正庚烷和正辛烷体系精馏浮阀塔设计
正己烷-正庚烷分离过程筛板精馏塔课程设计

课程设计说明书题目: 分离正戊烷-正己烷用筛板精馏塔设计院系:机械工程学院专业班级:过控11-1学号: 2011301936学生姓名:冒鹏飞指导教师:李雪斌2013 年 12 月30 日目录第一部分 概述 (4)一、设计目标 (4)二、设计任务 (4)三、设计条件 (4)四、设计内容 (4)五、工艺流程图 (4)第二部分 工艺设计计算 (6)一、设计方案的确定 (6)二、精馏塔的物料衡算 (6)1.原料液及塔顶、塔底产品的摩尔分数 (6)2.原料液及塔顶、塔底产品的平均摩尔质量和质量分数 (6)3.物料衡算原料处理量 (6)三、塔板数的确定 (7)1.理论板层数T N 的求取 (7)2.全塔效率T E (8)3.实际板层数的求取 (9)四、精馏塔的工艺条件及有关物性数据的计算 (9)1.操作压强计算 (9)2.操作温度计算 (9)3.平均摩尔质量计算 (9)4.平均密度计算 (10)5.液相平均表面张力计算 (11)6.液相平均粘度计算 (11)五、精馏塔的塔体工艺尺寸计算 (12)1.塔径的计算 (12)2.精馏塔的有效高度的计算 (13)六、塔板主要工艺尺寸的计算 (14)1.溢流装置计算 (14)2.塔板布置 (15)3.筛孔数n 与开孔率 (16)七、筛板的流体力学验算 (16)1.气体通过筛板压降相当的液柱高度P h (16)2.雾沫夹带量V e 的验算 (17)3.漏液的验算 (18)4.液泛验算 (18)八、塔板负荷性能图 (19)1.漏液线 (19)3.液相负荷下限线 (20)5.液泛线 (21)6. 操作线 (22)九、设计一览表 (24)十、操作方案的说明: (25)附表 (26)总结 (29)参考文献 (29)第一部分概述一、设计目标分离正己烷-正庚烷(正戊烷-正己烷)混合液的筛板式精馏塔设计二、设计任务试设计分离正己烷-正庚烷(正戊烷-正己烷)混合物的筛板精馏塔。
精馏分离含正己烷30%(正戊烷60%)的正己烷-正庚烷(正戊烷-正己烷)混合液,要求塔顶馏岀液中含正己烷(正戊烷)不小于96%,塔底釜液中含正己烷不高于2%(正己烷96%)。
浮阀塔课程设计说明书

题目拟建一浮阀塔用以分离苯-氯苯混合物(不易气泡),决定采用F1型浮阀,液相密度L 气相密度V液相流里L s 气相流里V S表面张力物系kg m 3kg m 33 1m s3 1m s N m 1苯-氯苯841.9 2.996 0.006 1.61 0.0209(1)进行塔板工艺设计计算及验算(2)绘制负荷性能图(3)绘制塔板结构图(4)给出设计结果列表(5)进行分析和讨论设计计算及验算1•塔板工艺尺寸计算(1)塔径欲求塔径应先给出空塔气速u,而u (安全系数)U max式中c可由史密斯关联图查出,横标的数值为取板间距H T0.45m,板上液层高度h L 0.05m,则图中参数值为H T h L 0.45 0.05 0.4m由图3 5查得c20 0.0825,表面张力20.9mN/m.C20 20)0.2 0.0832L h V h J_)0.5v0.006(841.9、1.612.9960.5 0.0625 U max___ cc [841.9 2.996 , U max 0.0832 . 1.399m/sV 2.996取安全系数为0.6,则空塔气速为u 安全系数U max 0.6 1.399 0.84m/s塔径D .. 4Vs 4 1.61 1.562mX u V3.14 0.84按标准塔径圆整D 1.6m,则2 3 14 2 2塔截面积A -D2(1.6)2 2.01m24 4实际空塔气速u 生1610.801m/sA T 2.01(2 )溢流装置选用单溢流弓形降液管,不设进口堰。
各项计算如下:①堰长I W :取堰长I W 0.66D,即I W 0.66 1.6 1.056m②出口堰咼% : h L h OW采用平直堰,堰上液层高度h ow可依下式计算:h ow 2叫宀)1 1000 l w近似取E 1,则可由列线图查出h ow值。
L h 0.006 3600 21.6m3/h,l w 1.056m,查得h ow 0.021m 则h w h L h OW0.05 0.021 0.029m③弓形降液管宽度W d和面积A f:—0.66D由图3 10查得:A 0.0721,池0.124,则A T DA f 0.0721 2.01 0.145m25s ,故降液管尺寸可用。
化工原理课程设计--分离正庚烷-正辛烷混合液的筛板精馏塔

化工原理课程设计一分离正庚烷-正辛烷混合液的筛板精馆塔课程设计说明书狸珀空戏分离正庚烷■正辛烷混合液味衽石称的筛板精帽塔设计姓名________________________学号________________________班级________________________指导教师_____________________ 校方_________________________ 企方设计地点_____________________设计时间2014年5月31日目录1.设计任务及要求 (3)11设计任务 (3)1.2设计内容 (3)2.主要基础数据 (3)3・设计计算 (4)3.1设计方案的确定 (4)3.2精憎塔的物料衡算 (4)3.3塔板数的确定 (5)3.4精馆塔工艺条件及有关物性数据 (6)3.5精馆塔塔体工艺尺寸计算 (8)3.6全凝器冷凝介质的消耗量 (9)3.7再沸器加热介质的消耗量 (10)4.筛板塔设计结果汇总 (11)5.工艺流程图 (11)6.设计感想 (12)7.参考文献 (12)设计题目:分离正庚烷-正辛烷混合液的筛板精馅塔1.设计任务及要求1.1设计任务在一常压操作的连续塔精馆塔内分离正庚烷-正辛烷混合物。
原料液年处理量为20000t,料液浓度为50% (正庚烷质量分数)。
要求塔顶产品正庚烷浓度为98. 5%(质量分数),塔底釜液中正辛烷浓度不低于98%(质量分数)。
设计条件如下:根据上述工艺条件进行筛板塔的设计计算。
1.2设计内容1 •设计方案的确定及流程说明;2.工艺计算;3.主要设备工艺尺寸设计;4.设计结果汇总;5.工艺流程图;6.设计感想。
2.主要基数数据以上为实验数据,也可用安托尼公式计算:三表3 A、B. C取值温度/° C A B C正庚烷 6.02 1263.91 216.432 正辛烷 6.05 1356.36 209.635表4液体密度(Kg/n?)表7液体汽化热(KJ/mol)温度/。
精馏塔的设计
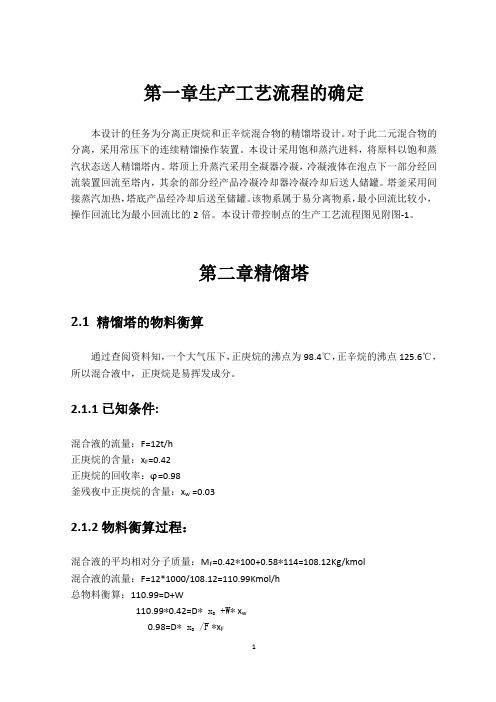
第一章生产工艺流程的确定本设计的任务为分离正庚烷和正辛烷混合物的精馏塔设计。
对于此二元混合物的分离,采用常压下的连续精馏操作装置。
本设计采用饱和蒸汽进料,将原料以饱和蒸汽状态送人精馏塔内。
塔顶上升蒸汽采用全凝器冷凝,冷凝液体在泡点下一部分经回流装置回流至塔内,其余的部分经产品冷凝冷却器冷凝冷却后送人储罐。
塔釜采用间接蒸汽加热,塔底产品经冷却后送至储罐。
该物系属于易分离物系,最小回流比较小,操作回流比为最小回流比的2倍。
本设计带控制点的生产工艺流程图见附图-1。
第二章精馏塔2.1 精馏塔的物料衡算通过查阅资料知,一个大气压下,正庚烷的沸点为98.4℃,正辛烷的沸点125.6℃,所以混合液中,正庚烷是易挥发成分。
2.1.1已知条件:混合液的流量:F=12t/h正庚烷的含量:x F=0.42正庚烷的回收率:φ=0.98釜残夜中正庚烷的含量:x w =0.032.1.2物料衡算过程:混合液的平均相对分子质量:M F=0.42*100+0.58*114=108.12Kg/kmol混合液的流量:F=12*1000/108.12=110.99Kmol/h总物料衡算:110.99=D+W110.99*0.42=D* x D +W* x w0.98=D* x D /F*x F计算结果:D=79.77 W=31.22 x=0.573D2.2 塔板数的确定2.2.1塔板理论数N T的求取正庚烷—正辛烷属于理想物系,采用图解法求理论板层数。
(1)由资料查得正庚烷—正辛烷在101.3KPa的气液平衡数据如下:温度(℃):98.4 105 110 115 120 125.6X: 1.0 0.656 0.487 0.311 0.157 0.0y: 1.0 0.810 0.673 0.491 0.280 0.0绘出x-y图,见附图2。
(2)求最小回流比及操作回流比采用作图法求最小回流比。
在附图2中对角线上,自点e(0.42,0.42)作垂线ef即为进料线,该线与平衡线的交点坐标y q = 0.42 x q=0.26最小回流比为R min= (x D- y q )/ (y q - x q)=(0.573-0.42) / ( 0.42-0.26) = 0.96取操作回流比为R=2 R min=2*0.96=1.92(3)求精馏塔的气液负荷线L=RD=1.96*79.77=156.35V=(R+1)D=(1+1.96)*79.77=232.93L=L=156.35V=V-F=232.93-110.99=122.0(4) 求操作线方程精馏段操作线方程为y=L x /V + D x D /V =0.658x+0.196提馏段操作线方程为y=L x /V -W x W /V =1.282x-0.008(5)图解法取理论板层数采用图解法取理论板层数,如附图2所示。
精馏塔设计化工原理课程设计

一、设计方案的确定1.塔型:选用重型浮阀塔F1型浮阀塔的结构简单,制造方便,节省材料,性能良好,广泛用于化工及炼油生产中,现已列入部颁标准(JB1118-68)内。
一般情况下采用重阀,只有在处理量大并且要求压强降得很低的系统(如减压塔)中,采用轻阀。
由于本设计采用常压操作即可完成任务故采用重阀。
重阀采用厚度未2mm的薄板冲制,每阀质量约为33g。
浮阀塔具有以下优点:生产能力大;操作弹性好;塔板效率高;气体压强及液面落差较小;使用周期长;结构简单,便于安装;塔的造价低等。
2.操作压力:常压精馏因为常压下乙醇—水湿液态混合物,其沸点较低(小于100℃),故采用常压精馏就可以分离。
3.进料状态:泡点进料泡点进料的操作容易控制,而且不受季节的影响;另外泡点进料时精馏段和提留段塔径相同,设计和制造比较方便。
4.加热方式:采用间接蒸汽加热5.冷却剂与出口温度:采用25℃常温水为冷却剂,出口温度是40℃6.回流方式:泡点回流泡点回流易于控制,设计和控制是比较方便,而且可以节约能源。
3.1工艺条件和物性参数的计算3.3.1将质量分数转换成摩尔分数质量分数:0.425F X = 0.8346=0.92580.8346+0.1718D X ⨯=⨯⨯B 0.146=0.22120.146+0.918X ⨯=⨯⨯摩尔分数:()F 0.425/46=0.22430.425/4610.425/18x =+- 0.8300D x = 0.1000B x =3.1.2物料衡算摩尔流量:原料处理量=20.0115 1.85/t h -⨯= 故摩尔流量()()185010.42518500.42576.19/4618F kmol h ⨯-⨯=+=由F D B Fx Dx Bx =+ B F D =+ ()0.22430.176.1912.97/0.830.1F B D B x x D Fkmol h x x --==⨯=--()76.1912.9763.22/B F D kmol h =-=-= 质量流量:1850/F kg h = F D B Fx Dx Bx =+ B F D =+471.84/D kg h = 1378.16/B kg h =3.1.3平均分子量()()0.22434610.22431824.28/F M kg kmol =⨯+-⨯= ()()0.834610.831841.24/D M kg kmol =⨯+-⨯= ()0.1460.91820.8/B M kg kmol =⨯+⨯=3.1.4理论塔板数T N 的求取(图解法)乙醇—水气液平衡数据做x-y 图 (1) 最小回流比从下图读得,精馏线的斜率为min min 83340.5904183R R -==+,故min 1.441R =(2) 精馏段方程()min =1.2~2R R ,故取min =1.8 1.8 1.441 2.5938R R =⨯= 则精馏段方程为:y=0.7220.23111D x Rx x R R +=+++ (3) 提留段方程RR D=, 2.593812.9733.64L RD ==⨯=()/kmol h ()()146.61/V L D D R kmol h =+=+=1q =,()'46.61/V V kmol h =='33.6476.19109.83L L qF =+=+=()/kmol h则提留段方程为:''' 2.360.058B L By x x x V V=-=-故得到下图:由图得到全塔共需理论塔板13块,扣除再沸器后理论塔板数12N ,其中精T馏段12块,提留段0块E3.1.5全塔效率T(1)作t-x-y图:(2)计算黏度从t-x-y 图查得78.3C D t =︒,86.5C B t =︒,83.0C F t =︒ 则78.386.582.4C 22D B m t t t ++===︒ 由《流体力学与传热》附录二和P257液体粘度共线图可得水和乙醇在不同温度下的粘度: ()L 82.4C =0.41mPa s μ︒⋅乙醇℃,()L 82.4C =0.3461mPa s μ︒⋅水℃()()()L L +1=0.22430.41+10.22430.34610.360Lm F F x x mPa s μμμ∴=⨯-⨯⨯-⨯=⋅乙醇水(3)相对挥发度:由t-x-y 图上查得,0.8300D x =, 0.84D y *= 0.1000B x =, 0.4385B y *=()()()()10.8410.83 1.07530.8310.841D D D D D y x x y α***-⨯-===⨯-- ()()()()10.438510.17.02850.110.43851B B B B B y x x y α***-⨯-===⨯--2.749m α∴=== 则计算全塔效率为:()0.2450.490.4913T m Lm E αμ-=⨯⋅=3.1.6实际塔板数1224.430.4913T P T N N E ===, 取整25P N = 其中,精馏段:12240.4913N ==精, 提留段:1N =精 3.1.7塔的工艺条件以及无聊数据计算(一)、操作压强因为常压下乙醇—水湿态混合物,其沸点较低(小于100C ︒),故采用常压精馏就可以分离。
正己烷-正庚烷分离过程筛板精馏塔课程设计

课程设计说明书题目: 分离正戊烷-正己烷用筛板精馏塔设计院系:机械工程学院专业班级:过控11-1学号: 2011301936学生姓名:冒鹏飞指导教师:李雪斌2013 年 12 月30 日目录第一部分 概述 (4)一、设计目标 (4)二、设计任务 (4)三、设计条件 (4)四、设计内容 (4)五、工艺流程图 (4)第二部分 工艺设计计算 (6)一、设计方案的确定 (6)二、精馏塔的物料衡算 (6)1.原料液及塔顶、塔底产品的摩尔分数 (6)2.原料液及塔顶、塔底产品的平均摩尔质量和质量分数 (6)3.物料衡算原料处理量 (6)三、塔板数的确定 (7)1.理论板层数T N 的求取 (7)2.全塔效率T E (8)3.实际板层数的求取 (9)四、精馏塔的工艺条件及有关物性数据的计算 (9)1.操作压强计算 (9)2.操作温度计算 (9)3.平均摩尔质量计算 (9)4.平均密度计算 (10)5.液相平均表面张力计算 (11)6.液相平均粘度计算 (11)五、精馏塔的塔体工艺尺寸计算 (12)1.塔径的计算 (12)2.精馏塔的有效高度的计算 (13)六、塔板主要工艺尺寸的计算 (14)1.溢流装置计算 (14)2.塔板布置 (15)3.筛孔数n 与开孔率 (16)七、筛板的流体力学验算 (16)1.气体通过筛板压降相当的液柱高度P h (16)2.雾沫夹带量V e 的验算 (17)3.漏液的验算 (18)4.液泛验算 (18)八、塔板负荷性能图 (19)1.漏液线 (19)3.液相负荷下限线 (20)5.液泛线 (21)6. 操作线 (22)九、设计一览表 (24)十、操作方案的说明: (25)附表 (26)总结 (29)参考文献 (29)第一部分概述一、设计目标分离正己烷-正庚烷(正戊烷-正己烷)混合液的筛板式精馏塔设计二、设计任务试设计分离正己烷-正庚烷(正戊烷-正己烷)混合物的筛板精馏塔。
精馏分离含正己烷30%(正戊烷60%)的正己烷-正庚烷(正戊烷-正己烷)混合液,要求塔顶馏岀液中含正己烷(正戊烷)不小于96%,塔底釜液中含正己烷不高于2%(正己烷96%)。
浮阀塔的设计示例
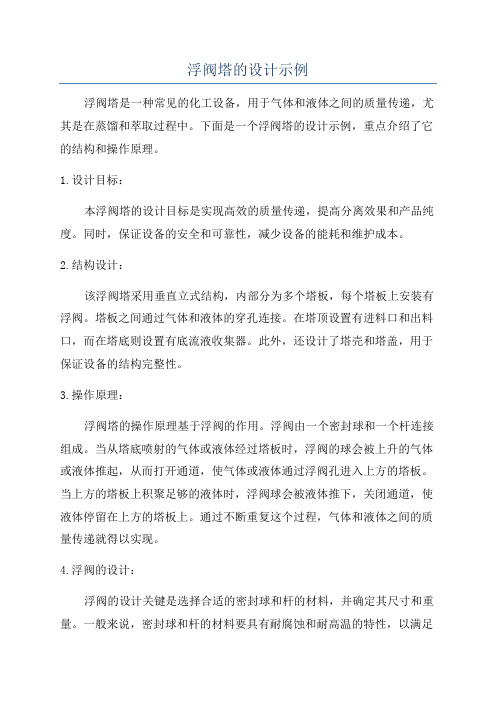
浮阀塔的设计示例浮阀塔是一种常见的化工设备,用于气体和液体之间的质量传递,尤其是在蒸馏和萃取过程中。
下面是一个浮阀塔的设计示例,重点介绍了它的结构和操作原理。
1.设计目标:本浮阀塔的设计目标是实现高效的质量传递,提高分离效果和产品纯度。
同时,保证设备的安全和可靠性,减少设备的能耗和维护成本。
2.结构设计:该浮阀塔采用垂直立式结构,内部分为多个塔板,每个塔板上安装有浮阀。
塔板之间通过气体和液体的穿孔连接。
在塔顶设置有进料口和出料口,而在塔底则设置有底流液收集器。
此外,还设计了塔壳和塔盖,用于保证设备的结构完整性。
3.操作原理:浮阀塔的操作原理基于浮阀的作用。
浮阀由一个密封球和一个杆连接组成。
当从塔底喷射的气体或液体经过塔板时,浮阀的球会被上升的气体或液体推起,从而打开通道,使气体或液体通过浮阀孔进入上方的塔板。
当上方的塔板上积聚足够的液体时,浮阀球会被液体推下,关闭通道,使液体停留在上方的塔板上。
通过不断重复这个过程,气体和液体之间的质量传递就得以实现。
4.浮阀的设计:浮阀的设计关键是选择合适的密封球和杆的材料,并确定其尺寸和重量。
一般来说,密封球和杆的材料要具有耐腐蚀和耐高温的特性,以满足不同工艺的要求。
此外,密封球的尺寸和重量需要根据气体和液体的流速和密度来确定,以保证浮阀的正常运行。
5.设备的操作与维护:为了确保浮阀塔的高效运行,需要进行定期的检查和维护工作。
首先,要检查浮阀是否正常工作,如有必要,需要更换损坏的浮阀。
其次,要及时清理塔板上的沉积物,以保证通道的畅通。
此外,还需要定期检查塔壳和塔盖的密封性,以防止气体或液体的泄漏。
6.设备的优化改进:针对该浮阀塔的优化改进措施主要包括以下几个方面:一是改善塔板的结构,增加塔板的布置密度,减小气液间的传质距离,从而提高质量传递效果。
二是采用节能技术,如加热和冷凝剂回收,减少能耗和环境污染。
三是引入自动控制系统,实现设备的自动化运行和监控,提高生产效率和安全性。
正戊烷正己烷精馏分离板式塔设计
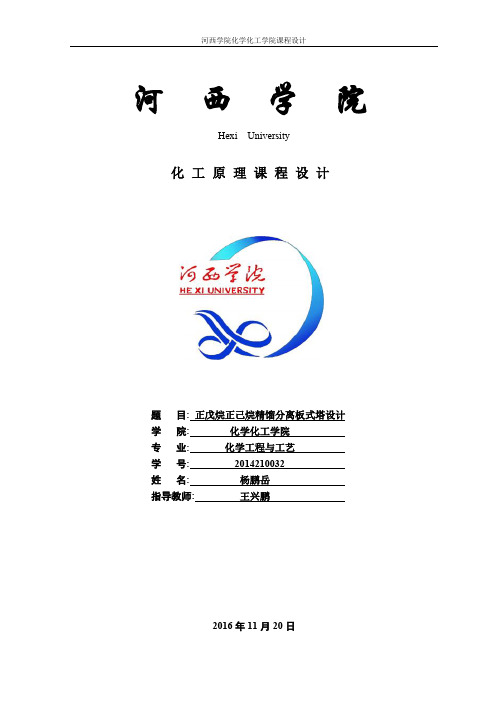
河西学院Hexi University化工原理课程设计题目: 正戊烷正己烷精馏分离板式塔设计学院:化学化工学院专业:化学工程与工艺学号:::2016年11月20日化工原理课程设计任务书一、设计题目正戊烷-正己烷混合液筛板(浮阀)精馏塔设计二、设计任务及操作条件1.设计任务生产能力(进料量)80000 吨/年操作周期7200 小时/年进料组成40% (正戊烷质量分率)塔顶产品组成≥98.5% (正戊烷质量分率)塔底产品组成≥98% (正己烷质量分率)2.操作条件料液初温20℃操作压力塔顶4 kpa(表压)单板压降≦0.7kPa冷却水温度20℃饱和水蒸汽压力0.25Mpa(表压)3.设备型式筛板(浮阀)塔4.厂址珠海(压力:1atm )三、设计内容1.设计方案的选择及流程说明2.塔的工艺计算3.主要设备工艺尺寸设计(1)塔径、塔高及塔板结构尺寸的确定(2)塔板的流体力学校核(3)塔板的负荷性能图(4)总塔高、总压降及接管尺寸的确定4.辅助设备选型与计算5.设计结果汇总6.工艺流程图及精馏工艺条件7.设计评述目录1 设计方案的确定 (1)1.1概述 (1)1.2设计方案确定原则 (1)1.3设计方案内容 (2)1.3.1 操作压力 (2)1.3.2 加热方式 (2)1.3.3 进料状态 (2)1.3.4 板式塔的常用塔型及其选用 (3)1.3.4 回流比 (4)1.3.5 热能利用 (4)2 精馏塔的工艺设计计算 (4)2.1设计任务和条件 (4)2.1.1 设计任务 (4)2.1.2 操作条件 (5)2.2工艺计算 (5)2.2.1 精馏塔的物料衡算 (5)2.3塔板数的确定 (6)的确定 (6)2.3.1 理论层数NT2.3.2 最小回流比的计算 (6)2.4操作线方程 (7)2.4.1 图解法求理论板层数 (7)2.5实际板数的计算 (8)3 工艺条件及有关物性的计算 (9)3.1操作压力 (9)3.2操作温度 (9)3.3平均摩尔质量 (9)3.3.1 塔顶汽液混合物平均摩尔质 (9)3.3.2 进料板汽、液混合物平均摩尔质量 ................................ 9 3.3.3 塔底汽液混合物平均摩尔质量 .................................... 9 3.3.4 精馏段汽、液混合物平均摩尔质量 ............................... 10 3.3.5 提馏段汽、液混合物 ........................................... 10 3.4 平均密度 ......................................................... 10 3.4.1 气相平均密度 ................................................. 10 3.4.2 液相平均密度 ................................................. 10 3.5 液相平均表面张力 ................................................. 11 4 精馏塔工艺尺寸计算 .................................................. 13 4.1 塔径的计算 ....................................................... 13 4.2 精馏塔有效高度的计算 ............................................. 15 4.3 溢流装置计算 ..................................................... 15 4.3.1 堰长 ......................................................... 15 4.3.2 溢流堰高度 ................................................... 15 4.3.3 弓形降液管的宽度d W 和横截面f A 的计算 ......................... 16 4.3.4 降液管底隙高度 ............................................... 17 4.3.5 塔板布置及筛孔数目的计算 ..................................... 17 4.3.6 边缘区宽度确定 ............................................... 17 4.3.7 开孔面积的计算 ............................................... 17 4.3.8 筛孔计算及其排列 ............................................. 18 5 筛板的流体力学验算 .................................................. 18 5.1 塔板压降 ......................................................... 18 5.1.1 精馏段 ....................................................... 18 5.2 气体通过液层的阻力计算 ........................................... 19 5.3 液体表面张力的阻力计算 ........................................... 19 5.4 液面落差 ......................................................... 20 5.5 液沫夹带 ......................................................... 20 5.6 漏液 . (20)5.7液泛验算 (20)6 塔板负荷性能图 (21)6.1漏液线 (21)6.2液沫夹带 (22)6.3液相负荷下限线 (24)6.4液相负荷上限线 (24)6.5液泛线 (24)7 塔附件设计 (27)7.1接管——进料管 (27)7.2筒体与封头 (27)7.2.1 筒体 (27)7.2.2 封头 (28)7.3人孔 (28)7.4裙座 (28)7.5塔釜料液排出管管径 (28)7.6回流管管径 (28)7.7塔顶蒸汽出料管 (29)7.8塔底进气管 (29)7.9法兰 (29)8 设计一览表 (29)设计评述 (31)参考文献 (31)致谢 (32)正戊烷-正己烷混合液筛板(浮阀)精馏塔设计杨鹏岳摘要:本设计任务为分离正戊烷一正己烷二元混合物,通过图解法计算得出理论板数为13块,取回流比为1.5,算出全塔效率为0.4263,实际板数为31块,进料位置为第13块塔板,在浮阀塔主要工艺尺寸的设计计算中得出塔径为1.6米,塔高20.525米,通过流体力学验算,证明各指标数据均符合标准。
化工原理课程设计---利用浮阀塔分离正戊烷与正己烷的工艺设计

安徽理工大学课程设计说明书设计题目:化工原理课程设计学院、系:机械工程学院专业班级:过程装备与控制工程11-2 学生姓名:指导教师:李雪斌成绩:2013年12月23日设计任务书(一)设计题目: 利用浮阀塔分离正戊烷与正己烷的工艺设计分离要求:试设计一座正戊烷—正己烷连续精馏浮阀塔,要求年产纯度98%的正己烷4.0万吨,塔顶馏出液中含正己烷不得高于2%,塔底釜液含正己烷不低于98%,原料液中含正戊烷60%(以上均为质量分数)。
(二)操作条件:塔顶压力:4kPa(表压)进料状态:泡点进料回流比:1.4Rmin塔釜加热蒸汽压力:0.5MPa(表压)单板的压降: 0.7kPa全塔效率:52%(3)塔板类型:浮阀塔板(F1型)(4)工作日: 330天/年(一年中有一个月检修)(5)厂址:淮南地区(六)设计内容①精馏塔的物料衡算②塔板数的确定③精馏塔的工艺条件及有关物性数据的计算④塔体工艺条件尺寸⑤塔板负荷性能图目录第1章序言 (3)第2章精馏塔的物料衡算 (6)2.1. 物料衡算 (6)2.2. 常压下正戊烷—正己烷气、液平衡组成与温度的关系 (7)第3章塔板数的确定 (8)N的确定 (8)3.1. 理论板数T3.2. 实际板数的确定 (9)第4章精馏塔的工艺条件及有关物性数据 (9)4.1. 操作压力的计算 (9)4.2. 密度的计算 (10)4.3. 表面张力的计算 (11)4.4. 混合物的粘度 (12)4.5. 相对挥发度 (12)第5章塔体工艺条件尺寸 (13)5.1. 气、液相体积流量计算 (13)5.2. 塔径的初步设计 (14)5.3. 溢流装置 (15)5.4. 塔板布置及浮阀数目与排列 (17)第6章塔板负荷性能图 (20)6.1. 物沫夹带线 (20)6.2. 液泛线 (21)6.3. 液相负荷上限 (22)6.4. 漏液线 (22)6.5. 液相负荷下限 (23)第7章结束语 (24)正戊烷—正己烷连续精馏浮阀塔的设计第1章序言精馏是分离液体混合物,一种利用回流使液体混合物得到高度分离的蒸馏方法,是工业上应用最广的液体混合物分离操作,广泛应用与石油、化工、轻工、食品、冶金等部门。
(完整word版)化工机械设备课程设计浮阀塔的设计

摘要 (3)1 前言 (3)1。
1 研究的现状及意义 (3)1.2 设计条件及依据 (10)1。
3 设备结构形式概述 (12)2 设计参数及其要求 (15)2.1 设计参数 (15)2。
2设计条件 (16)2.3设计简图 (17)3 材料选择 (18)3。
1 概论 (18)3。
2塔体材料选择 (18)3。
3裙座材料的选择 (18)4 塔体结构设计及计算 (19)4。
1塔体和封头厚度计算 (19)4.1。
1 塔体厚度的计算 (19)4.1。
2封头厚度计算 (20)4。
2塔设备质量载荷计算 (20)4。
3风载荷与风弯矩的计算 (24)4。
4地震弯矩的计算 (28)4.4。
1地震弯矩的计算 (28)4.4。
2偏心弯矩的计算 (30)4。
5各种载荷引起的轴向应力 (30)14.6塔体和裙座危险截面的强度与稳定校核 (32)4。
6.1塔体的最大组合轴向拉应力校核 (32)4。
6。
2。
塔体和裙座的稳定校核 (33)4.7塔体水压试验和吊装时的应力校核 (36)4。
7.1水压试验时各种载荷引起的应力 (36)4。
7.2水压试验时应力校核 (37)4。
8基础环的设计 (38)4.8.1 基础环尺寸 (38)4。
8。
2基础环的应力校核 (38)4。
8.3基础环的厚度 (39)4.9地脚螺栓计算 (40)4.9.1地脚螺栓承受的最大拉应力 (40)4.9。
2地脚螺栓的螺纹小径 (41)符号说明 (42)小结 (46)参考文献................................................................................................................... 错误!未定义书签。
谢辞........................................................................................................................... 错误!未定义书签。
精馏塔(浮阀塔)的设计
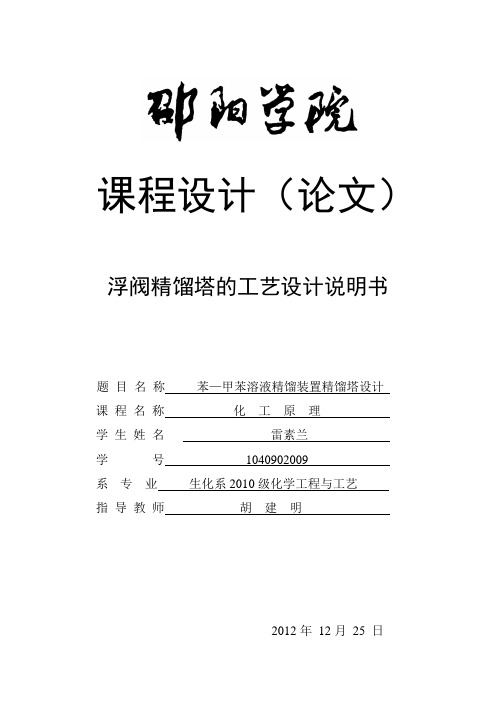
课程设计(论文)浮阀精馏塔的工艺设计说明书题目名称苯—甲苯溶液精馏装置精馏塔设计课程名称化工原理学生姓名雷素兰学号**********系专业生化系2010级化学工程与工艺指导教师胡建明2012年12月25 日目录一、设计任务书 (3)二、概述 (4)三、设计方案的确定和流程说明 (4)四、物料衡算 (5)1.设计条件 (5)2.全塔物料衡算 (6)五、设备设计与选型 (7)1. 精馏塔工艺设计 (7)2.塔内气液负荷 (11)3.计算塔径、确定板间距 (13)六、塔板结构设计 (14)1.溢流装置 (14)2.塔板布置 (15)七、浮阀塔流体力学验算 (17)1.塔板压降 (17)2.塔板负荷性能 (19)八、精馏塔结构尺寸设计 (23)九、参考文献 (26)十、总结 (27)十一、致谢 (27)十二、附工程图纸 (28)概述塔设备是化学工业,石油化工,生物化工,制药等生产过程中广泛采用的传质设备。
根据塔内气液接触构件的结构形式,可分为板式塔和填料塔两大类。
板式塔为逐级接触式气液传质设备,塔内设置一定数量的塔板,气体以鼓泡形式或喷射形式通过塔板上的液层,正常条件下,气相为分散相,液相为连续相,气相组成呈阶梯变化,它具有结构简单,安装方便,压降低,操作弹性大,持液量小等优点,被广泛的使用。
本设计的目的是分离苯—甲苯的混合液,故选用板式塔。
设计方案的确定和流程说明1.塔板类型:精馏塔的塔板类型共有三种:泡罩塔板,筛孔塔板,浮阀塔板。
浮阀塔板具有结构简单,制造方便,造价低等优点,且开孔率大,生产能力大,阀片可随气流量大小而上下浮动,故操作弹性大,气液接触时间长,因此塔板效率较高。
本设计采用浮阀塔板。
2. 加料方式:加料方式共有两种:高位槽加料和泵直接加料。
采用泵直接加料,具有结构简单,安装方便等优点,而且可以引入自动控制系统来实时调节流量及流速。
故本设计采用泵直接加料。
3. 进料状况:进料方式一般有两种:冷液进料及泡点进料。
化工原理课程设计任务及讲义课件

须满足板间距与塔径的关系外,还须进行空塔气速校核。
C20 exp[4.531 1.6562Z 5.5496Z 2 6.4695Z 3 (0.474675
0.079Z 1.39Z 2 1.3212Z 3 ) ln Lv (0.07291 0.088307Z
0.49123Z 2 0.43196Z 3 ) (ln Lv )2 ]
5~ 25
900
7 以下
7~ 50
1000
7 以下
45 以下
1200
9 以下
9~ 70
1400
9 以下
70 以下
1500
10 以下 70 以下
2000
11 以下 90 以下 90~160
3000
11 以下 110 以下 110~200 200~300
4000
11 以下 110 以下 110~230 230~350
表 1 板间距与塔径关系
塔径 D, m
0.3~0.5 0.5~0.8 0.8~1.6 1.6~2.0
塔板 间 距 HT mm 200~300 250~350 350~450 450~600
2、塔径 D 的初估与圆整
根据流量公式计算塔径,即 D 4V S
pu
式中 Vs —塔内的气相流量, m 3 s
5、绘制工整的设备结构图
5.注意事项: 写出详细计算步骤,并注明选用数据的来源; 每项设计结束后,列出计算结果明细表; 设计说明书要求字迹工整,装订成册上交。
第一章 综述 1.精馏原理及其在工业生产中的应用 2.精馏操作对塔设备的要求(生产能力、效率、流动阻力、操作 弹性、结构、造价和工艺特性等) 3.常用板式塔类型及本设计的选型 4.本设计所选塔的特性 第二章 工艺条件的确定和说明 1.确定操作压力 2.确定进料状态 3.确定加热剂和加热方式 第三章 流程的确定和说明(附流程简图) 1.流程的说明 2.设置各设备的原因(精馏设备、物料的储存和输送、必要的检 测手段、操作中的调节和重要参数的控制、热能利用)
正庚烷——正辛烷连续精馏塔设计

正庚烷——正辛烷连续精馏塔设计1.引言正庚烷和正辛烷是石油中较常见的两种烷烃化合物。
它们通常通过连续精馏过程从原油中分离出来。
在本文中,我们将设计一座连续精馏塔,以将正庚烷和正辛烷分离出来。
2.塔设计连续精馏塔是一种常用的分离设备,可以利用组分的不同挥发度将混合物分离成不同的组分。
在设计过程中,我们需要考虑以下几个方面:2.1塔型选择对于正庚烷和正辛烷的分离,通常选择塔顶回流塔。
这种塔型可以有效地分离轻质和重质组分,并提高分离效率。
2.2塔采用板式还是填料式?塔可以采用板式或填料式两种设计。
在本次设计中,我们选择填料式塔。
填料可以提供更大的表面积,增加相接触,从而提高分离效果。
2.3塔的电性能设计在连续精馏过程中,需要将混合物加热到适当的温度,以使其汽化。
此外,在塔中加入一定的沸点提升剂可以提高塔的分离效率。
因此,我们需要考虑塔的加热和冷却系统的设计。
2.4塔的操作参数在塔的操作中,我们需要确定适当的操作参数,包括进料温度、进料流量、塔顶回流比、底部回流比等。
这些参数将影响分离效率和产量。
3.热力学分析在进行连续精馏塔设计之前,我们需要进行热力学分析,以确定正庚烷和正辛烷的汽液平衡曲线和塔顶回流比与塔底回流比之间的关系。
这可以帮助我们确定最佳操作参数。
4.连续精馏塔的模拟在连续精馏塔的设计中,使用模拟软件进行仿真是非常有帮助的。
通过对塔的模拟,我们可以确定最佳的操作参数,并进行优化。
5.应用案例在连续精馏塔设计中,通过实际的应用案例,我们可以更好地理解设计原理和方法。
例如,可以选择一组原油成分,并基于该组分进行连续精馏塔的设计。
6.结论通过上述步骤,我们可以设计一座连续精馏塔,以将正庚烷和正辛烷有效地分离出来。
连续精馏塔的设计涉及到众多的参数和因素,需要综合考虑热力学和操作要求。
通过模拟和实际应用的结合,可以获得较为理想的设计结果。
中国石油大学课程设计-曹震-正戊烷-正己烷-正庚烷-正辛烷
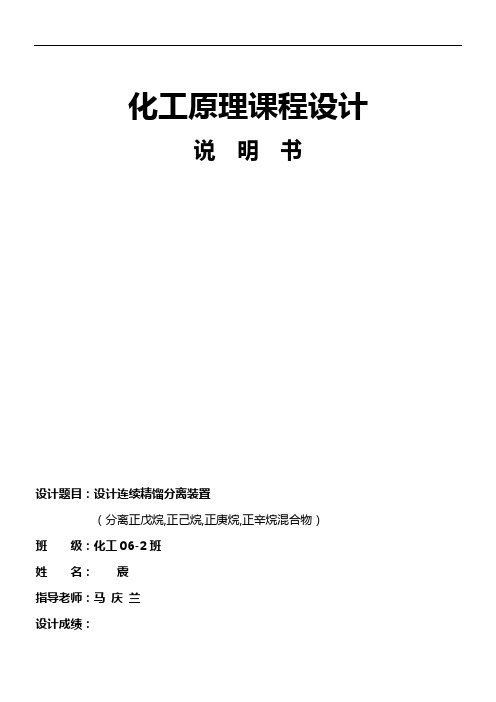
化工原理课程设计说明书设计题目:设计连续精馏分离装置(分离正戊烷,正己烷,正庚烷,正辛烷混合物)班级:化工06-2班姓名:震指导老师:马庆兰设计成绩:日期:2009年6月8日——2009年7月1日目录设计方案简介 (2)工艺流程简图 (3)第一章塔的工艺计算 (4)§1.1产品的组成及产品量的确定 (4)§1.2操作温度与压力的确定 (5)§1.3最小回流比的确定 (9)§1.4最小理论板数的确定 (11)§1.5适宜回流比的确定 (11)§1.6理论板数及理论加料位置的确定 (13)§1.7实际板数及实际加料位置的确定 (14)§1.8计算塔径 (14)§1.9全塔热量衡算 (18)§2.0第一章总结 (21)第二章塔板的结构设计 (22)§2.1塔板的布置 (22)§2.2塔板流体力学计算 (23)§2.3塔板负荷性能图 (30)第三章塔体结构设计 (33)§3.1塔体的尺寸、材料及开孔 (33)§3.2确定各接管的流速和直径 (34)§3.3塔的辅助设备选用 (35)计算结果汇总表 (41)自我评述 (44)工艺流程简图设计方案简介所设计的任务是:设计连续精馏分离装置,分离正戊烷、正己烷、正庚烷和正辛烷,是一个多元精馏过程,轻关键组分是正己烷,重关键组分是正庚烷。
根据工艺操作条件和分离任务,初步确定精馏方案,画出工艺流程草图。
确定方案流程后,逐步计算和确定多元混合物精馏塔的操作条件及装备设施。
首先,通过清晰分割法以及全塔物料衡算,确定塔顶、塔底的组分及其组成,根据回流罐的温度及泡露点方程,计算出塔顶、塔底和进料的压力和温度,进而确定精馏操作条件。
通过经验估算出达到分离目的所需的最少理论板数,再结合全塔操作条件,得出最小回流比,通过作理论板数与回流比的关系曲线图,得出适宜回流比,便可确定理论板数和实际板数,并得出实际加料位置。
化工原理课程设计--分离正庚烷-正辛烷混合液的筛板精馏塔

化工原理课程设计一分离正庚烷-正辛烷混合液的筛板精馆塔课程设计说明书狸珀空戏分离正庚烷■正辛烷混合液味衽石称的筛板精帽塔设计姓名________________________学号________________________班级________________________指导教师_____________________ 校方_________________________ 企方设计地点_____________________设计时间2014年5月31日目录1.设计任务及要求 (3)11设计任务 (3)1.2设计内容 (3)2.主要基础数据 (3)3・设计计算 (4)3.1设计方案的确定 (4)3.2精憎塔的物料衡算 (4)3.3塔板数的确定 (5)3.4精馆塔工艺条件及有关物性数据 (6)3.5精馆塔塔体工艺尺寸计算 (8)3.6全凝器冷凝介质的消耗量 (9)3.7再沸器加热介质的消耗量 (10)4.筛板塔设计结果汇总 (11)5.工艺流程图 (11)6.设计感想 (12)7.参考文献 (12)设计题目:分离正庚烷-正辛烷混合液的筛板精馅塔1.设计任务及要求1.1设计任务在一常压操作的连续塔精馆塔内分离正庚烷-正辛烷混合物。
原料液年处理量为20000t,料液浓度为50% (正庚烷质量分数)。
要求塔顶产品正庚烷浓度为98. 5%(质量分数),塔底釜液中正辛烷浓度不低于98%(质量分数)。
设计条件如下:根据上述工艺条件进行筛板塔的设计计算。
1.2设计内容1 •设计方案的确定及流程说明;2.工艺计算;3.主要设备工艺尺寸设计;4.设计结果汇总;5.工艺流程图;6.设计感想。
2.主要基数数据以上为实验数据,也可用安托尼公式计算:三表3 A、B. C取值温度/° C A B C正庚烷 6.02 1263.91 216.432 正辛烷 6.05 1356.36 209.635表4液体密度(Kg/n?)表7液体汽化热(KJ/mol)温度/。
- 1、下载文档前请自行甄别文档内容的完整性,平台不提供额外的编辑、内容补充、找答案等附加服务。
- 2、"仅部分预览"的文档,不可在线预览部分如存在完整性等问题,可反馈申请退款(可完整预览的文档不适用该条件!)。
- 3、如文档侵犯您的权益,请联系客服反馈,我们会尽快为您处理(人工客服工作时间:9:00-18:30)。
河西学院Hexi University化工原理课程设计题目: 正庚烷和正辛烷体系精馏浮阀塔设计学院:化学化工学院专业:_ 化学工程与工艺学号: 2014210012姓名:刘继麟指导教师:李守博2016年 11月 20日精馏塔设计任务书一设计题目正庚烷-正辛烷精馏分离板式塔设计二工艺条件与数据1.设计任务生产能力(进料量) 90000 吨/年操作周期 7920 小时/年进料组成 30% (正庚烷)(质量分率,下同)塔顶产品组成≥96% (正庚烷)塔底产品组成≤4% (正庚烷)回流比,自选单板压降≤700Pa2.操作条件操作压力塔顶为常压进料热状态进料温度50℃加热蒸汽 0.25Mpa(表压)冷却水温度30℃3.设备型式筛板或浮阀塔板4.厂址新疆地区(吐鲁番)三设计内容1.设计方案的选择及流程说明2.塔的工艺计算3.主要设备工艺尺寸设计(1)塔径、塔高及塔板结构尺寸的确定(2)塔板的流体力学校核(3)塔板的负荷性能图(4)总塔高、总压降及接管尺寸的确定4.辅助设备选型与计算5.设计结果汇总6.工艺流程图及精馏工艺条件图7.设计评述目录1.概述 (1)1.1精馏原理及其在化工生产上的应用 (1)1.2设计方案的选择和论证 (3)1.2.1设计思路 (3)1.2.2选定设计方案的原则 (3)1.3确定设计方案 (3)1.3.1精馏方式的选定 (3)1.3.2加热方式的选取 (3)1.3.3操作压力的选取 (4)1.3.4回流比的选择 (4)1.3.5塔顶冷凝器的冷凝方式与冷却介质的选择 (4)1.3.6板式塔的选择 (4)1.3.7 关于附属设备的设计 (5)1.3.8 流程的设计及说明 (5)2. 精馏塔工艺设计 (6)2.1精馏塔的物料衡算 (6)2.1.1原料液及其塔顶、塔底产品的摩尔分率 (6)2.1.2原料液及塔顶塔底产品的平均摩尔质量 (6)2.1.3物料衡算 (6)2.2塔板数的确定 (6)2.2.1 理论板层数NT的求取 (6)2.2.2 q线方程的计算 (7)2.2.2 塔板数的确定 (7)3.精馏塔的工艺条件及有关物性数据数据的计算 (9)3.1 操作压力的计算 (9)3.2操作温度的计算 (9)3.3 平均摩尔质量的计算 (10)3.4 平均密度的计算 (11)3.5平均粘度的计算 (12)3.6平均表面张力的计算 (13)4.精馏塔的塔体工艺尺寸计算 (14)4.1精馏段塔径计算 (14)4.2提馏段塔径计算 (15)4.3 精馏塔有效高度的计算 (15)5.塔板主要工艺尺寸的计算 (16)5.1精馏段 (16)5.2提馏段(计算公式和原理同精馏段) (19)6.筛板的流体力学验算 (21)6.1精馏段 (21)6.2 提馏段 (23)7.塔板负荷性能图 (26)7.1精馏段负荷性能图 (26)7.2 提馏段负荷性能图 (27)8.精馏塔的工艺设计结果一览表 (30)9、精馏塔的接管尺寸及附属设备 (33)9.1.接管尺寸 (33)9.1.1进料管 (33)9.1.2回流管 (33)9.1.3塔釜出料管 (33)9.1.4塔顶蒸汽出料管 (34)9.1.5塔釜进气管 (34)9.1.6法兰 (34)9.2塔体结构 (34)9.2.1筒体与封头 (34)9.2.2除沫器 (35)9.2.3裙座 (35)9.2.4吊柱 (35)9.2.5人孔 (35)9.3塔总体高度的设计 (36)9.3.1塔的顶部空间高度 (36)9.3.2塔的底部空间高度 (36)9.3.3塔总体高度 (36)9.4附属设备设计 (36)9.4.1冷凝器 (36)9.4.2再沸器 (37)10.设计评述 (39)附图 (39)参考文献 (40)正庚烷-正辛烷精馏分离浮阀塔设计刘继麟摘要:本设计采用浮阀塔分离正庚烷和正辛烷,通过逐板计算法计算得出理论板数为20块,回流比为2.067,算出塔板效率0.59,实际板数为34块,进料位置为第18块,在浮阀塔主要工艺尺寸的设计计算中得出精馏段塔径为1.4米,精馏段塔径为1.6米,总塔高20.74米,精馏段每层浮阀数目为85,提馏段每层浮阀数目为132。
通过浮阀塔的流体力学验算,证明各指标数据均符合标准。
同时还对精馏塔的辅助设备进行了选型计算。
塔的附属设备中,所有管线均采用无缝钢管。
再沸器采用卧式浮头式热器,确定了操作点符合操作要求。
关键词:正庚烷,正辛烷,精馏,浮阀塔1概述1.1精馏原理及其在化工生产上的应用化工生产中所处理的原料,中间产物,粗产品几乎都是由若干组分组成的混合物,而且其中大部分都是均相物质。
生产中为了满足储存,运输,加工和使用的需求,时常需要将这些混合物分离为较纯净或几乎纯态的物质。
精馏是分离液体混合物最常用的一种单元操作,在化工,炼油,石油化工等工业得到广泛应用。
精馏过程在能量计的驱动下,使气,液两相多次直接接触和分离,利用液相混合物中各相分挥发度的不同,使挥发组分由液相向气相转移,难挥发组分由气相向液相转移。
实现原料混合物中各组成分离该过程是同时进行传质传热的过程。
本次设计任务为设计一定处理量的分离正庚烷和正辛烷混合物精馏塔。
精馏所进行的是气(汽)、液两相之间的传质,而作为气(汽)、液两相传质所用的塔设备,首先必须要能使气(汽)、液两相得到充分的接触,以达到较高的传质效率。
但是,为了满足工业生产和需要,塔设备还得具备下列各种基本要求:⑴气(汽)、液处理量大,即生产能力大时,仍不致发生大量的雾沫夹带、拦液或液泛等破坏操作的现象。
⑵操作稳定,弹性大,即当塔设备的气(汽)、液负荷有较大范围的变动时,仍能在较高的传质效率下进行稳定的操作并应保证长期连续操作所必须具有的可靠性。
⑶流体流动的阻力小,即流体流经塔设备的压力降小,这将大大节省动力消耗,从而降低操作费用。
对于减压精馏操作,过大的压力降还将使整个系统无法维持必要的真空度,最终破坏物系的操作。
⑷结构简单,材料耗用量小,制造和安装容易。
⑸耐腐蚀和不易堵塞,方便操作、调节和检修。
⑹塔内的滞留量要小。
实际上,任何塔设备都难以满足上述所有要求,况且上述要求中有些也是互相矛盾的。
不同的塔型各有某些独特的优点,设计时应根据物系性质和具体要求,抓住主要矛盾,进行选型。
浮阀精馏塔也是很早出现的一种板式塔,20世纪50年代起对板式精馏塔进行了大量工业规模的研究,逐步掌握了浮阀塔的性能,并形成了较完善的设计方法。
与泡罩塔相比,浮阀精馏塔具有下列优点:⑴结构比泡罩塔更简单,易于加工,造价约为泡罩塔的60%。
⑵处理能力大,比同塔径的泡罩塔可增加10~15%。
⑶塔板效率高,比泡罩塔高15%左右。
⑷压降较低,每板压力比泡罩塔约低30%左右。
浮阀塔的缺点是:⑴塔板安装的水平度要求较高,否则气液接触不匀。
⑵操作弹性较小(约2~3)。
⑶造价比筛板塔高。
化工原理课程设计是培养学生化工设计能力的重要教学环节,通过课程设计使我们初步掌握化工设计的基础知识、设计原则及方法;学会各种手册的使用方法及物理性质、化学性质的查找方法和技巧;掌握各种结果的校核,能画出工艺流程、塔板结构等图形。
本课程设计的主要内容是过程的物料衡算,工艺计算,结构设计和校核。
1.2设计方案的选择和论证1.2.1设计思路在本次设计中,我们进行的是正庚烷和正辛烷二元物系的精馏分离,简单蒸馏和平衡蒸馏只能达到组分的部分增浓,如何利用两组分的挥发度的差异实现高纯度分离,是精馏塔的基本原理。
实际上,蒸馏装置包括精馏塔、原料预热器、蒸馏釜、冷凝器、釜液冷却器和产品冷却器等设备。
蒸馏过程按操作方式不同,分为连续蒸馏和间歇蒸馏,我们这次所用的就是浮阀式连续精馏塔。
蒸馏是物料在塔内的多次部分汽化与多次部分冷凝所实现分离的。
热量自塔釜输入,由冷凝器和冷却器中的冷却介质将余热带走。
在此过程中,热能利用率很低,有时后可以考虑将余热再利用。
要保持塔的稳定性,流程中除用泵直接送入塔原料。
流程参见附图塔顶冷凝器可采用全凝器、分凝器-全能器连种不同的设置。
在这里准备用全凝器,因为可以准确的控制回流比。
此次设计是在常压下操作。
因为这次设计采用间接加热,所以需要再沸器。
回流比是精馏操作的重要工艺条件。
选择的原则是使设备和操作费用之和最低。
在设计时要根据实际需要选定回流比。
从正庚烷—正辛烷的相关物性中可看出它们可近似地看作理想物系。
而且筛板与塔盘板之间的流通面积能随气体负荷的变动而自动调节,因而在较宽的气体负荷范围内,均能保持稳定操作。
气体在塔盘板上以水平方向吹出,气液接触时间长,雾沫夹带量少,液面落差也较小。
1.2.2选定设计方案的原则方案选定是指确定整个精馏装置的流程。
主要设备的结构形式和主要操作条件。
所以方案的选定必须:(1)能满足工艺要求,达到指定的产量和质量。
(2)操作平稳,易于调节。
(3)经济合理。
(4)生产安全。
在实际的设计问题中,上述四项都是必须考虑的。
1.3确定设计方案1.3.1精馏方式的选定本设计采用连续精馏操作方式,其特点是:连续精馏过程是一个连续定态过程,能耗小于间歇精馏过程,易得纯度高的产品。
1.3.2加热方式的选取本设计采用间接蒸汽加热,加热设备为再沸器。
本设计不易利用直接蒸汽加热,因为直接蒸汽的加入,对釜内溶液起一定稀释作用,在进料条件和产品纯度,轻组分收率一定前提下,釜液浓度相应降低,故需在提馏段增加塔板以达到生产要求,从而又增加了生产的费用,但也增加了间接加热设备。
1.3.3操作压力的选取本设计采用常压操作,一般,除了热敏性物料以外,凡通过常压蒸馏不难实现分离要求,并能用江河水或循环水将馏出物冷凝下来的系统都应采用常压蒸馏。
在化工设计中有很多加料状态,这次设计中采用冷液进料。
1.3.4回流比的选择对于一般体系最小回流比的确定可按常规方法处理,但对于某些特殊体系,如乙醇水体系则要特殊处理,该体系最小回流R min 的求取应通过精馏段操作线与平衡线相切得到。
而适宜回流比R 的确定,应体现最佳回流比选定原则即装置设备费与操作费之和最低,我们推荐以下简化方法计算各项费用,从而确定最佳回流比。
一般经验值为min )2~1.1(R R1.3.5塔顶冷凝器的冷凝方式与冷却介质的选择塔顶选用全凝器,因为后继工段产品以液相出料,但所得产品的纯度低于分凝器,因为分凝器的第一个分凝器相当于一块理论板。
塔顶冷却介质采用自来水,方便、实惠、经济。
1.3.6板式塔的选择板式塔工艺尺寸设计计算的主要内容包括:板间距、塔径、塔板型式、溢流装置、塔板布置、流体力学性能校核、负荷性能图以及塔高等。
其设计计算方法可查阅有关资料。
着重应注意的是:塔板设计的任务是以流经塔内气液的物流量、操作条件和系统物性为依据,确定具有良好性能(压降小、弹性大、效率高)的塔板结构与尺寸。