高温散体物料余热回收装置
一种高温固体散料余热回收大型换热器[发明专利]
![一种高温固体散料余热回收大型换热器[发明专利]](https://img.taocdn.com/s3/m/4306a409f8c75fbfc67db207.png)
专利名称:一种高温固体散料余热回收大型换热器
专利类型:发明专利
发明人:刘永启,王延遐,史俊瑞,孙鹏,齐晓霓,高海波,张雨秋申请号:CN202010499681.6
申请日:20200604
公开号:CN111637755A
公开日:
20200908
专利内容由知识产权出版社提供
摘要:一种高温固体散料余热回收大型换热器,属于固体散热器技术领域。
其特征在于:壳体(1)上下端面开口设置,上端面为入料口,下端面为出料口,所述换热元件为U型换热元件(2),多个U型换热元件(2)分成左右对称的两组安装在壳体(1)的两侧壁上;U型换热元件(2)的纵截面呈U型设置,U型换热元件(2)开口端包括进气端和出气端,进气端和出气端伸出壳体(1)外部,U型换热元件(2)封闭端朝向壳体(1)内部,且两组U型换热元件(2)之间留有膨胀间隙。
本发明换热器元件采用扁管,左右两部分,U型换热元件尾部之间留有足够的间隙,尾部可以自由膨胀,换热器不会产生很大的热应力,换热器工作可靠。
申请人:山东理工大学
地址:255086 山东省淄博市高新技术产业开发区高创园A座313室
国籍:CN
代理机构:淄博佳和专利代理事务所(普通合伙)
代理人:孙智慧
更多信息请下载全文后查看。
高温固体散料余热回收利用集成技术实施计划(四)
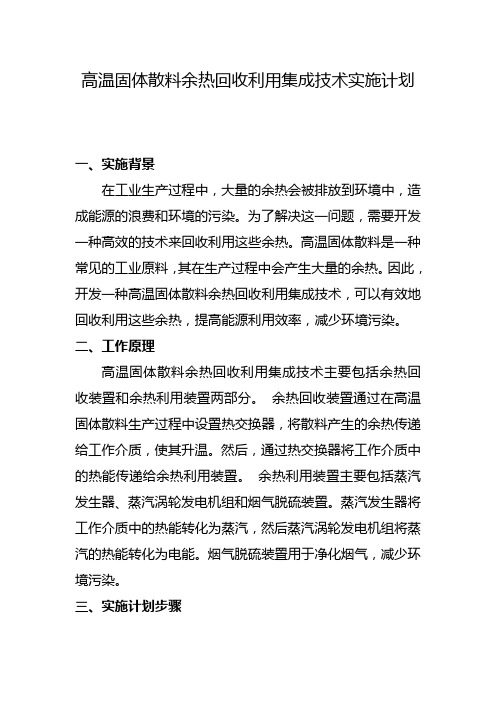
高温固体散料余热回收利用集成技术实施计划一、实施背景在工业生产过程中,大量的余热会被排放到环境中,造成能源的浪费和环境的污染。
为了解决这一问题,需要开发一种高效的技术来回收利用这些余热。
高温固体散料是一种常见的工业原料,其在生产过程中会产生大量的余热。
因此,开发一种高温固体散料余热回收利用集成技术,可以有效地回收利用这些余热,提高能源利用效率,减少环境污染。
二、工作原理高温固体散料余热回收利用集成技术主要包括余热回收装置和余热利用装置两部分。
余热回收装置通过在高温固体散料生产过程中设置热交换器,将散料产生的余热传递给工作介质,使其升温。
然后,通过热交换器将工作介质中的热能传递给余热利用装置。
余热利用装置主要包括蒸汽发生器、蒸汽涡轮发电机组和烟气脱硫装置。
蒸汽发生器将工作介质中的热能转化为蒸汽,然后蒸汽涡轮发电机组将蒸汽的热能转化为电能。
烟气脱硫装置用于净化烟气,减少环境污染。
三、实施计划步骤1.调研分析:对高温固体散料生产过程中的余热排放情况进行调研分析,确定余热回收利用的可行性。
2.设计方案:根据调研结果,设计高温固体散料余热回收利用集成技术的具体方案,包括余热回收装置和余热利用装置的设计。
3.建设安装:按照设计方案,进行余热回收装置和余热利用装置的建设和安装。
4.调试运行:对建设完毕的装置进行调试运行,确保其正常工作。
5.监测评估:对装置的运行情况进行监测和评估,评估其能源利用效率和环境效益。
6.优化改进:根据监测评估结果,对装置进行优化改进,提高其能源利用效率和环境效益。
四、适用范围高温固体散料余热回收利用集成技术适用于各类高温固体散料的生产过程,如钢铁、水泥、玻璃等行业。
这些行业在生产过程中产生大量的余热,利用该技术可以有效地回收利用这些余热,提高能源利用效率。
五、创新要点1.设计热交换器:根据高温固体散料的特点,设计一种高效的热交换器,提高余热回收的效率。
2.蒸汽涡轮发电机组:采用蒸汽涡轮发电机组,将余热转化为电能,提高能源利用效率。
高温固体散料余热回收利用集成技术实施计划(九)

高温固体散料余热回收利用集成技术实施计划实施背景:随着工业化进程的加快和能源紧缺问题的日益突出,高温固体散料的余热回收利用成为了一个重要的课题。
传统的余热回收技术存在着能量损失大、回收效率低、操作复杂等问题,因此需要开发一种新的集成技术来提高余热回收利用的效率和经济性。
工作原理:高温固体散料余热回收利用集成技术的工作原理是通过将散料的余热传递给工作介质,然后将工作介质中的余热转化为可利用的能量。
具体来说,该技术包括以下几个步骤:1.散料预处理:对高温固体散料进行预处理,包括除尘、破碎、干燥等操作,以提高余热回收的效率和安全性。
2.余热回收装置:设计和安装一套高效的余热回收装置,包括换热器、传热管、热交换器等设备,用于将散料中的余热传递给工作介质。
3.工作介质循环系统:建立一个完善的工作介质循环系统,包括泵、管道、阀门等设备,用于将工作介质循环输送到余热回收装置中进行热交换。
4.能量转化装置:设计和安装一套能量转化装置,用于将工作介质中的余热转化为可利用的能量,例如蒸汽、热水等。
实施计划步骤:1.进行市场调研,了解目前高温固体散料余热回收利用的现状和存在的问题。
2.设计和开发高温固体散料余热回收利用集成技术的关键设备和系统。
3.进行实验室试验,验证技术的可行性和效果。
4.在实际工业生产环境中进行试点应用,收集数据并进行分析。
5.根据试点结果进行技术改进和优化,提高余热回收利用的效率和经济性。
适用范围:该技术适用于各种高温固体散料的余热回收利用,例如钢铁、水泥、化工等行业。
创新要点:1.设计和开发了一套高效的余热回收装置,能够实现高温固体散料余热的快速传递和转化。
2.建立了完善的工作介质循环系统,能够实现工作介质的循环输送和热交换。
3.设计和开发了一套能量转化装置,能够将工作介质中的余热转化为可利用的能量。
预期效果:1.提高高温固体散料余热回收利用的效率和经济性,减少能源消耗和环境污染。
2.降低生产成本,提高企业的竞争力和可持续发展能力。
高温固体散料余热回收利用集成技术实施计划(七)

高温固体散料余热回收利用集成技术实施计划实施背景:随着工业化的进一步发展,大量的热能被浪费掉,其中包括高温固体散料的余热。
传统的余热回收利用技术存在效率低、成本高等问题,因此需要开发一种新的集成技术来提高余热的回收利用效率。
工作原理:高温固体散料余热回收利用集成技术是通过将高温固体散料中的余热进行回收和利用。
具体工作原理如下:1.收集余热:通过在高温固体散料的生产过程中设置余热收集装置,将散料中的余热收集起来。
2.余热传导:将收集到的余热传导到热交换器中。
3.热交换:在热交换器中,将余热传递给工作介质,使其温度升高。
4.功率产生:通过将温度升高的工作介质送入发电机组,产生电能。
实施计划步骤:1.调研分析:对目前的余热回收利用技术进行调研,分析其存在的问题和不足之处。
2.技术研发:基于调研结果,开展高温固体散料余热回收利用集成技术的研发工作,包括设备设计、工艺流程优化等。
3.实施试点:在一些具备条件的企业中进行试点实施,验证技术的可行性和效果。
4.优化改进:根据试点实施的结果,对技术进行优化改进,提高其回收利用效率和经济效益。
5.推广应用:将优化改进后的技术推广应用到更多的企业中,实现规模化应用。
适用范围:高温固体散料余热回收利用集成技术适用于各类高温固体散料的生产过程中,如钢铁、水泥、玻璃等行业。
创新要点:1.高效收集:通过优化余热收集装置,提高余热的收集效率。
2.高效传导:采用高效的热传导材料,提高余热的传导效率。
3.高效热交换:设计高效的热交换器,提高余热的传递效率。
4.高效发电:优化发电机组的设计,提高发电效率。
预期效果:1.提高能源利用效率:通过回收利用高温固体散料的余热,提高能源利用效率,减少能源浪费。
2.减少环境污染:减少高温固体散料的燃烧过程中产生的废气和废水,减少环境污染。
3.降低生产成本:通过回收利用余热,减少能源消耗,降低生产成本。
4.提高企业竞争力:降低生产成本和环境污染,提高企业的竞争力。
- 1、下载文档前请自行甄别文档内容的完整性,平台不提供额外的编辑、内容补充、找答案等附加服务。
- 2、"仅部分预览"的文档,不可在线预览部分如存在完整性等问题,可反馈申请退款(可完整预览的文档不适用该条件!)。
- 3、如文档侵犯您的权益,请联系客服反馈,我们会尽快为您处理(人工客服工作时间:9:00-18:30)。
高温散体物料余热回收装置
1 问题概述
在水泥烧成窑、石灰窑等各种散体物料烧成窑中,物料的出窑温度一般都很高,这些固体物料的预热回收有很好的节能效益和经济效益。
试设计一套散体物料间接换热的热回收系统和装置。
设计条件:小时处理量15吨/h。
提示:因为散料品质以及被加热介质洁净方面的要求,对于散料的热回收常常需要采用间接换热的方式。
但散料内部孔隙率高。
导热系数很小,强化散料内部的热传导成为换热器的设计难点。
2 分析与设计
2.1 设计思路
散体物料尺寸差异对其内部导热影响较大,因此对出窑后不同尺寸的物料需进行筛分,较细的粉料直接进入本装置进行换热,而较粗的块料需先粉状细化再进入换热器,或直接使用其他方法进行余热回收。
由于粗料在所有物料中所占比例较小,本装置只针对筛选后的细料进行处理。
图2-1 高温散体物料余热回收流程图
而高温散体物料间接换热器中的问题集中表现在以下几个方面:选取何种换热形式;如何避免对物料品质的损害;如何提高换热系数;如何强化散体物料内部的热传导。
由于固体物料难以流动,或者说即使使用流体带动散体物料流动,之后的换热过程过于复杂,且后期难以分离,因此本装置将散料固定装于圆柱管中,通过
管壁与管外的流体进行周期性间接对流换热。
选取空气作为换热的介质,一方面考虑到空气易于获取,另一方面考虑到很多比热容更大的流体包括水在高温环境中易损坏换热器。
若干根圆柱管竖直平行排列,管中填装散体物料;管间有一定的间距,保证空气从四周经过。
圆管的上端和下端做成类似漏斗的渐扩形状并互相吻合,可通过焊接固定在一起,这样即可以做到在便于装料和出料的同时,不会有散料漏入圆管间隙的空气通道中。
散料进口
图2-1 换热器纵向剖面示意图
图2-2 换热器顶面示意图
2.2 工作过程
图2-3 装置工作过程示意图
整个装置为周期性工作,过程如图所示,出炉后的物料经尺寸筛选处理后,换热器顶盖开启,底盖关闭,进料过程开始,从换热器上方进料;高温物料装满所有管道后,需进行若干次压实处理,以尽量减少物料内部空隙,提高导热效果。
进料过程结束后换热过程开始,顶盖关闭,风机启动,空气掠过管束进行热交换。
换热过程结束后底盖开启,物料落入下方传送带被运走,此工作周期结束。
同时
空 气 进 口
下一个工作周期开始,再次开始进料。
3 理论计算
本部分以散体物料为生石灰为例,将换热过程简化为空气与恒温管壁对流过程,对换热效果进行粗略计算,物料、空气的热物性和初始确认的换热器尺寸如下表所示。
表3-1 物料(生石灰)参数表
表3-2 换热器参数表
表3-3 换热介质(空气)参数表
换热器空气入口侧截面F积满足公式
F=N1S T H
(1)
N1,S T代入式(1)得F=2.4H(m2)
换热表面积A s满足公式
A s=πN1N2DH (2)
N1,N2,D代入式(2)得A s=40.2H(m2)
空气质量流量Q m满足公式
Q m=V·F·ρa
(3)
V,F代入式(3)得Q m=15.12H(kg/s)
空气最大流速V max满足公式
V max=S T
S T−D
·V (4)
V,S T,D代入式(4)得V max=21(m/s)
空气Reynolds number满足公式
Re D=V max·D
ν(5)
V max,D,v代入式(5)得Re D=200000
空气Nusselt number满足公式
Nu D=0.27Re D0.63Pr0.36(Pr
Pr s )
0.25
(6)
Re D,Pr,Pr s代入式(6)得Nu D=519.1
空气对流系数h满足公式
h=Nu Dλ
D
(7)
Nu D,D,λ代入式(7)得h=77.9W/(K·m2)
每周期处理物料质量m w满足公式
m w=π
4
N1N2ρw D2H
(8)
N1,N2,ρw,D代入(8)得m w=6635.04H(kg)
每周期换热量Q满足公式
Q=hA s∆T ln·∆t
(9)
Q=Q m C pa(T e−T i)·∆t
(10)
Q=m w C pw∆T w
(11)
△T ln可由对数平均温差法得到
∆T ln=(T s−T e)−(T s−T i)
ln(T s−T e)
(T s−T i)
(12)
联立式(9)(10)(12)可得到空气出口温度T e计算公式
T e=T s−(T s−T i)e(−A sℎ
Q m C pa
) (13)
T i,T s,A s,h,Q m,C pa代入式(13)得T e=385.5 K
生产率满足公式
(14)
G=m w
∆t
联立式(10)(11)可得到
G=Q m C pa(T e−T i)
C pw∆T w
(15)
Q m,C pa,T e,T i,C pw,△T w代入(15)得G=7.506H kg/s
目标单位小时处理量为15t/h,即
G≥4.17kg/s (△t≤3600s)
则H>=0.56(m),
取H=0.833(m),则每生产周期产量m w=7.5(t),每生产周期换热时间
△t=0.333(h),相邻生产周期间隔装料时间取t’=0.167(h)。
即可实现一小时经过2个完整生产周期,生产率为15t/h。
汇总可得换热器各项参数如下表所示:
表3-4 换热器各项参数表
4 总结
我们的高温散料余热回收系统,采用间接换热,避免空气与物料直接接触,保证了物料的品质;空气与管壁叉流的换热形式,尽量增大比表面积以增大对流系数;针对散料内部孔隙率高,导热系数很小的问题,通过筛分粗细料,与进料过程中若干次压实处理,一定程度上强化了物料内部导热。
漏斗形的设计,使物料从上端倒入时不会洒落到圆管中间的空隙中。
进行粗略的传热计算后,得出最后设计的方案,使得产率满足要求。
除此之外,本装置仍存在很多问题,首先本装置由于固体物料位置固定,只
能进行周期性工作,如何实现连续工作,进一步提高生产率仍有待考虑;并且工作周期受到散料窑的工作时间的限制,换热器与散料窑需实现配合;其次本装置理论上只能对筛分处理后的细料的换热效果与内部导热效果有一定提升,对于粗料,尤其是没有办法细化处理的粗料,仍无较好的换热方法;在强化换热方面,仍然有着提升空间,可以在本装置基础上增加肋片并优化流体流动过程;最后,本部分的计算过程较为粗略,进行了很大的理想化,只能粗略参考以判断方案的可行性,而在实际生产过程中空气的流场、温度场以及物料温度随时间的变化规律是极为复杂的,具体各项参数的确认还需要更精确的计算、建模与实验。
总的来说,本装置理论上可以实现,是一种散体物料余热回收的新思路,各方面仍有较大改进空间。
参考文献
[1] 彭家燕. 高温颗粒余热回收装置的研究概况[A]. 中国金属学会能源与热工
分会.第八届全国能源与热工学术年会论文集[C].中国金属学会能源与热工分会:中国金属学会能源与热工分会,2015:4.
[2] 夏德宏,肖琳姝,李一帆,薛根山.间壁式固体散料余热回收器的开发[J].冶金
能源,2009,28(04):47-50.
[3] 刘万旺. 外掠管束的流动和换热特性的数值模拟[D].华东理工大学,2018.
[4] Wiji Mangestiyono , Sutrisno , Sutrisno , Juli Mrihardjono . Pipe Blockage
Prediction of Shell and Tube Heat Exchanger under Linear and Cross Flow Operation[J]. Materials Today: Proceedings,2019,13.
[5] A. Safwat Wilson,M. Khalil Bassiouny. Modeling of heat transfer for flow
across tube banks[J]. Chemical Engineering & Processing: Process Intensification,2000,39(1).。