350万吨常减压车间工艺设计论文
35万吨重整350万吨常减压工程施工组织设计_最终版

(此文档为word格式,下载后您可任意编辑修改!)35万吨重整350万吨常减压工程施工组织设计目录1、编制说明2、编制依据3、工程概况3.1工程性质3.2工程简介3.3工程特点3.4主要实物工程量3.5 工程条件4、施工进度计划及工期保证措施4.1施工总进度控制计划4.2施工网络图4.3施工部署4.4工期保证措施5、施工组织5.1项目管理机构5.2主要管理人员简历5.3现场主要技术人员简历5.4劳动力组织5.5计划投入的主要施工机械设备6、施工方法及主要施工技术措施A钢结构工程B工艺管道工程C设备安装工程D加热炉安装工程E筑炉工程F管道、设备保温工程G焊接工程H电气工程I仪表工程J冬季及夜间施工技术措施7、质量目标及保证措施7.1质量方针及目标7.2质量体系及组织机构7.3质量保证措施8、安全生产及文明施工保证措施8.1 安全生产方针目标8.2安全生产保证体系8.3安全及文明施工保证措施9、施工总平面布置9.1布置原则9.2临时设施9.3施工现场平面布置10、项目管理及项目控制10.1项目管理10.2进度控制10.3质量控制10.4技术管理10.5 材料控制11、工程分包与转包12、拟执行的标准规范一览表1、编制说明本组织设计针对****炼油厂350万吨年常减压装置改造工程而编制。
它包括了钢结构、加热炉、设备、工艺管道及给排水、电气、仪表各工程的拆除、改造、移位、安装、施工全过程的工作内容。
它是该工程施工的全面性技术文件。
该设计在编制当中充分的进行了调查研究,广泛地发动技术人员及工人的建议,使施工组织设计切合实际,达到指导施工的目的。
2、编制依据2.1 ****炼油厂****号招标文件;2.2 ****炼油厂350万吨年常减压装置(改造)施工图;2.3 与本工程有关的工程施工验收规范及相关标准。
3、工程概况3.1 工程性质该工程性质为技术改造扩建。
3.2 工程简介该工程位于****炼油厂一联合常减压装置原位置。
设计一座年产350万吨良坯的转炉炼钢车间_本科毕业设计论文
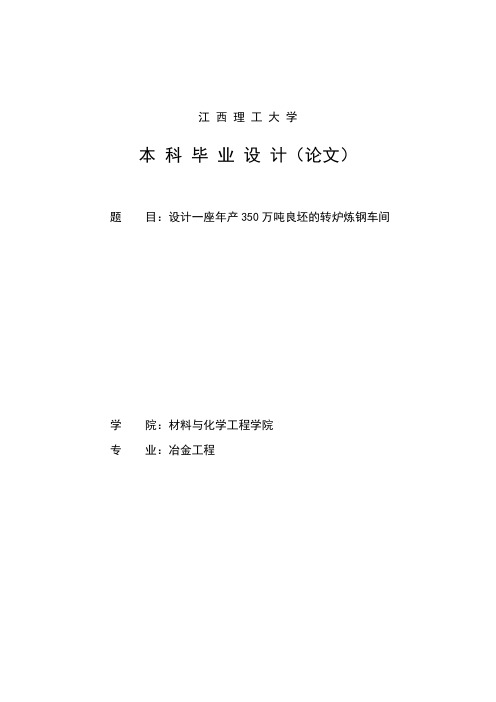
江西理工大学本科毕业设计(论文)题目:设计一座年产350万吨良坯的转炉炼钢车间学院:材料与化学工程学院专业:冶金工程江西理工大学毕业设计(论文)任务书冶金工程专业06 级(10届)3 班学生肖山题目:设计一座年产350万吨良坯的转炉炼钢车间原始依据(包括设计(论文)的工作基础、研究条件、应用环境、工作目的等):本设计是在学生系统学习钢铁冶金专业知识的基础上,以及认真仔细地钢铁厂实地实习考察的基础上进行的。
通过课程学习、实习考察使得学生掌握了大量的设计资料,具有良好的工作基础和设计条件。
近年来,我国钢铁行业得到迅猛发展,急需该方面专业的技术人才。
通过该设计使学生对钢铁厂生产工艺流程、主要技术条件、冶金计算、冶金设备等实际生产情况有比较全面的了解和掌握,使学生成为符合需要的合格专业技术人才。
主要内容和要求:(包括设计(研究)内容、主要指标与技术参数,并根据课题性质对学生提出具体要求):1、厂址与生产能力的选择2、物料平衡与热平衡计算:平衡计算以100Kg铁水为基础进行计算。
3、氧气转炉设计4、氧枪设计5、氧气转炉炼钢车间设计6、车间生产概述7、转炉车间人员编制8、技术经济分析图纸:转炉主体设备图一张;转炉车间平面、剖面示意图各一张。
其中剖面示意图要求用计算机CAD软件绘图。
日程安排:第4周—第6周收集原始资料并进行文献检索,撰写开题报告。
第7周—第10周冶金计算、设备选择计算第11周—第13周图纸绘制及论文编写第14周毕业答辩主要参考文献和书目:1、李传薪主编,《钢铁厂设计原理》,冶金工业出版社,2005.2、戴云阁等,《现代转炉炼钢》东北大学出版社,1998.3、王德全主编,《冶金工厂设计基础》东北大学,1998.4、杜挺等编,《钢铁冶炼新工艺》,北京大学出版社,19945、潘旒淳主编,《炼钢设备》,冶金工业出版社,1992。
6、陈家祥主编,《钢铁冶金学(炼钢部分)》,冶金工业出版社,1990。
7、其它相关科技期刊文章指导教师签字:年月日教研室主任签字:年月日教学院长签字:年月日注:1、本表可自主延伸 2、本表一式两份,一份下达给学生,一份装订在《指导教师日志》中。
毕业设计(论文)-年产350万吨热轧带钢厂工艺设计[管理资料]
![毕业设计(论文)-年产350万吨热轧带钢厂工艺设计[管理资料]](https://img.taocdn.com/s3/m/e1625e64dd88d0d232d46a7c.png)
年产350万吨热轧带钢厂工艺设计班级:金加092姓名:指导教师:摘要板带钢是钢铁产品的主要品种之一,广泛应用于工业,农业,交通运输和建筑业。
宽带钢在我国国民经济中的发展中需求量很大。
世界各国近年来都在注重研制和使用连铸连轧等新技术和新设备来生产板带钢。
本设计是年产350万吨的热轧板带钢车间工艺设计。
产品规格为:1400*。
所用钢种为:普碳钢、合金结构钢、不锈钢。
论文主要内容包括:原料的选择、生产工艺的制定、典型产品工艺计算、主要设备和辅助设备的选择,并且对主要设备(轧辊和电机)的能力进行了校核,对车间主要经济指标、生产车间布置和环境保护,进行了设计和规划目录摘要 (I)目录 (II) (1)热轧板带钢生产状况 (1) (1) (3)热轧带钢市场前景和需求概况 (3)今后热轧板带钢的发展趋势 (3)本设计的目的和意义 (4)热传送设备工艺 (4) (5) (5) (6) (7)确定计算产品的成品率 (7)编制金属平衡表 (8) (9) (10)粗轧前立轧机(E1、E2) (11)四辊粗轧机(两架)(R1、R2) (11)精轧前立轧机(FE) (11)精轧机组(F1~F7) (12) (12) (13) (14) (14) (16) (16) (16).精轧机速度制度 (18)温度制度 (20) (21) (22) (23) (24) (24) (24) (25) (26) (26) (26) (27) (27) (27) (27)R1轧辊强度校核 (29) (32) (33)电机功率校核 (33)9.轧钢机产量计算 (35)典型产品的工作图表 (35)典型产品小时产量计算 (36)轧机实际工作小时数 (36)年计划实际工作小时数 (36)轧机负荷率 (37) (37) (38)致谢 (38)热轧板带钢生产状况热轧带钢是重要的钢材品种,对整个钢铁工业的技术进步和经济效益有着重要影响。
发达国家热轧带钢产量约占热轧钢材的50%以上,并在国际市场竞争中居于领先地位。
35万吨重整350万吨常减压工程施工组织设计

35万吨重整350万吨常减压工程施工组织设计一、项目概况本项目为建设一个年处理能力为35万吨的重整厂和一个年处理能力为350万吨的常减压工程。
二、施工组织机构1.总指挥部总指挥部负责项目的总体协调、决策和督导工作,并负责与业主进行沟通和协调。
2.项目管理部项目管理部负责施工项目的管理和协调工作,包括项目计划的编制和实施、资源的调配和协调、施工技术的指导和监督等。
3.施工现场指挥部施工现场指挥部负责具体的施工现场管理工作,包括施工队伍的组织和管理、设备材料的调配和管理、施工安全的监督和控制等。
4.施工队伍施工队伍根据项目需要组织施工作业,包括土建施工队、设备安装队、管道焊接队、电气安装队等。
三、施工工序及施工方法1.土建施工工序及施工方法(1)场地平整:采用机械平整和人工清理相结合的方式,确保施工现场的平整和清洁。
(2)基础施工:按照设计要求进行基坑开挖、基础桩基施工和混凝土浇筑。
(3)主体结构施工:采用钢结构,先进行钢梁和钢柱的安装,再进行屋面和墙体的安装。
(4)室内装修:进行室内地面、墙面的装修工作,包括瓷砖贴贴、墙面涂料施工等。
2.设备安装工序及施工方法(1)设备吊装:采用起重机进行设备吊装安装,确保设备的安全和稳定。
(2)设备固定:使用膨胀螺栓对设备进行固定,保证设备的稳定和牢固。
(3)设备接口连接:根据设备接口要求进行管道连接和电缆接线等。
(4)设备调试:对安装好的设备进行逐一调试,确保设备的正常运行。
3.管道焊接工序及施工方法(1)管道准备:对管道进行切割、修整和清洗等准备工作。
(2)管道焊接:采用手工氩弧焊进行焊接作业,保证焊接质量和焊缝无损害。
(3)管道测试:对焊接好的管道进行压力测试和气密性测试,确保管道的安全和正常使用。
4.电气安装工序及施工方法(1)电缆敷设:根据设计要求进行电缆敷设和布线工作。
(2)电气设备安装:对电气设备进行定位安装和接线工作。
(3)接地系统:进行接地电阻测试和接地系统的安装。
年产350万吨连铸坯的转炉炼钢车间工艺设计毕业论文

年产350万吨连铸坯的转炉炼钢车间工艺设计毕业论文目录1 绪论 (1)1.1 转炉冶炼原理简介 (1)1.2 氧气转炉炼钢的特点 (2)1.3设计原则和指导思想 (2)1.4 产品方案 (3)2 氧气转炉炼钢车间 (5)2.1 初始条件 (5)2.2 公称容量选择 (5)2.3 转炉座数的确定 (5)2.4根据生产规模和产品方案计算出年需钢水量。
(6)2.5 根据生产规模和产品方案计算出年需钢水量 (6)3 转炉物料平衡和热平衡计算 (8)3.1 氧气顶底复吹转炉的物料平衡和热平衡 (8)3.2热平衡计算 (20)3.2.1热平衡计算所需数据 (20)3.2.2计算步骤 (21)4 氧气转炉及相关设备设计 (25)4.1 炉型设计 (25)4.1.1炉型选择 (25)4.1.2 主要参数的确定 (25)4.2 炉衬设计 (27)4.3 炉底供气构件的设计 (28)4.4 转炉炉体金属构件设计 (28)4.5 倾动机构 (29)4.6 氧枪喷头设计 (29)4.6.1喷头设计 (29)4.6.2 氧枪枪身设计 (31)4.6.3氧枪升降和更换机构 (34)4.6.4 副枪设计 (34)4.6.5 副枪的功能和要求 (35)4.7 底部供气元件设计 (36)4.7.1底气种类 (36)4.7.2供气构件的选择 (36)4.7.3喷嘴数量及布置 (36)5 转炉车间烟气净化和回收 (37)5.1 烟气量的计算 (37)5.2 烟气净化系统类型的选择 (38)5.3 烟气净化系统主要设备的选择 (39)5.4 含尘污水处理 (40)6 转炉炼钢的生产制度 (41)6.1主要原材料的技术要求 (41)6.1.1金属料 (41)6.1.2造渣材料 (42)6.1.3氧化剂 (43)6.2装料制度 (44)6.3供氧制度 (45)6.3.1供氧制度主要工艺参数 (45)6.3.2氧枪操作 (45)6.4造渣制度 (46)6.4.1采用单双渣操作 (47)6.4.2各种渣料用量计算及加 (47)6.4.3炉渣调整 (48)6.5 温度制度 (49)6.6 终点控制与出钢 (50)6.7 脱氧合金化 (51)6.7.1脱氧合金化操作 (51)6.7.2 影响合金元素吸收率的因素 (52)6.8 精炼与连铸 (52)7 连铸车间的设计 (54)7.1 连铸机机型的选择 (54)7.2 连铸机的主要工艺参数 (54)7.2.1 钢包允许的最大浇注时间 (54)7.2.2 铸坯断面 (54)7.2.3 拉坯速度 (54)7.2.4 连铸机的流数 (56)7.2.5 铸坯的液相深度和冶金长度 (56)7.2.6 弧形半径 (56)7.3 连铸机生产能力的确定 (57)7.3.1 理论小时产量 (57)7.3.2 连铸机的平均年产量 (57)7.3.3 连铸机台数的确定 (57)7.4 结晶器的设计 (58)7.4.1 结晶器的长度 (58)7.4.2 结晶器断面尺寸 (58)7.4.3 结晶器铜壁厚度 (58)7.4.4 结晶器锥度 (58)7.4.5 结晶器拉坯阻力 (59)7.5 二次冷却装置 (59)7.6 拉坯矫直装置及引锭装置 (59)7.7 钢包 (60)7.8 中间包 (62)8 炼钢车间其它设备的选择与计算 (63)8.1渣罐车 (63)8.1.1渣罐车型号的选取 (63)8.1.2渣罐车数量的确定 (63)8.2 混铁车 (63)8.3 铁水罐 (64)8.4 废钢供应系统 (64)8.4.1转炉车间昼夜所需废钢量 (64)8.4.2废钢贮仓容积或堆放场地所需面积计算 (64)8.4.3废钢料斗容量及数量 (65)8.5 散装材料供应系统 (65)8.5.1 地面料仓容积和数量的确定 (65)8.5.2 上料方式的选择 (66)8.5.3 高位料仓容积和数量的确定 (66)8.6 钢包的其他工艺参数 (67)8.7起重机的选用 (68)9 转炉车间的组成、类型和主厂房尺寸 (69)9.1 车间组成 (69)9.2主厂房主要尺寸的确定 (69)9.2.1加料跨 (69)9.2.2炉子跨 (71)9.2.3 浇铸跨 (75)10 炼钢车间人员编制 (78)11 炼钢车间经济指标 (82)参考文献 (83)致谢 (84)1 绪论1.1 转炉冶炼原理简介[1]转炉炼钢是把氧气鼓入熔融的生铁里,使杂质硅、锰等氧化。
常减压操作规程报告

第一章概述1 装置概述本装置是由中国石化总公司北京设计院设计,年加工大庆原油350万吨的润滑油型常减压蒸馏装置。
全装置共有设备232台,占地面积17100m2,1989年4月破土动工,于1991年7月投产,各项主要技术指标均已达到设计要求。
2 装置特点2.1本装置主要设计要求是能生产出优质润滑油料。
减压蒸馏采用了粗转油线(低速段直径2m)、大塔径(汽化段直径10m,精馏段直径8.2m),高效规整全填料(GEMPAK)等多种技术措施来实现减压操作的低炉温、高真空、窄馏份,提高润滑油料的品质。
2.2本装置生产的减压渣又作丙烷脱沥青装置生产150BS光亮润滑油料,装置总拔出率控制在62%左右。
2.3本装置减压渣油直接送到重油催化裂化装置作原料、对渣油的含盐量有一定限制,因此装置设有电脱盐系统。
2.4 本装置生产航空煤油要求符合3号航煤标准,因此设计了航煤脱硫醇系统。
2.5本装置采用集散型控制系统(DCS),以提高装置的管理水平并实现过程的部分优化控制,提高轻质油收率,降低能耗,确保润滑油质量,提高经济效益。
2.6废水排放:为减少含油污水的排放量,减少了含油污水的排放。
因为加工的是大庆原油,硫含量低,排放的污水无需脱硫,只需进行简单隔油,然后直接排放送到含油污水场。
2.7废气排放:本装置正常生产时排放的低压瓦斯,如初顶产品罐排放初顶气送到轻烃回收设施加以回收,常顶气和减顶气分别引到加热炉烧掉,因此本装置正常生产时,不向大气排放有污染性的废气。
塔和容器顶部油气的安全阀放空设有放空总管,引到装置外火炬烧掉;本装置的大气污染源主要是燃料在加热炉燃烧后排放的烟气,从烟气监测数据可知,其中不含SO2,NO X的排放量低于国家排放标准,对环境质量没有太大的影响。
2.8 本装置无废渣产生。
2.9噪声:经调查,该套装置的噪声污染主要来自加热炉火嘴、泵和风机的电机、空冷器风机。
加热炉火嘴在密闭的罩内操作,噪声低于85分贝。
万吨年常减压蒸馏装置工艺设计

万吨年常减压蒸馏装置工艺设计一、引言常减压蒸馏是一种重要的分离工艺,广泛应用于石油化工行业。
本文基于万吨年常减压蒸馏装置的设计要求,对工艺进行详细设计,旨在满足设备的高效运行和产品质量的要求。
二、装置工艺流程常减压蒸馏装置的主要工艺流程包括进料、预热、加热、分馏、冷却和产品收集等步骤。
2.1 进料进料是装置的起始步骤,原料从储罐经过输送管道进入装置。
进料过程需要考虑流量和温度的控制,以确保装置的正常运行。
2.2 预热进料经过加热器进行预热,提高进料的温度至蒸发温度。
预热过程需要控制加热温度和时间,以确保进料在进入分离塔前达到合适的温度。
2.3 加热预热后的进料进入分离塔,在分离塔内进行加热。
加热过程中需要控制加热温度和压力,使得进料能够充分蒸发并分离成不同的组分。
2.4 分馏在分馏塔中进行分离,通过不同组分的沸点差异,实现轻质组分和重质组分的分离。
分馏过程中需要控制塔底的温度和塔顶的压力,以确保合理的分离效果。
2.5 冷却分馏后的产品经过冷却器进行冷却,降低温度至合适的收集温度。
冷却过程中需要控制冷却温度和冷却时间,避免产品的过热或过冷。
2.6 产品收集冷却后的产品通过收集器进行收集,分离出所需的产物。
产品收集过程需要注意收集器的遮挡和密封,以防止产品的污染或泄露。
三、工艺参数设计为了保证装置的高效运行和产品质量的要求,需要对装置的工艺参数进行设计。
3.1 进料流量根据设备的设计要求和生产需求,确定进料的流量范围。
进料流量的选择需要考虑装置的生产能力和运行稳定性。
3.2 加热温度和压力根据进料组分的性质和分离要求,确定加热的温度和压力范围。
加热温度和压力的选择需要兼顾分离效果和能耗的平衡。
3.3 分馏塔底温度和塔顶压力根据产品要求和分离塔的结构特点,确定分馏塔底温度和塔顶压力的要求。
分馏塔底温度和塔顶压力的选择需要满足产品质量和工艺要求。
3.4 冷却温度和冷却时间根据产品的蒸发温度和收集温度,确定冷却的温度和时间范围。
400万吨年常减压蒸馏装置工艺设计

400万吨年常减压蒸馏装置工艺设计常减压蒸馏装置是一种常用的化工设备,用于对原料进行分离和提纯。
本文将介绍一种设计容量为400万吨年的常减压蒸馏装置的工艺设计。
首先,我们需要确定装置的原料和产品。
假设我们的装置用于石油精炼,原料是原油,产品是石油衍生品,如汽油、柴油和液化石油气等。
接下来,我们需要进行原料的预处理。
原油中含有杂质和不同碳链长度的烃类化合物,需要通过脱盐、脱水和脱硫等工艺步骤进行预处理。
这些步骤将有助于提高蒸馏塔的效率和避免设备的腐蚀。
然后,我们需要设计蒸馏塔的结构。
常减压蒸馏装置通常由多个塔组成,包括原料预热塔、主分馏塔和精馏塔等。
每个塔都有不同的功能和操作条件。
例如,原料预热塔用于将原料加热到合适的温度,以便进入主分馏塔进行分离。
在主分馏塔中,原料将经历不同温度的塔板,每个塔板上都有一定的压力和温度。
通过调节供料量、回流比和冷凝器温度等操作参数,可以实现不同组分的分离。
高沸点组分将在底部的液相中收集,而低沸点组分将在顶部的气相中收集。
精馏塔用于进一步提纯分离出的不同组分。
它通常会有更多的塔板和较低的操作压力和温度。
最后,产品将通过冷凝器冷却,并收集在不同的收集装置中。
收集的产品可以进一步处理或直接用作市售产品。
在整个装置的设计过程中,需要进行多次的热力学计算和模拟。
这些计算将帮助我们确定塔板数目、操作参数、回流比和冷凝温度等设计参数。
总之,400万吨年的常减压蒸馏装置的工艺设计需要根据原料和产品的特性进行合理的塔结构和操作参数的选择。
通过热力学计算和模拟,可以优化装置的设计,实现高效的分离和提纯过程。
继续写相关内容,1500字为了确保400万吨年常减压蒸馏装置的高效运行和优化设计,还需要考虑以下几个方面:首先是热能供应和回收利用。
蒸馏过程需要大量的热能来提供蒸汽和加热原料。
为了降低能耗和运行成本,装置需要考虑热能的供应和回收利用。
一种常见的做法是利用余热回收系统和换热器来回收废热,并将其用于加热原料或生成蒸汽。
常减压装置年产350万吨计算
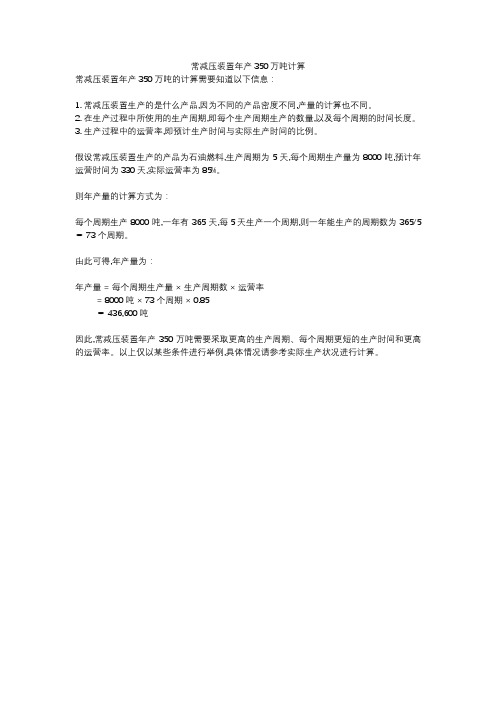
常减压装置年产350万吨计算
常减压装置年产350万吨的计算需要知道以下信息:
1. 常减压装置生产的是什么产品,因为不同的产品密度不同,产量的计算也不同。
2. 在生产过程中所使用的生产周期,即每个生产周期生产的数量,以及每个周期的时间长度。
3. 生产过程中的运营率,即预计生产时间与实际生产时间的比例。
假设常减压装置生产的产品为石油燃料,生产周期为5天,每个周期生产量为8000吨,预计年运营时间为330天,实际运营率为85%。
则年产量的计算方式为:
每个周期生产 8000 吨,一年有 365 天,每5天生产一个周期,则一年能生产的周期数为 365/5 ≈ 73 个周期。
由此可得,年产量为:
年产量 = 每个周期生产量× 生产周期数× 运营率
= 8000 吨× 73 个周期× 0.85
≈ 436,600 吨
因此,常减压装置年产 350 万吨需要采取更高的生产周期、每个周期更短的生产时间和更高的运营率。
以上仅以某些条件进行举例,具体情况请参考实际生产状况进行计算。
300万吨胜利原油常减压装置设计
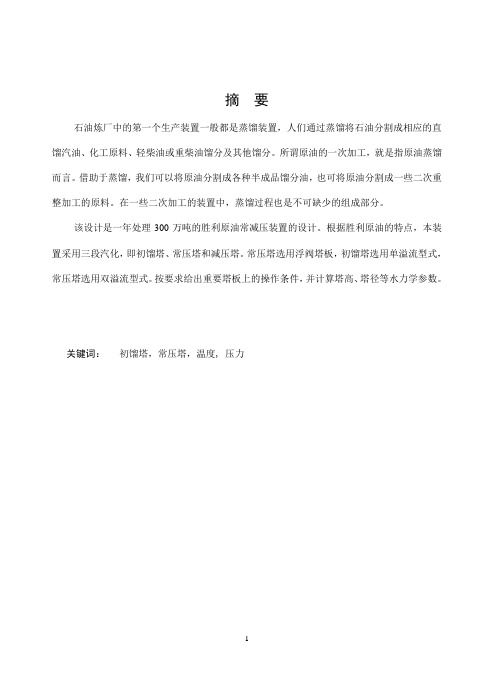
摘要石油炼厂中的第一个生产装置一般都是蒸馏装置,人们通过蒸馏将石油分割成相应的直馏汽油、化工原料、轻柴油或重柴油馏分及其他馏分。
所谓原油的一次加工,就是指原油蒸馏而言。
借助于蒸馏,我们可以将原油分割成各种半成品馏分油,也可将原油分割成一些二次重整加工的原料。
在一些二次加工的装置中,蒸馏过程也是不可缺少的组成部分。
该设计是一年处理300万吨的胜利原油常减压装置的设计。
根据胜利原油的特点,本装置采用三段汽化,即初馏塔、常压塔和减压塔。
常压塔选用浮阀塔板,初馏塔选用单溢流型式,常压塔选用双溢流型式。
按要求给出重要塔板上的操作条件,并计算塔高、塔径等水力学参数。
关键词:初馏塔,常压塔,温度, 压力AbstractIn the petroleum refinery first production installment all is the distilling apparatus generally. The people divide through the distillation the petroleum the corresponding straight run gasoline, the petroleum, the light diesel oil or the heavy oil fraction and other fractions. A so-called crude oil processing, Speaking of is refers to the crude distillation. With the aid of in distillation, we may divide the crude oil to the half-finished product fraction oil, also may divide the crude oil to some second reforming the processing the raw material. In some second processes in fixture, the distillation process also is the essential installment. This design is a year processes three million ton the Shengli crude oil atmospheric and vacuum distillation unit technological design. According to Shengli crude oil characteristic, this fixture uses three stage of vaporization, namely primary tower, atmospheric distillation tower and vacuum distillation tower. The atmospheric distillation tower selects the float valve column tray. The primary tower selects the single overflow pattern. The atmospheric distillation tower selects the double overflow pattern. According to the request, the operation condition on the important tower-board is provided, and such hydraulics parameters as the tower-high, tower-diameter, etc. are calculated.Key word: primary tower, atmospheric distillation tower, temperature , pressure目录第一章概述 (5)1.1石油蒸馏装置的简单介绍 (5)1.2 装置生产方案的确定 (5)1.3流程的确定 (6)1.4 设计的简单说明 (8)第二章基本数据计算 (11)2.1 油品物性 (11)2.1.1 相对密度指数ºAPI (11)2.1.2 体积平均沸点tv(ºC) (11)2.1.3 恩氏蒸馏90 % ~10 % 斜率 (12)2.1.4 中平均沸点tme = tv - me (12)2.1.5 特性因数K和相对分子量M (12)2.1.6 平衡汽化数据 (13)2.2 物料平衡 (15)2.2.1 油品实沸点切割 (15)2.2.2 物料平衡 (15)第三章初馏塔的设计 (16)3.1 初馏塔的工艺计算 (16)3.1.1 以塔为衡算系统,作出塔的物料平衡: (16)3.1.2 汽提水汽的用量 (16)3.1.3 初馏塔的汽化段温度 (17)3.1.4 塔顶温度的计算 (20)3.2 塔径与塔高的计算 (22)3.2.1初馏塔塔径的计算 (22)3.2.2 塔高的计算 (24)第四章常压塔的设计 (25)4.1 常压塔的工艺计算 (25)4.1.1 汽提蒸汽用量 (25)4.1.2 塔板型式和塔板数 (26)4.1.3 精馏塔计算草图 (26)4.1.4 操作压力 (28)4.1.5 汽化段温度 (28)4.1.6塔底温度 (31)4.1.7 塔顶及侧线温度的假设与回流热分配 (31)4.1.8 侧线及塔顶温度校核 (33)4.1.9全塔气液负荷分布图 (40)4.1.10常压塔塔板负荷计算结果 (61)4.1.11 气液相负荷图 (62)4.2 塔板的设计 (65)4.2.1 所需基本数据的计算 (65)4.2.2 塔径的计算 (66)4.2.3 塔高的计算 (66)4.2.4 溢流装置 (67)4.2.5 浮阀塔板布置 (68)4.3塔板水力学计算 (69)4.3.1气相通过浮阀塔塔板的压力计算 (69)4.3.2 淹塔 (70)4.3.3 雾沫夹带 (70)4.3.4 塔板负荷性能图 (71)结束语 (74)第一章概述1.1石油蒸馏装置的简单介绍石油是极其复杂的混合物。
年处理量420万吨常减压装置常压塔工艺设计

年处理量420万吨常减压装置常压塔工艺设计北京化工大学毕业设计(论文)题目:年处理量420万吨常减压蒸馏装置工艺设计院别:专业:化工工艺班级:学生:指导教师:摘要本设计主要是以某石化公司常减压为设计原型,主要计算数据取自生产实际。
所处理的原料为辽河混合原油,经过初馏塔初步分离后再经过常压塔和减压塔的分离得到不同馏程的馏分油。
在采用新工艺、新设备的同时优化了工艺流程,为了节能常压系统采用4台空冷器,为增加处理量,常压炉四路进料四路出料。
为使相当数量的中间馏分得到合理利用,因为它们是很多的二次加工原料,又能从中生产国民经济所需的各种润滑油、蜡、沥青的原料。
因此本设计采用三段汽化蒸馏,即预汽化—常压蒸馏—减压蒸馏。
关键词:常减压蒸馏;常压塔;工艺;设计目录第1章文献综述 (3)1.1 常减压蒸馏意义 (3)1.2 装置的概况和特点 (3)1.3 工艺流程概况 (4)1.4 主要原料、工艺及能耗指标 (7)第2章设计计算 (12)2.1 基础数据的换算 (12)2.1.1平均沸点 (12)2.1.2 确定各馏分相对分子质量和特性因数K (14)2.1.3 确定临界参数 (14)2.1.4 确定焦点参数 (15)2.1.5 确定平衡汽化温度 (15)2.1.6 确定实沸点温度 (19)2.1.7 原料及产品的有关参数汇总 (22)第三章物料衡算 (19)3.1 初馏塔的物料衡算 (23)3.2 常压塔的物料衡算 (20)第四章确定塔的相关参数和条件 (21)4.1 确定塔板数 (21)4.2 确定塔的操作条件 (21)4.2.1 确定塔的操作压力 (21)4.2.2 确定各侧线及塔底的气提蒸汽量 (23)4.2.3 确定过汽化段温度 (23)4.2.4 估算塔底温度 (27)4.2.5 假定塔顶及各侧线温度 (27)4.3 侧线及塔顶温度的校核 (28)4.4 塔经计算 (34)4.4.1 塔经的初算 (34)4.4.2计算出Wmax后再计算适宜的气速Wa (35)4.4.3计算气相空间截面积 (35)4.4.4 降液管内流体流速Vd (35)4.4.5计算降液管面积 (35)4.4.6塔横截面积Ft的计算 (36)4.5 塔高计算 (36)第五章存在的问题和设想 (37)5.1存在问题 (37)5.2设想 (37)5.3三废的处理情况及噪声的消除 (37)总结 (38)参考文献 (39)致谢 (40)北京工大学继续教育学院论文诚信承诺书本人郑重承诺:我所呈交的毕业设计《年处理量420万吨常减压蒸馏装置工艺设计》是在指导教师的指导下,独立开展研究取得的成果,文中引用他人的观点和材料,均在文后按顺序列出其参考文献,设计使用的数据真实可靠。
350万吨常减压车间工艺设计论文
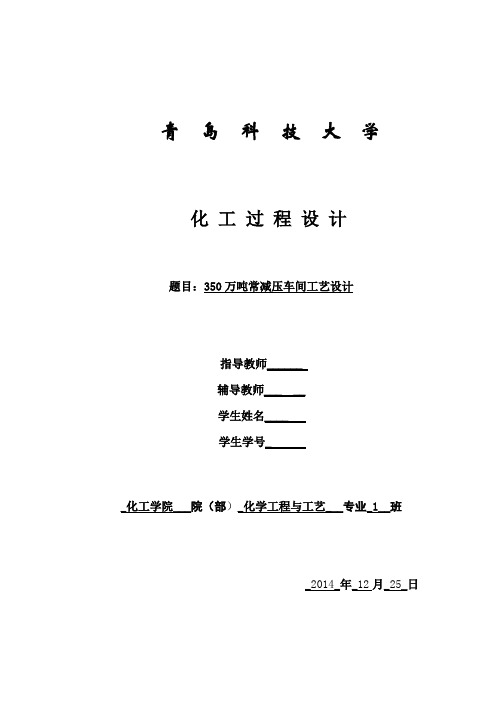
青岛科技大学化工过程设计题目:350万吨常减压车间工艺设计指导教师______辅导教师___ __学生姓名____学生学号__化工学院___院(部)_化学工程与工艺___专业_1__班_2014_年_12月_25_日目录中文摘要在本次设计中,我针对350万吨/年的常减压车间进行工艺设计。
内容主要包括:概述、工艺设计及计算、设备一览表、车间设备布置、非工艺部分设计、自动控制、安全与环境保护及个人的设计体会等。
其中最主要的部分是工艺设计及计算部分,其主要包含:物料衡算、能量衡算及主要设备的设计选型计算。
该计算主要利用Aspen Plus软件模拟的结果。
另外,我还用Auto CAD软件绘制了带控制点的工艺流程图、设备图和车间的平立面布置图。
关键词:工艺设计及计算;带控制点的工艺流程图;平立面布置图;ASPEN模拟1总论1.1胜利炼油厂简介中国石化集团齐鲁石化公司胜利炼油厂是全国颇具规模的炼油企业之一,于1966年4月动工建设,1967年10月投入生产,现已成为加工能力10500kt/a,占地面积587公顷的现代化石油加工企业。
该厂拥有生产装置和辅助生产装置60余套,拥有相应配套的科学研究、开发设计、计算机应用、环境保护等设施,是全国最具影响力的含硫原油加工以及沥青、硫磺生产和加氢工艺技术应用基地之一,生产的39种石油产品畅销全国27个省市,部分产品已进入国际市场。
胜利炼油厂坚持依靠科技求发展。
该厂VRDS-FCC组合工艺曾获联合国科技创新发明奖;石油苯、-10号军用柴油等产品曾获国家金奖;100号甲级道路沥青、1号喷气燃料、石油甲苯等产品曾获国家银奖;硫磺、90号车用汽油等18种产品曾获省(部)优名牌产品称号;汽油全部实现了高标号无铅系列化生产,其中97号无铅汽油填补了国内空白;1999年开发投产的高等级道路沥青,技术指标达到或超过了国外同类产品水平,从而标志着胜利炼油厂的沥青产品实现了系列化。
按照“质量第一,用户至上”的原则,胜利炼油厂建立了从原材料进厂、生产过程控制、新产品开发、标准化管理、产品出厂控制到售后服务的全过程质量控制保证体系。
推荐-年产350万吨连铸坯的转炉炼钢车间工艺设计-毕业论文

西安建筑科技大学华清学院本科毕业设计(论文)任务书题目:年产350万吨连铸坯的转炉炼钢车间工艺设计院(系):专业:冶金工程学生姓名:学号:指导教师(签名):主管院长(主任)(签名):时间:2013 年 2月 25 日年产350万吨全连铸坯的转炉炼钢车间设计专业:冶金工程姓名:指导老师:设计总说明当前的炼钢工艺中,较为普遍的是以高炉铁水为原料的转炉炼钢工艺和以预还原球团矿或高质量的工业废钢为原料的电弧(炉)工艺。
本设计为具有代表性的氧气顶底复吹工艺,预计年生产能力为350万吨良坯钢。
车间设有公称容量为150吨的转炉两座,LF精炼炉2座、板坯连铸机1台和方坯连铸机1台。
转炉的冶炼周期38分钟,吹氧时间16分钟。
根据国内外转炉炼钢技术的发展趋势,结合设计任务书中普碳钢和普碳钢的品种需要,选择了LF炉外精炼设备,进行全连铸生产。
最终确定如下的的工艺流程:铁水预处理→转炉炼钢→LF精炼→连铸。
本次设计在对转炉物料平衡和热平衡计算的基础上,对炼钢车间的主要设备参数进行了设计、选型,完成了主体设备选择、炼钢工艺设计、主厂房工艺布置和设备布置。
编制说明书一份,绘制转炉炉型图、车间平面图、剖面图各一张,并完成题目为炼钢节能技术思路与对策的专题。
关键词:炼钢,顶底复吹,工艺流程,精炼,连铸,Design DescriptionAt present, there are two main steel-making processes: converter steelmaking process with blast furnace hot metal and steel scrap as the raw materials and the arc (furnace) process with pre-reduction pellets or high-quality industrial steel scrap as raw materials. In this paper, the representative process combined-blowing oxygen converter process with a scale of 3.7×106 continuous casting billet annual is designed.. In the workshop, main equipments including 2×150t converters and its auxiliary equipments with 2 LF refining furnaces, 2 sets of slab continuous casting machines and a set of billet continuous casting machine are designed. The Smelting period is set for 38 minuter in which the actual oxygen blowing time is only 16 minutes.Depending on the development trend of steel-making process and the quality requirement of carbon steel and pressure vessel steel, LF refining is selected to fulfill continuous casting. Finally,the following process flow is choosed: Pretreatment→Converter→LF→CC.On the base of the material and heat equilibrim calculation,the size of steel-making plant workshop span and device assign, personnel placement is made .A project instruction is redacted ,furnace size graphic, a ground plane and a sectional view of the workshop are also submitted. And finally, the monograph which is about non-metallic inclusions in steel and its damagement is also finished.Key words:steel making, combined-blown, process, refining, continuous casting目录1 绪论 (1)1.1 转炉冶炼原理简介 (1)1.2 氧气转炉炼钢的特点 (2)1.3设计原则和指导思想 (2)1.4 产品方案 (3)2 氧气转炉炼钢车间 (5)2.1 初始条件 (5)2.2 公称容量选择 (5)2.3 转炉座数的确定 (5)2.4根据生产规模和产品方案计算出年需钢水量。
350吨剪切机的毕业设计

350吨剪切机的设计摘要本次毕业设计的题目是“350吨剪切机的设计”。
从传动形式上看可称为曲柄连杆式。
它的特点是下刀片固定不动,剪切过程是靠上刀片的运动来实现的。
其工作原理为电动机带动一轴转动,经第一级齿轮减速把运动传递到二轴,二轴再通过第二级齿轮减速把运动传递到曲轴,在离合器的作用下,曲轴通过它的偏心连杆带动滑块在机身的导轨内上下移动,上刃台固定在滑块的下端,随滑块一起移动实现剪切,下刃台与机身底座靠螺栓链接固定不动。
离合器每合一次,滑块上下往复运动一次,既东片完成一次剪切工作。
通过计算剪切机的结构参数和里能参数来确定主要零部件的尺寸,确定电动机的型号。
以材料力学的原理来校核主要部件的强度是否符合要求,最终确定剪切机的各部分的技术参数。
选择设备的润滑方式,在使用过程中的注意事项和简单的故障处理方法。
关键词:上浮动式;剪切机;里能参数;强度计算;润滑;维护Design for 350 tons of GuillotineAbstractThe graduation project is entitled“Design for 350 tons of Upper guillotine.”From the transmission link can be called crank.It is characterized by fixed underthe blade,the shear process of the blade by the campaign to achieve.Its workingprinciple for a motor driven rotating shaft,with the first-class sports gearto transfer to the second axis,the axis through the second stage transmissiongear to the crankshaft to movement:the role of the clutch,the crankshaft,throughits eccentric even slider stroke lead in the body moved up and down within theguide,on the edge of Taiwans fixed in the bottom of the slider,theslider,together with the realization of shear movement,under the edge of thebase p;atform an the body by bolts fixed link.Allthe clutch every time,a sliderup and down reciprocating motion,both completing a cut blade work.By calculatingthe shear plane in the structural parameters and parameters to determine thesize of the main components to determine the motor model.To the principles ofmechanics of materials to check whether the intensity of the main componentsto meet the requirements,and ultimately determine the shearing machine of thevarious parts of the technical parameters.Choice of lubrication equipment meansthe process in the use of note and simple failure handling.Key words:floating;shearing machine;force and energy parameters;strength calculation;lubrication;maintenance1绪论1.1选题背景与目的用于对轧件进行切头,切尾或剪切成规定尺寸的机械称为剪切机。
年产350万吨炼钢生铁高炉车间毕业设计

V1 =
2
= 炉腰体积 炉身体积
V3 =
12
2
3.5 (11 .9 2 11 .9 10.8 10.8 页 共 22 页
唐山科技职业技术学院(成)毕业设计(论文)
1 设计条件
1.1 主要技术经济指标 1.1.1 高炉有效容积利用系数(V ) 高炉有效容积利用系数即每昼夜生铁的产量与高炉有效容积之 比,即每昼夜 1m³有效容积的生铁产量。可用下式表示:
P V有
3
v
式中
v ---高炉有效容积利用系数,吨铁/米 ·昼夜
d = 0 . 23 I Vu = 0 . 23 i燃 0 . 95 2520 =10.73 1.1
取 d =10.8 m 合理
Vu 2520 = =27.5 A 2 10.8 4
第 5 页 共 22 页
唐山科技职业技术学院(成)毕业设计(论文)
2) 炉缸高度 渣口高度
hz = 1.27
第 4 页 共 22 页
唐山科技职业技术学院(成)毕业设计(论文)
2 高炉炉型设计
2.1 高炉炉型选择 高炉炉型选择五段式矮胖型。见图 1
图1
2520m 高炉炉型图
3
2.2 设计与计算 2.2.1 炉缸尺寸: 1) 炉缸直径 选定冶炼强度 I =0.95 t / m 3 d , 燃烧强度 i燃 =1.10 t / m 3 h 则 校核
年产量 年工作日
根据高炉炼铁车间日产量和高炉有效容积利用系数可以计算出炼 铁车间总容积( m 3 ): 高炉炼铁车间总容积=
年产350万吨炼钢生铁车间毕业设计

喷吹燃料系统 ●喷吹工艺:直接喷吹工艺 喷吹工艺: 喷吹工艺 喷吹设备: ●喷吹设备:由混合器或经 过分配器输送煤粉, 过分配器输送煤粉,通过喷枪送 到高炉直吹管吹入炉内
10
炉顶设备 ●并罐式无料钟炉顶 ●旋转溜槽布料
11
车间平面布置 • 半岛式布置 • 高炉和热风炉列线与车间调度线交角增 大到45° 大到 °; • 设有摆动流嘴,出一次铁可放置多个铁 设有摆动流嘴, 水罐车; 水罐车 • 在高炉两侧各有三条独立的有尽头的铁 水罐车停放线和一条辅助材料运输线。 水罐车停放线和一条辅助材料运输线。 出铁场与铁水罐车停放线垂直. 出铁场与铁水罐车停放线垂直
3
高炉炉型
★炉缸直径:d=10.8m ★死铁层厚度:1.5m ★ 炉腹角:810 ★炉喉直径 :8.1m ★炉身角:840 ★炉腰高度:2.8m ★炉缸高度 :h1=3.5m ★炉腰直径 :11.8m; ★炉腹高度:3.5m ★炉喉高度:2.0m ★炉身高度 :29.8m
4
高炉炉衬
• • • • • • 炉底: 炉底:采用全炭砖炉底 炉缸:采用炭砖炉缸, 炉缸:采用炭砖炉缸,以薄缝连接 炉腹:一层高铝砖, 炉腹:一层高铝砖,厚345mm 炉喉: 炉喉:炉喉钢砖 炉身: 炉身:冷却模块 炉腰:过度式, 炉腰:过度式,230+345高铝砖 高铝砖
8
送风系统、渣铁系统、 送风系统、渣铁系统、除尘系统 送风系统: ●送风系统: • 高炉鼓风机用离心式二座高炉装三座,一台备 高炉鼓风机用离心式二座高炉装三座 离心式二座高炉装三座, 用; • 每座高炉配备 座改进型内燃式热风炉。 每座高炉配备3座改进型内燃式热风炉 座改进型内燃式热风炉。 ●渣铁系统: 渣铁系统: 渣铁系统 • 采用轮法粒化渣处理工艺; 采用轮法粒化渣处理工艺; • 铁水处理采用铁水罐车和铸铁机。 铁水处理采用铁水罐车和铸铁机。 采用 ●除尘系统 : 除尘系统 • 高炉煤气为传统的湿法除尘; 高炉煤气为传统的湿法除尘; • 出铁均采用布袋
- 1、下载文档前请自行甄别文档内容的完整性,平台不提供额外的编辑、内容补充、找答案等附加服务。
- 2、"仅部分预览"的文档,不可在线预览部分如存在完整性等问题,可反馈申请退款(可完整预览的文档不适用该条件!)。
- 3、如文档侵犯您的权益,请联系客服反馈,我们会尽快为您处理(人工客服工作时间:9:00-18:30)。
青岛科技大学化工过程设计题目:350万吨常减压车间工艺设计指导教师______辅导教师___ __学生姓名____学生学号__化工学院___院(部)_化学工程与工艺___专业_1__班_2014_年_12月_25_日目录中文摘要在本次设计中,我针对350万吨/年的常减压车间进行工艺设计。
内容主要包括:概述、工艺设计及计算、设备一览表、车间设备布置、非工艺部分设计、自动控制、安全与环境保护及个人的设计体会等。
其中最主要的部分是工艺设计及计算部分,其主要包含:物料衡算、能量衡算及主要设备的设计选型计算。
该计算主要利用Aspen Plus软件模拟的结果。
另外,我还用Auto CAD软件绘制了带控制点的工艺流程图、设备图和车间的平立面布置图。
关键词:工艺设计及计算;带控制点的工艺流程图;平立面布置图;ASPEN模拟1总论1.1胜利炼油厂简介中国石化集团齐鲁石化公司胜利炼油厂是全国颇具规模的炼油企业之一,于1966年4月动工建设,1967年10月投入生产,现已成为加工能力10500kt/a,占地面积587公顷的现代化石油加工企业。
该厂拥有生产装置和辅助生产装置60余套,拥有相应配套的科学研究、开发设计、计算机应用、环境保护等设施,是全国最具影响力的含硫原油加工以及沥青、硫磺生产和加氢工艺技术应用基地之一,生产的39种石油产品畅销全国27个省市,部分产品已进入国际市场。
胜利炼油厂坚持依靠科技求发展。
该厂VRDS-FCC组合工艺曾获联合国科技创新发明奖;石油苯、-10号军用柴油等产品曾获国家金奖;100号甲级道路沥青、1号喷气燃料、石油甲苯等产品曾获国家银奖;硫磺、90号车用汽油等18种产品曾获省(部)优名牌产品称号;汽油全部实现了高标号无铅系列化生产,其中97号无铅汽油填补了国内空白;1999年开发投产的高等级道路沥青,技术指标达到或超过了国外同类产品水平,从而标志着胜利炼油厂的沥青产品实现了系列化。
按照“质量第一,用户至上”的原则,胜利炼油厂建立了从原材料进厂、生产过程控制、新产品开发、标准化管理、产品出厂控制到售后服务的全过程质量控制保证体系。
该厂于1998年通过了ISO9002国际质量体系贯标认证和ISO10012计量检测体系贯标认证;2001年3月被中国实验室国家认可委员会等机构评定为“沥青产品检验实验室”。
齐鲁石化坚持科技创新,1996年以来,累计完成科研课题950项,成果鉴定169项,获得专利授权93项,16项科技成果获国家级奖励。
先后与美国、德国、英国、日本、意大利、荷兰、韩国等多家国外公司进行了成功合作。
公司凭籍自身丰富的工程建设经验,依托雄厚的技术实力和可靠的服务质量,在国内树立了良好的企业形象,形成了可研、设计、采购、施工和开车服务管理等系统的服务网络。
自主开发的硫磺回收技术及催化剂、炼厂气等温绝热加氢技术、轻烃醚化技术等填补了国内空白。
为全国“科技进步百强企业”。
在中国石油和化学工业协会、中国化工企业管理协会、中国化工情报信息协会联合发布的2003年中国化工企业500强排行榜中,齐鲁分公司、齐鲁股份有限公司分别名列第7位和第27位。
1.2车间简介齐鲁分公司胜利炼油厂自2004年加工胜利高硫高酸原油以来,一、二套常减压装置存在着设备材质低、腐蚀严重等安全隐患,为消除这些安全隐患,提高装置的技术水平,实现节能降耗,增加炼油厂的经济效益和综合竞争力,炼油厂新建一套800万吨/年常减压装置,以取代原一、二套常减压装置。
新建常减压装置由中国石化集团洛阳石油化工工程公司设计,装置总占地为13320m2,设计规模为800万吨/年,年开工时间为8400小时。
装置为燃料−化工型蒸馏装置,主要由换热、闪蒸、常压蒸馏、减压蒸馏、一脱三注、不凝气脱硫等部分组成,采用电脱盐→闪蒸罐→常压塔→减压塔的工艺路线,设计加工的原油为高硫高酸原油和胜利原油的混合油,其中高硫高酸原油670万吨/年,胜利原油130万吨/年。
混合原油酸值为1.685mgKOH/g,硫含量为1.97%,属高硫高酸-中间基原油。
分馏、吸收部分西侧为主管廊,东侧布置立、卧式设备。
管廊下地面布置机泵,管廊上第一层布置冷换设备,第二层布置空气冷却器。
南头布置气压机部分。
与系统相关的原料及产品由主管廊西侧进出,水系统由装置南端进出。
1.3、产品介绍主要产品:石脑油、柴油、蜡油和减压渣油。
产品去向:气体:常顶不凝气增压后送焦化装置;减顶气经脱硫后送本装置加热炉;石脑油:去连续重整罐区;柴油(常一线油):去加氢罐区;柴油(常二线油):柴油加氢装置或加氢罐区;柴油(常三线油):去柴油加氢装置或加氢罐区;柴油(减顶油):去四罐区;柴油(减一线油):去一催化或三罐区或加氢装置;蜡油(减二线油):去SSOT(单段高压蜡油加氢裂化装置)或加氢裂化罐区;蜡油(减三线油):去一催化、去VRDS(渣油加氢处理)或加氢裂化罐区或蜡油加氢装置;蜡油(减四线油):去VRDS(渣油加氢处理);减压渣油:去南焦化、北焦化、一罐区。
表1-1 常减压装置产品说明1.4、工艺流程与生产原理1.4.1 工艺流程(一)工艺流程简述装置设计加工原油为高硫高酸原油和胜利原油的混和原油,混合原油酸值为1.685mgKOH/g,硫含量为1.98%(m),属高硫高酸-中间基原油。
装置生产石脑油、柴油(加氢原料)、蜡油(加氢原料、催化原料)和减压渣油(焦化原料)。
装置采取的工艺技术路线为原油换热→电脱盐→原油换热→闪蒸→闪底油换热→常压炉→常压塔→减压炉→减压塔的三级蒸馏路线,减压采用深拔工艺技术。
装置内设置不凝气脱硫设施,采用甲基二乙醇胺洗脱硫工艺。
一、常压部分原油自罐区来进装置后分4路。
第一路原油依次经E-102(原油-常一线换热器)、E-103(原油-常一中(Ⅱ)换热器)和E-104A.B.C(原油-减压渣油(Ⅵ)换热器)与热源换热到147℃。
第二路原油依次经E-101A(原油-常顶循换热器)、E-105(原油-减一中换热器)、E-106A.B(原油-常二线(Ⅱ)换热器)和E-107(原油-减三线换热器)与热源换热到145℃。
第三路原油依次经E-101B(原油-常顶循换热器)、E-109A.B(原油-减二线及二中(Ⅲ)换热器)与热源换热到150℃。
第四路原油依次经E-101C(原油-常顶循换热器)、E-110(原油-减二线换热器)、E-111A.B(原油-常三线(Ⅲ)换热器)和E-112(原油-常一中(Ⅰ)换热器)与热源进行换热到141℃。
上述四路原油混合后经E-113(原油-减压渣油(Ⅴ)换热器)与热源换热到155℃后进电脱盐部分进行脱盐脱水,原油经电脱盐后均分成三路,第一路脱后原油依次经E-114(原油-常二中(Ⅱ)换热器)、E-115 A.B(原油-减四线(Ⅱ)换热器)和E-116 A.B(原油-减渣(Ⅳ)换热器)与热源换热到237℃。
第二路脱后原油依次经E-117(原油-常三线(Ⅱ)换热器)、E-118A.B(原油-减二线及二中(Ⅱ)换热器)和E-119 A.B(原油-减三线及三中(Ⅲ)换热器)与热源换热到237℃。
第三路脱后原油依次经E-120(原油-常二线(Ⅰ)换热器)、E-121(原油-减三线及三中(Ⅳ)换热器)和E-122A.B(原油-减二线及二中(Ⅰ)换热器)与热源换热到237℃。
上述三路脱后原油合并后进T-101(闪蒸塔)。
T-101(闪蒸塔)塔顶油气进塔T-102(常压塔)。
闪底油由P-102A.B.C(闪底油泵)抽出均分两路与热源换热。
第一路闪底油依次经E-123(闪底油-常二中(Ⅰ)换热器)、E-124A.B.C.D(闪底油-减三线及三中(Ⅱ)换热器)、E-125 A.B.C.D(闪底油-减压渣油(Ⅱ)换热器)和E-126(闪底油-减四线(Ⅰ)换热器)换热到约306℃。
第二路闪底油依次经E-127(闪底油-常三线(Ⅰ)换热器)、E-128(闪底油-减压渣油(Ⅲ)换热器)、E-129 A.B.C.D(闪底油-减三线及三中(Ⅰ)换热器)和E-130 A.B.C.D (闪底油-减压渣油(Ⅰ)换热器)换热到约314℃。
上述两路闪底油合并后约310℃进入F-101(常压炉),加热至373℃后进入T-102(常压塔)。
T-102塔顶油气经EA-101A~L(常顶油气空冷器)及E-131(常顶油气冷却器)冷凝冷却到40℃后进入V-102(常压塔顶回流罐)进行气液分离。
分离出的常顶油经P-103A.B(常项油泵)抽出,一部分作为常顶回流,另一部分作为产品出装置。
分离出的含硫污水经泵P-119A.B(常顶排水泵)送往酸性水汽提装置。
分离出的不凝气经P-124 A.B(不凝气水环泵)加压后送至焦化。
常一线油从T-102第14层塔板自流进入T-103(常压汽提塔)上段,采用蒸汽进行汽提,常一线油由P-105A.B(常一线泵)抽出,经E-102、EA-102(常一线空冷器)和E-132(常一线油冷却器)换热冷却至40℃送到柴油加氢罐区。
常二线油从T-102第24层或第26层塔板自流进入T-103中段,采用蒸汽进行汽提(根据情况决定是否开),汽提后的常二线油由P-107A.B(常二线泵)抽出,经E-120、E-106 A.B、EA-103A.B(常二线空冷器)换热冷却至60℃送到柴油加氢装置。
加氢装置暂时不开时,再经E-133(常二线冷却器)冷却至50℃送到罐区。
常三线油从T-102第34层或36层塔板自流进入T-103下段,采用蒸汽进行汽提(根据情况决定是否开),汽提后的常三线油由P-109A.B(常三线泵)抽出,经E-127、E-117、E111A.B和EA-104A.B(常三线空冷器)换热和冷却至80℃,再经P-134A.B(常三线接力泵)加压送到柴油加氢装置。
加氢装置暂时不开时,常三线再经EA-105A.B(常三线空冷器)冷却至55℃后,经P-134A.B(常三线接力泵)加压送出装置。
常顶循油由泵P-104A.B(常顶循油泵)自T-102第4层塔盘抽出,经E-101A.B.C换热后返回第1层塔盘上。
常一中油由泵P-106A.B(常一中油泵)自T102第18层塔盘抽出经E-112、E-103换热后返回第15层塔盘上。
常二中油由泵P-108A.B(常二中油泵)自T102第30层塔盘抽出,经E-123、E-114换热后返回第27层塔盘上。
常压塔底油由泵P-110A.B.C(常底油泵)抽出送F-102(减压炉)升温到约403℃后进入减压塔。
二、减压部分减顶油气经EJ-101A.B(减顶增压器)、E-144 A.B(减顶增压冷凝器)后,液相(油和水)经大气腿进入V-103(减顶一级油水分离罐),未凝气体经EJ-102A.B(减顶一级抽空器)、E-145A.B(减项一级抽空冷凝器)后,液相(油和水)经大气腿进入V-103,未凝油气经P-125(减顶水环泵)增压后,气、油、水的混合物在V-104(减顶二级油水分离罐)中分离,不凝气经V-107(减顶气液封罐)、V-108(减顶气分液罐)至T-105(减顶不凝气脱硫塔)进行脱硫后,不凝气进V-126(减顶脱硫不凝气分液罐)分液后进加热炉燃烧。