periodical__swjstb__swjs2009__0907pdf__090711
periodical__kjqbkfyjj__kjqb2009__0901pdf__090142

不同阶段、不同层面都发挥着不同的角色作用。 2.3.2客体的特异性 教育信息服务的客体是十分明确的,就是所有有学习需要 的人。这一客体涉及的人群非常广泛,不同年龄、不同性别、不同 社会地位以及不同背景的人只要有学习需求,都可以享受教育 信息服务。因此,教育信息服务客体的特异性就是人群分布上的 普遍性和学习倾向上的同一性。同时,由于教育信息服务的客体 包括了各个年龄层次和不同社会背景的人,所以他们对于学习 内容和学习方式的追求必然各不相同。由此可以看出,教育信息 服务的客体义在学习需求和个人学习风格上呈现出多样化的特 异性。 2.3.3服务形式的特异性 教育信息服务面对的是层次背景各异、条件需求不同的所 有人。他们对于学习的需求是各种各样的.为了适应他们多种多 样的学习方式,教育信息服务提供的服务形式必须是不拘一格 的,要具有灵活开放的特异性。教育信息服务形式的多元化和灵 活性就是耍向人们提供尽可能多的、可行的以及个性化的学习 方式来适用于各个学习者。 2.3.4服务内容的特异性 一方面教育信息服务的内容量呈“海量”化。教育信息服务 体系为了满足客体纷繁复杂的学习需求,必须积累和提供大量 而且全面的教育信息。凶此。教育信息服务内容的一个明显的特 异性就是数量上多得惊人。 另一方面教育信息服务表征的内容类别繁多。教育信息服 务提供的信息类别包罗万象,涉及人文和自然科学的各个领域, 而且它所提供的信息不局限于纸质媒介的文字信息,还包括了 声音、图像等多媒体信息。实践证明信息表征的内容多样化可以 提高人们的学习兴趣和学习效果。 2.3.5服务技术方法的特异性 综合应用现代信息技术和各种高科技手段是教育信息服务 技术方法的特异性。通过现代信息技术和多种高科技手段综合 运用,可以实现信息的远距离传送、无线传输和完成庞杂的信息 编辑整理T^作和信息的瞬时调用,这为客体的学习提供了极大 的方便和便利。教育信息服务的特点见表1。 表l教育信息服务的特点
LabVIEW 2009 Manual Chapter 3

3. FOR Loops, Case Structures and Sequences___________________________FOR LoopsThe FOR loop within LabVIEW is very similar to the WHILE loop except that the loop iterates a given number of times instead of iterating until a given condition is met.The FOR loop structure is found within the “Structures” palette, figure 46 shows the basic details.Important notesAs when programming FOR loops in ‘C’, the ‘I’ counter starts at 0 and not 1 so.....If ‘N’ is set as 10 ....... ..... ‘I’ will count from 0 to 9.An example VI that finds the smallest of 100 random numbers will be used to demonstrate the use of a FOR loop.Front panelAdd two digital indicators, named “Number” and “Minimum”Block DiagramAdd a FOR loop structureSet the count to 100 by adding a constant (use the help system to ensure that you use the correct datarepresentation) and connecting it to the loop’s ‘N’ connector.Add a random number generator placing it within the loop.Continued .....Number of iterations the loop will make - thevalue has to be outside of the loop.Loop iteration counter.Figure 46 : Basic FOR loop structureAdd a “Max & Min” function (Comparisons palette), also placing it within the FOR loop.Add a shift register to the FOR loop.(See WHILE loop notes)Move the “Number” numeric indicator node so that it is within the FOR loop and connect the output of the random number generator to it.Take a second connection from the random number generator (or pick up from the above connecting wire) and connect to the ‘x’ input of the “Max & Min” function.Connect the “min(x,y)” output of “Max & Min” to the shift register element on the right hand side of the FOR loop structure.Initialise the shift register by placing a constant to the left of the loop and connecting it to the shift register element on the left hand side of the FOR loop. This initialising constant should be set as 1 (one)Make sure that the node “Minimum” is outside of the loop and to its right.Connect the left hand element of the shift register to the lower input of the “Max & Min” function.Connect the right hand element of the shift register to the “Minimum” node.Figures 47.a and 47.b show the front panel and block diagrams.Figure 47.a : FOR loop example front panel Figure 47.b : FOR loop example block diagramClick on “Run” and you will see the smallest of 100 values output.You should see that the results are produced almost instantaneously, LabVIEW is very fast!. Try changing the number of times the loop runs to 1000, 10,000 ...... Try adding a delay.Eventually you will see a time delay between starting the VI and the result being output in the “Minimum”, this is because the loop effectively “holds” the data within it until it finishes iteration (WHILE loops are the same). Once the iterations are completed data is “released” from the loop.Before leaving the FOR loop, consider why the shift register initialisation constant has been set at 1, also consider what changes you would have to make in order to make the VI output the maximum value or even both at the same time.CASE STRUCTUREThe CASE structure within LabVIEW operates in much the same manner as the Switch / Case structure within many textural programming languages such as ‘C’.The LabVIEW CASE structure can be found within the “Structures” palette, it basic use is shown in figure48 below.The different cases withinthe structure can beviewed by clicking onthese scrolling arrows.Alternatively, use thedrop down list.Input point for the valuesthat drive the CASEstructure.Figure 48 : Basic CASE structureWhen the CASE structure is initially instantiated, it will default to a Boolean driven structure with just two cases (one of “TRUE” and the other for “FALSE”), it will accept other data types (numeric and string) and will adjust accordingly.Additional cases can be added by right clicking and selecting to add a new case either before or after the case currently being shown. Other options including deletion are available via the right click facility.IMPORTANT - One of the cases must be set as the default case so that out of range values can be caught. It is often better to set the default case after wiring the input so that the structure is configured correctly before manipulating it. There is no default when the case structure is Boolean.CASE example - Square Root Calculation.Start a new, blank VI.Front panelAdd a Numeric Control - “Number” Add a Numeric Indicator - “Square Root”Block DiagramAdd a CASE function.Add a “³0” function from the Comparisons palette.Position it just to the left of the CASE input connection point. Position the “Number” node to the left of the greater than or equal function.Tip - A Boolean case structure is the equivalent of an “if, then, else”structure within textural programming languages.CASE Block Diagram continuedConnect the “Number” node to the input of the “³” function and then its output to the data input ofthe CASE structure (the little box on the left hand side that should be showing a question mark)Select the “True” case and place within it .....A “Square Root” function from the Numeric Palette.Connect “Number” to the input of the square root function.Notice how a little “tunnel appears in the structure wall, this is how values can be passed intostructures (WHILE and FOR loops also have this facility).Position the “Square Root” node to the right of the CASE structure and connect it to the output of thesquare root function.Notice how the little tunnel is created but, this time it only its boundary has been colouredorange to suit the data type. This indicates that not all of the possible outputs from the CASEstructure have been satisfied.Select the “False” case and place within it....A numeric constant set to “-9999”, use the correct data representation.A “One button Dialog” from the “Time & Dialog” palette. A string constant from the “String” palette set to “Error, negative value”A second string constant set to “OK - so I’m a big dummy”Connect “Error, negative value” to the top input of the “One Button Dialog” and “OK - so.....” to thebottom input.Connect “-9999” to the output tunnel on the right hand side of the CASE structure.Notice how the tunnel becomes solid orange, this indicates that all of the possible CASE out puts have been satisfied.Figures 49.a, 49.b and 49.c show the complete CASE VI.Error, negative value -9999OK - so I'm a big dum my Figure 49.a : CASE VI front panelFigure 49.a : CASE VI block diagram showing the “True” caseFigure 49.a : CASE VI block diagram showing the “False” caseSwitch to the front panel and save NOW!Enter positive a value in “Number” and run the VI by clicking on the “Run” button , try other values including negative,Try running the VI using the “Run Continuously” button, try a negative value, try getting out of the loop!Hint: Have a look at the key board short cuts.If you are really stuck a couple of solutions can be found at the end of this chapter. When using CASE structures it is also possible to use the value that drives it, just simply pick up from the connection point, figure 50 shows a simple example.Figure 50 : Using the CASE driving valueSEQUENCE STRUCTUREThe SEQUENCE structure allows the programming of a number of steps that will occur in a fixed sequence.The representation within LabVIEW appears as a film strip which helps to illustrate the concept, in the same way that a film strip contains a series of pictures that are shown consecutively in sequence, each frame of the SEQUENCE structure will contain functionality that will occur consecutively and in the same sequence each time.LabVIEW offers two styles of SEQUENCE structure, the “Stacked Sequence Structure” and the “Flat Sequence Structure”. The main difference between them is the the first is more suited to a sequence that requires many steps and / or steps that contain a moderate to large number of programming elements. The Flat structure is more suited to situations where on a small number of steps is required and each step contains only a few elements.To illustrate the use of this structure an example will be used that will indicate how fast LabVIEW runs, the same example will be programmed using each SEQUENCE structure.Stacked Sequence Structure - Sequence1.viStart a new, blank VI.Front Panel - see figure 51 below.Numeric Control - “Number to Match”Set the representation to “I32” - 32 bit signed integer.Data Range - Max 1,000,000 & Min 0 (right click at select “Data Range...”)Set increment to 1 and default value to 500,000Set Precision by right clicking and selecting “Format & Precision”From the dialogue select Automatic Formatting0 Digits of precision (drop down list at top right)Numeric Control - “Current Number”Set precision to 0.Numeric Indicator - “No. Of Iterations”Set to 32 bit unsigned integer.Numeric Indicator - “Time to Match”Set to 32 bit unsigned integer.Figure 51 : Sequence1.vi front panelBlock DiagramTemporarily move the front panel nodes to one side.Add a “Stacked Sequence Structure” from the “structures” palette.Right click on the SEQUENCE frame and select “Add Frame After”.Repeat this step so that the SEQUENCE has three framesFrames are numbered from zero and can be navigated using the scroll arrows.Figure 52 shows how the block diagram should appear at this stage.SEQUENCEframe.Drop down listalternativeFigure 52 : Sequence1.vi - initial placement of structureBlock Diagram continuedUsing the navigation facilities, select the first frame - numbered zero.It would appear that it is not possible to change the numbering.Add to this frame the function “Tick Count (ms)” from the “Time & Dialog” palette.Right click on the sequence frame (the bottom is a good place) and select “Add Sequence Local”.This will place a small box on the edge of the sequence structure to “carry” a value to theother frames within the structure.associated with it.As with shift registers on loop structures, it is possible to have an unlimited number of“Sequence Locals”, each being able to carry only one data type.Connect the output of the “Tick Count” to the “Sequence Local” that has just been added.Note the colour change and arrow.Select the next frame in the sequence.Note that the local variable now shows an arrow pointing inwards. You can only assigndata to a local variable once. It can, however, be read often but only in those frames thatfollow the one in which the value was assigned.Figures 53.a & 53.b shows how the Block Diagram should now appear.Note directions ofarrowsFigure 53.a : Sequence1.vi - first sequence frame Figure 53.b : Sequence1.vi - second sequence frame Into the second frame (numbered 1) add.....A WHILE loop.Within this loop place a random number generator, multiply its output by 1,000,000 (use a constant and a multiply function) and round the result to the nearest whole number.Place the “Current Number” node within the loop and connect the rounded value to it via a “To Long Integer” function that can be found within the “Conversions” palette which itself is a subpalette of the “Numeric” palette..Place the “No. Of Iterations” node within the loop. Connect the loop counter to this node via anincrement function so that the presentation of the loop count commences at “1” instead of “0”.Place a “Not Equal” comparison function together with the “Number to Match” node within the loop and connect them such that the rounded value is being tested against “Number to Match”.Connect the output of the “Not Equal” function to the loop control node.Check the logical operation of the loop control and adjust if necessary - you will have to work outthe logic of the loop contents first.Figure 54 : Sequence1.vi - completed second frame of sequence structureSelect the final frame in the sequence (No. 2)Add a “Tick Count (ms)” and a subtract functionMove the “Time to Match” node into this frame.Connect the output of the “Tick Count” to the “x” input of the subtract function.Connect the sequence local to the “y” input of the subtract function.Connect the output of the subtract function to “Time to Match”.The final frame should appear as figure 55.Figure 55 : Sequence1.vi - completed final sequence frameRun the VI using the “Run” button.Each time the VI is run it will display how long LabVIEW takes to match the value in “Number to Match”together with how many attempts (loop iterations) are used.Flat Sequence Structure example - Sequence2.viFront PanelAs that used in Sequence1.vi.Block DiagramTemporarily move the nodes representing the objects on the front panel to the left hand side of the window.Add a “Flat Sequence Structure” from the “Structures” palette.Right click on the sequence frame and select “Add Frame After”, repeat so that there are three frames.The block diagram should now resemble figure 56 on the following page.Figure 56 : Sequence2.vi with flat sequence structure outline Resize handles - use select / size / position tool to activate.As with most objects, the flat sequence structure can be easily resized, it is also possible to move the internal frame separations so that each frame within the sequence can be sized to suit the programming elements that are placed within them.It should be noted that the frames are not numbered.First FrameAdd a “Tick Count (ms) towards the top of the frame.Second FrameBuild as the second frame of Sequence1.viThird FrameBuild as the third frame of Sequence1.vi but without the Sequence Local connection. Try and keep the loop and its contents towards the bottom of the frame.Completing the wiringUsing a series of way points to keep the wiring tidy and well routed, connect the output of the “Tick Count (ms)” in the first frame to the “y” input of the subtract function in the third frame. Note how the wire “tunnels” through the frame walls instead of having to use a “Sequence Local” facility.The Block Diagram of Sequence2.vi should resemble figure 57 on the following page.Figure 57 : Sequence2.vi completed block diagramRun the VI.Sequence1.vi and Sequence2.vi show the same programming using the two different sequence structures, ultimately it is up to the programmer / developer to decide which of the two structure formats to use as circumstances change.SummaryThis section has consideredFOR loops and how they are used to carry out a predetermined number of operations.CASE structures and how they can be used to process any one of a number of operations asdetermined by an input value.SEQUENCE structures and how they can be used to ensure that processing states are carried out in a predetermined order.Two sequence structures have been shown that, essentially, operate in the same manner butpresent the programming in two different styles.Stopping the errant Case1.viWith one hand, use the keyboard shortcut for halting a VI (Control plus the full stop key), with the other hand use the mouse to click on the “OK - so I’m a big dummy” button. It may take a few tries.If that fails the only other solution is to use the task manager to kill the LabVIEW process.Using this technique will result in any unsaved work being lost - you were warned!Tutorial Work - Chapter 31: Using a combination of WHILE and FOR loops, create a VI that will generate numbers using a Random Number generator, calculate the Max and Min values for batches of 50 numbers and plot these Max an Min values to charts. Each chart should only show the Max or Min from each batch. The VI should run continuously when started using the “Run” button and have suitable controls to alter the rate of production and to stop.2: Create a VI that will allow the user to select a number in the range 0..5 and then when a connect button is pressed will display one of five messages as given below.Option 0 You are now being transferred to ReceptionOption 1 You are now being connected to the Accounts DepartmentOption 2 You are now being transferred to the Sales DepartmentOption 3 You are now being connected to the Technical DepartmentOption 4 You are now being transferred to the Manager’s OfficeOption 5 You are now being connected to the holding queue forever.The VI should use a combination of WHILE loop, CASE and SEQUENCE structures. By examining the option messages it should be possible to reduce the amount of text stored in strings and then combining using a SELECT function - you will need to use a “Concatenate Strings” functionfrom the “String” palette.Upon pressing the connect button the number of the extension should also be displayed as a combination of a configurable base number plus the extension number, e.g. if the base number is “1200” and the selected extension is “4”, the display should show “1204”Don’t forget to assign one of the cases as default. To do this, select the chosen case, right click on the case number and select “Make This The Default Case”3: Using either Sequence1.vi or Sequence2.vi, add functionality so that the time output is displayed in seconds and milliseconds.Hint: Consider the data representations.Ensure that you eliminate all data mismatch warnings (little grey “blobs”)4: Using the VI developed in 3, experiment with the setting within the “Format & Precision” so that the output in “Time to Match” is formatted into hours : minutes : seconds.。
iecee02
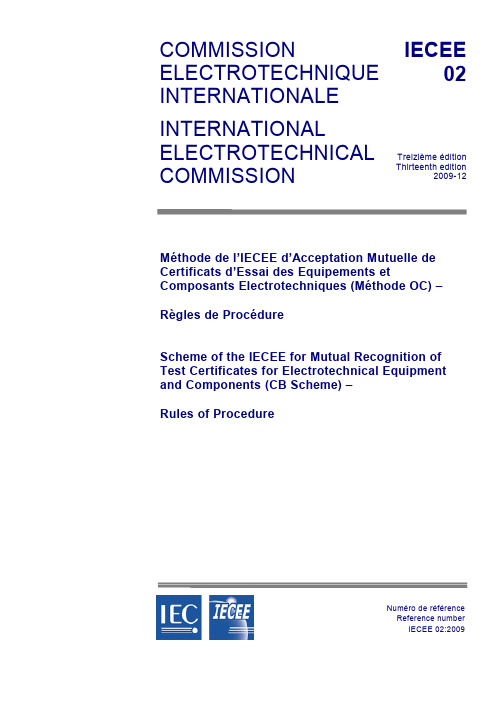
INTERNATIONALE INTERNATIONAL ELECTROTECHNICALCOMMISSION Treizième éditionThirteenth edition2009-12Méthode de l’IECEE d’Acceptation Mutuelle de Certificats d’Essai des Equipements etComposants Electrotechniques (Méthode OC) –Règles de ProcédureScheme of the IECEE for Mutual Recognition ofTest Certificates for Electrotechnical Equipmentand Components (CB Scheme) –Rules of ProcedureNuméro de référenceReference numberIECEE 02:2009INTERNATIONALE INTERNATIONAL ELECTROTECHNICAL COMMISSION Treizième édition Thirteenth edition 2009-12Méthode de l’IECEE d’Acceptation Mutuelle deCertificats d’Essai des Equipements etComposants Electrotechniques (Méthode OC) –Règles de ProcédureScheme of the IECEE for Mutual Recognition ofTest Certificates for Electrotechnical Equipmentand Components (CB Scheme) –Rules of Procedure Commission Electrotechnique InternationaleInternational Electrotechnical Commission Pour prix, voir catalogue en vigueur For price, see current catalogue© IEC 2009 Droits de reproduction réservés ⎯ Copyright - all rights reservedAucune partie de cette publication ne peut être reproduite niutilisée sous quelque forme que ce soit et par aucunprocédé, électronique ou mécanique, y compris la photo-copie et les microfilms, sans l'accord écrit de l'éditeur. No part of this publication may be reproduced or utilized in any form or by any means, electronic or mechanical, including photocopying and microfilm, without permission in writing from the publisher.International Electrotechnical Commission 3, rue de Varembé Geneva, SwitzerlandTelefax: +41 22 919 0300 e-mail: inmail@iec.ch IEC web site http: //www.iec.chCODE PRIX PRICE CODE ZZContentsForeword ....................................................................................................................... .. 4 Introduction.. (5)1 Scope (6)2 Normative references (6)3 Definitions (6)4 Rules (8)5 Acceptance of National Certification Bodies and of CB Testing Laboratories (12)6 Procedures for handling CB Test Certificates (18)INTERNATIONAL ELETROTECHNICAL COMMISSION_________IEC SYSTEM OF CONFORMITY ASSESSMENT SCHEMES FORELECTROTECHNICAL EQUIPMENT AND COMPONENTS (IECEE) IECEE CB SCHEME FOR MUTUAL RECOGNITION OF TEST CERTIFICATES FOR ELECTROTECHNICAL EQUIPMENT AND COMPONENTS(CB SCHEME)RULES OF PROCEDUREFOREWORDThis publication governs the Certification Body Scheme of the IECEE for testing and certification of electrotechnical equipment and components which includes appliances, systems, industrial and household equipment and sub-assemblies (CB Scheme).It cancels and replaces Publication IECEE 02, Twelfth edition, 2008.Changes from the second edition mainly concern the slimming-down of the organizational structure, whereby the former Management Committee (MC) and Committee of Certification Bodies (CCB) are replace by one committee, namely the Certification Management Committee (CMC).This publication is directly related to Publication IECEE 01 containing the Basic Rules of the IECEE.The annexe to this publication is normative.The text of the amendments of this edition (IECEE 02, Thirteenth edition 2008) is based on the following Document.Document Report on votingDecisionIECEE-CMC/1022/RM CMCFull information on the approval of this publication can be found in the Minutes of the CMC meeting held in Stockholm on June 24/25, 2009.________INTRODUCTIONNOTE This introduction provides an overview of the CB Scheme and is not part of the Rules.In recognition of the need to facilitate international trade in electrotechnical equipment, and components primarily intended for use in homes, offices, workshops healthcare facilities and similar locations, for benefit of consumers, industries, authorities etc, and to provide convenience for manufacturers and other users of the services provided by various National Certification Bodies (NCBs), an international Scheme is operated by the IECEE (IEC System for Conformity Testing and Certification of Electrotechnical Equipment and Components), known as the CB Scheme. The Scheme is based on the principle of mutual recognition (reciprocal acceptance) by its members of test results for obtaining certification or approval at national level.The Scheme is intended to reduce obstacles to international trade which arise from having to meet different national certification or approval criteria. Participation of the various NCBs within the Scheme is intended to facilitate certification or approval according to IEC standards. Where national standards are not yet completely based on IEC standards, declared national differences will be taken into account; however, successful operation of the Scheme presupposes that national standards are reasonably harmonized with the corresponding IEC standards. Use of the Scheme to its fullest extent will promote the exchange of information necessary in assisting manufacturers around the world to obtain certification or approval at national level.The operating units of the Scheme are the NCBs accepted according to these Rules. Those NCBs employ testing laboratories also accepted according to the Rules, known as CB Testing Laboratories (CBTLs). A list of NCBs is published in the CB Bulletin.The CB Scheme is based on the use of CB Test Certificates which provide evidence that representative specimens of the product have successfully passed tests to show compliance with the requirements of the relevant IEC standard. A supplementary report providing evidence of compliance with declared national differences in order to obtain national certification or approval may also be attached to the CB Test Report.The first step for an NCB, intending to operate in the CB Scheme, is to be accepted as a Recognizing NCB. Such an NCB is prepared to recognize CB Test Certificates as a basis for certification or approval at national level for one or more categories of productsThe second step for an NCB, which can be taken at the same time as the first step, is to be accepted as an Issuing and Recognizing NCB. Such an NCB is entitled to issue CB Test Certificates for the categories of equipment for which it recognizes CB Test Certificates. It should, however, be noted that an NCB may recognize CB Test Certificates for more categories of equipment than for which it is entitled to issue CB Test Certificates.The Rules are formulated in such a way as to make them applicable in different national certification structures.Definitions are given in clause 3.IEC SYSTEM OF CONFORMITY ASSESSMENT SCHEMES FORELECTROTECHNICAL EQUIPMENT AND COMPONENTS (IECEE) IECEE CB SCHEME FOR MUTUAL RECOGNITION OF TEST CERTIFICATES FOR ELECTROTECHNICAL EQUIPMENT AND COMPONENTS–RULES OF PROCEDURE1 ScopeThis publication contains the Rules of Procedure of the IECEE CB Scheme for Mutual Recognition of Test Certificates for Electrotechnical Equipment and Components (CB Scheme).The CB Scheme is applicable to Electrotechnical Equipment and Components primarily intended for use in homes, offices, workshops, healthcare facilities and similar locations.references2 NormativeThe following publications contain provisions which, through reference in this text, constitute provisions of these Rules of Procedure. At the time of publication, the editions indicated were valid. The IECEE Certification Management Committee (CMC) shall decide the timetable for the introduction of new publications or revised editions of existing publications.IECEE 01: 2008, IEC System of Conformity Assessment Schemes for Electrotechnical Equipmentand Components (IECEE)ISO/IEC Guide 2: 2004, Standardization and related activities - General vocabulary.ISO/IEC 17000: 2004 Conformity assessment - Vocabulary and general principlesISO/IEC 17025: 2005, General requirements for the competence of calibration and testing laboratories.ISO/IEC 17040: 2005 Conformity assessment - General requirements for peer assessment of conformity assessment bodies and accreditationISO/IEC Guide 65: 1996, General requirements for bodies operating product certification systems. ISO/IEC Guide 67: 2004,Conformity assessment — Fundamentals of product certification3 DefinitionsISO/IEC Guide 2 gives the basic definitions.For the purpose of the CB Scheme, the following special definitions apply:3.1 National Certification Body (NCB)a body which operates a national certification or approval scheme for Electrotechnical equipment and components in a country that has a Member Body of the IECEE3.2Recognizing NCBan NCB which is, or has been appointed by, a Member Body of the IECEE, and accepted according to these Rules, and which is prepared to recognize CB Test Certificates for specified IEC standards as a basis for national certification or approval3.3Issuing and Recognizing NCBa Recognizing NCB which has also been accepted according to these Rules for issuing CB Test Certificates for specified standards3.4CB Testing Laboratory (CBTL)a testing laboratory which, after having been proposed as a candidate by an Issuing and Recognizing NCB, and which, after having been successfully assessed according to these Rules, is accepted into the CB Scheme3.5national differencesthose requirements or test parameters in the corresponding national standard which, when applied to equipment complying only with the standard accepted for use in the IECEE, might entail non-compliance of that equipment with the relevant national standardNOTE 1 When a requirement in the IEC standard is not implemented in the corresponding national standard, that is also a national difference.NOTE 2 Those restrictive requirements in a national standard, which do not deviate from the criteria included in the corresponding standard accepted for use in the IECEE, but which limit the possibility to offer the relevant equipment for sale in the country concerned, are also considered to be national differences.3.6applicanta firm or a person who applies to an Issuing and Recognizing NCB for obtaining a CB Test Certificate or to a Recognizing or Issuing and Recognizing NCB for national certification or approval on the basis of a CB Test CertificateNOTE The applicant is the holder of the CB Test Certificate3.7manufactureran organisation, situated at a stated location or stated locations, that carries out or controls such stages in the manufacture, assessment, verification, handling and storage of a product.A Manufacturer has full responsibility for continued compliance of the product with the relevant requirements and undertakes all obligations in that connection.3.8standards used in the IECEE SchemesThe IECEE is based on the use of specific IEC standards for electrotechnical equipment and components accepted by the CMC for use in the IECEE.Specific CAB approval is required should the CMC propose to make use of normative documents, other than IEC standards.3.9factorythe location at which the product is produced or assembled and follow-up service is established by the NCB3.10approvalacceptance of a product by an authority having the appropriate jurisdiction3.11Acceptance of Standards used in the IECEE SchemesAt the time of application, a formal declaration made by the IECEE National Certification Body (NCB) to the IECEE Secretariat that the NCB accepts the relevant Standards used in the IECEE Schemes, as the basis for the national certification.3.12Extension of scopea formal application made by the NCB to the IECEE Secretariat, with copy to the responsible Member Body of the IECEE for that NCB, seeking the extension of its scope as a Recognizing or Issuing/Recognizing Body to declared standards.3.13operational documentsnormative documents approved by the CMC and used to cover the various operations within the CB Scheme such as applications, assessments, Test Report Format, etc. The Operational Documents are used in conjunction with the Basic Rules IECEE 01 and Rules of Procedure IECEE 02.3.14Scope of NCB and its associated CBTL(s)The standards for which the NCB and its associated CBTL(s) have been formally accepted by the IECEE.NOTE : The scope of the NCB and its associated CBTLs(s) is published on the IECEE website4 Rules4.1 General4.1.1 The IEC System of Conformity Assessment Schemes for Electrotechnical Equipment and Components (IECEE) operates a scheme with the aim of facilitating international trade by promoting and simplifying certification and approval at national level through mutual recognition of test results. CB Test Certificates according to 4.2.1 are used as the means for mutual recognition of test results.4.1.2The Scheme is called “IECEE CB Scheme for Mutual Recognition of Test Certificates for Electrotechnical Equipment and Components”, hereinafter referred to as “the CB Scheme”.4.134 The CB Scheme shall be governed by the CMC, whose responsibilities in this respect are defined in the Basic Rules of the IECEE, as given in Publication IECEE 01.4.1.4The IEC, IECEE and combination IEC/IECEE logos are copyrighted and belong to the IEC. Their use is restricted to official documents published by the IEC or the IECEE or both and shall not be reproduced or utilized in any form or by any means, electronic or mechanical, including photocopying and microfilm, without prior permission in writing from the IECEE Secretary.4.2 CB Test Certificates4.2.1 A CB Test Certificate is a document issued by an Issuing and Recognizing NCB to inform other NCBs, in conjunction with the attached CB Test Report, that one or more specimens of certain electrical products were fully tested according to the relevant requirements of one or more standard(s) applicable to the electrical products accepted for use in the IECEE, unless otherwise permitted by the relevant standard(s) and that the specimens were found to be in conformity with that (those) standard(s). A CB Test Certificate is valid only when the IECEE documented CB Test Report (in agreed harmonised form) is attached. The CB Test Report will fully and completely cover the applicable and relevant test results according to the requirements of the standard(s), and when requested also according to declared national differences.4.2.2 The CMC shall decide on the layout and content of CB Test Certificates. The CB Test Certificate shall always contain a clear description of the product, the name and address of the applicant, manufacturer and factory or factories (see definitions) and the edition of the IEC standard, and amendments, if any.The CB Test Certificate shall be signed by authorized person(s) operating within the Certification department of the responsible NCB.The name(s) and signature(s) of the authorized person(s) shall clearly appear on the CB Test Certificate and the names shall be declared to the IECEE Secretariat and listed in the Quality Procedure used by the NCB to process the CB Scheme.A Test Report shall be attached to each CB Test Certificate giving, as far as necessary, for each clause of the relevant standard a brief reference to the requirements, and the results of tests and examinations. The Test Report shall also contain the information necessary for identification of the product, such as type designation, ratings, description and photographs.4.2.3 CB Test Certificates shall not be used in any form of advertising or sales promotion.NOTE This subclause does not preclude the holder of a CB Test Certificate from making reference to the existence of that Certificate in business correspondence related to equipment for which a CB Test Certificate has been issued.4.2.4Modifications to products declared in a valid CB Test Certificate are limited to three, after which a new CB Test Certificate shall be issued and a new surcharge levied if applicable. This shall not preclude issuing a new CB Test Certificate at every modification if the Issuing NCB wishes to do so.When a product is subject to "Modifications" regardless of the suffix used to identify the CB Test Certificate, i.e. the letter "M" followed by 1, 2 or 3, the CB Test Certificate shall clearly identify the nature of such "Modifications" under "Additional Information".A re-issued CB Test Certificate shall include the original issue date and revision date under "Additional Information".4.2.5 A CB Test Certificate may be cancelled by the issuing NCB if−the Certificate is misused,−the Certificate has been issued in error, the equipment no longer corresponds to the specimens tested and described in the attached Test Report, or−the holder of the Certificate requests cancellation.4.2.6 When a CB Test Certificate has been cancelled, the Secretary of the IECEE shall be notified as soon as possible by the issuing NCB, which shall state the reason for cancellation.The Secretary of the IECEE shall inform the manufacturer and all NCBs participating in the CB Scheme for the standard concerned that the relevant CB Test Certificate has been cancelled, and give the reason for the cancellation.NOTE Each NCB concerned decides for itself if any certification or approval at national level based on that CB Test Certificate should be revoked.4.3 Participation in the CB Scheme4.3.1 Any Member Body of the IECEE shall have the right to nominate a candidate NCB under the conditions stated in 4.3.2. The membership is subject to acceptance by the CMC.When there is more than one accepted NCB in a country, national arrangements shall be made to provide the co-ordination necessary for the operation according to these Rules.An NCB shall not be, or be influenced by, a body which manufactures or trades in electrotechnical equipment and components.NOTE The Member Body of IECEE and the NCB may be the same body.4.3.2 An NCB shall be accepted by the CMC either as a Recognizing NCB according to5.1 or as an Issuing and Recognizing NCB according to 5.2.NOTE The acceptance described in this subclause may be made in two steps or in one step.4.3.3 When certification or approval is needed in a country as a condition to sell a product, it shall be declared by the candidate NCB that the national certification or approval can be based on a CB Test Certificate. When other conditions have to be fulfilled, they shall also be declared for later publication in the CB Bulletin.4.3.4 An NCB nominated by a Member Body of the IECEE to participate in the CB Scheme shall, via the Member Body of the IECEE, send a written application to the Secretary of the IECEE who shall submit the application to the CMC for decision.The application shall contain the following:a) information on legal status, address etc of the candidate NCB;b) a written declaration by the candidate NCB that it is ready to provide for recognition of CB TestCertificates as a basis for national certification or approval to specified standards as required by 4.3.3. The number, the edition, and amendments, if any, shall be specified for each standard. The date from which CB Test Certificates will be recognized at national level shall also be stated for each standard.c) a declaration by the candidate NCB that is willing to abide by these Rules.An Issuing and Recognizing NCB will not be authorized to issue CB Test Certificates for a standard until CB Test Certificates for that standard are recognized by that NCB.National differences, if any, from the specified standards, as well as other requirements (see 4.3.3), shall also be indicated in the application for later publication in the CB Bulletin.There shall not be more than one set of national differences for each country.NOTE Candidate NCBs are strongly recommended to keep the number of national differences as low as possible.The arrangements, when relevant, between the Member Body of the IECEE and the candidate NCB, shall be described, and a written statement from the NCB that it accepts the arrangement and permits the Member Body of the IECEE to act on its behalf according to these Rules shall be submitted.4.3.5 Each Member Body of the IECEE shall communicate the following information relevant to the recognition of CB Test Certificates to the Secretary of the IECEE:−whether or not written information on procedures and rules for certification or approval at national level is available;−whether or not a foreign manufacturer is required to make application for certification or approval at national level through representatives resident in that country.4.3.6 Each Member Body of the IECEE shall inform the Secretary of the IECEE about changes in the information given according to 4.3.4 and about the information according to 4.3.5.4.3.7 An NCB wishing to discontinue recognizing CB Test Certificates for certain standards shall, via the Member Body of the IECEE, notify the Secretary of the IECEE and shall indicate the date from which the discontinuation becomes effective at least one year in advance. Such a notice automatically cancels the right to issue CB Test Certificates to those standards. It is the duty of the Secretary to inform all other Member Bodies of the decision.4.3.8 An NCB wishing to withdraw from the CB Scheme shall notify the Secretary of the IECEE at least one year in advance and shall indicate the reason for the withdrawal and the date from which the withdrawal will become effective. The annual dues for that NCB shall be paid for the calendar year following the year during which the notice was given.4.3.9 Should, in the opinion of the CMC, an NCB hamper the aim, operation or development of the CB Scheme, fail to take action regarding misuse of CB Test Certificates or violate these Rules, the CMC has the right to exclude or to suspend that NCB from the CB Scheme.A decision to exclude or suspend an NCB shall be taken in accordance with the provisions of 5.6 of Publication IECEE 01.4.4 The CB Bulletin4.4.1 The CB Bulletin shall be made available at intervals decided by the CMC.4.4.2 The CB Bulletin shall contain information about−categories of products covered by the CB Scheme,−standards accepted for use in the CB Scheme,−the product standards for which NCBs in each country have declared recognition of CB Test Certificates,−national differences for each standard and country as declared by the NCB(s) and confirmed as detailed in clause 5.2.9 of this IECEE Rules of Procedure,−important rules in addition to the content of the standards which have to be fulfilled in the countries,−the product categories for which NCBs in each country are authorized to issue CB Test Certificates,−CB Test Certificates issued,−accepted NCBs, and−the operation of the CB Scheme, to assist the applicants.4.4.3 The information published in the CB Bulletin is based on information given by the Member Bodies of the IECEE. Neither the IEC nor the Secretary of the IECEE is therefore liable for the accuracy of that information.4.5 ComplaintsIf there are complaints concerning the behaviours of an NCB or CBTL, the case shall be reported tothe Secretary of the IECEE with due documentation of evidence. After review and acceptance of the complaint, the Secretary of the IECEE will submit the case to the Board of Appeal in accordance with the procedure as per the Basic Rules IECEE 01 Annex B.5 Acceptance of National Certification Bodies and of CB Testing LaboratoriesNCBs5.1 Recognizing5.1.1 Prerequisites for Acceptance5.1.1.1 The NCB shall operate a national certification scheme for electrotechnical equipment andcomponents that provides market access to the country of the NCB.5.1.1.2 The NCB shall be nominated to the IECEE by its IECEE Member BodyNote: Anyone in any country is free to recognize CB Test Certificate in the market place. However, only organizations that comply with these requirements are eligible to be accepted as IECEE RecognizingNCBs.Note:a A Recognizing NCB should not be, or be influenced by, a body which manufactures or trades inelectrotechnical equipment and components.b A Recognizing NCB should be impartial and not offer assistance or other services which maycompromise the objectivity of its certification activities and decisions.5.1.2. Application for Acceptance5.1.2.1An application for the acceptance of an NCB as a Recognizing NCB for one or more ProductCategories / Standards accepted for use in the IECEE (IECEE Categories) shall be made bythe candidate NCB through the Member Body the IECEE in the country of the candidateNCB.5.1.2.2 The application shall be submitted to the Executive Secretary of the IECEE and shall beaccompanied by the documentation as detailed in OD-CB2007 as far as applicable.5.1.3 Acceptance5.1.3.1 The Executive Secretary and two appointed Lead Assessors will perform an administrativeassessment of the application documentation to determine whether the candidate Recognizing NCB fulfils the Prerequisites for Acceptance (5.1.1) and complies with otherapplicable requirements of these Rules of Procedure.5.1.3.2 A positive outcome will result in a recommendation to the Peer Assessment Committee forthe acceptance of the Candidate NCB by the CMC.5.1.4 Suspension5.1.4.1 When it is determined that an NCB no longer fulfils the “Requirements for a RecognizingNCB” or if it violates these Rules of Procedure, the NCB shall be offered the opportunity totake corrective action over a period to be determined on a case-by-case following thenature of the infringement.5.1.4.2 The acceptance of a Recognizing NCB may be suspended or withdrawn by the CMC onrecommendation of the Executive Secretary if it no longer fulfil the “Requirements for aRecognizing NCB” or continues to violate these Rules of Procedure or attempts to inflictdamage upon the IECEE’s reputation or image.5.1.4.3 In case of a suspension or withdrawal, the Recognizing NCB shall no longer claim anyassociation with the IECEE.5.2 Acceptance of Issuing and Recognizing NCBsNOTE When an application is made for acceptance of an NCB that intends to employ already accepted CBTLs, assessment is made according to this subclause.Applications for acceptance of an NCB and an associated testing laboratory may be submitted together or as one combined application, and assessment according to 5.2 and 5.3 may be combined.5.2.1 An NCB may be given the right by the CMC to issue CB Test Certificates for specified individual product categories in compliance with specified standards according to the procedures stipulated in 5.2.2 to 5.2.10 and under the following conditions:a) the NCB shall be well established and fulfil the conditions of 5.1.1 for at least the standards forwhich acceptance to issue CB Test Certificates is sought. When the candidate NCB has not earlier been accepted as a Recognizing NCB according to 5.1, the conditions of 5.1.1 shall be included in the assessment;b) the NCB has within its organization, or has an agreement to employ, a CBTL accepted by theIECEE according to 5.3 of these Rules for the relevant product standards;NOTE See the Note to 5.2 under the headline.c) an Issuing and Recognizing NCB shall not be, or be influenced by, a body which manufacturesor trades in Electrotechnical equipment and components. Furthermore, the NCB shall be impartial and not offer assistance or other services which may compromise the objectivity of its certification activities and decisions;d) the competence of the NCB to comply with these Rules shall be demonstrated by assessment.The general competence, efficiency, experience, familiarity with the relevant standards and the products included in those standards as well as compliance with applicable parts of the relevant ISO/IEC Guide 65 shall be taken into consideration. Accreditation, if any, shall be taken into account when a recognized national accreditation body provides an accreditation service in the country.e) Experience is considered sufficient when, within the last 2 (two) years, at least 10 Certificates havebeen issued for the product category applied for but at least one Certificate for the specific part 2 standard applied forNOTE NCBs are encouraged to recognize CB Test Certificates over a wider product area than covered by their right to issue CB Test Certificates.5.2.2 An application for the acceptance of an NCB to issue CB Test Certificates for one or more specified individual products in compliance with specified standards accepted for use in the IECEE shall be made by the candidate NCB, via the Member Body of the IECEE in the country of the candidate NCB.The application shall be submitted to the Secretary of the IECEE and shall be accompanied by the relevant documentation as detailed in OD-CB2007.NOTE When a laboratory is integrated in the organization of the NCB, the application according to this subclause for the NCB and 5.3.2 for the testing laboratory may be combined.5.2.3 The candidate Issuing and Recognizing NCB shall be assessed by three experts to be appointed by the Secretary of the IECEE with a view to determining whether the conditions according to 5.2.1 are fulfilled. These assessors shall normally be recruited from Issuing and Recognizing NCBs.。
TES-77401 Hose_Draft_090506
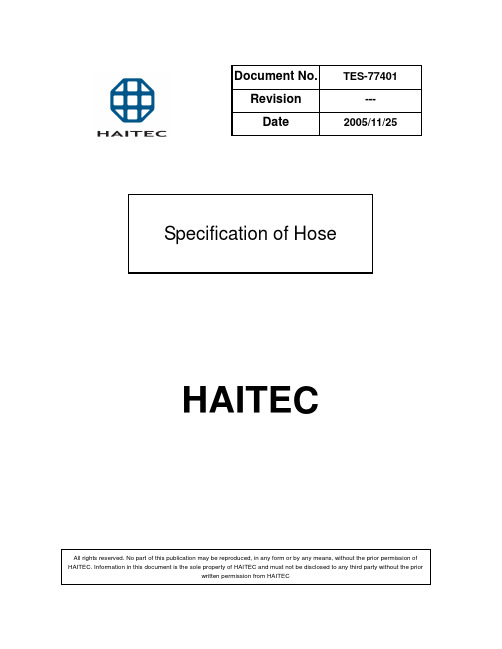
2. Conditions in Use No. Items 2-1 Working oil in use 2-2 Ambient temperature range in use 2-3 Working oil temperature range in use 2-4 Working oil flow range in use 2-5 High pressure Return Suction 2-6
Revision: --Specification of HOSE Date: 2005/11/25 Document Secret Rank:■Extremely Secret
Document No: TES-77401 Page: 4/ 50 □Secret □Ordinary
1. General No. Items Required Specifications 1-1 Part constitution and shapes Follow specification tender. 1-2 Materials of hose 1-3 Materials of tube (including surface treatment) 1-5 Materials of protector 1-6 Materials of insulation 1-7 Bracket specifications
---
Specification of SPR ( LEAF ) Description
Initial release
DOCU NO Date
2005/11/25
TES-77401 Rev by
Copyright © Hua-chuang Automobile Information Technical Center Co., Ltd. All Rights Reserved. After this document series printing is the reference file, only supplies the reference use.
健康档案基本数据集编制规范 2009试行

——表示类术语描述数据元有效值集合的格式。一个数据元需要有一个且仅有一个表示类术语。当表示类术语与特性类术语有重复或部分重复时,可从名称中将冗余词删除。通用表示类术语见表(2)。
死亡日期根本死因代码其他9900未能归入上述各类目的其他信息wstxxx200914附录b规范性附录健康档案相关卫生服务基本数据集分类编码表b1健康档案相关卫生服务基本数据集分类编码一级类目二级类目数据集名称数据集分类编码a基本信息00个人信息基本数据集hra0001公共卫生01儿童保健出生医学证明基本数据集hrb0101新生儿疾病筛查基本数据集hrb0102儿童健康体检基本数据集hrb0103体弱儿童管理基本数据集hrb010402妇女保健婚前保健服务基本数据集hrb0201妇女病普查基本数据集hrb0202计划生育技术服务基本数据集hrb0203孕产期保健服务与高危管理基本数据集hrb0204产前筛查与诊断基本数据集hrb0205出生缺陷监测基本数据集hrb020603疾病控制预防接种基本数据集hrb0301传染病报告基本数据集hrb0302结核病防治基本数据集hrb0303艾滋病防治基本数据集hrb0304血吸虫病病人管理基本数据集hrb0305慢性丝虫病病人管理基本数据集hrb0306职业病报告基本数据集hrb0307职业性健康监护基本数据集hrb0308伤害监测报告基本数据集hrb0309中毒报告基本数据集hrb0310行为危险因素监测基本数据集hrb0311死亡医学证明基本数据集hrb031204疾病管理高血压病例管理基本数据集hrb0401糖尿病病例管理基本数据集hrb0402肿瘤病例管理基本数据集hrb0403精神分裂症病例管理基本数据集hrb0404老年人健康管理基本数据集hrb0405医疗服务00门诊诊疗基本数据集hrc0001住院诊疗基本数据集hrc0002住院病案首页基本数据集hrc0003成人健康体检基本数据集hrc0004社凹积吧范围本标准规定了健康档案基本数据集的内容结构数据元描述规则分类代码和目录格式以及数据集元数据描述规数据集分类编码等
光缆竣工文档。。。。。
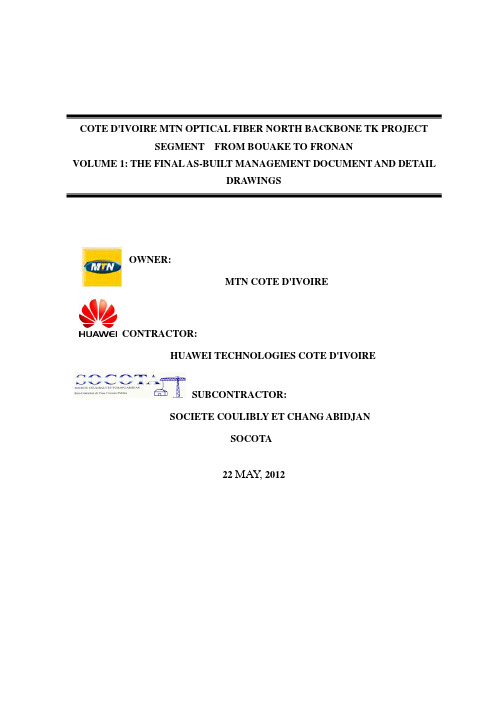
COTE D'IVOIRE MTN OPTICAL FIBER NORTH BACKBONE TK PROJECT SEGMENT FROM BOUAKE TO FRONANVOLUME 1: THE FINAL AS-BUILT MANAGEMENT DOCUMENT AND DETAILDRAWINGSOWNER:MTN COTE D'IVOIRECONTRACTOR:HUAWEI TECHNOLOGIES COTE D'IVOIRESUBCONTRACTOR:SOCIETE COULIBLY ET CHANG ABIDJANSOCOTA22 MAY, 2012CONTENTS1、General introduction of the FOB route2、Fiber Optical Cable Distribution3、The major materials checklist4、The major workload checklist5、Project implement instruction6、The relative signature of the project7、The project delivered report(1) The Delivered Cable Test Report(2) Spliciling test report(3) OTDR test report8. The detail drawing1、General introduction ofthe FOB routeThe ducts fiber route in this segment was from MTN site in Bouake to MTN site in Fronan along with the north backbone road to Ferkessedougou.Start point: Bouake MTN site Area through :Bouake metro ---Allakro MTN site----Kiola----Fronan MTN site Distance :1.Civil route:66839m2.Fiber route:73482mFiber Ducts type and area used:1.3ways PVC: Bouake, kiola2.1way HDPE: The rest route2. Fibre Optical Cable Distribution3.The major materials checklist4. The major workload checklist5. Project implement instruction::THE DELIVERED REPORT OF COTE D'IVOIRE MTN OPTICAL FIBER NORTHBACKBONE TK PROJECTThe Delivered Cable Test ReportSegment:BOUKÉ- FRONAN Date of Testing: 14 / 12/ 2011Signature :Signature:Signature:SOCOTA Representative Huawei Representative MTN RepresentativeThe Delivered Cable Test ReportSegment:BOUKÉ- FRONAN Date of Testing: 14 / 12 / 2011Signature :Signature:Signature:SOCOTA Representative Huawei Representative MTN RepresentativeSegment:BOUKÉ- FRONAN Date of Testing: 14 / 12 / 2011Signature :Signature:Signature:SOCOTA Representative Huawei Representative MTN RepresentativeSegment:BOUKÉ- FRONAN Date of Testing: 14 / 12 / 2011Signature :Signature:Signature:SOCOTA Representative Huawei Representative MTN RepresentativeSegment:BOUKÉ- FRONAN Date of Testing: 14 /12 / 2011Signature :Signature:Signature:SOCOTA Representative Huawei Representative MTN RepresentativeThe Delivered Cable Test ReportSegment:BOUKÉ- FRONAN Date of Testing: 14 /12 / 2011Signature :Signature:Signature:SOCOTA Representative Huawei Representative MTN RepresentativeSignature :Signature:Signature:SOCOTA Representative Huawei Representative MTN RepresentativeSignature :Signature:Signature:SOCOTA Representative Huawei Representative MTN RepresentativeThe Delivered Cable Test ReportSegment:BOUKÉ- FRONAN Date of Testing: 14 /12 / 2011Signature :Signature:Signature:SOCOTA Representative Huawei Representative MTN RepresentativeThe Delivered Cable Test ReportSegment:BOUKÉ- FRONAN Date of Testing: 14 /12 / 2011Signature :Signature:Signature:SOCOTA Representative Huawei Representative MTN RepresentativeThe Delivered Cable Test ReportSegment:BOUKÉ- FRONAN Date of Testing: 14 /12 / 2011Signature :Signature:Signature:SOCOTA Representative Huawei Representative MTN RepresentativeThe Delivered Cable Test ReportSegment:BOUKÉ- FRONAN Date of Testing: 14 /12 / 2011Signature :Signature:Signature:SOCOTA Representative Huawei Representative MTN RepresentativeThe Delivered Cable Test ReportSegment:BOUKÉ- FRONAN Date of Testing: 14 /12 / 2011Signature :Signature:Signature:SOCOTA Representative Huawei Representative MTN RepresentativeThe Delivered Cable Test ReportSegment:BOUKÉ- FRONAN Date of Testing: 14 /12 / 2011Signature :Signature:Signature:SOCOTA Representative Huawei Representative MTN RepresentativeThe Delivered Cable Test ReportSegment:BOUKÉ- FRONAN Date of Testing: 14 /12 / 2011Signature :Signature:Signature:SOCOTA Representative Huawei Representative MTN RepresentativeThe Delivered Cable Test ReportSegment:BOUKÉ- FRONAN Date of Testing: 14 /12 / 2011Signature :Signature:Signature:SOCOTA Representative Huawei Representative MTN RepresentativeThe Delivered Cable Test ReportSegment:BOUKÉ- FRONAN Date of Testing: 14 /12 / 2011Signature :Signature:Signature:SOCOTA Representative Huawei Representative MTN RepresentativeThe Delivered Cable Test ReportSegment:BOUKÉ- FRONAN Date of Testing: 14 /12 / 2011Signature :Signature:Signature:SOCOTA Representative Huawei Representative MTN RepresentativeThe Delivered Cable Test ReportSegment:BOUKÉ- FRONAN Date of Testing: 14 /12 / 2011Signature :Signature:Signature:SOCOTA Representative Huawei Representative MTN RepresentativeThe Delivered Cable Test ReportSegment:BOUKÉ- FRONAN Date of Testing: 14 /12 / 2011Signature :Signature:Signature:SOCOTA Representative Huawei Representative MTN RepresentativeThe Delivered Cable Test ReportSegment:BOUKÉ- FRONAN Date of Testing: 14 /12 / 2011Signature :Signature:Signature:SOCOTA Representative Huawei Representative MTN RepresentativeThe Delivered Cable Test ReportSegment:BOUKÉ- FRONAN Date of Testing: 14 /12 / 2011Signature :Signature:Signature:SOCOTA Representative Huawei Representative MTN RepresentativeThe Delivered Cable Test ReportSegment:BOUKÉ- FRONAN Date of Testing: 14 /12 / 2011Signature :Signature:Signature:SOCOTA Representative Huawei Representative MTN RepresentativeThe Delivered Cable Test ReportSegment:BOUKÉ- FRONAN Date of Testing: 14 /12 / 2011Signature :Signature:Signature:SOCOTA Representative Huawei Representative MTN RepresentativeThe Delivered Cable Test ReportSegment:BOUKÉ- FRONAN Date of Testing: 14 /12 / 2011Signature :Signature:Signature:SOCOTA Representative Huawei Representative MTN Representative(2)FIBER SPLICING LOSS MONITOR RECORDSegment: From Segment: From BOUKÉ to FRONANLocation: (N:06.88685°,W:05.010030°)Splicing Machine:FUJUKURA 60S Test Instrument:EXFO FTB-7300DSOCOTA Representative: Huawei Representative: MTN Representative:FIBER SPLICING LOSS MONITOR RECORDSegment: From Segment: From BOUKÉ to FRONANLocation: (N:07.693112°,W:05.025131°)Splicing Machine:FUJUKURA 60S Test Instrument:EXFO FTB-7300DSOCOTA Representative: Huawei Representative: MTN Representative:Segment: From Segment: From BOUKÉ to FRONANLocation: (N:07.714711°,W:05.026225°)Splicing Machine:FUJUKURA 60S Test Instrument:EXFO FTB-7300DSOCOTA Representative: Huawei Representative: MTN Representative:Segment: From Segment: From BOUKÉ to FRONAN Location: ()Location: (N:07.741203°,W:05.034034°)Splicing Machine:FUJUKURA 60S Test Instrument:EXFO FTB-7300DSOCOTA Representative: Huawei Representative: MTN Representative:Splicing Machine:FUJUKURA 60S Test Instrument:EXFO FTB-7300DSOCOTA Representative: Huawei Representative: MTN Representative:Splicing Machine:FUJUKURA 60S Test Instrument:EXFO FTB-7300DSOCOTA Representative: Huawei Representative: MTN Representative:Splicing Machine:FUJUKURA 60S Test Instrument:EXFO FTB-7300DSOCOTA Representative: Huawei Representative: MTN Representative:Splicing Machine:FUJUKURA 60S Test Instrument:EXFO FTB-7300DSOCOTA Representative: Huawei Representative: MTN Representative:Splicing Machine:FUJUKURA 60S Test Instrument:EXFO FTB-7300DSOCOTA Representative: Huawei Representative: MTN Representative:Splicing Machine:FUJUKURA 60S Test Instrument:EXFO FTB-7300DSOOCTA Representative: Huawei Representative: MTN Representative:Splicing Machine:FUJUKURA 60S Test Instrument:EXFO FTB-7300DSOOCTA Representative: Huawei Representative: MTN Representative:FIBER SPLICING LOSS MONITOR RECORDSegment: From Segment: From BOUKÉ to FRONANLocation: (N:07.9544°,W:05.0601°)Splicing Machine:FUJUKURA 60S Test Instrument:EXFO FTB-7300DSOCOTA Representative: Huawei Representative: MTN Representative:Splicing Machine:FUJUKURA 60S Test Instrument:EXFO FTB-7300DSOCOTA Representative: Huawei Representative: MTN Representative:Splicing Machine:FUJUKURA 60S Test Instrument:EXFO FTB-7300DSOOCTA Representative: Huawei Representative: MTN Representative:Splicing Machine:FUJUKURA 60S Test Instrument:EXFO FTB-7300DSOOCTA Representative: Huawei Representative: MTN Representative:Splicing Machine:FUJUKURA 60S Test Instrument:EXFO FTB-7300DSOOCTA Representative: Huawei Representative: MTN Representative:Splicing Machine:FUJUKURA 60S Test Instrument:EXFO FTB-7300DSOOCTA Representative: Huawei Representative: MTN Representative:。
IC datasheet pdf-TAS5705,pdf(20-W stereo Digital Audio Power Amplifier)
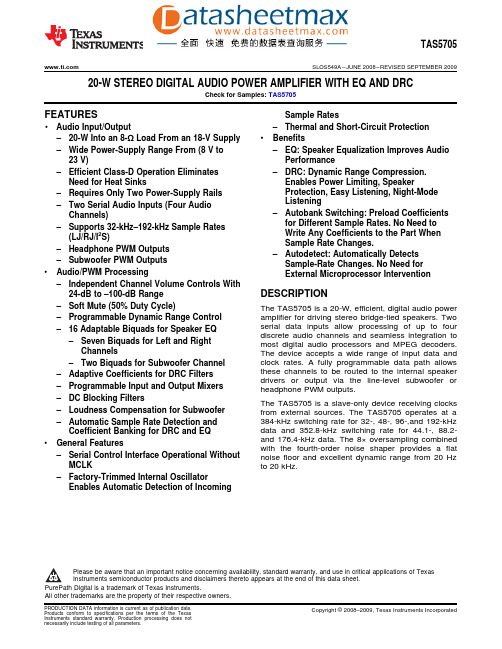
TAS5705................................................................................................................................................SLOS549A–JUNE2008–REVISED SEPTEMBER2009 20-W STEREO DIGITAL AUDIO POWER AMPLIFIER WITH EQ AND DRCCheck for Samples:TAS5705FEATURES Sample Rates•Audio Input/Output–Thermal and Short-Circuit Protection –20-W Into an8-ΩLoad From an18-V Supply•Benefits–Wide Power-Supply Range From(8V to–EQ:Speaker Equalization Improves Audio 23V)Performance–Efficient Class-D Operation Eliminates–DRC:Dynamic Range Compression.Need for Heat Sinks Enables Power Limiting,SpeakerProtection,Easy Listening,Night-Mode –Requires Only Two Power-Supply RailsListening–Two Serial Audio Inputs(Four Audio–Autobank Switching:Preload Coefficients Channels)for Different Sample Rates.No Need to –Supports32-kHz–192-kHz Sample RatesWrite Any Coefficients to the Part When (LJ/RJ/I2S)Sample Rate Changes.–Headphone PWM Outputs–Autodetect:Automatically Detects –Subwoofer PWM Outputs Sample-Rate Changes.No Need for •Audio/PWM Processing External Microprocessor Intervention –Independent Channel Volume Controls With24-dB to–100-dB Range DESCRIPTION–Soft Mute(50%Duty Cycle)The TAS5705is a20-W,efficient,digital audio poweramplifier for driving stereo bridge-tied speakers.Two –Programmable Dynamic Range Controlserial data inputs allow processing of up to four –16Adaptable Biquads for Speaker EQdiscrete audio channels and seamless integration to –Seven Biquads for Left and Right most digital audio processors and MPEG decoders.Channels The device accepts a wide range of input data andclock rates.A fully programmable data path allows –Two Biquads for Subwoofer Channelthese channels to be routed to the internal speaker –Adaptive Coefficients for DRC Filtersdrivers or output via the line-level subwoofer or –Programmable Input and Output Mixers headphone PWM outputs.–DC Blocking FiltersThe TAS5705is a slave-only device receiving clocks –Loudness Compensation for Subwoofer from external sources.The TAS5705operates at a384-kHz switching rate for32-,48-,96-,and192-kHz –Automatic Sample Rate Detection anddata and352.8-kHz switching rate for44.1-,88.2-Coefficient Banking for DRC and EQand176.4-kHz data.The8×oversampling combined •General Featureswith the fourth-order noise shaper provides a flat –Serial Control Interface Operational Without noise floor and excellent dynamic range from20Hz MCLK to20kHz.–Factory-Trimmed Internal OscillatorEnables Automatic Detection of IncomingPlease be aware that an important notice concerning availability,standard warranty,and use in critical applications of TexasInstruments semiconductor products and disclaimers thereto appears at the end of this data sheet.Digital is a trademark of Texas Instruments.All other trademarks are the property of their respective owners.PRODUCTION DATA information is current as of publication date.Copyright©2008–2009,Texas Instruments Incorporated Products conform to specifications per the terms of the TexasInstruments standard warranty.Production processing does notnecessarily include testing of all parameters.TAS5705SLOS549A–JUNE2008–REVISED SIMPLIFIED APPLICATION DIAGRAMB0264-012Submit Documentation Feedback Copyright©2008–2009,Texas Instruments IncorporatedProduct Folder Link(s):TAS5705TAS5705 ................................................................................................................................................SLOS549A–JUNE2008–REVISED SEPTEMBER2009 FUNCTIONAL VIEWCopyright©2008–2009,Texas Instruments Incorporated Submit Documentation Feedback3Product Folder Link(s):TAS5705TAS5705SLOS549A–JUNE2008–REVISED Figure1.Power Stage Functional Block Diagram4Submit Documentation Feedback Copyright©2008–2009,Texas Instruments IncorporatedProduct Folder Link(s):TAS5705BKND_ERR VALIDDVDDD V S SD V S S O S D I N 1S D I N 2L R C L K S C L K MCLK M U TE H P S E L O S C _R E SP D N S D A S C L V R _D I GV R E G _E N S T E S T T E S T 2HPL_PWM HPR_PWM SUB_PWM–SUB_PWM+GNDGND GVDD_CD V D D _B V D D _B V D D _C V D D _C PVDD_D PVDD_D G N D _A BG N D _A B G N D _C D G N D _C D VREG U T _AU T _B U T _B U T _C U T _C OUT_D U T _DS T _B S T _C BST_D P0071-01PAP Package (Top View)TAS5705 ................................................................................................................................................SLOS549A –JUNE 2008–REVISED SEPTEMBER 200964-PIN,HTQFP PACKAGE (TOP VIEW)TERMINAL FUNCTIONSTERMINAL TYPE5-V TERMINATIONDESCRIPTION(1)TOLERANT(2)NAME NO.AVDD 10P 3.3-V analog power supply.Needs close decoupling capacitor.AVSS 11P Analog 3.3-V supply groundBKND_ERR35DIPullupActive-low.A back-end error sequence is generated by applying logic LOW to this terminal.This pin is connected to an external power stage.If no external power stage is used,connect this pin directly to DVDD.BST_A 4P High-side bootstrap supply for half-bridge A BST_B 57P High-side bootstrap supply for half-bridge B BST_C 56P High-side bootstrap supply for half-bridge C BST_D 45PHigh-side bootstrap supply for half-bridge D(1)TYPE:A =analog;D =3.3-V digital;P =power/ground/decoupling;I =input;O =output(2)All pullups are 20-μA weak pullups and all pulldowns are 20-μA weak pulldowns.The pullups and pulldowns are included to assure proper input logic levels if the terminals are left unconnected (pullups →logic 1input;pulldowns →logic 0input).Devices that drive inputs with pullups must be able to sink 50μA while maintaining a logic-0drive level.Devices that drive inputs with pulldowns must be able to source 50μA while maintaining a logic-1drive level.Copyright ©2008–2009,Texas Instruments IncorporatedSubmit Documentation Feedback5Product Folder Link(s):TAS5705TAS5705SLOS549A–JUNE2008–REVISED TERMINAL FUNCTIONS(continued)TERMINAL TYPE5-V TERMINATIONDESCRIPTION(1)TOLERANT(2)NAME NO.DVDD15,33P 3.3-V digital power supplyDVSS20P Digital groundDVSSO26P Oscillator groundFAULT9DO Pullup Overtemperature,overcurrent,and undervoltage fault reporting.Active-low indicates fault.If high,normal operation.GND41,42P Analog ground for power stageGVDD_AB5P Gate drive internal regulated output for AB channelsGVDD_CD44P Gate drive internal regulated output for CD channelsHPL_PWM37DO Headphone left-channel PWM output.HPR_PWM38DO Headphone right-channel PWM output.HPSEL30DI5-V Headphone select,active-high.When a logic high is applied,deviceenters headphone mode and speakers are MUTED(HARD MUTE).When a logic LOW is applied,device is in speaker mode andheadphone outputs become line outputs or are disabled.When in lineout mode,this terminal functionality is disabled(see system controlregister2.LRCLK22DI5-V Input serial audio data left/right clock(sampling rate clock)MCLK34DI5-V MCLK is the clock master input.The input frequency of this clock canrange from4.9MHz to49.2MHz.MUTE21DI5-V Pullup Performs a soft mute of outputs,active-low.A logic low on this pinsets the outputs equal to50%duty cycle.A logic high on this pinallows normal operation.The mute control provides a noiselessvolume ramp to silence.Releasing mute provides a noiseless ramp toprevious volume.OC_ADJ8AO Analog overcurrent programming.Requires22-kΩresistor to ground. OSC_RES19AO Oscillator trim resistor.Connect an18.2-kΩ,1%tolerance resistor toDVSSO.OUT_A1,64O Output,half-bridge AOUT_B60,61O Output,half-bridge BOUT_C52,53O Output,half-bridge COUT_D48,49O Output,half-bridge DPDN17DI5-V Pullup Power down,active-low.PDN powers down all logic,stops all clocks,and stops output switching whenever a logic low is applied.WhenPDN is released,the device powers up all logic,starts all clocks,andperforms a soft start that returns to the previous configurationdetermined by register settings.PGND_AB62,63P Power ground for half-bridges A and BPGND_CD50,51P Power ground for half-bridges C and DPLL_FLTM12AO PLL negative loop filter terminalPLL_FLTP13AI PLL positive loop filter terminalPVDD_A2,3P Power supply input for half-bridge output A(8V–23V)PVDD_B58,59P Power supply input for half-bridge output B(8V–23V)PVDD_C54,55P Power supply input for half-bridge output C(8V–23V)PVDD_D46,47P Power supply input for half-bridge output D(8V–23V)RESET16DI5-V Pullup Reset,active-low.A system reset is generated by applying a logiclow to this terminal.RESET is an asynchronous control signal thatrestores the DAP to its default conditions,sets the VALID outputslow,and places the PWM in the hard-mute state(stops switching).Master volume is immediately set to full attenuation.Upon the releaseof RESET,if PDN is high,the system performs a4–5-ms deviceinitialization and sets the volume at mute.SCL29DI5-V I2C serial control clock input6Submit Documentation Feedback Copyright©2008–2009,Texas Instruments IncorporatedProduct Folder Link(s):TAS5705TAS5705 ................................................................................................................................................SLOS549A–JUNE2008–REVISED SEPTEMBER2009TERMINAL FUNCTIONS(continued)TERMINAL TYPE5-V TERMINATIONDESCRIPTION(1)TOLERANT(2)NAME NO.SCLK23DI5-V Serial audio data clock(shift clock).SCLK is the serial audio portinput data bit clock.SDA28DIO5-V I2C serial control data interface input/outputSDIN125DI5-V Serial audio data1input is one of the serial data input ports.SDIN1supports three discrete(stereo)data formats.SDIN224DI5-V Serial audio data2input is one of the serial data input ports.SDIN2supports three discrete(stereo)data formats.SSTIMER6AI Controls ramp time of OUT_X for pop-free operation.Leave this pinfloating for BD mode.Requires capacitor of2.2nF to GND in ADmode.The capacitor determines the ramp time of PWM outputs from0%to50%.For2.2nF,start/stop time is~10ms.STEST31DI Test pin.Connect directly to GND.SUB_PWM–39DO Subwoofer negative PWM outputSUB_PWM+40DO Subwoofer positive PWM outputTEST17DI Test pin.Connect directly to GND.TEST232DI Test pin.Connect directly to DVDD.VALID36DO Output indicating validity of ALL PWM channels,active-high.This pinis connected to an external power stage.If no external power stage isused,leave this pin floating.VR_ANA14P Internally regulated1.8-V analog supply voltage.This terminal mustnot be used to power external devices.VR_DIG27P Internally regulated1.8V digital supply voltage.This terminal must notbe used to power external devices.VREG43P 3.3Regulator output.Not to be used as s supply or connected to anyother components other than decoupling caps.Add decouplingcapacitors with pins42and41.VREG_EN18DI Pulldown Voltage regulator enable.Connect directly to GND.ABSOLUTE MAXIMUM RATINGSover operating free-air temperature range(unless otherwise noted)(1)VALUE UNIT DVDD,AVDD–0.3to3.6V Supply voltagePVDD_X–0.3to30VOC_ADJ–0.3to4.2VInput voltage 3.3-V digital input–0.5to DVDD+0.5V 5-V tolerant(2)digital input–0.5to DVDD+2.5VOUT_x to PGND_X32(3)VBST_x to PGND_X43(3)VInput clamp current,I IK(V I<0or V I>1.8V)±20mA Output clamp current,I OK(V O<0or V O>1.8V)±20mA Operating free-air temperature0to85°C Operating junction temperature range0to150°C Storage temperature range,T stg–40to125°C (1)Stresses beyond those listed under absolute ratings may cause permanent damage to the device.These are stress ratings only andfunctional operation of the device at these or any other conditions beyond those indicated under recommended operation conditions are not implied.Exposure to absolute-maximum conditions for extended periods may affect device reliability.(2)5-V tolerant inputs are SCLK,LRCLK,MCLK,SDIN1,SDIN2,SDA,SCL,and HPSEL.(3)DC voltage+peak ac waveform measured at the pin should be below the allowed limit for all conditions.Copyright©2008–2009,Texas Instruments Incorporated Submit Documentation Feedback7Product Folder Link(s):TAS5705TAS5705SLOS549A–JUNE2008–REVISED DISSIPATION RATINGSDERATING FACTOR T A≤25°C T A=70°C T A=85°C PACKAGEABOVE T A=25°C POWER RATING POWER RATING POWER RATING10-mm×10-mm QFP40mW/°C5W 3.2W 2.6W RECOMMENDED OPERATING CONDITIONSMIN NOM MAX UNIT Digital/analog supply voltage DVDD,AVDD3 3.3 3.6VHalf-bridge supply voltage PVDD_X823VV IH High-level input voltage 3.3-V TTL,5-V tolerant2 5.5VV IL Low-level input voltage 3.3-V TTL,5-V tolerant0.8VT A Operating ambient temperature range085°CT J Operating junction temperature range0150°CR L(BTL)68Load impedance Output filter:L=15μH,C=0.68μFΩR L(SE) 3.24L O(BTL)10Minimum output inductance underOutput-filter inductanceμHshort-circuit conditionL O(SE)10PWM OPERATION AT RECOMMENDED OPERATING CONDITIONSPARAMETER TEST CONDITIONS MODE VALUE UNIT32–kHz data rate±2%12×sample rate384kHz Output sample rate2×–1×44.1-,88.2-,176.4-kHz data rate±2%8×,4×,and2×sample rates352.8kHz oversampled48-,96-,192-kHz data rate±2%8×,4×,and2×sample rates384kHz PLL INPUT PARAMETERS AND EXTERNAL FILTER COMPONENTSPARAMETER TEST CONDITIONS MIN TYP MAX UNITf MCLKI Frequency,MCLK(1/t cyc2) 4.949.2MHzMCLK duty cycle40%50%60%MCLK minimum high time8nsMCLK minimum low time8nsLRCLK allowable drift before LRCLK reset4MCLKs External PLL filter capacitor C1SMD0603Y5V47nFExternal PLL filter capacitor C2SMD0603Y5V 4.7nFExternal PLL filter resistor R SMD0603,metal film470Ω8Submit Documentation Feedback Copyright©2008–2009,Texas Instruments IncorporatedProduct Folder Link(s):TAS5705TAS5705 ................................................................................................................................................SLOS549A–JUNE2008–REVISED SEPTEMBER2009 ELECTRICAL CHARACTERISTICSDC CharacteristicsT A=25°,PVCC_X=18V,DVDD=AVDD=3.3V,R L=8Ω,BTL mode(unless otherwise noted)PARAMETER TEST CONDITIONS MIN TYP MAX UNITV OH High-level output voltage 3.3-V TTL and5-V tolerant(1)I OH=–4mA 2.4VV OL Low-level output voltage 3.3-V TTL and5-V tolerant(1)I OL=4mA0.5V3.3-V TTL V I=V IL±2I IL(2)Low-level input currentμA5-V tolerant(1)V I=0V,DVDD=3V±23.3-V TTL V I=V IH±2I IH(2)High-level input currentμA5-V tolerant V I=5.5V,DVDD=3V±20Normal Mode6583Digital supply voltage(DVDD,Power down(PDN=823I DD Digital supply current mAAVDD)low)Reset(RESET=low)2338.5I PVDD Analog supply current No load(all PVDD inputs)3060Power down(PDN=5 6.3I PVDD(PDN)Power-down current No load(all PVDD inputs)mAlow)I PVDD(RESET)Reset current No load(all PVDD inputs)Reset(RESET=low)5 6.3Drain-to-source resistance,180T J=25°C,includes metallization resistanceLSr DS(on)mΩDrain-to-source resistance,T J=25°C,includes metallization resistance180HSI/O ProtectionV uvp Undervoltage protection limit PVDD falling7.2VV uvp,hyst Undervoltage protection limit PVDD rising7.6V OTE(3)Overtemperature error150°C Extra temperature dropOTE HYST(3)required to recover from30°C errorOLPC Overload protection counter f PWM=384kHz0.63msResistor—programmable,max.current, 4.5I OC Overcurrent limit protection AR OCP=22kΩI OCT Overcurrent response time150nsResistor tolerance=5%for typical value;the minimumOC programming resistorR OCP resistance should not be less than20kΩ.This value is2022kΩrangenot adjustable.It must be fixed at22kΩ.Internal pulldown resistor at Connected when RESET is active to provide bootstrapR PD3kΩthe output of each half-bridge capacitor charge.(1)5-V tolerant inputs are PDN,RESET,MUTE,SCLK,LRCLK,MCLK,SDIN1,SDIN2,SDA,SCL,and HPSEL.(2)I IL or I IH for pins with internal pullup can go up to50μA.(3)Specified by designCopyright©2008–2009,Texas Instruments Incorporated Submit Documentation Feedback9Product Folder Link(s):TAS5705TAS5705SLOS549A–JUNE2008–REVISED AC Characteristics(BTL)PVDD_X=18V,BTL mode,R L=8Ω,R OC=22KΩ,C BST=33nF,audio frequency=1kHz,AES17filter,f PWM=384kHz,T A=25°C(unless otherwise noted).All performance is in accordance with recommended operating conditions,unless otherwise specified.PARAMETER TEST CONDITIONS MIN TYP MAX UNITPVDD=18V,10%THD,1-kHz input signal20.0PVDD=18V,7%THD,1-kHz input signal18.6PVDD=12V,10%THD,1-kHz input9signalP O Power output per channel WPVDD=12V,7%THD,1-kHz input signal8.3PVDD=8V,10%THD,1-kHz input signal 3.9PVDD=8V,7%THD,1-kHz input signal 3.7PVDD=18V;P O=10W(half-power)0.12%THD+N Total harmonic distortion+noise PVDD=12V;P O=4.5W(half-power)0.1%PVDD=8V;P O=2W(half-power)0.24%V n Output integrated noise A-weighted50μV Crosstalk P O=1W,f=1kHz–73dBA-weighted,f=1kHz,maximum power atSNR Signal-to-noise ratio(1)105dBTHD<0.1%P D Power dissipation due to idle losses(I PVDD_X)P O=0W,4channels switching(2)0.6W(1)SNR is calculated relative to0-dBFS input level.(2)Actual system idle losses are affected by core losses of output inductors.AC Characteristics(Single-Ended Output)PVDD_X=18V,SE mode,R L=4Ω,R OC=22kΩ,C BST=33-nF,audio frequency=1kHz,AES17filter,f PWM=384kHz, ambient temperature=25°C(unless otherwise noted).All performance is in accordance with recommended operating conditions,unless otherwise specified.PARAMETER TEST CONDITIONS MIN TYP MAX UNITPVDD=18V,10%THD10PVDD=18V,7%THD9P O Power output per channel WPVDD=12V,10%THD 4.5PVDD=12V,7%THD4PVDD=18V,Po=5W(half-power)0.2THD+Total harmonic distortion+noise%N PVDD=12V,Po=2.25W(half-power)0.2V n Output integrated noise A-weighted50μV SNR Signal-to-noise ratio(1)A-weighted105dB DNR Dynamic range A-weighted,input level=–60dBFS using TAS5086modulator105dBPower dissipation due to idleP D P O=0W,4channels switching(2)0.6W losses(IPVDD_X)(1)SNR is calculated relative to0-dBFS input level.(2)Actual system idle losses are affected by core losses of output inductors.10Submit Documentation Feedback Copyright©2008–2009,Texas Instruments IncorporatedProduct Folder Link(s):TAS5705SERIAL AUDIO PORTS SLAVE MODEover recommended operating conditions(unless otherwise noted)TESTPARAMETER MIN TYP MAX UNITCONDITIONSf SCLKIN Frequency,SCLK32×f S,48×f S,64×f S C L=30pF 1.02412.288MHz t su1Setup time,LRCLK to SCLK rising edge10ns t h1Hold time,LRCLK from SCLK rising edge10ns t su2Setup time,SDIN to SCLK rising edge10ns t h2Hold time,SDIN from SCLK rising edge10ns LRCLK frequency3248192kHz SCLK duty cycle40%50%60%LRCLK duty cycle40%50%60%SCLK SCLK rising edges between LRCLK rising edges3264edgest(edge)SCLK LRCLK clock edge with respect to the falling edge of SCLK–1/41/4periodFigure2.Slave Mode Serial Data Interface TimingSCLSDAT0027-01 SCLSDAStart ConditionStopConditionT0028-01I2C SERIAL CONTROL PORT OPERATIONTiming characteristics for I2C Interface signals over recommended operating conditions(unless otherwise noted)PARAMETER TEST CONDITIONS MIN MAX UNIT f SCL Frequency,SCL No wait states400kHz t w(H)Pulse duration,SCL high0.6μs t w(L)Pulse duration,SCL low 1.3μs t r Rise time,SCL and SDA300ns t f Fall time,SCL and SDA300ns t su1Setup time,SDA to SCL100ns t h1Hold time,SCL to SDA0ns t(buf)Bus free time between stop and start condition 1.3μs t su2Setup time,SCL to start condition0.6μs t h2Hold time,start condition to SCL0.6μs t su3Setup time,SCL to stop condition0.6μs C L Load capacitance for each bus line400pFFigure3.SCL and SDA TimingFigure4.Start and Stop Conditions TimingRESETVALIDtStart systemSystem initialization.Enable via I C.2T0029-05PDNVALIDt T0030-04RESET TIMING (RESET)Control signal parameters over recommended operating conditions (unless otherwise noted)PARAMETERMIN TYP MAX UNIT t d(VALID_LOW)Time to assert VALID (reset to power stage)low 100ns t w(RESET)Pulse duration,RESET active 100200ns t d(I2C_ready)Time to enable I 2C3.5ms t d(run)Device start-up time (after start-up command via I 2C)10msNOTE:On power up,it is recommended that the TAS5705be held LOW for at least 100μs after DVDD has reached3.0V.RESET assertion is ignored if applied while part is powered downFigure 5.Reset TimingPOWER-DOWN (PDN)TIMINGControl signal parameters over recommended operating conditions (unless otherwise noted)PARAMETERMINTYP MAXUNIT t d(VALID_LOW)Time to assert VALID (reset to power stage)low 725μs t d(STARTUP)Device startup time650μs t wMinimum pulse duration required1μsNOTE:PDNZ assertion is ignored if applied when part is in RESETFigure 6.Power-Down TimingDVDD PVDDT0317-01DVDDRESETPDNT0318-01Figure7.Power Up and Power Down of Power SuppliesNOTE:t power_down=time to wait before powering down the supplies after assertion=725μs+power-stage stop time defined by register0x1AFigure8.Terminal Control and DVDDBKND_ERRVALIDVOLUMEMUTET0032-03BACK-END ERROR (BKND_ERR)Control signal parameters over recommended operating conditions (unless otherwise noted)PARAMETERMIN TYP MAX UNIT t w(ER)Minimum pulse duration,BKND_ERR active (active-low)350nst p(valid_high)Programmable.Time to stay in the VALID (reset to the power stage)low state.After t p(valid_high),the TAS5705attempts to bring the system out of the VALID low state if 300ms BKND_ERR is high.t p(valid_low)Time TAS5705takes to bring VALID (reset to the power stage)low after BKND_ERR ns400assertion.Figure 9.Error Recovery TimingMUTE TIMING Control signal parameters over recommended operating conditions (unless otherwise noted)PARAMETERMINTYP MAXUNIT Volume ramp time (=number of steps ×step size).Number of steps is defined by volume t d(VOL)configuration register 0x0E (see Volume Configuration Register ).Step size =4LRCLKs if 1024stepsf S ≤48kHz;else 8LRCLKs if f S ≤96kHz ;else 16LRCLKsFigure 10.Mute TimingHP VolumeHPSELVALIDSpkr VolumeSpkr VolumeHPSELVALIDHP VolumeHEADPHONE SELECT (HPSEL)PARAMETERMIN MAX UNIT t w(MUTE)Pulse duration,HPSEL active 350ns t d(VOL)Soft volume update timeSee(1)ms t (SW)Switch-over time (controlled by start/stop period register,0x1A)0.2ms(1)Defined by the volume slew rate setting (see the volume configuration register ,0x0E).Figure 11and Figure 12show functionality when bit 4in the HP configuration register is set to DISABLE (not in line-out mode).See register 0x05for details.If bit 4is not set,than the HP PWM outputs are not disabled when HPSEL is brought low.Figure 11.HPSEL Timing for Headphone InsertionFigure 12.HPSEL Timing for Headphone Extractionf − Frequency − Hz 201001k10k T H D +N − T o t a l H a r m o n i c D i s t o r t i o n + N o i s e − %20kG0030.0010.01100.11f − Frequency − Hz 201001k10k T H D +N − T o t a l H a r m o n i c D i s t o r t i o n + N o i s e − %20kG0020.0010.01100.11f − Frequency − Hz201001k10k T H D +N − T o t a l H a r m o n i c D i s t o r t i o n + N o i s e − %20kG0010.0010.01100.11P O − Output Power − W0.010.1110T H D +N − T o t a l H a r m o n i c D i s t o r t i o n + N o i s e − %40G006TYPICAL CHARACTERISTICS,BTL CONFIGURATIONTOTAL HARMONIC DISTORTION +NOISE (BTL)TOTAL HARMONIC DISTORTION +NOISE (BTL)vsvsFREQUENCYFREQUENCYFigure 13.Figure 14.TOTAL HARMONIC DISTORTION +NOISE (BTL)TOTAL HARMONIC DISTORTION +NOISE (BTL)vsvsFREQUENCY OUTPUT POWERFigure 15.Figure 16.P O − Output Power − W 0.010.111040G005P O − Output Power − W 0.010.111040G004P O − Total Output Power − W0.00.51.01.52.02.53.0510152025303540G008P O − Output Power (Per Channel) − W010203040506070809010002468101214161820E f f i c i e n c y − %G007TOTAL HARMONIC DISTORTION +NOISE (BTL)TOTAL HARMONIC DISTORTION +NOISE (BTL)vsvsOUTPUT POWEROUTPUT POWERFigure 17.Figure 18.EFFICIENCYSUPPLY CURRENTvsvsOUTPUT POWERTOTAL OUTPUT POWERFigure 19.Figure 20.PVDD − Supply Voltage − V051015202568101214161820P O − O u t p u t P o w e r − WG009−100−95−90−85−80−75−70−65−60 f − Frequency − Hz C r o s s t a l k − d BG012201001k10k 20kOUTPUT POWERCROSSTALKvsvsSUPPLY VOLTAGEFREQUENCYFigure 21.Figure 22.f − Frequency − Hz 201001k10k T H D +N − T o t a l H a r m o n i c D i s t o r t i o n + N o i s e − %0.0011020k0.1G01210.01f − Frequency − Hz 201001k10k T H D +N − T o t a l H a r m o n i c D i s t o r t i o n + N o i s e − %0.0011020k0.1G01210.01V CC − Supply Voltage − V369121518510152025P O − O u t p u t P o w e r − WG014P O − Output Power − W 0.010.111040G013TYPICAL CHARACTERISTICS,SE CONFIGURATIONTOTAL HARMONIC DISTORTION +NOISETOTAL HARMONIC DISTORTION +NOISEvsvsFREQUENCYFREQUENCYFigure 23.Figure 24.TOTAL HARMONIC DISTORTION +NOISEOUTPUT POWERvsvsOUTPUT POWER SUPPLY VOLTAGEFigure 25.Figure 26.TAS5705 ................................................................................................................................................SLOS549A–JUNE2008–REVISED SEPTEMBER2009DETAILED DESCRIPTIONPOWER SUPPLYTo facilitate system design,the TAS5705needs only a3.3-V digital supply in addition to the(typical)18-V power-stage supply.An internal voltage regulator provides suitable voltage levels for the gate drive circuitry. Additionally,all circuitry requiring a floating voltage supply,e.g.,the high-side gate drive,is accommodated by built-in bootstrap circuitry requiring only a few external capacitors.In order to provide good electrical and acoustical characteristics,the PWM signal path for the output stage is designed as identical,independent half-bridges.For this reason,each half-bridge has separate bootstrap pins (BST_X),and power-stage supply pins(PVDD_X).The gate drive voltages(GVDD_AB and GVDD_CD)are derived from the PVDD voltage.Separate,internal voltage regulators reduce and regulate the PVDD voltage to a voltage appropriate for efficient gave drive operation.Special attention should be paid to placing all decoupling capacitors as close to their associated pins as possible.In general,inductance between the power-supply pins and decoupling capacitors must be avoided.For a properly functioning bootstrap circuit,a small ceramic capacitor must be connected from each bootstrap pin (BST_X)to the power-stage output pin(OUT_X).When the power-stage output is low,the bootstrap capacitor is charged through an internal diode connected between the gate-drive power-supply pin(GVDD_X)and the bootstrap pin.When the power-stage output is high,the bootstrap capacitor potential is shifted above the output potential and thus provides a suitable voltage supply for the high-side gate driver.In an application with PWM switching frequencies in the range from352kHz to384kHz,it is recommended to use33-nF ceramic capacitors, size0603or0805,for the bootstrap supply.These33-nF capacitors ensure sufficient energy storage,even during minimal PWM duty cycles,to keep the high-side power stage FET(LDMOS)fully turned on during the remaining part of the PWM cycle.Special attention should be paid to the power-stage power supply;this includes component selection,PCB placement,and routing.As indicated,each half-bridge has independent power-stage supply pins(PVDD_X).For optimal electrical performance,EMI compliance,and system reliability,it is important that each PVDD_X pin is decoupled with a100-nF ceramic capacitor placed as close as possible to each supply pin.The TAS5705is fully protected against erroneous power-stage turnon due to parasitic gate charging.SYSTEM POWER-UP/POWER-DOWN SEQUENCEPowering UpThe outputs of the H-bridges remain in a low-impedance state until the internal gate-drive supply voltage (GVDD_XY)and external VREG voltages are above the undervoltage protection(UVP)voltage threshold(see the DC Characteristics section of this data sheet).It is recommended to hold PVDD_X low until DVDD(3.3V)is powered up while powering up the device.This allows an internal circuit to charge the external bootstrap capacitors by enabling a weak pulldown of the half-bridge output.The output impedance is approximately3kΩ. This means that the TAS5705should be held in reset for at least100μs to ensure that the bootstrap capacitors are charged.This also assumes that the recommended0.033-μF bootstrap capacitors are used.Changes to bootstrap capacitor values change the bootstrap capacitor charge time.See Figure7and Figure8.Powering DownApply PDN(assert low).Wait for the power stage to shut down.Power down PVDD.Then power down DVDD. Then de-assert See Figure8for recommended timing.ERROR REPORTINGThe pin is an active-low,open-drain output.Its function is for protection-mode signaling to a system-control device.Any fault resulting in device shutdown is signaled by the pin going low(see Table1).。
营销〔2009〕13号(附件)-三相载波电能表订货及验收技术条件-2009
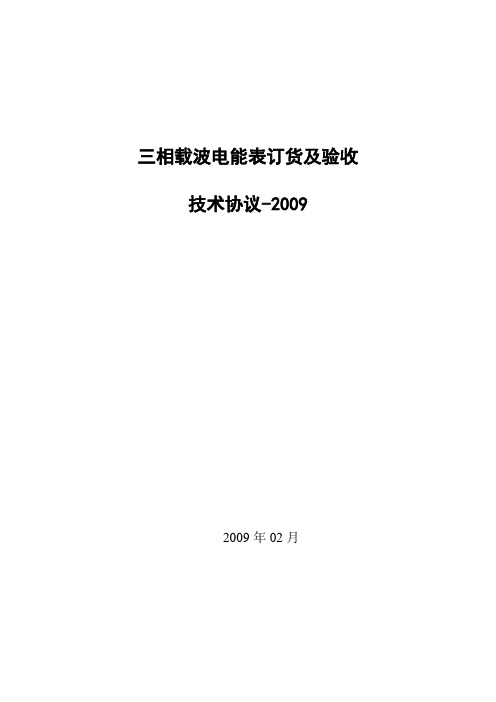
三相载波电能表订货及验收技术协议-20092009年02月1范围本技术条件规定了湖南省电力公司使用的三相载波电能表订货及验收的技术要求。
2总体说明下列标准中的条款通过本规范的引用而成为本规范的条款,其最新版本适用于本规范。
除本规范中规定的技术参数和要求外,其余均应遵循最新版本的国家标准、电力行业标准,这是对设备的最低要求。
如果投标方有自已的标准或规范,应提供标准号及其有关内容,并经招标方同意后方可采用。
但原则上采用更高要求的标准。
GB/T 15284-2002 《多费率电能表特殊要求》GB/T 17882-1999 《2级和3级静止式交流无功电度表》GB/T 9092-1998 《费率和负载控制内部时钟》(idt IEC 1038:1990)GB/T 17215.211-2006 《交流电测量设备-通用要求试验和试验条件》- 第11部分:测量设备GB/T 17215.301-2007 《多功能电能表特殊要求》IEC 62051:2004 《电能计量术语》IEC 62053-21 《1和2级静电式交流有功电能表的特殊要求》IEC 62053-23 《2和3级静电式交流无功电能表的特殊要求》DL/T 645-1997 《多功能电能表通信协议》DL/T 566-1995 《电压失压计时器技术条件》JB/T 6214-1992 《仪器仪表可靠性验证试验及测定试验(指数分布)导则》JB/T 50070-2002 《电能表可靠性要求及考核办法》JJG 596-1999 《电子式电能表》《全电子式电能表定型鉴定大纲》《国家电网公司电能表功能规范》《国家电网公司三相电能表型式规范》3.技术要求本技术条件是在国家和行业有关标准的基础上,针对湖南省电网的实际使用需要,提出了更高的技术要求。
在本技术条件中未作明确规定的内容,必须符合《GB/T 17215-2002 1级和2级静止式交流有功电度表》、《GB/T 17882-1999 2级和3级静止式交流无功电度表》、《GB/T15284-2002 复费率电能表》、《DL/T 614-1997多功能电能表》、《JJG596-1999 电子式电能表检定规程》和《DL/T 645-1997多功能电能表通信规约》的要求。
有质量评定的射频体声波滤波器 第2部分:使用指南-最新国标
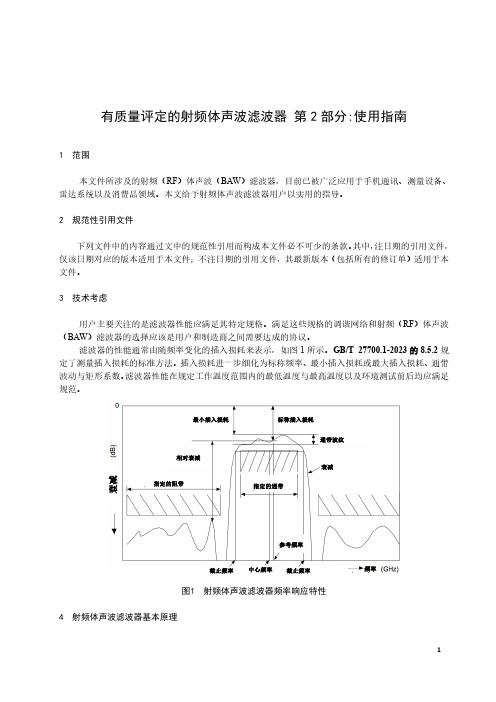
有质量评定的射频体声波滤波器 第2部分:使用指南1 范围本文件所涉及的射频(RF )体声波(BAW )滤波器,目前已被广泛应用于手机通讯、测量设备、雷达系统以及消费品领域。
本文给予射频体声波滤波器用户以实用的指导。
2 规范性引用文件下列文件中的内容通过文中的规范性引用而构成本文件必不可少的条款。
其中,注日期的引用文件,仅该日期对应的版本适用于本文件;不注日期的引用文件,其最新版本(包括所有的修订单)适用于本文件。
3 技术考虑用户主要关注的是滤波器性能应满足其特定规格。
满足这些规格的调谐网络和射频(RF )体声波(BAW )滤波器的选择应该是用户和制造商之间需要达成的协议。
滤波器的性能通常由随频率变化的插入损耗来表示,如图1所示。
GB/T 27700.1-2023的8.5.2规定了测量插入损耗的标准方法。
插入损耗进一步细化为标称频率、最小插入损耗或最大插入损耗、通带波动与矩形系数。
滤波器性能在规定工作温度范围内的最低温度与最高温度以及环境测试前后均应满足规范。
衰减频率中心频率截止频率截止频率相对衰减参考频率指定的通带指定的阻带减衰标称插入损耗通带波纹最小插入损耗图1 射频体声波滤波器频率响应特性4 射频体声波滤波器基本原理4.1 概述射频(RF )体声波(BAW )滤波器具有尺寸小、重量轻、无需调整、高稳定性、高可靠性的特点。
射频体声波滤波器在声表面波(SAW )滤波器与介质滤波器领域之外增加了新的特性与应用方向。
目前,具有低插入损耗的RF-BAW 滤波器广泛应用于吉赫兹(GHz )范围的多种应用领域。
RF-BAW 滤波器因其小型化与低插入损耗的特点在移动通讯应用中迅速占领市场。
与RF-SAW 滤波器相比,具有相同带宽的RF-BAW 滤波器可较易实现低插入损耗的特性,并且具有较小的体积。
但是BAW 滤波器可实现的带宽受限于所用的压电材料、设计方法等因素。
用户有必要理解这些因素对BAW 滤波器性能的影响。
测试测量解决方案
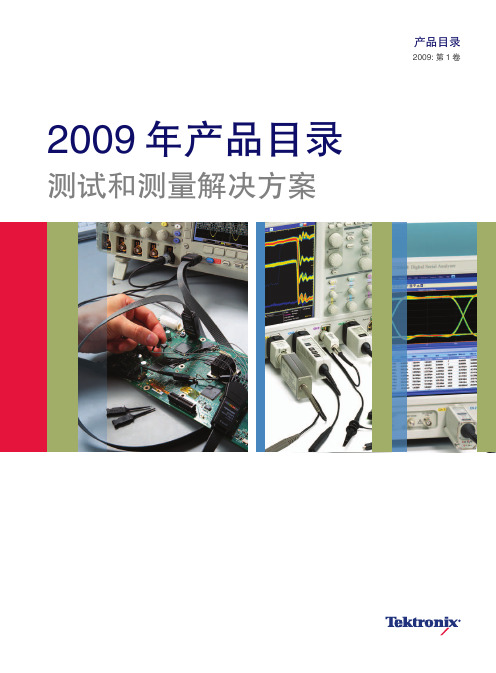
2009年产品目录测试和测量解决方案产品目录2009: 第1卷2 您只需敲敲键盘,就可以获得所需的信息,参阅泰克网站: 泰克网站为您获得完整的最新产品信息、应用解决方案、选型指南等提供了可靠的资源。
资源:详情请参阅泰克网站中提供的下述资源。
技术内容更好地了解产品基础知识或最新的技术和应用信息。
访问:/techpapers服务在线查找工具校准如需完整的服务信息,访问:/serviceMyTek 资源 下载手册获得软件和驱动程序查看订单状况 审核服务状况 我的产品支持 网上研讨会参阅/mytek产品演示通过网上演示,了解我们的部分产品。
我们的演示贯穿在整个网站的产品中心页面内。
访问网上研讨会帮助您解决应用问题。
参阅我们的网上研讨会网站:/webinar泰克RSS Feeds在您需要时提供各种最新信息。
详情请访问: /rs探头和附件利用互动探头选型工具,找到最适合您需求的探头。
访问: /probes技术和应用解决方案2009年产品目录技术和应用解决方案了解泰克最新技术和应用:/Measurement/applications/PCI Express迎接PCI Express 设计挑战需要采用快速准确的解决方案PCI Express 2.0测试要求双端口采集和1M 单位间隔分析能力。
泰克示波器在所有通道上为一致性测试提供了所需的全部采样率和深存储器。
DPO70000B 拥有通道仿真、均衡和高达20 GHz 的带宽,可以在高达8 Gb/s 数据速率的PCI Express 3.0上执行五次谐波测量。
推荐产品:示波器和应用软件:DSA70000B 系列实时示波器 DPOJET 抖动和眼图分析软件 DSA8200采样示波器,配有80E08模块TLA7Sxx 串行分析仪模块TLA 5.1版或更高版本软件及协议反汇 编软件信号发生器:AWG7000B 系列 AFG3000系列频谱分析仪RSA6000A 系列详情请访问:/Measurement/applications/serial_data/pci_express.html串行ATA强大的串行ATA 自动一致性测试系列工具,节约时间和工作量串行ATA 测试要求是当前串行数据标准中其中一个最复杂的。
periodical__jfjhlzz__jfjh2009__0902pdf__090213

低脑组织氧耗量,减少脑组织乳酸堆积;保护血脑屏障,减轻 脑水肿;抑制内源性毒性产物对脑细胞的损害作用;减少钙离 子内流,阻断钙对神经元的毒性作用;减少脑细胞结构蛋白
万方数据
破坏,促进脑细胞结构和功能修复;减轻弥漫性轴索损伤。 2亚低温的临床治疗方法[91
[12]郭京丽,宋丽华.护理管理学[M].吉林:吉林人民出版社,2005:8-9. [13]Kuokkanen J。,Leino-Kilpi H,Katajisto J.Nurse empowerment,
.
job—related satisfaction,and organizational commitment[J].J
1991年,Clifton等[1 3在国际上首先证实30~34℃低温 对实验性颅脑损伤的动物有显著的保护作用后,国内外神经 外科医师便将亚低温方法应用于临床治疗颅脑损伤患者,并 建立了一整套临床确实有效、简单实用、安全可靠的降温方 法。国内外大多数前瞻性临床应用研究L2胡结果表明,32~ 35℃亚低温能显著降低重型颅脑损伤患者的病死率,改善颅 脑损伤患者的神经功能预后,避免发生严重并发症。因此, 国内外有条件的医院已将亚低温治疗方法列为重型颅脑损 伤患者的治疗常规¨J。有文献口。81报道,亚低温治疗中肺部 感染的发生率位于其他并发症的首位,直接关系到患者的预 后和康复,故重度颅脑损伤患者在亚低温治疗期间防治肺部 感染的发生十分重要。现将亚低温治疗重度颅脑损伤并发 肺部感染的原因及护理进展综述如下。
3肺部感染的原因
3.1 机体免疫功能的下降 由于重型颅脑损伤对机体的细
收稿日期:2008—05—20;修回日期:2008—08—03 作者简介:沈春燕(1968一),女,上海人,主管护师,本科,主要从事神 经外科护理管理和临床护理工作
SAE J1085-1999 Testing Dynamic Properties of Elastomeric Isolators
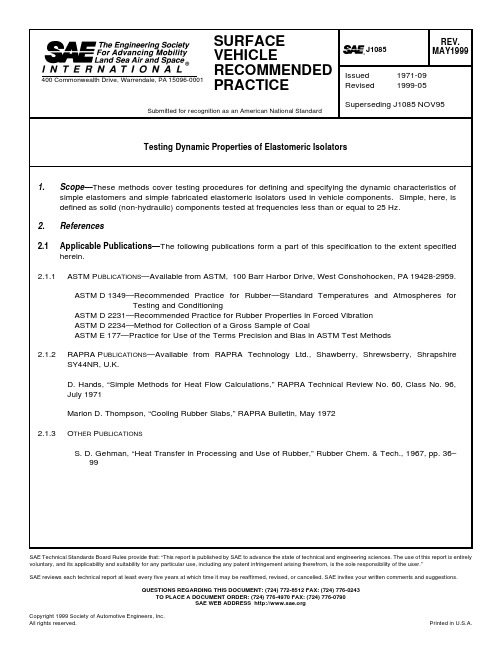
SAE Technical Standards Board Rules provide that: “This report is published by SAE to advance the state of technical and engineering sciences. The use of this report is entirely voluntary, and its applicability and suitability for any particular use, including any patent infringement arising therefrom, is the sole responsibility of the user.”SAE reviews each technical report at least every five years at which time it may be reaffirmed, revised, or cancelled. SAE invites your written comments and suggestions.QUESTIONS REGARDING THIS DOCUMENT: (724) 772-8512 FAX: (724) 776-0243TO PLACE A DOCUMENT ORDER: (724) 776-4970 FAX: (724) 776-0790SAE WEB ADDRESS 2.2Related Publications—The following publications are provided for information purposes only and are not arequired part of this document.2.2.1SAE P UBLICATION—Available from SAE, 400 Commonwealth Drive, Warrendale, PA 15096-0001.SAE SP-375, ASTM STP-535—The Measurement of the Dynamic Properties of Elastomers and Elastomeric Mounts, B. M. Hillberry and A. F. Hegerich, Proceedings of Symposium presented at SAEInternational Automotive Engineering Congress, Detroit, January 19732.2.2ASTM P UBLICATIONS—Available from ASTM, 100 Barr Harbor Drive, West Conshohocken, PA 19428-2959.ASTM D832—Recommended Practice for Rubber Conditioning for Low Temperature TestingASTM D1053—Test for Rubber Property—Stiffening at Low Temperature TestingASTM D1229—Test for Rubber Property—Compression Set at low TemperatureASTM D1329—Test for Rubber Property—Retraction at Low Temperatures (TR Test)ASTM D 1566—Definition of Terms Relating to RubberASTM E4—Verification of Testing MachinesASTM E74—Calibration of Force-Measuring Instruments for Verifying the Load Indication of Testing Machines3.Summary—These methods describe procedures for measuring the dynamic characteristics of automotiveelastomeric mountings using forced vibration testing machines. These characteristics are the elastic spring rate, damping coefficient, and loss tangent. Either fabricated mountings or elastomer specimens may be tested. Since measured dynamic properties are highly dependent upon test conditions, emphasis has been placed on the definition of suitable conditions.4.Description of Terms—These terms are in common use throughout the North American automotive industry.Alternate Terminology has been added to assist in cross-referencing terminology from other areas of the world.Please use SAE terminology to avoid confusion and data inaccuracies.4.1Test Temperature4.1.1A MBIENT T EMPERATURE—The temperature of the environment surrounding the test specimen. Unlessotherwise specified, it is assumed that the sample is at the ambient temperature before being subjected to dynamic flexing.4.1.2P ART T EMPERATURE—The temperature obtained by locating a temperature-sensing device in or on thespecimen. In most cases, temperature gradients that develop within flexing rubber specimens make it necessary to define the precise points and techniques used to measure temperature.4.2Frequency (f)—The number of complete cycles, whole periods, of forced vibrations per unit of time causedand maintained by a periodic excitation, usually sinusoidal.4.3Preload—An external static load producing a strain in a test specimen. Preload is imposed prior to forcedvibration testing. Preload is usually expressed in Newtons (pounds) of force instead of meters (inches) of deflection.4.4Double Amplitude (DA)—The peak-to-peak amplitude as applied to the elastomer specimen measured in thedirection of the applied vibration. Two times the single peak value in either the plus or minus direction may not be equivalent to the peak-to-peak value.4.5Complex Spring Rate (K *)—The effective spring rate of a part under sinusoidal dynamic stress. It is thepeak-to-peak force across the sample divided by the peak-to-peak displacement. The complex spring rate can be visualized as being the vector sum of an elastic component and a viscous damping component.4.5.1A LTERNATE T ERMINOLOGYa.Complex Stiffness b.K-dynamic (K d , K dyn )c.Dynamic Stiffness (sometimes confused with 4.6)4.6Dynamic Spring Rate (K)—The proportionality factor between the component of the applied force vector thatis in phase with the displacement and the displacement vector. The dynamic spring rate is equal to the elastic component of the complex spring rate.4.6.1A LTERNATE T ERMINOLOGYa.Elastic Spring Rate (K el )b.Dynamic Stiffness (K')c.Storage Stiffness (K")4.7Damping Coefficient (C)—The proportionality factor between the component of the applied force vectorwhich is in phase with velocity and the velocity vector.4.8Loss Rate (Cw)—The proportionality factor between the magnitude of the component of the applied force vector that is in phase with the velocity and the magnitude of the displacement vector, where:(Eq. 1)NOTE—The magnitudes of the complex spring rate, elastic spring rate, and loss rate are related by Equation2:(Eq. 2)(Eq. 3)Equation 3 is sometimes written as shown in Equation 4:(Eq. 4)whereK" = C ω4.8.1A LTERNATE T ERMINOLOGYa.Loss Stiffness (K")b.Viscous Stiffness (K")4.9Loss Tangent (tan δ)—The tangent of the phase angle between the applied force and the resultingdisplacement:(Eq. 5)ω2πf =K*complex spring rate=K*K ()2C ω()2+()=K ∗()2K ′()2K ″()2+=δC ωk --------=tan4.9.1A LTERNATE T ERMINOLOGYa.Loss factor5.General Testing Methods5.1Preparation Prior To Testing5.1.1Virgin specimens must be allowed to age between manufacturing and testing. Typically, a minimum of 24 his suggested. Elastomeric specimens that have undergone some permanent deformation (such as that due to an assembly operation) may require additional time to permit relaxation of any internal stresses that may exist.5.1.2Parts that have been kept at temperatures other than the test temperature (for example, during shipment,storage, or environmental testing) must be conditioned at the test temperature long enough to achieve uniform temperature stabilization throughout. Minimum conditioning time depends upon many factors, including temperature difference, specimen size and shape, and airflow around the specimen. Guidance for determining the required conditioning time is given in Appendix A.5.1.3All test equipment instrumentation should be fully stabilized per manufacturer's instructions. At least 1/2 h isrequired. Greater stability is obtained by leaving electronic equipment on permanently. It is recommended that at the start and conclusion of every test session or operator change, a quick check of calibration be performed with a control specimen.5.2Outline Of Test Procedure5.2.1Insert the specimen.5.2.2Apply the preload.5.2.3Apply and maintain the dynamic conditions of test.5.2.4Stabilize specimen properties.5.2.5Read data within 1 min.5.2.6Remove the specimen if no further measurements are to be made.5.3Preferred Test Conditions5.3.1Where a single measurement is to be made on a specimen, the following reference test conditions aresuggested in the interests of standardization. They take into account: the precision of equipment, stabilization of specimen dynamic properties, minimization of heat buildup, avoidance of regions in which elastomers are most sensitive to changes in test conditions, and relevance to most practical applications. 5.3.1.1Preload—Selected to correspond to that existing in the intended application. Sufficient preload should beapplied to prevent any separation of sample-to-machine interfaces unless all interfaces are securely attached. The preload should be chosen so that any sharp changes in the slope of the load-deflection curve are avoided.5.3.1.2Double Amplitude—0.50 mm (0.020 in).5.3.1.3Frequency—15 Hz.5.3.1.4Ambient Temperature—23 °C ± 2 °C (73.4 °F ± 3.6 °F).5.3.1.5Stabilization Period—2 min minimum.5.3.2Additional or alternate test conditions should follow the guidelines in ASTM D 2231 and ASTM D 1349. Theambient temperatures in Table 1 are suggested for testing elastomers used in automotive applications:5.3.3A LTERNATIVE C OLD T EST P ROCEDURE 5.3.3.1Discussion—When a specimen has been temperature stabilized at a test temperature such as −40 °C(−40 °F), any test data obtained in the first few thousand cycles will be transient data. Each unit of energy input will change the specimen's dynamic properties. The following procedure is suggested so data can be obtained in a repeatable manner when specimen response is changing.5.3.3.2Pretest Preparation5.3.3.2.1Prepare the test machine to record test data continuously during test so that information pertaining toany particular cycle can be determined. Include the following:a.Test Cycles Count b.Dynamic Spring Rate c.Damping Coefficient d.Test Chamber Ambient Temperature—Temperature sensor will be located to best sense the temperature of the test chamber ambient to which the sample is subjected.e.Energy Input f.Specimen Temperature—Is assumed the same as chamber ambient when correctly stabilized at startof test.5.3.3.2.2Prior to Test—Weigh the specimen (include all specimen elements that are molded together or fastenedtogether).5.3.3.2.3Insert the specimen.5.3.3.2.4Condition the specimen at test temperature.5.3.3.2.5Preload—There are two ways to soak the specimen at ambient temperature with or without preload.Measured dynamic characteristics are influenced by preload history. The desired condition should bespecified in test requests.TABLE 1—AMBIENT TEMPERATURES°C°F−40−40−10+14+23+73.4+100+212+150+302F t ()V t ()t d o t ∫()5.3.3.2.5.1Soak Period with Preload—The preload will be maintained until the entire soak period and test iscomplete.a.Start of Preload:Load Control—No stabilization required.Displacement Control—Preload stabilization period will be required.5.3.3.2.5.2Soak Period without Preload—The preload is added following the soak period and maintained until thetest is complete.5.3.3.2.6Precondition to Maximum Load/Deformation—Often precondition cycling to maximum load/deformationconditions is included prior to measurement of dynamic data. Dynamic properties will be influenced bythis preconditioning. If this preconditioning is desired, it should be specified in the test procedure.5.3.3.3Data Reduction—Should include the following information pertaining to the cycle of interest:5.3.3.3.1Number of Cycles5.3.3.3.2Spring Rate5.3.3.3.3Damping Coefficient5.3.3.3.4Total Energy Input5.3.3.3.5Total energy input per unit weight of specimen. When reading the dynamic spring rate or damping, usethe average for the specified cycle such as: cycle 100 equals the end of 99 to the beginning of 101.6.Specimens 6.1Standard Compression Specimens—Specimens used for comparing elastomer properties or standardizingtest machines in compression should be chosen based on the following considerations:6.1.1The size of the specimens shall be chosen to suit the load capacities of the test machine but should be no less than 12.7 mm (0.50 in) nor more than 50.8 mm (2.0 in) high; the recommended height is 25.4 mm (1.0in).6.1.2The preferred shape factor for comparing elastomer properties is 0.5 where:(Eq. 6)6.1.3The preferred shape is a right circular cylinder with faces parallel within 0.001 mm/mm or 0.001 in/in.6.1.4T EST I NTERFACE —For best reproducibility, the sample mentioned in 6.1.2 should have metal plates bondedto both faces during vulcanization.6.1.5O PTIONAL -TEST I NTERFACE —The test machine will be equipped with loading plates top and bottom of sufficient area to support the loaded specimen. The specimen will be held in place with 300 grit sandpaper,securely bonded to both loading plates. The sandpaper prevents specimen lateral movement and aids in bulge control. The two plates exciting the specimen shall be parallel within 0.001 mm/mm (0.001 in/in) of platen length in neutral position. Plate parallelism will be within tolerances on orthogonal lines.Shape factor area of one loaded face area free to bulge --------------------------------------------------------------=6.2Standard Shear Specimens—Shear specimens shall comply with ASTM D 2234 for general configuration.Dimensions may be adjusted to provide required spring rates. Supporting fixtures should be sufficiently rigid to maintain parallelism of all plates.6.3Fabricated Mountings or Bushings—The following considerations shall apply when fabricated mountings orbushings are tested:6.3.1Supporting fixtures shall be designed to restrain lateral movement of the top or bottom surfaces of themounting as a result of forces applied in the test direction.6.3.2It shall be carefully determined that any lateral forces which may develop as a result of forces applied in thetest direction do not influence the test readings.6.4Standard specimens to be tested must be clearly marked for identification.6.5Standard specimens used for standardizing test machines shall be aged no less than one month and shall beaccepted only after repetitive testing indicates that dynamic properties have stabilized.7.Preferred Test Apparatus—Forced Nonresonant System7.1General Description—A forced nonresonant system is comprised of a drive mechanism which forces thespecimen through a desired sinusoidal load, displacement, or energy. The desired frequency and amplitude of the test are not affected by the specimen's dynamic response; therefore, test conditions may be quite easily changed.7.1.1T HEORY—In a forced nonresonant system, the sample is excited with a sinusoidal oscillation which is eitherforce or displacement controlled. The forcing medium causing this sinusoidal oscillation can be an electromechanical, electrohydraulic system, or a pure mechanical system.This method assumes that the existing force or displacement and the response of the specimen can be considered to be sinusoidal. If this is not the case, special methods of analysis are required.The transmitted force is measured by a load cell in contact with the sample, preferably on the stationary side to minimize errors due to acceleration of the mass of the fixture. The component of this force which is in phase with velocity and the component that is in phase with the displacement are usually determined electronically. From this information, the values of C and K are usually determined. The vector phase relationships are illustrated in Figure 1.7.1.2C OMPONENTS—The basic elements of a forced nonresonant system are the drive system, the control system,a loading frame, transducers, and the instrumentation for readout.7.1.2.1Drive System—The system should be capable of providing sinusoidal dynamic operation, with minimumharmonic distortion, in the same direction as the applied force.7.1.2.2Control—A means of precise control over the input drive unit is required for repeatable test results.Controls for mean input, dynamic input, and frequency should be independently selectable for the desired test condition.FIGURE 1—VECTOR PHASE RELATIONSHIPS7.1.2.3Transducers and Instrumentation—Common transducer signals used in forced nonresonant systems forobtaining data are load, displacement, and/or velocity. Each transducer should be calibrated to the following minimum accuracies:a.Load—± 0.5% of full-scale for each calibrated rangeb.Displacement—± 0.5% of full-scale for each calibrated rangec.Velocity—± 0.1% of full-scale for each calibrated rangeReadout instrumentation for load, displacement, and velocity transducers should provide a sufficient number of ranges so that it will not be necessary to use less than 20% of range.Precautions listed in ASTM D 2231, paragraph 4.2 should be observed in selecting transducers, electronics, and techniques of calibration.7.1.2.4Preferred Location of Transducers—The load cell shall be mounted on the stationary side of the samplebeing tested.The displacement and/or velocity transducer should be located to accurately measure the motion of the dynamic surface of the sample. It should be located parallel to and as close as possible to the centerline ofthe existing force.7.1.2.5Load Path Compliance—A correction factor will be required unless the overall spring rate of the fixturesand the machine elements that are included in the measurement is sufficiently high. The machine and fixture spring rate should be at least 100 times greater than the nominal spring rate of the test specimen. If this degree of rigidity cannot be achieved, the correction factor shall be calculated and applied.7.1.2.6Fixture Mass—The mass of the fixture located on the stationary platen shall be minimized to reduce errorsdue to mass-inertia accelerations. The fixture located on the moving platen shall be rigid to eliminate any possibility of structural resonance near operating frequencies.8.Report8.1Test Conditions—The report shall include the following:8.1.1Type of testing machine used.8.1.2Test specimen(s) identification.8.1.3Type of specimen loading, for example, compression or shear. For specimens of complex configuration, fulldescription of fixtures used, with diagrams if necessary.8.1.4Date of test.8.1.5Preload1.8.1.6Frequency1 used at each test point in Hertz.8.1.7Double amplitude displacement1 used at each test point.8.1.8Ambient temperature1.8.1.9Specimen internal temperature (optional). If internal temperature is used, the following additional informationis required:8.1.9.1Internal temperature before flexing.8.1.9.2Ambient temperature.8.1.9.3Exact location of the temperature measuring transducer.8.1.9.4Time from start of flexing until temperature and dynamic property readings are taken.8.2Calculated Values—The method for computing C and K from the measured variable shall be described.8.2.1Dynamic (elastic) spring rate, K.8.2.2Damping coefficient, C.8.2.3Loss tangent, Cω/K1.Include both actual and specified, if different.8.2.4For all test machines, as applicable:8.2.4.1Range scale settings.8.2.4.2Mode of test control, that is, stroke or load.8.2.4.3All observed and recorded data on which calculations are based.9.Precision or Reproducibility—Precision as defined in ASTM E 177-71T is a function of the operator,compound, and maintenance of constant test conditions. The test conditions that can influence “level”are: preload, frequency, double amplitude displacement, temperature, and others not yet well defined.10.Test for Dynamic Properties of Elastomeric Isolators with Multi-Axis Preloads10.1General—The purpose of this section is to review the procedures to determine the dynamic characteristics ofautomotive elastomeric mounts with multi-axis preloads. To test the dynamic characteristics in its three principle axes of the engine mount is a typical example. The following reference calculation and test setups are suggested in the interests of standardization.10.2Multi-Axis Preloads—Figure 2 shows two sandwich mountings in a vee with an included angle of 2 αbetween the compression axes.FIGURE 2—MOUNTING ARRANGEMENTAssume a vertical static force F acts on the system. Figure 3 shows the static force diagram of one isolator.FIGURE 3—STATIC FORCE DIAGRAMNotationF - Static vertical force on the systemFc - Static compression force on one isolatorFs - Static shear force on one isolatorFh - Static horizontal force on one isolatorThe Fc and Fs can be calculated from the given F and α.10.3Preferred Test Conditions10.3.1The reference test conditions, suggested in 5.3, are applicable except the preload.The following reference test preloads for the three principle axes are suggested in the interests of standardization. The preload should be chosen so that any sharp changes in the slope of the load-deflection curve are avoided.10.3.2D YNAMIC C HARACTERISTICS IN C OMPRESSION A XIS—The applied excitation axis is in compression direction.The preload in this direction is Fc. There is an off-axis preload, Fs, should be applied on the test specimen.10.3.3D YNAMIC C HARACTERISTICS IN S HEAR A XIS—The excitation axis is in shear direction. The preload in thisdirection is Fs. There is an off-axis preload, Fc, should be applied on the test specimen.10.3.4D YNAMIC C HARACTERISTICS IN F ORE AND A FT A XIS—The excitation axis is in Fore and Aft direction that isperpendicular to compression and shear axis. Sufficient preload in Fore and Aft direction should be applied to prevent any separation of sample-to-machine interfaces unless all interfaces are securely attached.There are two off-axis preloads, Fc and Fs, should be applied on the test specimen.10.4Test Setup—There are several methods to apply the off-axis preloads. This section outlines three methods: 10.4.1M OVING L OAD C ELL—Figure 4 shows a test setup for shear and Fore and Aft characterization of isolators.The load cell is mounted on the actuator and the isolator is mounted on the mounting base. The DC conditioner shall compensate the moving load cell. This setup reduces actuator side load, bending moments on the load cell and fixturing mass attached to the load cell, and applies a more easily controlled preload. This method works up to about 15 Hz. The spherical bearings and links lower the amplitude of bending moments and side loads introduced to the actuator and load cell. The attachment to the load cell should be configured so that the dead load can be connected first and then the actuator can be attached to minimize misalignment.10.4.2T EST T WO S PECIMENS IN P ARALLEL—Use the arrangement shown in Figure 5. Two duplicate isolators aretested at the same time. A constant compression deflection is maintained on the mountings to simulate the results of a compression loading while the mountings are being tested in the shear direction. Special attention should be paid to the fixture design to minimize the fixture mass effect. This setup is not suitable for two off-axis preloads test.10.4.3MANUAL T RANSLATION P LATFORM—A manual translation platform is mounted on the load cell and the testisolator is mounted on the platform. Figure 6 shows the setup. By adjusting the translation platform, an off-axis preload is applied on the specimen against a hydrostatic bearing actuator. The test system design should minimize inertia effects.10.5Fixture—The resonant frequency of the fixture should be high enough so that these resonances do not affectthe dynamic property measurements of the isolators.FIGURE 4—MOVING LOAD CELLFIGURE 5—TWO ISOLATORS IN PARALLELFIGURE 6—MANUAL TRANSLATION PLATFORM11.Notes11.1Marginal Indicia——The change bar (l) located in the left margin is for the convenience of the user in locatingareas where technical revisions have been made to the previous issue of the report. An (R) symbol to the left of the document title indicates a complete revision of the report.PREPARED BY THE SAE VIBRATION ISOLATION COMPONENTS COMMITTEEAPPENDIX AA.1The following information is presented for guidance in determining the amount of time required for rubber partsto substantially reach equilibrium with the desired test temperature.Figure A1 shows the time required for the center of a rubber part to reach 90% of the desired temperature change under the following conditions:a.Unrestricted free convection.b.Thermal conductivity of the elastomer = 0.173 W/m °C (0.1 Btu/h-ft2°F/ft).c.Thermal diffusivity of the elastomer = 0.00024 m2/H (0.0026 ft2/H)—a conservative value for mostelastomer compositions.d.Film coefficients = 13.3 W/m2°C (2.35 Btu/h-ft2°F) and ∞.The curves apply to shapes approximating spheres, cylinders whose radii are less than 1/4 that of their lengths or slabs whose total thickness is less than 1/4 that of their length and width.For example, for a 1.27 cm (0.5 in) radius sphere in still air, 35 min are required to reach at least 90% of the desired temperature change throughout; for a 2.54 cm (1 in) thick slab, 2 h are required. Times for actual specimens may be estimated by relating them to these basic shapes or by calculations using the information in References 2.1.2 and 2.1.3. Reference 2.1.3 also discusses the effect of metal plates in, or attached to, elastomeric shapes.Extra time should be allowed if circulation around each part is restricted or if more precise part temperature control is required, as, for example, at low temperatures where dynamic response is most sensitive to temperature. Conditioning time may be shortened by forced convection, immersion in water baths, or other means suggested in Reference 2.1.2 RAPRA, Cooling Rubber Slabs. The curves for film coefficient equal to ∞show the minimum times that can be achieved by such methods.FIGURE A1—TIME TO REACH DESIRED TEMPERATURE CHANGERationale—Section 10 was added to this document.Relationship of SAE Standard to ISO Standard—Not applicable.Application—These methods cover testing procedures for defining and specifying the dynamic characteristics of simple elastomers and simple fabricated elastomeric isolators used in vehicle components. Simple, here is defined as solid (non-hydraulic) components tested at frequencies less than or equal to 25 Hz.Reference SectionASTM D 832—Recommended Practice for Rubber Conditioning for Low Temperature TestingASTM D†1053—Test for Rubber Property—Stiffening at low Temperature TestingASTM D 1229—Test for Rubber Property—Compression Set at low TemperatureASTM D1329—Test for Rubber Property—Retraction at Low Temperatures (TR Test)ASTM D1349—Recommended Practice for Rubber—Standard Temperatures and Atmospheres for Testing and ConditioningASTM D1566—Definition of Terms Relating to RubberASTM D2231—Recommended Practice for Rubber Properties in Forced VibrationASTM D2234—Method for Collection of a Gross Sample of CoalASTM E4—Verification of Testing MachinesASTM E74—Calibration of Force-Measuring Instruments for Verifying the Load Indication of Testing MachinesASTM E177—Practice for Use of the Terms Precision and Bias ASTM Test MethodsB. M. Hillberry and A. F. Hegerich, “The Measurement of the Dynamic Properties of Elastomers andElastomeric Mounts,”SAE SP-375, ASTM STP-535. Proceedings of Symposium presented at SAE International Automotive Engineering Congress, Detroit. January 1973.D. Hands, “Simple Methods for Heat Flow Calculations,”RAPRA Technical Review No. 60, Class No.96, July 1971.Marion D. Thompson, “Cooling Rubber Slabs,”RAPRA Bulletin, May 1972.S. D. Gehman, “Heat Transfer in Processing and Use of Rubber,”Rubber Chem. & Tech., 1967, pp. 36–99.Developed by the SAE Vibration Isolation Committee。
标准编写模板TCS_2009使用指南

在编写“章标题”和各级“条标题”后,如果敲 击“回车”,TCS2009自动将回车后光标所在位 置设置为“段”的格式
注意: 在编写“无标题条”后,如敲击回车, TCS2009自动将回车后光标所在位置设置 为本级的下一个“无标题条”;当不输入 任何内容,在无标题条的编号后紧跟着再 次回车,TCS则自动将再次回车后光标所 在的位置设置为上一级“条标题”或“章 标题”的格式(列项也相同)
安装与运行环境
硬件环境
主机为PC机,最低配置Pentium 100 1024×768及以上分辨率,16位色以上显示卡 内存16M以上,建议32M,最好64M以上 硬盘剩余空间100M以上 软件环境
中文版Windows 98以上操作系统 中文编辑软件Word 2007、 Word 2003、Word XP或Word 2000之一。推荐使用Word 2003 注意Word 2010不可以。
章标题
当需要将文本的某些内容设成章标题时, 请点击“章”按钮,TCS2009将自动生成 相应的章标题格式,章的编号无须手工输 入
当所编辑的页面处于正文时,点击“章” 按钮就会自动生成正文章标题编号,当所 编辑的页面处于附录时,则会自动生成附 录的章标题编号
条标题
条标题样式共分5级(条一、条二、条三、条 四、条五) 通过点击相应级别的“条”按钮即可自动生 成相应的条标题格式,条的编号无须手动输 入
列项
点击“项一”按钮,TCS2009会自动在光标所在的行首 插入“——”符号,并设定为一级列项格式 点击“项二”按钮,TCS2009会自动在光标所在的行首 插入“· ”符号,并设立为二级列项格式 点击“字母项”按钮,TCS2009会自动在光标所在的行 首插入“a)”、“b)”、“c)”等编号,并设定为一级字 母标号列项的格式 当不同的章、条或段有多个字母编号列项时,后面列项的 字母编号将接续前面的字母编号。这是如果某个列项需要 从a)开始编号,则需点击“首字母项”按钮 点击“数字项”安扭,TCS2009会自动在光标所在的行 首插入“1)”、“2)”、“3)”等编号,并设定为二 级数字编号列项的格式
GPS测量要求规范2009

目次1范围……………………………………………1 范围 (4) (1)2规范性引用文件 (1)3术语和定义 (1)4基本规定 (2)5级别划分和测量精度 (2)5.1级别划分 (2)5.2测量精度 (2)5.3用途 (3)6布设的原则 (3)6.1基本原则 (3)6.2 GPS点命名 (4)6.3技术设计 (4)7选点 (4)7.1选点准备 (4)7.2点位基本要求 (4)7.3辅助点与方位点………………………………………………………………..47.4选点作业 (5)7.5选点后应上交的资料 (5)8埋石 (5)8.2埋石作业 (5)8.3标石外部整饰 (6)8.4关键工序的控制 (6)8.5埋石后上交的资料 (6)9仪器 (6)9.1接收机选用 (6)9.2仪器检验 (6)9.3仪器维护 (7)10观测 (7)10.1基本技术规定 (7)10.2观测区的划分 (7)10.3观测计划 (8)10.4观测前的准备 (8)10.5观测作业的要求 (8)11外业成果记录 (9)11.1 A级GPS网外业成果记录 (9)11.2 B、C、D、E级GPS网外业成果记录 (9)12.1基本要求 (9)12.2外业数据质量检核 (9)12.3基线向量解算 (10)12.4 A、B级GPS网基线处理结果质量检核 (11)12.5重测和补测 (11)12.6 GPS网平差 (12)12.7数据处理成果整理和技术总结编写................................................l3 13成果验收与上交资料.....................................................................l3 13.1成果验收 (13)13.2上交资料 (13)附录A(资料性附录)大地坐标系有关说明………………………………………l4附录B(规范性附录)选点与埋石资料及其说明………………………………l5附录C(规范性附录)气象仪表的主要技术要求…………………………………l9附录D(规范性附录)测量手簿记录及有关要求 (20)附录E(资料性附录)归心元素测定与计算 (23)附录F(规范性附录) 同步观测环检核……………………………………………1 范围本标准规定了利用全球定位系统(GPS)静态测量技术,建立GPS控制网的布设原则、测量方法、精度指标和技术要求。
动态无功补偿装置(SVG)技术规范书

国电宣和光伏电站一期20MWP工程 35KV动态无功补偿装置(SVG)国电中卫宣和光伏电站一期20MWp工程35kV无功补偿成套装置技术规范书采购方:国电太阳能系统科技(上海)有限公司供货方:设计方:上海能辉电力科技有限公司批准:审核:校核:编写:国电宣和光伏电站一期20MWP工程 35KV动态无功补偿装置(SVG)第一章总的要求1.1.本技术协议适用于国电宣和光伏电站一期20MWp工程35kV静止型动态无功补偿成套装置,它提出了该设备的功能设计、结构、性能、安装和试验等方面的技术要求。
1.2.本设备技术协议书提出了最低限度的技术要求,并未对一切技术细节作出规定,也未充分引述有关标准和规范的条文,供方应提供符合工业标准和本协议书的优质产品。
1.3.供方提供的设备必须完全符合本协议书的要求。
1.4. 供方应执行本技术协议所列标准。
有不一致时,按较高标准执行。
1.5.若供方所提供的技术协议前后有不一致的地方,以有利于设备安装运行、工程质量为原则,由买方确定。
1.6.合同签订后1周内,按本协议要求,供方提出合同设备的设计、制造、检验/试验、装配、安装、调试、试运、验收、试验、运行和维护等标准清单给买方,由买方确认。
1.7.本设备技术协议书未尽事宜,由供、需双方在技术联络会时协商确定。
1.8.供方保证提供的产品符合安全、健康、环保标准的要求。
供方对成套设备(含辅助系统与设备)负有全部技术及质量责任,包括分包(或采购)的设备和零部件。
买方有权参加分包、外购设备的采购和技术谈判,供方和买方协商,最终买方确定分包厂家,但技术上由供方负责归口协调。
1.9.在签订合同之后,买方有权提出因规范标准和规程发生变化而产生的一些补充要求,在设备投料生产前,供方在设计上给予修改。
具体项目由买卖双方共同商定。
1.10. 本设备技术协议书经供、需双方确认后作为订货合同的技术附件,与合同正文具有同等的法律效力。
第二章工程概况本工程拟建在宁夏回族自治区中卫市宣和镇境内。
试验项目操作说明大众标准)

文档类型 产品类型 使用标准
TS 大众 VW80000:2009
试验项目操作说明 (大众标准)
Prepared by Weiwei Chen
Sign
Date
Revision History
Versions Revisions
Rห้องสมุดไป่ตู้0
Initial Version
Checked by
Sign Date
Approved by
Sign Date
Writer/Adapter Weiwei Chen
Release Date 2012.05.28
Customer Part NO. : KBD Part NO. :
Confidential
Page 1 of 57 2013,KEBODA
大众标准试验项目 操作说明
目录
文档类型 产品类型 适用标准
TS 大众 VW8000:2009
1 适用范围及说明...................................................................................................................................................5 1.1 参考标准 ..........................................................................................................................................................5 1.2 缩写定义 ....................
- 1、下载文档前请自行甄别文档内容的完整性,平台不提供额外的编辑、内容补充、找答案等附加服务。
- 2、"仅部分预览"的文档,不可在线预览部分如存在完整性等问题,可反馈申请退款(可完整预览的文档不适用该条件!)。
- 3、如文档侵犯您的权益,请联系客服反馈,我们会尽快为您处理(人工客服工作时间:9:00-18:30)。
striatula)的微卫星DNA 8个位点进行分析,以
研究它们之间的谱系和亲缘关系,并提出了维持这 种亲缘关系的机制。Keller等"¨通过微卫星DNA 分子标记和等位酶电泳技术,研究蚁属的Formica
exsecta和F trttncorum的野生种群,并对其繁殖规律
进行了阐释。Heinze等¨21运用微卫星分子标记技 术,对亚利桑那州举腹蚁属的(Grematogaster smithi) 进行种群遗传结构研究,发现蚁后的交配效率与种 群遗传结构密切相关。Bekkevold等心纠通过微卫星 (AG)n重复片段的遗传多样性分析,对1种可以存 在多雌制的刺切叶蚁(Acromyrmex echinatior)蚁后的 交配频率进行了研究。Else等Ⅲo以1种单雌制的 切叶蚁(Atta colomb/ca)为材料,通过微卫星DNA分
tandem repeat
级至科级阶元,已对许多类群昆虫的q玷基因序列
有过研究。但分子系统学的系统发育树与传统的分 类系统及形态支序分析结果不尽一致。 有关蚂蚁的分子生物学研究目前主要集中在线 粒体DNA上。Carew等旧。通过mtDNA的变异分 析,对澳大利亚肉食性虹臭蚁(1ridomyrmex
purpu.
和COII,可将举腹蚁属(Crematogaster)分为3个进 化支,该结果支持了形态学和生态学的特征。 Chiotis等¨4。运用3个线粒体基因片段(cyt2, cyt3和cytb)的序列及tRNAleu来构建臭蚁亚科 (dolichoderinae)的系统发育框架,以便从行为学和 系统学上对臭蚁亚科进行研究。Tsutsui等¨纠运用 cytb序列来探讨阿根廷蚂蚁Linepithema humile本土 种与引进种之间的关系及引进种的来源。 1.2微卫星DNA 微卫星DNA也称串联重复短序列的多态性 (short
A Summary
on
the Ant
Jiaojiao
Molecular Systematics
Xu
Chu
Zhenghui
Forestry
(Faculty of Conservation Biology,Southwest
group of social insects which
College。Kunming
l
列,分析2种红蚁Myrmica microrubra和Myrmica rubra是否为该分布区内的重叠物种,并探讨重叠物 种的形成及2个种之间蚁后的替代选择生殖策略。 Ross等”。通过分析mtDNA和COI序列来确定南美 洲本地火蚁的种间界线,同时探讨种问生殖隔离机 制和基因流。Miriam等"o同时运用mtDNA和微卫 星DNA序列来探讨欧洲广布寄生虫及其寄主(包 括7种蚂蚁)的协同进化与密度结构的关系。
1.1线粒体DNA(mtDNA)
mtDNA序列是目前研究昆虫系统发育、种群遗 传变异和分化,以及难以用外部形态特征来区别的 近缘种、种下分类单元鉴定中应用最为广泛的遗传 物质之一。mtDNA是快速进化序列,主要用于群体 水平及近缘种之间的系统发育研究的比较上。通过 对包含不同遗传信息的DNA序列的研究,可以对形 态分类不能解决的类群的系统关系进行分析和探 讨,也可对传统的分类系统进行验证。其中,COI、
(AP—PCR)和扩增片段长度多态性(AFLP)本质上 都是任意引物的随机扩增,只是所用引物的长度不 同,将它们统称为RAPD。RAPD.PCR技术可以在 对物种基因组没有任何分子生物学研究的情况下对 其进行DNA多态性分析,方法简便易行,省力省时, 无需克隆、转移杂交等繁琐程序。另一方面,RAPD— PCR技术也存在一些缺陷:几乎所有的RAPD标记 都呈显形遗传特征,所以无法区分杂合子和纯合子, 对群体水平的分析不利;由于扩增极其灵敏,易受外 源及污染DNA的干扰;RAPD图谱中某些弱带重复 性较差;目前该方法在引物长度和序列及应用引物 数目、扩增反应条件等实验技术方面未标准化,因而 不同方法获得的结果之间无法比较。 在昆虫学研究中,RAPD是一种重要的分子标 记,被大量地应用于昆虫学的研究中,并取得了丰硕 成果。RAPD—PCR对于近缘种和杂合种等都能进行 定性和性状的分析。但是,RAPD应用在昆虫分子 系统学上的准确性以及可重复性仍有争议¨¨。 谭声江等¨21对采自西安地区不同巢穴的日本 弓背蚁(Camponotus japonicus)进行攻击行为测试和 RAPD.PCR分析,探讨它们的亲系识别能力及遗传 背景,发现虽然环境因素对识别行为的影响不容忽 视,但是行为识别受遗传因素影响较大。Anna 等¨列用一种沙漠地带的切叶蚁(Acromyrmex
ant
new way
for
ant
systematics.Research
were
progresses
in contents,techniques and methods of Key words: Formicidae Ants
molecular systematics
al'e
summarized.Prospects for future studies Research progress
生物技术通报
・综述与专论・ B10TECHNOLOGY
BULLETlN
2009年第7期
蚂蚁分子系统学研究进展
褚姣娇徐正会
(西南林学院保护生物学学院,昆明650224)
摘要:
蚂蚁是分布广泛、种类和数量丰富的社会性昆虫。蚂蚁的传统分类学研究存在一定局限性,而分子生物学为
蚂蚁的系统学研究提供了新途径。概述了蚂蚁分子系统学在研究内容和技术方法上的研究进展,并对今后的研究做了展望。 关键词:蚁科蚂蚁分子系统学技术方法研究进展
650224)
Abstract:The
axe
aபைடு நூலகம்ts
ale
a
are
widely distributed and rich in species and individual numbers.There
a
some limitations in traditional taxonomy.However molecular systematics offers
consobrinusⅢ。时发展了合适的引物。Maca卜
anas等¨驯通过微卫星DNA研究了新南威尔士弓背 蚁属的Camponotus ephippium在地域水平上的遗传 变异。Suarez等¨刘运用微卫星DNA分子标记多样 性分析了阿根廷本土蚂蚁种与引进种之间的差异, 证明引进种在引入的一段时间内出现了瓶颈效应, 提出了阿根廷蚂蚁引入种成功地广泛传播的机制。 Giraud等四1对1种多雌制的曲颊猛蚁(Gnamptoge—
ell
万方数据
2009年第7期
褚姣娇等:蚂蚁分子系统学研究进展
43
间的系统关系。 种间的分类鉴定主要是针对近缘种和复合种, 种下阶元的分类鉴定主要是亚种和生态型的识别与 鉴定。种上阶元的系统发育分析是目前系统学研究 的热点。对传统形态分类不能解决的问题,可以通 过分子系统发育研究进行分析和探讨。目前,从种
万方数据
生物技术通报Biotechnology
Bulletin
2009年第7期
子标记对蚁后的后代进行分析,结果发现蚁后贮存 的精子数目与该蚁后交配的雄性个体数目之间呈正 相关,认为贮存更多的精子可以提高切叶蚁属Atta 蚁后的适合度,尽管多重交配代价昂贵。Jean等¨纠 通过微卫星DNA的5个基因位点,对印度南部的1 种无蚁后双刺猛蚁(Diacamma c弘舱妇en£re)的连续 多雌现象和种群的遗传结构进行了研究,并确定了 连续多雌制的水平及其对遗传结构的影响。 1.3核糖体DNA(rDNA) rDNA是目前为止对生命起源和发展、生物早 期演化关系贡献最大的分子。它们的应用范围从前 寒武纪(18S、5S和5.8S)、古生代和中生代(28S)到 新生代(间隔序列),跨越生物分类体系中的所有阶 层,是研究生命演化历史的万能序列。 rRNA的重复串联单位包括:非转录区(non—
transcribed
等唧1通过研究不同地域隆头蚁属(Strumigenys)11种 及3个未定种的ITS2序列变异并构建了系统发育树。 虽然ITS2序列的变异很高,但是对种间水平的分子进 化及生物地理学研究来说,这些数据仍然是主要的一 个潜在工具。
2蚂蚁分子系统学研究中的技术方法
2.1
RAPD.PCR技术 随机扩增多态性DNA(RAPD)、任意引物PCR
polymorphism,STRP),是包含一
段单拷贝DNA侧翼,由简单重复模块构成的一类重 复DNA。微卫星DNA重复单位小,有利于PCR扩 增检测,并可用于微量样品及部分降解样品DNA的 分析,便于电泳分析,遗传方式符合孟德尔规律,成 为近年来遗传多态性和遗传标记分析的主要分子 标记。 Pamilo等¨纠应用微卫星DNA分析研究蚂蚁的 比例差异性和基因流,并在研究了弓背蚁属的Cam.
proposed.
Molecular systematics
Technique and method
蚂蚁隶属于昆虫纲(insecta),膜翅目(hymenop— tera),蚁科(formicidae),是地球上分布最广泛、种类 和数量最多的社会性昆虫,全世界已知9 538种,分 为16亚科,296属¨1。据Holldobler等旧1估计,全球 蚂蚁约有350属,20 000种。传统的形态分类学在 近缘种鉴别和系统发育研究中存在一些不足,已经 不能完全满足系统学发展的需求。分子生物学越来 越广泛地应用于昆虫系统学,为蚂蚁的系统学研究 提供了新途径。国外在蚂蚁分子系统学领域已经有 大量研究报道,并主要集中在运用线粒体DNA和微 卫星DNA对红火蚁(Solenopsis invicta)、臭蚁、与菌 类共生蚂蚁种类及蚂蚁性别配置、基因流的研究,而 国内的类似研究尚处于起步阶段。