BP美国德州炼油厂火灾爆炸事故
最新BP德克萨斯炼油厂爆炸事故案例学习(教学版)解析ppt课件
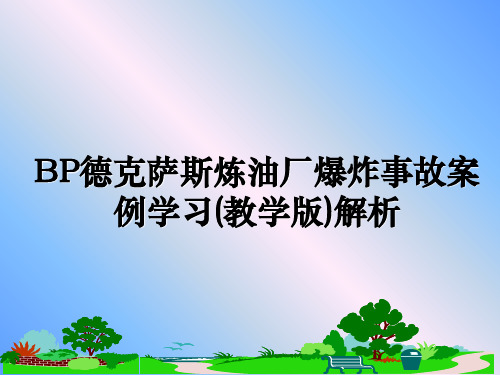
第二章 事故经过
爆炸后放空罐继续喷出烃类物质,装置持续燃烧。
第二章 事故经过
距离异构化装置数百 米远距离上拍摄的图 像-浓烟滚滚
第二章 事故经过
事故后的现场:异构化装置成为了废墟。
第二章 事故经过
2.4 学员观看事故录像 放映该事故的录像,该录像真实的还原了事故发生的
整个过程以及所造成的惨痛后果。 时间:35mintues
12 时40 分左右,发出了高压警报,加热炉的两个 火嘴被关闭以降低物料温度。
由于操作流程所规定的流量控制阀不能正常工作, 因此操作人员使用应急泄压阀将气体排到放空罐中,然 后排至大气。13 时左右,操作人员打开阀门将液体从 塔底送往储罐。
第二章 事故经过
13时左右,换热器出现异常,并且导致进入塔的原 料温度突然上升至150℃以上。
第二章 事故经过
2.5 事故细节的补充叙述
2005年3月23日,生产操作工约翰准时来到得克萨斯炼油厂异构化 装置上班。这是他连续工作的第29天。由于每天只能睡5到6个小时, 他的脑子稍微有点发木。自从BP公司施行人力资源管理的低成本战略 后,操作工人数被减少了,因此操作工常常加班,疲倦成为了普遍的 现象。在装置开车的过程中,约翰没有注意到液位的异常。3个小时后 由于液面超标导致分馏塔超压,大量物料进入放空烟囱,与空气混合 后发生了剧烈爆炸。更糟糕的是,装满回料的拖车也违章停在附近, 引起了连环爆炸,约翰和他的14位工友当场丧生,180多人不同程度地 被烧伤。“得克萨斯炼厂爆炸”事件是十年来,美国工业最为严重的 一次事故。
13 时5 分,进入塔中的液体开始膨胀并沸腾,导致 塔内的液位进一步上升;
13 时10 分左右,塔开始出现溢流,液体被排到塔 顶的排放管中;
BP美国德州炼油厂火灾爆炸事故(2005年3月23日)

BP美国德州炼油厂火灾爆炸事故(2005年3月23日)2005年3月23日13点20分左右,英国石油公司(BP)在美国德克萨斯州(Texas)炼油厂的异构化装置发生爆炸事故,15名工人被当场炸死,170余人受伤,直接经济损失超过15亿美元。
这是近20年来,美国发生的最严重的工业事故。
1 事故经过2005年3月23日早上,英国石油公司(BP)美国德克萨斯州(Texas)炼油厂的一套异构化装置(工艺流程见图1)的抽余油塔在经过2周的短暂维修后,重新开车。
开车过程中,操作人员将可燃的液态烃原料不断泵入抽余油塔。
抽余油塔是一个垂直的蒸馏塔,内径3.8m,高51.8m,容积约586100升,塔内有70块塔板,用于将抽余油分离成轻组分和重组分。
在3个多小时的进料过程中,因塔底馏出物管线上的液位控制阀未开,而报警器和控制系统又发出了错误的指令,使操作者对塔内液位过高毫不知情。
液体原料装满抽余油塔后,进入塔顶馏出管线。
塔顶的管线通往距塔顶以下45.1m的安全阀。
管线中充满液体后,压力迅速从144.8kPa上升到441.3kPa,迫使3个安全阀打开了6分钟,将大量可燃液体泄放到放空罐里。
液体很快充满了34.4m高的放空罐,并沿着罐顶的放空管,像喷泉一样洒落到地面上。
泄漏出来的可燃液体蒸发后,形成可燃气体蒸气云。
在距离放空罐7.6m的地方,停着一辆没有熄火的小型敞蓬载货卡车,发动机引擎的火花点燃了可燃蒸气云,引发了大爆炸,导致正在离放空罐7码远处工作的15名承包商雇员死亡。
2 事故原因美国化学安全局(CSB)通过广泛细致的调查,对事故原因从技术和管理两方面进行了分析。
2.1 技术原因1)抽余油塔上的液位控制阀能够将液体从塔内转移到储罐中。
但是,装置开车时,液位控制阀被一名工人关闭,塔里不断加入物料,却没有产品出来。
2)尽管早先已报告该塔的液位计、液位观察孔和压力控制阀出现故障,但装置仍按原计划开车。
3)放空罐设计不合理,排放气没有连接到火炬系统。
2005年BP德克萨斯州炼油厂爆炸事故
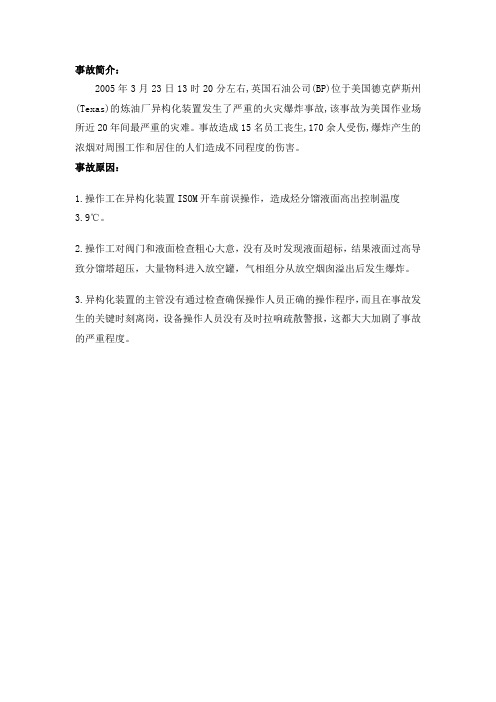
事故简介:
2005年3月23日13时20分左右,英国石油公司(BP)位于美国德克萨斯州(Texas)的炼油厂异构化装置发生了严重的火灾爆炸事故,该事故为美国作业场所近20年间最严重的灾难。
事故造成15名员工丧生,170余人受伤,爆炸产生的浓烟对周围工作和居住的人们造成不同程度的伤害。
事故原因:
1.操作工在异构化装置ISOM开车前误操作,造成烃分馏液面高出控制温度
3.9℃。
2.操作工对阀门和液面检查粗心大意,没有及时发现液面超标,结果液面过高导致分馏塔超压,大量物料进入放空罐,气相组分从放空烟囱溢出后发生爆炸。
3.异构化装置的主管没有通过检查确保操作人员正确的操作程序,而且在事故发生的关键时刻离岗,设备操作人员没有及时拉响疏散警报,这都大大加剧了事故的严重程度。
BP德克萨斯炼油厂爆炸事故案例学习(教学版)分析
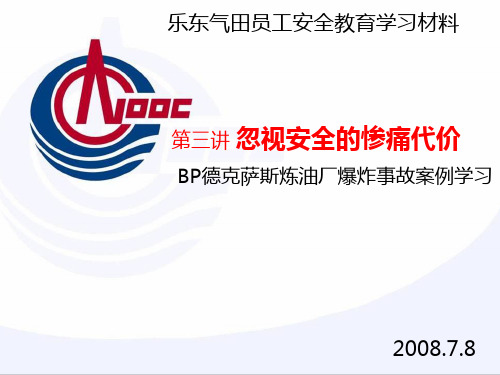
后果:由于削减成本,得克萨斯州炼厂很多设备年久失修, 无法更新;员工雇佣成本和设备更新维护方面的预算被大 量削减。这些削减对生产安全产生了负面影响。
第一章
概述
2005 年3 月23 日13 时20 分左右,英国石油公 司(BP)位于美国德克萨斯州(Texas)的炼油厂 异构化装置发生了严重的火灾爆炸事故,该事故为 美国作业场所近20年间最严重的灾难。事故造成15 名员工丧生,170 余人受伤,爆炸产生的浓烟对周围 工作和居住的人们造成不同程度的伤害。
第一章
概述
1999年之前,得克萨斯城炼油厂属于阿莫科石油公司。在 属于阿莫科石油公司管理期间的1994年,管理层决定减 少得克萨斯炼厂的人数以不断削减人力成本。
第一章
概述
根据当时被各大公司竞相追捧的一个用人原则,减少 18%的员工,就能节省2200万到3300万美元的人力成 本投资。如果减少31%的员工,就能节约4200万到 6100万美元的花销。 1999年,BP收购阿莫科石油公司 在得克萨斯城炼油厂的人员管理和设备投资方面,低 成本的战略得以维持并被BP公司继续维持下去。
第一章
概述
低成本的战略在得克萨斯城炼油厂人员管理方面所产 生的影响:
人手不足 相关机构的研究发现,在过去的四年里,得克萨斯 炼厂的操作工和维护人员加班时间占总工作时间的 27%,有些员工甚至高达68%。这么高的加班比率 远远超出正常水平,这是得克萨斯炼厂员工人数不 足的一种表现。
第一章
概述
BP低成本的战略在设备投资方面的表现: 1999年,BP收购阿莫科后削减了得克萨斯炼厂25%的固定 资产投资,两年后固定资产投资又削减了25%。
2.2 事故过程描述
2005 年3 月23 日凌晨2 时左右,异构化装置的操作人员将 液态烃原料导入分馏塔中。 凌晨3 时30 分,开始进料,当时液位计指示塔内液位在距离 塔底3.0 m 处。 9 时50 分左右,操作员开始将液态原料进行循环,并将更 多的液体打入液位已经过高的塔中,
BP炼油厂重大事故调查报告

重建与提升
针对事故原因,改进和提升生 产设施和安全性能。
04
事故调查
调查组织与程序
调查组织
BP炼油厂重大事故发生后,当地政府成立了专门的事故调查组,由相关部门 和专家组成,对事故进行全面调查。
调查程序
事故调查组制定了详细的调查计划,包括现场勘查、取证和技术鉴定等步骤 ,同时对相关人员进行问询和调查。
加强安全生产培训与教育
对员工进行定期的安全生产培训,提高员工的安 全意识和操作技能。
开展多种形式的安全教育活动,加强员工的安全 意识培养。
对安全生产培训和教育效果进行评估和反馈,不 断改进和提高培训教育质量。
完善安全生产责任制考核机制
建立和完善安全生产责任制 考核机制,明确各级管理人 员和员工的安全生产职责。
加强领导干部安全意识
加强领导干部的安全意识培养,使其能够起到表率作用,并 将安全生产纳入到企业整体战略中。
安全生产管理体制不健全
建立健全安全生产管理体系
建立完善的安全生产管理体系,明确各级管理人员在安全生产中的职责和权 限,形成科学有效的管理机制。
加强安全检查和隐患排查
定期进行安全检查和隐患排查,发现并解决存在的安全隐患,确保生产过程 的安全。
损失
BP炼油厂被迫关闭,周边企业生产受到不同程度的影响。
事故等级与性质
等级
美国国家应急管理局(NRC)将事故定为“重大”级别。
性质
爆炸、火灾、有毒化学物质泄漏等多种因素交织的复杂事故 。
02
事故原因分析
直接原因分析
操作失误
操作人员在进行催化剂注入时,未能按照规定步骤进行,导致催化剂注入量 过大。
炼油厂自燃火灾事故原因

炼油厂自燃火灾事故原因概述炼油厂是能源行业中的重要环节,其作用是将原油加工成各种石油产品,如汽油、柴油、润滑油等。
然而,由于炼油过程中涉及许多高温、高压、易燃易爆的化工物质,炼油厂自燃火灾事故是比较普遍的。
自燃火灾事故不仅会造成财产损失,还可能导致严重的人员伤亡和环境污染,因此必须引起高度重视。
本文将分析炼油厂自燃火灾事故的原因,探讨如何通过科学的管理和技术手段预防和控制自燃火灾事故的发生。
一、炼油厂自燃火灾事故的典型案例为了更好地了解炼油厂自燃火灾事故的原因,我们先看一下一些典型的事故案例。
1. 美国德州炼油厂自燃火灾事故2005年3月,美国德州一家炼油厂发生了一起严重的自燃火灾事故,导致15人死亡,数十人受伤。
据调查,事故发生时,炼油厂的一座储油罐发生了自燃,引发了爆炸和大火。
事后调查发现,该储油罐原本对硫化氢等有害气体进行处理,但由于设备老化,未能有效控制有害气体的排放,导致了事故的发生。
2. 俄罗斯炼油厂自燃火灾事故2010年,俄罗斯一家炼油厂发生了一起严重的自燃火灾事故,造成了严重的人员伤亡和环境污染。
据调查,事故发生时,炼油厂的一台精馏塔发生了自燃,引发了大火。
事后调查发现,该精馏塔因长期使用而出现了严重的老化和腐蚀,加上操作人员对设备运行状态的监测不力,导致了事故的发生。
以上两起炼油厂自燃火灾事故,都与设备老化、操作不当等因素有关。
下面我们将详细分析炼油厂自燃火灾事故的原因。
二、炼油厂自燃火灾事故的原因分析1. 设备老化、腐蚀炼油厂里的许多设备都需要长期承受高温、高压、腐蚀和磨损,这使得设备的老化和腐蚀问题十分严重。
一旦设备发生老化、腐蚀,就会导致其失去了原有的安全性能,容易发生自燃火灾事故。
2. 储油罐泄露炼油厂的储油罐是存放原油和石油产品的重要设施,然而由于储油罐的使用年限长和环境因素等原因,储油罐很容易发生泄露,一旦油品泄漏,很容易与空气中的氧气发生化学反应,导致自燃。
3. 作业疏忽炼油厂的作业条件复杂,需要操作人员严格按照操作规程和安全程序进行作业。
事故案例分析2013.1
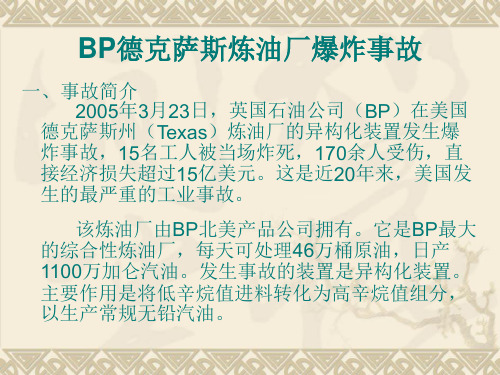
二、事故原因 1)912号储罐的自动测量系统(ATG)失灵,储罐装满时,液位计停止在储罐的 2/3液位处, ATG报警系统没能启动,储罐独立的高高液位开关也未能自动开启 切断储罐的进油阀门,致使油料从罐顶溢出,从罐顶泄漏的油料外溢,油料挥发, 形成蒸气云,遇明火发生爆炸、起火。 2)尽管邦斯菲尔德油库进行了三级设防,由于一级设防的缺陷使外溢的油料形成多 处瀑布,加速了蒸气云的形成,二级和三级设防主要是用于保护环境的,但由于 泄漏的油料形成大面积池火,高温破坏了防火堤,致使防火堤围墙倒塌和断裂, 同时殃及了第三级设防,大量的油料和消防泡沫流出库区。 3)部分储罐和管道系统的电子监控器以及相关的报警设备处在非正常工作状态。 4)储罐和管道系统附近的可燃气体检测仪器不灵敏。 5)对于某些处于非正常工作状态设备的检查不及时,响应迟钝,诸如储罐入口的自 动切断阀和管线入口的控制阀等。 6)储罐的结构设计(如罐顶的设计)不尽合理,这在一定程度上加剧了油料蒸气云 形成的可能性。 7)罐区应急设施(如消防泵房等)的选址和保护措施不合理。 三、 教训与启示 此次邦斯菲尔德油库事故除设计和操作的原因外,油库选址存在安全隐患也 是教训之一。英国健康安全署(HSE)在过去审批过程中,对油库选址与周围发 展问题考虑不够,只考虑储罐油料泄漏在防火堤内形成池火,未充分考虑油料蒸 气云爆炸的潜在危害性;只对汽车罐车装卸站台可能发生油料蒸气云爆炸的风险 在应急预案中作了相应的准备。邦斯菲尔德油库事故提示我们应对油库罐区和选 址的安全评估标准进行新的修改。
由于喷出的油气量比较大,油气从放空罐顶部的放空管喷 出(放空管直接排大气,高度34.4米左右),大量汽油流向罐 周围并迅速气化。在第一次小的爆炸后,在13:20发生大爆炸。 由于放空罐附近的临时活动房(为另一套检修装置服务)内仍 有很多人,在油气大量喷出并迅速气化的情况下也没有组织疏 散,导致事故伤亡人数大大增加。
BP美国炼油厂爆炸事故

BP美国德克萨斯(Texas)炼油厂爆炸事故高前进赵建民1、事故简介2005年3月23日下午1点20分,一系列猛烈的爆炸发生在BP美国德克萨斯(Texas)炼油厂的一个正在开工的异构化装置。
爆炸造成15人死亡,180人受伤,在爆炸现场的工艺泄放烟囱旁边当时放置了一些检修用的可移动拖车,这些死伤人员中的大多数当时都是在拖车的里面或外面。
爆炸冲击波摧毁了附近的50个大型化学品储罐,震碎了3/4英里外的居民窗户玻璃,滚滚黑烟从工厂翻腾而出,当局指示约4万4千德克萨斯(Texas)市的居民呆在室内不要外出。
异构化装置被迫停工超过两年,BP公司为此爆炸损失数十亿美元。
图1:事故后的异构化装置的现场3月23日早上,炼油厂的异构化装置的萃取油分馏塔在检修后重新开工进料,操作员用泵连续向分馏塔内送可燃物料超过三个小时,在这三个小时的过程中没有将物料从塔内送出,这和操作开工指导是相矛盾的。
关键的报警和控制仪表显示假值,没能提醒操作员分馏塔内物料的液位已经很高。
结果,在操作员不清楚的的情况下,高170英尺(52米)的分馏塔进料过多,液体进料溢流到了塔顶部的管道中。
分馏塔顶部管道向下走,在约148英尺(45米)高的位置安装有三个安全阀。
当塔顶部的管道充满液体时,塔底部的压力迅速地从21psi升高到64psi,三个安全阀起跳打开持续了6分钟,排放了大量的可燃液体到下游的排放收集罐,这个排放收集罐通过一个泄放烟囱和大气相连通。
排放收集罐和泄放烟囱都相继溢流,大量的可燃液体从113英尺(34米)高的泄放烟囱顶部象喷泉一样地喷涌而出。
排放收集系统是一种陈旧的且不安全的设计,它是在19世纪50年代安装的,这个系统从来也没有和火炬系统相连通,不能安全地收集从工艺装置泄放的液体和可燃易燃的气体。
这些喷涌出的易挥发的液体,流到地面后形成了可燃蒸汽云。
在离排放收集罐约25英尺(7.6m)的地方停了一辆没有熄火发动机空转的皮卡车,扩散的可燃蒸汽随即被点燃,火焰迅速扩散,可燃蒸汽云被点燃,接下来在装置区发生了一系列的爆炸。
BP德州炼油厂火灾爆炸事故
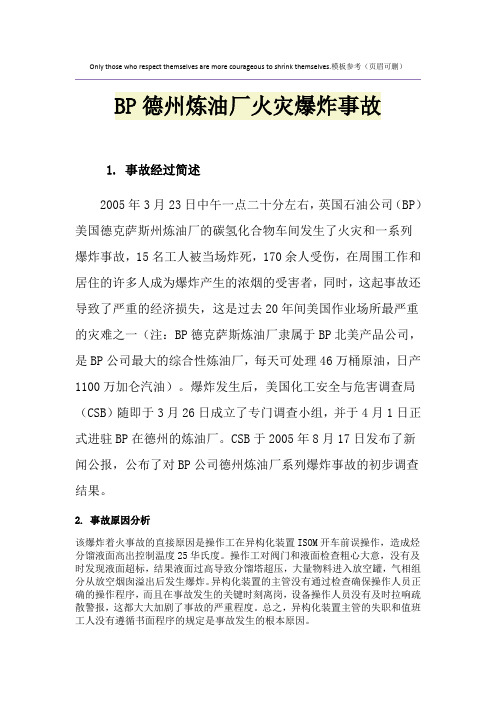
Only those who respect themselves are more courageous to shrink themselves.模板参考(页眉可删)BP德州炼油厂火灾爆炸事故1. 事故经过简述2005年3月23日中午一点二十分左右,英国石油公司(BP)美国德克萨斯州炼油厂的碳氢化合物车间发生了火灾和一系列爆炸事故,15名工人被当场炸死,170余人受伤,在周围工作和居住的许多人成为爆炸产生的浓烟的受害者,同时,这起事故还导致了严重的经济损失,这是过去20年间美国作业场所最严重的灾难之一(注:BP德克萨斯炼油厂隶属于BP北美产品公司,是BP公司最大的综合性炼油厂,每天可处理46万桶原油,日产1100万加仑汽油)。
爆炸发生后,美国化工安全与危害调查局(CSB)随即于3月26日成立了专门调查小组,并于4月1日正式进驻BP在德州的炼油厂。
CSB于2005年8月17日发布了新闻公报,公布了对BP公司德州炼油厂系列爆炸事故的初步调查结果。
2. 事故原因分析该爆炸着火事故的直接原因是操作工在异构化装置ISOM开车前误操作,造成烃分馏液面高出控制温度25华氏度。
操作工对阀门和液面检查粗心大意,没有及时发现液面超标,结果液面过高导致分馏塔超压,大量物料进入放空罐,气相组分从放空烟囱溢出后发生爆炸。
异构化装置的主管没有通过检查确保操作人员正确的操作程序,而且在事故发生的关键时刻离岗,设备操作人员没有及时拉响疏散警报,这都大大加剧了事故的严重程度。
总之,异构化装置主管的失职和值班工人没有遵循书面程序的规定是事故发生的根本原因。
德克萨斯城炼油厂的爆炸,还具有五个主要的间接原因:首先,历经多年的工作环境已被侵蚀到排斥变化的地步,而且缺乏信任、动力和目标。
监督和管理行为不清晰。
对条例的执行不彻底。
员工个人感觉没有提建议和进行改进的权力。
第二,管理者没有建立或强制实行流程安全、操作执行程序、系统的降低风险优先权等。
BP德克萨斯炼油厂爆炸事故案例学习(学生预习版)
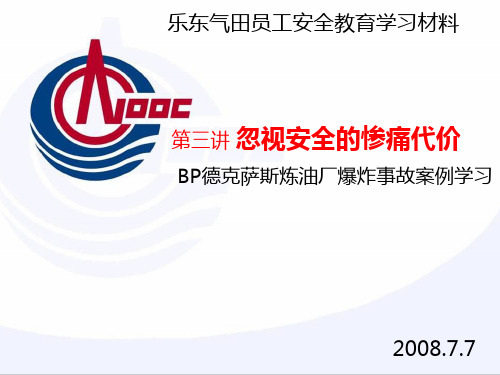
2.2 事故过程描述
2005 年3 月23 日凌晨2 时左右,异构化装置的操作人员将 液态烃原料导入分馏塔中。 凌晨3 时30 分,开始进料,当时液位计指示塔内液位在距离 塔底3.0 m 处。 9 时50 分左右,操作员开始将液态原料进行循环,并将更 多的液体打入液位已经过高的塔中,
第二章
事故经过
事故经过
个人记录区
4.从危险源辨识与风险分析来看
第二章
事故经过
个人记录区
5.你个人认为还需要改进的其他方面?
第三章
事故处理
事故发生后,BP 公司迅速做出反应,BP 首席执行官布 朗勋爵、BP 北美公司总裁罗斯- 费拉里等立即赶往德克萨斯 州,BP 网站也报道了关于事故的最新进展以及公司所采取 的应急措施。BP 公司成立了独立的事故调查小组对事故开 展调查,事故调查小组于2005 年5 月17 日公布了德州炼油 厂爆炸事故的初步调查报告。12 月又提出了最终报告,并通 过BP 公司全球网站向全世界发布。
第二章
事故经过
2.1 事故所处环境
炼油厂异构化装置
2.2 事故环境的工艺设施
1.异构化装置分馏塔 附属设施:来料流量控制阀,液位计,液位高高位报警系统,应急泄压阀BDV,溢流排放 管线,压力安全阀, 2.加热炉 3.换热器 4.放空罐,顶部有烟囱
第二章
2.3 事故背景
事故经过
操作工启动异构化装置
第五章
结束语
像这样一个有着良好安全业绩的世界级的大企业, 通过事故调查仍能发现在企业文化、领导层的个人行 为以及标准的准确度等诸多方面存在的问题。这也应 引起我们的思考,这起事故暴露的问题是不是我们的 企业也存在?
第二章
事故经过
BP炼油厂重大事故调查报告

事故经过与影响
事故经过
在炼油厂正常运营过程中,一个油罐突然发生爆炸,导致大 量原油泄漏。事故导致部分设备严重损坏,现场工作人员紧 急撤离。
影响
事故导致炼油厂部分区域被关闭,原油供应受到严重影响。 由于原油泄漏对环境和公共安全的影响,当地政府紧急启动 应急响应计划。
初步原因分析
原油泄漏的原因
初步分析表明,原油泄漏可能是由于油罐内部腐蚀导致。在油罐维护过程中,可 能存在一些不当操作导致内部腐蚀加剧。
现故障。
维护不到位
通过对设备进行检查和维护,发 现设备存在维护不到位的情况, 这也是导致事故发生的原因之一 。
管理问题
通过对公司管理流程的分析,发现 公司在设备维护和管理方面存在一 些问题,这也对事故的发生起到了 一定的影响。
验证过程与结果
模拟实验
通过对事故现场进行模拟实验,验证了操作不当和维护不到位是导致事故发生的主要原因。
环境的污染。
加强国际合作
炼油行业将加强国际合作,共 同应对全球能源和环境挑战。
感谢您的观看
THANKS
05
结论与展望
事故结论与设备维护不当,导致管道 破裂,大量原油泄漏。
影响范围
事故导致附近区域空气、 土壤和水质受到严重污染 ,部分动物栖息地受损。
人员伤亡
无人员伤亡,但附近居民 因环境污染受到不同程度 的影响。
安全措施改进建议
加强设备维护
定期对炼油厂设备进行检 查和维护,确保设备运行 正常。
BP炼油厂重大事故调查报 告
2023-11-06
contents
目录
• 引言 • 事故经过与初步分析 • 事故调查与验证 • 事故责任认定与教训 • 结论与展望
BP美国德州炼油厂火灾事故
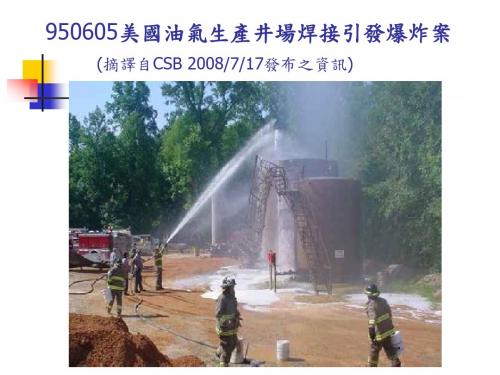
1.焊接前及作業中,未使用氣體偵測儀量測可燃性氣體濃 度。 2.動火作業前未將距離4英尺旁之鄰槽開口管線加帽蓋或 進行盲封隔離等。 3.四座儲槽內部連通,有些槽內仍有可燃性氣體及原油, 卻未先移除與清理,工作環境不安全。 4.將梯子橫置二儲槽作為焊接者的臨時工作平台,並由 維修人員站在槽頂協助穩定橫梯,不符高處作業之安全 程序。
事故原因分析
基本原因: 1.承商缺乏熱作之標準作業程序 承攬商未備製API規範之熱作SOP,以致
-在焊接前未先隔離含有可燃性蒸氣之#2與
#3槽。
-未移除#2號槽之原油。
-未將#3號槽之開口管線加帽蓋致油氣溢散。
-未偵測作業環境油氣濃度等。
事故原因分析
基本原因:
2.承商忽視高處作業之工作安全 未建造儲槽高處焊接之工作平台,僅以梯子橫放 #3及#4槽間以代替工作平台,致需有2名維修人 員在#3槽頂穩固梯子,而被爆炸波及死亡。
Partridge-Raleigh公司及其承攬商應 依API、NFPA提供之指引,並遵循OSHA 的規定執行熱作業,例如建立生產井場 熱作之SOP、工作手冊及製訂工作安全 計畫等,並落實執行。
Байду номын сангаас
3.Partridge-Raleigh及其承商均未建立工作許可 制度以管理動火作業
4.Partridge-Raleigh未建置井場員工之安全計 畫,亦未要求承商施工前應提出安全計畫並執行
改善措施
焊接區應與含可燃性液體(原油)、蒸氣之 儲槽及管線隔離,例如開口管線應設置管 帽或盲封或採取其他隔離措施。
950605美國油氣生產井場焊接引發爆炸案
(摘譯自CSB 2008/7/17發布之資訊)
事故摘要
2006年06月05日,位於美國密西西比州 Raleigh城的Partridge-Raleigh公司之生 產井場,有承攬商進行儲槽新設管線焊接 工作,欲將2個儲槽與第3個儲槽相接。當 天上午8時30分許,焊接火花引燃自鄰槽 未盲封管線溢散出的可燃性蒸氣(相對位 置參見圖示),導致兩個儲槽發生爆炸, 造成承攬商領班及維修人員3人死亡、焊 接工1人重傷的重大事故。
BP炼油厂爆炸事故的

一篇名为《BP炼厂爆炸事故的教训》的文章在石油业界广为流传,有的公司还将文章印发给高层管理人员,引起热烈反响。
《BP炼厂爆炸事故的教训》是篇什么样的文章,究竟是什么引起如此震动呢?其实文章没有什么特别新奇的地方,它最难能可贵的是,敢于让世界分享事故资源。
2005年3月23日,BP旗下最大的炼油厂——美国得克萨斯城炼油厂发生爆炸事故,造成15人死亡,170多人受伤,影响巨大,引起全世界广泛关注。
该文章的作者约翰·摩格福特是BP集团负责健康安全环保和运营工作的高级副总裁。
该文是根据他今年4月16日在一次行业安全会议上的发言整理出来的。
文章讲述了事故发生的经过,分析了事故原因,提出了整改的具体措施,既没有深奥的理论,也没有高超的技巧。
但态度坦诚,情感恳切。
尤其是在文章的最后说:“事实上得克萨斯城炼油厂的事故是可以避免的,不过我们的失误可以帮助其他公司免于陷入同样的险境。
请以我们为前车之鉴。
”BP炼厂爆炸事故的教训BP公司决定与社区、公司、监管部门、媒体和业界同仁一起分享我们的教训。
BP得克萨斯城炼厂爆炸事故原因相当复杂,包括超出炼油厂安全运作流程之外的许多因素——BP的授权文化,领导层的个人行为,以及我们标准的清晰度。
得克萨斯城炼油厂爆炸本来是一次可以预防的事故,这里既有操作失误,也有文化失误,还有管理失误。
我们经过调查,发现了得州炼油厂在工作和安全文化方面存在明显缺陷。
问题在于,为什么会出现这些缺陷?为什么爆炸发生之前这些缺陷没有及时查证和报告?回顾安全管理如果是2005年3月22日(也就是炼油厂爆炸前一天)我在这里作报告,我讲的肯定和今天谈的大不一样。
开头我可能表现出对BP集团安全文化、安全标准、安全管理系统和安全监控程序信心十足,会列举一些数据——例如,BP公司过去五年以来如何实现记录受伤率降低了70%,事故死亡率下降了75%。
我可能会断言,这种积极的趋势反映了我们协调一致的、系统化的安全措施取得了成效。
bp美国德州炼油厂爆炸事故观后感

bp美国德州炼油厂爆炸事故观后感英文版On March 23, 2005, an explosion occurred at the BP Texas City Refinery in Texas, USA. The explosion resulted in 15 deaths and injured over 180 people. The incident was a tragic reminder of the dangers that workers in the oil and gas industry face on a daily basis.The explosion was caused by the ignition of flammable liquid hydrocarbons that were being released from a blowdown stack. The investigation into the incident revealed a number of safety failures at the refinery, including inadequate training, poor maintenance practices, and a lack of oversight from BP management.In the aftermath of the explosion, BP faced intense scrutiny and criticism for its role in the disaster. The company was fined millions of dollars for safety violations and was forced to make significant changes to its safety procedures. The incident also led to a renewed focus on workplace safety in the oil and gas industry as a whole.The BP Texas City Refinery explosion serves as a stark reminder of the importance of prioritizing safety in the workplace. It is crucial for companies to invest in proper training, maintenance, and oversight to prevent similar tragedies from occurring in the future.观后感2005年3月23日,美国德克萨斯州的BP得克萨斯城炼油厂发生爆炸事故。
bp德克萨斯州炼油厂爆炸事故观后感

bp德克萨斯州炼油厂爆炸事故观后感英文版On March 23, 2005, a tragic explosion occurred at the BP Texas City Refinery in Texas, resulting in 15 deaths and injuring over 170 people. The incident was a stark reminder of the dangers associated with working in the oil and gas industry, as well as the importance of maintaining strict safety protocols.The explosion was caused by the ignition of hydrocarbon vapors that had accumulated in a vent stack. This was a result of a number of factors, including equipment malfunction, inadequate training, and a lack of proper safety procedures. The subsequent investigation revealed that BP had failed to adequately maintain its equipment and had not provided sufficient training to its employees.In the aftermath of the explosion, BP faced harsh criticism for its role in the incident. The company was fined millions of dollars and forced to pay compensation to the victims and their families. The incident also led to a renewed focus on safety in the oil and gas industry, with companies being urged to prioritize the well-being of their employees above all else.The BP Texas City Refinery explosion serves as a sobering reminder of the potential consequences of neglecting safety protocols in the workplace. It is a tragedy that should never have happened, and one that should serve as a wake-up call to all companies operating in high-risk industries.观后感2005年3月23日,在德克萨斯州的BP德克萨斯城炼油厂发生了一起悲剧性爆炸事故,造成15人死亡,170多人受伤。
BP德克萨斯州炼油厂火灾爆炸事故给我们的启示

BP 德克萨斯州炼油厂火灾爆炸事故给我们的启示唐彬 1 天津市居安企业管理咨询有限公司何琛 2 上海于睿商务咨询有限公司关键词 : 过程安全绩效指标(PSM KPI、过程安全管理、火灾、爆炸、美国化学品安全与危害调查委员会 (CSB摘要本文结合美国化学品安全与危害调查委员会对美国 BP 德克萨斯州炼油厂火灾爆炸事故的分析,从过程安全管理及过程安全绩效指标方面深刻分析产生爆炸事故的原因, 并提出改进措施。
1. 介绍目前很多企业都是执行 HSE 管理体系,把零伤亡作为企业安全管理的目标,所以我们管理的重点自然而然就变成对人身安全的管理, 但是对诸如操作工违反操作规程进行操作、报警的次数、联锁触发的次数、安全阀起跳的次数已经企业内出现的泄露事故关注的相对较少 , 但是这些看似微不足道的隐患往往最后导致了重大的过程安全事故的发生。
所以我们需要重视过程安全管理,重视过程安全管理的绩效。
本文通过美国化学品安全与危害调查委员会(CSB- Chemical Safety Board 对美国 BP 德克萨斯州炼油厂火灾爆炸事故的分析, 提出了企业应重视过程安全管理和过程安全管理绩效,并阐述过程安全管理绩效的划分和目的。
2. BP德克萨斯州炼油厂火灾爆炸事故经过2005年 3月 23日 13时 20分左右 , 英国石油公司 (BP位于美国德克萨斯州(Texas的炼油厂异构化装置发生了严重的火灾爆炸事故, 该事故为美国作业场所近 20年间最严重的灾难。
事故造成 15人死亡, 180余人受伤,爆炸产生的浓烟对周围工作和居住的人们造成不同程度的伤害, 直接经济损失超过 15亿美元。
德克萨斯州的炼油厂是 BP 公司最大和最复杂的炼油厂, 其每天生产汽油产量达 1000万加仑 (约占整个美国汽油销售总量的 2.5%。
此外 , 它还生产喷气式发动机燃料、柴油燃料和化学原料。
炼油厂有 29个炼油工艺装置和 4个化工装置 , 占地 1200英亩 , 拥有 1800名 BP 正式员工 ,事故发生时另外有大约 800名承包商员工在现场 , 正在进行检修作业。
观美国德州炼油厂爆炸事故有感
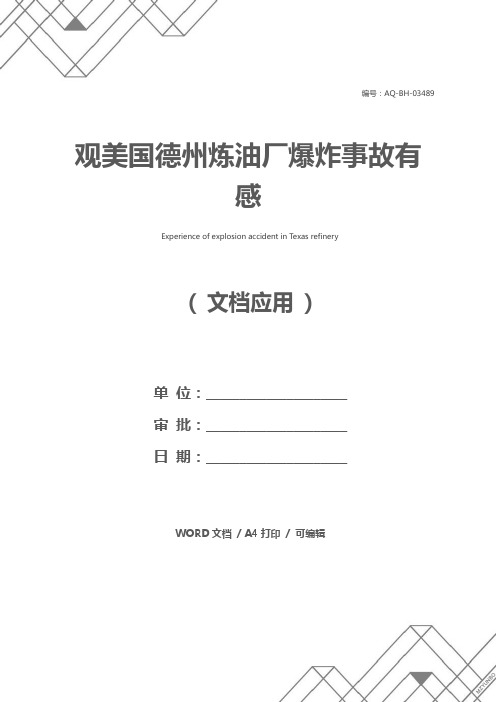
编号:AQ-BH-03489( 文档应用)单位:_____________________审批:_____________________日期:_____________________WORD文档/ A4打印/ 可编辑观美国德州炼油厂爆炸事故有感Experience of explosion accident in Texas refinery观美国德州炼油厂爆炸事故有感备注:每次经过学习之后总想着把自己学习到的经验记录下来,这会在潜移默化中濡染到生活中的其他事情,做事更加具有目的性,做事更加具有连贯性,不再是一股脑去做,步步摸棋。
2014年6月是安全生产月,11日部门进行安全生产事故警示教育活动,组织部门员工及外委运行人员观看美国德州炼油厂爆炸事故视频,并讨论分享观后感。
2005年3月23日13∶20左右,BP(英国石油公司)美国德克萨斯州炼油厂的一套异构化装置的抽余油裂解塔在经过短暂的维修后,重新开车。
启动过程中,操作人员将液态烃原料不断泵入裂解塔,但在3个多小时的加料过程中,没有任何产物馏出,而报警器和控制系统又提供了错误的指令,使操作者对塔内液位过高毫不知情。
液体原料装满裂解塔后,压力迅速上升,迫使塔顶3个安全阀打开,将大量可燃液体泄放并充满放空罐,并沿着罐顶的烟道,像喷泉一样洒落到地面上。
泄漏出来的可燃液体蒸发后,形成可燃气体蒸气云,更不幸的是,在距离放空罐不远的地方,停着一辆没有熄火的载货卡车,发动机引擎的火花点燃了可燃蒸气云,引发了大爆炸。
爆炸事故导致15名工人被当场炸死,170余人受伤,在周围工作和居住的许多人成为爆炸产生的浓烟的受害者。
同时,这起事故还导致了严重的经济损失。
这是过去20年间美国作业场所最严重的灾难之一。
著名的过程安全专家TrevorKletz说,把事故原因简单地归咎于人员误操作,就像不小心跌倒了责怪地心引力一样,无法帮助我们阻止事故再次发生。
为了避免类似事故重演,事故调查组认真分析了事故发生的深层次原因。
美国Dierpark炼油厂失火
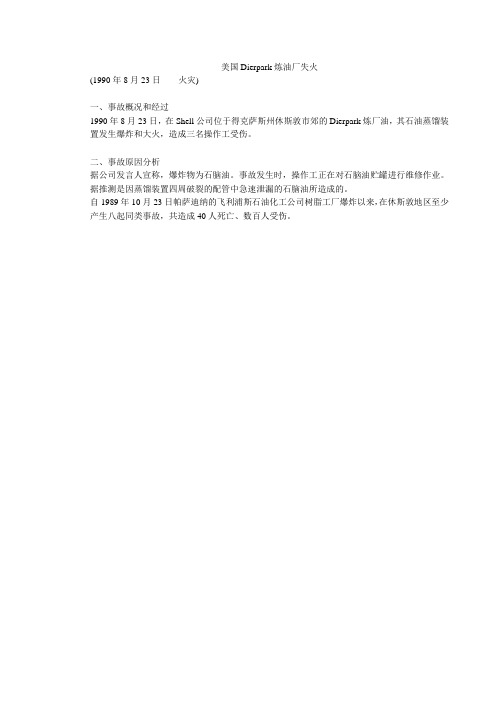
美国Dierpark炼油厂失火
(1990年8月23日火灾)
一、事故概况和经过
1990年8月23日,在Shell公司位于得克萨斯州休斯敦市郊的Dierpark炼厂油,其石油蒸馏装置发生爆炸和大火,造成三名操作工受伤。
二、事故原因分析
据公司发言人宣称,爆炸物为石脑油。
事故发生时,操作工正在对石脑油贮罐进行维修作业。
据推测是因蒸馏装置四周破裂的配管中急速泄漏的石脑油所造成的。
自1989年10月23日帕萨迪纳的飞利浦斯石油化工公司树脂工厂爆炸以来,在休斯敦地区至少产生八起同类事故,共造成40人死亡、数百人受伤。
- 1、下载文档前请自行甄别文档内容的完整性,平台不提供额外的编辑、内容补充、找答案等附加服务。
- 2、"仅部分预览"的文档,不可在线预览部分如存在完整性等问题,可反馈申请退款(可完整预览的文档不适用该条件!)。
- 3、如文档侵犯您的权益,请联系客服反馈,我们会尽快为您处理(人工客服工作时间:9:00-18:30)。
BP美国德州炼油厂火灾爆炸事故2005年3月23日中午1∶20左右,BP(英国石油公司)美国德克萨斯州炼油厂的碳氢化合物车间发生了火灾和一系列爆炸事故,15名工人被当场炸死,170余人受伤,在周围工作和居住的许多人成为爆炸产生的浓烟的受害者。
同时,这起事故还导致了严重的经济损失。
这是过去20年间美国作业场所最严重的灾难之一(注:BP德克萨斯州炼油厂隶属于BP北美产品公司,是BP公司最大的综合性炼油厂,每天可处理46万桶原油,日产1 100万加仑汽油)。
爆炸发生后,CSB(美国化工安全与危害调查局)随即于3月26日成立了专门调查小组,并于4月1日正式进驻BP 在德克萨斯州的炼油厂。
CSB于2005年8月17日发布了新闻公报,公布了对BP 公司德州炼油厂系列爆炸事故的初步调查结果。
BP美国德克萨斯州炼油厂火灾爆炸事故现场事故原因分析直接原因异构化装置主管的失职和值班工人没有遵循书面程序的规定操作是事故发生的直接原因。
具体表现在:误操作操作工在异构化装置ISOM开车前误操作,造成烃分馏液面高出控制温度3.9℃。
粗心大意操作工对阀门和液面检查粗心大意,没有及时发现液面超标,结果液面过高导致分馏塔超压,大量物料进入放空罐,气相组分从放空烟囱溢出后发生爆炸。
监管不力异构化装置的主管没有通过检查确保操作人员正确的操作程序。
应急反应主管在事故发生的关键时刻离岗,设备操作人员没有及时拉响疏散警报。
间接原因缺乏文化氛围历经多年的工作环境已被侵蚀到排斥变化的地步,而且缺乏信任、动力和目标。
监督和管理行为不清晰。
对条例的执行不彻底。
员工个人感觉没有提建议和进行改进的权利。
管理不利管理者没有建立或强制实行流程安全、操作执行程序、系统的降低风险优先权等。
没有从BP其他事故中吸取教训。
职责与责任不清复杂组织内的众多变化,包括组织结构和人员的调整,导致了责任不明和沟通不畅。
结果造成员工对角色、职责和优先顺序迷惑不清。
缺乏危害辨识要归咎于对危险辨识不足,对站点流程安全的理解知之甚少,这些导致了人们承受了更大的风险。
作业管理与沟通不善低水平的操作管理和炼油厂内由上至下缺乏沟通,意味着对于问题没有及时的早期警报系统。
而且缺乏独立的渠道,无法通过组织彻底的核查来了解这个工厂的水准下滑。
事故处理措施组建了一个新的管理团队进入德克萨斯州炼油厂,精简机构,促进沟通。
明晰岗位角色和职责,并采取措施验证了遵守操作规程。
创建了项目组,以协调并跟踪最终事故调查报告中的建议以及BP公司与OSHA(美国职业安全健康局)协商相关措施的执行。
在公司层面建立新的安全运行机构,这个机构的主要职能之一就是促进交流与协作,共享相关经验教训。
强化了独立的检查程序,当前的重点是确定系统与程序都被安排在适当的位置,并有效地工作。
已建立新的标准,以促进更严格、更有连续性地掌握BP集团的工作和完整性管理。
在未来的5年投入10亿美元,对德克萨斯州炼油厂进行升级维修。
此外,将在关键装置上安装先进的过程控制系统,取消在轻度维修中使用放空烟囱,同时加强员工培训。
推行了新的工程技术实务规范,以管理炼厂和其他加工厂内临时建筑物的使用。
BP德克萨斯州炼油厂火灾爆炸事故再次提醒我们:火灾和爆炸事故往往在人们意想不到的时候发生,根源在于管理上的缺陷。
在造成重大伤害和多人伤亡的同时,还会伴生设备炸毁、厂房倒塌、环境污染等事故,不但给诸多伤者及其家庭带来诸多精神上与生活上的困苦,还严重影响到生产的顺利进行,威胁到企业的声誉,甚至迫使企业面对较长时间的停产,面对官司纠纷、理赔及公众的抱怨等,致使企业财产蒙受巨大损失,一批领导倒台。
火灾和爆炸事故原因比较复杂,如误操作,可燃物种类繁多,引起事故的火源也有多种等。
该类事故因燃烧、爆炸的作用对证据具有毁灭性,这也给后续事故原因的调查与分析带来很大的困难。
火灾和爆炸事故对企业与社会的危害巨大,预防该类事故的发生,于民于国于企都事关重大。
通过采用一些提前预防的手段可以有效地预防和应对火灾爆炸事故的发生,如HAZOP分析及定期回顾,定期安全隐患排查,灾情分析、模拟及应对演练等。
通过结合本单位的实际,学习事故案例是一种很有效的方法。
事故经过2005年3月23日早上,得州炼厂一套异构化装置的抽余油裂解塔在经过短暂的维修后,重新开车。
启动过程中,操作人员将可燃的液态烃原料不断泵入抽余油裂解塔。
抽余油裂解塔是一个垂直的蒸馏塔,内径3.8m,高51.8m,容积约58.61万L,塔内有70块塔板,用于将抽余油分离成轻组分和重组分。
但是,在3个多h的加料过程中,没有任何产物馏出,而报警器和控制系统又提供了错误的指令,使操作者对塔内液位过高毫不知情。
这样,由于进料仍在继续,液体原料装满裂解塔后,进入塔顶的管线。
塔顶的管线通往距塔顶以下45.1m 的安全阀。
管线中充满液体后,压力迅速从144.8kPa上升到441.3kPa,迫使3个安全阀打开了6min,将大量可燃液体泄放到放空罐里。
液体很快充满了34.4m高的放空罐,并沿着罐顶的烟道,像喷泉一样洒落到地面上。
泄漏出来的可燃液体蒸发后,形成可燃气体蒸气云。
更不幸的是,在距离放空罐7.6m的地方,停着一辆没有熄火的小型敞蓬载货卡车,发动机引擎的火花点燃了可燃蒸气云,引发了大爆炸。
事故原因美国化学安全局(CSB)通过广泛细致的调查,对事故原因从技术和组织两方面进行了分析。
一、技术原因1. 抽余油裂解塔上的液位控制阀能够将液体从塔里转移到储罐中。
但是,异构化装置开车时,液位控制阀被一名工人关闭,塔里不断加入物料,却没有产品出来。
2. 尽管早先已报告该塔的液位计、液位观察孔和压力控制阀出现故障,但装置仍按原计划开车。
3. 放空罐的容积太小,不足以盛装安全阀排出的液体。
4.放空系统非常陈旧,在事故发生前的1年间,已经发生过8起严重的可燃物料泄漏事故。
但阿莫科公司和BP公司都没有对其进行更换,也没有连接点火系统。
5. 末熄火拖车距离有燃爆危险性的装置太近。
6. 以往在开车时,抽余油裂解塔经历过很多次液位过高的情况,但没有引起重视,阿莫科公司和BP公司都没有对这些情况展开调查。
7.开车过程非常危险,BP公司得州炼厂的管理人员没有遵从安全要求,将不相关人员从附近区域撤出。
二、组织原因1.尽管炼油厂的许多基础设施和过程设备已经年久失修,但BP公司继续削减成本,造成安全投入不足。
得州炼厂原本属于美国阿莫科公司,1999年BP集团收购阿莫科公司,得州炼厂也随之转至BP集团名下。
上世纪90年代,阿莫科公司实施了成本削减计划,BP 公司接管后延续了这种政策,1999年预算缩减25%,,2005年再度减少25%。
2. BP董事会没有对集团公司的安全文化和重大事故预防体系给予足够的关注,董事会中没有人专门负责评估和检验重大事故预防方案。
3.BP公司和得州炼厂的管理人员没有履行有效的领导和监督责任。
BP公司管理层没有设置足够的安全监督力量,没有提供足够的人力和财力,也没有建立作风一贯的安全管理模式,用于执行安全法规和操作规程。
得州炼厂存在的事故隐患,没有引起BP公司管理层的注意。
4.以人员伤害率作为安全指标,无法真实地反映过程安全性和安全文化是否健全。
5. 在得州炼厂,普遍的做法是,员工对操作过程进行文字记录,并与安全规定和操作规程进行核对,对有没有达到要求并不考核。
6. BP公司得州炼厂缺乏一种报告和学习传统。
BP公司不支持员工报告隐患,员工感觉没有提建议和实施改进的权力。
7.BP公司没有建立良好的事故调查管理系统,以便更好地汲取事故教训,对工艺进行必要的改进。
1994-2004年,BP公司这套异构化装置的放空罐已经发生了8次严重的事故,但公司只对3起事故进行了调查。
8.安全活动、目标和奖励集中在提高员工的安全操作和工人的安全行为上,没有对过程和管理安全系统加以关注。
仅依赖安全法规和操作规程,而不根据安全实践来进行安全管理的做法存在缺陷。
9. 人员、政策和组织结构的变动,可能导致责任不明和沟通不畅,造成员工对自身角色、职责和优先顺序迷惑不清,影响到过程安全性,但得州炼厂没有对这些变动的影响进行有效的评估。
过程安全系统存在的问题著名的过程安全专家Trevor Kletz说,把事故原因简单地归咎于人员误操作,就像不小心跌倒了责怪地心引力一样,无法帮助我们阻止事故再次发生。
为了避免类似事故重演,事故调查组认真分析了事故发生的深层次原因。
1. BP公司得州炼厂不注重更新安全操作规程,为操作者违反操作规程提供了条件。
经过维修,生产装置中的设备、工艺设计和功能都发生了改变,但开车操作程序没有及时更新。
操作规程里没有指出以前开车过程中曾发生过的危险,例如塔内液位的大幅波动,会对设备造成严重损害;也没有对开车阶段的操作提出特别要求,例如不正常停车和重启异构化装置的开车安全注意事项。
操作人员有很大的自由度,甚至可以不通过危害分析,就随意更改操作程序。
得州炼厂事故中几次违章操作,在以前的18次开车过程中都曾发生过。
2. 对交接班和开车等危险操作的信息沟通不畅,使产品进入储罐的时间被延迟。
BP公司没有严格的交接班信息传达制度,也不强制进行明晰的工作记录,以确保操作人员之间的信息沟通明确。
得州炼厂的管理人员和监督人员没有告诉操作者,应该将抽余油裂解产品导入储罐;夜班工作人员在交接班时,没有将装置工况,特别是塔里的液位高度告诉日班工作3. 故障报警仪器失灵,没有将实际工况反映给操作者。
发生事故前,抽余油裂解塔中的液位不断升高,但液位计显示的却是液位不断下降。
仪表显示加料量是78%,即液位为2.4m,而实际液位已经达到48.2m。
另外,由于观察液位的玻璃窗很脏,操作者无法观察到实际液位。
4.计算机控制系统设计缺陷,没能提供正确的信息,使操作者没有及时发现塔内已装满液体原料。
事故发生当日,计算机控制系统没有提供抽余油裂解装置的进出流量数据,以及物料平衡数据,使BP公司内部的操作人员(以下简称“内操”)不了解开车进展情况,没有指挥操作人员将产品导人储罐。
5监督人员和技术助理工作不力。
在抽余油裂解装置开车时,一名日班监督人员由于家人生病,离开了工作岗位,留下的一名监督员缺乏这套装置的相关技术知识,这样就没人能对内操的工作提供有力的支持和监督。
6.人手不足。
正常生产时,1名内操负责管理和控制石脑油脱硫装置、2号芳烃装置和异构化装置,每班12h,其中工作时间达10.5h。
但在事故发生时,这名内操同时还负责异构化装置抽余油裂解装置开车的监督和管理工作,工作超负荷。
7.工作人员过度疲劳。
截至发生事故当日,日班内操已经连续29天、每天工作12h,每天睡眠时间只有5~6h,严重不足。
夜班操作主管已经连续工作了33天,日班操作主管连续工作37天。