辊压机终粉磨系统在生料制备中的应用
辊压机联合粉磨系统在水泥生产中的应用
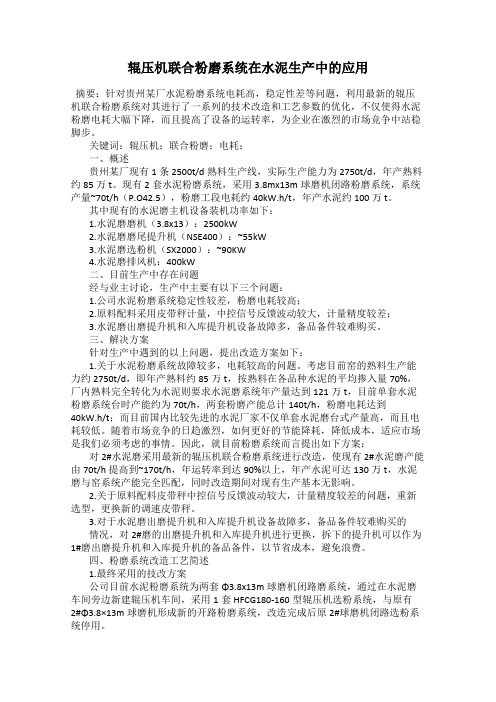
辊压机联合粉磨系统在水泥生产中的应用摘要:针对贵州某厂水泥粉磨系统电耗高,稳定性差等问题,利用最新的辊压机联合粉磨系统对其进行了一系列的技术改造和工艺参数的优化,不仅使得水泥粉磨电耗大幅下降,而且提高了设备的运转率,为企业在激烈的市场竞争中站稳脚步。
关键词:辊压机;联合粉磨;电耗;一、概述贵州某厂现有1条2500t/d熟料生产线,实际生产能力为2750t/d,年产熟料约85万t。
现有2套水泥粉磨系统,采用3.8mx13m球磨机闭路粉磨系统,系统产量~70t/h(P.O42.5),粉磨工段电耗约40kW.h/t,年产水泥约100万t。
其中现有的水泥磨主机设备装机功率如下:1.水泥磨磨机(3.8x13):2500kW2.水泥磨磨尾提升机(NSE400):~55kW3.水泥磨选粉机(SX2000):~90KW4.水泥磨排风机:400kW二、目前生产中存在问题经与业主讨论,生产中主要有以下三个问题:1.公司水泥粉磨系统稳定性较差,粉磨电耗较高;2.原料配料采用皮带秤计量,中控信号反馈波动较大,计量精度较差;3.水泥磨出磨提升机和入库提升机设备故障多,备品备件较难购买。
三、解决方案针对生产中遇到的以上问题,提出改造方案如下:1.关于水泥粉磨系统故障较多,电耗较高的问题。
考虑目前窑的熟料生产能力约2750t/d,即年产熟料约85万t,按熟料在各品种水泥的平均掺入量70%,厂内熟料完全转化为水泥则要求水泥磨系统年产量达到121万t,目前单套水泥粉磨系统台时产能约为70t/h,两套粉磨产能总计140t/h,粉磨电耗达到40kW.h/t;而目前国内比较先进的水泥厂家不仅单套水泥磨台式产量高,而且电耗较低。
随着市场竞争的日趋激烈,如何更好的节能降耗,降低成本,适应市场是我们必须考虑的事情。
因此,就目前粉磨系统而言提出如下方案:对2#水泥磨采用最新的辊压机联合粉磨系统进行改造,使现有2#水泥磨产能由70t/h提高到~170t/h,年运转率到达90%以上,年产水泥可达130万t,水泥磨与窑系统产能完全匹配,同时改造期间对现有生产基本无影响。
生料终粉磨系统中立磨和辊压机的应用对比
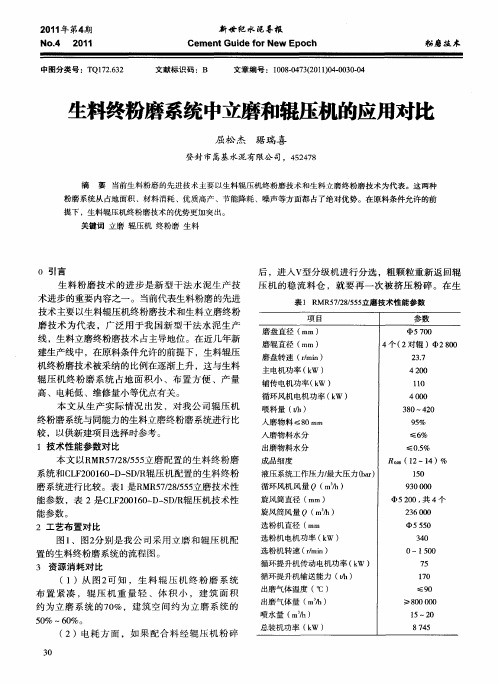
( 1)R 5 /85 5 MR 72 /5 立磨 属 料床 式粉 磨 ,磨辊 压 力较 大 ,双重 挤压 ,压 力油 缸属 单行 程拉 力式 , 磨 辊 能压 而不 能抬 ,这 就要 求 连续 、稳 定 喂料 , 料 床上 需要 有一 个平 整 的料垫 ,且 不能有 金 属等异 物 ,否 则 ,磨机 就不 能安 全高 效运 行 。辊压 一般控
1O 5
90 o 3 00 q52 0, 4个 b 0 共 2 6O 0 3 0 中550 5 3O 4 O~1 0 o 5
图1 、图2 分别 是 我 公 司采用 立 磨 和辊 压 机 配 置 的生 料终 粉磨 系统的流 程 图。
3 资源 消耗对 比
循环提升机传动电机功率 ( W ) k
本 文 从 生 产 实 际情 况 出发 ,对 我公 司辊 压 机 终粉 磨系 统与 同能 力 的生 料立 磨终 粉磨 系统进行 比 较 ,以供新建 项 目选择 时参考 。
1技 术性 能参数对 比
辅传电机功率 ( W ) k
循环风机电机功率 ( W ) k
喂料 量 (/ t h)
0 引 言
后 ,进 人V型分级 机进 行 分选 ,粗 颗粒 重新 返 回辊
压 机 的稳 流料 仓 ,就 要 再 一 次被 挤 压 粉 碎 。在 生
表 1 MR5/85 5 R 72/5 立磨 技 术 性 能 参 数
生料 粉 磨 技 术 的进 步 是 新 型 干法 水 泥 生 产 技 术进 步 的重 要 内容之一 。当前 代表 生料粉 磨 的先进 技术 主要 以生料辊 压机 终粉磨 技术 和生料 立磨终 粉 磨 技 术 为代 表 ,广 泛 用 于 我 国新 型干 法 水 泥 生 产 线 ,生 料立磨 终粉磨 技术 占主导 地位 。在近 几年新
辊压机生料终粉磨系统的生产调试及应用

辊压机生料终粉磨系统的生产调试及应用作者:吴君山么化民来源:《科技创新与应用》2013年第02期摘要:牡丹江北方水泥有限公司,其2#窑是由原牡丹江水泥厂自行设计的日产1848t/d熟料的预分解窑,生料制备为两台带烘干机的Φ3.0m×11m闭路磨系统,台时产量130t/h。
由于原生料制备系统产量低、出磨质量差、能耗高等问题,我单位引进一套Φ1800×1000生料辊压机终粉磨系统,台时产量200t/h。
现将该系统调试中出现的问题及解决方法与同仁分享。
关键词:辊压机;生产调试;应用1 工艺流程及主机设备表1.1 工艺流程简述从配料站来的混合料由胶带输送机(01)送至生料粉磨车间,胶带输送机上悬挂除铁器(02),将物料中混入的铁件除去;同时该皮带上装有金属探测器(03),发现有金属后气动三通阀(04)换向,将混有金属的物料由旁路卸出,以保证辊压机的安全运行。
不含金属的物料由气动三通经锁风阀(05)喂入V型选粉机(06),在V型选粉机中预烘干后,通过提升机(07)提升进入稳流仓(08),该稳流仓设有荷重传感器检测仓内料位,物料从稳流仓过饱和喂入辊压机(11)进行料床粉碎的挤压过程,挤压后料饼通过提升机(12)送入V型选粉机中打散、烘干、分级,细小颗粒被热风分选出来,粗颗粒与新喂入的混合料一同进入循环挤压过程。
V型选粉机中被打散分选出来的细颗粒被热风带至热风管道内继续烘干后进入XR选粉机(13),通过笼型转子进行分选,粗粉通过双层重锤锁风阀(13a)卸出至稳流仓(08)后继续挤压,选出的生料成品通过旋风除尘器(14)气料分离后,通过双层重锤锁风阀(14a)卸入生料成品输送斜槽(16)入生料库。
生料烘干热源来自窑尾废气,可通过电动阀门(20)控制窑尾热风量,同时冷风阀(21)可控制掺入冷风量,以控制入V型选粉机的热风温度。
生料磨系统含尘废气由旋风筒(14)经循环风机(15)排出后,一部分经调节阀(18)循环回V型选粉机进风管,大部分进入窑尾废气处理电收尘器(22),除尘净化后由风机排入大气。
生料终粉磨辊压机的应用实践与技术创新

-18-C€Ai€tiT2021.N〇.4生料终粉磨辊压机的应用实践与技术创新琚瑞喜,李彩峰(登封市嵩基水泥有限公司,河南登封452478)摘要:国内使用最广泛的生料终粉磨设备就是立磨和辊压机,这两种粉磨设备从占地面积、材料消耗、优质高产、节能 降耗、噪声影响等方面都占了绝对优势.本文介绍经过多年的应用实践,对生料终粉磨系统又进行了接料装置改造、下料溜子改造、原材料优化、新型铸钉辊的使用等一系列技术创新,最终实现了提高产量降低能耗的目的关键词:生料;终粉磨;辊压机;技术创新中图分类号:TQ172.632.5 文献标识码:B文章编号:1002-9877(2021)04-00丨8-03 DOI:丨0.13739/H-1899/tq.2021.04.006我公司4 500 t/d熟料生产线配置的CLF200160- D-SD/R生料辊压机终粉磨系统,投产初期存在台 时产量低、电耗高、选粉效果不佳、辊面磨损严重 等问题。
通过采取一系列技改措施,台时产量由 380 t/h增加到420 t/h,生料电耗由原来的15 kWh/t 降低到13.5 kWh/t,生料细度达到/?a2in m<2.2%、A i m彡20%,生料的供应可以满足回转窑的需求。
自2014年起,我公司又对生料粉磨系统进行了优化 和技术创新,具体措施如下。
1新型接料装置的改造2014年,我公司对接料装置进行了技术创新,接 料装置改造前后对比见图1。
改造前为传统技术往 复拔插型进料装置,调节插板沿座上下直线往复运 动,调节插板下端与辊面间隙不能恒定,虚线喂料开 大状态时,易出现漏料;改造后旋转摆动型进料装 置,调节插板绕轴转动,接料装置调整时漏料现象明 显减少[1]。
改造前:往复拔插型改造后:旋转摆动型图1接料装置改造前后对比2下料溜子变径稳流仓原下料管为1600 mm X700 mm长方形 管,我们考虑物料流速快,辊缝处料压小,2015年初,把下料管改为600 mm圆管,同时加高800 mm,改 造后稳流仓下料管实物见图2。
CDG辊压机生料终粉磨系统的设计特点及应用

粉过程 ,优化 了T艺 流程 ,降低 了系统 能耗 。
关键词 生料 辊压机 终粉磨
。 引言
的静 态选 粉机 中引入 窑 尾废气 作 为烘干 热源 ,综 合
平 时 注重积 累处 理 问题 的成功 经验 和方法 。 1 1结 束语 造 成 熟 料f a 偏 高 的原 因很 多 ,有 原燃 材 料 CO
结 皮时 ,fa 偏 高 已经 几个 小 时 了 。 CO ( 3)处理 问题 不 果 断 。 比如 开窑 时 窑速 提 的 过 快 ,正常 生产 时大 量生 料涌 进烧 成带 而慢 窑不 及 时 ,这 两种 情况 都容 易发 生跑 生料 ,造 成f a 含 量 CO
及 生料 质量 的客 观原 因 ,也有熟 料煅 烧过 程 中操作 员 的 主观原 因 。处理f a 偏 高 问题 时 ,一 定要结 合 CO
窑 的实 际生产 状 况进行 原 因分析 ,采 取相 应 的处 理
措施 ,这样才 能 达到 比较理 想 的效果 。
( 稿 日期 :2 1 3 01) 收 010 —
静 态 选 粉 机 内与物 料 逆 向 的气 流 携带 较 小 的 料粒经 过导 叶系统 从选粉 机顶部 排 出进入 动态选粉 机 。经 动态选 粉机 分离下 来 的粗 粉 由空气输 送斜槽
返 回称 重稳 流仓再 次喂人 辊压机 ,合格 生料 随气体 出动态 选粉机进 入双 旋风 收尘器 。双旋 风收 尘器收 集 的生料 经 回转 锁风 阀 、空气输 送斜槽 、提升 机等 输送 入生 料均化 库 。 出双 旋 风 收 尘器 的气 体 由生料 磨 循 环 风 机 排 出后 ,一部分 经循 环风 管与窑尾 来 的废 气混合 后进 人 静态选 粉机 作为烘 干热 源 ,其 余部分 进入 窑尾袋
节能型水泥生料降硫助剂辊压机终粉磨应用效果浅析

I 粉磨技术 Grinding 丁echnology节能型水泥生料降硫助剂辊压机终粉磨应用效果浅析兰文献,王兆祥,潘民夫,彭志福,潘东涛(广西都安西江鱼峰水泥有限公司,广西都安530700 )摘要:辊压机终粉磨节电效果明显,但对原料的水分、粘度适应性相对较差,0.2mm筛筛余偏粗;节能型水泥生料降硫助剂作为一种新型节能降耗减排产品,能够改善生料粒度分布、提高生料比表面积 及降低生料细度。
在辊压机生产过程中,生料助剂从辊压机前入磨石灰石皮带上加入,能够使V 型选粉 机、辊压机的工作效率上升,提高辊压机粉磨效率,使粉磨系统产量明显提高。
关键词:生料助剂;辊压机;颗粒分布;比表面积;细度;粉磨效率中图分类号:TQ 172 TQ 172.63; TQ 172.463 文献标识码:A 文章编号:1671—8321 (2021) 06—0102—031试验背景广西都安西江鱼峰水泥有限公司(简称:我司)生料粉磨采用C L F 200-160辊压机终粉磨系统,台时产量 维持在500l /h 左右,同时存在原材料品质波动及棍压机 运行不稳定、磨机产量偏低等问题。
为节省技改成本、 提高磨机产量,确保磨、窑稳定高产运行,我司与湖南 昌迪环境科技有限公司(简称:昌迪公司)就节能型水 泥生料降硫助剂(简称:生料助剂)应用技术进行了深 人交流,在昌迪公司提供的生料助剂《试验方案》、《安 全操作规程》、《中控操作技术要领》、《生料助剂检验 标准》和《作业指导书》等资料的基础上,双方对生产 运行、人员组织、安全等试验细节进行了沟通,确定于 2020年1月开始试验。
生料辊压机终粉磨系统工艺流程见图1。
图1生料辊压机终粉磨系统工艺流程图我司原料粉磨采用辊压机终粉磨系统,人磨物料粒度矣55mm,各种原料经人磨皮带入V 型选粉机分级打散,粗粉经提升机均化人喂料小仓,经过辊压机循环挤 压;细粉进入动态选粉机分选,合格品人旋风收尘器收 集,不合格品经空气斜槽入稳流仓回辊压机循环挤压, 挤压后的物料经提升机送入V 型选粉机,4个旋风筒下料 人空气斜槽,经提升机人均化库。
CDG辊压机生料终粉磨系统的设计特点及应用

CDG相压机生料终粉磨系统的设计特点及应用文章正文摘要:节能和降低成本是生料制备技术发展的原动力。
采用“辐压机+静态选粉机”组合方式的生料较压机终粉磨系统,由辐压机来完成对原料的粉碎、挤压和研磨过程,以提高系统产量并降低粉磨能耗;同时在完全没有动力消耗的静态选粉机中引入窑尾废气作为烘干热源,综合完成对原料的烘干、打散、分级和选粉过程,优化了工艺流程,降低了系统能耗。
关键词:生料辐压机终粉磨O引言生料制备技术的发展是新型干法水泥生产技术进步的一个重要部分。
节能和降低成本是生料制备技术发展的原动力。
在同样的物料特性和运行管理水平下,短压机终粉磨工艺的系统电耗相对于立磨粉磨工艺的系统电耗降低3~4kWh∕t o2010年4月,由成都建材工业设计研究院有限公司提供设计和装备的生料辐压机终粉磨系统在青海新型建材工贸有限公司成功投入运行。
该系统采用“辐压机+静态选粉机”的组合方式,由轮压机来完成对原料的粉碎、挤压和研磨过程,以提高系统产量并降低粉磨能耗;同时在完全没有动力消耗的静态选粉机中引入窑尾废气作为烘干热源,综合完成对原料的烘干、打散、分级和选粉过程,极大地优化了工艺流程,降低了系统能耗,系统各项技术指标达到先进技术水平。
本文就CDG转压机生料终粉磨系统的设计特点及应用进行介绍。
1系统主要工艺流程由原料配料带式输送机送来的配合原料,经气动正三通分料阀、单层双门重锤锁风阀锁风后,与轻压机出料混合后进静态选粉机。
静态选粉机分选后的粗颗粒经斗式提升机喂入称重稳流仓,出仓物料经单层棒闸、气动截断阀和电动插板阀喂入轻压机,物料经辐压机挤压破碎后喂入循环斗提机,与原料配料来的物料混合后喂入静态选粉机分选。
见图1。
图ICDG辐压机生料终粉磨系统1-皮带输送机;2-金属探测仪;3-气动正三通分料阀;4T型选粉机;5-斗式提升机;6-稳流仓;7~耨压机;8-循环斗式提升机;9-动态选粉机;10-旋风分离器;11-循环风机;12-空气输送斜槽.静态选粉机内与物料逆向的气流携带较小的料粒经过导叶系统从选粉机顶部排出进人动态选粉机。
生料中卸烘干粉磨系统改造为辊压机终粉磨系统的实践
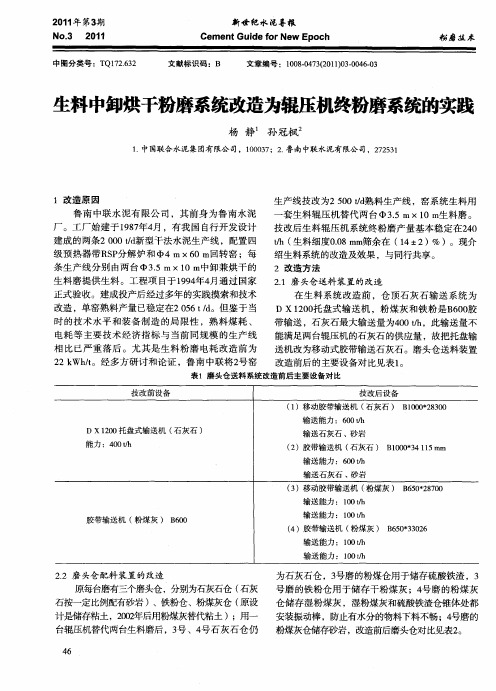
为石灰石仓 ,3 号磨的粉煤仓用于储存硫酸铁渣 ,3 号磨 的铁粉仓用于储存干粉煤灰 ;4 号磨的粉煤灰
仓储存湿粉煤灰 ,湿粉煤灰和硫酸铁渣仓锥体处都 安装振动棒 ,防止有水分的物料下料不畅 ; 号磨的 4 粉煤灰仓储存砂岩 ,改造前后磨头仓对比见表2 。
2 1年g3 01 期
N . 21 o3 01 杨静 ,等 :生料 中卸烘干粉磨系统改造为辊压机终粉磨系统的实践
2 号辊压机的湿粉煤灰
每台磨 主要设 备电机 功率 :中卸式提升循环 磨机电机功率1 0 旋风式选粉机7 w+ 0 w+ 6 k 5k 斗式 提升机电机功率7 w+ 5k 循环风机电机功率12 w+ 3k 磨排风机电机功率4 0k 2 8 W。则两台磨 的 0 W= 2k 2 主要设备电机功率为4 6 4 W。 5 k
输送能力 :10t 0 / h
( 4)胶带输送机 ( 粉煤灰 ) B 5 " 3 2 60 3 0 6 输送能力 :10t 0 / h
输送 能力 : 10 / 0 t h
22 磨 头仓 配 料装 置 的改造 .
原每台磨有三个磨头仓, 分别为石灰石仓 ( 石灰 石按一定 比例配有砂岩 ) 、铁粉仓 、 粉煤灰仓 ( 原设 计是储存粘土 , o2 2o ̄后用粉煤灰替代粘土 );用一 台辊压机替代两台生料磨后 ,3 、4 号 号石灰石仓仍
23 主机 设备 的 改 变 .
杉磨技术
表2 磨头仓贮存物料的变化 技改前 技改后
改造 前后 的 主机设 备对 比见 表3 。 231 改造 前 主要 设备 电机 功 率情 况 . .
3 、4号石灰石仓 ( 号 包含砂岩 ) 2号辊压机的石灰石仓
3号粉煤灰仓
4号粉煤灰仓
2 号辊压机的铁粉仓
辊压机生料终粉磨应用实例浅析
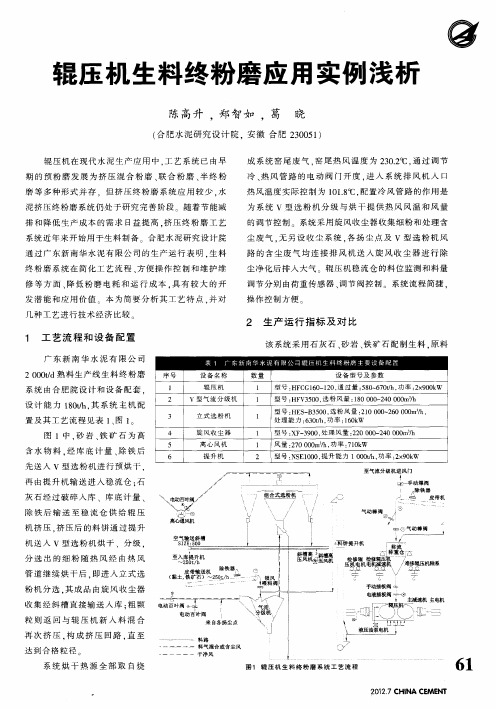
含 水 物 料 , 库 底 计 量 、 铁 后 经 除
先送入 V型选粉机进行 预烘干 .
6
提升机
2
型号:S I0 , N E O0提升能力 1 0t , : 9k 0/ 功率 2 0W 0 h x
再 由提 升 机 输 送 进 入 稳 流 仓 : 石 灰 石 经 过 破 碎 入 库 、库 底 计 量 、
粒 则 返 回 与 辊 压 机 新 人 料 混 合 再 次 挤 压 . 成 挤 压 回路 . 至 构 直
达 到 合 格 粒 径 系 统 烘 干 热 源 全 部 取 自烧
图 1 辊 压 机 生料 终 粉 磨 系统 工 艺 流 程
6 1
序 号 l 2
3
设 备 名 称 辊 压 机 v 型气 流 分 级 机
立 式 选 粉 机
数 量 l l
1
设 备 型 号及 参 数 型 号 : F G10 10 通 过 量 :8 ~ 7 t , 率 :x 0 k H C 6—2 , 5 0 6 0/ 功 h 2 9 O W 型 号 : V30 选 粉 风 量 :8 0 4 0 m3 HF 50, 100 0 2 00 0 / h
2O 0/ 料 生 产 线 生 料 终 粉 磨 0 t d熟 系 统 由 合 肥 院设 计 和 设 备 配 套 . 设 计 能 力 1 0/ 其 系 统 主 机 配 8t h. 置及其工艺流程见表 1图 l 、 图 l中 . 岩 、 矿 石 为 高 砂 铁
4 5 旋 风 收 尘 器 离 心 风 机 1 1
辊压机 生料 终粉磨应 用实例 浅析
陈 高升 , 智如 ,葛 晓 郑
( 肥水 泥研 究设 计 院 ,安徽 合 肥 2 0 5 ) 合 3 0 1
现代水泥生产生料制备与水泥粉磨工序节能技术方案探讨

术耗 电量大 , 系统耗 电量高达 2 0 2 2 k Wh / t , 这样一来提 高了生产 成本 , 不符合生产 的节能路线 , 因此此技术逐渐 被立磨系统或生 料终粉磨系统所取代。但是 , 目前 已开始采用烘干中卸式生料粉 磨系统 ,该系统的生产 设备耗 电量不高,完全符合经济技术要
自不 同, 该磨机根据含水量、 易 磨 性 配 置 相 关 的 风 扫 磨 系 统 与 尾
卸提升循环系统 ,此外还能根据 生产规模的大小设置有 中卸提 升循环系统 , 这类系统 的设置 , 在一定程度上促使水泥生料制备
工 作 的J i  ̄ l N进行, 并 能保 证 生 料 制 备 的 质 量 , 如 此 多 的 优 点 正 是 管磨 工 艺 技术 被 认 可 和 使用 的原 因 。但 不 可 逃 避 的 问题 是 , 该 技
或 是 从 实 际运 行 的 角 度 来 看 , 辊 压 机 终粉 制备 , 再 进 行 熟 料煅 烧 、 冷却 , 最后是制备水泥 , 包装 入 库 或 直 接 不 管 是 从耗 能 的角 度 , 磨 工 艺 技 术 都 具有 其 特 有 的优 势 ,在 我 国 该系 统 已 得 到广 泛 使 散装 出厂 , 每一道工序的进行 都需要消耗相应的能源 , 要降低生 产 成 本 必 须 降 低 能源 的消 耗 。
立磨 工艺技术 、 管磨工艺技术 以及辊压机终粉磨工 艺技术 , 每种 技术都具有其特点, 对水泥生产 生料制备都具有重要意义。
辊压机终粉磨系统在生料制备中的应用
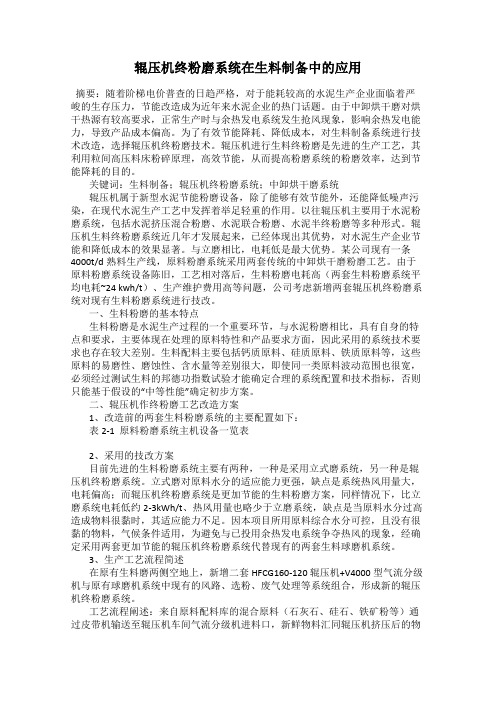
辊压机终粉磨系统在生料制备中的应用摘要:随着阶梯电价普查的日趋严格,对于能耗较高的水泥生产企业面临着严峻的生存压力,节能改造成为近年来水泥企业的热门话题。
由于中卸烘干磨对烘干热源有较高要求,正常生产时与余热发电系统发生抢风现象,影响余热发电能力,导致产品成本偏高。
为了有效节能降耗、降低成本,对生料制备系统进行技术改造,选择辊压机终粉磨技术。
辊压机进行生料终粉磨是先进的生产工艺,其利用粒间高压料床粉碎原理,高效节能,从而提高粉磨系统的粉磨效率,达到节能降耗的目的。
关键词:生料制备;辊压机终粉磨系统;中卸烘干磨系统辊压机属于新型水泥节能粉磨设备,除了能够有效节能外,还能降低噪声污染,在现代水泥生产工艺中发挥着举足轻重的作用。
以往辊压机主要用于水泥粉磨系统,包括水泥挤压混合粉磨、水泥联合粉磨、水泥半终粉磨等多种形式。
辊压机生料终粉磨系统近几年才发展起来,已经体现出其优势,对水泥生产企业节能和降低成本的效果显著。
与立磨相比,电耗低是最大优势。
某公司现有一条4000t/d熟料生产线,原料粉磨系统采用两套传统的中卸烘干磨粉磨工艺。
由于原料粉磨系统设备陈旧,工艺相对落后,生料粉磨电耗高(两套生料粉磨系统平均电耗~24 kwh/t)、生产维护费用高等问题,公司考虑新增两套辊压机终粉磨系统对现有生料粉磨系统进行技改。
一、生料粉磨的基本特点生料粉磨是水泥生产过程的一个重要环节,与水泥粉磨相比,具有自身的特点和要求,主要体现在处理的原料特性和产品要求方面,因此采用的系统技术要求也存在较大差别。
生料配料主要包括钙质原料、硅质原料、铁质原料等,这些原料的易磨性、磨蚀性、含水量等差别很大,即使同一类原料波动范围也很宽,必须经过测试生料的邦德功指数试验才能确定合理的系统配置和技术指标,否则只能基于假设的“中等性能”确定初步方案。
二、辊压机作终粉磨工艺改造方案1、改造前的两套生料粉磨系统的主要配置如下:表2-1 原料粉磨系统主机设备一览表2、采用的技改方案目前先进的生料粉磨系统主要有两种,一种是采用立式磨系统,另一种是辊压机终粉磨系统。
辊压机在生料粉磨系统中的应用

空气斜槽
XZ 4 0 0X 2 3 m 能力 :3 0 0 t / h 斜槽风机XQ I N0 5 . 4 1 风量 :8 0 0 m3 / h 全压:5 4 1 6 P a 2  ̄
,
证 来 料 不 存 在 金 属 ,减 少 对 辊 压 机 磨 辊 的 磨 损 ,二
是在 出料 提 升机 入 V 选 的溜 子 由捌 弯 变成 直 溜 子 ,保
1 1 O
辊压 机 ห้องสมุดไป่ตู้
C L F 1 8 0 — 1 0 0 一 S D / R 1 轧辊直径: 1 . 8 I l 1 ,车 l 辊宽度:1 m
l 0 o o ( 电机2 个)
图2 入料溜子改造 图 ( mm )
板 链 斗 式 提 升 机 N S E 8 0 0 H = 2 0 . 6 m ( 出料提升机 ) 能力 :8 0 0 f h 0 型 选 粉 机 旋 风 收 尘 器 X R 3 2 0 0风 量 :3 0 ~ 4 0 万m / h
辊压机在 生料粉磨 系统 中的应 用
于进 月 ,姜 宜 汹
( 天津水泥工业设计研究 院有 限公 司体系运行部 ,天津 3 0 0 4 0 0)
中图分类号:T O 1 7 2 . 6 3 2 文献标识码 :B 文章编 号:1 6 7 1 — 8 3 2 1( 2 0 1 4 )0 1 — 0 0 6 7 — 0 2
好 的节 能 、降耗 ,采用最 优的工艺 系统 ,最简洁 的工艺 配置 ,最新 的技术和装备 ;于2 0 1 1 年对该生料粉磨 系统进 行改造 ,由管磨更换为辊压磨生料粉磨 系统 ,采用 的是成 都利君专利技术 , 辊压机型号C L F 1 8 0 - 1 (  ̄ - - S D / R, 设计 台时
生料终粉磨辊压机的应用实践与技术创新研究
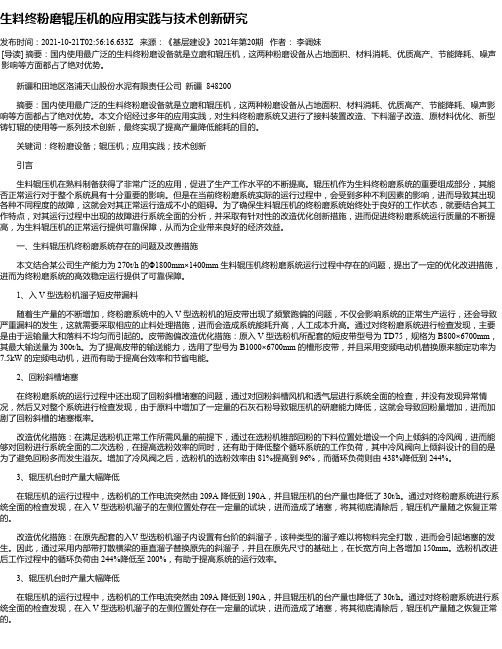
生料终粉磨辊压机的应用实践与技术创新研究发布时间:2021-10-21T02:56:16.633Z 来源:《基层建设》2021年第20期作者:李调妹[导读] 摘要:国内使用最广泛的生料终粉磨设备就是立磨和辊压机,这两种粉磨设备从占地面积、材料消耗、优质高产、节能降耗、噪声影响等方面都占了绝对优势。
新疆和田地区洛浦天山股份水泥有限责任公司新疆 848200摘要:国内使用最广泛的生料终粉磨设备就是立磨和辊压机,这两种粉磨设备从占地面积、材料消耗、优质高产、节能降耗、噪声影响等方面都占了绝对优势。
本文介绍经过多年的应用实践,对生料终粉磨系统又进行了接料装置改造、下料溜子改造、原材料优化、新型铸钉辊的使用等一系列技术创新,最终实现了提高产量降低能耗的目的。
关键词:终粉磨设备;辊压机;应用实践;技术创新引言生料辊压机在熟料制备获得了非常广泛的应用,促进了生产工作水平的不断提高。
辊压机作为生料终粉磨系统的重要组成部分,其能否正常运行对于整个系统具有十分重要的影响。
但是在当前终粉磨系统实际的运行过程中,会受到多种不利因素的影响,进而导致其出现各种不同程度的故障,这就会对其正常运行造成不小的阻碍。
为了确保生料辊压机的终粉磨系统始终处于良好的工作状态,就要结合其工作特点,对其运行过程中出现的故障进行系统全面的分析,并采取有针对性的改造优化创新措施,进而促进终粉磨系统运行质量的不断提高,为生料辊压机的正常运行提供可靠保障,从而为企业带来良好的经济效益。
一、生料辊压机终粉磨系统存在的问题及改善措施本文结合某公司生产能力为 270t/h 的Φ1800mm×1400mm 生料辊压机终粉磨系统运行过程中存在的问题,提出了一定的优化改进措施,进而为终粉磨系统的高效稳定运行提供了可靠保障。
1、入 V 型选粉机溜子短皮带漏料随着生产量的不断增加,终粉磨系统中的入 V 型选粉机的短皮带出现了频繁跑偏的问题,不仅会影响系统的正常生产运行,还会导致严重漏料的发生,这就需要采取相应的止料处理措施,进而会造成系统能耗升高,人工成本升高。
辊压机在水泥粉磨系统中的应用探讨

辊压机在水泥粉磨系统中的应用探讨摘要:目前国内水泥粉磨系统常采用的主要有两种工艺形势,一是传统的球磨机开路或闭路粉磨系统,二是辊压机+球磨机的挤压联合粉磨系统,辊压机、球磨机可以双闭路或单闭路。
辊压机+球磨机的挤压联合粉磨系统的核心是:物料经过辊压机挤压粉碎后再通过打散分级或选粉回路,将其粗颗粒返回辊压机与新给物料混合继续挤压直至合格粒径,以确保喂入球磨机的物料颗粒结构松散、粒度均匀,从而提高磨机台时产量。
文中对辊压机在水泥粉磨系统中的应用进行了分析。
关键词:辊压机;水泥粉磨系统;应用1导言在水泥生产过程中,粉磨系统电耗占全部生产用电的60%~70%,因此,降低粉磨系统电耗是水泥生产企业节能降耗的主要目标之一。
在常见的大型粉磨设备中,辊压机的能量利用率为600m2/kJ,球磨机为240~320m2/kJ。
新建或改造的粉磨系统,生料粉磨系统大多采用辊压机终粉磨系统,水泥粉磨系统辊压机与球磨机组成的联合粉磨系统。
2工程概况某地工程项目预分解窑水泥生产线,以将水泥制成工序。
工程建设人员采用两套大型机械设备,组成大型开路联合粉磨系统。
经分析,该系统应用的技术特点主要集中在,充分发挥了磨前辊压机段的高效率优势。
即挤压后,料饼进入了动态与静态两级高细气流分级设备,从而使物料分析更为精确、分级效率更高。
但由于当前运行的水泥粉磨生产线,其原配置辊压机规格偏小,因此,无法满足物料的处理能力、做功以及入磨入料中细粉使用等方面的需求。
为此,相关建设人员应在明确水泥粉磨系统预粉磨能力应用现状的情况下,找出优化实践控制的方法策略。
3辊压机系统设备分析气流分级机在使用过程中发现循环提升机入V选物料分布均匀性不好,通过分级机打散板磨损情况进行检查,出现偏料情况通过对现有入V选溜子内部增加打散板,调整物料在溜子内流速、流向,仍不能有效提升入V选溜子物料的均匀分布。
通过对V选下料取样分析,物料在通过V选后仍有0.08mm筛余在12%~15%左右,与先进公司数据通过提高V选效率,通过V选后物料0.08筛余能够达到5%~8%之间。
辊压机生料终粉磨系统的生产调试及应用

设备阻力 ( V 选+ 动选):1 . 0 ~1 . 5 k P a 电机功率:7 5 k - W
一
1 . 2主 要设 备 参 数表 表 1主要设备参数表
设备名称 规格 型号 性能 数量
1台 v型选粉 机 型号 :V X O 6 2 0 F风 量:3 0 0 0 0 0  ̄4 5 0 0 0 0 m ’ / h 设备 阻力I 1 . 0 ~1 . 5 k P a
图2 XR选粉 机 改 造 图
工 业 技 术
2 0 1 3 年 第2 期I 科技 创新 与应 用
辊压机生料终粉磨系统的生产调试及应用
吴 君 山 民
( 牡 丹江北方水泥有限公 司, 黑龙江 牡丹 江 1 5 7 0 4 1 )
摘 妻: 牡 丹江北方水泥有限公司, 其 窑是 由原牡丹江水泥广 自行设计 的 日产 1 8 4 8 t / d熟料 的预分解 窑 生料 制 备 为 两 台带 烘 干机的 3 . O m x l l m闭路磨 系统 , 台时产量 1 3 0 t / h o由于原 生料制备 系统 产量低 、 出磨质 量差、 能耗 高等 问题 我单位引进一套
, ,
1 8 o o  ̄1 o o o 生料辊压机 终粉磨 系 统, 台时产量 2 0 0 t / h 。现将该 系统调试 中出现的问 题及解决方法与 同仁分享。
关 键诃: 辊 机; 生产 调试; 应用 、
3 3 m m、 6 4  ̄ 6 7 m m。经查找 、 分析发现两方面原 因造成物料离析: 一是 新喂人的混合料和循环料存在偏料现象 , 进入“ v选” 物料未均匀分 布, 导致辊压机左右侧辊缝偏差 。 二是稳流仓 内安装的布料器 , 由于 原材料 中杂物较多 , 将布料器下料 口部分堵住 , 加剧 了离析现象。 针对 以上两种情况 , 采取 的改进措施分别为 : 一 将“ v选 ” 的进 料 口处用厚度 2 0 m m耐磨钢板三等分 , 保证 进入 “ v选” 物料均匀分 布, 减小离析现象 。 二是将稳 流仓 内的布料器拆除 , 仓顶中心向仓内 焊接 q b 8 0 0 x l 5 0 0 m m的卷制圆筒进一步减小物料离析 ,并加强进厂 原材料杂物清理工作, 减小物料离析现象。 经上 述改 造后 实 现辊 压机 台时 2 0 0 t / h ,工 作辊 缝 左 、右侧 4 3 m m、 4 7 m m, 动辊 、 定辊电流 6 7 A、 7 1 A 。 2 . 2生料细度指标 中 O . 2 m m筛余合格率低 我单 位出磨生料细 度指标为 0 . 0 8 m m方孔筛余 1 4  ̄ 2 %、 0 . 2 a r m 方孔筛余> 1 . 5 % 。辊压机喂料 2 0 0 t / h时 , 选粉机频率 1 8 2 2 H z , 无论 是怎么调整都难满足以上两个指标的同时合格。 和辊压机厂家技术 图 1 生料辊 压机 终粉 磨 系统 工 艺流程 人员探讨后 , 制定如下改造方案 : 从配料站来 的混合料 由胶带输送 机( 0 1 ) 送至生料粉磨车间 , 胶 2 . 2 . 1去掉进 风 口处弧形导风板 ,将进风 口均匀将风 口分为 9 带输送机上悬挂除铁器( 0 2 ) , 将物料中混入的铁件 除去 ; 同时该皮带 格 , 用 以对 风进 行 整 流 。 上装有金属探测器 ( 0 3 ) , 发现有金属后气动三通 阀( 0 4 ) 换向 , 将混有 2 . 2 . 2在涡壳进风侧的涡壳壁上, 加装两块迎风导风板 。 金属的物料由旁路卸出, 以保证辊压机的安全运行。不含金属的物 2 . 2 . 3在 出风侧壳体下部 , 转子端面加一 L型倒扣的导风板 , 减 料 由气动三通经 锁风阀( 0 5 ) 喂人 V型选粉机( 0 6 ) , 在 v型选粉机 中 少密封环受 冲刷的几率。 预烘干届 通过提升机( O 7 ) 提升进人稳流仓 ( O 8 ) , 该稳 流仓设有荷重 2 . 2 . 4将转子端面的工艺孔进行堵焊 , 评见下图
生料辊压机终粉磨系统提产改造
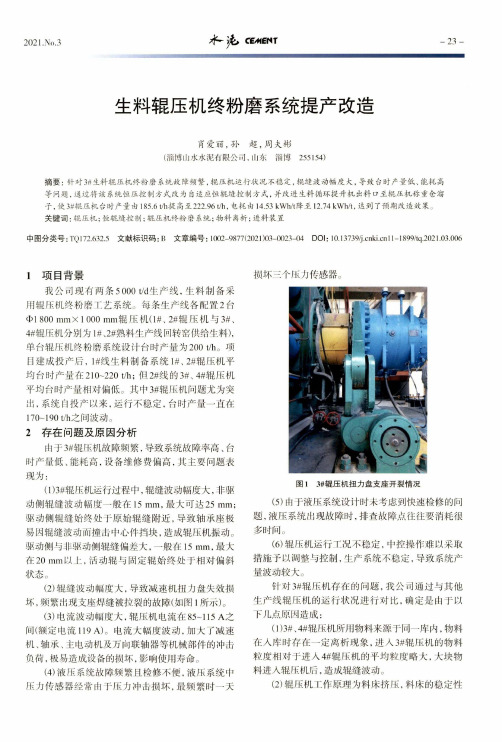
2021.N 〇.3♦务 CE/HENT-23-1敏翻生料辊压机终粉磨系统提产改造肖爱丽,孙超,周夫彬(淄博山水水泥有限公司,山东淄博255154)摘要:针对3#生料辊压机终粉磨系统故障频繁,辊压机运行状况不稳定,辊缝波动幅度大,导致台时产量低、能耗高 等问题,通过将该系统恒压控制方式改为自适应恒辊缝控制方式,并改进生料循环提升机出料口至辊压机称重仓溜 子,使3#辊压机台时产量由185.6 t/h 提高至222.96 t /h ,电耗由14.53 kWh/t 降至12.74 kWh /t ,达到了预期改造效果。
关键词:辊压机;恒辊缝控制;辊压机终粉磨系统;物料离析;进料装置中图分类号:T Q ) 172.632.5 文献标识码:B 文章编号:1002-9877(2021)03-0023-04 DOI : 10.13739/j l l -1899/tq .2021.03.0061项目背景我公司现有两条5000 t /d 生产线,生料制备采 用辊压机终粉磨工艺系统。
每条生产线各配置2台 01 800 mm X 1 000 mm 辊压机(1#、2#辊压机与 3#、 4#辊压机分别为1#、2#熟料生产线回转窑供给生料), 单台辊压机终粉磨系统设计台时产量为200 t /h 。
项 目建成投产后,1#线生料制备系统1#、2#辊压机平 均台时产量在210~220 t /h ;但2#线的3#、4#辊压机 平均台时产量相对偏低。
其中3#辊压机问题尤为突 出,系统自投产以来,运行不稳定,台时产量一直在 170〜190 t /h 之间波动。
2存在问题及原因分析由于3#辊压机故障频繁,导致系统故障率高、台 时产量低、能耗高,设备维修费偏高,其主要问题表 现为:(1)3#辊压机运行过程中,辊缝波动幅度大,非驱动侧辊缝波动幅度一般在15 mm ,最大可达25 mm ; 驱动侧辊缝始终处于原始辊缝附近,导致轴承座极 易因辊缝波动而撞击中心件挡块,造成辊压机振动。
生料辊压机终粉磨系统的提产措施

生料辊压机终粉磨系统的提产措施我公司生料粉磨采用的是CLF200-160辊压机终粉磨系统,于2014年10月1日投产,试生产初期台时产量一直徘徊在400t/h左右,辊压机运行不稳定,称重仓塌料频繁,辊压机因辊缝偏差超设定值频繁跳停。
通过调整技术参数,实地摸索数据,总结出了几种影响生料辊压机效率的因素,改造后取得了较好的效果。
1 主机设备参数及配料情况辊压机型号CLF200-160,主电动机功率2000kW,循环风机功率2000kW、处理风量800000m3/h、全压7000Pa,称重仓容量为35t,辊压机通过能力1400~1800t/h,料饼厚度40~60mm,设计台时产量420t/h。
我公司采用的是四组分配料,石灰石∶黏土∶砂岩∶硫酸渣=84∶7∶5∶4,其中砂岩采用的是硬质砂岩,结晶硅含量高,一般在90%以上,易磨性较差,物料水分除石灰石外一般都在10%以上。
生料粉磨系统工艺流程见图1。
2 导致辊压机台时产量低的原因通过对系统运行参数的观察研究,我们认为导致生料辊压机台时产量低的原因:1)V型选粉机打散效果不好,导致选粉效率仅55%左右,一直偏低;2)V型选粉机阻力大,出口负压比正常值高了400Pa左右,导致细粉不能被充分分离;图1 生料粉磨系统工艺流程3)称重仓下料不稳,频繁塌料,造成辊压机辊缝偏差大,最大偏差在20mm左右,压力波动大,两边最大相差5MPa,影响挤压效果,甚至导致辊压机频繁跳停;4)循环风机进口风门阀板增大系统阻力。
根据以上几点原因,我公司采取了相应的措施。
3 技改措施1)根据现场物料分布情况,发现入V型选粉机料饼提升机下料口出现物料分布不均,导致入V型选粉机出现偏料现象,造成物料进入V型选粉机后分散不开,选粉效果不好。
我们根据下料口尺寸和物料偏离情况,把下料管中间加两块隔板,将物料分成三部分下料,这样使物料均匀进入V型选粉机,起到间接打散的作用。
2)考虑到V型选粉机可调导风叶片已经可以起到导风打散作用,原有固定导风板与可调导风板过于密集,影响通风,直接增大了阻力,因此把右侧(见图2)调节叶片从下往上去掉5块,左侧导流板由下往上去掉2块,这样在不影响导风及打散的情况下在很大程度上减小了V 型选粉机阻力,使其选粉效果大大提高。
Φ1.8m×1.4m生料辊压机终粉磨系统的应用
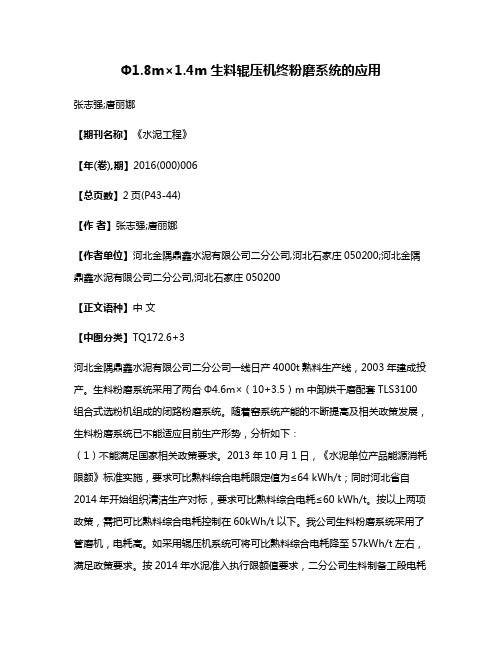
Φ1.8m×1.4m生料辊压机终粉磨系统的应用张志强;唐丽娜【期刊名称】《水泥工程》【年(卷),期】2016(000)006【总页数】2页(P43-44)【作者】张志强;唐丽娜【作者单位】河北金隅鼎鑫水泥有限公司二分公司,河北石家庄050200;河北金隅鼎鑫水泥有限公司二分公司,河北石家庄050200【正文语种】中文【中图分类】TQ172.6+3河北金隅鼎鑫水泥有限公司二分公司一线日产4000t熟料生产线,2003年建成投产。
生料粉磨系统采用了两台Φ4.6m×(10+3.5)m中卸烘干磨配套TLS3100组合式选粉机组成的闭路粉磨系统。
随着窑系统产能的不断提高及相关政策发展,生料粉磨系统已不能适应目前生产形势,分析如下:(1)不能满足国家相关政策要求。
2013年10月1日,《水泥单位产品能源消耗限额》标准实施,要求可比熟料综合电耗限定值为≤64 kWh/t;同时河北省自2014年开始组织清洁生产对标,要求可比熟料综合电耗≤60 kWh/t。
按以上两项政策,需把可比熟料综合电耗控制在60kWh/t以下。
我公司生料粉磨系统采用了管磨机,电耗高。
如采用辊压机系统可将可比熟料综合电耗降至57kWh/t左右,满足政策要求。
按2014年水泥准入执行限额值要求,二分公司生料制备工段电耗超出限额5.06kWh/t。
而采用辊压机系统可将生料工序电耗降至21kWh/t以下,满足要求(22 kWh/t)。
同时可以合理利用峰谷电价,进一步降低生产成本,提高企业竞争力。
(2)经过十多年的使用,现有球磨设备老化,存在一定隐患,为了维持运转每年需要增加大量投资。
(3)“十二五”期间要求完成节标煤11.08万t。
没有节能技改项目支撑,难以完成。
通过借鉴改造经验,结合对山东几家水泥公司生料辊压机终粉磨系统应用的实地考察,决定对我公司生料粉磨系统进行改造。
通过对比选择,我公司最终采用天津院设计、中材装备制造的RP180-140型辊压机配套立式动态选粉机组成的生料辊压机终粉磨系统,具体设备型号及参数见表1,工艺流程见图1。
浅谈辊压机生料终粉磨的操作

浅谈辊压机生料终粉磨的操作发布时间:2022-07-13T07:35:03.629Z 来源:《福光技术》2022年15期作者:杨吉鹏[导读] 生料制备工艺主要有管磨、立磨、辊压机终粉磨等粉磨系统,其中辊压机终粉磨与其他粉磨系统相比,粉磨电耗最低、节电效果显著。
新疆圣雄能源股份有限公司水泥厂新疆吐鲁番 838100 摘要:生料制备工艺主要有管磨、立磨、辊压机终粉磨等粉磨系统,其中辊压机终粉磨与其他粉磨系统相比,粉磨电耗最低、节电效果显著。
关键词:生料磨;辊压机终粉磨;窑磨一体运行;脱硫随着新型干法水泥生产技术的不断创新及新设备、新工艺的不断应用,现阶段推出的生料辊压机终粉磨工艺比立磨粉磨系统更节电(辊压机终粉磨电耗11~13kWh/t、立磨吨生料粉磨电耗一般18kWh/t左右)。
某公司5000t/d干法熟料生产线生料制备,首次采用辊压机终粉磨工艺,自2010年4月份投产运行以来,节电效果显著。
1 生产工艺流程及主要设备粉磨系统利用预热器的废气作为生料的烘干热源,按照质量控制要求配好的原料混合料由带式输送机送至生料粉磨车间,带式输送机上挂有除铁器,将物料中混入的铁件除去;同时在该皮带上装有金属探测器,发现有金属后气动三通阀换向,将混有金属的物料由旁路卸出,以保证辊压机的安全正常运行。
不含金属的物料由气动三通阀喂入V型选粉机内,在V型选粉机中预烘干和初选,大块物料经斗提送入稳流仓再入辊压机内进行挤压,小块物料随气流进入XR型选粉机再次分选,粗料通过帘式锁风阀卸出至稳流仓后继续回到辊压机进行二次挤压,细粉随热风进入旋风分离器,收集下来后经空气输送斜槽和斗式提升式机送入生料均化库。
通过辊压机的物料被挤压后经斗式提升机送入V型选粉机进行循环。
出旋风分离器的废气经窑尾袋收尘器净化处理后,经排风机排入大气。
增湿塔和袋收尘器收集的窑灰直接送往生料入窑系统或生料均化库。
当辊压机停止运行时,窑尾高温废气由增湿塔增湿降温后,直接进入袋收尘器,由增湿塔、袋收尘器收集下来的窑灰直接送往生料入窑系统或生料均化库。
- 1、下载文档前请自行甄别文档内容的完整性,平台不提供额外的编辑、内容补充、找答案等附加服务。
- 2、"仅部分预览"的文档,不可在线预览部分如存在完整性等问题,可反馈申请退款(可完整预览的文档不适用该条件!)。
- 3、如文档侵犯您的权益,请联系客服反馈,我们会尽快为您处理(人工客服工作时间:9:00-18:30)。
辊压机终粉磨系统在生料制备中的应用
发表时间:2019-12-17T09:10:48.577Z 来源:《基层建设》2019年第26期作者:文有强[导读] 摘要:随着阶梯电价普查的日趋严格,对于能耗较高的水泥生产企业面临着严峻的生存压力,节能改造成为近年来水泥企业的热门话题。
中建材(合肥)粉体科技装备有限公司安徽合肥 230051摘要:随着阶梯电价普查的日趋严格,对于能耗较高的水泥生产企业面临着严峻的生存压力,节能改造成为近年来水泥企业的热门话题。
由于中卸烘干磨对烘干热源有较高要求,正常生产时与余热发电系统发生抢风现象,影响余热发电能力,导致产品成本偏高。
为了有效节能降耗、降低成本,对生料制备系统进行技术改造,选择辊压机终粉磨技术。
辊压机进行生料终粉磨是先进的生产工艺,其利用粒间
高压料床粉碎原理,高效节能,从而提高粉磨系统的粉磨效率,达到节能降耗的目的。
关键词:生料制备;辊压机终粉磨系统;中卸烘干磨系统辊压机属于新型水泥节能粉磨设备,除了能够有效节能外,还能降低噪声污染,在现代水泥生产工艺中发挥着举足轻重的作用。
以往辊压机主要用于水泥粉磨系统,包括水泥挤压混合粉磨、水泥联合粉磨、水泥半终粉磨等多种形式。
辊压机生料终粉磨系统近几年才发展起来,已经体现出其优势,对水泥生产企业节能和降低成本的效果显著。
与立磨相比,电耗低是最大优势。
某公司现有一条4000t/d熟料生产线,原料粉磨系统采用两套传统的中卸烘干磨粉磨工艺。
由于原料粉磨系统设备陈旧,工艺相对落后,生料粉磨电耗高(两套生料粉磨系统平均电耗~24 kwh/t)、生产维护费用高等问题,公司考虑新增两套辊压机终粉磨系统对现有生料粉磨系统进行技改。
一、生料粉磨的基本特点生料粉磨是水泥生产过程的一个重要环节,与水泥粉磨相比,具有自身的特点和要求,主要体现在处理的原料特性和产品要求方面,因此采用的系统技术要求也存在较大差别。
生料配料主要包括钙质原料、硅质原料、铁质原料等,这些原料的易磨性、磨蚀性、含水量等差别很大,即使同一类原料波动范围也很宽,必须经过测试生料的邦德功指数试验才能确定合理的系统配置和技术指标,否则只能基于假设的“中等性能”确定初步方案。
二、辊压机作终粉磨工艺改造方案
1、改造前的两套生料粉磨系统的主要配置如下:表2-1 原料粉磨系统主机设备一览表
2、采用的技改方案目前先进的生料粉磨系统主要有两种,一种是采用立式磨系统,另一种是辊压机终粉磨系统。
立式磨对原料水分的适应能力更强,缺点是系统热风用量大,电耗偏高;而辊压机终粉磨系统是更加节能的生料粉磨方案,同样情况下,比立磨系统电耗低约2-3kWh/t、热风用量也略少于立磨系统,缺点是当原料水分过高造成物料很黏时,其适应能力不足。
因本项目所用原料综合水分可控,且没有很黏的物料,气候条件适用,为避免与已投用余热发电系统争夺热风的现象,经确定采用两套更加节能的辊压机终粉磨系统代替现有的两套生料球磨机系统。
3、生产工艺流程简述在原有生料磨两侧空地上,新增二套HFCG160-120 辊压机+V4000 型气流分级机与原有球磨机系统中现有的风路、选粉、废气处理等系统组合,形成新的辊压机终粉磨系统。
工艺流程阐述:来自原料配料库的混合原料(石灰石、硅石、铁矿粉等)通过皮带机输送至辊压机车间气流分级机进料口,新鲜物料汇同辊压机挤压后的物料送入新增的气流分级机内。
物料经过气流分级机的分选,粗粉通过皮带机和提升机返回辊压机稳流称重仓,细粉(半成品)被风带入原有组合式高效选粉机内,选出的粗粉也回到辊压机称重仓,细粉即为成品再由空气输送斜槽、提升机等送入生料均化库内。
窑尾热风仍作为整个系统的主要烘干热源,重新安装风管后将热风直接引入新增的气流分级机内,与循环风、自然风一起通过料幕,将物料中的细粉带出进入到原组合式选粉机内,通过选粉机分离后的含尘风部分返回到气流分级机内,其余气体进入窑尾收尘器。
整个风路系统仍由原组合式选粉机后的循环风机完成,在入V 型气流分级机的热风管、循环风管及冷风管上均设有电动风阀。
在上述系统中,在入辊压机系统的物料皮带及V 型气流分级机粗料返回皮带机上均设有自动除铁器,以去除原料及系统中的铁,有效保护辊压机。
工艺流程图如下:
三、项目评价及使用注意事项
在项目部成员的共同努力下,生料辊压磨顺利完成安装和空车调试,在原生料磨停产后,仅用短时间就把生料辊压机终粉磨系统带料调试正常,实现达产达标。
本项目改造完成后,维持原有产能不变的情况下,年产生料约125万吨,较改造前年节约用电量1000×104kWh。
技改后的生料细度降低,生料颗粒均齐,很好的改善了熟料的易烧性和易磨性,降低熟料煤耗,提高熟料强度,水泥混合材掺加量会进一步提高,提升了水泥磨台时产量,有效降低综合生产成本,提升市场竞争力。
生料供应充足,可以实现回转窑高效满负荷运转,每年可以多生产优质熟料,避免以往因生料磨能力不足导致的运转效率低的不利局面。
使用中的注意事项:①确保输送系统除铁器安装到位,进入生料终粉磨系统按比例配好的混合料不含金属杂物。
②各润滑点按照规定加油,润滑正常。
③保证液压系统正常,辊压机滚缝偏差过大会导致辊压机损严重和轴承损坏,同时系统会保护性跳停。
④加厚下料溜子的耐磨层,否则使用中极易磨穿漏料。
⑤严格控制入辊压机缓冲仓仓位,避免“塌料”等不良情况对系统运行的影响。
⑥岗位和中控室结合,开机后争取五分钟内带料运行能有效节能降耗。
本项目建成,提高生料易烧性,为下游煅烧工序降低热耗,熟料产品强度提升做好铺垫;提供了多种设备组合生产运行模式,为系统稳定高效运转提供保障;工艺先进、高效能设备使用,节能改造后设备运行稳定可靠,大幅降低维修费,节能降耗效果显著。
参考文献:
[1]刘成,赵文新.立磨和辊压机作生料终粉磨技术比较[J].水泥,2013(1 1):6.
[2]贾华平.辊压机生料终粉磨运用之调研分析[J] 新世纪水泥导报,2012(2).。