The Lean Enterprise 09_Intro_to_TPM_31_pgs(全员设备预防维护)
戴尔OpenManage部署工具包安装指南说明书

Dell OpenManage Deployment Toolkit Installation GuideNotes and CautionsNOTE: A NOTE indicates important information that helps you make better use of your computer.____________________Information in this publication is subject to change without notice.© 2012 Dell Inc. All rights reserved.Reproduction of these materials in any manner whatsoever without the written permission of Dell Inc. is strictly forbidden.Trademarks used in this text: Dell™ and OpenManage™, are trademarks of Dell Inc. Red Hat Enterprise Linux® and Enterprise Linux® are registered trademarks of Red Hat, Inc. in the United States and/or other countries. SUSE ™ is a trademark of Novell Inc. in the United States and other countries. Microsoft®, Windows®, Windows Vista® and Windows® 7 are either trademarks or registered trademarks of Microsoft Corporation in the United States and/or other countries. Linux®is a registered trademark of Linus Torvalds.Other trademarks and trade names may be used in this publication to refer to either the entities claiming the marks and names or their products. Dell Inc. disclaims any proprietary interest in trademarks and trade names other than its own.2012 – 02IntroductionThe Dell OpenManage Deployment Toolkit (DTK) includes a set of utilities, sample scripts, and sample configuration files that you need, to deploy and configure your Dell system. Y ou can use DTK to build script-based and RPM-based installation for deploying large number of systems on apre-operating system environment in a reliable way, without changing their current deployment processes.Documents You Will Need•Dell OpenManage Deployment T oolkit Command Line Interface Reference Guide•Dell OpenManage Deployment T oolkit User’s Guide•Operating system documentationFor a complete list of supported operating systems, BIOS firmware, and hardware, see the Dell Systems Software Support Matrix available at /manuals→Software→Systems Management→Dell OpenManage Releases. Click the appropriate product version to access the Support Matrix.PrerequisitesBefore using DTK to deploy Microsoft Windows Pre-installation Environment (PE) or embedded Linux environment (Red Hat Enterprise Linux or SUSE Linux Enterprise Server), ensure you have the following prerequisites:Table 1-1.Prerequisites for InstallationWindows PE Environment Embedded Linux EnvironmentThe DTK self-extracting zip file (DTKX.X-WINPE-XX.exe) available at .The DTK ISO image available at .A Windows workstation that has at least 512 MB of RAM.A workstation that has at least 512 MB of RAM.Quick Installation Guide3Deployment OverviewDTK offers a complete set of utilities, sample scripts, and RPM packages that can be used to automate the deployment of Dell systems.Before running the deployment, ensure that you create specific deployment media to facilitate the deployment method you choose. For more information, see the Dell OpenManage Deployment T oolkit User’s Guide available on /manuals→Software→Systems Management→Dell OpenManage Deployment Toolkit.Deployment PrerequisitesBefore beginning the deployment process for Windows PE, ensure that you have all of the following tools, software, and information ready to use or consult:•Windows Automated Installation Kit (AIK) 1.1 released with Microsoft Windows Vista SP1 and Windows Server 2008 to build Windows PE 2.0.•Windows AIK for Windows 7 to build Windows PE 3.0.•An unzip utility.•Working knowledge to build Windows PE 2.0 and Windows PE 3.0 (See the Microsoft documentation to customize Windows PE).•Working knowledge of Microsoft Remote Installation Services (RIS) and Automated Deployment Services (ADS) (including setting up of RIS and ADS environments) or any other third party deployment system or tool for Windows PE.•Working knowledge of Windows Deployment Services (WDS) or any other third party deployment system or tool for Windows PE.• A workstation with the following capabilities:–Writable media drive–Network access• A target system with a media drive, if performing a local deployment.• A target system with a media drive and network access, if performing a network deployment.•All DTK utilities, sample scripts, and sample configuration files.•Dell Systems Management Tools and Documentation DVD.4Quick Installation GuideQuick Installation Guide 5•Y our operating system software and documentation.•An optimally configured source system with network access. NOTE: You can also download the latest drivers from .For embedded Linux, ensure that you have all of the following tools, software, and information ready to use or consult:•Advanced knowledge of Linux and Linux scripting (bash), Linux networking, installing and working with RPM Package Managers (RPMs), and creating and modifying loop file systems.•Any third party deployment system or tool.• A workstation with the following capabilities:–A writable media drive –Network access •A target system with a media drive, if performing a local deployment.•A target system with a media drive and network access, if performing a network deployment.•All DTK utilities, sample scripts, sample configuration files, and RPM packages.•All operating system RPM packages that DTK RPMs require.NOTE: Tools such as Yellowdog Updater Modified (YUM), Yet Another Setup Tool (YAST), and Advanced Packaging Tool (APT) can be used to manage RPM dependency issues.•All other utilities and files necessary to perform the deployment, including all required Linux drivers, operating system drivers, and the Dell utility partition file.•Dell Systems Management Tools and Documentation DVD.•Y our operating system software and documentation.•An optimally configured source system with network access.NOTE: You can download the latest drivers from .6Quick Installation GuidePreparing for DeploymentIf you are using the Windows PE environment:1Copy or extract DTK utilities, sample scripts, sample configuration files, and drivers provided (in the zip file) to the Windows PE image.2Organize DTK utilities, script files, configuration files, the operating system installation files, and the requisite system files and drivers on a network share or local media.3Set up a Source System by using the Dell Systems Build and Update Utility (to install your operating system) and the Systems Service and Diagnostics Tools (to load drivers). The Source System acts as a masterserver that is used to replicate settings to the T argetServers .NOTE: You can also download the latest drivers from the Dell Support website at .4Generate a system BIOS, BMC, RAID, and/or RAC configuration profile from the Source System . Copy the generated configuration files to a read/write share on the workstation or server.NOTE: You can obtain the system BIOS, BMC, RAID, and/or RAC configuration files by booting from DTK Windows PE image and running the SYSCAP .BAT , RAIDCAP .BAT , and RACCAP .BAT scripts. 5Create an operating system answer file that contains unattended operating system software installation information.6Edit DTK sample script files that access the system configuration files to set up the system BIOS, BMC, RAID, and RAC and then, install an operating system on a Target Server .If you are using the embedded Linux environment:1Obtain the DTK Linux ISO image, which is a self-contained bootable ISO image.2Use and customize the sample scripts as per your requirements.3Set up a Source System by using the Systems Build and Update Utility on the Dell Systems Management T ools and Documentation DVD (to install your operating system) and the Systems Service and Diagnostics Tools (to load drivers).NOTE: You can also download the latest drivers from the Dell Support website at .4Generate a system BIOS, BMC, RAID, and/or RAC configuration profile from the optimally configured source system. Copy the generatedconfiguration files to a read/write share onto the workstation or server.NOTE: You can obtain the system BIOS, BMC, RAID, and/or RAC configurationfiles by booting from DTK Linux ISO image and running the syscap.sh,raidcap.sh, and raccap.sh scripts.5Create an operating system answer file that contains unattended operating system software installation information.6Install an operating system on a T arget Server.DeployingTo proceed with deployment, ensure that you have prepared all scripts, files, and utilities. Y ou can deploy the Win PE and embedded Linux using one of the following methods:•Deploy using removable boot media with a network connection (media-based)•Deploy using removable boot media without a network connection (media-based)•Network-based deployment (remote)For information on these methods, see the Dell OpenManage DeploymentT oolkit User’s Guide available on /manuals→Software→Systems Management→Dell OpenManage Deployment Toolkit.Upgrading Your DTK VersionWhen upgrading from a previous release of DTK, ensure that you create the environment for new DTK version separately from the previous version. This step is necessary because the environments and requirements for the new DTK versions are completely different.Quick Installation Guide78Quick Installation Guide。
MLC 9000+ 说明书
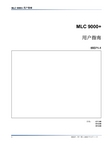
保修
我们可以担保这些产品在出厂之前,在材料和工艺方面无任何功能缺陷,并且可以担保此类 产品在三年内符合相关说明手册资料中所提到的技术规范。 除此处及上述所提及的保修条例外,无任何其他明示或暗示保修。WEST 不会因任何特殊原 因对该产品的适销性和适用性做任何担保。
限制
对于任何意外损坏、后续损坏、特殊损坏或任何其他损坏,或者除上述所提及的任何维修或 更换之外的成本或费用,供应商概不承担责任。用户必须按照说明安装和维护产品。对于因 腐蚀性而造成的产品损坏,供应商没有保修责任。用户自己对于这些产品与其应用程序的适 用性负责。对于一个有效的保修声明,产品在保修期内进行返修必须向供应商支付运费。产 品必须进行适当包装,以免在运输过程中因静电放电或其他形式的危害导致产品受损。
MLC 9000+ 用户指南
MLC 9000+ 用户指南
59371-1
价格:
£11.00 €15.00 $15.00
ii
59327,第 1 期 – 2003 年 5 月 4 日
本安装、接线和操作手册中的信息可能会有所变动,恕不另行通知。 Copyright © 2004 年 5 月,Danaher ICG,保留所有权利。未经厂商书面许可,不得以任何 形式或通过任何方式在检索系统中复制、传播、改写或存储本出版物的任何部分,或者将本 出版物的任何部分翻译成任何其他语言。 注意:
ii
59327,第 1 期 – 2003 年 5 月 4 日
MLC 9000+ 用户指南
目录
目录
1 2 MLC 9000+ 系统概述 ................................................................................
TPM介绍

An Introduction to Total Productive Maintenance (TPM)What is Total Productive Maintenance ( TPM ) ?It can be considered as the medical science of machines. Total Productive Maintenance (TPM) is a maintenance program which involves a newly defined concept for maintaining plants and equipment. The goal of the TPM program is to markedly increase production while, at the same time, increasing employee morale and job satisfaction.TPM brings maintenance into focus as a necessary and vitally important part of the business. It is no longer regarded as a non-profit activity. Down time for maintenance is scheduled as a part of the manufacturing day and, in some cases, as an integral part of the manufacturing process. The goal is to hold emergency and unscheduled maintenance to a minimum.Why TPM ?TPM was introduced to achieve the following objectives. The important ones are listed below.•Avoid wastage in a quickly changing economic environment.•Producing goods without reducing product quality.•Reduce cost.•Produce a low batch quantity at the earliest possible time.•Goods send to the customers must be non defective.Similarities and differences between TQM and TPM :The TPM program closely resembles the popular Total Quality Management (TQM) program. Many of the tools such as employee empowerment, benchmarking, documentation, etc. used in TQM are used to implement and optimize TPM.Following are the similarities between the two.1. Total commitment to the program by upper level management is required in both programmes2. Employees must be empowered to initiate corrective action, and3. A long range outlook must be accepted as TPM may take a year or more to implement and is an on-goingprocess. Changes in employee mind-set toward their job responsibilities must take place as well.The differences between TQM and TPM is summarized below.Category TQM TPMObject Quality ( Output and effects ) Equipment ( Input and cause )Mains of attaining goal Systematize the management. It issoftware orientedEmployees participation and it ishardware orientedTarget Quality for PPM Elimination of losses and wastes. Types of maintenance :1. Breakdown maintenance :It means that people waits until equipment fails and repair it. Such a thing could be used when the equipment failure does not significantly affect the operation or production or generate any significant loss other than repair cost.2. Preventive maintenance ( 1951 ):It is a daily maintenance ( cleaning, inspection, oiling and re-tightening ), design to retain the healthy condition of equipment and prevent failure through the prevention of deterioration, periodic inspection or equipment condition diagnosis, to measure deterioration. It is further divided into periodic maintenance and predictive maintenance. Just like human life is extended by preventive medicine, the equipment service life can be prolonged by doing preventive maintenance.2a. Periodic maintenance ( Time based maintenance - TBM) :Time based maintenance consists of periodically inspecting, servicing and cleaning equipment and replacing parts to prevent sudden failure and process problems.2b. Predictive maintenance :This is a method in which the service life of important part is predicted based on inspection or diagnosis, in order to use the parts to the limit of their service life. Compared to periodicmaintenance, predictive maintenance is condition based maintenance. It manages trend values, by measuring and analyzing data about deterioration and employs a surveillance system, designed to monitor conditions through an on-line system.3. Corrective maintenance ( 1957 ) :It improves equipment and its components so that preventive maintenance can be carried out reliably. Equipment with design weakness must be redesigned to improve reliability or improving maintainability4. Maintenance prevention ( 1960 ):It indicates the design of a new equipment. Weakness of current machines are sufficiently studied ( on site information leading to failure prevention, easier maintenance and prevents of defects, safety and ease of manufacturing ) and are incorporated before commissioning a new equipment.TPM - History:TPM is a innovative Japanese concept. The origin of TPM can be traced back to 1951 when preventive maintenance was introduced in Japan. However the concept of preventive maintenance was taken from USA. Nippondenso was the first company to introduce plant wide preventive maintenance in 1960. Preventive maintenance is the concept wherein, operators produced goods using machines and the maintenance group was dedicated with work of maintaining those machines, however with the automation of Nippondenso, maintenance became a problem as more maintenance personnel were required. So the management decided that the routine maintenance of equipment would be carried out by the operators. ( This is Autonomous maintenance, one of the features of TPM ). Maintenance group took up only essential maintenance works.Thus Nippondenso which already followed preventive maintenance also added Autonomous maintenance done by production operators. The maintenance crew went in the equipment modification for improving reliability. The modifications were made or incorporated in new equipment. This lead to maintenance prevention. Thus preventive maintenance along with Maintenance prevention and Maintainability Improvement gave birth to Productive maintenance.The aim of productive maintenance was to maximize plant and equipment effectiveness to achieve optimum life cycle cost of production equipment.By then Nippon Denso had made quality circles, involving the employees participation. Thus all employees took part in implementing Productive maintenance. Based on these developments Nippondenso was awarded the distinguished plant prize for developing andimplementing TPM, by the Japanese Institute of Plant Engineers ( JIPE ). Thus Nippondenso of the Toyota group became the first company to obtain the TPM certification. TPM Targets:PObtain Minimum 80% OPE.Obtain Minimum 90% OEE ( Overall Equipment Effectiveness )Run the machines even during lunch. ( Lunch is for operators and not for machines ! )QOperate in a manner, so that there are no customer complaints.CReduce the manufacturing cost by 30%.DAchieve 100% success in delivering the goods as required by the customer.SMaintain a accident free environment.MIncrease the suggestions by 3 times. Develop Multi-skilled and flexible workers.Motives of TPM 1. Adoption of life cycle approach for improving the overall performance ofproduction equipment.2. Improving productivity by highly motivated workers which is achieved by jobenlargement.3. The use of voluntary small group activities for identifying the cause of failure,possible plant and equipment modifications.Uniqueness of TPM The major difference between TPM and other concepts is that the operators arealso made to involve in the maintenance process. The concept of "I ( Productionoperators ) Operate, You ( Maintenance department ) fix" is not followed.TPM Objectives 1. Achieve Zero Defects, Zero Breakdown and Zero accidents in all functional areasof the organization.2. Involve people in all levels of organization.3. Form different teams to reduce defects and Self Maintenance.Direct benefits of TPM 1. Increase productivity and OPE ( Overall Plant Efficiency ) by 1.5 or 2 times.2. Rectify customer complaints.3. Reducethe manufacturing cost by 30%.4. Satisfy the customers needs by 100 % ( Delivering the right quantity at the righttime, in the required quality. )5. Reduce accidents.6. Follow pollution control measures.Indirect benefits of TPM 1. Higher confidence level among the employees.2. Keep the work place clean, neat and attractive.3. Favorablechange in the attitude of the operators.4. Achieve goals by working as team.5. Horizontaldeployment of a new concept in all areas of the organization.6. Share knowledge and experience.7. The workers get a feeling of owning the machine.OEE ( Overall Equipment Efficiency ) :OEE = A x PE x QA - Availability of the machine. Availability is proportion of time machine is actually available out of time it should be available.A = ( MTBF - MTTR ) / MTBF.MTBF - Mean Time Between Failures = ( Total Running Time ) / Number of Failures. MTTR - Mean Time To Repair.PE - Performance Efficiency. It is given by RE X SE.Rate efficiency (RE) : Actual average cycle time is slower than design cycle time because of jams, etc. Output is reduced because of jamsSpeed efficiency (SE) : Actual cycle time is slower than design cycle time machine output is reduced because it is running at reduced speed.Q - Refers to quality rate. Which is percentage of good parts out of total produced sometimes called "yield".Steps in introduction of TPM in a organization :Step A - PREPARATORY STAGE :STEP 1 - Announcement by Management to all about TPM introduction in the organization :Proper understanding, commitment and active involvement of the top management in needed for this step. Senior management should have awareness programmes, after which announcement is made to all. Publish it in the house magazine and put it in the notice board. Send a letter to all concerned individuals if required.STEP 2 - Initial education and propaganda for TPM :Training is to be done based on the need. Some need intensive training and some just an awareness. Take people who matters to places where TPM already successfully implemented.STEP 3 - Setting up TPM and departmental committees :TPM includes improvement, autonomous maintenance, quality maintenance etc., as part of it. When committees are set up it should take care of all those needs.STEP 4 - Establishing the TPM working system and target :Now each area is benchmarked and fix up a target for achievement.STEP 5 - A master plan for institutionalizing :Next step is implementation leading to institutionalizing wherein TPM becomes an organizational culture. Achieving PM award is the proof of reaching a satisfactory level. STEP B - INTRODUCTION STAGEThis is a ceremony and we should invite all. Suppliers as they should know that we want quality supply from them. Related companies and affiliated companies who can be our customers, sisters concerns etc. Some may learn from us and some can help us and customers will get the communication from us that we care for quality output.STAGE C - IMPLEMENTATIONIn this stage eight activities are carried which are called eight pillars in the development of TPM activity.Of these four activities are for establishing the system for production efficiency, one forinitial control system of new products and equipment, one for improving the efficiency of administration and are for control of safety, sanitation as working environment. STAGE D - INSTITUTIONALISING STAGEBy all there activities one would has reached maturity stage. Now is the time for applying for PM award. Also think of challenging level to which you can take this movement. Organization Structure for TPM Implementation :Pillars of TPMPILLAR 1 - 5S :TPM starts with 5S. Problems cannot be clearly seen when the work place is unorganized. Cleaning and organizing the workplace helps the team to uncover problems. Making problems visible is the first step of improvement.Japanese Term English Translation Equivalent 'S' termSortSeiri OrganisationSeiton Tidiness SystematiseSweepSeiso CleaningStandardiseSeiketsu StandardisationShitsuke Discipline Self - DisciplineSEIRI - Sort out :This means sorting and organizing the items as critical, important, frequently used items, useless, or items that are not need as of now. Unwanted items can be salvaged. Critical items should be kept for use nearby and items that are not be used in near future, should be stored in some place. For this step, the worth of the item should be decided based on utility and not cost. As a result of this step, the search time is reduced.Priority Frequency of Use How to useLow Less than once per year, Once per year< Throw away, Store away from the workplaceAverage At least 2/6 months, Once per month,Once per weekStore together but offlineHigh Once Per Day Locate at the workplaceSEITON - Organise :The concept here is that "Each items has a place, and only one place". The items should be placed back after usage at the same place. To identify items easily, name plates and colored tags has to be used. Vertical racks can be used for this purpose, and heavy items occupy the bottom position in the racks.SEISO - Shine the workplace :This involves cleaning the work place free of burrs, grease, oil, waste, scrap etc. No loosely hanging wires or oil leakage from machines.SEIKETSU - Standardization :Employees has to discuss together and decide on standards for keeping the work place / Machines / pathways neat and clean. This standards are implemented for whole organization and are tested / Inspected randomly.SHITSUKE - Self discipline :Considering 5S as a way of life and bring about self-discipline among the employees of the organization. This includes wearing badges, following work procedures, punctuality, dedication to the organization etc.PILLAR 2 - JISHU HOZEN ( Autonomous maintenance ) :This pillar is geared towards developing operators to be able to take care of small maintenance tasks, thus freeing up the skilled maintenance people to spend time on morevalue added activity and technical repairs. The operators are responsible for upkeep of their equipment to prevent it from deteriorating.Policy :1. Uninterrupted operation of equipments.2. Flexible operators to operate and maintain other equipments.3. Eliminating the defects at source through active employee participation.4. Stepwise implementation of JH activities.JISHU HOZEN Targets:1. Prevent the occurrence of 1A / 1B because of JH.2. Reduce oil consumption by 50%3. Reduce process time by 50%4. Increase use of JH by 50%Steps in JISHU HOZEN :1. Preparation of employees.2. Initial cleanup of machines.3. Take counter measures4. Fix tentative JH standards5. General inspection6. Autonomous inspection7. Standardization and8. Autonomous management.Each of the above mentioned steps is discussed in detail below.1. Train the Employees : Educate the employees about TPM, Its advantages, JH advantages and Steps in JH.Educate the employees about abnormalities in equipments.2. Initial cleanup of machines :o Supervisor and technician should discuss and set a date for implementing step1o Arrange all items needed for cleaningo On the arranged date, employees should clean the equipment completely with the help of maintenance department.o Dust, stains, oils and grease has to be removed.o Following are the things that has to be taken care while cleaning. They are Oil leakage, loose wires, unfastened nits and bolts and worn out parts.o After clean up problems are categorized and suitably tagged. White tags is place where problems can be solved by operators. Pink tag is placed where the aid of maintenance department is needed.o Contents of tag is transferred to a register.o Make note of area which were inaccessible.o Finally close the open parts of the machine and run the machine.3. Counter Measures :o Inaccessible regions had to be reached easily. E.g. If there are many screw to open a fly wheel door, hinge door can be used. Instead of opening a door for inspecting the machine, acrylic sheets can beused.o To prevent work out of machine parts necessary action must be taken.o Machine parts should be modified to prevent accumulation of dirt and dust.4. Tentative Standard :o JH schedule has to be made and followed strictly.o Schedule should be made regarding cleaning, inspection and lubrication and it also should include details like when, what and how.5. General Inspection :o The employees are trained in disciplines like Pneumatics, electrical, hydraulics, lubricant and coolant, drives, bolts, nuts and Safety.o This is necessary to improve the technical skills of employees and to use inspection manuals correctly.o After acquiring this new knowledge the employees should share this with others.o By acquiring this new technical knowledge, the operators are now well aware of machine parts.6. Autonomous Inspection :o New methods of cleaning and lubricating are used.o Each employee prepares his own autonomous chart / schedule in consultation with supervisor.o Parts which have never given any problem or part which don't need any inspection are removed from list permanently based on experience.o Including good quality machine parts. This avoid defects due to poor JH.o Inspection that is made in preventive maintenance is included in JH.o The frequency of cleanup and inspection is reduced based on experience.7. Standardization :o Upto the previous stem only the machinery / equipment was the concentration. However in this step the surroundings of machinery are organized. Necessary items should be organized, such that there isno searching and searching time is reduced.o Work environment is modified such that there is no difficulty in getting any item.o Everybody should follow the work instructions strictly.o Necessary spares for equipments is planned and procured.8. Autonomous Management :o OEE and OPE and other TPM targets must be achieved by continuous improve through Kaizen.o PDCA ( Plan, Do, Check and Act ) cycle must be implemented for Kaizen.PILLAR 3 - KAIZEN :"Kai" means change, and "Zen" means good ( for the better ). Basically kaizen is for small improvements, but carried out on a continual basis and involve all people in the organization. Kaizen is opposite to big spectacular innovations. Kaizen requires no or little investment. The principle behind is that "a very large number of small improvements are move effective in an organizational environment than a few improvements of large value. This pillar is aimed at reducing losses in the workplace that affect our efficiencies. By using a detailed and thorough procedure we eliminate losses in a systematic method using various Kaizen tools. These activities are not limited to production areas and can be implemented in administrative areas as well.Kaizen Policy :1. Practice concepts of zero losses in every sphere of activity.2. relentless pursuit to achieve cost reduction targets in all resources3. Relentless pursuit to improve over all plant equipment effectiveness.4. Extensive use of PM analysis as a tool for eliminating losses.5. Focus of easy handling of operators.Kaizen Target :Achieve and sustain zero loses with respect to minor stops, measurement and adjustments, defects and unavoidable downtimes. It also aims to achieve 30% manufacturing cost reduction.Tools used in Kaizen :1. PM analysis2. Why - Why analysis3. Summary of losses4. Kaizen register5. Kaizen summary sheet.The objective of TPM is maximization of equipment effectiveness. TPM aims at maximization of machine utilization and not merely machine availability maximization. As one of the pillars of TPM activities, Kaizen pursues efficient equipment, operator andmaterial and energy utilization, that is extremes of productivity and aims at achieving substantial effects. Kaizen activities try to thoroughly eliminate 16 major losses.16 Major losses in a organisation:Loss Category1. Failure losses - Breakdown loss2. Setup / adjustment losses3. Cutting blade loss4. Start up loss5. Minor stoppage / Idling loss.6. Speed loss - operating at low speeds.7. Defect / rework loss8. Scheduled downtime lossLosses that impede equipment efficiency9. Management loss10. Operating motion loss11. Line organization loss12. Logistic loss13. Measurement and adjustment lossLoses that impede human work efficiency14. Energy loss15. Die, jig and tool breakage loss16. Yield loss.Loses that impede effective use of production resourcesClassification of losses :Aspect Sporadic Loss Chronic LossCausation Causes for this failure can beeasily traced. Cause-effectrelationship is simple to trace.This loss cannot be easilyidentified and solved. Even ifvarious counter measures areappliedRemedy Easy to establish a remedialmeasureThis type of losses are causedbecause of hidden defects inmachine, equipment andmethods.Impact / Loss A single loss can be costly A single cause is rare - acombination of causes trendsto be a ruleFrequency of occurrence The frequency of occurrence is lowand occasional.The frequency of loss is more. Corrective action Usually the line personnel in the production can attend to this problem. Specialists in process engineering,quality assurance and maintenancepeople are required.PILLAR 4 - PLANNED MAINTENANCE :It is aimed to have trouble free machines and equipments producing defect free products for total customer satisfaction. This breaks maintenance down into 4 "families" or groups which was defined earlier.1. Preventive Maintenance2. Breakdown Maintenance3. Corrective Maintenance4. Maintenance PreventionWith Planned Maintenance we evolve our efforts from a reactive to a proactive method and use trained maintenance staff to help train the operators to better maintain their equipment. Policy :1. Achieve and sustain availability of machines2. Optimum maintenance cost.3. Reduces spares inventory.4. Improve reliability and maintainability of machines.Target :1. Zero equipment failure and break down.2. Improve reliability and maintainability by 50 %3. Reduce maintenance cost by 20 %4. Ensure availability of spares all the time.Six steps in Planned maintenance :1. Equipment evaluation and recoding present status.2. Restore deterioration and improve weakness.3. Building up information management system.4. Prepare time based information system, select equipment, parts and members and map out plan.5. Prepare predictive maintenance system by introducing equipment diagnostic techniques and6. Evaluation of planned maintenance.PILLAR 5 - QUALITY MAINTENANCE :It is aimed towards customer delight through highest quality through defect free manufacturing. Focus is on eliminating non-conformances in a systematic manner, much like Focused Improvement. We gain understanding of what parts of the equipment affect product quality and begin to eliminate current quality concerns, then move to potential quality concerns. Transition is from reactive to proactive (Quality Control to Quality Assurance).QM activities is to set equipment conditions that preclude quality defects, based on the basic concept of maintaining perfect equipment to maintain perfect quality of products. The condition are checked and measure in time series to very that measure values are within standard values to prevent defects. The transition of measured values is watched to predict possibilities of defects occurring and to take counter measures before hand.Policy :1. Defect free conditions and control of equipments.2. QM activities to support quality assurance.3. Focus of prevention of defects at source4. Focus on poka-yoke. ( fool proof system )5. In-line detection and segregation of defects.6. Effective implementation of operator quality assurance.Target :1. Achieve and sustain customer complaints at zero2. Reduce in-process defects by 50 %3. Reduce cost of quality by 50 %.Data requirements :Quality defects are classified as customer end defects and in house defects. For customer-end data, we have to get data on1. Customer end line rejection2. Field complaints.In-house, data include data related to products and data related to processData related to product :1. Product wise defects2. Severity of the defect and its contribution - major/minor3. Location of the defect with reference to the layout4. Magnitude and frequency of its occurrence at each stage of measurement5. Occurrence trend in beginning and the end of each production/process/changes. (Like pattern change,ladle/furnace lining etc.)6. Occurrence trend with respect to restoration of breakdown/modifications/periodical replacement of qualitycomponents.Data related to processes:1. The operating condition for individual sub-process related to men, method, material and machine.2. The standard settings/conditions of the sub-process3. The actual record of the settings/conditions during the defect occurrence.PILLAR 6 - TRAINING :It is aimed to have multi-skilled revitalized employees whose morale is high and who has eager to come to work and perform all required functions effectively and independently. Education is given to operators to upgrade their skill. It is not sufficient know only "Know-How" by they should also learn "Know-why". By experience they gain, "Know-How" to overcome a problem what to be done. This they do without knowing the root cause of the problem and why they are doing so. Hence it become necessary to train them on knowing "Know-why". The employees should be trained to achieve the four phases of skill. The goal is to create a factory full of experts. The different phase of skills arePhase 1 : Do not know.Phase 2 : Know the theory but cannot do.Phase 3 : Can do but cannot teachPhase 4 : Can do and also teach.Policy :1. Focus on improvement of knowledge, skills and techniques.2. Creating a training environment for self learning based on felt needs.3. Training curriculum / tools /assessment etc conductive to employee revitalization4. Training to remove employee fatigue and make work enjoyable.Target :1. Achieve and sustain downtime due to want men at zero on critical machines.2. Achieve and sustain zero losses due to lack of knowledge / skills / techniques3. Aim for 100 % participation in suggestion scheme.Steps in Educating and training activities :1. Setting policies and priorities and checking present status of education and training.2. Establish of training system for operation and maintenance skill up gradation.3. Training the employees for upgrading the operation and maintenance skills.4. Preparation of training calendar.5. Kick-off of the system for training.6. Evaluation of activities and study of future approach.PILLAR 7 - OFFICE TPM :Office TPM should be started after activating four other pillars of TPM (JH, KK, QM, PM). Office TPM must be followed to improve productivity, efficiency in the administrative functions and identify and eliminate losses. This includes analyzing processes and procedures towards increased office automation. Office TPM addresses twelve major losses. They are1. Processing loss2.Cost loss including in areas such as procurement, accounts, marketing, sales leading to high inventories3. Communication loss4. Idle loss5. Set-up loss6. Accuracy loss7. Office equipment breakdown8. Communication channel breakdown, telephone and fax lines9. Time spent on retrieval of information10. Non availability of correct on line stock status。
年产十万吨乙二醇项目-初步设计说明书
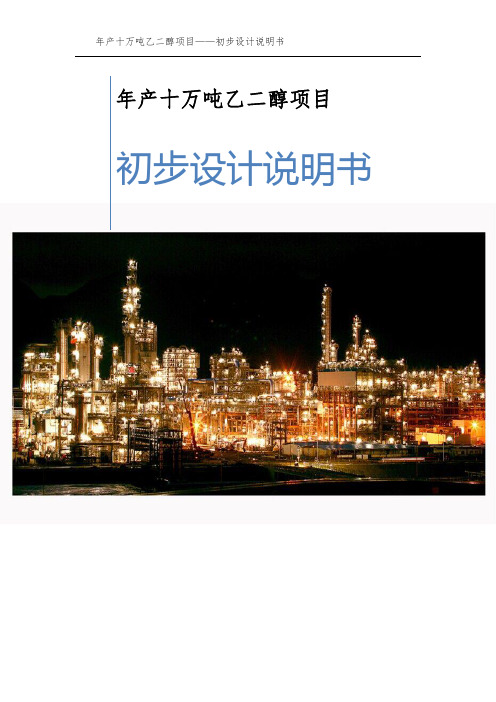
Lean-Boot-Camp-Day-1
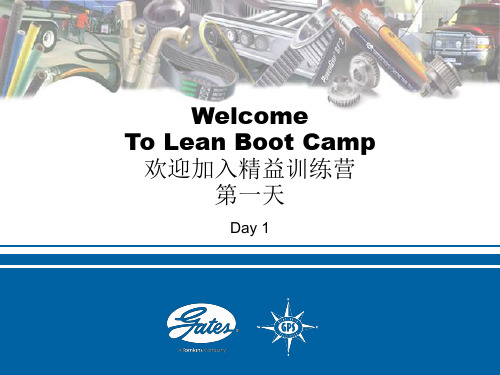
• Key elements of Lean manufacturing精益生产的要素 – Just in time 即时响应 – Zero defects零缺陷 ►
10
Basic Concepts of Lean Manufacturing 精益生产的基本概念
• The Gates Production System is based on the Toyota Production Model 盖茨生产系统基于丰田生 产模式
9
Basic Concepts of Lean Manufacturing精益生产的基本概念
• Lean Manufacturing was developed by Toyota in the early 1940’s精益生产由丰 田在上世纪四十年代初期发展起来 – Taiichi Ohno, Sakichi Toyoda and his son Kiichiro – Mass vs. Lean大批量对精益 – Many different products with small runs, efficiently很多不同的产品有效的 小批量生产
成本+利润=价格
Price
Price
Profit
Cost
Lean Thinking
Price – Cost = Profit 精益思想
U9环境配置及安装介绍

U9环境配置及安装介绍
正式环境配置流程
目录
U9环境配置
U9安装过程
U9系统管理
U9企业创建与配置
产品安装流程
DB:
1
SQL Server安装 App:
1
安装过程略
U9安装服务器
2
U9主控服务器
安装管理控制台
U9主控服务器
3
创建环境
4
U9主控服务器
1) 2) 3) 4)
生产环境 测试环境 二次开发环境 教学环境
安装服务
U9系统管理
参数设置,设置用户补丁服务器的获取U9补丁的参数。 包含用友U9补丁服务器的网络设置、补丁的存放位置、更新设置、安装设置。 使用户补丁服务器能够自动或者手动的方式来安装和部署U9提供的补丁。 如下图:
U9系统管理
测试环境下载安装补丁
U9系统管理
测试环境,在已安装补丁中将以验证的补丁进行标记才能在生产环境安装
U9系统管理 许可证监控包含两个方面的内容 一、查看本站点中使用的加密盒中授权的使 用情况。也就是每个应用的许可总数和已使 用的许可数量。 二、特征查看,查询本站点中使用的加密盒 中的特征的对应情况。 特征分两类:一类是U9的全局特征,即这个 特征对各个模块的应用均有影响;一类是局 部特征,即这个特征只对某个模块的应用有 影响。
2010年 9月 9日
概述
内容:本单元主要讲解 U9 安装的环境配
大华6017793门禁控制器用户手册说明书
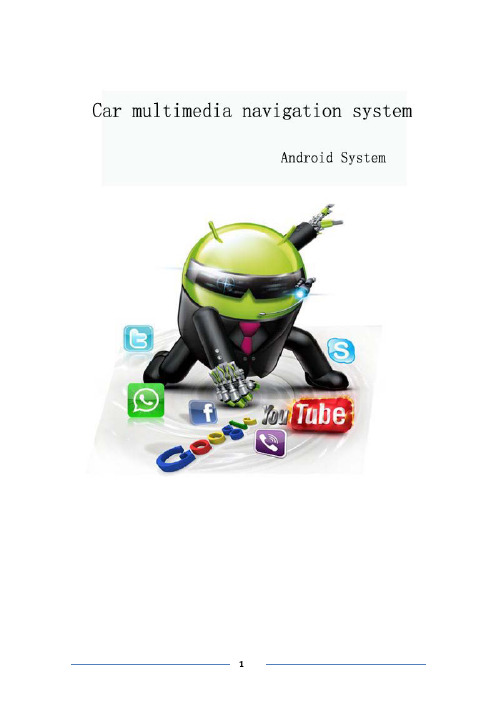
table of Contents1、matters needing attention (3)2、Basic operation (4)2.1、System reset (4)2.2、Start/off host (4)2.3、volume adjusting (4)2.4、Power Key (4)2.5、Backing camera (4)3、Main interface operation (5)4、Bluetooth (6)4.1、Bluetooth main interface (6)4.2、Bluetooth–dial (6)4.3、Outgoing state diagram (7)4.4、Call state diagram (7)4.5、Phone book and phone records (8)4.6、Bluetooth-Music (8)5、Vehicle setup (9)5.1、General settings (9)5.2、Factory settings (10)5.3、Touch learning (10)5.4、Sound settings (10)5.5、Navigation set (11)5.6、Square set (11)6、radio reception (12)7、Multimedia music (13)8、Multimedia video: (14)9、File management operation (14)10、Common troubleshooting wizard (15)1、matters needing attentionFor your safety,please try not to while driving to watch video and operate the machine.When you're driving the volume knob can clearly hear the sound of the outside world.Product change iterations,the system will be updated step by step.The contents of this manual are for reference only,please refer to the actual product.1.1First pay attention to traffic safety.1.2Please park your car in a safe place if you have difficulty in operating the system.1.3Do not allow children to operate the machine,in order to avoid damage to the adult or machine.1.4Please follow the traffic rules when using the satellite navigation system.1.5Please do not prohibit the use of electronic equipment or the use of open flame,such as:gas stations,wineries,strong electromagnetic interference areas,or may cause danger.1.6Do not self maintenance,maintenance,installation of the machine.In the power supply is switched on do not install or repair the machine,because of no electronic equipment or vehicle accessories installation training or lack of experienced personnel to install and repair the machine is very dangerous.1.7Don't put the machine storage or installed in direct sunlight.Don't make placed and other harmful substances into the environment,especially LCD screen.If installed,LCD screen just in air conditioning ventilation Road in the vicinity,please ensure cool or hot air not blowing directly on the machine,otherwise it might damage the machine,even the car or bodily harm.2、Basic operation2.1、System resetCaused by the improper operation of the crashes and other non normal phenomenon, please use the tip of the short by a panel reset hole,the machine can be restored to normal.(Note:due to the reset button panel on a small,please press this button),using the pen or similar pointed object point2.2、Start/off hostIn the ACC switch in the open position,according to the host panel"power"button to turn on the power,insert the CD into the trough dish,machine will automatically open, open access to read disk mode;when the phone is switched on,long press"power" button switch for host panel,or flameout pull bus key will shut closed the power of this machine.2.3、volume adjustingRotate the volume knob on the console panel(some models have the volume control keys on the panel"VOL+/VOL-"button),which can adjust the volume of the machine.2.4、Power KeyPress the Power key on the panel to mute the system,press again or adjust the volume to restore the sound.2.5、Backing cameraThe vehicle go into reverse,regardless of the machines in the boot or shutdown state, the display will immediately switch to reverse the camera screen.3、Main interface operationIn the main interface,a different function icon into the corresponding interface,the function of the detailed operating instructions.Please see the back.About touch sliding page can switch between multiple pages,as shown below:Click the icon to access the third-party application menu as follows,Long press the icon to drag to move the icon position4、Bluetooth4.1、Bluetooth main interfaceAs shown below:Search around the open Bluetooth device.Select the device that exists around the click on the link to wait for the match or match Will automatically link.Disconnect the connected device.Settings:mainly for the Bluetooth device function selection,automatic connection,auto answer,Bluetooth name modification and Bluetooth PIN code modification.4.2、Bluetooth–dialBluetooth connection is successful,the user can dial directly,through the touch screen number keys,as shown below:4.3、Outgoing state diagramAfter the Bluetooth connection is successful,you can enter the number by phonebook,dialing,and manually pressing the number keys on your keyboard use Dial outthe phoneThe voice of the other party's call is output from the machine(in-car speaker).Click this icon to switch the voice of the other party to the output of the paired mobile phone.The voice of the other party's call is output from the paired mobile phone.Click this icon to switch the voice of the other party to the output of the machine(in-car speaker).The microphone on the machine is turned on.During the call,the other party can hear the content of the user on the machine and the two parties talk normally.Click this icon to turn off the microphone on the machine.The microphone on the machine is off.During the call,the other party cannot hear the content of the user on the machine.Click this icon to turn on the microphone on the machine.Dial the call or hang up during the call to end the callIn the call interface,you can hide or display the dial pad4.4、Call state diagramBluetooth connection status,there will be incoming calls call interface as follows:Answer the call and enter the call state.4.5、Phone book and phone recordsBluetooth connection,can enter the phone book and phone records,as follows:number in the phone book.to dial the number to contact each other.Used to synchronize the phone book in this connected phoneHas been dialed out of the number recordList of numbers that have been answeredList of unanswered numbers4.6、Bluetooth-MusicBluetooth media media connection is successful,if the phone supports Bluetoothmusic player,the audio will be transmitted to the Bluetooth device,as shown below:You can control the phone through the three buttons to control the music on a song,pause playback and the next song function5、Vehicle setupSet the main settings,navigation settings,network settings,sound settings,time settings,brightness settings,language and input method, steering wheel settings,factory settings and on the car,as shown below:5.1、General settingsGeneral settings include brake warning,reverse volume switch,button tone,reverse mirror,default system volume,default call volume,home page style,as shown below:Brake Warning:Controls whether or not a traffic warning switch pops up when playing a video file.Reverse volume switch:control the volume when the reversing switch.Touch tone:Whether the control system has a tone switch when it touches.Reversing Mirror:Controls whether the camera is turned on.GPS mix:Switch function options,navigation work with music-video-Bluetooth music-mix outputGPS Mixing Ratio:Controls the mixing ratio of GPS.Default system volume:Controls the system volume size by default.Default call volume:Controls the default value of the Bluetooth call volume.5.2、Factory settingsFactory settings are mainly for production,installation,after-sales,maintenance,non-professionals,please do not use[Note]Non-professionals are not allowed to enter the factory settings.Improper settings may result in the product not working properly!!!5.3、Sound settingsSound settings are sound and balance two parts,as shown below:Sound effects:sound type settings,you can off,users,rock,pop,live,dance, classical and soft eight types to choose,according to their own preferences equal loudness,bass and treble to adjust.Balance:sound field balance mode settings,according to the different effects of the upper and lower left and right reverse adjustment.5.4、Navigation setSelect map application:press GPS key,will display the default navigation software5.5、Square setSteering wheel control button settings:enter the steering wheel learning interface,first press,And then long press the button on the steering wheel,select the appropriate key in the interface,when the settings are successful,the correspondinginterface button will be lit,after learning press Will save this learning content.6、radio receptionThe main radio interface,as shown below:[Note]The introduction is for reference only,please refer to the actual product.band,as:FM1、FM2、FM3、AM1、AM2Short press the button from the system will search the radio station step by step from high frequency to low frequency or from low frequency to high frequency until you find the radio frequency you want(FM band short press for FM1\FM2\FM3bandbetween the1-6units switch;long press to automatically scan the radio to the highfrequency;long press to the low-end scanning stationNote:If there is a tuner on some models of the front panel button,rotate it to the search frequency).The stronger the FM signal,the switch of the stereo,the radio broadcast effect is good,whereas in the remote area,the wireless signal is not stable,close the stereo switch to single channel,can improve the effect of the radio.When in a remote area,the radio signal is unstable,usually switching to the remote mode,the closer to the city center,the more powerful the FM broadcast signal, usually switching to the short range to improve the effect of the radio broadcast.Automatically browse stations and store up to six preset stations per band.The system can store up to30preset stations(18FM stations and12AM stations).(Click the browse button to browse the stations that have been memorized in the band(view a station every5seconds).After browsing to the appropriate station,click Browse and the selected station will play.Click on the button system will automatically search the radio from low to high frequency,during the search process,once again hit the button will stop the search,while the frequency of the screen will stop changing.Can enter the sound settings to switch the sound.7、Multimedia musicAfter inserting the USB flash drive,entering the music application will update all the audio files in the USB flash drive to the list,as shown below:Enter the song list,as shown below:You can select different paths to view music,and you can update the newly added audio files in the USB flash drive with the refresh button.Circle all the songs.Random play.Sound settings.previous track.Pause playback.next track.8、Multimedia video:After inserting the USB flash drive,the video will automatically detect the USB flash drive and enter the video playback screen.Music lists the video files in the USB drive.Enter the video playback page,as shown below:Function is similar to music,can be selected from U disk or local path(Note:This video player has a total of8interfaces,it supports MP4,AVI,RMVB,3GP,MKV,MOV, MPG,FLV and1080p HD video playback formatCan be displayed on the screen length and width to switch the ratio.9、File management operationEnter the file management interface,click Query the file to be found orclick Create a new folder,as shown below:Can be different from the path into the corresponding folder Long press the optional file on the file to copy,delete,cut and rename the details of the file,as shown below10、Common troubleshooting wizardIf you encounter the following problems in use,troubleshooting will help you quickly solve the problem,if the problem is still not resolved,it is recommended to contact our service department to help solve.phenomenon Reason HandleCan not boot The car key is not inserted intothe switch and the switch is notopenInsert the vehicle key and openthe door Power line insertion host Insert power cordTouch screen is not allowed Recalibrate the touch screen,press and hold the screen with fivefingers,and the system will automatically enter the calibrationscreen.The touch screen does notrespond The system is processing the transaction(road search,etc.),wait a moment,if it still can't be solved,please press the RST hole throughthe needle or the tip of the pen.Reversing without rear viewimageCamera not installed Install cameraCamera system is wrong Restart the machineThe system does not start,the rear view image appears after the reverse process,and thebutton is invalid.Pay attention to the principle ofdriving safety when designingproducts,and preset the rearview priorityYou must terminate the reverseaction before you can start thesystem by pressing the originalcar power button.Navigation cannot be located May be in the shielding area ofsome navigation signalsTry to drive the car out of a distance and observe whether the navigation resumes thesignal.If it is not restored,please restart or reset the machine.Cannot locate and navigate afterbootingNavigation map blind spots,some remote mountain areas orroads have not been built in thismapConfirm update mapFuzzy search can't find where togo First confirm that the entered Chinese character is correct,and then try to enter another name for the location.If it is not found,the location may not be in the map database.The navigation system gives the selected road"a far-reachingapproach"The navigation system will consider various factors in the road search.In addition to the distance,it will also consider the level of the road,the traffic regulations,the viaduct,the main line,etc.In short,it is convenient for the driver to reach the destination in the shortestpossible time.Blank on the map The machine has no network or no offline map data.It is alsopossible that the navigation scale is set too large or too small.Trychanging the scale to see if you can restore the map display.If it hasnot been resolved,it may be caused by the loss of positioning.Please re-select a marker point.FCC Radiation Exposure Statement:This equipment complies with FCC radiation exposure limits set forth for an uncontrolled environment. This equipment should be installed and operated with minimum distance 20cm between the radiator & your bodyFCC WarningThis device complies with Part 15 of the FCC Rules. Operation is subject to the following two conditions:(1) This device may not cause harmful interference, and (2) this device must accept any interference received, including interference that may cause undesired operation.NOTE 1: This equipment has been tested and found to comply with the limits for a Class B digital device, pursuant to part 15 of the FCC Rules. These limits are designed to provide reasonable protection against harmful interference in a residential installation. This equipment generates uses and can radiate radio frequency energy and, if not installed and used in accordance with the instructions, may cause harmful interference to radio communications. However, there is no guarantee that interference will not occur in a particular installation. If this equipment does cause harmful interference to radio or television reception, which can be determined by turning the equipment off and on, the user is encouraged to try to correct the interference by one or more of the following measures:- Reorient or relocate the receiving antenna.- Increase the separation between the equipment and receiver.-Connect the equipment into an outlet on a circuit different from that to which the receiver is connected.-Consult the dealer or an experienced radio/TV technician for help.NOTE 2: Any changes or modifications to this unit not expressly approved by the party responsible for compliance could void the user's authority to operate the equipment.。
Lean_Sigma_Integration
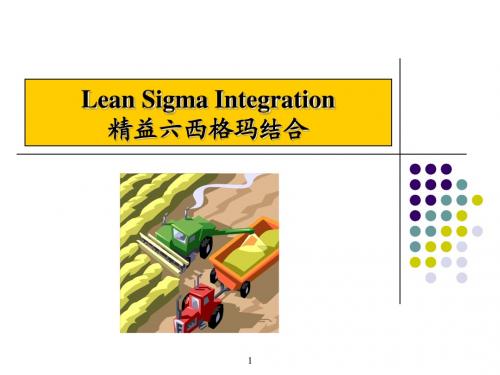
Pursuit of Perfection
A relentless pursuit of perfection through a culture driven at continuous improvement.
Six Sigma Application (Process Map, FMEA, SPC Control Charts, …)
SPEED
STABILITY & ACCURACY
LEAN + SIX SIGMA = A POWERFUL UNION
8
Lean Tools
Six Sigma Tools
s DOE (Optimizing) s Training s Change mgmt s Multi-Vari s DOE (Screening) s Control chart s ANOVA s FMEA
Lean Tools
Cell Design (Co-location) Kanban / Pull Product / Process Family (Group
Lean + Six Sigma Lean
Waste Elimination Standard Work Flow Customer PULL
Six Sigma
s Variation Reduction s Scrap / Rework Elimination s Process Optimization s Process Control
Operation
6s 6s
Test
6s 6s Customer
Administration
Materials
Support
汽车GPS防盗系统和GSM防盗系统有什么区别
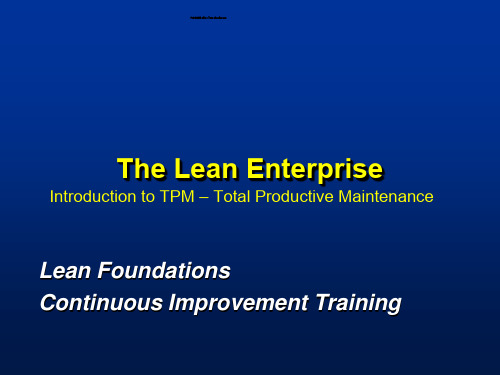
– Everyone has a role to make TPM work – Management to set policy – Middle management, staff to support and lead – Maintenance to maintain and train – Operators to take on new maintenance challenges
of the ‘six major losses’ while striving for a goal of zero unscheduled downtime
TPM - The Six Major Losses (Waste)
Downtime Losses
– (1) Equipment failures – (2) Set-up and adjustments
TPM – Operational Goals (Quantitative)
Cost Reductions
– Actual and to be reduced – Energy savings – Maintenance
Equipment Efficiencies
0.5/ unit x 400 units 400 minutes
= 50%
5. Defects in Process
]
6. Reduced Yield
Overall Equip. Effectiveness:
Ratio of Quality
Products
=
Processed Amount – Amount of Defects
戴尔易安信系统更新版本 1.9.2.0 安全配置指南说明书

Dell EMC System Update version 1.9.2.0 Security Configuration GuideNotes, cautions, and warningsA NOTE indicates important information that helps you make better use of your product.A CAUTION indicates either potential damage to hardware or loss of data and tells you how to avoidA WARNING indicates a potential for property damage, personal injury, or death.© 2021 Dell Inc. or its subsidiaries. All rights reserved. Dell, EMC, and other trademarks are trademarks of Dell Inc. or its subsidiaries. Other trademarks may be trademarks of their respective owners.Figures (4)Tables (5)Chapter 1: PREFACE (6)Terms used in this document (7)Chapter 2: Deployment models (8)Security profiles (8)Chapter 3: Product and Subsystem Security (9)Security controls map (9)Authentication (9)Access control (9)Login security settings (10)Failed login behavior (10)Remote connection security (10)User and credential management (10)Network security (10)Network exposure (10)Outbound ports (10)Inbound ports (11)Data security (11)Auditing and logging (11)Serviceability (11)Product code integrity (12)Chapter 4: Miscellaneous Configuration and Management (13)Dell EMC System Update licensing (13)Protect authenticity and integrity (13)Manage backup and restore in Dell EMC System Update (13)Contents31Security Controls Map (9)4Figures1Revision History (6)2Terms used in this document (7)3Outbound ports (10)4Inbound ports (11)Tables51PREFACE As part of an effort to improve its product lines, Dell EMC periodically releases revisions of its software and hardware. Some functions that are described in this document might not be supported by all versions of the software or hardware currently in use. The product release notes provide the most up-to-date information about product features.Contact your Dell EMC technical support professional if a product does not function properly or does not function as described in this document. This document was accurate at publication time. To ensure that you are using the latest version of this document, go to https:///support.Legacy disclaimersThe information in the publication is provided as-is. Dell Technologies makes no representations or warrantiesof any kind regarding the information in the publication, and specifically disclaims implied warranties of merchantability or fitness for a particular purpose. In no event shall Dell Technologies, its affiliates or suppliers, be liablefor any damages whatsoever arising from or related to the information contained herein or actions that you decide to take based thereon, including any direct, indirect, incidental, consequential, loss of business profits or special damages, even if Dell Technologies, its affiliates or suppliers have been advised of the possibility of such damages.The Security Configuration Guide intends to be a reference. The guidance is provided based on a diverse set of installed systems and may not represent the actual risk/guidance to your local installation and individual environment. It is recommended that all users determine the applicability of this information to their individual environments and take appropriate actions. All aspects of this Security Configuration Guide are subject to change without notice and on a case-by-case basis. Your use of the information that is contained in this document or materials that are linked herein is at your own risk. Dell reserves the right to change or update this document in its sole discretion and without notice at any time.Scope of the documentThis document includes information about security features and capabilities of Dell EMC System Update (DSU). AudienceThis document is intended for individuals who are responsible for managing security for Dell EMC System Update. Revision HistoryThe following table presents the revision history of this document.Table 1. Revision HistoryRevision Date DescriptionA00July 2021Initial release of the Dell EMCSystem Update 1.9.2.0 Security GuidelineDocument.A00March 2021Initial release of the Dell EMCSystem Update 1.9.1.0 Security GuidelineDocument.6PREFACEDocument ReferencesIn addition to this guide, you can access the other guides available at /support . Since DSU supports an Update to the Server through iDRAC, see Integrated Dell Remote Access Controller User's Guide for any configuration-related queries. For the information about supported PowerEdge Servers, see Dell EMC Systems Management - OpenManage Software Support Matrix. Go to support site, click product support -> Dell EMC system Update to access the following documents:●Dell EMC System Update Version 1.9 User's Guide●Dell System Update 1.9 Release NotesYou can find the technical artifacts including white papers at /supportSecurity resources●Dell Security Advisories (DSA) /support/security●Support knowledge base (KB) articles at /support/kbdoc/en-us/000130590/dell-emc-system-update-dsu Getting helpContact your Dell EMC technical support professional if a product does not function properly or does not function as described in this document. This document was accurate at publication time. To ensure that you are using the latest version of this document, go to /supportReporting security vulnerabilitiesDell EMC takes reports of potential security vulnerabilities in our products very seriously. If you discover a security vulnerability, you are encouraged to report it to Dell EMC immediately. For the latest on how to report a security issue to Dell, please see the Dell Vulnerability Response Policy on the site.Topics:•Terms used in this documentTerms used in this documentTable 2. Terms used in this documentTerminology DescriptionDSU Dell EMC System UpdateDUP Dell EMC Update PackageiDRAC Integrated Dell Remote Access ControllerWMI Windows Management InstrumentationSSH Secure ShellPREFACE7Deployment models You can deploy Dell EMC System Update on Microsoft Windows Server or Linux operating system through Dell Update Package (DUP) on supported Dell EMC PowerEdge servers. Dell EMC System Update supports online or offline method to deploy on the selected operating system through Dell Update Package. For more information on the deployment of Dell System Update, see Dell EMC System Update User's Guide at /supportTopics:•Security profilesSecurity profilesDell EMC System Update has a default security profile for secure HTTP or HTTPS access with self-signed certificate during installations. It is recommended to replace the Certificate Authority (CA) signed certificates for a better security environment. 8Deployment modelsProduct and Subsystem Security Topics:•Security controls map•Authentication•Login security settings•User and credential management•Network security•Data security•Auditing and logging•Serviceability•Product code integritySecurity controls mapDell EMC System Update is a script optimized update deployment tool that is used to apply Dell EMC updates such as applications, firmware, and drivers for Linux and Microsoft Windows operating systems. Using DSU, identifies the available updates, select the relevant updates, and deploy the updates on a single system or multiple systems through operating systems or integrated Dell Remote Access Controller(iDRAC) or iDRAC passthrough(connection to the iDRAC through redfish API to get relevant firmware update and deploy. System Credentials (share location credentials) used for repository or system (remote server) access are not stored within DSU.The following figure displays the DSU security controls map:Figure 1. Security Controls MapAuthenticationAccess controlDell EMC System Update allows only administrator console and root privilege console account to perform the operation.Product and Subsystem Security9Login security settingsFailed login behaviorDellEMC System Update (DSU) populate failed login message on console for wrong credential. For more information about failed login behavior of DSU, see the Dell EMC System Update User's Guide at /supportRemote connection securityDell EMC System Update uses open source library for remote connection using SSH and WMI and it does not log the credentials mentioned for connections.User and credential managementDell EMC System Update supports HTTPS and HTTP connections.Network securityDell System Update uses a pre-configured firewall to enhance security by restricting inbound and outbound network traffic to the TCP and UDP ports. The tables in this section lists the inbound and outbound ports that Dell System Update uses. Network exposureDell System Update uses inbound and outbound ports when communicating with remote systems.Outbound portsOutbound ports can be used by Dell System Update when connecting to a remote system..The ports that are listed in the following table are the Dell System Update outbound ports.Table 3. Outbound portsPort number Layer 4 Protocol Service7TCP, UDP ECHO22TCP SSH25TCP SMTP53UDP, TCP DNS67,68TCP DHCP80TCP HTTP88TCP, UDP Kerberos111TCP, UDP ONC RPC123TCP, UDP NTP161-163TCP, UDP SNMP389TCP, UDP LDAP443TCP HTTPS10Product and Subsystem SecurityTable 3. Outbound ports (continued)Port number Layer 4 Protocol Service448TCP Data Protection Search Admin REST API 464TCP, UDP Kerberos514TCP, UDP rsh587TCP SMTP636TCP, UDP LDAPS902TCP VMware ESXi2049TCP, UDP NFS2052TCP, UDP mountd, clearvisn3009TCP Data Domain REST APIInbound portsThe inbound ports that are available to be used by a remote system when connecting to Dell System Update remote.The ports that are listed in the following table are the Dell System Update inbound ports.Table 4. Inbound portsPort number Layer 4 Protocol Service22TCP SSH80TCP HTTP443TCP HTTPS135TCP WMIData securityDSU does not store any data in databases also from input dependencies libraries. DSU uses certificates for secure HTTP access (HTTPS). By default, DSU installs GPG keys and uses the self-signed certificate for the HTTPS secure transactions. For better security, it is recommended to use the Certificate Authority (CA) signed or custom certificates.Auditing and loggingDSU administration console generate all the relevant logs in default location or user provided location. DSU supports Log file retention , compression and file rollover. Log file sizes are defined to 5 MB limit. A descriptive and clear log messages are provided. For more information about Troubleshooting, Log files, see the Dell EMC System Update User's Guide available at /supportServiceabilityThe support website https:///support provides access to licensing information, product documentation, advisories, downloads, and troubleshooting information. This information helps you to resolve a product issue before you contact support team.Special login is not required to Dell EMC System Update for service personnel. If the troubleshooting bundle is not sufficient, the personnel can enable the root user to collect more information.Ensure that you install security patches and other updates when they are available, including the Dell EMC System Update.Product and Subsystem Security11Product code integrityThe Dell EMC System Update software installer is signed by Dell. It is recommended that you verify the authenticity of the Dell EMC System Update installer signature.12Product and Subsystem Security4Miscellaneous Configuration andManagement Topics:•Dell EMC System Update licensing•Protect authenticity and integrity•Manage backup and restore in Dell EMC System UpdateDell EMC System Update licensingDSU has open source approvals for the internal dependencies and gets installed with the application on the box. It can also be find at /releases/DSU/ For more information about licensing of Dell EMC System Update, see the Dell EMC System Update User's Guide available at /supportProtect authenticity and integrityTo ensure product integrity, the Dell EMC System Update installation and update components are signed.To ensure communication integrity, it is recommended to use CA-signed certificate.Manage backup and restore in Dell EMC System UpdateFor information about backup and restore, see the Dell EMC System Update User's Guide available at https:/// support/home/?app=knowledgebaseMiscellaneous Configuration and Management13。
Volume 9—OEM Product Guide CA08100011E—January 201

V9-T4-5444.3Operator InterfacePanel MetersProduct OverviewProduct Selection GuideFor our complete product offering, see Volume 7—Logic Control, Operator Interface and Connectivity Solutions, CA08100008E.DescriptionE5 Panel MetersEclipse Series Panel Meters Page V9-T4-55Page V9-T4-55Number of digits 54Display technology 7-segment LED 7-segment LED Display character height 8 mm14 mmPanel cut-out size 1/32 DIN (25 x 50 mm)1/8 DIN (45 x 92 mm)Available outputs NoneDual relay, analog, RS-485Available inputs 0–10V/2–10V/0–20 mA/4–20 mA DC volt, AC volt, DC amp, AC amp, 5A AC,Temperature (J, K, T, PT100 RTD), 4–20 mA/0–10V/1–5V Front panel protection IP65NEMA 4XConnection method Screw terminalDepluggable screw terminalsScalingProgrammable end points, linear interpolation Programmable end points, linear interpolation Input power options 10–30 Vdc 9–30 Vdc or 85–264 Vac Update time500 ms 400 ms Automatic min/max capture Yes Yes Input for display-holdYes—C o u r t e s y o f C M A /F l o d y n e /H y d r a d y n e ▪ M o t i o n C o n t r o l ▪ H y d r a u l i c ▪ P n e u m a t i c ▪ E l e c t r i c a l ▪ M e c h a n i c a l ▪ (800) 426-5480 ▪ w w w .c m a f h .c o mV9-T4-5544.3Operator InterfacePanel MetersDigital Panel MetersFeaturesE5-324-E digital panel meters ●Galvanic isolation with protection against incorrect polarity ●Automatic min/max value detection ●Freely programmable characteristic curve end points ●Input range:●Single current measuring input (0/4–20 mA)●Single voltage measuring input (0/2–10V)Eclipse Series digital panel meters ●Four full digits ●1/8 DIN size ●Red, LED display ●Scalable display ●Flashing alarms ●Min/max data hold ●Optional analog, relay and RS-485 outputs ●Type 4XCatalog Number SelectionDigital Panel MetersEclipse SeriesProduct SelectionE5-324-E0402Eclipse SeriesNote1 Output options 0, 2, 4 are not available for models -41X and -43X.DescriptionCatalog Number LED digital panel meter, 24 x 48 mmE5-324-E0402DescriptionCatalog Number Digital ammeter—5A AC, 85–264 Vac power57701440Digital ammeter—5A AC, 85–264 Vac power, 2 relay outputs 57701441Digital process meter—4–20 mA/0–10V, 85–264 Vac power57701450Digital process meter—4–20 mA/0–10V, 85–264 Vac power, 2 relay outputs57701451Digital process meter—4–20 mA/0–10V, 85–264 Vac power, 2 relay outputs and analog retransmission 57701453Digital temperature meter, 85–264 Vac power57701460Digital temperature meter, 85–264 Vac power, 2 relay outputs 57701461Power Supply0 = DC (9–30 Vdc)1= AC (85–265 Vac)Output Option 10 = No option 1 = Dual relay2 = Analog output (4–20 mA and 0–10V)3 = Dual relay, analog output (4–20 mA and 0–10V)4 = RS-485 communications 5 = Dual relay, RS-4856 = Analog, RS-485 (4–20 mA and 0–10V)7 = Dual relay, analog, RS-485 (4–20 mA and 0–10V)Input Option0 = DC volt1 = AC volt TRMS2 = DC amp3 = AC amp TRMS4 = 5A AC TRMS5 = Process (4–20 mA, 0–10V, 1–5V)6 = Temperature (J, K, T, PT100 RTD)5770X –4X XE5-324-E0402Eclipse SeriesC o u r t e s y o f C M A /F l o d y n e /H y d r a d y n e ▪ M o t i o n C o n t r o l ▪ H y d r a u l i c ▪ P n e u m a t i c ▪ E l e c t r i c a l ▪ M e c h a n i c a l ▪ (800) 426-5480 ▪ w w w .c m a f h .c o m。
精益生产之全面生产维护(TPM)
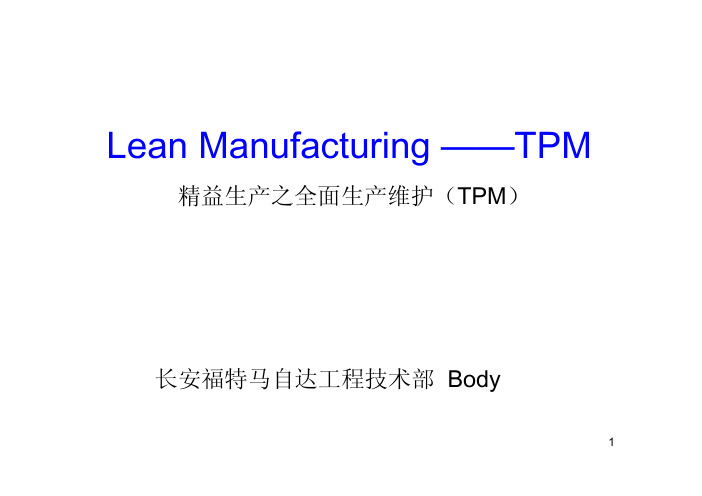
Lean Manufacturing ——TPM 精益生产之全面生产维护(TPM)长安福特马自达工程技术部Body1Lean manufacturing 精益生产Lean manufacturing is a total system.* Problem Solving & 6-σ* Standardized Work* 5S / Visual Factory* Value Stream Mapping* Kanban* Error Proofing* Total Productive Maintenance (TPM)* Quick Changeover* Kaizen2目录单元1、TPM概论单元2、TPM之自主维护活动单元3、TPM之计划维护活动单元4、TPM之个别改善活动单元5、TPM其他重要活动介绍单元6、现场6S活动实务* 供应商需要关注的问题点3⑥休止时间:作业时间中由于设备的非稼动而引起的损失时间(与设备的机能无关停止的时间)会议、早会:作业中因计划或必需的会议及早会而使设备停止的时间(例:月例会、早会, 参加活动, 故障, 车间、班组早会)教育训练:必须参加的公司内部、外部教育训练而引起的设备停止时间停电停水:电力供给(断水) 中断引起的设备不能稼动的时间以及生产过程中由于资材的品质问题引起的生产不能持续进行导致设备停止的时间(管理上的损失)⑦停止时间:由于以下的原因而引起的设备不能稼动的时间:机器故障:故障停机的时间机种变更:资材不良, 品质等偶发因素依据生产计划变更时发生的设备停止时间准备调整:产品生产结束或开始时工具类的调整, 整理, 清扫等相关的作业引起的停止时间资材不良:不良材料引起的投入前的选取、修理或生产过程中修正导致设备停止的情况不良再作业:不合格制品的修理和中间检查后修理作业需要的设备稼动时间工程不均衡:前、后工程(或前、后设备)中由于其他因素引起的作业停止或者担当设备后工程(设备)的生产数量或者目标量已达成而停止的时间其它:由上述原因以外的其他原因引发的设备停止时间⑧理论C.T.: 设备生产公司提示的或者设备设置后最佳的状态下单位产品的生产所需要的时间。
HP ALM 11.00功能对比指南-HP应用生命周期管理11.00-HP质量中心11.00-企业版
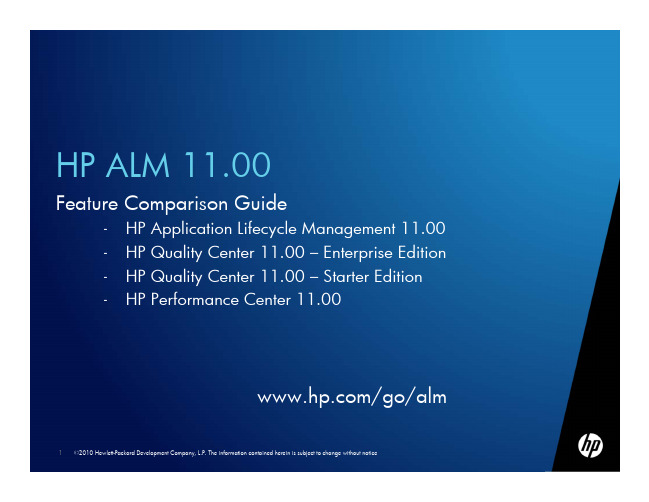
Baselining
HP Sprinter
HP Business Process Testing
HP Service Test Management
HP QAInspect
Test Assets Sharing/Reuse
(Cross-Project Library)
MyPC
(Thin Web Client)
/go/alm
1 ©2010 Hewlett-Packard Development Company, L.P. The information contained herein is subject to change without notice
Feature Comparison Guide
Included PC Lifecycle User (Reqs &D来自fects) Available
Feature Comparison Guide
NEW in Version 11.00 NEW in Version 10.00
Feature
Test Management
Test Plan
(Test Case Creation & Library)
Dashboard
Included
Included
Release & Cycle Mgmt
Included
Reporting
Included
Included
Project Planning & Tracking
Cross-Project Reporting
Requirements Management
Limited
TPM概述之持续改进工具
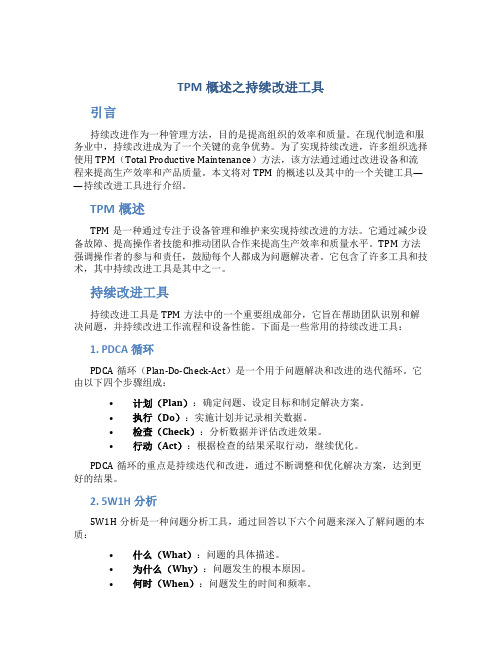
TPM概述之持续改进工具引言持续改进作为一种管理方法,目的是提高组织的效率和质量。
在现代制造和服务业中,持续改进成为了一个关键的竞争优势。
为了实现持续改进,许多组织选择使用TPM(Total Productive Maintenance)方法,该方法通过通过改进设备和流程来提高生产效率和产品质量。
本文将对TPM的概述以及其中的一个关键工具——持续改进工具进行介绍。
TPM概述TPM是一种通过专注于设备管理和维护来实现持续改进的方法。
它通过减少设备故障、提高操作者技能和推动团队合作来提高生产效率和质量水平。
TPM方法强调操作者的参与和责任,鼓励每个人都成为问题解决者。
它包含了许多工具和技术,其中持续改进工具是其中之一。
持续改进工具持续改进工具是TPM方法中的一个重要组成部分,它旨在帮助团队识别和解决问题,并持续改进工作流程和设备性能。
下面是一些常用的持续改进工具:1. PDCA循环PDCA循环(Plan-Do-Check-Act)是一个用于问题解决和改进的迭代循环。
它由以下四个步骤组成:•计划(Plan):确定问题、设定目标和制定解决方案。
•执行(Do):实施计划并记录相关数据。
•检查(Check):分析数据并评估改进效果。
•行动(Act):根据检查的结果采取行动,继续优化。
PDCA循环的重点是持续迭代和改进,通过不断调整和优化解决方案,达到更好的结果。
2. 5W1H分析5W1H分析是一种问题分析工具,通过回答以下六个问题来深入了解问题的本质:•什么(What):问题的具体描述。
•为什么(Why):问题发生的根本原因。
•何时(When):问题发生的时间和频率。
•谁(Who):问题涉及的人员和责任。
•哪里(Where):问题发生的位置。
•如何(How):问题导致的影响和可能的解决方案。
通过使用5W1H分析工具,团队可以更好地了解问题,并制定更有效的解决方案。
3. 故障模式和影响分析(FMEA)故障模式和影响分析(FMEA)是一种系统性的方法,用于识别和评估潜在的故障模式和它们对系统的影响。
TheLeanEnterprise20AllAboutKAIZEN(持续改善)
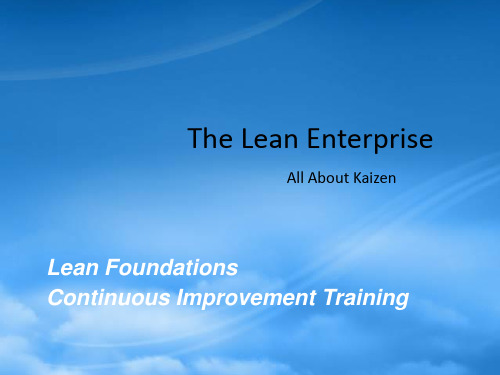
Identify Desired Result
Find a Solution
M
Do
Implement Solution (PILOT first)
A
Did not achieve
desired
result
I C
Check
Evaluate
Achieve desired result ?
Act
Standardize (ROLL-OUT SOLUTION)
Kaizens seek small daily improvements resulting in large yearly savings
Compared to a large-scale DMAIC project, Kaizens focus on short-term “blitzes” to make immediate impact and change (change for the better)
RR e v i s e S S ttaa n d a rrdd s s
S ta b iliz e P ro c e s s
AS CD
AP CD
E xpose P r o b le m s
E lim in a te P r o b le m s
Overview
Kaizen concentrates on improving several aspects of the business:
Kanban Cellular Layout
Set-up Reduction
Overview
Kaizen is one of the critical tools within a
TPM导入培训
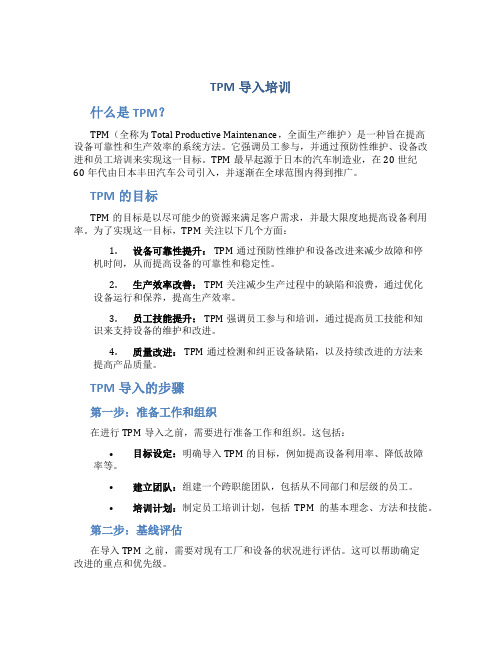
TPM导入培训什么是TPM?TPM(全称为Total Productive Maintenance,全面生产维护)是一种旨在提高设备可靠性和生产效率的系统方法。
它强调员工参与,并通过预防性维护、设备改进和员工培训来实现这一目标。
TPM最早起源于日本的汽车制造业,在20世纪60年代由日本丰田汽车公司引入,并逐渐在全球范围内得到推广。
TPM的目标TPM的目标是以尽可能少的资源来满足客户需求,并最大限度地提高设备利用率。
为了实现这一目标,TPM关注以下几个方面:1.设备可靠性提升: TPM通过预防性维护和设备改进来减少故障和停机时间,从而提高设备的可靠性和稳定性。
2.生产效率改善: TPM关注减少生产过程中的缺陷和浪费,通过优化设备运行和保养,提高生产效率。
3.员工技能提升: TPM强调员工参与和培训,通过提高员工技能和知识来支持设备的维护和改进。
4.质量改进: TPM通过检测和纠正设备缺陷,以及持续改进的方法来提高产品质量。
TPM导入的步骤第一步:准备工作和组织在进行TPM导入之前,需要进行准备工作和组织。
这包括:•目标设定:明确导入TPM的目标,例如提高设备利用率、降低故障率等。
•建立团队:组建一个跨职能团队,包括从不同部门和层级的员工。
•培训计划:制定员工培训计划,包括TPM的基本理念、方法和技能。
第二步:基线评估在导入TPM之前,需要对现有工厂和设备的状况进行评估。
这可以帮助确定改进的重点和优先级。
•设备评估:对现有设备进行评估,包括设备性能、故障率和维护历史。
•生产过程评估:评估生产过程中存在的问题,如停机时间、缺陷率等。
第三步:设备可靠性改善设备可靠性改善是TPM的核心之一。
在这一步骤中,重点关注以下方面:•预防性维护:建立定期的保养计划,包括清洁、润滑、紧固和检查等。
•故障模式分析:对设备故障进行分析,以了解根本原因并采取措施来防止再次发生。
•改进项目:根据设备评估结果和员工的参与,制定设备改进项目并跟踪实施的进展。
精益运营管理

15.2%已经在全球引发了一场向丰田生产模式(即“精益生产”)转变的运动,并扩展2014Lean Enterprise Management2014来源:丰田生产方式—大野耐一Waste 浪费Work 工作提示:设定工作区域,以便每个员工均能操作每个工位!传统方法 TPS 方法轧机MILLMILLMILLGRINDER 磨床GRINDERGRINDERDRILLDRILL 钻床PART FLOWLean Enterprise Management2014« Waste » 浪费Work 工作来源:丰田生产方式—大野耐一• Leaders are the Teachers and Developers • Problem Solving• Visual KPI Management• Stable and Standardized Work Processes3M’s:MURI MURA MUDA 无理=超负荷不均=不均衡、波动、变化浪费没有无理、不均和浪费缺陷 7Wastes 浪费过度加工库存运输过量生产动作 等待E L I MI NA TE消除Lean Enterprise Management2014运输(Transportation)多次的和不必要的材料、零件、Lean Enterprise Management认识7大浪费(T I M WOOD)库存(Inventory)购买或者持有不必要的原料、在制品或成品Lean Enterprise Management动作(Motion)不增加产品价值的人或者机器的动作劳动力使用效率低Lean Enterprise Management认识7大浪费(TIM W OOD)等待(Waiting)等来料,等机器完成操作,等维修,等料筐,等工具,等工装、等订单,等待计划指令,…• • • Lean Enterprise Management过量生产(Over production)生产数量超过客户需求数量,或者是比需要的时间提前产品或材料变坏Lean Enterprise Management认识7大浪费(TIM WO O过度加工(Over processing)没有算在产品成本内的额外的时间或材料,如检验、去毛刺、清洗、上防锈油、高出标准要求的额外加工等Lean Enterprise Management缺陷(Defect)产出的零件有缺陷,需要返修或报废生产力低和士气低产品大批量召回Lean Enterprise Management什么是增值活动?增值活动(3F):• 就是使原材料或原始信息改变或成型以满足客户的需要的活动• 消耗资源并对客户满意做贡献的活动,即增加价值的活动、客户愿意付钱的活动Lean Enterprise ManagementLean Enterprise ManagementPhysical 物质的44Lean Enterprise Management 2014 精益员工管理精益供应商管理质量(Q) 成本(c ) 交付(D)精益领导力 精益产品开发精益生产 精益客户管理精益企业数字化管理安全(S)精 益 人 才 培 养49Lean Enterprise Management 2014 精益运营系统的四大要素技术: 精益工具/方法 • 目视化管理 • 5S 及现场组织 • 过程设计• 标准化工作 • 内建质量 • 问题解决• KPIs 关键绩效指标• JIT 供货• … • 注重持续改进 • 领导者是其他人的老师 • 按事实管理(关键绩效指标) • 现场观察 •问题解决• 清晰的方向和优先权• 建立团队• 吸引他人• 一致性• 坚持不懈理念: • 顾客第一 • 聚焦增加价值 • 尊重员工• 最重要的资本• 成长和发展 • 聚焦现场 • 团队合作 • 战斗 • 诚实和尊重 • 持续改进• 消除浪费• 缩短供货周期• 减少变差人: 发展那些能在其负责区域内执行并保持持续改进的有知识、技能和领导力的人。
戴尔Latitude 5491固态硬盘安装指南说明书
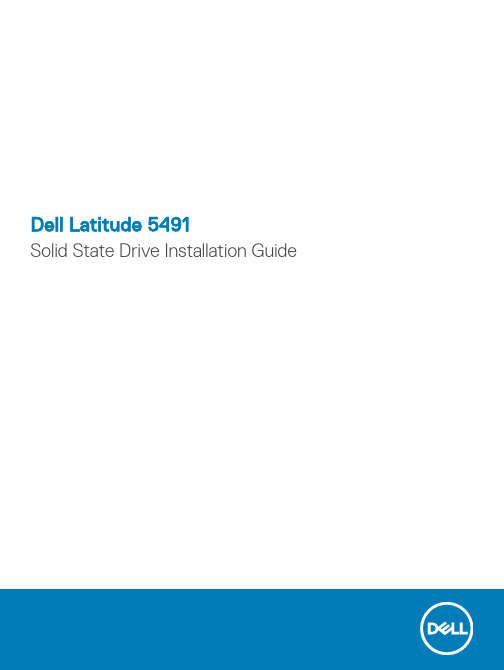
Dell Latitude 5491Solid State Drive Installation GuideNotes, cautions, and warningsNOTE: A NOTE indicates important information that helps you make better use of your product.CAUTION: A CAUTION indicates either potential damage to hardware or loss of data and tells you how to avoid the problem.WARNING: A WARNING indicates a potential for property damage, personal injury, or death.© 2018 Dell Inc. or its subsidiaries. All rights reserved. Dell, EMC, and other trademarks are trademarks of Dell Inc. or its subsidiaries. Other trademarks may be trademarks of their respective owners.2018 - 05Rev. A001 Before you begin (4)Safety instructions (4)Before working inside your computer (4)Safety precautions (5)Electrostatic discharge—ESD protection (5)ESD field service kit (6)Transporting sensitive components (7)After working inside your computer (7)2 Solid State Drive (8)Installing the Solid State Drive (8)3 Getting help (15)Contacting Dell (15)Contents3Before you begin Safety instructionsUse the following safety guidelines to protect your computer from potential damage and to ensure your personal safety. Unless otherwise noted, each procedure included in this document assumes that the following conditions exist:•You have read the safety information that shipped with your computer.•A component can be replaced or, if purchased separately, installed by performing the removal procedure in reverse order. WARNING: Disconnect all power sources before opening the computer cover or panels. After you finish working inside thecomputer, replace all covers, panels, and screws before connecting to the power source.WARNING: Before working inside your computer, read the safety information that shipped with your computer. For additional safety best practices information, see the Regulatory Compliance Homepage at /regulatory_complianceCAUTION: Many repairs may only be done by a certified service technician. You should only perform troubleshooting and simple repairs as authorized in your product documentation, or as directed by the online or telephone service and support team.Damage due to servicing that is not authorized by Dell is not covered by your warranty. Read and follow the safety instructions that came with the product.CAUTION: T o avoid electrostatic discharge, ground yourself by using a wrist grounding strap or by periodically touching an unpainted metal surface at the same time as touching a connector on the back of the computer.CAUTION: Handle components and cards with care. Do not touch the components or contacts on a card. Hold a card by its edges or by its metal mounting bracket. Hold a component such as a processor by its edges, not by its pins.CAUTION: When you disconnect a cable, pull on its connector or on its pull-tab, not on the cable itself. Some cables have connectors with locking tabs; if you are disconnecting this type of cable, press in on the locking tabs before you disconnect the cable. As you pull connectors apart, keep them evenly aligned to avoid bending any connector pins. Also, before you connect acable, ensure that both connectors are correctly oriented and aligned.NOTE: The color of your computer and certain components may appear differently than shown in this document.Before working inside your computer1 Ensure that your work surface is flat and clean to prevent the computer cover from being scratched.2 Turn off your computer.3 If the computer is connected to a docking device (docked), undock it.4 Disconnect all network cables from the computer (if available).CAUTION: If your computer has an RJ45 port, disconnect the network cable by first unplugging the cable from yourcomputer.5 Disconnect your computer and all attached devices from their electrical outlets.6 Open the display.7 Press and hold the power button for few seconds, to ground the system board.CAUTION:To guard against electrical shock unplug your computer from the electrical outlet before performing Step # 8.CAUTION: To avoid electrostatic discharge, ground yourself by using a wrist grounding strap or by periodically touching anunpainted metal surface at the same time as touching a connector on the back of the computer.8 Remove any installed ExpressCards or Smart Cards from the appropriate slots.1 4Before you beginSafety precautionsThe safety precautions chapter details the primary steps to be taken before performing any disassembly instructions.Observe the following safety precautions before you perform any installation or break/fix procedures involving disassembly or reassembly:•Turn off the system and all attached peripherals.•Disconnect the system and all attached peripherals from AC power.•Disconnect all network cables, telephone, and telecommunications lines from the system.•Use an ESD field service kit when working inside any notebook to avoid electrostatic discharge (ESD) damage.•After removing any system component, carefully place the removed component on an anti-static mat.•Wear shoes with non-conductive rubber soles to reduce the chance of getting electrocuted.Standby powerDell products with standby power must be unplugged before you open the case. Systems that incorporate standby power are essentially powered while turned off. The internal power enables the system to be remotely turned on (wake on LAN) and suspended into a sleep mode and has other advanced power management features.Unplugging, pressing and holding the power button for 15 seconds should discharge residual power in the system board.BondingBonding is a method for connecting two or more grounding conductors to the same electrical potential. This is done through the use of a field service electrostatic discharge (ESD) kit. When connecting a bonding wire, ensure that it is connected to bare metal and never to a painted or non-metal surface. The wrist strap should be secure and in full contact with your skin, and ensure that you remove all jewelry such as watches, bracelets, or rings prior to bonding yourself and the equipment.Electrostatic discharge—ESD protectionESD is a major concern when you handle electronic components, especially sensitive components such as expansion cards, processors, memory DIMMs, and system boards. Very slight charges can damage circuits in ways that may not be obvious, such as intermittent problems or a shortened product life span. As the industry pushes for lower power requirements and increased density, ESD protection is an increasing concern.Due to the increased density of semiconductors used in recent Dell products, the sensitivity to static damage is now higher than in previous Dell products. For this reason, some previously approved methods of handling parts are no longer applicable.Two recognized types of ESD damage are catastrophic and intermittent failures.•Catastrophic – Catastrophic failures represent approximately 20 percent of ESD-related failures. The damage causes an immediate and complete loss of device functionality. An example of catastrophic failure is a memory DIMM that has received a static shock and immediately generates a "No POST/No Video" symptom with a beep code emitted for missing or nonfunctional memory.•Intermittent – Intermittent failures represent approximately 80 percent of ESD-related failures. The high rate of intermittent failures means that most of the time when damage occurs, it is not immediately recognizable. The DIMM receives a static shock, but the tracing is merely weakened and does not immediately produce outward symptoms related to the damage. The weakened trace may take weeks or months to melt, and in the meantime may cause degradation of memory integrity, intermittent memory errors, etc.The more difficult type of damage to recognize and troubleshoot is the intermittent (also called latent or "walking wounded") failure. Perform the following steps to prevent ESD damage:•Use a wired ESD wrist strap that is properly grounded. The use of wireless anti-static straps is no longer allowed; they do not provide adequate protection. T ouching the chassis before handling parts does not ensure adequate ESD protection on parts with increased sensitivity to ESD damage.Before you begin5•Handle all static-sensitive components in a static-safe area. If possible, use anti-static floor pads and workbench pads.•When unpacking a static-sensitive component from its shipping carton, do not remove the component from the anti-static packing material until you are ready to install the component. Before unwrapping the anti-static packaging, ensure that you discharge static electricity from your body.•Before transporting a static-sensitive component, place it in an anti-static container or packaging.ESD field service kitThe unmonitored Field Service kit is the most commonly used service kit. Each Field Service kit includes three main components: anti-static mat, wrist strap, and bonding wire.Components of an ESD field service kitThe components of an ESD field service kit are:•Anti-Static Mat – The anti-static mat is dissipative and parts can be placed on it during service procedures. When using an anti-static mat, your wrist strap should be snug and the bonding wire should be connected to the mat and to any bare metal on the system being worked on. Once deployed properly, service parts can be removed from the ESD bag and placed directly on the mat. ESD-sensitive items are safe in your hand, on the ESD mat, in the system, or inside a bag.•Wrist Strap and Bonding Wire – The wrist strap and bonding wire can be either directly connected between your wrist and bare metal on the hardware if the ESD mat is not required, or connected to the anti-static mat to protect hardware that is temporarily placed on the mat. The physical connection of the wrist strap and bonding wire between your skin, the ESD mat, and the hardware is known as bonding. Use only Field Service kits with a wrist strap, mat, and bonding wire. Never use wireless wrist straps. Always be aware that the internal wires of a wrist strap are prone to damage from normal wear and tear, and must be checked regularly with a wrist strap tester in order to avoid accidental ESD hardware damage. It is recommended to test the wrist strap and bonding wire at least once per week.•ESD Wrist Strap T ester – The wires inside of an ESD strap are prone to damage over time. When using an unmonitored kit, it is a best practice to regularly test the strap prior to each service call, and at a minimum, test once per week. A wrist strap tester is the best method for doing this test. If you do not have your own wrist strap tester, check with your regional office to find out if they have one.T o perform the test, plug the wrist-strap's bonding-wire into the tester while it is strapped to your wrist and push the button to test. A green LED is lit if the test is successful; a red LED is lit and an alarm sounds if the test fails.•Insulator Elements – It is critical to keep ESD sensitive devices, such as plastic heat sink casings, away from internal parts that are insulators and often highly charged.•Working Environment – Before deploying the ESD Field Service kit, assess the situation at the customer location. For example, deploying the kit for a server environment is different than for a desktop or portable environment. Servers are typically installed in a rack within a data center; desktops or portables are typically placed on office desks or cubicles. Always look for a large open flat work area that is free of clutter and large enough to deploy the ESD kit with additional space to accommodate the type of system that is being repaired. The workspace should also be free of insulators that can cause an ESD event. On the work area, insulators such as Styrofoam and other plastics should always be moved at least 12 inches or 30 centimeters away from sensitive parts before physically handling any hardware components•ESD Packaging – All ESD-sensitive devices must be shipped and received in static-safe packaging. Metal, static-shielded bags are preferred. However, you should always return the damaged part using the same ESD bag and packaging that the new part arrived in.The ESD bag should be folded over and taped shut and all the same foam packing material should be used in the original box that the new part arrived in. ESD-sensitive devices should be removed from packaging only at an ESD-protected work surface, and parts should never be placed on top of the ESD bag because only the inside of the bag is shielded. Always place parts in your hand, on the ESD mat, in the system, or inside an anti-static bag.•Transporting Sensitive Components – When transporting ESD sensitive components such as replacement parts or parts to be returned to Dell, it is critical to place these parts in anti-static bags for safe transport.ESD protection summaryIt is recommended that all field service technicians use the traditional wired ESD grounding wrist strap and protective anti-static mat at all times when servicing Dell products. In addition, it is critical that technicians keep sensitive parts separate from all insulator parts while performing service and that they use anti-static bags for transporting sensitive components.6Before you beginTransporting sensitive componentsWhen transporting ESD sensitive components such as replacement parts or parts to be returned to Dell, it is critical to place these parts in anti-static bags for safe transport.Lifting equipmentAdhere to the following guidelines when lifting heavy weight equipment:CAUTION: Do not lift greater than 50 pounds. Always obtain additional resources or use a mechanical lifting device.1Get a firm balanced footing. Keep your feet apart for a stable base, and point your toes out.2Tighten stomach muscles. Abdominal muscles support your spine when you lift, offsetting the force of the load.3Lift with your legs, not your back.4Keep the load close. The closer it is to your spine, the less force it exerts on your back.5Keep your back upright, whether lifting or setting down the load. Do not add the weight of your body to the load. Avoid twisting your body and back.6Follow the same techniques in reverse to set the load down.After working inside your computerAfter you complete any replacement procedure, ensure that you connect external devices, cards, and cables before turning on your computer.CAUTION: T o avoid damage to the computer, use only the battery designed for this particular Dell computer. Do not use batteries designed for other Dell computers.1 Connect any external devices, such as a port replicator or media base, and replace any cards, such as an ExpressCard.2 Connect any telephone or network cables to your computer.CAUTION: To connect a network cable, first plug the cable into the network device and then plug it into thecomputer.3 Connect your computer and all attached devices to their electrical outlets.4 Turn on your computer.Before you begin7Solid State DriveInstalling the Solid State Drive1Follow the procedure in Before working inside your computer .2 Remove the base cover:aLoosen the M2.0x6 (8) captive screws that secure the base cover to the system [1].b Pry the base cover from the recess at the top edge [2] and continue prying throughout the outer sides of the base cover inclockwise direction to release the base cover.NOTE:Use a plastic scribe to pry the base cover from the edges.c Lift the base cover from the system.28Solid State Drive3 Remove the battery:a Disconnect the battery cable from the connector on the system board [1] and unroute the cable from the routing channel.b Loosen the M2x6 captive screw that secures the battery to the system [2].c Lift the battery away from the system [3].Solid State Drive94 Install the Solid State Drive (SSD) bracket:a Place the SSD bracket into the slot in the system [1].b Replace the M2x3 screw that secures the SSD bracket to the system [2].10Solid State Drive5 Install the SSD:a Insert the SSD into the connector on the system [1].b Replace the M2x3 screw that secures the SSD card to the system [2].c Place the Mylar shield over the SSD [3].Solid State Drive116 Replace the battery:a Insert the battery into the slot on the system [1].b Route the battery cable through the routing channel.c Tighten the M2x6 captive screw to secure the battery to the system [2].d Connect the battery cable to the connector on the system board [3].12Solid State Drive7 Replace the base cover:a Align the base cover with the screw holders on the system [1].b Press the edges of the base cover until it clicks into place.c Tighten the M2.0x6 (8) captive screws to secure the base cover to the system [1].Solid State Drive1314Solid State DriveGetting helpContacting DellNOTE: If you do not have an active Internet connection, you can find contact information on your purchase invoice, packing slip, bill, or Dell product catalog.Dell provides several online and telephone-based support and service options. Availability varies by country and product, and some services may not be available in your area. T o contact Dell for sales, technical support, or customer service issues:1Go to /support.2Select your support category.3Verify your country or region in the Choose a Country/Region drop-down list at the bottom of the page.4 Select the appropriate service or support link based on your need.3Getting help 15。
TPM设备升级八大举措
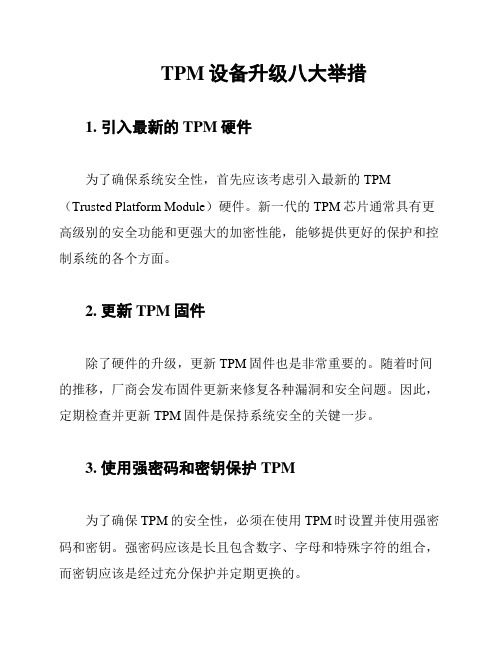
TPM设备升级八大举措1. 引入最新的TPM硬件为了确保系统安全性,首先应该考虑引入最新的TPM (Trusted Platform Module)硬件。
新一代的TPM芯片通常具有更高级别的安全功能和更强大的加密性能,能够提供更好的保护和控制系统的各个方面。
2. 更新TPM固件除了硬件的升级,更新TPM固件也是非常重要的。
随着时间的推移,厂商会发布固件更新来修复各种漏洞和安全问题。
因此,定期检查并更新TPM固件是保持系统安全的关键一步。
3. 使用强密码和密钥保护TPM为了确保TPM的安全性,必须在使用TPM时设置并使用强密码和密钥。
强密码应该是长且包含数字、字母和特殊字符的组合,而密钥应该是经过充分保护并定期更换的。
4. 启用TPM的硬盘加密功能TPM通常具有硬盘加密功能,可以提供更高级别的数据保护。
通过启用TPM的硬盘加密功能,可以有效防止数据泄露和未经授权的访问。
在系统启动时,TPM将自动解锁硬盘,使得数据只能在授权的情况下访问。
5. 定期备份TPM数据为了避免数据丢失和系统故障,定期备份TPM数据是非常重要的。
这样,即使发生故障或数据被破坏,也能够通过恢复备份数据来重新建立安全系统。
6. 定期更新TPM软件除了更新TPM固件外,同样重要的是定期更新TPM软件。
厂商会定期发布软件更新来修复漏洞和增强安全性能。
因此,及时安装并使用最新版本的TPM软件是保持系统安全的必要措施。
7. 发现和解决TPM故障在使用TPM设备时,可能会遇到各种故障和问题。
因此,应该建立一个完善的故障排除和解决方案,以及提供相应的技术支持。
系统管理员应该能够快速有效地检测并解决TPM故障,以确保系统安全。
8. 培训和教育用户最后,应该对所有系统用户进行培训和教育,以提高其对TPM设备和安全性的认识。
用户应该了解TPM的功能和工作原理,并注意安全操作措施,以避免不必要的风险和错误。
结论以上是TPM设备升级的八大举措,通过引入最新的硬件和软件、更新固件、加强密码和密钥保护、启用硬盘加密功能、定期备份数据、发现和解决故障、以及培训用户等措施,可以有效提升TPM设备的安全性和性能,保障系统的整体安全。
- 1、下载文档前请自行甄别文档内容的完整性,平台不提供额外的编辑、内容补充、找答案等附加服务。
- 2、"仅部分预览"的文档,不可在线预览部分如存在完整性等问题,可反馈申请退款(可完整预览的文档不适用该条件!)。
- 3、如文档侵犯您的权益,请联系客服反馈,我们会尽快为您处理(人工客服工作时间:9:00-18:30)。
Measure
Availability
Formula =
460 min – 60 min
460 The Theoretical Cycle
Metric
2. Set-up & adjustments
] ] ]
Load – Down Time x 100% Load Time
example:
= 87%
3. Idling and minor stoppages 4. Reduced speed
Identifies Design weaknesses and improves the equipment to error-free function (via poka-yoke) Improves technical maintenance skills for checks, inspections, and overhauls
Efficiency
=
Time x Processed Qty
x 100% = 50%
Operating Time
example:
0.5/ unit x 400 units 400 minutes
5. Defects in Process 6. Reduced Yield
Ratio of Quality Products example:
TPM – The Need
Process Industry relies heavily on equipment that is integrated and runs continuously When down, losses are costly With lower inventories, machines need to be reliable Machining and Assembly industries becoming more mechanized to save manpower and do difficult jobs – More machines to maintain – Need to save energy
Total Maintenance
– Involves the whole maintenance system inclusive of equipment manufacturer, equipment engineering, and equipment user to improve maintainability
TPM – Operational Goals, cont. (Quantitative)
Safety – Zero accidents
Quality – Zero failures – Zero complaints
Education – Hours of training/ number of sessions – Number of KAIZEN projects – Number of Suggestions
TPM – Role of Maintenance Function
Provides technical support for autonomous maintenance done by operators
Restores deteriorated equipment through checks, inspections, and overhauls
After
> 90% > 95% > 99% > 85%
TPM – Operational Goals (Qualitative)
Increase number of suggestions Improve level of teamwork of shop floor Improve cross-functional teamwork Establish maintenance throughout the total equipment life cycle People maintain their own equipment Machines available for just-in-time (JIT) application Improve machine availability Improve working environment (6S) Improve Corporate culture and image Improve Business performance
Material Losses
– Losses in yield due to „inherent waste‟ (cut-off stock, set-up pieces, prototype, etc) – Energy losses such as electricity, gas, and water when machinery is not doing valueadded work – Idling losses due to inadequate sensors and product buildup on conveyors and chutes
TPM – Role of Operator Function
Maintains basic condition (cleaning and lubrication) Maintains proper condition and standards for equipment usage Partially restores deterioration Basic skill levels in: – Changeover and set-up – Reduction of minor stoppages and adjustments
The Lean Enterprise
Introduction to TPM – Total Productive Maintenance
Lean Foundations Continuous Improvement Training
Learning Objectives
Learn the basic philosophy of TPM Explain OEE and how it contributes to a TPM project, explore OEE components; define and calculate OEE List 6 major components of equipment loss Review and adopt the 7 steps to Autonomous Maintenance
Yield (Quality)
TPM attacks 6 major “Losses” plus Elimination of other Wastes (Mura, Muri, Muda)
Operator Time Losses
– Manpower losses due to operation time being done more slowly than standard time (Cycle Time > Standard Time)
Total Participation
– – – – – Everyone has a role to make TPM work Management to set policy Middle management, staff to support and lead Maintenance to maintain and train Operators to take on new maintenance challenges
TPM – Definition of „Total‟
Total Effectiveness
– Reduction in losses of all equipment to optimize its effectiveness and improve costs
TPM – The Philosophy
TPM aims at using equipment to its maximum and aids in reducing Life Cycle Costs (LCC) In other words - going all out to eliminate the Losses (Waste) caused by the equipment TPM improves work activities that deal with Equipment Set-up, Operating parameters, Maintenance, Tear down, Repairs and Breakdowns It specifically aims at the complete elimination of the „six major losses‟ while striving for a goal of zero unscheduled downtime
=
Processed Amount – Amount of Defects Processed Amount 400 – 8 400
x 100% = 98%
Overall Equip. Effectiveness:
.87 x .50 46.2 % .98 =
OEE Pareto Analysis by Loss Category
Best Practices World-Class Goals (A TPM “Vision”)