典型上汽小机跳闸经过分析
300MW机组汽泵小机跳闸原因分析及处理

300MW 机组汽泵小机跳闸原因分析及处理摘要:汽动给水泵在火力发电热力系统中具有举足轻重的地位,它的正常与否,直接决定了火力发电机组整体的健康运行水平。
本文就汽泵小机一些不常见的跳闸原因如转速偏差值大、喷油飞锤误动、温度测点接线接反等进行分析、讨论,由表及里,摊出现象,捋出本质,给出处理对策及防范措施。
可借鉴于同类机组,用作参考预见,以维护运行。
关键词:汽泵小机;跳闸;转速偏差值;飞锤误动;测点接线;对策前沿重庆中机龙桥热电有限公司300MW供热式抽凝机组,给水系统配置两台50%BMCR容量的汽动给水泵及一台30%BMCR容量的电动调速给水泵,汽动给水泵型号:FK5F32M;小汽机型号:G6.6-0.8-2,单缸、单流、冲动式、纯凝汽汽轮机,东汽出品。
运行中当一些常规参数超限条件满足时,保护动作跳闸,如超速、润滑油压低、排汽真空低、轴瓦温度高、轴振、轴位移大等。
本文就常规跳闸条件里所不具有的,转速偏差值大、喷油飞锤误动、温度测点接线接反,三项现实事例原因进行分析,按照时间线索,务求明晣条理,分呈脉络,清醒意识,防患未然,未雨绸缪,举重若轻而具参考意义。
1.汽泵小机转速偏差值大跳闸1.事件经过2014年09月03日中班,18:21:37`负荷212MW,锅炉MFT,床温低于650℃且未投油首出;主机以20MW/min速率降负荷,18:22:13 `A汽泵3762.25r/min,开始降转速,18:23:58` 至2847.68r/min,关闭出口门,旋转备用。
此时B汽泵单独运行,电动给水泵检修无备用。
18:27:36` 负荷120MW,B小机入口压力低跳闸,MEHB排汽温度高首出、排汽温度高停机,而此时排汽温度53.8℃,系误发。
立即开启A汽泵出口门,并升速带负荷,但已来不及,18:27:42`给水泵均停主汽流量大于30%首出,锅炉BT。
18:31:52`汽包水位高BT,机组跳闸。
在此后恢复过程中,B小机冲转后旋转备用,出口门关闭。
跳闸事故分析报告

跳闸事故分析报告1. 引言跳闸事故是电力系统中常见的故障类型之一,其发生可能导致供电中断、设备损坏甚至人身伤亡等严重后果。
为了确保电力系统运行的安全和稳定,对跳闸事故进行深入分析和研究具有重要意义。
本文将从跳闸事故的定义和分类入手,通过实例分析和对相关因素的考察,探讨跳闸事故发生的原因和可能的预防措施。
2. 跳闸事故的定义和分类跳闸事故是指电力系统中某个或某些设备突然失去电源供应,导致电路中断的异常情况。
根据跳闸事故的发生原因和性质,可以将其分为以下几类:2.1 过载跳闸过载跳闸是由于电路或设备长时间承受超过其额定负荷的电流而引起的跳闸事故。
过载跳闸常见于电力系统负荷突然增加或设备老化损坏等情况下。
2.2 短路跳闸短路跳闸是指电路中出现短路故障,导致电流突然增大,超过设备的承受能力而引起的跳闸事故。
短路跳闸常见于电路故障、设备绝缘损坏或人为操作失误等情况下。
2.3 漏电跳闸漏电跳闸是指电路中出现漏电故障,导致电流异常泄漏,超过保护装置的动作阈值而引起的跳闸事故。
漏电跳闸常见于设备绝缘损坏或设备内部故障等情况下。
3. 跳闸事故的分析为了进一步了解跳闸事故的发生原因,本文将以一起过载跳闸事故为例进行分析。
3.1 事故描述该起事故发生在某工业区的配电房中,导致该区域的生产线全部停工。
事故发生时,供电房的电源突然中断,所有设备无法正常运行。
经过排查,工作人员发现是一台额定电流为100A的设备发生过载跳闸。
3.2 事故原因经过进一步调查和分析,确定该起跳闸事故的原因如下:•设备负荷超载:该设备长时间运行时,额定负荷已接近或超过其额定电流,导致设备过热,进而引发过载跳闸。
•配电线路老化:供电线路老化严重,电阻增大,导致电流通过线路时产生过大的电压降,进而导致线路负荷增加,设备过载跳闸。
3.3 预防措施为了避免类似的跳闸事故再次发生,需要采取以下预防措施:•定期检查设备负荷情况,确保设备运行在额定负荷范围内。
小汽轮机跳闸问题的分析

1B小机跳机与挂闸故障分析总结最终版
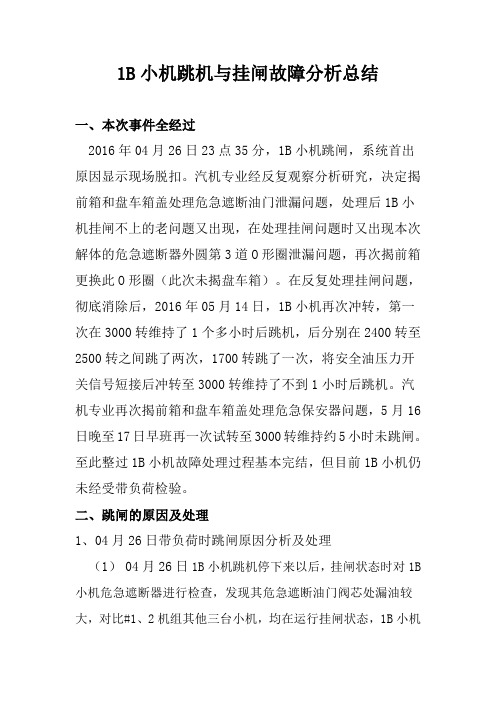
1B小机跳机与挂闸故障分析总结一、本次事件全经过2016年04月26日23点35分,1B小机跳闸,系统首出原因显示现场脱扣。
汽机专业经反复观察分析研究,决定揭前箱和盘车箱盖处理危急遮断油门泄漏问题,处理后1B小机挂闸不上的老问题又出现,在处理挂闸问题时又出现本次解体的危急遮断器外圆第3道O形圈泄漏问题,再次揭前箱更换此O形圈(此次未揭盘车箱)。
在反复处理挂闸问题,彻底消除后,2016年05月14日,1B小机再次冲转,第一次在3000转维持了1个多小时后跳机,后分别在2400转至2500转之间跳了两次,1700转跳了一次,将安全油压力开关信号短接后冲转至3000转维持了不到1小时后跳机。
汽机专业再次揭前箱和盘车箱盖处理危急保安器问题,5月16日晚至17日早班再一次试转至3000转维持约5小时未跳闸。
至此整过1B小机故障处理过程基本完结,但目前1B小机仍未经受带负荷检验。
二、跳闸的原因及处理1、04月26日带负荷时跳闸原因分析及处理(1)04月26日1B小机跳机停下来以后,挂闸状态时对1B 小机危急遮断器进行检查,发现其危急遮断油门阀芯处漏油较大,对比#1、2机组其他三台小机,均在运行挂闸状态,1B小机此处漏油明显比其它小机均大很多,因此危急遮断油门阀芯漏泄是主要原因。
(2)跳机时1B机运行的是#1主油泵, #1主油泵出口压力只有0.64Mpa,#2主油泵的出口压力可以达到0.72Mpa,2台油泵对应的安全油压分别是0.58Mpa和0.61Mpa左右,其他三台小机的安全油压都可以达到0.60Mpa以上;因此当时的1B小机安全油压偏低(具体多少无法核实)也是诱发跳闸的原因之一。
(3)在未研磨危急遮断油门阀芯及活塞密封面前,在挂闸的状态,用手轻轻左右触动危急遮断器拉钩,瞬间就脱扣,说明运行时挂闸状态时很不稳定。
安全油腔室危急遮断阀芯活塞飞锤间隙(4)4月26日带负荷时跳闸原因:(见上图)运行时#1主油泵运行安全油压偏低,挂闸状态时安全油腔室的的阀芯处漏油,使腔室形成的油压虽可压住活塞不跳机,但此时是处于一种弱平衡状态,系统油压稍有波动时,活塞后的弹簧克服油压给活塞的作用力,打开活塞大油口使小机跳闸。
燃气机组典型事故案例分析及基建生产期反事故措施

燃气机组典型事故案例分析及基建生产期反事故措施为了确保燃气机组安装、调试、运行期间安全生产,有效控制事故发生,把好安全生产这个关口,从在役燃气机组投运以来发生的故障案例中,选择了部分典型案例作为培训学习。
目的是希望燃气电厂相关人员能以身边发生的这些不安全事例为借鉴,举一反三、深刻反思、吸取教训、改进工作、加强管理、提前预控,做好详细的防范措施,避免类似事故再次发生。
反事故措施目录表第一章燃机系统案例1:#7叶片通道温差大自动停机1、经过:2006年8月3日℃,超过了设计的25℃,时间超过30秒,控制室来“BPT温度偏差大”信号,机组自动停机以保护燃机。
8月7日8时17分启动,8时53分并列。
2、原因分析:1)2005年11月份调试期间曾出现#7叶片通道温度高现象,报警值由20℃调到23℃,自动停机值、跳闸值未做改动。
其他叶片通道温度报警值维持20℃不变。
2)由于日方技术人员在对BPT温差定值进行调整时,考虑不周,设定值偏低(自动停机BPT温差定值实际是25℃,定值最高可小于40℃)导致自动停机。
3、防范措施:1)在控制系统中,修改燃机负荷35MW-65MW阶段的#1-20BPT温差定值(尤其#7BPT在启动期间报警由原来的23℃提高到30℃,自动停机由原来的25℃提高到33℃,跳闸由原来的30℃提高的35℃)。
2)其他19个BPT温差定值,在燃机负荷35MW-65MW启动期间报警由原来的20℃提高到25℃,自动停机由原来的25℃提高到30℃,跳闸保持原来的35℃。
案例2:燃烧器压力波动高高#1燃机跳机1、经过:2006年10月5日20时14分,#1燃机来“#20燃烧器压力波动传感器异常信息”及“燃烧器压力波动预报警”光字牌。
通知维护部检修班人员到场检查,之后此报警频发。
23时02分,来“燃烧器压力波动高高跳闸”光字牌(经查为#6、#7燃烧器压力波动高高),#1燃机跳闸。
停机后,技术人员查找压力传感器、信号回路未见异常,经与网局调度协商于6日2时50分#1燃机启动,3 时21分转速3000r/min观察,未见异常,于3时49分机组并列。
小机跳闸原因分析及处理

电子机械工程
小机 跳 闸原 因分 析 及 处 理
I I 刘 瑞英
嘉峪关宏 晟电热公 司 3 、# 4机 小汽轮机 为由杭 州汽轮机 厂生产的
N K 5 0 / 5 6型 变转 速凝 汽 式汽轮 机 ( 简称 小机 ) 。 该 小机 与哈 尔滨汽 轮 机 厂 生
阀卡涩致使小机跳 闸的原 因。
胶圈弹性较好 , 并 没有摩擦 、断裂之处 ,那么可以排 除速关油 泄入启 动
规定值最 大值 1 . 2 a r m,修复被摩擦 处 , 栓板 进行倒 角处理 。 2 ) 合理 利用 大小修机会 , 对 现有 小机前箱 部件进行检查 ,对紧固 件 、部件关联部 位检查要 到位 ,做好验收 。 3 ) 合理利用大小修机会 ,彻底清扫小ห้องสมุดไป่ตู้速关阀油缸 ,将速关 阀内
直接切断速关 油 ,关闭速关 阀。轴瓦温度 、轴振 动 、 轴位 移等停 机信 号
均通过 E T S实现遥控停机。
远远低于标准值。 后 吊出速关 阀阀台, 检查危机遮断装置栓板 间隙 , 发
现栓板两侧有明显的摩擦痕迹 ,结合在运 行时 , 前箱 内有异音 , 可 以得 出结论 :危机遮断装置栓板动作 ,致使速关油压力泄去 ,速关阀关闭 ,
2 . 1事件 经 过
R+
R一
要求
0 S 1 0
0 S l0
变测
1. OO
0 81 . 0
O 8 O
2 0 1 3年 1 0月 1 9 3上午 1 1 1 : l 0时 。新# 4机组 B小机速关 阀速关油
5 ) 危机遮 断装 置栓板 动作有两个方 面的原 因 :一是栓 板间隙明显 不符合杭 汽厂 家 0 . 8 a r m 一 1 . 0 a r m / 0 . 8 a r m 一 1 . 2 r n m的要求 ,安装 间隙过小而 使汽轮机轴 和栓 板进行 了摩擦 ;二是小机危机遮 断装置 自机组 投产 以 来, 就没有系统检修过 , 各部件 、 部套和螺栓部位松动 , 危机遮断装置 产生了微量的位移 ,遇有机组 压力 波动和负荷调整 时 , 机组振 动增 大 , 轴与栓板产生了摩擦 ,这个摩 擦是 时断时续 的 ,不会将机 组就 地打跳 , 只是仅仅将手动打闸装置油 口开启 , 速关油 压泄掉 , 速关 阀关 闭 , 从 而
汽轮机跳闸的原因分析及改造措施

启瞬间拉低了 6 k V厂用电压,导致部分设备低电
3 3 4 MW ,最 大功 率为 3 4 2 . 7 MW 。
汽量瞬时增大,造成汽轮机转速快速上升。
( 2 )机 组发生 异 常后无 法及 时掌 握安 全 门的动 作情 况 。 ( 3 ) ’ 由于 机组 跳 闸 ,四段抽 汽逆 止 门联关 ,四 抽 汽源压 力低 。手 动开启 辅 汽至 甲、乙小机 供 汽分
由于热工保护逻辑不完善,造成机组安全油压
降低后 主汽 门关 闭但不跳 闸汽 轮机 ,在安全 油压 建 立后 主汽 门直接 开启 , 容 易造 成汽 轮机 超速 。为此 ,
采取 了以下改造措施。 ( 1 )在 汽轮 机 跳 闸 条 件 中增 加 “ 安全 油 压
<1 . 2 MP a ” 。安 全 油压 压 力 开 关 取 自安 全 油母 管 , 按三 取二逻 辑设计 。
转速为 3 0 0 0 r / m i n ,切换调速油泵 时安全油压下 降。后开 启调 速油 泵 出 口门时 ,安 全油压 恢复 ,主
汽 门突然 开启 ,转 速上升 较快 ,即采取 手动打 闸停
( 2 )在 1 号、2 号机组疏油 门前后增加小 口径 旁路阀,机组启动时将疏油门完全关闭、开启旁路 小阀 ,油泵切换时操作小阀即可。 3 . 3 在安全门处加装动作指示器 之前 ,热控监测安全门的动作情况依靠压力开
动 作情 况。针对 此 问题 ,在 安全 门处加 装 了动 作指
示器 。
3 . 6 修改低旁快开触发条件 上述事故中,低旁实 际已经联开。但是,由于 低旁陕开触发条件为低旁人 H 压力 >4 MP a ,而入
口压 力 < 4 MP a时 快开 指令 立 即消 失 ;因此 ,造
关于2A小机跳闸的原因分析报告

关于2A小机跳闸的原因分析报告事故经过:3月4日9:05,#2机监盘人员发现2A小机跳闸,电泵联启,盘面无任何报警,给水自动跳手动。
运行人员立即调整2B汽泵、电泵出力,保持水位正常。
就地检查2A汽泵无异常,联系热工检查处理。
9:18热工检查无异常,汇报值长,启2A汽泵。
2A汽泵启动后运行正常。
原因分析:热工查相关运行参数后发现2A小机跳闸是由于安全油压低引起的。
热工检查该安全油压低开关,动作数值准确。
根据小机安全油系统结构,安全油压降低可能由EH油压降低、节流孔堵塞、隔膜阀油压降低引起。
由2B小机及主机EH系统运行正常,可排除EH油压降低引起安全油压降低的可能;根据隔膜阀油压突然降低特点,如果节流孔是堵塞引起的,堵塞物不会自行冲开;根据上述分析本次2A小机跳闸原因应为隔膜阀油压突然降低引发。
根据下图的数据:图中蓝色曲线为隔膜阀油压,粉色曲线为安全油压低开关量曲线,红色为小机转速。
图中粉色开关量曲线在9点05分30秒由0跳变为1,约0.5秒后,隔膜阀油压开始迅速降低。
由于安全油压低为开关量数据,隔膜阀油压为模拟量数据,由于数据采集的特点,在数据记录时间上模拟量数据普遍滞后于开关量数据,故实际情况应为隔膜阀油压降低在前,安全油压低开关动作在后。
本次事件是由于隔膜阀油压降低所引起的。
联系热工查找相关操作的历史记录,未发现有操作的痕迹,可以排除监盘人员误操作的可能。
2A小机主油泵出口压力及润滑油压也无明显变化,故隔膜阀动作只能是小机跳闸滑阀动作导致。
而2A小机挂闸后无异常,加之,我厂多台小机从未发生过跳闸滑阀误动作的先例,说明小机就地跳闸按钮被误碰动作是导致小机跳闸的最大可能原因。
三、吸取教训1、巡视检查人员及清扫人员应熟悉跳闸按钮位置,作业时避免触碰。
2、汽机分厂考虑增设保护罩的可能性。
小机跳闸技术原因分析

上汽ND84/79/07—1型小汽轮机主油泵故障造成小机跳闸的原因分析及处理故障现象:我厂机组四台小机均为上汽厂生产的,型号为ND84/79/07—1,液控调节系统采用上汽厂提供的配套液压调节系统,控制油采用高压抗燃油,低压安全油通过隔膜阀与高压抗燃油进行连接。
我厂#1机在2012年9月发生#1机A小机主油泵故障(轴承损坏)润滑油压下降(低压安全油压没有模拟量),备用泵、事故油泵自启成功,但该小机仍跳闸,针对上述情况将利用停机时对四台小机分别做主油泵停用试验(人为模拟主油泵跳闸)。
原因分析:2012年9月12日#1机B小机在运行中发生跳闸事故,当时该小机#1主油泵在运行,检查发现该小机#2油泵及直流油泵都自投,但该小机却跳机,针对上述现象,通过调看DCS 记录,发现该小机跳闸原因首出为润滑油压低、安全油压低保户动作,但检查发现当时润滑油压直线下降至0.09MPa后又快速回升至0.27MPa,未降至跳机值0.06 Mpa,而且润滑油压也未发出报警、启用备用泵信号,但备用泵自启,通过备用泵自启条件发现运行中的主油泵出口压力若低于0.58 Mpa时自启,事故油泵自启条件发现运行中的润滑油压力压力若低于0.093 Mpa 时自启,结合DSC中润滑油压未低至跳机值,及利用停机时对四台小机分别做主油泵停用试验(人为模拟主油泵跳闸故障),结果发现我厂四台小机均未发出跳闸信号,只有#2机B小机安全油压低信号一个压力开关动作(跳机为三选二),对应的应为低压安全油压低。
判断为当时主油泵故障,造成主油泵出口油压降低,备用泵虽然自启,因该型小机的油箱布置在0米层,而小机布置在13.7米层,并且主油泵出口经直径为φ45mm的管道节流后至润滑油母管,润滑油母管直径为φ133mm, 且润滑油母管上有一只80L的蓄能器(布置在0米层,充气压力为0.14 Mpa),运行中的润滑油母管压力若低于0.093 Mpa时事故油泵自启,结合DSC中润滑油压低至0.09Mpa后就未再下降,更未低至跳机值,判断为此次小机跳机与润滑油压低无关;而主油泵出口至低压安全油母管需经一只逆止门,另外低压安全油母管直径只有φ32mm,还有在设计上把主油泵出口手动门放在了逆止门前的缺陷,造成了备用主油泵出口至逆止门前那一段约1.25米长管道的空间无油,虽然运行中的主油泵出口压力若低于0.58 Mpa时备用主油泵自启,但备用主油泵出口的油必须先充满其出口至逆止门前那一段无油空间后方能向低压安全油母管供油,加上至低压安全油母管需经一只逆止门且管道较细和一定的高度差,造成备用主油泵提供的油压上升速度低于因油泵故障造成油压下降的速度,即低压安全油压低至隔膜阀动作压力,隔膜阀动作,卸去高压控制油,造成小机跳闸。
电厂#4机组跳闸事件分析报告

电厂#4机组跳闸事件分析报告1、事件经过(1)2005年5月18日16:23时,2204开关跳闸,值班员立即检查,发现#4机高、低旁快开至100%、主汽门全关,DCS有变压器压力释放、主变重瓦斯动作等SOE画面报警。
#3机负荷减到80MW,后经中调同意,17:02时#3机解列。
(2)检查SOE画面报警有:16:23:09:449 #4汽轮发电机故障16:23:09:450 #4汽机ETS已跳闸16:23:09:474 #4汽机发变组220KV断路器分状态16:23:09:539 #4汽机主变压器压力释放保护动作16:23:09:542 #4汽机发电机保护动作总信号16:23:09:617 #4汽机就地打闸16:23:28:475 #4汽机主变压器重瓦斯保护动作DCS报警有:16:23:09:615 #4汽轮发电机故障16:23:09:615 #4汽机ETS已跳闸16:23:09:621 #4汽机发变组220KV断路器分状态16:23:09:622 #4汽机发变组220KV断路器事故跳闸16:23:09:667 #4机ASP压力油压力低16:23:09:671 #4机OPC压力油压力低16:23:09:671 #4汽机联跳保护动作16:23:09:882 #4汽轮发电机逆变16:23:09:883 #4汽机就地打闸16:23:09:883 #4汽机主变压器压力释放保护动作16:23:09:884 #4汽轮发电机灭磁开关跳闸16:23:09:885 #4汽机发电机保护动作总信号16:23:09:890 #4汽机主汽门已关闭16:23:09:918 #4机OPC保护动作发变组保护柜动作信号:CPUO 灭磁联跳,汽机联跳16:21:00:360主变压力释放保护动作16:21:09:65主变重瓦斯16:21:19CPOE 相隔一秒有与CPUO相同报警(3)就地检查发现4B主变发生喷油。
17:10时,4B主变转检修,并联系ABB厂家工作人员到现场对4B主变进行检查。
一台600MW超临界机组2B小机跳闸原因分析、处理及防范措施

一台600MW超临界机组2B小机跳闸原因分析、处理及防范措施某电厂装机为2台600MW超临界机组,给水系统采用2台50%容量的汽动变速给水泵和1台30%容量的电动给水泵,小机设计有中、低压两路汽源,自动内切换。
小机型号TGQ10/6-1,连续运行转速为3000~5780r/min,危急保安器动作转速为6150~6213 r/min,电超速保护动作转速为6069 r/min。
汽泵额定扬程3060m,最小流量270m3/h,额定流量1141t/h。
1.事件经过201X年7月17日1:30,2号机组负荷424MW,给水流量1036t/h,煤量207t/h,AGC在投入状态,主汽压23.1MPa,2号机2A,2B小机转速分别为4623r/min,4608r/ min,2A,2B给水泵入口流量分别为732t/h,705t/h,2A汽泵调门开度指令28%,反馈29%;2B汽泵调门开度指令31%,反馈32%。
01:30:21,2号机2A小机转速突然上升至5803r/min,指令5800r/min。
2A小机高压进汽流量由零突然上升至39t/h(小机进汽调门实际全开),炉主给水流量由1066t/h上升至1567t/h,01:31:34,2A小机转速突降至4510r/min又迅速回升至5787r/min,2B转速4207r/min,2A小机进汽调门开度指令24.8%,反馈20.8%,给水流量突降至709t/h。
01:31:55,2B小机跳闸(保护动作原因为汽泵入口流量低保护跳闸)。
2号机电泵联锁启动正常,立即解除协调控制,加大电泵出力,联系热工值班人员查找原因,汇报值长。
01:36:00,2号机2A小机转速突降至3998.9r/min,指令3998r/min,给水流量突降至546t/h,随即回升至5800 r/min,01:36起2A小机进汽调门指令2.5%,反馈1.6%。
01:36,01:37,01:51,02:12,02:14,02:16共6次出现给水流量大幅突降突升,且变化越来越剧烈。
浅谈上汽660MW机组汽动给水泵跳闸事件原因分析及处理办法

4.2针对断裂的叶片,经专业锅炉压力容器检验中心检测后,对叶片断口进行了详细的分析,主要分为以下3部分。
3.4由于割除了4片末级叶片,相应的破坏了原始末级叶片拉筋,减小了叶片强度,改变了叶片频率;同时对碰伤的其它叶片只是进行简单的抛光处理,造成动叶栅流道轻微改变,产生新的激振力。最终随着机组运行,6A小汽轮机振动逐渐增大,为保证6A小机轴振在要求范围内,不得不通过开启电泵维持机组高负荷运行。
4原因分析
浅谈上汽660MW机组汽动给水泵跳闸事件原因分析及处理办法
摘要:某电厂上汽660MW汽轮机发电机组的给水泵小汽轮机汽泵运行中,“A小机2号轴承轴瓦振动大跳机”、“A小机给水泵主保护动作”,设备停机发现给水泵小汽轮机末级叶片断裂,造成轴瓦振动瞬间增大,机组跳机。
关键词:事件经过;处理过程;修复方案;原因分析;暴露问题;防范措施
给水泵小汽轮机为单缸、单流程、单轴、纯凝汽冲动式汽轮机,型号:N12.5-1.089,运行方式为变参数、变功率、变转速,小机转子共有6级动叶,第1-5级有叶顶围带,第6级无叶顶围带中间有拉筋的自由叶片,共有5级隔板静叶。转子、隔板为日本三菱进口,机组2007年11月正式投运。
1事件经过
1.1设备运行工况,锅炉负荷650MW,主汽压力24.8MPa,主汽温567/566℃,再热汽温565/566℃,真空-95kPa,6A-6F 6台制粉系统运行,6A、6B汽泵运行,电泵备用,六大风机运行,6A、6B循环水泵运行。
2处理过程
2.1 6A小机2号轴承轴瓦振动大机组跳机后,汽机和热控专业人员检查设备外观无异常,手动盘车正常,通过调取运行各参数曲线分析,A小机1、2号瓦轴振、瓦振都出现突增,瓦温较正常增大5℃左右,汽动给水泵振动稍有延后也出现突增,从曲线看属振动大跳闸,初步诊断转子可能出现部件脱落,需揭缸检查。
660MW超临界机组小机跳闸故障分析及对策

660MW超临界机组小机跳闸故障分析及对策摘要:大型燃煤机组的汽动给水泵,在运行中发生故障有多种,从热控专业的角度进行故障分析,为检修人员提供有价值的信息,能够提高故障处理效率。
关键词:小机;跳闸;分析;1.机组情况简介:京能宁东发电有限责任公司汽轮机为哈尔滨汽轮机厂生产的超临界、一次中间再热、单轴、三缸四排汽、间接空冷凝器式汽轮机,机组型号为:CLNJK-660-24.2/566/566。
机组给水系统主要包括两台50%容量的汽动给水泵,由两台杭汽生产的NK63/71/0型冷凝式小汽轮机驱动。
DCS控制系统为OVATION3.2版本。
2.三次跳闸情况1.2014年11月16日,#1机组负荷657MW,两台小机运行,08:02时#11小机跳闸,气动泵转速迅速下降,跳闸首出为“速关油压低”,同时RB正常动作,机组负荷下降,8:05时机组负荷降为340MW。
故障过程见图一图一:机组运行曲线1.第二次跳闸经过2012年3月12日8:35,运行白班接班时#1机负荷600MW,机组投入AGC控制方式,B、C、D、E、F制粉系统运行。
早上8:39,#1机#11小机#1轴承、#2轴承振动值同时达到300um,#11汽泵跳闸,机组RB动作,联跳E、C制粉系统。
8:46,#1机RB复位,此时主汽温度565℃,水煤比失调,运行人员将给水、煤量切手动调节控制机组主要运行参数。
9:16,经调整,#1机煤水比稳定,主再热汽温稳定,维持负荷290MW,投入机组CCS模式。
11:31,向中调申请#1机负荷限高300MW,获准。
12:30,值长令,执行#11小机汽侧隔离措施,关闭#11小机排气蝶阀,小机真空到零后退出#11小机轴封系统运行,#11小机排气管喷水注水4分钟后,关闭#11小机进汽电动门及门前手动门。
1.第三次跳闸简要经过2020年07月04日15:56:159,#2机组负荷456W,#21小机跳闻,转速迅速下降,跳闸首出为“速关油压低”,RB正常动作机组负荷下降,15:59时机组负荷降为390MW,运行人员通知设备部汽机室、发电部自控中心检査。
#1机跳闸分析报告
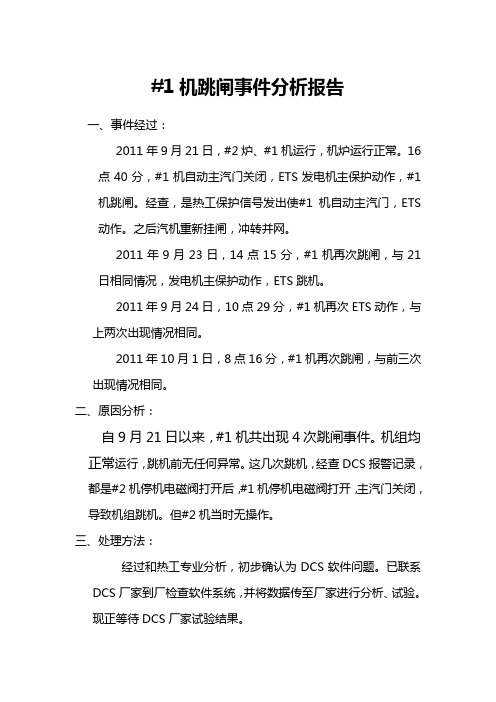
#1机跳闸事件分析报告
一、事件经过:
2011年9月21日,#2炉、#1机运行,机炉运行正常。
16点40分,#1机自动主汽门关闭,ETS发电机主保护动作,#1机跳闸。
经查,是热工保护信号发出使#1机自动主汽门,ETS 动作。
之后汽机重新挂闸,冲转并网。
2011年9月23日,14点15分,#1机再次跳闸,与21日相同情况,发电机主保护动作,ETS跳机。
2011年9月24日,10点29分,#1机再次ETS动作,与上两次出现情况相同。
2011年10月1日,8点16分,#1机再次跳闸,与前三次出现情况相同。
二、原因分析:
自9月21日以来,#1机共出现4次跳闸事件。
机组均正常运行,跳机前无任何异常。
这几次跳机,经查DCS报警记录,都是#2机停机电磁阀打开后,#1机停机电磁阀打开,主汽门关闭,导致机组跳机。
但#2机当时无操作。
三、处理方法:
经过和热工专业分析,初步确认为DCS软件问题。
已联系DCS厂家到厂检查软件系统,并将数据传至厂家进行分析、试验。
现正等待DCS厂家试验结果。
四、防范措施:
现#1机正稳定运行,应定期检查润滑油压、调节系统油压,不得随意触碰505控制器。
某电厂#3机组小机B速关阀试验时跳闸分析

某电厂#3机组小机B速关阀试验时跳闸分析摘要:某电厂600MW机组小汽轮机由杭汽生产,结合小机速关阀结构原理,以及小机调节油系统的特性,从热工角度对小机速关阀试验时跳闸原因进一步分析并提供解决方向,确保机组的安全运行。
关键词:速关阀;跳闸;热工;分析一、事件发生前状态9月7日22时00分,#3机组停机前,小机B运行正常,调节油压0.84Mpa,速关油压0.61Mpa,速关阀全开,系统各油压均稳定。
随后小机B速关阀试验时,速关阀突然关闭,速关油压到0.03Mpa,小机B跳闸,首出原因为“小机B速关油压低”。
二、事件过程小机B22:00:09,试验前,调节油压0.84Mpa,速关油压0.61Mpa,速关阀全开。
22:00:40,开始进行小机B速关阀活动试验,调节油压0.84Mpa,速关油压突降至0.03Mpa,速关阀全关,小机B跳闸。
小机A21:58:35,试验前,调节油压0.83Mpa,速关油压0.76Mpa,速关阀全开。
21:59:36,开始进行小机A速关阀活动试验,调节油压0.83Mpa,速关油压0.76Mpa,速关阀反馈80%。
21:58:35,试验后,调节油压0.83Mpa,速关油压0.76Mpa,速关阀全开,小机A速关阀活动试验正常。
三、原因分析(1)速关阀原理a 速关阀开启原理图2 二期小机油路图图3 速关阀结构图速关阀由油压控制。
开启速关阀时,1842速关电磁阀及1843启动电磁阀带电,则1842速关电磁阀的P与B导通,DG16插装阀关闭,切断E1与E2通道;同时1843启动电磁阀的P与B导通,启动油F通至活塞(13)右端,活塞在油压作用下克服弹簧力(14)被压向活塞盘(16),使活塞与活塞盘的密封面相接触,约15秒后,先让1842速关电磁阀失电,速关油E通入活塞盘左侧,随着速关油压的建立,约60秒后,让1843启动电磁阀失电,启动油与回油T口导通,启动油开始在节流孔及溢流板的作用下有控制的缓慢泄放,于是活塞盘和活塞如同一个整体构件在两侧油压差作用下,持续向右移动直至被试验活塞限位(12)。
上汽660mw超超临界汽轮机油动机动作异常造成跳闸的分析及处理
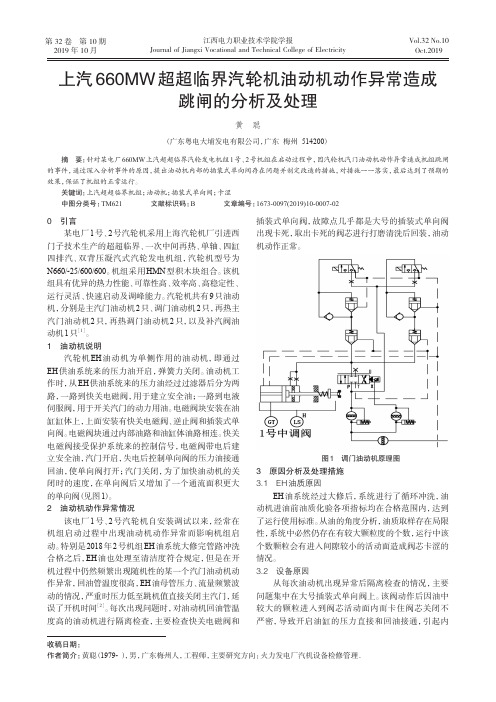
第 32 卷 第 10 期2019 年 10 月江西电力职业技术学院学报Journal of Jiangxi Vocational and Technical College of ElectricityVol.32 No.10Oct.2019上汽660MW超超临界汽轮机油动机动作异常造成跳闸的分析及处理黄聪(广东粤电大埔发电有限公司,广东梅州 514200)摘 要:针对某电厂660MW上汽超超临界汽轮发电机组1号、2号机组在启动过程中,因汽轮机汽门油动机动作异常造成机组跳闸的事件,通过深入分析事件的原因,提出油动机内部的插装式单向阀存在问题并制定改造的措施,对措施一一落实,最后达到了预期的效果,保证了机组的正常运行。
关键词:上汽超超临界机组;油动机;插装式单向阀;卡涩中图分类号:TM621 文献标识码:B 文章编号:1673-0097(2019)10-0007-020 引言某电厂1号、2号汽轮机采用上海汽轮机厂引进西门子技术生产的超超临界、一次中间再热、单轴、四缸四排汽、双背压凝汽式汽轮发电机组,汽轮机型号为N660/-25/600/600。
机组采用HMN型积木块组合。
该机组具有优异的热力性能、可靠性高、效率高、高稳定性、运行灵活、快速启动及调峰能力。
汽轮机共有9只油动机,分别是主汽门油动机2只、调门油动机2只,再热主汽门油动机2只,再热调门油动机2只,以及补汽阀油动机1只[1]。
1 油动机说明汽轮机EH油动机为单侧作用的油动机,即通过EH供油系统来的压力油开启,弹簧力关闭。
油动机工作时,从EH供油系统来的压力油经过过滤器后分为两路,一路到快关电磁阀,用于建立安全油;一路到电液伺服阀,用于开关汽门的动力用油。
电磁阀块安装在油缸缸体上,上面安装有快关电磁阀、逆止阀和插装式单向阀。
电磁阀块通过内部油路和油缸体油路相连。
快关电磁阀接受保护系统来的控制信号,电磁阀带电后建立安全油,汽门开启,失电后控制单向阀的压力油接通回油,使单向阀打开;汽门关闭,为了加快油动机的关闭时的速度,在单向阀后又增加了一个通流面积更大的单向阀(见图1)。
- 1、下载文档前请自行甄别文档内容的完整性,平台不提供额外的编辑、内容补充、找答案等附加服务。
- 2、"仅部分预览"的文档,不可在线预览部分如存在完整性等问题,可反馈申请退款(可完整预览的文档不适用该条件!)。
- 3、如文档侵犯您的权益,请联系客服反馈,我们会尽快为您处理(人工客服工作时间:9:00-18:30)。
11月2日2A小机跳闸经过分析
一、事件前运行方式
#2机负荷280MW,A、B汽泵组运行,电泵备用。
二、事件经过
13:47“#2A汽泵低压调门关闭”报警光字闪烁,杨善虎立即翻阅给水画面,发现2A汽泵组转速2200rpm并继续下降,电泵未联启,给水流量已由973T/H 骤然降至648T/H,立即手启电泵并汇报值长通知各岗位。
值长金树林令解除#2机组AGC手动控制机组负荷并要求#2机组退出“汽包水位保护”,对汽包水位进行手动控制;集控班长王帏迅速在盘前设定降负荷速率及目标值进行负荷干预,负荷降至250MW;锅炉副职吴积德手动调节汽包水位,汽机加强对电泵的检查,汽包水位最低降至-132mm。
三、事件分析
(一)、究竟是什么保护动作引起的2A小机跳闸?
事件后2A小机挂闸信号在,低主门、低调门关闭,而值班员并没有对其进行任何操作。
由于挂闸信号在,所以2A小机ETS面板没有任何异常信号,“给水泵首出”没有任何报警。
能够使小机跳闸的信号有:
一)、直接在ETS动作,通过20/TT电磁阀泄油动作:
1、低真空(61.3KPa);
2、润滑油压低(0.08MPa);
3、轴向位移大(±1.2mm);
4、电超速(6300r/min);
5、小机任一轴承振动大(125um)。
6、MEH画面手动打闸。
7、通过DCS和ETS的“Remote”接口动作:
1)、A前置泵进出口差压低保护投入、A小机低主门未全关且A小机未跳闸、A前置泵进出口差压低、A给水泵入口流量<80t/h;
2)、A前置泵跳闸;
3)、A前置泵入口电动门关闭;
4)、A给水泵入口流量低低保护投入、A给水泵再循环门全开、A给水泵入口流量<148t/h;
5)、A给水泵除氧器水位低低保护投入、除氧器水位低低、除氧器水位低;
6)、A给水泵温度保护投入且以下几个温度保护任意一个达到动作值:①、进水端径向轴承温度>95℃;②、进水端机械密封循环液温度>90℃;③、出水端机械密封循环液温度>90℃;④、出水端径向轴承温度>95℃;⑤、推力轴承温度>95℃;⑥、非驱动端径向轴承温度>95℃;
二)、通过MEH逻辑实现:
小机跳闸后,直接发脉冲信号去关闭低主门和低调门。
三)、就地打闸泄油。
四)、机械超速动作泄油(2005年4月3日投产时最高动作转速6307r/min)。
通过追查DCS工程师站SOE记录,一)、四)中的所有条件都没有可能。
由于整个事件的起因源于A小机A交流油泵电机BC相相间短路跳闸引起,所以排除人为就地打闸的可能。
那么就只有小机跳闸后MEH发指令去关闭低主门和低调门了。
从动作情况分析,除了二)这种情况外,其它的动作结果都是泄去安全油,也就是说,如果是其它原因引起的小机跳闸,跳闸后都必须通过20/RS复位电磁阀或就地按复位按钮去复位,否则“小机挂闸”信号不可能出现。
综合以上分析,小机跳闸原因是因为小机跳闸信号发出后,直接发脉冲信号去关闭低主门和低调门。
(二)、小机跳闸后为什么挂闸信号在?
我们小机挂闸、跳闸信号取的是安全油压力开关信号,小机挂闸信号取的是“安全油压力≥0.8MPa”,小机跳闸信号取的是“安全油压力≤0.5MPa”,从SOE 看,13:47:37.622时“A小机A交流油泵试验油压低”压力开关信号到,此时安全油压≤0.9MPa,联锁启动B交流油泵信号发出。
其后“A小机挂闸信号”失去,接着“B交流油泵跳闸”信号失去,此时B交流油泵联启。
在14:47:38.062时“A小机跳闸”信号来,此时安全油压力≤0.5MPa,但在此信号之后,“A小机挂闸信号”到,在14:47:38.387后“A小机B交流油泵试验油压低”压力开
关信号到,此时安全油压已正常。
由上可见:从“A小机A交流油泵试验油压低”信号发出至“A小机跳闸”信号来共440ms。
在A小机跳闸信号到至安全油压正常只有325ms时间。
也就是说B交流油泵联启至安全油压正常一共是765ms。
从历史趋势来看,A交流油泵电流由46A下降至38A后稳定了有0.8s时间,A小机润滑油压与其变化一致,但在A小机A交流油泵跳闸后油压即上升,结合DCS工程师站SOE记录的时间,两者基本一致,也就是说,实际在A交流油泵跳闸的同时B泵已经启动正常。
由于MEH是通过泄去低主门操纵座的启动油压从而关闭低主门,所以其对安全油压无影响。
实际系统当时并无去跳小机的信号发生,而仅仅是小机跳闸信号到后MEH逻辑动作,所以一旦油压≥0.8 MPa”后小机挂闸信号即到。
(三)、为什么小机跳闸后电泵未联启、RB未动作、直流油泵未联启?
前两者原因相同,主要是因为小机跳闸信号发出后很快“挂闸”信号到,DCS 未检测到小机跳闸信号。
直流油泵未联启是因为实际润滑油压一直在0.11Mpa以上。
(四)、B交流油泵联启是热控油压低联启还是硬接线联锁动作?
从SOE判断应该是热控低油压先动作。
四、建议
结合本次异常,建议将小机跳闸压力开关定值降低至安全油压低至0.3Mpa。