工艺卡片-铁塔
(完整版)工艺过程卡和工序卡卡片

机电学院机械加工工序卡片产品名称柴油机零件名称机油泵后盖共13 页第 1 页车间工序号工序名称材料牌号粗铣HT200毛坯种类毛坯外形尺寸每毛坯可制件数每台件数铸件120*78*40 1 1设备名称设备型号设备编号同时加工件数卧式铣床X61 1夹具编号夹具名称切削液虎钳工位器具编号工位器具名称工序工时(分)准终单件工步号工步内容工艺装备主轴转速切削速度进给量切削深度进给次数工步工时r/min m/s mm/r mm 机动辅助1 粗铣机盖顶端面,保证尺寸35mm 硬质合金端面铣刀、卡尺160 1 1.6 5 1 32.822标记处数更改文件号签字日期标记处数更改文件号签字日期设计(日期)校对(日期)审核(日期)标准化(日期)会签(日期)机电学院机械加工工序卡片产品名称柴油机零件名称机油泵后盖共13 页第 2 页车间工序号工序名称材料牌号粗铣、半精铣HT200毛坯种类毛坯外形尺寸每毛坯可制件数每台件数铸件120*78*35 1设备名称设备型号设备编号同时加工件数卧式铣床X61 1夹具编号夹具名称切削液虎钳工位器具编号工位器具名称工序工时(分)准终单件工步号工步内容工艺装备主轴转速切削速度进给量切削深度进给次数工步工时r/min m/s mm/r mm 机动辅助1 粗铣下端面,保证尺寸31mm 硬质合金端面铣刀、卡尺160 1 1.6 4 1 32.822 半精铣下端面,保证尺寸30.2mm 硬质合金端面铣刀、卡尺210 1.3 1.6 0.8 1 25.00标记处数更改文件号签字日期标记处数更改文件号签字日期设计(日期)校对(日期)审核(日期)标准化(日期)会签(日期)机电学院机械加工工序卡片产品名称柴油机零件名称机油泵后盖共13 页第 3 页车间工序号工序名称材料牌号HT200毛坯种类毛坯外形尺寸每毛坯可制件数每台件数铸件120*78*30.2 1设备名称设备型号设备编号同时加工件数摇臂钻床Z3040 1夹具编号夹具名称切削液专用夹具工位器具编号工位器具名称工序工时(分)准终单件工步号工步内容工艺装备主轴转速切削速度进给量切削深度进给次数工步工时r/min m/s mm/r mm 机动辅助1 钻6-Φ9mm孔Φ9高速钢麻花钻、塞规630 0.29 0.4 22.862 铰6-Φ9孔中对称轴上的两个孔至Φ9.1H8(022.0)做定位孔Φ9.1铰刀、塞规500 0.26 0.8 7.44标记处数更改文件号签字日期标记处数更改文件号签字日期设计(日期)校对(日期)审核(日期)标准化(日期)会签(日期)机电学院机械加工工序卡片产品名称柴油机零件名称机油泵后盖共13 页第 4 页车间工序号工序名称材料牌号HT200毛坯种类毛坯外形尺寸每毛坯可制件数每台件数铸件120*78*30.2 1设备名称设备型号设备编号同时加工件数摇臂钻床Z3040 1夹具编号夹具名称切削液专用夹具工位器具编号工位器具名称工序工时(分)准终单件工步号工步内容工艺装备主轴转速切削速度进给量切削深度进给次数工步工时r/min m/s mm/r mm 机动辅助1 钻一个2-Φ4.8mm孔模具、Φ4.8高速钢麻花钻、塞规250 0.13 0.25 9.32 铰此孔2-Φ4.8mm至2-Φ5mmΦ5铰刀、塞规500 0.13 0.4 4.653 通过模具以此孔定位钻另一个Φ4.8mm孔模具、Φ4.8高速钢麻花钻、塞规250 0.13 0.25 9.34 铰此孔2-Φ4.8mm至2-Φ5mm Φ5铰刀、塞规500 0.13 0.4 4.655 倒角2-Φ4.8mm孔1.1x45º高速钢锥面锪钻10x90º标记处数更改文件号签字日期标记处数更改文件号签字日期设计(日期)校对(日期)审核(日期)标准化(日期)会签(日期)机电学院机械加工工序卡片产品名称柴油机零件名称机油泵后盖共13 页第 5 页车间工序号工序名称材料牌号HT200毛坯种类毛坯外形尺寸每毛坯可制件数每台件数铸件120*78*30.2 1设备名称设备型号设备编号同时加工件数摇臂钻床Z3040 1夹具编号夹具名称切削液工位器具编号工位器具名称工序工时(分)准终单件工步号工步内容工艺装备主轴转速切削速度进给量切削深度进给次数工步工时r/min m/s mm/r mm 机动辅助1 锪6-Φ18mm螺钉凸台高速钢平底锪钻18x9、卡尺400 0.4 0.14 5 1 19.32234标记处数更改文件号签字日期标记处数更改文件号签字日期设计(日期)校对(日期)审核(日期)标准化(日期)会签(日期)机电学院机械加工工序卡片产品名称柴油机零件名称机油泵后盖共13 页第 6 页车间工序号工序名称材料牌号HT200毛坯种类毛坯外形尺寸每毛坯可制件数每台件数铸件120*78*30.2 1设备名称设备型号设备编号同时加工件数卧式铣床X61 1夹具编号夹具名称切削液专用夹具工位器具编号工位器具名称工序工时(分)准终单件工步号工步内容工艺装备主轴转速切削速度进给量切削深度进给次数工步工时r/min m/s mm/r mm 机动辅助1 铣下端面20*10*1.5槽硬质合金键槽铣刀10x60,卡尺945 0.5 0.2 1.5 3.812标记处数更改文件号签字日期标记处数更改文件号签字日期设计(日期)校对(日期)审核(日期)标准化(日期)会签(日期)机电学院机械加工工序卡片产品名称柴油机零件名称机油泵后盖共13 页第7 页车间工序号工序名称材料牌号HT200毛坯种类毛坯外形尺寸每毛坯可制件数每台件数铸件120*78*30.2 1设备名称设备型号设备编号同时加工件数摇臂钻床Z3040 1夹具编号夹具名称切削液专用夹具工位器具编号工位器具名称工序工时(分)准终单件工步号工步内容工艺装备主轴转速切削速度进给量切削深度进给次数工步工时r/min m/min mm/r mm 机动辅助1 钻Φ12mm孔Φ12高速钢麻花钻400 0.28 0.45 21.672 钻Φ14mm孔Φ14高速钢麻花钻320 0.28 0.5 11.443 钻Φ24mm孔Φ24高速钢麻花钻200 0.28 0.7 13.074标记处数更改文件号签字日期标记处数更改文件号签字日期设计(日期)校对(日期)审核(日期)标准化(日期)会签(日期)华侨大学机电学院机械加工工序卡片产品型号6120 零件图号6120-1011-016 姓名:林凌攀产品名称柴油机零件名称机油泵后盖共13 页第8 页车间工序号工序名称材料牌号HT200毛坯种类毛坯外形尺寸每毛坯可制件数每台件数铸件120*78*30.2 1设备名称设备型号设备编号同时加工件数摇臂钻床Z3040 1夹具编号夹具名称切削液专用夹具工位器具编号工位器具名称工序工时(分)准终单件工步号工步内容工艺装备主轴转速切削速度进给量切削深度进给次数工步工时r/min m/min mm/r mm 机动辅助1 钻侧面的Φ12mm的孔到铸件的铸孔约62mm深Φ12高速钢麻花钻,塞规400 0.28 0.45 88.47234标记处数更改文件号签字日期标记处数更改文件号签字日期设计(日期)校对(日期)审核(日期)标准化(日期)会签(日期)华侨大学机电学院机械加工工序卡片产品型号6120 零件图号6120-1011-016 姓名:林凌攀产品名称柴油机零件名称机油泵后盖共13 页第9 页车间工序号工序名称材料牌号HT200毛坯种类毛坯外形尺寸每毛坯可制件数每台件数铸件120*78*30.2 1设备名称设备型号设备编号同时加工件数卧式车床CA6140 1夹具编号夹具名称切削液专用夹具工位器具编号工位器具名称工序工时(分)准终单件工步号工步内容工艺装备主轴转速切削速度进给量切削深度进给次数工步工时r/min m/s mm/r mm 机动辅助1 Φ12粗镗到Φ16.5,深度为25,作为螺纹的底孔硬质合金镗刀、塞规1400 1.0 0.2 6.782 粗镗Φ16.5右端面,保证尺寸41mm 硬质合金端面镗刀,卡尺160 1 1.6 5 1 7.683 M18*1.5孔倒角硬质合倒角刀1120 0.25 0.644 攻丝内螺纹镗刀320 0.3 0.5 9.37标记处数更改文件号签字日期标记处数更改文件号签字日期设计(日期)校对(日期)审核(日期)标准化(日期)会签(日期)机电学院机械加工工序卡片产品名称柴油机零件名称机油泵后盖共13 页第10 页车间工序号工序名称材料牌号HT200毛坯种类毛坯外形尺寸每毛坯可制件数每台件数铸件120*78*30.2 1设备名称设备型号设备编号同时加工件数卧式车床CA6140 1夹具编号夹具名称切削液专用夹具工位器具编号工位器具名称工序工时(分)准终单件工步号工步内容工艺装备主轴转速切削速度进给量切削深度进给次数工步工时r/min m/s mm/r mm 机动辅助1 粗镗Φ14mm孔至Φ16.3mm硬质合金镗刀、塞规1120 1 0.2 2.3 8.172 粗镗Φ24mm孔至Φ26.3mm硬质合金镗刀、塞规900 1.33 0.4 2.3 5.083 半精镗Φ16.3mm孔至Φ17.8mm 硬质合金镗刀、塞规1400 1.33 0.1 1.5 13.064 半精镗Φ26.3mm孔至Φ27.8mm 硬质合金镗刀、塞规1018 1.5 0.2 1.5 8.985 倒角Φ27.8mm孔1.1x45º硬质合金倒角刀1120 0.25 0.646 倒角Φ17.8mm孔1.1x45º硬质合金倒角刀1120 0.25 0.64标记处数更改文件号签字日期标记处数更改文件号签字日期设计(日期)校对(日期)审核(日期)标准化(日期)会签(日期)机电学院机械加工工序卡片产品名称柴油机零件名称机油泵后盖共13 页第11 页车间工序号工序名称材料牌号HT200毛坯种类毛坯外形尺寸每毛坯可制件数每台件数铸件120*78*30.2 1设备名称设备型号设备编号同时加工件数卧式车床CA6140 1夹具编号夹具名称切削液专用夹具工位器具编号工位器具名称工序工时(分)准终单件工步号工步内容工艺装备主轴转速切削速度进给量切削深度进给次数工步工时r/min m/min mm/r mm 机动辅助1 把Φ12mm孔粗镗到Φ14.4mm,深58mm 硬质合金镗刀、塞规1400 1.0 0.2 2.4 6.782 把Φ14.4mm半精镗到Φ16mm,深58mm硬质合金镗刀、塞规1580 1.0 0.1 1.6 11.393 精镗Φ16底面硬质合金端面镗刀1580 1.33 0.2 0.38标记处数更改文件号签字日期标记处数更改文件号签字日期设计(日期)校对(日期)审核(日期)标准化(日期)会签(日期)机电学院机械加工工序卡片产品名称柴油机零件名称机油泵后盖共13 页第12 页车间工序号工序名称材料牌号HT200毛坯种类毛坯外形尺寸每毛坯可制件数每台件数铸件120*78*30.2 1设备名称设备型号设备编号同时加工件数卧式车床CA6140 1夹具编号夹具名称切削液专用夹具工位器具编号工位器具名称工序工时(分)准终单件工步号工步内容工艺装备主轴转速切削速度进给量切削深度进给次数工步工时r/min m/min mm/r mm 机动辅助1 精镗Φ17.8mm孔至Φ18mm硬质合金镗刀、塞规1400 1.33 0.1 0.2 13.062 精镗Φ27.8mm孔至Φ28mm硬质合金镗刀、塞规1018 1.5 0.2 0.2 8.98标记处数更改文件号签字日期标记处数更改文件号签字日期设计(日期)校对(日期)审核(日期)标准化(日期)会签(日期)机电学院机械加工工序卡片产品名称柴油机零件名称机油泵后盖共13 页第13 页车间工序号工序名称材料牌号HT200毛坯种类毛坯外形尺寸每毛坯可制件数每台件数铸件120*78*30.2 1设备名称设备型号设备编号同时加工件数磨床M7130 1夹具编号夹具名称切削液电磁铁吸盘工位器具编号工位器具名称工序工时(分)准终单件工步号工步内容工艺装备主轴转速切削速度进给量切削深度进给次数工步工时r/min m/min mm/r mm 机动辅助1 磨削下端面刚玉砂轮,百分表2标记处数更改文件号签字日期标记处数更改文件号签字日期设计(日期)校对(日期)审核(日期)标准化(日期)会签(日期)。
铁塔的制作工艺

铁塔的制作工艺
铁塔的制作工艺包括以下几个步骤:
1. 设计与规划:根据塔的用途和要求,设计师需要确定塔的高度、荷载能力、材料使用等参数,并进行塔的结构设计和规划。
2. 材料采购与准备:根据设计要求采购所需的材料,一般情况下,铁塔主要由角钢、钢管等钢材构成。
在材料使用前需要进行材料的质量检验,并根据设计要求进行切割和加工。
3. 拼装制作:根据设计图纸,将切割好的钢材进行拼装。
一般情况下,铁塔的主要结构由单元块组成,先制作好单元块,再将单元块进行组装。
4. 焊接处理:在拼装的过程中,需要进行钢材的塔身焊接。
焊接是将多个钢材部分连接在一起,确保铁塔的结构牢固和稳定。
焊接之后需要进行焊缝检查,确保焊接质量。
5. 表面处理:铁塔的表面需要经过除锈处理和防腐涂装。
除锈可以使用化学方法或机械手段,将钢材表面的氧化物和锈层去除。
防腐涂装是涂上一层防腐涂料,以保护铁塔不被氧化和腐蚀。
6. 安装调试:根据设计要求,将铁塔安装在预定位置。
在安装过程中需要确保
塔的垂直度和水平度,并对塔进行整体调试和检查。
7. 完工验收:在铁塔制作完成后,需要进行完工验收。
验收包括对铁塔的结构和质量进行检查和测试,确保塔能够满足设计和使用要求。
以上是一般情况下铁塔的制作工艺流程,具体工艺可能会因不同的塔类型和设计要求而有所不同。
概念解释

铁塔绘图及放样软件初学者需掌握的概念(暂行、欢迎指出错误之处。
)一、铁塔构造1、基本构造构件接头采用对接;不同规格的构件对接时,应以外边缘对齐,接头螺栓排列在各自准线上;主材接头设置在节点时,上、下段斜材的准线应交于各自主材准线(如铁塔瓶口、塔身变坡处),如图4.1所示:图4.1 铁塔瓶口处准线构图示意焊接构件应以斜材重心线交于主材的重心线;斜材与主材准线相交方式,应按下列方法确定:1. 所有斜材和辅助材以角钢基准线构图;2. 主材为单排螺栓时,主材以基准线构图,即主、斜材以基准线相交,如图4.2所示:3. 主材为双排螺栓时,主材以第一排准线构图,即斜材基准线交于主材第一排准线,如图4.3所示:4. 主材为组合角钢时,斜材准线交于主材中心,如图4.4所示;图4.2 主材单排准线构图示意 图4.3 主材双排准线构图示意图4.4 主材为组合角钢构图示意注:1、用两个以下螺栓连接的斜材与补助材,宜直接连于主材,不使用节点板连接;2、制弯构件,选择顺序应为连接板、短构件、长构件,火曲线与连接构件边缘距离设定为10mm ;3、热镀锌构件长度不宜超过12米,L100以下角钢构件长度不宜超过9米,宽度不宜超过0.75米;4、横担悬臂部分超过3米以上应采用预拱,预拱值一般可取横担悬臂长度的1/100~150,具体值可根据实际外荷载在无风情况下的验算查看其位移(*.DIS 文件)确定;5、塔腿各主材应设置一个接地孔(孔径17.5mm ),距基础顶面距离为500~1000mm ;地线支架上设置一个引流孔(孔径17.5mm )。
2、螺栓排列 角钢准线肢宽(mm)基准线(mm)第一排准线 (mm) 第二排准线 (mm)角钢最大使用孔径(Φ)mm∠40 20 17.5∠45 23∠50 25 (28) ∠56 28(32) ∠63 32(36) 21.5∠70 35(40) ∠75 38(40) ∠80 40 ∠9045∠100 50∠110 55 45 75∠125 60 50 80∠140 70 55 9025.5∠160 80 60 105∠180 90 65 120∠200 100 75 135注:1、根据需要,角钢准线需多排,则标出准线位置。
铁塔生产的主要工序及铁塔生产工艺流程图
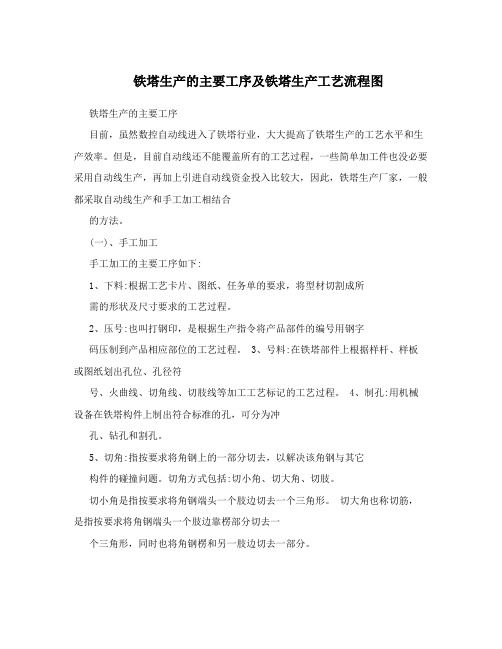
铁塔生产的主要工序及铁塔生产工艺流程图铁塔生产的主要工序目前,虽然数控自动线进入了铁塔行业,大大提高了铁塔生产的工艺水平和生产效率。
但是,目前自动线还不能覆盖所有的工艺过程,一些简单加工件也没必要采用自动线生产,再加上引进自动线资金投入比较大,因此,铁塔生产厂家,一般都采取自动线生产和手工加工相结合的方法。
(一)、手工加工手工加工的主要工序如下:1、下料:根据工艺卡片、图纸、任务单的要求,将型材切割成所需的形状及尺寸要求的工艺过程。
2、压号:也叫打钢印,是根据生产指令将产品部件的编号用钢字码压制到产品相应部位的工艺过程。
3、号料:在铁塔部件上根据样杆、样板或图纸划出孔位、孔径符号、火曲线、切角线、切肢线等加工工艺标记的工艺过程。
4、制孔:用机械设备在铁塔构件上制出符合标准的孔,可分为冲孔、钻孔和割孔。
5、切角:指按要求将角钢上的一部分切去,以解决该角钢与其它构件的碰撞问题。
切角方式包括:切小角、切大角、切肢。
切小角是指按要求将角钢端头一个肢边切去一个三角形。
切大角也称切筋,是指按要求将角钢端头一个肢边靠楞部分切去一个三角形,同时也将角钢楞和另一肢边切去一部分。
切肢是指按要求将角钢的一个面切去一部分。
下面是国网公司铁塔制图规定中的有关插图,可供参考,其中“切空角”即为“切肢”。
6、铲刨:包括铲背和刨根。
铲背是将角钢背按要求刨成圆弧形,刨根是将角钢内圆弧刨成直角,也称清根。
7、制弯:将角钢、钢板等构件,进行弯曲变形达到安装要求的工序。
分为热曲和冷曲。
有关术语:热曲:也叫火曲,指将构件加热到一定温度后的弯曲加工。
冷曲:指将构件在环境温度下的弯曲加工。
打扁:指将角钢的一肢边合到另一肢边的变形加工,也叫压扁。
曲线:产品部件上弯曲部位的弯曲基准线。
傍曲:指角钢向某一肢的方向弯曲。
曲筋:指角钢棱沿两肢角分线向某方向的弯曲。
正曲正号:是对钢板弯曲而言,指号料时将样板的无字面贴到钢板上进行号料,而弯曲时是面向样板的有字面向上弯曲。
工艺过程工序卡(范本)

附表1-1 机械加工工艺过程卡片*****学院机械加工工艺过程卡片产品型号零件图号产品名称零件名称共页第页材料牌号毛坯种类毛坯外形尺寸每毛坯件数 1 每台件数 1 备注工序号工序名称工序内容车间工段设备工艺装备工时准终单件描图描校底图号装订号设计(日期)审核(日期)标准化(日期)会签(日期)标记处数更改文件号签字日期标记处数更改文件号签字日期汽车与交通学院机械加工工艺过程卡片产品名称解放汽车第四及第五变速叉零件名称解放汽车第四及第五变速叉第1页车间工序号工序名称材料牌号1 粗铣16mm槽20钢毛坯种类毛坯外形尺寸每毛坯课制件数每台件数金属铸造件160 X 85 X 852000件每年 1设备名称设备型号设备编号同时加工件数万能升降台铣床XA6132 1夹具编号夹具名称切削液专用夹具工位器具编号工位器具名称工序时间准终单件描图工步号工步名称工艺装备主轴转速(r/min)切削速度(m/min)进给量(mm)被吃刀量(mm)工时(min)描校机动单件1 粗铣16mm槽454 22.8 0.18 22底图号装订号设计(日期)审核(日期)标准化(日期)会签(日期)标记处数更改文件号签字日期标记处数更改文件号签字日期汽车与交通学院机械加工工艺过程卡片产品名称解放汽车第四及第五变速叉零件名称解放汽车第四及第五变速叉第1页车间工序号工序名称材料牌号2 粗铣16mm槽两侧面20钢毛坯种类毛坯外形尺寸每毛坯课制件数每台件数金属铸造件160 X 85 X 852000件每年 1设备名称设备型号设备编号同时加工件数万能升降台铣床XA6132 1夹具编号夹具名称切削液专用夹具工位器具编号工位器具名称工序时间准终单件描图工步号工步名称工艺装备主轴转速(r/min)切削速度(m/min)进给量(mm)被吃刀量(mm)工时(min)描校机动单件1 粗铣16mm槽两侧面107.5 27 1.2 60底图号装订号设计(日期)审核(日期)标准化(日期)会签(日期)标记处数更改文件号签字日期标记处数更改文件号签字日期汽车与交通学院机械加工工艺过程卡片产品名称解放汽车第四及第五变速叉零件名称解放汽车第四及第五变速叉第1页车间工序号工序名称材料牌号3 粗铣Φ19mm孔上端两端面20钢毛坯种类毛坯外形尺寸每毛坯课制件数每台件数金属铸造件160 X 85 X 852000件每年 1设备名称设备型号设备编号同时加工件数万能升降台铣床XA6132 1夹具编号夹具名称切削液专用夹具工位器具编号工位器具名称工序时间准终单件描图工步号工步名称工艺装备主轴转速(r/min)切削速度(m/min)进给量(mm)被吃刀量(mm)工时(min)描校机动单件1 粗铣Φ19mm孔上端两端面108 27 1.2 12 0.11底图号装订号设计(日期)审核(日期)标准化(日期)会签(日期)标记处数更改文件号签字日期标记处数更改文件号签字日期2012.7.11汽车与交通学院机械加工工艺过程卡片产品名称解放汽车第四及第五变速叉零件名称解放汽车第四及第五变速叉第1页车间工序号工序名称材料牌号4 16mm槽1.5*45度倒角20钢毛坯种类毛坯外形尺寸每毛坯课制件数每台件数金属铸造件160 X 85 X 852000件每年 1设备名称设备型号设备编号同时加工件数车床C620-1 1夹具编号夹具名称切削液专用夹具工位器具编号工位器具名称工序时间准终单件描图工步号工步名称工艺装备主轴转速(r/min)切削速度(m/min)进给量(mm)被吃刀量(mm)工时(min)描校机动单件1 16mm槽1.5*45度倒角318 16 0.08 3 0.20底图号装订号设计(日期)审核(日期)标准化(日期)会签(日期)标记处数更改文件号签字日期标记处数更改文件号签字日期2012.7.11汽车与交通学院机械加工工艺过程卡片产品名称解放汽车第四及第五变速叉零件名称解放汽车第四及第五变速叉第1页车间工序号工序名称材料牌号5 钻铰Φ19mm孔20钢毛坯种类毛坯外形尺寸每毛坯课制件数每台件数金属铸造件160 X 85 X 852000件每年 1设备名称设备型号设备编号同时加工件数立式钻床Z5125 1夹具编号夹具名称切削液专用夹具工位器具编号工位器具名称工序时间准终单件描图工步号工步名称工艺装备主轴转速(r/min)切削速度(m/min)进给量(mm)被吃刀量(mm)工时(min)描校机动单件1 钻铰Φ19mm孔285 17 0.35 40 0.41底图号 2 钻铰Φ19mm孔246 14.7 0.7 40 0.28装订号设计(日期)审核(日期)标准化(日期)会签(日期)标记处数更改文件号签字日期标记处数更改文件号签字日期2012.7.11汽车与交通学院机械加工工艺过程卡片产品名称解放汽车第四及第五变速叉零件名称解放汽车第四及第五变速叉第1页车间工序号工序名称材料牌号6 钻M10mm螺纹孔并倒角120度20钢毛坯种类毛坯外形尺寸每毛坯课制件数每台件数金属铸造件160 X 85 X 852000件每年 1设备名称设备型号设备编号同时加工件数立式钻床Z5125 1夹具编号夹具名称切削液专用夹具工位器具编号工位器具名称工序时间准终单件描图工步号工步名称工艺装备主轴转速(r/min)切削速度(m/min)进给量(mm)被吃刀量(mm)工时(min)描校机动单件1 钻M10mm螺纹孔并倒角120度637 20 0.1 0.24底图号装订号设计(日期)审核(日期)标准化(日期)会签(日期)标记处数更改文件号签字日期标记处数更改文件号签字日期2012.7.11汽车与交通学院机械加工工艺过程卡片产品名称解放汽车第四及第五变速叉零件名称解放汽车第四及第五变速叉第1页车间工序号工序名称材料牌号7 攻螺纹M10 20钢毛坯种类毛坯外形尺寸每毛坯课制件数每台件数金属铸造件160 X 85 X 852000件每年 1设备名称设备型号设备编号同时加工件数丝锥M10 1夹具编号夹具名称切削液专用夹具工位器具编号工位器具名称工序时间准终单件描图工步号工步名称工艺装备主轴转速(r/min)切削速度(m/min)进给量(mm)被吃刀量(mm)工时(min)描校机动单件1 攻螺纹M10 238 8 0.08底图号装订号设计(日期)审核(日期)标准化(日期)会签(日期)标记处数更改文件号签字日期标记处数更改文件号签字日期2012.7.11汽车与交通学院机械加工工艺过程卡片产品名称解放汽车第四及第五变速叉零件名称解放汽车第四及第五变速叉第1页车间工序号工序名称材料牌号8 粗铣Φ82.2mm孔端面20钢毛坯种类毛坯外形尺寸每毛坯课制件数每台件数金属铸造件160 X 85 X 852000件每年 1设备名称设备型号设备编号同时加工件数万能升降台铣床XA6132 1夹具编号夹具名称切削液专用夹具工位器具编号工位器具名称工序时间准终单件描图工步号工步名称工艺装备主轴转速(r/min)切削速度(m/min)进给量(mm)被吃刀量(mm)工时(min)描校机动单件1 粗铣Φ82.2mm孔端面63.7 202 82.2 0.75底图号装订号设计(日期)审核(日期)标准化(日期)会签(日期)标记处数更改文件号签字日期标记处数更改文件号签字日期2012.7.11汽车与交通学院机械加工工艺过程卡片产品名称解放汽车第四及第五变速叉零件名称解放汽车第四及第五变速叉第1页车间工序号工序名称材料牌号9 粗镗Φ81.7mm孔20钢毛坯种类毛坯外形尺寸每毛坯课制件数每台件数金属铸造件160 X 85 X 852000件每年 1设备名称设备型号设备编号同时加工件数双面卧式金刚镗床T740 1夹具编号夹具名称切削液专用夹具工位器具编号工位器具名称工序时间准终单件描图工步号工步名称工艺装备主轴转速(r/min)切削速度(m/min)进给量(mm)被吃刀量(mm)工时(min)描校机动单件1 粗镗Φ81.7mm孔156 40 1 0.96底图号装订号设计(日期)审核(日期)标准化(日期)会签(日期)标记处数更改文件号签字日期标记处数更改文件号签字日期2012.7.11汽车与交通学院机械加工工艺过程卡片产品名称解放汽车第四及第五变速叉零件名称解放汽车第四及第五变速叉第1页车间工序号工序名称材料牌号10 精镗Φ82.2mm孔20钢毛坯种类毛坯外形尺寸每毛坯课制件数每台件数金属铸造件160 X 85 X 852000件每年 1设备名称设备型号设备编号同时加工件数万能升降台铣床XA6132 1夹具编号夹具名称切削液专用夹具工位器具编号工位器具名称工序时间准终单件描图工步号工步名称工艺装备主轴转速(r/min)切削速度(m/min)进给量(mm)被吃刀量(mm)工时(min)描校机动单件1 精镗Φ82.2mm孔136 35 0.6 0.64底图号装订号设计(日期)审核(日期)标准化(日期)会签(日期)标记处数更改文件号签字日期标记处数更改文件号签字日期2012.7.11汽车与交通学院机械加工工艺过程卡片产品名称解放汽车第四及第五变速叉零件名称解放汽车第四及第五变速叉第1页车间工序号工序名称材料牌号11 Φ82.2mm孔1*45度倒角20钢毛坯种类毛坯外形尺寸每毛坯课制件数每台件数金属铸造件160 X 85 X 852000件每年 1设备名称设备型号设备编号同时加工件数车床C620-1 1夹具编号夹具名称切削液专用夹具工位器具编号工位器具名称工序时间准终单件描图工步号工步名称工艺装备主轴转速(r/min)切削速度(m/min)进给量(mm)被吃刀量(mm)工时(min)描校机动单件1 Φ82.2mm孔1*45度倒角62 16 0.08 0.48底图号装订号设计(日期)审核(日期)标准化(日期)会签(日期)标记处数更改文件号签字日期标记处数更改文件号签字日期2012.7.11汽车与交通学院机械加工工艺过程卡片产品名称解放汽车第四及第五变速叉零件名称解放汽车第四及第五变速叉第1页车间工序号工序名称材料牌号12 精铣Φ82.2mm孔端面20钢毛坯种类毛坯外形尺寸每毛坯课制件数每台件数金属铸造件160 X 85 X 852000件每年 1设备名称设备型号设备编号同时加工件数万能升降台铣床XA6132 1夹具编号夹具名称切削液专用夹具工位器具编号工位器具名称工序时间准终单件描图工步号工步名称工艺装备主轴转速(r/min)切削速度(m/min)进给量(mm)被吃刀量(mm)工时(min)描校机动单件1 精铣Φ82.2mm孔端面98 31 0.6 1底图号装订号设计(日期)审核(日期)标准化(日期)会签(日期)标记处数更改文件号签字日期标记处数更改文件号签字日期2012.7.11。
工艺卡片模板100例
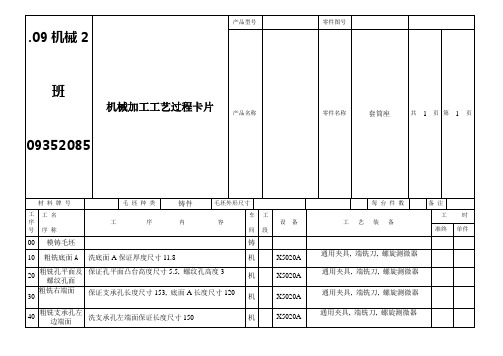
单件
设计(日期)
校对(日期)
审核(日期)
标准化(日期)
会签(日期)
标记
处数
更改文件号
签字
日期
标记
处数
更改文件号
签字
日期
机械加工工艺过程卡片
产品型号
零件图号
产品名称
零件名称
套筒座
共
1
页
第
1
页
材料牌号
毛坯种类
铸件
毛坯外形尺寸
每台件数
备注
工
序
号
工名
序称
工序内容
车
间
工
段
设备
工艺装备
工时
准终
单件
00
模铸毛坯
铸
10
粗铣底面A
洗底面A保证厚度尺寸11.8
机
X5020A
通用夹具,端铣刀,螺旋测微器
20
粗铣孔平面及螺纹孔面
保证孔平面凸台高度尺寸5.5,螺纹孔高度3
通用夹具,螺纹刀,扩孔钻,千分尺
130
检验入库
设计(日期)
校对(日期)
审核(日期)
标准化(日期)
会签(日期)
刘涛
标记
处数
更改文件号
签字
日期
标记
处数
更改文件号
签字
日期
机械加工工艺过程卡片
产品型号
零件图号
产品名称
零件名称
共
页
第
页
材料牌号
毛坯种类
毛坯外形尺寸
每毛坯件数
每台件数
备注
工
序
号
工名
序称
工序内容
车
铁塔制造基础知识

铁塔制造基础知识铁塔概述铁塔制造用钢材铁塔制造设备铁塔制造工艺产品质量事故及处理程序1.铁塔为实现承受某一空中载荷或通讯功能而架设的独立式的钢结构物通称为铁塔。
现在的铁塔一般都采用角钢、钢板部件制做用螺栓连接组合而成只是局部采用少量的焊接件如挂线角钢加强板等基础座板一般都采用电焊焊接。
塔上部件一般都采用热浸镀锌防腐。
2.输电线路输电线路通常是由基础、杆塔包括拉线、绝缘子、金具、导线、地线也称避雷线和接地装置等部分组成。
3.铁塔的呼称高度输电线路铁塔的呼称高度一般是指从地面到铁塔最低导线悬挂点的高度500KV铁塔到最低导线吊架挂线点处一般铁塔也可以是到最低导线横担下弦杆的准线处。
4.多接腿铁塔受地形地物地段的影响铁塔的四条腿的高度在标准塔腿高度上进行了全加长、全减短和部分腿加长或部分腿减短。
塔型中出现的这些长短级别不同的接腿称为多接腿铁塔。
5.档距两杆塔之间的距离称为两杆塔的档距。
1.按铁塔在线路中的位置和作用分类重要1.1直线塔用“Z”表示直线塔位于线路直线段的中间部分由于绝缘子串是悬垂式故称悬垂式铁塔。
在一条输电线路中直线塔占了很大的比重一般约占全线路铁塔总数的80左右。
这种塔只有在安装、事故断线和大风工况下承受着不平衡较大张力。
平时只承受导、地线、覆冰、金具、绝缘子串、塔上操作人员包括工具和塔的自重等垂直载荷。
直线塔的绝缘子串有单联悬垂、双联悬垂和“V”形悬垂三种。
直线塔总体要比同线路的承力塔较高塔身坡度较小塔材较小节点螺栓较少塔体较轻。
典型的塔型有ZGU51、ZGU52、ZGU53、ZGU54、SZ52、ZB15、ZB24、ZB34、ZB45等。
1.2跨越塔跨越塔用“K”表示跨越塔也是直线塔的一种特殊型这种塔一般都是成对地设立在江、河的两岸或用来跨越较大的沟谷或跨越铁路、公路及其他级别的中小型电力线路。
通常用于线路出现较大档距或要求跨越段具有较高的安全度这种塔比一般直线塔要高得多一般塔高都在50米250米之间构造也比较复杂。
工艺卡片模板
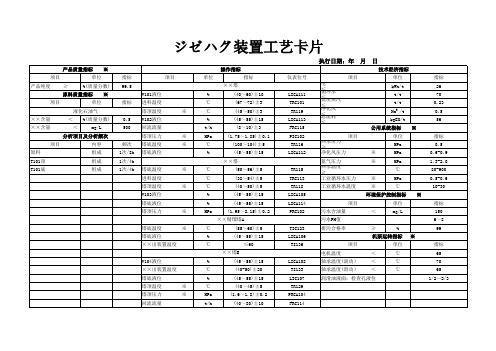
执行日期:年
产品质量指标 项目 产品纯度 项目 ××含量 ××含量 项目 原料 T101顶 T101底 < < ≥ 单位 %(质量分数) ※ 指标 0.5 500 频次 1次/8h 1次/4h 1次/4h 塔底温度 进料温度 塔顶温度 V103液位 塔底液位 塔顶压力 塔底温度 塔底液位 ××出装置温度 V104液位 ××出装置温度 塔底液位 塔顶温度 塔顶压力 回流流量 ※ ※ ※ ※ ※ ※ ℃ ℃ ℃ % % MPa ℃ % ℃ ××塔B % ℃ % ℃ MPa t/h (45~55)±15 (40-50)±20 (45~55)±15 (40~45)±5 (1.6~1.8)±0.2 (40~80)±10 LICA108 TI133 LIC107 TR129 PRCA104 FRC114 单位 液化石油气 %(质量分数) mg/L 内容 组成 组成 组成 原料质量指标 ※ 指标 99.5 V101液位 进料温度 塔顶温度 V102液位 回流流量 塔顶压力 塔底温度 塔底液位 ※ ※ ※ % ℃ ℃ % t/h MPa ℃ % 项目 单位 ××塔 (40~60)±10 (67~72)±3 (45~50)±3 (45~55)±15 (8~10)±3 (1.75~1.85)±0.1 (100~104)±5 (45~55)±15 ××塔 (50~56)±5 (38~54)±5 (40~50)±5 (45~55)±15 (45~55)±15 (1.95~2.15)±0.2 ××精馏塔A (55~60)±5 (45~55)±15 ≤60 TIC123 LICA106 TI136 电机温度 轴承温度(滚动) 轴承温度(滑动) 项目 < < < TR115 TRC113 TR118 LICA105 LICA114 PRC102 污水含油量 污水PH值 排污合格率 ≥ % ※ 指标 65 70 65 1/2—2/3 单位 ℃ ℃ ℃ 机泵运转指标 项目 < LICA111 TRC101 TR119 LICA113 FRC115 PIC102 TR116 LICA112 热水压力 净化风压力 氮气压力 热水温度 工业循环水压力 工业循环水温度 ※ ※ ※ ※ 项目 操作指标 指标 仪表位号 电 循环水 低压蒸汽 净化风 总能耗 项目
铁塔常识

铁塔生产常识随着电力建设的发展,数控设备和计算机放样的引进,乃至ERP 管理模式在行业内的推广,铁塔加工行业已逐步从劳动密集型向技术密集型转化。
行业内有关概念和专业术语的不统一,给行业的发展带来了极大的不便。
本文试图对铁塔加工行业的有关概念、术语进行归纳、整理和定义,供业内人员参考。
一、铁塔的分类所谓铁塔,就是用钢铁型材建成的用来架设高压输电线路的塔状钢构架。
铁塔按不同的归类方式有如下分类:1、按用途分为:直线塔(Z)、转角塔(J)、直线转角塔(ZJ)、换位塔(H)、终端塔(D)、分支塔(F)、跨越塔(K)等。
2、按结构形式分为:酒杯型(B)、三角型(J)、干字型(G)、上字型(S)、桥型(Q)、叉骨型(C)、门型(M e)、鱼叉型(Y u)、鼓型(G u)、V字型(V)、正伞型(Sz)、倒伞型(Sd)、田字型(T)、羊角型(Y)、王字型(W)等。
3、按组立方式分为:拉线式(L)和自立式(不表示)。
4、按电压等级分为:35、110、220、330、500、750(千伏)等。
5、按线路回路分为:双回路(S)、单回路(不表示)。
二、铁塔生产的前期工作铁塔生产的前期工作,包括签定合同、制定供货计划、审图、提料、备料、放样、制定生产计划等工作。
工作流程如下:1、定货合同铁塔产品是一种多品种小批量生产的产品,只能采取以销定产的方式,安排生产的依据只能是订货合同。
订货合同除了与甲方的经济往来方面的内容外,从生产系统的角度来要求,必须包括订货清单(杆塔明细)、供货期限、技术质量要求、工程图纸等。
对于生产系统来说,必须认真阅读合同文本,了解相关内容,并查对订货清单、图纸和有关合同附件的正确性。
根据合同要求、本厂生产现状、生产能力、材料库存等情况,制定出该项目的供货计划。
2、审图凡进入本厂,做为生产依据的铁塔图纸,必须经审图确认后方能投产。
审图工作由铁塔(放样)技术员进行,技术科(部)长审核,特殊工程项目由总工程师审核批准。
机械加工工艺卡片模板

零件图号
共8页
产品名称
零件名称
偏心轮
第3页
车间
工序号
工序名称
材料牌号
15
车
20cr
毛坯种类
毛坯外形尺寸
每件毛坯可制件数
每台件数
热轧圆钢
Φ
1
1
设备名称
设备型号
设备编号
同时加工件数
卧式车床
C620-1
夹具编号
夹具名称
切削液
1
三爪卡盘
工位器具编号
工位器具名称
工序工时/min
准终
单件
步号
工步内容
工艺装备
立钻
320
10
0.75
2
攻2-M10螺纹控 及与 孔对称
设计(日期)
校对(日期)
审核(日期)
标准化(日期)
会签(日期)
标记
处数
更改文件号
签字
日期
标记
处数
更改文件号
签字
日期
0.36
2
扩 孔为 ,偏心距为9
立钻
320
15.7
0.2
3
倒两面空口角
设计(日期)
校对(日期)
审核(日期)
标准化(日期)
会签(日期)
标记
处数
更改文件号
签字
日期
标记
处数
更改文件号
签字
日期
机械加工工序卡片
产品型号
零件图号
共8页
产品名称
零件名称
偏心轮
第7页
`
车间
工序号
工序名称
材料牌号
35
绞
20cr
[整理版]铁塔画图
![[整理版]铁塔画图](https://img.taocdn.com/s3/m/b18796cfd05abe23482fb4daa58da0116c171f4f.png)
铁塔概念角钢相关:心线:螺栓孔布置在角钢肢的一条直线上,这条直线称之为心线又叫准线。
楞线:角钢外皮相交的直线,又称角钢背或角钢劲线。
楞点:构成角钢楞线的两个端点。
楞线侧:在角钢肢平面内,心线向楞线的方向为楞线侧。
肢边侧:在角钢肢平面内,心线向楞线的反方向为肢边侧,又叫肢翼侧。
轧制边:如下图1所示。
切角边:如下图1所示。
图1图2图3心距:在角钢肢平面内,楞线与心线之间的垂直距离,又叫准距。
(见图2)间距:在角钢肢平面内,同一准线上相邻两螺栓孔中心之间的距离。
(见图2)端距:在角钢肢平面内,角钢端头与首个螺栓孔中心之间的距离。
(见图2)轧制边距:准线与轧制边之间的距离。
(见图3)切角边距:螺栓孔中心与切角边之间的距离。
(见图3)重心线:角钢两个截面的重力作用点的连线就是重心线,一般认为角钢1/2准线处即为其近似重心线。
切角:为防止角钢碰撞,将角钢端头一肢切去一角的工艺。
切肢:在角钢端头处,两肢同时被一平面切割形成的缺口或一肢被整个切去的工艺。
制弯:把角钢或板进行弯曲处理的工艺。
分冷曲和热曲,热曲又称之为火曲。
压扁:把角钢某处两肢压在一起的工艺。
开角:使角钢两肢夹角大于900的工艺,又叫开肢。
合角:使角钢两肢夹角小于900的工艺,又叫合肢。
铲背:去除角钢外楞直角的工艺,又叫铲棱。
清根:去除角钢内圆弧变为直角的工艺,又叫铲心或去弧。
正头:在图纸中,标注角钢为“+数”,就为正头(如下图中317角钢,注:315角钢与310角钢也为正头,因为是常规不进行标注,它们这时的正头是标准端距如315#角钢螺栓为M20,则正头为30mm,310角钢螺栓为M16,则正头为25mm)。
负头:在图纸中,标注角钢为“-数”,就为负头(如下图中318、311、205角钢)。
端连接:角钢上的首个螺栓孔位于各角钢心线交点处的情况称为端连接(如上图中315、310角钢)。
图4 图5专用名词:1、V面:一个塔脚上连的两根斜材组成的一个视图面称之为“V”面隔面:两根材展开组成的面,在机械制图上称之为剖面图。
钢结构(铁塔)生产工艺流程

钢结构(铁塔)生产工艺流程
A.L100×8以下:矫直,冲剪,冲孔,打钢印。
(如孔不在进线上,则用钻孔工序)
B.L100×8及以上:矫直,气割,划线,钻孔,打钢印。
注:若需切肢或切角,L100×8以下的冲剪;L100×8及以上
的气割
4.槽钢类:矫直,气割,划线,冲孔(或钻孔),打钢印。
注:a.若此槽钢切角或切肢则加入气割工序。
b.若孔在肢上,则只能钻孔。
c.若为弯曲槽钢工序为:矫直,弯曲,冲剪(气割),划线,钻孔。
5.圆钢类:
A.φ25以下:矫直,冲剪,割丝,弯曲(φ24以上的车丝)。
B.φ25以上:矫直,锯割,车丝(车削)。
C.爬梯中用圆钢:矫直,冲剪。
6.钢管类:
A、φ32以下:做样板,矫直,(砂轮)切割,划线,钻孔。
B、φ32~φ273:做样板,矫直,锯割(或气割),划线,钻孔。
注:φ114以下管若有需气割处应在切割(或锯割)工序后加入气割工序。
总说明:
以上各类零件中,凡是非组装件都加“镀锌”工序,组装件均
加“组装”工序。
工艺卡片-铁塔.doc

放样1 构件或零件放样,应以设计图纸确定的基准为依据。
2 放样和样板允许偏差按表1规定。
表1 放样和样板允许偏差3 放样时可通过适当调整爬梯孔位,避免馈线杆与爬梯支撑干涉。
4 放样时应注意是否存在平台构件与塔体构件干涉问题,如存在干涉问题不能解决时,应与设计单位协商解决。
5 放样时应考虑封闭构件或由于流锌不畅对热镀锌质量有影响的构件,在适当位置开工艺孔。
切断1 钢材切断后,其断口上不得有裂纹和超过1.0mm之缺棱,切断处切割平面度为0.05t(t 为厚度)且不大于2.0mm,割纹深度不大于0.3mm,局部缺口深度允许偏差1.0mm。
2 切断的允许偏差按表1规定。
3、标识(1)零件应按工程代号(必要时)、塔型、零件号的顺序,以钢字模压印作标识。
(2)标识的钢印应排列整齐,字形不得有缺陷。
字体高度为8mm~18mm,钢印深度0.5mm~1.0mm。
钢印附近的钢材表面不得产生凹凸面缺陷,并不得在边缘有裂纹或缺口。
表1 切断的允许偏差单位为毫米(3)焊接部件的钢印不得被覆盖。
(4)对于不宜直接用钢字模压印作标识的构件,应采用其它方法作标识。
制弯1 通信铁塔横隔面图中未注明零部件需开合角或制弯时,应保证横杆与隔面构件间的安装夹角不大于5°。
大于5°时,相应构件应开合角或制弯。
2 塔靴斜杆连接板与斜杆安装理论间隙大于3mm时,应根据塔靴具体结构,在组焊时使两斜杆连接板成90°角;或采取斜杆连接板制弯,保证两斜杆连接板成90°角。
3 其它需制弯的零部件由放样依据图纸确定。
4 零件制弯后,其边缘应圆滑过渡,表面不应有明显的折皱、凹面和损伤,划痕深度不应大于0.5mm。
5 制弯允许偏差按表规定。
表制弯允许偏差制孔1 制孔一般采用冲孔或钻孔。
制孔表面大于0.3mm的毛刺应清除。
冲孔表面不得有明显的凹面缺陷。
2 制孔的允许偏差按表规定。
表制孔的允许偏差单位为毫米5.3 不合格的螺栓孔必须经设计同意后才可扩钻或焊补后重新钻孔。
- 1、下载文档前请自行甄别文档内容的完整性,平台不提供额外的编辑、内容补充、找答案等附加服务。
- 2、"仅部分预览"的文档,不可在线预览部分如存在完整性等问题,可反馈申请退款(可完整预览的文档不适用该条件!)。
- 3、如文档侵犯您的权益,请联系客服反馈,我们会尽快为您处理(人工客服工作时间:9:00-18:30)。
1构件或零件放样,应以设计图纸确定的基准为依据
2放样和样板允许偏差按表1 规定。
表1 放样和样板允许偏差
3放样时可通过适当调整爬梯孔位,避免馈线杆与爬梯支撑干涉。
4放样时应注意是否存在平台构件与塔体构件干涉问题,如存在干涉问题不能解决时,应与设计单位协商解决。
5放样时应考虑封闭构件或由于流锌不畅对热镀锌质量有影响的构件,在适当位置开工
艺孔。
切断
1钢材切断后,其断口上不得有裂纹和超过1.0mm 之缺棱,切断处切割平面度为0.05t (t 为厚度)且不大于2.0mm ,割纹深度不大于0.3mm ,局部缺口深度允许偏差
1.0mm 。
2切断的允许偏差按表1 规定。
3、标识
(1 )零件应按工程代号(必要时)、塔型、零件号的顺序,以钢字模压印作标识。
(2)标识的钢印应排列整齐,字形不得有缺陷。
字体高度为8mm ~18mm ,钢印深度
0.5mm ~1.0mm 。
钢印附近的钢材表面不得产生凹凸面缺陷,并不得在边缘有裂纹或缺口。
表1 切断的允许偏差单位为毫米
3)焊接部件的钢印不得被覆盖。
4)对于不宜直接用钢字模压印作标识的构件,应采用其它方法作标识。
制弯
1通信铁塔横隔面图中未注明零部件需开合角或制弯时,应保证横杆与隔面构件间的安装夹角不大于5°。
大于5°时,相应构件应开合角或制弯。
2塔靴斜杆连接板与斜杆安装理论间隙大于3mm 时,应根据塔靴具体结构,在组焊时使两斜杆连接板成90°角;或采取斜杆连接板制弯,保证两斜杆连接板成90°角。
3其它需制弯的零部件由放样依据图纸确定。
4零件制弯后,其边缘应圆滑过渡,表面不应有明显的折皱、凹面和损伤,划痕深度不应大
于0.5mm 。
5制弯允许偏差按表规定。
表制弯允许偏差
单位为毫米
4
序号
项目 允许偏差
示意图
非镀锌件
孔径
镀锌件
孔垂直度 S
准距 a 1
多排孔
±0.7 a 2
接头处 ±0.7 其它
±1.0 排间距离 S
±1.0
制孔
1 制孔一般采用冲孔或钻孔。
制孔表面大于 0.3mm 的毛刺应清除。
冲孔表面不得有明显
的 凹面缺陷。
2 制孔的允许偏差按表规定。
表 制孔的允许偏差
单位为毫米
+0.
D
0 +0.
D
-D 1–
≤0.1
圆度
D
≤0.0
且
项目允许偏差示意图
同组内不相邻两孔距离S1 ±0.7
同组内相邻两孔距离S 2 ±0.5
相邻组两孔距离S3 ±1.0
不相邻组两孔距离S4 ±1.5
端距和边距S d ±1.5
7 端边距
切角边距S g ±1.5
注1 :序号1 、2 偏差不允许同时存在。
注2 :冲制孔的位置测量应在其小径所在平面进行
5.3 不合格的螺栓孔必须经设计同意后才可扩钻或焊补后重新钻孔。
扩钻后的孔径不得大于原设计孔径的2.0mm ;补孔应用与母材材质相同的焊条补焊,严禁用钢块填塞。
每组孔中焊补重新钻孔的数量不得超过20﹪。
处理后均应做出记录。
4
清根、铲背和开坡口
1清根、铲背和开坡口一般采用刨削或铣削加工,加工面表面粗糙度R a 不应大于25μm
2清根、铲背和开坡口的允许偏差按表规定。
表:清根、铲背和开坡口的允许偏差
单位为毫米
材料拼接
1 设计允许拼接时,应按设计要求进行,且应采取必要的措施,以保证拼接达到与母材等强度。
2 当设计未作规定时,对于爬梯、走线架主柱长度大于6m ,允许材料拼接且每根材料只许拼接一处,焊接处必须熔透,且应做探伤检查(拼接接头不应在同一断面)。
通信铁塔其他部位构件不允许材料拼接。
焊接件组装
1 组装前,连接表面及沿焊缝每边30 ~50mm 范围内的铁锈、毛刺和油污等必须清除干净。
2 组装应在工作台上进行, 并由胎板等辅助装置控制构件的尺寸、位置精度。
3组装点焊所用的焊接材料的型号应与后续焊接的焊接材料相同;焊点高度不宜超过设计焊缝高度的2/3,当焊缝高度大于12mm 时,焊点高度不得超过设计焊缝高度的1/2 ;点焊应牢固;当定位装置拆除后组件不应产生变形。
4焊接件组装允许偏差按表规定。
表装配的允许偏差
6 b≤50 1.0
b>50 2.0
搭接间隙m
序号项目允许偏差示意图
7
T 接板倾斜距离?
有孔±2.0
无孔±5.0
T 接板位移S
有孔±1.O
无孔±5.0
8
法兰面对轴线倾斜△ 1.5
续表
焊接
1焊条、焊丝、焊剂等焊接材料与母材的匹配应符合设计要求及现行行业标准《建筑钢结构焊接技术规程》JGJ81 的规定。
焊条、焊丝、焊剂在使用前应按其说明书及焊接工艺文件的规定进行烘焙和存放。
2焊工必须持有国家相关部门颁发的相应的上岗资格证书。
3设计要求全焊透的一、二级焊缝应采用超声波探伤进行内部缺陷检验,超声波不能对缺陷做出判断时,应采用射线探伤,其内部缺陷分级及探伤方法应符合现行国家标准GB11345 或GB3323 的规定。
4影响镀锌质量的焊缝缺陷应进行修磨或补焊,且补焊的焊缝应与原焊缝保持圆滑过渡。
5焊缝感观应达到:外形均匀、成型较好,焊道与焊道、焊道与基本金属间过渡较平滑,焊渣与飞溅物基本清除干净。
6一级、二级焊缝的质量等级及缺陷分级按表1 规定。
设计未注明的焊缝质量等级按三级焊缝质量检验。
表1 焊缝质量等级及缺陷分级
7 一级、二级、三级焊缝外观质量标准按表2 规定。
表2 焊缝质量等级及缺陷分级单位为毫米
8 对接焊缝及完全熔透组合焊缝尺寸允许偏差按表3 规定
9 部分焊透组合焊缝和角焊缝外形尺寸允许偏差按表4 规定。
表4 部分焊透组合焊缝和角焊缝外形尺寸允许偏差单位为毫米
序号项目允许偏差图例
1 焊脚尺寸
h f h f≤6:0~1.5 h f>6:0~3.0
2 角焊缝余
高C
h f≤6:0~1.5
h f>6:0~3.0
表3 对接焊缝及完全熔透组合焊缝尺寸允许偏单位为毫米项目允许偏差
对接焊缝余高C 一级、二级三级
B<20:0~
3.0
B≥20:0~
4.0
B<20:0~
4.0
B≥20:0~
5.0
对接焊缝错边d d≤0.15t
且≤2.0
图例
1 2 序号
矫正
矫正的允许偏差按表1 规定。
表1 矫正的允许偏差
镀锌
热浸镀锌工件的锌层质量要求:
1 外观:镀锌层表面应连续完整,并具有实用性光滑,不得有过酸洗、毛刺、结瘤、锐点、残留锌渣锌灰等缺陷。
漏镀总面积不应超过每个镀件总面积的0.5% ,每个漏镀面的面积不应超过10cm 2,所有漏镀面必须进行修复。
若漏镀面积较大,镀件应返镀。
修复的方法可以采用热喷涂锌或者涂富锌涂层进行修复,修复层的厚度应比镀锌层要求的最小厚度厚30μm 以上热浸镀锌件的颜色一般呈灰色及暗灰色,或灰色与暗灰色相间。
对于储运或使用过一段时间的镀锌件,有些镀锌件表面会出现储运斑点或白锈,这种储运斑点或白锈大多为碱性碳酸锌、氢氧化锌、氧化锌或者是它们的混合物,这是储运和使用中高温潮湿的环境造成的,与镀锌质量无关。
采用表面钝化工艺可阻滞储运斑点或白锈的生成。
2 通信铁塔结构件镀锌层厚度和镀锌层附着量见表1
表1 结构件镀锌层厚度和镀锌层附着量
3标准件镀锌层厚度和镀锌层附着量见表2 (离心处理时)
表2 标准件镀锌层厚度和镀锌层附着量
注:进行过二次攻丝的内螺纹部分,镀锌层厚度不作要求。
4镀锌层厚度的测量宜采用磁性涂层测厚仪测量,测量时,测量点应均匀分布,离边缘距离不小于10mm ,测量点数目按下列规定选择:
a)角钢试样每面3处各1点,4面共12点。
b)钢板试样每面6处各1点,2面共12点。
c)其它试样每个基本测量面内各测量6 次,且基准测量面不应小于0.001m 2,主要表面小于0.001m 2的构件,应选取足够数量的构件构成一个基本测量面,使基本测量面不小于0.001m 2。
测量结果按各测量点所测得的数值以算术平均值计算。
附着量可根据测量到的厚度通过计算得到。
如果对测量结果存在疑义,以溶解称重试验方法测量锌层附着量为准。
5镀锌层均匀性:镀锌层应均匀,作硫酸铜试验,耐浸蚀次数不少于4 次。
6镀锌层附着性:镀锌层应形成均匀的合金层,确保与金属基体结合牢固,应保证在无外力作用下没有剥落或起皮现象,经落锤试验镀锌层不凸起、不剥离。