工艺知识培训
机械加工工艺基础知识讲解培训课件

❖ 例如,在车床上加工轴,先从一端加工 出部分表面,然后调头再加工另一端,这 时的工序内容就包括两个安装。
15
❖ (3)工位
❖ 采用转位(或移位)夹具、回转工作 台或在多轴机床上加工时,工件在机床 上一次装夹后,要经过若干个位置依次 进行加工,工件在机床上所占据的每一 个位置上所完成的那一部分工序就称为 工位。
机械加工工艺系统由金属切削机床、刀具、 夹具和工件四个要素组成,它们彼此关联、互 相影响。
该系统的整体目的是在特定的生产条件下, 在保证机械加工工序质量的前提下,采用合理 的工艺过程,降低该工序的加工成本。
8
❖(3)机械制造系统
在工艺系统基础上以整个机械加 工车间为整体的更高一级的系统。该 系统的整体目的就是使该车间能最有 效地全面完成全部零件的机械加工任 务。
形状、尺寸、相对位置和性质等,使其成为成品 或半成品的过程称为工艺过程。 ❖ 工艺:就是制造产品的方法。 ❖ 机械加工工艺过程:采用机械加工的方法,直接 改变毛坯的形状、尺寸和表面质量等,使其成为 零件的过程称为机械加工工艺过程。
2
❖ 生产过程
❖ 工业产品的生产过程:是指由原材料到成品之 间的各个相互联系的劳动过程的总和。
❖ 例如轴类零件如果要切去的金属层很厚,则 需分几次切削,这时每切削一次就称为一次走刀。 因此在切削速度和进给量不变的前提下刀具完成 一次进给运动称为一次走刀。
❖ 下图是一个带半封闭键槽阶梯轴两种生产类 型的工艺过程实例,从中可看出各自的工序、安 装、工位、工步、走刀之间的关系。
19
20
基本概念
17
❖ (4)工步
❖ 在加工表面、切削刀具、切削速度 和进给量不变的条件下,连续完成的那 一部分工序内容称为工步。生产中也常 称为“进给”。
工艺基础知识培训

机床:加工设备,如车床、铣床、磨床等,也包括钳工台
等钳工设备; 工具:各种刀具、磨具、检具,如车刀、铣刀、砂轮等; 夹具:机床夹具,加工时如将工件直接装夹在机床工作台 上,则可以不要夹具。
二、影响加工精度的主要因素及改善措施
传动链的传 工艺系统与精度的关系 动误差 导轨导向误差 主轴回转误 差
影响零件加工表面 的几何形状精度
粗糙度过细,不易储存润滑油,加重磨损,同时过细的表面
还将大大提高制造成本。
三、加工表面质量
表面质量对零件性能的影响:
1.表面质量对零件耐磨性的影响 零件磨损分为三个阶段:初期磨损阶段、正常磨损阶段、 急剧磨损阶段。
表面粗糙度对摩擦副的 初期磨损影响巨大。
三、加工表面质量
表面纹理对耐磨性的影响: 它影响金属表面的实际接触面积和润滑液的存留情况。 轻载时两表面的纹理方向与相对运动方向一致时,磨损量
二、影响加工精度的主要因素及改善措施
改善措施:
1)减少热源的发热:移出热源如发动机、变速箱等、考虑
结构优化、改善摩擦特性、改变润滑材料采取冷却措施等。 2)用热补偿法减少热变形。 3)合理设计机床部件结构减少热变形的影响。 4)加速达到工艺系统的热平衡(预热)。 5)控制环境温度(恒温)。空运转机床至热平衡状态后再加工;进行充
完整的工艺系统。
工件和刀具安装在夹具和机床上,受到夹具和机床
的约束。 尺寸、几何形状和表面间相对位臵的形成,归结到 一点,取决于工件和刀具在切削运动过程中相互位臵的关系。 由于工艺系统各种原始误差的存在,使工件与道具 之间正确的几何关系遭到破坏,而产生加工误差。
8
二、影响加工精度的主要因素及改善措施
二、影响加工精度的主要因素及改善措施
工艺的概念培训知识

工艺的概念培训知识工艺是指将原材料或半成品通过一系列的操作、加工和装配等工艺过程,转化为成品的过程。
它是一项以技术和工程为基础的活动,涉及制造和加工的各个方面。
工艺培训是一种教育或训练活动,旨在向工人、操作员、技术人员和工程师等相关人员传授工艺方面的知识和技能。
通过培训,人们可以了解和掌握正确的操作方法和工艺流程,提高产品的质量和生产效率。
工艺培训的内容包括以下几个方面:1. 工艺基础知识:包括原材料的选择与使用、加工工艺和操作流程等基本概念。
学员需要了解原材料的性质和特点,掌握不同加工方法的优缺点,并了解操作过程中的安全要求。
2. 工装和设备的使用:工艺培训还包括对工装和设备的使用培训。
工装是指用于定位、固定和加工工件的装置,而设备是指用于完成加工和装配等工艺过程的机器和设备。
学员需要了解不同工艺过程中所需的工装和设备的使用方法和维护要求。
3. 质量控制和检测:工艺培训应该强调质量控制和检测的重要性。
学员需要掌握如何进行质量控制,并了解常用的检测方法和设备。
质量控制包括在加工过程中进行的各种操作和控制,以确保产品符合质量要求。
4. 故障排除与维护:工艺培训还应该包括故障排除和设备维护的知识。
学员需要学习如何分析和解决常见的故障,并了解设备的维护和保养方法。
这样可以减少生产中的停机时间,并提高设备的寿命和可靠性。
工艺培训可以通过不同的方式进行,包括理论讲座、实践演示和现场培训等。
培训内容应该符合实际工艺流程和企业的需求,同时注重培养学员的实际操作能力。
总之,工艺培训对于提高产品质量、提高生产效率和减少故障损失非常重要。
通过培训,可以提高工人和技术人员的技能水平,更好地适应企业发展的需要。
工艺培训是企业中非常重要的环节,它直接关系到产品的质量和生产效率。
通过有效的工艺培训,可以提高员工的技能水平,增强企业的竞争力。
首先,工艺培训可以提高员工的技能水平。
在工艺培训中,员工可以学习到最新的工艺技术和操作方法,了解最新的工艺设备和工具。
《工艺技术培训》课件
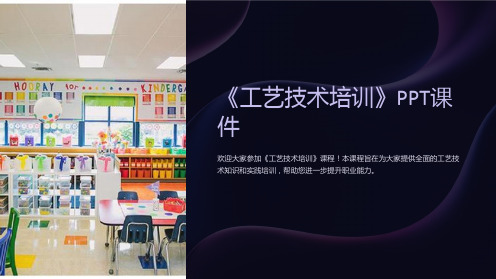
课程内容概述
工艺技术基础
介绍工艺技术的基本概念、 分类和应用领域。
工艺流程与流程控制
探讨工艺流程设计和流程控 制的关键要素和最佳实践。
团队协作与项目管理
培养团队协作精神,学习项 目管理技巧和团队沟通策略。
培训方法
讲授
通过专业讲师系统讲解工 艺技术理论和实践案例, 深入浅出。
《工艺技术培训》PPT课 件
欢迎大家参加《工艺技术培训》课程!本课程旨在为大家提供全面的工艺技 术知识和实践培训,帮助您进一步提升职业能力。
课程目标
1 全面掌握工艺技术知识
学习核心工艺技术概念、原理和应用,提高技术实践能力。
2 了解最新技术发展趋势
掌握行业前沿技术动态,提前了解并应用最新技术。
3 培养创新思维
学员反馈与总结
1 知识收获丰富
学员对工艺技术知识有了全新的认识和理解。
2 互动学习体验好
学员通过小组讨论和实践演练,与同行们共同交流学习。
3 实践效果显著
学员能够将所学知识应用于实际工作中,取得了可观的成果。
下一步行动计划
深入研究
继续学习工艺技术相关 文献和案例,不断提升 自己的技术水平。
实践实践再实践
案例分析
结合真实案例,分析解决 工艺技术难题的方法和策 略。
小组讨论
模拟工作场景,组织小组 讨论,促进经验分享和互 动学习。
实践演练
1
仿真实验
通过实验室仿真实验,艺技术实践。
指导学员自主设计工艺流程,提升
解决问题的能力。
3
实际操作
在真实工业环境中操作设备,掌握 工艺技术的应用技巧。
公司工艺知识培训计划

公司工艺知识培训计划一、培训目的本培训计划的目的是为了提高公司员工的工艺知识水平,增强员工对工艺流程和操作的理解和掌握,提高产品质量和生产效率,从而满足客户需求,提高公司的竞争力。
二、培训对象本次培训对象为公司生产部门、技术部门和质量部门的相关员工。
三、培训内容1. 基础工艺知识(1)工艺流程:生产过程中的每一个环节,包括原材料准备、加工制造、装配和包装等流程。
(2)工艺操作规程:各个环节的操作步骤和要求,如加工工艺、装配工艺以及使用工艺工具等。
(3)工艺设备:生产过程中所使用的各种机械设备和工艺工具,以及其操作和维护知识。
2. 产品工艺知识(1)产品结构和组成:对产品的结构和各个零部件的功能和作用进行分析和学习。
(2)产品加工工艺:对产品的加工工艺和生产工艺进行深入了解,包括原材料加工、零部件加工和总装工艺等。
(3)产品质量要求:了解产品的质量标准和检验要求,掌握产品质检方法和技巧。
3. 工艺管理知识(1)工艺改进与优化:学习如何对工艺流程进行改进和优化,提高生产效率和产品质量。
(2)工艺控制与监督:学习如何对工艺进行控制和监督,确保生产过程中的质量和效率。
(3)工艺安全与环保:学习如何从工艺角度出发,确保生产过程中的安全和环保要求。
四、培训方式本次培训将采用多种方式进行,包括课堂讲解、案例分析、实地考察和操作演练等形式。
1. 课堂讲解:安排专业的工艺专家进行课堂授课,介绍工艺知识和操作技能。
2. 案例分析:通过真实的生产案例进行分析和讨论,加深员工对工艺知识的理解和掌握。
3. 实地考察:安排员工到生产现场进行实地考察,了解实际生产过程和工艺操作。
4. 操作演练:通过模拟实际操作的方式,让员工进行操作演练,提高实际操作能力。
五、培训计划本次培训将分为基础知识培训和产品工艺知识培训两个阶段进行,每个阶段周期为一个月。
1. 基础知识培训阶段第一周:工艺流程和操作规程的讲解及案例分析。
第二周:工艺设备的认识和操作技能培训。
工艺知识培训课件

• 工艺基础知识 • 工艺技术及实践 • 工艺管理及优化 • 工艺安全与环保 • 工艺知识培训与提升 • 工艺知识应用与发展趋势
01
工艺基础知识
工艺的定义与分类
工艺定义
工艺是将原材料转化为成品的过 程,这个过程需要知识、技能和 工具的结合。
工艺分类
根据生产类型和目的,工艺可分 为制造工艺、装配工艺、维修工 艺等。
工艺环保的实践与策略
环保法规与标准
01
介绍国家和地方对环保的法规和标准,以及企业如何根据这些
法规和标准制定相应的环保管理制度。
废水、废气、废渣等污染物的处理与排放
02
讲解各种污染物的处理方法和排放标准,以及企业如何做到达
标排放。
节能减排与资源综合利用
03
介绍如何通过节能减排和资源综合利用,降低工艺过程对环境
工艺管理的案例分析
01
02
03
04
案例一
某制造企业通过引入自动化生 产线和精益生产理念,提高了
生产效率和产品质量。
案例二
某化工企业采用连续化生产工 艺,降低了能源消耗和环境污
染。
案例三
某医疗器械制造企业通过优化 生产线布局,提高了生产效率
和产品一致性。
案例四
某机械加工企业通过引入数字 化工艺管理系统,提高了生产 计划管理和数据分析能力。
在现代制造业中,工艺知识已经被广泛应用于产品研发、生产制造、质量控制等各 个环节,它对于企业的竞争力至关重要。
工艺知识也可以帮助企业实现生产过程的自动化和智能化,从而提高生产效率和降 低成本。
工艺技术的发展趋势与展望
随着科学技术的不断发展,工艺技术也在不断进 步和创新。目前,工艺技术的发展趋势主要包括 数字化、智能化、绿色化等方向。
机械制造工艺基础知识培训
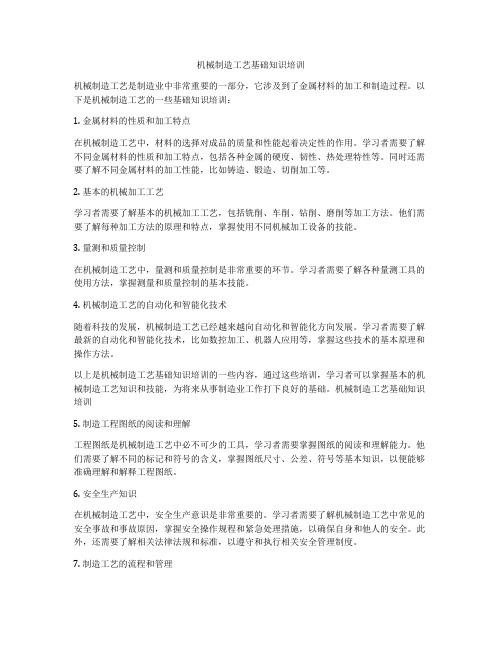
机械制造工艺基础知识培训机械制造工艺是制造业中非常重要的一部分,它涉及到了金属材料的加工和制造过程。
以下是机械制造工艺的一些基础知识培训:1. 金属材料的性质和加工特点在机械制造工艺中,材料的选择对成品的质量和性能起着决定性的作用。
学习者需要了解不同金属材料的性质和加工特点,包括各种金属的硬度、韧性、热处理特性等。
同时还需要了解不同金属材料的加工性能,比如铸造、锻造、切削加工等。
2. 基本的机械加工工艺学习者需要了解基本的机械加工工艺,包括铣削、车削、钻削、磨削等加工方法。
他们需要了解每种加工方法的原理和特点,掌握使用不同机械加工设备的技能。
3. 量测和质量控制在机械制造工艺中,量测和质量控制是非常重要的环节。
学习者需要了解各种量测工具的使用方法,掌握测量和质量控制的基本技能。
4. 机械制造工艺的自动化和智能化技术随着科技的发展,机械制造工艺已经越来越向自动化和智能化方向发展。
学习者需要了解最新的自动化和智能化技术,比如数控加工、机器人应用等,掌握这些技术的基本原理和操作方法。
以上是机械制造工艺基础知识培训的一些内容,通过这些培训,学习者可以掌握基本的机械制造工艺知识和技能,为将来从事制造业工作打下良好的基础。
机械制造工艺基础知识培训5. 制造工程图纸的阅读和理解工程图纸是机械制造工艺中必不可少的工具,学习者需要掌握图纸的阅读和理解能力。
他们需要了解不同的标记和符号的含义,掌握图纸尺寸、公差、符号等基本知识,以便能够准确理解和解释工程图纸。
6. 安全生产知识在机械制造工艺中,安全生产意识是非常重要的。
学习者需要了解机械制造工艺中常见的安全事故和事故原因,掌握安全操作规程和紧急处理措施,以确保自身和他人的安全。
此外,还需要了解相关法律法规和标准,以遵守和执行相关安全管理制度。
7. 制造工艺的流程和管理学习者需要了解制造工艺的整体流程,包括原材料采购、加工制造、质量控制、包装和运输等各个环节。
他们需要了解现代制造企业的管理理念和方法,包括精益生产、供应链管理等,以提高生产效率和降低成本。
焊接工艺知识培训教程

焊接工艺知识培训教程一、焊接工艺知识1. 焊接原理焊接是通过加热金属材料,在一定压力下使其熔化,然后冷却后形成牢固的连接。
焊接的原理是利用电弧能量和熔化的焊条将要连接的金属材料熔化,并形成连接。
2. 焊接分类按照焊接方式的不同,焊接可以分为手工焊接、自动焊接和半自动焊接。
按照焊接材料的不同,可以分为电弧焊、气体保护焊、激光焊等。
3. 焊接设备常见的焊接设备包括电弧焊机、气体保护焊机、激光焊机等。
不同的焊接设备适用于不同的焊接方式和材料。
4. 焊接安全焊接时需要注意安全,包括佩戴防护眼镜、手套、面具等个人防护装备,确保焊接作业环境通风良好,避免产生有害气体。
二、焊接工艺培训教程1. 熟悉焊接设备学习焊接首先需要熟悉各种焊接设备的使用方法和操作规程,包括电弧焊机、气体保护焊机等设备的使用方式和维护方法。
2. 学习焊接材料的选择和准备了解各种焊接材料的类型和特点,包括焊条、焊丝、气体保护剂等,学会正确选择和准备焊接材料。
3. 掌握焊接技术学习焊接技术是焊接培训的关键。
包括焊接姿势、焊接速度、焊接电流和电压的调节等技术要点。
4. 实践操作通过实际操作,掌握焊接技术,熟练掌握不同种类的焊接工艺,提高焊接质量和效率。
5. 安全意识培养焊接作业需要非常严格的安全措施,包括个人防护和作业环境的安全。
要培养焊接工作者的安全意识,确保在焊接过程中避免发生安全事故。
在焊接工艺培训教程中,学员除了需要掌握以上基本知识和技能外,还需要了解焊接工艺标准和规范,以及各种不同工况下的焊接质量要求和检验方法。
通过系统的培训教程,焊接工作者可以快速掌握焊接技能,提高工作效率和质量。
6. 焊接工艺标准和规范在焊接培训教程中,学员需要了解国家和行业制定的相关焊接工艺标准和规范,包括焊接工艺规范、焊接接头设计规范、焊接检测标准等。
掌握这些标准和规范可以帮助焊接工作者更好地理解焊接工艺要求,保证焊接质量。
7. 焊接质量要求和检验方法学员需要了解各种不同工况下的焊接质量要求和检验方法,包括焊缝外观、焊缝密度、焊接强度等方面的要求和检验方法。
工艺培训方案

工艺培训方案工艺培训是提升员工技能和知识的重要手段,对于企业的发展和生产力提升具有重要的作用。
本文将就工艺培训的内容、方法以及实施计划进行探讨和分析,旨在提供一套有效的工艺培训方案。
一、培训内容1. 员工基础技能培训:包括相关工具的使用、工装制作、操作规范等基础知识,使员工能够熟练进行常规工艺操作。
2. 工艺工程知识培训:包括产品结构、工艺设计、制造流程等专业知识,使员工能够理解整个工艺流程,具备问题诊断和解决能力。
3. 创新技术培训:包括新材料、新工艺、新设备的应用,使员工能够及时掌握和应用新技术,提升工艺创新能力。
4. 质量管理培训:包括质量控制、质量检验、质量改进等内容,使员工了解质量标准和要求,提高产品质量和合格率。
5. 安全环保培训:包括相关操作规范、安全知识、环保要求等内容,使员工意识到安全环保的重要性,保证生产过程安全和环境可持续。
二、培训方法1. 理论培训:通过讲座、培训课程等形式,传授相关理论知识和技能要点,使员工掌握基本概念和理论基础。
2. 实践培训:通过模拟实验、实际操作等方式,让员工亲身参与和实践,培养操作技能和应对实际问题的能力。
3. 团队合作培训:通过分组活动、团体讨论等形式,促进员工之间的交流和合作,培养团队合作精神和解决问题的能力。
4. 在岗培训:通过岗位轮换、实际操作等方式,让员工在实际工作中学习和实践,提升工作能力和应变能力。
5. 多元化培训:结合在线学习、外部培训等形式,拓宽员工的学习渠道和交流平台,提供多样化的学习机会和资源。
三、实施计划1. 培训需求调研:对员工的技能水平和学习需求进行调研,明确培训的重点和目标。
2. 培训计划制定:根据调研结果,制定详细的培训计划,包括培训内容、培训对象、培训时间等要素。
3. 培训资源准备:准备培训所需的教材、讲师、场地等资源,确保培训的顺利进行。
4. 培训活动组织:组织培训活动,包括理论授课、实践操作、团队合作等环节,确保培训效果。
生产工艺培训
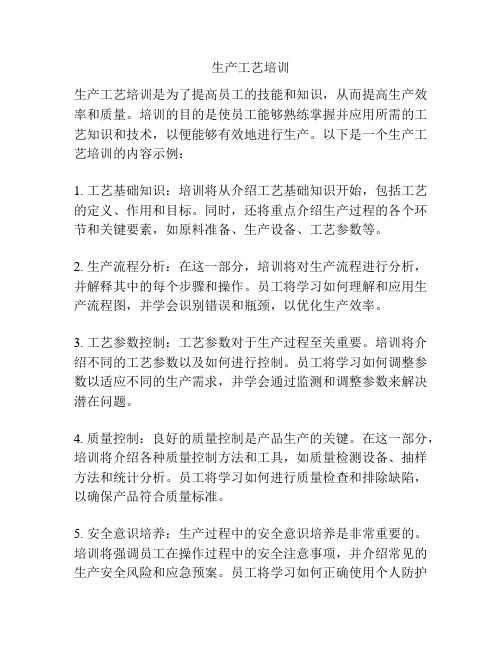
生产工艺培训生产工艺培训是为了提高员工的技能和知识,从而提高生产效率和质量。
培训的目的是使员工能够熟练掌握并应用所需的工艺知识和技术,以便能够有效地进行生产。
以下是一个生产工艺培训的内容示例:1. 工艺基础知识:培训将从介绍工艺基础知识开始,包括工艺的定义、作用和目标。
同时,还将重点介绍生产过程的各个环节和关键要素,如原料准备、生产设备、工艺参数等。
2. 生产流程分析:在这一部分,培训将对生产流程进行分析,并解释其中的每个步骤和操作。
员工将学习如何理解和应用生产流程图,并学会识别错误和瓶颈,以优化生产效率。
3. 工艺参数控制:工艺参数对于生产过程至关重要。
培训将介绍不同的工艺参数以及如何进行控制。
员工将学习如何调整参数以适应不同的生产需求,并学会通过监测和调整参数来解决潜在问题。
4. 质量控制:良好的质量控制是产品生产的关键。
在这一部分,培训将介绍各种质量控制方法和工具,如质量检测设备、抽样方法和统计分析。
员工将学习如何进行质量检查和排除缺陷,以确保产品符合质量标准。
5. 安全意识培养:生产过程中的安全意识培养是非常重要的。
培训将强调员工在操作过程中的安全注意事项,并介绍常见的生产安全风险和应急预案。
员工将学习如何正确使用个人防护装备,以及应急处理措施。
6. 环境保护意识:在今天的社会中,环境保护已成为一个重大问题。
培训将介绍生产过程中的环境保护措施和方法,如废水处理、废气排放控制等。
员工将学习如何正确处理产生的废弃物和污染物,以减少对环境的影响。
生产工艺培训对于提高生产效率、质量和安全性都具有重要意义。
通过培训,员工将能够获得必要的知识和技能,以适应不断变化的生产环境。
培训还将帮助员工更好地理解和掌握生产过程中的关键要素,从而更好地应对各种挑战。
最终,这将有助于提高企业的竞争力和可持续发展。
生产工艺培训的重要性不言而喻。
在竞争激烈的市场环境下,企业需要不断提高生产效率和产品质量,以增强竞争力。
工艺培训计划包含哪些内容

工艺培训计划包含哪些内容一、培训目的本培训旨在提升员工的工艺技能和品质意识,改善产品质量和生产效率,提升企业的竞争力和市场地位。
二、培训对象生产车间的操作工、技术员及相关管理人员。
三、培训内容1.基础工艺知识1) 工艺流程:包括原料准备、生产加工、成品质检等各个环节。
通过讲解、视频展示等方式,让员工了解产品的生产流程和每个环节的重要性;2) 工艺标准:介绍企业的工艺标准和要求,包括产品的尺寸、质量、外观等方面的要求;3) 原材料的选择和运用:培训员工如何选择合适的原材料,并正确使用、储存和保护原材料。
2.生产操作技能1) 设备操作技能:包括设备的开关操作、工作参数设定、设备日常维护等;2) 工艺流程掌握:培训员工掌握每个环节的要领和技巧,提高操作效率和产品质量;3) 产品质量控制:培训员工对产品进行质量检查,发现问题及时处理,最大程度避免次品的产生。
3.品质管理1) 品质意识培养:通过案例分析、品质标准介绍等方式,培养员工的品质意识,让其知道品质对企业的重要性;2) 品质管理方法:介绍企业品质管理的各种方法和工具,如PDCA循环、6σ、质量管理手册等;3) 品质改进机制:分享员工对品质改进的建议和意见,并给予相应奖励,促使员工积极参与品质改进。
4.安全生产1) 安全知识普及:介绍各类事故案例和避免事故的方法,提高员工的安全意识;2) 安全操作规程:讲解企业的安全操作规程和各种安全设备的使用方法,确保员工能够做到安全生产;3) 应急措施培训:对突发事件的处理方法进行培训,以确保员工能够及时、有效地应对各种突发事件。
四、培训方式1.理论讲解培训过程中,将采用讲解、案例分析、视频展示等形式,对培训内容进行系统全面地介绍,以便员工深入理解和掌握。
2.现场操作对于设备操作技能、工艺流程掌握等内容,将采用现场操作的方式进行培训,以便员工能够亲自动手学习和熟练掌握操作要领。
3.案例分析通过分析质量问题的案例,引导员工从事实中学习,从错误中汲取教训,以提升员工的品质意识和品质管理水平。
机械加工工艺知识培训

es(轴)下偏差= 最小极限尺寸—基本尺寸 EI(孔)、ei(轴) 3)尺寸公差——尺寸公差是指尺寸允许的变动量。
尺寸公差 = 最大极限尺寸—最小极限尺寸 = 上偏差—下偏差 4) 零线 ——零线是在公差带图中,确定偏差的一条基准 直线
4)毛面与加工面间的尺寸: 两组尺寸分别标注,各个方向要有 一个尺寸把它们联系起来。
5)便于测量的尺寸注法
四、零件尺寸标注的合理性
四、零件尺寸标注的合理性
四、零件尺寸标注的合理性
四、零件尺寸标注的合理性
四、零件尺寸标注的合理性
3、零件尺寸的标注方法步骤 选择基准: 考虑设计要求,标注出功能尺寸; 考虑工艺要求,标注出非功能尺寸; 用形体分析、结构分析法补全尺寸和检查尺寸,同 时计算三个方向(长、宽和高)的尺寸链是否正确,尺寸 数值是否符合标准数系。
螺纹连接键连接花键连接销连接弹性环连接等焊接铆接连接可拆连接不可拆连接一螺纹基本知识螺纹的主要参数小径d1中径d2螺距p一螺纹基本知识螺栓联接的基本类型一螺纹基本知识双头螺柱联接一螺纹基本知识螺钉联接一螺纹基本知识紧定螺钉联接一螺纹基本知识柴油机五大主要螺栓是指
机械加工工艺培训
姓名 2012年6月16日
目
录
一、螺纹基本知识
二、零件装配的合理性 三、零件设计的合理性
四、零件尺寸标注的合理性 五、零件的公差与配合
六、零件的材料与热处理 五、形位公差、表面粗糙度
一、螺纹基本知识
◆螺纹的类型
1. 一般分法:外螺纹、内螺纹;圆柱螺纹、圆锥螺纹;
左旋螺纹、右旋螺纹。 2、按牙型的不同分为: 三角螺纹、普通螺纹:效率低,易自锁,多用于连接。 矩形螺纹、梯形螺纹、锯齿形螺纹:效率较高,主要用于
工艺车间级安全知识培训
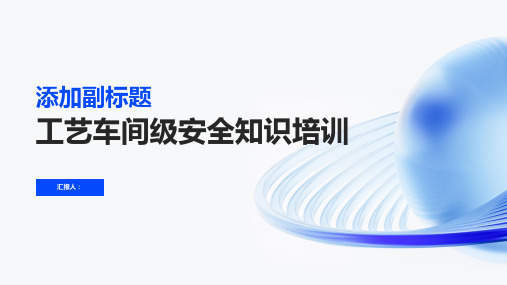
建立设备档案:对每台 设备建立档案,记录设 备的运行情况和维修历 史,方便对设备进行管 理。
设备操作的安全注意事项
严格遵守设备 操作规程,禁
止违规操作
设备运行时, 禁止进行维修
或清理工作
定期检查设备 安全防护装置, 确保其有效性
使用设备时, 应佩戴相应的 劳动防护用品
危险化学品的安全管理
危险化学品的分类与标识
持续改进:定期评估安全文化建设的成效,及时调整和完善相关措施,确保安全文化的持续发展和 提升
安全培训教育的形式与内容
形式:线上培训、线下培训、混合式培训 内容:安全意识教育、安全知识教育、安全技能培训
提高员工安全素质的方法与途径
建立完善的安全培训制度,定期开展安全培训课程,确保员工掌握必要的安全知识和技能。 开展安全文化宣传活动,如安全知识竞赛、安全文化周等,提高员工的安全意识和责任感。
危险化学品的储存:危险化学品应 存放在专用仓库内,并采取相应的 防火、防爆、防泄漏等安全措施。
危险化学品的储存与运输
储存要求:危险化学品应存放在专 用仓库,并配备相应的消防设施
应急处理:在储存和运输过程中如 发生危险情况,应立即采取相应的 应急措施
添加标题
添加标题
添加标题
添加标题
运输规定:危险化学品运输必须符 合国家相关法规和标准,并使用专 用车辆进行运输
添加副标题
工艺车间级安全知识培训
汇报人:
目录
CONTENTS
01 工艺车间安全概述
02 工艺操作规程与安 全规范
03 工艺设备安全与维 护
04 危险化学品的安全 管理
05 事故应急救援与处 理
06 安全文化与培训教 育
工艺车间安全概述
工艺培训资料
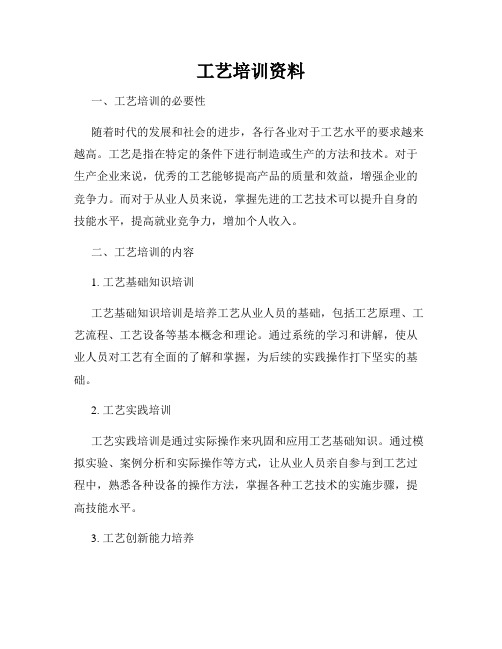
工艺培训资料一、工艺培训的必要性随着时代的发展和社会的进步,各行各业对于工艺水平的要求越来越高。
工艺是指在特定的条件下进行制造或生产的方法和技术。
对于生产企业来说,优秀的工艺能够提高产品的质量和效益,增强企业的竞争力。
而对于从业人员来说,掌握先进的工艺技术可以提升自身的技能水平,提高就业竞争力,增加个人收入。
二、工艺培训的内容1. 工艺基础知识培训工艺基础知识培训是培养工艺从业人员的基础,包括工艺原理、工艺流程、工艺设备等基本概念和理论。
通过系统的学习和讲解,使从业人员对工艺有全面的了解和掌握,为后续的实践操作打下坚实的基础。
2. 工艺实践培训工艺实践培训是通过实际操作来巩固和应用工艺基础知识。
通过模拟实验、案例分析和实际操作等方式,让从业人员亲自参与到工艺过程中,熟悉各种设备的操作方法,掌握各种工艺技术的实施步骤,提高技能水平。
3. 工艺创新能力培养工艺创新能力是指从业人员在运用现有工艺知识的基础上,能够进行创新改进,提高工艺效率和产品质量。
通过培训教育,提高从业人员的工艺创新意识,让其能够在实践中发现问题、解决问题,并提出改进方案,不断推动企业的技术创新和工艺改进。
三、工艺培训的方式1. 线下集中培训线下集中培训是指通过组织专业的培训机构或企事业单位进行培训,统一安排时间、地点和课程内容,让从业人员进行系统的学习和实践。
这种培训方式可以提供专业师资和完善的培训设施,保证培训的质量和效果。
2. 在线远程培训随着互联网的发展,在线远程培训成为一种越来越流行的方式。
通过网络平台提供在线教学和互动学习,从业人员可以根据自身的时间和地点选择合适的培训课程,灵活学习。
这种培训方式节省了时间和成本,提高了学习效率。
3. 实践导向培训实践导向培训是指将培训内容和实际工作相结合,让从业人员在实际工作中学习和实践。
通过安排实习或实训环节,让从业人员亲自参与到实际工艺过程中,不断实践和探索,提高技术水平。
这种培训方式可以使从业人员学以致用,更好地掌握和运用工艺技术。
机械加工工艺培训教材

上对一个(或同时几个)工件进行加工所连续完成的那部分 工艺过程。 D、一个完整工艺由一个或几个工序组成。 E、设计基准:用以标注尺寸和表面互相关系是所依据的要素。 F、工艺基准:零件在加工、度量和装配过程中所依据的要素。
第一部分 基础知识
一、公差与配合 二、形状和位置公差 三、图例解析
一、公差与配合
A、常用计量单位及换算
1、长度单位 公制:千米(km) 米(m) 厘米(cm) 毫米(mm) 微米(μm) 英制:码(yd) 英尺(ft) 英寸(in) 1码=3英尺=36英寸 1英寸=25.4毫米
2、平面角单位 弧度 1度=60分=3600 秒
二 工艺制定原则
A、基本原则:优质、高产、安全、低耗; B、工艺路线原则:
先粗后精,先主后次,先基准后其它; C、定位基准选择: 1、基准重合原则:将设计基准做为工艺基准; 2、基准统一原则:统一定位基准加工个表面; 3、互为基准原则:相互加工面互相做为工艺基准。
三 加工余量的确定
A、压铸件由于尺寸精度或形位公差达不到产品 图纸要求时,应首先考虑采用精整加工方法, 如校正、拉光、挤压、整形等。必须采用机加 工时应考虑选用较小的加工余量,并尽量以不 受分型面及活动成型影响的表面为毛坯基准面。
B、推荐采用的机加工余量及其偏差值。 1、端面加工余量见表1、 2、镗孔/铰孔加工余量见表2、
表1、推荐端面加工余量及其偏差(MM)
基本尺寸 每面余量
≤100
0.5
+0.4 -0.1
>100~250
0.75
+0.5 -0.2
> 250 ~400
工艺安全知识培训内容

水泥厂工艺操作安全生产及注意事项一、均化及喂料系统(1)工作场所应保持道路畅通,照明充足,严禁乱堆乱放杂物。
(2)开机前应认真检查所属机电设备的安全状况,确认正常后,方可开机.(3)生料均化时,应严格遵守各项操作规程。
(4)处理卸料器堵塞时,应将活动平台支稳,要防滑、防跌,打开检查门时,人应侧面作业,防止生料喷出造成伤害。
(5)绞刀机壳盖板必须完好、固定,严禁在上面行走;库内检查门、测量孔盖板必须安全可靠,做到谁开谁盖,严禁乱打开盖板。
(6)机电设备检修时,必须切断电源,挂警告牌,现场设专人监护。
(7)生料均化时,应经常检查库内容量,不可把库内物料进得过满,料位控制在60%~80%。
(8)加强机电设备的巡检工作,如发现缺油、超油、超电流、振动等异常情况,应及时停机处理,确保安全运行。
二、回转窑系统(1)严格遵守回转窑工艺技术操作规程,严格控制回转窑工艺技术参数。
(2)回转窑点火喷煤时,操作人员不得靠近窑门附近,非工作人员应撤离窑头平台,避免“放炮”回火伤人。
(3)在操作室外作业时,必须穿戴好劳动保护用品,禁止穿短袖衫及化纤工作服;看火时必须使用看火面罩,并戴好皮手套。
(4)烘窑点火时,须确认本系统所有设备、仪表处于良好状态,确认预热器、窑内无杂物(铁器),并通知有关生产岗位做好点火前的准备工作,符合点火条件才能点火.(5)遇阴雨天点窑时,应及时观察窑筒体变化,勤翻窑,并尽快连续转窑,防止窑筒体受热不均造成弯曲变形。
(6)点火升温时,及时掌握窑温,间歇翻窑,随着温度不断升高而减短翻窑间隔时间,从而达到连续转窑.(7)烘窑升温结束后,通知分解炉岗位,检查排灰阀及预热器锥体部分是否有积灰,并打开循环吹堵进行清理后,才能正式投料生产,避免投料造成堵塞。
(8)正常操作时,严格控制工艺技术参数,经常观察窑内火焰、窑状况和窑筒体温度,如发现异常时及时调整。
掉砖红窑应立即停窑,并及时向工段或厂部汇报。
(9)窑尾缩结皮和预热器堵塞处理时,必须严格遵守清理窑尾缩结皮及捅堵的安全操作规定.(10 )停窑检修时,应切断电源,并在操作台上挂“禁止启动“警告牌,确认窑的前后设备均处于停机状态时,才能进行检修作业。
- 1、下载文档前请自行甄别文档内容的完整性,平台不提供额外的编辑、内容补充、找答案等附加服务。
- 2、"仅部分预览"的文档,不可在线预览部分如存在完整性等问题,可反馈申请退款(可完整预览的文档不适用该条件!)。
- 3、如文档侵犯您的权益,请联系客服反馈,我们会尽快为您处理(人工客服工作时间:9:00-18:30)。
第一章:压铸基本知识一、压铸机本公司所用的是热室式压铸机。
基本结构有:1、固定机板2、移动机板3、顶出机构4、锁紧机构5、配电及数显6、操纵台7、射料机构8、熔料室压铸机的主要参数固定机板,用以固定压铸模的静模部分;移动机板,用以固定压铸模的动模部分;顶出机构,用以顶出压铸件。
二、材料1、合金啤件用料本公司生产的合金啤件所用的材料为3#锌合金和5#锌合金。
其化学成份如表所示2、锌合金性能(1)熔点较低;(2)压铸成型效果好;(3)啤件表面可镀金属;(4)缺点:啤件易老化,抗腐蚀性差。
3、3#锌合金与5#锌合金的比较(1)液态流动性:5#锌合金优于3#锌合金(2)结晶温度范围:3#锌合金为410—4400C(3)3#锌合金较5#锌合金的价格便宜4、原料中掺入水口料对啤件质量的影响在锌合金原料中,适当地掺入水口料,可使啤件的成本降低。
但也会给啤件带来质量问题。
首先,水口料的杂质多;其二,水口料中的化学成份已发生变化,铝镁等成份减少,使锌合金的理化性能变坏。
所以掺入水口料,将导致压铸成形效果变劣,花纹气泡等废品增多。
如果在掺有水口料的锌合金中适当地加入铝和镁,并改善压铸模的排溢条件,选择适当的压铸参数,也会提高啤件质量。
三、压铸模1、压铸模的基本结构压铸模是压铸成形的母体,其结构包括:(1)静模(2)动模(3)支承板(4)顶杆(5)推板(6)浇口套(7)静模板(8)静固板(9)动固板(10)变位杆(11)动模板压铸模由动模和静模两大部分组成,分型面以上为静模,分型面以下为动模。
静模与动模合在一起组成型腔。
静模上设有型腔的进料道,进料道由入料口、纵浇道、横浇道和浇口组成。
型腔的末端是排溢道。
动模上设有压铸件的顶出机构以及合模时的复位机构。
2、对压铸模的技术要求(1)压铸出来的铸件必须和设计上的技术要求相符合;(2)必须符合压铸机的使用参数;(3)使用方便,可靠,并能达到一定的使用寿命。
四、压铸工艺1、简要的压铸工艺流程开动压铸机,使压铸模合拢,顶针复位,开动压铸机,身料机构将金属熔液打入模具内,通过进料道,充入型腔,在充型时,将其废物排放到排溢道内。
然后经过持续加压,改善成形效果,冷却固化。
再由压铸机动作使模具打开,这时铸件附在动模上,最后由顶出机构完成一个压铸工艺流程。
2、影响压铸件质量的工艺因素压铸工艺的实施基础为:压铸机的功能及其可靠性;压铸模的质量及其结构的合理性;合金材料的合金含量及其熔料温度的稳妥性;以及压铸操作的技术素质等等。
影响压铸工艺的因素概括为:压力、温度、速度和时间。
压力分为压射力和压射比压,压射力是压铸机的总的射料力,单位为TON。
压射比压是金属熔液实际得到的作用压强,单位为KG/CM2温度包括金属熔液的压铸温度和模具工作温度,单位为T0C。
速度包括对金属熔液的压射速度和金属熔液对型腔的充填速度,单位为M/S时间分为射料时间、持续施压时间和冷却时间,单位为S。
持压是为了改善熔液的结晶效果而施加的压力。
在压铸工艺因素中,主要的是压铸工艺参数和参量的选定与应用。
3、压铸件(1)压铸件的质量要求,根据客户需要,内容主要包括:造型效果,精度,表面粗糙度,理化和机械性能等。
(2)压铸件的缺陷分析:(参见表格A)4、废品压铸件的某些缺陷,可以通过其它工艺方法予以挽救或消除,所以,有缺陷的压铸件不一定就是废品。
压铸件的报废标准,应依据其各自的使用技术要求而定。
5、成品压铸件仅仅是完成了产品件的基本造型,要达到成品件的技术要求,还需要一系列的后续工艺方法的处理。
其内容有:除去水口和垃圾位,批锋,机械加工,整形,打光,抛光,清洗,干燥表面处理等等表格A第二章:注塑基本知识注塑(又称注射模型或注射成形)是热塑性塑料成型制品的一种主要方法,注塑的过程是将粒状或粉状塑料从压炼机的料斗送进加热的料筒,经加热熔化至流动状态后由螺杆的推动通过料筒端部的喷嘴,注入温度较低的闭合塑胶模中,充满塑料模的熔料在受压的情况下,经过冷却固化后即可保持胶模型腔所赋予的形样。
本厂注塑机的型号和规格一、注塑机的基本结构:各种型号的压纯练机都是由注射系统、锁模系统和塑胶模三大部分组成的。
(1)注塑装置(2)合模装置(3)塑胶模1、注射系统,它是注射机最主要的部分,其作用是使塑料均化和塑化,并在很高的压力和较快的速度下,通过螺杆的推挤将均化和塑化好的塑料注射入模具。
注射系统包括有:加料装置、料筒、螺杆及喷嘴等部件。
2、在注射机上实现锁合模具,启闭模具和顶出制件的机构统称为锁模系统。
我厂所用的注塑机锁模系统为液压—双曲肘式。
二、注射模1、主流道它是模具中连接注射机喷口通至流道或型腔的一段通道,主流道进口顶部是凹形,以便与喷嘴连接。
主流道进口直径应略大于喷嘴直径(0.8mm),以免溢料,并防止两者因连接不准而发生的堵截。
进口直径根据制品大小而定,一般为4—8mm。
主流道直径应向内扩大,呈3—50 角度,以便流道积物的脱模。
2、冷料穴它是设在主流道末端的一个空穴,用以搜集喷嘴端部两次注射之间所产生的冷料,从而防止分流道或浇口的堵塞。
如果冷料一旦混入型腔,则所制制品中就容易产生内应力。
冷料穴的直径约为8—10mm,深度约为6mm,为了便于脱模,其底部常由脱模杆承担,脱模杆的顶部可设计成曲折钩形或设下陷沟槽,以便脱模时能顺利拉出主流道的积物。
3、分流道它是多腔模中连接主流道和各个型腔的通道,为使熔料以等速度充满各型腔,分流道在塑模上的排列应对称和等距离分布,分流道截面的尺寸对塑料熔体的流动、制品脱模和模具制造的难易都有影响。
如果按相对等料量的流动来说,则以圆形截面的流道阻力最小,但因圆柱形流道的壁表面小,对分流道赘物的冷却不利,而且这种分流道必须开设在两半模上,既费工又不易对准,因此,经常采用的都是用梯形或半圆形截面的分流道,而且是开设在带有脱模杆的一半模具上。
流道表面必须抛光以减少流动阻力而提供较快的充模速度。
流道的尺寸决定于塑料品种,制品的尺寸和厚度。
对大多数热塑性塑料来说,分流道截面宽度均不超过8mm,特大的可达10—12mm,特小的约为2—3mm。
在满足需要的前提下应尽量减小截面积,以免增加分流道赘物和延长冷却时间。
4、浇口它是接通主流道(或分流道)与型腔的通道。
通道的截面积可以是与主流道(或分流道)相等的,但通常都是缩小的。
所以它是整个流道系统中截面积最小的部分。
浇口的形状和尺寸对制品的质量影响很大。
浇口的作用是:(1)控制料流的速度(2)在注射中可以因为存于这部分的熔料早凝而防止倒流(3)使通过的熔料受到较强的剪切而升高温度,并从而降低其表观粘度以提高流动性(4)便于制品与流道系统分离。
因此浇口形状、尺寸和位置的设计都应根据塑料的性质、制品的大小和结构。
一般浇口的截面形状为矩形或圆形,截面可小而长度可短,这不仅是基于上拆作用,还因为小浇口变大比较容易,而大浇口变小则很困难。
浇口位置一般应选在制品最厚而又不影响外观的地方。
浇口尺寸的设计应考虑到塑料熔体的性质。
5、型腔它是模具中成形塑料制品的空间,而用作构成型腔的组件则统称为成型零件。
各个成型零件又常有专用的名称。
具体地说,构成制品外形的成形零件称为凹模(又称阴模)构成制品内部形状(如孔、槽等)的称为型芯或凸模(又称阳模)。
设计成形零件时首先要根据塑料的性能,制品的几何形状,尺寸公差和使用要求来确定型腔的总体结构。
其次是根据确定的结构选择分型面,浇口和排气孔的位置以及脱模方式。
最后则按制品尺寸进行各零件的设计,及确定各零件之间的组合方式。
由于塑料熔体进入型腔时具有很高的压力,故对成形零件要进行合理的选材及强度和钢度的校核。
为保证塑料制品表面的光洁美观和容易脱模,凡与塑料接触的表面,其表面粗糙度应在0.4以上,而且要求它具有耐腐蚀性。
成型零件一般都是通过热处理来提高硬度,并选用耐腐蚀的铜材来制造的。
6、排气口它是开设在模具中的一种槽形出气口,用以防止进入模具的熔料卷入气体物质。
熔料注入型腔时,原存于型腔内的空气以及由熔体卷入的气体必须在料流的尽头通过排气口向模外排气,否则将会使制品带有气孔、熔接不良、充填不满,甚至积存空气因压缩产生高温而制品烧伤。
在一般情况下,排气口既可设在型腔内熔料流动的尽头,也可设在塑模的分型面上。
后者是在凹模一侧开深00.3—0.06mm、宽1.5—6mm的浅。
注射中,排气口是不会有很多的熔料渗出的,因为熔料会在该处冷却固化而自动将通道堵死。
排气口的开设位置切勿对着操作人员,以防熔料意外喷出伤人,此外,亦可利用顶出杆与顶出孔的配合间隙,顶块和脱模板与型芯的配合间隙来排气。
7、结构零件它是指构成模具结构的各种零件,包括:导向、脱模、抽芯以及分型的各种零件。
诸如、前后夹模板,承压板,承压柱,导向柱,脱模板,脱模杆及回程杆等。
8、注塑模的冷却装置这是为熔料能在模具内冷却定型而设的一种装置,一般是在阴阳模内沟通冷却介质流动的通道,然后凭借冷却介质的循环流动来过到冷却目的。
通入的冷却介质随所用塑料的种类和制品的结构等而异,采用的冷却介质有冷水,热水,热油和蒸汽等。
塑模冷却的关键是要求高效率的均匀冷却,因为冷却不均匀会直接影响制品的质量和尺寸因此设计时应根据熔料的热性能(包括结晶)、制品的形状和模具结构,考试冷却通道的排布和冷却介质的选择。
二、常用热塑性塑料使用特性三、塑胶模的基本结构塑模亦称模具,是在成型中赋予塑料以形状时所用部件的组合体。
塑模的结构虽然由于塑料的品质和性能、塑料制品的形状和结构以及注射机的类型等的不同而可能千变万化,但是基本结构是一致的,塑模主要由浇系统、成型零件和结构零件三大部分所组成。
其中浇注系统和成型零件是与塑料直接接触部分,并跟塑料和制品而变化,是塑模中最复杂,变化最大,要求表面粗糙和精度最高的部分。
浇注系统是指塑料从喷嘴进入型腔前的流道部分,包括主流道、冷料穴、分流道和浇口等,成型零件是指构成制品形状的各种零件,包括动模、定模和型腔、型芯、成型杆以及排气口等,现简述如下。
典型塑模结构如下所示。
A充满阶段,这一阶段从螺杆开始向前移动起直至模腔塑料熔体充满为止。
B压实阶段,这是指容体充满模腔时起至螺杆拆回时为止的一段时间。
C倒流阶段,这一阶段是从螺杆后退时开始的,这时射模内的压力比流道内高,因此就会发生塑料熔体的倒流,从而使模腔内压力迅速下降。
D冻结后的冷却阶段,这一阶段指,浇口的塑料完全冻结时起到制品从模腔中顶出为止。
四成型工艺注射模塑最重要的工艺条件是影响塑化流动和冷却的温度,压力和相应的和个作用时间。
1 温度注塑过程需要控制的温度有料筒温度、喷嘴温度和模具温度。
前两者温度主要是影响塑料的塑化和流动,而后一种温度主要是影响塑料的流动和冷却。
A 料筒温度,料筒温度的选择与各种塑料的特性有关,每一种塑料都具有不同的流动温度,因此对无定型的塑料,料筒末端最高温度应高于流动温度,对结晶型塑料应高于熔点,但必须低于塑料的分解温度。