PFMEA 分析表
注塑件过程失效模式及后果分析表模板(PFMEA)

6
包装破损
零件污染,客户投 诉
5
产品碰伤砸伤 客户投诉
6
装箱时确认不足 货物堆积过高
搬运不规范
2
无
3
试验后制定合理堆 积标准
2
无
100目测 100目测 100目测
5 60 5 75 4 48
标签贴错 发错货,客户投诉 5
标签与实物未核对 2
无
100目测
4 40
产品数量不正确
客户投诉
6
80-出货检验
关键尺寸超差
第 1 页,共 2 页
注塑件过程失效模式及后果分析表模板(PFMEA)
零件号
设计责任部门
FMEA 编号
零件名称
关键日期
编制人
车型/年份
系统/子系统/部件
编制日期
核心小组
序号
过程
潜在的失效模式
严 潜在的失效后果 重
度
级 别
潜在的失效原因/机理
频 度 数
现行预防性设计控 制
现行探测性设计控 制
探 测 度
5 60 5 75
建议措施
责任人和目标 完成日期
无
采取的措施
严频探 R 重度测 P 度数度 N
无
无
无
无
不同产品分区放置, 并做好标识
6
2 5 60
无
对纸箱进行固定 6 2 5 60
无
无
无
无
无
不同产品分区放置, 并做好标识
6
2 5 60
无
对纸箱进行固定 6 2 5 60
无
40-原材料烘料
烘料时间不对 烘料温度不对
表面料花 色差
过程潜在失效模式与效果分析表(PFMEA)
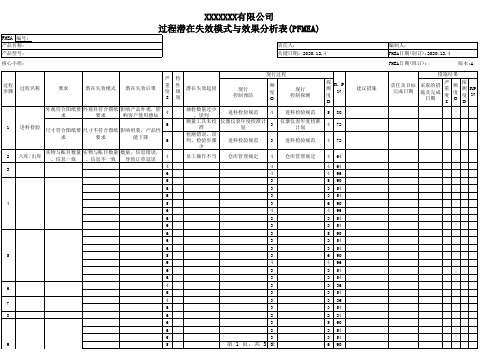
求
要求
响客户使用感知
4
1
进料检验 尺寸符合图纸要 尺寸不符合图纸 影响组装,产品性 6
求
要求
能下降
6
2
入库/出库
实物与账目数量 实物与账目数量 数量、信息错误, 、信息一致 、信息不一致 导致订单延误
4
抽检数量过少 、误判
进料检验规范
4
进料检验规范
5 80
测量工具未校 准
仪器仪表年度校准计 划
3
仪器仪表年度校准 计划
4 96
18
6
第 2 页,共 3 页4
4 96
18
6
4
4 96
5
4
4 80
19
5
4
4 80
6
3
4 72
6
4
4 96
20
6
4
4 96
6
4
4 96
21
4
4
5 80
4
4
4 64
22
4
4
5 80
23
4
4
4 64
备注:S、O、D评分标准详见《过程潜在失效模式后果分析PFMEA管理程序》,仅需对新部件进行评价分析,当RPN值超过200时要制定改善措施。
核准:
会签:
审查:
拟制:
表单 编 号:
第 3 页,共 3 页
6
4
4 96
6
3
3 54
6
3
3 54
6
3
5 90
6
3
3 54
6
3
3 54
13
5
3
pfmea分析表
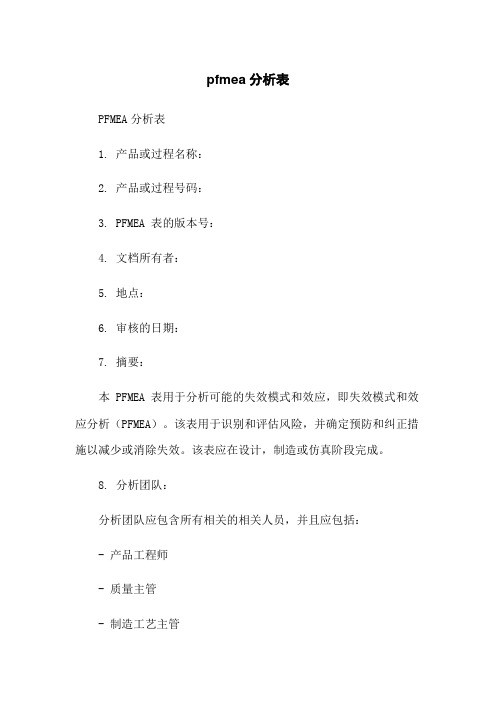
pfmea分析表PFMEA分析表1. 产品或过程名称:2. 产品或过程号码:3. PFMEA 表的版本号:4. 文档所有者:5. 地点:6. 审核的日期:7. 摘要:本 PFMEA 表用于分析可能的失效模式和效应,即失效模式和效应分析(PFMEA)。
该表用于识别和评估风险,并确定预防和纠正措施以减少或消除失效。
该表应在设计,制造或仿真阶段完成。
8. 分析团队:分析团队应包含所有相关的相关人员,并且应包括:- 产品工程师- 质量主管- 制造工艺主管- 安全主管- 故障分析师- 设计负责人- 制造工程师- 客户服务代表9. 步骤:步骤1:识别过程、组件或子组件- 识别过程、组件或子组件,该过程对产品性能,质量和可靠性的影响最大- 如果有多个过程,组件或子组件,请在单独的表中进行分析步骤2:确定失效模式- 对于每个识别的过程、组件或子组件,列出可能的失效模式步骤3:确定失效效应- 确定每种失效模式的影响,包括可能导致的产品或过程故障、风险和/或安全问题步骤4:确定失效严重性(S)- 确定失效对于产品功能和可靠性的影响严重性级别为S步骤5:确定失效发生概率(O)- 确定失效的发生概率级别为O步骤6:确定失效检出度(D)- 确定失效的检出度级别为D步骤7:计算风险优先级数(RPN)- 计算风险优先级数(RPN),即 RPN = S × O × D步骤8:制定预防和纠正措施- 针对高优先级数(RPN)的失效模式制定预防和纠正措施步骤9:跟踪措施有效性- 跟踪预防和纠正措施的实施,以确保其有效性。
10. 列举本文档所涉及简要注释如下:- 失效模式和效应分析(PFMEA):用于确定可能的失效模式和效应并采取纠正措施的过程。
- 风险优先级数(RPN): PFMEA 表中计算风险的指标。
RPN = S × O × D。
11. 列举如下本文档所涉及的法律名词及注释:无总结本文介绍了 PFMEA 分析表,该表用于识别和评估风险,并确定预防和纠正措施以减少或消除失效。
组装过程pfmea分析表
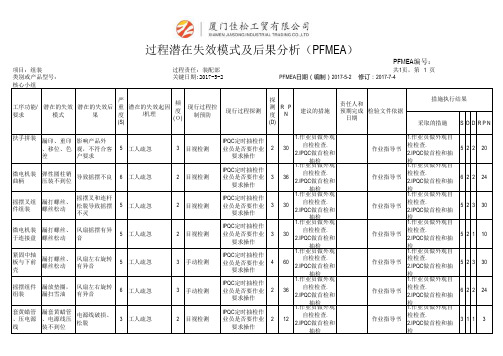
核心小组采取的措施S O D R P N扶手拼装漏印、重印、移位、色差影响产品外观,不符合客户要求5工人疏忽3目视检测IPQC定时抽检作业员是否要作业要求操作2301.作业员做外观自检检查.2.IPQC做首检和抽检作业指导书1.作业员做外观自检检查.2.IPQC做首检和抽检52220微电机装曲柄弹性圆柱销压装不到位导致摇摆不良6工人疏忽2目视检测IPQC定时抽检作业员是否要作业要求操作3361.作业员做外观自检检查.2.IPQC做首检和抽检作业指导书1.作业员做外观自检检查.2.IPQC做首检和抽检62224摇摆叉组件组装漏打螺丝、螺丝松动摇摆叉和连杆松脱导致摇摆不灵5工人疏忽2目视检测IPQC定时抽检作业员是否要作业要求操作3301.作业员做外观自检检查.2.IPQC做首检和抽检作业指导书1.作业员做外观自检检查.2.IPQC做首检和抽检52330微电机装于连接盘漏打螺丝、螺丝松动风扇摇摆有异音5工人疏忽2目视检测IPQC定时抽检作业员是否要作业要求操作3301.作业员做外观自检检查.2.IPQC做首检和抽检作业指导书1.作业员做外观自检检查.2.IPQC做首检和抽检52110紧固中轴板与下前壳漏打螺丝、螺丝松动风扇左右旋转有异音5工人疏忽3手动检测IPQC定时抽检作业员是否要作业要求操作4601.作业员做外观自检检查.2.IPQC做首检和抽检作业指导书1.作业员做外观自检检查.2.IPQC做首检和抽检52330摇摆组件组装漏放垫圈,漏扫雪油风扇左右旋转有异音6工人疏忽3手动检测IPQC定时抽检作业员是否要作业要求操作2361.作业员做外观自检检查.2.IPQC做首检和抽检作业指导书1.作业员做外观自检检查.2.IPQC做首检和抽检62224套黄蜡管、压电源线漏套黄蜡管、电源线压装不到位电源线破损、松脱3工人疏忽2目视检测IPQC定时抽检作业员是否要作业要求操作2121.作业员做外观自检检查.2.IPQC做首检和抽检作业指导书1.作业员做外观自检检查.2.IPQC做首检和抽检3113责任人和预期完成日期检验文件依据频度(O)现行过程控制预防现行过程探测探测度(D)R PN建议的措施类别或产品型号:关键日期:2017-5-2PFMEA日期(编制)2017-5-2 修订:2017-7-4措施执行结果工序功能/要求潜在的失效模式潜在的失效后果严重度(S)潜在的失效起因/机理过程潜在失效模式及后果分析(PFMEA)PFMEA编号:项目:组装过程责任:装配部共1页,第 1 页。
铝合金压铸件PFMEA分析

页码: 页
共页
关键日期:
编制者:龙健
FMEA日期:2014.2.20(编制)第 2 页,共(3修页订)
潜在 失效后果
严 重等 度级 S
潜在失效
频 度
起因/机理 O
现行预防
过程控制
(P)
(D)
预防措施
探测措施
探 风险 测 顺序
度数 D RPN
建议 措施
责任和目
措施执行结果
标完成日 期 采取的措 施
S O D RPN
3
1.定期校检 2.设备点检
检验设备使用环 境温度湿度不稳 2 温度湿度计控制 定
1锭/批,用光谱仪 检测
3
42批,用光谱仪 检测
2
20
漏判
同上
5 未报检/少检 2 进料检验流程
每批检验报告归档 2 20
未标示材质 铝锭入库/合格铝锭
用标识分开 表面卤化
领料至熔炼炉 牌号错误
零件报废
压铸/没有严重的缺 陷,如冷隔、开裂、 气孔
PFMEA评分表

PFMEA评分表PFMEA评分表》是一种常用的品质管理工具,用于进行潜在失效模式与效应分析(Process Failure Mode and Effects Analysis,简称PFMEA)。
它的目的是识别关键步骤或流程中的潜在失效模式,并评估其对产品或服务质量的影响程度。
PFMEA评分表可以帮助团队全面分析和评估可能发生的失效模式,并制定适当的预防和纠正措施,从而最大程度地降低产品或服务质量风险。
通过对各种失效模式和其效应的评估,可以提前发现潜在问题并采取相应的控制措施,以确保产品或服务质量的稳定和可靠。
在PFMEA评分表中,各个步骤或流程会被列出,并根据其对产品或服务的潜在失效的重要程度进行评分。
评分标准可以根据具体情况进行制定,但通常包括失效模式的严重性、发生频率和检测能力等方面的考量。
评分结果可以帮助团队确定哪些步骤或流程需要重点关注和改进,从而优化生产或服务流程,提高质量稳定性。
综上所述,《PFMEA评分表》是一种重要的品质管理工具,用于识别和评估潜在的失效模式,以确保产品或服务质量的稳定和可靠。
PFMEA评分表是一种用于进行过程故障模式与影响分析的工具。
它由以下几个组成部分构成,并且包含一些必填项。
1.项目信息在评分表的顶部,需要填写一些项目信息,以便对分析的过程进行标识和跟踪。
这些信息可能包括项目名称、项目编号、评分表编制人员等。
2.设计和工艺流程步骤在评分表中,需要列出与该过程相关的设计和工艺流程步骤。
这些步骤可以按照顺序进行排列,并且需要明确指出每个步骤的名称和内容。
3.故障模式与影响分析针对每个设计和工艺流程步骤,需要进行故障模式与影响分析。
这部分需要列出可能的故障模式,并对其进行评估。
评估可以基于指标如严重性、发生频率和可探测性等进行。
4.推理控制计划在评分表中,需要制定推理控制计划,以预防或控制故障模式对产品或过程的影响。
这部分需要明确列出控制措施、控制方式以及执行者。
新版PFMEA表格
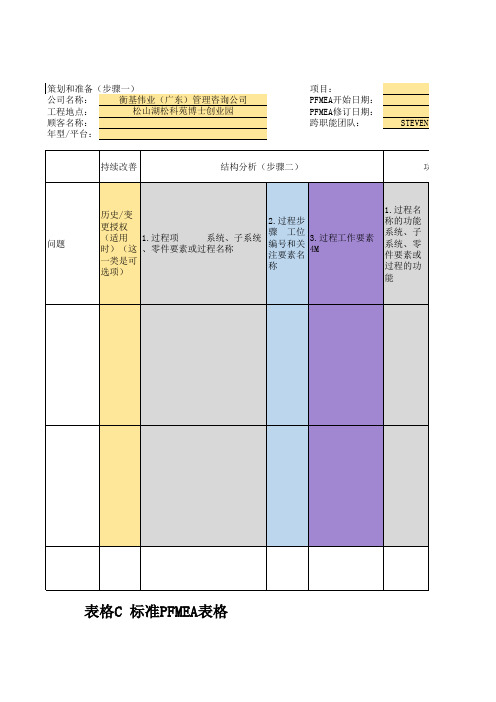
失效分析(步骤四)
PFMEA风险
2.过程步骤的功 能和产品特性 (量值为可选 项)
3.过程工 作要素的 功能和过 程特性
1.对于上
一较高级
2.关注
别要素和/ 失效影响的 要素的 3.工作要素的失效起因
或终端用 严重度(s) 失效模 (FC)
户的失效
式(FM)
影响(FE)
当前的 对失效 起因的 预防措 施(PC)
选)
施
A优化(步骤六)
频度 (O)
探测 度 (D)
DFME A措 施优 先级
筛选器代 码(可 备注 选)
策划和准备(步骤一)
公司名称:
衡基伟业(广东)管理咨询公司
工程地点:
松山湖松科苑博士创业园
顾客名称:
年型/平台:
项目: PFMEA开始日期: PFMEA修订日期: 跨职能团队:
STEVEN 13929414846
持续改善
结构分析(步骤二)
功能分析(步骤三
问题
历史/变
更授权
(适用 1.过程项
系统、子系统
时)(这 、零件要素或过程名称
一类是可
选项)
2.过程步
骤 工位 编号和关 注要素名
3.过程工作要素 4M
称
1.过程名 称的功能 系统、子 系统、零 件要素或 过程的功 能
表格C 标准PFMEA表格
STEVEN 13929414846 功能分析(步骤三)
过程失效模式及影响分析(过程FMEA)
PFMEA ID编号: 过程责任人: 保密级别: 加微信免费送案例及DFM分析(步骤五)
PFMEA优化(步骤六)
当前的
失效起 失效起
因/失效 模式的 频度
制程PFMEA分析表格
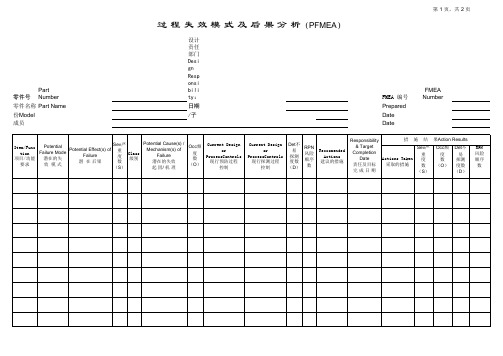
Occ频 度 数
(O)
Current Design or
ProcessControls 现行预防过程 控制
Current Design or
ProcessControls 现行探测过程 控制
Det不
易 探测 度数 (D)
RPN 风险 顺序 数
Reccomended Actions
建议的措施
Responsibility
措 施 结 果Action Results
& Target Completion
Date 责任及目标 完成日期
Actions Taken 采取的措施
Sev严 重 度 数
(S)
Occ频 度 数
(O)
Det不 易 探测 度数
(D)
RPN 风险 顺序
数
Part 零件号 Number
建议的措施
Responsibility
措 施 结 果Action Results
& Target Completion
Date 责任及目标 完成日期
Actions Taken 采取的措施
Sev严 重 度 数
(S)
Occ频 度 数
(O)
Det不 易 探测 度数
(D)
RPN 风险 顺序
数
FMEA Number
Item/Func tion
项目/功能 要求
Potential
Failure Mode 潜在的失 效 模式
Sev严
Potential Effect(s) of Failure
潜 在 后果
重 度 数
Class 级别
AIAG VDA PFMEA表格模板(自动计算AP)

1.对于上 一较高级 别要素和/ 或最终用 户的失效 影响 (FE)
失效 影响 2.关注要 的严 素的失效 重度 模式 (FM) (S)
3.下一较 低级别要 素或特性 的失效原 因 (FC)
对失效原 因的当前 预防控制
(PC)
失效 原因 的发 生度 (O)
对失效原 因 / 失效 模式的当 前探测控 制 (DC)
失效分析 (第4步)
PFMEA 风险分析 (第5步)
PFMEA 优化 (第6步)
问题#
1.过程项
历史/变 更授权 系统、子系 (适用时) 统、零件要
素或过程名 称
2.过程步 骤
工位编号和 关注要素名
称
3.过程工 作要素
4M类型
1.过程 名称的 功能
系统、子 系统、零 件要素或 过程的功
2.过程步 骤的功能 和产品特
PFMEA 优化 (第6步)
问题#
1.过程项
历史/变 更授权 系统、子系 (适用时) 统、零件要
素或过程名 称
2.过程步 骤
工位编号和 关注要素名
称
3.过程工 作要素
4M类型
1.过程 名称的 功能
系统、子 系统、零 件要素或 过程的功
2.过程步 骤的功能 和产品特
性
(量值为可 选项)
3.过程 工作要 素的功 能和过 程特性
(PC)
失效 原因 的发 生度 (O)
对失效原 因 / 失效 模式的当 前探测控 制 (DC)
失效原 因/失 效模式 的探测 度 (D)
AP
特殊 特性
筛选器 代码(选
填)
PFMEA 预防措
施
PFMEA 探测措
施
PFMEA分析标准表格模版

(过程PROCESS FMEA)
项目名称 Item: 主要参加人Core Team: 序号 NO. 过程功能要求 潜在的失效后果 潜在的失效模式 Process Function Potential Effect(S) of Potential Failure Mode Requirements Failure 严 级 重 别 度 Class Sev 潜在的失效原因/机理 Potential Cause(s)/ Mechanism(s) of Failure 频 现行过程预防控制 度 Current Process Controls 数 Prevention Occ 过程责任部门Process Responsibility: 关键日期Key Date:
准备人PrepareBiblioteka by审核Checked by
批准Approval by
1 of 1
工
现行过程检测控制 Current Process Controls Detection
措施结果Result 严 频 难 重 度 检 度 数 度 Sev Occ Det
风险 优先 指数 R.P.N.
out of 0.2 A spec.
偏小
版本 Rev. A0
变更内容Comment 新制/New
日期 Date
AND EFFECTS ANALYSIS
FMEA编号Number: 准备人Prepared By: FMEA日期Data(编制(orig): 责任及目标完 难 风险 建议的措施 成日期 检 优先 指数 Recommended Responsibility 度 Action(S) & Target Det R.P.N . Completion 页码Page:
第五版DFMEA和PFMEA表单
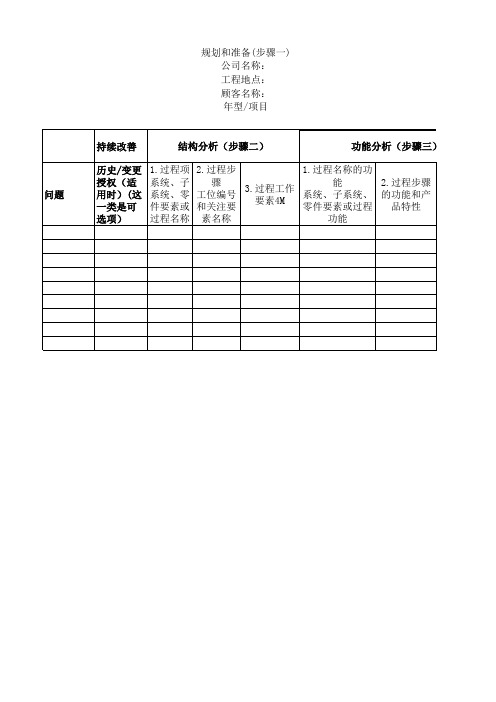
问题
持续改善
结构分析(步骤二)
功能分析(步骤三)
历史/变更 1.过程项 2.过程步
1.过程名称的功
授权(适 用时)(这 一类是可
系统、子 骤 系统、零 工位编号 件要素或 和关注要
3.过程工作 要素4M
能 系统、子系统、 零件要素或过程
2.过程步骤 的功能和产
品特性
选项) 过程名称 素名称
功能
项目: DFMEA开始日期: DFMEA开始日期: 跨职能团队:
(步骤三)
失效分析功能分析(步骤四)
风险评估功能分析(步骤五)
3.过程工作 要素的功能 或过程特性
1. 对于上一 较高级别要素 失效影响 和或最终用户 的严重度 的失效影响 (S) (FE)
2. 关注 要素的失 效模式 (FM)
3.工作要 素的失效 起因 (FC)
当前的对失 效起因的预
防控制 (PC)
失效起 因/失 效模式 的频度 (O)
当前的失 效起因或 失效模式 的探测控 制(DC)
DFMEA ID编号 设计职责: 保密级别:
评估功能分析(步骤五)
改进措施功能分析(步骤六)
失效起因ቤተ መጻሕፍቲ ባይዱ/失效模 式的探测 度(D)
PFMEA 措施 特殊 优先 特性 级
筛选 器代 码 (可 选)
预防措施
探测措施
负责人姓 名
目标完成 日期
状态
采取基于 证据的措
施
分析(步骤六)
完成日期
严重 度 (S)
频度 (O)
探测 度 (D)
PFMEA AP
特殊 特性
备注
过程失效模式及后果分析表(PFMEA)(第五版表格)
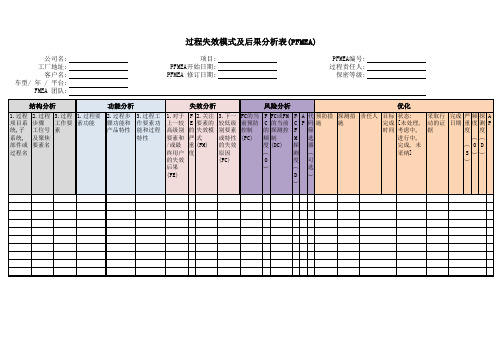
2.过程步 骤功能和 产品特性3.过程工 作要素功 能和过程 特性
1.对于 F 2.关注 3.下一 FC的当 F FC或FM F A 代 预防措 探测措 责任人 目标 状态:
上一较 E 要素的 较低级 前预防 C 的当前 C P 码 施
施
完成 [未处理,
高级别 的 失效模 别要素 控制 的 探测控 F 筛
时间 考虑中,
要素和 严 式
或特性 (PC) 频 制
M选
进行中,
/或最 重 (FM) 的失效
度 (DC) 探 器
完成, 未
()
终用户 度
原因
测
(
采纳]
的失效
(FC)
O
度可
后果
选
)
(FE)
D
采取行 完成 严 频 探 A
动的证 日期 重 度 测 P
据
度度
OD S
() ()
()
()
过程失效模式及后果分析表(PFMEA)
公司名: 工厂地址:
客户名: 车型/ 年 / 平台:
FMEA 团队:
项目: PFMEA开始日期: PFMEA 修订日期:
PFMEA编号: 过程责任人:
保密等级:
结构分析
功能分析
失效分析
风险分析
优化
1.过程 2.过程 3.过程 1.过程要 项目系 步骤 工作要 素功能 统,子 工位号 素 系统, 及聚焦 部件或 要素名 过程名
PFMEA分析表
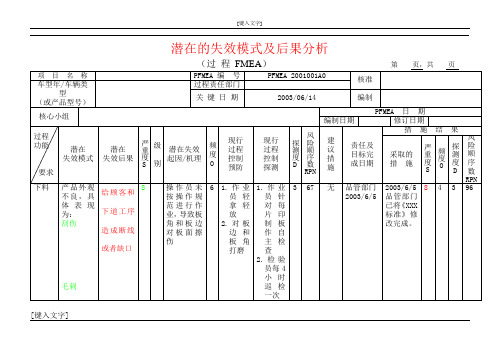
120
无
PP-705-2-01A0
XXX 有 限 公 司
过 程 F M E A 检 查 表
制定部门: 制定日期: 年 月 日
产品名称
规格/型号
顾客零件编号
问 题
是
否
所要求的意见 / 措施
负责部门/负责人
完成日期
1
是否使用克莱斯勒、福特和通用汽车公司的指南制定过程ห้องสมุดไป่ตู้MEA
2
所有影响配合、功能、耐久性、政府法规和安全性的操作是否已被识别并按顺序列出
潜在的失效模式及后果分析
(过程FMEA)第页,共页
项 目 名 称
PFMEA 编 号
PFMEA2001001A0
核准
车型年/车辆类型
(或产品型号)
过程责任部门
关 键 日 期
2003/06/14
编制
核心小组
PFMEA 日 期
编制日期
修订日期
过程
功能
要求
潜在
失效模式
潜在
失效后果
严
重
度
S
级
别
潜在失效
起因/机理
频
度
O
现行
过程
控制
预防
现行
过程
控制
探测
探测
度
D
风险
顺序
数RPN
建 议
措 施
责任及
目标完
成日期
措 施 结 果
采取的
措 施
严
重
度
S
频
度
O
探测
度
D
风险
顺序数
RPN
下料
产品外观不良,具体表现为:
PFMEA分析表

(过 程 FMEA)第 页,共 页
项 目 名 称
PFMEA 编 号
PFMEA2001001A0
核准
车型年/车辆类型
(或产品型号)
过程责任部门
关 键 日 期
2003/06/14
编制
核心小组
PFMEA 日 期
编制日期
修订日期
过程
功能
要求
潜在
失效模式
潜在
失效后果
严
重
度
S
级
别
潜在失效
起因/机理
频
度
O
现行
过程
控制
预防
现行
过程
控制
探测
探测
度
D
风险
顺序
数RPN
建 议
措 施
责任及Leabharlann 目标完成日期措 施 结 果
采取的
措 施
严
重
度
S
频
度
O
探测
度
D
风险
顺序数
RPN
下料
产品外观不良,具体表现为:
刮伤
毛刺
给顾客和下道工序造成断线或者缺口
8
操作员未按操作规范进行作业,导致板角和板边对板面擦伤
6
1.作业员轻拿轻放
3
是否考虑了类似零件的FMEA?
4
是否对已发生事件和保修数据进行了评审?
5
对高风险顺序数的项目是否已计划并采取了适当的纠正措施?
6
对严重度数高的项目是否已计划并采取了适当的纠正措施?
7
当纠正措施完成后,风险顺序数是否作了修改?
8
当完成设计更改时,是否修改了高严重度数?
制程PFMEA分析表格

第 1 页,共 1 页
FMEA 编号 FMEA Number 编制Prepared by: 编制日期Date (Orig.): 修订日期Date (Rev.):
Item/Func tion
项目/功能 要求
Potential
Failure Mode 潜在的失 效 模式
Sev严
Potential Effect(s) of Failure
Sev严 重 度 数
(S)
Occ频 度 数
(O)
Det不 易Βιβλιοθήκη 探测 度数(D)RPN 风险 顺序
数
潜 在 后果
重 度 数
Class 级别
(S)
Potential Cause(s) / Mechanism(s) of
Failure 潜在的失效 起 因/ 机 理
Occ频 度 数
(O)
Current Design or
ProcessControls 现行预防过程 控制
Current Design or
零件号 Part Number 零件名称 Part Name 车型/年份Model Year(s)/Vehicle(s) 核心小组成员Core Team Member
过 程 失 效 模 式 及 后 果 分 析(PFMEA)
设计责任部门Design Responsibility: 关键日期Key Date: 系统/子系统/部件System/Subsystem/Component
ProcessControls 现行探测过程 控制
Det不 易 探测 度数
(D)
RPN 风险 顺序 数
Reccomended Actions
建议的措施
Responsibility
- 1、下载文档前请自行甄别文档内容的完整性,平台不提供额外的编辑、内容补充、找答案等附加服务。
- 2、"仅部分预览"的文档,不可在线预览部分如存在完整性等问题,可反馈申请退款(可完整预览的文档不适用该条件!)。
- 3、如文档侵犯您的权益,请联系客服反馈,我们会尽快为您处理(人工客服工作时间:9:00-18:30)。
4.定期保养真空过滤棉时进行检查。
4
12
参阅《SMT设备保养计划》
1◎ 相机识别不清
3
每日保养对镜片进行擦拭,防止灰层,板 屑污染镜片,每日点检1次。 参阅《SMT设备点检记录表》
100%自检, IPQC抽检1次/天
4
12
1. 检查FEEDER MARK点识别坐标
1.供料器动作不到位; 2.Feeder取料中心位置偏移.
1、作业前按照标准设置4±0.5kgf.cm;
1、首件确认;
3
2、设置后实际测量,实际扭力需与标准一 致;
2、100%自检; 3、IPQC:2H/次
2
42
3、首件确认螺丝锁后是否锁紧及滑牙
抽检;
烧录
程序没烧录进芯 片
产品功能测试 失败
7 ● 烧录时程序调用错误
1.烧录前工程确认软件,确认无误后需先 1、首件确认;
7 ◎ 升温过快,导致器件两端受 3 升温斜率),参阅《回流焊炉温设定表 检; 2、IPQC抽 3 63
热不均匀;
》;
检2H/次
7
◎
回流焊升温区时间设定过 长;
3
根据炉温曲线设定SOP来设定炉温曲线的 各个参数,并参照锡膏规格书。
100%1、100%自 检; 2、IPQC抽 检2H/次
3
63
7 ◎ 作业员漏失;
3
湿敏元件的贮存环境进行控制,如温度、 湿度。参阅《温湿管理规范》。
行实时稽查。
3 63
锡膏存储 钢网管控
1.存储温度按照锡膏规格参数控制;
锡膏印刷品质 不良
存贮锡膏的冰箱温度不满足 锡膏存储条件。
2
2.对冰箱温度进行监控点检,2次/天; (参阅《锡膏存储使用规范》)
3.每天一次测试新开启的锡膏做粘度;
3
2. 调整机器取料位置 参阅《SMT设备保养计划》
100%自检, IPQC抽检4H/次
4
12
冷焊
回流焊
立碑
连锡 作业员错判
AOI检查
机器误判
测试盲点
功能失效
影响外观,功 能 影响外观,功 能 影响外观,功 能
PCB板上不同元器件在回流
1.制作测温板时,采用同型号的PCB来制 作根据测试温度数据来设定炉温曲线;
3
1、作业前查看样品板及SOP明确焊接标准 及外观要求
2 48
100%检查;
IPQC抽检2H/次
4 ● 过炉夹具未遮挡散热焊盘
将夹具散热焊盘位置遮挡,避免过炉焊盘 2 上沾锡
2 16
取夹具,补焊
焊接不良(多锡,少 锡,连锡)
焊接品质无保 证,影响产品使 用寿命
1.焊接温度不合适; 8 ● 2.焊接参数未调整到最佳状
自检、IPQC抽检 4H/次
3
42
(锡膏塌陷、
锡膏粘度不符合 连锡、少锡、
规格要求
漏印、拉尖 等,造成零件 连锡、少锡、 空焊/虚焊、少 件等)
7● 回温时间不足或过长。
1.使用《锡膏管制标签卡》对回温时间进
2
行管控;(记录起止时间); (参阅《锡膏存储使用规范》)
自检、IPQC抽检 1次/天
3
42
态
1.依据零件规格书定义焊接温度(370±20 3 ℃) ;
2.规范烙铁头和锡线型号;
1、100%自检; 2、IPQC抽检2H/ 2 次
48
测试架造成
1、收到测试架制作后进行验收确认定位柱
产品功能不良
8
●
测架定位柱距离零件距离过 近压伤零件
2
及顶针需距离零件有安全距离; 2、每4小时检查测试架测试功能及测试参
ห้องสมุดไป่ตู้
2 制作首件进行确认无误后方可生产;
2、IPQC,2H/次 2 28
进行抽检核对
漏检查 测试架造成
产品功能或外 观不良
7◎
未按照一定顺序检查
程序误用
不满足标准要 求
3 ◎ 贴片机精度不稳定
1. 对刮刀压力参数进行控制,参阅《印刷
工位参数设定指引》;
2. 首件及过程中每2hrs用SPI检测锡膏厚 100%1、100%自
2 度;
检; 2、IPQC抽 4 56
3. 设定机器自动清洗钢网;
检2H/次
参阅《印刷工位参数设定指引》、《锡膏
厚度测试指引》。
4 置;
2 64
焊点空焊,虚 焊,连锡
焊接外观标准不明确
1、作业前查看样品板,及SOP明确焊点外 2 观标准;
1、100%自检; 2、IPQC 2H/次
进行抽检
2
32
影响外观及功 能测试不通过
8●
1、未按照标准条件进行作 业
2
1、实际测量焊接温度,在标准范围; 2、焊接后检查焊点;
1、IPQC:4H/次
3 42
刷散热膏
DIP
散热油过少,过 多
影响散热或散 热油溢出影响
外观
5 ○ 刷散热膏夹具未调整合适
1、首件确认; 3 2、刷散热油后自检;
1、100%自检; 2、2H/次抽检
2
30
螺丝未打紧
漏锁螺丝 锁散热器螺丝
影响散热,降 低产品使用寿
命
8
●
1、散热片有碎屑,螺丝孔功 牙不良
2
1、来料管控,来料IQC按照AQL允收标准 1、IQC来料检
3 75
维修
零件损坏 冷焊
错件、反向等
影响外观,功 能
5 ○ 烙铁温度过高;
2 1.烙铁温度要参照SOP设定。
4 40
5 ○ 烙铁温度过低;
2.定时对烙铁温度点检。 2
100%1、100%自 4 40
检; 2、IPQC抽
7
○
更换物料出错或焊接时极性 错误。
3
1.领料及更换物料时,须核对BOM; 2.维修完毕的半成品,在检查确认后,须 从新AOI测试。参阅《半成品维修流程》
4H/次进行点检 测试架
2
32
数。
ICT测试
误放
产品功能不良
8
●
未按照要求标示及摆放待测 产品及已测产品
2
1、将已测产品与待测产品分区域摆放; 2、测试合格品在对应位置贴上二维码;
1、100%自检; 2、IPQC抽检2H/ 2 32
次
漏检查
产品功能或外 观不良
7◎
未按照一定顺序检查
2 1、按照指定的顺序检查;
1、100%自检; 2、IPQC抽检2H/ 3 42 次
焊线 分板
线材焊接错误
产品外观检验 不通过以及功 能不符合要求
8●
物料来料错误
作业前不明确焊接位置
2
在焊接前核对物料编码是否与BOM物料料号 的一致。
1、100%自检;
2
32
2、IPQC 2H/次
1、作业前查看样品板,及SOP明确焊线位
进行抽检
2 料号,品名描述;
2 32
3、加工前班长依照BOM核对物料料号及
品名描述事物与BOM一致
零件反向
1、产品功能失 效 2、产品寿命降 低
7
◎
1、不同方向的零件放在同 一工位作业
2 1、同一位置插同一方向的零件
3 42
装夹具,插件 错料
影响产品功能
7
◎
1、产线混料或错料; 2、
1、将已加工的物料加入写有标识的物料盒
进行点检温度及
接地; 2、焊后100%自
2 32
检焊点外观
板边有毛刺
外观不良
5 ○ 来料V-CUT槽切割过浅 2 首件确认来料V-CUT槽
目视100%自检; IPQC抽检2H/次
2
20
清洗焊点
漏清洗不良品流 出
外观不良
不明确外观标准 6◎
2
作业前查看样品板及SOP,明确该产品外 观要求及零件分布位置
3 作业员培训上岗;
4 84
7
●
设备特性决定设备会有误 判;
5 ◎ 设备特性
1.开拉前对设备进行样板点检;(空板、
良品板、不良板)
100%1、100%自
4 2.设备参数微调;(原件资料中的颜色提 检; 2、IPQC抽 3 84
取,等)
检2H/次
3.作业员复判。
制作测试盲点表,作业员对所有盲点逐一 5 确认。
检; 2、IPQC抽 4 56
检2H/次 1.依据《SMD程序命名规范》来命名程
序;
100%1、100%自
2 2.增加权限管理,非技术人员无权对程序 检; 2、IPQC抽 4 56
进行调用及修改;
检2H/次
3.首件确认。
1.定期使用校正吸嘴校正X/Y轴。参阅《
3
SMT设备保养计划》; 2.产前对CAD资料坐标校准;
中,加物料前需核对物料料号及品名描 1、首件确认,
2 述;
IPQC抽检2H/次 2 28
2、若有链条异常或认为打翻夹具需从拉头
重新流拉
零件歪斜浮高
1、影响装配; 2、外观不良
4
◎ 1、插件后零件未查到位;
3 插件后自检,炉前检查
3 36
过波峰焊
焊点不良
功能不良
底板散热焊盘上 沾锡
外观不良
波峰焊参数设置未达最佳状 8 ●态
IQC100%全检
4 84
元器件受潮、氧 化
器件性能的可 靠性; 2.影响焊接质 量
生产线对湿敏元件的使用、 7 ◎ 贮存、烘烤未按照要求执
行仓;库对湿敏元件的接收,贮
3
对湿敏元件的使用、贮存、烘烤等做控制 要求,参阅《温湿管理规范》;