络达AB1510模块资料
利达多格式同步信号发生器文档说明书

概要特点LT 4600A Multiformat Video GeneratorLT4600A多格式同步信号发生器是支持多标准SDI(3G-SDI/HD-SDI/SD-SDI)测试信号,1U高度半个机架宽小型的SDI视频信号发生器。
不仅有彩条、SDI测试场等测试图输出,还配备了ID字符、QVGA尺寸标识、安全框、嵌入音频叠加、外部基准输入信号的同步锁相功能、3组6路独立系统的模拟黑场同步信号输出等丰富的功能。
支持SDI信号支持3G(级别A、级别B)、HD(含双链路)、以及SD的独立的2个SDI输出接口。
可独立改变图像和相位。
(但3G-B和HD(DL)是1路输出)ID字符叠加可在图像上任意位置叠加ID字符。
并且为了确认静止状态,可采用左右滚动或者闪烁显示。
标识叠加图像的任意位置上用最大320(dot)×240(line)尺寸 (QVGA大小),可叠加由BMP格式转换而来的4阶段单色数据的标识。
安全框不但可在图像上叠加90%、80%的安全框,还可在3G、HD 信号时叠加4:3形态框。
图像滚动具有8个方向滚动图像的功能,还可调整速度。
嵌入式音频叠加3G-B中可叠加32ch(Link A、Link B、各4ch×4组)、3G-A、HD、SD中可叠加16ch(4ch×4组)嵌入式音频信号。
频率、电平等可按通道各自设置。
视音频延时图像输出视频和音频同步的视音频延时测试图像。
通过使用利达电子的多功能波形监视器设备,可正确地测量SDI信号视频和音频的延时。
同步锁相功能可同步NTSC/PAL黑场同步信号、以及HD 3电平同步信号。
也支持带场同步脉冲的NTSC/PAL黑场同步信号、以及带10场ID 字符的NTSC黑场同步信号。
并且支持外同步锁相信号出现异常也能保持原相位继续输出同步信号的STAY IN SYNC功能。
模拟黑场同步信号输出具有独立的3组黑场同步信号输出。
选择NTSC/PAL黑场同步信号、与SDI输出格式同系统时钟频率的HD 3电平同步信号,可更改相位。
LMZ10501和LMZ10500SIMPLE SWITCHER nano 模块评估板用户指南说明书
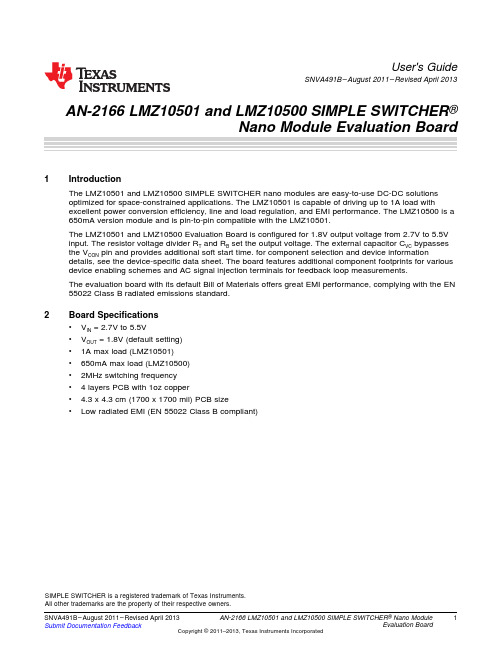
User's GuideSNVA491B–August2011–Revised April2013 AN-2166LMZ10501and LMZ10500SIMPLE SWITCHER®Nano Module Evaluation Board1IntroductionThe LMZ10501and LMZ10500SIMPLE SWITCHER nano modules are easy-to-use DC-DC solutionsoptimized for space-constrained applications.The LMZ10501is capable of driving up to1A load withexcellent power conversion efficiency,line and load regulation,and EMI performance.The LMZ10500is a 650mA version module and is pin-to-pin compatible with the LMZ10501.The LMZ10501and LMZ10500Evaluation Board is configured for1.8V output voltage from2.7V to5.5Vinput.The resistor voltage divider RT and RBset the output voltage.The external capacitor CVCbypassesthe VCON pin and provides additional soft start time.for component selection and device informationdetails,see the device-specific data sheet.The board features additional component footprints for various device enabling schemes and AC signal injection terminals for feedback loop measurements.The evaluation board with its default Bill of Materials offers great EMI performance,complying with the EN 55022Class B radiated emissions standard.2Board Specifications•VIN=2.7V to5.5V•VOUT=1.8V(default setting)•1A max load(LMZ10501)•650mA max load(LMZ10500)•2MHz switching frequency•4layers PCB with1oz copper• 4.3x4.3cm(1700x1700mil)PCB size•Low radiated EMI(EN55022Class B compliant)SIMPLE SWITCHER is a registered trademark of Texas Instruments.All other trademarks are the property of their respective owners.1 SNVA491B–August2011–Revised April2013AN-2166LMZ10501and LMZ10500SIMPLE SWITCHER®Nano ModuleEvaluation Board Submit Documentation FeedbackCopyright©2011–2013,Texas Instruments IncorporatedTypical Performance Characteristics 3Typical Performance CharacteristicsOutput RippleRadiated EMI2AN-2166LMZ10501and LMZ10500SIMPLE SWITCHER ®Nano Module SNVA491B–August 2011–Revised April 2013Evaluation BoardSubmit Documentation FeedbackCopyright ©2011–2013,Texas Instruments IncorporatedOPTIONAL COMPONENT FOR AC INJECTION FOR CONTROL LOOP MEASUREMENTSBOARD EDGE PAD ASSIGNMENTS FOR QUICK CONNECTIONOPTIONALPLACE CIN AS CLOSE AS POSSIBLE TO THE PVIN AND PGND PINS FOR GOOD BYPASSRESISTORS RT AND RB SET THE OUTPUTVOLTAGEPLACE C VC AS CLOSE AS POSSIBLE TO THE VCONAND SGND PINSENABLE OPTComponents marked with (*) are notpopulated on the board Evaluation Board Schematic and Bill of Materials4Evaluation Board Schematic and Bill of MaterialsFigure 1.Evaluation Board SchematicTable 1.LMZ10501and LMZ10500Bill of Materials,V IN =2.7V to 5.5V,V OUT =1.8V,I OUT (MAX)=1000mA /650mADesignatorDescription Case Size Manufacturer Manufacturer P/N QuantityU1SIMPLE SWITCHERSE08A Texas InstrumentsLMZ10501SE or 1Nano Module LMZ10500SE C IN ,C OUT10µF,X5R,10V0805KEMET C0805C106K8PACTU 2C VC 1000pF 0603TDK C1608C0G2A102J 1R B 82.5k Ω0603Vishay-Dale CRCW060382K5FKEA 1R T 187k Ω0603Vishay-Dale CRCW0603187KFKEA 1R EN1k Ω0603Vishay-Dale CRCW06031K00FKEA 1(optional)R INJ10Ω0603Vishay-DaleCRCW060310R0FKEA1(optional)3SNVA491B–August 2011–Revised April 2013AN-2166LMZ10501and LMZ10500SIMPLE SWITCHER ®Nano ModuleEvaluation BoardSubmit Documentation FeedbackCopyright ©2011–2013,Texas Instruments IncorporatedEvaluation Board Layout 4.1Optional Components and Footprints•RINJ resistor–allows for a network analyzer connection to measure the control loop response.Replacethis resistor with a short in a final design if control loop measurements are not needed.•RPU resistor–an optional footprint to pull EN up to VINwith an external resistor.EN is internally pulledup to VINby a790kΩresistor.•REN–an optional resistor in series with the EN pin.•RPD –an optional pull-down resistor for the QENgate.•QEN–an optional footprint to use an N-ch MOSFET as a pull-down device for EN.•J1–jumper to select how to drive EN.Connecting the jumper pins1and2allows for driving ENdirectly from the EN turret at the edge of the board.Connecting the jumper pins2and3allows fordriving the gate of the pull-down device QEN.•EC1–board edge connector for quick testing.•COUT footprints–the solder mask on the VOUTside of the board is removed to allow for different outputcapacitor configurations.5Evaluation Board LayoutFigure2.Evaluation Board Top View4AN-2166LMZ10501and LMZ10500SIMPLE SWITCHER®Nano Module SNVA491B–August2011–Revised April2013 Evaluation Board Submit Documentation FeedbackCopyright©2011–2013,Texas Instruments Incorporated Evaluation Board LayoutFigure3.Evaluation Board Bottom ViewFigure4.Evaluation Board Assembly(DNP=not populated components)5 SNVA491B–August2011–Revised April2013AN-2166LMZ10501and LMZ10500SIMPLE SWITCHER®Nano ModuleEvaluation Board Submit Documentation FeedbackCopyright©2011–2013,Texas Instruments Incorporated30 mV/Div250 MHz BW500 µs/DivCOUT = 10 F 10V 0805 X5RLOAD CURRENTOUTPUT VOLTAGE500 mA/Div 10 mV/Div500 MHz BW1 µs/DivCOUT = 10 F 10V 0805 X5RVOUT RIPPLETypical Performance for V OUT =1.8V6Typical Performance for V OUT =1.8VUnless otherwise specified the following conditions apply:V IN =5V,I OUT =1A,T A =25°C6AN-2166LMZ10501and LMZ10500SIMPLE SWITCHER ®Nano Module SNVA491B–August 2011–Revised April 2013Evaluation BoardSubmit Documentation FeedbackCopyright ©2011–2013,Texas Instruments IncorporatedCf = 0603YD105MAT AVXLf = VLS252015T-1R0N1R7 TDKTypical Performance for V OUT =1.8VInput LC Filter for Conducted EMI 7SNVA491B–August 2011–Revised April 2013AN-2166LMZ10501and LMZ10500SIMPLE SWITCHER ®Nano ModuleEvaluation BoardSubmit Documentation FeedbackCopyright ©2011–2013,Texas Instruments IncorporatedTypical Performance for V OUT =1.8V8AN-2166LMZ10501and LMZ10500SIMPLE SWITCHER ®Nano Module SNVA491B–August 2011–Revised April 2013Evaluation BoardSubmit Documentation FeedbackCopyright ©2011–2013,Texas Instruments Incorporated Other Output Voltage Settings7Other Output Voltage SettingsFigure 5.V OUT =1.2VFigure 6.V OUT =2.5VFigure 7.V OUT =3.3VFor other output voltages,choose R T =80k Ωto 300k ΩThen calculate R B usingR B =V OUT x R T /(5.875V –V OUT )(1)9SNVA491B–August 2011–Revised April 2013AN-2166LMZ10501and LMZ10500SIMPLE SWITCHER ®Nano ModuleEvaluation BoardSubmit Documentation FeedbackCopyright ©2011–2013,Texas Instruments IncorporatedIMPORTANT NOTICETexas Instruments Incorporated and its subsidiaries(TI)reserve the right to make corrections,enhancements,improvements and other changes to its semiconductor products and services per JESD46,latest issue,and to discontinue any product or service per JESD48,latest issue.Buyers should obtain the latest relevant information before placing orders and should verify that such information is current and complete.All semiconductor products(also referred to herein as“components”)are sold subject to TI’s terms and conditions of sale supplied at the time of order acknowledgment.TI warrants performance of its components to the specifications applicable at the time of sale,in accordance with the warranty in TI’s terms and conditions of sale of semiconductor products.Testing and other quality control techniques are used to the extent TI deems necessary to support this warranty.Except where mandated by applicable law,testing of all parameters of each component is not necessarily performed.TI assumes no liability for applications assistance or the design of Buyers’products.Buyers are responsible for their products and applications using TI components.To minimize the risks associated with Buyers’products and applications,Buyers should provide adequate design and operating safeguards.TI does not warrant or represent that any license,either express or implied,is granted under any patent right,copyright,mask work right,or other intellectual property right relating to any combination,machine,or process in which TI components or services are rmation published by TI regarding third-party products or services does not constitute a license to use such products or services or a warranty or endorsement e of such information may require a license from a third party under the patents or other intellectual property of the third party,or a license from TI under the patents or other intellectual property of TI.Reproduction of significant portions of TI information in TI data books or data sheets is permissible only if reproduction is without alteration and is accompanied by all associated warranties,conditions,limitations,and notices.TI is not responsible or liable for such altered rmation of third parties may be subject to additional restrictions.Resale of TI components or services with statements different from or beyond the parameters stated by TI for that component or service voids all express and any implied warranties for the associated TI component or service and is an unfair and deceptive business practice. TI is not responsible or liable for any such statements.Buyer acknowledges and agrees that it is solely responsible for compliance with all legal,regulatory and safety-related requirements concerning its products,and any use of TI components in its applications,notwithstanding any applications-related information or support that may be provided by TI.Buyer represents and agrees that it has all the necessary expertise to create and implement safeguards which anticipate dangerous consequences of failures,monitor failures and their consequences,lessen the likelihood of failures that might cause harm and take appropriate remedial actions.Buyer will fully indemnify TI and its representatives against any damages arising out of the use of any TI components in safety-critical applications.In some cases,TI components may be promoted specifically to facilitate safety-related applications.With such components,TI’s goal is to help enable customers to design and create their own end-product solutions that meet applicable functional safety standards and requirements.Nonetheless,such components are subject to these terms.No TI components are authorized for use in FDA Class III(or similar life-critical medical equipment)unless authorized officers of the parties have executed a special agreement specifically governing such use.Only those TI components which TI has specifically designated as military grade or“enhanced plastic”are designed and intended for use in military/aerospace applications or environments.Buyer acknowledges and agrees that any military or aerospace use of TI components which have not been so designated is solely at the Buyer's risk,and that Buyer is solely responsible for compliance with all legal and regulatory requirements in connection with such use.TI has specifically designated certain components as meeting ISO/TS16949requirements,mainly for automotive use.In any case of use of non-designated products,TI will not be responsible for any failure to meet ISO/TS16949.Products ApplicationsAudio /audio Automotive and Transportation /automotiveAmplifiers Communications and Telecom /communicationsData Converters Computers and Peripherals /computersDLP®Products Consumer Electronics /consumer-appsDSP Energy and Lighting /energyClocks and Timers /clocks Industrial /industrialInterface Medical /medicalLogic Security /securityPower Mgmt Space,Avionics and Defense /space-avionics-defense Microcontrollers Video and Imaging /videoRFID OMAP Applications Processors /omap TI E2E Community Wireless Connectivity /wirelessconnectivityMailing Address:Texas Instruments,Post Office Box655303,Dallas,Texas75265Copyright©2013,Texas Instruments Incorporated。
TB1510中文资料

15.0A Single-Phase Bridge RectifierFeatures• High forward surge current capability • Ideal for printed circuit board• High temperature soldering guaranteed: 260°C/10 seconds, 5 lbs (2.3kg) tension • RoHS CompliantMechanical DataCase: Molded plastic body with Metal Heat SinkPolarity: Polarity symbols marked on case Terminals: Plated 0.25" (6.35mm) lugMounting Position:Thru hole for #10 screw,20 in -lbs. torque maxWeight:0.53 ounce, 15 gramsMaximum Ratings & Electrical Characteristics (T Ambient =25ºC unless noted otherwise)SymbolsDescriptionTB1505TB151TB152TB154TB156TB158 TB1510UnitV RRM Max. recurrent peak reverse voltage50 100 200 400 600 800 1000 V V RMS Max. RMS voltage 35 70 140 280 420 560 700 V V DC Max. DC blocking voltage 501002004006008001000VIo (AV) Max. average forward rectified current @ T C=55° C 15.0 AI FSMPeak forward surge current (Note 1)300 A l²t Rating for Fusing (t<8.3ms) 373 A²secV ISOIsolation Voltage from case to lugs2500 VC j Typical CapacitanceJunction(per element)(Note 2) 300 pF T J Operating junction temperature range-65 to +150 ° C T STG Storage Temperature Range-65 to +150° CTB3515.0A SINGLE-PHASE BRIDGE RECTIFIERNOTES:1. 8.3ms single half sine-wave superimposed on rated load (JEDEC method).2. Measured at 1MHz and applied reverse voltage of 4.0Volts D.C.3. Thermal resistance junction to case mounted on heat sink.Typical Characteristics CurvesSymbolDescriptionTB1505TB151TB152TB154TB156 TB158 TB1510UnitV FMaximum Instantaneous Forward Voltage Drop Per Leg@7.5 A1.1 VT A =25° C 10.0 uAI RMaximum DC Reverse Current Rated DC Blocking VoltageT A =100° C 500 uAR θ-JCMaximum Thermal Resistance (Note 3)2.0 ° C/WI o (A V ) A v e r a g e F o r w a r d C u r r e n t (A )Case Temperature (°C)Fig.2-Max. Non-repetitive Peak Forward Surge Current Fig.1- Typical Forward Current Derating Curve15.0A SINGLE-PHASE BRIDGE RECTIFIERI F I n s t a n t a n e o u s F o r w a r d C u r r e n t (A )I R I n s t a n t a n e o u s R e v e r s e C u r r e n t (u A )15.0A SINGLE-PHASE BRIDGE RECTIFIERDimensions in inches (mm)TB3515.0A SINGLE-PHASE BRIDGE RECTIFIERHow to contact us。
LMX1501资料

TL W 12340LMX1501A LMX1511PLLatinum 1 1GHz Frequency Synthesizer for RF Personal CommunicationsNovember 1995LMX1501A LMX1511PLLatinum TM 1 1GHz Frequency Synthesizer for RF Personal CommunicationsGeneral DescriptionThe LMX1501A and the LMX1511are high performance fre-quency synthesizers with integrated prescalers designed for RF operation up to 1 1GHz They are fabricated using Na-tional’s ABiC IV BiCMOS processThe LMX1501A and the LMX1511contain dual modulus prescalers which can select either a 64 65or a 128 129divide ratio at input frequencies of up to 1 1GHz Using a proprietary digital phase locked loop technique the LMX1501A 11’s linear phase detector characteristics can generate very stable low noise local oscillator signalsSerial data is transferred into the LMX1501A and the LMX1511via a three line MICROWIRE TM interface (Data Enable Clock) Supply voltage can range from 2 7V to 5 5V The LMX1501A and the LMX1511feature very low current consumption typically 6mA at 3VThe LMX1501A is available in a JEDEC 16-pin surface mount plastic package The LMX1511is available in a TSSOP 20-pin surface mount plastic packageFeaturesY RF operation up to 1 1GHz Y 2 7V to 5 5V operation YLow current consumptionI CC e 6mA (typ)at V CC e 3VY Dual modulus prescaler 64 65or 128 129Y Internal balanced low leakage charge pumpYSmall-outline plastic surface mount JEDEC 0 150 wide (1501A)or TSSOP 0 173 wide (1511)packageApplicationsY Cellular telephone systems (AMPS NMT ETACS)YPortable wireless communications (PCS PCN Cordless)YAdvanced cordless telephone systems (CT-1 CT-1a CT-2 ISM902-928)YOther wireless communication systemsBlock DiagramTL W 12340–1TRI-STATE is a registered trademark of National Semiconductor CorporationMICROWIRE TM and PLLatinum TM are trademarks of National Semiconductor Corporation C 1995National Semiconductor CorporationRRD-B30M115 Printed in U S AConnection DiagramsLMX1501ATL W 12340–2JEDEC 16-Lead (0 150 Wide)SmallOutline Molded Package (M)Order Number LMX1501AM or LMX1501AMXSee NS Package Number M16ALMX1511TL W 12340–320-Lead (0 173 Wide)Thin ShrinkSmall Outline Package (TM)Order Number LMX1511TM or LMX1511TMXSee NS Package Number MTC20Pin DescriptionsPin No Pin No Pin Name I O Description1501A 15111501A 151111OSC INIOscillator input A CMOS inverting gate input intended for connection to a crystal resonator for operation as an oscillator The input has a V CC 2inputthreshold and can be driven from an external CMOS or TTL logic gate May also be used as a buffer for an externally provided reference oscillator 23OSC OUT OOscillator output34V P Power supply for charge pump must be t V CC45V CCPower supply voltage input Input may range from 2 7V to 5 5V Bypasscapacitors should be placed as close as possible to this pin and be connected directly to the ground plane56D o OInternal charge pump output For connection to a loop filter for driving the input of an external VCO 67GND Ground78LD O Lock detect Output provided to indicate when the VCO frequency is in ‘‘lock’’ When the loop is locked the pin’s output is HIGH with narrow low pulses 810f IN I Prescaler input Small signal input from the VCO911CLOCK I High impedance CMOS Clock input Data is clocked in on the rising edge into the various counters and registers1013DATA I Binary serial data input Data entered MSB first LSB is control bit High impedance CMOS input1114LEILoad enable input (with internal pull-up resistor) When LE transitions HIGH data stored in the shift registers is loaded into the appropriate latch (control bit dependent) Clock must be low when LE toggles high or low See Serial Data Input Timing Diagram1215FC I Phase control select (with internal pull-up resistor) When FC is LOW the polarity of the phase comparator and charge pump combination is reversed X 16BISW O Analog switch output When LE is HIGH the analog switch is ON routing the internal charge pump output through BISW (as well as through D o )13f r O Monitor pin of phase comparator input Programmable reference divider output 14f pO Monitor pin of phase comparator input Programmable divider output X 17f OUT O Monitor pin of phase comparator input CMOS Output1518w p O Output for external charge pump w p is an open drain N-channel transistor and requires a pull-up resistor1620w r OOutput for external charge pump w r is a CMOS logic output X2 9 12 19NCNo connect2Functional Block DiagramLMX1501ATL W 12340–403Functional Block Diagram(Continued)LMX1511TL W 12340–44Absolute Maximum Ratings(Note1)If Military Aerospace specified devices are required please contact the National Semiconductor Sales Office Distributors for availability and specifications Power Supply VoltageV CC b0 3V to a6 5V V P b0 3V to a6 5V Voltage on Any Pinwith GND e0V(V I)b0 3V to a6 5V Storage Temperature Range(T S)b65 C to a150 C Lead Temperature(T L)(solder 4sec )a260 C Recommended Operating ConditionsPower Supply VoltageV CC2 7V to5 5V V P V CC to5 5V Operating Temperature(T A)b40 C to a85 C Note1 Absolute Maximum Ratings indicate limits beyond which damage to the device may occur Operating Ratings indicate conditions for which the device is intended to be functional but do not guarantee specific perform-ance limits For guaranteed specifications and test conditions see the Elec-trical Characteristics The guaranteed specifications apply only for the test conditions listedElectrical Characteristics V CC e5 0V V P e5 0V b40 C k T A k85 C except as specifiedSymbol Parameter Conditions Min Typ Max Units I CC Power Supply Current V CC e3 0V6 08 0mAV CC e5 0V6 58 5mA f IN Maximum Operating Frequency1 1GHz f OSC Maximum Oscillator Frequency20MHz f w Maximum Phase Detector Frequency10MHz Pf IN Input Sensitivity V CC e2 7V to5 5V b10a6dBm V OSC Oscillator Sensitivity OSC IN0 5V PP V IH High-Level Input Voltage 0 7V CC V V IL Low-Level Input Voltage 0 3V CC V I IH High-Level Input Current(Clock Data)V IH e V CC e5 5V b1 01 0m A I IL Low-Level Input Current(Clock Data)V IL e0V V CC e5 5V b1 01 0m A I IH Oscillator Input Current V IH e V CC e5 5V100m A I IL V IL e0V V CC e5 5V b100m A I IH High-Level Input Current(LE FC)V IH e V CC e5 5V b1 01 0m A I IL Low-Level Input Current(LE FC)V IL e0V V CC e5 5V b1001 0m A Except f IN and OSC IN5Electrical Characteristics V CC e5 0V V P e5 0V b40 C k T A k85 C except as specified(Continued) Symbol Parameter Conditions Min Typ Max UnitsI Do-source Charge Pump Output Current V Doe V P 2b5 0mAI Do-sink V Doe V P 25 0mAI Do-Tri Charge Pump TRI-STATE Current0 5V s V D o s V P b0 5V b5 05 0nAT e25 CV OH High-Level Output Voltage I OH e b1 0mA V CC b0 8V V OL Low-Level Output Voltage I OL e1 0mA 0 4V V OH High-Level Output Voltage(OSC OUT)I OH e b200m A V CC b0 8V V OL Low-Level Output Voltage(OSC OUT)I OL e200m A0 4V I OL Open Drain Output Current(w p)V CC e5 0V V OL e0 4V1 0mA I OH Open Drain Output Current(w p)V OH e5 5V100m A R ON Analog Switch ON Resistance(1511)100X t CS Data to Clock Set Up Time See Data Input Timing50ns t CH Data to Clock Hold Time See Data Input Timing10ns t CWH Clock Pulse Width High See Data Input Timing50ns t CWL Clock Pulse Width Low See Data Input Timing50ns t ES Clock to Enable Set Up Time See Data Input Timing50ns t EW Enable Pulse Width See Data Input Timing50ns Except OSC OUT6Typical Performance CharacteristicsI CC vs V CCTL W 12340–5I DoTRI-STATE vs D o VoltageTL W 12340–6Charge Pump Current vs D o VoltageTL W 12340–7Charge Pump Current vs D o VoltageTL W 12340–8Charge Pump Current VariationTL W 12340–9Oscillator Input SensitivityTL W 12340–10 7Typical Performance Characteristics(Continued)Input Sensitivity vs FrequencyTL W 12340–11Input Sensitivity vs FrequencyTL W 12340–12Input Sensitivity at TemperatureVariation V CC e5VTL W 12340–13Input Sensitivity at TemperatureVariation V CC e3VTL W 12340–14LMX1501A Input Impedance vs FrequencyV CC e2 7V to5 5V f IN e100MHz to1 600MHzTL W 12340–15 Marker1e500MHz Real e67 Imag e b317Marker2e900MHz Real e24 Imag e b150Marker3e1GHz Real e19 Imag e b126Marker4e1 500MHz Real e9 Imag e b63LMX1511Input Impedance vs FrequencyV CC e2 7V to5 5V f IN e100MHz to1 600MHzTL W 12340–16 Marker1e500MHz Real e69 Imag e b330Marker2e900MHz Real e36 Imag e b193Marker3e1GHz Real e35 Imag e b172Marker4e1 500MHz Real e30 Imag e b1068Charge Pump Current Specification DefinitionsTL W 12340–17I1e CP sink current at V D o e V P b D V I2e CP sink current at V D o e V P 2I3e CP sink current at V D o e D VI4e CP source current at V D o e V P b D V I5e CP source current at V D o e V P 2I6e CP source current at V D o e D VD V e Voltage offset from positive and negative rails Dependent on VCO tuning range relative to V CC and ground Typical values are between 0 5V and 1 0V 1 I D o vs V D o e Charge Pump Output Current magnitude variation vs Voltage el I1l b l I3l l I1l a l I3l 100%and l I4l b l I6l l I4l a l I6l 100%2 I D o-sink vs I D o-source e Charge Pump Output Current Sink vs Source Mismatch el I2l b l I5l l I2l a l I5l 100%3 I D o vs T A e Charge Pump Output Current magnitude variation vs Temperature el I2 temp l b l I2 25 C l l I2 25 C l 100%and l I5 temp l b l I5 25 C l l I525 C l 100%4 K w e Phase detector charge pump gain constant e l I2l a l I5lRF Sensitivity Test Block DiagramTL W 12340–18Note 1 N e 10 000R e 50P e 64Note 2 Sensitivity limit is reached when the error of the divided RF output f OUT is greater than or equal to 1Hz9Functional DescriptionThe simplified block diagram below shows the 19-bit data register the 14-bit R Counter and the S Latch and the 18-bit N Counter (intermediate latches are not shown) The data stream is clocked (on the rising edge)into the DATA input MSB first If the Control Bit (last bit input)is HIGH the DATA is transferred into the R Counter (programmable reference divider)and the S Latch (prescaler select 64 65or 128 129) If the Control Bit (LSB)is LOW the DATA is transferred into the N Counter (programmable divider)TL W 12340–19PROGRAMMABLE REFERENCE DIVIDER (R COUNTER)AND PRESCALER SELECT (S LATCH)If the Control Bit (last bit shifted into the Data Register)is HIGH data is transferred from the 19-bit shift register into a 14-bit latch (which sets the 14-bit R Counter)and the 1-bit S Latch (S15 which sets the prescaler 64 65or 128 129) Serial data format is shown belowTL W 12340–2014-BIT PROGRAMMABLE REFERENCE DIVIDER RATIO (R COUNTER)Divide14S 13S 12S 11S 10S S 9S 8S 7S 6S 5S 4S 3S 2S1RatioR 30000000000001140000001001638311111111111111Notes Divide ratios less than 3are prohibitedDivide ratio 3to 16383S1to S14 These bits select the divide ratio of the programmable reference dividerC Control bit (set to HIGH level to load R counter and S Latch)Data is shifted in MSB first1-BIT PRESCALER SELECT (S LATCH)Prescaler 15S Select P 128 129064 65110Functional Description(Continued)PROGRAMMABLE DIVIDER(N COUNTER)The N counter consists of the7-bit swallow counter(A counter)and the11-bit programmable counter(B counter) If the Control Bit(last bit shifted into the Data Register)is LOW data is transferred from the19-bit shift register into a7-bit latch(which sets the7-bit Swallow(A)Counter)and an11-bit latch(which sets the11-bit programmable(B)Counter) Serial data format is shown belowTL W 12340–21 Note S8to S18 Programmable counter divide ratio control bits(3to2047)7-BIT SWALLOW COUNTER DIVIDE RATIO(A COUNTER)DivideS7S6S5S4S3S2S1RatioA00000000100000011271111111 Note Divide ratio 0to127B t A11-BIT PROGRAMMABLE COUNTER DIVIDE RATIO(B COUNTER)Divide18S17S16S15S14S13S12S11S10S S9S8 RatioB300000000011400000000100204711111111111 Note Divide ratio 3to2047(Divide ratios less than3are prohibited)B t APULSE SWALLOW FUNCTIONf VCO e (P c B)a A c f OSC Rf VCO Output frequency of external voltage controlled oscil-lator(VCO)B Preset divide ratio of binary11-bit programmablecounter(3to2047)A Preset divide ratio of binary7-bit swallow counter(0s A s127 A s B)f OSC Output frequency of the external reference frequencyoscillatorR Preset divide ratio of binary14-bit programmable ref-erence counter(3to16383)P Preset modulus of dual moduIus prescaler(64or 128)11Functional Description (Continued)SERIAL DATA INPUT TIMINGTL W 12340–22Notes Parenthesis data indicates programmable reference divider dataData shifted into register on clock rising edge Data is shifted in MSB firstTest Conditions The Serial Data Input Timing is tested using a symmetrical waveform around V CC 2 The test waveform has an edge rate of 0 6V ns withamplitudes of 2 2V V CC e 2 7V and 2 6V V CC e 5 5VPhase CharacteristicsIn normal operation the FC pin is used to reverse the polari-ty of the phase detector Both the internal and any external charge pump are affectedDepending upon VCO characteristics FC pin should be set accordinglyWhen VCO characteristics are like (1) FC should be set HIGH or OPEN CIRCUITWhen VCO characteristics are like (2) FC should be set LOWWhen FC is set HIGH or OPEN CIRCUIT the monitor pin of the phase comparator input f out is set to the reference divider output f r When FC is set LOW f out is set to the programmable divider output f pVCO CharacteristicsTL W 12340–23PHASE COMPARATOR AND INTERNAL CHARGE PUMP CHARACTERISTICSTL W 12340–24Notes Phase difference detection range b 2q to a 2qThe minimum width pump up and pump down current pulses occur at the D o pin when the loop is locked FC e HIGH12Analog Switch (1511only)The analog switch is useful for radio systems that utilize a frequency scanning mode and a narrow band mode The purpose of the analog switch is to decrease the loop filter time constant allowing the VCO to adjust to its new frequency in a shorter amount of time This is achieved by adding another filter stage in parallel The output of the charge pump is normally through the D o pin but when LE is set HIGH the charge pump output also becomes available at BISW A typical circuit is shown below The second filter stage (LPF-2)is effective only when the switch is closed (in the scanning mode)TL W 12340–25Typical Crystal Oscillator CircuitA typical circuit which can be used to implement a crystal oscillator is shown belowTL W 12340–26Typical Lock Detect CircuitA lock detect circuit is needed in order to provide a steady LOW signal when the PLL is in the locked state A typical circuit is shown belowTL W 12340–2713Typical Application ExampleTL W 12340–28 Operational NotesVCO is assumed AC coupledR IN increases impedance so that VCO output power is provided to the load rather than the PLL Typical values are10X to200X depending on the VCO power level f IN RF impedance ranges from40X to100X50X termination is often used on test boards to allow use of external reference oscillator For most typical products a CMOS clock is used and no terminating resistor is required OSC IN may be AC or DC coupled AC coupling is recommended because the input circuit provides its own bias (See Figure below)TL W 12340–29Proper use of grounds and bypass capacitors is essential to achieve a high level of performanceCrosstalk between pins can be reduced by careful board layoutThis is a static sensitive device It should be handled only at static free work stations14Application InformationLOOP FILTER DESIGNA block diagram of the basic phase locked loop is shownTL W 12340–30FIGURE1 Basic Charge Pump Phase Locked LoopAn example of a passive loop filter configuration includingthe transfer function of the loop filter is shown in Figure2TL W 12340–31Z(s)es(C2 R2)a1s2(C1 C2 R2)a sC1a sC2FIGURE2 2nd Order Passive FilterDefine the time constants which determine the pole andzero frequencies of the filter transfer function by lettingT2e R2 C2(1a)andT1e R2C1 C2C1a C2(1b)The PLL linear model control circuit is shown along with theopen loop transfer function in Figure3 Using the phasedetector and VCO gain constants K w and K VCO and theloop filter transfer function Z(s) the open loop Bode plotcan be calculated The loop bandwidth is shown on theBode plot(0p)as the point of unity gain The phase marginis shown to be the difference between the phase at the unitygain point and b180TL W 12340–33Open Loop Gain e i i i e e H(s)G(s)e K w Z(s)K VCO NsClosed Loop Gain e i o i i e G(s) 1a H(s)G(s)TL W 12340–32FIGURE3 Open Loop Transfer FunctionThus we can calculate the3rd order PLL Open Loop Gain interms of frequencyG(s) H(s)l s e j 0e b K wK VCO(1a j0 T2)02C1 N(1a j0 T1)T1T2(2)From equation2we can see that the phase term will bedependent on the single pole and zero such thatw(0)e tan b1(0 T2)b tan b1(0 T1)a180 (3)By settingd wd0eT21a(0 T2)2bT11a(0 T1)2e0(4)we find the frequency point corresponding to the phase in-flection point in terms of the filter time constants T1and T2This relationship is given in equation50p e1 0T2 T1(5)For the loop to be stable the unity gain point must occurbefore the phase reaches b180degrees We thereforewant the phase margin to be at a maximum when the magni-tude of the open loop gain equals1 Equation2then givesC1eK w K VCO T10p2 N T2(1a j0p T2)(1a j0p T1) (6)15Application Information(Continued) Therefore if we specify the loop bandwidth 0p and the phase margin w p Equations1through6allow us to calcu-late the two time constants T1and T2 as shown in equa-tions7and8 A common rule of thumb is to begin your design with a45 phase marginT1e sec w p b tan w p0p(7)T2e10p2 T1(8)From the time constants T1 and T2 and the loop band-width 0p the values for C1 R2 and C2are obtained in equations9to11C1e T1T2K w K VCO0p2 N01a(0p T2)21a(0p T1)2(9) C2e C1 T2T1b1J(10) R2eT2C2(11)K VCO(MHz V)Voltage Controlled Oscillator(VCO)Tuning Voltage constant The fre-quency vs voltage tuning ratioK w(mA)Phase detector charge pump gainconstant The ratio of the current out-put to the input phase differentialN Main divider ratio Equal to RF opt f ref RF opt(MHz)Radio Frequency output of the VCO atwhich the loop filter is optimizedf ref(kHz)Frequency of the phase detector in-puts Usually equivalent to the RFchannel spacing In choosing the loop filter components a trade off must be made between lock time noise stability and reference spurs The greater the loop bandwidth the faster the lock time will be but a large loop bandwidth could result in higher reference spurs Wider loop bandwidths generally improve close in phase noise but may increase integrated phase noise depending on the reference input VCO and division ratios used The reference spurs can be reduced by reduc-ing the loop bandwidth or by adding more low pass filter stages but the lock time will increase and stability will de-crease as a resultTHIRD ORDER FILTERA low pass filter section may be needed for some applica-tions that require additional rejection of the reference side-bands or spurs This configuration is given in Figure4 In order to compensate for the added low pass section the component values are recalculated using the new open loop unity gain frequency The degradation of phase margin caused by the added low pass is then mitigated by slightly increasing C1and C2while slightly decreasing R2The added attenuation from the low pass filter isATTEN e20log (2q f ref R3 C3)2a1 (12) Defining the additional time constant asT3e R3 C3(13) Then in terms of the attenuation of the reference spurs add-ed by the low pass pole we haveT3e010ATTEN 20b1(2q f ref)2(14) We then use the calculated value for loop bandwidth0c in equation11 to determine the loop filter component values in equations15–17 0c is slightly less than0p therefore the frequency jump lock time will increaseT2e10c2 (T1a T3)(15)0c etan w (T1a T3)(T1a T3)2a T1 T301a(T1a T3)2a T1 T3tan w (T1a T3) 2b1((16)C1e T1T2K w K VCO0c2 N(1a0c2 T22)(1a0c2 T12)(1a0c2 T32)((17)16Application Information (Continued)Example 1K VCO e 19 3MHz V K w e 5mA (Note 1)RF opt e 886MHz F ref e 25kHzN e RF opt f ref e 354400p e 2q 5kHz e 3 1415e4w p e 43ATTEN e 10dBT1e sec w p b tan w p0pe 1 38e b 5T3e10(10 20)b 1(2q 25e3)2e 9 361e b 60c e(tan 43 ) (1 38e b 5a 9 361e b 6)(1 38e b 5a 9 361e b 6)2a 1 38e b 59 361e b 61a(1 38e b 5a 9 361e b 6)2a 1 38e b 5 9 361e b 6(tan 43 ) (1 38e b 5a 9 361e b 6) 2b 1(e 1 8101e4T2e 1(1 8101e4)2(1 38e b 5a 9 361e b 6)e 1 318e b 4C1e1 38e b 51 318e b 4(5e b 3) 19 3e6(1 8101e4)2 (35440)1a (1 8101e4)2 (1 318e b 4)2 1a (1 8101e4)2 (1 38e b 5)2 1a (1 8101e4)2 (9 361e b 6)2 (e 2 153nFC2e 2 153nF1 318e b 41 384e b 5b 1Je 18 35nFR2e1 318e b 418 35e b 9e 7 18k Xif we choose R3e 120k then C3e9 361e b 6120e3e 78pFConverting to standard component values gives the follow-ing filter values which are shown in Figure 4 C1e 2200pF R2e 8 2k X C2e 0 018m F R3e 120k X C3e 78pFNote 1 See related equation for K w in Charge Pump Current SpecificationDefinitions For this example V P e 5 0V The value for K w can then be approximated using the curves in the Typical Performance Char-acteristics for Charge Pump Current vs D o Voltage The units for K w are in mA You may also use K w e (5mA 2q rad) but in this case you must convert K VCO to (rad V)multiplying by 2qTL W 12340–41FIGURE 4 E 5kHz Loop Filter17Application Information(Continued)TL W 12340–43 FIGURE5 PLL Reference SpursThe reference spurious level is k b66dBc due to the loop filter attenuation and the low spurious noise level of the LMX1511TL W 12340–45 FIGURE6 PLL Phase Noise3 5kHz OffsetThe phase noise level at3kHz offset is b65dBc HzTL W 12340–44 FIGURE7 PLL Phase Noise 150Hz OffsetThe phase noise level at150Hz offset is b75 5dBc HzTL W 12340–42 FIGURE8 Frequency Jump Lock Time Of concern in any PLL loop filter design is the time it takes to lock in to a new frequency when switching channels Fig-ure8shows the switching waveforms for a frequency jump of857MHz–915MHz By narrowing the frequency span of the HP53310A Modulation Domain Analyzer enables evalu-ation of the frequency lock time to within g1kHz The lock time is seen to be k1 6ms for a frequency jump of58MHz 18Application Information(Continued) EXTERNAL CHARGE PUMPThe LMX PLLatimum series of frequency synthesizers are equipped with an internal balanced charge pump as well as outputs for driving an external charge pump Although the superior performance of NSC’s on board charge pump elim-inates the need for an external charge pump in most appli-cations certain system requirements are more stringent In these cases using an external charge pump allows the de-signer to take direct control of such parameters as charge pump voltage swing current magnitude TRI-STATE leak-age and temperature compensationOne possible architecture for an external charge pump cur-rent source is shown in Figure9 The signals w p and w r in the diagram correspond to the phase detector outputs of the LMX1501 1511frequency synthesizers These logic signals are converted into current pulses using the circuitry shown in Figure9 to enable either charging or discharging of the loop filter components to control the output frequency of the PLLReferring to Figure9 the design goal is to generate a5mA current which is relatively constant to within5V of the power supply rail To accomplish this it is important to establish as large of a voltage drop across R5 R8as possible without saturating Q2 Q4 A voltage of approximately300mV pro-vides a good compromise This allows the current source reference being generated to be relatively repeatable in the absence of good Q1 Q2 Q3 Q4matching (Matched tran-sistor pairs is recommended )The w p and w r outputs are rated for a maximum output load current of1mA while5mA current sources are desired The voltages developed across R4 9will consequently be approximately258mV or42mV k R8 5 due to the current density differences 0 026 1n(5 mA 1mA) through the Q1 Q2 Q3 Q4pairsIn order to calculate the value of R7it is necessary to first estimate the forward base to emitter voltage drop(Vfn p)of the transistors used the V OL drop of w p and the V OH drop of w r’s under1mA loads (w p’s V OL k0 1V and w r s V OH k0 1V )Knowing these parameters along with the desired current allow us to design a simple external charge pump Separat-ing the pump up and pump down circuits facilitates the no-dal analysis and give the following equationsR4e V R5b V T 1n i source i p max Ji sourceR9e V R8b V T 1n i sink i n max Ji sinkR5eV R5 (b p a1)i p max (b p a1)b i sourceR8eV R8 (b n a1)i r max (b n a1)b i sinkR6e (V p b V VOL w p)b(V R5a Vfp)i p maxR7e (V P b V VOH w r)b(V R8a Vfn)i maxEXAMPLETypical Device Parameters b n e100 b p e50Typical System Parameters V P e5 0VV cntl e0 5V b4 5VV w p e0 0V V w r e5 0VDesign Parameters I SINK e I SOURCE e5 0mAV fn e V fp e0 8VI rmax e I pmax e1mAV R8e V R5e0 3VV OL w p e V OH w r e100mVTL W 12340–46FIGURE9Therefore selectR4e R9e0 3V b0 026 1n(5 0mA 1 0mA)5mAe51 6XR5e0 3V (50a1)1 0mA (50a1)b5 0mAe332XR8e0 3V (100b1)1 0mA (100a1)b5 0mAe315 6XR6e R7e(5V b0 1V)b(0 3V a0 8V)1 0mAe3 8k X1920Physical Dimensions inches(millimeters)JEDEC16-Lead(0 150 Wide)Small Outline Molded Package(M)Order Number LMX1501AMFor Tape and Reel Order Number LMX1501AMX(2500Units per Reel)NS Package Number M16A21L M X 1501A L M X 1511P L L a t i n u m 1 1G H z F r e q u e n c y S y n t h e s i z e r f o r R F P e r s o n a l C o m m u n i c a t i o n s Physical Dimensions (millimeters)(Continued)20-Lead (0 173 Wide)Thin Shrink Small Outline Package (TM)Order Number LMX1511TMFor Tape and Reel Order Number LMX1511TMX (2500Units per Reel)NS Package Number MTC20LIFE SUPPORT POLICYNATIONAL’S PRODUCTS ARE NOT AUTHORIZED FOR USE AS CRITICAL COMPONENTS IN LIFE SUPPORT DEVICES OR SYSTEMS WITHOUT THE EXPRESS WRITTEN APPROVAL OF THE PRESIDENT OF NATIONAL SEMICONDUCTOR CORPORATION As used herein1 Life support devices or systems are devices or2 A critical component is any component of a life systems which (a)are intended for surgical implantsupport device or system whose failure to perform can into the body or (b)support or sustain life and whosebe reasonably expected to cause the failure of the life failure to perform when properly used in accordancesupport device or system or to affect its safety or with instructions for use provided in the labeling caneffectiveness be reasonably expected to result in a significant injuryto the userNational SemiconductorNational Semiconductor National Semiconductor National Semiconductor CorporationEurope Hong Kong Ltd Japan Ltd 1111West Bardin Road Fax (a 49)0-180-530858613th Floor Straight Block Tel 81-043-299-2309。
MD-015 GNSS多星系统精准原子振子模块说明书

MD-015GNSS (GPS, GLONASS, Galileo)Disciplined Atomic Oscillator ModuleThe MD-015 is a Microchip GNSS disciplined atomic clock module. 1 PPS TTL, 10MHz sine wave, and 10 MHz square wave outputs are generated from an on-board low-power SA.65s Chip Scale Atomic Clock, a high-stability SA53, or a high-stability SA55 Miniature Atomic Clock which is disciplined to an embedded 72 channel multi-constellation GNSS receiver or an external reference input supporting input frequencies from 1Hz (1PPS) to 120 MHz.• Embedded GNSS Receiver - GPS, GLONASS, Galileo • 1pps TTL output signal• TTL (5.0V) Standard, LVTTL (3.3V) available • 10MHz sinewave and square wave output • Other RF output frequencies available• Adaptive aging correction during holdover • Barometric pressure correction • Evaluation kit with software• Serial Communications Interface• Basestation Communication • Digital Video Broadcast • E911 Location Systems• General Timing and Synchronization • Military Radio • Radar SystemsFeaturesBlock DiagramApplicationsAtomic Oscillator(SA53 MAC or SA.65s CSAC)Processor/ControllerOutput Frequency GenerationAntenna Input1PPS Output 10 MHz CMOS RF Output SerialFigure 1. Functional Block DiagramOutput Locked Module OKGNSS ReceiverHardwareResetManual Holdover External ReferenceInput10 MHz Sinewave RF OutputNotes:• RF and 1pps input and output connectors are MCX type (SMA, SMB, MMCX connectors require additional part numbers).• Keyed connector is Samtec FTSH-108-01LDVK type.• Dimensions: mm• Module height in part number is the sum of oscillator height, board, and clearancePackage OutlineAlthough ESD protection circuitry has been designed into the MD-015, proper precautions should be taken when handling and mounting. Microchip employs a human body model (HBM) and a charged-device model (CDM) for ESD susceptibility testing and design protectionMD-015-0001MD-015-0002 & MD-015-0003Ordering Information InstructionsCustomization to unique customer requirements is available and is common for this level of integration. Common customizations include alternate output frequencies, temperature ranges, differing values and methods of hold over specification, and holdover optimization in the frequency domain. The table below lists exisiting combinations available as of the date of publication of this data sheet. Please contact thefactory for additional options.Notes1) Aging performance is after 1 month of power-on time. Temperature and aging rates are when device is notlocked. Performance measured in still air.2) After customer applies correct offset using cable delay command while locked, after 24 hours of locked opera-tion3) The status locked indicator is intended to indicate when the module is fully locked to a reference.4) The Hardware OK indicator is intended to indicate when the module is operating properly without any failures, including hardware, software or parameter out of range.5) Antenna over current flag will be set if maximum current is exceeded. Circuit has overcurrent protection.6) The Rx pin is the serial interface input and the Tx pin is the serial interface output. 7)Serial configuration: 8 data bits, 1 stop bit, no parity, no flow controlUSA:100 Watts StreetMt Holly Springs, PA 17065Tel: 1.717.486.3411Fax: 1.717.486.5920Europe:Landstrasse74924 NeckarbischofsheimGermanyTel: +49 (0) 7268.801.0Fax: +49 (0) 7268.801.281Information contained in this publication regarding device applications and the like is provided only for your convenience and may be superseded by updates. It is your reasonability to ensure that your application meets with your specifications. MICRO-CHIP MAKES NO REPRESENTATION OR WARRANTIES OF ANY KIND WHETHER EXPRESS OR IMPLIED, WRITTEN OR ORAL, STATUTORY OR OTHERWISE, RELATED TO THE INFORMATION INCLUDING, BUT NOT LIMITED TO ITS CONDITION, QUALITY, PERFORMANCE, MERCHANTABILITY OR FITNESS FOR PURPOSE. Microchip disclaims all liability arising from this information and its use. Use of Microchip devices in life support and/or safety applications is entirely at the buyer’s risk, and the buyer agrees to defend, indemnify and hold harmless Microchip from any and all damages, claims, suits, or expenses resulting from such use. No licenses are conveyed, implicitly, or otherwise, under any Microchip intellectual property rights unless otherwise stated. TrademarksThe Microchip and Vectron names and logos are registered trademarks of Microchip Technology Incorporated in the。
MPS150 150mm手动测试平台说明书

Features / BenefitsOverviewThe MPS150 is an easy to use, yet highly-precise manual probe platform for wafers and substrates up to 150 mm. It supports a wide variety of applications and accessories. The modular and flexible design allows to configure and individualize the system to match application requirements. With the System Integration for Measurement Accuracy (SIGMA™) kit, MPS150 can be seamlessly integrated with third-party instrumentation, ensuring the shortest signal bining the MPS150 probe system with our measurement expertise, FormFactor provides pre-configured application-focused probing solutions for a variety of applications, and an integrated measurement solution for accurate S-parameter measurements, which include everything you need to achieve accurate measurement results in the shortest time, with maximum confidence.Note: For physical dimensions and facility requirements, refer to the MPS150 Facility Planning Guide.Mechanical PerformanceChuck StageTravel155 mm x 155 mm (6 in. x 6 in.)Resolution 5 µmPlanarity over 150 mm (6 inch)< 10 µmLoad stroke, Y axis90 mmZ height adjustment range10 mmZ contact / separation / load stroke0-3 mm adjustableTheta travel (standard)360°Theta travel (fine)± 8°Theta resolution7.5 x 10-3 gradientManual Microscope Stage (On Bridge)Travel range50 mm x 50 mm (2 in. x 2 in.) / 150 mm x 100 mm (6 in. x 4 in)Resolution≤ 5 µm (0.2 mils)Scope lift Manual, tilt-back or linear pneumaticProgrammable Microscope Stage*Travel range50 mm x 50 mm (2 in. x 2 in.)Resolution0.25 µm (0.01 mils)Scope lift Programmable 130 mm* Electronics box for manual systems (P/N 157-137) requiredPlaten SystemPlatenPlaten space (typical)Universal platen: space for up to four DPP2xx/DPP3xx/DPP4xx/RPP210 or up to twelve DPP105 positionersUniversal platen with optional probe card adapter: space for up to eight DPP2xx/DPP3xx/DPP4xx/RPP210or up to sixteen DPP105 positionersMMW platen: space for up to four RPP305 or two LAP positionersZ-Height adjustment range Maximum 40 mm (depending on configuration)Minimum platen-to-chuck height16 mm (universal platen)Separation lift200 µmSeparation repeatability< 1 µmVertical rigidity / force 5 µm / 10 N (0.2 mils / 2.2 lb.)Accessory mounting options Universal platen: magnetic, vacuumRF-platen: bolt-down, magneticWafer ChuckStandard Wafer ChuckDiameter150 mmMaterial Stainless steelDUT sizes supported Shards or wafers 25 mm (1 in.) through 150 mm (6 in.)Vacuum ring diameter Universal: 4 mm, 7 mm, 22 mm, 42 mm, 66 mm, 88 mm, 110 mm, 132 mmStandard: 22 mm, 42 mm, 66 mm, 88 mm, 110 mm, 132 mmVacuum ring actuation Universal: all connected in meander, center hole 1.5 mm diameterStandard: mechanically selected, center hole 1.0 mm diameterChuck surface Planar with centric-engraved vacuum groovesSurface planarity≤ ± 3 µmRigidity< 15 µm / 10 N @ edgeRF Wafer ChuckDiameter150 mm with two additional AUX chucksMaterial Stainless steel with HF/OPTO surface (flat with 0.7 mm holes)DUT sizes supported Main: single DUTs down to 3 mm x 5 mm size or wafers 25 mm (1 inch) through 150 mm (6 inch)AUX: up to 18 mm x 26 mm (1 in. x 0.7 inch) eachVacuum hole sections (diameter)22 mm, 42 mm, 66 mm, 88 mm, 110 mm, 132 mm (four holes in center with 2.5 mm x 4.3 mm distance) Vacuum hole actuation Mechanically selectedChuck surface Planar with 0.7 mm diameter holes in centric sectionsSurface planarity≤ ± 3 µmRigidity< 15 µm / 10 N @ edgeTriax Wafer ChuckDiameter150 mm with three additional AUX chucks (two with vacuum fixation)Material Stainless steelDUT sizes supported Main: wafers 50 mm through 150 mmAUX: up to 18 mm x 26 mm (1 inch x 0.7 inch) eachVacuum hole sections (diameter)50 mm, 100 mm, 150 mm (2 inch, 4 inch, 6 inch)Vacuum hole actuation3x vacuum switch unitChuck surface Planar with 0.4 mm diameter holes in centric sectionsSurface planarity≤ ±5 µmNon-Thermal ChucksNote: Results measured with non-thermal chuck at standard probing height (10,000 µm) with chuck in a dry environment. Moisture in the chuck may degrade performance.MPS-CHUCK150-COAXOperation voltage Standard: in accordance with EC 61010, certificates for higher voltages available upon requestIsolation*> 2 GΩCapacitance100 pF* Factory test with multimeter with maximum 2 GΩ range.Non-Thermal Chucks (continued)MPS-CHUCK150-RFOperation voltage Standard: in accordance with EC 61010, certificates for higher voltages available upon request Isolation (Signal-Shield)> 200 GΩCapacitance (Signal-Shield)80 pFMPS-CHUCK150-TRIAX1In Purged Shield Enclosure Open2Humidity2< 30%50%Leakage (1 sigma)< 50 fA< 200 fALeakage (average)NA NALeakage (P-P)< 100 fA< 1000 fAResistance (F-G)> 1 TΩ> 1 TΩResistance (G-S)> 1 TΩ> 1 TΩResistance (F-S)> 1 TΩ> 1 TΩResidual capacitance @ 3 pA Tx< 20 pF< 20 pFCapacitance @ 300 pA (F-G)< 400 pF< 400 pFCapacitance @ 300 pA (G-S)< 400 pF< 400 pFTRIAXIAL PROBE ARMS1Standard Triaxal Arm (PN 100525)Advanced Triax Option (PN 157-450 and DCP)In Purged Shield Enclosure In Purged Shield EnclosureHumidity3< 30%< 30%Leakage (1 sigma)< 5 fA< 2 fAResistance (F-G)> 20 TΩ> 50 TΩResistance (G-S)> 4 TΩNAResidual capacitance @ 3 pA Tx< 1 pF< 0.3 fFCapacitance @ 300 pA (F-G)< 300 pF< 150 pFCapacitance @ 300 pA (G-S)< 400 pF< 200 pFCOAXIAL PROBE ARMS1Coaxial Probe Arm (PN 100561)Open / Ambient2, 4Resistance (Signal-Shield)> 20 TΩCapacitance (Signal-Shield)< 200 pF1. T est conditions: B1500 with SMU B1517, triax test cables and adapter ground unit (104-337). Resistor test setup: 10 V HR Mode PCL Factor 15.Capacitor test setup: 3 pA / 300 pA HR Mode PCL Factor 4. Leakage test setup: 10 V HR Mode PCL Factor 40.2. Depending on DC-/AC-noise environment.3. Environment data (not specification data).4. Depending on humidity.Thermal Chuck PerformanceNote: For details on facility requirements, refer to the Facility Planning Guide for your thermal system.MPS-TC150-CTX-300C1Triax @ 30°C Triax @ 200°C Triax @ 300°C Breakdown voltage2a Force-to-guard≥ 500 V≥ 500 V≥ 500 VGuard-to-shield≥ 500 V≥ 500 V≥ 500 VForce-to-shield≥ 500 V≥ 500 V≥ 500 V Resistance3a Force-to-guard≥ 1 x 1012≥ 1 x 1011≥ 5 x 109Guard-to-shield≥ 1 x 1011≥ 1 x 1010≥ 1 x 109Force-to-shield≥ 5 x 1012≥ 2 x 1011≥ 5 x 109 Chuck leakage4≤ 100 fA≤ 10 pA≤ 300 pA Residual capacitance≤ 50 pFSettling time6 @ 10 V 50 fA500 ms (typical)MPS-TC150-CTX-300C (using coax-triax adapter)1, 5Coax @ 30°C Coax @ 200°C Coax @ 300°C Breakdown voltage2a≥ 500 V≥ 500 V≥ 500 V Resistance3a Signal-to-shield≥ 1 x 1012≥ 1 x 1011≥ 5 x 109 Chuck leakage4≤ 600 fA≤ 15 pA≤ 1 nA Residual capacitance≤ 600 pFMPS-TC150-RF-300C1, 5Coax @ 30°C Coax @ 200°C Coax @ 300°C Breakdown voltage2a≥ 500 V≥ 500 V≥ 500 V Resistance3a Signal-to-shield≥ 1 x 1012≥ 1 x 1011≥ 5 x 109 Chuck leakage4≤ 600 fA≤ 15 pA≤ 1 nA Residual capacitance≤ 600 pFMPS-TC150-200C1Triax @ 30°C Triax @ 200°CBreakdown voltage2b Force-to-guard≥ 500 V≥ 500 VGuard-to-shield≥ 500 V≥ 500 VForce-to-shield≥ 500 V≥ 500 VResistance3b Force-to-guard≥ 5 x 1012≥ 5 x 1011Guard-to-shield≥ 2 x 1012≥ 8 x 1010Force-to-shield≥ 7 x 1012≥ 5 x 1011Chuck leakage4≤ 35 fA≤ 40 fAResidual capacitance6≤ 20 pFSettling time7 @ 10 V 50 fA500 ms (typical)Thermal Chuck Performance (continued)MPS-TC150-200C (using coax-triax adapter)1, 5Coax @ 30°C Coax @ 200°CBreakdown voltage2b≥ 500 V≥ 500 VResistance3b Signal-to-shield≥ 5 x 1012≥ 5 x 1011Chuck leakage4≤ 600 fA≤ 7.5 pAResidual capacitance6≤ 600 pF1. P erformance values determined using EMV shielded chamber. Actual value depend on electromagnatic surrounding and shielding situation of the probestation.2a. For fully-baked chuck: 90°C for 60 minutes + 200°C for 240 minutes + 300°C for 480 minutes.2b. For fully-baked chuck: 90°C for 60 minutes + 200°C for 800 minutes3a. For fully-baked chuck: 90°C for 60 minutes + 200°C for 240 minutes + 300°C for 480 minutes; controller on; 21-23C° environment with ≤ 50% humidity.3b. For fully-baked chuck: 90°C for 60 minutes + 200°C for 800 minutes; 21-23C° environment with ≤ 50% humidity.4. O verall leakage current is comprised of two separate components: 1) offset, and 2) noise. Offset is the DC value of current due to instrument voltageoffset driving through isolation resistance. Noise is low frequency ripple superimposed on top of offset and is due to disturbances in the probe station environment.*****************************************************************************************************************(1σ).5. Chuck: Guard-Shield shorted, B1500: triax, guard open.6. Depends on test environment7. Settling time is measured with B1500 with SMUB1517 - ST@10V CMI program or equivalentTransition TimeHeating Cooling30°C to 100°C°100°C to 200°C200°C to 300°C300°C to 200°C200°C to 100°C100°C to 30°C MPS-TC150-CTX-300C145 sec155 sec300 sec145 sec245 sec1525 secMPS-TC150-RF-300C180 sec300 sec540 sec165 sec310 sec1650 secMPS-TC150-200C155 sec260 sec na na120 sec425 secMPS-TC150-CTX-300C and MPS-TC150-RF-300C SpecificationsTemperature range+ 30°C to 300°CTemperature accuracy± 0.1°C (with calibrated controller)Temperature resolution0.1°CTemperature uniformity≤ 0.5°C @ 30°C, ≤ 3.0°C @ 300°CChuck flatness≤ 30 μm (0.12 mils) @ +30°C to 300°CAudible noise< 58 dB(A) (normal operation); < 79 dB(A) (max. cooling mode)MPS-TC150-200CTemperature range+ 30°C to 200°CTemperature accuracy± 0.5°CTemperature resolution0.1°CTemperature uniformity≤ ±1°C (30°C - 200°C)Chuck flatness≤ 30 μm (0.12 mils) @ +30°C to 200°CAudible noise< 54 dB(A) (normal operation); < 68 dB(A) (max. cooling mode)Ordering InformationPre-Configured Application-Focused PackagesEPS150 COAX / COAX PLUS EPS150TRIAX EPS150RFEPS150MMW EPS150FA EPS150TESLAIntegrated Measurement SolutionRFgeniusPart Number DescriptionEPS150COAX150 mm manual probing solution for DC parametric testEPS150COAXPLUS150 mm manual probing solution for DC parametric test (including platen lift)EPS150TRIAX150 mm manual probing solution for low-noise measurementsEPS150RF150 mm manual probing solution for RF applicationsEPS150MMW150 mm manual probing solution for mmW, THz and load pull applicationsEPS150FA150 mm manual probing solution for failure analysisRFgenius-xx*RFgenius education kit, turn-key solution for measurements up to 4.5/6.5/9/14/20/26.5 GHz 181-669FormFactor certified laptop for RFgenius-xx (optional)*** Enter the frequency range for a VNA of your choice. Example: RFgenius-4 for 4.5 GHz. RFgenius-26 for 26.5 GHz.** M inimum requirement for a laptop to be supplied by a user: Windows 7 or 10 (64 bit), Intel i5 6th Gen or newer, 4 GB memory or more (16 GB recommended),2 GB disk space or more, 1024 x 768 resolution, USB 3.o port.Corporate Headquarters 7005 Southfront Road Livermore, CA 94551Phone: © Copyright 2018 FormFactor, Inc. All rights reserved. FormFactor and the FormFactor logo are trademarks of FormFactor, Inc. All other trademarks are the property of their respective owners.All information is subject to change without notice.MPS150-DS-0518Regulatory ComplianceCertificationCE, cNRTLus, CBWarrantyWarranty* Fifteen months from date of delivery or twelve months from date of installation Service contracts Single and multi-year programs available to suit your needs*See FormFactor’s T erms and Conditions of Sale for more details.。
降压型开关稳压器AP1510及其应用
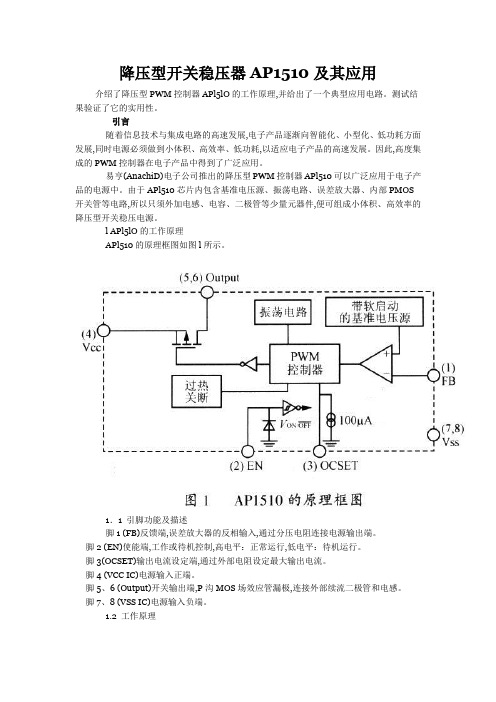
降压型开关稳压器AP1510及其应用介绍了降压型PWM控制器APl5lO的工作原理,并给出了一个典型应用电路。
测试结果验证了它的实用性。
引言随着信息技术与集成电路的高速发展,电子产品逐渐向智能化、小型化、低功耗方面发展,同时电源必须做到小体积、高效率、低功耗,以适应电子产品的高速发展。
因此,高度集成的PWM控制器在电子产品中得到了广泛应用。
易亨(AnachiD)电子公司推出的降压型PWM控制器APl510可以广泛应用于电子产品的电源中。
由于APl510芯片内包含基准电压源、振荡电路、误差放大器、内部PMOS 开关管等电路,所以只须外加电感、电容、二极管等少量元器件,便可组成小体积、高效率的降压型开关稳压电源。
l APl5lO的工作原理APl510的原理框图如图l所示。
1.1 引脚功能及描述脚1 (FB)反馈端,误差放大器的反相输入,通过分压电阻连接电源输出端。
脚2 (EN)使能端,工作或待机控制,高电平:正常运行,低电平:待机运行。
脚3(OCSET)输出电流设定端,通过外部电阻设定最大输出电流。
脚4 (VCC IC)电源输入正端。
脚5、6 (Output)开关输出端,P沟MOS场效应管漏极,连接外部续流二极管和电感。
脚7、8 (VSS IC)电源输入负端。
1.2 工作原理由图1可知,APl510由基准电压源、振荡电路、误差放大器、PWM控制器、过热关断控制电路以及P沟MOS场效应管等部件组成。
基准电压源为芯片内部电路提供稳定的供电电压,并为误差放大器的同相输入端提供0.8V的电压基准。
它具有软启动功能,可以防止电源启动时的冲击,它还具有欠压锁定功能,当输入电压低于3.3V时APl510停止工作;当输入电压高于3.5V时,它自动恢复工作。
振荡电路产生300 kHz的振荡波形,当发生过流保护或短路保护时,工作频率将从300 kHz减小到30kHz。
输出电压的取样信号进入误差放大器的反相输入端,经比较后进入PWM控制器,输出占空比变化的方波去驱动内部的P沟M0S管:APl510调节脉冲的占空比可以从O%~100%,这使得APl510可以在很宽的输入电压范围内正常工作。
RemoDAQ-8017A 16路模拟量输入模块用户手册说明书

V1.1 2008.11.4RemoDAQ-8017A16路模拟量输入模块用户手册北京集智达智能科技有限责任公司目录1 概述 (2)1.1 端子分布 (2)1.2 特性 (3)1.3 结构图 (3)1.4 接线说明 (4)1.5 默认设置 (4)1.6 跳线设置 (4)1.7 校准 (5)1.8 设置列表 (5)1.9 RemoDAQ-8000-9000 Series Utility软件介绍 (6)2 命令 (7)2.1 %AANNTTCCFF (9)2.2 #AA (10)2.3 #AAN (11)2.4 $AA0 (12)2.5 $AA1 (13)2.6 $AA2 (14)2.7 $AA5VVVV (15)2.8 $AA6 (16)2.9 $AA3V.VVVV (17)2.10 $AA4+VV (18)2.11 $AAF (19)2.12 $AAM (20)2.13 ~AAO(数据) (21)2.14 ~AAEV (22)3 应用注释 (23)3.1 INIT* 端子操作 (23)3.2 变送器 (23)1 概述RemoDAQ-8000系列是基于RS-485网络的数据采集和控制模块。
它们提供了模拟量输入、模拟量输出、数字量输入/输出、定时器/计数器、交流电量采集、无线通讯等功能。
这些模块可以由命令远程控制。
RemoDAQ-8017A是16通道电压/电流输入模块,除了支持ASCII命令集外,还支持MODBUS/RTU通信协议。
具有如下特点:●3000 VDC隔离●24位ADC提供极高的精确度●软件校准●TVS过压保护、RC滤波1.1 端子分布1.2 特性通道:16路单端输入类型:mA,V量程范围:0~20 mA,0~5V,0~10V跳线及软件配合选择采样速率:6.8次/秒(total)带宽:15.7Hz精确度:±0.1%零漂移:20uV/℃量程漂移:25ppm/℃CMR:86dB输入阻抗:10M Ohms 过电压保护:20V P-P隔离:3000VDC温度:-20℃~70℃湿度:5%~90%,无凝露电源输入:+10V ~ +30VDC 功耗:1.3W1.3 结构图1.4 接线说明REMODAQ-8017A 电压接线说明JP1~JP16:JP17(0~10V):REMODAQ-8017A 电流接线说明 JP1~JP16:JP17(0~20mA):注意:因为模块内部设有信号保护电路,在没有供电的情况下会 对正常信号产生影响,所以一定要在确保正常供电的情况下安装 和采集信号,并且在模块断电之前切断或停止采集信号。
安装说明-Compact 5000 I O 数字量 8 点安全拉出型输入模块说明书
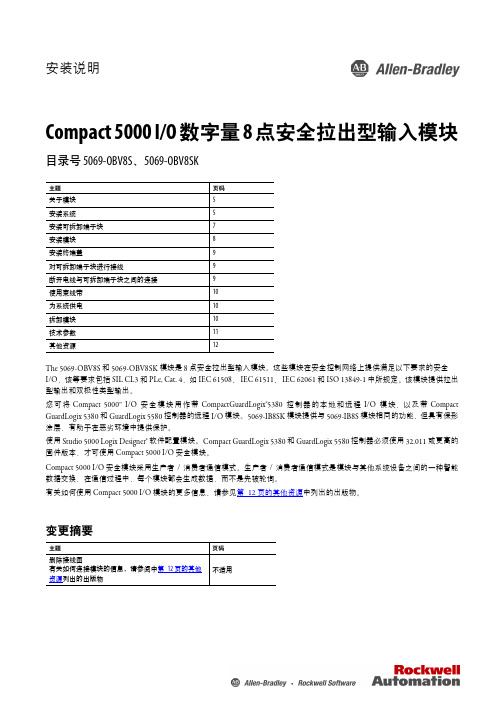
安装说明Compact 5000 I/O 数字量 8 点安全拉出型输入模块目录号 5069-OBV8S 、5069-OBV8SKThe 5069-OBV8S 和 5069-OBV8SK 模块是 8 点安全拉出型输入模块。
这些模块在安全控制网络上提供满足以下要求的安全 I/O ,该等要求包括 SIL CL3 和 PLe, Cat. 4,如 IEC 61508、IEC 61511、IEC 62061 和 ISO 13849-1 中所规定。
该模块提供拉出型输出和双极性类型输出。
您可将 Compact 5000™ I/O 安全模块用作带 CompactGuardLogix®5380 控制器的本地和远程 I/O 模块,以及带 Compact GuardLogix 5380 和 GuardLogix 5580 控制器的远程 I/O 模块。
5069-IB8SK 模块提供与 5069-IB8S 模块相同的功能,但具有保形涂层,有助于在恶劣环境中提供保护。
使用 Studio 5000 Logix Designer® 软件配置模块。
Compact GuardLogix 5380 和 GuardLogix 5580 控制器必须使用 32.011 或更高的固件版本,才可使用 Compact 5000 I/O 安全模块。
Compact 5000 I/O 安全模块采用生产者/消费者通信模式。
生产者/消费者通信模式是模块与其他系统设备之间的一种智能数据交换,在通信过程中,每个模块都会生成数据,而不是先被轮询。
有关如何使用 Compact 5000 I/O 模块的更多信息,请参见第12页的其他资源中列出的出版物。
变更摘要主题页码关于模块5安装系统5安装可拆卸端子块7安装模块8安装终端盖9对可拆卸端子块进行接线9断开电线与可拆卸端子块之间的连接9使用束线带10为系统供电10拆卸模块10技术参数11其他资源12主题页码删除接线图有关如何连接模块的信息,请参阅中第12页的其他资源列出的出版物不适用Compact 5000 I/O 数字量 8 点安全拉出型输入模块ATTENTION:Read this document and the documents listed in the Additional Resources section about installation, configuration and operation of this equipment before you install, configure, operate ormaintain this product. Users are required to familiarize themselves with installation and wiring instructions in addition to requirements of all applicable codes, laws, and standards.Activities including installation, adjustments, putting into service, use, assembly, disassembly, and maintenance are required to be carried out by suitably trained personnel in accordance with applicable code of practice.If this equipment is used in a manner not specified by the manufacturer, the protection provided by the equipment may be impaired.注意:在安装、配置、操作和维护本产品前,请阅读本文档以及“其他资源”部分列出的有关设备安装、配置和操作的相应文档。
2014年的Rockwell Automation 1715系列输入输出系统技术规格说明书

Emissions CISPR 11 (IEC 61000-6-4)
ESD immunity IEC 61000-4-2
Radiated RF immunity IEC 61000-4-3
Attribute
1715-IF16, 1715-A3IO, 1715-TASIF16, 1715-TADIF16
Operating voltage range, supply power and/or current ratings
1715-IF16 backplane: 260 mA @ 18…32V DC 1715-TASIF16, 1715-TADIF16 I/O: 0…24 mA per channel @ 18…32V DC
EFT/B immunity IEC 61000-4-4
Surge transient immunity IEC 61000-4-5
Conducted RF immunity IEC 61000-4-6
1715-IF16, 1715-A3IO, 1715-TASIF16, 1715-TADIF16 -25…70 °C (-13…158 °F)
166 x 42 x 118 mm (6.5 x 1.625 x 4.625 in.)
Wire size
1715-TASIF16, 1715-TADIF16 I/O connections: Single 0.33... 1.5 mm2 (22...16 AWG) solid or stranded shielded copper wire rated at 85 °C (185 °F), or greater
安全伯力护套模块说明书
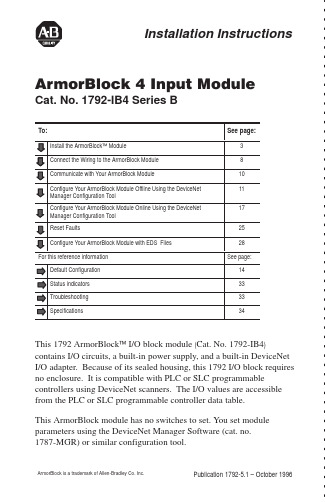
ArmorBlock 4 Input Module2Publication 1792-5.1 – October 1996European Union Directive ComplianceIf this product is installed within the European Union or EEA regions and has the CE mark, the following regulations apply.EMC DirectiveThis apparatus is tested to meet Council Directive 89/336/EECElectromagnetic Compatibility (EMC) using a technical construction file and the following standards, in whole or in part:•EN 50081-2EMC – Generic Emission Standard, Part 2 –Industrial Environment•EN 50082-2EMC – Generic Immunity Standard, Part 2 –Industrial EnvironmentThe product described in this manual is intended for use in an industrial environment.Low Voltage DirectiveThis apparatus is also designed to meet Council Directive 73/23/EEC Low V oltage, by applying the safety requirements of EN 61131–2Programmable Controllers, Part 2 – Equipment Requirements and Tests.For specific information that the above norm requires, see the appropriate sections in this manual, as well as the following Allen-Bradley publications:•Industrial Automation Wiring and Grounding Guidelines,publication 1770-4.1•Automation Systems Catalog, publication B1113ArmorBlock 4 Input Module Publication 1792-5.1 – October 1996Install Y our ArmorBlock ModuleInstallation of the ArmorBlock module consists of:•setting the node address in the ArmorBlock module •mounting the ArmorBlock module •connecting the wiring•communicating with your module •configuring the parametersSet the Node AddressEach ArmorBlock comes with its internal program set for node address 63. To set the node address, you need the following:•host computer with DeviceNet Manager Software (or similarconfiguration software tool)•1770-KFD RS-232 module (or similar interface)•suitable cables to connect the 1770-KFD to your module and to connect the 1770-KFD to your host computer Set the node address to meet your system requirements as follows:1.Set up a system (as shown below) to communicate with your ArmorBlock module.Power from 9V DC Power-Supply AdapterRS-232 moduleDeviceNet Manager software1770-KFDArmorBlock 4 Input Module4Publication 1792-5.1 – October 1996ing DeviceNet Manager Software, go online using the “SetupOnline Connection” selection on the utility pulldown menu.3.The DeviceNet Driver selection screen appears.Select the driver for your application and click onto go online.5ArmorBlock 4 Input Module Publication 1792-5.1 – October 19965.The bar at the bottom of the screen will tell you when you go online.ArmorBlock 4 Input Module6Publication 1792-5.1 – October 1996Mount the ArmorBlock ModuleMount the block module directly to the machine or device. Complete mounting dimensions are shown below. Note that the block dimensions allow direct connection of a T-port tap (cat. no. 1485P-P1N5-j ) to the DeviceNet connector. (Refer to publication 1485-6.7.1 for cabling details.)The ArmorBlock module has a sloping top and a gap at the rear to allow water or other liquids to run off during washdowns. The flow through the gap prevents buildup of debris under the block.Preferred mounting position is with the microconnectors pointing down. However, the block can be mounted in any orientation.7ArmorBlock 4 Input Module Publication 1792-5.1 – October 1996Mounting DimensionsBlock dimensions allow T -port tap connection directly onto connectorFor washdown installations,or excessively moist areas,mount block with micro connectors down.ArmorBlock 4 Input Module8Publication 1792-5.1 – October 1996Connect the Wiring to the ArmorBlock ModuleThe block module uses quick disconnect, screw-on style connectors for:•I/O input wiring•the DeviceNet connectorDeviceNet mini connectorseal unused portsMicro plugs are included with your module. Use these plugs to cover and seal unused ports.Pinout diagrams for these connectors are shown below.!ATTENTION: All connectors must be securelytightened to properly seal the connections against leaks and maintain NEMA 4X and 6P requirements.9ArmorBlock 4 Input Module Publication 1792-5.1 – October 1996Connecting the Input WiringConnect input wiring to the micro connectors which screw into mating connectors on the side of the block.Make connections as shown below.Pin 1 = Sensor Source Voltage Positive Pin 3 = Negative/Return Pin 4 = SignalPin 2 = Not used Connecting the DeviceNet WiringConnect DeviceNet wiring to the 5-pin mini connector on the end of the block. Connections are shown below.DeviceNet Mini Connector Pin 1 = Drain (Bare)Pin 2 = V+ (Red)Pin 3 = V– (Black)(View into pins)Pin 4 = CAN–HI (White)Pin 5 CAN–LO (Blue)Note: Colors are DeviceNet standardArmorBlock 4 Input Module10Publication 1792-5.1 – October 1996Communicate with Your ArmorBlock ModuleThis ArmorBlock module acts as a slave in a master/slave environment.It is both a “polled device” and a “change of state device.”When configured as a polled device, a master initiates communication by sending its polled I/O message to the ArmorBlock module. The 4input module scans the inputs and fault bit producing a response that reflects their status.When configured as a “change of state” device, productions occur when an input changes or an input source voltage fault occurs. If neither has occurred within the “expected packet rate,” a heartbeat production occurs. This heartbeat production tells the scanner module that the ArmorBlock module is alive and ready to communicate.S = Sensor source voltage faultConfigure Y our Armor Block Module Offline Using the DeviceNet Manager Configuration ToolTo configure your ArmorBlock module offline:•add the device to the network•set the parameters for the device•save the parameters to a fileNote: You cannot actually configure your device offline. You can set and save the parameters to a file for downloading to the device when you go online.Adding a Device to the Networkscreen, click on “discrete I/O” inthe device type box.Then click on the desired ArmorBlock device.Configure your Device ParametersAfter adding the devices to the network, you must configure them. You have 2 choices:•highlight the device, and click on the.Configuring the ParametersDefault settings for the 4 input module are:1.Double click on the parameter you want to change.The software displaysthe parameter number,name and value.Read only parameters(designated by an R)are also shown.Parameters can beviewed all at once,configuration only, orI/O only.The parameter screen appears.2.Click on the radio button. To cancel any changes, click on. A screen similar to this will appear. To continue, click onbutton. This returns you to the device configuration screen.You can save these parameters to a file for downloading to the device when online, or print them to a text file for hard copy use.Saving to a File1.To save those parameters to a file, click on thebutton.A screen similar to the following will appear.2.Choose the file name, file type (.TXT), directory and drive to whichyou want to save the file.3.Click on theto bring up pertinent information concerning the device configuration you are selecting.Additionally, help is available on each parameter screen by clicking on2.The configuration screen for your selected driver appears. You can:•set the node address•set the data rate•select the interface adapter serial port•set the interface adapter baud rate3.After setting the parameters, click on theOnlineAdd the Device to the Networkscreen, click on “discrete I/O” inthe device type box.Then click on the desired ArmorBlock device.4.Click once on the device you wish to configure on the project screenand choose5.Load parameters.If you want to load parameters Choose From a fileFrom default settings6.Modify the parameter.If you want to ChooseModify a parameterYou see a screen similar to this one.T o save these settings to the device,chooseYou can view parameters online by clicking onAny changes that occur for a parameter will be reflectedon the screen.7.Save parameters to a file, to the device, or print to a file.If you want to ChooseSave parametersto a fileYou see this screen.Print to a fileYou see this screen.Select the drive, file type, directory, and file name to which youwould like to save and choose8.To exit from the Enhanced Configuration screen,click onMonitoring Parameters OnlineYou can monitor parameters at the Device Configuration screen or at the selected parameter screen.The start monitor button on the Device Configuration screen allows you to monitor all of the parameters online. To monitor parameters:Click on the4.Click on the button to stop monitoring.Reset FaultsThere are various ways to reset faults on an ArmorBlock module.•cycle power to the module by disconnecting, then reconnecting the DeviceNet connector•use the Reset Faulted I/O feature on the parameter screen•use the explicit message program control featureNote:This module contains a circuit to protect the DeviceNet power supply from short circuits in an attached sensor or sensor cable. If you connect a sensor while the module is powered, the surge current produced by the sensor can cause themodule to fault. This operation is normal. If this occurs, reset the module.Reset Faults Online Using the Parameter ScreenTo reset faults online, return to the network screen and proceed as follows:1.Click on the faulted device.2.Then click on the ConfigureDevice button.The device configuration screen appears. Select the Reset Faulted I/Oparameter.After selectingthe parameter, click on themodify parameter button.The configuration screen for the selected parameter appears.2.Then click on theOK button to apply.3.You will be returned tothe configuration screen.Click on ”Save to Device”to apply the change.1.Click on the desired selection to reset.Reset Faults using Explicit Message Program ControlYou can also reset inputs using the Explicit Message Program Control feature on the Scanner module master. Refer to the specific scanner publications for information on using this feature.The format for the reset explicit message transaction block must contain 6 words as shown below:Configure Y our Armor Block Module Using EDS Files Current versions of DeviceNet Manager software include ArmorBlock module support. If you are using a version of DeviceNet Manager software that does not include ArmorBlock module Electronic Data Sheets (EDS) files in its library, you can use the following information to create the file.If you are using a configuration tool other than DeviceNet Manager, you can also use the following information to create the EDS file. (Note: This EDS file was current at the time of printing. Contact your nearest district office for information on later files.)$ Electronic Data Sheet for Armor Block I/O (1792–IB4)[File]DescText=”1792–IB4 Armor Block I/O EDS File”;CreateDate = 04–18–96;CreateTime = 12:00:00;ModDate = 09–17–96;ModTime = 16:00:00;Revision = 2.1;$ EDS revision.[Device]VendCode = 1;VendName = ”Allen–Bradley Company, Inc.”;ProdType = 7;ProdTypeStr = ”General Purpose Discrete I/O”;ProdCode = 1024;MajRev = 2;MinRev = 1;ProdName = ”Armor Block I/O 4 input”;Catalog = ”1792–IB4”;UCMM = 0;$ UCMM is not supported.[IO_Info]Default = 0x0001;$ The default I/O type is polled I/O.PollInfo =0x0001,$ Polled I/O device.1,$ Input1 entry is the default input connection.1;$ Output1 entry is the default output connection.Input1 =1,$ The size in bytes that this connection produces.0,$ All bits of this connection are significant.0x0001,$ Only Polled I/O is compatible.”IB4 Production Data”,$ Name of Connection.6,$ Path length.”20 04 24 0D 30 03”,$ Path to I/O Production Assembly.$$$$$$$$$$ Help string $$$$$$$$$$$”This connection contains data from inputs at bits 0–3 and the sensor source voltage status at bit 7.”;[ParamClass]MaxInst = 9;$ 4 configurable and 5 read–only parameters Descriptor = 0x09;$ Stub param instances in eeprom.CfgAssembly = 0x66;$ The config assembly is instance #102 of assy obj. [Params] $$$$$$$$$$$$$$$$$$$$$$$$$$$$$$$$$$$$$$$$$$$$$$$$$$$$$$$$$$$$$$$$$$$$$ $$$$$$$$$$Param1 =$ Disable Autobaud0,$ reserved6,$ Link Path Size”20 03 24 01 30 64”,$ Link Path to disable autobaud attribute.0x0002,$ No support for settable path, scaling, scaling links,$ or real time update of value. Value is gettable and$ Settable. Enumerated strings are supported.4,$ Data Type – boolean1,$ Data Size”Autobaud”,$ Parameter Name””,$ Units String$$$$$$$$$$ Help string $$$$$$$$$$$”Enable takes effect after next powerup. Disable is required to set fixed baud rate, no power cycle is required.”,0,1,0,$ Min, Max, and Default values1,1,1,0,0,0,0,0,0;$ Not Used $$$$$$$$$$$$$$$$$$$$$$$$$$$$$$$$$$$$$$$$$$$$$$$$$$$$$$$$$$$$$$$$$$$$$ $$$$$$$$$$Param2 =$ Input filter Off_to_On Delay selection0,$ reserved6,$ Link Path Size”20 0F 24 02 30 01”,$ Link Path to param instance. The param instance$ decodes the enumerated parameter into engineering$ units (micro seconds).0x0002,$ No support for settable path, scaling, scaling links,$ or real time update of value. Value is gettable and$ Settable. Enumerated strings are supported.2,$ Data Type – unsigned int2,$ Data Size – (in bytes)”Off–to–On Delay”,$ Parameter Name”ms”,$ Units String$$$$$$$$$$ Help string $$$$$$$$$$$”Signal must be present for this delay period before module detects the change.”,0,4,0,$ Min, Max (max enumeration #), and Default values 1,1,1,0,0,0,0,0,0;$ Not Used $$$$$$$$$$$$$$$$$$$$$$$$$$$$$$$$$$$$$$$$$$$$$$$$$$$$$$$$$$$$$$$$$$$$$ $$$$$$$$$$Param3 =$ Input filter On_to_Off Delay selection0,$ reserved6,$ Link Path Size”20 0F 24 03 30 01”,$ Link Path to param instance. The param instance$ decodes the enumerated parameter into engineering$ units (micro seconds).0x0002,$ No support for settable path, scaling, scaling links,$ or real time update of value. Value is gettable and$ Settable. Enumerated strings are supported.2,$ Data Type – unsigned int2,$ Data Size – (in bytes)”On–to–Off Delay”,$ Parameter Name”ms”,$ Units String$$$$$$$$$$ Help string $$$$$$$$$$$”Signal must be present for this delay period before module detects the change.”,0,4,0,$ Min, Max (max enumeration #), and Default values 1,1,1,0,0,0,0,0,0;$ Not Used $$$$$$$$$$$$$$$$$$$$$$$$$$$$$$$$$$$$$$$$$$$$$$$$$$$$$$$$$$$$$$$$$$$$$ $$$$$$$$$$Param4 =$ Reset Faulted I/O0,$ reserved6,$ Link Path Size”20 0F 24 04 30 01”,$ Link Path to param instance.0x0002,$ No support for settable path, scaling, scaling links,$ or real time update of value. Value is gettable and$ Settable. Enumerated strings are supported.8,$ Data Type – unsigned short int1,$ Data Size – (in bytes)”Reset Faulted I/O”,$ Parameter Name””,$ Units String$$$$$$$$$$ Help string $$$$$$$$$$$”This resets the voltage supplied to sensors. A reset will only be accepted if a fault exists.”,0,1,0,$ Min, Max (max enumeration #), and Default values 1,1,1,0,0,0,0,0,0;$ Not Used $$$$$$$$$$$$$$$$$$$$$$$$$$$$$$$$$$$$$$$$$$$$$$$$$$$$$$$$$$$$$$$$$$$$$ $$$$$$$$$$Param5 =$ Input 1 value0,$ reserved6,$ Link Path Size”20 08 24 01 30 03”,$ Link Path to Input 1 value attribute.0x0030,$ No support for settable path, scaling, or scaling$ links.$ Value is gettable only. Enumerated strings are not$ supported.8,$ Data Type – unsigned short int1,$ Data Size – (in bytes)”Input 1 Value”,$ Parameter Name””,$ Units String$$$$$$$$$$ Help string $$$$$$$$$$$”This parameter is the current value of Input 1.”,0,1,0,$ Min, Max, and Default values1,1,1,0,0,0,0,0,0;$ Not Used $$$$$$$$$$$$$$$$$$$$$$$$$$$$$$$$$$$$$$$$$$$$$$$$$$$$$$$$$$$$$$$$$$$$$ $$$$$$$$$$Param6 =$ Input 2 value0,$ reserved6,$ Link Path Size”20 08 24 02 30 03”,$ Link Path to Input 2 value attribute.0x0030,$ No support for settable path, scaling, or scaling$ links.$ Value is gettable only. Enumerated strings are not$ supported.8,$ Data Type – unsigned short int1,$ Data Size – (in bytes)”Input 2 Value”,$ Parameter Name””,$ Units String$$$$$$$$$$ Help string $$$$$$$$$$$”This parameter is the current value of Input 2.”,0,1,0,$ Min, Max, and Default values1,1,1,0,0,0,0,0,0;$ Not Used $$$$$$$$$$$$$$$$$$$$$$$$$$$$$$$$$$$$$$$$$$$$$$$$$$$$$$$$$$$$$$$$$$$$$ $$$$$$$$$$Param7 =$ Input 3 value0,$ reserved6,$ Link Path Size”20 08 24 03 30 03”,$ Link Path to Input 3 value attribute.0x0030,$ No support for settable path, scaling, or scaling$ links.$ Value is gettable only. Enumerated strings are not$ supported.8,$ Data Type – unsigned short int1,$ Data Size – (in bytes)”Input 3 Value”,$ Parameter Name””,$ Units String$$$$$$$$$$ Help string $$$$$$$$$$$”This parameter is the current value of Input 3.”,0,1,0,$ Min, Max, and Default values1,1,1,0,0,0,0,0,0;$ Not Used $$$$$$$$$$$$$$$$$$$$$$$$$$$$$$$$$$$$$$$$$$$$$$$$$$$$$$$$$$$$$$$$$$$$$ $$$$$$$$$$Param8 =$ Input 4 value0,$ reserved6,$ Link Path Size”20 08 24 04 30 03”,$ Link Path to Input 4 value attribute.0x0030,$ No support for settable path, scaling, or scaling$ links.$ Value is gettable only. Enumerated strings are not$ supported.8,$ Data Type – unsigned short int1,$ Data Size – (in bytes)Publication 1792-5.1 – October 1996”Input 4 Value”,$ Parameter Name””,$ Units String$$$$$$$$$$ Help string $$$$$$$$$$$”This parameter is the current value of Input 4.”,0,1,0,$ Min, Max, and Default values1,1,1,0,0,0,0,0,0;$ Not Used $$$$$$$$$$$$$$$$$$$$$$$$$$$$$$$$$$$$$$$$$$$$$$$$$$$$$$$$$$$$$$$$$$$$$ $$$$$$$$$$Param9 =$ Input status0,$ reserved6,$ Link Path Size”20 1D 24 01 30 05”,$ Link Path to Dicrete Input Group status attribute.0x0032,$ No support for settable path, scaling, or scaling$ links.$ Value is gettable only. Enumerated strings are$supported.8,$ Data Type – unsigned short int1,$ Data Size – (in bytes)”Input Status”,$ Parameter Name””,$ Units String$$$$$$$$$$ Help string $$$$$$$$$$$”This parameter is the current status of the sensor source voltage.”,0,1,0,$ Min, Max, and Default values1,1,1,0,0,0,0,0,0;$ Not Used[Groups]Group1=”Configuration”,3,1,2,3;Group2=”I/O”,6,4,5,6,7,8,9;[EnumPar]Param1=”Enable”,”Disable”;Param2=”0 ms”,”2 ms”,”4 ms”,”8 ms”,”16 ms”;Param3=”0 ms”,”2 ms”,”4 ms”,”8 ms”,”16 ms”;Param4=”Nothing Selected”,”Reset Sensor Source V oltage”;Param9=”Healthy”,”Faulted”;Publication 1792-5.1 – October 1996Troubleshoot with the IndicatorsThe ArmorBlock I/O module has 3 types of indicators:•Mod/Net status indicator•Input fault indicator•individual I/O status indicatorsNote:This module contains a circuit to protect the DeviceNet power supply from short circuits in an attached sensor or sensor cable. If you connect a sensor while the module ispowered, the surge current produced by the sensor can cause the module to fault. This operation is normal. If this occurs, reset the module (page 25).Publication 1792-5.1 – October 1996Specifications4 Input Module – Cat. No. 1792-IB4Publication 1792-5.1 – October 19964 Input Module – Cat. No. 1792-IB4This product has been tested at an Open DeviceNet V endor Association, Inc. (ODV A) authorized independent test laboratory and found to comply with ODVA Conformance Test Software V ersion FT 1.2/1.0.Publication 1792-5.1 – October 1996Publication 1792-5.1 – October 1996Publication 1792-5.1 – October 1996Supersedes publication 1792-5.1 – November 1995PN955126–02Copyright 1996 Allen-Bradley Company , Inc. Printed in USAWorldwide representation.Argentina • Australia • Austria • Bahrain • Belgium • Brazil • Bulgaria • Canada • Chile • China, PRC •Colombia • Costa Rica • Croatia • Cyprus • Czech Republic • Denmark • Ecuador • Egypt • El Salvador •Finland • France • Germany • Greece • Guatemala • Honduras • Hong Kong • Hungary • Iceland • India •Indonesia • Ireland •Israel • Italy • Jamaica • Japan • Jordan • Korea • Kuwait • Lebanon • Malaysia •Mexico • Netherlands •New Zealand • Norway • Pakistan • Peru • Philippines • Poland • Portugal •Puerto Rico • Qatar • Romania • Russia–CIS • Saudi Arabia • Singapore • Slovakia • Slovenia • South Africa, Republic • Spain • Sweden •Switzerland • T aiwan • Thailand • T urkey • United Arab Emirates •United Kingdom • United States • Uruguay • V enezuela • Y ugoslaviaAllen-Bradley Headquarters, 1201 South Second Street, Milwaukee, WI 53204 USA,Tel: (1) 414 382-2000 Fax: (1) 414 382-4444。
AD5940 AD5941 高精度阻抗和电化学前端数据手册说明书

Rev. BDocument FeedbackInformation furnished by Analog Devices is believed to be accurate and reliable. However, no responsibility is assumed by Analog Devices for its use, nor for any infringements of patents or other rights of third parties that may result from its use. Specifications subject to change without notice. No license is granted by implication or otherwise under any patent or patent rights of Analog Devices. Trademarks andregistered trademarks are the property of their respective owners.One Technology Way, P.O. Box 9106, Norwood, MA 02062-9106, U.S.A.Tel: 781.329.4700 ©2019-2020 Analog Devices, Inc. All rights reserved. Technical Support /cnADI 中文版数据手册是英文版数据手册的译文,敬请谅解翻译中可能存在的语言组织或翻译错误,ADI 不对翻译中存在的差异或由此产生的错误负责。
如需确认任何词语的准确性,请参考ADI 提供的最新高精度阻抗和电化学前端数据手册AD5940/AD5941特性模拟输入16位ADC ,提供800 kSPS 和1.6 MSPS 选项 电压、电流和阻抗测量能力 内部和外部电流和电压通道超低泄漏开关矩阵和输入多路复用器 输入缓冲器和可编程增益放大器 电压DACs输出范围为0.2 V 至2.4 V 的双通道输出电压DAC 12位V BIAS0输出到偏置恒电势器 6位V ZERO0输出到偏置TIA 超低功耗:1 µA1个高速、12位DAC传感器输出范围至:±607 mV输出上具有2和0.05增益设置的可编程增益放大器 放大器、加速器和基准电压源1个低功耗、低噪声恒电势器放大器,适合电化学检测中的恒电势器偏置1个低噪声、低功耗TIA ,适合测量传感器电流输出 50 pA 至3 mA 范围用于传感器输出的可编程负载和增益电阻 模拟硬件加速器 数字波形发生器 接收滤波器复数阻抗测量(DFT)引擎1个高速TIA ,可以处理0.015 Hz 至200 kHz 的宽带宽输入信号 数字波形发生器,用于生成正弦波和梯形波形 2.5 V 和1.82 V 内部基准电压源 降低系统级功耗能够快速上电和断电的模拟电路可编程AFE 序列器,最大程度地降低了主机控制器的工作负载6 kB SRAM ,可对AFE 序列进行预编程超低功耗恒电势器通道:上电且所有其他模块处于休眠模式时为6.5 µA 的电流消耗 智能传感器同步和数据采集 传感器测量的精确周期控制 受控于序列器的的GPIOs 片内外设SPI 串行输入/输出 唤醒定时器 中断控制器 电源电源电压:2.8 V 至3.6 V 1.82 V 输入/输出兼容 上电复位集成已上电的低功耗DAC 和恒电势器放大器的休眠模式,以保持传感器偏置 封装和温度范围3.6 mm ×4.2 mm 、56引脚WLCSP 7 mm × 7 mm 、48引脚LFCSP 封装 额定工作温度范围为-40°C 至+85°C应用电化学测量电化学气体传感器恒电势器/电流测量/伏安法/循环伏安法 生物阻抗应用 皮肤阻抗 人体阻抗 连续血糖监测 电池阻抗简化功能框图图1.AD5940/AD5941数据手册目录特性 (1)应用 (1)简化功能框图 (1)修订历史 (3)功能框图 (5)概述 (6)技术规格 (7)ADC RMS噪声规格 (16)SPI时序规格 (17)绝对最大额定值 (18)热阻 (18)ESD警告 (18)引脚配置和功能描述 (19)典型性能参数 (22)参考测试电路 (24)工作原理 (25)配置寄存器 (25)芯片标识 (28)标识寄存器 (28)系统初始化 (29)低功耗DAC (30)低功耗DAC开关选项 (30)12位和6位输出之间的关系 (31)低功耗DAC应用场景 (31)低功耗DAC电路寄存器 (32)低功耗恒电势器 (35)低功耗TIA (36)低功耗TIA保护二极管 (36)使用外部R TIA (36)各种工作模式的推荐开关设置 (36)低功耗TIA电路寄存器 (39)高速DAC电路 (42)高速DAC输出信号生成 (42)高速DAC核心的功耗模式 (42)高速DAC滤波器选项 (42)高速DAC输出衰减选项 (43)高速DAC激励放大器 (43)将来自高速DAC的交流信号耦合到低功耗DAC设置的直流电平 (43)在阻抗测量期间避免激励和测量频率之间的不一致性误差 (43)高速DAC校准选项 (44)高速DAC电路寄存器 (45)高速TIA电路 (48)高速TIA配置 (48)高速TIA电路寄存器 (50)高性能ADC电路 (52)ADC电路概述 (52)ADC电路图 (52)ADC电路特性 (53)ADC电路工作原理 (53)ADC转换函数 (53)ADC低功耗电流输入通道 (54)选择ADC多路复用器的输入 (54)ADC后处理 (55)内部温度传感器通道 (55)Sinc2滤波器(50 Hz/60 Hz交流电源滤波器) (55)ADC校准 (55)ADC电路寄存器 (56)ADC校准寄存器 (62)ADC数字后处理寄存器(可选) (68)ADC统计寄存器 (69)可编程开关矩阵 (70)开关描述 (70)休眠模式下的推荐配置 (70)控制所有开关的选项 (70)可编程开关寄存器 (73)精密基准电压源 (83)高功率和低功耗缓冲器控制寄存器—BUFSENCON (84)序列器 (85)序列器特性 (85)序列器概述 (85)序列器命令 (85)序列器操作 (87)序列器和FIFO寄存器 (89)波形发生器 (94)波形发生器特性 (94)波形发生器操作 (94)数据手册AD5940/AD5941波形发生器与低功耗DAC配合使用 (94)波形发生器寄存器 (95)SPI接口 (98)概述 (98)SPI引脚 (98)SPI工作原理 (98)命令字节 (98)写入和读取寄存器 (98)从数据FIFO读取数据 (99)睡眠和唤醒定时器 (100)睡眠和唤醒定时器特性 (100)睡眠和唤醒定时器概述 (100)配置一个确定的序列顺序 (100)睡眠和唤醒定时器建议操作 (100)睡眠和唤醒定时器寄存器 (101)中断 (105)中断控制器中断 (105)配置中断 (105)自定义中断 (105)外部中断配置 (105)中断寄存器 (106)外部中断配置寄存器 (111)数字输入/输出 (115)数字输入/输出特性 (115)数字输入/输出操作 (115)GPIO寄存器 (116)系统复位 (119)模拟芯片复位寄存器 (119)功耗模式 (120)有效高功率模式(>80 kHz) (120)有效低功耗模式(<80 kHz) (120)休眠模式 (120)关断模式 (120)低功耗模式 (120)功耗模式寄存器 (120)时钟架构 (123)时钟特性 (123)时钟架构寄存器 (123)应用信息 (127)使用低带宽环路进行EDA生物阻抗测量 (127)使用高带宽环路进行体阻抗分析(BIA)测量 (128)高精度恒电势器配置 (129)使用AD5940/AD5941、AD8232或AD8233进行生物阻抗和心电图(ECG)测量 (130)智能水质/液体质量AFE (131)外形尺寸 (132)订购指南 (133)修订历史2020年3月—修订版A至修订版B更改“产品特性”部分 (1)更改图2和图3 (5)更改表6 (18)更改表7 (20)删除图19;重新排序 (29)增加“系统初始化”部分和表14;重新排序 (29)更改“低功耗DAC开关选项”部分 (30)更改图21 (32)更改表17 (33)更改图22 (36)更改图23 (38)更改图29 (48)更改表36 (49)更改“ADC转换函数”部分 (53)更改图33 (54)更改“Sinc3滤波器”部分和“内部温度传感器通道”部分 ....... 55 更改“精密基准电压源”部分和图38 . (83)更改表93 (84)更改表101 (91)更改“配置一个确定的序列顺序”部分和图51 (100)2019年8月—修订版0至修订版A增加AD5941 ................................................................................ 通篇增加LFCSP封装 ........................................................................ 通篇更改图2,增加图3,按顺序重新编号 (4)更改表1的噪声(RMS)参数 (7)更改表3 (16)增加图6 (19)更改表7 (20)增加图16和图17 (23)更改“数字输入/输出”部分 (119)更改图20 (32)AD5940/AD5941数据手册更改表16 (33)更改表20中关于“短路开关使能的电流测量模式”的描述 (37)更改图28 (49)更改“选择ADC多路复用器的输入”部分 (55)更改“温度传感器0”部分和表40 (57)更改图35 .......................................................................................... 73 更改图47 .. (101)更改“配置一个确定的序列顺序”部分 (102)更改图53 (129)更新外形尺寸,增加图59 (139)更改“订购指南” (140)2019年3月—修订版0:初始版数据手册AD5940/AD5941功能框图图2. AD5940功能框图图3. AD5941功能框图AD5940/AD5941数据手册概述AD5940和AD5941均为高精度、低功耗模拟前端(AFE),专为需要基于电化学测量技术的高精度便携式应用而设计,如电流、伏安或阻抗测量。
CR1510 Datasheet - 080813

(Emitter and base shorted together; I = 1mA, R ȍ
C
EB
Collector current1
Collector peak current1 (tp < 1ms) Maximum junction temperature
Storage temperature /HDGWHPSHUDWXUHGXULQJ,5UHÀRZIRUVHFRQGV
Figure 3.2: CR1510 Typical Application Circuit (Isolated SSL Application)
L
+ N
U1 CR1510
1C
E8
2C 4 VCC
ISENSE 7 VSENSE 6
GND 5
VOUT +
GND
Figure 3.3: CR1510 Typical Application Circuit (Isolated Charger/Adapter Application)
4
V
Power Input 3RZHUVXSSO\IRUFRQWUROORJLF
CC
5
GND
Ground *URXQG
6
VSENSE
Analog Input $X[LOLDU\YROWDJHVHQVH XVHGIRUSULPDU\VLGHUHJXODWLRQ
3ULPDU\FXUUHQWVHQVH8VHGIRUF\FOHE\F\FOHSHDNFXUUHQWFRQWURODQGFXUUHQW
L
+ N
2.0 Description
The CR1510 is a high performance AC/DC power supply control device which uses digital control technology to EXLOG SHDN FXUUHQW PRGH 3:0 À\EDFN SRZHU VXSSOLHV This device includes an internal power BJT and operates in TXDVLUHVRQDQW PRGH WR SURYLGH KLJK HI¿FLHQF\ DORQJ ZLWK D number of key built-in protection features while minimizing the external component count, simplifying EMI design, and ORZHULQJWKHWRWDOELOORIPDWHULDOFRVW7KH&5UHPRYHV the need for secondary feedback circuit while achieving H[FHOOHQWOLQHDQGORDGUHJXODWLRQ,WDOVRHOLPLQDWHVWKHQHHG for loop compensation components while maintaining stability LQ DOO RSHUDWLQJ FRQGLWLRQV 7KH EXLOWLQ SRZHU OLPLW IXQFWLRQ enables optimized transformer design in universal off-line DSSOLFDWLRQVDQGDOORZVIRUDZLGHLQSXWYROWDJHUDQJH
Multi Micro Hornet - ORG1510-MK05 评估套件数据表 Revision

MULTI MICRO HORNET (ORG1510-MK-05) EVALUATION KIT(ORG1510-MK05-UAR)DatasheetO r i g i n G P S . c o mINDEX1. SCOPE (4)2. DISCLAIMER (4)3. SAFETY INFORMATION (4)4. ESD SENSITIVITY (4)5. CONTACT INFORMATION (4)6. RELATED DOCUMENTATION (4)7. REVISION HISTORY (5)8. ABOUT HORNET FAMILY (5)9. ABOUT MULTI MICRO HORNET MODULE (5)10. ABOUT ORIGINGPS (6)11. DESCRIPTION (6)12. SCHEMATICS (7)12.1. MAIN BOARD SCHEMATICS (7)12.2. INTERFACE ADAPTOR SCHEMATICS (8)13. BILL OF MATERIALS (9)13.1. MAIN BOARD BILL OF MATERIALS (9)13.2. INTERFACE ADAPTOR BILL OF MATERIALS (9)14. ASSEMBLY AND LAYOUT (10)14.1. MAIN BOARD PCB (10)14.2. INTERFACE ADAPTOR PCB (12)15. TTL-232R-3V3 USB-Serial CONVERTER CABLE (15)TABLE INDEXTABLE 1 – RELATED DOCUMENTATION (4)TABLE 2 – REVISION HISTORY (5)TABLE 3 – MAIN BOARD BILL OF MATERIALS (9)TABLE 4 – INTERFACE ADAPTOR BILL OF MATERIALS (9)TABLE 5 –USB-SERIAL CONVERTER CABLE HEADER PIN-OUT (15)TABLE 6 –USB-SERIAL CONVERTER CABLE OPERATING PARAMETERS (15)FIGURE INDEXFIGURE 1 – MAIN BOARD SCHEMATICS (7)FIGURE 2 – INTERFACE ADAPTOR SCHEMATICS (8)FIGURE 3 – MAIN BOARD COMPONENTS PLACEMENT (10)FIGURE 4 – MAIN BOARD SOLDER MASK (10)FIGURE 5 – MAIN BOARD TOP LAYER ROUTING (11)FIGURE 6 – MAIN BOARD BOTTOM LAYER ROUTING (11)FIGURE 7 –INTERFACE ADAPTOR BOARD COMPONENTS PLACEMENT (12)FIGURE 8 – INTERFACE ADAPTOR BOARD SOLDER MASK (12)FIGURE 9 – INTERFACE ADAPTOR BOARD TOP LAYER ROUTING (13)FIGURE 10 – INTERFACE ADAPTOR INNER LAYER 1 ROUTING (13)FIGURE 11 –INTERFACE ADAPTOR INNER LAYER 2 ROUTING (14)FIGURE 12 – INTERFACE ADAPTOR BOTTOM LAYER ROUTING (14)FIGURE 13 – PIN HEADER SOCKET BOTTOM VIEW (15)1. SCOPEThis document describes the features and specifications of Multi Micro Hornet ORG1510-MK-05 evaluation kit.2. DISCLAIMERAll trademarks are properties of their respective owners.Performance characteristics listed in this document do not constitute a warranty or guarantee of product performance. OriginGPS assumes no liability or responsibility for any claims or damages arising out of the use of this document, or from the use of integrated circuits based on this document.OriginGPS assumes no liability or responsibility for unintentional inaccuracies or omissions in this document. OriginGPS reserves the right to make changes in its products, specifications and other information at any time without notice.OriginGPS reserves the right to conduct, from time to time, and at its sole discretion, firmware upgrades.As long as those FW improvements have no material change on end customers, PCN may not be issued. OriginGPS navigation products are not recommended to use in life saving or life sustaining applications.3. SAFETY INFORMATIONImproper handling and use can cause permanent damage to the product.4. ESD SENSITIVITYThis product is ESD sensitive device and must be handled with care.5. CONTACT INFORMATIONSupport - *********************Marketing and sales - ***********************Web –6. RELATED DOCUMENTATION№DOCUMENT NAME1Multi Micro Hornet – ORG1510-MK-05 Datasheet2MTK NMEA Packet User ManualTABLE 1 – RELATED DOCUMENTATION7. REVISION HISTORYREVISION DATE CHANGE DESCRIPTION1.0September 2, 2018 First releaseTABLE 2 – REVISION HISTORY8. ABOUT HORNET FAMILYOriginGPS GNSS receiver modules have been designed to address markets where size, weight, stand-alone operation, highest level of integration, power consumption and design flexibility - all are very important. OriginGPS’ Hornet family breaks size barrier, offering the industry’s smallest fully-integrated, highly-sensitiveGPS and GNSS modules with integrated antennas or on-board RF connectors.Hornet family features OriginGPS' proprietary NFZ™ technology for high sensitivity and noise immunity evenunder marginal signal condition, commonly found in urban canyons, under dense foliage or when thereceive r’s position in space rapidly changes.Hornet family enables the shortest TTM (Time-To-Market) with minimal design risks.Just connect power supply on a single layer PCB.9. ABOUT MULTI MICRO HORNET MODULEMulti Micro Hornet is a complete SiP featuring miniature LGA SMT footprint designed to commit uniqueintegration features for high volume cost sensitive applications.Designed to support compact and traditional applications such as smart watches, wearable devices,asset trackers, Multi Micro Hornet ORG1510MK-05 module is a miniature multi-channel GPS/ GLONASS/ BEIDOU with SBAS, QZSS and other regional overlay systems receiver that continuously tracks all satellites in view, providingreal-time positioning data in industry’s standard NMEA format.Multi Micro Hornet ORG1510 module offers superior sensitivity and outstanding performance, achieving rapidTTFF in less than one second, accuracy of approximately two meters, and tracking sensitivity of -165dBm.Sized only 10mm x 10mm Multi Micro Hornet ORG1510MK-05 module is industry’s small sized, record breaking solution. Multi Micro Hornet module integrates OriginGPS proprietary on-board GNSS antenna, dual-stage LNA, RF LDO,SAW filter, TCXO, RTC crystal and RF shield with market-leading MT3333 GNSS SoC.Multi Micro Hornet ORG1510MK-05 module is introducing industry’s lowest energy per fix ratio, unparalleled accuracy and extremely fast fixes even under challenging signal conditions, such as in built-up urban areas, dense foliageor even indoor.Integrated GNSS SoC incorporating high-performance microprocessor and sophisticated firmware keepspositioning payload off the host, allowing integration in embedded solutions with low computing resources. Innovative architecture can detect changes in context, temperature, and satellite signals to achieve a stateof near continuous availability by maintaining and opportunistically updating its internal fine time, frequency,and satellite ephemeris data while consuming mere microwatts of battery power.10. ABOUT ORIGINGPSOriginGPS is a world leading designer, manufacturer and supplier of miniature positioning modules, antenna modules and antenna solutions. OriginGPS modules introduce unparalleled sensitivity and noise immunity by incorporating Noise Free Zone system (NFZ™) proprietary technology for faster position fix and navigation stability even under challenging satellite signal conditions.Founded in 2006, OriginGPS is specializing in development of unique technologies that miniaturize RF modules, thereby addressing the market need for smaller wireless solutions.11. DESCRIPTIONEvaluation Kit of the ORG1510-MK-05 GNSS Antenna Module comprises the Demo Board, USB to UART cable and memory stick ( USB) with GPS simulator software for PC and documentation.The Demo Board is built of Main Board, incorporating 3.3V LDO regulator, UART connector and various test points.The ORG1510-MK-05 GNSS Antenna Module is soldered onto the Main Board through the Interface Adaptor.Demo Board is connected to computer USB port through USB to UART adapter cable that also provides power to the board. Battery back-up (pin 8of ORG1510-MK05) is connected through yellow wire (battery plus) and black wire (GND). Red wire is used when there is no battery presents. In such a case yellow wire should be connected to red wire in order to supply power to pin 8 (Vbat) of module ORG1510-MK5Main BoardORG1510-MK-05 Adaptor ORG1510-MK513. BILL OF MATERIALS13.1 MAIN BOARD BILL OF MATERIALSReference Value Description P/N MFG 18pF CAP SMT 0402 18pF ±5% 50V COG GRM1555C1H180JZ01D MURATAC1, C2, C6, C9C10, C11C3,C7,C8 4.7µF CAP SMT 0603 4.7µF ±10% 6.3V X5R GRM188R60J475KE19D MURATAC5 1µF CAP SMT 0402 1µF ±10% 10V X5R GRM155R61A105KE15D MURATAD1 LED BLUE LED BLUE SMT 0805 20mA APT2012QBC/D KINGBRIGHT J3 ZIF CONN 10pos. 0.5mm pitch FPC ZIF SMT Conn. 52746-1071 MOLEXQ1 BSS138 N-CH 0.2A 50V SOT23 Power MOSFET BSS138LT1G ONR3, R4, R5 33R RES SMT 0402 33R ±1% RM04FTN033R TA-IR6 270R RES SMT 0402 270R ±1% RM04FTN270R TA-IJ1 HDR HEADER 6 POS. “0.1 RIGHT ANGLE 2211S-06G-F1 NELTRONU1 LDO 3.3V 200mA LDO W. Discharge Reg. SOT23 ADP160AUJZ-3.3-R7 ADJ2Connector 18 pin connectorTABLE 3 - MAIN BOARD BILL OF MATERIALS13.2 INTERFACE ADAPTOR BILL OF MATERIALSReference Value Description P/N MFGC1 18pF CAP SMT 0402 18pF ±5% 50V COG GRM1555C1H180JZ01D MURATAC4 100nF CAP SMT 0402 100nF ±10% 16V X7R GRM155R71C104KA88D MURATAC2,C3 1µF CAP SMT 0402 1µF ±10% 10V X5R GRM155R61A105KE15D MURATAR5 100ΩRES SMT 0402 100Ω ±1%RM04FTN1000 TA-IR1,R2,R3,10KΩRES SMT 0402 10KΩ ±1%RM04FTN1002 TA-I R4, R6R7 100KΩRES SMT 0402 100KΩ ±1%RM04FTN1003 TA-IQ1 2N7002 N-CH MOSFET SOT-23 2N7002KT1G ONU1 MODULE GNSS ANTENNA MODULE SMT LGA ORG1510–MK-05 ORIGINGPSU2 NLU1GT126 SINGLE BUFFER 3-STATE NLU1GT126CMX1TCG ONU3 TPS3808 LOW IQ POR SUPERVISOR W. MAN. RST TPS3808G18DRVR TITABLE 4 - INTERFACE ADAPTOR BILL OF MATERIALS14. ASSEMBLY AND LAYOUT14.1 MAIN BOARD PCBMain Board for the ORG1510-MK-05 GNSSS Antenna Module is 2 layers 1.6mm thickness FR4 PCB.FIGURE 3 - MAIN BOARD COMPONENTS PLACEMENTFIGURE 4 - MAIN BOARD SOLDER MASKFIGURE 5 – MAIN BOARD TOP LAYER ROUTING FIGURE 6 – MAIN BOARD BOTTOM LAYER ROUTING14.2 INTERFACE ADAPTOR PCBInterface Adaptor Board for the ORG1510-MK-05 GNSS Antenna Module is 17mm x 17mm 22 pads 4 layers 0.6mm thickness FR4 PCB.FIGURE 7 - INTERFACE ADAPTOR BOARD COMPONENTS PLACEMENTFIGURE 8 - INTERFACE ADAPTOR BOARD SOLDER MASKFIGURE 9 - INTERFACE ADAPTOR BOARD TOP LAYER ROUTINGFIGURE 10 - INTERFACE ADAPTOR INNER LAYER 1 ROUTINGFIGURE 11 - INTERFACE ADAPTOR INNER LAYER 2 ROUTINGFIGURE 12 - INTERFACE ADAPTOR BOTTOM LAYER ROUTING15. TTL-232R-3V3 USB-Serial CONVERTER CABLE*The TTL-232R-3V3 is a USB to Serial converter cable that provides a simple way to connect devices withUART interface to PC.The TTL-232R-3V3 uses an FTDI FT232RQ IC which is housed inside the USB Type 'A' connector and is terminated at the end of a 1.8 meter cable (6 ft.) with a 2.54mm (“0.1) pitch header socket which provides an access to UART standard Transmit Data (TxD) and Receive Data (RxD). These lines are operating at 3.3V LVTTL levels.Also brought out on the header are +5V and GND.FIGURE13-PIN HEADER SOCKET BOTTOM VIEWPin Number Name Type Colour Description1GND Power Black Ground supply pin2CTS Input Brown Clear To Send input – not in use3VCC Power Red+5V power source, USB specified4TXD Output Orange Asynchronous Data output – GPS input5RXD Input Yellow Asynchronous Data input – GPS output6RTS Output Green Request To Send output – not in useTABLE 5 - USB-SERIAL CONVERTER CABLE HEADER PIN-OUTParameter Symbol Test Conditions Min Typ Max Units Power Supply Voltage V CC Defined by USB V BUS 4.25 5.0 5.25V Power Supply Current I O--75mA Output Voltage Low State V OL I OL = 8mA0.30.40.6V Output Voltage High State V OH I OH = -3mA 2.2 2.8 3.2VInput Voltage State Switching Threshold V IN Low → HighHigh → Low 1.0 1.2 1.5VInput Voltage State Switching Hysteresis V HYST202530mV Operating Temperature T AMB-40+25+850CTABLE 6 - USB-SERIAL CONVERTER CABLE OPERATING PARAMETERS*Note: For more information refer to FTDI Ltd. TTL-232R TTL To USB Serial Converter Range Of Cables Datasheet, Document Reference No.: FT_000054。
Dual TBX10A 10 端口式封闭式柜体与内置音频放大器说明书

TBX10A INSTALLATION/OWNER'S MANUAL 10" Sealed Enclosure with Built-in AmplifierPREPARATIONGetting StartedThank you for purchasing the Dual TBX10A 10" ported enclosure with built-in amplifier. Although Dual has attempted to ensure the information in this manual is accurate, please be aware that any part of it is subject to change without notice. Please read entire manual before installation. Due to the technical nature of amplifiers, it is highly recommended that your Dual TBX10A is installed by a professional installer or an authorized dealer.Before You Start• Always disconnect the negative battery terminal. Consult a qualified technician for instructions if you are unsure.• Avoid installing the amplifier where it would be subject to high temperatures, such as from direct sunlight, or where it would be subject to dust, dirt or excessive vibration.• Use extreme caution when drilling holes to avoid damaging fuel lines or existing vehicle wiring.• All amplifier installations require power, signal and speaker wires (not included).• An amplifier installation kit (sold separately) is highly recommended to facilitate the installation. Consult your dealer for recommendations. Mounting Location• Choose a mounting location for the TBX10A. Suggested locations include behind a seat or in the trunk.• For optimum performance, make sure to provide at least 1" of space around all sides of the amplifier.• Do not mount the TBX10A under carpets or where airflow is restricted.• Do not install the TBX10A where it may be exposed to moisture.• The optimum mounting location varies between vehicles. Remember to test all amplifier functions before completing the final mounting procedure.The following installation instructions are intended to be used as a basicguideline. If you feel unsure about installing this speaker system yourself, Dual recommends acquiring the services of a professional car audio installation center.Before installation, please review the following guidelines:1. Be sure to carefully read and understand the instructions before attempting to install this product.2. If additional wiring is required, we recommend running all wires prior to mounting your enclosure in place.3. To ensure reliable performance and minimize signal or power loss, use the highest quality connectors available.4. Never run speaker wires underneath your vehicle. Running speaker wires inside the vehicle provides the best protection from exhaust, heat and environmental elements.5. Avoid running wires over, near or through sharp-edged surfaces. We suggest you also use rubber grommets to protect any wires routed through metal, especially the firewall.6. When running the speaker cable to the amplifier, avoid running it near sources of high current (i.e. wiring harnesses, battery cables).Safety FirstThe following instructions are designed to ensure safety during installation and use of the TBX10A. Failure to heed these instructions can result in injury or damage to the unit or vehicle.CAUTION!Connection DescriptionsNote: Be sure to follow specific instructions included with your amplifier installation kit (not included with this amplifier). The information below should be used a general guideline only.Power Wire (+12V)• D isconnect negative battery terminal before proceeding. Consult a qualified technician for instructions if you are unsure.• P lan wire routing before cutting any wires to length. Begin by routing the power +12V wire from the battery to the amplifier location. Use a grommet when running wires through the firewall or metal openings. Avoid running the power wire near existing vehicle wiring to prevent induced noise from entering the audio system.• U se extreme caution when drilling holes to avoid damaging fuel lines or existing vehicle wiring.• T he +12V wire MUST be fused within 18" of the battery for protection of the vehicle’s electrical system.Ground Wire (GND)• T he amplifier ground wire should be as short as possible. Choose a clean unpainted section of metal or the vehicle chassis when attaching the ground connection. Be sure to clean the area of any dirt or grease.Remote Turn-on Wire (REM)• T he remote turn-on wire connects to the head unit's amplifier turn-on lead or other switched 12 volt source.Input Signal • T he amplifier's input signal connects to the receiver's low level (RCA) or high level (speaker wire) outputs.CAUTION• N ever run any wires underneath or outside the vehicle.Phase Control Power Indicator Protect Indicator Input Level ControlCrossover Frequency Bass EQ Fuse (15A)Power / Input ConnectorConnections and ControlsHIGH LEVEL 12345678Main Power ConnectionsConnect BAT+, GND and REM wires accordingly. A suitable fuse MUST be installed on theBAT+ lead within 18" of the battery for protection of the vehicle’s electrical system.Power/Ground Wire SizeFor optimum performance, use only 12 gauge wire or larger. Make sure to use the same size power and ground wire.Typical Wire RoutingHigh Level Input (Speaker Wire)High level inputs should only be used when RCA outputs are not available from the head unit. Connect the head unit speaker outputs to the high level input connector as shown below. The black wire (signalreference ground) may or may not require a connection to chassis ground - depending on your particularinstallation. Do not use both low and high level inputs at the same time. Connect only one or the other. MountingPlace the TBX10A on the strapsScrew the mounting brackets securely to the floorboard of your car or tuck as illustratedLace the straps so that they pass through the brackets as illustrated.Lace the straps through thebrackets as illustrated.Fasten the buckles as tightlyas possible.Low level (RCA) input signal is preferred for best performance. Typical trunk-mount installations require a 17-20 foot RCA cable. Most trucks and behind-seat applications require a 6-12 foot RCA cable. Using twisted pair construction RCA cables will minimize noise.The adjustable crossover is used to filter outfrequencies above 50Hz ~ 250Hz. Adjust it to wherethe TBX10A sound output blends with the rest of the sound system.The phase control compensates for delay between the TBX10A output and the rest of the sound system. Begin with the phase control set to 0 degrees. If the sound is adequate from the normal listening position inside the vehicle, no further adjustment is necessary. If the sound is thin or lacking bass, adjust the phase control until the bass is full and punchy.The input level control (LEVEL) is used to obtain the best possible match between the head unit audio output and the amplifier input. Begin by turning the input level control fully counterclockwise. Next, turn up the head unit volume control around 3/4 of the way up. Adjust the input level control clockwise until audible distortion is heard, then slightly counterclockwise to provide the best match.The LED indicator illuminates green during normal operation.Input Signal ConnectionsLow Level (RCA)Crossover Frequency Control Phase ControlInput Level ControlLED IndicatorControl Setup and AdjustmentThis warranty gives you specific legal rights. You may also have other rights which vary from state to state.Dual Electronics Corp. warrants this product to the original purchaser to be free from defects in material and workmanship for a period of one year from the date of the original purchase.Dual Electronics Corp. agrees, at our option, during the warranty period,to repair any defect in material or workmanship or to furnish an equal new, renewed or comparable product (whichever is deemed necessary) in exchange without charges, subject to verification of the defect or malfunction and proof of the date of purchase. Subsequent replacement products are warranted for the balance of the original warranty period. Who is covered? This warranty is extended to the original retail purchaser for products purchased from an authorized Dual dealer and used in the U.S.A.What is covered? This warranty covers all defects in material and workmanship in this product. The following are not covered: software, installation/removal costs, damage resulting from accident, misuse, abuse, neglect, product modification, improper installation, incorrect line voltage, unauthorized repair or failure to follow instructions supplied with the product, or damage occurring during return shipment of the product. Specific license conditions and copyright notices for the software can be found via .What to do?1. Before you call for service, check the troubleshooting guide in your owner’s manual. A slight adjustment of any custom controls may save you a service call.2. If you require service during the warranty period, you must carefully pack the product (preferably in the original package) and ship it by prepaid transportation with a copy of the original receipt from the retailer to an authorized service center.3. Please describe your problem in writing and include your name, a return UPS shipping address (P.O. Box not acceptable), and a daytime phone number with your shipment.4. For more information and for the location of the nearest authorized service center please contact us by one of the following methods:• Call us toll-free at 1-866-382-5476•*********************** Exclusion of Certain Damages: This warranty is exclusive and in lieu of any and all other warranties, expressed or implied, including without limitation the implied warranties of merchantability and fitness for a particular purpose and any obligation, liability, right, claim or remedy in contract or tort, whether or not arising from the company’s negligence, actualor imputed. No person or representative is authorized to assume for the company any other liability in connection with the sale of this product. In no event shall the company be liable for indirect, incidental or consequential damages.Limited One-Year WarrantyWARRANTYPlease keep your original sales receipt and be prepared to provide this receipt in the event you require service, as your original receipt is considered the best proof of purchase and indicates the date you purchased your Dual product.Dealer Name Dealer Phone Purchase DateRegister your product online at For Your RecordsRegister Your Product NotesINSTALLATIONTroubleshooting11300 watts 100 watts 40-250Hz 11.0VDC ~ 14.4VDC Allowed 4 Ohms 50–250Hz Class A/B 0–180 degrees 15 amp ATO 11.5” (H) x 5.5” Bottom / 4” Top (D) x 16.5” (W)Design and specifications subject to change without notice.Maximum Output PowerContinuous Output PowerFrequency ResponseOperating VoltageImpedanceCrossover FrequencyAmplifier TypePhaseFuseDimensions SpecificationsINSTALLATIONDual Electronics Corp.Toll Free: 1-866-382-5476Monday-Friday, 9AM-5PM EST©2016 Dual Electronics Corp. All rights reserved.NSA0716-V01Printed in China。
D1511

D1511
D1511 □ □
司
Circuit Type
公Packing:
Blank:Tube
Package
限R:Type and Reel
P:SOP8
有
Function Block
技 科
安
达
众
市
圳
深
Figure 3 Function Block Diagram of D1511
电话:(0755)27858667 27858661 传真:(0755)27858707
z Built in Current Limit Function
current protection function and a short circuit protection function are built inside. An internal compensation block is built in to minimize external component count.
科TLEAD
260 2000
MSL Thermal Resistance-Junction to Ambient Thermal Resistance-Junction to Case
安 RθJA 达 RθJC
Level3 85 45
众 Recommended Operating Conditions 市
达Note:In PCB layout. Reserved an area for CFF.
4
mA
Feedback Voltage Feedback Bias Current Switch Current Limit
VFB
VIN = 3.6V to 18V
LAUREL电子1-4.20mA、0-10V多功能输出模块说明书

1- MAO14-20 mA - MAO20-10V- MAO3-10V to +10VMAGNA Analog Output OptionsLAUREL Electronics, Inc.3183-G Airway Ave, Costa Mesa, CA 92626, USA Tel +1 714-434-6131Fax +1 714-434-3766 *****************.WarrantyWe warrant our products against defects in materials or workmanship for a period of one year from the date of purchase.In the event of a defect during the warranty period, the unit should be returned, freight (and all duties and taxes) prepaid by the Buyer to the authorised distributor from where the unit was purchased.The Distributor, at its option, will repair or replace the defective unit. The unit will bereturned to the Buyer with freight charges prepaid by the distributor.LIMITATION OF WARRANTYThe foregoing warranty shall not apply to defects resulting from:1. Improper or inadequate maintenance by the buyer.2. Unauthorised modification or misuse.3. Operation outside the environmental specification of the product.4. Mishandling or abuse.The warranty set forth above is exclusive and no other warranty, whether written or oral is expressed or implied. We specifically disclaim the implied warranties of merchantability and fitness for a particular purpose.EXCLUSIVE REMEDIESThe remedies provided herein are the buyer’s sole and exclusive remedies.In no event shall we be liable for direct, indirect, incidental or consequential damages (including loss of profits) whether based on contract, tort or any other legal theory.2ContentsGeneral Description4 Installation Hints5Wiring Advice5Zener Barriers54-20 mA Available Responses60-10V Available Responses7-10V to +10V Available Responses8Analog Output Board - Configuring9Scaling the Analog Output10 Specifications11Record of Revisions12 Warranty2Connections and Installing into a MAGNA Display. See main MAGNA manual. Need a manual urgently? You can download manuals from our website.3General DescriptionThis manual only covers the setup of the MAGNA analog output option. Please refer to the main display’s operating manual for full specifications, installation methods, safety notices etc. You can download manuals from our website.The analog output option allows you to create an isolated analog signal which is propor-tional to the value shown on the front of your display.This can be used to feed remote devices such as data loggers, displays, PLCs and other peripheral equipment.The outputs are active. That means the outputs are available directly, without needing external excitation power.Two analog output boards are available:1.Unipolar output board -(options MAO1 or MAO2), which can be configured togive an output of 0-20 mA, 4-20 mA or 0-10V.2.Bipolar output board (option MAO3), which gives an output of -10V to+10V. These analog output options have high resolution and precision, thanks to their 16-bit D/A architecture.Scaling the output to cover your required measurement range is simple and only takes a few minutes.You will easily find the analog output setting button on the front of the display, it is the one marked OUTPUT, so you can get to the setting directly, without needing to find it in a menu. The analog output is derived from the displayed value, so if you adjust filtering for the display, the analog output will also be filtered and will respond to any input changes at the same speed as the display.The analog output is updated 10 times per second.45Installation Hints for Best PerformanceThis section offers several suggestions which will help you get the best performance from your analog output.1.Use good quality twisted-pair screened signal cable. Belden 8761NH (single pair), Belden 8777NH (multi-pair), Belden 9503 (multi-pair) or AlphaWire 6010C (multi-pair) are good choices available from many electrical distributors.2.The cable should be routed away from noisy wiring and devices such as power feeds from inverters, discharge-lighting cables, welder cabling etc,and should preferrably be routed in a dedicated low voltage signalling /instrumentation conduit or cable tray.3.Screened cable should be earthed at the destination end only.4.All wires and screens coming out of the screened cable should be kept as short as possible to minimise pickup of noise.5.If you are using barriers, you should earth your screen as shown below,paying particular care that you do not earth both ends of any run of of cable.6.If you are feeding the analog output to a PLC, data logger or other device with an A/D converter, you should set a sample time of around 100 mS and ensure that the signal is averaged during this period. This will ensure opti-mum noise performance without degrading response speed.Clean Earthu t p u t6MAO1 4-20 mA Output, Available ResponsesComplete flexibility and simplicity of scaling for your 4-20 mA analog output signal. Directly proportional and inversely proportional, symmetrical and assymetrical, zero based displayand offset display, all set with just 2 parameters!MAO2 0-10V Output, Available Responses Complete flexibility and simplicity of scaling for your 0-10V analog output signal. Directly proportional and inversely proportional, symmetrical and assymetrical, zero based display and offset display, all set with just 2 parameters!7MAO3 -10V to +10V Available ResponsesComplete flexibility and simplicity of scaling for your -10V to +10V analog output signal. Directly proportional and inversely proportional, symmetrical and assymetrical, zero based display and offset display, all set with just 2 parameters!89Analog Output Board ConfigurationYou can adjust your display to generate an analog output over a chosen numeric display range.For example you could have 4-20 mA output, where 4 mA occurs at 0 on the display and 20 mA occurs at 2500.0 on the display. Or, you may want the analog output to be reverse acting, so you could set 4 mA to occur at 500 on the display and 20 mA to occur at 125 on the display.You have complete freedom on the numeric display limits which correspond to your analog output. They can both be positive, one negative and one positive, or both negative.There are two board types, one for single polarity output such as 4-20 mA and 0-10V, the other for -10V to +10V output. The appropriate one will be fitted in your display, according to your order.MAO3 Bipolar -10V to +10V0-20 mA &4-20 mA DCMAO2 Voltage 0-10V DCScaling your Analog Output10SpecificationsOutput signal0-10VDC-10 to +10V0-20mA4-20mADrive capacity > 1K Ohms > 1K Ohms < 500 Ohms< 500 Ohms Isolation250 VAC optically isolated from input, logic, excitation, power,alarms and serial communications ports.Accuracy± 0.1% of range, ± 10 mV for MAO2 or MAO3, ± 10 µA for MAO1. Thermal stability± 50 ppm/°C stability.Linearity± 0.02% of rangeResolution16-bit D/A. Better than 0.2 mV for 0-10V range, 0.4 µA for 4-20 mA range. Scaling Fully adjustable direct or inverse. Can be derived from Net or Gross value. Response speed Derived from displayed value, which is updated 10 times per second. Any filtering applied to the display will be applied to the analog output also. Linearization The analog output is derived from the displayed value, so if your displayhas a non-linear response, and you are using the display’s linearizerfunction, the output will follow the display directly.11Record of Revisions20 August 2010Revision 0 version of manual released.26 November 2010Revision 2. Software F00.20 released2 February 2011Software F00.21 released28 February 2011Warranty increased to 3 years and terms added.Software version F00.21Revision:3 Dated: 28 February 2011 12。
西门子SCALANCE X101-1LD IE媒体转换器数据表说明书

/snst /simatic-net https://
6GK51011BC002AA3 Page 2/3
transfer rate transfer rate
interfaces number of electrical/optical connections / for network components or terminal equipment / maximum number of electrical connections ● for network components or terminal equipment ● for signaling contact ● for power supply ● for redundant voltage supply type of electrical connection ● for network components or terminal equipment ● for signaling contact ● for power supply number of optical interfaces ● for fiber optic cable / at 100 Mbit/s design of the optical interface ● for fiber optic cable / at 100 Mbit/s connectable optical power relative to 1 mW ● of the transmitter output / minimum ● of the transmitter output / maximum ● of the receiver input / maximum optical sensitivity relating to 1 mW / of the receiver input / minimum attenuation factor / of the FOC transmission link / minimum necessary range / at the optical interface / depending on the optical fiber used
AB-PLC5维护手册

AB PLC5/60系列PLC维护手册第一章PLC5/60处理器一、PLC5/60处理器前面板介绍①通道0是光耦合通道(具有较高的抗电气抗扰度),可以和大多数RS-422A设备一起使用:●不使用终端电阻●距离及传输速度将降低,以遵循RS-423需求②配置这三个端口用于:●远程I/O扫描器●远程I/O适配器●DH+通信链路●不使用二、PLC5/60处理器SW1及SW2拨码开关使用说明1、SW1介绍:2、SW2介绍三、使用钥匙改变处理器的操作模式如果用户想:把钥匙开关设置为:·运行程序 RUN (运行)输出有效(梯形图程序中寻址的I/O所控制的设备开始操作)·强置I/O·把用户程序保存到磁盘驱动器中·使输出有效·编辑数据表数值说明:·在运行模式下用户不能创建或删除程序文件创建或删除数据文件或通过编程软件改变操作模式。
使用6200 的5.2 版或A1.5 的7.21 版本时,通过设置用户控制位s:26/6 可以阻止强置功能和数据表改变。
·禁止输出(输出断开) PROG(编程)·创建、修改、删除梯形图文件、sFc 文件或数据文件。
·读/写存储器模块·保存/恢复程序说明:·处理器不扫描程序·在编程模式时用软件编程不能改变操作模式通过编程软件在远程编程、远程测试、 REM(远程)远程运行模式之间改变。
远程运行·使输出有效·保存/恢复程序·在线编辑远程编程请参阅面前的编程模式远程测试·在禁止输出的情况下执行梯形图程序·不能创建或删除梯形图程序或数据文件·保存/恢复程序·在线编辑四、程序和下载和上传无论是对处理器进行程序下载还是上传,首先都先建立和处理器之间的通讯。
(注意:如果编程器还未装Rslogix5和Rslinx-lite软件,就得先安装这两个软件包。
- 1、下载文档前请自行甄别文档内容的完整性,平台不提供额外的编辑、内容补充、找答案等附加服务。
- 2、"仅部分预览"的文档,不可在线预览部分如存在完整性等问题,可反馈申请退款(可完整预览的文档不适用该条件!)。
- 3、如文档侵犯您的权益,请联系客服反馈,我们会尽快为您处理(人工客服工作时间:9:00-18:30)。
DATASHEETB426-A B1510Wireless Stereo Speaker ModuleFor Intensive Audio ApplicationsSpecificationVERSION 0.10 25-Dec-2013 ArrayB426-AB1510 Stereo Speaker Module for IntensiveThis document is commercially confidential and must NOT be disclosed to thirdparties without prior consent.The information provided herein is believed to be reliable. But production testingmay not include testing of all parameters. AIROHA Technology Corp. reserves the right to change information at any time without notification.B426-AB1510 Stereo Speaker Module for IntensiveB426-AB1510Stereo Speaker Module For Intensive Audio ApplicationsB426-AB1510 Stereo Speaker Module for IntensiveAudio Applications Page 3 of 16 CONFIDENTIAL Revision HistoryVersion Change SummaryDate Author 0.10CreatedDec, 25th, 13LY Kuo1 System Overview1.1 General DescriptionB426-AB1510 is a stereo module, which are highly integrated, cost effective, low power consumptions with Airoha AB1510 chip for intensive audio applications. It complies with Bluetooth system version 3.0 with EDR function. The built-in noise reduction and echo cancellation functions enhance the voice quality. Advanced multipoint supports HFP connection to two handsets for voice, or two A2DP sources for music play back. The voice prompt function can be customized by customers for different voice commands.1.2 FeaturesBluetooth 3.0+EDR compliantA2DP 1.3 and AVRCP 1.5 profile enableHFP profile version 1.6 compliantHSP profile version 1.2 compliantAVRCP profile version 1.5 compliantSBC decodeClass 2 type output powerSupport for noise reduction and echo cancellationMulti-band configurable EQMultipoint for HFP and A2DPSupport for voice promptSupport SPI flash applicationSupport NFC application with wake-up and pairing functionAudio I/F:I2S and PCMIntegrated Li-ion battery charger supports 400mA fast chargingB426-AB1510 Stereo Speaker Module for IntensiveB426-AB1510 Stereo Speaker Module for IntensiveAudio Applications Page 5 of 16 CONFIDENTIAL 2 Module Package Information2.1 Module Pin DefinitionAB1510_Module with antennaVCHG_IN28BAT_IN 29LINE_IN_R 38SPK_LP 39LRVCM 40MIC_BIAS32MIC1_P 33MIC2_P 36LINE_IN_L 37WAKE 3V R E G O U T _M V25UART_TX 8UART_RX 7L E D 020L E D 121PIO1715PIO1614PIO1513PIO1412P I O 1224V C C I O 23PIO119PIO711PIO610P I O 522VREGOUT_HV30PIO36PIO25PIO14NC 1R S T26PIO431MIC2_N 35MIC1_N 34S D A17S C L18GND 2GND16GND 27SPK_RP 41W P /P I O 1819GND 42Figure 2-1 Pin DefinitionB426-AB1510 Stereo Speaker Module for IntensiveAudio Applications Page 6 of 16 CONFIDENTIAL 2.2 Pin DescriptionPIN SIGNAL TYPE DESCRIPTIONALTERNATIVE1 NC NC2 GND3 WAKE Input, Digital Input Pin with 125K pull up4 PIO1 Input, Digital Input Pin with 750K pull up5 PIO2 Input, Digital Input Pin with 750K pull up6 PIO3 Input, Digital Input Pin with 750K pull up7 UART_RX Input, Digital UART RX 8 UART_TX Output, Digital UART TX 9 PIO11 Input/Output, Digital Programmable IO 10 PIO6 Input/Output, Digital Programmable IO 11 PIO7 Input/Output, Digital Programmable IO 12 PIO14 Input/Output, Digital Programmable IO SPI/PCM/I2S 13 PIO15 Input/Output, Digital Programmable IO SPI/PCM/I2S 14 PIO16 Input/Output, Digital Programmable IO SPI/PCM/I2S 15 PIO17 Input/Output, DigitalProgrammable IOSPI/PCM/I2S16 GND17 SDA Input/Output, Digital I2C data line 18 SCL Input/Output, Digital I2C clock line 19 WP/PIO18 Output, Digital Write Protect Control forEEPROM WP 20 LED0 Open Drain LED 0 for Red Light 21 LED1 Open Drain LED 1 for Blue Light 22 PIO5 Input/Output, DigitalAIO,Analog Programmable IOUART_RTS23 VCCIO Supply, 1.8V~3.3V VCC for IO 24PIO12Input/Output, DigitalProgrammable IO LED3 25 VREGOUT_MV Analog LDO output 26 RST Input, DigitalGlobal reset27 GND28VCHG_INSupply, 5VVCC for ChargerB426-AB1510 Stereo Speaker Module for IntensiveAudio Applications Page 7 of 16 CONFIDENTIAL 29 BAT_IN Supply Battery input P , as Switching/Linear regulator input30 VREGOUT_HV Analog LDO output 31 PIO4 Input/Output, DigitalAIO,Analog Programmable IO UART_CTS32 MIC_BIAS Analog Microphone bias 33 MIC1_P Analog Microphone 1 P-path 34 MIC1_N Analog Microphone 1 N-path 35 MIC2_N Analog Microphone 2 N-path 36 MIC2_P Analog Microphone 2 P-path37 LINE_IN_L Analog Line in L-path 38 LINE_IN_R Analog Line in R-path 39 SPK_LP Analog Speaker output LP 40 LRVCM Analog Speaker output LRVCM 41 SPK_RP AnalogSpeaker output RP42GNDTable 2-1 Pin Description2.3 Module package and PCB footprint dimensionsFigure 2-2 Module package dimensions Figure 2-3 Module PCB footprint dimensions Dimesion:25mm(L)x14.5mm(W)x0.8mm(H)14121162742B426-AB1510 Stereo Speaker Module for IntensiveAudio Applications Page 8 of 16 CONFIDENTIAL 3 General Application SchematicB426-AB1510 Stereo Speaker Module for IntensiveAudio Applications Page 9 of 16 CONFIDENTIALPower on/off 1﹜Press ButtonPower on WAKEPower off≡3s ....≡3s ....2﹜Slide Switch3 second later,then Power onWAKEalways lowPower off at onceWAKETCB Connector for MPdownload and calibrationPIO7BAT_INJ15HEADER 9123456789VCHG_IN UART_RXRESET SDA WAKE UART_TXB426-AB1510 Stereo Speaker Module for IntensiveAudio Applications Page 10 of 16 CONFIDENTIALB426-AB1510 Stereo Speaker Module for IntensiveAudio Applications Page 11 of 16 CONFIDENTIAL 4 Electrical Characteristics4.1 Recommended Operating ConditionsItemMin.Typ.Max.UnitI/O supply voltage (VCCIO) 1.7 3.6 V Battery supply voltage (BAT_P)2.7 4.2 V Internal charger supply voltage (V_CHG)4.556.5VTable 4-1 Recommended Operating Conditions4.2 Power4.2.1 High-Voltage LDO (VREGOUT_HV)ItemCondition Min.Typ.Max.UnitInput Voltage (BAT_P)2.7 4.2 V Output VoltageInput voltage > 3.3V 3 V Rated Output Current (Iout)Input voltage = 4.2V300mATable 4-2 High-Voltage LDO4.2.2 Medium Voltage LDO (VREGOUT_MV)ItemCondition Min.Typ.Max.UnitInput Voltage (BAT_P) 2.7 4.2 V Output Voltage1.8 V Rated Output Current (Iout)Input voltage = 4.2V100mATable 4-3 Medium-Voltage LDO4.3 Battery ChargerB426-AB1510 Stereo Speaker Module for IntensiveAudio Applications Page 12 of 16 CONFIDENTIAL ItemMin.Typ.Max.UnitInput Voltage4.5 5 6.5 V Charge Current (CC Mode) 25 400 mA Trickle Charge Current4 mA Trickle Charge Threshold Voltage 2.92 V Regulated Output (Float) Voltage4.2VTable 4-4 Battery Charger4.4 Typical Current ConsumptionItemConditionMin.Typ.Max.UnitTransmit Peak Current TBD mA ReceivePeak Current TBD mA 10 msTBD mA 100 ms TBD mA Sniff mode 1.28 sTBDmADeep sleep (disconnected, link loss state, wake on interrupt)One battery/Li-Po battery solution, Vbat=3v, buck on, wake on by all GPIOsTBDuATable 4-5Typical Current Consumption4.5 Radio Characteristics4.5.1 TransmitterBasic Data RateCore Supply Voltage = 1.8V @ 25℃ItemMin.Typ.Max.UnitMaximum RF transmit Power *17 dBm RF power control range25 dB 20dB bandwidth for modulated carrier 900 KHz Adjacent channel transmit+2MHz-20dBmB426-AB1510 Stereo Speaker Module for IntensiveAudio Applications Page 13 of 16 CONFIDENTIAL -2MHz -20 dBm +3MHz -40 dBm power -3MHz-40 dBm ∆f1avg Maximum Modulation165 KHz ∆f2max Minimum Modulation 140 KHz Frequency deviation ∆f1avg/∆f2avg0.9 Initial carrier frequency tolerance-75 75 KHz DH1 packet-25 25 KHz DH3 packet -40 40 KHz Freq. DriftDH5 packet-40 40 KHz Freq. Drift Rate -20 20 KHz/50us Harmonic Content-45dBmTable 4-6 Transmitter Basic Data Rate*1 The maximum RF transmit power could reach to 8dBm with appropriate settingsEnhanced Data RateCore Supply Voltage = 1.8V @ 25℃ItemMin.Typ.Max.UnitRelative transmit power-1.5 dB π/4 DQPSK max carrier frequency stability |ωo | -10 10 KHz π/4 DQPSK max carrier frequency stability |ωi | -75 75 KHz π/4 DQPSK max carrier frequency stability |ωo +ωi | -75 75 KHz 8DPSK max carrier frequency stability |ωo | -10 10 KHz 8DPSK max carrier frequency stability |ωi | -75 75 KHz 8DPSK max carrier frequency stability |ωo +ωi |-75 75 KHz RMS DEVM20 % 99% DEVM 99 % π/4 DQPSK Modulation AccuracyPeak DEVM 35 % RMS DEVM13 % 99% DEVM 99 % 8DPSK Modulation AccuracyPeak DEVM25 % F > F0 + 3MHz -40 dBm F < F0 - 3MHz -40 dBm In-band spurious emissionsF = F0 + 3MHz-40dBmB426-AB1510 Stereo Speaker Module for IntensiveAudio Applications Page 14 of 16 CONFIDENTIAL F = F0 - 3MHz -40 dBm F = F0 + 2MHz -20 dBm F = F0 - 2MHz -20 dBm F = F0 + 1MHz -26 dB F = F0 - 1MHz-26 dB EDR Differential Phase Encoding99%Table 4-7 Transmitter Enhanced Data Rate4.5.2 ReceiverBasic Data RateCore Supply Voltage = 1.35V @ 25℃ItemMin.Typ.Max.Unit2.402GHz-92 dBm 2.441GHz -92 dBm Sensitivity at 0.1% BER2.480GHz-92 dBm Maximum input power at 0.1% BER -20 dBm Co-Channel interference11 dB F = F 0+1MHz 0 dB F = F 0-1MHz0 dB F = F 0+2MHz -30 dB F = F 0-2MHz -20 dB F = F 0+3MHz -40 dB Adjacent channel selectivity C/IF = F image-9 dB Maximum level of intermodulation interference-39 dBm 30-2000 MHz-10 dBm 2000-2400 MHz -27 dBm 2500-3000 MHz -27 dBm Blocking @Pin=-67dBm with 0.1%BER3000-12750 MHZ-10dBmTable 4-8 Receiver Basic Data RateEnhanced Data RateCore Supply Voltage = 1.8V @ 25℃B426-AB1510 Stereo Speaker Module for IntensiveAudio Applications Page 15 of 16 CONFIDENTIAL ItemMin. Typ. Max. Unit π/4 DQPSK -91 dBm Sensitivity at 0.01% EDR8DPSK-83 dBm π/4 DQPSK -20 dBm Maximum input power at 0.1% BER8DPSK -20 dBm π/4 DQPSK 13 dB Co-Channel interference8DPSK21 dB π/4 DQPSK0 dB F = F 0+1MHz8DPSK5 dB π/4 DQPSK0 dB F = F 0-1MHz8DPSK 5 dB π/4 DQPSK-30 dB F = F 0+2MHz8DPSK -25 dB π/4 DQPSK-20 dB F = F 0-2MHz8DPSK -13 dB π/4 DQPSK-40 dB F = F 0+3MHz8DPSK -33 dB π/4 DQPSK-7 dB Adjacent channel selectivity C/IF = F image8DPSKdBTable 4-9 Receiver Enhanced Data Rate4.6 Audio ADCItemConditionMin. Typ. Max. UnitMicrophone amplifier(A-Weighted 1kHz@ full scale, microphone input BW=20~20kHz)84dBSNRCodec bypass mode(A-Weighted 1kHz@ full scale, line-input BW=20~20kHz, VCCSPK=3V EAR_AMP=0dB)95dBTHD+NMicrophone amplifier gain=42dB(A-Weighted 1kHz@-10dBFS, microphone input BW=20~4kHz)-55dBB426-AB1510 Stereo Speaker Module for IntensiveAudio Applications Page 16 of 16 CONFIDENTIAL Microphone amplifier gain=21dB (A-Weighted 1kHz@-10dBFS, microphone input BW=20~20kHz)-66.7DBMicrophone amplifier gain=0dB (A-Weighted 1kHz@ -10dBFS, line-input BW=20~20kHz)0.05%Digital Gain -21 24 dB Analog Gain0 42 dB Input Full-Scale at MAX gain 2.24 MVrms Input Full-Scale at Min gain282 MVrms Microphone in level (Microphone input, full scale) 0.8 Vpp Input in level (Line-input, full scale) 1.7 Vpp Mic_bias_voltage2.7VTable 4-10 Audio ADC4.7 Stereo DACItemCondition Min.Typ.Max.UnitSNR94 dB THD+N16 ohm load Analog gain=0dB0.1%Output swingSPK_LP or SPK_RP Output Full-Scale at load=16OhmSPK_RP -- (16Ohm) LRVCMSPK_LP -- (16Ohm) speaker gain=3dB2.1VppDigital Gain -21 24 dB Analog Gain-12 9 dB Allow load VCCSPK=3V 8 16 Ohm Cross talk Load =16Ohm -50 dB Noise floor powerAnalog gain=0dB-100dBVTable 4-11 Stereo DAC。