精密和超精密加工技术及其发展展望
精密和超精密加工技术复习思考题答案
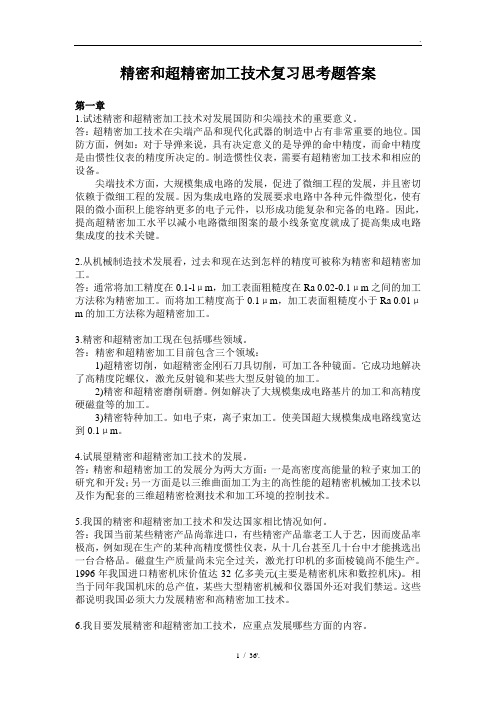
精密和超精密加工技术复习思考题答案第一章1.试述精密和超精密加工技术对发展国防和尖端技术的重要意义。
答:超精密加工技术在尖端产品和现代化武器的制造中占有非常重要的地位。
国防方面,例如:对于导弹来说,具有决定意义的是导弹的命中精度,而命中精度是由惯性仪表的精度所决定的。
制造惯性仪表,需要有超精密加工技术和相应的设备。
尖端技术方面,大规模集成电路的发展,促进了微细工程的发展,并且密切依赖于微细工程的发展。
因为集成电路的发展要求电路中各种元件微型化,使有限的微小面积上能容纳更多的电子元件,以形成功能复杂和完备的电路。
因此,提高超精密加工水平以减小电路微细图案的最小线条宽度就成了提高集成电路集成度的技术关键。
2.从机械制造技术发展看,过去和现在达到怎样的精度可被称为精密和超精密加工。
答:通常将加工精度在0.1-lμm,加工表面粗糙度在Ra 0.02-0.1μm之间的加工方法称为精密加工。
而将加工精度高于0.1μm,加工表面粗糙度小于Ra 0.01μm的加工方法称为超精密加工。
3.精密和超精密加工现在包括哪些领域。
答:精密和超精密加工目前包含三个领域:1)超精密切削,如超精密金刚石刀具切削,可加工各种镜面。
它成功地解决了高精度陀螺仪,激光反射镜和某些大型反射镜的加工。
2)精密和超精密磨削研磨。
例如解决了大规模集成电路基片的加工和高精度硬磁盘等的加工。
3)精密特种加工。
如电子束,离子束加工。
使美国超大规模集成电路线宽达到0.1μm。
4.试展望精密和超精密加工技术的发展。
答:精密和超精密加工的发展分为两大方面:一是高密度高能量的粒子束加工的研究和开发;另一方面是以三维曲面加工为主的高性能的超精密机械加工技术以及作为配套的三维超精密检测技术和加工环境的控制技术。
5.我国的精密和超精密加工技术和发达国家相比情况如何。
答:我国当前某些精密产品尚靠进口,有些精密产品靠老工人于艺,因而废品率极高,例如现在生产的某种高精度惯性仪表,从十几台甚至几十台中才能挑选出一台合格品。
先进制造技术的发展趋势
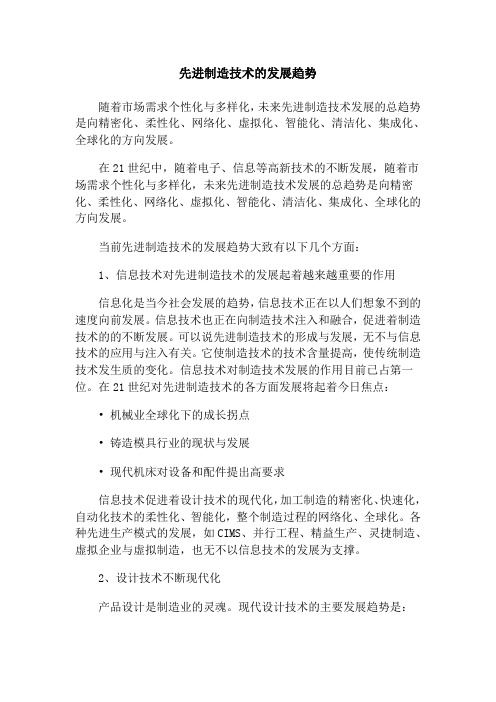
先进制造技术的发展趋势随着市场需求个性化与多样化,未来先进制造技术发展的总趋势是向精密化、柔性化、网络化、虚拟化、智能化、清洁化、集成化、全球化的方向发展。
在21世纪中,随着电子、信息等高新技术的不断发展,随着市场需求个性化与多样化,未来先进制造技术发展的总趋势是向精密化、柔性化、网络化、虚拟化、智能化、清洁化、集成化、全球化的方向发展。
当前先进制造技术的发展趋势大致有以下几个方面:1、信息技术对先进制造技术的发展起着越来越重要的作用信息化是当今社会发展的趋势,信息技术正在以人们想象不到的速度向前发展。
信息技术也正在向制造技术注入和融合,促进着制造技术的的不断发展。
可以说先进制造技术的形成与发展,无不与信息技术的应用与注入有关。
它使制造技术的技术含量提高,使传统制造技术发生质的变化。
信息技术对制造技术发展的作用目前已占第一位。
在21世纪对先进制造技术的各方面发展将起着今日焦点:• 机械业全球化下的成长拐点• 铸造模具行业的现状与发展• 现代机床对设备和配件提出高要求信息技术促进着设计技术的现代化,加工制造的精密化、快速化,自动化技术的柔性化、智能化,整个制造过程的网络化、全球化。
各种先进生产模式的发展,如CIMS、并行工程、精益生产、灵捷制造、虚拟企业与虚拟制造,也无不以信息技术的发展为支撑。
2、设计技术不断现代化产品设计是制造业的灵魂。
现代设计技术的主要发展趋势是:(1)设计手段的计算机化在实现了计算机计算、绘图的基础上,当前突出反映在数值仿真或虚拟现实技术在设计中的应用,以及现代产品建模理论的发展上,并且向智能化设计方向发展。
(2)新的设计思想和方法不断出现如并行设计、面向“X”的设计(Design For X--DFX)、健壮设计(Robust Design)、优化设计Optimal Design)、反求工程技术(Revese Engineering)等。
(3)向全寿命周期设计发展传统的设计只限于产品设计,全寿命周期设计则由简单的、具体的、细节的设计转向复杂的总体的设计和决策,要通盘考虑包括设计、制造、检测、销售、使用、维修、报废等阶段的产品的整个生命周期。
精密注塑模具设计加工及发展前景

精密注塑模具设计加工及发展前景摘要:随着技术的进步,模具的制作也变得更加精细。
在当前的整体模具制造中,精确注射模的设计与制造有着相当大的发展空间。
在精密注射成型工艺中,该工艺不仅能保证产品的品质,而且还能提高产品的产量。
文章重点阐述了该产品的开发和制造工艺,并对该产品的开发和制造进行了展望。
关键词:精密注塑模具;设计加工;发展前景;引言注塑模具是一种利用其特殊的型腔形状,通过塑料注塑机对其进行复现,或对其进行复现。
与一般的注塑模具不同之处,就是它的模具自身的设计和加工精度比较高,成型产品的精度也比较高。
因此,它具有高的品质和较长的使用寿命,可以适用于大规模的、快速的生产,因此,它被大量地用于现代制造业。
1.开发精密注塑模具的意义1.1提升模具的生产质量由于精密注射模的特殊设计和处理技术,提高了模具行业的产品质量,因此,研究和开发具有高精度和高质量的模具,对于提高模具制造业的发展具有重要意义。
随着现代工业生产对生产设备的要求越来越高,用户对产品的使用感受的需求也越来越多,因此,通过传统的模具加工技术生产出来的模具在使用率和寿命期限上都已经渐渐落后,很难满足日益增长的高标准的市场需求。
因此,研发出一套精确的注塑模具,能够有效地提升模具生产的整体品质,在一定程度上避免浪费,实现更长的寿命期限,这对模具生产企业的发展大有裨益。
1.2推动模具生产产业的发展进步在国内,精确注射模的设计与制造技术还没有得到很好的发展,它还在持续地进行着革新与构建,随着行业的发展,精密注塑技术逐渐完善、娴熟,该模型的设计与制造项目也将逐渐走上轨道。
伴随着国民经济的发展,对制造装备的要求越来越高,因此,精确注塑模具的发展潜力巨大,未来将给模具制造行业带来巨大的利润,还可以提高产品的品质,获得更高的品牌知名度。
因此,精确注射模具的持续发展,将会对模具制造工业的发展起到积极的作用,推动工业技术的发展,进而推动经济的发展。
2.精密注塑模具设计加工2.1设计方法毫无疑问,由于精确注射过程非常细致且非常复杂,因此在设计精确注射模具时,也就有了相当高的要求。
超精密制造技术论文
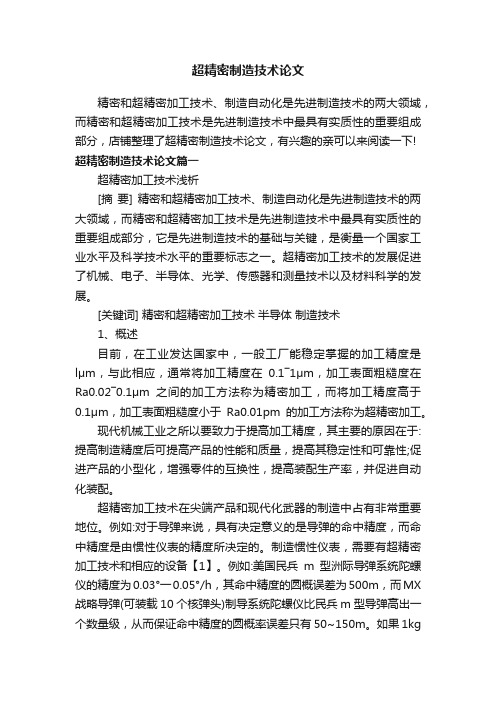
超精密制造技术论文精密和超精密加工技术、制造自动化是先进制造技术的两大领域,而精密和超精密加工技术是先进制造技术中最具有实质性的重要组成部分,店铺整理了超精密制造技术论文,有兴趣的亲可以来阅读一下! 超精密制造技术论文篇一超精密加工技术浅析[摘要] 精密和超精密加工技术、制造自动化是先进制造技术的两大领域,而精密和超精密加工技术是先进制造技术中最具有实质性的重要组成部分,它是先进制造技术的基础与关键,是衡量一个国家工业水平及科学技术水平的重要标志之一。
超精密加工技术的发展促进了机械、电子、半导体、光学、传感器和测量技术以及材料科学的发展。
[关键词] 精密和超精密加工技术半导体制造技术1、概述目前,在工业发达国家中,一般工厂能稳定掌握的加工精度是lμm,与此相应,通常将加工精度在0.1―1μm,加工表面粗糙度在Ra0.02―0.1μm之间的加工方法称为精密加工,而将加工精度高于0.1μm,加工表面粗糙度小于Ra0.01pm的加工方法称为超精密加工。
现代机械工业之所以要致力于提高加工精度,其主要的原因在于:提高制造精度后可提高产品的性能和质量,提高其稳定性和可靠性;促进产品的小型化,增强零件的互换性,提高装配生产率,并促进自动化装配。
超精密加工技术在尖端产品和现代化武器的制造中占有非常重要地位。
例如:对于导弹来说,具有决定意义的是导弹的命中精度,而命中精度是由惯性仪表的精度所决定的。
制造惯性仪表,需要有超精密加工技术和相应的设备【1】。
例如:美国民兵m型洲际导弹系统陀螺仪的精度为0.03°一0.05°/h,其命中精度的圆概误差为500m,而MX 战略导弹(可装载10个核弹头)制导系统陀螺仪比民兵m型导弹高出一个数量级,从而保证命中精度的圆概率误差只有50~150m。
如果1kg重的陀螺转子,其质量中心偏离其对称轴0.5nm,则会引起100m的射程误差和50m的轨道误差。
惯性仪表中有许多零件的制造精度都要求达到小于微米级。
答案精密加工课后习题—黄

.
.
液压喷砂法,用高压泵打出流量为20L/min、压力为150Pa的冷却液,进入喷嘴的漩涡室时,形成低压,从
边孔中吸入碳化硅或刚玉等磨粒及空气,与冷却液形成混合液,并以高速喷嘴喷射到转动的砂轮上。
晶面。
网面最小单元不同,100是正方形,110为矩形,111为三角形,网面密度100:110:111为1:1.414:2.308
网面距不同:100与110为均匀分布,分别为D/4=0.089mm,sqrt(2)D/4=0.126mm,111为宽窄交替宽为
sqrt(3)D/4=0.154mm,窄为sqrt(3)D/12=0.1051mm
光刃的长度对表面加工质量效果不大,对刀不易
圆弧刃容易对刀,半径可取R=2~5mm。可加工高质量的超光滑表面,缺点是刀具制造复杂
2-19试述金刚石刀具的前面应选哪个晶面
选用100面,111面硬度高,而微观破损强度并不高,研磨加工困难。
选用100面的原因:
1)100面耐磨性高于110面,刀具使用寿命长
2)100面微观破损强度高于110面,产生崩刃的机会小
解理现象:111面的面网宽面距比100和110都大,最易解理。
好磨难磨方向可用图表示:
.
.
好磨方向
难磨方向
100磨削率:111磨削率:110磨削率=5.8:1:12.8
2-15金刚石晶体有哪些定向方法?
1)人工目测定向2)X射线定向3)激光定向
2-16试述金刚石晶体的激光定向原理和方法。
利用金刚石在不同晶面方向上,晶体结构不同,对激光反射形成的衍射图像不同而进行。
小后面与加工表面间的摩擦
2-10工件材料的晶体方向对切削变形和加工表面质量的影响如何?
精密加工课后习题答案
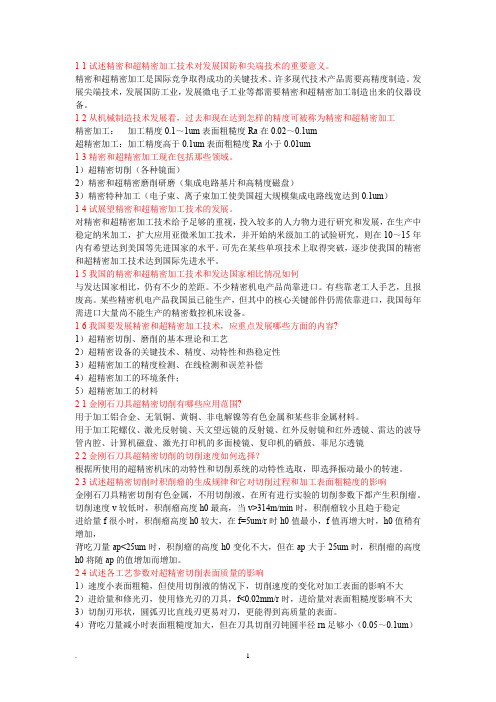
1-1试述精密和超精密加工技术对发展国防和尖端技术的重要意义。
精密和超精密加工是国际竞争取得成功的关键技术。
许多现代技术产品需要高精度制造。
发展尖端技术,发展国防工业,发展微电子工业等都需要精密和超精密加工制造出来的仪器设备。
1-2从机械制造技术发展看,过去和现在达到怎样的精度可被称为精密和超精密加工精密加工:加工精度0.1~1um表面粗糙度Ra在0.02~0.1um超精密加工:加工精度高于0.1um表面粗糙度Ra小于0.01um1-3精密和超精密加工现在包括那些领域。
1)超精密切削(各种镜面)2)精密和超精密磨削研磨(集成电路基片和高精度磁盘)3)精密特种加工(电子束、离子束加工使美国超大规模集成电路线宽达到0.1um)1-4试展望精密和超精密加工技术的发展。
对精密和超精密加工技术给予足够的重视,投入较多的人力物力进行研究和发展,在生产中稳定纳米加工,扩大应用亚微米加工技术,并开始纳米级加工的试验研究,则在10~15年内有希望达到美国等先进国家的水平。
可先在某些单项技术上取得突破,逐步使我国的精密和超精密加工技术达到国际先进水平。
1-5我国的精密和超精密加工技术和发达国家相比情况如何与发达国家相比,仍有不少的差距。
不少精密机电产品尚靠进口。
有些靠老工人手艺,且报废高。
某些精密机电产品我国虽已能生产,但其中的核心关键部件仍需依靠进口,我国每年需进口大量尚不能生产的精密数控机床设备。
1-6我国要发展精密和超精密加工技术,应重点发展哪些方面的内容?1)超精密切削、磨削的基本理论和工艺2)超精密设备的关键技术、精度、动特性和热稳定性3)超精密加工的精度检测、在线检测和误差补偿4)超精密加工的环境条件;5)超精密加工的材料2-1金刚石刀具超精密切削有哪些应用范围?用于加工铝合金、无氧铜、黄铜、非电解镍等有色金属和某些非金属材料。
用于加工陀螺仪、激光反射镜、天文望远镜的反射镜、红外反射镜和红外透镜、雷达的波导管内腔、计算机磁盘、激光打印机的多面棱镜、复印机的硒鼓、菲尼尔透镜2-2金刚石刀具超精密切削的切削速度如何选择?根据所使用的超精密机床的动特性和切削系统的动特性选取,即选择振动最小的转速。
超精密加工技术认识及发展前景
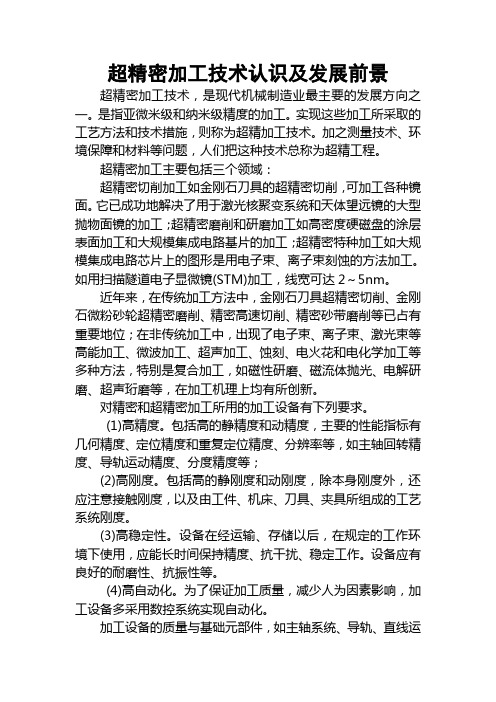
超精密加工技术认识及发展前景超精密加工技术,是现代机械制造业最主要的发展方向之一。
是指亚微米级和纳米级精度的加工。
实现这些加工所采取的工艺方法和技术措施,则称为超精加工技术。
加之测量技术、环境保障和材料等问题,人们把这种技术总称为超精工程。
超精密加工主要包括三个领域:超精密切削加工如金刚石刀具的超精密切削,可加工各种镜面。
它已成功地解决了用于激光核聚变系统和天体望远镜的大型抛物面镜的加工;超精密磨削和研磨加工如高密度硬磁盘的涂层表面加工和大规模集成电路基片的加工;超精密特种加工如大规模集成电路芯片上的图形是用电子束、离子束刻蚀的方法加工。
如用扫描隧道电子显微镜(STM)加工,线宽可达2~5nm。
近年来,在传统加工方法中,金刚石刀具超精密切削、金刚石微粉砂轮超精密磨削、精密高速切削、精密砂带磨削等已占有重要地位;在非传统加工中,出现了电子束、离子束、激光束等高能加工、微波加工、超声加工、蚀刻、电火花和电化学加工等多种方法,特别是复合加工,如磁性研磨、磁流体抛光、电解研磨、超声珩磨等,在加工机理上均有所创新。
对精密和超精密加工所用的加工设备有下列要求。
(1)高精度。
包括高的静精度和动精度,主要的性能指标有几何精度、定位精度和重复定位精度、分辨率等,如主轴回转精度、导轨运动精度、分度精度等;(2)高刚度。
包括高的静刚度和动刚度,除本身刚度外,还应注意接触刚度,以及由工件、机床、刀具、夹具所组成的工艺系统刚度。
(3)高稳定性。
设备在经运输、存储以后,在规定的工作环境下使用,应能长时间保持精度、抗干扰、稳定工作。
设备应有良好的耐磨性、抗振性等。
(4)高自动化。
为了保证加工质量,减少人为因素影响,加工设备多采用数控系统实现自动化。
加工设备的质量与基础元部件,如主轴系统、导轨、直线运动单元和分度转台等密切相关,应注意这些元部件质量。
此外,夹具、辅具等也要求有相应的高精度、高刚度和高稳定性。
航天、航空工业中,人造卫星、航天飞机、民用客机等制造中都有大量的精密和超精密加工的需求,如人造卫星用的姿态轴承和遥测部件对观测性能影响很大。
精密和超精密加工技术及其发展展望(精密加工)
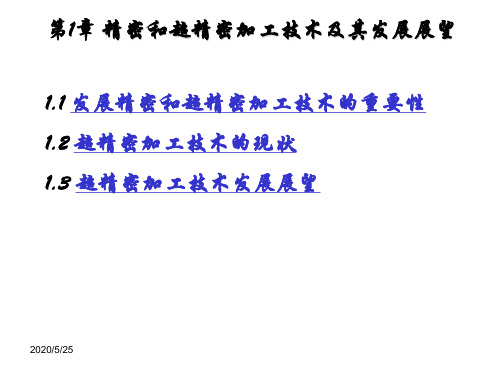
1.2 超精密加工技术的现状
4 加工工具
加工工具主要是指刀具、磨具及刃磨技术。用 金刚石刀具超精密切削,值得研究的问题有:金刚 石刀具的超精密刃磨,其刃口钝圆半径应达到2~ 4nm,同时应解决其检测方法,刃口钝圆半径与切 削厚度关系密切,若切削的厚度欲达到10nm,则刃 口钝圆半径应为2nm。
表面粗糙度可用电感式、压电晶体式表面形貌仪等
进行接触测量,或用光纤法、电容法、超声微波法和 隧道显微镜法进行非接触测量;
表面应力、表面变质层深度、表面微裂纹等缺陷,
可用X光衍射法、激光干涉法等来测量。检测可采取 离线的、在位的和在线的三种方式。
2013-9-22
1.2 超精密加工技术的现状
5 检测与误差补偿
在非传统加工中,出现了电子束、离子束、激
光束等高能加工、微波加工、超声加工、刻蚀、电 火花和电化学加工等多种方法,特别是复合加工, 如磁性研磨、磁流体抛光、电解研磨、超声珩磨等 ,在加工机理上均有所创新。
2013-9-22
1.2 超精密加工技术的现状
2 被加工材料
用精密和超精密加工的零件,其材料的化学成 分、物理力学性能、加工工艺性能均有严格要求。 例如,要求被加工材料质地均匀,性能稳定,无外 部及内部微观缺陷;其化学成分的误差应在10-2 ~ 10-3数量级,不能含有杂质;其物理力学性能,如拉 伸强度、硬度、延伸率、弹性模量、热导率和膨胀 系数等应达到10-5~10-6数量级;材料在冶炼、铸造 、辗轧、热处理等工艺过程中,应严格控制熔渣过 滤、辗轧方向、温度等,使材质纯净、晶粒大小匀 称、无方向性,能满足物理、化学、力学等性能要 求。
国家(中小零件加工) 。
我国的超精密加工技术在70年代末期有了长足
第一章 精密和超精密加工技术及发展展望要点

精密与超精密加工技术概述
◆精密加工 —— 在一定的发展时期,加工精度和表面质量 达到较高程度的加工工艺。
超精密加工 —— 在一定的发展时期,加工精度和表面质 量达到最高程度的加工工艺。
◆瓦特改进蒸汽机 —— 镗孔精度 1mm 20 世纪 40 年代 —— 最高精度 1μm 20 世纪 末 —— 精密加工:≤0.1μm,Ra ≤0.01μm(亚微米加工) 超精密加工:≤ 0.01μm ,Ra≤ 0.001μm(纳米加工)
◆微细加工 —— 微小尺寸的精密加工 超微细加工 ——微小尺寸的超精密加工
几种典型精密零件的加工精度
零件 激光光学零件
多面镜 磁头 磁盘 雷达导波管 卫星仪表轴承 天体望远镜
加工精度 形状误差 0.1μm 平面度误差 0.04μm 平面度误差 0.04μm 波度 0.01 ~0.02μm 平面度垂直度误差 < 0.1μm 圆柱度误差 <0.01μm 形状误差 < 0.03μm
• 超精密加工的对象
– 有色金属及合金 – 硬脆材料 – 黑色金属 – 复合材料
中小型精密零件的加工精度
加工零件 (μm)
激光光学零件 磁头 多面镜 磁盘 磁盘 非球面模具
Ra (μm)
0.01~0.006 0.02 0.01~0.02 0.01~0.004 0.01~0.004 0.01
形状精度
0.1
平面度 0.04 平面度 0.04 波度0.02~0.01 波度0.02~0.01
1~0.3
超精密加工的设备
• 美国LLL实验室的 DTM-3、LODTM超 精密金刚石车床
• 英国Cranfield的OAGM2500超精密金 刚石车床
精密和超精密加工技术的发展
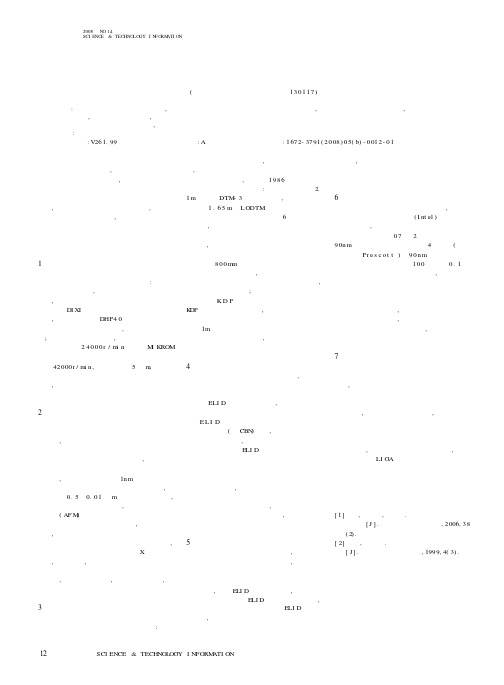
科技资讯科技资讯S I N &T NOL OGY I NFORM TI ON 2008N O .14SCI ENC E &TEC HNO LO GY I N F O RM ATI O N 工业技术国外已开发了多种精密和超精密车削、磨削、抛光等机床设备,发展了新的精密加工和精密测量技术。
目前,我国每年需进口大量国内尚不能生产的精密数控机床设备和仪器。
为了使我国的国防和科技发展不受制于人,我们必须投入必要的人力物力,自主发展精密和超精密加工技术,争取尽快将我国的精密和超精密加工技术水平提升到世界先进水平。
下面是对国内外精密和超精密加工技术的最新发展情况的介绍。
1精密机床技术的发展精密机床是精密加工的基础当今精密机床技术的发展方向是:在继续提高精度的基础上,采用高速切削以提高加工效率,同时采用先进数控技术提高其自动化水平。
瑞士DI XI 公司以生产卧式坐标镗床闻名于世,该公司生产的DHP40高精度卧式高速镗床已增加了多轴数控系统,成为一台加工中心;同时为实现高速切削,已将机床主轴的最高转速提高到24000r /m i n 。
瑞士M I KROM 公司的高速精密五轴加工中心的主轴最高转速为42000r /m i n,定位精度达5μm ,已达到过去坐标镗床的精度。
从这两台机床的性能可知,现在的加工中心与高速切削机床间已不再有严格的界限划分。
2使用金刚石刀具的超精密切削技术超精密切削技术的进展金刚石刀具超精密切削技术是超精密加工技术的一个重要组成部份,不少国防尖端产品零件都需要利用金刚石超精密切削来加工。
使用单晶金刚石刀具在超精密机床上进行超精密切削,可加工出光洁度极高的镜面。
超精密切削的切削厚度可极小,最小切削厚度可至1nm 。
超精密切削使用的单晶金刚石刀具要求刃口极为锋锐,刃口半径在0.5~0.01μm 。
因刃口半径甚小,过去对刃口的测量极为困难,现已可用原子力显微镜(AF M )进行测量。
机械工程前沿

机械工程前沿之精密超精密加工技术1 引言近些年,随着社会经济的不断发展,精密加工和超精密加工技术已成为机械制造技术的前沿标志。
它反映着一个工业国家机械加工的水平,它是六十年代应电子、计算机、宇航及激光尖端技术的发展而发展起来的一门新兴工艺技术。
在三十年的时间里,利用近代先进的技术和工艺使机械加工精度提高了一个数量级,目前正从微米、亚微米向纳米级精度迈进。
提高制造精度后可提高产品的性能和质量,提高其稳定性和可靠性;促进产品的小型化;增强零件的互换性,提高装配生产率,并促进自动化装配。
现如今,无论是科研领域还是生产领域,这项技术都得到了必要的应用。
这项技术的重要性是不言而喻的,直接关系到工艺事业的发展进程。
本文从精密超精密加工技术的相关理论、发展现状、运用三个角度,对该问题进行深入地分析与研究。
2 精密超精密加工技术理论众所周知,加工是一个非常宽泛的词汇。
在现实生活中,存在着普通加工、精密加工和超精密加工三种形式的加工。
普通加工是指一般技术水平就完成的精度;精密加工是指通过高精度的加工工具或器械,以及先进的加工技术才能实现的精度;超精密加工是指必须对先进加工技术进行实验、讨论、研究才能完成的精度。
每个时期的精度指标是不同的,因此,这三种形式的加工也会随着时间的变化而变化。
超精密加工技术以每个历史时期所能达到的最高加工精度值为衡量标准,只要超过了这个标准,我们就可将这些加工方法称之为超精密加工技术。
就目前的标准而言,精密加工技术的加工精度为1一0.1um、表面粗糙度为Ra0.2一0.01um;而超精密加工技术的加工精度高于0.1um、表面粗糙度Ra小于0.25um,以及所用机床定位精度的分辨率和重复性高于0.01um。
超精密加工主要包括三个领域:(1) 超精密切削加工如金刚石刀具的超精密切削,可加工各种镜面。
它已成功地解决了用于激光核聚变系统和天体望远镜的大型抛物面镜的加工。
(2) 超精密磨削和研磨加工如高密度硬磁盘的涂层表面加工和大规模集成电路基片的加工。
超精密加工的发展与展望
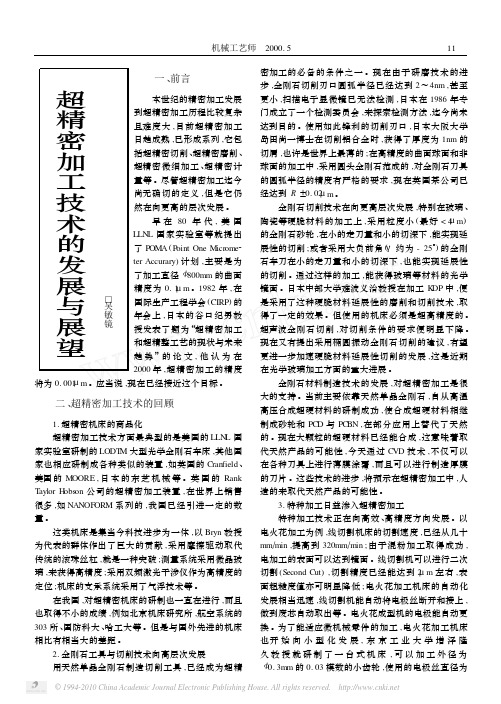
□吴敏镜 超精密加工技术的发展与展望 一、前言本世纪的精密加工发展到超精密加工历程比较复杂且难度大,目前超精密加工日趋成熟,已形成系列,它包括超精密切削、超精密磨削、超精密微细加工、超精密计量等。
尽管超精密加工迄今尚无确切的定义,但是它仍然在向更高的层次发展。
早在80年代,美国LLN L 国家实验室等就提出了POMA (P oint One Microme 2ter Accurary )计划,主要是为了加工直径<800mm 的曲面精度为0.1μm 。
1982年,在国际生产工程学会(CIRP )的年会上,日本的谷口纪男教授发表了题为“超精密加工和超精整工艺的现状与未来趋势”的论文,他认为在2000年,超精密加工的精度将为0.001μm 。
应当说,现在已经接近这个目标。
二、超精密加工技术的回顾1.超精密机床的商品化超精密加工技术方面最典型的是美国的LLN L 国家实验室研制的LODT M 大型光学金刚石车床,其他国家也相应研制成各种类似的装置,如英国的Cran field 、美国的MOORE ,日本的东芝机械等。
英国的Rank T aylor H obs on 公司的超精密加工装置,在世界上销售很多,如NANOFORM 系列的,我国已经引进一定的数量。
这类机床是集当今科技进步为一体,以Bryn 教授为代表的群体作出了巨大的贡献,采用摩擦驱动取代传统的滚珠丝杠,就是一种突破;测量系统采用微晶玻璃,来获得高精度;采用双频激光干涉仪作为高精度的定位;机床的支承系统采用了气浮技术等。
在我国,对超精密机床的研制也一直在进行,而且也取得不小的成绩,例如北京机床研究所,航空系统的303所、国防科大、哈工大等。
但是与国外先进的机床相比有相当大的差距。
2.金刚石工具与切削技术向高层次发展用天然单晶金刚石制造切削工具,已经成为超精密加工的必备的条件之一。
现在由于研磨技术的进步,金刚石切削刃口圆弧半径已经达到2~4nm ,甚至更小,扫描电子显微镜已无法检测,日本在1986年专门成立了一个检测委员会,来探索检测方法,迄今尚未达到目的。
超精密加工的发展和展望

超精密加工的发展和展望精密和超精密制造工程是适应前沿高技术发展需求而发展起来的。
它是一个国家重要经济和技术实力的体现,是其它高新技术实施的基础。
超精密制造技术是当前各个工业国家发展的核心技术之一,各技术先进国家在高技术领域(如国防工业、集成电路、信息技术产业等)之所以一直领先,与这些国家高度重视和发展超精密制造技术有极其重要的关系。
超精密制造技术是随着测量技术的发展而发展的。
Renishaw、Heidenhain及SONY等公司发展了分辨率均可以达到1nm的测量元件;美国HP公司、英国Taylor、美国zygo等公司的测量仪器均可以满足纳米测量的需求。
超精密制造技术在国际上已经得到广泛应用。
与国防工业有关的如人造卫星用的姿态轴承和遥测部件、被送入太空的哈勃望远镜(HST)、飞机发动机转子叶片等;与集成电路(IC)有关的硅片加工(要求硅片的加工表面粗糙度Ra一般小于2nm,精度要求达0.1nm);此外光刻设备和硅片加工设备的精度要求到亚微米和纳米级。
仪表的精度、激光陀螺仪的平面反射镜的精度、红外制导的反射镜等,其表面粗糙度均要求达到纳米级。
另外,光学非球曲面零件面形制造精度要求已达λ/(30—50),表面粗糙度要求≤0.5nm。
1、超精密制造技术的发展状况1962年美国Union Carbide公司研制出首台超精密车床。
在美国能源部支持下,LLI实验室和Y—12工厂合作,与1983年成功地研制出大型超精密金刚石车床(DTM—3型)。
该机床可加工直径¢2100mm,多路激光干涉测量系统分辨率为2.5nm。
1984年,LLL实验室成功地研制出LODTM大型金刚石车床。
该机床可加工的最大直径为¢1625mm x500mm,重量1360kg。
采用的双频激光测量系统分辨率为0.7nm,其主轴静态精度为:径向跳动≤25nm,轴向窜动≤51nm。
LLL实验室这两台机床是目前公认的国际上水平最高的超精密机床。
CUPE(Cranfield Unit for Precision Engineering)研制的Nanocenter超精密车床已批量生产,其主轴精度≤50nm,加工工件的面形精度≤0.1μm。
精密与超精密加工技术现状和发展展望

精密与超精密加工技术现状和发展展望精密加工技术是一种在当今制造业中非常重要的技术,它的发展与制造业的发展息息相关。
精密加工技术是通过对材料进行高精度的加工来制造出各种精密零部件,这些精密零部件被广泛应用于汽车、航空航天、医疗器械、电子产品等各个领域。
现阶段,精密加工技术已经取得了很大的进步,各种高精度的加工设备和加工工艺层出不穷。
在这些技术发展的基础上,超精密加工技术应运而生。
超精密加工技术是一种相对于精密加工技术更加高端、更加精密的加工技术,它可以实现对材料的超高精度加工,甚至可以达到纳米级的精度。
这种技术对于一些特殊材料的加工非常重要,比如硬质合金、钢、陶瓷等材料。
超精密加工技术的发展展望是非常乐观的。
随着科学技术的不断进步,各种先进的加工设备和工艺将不断涌现。
在这种趋势下,超精密加工技术将会得到更加广泛的应用。
在汽车工业中,超精密加工技术可以用于制造高压油泵的零部件,提高汽车发动机燃油的利用率;在医疗器械领域,超精密加工技术可以用于制造各种医疗器械的零部件,提高医疗器械的精度和安全性。
在未来的发展中,我们还可以看到超精密加工技术将会在航空航天领域得到更广泛的应用。
超精密加工技术可以制造出更加轻巧和高强度的航空零部件,提高航空器的性能和安全性。
超精密加工技术在电子产品领域也有很大的潜力,它可以制造出更小巧、更精密的电子元件,提高电子产品的性能和可靠性。
精密加工技术和超精密加工技术的发展是非常重要的。
它们直接关系到制造业的发展和产品的质量。
相信随着科学技术的不断进步,这些技术将会取得更大的突破,为各个领域带来更多的创新和发展。
精密与超精密加工技术的现状和发展展望精密加工技术是制造业中至关重要的一环,它的发展与制造业的发展密不可分。
精密加工技术通过对材料进行高精度的加工,制造出各种精密零部件,广泛应用于汽车、航空航天、医疗器械、电子产品等各个领域。
当前,精密加工技术已取得了长足的发展,各种高精度加工设备和工艺不断涌现。
精密和超精密加工技术PPT课件

精密和超精密加工技术
1
教材:《精密和超精密加工技术》(第2版) 袁哲俊、王先逵主编 机械工业出版社
➢ 学时:28 ➢ 周二下午5-6节(H514) ➢ 周四上午1-2节(H514)
参考材料: 1、张建华主编《精密与特种加工技术》 2、王先逵编《精密加工技术实用手册》,
8
1.1 发展精密和超精密加工技术的重要性
精密和超精密加工是先进制造技术的基础和关键
作为制造技术的主战场,作为真实产品的实 际制造,必然要靠精密加工和超精密加工技术, 例如,计算机工业的发展不仅要在软件上,还要 在硬件上,即在集成电路芯片上有很强的能力, 应该说,当前,我国集成电路的制造水平约束了 计算机工业的发展。美国制造工程研究者提出的 汽车制造业的“两毫米工程”使汽车质量赶上欧、 日水平,其中的举措都是实实在在的制造技术。
热流动加工(高频电流、热射流、电子束、激光) 液体、气体流动加工(压铸、挤压、喷射、浇铸) 微粒子流动加工
5
精密和超精密加工方法分类(2)
分类 切削加工 磨料加工
特种加工
复合加工
加工方法
等离子体切削 微细切削 微细钻削
微细磨削 研磨 抛光 弹性发射加工 喷射加工
电火花成形加工 电火花切割加工 电解加工 超声波加工 微波加工 电子束加工 粒子束去除加工 激光去除加工 光刻加工
段,通常,按加工精度划分,可将机械加工分为一般 加工、精密加工、超精密加工三个阶段。
➢精密加工:加工精度在0.1~1µm,加工表面粗糙
度在Ra0.02~0.1µm之间的加工方法称为精密加工;
➢超精密加工:加工精度高于0.1µm,加工表面粗糙
浅谈数控技术的国内外分析与发展趋势的展望

浅谈数控技术的国内外分析与发展趋势的展望摘要:新中国成立后,我国的工业化在六十多年的时间里得到长足发展,在日新月异的全球化潮流中勇创佳绩,已经成为了拥有独立且最为完整工业体系的国家。
“十四五”规划,我国开启了全面建设社会主义现代化国家新征程,也是我国制造强国建设的关键五年,我国的工业化正在逐步向“内生增长、创新驱动、智能绿色、协同开放”方向加快升级转变。
工业的发展离不开制造业的不断革新进步,而制造业又是我国的经济支柱性产业。
在“中国制造”向“中国智造”不断前行的征途上,对科学技术的依赖性越来越强,制造业潜能不断被发掘,数控技术就是推动制造业向智能化方向进一步发展的催化剂。
关键词:数控技术;现状;发展趋势数控技术是先进制造技术的核心,是在机械制造业中新兴的综合性技术,集合了微电子和计算机技术、信息处理技术、精密检测技术、自动控制技术、光机电技术、网络通信技术等高新技术于一体,不断推动传统制造业转型升级,同时也对数控技术不断优化提出新要求。
谋求进步就要理清发展脉络,本文将浅谈数控技术的发展现状,并对未来发展趋势做出合理预测。
一、数控技术的发展现状分析(一)国外数控技术发展自上世纪九十年代中期开始,国外数控技术大致经历了两阶段式发展。
第一阶段称为NC(Number control即数字控制),是由操作者自己运用文本符号等编程进而实现机器自动化运行。
第二阶段称为CNC(Computer number control即计算机数值控制),是通过计算机中高效的系统控制软件进行机器运行数值计算,直接发出运行和控制指令。
1952年,在美国麻省理工学院研制成功的电子管数控系统开启先河,随后又创造出晶体管数控系统,但由于装备零件昂贵难以得到广泛推广,科学家开始向集成电路控制系统研究,并在之后生产出小型计算机、微型计算机数控系统,随着信息处理技术和精度控制技术的不断发展,创造出开发式数控系统,不仅能够在不同平台运行,还可以与其他系统相互配合实现操作目标。
- 1、下载文档前请自行甄别文档内容的完整性,平台不提供额外的编辑、内容补充、找答案等附加服务。
- 2、"仅部分预览"的文档,不可在线预览部分如存在完整性等问题,可反馈申请退款(可完整预览的文档不适用该条件!)。
- 3、如文档侵犯您的权益,请联系客服反馈,我们会尽快为您处理(人工客服工作时间:9:00-18:30)。
电刷
工作台
绝缘板
磁力抛光
把磁性磨料放工件与磁 极间的入磁场中,磁性磨 振动运 料在延磁力线方向有序排 动 列成具有一定柔性的磁力 刷。加工时工件旋转,并 N 作相对磁极轴向振动;磁 性磨料使工件表面上极薄 工件 的金属层及毛边去除,将 (陶瓷滚柱) 表面逐步整平以达良好的 研磨效果
电极 放电管 冷却水进口 CO2气体 激光
反射 凹镜
冷却水出口 高压直流电源
反射平镜
◎混合气体:氦约80%,氮约15%,CO2 约5% ◎通过高压直流放电进行激励 ◎波长10.6μ m,为不可见光 ◎能量效率5%~ 15%
激光加工特点
加工材料范围广,适用各种金属/非金属材料,高 熔点材料,耐热合金及陶瓷、金刚石等硬脆材料。 加工性能好,工件可离开加工机进行加工,可透过 透明材料加工,可在不易达到的狭小空间加工。
普通灯光与激光的比较
激光产生过程及特性
自发吸收 - 电子透过吸收光子从低能阶跃迁到高能阶 自发辐射 - 电子自发地透过释放光子从高能阶跃迁到 较低能阶 受激辐射 - 光子射入物质诱发电子从高能阶跃迁到低 能阶,并释放光子。
激光器
固体激光器
YAG(钇、铝和石榴石构成)激光器,红宝石激光器 特点:器件小、坚固、使用方便、输出功率大
加工时无显著切削力,发热小,适于加工小 孔、薄壁、窄槽、形面、型腔及曲线孔等,且 加工质量较好。
脉冲参数调整方便,可一次装夹完成粗、精 加工。
易于实现数控加工。
电火花加工应用
电火花成形加工:电火花打孔常用于加工冷 冲模、拉丝模、喷嘴、喷丝孔等。型腔加工包 括锻模、压铸模、挤压模、塑料模等型腔加工, 以及叶轮、叶片等曲面加工。 电火花线切割:广泛用于加工各种硬质合金 和淬硬钢的冲模、样板、各种形状复杂的板类 零件、窄缝、栅网等。
电火花加工工作要素
脉冲宽度与间隔——影响加工速度、表面粗糙 度、电极消耗和表面组织等。脉冲频率高、持 续时间短,则每个脉冲去除金属量少,表面粗 糙度值小,但加工速度低。通常放电持续时间 在2μ s至2ms范围内,各个脉冲的能量2mJ到20J (电流为400A时)之间。
电火花加工类型
电火花成形加工:主要指孔加工,型腔加工等 电火花线切割
非接触加工方式,热变形小,加工精度较高。
可进行微细加工。激光聚焦直径理论上可至1μ m以 下,实际可实现φ 0.01mm的小孔加工和窄缝切割。
加工速度快,效率高。
激光加工不仅可以进行打孔和切割,也可进行焊接、 热处理等工作。 可控性好,易于自动控制。加工设备昂贵。
激光打孔
◎广泛应用于金刚石拉丝模、钟表宝石轴承、陶瓷、 玻璃等非金属材料,和硬质合金、不锈钢等金属材料 的小孔加工。 ◎激光打孔具有高效率、低成本的特点,特别适合 微小群孔加工。 ◎焦点位置对孔的质量影响:若焦点与加工表面之 间距离很大,则激光能量密度显著减小,不能进行加 工。如果焦点位置偏离加工表面1mm,可以进行加工, 此时加工出孔的断面形状随焦点位置不同而发生变化
气体激光器
CO2激光器,氦-氖激光器 结构简单、造价低;操作方便;工作介质均匀,光束质量好; 能长时间较稳定地连续工作(市场达60%左右)
半导体激光器
砷化镓激光器 体积小、质量轻、寿命长、结构简单而坚固
液体激光器
染料激光器 原理复杂,输出波长连续可调,且覆盖面宽
CO2气体激光器
232
激光加工 电火花加工 超声加工 电化学加工
EI 收录文章数比较
几种代表性特种加 工方法
电火花加工的原理示意图
电火花加工
原理:利用工具电极与工件电极之间脉冲性火花放电, 产生瞬时高温,工件材料被熔化和气化。同时,该处绝 缘液体也被局部加热,急速气化,体积发生膨胀,随之 产生很高的压力。在这种高压作用下,已经熔化、气化 的材料就从工件的表面迅速被除去
激 光 加 工 应 用焦点位置对孔形状影响激 光 打 孔 示 意 图
激光加工应用
激光切割 具有切缝窄、速度快、热影响区小、省材料、成本低等 优点,并可以在任何方向上切割,包括内尖角。 可以切割钢板、不锈钢、钛、钽、镍等金属材料,以及 布匹、木材、纸张、塑料等非金属材料。 激光焊接 与打孔相比,激光焊接所需能量密度较低,不需将材料 气化蚀除,只要将工件的加工区烧熔使其粘合在一起。 优点:无焊渣,不需去除工件氧化膜,可实现不同材料 之间的焊接,特别适宜微型机械和精密焊接。 激光热处理 原理:照射到金属表面上的激光使表面原子迅速蒸发, 产生微冲击波会导致大量晶格缺陷形成,达到硬化。 优点:快速、不需淬火介质、硬化均匀、变形小、硬化 深度可精确控制。
工具电极 直流 脉冲 电源
进给 系统
放电间隙 工件电极
工作液
电火花加工
◆ 4个阶段: 1.介质电离、击穿,形成放电通道; 2.火花放电产生熔化、气化、热膨胀; 3.抛出蚀除物; 4.间隙介质消电离(恢复绝缘状态)。
电火花加工机床
电火花加工工作要素
电极材料——要求导电,损耗小,易加工; 常用材料:紫铜、石墨、铸铁、钢、黄铜等, 石墨最常用。 工作液——主要功能压缩放电通道区域,提 高放电能量密度,加速蚀物排出;常用工作液 有煤油、机油、去离子水、乳化液等。 放电间隙——合理的间隙是保证火花放电的 必要条件。为保持适当的放电间隙,在加工过 程中,需采用自动调节器控制机床进给系统, 并带动工具电极缓慢向工件进给。
导轮
Y
储丝筒
X
电极丝
工件
电火花线切割原理图
电火花线切割
电火花线切割加工:用连续移动的钼丝(或 铜丝)作工具阴极,工件为阳极。机床工作 台带动工件在水平面内作两个方向移动,可 切割出二维图形。同时,丝架可作小角度摆 动,可切割出斜面。
电火花线切割机床
加工过程显示
电火花加工特点
不受加工材料硬度限制,可加工任何硬、脆、 韧、软的导电材料。
第三章 特种加工
本章内容
I. II.
III.
IV.
特种加工技术概述 电火花加工 电解加工 高能束加工
特种加工技术概述
非传统加工又称特种加工,通常被理解为别于传统切 削与磨削加工方法的总称。
非传统加工方法 产生于二次大战后。两方面问题传统 机械加工方法难于解决: 1)难加工材料的加工问题。宇航工业等对材料高强度、 高硬度、高韧性、耐高温、耐高压、耐低温等的要求,使 新材料不断涌现。 2)复杂形面、薄壁、小孔、窄缝等特殊加工问题。 非传统加工方法将电、磁、声、光等物理量及化学能量 或其组合直接施加在工件被加工的部位上,从而使材料被 去除、累加、变形或改变性能等。
磁极
S 磁性材料
磁力抛光
磁力线
研磨前
研磨后
工件
高能束加工
激光加工
光阑 激光器 反射镜
电源
聚焦镜 工件 工作台
激光加工原理图
激光加工工作原理
激光是一种受激辐射而得到的加强光。其基本特征: ◎强度高,亮度大 ◎波长频率确定,单色性好 ◎相干性好,相干长度长 ◎方向性好,几乎是一束平行光 当激光束照射到工件表面时,光能被吸收,转化成 热能,使照射斑点处温度迅速升高、熔化、气化而形 成小坑,由于热扩散,使斑点周围金属熔化,小坑内 金属蒸气迅速膨胀,产生微型爆炸,将熔融物高速喷 出并产生一个方向性很强的反冲击波,于是在被加工 表面上打出一个上大下小的孔。
特种加工方法特点
工具不受显著切削力的作用,对工具和工件的强度、硬 度和刚度均没有严格要求。
主要不是依靠机械能,而是用其它能量(如电能、光能、 声能、热能、化学能等)去除材料。
一般不会产生加工硬化现象。加工变形小,发热少(或 仅局限于工件表层加工部位很小区域内),工件热变形 小,加工应力小,易于获得好的加工质量。
头发直径70um 特征尺寸25um
激光切割
激光切割木工艺品
激光切割的不锈钢齿轮
激光切割有机玻璃电脑机箱面板
激光模具焊接
模具焊接
激光模具焊接
激光模具焊接
超 声 波 加 工
超声 波发 生器
换能器
振动方向
变幅杆
工作液 喷嘴
工具 工件
超声切割技术
加工力
磨料+工作液
工具振幅
超 声 波 加 工 原 理 图
激 光 加 工 的 各 种 应 用
激光加工的各种应用
切削
钻孔
表面处理
钻微孔
焊接
打标
激光加工应用
激光切割
激光焊接车身
激光修复刀具
激光打孔时孔实例
在铝上刻槽
在钼上打直径 为100um的孔
在厚度为1.1mm 的铝上打直径为 200um的孔
激光加工实例
在陶瓷上打 直径为25um 的孔阵列 在硅片上打直径 为6um的孔阵列
当工具以16 000 Hz以上的振动频率作用于 悬浮液磨料时,磨料便以极高的速度强力冲 击加工表面;同时由于悬浮液磨料的搅动, 使磨粒以高速度抛磨工件表面;此外,磨料 液受工具端面的超声振动而产生交变的冲击 波和“空化现象”。所谓空化现象,是指当 工具端面以很大的加速度离开工件表面时, 加工间隙内形成负压和局部真空,在磨料液 内形成很多微空腔;当工具端面以很大的加 速度接近工件表面时,空泡闭合,引起极强 的液压冲击波,从而使脆性材料产生局部疲 劳,引起显微裂纹。
特种加工分类
复合过程 利用机械、热、化学、电化学的复合作用,去除 材料。常见的复合形式有: ◎机械化学复合—如机械化学抛光、电解磨削、电镀 珩磨等。 ◎机械热能复合—如加热切削、低温切削等。
◎热能化学能复合—如电解电火花加工等。
◎其它复合过程—如超声切削、超声电解磨削、磁力 抛光等。
特种加工技术发展趋势
电解磨削