密炼机液压系统故障及诊断探究
液压系统故障的检查与排除范本

液压系统故障的检查与排除范本液压系统故障的检查与排除是维修液压设备的重要环节。
本文将分享一个液压系统故障的检查与排除的范本,旨在帮助读者更好地理解和解决液压系统故障。
一、液压系统压力不足液压系统压力不足是一种常见的故障现象,可以通过以下步骤进行检查和排除:1. 检查液压泵的工作状态。
检查液压泵是否正常运转,是否有异常噪声或震动。
如果存在异常情况,需要对液压泵进行检修或更换。
2. 检查液压泵的进油口和出油口。
确保进油口没有堵塞物,并且出油口没有泄漏。
如果有堵塞物或泄漏现象,需要进行清洁和修复。
3. 检查液压系统的油液质量和油液量。
确保油液质量符合要求,不含杂质和水分。
同时,检查油液量是否足够。
如有必要,需要更换油液或添加新的油液。
二、液压系统漏油液压系统漏油是另一种常见的故障现象,可以通过以下步骤进行检查和排除:1. 检查液压系统的密封件。
检查液压系统中的密封圈、密封垫等密封件是否完好无损。
如有磨损或老化现象,需要进行更换。
2. 检查液压系统的管路连接。
确保液压系统的管路连接牢固,没有松动现象。
如有松动,需要进行紧固。
3. 检查液压系统的油箱和油管。
检查油箱和油管是否有破损或渗漏的情况。
如有破损或渗漏,需要进行修复或更换。
三、液压系统工作不稳定液压系统工作不稳定是另一种常见的故障现象,可以通过以下步骤进行检查和排除:1. 检查液压系统的油液温度。
检查油液温度是否超过允许范围。
如超过范围,需要采取降温措施。
2. 检查液压系统的油液粘度。
检查油液粘度是否符合要求。
如不符合要求,需要更换合适的油液。
3. 检查液压系统的阀门和元件。
检查阀门和元件是否正常工作,是否存在卡滞或老化的情况。
如有必要,需要进行清洁或更换。
四、液压系统噪声过大液压系统噪声过大是一种常见的故障现象,可以通过以下步骤进行检查和排除:1. 检查液压泵和液压缸的工作状态。
检查液压泵和液压缸是否存在异常噪声或震动。
如存在异常情况,需要对相关部件进行检修或更换。
液压系统的故障诊断与维修

液压系统的故障诊断与维修液压系统是一种通过液体传递能量的系统,广泛应用于机械设备、工业生产以及航空航天等领域。
然而,由于液压系统的复杂性,故障的发生是不可避免的。
因此,了解液压系统的故障诊断与维修方法是非常重要的。
本文将详细介绍液压系统故障的常见原因和诊断方法,以及维修时需要注意的事项。
液压系统故障的常见原因:1.液压油污染:液压系统使用的液压油很容易受到外界污染物的影响。
污染物可能会阻塞液压油滤器,造成液压油的流动不畅,从而引起系统故障。
2.密封件老化:液压系统中的密封件容易随着时间的推移而老化。
老化的密封件会导致液压系统的泄漏,从而影响系统的正常运行。
3.高温问题:液压系统在长时间高温环境下运行,容易导致液压油温度过高,进而引起油封老化、内部泄漏等故障。
4.压力不稳定:液压系统的压力不稳定可能是由于泵的磨损、溢流阀不正常或是负载不平衡等原因造成的。
液压系统故障的常见诊断方法:1.检查液压油质量:首先需要检查液压系统中的液压油质量,判断是否被污染。
可以通过取样检测、化学分析等方法来确定液压油的质量,并及时更换污染严重的液压油。
2.检查泄漏问题:液压系统的泄漏问题是常见的故障之一。
通过检查液压系统中的密封件、管路连接等部位,找到泄漏的原因,并及时修复或更换受损的部件。
3.检查压力问题:如果液压系统的压力不稳定,可能是由于泵的磨损、溢流阀调节不当等原因造成的。
可以通过测量和调整压力来解决压力不稳定的问题。
4.检查液压系统的工作温度:液压系统长时间高温运行可能导致液压油老化,进而引起系统故障。
可以通过安装温度传感器,监测液压系统的工作温度,并及时采取降温措施。
液压系统维修需要注意的事项:1.安全第一:在进行液压系统维修时,必须确保安全。
断开电源,并将液压系统的压力释放完全,避免意外发生。
2.准备工具和备件:在进行液压系统维修前,需要准备好相应的工具和备件。
这样可以在需要时迅速更换受损的零部件,提高维修效率。
液压系统故障分析与排除方法浅析
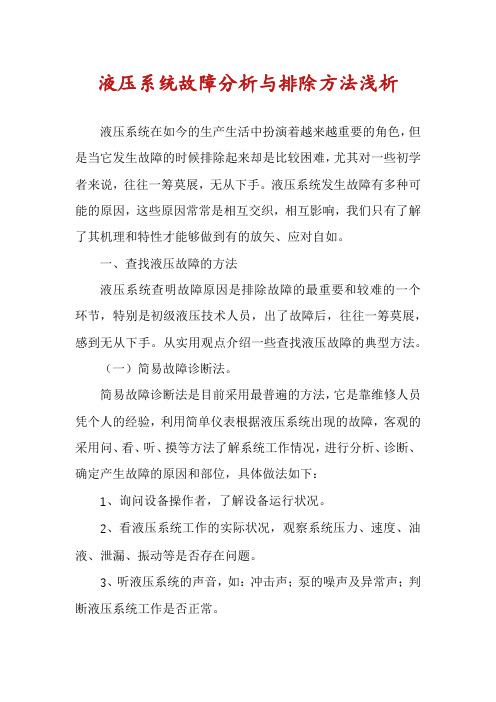
液压系统故障分析与排除方法浅析液压系统在如今的生产生活中扮演着越来越重要的角色,但是当它发生故障的时候排除起来却是比较困难,尤其对一些初学者来说,往往一筹莫展,无从下手。
液压系统发生故障有多种可能的原因,这些原因常常是相互交织,相互影响,我们只有了解了其机理和特性才能够做到有的放矢、应对自如。
一、查找液压故障的方法液压系统查明故障原因是排除故障的最重要和较难的一个环节,特别是初级液压技术人员,出了故障后,往往一筹莫展,感到无从下手。
从实用观点介绍一些查找液压故障的典型方法。
(一)简易故障诊断法。
简易故障诊断法是目前采用最普遍的方法,它是靠维修人员凭个人的经验,利用简单仪表根据液压系统出现的故障,客观的采用问、看、听、摸等方法了解系统工作情况,进行分析、诊断、确定产生故障的原因和部位,具体做法如下:1、询问设备操作者,了解设备运行状况。
2、看液压系统工作的实际状况,观察系统压力、速度、油液、泄漏、振动等是否存在问题。
3、听液压系统的声音,如:冲击声;泵的噪声及异常声;判断液压系统工作是否正常。
4、摸温升、振动、爬行及联接处的松紧程度判定运动部件工作状态是否正常。
(二)根据液压系统图纸查找液压故障。
从事液压设计、维修等方面的技术人员机维修工人,熟悉液压图纸是排除故障的基础,也是查找液压故障的最基本方法。
在液压系统图分析排除故障时,主要方法是“抓两头”即抓动力源(油泵)和执行元件(油缸),然后是“连中间”即从动力源到执行原件之间经过的管路和控制元件。
“抓两头”时要分析故障是否就出在油泵与液压缸本身。
“连中间”时除了要注意分析故障是否出在所连路线液压元件上,还要注意弄清系统从一个工作状态转换到另一个工作状态时有哪些原件发出信号,是不发信号还是发出信号不动作。
要对照实物逐個检查排除。
(三)通过滤油器查找液压故障。
通过对滤油器滤芯表面粘附的污物种类分析,可发现某些液压故障。
(四)故障实验法诊断。
由于故障现象各不相同,液压设备结构各异,所以实验方法往往千差万别。
浅谈液压系统的故障及排除方法
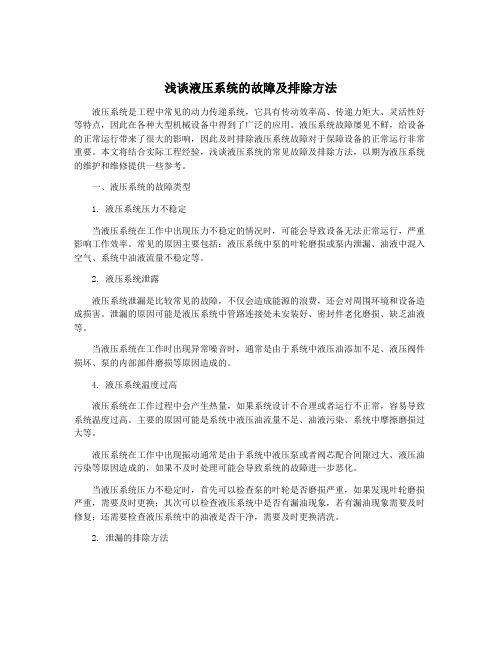
浅谈液压系统的故障及排除方法液压系统是工程中常见的动力传递系统,它具有传动效率高、传递力矩大、灵活性好等特点,因此在各种大型机械设备中得到了广泛的应用。
液压系统故障屡见不鲜,给设备的正常运行带来了很大的影响,因此及时排除液压系统故障对于保障设备的正常运行非常重要。
本文将结合实际工程经验,浅谈液压系统的常见故障及排除方法,以期为液压系统的维护和维修提供一些参考。
一、液压系统的故障类型1. 液压系统压力不稳定当液压系统在工作中出现压力不稳定的情况时,可能会导致设备无法正常运行,严重影响工作效率。
常见的原因主要包括:液压系统中泵的叶轮磨损或泵内泄漏、油液中混入空气、系统中油液流量不稳定等。
2. 液压系统泄露液压系统泄漏是比较常见的故障,不仅会造成能源的浪费,还会对周围环境和设备造成损害。
泄漏的原因可能是液压系统中管路连接处未安装好、密封件老化磨损、缺乏油液等。
当液压系统在工作时出现异常噪音时,通常是由于系统中液压油添加不足、液压阀件损坏、泵的内部部件磨损等原因造成的。
4. 液压系统温度过高液压系统在工作过程中会产生热量,如果系统设计不合理或者运行不正常,容易导致系统温度过高。
主要的原因可能是系统中液压油流量不足、油液污染、系统中摩擦磨损过大等。
液压系统在工作中出现振动通常是由于系统中液压泵或者阀芯配合间隙过大、液压油污染等原因造成的,如果不及时处理可能会导致系统的故障进一步恶化。
当液压系统压力不稳定时,首先可以检查泵的叶轮是否磨损严重,如果发现叶轮磨损严重,需要及时更换;其次可以检查液压系统中是否有漏油现象,若有漏油现象需要及时修复;还需要检查液压系统中的油液是否干净,需要及时更换清洗。
2. 泄漏的排除方法液压系统泄漏的排除方法主要包括检查管路连接处是否牢固,需要及时拧紧或更换液压管路连接件;检查液压系统中的密封件是否老化严重,需要及时更换;保证系统中油液的充足,避免系统缺油。
液压系统温度过高时,需要检查系统中的油液是否污染,需要定期更换液压油;需要检查系统中的摩擦部件是否磨损严重,需要及时更换润滑油或者润滑部件。
液压系统故障诊断与维修技术研究

液压系统故障诊断与维修技术研究液压系统作为工程机械等重要的动力传动系统,在工业制造中扮演着至关重要的角色。
然而,液压系统在长时间使用后,可能会遇到各种问题,如系统漏油、油压不稳定等故障。
这些故障不仅严重影响了设备的正常工作,也会导致机器损失和安全问题。
因此,液压系统故障诊断和维修技术的研究愈发重要。
一、液压系统常见故障1. 液压缸无法运动:这可能是因为传动机构或油马达故障,或者是油缸内有气体。
2. 油液温度升高:温度升高可能是由于油泵、马达或其他油液组件存在故障所致。
3. 液压泵无法正常工作:此时需要检查液压泵的吸入口是否有漏气、磨损或其他问题。
4. 漏油:很多时候漏油是导致液压系统故障的主要原因,可能是管路的密封性出现问题,也可能是其他部件产生泄漏。
二、液压系统故障诊断方法1. 分析故障现象:分析哪些部位存在问题,如感受到的异响、控制符号状态异常等。
2. 检查液压系统油道:检查油路是否通畅,如有阻塞就将对应的部件拆下来清洗或更换。
3. 检查控制系统:检查由仪表、阀门和传感器等构成的控制系统是否存在错误。
4. 测量压力:通过对液压系统各个部件压力的检测,容易找出故障点所在。
三、液压系统故障维修技术1. 适时更换液压油:经常更换液压油,不仅能保护液压系统的正常工作,而且还能提升其寿命。
2. 正确安装密封件:合适的密封件可以防止油液泄露,从而减少故障发生的机率。
安装时需要注意衬垫的位置和形状是否符合标准。
3. 确保管路清洁:管路中的杂质会堆积形成磨损,最终导致故障。
因此需要保证管路的清洁,及时进行维护。
4. 维护液压系统:长期使用液压系统后需要进行系统的维护,可以开展维护保养计划,定期清洗和保养各个部件。
总之,液压系统故障诊断和维修技术是液压技术领域中最为重要的技术之一。
液压系统故障的出现,不仅会导致设备的损失和维修成本的增加,也可能对人身安全带来威胁。
因此,我们需要不断地深入研究液压系统的故障诊断和维修技术,不断提高自己的专业水平,从而用更优质的服务来保障设备的正常运行和人身安全。
液压系统故障的检查与排除(三篇)

液压系统故障的检查与排除液压系统故障排除的五种基本方法:望、闻、摸、切、嗅一、望:看到什么。
1、看系统的配置是否正常,包括:泵、阀、执行元件、工作油液、滤油器、散热器等;2、看速度(流量):看执行机构运动速度是否有异常现象;3、看压力:看液压系统中各测压点的压力值大小及波动;4、看油液:观察油液容量是否合适,是否清洁,有无变质,油中是否有泡等;5、看泄漏:看液压管道各接头处、阀板结合处、液压缸端盖处、液压泵轴伸出处是否有渗漏、滴漏和油垢现象。
二、闻:听到什么。
1、听噪声:判断听到的声音是否属于噪声,噪声的源头在哪,是液压泵、马达、阀等液压件还是系统的管路或与元件连接的工作机构。
2、听冲击声:听系统的冲击声是否属于正常。
冲击声的时间:液压阀换向时冲击,还是莫名地发声。
冲击声的规律性:有节奏还是无规律。
3、听泄漏声:听油路内是否有细微不断的声音。
4、听敲打声:听液压件运转时是否有敲打声。
5、听相关人员反映。
三、摸:感觉到什么。
1、摸温升:用手摸运动部件表面,检查是否发热。
2、摸振动:感觉是否有振动现象。
3、摸爬行:感觉运动件有无“爬行”现象。
4、摸松紧程度:检验螺纹连接松紧程度。
5、摸密封性:对看不到的地方,检查是否有漏油现象。
四、切:用压力表判断。
1、各处的压力值是否正常:泵的吸油、出油,马达的进油、出油,油缸两腔的油压,阀的工作压力、控制压力等;2、压力是否有波动,波动是否在设计范围内。
五、用嗅觉判断。
1、闻一下油液是否发臭变质;旧车:使用时间长,油液成分会变质,发臭等怪味,新车:检查加油是否有误操作,防止加错油。
2、闻整系统是否有异味,出自何处。
液压系统故障的检查与排除(二)液压系统是一种利用液体传递能量和动量的技术,广泛应用于各种工程和机械设备中。
然而,由于使用条件和设备老化等原因,液压系统可能会出现故障。
本文将介绍液压系统故障的常见检查和排除方法。
首先,对于液压系统故障的检查,我们可以按照以下步骤进行。
液压系统常见故障以及排除

液压系统常见故障的诊断及消除方法
1 常见故障的诊断方法
1.1 简易故障诊断法
1〕询问设备操作者,了解设备运行状况。
其中包括:液压系统工作是否正常;液压泵有无异常现象;液压油检测清洁度的时间及结果;滤芯清洗和更换情况;发生故障前是否对液压元件进行了调节;是否更换过密封元件;故障前后液压系统出现过哪些不正常现象;过去该系统出现过什么故障,是如何排除的等,逐一进行了解。
2〕看液压系统压力、速度、油液、泄漏、振动等是否存在问题。
3〕听液压系统声音:冲击声;泵的噪声及异常声;判断液压系统工作是否正常。
4〕摸温升、振动、爬行及联接处的松紧程度判定运动部件工作状态是否正常。
1.2 液压系统原理图分析法
根据液压系统原理图分析液压传动系统出现的故障,找出故障产生的部位及原因,并提出排除故障的方法。
结合动作循环表对照分析、判断故障就很容易了。
1.3 其它分析法
液压系统发生故障时根据液压系统原理进行逻辑分析或采用因果分析等方
法逐一排除,最后找出发生故障的部位,这就是用逻辑分析的方法查找出故障。
为了便于应用,故障诊断专家设计了逻辑流程图或其它图表对故障进行逻辑判断,为故障诊断提供了方便。
2 系统噪声、振动大的消除方法
3 系统压力不正常的消除方法
4 系统动作不正常的消除方法
5 系统液压冲击大的消除方法
6 系统油温过高的消除方法
7 液压件常见故障及处理
7.3 液压缸常见故障及处理〔
7.4 压力阀常见故障及处理
7.4.1 溢流阀常见故障及处理。
液压系统故障的检查与排除

液压系统故障的检查与排除液压系统在工程和机械系统中扮演着重要的角色,常常用于输送能量和控制执行器等方面。
然而,由于长期使用或者部件磨损等原因,液压系统也会出现故障。
故障的及时检查和排除对于确保系统的正常运行非常重要。
本文将详细介绍液压系统故障的常见检查和排除方法。
1. 了解故障的表现:在检查和排除液压系统故障时,首先需要了解故障的表现。
常见的液压系统故障表现包括:液压执行元件(如液压缸、液压马达等)无法正常运行、液压系统压力异常高或低、液体温度过高、液体泄漏等。
根据故障的不同表现,可以针对性地进行检查和排除。
2. 检查液压系统压力:液压系统的压力是系统正常运行的基础,因此需要首先检查液压系统的压力。
可以使用压力表或压力传感器对系统的压力进行测量。
如果发现系统的压力异常高或低,可能是由于液压泵故障、压力阀故障或者泄漏引起的。
可以检查泵的吸入管路是否存在堵塞,检查压力阀是否工作正常,检查液体是否泄漏来排除这些故障。
3. 检查液体温度:液压系统的液体温度对于系统的正常运行至关重要。
如果液体温度过高,可能会导致液体粘度降低、润滑性能恶化,进而造成系统故障。
可以使用温度计或红外线测温仪来测量液体温度。
如果发现液体温度过高,可以检查冷却系统是否正常工作,液体是否过多或过少以及液体的质量等方面来排除故障。
4. 检查液体泄漏:液体泄漏是液压系统常见的故障之一。
泄漏的原因可能是由于密封件老化、部件松动或磨损、管路破裂等原因引起的。
可以使用光学方法或压力检测方法来检查和定位泄漏点。
在检查时,可以检查液压缸、液压阀、液压马达、管路连接件等部件的密封性能,并及时更换损坏的密封件或部件。
5. 检查液压执行元件:液压执行元件是液压系统的重要组成部分,包括液压缸、液压马达等。
如果液压执行元件无法正常工作,可能是由于密封件老化、部件磨损、液压泵供应不足等原因引起的。
可以检查液压执行元件的密封性能、清洁度以及液压泵供应情况来排除故障。
液压系统常见故障的诊断及消除方法
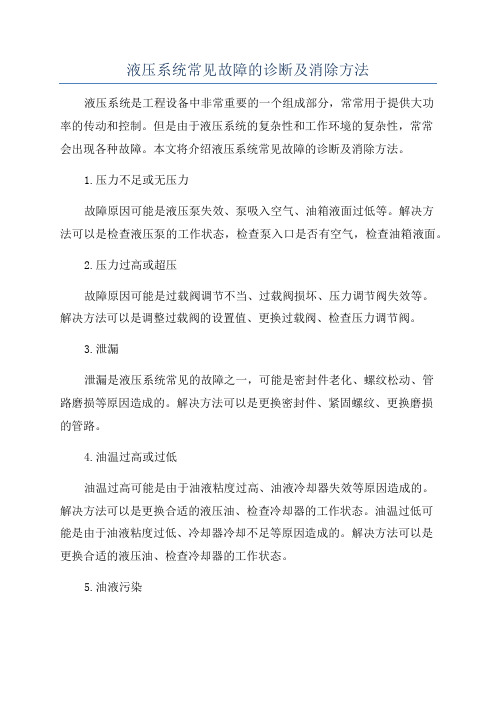
液压系统常见故障的诊断及消除方法液压系统是工程设备中非常重要的一个组成部分,常常用于提供大功率的传动和控制。
但是由于液压系统的复杂性和工作环境的复杂性,常常会出现各种故障。
本文将介绍液压系统常见故障的诊断及消除方法。
1.压力不足或无压力故障原因可能是液压泵失效、泵吸入空气、油箱液面过低等。
解决方法可以是检查液压泵的工作状态,检查泵入口是否有空气,检查油箱液面。
2.压力过高或超压故障原因可能是过载阀调节不当、过载阀损坏、压力调节阀失效等。
解决方法可以是调整过载阀的设置值、更换过载阀、检查压力调节阀。
3.泄漏泄漏是液压系统常见的故障之一,可能是密封件老化、螺纹松动、管路磨损等原因造成的。
解决方法可以是更换密封件、紧固螺纹、更换磨损的管路。
4.油温过高或过低油温过高可能是由于油液粘度过高、油液冷却器失效等原因造成的。
解决方法可以是更换合适的液压油、检查冷却器的工作状态。
油温过低可能是由于油液粘度过低、冷却器冷却不足等原因造成的。
解决方法可以是更换合适的液压油、检查冷却器的工作状态。
5.油液污染油液污染可能是由于油箱没有过滤装置、油液中杂质过多等原因造成的。
解决方法可以是安装合适的过滤装置、定期更换油液。
6.阀门卡死阀门卡死可能是由于阀芯与阀套间配合间隙过大、阀芯表面磨损等原因造成的。
解决方法可以是更换阀芯、研磨阀芯表面。
7.液压缸无法伸缩液压缸无法伸缩可能是由于缸内部部件损坏、密封件老化、液压系统压力不足等原因造成的。
解决方法可以是更换缸内部部件、更换密封件、检查液压系统压力。
8.油液乳化油液乳化可能是由于油液中含水过多、机械零件摩擦产生热量等原因造成的。
解决方法可以是更换干燥的液压油、检查液压系统的冷却状态。
以上是液压系统常见故障的诊断及消除方法的简要介绍,液压系统的故障诊断需要从系统整体入手,综合分析故障原因,采取相应的解决方法。
同时,定期检查和维护液压系统,保持系统的清洁和正常工作状态,可以预防故障的发生。
密炼机工作故障怎样查找分析和排除

密炼机工作故障怎样查找分析和排除?(1) 混炼室内转子工作出现异常声响转子轴的轴向调距装置中的铜垫磨损严重,使转子工作时轴向窜动量增大,转子端面与混炼室壁发生摩擦,从而出现异常声响。
拆卸调距装置,根据铜垫的磨损程度来决定是否更换。
如果磨损不严重,可修磨铜垫或旋转钢环的接触摩擦平面,然后重新装配。
装配后调整钢环与铜垫间的工作间隙。
(2) 转子轴密封处漏料正常工作中有少量油脂糊状物挤出。
如果挤出料量较大,可通过适当均匀用力紧各弹簧压紧螺钉来控制漏料。
如此办法不能控制漏料,则可能是石墨垫或铜环磨损较严重(如密封端面不光滑,间隙大)。
排除方法是拆卸密封装置,更换石墨垫和铜环,磨光固定环端面。
装配时注意均匀用力紧弹簧螺钉。
如果固定环端面硬度低于HRC40,则应先在端面上重新堆焊一层硬质合金,经磨光后再装配。
(3) 转子轴的轴承漏油主要是轴子轴与轴承衬的滑动摩擦表面磨损,变得粗糙,造成轴承漏油。
如果轴滑动面磨损,可用金属喷镀方法修补,然后再磨光至原直径尺寸。
轴衬磨损严重时要更换新轴衬。
(4) 上顶栓上下滑动出现阻滞现象①汽缸密封环磨损漏气,应更换密封环。
②压缩空气的压力不足,应检查输送管路是否有漏气部位,如无漏气现象应调节增加压缩空气的压力。
③控制阀有故障,动作不到位或阀芯磨损严重,应拆卸清洗维修。
④下移动滑道部位有油污异物,应清除干净并加注润滑油。
(5)进料翻板门动作不灵活①汽缸密封环磨损,漏气,应拆卸清洗或更换密封环。
②压缩空气压力不足,应检查输送管路有无漏气现象,修理漏气部位,调至工作所需压力。
③检查翻板门动作部位是否有异物或残料,应及时清除干净。
④压缩空气控制阀发生故障,可能阀芯有异物或磨损严重,应拆卸清洗维修。
浅谈液压系统的故障及排除方法

浅谈液压系统的故障及排除方法液压系统是现代机械领域中常见的一种动力传动系统,其通过油液的压力传递实现机械设备的运转。
但是,液压系统中也存在着一些故障问题,这些问题可能会影响到系统的工作性能,甚至导致设备的损坏。
因此,及时发现故障并采取有效的排除措施很重要。
下面,我们就来对液压系统的故障及排除方法进行浅谈。
一、故障种类1. 油液渗漏:液压系统中最常见的故障当属油液渗漏。
由于液压系统使用密封部件,如密封圈、油封等,当这些部件磨损或损坏时,油液就会从密封处泄漏出来。
2. 液压油污染:油液污染会导致液压系统中的各种元件、阀门、管路等部件的生锈或磨损。
3. 液压泵失效:液压泵失效通常是由于内部磨损或机械故障导致。
4. 液压阀故障:液压阀故障可能会引起系统中的某些部件无法正常工作,如油缸无法收缩或伸展等。
二、排除方法1. 油液渗漏:首先,需要寻找泄漏的位置和原因,确认后可以更换密封部件或进行维修。
2. 液压油污染:为防止液压油污染,需要在操作液压系统时保持清洁环境,并定期更换液压油。
3. 液压泵失效:出现液压泵失效时,需要找到泵的故障原因,如磨损、机械故障等。
可以更换泵或对泵进行修理。
4. 液压阀故障:对于液压阀的故障,可以首先更换阀芯,或者对阀芯进行清洗和修理。
如果更换阀芯或修理阀芯无法解决问题,就需要更换整个液压阀。
5. 液压缸失效:对于液压缸的问题,需要先检查密封部分是否破损或磨损。
若是密封部分的问题,需要更换相应的密封部件。
如果是其他内部元件的问题,则需要更换整个液压缸。
总之,液压系统故障的原因多种多样,但是解决问题的方法可以分为以上几类。
在使用液压系统时,需要经常检查和维护,及时发现故障并进行处理,以保证系统的长期稳定运行。
浅谈液压系统的故障及排除方法
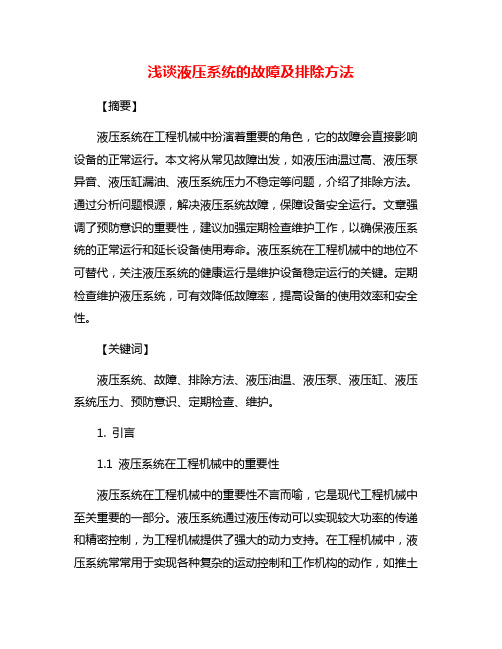
浅谈液压系统的故障及排除方法【摘要】液压系统在工程机械中扮演着重要的角色,它的故障会直接影响设备的正常运行。
本文将从常见故障出发,如液压油温过高、液压泵异音、液压缸漏油、液压系统压力不稳定等问题,介绍了排除方法。
通过分析问题根源,解决液压系统故障,保障设备安全运行。
文章强调了预防意识的重要性,建议加强定期检查维护工作,以确保液压系统的正常运行和延长设备使用寿命。
液压系统在工程机械中的地位不可替代,关注液压系统的健康运行是维护设备稳定运行的关键。
定期检查维护液压系统,可有效降低故障率,提高设备的使用效率和安全性。
【关键词】液压系统、故障、排除方法、液压油温、液压泵、液压缸、液压系统压力、预防意识、定期检查、维护。
1. 引言1.1 液压系统在工程机械中的重要性液压系统在工程机械中的重要性不言而喻,它是现代工程机械中至关重要的一部分。
液压系统通过液压传动可以实现较大功率的传递和精密控制,为工程机械提供了强大的动力支持。
在工程机械中,液压系统常常用于实现各种复杂的运动控制和工作机构的动作,如推土机的升降、挖掘机的铲斗开合,从而实现各种工程操作。
液压系统的高效性、稳定性和可靠性,直接影响到工程机械整体的工作效率和性能。
对液压系统的合理设计、运行维护和故障排除具有至关重要的意义,不仅可以保障工程机械的正常运行,还可以延长设备的使用寿命。
在现代工程机械应用中,液压系统已经成为不可或缺的核心技术之一,其重要性不容忽视。
1.2 液压系统的故障对设备运行的影响液压系统的故障对设备运行的影响是非常严重的。
一旦液压系统出现故障,设备将无法正常工作,造成生产受阻,影响工作效率,甚至可能导致设备损坏。
液压系统的故障会导致设备的运行不稳定,影响设备的工作性能,甚至可能引起安全事故。
液压系统的故障还会增加设备的维修成本和停机时间,影响企业的生产计划和经济效益。
特别是在工程机械这种需要高效运转的设备上,液压系统的故障更是不容忽视的。
液压系统故障的检查与排除

液压系统故障的检查与排除液压系统是现代工业的重要组成部分,广泛应用于机床、各类工业设备、航空、船舶等领域。
然而液压系统也会出现故障,如压力不足、漏油、噪音过大等问题,这些故障会影响到设备的正常工作,甚至会导致设备损坏。
因此,在液压系统应用过程中,必须及时检查及排除故障,保证系统的正常工作。
本文将介绍液压系统故障的检查与排除相关知识。
液压系统故障的检查要排除液压系统的故障,我们首先需要对故障进行检查。
针对不同的故障,需要进行相应的检查项目,以下为常见的故障检查项目。
压力不足故障检查如液压系统压力不足,具体检查步骤如下:1.检查液压泵是否正常工作。
2.检查液压泵是否与驱动源(电机等)连接牢固。
3.检查压力调节阀及其它压力控制元件是否正常工作。
4.检查液压油是否充足,油路连接是否正确。
漏油故障检查如液压系统存在漏油现象,具体检查步骤如下:1.检查液压油箱是否加油。
2.检查液压油路是否连接正确,油管上是否出现破裂、腐蚀、老化等现象。
3.检查密封件是否损坏,如液压缸老化、密封圈是否破裂等。
4.检查紧定件是否拧紧。
噪音过大故障检查如液压系统存在噪音过大的现象,具体检查步骤如下:1.检查液压油是否充足,油管是否连接不当。
2.检查附件及其它部件是否安装不当,如支架是否完整,附件拧紧程度是否充分。
3.检查流速过大是否导致噪音过大。
液压系统故障的排除在检查出故障后,需要对故障进行排除。
液压系统故障的排除涉及到多个方面,以下为常见的故障排除措施。
压力不足故障排除如液压系统压力不足,排除措施如下:1.检查液压泵是否存在异常声响,如存在,则修理或更换。
2.检查压力调节阀及其它控制元件的工作状态,如存在故障,及时维修或更换。
3.检查油路连接是否存在漏油,如存在漏油,及时修补。
4.检查油泵与驱动源的连接状态,进行牢固的连接。
漏油故障排除如液压系统存在漏油现象,排除措施如下:1.检查油路连接状态,如有松动或者破损,进行重新拧紧或更换。
液压系统故障的检查与排除
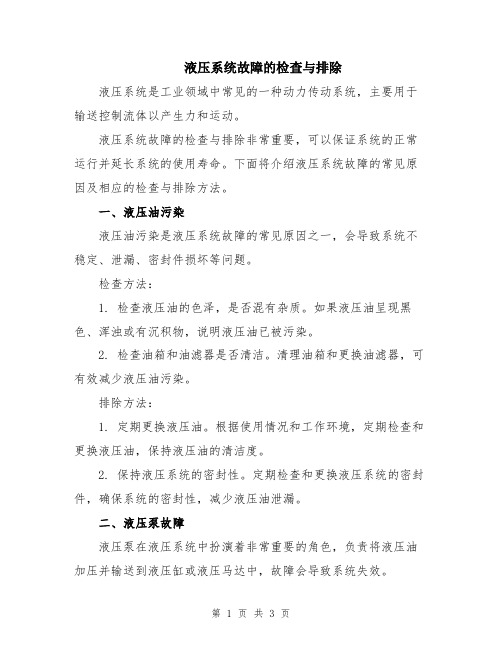
液压系统故障的检查与排除液压系统是工业领域中常见的一种动力传动系统,主要用于输送控制流体以产生力和运动。
液压系统故障的检查与排除非常重要,可以保证系统的正常运行并延长系统的使用寿命。
下面将介绍液压系统故障的常见原因及相应的检查与排除方法。
一、液压油污染液压油污染是液压系统故障的常见原因之一,会导致系统不稳定、泄漏、密封件损坏等问题。
检查方法:1. 检查液压油的色泽,是否混有杂质。
如果液压油呈现黑色、浑浊或有沉积物,说明液压油已被污染。
2. 检查油箱和油滤器是否清洁。
清理油箱和更换油滤器,可有效减少液压油污染。
排除方法:1. 定期更换液压油。
根据使用情况和工作环境,定期检查和更换液压油,保持液压油的清洁度。
2. 保持液压系统的密封性。
定期检查和更换液压系统的密封件,确保系统的密封性,减少液压油泄漏。
二、液压泵故障液压泵在液压系统中扮演着非常重要的角色,负责将液压油加压并输送到液压缸或液压马达中,故障会导致系统失效。
检查方法:1. 检查液压泵的噪音和振动。
异常的噪音和振动可能是液压泵内部损坏的征兆。
2. 检查液压泵的进、出口压力。
检查泵的进口压力是否正常,进口压力过低可能是油汇泵进口堵塞;检查出口压力是否达到设定值,出口压力过低可能是液压泵内部零部件损坏。
排除方法:1. 清洗液压泵。
定期清洗液压泵,清除泵内的沉积物和杂质,以保证泵的正常运行。
2. 更换液压泵的密封件。
定期检查液压泵的密封件,如发现磨损或损坏,及时更换。
三、液压阀故障液压阀用于调节流量和压力,控制液压系统的运行,故障会导致系统无法正常工作。
检查方法:1. 检查液压阀的工作状态。
观察阀是否关闭或打开,是否存在泄漏现象。
2. 检查液压阀的返回压力。
检查液压阀的回油通道,如存在堵塞或压力过高,说明阀有故障。
排除方法:1. 清洗液压阀。
通过拆卸液压阀并清洗其内部零部件,清除沉积物和杂质。
2. 更换液压阀的密封件。
定期检查液压阀的密封件,如发现磨损或损坏,及时更换。
液压系统的故障诊断及维护

液压系统的故障诊断及维护液压系统是现代机械、工程和设备中广泛应用的重要组成部分,掌握液压系统的故障诊断和维护技能对于保障设备的正常运转、提高设备的可靠性和安全性具有极为重要的意义。
本文将针对液压系统的故障诊断和维护,从多个方面进行探讨。
一、液压系统的故障液压系统的故障存在多种形式和原因,在实际应用中也非常常见。
常见的故障类型包括:1.液压油泄漏:由于管路连接不牢、密封不良、油封老化、油封悬挂角度过大等原因,液压油会发生泄漏,在严重的情况下将导致油量不足,影响系统的正常运行。
2.液压系统的压力不稳定或无法升压:常见原因包括泵的轴向偏移、泵的齿轮故障、泵体内部堵塞等。
3.液压系统的油温升高:原因可能是泵的排量过大、泵的转速过高、油道堵塞等。
4.执行机构的动作缓慢或无法动作:常见原因包括液压油中含有气泡、执行机构内部部件损坏等。
5.液压系统的噪音过大:常见原因包括系统内部出现震荡、过滤器故障等。
6.液压油的变质:由于工作环境和操作方式等原因,液压油可能会出现老化、污染、氧化等问题,导致液压系统失效。
以上仅列举了一些常见的液压系统故障类型,但是在实际工作中,液压系统出现故障的原因是多种多样的。
因此,采取科学有效的故障诊断方法是解决问题的关键。
二、液压系统的故障诊断1.故障的定位:在进行液压系统的故障诊断时,第一步需要明确故障部件的位置和原因。
可以通过观察液压系统的工作状况、听液压系统的声音、检查液压油的颜色和气味等,进行初步的判断和排查。
2.压力测试:压力测试是液压系统故障诊断中必不可少的一项。
通过测试系统内部的压力变化,可以判断液压系统的供油和执行工作是否正常。
采用压力表或示波器等设备进行检测。
3.液压油检测:液压油的变质不仅会影响到系统的正常运行,同时也会对系统内部部件造成损害。
因此,进行液压油检测、更换、维护工作是液压系统故障诊断中的重要环节。
可以通过观察液压油的颜色和气味、进行液压油的粘度测试、采取液压油的物理化学检测等方法进行检测。
浅谈液压系统的故障及排除方法

浅谈液压系统的故障及排除方法液压系统是工业生产中常见的一种动力传输和控制系统。
它通过液体传递能量,实现机械运动和各种动作控制。
液压系统在工作过程中可能会出现各种故障,这不仅影响生产效率,还可能引发安全隐患。
对液压系统的故障及排除方法进行深入了解是非常重要的。
本文将从液压系统的常见故障入手,探讨其可能的原因和处理方法,以期能够帮助读者更好地了解和排除液压系统的故障。
一、液压系统常见故障及排除方法1. 液压系统压力不稳定液压系统压力不稳定可能是由于液压泵内部泄漏引起的。
解决方法是检查液压泵是否有漏油现象,如果有漏油现象,需要及时更换密封件或修理液压泵。
2. 液压系统温升过高液压系统温升过高可能是由于液压油油温过高或液压泵内部泄漏引起的。
解决方法可以采取以下措施:(1)减小系统工作压力,适当增大冷却装置的容量,保证冷却液通畅,是解决液压油温升过高的有效方法。
(2)检查液压泵的密封件是否磨损或老化,必要时更换密封件。
液压系统噪音过大可能是由于液压泵内部零件磨损或液压泵进口气体引起的。
解决方法包括:(1)如果是液压泵内部零部件磨损引起的噪音过大,应及时更换液压泵的磨损零部件。
(2)如果是进口气体引起的噪音过大,应检查吸油口和油吸入管路是否漏气,并排除漏气现象。
4. 液压系统泄漏严重液压系统泄漏严重可能是由于密封件老化、液压管路损坏或液压泵内部故障引起的。
解决方法包括:(1)检查密封件是否老化,必要时及时更换密封件。
(2)检查液压管路是否损坏,必要时更换液压管路。
(3)检查液压泵内部是否有泄漏现象,必要时更换液压泵。
5. 液压系统缓慢运动或不运动以上仅是液压系统常见故障及排除方法的部分案例,实际工作中还可能遇到其他不同的故障情况。
在此,我将详细介绍液压系统故障的诊断方法,希望对读者有所帮助。
1. 装置故障诊断装置故障是指与液压系统相关的各种液压元件,比如液压泵、阀门、缸体等单元的故障。
当液压系统出现故障时,首先需要对装置进行诊断,检查这些液压元件是否有泄漏、异响、温升过高等现象。
浅谈液压系统的故障及排除方法
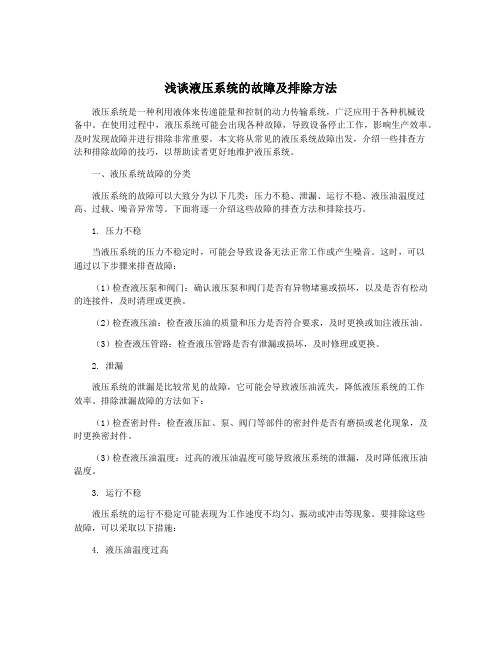
浅谈液压系统的故障及排除方法液压系统是一种利用液体来传递能量和控制的动力传输系统,广泛应用于各种机械设备中。
在使用过程中,液压系统可能会出现各种故障,导致设备停止工作,影响生产效率。
及时发现故障并进行排除非常重要。
本文将从常见的液压系统故障出发,介绍一些排查方法和排除故障的技巧,以帮助读者更好地维护液压系统。
一、液压系统故障的分类液压系统的故障可以大致分为以下几类:压力不稳、泄漏、运行不稳、液压油温度过高、过载、噪音异常等。
下面将逐一介绍这些故障的排查方法和排除技巧。
1. 压力不稳当液压系统的压力不稳定时,可能会导致设备无法正常工作或产生噪音。
这时,可以通过以下步骤来排查故障:(1)检查液压泵和阀门:确认液压泵和阀门是否有异物堵塞或损坏,以及是否有松动的连接件,及时清理或更换。
(2)检查液压油:检查液压油的质量和压力是否符合要求,及时更换或加注液压油。
(3)检查液压管路:检查液压管路是否有泄漏或损坏,及时修理或更换。
2. 泄漏液压系统的泄漏是比较常见的故障,它可能会导致液压油流失,降低液压系统的工作效率。
排除泄漏故障的方法如下:(1)检查密封件:检查液压缸、泵、阀门等部件的密封件是否有磨损或老化现象,及时更换密封件。
(3)检查液压油温度:过高的液压油温度可能导致液压系统的泄漏,及时降低液压油温度。
3. 运行不稳液压系统的运行不稳定可能表现为工作速度不均匀、振动或冲击等现象。
要排除这些故障,可以采取以下措施:4. 液压油温度过高液压油温度过高可能会降低液压系统的工作效率,甚至导致设备损坏。
要解决这一问题,可以采取以下方法:(1)调整液压系统工作压力:合理调整液压系统的工作压力,使其在合适的范围内工作。
(2)改善润滑条件:适当增加液压油的润滑性能,降低摩擦阻力,同时减少液压油的粘度,降低液压油的温度。
5. 过载(1)增加液压缸的数量:在液压系统中增加液压缸的数量,以减轻单个液压缸的负荷。
(2)检查液压缸的使用条件:检查液压缸的使用条件是否合理,及时调整液压系统的工作参数。
液压系统故障诊断及排除方法的研究分析

液压系统故障诊断及排除方法的研究分析车辆工程技术194机械电子1 前言液压技术属于流体动力学范畴,它始于17世纪Blaise Pascal提出的静液压力传动原理,1795年Joseph Braman发明了世界上第一台水压机。
1905年液压传动的工作介质由油替代了水,从而使液压系统整体性能得到进一步提高。
液压系统的广泛应用是从第一次世界大战以后开始,其中F.Vikers发明的叶片泵和GoConstantimsco对能量波传递的研究都对推动液压系统的研究作出了重要贡献。
液压系统出故障不易找出问题,维修困难,维修成本较高,因此对液压系统进行详细深入的研究就显得尤为重要。
本文将针对液压系统的故障诊断、故障排除方法进行研究分析。
2 液压系统故障特点分析由于液压系统的特殊性,它出现故障的种类非常多,其所表现的故障特点如下:2.1 发生率较低液压系统机械故障发生率较低,使用寿命长。
液压系统工作介质大部分是油液,润滑条件良好,再加上液压系统设计的有过载保护装置,所以液压系统的机械结构部分就不容易出现机械故障。
2.2 隐蔽性液压系统大部分的运动机械结构零件都被封装在壳体零件内部,因此运动结构部件一旦发生故障,将不容易被发现,并且也不容易被找到故障位置点,因此当液压系统出现故障时就要一点一点查找排除。
2.3 多因性液压系统常见的故障种类很多,它有独特的故障也有和其它普通机械相同的故障。
和普通机械故障一样,有些运动零部件之间由于磨损的原因出现了间隙扩大现象,从而导致传动精度降低,有些零部件长期在油液环境中性能发生改变,从而引起的使用寿命降低等,这些原因都可以称为渐发式的。
还有一些故障属于偶发式的,例如系统中突然出现异物,从而引起运动的组件被突然卡死,或是系统突然受力过大引起的结构件的变形等。
还有一些系统故障是由很多种因素综合到一起引起的,例如在设计过程中构件刚性不够,而选择的电动设备功率过大,引起的结构件破坏等。
2.4 非独立性采用液压系统的设备实际是一套综合系统,它往往会包括机械、电气、液压三个部分,它们三者之间功能相互影响,因此液压系统的故障往往不是独立存在的,一旦出现故障,就需要综合考虑这三个领域的相关技术知识,进行综合诊断分析。
液压系统故障分析与维修技术研究
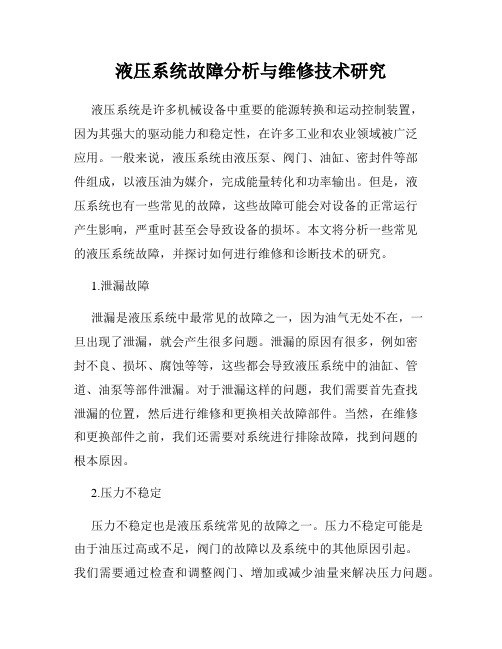
液压系统故障分析与维修技术研究液压系统是许多机械设备中重要的能源转换和运动控制装置,因为其强大的驱动能力和稳定性,在许多工业和农业领域被广泛应用。
一般来说,液压系统由液压泵、阀门、油缸、密封件等部件组成,以液压油为媒介,完成能量转化和功率输出。
但是,液压系统也有一些常见的故障,这些故障可能会对设备的正常运行产生影响,严重时甚至会导致设备的损坏。
本文将分析一些常见的液压系统故障,并探讨如何进行维修和诊断技术的研究。
1.泄漏故障泄漏是液压系统中最常见的故障之一,因为油气无处不在,一旦出现了泄漏,就会产生很多问题。
泄漏的原因有很多,例如密封不良、损坏、腐蚀等等,这些都会导致液压系统中的油缸、管道、油泵等部件泄漏。
对于泄漏这样的问题,我们需要首先查找泄漏的位置,然后进行维修和更换相关故障部件。
当然,在维修和更换部件之前,我们还需要对系统进行排除故障,找到问题的根本原因。
2.压力不稳定压力不稳定也是液压系统常见的故障之一。
压力不稳定可能是由于油压过高或不足,阀门的故障以及系统中的其他原因引起。
我们需要通过检查和调整阀门、增加或减少油量来解决压力问题。
如果检查后发现故障出现在阀门处,则需要更换或修理损坏的阀门。
除此之外,我们还需要对系统中的其他部件进行检查,以确保它们的正常工作。
3.迟滞现象迟滞现象可能导致流量不畅或不正常,这会使设备的运行效率下降。
迟滞的原因可能是系统中阀门的损坏或泄漏、损坏的油泵、堵塞的管道、过滤器堵塞等。
我们需要检查阀门、更换损坏的部件、清洗管道和更换过滤器来解决这些问题。
此外,我们还需要确保液压油干净并且质量良好。
4.运动部件闪烁、波动液压系统是机械设备中常见的驱动力和功率输出装置,如果它们的运动不流畅,就会对设备的正常运行产生影响。
闪烁或波动的原因可能是阀门的损坏或系统中的压力不稳定,此外还可能是泵、管道等部件所引起的问题。
我们需要检查系统中液压泵、管道、阀门等部件,并更换或修理损坏的部件。
- 1、下载文档前请自行甄别文档内容的完整性,平台不提供额外的编辑、内容补充、找答案等附加服务。
- 2、"仅部分预览"的文档,不可在线预览部分如存在完整性等问题,可反馈申请退款(可完整预览的文档不适用该条件!)。
- 3、如文档侵犯您的权益,请联系客服反馈,我们会尽快为您处理(人工客服工作时间:9:00-18:30)。
密炼机液压系统故障及诊断探究
作者:陈俊
来源:《中国化工贸易·下旬刊》2020年第01期
摘要:密炼机作为当前橡胶工业的主要生产设备,而液压系统作为设备的主要动力源,在制胶过程中举足轻重。
仔细分析故障现象与故障原因之间的内在联系。
有助于行业快速发展,基于此,本文将主要论述密炼机液压系统故障及诊断探究。
关键词:密炼机;液压系统;诊断探究
我国工业化起步较晚,而橡胶行业缺口巨大,市场供不应求。
液压系统的工作量较大,持续周期长,液压系统的故障频繁。
管理人员应该明确液压系统与故障之间存在的映射关系,采取多角度的监测手段,实现快速的液压系统故障诊断,保证橡胶生产质量。
1 密炼机液压系统的概述
密炼机又称为封闭式炼胶机,主要用于改变橡胶的形态。
密炼机内部含有持续回转的转子。
工作人员可以通过检测转子的运动状态,调节内部的温度、压力等重要参数,从而实现对橡胶的塑型。
密炼机主要由密炼室、加料压料设备、转子卸料设备、传动机等主要部分组成。
密炼机在工作过程中,转子发生相对回转,向物料施加特定参数的应力,胶料周转过程中受到内部的压力被拉伸变形。
管理人员要检测不同类型探测信号,匹配液压接口,维持电容量稳定,提高密炼机液压系统的抗干扰性。
将市场需求转化为橡胶参数,给予密炼机液压系统足够的工作空间,使密炼机液压系统可以快速完成制动。
2 密炼机液压系统故障分类
密炼机在长期运行过程中,受到磨损,温度,压力、多次拆装等影响,浪费资源同时造成了大量的安全隐患。
下面将主要论述故障的三种类型。
2.1 密炼机液压元件故障
密炼机液压系统作为系统的主要动力源,一般通过上下栓的往复运动控制回路。
目前大部分密炼机液压系统普遍采用进口的BOSCH电压比例阀,基本可以实现精准控制。
但由于大部分密炼机的工作环境比较恶劣,长期运行后封闭性能下降,外界污染物难免会混入液压系统之中,造成液压机阀芯卡死、阻塞孔塞等現象。
此外,液压系统内部的压力维持在在1MPa左右,长时间的负载工作,经常会出现变形、压裂,严重密封元件损坏,甚至会出现大量泄漏橡胶原料的问题。
2.2 外界压力与内部流量供给不匹配
在炼制橡胶过程中,液压上顶栓需要给予胶料固定的压力,以满足日常生产的各种工艺要求。
但在系统传动过程中,可能出现PLC系统传动不灵,传动器精度失调等问题。
内部工作压力出现震荡变化,直接影响了胶料质量。
此外,一旦内部压强过大,分子运动过于剧烈、内部油温急速上升,继电器发出错误信号,导致整体的液压系统失灵。
2.3 液压系统本身存在联动机制
在一般情况下液压机的工作强度较高,循环周期较长,在工作时需要密闭。
出现微小问题时,很难观察到,因此给液压系统检验带来了麻烦,当出现异常发热、震动时。
内部可能存在多点故障。
机械、电气、液压部分的故障的症状与原因之间存在着重叠与交叉。
3 密炼机液压系统故障诊断措施
3.1 完成可视化模式
综合完成液压的集成设计,首先要分析密炼机全液压系统的工作原理,在完成一个工作循环后,向PLC发射信号,执行后续的排料步骤。
通过调节松紧装置,使开关能够快速检测到松紧信号,并在15秒内完成排料输过,最后卸料是关闭电磁阀下顶栓。
在循环往复过程中,各个元件依次完成设定动作。
管理人员可以基于此,通过大量的现场实验,查阅说明书等办法,以现实数据为依据设计可视化的CAD模型,为后续的液压机集成提供理论支持。
集成的液压系统结构更加紧促,更换元件方便,持续简化工作流程。
能用全PLC的控制体系保证传动力巨大,制胶过程平稳,自动化水平高,并能够实现远程的监控与操作,切实提高了炼焦质量。
例如,管理人员利用一些电阻较小阻抗元件,来降低液压系统的损耗过快问题,确保制胶过程安全,针对不同批次的材料进行全面检查,确保同一位置上没有三条以上的交叉线路,禁止线路并排捆绑,密切管理电线捆绑的零件,动态监测密炼机液压系统的运行效率,从根本上解决故障的起始点。
及时记录转子的准确值,完成密炼机液压系统的检测,但在具体操作过程中一定要采取平行实验的方法。
综合利用q值检验法剔除误差数据,保证实验精度提高液压系统的工作效率。
3.2 实现密炼机液压系统的参数检测
管理人员要明确内部的主要参数,通过转子的转速,确定填充系数与上顶栓对于物料的单位压力。
形成整体的信息化管理,将密炼机液压系统的各项数据录入到数据模型中,通过计算机控制系统对不同数据进行拆分、统计、对比形成一个完整的3D数据共享平台,实现数据的
自动录入、检验、输出。
综合利用PLC技术作为核心的监控系统,及时调整内部温度、压强等重要数据,保证橡胶压缩环节数据的准确性与实用性,为后续的决策提供理论支持。
配合计算机对现场温度参数进行实时的数据监控。
以自动化监控提醒、调动信息等方式传递到控制中心,督促并引导基层人员,完成操作标准,从而履行异常处理规则。
例如,设计人员可以通过建立故障知识库进行推理,研究液压故障问题存在的原因,获取综合的维护管理知识。
将目前存在的故障输入到access中,实现故障与维修的一一对应,或者是一对多对应,形成完整的知识体系。
快速解放生产力,推动国内橡胶事业快速发展。
通过上顶栓液压活塞缸的位置信号,进行故障参数处理。
综合不同系统的油压检测方式,直接定位液压系统内的故障部位和原因,判断回路之后的动作,完成后续的故障诊断。
3.3 实现细化的密炼机的步骤管理
密炼机在启动过程中需要一系列的步骤,管理人员应该强化操作方法。
检测转子轴承温、减速器轴承温,保证转子端面密封装置定圈最高温度≤85℃。
快速调动密炼机液压系统,采用集成性控制手段,提高密炼机液压系统的效率,依照生产要求,持续优化网络智能方案,在提高整体橡胶强度,延长液压系统的使用寿命。
例如,在添料过程中,应该按照工业配方将氧化锌、防老剂、固体软化剂等等试剂,分别放置在打开密炼机时要,做好前期的预热,检验内部的压力是否符合工艺要求。
综合监测内部的温度功率指标是否正常,在保证一切正常的前提下。
提起上顶栓,将符合规格的橡胶原料加料口投入密炼机后,及时落下上顶栓,将时间维持在1min左右。
分别加入小料炭黑,液体软化剂等。
在最后排胶过程中一定要明确内部胶料的温度,通过对比初始温度与最终温度,确定好排胶系数。
3.4 保证密炼机液压系统的清洁
密炼机在长时间工作中,内部难免会出现磨料、焊渣、等固体颗粒,会严重威胁整体液压系统的稳定性。
因此管理人员必须强化管理控制污染源,确保液压系统安全稳定的运行。
同时升级密炼机液压系统的适应能力。
开展定期的检修工作,使密炼、液压系统适应多元化的工作路径,为制胶过程的灵活性提供保障。
并根据量化的行为规范,全过程监管,在规定时间内通过观察密炼机压系统的操作习惯,计算出最小单元的平均完成时间。
此外,在日常情况中要建立完善的管理制度,将系统检测落实到个人身上,明确责任与义务之间的相对关系。
提高基层人员的专业化水平,并聘请专门的技术员进行现场故障排查。
例如,在安装新组件之前要做好整体水平的倾斜,将液压件放在专业的清洗台上深度清洗,保证清洗台的清洁程度,在清洗过程中要用与液压机油排相同的液压油,洗过后的部件应该马上吹干,不允许直接放在地上、装配工作台,防止出现交叉感染。
要及时放入带盖子的密闭空间中,并采取一定的密封手段,做好入库管理。
检查液压机的安装人员的衣服是否符合质
量要求,不能穿戴易脱落的纤维制品。
以防止纤维灰尘头发等物品落入到液压系统内,造成二次污染。
4 总结
近年来我国橡胶工业快速发展,而密炼机液压系统作为生产橡胶的主要动力端,管理人员应该综合液压机的故障机理,建立数据化的排查体系,联合开发液压机故障诊断系统,节约实验成本,快速解放生产力,降低劳动强度,推动国内橡胶市场快速发展。
参考文献:
[1]赵云.GK250E密炼机液压系统工作原理及故障探究[J].中国化工贸易,2019,11(4):211.
[2]宋宝玉.密炼机转子密封装置与故障排除实例[J].润滑与密封,2016(3):146-148.。