单面板和双面板制作流程
双面板小型工业制版

小型工业制版一、简易流程:底片输出→裁板→钻孔→抛光→(整孔)→预浸→水洗→烘干→活化→通孔→热固化→微蚀→水洗→抛光→加速→镀铜→水洗→抛光→烘干→刷感光线路油墨→烘干→曝光→显影→水洗→微蚀→水洗→镀锡→水洗→脱膜→水洗→蚀刻→水洗→褪锡→水洗→烘干→刷感光阻焊油墨→烘干→曝光→显影→水洗→烘干→刷感光字符油墨→烘干→曝光→显影→水洗→热固化→切边。
二、制作流程:1.打印底片(打印机菲林膜出图《CAM350或其他》)2.裁板(建议保留20㎜的工艺边)3.钻孔(设置板厚2.0㎜或1.6㎜,钻头尖离待加工的PCB板1-1.5㎜《利用Create-DCM双面电路板雕刻软件生成雕刻机能识别的U00格式的钻孔文件》)4.抛光(去除覆铜板表面的氧化物及油污,去除钻孔时产生的毛刺)5.整孔(要保证孔的通透,帮助药水更好的浸到孔内《将钻好孔抛光的板子对光看孔是否通透》)6.预浸(除油,除氧化物毛刺铜粉,调整电荷,有利于碳颗粒的吸附)7.水洗(水洗都是为除去药水的残留《务必反复用清水冲洗干净》)8.烘干(除去孔内残留水分《烘干机或电吹风均可》)9.活化(纳米碳粒附在孔内壁《主要是为了过孔》)10.通孔(将孔内多余的活化液去除,保证每个孔均通透《轻轻敲击板子》)11.固化(使碳颗粒更好的吸附在孔内)12.微蚀(去除表面的碳颗粒《也可用抛光机抛光》)13.水洗14.抛光15.加速(可省略)16.水洗17.镀铜(20-30分钟,电流约3-4A/d㎡(有效面积)《具体视情况增减电流大小》,主要是针对双面板上下电路的通孔导通,在孔内壁镀上铜)18.水洗19.抛光20.烘干(烘干表面及孔内水分)21.刷感光线路油墨(90T的丝网框《主要用到线路板丝印机》)22.烘干(75℃,20-30分钟《优先使用烘干机,可用电吹风,但必须确保能将油墨烘干不粘手》)23.曝光(曝光时间10-40S,先将底片对位,双面板应注意电路的正反面)24.显影(45-50℃,注意观察板子上面的变化)25.水洗26.放入微蚀液中去油(5-10S)27.水洗28.镀锡(20-30分钟,电流约1.5-2A/d㎡有效面积《焊盘及线路部分镀上锡,以达到PCB板在碱性腐蚀液中保护线路部分不被腐蚀》)29.水洗30.脱膜(强碱性液体,除去板上面的线路油墨)31.水洗32.蚀刻(建议温度55℃)33.水洗(务必清洗干净保证电路不会被残留腐蚀液腐蚀掉)34.褪锡(褪锡夜,去除电路上面的锡)35.水洗36.烘干37.刷感光阻焊油墨(90T丝网框,感光阻焊油墨:固化剂=3:1,并加入少量稀释剂调整其粘度《类似洗发水》)38.静置(在阴凉环境,目的是让油墨预干,可用微热的电吹风慢烘)39.油墨烘干(75℃,30分钟)40.曝光(60-120S,光绘底片)41.显影42.水洗43.烘干44.刷感光字符油墨(120T丝网框,感光字符油墨:固化剂=3:1,并加少量的稀释剂调整其粘度《类似洗发水》)45.油墨烘干(75℃,20分钟)46.曝光(90-120S光绘底片)47.显影(字符油墨在显影的时候必须缩短显影时间,不能太久,防止文字掉落)48.水洗49.热固化(150℃,5分钟,固化剂在150℃起作用)50.沉锡(除油-微蚀-水洗-沉锡,主要是在焊盘部分镀上助焊锡,可防氧化,也有利于后面的焊接《镀锡机》)51.切边(根据已做好的电路板切除多余部分,再用手动打磨机将板子边缘部分打磨光滑)注意:以上主要是针对双面板的制作,制作单面板可省略其中的某些步骤。
单面板工艺流程

*单面板工艺流程开料磨边→钻孔→外层图形→(全板镀金)→蚀刻→检验→丝印阻焊→(热风整平)→丝印字符→外形加工→测试→检验*双面板喷锡板工艺流程开料磨边→钻孔→沉铜加厚→外层图形→镀锡、蚀刻退锡→二次钻孔→检验→丝印阻焊→镀金插头→热风整平→丝印字符→外形加工→测试→检验*双面板镀镍金工艺流程开料磨边→钻孔→沉铜加厚→外层图形→镀镍、金去膜蚀刻→二次钻孔→检验→丝印阻焊→丝印字符→外形加工→测试→检验*多层板喷锡板工艺流程开料磨边→钻定位孔→内层图形→内层蚀刻→检验→黑化→层压→钻孔→沉铜加厚→外层图形→镀锡、蚀刻退锡→二次钻孔→检验→丝印阻焊→镀金插头→热风整平→丝印字符→外形加工→测试→检验*多层板镀镍金工艺流程开料磨边→钻定位孔→内层图形→内层蚀刻→检验→黑化→层压→钻孔→沉铜加厚→外层图形→镀金、去膜蚀刻→二次钻孔→检验→丝印阻焊→丝印字符→外形加工→测试→检验*多层板沉镍金板工艺流程开料磨边→钻定位孔→内层图形→内层蚀刻→检验→黑化→层压→钻孔→沉铜加厚→外层图形→镀锡、蚀刻退锡→二次钻孔→检验→丝印阻焊→化学沉镍金→丝印字符→外形加工→测试→检验一、工艺简介沉金工艺之目的的是在印制线路表面上沉积颜色稳定,光亮度好,镀层平整,可焊性良好的镍金镀层。
基本可分为四个阶段:前处理(除油,微蚀,活化、后浸),沉镍,沉金,后处理(废金水洗,DI水洗,烘干)。
二、前处理沉金前处理一般有以下几个步骤:除油(30%AD-482),微蚀(60g/InaPS,2%H2SO4),活化(10%Act-354-2),后浸(1%H2S04)。
以除去铜面氧化物,并在铜面沉钯,以作沉镍活化中心。
其中某个环节处理不好,将会影响随后的沉镍和沉金,并导致批量性的报废。
生产过程中,各种药水必须定期分析和补加,控制在要求范围内。
较重要的比如:微蚀速率应控制在“25U—40U”,活化药水铜含量大于800PPM时必须开新缸,药水缸的清洁保养对联PCB的品质影响也较大,除油缸,微蚀缸,后浸缸应每周换缸,各水洗缸也应每周清洗。
软硬结合板做法

FPCB板的常规做法以及特例分析常规做法:软板(单双面板、多层板)和软硬结合板。
软板(单双面板、多层板)一.单面板:普通单面板和单面双接触板1.普通单面板:有胶基材和无胶基材叠构:①有胶基材②无胶基材基本流程:下料→化学清洗→贴干膜→曝光→显影→首检/每小时抽检→蚀刻→首检/每小时抽检→去膜→首检/每小时抽检→AOI→化学清洗→烘干120℃15Min→下料→贴上保护膜→层压→首检/每小时抽检→下料→贴补强→层压→首检/每小时抽检→自动认位打孔→首检/每小时抽检→化学清洗→表面处理→首检/每小时抽检→刀模分割→首检/每小时抽检→ET →钢模冲切外形→首检/每小时抽检→FQC→QA→包装出货。
2.单面双接触板⑴上下保护膜开口在同一区域时的做法:CC+CU+CC(纯铜箔+保护膜)。
此时镂空处线宽不能小于8mil;且为防止飘线,CC要压住线路至少20mil;另外要注意上下保护膜错开防止断线。
叠构:纯铜箔+保护膜基本流程:下料→钻孔包装→钻孔→首检/每小时抽检→下料→贴下保护膜→层压→首检/每小时抽检→化学清洗→两面贴干膜→曝光→显影→首检/每小时抽检→蚀刻→首检/每小时抽检→去膜→首检/每小时抽检→AOI→化学清洗→烘干120℃15Min→下料→贴上保护膜→层压→首检/每小时抽检→自动认位打孔→首检/每小时抽检→化学清洗→表面处理→首检/每小时抽检→刀模分割→首检/每小时抽检→ET→钢模冲切外形→首检/每小时抽检→FQC→QA→包装出货。
⑵上下保护膜开口不在同一区域时的做法:CU+CC(无胶基材+保护膜)。
此时CC的胶只能用环氧胶,不可用压克力胶;是走蚀刻PI线。
叠构:无胶基材+保护膜基本流程:下料→化学清洗→贴干膜→曝光→显影→首检/每小时抽检→蚀刻→首检/每小时抽检→去膜→首检/每小时抽检→AOI→化学清洗→烘干120℃15Min→下料→贴上保护膜→层压→首检/每小时抽检→化学清洗→两面贴抗KAPTON ETCH干膜→曝光→显影→首检/每小时抽检→预浸→蚀刻KAPTON→首检/每小时抽检→去膜→首检/每小时抽检→自动认位打孔→首检/每小时抽检→化学清洗→表面处理→首检/每小时抽检→刀模分割→首检/每小时抽检→ET→钢模冲切外形→首检/每小时抽检→FQC→QA→包装出货。
线路板生产工艺流程
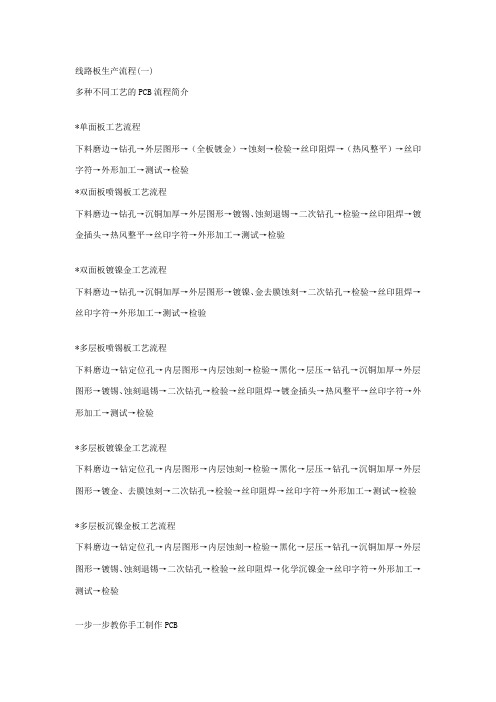
线路板生产流程(一)多种不同工艺的PCB流程简介*单面板工艺流程下料磨边→钻孔→外层图形→(全板镀金)→蚀刻→检验→丝印阻焊→(热风整平)→丝印字符→外形加工→测试→检验*双面板喷锡板工艺流程下料磨边→钻孔→沉铜加厚→外层图形→镀锡、蚀刻退锡→二次钻孔→检验→丝印阻焊→镀金插头→热风整平→丝印字符→外形加工→测试→检验*双面板镀镍金工艺流程下料磨边→钻孔→沉铜加厚→外层图形→镀镍、金去膜蚀刻→二次钻孔→检验→丝印阻焊→丝印字符→外形加工→测试→检验*多层板喷锡板工艺流程下料磨边→钻定位孔→内层图形→内层蚀刻→检验→黑化→层压→钻孔→沉铜加厚→外层图形→镀锡、蚀刻退锡→二次钻孔→检验→丝印阻焊→镀金插头→热风整平→丝印字符→外形加工→测试→检验*多层板镀镍金工艺流程下料磨边→钻定位孔→内层图形→内层蚀刻→检验→黑化→层压→钻孔→沉铜加厚→外层图形→镀金、去膜蚀刻→二次钻孔→检验→丝印阻焊→丝印字符→外形加工→测试→检验*多层板沉镍金板工艺流程下料磨边→钻定位孔→内层图形→内层蚀刻→检验→黑化→层压→钻孔→沉铜加厚→外层图形→镀锡、蚀刻退锡→二次钻孔→检验→丝印阻焊→化学沉镍金→丝印字符→外形加工→测试→检验一步一步教你手工制作PCB制作PCB设备与器材准备(1)DM-2100B型快速制板机1台(2)快速腐蚀机1台(3)热转印纸若干(4)覆铜板1张(5)三氯化铁若干(6)激光打印机1台(7)PC机1台(8)微型电钻1个(1)DM-2100B型快速制板机DM一2100B型快速制板机是用来将打印在热转印纸上的印制电路图转印到覆铜板上的设备,1)【电源】启动键一按下并保持两秒钟左右,电源将自动启动。
2)【加热】控制键一当胶辊温度在100℃以上时,按下该键可以停止加热,工作状态显示为闪动的“C”。
再次按下该键,将继续进行加热,工作状态显示为当前温度;按下此键后,待胶辊温度降至100℃以下,机器将自动关闭电源;胶辊温度在100℃以内时,按下此键,电源将立即关闭。
单双及普通多层板的制作工艺
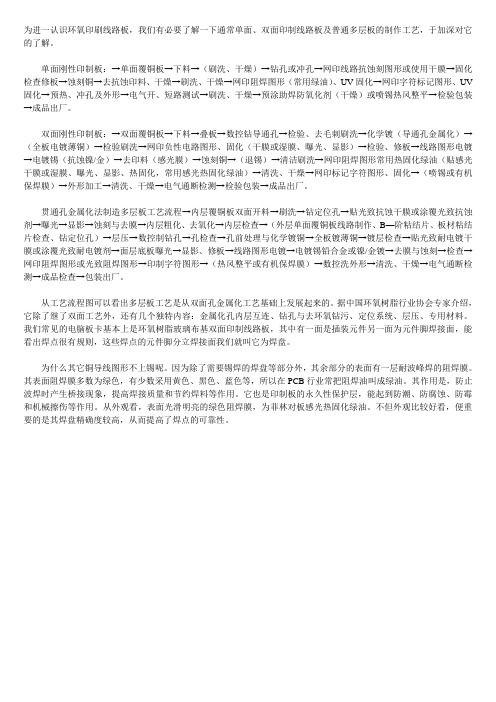
为进一认识环氧印刷线路板,我们有必要了解一下通常单面、双面印制线路板及普通多层板的制作工艺,于加深对它的了解。
单面刚性印制板:→单面覆铜板→下料→(刷洗、干燥)→钻孔或冲孔→网印线路抗蚀刻图形或使用干膜→固化检查修板→蚀刻铜→去抗蚀印料、干燥→刷洗、干燥→网印阻焊图形(常用绿油)、UV固化→网印字符标记图形、UV 固化→预热、冲孔及外形→电气开、短路测试→刷洗、干燥→预涂助焊防氧化剂(干燥)或喷锡热风整平→检验包装→成品出厂。
双面刚性印制板:→双面覆铜板→下料→叠板→数控钻导通孔→检验、去毛刺刷洗→化学镀(导通孔金属化)→(全板电镀薄铜)→检验刷洗→网印负性电路图形、固化(干膜或湿膜、曝光、显影)→检验、修板→线路图形电镀→电镀锡(抗蚀镍/金)→去印料(感光膜)→蚀刻铜→(退锡)→清洁刷洗→网印阻焊图形常用热固化绿油(贴感光干膜或湿膜、曝光、显影、热固化,常用感光热固化绿油)→清洗、干燥→网印标记字符图形、固化→(喷锡或有机保焊膜)→外形加工→清洗、干燥→电气通断检测→检验包装→成品出厂。
贯通孔金属化法制造多层板工艺流程→内层覆铜板双面开料→刷洗→钻定位孔→贴光致抗蚀干膜或涂覆光致抗蚀剂→曝光→显影→蚀刻与去膜→内层粗化、去氧化→内层检查→(外层单面覆铜板线路制作、B—阶粘结片、板材粘结片检查、钻定位孔)→层压→数控制钻孔→孔检查→孔前处理与化学镀铜→全板镀薄铜→镀层检查→贴光致耐电镀干膜或涂覆光致耐电镀剂→面层底板曝光→显影、修板→线路图形电镀→电镀锡铅合金或镍/金镀→去膜与蚀刻→检查→网印阻焊图形或光致阻焊图形→印制字符图形→(热风整平或有机保焊膜)→数控洗外形→清洗、干燥→电气通断检测→成品检查→包装出厂。
从工艺流程图可以看出多层板工艺是从双面孔金属化工艺基础上发展起来的。
据中国环氧树脂行业协会专家介绍,它除了继了双面工艺外,还有几个独特内容:金属化孔内层互连、钻孔与去环氧钻污、定位系统、层压、专用材料。
FPCB工艺制造流程介绍

蚀刻
1-1 RTR单面显影蚀刻 1-2 RTR双面显影蚀刻 1-3 RTS双面显影蚀刻
1-4 STS双面显影蚀刻
二.FPC的生产工序简介
蚀刻: 利用腐蚀技术将显影后的板子将线 路以外多余的铜腐蚀掉得到有线路 的半成品
去膜: 利用强碱将时刻后残留在板面上的 干膜溶解剥离掉
二.FPC的生产工序简介
叠层
RTR蚀刻
补强快压
补强
快压
RTR靶冲
RTR假贴
表面处理
电测
冲裁
FQC/FQA
包装
FQC/FQA
功能测试
冲裁2
SMT
普通双面板(片材生产)
计划投料
开料
靶冲
快压
钻孔 叠层
补强
补强快压
表面处理
装配
冲裁2
功能测试
FQC/FQA
SMT
包装
黑孔
蚀刻
VCP镀铜
光致
文字
电测
FQC/FQA
冲裁
普通双面板(RTR化生产)
补强厚度:小于0.3mm; 贴合精度:偏移100um内; 贴合效率:0.15S/贴次
二.FPC的生产工序简介
电测: 通过测试治具以及电测机,将不符合
客户电气性能要求的线路板挑选出 来报废处理
二.FPC的生产工序简介
外形加工: 通过精密的模具,将客户需要的零件
外形冲制出来 加工方式:
模具+冲床 激光机切割
1- 3 STS开料
剪成单片
二.FPC的生产工序简介
已钻OK的产品
局部大
钻咀/钻头
钻孔:
① 双面板以及多
层板通孔的加工
② 辅料工具孔的 加工
制作单面板的步骤

单面板制作流程说明书华中科技大学电信系实验室龚 军 罗志强 制作2010年5月目录一、 单面板制作流程概述----------------------------------------------- 3二、 单面板制作流程各步骤详细说明-------------------------------- 31、制作感光负片 ------------------------------------------------------- 32、覆膜 ------------------------------------------------------------------- 63、曝光 ----------------------------------------------------------------- 84、显影 ----------------------------------------------------------------- 95、蚀刻 ---------------------------------------------------------------- 116、退膜 ---------------------------------------------------------------- 117、打孔 ---------------------------------------------------------------- 128、焊接 ---------------------------------------------------------------- 12附录 --------------------------------------------------------------------- 13一、 单面板制作流程概述单面板的制作流程较为简单,具体的流程如下图1所示。
单面板和双面板制作流程

概述PCB(Printed Circuit Board),中文名称为印制线路板,简称印制板,是电子工业的重要部件之一。
几乎每种电子设备,小到电子手表、计算器,大到计算机,通讯电子设备,军用武器系统,只要有集成电路等电子元器件,为了它们之间的电气互连,都要使用印制板。
在较大型的电子产品研究过程中,最基本的成功因素是该产品的印制板的设计、文件编制和制造。
印制板的设计和制造质量直接影响到整个产品的质量和成本,甚至导致商业竞争的成败。
印制电路在电子设备中提供如下功能:提供集成电路等各种电子元器件固定、装配的机械支撑。
实现集成电路等各种电子元器件之间的布线和电气连接或电绝缘。
提供所要求的电气特性,如特性阻抗等。
为自动焊锡提供阻焊图形,为元件插装、检查、维修提供识别字符和图形。
有关印制板的一些基本术语在绝缘基材上,按预定设计,制成印制线路、印制元件或由两者结合而成的导电图形,称为印制电路。
在绝缘基材上,提供元、器件之间电气连接的导电图形,称为印制线路。
它不包括印制元件。
印制电路或者印制线路的成品板称为印制电路板或者印制线路板,亦称印制板。
印制板按照所用基材是刚性还是挠性可分成为两大类:刚性印制板和挠性印制板。
今年来已出现了刚性-----挠性结合的印制板。
按照导体图形的层数可以分为单面、双面和多层印制板。
导体图形的整个外表面与基材表面位于同一平面上的印制板,称为平面印板。
有关印制电路板的名词术语和定义,详见国家标准GB/T2036-94“印制电路术语”。
电子设备采用印制板后,由于同类印制板的一致性,从而避免了人工接线的差错,并可实现电子元器件自动插装或贴装、自动焊锡、自动检测,保证了电子设备的质量,提高了劳动生产率、降低了成本,并便于维修。
印制板从单层发展到双面、多层和挠性,并且仍旧保持着各自的发展趋势。
由于不断地向高精度、高密度和高可靠性方向发展,不断缩小体积、减轻成本、提高性能,使得印制板在未来电子设备地发展工程中,仍然保持强大的生命力。
pcb单面板制作流程及oqc职责

pcb单面板制作流程及oqc职责
PCB单面板是一种用于嵌入电子元件的基础结构。
它是由不同厚度的铜箔层、阻焊剂层及陶瓷层等组成,其中的铜箔层可以通过钻头孔连接电子元件。
PCB单面板制作流程由准备、成型、焊接、清理4个步骤构成:
1、准备:首先,应检查工艺图、配料表等材料,根据要求准备铜箔片、陶瓷和阻焊剂,并将其进行分类处理。
2、成型:根据工艺图中的尺寸要求,将铜箔片通过压力、温度等手段制成单面板。
3、焊接:将电子元件焊接在铜箔片上,并将它们连接起来。
4、清理:清理单面板表面,删除多余的未焊接部分,使其表面光滑,便于进行下一道工序。
OQC(过程质量控制)是在产品生产过程中对质量的监控和控制,它的职责包括:
1、监控制造过程的质量控制指标,检测制造设备的性能及其它参数,确保一致性。
2、检查制造过程的操作流程,检查管理系统的实施情况,确保质量把关政策的落实。
3、检查生产设备的运行状况,及时发现故障,避免不良品的
产生。
4、定期进行抽样检测,确保生产质量满足规定的要求。
5、及时发现与质量相关的问题,并采取有效措施,针对不合格品,采取相应的控制办法,以避免其进入市场。
精选FPCB工艺制造流程介绍ktt

FPC流程工序—表面处理
表面处理: 通过化学或者电化学方式,完成手指焊盘通孔等表面处理 其中有:化金、镀金、镀锡、OSP、喷锡
二.FPC的生产工序简介
FPC流程工序—靶冲
靶冲: 通过靶冲机,冲制出后工序需要使用的工具孔
二.FPC的生产工序简介
FPC流程工序—丝印
二.FPC的生产工序简介
FPC流程工序—黑孔
黑孔线
黑孔: 在孔壁上沉积上一层导电的碳膜,通过碳膜的导电性,实现电镀
二.FPC的生产工序简介
FPC流程工序—镀铜
龙门镀铜线
镀铜: 利用电化学反应方法在孔内及板面电镀上铜。增加铜面及孔壁金属厚度
二.FPC的生产工序简介
环形镀铜线
FPC流程工序—光致前清洗
二.FPC的生产工序简介
FPC流程工序—机械钻孔
局部放大
钻咀/钻头
已钻OK的产品
钻孔: ① 双面板以及多层板通孔的加工 ② 辅料工具孔的加工 ③ 工装治具的加工
二.FPC的生产工序简介
FPC流程工序—CO2激光机钻孔
二.FPC的生产工序简介
CO2 LASER原理: 利用红外线的热能,当温度升高或能量增加到一定程度后,如有机物的熔点、燃点或沸点时,则有机物分子的相互作用力或束缚力将大为减小到使有机物分子相互脱离成自由态或游离态,由于激光的不断提供能量,而使有机分子逸出或者与空气中的氧气燃烧而成为二氧化碳或水气体而散离去,由于激光是以一定直径的红外光束来加工的,因而形成微小孔。
丝印 利用印刷技术,在FPC板上印上文字、字符等符号,作为客户识别用; 或者丝印上一层油墨,作为线路板的覆盖阻焊层
二.FPC的生产工序简介
FPC流程工序—装配
制作双面板流程

双面板制作流程注意:刷油墨操作须在弱光环境操作,且刷油墨后立即清洗丝网。
一:打孔1 开机2 是否回原点?确定3 轴启4 移动X、Y、Z,使钻头位于覆铜板左下角定位孔、且垂直距覆铜板2mm以内。
5 对准后X、Y—0,Z—06 按“运行”键7 U盘文件8 选择钻孔文件9 加工速度(150-200),确定。
注:手柄设置请见文后附录一(雕刻机使用)二:抛光三:智能沉铜机预浸→水洗(可省)→活化(黑孔夹子轻轻晃动)→通孔→烘干→微蚀(可省)→水洗(可省)→烘干四:智能镀铜机设置运行电流4A~5A,时间20分钟,10*10com的板子,如果板子大电流大,时间长些,约30分钟。
注:使用时,刚开始电流稍小些,运行一定时间后电流上升五:刷线路油墨选用90的丝网,且需注意用铝角尺将线路板卡住,刷完后立即用油墨显影粉清洗丝网,该过程应在弱光环境下进行,关闭灯。
六:烘干(75度,15~20分钟)七:爆光开电源→抽气开(约5秒)→开灯(电流从40A降到20A)→爆光(正反面时间均设为6秒,十分关键)→关排气、关灯(如后面还需曝光无须关灯直接关排气即可,因灯重启需要三分钟)如显影后出现脱膜现象请适量增加曝光时间如显影后线路部分油墨不能很好的脱落请适量减少曝光时间。
八:显影自动喷淋显影机(水和油墨显影粉混合的,刚开机先空喷几次,温度40—45度,时间40~60秒)显影一次后用手轻擦线路上的墨点,如轻擦不落再次显影,直至线路部分露出光亮铜面。
九:水洗轻擦洗去显影液十:烘干十一:镀锡电流=0.6A,时间=4~5分钟,预镀锡时间为30秒。
镀锡过程中要常看,锡的厚度要比绿膜要薄。
十二:水洗十三:去膜*脱模机去膜,一定要用手套,去膜液为强碱性十四:水洗十五:腐蚀(时间:50秒,温度:45℃。
防止腐蚀过头。
)十六:水洗十七:去锡(时间:30秒,温度:室温)十八:水洗十九:刷阻焊油墨阻焊丝网选用100很重要,要均匀。
(阻焊油墨中可加固化剂,增加固化能力)二十:烘干(时间:30分钟温度:75℃)二十一:曝光(正反面均为40秒)二十二:显影显影一次,时间为60秒,显影结束观察焊盘部分油墨,如留有墨点用手轻擦之,如不掉落再次进行显影。
PCB双面板制作流程

印刷电路知识简介印刷电路板(Print Circuit Board)简称PCB,也称为印刷线路板Print Wiring Board(PWB)它用影像转移的方式将线路印在基板上,经过化学蚀刻后产生线路。
印刷电路板可作为零件在电路中的支架(Supporting) 也可做为零件的连接体。
使得板上各组件电性能相连.于1960年以后才有专业制造厂以甲醛树脂铜箔为基材,制作单面PCB进军电唱机、录音机、录像机等市场,之后因双面贯孔镀铜制造技术兴起,于是耐热、尺寸安定之玻璃环氧基板大量被应用至今。
现在用得比较多的有FR4,FR2,CEM3,陶瓷板,铁氟龙板等,公司现在使用的一般为FR4板.电路板的分类:1.根据硬度分:软板、硬板、软硬板2.根据层数分:单面板、双面板、多层板单面板就是只有一层导电图形层双面板是有两层导电图形层多层印刷线路板是指由三层及以上的导电图形层与绝缘材料交替层压粘结在一起制成的印刷电路板。
总体流程介绍客户要求→工程设计资料→制作工单MI →开料/烤板→钻孔→沉铜/板面电镀→磨刷→线路→电镀铜锡→退膜/蚀刻→退锡→阻焊→沉镍金→成型/冲压→成测→高温整平→成品检验→成品仓流程说明1)下料:从一定板厚和铜箔厚度的整张覆铜板大料上剪出便于加工的尺寸2)钻孔:在板上按电脑钻孔程序钻出导电孔或插件孔3)沉铜:在钻出的孔内沉积一层薄薄的化学铜,目的是在不导电的环氧玻璃布基材(或其他基材)通过化学方法沉上一层铜,便于后面电镀导通形成线路;4)全板镀铜:主要是为加厚保护那层薄薄的化学铜以防其在空气中氧化,形成孔内无铜或破洞;5)线路(图形转移):在板上贴上干膜或丝印上图形抗电镀油墨,经曝光,显影后,做出线路图形6)图形电镀:在已做好图形线路的板上进行线路加厚镀铜,使孔内和线路铜厚达到一定厚度,可以负载一定的电流7)蚀刻:褪掉图形油墨或干膜,蚀刻掉多余的铜箔从而得到导电线路图形8)退锡:将所形成图形上的锡层退掉,以便露出所需的线路9)丝印阻焊油墨或贴阻焊干膜:在板上印刷一层阻焊油墨,或贴上一层阻焊干膜,经曝光,显影后做成阻焊图形,主要目的在于防止在焊接时线路间发生短路10)化金/喷锡:在板上需要焊接的地方沉上金或喷上一层锡,便于焊接,同时也可防止该处铜面氧化11)字符:在板上印刷一些标志性的字符,主要便于客户安装元器件12)冲压/成型:根据客户要求加工出板的外形13)电测:通过闭合回路的方式检测PCB中是否有开短路现象。
FPC生产流程(全流程)

FPC生产流程(全流程)1. FPC生产流程:1.1 双面板制程:开料→ 钻孔→ PTH → 电镀→ 前处理→ 贴干膜→ 对位→曝光→ 显影→ 图形电镀→ 脱膜→ 前处理→ 贴干膜→对位曝光→ 显影→蚀刻→ 脱膜→ 表面处理→ 贴覆盖膜→ 压制→ 固化→ 沉镍金→ 印字符→ 剪切→ 电测→ 冲切→ 终检→包装→ 出货1.2 单面板制程:开料→ 钻孔→贴干膜→ 对位→曝光→ 显影→蚀刻→ 脱膜→ 表面处理→ 贴覆盖膜→ 压制→ 固化→表面处理→沉镍金→ 印字符→ 剪切→ 电测→ 冲切→ 终检→包装→ 出货2. 开料2.1. 原材料编码的认识NDIR050513HJY: D→双面, R→ 压延铜, 05→PI厚0.5mil,即12.5um, 05→铜厚18um, 13→胶层厚13um.XSIE101020TLC: S→单面, E→电解铜, 10→PI厚25um, 10→铜厚度35um, 20→胶厚20um.CI0512NL:(覆盖膜) :05→PI厚12.5um, 12→胶厚度12.5um. 总厚度:25um.2.2.制程品质控制A.操作者应带手套和指套,防止铜箔表面因接触手上之汗而氧化.B.正确的架料方式,防止皱折.C.不可裁偏,手对裁时不可破坏沖制定位孔和测试孔.D.材料品质,材料表面不可有皱折,污点,重氧化现象,所裁切材料不可有毛边,溢胶等.3钻孔3.1打包: 选择蓋板→組板→胶帶粘合→打箭头(记号)3.1.1打包要求: 单面板 30张 ,双面板 6张 , 包封15张.3.1.2蓋板主要作用:A: 防止钻机和压力脚在材料面上造成的压伤B::使钻尖中心容易定位避免钻孔位置的偏斜C:带走钻头与孔壁摩擦产生的热量.减少钻头的扭断.3.2钻孔:3.2.1流程: 开机→上板→调入程序→设置参数→钻孔→自检→IPQA检→量产→转下工序.3.2.2. 钻针管制方法:a. 使用次数管制 b. 新钻头之辨认,检验方法3.3. 品质管控点: a.钻带的正确 b.对红胶片,确认孔位置,数量,正确. c确认孔是否完全导通. d. 外观不可有铜翘,毛边等不良现象.3.4.常见不良现象3.4.1断针: a.钻机操作不当 b.钻头存有问题 c.进刀太快等.3.4.2毛边 a.蓋板,墊板不正确 b.靜电吸附等等4.电镀4.1.PTH原理及作用: PTH即在不外加电流的情況下,通过镀液的自催化(钯和铜原子作为催化剂)氧化还原反应,使铜离子析镀在经过活化处理的孔壁及铜箔表面上的过程,也称为化学镀铜或自催化镀铜.4.2.PHT流程: 碱除油→水洗→微蚀→水洗→水洗→预浸→活化→水洗→水洗→速化→水洗→水洗→化学铜→水洗.4.3.PTH常见不良状况之处理4.3.1.孔无铜 :a活化钯吸附沉积不好. b速化槽:速化剂浓度不对. c化学铜:温度过低,使反应不能进行反应速度过慢;槽液成分不对.4.3.2.孔壁有颗粒,粗糙: a化学槽有颗粒,铜粉沉积不均,开过滤机过滤. b板材本身孔壁有毛刺.4.3.3.板面发黑: a化学槽成分不对(NaOH浓度过高).4.4镀铜镀铜即提高孔内镀层均匀性,保证整个版面(孔内及孔口附近的整个镀层)镀层厚度达到一定的要求.4.4.1电镀条件控制a电流密度的选择b电镀面积的大小c镀层厚度要求d电镀时间控制4.4.1品质管控 1 贯通性:自检QC全检,以40倍放大镜检查孔壁是否有镀铜完全附着贯通.2 表面品质:铜箔表面不可有烧焦,脱皮,颗粒状,针孔及花斑不良等现象.3 附着性:于板边任一处以3M胶带粘贴后,以垂直向上接起不可有脱落现象.5.线路5.1干膜干膜贴在板材上,经曝光后显影后,使线路基本成型,在此过程中干膜主要起到了影象转移的功能,而且在蚀刻的过程中起到保护线路的作用.5.2干膜主要构成:PE,感光阻剂,PET .其中PE和PET只起到了保护和隔离的作用.感光阻剂包括:连接剂,起始剂,单体,粘着促进剂,色料.5.3作业要求 a保持干膜和板面的清洁, b平整度,无气泡和皱折现象.. c附着力达到要求,密合度高.5.4作业品质控制要点5.4.1为了防止贴膜时出现断线现象,应先用无尘纸粘尘滚轮除去铜箔表面杂质.5.4.2应根据不同板材设置加热滚轮的温度,压力,转数等参数.5.4.3保证铜箔的方向孔在同一方位.5.4.4防止氧化,不要直接接触铜箔表面.5.4.5加热滚轮上不应该有伤痕,以防止产生皱折和附着性不良5.4.6贴膜后留置10—20分钟,然后再去曝光,时间太短会使发生的有机聚合反应未完全,太长则不容易被水解,发生残留导致镀层不良.5.4.7经常用无尘纸擦去加热滚轮上的杂质和溢胶.5.4.8要保证贴膜的良好附着性.5.5贴干膜品质确认5.5.1附着性:贴膜后经曝光显影后线路不可弯曲变形或断等(以放大镜检测)5.5.2平整性:须平整,不可有皱折,气泡.5.5.3清洁性:每张不得有超过5点之杂质.5.6曝光5.6.1.原理:使线路通过干膜的作用转移到板子上.5.6.2作业要点: a作业时要保持底片和板子的清洁.b底片与板子应对准,正确.c不可有气泡,杂质.*进行抽真空目的:提高底片与干膜接触的紧密度减少散光现象.*曝光能量的高低对品质也有影响:1能量低,曝光不足,显像后阻剂太软,色泽灰暗,蚀刻时阻剂破坏或浮起,造成线路的断路.2.能量高,则会造成曝光过度,则线路会缩小或曝光区易洗掉.5.7显影5.7.1原理:显像即是将已经曝过光的带干膜的板材,经过(1.0+/-0.1)%的碳酸钠溶液(即显影液)的处理,将未曝光的干膜洗去而保留经曝光发生聚合反应的干膜,使线路基本成型.5.7.2影响显像作业品质的因素: a﹑显影液的组成 b﹑显影温度. c﹑显影压力. d﹑显影液分布的均匀性.e﹑机台转动的速度.5.7.3制程参数管控:药液溶度,显影温度,显影速度,喷压.5.7.4显影品质控制要点:a﹑出料口扳子上不应有水滴,应吹干净.b﹑不可以有未撕的干膜保护膜.c﹑显像应该完整,线路不可锯齿状,弯曲,变细等状况.d﹑显像后裸铜面用刀轻刮不可有干膜脱落,否则会影响时刻品质.e﹑干膜线宽与底片线宽控制在+/-0.05mm以内的误差.f﹑线路复杂的一面朝下放置,以避免膜渣残留,减少水池效应引起的显影不均.g﹑根据碳酸钠的溶度,生产面积和使用时间来及时更新影液,保证最佳的显影效果.h﹑应定期清洗槽内和喷管,喷头中之水垢,防止杂质污染板材和造成显影液分布不均匀性. i﹑防止操作中产生卡板,卡板时应停转动装置,立即停止放板,并拿出板材送至显影台中间,如未完全显影,应进行二次显影.j﹑显影吹干后之板子应有绿胶片隔开,防止干膜粘连而影响到时刻品质.5.8蚀刻脱膜5.8.1原理:蚀刻是在一定的温度条件下(45—50)℃蚀刻药液经过喷头均匀喷淋到铜箔的表面,与没有蚀刻阻剂保护的铜发生氧化还原反应,而将不需要的铜反应掉,露出基材再经过脱膜处理后使线路成形.5.8.2蚀刻药液的主要成分:酸性蚀刻子液(氯化铜),双氧水,盐酸,软水5.9蚀刻品质控制要点:5.9.1以透光方式检查不可有残铜, 皱折划伤等5.9.2线路不可变形,无水滴.5.9.3时刻速度应适当,不允收出现蚀刻过度而引起的线路变细,和蚀刻不尽.5.9.4线路焊点上之干膜不得被冲刷分离或断裂5.9.5时刻剥膜后之板材不允许有油污,杂质,铜皮翘起等不良品质。
单面板工艺流程

*单面板工艺流程开料磨边→钻孔→外层图形→(全板镀金)→蚀刻→检验→丝印阻焊→(热风整平)→丝印字符→外形加工→测试→检验*双面板喷锡板工艺流程开料磨边→钻孔→沉铜加厚→外层图形→镀锡、蚀刻退锡→二次钻孔→检验→丝印阻焊→镀金插头→热风整平→丝印字符→外形加工→测试→检验*双面板镀镍金工艺流程开料磨边→钻孔→沉铜加厚→外层图形→镀镍、金去膜蚀刻→二次钻孔→检验→丝印阻焊→丝印字符→外形加工→测试→检验*多层板喷锡板工艺流程开料磨边→钻定位孔→内层图形→内层蚀刻→检验→黑化→层压→钻孔→沉铜加厚→外层图形→镀锡、蚀刻退锡→二次钻孔→检验→丝印阻焊→镀金插头→热风整平→丝印字符→外形加工→测试→检验*多层板镀镍金工艺流程开料磨边→钻定位孔→内层图形→内层蚀刻→检验→黑化→层压→钻孔→沉铜加厚→外层图形→镀金、去膜蚀刻→二次钻孔→检验→丝印阻焊→丝印字符→外形加工→测试→检验*多层板沉镍金板工艺流程开料磨边→钻定位孔→内层图形→内层蚀刻→检验→黑化→层压→钻孔→沉铜加厚→外层图形→镀锡、蚀刻退锡→二次钻孔→检验→丝印阻焊→化学沉镍金→丝印字符→外形加工→测试→检验一、工艺简介沉金工艺之目的的是在印制线路表面上沉积颜色稳定,光亮度好,镀层平整,可焊性良好的镍金镀层。
基本可分为四个阶段:前处理(除油,微蚀,活化、后浸),沉镍,沉金,后处理(废金水洗,DI水洗,烘干)。
二、前处理沉金前处理一般有以下几个步骤:除油(30%AD-482),微蚀(60g/InaPS,2%H2SO4),活化(10%Act-354-2),后浸(1%H2S04)。
以除去铜面氧化物,并在铜面沉钯,以作沉镍活化中心。
其中某个环节处理不好,将会影响随后的沉镍和沉金,并导致批量性的报废。
生产过程中,各种药水必须定期分析和补加,控制在要求范围内。
较重要的比如:微蚀速率应控制在“25U—40U”,活化药水铜含量大于800PPM时必须开新缸,药水缸的清洁保养对联PCB的品质影响也较大,除油缸,微蚀缸,后浸缸应每周换缸,各水洗缸也应每周清洗。
FPCB工艺制造流程介绍

二.FPC的生产工序简介
沉铜: 利用氧化还原方法在孔内及板面沉积上 上一层薄铜,通过孔壁上的铜连接两面 铜皮
沉铜线
二.FPC的生产工序简介
黑孔线
黑孔:
在孔壁上沉积上一层导电的 碳膜,通过碳膜的导电性,实 现电镀
二.FPC的生产工序简介
龙门镀铜线
环形镀铜线
镀铜:
利用电化学反应方法在孔内及板 面电镀上铜。增加铜面及孔壁金 属厚度
1- 3 STS开料
剪成单片
二.FPC的生产工序简介
已钻OK的产品
局部放大
钻咀/钻头
钻孔:
① 双面板以及多
层板通孔的加工
② 辅料工具孔的 加工
③ 工装治具的加 工
二.FPC的生产工序简介
CO2 LASER原理: 利用红外线的热能,当温度升高或能量增加到一定程度后,如有 机物的熔点、燃点或沸点时,则有机物分子的相互作用力或束缚 力将大为减小到使有机物分子相互脱离成自由态或游离态,由于 激光的不断提供能量,而使有机分子逸出或者与空气中的氧气燃 烧而成为二氧化碳或水气体而散离去,由于激光是以一定直径的 红外光束来加工的,因而形成微小孔。
计划投料
开料
RTR光致
RTR蚀刻
补强快压
补强
快压
RTR靶冲
RTR假贴
表面处理
电测
冲裁
FQC/FQA
包装
FQC/FQA
功能测试
冲裁2
SMT
普通双面板(片材生产)
计划投料
开料
钻孔
靶冲
快压
叠层
补强
补强快压
表面处理
装配
冲裁2
功能测试
FQC/FQA
FPC工艺

FPCFPC是Flexible Printed Circuit的简称,又称软性线路板、柔性印刷电路板,挠性线路板,简称软板或FPC,具有配线密度高、重量轻、厚度薄的特点,主要使用在手机、笔记本电脑、PDA、数码相机、LCM等很多产品。
目录FPC特点FPC生产流程FPC制程要点FPC贴装工艺要求和注意事项FPC特点1.可自由弯曲、折叠、卷绕,可在三维空间随意移动及伸缩。
2.2.散热性能好,可利用F-PC缩小体积。
3.3.实现轻量化、小型化、薄型化,从而达到元件装置和导线连接一体化。
FPC生产流程1. FPC生产流程:1.1 双面板制程:开料→钻孔→ PTH →电镀→前处理→贴干膜→对位→曝光→显影→图形电镀→脱膜→前处理→贴干膜→对位曝光→显影→蚀刻→脱膜→表面处理→贴覆盖膜→压制→固化→沉镍金→印字符→剪切→电测→冲切→终检→包装→出货1.2 单面板制程:开料→钻孔→贴干膜→对位→曝光→显影→蚀刻→脱膜→表面处理→贴覆盖膜→压制→固化→表面处理→沉镍金→印字符→剪切→电测→冲切→终检→包装→出货2. 开料2.1. 原材料编码的认识NDIR050513HJY: D→双面, R→压延铜, 05→PI厚0.5mil,即12.5um, 05→铜厚18um, 13→胶层厚13um.XSIE101020TLC: S→单面, E→电解铜, 10→PI厚25um, 10→铜厚度35um, 20→胶厚20um.CI0512NL:(覆盖膜) :05→PI厚12.5um, 12→胶厚度12.5um. 总厚度:25um.2.2.制程品质控制A.操作者应带手套和指套,防止铜箔表面因接触手上之汗而氧化.B.正确的架料方式,防止皱折.C.不可裁偏,手对裁时不可破坏冲制定位孔和测试孔.D.材料品质,材料表面不可有皱折,污点,重氧化现象,所裁切材料不可有毛边,溢胶等.3钻孔3.1打包: 选择盖板→组板→胶带粘合→打箭头(记号)3.1.1打包要求: 单面板30张,双面板6张, 包封15张.3.1.2盖板主要作用:A: 防止钻机和压力脚在材料面上造成的压伤B::使钻尖中心容易定位避免钻孔位置的偏斜C:带走钻头与孔壁摩擦产生的热量.减少钻头的扭断.3.2钻孔:3.2.1流程: 开机→上板→调入程序→设置参数→钻孔→自检→IPQA检→量产→转下工序.3.2.2. 钻针管制方法:a. 使用次数管制b. 新钻头之辨认,检验方法3.3. 品质管控点: a.钻带的正确b.对红胶片,确认孔位置,数量,正确. c确认孔是否完全导通. d. 外观不可有铜翘,毛边等不良现象.3.4.常见不良现象3.4.1断针: a.钻机操作不当b.钻头存有问题c.进刀太快等.3.4.2毛边a.盖板,垫板不正确b.静电吸附等等4.电镀4.1.PTH原理及作用: PTH即在不外加电流的情况下,通过镀液的自催化(钯和铜原子作为催化剂)氧化还原反应,使铜离子析镀在经过活化处理的孔壁及铜箔表面上的过程,也称为化学镀铜或自催化镀铜.4.2.PHT流程: 碱除油→水洗→微蚀→水洗→水洗→预浸→活化→水洗→水洗→速化→水洗→水洗→化学铜→水洗.4.3.PTH常见不良状况之处理4.3.1.孔无铜:a活化钯吸附沉积不好. b速化槽:速化剂浓度不对. c化学铜:温度过低,使反应不能进行反应速度过慢;槽液成分不对.4.3.2.孔壁有颗粒,粗糙: a化学槽有颗粒,铜粉沉积不均,开过滤机过滤. b板材本身孔壁有毛刺.4.3.3.板面发黑: a化学槽成分不对(NaOH浓度过高).4.4镀铜镀铜即提高孔内镀层均匀性,保证整个版面(孔内及孔口附近的整个镀层)镀层厚度达到一定的要求.4.4.1电镀条件控制a电流密度的选择b电镀面积的大小c镀层厚度要求d电镀时间控制4.4.1品质管控1 贯通性:自检QC全检,以40倍放大镜检查孔壁是否有镀铜完全附着贯通.2 表面品质:铜箔表面不可有烧焦,脱皮,颗粒状,针孔及花斑不良等现象.3 附着性:于板边任一处以3M胶带粘贴后,以垂直向上接起不可有脱落现象.5.线路5.1干膜干膜贴在板材上,经曝光后显影后,使线路基本成型,在此过程中干膜主要起到了影象转移的功能,而且在蚀刻的过程中起到保护线路的作用.5.2干膜主要构成:PE,感光阻剂,PET .其中PE和PET只起到了保护和隔离的作用.感光阻剂包括:连接剂,起始剂,单体,粘着促进剂,色料.5.3作业要求a保持干膜和板面的清洁, b平整度,无气泡和皱折现象.. c附着力达到要求,密合度高.5.4作业品质控制要点5.4.1为了防止贴膜时出现断线现象,应先用无尘纸粘尘滚轮除去铜箔表面杂质.5.4.2应根据不同板材设置加热滚轮的温度,压力,转数等参数.5.4.3保证铜箔的方向孔在同一方位.5.4.4防止氧化,不要直接接触铜箔表面.5.4.5加热滚轮上不应该有伤痕,以防止产生皱折和附着性不良5.4.6贴膜后留置10—20分钟,然后再去曝光,时间太短会使发生的有机聚合反应未完全,太长则不容易被水解,发生残留导致镀层不良.5.4.7经常用无尘纸擦去加热滚轮上的杂质和溢胶.5.4.8要保证贴膜的良好附着性.5.5贴干膜品质确认5.5.1附着性:贴膜后经曝光显影后线路不可弯曲变形或断等(以放大镜检测)5.5.2平整性:须平整,不可有皱折,气泡.5.5.3清洁性:每张不得有超过5点之杂质.5.6曝光5.6.1.原理:使线路通过干膜的作用转移到板子上.5.6.2作业要点:a作业时要保持底片和板子的清洁.b底片与板子应对准,正确.c不可有气泡,杂质.*进行抽真空目的:提高底片与干膜接触的紧密度减少散光现象.*曝光能量的高低对品质也有影响:1能量低,曝光不足,显像后阻剂太软,色泽灰暗,蚀刻时阻剂破坏或浮起,造成线路的断路.2.能量高,则会造成曝光过度,则线路会缩小或曝光区易洗掉.5.7显影5.7.1原理:显像即是将已经曝过光的带干膜的板材,经过(1.0+/-0.1)[%]的碳酸钠溶液(即显影液)的处理,将未曝光的干膜洗去而保留经曝光发生聚合反应的干膜,使线路基本成型.5.7.2影响显像作业品质的因素:a﹑显影液的组成b﹑显影温度. c﹑显影压力. d﹑显影液分布的均匀性.e﹑机台转动的速度.5.7.3制程参数管控:药液溶度,显影温度,显影速度,喷压.5.7.4显影品质控制要点:a﹑出料口扳子上不应有水滴,应吹干净.b﹑不可以有未撕的干膜保护膜.c﹑显像应该完整,线路不可锯齿状,弯曲,变细等状况.d﹑显像后裸铜面用刀轻刮不可有干膜脱落,否则会影响时刻品质.e﹑干膜线宽与底片线宽控制在+/-0.05mm以内的误差.f﹑线路复杂的一面朝下放置,以避免膜渣残留,减少水池效应引起的显影不均.g﹑根据碳酸钠的溶度,生产面积和使用时间来及时更新影液,保证最佳的显影效果.h﹑应定期清洗槽内和喷管,喷头中之水垢,防止杂质污染板材和造成显影液分布不均匀性.i﹑防止操作中产生卡板,卡板时应停转动装置,立即停止放板,并拿出板材送至显影台中间,如未完全显影,应进行二次显影.j﹑显影吹干后之板子应有绿胶片隔开,防止干膜粘连而影响到时刻品质.5.8蚀刻脱膜5.8.1原理:蚀刻是在一定的温度条件下(45—50)℃蚀刻药液经过喷头均匀喷淋到铜箔的表面,与没有蚀刻阻剂保护的铜发生氧化还原反应,而将不需要的铜反应掉,露出基材再经过脱膜处理后使线路成形.5.8.2蚀刻药液的主要成分:酸性蚀刻子液(氯化铜),双氧水,盐酸,软水5.9蚀刻品质控制要点:5.9.1以透光方式检查不可有残铜, 皱折划伤等5.9.2线路不可变形,无水滴.5.9.3时刻速度应适当,不允收出现蚀刻过度而引起的线路变细,和蚀刻不尽.5.9.4线路焊点上之干膜不得被冲刷分离或断裂5.9.5时刻剥膜后之板材不允许有油污,杂质,铜皮翘起等不良品质。
单面板工艺流程教程文件

"单面板工艺流程开料磨边•钻孔•外层图形・(全板镀金)•蚀刻•检验•丝印阻焊・(热风整平)一丝印字符一外形加工一测试一检验W双面板喷锡板工艺流程开料磨边•钻孔•沉铜加厚•外层图形•镀锡、蚀刻退锡•二次钻孔•检验•丝印阻焊•镀金插头•热风整平•丝印字符•外形加工•测试•检验W双面板镀镰金工艺流程开料磨边•钻孔•沉铜加厚•外层图形•镀鎳、金去膜蚀刻•二次钻孔•检验•丝印阻焊•丝印字符•外形加工•测试・检验"多层板喷锡板工艺流程开料磨边•钻定位孔•内层图形•内层蚀刻•检验•黑化•层压•钻孔•沉铜加厚•外层图形•镀锡、蚀刻退锡•二次钻孔•检验•丝印阻焊•镀金插头・热风整平•丝印字符-外形加工•测试•检验"多层板镀银金工艺流程开料磨边•钻定位孔•内层图形•内层蚀刻•检验•黑化•层压•钻孑L•沉铜加厚•外层图形•镀金、去膜蚀刻•二次钻孔•检验•丝印阻焊•丝印字符・外形加工•测试•检验円多层板沉银金板工艺流程开料磨边•钻定位孔•内层图形•内层蚀刻•检验•黑化•层压•钻孔•沉铜加厚•外层图形•镀锡、蚀刻退锡•二次钻孔•检验•丝印阻焊•化学沉银金-丝印字符-外形加工•测试-检验工艺简介沉金工艺之目的的是在印制线路表面上沉积颜色稳定,光亮度好,镀层平整,可焊性良好的魂金镀层。
基本可分为四个阶段:前处理(除油,微蚀,活化、后浸),沉镰,沉金,后处理(废金水洗,DI水洗,烘干)。
二、前处理沉金前处理一般有以下几个步骤:除油(30%AD-482),微蚀(60g/lnaPS,2%H2SO4),活化(10%Act-354-2),后浸(1%H2S04)。
以除去铜面氧化物,并在铜面沉锂,以作沉镣活化中心。
其中某个环节处理不好,将会影响随后的沉镰和沉金,并导致批量性的报废。
生产过程中,各种药水必须定期分析和补加,控制在要求范围内。
较重要的比如:微蚀速率应控制在“25U 40U',活化药水铜含量大于800PPM时必须开新缸,药水缸的清洁保养对联PCB的品质影响也较大,除油缸,微蚀缸,后浸缸应每周换缸,各水洗缸也应每周清洗。
- 1、下载文档前请自行甄别文档内容的完整性,平台不提供额外的编辑、内容补充、找答案等附加服务。
- 2、"仅部分预览"的文档,不可在线预览部分如存在完整性等问题,可反馈申请退款(可完整预览的文档不适用该条件!)。
- 3、如文档侵犯您的权益,请联系客服反馈,我们会尽快为您处理(人工客服工作时间:9:00-18:30)。
概述PCB(Printed Circuit Board),中文名称为印制线路板,简称印制板,是电子工业的重要部件之一。
几乎每种电子设备,小到电子手表、计算器,大到计算机,通讯电子设备,军用武器系统,只要有集成电路等电子元器件,为了它们之间的电气互连,都要使用印制板。
在较大型的电子产品研究过程中,最基本的成功因素是该产品的印制板的设计、文件编制和制造。
印制板的设计和制造质量直接影响到整个产品的质量和成本,甚至导致商业竞争的成败。
印制电路在电子设备中提供如下功能:提供集成电路等各种电子元器件固定、装配的机械支撑。
实现集成电路等各种电子元器件之间的布线和电气连接或电绝缘。
提供所要求的电气特性,如特性阻抗等。
为自动焊锡提供阻焊图形,为元件插装、检查、维修提供识别字符和图形。
有关印制板的一些基本术语在绝缘基材上,按预定设计,制成印制线路、印制元件或由两者结合而成的导电图形,称为印制电路。
在绝缘基材上,提供元、器件之间电气连接的导电图形,称为印制线路。
它不包括印制元件。
印制电路或者印制线路的成品板称为印制电路板或者印制线路板,亦称印制板。
印制板按照所用基材是刚性还是挠性可分成为两大类:刚性印制板和挠性印制板。
今年来已出现了刚性-----挠性结合的印制板。
按照导体图形的层数可以分为单面、双面和多层印制板。
导体图形的整个外表面与基材表面位于同一平面上的印制板,称为平面印板。
有关印制电路板的名词术语和定义,详见国家标准GB/T2036-94“印制电路术语”。
电子设备采用印制板后,由于同类印制板的一致性,从而避免了人工接线的差错,并可实现电子元器件自动插装或贴装、自动焊锡、自动检测,保证了电子设备的质量,提高了劳动生产率、降低了成本,并便于维修。
印制板从单层发展到双面、多层和挠性,并且仍旧保持着各自的发展趋势。
由于不断地向高精度、高密度和高可靠性方向发展,不断缩小体积、减轻成本、提高性能,使得印制板在未来电子设备地发展工程中,仍然保持强大的生命力。
三.印制板技术水平的标志:印制板的技术水平的标志对于双面和多层孔金属化印制板而言:既是以大批量生产的双面金属化印制板,在2.50或2.54mm标准网格交点上的两个焊盘之间,能布设导线的根数作为标志。
在两个焊盘之间布设一根导线,为低密度印制板,其导线宽度大于0.3mm。
在两个焊盘之间布设两根导线,为中密度印制板,其导线宽度约为0.2mm。
在两个焊盘之间布设三根导线,为高密度印制板,其导线宽度约为0. 1-0.15mm。
在两个焊盘之间布设四根导线,可算超高密度印制板,线宽为0.05--0.08mm。
国外曾有杂志介绍了在两个焊盘之间可布设五根导线的印制板。
对于多层板来说,还应以孔径大小,层数多少作为综合衡量标志。
PCB先进生产制造技术的发展动向综述国内外对未来印制板生产制造技术发展动向的论述基本是一致的,即向高密度,高精度,细孔径,细导线,细间距,高可靠,多层化,高速传输,轻量,薄型方向发展,在生产上同时向提高生产率,降低成本,减少污染,适应多品种、小批量生产方向发展。
印制电路的技术发展水平,一般以印制板上的线宽,孔径,板厚/孔径比值为代表,其发展历程和水平如下表:印制电路的技术发展水平:孔径(mm)线宽(mm)板厚/孔径比孔密度,孔数/CM211.00.25 1.5497010.80.17 2.57.597510.60.1351598010.40.10102598510.30.08204099010.150.054055995一、菲林底版菲林底版是印制电路板生产的前导工序,菲林底版的质量直接影响到印制板生产质量。
在生产某一种印制线路板时,必须有至少一套相应的菲林底版。
印制板的每种导电图形(信号层电路图形和地、电源层图形)和非导电图形(阻焊图形和字符)至少都应有一张菲林底片。
通过光化学转移工艺,将各种图形转移到生产板材上去。
菲林底版在印制板生产中的用途如下:图形转移中的感光掩膜图形,包括线路图形和光致阻焊图形。
网印工艺中的丝网模板的制作,包括阻焊图形和字符。
机加工(钻孔和外型铣)数控机床编程依据及钻孔参考。
随着电子工业的发展,对印制板的要求也越来越高。
印制板设计的高密度,细导线,小孔径趋向越来越快,印制板的生产工艺也越来越完善。
在这种情况下,如果没有高质量的菲林底版,能够生产出高质量的印制电路板。
现代印制板生产要求菲林底版需要满足以下条件:菲林底版的尺寸精度必须与印制板所要求的精度一致,并应考虑到生产工艺所造成的偏差而进行补偿。
菲林底版的图形应符合设计要求,图形符号完整。
菲林底版的图形边缘平直整齐,边缘不发虚;黑白反差大,满足感光工艺要求。
菲林底版的材料应具有良好的尺寸稳定性,即由于环境温度和湿度变化而产生的尺寸变化小。
双面板和多层板的菲林底版,要求焊盘及公共图形的重合精度好。
菲林底版各层应有明确标志或命名。
菲林底版片基能透过所要求的光波波长,一般感光需要的波长范围是3000--4000A。
以前制作菲林底版时,一般都需要先制出照相底图,再利用照相或翻版完成菲林底版的制作。
今年来,随着计算机技术的飞速发展,菲林底版的制作工艺也有了很大发展。
利用先进的激光光绘技术,极大提高了制作速度和底版的质量,并且能够制作出过去无法完成的高精度、细导线图形,使得印制板生产的CAM技术趋于完善。
基板材料覆铜箔层压板(Copper Clad Laminates,简写为CCL),简称覆铜箔板或覆铜板,是制造印制电路板(以下简称PCB)的基板材料。
目前最广泛应用的蚀刻法制成的PCB,就是在覆铜箔板上有选择的进行的蚀刻,得到所需的线路的图形。
覆铜箔板在整个印制电路板上,主要担负着导电、绝缘和支撑三个方面的功能。
印制板的性能、质量和制造成本,在很大程度上取决于覆铜箔板。
基本制造工艺流程印制板按照导体图形的层数可以分为单面、双面和多层印制板。
单面板的基本制造工艺流程如下:覆箔板-->下料-->烘板(防止变形)-->制模-->洗净、烘干-->贴膜(或网印) —>曝光显影(或抗腐蚀油墨) -->蚀刻-->去膜--->电气通断检测-->清洁处理-->网印阻焊图形(印绿油)-->固化-->网印标记符号-->固化-->钻孔-->外形加工-->清洗干燥-->检验-->包装-->成品。
双面板的基本制造工艺流程如下:近年来制造双面孔金属化印制板的典型工艺是SMOBC法和图形电镀法。
在某些特定场合也有使用工艺导线法。
1、图形电镀工艺流程覆箔板-->下料-->冲钻基准孔-->数控钻孔-->检验-->去毛刺-->化学镀薄铜-->电镀薄铜-->检验-->刷板-->贴膜(或网印)-->曝光显影(或固化)-->检验修板---->图形电镀(Cn十Sn/Pb)-->去膜-->蚀刻-->检验修板-->插头镀镍镀金-->热熔清洗-->电气通断检测-->清洁处理-->网印阻焊图形-->固化-->网印标记符号-->固化-->外形加工-->清洗干燥-->检验-->包装-->成品。
流程中“化学镀薄铜--> 电镀薄铜”这两道工序可用“化学镀厚铜”一道工序替代,两者各有优缺点。
图形电镀--蚀刻法制双面孔金属化板是六、七十年代的典型工艺。
八十年代中裸铜覆阻焊膜工艺(SMOBC)逐渐发展起来,特别在精密双面板制造中已成为主流工艺。
2、裸铜覆阻焊膜(SMOBC)工艺SMOBC板的主要优点是解决了细线条之间的焊料桥接短路现象,同时由于铅锡比例恒定,比热熔板有更好的可焊性和储藏性。
制造SMOBC板的方法很多,有标准图形电镀减去法再退铅锡的SMOBC工艺;用镀锡或浸锡等代替电镀铅锡的减去法图形电镀SMOBC工艺;堵孔或掩蔽孔法SMOBC 工艺;加成法SMOBC工艺等。
下面主要介绍图形电镀法再退铅锡的SMOBC工艺和堵孔法SMOBC工艺流程。
图形电镀法再退铅锡的SMOBC工艺法相似于图形电镀法工艺。
只在蚀刻后发生变化。
双面覆铜箔板-->按图形电镀法工艺到蚀刻工序-->退铅锡-->检查---->清洗--->阻焊图形-->插头镀镍镀金-->插头贴胶带-->热风整平---->清洗--->网印标记符号--->外形加工--->清洗干燥--->成品检验-->包装-->成品。
堵孔法主要工艺流程如下:双面覆箔板-->钻孔-->化学镀铜-->整板电镀铜-->堵孔-->网印成像(正像)-->蚀刻-->去网印料、去堵孔料-->清洗-->阻焊图形-->插头镀镍、镀金-->插头贴胶带-->热风整平-->下面工序与上相同至成品。
此工艺的工艺步骤较简单、关键是堵孔和洗净堵孔的油墨。
在堵孔法工艺中如果不采用堵孔油墨堵孔和网印成像,而使用一种特殊的掩蔽型干膜来掩盖孔,再曝光制成正像图形,这就是掩蔽孔工艺。
它与堵孔法相比,不再存在洗净孔内油墨的难题,但对掩蔽干膜有较高的要求。
SMOBC工艺的基础是先制出裸铜孔金属化双面板,再应用热风整平工艺。
PCB工程制作对于PCB印制板的生产来说,因为许多设计者并不了解线路板的生产工艺,所以其设计的线路图只是最基本的线路图,并无法直接用于生产。
因此在实际生产前需要对线路文件进行修改和编辑,不仅需要制作出可以适合本厂生产工艺的菲林图,而且需要制作出相应的打孔数据、开模数据,以及对生产有用的其它数据。
它直接关系到以后的各项生产工程。
这些都要求工程技术人员要了解必要的生产工艺,同时掌握相关的软件制作,包括常见的线路设计软件如:Protel、Pads2000、Autocad等等,更应熟悉必要的CAM软件如:View2001、CAM350;GCCAM等等,CAM应包括有PCB设计输入,可以对电路图形进行编辑、校正、修理和拼版,以磁盘为介质材料,并输出光绘、钻孔和检测的自动化数据。
基本制造工艺流程印制板按照导体图形的层数可以分为单面、双面和多层印制板。
单面板的基本制造工艺流程如下:覆箔板-->下料-->烘板(防止变形)-->制模-->洗净、烘干-->贴膜(或网印) —>曝光显影(或抗腐蚀油墨) -->蚀刻-->去膜--->电气通断检测-->清洁处理-->网印阻焊图形(印绿油)-->固化-->网印标记符号-->固化-->钻孔-->外形加工-->清洗干燥-->检验-->包装-->成品。