P8279-5中文资料
uPC2791TB中文资料

NEC's UPC2791TB and UPC2792TB are Silicon MMIC Wideband Amplifiers manufactured using NEC's 10 GHz f T NESAT TM II silicon bipolar process. These devices are de-signed for use as second IF buffer amps in DBS tuners. The UPC2791/92TB are pin compatible and their performance is comparable to the larger UPC1675/76G, so they are suitable for use as a replacement to help reduce system size. These IC's are housed in a 6 pin super minimold or SOT-363 pack-age.NEC's stringent quality assurance and test procedure ensure the highest reliability and performance.DESCRIPTIONFEATURES• HIGH DENSITY SURFACE MOUNTING:6 pin super minimold or SOT- 363 package •SUPPLY VOLTAGE: V CC = 4.5 to 5.5 V •WIDEBAND RESPONSE:UPC2791TB: fu = 1.9 GHz TYP UPC2792TB: fu = 1.2 GHz TYP •POWER GAIN:UPC2791TB: G P = 12 dB TYP UPC2792TB: G P = 20 dB TYPPRELIMINARY DATA SHEETGAIN vs. FREQUENCYFrequency, f (GHz)G a i n , G P (d B )TYPICAL PERFORMANCE CURVES201510500.51.01.52.0PART NUMBER UPC2791TBUPC2792TBPACKAGE OUTLINES06S06SYMBOLSPARAMETERS AND CONDITIONS UNITS MIN TYP MAX MIN TYP MAX I CC Circuit Current (no signal)mA 121722141924G P Power Gain, f = 500 MHzdB 101214172022f U Upper Limit Operating Frequency(The gain at f U is 3 dB down from the gain at 100 MHz)GHz 1.6 1.9 1.0 1.2P O (SAT)Maximum Output Level, f = 500 MHz, P IN = 0 dBm dBm +2+4+3+5NF Noise Figure, f = 500 MHz dB 5.57.03.56RL IN Input Return Loss, f = 500 MHz dB 9121215RL OUT Output Return Loss, f = 500 MHz dB 811912ISOLIsolation, f = 500 MHzdB20242428ELECTRICAL CHARACTERISTICS (T A = +25 °C, V CC = 5.0 V, Z L = Z S = 50 Ω)Date Published: June 28, 2005The information in this document is subject to change without notice. Before using this document, please confirmthat this is the latest version.ABSOLUTE MAXIMUM RATINGS1(T A = 25°C) SYMBOLS PARAMETERS UNITS RATINGS V CC Supply Voltage V6P IN Input Power dBm+10P T Total Power Dissipation2mW200T OP Operating Temperature°C-40 to +85 T STG Storage Temperature°C-55 to +150RECOMMENDEDOPERATING CONDITIONSSYMBOL PARAMETER UNITS MIN TYP MAX V CC Supply Voltage V 4.5 5.0 5.5 T OP Operating Temperature˚C-40+25+85Notes:1.Operation in excess of any one of these parameters may resultin permanent damage.2.Mounted on double sided copper clad 50 x 50 x 1.6 mm epoxyglass PWB (T A = +85°C).PIN DESCRIPTIONOUTLINE DIMENSIONS (Units in mm)PACKAGE OUTLINE S06PIN CONNECTIONSINOUTV CCTEST CIRCUITPART NUMBER MARKING QTY UPC2791TB-E3C2S 3K/reel UPC2792TB-E3C2T3K/reelORDERING INFORMATION (Solder Contains Lead)Note:Embossed tape, 8 mm wide. Pins 1, 2, and 3 face perforatedside of tape.(Top View)(Bottom View)1.GND2.GND3.Output Marking is an example of UPC2791TB4.V CC5.GND6.Input214562145633C 2CPART NUMBER MARKING QTY UPC2791TB-E3-A C2S 3K/reel UPC2792TB-E3-AC2T3K/reelORDERING INFORMATION (Pb-Free)Note:Embossed tape, 8 mm wide. Pins 1, 2, and 3 face perforatedside of tape.Life Support ApplicationsThese NEC products are not intended for use in life support devices, appliances, or systems where the malfunction of these products can reasonably be expected to result in personal injury. The customers of CEL using or selling these products for use in such applications do so at their own risk and agree to fully indemnify CEL for all damages resulting from such improper use or sale.A Business Partner of NEC Compound Semiconductor Devices, Ltd.4590 Patrick Henry DriveSanta Clara, CA95054-1817Telephone: (408)919-2500Facsimile:(408) 988-0279Subject:Compliance with EU DirectivesCEL certifies, to its knowledge, that semiconductor and laser products detailed below are compliant with the requirements of European Union (EU) Directive 2002/95/EC Restriction on Use of Hazardous Substances in electrical and electronic equipment (RoHS) and the requirements of EU Directive 2003/11/EC Restriction on Penta and Octa BDE.CEL Pb-free products have the same base part number with a suffix added. The suffix –A indicates that the device is Pb-free. The –AZ suffix is used to designate devices containing Pb which are exempted from the requirement of RoHS directive (*). In all cases the devices have Pb-free terminals. All devices with these suffixes meet the requirements of the RoHS directive.This status is based on CEL’s understanding of the EU Directives and knowledge of the materials that go into its products as of the date of disclosure of this information.Restricted Substanceper RoHS Concentration Limit per RoHS(values are not yet fixed)Concentration containedin CEL devices-A-AZLead (Pb)< 1000 PPMNot Detected(*) Mercury< 1000 PPM Not DetectedCadmium< 100 PPM Not Detected Hexavalent Chromium< 1000 PPM Not DetectedPBB< 1000 PPM Not DetectedPBDE< 1000 PPM Not DetectedIf you should have any additional questions regarding our devices and compliance to environmental standards, please do not hesitate to contact your local representative.Important Information and Disclaimer: Information provided by CEL on its website or in other communications concerting the substance content of its products represents knowledge and belief as of the date that it is provided. CEL bases its knowledge and belief on information provided by third parties and makes no representation or warranty as to the accuracy of such information. Efforts are underway to better integrate information from third parties. CEL has taken and continues to take reasonable steps to provide representative and accurate information but may not have conducted destructive testing or chemical analysis on incoming materials and chemicals. CEL and CEL suppliers consider certain information to be proprietary,and thus CAS numbers and other limited information may not be available for release.In no event shall CEL’s liability arising out of such information exceed the total purchase price of the CEL part(s) at issue sold by CEL to customer on an annual basis.See CEL Terms and Conditions for additional clarification of warranties and liability.。
27938;中文规格书,Datasheet资料
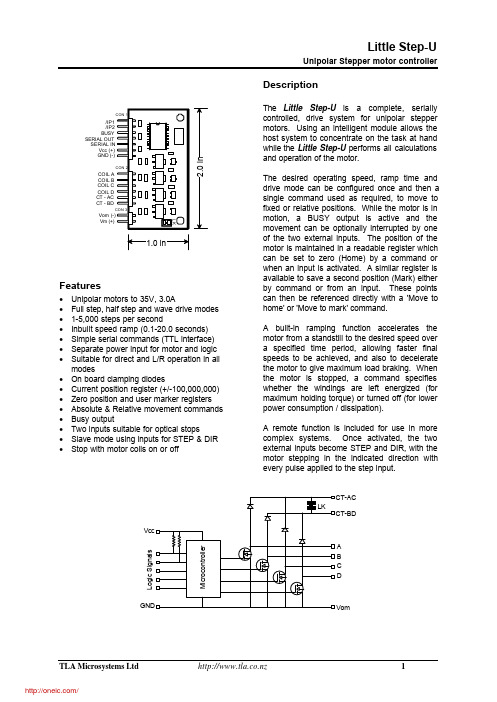
Little Step-UUnipolar Stepper motor controllerTLA Microsystems Ltd 1Features• Unipolar motors to 35V, 3.0A• Full step, half step and wave drive modes • 1-5,000 steps per second• Inbuilt speed ramp (0.1-20.0 seconds)• Simple serial commands (TTL interface)• Separate power input for motor and logic • Suitable for direct and L/R operation in all modes• On board clamping diodes• Current position register (+/-100,000,000)• Zero position and user marker registers • Absolute & Relative movement commands • Busy output• Two inputs suitable for optical stops• Slave mode using inputs for STEP & DIR •Stop with motor coils on or offDescriptionThe Little Step-U is a complete, serially controlled, drive system for unipolar stepper motors. Using an intelligent module allows the host system to concentrate on the task at hand while the Little Step-U performs all calculations and operation of the motor.The desired operating speed, ramp time and drive mode can be configured once and then a single command used as required, to move to fixed or relative positions. While the motor is in motion, a BUSY output is active and the movement can be optionally interrupted by one of the two external inputs. The position of the motor is maintained in a readable register which can be set to zero (Home) by a command or when an input is activated. A similar register is available to save a second position (Mark) either by command or from an input. These points can then be referenced directly with a 'Move to home' or 'Move to mark' command.A built-in ramping function accelerates the motor from a standstill to the desired speed over a specified time period, allowing faster final speeds to be achieved, and also to decelerate the motor to give maximum load braking. When the motor is stopped, a command specifies whether the windings are left energized (for maximum holding torque) or turned off (for lower power consumption / dissipation).A remote function is included for use in more complex systems. Once activated, the two external inputs become STEP and DIR, with the motor stepping in the indicated direction withevery pulse applied to the step input./IP1/IP2BUSYSERIAL OUT SERIAL INVcc (+)GND (-)COIL A COIL B COIL C COIL D CT - AC CT - BDVm (+)A B C D VomL o g i c S i g n a l s/DC CharacteristicsCharacteristic Symbol Min Typ Max Unit NotesLogic Supply Voltage V CC 4.5 5.0 5.5VVcc risetime t VCC0.05V/ms1Logic supply current I CC 1.5 3.0mAInput Low Voltage V IL0.0 1.0VInput High Voltage V IH 4.3Vcc VOutput Low Voltage V OL0.6VOutput High Voltage V OH 4.3VIP1/2 Source Current I OL 1.0mAMotor Voltage V M50VMotor current I M 3.0AMotor resistance R M 2.8ΩClamp diode current I CL250mAStep rate F STEP15000steps/secSpeed Error F ERR+/- 0.5%2Comms bit rate F BIT2400bpsBUSY rise/fall time T RF1025nsResponse time to IP1/2T INP1ms3DIR hold time T DIR8usMax Slave step rate F EXT10000steps/sec4Operating temp t OP070°C5Storage temp t ST-40100°C[1]Required to ensure reliable startup.[2]As a percentage of requested speed[3]Response to IP is lesser of 1ms or 1 step[4]If no comms while stepping. Max = 6000 steps/sec with comms[5]Refer loading derating graphPin functionsConnector 1Pin Function/IP1Optional input 1. Set home. Emergency stop./IP2Optional input 2. Set mark. Emergency stop.BUSY Output - High when motor movingSERIAL OUT Data from Little step-U to controller. TTLSERIAL IN Data from controller to Little Step-U. TTLVcc Supply to logic circuitsGND Supply ground. Common with motor circuits.Connector 2Pin FunctionA Winding A outputB Winding B outputC Winding C outputD Winding D outputCT-AC Common for windings A & CCT-BD Common for windings B & DConnector 3Pin FunctionV OM Motor supply ground. Common with logic circuitsV M Motor Supply +2Little Step-U /Hardware ConnectionPower SupplyThe Little Step-U divides the circuitry into two distinct sections with separate power suppliesrequired for the motor drive and the logic. The logic/control section must be powered by aregulated 5V supply applied to the VCC and GND pins. The motor power supply voltage isdictated by the motor characteristics and is connected to the VM(+) and VOM(-) pins. TheGND and VOM pins are connected on the circuit board as a common reference. The motorpower supply must have sufficient capacity for the motor and if the power supply is notphysically close to the motor/controller, a capacitor (eg. 4700uF) may be required at thecontroller to ensure smooth operation of the motor.Motor ConnectionThe motor connector has 4 connections (A, B, C & D) that are switched to ground in thesequence required to cause the motor to step. Note that stepper motor manufacturers haveseveral methods of labelling the connections to the motor. The Little Step-U labels the pins inthe sequence they are switched when operating the motor with one coil on at a time and drivingin a clockwise direction. ie. A, then B, then C, then D and back to A. The centre taps of thetwo coils are connected to CT-AC and CT-BD, corresponding to the common connection of coilsA & C and coilsB & D respectively. These two connections provide the freewheel diodes foreach of the motor coils and are connected on the circuit board.IMPORTANT: A poor or intermittent connection to any of the stepper motor terminals can resultin destructive voltages being generated and causing permanent damage to the Little Step-U.Similarly, do not connect or disconnect any stepper motor connections while power is applied.The connection point between CT-AC and CT-BD is indicated on the circuit board by thedesignator "LK". This track can be cut and rejoined by soldering a wire between two pads ifneeded. In most cases this isn't required but is provided for applications using and L/xRconfiguration in half step mode.Interface connectionsThe Little Step-U acts on commands received serially from a host controller via the SERIAL INpin. This is an asynchronous interface operating at 2400 bits per second, 8 data bits (LSBfirst), 1 stop bit and no parity. The signal levels are TTL. Some commands illicit a responseand these are sent via the SERIAL OUT pin using the same protocol and signal levels as theSERIAL IN pin.When a command has been sent to the Little Step-U that causes the motor to move, the BUSYpin will be high while the motor is in motion.Two input pins are provided for use with stepper operation in the form of limit or home switchesor can be used as general inputs which can be read by software. These pins accept logic levelinputs and will source 1mA when pulled low, making them suitable for direct connection to theoutput of opto-couplers.TLA Microsystems Ltd 3 /Software commandsCommunication with the Little Step-U is by a TTL level serial interface at 2400bps. Allcommands must begin with a "{" character and end with a "}" Characters outside of the braces(including carriage return and line feeds) are ignored. Responses are enclosed by "[" and "]"characters.A - SET SPEEDSyntax{Axxxxx}Default value100 steps/secSets the maximum speed in steps per second for any commands that follow. Thenumeric value can be any number from 1 to 5000.B - SET RAMP TIMESyntax{Bxxx}Default value0 secondsThe Little Step-U has a built in function to accelerate and decelerate the stepper motorto/from the speed specified by the command above. This command sets the amount oftime in tenths of a second that the motor will accelerate to that speed. Valid numbersare 0 to 200 being 0.0 to 20.0 seconds in 0.1 second increments.Any move function that utilises the ramping facility will accelerate and decelerate at therate defined by this command. The distance moved includes the steps used to ramp upand ramp down so a move of 1000 steps will move exactly that amount. If the number ofsteps requested is less than the number required to ramp to full speed and ramp downagain, the Little Step-U will accelerate at the same rate until it is half way to itsdestination and then ramp down again to stop at the commanded position.See the discussion on ramping after the command descriptions.C - SET STEP MODESyntax{Cx}Default value0 (Full step drive)Stepper motors can be driven by powering the windings sequentially using three differenttechniques. The method used is specified by this command with x being 0, 1 or 2.{C0}Full stepFor every step, two windings are energised.Step Coil A Coil B Coil C Coil D1ON ON Off Off2Off ON ON Off3Off Off ON ON4ON Off Off ON{C1}WaveEach step has only one winding energised.Step Coil A Coil B Coil C Coil D1ON Off Off Off2Off ON Off Off3Off Off ON Off4Off Off Off ON4Little Step-U /{C2}Half stepEach alternate step has one or two windings energised giving the motor twicethe number of steps per revolution.Step Coil A Coil B Coil C Coil D1ON Off Off Off2ON ON Off Off3Off ON Off Off4Off ON ON Off5Off Off ON Off6Off Off ON ON7Off Off Off ON8ON Off Off ONWhen the mode is changed to or from Half step, the position, mark and speed values areadjusted accordingly so that the motor will turn at the same rotational speed and themechanical positions remain unchanged.Example: A 200 step/rev motor is being used. The current position is 3600, speed is setat 200 steps per second and there is a mark at 1200. When the mode is changed fromfull-step to half step, the speed value will be 400 (giving the same number of revolutions ofthe motor per second). The current position register and the mark register will containthe values 7200 and 2400 respectively.D - GO TO ABSOLUTE POSITIONSyntax{Dxxxxxxxx}At anytime after powerup, the Little Step-U keeps track of its current position in steps.This command instructs the Little Step-U to calculate the direction and number of stepsrequired to move to another position and then it performs the move. At the end of themove, the position will be the number specified in this command. The value can be anynumber from -10000000 to +10000000, including 0. The number may be preceded by a"+" or "-" as required, but must not include a comma or decimal point.Example: If the current position is 2500, a command of {D-1000} will cause the motor torun counter-clockwise for 1500 steps, stopping at position 1000.E - GO TO RELATIVE POSITIONSyntax{Exxxxxx}This command is similar to the "D" command in respect to the numeric parameter, butcommands the motor to move to a position relative to its current position. Positivenumbers are clockwise and negative numbers are counter-clockwise.Example: If the current position is 2500, a command of {E1000} will cause the motor torun 1000 steps clockwise to end at position 3500.F - GO TO ABSOLUTE POSITION WITH INPUTS 1 & 2 AS STOPSSyntax{Fxxxxxx}This command is the same as the "D" command except that the two input pins aremonitored. If either of them is pulled low during the move, the motor will be deceleratedto a stop at the rate defined in the RAMP command (B). The position register will reflectthe current position when the motor has stopped. These inputs are level sensitive so if a“F” command is used when one of the inputs is low, the motor will stop immediately.Note: Allowing the motor to continue to running past a stop indicator is done for tworeasons; This method allows the motor to provide maximum braking torque duringdeceleration and the position register integrity is maintained.TLA Microsystems Ltd 5 /Example: If the current position is 2500 and a limit switch attached to I/P2 is at position5000, the command {F8000} will result in the motor stopping at position 5087 (dependingon the SPEED and RAMP settings).G - GO TO RELATIVE POSITION WITH INPUTS 1 & 2 AS STOPSSyntax{Gxxxxxx}This command is the same as the "E" command except that the two input pins aremonitored as in the command above.Example: If the current position is 2500 and a limit switch attached to I/P1 is at the homeposition (0), the command {G-5000} will result in the motor stopping at position -87(depending on the SPEED and RAMP settings).H - GO CLOCKWISE UNTIL INPUT 2Syntax{H}This command is used to find a limit stop connected to I/P2 and has no numericparameter. The motor will accelerate at the rate determined by the RAMP setting, up tothe SPEED setting and not stop (ramp down) until I/P2 is pulled low.Example: The motor is at position 28 and a limit switch is at position 1000. The SPEEDhas been set to a slow value and RAMP set to 0. After an {H} command the position is1000.J - GO COUNTER-CLOCKWISE UNTIL INPUT 1 AND ZERO POSITIONSyntax{J}The J command is similar to the H command above except that the direction is reversedand I/P1 is used to halt the movement. When the movement is stopped, the positionregister is cleared to 0 to mark this position as "Home".Example: The motor is at an unknown position and a {J} command is used at a slowspeed and 0 RAMP rate. At the end of the movement (dictated by I/P1) the positionregister is 0.K - GO CLOCKWISE UNTIL INPUT 2 AND MARK POSITIONSyntax{K}The motor runs continuously in a clockwise direction until stopped by I/P2 being pulledlow. When this occurs, the position is recorded in the MARK register.Example: The motor has been moved to the home position using the {J} command.Issuing a {K} command will run the motor and when it has stopped, the position of theother limit switch has been recorded.M - GO TO THE MARK POSITIONSyntax{M}This command instructs the Little Step-U to move to the absolute position held in the"Mark" register. The contents of this register is set to 0 when the device is powered onand can be set using the "K" or "R" commands. As with the "D" (Go to absoluteposition) command, the controller will determine the direction and will use the Ramp andSpeed settings to move to that position.Example: The Little Step-U is being used in a component placement machine and theposition to pick up the next component is known to always be 123456. After eachplacement, a {M} command will place the pickup head over the next component to beplaced.6Little Step-U /N - GO TO THE HOME POSITIONSyntax{N}Sending an "N" command will cause the Little Step-U to move the motor to the 0, orhome position. The position register defaults to 0 when the device is powered on and canbe set to 0 by the "J" or "Q" commands.Example: A Little Step-U is being used to position a print head in a dot matrix printer. Ateach Carriage Return in the data being printed, an {N} command is issued to return thehead to the left margin, ready for the next line.P - SET OFF STATE POWERSyntax{Px}When the motor is not being moved, the coils can be left energised for maximum holdingtorque or turned off to reduce power consumption and motor heating. This command setsthe state as off {P0} or on {P1} and will remain that way until changed with another "P"command. Power on default is off.Example: A motor is being used in a high vibration environment and retaining position ismore important than power consumption. The {P1} command ensures maximum holdingtorque.Q - SET HOME POSITIONSyntax{Q}This command unconditionally sets the position register to 0. All position information andabsolute moves become relative to this new home position.Example: A drilling sequence needs to be repeated several times over a panel. The totalsize of the program can be reduced by moving the offset amount, resetting the homeposition with the {Q} command and repeating the same sequence.R - SET MARKSyntax{R}This command instructs the Little Step-U to remember the current position. It is used inconjunction with the {M} command which will return the motor to this same positionregardless of any intervening moves.Example: A stepper motor is being used in a piece of hastily constructed test equipmentto rub an abrasive over a surface. The distance is found by trial and error and a mark isset with the {R} command. The experiment can then be run using the {Q} (Go to home)and {R} (Go to mark) commands in a loop.S - SWITCH TO REMOTE MODESyntax{S}The Little Step-U can be operated as simple translator/drive for use in systems withenhanced motion control capability or for the purposes of experimentation. This mode ofoperation is entered by sending the {S} command. Input pin 1 will then act as the STEPinput and Input pin 2 will act as a DIRection input.On each high to low transition (falling edge) of the STEP input, the motor will move onestep in the direction indicated by the DIR input. A high on the DIR input will cause themotor to step clockwise and a low, counter-clockwise. This input must be stable whenSTEP is taken low and for tDIR afterwards. When in REMOTE mode, the mode settingsthat were set with the {C} command (wave, full, half step) remain in force and the position TLA Microsystems Ltd 7 /register is updated with each step. The {S} command will turn the motor windings on,regardless of the value set by the {P} command.Example: During the commissioning phase of a machine, the operator wishes to move toa target position one step at a time using a pushbutton. The {S} command is sent andthe microcontroller is used to debounce each button press and apply a single pulse.When the desired destination is reached, the position is read using the {U} command.T - RETURN FROM REMOTE MODESyntax{T}When the Little Step-U is operating in the REMOTE mode, sending a {T} will return to thestandard operating mode. The position register contents are valid and the motor windingswill be powered on or off according to the value previously set by the {P} command.Example: Once the setup phase described above has been completed, a {T} commandreadies the controller for full speed operation.U - SHOW CURRENT STATUSSyntax{U}Returns[aaaa,bbbb,ccc]The {U} command instructs the Little Step-U to send the current values of the Position,Speed and Ramp registers back to the controller. The data consists of enclosing squarebrackets ("[" and "]") containing the three (decimal) values separated by commas.Example: A stepper is being used to move a print head mechanism. In order todetermine the paper width the user has selected, the motor is moved to one stop andzeroed and then moved slowly to the other stop with RAMP set to 0. When the motorstops (BUSY goes low), the position is retrieved with the {U} command. The controllercan then use this value to scale the print head movement commands and ensure that animage will fit on the page.V - SHOW STATE OF INPUT PINSSyntax{V}Returns[a,b]The {V} command returns the current state of the two input pins in the form of "0" for alow input and "1" for a high.Example: An {G-1000} command is issued which instructs the Little Step-U to move1000 steps counter-clockwise from the current position and to stop if it encounters a lowinput on either IP1 or IP2. Checking that the complete move was made successfully ismade easier by only having to check two single digits with the {V} command, thansubtracting the current position from the earlier position and checking the result.Multi-parameter commandsMovement related commands have the option of including speed, ramp time and/or step modevalues in the form of {X,speed,ramp,mode} where X is the command listed below and speed,ramp and mode are valid values as described for the A, B and C commands above. Eachparameter is separated by a comma and may either be a value or no value (without spaces) ifthat parameter is to remain unchanged. Any setting changed by using a command in this formwill remain at the new value for any subsequent commands unless explicitly changed.D GO TO ABSOLUTE POSITIONE GO TO RELATIVE POSITION8Little Step-U /TLA Microsystems Ltd 9F GO TO ABSOLUTE POSITION WITH INPUTS 1 & 2 AS STOPSG GO TO RELATIVE POSITION WITH INPUTS 1 & 2 AS STOPS H GO CLOCKWISE UNTIL INPUT 2J GO COUNTER-CLOCKWISE UNTIL INPUT 1 AND ZERO POSITION K GO CLOCKWISE UNTIL INPUT 2 AND MARK POSITION M GO TO THE MARK POSITION N GO TO THE HOME POSITIONExamples:{D-2000,200,5}Go to absolute position -2000 with a maximum speed of 200 steps per second, accelerating to that speed over a period of 0.5 seconds and use the currently set drive mode.{N,,,0}Go to the HOME position using the current speed and ramp settings but change the drive mode to full step.Ramping or Trapezoidal speed profile.The ability to accelerate a stepper motor over a period of time, greatly improves the useful range of operations the motor can perform. Not only does this allow the motor to reach higher speeds,but also reduces wear on mechanical components. While acceleration is defined as a change in speed over a period of time (steps/sec/sec), it is easier to think of the motor accelerating to a desired speed over a defined time period, so the B command is used in this manner.The graph below illustrates a typical move where the final speed, ramp time and destination position have been specified. Both the position (in steps) and the speed (in steps per second)show how the motor moves slowly at the beginning, at the maximum rate for the majority of the move and then transitions smoothly into the deceleration phase, before coming to a stop at the desired position. Because of the shape of the curve, the speed plot is known as a trapezoidal speed profile.When the distance to be moved is less than that required to ramp up to full speed and then ramp down again, the acceleration rate is kept the same and half way through the move, the Little Step-U will begin the deceleration. An example is illustrated below. The speed and ramp values are unchanged for two discrete move operations. The first is long (far) enough for the motor to reach the specified operating speed but because Move 2 is shorter, the motor transitions directly from accelerating in speed to the deceleration profile.Final Speed/PositionMove 1Move 2TimeThe ramp function used in the Little Step-U is a piecewise, linear ramp of frequency in 64 steps.The motor is run at each of these speeds for a period that is 1/64 of the ramp time requestedwith the {B} command.If long ramp periods are used with a high final speed, the steps are discernible to the ear but stillachieve the desired effect of not accelerating the motor at excessive rates.When using relatively slow final speed settings with short ramp times, the situation arises wherethe first few steps take longer than the allocated time.For example, a motor accelerating to a final speed of 640 steps/sec will run at 10 steps/sec, 20,30, etc. At 10 steps/sec, each step takes 100ms. If the ramp time setting is 2 (for 200ms),clearly a problem has arisen as the first step has used half of the ramp time for one step.The Little Step-U addresses this situation by dividing the ramp time into 64ths. If the length ofone step at the required speed is less than 1/64 of the ramptime, that step rate is skipped.In the example above, 1/64 of the total ramp time (200ms) is 3.1ms which is the period of onestep at 320 steps/sec, so the first step will be at the 320 steps/sec rate, the next at 330steps/sec, etc. This means that the motor doesn’t actually turn until halfway through theramping period (320 = half of the final speed 640). Rather than have the motor doing nothing forthe duration of this dead period, the delay is bypassed and the motor will appear to startimmediately at 320 steps/sec and take only 100ms to get to the final speed, even though the Bcommand specified 200ms.The net result is that the motor acceleration in steps per second per second is still the sameand this is the important parameter. Having it specified as a time to reach final speed is aneasier concept to grasp and is also a simple figure to calculate from a required accelerationrate.Ramping and forced stopsWhen the motor is forced to a stop from an external input (IP1 or IP2) and a ramp value otherthan zero has been specified, the motor will begin decelerating at that point. Obviously the finalresting position will be different from that when the input occurred. Where the input is used tospecify a position, the register is updated when the input occurs, not when the motor completesthe ramp down.For example, the {J} command runs the motor counter-clockwise until IP1 is pulled low andmarks that position as zero. If the ramp value is 0, the motor will stop there and the positionregister will hold 0. If a ramp period has been specified, the position register will hold a negativevalue, indicating the number of steps used to decelerate to a stop. The {N} command (Go to theHome position) can then be used to move the motor to where the input occurred.10Little Step-U /分销商库存信息: PARALLAX 27938。
单片机应用技术1 单片机硬件基础
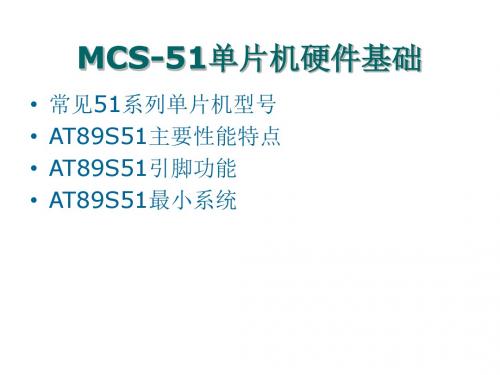
复位电路
AT89S51最小系统之ROM选择
51单片机内部集成有4K字节的 程序存储器(标准型),可以外 接存储器芯片扩展容量。 EA=0时:不使用内部ROM, 外部地址从0开始。 EA=1时:内+外。超过内部 地址后自动使用外部ROM地址, 内外的地址连续。 根据程序编译后的代码长度考 虑选择不同内部ROM容量的单片 机型号。故EA固定为高电平。
AT:(美)ATMEL公司 P:(荷)Philips公司 STC:(大陆)宏晶科技 W:(台)华邦公司
0343:2003年43周制 造
AT89S51封装形式
PLCC44
TQFP44式封装。 PLCC44:特殊引脚芯片塑料封装,贴片封 装的一种,引脚在芯片底部向内弯曲,焊接 采用回流焊工艺,在调试时有插座可用。 TQFP44:薄四方扁平封装,低成本,低高 度引线框封装,适合用SMT表面安装技术。
PDIP40封装
端口的几个操作注意点
1.驱动能力不同,P0每引脚可以驱动8个TTL负载, 其余端口每引脚只能带4个。
2.P0口内部无上拉电阻,其余口有弱上拉,电路设计 时需要注意P0口漏极开路,做IO输出时,需外加上 拉电阻才会有高电平输出。
3.P0在做数据线时才是真正的双向口 P0-P3在做输入接口时,需要先置1再读入(打 开内部锁存器)
AT89S51
PDIP40 封装
AT89S51
PLCC44封装
注:NC表示该脚无用
AT89S51
TQFP44封装
注:NC表示该脚无用
AT89S51引脚功能
P0/P1/P2/P3:
4个并行端口,每口8脚,可做IO接口, 也可做第二功能;
IO功能:
输入输出引脚,用户灵活DIY
27971;中文规格书,Datasheet资料

Web Site: Forums: Sales: sales@Technical: support@Office: (916) 624-8333Fax: (916) 624-8003Sales: (888) 512-1024Tech Support: (888) 997-8267Motor Mount and Wheel Kit (#27971) withPosition Controller (#29319)Featuresy Powerful DC motors for plenty of torque~150 RPM @ 12.0 VDC, 1.50 A, no load~190 RPM @ 14.5 VDC, 1.60 A, no loady Precision machined 6061 aluminumhardwarey Conveniently positioned screw holes makemounting this kit a breeze.y Rugged pneumatic tires are well-suited fora variety of terrainsy+5 volt Supply for Position Controllersy36 encoder positions per revolution;approx 0.5 inch resolution with 6” wheely Compatible with any microcontrollery Single I/O line can control up to 4 PositionControllersy Strong but light: only 3.2 lbs (1.45 kg) perwheel assembly (kit contains two).Application Ideasy Sturdy and stylish midsize robot platformsy Accurate distance trackingy Autonomous exploration and datacollectiony Part of a robust navigation system whenincorporated with GPS and compassmodulesGeneral DescriptionThe Motor Mount and Wheel Kit combinespowerful 12 VDC motors and precision machinedaluminum hardware to provide the power,strength, and beauty demanded by midsizedrobots. All custom parts are CNC machined atParallax headquarters in Rocklin, California from6061 billet aluminum. Conveniently positionedscrew holes on the top, bottom, and front face ofthe bearing blocks provide a variety of quick andeasy mounting options. The included 6 inch (15.3cm) pneumatic rubber tires are durable enough tohandle a variety of smooth or rugged terrainswithout hesitation.The Position Controllers use a quadrature encodersystem to reliably track the position and speed ofeach wheel at all times. With the included plasticencoder disks, each Position Controller has aresolution of 36 positions per rotation; thisequates to approximately 0.5 inches of lineartravel per position using the included 6 inch tires.The Position Controllers calculate and reportposition and average speed data on command.This leaves the main processor free to handlemore important tasks like reading GPScoordinates, processing sensor information, andmaneuvering complex environments.The Position Controllers are compatible with anymicrocontroller via a single-wire half-duplexasynchronous serial communication (UART) bus.Up to four Position Controller devices can becontrolled on the same bus to minimize I/Orequirements.For increased functionality, Position Controllerscan be interfaced with HB-25 motor controllers(#29144; sold separately) to control the positionof the wheel and automatically provide smoothspeed ramping as well as accurate positionadvancement capability.Table of ContentsBill of Materials (2)Assembly Instructions (3)Position Controller Device Information (8)Pin Description (8)Absolute Maximum Ratings (8)DC Electrical Characteristics (8)Theory of Operation (9)Setting the Device ID (10)Interfacing with the HB-25 Motor Controller (11)Command Set Summary (11)Command Set Summary Table (12)Command Set Details (12)QPOS – Query Position (12)QSPD – Query Speed (13)CHFA – Check for Arrival (13)TRVL – Travel Number of Positions (13)CLRP – Clear Position (14)SREV – Set Orientation as Reversed (15)STXD – Set Tx Delay (15)SMAX – Set Speed Maximum (16)SSRR – Set Speed Ramp Rate (16)Communication Protocol (17)Module Schematic (18)Dimensions (18)Example Code (19)Hardware Dimensional Drawings appended.Bill of MaterialsPart # Description Quantity 27958 Motor, 12 VDC Left Hand1 27959 Motor, 12 VDC Right Hand1 29319 Dual Position Controller Assembly–Contains the following: 1550-29319 Position Controller PCB Assy. 2710-00005 #4-40 x 3/16” Flat Head Screw 4721-00005 Plastic Encoder Disk 2805-00002 Servo Extension Cable, 14” 2Bearing Block –6061 Aluminum2 34010 Motor34015 Wheel, main rim section –6061 Aluminum2 34016 Wheel, rim ring section –6061 Aluminum2 34021 Axle – 6061 Aluminum2700-00100 1/8” x 1” Roll Pin2710-00015 #4-40 x 0.5” Flat Head Screw12710-00105 1/4”-20 x 0.625” Button Cap Screw2710-00110 M4 x 50 mm Socket Cap Screw 6713-00012 3/8”-OD, #8-ID x 1” Aluminum Spacer6721-00004 Inner Tube, 6” x 1-1/4” Pneumatic, with valve stem cap2721-00006 Knobby Tire, 6” x 1-1/4” Rubber2724-00001 0.5” ID x 1.125” OD Ball Bearing2Assembly InstructionsThe following directions apply to both right-hand and left-hand assemblies. Tools Required (not included)•Size 1 Philips-tip screwdriver• 3 mm Hex key•5/32” Hex key•Hammer•Wood block•Dish soap•Tire pumpStep 1: Slide encoder disk and bearing on axleSlide the plastic encoder disk for thePosition Controller on the axle withthe tapered sleeve oriented awayfrom the larger axle end. Then slidethe bearing onto the axle.Step 2: Insert bearing into mounting blockCarefully slide the axle and bearingassembly into the bearing pocket ofthe mounting block.Important: Do not force thebearing into the bearing pocket.The pocket is precision machined tofit the bearing exactly. If the bearingdoes not slide in with delicatepressure, slightly adjust the insertionangle and try again. Using excessiveforce can cause the bearing to bind inthe pocket and become very difficultto insert.Step 3: Align axle and assemble mounting block with motorAlign the drive shaft of the motor with thecorresponding square cutout in the axle. Ifnecessary, turn the axle by hand until it mesheswith the motor shaft.Align the mounting block so that the appropriatecounter-bored holes in the block align with thescrew holes in the motor casing. Using a 3 mmhex key, install the three M4 x 50 mm socket capscrews with three 3/8” OD x 1” round spacers tofasten the block to the motor.Step 4: Insert roll pin in axlePosition the end of the axle so the roll pin can be inserted vertically through the side of the shaft. Using a small hammer, tap the roll pin through the hole until the pin is centered in the axle (simultaneously avoid striking fingers with hammer). It is advisable to perform this operation against a scrap wooden block to prevent possible damage to the axle.Step 5: Assemble tire, tube, and wheelInsert the pneumatic tube into the tire. It may help to slightly inflate the tube so it holds its shape in the tire. Mount the tube and tire onto the main wheel section, making sure the valve stem projects through the cutaway in the wheel. Note: it is entirely personal preference whether the valve stem extends toward the inside or outside of the wheel. If there is any resistance when sliding the tire on the rim, apply a small amount of dish soap and water to the inside rim of the tire as lubrication.Mount the inside rim ring section using six #4-40 x ½” flat head screws as shown above. Make sure the rubber tube and tire do not get pinched when tightening down the rim. This can be accomplished by compressing the side wall of each tire while tightening the screws.Step 6: Inflate tire to desired pressureThe recommended tire pressure is 36 PSI; however, ideal tire pressure may vary depending on the intended terrain. For example, in more rugged outdoor environments, a lower tire pressure may improve traction and result in a smoother ride. For solid, flat ground, and for most indoor floor surfaces, a firm tire is preferable and will generally be most efficient. Experimentation is recommended to find the ideal pressure depending on robot weight and intended terrain.Step 7: Mount the wheel on the axle Slide the wheel onto the axle, aligningthe slot in the wheel with the roll pin inthe axle as shown at right.Fasten the wheel to the axle using the1/4"-20 button cap screw and a 5/32”hex key.WARNING!! Do not insert fingersinto the wheel holes. Do not allowhair or clothing to become entangled in the motor mount assembly.Step 8: Mount the Position Controller circuit boardUsing two #4-40 x 3/16” flat head screws,mount the Position Controller circuit boardin the cutout on the top side of themounting block. Check the alignment ofthe plastic encoder disk to make sure itwill not interfere with the optical sensorsas the axle rotates.Adjust the position of the plastic encoderdisk on the axle so it passes through thesensor gap with roughly equal clearanceon each side. If the encoder disk cannotbe adjusted enough to avoid interferencewith the sensor, or if the sensors are notsymmetrically aligned, it is possible toslightly re-align the sensors on the circuitboard. Apply just enough finger pressureto nudge the sensor to the ideal location.Completed Motor Mount and WheelKit Assembly with Position ControllerPosition Controller Device InformationPin DescriptionAbsolute Maximum RatingsNOTICE: These values are the limit before permanent damage may occur, but proper operation of the device is not guaranteed all the way up to these values. See the “Electrical Characteristics” section for recommended operating conditions for the Position Controller.ParameterMin.Max.UnitsOperating Temperature (1) -55 125 °C Storage Temperature (1) -65 150 °CVoltage on Data Pin (with respect to Ground) (1) -0.5 V CC +0.5 VMaximum Operating Voltage (1) -- 6.0 V (1) These values are taken from the Atmel ATtiny2313 device documentation.DC Electrical CharacteristicsAmbient Temperature = -40°C to 85°C ParameterMin. Typ. Max.UnitsOperating Voltage (V CC )4.55.0 5.5(1)V Average Power Supply Current (I CC ) -- 50 -- mA Ground (GND)----V Data Pin Input Low Voltage (1)(2) -0.5 -- 0.3V CC VData Pin Input High Voltage(1)(2)0.6V CC -- V CC + 0.5VSignal Pin Output Low Voltage (1) -- GND 0.7(3) V Signal Pin Output High Voltage (1) 4.2(3)V CC -- VNotes:(1) These values are taken from the Atmel ATtiny2313 device documentation. (2) V CC = 4.5 V to 5.5 V (3) V CC = 5 V; I PIN = 20 mAPin Name FunctionDATA Communication line used to send and receive data – Connect to single-wire UART bus+5VRegulated DC Supply Voltage (V CC )GND Common GroundSIGNALPulse output line to control anoptional HB-25 motor controller ToController +5 VDC SIGNAL GNDTo HB-25N/CTheory of OperationThe Position Controller is designed to manage certain operations associated with wheel motion that traditionally consumed system resources, processing power, and execution time in the main microcontroller. By using the Position Controller to manage these functions instead, the main microcontroller is free to focus on more important tasks.Each Position Controller has an on-board microcontroller which continually tracks the position and average speed of the wheel. In conjunction with the plastic encoder disk, two optical interrupter switches generate a quadrature encoded waveform which is processed by the microcontroller. Based on the rate and specific sequence of the pulses, it is possible for the Position Controller to determine how fast, and in which direction, the wheel is turning.Figure 1Quadrature encoded voltage waveforms for a wheel rotating at 4 positions per second. Notice that rising edges occur first on Sensor 1, signifying that the wheel is rotating in the positive direction.Figure 2Quadrature encoded voltage waveforms for a wheel rotating at 2positions per second. In this case, rising edges are seen on Sensor 2 first, signifying a negative direction of rotation.The current position value appropriately increments or decrements by 1 each time there is a waveform transition. The current average speed value is updated every 20 ms and is an accumulated average over the previous 0.5 seconds. It is important to note that this is an average speed value, not the instantaneous speed of the wheel. See the Command Set Details section on page 12 for more information.The Position Controller automatically generates the appropriate pulses to drive an HB-25 motor controller (#29144; sold separately). See Interfacing with the HB-25 Motor Controller on page 11 for more information. This configuration dramatically increases the Position Controller’s functionality since it gains control over the wheel’s position and speed rather than simply measuring them. The Position Controller stores the desired location as a set point which it continually seeks. If the wheel is rotated away from the current set point, it increases power to the motor in the opposite direction in order to return back to the original position. Additionally, when the wheel is being driven on an incline or decline, the Position Controller automatically increases or decreases power to the motor to maintain the true desired speed.1 second2 seconds0 seconds Sensor 1Sensor 21 second2 secondsSensor 1Sensor 20 secondsThe position advancement scheme is designed to move the wheel a user-set distance (TRVL command) at a user-set maximum speed (SMAX command) with smooth user-set acceleration and deceleration (SSRR command) along the way. Each variable has a default value when powered on, but can be directly modified with specific commands (see the Command Set Details section on page 12 for more information). A typical speed profile for traveling a certain distance is shown in Figure 3 below.Figure 3Typical speed profile fortraveling a certaindistance. The set point is advanced incrementally until it reaches the endpoint.When the wheel advances toward the end point, it is really the set point that is being incrementally advanced. Higher speeds are achieved by advancing the set point by a greater distance each increment than for lower speeds. Since the Position Controller constantly drives the wheel to match its set point, it is able to achieve the true overall user-set speed.The Position Controller accelerates at the user-set speed ramp rate until it reaches the user-set speed. Then it uses the current average speed to calculate the distance required to decelerate smoothly to the final end point without overshoot. When traveling in one direction, if a new position advancement value requires the wheel to reverse direction, it will still decelerate smoothly to a stop at the user-set ramp rate before re-accelerating in the opposite direction toward the new end point.The main microcontroller communicates easily with up to four Position Controllers over a single-wire universal asynchronous serial receiver and transmitter (UART) bus. The UART operates at 19.2 kbits/sec data rate, 8-bit frame, 1 stop bit, no parity. See the Module Schematic section on page 18 for details on how the bus is electrically connected. In most cases, the data line on the Position Controller can be directly connected to the main microcontroller with no additional external components required.Setting the Device IDWhen more than one device is connected on the same bus, it is necessary to give each device a unique device ID. Each device’s ID value is physically set by its corresponding jumper configuration read when powered on (see table below). Notice that the possible values are 1 through 4. Commands can address ID 0 as a special case address to send commands to all devices at once. Devices are shipped with both jumpers installed (ID value 1).devices at once.Start PointEnd Distance (in positions)分销商库存信息: PARALLAX 27971。
IRS27951STRPBF;IRS27951SPBF;IRS27952STRPBF;IRS27952SPBF;中文规格书,Datasheet资料
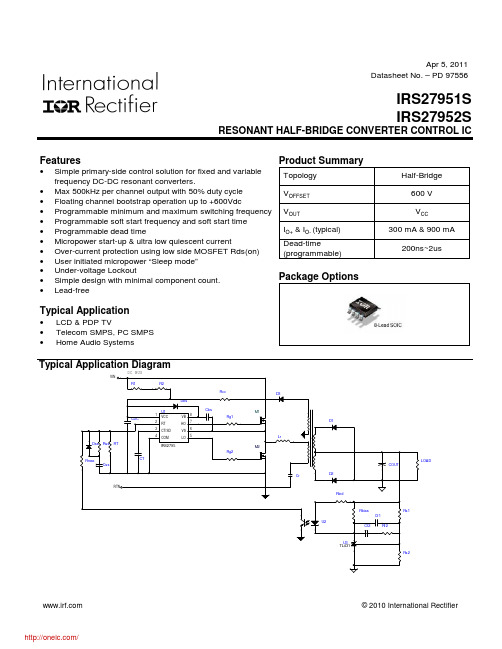
Apr 5, 2011Datasheet No. – PD 97556IRS27951SIRS27952S RESONANT HALF-BRIDGE CONVERTER CONTROL ICFeatures•Simple primary-side control solution for fixed and variable frequency DC-DC resonant converters.•Max 500kHz per channel output with 50% duty cycle •Floating channel bootstrap operation up to +600Vdc •Programmable minimum and maximum switching frequency •Programmable soft start frequency and soft start time •Programmable dead time•Micropower start-up & ultra low quiescent current•Over-current protection using low side MOSFET Rds(on) •User initiated micropower “Sleep mode”•Under-voltage Lockout•Simple design with minimal component count.•Lead-freeTypical Application•LCD & PDP TV•Telecom SMPS, PC SMPS•Home Audio Systems Product SummaryTopologyHalf-BridgeV OFFSET 600 VV OUT V CCI O+ & I O- (typical) 300 mA & 900 mA Dead-time(programmable)200ns~2us Package OptionsTypical Application DiagramDC BUSTable of Contents Page Typical Application Diagram 1 Qualification Information 4 Absolute Maximum Ratings 5 Recommended Operating Conditions 5 Electrical Characteristics 6 Functional Block Diagram 8 Input/Output Pin Equivalent Circuit Diagram 9 Lead Definitions 10 Lead Assignments 10 State Diagram 12 Application Information and Additional Details 13 Package Details 23 Tape and Reel Details 24 Part Marking Information 25 Ordering Information 26DescriptionThe IRS2795(1,2) is a self oscillating half-bridge driver IC for DC-DC resonant converter applications, especially the LLC resonant half-bridge converter. The frequency and dead time can be programmed externally using two external components. The IC offers over current protection using the on state resistance of the low-side MOSFET. The IC can be disabled by externally pulling the voltage at the CT/SD pin below its enable voltage threshold.Qualification Information†Qualification LevelIndustrial††Comments: This family of ICs has passed JEDEC’s Industrial qualification. IR’s Consumer qualification level is granted by extension of the higher Industrial level.Moisture Sensitivity LevelMSL2††† 260°C(per IPC/JEDEC J-STD-020C)ESD Machine ModelClass B(per JEDEC standard EIA/JESD22-A115-A) Human Body ModelClass 2(per EIA/JEDEC standard JESD22-A114-B)IC Latch-Up Test Class I, Level A (per JESD78A)RoHS Compliant Yes†Qualification standards can be found at International Rectifier’s web site /††Higher qualification ratings may be available should the user have such requirements. Please contact your International Rectifier sales representative for further information.†††Higher MSL ratings may be available for the specific package types listed here. Please contact your International Rectifier sales representative for further information.Absolute Maximum RatingsAbsolute maximum ratings indicate sustained limits beyond which damage to the device may occur. All voltage parameters are absolute voltages referenced to COM, all currents are defined positive into any lead. The thermal resistance and power dissipation ratings are measured under board mounted and still air conditions.SymbolDefinitionMin. Max. UnitsV CC Supply Voltage-0.3 25 VV B High-side Floating Supply Voltage-0.3 625 V S High-side Floating Supply Offset Voltage V B – 25 V B + 0.3 V HO High-side Floating Output Voltage V S – 0.3 V B + 0.3 V LO Low-side Output Voltage -0.3 V CC + 0.3 V CT CT/SD Pin Voltage -0.3 V CC + 0.3 V RT RT Pin Voltage-0.3 V CC + 0.3I RT RT pin source current--- 2 mA dV s /dt Allowable offset voltage slew rate -50 50 V/ns T J Operating Junction Temperature -40 150 °C T S Storage Temperature-55 150 R θJA Thermal Resistance, junction to ambient --- 150 °C/W P D Package Power Dissipation @ TA ≤ +25 ºC--- 833mWRecommended Operating ConditionsFor proper operation the device should be used within the recommended conditions.Symbol Definition Min. Max. Units V BS High-side floating supply voltage 10 VccVV S Steady-state high-side floating supply offset voltage -3.0†600 V CC Supply voltage 12 18 fsw Switching Frequency --- 500 kHz † Care should be taken to avoid output switching conditions where the V S node flies inductively below groundby more than 5 V.Recommended Component ValuesSymbol ComponentMin. Max. Units R RT RT pin resistor value 2 100 k Ω C CTCT pin capacitor value 200 2000pFElectrical CharacteristicsVCC=VBS=15V, VS=0V, CVCC=CBS=0.1uF, CLO=CHO=1nF, RT=50.5k Ω, CT=200pF and TA = 25°C unless otherwise specified. The output voltage and current (VO and IO) parameters are referenced to COM and are applicable to the respective HO and LO output leads.Symbol Definition Min Typ Max Units Test Conditions Low Voltage Supply Characteristics V CCUV + V CC turn on threshold 10.1 11 11.9 VN/AV CCUV - V CC turn off threshold (Under Voltage Lock Out)8.1 9 9.9 V CCUVHYS V CC undervoltage lockout hysteresis --- 2 --- I CCSTART V CC startup current--- 50 100 µAV CC = V CCUV+-0.1VI SLEEP Sleep mode V CC supply current --- 150 200 V CT/SD <V EN2, V BS =0V I QCC Quiescent V CC supply current --- 2 2.5 mAV EN1 < V CT/SD < 4.5VI CC46KHz V CC operating current @ f osc = 46KHz --- 3.1 4.5 RT=50.5k Ω I CC285KHzV CC operating current @ f osc = 285KHz---8.711RT=7.32k ΩFloating Supply CharacteristicsV BSUV+V BS turn on threshold 7.6 8.5 9.4 VN/AV BSUV- V BS turn on threshold(Under Voltage Lock Out)7 7.9 8.8 V BSUVHYS V BS undervoltage lockout hysteresis --- 0.6 --- I LKVS VS Offset supply leakage current --- --- 50 µAV B = V S = 600 V I BSSTART V BS startup current--- 50 100 V BS ≤ V BSUV+ - 0.1V I QBS Quiescent V BS supply current --- 50 100 V EN1 < V CT/SD < 4.5VI BS46KHz V BS operating current @ f osc = 46KHz --- 1 1.5 mA RT=50.5k Ω I BS285KHzV BS operating current @ f osc = 285KHz---5.77RT=7.32k Ω Oscillator I/O Characteristicsf SW Oscillator frequency44.346.648.9kHzCT=200pF,RT=50.5k Ω 271285 299 CT=200pF, RT=7.32k Ω V CT+ Upper CT ramp voltage threshold --- 5.0 --- V GBD V CT- Lower CT ramp voltage threshold --- 3.0 --- I CTSTART CT/SD pin startup current --- 10 --- µA V CT/SD < V EN1V RT Voltage reference at RT pin 1.92 2.0 2.08 V CM Current mirror ratio--- 1 --- A/A D Output duty cycle (LO and HO) 48 50 52 % t DTHigh/low output dead time170210250nsCT=200pFElectrical CharacteristicsVCC=VBS=15V, VS=0V, CVCC=CBS=0.1uF, CLO=CHO=1nF, RT=50.5kΩ, CT=200pF and TA = 25°C unless otherwise specified. The output voltage and current (VO and IO) parameters are referenced to COM and are applicable to the respective HO and LO output leads.Symbol Definition Min Typ Max Units Test Conditions Protection CharacteristicsR RTD RT discharge resistance ---115 ---ΩR CTD CT/SD discharge resistance --- 115 ---V EN1CT/SD rising enable voltage 0.75 1.05 1.4VV EN2CT/SD standby voltage 0.60.85 1.1V ENHYST CT/SD enable hysteresis voltage --- 0.2 ---V OCP Overcurrent VS threshold1.9 22.1VIRS27951 2.85 3 3.15 IRS27952t BLANK Leading edge blanking on LO --- 300 ---ns GBDt SD Shutdown propagation delay --- 300 --- GBD Gate Driver Output CharacteristicsV OH Gate High Voltage Vcc-1 --- ---VI GATE = 20mAVOLGate Low Voltage --- 0.05 0.15 I GATE = -20mAt r Output rise time --- 60 ---ns C LOAD=1nFt r Output rise time --- 200 --- C LOAD=4.7nF t f Output fall time --- 16 --- C LOAD=1nF t f Output fall time --- 65 --- C LOAD=4.7nFM DT Output deadtime matching|(DTLO-HO) – (DTHO-LO)|------25 nsI O+Output source current --- 300 ---mA GBD I O-Output sink current --- 900 ---R UP Pull up Resistance --- 20 ---ΩI GATE = 20mAR DOWN Pull down Resistance --- 3 --- IGATE=-20mA †GBD: Guaranteed by design.Functional Block DiagramInput/Output Pin Equivalent Circuit Diagrams:Lead DefinitionsSymbolDescriptionVCC Supply VoltageRT Oscillator timing resistorCT/SD Oscillator timing capacitor / shutdown COM GroundLO Low-side gate driveVSHigh-side gate drive return / HV current Sense HO High-side gate driveVBHigh-side floating supply voltageLead AssignmentsVCC: Power Supply VoltageThis is the supply voltage pin of the IC and sense node for the under-voltage lock out circuit. It is possible to turn off the IC by pulling this pin below the minimum turn off threshold voltage, V CCUV- without damage to the IC. This pin is not internally clamped.RT: Oscillator timing resistorThis pin provides a precise 2V reference and a resistor connected from this pin to COM defines a current that is used to set the minimum oscillator frequency. To close the feedback loop that regulates the converter output voltage by modulating the oscillator frequency, the phototransistor of an optocoupler will be connected to this pin through a resistor. The value of this resistor will set the maximum operating frequency. An R-C series connected from this pin to COM sets frequency shift at start-up to prevent excessive energy inrush (soft-start).CT/SD: Oscillator timing capacitor /ShutdownAn external capacitor CT from this pin to COM sets the dead time and frequency of the oscillator. The CT pin has sawtooth waveform, which is charged up by the current reference programmed at RT pin during rising slope and is discharged by an internal fixed 2mA current source during the falling slope. The falling time of the sawtooth defines the dead-time.At start-up, a 10uA current source charges this capacitor and the oscillator is enabled only when the voltage at this pin exceeds VEN1. The IC can also be used to enter sleep mode by externally pulling this pin below VEN2.COM: Logic and Gate drive GroundThis is ground potential pin of the integrated control circuit. All internal circuits are referenced to this point.分销商库存信息:IRIRS27951STRPBF IRS27951SPBF IRS27952STRPBF IRS27952SPBF。
研华工业显示器SPC-815(M) SPC-821(M) BOR-DE115W BOR-DE121W

版权声明随附本产品发行的文件为研华公司 2020 年版权所有,并保留相关权利。
针对本手册中相关产品的说明,研华公司保留随时变更的权利,恕不另行通知。
未经研华公司书面许可,本手册所有内容不得通过任何途径以任何形式复制、翻印、翻译或者传输。
本手册以提供正确、可靠的信息为出发点。
但是研华公司对于本手册的使用结果,或者因使用本手册而导致其它第三方的权益受损,概不负责。
认可声明Intel® 和 Pentium® 为 Intel Corporation 的商标。
Microsoft Windows 和 MS-DOS 为 Microsoft Corp. 的注册商标。
所有其它产品名或商标均为各自所属方的财产。
http:///本手册适用于以下型号:⏹SPC-821-MSPC-821-MXXXXXXXXXXXXXXXXSPC821MXXXXXXXXXXXXXXXX(“x”为任意数字字母组合,-或空格。
)⏹SPC-815-MSPC-815-MXXXXXXXXXXXXXXXXSPC8156MXXXXXXXXXXXXXXX(“x”为任意数字字母组合,-或空格。
)产品质量保证(两年)从购买之日起,研华为原购买商提供两年的产品质量保证。
但对那些未经授权的维修人员维修过的产品不予提供质量保证。
研华对于不正确的使用、灾难、错误安装产生的问题有免责权利。
如果研华产品出现故障,在质保期内我们提供免费维修或更换服务。
对于出保产品,我们将会酌情收取材料费、人工服务费用。
请联系相关销售人员了解详细情况。
如果您认为您购买的产品出现了故障,请遵循以下步骤:1.收集您所遇到的问题信息(例如,CPU 主频、使用的研华产品及其它软件、硬件等)。
请注意屏幕上出现的任何不正常信息显示。
2.打电话给您的供货商,描述故障问题。
请借助手册、产品和任何有帮助的信息。
3.如果您的产品被诊断发生故障,请从您的供货商那里获得 RMA(ReturnMaterial Authorization) 序列号。
Sharp SJ-PG51P2 SJ-PG55P2 SJ-PG60P2 SJ-FTG18CVP SJ
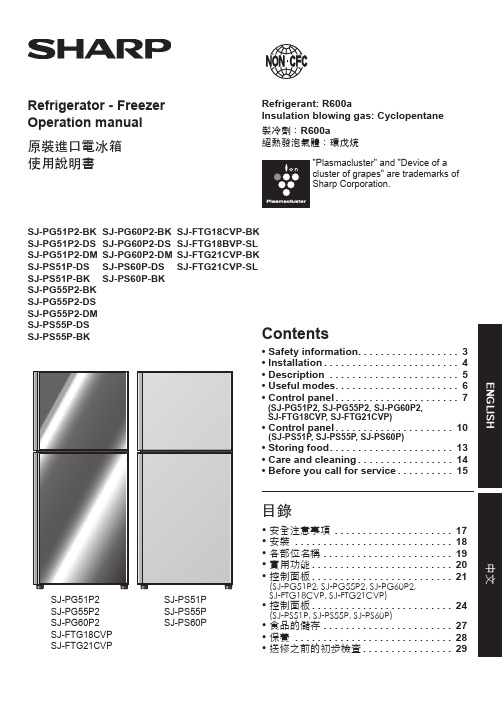
"Plasmacluster" and "Device of a cluster of grapes" are trademarks of Sharp Corporation.SJ-PG51P2SJ-PG55P2SJ-PG60P2SJ-FTG18CVPSJ-FTG21CVP SJ-PS51P SJ-PS55P SJ-PS60P Refrigerator - FreezerOperation manual原裝進口電冰箱使用說明書Contents• Safety information. . . . . . . . . . . . . . . . . . 3• Installation. . . . . . . . . . . . . . . . . . . . . . . . 4• Description . . . . . . . . . . . . . . . . . . . . . . . 5• Useful modes. . . . . . . . . . . . . . . . . . . . . . 6• Control panel. . . . . . . . . . . . . . . . . . . . . . 7 (SJ-PG51P2, SJ-PG55P2, SJ-PG60P2, SJ-FTG18CVP , SJ-FTG21CVP)• Control panel. . . . . . . . . . . . . . . . . . . . . 10(SJ-PS51P , SJ-PS55P , SJ-PS60P)• Storing food . . . . . . . . . . . . . . . . . . . . . . 13• Care and cleaning. . . . . . . . . . . . . . . . . 14• Before you call for service . . . . . . . . . . 15目錄• 安全注意事項 . . . . . . . . . . . . . . . . . . . . . 17• 安裝 . . . . . . . . . . . . . . . . . . . . . . . . . . . . 18• 各部位名稱 . . . . . . . . . . . . . . . . . . . . . . . 19• 實用功能. . . . . . . . . . . . . . . . . . . . . . . . . 20• 控制面板. . . . . . . . . . . . . . . . . . . . . . . . . 21(SJ-PG51P2, SJ-PG55P2, SJ-PG60P2, SJ-FTG18CVP, SJ-FTG21CVP)• 控制面板. . . . . . . . . . . . . . . . . . . . . . . . . 24 (SJ-PS51P, SJ-PS55P, SJ-PS60P)• 食品的儲存 . . . . . . . . . . . . . . . . . . . . . . . 27• 保養 . . . . . . . . . . . . . . . . . . . . . . . . . . . . 28• 送修之前的初步檢查. . . . . . . . . . . . . . . . 29中文ENGLISH SJ-FTG18CVP-BK SJ-FTG18BVP-SL SJ-FTG21CVP-BK SJ-FTG21CVP-SL SJ-PG60P2-BK SJ-PG60P2-DS SJ-PG60P2-DM SJ-PS60P-DS SJ-PS60P-BK SJ-PG51P2-BK SJ-PG51P2-DS SJ-PG51P2-DM SJ-PS51P-DS SJ-PS51P-BK SJ-PG55P2-BK SJ-PG55P2-DS SJ-PG55P2-DM SJ-PS55P-DS SJ-PS55P-BK Refrigerant: R600a Insulation blowing gas: Cyclopentane 製冷劑:R600a 絕熱發泡氣體:環戊烷2Dear Customer尊敬的客戶僅限於家庭用途感謝您購買SHARP 產品。
超长混凝土结构无缝设计及裂缝控制技术
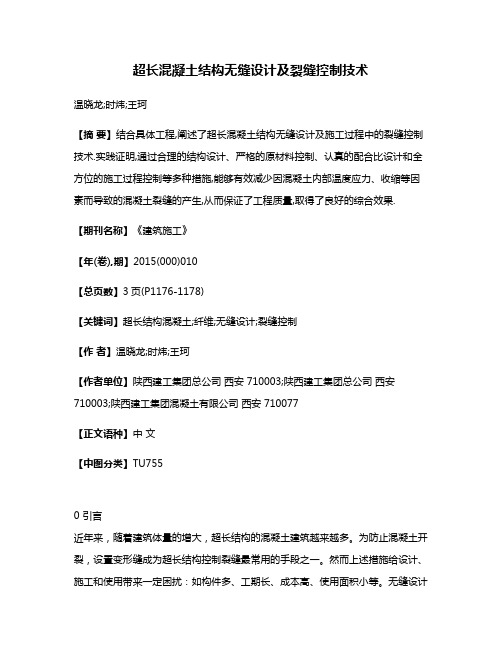
超长混凝土结构无缝设计及裂缝控制技术温晓龙;时炜;王珂【摘要】结合具体工程,阐述了超长混凝土结构无缝设计及施工过程中的裂缝控制技术.实践证明,通过合理的结构设计、严格的原材料控制、认真的配合比设计和全方位的施工过程控制等多种措施,能够有效减少因混凝土内部温度应力、收缩等因素而导致的混凝土裂缝的产生,从而保证了工程质量,取得了良好的综合效果.【期刊名称】《建筑施工》【年(卷),期】2015(000)010【总页数】3页(P1176-1178)【关键词】超长结构混凝土;纤维;无缝设计;裂缝控制【作者】温晓龙;时炜;王珂【作者单位】陕西建工集团总公司西安 710003;陕西建工集团总公司西安710003;陕西建工集团混凝土有限公司西安 710077【正文语种】中文【中图分类】TU7550 引言近年来,随着建筑体量的增大,超长结构的混凝土建筑越来越多。
为防止混凝土开裂,设置变形缝成为超长结构控制裂缝最常用的手段之一。
然而上述措施给设计、施工和使用带来一定困扰:如构件多、工期长、成本高、使用面积小等。
无缝设计及裂缝控制技术成为解决上述问题的有效途径。
1 工程概况西安市某工程为地下2层,地上9层。
建筑面积58 520 m2,采用“天然地基+筏形基础”,框架-剪力墙结构(局部为型钢混凝土组合结构)。
主楼结构总长度156 m,总宽度28.20 m;地下室筏板总长度156.90 m,总宽度56.50 m。
柱间距以8.40 m为主,柱网尺寸为8.40 m×9.60 m~6.00 m×9.00 m不等。
基础筏板厚700 mm(局部500 mm),地下室楼板厚180~200 mm,地下室顶板厚180 mm,地上部分楼板厚120~150 mm,屋面结构板厚150~200 mm,地下室外墙厚400 mm。
混凝土强度等级分别为C45(5层以下墙、柱)、C40(5层及以下梁、板,5~8层墙、柱)和C35(基础梁,筏板,5层以上梁、板,8层以上墙、柱)。
U2790B-MFP中文资料

4, 5
IPU
6 to 3
tsPU
10
1
µA
D
10
µs
D
6.1 Power-on
1
VPUon
4
V
D
6.2 Power-up
1
VPUdown
1
V
D
*) Type means: A = 100% tested, B = 100% correlation tested, C = Characterized on samples, D = Design parameter
Saving
Electrostatic sensitive device. Observe precautions for handling.
1000-MHz Quadrature Modulator
U2790B
1. Description
The U2790B is a 1000-MHz quadrature modulator using Atmel®’s advanced UHF process. It features a frequency range from 100 MHz up to 1000 MHz, low current consumption, and single-ended RF and LO ports. Adjustment-free application makes the direct converter suitable for all digital radio systems up to 1000 MHz, e.g., GSM, ADC, JDC.
Benefits
• No External Components Required for Phase Shifting • Adjustment Free, Hence Saves Manufacturing Time • Only Three External Components Necessary, this Results in Cost and Board Space
ASUS PG279Q系列LCD监视器用户指南第二版九月2015年版权所有说明书
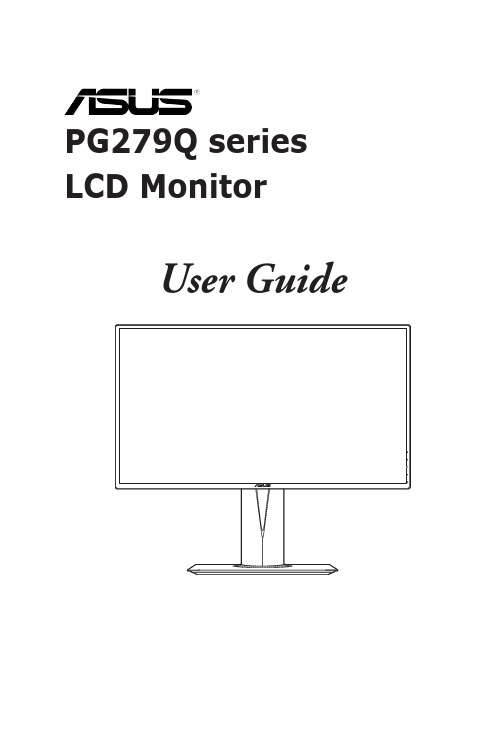
PG279Q series LCD MonitorUser GuideFirst EditionSeptember 2015Copyright © 2015 ASUSTeK COMPUTER INC. All Rights Reserved.No part of this manual, including the products and software described in it, may be reproduced,transmitted, transcribed, stored in a retrieval system, or translated into any language in any form or by any means, except documentation kept by the purchaser for backup purposes, without the express writtenpermission of ASUSTeK COMPUTER INC. (“ASUS”).Product warranty or service will not be extended if: (1) the product is repaired, modified or altered, unless such repair, modification of alteration is authorized in writing byASUS; or (2) the serial number of theproduct is defaced or missing.ASUS PROVIDES THIS MANUAL “AS IS” WITHOUT WARRANTY OF ANY KIND, EITHER EXPRESS OR IMPLIED, INCLUDING BUT NOT LIMITED TO THE IMPLIED WARRANTIES OR CONDITIONS OF MERCHANTABILITY OR FITNESS FOR A PARTICULAR PURPOSE. IN NO EVENT SHALL ASUS, ITS DIRECTORS, OFFICERS, EMPLOYEES OR AGENTS BE LIABLE FOR ANY INDIRECT, SPECIAL,INCIDENTAL, OR CONSEQUENTIAL DAMAGES (INCLUDING DAMAGES FOR LOSS OF PROFITS, LOSS OF BUSINESS, LOSS OF USE OR DATA, INTERRUPTION OF BUSINESS AND THE LIKE),EVEN IF ASUS HAS BEEN ADVISED OF THE POSSIBILITY OF SUCH DAMAGES ARISING FROMANY DEFECT OR ERROR IN THIS MANUAL OR PRODUCT.SPECIFICATIONS AND INFORMATION CONTAINED IN THIS MANUAL ARE FURNISHED FORINFORMATIONAL USE ONLY, AND ARE SUBJECT TO CHANGE AT ANY TIME WITHOUT NOTICE, AND SHOULD NOT BE CONSTRUED AS A COMMITMENT BY ASUS. ASUS ASSUMES NORESPONSIBILITY OR LIABILITY FOR ANY ERRORS OR INACCURACIES THAT MAY APPEAR INTHIS MANUAL, INCLUDING THE PRODUCTS AND SOFTWARE DESCRIBED IN IT.Products and corporate names appearing in this manual may or may not be registered trademarks orcopyrights of their respective companies, and are used only for identification or explanation nd to theowners’ benefit, without intent to infringe.iiContents Notices (iv)rmation (v)Care.&.Cleaning (vi)Takeback.Services (vii)Chapter.1:.....Product.introduction1.1.Welcome!.......................................................................................1-11.2.Package.contents..........................................................................1-11.3.1 Front view .......................................................................1-21.3.2 Back view ........................................................................1-31.3.3 GamePlus Function ........................................................1-41.3.4 TURBO Function (only for DisplayPort input) .................1-5 Chapter.2:.....Setup2.1.Adjusting.the.monitor...................................................................2-12.2.Detaching.the.arm.(for.VESA.wall.mount)..................................2-22.3.Connecting.the.cables..................................................................2-22.4.Turning.on.the.monitor.................................................................2-3 Chapter.3:.....General.instructions3.1.OSD.(On-Screen.Display).menu..................................................3-13.1.1 How to reconfigure ..........................................................3-13.1.2 OSD function introduction ...............................................3-13.2.Specifications.summary...............................................................3-63.3.Supported.operating.mode..........................................................3-8iiiNoticesmission.StatementThis device complies with Part 15 of the FCC Rules. Operation is subject to the following two conditions:• This device may not cause harmful interference, and• This device must accept any interference received including interference that may cause undesired operation.This equipment has been tested and found to comply with the limits for aClass B digital device, pursuant to Part 15 of the FCC Rules. These limits are designed to provide reasonable protection against harmful interference in a residential installation. This equipment generates, uses and can radiate radio frequency energy and, if not installed and used in accordance with manufacturer’s instructions, may cause harmful interference to radio communications. However, there is no guarantee that interference will not occur in a particular installation. If this equipment does cause harmful interference to radio or television reception, which can be determined by turning the equipment off and on, the user is encouraged to try to correct the interference by one or more of the following measures:• Reorient or relocate the receiving antenna.• Increase the separation between the equipment and receiver.• Connect the equipment to an outlet on a circuit different from that to which the receiver is connected.• Consult the dealer or an experienced radio/TV technician for help.The use of shielded cables for connection of the monitor to the graphics card isrequired to assure compliance with FCC regulations. Changes or modificationsto this unit not expressly approved by the party responsible for compliancecould void the user’s authority to operate this equipment.As an Energy Star® Partner, our company has determined that thisproduct meets the Energy Star® guidelines for energy efficiency.munications.StatementThis digital apparatus does not exceed the Class B limits for radio noise emissions from digital apparatus set out in the Radio Interference Regulations of theCanadian Department of Communications.This class B digital apparatus complies with Canadian ICES-003.This Class B digital apparatus meets all requirements of the Canadian Interference - Causing Equipment Regulations.Cet appareil numérique de la classe B respecte toutes les exigences du Réglementsur le matériel brouiller du Canada.ivvSafety information•Before setting up the monitor, carefully read all the documentation that came with the package. •To prevent fire or shock hazard, never expose the monitor to rain or moisture. •Never try to open the monitor cabinet. The dangerous high voltages inside the monitor may result in serious physical injury. •If the power supply is broken, do not try to fix it by yourself. Contact a qualified service technician or your retailer. • Before using the product, make sure all cables are correctly connected and the power cables are not damaged. If you detect any damage, contact your dealer immediately.• Slots and openings on the back or top of the cabinet are provided for ventilation. Do not block these slots. Never place this product near or over a radiator or heat source unless proper ventilation is provided.• The monitor should be operated only from the type of power source indicated on the label. If you are not sure of the type of power supply to your home, consult your dealer or local power company.• Use the appropriate power plug which complies with your local power standard. • Do not overload power strips and extention cords. Overloading can result in fire or electric shock.• Avoid dust, humidity, and temperature extremes. Do not place the monitor in any area where it may become wet. Place the monitor on a stable surface. • Unplug the unit during a lightning storm or if it will not be used for a long period of time. This will protect the monitor from damage due to power surges.• Never push objects or spill liquid of any kind into the slots on the monitor cabinet.• To ensure satisfactory operation, use the monitor only with UL listed computers which have appropriate configured receptacles marked between 100-240V AC.• If you encounter technical problems with the monitor, contact a qualified service technician or your retailer.•The adapter is only used for this monitor, do not use it for other purpose. Your device uses one of the following power supplies: - Manufacturer: Delta Electronics Inc., Model: ADP-90YD B / ADP-120RH BThis symbol of the crossed out wheeled bin indicates that the product (electrical, electronic equipment, and mercury-containing button cell battery) should not be placed in municipal waste. Please check local regulations for disposal ofelectronic products.AEEE.yönetmeliğine.uygundurviCare & Cleaning• Before you lift or reposition your monitor, it is better to disconnect the cables and power cord. Follow the correct lifting techniques when positioning the monitor. When lifting or carrying the monitor, grasp the edges of the monitor. Do not lift the display by the stand or the cord.• Cleaning. Turn your monitor off and unplug the power cord. Clean the monitor surface with a lint-free, non-abrasive cloth. Stubborn stains may be removed with a cloth dampened with mild cleaner.•Avoid using a cleaner containing alcohol or acetone. Use a cleaner intended for use with the monitor. Never spray cleaner directly on the screen, as it may drip inside the monitor and cause an electric shock. The.following.symptoms.are.normal.with.the.monitor:• The screen may flicker during the initial use due to the nature of the fluorescent light. Turn off the Power Switch and turn it on again to make sure that the flicker disappears.• You may find slightly uneven brightness on the screen depending on the desktop pattern you use.• When the same image is displayed for hours, an afterimage of the previous screen may remain after switching the image. The screen will recover slowly or you can turn off the Power Switch for hours.•When the screen becomes black or flashes, or cannot work anymore, contact your dealer or service center to fix it. Do not repair the screen by yourself!ed.in.this.guideWARNING: Information to prevent injury to yourself when trying tocomplete a task.CAUTION: Information to prevent damage to the components when tryingto complete a task.IMPORTANT: Information that you MUST follow to complete a task.NOTE: Tips and additional information to aid in completing a task.rmationRefer to the following sources for additional information and for product and software updates.1..ASUS.websitesThe ASUS websites worldwide provide updated information on ASUShardware and software products. Refer to 2..Optional.documentationYour product package may include optional documentation that may havebeen added by your dealer. These documents are not part of the standardpackage.Takeback ServicesASUS recycling and takeback programs come from our commitment to the highest standards for protecting our environment. We believe in providing solutions forour customers to be able to responsibly recycle our products, batteries and other components as well as the packaging materials.Please go to /english/Takeback.htm for detail recycling information in different region.viiviii1.1 Welcome!Thank you for purchasing the ASUS® LCD monitor!The latest widescreen LCD monitor from ASUS provides a broader, brighter and crystal-clear display, plus a host of features that enhance your viewing experience. With these features, you can enjoy the convenience and delightful visual experience that the monitor brings to you!1.2 Package contentsCheck your package for the following items:LCD monitorDriver and Manual discQuick start guideWarranty cardPower adapterPower cordDP cableHDMI cableUSB cableIf any of the above items is damaged or missing, contact your retailerimmediately.Select “ON” when you see the message “LIGHT IN MOTION ON/OFF” appearsif you want to turn on the red light on the base. Select “OFF” if you want it toturn off. If you disable this function but later wish to reactivate it, please usethe OSD menu to turn it on. The monitor is Energy Star 6.0 compatible when“LIGHT IN MOTION” is “OFF”.If no signal is detected for 120 seconds, the monitor automatically enters savingmode.It is recommended that you set the DisplayPort Deep Sleep and HDMI DeepSleep functions to “OFF”.1-1 ASUS PG279Q Series LCD Monitor1-2Chapter 1: Product introduction 1.3 Monitor introduction1.3.1.Front.view1.2. • Exits the OSD menu item.• Turns on the OSD menu when the monitor enters standby mode or displays the “NO SIGNAL“ message.3. button:• GamePlus hotkey. Move the press • Turns on the OSD menu when the monitor enters standby mode or displays the “NO SIGNAL“ message.4. button• TURBO hotkey. Press the button to select among different refresh rates. (Only for DisplayPort input)• Turns on the OSD menu when the monitor enters standby mode or displays the “NO SIGNAL“ message.5.• Turns the monitor on/off.The color definition of the power indicator is as the below table.•1.3.2.Back.viewRear.connectors1..DC-IN.port. This port connects the power cord.2..Earphone.jack. This port is only available when an HDMI/DisplayPort cableis connected.3..DisplayPort. This port is for connection for a DisplayPort compatible device.4..HDMI.port. This port is for connection with an HDMI compatible device.B.3.0.upstream.port. This port is for connection with a USB upstreamcable. The connection enables the USB ports on the monitor.B.3.0.downstream.ports. These ports are for connection with USBdevices, such as USB keyboard/mouse, USB flash drive, etc.7. For service personnel only.8..Kensington.lock.slot.9..Control.buttons.ASUS PG279Q Series LCD Monitor1-31.3.3.GamePlus.FunctionThe GamePlus function provides a toolkit and creates a better gaming environment for users when playing different types of games. In addition, Crosshair function is specially designed for new gamers or beginners interested in First Person Shooter (FPS) games.To active GamePlus:1. Press the GamePlus hotkey.2. Move the3. Press the) button or move thefunction you choose, and move thethrough the settings. Move the4. Highlight the desired setting and press thePress the button to inactivate it.1-4Chapter 1: Product introduction1.3.4.TURBO.Function.(only.for.DisplayPort.input)The TURBO function helps you select among different refresh rates in a convenient way.To active TURBO:Press the TURBO hotkey repeatedly to select.ASUS PG279Q Series LCD Monitor1-51-6Chapter 1: Product introduction2-1ASUS PG279Q Series LCD Monitor 2.1Adjusting the monitor• For optimal viewing, we recommend that you look at the full face of the monitor, then adjust the monitor to the angle that is most comfortable for you.• Hold the stand to prevent the monitor from falling when you change its angle.•The recommended adjusting angle is +20˚ to -5˚ (for tilt)/+60˚ to -60˚ (for swiveling/ +120 mm (for height adjustment)/90˚ (for portrait view).-5° ~ +20°It is normal that the monitor slightly shakes while you adjust the viewing angle.Pivoting.the.monitor 1. Lift the monitor to the highest position.2 Tilt the monitor to its maximum angle.3.Pivot the monitor clockwise to the angle you need.-5° ~ +20°It is normal that the monitor slightly shakes while you adjust the viewing angle.Figure 1Figure 2Figure 32-2Chapter 2: Setup2.2Detaching the arm (for VESA wall mount)The detachable arm of this monitor is specially designed for VESA wall mount. To detach the arm:1. Have the front of the monitor face down on a table.2.Loosen the four screws on the back of the monitor and remove the arm/base.We recommend that you cover the table surface with soft cloth to preventdamage to the monitor.2.3 Connecting the cablesConnect the cables as the following instructions:•.To.connect.the.power.cord :a. Connect the power adapter securely to the monitor’s DC input.b. Connect one end of the power cord to the power adapter and the otherend to a power outlet.•.To.connect.the.DisplayPort/HDMI.cable:a. Plug one end of the DisplayPort cable to the monitor’s DisplayPort/HDMIport.b. Connect the other end of the DisplayPort/HDMI cable to your computer'sDisplayPort port.•e.the.earphone: connect the end with plug type to the monitor’s earphone jack when an HDMI or DisplayPort signal is fed.•B.3.0.ports: Take the supplied USB 3.0 cable, and plug the smaller end (type B) of the USB upstream cable to the monitor’s USBupstream port, and the larger end (type A) to your computer’s USB 3.0 port.Make sure your computer is installed with the lastest Windows 7/Windows 8operating system. That will enable the USB ports on the monitor to work.2.4 Turning on the monitorASUS PG279Q Series LCD Monitor2-32-4Chapter 2: Setup3-1ASUS PG279Q Series LCD Monitor 3.1OSD (On-Screen Display) menu3.1.1.How.to.reconfigure1. Press the2.Move the ) button up/down to navigate through the functions. Highlight the desired function and press the (the function selected has a sub-menu, move the again to navigate through the sub-menu functions. Highlight the desired sub-menu function and press the right to activate it. 3. Move the function.4.To exit and save the OSD menu, press the button or move the ) left repeatedly until the OSD menu disappears. To adjust other functions, repeat steps 1-3.3.1.2.OSD.function.introduction1..Over.ClockingThis function allows you to adjust the refresh rate.• Select “ON” if you want to enable this function.3-2Chapter 3: General Instructions•.Max.Refresh.Rate : After activating this function, you can select one refresh rate to be displayed along with 60 Hz and 120 Hz when pressing the TURBO hotkey (Only for DisplayPort input).After reboot, test the new Max Refresh Rate by enabling it in the NVIDIAControl Panel. If you don’t see an image, disconnect the DP cable and use themonitor OSD to try again with a safer Max Refresh Rate.2..GameVisualThis function contains 6 sub-functions you can select for your preference. Each mode has the Reset selection, allowing you to maintain your setting or return to the preset mode.•.Scenery.Mode : This is the best choice for scenery photo displaying with GameVisual TM Video intelligence Technology.•.Racing.Mode : This is the best choice for racing game playing with GameVisual TM Video intelligence Technology.•.Cinema.Mode : This is the best choice for movie watching with GameVisual TM Video intelligence Technology.•.RTS/RPG.Mode : This is the best choice for Real-Time Strategy (RTS)/Role-Playing Game (RPG) playing with GameVisual TM Video intelligence Technology.•.FPS.Mode : This is the best choice for First Person Shooter game playing with GameVisual TM Video intelligence Technology.•.sRGB.Mode : This is the best choice for viewing photos and graphics from PCs.• In the Racing mode, the following function(s) are not user-configurable: Saturation.• In the sRGB mode, the following function(s) are not user-configurable: Saturation, Color Temp., Brightness, Contrast.3..Blue.Light.FilterIn this function, you can adjust the blue light filter level.•.Level.0:.No change.•.Level.1~4: The higher the level, the less blue light is scattered.When Blue Light Filter is activated,the default settings of Racing Modewill be automatically imported. Between Level 1 to Level 3, the Brightnessfunction is user-configurable. Level 4 is optimized setting. It is compliancewith TUV Low Blue Light Certification. The Brightness function is not user-configurable.4..ColorYou can adjust Brightness, Contrast, Saturation and Color temperature from this menu.•.Brightness: the adjusting range is from 0 to 100.•.Contrast: the adjusting range is from 0 to 100.•.Saturation: The adjusting range is from 0 to 100.•.Color.Temp.: contains 4 modes including Cool, Normal, Warm, and User Mode.5..Image.You can adjust OD and ULMB from this menu.•.OD: Improves the gray level response time of the LCD panel.•.ULMB.(Ultra Low Motion Blur) (only for DisplayPort input): Adjusts the level of motion blur reduction. This function is available when the refreshrate is 85Hz, 100Hz or 120Hz.6..Input.Select.In this function, you can select your desired input source.7..System.Setup.Allows you to adjust the system.•.Language: There are 21 languages for your selection, including English, French, German, Italian, Spanish, Dutch, Portuguese, Russian, Czech,Croatian, Polish, Romanian, Hungarian, Turkish, Simplified Chinese,Traditional Chinese, Japanese, Korean, Thai, Indonesia, Persian.•.OSD.Position: Adjusts the horizontal position (H-Position)/the vertical position (V-Position) of the OSD.•.Transparency: Adjusts the OSD background from opaque to transparent.•.OSD.Timeout: Adjusts the OSD timeout from 10 to 120 seconds.•.Keylock: To disable all function keys. Press over 5 seconds to cancel the key lock function.•.Information: Shows the monitor information.•.LIGHT.IN.MOTION: Select“ON” if you want to turn on the red light on the base.•.Sound:*.Volume: the adjusting range is from 0 to 100.*.Mute: toggles the monitor sound between on and off.•.All.Reset: “Yes” allows you to restore the default settings.•.DisplayPort.Deep.Sleep: puts the DisplayPort port into deep sleep.•.HDMI.Deep.Sleep: puts the HDMI port into deep sleep.In order to be Energy Star compliant, the default setting for DisplayPort DeepSleep and HDMI Deep Sleep is “On”.If the monitor cannot wake up after going into deep sleep, do one of thefollowings:3.2 Specifications summary*Specifications are subject to change without notice.3.3 Troubleshooting (FAQ)3.4 Supported operating modeHDMI inputNote:Do not support interlace.DisplayPort inputNote:Do not support interlace.G-SYNC (only for DisplayPort input) supported NVIDIA GPUs: GeForce GTX TITAN X, GeForce GTX 980 Ti, GeForce GTX 980, GeForce GTX 970, GeForce GTX 960, GeForce GTX TITAN Z, GeForce GTX TITAN Black, GeForce GTX TITAN, GeForce GTX 780 Ti, GeForce GTX 780, GeForce GTX 770, GeForce GTX 760, GeForce GTX 750 Ti, GeForce GTX 750, GeForce GTX 745 (OEM), GeForce GTX 690, GeForce GTX 680, GeForce GTX 670, GeForce GTX 660 Ti, GeForce GTX 660, GeForce GTX 650 Ti BOOST. For other GPUs, please contact the manufactures to see if they are compatible.DisplayPort.input--Over.clockingNote:.Do.not.support.interlace.Over.Clocking.supported.GPUs:.NVIDIA.Maxwell.GPU.Graphics.Card.like.GTX745,.GTX750,.GTX750. Ti,.GTX.960,.GTX970,.GTX980,.GTX980.Ti.and.GTX.Titan.X..For.other.GPUs,.please.contact.the. patible.The.monitor.is.purposely.supporting.the.NVIDIA.G-SYNC.technology.and.targeting.NVIDIA.graphics. solutions..Please.note.that.Over.Clocking.function/performance.depends.on.the.GPUs.or.contents.displayed.. ASUS.only.provides.this.function..The.performance.or.any.side.effect.after.activation.is.not. guaranteed...。
LG 液晶显示器型号说明.pdf_1702033596.4889665说明书
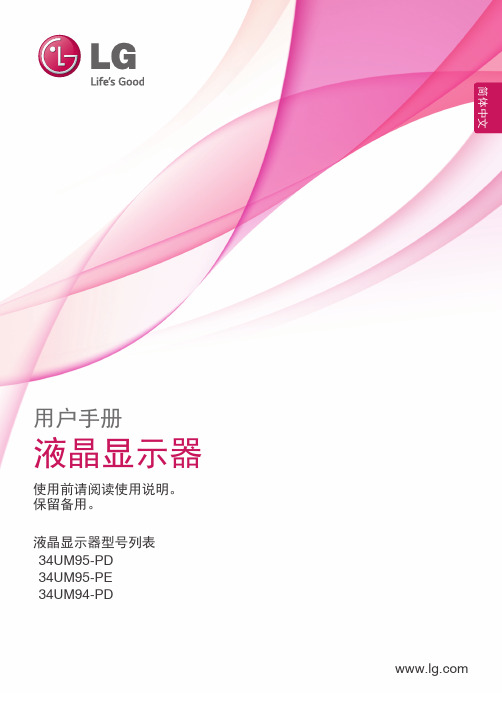
简体中文用户手册液晶显示器使用前请阅读使用说明。
保留备用。
液晶显示器型号列表34UM95-PD34UM95-PE34UM94-PD2目录3 重要预防措施3 安全警告3 - 请勿打开显示器:3 - 为避免人身伤害:3 - 为避免火灾或危险:4 关于安装5 关于清洁5 关于重新包装5 关于处置6 许可证7 组装和准备工作7 产品组件8 产品和按钮描述20 - HDMI 连接20 连接外部设备20 - USB电缆连接- PC21 - 耳机端口连接22 安装软件25 用户设置25 激活主菜单25 - 主菜单26 用户设置26 - 菜单设置27 - -比率28 - -功能29 - -PBP30 - -画面31 - -色彩32 - -设置33 - -初始化34 - -阅读3重要预防措施重要预防措施设计和制造本设备旨在确保您的个人安全,但使用不当可能造成潜在的触电或火灾危险。
为了使本显示器中包含的所有防护措施都能正确运行,请遵守以下有关其安装、使用和维修的基本规则。
安全警告仅使用随本设备提供的电源线。
如果您使用其他电源线,且如果不是由供应商提供,请确保其经过适用国家标准的认证。
如果电源线在任何情况下发生故障,请联系制造商或最近的授权维修服务提供商,以进行更换。
产品耦合器用作断开连接设备。
请确保设备安装在其连接的墙上插座附近并可轻松使用墙上插座。
只能根据本手册规格中指明的或显示器上列出的电源运行显示器。
如果不确定您家里的电源类型,请咨询您的经销商。
交流电源插座过载和延长线都会产生危险。
电源线磨损和插头破损也是如此。
它们可能会造成触电或火灾危险。
请联系维修技术人员进行更换。
只要此设备连接到交流电墙上插座,则即使设备关闭,与交流电源的连接也不会断开。
请勿打开显示器:� 设备内无用户可维修的组件。
� 即使电源关闭时,设备内也有非常危险的高压。
� 如果显示器无法正常运行,请联系您的经销商。
为避免人身伤害:� 不要将显示器放置在倾斜的支架上,除非已正确固定。
Philips 279P1 4K UHD USB-C 笔记本屏幕说明书
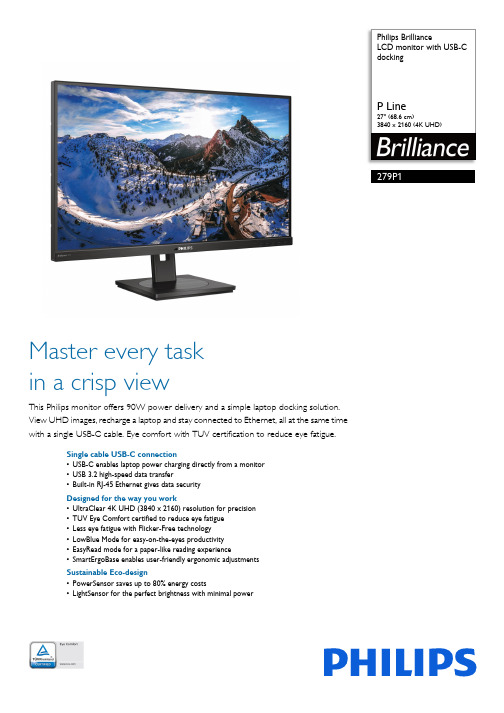
Philips BrillianceLCD monitor with USB-C dockingP Line27" (68.6 cm)3840 x 2160 (4K UHD)279P1Master every task in a crisp viewThis Philips monitor offers 90W power delivery and a simple laptop docking solution. View UHD images, recharge a laptop and stay connected to Ethernet, all at the same time with a single USB-C cable. Eye comfort with TUV certification to reduce eye fatigue.Single cable USB-C connection•USB-C enables laptop power charging directly from a monitor •USB 3.2 high-speed data transfer•Built-in RJ-45 Ethernet gives data securityDesigned for the way you work•UltraClear 4K UHD (3840 x 2160) resolution for precision •TUV Eye Comfort certified to reduce eye fatigue •Less eye fatigue with Flicker-Free technology •LowBlue Mode for easy-on-the-eyes productivity •EasyRead mode for a paper-like reading experience•SmartErgoBase enables user-friendly ergonomic adjustments Sustainable Eco-design•PowerSensor saves up to 80% energy costs•LightSensor for the perfect brightness with minimal powerHighlightsUSB Type-C connectionThis Philips display features a built-in USB type-C docking station with power delivery. With intelligent and flexible power management, you can power charge your compatible* laptop directly. Its slim, reversible USB-C connector allows for easy, one-cable docking. Simplify by connecting all your peripherals like keyboard, mouse and your RJ-45 Ethernet cable to the monitor's docking station. You can watch high-resolution video and transfer data at super-speed, while powering up and re-charging your notebook at the same time.UltraClear 4K UHD ResolutionThese Philips displays utilise high-performance panels to deliver UltraClear, 4K UHD (3840 x 2160) resolution images. Whether you are a demanding professional requiring extremely detailed images for CAD solutions, a user of 3D graphics applications or a financial wizard working on huge spreadsheets, Philips displays will make your images and graphics come alive.TUV Rheinland Eye Comfort Philips displays meet TUV Rheinland EyeComfort standard to prevent eye strain caused by prolonged computer use. With TUV Eye Comfort certification, Philips displays ensure flicker-free, low-blue mode, no disturbing reflections, a wide viewing angle, less reduction of image quality from different angles and ergonomic stand designs for an ideal viewing experience. Keep your eyes healthy and boost work productivity.Flicker-Free technologyDue to the way brightness is controlled on LED-backlit screens, some users experience flicker on their screen which causes eyefatigue. Philips Flicker-Free technology applies a new solution to regulate brightness and reduce flicker for more comfortable viewing.LowBlue ModeStudies have shown that just as ultra-violet rays can cause eye damage, shortwave-length blue light rays from LED displays can cause eye damage and affect vision over time. Developed for wellbeing, the Philips LowBlue Mode setting uses a smart software technology to reduce harmful shortwave blue light.EasyRead modeEasyRead mode for a paper-like reading experienceSmartErgoBaseThe SmartErgoBase is a monitor base that delivers ergonomic display comfort and provides cable management. The base can swivel, tilt and rotate to various angles to ensure maximum comfort. The height-adjustable stand guarantees the optimalviewing level, reducing the physical strains of a long workday, while cable managementreduces cable clutter and keeps the workspaceneat and professional.Issue date 2023-03-22 Version: 8.0.312 NC: 8670 001 65131 EAN: 87 12581 76438 8© 2023 Koninklijke Philips N.V.All Rights reserved.Specifications are subject to change without notice. Trademarks are the property of Koninklijke Philips N.V. or their respective owners.SpecificationsPicture/Display•LCD panel type: IPS technology•Backlight type: W-LED system•Panel Size: 27 inch/68.6 cm•Display Screen Coating: Anti-Glare, 3H, Haze 25%•Effective viewing area: 596.736 (H) x 335.664 (V)•Aspect ratio: 16:9•Maximum resolution: 3840 x 2160 @ 60 Hz*•Pixel Density: 163 PPI•Response time (typical): 4 ms (Grey to Grey)*•Brightness: 350 cd/m²•Contrast ratio (typical): 1000:1•SmartContrast: 50,000,000:1•Pixel pitch: 0.1554 x 0.1554 mm•Viewing angle: 178º (H) / 178º (V), @ C/R > 10•Flicker-free•Picture enhancement: SmartImage•Display colours: Colour support 1.07 billion colours•Colour gamut (typical): NTSC 93%*, sRGB 112%*•Scanning Frequency: 30–140 kHz (H) / 23–60 Hz (V)•SmartUniformity: 97 ~ 102%•Delta E: < 2 (sRGB)•sRGB•LowBlue Mode•EasyReadConnectivity•Signal Input: DisplayPort 1.4 x 1, HDMI 2.0 x 2, USB-C 3.2 Gen 2 x 1 (upstream, power delivery up to 90 W)•HDCP: HDCP 2.2 (HDMI/DP/USB-C)•HBR3•USB:: USB-C x 1 (upstream), USB 3.2 x 4 (downstream with 1 fast charge B.C 1.2)•Audio (In/Out): Audio out•RJ45: Ethernet LAN (10 M/100 M/1 G)*, Wake on LAN•Sync Input: Separate SyncUSB•USB-C: Reversible plug connector•Super speed: Data and Video transfer•DP: Built-in Display Port Alt mode•Power delivery: USB PD version 3.0•USB-C max. power delivery: Up to 90 W (5 V/3 A;7 V/3 A; 9 V/3 A; 10 V/3 A; 12 V/3 A; 15 V/3 A;20 V/4.5 A)Convenience•Built-in Speakers: 3 W x 2•User convenience: SmartImage, Input, PowerSensor, Menu, Power On/Off•Control software: SmartControl•OSD Languages: Brazil Portuguese, Czech, Dutch, English, French, Finnish, German, Greek, Hungarian, Italian, Japanese, Korean, Portuguese, Polish, Russian, Simplified Chinese, Spanish, Swedish, Traditional Chinese, Turkish, Ukrainian •Other convenience: Kensington lock, VESA mount (100 x 100 mm)•Plug and Play Compatibility: DDC/CI, Mac OS X, sRGB, Windows 10 / 8.1 / 8 / 7Stand•Height adjustment: 150 mm•Pivot: -/+90 degree•Swivel:-/+ 180 degree•Tilt: -5/35 degreePower•ECO mode: 20.9 W (typ.)•On mode: 25.9 W (typ.) (EnergyStar test method)•Standby mode: 0.3 W•Off mode: Zero watts with Zero switch•Energy Label Class: G•Power LED indicator: Operation - White, Standbymode - White (flashing)•Power supply: Built-in, 100–240 VAC, 50–60 HzDimensions•Product with stand (max height): 613 x 537 x225 mm•Product without stand (mm): 613 x 366 x 54 mm•Packaging in mm (W x H x D): 730 x 471 x 193 mmWeight•Product with stand (kg): 7.52 kg•Product without stand (kg): 5.73 kg•Product with packaging (kg): 11.20 kgOperating conditions•Temperature range (operation): 0°C to 40°C °C•Temperature range (storage): -20°C to 60°C °C•Relative humidity: 20%-80 %•Altitude: Operation: +12,000 ft (3658 m), Non-operation: +40,000 ft (12,192 m)•MTBF (demonstrated): 70,000 hrs (excludedbacklight)Sustainability•Environmental and energy: PowerSensor,LightSensor, EnergyStar 8.0, EPEAT*, TCOCertified Edge, RoHS•Recyclable packaging material: 100 %•Post-consumer recycled plastic: 85%•Specific Substances: Mercury free, PVC/BFR freehousingCompliance and standards•Regulatory Approvals: cETLus, CB, TUV/GS, TUVErgo, SEMKO, CU-EAC, EAEU RoHS, CE Mark,UKRAINIAN, FCC Class B, ICES-003, TUV EyeComfort certifiedCabinet•Front bezel: Black•Rear cover: Black•Foot:Black•Finish: TextureWhat's in the box?•Monitor with stand•Cables: HDMI cable, DP cable, USB-C to C/A Ycable, Power cable•User Documentation*The maximum resolution works for either USB-C, DP or HDMIinput.*Response time value equal to SmartResponse*NTSC Area based on CIE 1976*sRGB Area based on CIE1931*For Video transmission via USB-C, your Notebook/device mustsupport USB-C DP Alt mode*Activities such as screen sharing and online streaming over theInternet can impact your network performance. Your hardware andnetwork bandwidth will determine the overall audio and videoquality.*For USB-C power and charging function, your Notebook/devicemust support USB-C standard Power Delivery specifications. Pleasecheck with your Notebook user manual or manufacturer for moredetails.*If your Ethernet connection seems slow, please enter the OSD menuand select USB 3.0 or a higher version that can support the LANspeed up to 1G.*EPEAT rating is valid only where Philips registers the product. Pleasevisit https:/// for registration status in your country.*The monitor may look different from feature images.。
酶解菊芋生产低聚果聚糖
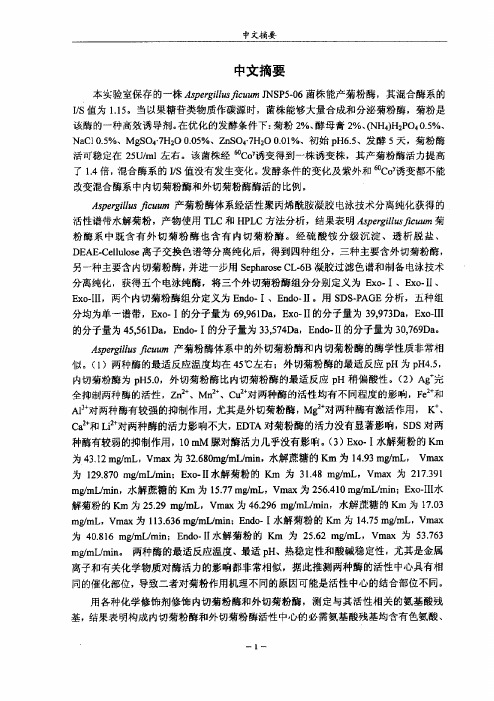
m/L i g /n m m 。两种酶的 最适反 温度、 应 最适叫、 稳定性 热 和酸碱稳定性, 尤其是金 属
离子和有关化学物质对酶活力的影响都非常相似,据此推测两种酶的活性中心具有相 同的催化部位, 导致二者对菊粉作用机理不同的原因可能是活性中心的结合部位不同。
用各种化学修饰剂修饰 内切菊粉酶和外切菊粉酶,测定与其活性相关的氨基酸残 基, 结果表明构成内切菊粉酶和外切菊粉酶活性中心的必需氨基酸残基均含有色氨酸、
粉酶系中既含有外切菊粉酶也含有内切菊粉酶。经硫酸按分级沉淀、透析脱盐、
D A -eu s离子交换色谱等分离纯化后, E E lle C lo 得到四种组分, 三种主要含外切菊粉酶, 另一 种主要 切菊粉酶, 进一 用S h o C - 凝胶过滤色谱和制备电 技术 含内 并 步 e as L B p re 6 泳
一 2一
中文摘要
菊芋汁酶解后的低聚果糖得率最高。因此,内切菊粉酶酶解菊芋制备低聚果糖宜选择 菊芋汁作底物.
根 s rl 介, 株内 菊粉酶酶解动力 研究结果, i s 。 菌 切 据A e l pg u 学的 提出了内 粉 切菊
酶酶解菊芋制备低聚果糖的工艺路线。由 此工艺路线,可以 得到两种低聚果糖产品:
A ei s u 介u s rl p gl u m产菊粉酶 体系中的 外切菊 粉酶和内 切菊粉酶的酶学 质非常相 性 似。 1 两种酶的最适反应温度均在4℃ () 5 左右:外切菊粉酶的最适反应p H为p4 , H. 5 内 菊粉 切 酶为p 5 , 菊粉酶比 切菊 H . 外切 0 内 粉酶的 最适反 H稍偏酸 () 完 应p 性. 2 A 『 全抑制两种酶的活性, n , " Ce Z2 M , + + n u 对两种酶的活性均有不同程度的影响, e和 Fz +
851-279 Rev. F 重量级90°工业60Hz螺栓电动机底座驱动套装维修及配件说明书
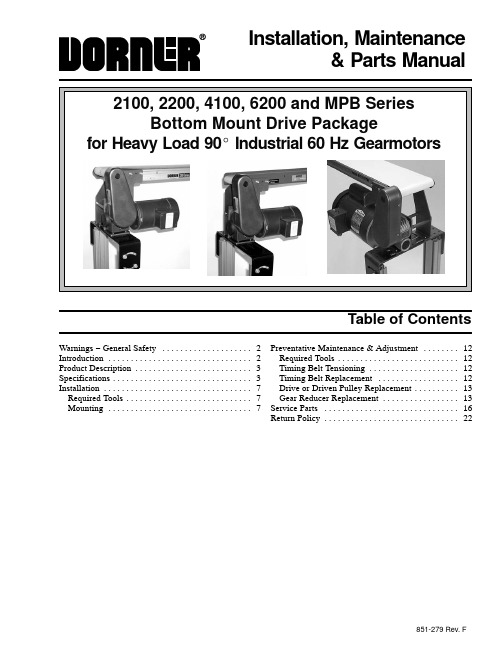
851-279 Rev. FInstallation, Maintenance& Parts ManualTable of ContentsWarnings − General Safety 2. . . . . . . . . . . . . . . . . . . . Introduction 2. . . . . . . . . . . . . . . . . . . . . . . . . . . . . . . . Product Description 3. . . . . . . . . . . . . . . . . . . . . . . . . . Specifications 3. . . . . . . . . . . . . . . . . . . . . . . . . . . . . . . Installation 7. . . . . . . . . . . . . . . . . . . . . . . . . . . . . . . . . Required Tools 7. . . . . . . . . . . . . . . . . . . . . . . . . . . . Mounting 7. . . . . . . . . . . . . . . . . . . . . . . . . . . . . . . .Preventative Maintenance & Adjustment 12. . . . . . . . Required Tools 12. . . . . . . . . . . . . . . . . . . . . . . . . . . Timing Belt Tensioning 12. . . . . . . . . . . . . . . . . . . . Timing Belt Replacement 12. . . . . . . . . . . . . . . . . . Drive or Driven Pulley Replacement 13. . . . . . . . . . Gear Reducer Replacement 13. . . . . . . . . . . . . . . . . Service Parts 16. . . . . . . . . . . . . . . . . . . . . . . . . . . . . . Return Policy 22. . . . . . . . . . . . . . . . . . . . . . . . . . . . . .IntroductionIMPORTANT: Some illustrations may show guardsremoved. Do NOT operate equipment without guards.Upon receipt of shipment:D Compare shipment with packing slip. Contact factory regard-ing discrepancies.D Inspect packages for shipping damage. Contact carrier regardingdamage.D Accessories may be shipped loose. See accessory instructionsfor installation.Dorner 2100 Series conveyors are covered by the followingpatent numbers: 5131529, 5174435, and corresponding patentsand patent applications in other countries.Dorner 2200 and MPB Series conveyors are covered by patentnumber 5174435 and corresponding patents and patent applica-tions in other countries.Dorner 4100 Series conveyors are covered by patent number3923148 and corresponding patents and patent applications inother countries.Dorner 6200 Series conveyors are covered by patent numbers:6685009, 5174435, 6109427 and corresponding patents andpatent applications in other countries.Dorner’s Limited Warranty applies.Dorner reserves the right to make changes at any time without noticeor obligation.Dorner has convenient, pre−configured kits of Key Service Partsfor all conveyor products. These time saving kits are easy to order,designed for fast installation, and guarantee you will have whatyou need when you need it. Key Parts and Kits are marked in theService Parts section of this manual with the Performance PartsKits logo .Warnings − General Safety2100, 2200, 4100, 6200 and MPB Series Bottom Mount Drive Package for Heavy Load 90_ Industrial 60 Hz Gearmotors 851-279 Rev. F2Dorner Mfg. Corp.2100, 2200, 4100, 6200 and MPB Series Bottom Mount Drive Package for Heavy Load 90_ Industrial 60 Hz Gearmotors Dorner Mfg. Corp.3851-279 Rev. FRefer to Figure 1 for typical components.A ConveyorB Mounting BracketC GearmotorD Timing Belt TensionerE CoverF Timing BeltG Drive Pulley HDriven PulleyTypical ComponentsFigure 1ABCDEHFGSpecificationsGearmotor Mounting Package Models:Example:5 Industrial 22 = 2200 Series Conveyor 4 = 4100 Series Conveyor6 = 6200 Series Conveyor 2P = MPB Series ConveyorDriven Pulley (see Table 2 & 3)− = flat belt, A through J = cleated belt )* See “Ordering and Specifications” Catalog for details.Table 1: Gearmotor SpecificationsSingle PhaseThree Phase DC Variable SpeedVFD Variable SpeedOutput Power 0.50 hp (0.37 kw)Input Voltage 115 VAC208–230/460 VAC90 VDC 230 VAC Input Frequency 60 HzN/A 10–60 Hz Input Current 7.4 Amperes 2.1–2/1 Amperes 5.0 Amperes1.6 AmperesMotor RPM 172525001725Gearmotor Ratios 5:1, 10:1, 20:1, 40:1, 60:1Frame Size NEMA 56CMotor TypeTotally enclosed, Fan-cooledProduct DescriptionSpecificationsTable 2: Belt Speeds for Heavy Load Fixed Speed 905 60 Hz Gearmotors on 2100, 2200 (Gang Drive), 4100 and 6200 Series ConveyorsBelt Speed Gearmotors Drive Driven Ft/min M/min Part Number Gear Ratio RPM In-lb N-m Pulley Pulley6 1.732M060HS4(vp)F(n)60:12927030.522328 2.432M060HS4(vp)F(n)60:12927030.5323212 3.732M060HS4(vp)F(n)60:12927030.5483212 3.732M040HS4(vp)F(n)40:14324727.9323218 5.532M040HS4(vp)F(n)40:14324727.94832257.632M020HS4(vp)F(n)20:1869010.232323711.332M020HS4(vp)F(n)20:1869010.24832 4914.932M010HS4(vp)F(n)10:117345 5.132327422.632M010HS4(vp)F(n)10:117345 5.148329930.232M005HS4(vp)F(n)5:134525 2.8323214845.132M005HS4(vp)F(n)5:134525 2.84832 16951.532M005HS4(vp)F(n)5:134525 2.8482819760.032M005HS4(vp)F(n)5:134525 2.8442221565.532M005HS4(vp)F(n)5:134525 2.8482224975.932M005HS4(vp)F(n)5:134525 2.84819 (vp) = voltage and phase:(n) = reversing capability:11 = 115 V, 1-phase N = no reversing switch23 = 230V, 3-phase R = with reversing switch (115V, 1 phase only)Table 3: Belt Speeds for Heavy Load Fixed Speed 905 60 Hz Gearmotors on 2200 Series Conveyors (Excluding Gang Drive)Belt Speed Gearmotors *DrivenDrivePulley Ft/min M/min Part Number Gear Ratio RPM In-lb N-m Pulley6 1.732M060HS4(vp)F(n)60:12927030.5193210 3.032M060HS4(vp)F(n)60:12927030.5282815 4.632M040HS4(vp)F(n)40:14324727.9282816 4.932M060HS4(vp)F(n)60:12927030.54428247.332M040HS4(vp)F(n)40:14324727.94428309.132M020HS4(vp)F(n)20:1869010.228284814.632M020HS4(vp)F(n)20:1869010.244286118.632M010HS4(vp)F(n)10:117345 5.128289529.032M010HS4(vp)F(n)10:117345 5.1442810431.732M010HS4(vp)F(n)10:117345 5.1482812136.932M005HS4(vp)F(n)5:134525 2.8282813842.132M005HS4(vp)F(n)5:134525 2.8322817653.632M005HS4(vp)F(n)5:134525 2.8322220863.432M005HS4(vp)F(n)5:134525 2.8482824273.832M005HS4(vp)F(n)5:134525 2.8442226480.532M005HS4(vp)F(n)5:134525 2.84822 (vp) = voltage and phase:(n) = reversing capability:11 = 115 V, 1-phase N = no reversing switch23 = 230V, 3-phase R = with reversing switch (115V, 1 phase only)2100, 2200, 4100, 6200 and MPB Series Bottom Mount Drive Package for Heavy Load 90_ Industrial 60 Hz Gearmotors 851-279 Rev. F4Dorner Mfg. Corp.Specifications Table 4: Belt Speeds for Heavy Load Fixed Speed 905 60 Hz Gearmotors on MPB Series ConveyorsBelt Speed Gearmotors Drive Driven Ft/min M/min Part Number Gear Ratio RPM In-lb N-m Pulley Pulley13 4.032M060HS4(vp)F(n)60:12927030.5223220 6.032M060HS4(vp)F(n)60:12927030.52828298.932M040HS4(vp)F(n)40:14324727.92828 4413.432M040HS4(vp)F(n)40:14324727.94832 5917.932M020HS4(vp)F(n)20:1869010.22828 (vp) = voltage and phase(n) = reversing capability11 = 115 V, 1-phase N = no reversing switch23 = 230V, 3-phase R = with reversing switch (115V, 1 phase only)Table 5: Belt Speeds for Heavy Load Variable Speed 905 VFD Gearmotors on 2100, 4100 and 6200 Series ConveyorsBelt Speed Gearmotors Drive Driven Ft/min M/min Part Number Gear Ratio RPM*In-lb*N-m*Pulley Pulley .6−5.6.2−1.732M060HS423EN60:12922635.52232 .8−8.2.3−2.532M060HS423EN60:12922635.532321.2−12.4−3.832M040HS423EN40:14324727.928282.5−25.8−7.532M020HS423EN20:18624827.932324.9−49 1.5−1532M010HS423EN10:117315617.632329.9−993−3032M005HS423EN5:1345819.1323214−148 4.5−4532M005HS423EN5:1345819.14832 19−1976−6032M005HS423EN5:134558 6.54422 24−2497.6−7632M005HS423EN5:134558 6.54819* At 60 HzTable 6: Belt Speeds for Heavy Load Variable Speed 905 VFD Gearmotors on 2200 Series Conveyors (Excluding Gang Drive)Belt Speed Gearmotors *Drive Driven Ft/min M/min Part Number Gear Ratio RPM*In-lb*N-m*Pulley Pulley .6−6.2−1.832M060HS423EN60:12927030.51932 1−10.3−3.132M060HS423EN60:12927030.528281.5−15.5−4.632M040HS423EN40:14324727.928283−30.9−9.232M020HS423EN20:18616718.92828 6−60 1.8−1832M010HS423EN10:1173115132828 10−104 3.2−3232M010HS423EN10:1173115134828 12−121 3.7−3732M005HS423EN5:134558 6.52828 26−2648.1−8132M005HS423EN5:134558 6.54822* At 60 Hz2100, 2200, 4100, 6200 and MPB Series Bottom Mount Drive Package for Heavy Load 90_ Industrial 60 Hz Gearmotors Dorner Mfg. Corp.5851-279 Rev. FSpecificationsTable 7: Belt Speeds for Heavy Load Variable Speed 905 VFD Gearmotors on MPB Series ConveyorsBelt Speed Gearmotors Drive Driven Ft/min M/min Part Number Gear Ratio RPM*In-lb*N-m*Pulley Pulley 1.3−13.4.4−4.132M060HS423EN60:12927030.522322−19.9−5.932M060HS423EN60:12927030.528282.9−29.9−8.932M040HS423EN40:14324727.928285.9−59 1.8−1832M020HS423EN20:18616718.9282811−117 3.6−3632M010HS423EN10:1173115132828 17−175 5.4−5432M010HS423EN10:1173115134832 23−2347.1−7132M005HS423EN5:134558 6.52828* At 60 HzTable 8: Belt Speeds for Heavy Load Variable Speed 905 DC Gearmotors on 2100, 2200 (Gang Drive), 4100 and 6200 Series ConveyorsBelt Speed Gearmotors Drive Driven Ft/min M/min Part Number Gear Ratio RPM In-lb N-m Pulley Pulley1.0−8.2.3−2.532M060PSD3DEN60:14227030.522321.4−12.4−3.632M060PSD3DEN60:14227030.532322.1−18.7−5.432M040PSD3DEN40:16321524.332324.3−36 1.3−1132M020PSD3DEN20:11259010.232329−71 2.6−2232M010PSD3DEN10:1250728.13232 17−143 5.2−4332M005PSD3DEN5:150025 2.83232 26−2147.8−6532M005PSD3DEN5:150025 2.84832 29−2459.0−7532M005PSD3DEN5:150025 2.84828Table 9: Belt Speeds for Heavy Load Variable Speed 905 DC Gearmotors on 2200 Series Conveyors (Excluding Gang Drive)Belt Speed Gearmotors Drive Driven Ft/min M/min Part Number Gear Ratio RPM In-lb N-m Pulley Pulley1.8−14.5−4.532M060PSD3DEN60:14227030.528282.6−22.8−6.732M040PSD3DEN40:16321524.328282.8−23.8−732M060PSD3DEN60:14227030.544285.3−44 1.6−1332M020PSD3DEN20:11259010.2282810−88 3.2−2732M010PSD3DEN10:1250728.12828 17−1385−4232M005PSD3DEN5:150025 2.84428 21−176 6.4−5432M005PSD3DEN5:150025 2.82828 33−27610−8432M005PSD3DEN5:150025 2.844282100, 2200, 4100, 6200 and MPB Series Bottom Mount Drive Package for Heavy Load 90_ Industrial 60 Hz Gearmotors 851-279 Rev. F6Dorner Mfg. Corp.Table 10: Belt Speeds for Heavy Load Variable Speed 905 DC Gearmotors on MPB Series ConveyorsBelt Speed Gearmotors Drive DrivenFt/min M/min Part Number Gear RatioRPM In-lb N-m Pulley Pulley2.3−19.7−5.932M060PSD3DEN60:14227030.522323.4−281−8.632M060PSD3DEN60:14227030.528285.1−42 1.6−12.932M040PSD3DEN40:16321524.328285.3−44 1.6−1332M060PSD3DEN60:14227030.5442810−853−2632M020PSD3DEN20:11259010.22828 15−127 4.7−3932M020PSD3DEN20:11259010.24832 20−1706−5232M010PSD3DEN10:1250728.12828 31−2559−7732M010PSD3DEN10:1250728.14832* = Cleated and Sidewall Cleated belts opperate at a maximum of 150 Ft/min (45.7 m/min)NOTE: For belt speed other than those listed, contactfactory for details.InstallationRequired ToolsD Hex key wrenches:2 mm, 2.5 mm,3 mm, 5 mmD Torque wrench MountingInstallation Component ListI Bottom Mount AssemblyJ Drive PulleyK CoverL M4 Socket Head Screws (4x)M Driven PulleyN KeyO Timing BeltP M6 Socket Head Screws (2x)Q M6 Socket−Head Screws & Hard Washers (4x)R End Support BracketS Hex Support Posts (2x)T Gearhead/Conveyor Support PlateU Support Plate SpacerV M6 Socket Head Screws (2x)W M6 Socket Head Screws (2x)Specifications2100, 2200, 4100, 6200 and MPB Series Bottom Mount Drive Package for Heavy Load 90_ Industrial 60 Hz Gearmotors Dorner Mfg. Corp.7851-279 Rev. F2100, 2200, 4100, 6200 and MPB Series Bottom Mount Drive Package for Heavy Load 90_ Industrial 60 Hz Gearmotors 851-279 Rev. F 8Dorner Mfg. Corp.1.Typical components (Figure 2)Figure 2M KL Q NOTE: 2100, 2200, MPB and 6200 2” & 3” (51mm &76mm) and 4100 1” through 6” (25mm –152mm)conveyors do not include parts R through W of Figure 2.NOTE: Gearmotor may be operated in positions 1 & 3(Figure 3).Figure 3132.If required, change gearmotor position by removingfour screws (X of Figure 4) from bottom mount assembly and two screws (Y of Figure 5) from gear reducer support. Rotate gearmotor to other position and install screws. Tighten screws to 103 in-lb (12 Nm).Figure 4XXFigure 5YInstallation2100, 2200, 4100, 6200 and MPB Series Bottom Mount Drive Package for Heavy Load 90_ Industrial 60 Hz Gearmotors Dorner Mfg. Corp.9851-279 Rev. F3.For your reference, the following figures show theattachment area of complete mounting packages forthe various conveyor series.Figure 6 −2200 SeriesFigure 7 − 6200 SeriesFigure 8 − 4100 SeriesFigure 9 − 2100 SeriesFigure 10 − MPB SeriesGearmotor bottom mount assembly is mounted to Head PlateGearmotor bottom mount assembly is mounted to Drive SpacerGearmotor bottom mount assembly is mounted to Drive Adapter PlateGearmotor bottom mount assembly is mounted to Head PlateGearmotor bottom mount assembly is mounted to Head PlateNOTE: 6200 conveyor shown, other Series similar.4.Locate drive output shaft (Z of Figure 11) andremove two screws (AA).Figure 11AAZFor 2100, 2200 and 6200 − 2”&3” (51mm & 76mm)wide conveyors and 4100 − 1” through 6”(25mm –152mm) wide conveyors:5.Attach bottom mount assembly (I of Figure 12) withscrews (P). Tighten to 80 in-lb (9 Nm). Proceed to step 10.Figure 12IPADFor 2100, 2200, 6200 and MPB − 4” (102mm) and wider conveyors and 4100 − 8” (203mm) and wider conveyors:6.On side opposite drive output shaft, remove two screws (AB of Figure 13).Figure 13ABInstallation2100, 2200, 4100, 6200 and MPB Series Bottom Mount Drive Package for Heavy Load 90_ Industrial 60 Hz Gearmotors 851-279 Rev. F 10Dorner Mfg. Corp.NOTE: Refer to Figures 6 through 10 while doing step7.7.Attach bottom mount assembly (I of Figure 12) withtwo screws (P). Tighten to 80 in-lb (9 Nm).8.Install hex support posts (S of Figure 14). Tightenposts to 80 in-lb (9 Nm).Figure 14S9.Install spacer (U of Figure 15) (2100 & 6200 Only)and gearhead/conveyor support plate (T) with screws (V). Install end support bracket (R) with screws (W). Tighten screws (V & W) to 80 in-lb (9Nm).Figure 15URTVW10.Install key (N of Figure 16).Figure 16NOJM11.Wrap timing belt (O) around driven pulley (M) and drive pulley (J). Install driven pulley (M) onto conveyor shaft.12.Remove cam bearing and spacer (AD of Figure 12).Place cam bearing and spacer (AD of Figure 17) next to driven pulley (M). Ensure flanges of driven pulley are aligned with cam bearing. Tighten driven pulley set screws (AA). This will allow for proper belt alignment while conveyor is in use. Install cam bearing and spacer (AD).Figure 17MInstallation13.Depending on direction of conveyor belt travel (1 or 2of Figure 18), position belt tensioner (AE) as shown.Tension belt to obtain 0.125¨ (3 mm) deflection for 1.0lb (456 grams) of force at belt mid-point (AF). Tightentensioner screw to 103 in-lb (12 Nm).AFFigure 1814.Install cover (K of Figure 19) with four screws (L).Tighten to 35 in-lb (4 Nm).Figure 19KL15.Mount assembly to support structure with four hardwashers and screws (Q of Figure 20). Tighten to 80in-lb (9 Nm).Figure 20QInstallationRequired ToolsD Hex key wrenches:2 mm, 2.5 mm,3 mm, 5 mmD Adjustable wrench (for hexagon head screws)D Torque wrenchTiming Belt Tensioning1.Remove four (4) screws (L of Figure 19) and removecover (K).2.Loosen tensioner (AE of Figure 21).Figure 21AE O3.Depending on direction of conveyor belt travel (1 or2 of Figure 18), position belt tensioner (AE) asshown. T ension belt to obtain 0.125¨ (3 mm) deflection for 1.0 lb (456 grams) of force at belt mid-point (AF).Tighten tensioner screw to 103 in-lb (12 Nm).4.Install cover (K of Figure 19) with four (4) screws(L). Tighten to 35 in-lb (4 Nm).Timing Belt Replacement1.Remove four (4) screws (L of Figure 19) and removecover (K).2.Loosen tensioner (AE of Figure 21).3.Remove timing belt (O of Figure 22).NOTE: If timing belt does not slide over pulley flange, loosen driven pulley set screws (AG of Figure 22) and remove pulley with belt (O). For re-installation, see steps 11 and NO TAG on page 10.Figure 22AGO4.Install new timing belt.5.Depending on direction of conveyor belt travel (1 or2 of Figure 18), position belt tensioner (AE) asshown. T ension belt to obtain 0.125¨ (3 mm) deflection for 1.0 lb (456 grams) of force at belt mid-point (AF).Tighten tensioner screw to 103 in-lb (12 Nm).6.Install cover (K of Figure 19) with four (4) screws(L). Tighten to 35 in-lb (4 Nm).Preventive Maintenance and AdjustmentDrive or Driven Pulley Replacementplete steps 1 through 3 of “Timing BeltReplacement” section on page 12.2.Loosen set screws and remove drive or driven pulley.NOTE: If drive pulley (J of Figure 23) is replaced, wrap timing belt around drive pulley and complete step 3.plete steps 11 through 14 of “Installation”section on page 10.Gear Reducer Replacement1.Remove four (4) screws (L of Figure 19) and removecover (K).2.Loosen tensioner (AE of Figure 21).3.Loosen drive pulley set screws (AG of Figure 23).Remove drive pulley (J) and timing belt (O).Figure 23OJAG4.Remove screws (V & W of Figure 24) and removesupport bracket (R), support plate (T) andspacer (U).Figure 24URTVW5.Remove hex support posts (S of Figure 25).Figure 25S6.Remove two (2) bracket screws (AL of Figure 26)and remove bracket (AM).Figure 26AMALPreventive Maintenance and Adjustment7.Remove four (4) gear reducer mounting screws (ANof Figure 27). Remove gearmotor.Figure 27AN8.Remove four screws (AO of Figure 28). Detachmotor (AP) from gear reducer (AQ). Retain motor output shaft key (AR).Figure 28APAQATASAO9.Remove two (2) screws (AS) and detach output shaftcover (AT).10.Remove gear reducer output shaft key (AU).11.Loosen six (6) set screws (A V of Figure 29). Removedrive shaft (AW) and key (AX).Figure 29AVAWAX12.Apply grease (AY of Figure 30) to shaft.Figure 30AY13.Replace the original shaft components into new gearreducer (see Figure 29). Tighten set screws (A V) to 26 in-lb (3 Nm).IMPORTANT: Be extremely careful when couplingmotor to gear reducer. Avoid misalignment and forcing the connection causing possible permanent gear reducer seal damage.14.With key (AR of Figure 28) in keyway, slide motor(AP) and gear reducer (AQ) together. Install screws (AO) and tighten.Preventive Maintenance and Adjustment15.Reverse steps 4 through 7 beginning on page 13.NOTE: Drive pulley (J of Figure 23) is removed.Wrap timing belt around drive pulley and complete step 16.plete steps 11 through 15 of “Installation”section on page 10.Motor Replacement1.For single phase motor, unplug power cord fromoutlet.2.For three phase and VFD variable speed motor:a .Loosen terminal box screws (AZ of Figure 31) andremove cover (BA).Figure 31AZb .Record wire colors on terminals 1, 2 and 3.Loosen wire nuts and remove wires 1, 2 and 3.c .Loosen cord grip and remove cord.3.For DC variable speed motor, unplug motor cord at disconnect (BB of Figure 32).Figure 324.Remove four screws (AO of Figure 33). Detachmotor (AP) from gear reducer (AQ). Retain motor output shaft key (AR).Figure 33APARIMPORTANT: Be extremely careful when couplingmotor to gear reducer. Avoid misalignment and forcing the connection causing possible permanent gear reducer seal damage.5.With key (AR of Figure 34) in keyway, slide motorand gear reducer together. Install screws (AO) and tighten.Figure 34ARAO6.Replace wiring:D For a single phase motor, reverse step 1 on this page.D For a three phase and VFD variable speed motor, re-verse step 2, on this page.D For a DC variable speed motor, reverse step 3 on this page.Preventive Maintenance and AdjustmentNOTE: For replacement parts other than those shown in this section, contact an authorized Dorner ServiceCenter or the factory. Key Service Parts and Kits are identified by the Performance Parts Kits logo . Dorner recommends keeping these parts on hand.2100, 2200, 4100, 6200 Series (All) and MPB Series (Flat Belt) Bottom Mount Drive Package1211724394525141813267286282930102711122100, 2200, MPB & 6200 − 2”−3” (52mm −76mm) and 4100 − 1”−6” (25mm −152mm)2100, 2200 & MPB − 4”−24” (102mm −610mm), 4100 − 8”−12” (203mm −305mm) and 6200 − 4”−18” (102mm −457mm)4100 Only2100, 2200, 6200 & MPB151920202316221414161423Service PartsItem Part Number Description1202390M Nut2920625M Socket Head Screw M6x25mm(2100 & 2200)920616M Socket Head Screw M6x16mm(4100)920630M Socket Head Screw M6x30mm(6200)3450375M Cover Mounting Bracket 4450445Spacer5802−046Bearing6920845M Socket Head Screw M8x45mm 7920410M Socket Head Screw M4x10mm 8920693M Socket Low Head Screw M6x16mm 9450443M Grove Mounting Plate10980422M Square Key 4mm x 22mm11912−084Square Key .188 x 1.5”12450444M Grove Output Shaft 12mm 13300139M Drive−Bearing Shaft Cover 14920616M Socket Head Screw M6x16mm 15920608M Socket Head Screw M6x8mm 16605279P Hard Washer17450441M Gearhead Support Bracket 184533WWM Gearhead Support Hex Post 19450440M End Support Bracket20450442M Gearhead/Conveyor Support Plate 697869M Gearhead/Conveyor Support Platew/Spacer (4100 Only)21450027M Drive Spacer [2100 −4”−24”(102mm − 610mm) and All 6200]22807−952Grooved Pin [2100 − 4”−24”(102mm − 610mm) and All 6200] 23920620M Socket Head Screw M6x20mm 24450376M Drive Guard25807−226Snap−out Plastic Plug26920406M Socket Head Screw M4x6mm 27980422M Square Key 4mm x 22mm912−053Square Key .125 x .75” [4100 − 1”(25mm) Conveyor Only]28814-104Timing Belt, 15mm W x 450mm L 814-105Timing Belt, 15mm W x 460mm L814-065Timing Belt, 15mm W x 475mm L814-112Timing Belt, 15mm W x 495mm L814-101Timing Belt, 15mm W x 500mm L814-108Timing Belt, 15mm W x 520mm L814-064Timing Belt, 15mm W x 535mm L814-099Timing Belt, 15mm W x 565mm L 29450365MP Driven Pulley, 19Tooth, 12mm bore 450366MP Driven Pulley, 22T ooth, 12mm bore450367MP Driven Pulley, 28T ooth, 12mm bore450368MP Driven Pulley, 32T ooth, 12mm bore 30450365MP Drive Pulley, 19T ooth, 12mm bore 450366MP Drive Pulley, 22T ooth, 12mm bore450367MP Drive Pulley, 28T ooth, 12mm bore450368MP Drive Pulley, 32T ooth, 12mm bore450369MP Drive Pulley, 44T ooth, 12mm bore450370MP Drive Pulley, 48T ooth, 12mm bore WW = Conveyor width ref.: 01, 02, 03, 04, 06, ,08, 10, 12, 18, 21, 24Service PartsMPB Series Cleated Belt Bottom Mount Drive Package1582325267427241139610213141216181521221620171619161712Service PartsItem Part Number Description1202390M Nut2920692M Socket Low Head Screw M6 x 12mm 3920625M Socket Head Screw M6x25mm 4802−046Bearing5807−1133Washer6920845M Socket Head Screw M8x45mm 7450445Spacer8243402Cover Mounting Angle9920693M Socket Low Head Screw M6x16mm 10243401Mounting Plate11920416M Socket Head Screw M4x16mm 12980422M Square Key 4mm x 22mm13912−084Square Key .188 x 1.5”14450444M Grove Output Shaft 12mm 15300139M Drive−Bearing Shaft Cover 16920616M Socket Head Screw M6x16mm 17605279P Hard Washer18450441M Gearhead Support Bracket194533WWM Gearhead Support Hex Post 20450440M End Support Bracket21243403Gearhead/Conveyor Support Plate 22920620M Socket Head Screw M6x20mm 23300871M Drive Cover24920408M Socket Head Screw M4x8mm 25450367MP Driven Pulley, 28T ooth, 12mm bore 450368MP Driven Pulley, 32T ooth, 12mm bore 26450366MP Drive Pulley, 22T ooth, 12mm bore 450367MP Driven Pulley, 28T ooth, 12mm bore450369MP Drive Pulley, 44T ooth, 12mm bore450370MP Drive Pulley, 48T ooth, 12mm bore 27814-101Timing Belt, 15mm W x 500mm L 814-108Timing Belt, 15mm W x 520mm L814-064Timing Belt, 15mm W x 535mm L814-099Timing Belt, 15mm W x 565mm L814-109Timing Belt, 15mm W x 580mm L814-115Timing Belt, 15mm W x 600mm L814-110Timing Belt, 15mm W x 615mm LWW = Conveyor width ref.: 04, 06, 12, 18, 24Service Parts4100 Series Adapter Package32541Item Part No.Part Description1609486Mounting Block 1” (25mm)609487Mounting Block 2” (51mm)609488Mounting Block 3” (76mm)609479Mounting Block 4” (102mm)609480Mounting Block 5” (127mm)609481Mounting Block 6” (152mm)609482Mounting Block 7” (178mm)609483Mounting Block 8” (203mm)609484Mounting Block 10” (254mm)609485Mounting Block 12” (305mm) 2613602P Bolt & Flat Washer Assembly 3450374Drive Adapter Plate4910−126Hex Nut with Lock Washer5930612M Flat Head Screw M6 x 12mm Gear Motor21Item Part No.Part Description62MH411FN Motor, 0.5 hp (0.37 Kw) 115/230 Volts,60 Hz, 1-Phase, non−reversing162MH411FRMotor, 0.5 hp (0.37 Kw) 115/230 Volts,60 Hz, 1-Phase, reversing62MHD9DEN Motor, 0.5 hp (0.37 Kw) 90 Volts DC32MS423EN Motor, 0.5 hp (0.37 Kw) 230V, 10–60Hz,Inverter Duty, 3 Phase62MH423Motor, 0.5 hp (0.37 Kw)208−230/460 Volts,60 Hz, 3-Phase32M005HS Gear Reducer, 5:1, 56C32M010HS Gear Reducer, 10:1, 56C232M020HS Gear Reducer, 20:1, 56C32M040HS Gear Reducer, 40:1, 56C32M060HS Gear Reducer, 60:1, 56CService PartsNotes2100, 2200, 4100, 6200 and MPB Series Bottom Mount Drive Package for Heavy Load 90_ Industrial 60 Hz Gearmotors Dorner Mfg. Corp.21851-279 Rev. FNo returns will be accepted without prior written factory authorization. When calling for authorization, please have the following information ready for the Dorner Factory representative or your local distributor: and address of customer.2.Item(s) being returned.3.Reason for return.4.Customer’s original order number used when ordering the item(s).5.Dorner or distributor invoice number.A representative will discuss action to be taken on the Returned items and provide a Returned Goods Authorization Number to reference.There will be a 15% restocking charge on all new items returned for credit where Dorner was not at fault. These will not be accepted after 60 days from original invoice date. The restocking charge covers inspection, cleaning,disassembly, and reissuing to inventory.If a replacement is needed prior to evaluation of returned item, a purchase order must be issued. Credit (if any) is issued only after return and evaluation is complete.Dorner has representatives throughout the world. Feel free to contact Dorner for the name of your local representative.Our technical sales and service staff will gladly help with your questions on Dorner products.For a copy of Dorner’s Limited Warranty, contact factory, distributor, service center or visit our website at 851-279 Rev. F Printed in U.S.A.For replacement parts, contact an authorizedDorner Service Center or the factory.Return Policy。
华硕MX279H液晶显示器使用说明书
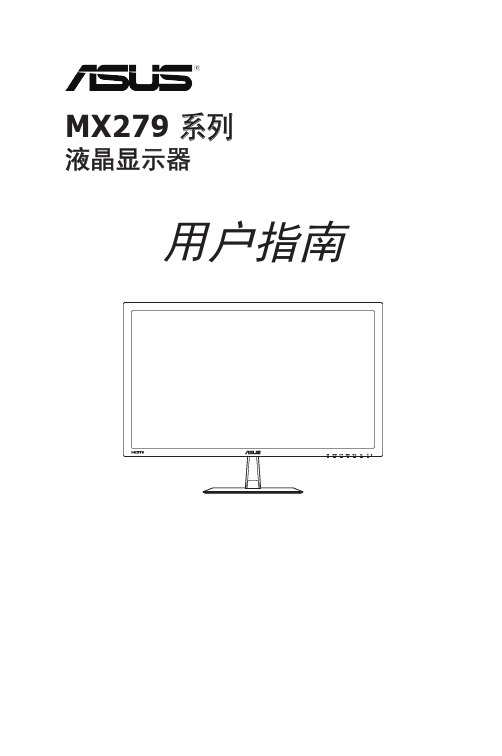
联系。 • 在使用本产品之前,确保所有线缆均连接正确并且电源线没有损坏。如
有任何损坏,请立即与经销商联系。 • 机壳后部和顶部的槽和开口用于通风目的。不要堵塞这些开口。除非通
风良好,否则不要将本产品放置在散热器或热源上部或附近。 • 本显示器只应使用标签上注明的电源类型。如果您不了解家中的电源类
1ascr开启色饱和度ntsc72典型视角水平垂直cr10178显示颜色数167ms灰色到灰色像素点距03114mm全高清1080p无残影技术splendidtm视频增强技术splendidtm选择种视频预设模式用热键自动调整是用热键色温选择种色温肤色选择种肤色数字输入hdmiv13x2模拟输入dsub音频输入端口35mm迷你插孔耳机插孔是仅限hdmikensington锁槽颜色黑色扬声器内置电源led白色开机黄色待机倾斜52035一般说明额定电压ac100240vac5060hz交流适配器
vii
1.1 欢迎使用!
感谢您购买 ASUS® 液晶显示器! 这是 ASUS 最新推出的宽屏液晶显示器,它不但提供更艳丽、更宽、更亮 的显示屏,而且通过一些有用的功能丰富您的观看体验。 通过这些功能,本显示器为您提供方便愉快的视觉体验!
1.2 物品清单
检查是否包括了以下物品:
液晶显示器 1 x 适配器 1 x 电源线 1 x VGA 线 1 x DVI-HDMI 线 1 x 音频线 1 x 快速入门指南 1 x 保修卡
进行修理。不要自行修理屏幕! 本指南中使用的约定
警告:这些信息旨在防止您在试图完成一项任务时受伤。
小心:这些信息旨在防止当试图完成一项任务时损坏组件。
重要:您在完成一项任务时必须遵循这些信息。 注:这些提示和附加信息旨在帮助您完成一项任务。
再谈“似的”及其相关问题
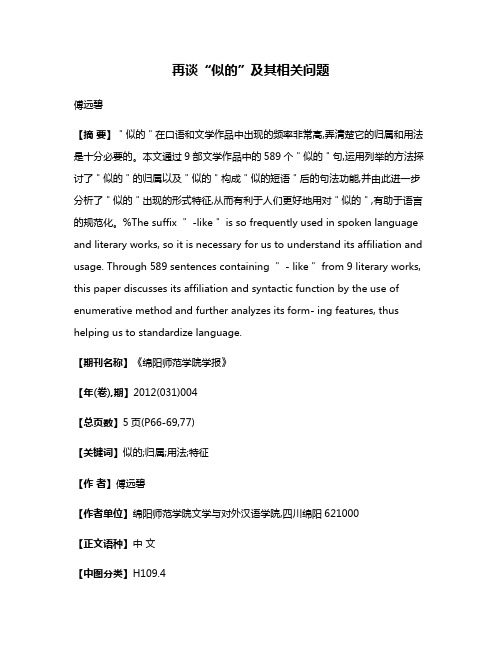
再谈“似的”及其相关问题傅远碧【摘要】"似的"在口语和文学作品中出现的频率非常高,弄清楚它的归属和用法是十分必要的。
本文通过9部文学作品中的589个"似的"句,运用列举的方法探讨了"似的"的归属以及"似的"构成"似的短语"后的句法功能,并由此进一步分析了"似的"出现的形式特征,从而有利于人们更好地用对"似的",有助于语言的规范化。
%The suffix " -like" is so frequently used in spoken language and literary works, so it is necessary for us to understand its affiliation and usage. Through 589 sentences containing " - like" from 9 literary works, this paper discusses its affiliation and syntactic function by the use of enumerative method and further analyzes its form- ing features, thus helping us to standardize language.【期刊名称】《绵阳师范学院学报》【年(卷),期】2012(031)004【总页数】5页(P66-69,77)【关键词】似的;归属;用法;特征【作者】傅远碧【作者单位】绵阳师范学院文学与对外汉语学院,四川绵阳621000【正文语种】中文【中图分类】H109.4近来笔者阅读了《咬文嚼字》(2006年第3期,p20)中的一篇文章《似的不能写成“似地”》,文章很短,照录如下:“似的”?“似地”?热线电话栏目姚博士问:我是一名期刊校对,有一个一直觉得头痛的问题,就是“似的”和“似地”是否要严格区分。
比如:“他一阵风似de溜走了。