cven9888 Week03 EMS env repor
MIL-S8TA 8-Port 10 100 1000 BASE-T 未管理开关用户指南(Rev.

MIL-S8TA8-Port 10/100/1000 BASE-T Unmanaged Switch User GuideRev. A22012-09-17Regulatory Approval- FCC Class A- UL 1950- CSA C22.2 No. 950- EN60950- CE- EN55022 Class A- EN55024Canadian EMI NoticeThis Class A digital apparatus meets all the requirements of the Canadian Interference-Causing Equipment Regulations.Cet appareil numerique de la classe A respecte toutes les exigences du Reglement sur le materiel brouilleur du Canada.European NoticeProducts with the CE Marking comply with both the EMC Directive (89/336/EEC) and the Low Voltage Directive (73/23/EEC) issued by the Commission of the European Community Compliance with these directives imply conformity to the following European Norms:EN55022 (CISPR 22) - Radio Frequency InterferenceEN61000-X - Electromagnetic ImmunityEN60950 (IEC950) - Product SafetyFive-Year Limited WarrantyTransition Networks warrants to the original consumer or purchaser that each of it's products,and all components thereof, will be free from defects in material and/or workmanship for aperiod of five years from the original factory shipment date. Any warranty hereunder isextended to the original consumer or purchaser and is not assignable.Transition Networks makes no express or implied warranties including, but not limited to, anyimplied warranty of merchantability or fitness for a particular purpose, except as expressly setforth in this warranty. In no event shall Transition Networks be liable for incidental orconsequential damages, costs, or expenses arising out of or in connection with theperformance of the product delivered hereunder. Transition Networks will in no case coverdamages arising out of the product being used in a negligent fashion or manner.TrademarksThe MiLAN logo and Transition Networks trademarks are registered trademarks of Transition Networks in the United States and/or other countries.To Contact Transition NetworksFor prompt response when calling for service information, have the following information ready:- Product serial number and revision- Date of purchase- Vendor or place of purchaseYou can reach Transition Networks technical support at:E-mail:**********************Telephone: +1.800.260.1312 x 200Fax: +1.952.941.2322Transition Networks6475 City West ParkwayEden Prairie, MN 55344United States of AmericaTelephone: +1.800.526.9267Fax: : +1.952.941.2322*******************© Copyright 2006 Transition NetworksThis equipment has been tested and found to comply with the limits for a class A device, pursuant to part 15 of the FCC rules. These limits are designed to provide reasonable protection against harmful interference in a commercial installation. This equipment generates uses and can radiate radio frequency energy and, if not installed and used in accordance with instructions, may cause harmful interference on radio communications. Operation of this equipment in a residential area is likely to cause harmful interference, in which case, the user will be requires to correct the interference at the user’s own expense.Content Introduction (1)Features (1)Package Contents (2)Hardware Description (3)Physical Dimensions (3)Front Panel (3)LEDs Indicators (3)Rear Panel (4)Installation (6)Attaching Rubber Feet (6)Mounting on the Wall (6)Power On (7)Technical Specification (8)IntroductionThe 8-port 10/100/1000BASE-T Switch with Auto MDI/MDIX is an unmanaged multi-port Switch that can be used to build high-performance switched networks. This switch is a store-and-forward device that offers low latency for high-speed networking. The Switch is designed for the core of the network backbone computing environment to solve traffic block problems at SME (small, medium enterprise) businesses.The 8-port 10/100/1000BASE-T Switch features a “store-and-forward”switching technology. This allows the switch to auto-learn and store source addresses in an 8K-entry MAC address table.Features⏹Conforms to IEEE 802.3, 802.3u, 802.3ab and 802.3x⏹8 Gigabit copper SOHO switch, compact size with universal internalpower⏹Auto-MDIX on all ports⏹16 Gbps back-plane⏹ N-Way Auto-Negotiation⏹8K MAC address table⏹Back pressure half duplex⏹Flow control full duplex⏹ Store-and-Forward switching architecture⏹ 144Kbytes memory buffer⏹True non-blocking switching⏹Support 8Kbytes Jumbo Frame1Package ContentsUnpack the contents of the switch and verify them against the checklist below.⏹ 8-port Switch⏹Power Cord.⏹User Guide.8-port Switch Power Cord User manualPackage ContentCompare the contents of your switch package with the standard checklist above. If any item is missing or damaged, please contact your local dealerfor service.23Hardware DescriptionPhysical DimensionsThe physical dimensions of the Switch is 165mm x 100mm x 32.5 mm (L x W x H)Front PanelThe front panel of the 8-Port Gigabit switch consists of LED-indicators (100/1000, Link/Activity, Full duplex/Collision) for each Gigabit port and power LED-indicator for unit.RJ-45 Ports (Auto MDI/MDIX): 8 10/100/1000 N-way auto-sensing for 10Base-T, 100Base-TX or 1000Base-T connections. (In general, MDI means connecting to another Hub or Switch while MDIX means connecting to a workstation or PC. Therefore, Auto MDI/MDIX allows you to connect to another Switch or workstation without changing to non-crossover or crossover cabling.)LEDs IndicatorsThe LED Indicators gives real-time information of systematic operation status. The following table provides descriptions of LED status and their meaning.Green PowerOnOff Power is not connectedGreen The port is operating at the speed of 1000Mbps.Orange The port is operating at the speed of 100Mbps.Off No device attached or in 10Mbps modeGreen The port is connecting with the device.Blinking The port is receiving or transmitting data.Off Nodeviceattached.Orange The port is operating in Full-duplex mode.Blinking Packet collision occurred on this port.Off No device attached or in half-duplex mode. Rear PanelThe rear panel of the 8-port Gigabit Switch consists of 8 auto-negotiation 10/100/1000Mbps Ethernet RJ-45 connectors (support Automatic4MDI/MDIX function).RJ-45 Ports (Auto MDI/MDIX): 8 port auto-negotiation 10/100/1000 Mbps Ethernet RJ-45 connectors[Auto MDI/MDIX means that you can connect to another Switch or workstation without changing non-crossover or crossover cabling.]5InstallationThis section shows the installation procedures of the switch.Set the Switch on a sufficiently large flat space with a power outlet nearby.The surface where you put your Switch should be clean, smooth, level, and sturdy. Make sure there is enough clearance around the Switch to allow attachment of cables, power cord and air circulation.Attaching Rubber FeetA. Make sure mounting surface on the bottom of the Switch is grease anddust free.B. Remove adhesive backing from your Rubber Feet.C. Apply the Rubber Feet to each corner on the bottom of the Switch.These footpads can prevent the Switch from shock/vibration. Mounting on the WallThe switch can be mounted on the wall. The switch has two wallmountbrackets included in the package.Power OnConnect the cord of power to the power socket on the rear panel of the Switch. The other side of power cord connects to the power outlet. Check the power indicator on the upper panel to see if power is properly supplied.7Technical SpecificationThe following table provides the technical specification of 8-ports Gigabit Switch.IEEE 802.3 10BASE-T EthernetIEEE 802.3u 100BASE-TX Fast EthernetIEEE 802.3ab Gigabit EthernetIEEE 802.3x Flow Control and Back-pressureCSMA/CDStore-and-Forward switching architecture14,880 pps for 10Mbps148,800 pps for 100Mbps1,488,000 pps for 1000MbpsRJ-45; Auto-MDIX on all ports8K Mac address table144Kbytes memory bufferSupports 8Kbytes jumbo packet size16Gbps810BASE-T: 2-pair UTP/STP Cat. 3, 4, 5 cable EIA/TIA-568 100-ohm (100m)100BASE-TX: 2-pair UTP/STP CAT. 5 cable EIA/TIA-568 100-ohm (100m)Gigabit Copper: 4 pair UTP/STP CAT. 5 cable EIA/TIA 568 100-ohm (100M)Per port: 100/1000, Link/Activity, Full duplex/ CollisionPer unit: PowerAC 110~240V, 50/60Hz7.6 Watt (maximum)0℃ to 45℃ (32℉ to 113℉)-40℃ to 70℃ (-40℉ to 158℉)10% to 90% (Non-condensing)0% to 95% (Non-condensing)165mm x 100mm x 32.5mm (L x W x H) Compliance with FCC Class A, CE Compliance UL, cUL,CE/EN609509。
en50288标准 -回复

en50288标准-回复the following questions and discuss the EN 50288 standard.Introduction:The EN 50288 standard, often referred to as the Industrial Ethernet Cable standard, provides guidelines for the construction and performance requirements of Ethernet cables used in industrial environments. In this article, we will explore the various aspects of this standard, including its background, scope, key provisions, and benefits. Let's get started.1. What is the background of EN 50288 standard?The EN 50288 standard was developed by the European Committee for Electrotechnical Standardization (CENELEC) to cater specifically to the industrial sector's networking needs. Traditional Ethernet cables designed for office environments were unable to withstand the harsh conditions in industrial settings, such as extreme temperatures, vibrations, and chemicals. Therefore, there was a need to establish a standard that addresses these challenges and ensures reliable communication in industrial Ethernet networks.2. What is the scope of the EN 50288 standard?The EN 50288 standard covers both copper and fiber-optic Ethernet cables used in industrial applications. It specifies the construction, materials, electrical, and mechanical requirements for these cables to ensure their performance in challenging industrial environments. The standard defines different categories and types of cables based on their capabilities, such as data transmission speed, temperature resistance, and shielding effectiveness.3. What are the key provisions of the EN 50288 standard?The EN 50288 standard provides comprehensive guidelines for industrial Ethernet cables, including the following key provisions:a. Construction Requirements: It specifies the physical construction of the cables, including the number and type of conductors, insulation, shielding, and jacket material. These requirements ensure the cables' durability, flexibility, and resistance to external factors like moisture, chemicals, and physical stress.b. Electrical Performance: The standard defines various electrical parameters, such as impedance, capacitance, and attenuation, to ensure reliable signal transmission and minimize signal degradation. It also specifies the maximum allowable signal lossover certain distances to guarantee the desired data transmission speed.c. Mechanical Performance: The standard outlines mechanical tests that cables must undergo, such as tensile strength, bending radius, and resistance to crush and impact forces. These tests ensure that the cables can withstand harsh installation and operating conditions commonly found in industrial environments.d. Environmental Performance: The standard sets requirements for cables' resistance to temperature variations, humidity, oil, and other chemicals commonly encountered in industrial settings. These provisions help ensure that the cables can operate reliably under extreme environmental conditions.e. Compatibility: The EN 50288 standard ensures backward compatibility with existing Ethernet standards, allowing industrial Ethernet networks to integrate smoothly with traditional office networks. This enables seamless communication between different systems and devices within an industrial facility.4. What are the benefits of using cables compliant with the EN50288 standard?By using industrial Ethernet cables compliant with the EN 50288 standard, businesses can enjoy several benefits, including:a. Enhanced Reliability: The standard's requirements for physical construction, electrical and mechanical performance, and environmental resistance ensure that the cables can withstand the challenges of industrial environments. This results in a highly reliable network infrastructure, minimizing network downtime and costly disruptions.b. Improved Performance: The EN 50288 standard guarantees the cables' compliance with the desired data transmission speeds, allowing businesses to achieve high throughput and low latency in their industrial Ethernet networks. This translates into faster and more efficient communication between devices, enabling better productivity and operational efficiency.c. Safety Assurance: The standard's provisions for shielding and environmental resistance protect against electromagnetic interference (EMI) and other potential hazards, ensuring safe operation of the network and minimizing the risk of equipmentdamage or failures.d. Future-Proofing: Compliance with the EN 50288 standard ensures compatibility with both existing and future Ethernet standards, allowing businesses to easily upgrade and expand their network infrastructure while maintaining interoperability.Conclusion:The EN 50288 standard plays a crucial role in ensuring reliable and efficient communication in industrial Ethernet networks. By providing guidelines for the construction and performance requirements of Ethernet cables used in industrial environments, this standard enables businesses to deploy robust and future-proof network infrastructures. Compliance with the EN 50288 standard not only enhances operational reliability and performance but also ensures safety and compatibility, ultimately benefiting businesses across various industrial sectors.。
GCF Field Trial requirements for GSM_GPRS_EGPRS

GLOBAL CERTIFICATION FORUM (GCF) LtdWork Item DescriptionField Trial requirements for GSM/GPRS/EGPRSReference: GCF WI-108Version: v3.1.0Date: 29.01.2010Document Type: Technical1 ScopeThe scope of this work item covers the renewal of Field Trial requirements for GSM/(E)GPRS including SIM/USIM.2 DescriptionThis Work Item description has been created to handle the renewal of GSM/(E)GPRS including SIM/USIM Field Trial requirements.3 JustificationField Trials are an integral part of the GCF scheme and therefore are required to evolve in conjunction with the implementation of associated mobile technology.4 Supporting companiesCSR, Ericsson Mobile Platforms, Motorola, NEC, Nokia, O2 UK, Orange France, RIM, Sony Ericsson, Vodafone Group, Broadcom, TIM, TeliaSonera5 RapporteurMarc OuwehandNokia CorporationTelephone: +358 40828 0908E-mail: marc.ouwehand@6 Affected bandsNote: GSM 850 and 1900 are outside the GCF certification scheme.7 Core Specifications8 Test SpecificationsNote: The operator expectations on each identified Field Trial Requirement can be derived from the GSMA PRD DG 11 ‘DG Field and Lab Trial Guidelines’, It is emphasised that DG.11 is only a guideline and that manufacturers may use their own test procedures.9 Work Item Certification Entry9.1 Work Item Certification Entry Criteria (CEC)N/A.9.2 Target Work Item Certification Entry Date / GCF-CC versionN/A10 Work Item Freeze and Completion CriteriaDuring the next PRP review this WI should be set to ‘Completed’.11 Conformance Test RequirementsN/A12 IOP Test RequirementsN/A13 Field Trial RequirementsFor BSS/MSC network dependent Field Trial Requirements (BM)For GPRS network dependent Field Trial Requirements (GPRS)For SIM/UICC dependent Field Trial Requirements (2GSIM)For SMSC dependent Field Trial Requirements (SMS)For Network/SIM/UICC/Client independent Field Trial Requirements (NI)14 Periodic Review PointsThe next PRP-review for this WI will be held at the t FT AG meeting during Q3 2010.15 Other commentsThe information below is coming from both WI’s, which during the FT AG #15 meeting has been merged into this WI.Former WI-028 Comments:- During the SG 25 meeting a concern was raised about the approval of this Work Item as well as the CR’s attached to this Work Item via 10 day rule process. The SG made clear that this approval process is not conform the official GCF rules. The SG supposed to approve this Work Item and CR’s. During the SG 25 meeting document S-06-053 was created and approved by the SG to give a mandate for approval via 10 day rule. This mandate applies only for CR’s concerning this Work Item.- Due to the introduction of this Work Item and Work Item 27 (HSDPA) it is required that GCF operators re-declare their status as GCF Qualified operator by using the new Annex B, which should be available in thePRD GCF-OP released in April 2006. The CR for this renewed Annex B is a part of this Work Item and will be uploaded as CR FT-06-022r4During the teleconference of 20.3.2006 there was agreed that an agenda point will be made for FT AG #04,3-4 May 2006 concerning re-declaration.- During the teleconference of 20.3.2006, there was noticed that the mandate for this Work Item didn’t include the EGPRS feature. Therefore it was agreed that the EGPRS topic will be put on the agendafor FT AG #04.Mr. M. Ouwehand (Nokia) will take care that there will be a discussion/input documentavailable for the FT AG #04.When WI-028 has been activated there was agreed to put a ‘transition period’ in place, due the fact that bythat time there were no enough FTQ ANNEX B documents available.During the FT AG #08, 2-3 May 2007, there has been agreed that the ‘transition period’ is ended by therelease of GCF-CC 3.26.0.Former WI-048 Comments:It was suggested during the FTAG meeting discussions of this WI that the most effective method ofadministrating and executing the EDGE classified test requirements while maintaining confidence in GCF FTfor both GPRS and EDGE networks is:a) Introduce a new classification called EDGEb) Copy all existing GPRS requirements to the EDGE Requirements.c) FT on GPRS NW Configurations do not need to perform the EDGE classified test requirementsd) FT on EDGE NW Configurations do not need to perform the GPRS classified test requirements.When this WI meet the CEC and therefore will be activated, it should be considered by FT AG to merge the EDGE Field Trial requirements table into the existing GPRS Field Trial requirements table as has been done with PS, HSDPA & EUL requirements table merge.The CR’s to GCF-CC related to this Work Item need to be submitted at the same time that CR to activate this Work item will be submitted.16 Document Change Record。
J-11OMEGA 无线红外温度传感器说明书
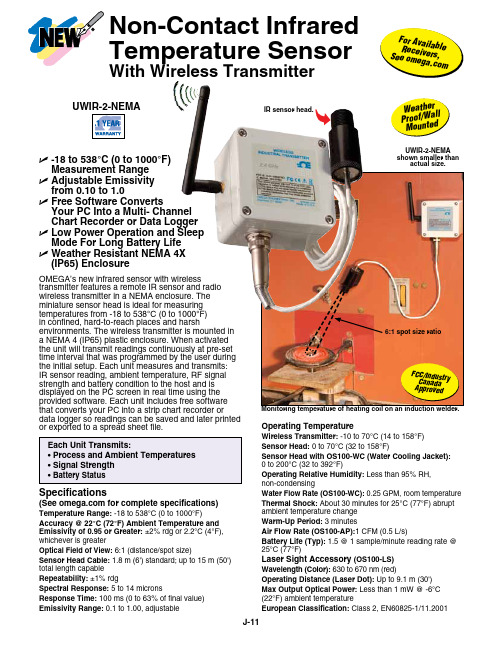
OMEGA’s new infrared sensor with wirelesstransmitter features a remote IR sensor and radio wireless transmitter in a NEMA enclosure. The miniature sensor head is ideal for measuring temperatures from -18 to 538°C (0 to 1000°F) in confined, hard-to-reach places and harshenvironments. The wireless transmitter is mounted in a NEMA 4 (IP65) plastic enclosure. When activated the unit will transmit readings continuously at pre-set time interval that was programmed by the user during the initial setup. Each unit measures and transmits: IR sensor reading, ambient temperature, RF signal strength and battery condition to the host and is displayed on the PC screen in real time using the provided software. Each unit includes free software that converts your PC into a strip chart recorder ordata logger so readings can be saved and later printed or exported to a spread sheet file.Operating TemperatureWireless Transmitter: -10 to 70°C (14 to 158°F)Sensor Head: 0 to 70°C (32 to 158°F)Sensor Head with OS100-WC (Water Cooling Jacket): 0 to 200°C (32 to 392°F)Operating Relative Humidity: Less than 95% RH, non-condensingWater Flow Rate (OS100-WC): 0.25 GPM, room temperature Thermal Shock: About 30 minutes for 25°C (77°F) abrupt ambient temperature change Warm-Up Period: 3 minutesAir Flow Rate (OS100-AP):1 CFM (0.5 L/s)Battery Life (Typ): 1.5 @ 1 sample/minute reading rate @ 25°C (77°F)Laser Sight Accessory (OS100-LS)Wavelength (Color): 630 to 670 nm (red)Operating Distance (Laser Dot): Up to 9.1 m (30')Max Output Optical Power: Less than 1 mW @ -6°C (22°F) ambient temperatureEuropean Classification: Class 2, EN60825-1/11.2001Specifications(See for complete specifications)Temperature Range: -18 to 538°C (0 to 1000°F)Accuracy @ 22°C (72°F) Ambient Temperature and Emissivity of 0.95 or Greater: ±2% rdg or 2.2°C (4°F), whichever is greaterOptical Field of View: 6:1 (distance/spot size)Sensor Head Cable: 1.8 m (6') standard; up to 15 m (50') total length capable Repeatability: ±1% rdgSpectral Response: 5 to 14 micronsResponse Time: 100 ms (0 to 63% of final value)Emissivity Range: 0.1 to 1.00, adjustableU -18 to 538°C (0 to 1000°F) Measurement Range U A djustable Emissivity from 0.10 to 1.0U F ree Software ConvertsYour PC Into a Multi- Channel Chart Recorder or Data Logger U L ow Power Operation and Sleep Mode For Long Battery Life U W eather Resistant NEMA 4X (IP65) EnclosureF C C /I n d u str y C a n a d a A p p r o v e dF o r A v ai l a b l e R e c e i v er s , S e e o me g a .c o mUWIR-2-NEMA shown smaller thanactual size.IR sensor head.W e a t h e rP r o o f /W al lM o u n t ed Non-Contact Infrared Temperature SensorWith Wireless Transmitter6:1 spot size ratioOS100-AP air purge collar to keep the lens free of particles or debris.Both shown smallerthan actual size.Maximum Operating Current: 45 mA @ 3 VdcFDA Classification: Complies with 21 CFR 1040.10, Class II laser product Beam Diameter: 5 mm (0.20")Beam Divergence: <2 mradOperating Temperature: 0 to 50°C (32 to 122°F)Operating Relative Humidity: Less than 95% RH, non-condensingbattery assembly.Ordering Examples: UWIR-2-NEMA, wireless infrared transmitter, UWTC-REC1, 48-channel USB receiver, UWTC-BATT-C, spare battery, and OS100-MB, sensor head bracket.UWIR-2-NEMA, wireless infrared transmitter, UWTC-REC2-D-MA, 48-channel transceiver/host with 1-channel 4 to 20 mA analog output, alarm and local display, UWTC-BATT-C, spare battery, and OS100-MB, sensor head bracket. OCW-3, OMEGACARE SM extends standard 1-yearwarranty to a total of 4 years.Power:(1.5 x 2")LASER RADIATION - DO NOT STARE INTO BEAM CAUTIONTYPE AND RULES PRINT BLACK 100%BACKGROUND YELLOW 100%Shown actual size.OS100-LS laser sight fits in front of the IR head for accurate positioning.。
Speedybee F405 WING FC Board User Manual

Specification overviewSpeedybeeF405 WING APPPart1 -OverViewSpeedybee APP Installation guide FacebookAssembly InstructionsM2x4 smallhead cross screwThe direction ofthe arrow is themachine headWireless BoardFC BoardPDB BoardM3x8.1 mmSilicone GrommetsM2 x 12 copperStandoff SpacerM3x4 mmSilicone GrommetsABC1.Align the pin headers between boards andthen press the two boards together tightly.2.Install both boards and onto board ,and tighten the screws.A BA B CAssembly orderABCCFC Board FrontPart2-hardware descriptionLayoutDigital airspeedsensor connectorAnalog VTX solder padsThe default power supply is 9V. Ifthe VTX can only be powered by5V, please change the PDB board'sVTX BEC to output 5V.Telemetry modulesolder padsTelemetry moduleconnectorRS SI sol de r p ad sSBUS inputpin headersMotor and servo outputpin headers MicroSD cardslotDigital VTXsolder padsAnalog camera solder padsAnalog airspeedsensor connectorELRS receiver pin headers same asthe Telemetrymodule connectorAnalog RSSI signalinput, supportsup to 3.3VWith inversioncircuit, connectedto RX2PWM1-11The default power supply is 9V. Ifthe camera can only be poweredby 5V, please connect the powersupply to the 5V solder pad.Built-in voltage divider circuit,supports up to 6.6V.Use these pin headers to connectthe ELRS/TBS receiver.GPS moduleFC Board BackSH1.0 6PAnalog cameraconnectorGPS module connectorAirspeed sensorsolder padsUSB extenderconnectorDigital VTXconnectorConnect to the PDBboardUART6 solderpadsVTXT G9VNCCAMGND9VSBUSGNDRX5TX5G9SDASCL4V5G T RSH1.0 4PThe signals are thesame as theairspeed sensorconnector.Analog VTX connectorUSB extender frontBuzzer USB TYPE-C PortBuzzer mute switchoperating state, the BOOTbutton is also used forcontrolling otherfunctions of thewireless board.FC RGB statusindicator BOOT buttonFC board connectorPDB board FrontConnect as shownin the diagramNote: TX800 requires5V power supply.VTX BEC voltageselection jumperServo BEC voltageselection jumper 12V outputDefault 9V output5V output6V outputDefault 5V output7.2V outputDO NOT connect ESC BEC outputto Vx pad (Red wire in middle ofconnector).4-level battery level indicator.Note: disconnect the UART6 jumper onthe back of the wireless board to useTX6 RX6. TX1 RX1 shares the same signalas the ELRS/TBS receiver pin header.Wireless status indicator (RGB LED)LED mode indicator(orange LED):, and Wireless board FrontLED mode indicator(orange LED)Battery LED:BLE not connectedGreen solid:BLE connected successfullyWhite slow flashing :Wi-Fi not connectedWhite Solid:Wi-Fi connected successfullyBlue slow flashing:Classic Bluetooth SPP not connectedBlue Solid:Classic Bluetooth SPP not connectedRGB LED off: Wireless module turned offPressing the BOOT button for 6 seconds can switch between the 4wireless modes. When the yellow LED flashes rapidly and the boardautomatically restarts, the switch is successful.Orange light always on:Solid orange LED means the 4 sets of LEDstrips are in SB_LED mode, controlled by the wireless chip.A short press of the BOOT button cycles through different displayeffects when the FC is operating normally.Orange light is off - Off orange LED indicates FC_LED mode, wherethe FC controls the 4 sets of LED strips directly.Press and hold the BOOT button for 3 seconds to switch betweenFC_LED mode and SB_LED mode.The maximum power supply for theLED connector is about 5.2V 1.3A.When the power exceeds the limit,the resettable fuse will cut off thepower supply. Please reduce thenumber of light beads appropriatelywhen the power exceeds the limit.Taking SpeedyBee Programable2812 Arm LED strips as an example,a total of 17 LED strips can beinstalled, including approximately68 light beads.LED strip connectorUART6 jumperSH1.0 3PSH1.0 3PSH1.0 3PWiring DiagramUSB extenderSR ST4S2S1VX VX4V5G G GGGGGGGVXVXVXVXVXVXS3S4S5S6S7S8SR14V5GND5VT4R4G8I428P7AA12203T E L EM2/4Wireless boardFC boardPDB boardPower supplyThe power distribution logic for the F405 WING APP is as follows:1、 The 9V pad uses a VTX&CAM BEC for power supply. When the VTX&CAM BEC switches to another voltage through the pad jumper, the 9V pad will output the corresponding voltage.2、The Vx pin headers use a Servo BEC for power supply. When the Servo BEC switches to anothervoltage through the pad jumper, the Vx pin headers will output the corresponding voltage.3、The default voltage for the FC BEC is 5.2V, with power output divided into three directions:·The first path directly outputs to the 5V pad.·The second path outputs to the onboard chip and 4V5 pad through a diode.·The third path outputs to the LED connector through a self-recovering fuse and reverse connection protection circuit.The limit for the LED connector power supply is approximately 68 pieces of SpeedyBee 5050 LED strip beads. Do not exceed this limit.To test if other brands of LED strips meet the power requirements, you can take the following steps:·After connecting the LED strip, let the flight controller be powered and idle for 10 minutes. Observe if the color of the LED strip suddenly dims and feel the wireless board with your hand. If it feels very hot, the power supply is insufficient, and you need to reduce the number of LED beads.·You can also use a multimeter to test the voltage of the 5V pad or the LED strip power pad. If thevoltage is below 5V, it indicates that the power supply is insufficient, and you need to reduce thenumber of LED beads.Note: If your ESC supports BEC output, do not connect the ESC BEC red wire to the Vx pinheaders, as this may burn the ESC or Servo BEC.Please note that the FC BEC can provide a continuous current of 2.4-2.5A and a peak current of 3A. The onboard chip requires less than 1A of power, GPS and receivers generally require less than 0.1A, and the wireless controller requires 0.1A.If the LED connector uses a maximum of 1.3A, the 5V pad will have no remaining capacity.If the LED connector is not used, the 5V pad will have a 1.3A surplus.APP connectionPart3-Firmware upgrade andAPP connection①Press and hold the BOOT button , andconnect the FC to the computer viaUSB cable.②Open the INAV Configurator on yourcomputer, go to the "Firmware Flasher "page, select the flight controller targetas "SPEEDYBEEF405WING", and thenflash the firmware.③To flash Ardupilot firmware, follow thesame steps as above, select "LoadFirmware [local]", and then flashthe firmware.SpeedyBee F405 WING APP not supportingwireless firmware flashing, please update thefirmware on a computer. Follow these steps:Check the color of the wireless status indicator. If it's not flashingwhite, press the BOOT button for 6 seconds to switch to white.Then connect to the "Speedybee F405Wing" Wi-Fi and openQGroundControl, it will automatically connect.Firmware upgradeConnecting Ardupilot firmware to QGroundControl app.Check the color of the wireless statusindicator .If it's slow flashing green, open theSpeedyBee app and follow thesteps to connect to thecorresponding product.Connecting INAV Firmware toSpeedybee APP.23APP ConnectionSuitable for different flight control firmware and Configurator. The supported apps are listed in thefollowing table. It is recommended to use Bluetooth BLE mode for iNav and WiFi mode for Ardupilot.Part4-SpecificationsSpeedyBee F405 WING FC board STM32F405,168MHz,1MB FlashICM-42688-P SPL006-001AT7456EMicroSD Card Slot6 sets(USART1, USART2, USART3, UART4, UART5, UART6(Dedicated for Wireless board Telemetry connection))1x Used for magnetometer, digital airspeed sensor 4x (VBAT, Current, RSSI, Analog AirSpeed)12x (11+1“LED”pad)Supported,connected to UART1Built in inverter for SBUS input (UART2-RX)3x LEDs for FC STATUS (Blue, Green) and 3.3V indicator(Red) 1x RGB Supported,Named as RS .INAV:SpeedyBeeF405WING(default)ArduPilot: SpeedyBeeF405WINGMCUIMU(Gyro&Accelerometer) Barometer OSD Chip Blackbox UART I2C ADC PWMELRS/CRSF receiver SBUS LED RSSISupported FC FirmwareSpeedyBee F405 WING PDB boardInput voltage range Battery Voltage Sensor Battery Current Sensor TVS Protective diode FC BEC outputVTX BEC output OutputServo BEC output 7~36V (2~6S LiPo)Connect to FC board VBAT, 1K:10K (Scale 1100 in iNav, BATT_VOL T_MUL T 11.0 in ArduPilot)90A continuous, 215A peak Connect to FC board Current (Scale 195 in iNav, 50 A/V in ArduPilot)YesOutput 5.2V +/- 0.1V DC Continuous current 2.4 Amps, 3A Peak Designed for FC, Receiver, GPS module, AirSpeed module, Telemetry module, WS2812 LED_StripOutput 9V +/- 0.1V DC Continuous current 1.8 Amps, 2.3A Peak Voltage adjustable, 9V Default, 12V or 5V via jumper Designed for Analog Video Transmitter,Digital Video Transmitter, Camera.Output 4.9V +/- 0.1V DC Continuous current 4.5 Amps, 5.5A PeakVoltage adjustable, 4.9V Default, 6V or 7.2V via jumper Designedfor Servos.BLE mode, connect to Speedybee APPClassic Bluetooth SPP mode, connect to QGroundControl APP , MissionPlanner4x WS2812 LED strip connectors, adjustable colors and flashing modesMax 5.2V 1.3A, supports around 68pcs 5050 WS2812 LED beads4x RGB indicator LED for battery level display by number of lightsWireless Configuration(long press BOOT button for 6 seconds to switch modes)LED strip controller (short press BOOT button to switch effects, long press 3 seconds to switch modes)On-board battery level indicator Wi-Fi mode, connect to QGroundControl APP , Speedybee APP , MissionPlanner, etc.SpeedyBee F405 WING Wireless boardPart5-pin mappingUART USB TX1 RX15V tolerant I/OUART1ELRS/TBS receiverSBUS receiver, SBUS pad = RX2 with inverter SmartPort Telemetry,enable Softserial_Tx2GPS USER DJI OSD/VTXOnboard wireless controllerTX3 RX35V tolerant I/O UART3TX4 RX45V tolerant I/O UART4TX5 RX55V tolerant I/O UART5TX6 RX65V tolerant I/OUART6TX2 RX2SBUS 5V tolerant I/OSBUS padTX2USB INAV mappingPWM TIMER INAV Plane INAV MultiRotor S1TIM4_CH2Motor Motor 5V tolerant I/O S2TIM4_CH1Motor Motor 5V tolerant I/O S3TIM3_CH3Servo Motor 5V tolerant I/O S4TIM3_CH4Servo Motor 5V tolerant I/O S5TIM8_CH3Servo Motor 5V tolerant I/O S6TIM8_CH4Servo Motor 5V tolerant I/O S7TIM8_CH2N Servo Servo 5V tolerant I/O S8TIM2_CH Servo Servo 5V tolerant I/O S9TIM2_CH4Servo Servo 5V tolerant I/O S10TIM2_CH1Servo Servo 5V tolerant I/O S11TIM12_CH2Servo Servo 5V tolerant I/O LEDTIM1_CH1WS2812LEDWS2812LED5V tolerant I/OADCVBAT CURR AIRSPD RSSIVBAT ADCADC_CHANNEL_1CURRENT_METER ADC ADC_CHANNEL_2AIRSPEED ADC ADC_CHANNEL_3RSSI ADCADC_CHANNEL_4voltage scale 11001K:10K divider builtin 0~30V 0~3.3V10K:10K divider builtin 0~6.6V 0~3.3VCurrent scale 195Analog Airspeed Analog RSSII2CI2C1onboard BarometerCompassDigital Airspeed sensor OLEDSPL06-001QMC5883 / HMC5883 /MAG3110 / LIS3MDL MS45250.96″5V tolerant I/OArduPilot mappingUSB TX1 RX1TX2 RX2SBUSTX3 RX3TX4 RX4TX5 RX5TX6 RX6USBUSART1(With DMA)SBUS pad RX2USART2USART3UART4UART5USART6SERIAL0SERIAL1BRD_AL T_CONFIG 0DefaultBRD_AL T_CONFIG 1SERIAL2SERIAL3SERIAL4SERIAL5SERIAL6ConsoleELRS/TBS receiver Serial RC inputSBUS receiver,SBUS pad = RX2 with inverter IBUS/DSM/PPM USER GPS1USER DJI OSD/VTX Telem1*If sending highspeed serial data (eg. 921600 baud) to the board, use USART1(Serial1).PWM S1S2S3S4S5S6S7S8S9S10S11LEDPWM1 GPIO50PWM2 GPIO51PWM3 GPIO52PWM4 GPIO53PWM5 GPIO54PWM6 GPIO55PWM7 GPIO56PWM8 GPIO57PWM9 GPIO58PWM10 GPIO59PWM11 GPIO60PWM12 GPIO61TIMER TIM4_CH2TIM4_CH1TIM3_CH3TIM3_CH4TIM8_CH3TIM8_CH4TIM8_CH2N TIM2_CH3TIM2_CH4TIM2_CH1TIM1_CH3N TIM1_CH1PWM/DShot(DMA)PWM/DShot(DMA)PWM/DShot(DMA)PWM/DShot(DMA)PWM/DShot(DMA)PWM/DShot(DMA)PWM/DShot(DMA)PWM/DShot(DMA)PWM/DShot(DMA)PWM/DShot(DMA)PWM/DShot(DMA)PWM/DShot(DMA)Group1Group2Group3Group4Group5*All motor/servo outputs are DShot and PWM capable. However, mixing DShot and normal PWM operation for outputs is restricted into groups, ie. enabling DShot for an output in a group requires that ALL outputs in that group be configured and used as DShot, rather than PWM outputs. LED, which corresponds to PWM12, is set as the default output for NeoPixel1. Therefore, if you need to use PWM11 as an output, you need to disable the NeoPixel1 function on PWM12.ADCVBATCURRAIRSPDRSSIBattery voltageCurrent senseAnalog AirspeedAnalog RSSIBATT_VOL T_PINBATT_VOL T_MUL TBATT_CURR_PINBATT_AMP_PERVL TARSPD_ANA_PINARSPD_TYPERSSI_ANA_PINRSSI_TYPE1011.051150152142 1K:10K divider builtin0~30V0~3.3V10K:10K divider builtin0~6.6V0~3.3VI2CI2C1onboard BarometerCompassDigital Airspeed sensorMS4525ASP5033SPL06-001COMPASS_AUTODECARSPD_BUSARSPD_TYPEARSPD_TYPE115 5V tolerant I/OPart7-PackageM2x4 small head4pin Dupont single-headCable(150mm) x18pin SH1.0 USB4pin SH1.0 to 3+2pin JST1.25 FPV CamCable(250mm) x1。
INTERNORMEN-electronics Bottle Sampling System BSS
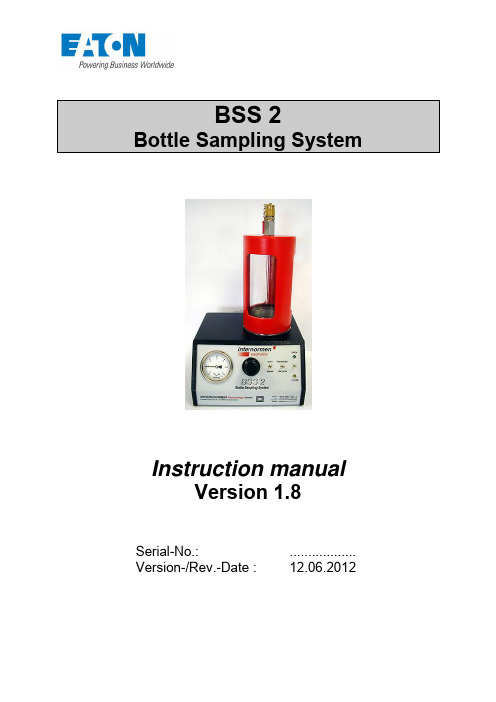
Instruction manualVersion 1.8Serial-No.: .................. Version-/Rev.-Date : 12.06.2012Contents1. General (3)2. Safety Instructions (4)3. Extent of Delivery (5)4. Switch Panel (6)5. Bottle Sampling (7)5.1. Reservoir (7)5.2. Sampling (7)6. Commissioning (8)6.1. Power supply (8)6.2. Compressed Air Supply (9)6.2.1. Operation with the Compressor from INTERNORMEN-electronics (10)6.2.2. Operation with Existing Compressed Air Supply (11)6.3. Connection to CCS 1 / CCS 2 (12)7. Before the Analysis (13)7.1. Conditioning of the Sample (14)8. Analysis of sample (14)8.1. Degassing (14)8.2. Sample Feed (17)9. Cleaning and Maintenance (19)10. Technical Data (20)10.1. Connections (20)10.1.1. Electrical (20)10.1.2. Pneumatic (20)1. GeneralDear CustomerWe congratulate you on buying the INTERNORMEN-electronics Bottle Sampling System BSS 2. Before commissioning please read this manual carefully to prevent damages to the BSS 2.You have purchased a product which is technically up-to-date and which enables you to perform a particle count in lab quality, at any points of your plant where an online-analysis is not possible.The sampling and the output of results only take a few minutes.In general an online-measurement is to be preferred rather than a bottle sample analysis. The process from sampling to particle counting involves many possibilities of mistakes. Therefore this kind of analysis should be carried out only by trained per-sonal.2. Safety Instructions☝To prevent accidents it is important to keep strictly to the manual during the oper-ation of the BSS 2.☝Never try to open the pressure chamber, when the system pressure varies from the ambient air pressure.☝Never try to pressurise the chamber before being sure that it is tightly closed (see the lighting diode!)☝ Never use damaged or defective components (threaded joints, hoses, connect-ors etc.)!☝ A damaged pressure vessel (scratches in the glass, bent housing etc.) must not be used.☝Never open the BSS 2 housing !3. Components of BSS 2The BSS 2 includes :- Case [1]- Instrument base with integrated service unit [2] - Pressure vessel [3] - Power supply unit [4] - Connector for pneumatics [5]- High pressure hose with mini-measuring connection M 16x2 [6] - Compressor [7] (optional) -Spiral hose [8] (optional)Illustration 1178235464. Switch PanelIllustration 2B1 – Vacuum + pressure gauge B2 – Regulator (pressure + vacuum) B3 – Switch VENT / WORKB4 – Switch PRESSURE / VACUUM B5 – Switch OPEN / CLOSEB6 – Green light emitting diode OPEN B7 – Yellow light emitting diode CLOSEB1B5 B3B2B6 B4B75. Bottle Sampling5.1. ReservoirBefore sampling make sure that the reservoir to be used can be put into the pressure chamber of the BSS 2.To guarantee reliable results of measurement you should only use reservoirs whose cleanliness according to ISO 3722 is proved. You can buy them directly from INTERNORMEN Technology GmbH (two sample bottle set, Best. Nr. 313427). These glasses should be used only once.5.2. SamplingThe bottle sampling requires a very careful handling. First flush the sampling point for a few seconds. Open the sample reservoir just directly before taking the sample, and close it immediately afterwards. Only this way the ambient influences do not impact your measuring results.Label your samples carefully. Note:Sampling pointDate and time of samplingSampler (name, first name)Special notes, if applicableThis is important for samplings at different plants, respectively different points of the plant to help prevent any unclearness.6. Commissioning6.1. Power supplyFor the operation of the BSS 2 you should only use the plug-in power supply supplied by INTERNORMEN-electronics, which is included in the system. Make sure that this power supply unit is set to the required output voltage of 12 V DC. (Illustration 3).Illustration 3Put the plug of the power supply unit into the current outlet (230 V~ 50 Hz) and the connection cable into the socket of the BSS 2 (Illustration 4) on the backside of the device. The actual unit might vary depending on the respective country's voltage.Illustration 4When correctly connected, one of the light emittingdiodes OPEN respectively CLOSE should light upafter a few seconds.Turn the switch VENT / WORK to the directionVENT, if it is in WORK.6.2. Compressed Air SupplyIn addition to the electric connection, the BSS 2 of INTERNORMEN-electronics also requires an external compressed air supply. This is provided either by an existing compressed air piping or the compressor optionally available.6.2.1. Operation with the Compressor from INTERNORMEN-electronics Instructions for the handling of the compressor are given in the enclosed manual.Connect the BSS 2 with the com-pressor. For this use the spiral hose(Pos. 8, Illustration 1) which is op-tionally available. Put the hose pluginto the coupler of the compressor.(Illustration 5).Illustration 5Now put the other end (coupler) into the quick con-nect plug at the backside of the BSS 2 (Illustration6). The coupler is locked, when you hear a clickingnoise while putting into one another.To release the plug connectors, pull back the lock-ing ring of the closing coupler.Before releasing make sure that the system is notunder pressure.Illustration 6Integrated service unitThe serialize inserted service unit prevents the entryof dirt and humidity into the BSS 2.To empty the container over knurled screw duringaccumulation of liquid.6.2.2. Operating with Existing Compressed Air SupplyConnect the BSS 2 to the pressure air supply. For this please use the optional attached plug-in connection to be connected with the device. This plug-in connection has an internal screw thread G 1/4 for the hose. Please make sure a firm seat and sealing between the hose and connector.Now slip the connection cap over the plug at thebackside of the BSS 2 (Illustration 7).To release the plug connectors, pull back thelocking ring of the closing coupler.Before releasing make sure that the system isnot under pressure.Illustration 7Integrated service unitThe serialize inserted service unit prevents the entryof dirt and humidity into the BSS 2.To empty the container over knurled screw duringaccumulation of liquid.6.3. Connection to CCS 1 / CCS 2Connect the BSS 2 to the contamination control system by means of the pressure hose (6, Illustration 1) included in the BSS 2. First remove the screw cap of the mini-measuring connection at the top of the pressure vessel (Illustration 8). Now you can mount the hose. The same way of connection applies to the CCS 1 as well as the CCS 2.Illustration 87. Before the AnalysisAfter following the instructions you are ready to operate the BSS 2. Make sure that you have sufficient air supply and pressure (max. 10 bar).Turn the compressor on (if operated by compressor), respectively open thefeeding main to the BSS 2 (existing compressed air supply). Set the pressure control valve to a rate between 6,0 and 6,5 bar. A different pressure rate might cause malfunctions or damages to the BSS 2.Turn the switch OPEN / CLOSE to the position OPEN. When the diodeOPEN (green) lights up, the pressure chamber lock is released. Now youcan remove the pressure vessel.Make sure that an O-ring (90x2,5) is inside the locking device (Illustration 9).Illustration 97.1. Conditioning of the SampleBefore putting the bottle into the BSS 2 for examination, homogenize thoroughly and ½ - 1 minute in the ultrasonic bath place. For exact measuring results an equal distribution of the particles is important. The following shakingprocedure should take about two minutes, dependent on the fluid viscosity, contamination and time interval between sampling and analysis.The vibration time depends directly on the fluid viscosity.< ISO-VG-32 2 minISO-VG-46 ... 100 3 ... 4 min> ISO-VG-100 5 ... 10 min (additional warming-up is indicated)8. Analysis of sampleInstructions for the operation of the CCS1, respectively the CCS2 can be taken from their manuals.Immediately after termination of the sample conditioning the analysis should be done.8.1. DegassingPlace the sample on the cover plate of the pressure chamber at the topside of the device. Please make sure once again that the O-ring is in proper position. Place the pressure vessel over the sample. Be aware of the correct position, i.e. it has to have slipped completely downwards. Now you can turn the switch OPEN / CLOSE to the position CLOSE (Illustration 12, 1). Wait until after a few seconds the diode CLOSE (yellow) lightens. Close the ball valve at the topside of the pressure vessel (Illustra-tion 10).Illustration 10Turn the switch VENT / WORK to the position WORK (Illustration 11, 2). Turn the switch PRESSURE / VACUUM to the position VACUUM (Illustration 11, 3).Illustration 11Pull out the handle of the pressure regulator.Illustration 12closeopen123Now turn the handle clockwise (Illustration 13) until – 1,0 bar. This will produce a vacuum in the pressure chamber. The more you turn, the lower the pressure in the chamber. You can observe this on the vacuum / pressure gauge (Illustration 13).Illustration 13Keep the vacuum in the chamber until there are no gas bub-bles in the fluid anymore.Illustration 14Turn the handle (illustration 15) anticlockwise until 0,0.Illustration 158.2. Sample FeedTurn the switch PRESSURE / VACUUM to the position PRESSURE (Illustration 16, 1).Now turn the handle (Illustration 16, 2) slowly clockwise. This will increase the pres-sure in the chamber. Continue turning until the gauge (Illustration 16) indicates a pressure of about approximate 3,0 bar. When you hear a hissing noise, the pressure in the chamber is too high. In this case turn the handle anticlockwise until this noise stops.Illustration 1612Open the ball valve at the top of the pressure vessel (Illustration 15). Turn the switch PRESSURE / VACUUM to the position PRESSURE (Illustration 16, 1).Illustration 15Now you can start the measurement at your particle counter. Please observe the in-st ructions for …Bottle Sampling“ in the manual of your contamination co ntroller.Illustration 17closeopenAfter finishing the measurements turn the switch VENT / WORK to the position VENT. You will then hear a hissing noise produced by the air escaping from the pressure chamber. Wait until this is ended, and then turn the switch OPEN / CLOSE to the position OPEN. When the green diode OPEN lights up, the vessel is unlocked and you can remove it by lifting upwards. Remove the sample glass.9. Cleaning and MaintenancePlease keep the device and the feeding tubes absolutely clean. After every use the device has to be flushed. For the flushing please use fine filtered low viscosity oil (e.g. ISOVG22 / ISOVG32). Before operating the BSS2 after a long time of not using it (about 2 weeks), the particle counting device should be flushed properly.For the cleaning of the pressure dome and the device housing please use a soft, fuzz-free cloth.Take care that the ascending tube is not bent while cleaning the pressure cham-ber. A contamination especially of this component would have negative affects on correct counting results, as it is in direct contact with the sample.Wipe the oil remains away from the plate of the pressure chamber lock and from the sealing area. For the cleaning do not use any aggressive chemical or rubbing agents.10. Technical DataDimensions: 220 x 240 x 390Weight: 6,5 kgInitial pressure: 0...4 barVacuum: 0...-0,95 bar10.1. Connections10.1.1. ElectricalPower supply / mains: 230V ~ 50 Hz or 110 V ~ 60 HzPower supply / device: 12 V DC10.1.2. PneumaticPressure range: 5...7 barFlow rate: min. 40 l/min airConnections: Rapid action coupling NW 7,2 with internal thread G ¼Mini-measuring connection with screw coupling M16 x 2 Subject to technical alterations!North America — HQ70 Wood Ave., South, 2nd Floor Iselin, NJ 08830Toll Free: (800) 656-3344 (North America Only)Voice: (732) 767-4200ChinaNo. 3, Lane 280, Linhong Road Changning District, 200335 Shanghai, P.R. ChinaVoice: +86-21-5200-0099 Singapore4 Loyang Lane #04-01/02 Singapore 508914Voice: +65-6825-1668Europe/Africa/Middle EastFriedensstraße 41D-68804 Altlussheim, GermanyVoice: +49-6205-2094-0Auf der Heide 253947 Nettersheim, GermanyVoice: +49-2486-809-0An den Nahewiesen 2455450 Langenlonsheim, GermanyVoice: +49 6704 204-0BrazilAv. Julia Gaioli, 474 –Bonsucesso07251-500 – Guarulhos, BrazilVoice: +55 (11) 2465-8822For more information, please e-mail us at filtra-******************Visit us online /filtration for a completelist of Eaton´s filtration products.©2012 Eaton Corporation. All Rights Reserved.All trademarks and registered trademarks are the property of their respectiveowners. Litho USA.All information and recommendations appearing in this brochure concerning theuse of products described herein are based on tests believed to be reliable.However, it is the user’s responsibility to determine the suitability for his own useof such products. Since the actual use by others is beyond our control, no guaran-tee, expressed or implied, is made by Eaton as to the effects of such use or theresults to be obtained. Eaton assumes no liability arising out of the use by othersof such products. Nor is the information herein to be construed as absolutelycomplete, since additional information may be necessary or desirable whenparticular or exceptional conditions or circumstances exist or because of applica-ble laws or government regulations.。
NEP988说明书

N E P988说明书(总32页) -CAL-FENGHAI.-(YICAI)-Company One1-CAL-本页仅作为文档封面,使用请直接删除NEP988数字式备用电源自动投切装置说明书国电南京自动化股份有限公司NEP 988数字式备用电源自动投切装置说明书编写:黄作兵审核:陈雪峰批准:郭效军国电南京自动化股份有限公司二OO三年五月目次1 装置概述........................................................................................................... 错误!未定义书签。
2 主要技术指标................................................................................................... 错误!未定义书签。
3功能介绍........................................................................................................... 错误!未定义书签。
NEP988A母联备自投功能说明 ........................................................................ 错误!未定义书签。
NEP988B进线互投功能说明 ............................................................................ 错误!未定义书签。
NEP988C内桥开关备自投功能说明 ................................................................ 错误!未定义书签。
cve-2006-0987 2008r2

CVE-2006-0987 漏洞及其对 Windows Server 2008 R2 的影响一、漏洞概述1. CVE-2006-0987 漏洞是指在软件或操作系统中存在的安全漏洞,可以被黑客利用进行远程攻击或其他恶意行为。
2. 该漏洞最初在2006年被发现,并被赋予CVE编号2006-0987。
它存在于某些版本的操作系统中,包括Windows Server 2008 R2。
二、漏洞的具体影响3. CVE-2006-0987 漏洞对Windows Server 2008 R2 的影响主要体现在以下几个方面:3.1. 可能导致系统崩溃或死机3.2. 可能会泄露敏感信息3.3. 可能被黑客利用进行远程攻击三、漏洞修复措施4. 针对CVE-2006-0987 漏洞,微软公司于发现后采取了一系列修复措施,以减轻漏洞带来的危害:4.1. 发布安全补丁4.2. 更新操作系统4.3. 提供相关的安全建议和指南四、Windows Server 2008 R2 的安全加固建议5. 除了及时应用微软发布的安全补丁外,针对 Windows Server 2008 R2 系统,我们还可以采取以下措施进行安全加固:5.1. 启用防火墙,限制对端口的访问5.2. 定期备份数据,以应对可能的攻击或数据丢失5.3. 安装可信的安全软件,对系统进行实时监控和防护五、如何预防类似漏洞的发生6. 为了预防类似漏洞的发生,我们还应该培养安全意识,加强对系统的监控和管理,做好以下工作:6.1. 及时了解漏洞信息,关注软件或操作系统的安全公告6.2. 定期对系统进行安全扫描和漏洞检测6.3. 加强对系统管理员的培训和管理,防止人为失误或疏忽导致安全漏洞的发生在使用 Windows Server 2008 R2 系统时,我们应当对系统的安全性给予足够的重视,及时更新补丁、加强安全加固措施、培养安全意识,从而有效预防 CVE-2006-0987 漏洞对系统的影响。
DuplineSafe 安全中继输出模块说明说明书
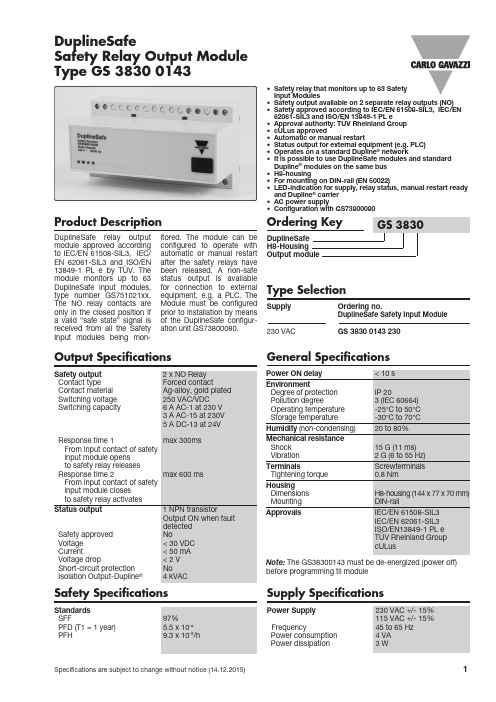
• Safety relay that monitors up to 63 Safety Input Modules• Safety output available on 2 separate relay outputs (NO)• Safety approved according to IEC/EN 61508-SIL3, IEC/EN 62061-SIL3 and ISO/EN 13849-1 PL e• Approval authority: TÜV Rheinland Group • cULus approved• Automatic or manual restart• Status output for external equipment (e.g. PLC)• Operates on a standard Dupline ® network• It is possible to use DuplineSafe modules and standard Dupline ® modules on the same bus • H8-housing• For mounting on DIN-rail (EN 50022)• LED-indication for supply, relay status, manual restart ready and Dupline ® carrier • AC power supply• Configuration with GS73800080Product DescriptionDuplineSafe relay output module approved according to IEC/EN 61508-SIL3, IEC/EN 62061-SIL3 and ISO/EN 13849-1 PL e by TÜV. The module monitors up to 63 DuplineSafe input modules, type number G S751021xx. The NO relay contacts are only in the closed position if a valid “safe state” signal is received from all the Safety Input modules being mon-itored. The module can be configured to operate with automatic or manual restart after the safety relays have been released. A non-safe status output is available for connection to external equipment, e.g. a PLC. The Module must be configured prior to installation by means of the DuplineSafe configur-ation unit GS73800080. Type SelectionSupply Ordering no.DuplineSafe Safety Input Module230 VACGS 3830 0143 230DuplineSafeSafety Relay Output ModuleType GS 3830 0143Safety SpecificationsStandards SFF97% PFD (T1 = 1 year)5.5 x 10-6 PFH9.3 x 10-9/hOutput SpecificationsNote: The GS38300143 must be de-energized (power off) before programming til moduleGeneral SpecificationsSupply SpecificationsPower Supply 230 VAC +/- 15%115 VAC +/- 15% Frequency45 to 65 Hz Power consumption 4 VA Power dissipation3 WWiring DiagramMode of OperationThe Safety Output module G S3******* monitors up to 63 Safety Input modules, type number G S751021xx. Each Safety Input module is monitoring the status of one potential-free contactin a safety device, e.g. anemergency stop palm but-ton or pull cord switch. The Safety Input modules arecontinuously transmitting on the Dupline ® bus the status of the safety contacts using a dynamic signaling princi-ple on two Dupline ® channel addresses (please refer to G S751021xx datasheet for more details). During configuration of theSafety Output module, theuser must define on whichDupline ® channel address-es Safety Input modules shall be monitored. If all themodules are sending avalid “safe-state” signal,then the relay contacts ofthe Safety Output modulewill be closed. In any other situation (non-safe signal received from one or moreSafety Input modules or bus fault), the relay contacts willbe open, thus keeping the system in a safe state. Find below a principle diagram of a DuplineSafe system.The Channel Generator Any type of Dupline ® Chan-nel G enerator can be used, as this component is not part of the safety function. However, it is important to note that all Dupline ® chan-nel addresses used for Safe-ty Input modules must be monostable. Split I/O mode and intelligent channel func-tions are not allowed. If this rule is not obeyed, the relay contacts of the Safety Out-put module will remain in the open position in any situa-tion.Combined SystemsIt is allowed to use stan-dard Dupline ® modules on the channel addresses not used for safety signals, thus allowing combined systems.Monitoring from a PLC, PC or Text DisplayThere are two products available for interfacing a DuplineSafe system to a PLC, PC, Text Display or Touchscreen. One possi-bility is the Profibus-DP gateway (G S3*******), the other possibility is the small Modbus inter-face G STI50 for Text dis-plays and Touchscreens. Using these products, it is possible to monitor theIndicatorsSupply OK Dupline ® OK Relay statusManual restart ready Configuration modeGS 3830 0143DuplineSafe Principle Diagram Input SpecificationsGS 3830 0143Mode of Operation (cont.)status of all the inputs of the Safety Input modules from e.g. a PLC or Text Display. It is not allowed to perform any control function on the channel addresses used for safety signals.Automatic or manual restart Two different operation modes for restart can be configured. A restart is needed whenever the Safety output has been brought to the safe state (relay con-tacts open). If “automatic restart” is selected then the Safety Output module will automatically close the relay contacts as soon as a valid “safe-state” signal is received from all the Safe-ty Input modules. If “manu-al restart” is selected, an activation of the “manu-al restart” input is required to make a restart, and the restart will only happen ifall Safety Input modules aresending a “safe-state” signal.Status outputThe status output is ONwhen a fault or a safetytransmitter is actuated. Thisoutput can be used as anindication by using a LEDor buzzer/horn to sound analarm.Synchronization ChannelThe synchronization channelis used by the Safety Relayto send out a synchroniz-ation signal to the SafetyInput modules on the bus.Therefore, all the SafetyInput modules and the Safe-ty Relay, which together areperforming a safety function,must be coded for the samesynchronization channel.But in case there is alreadyanother safety output mod-ule on the bus sending asynchronization signal onthis channel, then this signalcan be used by other safetyoutput modules.Configuration of the SafetyOutput modulePrior to installation, theSafety Output module needsto be configured by theDuplineSafe configurationunit G S7*******. The fol-lowing parameters need tobe selected:Number of channels on theDupline® busThe “number of channels”is actually selected on thechannel generator, but theRelay Output Module needto know this figure to ensurecorrect operation.Channel addresses of SafetyInput modules to be mon-itoredEach Safety Input Module isusing two channel address-es to send its signal. Thepossible selections are inthe range A3/A4 .. P7/P8.It must be defined whichchannel addresses the Safe-ty Output module shall mon-itor. (Please note that thechannel address A1/A2 isnot allowed in the system).Synchronization channelPlease refer to abovedescriptionPlease refer to the usermanual for the Dup-lineSafe Configuration UnitG S7******* for detailedinstructions on how to con-figure the Safety Outputmodule GS38300143 to per-form the desired function.DuplineSafe - System Characteristics and RulesReaction timeThe reaction time for the total Dupline® safety-loop depends of the num-ber of Dupline® channels. The response time can be calculated as:Reaction time on r elay r elease (wo r st-case): 2 x Number of Dupline® chan-nels + 40 [ms]Note: Reaction time is for the total Dupline® safe-ty-loop; from a safety input goes to non-safe state until the output relay is released. Reaction time on r elay acti-vate (wor st-case): 4 x Num-ber of Dupline® channels + 80 [ms]Note: Reaction time is for the total Dupline® safe-ty-loop; from a safety input goes to safe state until the output relay is activatedTopologyThe Dupline® system has free topology, so cable branches can freely be made at any point in the system. There are no specif-ic length restriction on cablebranches.Cable typesA non-shielded twisted paircable with a cross-sec-tion of 1.5 mm2 is recom-mended, but the Dup-line® bus can also run oncable without twistingand with lower cross-sections. However, the rulesmentioned below must beobeyed.Cabling rulesThe Dupline® system is anextremely robust transmis-sion system, but the followingrules should be obeyed:Rule no. 1The two Dupline® wires mustbe “floating” (none of thetwo wires may be connect-ed to any other potential).Specifically it should bemade sure that the Dupline®common is not connect-ed to protective earth, e.g.through the power supply.Rule no. 2If the longest cable pathexceeds 1.5 km a DT01 ter-mination unit needs to beinstalled at the point farthestaway from the channel gen-erator.If above rules are notobeyed, noise may beinduced in the system, andas a result the relay contactsof the safety output mod-ule will remain in the openposition.Distance, cable and num-ber of Safety input modulesIt is not always the full cap-acity of 63 Safety Inputmodules can be utilized. Itdepends on the cable typeand the length of the cable.The following rule applies:Total current x cable loopresistance < 3,7 VThe total current is the sum-marized current consump-tion of all Dupline®-poweredmodules on the bus. A SafetyInput module typ. uses 1mA.Cable loop esistance = 2x Length of cable (km) xresistance/km (for the cabletype used)Please note that the “lengthof cable” in this calculationis not necessarily the totallength of cable used, it is thecable path from the chan-nel generator to the farthestSafety Input module. In otherwords, only the longestcable path counts.If the above rule is notobeyed, the relay contactsof the Safety Output mod-ule will remain open in anysituation.Example: How many safe-ty Input modules can beinstalled on a 3 km of 1.5mm2 cable ?Cable loop resistance = 2 x3 km x 13,6 Ω/km = 81,6 ΩMax total current = 3,7 V /81,6 Ω = 45,3 mA.Conclusion: In this systemthe max capacity is 45 Safe-ty Input modules, since eachinput module uses 1 mA.DuplineSafe Safety ProcedureIn order to ensure correct safety function of a Dup-line®Safe system, the steps below need to be carried out:1.Identify the exact numberof Safety Input modulesrequired2.Make a table defining thechannel address of each Safety Input module (addresses to be selectedin the range A3/A4 ..P7/ P8)3. Physically allocate thenumber of Safety Inputmodules required andprogram them one by oneaccording to the addresstable, using the Dupline®-Safe Configuration unitGS73800080.4. Configure carefully theSafety Output module tomonitor exactly thechannel addressesselected for the Dupline®Input modules5. Connect all the SafetyInput modules and theSafety Output module tot h e D u p-line® two-wire busand bring all the inputs tothe safe state.6. Now the Safety RelayOutput should haveclosed the contacts. Ifthis is not the case,please review if theaddressing of the safetyinput modules and theconfiguration of the safe-ty output module complieswith each other. If thisdoes not solve theproblem, please checkthat all the DuplineSaferules have been obeyed.7. Now checkeach individualSafety Input module by:a.Remove the busconnection from SafetyInput module and checkthat the safety relayoutput releases.b. Re-connect the safetyinput module to the busand open the inputcontacts. Check that thesafety relay outputreleasesWhen all safety inputmodules have been checkedthis way, the DuplineSafesystem is ready to operate.GS 3830 0143。
Simplex
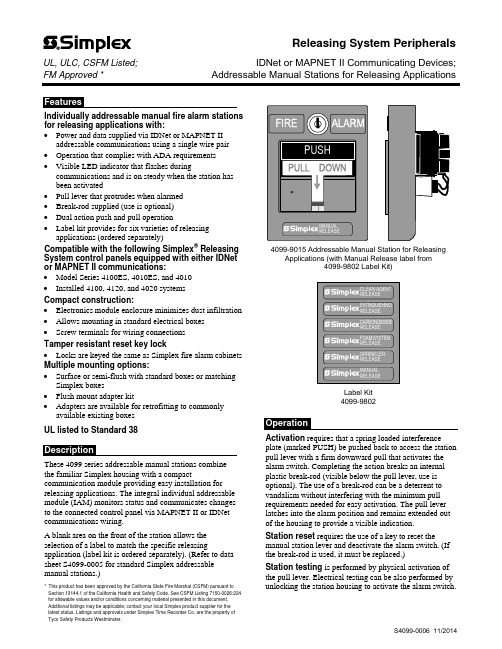
Individually addressable manual fire alarm stations for releasing applications with:∙Power and data supplied via IDNet or MAPNET II addressable communications using a single wire pair∙Operation that complies with ADA requirements∙Visible LED indicator that flashes duringcommunications and is on steady when the station hasbeen activated∙Pull lever that protrudes when alarmed∙Break-rod supplied (use is optional)∙Dual action push and pull operation∙Label kit provides for six varieties of releasing applications (ordered separately)Compatible with the following Simplex® Releasing System control panels equipped with either IDNet or MAPNET II communications:∙Model Series 4100ES, 4010ES, and 4010∙Installed 4100, 4120, and 4020 systemsCompact construction:∙Electronics module enclosure minimizes dust infiltration ∙Allows mounting in standard electrical boxes∙Screw terminals for wiring connectionsTamper resistant reset key lock∙Locks are keyed the same as Simplex fire alarm cabinets Multiple mounting options:∙Surface or semi-flush with standard boxes or matching Simplex boxes∙Flush mount adapter kit∙Adapters are available for retrofitting to commonly available existing boxesUL listed to Standard 38These 4099 series addressable manual stations combinethe familiar Simplex housing with a compact communication module providing easy installation for releasing applications. The integral individual addressable module (IAM) monitors status and communicates changes to the connected control panel via MAPNET II or IDNet communications wiring.A blank area on the front of the station allows the selection of a label to match the specific releasing application (label kit is ordered separately). (Refer to data sheet S4099-0005 for standard Simplex addressable manual stations.)* This product has been approved by the California State Fire Marshal (CSFM) pursuant to Section 13144.1 of the California Health and Safety Code. See CSFM Listing 7150-0026:224 for allowable values and/or conditions concerning material presented in this document. Additional listings may be applicable; contact your local Simplex product supplier for the latest status. Listings and approvals under Simplex Time Recorder Co. are the property of Tyco Safety Products Westminster.4099-9015 Addressable Manual Station for Releasing Applications (with Manual Release label from4099-9802 Label Kit)Label Kit4099-9802Activation requires that a spring loaded interference plate (marked PUSH) be pushed back to access the station pull lever with a firm downward pull that activates the alarm switch. Completing the action breaks an internal plastic break-rod (visible below the pull lever, use is optional). The use of a break-rod can be a deterrent to vandalism without interfering with the minimum pull requirements needed for easy activation. The pull lever latches into the alarm position and remains extended out of the housing to provide a visible indication.Station reset requires the use of a key to reset the manual station lever and deactivate the alarm switch. (If the break-rod is used, it must be replaced.)Station testing is performed by physical activation of the pull lever. Electrical testing can be also performed by unlocking the station housing to activate the alarm switch.Releasing System PeripheralsUL, ULC, CSFM Listed;IDNet or MAPNET II Communicating Devices; FM Approved *Addressable Manual Stations for Releasing ApplicationsAddressable Manual StationsModelDescription4099-9015 Double action, Push operation, Addressable manual station; red housing with white letters and white pulllever; requires label kit 4099-98024099-9802Label kit, white lettering on red background; select the label required for the specific releasing application; types include: Clean Agent, Extinguishing, Carbon Dioxide, Foam System, Sprinkler, and ManualAccessoriesModelDescriptionReference2975-9178 Surface mount steel box, redRefer to page 3 for dimensions 2975-9022 Cast aluminum surface mount box, red2099-9813 Semi-flush trim plate for double gang switch box, red Typically for retrofit, refer to page 4 2099-9814 Surface trim plate for Wiremold box V5744-2, red 2099-9819 Flush mount adapter kit, black Refer to page 4 for details2099-9820Flush mount adapter kit, beige2099-9804 Replacement break-rodPower and Communications IDNet or MAPNET II communications, 1 address per station, up to 2500 ft (762 m) from fire alarm control panel, up to 10,000 ft (3048 m) total wiring distance (including T-Taps)Address Means Dipswitch, 8 positionWire ConnectionsScrew terminal for in/out wiring, for 18 to 14 AWG wire (0.82 mm 2 to 2.08 mm 2)UL Listed Temperature Range 32° to 120° F (0° to 49° C) intended for indoor operation Humidity Range Up to 93% RH at 100° F (38° F) Housing Color Red with white raised letteringMaterialHousing and pull lever are Lexan polycarbonate or equal Pull Lever ColorWhite with red raised letteringHousing Dimensions 5” H x 3 ¾” W x 1” D (127 mm x 95 mm x 25 mm) Installation Instructions579-11354" (102 mm) square box, 2-1/8" (54 mm) minimum 4" Square Box MountSemi-Flush Mount Side ViewSingle Gang Box MountSingle gang box, 2-1/2" deepPreferred Mounting. For surface mounting of theseaddressable manual stations, the preferred electrical boxes are shown in the illustration to the right.Additional MountingReference. Refer to page 4 for Wiremold box mounting compatibility.2975-9178 Box5-3/16" H x 4" W x 2-3/16" D (132 mm x 102 mm x 56 mm)Knockouts located top and bottom2975-9022 Cast Box 5" H x 3-7/8" W x 2-3/16" D (127 mm x 98 mm x 56 mm)4099-9015 Addressable Manual StationFor retrofit and new installations, additional compatible mounting boxes and the required adapter plates are shown in the illustration to the right.Front ViewFlush mount adapter kit Side ViewTyco Fire Protection Products • Westminster, MA • 01441-0001 • USAS4099-0006 11/2014TYCO, SIMPLEX, and the product names listed in this material are marks and/or registered marks. Unauthorized use is strictly prohibited. Lexan is a trademark of the General Electric Co. Wiremold is a trademark of the Wiremold Company.。
安全数据表(SDS)单号:1796009-ENG-06,发布日期:1998年2月18日,修订日期:2

Safety Data SheetDocument number First issued Revised date Revision Issued by Page 1796009-ENG-06 1998-02-18 2008-01-29 5 Jeanette Hasseson 1 of 4Alpacon 0091. Identification of the substance/preparation and of the company/undertakingTrade Name: Supplier:Alpacon 009 ALFA LAVAL ABHans Stahles vägProduct Type: S-147 80 TumbaEmulsion breaker SwedenTel: +46 8 530 650 00e-mail:Emergency number: +46 8 33 70 43 open 24 h2. Hazard identificationThe surfactant might cause serious damage to eyes and may cause long-term adverse effects in the aquatic environmentIf the product is used as recommended the surfactants will be soluble in oil and therefore they will be excluded in the water- phase.3. Composition/information on the ingredientsHazardous ingredients Weight-% CAS No ECNoClassification Risk PhrasesPolymer 5 – 15 - - NoneSurfactants 5 – 10 68989-03-7 - Xi, N R41, 51/53 See section 16 for explanations to R-phrases.4. First –aid measuresFirst aid – Inhalation Move to fresh air.First aid – Skin contact Wash off with plenty of water.First aid – Eye contact Rinse immediately with tepid water for several minutes. Proceedthe rinse during transport to hospital.Obtain medical attention.First aid – Ingestion Rinse mouth and drink at least 1-2 glasses of water. Do notinduce vomiting.Obtain medical attention.5. Fire- fighting measuresExtinguishing media All extinguishing media are suitable.Special hazards of product The product is not flammable. In case of fire the product mightform hazardous gases as NOx and COx.Protective equipment for fire fighting Not applicable.Fire –fight If the fire is extinguished with water environmental dangeroussubstances might be entering the environment.6. Accidental release measuresPersonal precautions Wear suitable goggles and gloves.Environmental precautions Prevent spills from reaching sewage, wells and watercourses. Spillage Absorb spills with sand, earth or other inert material. Collect andremove for destruction.Large spillage Contact local authority7. Handling and storageHandling Do not mix with other chemicals. Use recommended personalprotection according to section 8.Storage Store in a closed container.8. Exposure control / personal protectionRespiratory protection Appropriate ventilation. Provide facilities for rinsing eyes.Skin protection Protective gloves of nitrile.Eye protection Safety goggles.Ingestion Do not eat or drink during use. Wash hands before eating.9. Physical and chemical propertiesPhysical state Clear liquid.Colour Slightly yellow.Odour Weak smell.Density at 20 °C (g/ml) 1.025± 0.005.pH (as is) at 20 °C 7-9°brix 17.8±0.6.Viscosity at 25 °C (SP01/20 rpm) (cP) 1368±130.Cloud point during heating (°C) 50ºC.Flash point >100 º C10. Stability and reactivityStability The product is stable under normal conditions, but it decomposesat high temperatures.Conditions to avoid Extreme heatMaterials to avoid None knownHazardous decomposition products None known if the product is handled as recommended. In caseof fire the product might form hazardous gases as NOx and COx.11. Toxicological informationSkin At prolonged or frequently use of the product blush might occur.Eyes The product might cause serious damage to eyes.Consumption Low acute toxicity . Might be irritating to mucous membrane.LD50 oral rat 4500mg/kgSkin irritation test rabbit Slightly irritatingEye irritation test rabbit Strongly irritatingSensibillisation Not allergenicGen toxicity Not mutagenic12. Ecological informationLC50 96h (fish) >100mg/lNOEC 96 h (fish) > 100mg/lEC50 48h (Daphnia magna) > 100mg/lNOEC 48 h (Daphnia magna) > 100 mg/lDegradation No readily bodegradable13. Disposal considerationsDisposal of product: State and local disposal regulations may differ from federaldisposal regulations. Always dispose in accordance with federal,state and local requirements.Disposal of containers: Containers should be reused or disposed of by landfill orincineration as appropriate.14. Transport informationNot classified as a hazardous substance according to transport regulations.15. Regulatory informationLabel Symbol(s): XiIrritantRisk Phrases: R36 Irritating to eyes.R52/53 Harmful to aquatic organisms, may cause long-termadverse effects in the aquatic environment.Safety Phrases: S39 Wear eye/ face protection.16. Other informationExplanations to R-phrases in section 2 R41 Risk of serious damage to eyes.R51/53 Toxic to aquatic organisms, may cause long-term adverse effects in the aquatic environment.See also product label for product applications.Important changes have been made in section: 1, 2, 3, 4, 5, 6, 7, 8, 9, 10, 11, 12 and 15.DISCLAIM OF RESPONSIBILITYAlfa Laval provides the information contained herein in good faith but makes no representation as to its comprehensiveness or accuracy. This document is only a guide to the potential hazards of the product. All individuals working with or around the product should be properly trained. Persons coming into contact with the product must be capable of exercising their own independent judgment concerning the conditions or methods of handling, storage and usage of the product. Alfa Laval will not be responsible for claims, losses, or damages of any kind resulting from the information provided in this Safety Data Sheet or the use, handling, storage or disposal of the product. Alfa Laval makes no representations or warranties, either express or implied, including without limitation any warranties of merchantability or fitness for a particular purpose with respect to the information set out herein or the product to which the information refers.。
ATTO Celerity FC Host Adapter Getting Started Guid
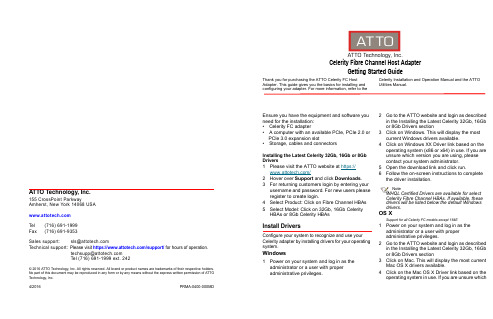
ATTO Technology, Inc.155 CrossPoint ParkwayAmherst, New York 14068 USATel (716) 691-1999Fax (716) 691-9353Sales support:****************Technical support: Please visit https:///support/ for hours of operation.*********************Tel (716) 691-1999 ext. 242© 2016 ATTO Technology, Inc. All rights reserved. All brand or product names are trademarks of their respective holders. No part of this document may be reproduced in any form or by any means without the express written permission of ATTO Technology, Inc.4/2016 PRMA-0400-000MDCelerity Fibre Channel Host AdapterGetting Started GuideThank you for purchasing the ATTO Celerity FC HostAdapter. This guide gives you the basics for installing andconfiguring your adapter. For more information, refer to theCelerity Installation and Operation Manual and the ATTOUtilities Manual.Ensure you have the equipment and software youneed for the installation:•Celerity FC adapter• A computer with an available PCIe, PCIe 2.0 orPCIe 3.0 expansion slot•Storage, cables and connectorsInstalling the Latest Celerity 32Gb, 16Gb or 8GbDrivers1Please visit the ATTO website at https:///2Hover over Support and click Downloads.3For returning customers login by entering yourusername and password. For new users pleaseregister to create login.4Select Product: Click on Fibre Channel HBAs5Select Model: Click on 32Gb, 16Gb CelerityHBAs or 8Gb Celerity HBAsInstall DriversConfigure your system to recognize and use yourCelerity adapter by installing drivers for your operatingsystem.Windows1Power on your system and log in as theadministrator or a user with properadministrative privileges.2Go to the ATTO website and login as describedin the Installing the Latest Celerity 32Gb, 16Gbor 8Gb Drivers section3Click on Windows. This will display the mostcurrent Windows drivers available.4Click on Windows XX Driver link based on theoperating system (x86 or x64) in use. If you areunsure which version you are using, pleasecontact your system administrator.5Open the download link and click run.6Follow the on-screen instructions to completethe driver installation.NoteWHQL Certified Drivers are available for selectCelerity Fibre Channel HBAs. If available, thesedrivers will be listed below the default Windowsdrivers.OS XSupport for all Celerity FC models except 164E1Power on your system and log in as theadministrator or a user with properadministrative privileges.2Go to the ATTO website and login as describedin the Installing the Latest Celerity 32Gb, 16Gbor 8Gb Drivers section3Click on Mac. This will display the most currentMac OS X drivers available.4Click on the Mac OS X Driver link based on theoperating system in use. If you are unsure whichversion you are using, please contact your system administrator.5Open the download.6Launch the installer package.7Follow the on-screen instructions.LinuxNoteNote: These steps assume a basic knowledge of Linux terminal commands. You must also have the correct kernel source files for the appropriate kernel already installed.1Power on your system and log in as the administrator or a user with properadministrative privileges.2Go to the ATTO website and login as described in the Installing the LatestCelerity 32Gb, 16Gb or 8Gb Driverssection.3Click on Linux. This will display the most current Linux drivers available.4Click on Linux XX Driver link based on the operating system in use. If you are unsure which version you are using, pleasecontact your system administrator.5Copy the .tgz file to a temporary folder.6Open a terminal window and change to the location of copied tgz from step 5.7Extract the file using the command tar -xfz <filename.tgz>.8Change to the directory created above then run the installer script ./install.sh.9Click on Y to load driver.10Click on Y to install CLI tools.11Confirm location.VMware (ESXi 5.x/6.0)NoteNote: ESXi 5.0 & later: 8Gb Celerity supportESXi 5.1 & later: 16Gb Celerity support1Download the correct Driver Bundle from the VMware or ATTO website.2Within the bundle unzip the Driver VIB file (.vib) for your ATTO Adapter.3Use the Datastore Browser in the vSphere Client to upload the VIB file to your ESXihost.4Log in to the ESXi host on the Local Tech Support Console (ESXi), or through anSSH client.5Install the VIB using the followingcommand on the ESXi host: # esxclisoftware vib install -v <full path to VIB file> 6Once the VIB is installed, reboot the ESXihostFreeBSDNoteRefer to the Celerity Installation and Operation Manual forinstructions on installing FreeBSD driversInstalling the ATTO ConfigToolThe ATTO ConfigTool is a free utility. Visit theATTO website (/downloads.php) for specific operatingsystem support information and downloads.The ATTO ConfigTool includes twocomponents: a GUI Application and a systemservice. Either, or both, of these componentscan be installed on a host, depending on thefunctionality desired. Refer to the Utilitiesmanual for additional details.NoteLogging and other important features are only available if theATTO ConfigTool service is installed. We recommendinstalling the service as a minimum configuration.NoteThe vConfigTool supports VMware VCenter Server. Refer tothe ATTO website for information on downloading and usingthis free utility.Windows Installation Instructions:1Double-click thewin_app_configtool_xxx.exe package file2Click "Unzip" to extract the installer files.The files are put in "C:\ATTO\ConfigTool\4.xx" directory.2.1To install the Full Application orApplication Only:•Navigate to the "C:\ATTO\ConfigTool\4.xx\Service"directory•Double-click on the ConfigTool_xxx.exeinstaller executable•Select Full Installation or ApplicationOnly as desired.•Follow the on-screen instructions2.2To install the System Service only:•Navigate to the"C:\ATTO\ConfigTool\4.xx\Service"directory•Double-click on the "attocfgd.msi"installer executable•Follow the on-screen instructionsOS X Installation Instructions:1Double-click theosx_app_configtool_xxx.exe package file.2 A Finder window appears.2.1To install the Full Application orApplication Only:•In the Finder window that appears,double-click on the ConfigTool_xxx.appinstaller executable.•Select Full Installation or ApplicationOnly as desired.•Follow the on-screen instructions.2.2To install the System Service only:•Navigate to the “Service” folder in theFinder window that appears.•Double-click on the "attocfgd.mpkg"installer executable file.•Follow the on-screen instructions.Linux Installation Instructions:1Extract the package file by running thefollowing command in a terminal: tar -xvzflnx_app_configtool_xxx.tgz2Navigate to the extracted folder“lnx_app_configtool_xxx”2.1To install the Full Application orApplication Only:•Run the ConfigTool_xxx.bin installerexecutable as root or superuser.•Select Full Installation or ApplicationOnly as desired.•Follow the on-screen instructions.2.2To install the System Service only:•Navigate to the “Service” directorylocated inside thelnx_app_configtool_xxx directory•Double-click on the "attocfgd.msi"installer executableRun the “attocfgd.sei” installer executable asroot or superuser using the followingcommand line: ./attocfgd.sei -i.Hardware InstallationBack up your system data before changing orinstalling any hardware.CAUTIONCelerity FC host adapters containcomponents that are sensitive toelectrostatic discharge (ESD). ESDcan Cause damage to the Celerity FChost adapter. Please follow standardmethods to avoid ESD.1Install the latest drivers. Refer to InstallDrivers of your Celerity Fibre Channel HostAdapter Getting Started Guide.2Power down the computer and unplug thecomputer from all power sources.3Open the case.4Install the Celerity FC host adapter in anyopen PCI Express expansion slot. ForCelerity 164E only, install the appropriateexternal power cable (supplied). If youhave questions about how to install anexpansion card in your system, consultyour computer’s documentation.NoteAll Celerity cards fit in x8 or x16 mechanicalslots.CAUTIONCelerity 16Gb Quad Fibre ChannelHost Adapters (FC-164E) requireexternal power supply and adequatecooling to ensure proper systemoperation and prevent data loss.5Connect Fibre Channel devices byinserting a Fibre Channel cable from thedevices to the connectors on the CelerityFC host adapter until you hear a click.6Close the case on the computer and powerit up.Configure your storage and adapterDefault settings are appropriate for mostsystems but you may change settings usingthe ATTO Configuration Tool on the ATTOwebsite.Please see ATTO Utilities Installation andOperations Manual for further information.。
MCD 988 用户手册说明书

MCD 988 Guida RapidaCosa c'è nella confezione?Nella confezione si dovrebbero trovare i seguenti articoli.12435Collegare il subwoofer all'unità principale tramite il cavo DIN in dotazione.Collegare gli altoparlanti.Collegare l'antenna FM.Collegare il cavo AV al televisore.Collegare il cavo di alimentazione del sistema e della TV .Tips–Cfr. il Manuale Utente per ulteriori opzioni di collegamento TV.–Per collegarsi a una TV con Scansione Progressiva, fare riferimento al manuale per effettuare collegamenti corretti e per i particolari dell'impostazione.Impostare l'orologio123Nella modalità standby, tenere premuto CLOCK/RDS sul telecomando.Premere VOLUME +/ - (VOL+/- sul telecomando) per impostare l'ora e CLOCK/RDS per completare l'impostazione.Premere VOLUME -/+ (VOL +/- sul telecomando) per impostare i minuti e CLOCK/RDS per completare l'impostazione.Impostare le opzioni del menu DVDAVVERTENZA!Se la funzione di scansione progressiva è attiva, ma non è supportata daltelevisore o i cavi non sono collegati correttamente, vedere Manuale d'uso per verificare la configurazione della scansione progressiva oppure disattivarla attenendosi a quanto riportato di seguito:1) Disattivare la modalità scansione progressiva del televisore oppure attivare la modalità interlacciata.2) Premere SYSTEM MENU sul telecomando per uscire dal menù del sistema e poi DISC 1 (DISC 2) e “1” per uscire dalla scansione progressiva.Riprodurre un disco 123Premere il pulsante DISC 1 ç/ DISC 2 çsul telecomando per aprire il comparto del disco e caricare un disco, quindi chiudere il comparto del disco.➜Assicurarsi che il lato del disco con l'etichetta sia rivolto verso l'esterno.Se la riproduzione non si avvia automaticamente, premere ÉÅ .Premere STOP 9 (9 sul telecomando) Per arrestare la riproduzione.Programmare e sintonizzare le stazioni radio 123Premere SOURCE (TUNER sul telecomando) per selezionare la fonte tuner.Premere PROGRAM per più di due secondi per programmare tutte le stazioni disponibili in ordine di gamma di frequenze.Premere ¡ / ™ sino a visualizzare il numero prestabilito della stazione desiderata.PDCC-JS/JW-0736TipLe funzioni di riproduzione dettagliate ed altre funzioni sono descritte nell’accluso manuale dell’utente.Note per il telecomando:–Per prima cosa, selezionare la sorgente che si desidera comandare premendo uno dei tasti di selezione di sorgente sul telecomando (ad esempio DISC o TUNER).–Quindi selezionare la funzione desiderata ( ad esempio 2;, í, ë).Royal Philips Electronics N.V . 2007All rights reserved.。
MASTR II BASE STATION COMBINATIONS 产品说明书

LBI-31899FDESCRIPTION AND MAINTENANCE MASTR ® II BASE STATION COMBINATIONSTABLE OF CONTENTSPage SPECIFICATIONS . . . . . . . . . . . . . . . . . . . . . . . . . . . . . . . . . . . . . . . . . . . . 1FCC FILING NUMBERS . . . . . . . . . . . . . . . . . . . . . . . . . . . . . . . . . . . . . . . . 1COMBINATION NOMENCLATURE . . . . . . . . . . . . . . . . . . . . . . . . . . . . . . . . . 1DESCRIPTION . . . . . . . . . . . . . . . . . . . . . . . . . . . . . . . . . . . . . . . . . . . . . . 2SYSTEM DESCRIPTION . . . . . . . . . . . . . . . . . . . . . . . . . . . . . . . . . . . . . . . .2Receiver . . . . . . . . . . . . . . . . . . . . . . . . . . . . . . . . . . . . . . . . . . . . . . . . 2Transmitter . . . . . . . . . . . . . . . . . . . . . . . . . . . . . . . . . . . . . . . . . . . . . . 2System Board A1 . . . . . . . . . . . . . . . . . . . . . . . . . . . . . . . . . . . . . . . . . . . 2DC Remote Control . . . . . . . . . . . . . . . . . . . . . . . . . . . . . . . . . . . . . . . . . 3Tone Remote Control . . . . . . . . . . . . . . . . . . . . . . . . . . . . . . . . . . . . . . . . 3Channel Guard . . . . . . . . . . . . . . . . . . . . . . . . . . . . . . . . . . . . . . . . . . . . 3INITIAL ADJUSTMENT . . . . . . . . . . . . . . . . . . . . . . . . . . . . . . . . . . . . . . . . 3MAINTENANCE . . . . . . . . . . . . . . . . . . . . . . . . . . . . . . . . . . . . . . . . . . . . . 3OUTLINE DIAGRAMSSystem Board A901 . . . . . . . . . . . . . . . . . . . . . . . . . . . . . . . . . . . . . . . . . 5Harness 19C320811 . . . . . . . . . . . . . . . . . . . . . . . . . . . . . . . . . . . . . . . . . 5SCHEMATIC DIAGRAMSSystem Board A901 W/Cable Interconnect . . . . . . . . . . . . . . . . . . . . . . . . . . . . . 6STATION INTERCONNECT DIAGRAMSSystem Block Diagram . . . . . . . . . . . . . . . . . . . . . . . . . . . . . . . . . . . . . . . . 4Continuous Duty Station Harness Without Metering . . . . . . . . . . . . . . . . . . . . . . . 8Continuous Duty Station Harness With Metering . . . . . . . . . . . . . . . . . . . . . . . . . 10PARTS LISTContinuous Duty Station Harness Without Metering . . . . . . . . . . . . . . . . . . . . . . . 7Continuous Duty Station Harness With Metering . . . . . . . . . . . . . . . . . . . . . . . . . 7MASTR II Station Radio Panel . . . . . . . . . . . . . . . . . . . . . . . . . . . . . . . . . . . 7PRODUCTION CHANGES . . . . . . . . . . . . . . . . . . . . . . . . . . . . . . . . . . . . . . . 7MECHANICAL PARTS BREAKDOWNRadio Panel Front Door Assembly . . . . . . . . . . . . . . . . . . . . . . . . . . . . . . . . . 12Transmitter Power Amplifier . . . . . . . . . . . . . . . . . . . . . . . . . . . . . . . . . . . . 13Station Cabinets . . . . . . . . . . . . . . . . . . . . . . . . . . . . . . . . . . . . . . . . . . .14-15ILLUSTRATIONSFIGURE 1 - Radio Panel Front Door . . . . . . . . . . . . . . . . . . . . . . . . . . . . . . . . . . 2FIGURE 2 - Typical Station Assembly . . . . . . . . . . . . . . . . . . . . . . . . . . . . . . . . .2EEricsson Inc.Private Radio Systems Mountain View RoadLynchburg, Virginia 245021-800-528-7711 (Outside USA, 804-528-7711)Printed in U.S.A.Copyright © October 1987, General Electric CompanyNo one should be permitted to handle any portion of the equipment that is supplied with high voltage; or to connect any external apparatus to the units while the units are supplied with power. KEEP AWAY FROM LIVE CIRCUITS.High level RF energy in the transmitter Power Amplifier assembly can cause RF burns KEEP AWAY FROM THESE CIRCUITS WHEN THE TRANSMITTER IS KEYED.WARNINGSPECIFICATIONS*EIA DIMENSIONS (H X W X D)DESK MATE (30-INCH)30-1/4" X 21-1/2" X 15.5"DESK MATE (44-INCH)44-1/4" X 21-1/2" X 15.5"POLE MOUNT 45" X 21-l/2" X 21"FLOOR MOUNT 69" X 23" X 21"WEIGHTDESK MATE (30-INCH)160 lbs DESK MATE (44-INCH)180 lbs POLE MOUNT 225 lbs FLOOR MOUNT 290 lbsINPUT VOLTAGE121/242 VAC, 60 Hz Only (50 Hz Optional)AC INPUT POWERRF OUTPUT POWER TRANSMIT RECEIVE STANDBY LOW BAND100 WATTS 260 WATTS 105 WATTS 65 WATTS HIGH BAND40 WATTS 270 WATTS 75 WATTS 40 WATTS 110 WATTS 560 WATTS 105 WATTS 65 WATTS UHF40 WATTS 270 WATTS 75 WATTS 40 WATTS 100 WATTS560 WATTS105 WATTS65 WATTSTEMPERATURE RANGE-30° TO + 60°C (-22 to + 140 F)* These specifications are intended primarily for the use of the serviceman. Refer to the appropriate Specification Sheet for the complete specifications.FCC FILING NUMBERSMODEL SERIES FCC FILING NO.DUTY CYCLE POWER OUTPUT LOW BANDC74KT-61-A CONTINUOUS 50 - 100 WATTS HIGH BANDC56KT-47-J CONTINUOUS 10 - 40 WATTS C76KT-49-J CONTINUOUS 20 - 110 WATTS UHFC55KT-55-K CONTINUOUS1 - 40 WATTS C75KT-114-KCONTINUOUS30 - 100 WATTS(o) /CABINET/STYLE (1st Digit "D", "S", "P", or "V")NOTE: FCC Filing number not relevant to equipment operating in the 406 - 420 MHz frequency range.COMBINATION NOMENCLATURELBI-31899F1DESCRIPTIONThe MASTR II radio station combinations are designed for either DC or Tone Remote Control or Repeater operation. The station receiver is mounted on a shielded enclosure on the radio panel front door, along with a receiver system board which accommodates Channel Guard and other op-tion boards. Jacks are provided on the system board for plug-in interface with the options and control functions. The transmitter exciter is located in a separate shielded compartment on the radio panel front door. See Figure l. The continuous duty transmitter power amplifier hinges from the bottom of the radio housing. The PA assembly consists of a frame mounted to a heat sink. A cover snaps over the frame to form an RF-tight enclosure for the PA board assembly.Directly above the PA assembly is the station control shelf. This shelf houses the Control Panel and the Mini Backplane option S3MB01. The option cards used with the Control Shelf are installed in the Mini-backplane housing. These options include: Auxiliary Control, Auxiliary Receiver (DC or Tone), and Scan functions. Refer to LBI-31877 for a complete description of Mini Backplane option S3MB01. Two front panels are used: one for all station applications and one for repeater applications. A Front Panel is shown in Figure 2. Typical Front Panel controls include the trans-mit (TF1-TF4) and receive (RF1-RF4) frequency select, REM PTT, Speaker, Auxiliary receiver, ICOM (Intercom) and TEST switches, and the VOLUME Control. Indicators include the TX (transmit), RPTR Disable, and Frequency Select (F1-F4).External control connections are made to TB1201 located on the back of the Control Shelf.The station power supply is connected to a 121 VAC power source. Conversion from 121 VAC to 242 VAC is made by jumper changes on the back of the power supply front panel. The input voltage is stepped down to 12 Volts by a ferro-resonant transformer which provides line regulation of 2% for a 20% primary change. A power switch, primary and secondary fuses and two AC outlets are located on the front panel. A high-current fuse is located on the back panel.SYSTEM DESCRIPTIONRECEIVERThe station receiver consists of an oscillator/multiplier as-sembly (OSC/MULT), RF Assembly, Mixer/IF Assembly(MIF) and IF-Audio Squelch Assembly (IFAS). In receiverswith noise blankers, the noise blanker circuit replaces thestandard MIF board. Refer to the Receiver MaintenanceManual for a complete description of the station receiver.TRANSMITTERThe station transmitter consists of an exciter board assem-bly and a power amplifier assembly. In continuous dutytransmitters, the PA assembly consists of a printed wiringboard mounted on a heat sink at the rear of the radiohousing. In intermittent duty stations, the heat sink assem-bly is fastened to two sheet metal adaptor plates which hingeat the radio panel. Refer to the transmitter MaintenanceManual for a complete description of the station transmit-ters.SYSTEM BOARD A1The station System Board is located on the Radio PanelFront Door and the receiver modules plug directly into theboard. Along the edge of the System Board are two connec-tors which interconnect with the Remote Control Shelf andPower-Supply. Plug-in Channel Guard and Carrier Control~ Timer option jacks are provided. A metering jack isprovided for accommodating the General Electric Model4EX3A11 Test Set. VOLUME Control R3 is located on theSystem Board. SQUELCH Control R901 is located on theRadio Panel Front Door.A jumper is normally present between J933-4 and J933-8in single-frequency transmit stations. A jumper is also pre-sent between H47 and H48 on A901 in single-frequencyreceive stations. In multiple-frequency receive stations, se-lecting a particular receive frequency at the remote controlunit applies a ground to the particular pin at J931 corre-sponding to the frequency selected. The ground is thenconnected via the System Board printed wiring to the re-ceiver. OSC/MULT to select the desired oscillator.VOLUME/SQUELCH from the receiver Audio PreAmp isconnected via J904-12 to the VOLUME (R3) andSQUELCH (R901) controls. The VOLUME arm is returnedto the receiver IFAS Board where the signal is amplified bythe receiver audio power amplifier circuit. The audio outputof the PA is then connected to the speaker leads at J904-18& 19. The station VOLUME control (R3) is normally ad-justed for 1-watt output and the station speaker level iscontrolled by the service speaker VOLUME control.Figure 1 - Radio Panel Front DoorFigure 2 - Typical Station AssemblyLBI-31899F 2DC REMOTE CONTROLIn DC Remote Control Systems, DC currents are selectively applied to a telephone pair at a remote control console to set the system operating characteristics. Items that are controlled by the DC Remote Control system include selecting the num-ber of channels, scan option, Channel Guard Disable, Re-peater Disable, and Auxiliary Receiver. In some cases combinations of the above may be selected. Refer to the Control Panel Manual for details.TONE REMOTE CONTROLUp to 13 functions may be controlled in the Tone Remote Control system. This is accomplished by applying the speci-fied tone frequency at the prescribed level to the transmission medium at a remote control console for detection by the Tone Remote Control system on the Control Shelf. The controlled functions include transmitter/receiver selection, Rx Channel Guard Disable, Channel Guard or Repeater Enable/Disable, Auxiliary function on/off, repeater enable, scan or sim. moni-tor or repeater disable, and Tx hold. Refer to the Maintenance Manual for the Control Shelf for a complete description of the system.CHANNEL GUARDIn stations equipped with Channel Guard, the Channel Guard Board is plugged into the System Board at P908 and P909. Each MASTR II receiver is equipped with a tone reject filter to prevent the CG tone from being heard in the speaker. In addition, all transmitters are provided with a Channel Guard Modulation control which is adjusted for proper deviation. Channel Guard is a continuous tone controlled squelch system that provides communications control in accordance with EIA standard RS-220. The system utilizes standard tone frequen-cies from 721.9 to 203.5 Hz with both the encoder and oper-ating on the same frequency. The STE circuit (Squelch Tail Eliminator) employs a phase shift of approximately 180 de-grees in the encode function to eliminate an undesirable noise burst after each transmission.The decoder operates in conjunction with the receiver to inhibit all calls that are not tone coded with the proper Channel Guard tone frequency. The Volume/Squelch output of the receiver is applied to the Channel Guard decoder at P908-1. When the received signal is not properly coded with the CG tone, a ground is supplied through P908-5 to mute the re-ceiver. When a properly coded signal is received, the receiver unsquelches and the desired signal is heard. In duplex combi-nations, a separate encoder is used in the exciter and a separate decoder is used in the receiver.A Channel Guard Filter is used in the remote audio to attenu-ate frequencies below 203.5 Hertz to prevent the ChannelGuard tone from being applied to the remote audio pair.A repeater will not key in Channel Guard systems unless thereceived signal is coded with the proper Channel Guard tone.The CG MONITOR function when selected will not allow therepeater to key on an encoded signal but will allow theoperator to hear all channel activity.INITIAL ADJUSTMENTAfter the MASTR II station has been installed as described inthe Installation Manual, the following adjust-ments should bemade by an authorized electronics technician before the sta-tion is placed in service.TEST EQUIPMENT REQUIRED1.Deviation Monitor2.Wattmeter, 50 ohms, rated power3.RF Generator, (Station RF Frequencies)4.AC Voltmeter5.30 dB CouplerTRANSMITTER ADJUSTMENTTransmitter adjustment includes measuring the forward andreflected power and adjusting the antenna length for optimumratio, then setting the transmitter to the rated power output.Next measure and record the frequency and modulation forfuture reference. For complete transmitter adjustment proce-dures, refer to the Alignment Procedure in the applicable radioMaintenance Manual.RECEIVER ADJUSTMENTInitial adjustment of the receiver includes tuning the inputcircuit to match the antenna, adjusting the station volumecontrol, and setting the station squelch control. Refer to theFront End Alignment and Adjustment Procedures in the Main-tenance Manual.STATION VOLUME (R3 on System Board)1.Apply a 1000 microvolt on-frequency test signal modulatedby 1000 Hz with 3 kHz deviation to the receiver antennajack J937.2.Turn service speaker switch (S1) to desired RCVR posi-tion.3.Connect an AC Voltmeter across J905 terminals 1 & 2and adjust R3 for a reading of 6.3 Volts RMS on the meter.4.Set VOLUME switch S2 on the service speaker to thedesired listening level.STATION SOUELCH (R901 on ReceiverExciter Door)1.Turn the SQUELCH control clockwise as far as possible.2.Turn the SQUELCH control counterclockwise until thenoise just disappears, then advance the control (clock-wise) another 20 degrees.LOCAL CONTROL MODULATIONADJUSTMENT1.Apply a 1000 Hz, 1 VRMS signal across P3-2 (MIC HI)and P3-1 (low). Connect a 0.5 microfarad (or larger) DCblocking capacitor in series with the MIC HI lead, P3-2.2.Set MOD ADJUST control R127 on the exciter for 4.5kHz deviation as indicated on a frequency modulationmonitor.3.While talking in a normal voice, at the station microphoneadjust LOCAL TX MOD LEVEL R222 (Tone Panel) orR46 (DC Panel) on the Control Panel for a deviation of 3to 4 kHz as measured on the deviation monitor.REPEATER CONTROL ADJUSTMENT1.Apply a 1000 Hz, on frequency signal modulated with1000 Hz tone at 3 kHz deviation to the station receiver.2.Adjust TX MOD control R60 on the Control Panel for a3.0 kHz deviation as indicated on the deviation monitor.REMOTE CONTROL ADJUSTMENTSThe transmitter modulation gain, the remote audio input andline output must be adjusted before placing the station inoperation. Refer to the DC Remote Control or the ToneRemote Control Maintenance Manual for these adjust-ments.REPEATER CONTROL ADJUSTMENTThe repeater drop out delay timing may be adjusted beforeplacing the station in operation. Refer to the MASTR IIRepeater Station Control Panel Maintenance Manual forthese adjustments.MAINTENANCETo insure high operating efficiency and to prevent mechani-cal and electrical failures from interrupting system opera-tion, routine checks should be made of all mechanical andelectrical parts at regular intervals. This preventive mainte-nance should include the checks listed in the table of Main-tenance Checks.TEST AND TROUBLESHOOTINGPROCEDURESThe individual Maintenance Manuals for the transmitterand receiver describe standard test procedures which thetechnician can use to compare the actual performance of thetransmitter or receiver against the specifications of the unitwhen shipped from the factory. In addition, specific trou-bleshooting procedures are available to assist the technicianwhen servicing the transmitter and receiver.Removing IC "s and other soldered-in components can beeasily accomplished by using a de-soldering tool. To re-move an IC, heat each lead separately on the solder side andremove the old solder with the de-soldering tool.An alternate method is to use a special soldering tip thatheats all of the pins simultaneously.Adjusting the VOLUME control for levels higher thanspecified may cause damage to the speaker.CAUTIONLBI-31899F3SYSTEM INTERCONNECTION DIAGRAMMAINTENANCE CHECKS INTERVAL BETWEENCHECKSEvery 6monthsAs RequiredTransmitter Alignment: Compare meter readings at transmittermultiplier metering jacks with voltages read during initial tune up.Touch up multiplier tuning. Check power output. (See AlignmentProcedure for Transmitter).XReceiver: While receiving an unmodulated signal on the stationfrequency(s), adjust OSC-1 trimmer for each operating frequencyfor a zero discriminator reading. (See the Receiver AlignmentProcedure).XTransmission Line: Check for positive indication of pressure ontransmission line pressure gauge (if pressurized line is used).XAntenna: Check antenna & mast for mechanical stability.XMechanical Inspection: Visually check cables, plugs, sockets, ter-minal boards & components for good electrical connections. Checkfor tightness of nuts, bolts, & screws to make sure that nothing isworking loose from its mounting.XCleaning: Use a vacuum cleaner to remove dust which may haveaccumulated inside the cabinet.XFrequency Check: Check transmitter frequency & deviation.X LBI-31899F4WIRING HARNESS 19C320811SYSTEM BOARD A901OUTLINE DIAGRAM(19D423147, Rev. 3)(19D417205, Sh. 2. Rev. 4)COMPONENT SIDE(19D423147, Rev. 2)(19D417205, Sh. 2. Rev. 4)SOLDER SIDE(19C328112, Rev. 2)LBI-31899F5SCHEMATIC DIAGRAM LBI-31899FSYSTEM BOARD A90119D417262G1(19E501154, Rev. 25)6MASTR II STATION RADIO PANELFRONT DOOR ASSEMBLY19D417262G1DESCRIPTION AND MAINTENANCEPARTS LIST & PRODUCTION CHANGESSYMBOL PART NUMBERDESCRIPTION A901COMPONENT BOARD19D417213G1— — — — CAPACITORS — — — — —C119A116080P107Polyester: 0.1 uF ±10%, 50 VdcW.C219A115680P24Electrolytic: 400 uF +150% -10%, 18 VdcW; sim to Mallory Type TTX.C319A116080P106Polyester: 0.068 uF ±10%, 50 VdcW.C419A701534P4Tantalum: 1 uF ±20%, 35 VdcW.thru C7C819A701534P8Tantalum: 22 uF ±20%, 16 VdcW.— — — — —JACKS — — — — — —J903Connector. Includes:and J90419A116659P1Connector, printed wiring: 3 contacts rated at 5 amps; sim to Molex 09-52-3032.19A116659P4Connector, printed wiring: 6 contacts rated at 5 amps; sim to Molex 09-52-3062.J90519B219374G2Connector, 9 contacts. Includes: Shell.J9364033513P4Contact, electrical: sim to Bead Chain L93-3.J937Part of W901 & W905.J938Part of W902 & W906.J95119A116659P13Connector, printed wiring: 4 contacts rated at 5 amps; sim to Molex 09-64-1041.J952Connector includes:19A116659P11Connector, printed wiring: 7 contacts rated at 5 amps; sim to Molex 09-64-1071.19A116659P12Connector, printed wiring: 6 contacts rated @ 5amps; sim to Molex 09-64-1061.— — — — — PLUGS — — — — — —P907Part of A901thru P909P934Part of A901and P935— — — —RESISTORS — — — — —R119A701250P444Metal film: 280K ohms ±1%, 1/4 w.and R2R319B209358P106Variable: 10K ohms ±5%, 1/4 w; sim to CTS X-201.R419A700106P71Composition: 2.2K ohms ±5%, 1/4 w.R519A700106P75Composition: 3.3K ohms ±5%, 1/4 w.R619A700113P3Composition: 3.3 ohms ±5%, 1/2 w.— — — MISCELLANEOUS — — — —5491541P302Spacer. (Used in G1).19B219761P3Jumper (Used in G1).— — — — — CABLES — — — — — —W90119B233742G1Cable, RF: approx 14 inches long, 350 VRMS, 500 Vdc operating voltage.W9025491689P104Cable, RF: approx 4 inches long, 350 VRMS, 500 Vdc operating voltage.W903CABLE ASSEMBLY 19D417262G2— — — — —JACKS — — — — — —J93119C851861P1Assembly.and J932*COMPONENTS, ADDED, DELETED OR CHANGED BY PRODUCTION CHANGESSYMBOL PART NUMBERDESCRIPTION19C317957P2Connector, Includes: Shell.19A700237P1Contact, electrical: sim to Malco 003-0132-001.19A116781P3Contact: 16-20 AWG; sim to Molex 08-50-0105.— — — — — — PLUGS — — — — — — — P101Part of W902 & W906 (Used in G1).P301Part of W901&W905 (Used in G1).P907Part of AX01 (Used in G1).P908Part of A901 (Used in G1).and P909P934Part of A901 (Used in G1).and P935P95119A116659P25Shell.and P952— — — — — RESISTORS — — — — — —R9015496870P31Variable, carbon film: 10K ohms ±20%, sim to Mallory LC(25K). (Used in G2).W904EXCITER CABLE 19D417262G3J93319C851861P1Assembly.— — — — — — PLUGS — — — — — — —P90119A116659P25Shell.P90619A127042P1Terminal, solderless: sim to Malco 12093-12.— — — — MISCELLANEOUS — — — — —7878455P1Lug terminal; sim to GE89473. (Used in G1).19A116781P4Contact: 22-26 AWG; sim to Molex 08-50-0107.(Used in G2 and G3).19A701785P1Contact, electrical; sim to Molex 08-50-0404.(Used with P907, P908, P909).19C320679G1Door. (Used in G1).19C320664P1FR (Used in G1).19B226035G1Support (Used in G1).19B226105G2Support (Used in G1).19B234589P1Pawl. (Used in G1).19C336435P1Knob. (Used in G1).N193P808B6Tap Screw;, Phillips POZIDRIV: No. 6-20X 1/2 (Part of door latch)5493361P8Washer, spring tension.(Part of door latch)4035664P8Nut, self locking. (Used on hinge).19A115161P2Sleeving. (Used in G1).19B226035G2Support (Used in G1).N402P39B6Flatwasher: No. 10. (Used in G1).19A115874P1Catch, friction. (Used in G1).19B201074P204Tap screw, phillips POZIDRIV: No. 4-40 x 1/4.(Used with P101).19A116686P2Nut, sheet spring. (Used in G1).N529P11B6Plug Button (Used in 3/8 inch hole).19B201074P305Tap screw, Phillips POZIDRIV: No. 6-32 x 5/16.(Used to secure J937).19B209519P1Polarity tab. (Used with P901, P951, and P952.19A121676P2Guide Pin (Used with J931-J933).19A116496P1Cable clip. (Used in G1).7115130P9Lockwasher, Internal tooth: No. 3/8. (Used in G1).7165075P2Hex nut, brass: thread size No. 3/8-32. (Used in G1).4037158P4Rubber channel. (Used in G1).N529P18B6Plug button (Used in G1).LBI-31899F7INTERCONNECTION DIAGRAM LBI-31899FCONTINUOUS DUTY STATION HARNESSWITHOUT METERING 19C320811G1(19R622032, Rev. 15)8INTERCONNECTION DIAGRAM CONTINUOUS DUTY STATION HARNESSWITHOUT METERING 19C320811G1(19R622032, Rev. 15)LBI-31899F9INTERCONNECTION DIAGRAM LBI-31899FCONTINUOUS DUTY STATION HARNESS (CONT.)WITH METERING 19C320811G4(19R622055, Rev. 14)LBI-31899F INTERCONNECTION DIAGRAMCONTINUOUS DUTY STATION HARNESSWITH METERING 19C320811G4(19R622055, Rev. 14)RADIO PANEL FRONT DOORMECHANICAL PARTS BREAKDOWN LBI-31899FLBI-31899F MECHANICAL PARTS BREAKDOWNTRANSMITTER POWER AMPLIFIERMECHANICAL PARTS BREAKDOWN LBI-31899FSTATION CABINETSLBI-31899FSTATION CABINETS。
FortiClient EMS 使用指南说明书

Course Description FortiClient EMSIn this course,you will learn how to use the FortiClient EMS feature,provisionFortiClient endpoints,FortiClient EMS Security Fabric integration,explore differenteditions of FortiClient,and deploy and configure ZTNA agent and endpoint securityfeatures.These fundamentals of the product will provide you with a solidunderstanding of how to deploy,manage and maintain endpoint security usingFortiClient EMS products.Product Versionl FortiClient EMS7.0.1l FortiClient7.0l FortiOS7.0.1Course Durationl Lecture time(estimated):6hoursl Lab time(estimated):4hoursl Total course duration(estimated):10hours/2daysWho Should AttendIT and security professionals involved in the management,configuration,and administration of FortiClient EMSendpoints used to secure devices for their organizations should attend this course.Participants should have a thorough understanding of endpoint solutions.CertificationThis course is intended to help you prepare for the FortiClient7.0specialist exam.This is one of the courses thatprepares you to take the NSE5certification exam.12/13/2021https://FortiClient EMS7.0Course DescriptionPrerequisitesA basic understanding of endpoint protection solutions. Agenda1.Introduction to FortiClient and FortiClient EMS2.Installation and Licensing3.FortiClient EMS configuration and Administration4.FortiClient Deployment5.FortiClient Provisioning Using FortiClient EMS6.ZTNA7.Diagnostics and TroubleshootingObjectivesAfter completing this course,you will be able to:l Understand the purpose of FortiClient EMS and identify FortiClient EMS componentsl Understand FortiClient EMS administration and database managementl Identify and explore FortiClient editionsl Understand FortiClient installationl Identify FortiClient features and settingsl Provision and deploy FortiClient using FortiClient EMSl Explore different deployment methods and typesl Understand and configure endpoint policies and profiles l Configure endpoint profile referencesl Understand the use of the ZTNAl Configure and deploy FortiClient ZTNA solutionl Understand compliance verification rules and manage tagsl Explore diagnostic tools and troubleshooting of FortiClient and FortiClient EMS Training Delivery Options and SKUs Instructor-Led TrainingIncludes standard NSE training content delivered in person onsite,or live online using a virtual classroom application.Training is delivered within public classesor as a private class.Private requests are scoped, quoted,developed,and delivered by Fortinet Training (minimum quantities apply).Use the following ILT Training SKU to purchase scheduled public classes of this course throughFortinet Resellers or Authorized Training Partners:FT-FCTSelf-Paced TrainingIncludes online training videos and resources throughthe NSE Training Institute library,free of charge.You can purchase on-demand lab access with interactive,hands-on activities using a purchase order (PO)through Fortinet Resellers or Authorized Training Partners.After you complete the purchase,you receive labaccess and the accompanying lab guide within the self-paced course.Use the following on-demand lab training SKU to purchase lab access using a PO:FT-FCT-LABSee Purchasing Process for more information about purchasing Fortinet training products.(ISC)2l CPE training hours:6l CPE lab hours:4l CISSP domains:Communication and Network Security Program Policies and FAQsFor questions about courses,certification,or training products,refer to Program Policy Guidelines or Frequently Asked Questions.。
FR9888-2010 datasheet
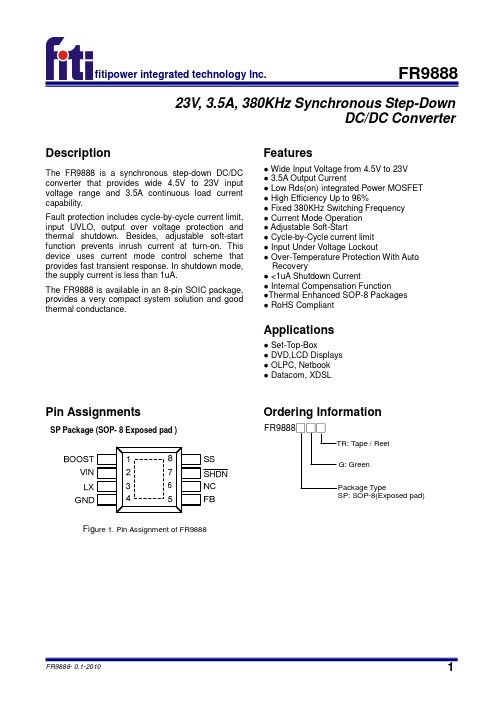
2
SHDN VIN
7
BOOST LX
1
3
L1 4.7uH~15uH VOUT C6 C2 100uF/6.3V EC x 1
FR9888
6
NC GND 4
FB SS
5
R1
(optional)
8
R2
C3 NC ~ 0.1uF
Figure 3. CIN /COUT use Electrolytic Capacitors Application Circuit
Features
● Wide Input Voltage from 4.5V to 23V ● 3.5A Output Current ● Low Rds(on) integrated Power MOSFET ● High Efficiency Up to 96% ● Fixed 380KHz Switching Frequency ● Current Mode Operation ● Adjustable Soft-Start ● Cycle-by-Cycle current limit ● Input Under Voltage Lockout ● Over-Temperature Protection With Auto Recovery ● <1uA Shutdown Current ● Internal Compensation Function ●Thermal Enhanced SOP-8 Packages ● RoHS Compliant
FR9888- 0.1-2010
4
fitipower integrated technology lnc.
FR9888
Electrical Characteristics
SafeCheck 8 安全检查器8说明书

This tester is ideal for use in the hire and service industry.SafeCheck8is a bench-mounted instrument for those who need a comprehensive tester memory which can provide result traceability.Operators can select one of the following tests from its clear user interface:Class I,Class Extension Power Cord.Equipment and tools are automatically sequenced through the test routine.The results are recorded, and information is displayed on a large clear LCD screen.SPECIFICATIONFlash/Hipot Test(Class I)Test Voltage Class l 1.25kV ACDisplay Range0.1-10mA ACResolution0.01mAAccuracy+/-5%+/-2digitsPass Levels selectable up to10mAFlash/Hipot Test(Class II)Test Voltage Class ll 2.5kV ACDisplay Range0.1-10mA AC.Resolution0.01mAAccuracy+/-5%+/-2digitsPass Levels selectable up to10mADC Insulation TestTest Voltage500VDisplay Range0.1-99.99MΩAccuracy+/-5%+/-2digits(up to19.99MΩ) Earth/Ground Bond TestTest Voltage6V AC(open circuit)Test Current25A,10A,4A,100mA AC into short circuit Range0.04Ω-20ΩResolution1mΩAccuracy+/-5%+/-2digitsPass Levels user selectableSubstitute Leakage(Short to Case Test)Test Voltage40V AC o/cDisplay Range0.1-20.0mA ACResolution0.01mAAccuracy+/-10%+/-2digits(1.00-20mA)Pass Levels selectable up to15mAEarth LeakageTest Voltage Mains SupplyDisplay Range0.1-20.0mA ACResolution0.01mAAccuracy+/-10%+/-2digits(1.00-20mA)Pass Levels selectable up to10mAPower/Run/Load TestsResolution0.01kVAMeasured Load0-4kVAAccuracy+/-10of reading,+/-2digits Optional ExtrasHardware194A922Barcode scanner312A912Desk Test n Tag printer3PHA Three phase adaptorSoftware352A910PATGuard Elite2-Premier352A920PATGuard Pro2-Professional 352A930PATGuard Lite2-Entry levelServicesService and CalibrationOrder NumberSC08UKSC08USASC08UKPackage Includes Test n Tag Printer and labelsSC08USAPackage Includes Test n Tag Printer and labelsIEC Power Cord Test Test Voltage 40V ACDetectsGood,Open,Short,ReversedADDITIONAL INFORMATION Mechanical Dimensions 450W x 410H x 155D mm Weight Approx 8.8kgElectricalSupply VoltageSelectable 115V /230V 50or 60Hz Operating Temperature 0°C to +40°C Storage Temperature -10°C to +50°CEN50191Compliant when used with appropriate accessories Supplied WithHT Probe3pin guard link connector Earth bond clip Mains leadInstruction ManualSafeCheck 8Solutions package for automation and traceability,includes:SafeCheck 8Desk Test n Tag printer Barcode Scanner 1000white labels PATGuard Lite 2CropicoHampton Road,Croydon,Surrey,United Kingdom,CR92RU T el:+44(0)2086844025Fax:+44(0)2086844094Web: Email:info@WORLD LEADERs IN SAFETY TEST AND MEASUREMENTG R O U PSEA W ARDPRECISION INSTRUMENTSCROPICOMEDICAL RIGELINDUSTRIAL SAFETY INSTRUMENTS CLAREPORTABLE ELECTRICAL SAFETY INSTRUMENTS SEA W ARD Seaward test and measurement companies include:。
标准报文83

标准报文83
标准报文83是一种用于数据传输和通信的标准格式,通常
用于金融交易、银行系统和其他需要高可靠性、安全性和数据一致性的领域。
这种报文格式被广泛采用,并具有严格的规范和标准,以确保数据的准确性和可靠性。
标准报文83通常采用ASCII码或二进制格式,包含了各种信息元素,如交易日期、交易时间、交易金额、账户信息等。
这些信息元素按照规定的格式进行组织和编码,以便在传输和接收过程中能够被正确地解析和处理。
标准报文83具有以下特点:
1.标准化:标准报文83是一种标准化的数据格式,具有
统一的规范和标准,使得不同系统之间可以相互通信和交换数据。
2.可靠性:标准报文83采用了各种错误检测和校验机制,以确保数据的完整性和准确性。
同时,它还支持重传和确认机制,以确保数据能够可靠地传输和接收。
3.安全性:标准报文83采用了加密和安全认证机制,以
确保数据传输和通信的安全性。
它还支持数字签名和验签机制,以确保数据的完整性和真实性。
4.高效性:标准报文83采用了高效的编码和传输方式,以尽可能地减少数据传输的开销和延迟。
同时,它还支持批量处理和并发处理,以提高数据处理效率。
5.可扩展性:标准报文83的设计允许在原有基础上进行扩展和改进,以适应新的业务需求和技术发展。
这有助于保持系统的灵活性和可维护性。
总之,标准报文83是一种高效、安全、可靠的数据传输和通信格式,广泛应用于各种需要高可靠性、安全性和数据一致性的领域。
主动网络安全风险管理系统

主动网络安全风险管理系统
颉钰;李卫
【期刊名称】《微电子学与计算机》
【年(卷),期】2004(21)6
【摘要】针对日益严峻的网络安全威胁,文章从加强内部安全管理入手,依据
BS7799信息安全管理体系标准的规范及指标,提出了一个主动网络安全风险管理
系统。
该系统利用信息侦察代理获得园区网的基本配置及漏洞信息,在此基础上建
立潜在入侵事件扩散模型,分析模型并对网络所面临的安全风险进行定性和定量评估,最后根据评估结果执行相应的风险控制措施,使风险等级降低到可接受的水平。
文章还介绍了主动安全风险管理系统的结构,入侵扩散模型以及风险评估算法的具
体细节,实验结果表明该系统能够有效地协助管理员建立完善的安全风险管理体系。
【总页数】6页(P1-5)
【关键词】网络安全;风险评估;入侵扩散模型;风险管理;BS7799
【作者】颉钰;李卫
【作者单位】西安交通大学计算机科学与工程系网络信息安全研究中心
【正文语种】中文
【中图分类】TP393.08
【相关文献】
1.基于心理动因模型的员工主动离职风险管理系统研究 [J], 李永华;石金涛;王莉
2.基于主动风险控制理论的内审辅助管理系统开发与实践 [J], 白宇
3.基于教学管理系统的网络安全风险监测方法研究 [J], 张丽红
4.高速公路风险防控主动交通管理系统及应用 [J], 齐建宇;马浩;李宇轩;张俊杰;李海舰
5.高速公路风险防控主动交通管理系统及应用 [J], 齐建宇;马浩;李宇轩;张俊杰;李海舰
因版权原因,仅展示原文概要,查看原文内容请购买。
- 1、下载文档前请自行甄别文档内容的完整性,平台不提供额外的编辑、内容补充、找答案等附加服务。
- 2、"仅部分预览"的文档,不可在线预览部分如存在完整性等问题,可反馈申请退款(可完整预览的文档不适用该条件!)。
- 3、如文档侵犯您的权益,请联系客服反馈,我们会尽快为您处理(人工客服工作时间:9:00-18:30)。
Overview
Sustainability review:
aims and principles Sustainability from a materials flow view Sustainability: policy, criteria, implementation
Environmental Management Systems Environmental reporting Sustainability: monitoring and control
or, Material Accounting Criteria
10
Environmental Management Systems in Organisations: Background: see paper by Moore & Scaife ICC Principles, ACM guidelines in early 1990’s
18
UNSW Environmental Policy: does it comply with ISO14001?
19
ISO14001 EMS: Question on approach
Is the approach of ISO14001 reasonable and will it deliver improvements in the environmental performance of organizations – is there too high a risk for organizations to define easy and trivial objectives and targets and still get commercial benefits through certification?
.au/soe/2000 .au/soe/97/index.htm .au/soe/95/
.au/soe/soe2003/ Regional SoE: Hurstville, Newcastle
Controls on Resource Utilisation
Renewable
Non- Renewable
Carrying Capacity of the Environment
Sustainable Yield
Optimal Rate
Best Available Technology
or, Environmental Risk Assesst
11
Environmental Management Systems ISO 14001
12
Environmental Management Systems
"the organisational structure, responsibilities, practices, procedures, processes and resources for implementing environmental management, which shall be documented. For regulatory and assessment purposes, demonstration of the implementation of identified elements in the system is required."
.au/plb/libs/hurstville/report/9596/96env.htm
Corporate environmental reports: BHP, WMC, UNSW
.au/eac/env99/default.htm .au/sustain/environ.htm
7
Sustainability from a materials flow view
8
Corporate interdisciplinary sustainability indicators
9
Sustainability: policy, criteria, implementation
ESD Principles
Where are most Australian companies now?
16
17
ISO14001 EMS: key issues
Read ISO14001 EMS standard The organisation shall….. The organisation shall define its environmental policy.. The organisation shall establish and maintain a procedure to identify the environmental aspects of its activities… The organisation shall establish and … objectives and targets… The organisation shall establish and maintain programs for achieving its objectives and targets.. …….. The organisation shall establish and maintain programs and procedures for periodic….audits. The organization's management shall review and change if necessary policy…..
Environmental policy developed
EMS system could be developed with : organisation in place priorities identified
24
Environmental reporting
25
Environmental reporting
Exercise ??
A limestone hill in a leasehold pastoral grazing area has been identified by a cement manufacturer as a desirable supply of limestone for a nearby kiln when the existing mine is depleted. Local environmental groups want to have a cave in the hill, with a rare bat/python community preserved. The cement company seek your services to prepare an EIS for their proposed development. What is your initial advice to the company?
13
Regional Share of EMS certification in %
What does this trend show?
14
New ISO14001 certificates issued in 1999
Current trends…East Asia USA???
15
Implementation within Companies 2000
3
Sustainability review
4
Sustainability: Aims
?? Conservation of resources
Renewable Non-renewable
Protection of the environment
5
Sustainability: Principles
26
27
Environmental reporting
Teaching/S.Moore/cven8888/GLU03 EMS/Public Env Reports framework.pdf
28
National SoE 1996
Executive Summary (pdf - 1.8M) Chapter 1 - Introduction (pdf - 133K) Chapter 2 - Portrait of Australia (pdf - 1.7M) Chapter 3 - Human Settlements (pdf - 1.4M) Chapter 4 - Biodiversity (pdf - 5.9M) Chapter 5 - The Atmosphere (pdf - 1.2M) Chapter 6 - Land Resources (pdf - 4.5M) Chapter 7 - Inland waters (pdf - 1.8M) Chapter 8 - Estuaries and the Sea (pdf - 1.3M) Chapter 9 - Natural and Cultural Heritage (pdf2.1M) Chapter 10 - Towards Ecological Sustainability (pdf - 548K) Appendix (pdf - 233K)
Teaching/S.Moore/cven8888/….
National State of the Environment report
.au/soe/soe96/soe96.html
.au search for SoE 2001 NSW SoE:
1
CVEN9888 Environmental Managms & Reporting on Sustainability