MAX1805MEE中文资料
MAX13085EESA-T中文资料

General DescriptionThe MAX13080E–MAX13089E +5.0V, ±15kV ESD-protect-ed, RS-485/RS-422 transceivers feature one driver and one receiver. These devices include fail-safe circuitry,guaranteeing a logic-high receiver output when receiver inputs are open or shorted. The receiver outputs a logic-high if all transmitters on a terminated bus are disabled (high impedance). The MAX13080E–MAX13089E include a hot-swap capability to eliminate false transitions on the bus during power-up or hot insertion.The MAX13080E/MAX13081E/MAX13082E feature reduced slew-rate drivers that minimize EMI and reduce reflections caused by improperly terminated cables, allowing error-free data transmission up to 250kbps. The MAX13083E/MAX13084E/MAX13085E also feature slew-rate-limited drivers but allow transmit speeds up to 500kbps. The MAX13086E/MAX13087E/MAX13088E driver slew rates are not limited, making transmit speeds up to 16Mbps possible. The MAX13089E slew rate is pin selectable for 250kbps,500kbps, and 16Mbps.The MAX13082E/MAX13085E/MAX13088E are intended for half-duplex communications, and the MAX13080E/MAX13081E/MAX13083E/MAX13084E/MAX13086E/MAX13087E are intended for full-duplex communica-tions. The MAX13089E is selectable for half-duplex or full-duplex operation. It also features independently programmable receiver and transmitter output phase through separate pins.The MAX13080E–MAX13089E transceivers draw 1.2mA of supply current when unloaded or when fully loaded with the drivers disabled. All devices have a 1/8-unit load receiver input impedance, allowing up to 256transceivers on the bus.The MAX13080E/MAX13083E/MAX13086E/MAX13089E are available in 14-pin PDIP and 14-pin SO packages.The MAX13081E/MAX13082E/MAX13084E/MAX13085E/MAX13087E/MAX13088E are available in 8-pin PDIP and 8-pin SO packages. The devices operate over the com-mercial, extended, and automotive temperature ranges.ApplicationsUtility Meters Lighting Systems Industrial Control Telecom Security Systems Instrumentation ProfibusFeatures♦+5.0V Operation♦Extended ESD Protection for RS-485/RS-422 I/O Pins±15kV Human Body Model ♦True Fail-Safe Receiver While Maintaining EIA/TIA-485 Compatibility ♦Hot-Swap Input Structures on DE and RE ♦Enhanced Slew-Rate Limiting Facilitates Error-Free Data Transmission(MAX13080E–MAX13085E/MAX13089E)♦Low-Current Shutdown Mode (Except MAX13081E/MAX13084E/MAX13087E)♦Pin-Selectable Full-/Half-Duplex Operation (MAX13089E)♦Phase Controls to Correct for Twisted-Pair Reversal (MAX13089E)♦Allow Up to 256 Transceivers on the Bus ♦Available in Industry-Standard 8-Pin SO PackageMAX13080E–MAX13089E+5.0V , ±15kV ESD-Protected, Fail-Safe, Hot-Swap, RS-485/RS-422 Transceivers________________________________________________________________Maxim Integrated Products 1Ordering Information19-3590; Rev 1; 4/05For pricing, delivery, and ordering information,please contact Maxim/Dallas Direct!at 1-888-629-4642, or visit Maxim’s website at .Selector Guide, Pin Configurations, and Typical Operating Circuits appear at end of data sheet.Ordering Information continued at end of data sheet.M A X 13080E –M A X 13089E+5.0V , ±15kV ESD-Protected, Fail-Safe, Hot-Swap, RS-485/RS-422 Transceivers 2_______________________________________________________________________________________ABSOLUTE MAXIMUM RATINGSDC ELECTRICAL CHARACTERISTICS(V CC = +5.0V ±10%, T A = T MIN to T MAX , unless otherwise noted. Typical values are at V CC = +5.0V and T A = +25°C.) (Note 1)Stresses beyond those listed under “Absolute Maximum Ratings” may cause permanent damage to the device. These are stress ratings only, and functional operation of the device at these or any other conditions beyond those indicated in the operational sections of the specifications is not implied. Exposure to absolute maximum rating conditions for extended periods may affect device reliability.(All Voltages Referenced to GND)Supply Voltage (V CC ).............................................................+6V Control Input Voltage (RE , DE, SLR,H/F , TXP, RXP)......................................................-0.3V to +6V Driver Input Voltage (DI)...........................................-0.3V to +6V Driver Output Voltage (Z, Y, A, B).............................-8V to +13V Receiver Input Voltage (A, B)....................................-8V to +13V Receiver Input VoltageFull Duplex (A, B)..................................................-8V to +13V Receiver Output Voltage (RO)....................-0.3V to (V CC + 0.3V)Driver Output Current.....................................................±250mAContinuous Power Dissipation (T A = +70°C)8-Pin SO (derate 5.88mW/°C above +70°C).................471mW 8-Pin Plastic DIP (derate 9.09mW/°C above +70°C).....727mW 14-Pin SO (derate 8.33mW/°C above +70°C)...............667mW 14-Pin Plastic DIP (derate 10.0mW/°C above +70°C)...800mW Operating Temperature RangesMAX1308_EC_ _.................................................0°C to +75°C MAX1308_EE_ _..............................................-40°C to +85°C MAX1308_EA_ _............................................-40°C to +125°C Junction Temperature......................................................+150°C Storage Temperature Range.............................-65°C to +150°C Lead Temperature (soldering, 10s).................................+300°CMAX13080E–MAX13089E+5.0V , ±15kV ESD-Protected, Fail-Safe, Hot-Swap, RS-485/RS-422 Transceivers_______________________________________________________________________________________3DC ELECTRICAL CHARACTERISTICS (continued)(V CC = +5.0V ±10%, T A = T MIN to T MAX , unless otherwise noted. Typical values are at V CC = +5.0V and T A = +25°C.) (Note 1)M A X 13080E –M A X 13089E+5.0V , ±15kV ESD-Protected, Fail-Safe, Hot-Swap, RS-485/RS-422 Transceivers 4_______________________________________________________________________________________DRIVER SWITCHING CHARACTERISTICSMAX13080E/MAX13081E/MAX13082E/MAX13089E WITH SRL = UNCONNECTED (250kbps)(V CC = +5.0V ±10%, T A = T MIN to T MAX , unless otherwise noted. Typical values are at V CC = +5.0V and T A = +25°C.)RECEIVER SWITCHING CHARACTERISTICSMAX13080E/MAX13081E/MAX13082E/MAX13089E WITH SRL = UNCONNECTED (250kbps)(V CC = +5.0V ±10%, T A = T MIN to T MAX , unless otherwise noted. Typical values are at V CC = +5.0V and T A = +25°C.)MAX13080E–MAX13089E+5.0V , ±15kV ESD-Protected, Fail-Safe, Hot-Swap, RS-485/RS-422 Transceivers_______________________________________________________________________________________5DRIVER SWITCHING CHARACTERISTICSMAX13083E/MAX13084E/MAX13085E/MAX13089E WITH SRL = V CC (500kbps)(V CC = +5.0V ±10%, T A = T MIN to T MAX , unless otherwise noted. Typical values are at V CC = +5.0V and T A = +25°C.)RECEIVER SWITCHING CHARACTERISTICSMAX13083E/MAX13084E/MAX13085E/MAX13089E WITH SRL = V CC (500kbps)(V CC = +5.0V ±10%, T A = T MIN to T MAX , unless otherwise noted. Typical values are at V CC = +5.0V and T A = +25°C.)M A X 13080E –M A X 13089E+5.0V , ±15kV ESD-Protected, Fail-Safe, Hot-Swap, RS-485/RS-422 Transceivers 6_______________________________________________________________________________________DRIVER SWITCHING CHARACTERISTICSMAX13086E/MAX13087E/MAX13088E/MAX13089E WITH SRL = GND (16Mbps)(V CC = +5.0V ±10%, T A = T MIN to T MAX , unless otherwise noted. Typical values are at V CC = +5.0V and T A = +25°C.)RECEIVER SWITCHING CHARACTERISTICSMAX13086E/MAX13087E/MAX13088E/MAX13089E WITH SRL = GND (16Mbps)(V CC = +5.0V ±10%, T A = T MIN to T MAX , unless otherwise noted. Typical values are at V CC = +5.0V and T A = +25°C.)Note 2:∆V OD and ∆V OC are the changes in V OD and V OC , respectively, when the DI input changes state.Note 3:The short-circuit output current applies to peak current just prior to foldback current limiting. The short-circuit foldback outputcurrent applies during current limiting to allow a recovery from bus contention.MAX13080E–MAX13089E+5.0V , ±15kV ESD-Protected, Fail-Safe, Hot-Swap, RS-485/RS-422 Transceivers_______________________________________________________________________________________70.800.901.501.101.001.201.301.401.60-40-10520-253550958011065125SUPPLY CURRENT vs. TEMPERATURETEMPERATURE (°C)S U P P L Y C U R R E N T (m A )0201040305060021345OUTPUT CURRENTvs. RECEIVER OUTPUT-HIGH VOLTAGEM A X 13080E -89E t o c 02OUTPUT HIGH VOLTAGE (V)O U T P U T C U R R E N T (m A )20104030605070021345OUTPUT CURRENTvs. RECEIVER OUTPUT-LOW VOLTAGEM A X 13080E -89E t o c 03OUTPUT LOW VOLTAGE (V)O U T P U T C U R R E N T (m A )4.04.44.24.84.65.25.05.4RECEIVER OUTPUT-HIGH VOLTAGEvs. TEMPERATURETEMPERATURE (°C)O U T P U T H I G H V O L T A G E (V )-40-10520-2535509580110651250.10.70.30.20.40.50.60.8RECEIVER OUTPUT-LOW VOLTAGEvs. TEMPERATURETEMPERATURE (°C)O U T P U T L O W V O L T A G E (V )-40-10520-25355095801106512502040608010012014016012345DRIVER DIFFERENTIAL OUTPUT CURRENT vs. DIFFERENTIAL OUTPUT VOLTAGEDIFFERENTIAL OUTPUT VOLTAGE (V)D I F FE R E N T I A L O U T P U T C U R R E N T (m A )2.02.82.43.63.24.44.04.8DRIVER DIFFERENTIAL OUTPUT VOLTAGE vs. TEMPERATURED I F FE R E N T I A L O U T P U T V O L T A G E (V )-40-10520-253550958011065125TEMPERATURE (°C)40201008060120140180160200-7-5-4-6-3-2-1012354OUTPUT CURRENT vs. TRANSMITTEROUTPUT-HIGH VOLTAGEOUTPUT HIGH VOLTAGE (V)O U T P U T C U R R E N T (m A )60402080100120140160180200042681012OUTPUT CURRENT vs. TRANSMITTEROUTPUT-LOW VOLTAGEOUTPUT-LOW VOLTAGE (V)O U T P U T C U R R E N T (m A )Typical Operating Characteristics(V CC = +5.0V, T A = +25°C, unless otherwise noted.)M A X 13080E –M A X 13089E+5.0V , ±15kV ESD-Protected, Fail-Safe, Hot-Swap, RS-485/RS-422 Transceivers 8_______________________________________________________________________________________21543679810SHUTDOWN CURRENT vs. TEMPERATUREM A X 13080E -89E t o c 10S H U T D O W N C U R R E N T (µA )-40-10520-253550958011065125TEMPERATURE (°C)600800700100090011001200DRIVER PROPAGATION DELAY vs. TEMPERATURE (250kbps)D R I VE R P R O P A G A T I O N D E L A Y (n s )-40-10520-253550958011065125TEMPERATURE (°C)300400350500450550600DRIVER PROPAGATION DELAY vs. TEMPERATURE (500kbps)D R I VE R P R O P A G A T I O N D E L A Y (n s )-40-10520-253550958011065125TEMPERATURE (°C)1070302040506080DRIVER PROPAGATION DELAY vs. TEMPERATURE (16Mbps)D R I VE R P R O P A G A T I O N D E L A Y (n s )-40-10520-253550958011065125TEMPERATURE (°C)40201008060120140160180RECEIVER PROPAGATION DELAYvs. TEMPERATURE (250kpbs AND 500kbps)R E C E I V E R P R O P A G A T I O N D E L A Y (n s )-40-10520-253550958011065125TEMPERATURE (°C)40201008060120140160180RECEIVER PROPAGATION DELAYvs. TEMPERATURE (16Mbps)R EC E I V E R P R O P A G AT I O N D E L A Y (n s )-40-10520-253550958011065125TEMPERATURE (°C)2µs/div DRIVER PROPAGATION DELAY (250kbps)DI 2V/divV Y - V Z 5V/divR L = 100Ω200ns/divRECEIVER PROPAGATION DELAY(250kbps AND 500kbps)V A - V B 5V/divRO 2V/divTypical Operating Characteristics (continued)(V CC = +5.0V, T A = +25°C, unless otherwise noted.)MAX13080E–MAX13089E+5.0V , ±15kV ESD-Protected, Fail-Safe, Hot-Swap, RS-485/RS-422 Transceivers_______________________________________________________________________________________9Test Circuits and Waveforms400ns/divDRIVER PROPAGATION DELAY (500kbps)DI 2V/divR L = 100ΩV Y - V Z 5V/div10ns/div DRIVER PROPAGATION DELAY (16Mbps)DI 2V/divR L = 100ΩV Y 2V/divV Z 2V/div40ns/divRECEIVER PROPAGATION DELAY (16Mbps)V B 2V/divR L = 100ΩRO 2V/divV A 2V/divTypical Operating Characteristics (continued)(V CC = +5.0V, T A = +25°C, unless otherwise noted.)Figure 2. Driver Timing Test CircuitM A X 13080E –M A X 13089E+5.0V , ±15kV ESD-Protected, Fail-Safe, Hot-Swap, RS-485/RS-422 Transceivers 10______________________________________________________________________________________Test Circuits and Waveforms (continued)Figure 4. Driver Enable and Disable Times (t DHZ , t DZH , t DZH(SHDN))DZL DLZ DLZ(SHDN)MAX13080E–MAX13089E+5.0V , ±15kV ESD-Protected, Fail-Safe, Hot-Swap, RS-485/RS-422 TransceiversTest Circuits and Waveforms (continued)Figure 6. Receiver Propagation Delay Test CircuitM A X 13080E –M A X 13089E+5.0V , ±15kV ESD-Protected, Fail-Safe, Hot-Swap, RS-485/RS-422 TransceiversMAX13080E–MAX13089E+5.0V , ±15kV ESD-Protected, Fail-Safe, Hot-Swap, RS-485/RS-422 TransceiversMAX13080E/MAX13083E/MAX13086EMAX13081E/MAX13084E/MAX13086E/MAX13087EFunction TablesM A X 13080E –M A X 13089E+5.0V , ±15kV ESD-Protected, Fail-Safe, Hot-Swap, RS-485/RS-422 Transceivers MAX13082E/MAX13085E/MAX13088EFunction Tables (continued)MAX13089EDetailed Description The MAX13080E–MAX13089E high-speed transceivers for RS-485/RS-422 communication contain one driver and one receiver. These devices feature fail-safe circuit-ry, which guarantees a logic-high receiver output when the receiver inputs are open or shorted, or when they are connected to a terminated transmission line with all dri-vers disabled (see the Fail-Safe section). The MAX13080E/MAX13082E/MAX13083E/MAX13085E/ MAX13086E/MAX13088E/MAX13089E also feature a hot-swap capability allowing line insertion without erroneous data transfer (see the Hot Swap Capability section). The MAX13080E/MAX13081E/MAX13082E feature reduced slew-rate drivers that minimize EMI and reduce reflec-tions caused by improperly terminated cables, allowing error-free data transmission up to 250kbps. The MAX13083E/MAX13084E/MAX13085E also offer slew-rate limits allowing transmit speeds up to 500kbps. The MAX13086E/MAX13087E/MAX13088Es’ driver slew rates are not limited, making transmit speeds up to 16Mbps possible. The MAX13089E’s slew rate is selectable between 250kbps, 500kbps, and 16Mbps by driving a selector pin with a three-state driver.The MAX13082E/MAX13085E/MAX13088E are half-duplex transceivers, while the MAX13080E/MAX13081E/ MAX13083E/MAX13084E/MAX13086E/MAX13087E are full-duplex transceivers. The MAX13089E is selectable between half- and full-duplex communication by driving a selector pin (H/F) high or low, respectively.All devices operate from a single +5.0V supply. Drivers are output short-circuit current limited. Thermal-shutdown circuitry protects drivers against excessive power dissi-pation. When activated, the thermal-shutdown circuitry places the driver outputs into a high-impedance state.Receiver Input Filtering The receivers of the MAX13080E–MAX13085E, and the MAX13089E when operating in 250kbps or 500kbps mode, incorporate input filtering in addition to input hysteresis. This filtering enhances noise immunity with differential signals that have very slow rise and fall times. Receiver propagation delay increases by 25% due to this filtering.Fail-Safe The MAX13080E family guarantees a logic-high receiver output when the receiver inputs are shorted or open, or when they are connected to a terminated transmission line with all drivers disabled. This is done by setting the receiver input threshold between -50mV and -200mV. If the differential receiver input voltage (A - B) is greater than or equal to -50mV, RO is logic-high. If (A - B) is less than or equal to -200mV, RO is logic-low. In the case of a terminated bus with all transmitters disabled, the receiv-er’s differential input voltage is pulled to 0V by the termi-nation. With the receiver thresholds of the MAX13080E family, this results in a logic-high with a 50mV minimumnoise margin. Unlike previous fail-safe devices, the-50mV to -200mV threshold complies with the ±200mVEIA/TIA-485 standard.Hot-Swap Capability (Except MAX13081E/MAX13084E/MAX13087E)Hot-Swap InputsWhen circuit boards are inserted into a hot or powered backplane, differential disturbances to the data buscan lead to data errors. Upon initial circuit board inser-tion, the data communication processor undergoes itsown power-up sequence. During this period, the processor’s logic-output drivers are high impedanceand are unable to drive the DE and RE inputs of these devices to a defined logic level. Leakage currents up to±10µA from the high-impedance state of the proces-sor’s logic drivers could cause standard CMOS enableinputs of a transceiver to drift to an incorrect logic level. Additionally, parasitic circuit board capacitance couldcause coupling of V CC or GND to the enable inputs. Without the hot-swap capability, these factors could improperly enable the transceiver’s driver or receiver.When V CC rises, an internal pulldown circuit holds DElow and RE high. After the initial power-up sequence,the pulldown circuit becomes transparent, resetting thehot-swap tolerable input.Hot-Swap Input CircuitryThe enable inputs feature hot-swap capability. At theinput there are two NMOS devices, M1 and M2 (Figure 9). When V CC ramps from zero, an internal 7µstimer turns on M2 and sets the SR latch, which alsoturns on M1. Transistors M2, a 1.5mA current sink, andM1, a 500µA current sink, pull DE to GND through a5kΩresistor. M2 is designed to pull DE to the disabledstate against an external parasitic capacitance up to100pF that can drive DE high. After 7µs, the timer deactivates M2 while M1 remains on, holding DE low against three-state leakages that can drive DE high. M1 remains on until an external source overcomes the required input current. At this time, the SR latch resetsand M1 turns off. When M1 turns off, DE reverts to a standard, high-impedance CMOS input. Whenever V CCdrops below 1V, the hot-swap input is reset.For RE there is a complementary circuit employing two PMOS devices pulling RE to V CC. MAX13080E–MAX13089E+5.0V, ±15kV ESD-Protected, Fail-Safe, Hot-Swap, RS-485/RS-422 TransceiversM A X 13080E –M A X 13089EMAX13089E ProgrammingThe MAX13089E has several programmable operating modes. Transmitter rise and fall times are programma-ble, resulting in maximum data rates of 250kbps,500kbps, and 16Mbps. To select the desired data rate,drive SRL to one of three possible states by using a three-state driver: V CC , GND, or unconnected. F or 250kbps operation, set the three-state device in high-impedance mode or leave SRL unconnected. F or 500kbps operation, drive SRL high or connect it to V CC .F or 16Mbps operation, drive SRL low or connect it to GND. SRL can be changed during operation without interrupting data communications.Occasionally, twisted-pair lines are connected backward from normal orientation. The MAX13089E has two pins that invert the phase of the driver and the receiver to cor-rect this problem. F or normal operation, drive TXP and RXP low, connect them to ground, or leave them uncon-nected (internal pulldown). To invert the driver phase,drive TXP high or connect it to V CC . To invert the receiver phase, drive RXP high or connect it to V CC . Note that the receiver threshold is positive when RXP is high.The MAX13089E can operate in full- or half-duplex mode. Drive H/F low, leave it unconnected (internal pulldown), or connect it to GND for full-duplex opera-tion. Drive H/F high for half-duplex operation. In full-duplex mode, the pin configuration of the driver and receiver is the same as that of a MAX13080E. In half-duplex mode, the receiver inputs are internally connect-ed to the driver outputs through a resistor-divider. This effectively changes the function of the device’s outputs.Y becomes the noninverting driver output and receiver input, Z becomes the inverting driver output and receiver input. In half-duplex mode, A and B are still connected to ground through an internal resistor-divider but they are not internally connected to the receiver.±15kV ESD ProtectionAs with all Maxim devices, ESD-protection structures are incorporated on all pins to protect against electro-static discharges encountered during handling and assembly. The driver outputs and receiver inputs of the MAX13080E family of devices have extra protection against static electricity. Maxim’s engineers have devel-oped state-of-the-art structures to protect these pins against ESD of ±15kV without damage. The ESD struc-tures withstand high ESD in all states: normal operation,shutdown, and powered down. After an ESD event, the MAX13080E–MAX13089E keep working without latchup or damage.ESD protection can be tested in various ways. The transmitter outputs and receiver inputs of the MAX13080E–MAX13089E are characterized for protec-tion to the following limits:•±15kV using the Human Body Model•±6kV using the Contact Discharge method specified in IEC 61000-4-2ESD Test ConditionsESD performance depends on a variety of conditions.Contact Maxim for a reliability report that documents test setup, test methodology, and test results.Human Body ModelFigure 10a shows the Human Body Model, and Figure 10b shows the current waveform it generates when dis-charged into a low impedance. This model consists of a 100pF capacitor charged to the ESD voltage of interest,which is then discharged into the test device through a 1.5k Ωresistor.IEC 61000-4-2The IEC 61000-4-2 standard covers ESD testing and performance of finished equipment. However, it does not specifically refer to integrated circuits. The MAX13080E family of devices helps you design equip-ment to meet IEC 61000-4-2, without the need for addi-tional ESD-protection components.+5.0V , ±15kV ESD-Protected, Fail-Safe, Hot-Swap, RS-485/RS-422 TransceiversThe major difference between tests done using the Human Body Model and IEC 61000-4-2 is higher peak current in IEC 61000-4-2 because series resistance is lower in the IEC 61000-4-2 model. Hence, the ESD with-stand voltage measured to IEC 61000-4-2 is generally lower than that measured using the Human Body Model. Figure 10c shows the IEC 61000-4-2 model, and Figure 10d shows the current waveform for IEC 61000-4-2 ESD Contact Discharge test.Machine Model The machine model for ESD tests all pins using a 200pF storage capacitor and zero discharge resis-tance. The objective is to emulate the stress caused when I/O pins are contacted by handling equipment during test and assembly. Of course, all pins require this protection, not just RS-485 inputs and outputs.Applications Information256 Transceivers on the BusThe standard RS-485 receiver input impedance is 12kΩ(1-unit load), and the standard driver can drive up to 32-unit loads. The MAX13080E family of transceivers has a1/8-unit load receiver input impedance (96kΩ), allowingup to 256 transceivers to be connected in parallel on one communication line. Any combination of these devices,as well as other RS-485 transceivers with a total of 32-unit loads or fewer, can be connected to the line.Reduced EMI and ReflectionsThe MAX13080E/MAX13081E/MAX13082E feature reduced slew-rate drivers that minimize EMI and reduce reflections caused by improperly terminated cables, allowing error-free data transmission up to250kbps. The MAX13083E/MAX13084E/MAX13085Eoffer higher driver output slew-rate limits, allowing transmit speeds up to 500kbps. The MAX13089E withSRL = V CC or unconnected are slew-rate limited. WithSRL unconnected, the MAX13089E error-free data transmission is up to 250kbps. With SRL connected toV CC,the data transmit speeds up to 500kbps. MAX13080E–MAX13089E+5.0V, ±15kV ESD-Protected, Fail-Safe, Hot-Swap, RS-485/RS-422 TransceiversM A X 13080E –M A X 13089ELow-Power Shutdown Mode (Except MAX13081E/MAX13084E/MAX13087E)Low-power shutdown mode is initiated by bringing both RE high and DE low. In shutdown, the devices typically draw only 2.8µA of supply current.RE and DE can be driven simultaneously; the devices are guaranteed not to enter shutdown if RE is high and DE is low for less than 50ns. If the inputs are in this state for at least 700ns, the devices are guaranteed to enter shutdown.Enable times t ZH and t ZL (see the Switching Characteristics section) assume the devices were not in a low-power shutdown state. Enable times t ZH(SHDN)and t ZL(SHDN)assume the devices were in shutdown state. It takes drivers and receivers longer to become enabled from low-power shutdown mode (t ZH(SHDN), t ZL(SHDN))than from driver/receiver-disable mode (t ZH , t ZL ).Driver Output ProtectionTwo mechanisms prevent excessive output current and power dissipation caused by faults or by bus contention.The first, a foldback current limit on the output stage,provides immediate protection against short circuits over the whole common-mode voltage range (see the Typical Operating Characteristics ). The second, a thermal-shut-down circuit, forces the driver outputs into a high-imped-ance state if the die temperature exceeds +175°C (typ).Line LengthThe RS-485/RS-422 standard covers line lengths up to 4000ft. F or line lengths greater than 4000ft, use the repeater application shown in Figure 11.Typical ApplicationsThe MAX13082E/MAX13085E/MAX13088E/MAX13089E transceivers are designed for bidirectional data commu-nications on multipoint bus transmission lines. F igures 12 and 13 show typical network applications circuits. To minimize reflections, terminate the line at both ends in its characteristic impedance, and keep stub lengths off the main line as short as possible. The slew-rate-lim-ited MAX13082E/MAX13085E and the two modes of the MAX13089E are more tolerant of imperfect termination.Chip InformationTRANSISTOR COUNT: 1228PROCESS: BiCMOS+5.0V , ±15kV ESD-Protected, Fail-Safe, Hot-Swap, RS-485/RS-422 TransceiversFigure 11. Line Repeater for MAX13080E/MAX13081E/MAX13083E/MAX13084E/MAX13086E/MAX13087E/MAX13089E in Full-Duplex Mode+5.0V, ±15kV ESD-Protected, Fail-Safe, Hot-Swap, RS-485/RS-422 TransceiversMAX13080E–MAX13089EM A X 13080E –M A X 13089E+5.0V , ±15kV ESD-Protected, Fail-Safe, Hot-Swap, RS-485/RS-422 TransceiversPin Configurations and Typical Operating CircuitsMAX13080E–MAX13089E+5.0V , ±15kV ESD-Protected, Fail-Safe, Hot-Swap, RS-485/RS-422 Transceivers______________________________________________________________________________________21Pin Configurations and Typical Operating Circuits (continued)M A X 13080E –M A X 13089E+5.0V , ±15kV ESD-Protected, Fail-Safe, Hot-Swap, RS-485/RS-422 Transceivers 22______________________________________________________________________________________Ordering Information (continued)MAX13080E–MAX13089E+5.0V , ±15kV ESD-Protected, Fail-Safe, Hot-Swap, RS-485/RS-422 Transceivers______________________________________________________________________________________23Package Information (continued)(The package drawing(s) in this data sheet may not reflect the most current specifications. For the latest package outline information,go to /packages .)。
LA1805中文资料
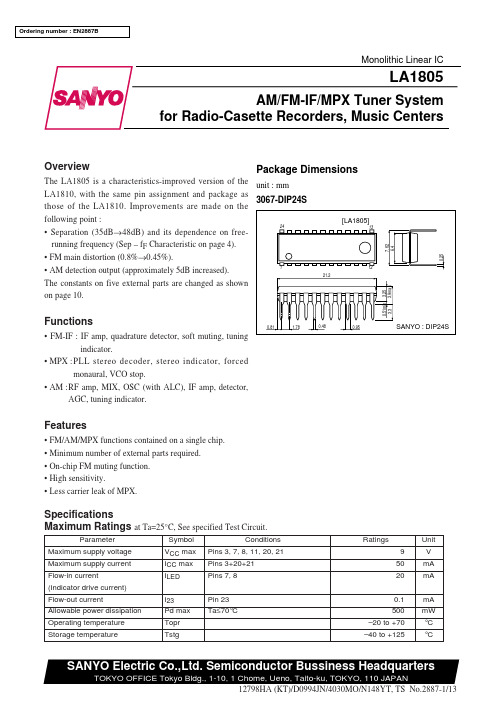
THD1
VIN=80dBµ, 30% mod.
THD2
VIN=100dBµ, 30% mod.
LED on sensitivity
VLED
IL=1mA
Note : Be fully careful of dielectric breakdown.
27
50
70 113
17
21
50
55
0.45
0.6
16
How to use the LA1805
Unit (resistance : Ω, capacitance : F)
1. Forced monaural mode.
Figures 1 and 2 show how to cause the forced monaural mode to be entered.
Forced Monaural Mode Setting Resistance FreeRunning Frequency
Free-running frequency – kHz
Figure 3 No.2887-3/13
元器件交易网
LA1805
2. VCO Stop The VCO is so designed as to stop automatically at the AM mode. (when pin 11 and pin 21 are at the same potential) There is no pin available for stopping the VCO at the FM mode. However, the method shown right can be used to stop the VCO at the FM mode, causing the forced monaural mode to be entered.
Datasheet MLX90614 中文 数据手册 rev008

单区视场和双区视场 TO-39 封装 红外温度传感器
特性和优点
尺寸小,成本低 易集成 在极宽温度范围内工作,带出厂校准: 传感器工作温度范围:-40…+125˚C 被测目标温度范围:-70…+380˚C Ta 和 To 在 0 到 50° C 时,测量精度可达 0.5° C 高(医疗)精度校准 测量值分辨率 0.02° C 单区视场和双区视场可选 SMBus 兼容数字接口 可配置 PWM 连续输出 3V 或 5V 供电,也可使用 8…16V 供电调制 支持睡眠模式 适合不同应用领域的多种封装方式和测试方式 车用级别标准
3901090614 Rev 008
第 2ห้องสมุดไป่ตู้/ 52 页
数据手册 2013/2/28
MLX90614 系列
单区视场和双区视场 TO-39 封装 红外温度传感器
3 目录
1 功能图 ........................................................................................................................................................................................................ 1 2 概述 ......................................................................................................................................................................
MAX9850中文资料

MAX9850
Ordering Information
PART MAX9850ETI TEMP RANGE -40°C to +85°C PIN-PACKAGE 28 Thin QFN-EP*
*EP = Exposed Paddle. Package code T2855-6 (see Package Information section). Pin Configuration appears at end of data sheet.
1
For pricing, delivery, and ordering information, please contact Maxim/Dallas Direct! at 1-888-629-4642, or visit Maxim’s website at .
元器件交易网
Stereo Audio DAC with DirectDrive Headphone Amplifier MAX9850
ABSOLUTE MAXIMUM RATINGS
(Voltages with respect to AGND.) DVDD, AVDD, PVDD ..................................................-0.3V to +4V AVDD Referenced to PVDD ....................................-0.3V to +0.3V SVSS, PVSS ...............................................................-4V to +0.3V SVSS Referenced to PVSS .....................................-0.3V to +0.3V DGND, PGND........................................................-0.3V to +0.3V BCLK, LRCLK, HPS, SDIN.......................-0.3V to (DVDD + 0.3V) GPIO, MCLK.............................................................-0.3V to +4V REF, PREG ...............................................-0.3V to (AVDD + 0.3V) NREG ........................................................+0.3V to (SVSS - 0.3V) SDA, SCL, ADD ........................................................-0.3V to +4V INL, INR .......................................................................-2V to +2V HPR, HPL.....................................(SVSS - 0.3V) to (AVDD + 0.3V) OUTL, OUTR .............................(NREG - 0.3V) to (PREG + 0.3V) C1N ............................................(PVSS - 0.3V) to (PGND + 0.3V) C1P ............................................(PGND - 0.3V) to (PVDD + 0.3V) Current Into/Out of Any Pin ...............................................100mA Duration of HPL, HPR, OUTL, OUTR Short Circuit to AGND .................................Continuous Continuous Power Dissipation (TA = +70°C) 28-Pin Thin QFN (derate 35.7mW/°C above +70°C) .....2857mW Junction Temperature ......................................................+150°C Operating Temperature Range ...........................-40°C to +85°C Storage Temperature Range .............................-65°C to +150°C Lead Temperature (soldering, 10s) .................................+300°C
MAXIM MAX13335E 电动汽车评估套件 (EV 套件) 使用手册说明书

General Description The MAX13335E evaluation kit (EV kit) is a fully assembled and tested PCB that evaluates the MAX13335E automotive audio receiver. The IC features a dual automotive differential audio receiver with I2C control and diagnostics. The EV kit features an on-board microcontroller for communicating with the I2C interface of the device. PCB pads are provided for accessing the analog inputs/outputs and the diagnostic I/O ports.The EV kit operates from a +3.3V or +5V power supply that provides 100mA of current. The EV kit can also operate from the on-board USB +5V supply. The EV kit delivers the audio outputs with programmable gain between -14dB and +16dB. The EV kit can also evaluate the MAX13336E after IC replacement of U1.Windows XP M-, Windows Vista M-, and Windows M 7-compatible software is provided to facilitate configuration. The EV kit software controls the on-board microcontroller over the USB, which generates I2C commands.Features S +3.3V or +5V Single-Supply OperationS Proven Audio PCB LayoutS On-Board USB Interface Circuit GeneratesI2C-Compatible SignalsS PCB Pads for User-Supplied I2C-Compatible SignalsS Surface-Mount ComponentsS Evaluates the MAX13336E After IC ReplacementS Windows XP-, Windows Vista-, and Windows7-Compatible SoftwareS Fully Assembled and TestedDESIGNATION QTY DESCRIPTIONC1–C444.7F F Q10%, 25V X7R ceramic capacitors (1206)Murata GRM31CR71E475KC5, C6, C731F F Q10%, 25V X7R ceramic capacitors (0805)Murata GRM21BR71E105KC8, C102, C113, C115410F F Q20%, 6.3V X5R ceramiccapacitors (0805)Murata GRM21BR60J106MC910.1F F Q10%, 50V X7R ceramic capacitor (0603)Murata GRM188R71H104KC10–C17, C1170Not installed, ceramic capacitors(0603)C101,C103–C110,C121100.1F F Q10%, 16V X7R ceramiccapacitors (0603)Murata GRM188R71C104KC111, C112210pF Q5%, 50V C0G ceramiccapacitors (0603)Murata GRM1885C1H100JDESIGNATION QTY DESCRIPTIONC114,C122–C12551F F Q10%, 10V X5R ceramiccapacitors (0603)Murata GRM188R61A105KC11612.2F F Q10%, 6.3V X5R ceramiccapacitor (0603)Murata GRM188R60J225KC118, C119222pF Q5%, 50V C0G ceramiccapacitors (0603)Murata GRM1885C1H220JC12013300pF Q10%, 50V X7R ceramiccapacitor (0603)Murata GRM188R71H332KD11Bidirectional quad TVS (SOT563)ON Semi NUP4102XV6D1011Green LED (0603)FB1010Not installed, ferrite bead—short(PC trace) (0603)JU113-pin headerJU2–JU542-pin headersP1011-20V, -2.4A p-channel MOSFET(3 SuperSOT)Fairchild FDN304P_NLMAX13335E Evaluation Kit Evaluates: MAX13335E/MAX13336E19-6290; Rev 0; 4/12Ordering Information appears at end of data sheet.Windows, Windows XP and Windows Vista are registeredtrademarks of Microsoft Corp.Component ListDESIGNATIONQTY DESCRIPTIONR1–R441k I Q 1% resistors (0603)R5, R6, R11, R12, R19–R22, R103, R104,R1090Not installed, resistors (0603)R7, R23, R24, R25420I Q 1% resistors (0603)R8, R9, R103 4.7k I Q 5% resistors (0603)R13–R164100k I Q 1% resistors (0603)R17, R18, R10130I Q 5% resistors (0603)R1021220I Q 5% resistor (0603)R1051 1.5k I Q 5% resistor (0603)R106, R107227I Q 5% resistors (0603)R10811k I Q 5% resistor (0603)U11Auxiliary input audio amplifier with I 2C (16 QSOP)Maxim MAX13335EGEE/V+U101132-bit microcontroller (68 QFN-EP*)Maxim MAXQ2000-RAX+U102Not installed EEPROM (8 SO)DESIGNATIONQTY DESCRIPTIONU1031UART-to-USB converter (32 TQFP, 7mmx7mm)U10413.3V, 300mA regulator (5 SOT23)Maxim MAX8888EZK33+T U1051 2.5V, 120mA regulator (5 SC70)Maxim MAX8511EXK25+T U106, U1072Level translators (10 F MAX M )Maxim MAX1840EUB+USB1USB type-B, right-angle female connectorY101116MHz crystal Hong Kong X’talsSSM16000N1HK188F0-0Y10216MHz crystalHong Kong X’talsSSL60000N1HK188F0-0—1USB-A male to USB-B male cable, 6ft —5Shunts—1PCB: MAX13335E EVALUATION KITSUPPLIERPHONE WEBSITEFairchild Semiconductor Hong Kong X’tals Ltd.852-******** Murata Electronics North America, ON Semiconductor602-244-6600FILE DESCRIPTIONInstall.exe Installs the EV kit files on your computerMAX13335E.exe Application programCDM20600.exe Installs the USB device driver Uninstall.exe Uninstalls the EV kit software USB_Driver_Help_200.pdfUSB driver installation help fileComponent List (continued)*EP = Exposed pad.Note: Indicate that you are using the MAX13335E when contacting these component suppliers.Component SuppliersµMAX is a registered trademark of Maxim Integrated Products, Inc.MAX13335E EV Kit FilesJUMPER SHUNT POSITION DESCRIPTIONJU11-2*On-board VDD supply. Connects the on-board USB +5V to VDD. 2-3External VDD supply. Externally supply VDD with +3.3V or +5V.JU21-2*On-board VL supply. Connects the on-board VDD to the logic-level translator output supply VL. Pin 1External VL supply. Externally supply VL with +3.3V or +5V.JU31-2*On-board I2C. Connects the IC’s INT output to the on-board microcontroller.Pin 1User-supplied I2C. Connects the IC’s INT output to the user-supplied microcontroller.JU41-2*On-board I2C. Connects the on-board SDA signal to the SDA PCB pad.Pin 1User-supplied I2C. Open the jumper and apply the SDA signal to the SDA PCB pad.JU51-2*On-board I2C. Connects the on-board SCL signal to the SCL PCB pad.Pin 1User-supplied I2C. Open the jumper and apply the SCL signal to the SCL pad.Quick StartRecommended Equipment• MAX13335E EV kit (USB cable included)• Function generator• Oscilloscope• User-supplied Windows XP, Windows Vista, or Windows 7 PC with an available USB portNote: In the following sections, software-related items are identified by bolding. Text in bold refers to items directly from the EV kit software. Text in bold and underlined refers to items from the Windows operating system.Procedure The EV kit is fully assembled and tested. Follow the steps below to verify board operation. Do not turn on the power supply until all connections are completed.1) Visit /evkitsoftware to down-load the latest version of the EV kit software, 13335ERxx.ZIP. Save the EV kit software to a temporary folder and uncompress the ZIP file.2) Install the EV kit software on your computer by run-ning the INSTALL.EXE program inside the temporaryfolder. The program files are copied and icons are created on the desktop and in the Windows Start | Programs| Maxim EVKIT Software menu.3) Verify that all jumpers are in their default positions,as shown in Table 1.4) Set the function generator output to high impedanceand to output a 1kH z, 10V P-P, sine wave with 0V offset. Disable the function generator.5) Connect the function generator output to theINPUTL+ and INPUTR+ PCB pads.6) Connect the function generator ground to the GNDPCB pad.7) Connect the INPUTL- and INPUTR- PCB pads to theGND PCB pad.8) Connect the oscilloscope channel 1 to the OUTLPCB pad.9) Connect the oscilloscope channel 2 to the OUTRPCB pad.10) Connect a USB cable between the PC and the Mini-USB port on the EV kit. A New Hardware Foundwindow pops up when installing the USB driver for the first time. If a window that is similar to the one described above is not seen after 30s, remove the USB cable from the board and reconnect it.Administrator privileges are required to install the USB device driver on Windows.11) Follow the directions of the Found New Hardwarewindow to install the USB device driver. Refer to the USB_Driver_Help_200.PDF document included with the software for additional information.12) Start the EV kit software by opening its icon onthe desktop or in the Start | Programs | Maxim EVKITSoftware menu. The EV kit software main window appears, as shown in Figure 1.13) Wait while the software connects to the EV kit. Oncethe connection is established, the bottom-left status bar displays Hardware: Connected.14) Enable the function generator.15) Verify that the oscilloscope channels 1 and 2 eachoutput a 1kHz, 2V P-P, sine wave with 0V offset.Detailed Description of SoftwareGraphical User Interface (GUI) The MAX13335E EV kit software GUI provides a convenient way to test the features of the MAX13335E IC. Figure 1 shows the EV kit software’s main window. The EV kit software main window divides the EV kit functions into logical blocks. Actions on this software window generate I2C commands to update the IC’s internal memory registers.Table 1. Jumper Positions (JU1–JU5) *Default position.Figure 1. MAX13335E EV Kit Software Main WindowSoftware Startup Upon starting the program, the EV kit software automatically searches for the USB interface circuit and then for the IC’s device address. The EV kit enters the normal operating mode when the USB connection is detected and has found the device address. If the USB connection is not detected, the software prompts the user to retry or enter the demo mode.Demo Mode The EV kit software enters demo mode when the USB connection is not detected, or by selecting the Options | Demo Mode menu item in the main window. When in demo mode, all software communication to the EV kit circuit is disabled; however, most of the software GUI is functional. Demo mode allows the user to evaluate the software without hardware connectivity.Main Controls The EV kit software’s Main Controls group box provides checkboxes to control the IC’s Shutdown, Mute, Zero Crossing Detection Enabled, Jack Sense Interrupt Enabled, Clip Detected Interrupt Enabled, and Audio Present Detected Interrupt Enabled features.I2C Interface The EV kit software’s Device Read/Write Addr radio group box selects the device address to perform read or write functions. The device’s I2C read and write addresses are internally set to 0xD1 and 0xD0, respectively.The I2C Register/Data group box contains the Register Address to display the last register that was read from or written to and the Data Sent, which displays the last data that was sent or received.Status The Status group box displays the IC’s Die Revision, Thermal SHDN status, Jack Inserted status, Clip Detected status, Audio Present status, and INT interrupt output logic level.Amplifier Gain The Amplifier Gain group box provides the Right Channel Amplifier Gain track bar/edit box and the Left Channel Amplifier Gain track bar/edit box to configure the IC’s amplifier output gain. The Track checkbox locks the Right Channel Amplifier Gain track bar/edit box to the Left Channel Amplifier Gain track bar/edit box when it is checked. The IC’s amplifier gain range is between -14dB and +16dB.Diagnostic I/O Ports The EV kit software Diagnostic I/O Ports group box provides combo boxes to configure the IC’s diagnostic I/O ports (D0–D3). Refer to the Detailed Description,Diagnostics, Applications Information, and Diagnostic Configurations sections in the MAX13335E/MAX13336E IC data sheet for additional details.Write All/Read All/Reset The Write All button writes the current settings to all the registers on the GUI. The EV kit software GUI performs I2C write commands as changes occur on the GUI. The Read All button changes the GUI settings to match the IC register settings. To change settings one time, enter demo mode by selecting the Options | Demo Mode menu item, change the GUI to the required settings, exit demo mode by selecting Options | Demo Mode, and then press the Write All button. To obtain the IC settings, press the Read All button and the GUI is updated to reflect the current register states of the IC. In addition, the EV kit software can be set to automatically read back the IC registers every two seconds by selecting the Auto Read checkbox. The Reset button clears the EV kit software GUI and reprograms the IC to the default values.Registers The EV kit software Registers group box displays each register’s individual bit logic-level status. A data bit in bold indicates a logic-high, while a data bit that is not bold indicates a logic-low. Clicking on the individual data bit toggles the bit and performs a write command. The new command is shown in the edit box at the right. Alternatively, write commands can be written to the registers by typing a hex value in the edit box and pressing the Enter key on the keyboard.Simple I2C Commands There are three methods for communicating with the EV kit, through the GUI components in the software main window, the Registers group box in the main window, or by using low-level SMBus commands available in the Advanced User Interface window (Figure 2). Select Options | Interface (Advanced Users) to display the Advanced User Interface window that allows I2C operations, such as SMBusReadByte and SMBusWriteByte.Detailed Description of HardwareThe MAX13335E EV kit evaluates the MAX13335E dual automotive differential audio receivers with diagnostics that communicate over I2C. The EV kit demonstrates the IC’s features, such as user-defined amplifier gains, interrupt enables, and diagnostic I/O configurations. The EV kit uses the IC in a 16-pin QSOP package on a proven, four-layer PCB design. The EV kit operates from a +3.3V or +5V, 100mA DC power supply. The EV kit can also operate from the on-board USB +5V available from a PC.Figure 2. MAX13335E EV Kit Software (Advanced User Interface)Amplifier Inputs/Outputs The EV kit provides PCB pads for connecting the amplifier I/O signals to the EV kit. The EV kit accepts fully differential inputs up to 7V RMS, and quasi-differential inputs up to 3.5V RMS. The EV kit delivers the amplified outputs with programmable gain between -14dB to +16dB.Diagnostic I/O Ports The IC’s diagnostic I/O ports (D0–D3 are accessible at the INPUTL-, INPUTL+, INPUTR-, and INPUTR+ PCB pads, respectively. Each diagnostic I/O port is connected to its respective input PCB pad through a resistor-divider network. The diagnostic I/O ports can be configured to perform jack-sense detection, short-to-ground, short-to-battery, open load, and short between channels when configured correctly. Refer to the Detailed Description, Diagnostics, Applications Information, and Diagnostic Configurations sections in the MAX13335E/MAX13336E IC data sheet for additional details.Evaluating the MAX13336E The EV kit can also be used to evaluate the MAX13336E after IC replacement. To evaluate the MAX13336E, replace U1 with the MAX13336E IC and refer to the MAX13335E/MAX13336E IC data sheet for additional details.Figure 3a. MAX13335E EV Kit Schematic (Sheet 1 of 2)Figure 3b. MAX13335E EV Kit Schematic (Sheet 2 of 2)Figure 4. MAX13335E EV Kit Component Placement Guide—Component SideFigure 5. MAX13335E EV Kit PCB Layout—Component SideFigure 6. MAX13335E EV Kit PCB Layout—GND Layer 2Figure 7. MAX13335E EV Kit PCB Layout—PWR Layer 3Figure 8. MAX13335E EV Kit PCB Layout—Solder SideOrdering InformationPART TYPEMAX13335EEVKIT#EV Kit#Denotes RoHS compliant.________________________________________________________________Maxim Integrated Products 11REVISION NUMBER REVISIONDATEDESCRIPTIONPAGESCHANGED04/12Initial release—Maxim cannot assume responsibility for use of any circuitry other than circuitry entirely embodied in a Maxim product. No circuit patent licenses are implied. Maxim reserves the right to change the circuitry and specifications without notice at any time.Maxim Integrated Products, 120 San Gabriel Drive, Sunnyvale, CA 94086 408-737-7600 12©2012 Maxim Integrated Products Maxim is a registered trademark of Maxim Integrated Products, Inc.Revision History。
MAX13085E美信中文版
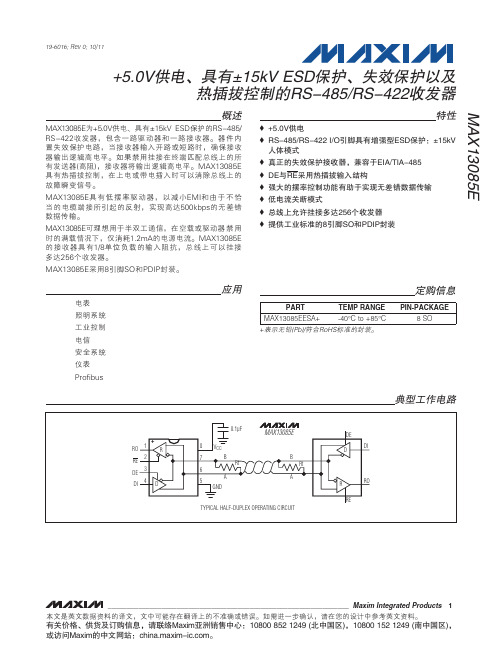
Stresses beyond those listed under “Absolute Maximum Ratings” may cause permanent damage to the device. These are stress ratings only, and functional operation of the device at these or any other conditions beyond those indicated in the operational sections of the specifications is not implied. Exposure to absolute maximum rating conditions for extended periods may affect device reliability.
19-6016; Rev 0; 10/11
+5.0V供电、具有±15kV ESD保护、失效保护以及 热插拔控制的RS-485/RS-422收发器
概述
MAX13085E为+5.0V供电、具有±15kV ESD保护的RS-485/ RS-422收发器,包含一路驱动器和一路接收器。器件内 置失效保护电路,当接收器输入开路或短路时,确保接收 器输出逻辑高电平。如果禁用挂接在终端匹配总线上的所 有发送器(高阻),接收器将输出逻辑高电平。MAX13085E 具有热插拔控制,在上电或带电插入时可以消除总线上的 故障瞬变信号。 MAX13085E具有低摆率驱动器,以减小EMI和由于不恰 当的电缆端接所引起的反射,实现高达500kbps的无差错 数据传输。 MAX13085E可理想用于半双工通信,在空载或驱动器禁用 时的满载情况下,仅消耗1.2mA的电源电流。MAX13085E 的接收器具有1/8单位负载的输入阻抗,总线上可以挂接 多达256个收发器。 MAX13085E采用8引脚SO和PDIP封装。 S +5.0V供电 S RS-485/RS-422 I/O引脚具有增强型ESD保护:±15kV 人体模式 S 真正的失效保护接收器,兼容于EIA/TIA-485 S DE与RE采用热插拔输入结构 S 强大的摆率控制功能有助于实现无差错数据传输 S 低电流关断模式 S 总线上允许挂接多达256个收发器 S 提供工业标准的8引脚SO和PDIP封装
米歇尔电子欧洲有限公司产品说明-GT2105-QMBDS HMI小型HMI扩展材料说明书

MITSUBISHI ELECTRIC EUROPE B.V.Industrial AutomationMitsubishi-Electric-Platz 1 40882 Ratingen DeutschlandTelefon +49 (0) 2102 486-0 Fax +49 (0) 2102 486-1120https:///faMATERIAL FACT SHEET297852GT2105-QMBDSGeneral DataProduct Hierarchy IAT93001HMISmall HMI Ext. Material Group10 STANDARD ITEM ABC Indicator B (Limited Availability from Stock) e-shop:https:///mee/FA_IA/EUR/en/p/000000000000297852FA-HMI: Human Machine InterfaceSeries GOT2000 SERIES Type GT21 MODEL Power Supply (V)24 Current Type DC Display TFT Display Colour MONOCHROME Display Size (Inch)5,7 Resolution (Pixels)320X240 Internal Memory Capacity (MB)9 Memory Card Slot SD USB1 RS-2321 RS-422/4851 Network Options MODBUS, ETHERNET Protection Class IP67FProduct Dimensions & WeightWidth (mm)164 Height (mm)135 Depth (mm)56 Weight (kg)0,7Logistic Dimensions & Gross WeightLength (cm)23,5 Width (cm)15,5 Height (cm)9,0 Gross Weight (kg)0,833 Volume (cdm)3,278Stock DataPlanned Delivery Time (Days)221Life CycleSales Start01.07.2016 Predecessor218492 / GT1050-QBBDAdditional Product InformationBinding Tariff Information DEBTI-10694/21-1 BTI validity date10.10.2024 Battery included YES – CHECK SPARE PART LISTExport DataCommodity Code85371091 Legal Control (Dual Use List)Not Listed Country of Origin Japan (JP) Preference Status (Supplier Declaration)Non EUEnvironmentalDangerous Goods Class NO Dangerous Goods Identifier NO RoHS Compliance COMPLIANT WEEE B2BConformityCE COMPLIANT UL/cUL COMPLIANT EAC COMPLIANT Shipping Approvals ABS,BV,DNV,LR,NK,RINA UKCA COMPLIANTDocumentation & Media DataManual URL Indicator https:///fa/advanced-search?ct=document&doc-cats=bltdae25c2bd5f2ff94&q=GT2105-QMBDS&doc-lang=en Certificates URL Indicator https:///fa/advanced-search?ct=document&doc-cats=blt8050dd1408c11cc2&q=GT2105-QMBDS&doc-lang=en Product PackagingCardboard (g)201 Other paper (g)0 Aluminum (g)0 Steel (g)0 Styrofoam (g)0 Other plastic (g)1 Wood (g)0 Glass (g)0 Others (g)0Spare partsMaterial Description Quantity Unit306884GT2105-QxBDS REAR COVER1PC306895GT2105-QxBDS FRONT COVER1PC306896GT2105-QxBDS ENVIRONMENT SHEET1PC306897GT2105-QxBDS TOUCHPANEL1PC306898GT2105-QxBDS POWER CONNECTOR1PC306899GT2105-QxBDS FASTENING PLATE1PC306900GT2105-QMBDS LCD DISPLAY1PC306902GT2105-QxBDS SD-CARD BOARD1PC306903GT2105-QMBDS CPU + INTERFACE BOARD1PC306904GT2105-QMBDS POWER + INTERFACE BOARD1PCCompatible productsMaterial Description / Price List Text / Classification163953GT01-C30R4-25PConn.cable AnS/QnAS/A/QnA/F-CPU+GOT2000/GOT1000/GOT Simple;3mClass 100100303: FA-HMI: Cable163954GT01-C100R4-25PGOT Connection cable for CPU (MELSEC AnS/QnAS or A/QnA) and GOT1000-series; 10 mClass 100100303: FA-HMI: Cable163955GT01-C200R4-25PGOT Connection cable for CPU (MELSEC AnS/QnAS or A/QnA) and GOT1000-series; 20 mClass 100100303: FA-HMI: Cable163956GT01-C300R4-25PGOT Connection cable for CPU (MELSEC AnS/QnAS or A/QnA) and GOT1000-series; 30 mClass 100100303: FA-HMI: Cable200496GT10-C30R4-25PGOT Connection cable for CPU (MELSEC AnS/QnAS/A/QnA) and GT1020/GT1030; 3 mClass 100100303: FA-HMI: Cable200497GT10-C100R4-25PGOT Connection cable for CPU (MELSEC AnS/QnAS/A/QnA) and GT1020/GT1030; 10 mClass 100100303: FA-HMI: Cable280470GT21-C30R4-25P5GOT2000;RS-422 connection cable between Q CPU and GT2103-PMBD;3mClass 100100303: FA-HMI: CableMaterial Description / Price List Text / Classification280471GT21-C100R4-25P5GOT2000;RS-422 connection cable between Q CPU and GT2103-PMBD;10mClass 100100303: FA-HMI: Cable280474GT21-C200R4-25P5GOT2000;RS-422 connection cable between Q CPU and GT2103-PMBD;20mClass 100100303: FA-HMI: Cable280475GT21-C300R4-25P5GOT2000;RS-422 connection cable between Q CPU and GT2103-PMBD;30mClass 100100303: FA-HMI: Cable293474Ethernetcable GOT Add on KitEthernetcable GOT Add on KitClass 100100303: FA-HMI: Cable。
马拉松MX系列发电机英文说明书
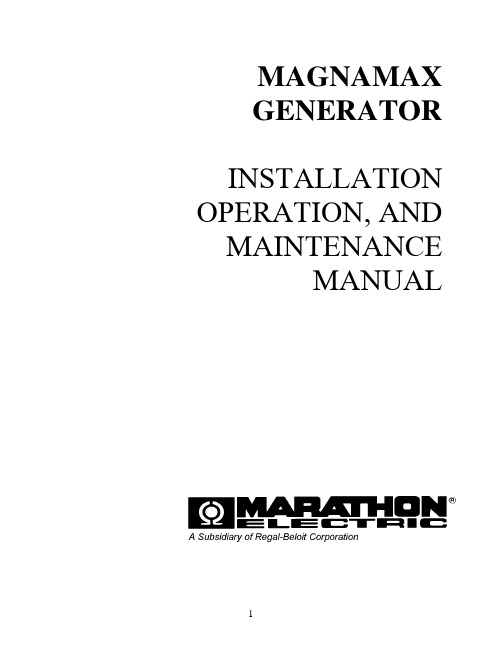
MAGNAMAXGENERATOR INSTALLATION OPERATION, AND MAINTENANCEMANUALTABLE OF CONTENTSTABLE OF CONTENTS (2)SAFETY (6)GENERAL INFORMATION (7)MECHANICAL DESIGN (7)General (7)Conduit Box (7)MagnaMAX Unirotor TM Construction (7)Adapters and Drive Discs (7)ELECTRICAL DESIGN (8)Temperature Rise (8)Standby Generator Ratings (8)Premium Insulation System (8)Power Factor (8)MagnaMAX Voltage Regulator (8)HOW TO READ A MODEL NUMBER (9)INSTALLATION (10)RECEIVING YOUR MAGNAMAX GENERATOR (10)UNPACKING AND HANDLING (10)STORAGE (10)PREPARATION FOR USE (10)GENERATOR MOUNTING - SINGLE BEARING (10)GENERATOR MOUNTING-TWO BEARING (11)BELT DRIVE (11)ENVIRONMENTAL CONCERNS (11)ELECTRICAL CONNECTIONS (12)GENERATOR LEAD CONNECTIONS (12)12 LEAD HIGH WYE CONNECTION (13)12 LEAD LOW WYE CONNECTION (13)12 LEAD HIGH DELTA CONNECTION (14)12 LEAD LOW DELTA CONNECTION (14)10 LEAD HIGH WYE CONNECTION (15)10 LEAD LOW WYE CONNECTION (15)6 LEAD WYE CONNECTION (16)6 LEAD DELTA CONNECTION (16)3 LEAD DELTA CONNECTION (17)4 LEAD WYE CONNECTION (17)DOUBLE DELTA -- SINGLE PHASE CONNECTION (18)LOW ZIG ZAG -- SINGLE PHASE CONNECTION (18)HIGH ZIG ZAG -- SINGLE PHASE CONNECTION (18)PARALLELING OPERATIONS (19)PRIME MOVER (19)VOLTAGE REGULATOR (19)SWITCHGEAR (19)PARALLELING BASICS (19)REACTIVE LOAD CONTROL (20)PARALLELING CIRCUITRY (20)THYRISTOR OR SCR LOADING (21)OPERATION (21)PRE-START INSPECTION (21)STARTING-UP THE GENERATOR (22)FIELD FLASHING (22)VOLTAGE ADJUSTMENTS (22)OTHER ADJUSTMENTS (23)MAINTENANCE (23)GENERAL INFORMATION (23)AIR INTAKE AND EXHAUST (23)ELECTRICAL CONNECTIONS, WINDINGS (24)LUBRICATION (24)DRYING ELECTRICAL INSULATION (26)Space Heaters (26)Oven (26)Forced Air (26)“Short Circuit” Method (26)CLEANING METHODS (27)Solvents (27)Cloth and Compressed Air (27)Brushing and Vacuum Cleaning (27)Shell Blasting (27)Steam Cleaning (27)DISASSEMBLY (28)REMOVAL FROM PRIME MOVER (28)CONDUIT BOX REMOVAL (29)EXCITER STATOR (FIELD) REMOVAL (30)EXCITER ARMATURE (ROTOR) REMOVAL (30)PMG STATOR REMOVAL (31)MAIN ROTOR REMOVAL (33)FRONT END BRACKET REMOVAL (35)EXCITER INSPECTION (35)EXCITER STATOR (35)EXCITER (ROTOR) ARMATURE (36)PMG INSPECTION (37)PMG STATOR (37)PMG ROTOR (37)MAIN ROTOR INSPECTION (37)BEARING (37)FAN (38)MAIN ROTOR CORE AND WINDINGS (40)DRIVE DISCS (SINGLE BEARING GENERATORS ONLY) (40)FRONT (EXCITER) END BRACKET INSPECTION (40)DRIVE END BRACKET OR SAE ADAPTER INSPECTION (41)MAIN STATOR INSPECTION (42)FRONT END BRACKET INSTALLATION (42)MAIN ROTOR INSTALLATION (42)PMG INSTALLATION (45)EXCITER INSTALLATION (46)CONDUIT BOX INSTALLATION (47)ASSEMBLY TO PRIME MOVER (48)TROUBLESHOOTING (50)INTRODUCTION (50)SYMPTOM: (51)NO VOLTAGE OR RESIDUAL VOLTAGE (51)LOW VOLTAGE - (52)NO LOAD (52)LOW VOLTAGE WHEN LOAD IS APPLIED (53)HIGH VOLTAGE (53)VOLTAGE IS FLUCTUATING (54)OPERATES SATISFACTORILY WHEN COLD, BUT SHUTS DOWN WHEN WARM (54)BUILDS VOLTAGE FROM STARTUP,THEN GOES TO LOW (RESIDUAL) VOLTAGE (54)EQUIPMENT RUNS NORMALLY ON UTILITY POWER, BUT WILL NOT RUN ON GENERATOR SET (54)GENERATOR TESTING (55)VISUAL INSPECTION (55)CONSTANT EXCITATION (12V BATTERY) TEST (55)MEASURING VOLTAGES (56)TYPICAL VOLTAGE MEASUREMENTS (57)Generator Output Voltage (57)Regulator Output (Exciter Stator Input) (57)Regulator Sensing (57)Regulator Input Volts (PMG Output Volts) (57)CURRENT (AMP) MEASUREMENTS (57)MEASURING RESISTANCE (58)Main Stator (58)Exciter Rotor (58)TESTING DIODES (RECTIFIERS) (58)INSULATION RESISTANCE - MAIN STATOR (59)GENERATOR TESTING (59)INSULATION RESISTANCE - MAIN ROTOR (59)INSULATION RESISTANCE - EXCITER STATOR (60)INSULATION RESISTANCE - EXCITER ROTOR (60)MAIN ROTOR FIELD AC IMPEDANCE TEST (60)MAGNAMAX EXPLODED VIEW (61)STANDARD TOOLS (64)SPECIAL TOOLS (65)MISCELLANEOUS (66)PREPARATION FOR SHIPMENT OR EXTENDED STORAGE (66)SHIPPING INSTRUCTIONS (66)STORAGE INSTRUCTIONS (66)TABLE 12-1: MAGNA MAX - FASTENER AND TORQUE SPECIFICATIONS (68)TABLE 12-2: CAPSCREW TORQUE VALUES (69)TABLE 12-3:EXCITATION DATA -60 HZ - 1800 RPM (70)TABLE 12-3:EXCITATION DATA -50 HZ - 1500 RPM (71)TABLE 12-5: RESISTANCE VALUES - MAIN WINDINGS (72)TABLE 12-6: RESISTANCE VALUES - EXCITER WINDINGS (73)SAFETYPLEASE REMEMBER SAFETY FIRST. If you are not sure of the instructions or procedures, seek qualified help before continuing.This service manual emphasizes the safety precautions necessary during the installation, opera-tion, and maintenance of your generator.Each section has caution and warning messages. These messages are for your safety and the safety of the equipment involved. If any of the cautions or warnings is not readily understood, seek clarification from qualified personnel before proceeding.Before any service work is done, disconnect all power sources and, where appropriate, lock out all controls, to prevent an unexpected start-up of the generator set. Proper grounding in compliance with local and national electrical codes must be provided. These safety precautions are necessary to prevent potential serious personal injury, or even death.The hazards associated with lifting or moving the generator are pointed out in the installation and service sections; incorrect lifting or moving can result in personal injury or property damage.Whenever the generator is running, always assume and proceed as if voltage is present. Residual voltage is present at the generator leads and at the regulator panel connections, even with the regulator fuse removed. Caution must be observed, or serious personal injury or death can result.Whenever solvents, cleaners, or flammable liquids are present, adequate ventilation must be available to avoid fire, explosion, and health hazards. Always avoid breathing vapors and use suitable personal protective equipment to prevent personal injuries. (Such as eyes, face, and hand protection.)This manual is not intended to be a substitute for properly trained personnel. Only qualified trained people should attempt repairs. The cautions and warnings point out known conditions that are potentially dangerous. Each installation will create its own set of circumstances. No manual can cover every possible situation.When in doubt, ask. Don’t be embarrassed to ask, “dumb questions”. Remember that dumb questions are much easier to handle than dumb mistakes.GENERAL INFORMATION MECHANICAL DESIGNGeneralAll single and two bearing units are manufactured with cast iron end brackets and adapters, and fabricated steel frames. Flexible drive discs and SAE adapters are machined to SAE standards. Pre-lubricated, regreasable, shielded ball bearings are used on MagnaMAX generators. Standard units are fully guarded. Drip proof shields are available as an option.Conduit BoxThe large end mounted conduit box is con-structed of formed sheet steel that will allow the addition of top mounted control packages. Refer to Marathon Electric for top mounted controls of more than 240 lbs. There is ample room inside the conduit box for a circuit breaker (through 800A Frame) and other options. The conduit box cover properly directs outside ventilating air through the generator.MagnaMAX Unirotor TM Construction An aluminum die cast rotor core affords high mechanical integrity and low vibration at operating speeds. Amortisseur winding and coil supports are die cast as an integral part of the rotor. Laminations are 4-pole, one piece laminations which are shrunk fit and keyed to the shaft. No dovetails, cross bolts or other pole to shaft connecting devices are used. The cast unidirectional aluminum alloy ventilation fan provides even air distribution to maximize cooling and generator efficiency.Adapters and Drive DiscsAll single bearing units are available with several adapters and drive disc arrangements. These can be shipped to order or can be changed in the field with standard shop tools. When changing flexible drive discs, spacers are used between the discs and the cast iron hub to maintain SAE standard dimensions.ELECTRICAL DESIGNAll standard products have 2/3 pitch main windings to eliminate the third harmonic. This serves to lower operating temperatures, give lower harmonic content and better waveform, and extend the overall life of the generator.Temperature RiseAll ratings and frame sizes are based on NEMA and CSA Class F and Class H temperature rises on both the rotor and stator windings. Ratings for British, German, French, IEC and all popular marine agencies are available.Standby Generator Ratings Synchronous generators used on emergency backup power can have temperature rises up to 25°C above those for continuous operation. (NEMA MG1 -22.40 and MG 1-22.84).Premium Insulation SystemAll MagnaMAX generators are built with Class H or better insulation materials. All standard generators are suitable for continuous duty at Class F temperature rise and will give equivalent or better winding life expectancy to generators supplied with Class A or B insulation systems operated within their temperature limits. The varnishes and epoxies used are synthetic, non-hygroscopic. Multiple dip and bake cycles of the main winding, plus a final coat of epoxy, make the standard winding moisture and fungus resistant. The MagnaMAX rotor is wet wound with thermo-setting epoxy applied between each layer, plus a final coating of epoxy for moisture and abrasion resistance. MagnaMAX generators can be ordered with an epoxy vacuum pressure impregnated insulation system as an option. (MagnaMAX generators with form wound coils include VPI as standard.)Power FactorAll standard generators are designed for operation at rated kVA at 0.8 lagging power factor but can be operated at rated kVA over the 0.8 to 1 .0 power factor range. MagnaMAX Voltage RegulatorThe standard voltage regulator is a fully encapsulated, static types with a solid state build up circuit. Standard features include 3-phase RMS sensing, paralleling, adjustable under frequency protection, and over excitation protection. The regulator meets EMI suppression to Mil Std-461B, part 9. An optional feature is adjustable armature current limiting. See the regulator manual for more information.HOW TO READ A MODEL NUMBERIt is extremely important to properly identify the machine when requesting parts or service. Always have the generator model number and serial number when requesting information from the factory. We cannot help you without this information.An Example For MagnaMAX Generators 431RSL 2000 AA - 000Character Category Description1st three characters Frame Number4th character Winding type R—Random WoundF—Form Wound5th character Bearing arrangement S—1 BearingD—2Bearings6th character Voltage range L—Up to 480 voltsM—1000-6600 voltsS—600 volts7th Character Product style4-Magna8th Character Type9th & 10th Character Wk2 Code11th Character Modification A-Z assigned sequentially 12th Character Mounting Arrangement A-Y see chart figurer 2-1 13th, 14th & 15th characters Modification numbers For internal use only Arrangement Adapter SAE Size Drive Disc SAE SizeA311-1/2B211-1/2C48D310E111-1/2F114G47-1/2H1DelcoJ1/214K210L1/2DelcoM014N2Small Delco0None NoneP018S0DelcoU0018V46-1/2W0021Y410Figure 2-1INSTALLATIONRECEIVING YOUR MAGNAMAX GENERATORUpon receipt of the generator, it is recommended that it be carefully examined for possible damage incurred in shipment. The generator was given to the Freight Company in good condition, and they are responsible for the product from our dock to yours. Any damage should be noted on the freight bill before accepting the shipment. Claims for damages must be promptly filed with the Freight Company. UNPACKING AND HANDLINGRead all instruction cards carefully. When lifting, attach an overhead crane to the lifting lugs on the generator frame. Apply lifting forces in a vertical direction.WARNINGTHE LIFTING LUGS ON THE GENERATOR ARE DESIGNED TO SUPPORT THE GENERATOR ONLY.DO NOT LIFT COMPLETE GENERATOR SET BY MEANS OF LIFTING DEVICES ON THE GENERATOR. PERSONAL INJURYOR QUIPMENT DAMAGE MAYOCCUR.STORAGEIn the event that the generator is not to be installed on the prime mover immediately, it is recommended that it be stored in a clean, dry area that is not subject to rapid changes in temperature and humidity. See "STORAGE INSTRUCTIONS" for more information.PREPARATION FOR USEAlthough the generator is carefully inspected and tested in operation before it leaves the factory, it is recommended the unit be thoroughly inspected. The insulation on the wire should be inspected and all bolts should be checked for tightness.Remove all shipping tapes, bags, blocks, and skids, which are used to prevent vibration and rotor movement during shipment. Dry, low-pressure compressed air of approximately 30 PSI (206 KPA) can be used to blow out the interior of the generator. In the case of two bearing machines, it is possible to turn the rotor by hand to make sure that it rotates smoothly without binding.If the machine has been in storage for a year or longer it is recommended that it be lubricated according to the lubrication instructions and chart supplied in the maintenance section.If the machine has been exposed to damp, humid conditions the insulation resistance should be checked. Refer to the instructions supplied in this manual.GENERATOR MOUNTING - SINGLE BEARINGSingle bearing generators are provided with an SAE flywheel adapter and flexible drive discs. Very close tolerances are maintained in the manufacture of the generator so that the alignment procedure is extremely simple. A coupling hub of nodular iron is shrunk on the shaft and special steel drivediscs are bolted to the hub. Holes are provided in the periphery of the coupling disc, which correspond to tapped holes inthe flywheel. The outside diameter of the discs fits in a rabbet in the flywheel so that concentricity is assured in all cases.WARNINGDO NOT APPLY ANY FORCE TO THE GENERATOR FAN FOR LIFITNG OR FOR ROTATING THE GENERATORROTOR. DISREGARDING THESEINSTRUCTIONS MAY CAUSE PERSONAL INJURY OR EQUIPMENTDAMAGECAUTION:GRADE 8 CAPSCREWSOR GRADE 8 PLACE-BOLTS AND HARDENED WASHERS ARE REC-OMMENDED TO MOUNT THE DRIVE DISCS TO THE FLYWHEEL.DO NOT USE HELICAL OR OTHER LOCKING DEVICES UNLESS APPROVED.The SAE adapter and the flywheel housing are designed to match each other with no further alignment necessary. Shims may be necessary under the feet of the generator to insure a solid mounting. See THE SERVICE SECTION for more information. GENERATOR MOUNTING-TWOBEARINGTwo bearing generators are provided with a shaft extension and key way. For direct-coupled sets the assembler furnishes a flexible coupling which is installed between the driver and the generator shaft.IMPORTANT: Aligning the two machinesas accurately as possible will reduce vibration, increase-bearing life, and insures minimum coupling wear. It may be necessary to shim the generator feet for proper support and alignment. Consult the coupling manufacturer’s instructions for alignment specifications and procedures. BELT DRIVEPlease refer to Marathon Electric for applications involving belt driven installations.ENVIRONMENTAL CONCERNSDirt, moisture, heat, and vibration are enemies of electrical equipment. The ambient temperature should not exceed the value shown on the generator nameplate. Generators for outdoor application should be protected from the elements by housings with proper openings for ventilation. This protection should be designed to prevent the direct contact of wind driven rain, snow, or dust with the generator. In moist or humid areas, such as the Tropics and marine serv-ice, additional protection is recommended. Although the standard windings are humidity and moisture resistant, special insulation and accessories such as space heaters can increase generator life. In extremely dirty and dusty environments a means of providing filtered cooling air to the generator is recommended. Please refer to Marathon Electric for filter kits that are available.ELECTRICAL CONNECTIONSThe generator conduit box construction allows conduit to enter the top, bottom, or either side of the box. A hole-saw or any suitable tool can be used to provide for the conduit entrance. Protect the interior of the generator from shavings when drilling or sawing. An approved connector must be used in conjunction with the conduit.To minimize the transmission of vibration, it is essential that flexible conduit be used for all electrical cable entrance to the generator. Refer to the connection diagram supplied with the generator and / or the proper diagrams shown in this section. Install all intercomponent and external wiring in accordance with the regulations of the national and local electrical codes. Clean all contact surfaces to assure good electrical bonding with the generator lugs or bus bars. Use heavy-duty terminal lugs or good quality clamps for making all connections. Insulate all connections in accordance with national and local regulations.Be sure the generator frame is grounded to all the other components of the system with a ground wire in accordance with national and local regulations.GENERATOR LEAD CONNECTIONS The electrical connections in the conduit box should be made in accordance with the appropriate “connection diagram.” Use the diagram appropriate for the number of leads and voltage range required. Refer to the drawings supplied with the generator and to drawings in this section.The final voltage setting is established within the selected range by an adjustment of the voltage regulator.CAUTION:SOME GENERATORS HAVE MULTIPLE, IDENTICALLY MARKED, CABLES FOR EACH LEAD. CONNECT ALL IDENTICALLY MARKED CABLES TOGETHER WHEN MAKING CONNECTIONS.PARALLELING OPERATIONSMagnaMAX generators come standard with amortisseur windings die cast as an integral part of the rotor. This exclusive, Unirotor TM, construction makes all MagnaMAX generators suitable for paralleling operations when the proper control equipment is added. Paralleling with other generator sets and / or with the utility power grid offers a number of advantages. Multiple unit installations increase power capacity; they can be added or removed from the line depending on the load requirements; they can be better maintained and repaired (since single source breakdown would mean total loss of power), and they often provide more reliable, efficient, and economical operation.Successful parallel operation means that the generators deliver power to the external system without delivering power to each other, or accepting power from the load bus or power grid. Additional equipment is necessary to insure safe and successful operation. PRIME MOVERThe prime mover provides the speed and torque which will be necessary to keep the machines in synchronized operation. A governor controls the prime mover's speed. The governor will directly control the watt or kW output and frequency of the unit. The governor must have special paralleling provisions to permit parallel operation with the other machines.VOLTAGE REGULATORThe voltage regulator controls the generator output voltage and the reactive power supplied by the generator. When two or more ac generators operate in parallel, the voltage regulator must have paralleling provisions (either internally or external to the regulator) to control the reactive or VAR load while it is in parallel operation. A separate paralleling current transformer is required to sense the reactive current and signal the voltage regulator. This additional paralleling circuitry is absolutely necessary to control the reactive current flowing between the generator sets. SWITCHGEARThere are additional relays and breaker controls that are necessary to insure safe, trouble free operation of paralleled units. Reverse power relays monitor the direction of power flow to insure that the generator is delivering power, not accepting it. These power relays control breakers, which are a means of connecting and disconnecting the gen-erator from the load. The total system can include over-voltage, over-current protection, under fre-quency protection, power factor correction provi-sion and a variety of associated control equipment from manual switchgear to microprocessors. The amount of control gear and level of sophistication will be determined by the needs and requirements of the particular application.PARALLELING BASICSThe following points are basic criteria which must be met before two units can be paralleled. THIS IS NOT MEANT TO BE SPECIFIC INSTRUCTIONS FOR PARALLELING OPERATION.1. Additional paralleling circuitryA. Voltage regulator-paralleling provisionsB.Paralleling current transformer(s)C. Paralleling provisions on governor controlsD. Switchgear2. The voltage and frequency must be the same for all sets with voltages in phase.3. The voltage regulation characteristics of the individual generators should be similar.4. The generators must have the same phase rotation.5.The driving engines should have the same speed regulation characteristics and the governors should be adjusted to give the same speed regulation.Before operating generator sets in parallel, each set should be checked by starting, operating, and adjusting the sets as individual units before attempting paralleling. REACTIVE LOAD CONTROLWhen two identical generators are operating together in parallel and an unbalance occurs in field excitation, circulating currents begin to flow between the generators. This current will appear as a lagging power factor or inductive load to the highly excited generator, and as a leading power factor or capacitive load to the generator with the lower field current. This is known as the reactive circulating current and there are two methods of controlling it in parallel operation:1. Reactive droop compensation. (Formerly known as parallel droop compensation.)The bus voltage droops, or decreases, as the reactive lagging power factor load is increased.2. Reactive differential compensation. (Formerly known as cross current compensation.) The reactive differential compensation circuit allows parallel generators to share reactive loads with no decrease or droop in generator voltage.The circuit must meet the following criteria:A.All paralleling current transformers for all the generators being paralleled must be included in the secondary interconnection loop.B. When different size generators are paralleled all paralleling current transformers must have the same proportional ratios that give approximately the same secondary current.C. Voltage regulator paralleling circuitry must be the same.D. Current transformer secondary and the generator lines must be isolated electrically.E. It is also desirable to have an auxiliary contact on the main generator breaker to short the parallel CT secondary when that breaker is open (not connected to the load bus).Because of the above criteria, reactive differential compensation cannot be used when paralleling with the utility power grid. There is no limit, however, in the number of generators that can be included in this type of circuit. PARALLELING CIRCUITRYBecause of the number of variables involved in paralleling generator sets, every installation will have its own circuitry and methods or procedure of bringing paralleled units on line. There are numerous ways of connecting paralleled units and an almost unlimited variety of applications and associated equipment.When parallel operation is desired, it is important that the control manufacturer, the generator manu-facturer, and the systems engineer work together to insure the proper selection of all components. Please refer to Marathon Electric for application assistance.THYRISTOR OR SCR LOADING Solid state electronic control devices which utilize thyristors or SCR firing circuits (such as variable frequency induction motor controls, precision motor speed controls, no-break powered battery chargers, etc.) can introduce high frequency harmonics which adversely affect or destroy the normal waveform of the generator. This creates additional heat in the generator stator and rotor, and can cause overheating. These devices can and do present problems to non-utility power generating equipment or any limited power bus system. The problems that can occur are not limited to the generator itself, but can effect the solid state control device, the equipment it controls, other associated loads, monitoring devices or a number of combinations over the entire system.MagnaMAX generators can supply power to thyristor or SCR loads when properly applied. The standard voltage regulator is PMG powered and senses 3 phase RMS voltages for maximum stability against severely distorted waveforms. SCR type applications such as cranes, shovels, etc., require special consideration of the generator insulation system due to greater dielectric stress and severe environmental conditions. It is impor-tant that the control manufacturer, the generator manufacturer, and the systems engineer work together to insure the proper selection of all components. Please refer to Marathon Electric for application assistance. OPERATIONPRE-START INSPECTIONBefore operating the generator for the first time, the following checks are recommended.1. A visual inspection should be made to check for any loose parts, connections, or foreign materials2. Check for clearance in the generator and exciter air gap. Be sure the generator set turns over freely. Bar the generator over by hand at least 2 revolutions to be sure there is no interference.WARNINGDO NOT APPLY ANY FORCE TO THEGENERATOR FAN FOR LIFITNG ORFOR ROTATING THE GENERATORROTOR. DISREGARDING THESEINSTRUCTIONS MAY CAUSE PERSONAL INJURY OR EQUIPMENTDAMAGE3. Check all wiring against the proper connection diagrams and make sure all connections are properly insulated. Support and tie leads to keep them from being damaged by rotating parts or by chafing on sharp corners.4. Be sure the equipment is properly grounded.5. Inspect for any remaining packing materials and remove any loose debris, building materials, rags, etc. that could be drawn into the generator.6. Check fasteners for tightness.7. Check to be sure no tools or other hardware have been left inside or near the machine.8. Install and check to be sure all covers and guards are in place and secure.WARNINGRESIDUAL VOLTAGE IS PRESENT AT THE GENERATOR LEADS AND AT THE REULATOR PANEL CONNECTIONS EVEN WITH THE REGULATOR FUSE REMOVED.CAUTION MUST BE OBSERVED OR SERIOUS PERSONAL INJURY OR DEATHCAN RESULT.STARTING-UP THE GENERATORThe following procedure should be followed for starting-up the generator for the first time:1.The generator output must be disconnected from the load. Be certain that the main circuit breaker is open.2.D isable the voltage regulator by removing the fuse.WARNINGDO NOT OVERSPEED THEGENERATOR. EXCESSIVE CENTRIFUGAL FORCES COULD DAMAGE THE ROTATING FIELDS. BE PREPARED FOR AN EMERGENCYSHUTDOWN.3.F ollow the manufacturer's instructions and start the prime mover. Check the speed and adjust to the RPM shown on the generator nameplate.4.Replace the regulator fuse and adjust the voltage to the required. Check all line to line and line to neutral voltages to be sure they are correct and balanced. If the voltages are not correct shut down immediately and recheck all connections.5. Close the main circuit breaker and apply the load.6. Monitor the generator output current to verify it is at or below nameplate amps.7. Adjust engine speed at full load to 1800 rpm for 60 hertz, 1500 rpm for 50 hertz. (Refer to prime mover/governor instruction manuals.)8. Before stopping the engine, remove the load by tripping the main circuit breaker.FIELD FLASHINGThe standard MagnaMAX generator is supplied with a PMG (permanent magnet generator). It will never require field flashing. In rare cases where a special generator may be furnished without a PMG, refer to the factory for more detailed information. Include the complete generator model and serial number.VOLTAGE ADJUSTMENTSThe voltage regulator controls the generator output voltage. There is a cover to access the controlpanel on the side of the generator conduit boxFigure 4-1Figure 4-2 Regulator Access Refer to the regulator manual for detailed information. In cases where special or remote mounted regulators are used, refer to instructions supplied by the generator set assembler and to the voltage regulator manual.。
MAX1986ETE中文资料

MAX1984/MAX1985/MAX1986
The MAX1984/MAX1985/MAX1986 are white light-emitting diode (LED) drivers that use individual regulators to control the current of up to eight LEDs. A high-efficiency step-up regulator generates just enough voltage to keep all the current regulators in regulation. A versatile dimming interface accommodates analog, digitally adjusted pulse-width modulation (DPWM), or parallel control. The individual current regulators allow good current matching between LEDs. Open or shorted LEDs cannot affect the performance of other LEDs. The step-up regulator achieves high efficiency by using synchronous rectification. The internal N-channel switch and P-channel synchronous rectifier eliminate the need for external MOSFETs and diodes. The 1MHz switching frequency allows the use of low-profile inductors and ceramic capacitors. The brightness can be easily adjusted using a multimode dimming interface, which allows brightness control through a DPWM signal, a 2- or 3-bit parallel control interface, or an analog signal. The DPWM signal can be connected directly to the control pin without the need for an external RC filter if its frequency is 10kHz or above. The MAX1984 drives up to eight LEDs, the MAX1985 drives up to six LEDs, and the MAX1986 drives up to four LEDs. Each device has an LED select pin (SEL) that allows one subset, the other subset, or all LEDs to be illuminated. All three devices are available in a 4mm ✕ 4mm thin QFN package.
MAX490EEPA中文资料
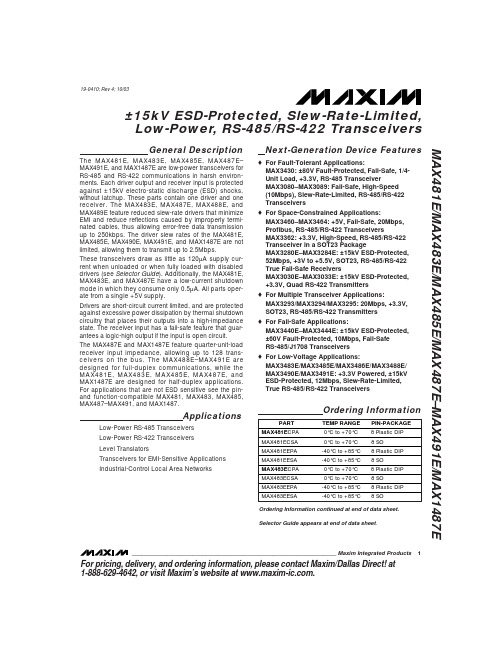
元器件交易网
MAX481E/MAX483E/MAX485E/MAX487E–MAX491E/MAX1487E
19-0410; Rev 4; 10/03
±15kV ESD-Protected, Slew-Rate-Limited, Low-Power, RS-485/RS-422 Transceivers
Ordering Information
PART MAX481ECPA MAX481ECSA MAX481EEPA MAX481EESA MAX483ECPA MAX483ECSA MAX483EEPA MAX483EESA
TEMP RANGE 0°C to +70°C 0°C to +70°C -40°C to +85°C -40°C to +85°C 0°C to +70°C 0°C to +70°C -40°C to +85°C -40°C to +85°C
Maxwell超级电容器改变全世界的能量储存和使用方式

1 - 150310 - 350650 – 3,40058 - 5002.3 - 2.7max图像不按比例缩放。
本手册所含信息仅为印刷当时的正确信息。
如欲了解最新信息和产品更新,敬请访问: 。
*有关适用的操作条件,敬请访问: ,参见产品说明书了解适用性细则。
新标准超级电容器为优化能源利用设立了全新的标准。
对于风机、公共交通、混合动力汽车、消费类电子产品和工业设备等应用而言,超级电容器都是理想的选择。
超级电容器有多种尺寸、容量和模块配置可供选择,是电池的低成本补充方案,不仅可延长电池使用寿命,在某些情况还能完全替代电池。
降低成本,提升价值专利材料技术的不断发展,加上工艺优化和全球制造,使Maxwell 能够在不断降低成本的同时确保高品质。
并且Maxwell 的产品团队还能针对各行业应用的特殊需求,灵活机动地提供设计与性能量身定制的产品。
Maxwell 超级电容器改变全世界的能量储存和使用方式Maxwell 业界领先的超级电容器是突破性创新型的储能和输电器件,其电容量是传统电容器的百万倍。
它能够快速可靠地释放大功率。
即便在苛刻的条件下,超级电容器也具有数十万次的工作周期。
文档编号:3000615-CN.2 MAXWELL TECHNOLOGIES 、MAXWELL 、MAXWELL CERTIFIED INTEGRATOR 、ENABLING ENERGY ’S FUTURE 、BOOSTCAP 、C CELL 、D CELL 及其对应的设计和/或标识均为Maxwell 技术公司的商标或注册商标,没有Maxwell 技术公司的事先书面许可,不得复制、伪造或使用其全部或部分内容。
本文所有内容均为©2014年Maxwell 技术公司版权所有。
保留一切权利。
没有Maxwell 技术公司的事先书面许可,不得以任何形式或方式复制上述材料的任何内容。
***包括有限质保在内的附加条款在购买时开始生效。
有关适用的操作与使用要求,参见产品说明书和质保详细说明。
Eaton Memera全金属消费者单元和保护设备说明书

EatonMemera full metal consumer units and protective devices Consumer unit solutionsto meet the requirements of the18th edition wiring regulations2EATON Memera full metal consumer units and protective devices - August 2020Memera full metal consumer unitsand protective devicesBS7671:2018Tested to BS EN 61439-3Fully complies with BS7671:2018(IET wiring Regulations 18th Edition)Contents1. Product overview (3)2. Memera full metal consumer unit range (6)3. Circuit protection devices and accessories (7)4. Consumer unit accessory selection (8)5. T echnical data (9)1 Product overview100A type A RCCB’s• Three new versions of the Memera 10, 14 and16 way dual RCCB boards are now also availablepre fitted with 100A type A RCCB’s for usewhere the installation is required to have type ARCD protection.Memera full metal consumer unitsThe Eaton range of full metal consumer units provide asuite of products to meet the requirements of BS7671:201818th Edition IET wiring regulations.Todays 18th edition consumer units incorporate anenclosure manufactured from non-combustible material,i.e. a full metal enclosure.Eaton consumer unit features• Full compliance with BS EN 61439-3.• All metal enclosure to meet requirements of BS7671regulation 421.1.201.• Sturdy steel enclosure with ample cable entry knockoutsto accommodate cable entry from top, bottom or rearface of the enclosure.• Multiple large apertures in rear face of enclosure to allowflexible cable entry from the rear, with dual knockouts toaccommodate both round glands as well as trunking ontop/bottom faces.• “Snap - able” busbars enabling easy on-site configuration.• Dual RCCB units come with three Neutral bars asstandard for High Integrity configuration.• Comprehensive label kit to complete the installation.• Polyester powder coat paint finish which complieswith industry standards for low smoke density, flamepropagation and toxic fume emission. RAL 9010 (Purewhite).• Available in single rail and dual rail surface and flushmounting variants up to a maximum of 38 outgoing ways.Arc Fault Detection Device (AFDD) solutionsSurge Protection Device (SPD) solutions• A 280V 20kA 2 pole type 2 Surge Protection Device isalso available as a kit to enable an Eaton SPD to be fittedinto any consumer unit even when fitted with AFDD’s.Installation kits are detailed in section 5.Command and control devices• The full range of Eaton modular command and controldevices such as transformers, timers, contactors andrelays can be installed in any unused ways. For detailssee main Single phase product catalogue.• Bus bars and connection links are available to simplify theinstallation of Eaton’s AFDD’s within Memera consumerunits as detailed in section 5.• Additional accessory connection kits are also available toprovide internal connectivity for consumer units equippedwith AFDD’s as well as MCB’s, RCBO’s and SPD’s.3EATONMemera full metal consumer units and protective devices - August 20204.1Circuit Protection devicesThe Eaton Memera range of consumer units can be equipped with the standard range of EAD 6kA MCB’s with ratings up to 63A at 6KA in both B and C curve, along with a full range of single module 6kA RCBO’s rated up to 45A in B and C curve with both AC and A current type characteristics.A new addition to the circuit protection portfolio is Eaton’s range of AFDD’s rated up to 40A can now also be accommodated using the additional accessory kits detailed further in this guide.In addition to the protection devices above the wide range of Eaton DIN rail modular accessories including SPD’s, timers and contactors etc., can also be accommodated within the consumer unit enclosure due to the flexible nature of the design. Fitting of AFDD’s into consumer unitsIn order to comply with the requirements of BS7671 for the inclusion of AFDD’s when deemed necessary, Eaton can provide a range of AFDD installation accessory kits to simplify the fitting of these devices into our Memera metal consumer units along with other protective devices as required.The kits include a special 3-4 way AFDD 2 pole busbar kit as well as a number of other interconnection accessory kits that may be required depending upon the consumer unit configuration selected and the devices to be fitted.Full details can be found in section 4 & 5 of this brochure.Requirements for Surge Protection devicesBS7671: 2018 also now places a greater emphasis on Chapter 44 – Protection against voltage disturbances and electromagnetic disturbances.Such disturbances can be temporary as a result of system faults in the LV or HV supply network, or perhaps transient overvoltages of atmospheric origin or else due to switching.The need for the inclusion of a surge protection device in an installation is dependent upon the perceived risk to an installation. The regulations in BS7671 provide detailed guidance on the application of Surge Protection devices and the methodologies relating to risk management and assessment.To make it simple for Installers, Eaton has introduced an SPD kit which includes a standard 2 pole 2 module Type 2 SPD rated at 280 V 20kA complete with the necessary interconnections.Full details can be found in section 5 of this brochure.EAS2PT2SPD - SPD KitEAS2PT2SPD kit includes the SPD and the the 3 pre made connectionsrequired to facilitate the installation of the 2pole SPD into any standardIsolator controlled Memera Consumer unit.EarthNeutralLiveFor SPDoperatinginstructionsconsult literaturesupplied withSPCT2-280/25 EATON Memera full metal consumer units and protective devices - August 20202 Memera metal consumer unit rangeModules Eaton list numberIsolator controlled RCCB controlled Split load Dual RCD Dual tariff Dimensions (mm)Modules Eaton list numberIsolator controlled RCCB controlled Split load Dual RCD Dual tariff Cover dimensions (mm)Back boxdimensions (mm)Full metal consumer unit rangeSurface mountedFlush mounted6EATON Memera full metal consumer units and protective devices - August 20203 Consumer unit circuit protection Devices & AccessoriesEaton Memera MCB’sEaton arc fault detection devices - T ype AEaton Memera RCBO’sTrip curve BTrip curve BAC type trip curve BA type trip curve BConsumer unit SPD and AFDD accessory kitsTrip curve CTrip curve CAC type trip curve CA type trip curve Cote: N Also available as type AC and type A with short time delay.7EATON Memera full metal consumer units and protective devices - August 20208EATON Memera full metal consumer units and protective devices - August 20204 Consumer unit accessory selection tables5 T echnical dataFitting of Consumer unit SPD with and without AFDD’sEarthNeutralLiveFor SPD operating instructionsconsult literature supplied with SPCT2-280/2Neutral NeutralEarthEarthLiveLive EAS2PT2SPD - SPD KitExample EAS10S - EAS10F1615141312LN 11109876543L N 21P DRCD AFDD 3AFDD 2AFDD 1lx AFDD 3AFDD 2AFDD 1S P DS P D2625242322212019181716151413AFDD 7AFDD 6AFDD 5AFDD 4S P D14131211109876543L N 211817161514131211109876543L N 21AFDD 3AFDD 2AFDD 1S P D AFDD 4S P DAFDD 4AFDD 3AFDD 2AFDD 1xAFDD 3AFDD 2AFDD 1S P DS P D14131211109876543LN 211817161514131211109876543LN 211211109876543L N 21AFDD 1S P D xAFDD 3AFDD 2S P DAFDD 4AFDD 3AFDD 2AFDD 1AFDD 3AFDD 2AFDD 1S P D AFDD 4S P D AFDD 4AFDD 3AFDD 2AFDD 1EASAFDDBB3S P D14131211109876543LN 211817161514131211109876543L N 2188171615141312LN 11109876543L N 21EASAFDDBB3AFDD 3AFDD 2AFDD 1S P D AFDD 4S P D AFDD 4AFDD 3AFDD 2AFDD 1x AFDD 3AFDD 2AFDD 1S P D 1817161514131211109876543L N 213L N 211716151413S P DS P DS P DAFDD 4S P DAFDD 4AFDD 3AFDD 2AFDD 1AFDD 3AFDD 2AFDD 1S P DAFDD 4S P DAFDD 4AFDD 3AFDD 2AFDD 1xAFDD 3AFDD 2AFDD 1S P DEASSPCONSPD – SPD/AFDD KitEASRCDCONSPD – SPD/AFDD KitFor use with EAS18 - 20S/EAS18 - 20FFor use with EAS26S/EAS26Fand Split Load BoardsFitting instructions for SPD with AFDD to specific Memera boards see overleaf9EATON Memera full metal consumer units and protective devices - August 2020Fitting of consumer unit with AFDD’sEASSPCON - AFDD Single Pole T erminalEASAFDDBB3 - AFDD BusbarEASDPCON - AFDD Double Pole T erminalEASAFDDTB - AFDD Busbar Stab ShieldNeutralLive X3 AFFD’s - Busbar connected directly to isolatorORX4 AFFD’s - Busbar connected to isolator via cablesFacility to fit mcb’s withAFDD’s X6 AFFD’s - Busbar connected directly to isolatorShield all un-used AFDD busbar stabsNote: Unless otherwise specified, all internal cabling supplied in the consumer unit is left unmodofied.*2 - Remove x2 (blue) pre-installed isolator to neutral terminal block cables and x1 (brown) isolator to lower busbar cable181716151413121110987654321L N555121110987654321L N AFDD 5DD 6321L N321L N 2625242322212019181716151413EASAFDDBB3AFDD 1AFDD 1AFDD 2AFDD 1xAFDD 316151413121110L N 987654321LNAFDD 2AFDD 1x AFDD 3AFDD 4AFDD 3121110987654321L N1211109262524232216151413121110L N 987654321L N AFDD 8AFDD 7xAFDD 3AFDD 4AFDD 3AFDD 2AFDD 11413121110987654321L N26252423222625242322AFDD 3AFDD 2AFDD 1RCDAFDD 8AFDD 7AFDD 2AFDD 1x AFDD 3AFDD 4AFDD 3AFDD 2AFDD 11413121110987654321L N181716151413121110987654321L N121110987654321L NAFDD 4AFDD 3AFDD 2AFDD 1RCD AFDD 6AFDD 3AFDD 2AFDD 1AFDD 4AFDD 2AFDD 1AFDD 2AFDD 1xAFDD 3AFDD 4AFDD 3AFDD 4AFDD 3AFDD 2AFDD 11413121110987654321L N181716151413121110987654321L NAFDD 3AFDD 2AFDD 1AFDD 4AFDD 2AFDD 1AFDD 2AFDD 1x AFDD 3AFDD 4AFDD 3AFDD 4AFDD 3AFDD 2AFDD 1Isolator Controlled -Split Load1413121110987654321L N151413121110987654321L NAFDD 5AFDD 4AFDD 6AFDD 4AFDD 3AFDD 2AFDD 1AFDD 3AFDD 2AFDD 1AFDD 3AFDD 2AFDD 1AFDD 4AFDD 2AFDD 1AFDD 2AFDD 1x AFDD 3AFDD 4AFDD 3AFDD 4AFDD 3AFDD 2AFDD 1Isolator controlledSplit load10EATON Memera full metal consumer units and protective devices - August 2020Miniature circuit breakers (MCBs)Eaton’s range of 6kA high performance MCBs meet the latest UK and European standards IEC/EN 60898, with ratings up to 63A in both B & C curve characteristics. Features include:• Box clamp barrier to prevent incorrect cable insertion• Positive contact indication Residual current circuitbreakers - with overloadprotection (RCBOs)Eaton’s range of 6kA, 30mA highperformance compact RCBOs meetthe latest UK and European standardsIEC/EN 61009, combining ResidualCurrent Circuit Breaker protectionwith integral overload protection inone compact modular device. Ratingsavailable from 6A to 45A in both B &C curve characteristics.Features include:• Compact modular design, only102mm tall, giving enhanced wiringspace• Single module width with solidneutral• Box clamp barrier to preventincorrect cable insertion• Positive contact indication• Devices available as both AC and Acurrent typesArc Fault DetectionDevices (AFDD +)Eaton’s range of AFDD’s combine thefunctionality of an MCB, RCD andAFDD in one package designed inaccordance to IEC/EN 62606 & IEC/EN 61009. Ratings are available up to40A with B & C curve characteristicsand 10mA and 30mA sensitivity.Devices are available in current typesA, AC and short time delayed type A.Features include:• Variable installation of N on eitherleft or right• Tripped indication : MCB, RCCB orAFDD with LED indication of arcfaults• Permanent self monitoring includingover heating and over voltage• Rated breaking capacity up to 10kA(6kA above 25A)Consumer unitsThe 2019 Memera full metal consumer units range fully complies with BS EN 61439-3 and meetsthe requirements of BS7671:2018 clause 421.1.201 i.e. non-combustible enclosure.In accordance with BS7671, installation of these units should use proper materials and follow good workmanship and industry practices. The correct use of grommets, grommet strip or glands should be considered to minimise the risk of damage arising from mechanical stress or damage to wiring whereit enters the metal enclosure. In addition, the horizontal top surface of the consumer unit if readily accessible shall provide a degree of protection of at least IPXXD or IP4X. T erminal capacity and torque settingsNote: A ll terminals should be tightened to the recommended torque values below using an appropriate torque driver.• Device torque cable capacity• Isolator 2.5 – 5.0 Nm 2.5 – 50 mm2• RCCB 2.0 – 2.4 Nm 1.5 – 35 mm2• MCB 2.0 – 2.4 Nm 1 – 25 mm2• RCBO Line 2.0 – 2.5 Nm Load 1.2 -1.5 Nm 1 -16 mm2• AFDD - 2.0 – 2.4 Nm 1.5 – 25 mm2• SPD - 2.0 – 2.4 Nm 1.5 – 35 mm2• Neutral / Earth bars 2.0 Nm 1 -16 mm2• Other devices: see appropriate installation instructions11 EATON Memera full metal consumer units and protective devices - August 2020At Eaton, we’re energized by the challenge of powering a world that demands more. With over 100 years experience in electrical power management, we have the expertise to see beyond today. From ground breaking products to turnkey design and engineering services, critical industries around the globe count on Eaton. We power businesses with reliable, efficient and safe electrical power management solutions. Combined with our personal service, support and bold thinking, we are answering tomorrow’s needs today. Follow the charge with Eaton. Visit /uk.Eaton Electric Limited252 Bath RoadSloughSL1 4DXCustomer Support CentreTel: +44 (0)8700 545 333Fax: +44 (0)8700 540 333email:**********************© 2020 Eaton CorporationAll Rights ReservedPrinted in UKPublication No. BR012018ENEAN Code 9010August 2020。
MAX1978中文数据手册

用于Peltier模块的集成温度控制器概论MAX1978 / MAX1979是用于Peltier热电冷却器(TEC)模块的最小, 最安全, 最精确完整的单芯片温度控制器。
片上功率FET和热控制环路电路可最大限度地减少外部元件, 同时保持高效率。
可选择的500kHz / 1MHz开关频率和独特的纹波消除方案可优化元件尺寸和效率, 同时降低噪声。
内部MOSFET的开关速度经过优化, 可降低噪声和EMI。
超低漂移斩波放大器可保持±0.001°C的温度稳定性。
直接控制输出电流而不是电压, 以消除电流浪涌。
独立的加热和冷却电流和电压限制提供最高水平的TEC保护。
MAX1978采用单电源供电, 通过在两个同步降压调节器的输出之间偏置TEC, 提供双极性±3A输出。
真正的双极性操作控制温度, 在低负载电流下没有“死区”或其他非线性。
当设定点非常接近自然操作点时, 控制系统不会捕获, 其中仅需要少量的加热或冷却。
模拟控制信号精确设置TEC 电流。
MAX1979提供高达6A的单极性输出。
提供斩波稳定的仪表放大器和高精度积分放大器, 以创建比例积分(PI)或比例积分微分(PID)控制器。
仪表放大器可以连接外部NTC或PTC热敏电阻, 热电偶或半导体温度传感器。
提供模拟输出以监控TEC温度和电流。
此外, 单独的过热和欠温输出表明当TEC温度超出范围时。
片上电压基准为热敏电阻桥提供偏置。
MAX1978 / MAX1979采用薄型48引脚薄型QFN-EP 封装, 工作在-40°C至+ 85°C温度范围。
采用外露金属焊盘的耐热增强型QFN-EP封装可最大限度地降低工作结温。
评估套件可用于加速设计。
应用光纤激光模块典型工作电路出现在数据手册的最后。
WDM, DWDM激光二极管温度控制光纤网络设备EDFA光放大器电信光纤接口ATE特征♦尺寸最小, 最安全, 最精确完整的单芯片控制器♦片上功率MOSFET-无外部FET♦电路占用面积<0.93in2♦回路高度<3mm♦温度稳定性为0.001°C♦集成精密积分器和斩波稳定运算放大器♦精确, 独立的加热和冷却电流限制♦通过直接控制TEC电流消除浪涌♦可调节差分TEC电压限制♦低纹波和低噪声设计♦TEC电流监视器♦温度监控器♦过温和欠温警报♦双极性±3A输出电流(MAX1978)♦单极性+ 6A输出电流(MAX1979)订购信息* EP =裸焊盘。
Maxcell称重显示器使用说明书

.................................. 37
1
Maxcell
2-3-12 RS485 ID 输入 (选配功能)
............................................. 38
命令格式说明 ...................................................................................................................... 39
2-3-9 RS232 一般或简易输出重量 6 位或 7 位选择
..................... 35
2-3-10 RTC 时间调整
............................................................... 36
2-3-11 调整打印时年月日或日月年显示方式
2-3-3 输出格式选择
.................................................................... 29
2-3-4 传送方式设定
.................................................................... 30
使用前之准备工作
一. 请将本机放置于稳固且平坦之桌面上使用,勿放于摇动或振动之台架上。 二. 避免将本机放置于温度变化过大或空气流动剧烈之场所,如日光直射或冷气机之出风口。 三. 请使用独立之电源插座,以避免其它电器用品干扰。 四. 打开电源时,秤盘上请勿放置任何东西。 五. 产品使用时,秤物之重心须位于秤盘之中心点,且秤物不超出秤盘范围,以确保其准确度。 六. 使用本机前,请先温机 15 ~ 20 分钟。 七. 请注意当低电源警示之符号( )闪烁时,则表示须再行充电。 八. 如对本产品有任何建议,请不吝指正。
MAX打印机说明书LM-380 AMANUAL (第1部分共5部)
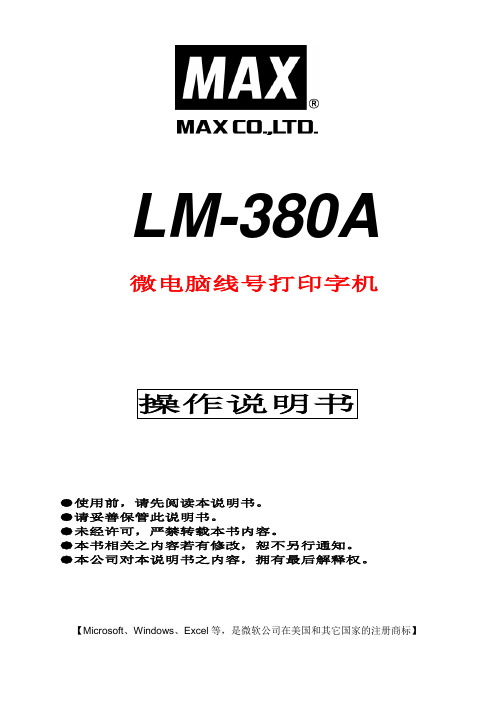
LM-380A微电脑线号打印字机操作说明书●使用前,请先阅读本说明书。
●请妥善保管此说明书。
●未经许可,严禁转载本书内容。
●本书相关之内容若有修改,恕不另行通知。
●本公司对本说明书之内容,拥有最后解释权。
【Microsoft、Windows、Excel等,是微软公司在美国和其它国家的注册商标】1. 请仔细阅读1-1 前言感谢您购买MAX LETATWIN LM-380A。
本机器具备多样化的设计功能,可在贴纸和套管上印字。
特别是在大量的贴纸和套管的印字上,有其独特的功能。
请妥善保管机器和阅读本说明书,接下来的介绍,将使您能完全的操作本机器。
1-2 使用上的注意■指示图本操作说明书用不同的符号显示,来帮助您安全和正确的使用LM-380A线号印字机。
在本节里将说明,这些符号所代表的意义。
警告如果不注意此警告,可能会导致使用者受到伤害。
注意如对此注意不加留意,将使操作人员受到伤害,损失您的设备,或流失所输入的资料。
表示机器出状况,需要修理,或要重新设定等,以使本机器能顺利的运作。
帮助您了解工作的要点,或给予一些指导。
★功能之注意事项。
■符号: 需注意事项。
:〝不能做的事〞。
在此显示中,您要特别留心。
:〝必须做的事〞。
此符号出现时,您必须跟随他的指示去做。
警告•千万别拆解或重组机器,这可能会引起火灾、电击或其它问题。
•请勿插入外来物品到本机器里面,如手指、笔、电线等。
这可能会损坏机器,或引起火灾。
•请使用正确的电压,否则将导致机器的损坏。
•请勿将重物至于电源线上,这会容易导致火灾或电线走火。
•请勿用湿的手去插或拔插头,此动作会引起电击。
•请勿洒水或化学药剂在机器上,以避免机器损坏、引起火灾或电击。
万一液体进入机器时,请立即切断电源,并联络您的经销商。
•机器故障时请勿再使用。
如机器在故障时使用,比如有异声或异味时,这可能会引起火灾或触电。
此时请立即切断电源,并联络您的经销商。
注意•资料不能保证永久储存在记忆卡或机器的内部存储器。
MAX490EESA+资料
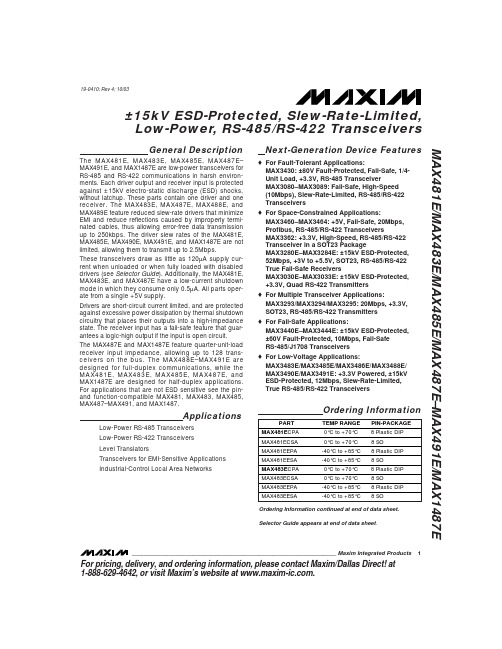
Supply Control
Voltage (VCC) Input Voltage
.(.–R—..E.–..,..D..E..)........................................-.0....5..V...t.o...(.V..C...C...+...0...152VV)
♦ For Low-Voltage Applications: MAX3483E/MAX3485E/MAX3486E/MAX3488E/ MAX3490E/MAX3491E: +3.3V Powered, ±15kV ESD-Protected, 12Mbps, Slew-Rate-Limited, True RS-485/RS-422 Transceivers
General Description
The MAX481E, MAX483E, MAX485E, MAX487E– MAX491E, and MAX1487E are low-power transceivers for RS-485 and RS-422 communications in harsh environments. Each driver output and receiver input is protected against ±15kV electro-static discharge (ESD) shocks, without latchup. These parts contain one driver and one receiver. The MAX483E, MAX487E, MAX488E, and MAX489E feature reduced slew-rate drivers that minimize EMI and reduce reflections caused by improperly terminated cables, thus allowing error-free data transmission up to 250kbps. The driver slew rates of the MAX481E, MAX485E, MAX490E, MAX491E, and MAX1487E are not limited, allowing them to transmit up to 2.5Mbps.
MAX1989MEE+中文资料

________________General DescriptionThe MAX1668/MAX1805/MAX1989 are precise multi-channel digital thermometers that report the tempera-ture of all remote sensors and their own packages. The remote sensors are diode-connected transistors—typi-cally low-cost, easily mounted 2N3904 NPN types—that replace conventional thermistors or thermocouples.Remote accuracy is ±3°C for multiple transistor manu-facturers, with no calibration needed. The remote chan-nels can also measure the die temperature of other ICs,such as microprocessors, that contain an on-chip,diode-connected transistor.The 2-wire serial interface accepts standard system management bus (SMBus™) write byte, read byte, send byte, and receive byte commands to program the alarm thresholds and to read temperature data. The data for-mat is 7 bits plus sign, with each bit corresponding to 1°C, in two’s-complement format.The MAX1668/MAX1805/MAX1989 are available in small, 16-pin QSOP surface-mount packages. The MAX1989 is also available in a 16-pin TSSOP.________________________Applications____________________________Featureso Multichannel4 Remote, 1 Local (MAX1668/MAX1989)2 Remote, 1 Local (MAX1805)o No Calibration Required o SMBus 2-Wire Serial Interfaceo Programmable Under/Overtemperature Alarms o Supports SMBus Alert Response o Accuracy±2°C (+60°C to +100°C, Local)±3°C (-40°C to +125°C, Local)±3°C (+60°C to +100°C, Remote)o 3µA (typ) Standby Supply Current o 700µA (max) Supply Currento Small, 16-Pin QSOP/TSSOP PackagesMAX1668/MAX1805/MAX1989†Multichannel Remote/LocalTemperature Sensors________________________________________________________________Maxim Integrated Products119-1766; Rev 2; 5/03SMBus is a trademark of Intel Corp.†Patents PendingDesktop and Notebook Computers LAN Servers Industrial ControlsCentral-Office Telecom EquipmentTest and Measurement Multichip ModulesFor pricing, delivery, and ordering information,please contact Maxim/Dallas Direct!at 1-888-629-4642, or visit Maxim’s website at .M A X 1668/M A X 1805/M A X 1989†Multichannel Remote/Local Temperature Sensors 2_______________________________________________________________________________________ABSOLUTE MAXIMUM RATINGSELECTRICAL CHARACTERISTICS(V CC = +3.3V, STBY = V CC , configuration byte = X0XXXX00, T A = 0°C to +125°C , unless otherwise noted.)Stresses beyond those listed under “Absolute Maximum Ratings” may cause permanent damage to the device. These are stress ratings only, and functional operation of the device at these or any other conditions beyond those indicated in the operational sections of the specifications is not implied. Exposure to absolute maximum rating conditions for extended periods may affect device reliability.V CC to GND..............................................................-0.3V to +6V DXP_, ADD_, STBY to GND........................-0.3V to (V CC + 0.3V)DXN_ to GND ........................................................-0.3V to +0.8V SMBCLK, SMBDATA, ALERT to GND......................-0.3V to +6V SMBDATA, ALERT Current.................................-1mA to +50mA DXN_ Current......................................................................±1mA Continuous Power Dissipation (T A = +70°C)QSOP (derate 8.30mW/°C above +70°C)....................667mW TSSOP (derate 9.40mW/°C above +70°C)..................755mWOperating Temperature Range .........................-55°C to +125°C Junction Temperature......................................................+150°C Storage Temperature Range.............................-65°C to +150°C Lead Temperature (soldering, 10s).................................+300°CMAX1668/MAX1805/MAX1989†Multichannel Remote/LocalTemperature Sensors_______________________________________________________________________________________3ELECTRICAL CHARACTERISTICS (continued)(V CC = +3.3V, STBY = V CC , configuration byte = X0XXXX00, T A = 0°C to +125°C , unless otherwise noted.)ELECTRICAL CHARACTERISTICS(V CC = +5V, STBY = V CC , configuration byte = X0XXXX00, T A = -55°C to +125°C , unless otherwise noted.) (Note 6)08416122024FREQUENCY (MHz)T E M P E R A T U R E E R R O R (°C )TEMPERATURE ERROR vs. SUPPLY NOISE FREQUENCY0.111010020-20110100TEMPERATURE ERROR vs. PC BOARD RESISTANCE-10LEAKAGE RESISTANCE (M Ω)T E M P E R A T U R E E R R O R (°C )10-2-101234-50-10-301030507090110TEMPERATURE ERROR vs. TEMPERATURETEMPERATURE (°C)T E M P E R A T U R E E R R O R (°C )Typical Operating Characteristics(Typical Operating Circuit , V CC = +5V, STBY = V CC , configuration byte = X0XXXX00, T A = +25°C, unless otherwise noted.)M A X 1668/M A X 1805/M A X 1989†Multichannel Remote/Local Temperature Sensors 4_______________________________________________________________________________________ELECTRICAL CHARACTERISTICS (continued)(V= +5V, STBY = V , configuration byte = X0XXXX00, T = -55°C to +125°C , unless otherwise noted.) (Note 6)Note 1:Guaranteed by design, but not production tested.Note 2:Quantization error is not included in specifications for temperature accuracy. For example, if the MAX1668/MAX1805/MAX1989 device temperature is exactly +66.7°C, the ADC may report +66°C, +67°C, or +68°C (due to the quantization error plus the +0.5°C offset used for rounding up) and still be within the guaranteed ±1°C error limits for the +60°C to +100°C temperature range. See Table 2.Note 3: A remote diode is any diode-connected transistor from Table 1. T R is the junction temperature of the remote diode. See theRemote-Diode Selection section for remote-diode forward-voltage requirements.Note 4:The SMBus logic block is a static design that works with clock frequencies down to DC. While slow operation is possible, itviolates the 10kHz minimum clock frequency and SMBus specifications, and can monopolize the bus.Note 5:Note that a transition must internally provide at least a hold time in order to bridge the undefined region (300ns max) ofSMBCLK’s falling edge t HD:DAT.Note 6:Specifications from -55°C to +125°C are guaranteed by design, not production tested.020406080100120140160012345STANDBY SUPPLY CURRENT vs. SUPPLY VOLTAGESUPPLY VOLTAGE (V)S U P P L Y C U R R E N T (µA )257550100125-220468RESPONSE TO THERMAL SHOCKTIME (s)T E M P E R A T U R E (°C )MAX1668/MAX1805/MAX1989†Multichannel Remote/LocalTemperature Sensors_______________________________________________________________________________________50.111000TEMPERATURE ERRORvs. COMMON-MODE NOISE FREQUENCYFREQUENCY (MHz)T E M P E R A T U R E E R R O R (°C )1010000.60.40.20.81.01.21.41.61.82.0Typical Operating Characteristics (continued)(Typical Operating Circuit , V CC = +5V, STBY = V CC , configuration byte = X0XXXX00, T A = +25°C, unless otherwise noted.)TEMPERATURE ERRORvs. DXP_ TO DXN_ CAPACITANCEM A X 16681805 t o c 05DXP_ TO DXN_ CAPACITANCE (nF)T E M P E R A T U R E E R R O R (°C )-10-6-8-2-42040203010405060STANDBY SUPPLY CURRENT vs. CLOCK FREQUENCYSMBCLK FREQUENCY (kHz)S U P P L Y C U R R E N T (µA )6010203040501101001000M A X 1668/M A X 1805/M A X 1989†Multichannel Remote/Local Temperature Sensors 6______________________________________________________________________________________________________Detailed DescriptionThe MAX1668/MAX1805/MAX1989 are temperature sensors designed to work in conjunction with an exter-nal microcontroller (µC) or other intelligence in thermo-static, process-control, or monitoring applications. The µC is typically a power-management or keyboard con-troller, generating SMBus serial commands by “bit-banging” general-purpose input-output (GPIO) pins or through a dedicated SMBus interface block.These devices are essentially 8-bit serial analog-to-digi-tal converters (ADCs) with sophisticated front ends.However, the MAX1668/MAX1805/MAX1989 also contain a switched current source, a multiplexer, an ADC, an SMBus interface, and associated control logic (Figure 1).In the MAX1668 and MAX1989, temperature data from the ADC is loaded into five data registers, where it is automatically compared with data previously stored in 10 over/undertemperature alarm registers. In the MAX1805, temperature data from the ADC is loaded into three data registers, where it is automatically compared with data previously stored in six over/undertemperature alarm registers.ADC and MultiplexerThe ADC is an averaging type that integrates over a 64ms period (each channel, typical), with excellent noise rejection.The multiplexer automatically steers bias currents through the remote and local diodes, measures their forward voltages, and computes their temperatures.Each channel is automatically converted once the con-version process has started. If any one of the channels is not used, the device still performs measurements on these channels, and the user can ignore the results of the unused channel. If any remote-diode channel is unused, connect DXP_ to DXN_ rather than leaving the pins open.The DXN_ input is biased at 0.65V above ground by an internal diode to set up the A/D inputs for a differential measurement. The worst-case DXP_ to DXN_ differential input voltage range is 0.25V to 0.95V.Excess resistance in series with the remote diode caus-es about +0.5°C error per ohm. Likewise, 200µV of offset voltage forced on DXP_ to DXN_causes about 1°C error.MAX1668/MAX1805/MAX1989†Multichannel Remote/LocalTemperature Sensors_______________________________________________________________________________________7Figure 1. MAX1668/MAX1805/MAX1989 Functional DiagramA/D Conversion SequenceIf a start command is written (or generated automatically in the free-running autoconvert mode), all channels are converted, and the results of all measurements are available after the end of conversion. A BUSY status bit in the status byte shows that the device is actually per-forming a new conversion; however, even if the ADC is busy, the results of the previous conversion are always available.Remote-Diode SelectionTemperature accuracy depends on having a good-qual-ity, diode-connected small-signal transistor. Accuracy has been experimentally verified for all of the devices listed in Table 1. The MAX1668/MAX1805/MAX1989 can also directly measure the die temperature of CPUs and other ICs having on-board temperature-sensing diodes.The transistor must be a small-signal type, either NPN or PNP, with a relatively high forward voltage; other-wise, the A/D input voltage range can be violated. The forward voltage must be greater than 0.25V at 10µA;check to ensure this is true at the highest expected temperature. The forward voltage must be less than 0.95V at 100µA; check to ensure this is true at the low-est expected temperature. Large power transistors do not work at all. Also, ensure that the base resistance is less than 100Ω. Tight specifications for forward-current gain (+50 to +150, for example) indicate that the manu-facturer has good process controls and that the devices have consistent VBE characteristics.F or heat-sink mounting, the 500-32BT02-000 thermal sensor from Fenwal Electronics is a good choice. This device consists of a diode-connected transistor, an aluminum plate with screw hole, and twisted-pair cable (Fenwal Inc., Milford, MA, 508-478-6000).Thermal Mass and Self-HeatingThermal mass can seriously degrade the MAX1668/MAX1805/MAX1989s’ effective accuracy. The thermal time constant of the 16-pin QSOP package is about 140s in still air. F or the MAX1668/MAX1805/MAX1989junction temperature to settle to within +1°C after a sudden +100°C change requires about five time con-stants or 12 minutes. The use of smaller packages for remote sensors, such as SOT23s, improves the situa-tion. Take care to account for thermal gradients between the heat source and the sensor, and ensure that stray air currents across the sensor package do not interfere with measurement accuracy.Self-heating does not significantly affect measurement accuracy. Remote-sensor self-heating due to the diode current source is negligible. F or the local diode, theworst-case error occurs when sinking maximum current at the ALERT output. For example, with ALERT sinking 1mA, the typical power dissipation is V CC x 400µA plus 0.4V x 1mA. Package theta J-A is about 150°C/W, so with V CC = 5V and no copper PC board heat sinking,the resulting temperature rise is:dT = 2.4mW x 150°C/W = 0.36°CEven with these contrived circumstances, it is difficult to introduce significant self-heating errors.ADC Noise FilteringThe ADC is an integrating type with inherently good noise rejection, especially of low-frequency signals such as 60Hz/120Hz power-supply hum. Micropower opera-tion places constraints on high-frequency noise rejec-tion; therefore, careful PC board layout and proper external noise filtering are required for high-accuracy remote measurements in electrically noisy environments. High-frequency EMI is best filtered at DXP_ and DXN_with an external 2200pF capacitor. This value can be increased to about 3300pF (max), including cable capacitance. Higher capacitance than 3300pF intro-duces errors due to the rise time of the switched cur-rent source.Nearly all noise sources tested cause additional error measurements, typically by +1°C to +10°C, depending on the frequency and amplitude (see the Typical Operating Characteristics ).PC Board Layout1)Place the MAX1668/MAX1805/MAX1989 as close aspractical to the remote diode. In a noisy environment,such as a computer motherboard, this distance canM A X 1668/M A X 1805/M A X 1989†Multichannel Remote/Local Temperature Sensors 8_______________________________________________________________________________________Table 1. Remote-Sensor Transistor ManufacturersNote:Transistors must be diode connected (base shorted to collector).be 4in to 8in (typ) or more as long as the worst noise sources (such as CRTs, clock generators, memory buses, and ISA/PCI buses) are avoided.2)Do not route the DXP_ to DXN_ lines next to thedeflection coils of a CRT. Also, do not route the traces across a fast memory bus, which can easily introduce +30°C error, even with good filtering.Otherwise, most noise sources are fairly benign.3)Route the DXP_ and DXN_ traces in parallel and inclose proximity to each other, away from any high-voltage traces such as +12VDC. Leakage currents from PC board contamination must be dealt with carefully, since a 20M Ωleakage path from DXP_ to ground causes about +1°C error.4)Connect guard traces to GND on either side of theDXP_ to DXN_ traces (Figure 2). With guard traces in place, routing near high-voltage traces is no longer an issue. 5)Route through as few vias and crossunders as possi-ble to minimize copper/solder thermocouple effects. 6)When introducing a thermocouple, make sure thatboth the DXP_ and the DXN_ paths have matching thermocouples. In general, PC board-induced ther-mocouples are not a serious problem. A copper-sol-der thermocouple exhibits 3µV/°C, and it takes about 200µV of voltage error at DXP_ to DXN_ to cause a +1°C measurement error. So, most para-sitic thermocouple errors are swamped out.7)Use wide traces. Narrow ones are more inductiveand tend to pick up radiated noise. The 10mil widths and spacings recommended in Figure 2 are not absolutely necessary (as they offer only a minor improvement in leakage and noise), but try to use them where practical.8)Copper cannot be used as an EMI shield, and onlyferrous materials such as steel work well. Placing a copper ground plane between the DXP_ to DXN_traces and traces carrying high-frequency noise sig-nals does not help reduce EMI.PC Board Layout Checklist•Place the MAX1668/MAX1805/MAX1989as close as possible to the remote diodes.•Keep traces away from high voltages (+12V bus).•Keep traces away from fast data buses and CRTs.•Use recommended trace widths and spacings.•Place a ground plane under the traces.•Use guard traces flanking DXP_ and DXN_ and con-necting to GND.•Place the noise filter and the 0.1µF V CC bypass capacitors close to the MAX1668/MAX1805/MAX1989.•Add a 200Ωresistor in series with V CC for best noise filtering (see the Typical Operating Circuit ).Twisted-Pair and Shielded CablesFor remote-sensor distances longer than 8in, or in partic-ularly noisy environments, a twisted pair is recommend-ed. Its practical length is 6ft to 12ft (typ) before noise becomes a problem, as tested in a noisy electronics lab-oratory. F or longer distances, the best solution is a shielded twisted pair like that used for audio micro-phones. For example, Belden #8451 works well for dis-tances up to 100ft in a noisy environment. Connect the twisted pair to DXP_ and DXN_ and the shield to GND,and leave the shield’s remote end unterminated.Excess capacitance at DX_ _ limits practical remote-sen-sor distances (see the Typical Operating Characteristics ).F or very long cable runs, the cable’s parasitic capaci-tance often provides noise filtering, so the 2200pF capac-itor can often be removed or reduced in value.Cable resistance also affects remote-sensor accuracy;1Ωseries resistance introduces about +0.5°C error.Low-Power Standby ModeStandby mode disables the ADC and reduces the sup-ply-current drain to less than 12µA. Enter standby mode by forcing the STBY pin low or through the RUN/STOP bit in the configuration byte register.Hardware and software standby modes behave almost identically: all data is retained in memory, and the SMB interface is alive and listening for reads and writes.Activate hardware standby mode by forcing the STBY pin low. In a notebook computer, this line can be con-nected to the system SUSTAT# suspend-state signal. The STBY pin low state overrides any software conversion command. If a hardware or software standby command is received while a conversion is in progress, the conver-MAX1668/MAX1805/MAX1989†Multichannel Remote/LocalTemperature Sensors_______________________________________________________________________________________9Figure 2. Recommended DXP_/DXN_ PC Tracession cycle is truncated, and the data from that conversion is not latched into either temperature-reading register. The previous data is not changed and remains available.In standby mode, supply current drops to about 3µA.At very low supply voltages (under the power-on-reset threshold), the supply current is higher due to the address pin bias currents. It can be as high as 100µA,depending on ADD0 and ADD1 settings.SMBus Digital InterfaceF rom a software perspective, the MAX1668/MAX1805/MAX1989appear as a set of byte-wide registers that contain temperature data, alarm threshold values, or control bits. A standard SMBus 2-wire serial interface is used to read temperature data and write control bits and alarm threshold data. Each A/D channel within the devices responds to the same SMBus slave address for normal reads and writes.The MAX1668/MAX1805/MAX1989employ four standard SMBus protocols: write byte, read byte, send byte, and receive byte (Figure 3). The shorter receive byte protocol allows quicker transfers, provided that the correct data register was previously selected by a read byte instruc-tion. Use caution with the shorter protocols in multimaster systems, since a second master could overwrite the com-mand byte without informing the first master.The temperature data format is 7 bits plus sign in two’s-com-plement form for each channel, with each data bit represent-ing 1°C (Table 2), transmitted MSB first. Measurements are offset by +0.5°C to minimize internal rounding errors; for example, +99.6°C is reported as +100°C.Alarm Threshold RegistersTen (six for MAX1805) registers store alarm threshold data, with high-temperature (T HIGH ) and low-tempera-ture (T LOW ) registers for each A/D channel. If either measured temperature equals or exceeds the corre-sponding alarm threshold value, an ALERT interrupt is asserted.The power-on-reset (POR) state of all T HIGH registers of the MAX1668 and MAX1805 is full scale (0111 1111, or +127°C). The POR state of the channel 1 T HIGH register of the MAX1989 is 0110 1110 or +110°C, while all other channels are at +127°C. The POR state of all T LOW reg-isters is 1100 1001 or -55°C.M A X 1668/M A X 1805/M A X 1989†Multichannel Remote/Local Temperature Sensors 10______________________________________________________________________________________Figure 3. SMBus ProtocolsThere is a continuity fault detector at DXP_ that detects whether the remote diode has an open-circuit condi-tion. At the beginning of each conversion, the diode fault is checked, and the status byte is updated. This fault detector is a simple voltage detector; if DXP_ rises above V CC - 1V (typ) due to the diode current source, a fault is detected. Note that the diode fault is not checked until a conversion is initiated, so immediately after power-on reset, the status byte indicates no fault is present, even if the diode path is broken.If any remote channel is shorted (DXP_ to DXN_ or DXP_ to GND), the ADC reads 0000 0000 so as not to trip either the T HIGH or T LOW alarms at their POR set-tings. In applications that are never subjected to 0°C in normal operation, a 0000 0000 result can be checked to indicate a fault condition in which DXP_ is acciden-tally short circuited. Similarly, if DXP_ is short circuited to V CC , the ADC reads +127°C for all remote and local channels, and the device alarms.A L E R T InterruptsThe ALERT interrupt output signal is latched and can only be cleared by reading the alert response address.Interrupts are generated in response to T HIGH and T LOW comparisons and when a remote diode is disconnected (for continuity fault detection). The interrupt does not halt automatic conversions; new temperature data continues to be available over the SMBus interface after ALERT is asserted. The interrupt output pin is open drain so that devices can share a common interrupt line. The interrupt rate can never exceed the conversion rate.The interface responds to the SMBus alert response address, an interrupt pointer return-address feature (see Alert R esponse Address section). Prior to taking corrective action, always check to ensure that an inter-rupt is valid by reading the current temperature.Alert Response AddressThe SMBus alert response interrupt pointer provides quick fault identification for simple slave devices that lack the complex, expensive logic needed to be a bus master. Upon receiving an ALERT interrupt signal, the host master can broadcast a receive byte transmission to the alert response slave address (0001 100). Then any slave device that generated an interrupt attempts to identify itself by putting its own address on the bus (Table 3).The alert response can activate several different slave devices simultaneously, similar to the I 2C general call. If more than one slave attempts to respond, bus arbitra-tion rules apply, and the device with the lower address code wins. The losing device does not generate an acknowledge and continues to hold the ALERT line low until serviced (implies that the host interrupt input isMAX1668/MAX1805/MAX1989†Multichannel Remote/LocalTemperature Sensors______________________________________________________________________________________11Table 3. Read Format for Alert Response Address (0001100)ADD66Provide the currentMAX1668/MAX1805/MAX1989slave address that was latched at POR (Table 8)FUNCTIONADD55ADD44ADD33ADD22ADD11ADD77(MSB)10(LSB)Logic 1BIT NAMElevel sensitive). Successful reading of the alert response address clears the interrupt latch.Command Byte FunctionsThe 8-bit command byte register (Table 4) is the master index that points to the various other registers within the MAX1668/MAX1805/MAX1989. The register ’s PORstate is 0000 0000, so that a receive byte transmission (a protocol that lacks the command byte) that occurs immediately after POR returns the current local temper-ature data.M A X 1668/M A X 1805/M A X 1989†Multichannel Remote/Local Temperature Sensors 12______________________________________________________________________________________**Not available for MAX1805.MAX1668/MAX1805/MAX1989†Multichannel Remote/LocalTemperature Sensors______________________________________________________________________________________13Manufacturer and DeviceID CodesTwo ROM registers provide manufacturer and device ID codes. Reading the manufacturer ID returns 4Dh,which is the ASCII code M (for Maxim). Reading the device ID returns 03h for MAX1668, 05h for MAX1805,and 0Bh for MAX1989. If the read word 16-bit SMBus protocol is employed (rather than the 8-bit Read Byte),the least significant byte contains the data and the most significant byte contains 00h in both cases.Configuration Byte FunctionsThe configuration byte register (Table 5) is used to mask (disable) interrupts and to put the device in soft-ware standby mode.Status Byte FunctionsThe two status byte registers (Tables 6 and 7) indicate which (if any) temperature thresholds have been exceeded. The first byte also indicates whether the ADC is converting and whether there is an open circuit in a remote-diode DXP_ to DXN_ path. After POR, the normal state of all the flag bits is zero, assuming none of the alarm conditions are present. The status byte is cleared by any successful read of the status byte,unless the fault persists. Note that the ALERT interrupt latch is not automatically cleared when the status flag bit is cleared.When reading the status byte, you must check for inter-nal bus collisions caused by asynchronous ADC timing,or else disable the ADC prior to reading the status byte (through the RUN/STOP bit in the configuration byte).To check for internal bus collisions, read the status byte. If the least significant 7 bits are ones, discard the data and read the status byte again. The status bits LHIGH, LLOW, RHIGH, and RLOW are refreshed on the SMBus clock edge immediately following the stop con-dition, so there is no danger of losing temperature-relat-ed status data as a result of an internal bus collision.The OPEN status bit (diode continuity fault) is only refreshed at the beginning of a conversion, so OPEN data is lost. The ALERT interrupt latch is independent of the status byte register, so no false alerts are generated by an internal bus collision.If the THIGH and TLOW limits are close together, it ’s possible for both high-temp and low-temp status bits to be set, depending on the amount of time between sta-tus read operations (especially when converting at the fastest rate). In these circumstances, it ’s best not to relyon the status bits to indicate reversals in long-term tem-perature changes and instead use a current tempera-ture reading to establish the trend direction.Conversion RateThe MAX1668/MAX1805/MAX1989 are continuously measuring temperature on each channel. The typical conversion rate is approximately three conversions/s (for both devices). The resulting data is stored in the temperature data registers.Slave AddressesThe MAX1668/MAX1805/MAX1989 appear to the SMBus as one device having a common address for all ADC channels. The device address can be set to one of nine different values by pin-strapping ADD0 and ADD1 so that more than one MAX1668/MAX1805/MAX1989 can reside on the same bus without address conflicts (Table 8).The address pin states are checked at POR only, and the address data stays latched to reduce quiescent supply current due to the bias current needed for high-Z state detection.The MAX1668/MAX1805/MAX1989 also respond to the SMBus alert response slave address (see the Alert Response Address section).POR and Undervoltage LockoutThe MAX1668/MAX1805/MAX1989 have a volatile memory. To prevent ambiguous power-supply condi-tions from corrupting the data in memory and causing erratic behavior, a POR voltage detector monitors V CC and clears the memory if V CC falls below 1.8V (typ, see the Electrical Characteristics table). When power is first applied and V CC rises above 1.85V (typ), the logic blocks begin operating, although reads and writes at V CC levels below 3V are not recommended. A second V CC comparator, the ADC UVLO comparator, prevents the ADC from converting until there is sufficient head-room (V CC = 2.8V typ).Power-Up Defaults•Interrupt latch is cleared.•Address select pins are sampled.•ADC begins converting.•Command byte is set to 00h to facilitate quick remote receive byte queries.•T HIGH and T LOW registers are set to max and min limits, respectively.。
- 1、下载文档前请自行甄别文档内容的完整性,平台不提供额外的编辑、内容补充、找答案等附加服务。
- 2、"仅部分预览"的文档,不可在线预览部分如存在完整性等问题,可反馈申请退款(可完整预览的文档不适用该条件!)。
- 3、如文档侵犯您的权益,请联系客服反馈,我们会尽快为您处理(人工客服工作时间:9:00-18:30)。
________________General DescriptionThe MAX1668/MAX1805/MAX1989 are precise multi-channel digital thermometers that report the tempera-ture of all remote sensors and their own packages. The remote sensors are diode-connected transistors—typi-cally low-cost, easily mounted 2N3904 NPN types—that replace conventional thermistors or thermocouples.Remote accuracy is ±3°C for multiple transistor manu-facturers, with no calibration needed. The remote chan-nels can also measure the die temperature of other ICs,such as microprocessors, that contain an on-chip,diode-connected transistor.The 2-wire serial interface accepts standard system management bus (SMBus™) write byte, read byte, send byte, and receive byte commands to program the alarm thresholds and to read temperature data. The data for-mat is 7 bits plus sign, with each bit corresponding to 1°C, in two’s-complement format.The MAX1668/MAX1805/MAX1989 are available in small, 16-pin QSOP surface-mount packages. The MAX1989 is also available in a 16-pin TSSOP.________________________Applications____________________________Featureso Multichannel4 Remote, 1 Local (MAX1668/MAX1989)2 Remote, 1 Local (MAX1805)o No Calibration Required o SMBus 2-Wire Serial Interfaceo Programmable Under/Overtemperature Alarms o Supports SMBus Alert Response o Accuracy±2°C (+60°C to +100°C, Local)±3°C (-40°C to +125°C, Local)±3°C (+60°C to +100°C, Remote)o 3µA (typ) Standby Supply Current o 700µA (max) Supply Currento Small, 16-Pin QSOP/TSSOP PackagesMAX1668/MAX1805/MAX1989†Multichannel Remote/LocalTemperature Sensors________________________________________________________________Maxim Integrated Products119-1766; Rev 2; 5/03SMBus is a trademark of Intel Corp.†Patents PendingDesktop and Notebook Computers LAN Servers Industrial ControlsCentral-Office Telecom EquipmentTest and Measurement Multichip ModulesFor pricing, delivery, and ordering information,please contact Maxim/Dallas Direct!at 1-888-629-4642, or visit Maxim’s website at .M A X 1668/M A X 1805/M A X 1989†Multichannel Remote/Local Temperature Sensors 2_______________________________________________________________________________________ABSOLUTE MAXIMUM RATINGSELECTRICAL CHARACTERISTICS(V CC = +3.3V, STBY = V CC , configuration byte = X0XXXX00, T A = 0°C to +125°C , unless otherwise noted.)Stresses beyond those listed under “Absolute Maximum Ratings” may cause permanent damage to the device. These are stress ratings only, and functional operation of the device at these or any other conditions beyond those indicated in the operational sections of the specifications is not implied. Exposure to absolute maximum rating conditions for extended periods may affect device reliability.V CC to GND..............................................................-0.3V to +6V DXP_, ADD_, STBY to GND........................-0.3V to (V CC + 0.3V)DXN_ to GND ........................................................-0.3V to +0.8V SMBCLK, SMBDATA, ALERT to GND......................-0.3V to +6V SMBDATA, ALERT Current.................................-1mA to +50mA DXN_ Current......................................................................±1mA Continuous Power Dissipation (T A = +70°C)QSOP (derate 8.30mW/°C above +70°C)....................667mW TSSOP (derate 9.40mW/°C above +70°C)..................755mWOperating Temperature Range .........................-55°C to +125°C Junction Temperature......................................................+150°C Storage Temperature Range.............................-65°C to +150°C Lead Temperature (soldering, 10s).................................+300°CMAX1668/MAX1805/MAX1989†Multichannel Remote/LocalTemperature Sensors_______________________________________________________________________________________3ELECTRICAL CHARACTERISTICS (continued)(V CC = +3.3V, STBY = V CC , configuration byte = X0XXXX00, T A = 0°C to +125°C , unless otherwise noted.)ELECTRICAL CHARACTERISTICS(V CC = +5V, STBY = V CC , configuration byte = X0XXXX00, T A = -55°C to +125°C , unless otherwise noted.) (Note 6)08416122024FREQUENCY (MHz)T E M P E R A T U R E E R R O R (°C )TEMPERATURE ERROR vs. SUPPLY NOISE FREQUENCY0.111010020-20110100TEMPERATURE ERROR vs. PC BOARD RESISTANCE-10LEAKAGE RESISTANCE (M Ω)T E M P E R A T U R E E R R O R (°C )10-2-101234-50-10-301030507090110TEMPERATURE ERROR vs. TEMPERATURETEMPERATURE (°C)T E M P E R A T U R E E R R O R (°C )Typical Operating Characteristics(Typical Operating Circuit , V CC = +5V, STBY = V CC , configuration byte = X0XXXX00, T A = +25°C, unless otherwise noted.)M A X 1668/M A X 1805/M A X 1989†Multichannel Remote/Local Temperature Sensors 4_______________________________________________________________________________________ELECTRICAL CHARACTERISTICS (continued)(V= +5V, STBY = V , configuration byte = X0XXXX00, T = -55°C to +125°C , unless otherwise noted.) (Note 6)Note 1:Guaranteed by design, but not production tested.Note 2:Quantization error is not included in specifications for temperature accuracy. For example, if the MAX1668/MAX1805/MAX1989 device temperature is exactly +66.7°C, the ADC may report +66°C, +67°C, or +68°C (due to the quantization error plus the +0.5°C offset used for rounding up) and still be within the guaranteed ±1°C error limits for the +60°C to +100°C temperature range. See Table 2.Note 3: A remote diode is any diode-connected transistor from Table 1. T R is the junction temperature of the remote diode. See theRemote-Diode Selection section for remote-diode forward-voltage requirements.Note 4:The SMBus logic block is a static design that works with clock frequencies down to DC. While slow operation is possible, itviolates the 10kHz minimum clock frequency and SMBus specifications, and can monopolize the bus.Note 5:Note that a transition must internally provide at least a hold time in order to bridge the undefined region (300ns max) ofSMBCLK’s falling edge t HD:DAT.Note 6:Specifications from -55°C to +125°C are guaranteed by design, not production tested.020406080100120140160012345STANDBY SUPPLY CURRENT vs. SUPPLY VOLTAGESUPPLY VOLTAGE (V)S U P P L Y C U R R E N T (µA )257550100125-220468RESPONSE TO THERMAL SHOCKTIME (s)T E M P E R A T U R E (°C )MAX1668/MAX1805/MAX1989†Multichannel Remote/LocalTemperature Sensors_______________________________________________________________________________________50.111000TEMPERATURE ERRORvs. COMMON-MODE NOISE FREQUENCYFREQUENCY (MHz)T E M P E R A T U R E E R R O R (°C )1010000.60.40.20.81.01.21.41.61.82.0Typical Operating Characteristics (continued)(Typical Operating Circuit , V CC = +5V, STBY = V CC , configuration byte = X0XXXX00, T A = +25°C, unless otherwise noted.)TEMPERATURE ERRORvs. DXP_ TO DXN_ CAPACITANCEM A X 16681805 t o c 05DXP_ TO DXN_ CAPACITANCE (nF)T E M P E R A T U R E E R R O R (°C )-10-6-8-2-42040203010405060STANDBY SUPPLY CURRENT vs. CLOCK FREQUENCYSMBCLK FREQUENCY (kHz)S U P P L Y C U R R E N T (µA )6010203040501101001000M A X 1668/M A X 1805/M A X 1989†Multichannel Remote/Local Temperature Sensors 6______________________________________________________________________________________________________Detailed DescriptionThe MAX1668/MAX1805/MAX1989 are temperature sensors designed to work in conjunction with an exter-nal microcontroller (µC) or other intelligence in thermo-static, process-control, or monitoring applications. The µC is typically a power-management or keyboard con-troller, generating SMBus serial commands by “bit-banging” general-purpose input-output (GPIO) pins or through a dedicated SMBus interface block.These devices are essentially 8-bit serial analog-to-digi-tal converters (ADCs) with sophisticated front ends.However, the MAX1668/MAX1805/MAX1989 also contain a switched current source, a multiplexer, an ADC, an SMBus interface, and associated control logic (Figure 1).In the MAX1668 and MAX1989, temperature data from the ADC is loaded into five data registers, where it is automatically compared with data previously stored in 10 over/undertemperature alarm registers. In the MAX1805, temperature data from the ADC is loaded into three data registers, where it is automatically compared with data previously stored in six over/undertemperature alarm registers.ADC and MultiplexerThe ADC is an averaging type that integrates over a 64ms period (each channel, typical), with excellent noise rejection.The multiplexer automatically steers bias currents through the remote and local diodes, measures their forward voltages, and computes their temperatures.Each channel is automatically converted once the con-version process has started. If any one of the channels is not used, the device still performs measurements on these channels, and the user can ignore the results of the unused channel. If any remote-diode channel is unused, connect DXP_ to DXN_ rather than leaving the pins open.The DXN_ input is biased at 0.65V above ground by an internal diode to set up the A/D inputs for a differential measurement. The worst-case DXP_ to DXN_ differential input voltage range is 0.25V to 0.95V.Excess resistance in series with the remote diode caus-es about +0.5°C error per ohm. Likewise, 200µV of offset voltage forced on DXP_ to DXN_causes about 1°C error.MAX1668/MAX1805/MAX1989†Multichannel Remote/LocalTemperature Sensors_______________________________________________________________________________________7Figure 1. MAX1668/MAX1805/MAX1989 Functional DiagramA/D Conversion SequenceIf a start command is written (or generated automatically in the free-running autoconvert mode), all channels are converted, and the results of all measurements are available after the end of conversion. A BUSY status bit in the status byte shows that the device is actually per-forming a new conversion; however, even if the ADC is busy, the results of the previous conversion are always available.Remote-Diode SelectionTemperature accuracy depends on having a good-qual-ity, diode-connected small-signal transistor. Accuracy has been experimentally verified for all of the devices listed in Table 1. The MAX1668/MAX1805/MAX1989 can also directly measure the die temperature of CPUs and other ICs having on-board temperature-sensing diodes.The transistor must be a small-signal type, either NPN or PNP, with a relatively high forward voltage; other-wise, the A/D input voltage range can be violated. The forward voltage must be greater than 0.25V at 10µA;check to ensure this is true at the highest expected temperature. The forward voltage must be less than 0.95V at 100µA; check to ensure this is true at the low-est expected temperature. Large power transistors do not work at all. Also, ensure that the base resistance is less than 100Ω. Tight specifications for forward-current gain (+50 to +150, for example) indicate that the manu-facturer has good process controls and that the devices have consistent VBE characteristics.F or heat-sink mounting, the 500-32BT02-000 thermal sensor from Fenwal Electronics is a good choice. This device consists of a diode-connected transistor, an aluminum plate with screw hole, and twisted-pair cable (Fenwal Inc., Milford, MA, 508-478-6000).Thermal Mass and Self-HeatingThermal mass can seriously degrade the MAX1668/MAX1805/MAX1989s’ effective accuracy. The thermal time constant of the 16-pin QSOP package is about 140s in still air. F or the MAX1668/MAX1805/MAX1989junction temperature to settle to within +1°C after a sudden +100°C change requires about five time con-stants or 12 minutes. The use of smaller packages for remote sensors, such as SOT23s, improves the situa-tion. Take care to account for thermal gradients between the heat source and the sensor, and ensure that stray air currents across the sensor package do not interfere with measurement accuracy.Self-heating does not significantly affect measurement accuracy. Remote-sensor self-heating due to the diode current source is negligible. F or the local diode, theworst-case error occurs when sinking maximum current at the ALERT output. For example, with ALERT sinking 1mA, the typical power dissipation is V CC x 400µA plus 0.4V x 1mA. Package theta J-A is about 150°C/W, so with V CC = 5V and no copper PC board heat sinking,the resulting temperature rise is:dT = 2.4mW x 150°C/W = 0.36°CEven with these contrived circumstances, it is difficult to introduce significant self-heating errors.ADC Noise FilteringThe ADC is an integrating type with inherently good noise rejection, especially of low-frequency signals such as 60Hz/120Hz power-supply hum. Micropower opera-tion places constraints on high-frequency noise rejec-tion; therefore, careful PC board layout and proper external noise filtering are required for high-accuracy remote measurements in electrically noisy environments. High-frequency EMI is best filtered at DXP_ and DXN_with an external 2200pF capacitor. This value can be increased to about 3300pF (max), including cable capacitance. Higher capacitance than 3300pF intro-duces errors due to the rise time of the switched cur-rent source.Nearly all noise sources tested cause additional error measurements, typically by +1°C to +10°C, depending on the frequency and amplitude (see the Typical Operating Characteristics ).PC Board Layout1)Place the MAX1668/MAX1805/MAX1989 as close aspractical to the remote diode. In a noisy environment,such as a computer motherboard, this distance canM A X 1668/M A X 1805/M A X 1989†Multichannel Remote/Local Temperature Sensors 8_______________________________________________________________________________________Table 1. Remote-Sensor Transistor ManufacturersNote:Transistors must be diode connected (base shorted to collector).be 4in to 8in (typ) or more as long as the worst noise sources (such as CRTs, clock generators, memory buses, and ISA/PCI buses) are avoided.2)Do not route the DXP_ to DXN_ lines next to thedeflection coils of a CRT. Also, do not route the traces across a fast memory bus, which can easily introduce +30°C error, even with good filtering.Otherwise, most noise sources are fairly benign.3)Route the DXP_ and DXN_ traces in parallel and inclose proximity to each other, away from any high-voltage traces such as +12VDC. Leakage currents from PC board contamination must be dealt with carefully, since a 20M Ωleakage path from DXP_ to ground causes about +1°C error.4)Connect guard traces to GND on either side of theDXP_ to DXN_ traces (Figure 2). With guard traces in place, routing near high-voltage traces is no longer an issue. 5)Route through as few vias and crossunders as possi-ble to minimize copper/solder thermocouple effects. 6)When introducing a thermocouple, make sure thatboth the DXP_ and the DXN_ paths have matching thermocouples. In general, PC board-induced ther-mocouples are not a serious problem. A copper-sol-der thermocouple exhibits 3µV/°C, and it takes about 200µV of voltage error at DXP_ to DXN_ to cause a +1°C measurement error. So, most para-sitic thermocouple errors are swamped out.7)Use wide traces. Narrow ones are more inductiveand tend to pick up radiated noise. The 10mil widths and spacings recommended in Figure 2 are not absolutely necessary (as they offer only a minor improvement in leakage and noise), but try to use them where practical.8)Copper cannot be used as an EMI shield, and onlyferrous materials such as steel work well. Placing a copper ground plane between the DXP_ to DXN_traces and traces carrying high-frequency noise sig-nals does not help reduce EMI.PC Board Layout Checklist•Place the MAX1668/MAX1805/MAX1989as close as possible to the remote diodes.•Keep traces away from high voltages (+12V bus).•Keep traces away from fast data buses and CRTs.•Use recommended trace widths and spacings.•Place a ground plane under the traces.•Use guard traces flanking DXP_ and DXN_ and con-necting to GND.•Place the noise filter and the 0.1µF V CC bypass capacitors close to the MAX1668/MAX1805/MAX1989.•Add a 200Ωresistor in series with V CC for best noise filtering (see the Typical Operating Circuit ).Twisted-Pair and Shielded CablesFor remote-sensor distances longer than 8in, or in partic-ularly noisy environments, a twisted pair is recommend-ed. Its practical length is 6ft to 12ft (typ) before noise becomes a problem, as tested in a noisy electronics lab-oratory. F or longer distances, the best solution is a shielded twisted pair like that used for audio micro-phones. For example, Belden #8451 works well for dis-tances up to 100ft in a noisy environment. Connect the twisted pair to DXP_ and DXN_ and the shield to GND,and leave the shield’s remote end unterminated.Excess capacitance at DX_ _ limits practical remote-sen-sor distances (see the Typical Operating Characteristics ).F or very long cable runs, the cable’s parasitic capaci-tance often provides noise filtering, so the 2200pF capac-itor can often be removed or reduced in value.Cable resistance also affects remote-sensor accuracy;1Ωseries resistance introduces about +0.5°C error.Low-Power Standby ModeStandby mode disables the ADC and reduces the sup-ply-current drain to less than 12µA. Enter standby mode by forcing the STBY pin low or through the RUN/STOP bit in the configuration byte register.Hardware and software standby modes behave almost identically: all data is retained in memory, and the SMB interface is alive and listening for reads and writes.Activate hardware standby mode by forcing the STBY pin low. In a notebook computer, this line can be con-nected to the system SUSTAT# suspend-state signal. The STBY pin low state overrides any software conversion command. If a hardware or software standby command is received while a conversion is in progress, the conver-MAX1668/MAX1805/MAX1989†Multichannel Remote/LocalTemperature Sensors_______________________________________________________________________________________9Figure 2. Recommended DXP_/DXN_ PC Tracession cycle is truncated, and the data from that conversion is not latched into either temperature-reading register. The previous data is not changed and remains available.In standby mode, supply current drops to about 3µA.At very low supply voltages (under the power-on-reset threshold), the supply current is higher due to the address pin bias currents. It can be as high as 100µA,depending on ADD0 and ADD1 settings.SMBus Digital InterfaceF rom a software perspective, the MAX1668/MAX1805/MAX1989appear as a set of byte-wide registers that contain temperature data, alarm threshold values, or control bits. A standard SMBus 2-wire serial interface is used to read temperature data and write control bits and alarm threshold data. Each A/D channel within the devices responds to the same SMBus slave address for normal reads and writes.The MAX1668/MAX1805/MAX1989employ four standard SMBus protocols: write byte, read byte, send byte, and receive byte (Figure 3). The shorter receive byte protocol allows quicker transfers, provided that the correct data register was previously selected by a read byte instruc-tion. Use caution with the shorter protocols in multimaster systems, since a second master could overwrite the com-mand byte without informing the first master.The temperature data format is 7 bits plus sign in two’s-com-plement form for each channel, with each data bit represent-ing 1°C (Table 2), transmitted MSB first. Measurements are offset by +0.5°C to minimize internal rounding errors; for example, +99.6°C is reported as +100°C.Alarm Threshold RegistersTen (six for MAX1805) registers store alarm threshold data, with high-temperature (T HIGH ) and low-tempera-ture (T LOW ) registers for each A/D channel. If either measured temperature equals or exceeds the corre-sponding alarm threshold value, an ALERT interrupt is asserted.The power-on-reset (POR) state of all T HIGH registers of the MAX1668 and MAX1805 is full scale (0111 1111, or +127°C). The POR state of the channel 1 T HIGH register of the MAX1989 is 0110 1110 or +110°C, while all other channels are at +127°C. The POR state of all T LOW reg-isters is 1100 1001 or -55°C.M A X 1668/M A X 1805/M A X 1989†Multichannel Remote/Local Temperature Sensors 10______________________________________________________________________________________Figure 3. SMBus ProtocolsThere is a continuity fault detector at DXP_ that detects whether the remote diode has an open-circuit condi-tion. At the beginning of each conversion, the diode fault is checked, and the status byte is updated. This fault detector is a simple voltage detector; if DXP_ rises above V CC - 1V (typ) due to the diode current source, a fault is detected. Note that the diode fault is not checked until a conversion is initiated, so immediately after power-on reset, the status byte indicates no fault is present, even if the diode path is broken.If any remote channel is shorted (DXP_ to DXN_ or DXP_ to GND), the ADC reads 0000 0000 so as not to trip either the T HIGH or T LOW alarms at their POR set-tings. In applications that are never subjected to 0°C in normal operation, a 0000 0000 result can be checked to indicate a fault condition in which DXP_ is acciden-tally short circuited. Similarly, if DXP_ is short circuited to V CC , the ADC reads +127°C for all remote and local channels, and the device alarms.A L E R T InterruptsThe ALERT interrupt output signal is latched and can only be cleared by reading the alert response address.Interrupts are generated in response to T HIGH and T LOW comparisons and when a remote diode is disconnected (for continuity fault detection). The interrupt does not halt automatic conversions; new temperature data continues to be available over the SMBus interface after ALERT is asserted. The interrupt output pin is open drain so that devices can share a common interrupt line. The interrupt rate can never exceed the conversion rate.The interface responds to the SMBus alert response address, an interrupt pointer return-address feature (see Alert R esponse Address section). Prior to taking corrective action, always check to ensure that an inter-rupt is valid by reading the current temperature.Alert Response AddressThe SMBus alert response interrupt pointer provides quick fault identification for simple slave devices that lack the complex, expensive logic needed to be a bus master. Upon receiving an ALERT interrupt signal, the host master can broadcast a receive byte transmission to the alert response slave address (0001 100). Then any slave device that generated an interrupt attempts to identify itself by putting its own address on the bus (Table 3).The alert response can activate several different slave devices simultaneously, similar to the I 2C general call. If more than one slave attempts to respond, bus arbitra-tion rules apply, and the device with the lower address code wins. The losing device does not generate an acknowledge and continues to hold the ALERT line low until serviced (implies that the host interrupt input isMAX1668/MAX1805/MAX1989†Multichannel Remote/LocalTemperature Sensors______________________________________________________________________________________11Table 3. Read Format for Alert Response Address (0001100)ADD66Provide the currentMAX1668/MAX1805/MAX1989slave address that was latched at POR (Table 8)FUNCTIONADD55ADD44ADD33ADD22ADD11ADD77(MSB)10(LSB)Logic 1BIT NAMElevel sensitive). Successful reading of the alert response address clears the interrupt latch.Command Byte FunctionsThe 8-bit command byte register (Table 4) is the master index that points to the various other registers within the MAX1668/MAX1805/MAX1989. The register ’s PORstate is 0000 0000, so that a receive byte transmission (a protocol that lacks the command byte) that occurs immediately after POR returns the current local temper-ature data.M A X 1668/M A X 1805/M A X 1989†Multichannel Remote/Local Temperature Sensors 12______________________________________________________________________________________**Not available for MAX1805.MAX1668/MAX1805/MAX1989†Multichannel Remote/LocalTemperature Sensors______________________________________________________________________________________13Manufacturer and DeviceID CodesTwo ROM registers provide manufacturer and device ID codes. Reading the manufacturer ID returns 4Dh,which is the ASCII code M (for Maxim). Reading the device ID returns 03h for MAX1668, 05h for MAX1805,and 0Bh for MAX1989. If the read word 16-bit SMBus protocol is employed (rather than the 8-bit Read Byte),the least significant byte contains the data and the most significant byte contains 00h in both cases.Configuration Byte FunctionsThe configuration byte register (Table 5) is used to mask (disable) interrupts and to put the device in soft-ware standby mode.Status Byte FunctionsThe two status byte registers (Tables 6 and 7) indicate which (if any) temperature thresholds have been exceeded. The first byte also indicates whether the ADC is converting and whether there is an open circuit in a remote-diode DXP_ to DXN_ path. After POR, the normal state of all the flag bits is zero, assuming none of the alarm conditions are present. The status byte is cleared by any successful read of the status byte,unless the fault persists. Note that the ALERT interrupt latch is not automatically cleared when the status flag bit is cleared.When reading the status byte, you must check for inter-nal bus collisions caused by asynchronous ADC timing,or else disable the ADC prior to reading the status byte (through the RUN/STOP bit in the configuration byte).To check for internal bus collisions, read the status byte. If the least significant 7 bits are ones, discard the data and read the status byte again. The status bits LHIGH, LLOW, RHIGH, and RLOW are refreshed on the SMBus clock edge immediately following the stop con-dition, so there is no danger of losing temperature-relat-ed status data as a result of an internal bus collision.The OPEN status bit (diode continuity fault) is only refreshed at the beginning of a conversion, so OPEN data is lost. The ALERT interrupt latch is independent of the status byte register, so no false alerts are generated by an internal bus collision.If the THIGH and TLOW limits are close together, it ’s possible for both high-temp and low-temp status bits to be set, depending on the amount of time between sta-tus read operations (especially when converting at the fastest rate). In these circumstances, it ’s best not to relyon the status bits to indicate reversals in long-term tem-perature changes and instead use a current tempera-ture reading to establish the trend direction.Conversion RateThe MAX1668/MAX1805/MAX1989 are continuously measuring temperature on each channel. The typical conversion rate is approximately three conversions/s (for both devices). The resulting data is stored in the temperature data registers.Slave AddressesThe MAX1668/MAX1805/MAX1989 appear to the SMBus as one device having a common address for all ADC channels. The device address can be set to one of nine different values by pin-strapping ADD0 and ADD1 so that more than one MAX1668/MAX1805/MAX1989 can reside on the same bus without address conflicts (Table 8).The address pin states are checked at POR only, and the address data stays latched to reduce quiescent supply current due to the bias current needed for high-Z state detection.The MAX1668/MAX1805/MAX1989 also respond to the SMBus alert response slave address (see the Alert Response Address section).POR and Undervoltage LockoutThe MAX1668/MAX1805/MAX1989 have a volatile memory. To prevent ambiguous power-supply condi-tions from corrupting the data in memory and causing erratic behavior, a POR voltage detector monitors V CC and clears the memory if V CC falls below 1.8V (typ, see the Electrical Characteristics table). When power is first applied and V CC rises above 1.85V (typ), the logic blocks begin operating, although reads and writes at V CC levels below 3V are not recommended. A second V CC comparator, the ADC UVLO comparator, prevents the ADC from converting until there is sufficient head-room (V CC = 2.8V typ).Power-Up Defaults•Interrupt latch is cleared.•Address select pins are sampled.•ADC begins converting.•Command byte is set to 00h to facilitate quick remote receive byte queries.•T HIGH and T LOW registers are set to max and min limits, respectively.。