无铅SMT工艺中网板的优化设计
无铅喷锡SMT上锡不良的几种分析思路

无铅喷锡在SMT上锡不良的几种分析思路1、无铅喷锡的历史演变:热风整平作为一种PCB焊锡面的表面处理方式在PCB行业已广泛应用了数十年,然而自WEEE(Waste from Electrical and Electronic Equipment)和ROHS(Restriction of Use of Hazardous Substances)的先后出台,所有电子产品无铅化的转变让所有人意识到有铅制程的气数已尽。
国内也于2007年6月份开始了无铅化的进程推进,无铅的表面处理方式也随之发展。
于是出现了多种无铅表面处理方式:(1)化学浸镍金(ENIG:Electroless Nickel and Immersion Gold)。
(2)化学浸锡(I—Tin:Immersion Tin)。
(3)化学浸银(I.Ag:Immersion Sliver)。
(4)有机保护膜(OSP:Organic Solderability Preservatives)。
(5)无铅焊料热风整平(HASL:Tot Air Solder Levelling)。
本文重点介绍此种表面处理方法在SMT 生产过程中上锡不良的几种因素及处理对策。
2、无铅喷锡的工艺方法:要解决无铅喷锡在SMT生产时出现上锡不良,首先得对无铅喷锡工艺有个详细的了解。
下面介绍的为无铅喷锡工艺方法。
无喷锡分为垂直喷锡和水平喷锡两种,其主要作用为:A、防治裸铜面氧化;B、保持焊锡性.喷锡的工艺流程为:前清洗处理→预热→助焊剂涂覆→垂直喷锡→热风刀刮锡→冷却→后清洗处理A.前清洗处理:主要是微蚀铜面清洗,微蚀深度一般在0.75—1。
0微米,同时将附着的有机污染物除去,使铜面真正的清洁,和融锡有效接触,而迅速的生成IMC;微蚀的均匀会使铜面有良好的焊锡性;水洗后热风快速吹干;B.预热及助焊剂涂敷预热带一般是上下约1.2米长或4英尺长的红外加热管,板子传输速度取决于板子的大小,厚度和其复杂性;‘60mil(1。
无铅波峰焊接工艺的优化
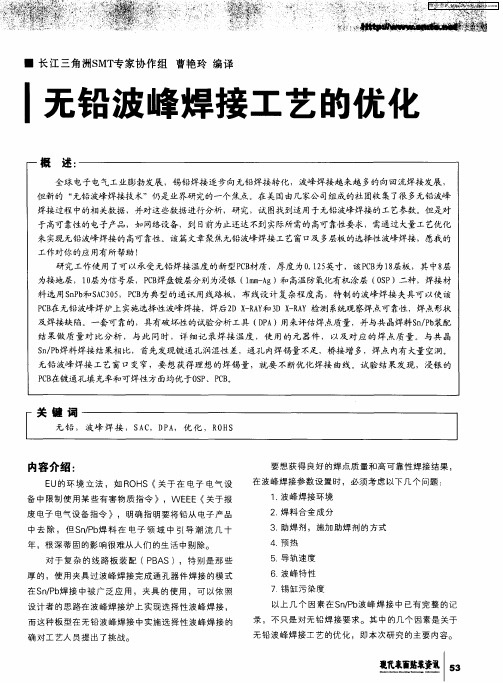
为接地层,1层为信号层,PB 0 C焊盘镀层分别为浸银 (m -g 和高温防氧化有机涂层 ( S ) 1m A ) OP 二种,焊接材 料选用SP和 SC 0,PB nb A 35 C 为典型的通讯用线路板 ,布线设计复杂程度 高,特制的波峰焊接 夹具可以使该 PB C在无铅波峰焊炉上实施选择性波峰焊接,焊后2 - A和3 -A D XRY D XRY检测系统观察焊点可靠性,焊点形状 及焊接缺陷。一套可靠的,具有破坏性的试验分析工具 ( P ) DA 用来评估焊点质量,并与共晶焊料S/b nP装配
无铅波峰焊接 工艺窗口变窄 ,要想获得理想的焊锡量,就要 不断优化焊接 曲线。试验结果发现,浸银 的
PB C 在镀通孔 填充率和 可焊性 方面均优 境 立 法 ,如 R S《关于 在 电子 电气 设 OH
要 想获得 良好 的焊点质 量和 高可靠性 焊接结 果 , 在 波峰焊 接参数 设置时 ,必须考 虑 以下几 个 问题 :
厚 的 ,使 用夹具 过波 峰焊 接完成 通孔器 件焊 接的模 式
2 焊料 合金成 分 . 3 助焊 剂 ,施加 助焊剂 的 方式 .
4 预 热 .
5 导轨 速度 .
6 波 峰特性 .
7 锡 缸污染度
在S / b nP 焊接 中被 广 泛应 用 ,夹 具 的使 用 ,可 以依 照 设 计者 的思路 在波 峰焊接炉 上 实现选择 性波 峰焊 接 , 而这种板 型在 无铅 波峰焊 接 中实施选择 性 波峰焊 接 的 确 对工 艺人 员 提 出了挑战。
无铅焊接控制与改进工艺

无铅焊接控制与改进工艺 Prepared on 22 November 2020无铅焊接:控制与改进工艺--------------------------------------------------------------------------------本文描述怎样控制与改进无铅工艺...。
在实施无铅工艺之后,我们必须经常跟进、监察和分析数据,以保持工艺在控制之中。
无铅焊接已经引入了,因此无数的问题也提出来了。
尽管如此,许多问题还是必须回答的,包括无铅的定义、它的实施成本、和甚至是否所有技术问题已经解决。
但是,实验继续在新的无铅合金的可靠性上提供好的数字。
本文讨论成本与能量效应,并展示工艺必须不断地检验,因为技术与工艺知识在将来会改进的。
一个标准改进模式,比如德明循环(Deming cycle),可用来维护无铅焊接工艺的控制,作出调整和改进,并在可能的时候实现成本的节约。
材料成本焊锡作为一个例子,某种焊接机的锡锅含有大约760公斤的锡铅(SnPb)合金。
用SnPb来填满锡锅将花大约$3,960美元。
SnPb的密度为8.4 g/mm3。
用锡铜(SnCu)合金填满相同的锡锅需要661公斤,其密度为7.31g/mm3 :质量 = ÷ x 760 = 661.结果是焊锡成本增加28%或$5,063美元。
其它无铅替代方案,如锡银(SnAg, 135%)和锡银铜(SnAgCu, 145%)对焊锡成本的影响甚至更大。
考虑到焊接点和将SnPb与无铅进行比较,我们可以作下列计算。
如果形状相同,那么无铅合金的质量将较少,由于其密度较大。
对于一个SnCu焊接的通孔引脚连接器,焊锡质量为:(ρSnCu x ρSnPb) x massSnPb因为焊点看上去不同,湿润可能较差,焊点的角度不同,我们必须验证是否计算的质量差别大约等于焊接点的实际质量增加。
为了证实,我们焊接一块有连接器的板(每块板总共192个引脚),称出焊接前后的重量差别(表一)。
无铅SMT网板设计解析

无铅SMT网板设计优化无铅SMT网板设计摘要:任何新技术的出现,势必产生对精细加工的更高要求,从而有利于采用主流技术和持续改进工艺过程。
在无铅制造中,第一个障碍就是合金和化学制剂的选择,这也是一个基本的过程。
根据早期对合金和化学制剂选择方面的工作的理解,我们对影响产能的主要因素作了进一步优化。
这些因素包括温度曲线、PWB的表面处理、元器件的金属喷镀、阻焊膜的选择或网板设计。
由于网印对直通率的影响很大,而且与基于铅的焊料相比,无铅合金在湿润性方面表现出很大的差异,本文作者对网板的几何开孔方法进行了研究,旨在优化出理想的SMT特性。
我们系统的研究了无铅合金在部分表面处理上浸润性较差的问题;同时,尝试了最大化焊盘覆盖率面的开孔设计,这样可以减少缺陷―――像MCSB(mid-chip solder balls)。
除了参考网板开孔设计指南,还将重新评估整个网板设计的优化方法。
关键词:无铅,网印,开孔设计,过程控制。
前言网印的主要目的就是周而复始的把适量的锡膏印刷到正确的位置上。
网板开孔的尺寸、形状和网板的厚度决定了锡膏的沉积量,而孔开的位置决定了锡膏沉积在什么地方。
我们有特定的方法来确保开孔位置的准确度【1】,并将在稍后介绍。
这次研究的目的是为无铅锡膏确定最为合适的开孔尺寸和形状。
无铅焊料不像有铅焊料那样容易润湿或浸润,这是不争的事实。
这种行为差异给一线的组装带来了几个问题:靠近焊盘四周的裸铜(或者基层表面处理),MCSB缺陷率,以及立碑。
为了确定不同的焊料浸润性对典型表面贴装缺陷的影响程度,我们设计了一个试验。
试验的第一部分以无铅和有铅焊料的浸润性和缺陷率为基础,网板开孔方法采用的是传统的有铅SMT开孔方法。
试验的第二部分,在使用到无铅焊料时,试图通过优化网板开孔来降低缺陷率。
在试验的第一部分,PCB的表面处理包括:有机可焊性保护膜(OSP),化镍浸金(ENIG),浸银(ImAg),浸锡(ImSn)。
第二部分用到了OSP和ImSn。
1-2-SMT概述如何提高无铅产品组装质量
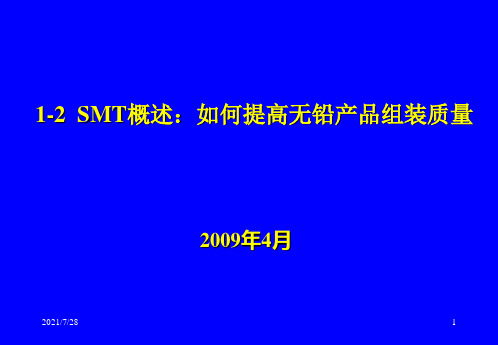
2021/7/28
23
(g)根据PCB的组装密度(有无窄间距)来选择合金粉末颗粒度
常用合金粉末的类型和颗粒尺寸
分为六种粒度等级(原四种) (目前已推出适应高密度的<20μm微粉颗粒)
合金粉末 80%以上粉 类型 末颗粒尺寸 (µm)
< 0.005% 质量< 的粉末尺寸 1%的粉 (µm) ﹡ 末尺寸
• 注意:
紧固金属刮刀时,紧固程度要适当。用力过大由于应 力会造成刮刀变形,影响刮刀寿命。
2021/7/28
29
• 金属刮刀
• 橡胶刮刀
2021/7/28
30
⑤印刷速度——由于刮刀速度与焊膏的粘稠度呈反比关 系,有窄间距,高密度图形时,速度要慢一些。速度 过快,刮刀经过模板开口的时间太短,焊膏不能充分 渗入开口中,容易造成焊膏图形不饱满或漏印的印刷 缺陷。
2021/7/28
2
一. 提倡DFM,使设计规范化
1、对客户:原始设备制造商(OEM)的要求 • 按照DFM设计 • 审核 • 对PCB加工厂商提出加工要求,确保PCB加工质量 2、对SMT加工厂:电子制造服务(EMS)的要求 • 根据本企业生产线的设备条件,写出本企业SMT设
备对PCB设计的要求(规范),并交给客户 • 客户(OEM)应按照SMT加工厂(EMS)“SMT设备对
表面,印刷时由于刮刀与PCB之间存在微小的间隙,因
此相当于增加了印刷厚度。另外压力过小会使模板表面
留有一层焊膏,容易造成图形粘连等印刷缺陷。因此理
想的刮刀压力应该恰好将焊膏从模板表面刮干净。
2021/7/28
28
• 金属刮刀的压力应比橡胶刮刀的压力大一些,一般大 1.2~1.5倍。橡胶刮刀的压力过大,印刷时刮刀会压入开 口中,造成印刷量减少,特别是大尺寸的开口。因此加 工模板时,可将大开口中间加一条小筋(架桥)。
无铅SMT工艺中网板的优化设计

无铅SMT工艺中网板的优化设计无铅SMT(表面贴装技术)工艺是一种环保型的电子元器件生产技术,其主要以无铅钎料代替传统的含铅钎料,减少对环境的污染。
其中网板作为起到电子元器件布局和连接作用的基本组成部分,其优化设计对于无铅SMT工艺的实施十分重要。
下文将从网板性质特点、网板设计方法、优化设计案例三个方面进行探讨。
一、网板性质特点网板即印制电路板(Printed Circuit Board,PCB),是电子元器件制作中的基本组成部分。
网板的性质特点直接影响着无铅SMT工艺的质量、效率和稳定性。
主要包括以下几个方面:1、导电性好网板的主要目的是为不同形态、大小的电子元器件提供布局和连接平台。
因此,网板需要具备良好的导电性能,以确保电路中各个元件之间的连接质量和通电情况。
同时,网板的导电性还与电路板的阻抗和纹波等特性相关。
2、耐化学腐蚀性强在无铅SMT工艺中,许多有机酸物质都会对网板造成一定的化学腐蚀,从而损害网板表面和内部的金属线路。
因此,网板的设计需要考虑其防腐蚀、耐久性等方面局限。
3、适应不同温度环境无铅SMT工艺通常需要进行高温处理,以确保电子元件和网板的黏合情况、钎焊效果等。
对于网板而言,需要具备一定的抗高温能力,同时在放置元器件时还需要尽量保证同一温度环境下的均匀性。
二、网板设计方法1、网格布局网格布局是一种比较常见的网板设计方法,主要思想是将网板分为不同的区域,每个区域内布置不同的电子元器件。
在这种布局方式下,具备以下优势:(1)网格布局可以让电子元件之间彼此独立,从而减少元件之间的干扰;(2)在进行布局设计时,可以将元器件按照功能分类,从而提高布局和调试的效率;(3)网格布局能够为不同功能的元器件提供多个接口,以保证电路的稳定性和可靠性。
2、单面/双面设计单面设计是指将电子元件布置在网板的一侧,而另一侧则为线路图案。
这种设计方式比较简单实用,对于元器件的连接也比较方便,但是通常由于元件的种类和数量过多,单面设计需要占用较大的空间,因此不适用于更为复杂的电路。
SMT钢网、网板设计

SMT钢网、网板设计简介在表面贴装技术(SMT)领域,钢网和网板是两个关键的组成部分。
钢网用于印刷焊膏,而网板则用于支撑和保护电子元件。
本文将详细介绍SMT钢网和网板的设计过程,包括设计要点、工艺参数和注意事项。
设计要点钢网设计钢网设计是确保焊膏正确印刷到PCB上的重要步骤。
以下是一些钢网设计的要点:1.孔径选择: 孔径的选择要根据焊膏的粘度和电子元件的封装密度进行。
一般来说,焊膏的粘度较高时,孔径应该较大,以确保能够顺利流过孔径;而电子元件封装越密集,孔径应更小。
2.网框尺寸: 网框尺寸要与PCB尺寸相匹配,以确保钢网能够完全覆盖焊膏印刷区域。
一般来说,网框的尺寸应大于PCB的尺寸,留出一定的余量。
3.网眼数量和布局: 网眼数量和布局也是需要考虑的因素。
通常,为了确保焊膏能够均匀印刷,网眼的数量应足够且均匀分布在整个钢网上。
网板设计网板是支撑和保护电子元件的重要组成部分。
以下是一些网板设计的要点:1.材料选择: 网板的材料选择要考虑刚性、导电性和耐热性。
常见的网板材料包括不锈钢和镍钛合金。
这些材料可以提供足够的刚性,并且具有良好的导电性能和耐高温能力。
2.开孔设计: 网板上的开孔设计要考虑到元件的布局和尺寸。
通常,开孔的位置和数量要与PCB上的元件一一对应,并且尺寸要稍微大一些,以便元件能够顺利通过。
3.边框设计: 网板的边框设计要考虑到安装和固定的需要。
一般来说,网板的边框应足够宽,以便于夹持和固定。
此外,边框上还可以添加一些标记或指示,方便组装操作。
工艺参数在SMT钢网和网板设计过程中,还需要设定一些工艺参数。
以下是一些常见的工艺参数:1.钢网厚度: 钢网的厚度影响焊膏的印刷效果。
一般来说,钢网的厚度应根据焊膏的粘度和元件的封装密度选择。
2.网框材料: 网框材料通常选择铝合金或不锈钢。
不锈钢更常用,因为它具有良好的刚性和导电性能。
3.网眼尺寸: 网眼尺寸要根据焊膏的颗粒大小选择。
网眼尺寸太大会导致焊膏流失,太小则可能造成堵塞。
无铅产品PCB设计及工艺控制.
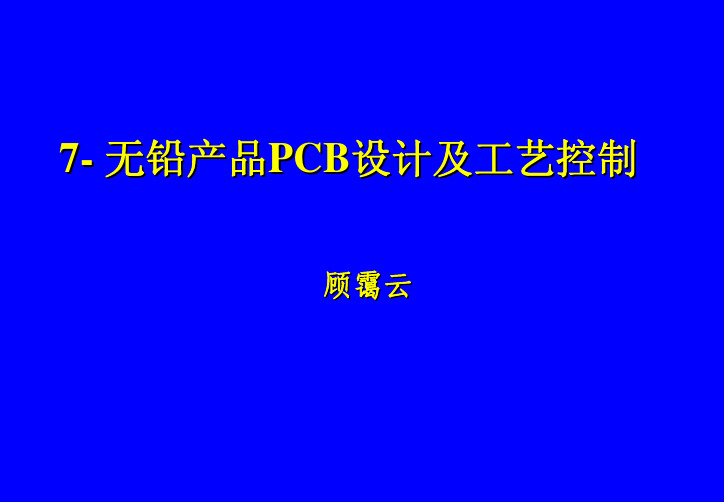
无铅工艺流程设计
• 尽量采用再流焊方式 (不采用或少采用波峰焊、手工焊工艺) • 通孔元件再流焊工艺 (适用于少量通孔插装元件(THC)时) • 选择性波峰焊机是无铅波峰焊的良好选择 (适用于高可靠、及无铅) • 一些单面板以及通孔元件非常多的情况,还是需 要采用传统波峰焊工艺。(适用于消费类产品)
• 化学镀Ni和浸镀金(ENIG)具有良好的可焊性,用于印制 插头(金手指)、触摸屏开关处。 • Ni作为隔离层和可焊的镀层,要求厚度≥3um ; • Au是Ni的保护层 ,Au能与焊料中的Sn形成金锡间共价化 合物(AuSn4),在焊点中金的含量超过3%会使焊点变 脆,过多的Au原子替代Ni原子,因为太多的Au溶解到焊点 里(无论是Sn-Pb还是Sn-Ag-Cu)都将引起“金脆”。所 以一定要限定Au层的厚度,用于焊接的Au层厚度≤1µm (ENIG :0.05~0.3µm); • 如果镀镍工艺控制不稳定,会造成“黑焊盘”现象。
② 无铅焊料合金介绍
• 无铅化的核心和首要任务是无铅焊料。全球范围内共 研制出 100 多种无铅焊料(焊膏 33 种,波峰焊棒材 62 种,丝49种),但真正公认能用的只有几种。 目前最有可能替代Sn/Pb焊料的合金材料 • 最有可能替代Sn/Pb焊料的无毒合金是Sn基合金,以Sn 为主,添加Ag、Zn、Cu、Bi、In等金属元素,通过添 加金属元素来改善合金性能,提高可焊性、可靠性。
7- 无铅产品PCB设计及工艺控制
顾霭云
1. 无铅产品组装方式与工艺设计
首先要确定组装方式及工艺流程 • 组装方式与工艺流程设计合理与否,直接影响: • 组装质量 • 生产效率 • 制造成本
印制板的组装形式
组装方式与工艺流程设计原则:
• 选择最简单、质量最优秀的工艺 • 选择自动化程度最高、劳动强度最小的工艺 • 工艺流程路线最短 • 工艺材料的种类最少 • 选择加工成本最低的工艺
基于无铅SMT焊膏印刷参数优化控制研究

( a’HC l g i om t nTcn l y Hu i n2 3 0 ,hn ) Hu i ol e f n r ai eh oo , a’ 2 0 3C ia O e o f o g a
Abs r t t ac :Th r du to y t m fSM T m an y i c u e i tpswh c r tncl rn i g c m p n n e p o ci n s se o i l n l d ssx se i h a ese i p i tn , o o e t p a e e t rfo s l e ig a he i ip n e w a es l e ig a di s e t n. t n i p i t g a t st efrt lc m n , e w o d rn , d sved s e s , v o d rn n p c i S e cl rn i c sa h s l n o n i
Th t yo o de sePrntn r m e e p i ii o t o a e n eS ud fS l rPa t i i gPa a t rO tm zngC n r l s d o b Le d-r eSo f e o a f e ur a eM unt c no o y Te h l g
Lo t et eLF 2 n-e ds l ei gp se ci h 3 0no la o d rn a t . t K e o ds tn ip itn la — e ; p i ii g yw r :se cl rn i g;e d f e o t zn l m
徐 建 丽
( 淮安信息职业技术学院 ,江苏 准安 2 3 0 ) 2 0 3
电子器件制造中的SMT工艺流程优化技巧

电子器件制造中的SMT工艺流程优化技巧在电子器件制造过程中,表面贴装技术(Surface Mount Technology,SMT)被广泛应用于电子产品的制造。
SMT工艺流程的优化是提高产品质量和生产效率的关键。
本文将介绍一些SMT工艺流程优化的技巧,以帮助制造商更好地提高其生产效率和产品质量。
1. 设计优化在SMT工艺流程中,设计优化是关键的一步。
设计工程师应该考虑组件的布局和放置,确保元件之间的间距合适,并避免过于密集的布局。
此外,正确选择元件的尺寸和形状也是至关重要的,以确保元件能够正确放置在印刷电路板(PCB)上。
2. 材料选择材料选择在SMT工艺流程的优化中起着重要作用。
制造商应选择高质量的贴装材料,如贴片元件、焊锡膏和PCB等。
同时,保证供应商的稳定性和可靠性也非常重要,以确保所用材料的一致性和品质。
3. 焊接工艺优化在SMT工艺流程中,焊接是一个关键步骤。
优化焊接工艺可以提高产品的可靠性和质量。
以下是一些优化焊接工艺的技巧:- 控制焊锡膏的厚度和平整度,确保良好的涂布效果和均匀的覆盖。
- 确保加热温度和时间的准确控制,以确保焊锡膏能够充分熔化和流动。
- 进行适当的冷却过程,以避免焊接后的热应力对产品的影响。
4. 质量检验与控制质量检验与控制是确保产品质量的一项重要步骤。
制造商应该实施严格的质量检验控制措施,以确保检测和预防可能的缺陷和故障。
以下是一些质量检验与控制的技巧:- 使用自动光学检测(Automated Optical Inspection,AOI)等精密设备对焊接质量进行检查,提高检测的准确性和效率。
- 进行原材料和半成品的抽样检验,确保它们符合质量标准。
- 建立可追溯性的制度,追踪产品的生产和质量数据,以便及时发现和解决潜在问题。
5. 过程自动化和优化过程自动化和优化是提高生产效率的关键。
制造商应该考虑引入自动化设备和系统,如自动贴片机和追踪系统,以提高生产效率和精确性。
SMT钢网设计规范

SMT钢网设计规范编号:修订记录目录1目的 ......................................................................... 错误!未定义书签。
2使用范围...................................................................... 错误!未定义书签。
3权责........................................................................................................................................................ 错误!未定义书签。
4定义 ......................................................................... 错误!未定义书签。
5操作说明...................................................................... 错误!未定义书签。
5.1材料和制作方法 (4)5.2钢网外形及标识的要求 (5)5.3钢片厚度的选择 (7)5.4印锡膏钢网钢片开孔设计 (8)5.5印胶钢网开口设计 (27)6附件 (30)1目的本规范规定了本公司钢网外形,钢网标识,制作钢网使用的材料,钢网焊盘开口的工艺要求。
2范围本规范适用于钢网的设计和制作。
3权责工程部:负责的钢网开口进行设计。
4定义钢网:亦称模板,是SMT印刷工序中,用来漏印焊膏或胶水的平板模具。
MARK点:为便于印刷时钢网和PCB准确对位设计的光学定位点。
5详细内容5.1材料和制作方法5.1.1网框材料钢网边框材料可选用空心铝框或实心铝框,网框边长为736*736±5mm的正方形,网框的厚度为40±3mm。
电子产品加工的SMT工艺如何优化

电子产品加工的SMT工艺如何优化在当今数字化和智能化的时代,电子产品已经成为我们生活中不可或缺的一部分。
从智能手机到智能家居设备,从汽车电子到医疗仪器,电子产品的广泛应用对其质量和性能提出了更高的要求。
而表面贴装技术(SMT)作为电子产品制造中的关键工艺,其优化对于提高产品质量、降低成本、提升生产效率具有重要意义。
SMT 工艺是一种将无引脚或短引脚的表面组装元器件安装在印制电路板(PCB)表面的组装技术。
它具有组装密度高、电子产品体积小、重量轻、可靠性高、生产效率高等优点。
然而,在实际生产中,SMT工艺仍然面临着一些挑战,如元器件贴装精度、焊接质量、生产效率等问题。
为了解决这些问题,需要对 SMT 工艺进行不断的优化。
一、优化 PCB 设计PCB 设计是 SMT 工艺的基础,一个良好的 PCB 设计可以大大提高SMT 生产的效率和质量。
在 PCB 设计时,需要考虑以下几个方面:1、布局合理性元器件的布局应遵循信号流向原则,尽量减少信号传输的距离和干扰。
同时,应将发热量大的元器件分散布置,避免局部过热。
2、焊盘设计焊盘的尺寸和形状应根据元器件的封装类型和尺寸进行合理设计。
焊盘过大或过小都会影响焊接质量,一般来说,焊盘的尺寸应比元器件引脚尺寸略大。
3、孔径设计PCB 上的孔径应根据元器件引脚的直径进行设计,孔径过小会导致引脚插入困难,孔径过大则会影响焊接的可靠性。
4、层数选择根据电路的复杂度和性能要求,合理选择PCB 的层数。
层数越多,成本越高,但可以提高电路的性能和抗干扰能力。
二、优化元器件选择元器件的质量和性能直接影响SMT 工艺的效果。
在选择元器件时,应考虑以下几个方面:1、元器件的封装类型应根据 PCB 的布局和生产设备的能力选择合适的封装类型。
常见的封装类型有 QFP、BGA、SOP 等,不同的封装类型对贴装精度和焊接工艺的要求不同。
2、元器件的质量选择质量可靠、一致性好的元器件供应商,确保元器件的性能稳定。
SMT钢网、网板设计

▪ 电铸工艺:质量较好,但成本很高,供应商少 不适合用于厚度变化钢网 不需使用抛光等技术也有很好的释放质量
▪ 抛光和镀镍:使孔壁更光滑的工艺,用在化学腐蚀和激光工 艺后,影响开孔尺寸,必须给予补偿
0.12mm
0.15mm
0.18~0.2mm
细间 距长 方形 开口
宽度≥0.18mm (长宽比<10) 且最近开口中心
距≥0.4mm
宽度≥0.225mm (长宽比<10) 且最近开口中心
距≥0.5mm
宽度≥0.225mm (长宽比<10)且 最近开口中心距
≥0.5mm
宽度≥0.27mm (长宽比<10)且 最近开口中心距
SMT工艺制程控制
钢网设计
钢网设计
SMT过程
印刷或滴注 贴片 回流
70%↑ 印刷引起的工艺问题占:
钢网设计
▪ 钢网的设计要求 ▪ 钢网材料和制造工艺 ▪ 钢网的开孔设计 ▪ 钢网的制作指标
一. 钢网的设计要求
正确的锡膏量或胶量 →可靠的焊点或粘结强度 良好的释放后外形 →可靠稳定的接触 容易定位和印刷 →良好的工艺管制能力
三. 钢网的开孔设计
L W
开孔尺寸设计的基本原则 Lmax=W+0.3W/D2 Wmin = 5 × solder powder size
印刷不良造成的焊接缺陷
少锡
锡珠
立碑
连锡
红胶上焊盘
掉件
钢网开口的一般原则
L
W
以化学腐蚀方法制作:W/D≥1.6 激光切割(用“钼”制作)W/D≥1.2 激光切割(无抛光工艺,用不锈钢片制作)W/D≥1.5 开口面积与孔壁面积之比: Area ratio=L*W/(2*(L+W)*D)≥0.66
SMT钢网的优化设计

钢网开孔设计
钢网开孔首先要优先考虑面积比和宽厚比,但开孔一般不会完全按照焊盘形状或 大小来设计,有时为了减少焊接缺陷,不得不对开孔形状和尺寸进行优化。 防锡珠开孔 生产过程中,经常会发现片式元件侧面有锡珠问题。
锡珠问题发生的原因很多,比如锡膏管控,回流温度曲线等,但主要的原因 还是在钢网开孔方面。对于一些新手来说,在钢网开孔设计时,不做任何的优化 而直接按照焊盘全比例开孔。这样的全开孔锡膏印刷,在元件贴装时,会将锡膏 挤压出焊盘。由于元件本体和PCB表面的阻焊膜与锡膏不兼容,不能产生润湿, 锡膏熔化后,在元件本体重量挤压作用下,锡膏不能完全依靠其表面张力聚拢回 到焊盘上,部分残留在元件底部,锡膏冷却固化时,元件下沉将这部分残留熔锡 挤压出来,在元件侧面中间位置形成锡珠。如果锡珠没有违反最小电气间隙要求, 而且被固定不会移动,按IPC-610标准是可接受的,可以不作处理。但是,没有 人能保证这些锡珠在产品的使用过程中不会脱离残留助焊剂的束缚而成为自由导 电粒子。如果这些能够自由移动的金属粒子卡在元件的引脚或相邻元件之间,就 会导致电气问题,甚至出现产品功能失效问题。由于产品的使用环境不可预测, 而且产品使用过程中的发热都可能导致束缚锡珠的助焊剂残留消耗而出现锡珠移 动。所以,一般客户都不允许锡珠留存在PCBA上。 既然说锡珠的产生是因为元件底部的锡溢出焊盘而形成,所以我们在钢网开孔设 计时就需要考虑避免这种情况,在元件底部减少锡膏量,从而减少锡膏溢出焊盘 的几率。常见的有以下一些开孔设计。
如何设计一张优良的钢网? 钢网设计基本原则是什么,如何解读? 如何优化钢网开孔以避免锡珠、短路、少锡问题?
锡膏印刷工艺事关SMT组装质量成败,其中钢网的设计和制造又是锡膏印刷 质量好坏的一个关键因子,设计适当可以得到良好的锡膏印刷结果,否则就会导 致制程质量不稳定,缺陷问题难以控制。本文将列举一些常见的钢网开孔优化设 计供大家参考。
SMT钢网的优化设计

• SMT钢网概述 • SMT钢网优化设计方法 • SMT钢网设计案例分析 • SMT钢网发展趋势与挑战 • SMT钢网优化设计实践建议
目录
01
SMT钢网概述
SMT钢网定义
SMT钢网是表面贴装技术(Surface Mount Technology,简称SMT)中 用于辅助电子元件焊接的金属模板, 通常由不锈钢制成。
在航空航天领域,由于对 产品精度和可靠性的高要 求,SMT钢网也得到了广 泛应用。
SMT钢网的重要性
提高焊接质量
通过精确控制锡膏的印刷,SMT 钢网能够确保焊接的一致性和可
靠性,从而提高产品质量。
降低制造成本
SMT钢网的使用可以减少人工操作, 提高生产效率,从而降低生产成本。
保证产品精度
SMT钢网具有高精度开口尺寸和位 置控制能力,能够确保电子元件焊 接位置的准确性,提高产品精度。
案例二:高精度钢网设计
总结词
高精度开口,提高焊接质量
VS
详细描述
在高精度钢网设计中,对开口的精度要求 极高,以确保焊料的准确释放和分布。通 过精确计算和精细加工,实现了高精度的 开口设计,显著提高了焊接质量。
案例三:大尺寸钢网设计
总结词
强化支撑结构,防止变形
详细描述
在大尺寸钢网设计中,由于面积较大,支撑 结构显得尤为重要。通过强化支撑结构并采 用特殊的材料,有效地防止了钢网的变形, 确保了焊接过程的稳定性和可靠性。
材料选择建议
选择合适的材料
根据实际需求选择合适的材料,如不锈钢、 铜等,以确保钢网的耐用性和稳定性。
考虑材料的加工性能
在选择材料时,还需考虑其加工性能,以确 保制造过程的顺利进行。
无铅技术系列文章八:无铅焊接工艺的优化和监控

无铅技术系列文章八:无铅焊接工艺的优化和监控薛竞成撰写前言:在以往的7篇文章中,我们谈到无铅技术带来的最大变化是材料上的改变。
而材料特性上的改变,也连带来工艺上调整的需求。
常用的SMT工艺中,受到无铅技术影响最大的是焊接工艺,包括所有常用的波峰、回流和手工焊接。
在本文中,我们针对回流工艺技术来进行探讨,看看在无铅技术的更严格要求下,如何对工艺进行优化和监控。
无铅的焊接挑战:铅是种特性十分适合焊接工艺的材料。
当我们将它除去后,到目前还无法找到一种能够完满取代它的金属或合金。
当我们在工艺、质量、资源和成本等考虑上找到比较满意的代用品时,我们在工艺和成本上都不得不做出让步。
而在工艺上较不理想的有以下几个方面。
1.较高的焊接温度。
大多数的无铅焊料合金的熔点都较传统锡铅焊料合金高。
业界有少部份溶点低的合金,但由于其中采用如铟之类的昂贵金属而成本高。
熔点高自然需要更高的温度来处理,这就带来了需要较高的焊接温度。
不过熔点只是决定焊接温度的一个因素。
例如目前被推荐的SAC305材料,其熔点为217℃,而事实上我们目前处理锡铅焊料时多数的焊接温度是达到225℃,甚至是235℃。
这已经是超出了SAC305合金的熔点,为什么我们还需要提高呢?就是因为熔点并非唯一的考虑。
2.较差的润湿性。
无铅合金也被发现具有较不良的润湿性能。
这不利于焊点的形成,并对锡膏印刷工艺有较高的要求。
由于润湿效果可以通过较高的温度来提高,这又加强了无铅对较高温度的需求。
熔化的金属,一般在其熔点温度上的润湿性是很差的,所以实际焊接中我们都需要在熔点温度上加上20度或以上的温度以确保能有足够的润湿。
这也说明了以上我们提到为什么SAC305不能使用刚过217℃的温度来进行焊接的原因。
美国推荐245到255℃。
3.较长的焊接时间。
由于温度提高了,为了避免器件或材料经受热冲击和确保足够的恒温以及预热,焊接的时间一般也需要增长。
以上这些不理想的地方带给用户什么呢?总结来说就是器件或材料的热损坏、焊点的外形和形成不良、以及因氧化造成的可焊性问题等工艺故障。
- 1、下载文档前请自行甄别文档内容的完整性,平台不提供额外的编辑、内容补充、找答案等附加服务。
- 2、"仅部分预览"的文档,不可在线预览部分如存在完整性等问题,可反馈申请退款(可完整预览的文档不适用该条件!)。
- 3、如文档侵犯您的权益,请联系客服反馈,我们会尽快为您处理(人工客服工作时间:9:00-18:30)。
无铅SMT工艺中网板的优化设计摘要随着新技术的不断涌现,需要进行不断的完善来促进主流应用以及持续的改进。
就无铅工艺而言,初期合金和化学品选择的障碍在起步阶段已经得以解决,提供了基础工艺。
来源于早期基础工艺工作的经验被进一步完善用来优化影响良率的要素。
这些要素包括温度曲线、PWB表面最终处理、元器件镀层、阻焊膜选择,或者网板的设计。
由于网板印刷对首次通过率的影响很大,而且锡铅合金与无铅合金的润湿性也有所不同,作者就此进行了专门的研究,以确定针对所需的SMT特性,对网板的开孔形状进行优化。
对无铅合金在一些替代表面处理上的低扩展性也需要进行考虑。
为达到焊盘的覆盖率最大化而进行的孔径设计,有可能导致片式元件间锡珠缺陷的产生。
除了开孔设计指南,我们还将讨论优化整个网板设计的方法。
关键词:无铅,网板印刷,开孔设计,工艺控制简介网板印刷的基本目标是重复地将正确量的焊膏涂敷于正确的位置。
开孔尺寸、形状,以及网板厚度,决定了焊膏沉积的量,而开孔的位置决定了沉积的位置。
关于有效控制穿孔位置的方法早已有了定论,将在后面的文章中讨论。
此研究的目的是找到对无铅焊膏的开孔的最佳尺寸和形状。
通常来说,无铅焊膏的润湿性或扩展性较锡铅焊膏要差;因此,组装者须考虑以下几个方面的问题:焊盘周边的裸铜(或板的表面处理),锡珠以及立碑的不同缺陷率为此,我们专门设计了一项试验,来量化不同焊膏对典型表面贴装缺陷的影响。
试验I部分,是使用传统锡铅SMT工艺,研究网板开孔大小对锡铅和无铅焊膏基准扩展性和缺陷率的影响。
试验II部分,优化网板开孔,以降低使用无铅焊膏时的缺陷率。
在I部分,板表面最终处理包括有机可焊性保护膜(OSP),化学镍金(ENIG),化学银(IMAG)以及化学锡(IMSN)。
试验的II部分使用OSP及IMSN。
试验设计润湿性及扩展性——焊膏的扩展性可以用两种方法测试。
第一种是在金属裸板上印刷一个已知面积的圆形焊料点(胶点),然后对样件进行回流,并测量回流后的胶点面积。
回流后的面积与原有面积之比,可以计算出焊膏的扩散率,并显示出不同表面处理的电路板的润湿性能。
另一种焊膏扩展性/润湿性的测试包括在一列相同厚度(30 mil)印刷成对的相同厚度(40 mil)的焊膏带,带的间距也相同。
如图1所示,焊膏带的间距逐渐扩大,以正交的方法印刷在线路板上。
在回流中,熔化的焊膏在板上沿着金属线扩张。
如果扩展性足够,邻近的焊点之间的缝隙将被桥连。
焊膏带之间的空隙从0.1mm到0.8mm之间不等。
每个空隙之间最多可产生20个桥连。
方型扁平封装——对于间距小于20mil的器件,当开孔与焊盘的比率为1:1时,会增大桥连的风险。
要降低风险,通常的做法是减少一定量的印刷面积。
将开孔面积减少10%,孔自然减小。
然而,当印刷面积减少10%,焊盘暴露的风险也会提高。
虽然暴露焊盘不会损害可靠性,但它影响到组件的外观。
如果锡铅工艺中需要关注裸露的焊盘,那么在无铅工艺中则更需要关注。
为了量化开孔大小的影响,我们在每块测试板上贴装2个20mil间距的方形QFP。
研究中I部分,QFP’s之一开孔与焊盘的比率为1:1,另一个减少了10%。
研究中部分II,开孔设置被定为1:1,减少5%和减少10%。
两部分测试中都用到了5mil和6mil厚的金属网片(分别为125和150μM)。
总的来说,I部分进行了面积及网片厚度的四种组合的测试;II 部分则进行了六种组合的测试。
测试板如图3所示。
片式元件间锡珠(Mid-chip solder ball, MCSB)也是一个常见缺陷,很容易受到网板设计的影响。
虽然形成片式元件间锡珠的因素很多——包括焊盘设计、阻焊膜形态、贴装压力、电极形状和金属化、焊盘最终处理和回流曲线——焊膏印刷图形的尺寸和形状,也正面或负面地影响到片式元件间锡珠的形成。
如果焊膏的相对体积较大,特别是在贴放元件的区域,贴装时会把柔软的焊膏挤出去。
印刷到器件本体下面的焊膏,在回流时可能会被拉回到焊盘上,也有可能不会。
如果焊膏没有被拉回,在其液态时由于毛细作用能够转移到元件的边上,在冷却后形成锡珠。
图4为典型的片式元件间锡珠。
采用锡铅焊膏进行几百次MCSB测试,其数据统计结果显示,效果最差的网板设计是1:1焊盘开孔比例、矩形开孔、6mil 网板厚度的组合。
效果最好的情况是所谓的“本垒板” (homeplate) 型开孔,加上10% 的面积缩减,和5mil网板厚度。
图5表示矩形、本垒板形和反本垒板形开孔。
而且,以往数据表明,采用均热式温度曲线的效果不如斜升式温度曲线,因为焊膏会在达到液相线之前持续软化并塌落(热坍塌)。
MCSB测试包括最佳和最差的网板设计。
在I部分,结合了每一种表面处理方式,焊膏型号及温度曲线类型(斜升和均热)。
每种元件贴装300个:1206、0805、0603、0402。
150个为垂直贴装,150个为水平贴装。
使用了IPC推荐的焊盘标准。
研究中并未包括0201元件,因为许多适合于较大无源元件的原则不一定能够适用于密间距微小元件的贴装。
作者认为应该单独对0201进行更深层次的研究。
在第II部分,采用了三种新的开孔设计。
如图6所示,第一个是尖角倒圆的本垒板形,后两个是带有三个圆弧的反本垒板形。
同样,对300个与上面尺寸相同的元件进行组装,两种表面处理方式/网板厚度,以及两种回流曲线。
立碑与MCSB一样,是SMT中另一个常见的缺陷,它们的形成有多种因素,但也会受网板设计的影响。
立碑,也被称作“吊桥现象”或“曼哈顿现象”(Manhattan effect)。
当作用在一端的焊膏的表面张力大于另一端的表面张力时就会产生;不平均的力瞬间作用于器件造成抬起,站立,像打开的吊桥。
影响立碑的设计因素包括焊盘形状和热容的不同。
影响立碑的组装因素包括焊膏印刷的位置精度,元件的贴装精度,以及在回流焊中进入液相时的温升斜率。
开孔设计与其他组装因素互相影响,也会造成立碑。
如果元件没有放在中心,它的一端会比另一端接触更多的焊膏,由于焊膏熔化,这会导致元件两端的张力差。
图7为一典型的立碑缺陷。
锡铅焊膏的历史数据表明,一些开孔形状更易造成立碑(例如矩形),而有些却不会(如“本垒板”形)。
片式元件间锡珠与立碑的比较:平衡的结果从前两个研究中可以知道,立碑和片式元件间锡珠的网板设计参数完全不同。
事实上生产过程中必须要折衷。
用来研究片式元件间锡珠的器件也被用来检查立碑。
虽然此项研究不是为了减少立碑,但仍然要观察其缺陷率,因为研究人员不希望在优化MCSB的性能的同时,以增加立碑的缺陷率为代价。
组装——全部174块线路板在一条小的试验线上进行组装。
此研究中使用的设备包括MPM UltraFlex 3000网板印刷机,环球仪器Advantis贴片机,和一台Electrovert OmniFlow 七温区回流炉。
图8-11为回流曲线。
使用的焊膏为3号粉,免清洗焊膏。
锡铅合金为6337,无铅合金为锡96.5/银3.0/铜0.5 (SAC 305)。
结果及讨论扩展性正如前面描述的,扩展性测试用两种不同的方法进行。
结果已用图12到14总结。
图13和14表示了回流后焊点面积与焊膏印刷面积之间的比率。
此扩展性测试的结果表明无铅和锡铅焊膏的扩展性非常接近,无铅的扩展性更好一些。
显然,这些测试结果有些奇怪,因为有很多文献可以证明锡铅焊膏的扩展性比无铅焊膏好,而且此观点也被普遍接受。
数据反常的潜在原因包括测试的种类和测试的方法。
由于焊膏印刷面积远小于焊盘面积,扩展不受焊盘边角的影响。
焊点周围的不平均的扩展性没有被计算。
测试结果只是来源于简单面积比率计算,没有考虑焊膏的形成或流动。
由于比较电子显微镜测量的面积是由人工定义的,这种给测试带来了不同程度的主观性,尤其是不同的人在不同的时间测试不同的样品。
作者对这种测试方法的合理性持一定的怀疑,这也是介绍交叉印刷方法的原因。
交叉印刷测试比普通扩展性测试对润湿性的定义更好。
图15列出在所有表面处理板上无铅焊膏的桥连数量。
图16列出锡铅焊膏的同样测试结果。
图17举例说明锡铅焊膏与无铅焊膏在最难润湿的OSP表面上的润湿性上的差别。
毫无疑问,测试量化的扩展性差异与业内公认的情况相符。
一如所料,ENIG表面涂层显示了完美的扩展性,甚至达到本测试的上限;IMSN也显示出了类似的情况,只是在最大间隙处有几个点没有桥连。
OSP和IMAG对锡铅和无铅焊膏都显示了较低的扩展特性,这同样在预料之中。
今后,作者将利用交叉测试来证明扩展性。
与原来的方法进行比较,这种测试方法提高了精确性,更为客观和清晰,实施起来更加快速、经济。
QFP的润湿性本测试检验了QFP 的焊盘裸露和桥连缺陷,总共贴装和测试了348次,却只发现了4个桥连。
作者不敢轻易根据如此小的样本量和似乎无统计意义的测试结果妄下结论。
由于组装工艺在实验室中进行,印刷和贴装设备都被调整得非常好,不存在典型生产环境中的干扰因素。
作者认为如果在典型生产设备公差下,制造的样板越多,得到的数据越有意义。
不管开孔如何,ENIG和IMSN如预期的那样表现出完全的扩展性,因此它被认为在ENIG或IMSN表面最终处理上进行组装时,组装者可以继续使用现在缩小的QFP开孔。
同样,OSP和IMAG在焊盘的角落的扩展性并不完全,但都符合IPC的可接受标准。
在焊盘的边缘,IMAG较OSP为好,但比不上ENIG或IMSN。
片式元件间锡珠片式元件间锡珠的计算包括板上所有的元器件。
共有6960个元件进行了组装和检测。
图19概括了全部MCSB的数量。
结果如下:l总体来说,无铅焊膏MCSB的数量比锡铅焊膏的少l化学锡所产生的MCSB的数量最少,接下来是ENIG,OSP和化学银l均热式曲线比斜升式曲线的MCSB少。
l 6 mil的网板所产生的MCSB远远多于5mil板。
需要注意的是,为了比较出“最好”和“最差”的情况,6 mil网板使用的是开孔与焊盘为1:1矩形开孔,5mil使用的是“本垒板”开孔,面积减少10%。
以元件尺寸来细分,图19显示了使用无铅焊膏,对于每种封装类型在所有四种表面处理板上的MCSB的总和。
图20是锡铅焊膏的结果。
元件类型后的字母H和V各自代表水平及垂直放置的元件。
这里的数据使用的是斜升式回流曲线。
对于无铅焊膏,中间尺寸的元件会产生较多的元件间锡珠,尤其是在IMAG 和ENIG板上。
OSP和IMSN板上的分布较为均匀。
锡铅焊膏的片式元件间锡珠的数量总体来说随着元件尺寸的减小而减少,只有在使用化学银板时,对于0603元件MCSB的比率开始上升。
在化学银的72个MCSB记录中,有67个是在连续的两块板上发现的。
其中的一块板在垂直排列的元件中出现了28个MCSB。
研究人员猜测这是由于特殊原因造成的反常数据,很可能是因为机器贴装造成的。