NM24W16UFTLEN中文资料
FM24W256-GTR;FM24W256-G;中文规格书,Datasheet资料
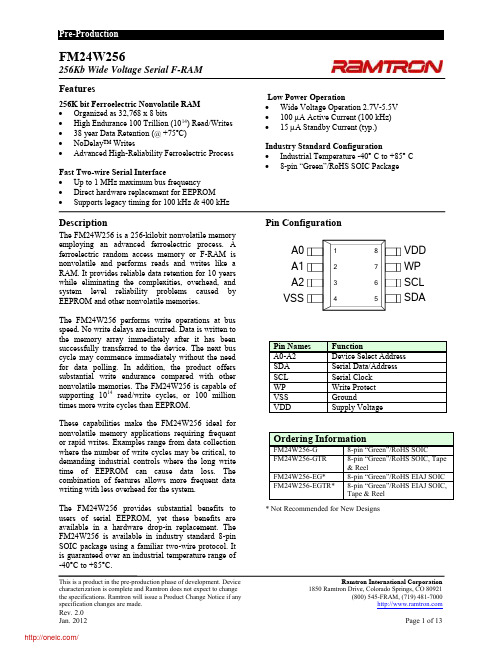
Rev. 2.0 Jan. 2012 /
Page 1 of 13
FM24W256 - 256Kb Wide Voltage I2C F-RAM
Counter
Address Latch
4,096 x 64 FRAM Array
8 SDA Serial to Parallel Converter
Description
The FM24W256 is a 256-kilobit nonvolatile memory employing an advanced ferroelectric process. A ferroelectric random access memory or F-RAM is nonvolatile and performs reads and writes like a RAM. It provides reliable data retention for 10 years while eliminating the complexities, overhead, and system level reliability problems caused by EEPROM and other nonvolatile memories. The FM24W256 performs write operations at bus speed. No write delays are incurred. Data is written to the memory array immediately after it has been successfully transferred to the device. The next bus cycle may commence immediately without the need for data polling. In addition, the product offers substantial write endurance compared with other nonvolatile memories. The FM24W256 is capable of supporting 1014 read/write cycles, or 100 million times more write cycles than EEPROM. These capabilities make the FM24W256 ideal for nonvolatile memory applications requiring frequent or rapid writes. Examples range from data collection where the number of write cycles may be critical, to demanding industrial controls where the long write time of EEPROM can cause data loss. The combination of features allows more frequent data writing with less overhead for the system. The FM24W256 provides substantial benefits to users of serial EEPROM, yet these benefits are available in a hardware drop-in replacement. The FM24W256 is available in industry standard 8-pin SOIC package using a familiar two-wire protocol. It is guaranteed over an industrial temperature range of -40°C to +85°C.
NTE电子有限公司的NTE NEV NEH系列微型铝电容器说明说明书

NEV, NEH SERIES32NTE Electronics, Inc. Voice (973) 748−5089 FAX (973) 748−6224 SUBMINIATURE(NEV: Radial Lead, NEH: Axial Leads)The NEV and NEH series subminiature aluminum electrolytic ca-pacitors are especially suitable for applications requiring high ca-pacitance, low cost, and very small size. In fact, you’ll find these capacitors in some of the most demanding applications, from precision medical electronics and automobiles to the newest personal computers and disk drives.They operate over a broad temperature range and are available in either blister pack or bulk.RATINGSCapacitance Range: 0.1f to 22,000f Tolerance: 20%Voltage Range: 6.3V to 100VPERFORMANCE SPECIFICATIONSOperating Temperature Range:−40C to +85C (−40F to +185F)Leakage Current: I 0.01CV + 3A (measured after3 minutes of applied voltage)I =Leakage Current (A)C =Nominal Capacitance (f)V =Rated Voltage (V)Capacitance Tolerance (M): 20%measured at +20C (+68F), 120HzDissipation Factor: measured at +20C (+68F),120HzRated Voltage 6.31016253550−801000.1f to 1000f 0.240.20.170.150.120.100.081000f to 22,000f Values above plus 0.02 for each 1000f Impedance Ratio at Low Temperature: 120HzComparison Z WV 6.31016253550−100Z @ −25C (−13F)/Z @ +20C (+68F)432222Z @ −40C (−40F)/Z @ +20C (+68F)864444Surge Voltage:DC Rated Voltage 6.3101625355063100Surge Voltage8132032446379125Load Life: 1000 12Hrs @ +85C (+185F),at rated voltageLeakage Current: Within values specified above Dissipation Factor: Within 150% of specified value Capacitance Change Max: See TableRated Voltage Capacitance Change Max6.3V to 16V Within 30% of the initial value 25V to 100VWithin 20% of the initial valueShelf Life: 1000 Hrs @ +85C (+185F),no voltage appliedLeakage Current: Within 200% of specified value Dissipation Factor: Within 150% of specified value Capacitance Change Max: Within 20% of initial valueMECHANICAL SPECIFICATIONSLead Solderability:Meets the requirements of MIL −STD 202, Method 208Marking:Consists of series type, nominal capacitance, rated voltage, temperature range, anode and/or cathode identification, vendor identification.Recommended Cleaning Solvents:Methanol, isopropanol ethanol, isobutanol, petroleum ether, propanol and/or commercial detergents. Halo-genated hydrocarbon cleaning agents such as Freon (MF, TF, or TC), trichloroethylene, trichloroethane, or methylchloride are not recommended as they may damage the capacitor.CASE SIZE AND DIMENSIONS:D’ Ø = D Ø + 0.5 MaxL’ = L + 1.0 Max at D Ø 8.0L’ = L + 2.0 Max at D Ø 10.0D’ Ø = D Ø + 0.5 Max L’ = L + 1.0 Max at D Ø 8.0L’ = L + 2.0 Max at D Ø 10.0NEV SERIESNEH SERIES(Insulating Bar = Negative)ORDERING INFORMATIONNEV47M50Series Capacitance Tolerance VoltageNEV Series (Radial Type) Dimensions: Diameter (D Ø) x Length (L): mmNEV Series (Radial Type) Mechanical Specifications: mmOutside Diameter (D Ø)5 6.381013161822 Lead Spacing (A)2 2.5 3.5557.57.510 Lead Diameter (d Ø)0.50.60.60.60.60.80.8 1.0*These dimensions are for reference only, please consult the factory for actual size.NTE Electronics, Inc. Voice (973) 748−5089 FAX (973) 748−6224 33NEH Series (Axial Type) Dimensions: Diameter (D Ø) x Length (L): mmNEH Series (Axial Type) Mechanical Specifications: mmOutside Diameter (D Ø)5 6.38101316182225 Lead Diameter (d Ø)0.60.60.60.60.80.80.80.80.8*These dimensions are for reference only, please consult the factory for actual size.34NTE Electronics, Inc. Voice (973) 748−5089 FAX (973) 748−6224 。
钽电容参数介绍及使用技巧
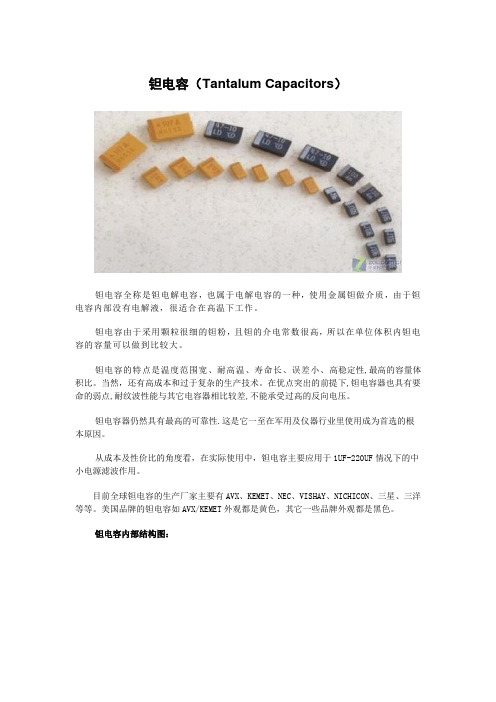
钽电容(Tantalum Capacitors)钽电容全称是钽电解电容,也属于电解电容的一种,使用金属钽做介质,由于钽电容内部没有电解液,很适合在高温下工作。
钽电容由于采用颗粒很细的钽粉,且钽的介电常数很高,所以在单位体积内钽电容的容量可以做到比较大。
钽电容的特点是温度范围宽、耐高温、寿命长、误差小、高稳定性,最高的容量体积比。
当然,还有高成本和过于复杂的生产技术。
在优点突出的前提下,钽电容器也具有要命的弱点,耐纹波性能与其它电容器相比较差,不能承受过高的反向电压。
钽电容器仍然具有最高的可靠性.这是它一至在军用及仪器行业里使用成为首选的根本原因。
从成本及性价比的角度看,在实际使用中,钽电容主要应用于1UF-220UF情况下的中小电源滤波作用。
目前全球钽电容的生产厂家主要有AVX、KEMET、NEC、VISHAY、NICHICON、三星、三洋等等。
美国品牌的钽电容如AVX/KEMET外观都是黄色,其它一些品牌外观都是黑色。
钽电容内部结构图:钽电容内部等效电路:钽电容MARK标识:钽电容主要参数:1、容值范围:钽电容的容值参数范围一般在0.47UF-680UF,不同厂家根据工艺能力,稍微有区别。
一般情况下钽电容使用参数范围在1UF-220UF左右。
从下面图表可以看出,钽电容在超过100K以上频率时,电容参数急剧减小。
所以,钽电容一般情况下只适合低频情况下中大电流滤波。
2、额定电压:一般钽电容的额定电压范围在4V-50V,考虑到125度环境需要做降额使用,参考下表。
在常规-55°C to + 125°C环境下,额定电压需要降额到2/3左右使用。
具体降额可以用下列公式计算:Vmax=( 1-(T-85)/125)×VRVmax是最大工作电压T 是要求的工作温度VR是额定电压值得注意的是上述公式只适用于高阻抗的放电电路。
同时,上述公式并没有考虑交流分量和浪涌的影响,因此当使用温度较高时,必须使用更大的降额电压才能稳定可靠地工作。
24LC16资料

I2C is a trademark of Philips Corporation.
© 1996 Microchip Technology Inc.
DS20070G-page 1
This document was created with FrameMaker 4 0 4
元器件交易2网
• Factory programming (QTP) available
• ESD protection > 4,000V
• 10,000,000 erase/write cycles guaranteed
• Data retention > 200 years
• 8-pin DIP, 8-lead or 14-lead SOIC packages
Parameter
Symbol
STANDARD MODE
Vcc = 4.5V - 5.5V FAST MODE Units
Remarks
Min Max Min Max
Clock frequency
FCLK
—
100
—
400 kHz
Clock high time
THIGH 4000
—
600
—
ns
Clock low time
13
VCC
12
WP
11
NC
10
SCL
9
SDA
8
NC
BLOCK DIAGRAM
WP
HV GENERATOR
I/O CONTROL
LOGIC
MEMORY CONTROL
LOGIC
XDEC
SDA SCL
NM24W16UTVN中文资料

Temp. Range
Voltage Operating Range
Blank T SCL Clock Frequency Blank F Ultralite Density 16 17 C W Interface 24 NM
3
NM24C16U/17U Rev. B.1
1
元器件交易网
NM24C16U/NM24C17U – 16K-Bit Serial EEPROM 2-Wire Bus Interface
Connection Diagrams
Dual-In-Line Package (N), 8-Pin SO Package (M8)
元器件交易网
NM24C16U/NM24C17U – 16K-Bit Serial EEPROM 2-Wire Bus Interface
Product Specifications Absolute Maximum Ratings
Ambient Storage Temperature All Input or Output Voltages with Respect to Ground Lead Temperature (Soldering, 10 seconds) ESD Rating –65°C to +150°C 6.5V to –0.3V +300°C 2000V min.
General Description
The NM24C16U/17U devices are 16K (16,384) bit serial interface CMOS EEPROMs (Electrically Erasable Programmable ReadOnly Memory). These devices fully conform to the Standard I2C™ 2-wire protocol which uses Clock (SCL) and Data I/O (SDA) pins to synchronously clock data between the "master" (for example a microprocessor) and the "slave" (the EEPROM device). In addition, the serial interface allows a minimal pin count packaging designed to simplify PC board layout requirements and offers the designer a variety of low voltage and low power options. NM24C17U incorporates a hardware "Write Protect" feature, by which, the upper half of the memory can be disabled against programming by connecting the WP pin to VCC. This section of memory then effectively becomes a ROM (Read-Only Memory) and can no longer be programmed as long as WP pin is connected to VCC. Fairchild EEPROMs are designed and tested for applications requiring high endurance, high reliability and low power consumption for a continuously reliable non-volatile solution for all markets.
NTE2716集成电路NMOS,16K UV可抹除PROM说明说明书

NTE2716Integrated CircuitNMOS, 16K UV Erasable PROMDescription:The NTE2716 is a 16,384–bit (2048 x 8–bit) Erasable and Electrically Reprogrammable PROM in a 24–Lead DIP type package designed for system debug usage and similar applications requiring non-volatile memory that could be reprogrammed periodically. The transparent lid on the package allows the memory content to be erased with ultraviolet light.The NTE2716 operates from a single power supply and has a static power down mode.Features:D Single 5V Power SupplyD Automatic Power–Down Mode (Standby)D Organized as 2048 Bytes of 8BitsD TTL Compatible During Read and ProgramD Access Time: 350nsD Output Enable Active Level is User SelectableAbsolute Maximum Ratings: (Note 1). . . . . . . . . . . . . . . . . . . . . . . . . . . . . . . .All Input or Output Voltages (with respect to V SS)+6 to –0.3V. . . . . . . . . . . . . . . . . . . . . . . . . . . . . . . . . . . . . .V PP Supply Voltage (with respect to V SS)+28 to –0.3V. . . . . . . . . . . . . . . . . . . . . . . . . . . . . . . . . . . . . . . . . Temperature Under Bias (V PP = 5V)–10° to +80°C. . . . . . . . . . . . . . . . . . . . . . . . . . . . . . . . . . . . . . . . . . .Operating Temperature Range, T opr0° to +70°C. . . . . . . . . . . . . . . . . . . . . . . . . . . . . . . . . . . . . . . . . .Storage Temperature Range. T stg–65° to +125°C Note 1.Permanent device may occur if “Absolute Maximum Ratings” are exceeded. Functional op-eration should be restricted to “Recommended Operating Conditions”. Exposure to higher than recommended voltages for extended periods of time could affect device reliability. Note 2.This device contains circuitry to protect the inputs against damage due to high static voltages or electric fields; however, it is advised that normal precautions be taken to avoid application of any voltage higher than maximum rated voltages to this high–impedance circuit.C =I ∆t∆VMode Selection:Note 3.In Read Mode if V PP ≥ V IH , then G (active low)V PP ≤ V IL , then G (active high)Capacitance: (f = 1MHz, T A = +25°C, periodically sampled rather than 100% tested)Note 4.Capacitance measured with a Boonton Meter oreffective capacitance calculated from the equation:DC Operating Conditions and Characteristics:(Full Operating Voltage and T emperature Rangeunless otherwise specified)Note 5.V CC must be applied simultaneously or prior to V PP . V CC must also be switched off simulta-neously with or after V PP . With V PP connected directly to V CC during the read operation, the supply current would then be the sum of I PP1 and I CC .AC Operating Conditions and Characteristics:(Full Operating Voltage and T emperature Range,Note 6, unless otherwise specified). . . . . . . . . . . . . .Note 6.Input Pulse Levels0.8V and 2.2V. . . . . . . . . . . . . . . . .Input Rise and Fall Times20ns. . . .Input and Output Timing Levels 2.0 and 0.8VNote7.t ELQV is referenced to E/Progr or stable address, whichever occurs last.DC Programming Conditions and Characteristics: (T = +25°C ±5°C)AC Programming Operating Conditions and Characteristics:Note8.If shorter than 45ms (min) pulses are used, the same number of pulses should be applied after the specific data has been verified to ensure that good programming levels have been written.Programming Instructions:Before programming, the memory should be submitted to a full ERASE operation to ensure every bit in the device is in the “1” state (represented by Output High). Data are entered by programming zeros (Output Low) into the required bits. The words are addressed the same way as in the READ operation.A programmed “0” can only be changed to a “1” by ultraviolet light erasure.To set the memory up for Program Mode, the V PP input (Pin21) should be raised to +25V. The V CC supply voltage is the same as for the Read operation and G is at V IH. Programming data is entered in 8–bit words through the data out (DQ) terminals. Only “0 s” will be programmed when “0 s” and “1 s” are entered in the 8–bit data word.After address and data setup, a program pulse (V IL to V IH) is applied to the E/Progr input. A program pulse is applied to each address location to be programmed. To minimize programming time, a 2ms pulse width is recommended. The maximum program pulse width is 55ms; therefore, programming must not be attempted with a DC signal applied to the E/Progr input.Multiple NTE2716s may be programmed in parallel by connecting together like inputs and applying the program pulse to the E/Progr inputs. Different data may be programmed into multiple NTE2716s connected in parallel by using the PROGRAM INHIBIT mode. Except for the E/Progr pin, all like inputs (including Output Enable) may be common.The PROGRAM VERIFY mode with V PP at +25V is used to determine that all programmed bits were correctly programmed.Read Operation:After access time, data is valid at the outputs in the READ mode. With stable system addresses, effec-tively faster access time can be obtained by gating the data onto the bus with Output Enable. The Standby mode is available to reduce active power dissipation. The outputs are in the high imped-ance state when the E/Progr input pin is high (V IH) independent of the Output Enable input. Erasing Instructions:The NTE2716 can be erased by exposure to high intensity shortwave ultraviolet light, with a wave-length of 2537 angstroms. The recommended integrated dose (i.e. UV–intensity X exposure time) is 15Ws/cm2. As an example, using the “Model 30–000” UV–Eraser (Turner Designs, Mountain View, CA 94043) the ERASE–time is 36 minutes. The lamps should be used without shortwave filters and the NTE2716 should be positioned about one inch away from the UV–tubes.Recommended Operating Procedures:After erasure and reprogramming of the EPROM, it is recommended that the quartz window be cov-ered with an opaque self–adhesive cover. It is important that the self–adhesive cover not leave any residue on the quartz if it is removed to allow another erasure.。
HT24LC16中文资料

4000
¾
600 ¾
ns
tHD:DAT Data Input Hold Time
¾
0
¾
0
¾
ns
tSU:DAT Data Input Setup Time
¾
200
¾
100 ¾
ns
tSU:STO STOP Condition Setup Time
¾
4000
¾
600 ¾
ns
Rev. 1.30
2
November 25, 2003
VIL
Input Low Voltage
¾
¾
VIH
Input High Voltage
¾
¾
VOL
Output Low Voltage
2.4V IOL=2.1mA
ILI
Input Leakage Current
5V VIN=0 or VCC
ILO
Output Leakage Current
5V VOUT=0 or VCC
ISTB1
Standby Current
5V VIN=0 or VCC
ISTB2
Standby Current
2.4V VIN=0 or VCC
CIN
Input Capacitance (See Note)
¾ f=1MHz 25°C
COUT Output Capacitance (See Note)
I/O
A0~A2
I
SDA
I/O
SCL
I
WP
I
VSS
¾
VCC
¾
Description Address input Serial data Serial clock input Write protect Negative power supply, ground Positive power supply
钽电容标示说明书

钽电容耐压值的表示方法钽电容上面标着106F表示: 106是容量为10UfF应是耐压值为2.5V钽电容耐压用不同的字母来标注,如下:F: 2.5G: 4L、J: 6.3A: 10C: 16D: 20E:25V:35T:50在体积一定的情况下,容值越大,耐压值越小。
目前全球主要有以下几个品牌的钽电容:AVX、KEMET、VISHAY、NEC、NICHICON。
市场上的钽电容,分为黄钽和黑钽两种。
黄钽品牌主要是:AVX KEMET 黑钽主要品牌是:NEC、NICHICON。
市场占有方面:AVX远高于KEMET,NEC高于NICHICON。
现在市场上的钽电价格变化比较大。
AVX涨价20%--30% , KEMET涨价15%-20%,NEC涨价10%--20%。
涨价的主要原因个人认为有这么几个原因:1.市场上原料钽价格上涨 2.劳动力成本的增加。
另外可能有朋友要问黄钽与黑钽的区别。
简单来说,黑钽是开模将钽粉压成型,而黄钽,是在表面用聚氧树脂包裹而成。
由于生产工艺的原因,黑钽的部空间没有得到最有效的利用,所以黄钽能做的容量会比黑钽要大,也就是说有些黄钽能做到的规格型号,黑钽做不了。
另外,前面有朋友说到Polymer,Polymer现在主要是 AVX与KEMET在做。
Polymer与比普通的二氧化锰的优势在于:普通的钽电他的实际使用电压一般是50%,Polymer一般在80%以上。
举个例子来说:100uf 10v的普通电容,在实际使用的时候,额定电压不能超过5V,如果使用Polymer材料的电容,那么只需要100uf 6.3v的。
但由于价格问题,Polymer现在在普通的电子产品上用的不是很多。
我所知道的,在笔记本电脑上有些有用到。
AVX与KEMET的优劣:AVX在军用,民用市场上的占有量都很大,在普通电容的市场上,AVX无论品质还是市场占有量都远强与KEMET。
价格上,AVX比KEMET 更贵。
KEMET他主要问题是其电容的耐压值不够,举例说:100uf 10v的电容,测试的电压按道理应该能达到5V,但若真用5V电压去测试的话,很可能会击穿。
详解铝电解电容器的参数

详解铝电解电容器的参数详解铝电解电容器的参数铝电解电容器的参数详解之一铝电解电容器的基本参数主要有电压、电容量、最高工作温度及寿命、漏电流和损耗因数,有的铝电解电容器,如开关电源输出滤波用的铝电解电容器还有额定纹波电流、ESR等参数。
电压铝电解电容器的电压指标主要有额定DC电压、额定浪涌电压、瞬间过压和反向电压,下面将逐一介绍。
1.反向电压钽电容是有极性电容器,通常不允许工作在反向电压。
在需要的地方,可通过连接一个二极管来防止反极性。
通常,采用导通电压约为0. 8V的二极管是允许的。
在短于Vs的时间内,小于或等于1.5V的反向电压也是可以承受的,但仅仅是短时间,绝不能是连续工作状态。
2.工作电压V OP工作电压是电容器在额定温度范围内所允许的连续工作的电压。
在整个工作温度范围内,电容器既可以在满额定电压(包括叠加的交流电压)下连续工作,也可以连续工作在0V与额定电压之间任何电压值。
在短时间内,电容器也可承受幅值不高于-1. 5V的反向电压。
反向电压的危害主要是反向电压将产生减薄氧化铝膜的电化学过程,从而不可逆地损坏铝电解电容器。
3.额定DC电压VR额定DC电压VR是电容器在额定温度范围内所允许的连续工作电压,它包括在电容器两电极间的直流电压和脉动电压或连续脉冲电压之和。
通常,钽电容的额定电压在电容器表面标明。
通常额定电压≤100V为“低压”铝电解电容器,而额定电压≥150V为“高压”铝电解电容器。
额定电压的标称电压为:3V、4V、6.3V、(7.5V)、10V、16V、25V、35V、(40V)、50V、63V、80V、100V、160V、200V、250V、300V、(315V)、350V、(385V)、400V、450V、500V、(550V)。
其中括号中的电压值为我国不常见的。
4.额定浪涌电压Vs额定浪涌电压Vs是铝电解电容器在短时间内能承受的电压值,其测试条件是:电容器工作在25℃,在不超过30s,两次间隔不小于5min。
GC65_硬件设计手册_V1.0(1)

e tia 3.3.3. 供电参考电路............................................................................................................... 20
上海移远通信技术有限公司
1 / 68
GC65 硬件设计手册
文档历史
修订记录
版本 1.0
日期
CQouneficdteenl tial 2013-09-16
作者 郝竹青
变更表述 初始版本
上海移远通信技术有限公司
2 / 68
GC65 硬件设计手册
目录
文档历史 ........................................................................................................................................................ 2 目录 ............................................................................................................................................................... 3 表格索引 ........................................................................................................................................................ 5 图片索引 ........................................................................................................................................................ 6
mn2488mp1620对管的参数

mn2488mp1620对管的参数mn2488mp1620是一种功率管,广泛应用于各种电子设备中,具有高性能和稳定性。
本文将从mn2488mp1620对管的参数、特点和应用领域等方面进行详细介绍,以便读者对该器件有更全面的了解。
mn2488mp1620是一种n沟道功率MOSFET管,它具有源极和漏极,以及一个控制极。
其参数包括最大漏极-源极电压(VDS)为800V,最大门极-源极电压(VGS)为±30V,最大漏极电流(ID)为8A,最大功耗(PD)为82W。
此外,mn2488mp1620的导通电阻(RDS(on))为3.9Ω,极限工作温度(Tj)为150°C。
mn2488mp1620具有较低的导通电阻和高的耐压能力,能够在高电压和高频率下稳定工作,具有较高的开关速度和较低的开关损耗。
此外,mn2488mp1620还具有良好的线性特性和低的开关噪声,能够提供稳定的功率输出。
mn2488mp1620的优点还包括其可靠性和稳定性高,能够长时间稳定工作而不易损坏,具有较长的使用寿命。
此外,mn2488mp1620还具有较小的尺寸和重量,便于安装和维护。
mn2488mp1620广泛应用于电源管理、电动车充电桩、逆变器、伺服驱动器、UPS、太阳能逆变器、蓄电池管理系统等领域。
其稳定的性能和高效的功率输出,使其成为这些领域中不可或缺的组件。
同时,mn2488mp1620还可以与其他器件配合使用,如IGBT、二极管等,实现更复杂的功率控制和转换功能。
mn2488mp1620还可以根据具体的应用需求进行定制,以满足不同用户的需求。
总之,mn2488mp1620作为一种高性能的功率管,具有较高的稳定性、可靠性和效率,适用于多种电子设备中,并且具有广泛的应用前景。
希望本文能够对读者对mn2488mp1620有更深入的了解,并为其在实际应用中提供一定的参考价值。
ST24W16资料

ST24C16, ST25C16 ST24W16, ST25W1616 Kbit Serial I 2C Bus EEPROMwith User-Defined Block Write ProtectionFebruary 19991/17AI00866B2PB0-PB1SDAV CCST24x16ST25x16MODE/WC*SCLV SSPRE Figure 1. Logic Diagram1 MILLION ERASE/WRITE CYCLES, with 40 YEARS DATA RETENTION SINGLE SUPPLY VOLTAGE:–4.5V to 5.5V for ST24x16 versions –2.5V to 5.5V for ST25x16 versionsHARDWARE WRITE CONTROL VERSIONS:ST24W16 and ST25W16TWO WIRE SERIAL INTERFACE, FULLY I 2C BUS COMPATIBLEBYTE and MULTIBYTE WRITE (up to 8BYTES) for the ST24C16PAGE WRITE (up to 16 BYTES)BYTE, RANDOM and SEQUENTIAL READ MODESSELF TIMED PROGRAMING CYCLEAUTOMATIC ADDRESS INCREMENTING ENHANCED ESD/LATCH UP PERFORMANCESDESCRIPTIONThis specification covers a range of 16 Kbit I 2C bus EEPROM products, the ST24/25C16 and the ST24/25W16. In the text, products are referred to as ST24/25x16 where "x" is: "C" for Standard ver-sion and "W" for hardware Write Control version.The ST24/25x16 are 16 Kbit electrically erasable programmable memories (EEPROM), organized as 8 blocks of 256 x8 bits. These are manufactured in STMicroelectronics’s Hi-Endurance Advanced CMOS technology which guarantees an endur-PRE Write Protect Enable PB0, PB1Protect Block SelectSDA Serial Data Address Input/Output SCL Serial ClockMODE Multybyte/Page Write Mode (C version)WC Write Control (W version)V CC Supply Voltage V SSGroundTable 1. Signal Names81PSDIP8 (B)0.25mm Frame81SO8 (M)150mil WidthNote: WC signal is only available for ST24/25W16 products.SDAV SSSCL MODE/WC PB0PRE V CCPB1AI00867BST24x16ST25x1612348765Figure 2A. DIP Pin Connections1AI00500B2348765SDAV SSSCL MODE/WC PB0PRE V CCPB1ST24x16ST25x16Figure 2B. SO8 Pin Connectionsance of one million erase/write cycles with a data retention of 40 years. The ST25x16 operates with a power supply value as low as 2.5V. Both Plastic Dual-in-Line and Plastic Small Outline packages are available.The memories are compatible with the I 2C stand-ard, two wire serial interface which uses a bi-direc-tional data bus and serial clock. The memoriesDESCRIPTION (cont’d)carry a built-in 4 bit, unique device identification code (1010) corresponding to the I 2C bus defini-tion. The memories behave as slave devices in the I 2C protocol with all memory operations synchro-nized by the serial clock. Read and write operations are initiated by a START condition generated by the bus master. The START condition is followed by a stream of 4 bits (identification code 1010), 3 block select bits, plus one read/write bit and terminated by an acknowledge bit. When writing data to theSymbol ParameterValue Unit T A Ambient Operating Temperature –40 to 125 °C T STG Storage Temperature –65 to 150°C T LEAD Lead Temperature, Soldering (SO8)(PSDIP8)40 sec 10 sec215260°C V IO Input or Output Voltages –0.6 to 6.5 V V CC Supply Voltage–0.3 to 6.5V V ESDElectrostatic Discharge Voltage (Human Body model) (2)4000V Electrostatic Discharge Voltage (Machine model) (3)500VNotes:1. Except for the rating "Operating T emperature Range", stresses above those listed in the Table "Absolute Maximum Ratings"may cause permanent damage to the device. These are stress ratings only and operation of the device at these or any other conditions above those indicated in the Operating sections of this specification is not implied. Exposure to Absolute Maximum Rating conditions for extended periods may affect device reliability. Refer also to the STMicroelectronics SURE Program and other relevant quality documents.2.100pF through 1500Ω; MIL-STD-883C, 3015.73.200pF through 0Ω; EIAJ IC-121 (condition C)Table 2. Absolute Maximum Ratings (1)2/17ST24/25C16, ST24/25W16ModeRW bit MODE pinBytes Initial SequenceCurrent Address Read ’1’X 1START, Device Select, RW = ’1’Random Address Read ’0’X 1START, Device Select, RW = ’0’, Address,’1’reSTART, Device Select, RW = ’1’Sequential Read ’1’X 1 to 2048As CURRENT or RANDOM Mode Byte Write ’0’X 1START, Device Select, RW = ’0’Multibyte Write ’0’V IH 8START, Device Select, RW = ’0’Page Write’0’V IL16START, Device Select, RW = ’0’Note: X = V IH or V IL .Table 4. Operating ModesDevice CodeMemory MSB AddressesRW Bitb7b6b5b4b3b2b1b0Device Select11A10A9A8RWNote: The MSB b7 is sent first.Table 3. Device Select Codememory it responds to the 8 bits received by as-serting an acknowledge bit during the 9th bit time.When data is read by the bus master, it acknow-ledges the receipt of the data bytes in the same way. Data transfers are terminated with a STOP condition.Data in the 4 upper blocks of the memory may be write protected. The protected area is programma-ble to start on any 16 byte boundary. The block in which the protection starts is selected by the input pins PB0, PB1. Protection is enabled by setting a Protect Flag bit when the PRE input pin is driven High.Power On Reset: V CC lock out write protect. In order to prevent data corruption and inadvertent write operations during power up, a Power On Reset (POR) circuit is implemented. Untill the V CC voltage has reached the POR threshold value, the internal reset is active: all operations are disabled and the device will not respond to any command.In the same way, when V CC drops down from the operating voltage to below the POR threshold value, all operations are disabled and the device will not respond to any command. A stable V CC must be applied before applying any logic signal.3/17ST24/25C16, ST24/25W16AI01100V CCC BUSSDA R LMASTERR LSCLC BUS10020030040048121620C BUS (pF)R L m a x (k Ω)V CC = 5VFigure 3. Maximum R L Value versus Bus Capacitance (C BUS ) for an I 2C BusSIGNALS DESCRIPTIONSerial Clock (SCL). The SCL input signal is used to synchronise all data in and out of the memory. A resistor can be connected from the SCL line to V CC to act as a pull up (see Figure 3).Serial Data (SDA). The SDA signal is bi-directional and is used to transfer data in or out of the memory.It is an open drain output that may be wire-OR’ed with other open drain or open collector signals on the bus. A resistor must be connected from the SDA bus line to V CC to act as pull up (see Figure 3).Protected Block Select (PB0, PB1). PB0 and PB1input signals select the block in the upper part of the memory where write protection starts. These inputs have a CMOS compatible input level.Protect Enable (PRE). The PRE input signal, in addition to the status of the Block Address Pointer bit (b2, location 7FFh as in Figure 7), sets the PRE write protection active.Mode (MODE). The MODE input is available on pin 7 (see also WC feature) and may be driven dynami-cally. It must be at V IL or V IH for the Byte Write mode, V IH for Multibyte Write mode or V IL for Page Write mode. When unconnected, the MODE input is internally read as V IH (Multibyte Write mode).Write Control (WC). An hardware Write Control feature is offered only for ST24W16 and ST25W16versions on pin 7. This feature is usefull to protect the contents of the memory from any erroneous erase/write cycle. The Write Control signal is used to enable (WC at V IH ) or disable (WC at V IL ) the internal write protection. When unconnected, the WC input is internally read as V IL . The devices with this Write Control feature no longer supports the Multibyte Write mode of operation, however all other write modes are fully supported.Refer to the AN404 Application Note for more de-tailed information about Write Control feature.4/17ST24/25C16, ST24/25W16Symbol ParameterTest ConditionMinMax Unit C IN Input Capacitance (SDA)8pF C IN Input Capacitance (other pins)6pF Z WCL WC Input Impedance (ST24/25W16)V IN ≤ 0.3 V CC 520k ΩZ WCH WC Input Impedance (ST24/25W16)V IN ≥ 0.7 V CC500k Ωt LPLow-pass filter input time constant (SDA and SCL)100nsNote: 1. Sampled only, not 100% tested.Table 5. Input Parameters (1) (T A = 25 °C, f = 100 kHz )Symbol ParameterTest Condition MinMax Unit I LI Input Leakage Current 0V ≤ V IN ≤ V CC ±2µA I LOOutput Leakage Current 0V ≤ V OUT ≤ V CC SDA in Hi-Z ±2µA I CCSupply Current (ST24 series)V CC = 5V, f C = 100kHz (Rise/Fall time < 10ns)2mA Supply Current (ST25 series)V CC = 2.5V, f C = 100kHz 1mA I CC1Supply Current (Standby)(ST24 series)V IN = V SS or V CC ,V CC = 5V 100µA V IN = V SS or V CC , V CC = 5V, f C = 100kHz 300µA I CC2Supply Current (Standby) (ST25 series)V IN = V SS or V CC , V CC = 2.5V 5µA V IN = V SS or V CC , V CC = 2.5V, f C = 100kHz50µA V IL Input Low Voltage (SCL, SDA)–0.30.3 V CC V V IH Input High Voltage (SCL, SDA)0.7 V CC V CC + 1V V IL Input Low Voltage(PB0 - PB1, PRE, MODE, WC)–0.30.5V V IH Input High Voltage(PB0 - PB1, PRE, MODE, WC)V CC – 0.5V CC + 1V V OLOutput Low Voltage (ST24 series)I OL = 3mA, V CC = 5V 0.4V Output Low Voltage (ST25 series)I OL = 2.1mA, V CC = 2.5V0.4VTable 6. DC Characteristics(T A = 0 to 70 °C or –40 to 85 °C; V CC = 4.5V to 5.5V or 2.5V to 5.5V)5/17ST24/25C16, ST24/25W16Symbol Alt ParameterMinMax Unit t CH1CH2t R Clock Rise Time 1µs t CL1CL2t F Clock Fall Time 300ns t DH1DH2t R Input Rise Time 1µs t DL1DL1t F Input Fall Time300ns t CHDX (1)t SU:STA Clock High to Input Transition 4.7µs t CHCL t HIGH Clock Pulse Width High4µs t DLCL t HD:STA Input Low to Clock Low (START)4µs t CLDX t HD:DAT Clock Low to Input Transition 0µs t CLCH t LOW Clock Pulse Width Low4.7µs t DXCX t SU:DAT Input Transition to Clock Transition 250ns t CHDH t SU:STO Clock High to Input High (STOP) 4.7µs t DHDL t BUF Input High to Input Low (Bus Free) 4.7µs t CLQV (2)t AA Clock Low to Next Data Out Valid 0.3 3.5µs t CLQX t DH Data Out Hold Time 300ns f C f SCL Clock Frequency 100kHz t W (3)t WRWrite Time10msNotes:1.For a reSTART condition, or following a write cycle.2.The minimum value delays the falling/rising edge of SDA away from SCL = 1 in order to avoid unwanted START and/or STOP conditions.3.In the Multibyte Write mode only, if accessed bytes are on two consecutive 8 bytes rows (5 address MSB are not constant)the maximum programming time is doubled to 20ms.Table 7. AC Characteristics(T A = 0 to 70 °C or –40 to 85 °C; V CC = 4.5V to 5.5V or 2.5V to 5.5V)DEVICE OPERATION I 2C Bus BackgroundThe ST24/25x16 support the I 2C protocol. This protocol defines any device that sends data onto the bus as a transmitter and any device that reads the data as a receiver. The device that controls the data transfer is known as the master and the other as the slave. The master will always initiate a data transfer and will provide the serial clock for syn-chronisation. The ST24/25x16 are always slave devices in all communications.Start Condition. START is identified by a high to low transition of the SDA line while the clock SCL is stable in the high state. A START condition must precede any command for data transfer. Except during a programming cycle, the ST24/25x16 con-tinuously monitor the SDA and SCL signals for a START condition and will not respond unless one is given.AI008250.8V CC0.2V CC0.7V CC 0.3V CCFigure 4. AC Testing Input Output WaveformsInput Rise and Fall Times ≤ 50nsInput Pulse Voltages 0.2V CC to 0.8V CC Input and Output Timing Ref.Voltages0.3V CC to 0.7V CCTable 8. AC Measurement Conditions6/17ST24/25C16, ST24/25W16SCL SDA INSCL SDA OUTSCL SDA INtCHCLtDLCLtCHDXSTARTCONDITIONtCLCHtDXCXtCLDXSDAINPUTSDACHANGEtCHDHtDHDLSTOP &BUS FREEDATA VALIDtCLQV tCLQXDATA OUTPUTtCHDHSTOPCONDITIONtCHDXSTARTCONDITIONWRITE CYCLEtWAI00795BFigure 5. AC Waveforms7/17ST24/25C16, ST24/25W16Stop Condition. STOP is identified by a low to high transition of the SDA line while the clock SCL is stable in the high state. A STOP condition termi-nates communication between the ST24/25x16and the bus master. A STOP condition at the end of a Read command forces the standby state. A STOP condition at the end of a Write command triggers the internal EEPROM write cycle.Acknowledge Bit (ACK). An acknowledge signal is used to indicate a successful data transfer. The bus transmitter, either master or slave, will release the SDA bus after sending 8 bits of data. During the 9th clock pulse period the receiver pulls the SDA bus low to acknowledge the receipt of the 8 bits of data.SCLSDASCLSDASDASTART CONDITIONSDA INPUTSDA CHANGEAI00792STOP CONDITION123789MSB ACKSTART CONDITIONSCL123789MSB ACKSTOP CONDITIONFigure 6. I 2C Bus ProtocolData Input. During data input the ST24/25x16samples the SDA bus signal on the rising edge of the clock SCL. Note that for correct device opera-tion the SDA signal must be stable during the clock low to high transition and the data must change ONLY when the SCL line is low.Memory Addressing. To start communication be-tween the bus master and the slave ST24/25x16,the master must initiate a START condition. The 8bits sent after a START condition are made up of a device select of 4 bits that identifie the device type (1010), 3 Block select bits and one bit for a READ (RW = 1) or WRITE (RW = 0) operation.There are three modes both for read and write.They are summarised in Table 4 and described hereafter. A communication between the master and the slave is ended with a STOP condition.8/17ST24/25C16, ST24/25W16Write OperationsThe Multibyte Write mode (only available on the ST24/25C16 versions) is selected when the MODE pin is at V IH and the Page Write mode when MODEpin is at V IL. The MODE pin may be driven dynami-cally with CMOS input levels.Following a START condition the master sends a device select code with the RW bit reset to ’0’. The memory acknowledges this and waits for a byte address. The byte address of 8 bits provides ac-cess to any of the 256 bytes of one memory block. After receipt of the byte address the device again responds with an acknowledge.For the ST24/25W16 versions, any write command with WC = ’1’ (during a period of time from the START condition untill the end of the Byte Address) will not modify data and will NOT be acknowledged on data bytes, as in Figure 10.Byte Write. In the Byte Write mode the master sends one data byte, which is acknowledged by the memory. The master then terminates the transfer by generating a STOP condition. The Write mode is independant of the state of the MODE pin which could be left floating if only this mode was to be used. However it is not a recommended operating mode, as this pin has to be connected to either V IH or V IL, to minimize the stand-by current. Multibyte Write (ST24/25C16 only). For the Mul-tibyte Write mode, the MODE pin must be at V IH. The Multibyte Write mode can be started from any address in the memory. The master sends from one up to 8 bytes of data, which are each acknowledged by the memory. The transfer is terminated by the master generating a STOP condition. The duration of the write cycle is t W = 10ms maximum except when bytes are accessed on 2 contiguous rows (one row is 16 bytes), the programming time is then doubled to a maximum of 20ms. Writing more than 8 bytes in the Multibyte Write mode may modify data bytes in an adjacent row (one row is 16 bytes long). However, the Multibyte Write can properly write up to 16 consecutive bytes only if the first address of these 16 bytes is the first address of the row, the 15 following bytes being written in the 15 following bytes of this same row.AI00870B7FFh b7b4b2X X700hBlock 7Protect FlagEnable = 0Disable = 116 byteboundaryaddressProtect Location600h 500h 400h1BlockSelectPB1PB0Block 6Block 5Block 41111PB1PB0Figure 7. Memory Protection9/17ST24/25C16, ST24/25W16Page Write. For the Page Write mode, the MODE pin must be at V IL . The Page Write mode allows up to 16 bytes to be written in a single write cycle,provided that they are all located in the same ’row’in the memory: that is the same Block Address bits (b3, b2, b1 of Device Select code in Table 3) and the same 4 MSBs in the Byte Address. The master sends one up to 16 bytes of data, which are each acknowledged by the memory. After each byte is transfered, the internal byte address counter (4Least Significant Bits only) is incremented. The transfer is terminated by the master generating a STOP condition. Care must be taken to avoid ad-dress counter ’roll-over’ which could result in data being overwritten. Note that for any write mode, the generation by the master of the STOP condition starts the internal memory program cycle. All inputs are disabled until the completion of this cycle and the memory will not respond to any request.WRITE Cycle in ProgressAI01099BNext Operation is Addressing the MemorySTART Condition DEVICE SELECT with RW = 0ACK ReturnedYESNOYESNOReSTARTSTOPProceedWRITE OperationProceedRandom Address READ OperationSend Byte AddressFirst byte of instruction with RW = 0 already decoded by ST24xxxFigure 8. Write Cycle Polling using ACKMinimizing System Delay by Polling On ACK.During the internal Write cycle, the memory discon-nects itself from the bus in order to copy the data from the internal latches to the memory cells. The maximum value of the Write time (t W ) is given in the AC Characteristics table, this timing value may be reduced by an ACK polling sequence issued by the master.The sequence is:–Initial condition: a Write is in progress (see Fig-ure 8).–Step 1: the Master issues a START condition followed by a Device Select byte (1st byte of the new instruction).–Step 2: if the memory is internally writing, no ACK will be returned. The Master goes back to Step1. If the memory has terminated the in-ternal writing, it will issue an ACK indicating that the memory is ready to receive the sec-ond part of the instruction (the first byte of this instruction was already sent during Step 1).10/17ST24/25C16, ST24/25W16Write Protection. Data in the upper four blocks of 256 bytes of the memory may be write protected.The memory is write protected between a boundary address and the top of memory (address 7FFh).The boundary address is user defined by writing it in the Block Address Pointer (location 7FFh).The Block Address Pointer is an 8 bit EEPROM register located at the address 7FFh. It is com-posed by 4 MSBs Address Pointer, which defines the bottom boundary address, and 4 LSBs which must be programmed at ’0’. This Address Pointer can therefore address a boundary by page of 16bytes.The block in which the Block Address Pointer de-fines the boundary of the write protected memory is defined by the logic level applied on the PB1 and PB0 input pins:–PB1 =’0’and PB0 =’0’ select block 4–PB1 =’0’and PB0 =’1’ select block 5–PB1 =’1’and PB0 =’0’ select block 6–PB1 =’1’and PB0 =’1’ select block 7The following sequence should be used to set the Write Protection:–write the data to be protected into the top of the memory, up to, but not including, location 7FFh;–select the block by hardwiring the signals PB0& PB1;–set the protection by writing the correct bottom boundary address in the Address Pointer (4MSBs of location 7FFh) with bit b2 (Protect Flag) set to ’0’.Note that for a correct fonctionality of the memory,all the 4 LSBs of the Block Address Pointer must also be programmed at ’0’. The area will be pro-tected when the PRE input is taken High.Remark: The Write Protection is active if and only if the PRE input pin is driven High and the bit 2 of location 7FFh is set to ’0’. In all the other cases, the memory Block will not be protected. While the PRE input pin is read at ’0’ by the memory, the location 7FFh can be used as a normal EEPROM byte.Caution: Special attention must be used when using the protect mode together with the Multibyte Write mode (MODE input pin High). If the Multibyte Write starts at the location right below the first byte of the Write Protected area, then the instruction will write over the first 7 bytes of the Write Protected area. The area protected is therefore smaller than the content defined in the location 7FFh, by 7 bytes.This does not apply to the Page Write mode as the address counter ’roll-over’ and thus cannot go above the 16 bytes lower boundary of the protected area.S T O PS T A R TBYTE WRITEDEV SELBYTE ADDR DATA INS T A R TMULTIBYTE ANDPAGE WRITEDEV SEL BYTE ADDR DATA IN 1DATA IN 2AI00793S T O PDATA IN NACKACKACKR/W ACKACKACKR/WACKACKFigure 9. Write Modes Sequence (ST24/25C16)11/17S T O PS T A R TBYTE WRITEDEV SELBYTE ADDR DATA INWCS T A R TPAGE WRITEDEV SELBYTE ADDR DATA IN 1WCDATA IN 2AI01161BPAGE WRITE (cont'd)WC (cont'd)S T O PDATA IN NACKACKNO ACKR/WACKACKNO ACKR/WNO ACKNO ACKFigure 10. Write Modes Sequence with Write Control = 1 (ST24/25W16)Read OperationRead operations are independent of the state of the MODE signal. On delivery, the memory content is set at all "1’s" (or FFh).Current Address Read. The memory has an in-ternal byte address counter. Each time a byte is read, this counter is incremented. For the Current Address Read mode, following a START condition,the master sends a memory address with the RW bit set to ’1’. The memory acknowledges this and outputs the byte addressed by the internal byte address counter. This counter is then incremented.The master does NOT acknowledge the byte out-put, but terminates the transfer with a STOP con-dition.Random Address Read. A dummy write is per-formed to load the address into the address counter (see Figure 11). This is followed by another START condition from the master and the byte address repeated with the RW bit set to ’1’. The memory acknowledges this and outputs the byte ad-dressed. The master does NOT acknowledge the byte output, but terminates the transfer with a STOP condition.Sequential Read. This mode can be initiated with either a Current Address Read or a Random Ad-dress Read. However, in this case the master DOES acknowledge the data byte output and the memory continues to output the next byte in se-quence. To terminate the stream of bytes, the master must NOT acknowledge the last byte out-12/17S T A R TDEV SEL *BYTE ADDRS T A R TDEV SELDATA OUT 1AI00794CDATA OUT NS T O PS T A R TCURRENT ADDRESS READDEV SELDATA OUTRANDOM ADDRESS READS T O PS T A R TDEV SEL *DATA OUTSEQUENTIAL CURRENT READS T O P DATA OUT NS T A R TDEV SEL *BYTE ADDR SEQUENTIAL RANDOM READS T A R TDEV SEL *DATA OUT 1S T O PACKR/WNO ACKACKR/W ACKACK R/WACKACK ACK NO ACKR/WNO ACKACKACKR/WACK ACKR/WACK NO ACKFigure 11. Read Modes SequenceNote:*The 7 Most Significant bits of DEV SEL bytes of a Random Read (1st byte and 3rd byte) must be identical.put, but MUST generate a STOP condition. The output data is from consecutive byte addresses,with the internal byte address counter automat-ically incremented after each byte output. After a count of the last memory address, the address counter will ’roll- over’ and the memory will continue to output data.Acknowledge in Read Mode. In all read modes the ST24/25x16 wait for an acknowledge during the 9th bit time. If the master does not pull the SDA line low during this time, the ST24/25x16 terminate the data transfer and switches to a standby state.13/17Operating Voltage 24 4.5V to 5.5V 25 2.5V to 5.5VRange C Standard W HardwareWrite ControlPackage B PSDIP80.25mm Frame M SO8150mil WidthTemperature Range 10 to 70 °C 6–40 to 85 °C3 (1)–40 to 125 °COption TR Tape & ReelPackingExample: ST24C16 M 1 TRORDERING INFORMATION SCHEMENote: 1.T emperature range on special request only.Devices are shipped from the factory with the memory content set at all "1’s" (FFh).For a list of available options (Operating Voltage, Package, etc...) or for further information on any aspect of this device, please contact the STMicroelectronics Sales Office nearest to you.14/17PSDIP-aA2A1A Le1DE1EN1CeA eBB1BSymbmm inches TypMin Max TypMin Max A 3.90 5.900.1540.232A10.49–0.019–A2 3.30 5.300.1300.209B 0.360.560.0140.022B1 1.15 1.650.0450.065C 0.200.360.0080.014D 9.209.900.3620.390E 7.62––0.300––E1 6.00 6.700.2360.264e1 2.54––0.100––eA 7.80–0.307–eB –10.00–0.394L 3.00 3.800.1180.150N88Drawing is not to scale.PSDIP8 - 8 pin Plastic Skinny DIP , 0.25mm lead frame15/17SO-aENCPBe ADCLA1α1Hh x 45˚Symbmm inches TypMin Max TypMin Max A 1.35 1.750.0530.069A10.100.250.0040.010B 0.330.510.0130.020C 0.190.250.0070.010D 4.80 5.000.1890.197E 3.80 4.000.1500.157e 1.27––0.050––H 5.80 6.200.2280.244h 0.250.500.0100.020L 0.400.900.0160.035α0°8°0°8°N 88CP0.100.004Drawing is not to scale.SO8 - 8 lead Plastic Small Outline, 150 mils body width16/17Information furnished is believed to be accurate and reliable. However, STMicroelectronics assumes no responsibility for the consequences of use of such information nor for any infringement of patents or other rights of third parties which may result from its use. No license is granted by implication or otherwise under any patent or patent rights of STMicroelectronics. Specifications mentioned in this publication are subject to change without notice. This publication supersedes and replaces all information previously supplied. STMicroelectronics products are not authorized for use as critical components in life support devices or systems without express written approval of STMicroelectronics.The ST logo is a registered trademark of STMicroelectronics© 1999 STMicroelectronics - All Rights ReservedAll other names are the property of their respective ownersPurchase of I2C Components by STMicroelectronics, conveys a license under the PhilipsI2C Patent. Rights to use these components in an I2C system, is granted provided that the system conforms tothe I2C Standard Specifications as defined by Philips.STMicroelectronics GROUP OF COMPANIESAustralia - Brazil - Canada - China - France - Germany - Italy - Japan - Korea - Malaysia - Malta - Mexico - Morocco - The Netherlands - Singapore - Spain - Sweden - Switzerland - Taiwan - Thailand - United Kingdom - U.S.A.17/17。
威尔恩灯条产品说明书
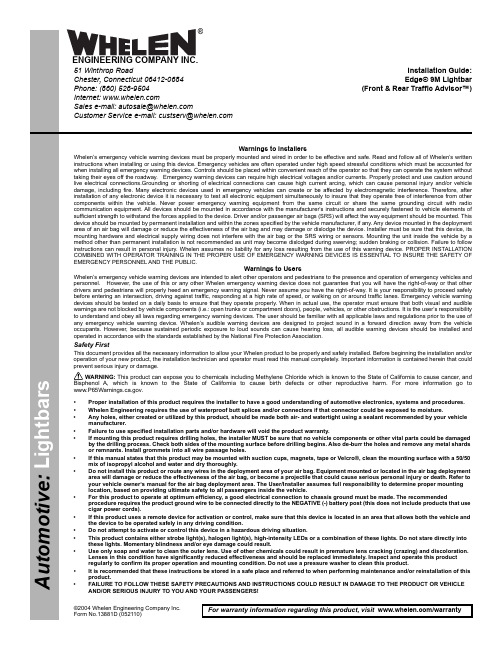
©2004 Whelen Engineering Company Inc.Form No.13881D (052110)A u t o m o t i v e : For warranty information regarding this product, visit /warranty•Proper installation of this product requires the installer to have a good understanding of automotive electronics, systems and procedures.•Whelen Engineering requires the use of waterproof butt splices and/or connectors if that connector could be exposed to moisture.•Any holes, either created or utilized by this product, should be made both air- and watertight using a sealant recommended by your vehicle manufacturer.•Failure to use specified installation parts and/or hardware will void the product warranty.•If mounting this product requires drilling holes, the installer MUST be sure that no vehicle components or other vital parts could be damaged by the drilling process. Check both sides of the mounting surface before drilling begins. Also de-burr the holes and remove any metal shards or remnants. Install grommets into all wire passage holes.•If this manual states that this product may be mounted with suction cups, magnets, tape or Velcro®, clean the mounting surface with a 50/50 mix of isopropyl alcohol and water and dry thoroughly.•Do not install this product or route any wires in the deployment area of your air bag. Equipment mounted or located in the air bag deployment area will damage or reduce the effectiveness of the air bag, or become a projectile that could cause serious personal injury or death. Refer to your vehicle owner’s manual for the air bag deployment area. The User/Installer assumes full responsibility to determine proper mounting location, based on providing ultimate safety to all passengers inside the vehicle.•For this product to operate at optimum efficiency, a good electrical connection to chassis ground must be made. The recommendedprocedure requires the product ground wire to be connected directly to the NEGATIVE (-) battery post (this does not include products that use cigar power cords).•If this product uses a remote device for activation or control, make sure that this device is located in an area that allows both the vehicle and the device to be operated safely in any driving condition.•Do not attempt to activate or control this device in a hazardous driving situation.•This product contains either strobe light(s), halogen light(s), high-intensity LEDs or a combination of these lights. Do not stare directly into these lights. Momentary blindness and/or eye damage could result.•Use only soap and water to clean the outer lens. Use of other chemicals could result in premature lens cracking (crazing) and discoloration. Lenses in this condition have significantly reduced effectiveness and should be replaced immediately. Inspect and operate this product regularly to confirm its proper operation and mounting condition. Do not use a pressure washer to clean this product.•It is recommended that these instructions be stored in a safe place and referred to when performing maintenance and/or reinstallation of this product.•FAILURE TO FOLLOW THESE SAFETY PRECAUTIONS AND INSTRUCTIONS COULD RESULT IN DAMAGE TO THE PRODUCT OR VEHICLE AND/OR SERIOUS INJURY TO YOU AND YOUR PASSENGERS!Warnings to InstallersWhelen’s emergency vehicle warning devices must be properly mounted and wired in order to be effective and safe. Read and follow all of Whelen’s written instructions when installing or using this device. Emergency vehicles are often operated under high speed stressful conditions which must be accounted for when installing all emergency warning devices. Controls should be placed within convenient reach of the operator so that they can operate the system without taking their eyes off the roadway. Emergency warning devices can require high electrical voltages and/or currents. Properly protect and use caution around live electrical connections.Grounding or shorting of electrical connections can cause high current arcing, which can cause personal injury and/or vehicle damage, including fire. Many electronic devices used in emergency vehicles can create or be affected by electromagnetic interference. Therefore, after installation of any electronic device it is necessary to test all electronic equipment simultaneously to insure that they operate free of interference from other components within the vehicle. Never power emergency warning equipment from the same circuit or share the same grounding circuit with radio communication equipment. All devices should be mounted in accordance with the manufacturer’s instructions and securely fastened to vehicle elements of sufficient strength to withstand the forces applied to the device. Driver and/or passenger air bags (SRS) will affect the way equipment should be mounted. This device should be mounted by permanent installation and within the zones specified by the vehicle manufacturer, if any. Any device mounted in the deployment area of an air bag will damage or reduce the effectiveness of the air bag and may damage or dislodge the device. Installer must be sure that this device, its mounting hardware and electrical supply wiring does not interfere with the air bag or the SRS wiring or sensors. Mounting the unit inside the vehicle by a method other than permanent installation is not recommended as unit may become dislodged during swerving; sudden braking or collision. Failure to follow instructions can result in personal injury. Whelen assumes no liability for any loss resulting from the use of this warning device. PROPER INSTALLATION COMBINED WITH OPERATOR TRAINING IN THE PROPER USE OF EMERGENCY WARNING DEVICES IS ESSENTIAL TO INSURE THE SAFETY OF EMERGENCY PERSONNEL AND THE PUBLIC.Warnings to UsersWhelen’s emergency vehicle warning devices are intended to alert other operators and pedestrians to the presence and operation of emergency vehicles and personnel. However, the use of this or any other Whelen emergency warning device does not guarantee that you will have the right-of-way or that other drivers and pedestrians will properly heed an emergency warning signal. Never assume you have the right-of-way. It is your responsibility to proceed safely before entering an intersection, driving against traffic, responding at a high rate of speed, or walking on or around traffic lanes. Emergency vehicle warning devices should be tested on a daily basis to ensure that they operate properly. When in actual use, the operator must ensure that both visual and audible warnings are not blocked by vehicle components (i.e.: open trunks or compartment doors), people, vehicles, or other obstructions. It is the user’s responsibility to understand and obey all laws regarding emergency warning devices. The user should be familiar with all applicable laws and regulations prior to the use of any emergency vehicle warning device. Whelen’s audible warning devices are designed to project sound in a forward direction away from the vehicle occupants. However, because sustained periodic exposure to loud sounds can cause hearing loss, all audible warning devices should be installed and operated in accordance with the standards established by the National Fire Protection Association.Safety FirstThis document provides all the necessary information to allow your Whelen product to be properly and safely installed. Before beginning the installation and/or operation of your new product, the installation technician and operator must read this manual completely. Important information is contained herein that could prevent serious injury or damage.WARNING: This product can expose you to chemicals including Methylene Chloride which is known to the State of California to cause cancer, and Bisphenol A, which is known to the State of California to cause birth defects or other reproductive harm. For more information go to .Installation Guide:Edge® 9M Lightbar(Front & Rear Traffic Advisor™)51 Winthrop RoadChester, Connecticut 06412-0684Phone: (860) 526-9504Internet: Salese-mail:*******************CustomerServicee-mail:*******************®ENGINEERING COMPANY INC.Strap Mounting:1.Locate the mounting foot, mounting plate and tinnerman plate included with your lightbar. If not already present, install the mounting plate onto the mounting foot. When properly positioned, this plate is centered from side to side on the mounting foot.2.Flip the lightbar upside-down to expose the bottom of the extrusion and place the mounting foot onto the extrusion.3.Rotate the mounting foot 90° in a counter-clockwise direction. Make sure that the edges of the mounting foot swing into position under the extrusion mounting lip. Install a tinnerman plate onto the extrusion in the same manner.IMPORTANT! The lightbar should be located a minimum of 16" from any radio antennas!Permanent Mounting:1.Locate the mounting foot and mounting plate included with your lightbar. If not already present, install the mounting plate onto the mounting foot. When properly positioned, this plate is centered from side to side on the mounting foot.2.Flip the lightbar upside-down to expose the bottom of the extrusion and place the mounting foot onto the extrusion.3.Rotate the mounting foot 90° in a counter-clockwise direction. Make sure that the edges of the mounting foot swing into position under the extrusion mounting lip.4.Repeat this procedure for the remaining mounting foot and return the lightbar to its right side-up position.5.Position the lightbar onto the vehicle roof in the desired mounting location. One often selected location is directly above the B-pillars.This area is the strongest part of the roof. Refer to your lightbar manual for cable exit location, to be sure that the lightbar is facing the proper direction.6.Adjust the two mounting feet outwards so that they are as close to the edge of the roof as possible. Make sure that both mounting feet are in full contact with the roof. Be sure that there is no less than 1/2”clearance between the roof and the lightbar at their closest point.When the mounting feet are in their proper position, lightly tighten the mounting foot allen head set screws.7.Turn the lightbar upside down and firmly tighten all of the set screws from step 6 (2 or 4 per side).8.Note that on the adjustable foot, use the hole in the pad as a guide to drill the two holes into the mounting foot at the locations shown.9.Place the lightbar in its final mounting position on the vehicle, mark the mounting hole locations off onto the mounting surface, remove the lightbar and drill the mounting holes.10.Place the lightbar back onto the vehicle lined up with the mountingholes and secure the mounting feet to the vehicle using the supplied hardware as shown.4.Repeat this procedure for the remaining mounting foot and tinnerman plate and return the lightbar to its right side-up position.5.Position the lightbar onto the vehicle roof in the desired mounting location.One often selected location is directly above the B-pillars. This area is the strongest part of the roof. Refer to your lightbar manual for cable exit location, to be sure that the lightbar is facing the proper direction.6.Adjust the two mounting feet outwards so that they are as close to the edge of the roof as possible. Both mounting feet must be in full contact with the roof. Be sure that there is no less than 1/2” clearance between the roof and the lightbar at their closest point. When the mounting feet are in their proper position, lightly tighten the mounting foot allen head set screws.7.Return the lightbar to an upside down position. Slide each tinnerman plate outwards until it is fully engaged with its corresponding mounting foot.With the mounting feet and tinnerman plates in their proper positions firmly tighten all of the set screws (2 or 4 per side). Flip the lightbar right side-up and return it to its mounting position.8.Open both drivers side doors. In the area directly below the mounting foot, carefully pull the drivers side weatherstrip away from the vehicle.Remove enough so that the area where the mounting strap will be secured to the vehicle is exposed. Repeat procedure for passenger side.9.Insert the mounting strap through the mounting foot. Be sure that the strap fits flush against the area where it will be secured onto the vehicle.Insert the tension bolt through the mounting strap and into the tinnerman nut on the tinnerman plate. Tighten slightly with a long shafted, Phillips screwdriver. Repeat procedure for passenger side.10.If your mounting strap has mounting holes in the end of the strap, use these holes as a template to drill appropriately sized pilot holes through the strap and into the vehicle. Repeat for passenger side of the vehicle.11.Firmly tighten the tension bolts to secure the lightbar to the vehicle.NOTE: Model MKAJ is an adjustable mounting foot. On this model you may loosen the screws on the rear of the foot and adjust the angle of the lightbar. This feature can be used if the angle of the roof is not level with the road.IMPORTANT: To adjust the leveling screws you must use a torque wrench set at 35 to 40 ft. lbs.If2.Connect the control wires to this switch panel using the Array information provided on the following page.Understanding TA Operation & Scan-Lock™To change TA sequences, momentarily apply +12VDC to the Scan-Lock™ wire for the TA in question (front or rear) while that TA is flashing Left, Right or Split. For example, with the Front TA in ‘sequence to left’ mode (+12VDC applied to the BLUE/ WHITE wire), apply +12VDC to the front Scan-Lock™ wire (WHITE/VIOLET) for less than 1 second. The next sequence will now be displayed. Repeat to advance to the next sequence. Applying +12VDC for more than 1 second will cycle to the previous sequence. Allow the sequence to run uninterrupted for at least 5 seconds to set it as the default sequence.TA Sequences:1. 1-lamp sequence to Triple Flash™.2. 2-lamp sequence to Triple Flash™.3. 3-lamp sequence to Triple Flash™.4. Sequence to Solid5. Sequence to Solid - Sequence OffChanging TA Patterns while in Flash mode uses the appropriate Scan-Lock™ wire in the same manner as outlined above. Refer to the TA Patterns (for Flash mode Only) table below for pattern order.For example, with the Rear TA in Flash Mode (+12VDC applied to the WHITE/BROWN wire), momentarily apply +12VDC to the rear Scan-Lock™ wire (WHITE/GREEN). If previously set to pattern 1 (see below), the front TA will now display pattern 2. Repeat to advance to the next pattern.TA Patterns (for Flash Mode Only):1. SignalAlert™75 6. RapidRate™1502. CometFlash®757. RapidRate™753. DoubleFlash 1208. ComAlert™754. DoubleFlash 759. ActionFlash™5. RapidRate™37510. ActionScan™TO RESET TO THE FACTORY DEFAULT PATTERN: Turn off the option you want to reset, apply +12 volts to the Scan-Lock™function wire of that option then turn the option back on.Troubleshooting:Your lightbar should now be fully operational. If your lightbar is not functioning properly, check the following:•The positive wire (RED) is properly connected to the battery, by way of the user supplied fuse block.• A working fuse of the correct amperage (30 amp) is installed in the fuse block.•The ground wire (BLACK) is properly connected to the factory ground.If all of these connections are good, contact your Whelenrepresentative for further assistance.。
IN24LC16资料

Note 2
1. As a transmitter, the device must provide an internal minimum delay time to bridge the undefined region (minimum 300 ns) of the falling edge of SCL to avoid unintended generation of START or STOP conditions. 2. This parameter is not tested but guaranteed by characterization.
FEATURES
• Single supply with operation down to 2.5V • Low power CMOS technology - 1 mA active current typical - 10 µA standby current typical at 5.5V - 5 µA standby current typical at 3.0V • Organized as 8 blocks of 256 bytes (8 x 256 x 8) • 2-wire serial interface bus, I2C compatible • Schmitt trigger inputs for noise suppression • Output slope control to eliminate ground bounce • 100 kHz (E-temp) and 400 kHz (C/I-temp) compatibility • Self-timed write cycle (including auto-erase) • Page-write buffer for up to 16 bytes • 2 ms typical write cycle time for page-write • Hardware write protect for entire memory • Can be operated as a serial ROM • 1,000,000 erase/write cycles guaranteed • Data retention > 200 years • 8-pin DIP, 8-lead SOIC,
HE-24W 24W 单组输出电源模块 技术参数说明说明书
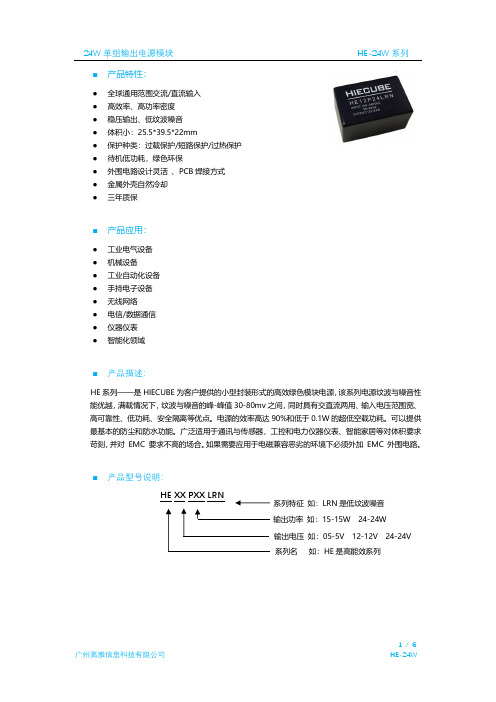
■ 产品特性:● 全球通用范围交流/直流输入 ● 高效率、高功率密度● 稳压输出、低纹波噪音 ● 体积小:25.5*39.5*22mm ● 保护种类:过载保护/短路保护/过热保护 ● 待机低功耗,绿色环保● 外围电路设计灵活 、PCB 焊接方式 ● 金属外壳自然冷却 ●三年质保■ 产品应用:● 工业电气设备 ● 机械设备 ● 工业自动化设备 ● 手持电子设备 ● 无线网络 ● 电信/数据通信 ● 仪器仪表●智能化领域■ 产品描述:HE 系列——是HIECUBE 为客户提供的小型封装形式的高效绿色模块电源,该系列电源纹波与噪音性能优越,满载情况下,纹波与噪音的峰-峰值30-80mv 之间,同时具有交直流两用、输入电压范围宽、 高可靠性、低功耗、安全隔离等优点。
电源的效率高达90%和低于0.1W 的超低空载功耗。
可以提供最基本的防尘和防水功能。
广泛适用于通讯与传感器,工控和电力仪器仪表、智能家居等对体积要求苛刻,并对 EMC 要求不高的场合。
如果需要应用于电磁兼容恶劣的环境下必须外加 EMC 外围电路。
■ 产品型号说明:HE XX PXX LRN系列名 如:HE 是高能效系列输出电压 如:05-5V 12-12V 24-24V 输出功率 如:15-15W 24-24W系列特征 如:LRN 是低纹波噪音■输入电气规格:■输出电气规格:■纹波与噪音特性:■通用特性:项目工作条件@测试结论开关频率65KHz短路保护可长期短路,自恢复过载保护>Load110%,可恢复过热保护模块表面温度在80℃(±4℃),进入过热保护耐压测试Input-Output 3000VAC /1min (耐压测试属于极限破坏实验,不可多次测试)工作温度-30~70℃(详细使用情况参考温度&降额曲线)存储温度-40~70℃模块重量47g(±2g)外壳尺寸25.5*39.5*22mm外壳材质铝外壳冷却方式自然冷却安全等级CLASS Ⅱ备注如未特别说明,所有规格参数均在输入电压为220VAC,环境温度25℃下测试。
电容容量标注法
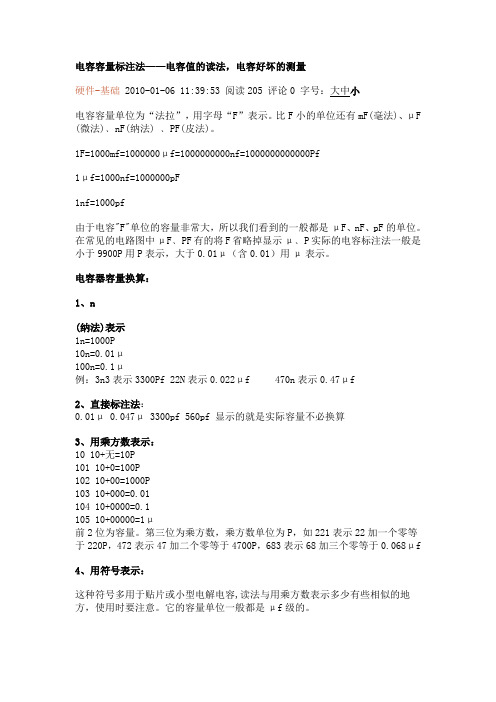
电容容量标注法——电容值的读法,电容好坏的测量硬件-基础 2010-01-06 11:39:53 阅读205 评论0 字号:大中小电容容量单位为“法拉”,用字母“F”表示。
比F小的单位还有mF(毫法)、μF (微法)﹑nF(纳法) ﹑PF(皮法)。
1F=1000mf=1000000μf=1000000000nf=1000000000000Pf1μf=1000nf=1000000pF1nf=1000pf由于电容"F"单位的容量非常大,所以我们看到的一般都是μF、nF、pF的单位。
在常见的电路图中μF﹑PF有的将F省略掉显示μ﹑P实际的电容标注法一般是小于9900P用P表示,大于0.01μ(含0.01)用μ表示。
电容器容量换算:1、n(纳法)表示1n=1000P10n=0.01μ100n=0.1μ例:3n3表示3300Pf 22N表示0.022μf 470n表示0.47μf2、直接标注法:0.01μ 0.047μ 3300pf 560pf 显示的就是实际容量不必换算3、用乘方数表示:10 10+无=10P101 10+0=100P102 10+00=1000P103 10+000=0.01104 10+0000=0.1105 10+00000=1μ前2位为容量。
第三位为乘方数,乘方数单位为P,如221表示22加一个零等于220P,472表示47加二个零等于4700P,683表示68加三个零等于0.068μf4、用符号表示:这种符号多用于贴片或小型电解电容,读法与用乘方数表示多少有些相似的地方,使用时要注意。
它的容量单位一般都是μf级的。
表示字符容量单位μf 表示字符容量单位μf 0R1 0.1μf 100 10μf R15 0.15μf 150 15μf R22 0.22μf 220 22μf R33 0.33μf 330 33μf R39 0.39μf 390 39μf R47 0.47μf 470 47μf R56 0.56μf 560 56μf R68 0.68μf 680 68μf R82 0.82μf 820 82μf 010 1μf 101 100μf 1R5 1.5μf 151 150μf 2R2 2.2μf 221 220μf 3R3 3.3μf 331 330μf 3R9 3.9μf 391 390μf 4R7 4.7μf 471 470μf 5R6 5.6μf 561 560μf 6R8 6.8μf 681 680μf 8R2 8.2μf 821 820μf电容器误差精度值代号标识法:电容误差值 A:-0+5%﹑J:±5%﹑K:±10%﹑M:±20%﹑Z:-20%+50%电容器耐压值标示方法:电容耐压等极:16V﹑25V﹑35V﹑50V﹑63V﹑100V﹑160V﹑250V﹑400V﹑630V﹑1000V﹑1250V﹑2000V﹑3000V 到更高耐压,实际的电容有的电容器耐压值只写上"1250" 不写1250V 。
- 1、下载文档前请自行甄别文档内容的完整性,平台不提供额外的编辑、内容补充、找答案等附加服务。
- 2、"仅部分预览"的文档,不可在线预览部分如存在完整性等问题,可反馈申请退款(可完整预览的文档不适用该条件!)。
- 3、如文档侵犯您的权益,请联系客服反馈,我们会尽快为您处理(人工客服工作时间:9:00-18:30)。
DS800010-2
8-Pin TSSOP Package (MT8) Rotated Die (24C16UT)
NC VCC NC NC 1 2 3 4 8 7 SCL SDA VSS NC
DS800010-3
NM24C16U
Block Diagram
VCC VSS WP H.V. GENERATION TIMING &CONTROL START STOP LOGIC CONTROL LOGIC SLAVE ADDRESS REGISTER & COMPARATOR E2PROM ARRAY
SDA
SCL
XDEC
WORD ADDRESS COUNTER
元器件交易网
NM24C16U/NM24C17U – 16K-Bit Serial EEPROM 2-Wire Bus Interface
August 1999
NM24C16U/NM24C17U 16K-Bit Serial EEPROM 2-Wire Bus Interface
1
元器件交易网
NM24C16U/NM24C17U – 16K-Bit Serial EEPROM 2-Wire Bus Interface
Connection Diagrams
Dual-In-Line Package (N), 8-Pin SO Package (M8)
Dual-In-Line Package (N), 8-Pin SO Package (M8)
NC NC NC VSS 1 2 3 4 8 7 VCC WP SCL SDA
DS800010-4
8-Pin TSSOP Package (MT8) Rotated Die (24C17UT)
WP VCC NC NC 1 2 3 4 8 7 SCL SDA VSS NC
ICCA ISB Active Power Supply Current fSCL = 400 KHz fSCL = 100 KHz Standby Current VIN = GND or VCC VCC = 2.7V - 4.5V VCC = 2.7V - 4.5V VCC = 4.5V - 5.5V
Temp. Range
Voltage Operating Range
Blank T SCL Clock Frequency Blank F Ultralite Density 16 17 C W Interface 24 NM
3
NM24C16U/17U Rev. B.1
www.fairchildБайду номын сангаас
R/W
YDEC
CK DIN DATA REGISTER DOUT
DS800010-1
I2C™ is a registered trademark of Philips Electronics N.V.
© 1999 Fairchild Semiconductor Corporation NM24C16U/17U Rev. B.1
Limits Typ (Note 1)
0.2 10 0.1 0.1
Units Max
1.0 50 1 1 VCC x 0.3 VCC + 0.5 0.4 mA µA µA µA V V V
Low VCC (2.7V to 5.5V) DC Electrical Characteristics
Symbol Parameter Test Conditions Min
General Description
The NM24C16U/17U devices are 16K (16,384) bit serial interface CMOS EEPROMs (Electrically Erasable Programmable ReadOnly Memory). These devices fully conform to the Standard I2C™ 2-wire protocol which uses Clock (SCL) and Data I/O (SDA) pins to synchronously clock data between the "master" (for example a microprocessor) and the "slave" (the EEPROM device). In addition, the serial interface allows a minimal pin count packaging designed to simplify PC board layout requirements and offers the designer a variety of low voltage and low power options. NM24C17U incorporates a hardware "Write Protect" feature, by which, the upper half of the memory can be disabled against programming by connecting the WP pin to VCC. This section of memory then effectively becomes a ROM (Read-Only Memory) and can no longer be programmed as long as WP pin is connected to VCC. Fairchild EEPROMs are designed and tested for applications requiring high endurance, high reliability and low power consumption for a continuously reliable non-volatile solution for all markets.
Features
I The I2C™ interface allows the smallest I/O pincount of any EEPROM interface I 16 byte page write mode to minimize total write time per byte I Typical 200µA active current (ICCA) I Typical 1µA standby current (ISB) for "L" devices and 0.1µA standby current for "LZ" devices I Endurance: Up to 1,000,000 data changes I Data retention greater than 40 years
DS800010-5
NM24C17U
6 5
NM24C17UT
6 5
Top View See Package Number N08E, M08A and MTC08
Pin Names
VSS SDA SCL WP VCC NC Ground Serial Data I/O Serial Clock input Write Protect Power Supply No Connection
Standard VCC (4.5V to 5.5V) DC Electrical Characteristics
Symbol Parameter Test Conditions Min
ICCA ISB ILI ILO VIL VIH VOL Active Power Supply Current Standby Current Input Leakage Current Output Leakage Current Input Low Voltage Input High Voltage Output Low Voltage IOL = 3 mA fSCL = 400 KHz fSCL = 100 KHz VIN = GND or VCC VIN = GND to VCC VOUT = GND to VCC –0.3 VCC x 0.7
Package
Letter
N M8 MT8 None V E Blank L LZ
Description
8-pin DIP 8-pin SOIC 8-pin TSSOP 0 to 70°C -40 to +125°C -40 to +85°C 4.5V to 5.5V 2.7V to 5.5V 2.7V to 5.5V and <1µA Standby Current Normal Pin Out Rotated Die Pin Out 100KHz 400KHz CS100UL Process 16K 16K with Write Protect CMOS Technology Total Array Write Protect IIC Fairchild Non-Volatile Memory
2
NM24C16U/17U Rev. B.1
元器件交易网
NM24C16U/NM24C17U – 16K-Bit Serial EEPROM 2-Wire Bus Interface
Ordering Information NM 24 C XX U F T LZ E XX
Operating Conditions
Ambient Operating Temperature NM24C16U/17U NM24C16UE/17UE NM24C16UV/17UV Positive Power Supply NM24C16U/17U NM24C16UL/17UL NM24C16ULZ/17ULZ 0°C to +70°C -40°C to +85°C -40°C to +125°C 4.5V to 5.5V 2.7V to 5.5V 2.7V to 5.5V