
在涂布过程中,可以根据需要进行干燥、固化和退火等处理。
7.导电性能测试:对涂膜进行导电性能测试,如电阻率、导电性等的测量,以确保涂层具
有所需的导电性能。
8.品质控制和调整:根据导电性能测试结果,对涂料的配方进行必要的调整,以满足预期
的导电性能和其他要求。
9.包装和储存:将制备好的导电涂料进行包装和标识,并储存在适当的条件下,以确保其
稳定性和长期使用效果。
以上是一个简要的导电涂料合成工艺技术路线,不同的导电涂料可能会有一些差异,具体的生产流程还需要根据实际情况进行调整和优化。
线路板直接电镀DMSE的技术问题
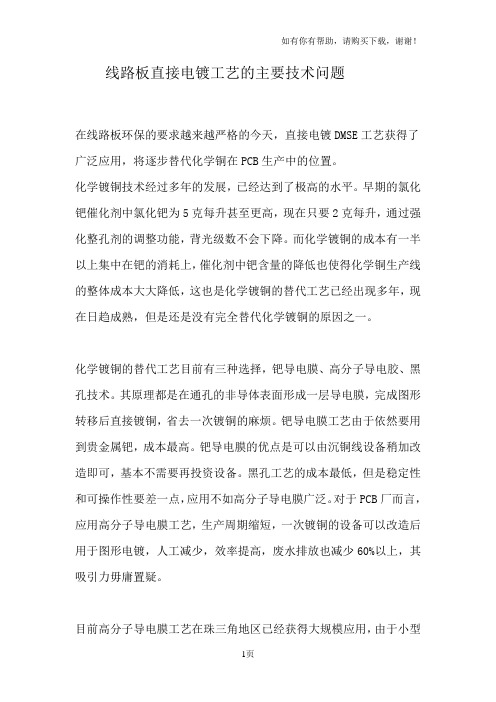
线路板直接电镀工艺的主要技术问题在线路板环保的要求越来越严格的今天,直接电镀DMSE工艺获得了广泛应用,将逐步替代化学铜在PCB生产中的位置。
化学镀铜技术经过多年的发展,已经达到了极高的水平。
早期的氯化钯催化剂中氯化钯为5克每升甚至更高,现在只要2克每升,通过强化整孔剂的调整功能,背光级数不会下降。
而化学镀铜的成本有一半以上集中在钯的消耗上,催化剂中钯含量的降低也使得化学铜生产线的整体成本大大降低,这也是化学镀铜的替代工艺已经出现多年,现在日趋成熟,但是还是没有完全替代化学镀铜的原因之一。
化学镀铜的替代工艺目前有三种选择,钯导电膜、高分子导电胶、黑孔技术。
其原理都是在通孔的非导体表面形成一层导电膜,完成图形转移后直接镀铜,省去一次镀铜的麻烦。
钯导电膜工艺由于依然要用到贵金属钯,成本最高。
钯导电膜的优点是可以由沉铜线设备稍加改造即可,基本不需要再投资设备。
黑孔工艺的成本最低,但是稳定性和可操作性要差一点,应用不如高分子导电膜广泛。
对于PCB厂而言,应用高分子导电膜工艺,生产周期缩短,一次镀铜的设备可以改造后用于图形电镀,人工减少,效率提高,废水排放也减少60%以上,其吸引力毋庸置疑。
目前高分子导电膜工艺在珠三角地区已经获得大规模应用,由于小型PCB厂商不愿意投资设备,导电胶加工厂有了一定的生存空间。
目前导电胶加工厂也存在一些问题,高密度微小孔径的板子无法保证品质,采用导电胶加工的板子后期焊接爆孔的问题也不少见。
做导电胶药水的厂家往往因此而赔款。
如果孔内镀铜层的平均厚度是达标的,药水商基本无话可说,只能接受赔款。
事实上,影响爆孔的因素很多,钻孔的品质、铜光亮剂的分散能力、镀铜层的应力等因素都会关系到爆孔。
导电膜的品质对孔壁的附着力有着重大影响。
使用EDOT为单体的导电胶药水往往存在分散不好的情况,EDOT本身的原料品质和与之配合的乳化分散材料都能影响最后PEDOT导电膜的厚度和附着力。
这方面的详情可以联系本文作者ZLMPCB。
高分子导电膜孔化直接电镀新型工艺
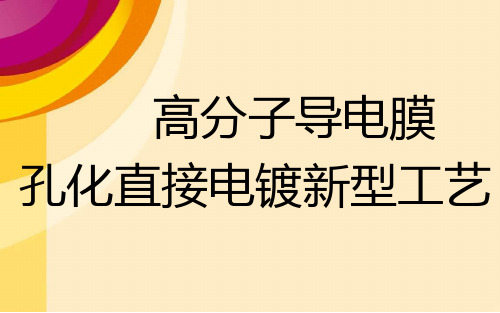
高分子导电膜孔化技术取代 PCB/FPC制程中的传统PTH 和Panel Plating 等工序的直 接进行Pattern plating的工艺
高分子导电膜孔化流程图如下:
钻孔 去毛刺 高分子单体 聚合吸附 清洁整平 两道水洗 微蚀 两道水洗 两道水洗 氧化 两道水洗
烘干
铜面磨刷
图形印刷
Hale Waihona Puke 酸浸两道水洗电镀纯锡
酸浸
两道水洗
图形电镀
经过清洁整平剂和高锰酸钾氧化反应在孔壁樹脂的表面和銅表 面上均勻地吸附形成厚度約1μm 的二氧化錳吸附層與導電聚合物 單體吡咯反應被還原成二價錳離子,而吡咯單體被氧化並聚合在一 起形成單鍵和雙鍵交替存在的聚合物。正是由於單雙鍵交替存在, 可以通過共振作用使電子在聚合物中自由移動而形成緻密光滑的有 机高分子聚吡咯導電黑膜,从而为直接图形电镀铜提供导电层:
热冲击测试(288degC/10sec):
通过有机高分子聚合催化反应形成 黑色导电膜直接进行图形电镀铜处 理的导通孔纵切面SEM图如下:
长期可靠性:热循环和热冲击测试
通过敝司CSM-3200铜光剂和有机高分子导电膜 CSM-2400已经被一些OEM所认可并且通过了 PCB/FPC的电镀行业热循环和热冲击测试,测试内 容如下:
长期可靠性:客户测试结果
导电薄膜生产工艺
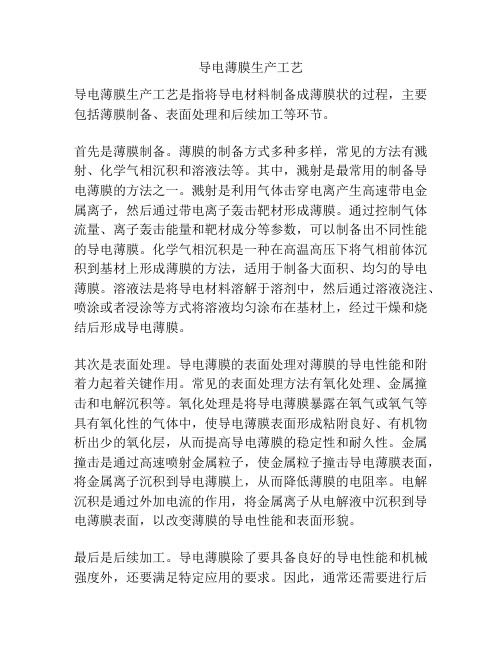
导电薄膜生产工艺导电薄膜生产工艺是指将导电材料制备成薄膜状的过程,主要包括薄膜制备、表面处理和后续加工等环节。
首先是薄膜制备。
薄膜的制备方式多种多样,常见的方法有溅射、化学气相沉积和溶液法等。
其中,溅射是最常用的制备导电薄膜的方法之一。
溅射是利用气体击穿电离产生高速带电金属离子,然后通过带电离子轰击靶材形成薄膜。
通过控制气体流量、离子轰击能量和靶材成分等参数,可以制备出不同性能的导电薄膜。
化学气相沉积是一种在高温高压下将气相前体沉积到基材上形成薄膜的方法,适用于制备大面积、均匀的导电薄膜。
溶液法是将导电材料溶解于溶剂中,然后通过溶液浇注、喷涂或者浸涂等方式将溶液均匀涂布在基材上,经过干燥和烧结后形成导电薄膜。
其次是表面处理。
导电薄膜的表面处理对薄膜的导电性能和附着力起着关键作用。
常见的表面处理方法有氧化处理、金属撞击和电解沉积等。
氧化处理是将导电薄膜暴露在氧气或氧气等具有氧化性的气体中,使导电薄膜表面形成粘附良好、有机物析出少的氧化层,从而提高导电薄膜的稳定性和耐久性。
金属撞击是通过高速喷射金属粒子,使金属粒子撞击导电薄膜表面,将金属离子沉积到导电薄膜上,从而降低薄膜的电阻率。
电解沉积是通过外加电流的作用,将金属离子从电解液中沉积到导电薄膜表面,以改变薄膜的导电性能和表面形貌。
最后是后续加工。
导电薄膜除了要具备良好的导电性能和机械强度外,还要满足特定应用的要求。
因此,通常还需要进行后续加工,如切割、印刷和膜转移等。
切割是将大面积的导电薄膜切割成特定的形状和尺寸,以适应具体的应用。
印刷是将导电薄膜印刷到基材上,从而形成柔性电子元件,如柔性电路板和柔性显示屏等。
膜转移是将导电薄膜从生长基材上转移到另一个基材上,以实现多种材料的组合和功能的实现。
综上所述,导电薄膜生产工艺是一个复杂的过程,需要进行薄膜制备、表面处理和后续加工等环节,以实现导电薄膜的具体应用。
随着科学技术的不断进步,导电薄膜的制备工艺也在不断演进,以满足越来越多的应用需求。
导电膜工艺
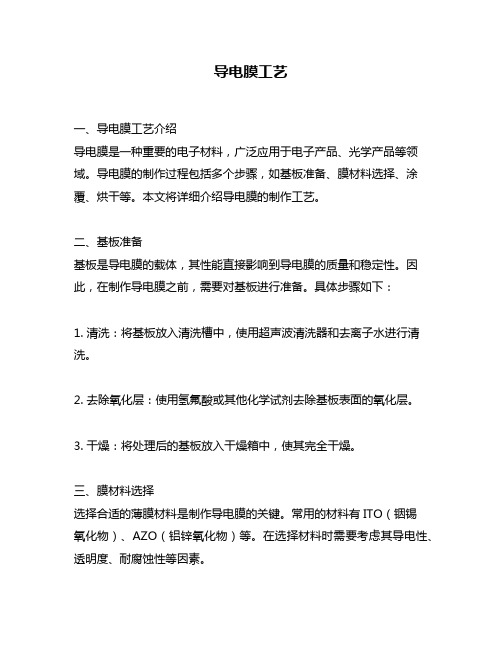
导电膜工艺一、导电膜工艺介绍导电膜是一种重要的电子材料,广泛应用于电子产品、光学产品等领域。
导电膜的制作过程包括多个步骤,如基板准备、膜材料选择、涂覆、烘干等。
本文将详细介绍导电膜的制作工艺。
二、基板准备基板是导电膜的载体,其性能直接影响到导电膜的质量和稳定性。
因此,在制作导电膜之前,需要对基板进行准备。
具体步骤如下:1. 清洗:将基板放入清洗槽中,使用超声波清洗器和去离子水进行清洗。
2. 去除氧化层:使用氢氟酸或其他化学试剂去除基板表面的氧化层。
3. 干燥:将处理后的基板放入干燥箱中,使其完全干燥。
三、膜材料选择选择合适的薄膜材料是制作导电膜的关键。
常用的材料有ITO(铟锡氧化物)、AZO(铝锌氧化物)等。
在选择材料时需要考虑其导电性、透明度、耐腐蚀性等因素。
四、涂覆涂覆是导电膜制作的核心步骤,其质量直接影响到导电膜的性能。
常用的涂覆方法有旋涂法、喷雾法、离子束溅射法等。
以ITO为例,具体涂覆步骤如下:1. 准备溶液:将ITO粉末与乙酸丁酯等有机溶剂混合,制成ITO溶液。
2. 涂覆:将基板放入旋转台上,使用注射器将ITO溶液滴在基板上,并启动旋转台使其均匀分布。
3. 烘干:将涂覆后的基板放入烘箱中进行烘干,使其完全固化。
五、烘干烘干是导电膜制作过程中必不可少的步骤。
在烘干过程中需要注意以下几点:1. 温度控制:根据所选材料和工艺要求,设定适当的烘干温度和时间。
2. 通风控制:在烘干过程中需要保持通风良好,以避免产生有害气体。
3. 检查质量:烘干后需对导电膜的质量进行检查,如有缺陷需要进行修补或重新制作。
六、电极制作导电膜通常需要与电极相连,以实现其导电功能。
常用的电极制作方法有蒸镀法、溅射法等。
具体步骤如下:1. 准备金属材料:选择合适的金属材料,如铝、银等。
2. 制作电极:将金属材料蒸镀或溅射在导电膜上,形成电极。
3. 烘干:将制作好的导电膜和电极放入烘箱中进行烘干,使其完全固化。
七、测试与包装在制作完成后,需要对导电膜进行测试和包装。
- 1、下载文档前请自行甄别文档内容的完整性,平台不提供额外的编辑、内容补充、找答案等附加服务。
- 2、"仅部分预览"的文档,不可在线预览部分如存在完整性等问题,可反馈申请退款(可完整预览的文档不适用该条件!)。
- 3、如文档侵犯您的权益,请联系客服反馈,我们会尽快为您处理(人工客服工作时间:9:00-18:30)。
水平直接电镀之导电膜配方工艺DMSE操作方法
(周生电镀导师)
高分子导电膜工艺,又称导电胶工艺或水平环保通孔,都是在PCB孔内形成一层高分子导电膜层,然后直接电镀的工艺,最新的DMSE配方已经发展了四代,目前的工艺更加稳定,使用周期更长了。
本工艺可以替代化学镀铜工艺。
但是目前看DMSE 并不能完全替代化学镀铜,主要是附着力及可靠性问题,对于要求较高的汽车、军工等PCB还是需要传统化学铜。
一、开缸参数
.周生电镀导师之【(@q)】:(3)(8)(0)(6)(8)(5)(5)(0)(9)
.电镀导师之[(微)(Xin)]:(1)(3)(6)(5)(7)(2)(0)(1)(4)(7)(0)
需要注意的是:我们的配方是量产的成熟商业配方,网上是找不到的,电镀手册也没有。
网上卖配方百个配方,那种资料只能当做书籍读读,没有商业价值。
有些用户嫌贵了,尽管买书好了。
●配方平台不断发展完善
我们的配方平台包含的成熟量产商业配方种类多,已有AN美特、乐思、罗哈、麦M德美、国内知名公司我们的配方平台帮助了很多中小企业提高产品技术水平,也有不少个人因此创业成功,帮助国内企业提升国产占有率是我们长期追求的目标。
●配方平台说明
目前市场上有很多类似抄袭的,或者是买过部分配方后再次转卖的,他们有时候会改动数据,而且不还有建立Q群或者微@信群推广配方,我们没有建立任何群。
一切建&群的都是假冒。
(本*公*
二、新设备清洗及开缸
一、缸体清洗方法:
二、开缸方法:
流程操作条件水平环保通孔控制条件
生产开缸量及千尺添加量
分析、加药、产量记录
为有效监测水平环保通孔工艺之稳定性, 化验室及生产部必须详细记录分析/加药数据于报表中:
换缸条件及步骤
生产注意事项
1、每次生产前必须事先补充好液位,分析并调整好药水各参数到最佳范围后才能进行生产;
2、生产首板前用测试板做哈林槽实验,检查基材上铜速率和孔内上膜状况;除胶线做除胶速率。
3、出板后需插架,待板面温度冷却至室温,方可叠板送至下工序;
4、水平环保通孔后的板需要在7天内完成干菲林工序。
经干菲林显影后的合格板需要在3天内完成,
图形电镀工序,超出时间则按水平通孔返工方法处理;
5、各药水缸添加药水所使用的量具需严格分开使用;
6、除胶缸再生器使用是电流要求600A,停产时保持温度45-50℃,电流300A。
7、水平环保通孔前后工序之工艺参数、生产物料或生产线变更时须考虑对水平环保通孔的影响,需先
行试板,无品质问题后方可量产。
返工方法和步骤
1、已贴干膜未曝光板返工方法:
按干菲林正常流程返工和生产,但返工次数不能超过两次且必须在三天内完成图形电镀;
2、已贴干膜并曝光板返工方法:
褪干膜---粗磨---水平环保通孔---干菲林工序
3、已经完成水平环保通孔的板子若经过氢氧化钠处理过后,需按第二条的方法返工。
设备日常保养
药水分析方法
二、水平环保通孔
整孔缸:
1、Na2CO3的分析
需要的试剂:
0.1mol/L HCl
甲基橙混合指示剂
需要的仪器:
1.250mL烧杯
2.10mL移液管
3.50mL滴定管
分析步骤:
a. 工作液取样;
b. 吸取10mL样品于250mL容量瓶中,用100毫升DI水稀释;
c. 加3~5滴混合指示剂,样品变黄;
d. 摇匀后,缓慢滴加0.1N HCl,黄色变成红色时便为滴定终点(pH4.0);
计算方法:
ml 0.1N x 0.53 = g/L Na2CO3
2、pH值的分析
需要的仪器:
1.250mL烧杯
2.磁力搅拌器
3.pH计
分析步骤:
1.工作液取样;
2.吸取200ml工作液到250ml烧杯内;
3.放置温度计到样品内并加热到操作温度50℃;
4.在样品内放置标准的pH电极去读取pH值;
调整:PH值低时添加碳酸钠进行调整,每次按1g/L添加,直至PH值达中值。
PH值偏高则停加碳酸钠。
氧化缸:
1、PM6920的分析
需要的仪器:
1.1mL移液管
2.5mL移液管
3.2个100mL容量瓶
4.UV仪器(526nm/603nm)(752N型分光光度计)
5.2个规格为1cm的石英比色皿
分析步骤:
1.移取5mL未冷却的工作药水置于100mL的容量瓶,并用DI水混合稀释至刻度;
2.移取1mL步骤1中的稀释溶液置于100mL的容量瓶,并用DI水混合稀释至刻度;
3.用DI水为参比液,在波长526nm和603nm处分别测量其吸光值,记录读数。
计算方法:
[(吸光度 526 nm x 129.34) – (吸光度 603 nm x 42.22)] x 1.62 = mL/L 备注::稀释后的待测液应尽快进行测量
2、pH值的分析
需要的仪器:
1.250mL烧杯
2.磁力搅拌器
3.pH计
分析步骤:
1.工作液取样;
2.吸取200ml工作液到250ml烧杯内;
3.放置温度计到样品内并加热到操作温度85℃;
4.在样品内放置标准的pH电极去读取pH值;
调整:PH值偏高则按2g/L添加硼酸粉,直至PH值达中值。
PH值偏低则停加硼酸。
注意:PH值趁热测量。
催化缸:
1、PM6930A的分析
需要的仪器:
1.1mL移液管
2.1个100mL容量瓶
3.UV仪器(254nm)
4.2个规格为1cm的石英比色皿
需要的试剂:
DI水
分析步骤:
1.调整UV波长到254nm,两只比色皿注入DI水作为空白,调整吸光值为0;
2.吸取1mL工作药水于100mL容量瓶中,用DI水稀释至刻度,混合均匀;
3.用比色皿装上稀释液,于254nm处测量吸光值,并记录。
计算方法:
吸光值x 21.2 = mL/L YF6930 A
补料:PM 6930A的补充量=(16-分析值)×缸体积
2、pH值的分析
需要的仪器:
1.250mL烧杯
2.磁力搅拌器
3.pH计
分析步骤:
1.工作液取样;
2.吸取200ml工作液到250ml烧杯内;
3.在样品内放置标准的pH电极去读取pH值;
调整:PH值偏高按2ml/L添加YF6930C,直至PH值达中值2.0。
PH值偏低则停加YF6930C。
上铜速率测试:
需要的仪器:
1.哈林槽(长250mm x 宽65mm x 高120mm)和RS-148 打气泵
2.整流器:电流范围在1-20A
3.两片阳极片:长150mm x 宽60mm x 厚度5mm
4.上铜速率专用测试片,尺寸:5英寸×1英寸,一端带双面铜皮,其余为基材
测试步骤:
1.取1.8L电镀液分析调整至:硫酸铜70±5g/L、硫酸200±10g/L、氯离子60±10ppm;
2.用哈氏槽片将光剂调整到最佳值;
3.将专用测试片用20ASF电流电镀5分钟后取出烘干;
4.测量基材两面(每面三点)的上铜长度mm;
计算方法:
所有测量数据之和mm÷6÷5min = mm/min
孔铜测试:
需要的仪器:
1.哈林槽(长250mm x 宽65mm x 高120mm)和RS-148 打气泵
2.整流器:电流范围在1-20A
3.两片阳极片:长150mm x 宽60mm x 厚度5mm
4.孔铜测试专用测试片(含0.4、0.6、0.8mm的孔),具体尺寸见我司提供之样品
测试步骤:
1.取1.8L电镀液分析调整至:硫酸铜70±5g/L、硫酸200±10g/L、氯离子60±10ppm;
2.用哈氏槽片将光剂调整到最佳值;
3.将专用测试片用20ASF电流电镀10分钟后取出烘干;
4.观察测试片,要求无孔内无铜,做切片观察孔内铜厚状况;
除胶速率分析方法:
1. 取约7.5cm*7.5cm板料,去毛边。
(没有钻孔及将铜皮蚀去)
2. 放入120℃的烘箱内干燥15分钟
3. 取出板料,冷却后称重精确至0.0001g;(Gl)
4. 将试板入生产线进行除胶,经中和缸后取出样板
5. 将样板放入120℃的烘箱内干燥15分钟
6. 取出冷却称量精确至0.0001g;(G2)
计算方法:
除胶渣速率(mg/cm2)=(G1-G2)÷板面积(双面)
控制范围:0.1-0.30mg/cm2
周生电镀导师--线路板原材料及湿式制程药水专业供应商
申明:本操作指引仅适用于水平环保通孔线,本公司有权对此指引内容进行完善及修订,修订后旧版资料失效,以最新版本为准。
11。