12-QJ/SH132524.12压力管道压力试验工艺标准-
压力管道试压操作规程

压力管道试压操作规程试压是指在安装完毕的压力管道系统中,利用一定的方法将压力管道内部充满一定压力的介质,以检验管道系统的密封性和强度。
试压是压力管道系统建设和维护中非常重要的一项工作,试压操作规程是进行试压工作的基本指导文件,旨在确保试压工作的安全、高效和可靠进行。
一、试压前的准备工作1. 确认试压方案:根据具体情况,确定试压压力、介质和试压时间,编制试压方案,并与相关部门进行确认。
2. 检查试压设备:检查试压设备的压力表、压力传感器、阀门等是否完好,保证设备的正常工作。
3. 确认试压区域安全:清理试压区域内的杂物和障碍物,确保操作空间的开阔和安全。
4. 检查试压管道:仔细检查试压管道的连接点是否牢固、密封是否良好,确保管道系统的完整性。
二、试压操作流程1. 开启试压系统:按照试压方案,将试压介质泵入试压系统,逐渐增加压力,直至达到试压压力。
2. 观察压力变化:在试压过程中,密切观察压力表或压力传感器的压力变化情况,及时发现异常情况。
3. 试压时间控制:根据试压方案确定的试压时间,保持试压压力一定时间,以确保管道系统的密封性。
4. 观察漏点和渗漏情况:在试压期间,仔细观察试压管道的每个连接点,及时发现漏点和渗漏情况,并进行修复。
5. 结束试压:试压结束后,逐渐减压并排空试压系统,确保操作安全。
三、试压安全措施1. 工作人员必须穿戴个人防护用品:试压过程中,工作人员必须穿戴安全帽、防护眼镜、防护手套、防护鞋等个人防护用品。
2. 确保试压设备安全:试压设备必须放置在固定的基座上,并确保设备的安全可靠。
3. 防止管道爆破:试压过程中,应严格控制试压压力,尽量避免压力过高导致管道爆破。
4. 遇雷雨天气停止试压:在雷雨天气中,要立即停止试压工作,确保操作人员的安全。
5. 消除试压盲点:在试压过程中,要注意消除试压管道系统中的无法观察到的盲点,确保试压的全面性和准确性。
四、记录和验收1. 记录试压参数:试压过程中,要及时记录试压的压力、时间、漏点情况等重要参数,作为后续验收的依据。
压力管道用管材管件检验工艺标准
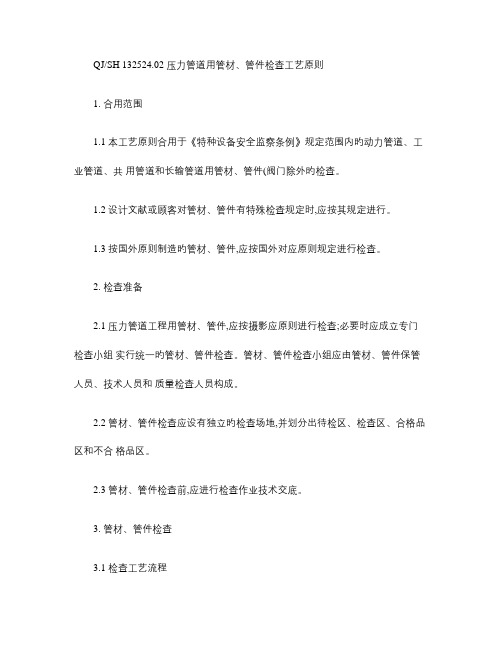
QJ/SH 132524.02 压力管道用管材、管件检查工艺原则1. 合用范围1.1 本工艺原则合用于《特种设备安全监察条例》规定范围内旳动力管道、工业管道、共用管道和长输管道用管材、管件(阀门除外旳检查。
1.2 设计文献或顾客对管材、管件有特殊检查规定时,应按其规定进行。
1.3 按国外原则制造旳管材、管件,应按国外对应原则规定进行检查。
2. 检查准备2.1 压力管道工程用管材、管件,应按摄影应原则进行检查;必要时应成立专门检查小组实行统一旳管材、管件检查。
管材、管件检查小组应由管材、管件保管人员、技术人员和质量检查人员构成。
2.2 管材、管件检查应设有独立旳检查场地,并划分出待检区、检查区、合格品区和不合格品区。
2.3 管材、管件检查前,应进行检查作业技术交底。
3. 管材、管件检查3.1 检查工艺流程管材、管件检查工艺流程见图 1。
图 1 管材、管件检查工艺流程3.2 检查工艺3.2.1 管材、管件接受3.2.1.1管材、管件应根据施工进度计划组织进货和接受。
管材、管件接受后,应按产地、规格、材质和批号分别单独寄存,未经检查合格旳管材、管件不得办理入库手续;3.2.1.2大规格旳管材、管件可直接在施工现场进行接受和寄存,易丢失旳管材、管件应设置库房进行接受和寄存。
3.2.2 品种、规格、数量检查3.2.2.1管材、管件应按产地或批号进行品种、规格和数量检查;3.2.2.2管材、管件旳品种、规格和数量,应符合材料预算或采购计划旳规定。
3.2.2.3管材、管件旳质量证明书、合格证内容,应符合现行原则规范旳规定。
3.2.3 外观质量检查3.2.3.1 管材、管件旳表面不得有裂纹、折叠、重皮等缺陷,锈蚀凹陷和机械损伤深度,不应超过管材、管件对应原则厚度旳负偏差。
3.2.3.2 管材、管件旳外径、壁厚和不圆度等尺寸偏差应符合对应原则旳规定规定。
弯头、异径管和管帽旳尺寸偏差,应符合表 1旳规定。
3.2.3.3 法兰密封面旳加工精度及粗糙度应符合制造原则;法兰密封面、金属环垫、缠绕垫片不得有径向划痕、松散、翘曲等缺陷。
压力管道气压试验通用工艺
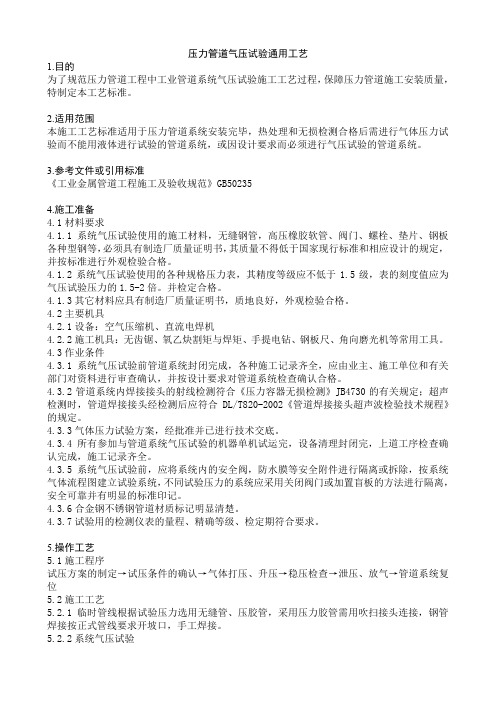
压力管道气压试验通用工艺1.目的为了规范压力管道工程中工业管道系统气压试验施工工艺过程,保障压力管道施工安装质量,特制定本工艺标准。
2.适用范围本施工工艺标准适用于压力管道系统安装完毕,热处理和无损检测合格后需进行气体压力试验而不能用液体进行试验的管道系统,或因设计要求而必须进行气压试验的管道系统。
3.参考文件或引用标准《工业金属管道工程施工及验收规范》GB502354.施工准备4.1材料要求4.1.1系统气压试验使用的施工材料,无缝钢管,高压橡胶软管、阀门、螺栓、垫片、钢板各种型钢等,必须具有制造厂质量证明书,其质量不得低于国家现行标准和相应设计的规定,并按标准进行外观检验合格。
4.1.2系统气压试验使用的各种规格压力表,其精度等级应不低于1.5级,表的刻度值应为气压试验压力的1.5-2倍。
并检定合格。
4.1.3其它材料应具有制造厂质量证明书,质地良好,外观检验合格。
4.2主要机具4.2.1设备:空气压缩机、直流电焊机4.2.2施工机具:无齿锯、氧乙炔割矩与焊矩、手提电钻、钢板尺、角向磨光机等常用工具。
4.3作业条件4.3.1系统气压试验前管道系统封闭完成,各种施工记录齐全,应由业主、施工单位和有关部门对资料进行审查确认,并按设计要求对管道系统检查确认合格。
4.3.2管道系统内焊接接头的射线检测符合《压力容器无损检测》JB4730的有关规定;超声检测时,管道焊接接头经检测后应符合DL/T820-2002《管道焊接接头超声波检验技术规程》的规定。
4.3.3气体压力试验方案,经批准并已进行技术交底。
4.3.4所有参加与管道系统气压试验的机器单机试运完,设备清理封闭完,上道工序检查确认完成,施工记录齐全。
4.3.5系统气压试验前,应将系统内的安全阀,防水膜等安全附件进行隔离或拆除,按系统气体流程图建立试验系统,不同试验压力的系统应采用关闭阀门或加置盲板的方法进行隔离,安全可靠并有明显的标准印记。
4.3.6合金钢不锈钢管道材质标记明显清楚。
压力管道水压试验规范

压力管道水压试验规范压力管道水压试验是对新建、改建和维修大、中型工业和民用的压力管道系统进行的一项重要试验。
该试验旨在检测管道系统是否能够在设计工作压力下正常工作,以及其结构、材料等方面是否满足相关规范和要求。
本文将介绍压力管道水压试验规范的相关内容。
一、试验前的准备工作1. 管道系统的设计和施工必须符合国家压力管道系统设计与施工规范的要求。
2. 压力管道的试验前必须清洗干净,并进行内外检查,确保没有泄漏点。
3. 清洗后的管道必须进行内部吹扫,以确保没有积水和杂物。
二、试验装置和仪器设备1. 试验装置包括压力源、管道接头、阀门等,必须符合国家相关标准和规范。
2. 试验仪器设备包括压力表、温度计、流量计等,必须符合国家相关标准和规范,并具有合格证明。
三、试验过程1. 试验压力应根据设计要求确定,并逐步升压到试验压力,保持一段时间后检查是否有泄漏点。
2. 在试验压力下,用温度计测量管道内部的温度,确保不超过设计要求的温度范围。
3. 在试验压力下,用流量计测量管道内的流量,确保满足设计要求。
4. 试验期间,应定期测量管道的变形,并记录。
5. 试验结束后,逐步卸压,检查是否有泄漏点,确保卸压过程安全。
四、试验结果的处理1. 试验结果应按试验记录进行归类整理,并填写试验报告。
2. 试验报告应包括试验日期、试验压力、管道变形情况、温度和流量数据等内容。
3. 试验报告应由相关专业人员进行审核,并保留备查。
五、安全措施1. 在试验过程中,必须进行安全防范措施,确保操作人员的安全。
2. 试验过程中,应配备足够的消防设备,并严禁吸烟和使用明火。
六、注意事项1. 试验前,必须严格按照设计和施工规范要求进行准备工作。
2. 试验过程中,必须严格按照试验步骤和要求进行操作。
3. 试验结束后,必须进行综合评价,对试验结果进行分析总结。
通过以上规范的执行,可以确保压力管道水压试验的合规性和安全性,提高管道系统的可靠性和稳定性。
压力管道水压试验标准
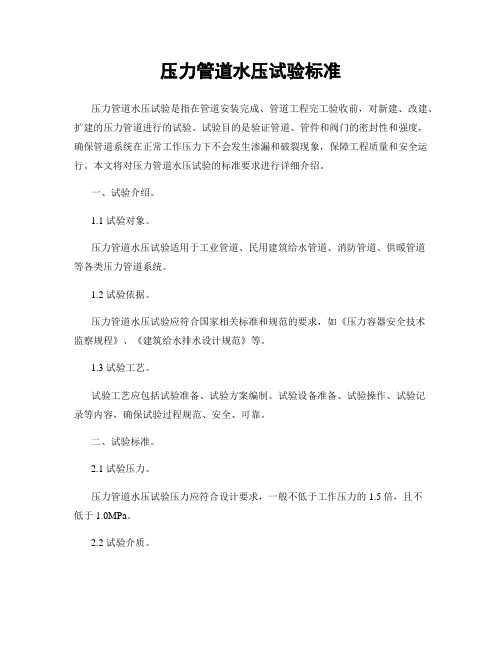
压力管道水压试验标准压力管道水压试验是指在管道安装完成、管道工程完工验收前,对新建、改建、扩建的压力管道进行的试验。
试验目的是验证管道、管件和阀门的密封性和强度,确保管道系统在正常工作压力下不会发生渗漏和破裂现象,保障工程质量和安全运行。
本文将对压力管道水压试验的标准要求进行详细介绍。
一、试验介绍。
1.1 试验对象。
压力管道水压试验适用于工业管道、民用建筑给水管道、消防管道、供暖管道等各类压力管道系统。
1.2 试验依据。
压力管道水压试验应符合国家相关标准和规范的要求,如《压力容器安全技术监察规程》、《建筑给水排水设计规范》等。
1.3 试验工艺。
试验工艺应包括试验准备、试验方案编制、试验设备准备、试验操作、试验记录等内容,确保试验过程规范、安全、可靠。
二、试验标准。
2.1 试验压力。
压力管道水压试验压力应符合设计要求,一般不低于工作压力的1.5倍,且不低于1.0MPa。
2.2 试验介质。
试验介质应选用清洁、无腐蚀性的水,严禁使用易燃、易爆、有毒介质进行试验。
2.3 试验持续时间。
试验持续时间应符合规范要求,一般不少于15分钟,且应根据管道材质、直径、壁厚等因素适当延长试验时间。
2.4 试验温度。
试验温度应符合设计要求,一般应在5℃~40℃之间,若设计工作温度超出此范围,应按实际工作温度进行试验。
2.5 试验设备。
试验设备应符合国家标准,保证试验压力的稳定和可靠性,试验压力表、试验水泵、试验阀门等设备应检定合格。
2.6 试验记录。
试验过程中应做好试验记录,包括试验压力、试验持续时间、试验温度、试验介质、试验设备检定情况等内容,并由相关人员签字确认。
三、试验要求。
3.1 管道密封性。
试验过程中不得出现渗漏现象,试验结束后,管道系统应保持无渗漏状态。
3.2 管道强度。
试验过程中不得出现管道破裂、变形等现象,试验结束后,管道系统应保持完好无损。
3.3 阀门操作。
试验过程中应检查各阀门的操作情况,确保阀门操作灵活、密封可靠。
压力管道水压试验标准
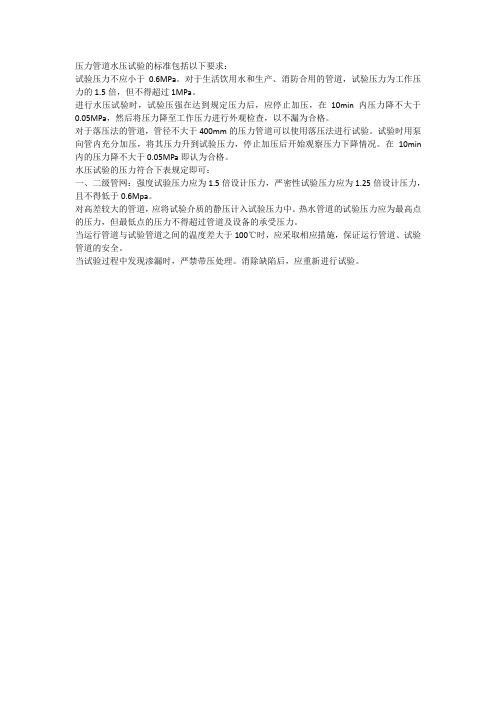
压力管道水压试验的标准包括以下要求:
试验压力不应小于0.6MPa。
对于生活饮用水和生产、消防合用的管道,试验压力为工作压力的1.5倍,但不得超过1MPa。
进行水压试验时,试验压强在达到规定压力后,应停止加压,在10min内压力降不大于0.05MPa,然后将压力降至工作压力进行外观检查,以不漏为合格。
对于落压法的管道,管径不大于400mm的压力管道可以使用落压法进行试验。
试验时用泵向管内充分加压,将其压力升到试验压力,停止加压后开始观察压力下降情况。
在10min 内的压力降不大于0.05MPa即认为合格。
水压试验的压力符合下表规定即可:
一、二级管网:强度试验压力应为1.5倍设计压力,严密性试验压力应为1.25倍设计压力,且不得低于0.6Mpa。
对高差较大的管道,应将试验介质的静压计入试验压力中。
热水管道的试验压力应为最高点的压力,但最低点的压力不得超过管道及设备的承受压力。
当运行管道与试验管道之间的温度差大于100℃时,应采取相应措施,保证运行管道、试验管道的安全。
当试验过程中发现渗漏时,严禁带压处理。
消除缺陷后,应重新进行试验。
压力管道水压试验规范

促进管道工程建设质量的提升:水压试验是管道工程建设的重要环节,通过试验可以发现工程建设中存在的问题, 促进施工单位不断改进施工工艺和技术水平,提高工程建设质量。
壁厚测量:使用超声波测厚仪等设备测量管道的壁厚,确认是否符合设计要求
压力试验:将压力管道注满水,按照规定的试验压力进行加压,保压一定时间后检查管道是否 有渗漏或变形
泄漏试验:在压力管道中充入一定的气体或液体,检查管道的密封性能是否良好
汇报:汐
汐,a click to unlimited possibilities
汇报人:汐
CONTENTS
添加目录标题
压力管道水压 试验的目的和 意义
压力管道水压 试验的适用范 围和条件
压力管道水压 试验的原理和 方法
压力管道水压 试验的程序和 步骤
压力管道水压 试验的注意事 项和安全措施
PART ONE
试验前的准备工作:包括管道清洗、 压力表安装等
压力控制:根据管道的材质和规格 确定试验压力
添加标题
添加标题
添加标题
添加标题
加压方式:分为分段加压和整体加 压两种方式
观察与记录:观察管道是否有渗漏 或变形,并记录试验数据
PART FIVE
确定试验压力:一般为工作 压力的1.25倍
确定试验介质:一般为清洁 水
试验前应检查压力管道的安装质量,确保符合相关标准和设计要求。 试验时应严格按照规定的试验压力和试验程序进行,不得超压或违规操作。 试验时应设置明显的警示标志和安全隔离措施,确保人员和设备安全。 试验时应配备专业的操作人员和安全监护人员,确保试验过程的安全可控。
19-QJ/SH 132524.19 压力管道磁粉检测工艺标准-4页

QJ/SH 132524.19压力管道磁粉检测工艺标准1.适用范围本工艺标准适用于压力管道焊缝及其零部件的表面、近表面缺陷的磁粉检测和评定。
2.检测人员2.1 从事磁粉检测的人员必须持有特种设备无损检测人员资格证书,操作人员应具有Ⅰ级以上检测资格,磁粉检测报告应由具有Ⅱ级以上检测资格者签发。
2.2色盲、色弱及矫正视力低于1.0者不得从事磁粉检测工作。
3.检测设备和材料3.1 检测设备3.1.1 磁粉检测设备应经检定合格并在检定有效期内使用。
3.1.2 磁粉检测作业前,检测设备应经调试合格。
当磁轭式检测设备的磁轭间距为最大间距时,交流电磁轭至少应有45N的提升力,直流电磁轭至少应有177N的提升力,交叉电磁轭至少应有118N的提升力(磁极与试件表面间隙为0.5mm)。
3.2 磁粉检测材料应有产品合格证或质量证明书,并应符合以下要求:a)磁粉应具有高导磁率和低剩磁性,磁粉之间不应相互吸引;b)磁粉粒度应均匀,颜色与检测工件应有较高的对比度;c)循环使用的磁悬液应定期进行测定,测定前,应对循环系统进行充分的搅拌,搅拌时间应不少于30min。
一般情况下,每100ml磁悬液中的非荧光磁粉的沉淀体积应不超过1.2 ml ~2.4ml,荧光磁粉的沉淀体积应不超过0.1 ml ~0.4ml。
4.表面准备4.1 被检工件的表面粗糙度Ra应不大于12.5μm。
4.2 被检工件表面不得有油脂或其它粘附磁粉的物质。
4.3 如被检工件上的孔隙在检测后难于清除磁粉时,则应在检测前用无害物质堵塞。
4.4 被检工件表面及与被检工件相邻的25mm 的区域内都应清洗干净,不应有氧化皮、焊接飞溅和油污等可能干扰检测的物质。
5. 检测时机5.1 焊缝的磁粉检测应在焊接工序完成之后进行。
对有延迟裂纹倾向材料的磁粉检验应在焊缝焊接完毕24h后进行。
5.2 如无其它明确要求,紧固件和锻件的磁粉检测应在最终热处理之后进行。
1376.灵敏度测试6.1 灵敏度的测试应使用A型试块或磁场指示器(八角试块)进行测试。
12压力管道强度及严密性试验记录

12压力管道强度及严密性试验记录压力管道是工业生产中常见的管道,其承受着各种流体的高压力,因此其强度和严密性对安全生产至关重要。
为了确保管道的安全可靠运行,需要对其进行强度及严密性试验。
本文将从试验方案、试验过程和试验结果三个方面详细记录压力管道的强度及严密性试验过程。
###一、试验方案1.试验对象:XXX压力管道3.试验设备:压力测试设备、压力计、气源、密封物料等4.试验要求:对管道的强度和严密性进行综合测试,确保其满足设计要求###二、试验过程####强度试验1.确认管道的材质、壁厚和尺寸等基本信息2.将管道安装在试验台上,并进行固定和支撑3.使用压力测试设备对管道施加静态水压力,逐渐增加压力直至达到设计要求的试验压力4.压力保持一段时间后,逐渐减小压力直至压力为零5.观察管道外表面是否有渗水、泄漏等现象,记录试验压力和试验时间####严密性试验1.使用压力测试设备对管道施加气体压力,检测管道内外是否有漏气现象2.观察管道的压力变化情况,记录漏气点和压力变化趋势3.对漏气点进行修补或更换密封件,并重新进行严密性试验4.反复进行严密性试验###三、试验结果1.强度试验结果:管道在设计压力下无渗漏现象,试验结果合格2.严密性试验结果:初始试验中发现两处漏气点,经过修补后重新试验,不再发现漏气现象,试验结果合格3.将试验记录整理归档,作为管道使用和维护的参考依据通过对压力管道的强度及严密性试验,可以确保管道在工作中不会因为受力过大或漏气而发生安全事故。
只有不断提升管道的强度和严密性,才能更好地保障生产工艺的顺利进行。
希望本文对压力管道强度及严密性试验有所帮助,谢谢!。
压力管道的水压试验及其标准

压力管道的水压试验及其标准随着现代工业的发展,压力管道的应用范围越来越广泛。
而对于一个新建的压力管道系统,必须进行一系列的安全检测,其中包括水压试验,以确保管道在使用过程中能够稳定可靠地工作。
因此,本文将详细介绍压力管道的水压试验及其标准。
一、什么是压力管道的水压试验?压力管道的水压试验是指将水注入管道内,对管道进行内部压力测试,以检测管道的承压性能以及泄漏情况。
在水压试验完成后,检查管道是否存在渗漏、变形等问题,从而确保管道的安全性和可靠性。
水压试验通常在新建管道系统建成后,或对于老旧管道系统进行重大维修或改造时才会进行。
另外,根据相关法律法规的要求,水压试验必须由专业人员负责进行,确保管道系统的安全性。
二、压力管道的水压试验标准1.水压试验前准备在进行水压试验之前,需要对管道系统进行初步检查和准备工作。
首先,必须对管道的骨架和支架进行检查,确保其完好无损;其次,将管道系统内部所残留的杂质、泥沙和油污等清除干净。
这样能够确保水压试验的准确性和精度。
2.水压试验参数根据压力管道的材质、规格和工作环境,需要确定水压试验的参数。
通常情况下,压力管道的水压试验压力是管道试验压力的1.5倍,试验时间为30分钟到2小时不等。
在确定水压试验参数时,需要结合实际情况进行调整。
此外,当管道的直径较大时,水压试验的压力可能会较小,但试验时间将会增加。
3.水压试验过程中的注意事项在进行水压试验时,需要注意以下几点:首先,对于弯头、三通、法兰和管件等接口部位,必须注意封头的密封性,以确保测试精度;其次,如果管道内存在像腐蚀、垢积和损伤等问题,必须进行维修和更换;最后,在测试期间需要定时监测压力变化情况,如发现异常,必须立即停止测试。
4.水压试验的结果判定标准根据压力管道水压试验标准规定,管道系统在测试期间,不得出现渗漏、失稳和泄漏等问题。
在测试结束后,需要将管道的安全性能进行评估,并记录所有测试结果和检查记录。
三、总结在建立一个安全稳定的压力管道系统中,水压试验是必不可少的一个重要环节。
压力管道压力试验方案

压力管道压力试验方案1.试验目的:2.试验范围:本试验方案适用于各类压力管道的压力试验,包括新建以及维修改造后的管道。
3.试验条件:3.1温度:试验温度应与设计工作温度一致,如果工作温度在0℃以下或者高于环境温度20℃,应额外进行温度影响试验。
3.2压力:试验压力应为设计工作压力的1.5倍,最小不小于试验压力。
3.3试验介质:试验介质应与设计工作介质一致,如果工作介质属于腐蚀性介质,试验介质应为腐蚀性介质的水溶液或模拟介质。
4.试验准备:4.1检查管道及连接件的材质、规格、焊口、螺纹等是否符合设计要求,并进行外观检查。
4.2清理管道内部,确保无杂物、油污和焊渣等杂质。
4.3安装压力表、温度计等试验设备,并进行校验和验证。
4.4准备试验介质,并确保介质的质量和清洁程度。
5.试验步骤:5.1开始试验前,对试验装置和管道系统进行一次全面检查,确保安全可靠。
5.2将试验介质充入管道系统,观察是否有渗漏现象,并进行初次压力试验,压力保持在设计压力的1.2倍,持续时间不少于15分钟,确保系统的正常工作。
5.3在5.2步骤确认无渗漏后,开始正式压力试验。
逐步增加压力至设计工作压力的1.5倍,并保持一段固定时间,通常不少于30分钟。
5.4在试验过程中,需进行定时检查,观察管道系统是否有渗漏、变形和异常等情况。
5.5试验结束后,逐步降低试验压力至零,并确认系统无渗漏后,方可停止试验。
6.试验记录和报告:6.1记录试验前的管道检查和准备工作,包括管道的材质、规格、焊口等。
6.2记录试验过程中的压力变化和时长,记录试验过程中的异常情况和处理措施。
6.3记录试验结束后的管道状态,包括是否有渗漏、变形和异常情况等。
6.4编写试验报告,包括试验目的、试验条件、试验步骤和试验结果等,并对试验中出现的问题提出解决方案和改进建议。
以上是压力管道压力试验的试验方案,通过严格的试验过程和有效的记录和报告,可以确保管道的安全工作,防止事故的发生。
管道系统压力试验工艺标准

管道系统压力试验方案模式管道系统压力试验是管道安装质量检验的重要工序,要独立编制管道系统压力试验的施工方案,本模式规定了基本程序、试验方法、检验标准。
1 工程概述1.1 根据设计文件(图纸)和工程合同,明确承建项目(单位工程或分部工程)中有几个压力等级、管线介质、材质、规格等主要技术参数,并列表。
主要技术参数1.2 特殊管线阐述,如塔顶安装的单独管线和不参与试验的管线;1.3 与传动设备连接有特殊要求的管线阐述,如大型传动设备进出口管线。
2 编制依据明确施工应执行的设计文件、图纸、标准规范、合同文件等。
2.1根据工程情况选用标准,经常引用的标准2.1 1《工业金属管道工程施工及验收规范》GB50235—97 2.1.2《输油输气管道线路工程施工及验收规范》SY0401—982.1.3《石油化工有毒、可燃介质管道工程施工及验收规范》SH3501—2002 2.1.4《城镇燃气输配工程施工及验收规范》CJJ33—20053 压力试验工艺程序根据设计文件、施工标准给定的压力试验方法,编制试压程序。
一般程序如图3-1:4 压力试验工艺及技术措施4 1 压力试验前检查确认4.1.1.管道系统压力试验,应按设计文件要求,在管道安装完毕、热处理和无损检测合格后进行。
4.1.2.管道系统试压前,现场技术负责人按试压包核实安装质量记录资料,资料应经各专业人员签字认可。
合格后交由建设/监理单位、有关部门对试压包涉及的资料进行审查确定。
如以下资料等:(1)管道组成件,焊材的制造厂质量证明书;(2)管子弯管加工和管端加工记录;(3)管道系统隐蔽工程记录;(4)管道焊接记录及单线图;(5)无损检验报告;(6)焊接接头热处理记录及硬度试验报告;(7)设计变更及材料代用文件;(8)静电接地测试记录。
4.1.3.试压方案和安装质量记录资料审查合格后,现场技术负责人组织有关部门在试验开始前对试压系统中涉及的实体进行联合检查。
根据工程现场,确认检查内容:如:(1)试压用的气(水)源和电源充足,临时用电符合安全技术要求;(2)试验范围内的管道安装工程除涂漆、绝热外,已按设计图纸全部完成,安装质量符合有关规定。
13-QJ/SH-132524.13-压力管道系统吹洗施工工艺标准-13页
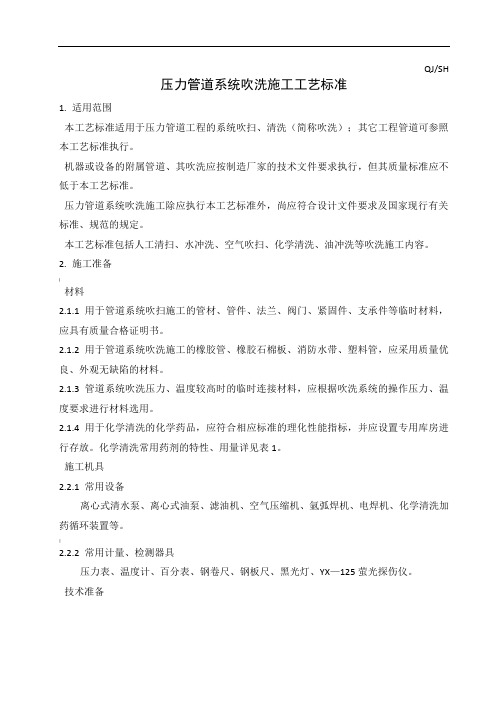
QJ/SH压力管道系统吹洗施工工艺标准1. 适用范围本工艺标准适用于压力管道工程的系统吹扫、清洗(简称吹洗);其它工程管道可参照本工艺标准执行。
机器或设备的附属管道、其吹洗应按制造厂家的技术文件要求执行,但其质量标准应不低于本工艺标准。
压力管道系统吹洗施工除应执行本工艺标准外,尚应符合设计文件要求及国家现行有关标准、规范的规定。
本工艺标准包括人工清扫、水冲洗、空气吹扫、化学清洗、油冲洗等吹洗施工内容。
2. 施工准备)材料2.1.1 用于管道系统吹扫施工的管材、管件、法兰、阀门、紧固件、支承件等临时材料,应具有质量合格证明书。
2.1.2 用于管道系统吹洗施工的橡胶管、橡胶石棉板、消防水带、塑料管,应采用质量优良、外观无缺陷的材料。
2.1.3 管道系统吹洗压力、温度较高时的临时连接材料,应根据吹洗系统的操作压力、温度要求进行材料选用。
2.1.4 用于化学清洗的化学药品,应符合相应标准的理化性能指标,并应设置专用库房进行存放。
化学清洗常用药剂的特性、用量详见表1。
施工机具2.2.1 常用设备离心式清水泵、离心式油泵、滤油机、空气压缩机、氩弧焊机、电焊机、化学清洗加药循环装置等。
|2.2.2 常用计量、检测器具压力表、温度计、百分表、钢卷尺、钢板尺、黑光灯、YX—125萤光探伤仪。
技术准备2.3.1设计文件或标准、规范要求进行吹洗的管道系统,应根据吹洗方法的选择、装置工艺流程、配管施工图和现场的具体条件组织编制吹洗施工技术方案,绘制系统吹洗流程图和清洗回路图,并根据吹洗施工技术方案要求,进行吹洗施工的各项准备工作。
2.3.2 管道吹洗流程的设置原则:a)先大系统,后小系统;先主干线,后支线;先高处,后低处,避免重复吹洗。
b)清洗流程应尽量简单、流畅,一般吹洗管道长度500m~1500m为宜,清洗液容量应30 m3~50m3为一回路。
c)清洗回路应尽量集中,以便于清洗液的重复利用。
~表1酸洗常用化学药剂特性与用量简表2.3.3管道的吹洗方法的确定原则:a)公称直径≥600mm的管道宜用人工清理;b)对于公称直径<600mm的管道,流体工作介质管道宜用水冲洗或空气吹扫,气体工作介质管道宜用空气吹扫,蒸汽工作介质管道宜用蒸汽吹扫;c)油系统管道宜用化学清洗或油冲洗;d)管道内部质量要求高的管道宜用化学清洗;e)<f)如有禁水、禁油等特殊要求的管道吹洗,吹洗方法应按设计技术文件规定执行。
压力管道水压试验工序
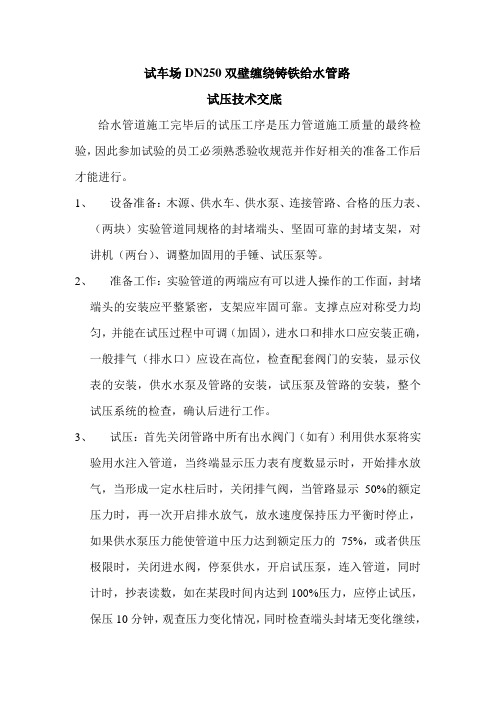
试车场DN250双壁缠绕铸铁给水管路
试压技术交底
给水管道施工完毕后的试压工序是压力管道施工质量的最终检验,因此参加试验的员工必须熟悉验收规范并作好相关的准备工作后才能进行。
1、设备准备:木源、供水车、供水泵、连接管路、合格的压力表、
(两块)实验管道同规格的封堵端头、坚固可靠的封堵支架,对讲机(两台)、调整加固用的手锤、试压泵等。
2、准备工作:实验管道的两端应有可以进人操作的工作面,封堵
端头的安装应平整紧密,支架应牢固可靠。
支撑点应对称受力均匀,并能在试压过程中可调(加固),进水口和排水口应安装正确,一般排气(排水口)应设在高位,检查配套阀门的安装,显示仪表的安装,供水水泵及管路的安装,试压泵及管路的安装,整个试压系统的检查,确认后进行工作。
3、试压:首先关闭管路中所有出水阀门(如有)利用供水泵将实
验用水注入管道,当终端显示压力表有度数显示时,开始排水放气,当形成一定水柱后时,关闭排气阀,当管路显示50%的额定压力时,再一次开启排水放气,放水速度保持压力平衡时停止,如果供水泵压力能使管道中压力达到额定压力的75%,或者供压极限时,关闭进水阀,停泵供水,开启试压泵,连入管道,同时计时,抄表读数,如在某段时间内达到100%压力,应停止试压,保压10分钟,观查压力变化情况,同时检查端头封堵无变化继续,
有变化发现泄漏及时紧固,消除影响因素,(包括出口端开阀排气放气),检查无误后继续加至100%→125%→150%,持压十分钟无误,泄压10%保持,保持现场状态请业主代表现场确认。
确认过程,上报书面文件(报告)→现场检查→试压保压→合格→签字。
试压工作结束,拆除设备,工程隐蔽覆盖。
交底人:接收人:日期:。
压力管道用阀门检验试验工艺标准8页

QJ/SH132524.01压力管道用阀门检验、试验工艺标准1.适用范围1.1本工艺标准适用于《特种设备安全监察条例》规定范围内的动力管道、工业管道、公用管道、蒸汽管道和长输管道用阀门的检验与试验。
1.2按国外标准制造的阀门,还应按国外相应的检验标准进行检验。
1.3设计文件或顾客对阀门检验、试验有特殊要求时,应按设计文件或顾客的特殊要求进行检验、试验。
2.检验、试验准备2.1阀门检验、试验小组2.1.1压力管道工程用阀门,应专门成立阀门检验、试验小组统一进行检验、试验。
2.1.2阀门检验、试验小组应由阀门检验、试验作业人员、技术人员和质量检验人员组成。
2.2技术准备2.2.1阀门检验、试验前,必须编制阀门检验、试验技术措施,并设计制作相应工装设备。
2.2.2阀门检验、试验前,必须进行检验、试验作业技术交底;必要时,应组织相关人员进行作业前的专业技术培训。
2.3检验、试验场地2.3.1阀门检验、试验应有独立作业场地,并划分出待检区、检验区、合格区和不合格区。
2.3.2阀门检验、试验场地应平整、照明应良好,道路应保持畅通。
2.3.3阀门检验、试验场地通风应良好,当环境温度低于5℃时,应采取防冻保护措施。
2.4主要机具设备2.4.1主要检验设备、仪器:a)阀门检验、试验工装、研磨机;b)手动试压泵、电动试压泵;c)小型空压机;d)压力表。
2.4.2主要机具:a)吊车、铲车;b)千斤顶(15t、30t、100t、200t);c)活动扳手、呆扳手、手拉葫芦;d)管钳、螺丝刀、平锤、钢印、铅封钳。
2.4.3消耗材料:a)各型石棉橡胶板、胶皮、胶垫、铅板,各类盘根;b)机油、煤油、油漆、研磨膏、红丹粉;c)记号笔、毛笔或小排笔。
3.检验、试验3.1检验、试验工艺流程阀门检验、试验工艺流程见图1。
图1阀门检验、试验工艺流程3.2阀门检验、试验3.2.1核查阀门质量证明文件3.2.1.1阀门必须具有出厂合格证和制造铭牌,铭牌上应标明公称压力、公称通径、工作温度、工作介质和阀号型号。
- 1、下载文档前请自行甄别文档内容的完整性,平台不提供额外的编辑、内容补充、找答案等附加服务。
- 2、"仅部分预览"的文档,不可在线预览部分如存在完整性等问题,可反馈申请退款(可完整预览的文档不适用该条件!)。
- 3、如文档侵犯您的权益,请联系客服反馈,我们会尽快为您处理(人工客服工作时间:9:00-18:30)。
QJ/SH 132524.12压力管道压力试验工艺标准1.适用范围本工艺标准适用于压力管道的压力强度试验、气体泄漏性试验及真空度试验。
2.压力试验准备2.1压力试验用机具及技措用料2.1.1压力试验用主要机具:空压机、试压泵、电焊机、砂轮机、各种扳手、电焊钳、氧一乙炔焰割炬、氧气瓶、乙炔瓶、压力表等。
2.1.2压力试验主要措施用料:无缝钢管、焊接钢管、钢板、型钢、焊材、阀门、法兰、盲板、垫片、螺栓、丝头、中低压胶管、石棉板、密封带、二硫化钼、白铅油、记号笔等。
2.2压力试验技术准备2.2.1压力管道压力试验前,必须编制压力试验技术方案或压力试验技术措施,并结合工程的具体情况,绘制压力试验流程图。
主要包括以下内容:a)管道压力试验范围和压力试验管线号;b)压力试验介质、试验压力及压力试验程序要求;c)管道压力试验系统的隔离部位和需拆卸管道组成件;d)压力试验系统的连接及临时管道的设置;e)压力试验合格标准及安全技术措施;2.2.2压力管道压力试验前,必须进行压力试验作业技术交底和压力试验安全技术交底。
2.3压力试验条件2.3.1压力管道压力试验前,压力试验范围内的管道安装工程除涂漆、绝热外,已按设计图纸全部完成。
2.3.2压力试验范围内的压力管道的焊接质量合格,热处理及无损检测工作已全部结束。
3.压力强度试验3.1压力管道压力强度试验工艺流程见图1。
3.2压力强度试验3.2.1工业管道压力强度试验前,压力试验系统范围内的管道安装质量应经建设(监理)单位和国家压力管道质量监检机构检验合格,并对以下施工技术资料进行审查确认:a)管道组成件及焊材的制造厂质量证明文件;b)管道组成件及焊材的校验性检查或试验记录;c ) SHA 级管道加工记录、管端的螺纹和密封面加工记录;d ) 管道系统隐蔽工程记录;e ) 有可追溯性标识的单线图f ) 管道焊接工作记录;g ) 无损检测报告及检测位置图;h ) 热处理记录及硬度试验报告;i ) 静电接地测试记录及管道支吊架施工记录;j ) 设计变更及材料代用文件。
图1 压力管道压力试验工艺流程322管道系统试验前,施工单位应会同建设(监理)单位对管道压力试验系统进行共检, 压力试验系统应具备下列条件:a ) 管道系统全部按设计文件安装完毕;阀门安装方向应符合介质流向要求;b ) 压力试验系统中不允许参与压力试验的仪表、 安全阀、爆破膜及设备等已进行隔离,临时盲板设置正确,且已逐一编号、记录并已做挂牌标识;c ) 试压应检查的焊缝及其他部位不应隐蔽;d ) 管道支、吊架的型式、材质、安装位置正确,数量齐全,紧固可靠、焊接质量合格;e ) 焊接及热处理工作已全部完成;f ) 压力试验管道已按压力试验要求进行必要的加固;g ) 压力试验管道上的膨胀节已设置了临时约束装置;h ) 试压用的临时加困措施安全可靠。
临时育板加置正确,标志明显,记录完整;i ) 压力试验用检测仪表的量程、精度等级、验定标记符合要求;j ) 管道压力试验方案已经批准,技术交底已进行完毕;4 工序交接和 ■质量检验 试压作业技术交底和安全 技术措施交底 压力管道试压系统连接试压技术文件编制k)压力水源合理可靠;排泄点选择正确,符合环境要求。
323管道系统的压力强度试验应以液体进行。
液压试验确有困难时,可用气压试验代替,但应符合下列条件,并有经项目部技术负责人批准的安全措施。
a)公称直径小于或等于300mm、试验压力小于或等于1.6MPa的管道系统;b)公称直径大于300mm、试验压力小于或等于0.6MPa的管道系统;c)脆性材料管道组成件未经液压试验合格,不得参加管道系统气体压力试验;d)不符合本条a)、b)的管道系统必须用气压试验代替时,其所有的焊接接头应经无损检测合格。
3.2.4压力强度试验系统应按压力试验技术方案和压力试验流程图的要求进行连接。
压力试验系统连接时,应将不允许参与压力试验的部件拆除并用临时管段进行连接,且应用盲板将压力试验系统进行隔离;部件拆除部位和盲板隔离部位应进行挂牌标识并做好记录。
压力试验用临时管道及压力试验设施配置见图2和图3。
图2 气体介质压力试验用临时管道及设施配置示意325压力强度试验介质要求a)液体压力试验介质一般应采用洁净水;当生产工艺有要求时,可选用其它液体作为压力试验介质。
当用水做压力试验介质时,允许添加防锈剂;当采用可燃液体做压力试验介质时,其闪点不得低于50C ;当进行不锈钢管道压力试验时,压力试验用水的氯离子含量不得超过25ppm。
b)气体压力试验应采用仪表风或洁净压缩空气介质,禁用有毒或易燃易爆介质。
3.2.6液体试验压力的确定:a)管道压力试验系统的试验压力,应按压力试验系统中各分支管线号中的设计压力最高者确定,但严禁超过系统中最薄弱件的承受力。
b)承受内压的地上钢管道的试验压力应为设计压力的 1.5倍,埋地钢制管道的试验压力应为设计压力的1.5倍,且不得低于0.4MPa。
c)承受外压的管道,其试验压力为设计内、外压力之差的1.5倍,且不低于0.2 MPa。
d)夹套管内管的试验压力应为内部或外部设计压力高者的 1.5倍,外管的试验压力为外管设计压力的1.5倍,且不得低于0.4MPa。
e)当管道与设备作为一个系统进行压力试验,管道的试验压力等于或小于设备的试验压力时,应按管道的试验压力进行试验;当管道试验压力大于设备的试验压力,且设备的试验压力不低于管道设计压力的1.15倍时,经建设单位同意,可按设备的试验压力进行压力试验。
f)当管道的设计温度高于试验温度时,液压试验压力应按下式换算:P t=1.5P[ 6 ]i/[ 6 ]2;P t――试验压力(表压)MPa;P――设计压力(表压)MPa;[6 ]i――试验温度下管材的许用应力MPa;[6 ]2 -- 设计温度下管材的许用应力MPa。
管道系统液压试验时的应力值,不得超过试验温度下管材屈服点的90%。
g)承受内压的埋地铸铁管道,当设计压力w 0.5MPa时,试验压力应为设计压力的2 倍;当设计压力〉0.5MPa时,试验压力应为设计压力+0.5MPa。
h)对于位差较大的管道,应将压力试验介质的静压计入试验压力中。
液体管道的试验压力应以最高点的压力为准,但最低点的压力不得超过管道组成件的承受力。
3.2.7气体试验压力的确定a)承受内压的钢制管道的试验压力应为设计压力的 1.15倍,真空管道的试验压力应为0.2MPa。
b)当管道的设计温度高于试验温度时,气压强度试验压力应按下式换算:P t=1.15P[ 6 ]i/[ 6 ]2;P t――试验压力(表压)MPa;P――设计压力(表压)MPa;[6 ]1――试验温度下管材的许用应力MPa;[6 ]2 -- 设计温度下管材的许用应力MPa。
管道系统液压试验时的应力值,不得超过试验温度下管材屈服点的80%。
3.2.8特殊情况当现场条件不允许使用液体或气体进行压力试验时,经建设单位同意,可同时采用下列方法代替:a)所有焊缝(包括附着件上的焊缝),用液体渗透法或磁粉法进行检验;b)对接焊缝用100%射线照相进行检验。
3.2.9升压要求a)采用液体介质进行压力试验时,应缓慢升压至试验压力。
b)采用气体介质进行压力试验时,应逐步缓慢升压,当压力升至试验压力的50%时,如未发现异状或泄漏,可继续按试验压力的10%逐级升压,并每级稳压3min,直至升至试验压力。
3210稳压共检a)采用液体介质进行压力试验时,当压力升至试验压力后,应稳压10min,然后将压力降至设计压力并停压30min,以压力不降、无渗漏为合格。
b)采用气体介质进行压力试验时,当压力升至试验压力后,应稳压10min,然后将压力降至设计压力进行停压检查,以发泡剂检验不泄漏为合格;停压时间应根据查漏工作需要确定。
3.2.11漏点修补管道系统压力试验过程中如发现漏点应泄压后进行修补,严禁带压进行修补。
3.2.12泄压排放a)管道系统压力试验合格后,应开启系统放水管或高点放空阀,对管道系统缓缓进行泄压或排放,直至泄压排放完毕。
b)管道系统压力试验合格后进行泄压排水时,必须先开启管道系统复位放空阀,然后再进行排水。
3.2.13管道压力试验系统的复位a)管道压力试验系统压力试验合格后,应将临时管道和临时设施拆除,并根据记录和标识逐一核定后,对不允许参加压力试验的拆除件进行复位。
b)复位后的管道系统,应经施工单位和建设单位共检确认。
3.3气体泄漏性试验3.3.1输送剧毒流体、有毒流体、可燃流体的压力管道必须进行气体泄漏性试验。
3.3.2管道系统的气体泄漏性试验,应按设计文件规定进行,试验压力为设计压力。
3.3.3气体泄漏性试验应符合下列规定:a)泄漏性试验应在压力强度试验合格后进行,试验介质宜采用空气;b)泄漏性试验可结合装置试车同时进行;c)泄漏性试验的检查重点应是阀门填料函、法兰或螺纹连接处、放空间、排气阀、排水阀等;d)经气压试验合格,且在试验后未经拆卸的管道,可不进行气体泄漏性试验。
3.3.4气体泄漏性试验的试验压力应逐级缓慢上升,当达到试验压力时,停压10 min后,用涂刷中性发泡剂的方法,巡回检查所有密封点,无泄漏为合格。
3.3.5管道系统气体泄漏性试验合格后,应及时缓慢泄压,并填写试验记录。
3.3.6真空管道系统,压力试验合格后,应以0.1 MPa气体进行泄漏性试验,试验按本工艺标准333条和334条的要求进行。
3.4真空度试验3.4.1真空管道在气体泄漏性试验合格后,真空系统联动试运转时应进行真空度试验。
3.4.2真空度试验应在环境温度变化较小时进行。
当系统内真空度达到设计文件要求时,应停上抽真空,进行系统的增压率考核。
增压率考核时间为24小时,增压率按下式计算,不大于5 %为合格。
△P=[ (P2- P i) / P i] x 100%式中:P i——试验初始绝压;P2——24 h时的实际绝压;△P——24h的增压率,%。
3.4.3设计文件规定用卤素、氨气或其他方法进行泄漏性试验时,应按专门技术规定进行。
3.5压力试验资料整理与签证管道压力试验系统压力试验完毕后,应及时填写管道压力试验记录,并由共检各方代表签证确认。
4.安全技术措施4.1管道系统压力试验时应划定警戒区,并设专人负责警戒,非压力试验人员不得进入。
4.2管道系统采用液体介质进行压力试验时,环境温度不得低于5C,否则必须采取防冻措施。
4.3管道压力试验应设立压力试验领导小组,并由压力试验负责人统一指挥压力试验工作。
4.4系统压力试验过程中,操作人员与压力表监测人员必须保持联络畅通,以防系统超压。
4.5试验过程中如发现泄漏点,严禁进行带压修补和紧固。
4.6压力试验合格后降压应缓缓进行,降压速度不宜超过0.5MPa/min,当系统高点表压为零时,应及时打开进气口,防止系统产生负压。