9第9讲:零件制造工艺过程常识
第九章 零件生产过程基础知识
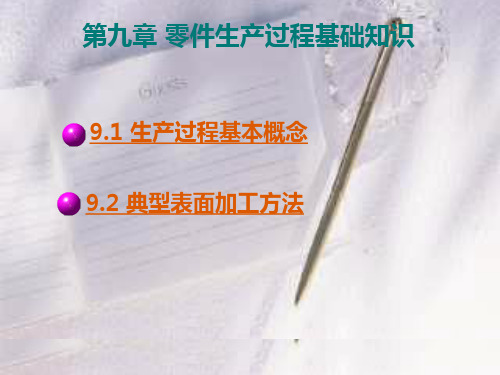
小常识:关于CAPP
制订零件工艺过程
复杂、繁琐、依靠经验、重点在管理
CAPP(Computer Aided Process Planning)
最低目标:工艺过程管理信息系统 标:代替经验丰富的工艺人员 智能生成零件的工艺过程
创成式、检索式
核心理论:成组技术+企业基础信息的统筹管理
二、套筒类零件加工工艺
1、套筒类零件的功用及结构特点 套筒类零件是指在回转体零件中的空心薄壁 件,是机械加工中常见的一种零件,在各类机器 中应用很广,主要起支承或导向作用。由于功用 不同,其形状结构和尺寸有很大的差异,常见的 有支承回转轴的各种形式的轴承圈、轴套;夹具 上的钻套和导向套;内燃机上的气缸套和液压系 统中的液压缸、电液伺服阀的阀套等都属于套类 零件。其大致的结构形式如图9-3所示。
画出并分析一专用铣削夹具,指出定位元件、夹紧元 件和夹具体并指出它们的作用。
答:左边固定钳口是定位元件,起到定位作用, 右边的活动钳口是夹紧元件起到夹紧,作用是装夹小而规则的零件。
安装举例 机械制造工艺学中,安装指齿轮毛坯经一次定位夹紧后,在工 件没有取下来,所进行的切削加工(铣齿)内容。
3. 工位
生产类型划分
二、机械加工工艺过程
机械制造过程是机械产品从原材料开始到成品之间各相互关联的劳动过 程的总和。它包括毛坯制造、零件机械加工、热处理、机器的装配、检验、 测试和油漆包装等主要生产过程,也包括专用夹具和专用量具制造、加工设 备维修、动力供应(电力供应、压缩空气、液压动力以及蒸汽压力的供给 等)。 工艺过程是指在生产过程中,通过改变生产对象的形状、相互位置和性 质等,使其成为成品或半成品的过程。 机械产品生产工艺过程又可分为铸造、锻造、冲压、焊接、机械加工、 热处理、装配、涂装等。其中与原材料变为成品直接有关的过程,称为直接 生产过程,是生产过程的主要部分。 而与原材料变为产品间接有关的过程,如生产准备、运输、保管、机床 与工艺装备的维修等,称为辅助生产过程。
零件生产工艺过程的基本知识_PPT74页
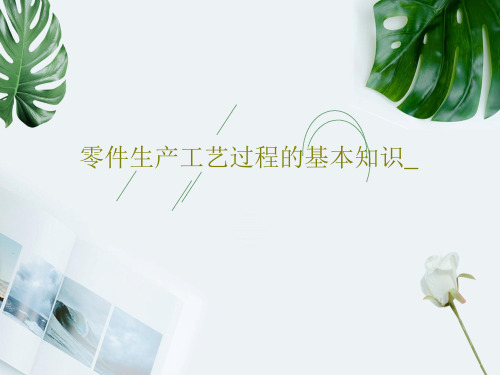
零件生产工艺过程的基本知识_
56、极端的法规,就是极端的不公。 ——西 塞罗 57、法律一旦成为人们的需要,人们 就不再 配享受 自由了 。—— 毕达哥 拉斯 58、法律规定的惩罚不是为了私人的 利益, 而是为 了公共 的利益 ;一部 分靠有 害的强 制,一 部分靠 榜样的 效力。 ——格 老秀斯 59、假如没有法律他们会更快乐的话 ,那么 法律作 为一件 无用之 物自己 就会消 灭。— —洛克
机械零件加工工艺过程的基本知识
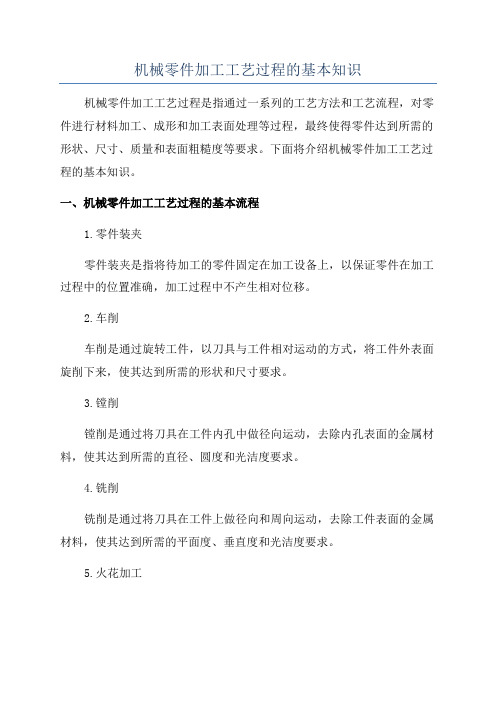
机械零件加工工艺过程的基本知识机械零件加工工艺过程是指通过一系列的工艺方法和工艺流程,对零件进行材料加工、成形和加工表面处理等过程,最终使得零件达到所需的形状、尺寸、质量和表面粗糙度等要求。
下面将介绍机械零件加工工艺过程的基本知识。
一、机械零件加工工艺过程的基本流程1.零件装夹零件装夹是指将待加工的零件固定在加工设备上,以保证零件在加工过程中的位置准确,加工过程中不产生相对位移。
2.车削车削是通过旋转工件,以刀具与工件相对运动的方式,将工件外表面旋削下来,使其达到所需的形状和尺寸要求。
3.镗削镗削是通过将刀具在工件内孔中做径向运动,去除内孔表面的金属材料,使其达到所需的直径、圆度和光洁度要求。
4.铣削铣削是通过将刀具在工件上做径向和周向运动,去除工件表面的金属材料,使其达到所需的平面度、垂直度和光洁度要求。
5.火花加工火花加工是利用电火花放电原理进行零件加工的一种加工方法。
通过电极与工件之间产生电火花放电,将工件上的材料溶解和熔化,并通过水冷剂迅速冷却,使其达到所需的形状和尺寸要求。
6.磨削磨削是通过在工件表面和砂轮之间进行相对运动,将工件表面的金属材料去除,以达到所需的平面度、圆度、光洁度和尺寸要求。
7.锤击锤击是通过将锤击力作用于工件上,去除工件上的金属材料,以达到所需的形状和尺寸要求。
8.切割切割是通过机械力或热能,将工件切割成所需的形状和尺寸。
常用的切割方法有剪切、火焰切割、激光切割等。
二、常见机械零件加工工艺方法1.塑性加工塑性加工是通过在零件上施加外力,使其发生塑性变形,以改变其形状和尺寸。
常见的塑性加工方法有拉伸、压缩、弯曲、冲压等。
2.热处理热处理是通过加热和冷却过程,改变零件内部组织结构,以改变其性能和硬度。
常见的热处理方法有淬火、回火、退火、时效等。
3.表面处理表面处理是对零件表面进行物理或化学处理,以提高其耐磨性、耐腐蚀性及美观度。
常见的表面处理方法有镀铬、镀镍、镀锌、喷涂、抛光等。
零件生产工艺过程基本知识
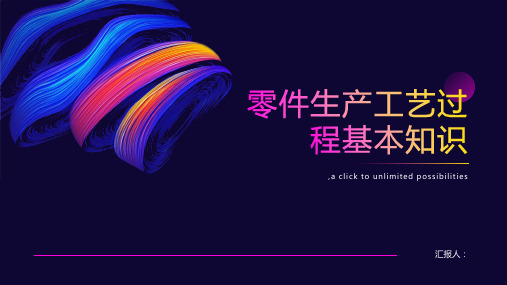
设计阶段:确定零件的尺寸、形状、材料等参数,并绘制图纸 制造阶段:根据图纸进行零件的加工和制造,包括切割、焊接、铸造等 检验阶段:对制造出来的零件进行质量检验,确保其符合设计要求 装配阶段:将零件组装成成品,并进行调试和测试 包装阶段:对成品进行包装和运输,确保其安全到达目的地
PART THREE
PART SIX
提高生产效率:通过改进和创新,可以提高生产效率,降低生产成本。
提高产品质量:通过改进和创新,可以提高产品质量,满足市场需求。
提高市场竞争力:通过改进和创新,可以提高企业的市场竞争力,增强企业的生存和发展能力。
遵循可持续发展原则:在改进和创新过程中,要遵循可持续发展原则,注重环境保护和资源节 约。
收集和分析现有工艺数据,找出存在的 问题和瓶颈
确定改进和创新的目标和方向,如提高 生产效率、降低成本、提高产品质量等
研究新技术、新工艺、新材料等,寻找 可能的改进和创新方案
制定改进和创新的具体方案,包括技术 方案、设备方案、工艺方案等
实施改进和创新方案,并进行试验和验 证
总结改进和创新的经验和教训,形成可 推广的案例和经验
PART TWO
设计阶段:确定零件的尺寸、形状、材料等基本参数 制造阶段:将设计阶段的参数转化为实际产品 检验阶段:检查产品的质量是否符合设计要求 包装阶段:将产品包装好,准备运输或销售 售后服务阶段:提供产品的售后服务,解决客户问题
设计阶段:确定零件的尺寸、形状、材料等 制造阶段:将设计转化为实物,包括铸造、锻造、冲压、焊接等 加工阶段:对制造出的零件进行精细加工,包括车削、铣削、磨削等 装配阶段:将加工好的零件组装成成品,包括装配、调试、检验等
,a click to unlimited possibilities
零件加工工艺流程

零件加工工艺流程零件加工是指将原材料经过一系列工艺加工,将其转化为具有特定形状和尺寸的产品。
下面是一篇关于零件加工工艺流程的介绍。
零件加工工艺流程是一个基于设计图纸的生产流程,它通常包括以下几个步骤:设计分析、工艺规划、加工准备、加工操作和质量控制。
首先是设计分析。
在这一步骤中,工艺师会仔细分析设计图纸,并确定零件的材料、工艺特点、尺寸和形状等关键要素。
他们还会进行模拟分析,以确保加工过程的可行性和结果的准确性。
接下来是工艺规划。
基于设计分析的结果,工艺师会制定出零件加工的具体方案。
这个方案包括选择适当的加工设备、工艺参数和工艺顺序。
工艺规划还涉及到工艺的经济性和工期的控制,以确保加工过程的效率和成本的可控性。
然后是加工准备。
在这一步骤中,工艺师会准备好所需的加工设备和工装夹具。
他们会检查和调整设备的性能,并进行所需的维护。
此外,他们还会准备好所需的刀具、磨具和润滑剂等加工工具和辅助材料。
接下来是加工操作。
在这一步骤中,工艺师会根据工艺规划的要求,进行具体的加工操作。
这包括将设备和工装夹具设置到合适的位置和状态,安装和调整刀具和磨具,控制加工参数,进行零件的切削、成型、抛光和检测等操作。
最后是质量控制。
在加工过程中,工艺师会进行各种质量控制措施,以确保加工结果的准确性和一致性。
这包括对加工后的零件进行尺寸和形状的测量和检测,并与设计要求进行比较。
如果发现问题,工艺师会采取相应的纠正措施,以确保零件的质量和性能达到要求。
总结起来,零件加工工艺流程是一个严谨而复杂的过程,它需要工艺师具备扎实的专业知识和技能。
通过设计分析、工艺规划、加工准备、加工操作和质量控制等环节的有效协作,可以实现零件加工过程的高效、高质和可控。
零件制造工艺过程常识
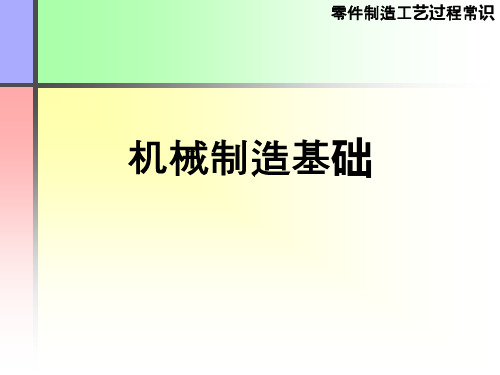
– 第一道切削加工工序所使用的基准 – 不是(粗加工时使用的基准)
• 精基准
– 第一道工序以后使用的基准
(1)粗基准
• 第一道切削加工工序所使用的基准
– 不是(粗加工时使用的基准)
• 第一道工序只能使用未加工表面作基准 • 选择粗基准的基础
– 保证各个加工表面都有足够加工余量 – 保证不加工表面的位置精度
– V型铁、挡块 – 平面用:支承钉、支承板 – 孔用:心轴、定位销
• 每种元件限制的自由度数量不同
– 形状决定的
• 钉(1),板(2),销(4、2、1) • V型铁(4、2),心轴(4、2)
支承钉
• 限制1个自由度
支承板
• 较长时,限制2个自由度
定位销
• 圆柱销:(长销:4,短销或圆锥销:2 ) • 菱形销(削边销):1 • 一面两销:用于箱体的完全定位
• 外圆、内圆
– 长(4)、短(2)
• 锥面
– 长(5)、短(3)
• 一般判断原则
– 观察小1、长2
定位基准:圆柱(内外圆)
• 长4、短2
定位基准:锥面
• 长5、短3
6、定位基准的选择原则
• 定位基准选择的出发点
– 保证加工精度、提高加工效率 – 从加工精度要求高的表面中选择
V型铁
• 长V型铁(4) • 短V型铁(2)
• 长心轴(4) • 短心轴(2)
心轴
5、基准:工件上定位的几何元素
• 基准
– 零件的设计制造中,用于确定零件上点线面 等几何要素的依据(也是一些点线面)
• 基准的种类
– 设计基准
• 设计时使用的基准
– 工艺基准
• 制造零件或者装配机器时使用 • 定位基准、度量基准、装配基准
零件加工工艺步骤

零件加工工艺步骤在零件加工过程中,正确的工艺步骤是确保产品质量和提高生产效率的关键。
本文将介绍零件加工的一般工艺步骤,以帮助读者更好地理解这一过程。
1. 设计和规划在加工工艺开始之前,首先需要进行设计和规划。
根据产品的要求,绘制出详细的零件图纸,并确定所需的材料和机械设备。
同时,考虑到生产成本和时间,确保设计方案的可行性和优化。
2. 材料准备在加工过程中,正确的材料选择和准备是至关重要的。
根据零件图纸要求,选择适当的材料,并确保其质量和供应。
材料准备包括切割、锻造、热处理等步骤,以确保材料达到所需的硬度和强度。
3. 加工工序在零件加工的实际步骤中,通常会包括以下几种工序:3.1 车削车削是一种通过旋转工件并用刀具去除材料的工艺。
它可以用于加工各种形状的零件,如轴、套筒等。
车削过程中需要根据零件图纸操作机床,实现精确的尺寸和表面质量要求。
3.2 铣削铣削是一种通过旋转刀具进行切削的工艺。
它可以用于加工平面、曲面以及一些特殊形状的零件。
铣削过程中需要进行刀具的选型和刀具路径的规划,以确保加工出理想的形状和尺寸。
3.3 钻削钻削是一种通过旋转刀具进行穿孔的工艺。
它常用于加工孔洞、螺纹等零件。
钻削前需要进行定位和固定零件,根据图纸确定孔洞的位置和尺寸,然后进行钻孔操作。
3.4 焊接焊接是一种通过高温熔化填充材料使两个零件连接的工艺。
焊接常用于加工金属零件,在零件加工过程中常涉及到的是电弧焊和气体保护焊等方法。
4. 表面处理在零件加工完成之后,有时需要进行表面处理以改善零件的外观和耐腐蚀性能。
常见的表面处理包括电镀、喷涂和抛光等。
根据零件的要求选择合适的表面处理方法,并进行相应的操作。
5. 检验和质量控制最后,零件加工的工艺步骤还包括检验和质量控制。
在每个加工步骤完成后,应进行相应的检验,确保零件尺寸和质量满足要求。
同时,建立完善的质量控制体系,监控整个加工过程的质量,并及时进行调整和改进。
总结零件加工工艺步骤的正确执行对保证产品质量和生产效率至关重要。
零件制造工艺过程常识共59页
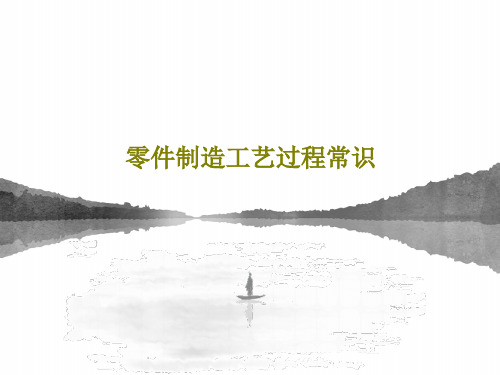
6、最大的骄傲于最大的自卑都表示心灵的最软弱无力。——斯宾诺莎 7、自知之明是最难得的知识。——西班牙 8、勇气通往天堂,怯懦通往地狱。——塞内加 9、有时候读书是一种巧妙地避开思考的方法。——赫尔普斯 10、阅读一切好书如同和过去最杰出的人谈话。——笛卡儿
零件制造工艺过程常识
1、战鼓一响,法律无声。——英国 2、任何法律的根本;不,不成文法本 身就是 讲道理 ……法 律,也 ----即 明示道 理。— —爱·科 克
3、法律是最保险的头盔。——爱·科 克 4、一个国家如果纲纪不正,其国风一 定颓败 。—— 塞内加 5、法律不能使人人平等,但是在法律 面前人
零件生产工艺过程基本知识

零件生产工艺过程基本知识零件生产工艺是指将原材料加工成符合设计要求的零件的过程。
在制造业中,零件生产工艺是非常重要的环节,它直接影响着产品的质量、成本和交货周期。
因此,了解零件生产工艺的基本知识对于提高生产效率和产品质量至关重要。
1. 材料选择零件生产工艺的第一步是材料选择。
不同的零件需要选择不同的材料,常见的材料包括金属、塑料、陶瓷等。
在选择材料时,需要考虑零件的使用环境、负荷、耐磨性等因素,以确保零件具有良好的性能和耐久性。
2. 设计在确定了材料之后,需要进行零件的设计。
设计师需要根据零件的功能要求和使用环境,绘制出详细的零件图纸。
在设计过程中,需要考虑到材料的加工性能、成本和生产工艺等因素,以确保设计的合理性和可制造性。
3. 加工工艺加工工艺是零件生产的核心环节,它包括多种加工方法,如铣削、车削、钻孔、磨削等。
不同的零件需要采用不同的加工工艺,以确保零件的精度和表面质量。
在加工过程中,需要根据零件的特点和要求,选择合适的工艺参数和加工设备,以确保加工质量和效率。
4. 检测与质量控制在零件生产过程中,需要进行多次检测和质量控制,以确保零件的质量符合设计要求。
常见的检测方法包括三坐标测量、硬度测试、表面粗糙度检测等。
通过严格的质量控制,可以及时发现和解决生产过程中的质量问题,确保零件的合格率和稳定性。
5. 表面处理一些零件需要进行表面处理,以提高其耐腐蚀性、耐磨性和美观性。
常见的表面处理方法包括镀锌、喷涂、阳极氧化等。
通过合适的表面处理,可以提升零件的使用寿命和外观质量。
6. 组装最后一步是零件的组装。
在组装过程中,需要将各个零件按照设计要求进行组合,以形成最终的产品。
在组装过程中,需要注意零件之间的配合精度和间隙,以确保产品的功能和性能。
总之,零件生产工艺是一个复杂而严谨的过程,它涉及材料选择、设计、加工工艺、检测与质量控制、表面处理和组装等多个环节。
只有在每个环节都做到精益求精,才能生产出高质量、高性能的零件和产品。
零件加工工艺流程
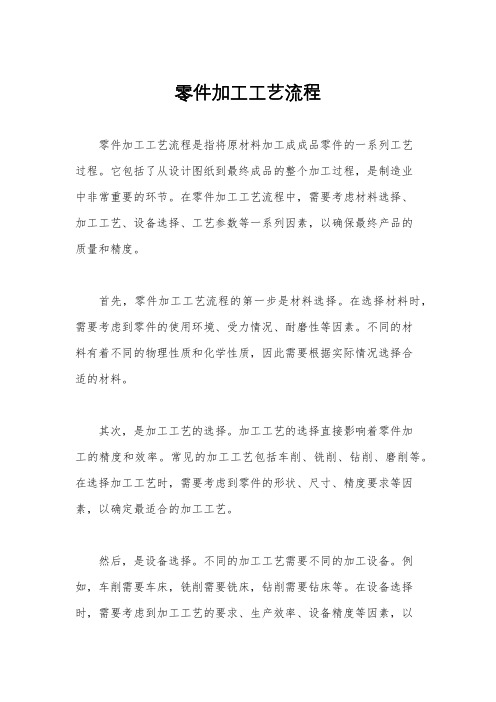
零件加工工艺流程零件加工工艺流程是指将原材料加工成成品零件的一系列工艺过程。
它包括了从设计图纸到最终成品的整个加工过程,是制造业中非常重要的环节。
在零件加工工艺流程中,需要考虑材料选择、加工工艺、设备选择、工艺参数等一系列因素,以确保最终产品的质量和精度。
首先,零件加工工艺流程的第一步是材料选择。
在选择材料时,需要考虑到零件的使用环境、受力情况、耐磨性等因素。
不同的材料有着不同的物理性质和化学性质,因此需要根据实际情况选择合适的材料。
其次,是加工工艺的选择。
加工工艺的选择直接影响着零件加工的精度和效率。
常见的加工工艺包括车削、铣削、钻削、磨削等。
在选择加工工艺时,需要考虑到零件的形状、尺寸、精度要求等因素,以确定最适合的加工工艺。
然后,是设备选择。
不同的加工工艺需要不同的加工设备。
例如,车削需要车床,铣削需要铣床,钻削需要钻床等。
在设备选择时,需要考虑到加工工艺的要求、生产效率、设备精度等因素,以选择最合适的加工设备。
接着,是工艺参数的确定。
在进行零件加工时,需要确定一系列工艺参数,如切削速度、进给速度、切削深度等。
这些工艺参数直接影响着加工效率和零件质量,因此需要根据实际情况进行合理的确定。
最后,是加工过程中的质量控制。
在零件加工过程中,需要进行质量检测和控制,以确保加工出来的零件符合设计要求。
常见的质量控制手段包括尺寸测量、表面质量检查、材料成分分析等。
综上所述,零件加工工艺流程是一个复杂而严谨的过程,需要考虑到诸多因素。
只有在材料选择、加工工艺选择、设备选择、工艺参数确定和质量控制等方面做到科学合理,才能够保证最终加工出的零件质量和精度。
在今后的工作中,我们需要不断学习和积累经验,以提高零件加工工艺的水平,为企业的发展做出贡献。
零件的加工工艺流程

零件的加工工艺流程零件的加工工艺流程是指将原材料按照要求进行加工和组装,制造成最终的零件产品的一系列工艺流程。
下面以某个零件的加工工艺流程为例,介绍零件加工的大致步骤。
首先,进行材料的选择。
根据零件的要求和使用环境,选择合适的材料进行加工。
材料的选择要考虑到强度、耐磨性、耐腐蚀性等因素,确保最终产品的质量和可靠性。
第二步,进行原材料的切割。
根据零件的尺寸和形状要求,使用切割设备(如剪切机、钢板切割机等)将原材料切割成适当的尺寸。
这一步骤需要精确测量和准确操作,确保切割出的原材料大小和形状与设计要求相符。
第三步,进行零件的粗加工。
在粗加工阶段,使用机床(如车床、铣床、镗床等)对原材料进行粗加工,以得到大致的形状和尺寸。
粗加工需要根据设计图纸进行操作,控制好工件的尺寸和表面质量。
第四步,进行零件的精加工。
在精加工阶段,使用精密机床(如磨床、铣床等)对零件进行加工,以获得更高的精度和表面质量。
精加工通常需要采用多道工序,如车削、钻孔、镗孔、镗座等,确保零件的尺寸、平整度和精度达到要求。
第五步,进行零件的热处理。
针对不同的材料性质和零件要求,在加工过程中可能需要进行热处理。
热处理过程通常包括淬火、回火、退火、正火等,以改变材料的组织结构和性能,提高零件的强度和硬度。
第六步,进行零件的表面处理。
为了提高零件的耐腐蚀性、表面光洁度和装饰效果,常常需要进行表面处理。
常见的表面处理方法包括镀锌、电镀、喷涂、抛光、喷砂等,使零件的外观更加美观并且延长使用寿命。
第七步,进行零件的装配。
在零件加工的最后阶段,根据设计要求和生产流程,使用合适的方法将零件组装起来。
组装过程需要仔细分析和操作,保证零件之间的配合度和安装质量。
最后,对零件加工的质量进行检测和检验。
通过检测和检验,确保加工出的零件满足设计要求和产品标准。
常用的检测方法包括尺寸测量、硬度测试、化学检验、无损检测等。
以上就是零件加工的大致流程,不同类型和要求的零件加工过程可能会有所不同。
零件生产工艺流程

零件生产工艺流程零件生产工艺流程是指生产一个零件的各个环节和步骤,包括材料采购、设计制定、加工生产、质量检验等。
下面将对零件生产工艺流程进行详细描述。
首先,零件生产的第一步是材料采购。
根据设计要求,采购人员需要与供应商联系并确定所需的材料规格、数量和交货时间。
在选择供应商时,需要考虑价格、质量、供货能力等因素。
一旦与供应商达成协议,就可以将材料运送到生产现场。
接下来,设计部门需要根据产品的要求进行制定设计方案。
设计工程师通过使用CAD或其他设计软件,绘制出精确的三维模型和技术图纸。
这些图纸将包含零件的几何尺寸、几何形状、材料要求等详细信息,以供后续加工生产使用。
一旦设计方案制定完成,工艺工程师将根据设定的生产要求,制定出具体的加工工艺。
这将包括选择适当的加工方法、工艺参数、工装夹具的设计等。
工艺工程师需要充分考虑材料的特性和工艺的可行性,以确保产品能够满足设计要求并且能够高效率、高质量地生产出来。
加工生产阶段是零件生产的核心环节。
根据加工工艺,操作工人将使用各种机床设备,如铣床、车床、钻床等,对材料进行切削、锻造、焊接等操作。
在这个阶段,操作工人需要具备一定的技术和经验,以确保加工过程的严密性、稳定性和安全性。
完成加工后,零件进入质量检验阶段。
质检人员将对零件进行外观检查、尺寸检测、硬度测量、材料成分分析等多项检测,以确保零件符合设计要求。
质检人员还需要记录和报告检测数据,并对不合格零件进行分类和处理。
最后,合格的零件将进行清洗、涂漆、包装等各个环节,以最终完成生产。
清洗操作可以去除加工过程中产生的油污和金属屑,涂漆可以提高零件的耐腐蚀性和美观度,而包装则可以保护零件免受损坏和污染。
以上就是零件生产工艺流程的主要步骤。
通过科学合理地组织和实施这些工艺流程,可以确保零件的质量和工期的达到预期效果,并为产品的正常生产提供支持。
零件生产工艺流程

零件生产工艺流程
《零件生产工艺流程》
零件生产工艺流程是指在零件加工生产过程中,根据零件的特性和要求,制定出合理有效的加工工艺方案,包括加工工艺流程、加工工艺参数、加工工艺设备等内容。
在零件生产过程中,工艺流程的合理性直接影响着零件加工的质量、效率和成本,因此在零件加工过程中,尤为重要。
首先,零件的生产工艺流程包括加工工艺计划、工艺数据编制、工艺过程设计等。
在加工工艺计划中,需要根据零件的结构特点、材料性能、加工技术要求等因素,制定出合理的工艺方案,确定零件的加工工艺路线。
在工艺数据编制中,需要编制出符合零件加工要求的加工工艺参数,包括切削速度、进给量、切削深度、刀具选择等内容。
在工艺过程设计中,需要设计出符合零件加工要求的工艺过程,包括工艺装夹、夹具设计、工艺检验等内容。
其次,零件的生产工艺流程还包括加工设备选择、工艺优化改进等内容。
在加工设备选择中,需要根据零件的加工要求、质量要求、生产效率要求等因素,选择适合的加工设备。
在工艺优化改进中,需要根据零件加工的实际情况,对加工工艺流程进行优化改进,以提高零件加工的质量和效率。
总的来说,零件生产工艺流程是零件加工生产中的重要环节,对于提高零件加工的质量、效率和成本具有重要意义,因此在零件加工生产中,必须认真制定和实施好零件生产工艺流程。
零件生产工艺流程

零件生产工艺流程
零件生产工艺流程是指将材料加工成符合产品要求的零件的过程。
下面是一个零件生产工艺流程的简要描述:
1. 材料准备:首先,需要准备好所需的材料,包括金属、塑料、橡胶等。
根据产品的要求选择合适的材料,并进行清洗和切割,以便后续加工。
2. 粗加工:接下来,进行粗加工,包括铣削、车削、钻孔等。
通过这些加工步骤,将材料的尺寸和形状加以调整,以便后续的加工。
3. 热处理:某些材料需要进行热处理,以改善其物理性能。
热处理过程包括退火、淬火、回火等,通过控制温度和时间,使材料的性能得到优化。
4. 精加工:在完成粗加工后,需要进行进一步的精加工,以获得更高的精度和表面质量。
精加工的方法包括磨削、铣削、镗削等。
5. 组装:如果零件需要多个部分组合成整体,需要进行组装操作。
组装包括焊接、螺纹连接、机械连接等方式,将不同部分正确地组合起来,以形成完整的零件。
6. 表面处理:有些零件需要进行表面处理,以保护和美化其外观。
表面处理的方法包括镀锌、喷涂、阳极氧化等,通过这些方式增加零件的耐腐蚀性和外观质量。
7. 检验:完成零件的加工后,需要进行质量检验。
检验过程包括外观检查、尺寸测量、物理性能测试等,确保零件符合设计要求。
8. 包装和出货:最后,将合格的零件进行包装,并按照订单要求进行出货。
包装可以采用纸箱、木箱、托盘等,以保护零件在运输过程中不受损坏。
以上是一个零件生产工艺流程的简要描述,不同的产品和工艺流程可能会有所差异。
在实际生产中,还需要根据具体情况进行工艺参数的优化和调整,以提高生产效率和产品质量。
零件工艺流程

零件工艺流程
零件工艺流程是指对零件进行加工的全过程,包括设计、加工、装配等环节。
在制造业中,零件工艺流程的设计和实施直接影响着
产品的质量、成本和交货周期。
因此,合理高效的零件工艺流程对
于企业的生产效率和竞争力至关重要。
首先,零件工艺流程的设计需要充分考虑零件的形状、尺寸、
材料、工艺要求等因素。
设计师需要根据零件的实际情况选择合适
的加工工艺和设备,确保零件在加工过程中能够满足产品的质量要求。
同时,设计师还需要考虑到生产成本和加工周期,尽可能降低
生产成本,缩短加工周期,提高生产效率。
其次,零件工艺流程的实施需要严格按照设计要求进行。
在加
工过程中,操作人员需要严格按照工艺要求进行操作,确保零件的
加工精度和表面质量。
同时,对于复杂的零件,还需要进行装配、
调试等环节,确保零件能够正常使用。
在实施过程中,需要不断对
工艺流程进行优化和改进,以适应市场需求和技术变化。
最后,零件工艺流程的管理和控制是保证产品质量的重要环节。
企业需要建立完善的质量管理体系,对零件工艺流程进行全面监控
和控制,确保产品的质量稳定性。
同时,企业还需要加强对员工的培训和管理,提高员工的技术水平和责任意识,减少人为因素对产品质量的影响。
总之,零件工艺流程的设计、实施和管理是企业生产的关键环节,对于提高产品质量、降低成本、缩短交货周期具有重要意义。
企业需要重视零件工艺流程的优化和改进,不断提高自身的竞争力和市场地位。
只有不断完善零件工艺流程,才能适应市场的需求,赢得客户的信赖。
- 1、下载文档前请自行甄别文档内容的完整性,平台不提供额外的编辑、内容补充、找答案等附加服务。
- 2、"仅部分预览"的文档,不可在线预览部分如存在完整性等问题,可反馈申请退款(可完整预览的文档不适用该条件!)。
- 3、如文档侵犯您的权益,请联系客服反馈,我们会尽快为您处理(人工客服工作时间:9:00-18:30)。
• 简单实例
© 2004 金工教研室 机械制造基础
一、工艺过程的有关概念
• 生产过程
– 机器制造时,由原材料到成品之间各个相互 关联的劳动过程的总和 – 例如,可能包括
• • • • 原材料运输和保管(库存) 生产准备工作 毛坯制造、零件加工和热处理 产品装配、调试、检验、油漆、包装
© 2004 金工教研室
机械制造基础
粗基准选择原则
• 所有表面都要加工时,选择余量和公差 最小的表面,避免出现废品 • 其它原则
– 表面光洁、平整、面积足够大、装夹稳固
• 重要常识
– 粗基准只能使用一次
© 2004 金工教研室
机械制造基础
(2)精基准
• 第一道工序后应该使用已加工表面作为 基准:精基准 • 选择的基础
© 2004 金工教研室
机械制造基础
工艺过程
© 2004 金工教研室
机械制造基础
工艺过程
© 2004 金工教研室
机械制造基础
工艺过程
© 2004 金工教研室
机械制造基础
工艺过程
© 2004 金工教研室
机械制造基础
总结
• • • • • • 工艺过程的有关概念 装夹与定位 零件加工工艺制订的有关常识 简单实例 工艺人员更多的是靠长期积累的经验 CAPP更像一个工艺过程的信息管理系统
© 2004 金工教研室 机械制造基础
设计基准
• 面2、3、孔4的设计 基准是面1 • 孔5的基准是孔4 • 实际上全部都是面1
© 2004 金工教研室
机械制造基础
定位基准
• 观察图示零件
– 加工外圆和端面时的 定位基准
• 孔的轴线
• 定位基准通常都以面 的形式体现
– 轴线->孔面 – 因此基准面要求有更 高的加工精度
– 将这些内容用工艺文件形式表示出来
• 机械加工工艺规程(机械加工工艺卡片)
© 2004 金工教研室 机械制造基础
制定零件加工工艺必须满足的要求
• • • • 确保零件的全部技术要求 生产效率高 生产成本低 劳动生产条件好
• 重要原则
– 要根据客观生产条件,经过反复实践反复修 改,才能使之合理与完善
© 2004 金工教研室
机械制造基础
工艺过程
• 工艺过程
– 生产过程的主要部分 – 机械加工工艺过程
• 用机械加工方法直接改变原材料或毛坯形状、 尺寸,使之变成成品
– 装配工艺过程
• 在装配车间将零件装配成机器的过程
© 2004 金工教研室
机械制造基础
工艺过程的组成
• 工序
– 三定一连续:
• 定机床、定工件、定工人 • 连续完成的加工内容
• 不受约束的物体
– 六个自由度:三个方向移动、三个方向转动
© 2004 金工教研室
机械制造基础
六点定位原理
• 六点定位原理
– 要完全确定工件位置, 必须有六个相应的支 承点来限制工件的六 个自由度
© 2004 金工教研室
机械制造基础
定位情况
• • • • 完全定位 不完全定位 超(过)定位 欠定位:绝对不允许
– 夹紧
• 在加工过程中,为使工件能承受切削力,并使 之保持正确位置,必须将工件压紧夹牢
– 从定位到夹紧的整个过程:安装
© 2004 金工教研室
机械制造基础
1、工件安装的方法
• 工件的安装
– 一般均使用夹具
• 机床上自带的通用夹具、专门制作的专用夹具
• 直接安装
– 使用机床自带的通用夹具安装
• 有时需画线找正位置、费时、适用于单件小批
• 通用机床、工夹量具、工序集中、需要熟练工
– 成批生产
• 专用机床、工夹量具、工序分散、工人技能要求一般
– 大量生产
• 广泛采用专用生产线、重复劳动、工人技能要求不高
• 无论那种批量,均可使用数控机床
– 尽量工序集中
© 2004 金工教研室 机械制造基础
二、安装与夹具
• 安装包括的概念
– 定位
• 进行机械加工前,必须将工件放在机床上,使 之在夹紧前占据正确的位置
• δB
© 2004 金工教研室 机械制造基础
以M定位
• 考虑基准不重合产生 的误差 • εA= δB + δc • 当然,还有这次加工 产生的加工误差
© 2004 金工教研室
机械制造基础
精基准选择的其它原则
• 基准同一原则
– 加工位置精度要求较高的一组表面,尽可能 选择同一个基准定位 – 有利于保证这些表面的相互位置精度
© 2004 金工教研室
机械制造基础
工艺文件编制
• 2、机械加工工序卡片
– 大批大量生产时,要求工艺文件更加完整和详细 – 每个零件的各个工序都要有工序卡片 – 工序卡片的主要表达形式:工序图
• 表示本工序完成后工件的形状、尺寸及其技术要求 • 表示出工件的装夹方式、刀具的形状及其位置
– 工序卡片的格式和填写要求可参阅原机械上业部指 导性技术文件“工艺规程格式及填写规则”
• 利用专用夹具安装
• 安装迅速可靠、精度高、成本高、批量生产
• 哲学问题?
• 单件小批生产、如果通用夹具不能保证精度或者非常费时, 怎么办?
© 2004 金工教研室 机械制造基础
2、关于专用夹具
导向元件 定位元件 夹紧机构
夹具体和其它部分
专用镗模通孔夹具
© 2004 金工教研室 机械制造基础
3、六点定位原理:自由度
© 2004 金工教研室 机械制造基础
四、简单实例:盘套类零件
© 2004 金工教研室
机械制造基础
工艺分析
• 典型组成型面
– 孔、外圆、端面、沟槽
• 技术要求的重点
– 相互位置精度
• 毛坯选择
– 铸件、锻件、型材
• 工艺原则重点
– 孔为基准、“一刀活”
© 2004 金工教研室 机械制造基础
工艺过程
© 2004 金工教研室
机械制造基础
4、夹具上的定位元件
• 夹具上用于限制工件自由度的元件
– V型铁、挡块 – 平面用:支承钉、支承板 – 孔用:心轴、定位销
• 每种元件限制的自由度数量不同
– 形状决定的
• 钉(1),板(2),销(4、2、1) • V型铁(4、2),心轴(4、2)
© 2004 金工教研室 机械制造基础
机械制造基础
制定零件加工工艺的步骤
• 3、零件的工艺分析
– (1) 确定主要表面的加工方法和步骤 – (2) 确定定位基面
• 轴类(两端面的中心孔) • 盘套类(孔) • 箱体支架类(装配基准平面)
– (3) 确定各工序加工余量、切削用量和工时 定额
© 2004 金工教研室 机械制造基础
制定零件加工工艺的步骤
• 4、安排热处理工序 • 5、拟定工艺过程
– 合理安排零件各表面的加工先后顺序 – 安排工艺过程时考虑的一般原则
• • • • 先基准后其他(基准先行原则) 先粗后精(粗精加工分开原则) 先重要后其他 先面后孔
© 2004 金工教研室
机械制造基础
工艺文件编制
• 1、机械加工工艺过程卡片(单件小批)
© 2004 金工教研室
机械制造基础
粗基准选择原则
• 选择不加工表面
– 保证不加工表面的位 置精度 – 多个不加工表面
• 选择位置精度要求高 的
© 2004 金工教研室
机械制造基础
粗基准选择原则
• 选择要求加工余量均 匀的表面
– 该基准面的加工均匀 – 机床导轨表面要求
• 金相、性能一致 • 去处一层很薄 金工教研室
机械制造基础
工艺文件编制
• 3、机械加工工艺(综合)卡片
– – – – 主要用于成批生产 它比工艺过程卡片详细 比工序卞片简单且较灵活 足介于两者之间的一种格式
© 2004 金工教研室
机械制造基础
关于CAPP的常识
• 制订零件工艺过程
– 复杂、繁琐、依靠经验、重点在管理
– 保证精度
• 基准重合、基准同一、自为基准、互为基准
– 基准面的精度应该较高
• 选定基准面后,即使该表面设计精度不高,也 应该提高加工精度
© 2004 金工教研室
机械制造基础
基准重合原则
• 考查3种定位基准下尺寸A的公差
– 以M定位 – 以H定位 – 以K定位
• 已知
– M-H的公差
• δc
– H-K的公差
– 第一道切削加工工序所使用的基准 – 不是(粗加工时使用的基准)
• 精基准
– 第一道工序以后使用的基准
© 2004 金工教研室 机械制造基础
(1)粗基准
• 第一道切削加工工序所使用的基准
– 不是(粗加工时使用的基准)
• 第一道工序只能使用未加工表面作基准 • 选择粗基准的基础
– 保证各个加工表面都有足够加工余量 – 保证不加工表面的位置精度
© 2004 金工教研室
机械制造基础
常见定位基准表面确定的自由度
• 平面
– 大平面(3)、小平面(1)、狭长平面(2)
• 外圆、内圆
– 长(4)、短(2)
• 锥面
– 长(5)、短(3)
• 一般判断原则
– 观察哪些自由度没有限制
© 2004 金工教研室 机械制造基础
定位基准:平面
• 大3、小1、长2
第八讲:零件制造工艺过程常识
机械制造基础
金工教研室 制造科学与工程学院 2007年春季学期
© 2004 金工教研室 机械制造基础
第八讲:零件制造工艺过程常识