一种2.5轴曲面粗加工环切轨迹规划方法
CAXA制造工程师练习题.doc

CAXA制造工程师练习题CAXA制造工程师基础知识综合练习(一)首先,填空。
1.CAXA制造工程师采用精确特征实体建模技术,可以用特征描述设计信息,简单、准确。
2.CAXA制造工程师的“轨迹再生”功能可以实现轨迹编辑。
用户只需选择现有的数控加工轨迹,修改原始定义的加工参数表,即可重新生成加工轨迹。
3.3常用的命令。
CAXA制造工程师以图标的形式显示在绘图区域的顶部。
4.CAXA制造工程师可以根据加工顺序自动生产。
5.曲线过渡是指指定两条曲线的圆弧过渡、锐角过渡或两条直线的倒角。
6.尖角过渡用于在两条给定曲线之间进行过渡,在过渡后,它显示在两条曲线的交点处。
7.平移是相对于原始场地移动或复制拾取的曲线。
8.有两种方法可以生成等距线:等距线和可变距离线。
9.在生成旋转曲面时,CAXA制造工程师需要在即时菜单中输入两个相关参数:(1)起始角度:生成的曲面的初始位置与母线和转轴形成的平面形成夹角;(2)终止角:生成曲面的末端位置与母线和旋转轴形成的平面形成夹角。
10.在CAXA制造工程师中,扫描表面实际上是一种直纹面,它是一种空间曲线扫描,以沿着指定方向从给定的起始位置生成具有一定锥度的表面。
第二,选择题。
1.计算机辅助工艺规划的英文缩写是(B)。
在CAXA制造工程师的导向功能中,剖面线和导向线保持固定连接,称为(D)。
a .单导轨b .双导轨c .平行导轨d .固定关节导轨3。
3 .粗加工轮廓。
CAXA制造工程师属于(b)轴加工。
A.2b.2.5 c.3 d.44 .根清洗是一个()过程。
a .半精加工b .精加工c .精加工d .其他5。
修剪是拾取一条或多条曲线,如(b)修剪一系列修剪后的曲线。
a .切割点b .剪刀线c .切割面d .切割体第三,判断问题。
1.安全高度是指刀具可以快速进给而不会过度切割的高度。
(错)2。
慢速切削距离是指当快速前进(G01)变为向前工作(G00)时的位置长度。
(错)3。
CAXA制造工程师练习试题

基础知识部分CAXA制造工程师综合练习题(一)一、填空题。
2.CAXA制造工程师的“轨迹再生成”功能可实现轨迹编辑。
用户只需要选中已有的数控加工轨迹,修改原定义的加工参数表,即可重新生成加工轨迹。
4.CAXA制造工程师可自动按照加工的先后顺序产生。
条直线倒角。
6.尖角过渡用于在给定的两根曲线之间进行过渡,过渡后在两曲线的交点处呈。
9.CAXA制造工程师生成旋转曲面时,需要在立即菜单中输入两个相的夹角。
是一条空间曲线沿指定方向从给定的起始位置开始以一定的锥度扫描生成曲面。
二、选择题。
1.计算机辅助工艺规划的英文缩写是( B )。
A.CADB.CAMC.CAED.CAPP2.在CAXA制造工程师导动特征功能中,截面线与导动线保持固接关系,该方式称为( D )。
A.单向导动B.双向导动C.平行导动D.固接导动3.CAXA制造工程师等高线粗加工属于( B )轴加工。
A.2B.2.5C.3D.44.清根加工属于()加工。
A.半精加工 B精加工 C.补加工 D.其他5.修剪是用拾取一条曲线或多条曲线作为( B ),对一系列被裁剪曲线进行裁剪。
A.裁减点B.剪刀线C.裁减面D.裁减体三、判断题。
1.安全高度是指保证在此高度以上可以快速走刀而不发生过切的高度。
(错)2.慢速下刀距离是指由快进(G01)转为工进(G00)时的位置长度。
(错)3.加工余量车、铣加工均是去除余量的过程,即从毛坯开始逐步去除多余的材料,以得到需要的零件。
()4.实际的加工模型是制定的加工模型按给定的加工余量进行等距的结果。
()5.在两轴联动控制中,对于直线和圆弧的加工存在误差,加工误差是指对样条线进行加工时用折线段逼近样条线时的误差。
()四、简答题。
1.简述CAXA制造工程师的基本功能。
2.简述CAXA制造工程师提供的特征造型方式。
3.简述CAXA制造工程师中曲面过渡的概念及其种类。
CAXA制造工程师综合练习题(二)一、填空题。
1.CAXA制造工程师2轴或2.5轴加工方式:可直接利用零件的轮廓曲线生成加工轨迹指令,而无须建立其。
五轴数控加工的刀具路径规划与动力学仿真
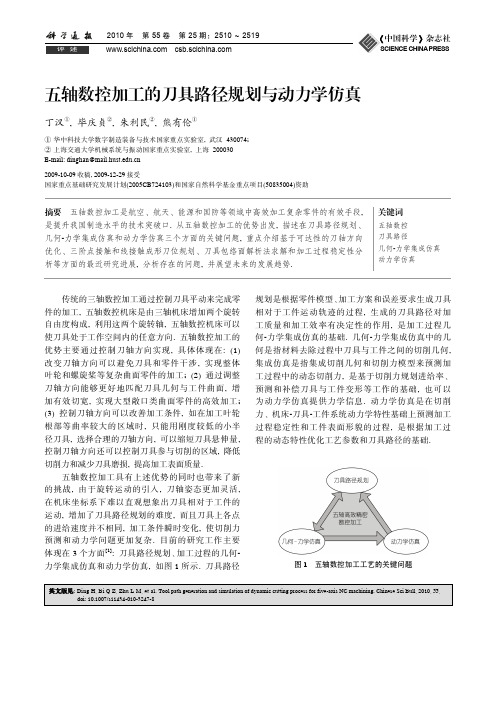
2010年 第55卷 第25期:2510 ~ 2519 英文版见: Ding H, Bi Q Z, Zhu L M, et al. Tool path generation and simulation of dynamic cutting process for five-axis NC machining. Chinese Sci Bull, 2010, 55,doi: 10.1007/s11434-010-3247-8评 述《中国科学》杂志社SCIENCE CHINA PRESS五轴数控加工的刀具路径规划与动力学仿真丁汉①, 毕庆贞②, 朱利民②, 熊有伦①① 华中科技大学数字制造装备与技术国家重点实验室, 武汉 430074; ② 上海交通大学机械系统与振动国家重点实验室, 上海 200030 E-mail: dinghan@ 2009-10-09收稿, 2009-12-29接受国家重点基础研究发展计划(2005CB724103)和国家自然科学基金重点项目(50835004)资助摘要 五轴数控加工是航空、航天、能源和国防等领域中高效加工复杂零件的有效手段, 是提升我国制造水平的技术突破口. 从五轴数控加工的优势出发, 描述在刀具路径规划、几何-力学集成仿真和动力学仿真三个方面的关键问题, 重点介绍基于可达性的刀轴方向优化、三阶点接触和线接触成形刀位规划、刀具包络面解析法求解和加工过程稳定性分析等方面的最近研究进展, 分析存在的问题, 并展望未来的发展趋势.关键词五轴数控 刀具路径几何-力学集成仿真 动力学仿真传统的三轴数控加工通过控制刀具平动来完成零件的加工, 五轴数控机床是由三轴机床增加两个旋转自由度构成, 利用这两个旋转轴, 五轴数控机床可以使刀具处于工作空间内的任意方向. 五轴数控加工的优势主要通过控制刀轴方向实现, 具体体现在: (1) 改变刀轴方向可以避免刀具和零件干涉, 实现整体叶轮和螺旋桨等复杂曲面零件的加工; (2) 通过调整刀轴方向能够更好地匹配刀具几何与工件曲面, 增加有效切宽, 实现大型敞口类曲面零件的高效加工; (3) 控制刀轴方向可以改善加工条件, 如在加工叶轮根部等曲率较大的区域时, 只能用刚度较低的小半径刀具, 选择合理的刀轴方向, 可以缩短刀具悬伸量, 控制刀轴方向还可以控制刀具参与切削的区域, 降低切削力和减少刀具磨损, 提高加工表面质量.五轴数控加工具有上述优势的同时也带来了新的挑战, 由于旋转运动的引入, 刀轴姿态更加灵活, 在机床坐标系下难以直观想象出刀具相对于工件的运动, 增加了刀具路径规划的难度, 而且刀具上各点的进给速度并不相同, 加工条件瞬时变化, 使切削力预测和动力学问题更加复杂. 目前的研究工作主要体现在3个方面[1]: 刀具路径规划、加工过程的几何-力学集成仿真和动力学仿真, 如图1所示. 刀具路径规划是根据零件模型、加工方案和误差要求生成刀具相对于工件运动轨迹的过程, 生成的刀具路径对加工质量和加工效率有决定性的作用, 是加工过程几何-力学集成仿真的基础. 几何-力学集成仿真中的几何是指材料去除过程中刀具与工件之间的切削几何,集成仿真是指集成切削几何和切削力模型来预测加工过程中的动态切削力, 是基于切削力规划进给率、预测和补偿刀具与工件变形等工作的基础, 也可以为动力学仿真提供力学信息. 动力学仿真是在切削力、机床-刀具-工件系统动力学特性基础上预测加工过程稳定性和工件表面形貌的过程, 是根据加工过程的动态特性优化工艺参数和刀具路径的基础.图1 五轴数控加工工艺的关键问题国内外对五轴数控加工进行了大量的理论和应用研究, 目前已有通用CAM软件(如UG和Catia)、专用CAM软件(如加工叶轮的Max和加工叶片的TurboSoft)和动力学仿真软件(如CutterPro). 欧盟在2001年开展了“Flamingo (flank milling optimization)”项目, 联合了SNECMA, Rolls Royce, Dassault Systè- mes等著名公司和高校研究了高效侧铣加工方法. 美国联合技术公司、普惠(Pratt & Whitney)公司和Concepts NREC公司一直在研究五轴高效精密加工技术. 国内也开发了如开目、5BDM和DynaCut等软件, 但在理论研究和应用方面尚处于起步阶段.目前的商业软件在刀具路径规划和仿真方面提供了丰富的策略, 但在智能性、工艺性和计算效率等方面还不完善, 如刀轴方向控制策略主要依靠编程人员的输入, 难以做到自动优化刀轴方向来同时满足干涉避免、宽行加工、刀具路径整体光顺和缩短刀具长度等需求; 在动力学仿真方面主要针对三轴数控加工, 亟需针对五轴高速加工的切削力和切削过程动力学建模与仿真.1 刀具路径规划刀具路径规划是数控编程的核心技术, 在复杂曲面五轴高效加工的刀具路径规划中, 最大的难点是除满足几何约束外, 还需要考虑加工过程中的动态特性和物理因素, 尤其对于难加工材料的工件, 动态特性和物理因素很大程度上决定了加工效率和加工质量, 是在刀具路径规划阶段必须考虑的. 规划刀具路径时, 需要在保证无干涉前提下, 通过调整刀轴方向来扩大刀具有效切削面积、改善工艺条件.1.1 干涉避免干涉避免是加工复杂曲面零件时需要首先考虑的几何约束, 目前的无干涉刀位规划方法可以分为先生成后检测的规划方法和基于可达性的规划方法. 先生成后检测是指先生成刀具路径然后检测干涉, 通过调整刀轴方向来避免干涉, 如图2所示; 而基于可达性的刀具路径规划方法是直接在可达空间中生成无干涉刀具路径, 如图3所示.先生成后检测方法的工作集中在干涉检查和刀轴方向调整两方面. 数控程序中刀位点一般有几万行甚至十几万行, 干涉检查往往花费大量的计算时间和资源,因此研究重点在提高全局干涉检查的效图2 先生成后调整的干涉避免方法[2](a) 干涉发生; (b)调整刀轴方向图3 基于可达性的干涉避免方法(a) 可达方向锥; (b) 无干涉刀具路径率方面[2,3]. 在加工复杂零件时, 先产生后检测方法往往需要反复的检查干涉和调整刀轴方向, 在这个过程中主要考虑几何约束, 难以根据工艺需求优化刀轴方向.基于可达性的规划方法首先在离散的刀触点处计算出刀具的可达方向锥, 然后在可达方向中规划刀具路径, 这种方法的优点是可以直接判断零件的可加工性, 减少甚至可以避免对刀具路径进行反复的调整和检测, 因此能够在刀具无干涉空间中优化刀具路径, 例如可以根据机床运动学性能优化刀轴方向, 克服在优化刀轴方向时难以避免全局干涉的难题. 但在加工复杂零件时, 障碍物模型往往由十几万甚至几十万个多边形组成, 计算可达刀轴方向往往需要庞大的计算资源和时间, 所以研究的重点集中在如何快速计算刀具可达方向锥方面, 主要有C(configuration space)空间法[4,5]和可视锥法[6~10]. C-空间法的关键是如何将障碍物表面快速映射到C-空间, 计算效率是该类算法的主要问题. Wang等人[5]的计算结果表明, 当障碍物模型包含10000个三角形时,即使不考虑刀柄的干涉检查, 计算可达方向锥的时25112010年9月 第55卷 第25期2512间会达到1190.33 min. 为了提高计算效率, 先忽略刀具半径, 把刀具抽象为一根从刀位点出发的射线, 可达性问题就转化为可视性问题. 本文作者[6~8]用C-空间方法描述了刀具的可视锥, 利用图形学中的消隐算法提出了3种提高可视锥计算速度的策略, 并提出了基于可视锥的曲面可制造性分析方法. 但可视性没有考虑刀具和刀柄的半径, 仅仅是刀具无干涉的必要条件, 因此需要耗时的后处理来进行精确的干涉检查[9]. 如果将加工曲面和干涉检查面做等距偏置, 球头刀的可达性问题可以等效为可视性问题[10], 但是引出的等距面计算是一项复杂的任务, 而且该方法仍然无法准确考虑刀柄的半径, 只适用于球头刀, 因此很难有通用性. 本文作者[11,12]推广了传统可视锥的概念, 提出了高效计算刀具全局可达方向锥的方法, 具有近似线性的时间复杂度. 对于工业中常用的平底铣刀和圆环铣刀, 根据刀触点、曲面外法线方向和刀轴方向一般能够确定唯一的刀位点, 当沿刀轴方向的反方向观察刀位点时, 刀具的全局可达问题可以等价为一组圆盘面和圆锥面的完全可视问题, 利用图形显卡(GPU)中的遮挡查询功能可以快速检测该圆盘和圆锥面的完全可视性, 进而判断刀具的完全可达性. 表1对比了3种算法的计算时间, 可以发现, 当输入障碍物模型的三角形数和刀轴方向数都是文献[9]中的10多倍时, 基于GPU 算法的计算时间仅为文献[9]中算法的2%, 单个刀位的平均计算时间小于文献[9]中算法的2‰. 即使输入三角形个数大于文献[3]的10倍, 基于GPU 算法的单个刀位平均检测时间小于文献[3]中算法的3%.1.2 加工效率五轴数控加工至今仍广泛采用球头刀, 球头刀加工刀位规划简单, 但效率比较低, 而非球头刀通过调整其位置和姿态, 可以使刀触点轨迹线附近带状区域内的刀具包络曲面充分逼近理论设计曲面, 从而显著提高给定精度下的加工带宽, 在加工平坦、敞口类曲面时能充分发挥五轴联动机床的潜力, 成为近些年来研究的热点. 研究工作主要集中在平底刀和圆环刀的端铣加工, 以及圆柱刀和圆锥刀的侧铣加工. 端铣加工中依靠点接触成形, 通过增大刀具的有效切削面积可以获得高材料去除率, 提高加工效率, 而侧铣加工中使用线接触成形, 直接实现宽行加工.五轴数控加工的成形原理为单参数面族包络原理, 真实的加工误差为刀具包络面相对于工件曲面的法向误差. 由于只有在所有刀位都确定之后才能计算刀具包络面[13,14], 因此如何在单个刀位规划的时候考虑刀具包络面与工件曲面之间的偏差是个非常关键的问题, 它直接关系到刀位计算的精度. 由于操作上的难度及复杂性, 多数文献都采用了近似的简化处理[15], 将刀位规划转化为单个刀位下, 刀具曲面与工件曲面间的优化逼近问题, 给出的各种刀位优化模型并不能真实地反映实际加工过程, 并且现有的方法仅仅适合某种曲面或某种刀具的刀位计算, 在通用性、可操作性、稳定性或加工精度方面还有许多需要改进的地方.针对端铣加工, 王小椿等人[15~17]相继从刀具包络面与设计曲面在刀触点处高阶切触的角度研究了刀位规划问题. 王小椿等人[15]提出了中凹盘形铣刀的密切曲率法, 在垂直于进给方向的法截面中, 由刀尖轨迹圆形成的包络面与理论曲面的法截线具有相同的1~3阶导数, 从而在保持精度的情况下, 加大了每次走刀的加工带宽. Rao 等人[16]通过讨论设计曲面与刀具包络面的曲率匹配, 给出了消除平底刀五轴加工自由曲面的局部干涉的方法. 上述两种方法均是基于刀具包络面的局部近似模型进行刀位优化, 但仅适用于盘形铣刀或平头刀, 而不能扩展到其他类型的刀具. Gong 等人[17]建立了描述刀具曲面、刀具包络面和设计曲面之间关系的模型, 提出了带状密切意义下刀具包络面逼近设计曲面的原理与方法. 该方法适用于一般的回转刀具, 但它是建立在刀具包络面的二阶局部重建的基础上的, 仅能做到刀具包络面与工件曲面的二阶切触. 对于五轴加工而言, 理表1 可达空间计算时间的对比输入模型 方法计算平台三角形刀位点 刀轴方向计算时间单个刀位的平均计算时间 Sarma 等人[9]SGI 工作站, Dual CPU 250M 10665 1500 80 51.63 min 2.58×10−2 s Elber 等人[3] CPU 2.4G, RAM 512M12600 50000 1 61.61 s 1.23×10−3 s 本文作者的方法[12]CPU2.4G, RAM 512M 1397542000 1026 60.53 s 2.95×10−5 s论上可以实现两者的三阶切触, 因此二阶模型未能充分发挥五轴联动加工的潜力. 这些方法的理论模型也互不兼容, 并且均是将切触条件转化为等式方程, 然后严格计算出满足切触条件的刀位. 但在实际应用中, 由于刀具和设计曲面的复杂性, 以及无干涉约束、机床工作空间约束以及刀具路径光顺性约束的存在, 往往无法实现精确的高阶切触加工. 本文作者[18,19]研究了两线接触曲面间的几何学特性, 刀具包络面的基本条件是沿特征线和刀触点轨迹线分别与刀具曲面和设计曲面线接触, 提出了回转刀具扫掠包络面的局部重建原理. 建立了由单个刀位重建刀具包络面局部三阶近似曲面的数学模型, 刻画了刀具曲面、刀具包络面与设计曲面在刀触点邻域内的三阶微分关系, 在此基础上提出了非球头刀宽行五轴数控加工自由曲面的刀位规划新方法——三阶切触法. 该方法通过优化刀具的前倾角和侧倾角使得在刀触点处刀具包络曲面与设计曲面达到三阶切触, 适用于任意回转面刀具、任意设计曲面及各种加工方式, 并且可以自然地处理各种几何学和运动学约束. 采用环心圆半径为10 mm, 母圆半径为2.5 mm的圆环刀加工某螺旋面, 在某一刀触点处限定加工误差δ为0.005, 0.01 mm时, 3种刀位(球头刀一阶切触、圆环刀二阶、三阶切触)的加工带宽如表2所示, 可以看出三阶切触加工实现了刀具包络曲面与设计曲面的局部最佳逼近, 即使与二阶切触加工相比也显著提高了加工效率.针对侧铣加工, Lartigue等人[20]首次从控制整体误差入手研究了刀位优化问题, 通过调整轴迹面使得刀具包络面在最小二乘意义下逼近设计曲面, 但他们所采用的误差度量经过了一定的简化. 针对柱刀加工, Gong等人[21]应用等距包容原理将该问题转化为轴迹面向设计曲面的等距面的最小二乘逼近问题. 这种方法不拘泥于局部误差的大小, 而是着眼于控制刀具面族包络在整体上向设计曲面的逼近误差, 因此被称为整体优化方法. 虽然最小二乘曲面拟合可以直接沿用曲面反求的有关理论和方法, 从计算的角度来说更容易实现, 但是不符合ISO和ANSI标准推荐的轮廓度误差评定准则, 而且这两种方法不能处理无过切约束, 不适用于半精加工规划. 此外, 包络面与设计曲面间的法向误差的解析描述以及轴迹面形状改变对法向误差的影响等基础问题也没有很好地解决. 本文作者[22,23]将柱刀侧铣加工刀具路表2 加工带宽比较加工误差δ/mm球头刀(R=5.5 mm)环刀二阶密切环刀三阶密切0.005 0.69 2.48 5.280.01 0.98 3.12 6.14径整体优化问题归结为刀具包络面向设计曲面的最佳一致逼近问题, 定义了点-轴迹面法向误差函数,并推导出其关于轴迹面形状控制参数的一阶梯度和二阶海色矩阵表达式, 在此基础上构造了高效的离散点云轴迹面逼近算法, 应用于非可展直纹面的侧铣加工, 几何精度比国际上现有的方法提高了30%以上, 并且可以自然地处理无过切约束, 对比结果如表3所示. 这一方法利用了柱刀包络面与其轴迹面互为等距面这一几何性质, 因此无法推广应用于锥刀的情形. 在某些应用场合下, 锥刀可在保证刚性的前提下实现端部的小半径切削, 从而避免刀具端部与工件的干涉以及小半径柱刀刚性不足的困难, 因此关于锥刀侧铣加工的刀位优化方法近年来引起重视.本文作者[24,25]基于刀具包络面的双参数球族包络表示, 提出了无须构造包络面而直接计算其与设计曲面间法向误差的方法, 并推导出法向误差关于刀轴轨迹面形状控制参数的一阶梯度表达式, 揭示了刀位微小调整对设计曲面和刀具包络面间整体逼近误差的影响规律, 在此基础上构造了基于导数信息的刀具包络面向设计曲面的离散点云的最佳一致逼近算法, 实现了圆锥刀五轴侧铣加工刀具路径的整体优化. 有关理论和方法同样也适用于一般回转刀具的侧铣加工规划. 以圆锥刀侧铣加工某叶轮叶片为例, 叶片直纹面的两条边界曲线均为3次B样条曲线,圆锥刀的底面圆半径为6.25 mm, 高度为30 mm, 半锥角为10°. 在待加工直纹面上均匀选取50×100个离散点. 由Chiou的方法[26]生成初始轴迹面, 此时刀具包络面与设计曲面间的最大过切量为0.0896 mm, 最大欠切量为0.0239 mm, 对轴迹面进行优化后, 最大过切量和欠切量分别减小到0.0062和0.0061 mm, 可以看出刀具路径整体优化显著提高了零件的几何精度.表3 几种不同方法结果的比较a)RRD[27]MBM[28]Gong等人[21]本文作者的方法[22]最大欠切量/mm 0.220 0.264 0.093(0.228) 0.068(0.228)最大过切量/mm 0.220 0.211 0.119(0.172) 0.067(0.172)a) 括号中的为优化前的结果25132010年9月 第55卷 第25期25141.3 工艺条件改善高速加工对刀具轨迹的光顺性和加工系统的整体刚度提出了更高的要求. 刀轴方向光顺性和刀具长度影响五轴数控加工过程的动态特性; 不同刀轴方向也会改变有效切削速度等切削参数, 影响切削力等物理因素. 在刀具路径规划中需要综合这些因素, 改善工艺条件.(ⅰ) 刀轴方向光顺. 刀轴方向的光顺性对运动学非线性误差、加工效率、进给运动平稳性和切削条件[29,30]都有直接的影响, 因此刀轴方向的光顺性是评价刀具路径的一个重要指标. 刀轴方向光顺性的度量可以在机床坐标系中、工件坐标系中或者进给坐标系中定义, 分别对应机床旋转轴的运动、刀轴方向相对于工件的变化和切削条件的变化.现有研究中大多考虑机床坐标系下的度量, Ker- sting 等人[31]研究了在自由C-空间中根据机床坐标系下的度量光顺刀轴方向的方法. Castagnetti 等人[29]以旋转轴进给运动的平稳性和加工效率为目标定义了机床坐标系下的度量, 证明优化刀轴方向后可以明显缩短加工时间. 本文作者[11,12]研究了在刀轴可行空间中整体光顺刀轴方向的算法, 该算法考虑了相邻刀位之间的角速度约束, 把刀轴方向整体光顺问题定义为离散域的约束最优化问题, 用有向图的最短路径算法求解该优化问题获得了整体光顺的刀具路径.根据工件坐标系下的度量光顺刀轴方向的方法主要集中在NURBS 刀具路径规划方面, Dassault 公司[32]研究了用双样条曲线描述五轴加工刀具路径的方式, 通过插值获得光滑的刀轴方向. Siemens 的840D 数控系统推出了支持等距双NURBS 刀具路径的接口, 刀轴方向为球面上的有理样条曲线, 保证了刀轴方向的光滑. 本文作者1)[33]提出了生成等距双NURBS 刀具路径的方法, 基于“点-线”运动学, 引入对偶四元数超平面描述刀具位形空间, 将“离散刀位→ 连续刀具路径”生成问题转化为对偶四元数空间中的平面插值型曲线设计问题, 采用B 样条曲线设计出有理运动表达形式的刀具路径, 可方便地转化为固定间距双NURBS 曲线的表达形式.进给坐标系下的度量反映了切削条件的变化, 根据进给坐标系下的度量光顺刀轴方向有助于实现切削力平滑. Ozturk 等人[34]针对球头铣刀加工分析了刀轴方向与切削力的关系, 证明刀轴方向对球头铣刀的加工质量有明显影响. 本文作者[30,35]提出了在刀触点网格上整体光顺刀轴方向的算法, 该算法综合考虑了工件坐标系下、机床坐标系下和进给坐标系下的三种度量, 可以同时保证沿进给方向和相邻行方向上刀轴方向的整体光顺性, 而且只需要计算刀触点网格上的刀具可达方向锥, 具有较高的计算效率, 仿真表明, 整体优化刀轴方向可以提高加工效率, 使机床进给运动更加平稳, 有利于实现加工过程中切削力的平滑.(ⅱ) 缩短刀具长度. 可以用更短的刀具加工复杂零件是五轴数控加工的一个重要优势, 缩短刀具悬伸长度可以提高整个加工系统的刚度. 刀具最短安全长度一般在数控程序仿真阶段计算, 如数控仿真软件Vericut 在6.2版本中提供了计算安全最短刀具长度的功能. 在仿真过程中计算安全最短刀具长度需要首先规划出刀具路径, 只能针对已有刀具路径计算安全的刀具悬伸量, 然而在加工复杂零件时,安全最短的刀具长度往往由刀轴方向决定, 因此应该在刀具路径规划阶段考虑刀具的安全最短长度.如何在规划五轴数控加工刀具路径时考虑安全最短刀具长度, 在现有研究中考虑较少. Morimoto 等人[10]针对球头铣刀的固定角度加工提出了调整刀轴方向来缩短刀具长度的算法, 该方法需要首先求被加工曲面和干涉检查曲面的等距偏置面, 而且在计算安全刀具长度时过于保守. 本文作者[36]在基于GPU 检测刀具可达性的基础上, 提出了计算可达方向上安全最短刀具长度的方法, 为3+2数控加工提供了高效的刀具安全长度规划方法. 在此基础上, 进一步探索了以刀具长度最短为目标的五轴联动数控加工刀具路径规划算法[37,38], 以刀具路径的无干涉和相邻刀位之间刀轴方向的光顺性作为约束, 把刀具长度优化问题转化为约束组合优化问题, 并给出了有效的求解方法.2 几何-力学集成仿真动态切削力仿真是物理仿真的基础, 在进给速1) Zhang X M, Zhu L M, Ding H, et al. Kinematic generation of ruled surface based on rational motion of line and point-line. Comput Aided Geom D, (Submitted)度、主轴转速等切削参数优化, 切削颤振预报, 加工过程自适应控制, 刀具磨损和破损监测, 加工表面形貌预测, 加工误差分析与补偿中有着广泛的应用. 几何-力学集成仿真是根据材料去除过程中的瞬时切削条件来预测动态切削力, 包含切削力系数和瞬时切削几何两方面的工作, 其中切削力系数一般采用实验标定的方法求得[39,40], 因此主要工作为刀具扫描体和刀具-工件切削几何建模.2.1 几何仿真与切削力预测的集成刀具扫掠体建模的关键是求解其包络面. 对于五轴运动下的刀具扫掠体包络面的建模, 目前常用的方法是数值法[41], 包括Jacobian秩亏损方法、扫掠微分方程方法、隐式建模方法及Minkowski和方法, 这些方法需要数值求解高阶常微分方程或超越方程, 计算量很大. Chiou等人[42]推导了环刀和由上、下锥面和中间环面组成的APT刀具在五轴线性插补运动下的瞬时特征线的求解公式. Du和Ye等人[43,44]通过引入瞬时标架和刚体速度表示简化了Chiou的结果. 之后, Chiou等[45]通过引入刀触点处的瞬时标架得到了APT刀具在一般空间刚体运动下的瞬时特征线的求解公式. 上述方法需要逐点计算包络面上的点, 解的判别过程比较复杂. 本文作者[13,14]提出了两种回转刀具切削刃扫描面的解析表达方法: (1) 将锥刀、鼓刀和环刀的切削刃回转面表示为单参数可变半径球族的包络面, 利用双参数球族包络理论推导出了这3种刀具在一般空间运动下的扫掠体包络面及其单位外法矢的解析表达式; (2) 应用包络条件和刚体运动的速度表示方法推导出任意回转刀具在一般空间运动下扫掠包络面特征线的解析表达式, 在方法上具有无须引入附加瞬时标架、公式简洁明了的优点.刀具-工件的切削几何是五轴加工铣削力仿真的基础. 目前常用的切削几何建模方法主要分为实体建模法、解析模型法和离散几何建模法3类: (1) 实体建模法, Altintas等人[46]采用ACIS实体建模工具确定五轴侧铣加工圆锥铣刀与工件的瞬时啮合状态和切厚; (2) 解析模型法, Elbestaw等人[47,48]将刀刃曲线表示为NURBS曲线, 通过计算该曲线与工件几何的相交确定瞬时参与切削的刀刃微元与瞬时切厚; (3) 离散几何建模法, Jerard等[40]使用扩展的Z-buffer方法表示工件几何, 通过刀具扫描体与Z-buffer单元的相交关系计算瞬时啮合区域与瞬时切厚. 2.2 切削力约束下的进给率规划在五轴铣削过程几何-力学集成仿真的基础上,可以根据切削力优化进给率. 目前商用CAM软件的进给率优化算法均基于体积分析(也称为材料去除率). 在这种传统的方法中, 通常把进给率设置为反比于瞬时材料去除率或者与材料去除率成指数函数关系. 该方法的两个主要缺点是: (1) 瞬时材料去除率虽然从一定程度上可以反映切削力的大小, 但不能反映切削力的方向, 故基于材料去除率的进给率优化不能反映切削力的本质; (2) 由这种方法规划出的进给率所产生的切削力的大小难以保持恒定. 针对基于材料去除率规划进给率的缺点, Bailey等人[47,48]提出了基于切削力模型的五轴加工进给率规划方法.Erdim等人[49]对基于切削力模型的与基于材料去除率模型的两种进给率优化策略做了详细比较研究.本文作者[50]提出了切削力约束的五轴数控侧铣加工进给率离线规划方法: 基于机床各轴立方样条多项式插补格式, 建立以各轴相邻位置点之间的时间序列为设计变量, 以各轴相邻位置点之间的运行时间序列之和极小为目标函数, 以各轴的速度、加速度、跃度极限为约束, 同时以刀具切削过程中的最大切削力小于阀域值为约束的优化模型, 并以全局最优算法求解获取最优进给率. 该方法适用于自由曲面粗加工及直纹面或类直纹面曲面半精加工.3 加工过程动力学仿真五轴铣削过程动力学仿真是为加工过程工艺优化提供过程状态变量的时间历程数据, 核心工作包括动力学建模、加工过程稳定性分析和工艺参数优化.3.1 动力学建模刀具-工件系统结构动力学模型分为: (1) 刀具-工件耦合振动模型, 对于薄板类零件加工, Ratchev的研究小组[51]提出了基于FEM的薄板-刀具耦合振动模型; Kovecses等人[52]提出了基于解析法建模的薄板类零件铣削振动模型. 然而, 对于薄壳类零件铣削加工,工件振动模型、刀具-工件耦合振动模型极少见诸国际期刊. (2) 工件-夹具接触动力学建模, Hu等人[53]在柔性多体动力学框架下, 使用集总参数模型分析了夹具的动态稳定性; Kapoor等人[54]研究了夹具-工件动态摩擦接触模型, 并分析了该动态效应对加工性能的影响; Rong等人[55]在FEM的框架下, 建立了夹具-工2515。
CATIA教程NC

加工轨迹的计算与编辑。 工艺参数设置。
加工仿真。
数控程序后处理、数据管理、数据传输等。
数控编程及加工工艺基础
2. 加工原理
机床上的刀具和工件间的相对运动,称为表面成形运动。数控加工是指数 控机床按照数控程序所确定的轨迹(刀轨或刀路)进行表面成形运动,从而加工 出产品的表面形状。
平面轮廓加工
对于不同的加工类型,CATIA的数控编程过程都需要经过获取零件模型、加 工工艺分析及规划、完善零件模型、设置加工参数、生成数控加工刀路、检验数 控刀路和生成数控加工程序七个步骤。其流程如下图所示。
CAD系统 建立零件
模型
数控 加工
加工工艺分析及规划 完善零件模型 设置加工参数 生成数控刀路 检验数控刀路
理想刀轨 实际刀轨
刀具
插补误差
残余高度
数控编程及加工工艺基础
3. 刀位计算
数控加工刀位点的计算过程可分为3个阶段: 加工表面偏置 刀位点计算的前提是根据刀具的类型和尺寸计算
出加工表面的偏置面。
表面偏置
数控编程及加工工艺基础
刀轨形式的的刀轨形式一是行切刀轨,即所有刀位点都分布在一组与刀轴 (Z轴)平行的平面内;二是等高线刀轨(环切刀轨),即所有刀位点 都分布在一组与Z轴垂直的平面内。
加工对象的确定 通过对模型的分析,确定工件上哪些部位需要在 数控铣床上或加工中心上加工。
加工区域规划 即按照形状特征、功能特征及精度、粗糙度等要求, 将加工对象划分为若干个加工区域,以此来提高加工效益与质量。
加工工艺路线规划 即从粗加工到精加工,再到清根加工的加工流 程规划,以及加工余量的分配。
加工工艺和加工方式确定 如刀具选择、加工工艺参数和切削方式 的选择等。
CATIA V5 数控加工

第1章 CATIA 数控加工基础知识1.1 概述CATIA数控加工模块包括车削加工(Lathe Machining)、2.5轴铣削加工(Prismatic Machining)、曲面加工(Surface Machining)、高级加工(Advanced Machining)、NC加工审视(NC Manufacturing Review)、STL快速成型(STL Rapid Prototyping)等部分。
CATIA数控加工模块用来定义和管理数控加工程序,使应用三维线框或实体造型设计完成的零件,能用2.5~5轴的数控加工技术加工出来。
它提供了便于应用和便于学习的图形界面,非常适合面向生产现场的情况下使用。
此外,CATIA的领先技术,加之V5版本的技术方法与DELMIA(达索公司的一种制造过程规划和模拟的软件工具)的数字加工环境的紧密集成,可很好地满足办公室编程的需要。
因此,CATIA数控加工是协调办公室和生产现场制造活动的很好的解决方法。
CATIA的集成后处理器使NC加工模块覆盖了从刀具轨迹(APT数据和Clfile文件)产生到NC数据输出的全部过程。
CATIA NC加工模块提供了下列基本功能:⑴从2.5到5轴的数控加工的公共平台,它们包括铣削、钻削和车削;⑵刀具和刀具目录的管理;⑶基于图形对话框的直观和易于学习的加工程序柔性管理;⑷刀具轨迹的定义、验证和生成的紧密集成;⑸通过f(x)方程和编辑搜索工具实现的软件智能用户化工具;⑹通过后置处理数据库实现的无缝的数控数据生成;⑺CATIA V5建模能力集成所促成的加工程序高水平关联性,保证了产品设计改变时对其进行有效管理;⑻自动生成HTML格式的NC加工报表文件;⑼基于过程—产品—资源(Process-Product-Resources )模型,使制造过程应用与制造数字处理(Digital Process for Manufacturing )紧密集成。
复杂曲面零件加工加工路径规划研究

复杂曲面零件加工加工路径规划研究在现代制造业中,复杂曲面零件的加工与制造是一项非常重要的任务。
随着科技的不断发展和各行业对零件精度和质量的要求不断提高,如何有效地进行复杂曲面零件加工成为了一个具有挑战性的问题。
为了提高加工效率和质量,研究人员一直在探索并改进加工路径规划技术。
1. 加工路径规划的重要性复杂曲面零件由于其曲面形状复杂多变,传统的加工方法难以满足要求。
而加工路径规划作为一种高级加工方法,可以根据零件的几何形状、材料性质和加工要求,通过优化路径来实现高效加工。
合理的路径规划可以最大限度地减少加工时间、降低加工成本,并保证加工质量,因此具有重要的实际意义。
2. 加工路径规划的难点复杂曲面零件加工路径规划的难点在于如何确定最优路径。
首先,需要根据零件的几何形状和加工要求,构建加工模型。
然后,在考虑加工介质和工具的情况下,通过算法优化得到最优加工路径。
这一过程中需要充分考虑多种因素,如切削力、切削热、刀具磨损等,以及零件上的不同曲面特征,如曲率半径等。
同时,由于复杂曲面零件的加工时间往往较长,对路径规划的实时性要求较高。
3. 加工路径规划的方法目前,常用的加工路径规划方法主要包括基于光学成像的方法、基于矢量法的方法以及基于仿真模拟的方法等。
基于光学成像的方法通过光学传感器对零件进行扫描和测量,从而获取其几何形状和曲率半径等信息,再进行路径规划。
而基于矢量法的方法则通过构建加工模型,并计算刀具的最佳轨迹,以实现路径规划。
基于仿真模拟的方法可以在计算机上建立零件的虚拟模型,并利用特定算法进行路径模拟和仿真,最终生成最优加工路径。
4. 加工路径规划的应用领域加工路径规划技术在航空航天、汽车制造、船舶制造等领域有着广泛的应用。
例如,在飞机的涡轮叶片制造过程中,采用加工路径规划技术可以实现高效率、高精度的加工,进而提高涡轮叶片的性能和可靠性。
另外,在汽车车身的冲压过程中,通过加工路径规划可以有效地减少试验模具制造成本,提高生产效率和产品质量。
CATIA+V5+数控加工
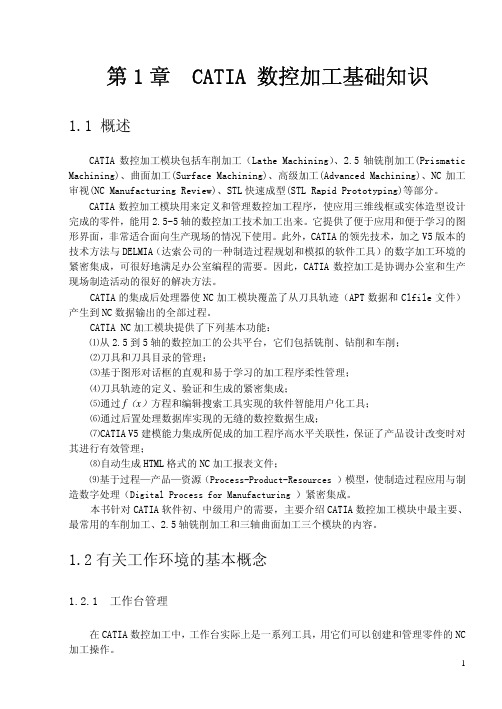
第1章 CATIA 数控加工基础知识1.1 概述CATIA数控加工模块包括车削加工(Lathe Machining)、2.5轴铣削加工(Prismatic Machining)、曲面加工(Surface Machining)、高级加工(Advanced Machining)、NC加工审视(NC Manufacturing Review)、STL快速成型(STL Rapid Prototyping)等部分。
CATIA数控加工模块用来定义和管理数控加工程序,使应用三维线框或实体造型设计完成的零件,能用2.5~5轴的数控加工技术加工出来。
它提供了便于应用和便于学习的图形界面,非常适合面向生产现场的情况下使用。
此外,CATIA的领先技术,加之V5版本的技术方法与DELMIA(达索公司的一种制造过程规划和模拟的软件工具)的数字加工环境的紧密集成,可很好地满足办公室编程的需要。
因此,CATIA数控加工是协调办公室和生产现场制造活动的很好的解决方法。
CATIA的集成后处理器使NC加工模块覆盖了从刀具轨迹(APT数据和Clfile文件)产生到NC数据输出的全部过程。
CATIA NC加工模块提供了下列基本功能:⑴从2.5到5轴的数控加工的公共平台,它们包括铣削、钻削和车削;⑵刀具和刀具目录的管理;⑶基于图形对话框的直观和易于学习的加工程序柔性管理;⑷刀具轨迹的定义、验证和生成的紧密集成;⑸通过f(x)方程和编辑搜索工具实现的软件智能用户化工具;⑹通过后置处理数据库实现的无缝的数控数据生成;⑺CATIA V5建模能力集成所促成的加工程序高水平关联性,保证了产品设计改变时对其进行有效管理;⑻自动生成HTML格式的NC加工报表文件;⑼基于过程—产品—资源(Process-Product-Resources )模型,使制造过程应用与制造数字处理(Digital Process for Manufacturing )紧密集成。
第3章 2.5 轴加工

第3章2.5轴加工本章主要内容:3.1 概述3.2 工件分析与工艺规划3.3 初始设置(实例)3.4 参数设置(实例)3.5 仿真检验与后处理3.6 思考题3.7 练习题3.1 概述2.5轴的铣床加工基本上是依靠二维图形的轮廓、高度来控制的。
在加工时X、Y轴根据水平方向联动,Z轴方向在加工完同一高度后再进行下一个高度才做的运动,所以2.5轴不能进行复杂的曲面加工。
但是2.5轴可以加工四周斜度一致的工件,并且2.5轴相对与3轴的程序计算要快很多。
2.5轴加工是根据二维图形控制,并不受3D图形的影响,在加工时一定要注意刀路的轨迹,不要产生过切等。
2.5轴加工可分为粗加工、光底平面和精加工。
粗加工也称为体积铣,可分为形腔切削—毛坯环切、平行切削、环切。
光底平面也使用上述功能,在粗加工时因进给、主轴转速等原因,造成加工表面比较粗糙,底平面达不到加工要求,因此将光底平面单独执行一个程序。
在光底平面时要求主轴转速加快、进给相对减慢,这样底平面加工才会达到要求。
精加工时采用轮廓铣(分为封闭轮廓和开放轮廓),利用二维图形控制轮廓,加工深度按高度控制。
以上加工方法会在以下几节将做详细的说明。
3.2. 工件分析与工艺规划2.5轴加工在实际应用中,主要用于一些形状简单的、模型特征可以是二维图形决定的、侧壁是垂直或同一斜度的、底面是平的工件。
如模具中用来镶嵌模芯的座框、图形简单的凹凸模等,如图10-1所示。
在2.5轴加工时,可选择多重嵌套的轮廓线,在两条轮廓之间为轮廓铣的加工区域。
在选择轮廓的时候没有先后次序的区分,它只按照轮廓的区域来计算,如图10-2所示,在图中的阴影部分为加工区域。
模具数控加工一般分为粗加工、半精加工和精加工3个基本工序。
在2.5轴的加工中,因图形较为简单,基本可不用半精加工这个程序。
在加工时因零件不同区域的尺寸差异、形状差异等因素,分别采用不同的加工工艺和加工方式进行加工,这是工艺分析与工艺规划,直接影响加工的效率和加工的质量。
数控铣削加工曲面刀具轨迹的规划

况。 然, 显 刀具 轨 迹 的 规 划 应 该 沿 着 曲 面 法 曲 率 变 化 较
小 的 方 向 , 而 使 其 切 线 方 向 和 法 矢 方 向 的 变 化 量 尽 从
可能 小 。
收 稿 日期 :o 7 7 2o 年 月
沿 参 数 方 向 的 几 何 尺 寸 变 化 比 较 大 , 以 实 际 得 到 刀 所
即 对 零 件 加 工 的 刀 具 轨 迹 的 总 长 度 , 中 包 括 刀 其 具有 效 切 削路 径 的 长 度 和不 进行 切 削 的空行 程 长 度 。 显而 易见 , 具 轨 迹 的 长度 越 短 , 加 工效 率 则 越 高 。 刀 其 锯 齿 形 的 往 复 式 双 向 切 削 刀 具 轨 迹 或 螺 旋 线 形 的环 切
参 数 曲 面 加 工 的 刀 具 轨 迹 生 成 方 法 多 种 , 等 如
距 截 平 面 法 、 距 偏 置 法 、 参 数 线 法 、 残 留高度 法 等 等 等
等 【 ( 图 1 示 ) 如 】 所 。
1 数控加工 刀具 轨迹的规划
1 1 刀 具 轨 迹 优 劣 的 评 价 指 标 .
刀 具 轨 迹 要 比单 向 切 削 的 刀 具 轨 迹 短 。
1 12 .. 刀具轨 迹 的连 续性
不 连 续 的轨 迹 会 因 经 常 性 的 抬 刀 使 得 刀 具 往 返 时
留高度 最大 处决 定 , 而加 工 效率 有 时较 低 【 因 引。
1 2 2 等 距 偏 置 法 .. 求 边 界 曲 线 的 等 距 离 曲 线 作 为 刀 具 轨 迹 线 , 间 其 距也 只 能 根据 残 留高 度最 大处 决 定 , 种 方 法 与 等距 这 截平 面法 相似 , 而加工 效 率有 时也 比较低 。 因
精密复杂曲面零件多轴数控加工技术研究进展
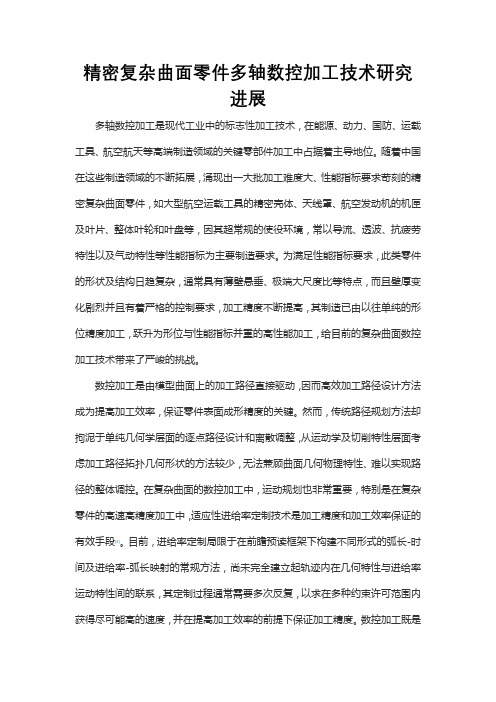
精密复杂曲面零件多轴数控加工技术研究进展多轴数控加工是现代工业中的标志性加工技术,在能源、动力、国防、运载工具、航空航天等高端制造领域的关键零部件加工中占据着主导地位。
随着中国在这些制造领域的不断拓展,涌现出一大批加工难度大、性能指标要求苛刻的精密复杂曲面零件,如大型航空运载工具的精密壳体、天线罩、航空发动机的机匣及叶片、整体叶轮和叶盘等,因其超常规的使役环境,常以导流、透波、抗疲劳特性以及气动特性等性能指标为主要制造要求。
为满足性能指标要求,此类零件的形状及结构日趋复杂,通常具有薄壁悬垂、极端大尺度比等特点,而且壁厚变化剧烈并且有着严格的控制要求,加工精度不断提高,其制造已由以往单纯的形位精度加工,跃升为形位与性能指标并重的高性能加工,给目前的复杂曲面数控加工技术带来了严峻的挑战。
数控加工是由模型曲面上的加工路径直接驱动,因而高效加工路径设计方法成为提高加工效率,保证零件表面成形精度的关键。
然而,传统路径规划方法却拘泥于单纯几何学层面的逐点路径设计和离散调整,从运动学及切削特性层面考虑加工路径拓扑几何形状的方法较少,无法兼顾曲面几何物理特性、难以实现路径的整体调控。
在复杂曲面的数控加工中,运动规划也非常重要,特别是在复杂零件的高速高精度加工中,适应性进给率定制技术是加工精度和加工效率保证的有效手段[4]。
目前,进给率定制局限于在前瞻预读框架下构建不同形式的弧长-时间及进给率-弧长映射的常规方法,尚未完全建立起轨迹内在几何特性与进给率运动特性间的联系,其定制过程通常需要多次反复,以求在多种约束许可范围内获得尽可能高的速度,并在提高加工效率的前提下保证加工精度。
数控加工既是一个零件的几何成形过程,也是一个复杂的动态物理切削过程,特别是随着高档数控机床切削速度不断提高,对数控加工技术的研究不能仅关注常规几何学层面的走刀路径设计和运动学层面的运动规划,必须转向实际的物理加工过程,解决大进给量、高转速所带来的刀具负载波动、变形、破损失效,特别是解决加工过程中由于切削力变化所引起的切削系统的不稳定等问题。
复杂曲面零件数控加工的关键问题——解读《复杂曲面零件五轴数控加工理论与技术》

1五轴数控加工简介复杂曲面零件作为数字化制造的主要研究对象之一,在航空、航天、能源和国防等领域中有着广泛的应用,其制造水平代表着一个国家制造业的核心竞争力。
复杂曲面零件往往具有形状和结构复杂、质量要求高等难点,是五轴数控加工的典型研究对象。
当前,复杂曲面零件主要包括轮盘类零件、航空结构件以及火箭贮箱壁板等,如图1所示。
轮盘类零件是发动机完成对气体的压缩和膨胀的关键部件,主要包括整体叶盘类零件和叶片类零件。
整体叶盘类零件的叶展长、叶片薄且扭曲度大,叶片间的通道深且窄,开敞性差,零件材料多为钛合金、高温合金等难加工材料,因此零件加工制造困难。
叶片是一种特殊的零件,数量多、形状复杂、要求高、加工难度大且故障多发,一图1复杂曲面零件直以来都是各发动机厂生产的关键。
航空整体结构件由整块大型毛坯直接加工而成,在刚度、抗疲劳强度以及各种失稳临界值等方面均比铆接结构胜出一筹,但由于其具有尺寸大、材料去除率大、结构复杂、刚性差等缺点,因此加工后会产生弯扭组合等加工变形。
随着新一代大型运载火箭设计要求的提高,为保证火箭的可靠性,并减轻结构质量,提高有效载荷,对火箭贮箱壁板网格壁厚精度和根部圆弧过渡尺寸都提出了更严格的要求。
五轴数控铣削加工具有高可达性、高效率和高精度等优势,是加工大型与异型复杂零件的重要手段。
五轴数控机床在3个平动轴的基础上增加了2个转动轴,不但可以使刀具相对于工件的位置任意可控,而且刀具轴线相对于工件的方向也在一定的范围内任意可控。
五轴数控加工的主要优势包括:①提高刀具可达性。
通过改变刀具方向可以提高刀具可达性,实现叶轮、叶片和螺旋桨等复杂曲面零件的数控加工。
②缩短刀具悬伸长度。
通过选择合理刀具方向可以在避开干涉的同时使用更短的刀具,提高铣削系统的刚度,改善数控加工中的动态特性,提高加工效率和加工质量。
③可用高效加工刀具。
通过调整刀轴方向能够更好地匹配刀具与工件曲面,增加有效切宽,实现零件的高效加工。
五轴联动数控车床刀具路径优化算法研究

五轴联动数控车床刀具路径优化算法研究引言:随着制造业的快速发展,数控车床在工业生产中扮演着至关重要的角色。
尽管五轴联动数控车床具有更高的加工精度和复杂零件加工能力,但是其刀具路径的优化仍然是一个具有挑战性的问题。
本文将探讨五轴联动数控车床刀具路径优化算法的研究,旨在提高工件的质量、减少加工时间和工具的磨损,从而提高生产效率。
一、概述五轴联动数控车床是一种具有五个坐标轴的先进机床,它可以使刀具在空间中自由移动,从而能够加工出形状复杂的工件。
然而,由于运动轴之间的互相制约以及工具长短等因素,刀具路径的选择变得相当复杂,容易出现冗余运动、工具干涉等问题。
二、相关算法1. 路径规划算法路径规划是五轴联动数控车床刀具路径优化算法中的一个关键环节。
传统的路径规划算法包括最小切削路径法、均匀切削路径法和建模路径法等。
近年来,基于智能优化算法的路径规划算法也得到了广泛的研究和应用,如遗传算法、模拟退火算法和粒子群算法等。
这些算法通过对初始路径进行优化,能够有效地避免干涉和冗余运动,提高加工效率。
2. 工具轨迹生成算法工具轨迹生成算法是在路径规划的基础上,生成实际刀具在加工过程中的运动轨迹。
最常用的方法是维护一个工具刀具轨迹的路径规划或点云生成,然后根据路径规划的结果生成实际的刀具轨迹。
3. 轨迹优化算法轨迹优化算法是指在生成刀具轨迹后,对其进行进一步优化,以减少刀具的运动路径长度、降低加工时间和减少工具的磨损。
常用的优化算法包括动态规划、最优控制和遗传算法等。
这些算法能够通过对轨迹进行分段或局部优化,使刀具的运动更加高效,提高生产效率。
三、优化效果与评价指标五轴联动数控车床刀具路径优化算法的最终目标是提高工件的加工质量、减少加工时间和降低工具的磨损。
为了评价优化算法的效果,可以根据以下指标进行评估:1. 加工精度:通过与设计要求进行对比,评估优化算法对加工精度的影响。
2. 加工时间:比较优化算法前后的加工时间,通过减少不必要的运动来提高加工效率。
闭式叶轮几何造型与粗加工刀位轨迹规划的研究
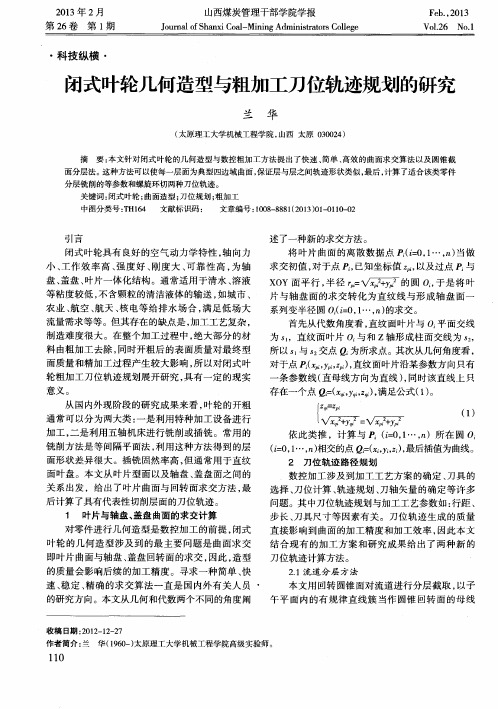
即叶片曲面与轴盘 、 盖盘 回转面 的求交 , 因此 , 造型 的质量会影响后续的加工精度。寻求一种 简单 、 快 速、 稳定 、 精 确的求交算法一 直是 国内外 有关人员 的研究方向。本文从几何 和代数两个不同的角度阐
数 控加 工 涉及 到加 工 工艺 方 案 的确定 、 刀 具 的
对零件进行几何造型是数控加工的前提 , 闭式
叶轮 的几 何 造 型涉 及 到 的最 主要 问题 是 曲 面求 交
选择 、 刀位计算 、 轨迹规划 、 刀轴矢量的确定等许多 问题 。其 中刀 位轨 迹规 划 与加工 工 艺参数 如 : 行距 、 步长 、 刀具尺寸等因素有关 。刀位轨迹生成 的质量 直接影响到曲面的加工精度和加工效率 , 因此本文
2 0 1 3年 2月
山西煤炭管理干部学院学报
J o u r n a l o f S h a n x i C o a l - Mi n i n g Ad mi n i s t r a t o r s Co l l e g e
Fe b . , 2 01 3 V0 1 . 2 6 No . 1
{ 【 、 = 一 瓜
2 刀位轨 迹 路径规 划
( … 1 )
加工 , 二是利用五轴机床进行铣削或插铣 。常用的 铣削方法是等间隔平面法 , 利用这种方法得到的层 面形状差异很大。插铣 固然率 高, 但通常用于直纹 面 叶盘 。本 文从 叶片 型 面 以及 轴 盘 、 盖 盘 面 之 间 的 关 系 出发 ,给 出 了叶 片 曲面 与 回转 面求 交 方 法 , 最
绕 叶轮 回转 轴线 回转 形成 。计算 圆锥 面截 面 与 围成 粗加 工 区域 的 四个 等 距 面 S l d  ̄ S S S 的 四条 交 线
《五轴数控系统轨迹平滑处理技术的研究与实现》

《五轴数控系统轨迹平滑处理技术的研究与实现》一、引言五轴数控系统广泛应用于机械制造、航空航天、医疗器械等领域,其精度和效率直接影响到产品的质量和生产效率。
轨迹平滑处理技术是五轴数控系统中的重要技术之一,能够有效提高加工轨迹的平滑性和加工精度,从而提升加工质量和效率。
本文将针对五轴数控系统轨迹平滑处理技术进行研究与实现,以期为相关领域的研究和应用提供参考。
二、五轴数控系统概述五轴数控系统是一种高精度、高效率的加工设备,其通过五个轴向的运动实现复杂零件的加工。
五轴数控系统的核心是控制系统,其中轨迹规划与平滑处理是控制系统的关键技术之一。
轨迹规划是指根据零件的加工要求,生成合理的加工轨迹;而轨迹平滑处理则是对生成的加工轨迹进行优化,以提高加工精度和表面质量。
三、轨迹平滑处理技术的研究1. 传统轨迹平滑处理方法传统的轨迹平滑处理方法主要包括参数曲线拟合、离散点插值等。
这些方法虽然能够实现一定程度的轨迹平滑,但在处理复杂轨迹时,往往存在计算量大、精度不高、轨迹不平滑等问题。
2. 现代轨迹平滑处理方法随着计算机技术和控制理论的不断发展,现代轨迹平滑处理方法逐渐成为研究热点。
其中,基于优化算法的轨迹平滑处理方法具有较高的精度和效率。
该方法通过建立优化模型,将轨迹平滑问题转化为优化问题,利用优化算法求解最优轨迹。
此外,还有一些智能算法如神经网络、遗传算法等也被应用于轨迹平滑处理中。
四、五轴数控系统轨迹平滑处理的实现1. 确定优化目标在五轴数控系统轨迹平滑处理中,优化目标主要包括提高加工精度、降低表面粗糙度、减小加工力等。
根据具体需求,确定合适的优化目标。
2. 建立优化模型根据优化目标,建立相应的优化模型。
优化模型包括目标函数和约束条件。
目标函数用于描述优化目标,约束条件用于限制变量的取值范围。
3. 选择合适的算法根据优化模型的特点,选择合适的算法进行求解。
对于复杂的优化问题,可以采用智能算法如神经网络、遗传算法等。
CAXA制造工程师练习题

封面作者:Pan Hongliang仅供个人学习基础知识部分CAXA制造工程师综合练习题(一)一、填空题。
2.CAXA制造工程师的“轨迹再生成”功能可实现轨迹编辑。
用户只需要选中已有的数控加工轨迹,修改原定义的加工参数表,即可重新生成加工轨迹。
4.CAXA制造工程师可自动按照加工的先后顺序产生。
条直线倒角。
6.尖角过渡用于在给定的两根曲线之间进行过渡,过渡后在两曲线的交点处呈。
9.CAXA制造工程师生成旋转曲面时,需要在立即菜单中输入两个相的夹角。
是一条空间曲线沿指定方向从给定的起始位置开始以一定的锥度扫描生成曲面。
二、选择题。
1.计算机辅助工艺规划的英文缩写是( B )。
A.CADB.CAMC.CAED.CAPP2.在CAXA制造工程师导动特征功能中,截面线与导动线保持固接关系,该方式称为( D )。
A.单向导动B.双向导动C.平行导动D.固接导动3.CAXA制造工程师等高线粗加工属于( B )轴加工。
A.2B.2.5C.3D.44.清根加工属于()加工。
A.半精加工 B精加工 C.补加工 D.其他5.修剪是用拾取一条曲线或多条曲线作为( B ),对一系列被裁剪曲线进行裁剪。
A.裁减点B.剪刀线C.裁减面D.裁减体三、判断题。
1.安全高度是指保证在此高度以上可以快速走刀而不发生过切的高度。
(错)2.慢速下刀距离是指由快进(G01)转为工进(G00)时的位置长度。
(错)3.加工余量车、铣加工均是去除余量的过程,即从毛坯开始逐步去除多余的材料,以得到需要的零件。
()4.实际的加工模型是制定的加工模型按给定的加工余量进行等距的结果。
()5.在两轴联动控制中,对于直线和圆弧的加工存在误差,加工误差是指对样条线进行加工时用折线段逼近样条线时的误差。
()四、简答题。
1.简述CAXA制造工程师的基本功能。
2.简述CAXA制造工程师提供的特征造型方式。
3.简述CAXA制造工程师中曲面过渡的概念及其种类。
CAXA制造工程师综合练习题(二)一、填空题。
复杂曲面零件的五轴数控加工技术研究

复杂曲面零件的五轴数控加工技术研究
张映故
【期刊名称】《现代制造技术与装备》
【年(卷),期】2024(60)3
【摘要】随着科技水平的不断提升,精密复杂曲面零件的应用越来越广泛。
曲面驱动是复杂曲面零件加工的重要方法,驱动刀轨的规划直接关系到曲面物理特性的调控,应用五轴数控加工技术能够提升复杂曲面零件的加工质量。
文章主要研究复杂曲面零件的五轴数控加工技术,以佛像这个复杂曲面零件为例,分析了曲面驱动刀轨规划、工装方案设计、加工策略以及试制加工过程。
在实际加工过程中,技术人员应充分理解驱动刀轨规划思路与原理,在粗加工、精加工中完善刀轨设计,并进行试制加工。
【总页数】3页(P63-65)
【作者】张映故
【作者单位】柳州职业技术学院
【正文语种】中文
【中图分类】TP3
【相关文献】
1.基于UG的复杂曲面叶轮三维造型及五轴数控加工技术研究
2.复杂曲面五轴数控加工关键技术研究
3.复杂曲面零件数控加工的关键问题r——解读《复杂曲面零件
五轴数控加工理论与技术》4.五轴数控机床高效加工多曲面零件工艺5.基于五轴数控加工工艺的复杂曲面零件加工轨迹分析
因版权原因,仅展示原文概要,查看原文内容请购买。
浅谈精雕编程--五轴曲线加工
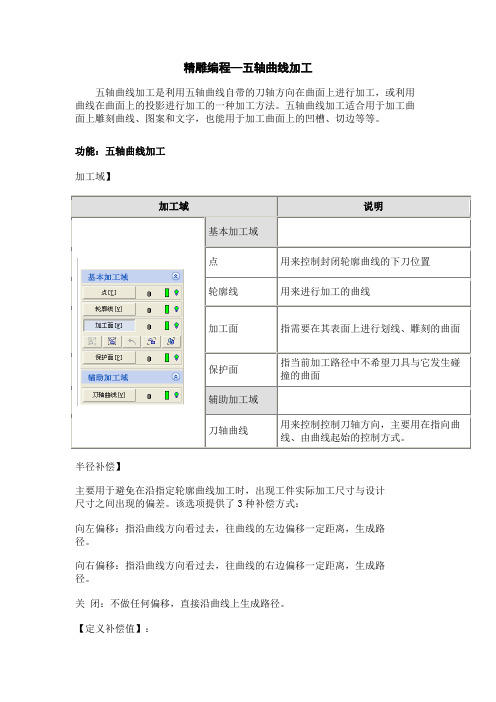
精雕编程—五轴曲线加工五轴曲线加工是利用五轴曲线自带的刀轴方向在曲面上进行加工,或利用曲线在曲面上的投影进行加工的一种加工方法。
五轴曲线加工适合用于加工曲面上雕刻曲线、图案和文字,也能用于加工曲面上的凹槽、切边等等。
功能:五轴曲线加工加工域】半径补偿】主要用于避免在沿指定轮廓曲线加工时,出现工件实际加工尺寸与设计尺寸之间出现的偏差。
该选项提供了3种补偿方式:向左偏移:指沿曲线方向看过去,往曲线的左边偏移一定距离,生成路径。
向右偏移:指沿曲线方向看过去,往曲线的右边偏移一定距离,生成路径。
关闭:不做任何偏移,直接沿曲线上生成路径。
【定义补偿值】:通常情况下,补偿值根据选用的刀具自动计算的。
用户也可以选中该复选框,自定义一个半径补偿值。
当半径补偿方式为关闭时,该项不可用。
【锥度补偿】该选项适用于锥刀或自定义刀具,选中该选项后,将自动计算出半锥角并以侧倾角度的方式补偿到路径刀轴方向上,如下图所示。
五轴曲线控制点的刀轴方向一般比较容易依据几何图形得到,但是这种方向一般代表的是刀具侧刃加工位置的方向,对于锥刀或自定义刀具来说,生成路径的刀轴方向还要在五轴曲线方向的基础上加上一个半锥角补偿值。
设置侧倾角度可以自动实现这一功能。
另外,通过改变侧倾角度值可以根据需要适当改变加工效果。
【端点延伸】沿曲线的首末端点的切向方向延伸一定的距离,主要用于改变路径的切入和切出位置。
•首端延长:在曲线的起点位置延伸一定距离。
•末端延长:在曲线的末点位置延伸一定距离。
说明:延伸长度支持正负值,当值为正,路径变长;反之变短;【线面最大间距】指曲线和曲面之间的允许存在的最大距离,当曲线和曲面之间的距离超出设定值,则不能生成有效的加工路径,需要调整该参数,只有线面之间的距离满足该范围才能生成路径。
【轴向分层】五轴曲线加工为了避免刀具划槽深度过大而断刀,支持轴向分层加工,并提供了限定层数、限定深度、自定义三种分层方式,控制钻孔路径的分层。
- 1、下载文档前请自行甄别文档内容的完整性,平台不提供额外的编辑、内容补充、找答案等附加服务。
- 2、"仅部分预览"的文档,不可在线预览部分如存在完整性等问题,可反馈申请退款(可完整预览的文档不适用该条件!)。
- 3、如文档侵犯您的权益,请联系客服反馈,我们会尽快为您处理(人工客服工作时间:9:00-18:30)。
A .一 xss ra er u h tae t r ln igmeh dcru cs n 25 a i u fc o g rjcoypa nn t o ic m i o i
LiH a i nq ng,N iW e ,W a pi i ng Ya ng
( in ies yo r n u isa dAsr n u is Be i gUnv ri fAe o a t n to a t ,1 0 ) j t c c 011 9
Ke or : R o h a hi i yW ds ug m c n ng;S r lt l pia oo —pa h;Too —pa h p a ni t l t l n ng
1引 言
.
2 5 曲面 粗 加 工 轨 迹 生 成 方 法 , 平 雪 良 提 出 了一 种 .轴 通 过 与 加 工 曲 面 求 交 获 取 加 工 区 域 边 界 , 然 后 在 加 工 区 域 内 规 划 刀 具 轨 迹 的 方 法 。 但 当 前 已 有 的 方 法 均 未
1
厂 、
图5 初 始 轨 迹 环
2 2 轨迹 环 的分 解 .
、
经过上 述操 作得到的轨迹环都是封 闭的,且通过与
外 边 界 做 交 操 作 得 到 的 轨 迹 环 间 存 在 许 多 重 叠 , 这 无
疑将 增加走 刀路 径 的长度 , 降低 加 工效率 。轨迹环 分
解 的 作 用 是 将 轨 迹 环 中 与 外 边 界 重 叠 的 部 分 删 除 , 从
廓 ) , 如 图2 示 , 以某 一 内边 界 为 基 础 , 根 据 加 工 步 所
距 向外等距 ( 闭轮廓的等距算法在文献 刮 封 儿 中有较为 详 细 的介 绍 ),得 到等 距轨迹 环l o s 后 ,首先 判断 opO
该 轨 迹 环 与 其 它 内轮 廓 是 否 发 生 干 涉 , 如 果 发 生 干 涉
加加工成本 。
本 文 提 出 了一 种 环 形 切 削 轨 迹 生 成 方 法 ,不 同于 传
( 图4 示 ),然后将交操 作的结果l o s 添加 到轨 如 所 op 1 迹 环链表p h L o s 中,否则将之前 的轨迹环 l o s a to p O op O
添 加 到 轨 迹 环 链 表 p h L o s 中 。经 过 这 些 操 作 便 得 a t op O
CA D/CAM 。
图 1 全 吃 刀
2 1年 第 8期 ( 01 总第 1 3期 )www MO D C T模 具 工程 2 UL — NNE 61
.
先进 测量技 术
f
2轨 迹 段 的 形成
2 1轨 迹 环等 距 . 在 某 一 加 工 区域 内 ( 加 工 区 域 必 须 包 含 内轮 该
5 曲面粗 加工 ,又名 分层粗加 工或等高线粗 加 轴
2
工 ,是 种利 用垂直于 刀轴的虚平面 同待加工 曲
面 集 以及 毛 坯 模 型 求 交 , 获 取 到 加 工 边 界 形 成 可
考 虑在 切 削过 程 中 出现 全 吃刀 时会 加剧 对 刀具 的磨损
加 工 区域 , 然 后 在 可 加 工 区 域 内 规 划 粗 加 工 刀 具 轨 迹 的 粗 加 工 轨 迹 生 成 方 法 。根 据 规 划 方 式 的 不 同 ,分 为
到 了一次 等距后 的轨迹环 ,然 后再 以轨迹环 1 o s 为 opO
基 础 , 重 复 上 述 操 作 直 到 l o s 的 等 距 结 果 包 含 外 边 opO 界 为 止 。如 图5 示 ,为 该 加 工 区 域 的轨 迹 环 。 所
统 的环切轨 迹 的基 本 形式 是封 闭的轨 迹环 ( 轨迹 环指
专题 ・ 先进测量技术一
ww w. oud— ne m I ∞ t
粗 加 工 环 切 轨 迹 规 划 方 法
李 汉 瓣 倪 伟 I亚 平 ( 京 航 空航 天 大 学 ,10 9 ) 北 0 1 1
摘
要 :本文 介绍 r ‘ 种杠 含有内边界 的加工区域 内按环 形切削 方式规划刀具轨 迹的方法 。首先 ,取加 l Ⅸ域 某 ‘ I : 内边 界按 等距步距 向外
具 的 磨 损 。 此 方 法 主 要 包 括 两 方 面 的 内容 : 一 是 得 到
基本 的轨迹 环 ,包括 封 闭或 者 非封 闭的轨迹 环 ,二是 将 这些 轨迹 环按 一定 方式连 接形 成加工 轨迹 。本 文 的 核 心是 介绍 在加工 区域 内规 划刀 具轨迹 ,因此加 工区
域 的 生成 方 法 在 这 里 不 再赘 述 , 可参 考 文献 。 儿
则做环 间的并操作 ( 如图3 所示) ,并用并操作 的结果代
圈 2 加 I 区 域
替 等 距 轨 迹 环 1 o s 。其 次 , 判 断轨 迹 环 l o s 与 外 op O opO
边界 是否发 生干涉 ,如果发 生干涉 则做 环 问的交操 作 的情况 ,尤其 是环 形切 削时 ,全 吃刀 的情 况较 多 ,如 图1 示红色轨迹 部分 ,这将 无形 中降低加 工效率 ,增 所
A bsr c : I h spa r e ho t ti e o pln oo —pa h fr t a t n t i pe ,a m t d ha s us d t a t l t o oug a hi i s d on s r lc tng h m c n ng ba e pia uti i he m a hi i r a w hi h ha nne unda i s i e e e n t c n ng a e c si r bo re s pr s nt d.Fisl rty,ofs ti f e tng one oft nne und re he i r bo a is w ih t fne t p outi e a f t o t he de i d se sd nd i he l ops he r s t oft fs ti pe a i n,i e v ne w ih he nne ,t e ul he of e tng o r to nt r e t ot r i r bou nda i s he un o re ,t i n ope a i s e e u e n he ;i he l ops a e i e f r d wih t t r bo r ton i x c t d o t m ft o r nt r e e t he ou e und r ,t a y he
图 3 环 间 并 操 作
图4 环 闻 交 操 作
62 模 具 工 程 www MOU D— E 0 1 第 8期 ( L CNN T 2 1年 总第 13期 2
图6 非 封 闭 轨 迹 环
先进测量技术 嚣 w w来自. u - n n t mo l c e d
而 得 到 一 系 列 非 封 闭 的 轨 迹 环 ,如 图 6 示 。其 实 现 流 所 程 如 图7 示 , 首先 ,从 上 述 轨 迹 环 链 表 p h L o s 中 所 a top O 分 离 出 通 过 与 外 边 界 做 交 操 作 得 到 的 轨 迹 环 , 插 入 到
环 形 切 削 和 平 行 切 削 两 种 方 式 。 目前 , 已 有 许 多 相 关 文 献 介 绍 了2 5 曲面 粗 加 工 的 刀 具 轨 迹 生 成 方 法 , 如 .轴
杨 建 中n在 其博 士 论文 中介 绍 了一种 基 于Z a 模 型 的 Mp
作 者 简 介 : 李 汉 卿 , 男 , 1 5 6月 生 、 研 究 生 在 读 、 98 年
是 外 边 界 上 点 , 则 新 生 成 一 轨 迹 环 n w o p 以c r t eLo , u P 为 起 点 ,然 后 继 续 遍 历 轨 迹 环 l o , 将 未 被 标 识 为 外 op 边 界 上 的 点 依 次 插 入 到 n w o p 点 链 表 中 , 直 到 遍 e Lo 的 历到 被标 识为 外边 界 上 的 点为止 ,然 后将 n w o p e L o 插 入 到 轨 迹 环 链 表 p t L o S 中 , 重 复 这 一 操 作 , 从 a h o p 1 而 得 到 轨 迹 环 l o 的 分 解 轨 迹 环 。 依 次 对 轨 迹 环 链 表 op 对 于 封 闭 轨 迹 环 的连 接 , 按 照 其 在 链 表 中 的位 置 依 次 连 接 即 可 , 而 非 封 闭 轨 迹 环 的 连 接 则 需 要 根 据 其 所 处
的是 由一系 列刀位 点组 成 的点链 表 ),该方 法生 成 的
轨 迹 的基本 形式包 括封 闭的和 非封 闭轨 迹环 ,利用 此 方法 生成 的粗 加工 环切 轨迹 ,一方 面能 够有效 地减 小
走 刀 路 径 的 长 度 ,避 免 不 必 要 的 抬 刀 或 者 绕 刀 , 另 一
方面 能够 有效 地 降低 全 吃刀情 况 的出现 比例 ,降低 刀
i e s ci nt r e tng ope a i s a ple n he .Se ond y,r m o ng t ve l ppi nt r a s f o he l ps whi h r ton i p i d o t m c l e vi he o r a ng i e v l r m t oo c r s l r m he i e s c i pe a i n nd c e u tf o t nt r e tng o r t o a onsr c i o e unc os d l t u tng s m l e oop ,t e i h s l e r unc os d s h n l nk t e e c os d o l e l p t ne a e t oo -pa h f t a h ni r a oo o ge r t he t l t o he m c i ng a e .The t l oo —pa h s d o t i e hod r d e he st ton t ba e n h s m t e uc s t i ua i t a he t l c st a e i li l d r c i h t t oo ut he m t r a n a l i e tonsva i l nd pr ld y a om o e he m a h ni g e c e y sg fc n l t st c i n m i nc i ni a ty. i