NI4882RTReadme
MEMORY存储芯片MT47R128M8CF-25 H中文规格书

Temperature-Controlled Refresh ModeDuring normal operation, temperature-controlled refresh (TCR) mode disabled, the de-vice must have a REFRESH command issued once every t REFI, except for what is al-lowed by posting (see REFRESH Command section). This means a REFRESH command must be issued once every 7.8μs if T C is less than or equal to 85°C, once every 3.9μs if T C is greater than 85°C, once every 1.95μs if T C is greater than 95°C, regardless of which Temperature Mode is selected (MR4[2]). TCR mode is disabled by setting MR4[3] = 0while TCR mode is enabled by setting MR4[3] = 1. When TCR mode is enabled (MR4[3]= 1), the Temperature Mode must be selected where MR4[2] = 0 enables the Normal Temperature Mode while MR4[2] = 1 enables the Extended Temperature Mode.When TCR mode is enabled, the device will register the externally supplied REFRESH command and adjust the internal refresh period to be longer than t REFI of the normal temperature range, when allowed, by skipping REFRESH commands with the proper gear ratio. TCR mode has two Temperature Modes to select between the normal tem-perature range and the extended temperature range; the correct Temperature Mode must be selected so the internal control operates correctly. The DRAM must have the correct refresh rate applied externally; the internal refresh rate is determined by the DRAM based upon the temperature.Normal Temperature ModeREFRESH commands should be issued to the device with the refresh period equal to t REFI of normal temperature range (-40°C to 85°C). The system must guarantee that the T C does not exceed 85°C when t REFI of the normal temperature range is used. The de-vice may adjust the internal refresh period to be longer than t REFI of the normal tem-perature range by skipping external REFRESH commands with the proper gear ratio when T C is below 85°C. The internal refresh period is automatically adjusted inside the DRAM, and the DRAM controller does not need to provide any additional control.Extended Temperature ModeREFRESH commands should be issued to the device with the refresh period equal to t REFI of extended temperature range (85°C to 95°C, or 95°C to 105°C) . The system must guarantee that the T C does not exceed 95°C, or 105°C. Even though the external refresh supports the extended temperature range, the device may adjust its internal refresh pe-riod to be equal to or longer than t REFI of the normal temperature range (-40°C to 85°C)by skipping external REFRESH commands with the proper gear ratio when T C is equal to or below 85°C. The internal refresh period is automatically adjusted inside the DRAM, and the DRAM controller does not need to provide any additional control.Table 49: Normal t REFI Refresh (TCR Enabled)8Gb: x4, x8, x16 DDR4 SDRAM Temperature-Controlled Refresh ModeRAS lockout circuit feature allows the PRECHARGE operation to be partially or com-pletely hidden during burst READ cycles when the auto precharge feature is engaged.The PRECHARGE operation will not begin until after the last data of the burst write se-quence is properly stored in the memory array.REFRESH CommandThe REFRESH command (REF) is used during normal operation of the device. This command is nonpersistent, so it must be issued each time a refresh is required. The de-vice requires REFRESH cycles at an average periodic interval of t REFI. When CS_n,RAS_n/A16, and CAS_n/A15 are held LOW and WE_n/A14 HIGH at the rising edge of the clock, the device enters a REFRESH cycle. All banks of the SDRAM must be pre-charged and idle for a minimum of the precharge time, t RP (MIN), before the REFRESH command can be applied. The refresh addressing is generated by the internal DRAM re-fresh controller. This makes the address bits “Don’t Care” during a REFRESH command.An internal address counter supplies the addresses during the REFRESH cycle. No con-trol of the external address bus is required once this cycle has started. When the RE-FRESH cycle has completed, all banks of the SDRAM will be in the precharged (idle)state. A delay between the REFRESH command and the next valid command, except DES, must be greater than or equal to the minimum REFRESH cycle time t RFC (MIN),as shown in Figure 84 (page 147).Note: The t RFC timing parameter depends on memory density.In general, a REFRESH command needs to be issued to the device regularly every t REFI interval. To allow for improved efficiency in scheduling and switching between tasks,some flexibility in the absolute refresh interval is provided for postponing and pulling-in the REFRESH command. A limited number REFRESH commands can be postponed depending on refresh mode: a maximum of 8 REFRESH commands can be postponed when the device is in 1X refresh mode; a maximum of 16 REFRESH commands can be postponed when the device is in 2X refresh mode; and a maximum of 32 REFRESH commands can be postponed when the device is in 4X refresh mode.When 8 consecutive REFRESH commands are postponed, the resulting maximum inter-val between the surrounding REFRESH commands is limited to 9 × t REFI (see Figure 85(page 147)). For both the 2X and 4X refresh modes, the maximum interval between sur-rounding REFRESH commands allowed is limited to 17 × t REFI2 and 33 × t REFI4, re-spectively.A limited number REFRESH commands can be pulled-in as well. A maximum of 8 addi-tional REFRESH commands can be issued in advance or “pulled-in” in 1X refresh mode,a maximum of 16 additional REFRESH commands can be issued when in advance in 2X refresh mode, and a maximum of 32 additional REFRESH commands can be issued in advance when in 4X refresh mode. Each of these REFRESH commands reduces the number of regular REFRESH commands required later by one. The resulting maximum interval between two surrounding REFRESH commands is limited to 9 × t REFI (Fig-ure 86 (page 147)), 17 × t RFEI2, or 33 × t REFI4. At any given time, a maximum of 16 REF commands can be issued within 2 × t REFI, 32 REF2 commands can be issued within 4 ×t REFI2, and 64 REF4 commands can be issued within 8 × t REFI4 (larger densities are limited by tRFC1, tRFC2, and tRFC4, respectively, which must still be met).8Gb: x4, x8, x16 DDR4 SDRAM REFRESH CommandFigure 84: REFRESH Command TimingCK_tCK_cCommand Don’t CareNotes: 1.Only DES commands are allowed after a REFRESH command is registered until t RFC(MIN) expires.2.Time interval between two REFRESH commands may be extended to a maximum of 9 ×t REFI.Figure 85: Postponing REFRESH Commands (Example)WFigure 86: Pulling In REFRESH Commands (Example)W8 REF-Commands pulled-in8Gb: x4, x8, x16 DDR4 SDRAM REFRESH Command。
NI-488.2

© 2002–2019 National Instruments. All rights reserved.
371333F-01
May19
4 | | NI-488.2™ for macOS Getting Started Guide
NI corporate headquarters is located at 11500 North Mopac Expressway, Austin, Texas, 78759-3504. NI also has offices located around the world. For telephone support in the United States, create your service request at /support or dial 1 866 ASK MYNI (275 6964). For telephone support outside the United States, visit the Worldwide Offices section of / niglobal to access the branch office websites, which provide up-to-date contact information, support phone numbers, email addresses, and current events.
T420HW04 V0 Preliminary Spec Ver.1.1

T420HW04 V0
0/30
Product Functional Specification 42” Full-HD Color TFT-LCD Module Model Name: T420HW04 V0
(*) Preliminary Specification ( ) Final Specification
T420HW04 V0
1/30
Contents
No
COVER CONTENTS RECORD OF REVISIONS 1 2 3 GENERAL DESCRIPTION ABSOLUTE MAXIMUM RATINGS ELECTRICAL SPECIFICATIONS
ITEM
3-1 3-2 3-3 3-4 3-5 3-6 4 5 6 7 7-1 7-2 8பைடு நூலகம்
Version 1.0 Date 2008/9/2 Page Old Description Preliminary specification first release 1.1 2008/9/9 10 Operating frequency typical value is 62KHz Modify operating frequency typical value to 58KHz New Description Remark
o o
Note 1 1 2 2 2 2 3 4 5 6
℃ and No condensation.
Note 3 : Half sine wave, shock level : 50G(11ms), direction : ±x, ±y, ±z (one time each direction) Note 4 : Wave form : Random, vibration level : 1.5G RMS, Bandwidth : 10~500Hz Duration : X,Y,Z 30min (one time each direction) Note 5 : -20C/1hr ~ 60C/1hr, 100 cycles Note 6 :Panel only (without TV set), Ambient temp 25C
NI推出NI-488.2驱动软件的中文版本

NI推出NI-488.2驱动软件的中文版本
无
【期刊名称】《自动化信息》
【年(卷),期】2005(000)001
【摘要】2004年来,美国国家仪器有限公司宣布推出行业标准的NI-488.2驱动软件的中文版本,该软件可用于控制Windows 2000/XP系统中的IEEE 488(GPIB)可编程仪器,中文版的软件可以帮助本地工程师在开发基于GPIB的自动化测试应用时,极大地提高工作效率,节省宝贵的时间,并减少工作失误。
【总页数】1页(P7)
【作者】无
【作者单位】无
【正文语种】中文
【中图分类】TP274.2
【相关文献】
1.NI为350余种Ethernet/LAN和USB接口仪器推出全新驱动软件 [J],
2.NI推出NI-DAQmx数据采集驱动软件 [J], 无
3.NI中文版NI-488.2驱动软件问世 [J], 无
4.NI推出Linux专用数据采集驱动软件NI-DAQmx Base [J], 无
5.NI中文版GPIB软件加速自动化测试系统的开发——仪器控制软件现已推出中文版本 [J],
因版权原因,仅展示原文概要,查看原文内容请购买。
ni4882 ibdev函数详解

ni4882 ibdev函数详解ni4882是一种在测试和测量设备中用于进行通信的标准接口,它是IEEE-488(通常称为GPIB)总线的一部分。
在GPIB总线上,设备可以使用一组命令进行通信,其中包括读写数据、查询设备状态等操作。
而在进行这些通信操作时,开发人员可以使用IB(Instrument Control)库来调用一系列的函数来完成操作。
其中,ibdev函数是用来建立与GPIB设备通信连接的函数。
本文将详细解释ibdev函数的用法及其参数含义。
1. ibdev函数概述ibdev函数是GPIB通信中用来打开设备连接的函数,它的原型如下所示:int ibdev(int boardID, int pad, int sad, int timeout, int send_eoi, int eos_mode)其中,各参数的含义分别是:- boardID:GPIB控制器的板号,对应不同的GPIB控制器- pad:设备位置区域,在GPIB总线上,每个设备都有一个唯一的位置区域- sad:辅助位置区域,有些设备具有两个位置区域,sad用来指定设备的第二个位置区域- timeout:超时时间,超过这个时间没有通信则会返回错误- send_eoi:表示是否在发送最后一个数据字节后自动发送结束信号- eos_mode:结束符模式,用于设定接收到何种字符时停止接收数据2. ibdev函数的使用方法在使用ibdev函数之前,首先需要通过ibfind函数找到GPIB控制器的位置区域。
然后才可以使用ibdev函数建立与设备的连接。
以下是一个简单的使用示例:#include <gpib.h>// 打开与GPIB设备连接int dev = ibdev(boardID, pad, sad, timeout, send_eoi,eos_mode);if (dev < 0) {// 连接失败} else {// 连接成功}在示例代码中,首先通过gpib.h头文件引入了GPIB通信相关的函数和数据类型,然后使用ibdev函数打开了与GPIB设备的连接。
ARTISAN技术组合购买指南说明书

INSTALLATION GUIDENI PXI-8186/8187This document contains information about installing yourNI PXI-8186/8187 controller in a PXI chassis.For complete configuration and troubleshooting information (includinginformation about BIOS setup, adding RAM, and so on), refer to theNI PXI-8186/8187 User Manual. The manual is in PDF format on therecovery CD included with your controller and on the National InstrumentsWeb site, .Installing the NI PXI-8186/8187This section contains general installation instructions for theNI PXI-8186/8187. Consult your PXI chassis user manual for specificinstructions and warnings.1.Plug in your chassis before installing the NI PXI-8186/8187. Thepower cord grounds the chassis and protects it from electrical damagewhile you install the module. (Make sure the power switch isturned off.)Caution To protect both yourself and the chassis from electrical hazards, leave the chassispowered off until you finish installing the NI PXI-8186/8187 module.2.Remove any filler panels blocking access to the system controller slot(Slot 1) in the chassis.3.Touch the metal part of the case to discharge any static electricity thatmight be on your clothes or body.4.Remove the protective plastic covers from the four bracket-retainingscrews as shown in Figure1.NI PXI-8186/8187 Installation Guide Figure 1. Removing Protective Screw Caps5.Make sure the injector/ejector handle is in its downward position.Align the NI PXI-8186/8187 with the card guides on the top andbottom of the system controller slot.CautionDo not raise the injector/ejector handle as you insert the NI PXI-8186/8187. Themodule will not insert properly unless the handle is in its downward position so that it doesnot interfere with the injector rail on the chassis.6.Hold the handle as you slowly slide the module into the chassis until the handle catches on the injector/ejector rail.7.Raise the injector/ejector handle until the module firmly seatsinto the backplane receptacle connectors. The front panel of theNI PXI-8186/8187 should be even with the front panel of the chassis.8.Tighten the four bracket-retaining screws on the top and bottom of thefront panel to secure the NI PXI-8186/8187 to the chassis.9.Check the installation.10.Connect the keyboard and mouse to the appropriate connectors. If youare using a PS/2 keyboard and a PS/2 mouse, use the Y-splitter adapterincluded with your controller to connect both to the PS/2 connector.11.Connect the VGA monitor video cable to the VGA connector.12.Connect devices to ports as required by your system configuration.13.Power on the chassis.14.Verify that the controller boots. If the controller does not boot, refer tothe What If the NI PXI-8186/8187 Does Not Boot? section.Figure2 shows an NI PXI-8186 installed in the system controller slot of aNational Instruments PXI-1042 chassis. You can place PXI devices in anyother slot.1PXI-1042 Chassis2NI PXI-8186 Controller3Injector/Ejector RailFigure 2. NI PXI-8186 Controller Installed in a PXI ChassisHow to Remove the Controller from the PXI ChassisThe NI PXI-8186/8187 controller is designed for easy handling. Completethe following steps to remove the unit from the PXI chassis:1.Power off the chassis.2.Remove the bracket-retaining screws in the front panel.3.Press the injector/ejector handle down.4.Slide the unit out of the chassis.© National Instruments Corporation3NI PXI-8186/8187 Installation GuideNational Instruments™, NI™, and ™ are trademarks of National Instruments Corporation. Product and company names mentioned herein are trademarks or trade names of their respective companies. For patents covering National Instruments products, refer to the appropriate location:Help»Patents in your software, the patents.txt file on your CD, or /patents.© 2003–2004 National Instruments Corp. All rights reserved.323683B-01Jun04 *323683B-01*What If the NI PXI-8186/8187 Does Not Boot?Several problems can cause a controller not to boot. Here are some thingsto look for and possible solutions.Things to Notice:•Which LEDs come on? The Power OK LED should stay lit.The Drive LED should blink during boot as the disk is accessed.•What appears on the display? Does it hang at some particular point(BIOS, Operating System, and so on)? If nothing appears on thescreen, try a different monitor. Does your monitor work with adifferent PC? If it hangs, note the last screen output that you saw forreference when consulting National Instruments technical support.•What has changed about the system? Did you recently move thesystem? Was there electrical storm activity? Did you recently adda new module, memory chip, or piece of software?Things to Try:•Make sure the chassis is plugged in to a working power source.•Check any fuses or circuit breakers in the chassis or other powersupply (possibly a UPS).•Make sure the controller module is firmly seated in the chassis.•Remove all other modules from the chassis.•Remove any nonessential cables or devices.•Try the controller in a different chassis.•Try a similar controller in this same chassis.•Recover the hard drive on the controller.•Clear the CMOS.。
国际电子(National Instruments)USB-7845R OEM 多功能数字实时接口设

SPECIFICATIONSNI USB-7845R OEMR Series for USB Multifunction RIO with Kintex-7 70T FPGA Français Deutsch日本語한국어简体中文/manualsThis document contains the specifications for the National InstrumentsUSB-7845R OEM device. Specifications are typical at 25 °C unless otherwise noted.Caution Using the NI USB-7845R OEM device in a manner not described in thisdocument may impair the protection the NI USB-7845R OEM device provides. Analog InputNumber of channels8 ............................................................................Input modes DIFF, NRSE, RSE (software-selectable; ............................................................................selection applies to all channels)Type of ADC Successive approximation register (SAR) ............................................................................Resolution16 bits ............................................................................Conversion time 2 µs ............................................................................Maximum sampling rate500 kS/s (per channel) ............................................................................Input impedancePowered on 1.25 GΩ ║ 2 pF....................................................................Powered off/overload 4.0 kΩ min....................................................................Input signal range±1 V, ±2 V, ±5 V, ±10 V (software-selectable) ............................................................................Input bias current±5 nA ............................................................................ ............................................................................Input offset current±5 nAInput coupling DC ............................................................................Overvoltage protection....................................................................Powered on±42 V maxPowered off±35 V max....................................................................Table 1. AI Operating Voltage Ranges Over TemperatureAI Absolute AccuracyAbsolute accuracy at full scale numbers is valid immediately following internal calibration and assumes the device is operating within 10 °C of the last external calibration. Accuracies listed are valid for up to one year from the device external calibration.Absolute accuracy at full scale on the analog input channels is determined using the following assumptions:•TempChangeFromLastExternalCal = 10 °C •TempChangeFromLastInternalCal = 1 °C•number_of_readings = 10,000•CoverageFactor = 3 σ1The minimum measurement voltage range is the largest voltage the NI USB-7845R OEM device is guaranteed to accurately measure.2| | NI USB-7845R OEM SpecificationsTable 2. AI Absolute Accuracy (Calibrated) (Continued)Table 3. AI Absolute Accuracy (Uncalibrated)Calculating Absolute AccuracyAbsoluteAccuracy=Reading⋅(GainError)+Range*(OffsetError)+NoiseUncertaintyGainError=ResidualGainError+GainTempco*(TempChangeFromLastInternalCal)+ReferenceTempco*(TempChangeFromLastExternalCal)OffsetError=ResidualOffsetError+OffsetTempco*(TempChangeFromLastInternalCal)+INL_ErrorNoiseUncertainty=Refer to the following equation for an example of calculating absolute accuracy.NI USB-7845R OEM Specifications| © National Instruments| 3Absolute accuracy at full scale on the analog input channels is determined using the following assumptions:•TempChangeFromLastExternalCal = 10 °C •TempChangeFromLastInternalCal = 1 °C•number_of_readings = 10,000•CoverageFactor = 3 σGainError=104.4ppm+20ppm*1+4ppm*10GainError=164.4ppmOffsetError=16.4ppm+4.18ppm*1+42.52ppmOffsetError=63.1ppmNoiseUncetainty=NoiseUncertainty=7.89µVAbsoluteAccuracy=10V*(GainError)+10V*(OffsetError)+NoiseUncertaintyAbsoluteAccuracy=2,283µVDC Transfer Characteristics ............................................................................INL Refer to the AI Accuracy TableDNL±0.4 LSB typ, ±0.9 LSB max ............................................................................No missing codes16 bits guaranteed ............................................................................CMRR, DC to 60 Hz-100 dB ............................................................................Dynamic CharacteristicsBandwidthSmall signal 1 MHz........................................................................................................................................Large signal500 kHz4| | NI USB-7845R OEM Specifications............................................................................Crosstalk-80 dB, DC to 100 kHzAnalog Output ............................................................................Output type Single-ended, voltage output ............................................................................Number of channels8 ............................................................................Resolution16 bits ............................................................................Update time 1.0 µs ............................................................................Maximum update rate 1 MS/sType of DAC Enhanced R-2R ............................................................................ ............................................................................Range±10 V ............................................................................Output coupling DCOutput impedance0.5 Ω............................................................................NI USB-7845R OEM Specifications| © National Instruments| 5............................................................................Minimum current drive±2.5 mAProtection Short circuit to ground ............................................................................Overvoltage protectionPowered on±15 V max....................................................................Powered off±10 V max....................................................................Power-on state User-configurable ............................................................................Power-on glitch-1 V for 1 µs ............................................................................Table 4. AO Operating Voltage Ranges for Over TemperatureAO Absolute AccuracyAbsolute accuracy at full scale numbers is valid immediately following internal calibration and assumes the device is operating within 10 °C of the last external calibration. Accuracies listed are valid for up to one year from the device external calibration.Absolute accuracy at full scale on the analog output channels is determined using the following assumptions:•TempChangeFromLastExternalCal = 10 °C •TempChangeFromLastInternalCal = 1 °C2The minimum measurement voltage range is the largest voltage the NI USB-7845R OEM device is guaranteed to accurately measure.6| | NI USB-7845R OEM SpecificationsTable 5. AO Absolute Accuracy (Calibrated) (Continued)Calculating Absolute AccuracyAbsoluteAccuracy=OutputValue*(GainError)+Range*(OffsetError)GainError=ResidualGainError+GainTempco*(TempChangeFromLastInternalCal)+ReferenceTempco*(TempChangeFromLastExternalCal)OffsetError=ResidualOffsetError+AOOffsetTempco*(TempChangeFromLastInternalCal)+INL_Error Refer to the following equation for an example of calculating absolute accuracy.Absolute accuracy at full scale on the analog output channels is determined using thefollowing assumptions:•TempChangeFromLastExternalCal = 10 °C•TempChangeFromLastInternalCal = 1 °CGainError=87.3ppm+12.6ppm*1+4ppm*10GainError=139.9ppmNI USB-7845R OEM Specifications| © National Instruments| 7OffsetError=41.1ppm+7.8ppm*1+61ppmOffsetError=109.9ppmAbsoluteAccuracy=10V*(GainError)+10V*(OffsetError)AbsoluteAccuracy=2,498µVDC Transfer CharacteristicsINL Refer to the AO Accuracy Table ............................................................................DNL±0.5 LSB typ, ±1 LSB max ............................................................................Monotonicity16 bits, guaranteed ............................................................................Dynamic CharacteristicsSlew rate-10 V/µs ............................................................................Noise250 µV rms, DC to 1 MHz ............................................................................Glitch energy at midscale transition±10 mV for 3 µs ............................................................................5V OutputOutput voltage 4.75 V to 5.1 V ............................................................................Output current0.5 A max ............................................................................Overvoltage protection±30 V ............................................................................ ............................................................................Overcurrent protection650 mA8| | NI USB-7845R OEM SpecificationsDigital I/OCompatibility LVTTL ............................................................................Logic family User-selectable ............................................................................Default software setting 3.3 V ............................................................................Maximum input 3.6 V ............................................................................NI USB-7845R OEM Specifications| © National Instruments| 9Table 10. Digital Output Logic Levels (Continued)Output currentSource 4.0 mA....................................................................Sink 4.0 mA....................................................................Input leakage current±15 µA max ............................................................................Input impedance50 kΩ typ, pull-down ............................................................................Power-on state Programmable, by line ............................................................................Protection±20 V, single line ............................................................................Digital I/O voltage switching time 2 ms max ............................................................................Note Refer to NI RIO Software Help for more information about switching times.Reconfigurable FPGAFPGA type Kintex-7 70T ............................................................................Number of flip-flops82,000 ............................................................................Number of LUTs41,000 ............................................................................Embedded block RAM4,860 kbits ............................................................................Number of DSP48 slices240 ............................................................................Timebase40, 80, 120, 160, or 200 MHz ............................................................................Timebase accuracy, onboard clock±100 ppm ............................................................................Calibration ............................................................................Recommended warm-up time15 minutesCalibration interval 1 year ............................................................................10| | NI USB-7845R OEM SpecificationsOnboard calibration referenceDC level3 5.000 V (±2 mV)....................................................................Temperature coefficient±4 ppm/°C max....................................................................Long-term stability±25 ppm/1,000 h....................................................................Note Refer to Calibration Certifications at /calibration to generate acalibration certificate for the NI USB-7845R OEM deviceBus Interface ............................................................................USB compatibility USB 2.0 Hi-Speed or Full-Speed4Data transfers DMA, interrupts, programmed I/O ............................................................................Number of DMA channels3 ............................................................................Power RequirementInput voltage9 V to 30 V ............................................................................Max power20 W ............................................................................ ............................................................................Overvoltage protection40 VNote You must use a UL Listed ITE power supply marked LPS with theNI USB-7845R OEM device.PhysicalNote If you need to clean the device, wipe it with a dry, clean towel.Dimensions (PCB)17.5 cm × 16.3 cm (6.9 in. × 6.4 in.) ............................................................................Weight183 g (6.45 oz) ............................................................................I/O connectors Analog- 1 × 50 pin box header, ............................................................................Digital- 3 × 34 pin box header3Actual value stored in Flash memory4Operating on a full-speed bus will result in lower performance and you might not be able to achieve maximum sampling/update rates.NI USB-7845R OEM Specifications| © National Instruments| 11Maximum Working VoltageMaximum working voltage refers to the signal voltage plus the common-mode voltage. Channel-to-earth±12 V, Measurement Category I ............................................................................Channel-to-channel±24 V, Measurement Category I ............................................................................Measurement Category I is for measurements performed on circuits not directly connected to the electrical distribution system referred to as MAINS voltage. MAINS is a hazardous live electrical supply system that powers equipment. This category is for measurements of voltages from specially protected secondary circuits. Such voltage measurements include signal levels, special equipment, limited-energy parts of equipment, circuits powered by regulated low-voltage sources, and electronics.Caution Do not use the NI USB-7845R OEM device for connection to signals inMeasurement Categories II, III, or IV.Note Measurement Categories CAT I and CAT O (Other) are equivalent. Thesetest and measurement circuits are not intended for direct connection to the MAINSbuilding installations of Measurement Categories CAT II, CAT III, or CAT IV. Environmental-40 °C to 70 °COperating temperature ............................................................................(IEC 60068-2-1, IEC 60068-2-2)Storage temperature-40 °C to 85 °C ............................................................................(IEC 60068-2-1, IEC 60068-2-2)10% to 90% RH, noncondensingOperating humidity ............................................................................(IEC 60068-2-56)Storage humidity (IEC 60068-2-56)5% to 95% RH, noncondensing ............................................................................ ............................................................................Pollution Degree2Maximum altitude2,000 m ............................................................................Indoor use only.Online Product CertificationTo obtain product certifications and the DoC for this product, visit /certification, search by model number or product line, and click the appropriate link in the Certification column.12| | NI USB-7845R OEM SpecificationsEnvironmental ManagementNI is committed to designing and manufacturing products in an environmentally responsible manner. NI recognizes that eliminating certain hazardous substances from our products is beneficial to the environment and to NI customers.For additional environmental information, refer to the Minimize Our Environmental Impact web page at /environment. This page contains the environmental regulations and directives with which NI complies, as well as other environmental information not included in this document.Waste Electrical and Electronic Equipment (WEEE)EU Customers At the end of the product life cycle, all products must be sent to aWEEE recycling center. For more information about WEEE recycling centers,National Instruments WEEE initiatives, and compliance withWEEE Directive 2002/96/EC on Waste Electrical and Electronic Equipment, visit/environment/weee.电子信息产品污染控制管理办法(中国RoHS)中国客户National Instruments符合中国电子信息产品中限制使用某些有害物质指令(RoHS)。
第三次作业带有GPIB接口的芯片TNT4882

TNT4882芯片名称:TNT4882生厂商:美国NI公司芯片功能:TNT4882是美国NI公司的一款单芯片、高速、听/讲功能的兼备的GPIB 接口专用芯片。
它内部集成了Turbo488 (高速传输电路)以及NAT4882(IEEE4 88.2兼容电路),并拥有诸多新的特性,能够兼容ANSI IEEE Standard 488.1和ANSI IEEE Standard 488.2规范,因而可以为GPIB系统提供一套完整的解决方案。
为了达到更高的传输速率。
TNT4882采用了单芯片FIFO缓存电路设计,其内置的16个增强型IEEE 488.1兼容收发器可以直接连接GPIB总线,以实现HS488传输模式(一种新的GPIB高速传输模式)。
在兼容性方面,它与以往使用的“PD7216 TMS9914A 中的寄存器设置完全兼容,用户可以将以前所用的代码直接移植到TNT4882上。
同时,它所包含的Turbo488电路及其诸多新特性也可以在一定程度上减少软件的开销。
另外,TMT4882还具有灵活的CPU 接口,可以方便地连接各种16位或8位微处理器,并将CPU发出的消息和信号转化成相应的GPIB消息和信号,以使实现GPIB设备和CPU及内存之间的通信。
GPIB (General Purpose Interface Bus)接口总线最早由美国HP公司倡导实施,命名为HPIB。
由于它良好的接口特性,很快在国际范围内得到广泛的应用,并被美国电气与电子工程学会命名为IEEE488,在英国和日本等国家则称为GPIB。
虽然有多种叫法,但实际上除了机械标准有所不同外,其实质完全相同。
它犹如一座桥梁,将配置GPIB总线接口的仪器与计算机紧密地结合起来。
用它组成的系统方便、灵活、功能强及适应性好,可方便地应用到科研、工程、医药工程、医药及测试等领域。
管脚定义及管脚功能:明向n 罢5n 30C S n E n 詈s n s> n 90- n s> n s> n s> n Eo n L r -'J."t,J .II .o n =8- n £§- n 30- n Msss 一n .L3S 咨n §3 n 8> n 雷h n ha 口 n 8 n 3f< n 盲o n 9U n M £5 n g c n 白5n n南口口n DATA7 DATA6 GND DATA5 DATA4 □ND DATAJDATA2DATA1 GND VDDDATAD lOCtlRDY AFN _N VDD GNDINTRQftCKN DRQ ADDR9M 79 T-3 77 Tfi 75 74 75 72 11 7D 03 CT W 65 2 03 02 b 1 6口 第 H 57 36 « E >3 52 31SI 值S 叫&4 ■c g45。
TNT4882手册

TNT4882Single-Chip IEEE 488.2 Talker/Listener ASIC National InstrumentsPhone: (512) 794-0100 • Fax: (512) 683-9300 • info@ • 3D I O 6N G N DL A D C S D I O 8NG N D I F C N D I O 5NS R Q N G N D D I O 7N A T N NR E N NG N D R E S E T NG N D DATA5DATA4GND GND VDD GND DATA0INTR DACKN DRQ BURST_RDN DAVNGNDVDDGNDDIO2NDIO3NVDDXTAL1EOINW R N G N D V D DT R I G C P U A C C T A D C S A B U S _O E N A D D R 4A D D R 3A D D R 2A D D R 1A D D R 0A B U S N P A G E D G N D R E M S W A P N F I F O _R D Y GNDXTAL0GNDKEYDQKEYRSTN DATA3DATA2DATA1GND VDD RDY1V D D D A T A 10G N D D A T A 11D A T A 12D A T A 13G N D D A T A 14D A T A 15B B U S _O E N D A T A 9D A T A 8V D D G N D GND DATA6DATA7R D N B B U S N G N D V D D G N D V D D G N D G N D C S N G N D M O D E N C D C A SGNDNRFDNNDACNGeneric Pin ConfigurationFigure 3. TNT4882 Generic Pin ConfigurationTable continued on page 4Generic Pin DescriptionAll pins with names that end in ‘N’ are active low; all others are active high. All input (I) and bidirectional (I/O) pins have an internal pull-up resistor between 50 k Ωand 150 k Ω.Note: You can also see the “Hardware Considerations” chapter of the “TNT Programmer Reference Manual” (P/N 320724-01) for more information.TNT4882Single-Chip IEEE 488.2 Talker/Listener ASIC National InstrumentsPhone: (512) 794-0100 • Fax: (512) 683-9300 • info@ • 4Pin No.(s)Name(s)Type Description 51DCAS O Asserts when the device clear state machine is in DCAS 52NC O Leave this pin unconnected 53MODE I Determines whether the TNT4882 powers up in 7210 or 9914 emulation mode – High = 7210 mode, Low = 9914 mode 55CSN I Chip Select enables I/O transfers between the CPU and the TNT488262BBUSN I Enables register accesses through the B bus (DATA7-0)63RDN I Enables the contents of the registers selected by ADDR 4:0 and CSN or the FIFOs to appear on the data bus selected by ABUSN and BBUSN 64WRN I Latches data on the bus selected by ABUSN and BBUSN into an internal TNT4882 register on the trailing (rising) edge of WRN 66LADCS O Asserts when the TNT4882 is addressed as a Listener 67RESETN I Holds the TNT4882 in its idle state 71,74,77,80,88,DIO8-1N I/O 8-bit bidirectional IEEE 488 data bus 89,91,9270,73,76,79,RENN, ATNN, SRQN, I/O IEEE 488 control signals 81,82,84,85IFCN, NDACN, NRFDN, DAVN, EOIN 95XTAL0O Output of crystal circuit – use only for driving a quartz crystal 96XTAL1I Crystal oscillator input – drive with a 40 MHz CMOS input level clock signal 98KEYCLKN O Strobes data to or from a DS1204 electronic key 99KEYDQ I/O Transmits serial data between the TNT4882 and a DS1204 key 100KEYRSTN O Resets a DS1204 key 4,8,13,25,27,35,37GND _Ground pins – 0 V 41,45,48,54,56,57,59,61,65,68,72,75,78,83,86,90,93,9712,24,36,40,58,VDD _Power pins – +5 V (±5%)60,69,87,94D I O 6N G N D I O C S 16N D I O 8NG N D I F C N D I O 5NS R Q NG N D D I O 7N A T N N R E N NG N D R E S E T G N D DATA5DATA4GND AEN_N VDD GND DATA0INTR DACKN DRQ ADDR9DAVNGNDVDDGNDDIO2NDIO3NVDDXTAL1EOINI O W N G N D V D D S W 7S W 6N C D 15_8_O E N A D D R 4A D D R 3A D D R 2A D D R 1A D D R 0B H E N _N A D D R 5G N D A D D R 6A D D R 7A D D R 8GNDXTAL0GNDKEYDQKEYRSTN DATA3DATA2DATA1GND VDD IOCHRDY V D D D A T A 10G N D D A T A 11D A T A 12D A T A 13G N D D A T A 14D A T A 15D 7_0_O E N D A T A 9D A T A 8V D D G N D GND DATA6DATA7I O R N S E N S E _8_16N G N D V D D V D D V D D G N D V D D S W 5N C M O D E S W 9S W 8GNDNRFDNNDACNISA Pin Configuration Figure 4. TNT4882 ISA Pin ConfigurationTable continued from page 3TNT4882 Single-Chip IEEE 488.2 Talker/Listener ASICNational Instruments Phone: (512) 794-0100 • Fax: (512) 683-9300 • info@ • 5ISA Pin DescriptionAll input (I) and bidirectional (I/O) pins have an internal pull-up resistor between 50 kΩand 150 kΩ. Pins with names that end in “N” are active low signals – all others are active high. Open-collector outputs are type “OC.”Note: You can also see the “Hardware Considerations” chapter of the “TNT Programmer Reference Manual” (P/N 320724-01) for more information.Pin No.(s)Name(s)Type Description1D7_0_OEN O Asserts when DATA7-0 bus is enabled for output – may be left unconnected2,3,5,6,7,9,10,11DATA15-8I/O Upper eight bits of bidirectional three-state data bus for transfer of commands,data, and status between TNT4882 and CPU – can connect directly to the AT bus –DATA15 is the most significant bit14BHEN_N I Enables access to upper eight bits of data bus when asserted19-15ADDR4-0I Determines which register will be accessed during an I/O access31,30,29,28,26ADDR9-5I Determines if an I/O address is within the range occupied by the TNT4882 –the chip is selected and an I/O access occurs when ADDR9-5 match SW9-5 andAEN_N is asserted20D15_8_OEN O Asserts when DATA15:8 bus is enabled for output – may be left unconnected21,54NC O Leave unconnected52,51,23,22,55SW9-5I Determines the base address of the TNT488232DRQ O Asserts to request a DMA transfer cycle33DACKN I Enables FIFO accesses during a DMA transfer cycle34INTR O Asserts when one or more of the unmasked interrupt conditions becomes true37AEN_N I Enables I/O accesses to the TNT488238IOCHRDY OC When the TNT4882 is not accessed, this open-collector signal is not driven, and apull-up resistor on the system board keeps it pulled high – at the start of someTNT4882 accesses, the TNT4882 may drive it low, then pull it high again during thecycle to indicate that the TNT4882 is ready for the CPU to end that cycle50,49,47,46,44,DATA7-0I/O Lower eight bits of bidirectional three-state data bus for transfer of commands, data, 43,42,39and status between TNT4882 and CPU – can connect directly to the AT bus – DATA7is the most significant bit53MODE I Forces the TNT4882 to 7210 (high) or 9914 (low) emulation mode on a hardwarereset – may be left unconnected62SENSE_8_16N I Pull this pin low to tell the TNT4882 that it is connected to a 16-bit bus – leave itunconnected if the TNT4882 is connected to an 8-bit bus63IORN I Drives the contents of the register selected by ADDR4-0 on the data bus when theTNT4882 is selected64IOWN I The value on the data bus is latched into the register selected by ADDR4-0 on therising edge of IOWN when you select the TNT488266IOCS16N OC Driven low during an access to the upper data bus67RESET I Causes a hardware reset and holds the TNT4882 in its idle state while asserted 71,74,77,80,88,DIO8-1N I/O8-bit bidirectional IEEE 488 data bus89,91,9270,73,76,79,81,RENN, ATNN, SRQN,I/O IEEE 488 control signals82,84,85IFCN, NDACN, NRFDN,DAVN, EOIN95XTAL0O Output of crystal circuit – use only for driving a quartz crystal96XTAL1I Crystal oscillator input – drive with a 40 MHz CMOS input level clock signal98KEYCLKN O Strobes data to or from the DS1204 electronic key99KEYDQ I/O Transmits serial data between the TNT4882 and a DS1204 key100KEYRSTN O Resets a DS1204 key4,8,13,25,27,35,41,GND–Ground pins – 0 V45,48,57,61,65,68,72,75,78,83,86,90,93,9712,24,36,40,56,58,VDD–Power pins – +5 V (±5%)59,60,69,87,94TNT4882Single-Chip IEEE 488.2 Talker/Listener ASIC National InstrumentsPhone: (512) 794-0100 • Fax: (512) 683-9300 • info@ • 6TNT4882 Register MapNotes on Register Map1. For complete register descriptions, see the “TNT4882Programmer Reference Manual” (320724-01)2. Some of the 7210 mode registers, such as the ISR1, havethe same names as some of the 9914 mode registers. The7210 mode registers are NOT the same as their 9914 modecounterparts. Be sure to refer to the appropriate bit map forthe chip emulation mode you are using when programmingthese registers.3. The shaded registers are “paged-in registers.” Paged-inregisters only exist in 9914 mode. Writing to the address of the9914 mode ADSR normally does not access any registers.Writing one of four page-in commands to the AUXCR changesall subsequent writes to that address to that of the corresponding paged-in register . The two readable paged-in registers, the 9914 mode SPSR and ISR2, are both paged in whenever any one of the four writable paged-in registers is paged in. When you write the clear page-in command to the AUXCR, all paged-in registers are paged out again and are no longer accessible.4.There are several unused bytes in the address space of the TNT4882. These addresses are reserved for adding new features to the chip. You should not map any external hardware into these addresses or access them at any time, as this may cause compatibility problems with future versions of the TNT4882.TNT4882 Single-Chip IEEE 488.2 Talker/Listener ASICNational Instruments Phone: (512) 794-0100 • Fax: (512) 683-9300 • info@ • 7zero; leaving them unconnectedcauses those address lines to becompared to one. (Base I/Oaddress 2C0 hex shown.)to be compared to zero;leaving them u nconnectedcauses those address linesto be compared to one. (BaseI/O address 2C0 hex shown.) Figure 5. PC/XT and AT (ISA) Bus to ISA Mode TNT4882Hardware Interfacing – ISA Mode TNT4882TNT4882Single-Chip IEEE 488.2 Talker/Listener ASIC National InstrumentsPhone: (512) 794-0100 • Fax: (512) 683-9300 • info@ • 8SENSE_8_16N BHEN_N ADDR4-0IORN IOWN DATA15-8DATA7-001100001FIFOA FIFOB 001100010FIFOA FIFOB 00XXXX101Read Not Driven 00XXXX110Written Ignored 01XXXX001Not Driven Read 01XXXX010Ignored Written 11XXXX001Not Driven Read 11XXXX010Ignored Written 11XXXX101Not Driven Read 11XXXX110Ignored WrittenISA Pin Configuration Byte Lane TableThis table shows which byte lane accesses the TNT4882 internalregisters during an I/O access when you use the ISA pinconfiguration. All combinations of ADDR4-1, SENSE_8_16N,and BHEN_N not shown in this table are illegal. You should notapply these combinations to the TNT4882 while the chip isselected. The accessed register is determined only by ADDR4-0,not SENSE_8_16N or BHEN_N.TNT4882Single-Chip IEEE 488.2 Talker/Listener ASIC National InstrumentsPhone: (512) 794-0100 • Fax: (512) 683-9300 • info@ • 9Generic Pin Configuration Byte Lane TableThis table shows which byte lanes will access TNT4882 registersduring I/O accesses.Figure 6. Intel CPU to Generic Mode TNT4882Hardware Interfacing – Generic Mode TNT4882ABUSN BBUSN ADDR4-0D15-8D7-00111000FIFOB unused1011000unused FIFOB0011000FIFOA FIFOB01XXXXX*used unused10XXXXX*unused used*Any address except 11000TNT4882Single-Chip IEEE 488.2 Talker/Listener ASIC National InstrumentsPhone: (512) 794-0100 • Fax: (512) 683-9300 • info@ • 10Generic Mode DC CharacteristicsParameterSymbol Min Max Unit Notes Supply voltageV DD 4.75 5.25V Voltage input lowV IL -0.5 0.8V Voltage input highV IH 2.0V CC V Voltage output lowV OL 0.00.4V Voltage output highV OH 2.4V DD V Supply currentI DD 90mA 50 mA, typical Output current lowI OL 24mA V OL = 0.4 V DATA15-0, LADCS, DRQ, INTR, RDY1Output current lowI OL 8mA V OL = 0.4 V BBUS_OEN, ABUS_OEN, TADCS,CPUACC, REM, TRIG, DCAS, CICFIFO_RDYI OL 4mA V OL = 0.4 V Output current lowI OL 2mA V OL = 0.4 V KEYDQ, KEYRSTN, KEYCLKNDIO8-1N, IFCN, SRQN, EOIN, ATNN,I OL 48mA V OL = 0.4 V RENN, DAVN, NRFDN, NDACNOutput current highI OH -12mA V OH =V DD -0.5 V DATA15-0, LADCS, DRQ, INTR, RDY1-24mA V OH = 2.4 V Output current highI OH -4mA V OH = V DD -0.5 V BBUS_OEN, ABUS_OEN, TADCS,CPUACC, REM, TRIG, DCAS-8mA V OH = 2.4 V FIFO_RDYI OH -2mA V OH = V DD -0.5 V -4V OH = 2.4 V Output current highI OH -1mA V OH = V DD -0.5 V KEYDQ, KEYRSTN, KEYCLKN-2mA V OH = 2.4 V DIO8-1N, IFCN, SRQN, EOIN, ATNN,I OH 16mA V OH = 2.4 V RENN, DAVN, NRFDN, NDACNInput leakage current – all pinsI IH±10µA V DD = 5.5 VOutput leakage current – all pins I OZ±10µA V DD = 5.5 V Generic Mode CapacitanceParameterSymbol Min Typ Max Unit Notes Pin capacitanceC 50pF DIO8-1N, RENN, ATNN, IFCN, SRQN, DAVN, EOIN, NDACN, NRFDNPin capacitance all other pins C 3.6pF Generic Mode AC CharacteristicsCommercial Industrial ParameterSymbol Min Max Min Max Unit Address setup to RDN = 0, WRN = 0t AS 2427ns Data delay from RDN = 0, CSN = 0 (one-chip mode access)t RD 7178ns Data float from RDN = 1t DF 4044ns RDN pulsewidth (I/0 access)t RW 7178ns RDN recovery widtht RR 4044ns Address hold from RDN = 1, WRN = 1t AH 00ns DRQ unassertiont DU 7886ns Data delay from RDN = 0, DACKN = 0t DR 4044ns Data setup to WRN = 1t WS 1416ns Data hold from WRN = 1t WH 00ns CSN setup to RDN or WRNt CS 00ns CSN hold from RDN or WRNt CH 00ns DACKN setup to RDN or WRNt DS 00ns DACKN hold from RDN or WRNt DH 00ns RDN or WRN to CPUACC (two-chip mode NAT4882 access only)t CPU 2629ns RDN or WRN to RDY1 assertt ARDY Two-chip mode NAT4882 access1010clock periods Other accesses2528ns RDN or WRN to RDY1 unassertt URDY 2225ns WRN pulse width (DMA access)t WP4044ns RDN pulse width (DMA access)t RP4044nsNational InstrumentsPhone: (512) 794-0100 • Fax: (512) 683-9300 • info@ • 11Figure 8. DMA ReadFigure 7. CPU ReadFigure 9. CPU WriteGeneric Mode AC Characteristics WaveformsWaveforms continued on page 12DATAWRNCSNABUSN,BBUSN, ADDR4-0RDY1CPUACC †††† CPUACC asserts during two-chip modeNAT4882 accesses onlyDRQ DACKNRDN DATA15-0RDY1ABUSN, BBUSN,ADDR4-0CSNRDNDATARDY1CPUACC ††††NAT4882 accesses onlyNational InstrumentsPhone: (512) 794-0100 • Fax: (512) 683-9300 • info@ • 12WRNDRQ DACKN DATA15-0Figure 10. DMA WriteWaveforms continued from page 11ISA Mode DC CharacteristicsParameterSymbolMin Max UnitNotesSupply voltage V DD 4.75 5.25V Voltage input low V IL -0.5 0.8V Voltage input high V IH 2.0V CC V Voltage output low V OL 0.00.4V Voltage output high V OH 2.4V DD V Supply current I DD 90mA 50 mA, typical Output current low I OL24mAV OL = 0.4 VDATA15-0DRQ, INTR, IOCS16, IOCHRDY Output current low I OL 16mA V OL = 0.4 V D7_0_OENOutput current lowI OL 8mA V OL = 0.4 V D15_8_OEN, TP_INTWTN Output current lowI OL2mAV OL = 0.4 VKEYDQ, KEYRSTN, KEYCLKN Output current lowDIO8-1N, RENN, ATNN, IFCN, SRQN,I OL 48mA V OL = 0.4 V DAVN, EOIN, NDACN, NRFDN Output current high I OH-12mA V OH = V DD -0.5 V DATA15-0DRQ, INTR-24mA V OH = 2.4 V Output current high I OH-8mA V OH = V DD -0.5 V D7_0_OEN-16mA V OH = 2.4 V Output current high I OH-4mA V OH = V DD -0.5 V D15_8_OEN,TP_INTWTN-8mA V OH = 2.4 V Output current high I OH-1mA V OH = V DD -0.5 V KEYDQ, KEYRSTN,KEYCLKN-2mA V OH = 2.4 V Output current highDIO8-1N, RENN, ATNN, IFCN, SRQN,I OH -16mA V OH = 2.4 V DAVN, EOIN, NDACN, NRFDN Input leakage current – all pins I IH ±10mA V DD = 5.5 V Output leakage current – all pinsI OZ±10mAV DD = 5.5 VNational InstrumentsPhone: (512) 794-0100 • Fax: (512) 683-9300 • info@ • 13Figure 11. I/O Read Access Waveforms continued on page 14ISA Mode CapacitanceParameterSymbolMin TypMax UnitNotesPin capacitanceC3.6pFDATA15-0, DRQ, INTR, IOCS16N, IOCHRDY, ADDR6Pin capacitanceC 3.0pFD7_0_OEN, D15_8_OEN, TP_INTWTN,KEYDQ, KEYRSTN, KEYCLKN, ADDR4, ADDR8, ADDR9Pin capacitanceC 3.5pFBHEN_N, ADDR3-0, ADDR5, ADDR7, DACKN, AEN_N, MODE, TESTMODE,PWBSEL2-0, SW9, SENSE_8_16N,IORN, IOWN, RESET Pin capacitanceC 50pFDIO8-1N, RENN, ATNN, IFCN, SRQN,DAVN, EOIN, NDACN, NRFDNParameterSymbol Min MaxUnit NotesADDR9-0 setup to IORN, IOWN t AS30ns ADDR9-0 hold from IORN, IOWN t AH 0ns DACKN setup to IORN, IOWN t DS 0ns DACKN hold from IORN, IOWN t DH 20ns Data setup time to IOWN rising t SU 22ns Data hold time from IOWN rising t WH 0ns IORN low pulse width t RPWL 100ns IORN high pulse width t RPWH 42ns IOWN low pulse width t WPWL 100ns IOWN high pulse widtht WPWH 100ns IORN or IOWN held from IOCHRDY t TD 20ns DRQ unassertion time t DU 73ns Due to FIFO full/empty DRQ unassertion timet DU 48ns Due to byte count reachedData access time from IORN falling, DMA t DACC 80ns Data access time from IORN falling, I/O t ACC 80ns Data hold time from IORN rising t RH 0ns Data float time from IORN rising t DF 30ns IOCS16N assertion after valid address t DEC 30ns IOCS16N negation after invalid address t DECN 20ns IOCHRDY negation from IORN or IOWN t RDYN 40ns IOCHRDY release after IORN or IOWNt RDY350nsISA Mode AC CharacteristicsADDR9-0, AEN_NIORN DATA15-0IOCS16N IOCHRDYNational InstrumentsPhone: (512) 794-0100 • Fax: (512) 683-9300 • info@ • 14Waveforms continued from page 13Figure 13. DMA Read AccessFigure 14. DMA Write AccessFigure 12. I/O Write AccessADDR9-0, AEN_NIOWN DATA15-0IOCS16N IOCHRDYIORN DRQDACKNDATA15-0IOWN DRQ DACKNDATA15-0National InstrumentsPhone: (512) 794-0100 • Fax: (512) 683-9300 • info@ • 15Figure 16. Mechanical DataFigure 17. Recommended Land Pattern (not to scale)Absolute Maximum RatingsProperty RangeUnitsSupply voltage, V DD - 0.5 to + 7.0 V Input voltage, V IN- 0.5 to V CC + 0.5V Output voltage, V OUT- 0.5 to V CC + 0.5V Storage temperature, T STG- 55 to 150˚ CFRONT VIEW SIDE VIEWPIN 1PIN 300.650.22 (MIN)0.38 (MAX)17.90 ± 3.40 (MAX.)2.80 ±0.250.23 ±0.13SEE DETAIL A0°0.80 ±0.15NOTES:1. All dimensions are shown in millimeters.2. Unless otherwise specified, all dimensions are nominal.3. When converting from millimeters to inches, four significant digits to the right of the decimal point are necessary.Technical SupportNational Instruments strives to provide you with quality technical assistance worldwide. We currently offer electronic technical support along with our technical support centers staffed by Applications Engineers.Access information from our Web site at Our FTP site is dedicated to 24-hour support, with a collection of files and documents to answer your questions. Log on to our Internet host at You can fax questions to our Applications Engineers anytime at (800) 328-2203 or (512) 683-5678. Or , you can call from 8:00 a.m. to 6:00 p.m. (central time) at (512) 795-8248.Internationally, contact your local office. National Instruments sponsors a wide variety of group activities, such as user group meetings at trade shows and at large industrial sites. Our users also receive our quarterly Instrumentation Newsletter with the latest information on new products, product updates, application tips,and current events. In addition, sign up for NI News , our electronic news service at /newsWarrantyAll National Instruments data acquisition, computer-based instrument, VXIbus, and MXIbus products are covered by a one-year warranty. GPIB hardware products are covered by a two-year warranty from the date of shipment. The warranty covers board failures, components, cables, connectors, and switches, but does not cover faults caused by misuse. The owner may return a failed assembly to National Instruments for repair during the warranty period. Extended warranties are available at an additional charge.Information furnished by National Instruments is believed to be accurate and reliable. National Instruments reserves the right to change product specifications without notice.Seminars/TrainingFree and fee-paid seminars are presented several times a year in cities around the world. Comprehensive, fee-paid training courses are available at National Instruments offices or at customer sites. Call for training schedules.For More InformationContact National Instruments for Application Notes such as:”Using the TNT4882 in a MC68340 System“”Factors to Consider When Clocking the TNT4882 at Frequencies Less than 40 MHz“”Porting a 9914 GPIB Design to Use the TNT4882“Ordering InformationTNT4882-BQTNT4882 Developer Kit..........................................776866-01Includes 2 TNT4882 ASICs, PC AT evaluation board, ESP-488TL source code software, and documentation.TNT4882 Programmer Reference Manual..............320724-01Part Number Legenda.Family name TNT = Single-chip, high-speed, GPIB Talker/Listener interfaceb.Device-number 4882 = IEEE 488.2 compatiblec.Reservedd.Revisione.Package type Q = Quad flat packU.S. Corporate Headquarters Fax (512) 683-9300 • info@Branch Offices: Australia 03 9879 5166 • Austria 0662 45 79 90 0 • Belgium 02 757 00 20 • Brazil 000 811 781 0559• Canada 905 785 0085China 86 21 6555 7838 • Denmark 45 76 26 00 • Finland 09 725 725 11 • France 01 48 14 24 24 • Germany 089 741 31 30 • Hong Kong 2645 3186India 91805275406• Israel 03 6120092 • Italy 02 413091 • Japan 03 5472 2970 • Korea 02 596 7456 • Mexico 001 800 010 0793Netherlands 0348 433466 • New Zealand 09 914 0488• Norway 32 27 73 00 • Singapore 2265886 • Spain 91 640 0085 • Sweden 08 587 895 00Switzerland 056 200 51 51 • Taiwan 02 2377 1200 • U.K . 01635 523545© Copyright 1999 National Instruments Corporation. All rights reserved. Product and company names listed are trademarks or trade names of their respective companies.0305599(512) 794-0100*000000A-01*340570D-01。
NI4882-Readme
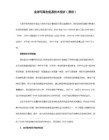
Power Management - NI-488.2 for Windows, Version 2.2, adds the EPWR
error code. This error indicates that the interface lost power.
This may occur when the system goes to standby or hibernate mode.
Controller/Analyzer board. Support for the obsolete GPIB-USB-A
interface has been dropped in this release.
Driver version 2.3 performance during IBCMD and serial poll calls was
lower than version 2.2. This has been fixed and improved over
version 2.2.
Documentation has been updated for various features.
Enhancements and Bugfixes in Version 2.3
to English and Japanese languages supported by the previous versions
of NI-488.2 for Windows. All Components of this release have been
localized with the exception of:
This driver version has been tested with the following software.
TiWi-uB2 EM BOARD User Guide
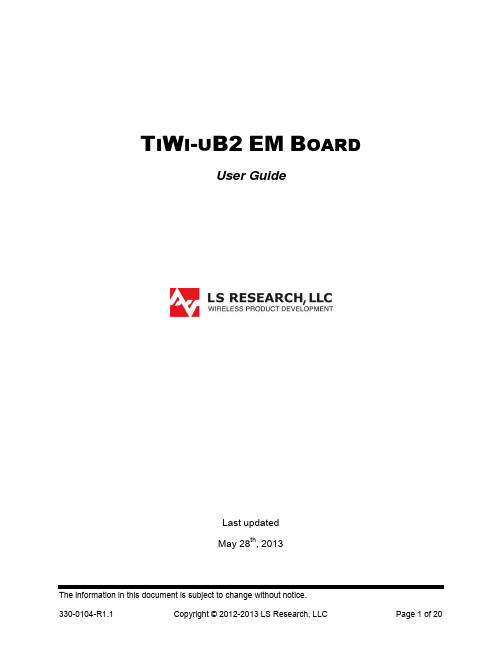
T I W I-U B2EM B OARDUser GuideLast updatedMay 28th, 2013Table of Contents1Introduction (3)1.1Purpose & Scope (3)1.2Applicable Documents (3)1.3Revision History (3)2TiWi-uB2 Module Description (4)3TiWi-uB2 EM Board Hardware (5)3.1Antenna (5)3.2Connectors (5)3.3Required Signals between EM Board and Host Device (6)3.4Connecting EM Board to Host Platform (7)3.5Power Supply (7)3.6Serial Interfaces (7)3.7HCI UART (8)3.8PCM Interface (8)3.9Option 1: Using EM Connectors (8)3.10Option 2: Using Single Row Headers (11)3.11Using J7 with USB to Serial Converter (12)4Schematic (13)4.1Bill Of Material (BOM) (14)5Application Development (15)5.1Overview (15)5.2Development Tools (15)6Contacting LS Research (20)1Introduction1.1 Purpose & ScopeThe purpose of this document is to provide details regarding the setup and use of theTiWi-uB2 module on an EM board. This document covers a description of the EM board and its features and a brief tutorial on how to operate the module EM board.1.2 Applicable Documents∙TiWi-uB2 Datasheet (330-0100)∙TiWi-uB2 Antenna Design Guide (330-0106)1.3 Revision HistoryTable 1 Revision History2TiWi-uB2 Module DescriptionThe TiWi-uB2 EM “Evaluation Module” Board is an evaluation platform for the LSResearch TiWi-uB2 Bluetooth and Bluetooth Low Energy (BLE) module.Communication between the TiWi-uB2 module, which is a slave, and the host device is through a UART interface.The TiWi-uB2 EM Board contains an on board chip antenna and U.FL connector. The EM board is intended for evaluation purposes when used in conjunction with variousTexas Instruments MSP430 and Stellaris development boards.Figure 1 TiWi-uB2 EM Board TopFigure 2 TiWi-uB2 EM Board Bottom3 TiWi-uB2 EM Board Hardware 3.1 AntennaThe TiWi-uB2 EM Board contains an on board chip antenna which is modular certified for FCC 15.247 and IC RSS-210, as well as compliant to the RF requirements for ETSI EN 300 328 and ETSI EN 301 489. The antenna layout and circuitry on the EM Board can be replicated on a custom designed PCB assembly. Assuming the design/layout is followed exactly as that which is on the EM Board, the custom PCB will retain the modular certification. Below are details on the certifications.FCC ID: TFB-BT1, 15.247 IC ID: 5969A-BT1, RSS 2103.2 ConnectorsThere are two primary connectors on the TiWi-uB2 EM Board (J1 & J2). These provide a standard interface to Texas Instruments development platforms (See Section 3.9). Two additional non populated connectors (J4 & J5) provide access to all of the significant signals on the module on a standard, single row 2mm pitch header.165423789Figure 3 TiWi-uB2 EM Board Top Side ConnectorsTable 2 TiWi-uB2 EM Board Top Side Connectors3.3 Required Signals between EM Board and Host DeviceIn addition to power and ground, there are three signals required for connecting a TiWi-uB2 module to a host device. See Table 3 below for details on these connections.Table 3 TiWi-uB2 Required Connections3.4 Connecting EM Board to Host PlatformThe TiWi-uB2 EM Board is intended to allow for evaluation of and early developmentwith a TiWi-uB2 module. The EM Board has two “EM” connectors on the bottom of the board that allows for easy connection to various Texas Instruments microcontrollerdevelopment platforms. The primary development platform is the MSP430F5438Experimenter Board.It is also possible to adapt the TiWi-uB2 EM Board to work with microcontroller platforms that do not have support for the EM connectors. Sections 3.9 and 3.10 describe the two options for adapting an EM Board to work with other microcontroller platforms.3.5 Power Supply3.5.1 VBATVBAT requires a 3.0V to 4.8V DC power supply.3.5.2 VDD_IOVDD_IO requires a 1.8V DC power supply.Figure 4 Power Supply3.6 Serial InterfacesThere are two serial interfaces to the module, HCI UART and PCM. Each interface isdescribed below.Figure 5 Serial Interfaces3.7 HCI UARTThis is the main interface between the host microcontroller and the module. TheBluetooth UART may also be used to download external patches from the host to theTiWi-uB2. The UART interface supports baud rates from 9600bps to 4Mbps.BT debug pin: The debug interface (TX_DBG) helps customers to debug the HW/SWissues for their application (not pictured).3.8 PCM InterfaceThe PCM Interface can connect to linear PCM Codec devices in master or slave mode.In master mode, the TiWi-uB2 generates the PCM_CLK and PCM_SYNC signals, and in slave mode, these signals are provided by another master on the PCM interface and are inputs to the TiWi-uB2.Figure 6 PCM Interface3.9 Option 1: Using EM ConnectorsEither build a PCB which has the EM Board mating connectors which will allow forplugging the TiWi-uB2 EM Board into, or solder wires to EM Board mating connectorsthat can then be wired into whatever development platform is being used.Below are two suggestions for the mating EM connectors.Through hole connector: Samtec TFM-110-01-S-D-WTSurface Mount connector: Samtec SFM-110-02-L-D-AIf building a PCB that has the mating EM Board connectors, the connectors need to be lined up and spaced 1.2” apart as shown in Figure 7.Figure 7 Host PCB EM Mating Connector Arrangement (Top View)Refer to Table 4 and Table 5 below for details on the signals brought out to the EM connectors J1 and J2.Table 4 EM Connector J1Table 5 EM Connector J2DI = Digital Input; DO = Digital Output; DIO = Digital Input/Output; PI = Power Input3.10 Option 2: Using Single Row HeadersSolder single row 12 pin 2mm headers into locations J4 and J5 on the EM Board, and then build a wiring harness between the headers on the EM Board and themicrocontroller development platform of interest.Below is a suggestion for the 12 pin 2mm headers.Sullins NRPN121PAEN-RCRefer to Table 6 and Table 7 below for details on the signals brought out to the single row headers J4 and J5.Table 6 Single Row Header J4DI = Digital Input; DO = Digital Output; PI = Power InputTable 7 Single Row Header J5DI = Digital Input; DO = Digital Output; DIO = Digital Input/Output; PI = Power Input3.11 Using J7 with USB to Serial ConverterJ7 is provided for interfacing the TiWi-uB2 Module to a USB-to-Serial converter, or similar serial device capable of providing 1.8V logic level data.Table 8 Single Row Header J7DI = Digital Input; DO = Digital Output; DIO = Digital Input/Output; PI = Power Input;4.1 Bill Of Material (BOM)Table 9 TiWi-uB2 EM Board BOM5Application Development5.1 OverviewThe TiWi-uB2 EM Board used in conjunction with a Bluetooth stack running on TI’sMSP430BT5438 or Stellaris LM3S9B96microcontroller (MCU) will reduce designbarriers and provides a highly flexible platform to enable customer’s early prototyping capabilities of embedded Bluetooth applications. The ready-to-go wireless platforms simplify the development process of pre-integrated and pre-validated Bluetooth serial link on an MSP430BT5438 or LM3S9B96system.For an overview of development platforms and software examples see CC256xBluetooth.5.2 Development Tools5.2.1 MSP430 HardwareHardware required for initial evaluation and development include:∙ 2 - TiWi-uB2 EM Boards∙ 1 - TI MSP430 USB Debugging Interface∙ 2 - TI MSP430F5438 Experimenter Boards5.2.2 Stellaris Hardware∙ 1 - TiWi-uB2 EM Board∙ 1 - TI MSP430 USB Debugging Interface∙ 1 - TI Stellaris LM3S9B96 EM2 Expansion Board∙ 1 - TI DK-LM3S9D965.2.3 SoftwareSoftware required for initial evaluation and development include:Stellaris∙Bluetopia®+LE SDK∙CC256x_Bluetopia_Stack∙Stellaris DK-LM3S9B96 SDKIntegrated BT Profiles∙Classic Bluetooth∙SPP∙A2DPFigure 9 TiWi-uB2 EM Board with Stellaris DK-LM3S9B96MSP430Bluetopia∙Bluetopia®+LE SDK∙CC256x_Bluetopia_Stack∙CC256x MSP430 Bluetopia Basic Demo APPSIntegrated BT Profiles∙Classic Bluetooth∙SPP∙Bluetooth Low Energy∙GATT∙ANP∙HRP∙HTP∙PASPThis Bluetooth software solution is licensed from Stonestreet One. The Bluetopia®+LE SDK is comprised of Single Mode and Dual Mode offering implementing the Bluetooth 4.0 specification. Bluetopia®+LE stack is built upon the solid foundation of the Bluetopia protocol stack that is currently being used in millions of consumer and industrial devices and that was first qualified in 2000 `TiWi-uB2 + MSP430 Bluetopia Basic Demo APPS allows users to evaluate TI's CC256x Bluetooth device by using the TiWi-uB2 EM board and the MSP-EXP430F5438 board. The CC256x+MSP430 Bluetooth sample applications code are provided to enable a rich out-of-box experience to the user. The application allows the user to use a console to send Bluetooth commands, setup a Bluetooth Device to accept connections, connect to a remote Bluetooth device and communicate over Bluetooth.Figure 10 TiWi-uB2 EM Board with MSP430F5438 Experimenter Board6Contacting LS ResearchHeadquarters LS Research, LLCW66 N220 Commerce CourtCedarburg, WI 53012-2636USATel: 1(262) 375-4400Fax: 1(262) 375-4248Website Wiki /products-wikiTechnical Support /products-forumSales Contact*************The information in this document is provided in connection with LS Research (hereafter referred to as “LSR”) products. No license, express or implied, by estoppel or otherwise, to any intellectual property right is granted by this document or in connection with the sale of LSR products. EXCEPT AS SET FORTH IN LSR’S TERMS AND CONDITIONS OF SALE LOCATED ON LSR’S WEB SITE, LSR ASSUMES NO LIABILITY WHATSOEVER AND DISCLAIMS ANY EXPRESS, IMPLIED OR STATUTORY WARRANTY RELATING TO ITS PRODUCTS INCLUDING, BUT NOT LIMITED TO, THE IMPLIED WARRANTY OF MERCHANTABILITY, FITNESS FOR A PARTICULAR PURPOSE, OR NON-INFRINGEMENT. IN NO EVENT SHALL LSR BE LIABLE FOR ANY DIRECT, INDIRECT, CONSEQUENTIAL, PUNITIVE, SPECIAL OR INCIDENTAL DAMAGES (INCLUDING, WITHOUT LIMITATION, DAMAGES FOR LOSS OF PROFITS, BUSINESS INTERRUPTION, OR LOSS OF INFORMATION) ARISING OUT OF THE USE OR INABILITY TO USE THIS DOCUMENT, EVEN IF LSR HAS BEEN ADVISED OF THE POSSIBILITY OF SUCH DAMAGES. LSR makes no representations or warranties with respect to the accuracy or completeness of the contents of this document and reserves the right to make changes to specifications and product descriptions at any time without notice. LSR does not make any commitment to update the information contained herein. Unless specifically provided otherwise, LSR products are not suitable for, and shall not be used in, automotive applications. LSR’s products are not intended, authorized, or warranted for use as components in applications intended to support or sustain life.Mouser ElectronicsAuthorized DistributorClick to View Pricing, Inventory, Delivery & Lifecycle Information:L S Research:450-0105。
PCI接口的高性能IEEE

USB 接口的高性能IEEE-488 GPIB 卡特点▪方便连接笔记本电脑的GPIB ▪API 兼容NI-488.2 驱动软件* ▪完全兼容IEEE-488标准 ▪完全兼容工业标准VISA 库 ▪仪器连接时不需要GPIB 线缆 ▪即插即用接口 ▪ 兼容USB 2.0PCI 接口的高性能IEEE-488 GPIB 卡▪支持32位3.3V 或5V PCI 总线 ▪完全兼容IEEE-488标准 ▪数据传输率最高达1.5 MB/s ▪API 兼容NI-488.2 驱动软件* ▪内置2 KB FIFO 用于读/写操作 ▪支持工业标准VISA 库 ▪支持测试和诊断的交互式工具简介凌华科技LPCI-3488A GPIB 控制器接口卡与IEEE-488.2仪器控制和通信标准完全兼容,并能够通过IEEE-488线缆来控制最多14个独立仪器。
为了满足用户对高性能和测量便携性的需要,凌华科技最新研发了LPCI-3488A 。
凭借凌华科技在FPGA 方面的核心技术,LPCI-3488A 提供了可靠的GPIB 总线控制能力,支持最高达1.5 MB/s 的数据传输率。
通过完全兼容NI- 488.2*驱动软件并支持VISA 的API ,LPCI-3488A 可完全兼容您现有的应用和仪器驱动程▪数据传输率最高达1.5 MB/s▪简介凌华科技GPIB接口卡配备了完整的软件支持,包括与NI-488.2*驱动软件完全二进制兼容的API驱动。
所有基于GPIB-32.DLL编写的程序在不需要任何修改与编译的情况下直接使用USB-3488A。
它还提供了VISA库以保证兼容基于VISA的应用。
因此凌华科技USB-3488A完全兼容您现有的应用程序,并可即插即用。
USB-3488A GPIB接口在GPIB仪器和电脑之前提供一个直接的接口,由于可以即插即用,GPIB仪器连接到电脑不需要关机,也不需要额外的电源供应。
USB-3488A GPIB接口卡配备一根2米长的USB线缆,它兼容USB 2.0规范。
Artisan Technology Group NI PXIe-7820R获取开始指南说明书

GETTING STARTED GUIDENI PXIe-7820RR Series for PXI Express Digital RIO with Kintex-7 160T FPGA Français Deutsch日本語한국어简体中文/manualsThis document explains how to install and configure the NI PXIe-7820R.Safety GuidelinesCaution Do not operate the NI PXIe-7820R in a manner not specified in this usermanual. Product misuse can result in a hazard. You can compromise the safetyprotection built into the product if the product is damaged in any way. If the productis damaged, return it to National Instruments for repair.Electromagnetic Compatibility GuidelinesThis product was tested and complies with the regulatory requirements and limits for electromagnetic compatibility (EMC) as stated in the product specifications. Theserequirements and limits are designed to provide reasonable protection against harmful interference when the product is operated in its intended operational electromagnetic environment.This product is intended for use in residential, commercial, and industrial locations. However, harmful interference may occur in some installations or when the product is connected to a peripheral device or a test object. To minimize interference with radio and television reception and prevent unacceptable performance degradation, install and use this product in strict accordance with the instructions in the product documentation.Furthermore, any changes or modifications to the product not expressly approved by National Instruments could void your authority to operate it under your local regulatory rules.Caution To ensure the specified EMC performance, operate this product only withshielded cables and accessories. Do not use unshielded cables or accessories unlessthey are installed in a shielded enclosure with properly designed and shielded input/output ports and connected to the product using a shielded cable. If unshieldedcables or accessories are not properly installed and shielded, the EMC specificationsfor the product are no longer guaranteed.Caution To ensure the specified EMC performance, install two (2) snap-on, ferritebeads (777297-01) per connected I/O cable in accordance with the productinstallation instructions.Caution To ensure the specified EMC performance, the length of any cableconnected to the input port(s) must be no longer than 3 m (10 ft).Unpacking the KitCaution To prevent electrostatic discharge (ESD) from damaging the device,ground yourself using a grounding strap or by holding a grounded object, such asyour computer chassis.1.Touch the antistatic package to a metal part of the computer chassis.2.Remove the device from the package and inspect the device for loose components or anyother sign of damage.Caution Never touch the exposed pins of connectors.Note Do not install a device if it appears damaged in any way.3.Unpack any other items and documentation from the kit.Store the device in the antistatic package when the device is not in use.Verifying the Kit ContentsVerify that the following components are in your kit.2| | NI PXIe-7820R Getting Started GuideFigure 1. Kit Contents for the NI PXIe-7820R1.Hardware2.NI-RIO Media3.Getting Started GuidePreparing the EnvironmentEnsure that the environment in which you are using the NI PXIe-7820R meets the following specifications.0° C to 55° C ............................................................................Operating temperature(IEC 60068-2-1, IEC 60068-2-2)10% RH to 90% RH, noncondensing Operating humidity ............................................................................(IEC 60068-2-56)Pollution degree2 ............................................................................Maximum altitude2,000 m ............................................................................Indoor use only.Note Refer to the device datasheet on /manuals for complete specifications.Installing Software on the Host ComputerBefore using the NI PXIe-7820R, you must install the following application software and device drivers on the host computer.bVIEW 2014 SP1 or laterbVIEW Real-Time Module 2014 SP1 or later1bVIEW FPGA Module 2014 SP1 or later4.NI-RIO Device Drivers February 2015 or later1LabVIEW Real Time Module is only required if the R Series board is being used on a PXIecontroller with a real-time operating system.NI PXIe-7820R Getting Started Guide| © National Instruments| 3Visit /info and enter the Info Code softwareversion for minimum software support information.Installing the NI PXIe-7820RCaution To prevent damage to the device caused by ESD or contamination, handlethe device using the edges or the metal bracket.1.Ensure the AC power source is connected to the chassis before installing the modules.The AC power cord grounds the chassis and protects it from electrical damage while you install the modules.2.Power off the chassis.3.Inspect the slot pins on the chassis backplane for any bends or damage prior toinstallation. Do not install a module if the backplane is damaged.4.Remove the black plastic connectors from all the captive screws on the module frontpanel.5.Identify a supported slot in the chassis. The following figure shows the symbols thatindicate the slot types.Figure 2. Chassis Compatibility Symbols1.PXI Express System Controller Slot2.PXI Peripheral Slot3.PXI Express Hybrid Peripheral Slot4.PXI Express System Timing Slot5.PXI Express Peripheral SlotNI PXIe-7820R modules can be placed in PXI Express peripheral slots, PXI Expresshybrid peripheral slots, or PXI Express system timing slots.6.Touch any metal part of the chassis to discharge static electricity.7.Ensure that the ejector handle is in the unlatched (downward) position.8.Place the module edges into the module guides at the top and bottom of the chassis. Slidethe device into the slot until it is fully inserted.4| | NI PXIe-7820R Getting Started GuideFigure 3. Module Installation1.Chassis2.Hardware3.Ejector Handle in Down (Unlatched) Positiontch the module in place by pulling up on the ejector handle.10.Secure the device front panel to the chassis using the front-panel mounting screws.Note Tightening the top and bottom mounting screws increases mechanical stability and also electrically connects the front panel to the chassis, which canimprove the signal quality and electromagnetic performance.11.Cover all empty slots using filler panels or slot blockers to maximize cooling air flow.12.Power on the chassis.Verifying Hardware Installation for Host Targets You can verify that the system recognizes the NI PXIe-7820R by using Measurement &Automation Explorer (MAX).unch MAX by navigating to Start »All Programs »National Instruments »MAX or byclicking the MAX desktop icon.2.Expand Devices and Interfaces .3.Verify that the device appears under Devices and Interfaces .If the device does not appear, press <F5> to refresh the view in MAX. If the device does not appear after refreshing the view, visit /support for troubleshootinginformation.NI PXIe-7820R Getting Started Guide | © National Instruments | 5Verifying Hardware Installation for RemoteT argetsYou can verify that the system recognizes the NI PXIe-7820R by using Measurement & Automation Explorer (MAX).unch MAX on the host computer.2.Expand Remote Targets in the configuration tree and locate your system.3.Install LabVIEW Real-Time Module 2014 SP1 and NI RIO Device Drivers February2015 or later on your Remote Target.a)Refer to the Installing Software on the Host Computer section for information aboutinstalling software on the host.b)Refer to the PXI Express Controllers User Manual at /manuals forinformation on installing software on the target.4.Under Remote Targets, find and expand Devices and Interfaces.If the device does not appear, press <F5> to refresh the view in MAX. If the device does not appear after refreshing the view, visit /support for troubleshootinginformation.Connecting the NI PXIe-7820RNI recommends using the following cables and accessories with the NI PXIe-7820R:•EMI suppression ferrites (777297-01)•Shielded 68-Pin Connector Block for R Series DIO & HSDIO Products (782914-01)•Shielded R Series High Speed Digital Cable, 1m (156166-01)•Shielded R Series High Speed Digital Cable, 2m (156166-02)Note NI is not liable for connections that exceed any of the maximum ratings ofinput or output signals on the NI PXIe-7820R and on the computer chassis. Refer tothe NI PXIe-7820R Specifications, available at /manuals for the maximuminput and output ratings for each signal.6| | NI PXIe-7820R Getting Started GuideThe NI PXIe-7820R is protected from overvoltage and overcurrent conditions. Refer to theNI PXIe-7820R Specifications, available at /manuals, for more information on overvoltage and overcurrent conditions.NI PXIe-7820R Getting Started Guide| © National Instruments| 7Digital I/OThe NI PXIe-7820R provides connections for 128 digital input/output (DIO) channels.Connectors 0 through 3 each contain 32 high-speed DIO channels that can run up to 80 MHz signal frequencies. Each connector has selectable logic levels that you can configure as 1.2 V ,1.5 V , 1.8 V ,2.5 V , or3.3 V . You can configure each channel as input or output.Figure 4. Connecting to the DIO Channels1.High-speed signal frequencies up to 80 MHz with logic levels configured as 1.2 V , 1.5 V , 1.8 V ,2.5 V , or3.3 V2.LEDThe DIO channels connect to the FPGA through protection circuitry, which has overvoltage and undervoltage protection as well as overcurrent protection. Refer to the NI PXIe-7820R Specifications for more information about the maximum voltage and current.When the system powers on, the DIO channels are set as input low with pull-down resistors.To set another power-on state, you can configure the NI PXIe-7820R to load a VI when the system powers on. The VI can then set the DIO lines to any power-on state.All the DIO channels on Connectors 0 through 3 are routed with a 50 Ω characteristic trace impedance. Route all external circuitry with a similar impedance to ensure best signal quality.NI recommends performing signal integrity measurements to test the affect of signal routing with the cable and connection accessory for your application.Installing Noise Suppression FerritesCaution To ensure the specified EMC performance, operate this product only with shielded cables and accessories. Do not use unshielded cables or accessories unless they are installed in a shielded enclosure with properly designed and shielded input/output ports and connected to the product using a shielded cable. If unshielded 8 | | NI PXIe-7820R Getting Started Guidecables or accessories are not properly installed and shielded, the EMC specificationsfor the product are no longer guaranteed.Caution To ensure the specified EMC performance, install two (2) snap-on, ferritebeads (777297-01) per connected I/O cable in accordance with the productinstallation instructions.Caution To ensure the specified EMC performance, the length of any cableconnected to the input port(s) must be no longer than 3 m (10 ft).For each connected I/O cable, install two (2) snap-on, ferrite beads (777297-01), one on each end of the cable, as close to the connector as practical.Two (2) snap-on, ferrite beads (777297-01) are included in ach of the following recommended cable kits:•Shielded R Series High Speed Digital Cable, 1m (156166-01)•Shielded R Series High Speed Digital Cable, 2m (156166-02)For user-supplied cables, the ferrite beads can be ordered directly from NI by visiting / info and entering RDIO2FERRITE.Figure 5. Ferrite Installation1.I/O cable2.FerritesNI PXIe-7820R Getting Started Guide| © National Instruments| 9Where to Go NextRefer to the following figure for information about other product tasks and associatedresources for those tasks.Where to Go for SupportThe National Instruments website is your complete resource for technical support. At /support you have access to everything from troubleshooting and application development self-help resources to email and phone assistance from NI Application Engineers.National Instruments corporate headquarters is located at 11500 North Mopac Expressway,Austin, Texas, 78759-3504. National Instruments also has offices located around the world tohelp address your support needs. For telephone support in the United States, create yourservice request at /support and follow the calling instructions or dial 512 795 8248. Fortelephone support outside the United States, visit the Worldwide Offices section of /niglobal to access the branch office websites, which provide up-to-date contact information,support phone numbers, email addresses, and current events.10| | NI PXIe-7820R Getting Started GuideArtisan Technology Group - Quality Instrumentation ... Guaranteed | (888) 88-SOURCE | Refer to the NI Trademarks and Logo Guidelines at /trademarks for information on National Instruments trademarks.Other product and company names mentioned herein are trademarks or trade names of their respective companies. For patentscovering National Instruments products/technology, refer to the appropriate location: Help»Patents in your software, thepatents.txt file on your media, or the National Instruments Patent Notice at /patents. Y ou can find information aboutend-user license agreements (EULAs) and third-party legal notices in the readme file for your NI product. Refer to the ExportCompliance Information at /legal/export-compliance for the National Instruments global trade compliance policy andhow to obtain relevant HTS codes, ECCNs, and other import/export data. NI MAKES NO EXPRESS OR IMPLIED WARRANTIESAS TO THE ACCURACY OF THE INFORMA TION CONT AINED HEREIN AND SHALL NOT BE LIABLE FOR ANY ERRORS.U.S. Government Customers: The data contained in this manual was developed at private expense and is subject to theapplicable limited rights and restricted data rights as set forth in FAR 52.227-14, DFAR 252.227-7014, and DFAR 252.227-7015.© 2015 National Instruments. All rights reserved.376820A-01Feb15Artisan Technology Group - Quality Instrumentation ... Guaranteed | (888) 88-SOURCE | 。
NVIDIA nForce 220 420平台下安装nForce核心驱动程序(Windows 98)

Application Note nForce 220/420 Platform Installing nForce Core Drivers Under Windows 98Installing Core DriversUnder Windows 98 This application note provides instructions to install the NVIDIA nForce coredrivers (GART, Ethernet, Audio, Audio Utilities, SMBUS and Memory Controller)under Windows 98. Currently, the NVIDIA installer supports Windows XP,Windows 2000 and Windows ME. Use the following procedure to install allNVIDIA devices under Windows 98 until the release of Windows 98 installersupport.To install the nForce integrated video driver, use the standard Windows installationsteps for ‘Updating a Video Driver.’Driver Package ContentsIt is recommended to have the following nForce drivers before proceeding:q GART Driverq Audio Drivers with Audio Utilitiesq Ethernet Driverq SMBUS Driver (System Management Bus)q Memory Controller DriverInstalling GART DriversWhen a Windows 98 operating system is installed, there are a series of unknowndevices in Windows 98 Device Manager. To install the nForce GART drivers, usethe following procedure:1. Extract the GART driver package to a temporary location.GART Manager is present in Device Manager under: PCI Standard Host CPUBridge. Microsoft Generic Drivers are used until you upgrade with the properGART drivers.2. Go to the Device Manager (STARTØCONTROL PANELØSYSTEMØDEVICE MANAGER).3. Look for the following devices:- NVIDIA nForce GART Manager- PCI Standard Host CPU Bridge- PCI standard PCI-to-PCI bridge device4. Update the drivers using the ones saved into the temporary location instep 1.5. Restart your system.Installing the Audio DriversUse the following procedure to install nForce Audio drivers:1. Extract the Audio driver package to a temporary location.Use the drivers from Audio Driver package to enumerate all unknown mediaclass devices.2. Go to the Device Manager (STARTØCONTROL PANELØSYSTEMØDEVICE MANAGER).3. Look for the following devices:Unknown Drivers- NVIDIA Audio Codec Interface- NVIDIA Media Controller ProcessorSound, Video, and Game Controllers- NVIDIA nForce Audio Codec Interface- NVIDIA nForce MCP Audio Processing UnitNote: Various nForce Audio items Under Sound, Video and GameControllers will be replaced when the System Devices are updated.4. Update the drivers using the ones saved into the temporary location instep 1.5. Restart your system.Installing Ethernet DriversUse the following procedure to install Ethernet drivers:1. Extract the Ethernet driver package to a temporary location.Use the drivers from the Ethernet Driver package to enumerate the unknownEthernet Device.2. Go to the Device Manager (STARTØCONTROL PANELØSYSTEMØDEVICE MANAGER).3. Look for the following devices:Unknown Drivers- NVIDIA Ethernet DeviceNetwork Adapters- NVIDIA nForce MCP Networking Adapter4. Update the drivers using the ones saved into the temporary location instep 1.5. Restart your system.Installing SMBus DriversUse the following procedure to install Ethernet drivers:1. Extract the SMBus driver package to a temporary location.SMBus needs to be enabled for DDC to function correctly and systemmanagement functions to be enabled.2. Go to the Device Manager (STARTØCONTROL PANELØSYSTEMØDEVICE MANAGER).3. Go to Unknown Devices / PCI System Management Bus4. Update the drivers using the ones saved into the temporary location instep 1.5. Restart your system.Updating MemoryController Drivers1. Extract the files from the (os)\memory directory of the driver package to atemporary location.Microsoft Generic Drivers will be used. To replace the Microsoft drivers withNVIDIA drivers, continue with Step 2.Note: Several instances of Memory Controller may be present in DeviceManager under:- Windows 9x/ME or Windows 2000/XP- PCI Standard RAM Controller2. Go to the Device Manager (STARTØCONTROL PANELØSYSTEMØDEVICE MANAGER).3. Look for the following devices:System Devices- PCI Standard RAM Controller- NVIDIA nForce 420 Memory Controller- NVIDIA nForce 220/420 Memory Controller4. Update all instances of these drivers using the ones saved into the temporarylocation in step 1.5. Restart your system.Note: It is important to restart your computer after all drivers are installed.Information furnished is believed to be accurate and reliable. However, NVIDIA Corporation assumes no responsibility for the consequences of use of such information or for any infringement of patents or other rights of third parties that may result from its use. No license is granted by implication or otherwise under any patent or patent rights of NVIDIA Corporation. Specifications mentioned in this publication are subject to change without notice. This publication supersedes and replaces all information previously supplied. NVIDIA Corporation products are not authorized for use as critical components in life support devices or systems without express written approval of NVIDIA Corporation.TrademarksNVIDIA, the NVIDIA logo, and nForce are trademarks of NVIDIA Corporation.Microsoft, Windows and the Windows logo are registered trademarks of Microsoft Corporation Other company and product names may be trademarks of the respective c ompanies with which they are associated.CopyrightCopyright NVIDIA Corporation 2001NVIDIA Corporation2701 San Tomas ExpresswaySanta Clara, CA 95050。
NI PXIe-6592R高速序列模块安装指南说明书
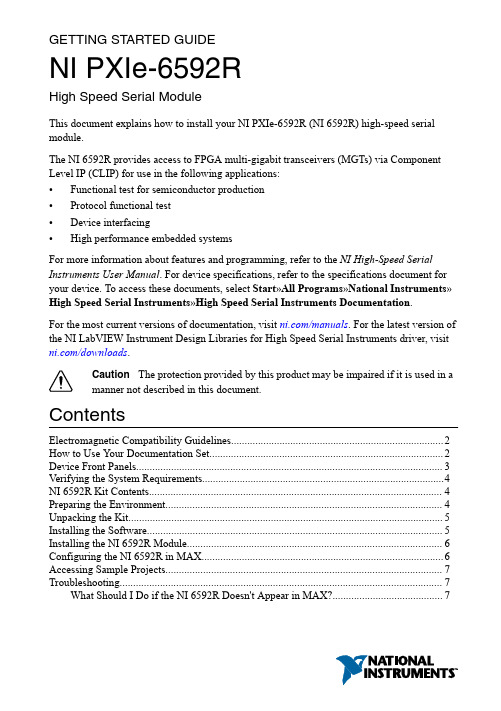
GETTING STARTED GUIDENI PXIe-6592RHigh Speed Serial ModuleThis document explains how to install your NI PXIe-6592R (NI 6592R) high-speed serial module.The NI 6592R provides access to FPGA multi-gigabit transceivers (MGTs) via Component Level IP (CLIP) for use in the following applications:•Functional test for semiconductor production•Protocol functional test•Device interfacing•High performance embedded systemsFor more information about features and programming, refer to the NI High-Speed Serial Instruments User Manual. For device specifications, refer to the specifications document for your device. To access these documents, select Start»All Programs»National Instruments»High Speed Serial Instruments»High Speed Serial Instruments Documentation.For the most current versions of documentation, visit /manuals. For the latest version of the NI LabVIEW Instrument Design Libraries for High Speed Serial Instruments driver, visit /downloads.Caution The protection provided by this product may be impaired if it is used in amanner not described in this document.ContentsElectromagnetic Compatibility Guidelines (2)How to Use Your Documentation Set (2)Device Front Panels (3)Verifying the System Requirements (4)NI 6592R Kit Contents (4)Preparing the Environment (4)Unpacking the Kit (5)Installing the Software (5)Installing the NI 6592R Module (6)Configuring the NI 6592R in MAX (6)Accessing Sample Projects (7)Troubleshooting (7)What Should I Do if the NI 6592R Doesn't Appear in MAX? (7)Where to Go Next (8)Worldwide Support and Services..............................................................................................8Electromagnetic Compatibility GuidelinesThis product was tested and complies with the regulatory requirements and limits forelectromagnetic compatibility (EMC) stated in the product specifications. These requirements and limits provide reasonable protection against harmful interference when the product is operated in the intended operational electromagnetic environment.This product is intended for use in industrial locations. However, harmful interference may occur in some installations, when the product is connected to a peripheral device or test object,or if the product is used in residential or commercial areas. To minimize interference with radio and television reception and prevent unacceptable performance degradation, install and use this product in strict accordance with the instructions in the product documentation.Furthermore, any changes or modifications to the product not expressly approved by NationalInstruments could void your authority to operate it under your local regulatory rules.Caution To ensure the specified EMC performance, operate this product only withshielded cables and accessories.Caution To ensure the specified EMC performance, the length of all I/O cablesmust be no longer than 3 m (10 ft).Caution To ensure the specified EMC performance, you must install PXI EMCFiller Panels, National Instruments part number 778700-01, in all open chassis slots.A kit of six single slot EMC Filler Panels can be ordered directly from NI by visiting /info and entering partnumber .How to Use Y our Documentation SetRefer to the following table to learn how to use your documentation set.Table 1. NI 6592R Document Locations and Descriptions2 | | NI PXIe-6592R Getting Started GuideTable 1. NI 6592R Document Locations and Descriptions (Continued)Device Front PanelsThe following figure shows the available signals on the NI 6592R.Figure 1. NI 6592R Front Panel and Connector PinoutsNI PXIe-6592R Getting Started Guide| © National Instruments| 3Verifying the System RequirementsTo use the NI LabVIEW Instrument Design Libraries for High Speed Serial Instruments instrument driver, your system must meet certain requirements.For more information about minimum system requirements, recommended system, and supported application development environments (ADEs), refer to the product readme, which is available on the driver software media or online at /updates.NI 6592R Kit ContentsThe following items are included in the device kit:•The NI 6592R•The NI LabVIEW Instrument Design Libraries for High Speed Serial Instruments driver software media•Other included items:–Read Me First: Safety and Electromagnetic Compatibility–Maintain Forced-Air Cooling Note to UsersPreparing the EnvironmentEnsure that the environment you are using the NI 6592R in meets the following specifications.0 °C to 45 °C ............................................................................Operating ambient temperature(IEC-60068-2-1, IEC-60068-2-2) ............................................................................10% to 90%, noncondensingOperating relative humidity(IEC-60068-2-56)Maximum altitude2,000 m (800 mbar) ............................................................................(at 25 °C ambient temperature)Pollution degree2 ............................................................................Indoor use only.Caution Clean the hardware with a soft, nonmetallic brush. Make sure that thehardware is completely dry and free from contaminants before returning it toservice.Note Refer to the NI PXIe-6592R Specifications at /manuals for completespecifications.4| | NI PXIe-6592R Getting Started GuideUnpacking the KitCaution To prevent electrostatic discharge (ESD) from damaging the device,ground yourself using a grounding strap or by holding a grounded object, such asyour computer chassis.1.Touch the antistatic package to a metal part of the computer chassis.2.Remove the device from the package and inspect the device for loose components or anyother sign of damage.Caution Never touch the exposed pins of connectors.Notify NI if the device appears damaged in any way. Do not install a damaged device. 3.Unpack any other items and documentation from the kit.Store the device in the antistatic package when the device is not in use.Installing the SoftwareYou must install the NI LabVIEW Instrument Design Libraries for High Speed Serial Instruments driver software before installing the NI 6592R.1.Install LabVIEW. Refer to the LabVIEW Installation Guide for installation instructionsfor LabVIEW and system requirements for the LabVIEW software. Refer to theLabVIEW Upgrade Notes for additional information about upgrading to the most recent version of LabVIEW for Windows.Documentation for LabVIEW is available at /manuals and by selecting Start»All Programs»National Instruments»LabVIEW»LabVIEW Manuals.2.Install the LabVIEW FPGA Module. Refer to the LabVIEW FPGA Module Release andUpgrade Notes for installation instructions and information about getting started with the LabVIEW FPGA Module.Documentation for the LabVIEW FPGA Module is available is available at /manuals and by selecting Start»All Programs»National Instruments»LabVIEW»LabVIEW Manuals.3.Install the NI LabVIEW Instrument Design Libraries for High Speed Serial InstrumentsHelp driver. Refer to the NI High Speed Serial Instruments Readme on the NI LabVIEW Instrument Design Libraries for High Speed Serial Instruments installation media forsystem requirements and installation instructions for the NI LabVIEW Instrument Design Libraries for High Speed Serial Instruments driver.Documentation for the NI LabVIEW Instrument Design Libraries for High Speed Serial Instruments driver is available at /manuals and by selecting Start»All Programs»National Instruments»High Speed Serial Instruments»High Speed SerialInstruments Documentation.NI PXIe-6592R Getting Started Guide| © National Instruments| 5Installing the NI 6592R ModuleNote You must install the software before you install the hardware.1.Power off and unplug the chassis. Refer to your chassis manual to install or configure thechassis.2.Identify a supported module slot in the chassis. The figure below shows the symbols thatindicate the slot types in the chassis.Figure 2. Symbols for Module Slots1.PXI Express System Controller Slot2.PXI Peripheral Slot3.PXI Express Hybrid Peripheral Slot4.PXI Express System Timing Slot5.PXI Express Peripheral SlotPXI Express devices can be placed only in PXI Express slots and PXIe Express Hybrid slots. Refer to the chassis documentation for details.3.Remove the filler panel of an unused module slot.4.Touch any metal part of the chassis to discharge any static electricity. Place the moduleedges into the module guides at the top and bottom of the chassis, and slide the module into the chassis until the module is fully inserted.5.Secure the device front panel to the chassis front panel mounting rail using the front panelmounting screws.6.Plug in and power on the chassis.Configuring the NI 6592R in MAXUse Measurement & Automation Explorer (MAX) to configure your National Instruments hardware. MAX informs other programs about which devices reside in the system and how they are configured. MAX is automatically installed with NI LabVIEW Instrument Design Libraries for High Speed Serial Instruments.unch MAX by navigating to Start»All Programs»National Instruments»NI MAX orby clicking the NI MAX desktop icon.2.In the Configuration pane, double-click Devices and Interfaces to see the list of installeddevices. Installed devices appear under the name of their associated chassis.6| | NI PXIe-6592R Getting Started Guide3.Expand your Chassis tree item. MAX lists all devices installed in the chassis. Yourdefault device names may vary.Note If you do not see your device listed, press <F5> to refresh the list ofinstalled devices. If the device is still not listed, power off the system, ensurethe device is correctly installed, and restart.4.Record the device identifier MAX assigns to the hardware. Use this identifier whenprogramming the NI 6592R.5.Close MAX.Accessing Sample ProjectsNI LabVIEW Instrument Design Libraries for High Speed Serial Instruments includes sample projects to help you get started designing for the NI 6592R.1.Open LabVIEW and select Create Project.2.In the Create Project dialog box, select High-Speed Serial and select a sample projectfor your device.3.Click Next.4.Configure the Project Name, Project Root, and File Name Prefix (Optional) fields.5.Click Finish.TroubleshootingWhat Should I Do if the NI 6592R Doesn't Appear in MAX?1.In the MAX configuration tree, click Devices and Interfaces.2.Expand the Chassis tree to see the list of installed devices, and press <F5> to refresh thelist.3.If the module is still not listed, power off the system, ensure that all hardware is correctlyinstalled, and restart the system.4.Navigate to the Device Manager.5.If you are using a PXI controller, verify that a National Instruments entry appears in thesystem device list. Reinstall NI LabVIEW Instrument Design Libraries for High Speed Serial Instruments and the device if error conditions appear in the list. If you are using an MXI controller, right-click PCI-to-PCI Bridge, and select Properties from the shortcut menu to verify that the bridge is enabled.NI PXIe-6592R Getting Started Guide| © National Instruments| 7Where to Go NextRefer to the following figure for information about other product tasks and associated resources for those tasks.Worldwide Support and ServicesThe National Instruments website is your complete resource for technical support. At / support, you have access to everything from troubleshooting and application development self-help resources to email and phone assistance from NI Application Engineers.Visit /services for NI Factory Installation Services, repairs, extended warranty, and other services.Visit /register to register your National Instruments product. Product registration facilitates technical support and ensures that you receive important information updates from NI.8| | NI PXIe-6592R Getting Started GuideA Declaration of Conformity (DoC) is our claim of compliance with the Council of the European Communities using the manufacturer’s declaration of conformity. This system affords the user protection for electromagnetic compatibility (EMC) and product safety. You can obtain the DoC for your product by visiting /certification. If your product supports calibration, you can obtain the calibration certificate for your product at /calibration. National Instruments corporate headquarters is located at 11500 North Mopac Expressway, Austin, Texas, 78759-3504. National Instruments also has offices located around the world. For telephone support in the United States, create your service request at /support or dial 1 866 ASK MYNI (275 6964). For telephone support outside the United States, visit the Worldwide Offices section of /niglobal to access the branch office websites, which provide up-to-date contact information, support phone numbers, email addresses, and current events.NI PXIe-6592R Getting Started Guide| © National Instruments| 9Refer to the NI Trademarks and Logo Guidelines at /trademarks for information on National Instruments trademarks. Other product and company names mentioned herein are trademarks or trade names of their respective companies. For patents covering National Instruments products/technology, refer to the appropriate location: Help»Patents in your software, the patents.txt file on your media, or the National Instruments Patent Notice at /patents. Y ou can find information about end-user license agreements (EULAs) and third-party legal notices in the readme file for your NI product. Refer to the ExportCompliance Information at /legal/export-compliance for the National Instruments global trade compliance policy and how to obtain relevant HTS codes, ECCNs, and other import/export data. NI MAKES NO EXPRESS OR IMPLIED WARRANTIES AS TO THE ACCURACY OF THE INFORMA TION CONT AINED HEREIN AND SHALL NOT BE LIABLE FOR ANY ERRORS. U.S. Government Customers: The data contained in this manual was developed at private expense and is subject to the applicable limited rights and restricted data rights as set forth in FAR 52.227-14, DFAR 252.227-7014, and DFAR 252.227-7015.© 2014—2015 National Instruments. All rights reserved.374805B-01Jan15。
National Instruments NI-488.2 for LabVIEW Real-Tim

NI-488.2 for LabVIEW Real-Time, Version 19.0 ReadmeApril 2019This file contains important information about NI-488.2, including new features and a partial list of bugs fixed for NI-488.2 Version 19.0.Compatible SoftwareSupported HardwareEnhancements and Bug FixesVersion 19.0Version 18.5Version 17.6Version 17.0Version 16.0Version 15.5Version 15.0.1Version 15.0Version 14.0Driver Version Naming ChangesLegal InformationCompatible SoftwareThis driver version is recommended for use with the following National Instruments software:NI-VISA 19.0Any version of NI-VISA prior to 5.1 on your system may cause NI-488.2 usability issues. Upgrade to NI-VISA version 5.1 or later before using any NI-488.2 devices.LabVIEW 2016, 2017, 2018, and 2019Supported HardwareNI-488.2 for LabVIEW Real-Time, Version 19.0, supports the following GPIB interfaces:Desktop RT with NI PCI-GPIBDesktop RT with NI PCIe-GPIBNI PXI controller with built-in GPIBNI PMC-GPIBNI PXI-8232NI PXI-GPIBEnhancements and Bug Fixes in Version 19.0NI-488.2 for LabVIEW Real-Time, Version 19.0, adds support for LabVIEW Real-Time 2019 and LabVIEW Real-Time on Linux. Added support for 32-bit Package Manager and deprecated the previous install process.Enhancements and Bug Fixes in Version 18.5LabVIEW Real-Time 2018NI-488.2 for LabVIEW Real-Time, Version 18.5, adds support for LabVIEW Real-Time 2018.Enhancements and Bug Fixes in Version 17.6The following issues were resolved in NI-488.2 17.6670170: A hang might occur during an I/O operation if a Service Request is stuck when Autopolling is happening.Enhancements and Bug Fixes in Version 17.0LabVIEW Real-Time 2017NI-488.2 for LabVIEW Real-Time, Version 17.0, adds support for LabVIEW Real-Time 2017.Enhancements and Bug Fixes in Version 16.0LabVIEW Real-Time 2016NI-488.2 for LabVIEW Real-Time, Version 16.0, adds support for LabVIEW Real-Time 2016.Enhancements and Bug Fixes in Version 15.5The following issues were resolved in NI-488.2 15.5Issues resolved in NI-488.2 15.0.1 were ported to the NI-488.2 for LabVIEW Real-Time, Version 15.5 release.Enhancements and Bug Fixes in Version 15.0.1The following issues were resolved in NI-488.2 15.0.1547340: GPIB ports may not be reported in NI MAX, Web Configuration, and System Configuration API with NI-488.2 15.0.0.Enhancements and Bug Fixes in Version 15.0Updated experience in Measurement & Automation Explorer (MAX)The configuration experience in MAX has been updated to improve consistency with other NI products. Self-Test has also been added for GPIB interfaces.Web configurationGPIB interfaces are now fully configurable through the NI Web Configuration interface. Self-Test has also been added.The following issues were resolved in NI-488.2 15.0121091: Calling ibonl when a board level ibwait is in progress could result in application crash.121181: A deadlock might occur when attempting to use a board handle with pending ibonl call on another thread.Enhancements and Bug Fixes in Version 14.0The following issues were resolved in NI-488.2 14.0122997: The EOIP status bit could remain set incorrectly if an ibwrta or ibrda call returned an EDVR error.205182: Asynchronous transfers could sometimes report EABO even though the transfer completed successfully.405414: In some cases the DCAS bit was not correctly cleared after being reported, causing it to be reported with subsequent calls.Driver Version Naming ChangesNI-488.2 versions are now aligned with the versions of major NI application software products. This alignment gives you information about the year the driver was released and the most recent software version the driver was designed to work with. Driver versions now start with a two-digit year indicator: <ProductName><Year-BasedVersion>. The last version released under the old numbering scheme was NI-488.2 3.1.2. The first version released under the new numbering scheme was NI-488.2 14.0. Legal InformationCopyright© 1995–2019 National Instruments. All rights reserved.Under the copyright laws, this publication may not be reproduced or transmitted in any form, electronic or mechanical, including photocopying, recording, storing in an information retrieval system, or translating, in whole or in part, without the prior written consent of National Instruments Corporation.NI respects the intellectual property of others, and we ask our users to do the same. NI software is protected by copyright and other intellectual property laws. Where NI software may be used to reproduce software or other materials belonging to others, you may use NI software only to reproduce materials that you may reproduce in accordance with the terms of any applicable license or other legal restriction.End-User License Agreements and Third-Party Legal NoticesYou can find end-user license agreements (EULAs) and third-party legal notices in the following locations after installation: Notices are located in the <National Instruments>\_Legal Information and <National Instruments>directories.EULAs are located in the <National Instruments>\Shared\MDF\Legal\license directory.Review <National Instruments>\_Legal Information.txt for information on including legal information ininstallers built with NI products.U.S. Government Restricted RightsIf you are an agency, department, or other entity of the United States Government ("Government"), the use, duplication, reproduction, release, modification, disclosure or transfer of the technical data included in this manual is governed by the Restricted Rights provisions under Federal Acquisition Regulation 52.227-14 for civilian agencies and Defense Federal Acquisition Regulation Supplement Section 252.227-7014 and 252.227-7015 for military agencies.IVI Foundation Copyright NoticeContent from the IVI specifications reproduced with permission from the IVI Foundation.The IVI Foundation and its member companies make no warranty of any kind with regard to this material, including, but not limited to, the implied warranties of merchantability and fitness for a particular purpose. The IVI Foundation and its member companies shall not be liable for errors contained herein or for incidental or consequential damages in connection with the furnishing, performance, or use of this material.TrademarksRefer to the NI Trademarks and Logo Guidelines at /trademarks for information on NI trademarks. Other product and company names mentioned herein are trademarks or trade names of their respective companies.PatentsFor patents covering the NI products/technology, refer to the appropriate location: Help»Patents in your software, the patents.txt file on your media, or the NI Patent Notice at /patents.375741F-01。
NI GPIB安装
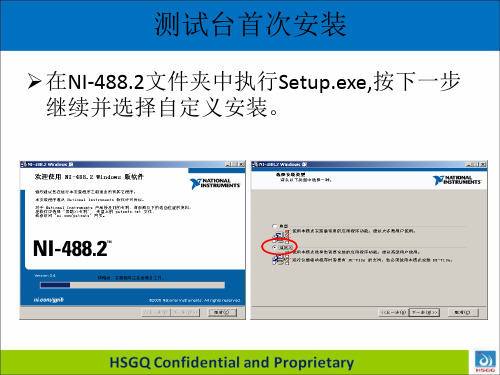
测试台首次安装
• 计算机重启之后即安装驱动成功,首次会出现入门先到,先选择“验 证硬件安装”,待出现下一个验证窗口时直接关闭即可(即不需要刻 意验证),接着向导自动进入“与仪器通信”,不理会,直接点退出 按钮即可,注意要勾选“在WINDOWS启动时不显示”。 • 至此GPIB驱动安装成功。
测试台首次安装
在NI-488.2文件夹中执行Setup.exe,按下一步 继续并选择自定义安装。
测试台首次安装
选择NI-VISA3.2(其他版本也可),需要安装此项目,其 他默认即可。 依次点击下一步…,完成安装。 选择“PCI-GPIB”,如果USB的选择“GPIB-USB-HS”进入 硬件向导,图2
- 1、下载文档前请自行甄别文档内容的完整性,平台不提供额外的编辑、内容补充、找答案等附加服务。
- 2、"仅部分预览"的文档,不可在线预览部分如存在完整性等问题,可反馈申请退款(可完整预览的文档不适用该条件!)。
- 3、如文档侵犯您的权益,请联系客服反馈,我们会尽快为您处理(人工客服工作时间:9:00-18:30)。
\Program Files\National Instruments\RT Images\NI-488.2\2.4, and
select either the PCI or ISA install script in this directory.
PXI-817x Controller
ISA Support
-----------
NI-488.2 for LabVIEW Real Time, Version 2.4 supports plug-in PXI
GPIB interfaces as well as the built-in PCI-compatible GPIB
After selecting the install script, right-click once more on the
NI-488.2 RT entry and select Install software... Follow the prompts
to complete the download process.
Release Notes
-------------
NI-488.2 for LabVIEW Real Time, Version 2.4, is the latest
driver offering from National Instruments. Every attempt has
launch Measurement and Automation Explorer, select the Software
tab for your Remote System, right-click on the NI-488.2 RT entry,
and select Choose new install script... You will be prompted for
patents.txt file on your CD, or /patents.
NI-488.2 for LabVIEW Real Time, Version 2.4
Copyright 2005 National Instruments Corporation.
All Rights Reserved.
This file contains release notes, patent information, and
interfaces on PXI controllers (PXI-8176 and later). It does not
directly support the built-in ISA-compatible GPIB interface on
the PXI-8146 and PXI-8156/8156B PXI controllers. You may need
specific interface.
PXI-GPIB Interface
PXI-8212 Interface
PMC-GPIB Interface
PXI-814x Controller (See ISA Support section below.)
PXI-815x Controller (See ISA Support section below.)
Patent Information
------------------
For patents covering National Instruments products, refer to the
appropriate location: Help籔atents in your software, the
been made to maintain backward compatibility with the installed
base of existing NI-488.2 applicቤተ መጻሕፍቲ ባይዱtions for LabVIEW Real Time.
Supported Interfaces
last-minute information for NI-488.2 for LabVIEW Real Time,
Version 2.4. Information in this file is too recent to be
included in the official documentation set.
--------------------
NI-488.2 for LabVIEW Real Time, Version 2.4, supports the
following hardware using LabVIEW Real Time, Version 7.0 or higher.
Any special requirements or conditions are stated beside the
to transition between these two types of interfaces on a periodic
and ongoing basis. Version 2.4 includes install scripts to make
this task easier. To change from ISA to PCI support or vice versa,