BATTERY TEST REPORT
batteryreport解读

batteryreport解读
电池报告解读
电池报告是一种提供设备电池使用情况的分析和解读的工具。
它为用户提供了详细的信息,包括电池的健康状态、充电周期、
容量以及其他相关参数。
通过解读电池报告,用户可以更好地了
解自己设备的电池使用情况,并根据报告提供的建议来优化电池
的寿命和性能。
电池报告中最常见的参数是电池的健康状态。
健康状态表示电
池的剩余容量与设计容量之间的比例。
通常,当健康状态低于80%时,意味着电池已经经历了一定程度的衰减,可能需要替换。
电
池报告还可以提供电池的充电周期信息,即电池从0%充电到100%所需要的充电次数。
较高的充电周期通常意味着电池的寿命已经
减少。
此外,电池报告还可以显示电池的容量,即电池可以储存
的电荷量。
容量越大,电池的续航时间越长。
通过分析电池报告,用户可以获得一些优化电池寿命和性能的
建议。
例如,可以减少频繁充电的次数,因为充电周期的增加会
对电池的寿命产生负面影响。
同时,避免将电池充放至极限,适
当控制电池的使用温度,也是保护电池寿命的重要措施。
此外,
定期进行软件更新以及关闭不必要的后台应用程序也有助于减少
电池的耗电量。
总之,电池报告是用户了解设备电池使用情况的重要工具。
通过详细分析报告中的参数和提供的建议,用户可以更好地管理和优化电池寿命和性能,从而提高设备的使用体验。
UPS蓄电池检测报告

UPS蓄电池检测报告英文回答:UPS Battery Testing Report。
(For Example, a report from a UPS battery testing company)。
Company Name: UPS Battery Testing Company。
Date: March 8, 2023。
Client: Acme Corporation。
Site: 123 Main Street, Anytown, CA 12345。
Equipment: UPS Battery System。
Model: XYZ-12345。
Serial Number: 1234567890。
Test Date: March 7, 2023。
Test Procedure:The UPS battery system was tested in accordance with the manufacturer's specifications. The following procedures were performed:Visual inspection of the battery system。
Electrical testing of the battery system。
Capacity testing of the battery system。
Test Results:The visual inspection revealed no signs of damage or defects. The electrical testing showed that the battery system was operating within the manufacturer's specifications. The capacity testing showed that thebattery system was able to provide the required backup power for the connected load.Conclusion:The UPS battery system is in good condition and is capable of providing the required backup power for the connected load.Recommendations:No recommendations at this time.中文回答:UPS蓄电池检测报告。
LIR1254-222mWh检测报告

Standard 标准
Under the temperature of 55±2℃, the discharging time of battery at current of 1C5A shall not be shorter than 51 minutes; the appearance of battery shall be free of deformation and explosive disruption. 在 55±2℃温度下,电池 1C5A 放电时间应不少于 51 分钟;电池不变形、不爆炸。
深圳市利汛葆实业有限公司
SHENZHEN LSB INDUSTRY CO., LTD.
High Temperature Performance Testing Report
高温性能测试报告
Battery Type/电池型号: Testing Number/测试数量: LIR1254-222 4pcs Nominal Capacity/标称容量: Testing Date/测试日期 : 60mAh 2018-01-05
Appearance 外观
5.44 5.42 5.45 5.42
369 374 377 373
4.201 4.203 4.201 4.203
5.45 5.44 5.45 5.43
374 373 380 375
54.4 55.1 54.7 53.9
No blasting, no fire 不爆炸、不起火
Result 结果 No. 序号 1 2 3 4 Conclusion 结论
Before testing 测试前
Thickness 厚度(mm) Internal resistance 内阻(mΩ) Voltage 电压(V) Thickness 厚度(mm)
UPS蓄电池检测报告

UPS蓄电池检测报告英文回答:Having your UPS battery system tested regularly is crucial to ensure that it is functioning properly and will provide the required backup power in the event of a power outage. Here are some key points to consider:Benefits: Regular battery testing can help identify potential problems early on, prevent unexpected failures, and extend the lifespan of your UPS battery system.Frequency: The recommended frequency for UPS battery testing varies depending on the manufacturer and thespecific battery type. However, most experts recommend testing your batteries every two to three years.Types of Tests: There are several different types of UPS battery tests, including load testing, capacity testing, and impedance testing. Each test provides differentinsights into the health of your batteries.Documentation: It is important to keep a record ofyour UPS battery test results. This documentation can help you track the performance of your batteries over time and make informed decisions about maintenance and replacement.Example:Let's say you have a UPS system that is used to power your critical IT equipment. You decide to have yourbatteries tested as part of your regular maintenance routine. The test results show that one of the batterieshas a lower capacity than the others. This indicates thatthe battery may be nearing the end of its lifespan and should be replaced soon. By catching this issue early, you can prevent an unexpected power outage and ensure that your critical equipment remains protected.中文回答:定期对UPS蓄电池进行检测非常重要,这可以确保它正常运行,并在停电时提供所需的备用电源。
电池检测报告,英文

Battery Detection ReportTest Parameters:The following parameters were evaluated during the battery detection process:1. Voltage: The voltage of each battery was measured to determine its charge status.2. Capacity: The capacity of each battery was tested to assess its energy storage capability.3. Internal Resistance: The internal resistance of each battery was measured to evaluate its electrical efficiency.4.漏电电流: The leakage current of each battery was measured to ensure safety.5. Temperature: The temperature of each battery was monitored during the testing process.Results and Analysis:1. Voltage Testing:All tested batteries met the specified voltage requirements.A slight deviation in voltage was observed in some batteries, which is within the acceptable range.2. Capacity Testing:Most batteries performed well in terms of capacity, with results close to their rated values.A few batteries showed a decrease in capacity, indicating potential performance issues.3. Internal Resistance Testing:The internal resistance of the tested batteries was found to be within the normal range.Higher internal resistance values were detected in some batteries, which may affect their performance in highdrain applications.4. Leakage Current Testing:Leakage current levels were well below the safety threshold for all tested batteries.No significant concerns were identified regarding leakage current.5. Temperature Testing:Temperature variations during the testing process were minimal, indicating stable battery performance.No abnormal temperature increases were observed.Conclusion:moving forward, we suggest the following actions to enhance battery performance and safety:1. Routine Inspection: Implement a regular inspection schedule for all batteries to catch any early signs of degradation or malfunction.2. Battery Management Systems: Utilize advanced battery management systems (BMS) to monitor battery performance in realtime, providing alerts for maintenance or replacement when needed.4. Charging Practices: Educate users on proper charging techniques to avoid overcharging, which can lead to reduced battery life and increased safety risks.5. Quality Assurance: Strengthen quality control measures during the manufacturing process to minimize the occurrence of defects in batteries.6. User Training: Provide training for users on how to handle and maintain batteries safely to prevent accidents and extend the life of the batteries.7. Record Keeping: Maintain detailed records of battery testing, maintenance, and replacement to track the performance history and lifecycle of each battery.8. Emergency Preparedness: Develop and implement emergency response plans for incidents involving battery failure or malfunction.Future Testing:1. Cycle Life Testing: Conduct longterm cycle life tests to evaluate how batteries perform over multiple charge and discharge cycles.2. Abuse Testing: Perform tests to simulate extreme conditions such as overcharging, overdischarging, and mechanical abuse to assess battery safety under adverse scenarios.3. Environmental Impact Assessment: Evaluate the environmental impact of battery disposal and explore opportunities for recycling and responsible battery disposal methods.4. Advanced Materials Research: Invest in research for new battery materials that can improve energy density, reduce costs, and enhance overall battery performance.Conclusion:Documentation and Reporting Enhancements:2. Data Visualization: Incorporate charts and graphs into the report to visually represent the test results. This will make it easier for stakeholders to quickly understand the performance metrics and identify trends.3. Risk Assessment: Include a risk assessment section in the report that evaluates the potential risks associated with the batteries under test and provides a clear indication of any urgent actions required.6. Continuous Improvement: Implement a feedback loop within the reporting process to continuously improve thetesting procedures based on the latest findings and industry advancements.7. Training Materials: Develop training materials for technicians and engineers involved in the battery testing process to ensure consistency and accuracy in the execution of tests.8.档案管理: Implement a robust document management system to store and organize all battery detection reports for easy retrieval and future reference.Conclusion:The battery detection report serves as a critical toolfor maintaining the integrity and performance of batteries across various applications. By enhancing the documentation and reporting process, we can provide clearer insights into battery health, improve decisionmaking, and ultimately, enhance user satisfaction and safety. It is through these ongoing efforts that we can continue to advance the field of battery technology and its safe deployment in our everyday lives.。
电池常用英文单词

电池常用英文单词电池常用英文单词Specification 规格书Dimension Drawing, Configuration Drawing 尺寸图,结构图Approval Sheet 承认书Data Sheet 电池参数表,也叫规格书。
Bill of Materials (BOM) 原材料清单Nominal Voltage 标称电压Nominal Capacity 标称容量Minimum/Minimal Capacity 最低容量Standard Charge 标准充电Rapid/ Fast Charge 快速充电Maximum Charge Voltage 最大充电电压CC/CV: Constant Current/Constant Charge 恒流/恒压充电Maximum Continuous Discharge Current最大连续放电电流Final Charge Current, Cut-off Current充电截止电流Final Discharge Voltage Cut-off Voltage放电截止电压Initial Internal Resistance / internal impedance 内阻Service Life, Circle Life 循环寿命Charge/ Discharge/Circle Life Curve 充电/放电/循环寿命曲线Lithium ion Battery锂离子电池Lithium Metal Battery 锂金属电池Lithium Ion Cylindrical Battery 锂离子圆柱电池Lithium Ion Prismatic Battery 锂离子方形电池Lithium Ion Polymer Battery 锂离子聚合物电池Lithium Phosphate Battery 磷酸铁锂电池Chemistry System 化学体系LiCoO2钴酸锂LiCoMnNiO2 锂钴锰镍,即三元锂电池Ambient Temperature 环境温度Charge Temperature Range 充电温度范围Discharge Temperature Range 放电温度范围Open Circuit Voltage 开路电压Capacity Retention 容量保持Self-Discharge 自放电Safety Test 安全测试Over Charge 过充电Over Discharge 过放电Short Circuit 短路Heating Test 热冲击测试Impact Test 冲击测试Environmental Test 环境测试Drop Test 自由跌落测试Vibration Test 振动测试Test Report 测试报告Constant Humidity and Temperature Test 恒温恒湿测试Protection Circuit Module (PCM) or Battery Manager Systems (BMS) 保护电路或者电池管理系统integrated circuit (IC) 集成电流Mosfet场效应管Over Charge Protection Voltage过充电保护电压Over Charge Protection Delay 过充电保护延迟Over Charge release Voltage 过充电恢复电压Over Discharge Protection Voltage 过放电保护电压Over Discharge Protection Delay 过放电保护延迟Over Discharge Release Voltage 过放电恢复电压Over Current Protection 过电流保护Over Current Protection Delay过电流保护延迟Short Circuit protection 短路保护Consumption 自耗电State Of Charge Indication (SOC Indication) 剩余容量显示Balance Charge 平衡充电Temperature Detection 温度检测Communication Bus or SMbus 通讯总线Thermistor or Negative Temperature Coefficient (NTC) 热敏电阻Thermostat 温度开关Polymer Positive T emperature Coefficient (PPTC) 过流保护器Circuit Diagram电路原理图Component List 元器件清单Charging Characteristics 充电特性Discharge CharacteristicsWeight: 重量 Gross Weight (G. WT)毛重,Net Weight (N. WT) 净重Dimension 尺寸Model No., Size 型号Part NumberPurchase Order (PO)采购订单Manufacture Order (MO) 生产订单L/C (LETTER OF CREDIT)信用证T/T (TELEGRAFIC TRANSFER) 电汇D/P (DOCUMENT AGAINST PAYMENT) 远期付款交单D/A (DOCUMENT AGAINST ACCEPTION) 承兑交单30% In Advance,30% deposit预付30%订金70% of the balance due 70%的余款10% Discount 10%折扣FOB (free on board) 离岸价(不含运费的价格)CIF (cost, insurance and freight) 到岸价(含运费和保险费)C&F (cost and freight) 成本加运费价(含运费不含保险费)Certification 认证Warranty 保质期External Appearance 外观Handling Instructions 操作指示Cautions 注意事项Samples 样品Fatal Defects 致命缺陷Major defect 严重缺陷Minor defect 次要缺陷Random Inspection 抽样检查Inspection Report 检验报告Final Quality Control (FQC), Outgoing Quality Control (OQC) 出货检验Input Process Quality Control (IPOC) 品质巡检Incoming Quality Control (IQC) 来料检查Sample inspectionFully inspection, Total InspectionACCEPTANCE QUALITY LIMIT (AQL) 允收水准Minimum Order Quantity (MOQ) 最低订单量Expected Time of Arrival 预计到港时间estimated time of departure 估计离港时间Lead time 交货周期。
BatteryTest

BatteryTestcopyright © 2000, Ben EzzellBatteryTest is a simple utility created to monitor your laptop computer’s battery usage. The BatteryTest.exe program – together with BatteryTest.pdf – is provided as freeware and may be distributed so long as this distribution is made without charge except for nominal fees when distributed in a media format. Any distribution of BatteryTest must include this document. If necessary, the complete BatteryTest program and documentation can be downloaded in .zip format from /.BatteryTest FeaturesThe BatteryTest program is most useful with modern laptops which incorporate ‘smart’ batteries – i.e., batteries which are capable of fully reporting their state of charge. Depending on the type of battery in your laptop, the features provided may vary and, on older models, may be limited solely to displaying a percentage of charge and/or discharge. In such cases, the display may be limited to the Battery Status report (left) while the Battery Life display may be limited only to the percentage bar.Modern laptop batteries – depending on the model – may also report an estimated remaining time (see “Remaining:” above) and, in some cases, may report a total battery life (see “Time total:” above). Because this last feature is less than common, however, a provision has been included here – when the battery proper does not report a total capacity – to estimate the battery life for a fully charged battery and to report this figure. When a laptop is initially disconnected from the charger (AC power is removed), the time remaining reported by a smart battery may be rather fantastically erroneous (initial values may range to hundreds of hours). After five minutes or so of battery operation, however, the reported values will normally stabilize and will report relatively authentic expectations.Note: actual battery life depends on usage demands and extensive hard drive access or CD/DVD-ROM usage can decrease the overall battery life. Because of this, the value shown for time remaining may fluctuate during periods of high demand.Because of these initial grossly invalid reports of capacity, when a smart battery is not able to report a time total, the time remaining at 95% charge is used to estimate the 100% capacity level and this value is recorded in your system registry. If, for any reason, this value appears to be reported incorrectly, the value used is recorded in the key[HKEY_LOCAL_MACHINE\SOFTWARE\Battery Watch] using the “Full Battery Time” value. This key can be deleted or the value can be reset to 0 if necessary. If this is done, the battery life for a fully charged battery will be recreated at a later time after the battery has been fully charged and after it discharges to the 95% level.New Features (Version 1.0.5)BatteryTest version 1.0.5 adds a new feature which displays an estimated time required for recharge when the laptop is connected to AC power (or other charging source). This feature is not provided by the battery (even the ‘smart’ batteries) but is estimated by the BatteryTest program based on the charge percentage (level) and the elapsed interval between reported changes in the charge level.Because batteries do not accept recharge in a linear fashion, the reported times are estimates only. For example, if a battery is fully discharged, the total charge time estimated may be relatively fast simply because the time to charge the battery from 10% to 20% is much less than the time required to change from 90% to 100% of capacity. This non-linear effect may be particular noticeable when the battery reaches the 97% to 100% range.BatteryTest uses an entry in the [HKEY_LOCAL_MACHINE\SOFTWARE\Battery Watch] key as “Battery Charge Interval” to average reported intervals using a weighting formula. Thus, while the charge time estimates are a highly empirical process; overall, you should find that BatteryTest does provide a reasonable guide to the time needed to recharge your laptop battery.You should also be aware that – in most cases – your laptop battery will recharge faster when the laptop is not in use.Version 1.0.6Repaired minor bug in time-to-charge reporting algorithm.Version 1.0.8Improved time-to-charge reporting algorithms, other minor performance issues. Known BugsWhen the ‘smart battery’ does not support reporting a total battery life, if the laptop uses a ‘speedstep’ CPU and is in standby when BatteryTest records the total battery life, the recorded value (Total Life) will reflect standby battery lifetime rather than the battery’s working lifetime. I.e., for a battery with a nominal charge life of 3 hours, 45 minutes during normal operations, the standby lifetime might appear as 20 to 30 hours (or higher). This aberration should correct itself during subsequent operations but the incorrect value can be manually cleared by resetting the “Full Battery Time” value in the[HKEY_LOCAL_MACHINE\SOFTWARE\Battery Watch] key.– Ben Ezzell –。
BAT 135 Battery Tester 操作说明书

EN2Contents1 Introduction 32 Safety Warnings and Instructions 33 Paper Loading 44 Test Preparation 45 Battery Testing 56 Start/Stop Test 67 System Test 78 Glossary 109 Warranty Terms and Conditions 11Appendix A - System Analyzer Screens 12 Appendix B - Surface Charge Notice 13 Appendix C - Decoding Test Codes 15BAT 135 | REV. C | APRIL 201931 Introduct i onThe BAT 135 Battery Tester is used to test 6 and 12 volt batteries, and to test 12 and 24 volt charging systems. The suggested operation range is from 0 degrees Centigrade (32 degrees Fahrenheit) to 50 degrees Centigrade (122 degrees Fahren-heit) in ambient temperature.2Safety Warnings and Instructions WARNINGThis product can expose you to chemicals including arsenic, which is known to the State of California to cause cancer. For more information,go to .CAUTIONDo not expose the tester to rain or snow.} Working in the vicinity of a lead acid battery is dangerous. Batteries generate explosive gases during normal operation. For this reason it is important that you refer back to these instructions if you have any questions on tool operation.} To reduce risk of battery explosion, follow these instructions, those published by the battery manufacturer, and the manufacturer of any equipment you intend to use in the vicinity of the battery. Observe cautionary markings on theseitems.} Another person should be within range of your voice or close enough to come to your aid when you work near a lead acid battery.} Have plenty of fresh water and soap nearby in case battery acid contacts skin, clothing, or eyes.} Wear safety glasses and protective clothing.} If battery acid contacts your skin or clothing, wash immediately with soap and water. If acid enters your eye, immediately flood the eye with running cold water for at least ten minutes and seek immediate medical attention.} NEVER smoke or allow a spark or flame in vicinity of the battery or engine.} Be extra cautious to reduce the risk of dropping a metal tool onto the battery. It could spark or short-circuit the battery or other electrical parts and could cause an explosion.} Remove personal metal items such as rings, bracelets, necklaces, and watches when working with a lead acid battery. These items can produce a short-circuit current high enough to weld a ring or like to metal causing a severe burns.BAT 135 | REV. C | APRIL 2019BAT 135 | REV. C | APRIL 201943 Paper Loading/ReplacementDo the following to load paper:1. Connect BAT 135 to battery. (See Pg. 5 for connection instructions.)2. Open the clear cover. Insert a new paper roll into the clear portion of thecover with the leading edge coming out from under the paper roll. Insert the end of the paper into the auto-feed slot of the printer. The paper should automatically load. (See Fig. 1)3. Slowly pull approximately 1 in. of paper straight up from the top of thetester. Feed the 1 in. strip of paper through the serrated slot in the clear cover as it is being closed. (See Fig. 2)Note: The battery clamp replacement part number is PN 1699501731. Replace-ment thermal paper rolls are available at most office supply retailers. The paper is 2 1/4 in. wide, with a maximum roll length of 98 ft.4 Test Preparation1. Ensure that the area around the battery is well ventilated while the batteryis being tested.2. Clean battery terminals. Be careful to keep corrosion from coming incontact with your eyes.3. Inspect the battery for cracked or broken case or cover. If the battery isdamaged, do not use the tester.4. If the battery is not a sealed maintenance free type, add distilled water ineach cell until the battery acid reaches the level specified by themanufacturer. This helps purge excessive gas from cells. Do not overfill.5. If necessary to remove battery from vehicle to test, always remove theground terminal from the battery first. Make sure all accessories in thevehicle are off to prevent arcing.(Figure 1)(Figure 2)5Battery TestingCAUTIONBefore you test a battery in a vehicle, turn off the ignition and allaccessories and loads. Close all vehicle doors and the trunk lid.Note: Each time you connect the tester to a battery, the tester will run a quick cable verification to ensure a proper connection through the output cables to sensors in the clamp jaws. If the connection checks out OK, the display will momentarily flash and proceed to the Home Screen. In operation the tester will only show three results: CHECK CLAMPS / VOL TAGE HIGH / VOL TAGELOW.1. Make sure you have put 6 AA alkaline 1.5V batteries into the battery chamber.Li-Ion or lithium batteries are not recommended because of the initial 1.7 Volt output. When the batteries are weak, the screen will display “POWER LOW.”Replace all 6 batteries at one time.Note: Nothing will be seen on the display until the tester is connected to a vehicle battery.2. Make sure the battery terminals are clean. Wire brush them if necessary.Clamp the black load lead to the vehicle negative battery terminal. Clamp the red load lead to the vehicle positive battery terminal.3. View the System Analyzer Screens diagram (Appendix A) for selection options.4. Press to select Battery Test, then press ENTER.5. Press to select one of the following battery types:}FLOODED}AGM FLAT}AGM SPIRAL}VRLA/GELPress ENTER to confirm choice.6. Press to select one of the following battery ratings.}CCA/SAE}EN}JIS}DIN}IEC}CA/MCAPress ENTER to confirm choice.BATTERY TYPE t uAGM FLAT PLATEExampleSELECT RATING t uCCA/SAEExampleBAT 135 | REV. C | APRIL 2019BAT 135 | REV. C | APRIL 201967. Press to select the battery capacity of SAE from one of the following:}CCA/SAE: 40~2000 }EN: 40~1885 }DIN: 25~1120 }IEC: 30~1320}JIS: By battery type number}CA/MCA: 50~2400Press ENTER to begin the test.8. Press to confirm the temperature.Press ENTER to begin the test.Note: Before the test is started, you can always return to the previous page by pressing and holding ENTER for two seconds.Important: If prompted by the tester to remove a surface charge, refer to Appendix B, Surface Charge Notice .6 Start/Stop Test1. Press to select Start/Stop Test, then press ENTER .2. Press to select one of the following the battery types:}EFB}AGM FLATPress ENTER to confirm choice.3. Press to select one of the following battery ratings:}CCA/SAE }EN }JIS }DIN }IEC}CA/MCAPress ENTER to confirm choice.SET CAPACITY t u xxxx CCA/SAEExampleAbove 32°F/0°C t u Yes / NoExampleBATTERY TYPE t u EFBExampleSELECT RATING t u CCA/SAEExampleBAT 135 | REV. C | APRIL 201974. Press to input one of the following battery capacities of SAE:}CCA/SAE: 40~2000 }EN: 40~1885 }DIN: 25~1120 }IEC: 30~1320}JIS: By battery type number}CA/MCA: 50~2400Press ENTER to begin test.5. Press to confirm temperature.Press ENTER to begin test.Note: Before the test is started, you can always return to the previous page by pressing and holding ENTER for two seconds.Important: If prompted by the tester to remove a surface charge, refer to Appendix B, Surface Charge Notice .7 System Test1. Press ENTER to view the System Test screen.2. Turn off all vehicle accessory loads such as lights, air conditioning, radio, etc.before starting the engine.SET CAPACITY t u xxxx CCA/SAEExampleAbove 32°F/0°C t u Yes / NoExampleSYSTEM TEST x x.x x VExampleTURN OFF LOADS START ENGINEExampleBAT 135 | REV. C | APRIL 201983. When the engine is started, one of three results will be displayed, along withthe reading taken:}Cranking Volts PassThe system is showing normal draw. Press ENTER to start the charging system test.}Cranking Volts FailThe cranking voltage is below normal limits. Troubleshoot the starter with the manufacturer’s recommended procedure.}Cranking Volts Not DetectedThe cranking voltage is not detected.4. If the cranking voltage is normal, press ENTER to begin the charging systemtest.5. Press ENTER . The following screen appears.6. Press ENTER . One of the following two results for the Charging Volts Test atIdle will be displayed.}PASS }FAIL7. Monitoring the charging system at idle, press ENTER for the charging systemwith accessory loads. Turn on the blower to High (heat), High Beam headlights, and Rear Defogger. Do not use cyclical loads such as airCRANKING VOLTS x x.x x V PASSExampleCRANKING VOLTS x x.x x V FAILExampleCRANKING VOLTS NOT DETECTEDExampleMAKE SURE ALL LOADS ARE OFFExample9conditioning or windshield wipers.8. When testing older model diesel engines, run up the engine to 2500 rpm for15 seconds. You will view the following screen:9. Press ENTER to determine the amount of ripple from the charging system tothe battery. One of two testing results will be displayed, along with thereading taken.}Ripple DetectedDiodes function well in the alternator / stator.}No Ripple DetectedOne or more diodes in the alternator are not functioning or there is statordamage. Ensure that the alternator mounting is sturdy and that the beltsare in good shape and functioning properly. If the mounting and belts aregood, replace the alternator.10. Press ENTER to continue testing the charging system with accessory loads.One of two results will be displayed.}PASS}FAIL11. Press ENTER when the charging system test is completed. Turn all accessoryloads and engine off. Press ENTER to return to Step 1 or remove the testclamps from the battery posts after completion of testing to end test.TURN ON LOADSAND PRESS ENTERExampleRUN ENGINE UP TO2500 RPM 15 SEC.ExampleRIPPLE DETECTEDx x.x x V NORMALExampleNO RIPPLE DETECTEDExampleTEST OVER. TURNOFF LOADS & ENGINEExampleBAT 135 | REV. C | APRIL 2019108 GlossaryGelled Electrolyte (GEL) BatteryA lead-acid electric storage battery that:}Is sealed using special pressure valves and should never be opened.}Is completely maintenance-free. (However, connections must be retorqued and the battery cleaned periodically.)}Uses thixotropic gelled electrolyte.}Uses a recombination reaction to prevent the escape of hydrogen and oxygen gases normally lost in a flooded lead-acid battery (particularly in deep-cycle applications).}Is non-spillable, and therefore can be operated in virtually any position.(However, upside-down installation is not recommended.)Absorbent Glass Mat (AGM) BatteryA lead-acid electric storage battery that:}Is sealed using special pressure valves and should never be opened.}Is completely maintenance-free. (However, connections must be retorqued and the battery cleaned periodically.)}Has all of its electrolyte absorbed in separators consisting of a sponge-like mass of matted glass fibers.}Uses a recombination reaction to prevent the escape of hydrogen and oxygen gases normally lost in a flooded lead-acid battery (particularly in deep-cycle applications).}Is non-spillable, and therefore can be operated in virtually any position.(However, upside-down installation is not recommended.)Valve Regulated Lead Acid (VRLA) BatteryA battery that is sealed Maintenance Free with a “Bunce” Valve or Valves in the top that opens when a preset pressure is realized inside the battery and lets the excess gas pressure out. Then the valve resets itself.Starting, Lighting, Ignition (SLI) BatteryA battery that performs three basic functions on all normal vehicles. Batteries given this description will have been specifically designed for service on cars and trucks within a voltage controlled electrical system. Those SLI batteries which are intended for heavy haulage vehicles fitted with large diesel motors may often be called COMMERCIAL batteries. They have to be much more powerful and more robust than batteries intended for cars.State of Health (SOH)Percent of battery capacity remaining compared with the marked original battery capacity.BAT 135 | REV. C | APRIL 201911 State of Charge (SOC)Percent of battery actually charged.Cold Cranking Amps (CCA)The current in amperes which a new fully charged battery can deliver for 30 se-conds continuously without the terminal voltage falling below 1.2 volts per cell, after it has been cooled to 0 degrees F and held at that temperature. This rating reflects the ability of the battery to deliver engine starting currents under winter conditions.Ampere-HourThe unit of measurement of electrical capacity. A current of one ampere for one hour implies the delivery or receipt of one ampere-hour of electricity. Current multiplied by time in hours equals ampere-hours.9 Warranty Terms and ConditionsAny battery tester found defective in material or workmanship within one year from the date of purchase by a retail customer will be repaired or replaced accord-ing to published defective return test repair procedures. The existence of a defect shall be determined by the manufacturer in accordance with published warranty repair procedures. The warranty repair procedures are available upon request. This warranty does not cover any unit that has been damaged due to accident, abuse, alternation, use for a purpose other than that for which it was intended, or failure to follow operating instructions. This warranty is expressly limited to origi-nal retail buyers. This warranty is not assignable or transferable. Proof of purchase is required for all alleged claims. Warranty cannot be authorized without proof of purchase. Warranty claims must be sent pre-paid with dated proof of purchase. Damage incurred during shipment is the responsibility of the shipper (customer returning unit) If the returned unit qualifies for warranty, the shipper will only incur shipping cost. The manufacturer reserves the right to substitute or offer alternative warranty options at its discretion.The sole and exclusive remedy for any unit found to be defective is repair or replacement, at the option of the manufacturer. In no event shall the manufacturer be liable for any direct, indirect, special, incidental, or consequential damages (including lost profit) whether based on warranty, contract, tort, or any other legal theory.Return GoodsPack with sufficient over-pack to prevent damage during shipment. DamageBAT 135 | REV. C | APRIL 2019BAT 135 | REV. C | APRIL 201912incurred during return shipment is not covered under this warranty. Repair costs for such damages will be charged back to shipper.WHEN RETURNING GOODS, INDICATE “RETURN GOODS” ON ALL INVOICES AND RELATED SHIPPING DOCUMENTS TO PREVENT ANY EXTRA CHARGE.Appendix A System Analyzer ScreensThe following screens are available for system analysis, testing, and customization.Note: Current language is displayed initially.SYSTEM ANALYZER BATTERY TEST t u xx.xx V SYSTEM TEST t u xx.xx V LANGUAGE t u SELECT LANGUAGE t uENGLISHDATE & TIME2006/11/25 t u(Time Setting)TEST COUNTERBATTERY /SYSTEM / STARTSTOP TESTDISPLAY START STOP TEST t u xx.xx V *Press t /u to select language, start-stop test or system test. *Press «ENTER» to do battery test.*Press «ENTER»to do a system test. *Press t /u to select battery test, system test or start-stop test.*Press «ENTER» to do a start-stop test. *Press t /u to select system test, start-stop test or language.*Press «ENTER»to set language.*Press t /u to select language. (English, French, Spanish, Portuguese)*Press «ENTER» to confirm choice & go back to battery test.*Press «ENTER» to see how many times you tested in battery/system/start stop test.*Press «ENTER» to confirm Time Setting.(continued on next page)BAT 135 | REV. C | APRIL 201913Appendix B Surface Charge Notice The tester will resume testing after it detects that the surface charge is removed.1. Test the battery for a few seconds. TESTING2. Press to select battery fully charged or not if tester asks, then press ENTER to confirm choice.IS BATTERY t u CHARGED? YES The battery will hold a surface charge if the engine has been running or after the battery has been charged. The tester may prompt you to remove the surface charge. Follow the instructions indicating when to turn the headlights on and off or apply a load into the battery.In VehicleOut of VehicleBRIGHTNESSt ADJUST u CUSTOMIZE*Press t /u to adjust “Year.” *Press «ENTER» to finish “Year.” Repeat previous step to finish “Month,” “Day,” “Hour” and “Minute.”*Press «ENTER» to confirm the bright-ness setting.*Press t /u to adjust the brightness of the display.*Press «ENTER» to edit customized info.BAT 135 | REV. C | APRIL 2019143. When the test is completed, the display shows the actual volts and the actual SAE or %. Press to select:}SOH (STATE OF HEAL TH) or }SOC (STATE OF CHARGE)One of 6 results will be displayed.Good & Pass The battery is good and capable of holding a charge.GOOD & PASS xx.xxV xxxx CCA/SAE xx.xx mΩMarginal Battery A Marginal battery indicates that your battery is functioning properly, but its life expectancy is compromised. The battery should be closely monitored with more frequent battery checkups.Recharge & Retest The battery is discharged, the battery condition cannot be determined until it is fully charged. Recharge and retest the battery.Bad & Replace The battery will not hold a charge. It should be replaced immediately.Bad Cell & Replace The battery has at least one cell short circuit. It should be replaced immediately.Load Error The tested battery is bigger than 2000SAE or 200AH. Or the clamps are not connected properly. Fully charge the battery and retest after excluding both previous reasons. If reading is the same, the battery should be replaced immediately.MARGINAL BATTERY xx.xxV xxxx CCA/SAE xx.xx mΩBAD & REPLACE xx.xxV xxxx CCA/SAE xx.xx mΩBAD CELL & REPLACE xx.xxV xxxx CCA/SAE xx.xx mΩLOAD ERRORRECHARGE & RETEST xx.xxV xxxx CCA/SAE xx.xx mΩBAT 135 | REV. C | APRIL 2019154. Press ENTER to get a test code for record.Note: A BARCODE will appear after printing. Pay attention to the BARCODE Scanner, which only supports CODE39 format. See Appendix C, Generating Test Codes .5. Press to select result printing: YES or NO. Press ENTER to confirm your choice.6. Press ENTER to return to Step 5, or remove the test clamps from the battery posts after completion of testing batteries to end test.CODE xxxxxxxxxxxDo the following to decode test codes:1. Download the decoding software via: https:///pro/products/bat1352. Click the icon labeled “BT/RTxxx” and the sheet below will appear.3. Input the test code into the chart manually or by barcode scanner.4. Test results will appear in the chart after decoding, as shown above.Appendix CDecoding Test CodesBoschAutomotive Service Solutions, Inc.655 Eisenhower Drive Owatonna, MN 55060 USA Phone: (800) 533-6127PN 1699200248。
UPS蓄电池检测报告

UPS蓄电池检测报告英文回答:UPS Battery Inspection Report。
Introduction:Uninterruptible Power Supplies (UPS) are critical components of any data center or other mission-critical environment. They provide backup power in the event of a power outage, ensuring that critical systems continue to operate without interruption. As such, it is important to regularly inspect and maintain UPS batteries to ensure they are in good working condition and can provide the necessary backup power when needed.Inspection Procedure:UPS battery inspections should be performed byqualified personnel and should include the following steps:Visual inspection of the batteries and battery terminals for any signs of damage, corrosion, or leakage.Measurement of the battery voltage and current to ensure they are within the manufacturer's specifications.Load testing of the batteries to simulate a power outage and verify that they can provide the necessary backup power.Inspection of the battery connections to ensure they are secure and free of corrosion.Cleaning of the battery terminals and connectors to remove any corrosion or debris.Inspection Findings:The following are some common findings from UPS battery inspections:Loose connections: Loose connections can lead to high resistance and poor battery performance.Corrosion: Corrosion can damage battery terminals and connectors, leading to poor electrical contact.Leaking batteries: Leaking batteries can release harmful chemicals and damage other components in the UPS.Low voltage: Low battery voltage can indicate a problem with the battery or the charger.High impedance: High impedance can indicate a problem with the battery or the connections.Corrective Actions:If any problems are identified during a UPS battery inspection, corrective actions should be taken immediately. These actions may include:Tightening loose connections。
UN38.3报告样本
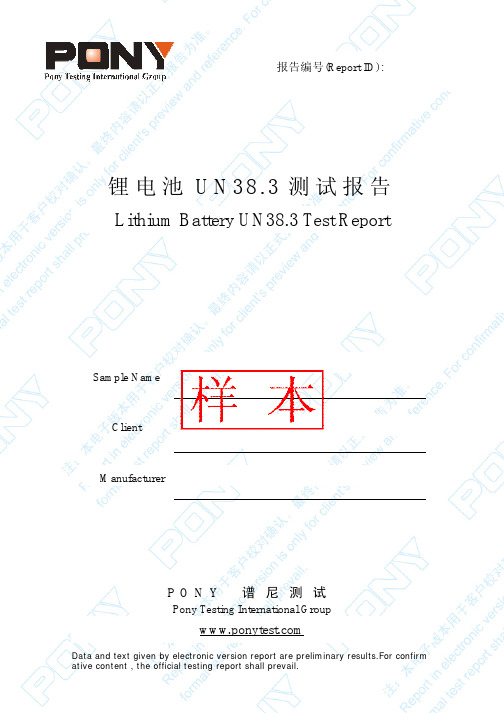
Batteries of N1~N8 are full charged after one cycle; Batteries of C1~C8 are full charged after fifty cycles;
V、 PHOTO OF THE SAMPLE
Authenticate the photo on original report only
at least 12 hours.
3. Vibration Cells and batteries are firmly secured to the platform of the vibration machine without distorting the cells in such a manner as to faithfully transmit the vibration. The vibration shall be a sinusoidal waveform with a logarithmic sweep between 7 Hz and 200 Hz and back to 7 Hz traversed in 15minutes. This cycle shall be repeated 12 times for a total of 3 hours for each of three mutually perpendicular mounting positions of the cell. One of the directions of vibration must be perpendicular to the terminal face. The logarithmic frequency sweep is as follows: from 7 Hz a peak acceleration of 1 g is maintained until 18 Hz is reached. The amplitude is then maintained at 0.8 mm (1.6 mm total excursion) and the frequency increased until a peak acceleration of 8 g occurs (approximately 50 Hz). A peak acceleration of 8 g is then maintained until the frequency is increased to 200 Hz.
中英文电池充电器测试报告

提交日期型号电池零件号充电器零件号Charger Part#序列号电池类型充电器类型检测组件Component Being电池电流充电器电流Charger Amps充电器样式描述Description检测员热电偶位置Thermal Couple Location 室温Ambient Temperature检测站Station 提供手册?Manual Provided?阅览手册?Manual Reviewed?报告日期Report Date第三方实验室测试? Tested by a 3rd party lab?IEC60335-29 或 IEC60601-1 报告引用电池组Reference Batteries Set 如果是,请说明依照标准If so, to what standard?附件Attachment保护装置Protection Device漏电流不得超过0.1毫安。
Leakage current should not exceed 0.1mA.认证类型Type of Certifications测试结果 TEST RESULTS最大电压Max Voltage充电周期 Charge Cycle浮动电压 Float Voltage充电周期Charge Cycle最大电流Max Current 充电周期Charge Cycle浮动电流Float Current 充电周期Charge Cycle最大外壳温度Max Case Temp 室温应小于:塑料35K+ ,金属25K+Should be less than:35K+ Ambient for plastic;25K+Amebient for metal充电周期Charge Cycle充电至80%容量80% Capacity Reached 评论显示结果检测技术员Test Technician 日期Date审阅人Reviewer 日期Date电池/充电器参考资料(容量,C/5等级,等等)REFERENCE BATTIERY/CHARGER INFORMATION (CAPACITY, C/5 RATING, etc.)样品编号NUMBER OF SAMPLES使用装置DEVICE TO BE USED IN电池是否标明生产厂家?IS THE BATTERY MARKED WITH THE MANUFACTURER?电池是否标明类型(AGM,胶体)?IS THE BATTERY MARKED WITH THE TYPE(AGM,GEL)?电池是否标明额定电压?IS THE BATTERY MARKED WITH THE NOMINAL VOLTAGE?电池是否标明额定容量(C20和C5)?IS THE BATTERY MARKED WITH THE RATED CAPACITIES (C20 AND C5)?电池是否标明生产日期?(IS THE BATTERY MARKED WITH THE DATE OF MANUFACTURE?)电池相邻端子是否标明极性?IS THE BATTERY MARKED WITH THE POLARITY MARKINGS ADJACENTTO EACH TERMINAL?参考文献(References)1.RESNA 71762.IEC 60335-13.IEC 60335-2-294.IEC 60601-15.IEC 529合格/不合格Pass/Fail分析清单PROFILING CHECKLIST如果充电器反极性连接,不应有大于100毫安的电流流动,也不会损坏充电器。
UPS蓄电池检测报告

UPS蓄电池检测报告英文回答:UPS Battery Testing Report。
As a seasoned UPS professional, I have extensive experience in conducting thorough battery testing and analysis. I'm proficient in utilizing advanced diagnostic tools and techniques to evaluate the health and performance of UPS batteries. My comprehensive testing reports provide valuable insights into the battery's current condition and its projected lifespan.Key Elements of a UPS Battery Test Report:Battery Specifications: This section details the make, model, and physical characteristics of the battery,including its voltage, capacity, and terminal configuration.Visual Inspection: I carefully examine the battery'sexterior for signs of physical damage, corrosion, or leaks. Any anomalies are documented and analyzed for potential implications.Load Testing: The battery is subjected to a controlled load test to assess its ability to deliver power under various load conditions. This test provides insights into the battery's capacity, internal resistance, and voltage stability.Discharge Testing: A discharge test simulates the battery's discharge under real-world conditions. The test duration and load profile are customized to replicate the specific application requirements. This data is crucial for determining the battery's runtime and overall reliability.Charge Testing: The battery's charge acceptance and efficiency are evaluated through a series of charge cycles. This test reveals any potential charging issues or limitations that could affect the battery's performance.Data Analysis and Interpretation: The collected datais meticulously analyzed to identify trends, patterns, and any deviations from expected norms. I correlate the results with industry benchmarks and the battery manufacturer's specifications to provide a comprehensive assessment of the battery's health.Recommendations: Based on the test findings, I formulate specific recommendations for battery maintenance, replacement, or further investigation. I clearly articulate the rationale behind my recommendations and provide guidance on the necessary actions to ensure optimal UPS performance.Example:Recently, I conducted a comprehensive battery test on a 3-year-old, 12-volt, 100Ah lead-acid battery used in a critical data center application. The visual inspection revealed minor corrosion on the terminals, which I cleaned thoroughly. The load test results indicated a slightly lower capacity than the rated value, suggesting some degradation. However, the discharge test demonstrated aruntime of 90 minutes at 75% load, which met the required specifications. The charge test revealed a higher-than-expected charging current, indicating a potential charging issue.Conclusion:My UPS battery testing reports provide a detailed and actionable assessment of the battery's health and performance. They empower decision-makers with the information they need to optimize UPS performance, ensure reliability, and minimize the risk of downtime. By leveraging my expertise and utilizing state-of-the-art testing equipment, I deliver comprehensive reports that are tailored to meet the specific requirements of each client.中文回答:UPS电池检测报告。
UPS蓄电池检测报告

UPS蓄电池检测报告英文回答:I recently had my UPS battery tested and I'm happy to share the results with you. The test was conducted by a qualified technician using state-of-the-art equipment.The first step in the testing process was to visually inspect the battery. The technician looked for any signs of damage or leakage. The battery was also tested for voltage and capacity. The voltage test measures the amount of electrical potential difference between the positive and negative terminals of the battery. The capacity test measures the amount of current that the battery can deliver over a period of time.The results of the test showed that my UPS battery isin good condition. The voltage and capacity tests were both within the acceptable range. The technician also found no signs of damage or leakage.I'm glad to know that my UPS battery is in good condition. This gives me peace of mind knowing that my UPS will be able to provide backup power in the event of a power outage.Here are some tips for maintaining your UPS battery:Keep the battery in a cool, dry place.Avoid exposing the battery to extreme temperatures.Charge the battery regularly, even if you're not using it.Replace the battery every 3-5 years.By following these tips, you can help extend the life of your UPS battery and ensure that it's always ready to provide backup power when you need it.中文回答:我最近对我的UPS电池进行了检测,我很乐意与你分享检测报告。
小技巧笔记本电池健康报告建立与解读
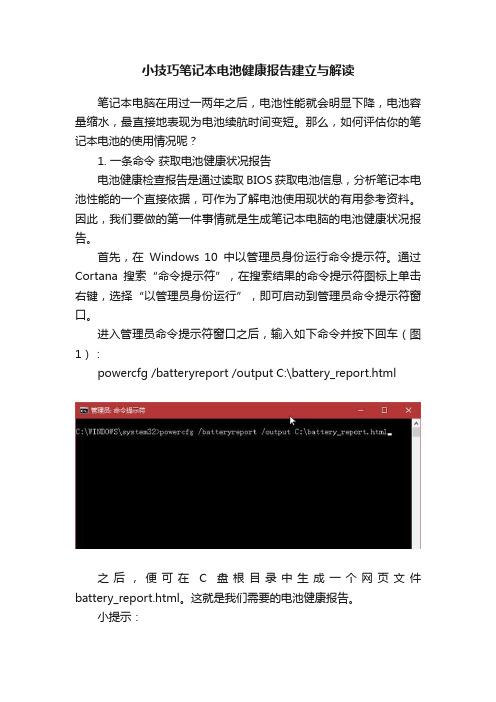
小技巧笔记本电池健康报告建立与解读笔记本电脑在用过一两年之后,电池性能就会明显下降,电池容量缩水,最直接地表现为电池续航时间变短。
那么,如何评估你的笔记本电池的使用情况呢?1. 一条命令获取电池健康状况报告电池健康检查报告是通过读取BIOS获取电池信息,分析笔记本电池性能的一个直接依据,可作为了解电池使用现状的有用参考资料。
因此,我们要做的第一件事情就是生成笔记本电脑的电池健康状况报告。
首先,在Windows 10中以管理员身份运行命令提示符。
通过Cortana搜索“命令提示符”,在搜索结果的命令提示符图标上单击右键,选择“以管理员身份运行”,即可启动到管理员命令提示符窗口。
进入管理员命令提示符窗口之后,输入如下命令并按下回车(图1):powercfg /batteryreport /output C:\battery_report.html之后,便可在C盘根目录中生成一个网页文件battery_report.html。
这就是我们需要的电池健康报告。
小提示:如果仅执行“powercfg /batteryreport”命令,则在当前目录下生成报告文件battery_report.html。
命令中最后一个字段“C:\battery_report.html”为报告输出的路径和文件名,用户可按需改变。
powercfg为电源配置命令,“/batteryreport”参数表示形成电池报告,“/output”参数后附路径和文件名表示以文件形式输出报告。
2. 有理有据解读电池健康报告参数电池健康情况的解读,是通过阅读电池健康报告文件battery_report.html来完成的。
双击该文件或将该文件拖动到任一款网页浏览器中,打开报告进行解读。
电池健康报告分为多个部分,分别解读每个部分,可获得相应部分的情况说明。
在报告的最上部分,在给出当前PC的名称、BIOS版本、系统版本等信息之后,接下来的已安装电池列表下,可以看到两个关键信息,电池设计能力(The Design Capacity)和最大充电能力(Full Charge Capacity)(图2)。
电池测试指南说明书

1A RECTIFIER Test by performing a continuity test.TERMINALCIRCUIT PROTECTOR INSPECTIONBENT TERMINALREGULATOR/RECTIFIER TESTINGInspect the rectifier by checking continuity following the inspection chart in the appropriate shop manual.Replace the rectifier if necessary and retest the system starting at step .Regulator/rectifiers have resistance tests in theappropriate shop manual. These tests are somewhat inconclusive because of the electronic regulationmechanism. If all other tests and inspections are made with no problems found, replace the regulator/rectifier with a known good one and retest the system starting at step .© American Honda Motor Co., Inc. Date of Issue: September 2011 (OTR53983-A)Charge Coil SpecificationsSystem Resistance () VAC output (3,600 rpm)1 Amp 58 ~ 623 Amp 0.20 ~ 0.9324 ~ 287 Amp 0.10 ~ 0.2028 ~ 3210 Amp 0.16 ~ 0.2424 ~ 2818 Amp 2 1626 ~ 3020 Amp 0.08 34 83.0~4.00.1~0.~ 0.12~ 3Lamp Coil SpecificationsSystemV (3,600 rpm)6V/15W 0.21 ~ 0.277 ~ 86V/25W 0.09 12V/15W 1.24 ~ 1.44 14 ~ 1612V/25W 12V/50W 0.1 Resistance ()AC Output ~ 0.157 ~ 80.36~0.4614 ~ 168 ~ 0.2314 ~ 16A 1-amp charging system is shown.Identify the system to be tested.CHARGING SYSTEM TROUBLESHOOTINGLamp coil system typically contains:LAMP COIL SYSTEM INSPECTION •Lamp coil (Honda)•Rectifier (OEM)•Load(s) (OEM)1.Perform only step to verify that the lamp coil is functioning properly.2.If OK, the problem is in the OEM’s system.Charging coil system typically contains:CHARGING SYSTEM INSPECTION•Battery (OEM)•Switch (Honda or OEM)•Fuse or circuit protection (Honda or OEM)•Charge coil (Honda)•Rectifier/regulator (Honda)•Load(s) (OEM)1.Isolate all loads from the battery before testing the charging system.2.Perform steps ~ .Charge coil – used to charge the battery to operate the starter motor and other DC mp coil – used to power loads without the need for a battery.Use the engine’s model and type information and the parts catalog to determine the engine’s charging system rated capacity.These readings were obtained using a Fluke® 88 DMM (Digital MultiMeter). Understand how to use your meter before conducting these tests.7A and 10AREGULATOR/RECTIFIERSInstall a known good regulator/rectifier and r .etest the system CHARGE COIL OR LAMP COIL INSPECTIONThe illustrations demonstrate charge coil inspection.Locate and disconnect the coil (charge coil or lamp coil) wire connector(s).Connect a DMM (set to measure AC volts) across the coil wires, or across the single coil wire and engine Start the engine and slowly raise the throttle to its normal maximum operating position while observing the voltage.The output voltage should start low at idle, then rise and level off at full throttle (see the table in the center column). If this is the case, the coil is functioning properly. Reconnect the wires and proceed to step .If the measured output voltage is low (or zero) and does not rise at full throttle, proceed to step “d.”Stop the engine. Use a DMM (set to measure ohms)and check the resistance of the coil (see the table in the center column).If the resistance is good but the output voltage is low, inspect the flywheel. If OK, replace the coil, reconnect the wires, and proceed to step .If the resistance is not normal and the output voltage is low or zero, replace the coil, reconnect the wires, and proceed to step .CHARGE COIL WIRESVCHARGE COIL WIRESMeasure to ground if only one coil lead.Measure to ground if only one coil lead.3A RECTIFIER Test by performing a continuity test.18A and 20AREGULATOR/RECTIFIERS Install a known good regulator/rectifierand retest the system.OUTPUT TESTa.Connect a DMM (set to measure DC volts) between the battery terminals as shown in step .b.Start the engine and run at the maximum throttle position while observing the DC voltage.c.With the engine still running, disconnect the DMM. Set the DMM to measureDC amps and connect the DMM to the battery as shown in step . Use a shunt if the system you are testing produces more current than your meter’s DC amps rating.d.Run the engine at its maximum throttle while observing the charging DC amperage output on your meter.e.Check that the battery voltage and charging current meet the following specifications:The battery voltage should rise above 13.0 VDC.Charging current should remain constant.The battery voltage should start low, then quickly rise and level off at approximately 14.5 VDC.Charging current should start high, and then begin to lower as the voltage approaches 14.5 VDC.–If the above results are obtained, the charging system is OK and the problem is the battery. Replace the battery and perform step again.–If the above results are not obtained, proceed to step .Units with a rectifier only:Units with a regulator/rectifier:•••••• Ω。
(XLS)锂电池产品测试报告

开路电压(V)充电 4.2/1A充电CC1A放电过流(A)短路保护内阻(m Ω)容量(mAh)3.82OK OK 6.5OK 58.144593.82OK OK 6OK 61.445183.82OKOK6.3OK61.44501日期/Datecell_3◆电池_3温度检测/Temperature Sensor 二级保护/2nd Protection0V 充电/0V Charge Function 测试报告/test report型号/Typecell_1cell_2内阻(m Ω)短路其它/Others3 电池使用及测试要求/Operation Conditions (If not specified, it will base on cell’s Spec.)过放保护电压/Under Voltage Protection 单cell : 2.50V+/-25mV过充保护电压/Over Voltage Protection 品牌/Vendor循环寿命要求/Cycle Life产品基本信息及设计要求6 其它/Others5 测试结果◆电池_2◆电池_1日期 Date2010/11/24200mAh2 电芯/Cell客户/Customer充电过流/Over Charge Current Protection NO1 ◆基本参数数量6.4A 项目名/Project Name2.如果客户对规格没有要求,请在表中填上"N/A"(Please fill in "N/A" if customer have not specified for this item);说明: 1. 标有"◆"号项的规格要求,营业或研发必须与客户确认(The item signed with "◆" need PM or RD to confirm with customer) ;最小容量/Min.Capacity4 测试内容@25℃NO NO放电过流/Over Discharge Current 单cell : 4.25V+/-25mV审批/Approved by 2010.11.2编制/Prepared by 日期/Date 70YES NOOK NG 其它/Others:OKNG其它/Others:OK NG 其它/Others:OKNG其它/Others:YesNoN/A。
电池测试手册(英文版)

INL/EXT-07-12536Rev. 1 Battery Test Manual for Plug-In Hybrid Electric VehiclesSeptember 2010The INL is a U.S. Department of Energy National Laboratoryoperated by Battelle Energy AllianceINL/EXT-07-12536Rev. 1 Battery Test Manual for Plug-In Hybrid ElectricVehiclesSeptember 2010Idaho National LaboratoryIdaho Falls, Idaho 83415Prepared for theU.S. Department of EnergyAssistant Secretary for Energy Efficiency and Renewable EnergyUnder DOE Idaho Operations OfficeContract DE-AC07-05ID14517INL/EXT-07-12536 U.S. Department of EnergyVehicle Technologies ProgramBattery Test ManualFor Plug-In Hybrid Electric VehiclesREVISION 1SEPTEMBER 2010The Idaho National Laboratory is a U.S. Department of Energy NationalLaboratoryOperated by Battelle Energy AllianceFOREWORDThis battery test procedure manual was prepared for the United States Department of Energy (DOE), Office of Energy Efficiency and Renewable Energy (EERE), Vehicle Technologies Program. It is based on technical targets established for energy storage development projects aimed at meeting system level DOE goals for Plug-in Hybrid Electric Vehicles (PHEV). The specific procedures defined in this manual support the performance and life characterization of advanced battery devices under development for PHEV’s. However, it does share some methods described in the previously published battery test manual for power-assist hybrid electric vehicles.Due to the complexity of some of the procedures and supporting analysis, future revisions including some modifications and clarifications of these procedures are expected. As in previous battery and capacitor test manuals, this version of the manual defines testing methods for full-size battery systems, along with provisions for scaling these tests for modules, cells or other subscale level devices.The DOE-United States Advanced Battery Consortium, Electrochemical Energy Storage Technical Team supported the development of the manual. Technical Team points of contact responsible for its development and revision are Harshad Tataria of General Motors Corporation and Jeffrey R. Belt of the Idaho National Laboratory.The development of this manual was funded by the Unites States Department of Energy, Office of Energy Efficiency and Renewable Energy, Vehicle Technologies Program. Technical direction from DOE was provided by David Howell, Energy Storage R&D Manager and Hybrid Electric Systems Team Leader. Comments and questions regarding the manual should be directed to Jeffrey R. Belt at the Idaho National Laboratory. (jeffrey.belt@).CONTENTSFOREWORD (v)CONTENTS (vii)FIGURES (ix)TABLES (x)ACRONYMS (xi)GLOSSARY (xii)1. PURPOSE AND APPLICABILITY (1)1.1Energy Storage Targets For Plug-In Hybrid Electric Vehicles (1)2. TEST PROFILES DERIVED FROM TARGETS (3)3. TESTPROCEDURES (3)3.1General Test Conditions and Scaling (3)3.1.1Temperature Control (3)3.1.2Scaling of Performance and Cycle Life Test Profile (3)3.1.3Scaling of HPPC-Current (4)3.1.4Charging Procedure (4)3.2Static Capacity Test (5)3.3Constant Power Discharge Tests (5)3.4Hybrid Pulse Power Characterization Test (5)3.4.1Hybrid Pulse Power Characterization Test Profile (5)3.4.2Test Procedure Description (6)3.4.3Charge-Sustaining Available Energy Verification Test (8)3.4.4Charge-Depleting Available Energy Verification Test (9)3.5Self-Discharge Test (9)3.6Cold Cranking Test (9)3.6.1Cold Cranking Test Profile (10)3.7Thermal Performance Test (11)3.8Energy Efficiency Test (12)3.9Charge-Sustaining Cycle Life Tests (12)3.9.1Cycle Life Test Procedure Outline (12)3.9.2Charge-Sustaining Cycle Life Test Profiles (13)3.9.3Operating Set Point Stability Test (16)3.10Charge-Depleting Cycle Life Tests (17)3.10.1Cycle Life Test Procedure Outline (18)3.10.2Charge-Depleting Cycle Life Test Profile (20)3.10.3Combined Cycle Life Test (22)3.11Calendar Life Test (23)3.11.1Calendar Life Test Planning (23)3.11.2Calendar Life Test Procedure (24)3.11.3Calendar Life Test Profile .................................................................................... 263.11.4Alternative Calendar Life Test ............................................................................ 263.12Reference Performance Tests . (27)4. ANALYSIS AND REPORTING OF TEST RESULTS ......................................................284.1General .. (28)4.2Static Capacity Test and Constant Power Discharge Test (28)4.2.1Capacity Fade (28)4.3Hybrid Pulse Power Characterization Test (28)4.3.1Open-Circuit Voltage (29)4.3.2Calculated Resistance Characteristics as a Function of Depth-of-Discharge (29)4.3.3Pulse Power Capability (30)4.3.4Useable and Available Energies (34)4.3.5CD and CS Available Energy Margins (36)4.3.6CS Available Power (38)4.3.7Power and Energy Fade (39)4.3.8Minimum and Maximum DOD Values (40)4.3.9Two-Second Discharge Target Verification (41)4.3.10Pulse Power Characterization Profile Voltage Response (41)4.3.11Other Laboratory Cell Performance Characteristics (41)4.3.12Determining Battery Size Factor When Not Supplied By Manufacturer (41)4.4Self-Discharge Test (44)4.5Cold Cranking Test (45)4.6Thermal Performance Tests (45)4.7Energy Efficiency Test (46)4.8Operating Set Point Stability Test (46)4.9Cycle Life Tests (46)4.10Calendar Life Test (47)4.11Reference Performance Tests (48)4.12Module Controls Verification Tests (49)4.13System-Level Testing ............................................................................................................ 495. REFERENCES (50)6. Appendix A (51)7. Appendix B (56)FIGURESFigure 1. Hybrid Pulse Power Characterization Test Profile. (6)Figure 2. Hybrid Pulse Power Characterization Test (start of test sequence). (7)Figure 3. Hybrid Pulse Power Characterization Test (complete HPPC sequence). (7)Figure 4. Cold Cranking Test Profiles. (11)Figure 5. Charge-Sustaining Minimum PHEV Battery (50 Wh) Cycle Life Test Profile. (14)Figure 6. Charge-Sustaining Medium PHEV Battery (50 Wh) Cycle Life Test Profile. (15)Figure 7. Charge-Sustaining Maximum PHEV Battery (50 Wh) Cycle Life Test Profile. (16)Figure 8. Charge-Depleting Cycle Life Test Profile for the Minimum PHEV Battery. (17)Figure 9. Charge-Depleting Cycle Life Test Profile for the Medium PHEV Battery. (19)Figure 10. Charge-Depleting Cycle Life Test Profile for the Maximum PHEV Battery. (21)Figure 11. Calendar Life Test Profile. (26)Figure 12. Resistance Calculation Time Points. (29)Figure 13. Open-Circuit Voltage and Pulse Resistances versus Depth-of-Discharge. (30)Figure 14. Pulse Power Capability vs. Depth-of-Discharge. (31)Figure 15. Relationship Between Energy and DOD in a 10-kW Discharge. (32)Figure 16. Unscaled HPPC Cell Power Capability vs. Energy Removed. (33)Figure 17. HPPC Power vs. HPPC-Current Discharge Energy Scaled by the Battery Size Factor. (34)Figure 18. PHEV Operating Philosophy. (35)Figure 19. CS and CD Useable Energy Determination. (36)Figure 20. Charge-Depleting and Sustaining Useable Energy Margin Determination. (37)Figure 21. CD and CS Available Energy and Power Margins Over Life. (38)Figure 22. Useable Energy versus Power Curve. (39)Figure 23. Minimum and Maximum DOD Values Where Targets Are Met. (40)Figure 24. Finding the CD Useable Energy Using Device-Level Results. (43)Figure 25. Finding a Battery Size Factor Using Device-Level Results. (44)Figure 26. Cold Cranking Test Resistance Calculation Points. (45)TABLESTable 1. Energy Storage System Performance Targets for Plug-In Hybrid Electric Vehicles (November 2009). (2)Table 2. Hybrid Pulse Power Characterization Test Profile. (6)Table 3. Cold Cranking Test Profile for Plug-In Hybrid Targets. (10)Table 4. Charge-Sustaining Minimum PHEV Battery (50 Wh) Cycle Life Test Profile. (14)Table 5. Charge-Sustaining Medium PHEV Battery (50 Wh) Cycle Life Test Profile. (14)Table 6. Charge-Sustaining Maximum PHEV Battery (50 Wh) Cycle Life Test Profile. (15)Table 7. Charge-Depleting Cycle Life Test Profile for the Minimum PHEV Battery. (18)Table 8. Charge-Depleting Cycle Life Test Profile for the Medium PHEV Battery. (20)Table 9. Charge-Depleting Cycle Life Test Profile for the Maximum PHEV Battery. (22)Table 10. Calendar Life Test Profile. (26)Table 11. Reference Performance Tests and Test Intervals for Life Testing. (27)Gap Analysis (56)ACRONYMSAE CS Available Energy for charge-sustainingAE CS Target Available Energy Target for charge-sustaining AE CD Available Energy for charge-depletingAE CD Target Available Energy Target for charge-depleting ASI area-specificimpedanceBSF battery size factorBOL beginning-of-lifeCD charge-depletingCS charge-sustainingDOD depth-of-dischargeEOL end-of-lifeEV electricvehicleHEV hybrid electric vehicleHPPC hybrid pulse power characterizationOCV open-circuitvoltageOSPS operating set point stabilityPHEV plug-in hybrid electric vehiclePNGV Partnership for a New Generation of Vehicles RPT reference performance testSOC state-of-chargeTLVT technology life verification testsUE CD Useable Energy for charge-depletingUE CD Margin Useable Energy Margin for charge-depleting UE CS Useable Energy for charge-sustainingUE CS Margin Useable Energy Margin for charge-sustaining USABC United States Advanced Battery ConsortiumGLOSSARYCS Available Power –the discharge pulse power at which the useable energy is equal to the Charge-Sustaining Available Energy target for a given mode (Minimum, Medium, or Maximum PHEV).Battery Size Factor (BSF) – for a particular cell or module design, an integer which is the minimum number of cells or modules expected to be required to meet all theperformance and life targets. If this value cannot be determined prior to testing, theBattery Size Factor is chosen as the minimum number of cells or modules that canboth satisfy the CS energy target with a 30% power margin and provide a 20% energy margin for Charge Depleting Available Energy at beginning-of-life . Battery SizeFactor is determined separately for each mode.Beginning-of-Life (BOL) – the point at which life testing begins. A distinction is made in this manual between the performance of a battery at this point and its initial performance, because some degradation may take place during early testing prior to the start of life testing. Analysis of the effects of life testing is based on changes from the BOLperformance.C1/1 Rate – a current corresponding to the manufacturer’s rated capacity (in ampere-hours) for a one-hour discharge at 30°C. For example, if the battery’s rated one-hourcapacity is 40Ah, then C1/1 is 40A.Charge – any condition in which energy is supplied to the device rather than removed from the device. Charge includes both recharge and regen conditions. Charge is indicated in this manual as a negative value (from the perspective of the battery)Charge-Depleting Available Energy –the discharge energy available at a 10-kW constant power discharge rate between an arbitrarily defined upper limit (nominally 10%DOD) and the minimum DOD. (See Section 4.3.4)Charge-Sustaining Available Energy –the discharge energy available over the DOD range where both the discharge and regen pulse power targets for a given mode (Minimum, Medium, or Maximum PHEV) are precisely met. This energy is measured using a10-kW discharge rate, and the limiting power conditions are calculated using theprocedure defined in this manual (section 4.3.4).Depth-of-Discharge (DOD) – the percentage of a device’s rated capacity removed by discharge relative to a fully charged condition, normally referenced to a constantcurrent discharge at the HPPC-Current rate.Device – a cell, module, sub-battery or battery pack, depending on the context. The generic term “device” is normally used in test procedures except where a specific type ofdevice is meant. (Most test procedures are intended to apply to any of these types). Discharge – any condition in which energy is removed from the device rather than supplied to the device. Discharge is indicated in this manual as a positive value (from theperspective of the battery)End-of-Life (EOL) – a condition reached when the device under test is no longer capable of meeting the targets. This is normally determined from HPPC Test results scaledusing the Battery Size Factor, and it may not coincide exactly with the ability toperform the life test profile (especially if cycling is done at elevated temperatures).The number of test profiles executed at end of test is not necessarily equal to the cycle life per the targets.End of Test – a condition where life testing is halted, either because criteria specified in the test plan are reached, or because it is not possible to continue testing.Energy Margin – for a given HPPC Test data set, the difference between either the CS or the CD Available Energy and the energy target for a given application and operatingmode.Fully Charged – The condition reached by a device when it is subjected to the manufacturer’s recommended recharge algorithm. This state is defined as 100%state-of-charge, or 0% depth-of-discharge.HPPC-Current rate – the constant current equivalent of a BSF-scaled 10-kW rate (see Section 3.1.3).Hybrid Pulse Power Characterization (HPPC) Test – a test procedure whose results are used to calculate pulse power and energy capability under operating conditions. Maximum Rated Current (Imax) – the maximum discharge current that a manufacturer will permit to be sustained by a device for 10 seconds. (This value need not be achievable at all DOD values).PHEV Charge Target—the upper regen limit used during PHEV operation, also known as the charge limit during charging.Power Fade—the change in CS Available Power from the beginning-of-life value to the value determined at some later time, expressed as a percentage of the BOL value.(Similar definitions apply to Capacity Fade and CS or CD Available Energy Fade,although these are not included in this glossary).Power Margin – for a given HPPC Test data set, the difference between the maximum power at which the applicable energy target can be met and the power target for a givenapplication.Profile – a connected sequence of pulses used as the basic ‘building block’ of many test procedures. A test profile normally includes discharge, rest and charge steps in aspecific order, and each step is normally defined as having a fixed time duration and a particular (fixed) value of current or power.Recharge – any device charge interval corresponding to the sustained replenishment of energy by a continuous power source (such as an engine-generator or off-boardcharger).Regen – any device charge interval corresponding to the return of vehicle kinetic energy to a device (typically from braking). Because of physical limitations, high rates of regen can only persist for a few seconds at a time.Rest –the condition in which energy is neither supplied to the device nor removed from the device. Rest is indicated by zero currentState- of-Charge (SOC)—the available capacity in a battery expressed as a percentage of rated capacity (Handbook of Batteries, 3rd Edition).Useable Energy – a value (calculated from HPPC Test results) that represents the discharge energy available over a DOD range corresponding to any pair of discharge and regen power values whose ratio is that of the corresponding power targets. Charge-Sustaining Available Energy is the value of useable energy at the actual power target values. (Useable energy has been frequently but inaccurately called “AvailableEnergy”).Battery Test ManualFor Plug-In Hybrid Electric Vehicles1.PURPOSE AND APPLICABILITYThis manual defines a series of tests to characterize aspects of the performance or life behavior of batteries for plug-in hybrid electric vehicle (PHEV) applications. Tests are defined based on the Vehicle Technologies Program targets for plug-in hybrid electric vehicles, though it is anticipated these tests may be generally useful for testing energy storage devices for plug-in hybrid vehicles. The test procedures in this manual are directly applicable to complete battery systems. However, most can also be applied with appropriate scaling to the testing of modules, cells or sub-scale cells. Much of the rationale for the test procedures and analytical methodologies utilized in this manual evolved from the USABC Electric Vehicle Battery Test Procedure Manual (Reference 1), the PNGV Battery Test Manual (Reference 2) and the FreedomCAR Battery Test Manual for Power-Assist Hybrid Electric Vehicles (Reference 3).1.1Energy Storage Targets For Plug-In Hybrid Electric Vehicles Vehicle Technologies Program Energy Storage Targets are the primary driving force for the test procedures and methods defined in this manual. These targets are outlined in Table 1 for a Minimum PHEV Battery, Medium PHEV Battery, and a Maximum PHEV Battery performance specified for the Vehicle Technologies Program. Note that this table of targets is presented as the primary basis for this test manual. Establishing or verifying battery performance in comparison to these targets is a principal objective of the test procedures defined in this document. The intended vehicle platform for the Minimum PHEV Battery target is a sport utility vehicle with a vehicular mass of 2000 kg with an equivalent electric range of 10 miles; the Medium PHEV Battery target is a car with a vehicular mass of 1600 kg with an equivalent electric range of 20 miles; and the Maximum PHEV Battery target is a car with a vehicular mass of 1500 kg with an equivalent electric range of 40 miles. Unless otherwise stated, these targets all pertain to devices operating at 30°C.This manual defines two operational modes for plug-in hybrid electric vehicles, Charge-Depleting (CD) and Charge-Sustaining (CS). The Charge-Depleting mode is intended to allow the vehicle to operate in hybrid mode (propulsion and accessories are powered by the electric drive and/or engine) and electric mode (propulsion and accessories powered by the electric drive and onboard electric energy storage), with a net decrease in battery state-of-charge (SOC). The Charge-Sustaining mode only allows the vehicle to operate in hybrid mode with a relatively constant battery state-of-charge.Table 1. Energy Storage System Performance Targets for Plug-In Hybrid Electric Vehicles(November 2009).Characteristics at EOL (End-of-Life) UnitMinimumPHEV Battery1MediumPHEV BatteryMaximumPHEV BatteryReference Equivalent Electric Rangemiles 10 20 40 Peak Discharge Pulse Power (2 sec /10sec) 2kW 50/45 45/37 46/38Peak Regen Pulse Power (10 sec) kW 30 25 25Max. Current (10 sec pulse) A 300 300 300Available Energy for CD (Charge-Depleting) Mode, 10-kW RatekWh 3.4 5.8 11.6 Available Energy for CS (Charge-Sustaining) Mode, 10-kW Rate 3kWh 0.5 0.3 0.3 Minimum Round-trip Energy Efficiency(CS 50 Wh profile)% 90 90 90 Cold cranking power at -30°C, 2 sec, 3PulseskW 7 7 7 CD Life / Discharge Throughput Cycles/MWh 5,000 / 17 5,000 / 29 5,000 / 58CS HEV Cycle Life, 50 Wh Profile Cycles 300,000 300,000 300,000Calendar Life, 35°C year 15 15 15 Maximum System Weight kg 60 70 120Maximum System Volume Liter 40 46 80Maximum Operating Voltage Vdc 400 400 400Minimum Operating Voltage Vdc>0.55 x Vmax4>0.55 x Vmax4>0.55 x Vmax4 Maximum Self-discharge Wh/day505050Maximum System Recharge Rate at 30°C kW1.4(120V/15A)51.4(120V/15A)51.4(120V/15A) 5Unassisted Operating & ChargingTemperature Range52°C >100% Available Power0°C >50% Available Power-10°C >30% Available Power-30°C >10% Available Power°C -30 to +52 -30 to +52 -30 to +52Survival Temperature Range °C -46 to +66 -46 to +66 -46 to +66 Suggested Total Energy kWh 5.6 8.7 17.0 Maximum System Production Price @100k units/yr$ $1,700 $2,200 $3,400 1 Minimum,Medium and Maximum PHEV Battery are also referred to as High Power/Energy Ratio Battery,Moderate Energy/Power Ratio Battery, and High Energy/Power Ratio Battery.2 The Peak Discharge Pulse Power and Peak Regen Pulse Power targets are applicable for the Charge-Sustainingmode.3 The HPPC-Current rate is used to approximate the required 10-kW rate during the HPPC Test and the StaticCapacity test.4 This value can be reduced to 45% of Vmax for temperatures lower than 0°C.5 With the battery manufacturer’s concurrence, an increase recharge rate can be used to accelerate life testing.Maximum System Recharge Rate refers to the maximum power expected from a standard garage outlet.2.TEST PROFILES DERIVED FROM TARGETSThe test procedures described in this manual are intended for use over a broad range of devices at various stages of developmental maturity. Application of the procedures is further complicated by the existence of three different sets of performance targets. The approach taken for these procedures is to define a small set of test profiles based on the overall vehicle characteristics, independent of the size or capability of the device to be tested. These profiles are specified in terms of the characteristics of vehicle power demand. They can be used in various combinations, with the appropriate scaling factors, to define specific performance or cycle life tests for cells, modules or battery systems. Each profile is defined within the respective procedure described, because there is essentially a one-to-one relationship between test profiles and test procedures.3.TEST PROCEDURES3.1General Test Conditions and ScalingIn general, testing is divided into three broad phases, i.e., characterization, life, and reference performance testing. Characterization testing establishes the baseline performance and includes static capacity, hybrid pulse power characterization, self-discharge, cold cranking, thermal performance, and efficiency tests.6 Life testing establishes behavior over time at various temperatures, states of charge and other stress conditions and includes both cycle life and calendar life testing. Reference Performance Tests establish changes in the baseline performance and are performed periodically during life testing, as well as at the start- and end-of-life testing. A generic test plan for testing is outlined in Appendix A; this outline can be used as a starting point for device-specific test plans.3.1.1Temperature ControlUnless otherwise specified in a device-specific test plan, the ambient temperature for all tests should be controlled at a default nominal temperature of 30ºC. Also, to the extent possible, all testing should be conducted using environmental chambers. As a general practice, a rest of 60 minutes (or more if required) should be observed after each charge and each discharge prior to proceeding with further testing, to allow devices to reach stable voltage and temperature conditions.3.1.2Scaling of Performance and Cycle Life Test ProfileWith the exception of the Hybrid Pulse Power Characterization Test (HPPC) and Calendar Life Test, all performance and cycle life test profiles are defined in terms of required power levels at the system (i.e., full-size vehicle battery) level. Testing any device smaller than a full-size system requires a method for scaling these test profiles to a level appropriate to the size of the device (cell, module, or sub-battery) under test. This is done by using a battery size factor. For purposes of this manual, the Battery Size Factor (BSF) is defined as the minimum number of units (cells, modules or sub-batteries) of a given design required for a device to meet all targets, including cycle life and calendar life. Wherever possible, the Battery Size Factor will be specified by the manufacturer, based on the 6 In this manual, unless specifically stated otherwise, the desired state-of-charge for a test is established as a depth-of-discharge (DOD) value, which is always reached by removing the appropriate fraction of the rated capacity from a fully charged device (normally at a constant HPPC current discharge rate.) Also, the term “fully charged” means “charged in accordance with the manufacturer’s recommended procedure”.manufacturer’s testing and best estimates of any allowances needed for system burdens and degradation over life.If insufficient data exist to allow the manufacturer to determine a meaningful value, the Battery Size Factor will be determined from the beginning-of-life Low Current HPPC Test results using a C1/1 rate for the HPPC-Current rate by applying the larger BSF from either a nominal power margin of 30% or a nominal CD Energy Margin of 20% to allow for degradation resulting from cycle life and calendar life effects. See Section 4.3.12 for details of this determination.7Once the Battery Size Factor is determined, it becomes a constant (i.e., fixed over life) scaling factor for all subsequent performance and cycle life tests. Any test profile (except HPPC or calendar life) is then scaled by dividing the nominal profile power levels by the Battery Size Factor. For example, if the Battery Size Factor is 100 for a particular cell design, the 7-kW Cold Cranking Test would then be performed at a pulse power level of 7000/100 = 70 W for such cells. Note that there is a different mode-specific Battery Size Factor for Minimum, Medium and Maximum PHEV Battery operation. 3.1.3Scaling of HPPC-CurrentThe HPPC-Current is a constant current that will closely resemble the steady state current during the 10-kW Constant Power Discharge Test. In order to relate the energy removed at the 10-kW rate and the energy removed during the HPPC Test, the “HPPC current” will be used for the 10% DOD (depth-of-discharge) constant current discharge segments.The HPPC-Current is calculated using the formula below.I HPPC = P CPDT/(V avg * BSF) (1)where I HPPC is the HPPC discharge current between pulses, P CPDT is the Constant Power Discharge Test power, and V avg is the average voltage between V max and V min. For example, if V max = 4V andV min = 3V, and V avg = (V max-V min)/2 = 3.5V, and the BSF = 100, and where P CPDT = 10-kW, then I HPPC = 10,000W/(3.5V * 100) = 28.6 A. Note that if the Battery Size Factor has not been determined, aC1/1 rate can be used as an approximate rate for the HPPC-Current during the first iteration of the HPPC Test to determine an appropriate Battery Size Factor. This value is used extensively once the BSF is determined for the Static Capacity and HPPC tests8.3.1.4Charging ProcedureThe manufacturer is responsible for defining a reasonable charging procedure with the assistance of the Program Manager. In order to speed up testing and avoid the degradation that may accompany the fully charged condition, the manufacturer may specify a charging procedure to charge up to the manufacturer’s specified DOD min during life testing and Reference Performance Tests. This charging procedure should specify rest periods required before and after (1 hour recommended) charging is performed. During CD cycle life testing a rest period of 15 minutes can be used to accelerate testing before and after charging. This is a default value can be adjusted based on the needs of the chemistry.7 In some cases, this value and/or the associated voltage limits may require modification to ensure that the round-trip efficiency targets are also met.8The HPPC current should be compared with the average current for a scaled 10-kW discharge. An alternate method to determine the HPPC current is as follows (HPPC Current = 10 kW / (BSF *(Device Energy/ Device Capacity)).。
锂电池出货检验报告

型号
Model
订单数量
Order form Q'TY
检验内容及结果 Inspection content and Result
工艺标准
检验数据记录
Spec
Test result
日期(Date):______________
额定容量(mAh)
Rated capacity
送检数量
Lot Q'TY
判定 Judgement PASS NG
是否符合环保
Complacence with environmental protection
□ 符合(Yes) □ 不符合(No)
最终判定
□ 合格 (Pass)
Final Judgement □ 不合格 (Fail)
备注(Remark):
环保标示
Environmental protection label
检验员(Inspector): ___________
QMS-0024-006D VER 02
审核(Auditing):___________
第一联(The first): OQC (白色 White)
第二联(The second):客户联 Customer(黄色Yellow)
备注
Remark
极 耳
T a b
长度
Length
宽度
Width
间距
Distance
Ⅱ、电 性 功 能 ( Characteristics )
容量
Capacity
开路电压
Open Circuit Voltage
内阻 Impedance
Ⅲ、外 观 检 验 (Appearance Inspection)
中英文电池充电器测试报告

提交日期型号电池零件号充电器零件号 Charger Part#序列号电池类型充电器类型检测组件Component Being电池电流充电器电流Charger Amps充电器样式描述Description检测员 热电偶位置Thermal Couple Location 室温Ambient Temperature检测站Station 提供手册?Manual Provided?阅览手册?Manual Reviewed?报告日期Report Date第三方实验室测试? Tested by a 3rd party lab?IEC60335-29 或 IEC60601-1 报告引用电池组Reference Batteries Set 如果是,请说明依照标准If so, to what standard?附件Attachment保护装置Protection Device漏电流不得超过0.1毫安。
Leakage current should not exceed 0.1mA.认证类型Type of Certifications测试结果 TEST RESULTS最大电压Max Voltage 充电周期Charge Cycle 浮动电压Float Voltage充电周期Charge Cycle最大电流Max Current 充电周期Charge Cycle浮动电流Float Current 充电周期Charge Cycle最大外壳温度Max Case Temp 室温应小于:塑料35K+ ,金属25K+Should be less than:35K+ Ambient for plastic;25K+Amebient for metal充电周期Charge Cycle充电至80%容量80% Capacity Reached 评论显示结果检测技术员Test Technician 日期Date审阅人Reviewer 日期Date电池/充电器参考资料(容量,C/5等级,等等)REFERENCE BATTIERY/CHARGER INFORMATION (CAPACITY, C/5 RATING, etc.)样品编号NUMBER OF SAMPLES使用装置DEVICE TO BE USED IN电池是否标明生产厂家?IS THE BATTERY MARKED WITH THE MANUFACTURER?电池是否标明类型(AGM,胶体)?IS THE BATTERY MARKED WITH THE TYPE(AGM,GEL)?电池是否标明额定电压?IS THE BATTERY MARKED WITH THE NOMINAL VOLTAGE?电池是否标明额定容量(C20和C5)?IS THE BATTERY MARKED WITH THE RATED CAPACITIES (C20 AND C5)?电池是否标明生产日期?(IS THE BATTERY MARKED WITH THE DATE OF MANUFACTURE?)电池相邻端子是否标明极性?IS THE BATTERY MARKED WITH THE POLARITY MARKINGS ADJACENTTO EACH TERMINAL?参考文献(References)1.RESNA 71762.IEC 60335-13.IEC 60335-2-294.IEC 60601-15.IEC 529合格/不合格Pass/Fail分析清单PROFILING CHECKLIST如果充电器反极性连接,不应有大于100毫安的电流流动,也不会损坏充电器。
- 1、下载文档前请自行甄别文档内容的完整性,平台不提供额外的编辑、内容补充、找答案等附加服务。
- 2、"仅部分预览"的文档,不可在线预览部分如存在完整性等问题,可反馈申请退款(可完整预览的文档不适用该条件!)。
- 3、如文档侵犯您的权益,请联系客服反馈,我们会尽快为您处理(人工客服工作时间:9:00-18:30)。
LAB NO. DATE PAGE
: (5509)082-1972 : March 31, 2009 : 2 OF 3
Photo of the Submitted Sample
The content of this PDF file is in accordance with the original issued reports for reference only. This Test Report cannot be reproduced, except in full, without prior written permission of the company.
Alkaline button cell (LR44G style)
“<” = less than Limit of Mercury:
Battery Type I II III Battery Alkaline Manganese Battery Alkaline Manganese Button Cell Zinc-Carbon Battery Maximum Allowableally introduced <25mg/cell Not be intentionally introduced
(852) 2494 4383 / (852) 2494 1263 rohs.enquiry@
BUREAU VERITAS HONG KONG LIMITED
PREPARED BY:
Ed DR. LEE SIU MING SENIOR MANAGER, CHEMICAL AND ANALYTICAL SERVICES
TEST REPORT
LAB NO. DATE PAGE APPLICANT : (5509)082-1972 : March 31, 2009 : 1 OF 3 : Golden Power Corporation (HK) Ltd Flat C, 20/F, Block 1, Tai Ping Industrial Centre, 57 Ting Kok Road, Tai Po, N.T., Hong Kong : Raymond Chung : March 23, 2009 : March 23, 2009 to March 31, 2009 : 7 : Alkaline Button Cell Model no.: LR44G, LR44GD LR44GH Manufacturer: Golden Power Country of origin: China SUMMARY OF TEST RESULTS TEST REQUESTED Mercury Content - US Public Law 104-142, Title II PASS X FAIL REMARK
LAB NO. DATE PAGE
: (5509)082-1972 : March 31, 2009 : 3 OF 3
TEST RESULT
Mercury Content - US Public Law 104-142, Title II Parameter Total Mercury (Hg) Conclusion Test Item 1: Note: Battery Type II Unit mg/ cell Result 1 <5 PASS
CONTACT PERSON DATE OF SUBMISSION TEST PERIOD NO. OF WORKING DAYS SAMPLE DESCRIPTION
REMARK If there are questions or concerns on this report, please contact:
Method:
Sample was digested with acid mixtures and then analyzed by Atomic Absorption Spectrometer. END
The content of this PDF file is in accordance with the original issued reports for reference only. This Test Report cannot be reproduced, except in full, without prior written permission of the company.
RW
The content of this PDF file is in accordance with the original issued reports for reference only. This Test Report cannot be reproduced, except in full, without prior written permission of the company.