第四章 拉延模设计3-导向
拉延模设计顺序标准
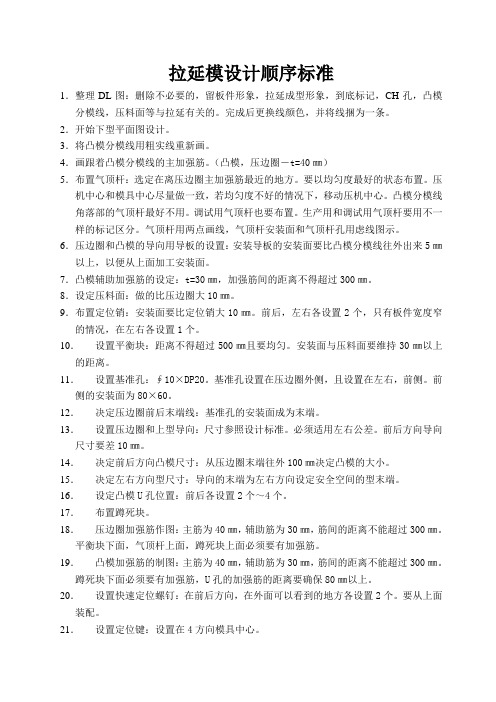
拉延模设计顺序标准1.整理DL图:删除不必要的,留板件形象,拉延成型形象,到底标记,CH孔,凸模分模线,压料面等与拉延有关的。
完成后更换线颜色,并将线捆为一条。
2.开始下型平面图设计。
3.将凸模分模线用粗实线重新画。
4.画跟着凸模分模线的主加强筋。
(凸模,压边圈-t=40㎜)5.布置气顶杆:选定在离压边圈主加强筋最近的地方。
要以均匀度最好的状态布置。
压机中心和模具中心尽量做一致,若均匀度不好的情况下,移动压机中心。
凸模分模线角落部的气顶杆最好不用。
调试用气顶杆也要布置。
生产用和调试用气顶杆要用不一样的标记区分。
气顶杆用两点画线,气顶杆安装面和气顶杆孔用虑线图示。
6.压边圈和凸模的导向用导板的设置:安装导板的安装面要比凸模分模线往外出来5㎜以上,以便从上面加工安装面。
7.凸模辅助加强筋的设定:t=30㎜,加强筋间的距离不得超过300㎜。
8.设定压料面:做的比压边圈大10㎜。
9.布置定位销:安装面要比定位销大10㎜。
前后,左右各设置2个,只有板件宽度窄的情况,在左右各设置1个。
10.设置平衡块:距离不得超过500㎜且要均匀。
安装面与压料面要维持30㎜以上的距离。
11.设置基准孔:∮10×DP20。
基准孔设置在压边圈外侧,且设置在左右,前侧。
前侧的安装面为80×60。
12.决定压边圈前后末端线:基准孔的安装面成为末端。
13.设置压边圈和上型导向:尺寸参照设计标准。
必须适用左右公差。
前后方向导向尺寸要差10㎜。
14.决定前后方向凸模尺寸:从压边圈末端往外100㎜决定凸模的大小。
15.决定左右方向型尺寸:导向的末端为左右方向设定安全空间的型末端。
16.设定凸模U孔位置:前后各设置2个~4个。
17.布置蹲死块。
18.压边圈加强筋作图:主筋为40㎜,辅助筋为30㎜,筋间的距离不能超过300㎜。
平衡块下面,气顶杆上面,蹲死块上面必须要有加强筋。
19.凸模加强筋的制图:主筋为40㎜,辅助筋为30㎜,筋间的距离不能超过300㎜。
拉延模设计手册

拉延模设计手册一、拉延模的分类拉延模分双动拉延模与单动拉延模两类1、双动拉延模是在专用的双动压力机上生产的拉延模,通常上模为凸模,下模为凹模,压边圈安装在压机的外滑块上,其结构如下图,此种结构拉延模压边力较为稳定,但由于需要专用的压机,安装较为烦琐,且结构尺寸较大,现在已经运用的越来越少。
2、单动拉延模是在单动压机上生产的拉延模,通常上模是凹模,下模是凸模,压边圈由下气垫或其它压力源(例于氮气弹簧)提供压料力,其结构如下图,由于模具通用性好,现大部分拉延模为此种结构。
工作台下模上模压边圈上模垫板内滑块外滑块下模上模工作台压边圈上滑块二、拉延模的主要零件(主要为单动拉延模)拉延模一般有上模、下模、压边圈三大部件组成(根据结构的不同要求,可能增加一此部件,例于局部的小压料板),以及安装这三大部件上的其它功能零件,主要有以下零件:1、导向零件:耐磨板、导向腿,导柱;2、限位调压零件:平衡块、到底块;3、坯料定位零件:定位具、气动定位具;4、安全装置:卸料螺钉(等向套筒,也起锁付的作有)、安全护板;5、拉延功能零件:到底印记、弹顶销、通气管、CH孔合件;6、取送料辅助零件:辅助送出料杆、打料装置。
三、单动拉延模的设计(一)模具中心的确认与顶杆的分布模具中心的确认通常依据顶杆的布置的需要设定。
一般在工艺设计时,会按钣件的中心确定一个数模中心。
顶杆的分布需尽量靠近分模线,并均匀布,通常两根顶杆之间最多空一个顶杆位,顶杆数量要尽可能多。
在模具设计时首先以数模中心与压机工作台中心重合,如顶杆分布满足上述要求,则以数模中心做为模具中心。
如无法满足上述要求,侧在需要更改的方向上移动(最大1/2顶杆间距),确认一个最优化的方案,同时以工作台的中心做为模具的中心。
(注:在试模压力机与工作压力机顶杆孔不致时,需设置试模顶杆,并在优先保证生产顶杆的要求下,优化顶杆部置)模具中心与数模中心重合如厂家要求使用顶杆以外的压力源,例于氮气弹簧等,则一般直接以数模中心做为模具中心,压力源沿分模线均匀分布,并需确认压力源的大小是否足够。
拉延模

拉延模Posted on 2009-05-08 by一、拉延模的典型结构拉延形状复杂的覆盖件必须采用双动压力机。
这是由于:(1)单动压力机的压紧力不够,一般有汽垫的单动压力机其压紧力等于压力机压力的20%~25~,而双动压力机的外滑块压紧力为内滑块压力的65%~70%。
(2)单动压力机的压紧力只能整个调节,而双动压力机的外滑块压力可用调节螺母调节外滑块四角的高低,使外滑块成倾斜状,调节模压料面上各部位的压料力,控制压料面上材料的流动。
(3)单动压力机的拉延深度不够。
(4)单动拉延模的压料板不是刚性的,如果压料面是立体曲面形状,在开始拉延预弯成压料面形状时由于压料面形状的不对称致使压料板偏斜,严重时失掉压料作用。
覆盖件拉延模的结构是由双动压力机决定的,虽然在确定拉延件工艺方案和绘制拉延件图时比较复杂,但其结构比较简单。
拉延模的结构,由主要的三大件或四大件组成:即凸模、凹模、压边圈或凸模、凹模、压边圈和固定座。
凸模通过固定座安装在双动压力机的内滑块上,压边圈安装在双动压力机外滑块上,凹模安装在双动压力机下台面上,凸模与压料圈之间、凹模与压料圈之间都有导板导向。
拉延模主要由五件组成,固定座、压边圈、顶出器、凹模和凸模。
凸模、凹模、压料圈是由钼钒铸铁铸成,经加工后棱线、凹模拉延圆角等处根据需要可以进行表面火焰淬火,淬火硬度50~55HRC。
固定座1由灰铸铁铸造。
拉延模铸造后都应经退火处理以消除铸造应力。
顶出器是在拉延完成后顶出拉延件便于让机械手取件。
图12-20所示为散热器罩拉延模。
图12-20a为覆盖件图,图12-20b为拉延件图。
该制件的拉延方向是按汽车位置翻转90°,其投影关系不改变。
考虑到制件两边有孔,因此两边采取倾斜修边,前后采取垂直修边,在第二工序修边冲孔模中一次行程完成。
这样两边的折边沿制件斜壁展开,前边按边缘提高5㎜做30°补充,见放大图Ⅱ。
修边后该处印痕不明显,后边将翻边90°展开,见放大图Ⅰ压料面中部与拉深件底部平行,拉延深度为55㎜,两端由R与直线组成。
模具培训:拉延模几大要素的设计原则
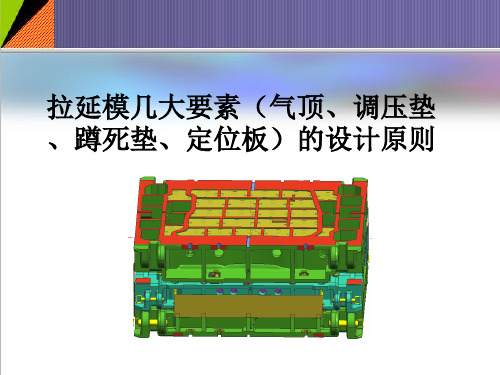
定位板的定位方向安装面留出
3mm间隙,待试料后确定最终 位置。
结束
1.内导向拉延模—压边圈的导向形式在分模线以里的拉延模
三、拉延模的分类
2.外导向拉延模—压边圈的导向形式在分模线以外的拉延模
三、拉延模的分类
双动拉延
三、拉延模的分类
另外,根据工作内容的不同及成型的需要,拉延模中还会增加不同的内 容,例如增加切角,破裂刀等,根据料厚的不同,还会采用镶块结构
切角拉延局部
定位板
▪ 定位板—用于放入制件时使其与
下模型面相对位置固定贴紧的部 件。
▪ 定位板的布置及有关事项: 定位板一般设置于下模、下圈或
下芯上。
拉延模需要四面布置定位板,数
量视模具大小确定,长方件车门 等一侧2处,细长件柱类1处。 定位板间距大于制件定位方向 2/3以上。
对于自动线模具,一般XY方向
若St+H’+D>ST应加接柱, 使St+H+D≤ST,则H=ST-StD
注:St:压边圈行程 ST:气垫行程 A:工作台厚 D:=(A+B)-L L:气顶杆长 H、H’:气顶承接面距工作台距离
调压垫
▪ 调压垫—用于压边圈与上模控
制二者之间局部压力的垫块。
▪ 调压垫布置及有关事项:
调压垫应延分模线均匀分布,
拉延模几大要素(气顶、调压垫 、蹲死垫、定位板)的设计原则
一、拉延模的定义
定义:拉延模就是使平面板料拉伸成具有一定形状 的空心零件的模具
拉延模
平面坯料
空心零件
二、拉延的运动过程
三、拉延模的Leabharlann 类▪ 拉延模分为单动拉延、双动拉延和三动拉延,由于三动拉
拉延类模具三维设计流程

PPT文档演模板
拉延类模具三维设计流程
•利用基准面进行装配位置的调整,图中为调整 定位板位置。
PPT文档演模板
拉延类模具三维设计流程
装配完各种标准件后,压边圈的基本结构就已经清楚了。但由于 我们的标准件是装配进来的,其安装部分也是装配进来的,而它
们本来属于铸件,而且可能还需要和模具本体进行布尔运算。所 以我们必须运用ASSEMBLIES 中WAVE GEOMETRY LINKER命 令将装配进来的标准件中属于铸件的部分LINK到模具本体上。
w 由于压边圈上的挖空大部分是侧挖空,所以先通过草图中的各个 曲线拉伸出下底板,导腿。
w 调整局部可能需要补出的下挖空。圈的铸件轮廓基本完成。如图:
PPT文档演模板
拉延类模具三维设计流程
装配标准件,运用ASSEMBLIES 中ADD EXISTING COMPONENT命令
w 压边圈中的导板、起重棒、定位板、调整垫块等标准件的安装是 通过装配命令来实现的。装配时应注意用基准面进行位置约束。 图示为装配刚刚开始时,导入起重棒。
PPT文档演模板
拉延类模具三维设计流程
从起重棒上 LINK过来的 补肉,可以与 模具本体进 行布尔运算
标准件的安装不可能一步到位,许多标准件如定位板,调
整垫块,导板等位置需要经常调整,而且这些标准件与铸件结 构有很多的关联。LINK过来的部分是与标准件有关联的,会 跟随标准件位置的变化而变化,因而无需另外调整。
PPT文档演模板
拉延类模具三维设计流程
LINK完成以后,可以将原标准件上的此部分移动到不可见的图 层中,此时LINK的部分就可以与模具本体进行布尔运算了。
w 将压边圈,上模和下模装配为一个文件。
w 出工程图。
拉延模设计..
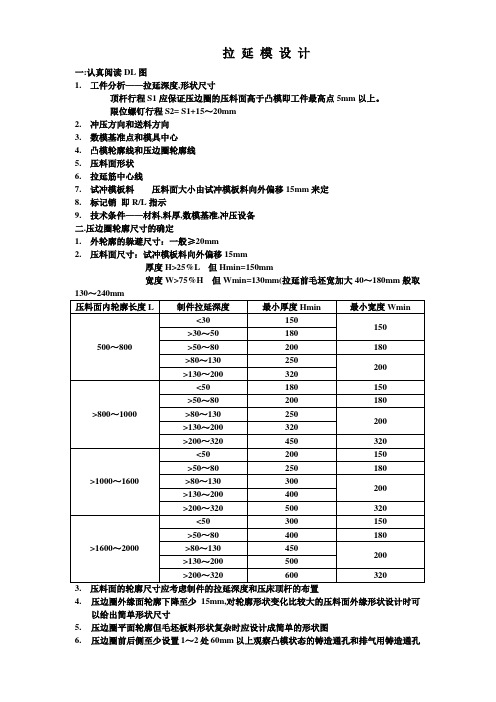
拉延模设计一:认真阅读DL图1. 工件分析——拉延深度,形状尺寸顶杆行程S1应保证压边圈的压料面高于凸模即工件最高点5mm以上。
限位螺钉行程S2= S1+15~20mm2. 冲压方向和送料方向3. 数模基准点和模具中心4. 凸模轮廓线和压边圈轮廓线5. 压料面形状6. 拉延筋中心线7. 试冲模板料压料面大小由试冲模板料向外偏移15mm来定8. 标记销即R/L指示9. 技术条件——材料,料厚,数模基准,冲压设备二.压边圈轮廓尺寸的确定1. 外轮廓的躲避尺寸:一般≥20mm2. 压料面尺寸:试冲模板料向外偏移15mm厚度H>25%L 但Hmin=150mm宽度W>75%H 但Wmin=130mm(拉延前毛坯宽加大40~180mm般取3. 压料面的轮廓尺寸应考虑制件的拉延深度和压床顶杆的布置4.压边圈外缘面轮廓下降至少15mm,对轮廓形状变化比较大的压料面外缘形状设计时可以给出简单形状尺寸5.压边圈平面轮廓但毛坯板料形状复杂时应设计成简单的形状图6.压边圈前后侧至少设置1~2处60mm以上观察凸模状态的铸造通孔和排气用铸造通孔三导向设计1. 气垫顶起时至少应有50mm导向接触面,大模具可延伸至100mm(1)导向腿设置在模具中部的尺寸规格①用于小型模具注: 1. 图为单独使用导向腿和导向腿+导柱二者共用形式2. 图中B,D,M处为设置导柱衬套时使用的尺寸②用于中大型模具注: 1. 图为单独使用导向腿和导向腿+导柱二者共用形式2. 图中B,D,M处为设置导柱衬套时使用的尺寸(2)导向腿设置在木角部形式的尺寸规格注: 1. 图为单独使用导向腿和导向腿+导柱二者共用形式2. 图中B,D,M处为设置导柱衬套时使用的尺寸三.上下模板高度尺寸确定依据1.制件的拉延深度2.既要满足压床允许闭合高度的范围又要确保模具的强度3.模具的装模高度取决于送料线的高度并考虑压边圈的强度(覆盖件模具压料圈厚度要在250mm以上)确定下模的高度4.一般在使用机械手的情况下,送料高度应该距压床工作台面1000±70mm 之间,手工操作要在450~600mm之间四.凸模,压遍圈,压料面尺寸1.前面定位⑴毛坯在模具中要设置四个方向的定位,前后和两侧⑵前后送料时前面定位低于送料线高度30mm防止干涉⑶手工送料时毛坯板料会形成一定的弯曲,送料的水平面与定位最高部至少留10mm的空间,要求定位块前面设置一定长度的斜面⑷定位块(或销)原则上每侧设置2个,板料毛坯较窄时可以设置1个.两定位块(销)的位置:距毛坯板料端边1/5处但要大于50mm.2.侧面定位⑴侧面定位高度:在使用夹钳形式和真空吸盘送料时定位块的最高处与送料线留50mm的空间.⑵进侧的定位块需倒角以便于板料推进.⑶面定位的长度要大于板料的1/2长度⑷对板料弯曲度比较大的定位要考虑弯曲后的位移量六出气孔的设置1.型面上的出气孔对外板制件的凸模取直径Φ4mm,对内板制件取Φ6mm2.在后工序要修掉的废料部分钻直径Φ20~30mm通气孔2~6个或直接铸出直径Φ60~120mm通气孔通气孔设置原则:①凸凹模成型处不设②曲率半径小,材料移动大处不设③外板懂得凹模排气孔面斜度在5‰以下时可以设置排气孔④上模排气孔设置时要加出气管,或在出气孔上方整体家盖板,以防止杂物落入七拉延标记销1.单动拉延模原则上设置在凹模上,材料变化小的位置上2.尽量在制件轮廓以外的拉延凸模的轮廓内设置,不得使制件产生压痕3.设置在修边和冲孔的废料上4.位置最好设置在对角方向2处,对角线长度在500mm以下时可以设置1处5.设置标记销处必须呈水平面,或较小斜面的法向方向的平面上,起平面必须大于标记销直径;制件上没有平面处工艺补充部分可以设置工艺平台6.标记的位置必须在D/L图中明确注明7.切入拉延深度:0.3mm七平衡块设置1.距压边圈加工面外端至少留30mm的空间2.安装平衡块的底板下面必须设置加强筋3.安装面的最高面不得高于模具压料面高度4.平衡块基本上设置在下模上5.单动拉延模为了保持压边圈力的平衡,在托杆附近平衡块的下方设置垫块6.小型模具设置6个,大型模具设置8个以上,一般400mm布置一个八装夹槽注:A为设置装夹槽侧的模具长,上模装夹槽数>下模装夹槽数九起重装置1.铸入式吊杆:强度高,外形小,安全可靠3.螺钉连接式吊杆:使用于中小型模具4.专用起吊器5.起重臂6.起重孔一○模具定位1.键定位2. 挡料销式定位设置在模具后侧二个(一组),距离尽量大。
拉延模的设计
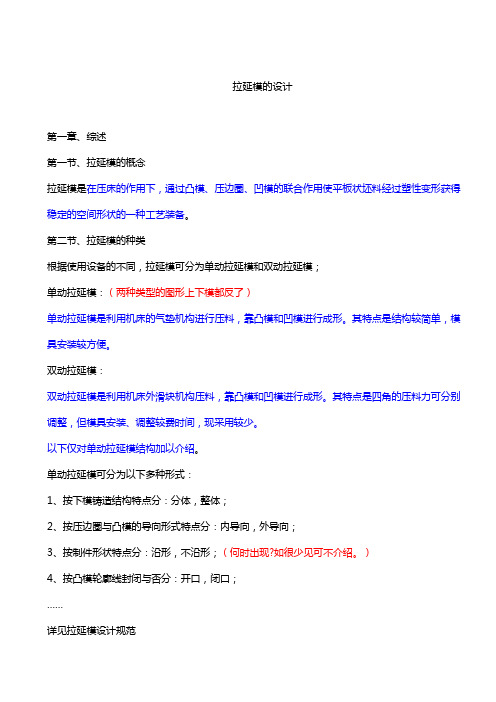
拉延模的设计第一章、综述第一节、拉延模的概念拉延模是在压床的作用下,通过凸模、压边圈、凹模的联合作用使平板状坯料经过塑性变形获得稳定的空间形状的一种工艺装备。
第二节、拉延模的种类根据使用设备的不同,拉延模可分为单动拉延模和双动拉延模;单动拉延模:(两种类型的图形上下模都反了)单动拉延模是利用机床的气垫机构进行压料,靠凸模和凹模进行成形。
其特点是结构较简单,模具安装较方便。
双动拉延模:双动拉延模是利用机床外滑块机构压料,靠凸模和凹模进行成形。
其特点是四角的压料力可分别调整,但模具安装、调整较费时间,现采用较少。
以下仅对单动拉延模结构加以介绍。
单动拉延模可分为以下多种形式:1、按下模铸造结构特点分:分体,整体;2、按压边圈与凸模的导向形式特点分:内导向,外导向;3、按制件形状特点分:沿形,不沿形;(何时出现?如很少见可不介绍。
)4、按凸模轮廓线封闭与否分:开口,闭口;……详见拉延模设计规范第三节、拉延模的设计要点一、根据制件的大小、形状、受力情况确定采用哪种形式的结构二、确定数模中心、压床中心、模具中心三者之间的关系,尽量使三心重合三、确定压边圈的行程四、确定气垫顶杆的数量、位置以及长度……1、充分分析工艺要求,了解制件的产品部分和工艺补充部分,确定拉延是否必须镦实,以及冲压方向、送料方向、料厚及方向等。
2、建立模具中心、数模中心、压床中心之间的关系,尽量使三心重合。
3、分析拉延所需行程,确定压边圈工作行程。
4、气垫顶杆布置。
5、其它结构设计。
第二章、单动拉延模的设计第一节、单动拉延模的基本结构基本结构简图第二节、单动拉延模的行程计算一、压料行程1、定义:当压料面为曲面时,从凹模接触板料到被凹模与压边圈固定住,上模在垂直方向运动的距离。
(当制件比较大或者拉延深度较深时)当压料面起伏较大时(如行李箱盖板),压料过程中如果不对板料加以约束,将会影响坯料定位。
(压料行程的确定对于板料的定位有着决定性作用。
拉延模具设计

设计步骤:1分析工艺文件首先拿到工艺后要分析各部分,分模线、坯料线、拉延后坯料线、重力坯料线、拉延筋、到底标记、左右标记、CH孔,有时还有弹顶销、穿刺孔和破裂刀位置分模线决定了凸模的外圈轮廓大小;坯料线决定了压料面的大小;从拉延前后坯料线可以看出板料在压料面上的流入情况;重力坯料线决定了定位板定位位置和高度;拉延筋可以控制板料的流入量;到底标记用来检测是否拉伸到位(设计在废料区);左右标记是产品左右件的标识,来实现焊装白车身的目的;CH 孔是在拉延(序)模上的拉延件上冲制的两个模具制造调试用的研模(定位)工艺孔。
是带件研合各序模具型面(和形状)的基准确认拉延模行程和气顶位置:参考工艺文件确定导向形式:根据制件形状确定模具的导向形式,大致分为外导向拉延,内导向拉延,四角导向拉延。
本套模具采用内导向。
暂定基准高:根据机床对操作高的要求自动线看是否要前后序操作高一致或是浮动范围。
本套模具选择闭合高度为800mm。
下图为工艺曲面2图层的设置用ug2.0打开工艺曲面进入建模模块。
把第1层的工艺面复制到11层把第2层的胚料线,分模线复制到12层。
3面的缝合打开11层,其它层全部关闭。
用缝合命令缝合曲面缝合的时候注意不要直接点击确定,应该点击应用看他是否报错如果报错看是那些地方有错然后更改更改好以后再缝补,检查报错,如果没报错,再拉伸一个通过曲面的体A。
用缝补好的曲面裁剪A,如果成功说明缝补成功。
下面是封面操作截图:注意缝合公差红点的地方表示有错修改完成无报错裁剪实体成功,删除实体保存一次图档,进入下一步4偏置工艺面用大致偏移命令偏移Z向-60.-50和60的三个面。
下面是操作截图:三个偏置的面如图所示5凸模本体的制作把12层设置为工作层,其它层关闭。
投影分模线到XY平面如图用分模线拉伸实体上下各500mm 如图:把11层设置为可选用工艺面把刚拉伸的实体上部分裁减掉如图:把得到的实体移动到62层。
然后用分模线拉伸一个上下各500mm,里外分别10mm 的实体环如图:用向Z方向偏置-50mm的面裁减掉这个体的上部分如图:把所得到的实体移动到62层。
拉延模设计规范

模具类别
特大型
大型
中型
小型
50X150
120X120
注:1.中型模具空间有限时可设成120X120或120X150;
2.上下模安全平面在闭合状态下相距110。
1-2
通用设计标准
5
连模板
连模板使用范例及安装凸台尺寸如下:
模具类别
特大型
大型
中型
小型
连模板尺寸
5
凹模与压边圈的设计
1.凹模与压边圈一般情况下仅用导板导向;当工件拉延困难需在拉延模上设置预切边结构时,应增加导柱导向;
2.凹模与压边圈的导向宽度尽量大于模具宽度的1/2,最小不小于200mm;
3.凹模上定位具避让孔80X70,平衡块位置要有筋条;
4.压边圈与凸模为内导时,凹模上安全区与压料圈对应;压边圈与凸模为外导时,凹模上安全区与凸模(下模座)对应;
拉延模设计规范
1-2
通用设计标准
5
模具大小分类上下模导向型式选用原则
1.模具大小分类:
按模具的外型尺寸大小,模具分类如下:
模具类别
外型尺寸
小型模具
长+宽≤2400,且长≤1500
中型模具
2400≤长+宽≤3200,且长≤2000
大型模具
3200≤长+宽≤4200,且长≤3000
特大型模具
4200≤长+宽
100导板
A=145
100导板
A=120
Ø40导柱
Ø32导柱
CAM+修边或冲孔
150导板+Ø100导柱
125导板+Ø80导柱
100导板+Ø60导柱
拉延模的设计

拉延模的设计第一章、综述第一节、拉延模的概念拉延模是在压床的作用下,通过凸模、压边圈、凹模的联合作用使平板状坯料经过塑性变形获得稳定的空间形状的一种工艺装备。
第二节、拉延模的种类根据使用设备的不同,拉延模可分为单动拉延模和双动拉延模;单动拉延模:(两种类型的图形上下模都反了)单动拉延模是利用机床的气垫机构进行压料,靠凸模和凹模进行成形。
其特点是结构较简单,模具安装较方便。
双动拉延模:双动拉延模是利用机床外滑块机构压料,靠凸模和凹模进行成形。
其特点是四角的压料力可分别调整,但模具安装、调整较费时间,现采用较少。
以下仅对单动拉延模结构加以介绍。
单动拉延模可分为以下多种形式:1、按下模铸造结构特点分:分体,整体;2、按压边圈与凸模的导向形式特点分:内导向,外导向;3、按制件形状特点分:沿形,不沿形;(何时出现?如很少见可不介绍。
)4、按凸模轮廓线封闭与否分:开口,闭口;……详见拉延模设计规范第三节、拉延模的设计要点一、根据制件的大小、形状、受力情况确定采用哪种形式的结构二、确定数模中心、压床中心、模具中心三者之间的关系,尽量使三心重合三、确定压边圈的行程四、确定气垫顶杆的数量、位置以及长度……1、充分分析工艺要求,了解制件的产品部分和工艺补充部分,确定拉延是否必须镦实,以及冲压方向、送料方向、料厚及方向等。
2、建立模具中心、数模中心、压床中心之间的关系,尽量使三心重合。
3、分析拉延所需行程,确定压边圈工作行程。
4、气垫顶杆布置。
5、其它结构设计。
第二章、单动拉延模的设计第一节、单动拉延模的基本结构基本结构简图第二节、单动拉延模的行程计算一、压料行程1、定义:当压料面为曲面时,从凹模接触板料到被凹模与压边圈固定住,上模在垂直方向运动的距离。
(当制件比较大或者拉延深度较深时)当压料面起伏较大时(如行李箱盖板),压料过程中如果不对板料加以约束,将会影响坯料定位。
(压料行程的确定对于板料的定位有着决定性作用。
拉延模的典型结构

一.按拉延模的结构形式,一般分为单动拉延模和双动拉延模。
1.单动拉延模。
参考图:单动(内导向)拉延模2.双动拉延模。
参考图:双动拉延模二.按拉延模导向形式,一般分为内导向和外导向。
1.内导向:优点:1)可在使模具变得小型。
2)比较容易保证同凸模的配合精度。
缺点:1)由于凸模需要紧固的螺栓、平行销较多,因此,当压料圈上加有侧向力时较为不利。
2)加工困难。
参考图:单动(内导向)拉延模2.外导向:1)箱式结构参考图:箱式结构拉延模2)四角导向参考图:四角导向拉延模优点:1)加工简便。
2)对细长部分有利。
缺点:1)模具增大。
拉延模一般采用内导向,即压边圈内与凸模导向、外与凹模导向。
特点是结构紧凑,模具尺寸小,造价低,是一种常用的结构。
对于细长柱类件和周边为不规则曲线类件,导板位确定困难的可以采用外导向即:凸模和凹模都与压边圈的外部导向;或者采用箱式结构:即凸模与压边圈外部导向,凸模与凹模直接导向,提高了导向的精度。
但采用箱式结构增大了模具尺寸,制造成本提高。
补充:凸模和下底板分为整体和分体两种形式(根据客户要求,一般为分体)分体结构三. 工艺切口拉延模 1. 内侧切口(刺破刀)使用目的:在难于成形的位置加切口,以使板易于流动注意:在内侧进行切口(冲孔)时,应在考虑冲压件成形性的前提下,决定切入。
参考图:内侧切口拉延模整体结构2.外侧切角外侧进行切角时,应注意废料飞溅、滑出是否顺畅。
注意:导向形式导腿+导柱。
参考图:外侧切角拉延模四.厚板料镶块拉延模拉延镶块通常反把螺钉,如果采用正把螺钉,往往会造成压料面破坏,拉延成型过程中会划伤产品,影响产品表面质量,所以凹模和压料圈上的镶块必须反把螺钉。
为了螺钉的合理布置和保障筋的强度,通常有以下三种结构形式。
1.沿分模线向外侧留出单排螺钉孔的位置,布置随型筋,同时在每个镶块下加小立筋支撑。
随后在随型筋外侧布置第二排螺钉孔。
特点:此种结构模具强度好,但是镶块会比较大,适用于拉延面较大的模具。
- 1、下载文档前请自行甄别文档内容的完整性,平台不提供额外的编辑、内容补充、找答案等附加服务。
- 2、"仅部分预览"的文档,不可在线预览部分如存在完整性等问题,可反馈申请退款(可完整预览的文档不适用该条件!)。
- 3、如文档侵犯您的权益,请联系客服反馈,我们会尽快为您处理(人工客服工作时间:9:00-18:30)。
凸模—压边圈 (导板) 0.05±0.022 凹模—压边圈 (导板) 0.05±0.02 注单动和双动拉 延同此要求;含 切角工序内容时, 按剪切类标准。
拉延模导向
端头结构设计
中间导向腿
中小型模具
A B 135 135 155 B′ 180 180 180 C 150 150 200 D 100 100 100 D1 110 110 110 E 100 100 125 J 50 50 50 K 40 40 40 M 60 60 60 d 50 50 50
类别 Ⅳ Ⅴ Ⅵ Ⅶ Ⅷ
A 450 700 1000 1200 1500
拉延模导向
端头结构设计
角部导向腿
拉延模导向
端头结构设计
角部导向腿
拉延模导向
端头结构设计
类别 Ⅰ Ⅱ Ⅲ Ⅳ Ⅴ Ⅵ Ⅶ Ⅷ
角部导向腿
R 55 55 55 60 60 70 70 70 B 135 135 135 160 160 185 185 185 B′ 195 195 195 205 205 225 225 225 C 100 100 100 125 125 150 150 150 D 120 120 120 140 140 180 180 180 D1 110 110 110 120 120 140 140 140 E 100 100 100 125 125 150 150 150 J 50 50 50 50 50 60 60 60 K 40 40 40 40 40 50 50 50 M 60 60 60 70 70 90 90 90 d 50 50 50 60 60 80 80 80
上下模直接导向结构
凸模和凹模导向
原则上使凸模和凹模 导向
4-8 拉延模的导向
上下模直接导向结构
4-8 拉延模的导向
ห้องสมุดไป่ตู้
上下模直接导向结构
4-8 拉延模的导向
上下模直接导向结构
4-8 拉延模的导向
上下模直接导向结构
4-8 拉延模的导向
上下模直接导向结构
第十一章 拉延模设计
拉延模导向
上下模导向
端头 导板
拉延模导向
端头结构设计
拉延模导向
端头结构设计
模具分类(按模具外形长宽尺寸L1及L2可分 为八类)
拉延模导向
端头结构设计
模具分类(按模具外形长宽尺寸L1及L2可分 为八类)
拉延模导向
端头结构设计
中间导向腿
拉延模导向
导向间隙
间隙是指单侧间 隙。
拉延模导向
端头结构设计
角部导向腿
拉延模导向
端头结构设计
角部导向腿
拉延模导向
防反设计
拉延模导向
防反设计
类别 Ⅰ Ⅱ Ⅲ
260 260 300
拉延模导向
端头结构设计
中间导向腿
中小型模具
拉延模导向
端头结构设计
中间导向腿
中大型模具
B 160 160 185 185 185 B′ 205 205 225 225 225 C 100 100 150 150 200 D 140 140 180 180 180 D1 120 120 150 150 150 E 100 100 125 150 150 J 50 50 60 60 60 K 40 40 50 50 50 M 70 70 90 90 90 d 60 60 80 80 80
存放状态 下死点状态
4-8 拉延模的导向
导向面的搭接量
板料定位后,凸模行程开始时压边圈和凸模的 导滑面搭接量应为100mm以上。
4-8 拉延模的导向
拉延模导向
上下模导向
直接导向(凸模和凹模导向) 间接导向(压料圈和凹模导向) 内部导向 外部导向
凸模和压料圈之间导向
4-8 拉延模的导向
汽车覆盖件模具设计讲 稿
湖北汽车工业学院材工系 李芳华
第四章 拉延模设计-3
理论学习
4-7 汽车覆盖件模具导向方式 4-8 拉延模的导向
4-7 汽车覆盖件模具导向方式
4-7 汽车覆盖件模具导向方式
4-7 汽车覆盖件模具导向方式
模具导向件啮合尺寸的设定
上、下模开始接触时,导向件应啮合50mm以上。 模具保管时,上下导向件应啮合50mm以上。
导板面原则上与中心 线平行
拉延模导向
内导向
导向面长度选定 t1+t2≥0.2×t
拉延模导向
内导向
a<300时/1处 a>300时/2处 b<300时/1处 b>300时/2处 · 导板装在易加工的部位。 · 导板尽量对称布置。 · 导板部应设检测孔。
拉延模导向
上下模导向
端头 导板
11-2 拉延模工作零件
1.
拉延凸、凹模
导向板
第十一章 拉延模设计
11-2 拉延模工作零件 导向板
4-8 拉延模的导向
上下模间接导向结构
凹模和压料圈的导向
4-8 拉延模的导向
凸模与压料圈之间的导向
内导 外导
4-8 拉延模的导向
外导向
优点
加工简便。 对细长零件有利。 模具增大。
缺点
4-8 拉延模的导向
内导向
拉延模导向
内导向
拉延模导向
内导向
优点
可使模具变小。 比较容易保证同凸模的配合精度。 当分体凸模时,需要螺钉、柱销固定,因此,当 压料圈上加有侧向力时较为不利。 加工比外导向困难。
缺点
拉延模导向
内导向
导板的位置选定
拉延模导向
内导向