汽车内饰:热塑性聚烯烃弹性体(TPO)搪塑表皮性能及工艺研究
汽车软质内饰用搪塑表皮技术条件
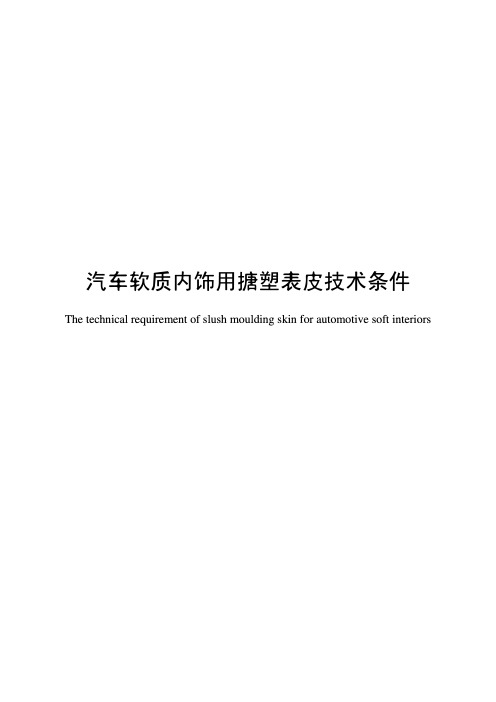
按Q/CC JT097的规定进行。 示例: 聚氯乙烯: >PVC<
聚氨酕弹性体: >TPU<
5 技术要求
表皮材料应满足表1中的技术要求。
表1 技术要求
项目
试验方法
外观
见 6.2.1
厚度 光泽度 密度 抗张强度 断裂伸长率 撕裂强度
见 6.2.2 见 6.2.3 见 6.2.4
见 6.2.5
见 6.2.6
2 规范性引用文件
下列文件对于本文件的应用是必不可少的。凡是注日期的引用文件,仅所注日期的版本适用千本文 件。 凡是不注日期的引用文件, 其最新版本(包括所有的修改单)适用于本文件。
GB/T 250—2008 纺织品色牢度试验评定变色用灰色样卡 GB/T 251—2008 纺织品色牢度试验评定沾色用灰色样卡 GB/T 1033. 1—2008 塑料 非泡沫塑料密度的测定第1部分:浸渍法、 液体比重瓶法和滴定法 GB/T 1040. 2—2006 塑料拉伸性能的测定第2部分:模塑和挤塑塑料的试验条件 QB/T 2537—2001 皮革色牢度试验往复式摩擦色牢度 QB/T 2709—2005 皮革物理和机械试验厚度的测定 QB/T 2711—2005 皮革物理和机械试验撕裂力的测定:双边撕裂 GB/T 7141—2008 塑料热老化试验方法 GB 8410—2006 汽车内饰材料的燃烧特性 GB/T 9754—2007 色漆和清漆不含金属颜料的色漆漆膜的20 ° 、 60 ° 和85 ° 镜面光泽的测定 QC/T 15—1992 汽车塑料制品通用试验方法 Q/CC JTOOl 汽车内饰材料气味散发性试验方法和限值 Q/CC JT097 汽车塑料件、 橡胶件和热塑性弹性体件的材料标识和标记 Q/CC JT098 汽车产品中有毒有害物质限晕要求 Q/CC JTll7—2009 汽车车辆内饰零件颜色评价技术条件 Q/CC JT146 汽车内饰材料雾化特性试验方法和限值 Q/CC SY335—2012 汽车非金属部件及材料侃灯加速老化测试方法
tpo是什么材料
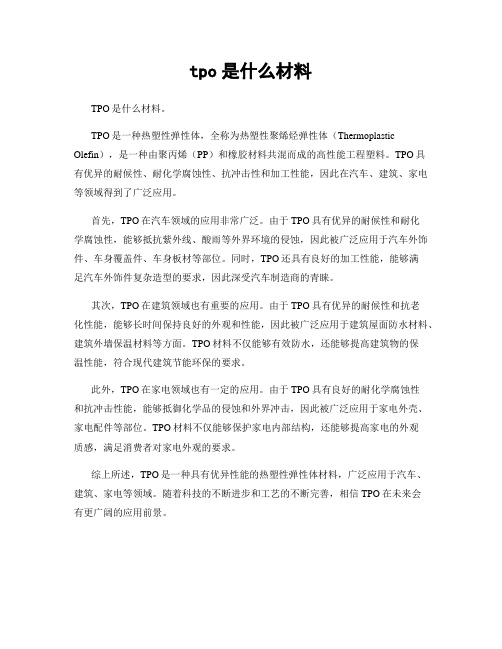
tpo是什么材料
TPO是什么材料。
TPO是一种热塑性弹性体,全称为热塑性聚烯烃弹性体(Thermoplastic Olefin),是一种由聚丙烯(PP)和橡胶材料共混而成的高性能工程塑料。
TPO具
有优异的耐候性、耐化学腐蚀性、抗冲击性和加工性能,因此在汽车、建筑、家电等领域得到了广泛应用。
首先,TPO在汽车领域的应用非常广泛。
由于TPO具有优异的耐候性和耐化
学腐蚀性,能够抵抗紫外线、酸雨等外界环境的侵蚀,因此被广泛应用于汽车外饰件、车身覆盖件、车身板材等部位。
同时,TPO还具有良好的加工性能,能够满
足汽车外饰件复杂造型的要求,因此深受汽车制造商的青睐。
其次,TPO在建筑领域也有重要的应用。
由于TPO具有优异的耐候性和抗老
化性能,能够长时间保持良好的外观和性能,因此被广泛应用于建筑屋面防水材料、建筑外墙保温材料等方面。
TPO材料不仅能够有效防水,还能够提高建筑物的保
温性能,符合现代建筑节能环保的要求。
此外,TPO在家电领域也有一定的应用。
由于TPO具有良好的耐化学腐蚀性
和抗冲击性能,能够抵御化学品的侵蚀和外界冲击,因此被广泛应用于家电外壳、家电配件等部位。
TPO材料不仅能够保护家电内部结构,还能够提高家电的外观
质感,满足消费者对家电外观的要求。
综上所述,TPO是一种具有优异性能的热塑性弹性体材料,广泛应用于汽车、
建筑、家电等领域。
随着科技的不断进步和工艺的不断完善,相信TPO在未来会
有更广阔的应用前景。
仪表台成型工艺简介
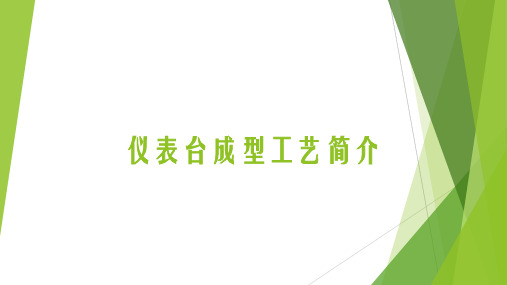
1.06 80~85 6 350 42
(TPU)
四、仪表板表皮的阴模吸塑成型
阴模吸塑成型技术是阳模真空吸塑与搪塑技术的有机结合,它是一种热模成型技术, 即将不带皮纹的热片材(0.8mm TPO表皮+2.0mm泡沬)放置在发泡层与阴模的型腔之间, 通过真空吸附使片材与模具型腔(模具型腔已做出了皮纹)接触成型。冷却时片材收缩, 并与发泡层吸附贴合成型。与传统的成型和复合工艺相比,该工艺不会出现皮纹拉伸现象, 而且可以在一个零件上实现不同的皮纹形式,皮纹均匀、清晰且手感好,与搪塑效果相当。
搪塑表皮一般具有如下优点:由于搪塑表皮的表面花纹是在表皮成型过程中形成的, 因此花纹表面的一致性好;在产品设计上,只要照顾到模具的局部加热性,即可将模具做 成较深的凹陷,甚至做成一定的负角,以加大产品造型设计的裕度;材料成本相对较低。 其缺点是:模具投资大,寿命短(一般模具的质量保证只有20000次表皮寿命);设备投 资大;需要不断地清理模具,导致辅助工时较长。
聚氨酯喷涂仪表板的工艺流程为:注塑成型仪表板骨架→PU喷涂→发泡层 发泡→切割孔和边→焊接主要零件(如需要)→组装相关零件。(高端车型采 用)
一、仪表板的注塑成型
对于全塑的硬质仪表板和发泡仪表板而言,其骨架的注塑成型一般需要使用锁模 力为2000~3000T的注塑机,骨架材料可以采用PC/ABS、SMA或PP+GF,下表对这3 种材料的成型性、成本和使用性能做了比较。片材切割阳模吸塑源自型三、仪表板表皮的搪塑成型
搪塑表皮的制造过程是:首先将带有表面花纹的搪塑模具加热到搪塑表皮的成 型温度,然后将粉箱与搪塑模扣合,使之按设定的程序旋转。当粉料熔化并粘附 于模具表面达到一定厚度后,脱开粉箱。接着,继续加热模具外表面,以使模具 内表面的搪塑表皮得到塑化烧结。最后,快速冷却模具外表面(不喷淋),使表 皮冷却成型。
汽车软质仪表板表皮成型工艺研究
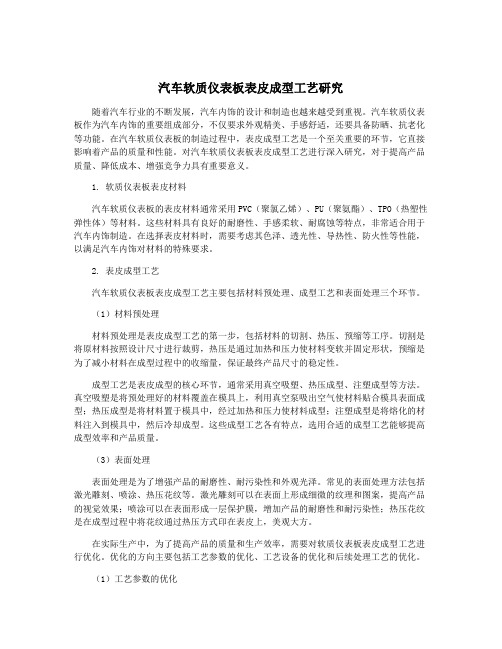
汽车软质仪表板表皮成型工艺研究随着汽车行业的不断发展,汽车内饰的设计和制造也越来越受到重视。
汽车软质仪表板作为汽车内饰的重要组成部分,不仅要求外观精美、手感舒适,还要具备防晒、抗老化等功能。
在汽车软质仪表板的制造过程中,表皮成型工艺是一个至关重要的环节,它直接影响着产品的质量和性能。
对汽车软质仪表板表皮成型工艺进行深入研究,对于提高产品质量、降低成本、增强竞争力具有重要意义。
1. 软质仪表板表皮材料汽车软质仪表板的表皮材料通常采用PVC(聚氯乙烯)、PU(聚氨酯)、TPO(热塑性弹性体)等材料。
这些材料具有良好的耐磨性、手感柔软、耐腐蚀等特点,非常适合用于汽车内饰制造。
在选择表皮材料时,需要考虑其色泽、透光性、导热性、防火性等性能,以满足汽车内饰对材料的特殊要求。
2. 表皮成型工艺汽车软质仪表板表皮成型工艺主要包括材料预处理、成型工艺和表面处理三个环节。
(1)材料预处理材料预处理是表皮成型工艺的第一步,包括材料的切割、热压、预缩等工序。
切割是将原材料按照设计尺寸进行裁剪,热压是通过加热和压力使材料变软并固定形状,预缩是为了减小材料在成型过程中的收缩量,保证最终产品尺寸的稳定性。
成型工艺是表皮成型的核心环节,通常采用真空吸塑、热压成型、注塑成型等方法。
真空吸塑是将预处理好的材料覆盖在模具上,利用真空泵吸出空气使材料贴合模具表面成型;热压成型是将材料置于模具中,经过加热和压力使材料成型;注塑成型是将熔化的材料注入到模具中,然后冷却成型。
这些成型工艺各有特点,选用合适的成型工艺能够提高成型效率和产品质量。
(3)表面处理表面处理是为了增强产品的耐磨性、耐污染性和外观光泽。
常见的表面处理方法包括激光雕刻、喷涂、热压花纹等。
激光雕刻可以在表面上形成细微的纹理和图案,提高产品的视觉效果;喷涂可以在表面形成一层保护膜,增加产品的耐磨性和耐污染性;热压花纹是在成型过程中将花纹通过热压方式印在表皮上,美观大方。
在实际生产中,为了提高产品的质量和生产效率,需要对软质仪表板表皮成型工艺进行优化。
电子交联对TPO类汽车内饰性能的影响
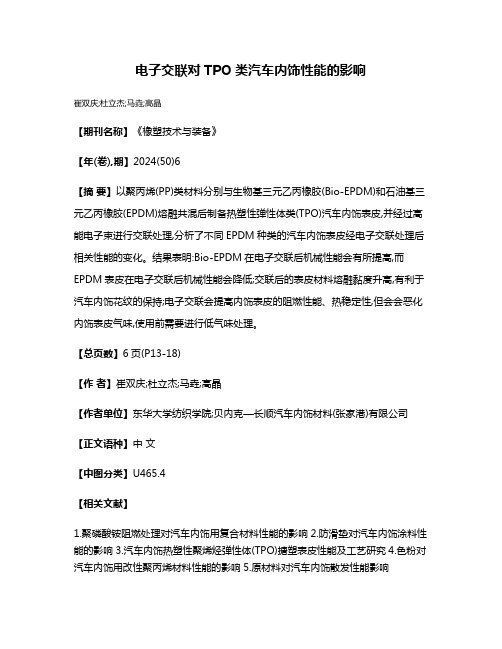
电子交联对TPO类汽车内饰性能的影响
崔双庆;杜立杰;马垚;高晶
【期刊名称】《橡塑技术与装备》
【年(卷),期】2024(50)6
【摘要】以聚丙烯(PP)类材料分别与生物基三元乙丙橡胶(Bio-EPDM)和石油基三元乙丙橡胶(EPDM)熔融共混后制备热塑性弹性体类(TPO)汽车内饰表皮,并经过高能电子束进行交联处理,分析了不同EPDM种类的汽车内饰表皮经电子交联处理后相关性能的变化。
结果表明:Bio-EPDM在电子交联后机械性能会有所提高,而EPDM表皮在电子交联后机械性能会降低;交联后的表皮材料熔融黏度升高,有利于汽车内饰花纹的保持;电子交联会提高内饰表皮的阻燃性能、热稳定性,但会会恶化内饰表皮气味,使用前需要进行低气味处理。
【总页数】6页(P13-18)
【作者】崔双庆;杜立杰;马垚;高晶
【作者单位】东华大学纺织学院;贝内克—长顺汽车内饰材料(张家港)有限公司【正文语种】中文
【中图分类】U465.4
【相关文献】
1.聚磷酸铵阻燃处理对汽车内饰用复合材料性能的影响
2.防滑垫对汽车内饰涂料性能的影响
3.汽车内饰热塑性聚烯烃弹性体(TPO)搪塑表皮性能及工艺研究
4.色粉对汽车内饰用改性聚丙烯材料性能的影响
5.原材料对汽车内饰散发性能影响
因版权原因,仅展示原文概要,查看原文内容请购买。
汽车内饰蒙皮加工工艺
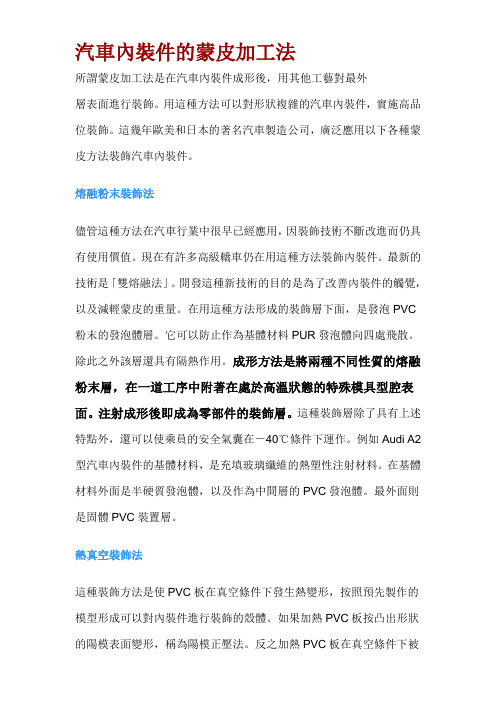
汽車內裝件的蒙皮加工法所謂蒙皮加工法是在汽車內裝件成形後,用其他工藝對最外層表面進行裝飾。
用這種方法可以對形狀複雜的汽車內裝件,實施高品位裝飾。
這幾年歐美和日本的著名汽車製造公司,廣泛應用以下各種蒙皮方法裝飾汽車內裝件。
熔融粉末裝飾法儘管這種方法在汽車行業中很早已經應用,因裝飾技術不斷改進而仍具有使用價值。
現在有許多高級轎車仍在用這種方法裝飾內裝件。
最新的技術是「雙熔融法」。
開發這種新技術的目的是為了改善內裝件的觸覺,以及減輕蒙皮的重量。
在用這種方法形成的裝飾層下面,是發泡PVC 粉末的發泡體層。
它可以防止作為基體材料PUR發泡體向四處飛散。
除此之外該層還具有隔熱作用。
成形方法是將兩種不同性質的熔融粉末層,在一道工序中附著在處於高溫狀態的特殊模具型腔表面。
注射成形後即成為零部件的裝飾層。
這種裝飾層除了具有上述特點外,還可以使乘員的安全氣囊在-40℃條件下運作。
例如Audi A2型汽車內裝件的基體材料,是充填玻璃纖維的熱塑性注射材料。
在基體材料外面是半硬質發泡體,以及作為中間層的PVC發泡體。
最外面則是固體PVC裝置層。
熱真空裝飾法這種裝飾方法是使PVC板在真空條件下發生熱變形,按照預先製作的模型形成可以對內裝件進行裝飾的殼體。
如果加熱PVC板按凸出形狀的陽模表面變形,稱為陽模正壓法。
反之加熱PVC板在真空條件下被吸附在凹入形狀的陰模表面,稱為陰模負壓法。
用正壓法裝飾的內裝件,耐擦刮性能較差。
用負壓法裝飾內裝件在-40℃溫度條件下也不會飛散,所以特別適合用於對車內氣囊覆蓋板進行裝飾。
PUR噴塗法這種方法的特點是,用單層就可以滿足使用要求。
現在賓士和大眾汽車公司的很多內裝件是用這種方法裝飾。
最近又開發了廣受用戶青睞的直接後發泡工藝。
這是在噴塗結束後,由第二機器人控制PUR 混合頭與半硬質發泡體相結合,可進一步提高內裝件的質量。
除了上面介紹的裝飾方法以外,還有PUR鑄造蒙皮、PUR反應注射、吹塑成形和雙蒙皮成形等方法,也都廣泛用於裝飾現代汽車的內裝件。
热塑性聚烯烃弹性体在汽车中的应用
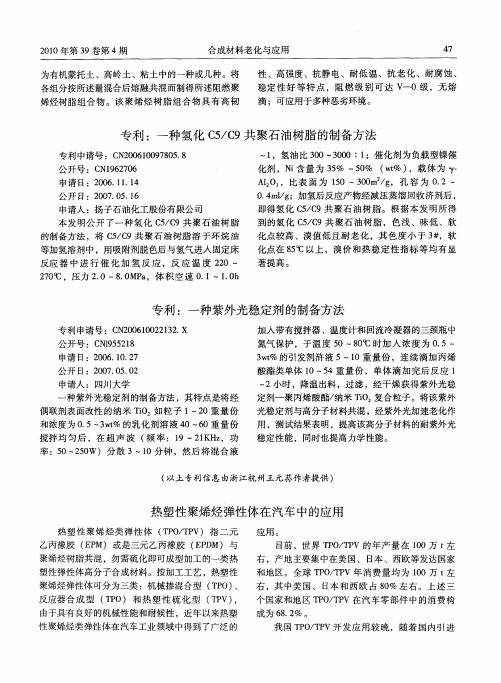
合 成材 料老化 与应 用
4 7
为有机 蒙托土 、高岭 土 、粘 土 中的一种或 几种 。将 各组分按所 述量 混合后 熔融共 混而制 得所述 阻燃 聚
性 、高强度 、抗静 电 、耐 低 温 、抗 老 化 、耐腐 蚀 、 稳 定 性 好 等 特 点 ,阻 燃 级 别 可 达 V ’ -0级 ,无 熔 滴 ;可应用 于多种 恶劣环境 。
( 以上 专利信 息 由浙江杭 州王元 荪作 者提 供 )
热塑性聚烯烃 弹性体在汽车中的应用
热 塑 性 聚烯 烃 类 弹性 体 ( P / P T 0 T V) 指 二 元 乙丙橡 胶 ( P E M)或 是三元 乙丙 橡胶 ( P M)与 ED 聚烯 烃树脂共 混 ,勿 需硫化 即可 成型加工 的一类 热 塑性 弹性体高 分子合 成材料 。按加 工工艺 ,热 塑性 聚烯烃 弹性体 可分为 三类 :机 械掺 混合 型 ( P 、 T O) 反应器 合 成 型 ( P T O) 和 热 塑 性 硫 化 型 ( P , T V) 由于具 有 良好 的机械 性能 和耐候性 ,近年 以来热 塑 性 聚烯烃类 弹性 体在 汽车工业 领域 中得到 了广泛 的
公 开 日 :2 0 . 5 1 0 7 0 .6
申请人 :扬 子石油 化工股 份有 限公 司
即得氢 化 C / 9共 聚石 油 树 脂 。根 据 本 发 明所 得 5C 到 的氢 化 C / 9共 聚石 油 树 脂 ,色 浅 、味 低 、软 5C 化 点较 高 、溴值 低 且 耐 老化 ,其 色 度小 于 3 ,软 # 化 点在 8  ̄ 5C以上 ,溴 价 和 热稳 定 性 指 标 等 均物。该 聚烯烃树脂 组合 物具 有高 韧
专利 :一种氢化 C / 9共聚石油树脂 的制备方法 5C
汽车软质仪表板表皮成型工艺研究
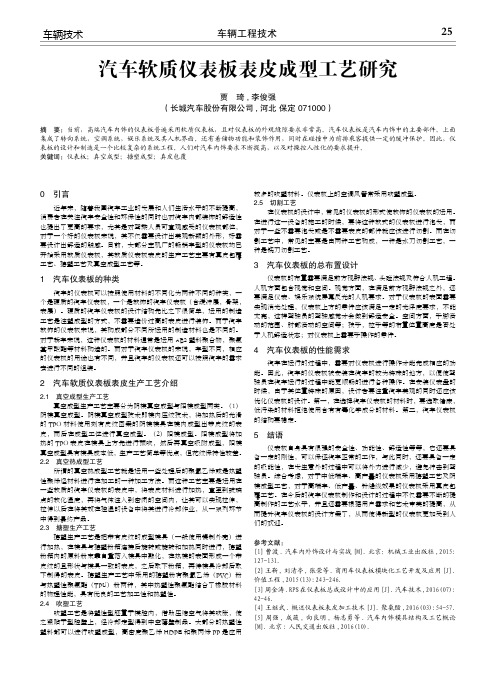
车辆工程技术25车辆技术0 引言 近年来,随着我国汽车工业的发展和人们生活水平的不断提高,消费者在关注汽车安全性和环保性的同时也对汽车内部装饰的舒适性也提出了更高的要求,尤其是对驾乘人员可直观感受的仪表板部位,对于一个好的仪表板来说,其不仅需要设计出美观新颖的外形,好需要设计出舒适的触感。
目前,大部分主机厂的畅销车型的仪表板均已开始采用软质仪表板,其软质仪表板表皮的生产工艺主要有真皮包覆工艺、搪塑工艺及真空成型工艺等。
1 汽车仪表板的种类 汽车的仪表板可以按照使用材料的不同化为两种不同的种类,一个是硬质的汽车仪表板,一个是软饰的汽车仪表板(含缓冲层,骨架,表层)。
硬质的汽车仪表板的设计结构先比之下很简单,运用的制造工艺是注塑成型的方式,不需要造价过高的表皮进行装饰。
而于汽车软饰的仪表板来说,其构成部分不同所运用的制造材料也是不同的。
对于轿车来说,这种仪表板的材料通常是运用ABS塑料聚合物,聚氨基甲酸酯等材料构造的。
而对于汽车仪表板的来说,车型不同,相应的仪表板的用途也有不同,并且汽车的仪表板还可以按照汽车的需求去进行不同的组装。
2 汽车软质仪表板表皮生产工艺介绍2.1 真空成型生产工艺 真空成型生产工艺主要分为阴模真空成型与阳模成型两类。
(1)阴模真空成型。
阴模真空成型技术即模内压纹技术,将加热后的光滑的TPO材料使用刻有皮纹图案的阴模模具在模内成型出带皮纹的表皮,而后在成型工位进行真空成型。
(2)阳模成型。
阳模成型将加热的TPO表皮在模具上方先进行预吹,然后再真空吸附成型,阳模真空成型具有模具成本低,生产工艺简单等优点,但花纹保持性较差。
2.2 真空热成型工艺 所谓的真空热成型工艺就是运用一些处理后的聚氯乙烯或是热塑性聚烯烃材料进行在加工的一种加工方法。
而这种工艺主要是运用在一些软质的汽车仪表板的表皮中,将表皮材料进行加热,直至到玻璃点的软化温度,再将气体注入到密闭的空间内,让其可以实现拉伸,拉伸以后在将其放在控温的设备中将其进行冷却作业,从一系列环节中得到最终产品。
汽车内饰常用表皮材料

汽车内饰常用表皮材料随着汽车在安全和环保方面的发展,人们对汽车饰件在安全性及环保性方面的要求也越来越高。
以汽车仪表板来说,一个好的仪表板不仅要有设计新颖美观的外形,舒适的手感,而且还需具有优良的高低温性能及优良的散发特性。
鉴于此,对仪表板表皮制造的材料及工艺就提出了更高的要求。
以下以仪表板为例对内饰常用的表皮材料及成型工艺进行介绍。
1.搪塑成型工艺表皮搪塑工艺是对带皮纹的搪塑模具背面或整体进行加热,模具和搪塑粉末的粉箱对接后旋转或一边加热一边旋转,粉箱中的塑料粉体自然落入模具中熔化,热模表面上就会形成一个形状与模具一致的带皮纹的表皮,然后取下粉箱,对模具进行冷却后人工取下得到的表皮。
搪塑工艺是当前一项成熟并使用广泛的成型工艺,其加工成型工艺简单,是目前应用最广的工艺。
目前,搪塑模可采用的皮纹也越来越广,如缝纫线( Stitch line),主要材料有PVC、TPO、TPU粉料,但由于其传统的冷却方式为水冷却,因此造成了模具使用寿命较短,搪塑模成本很高,目前随着加工设备的改进,采用了空气冷却的冷却方式,搪塑模的使用寿命已经得到很大的提高。
1)PVC材料PVC材料具有良好的手感、花纹成型性,以及耐热、耐光老化、防起雾等性能,而且PVC 材料价格便宜,因此,目前PVC占据了搪塑成型工艺的绝大部分市场。
但由于PVC在抗老化性、增塑剂迁移等方面存在问题,并且PVC材料的玻璃化温度较高,材料在低温环境下发脆易造成无缝气囊仪表板在低温(-35℃)状态爆破时,气囊区域PVC表皮碎裂而飞出,对乘客产生安全隐患。
因此,出于安全及环保原因,PVC搪塑的占有率正逐渐下降,目前世界市场上正在开发PVC的替代材料,如玻璃化温度低且环保的搪塑材料TPU、TPO搪塑粉料。
2)热塑性聚氨酯TPU热塑性聚氨酯TPU是一种热塑性弹性体,它结合了橡胶的物理和力学性能,具有优良热塑性及工艺加工性,是PVC材料的一种理想的环保型替代材料,TPU具有以下优点:(1)TPU是一种环保型的材料,可回收循环使用。
汽车搪塑PVC表皮再利用研究
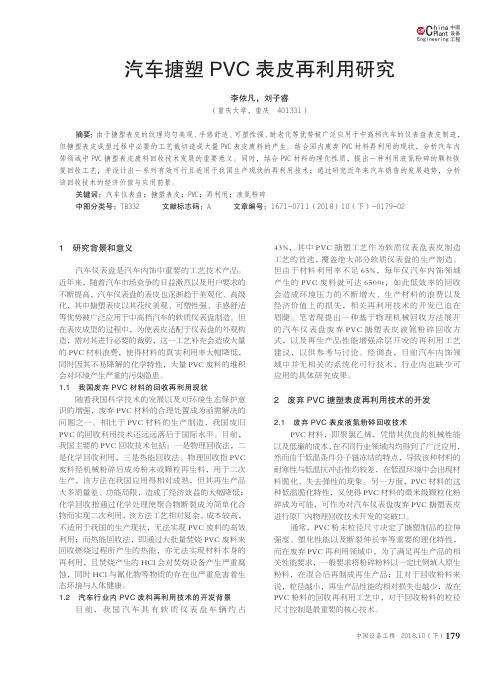
179中国设备工程Engineer ing hina C P l ant中国设备工程 2018.10 (下)1 研究背景和意义汽车仪表盘是汽车内饰中重要的工艺技术产品。
近年来,随着汽车市场竞争的日益激烈以及用户要求的不断提高,汽车仪表盘的表皮也逐渐趋于美观化、高级化,其中搪塑表皮以其花纹美观、可塑性强、手感舒适等优势被广泛应用于中高档汽车的软质仪表盘制造。
但在表皮成型的过程中,为使表皮适配于仪表盘的外观构造,需对其进行必要的裁剪,这一工艺补充会造成大量的PVC 材料浪费,使得材料的真实利用率大幅降低,同时因其不易降解的化学特性,大量PVC 废料的堆积会对环境产生严重的污染隐患。
1.1 我国废弃PVC 材料的回收再利用现状随着我国科学技术的发展以及对环境生态保护意识的增强,废弃PVC 材料的合理处置成为亟需解决的问题之一。
相比于PVC 材料的生产制造,我国废旧PVC 的回收利用技术还远远落后于国际水平。
目前,我国主要的PVC 回收技术包括:一是物理回收法,二是化学回收利用,三是热能回收法。
物理回收指PVC 废料经机械粉碎后成为粉末或颗粒再生料,用于二次生产,该方法在我国应用得相对成熟,但其再生产品大多质量差、功能局限,造成了经济效益的大幅降低;化学回收指通过化学处理使聚合物断裂成为简单化合物而实现二次利用,该方法工艺相对复杂,成本较高,不适用于我国的生产现状,无法实现PVC 废料的高效利用;而热能回收法,即通过大批量焚烧PVC 废料来回收燃烧过程所产生的热能,亦无法实现材料本身的再利用,且焚烧产生的HCl 会对焚烧设备产生严重腐蚀,同时HCl 与氰化物等物质的存在也严重危害着生态环境与人体健康。
1.2 汽车行业内PVC 废料再利用技术的开发背景目前,我国汽车具有软质仪表盘车辆约占43%,其中PVC 搪塑工艺作为软质仪表盘表皮制造工艺的首选,覆盖绝大部分软质仪表盘的生产制造。
但由于材料利用率不足65%,每年仅汽车内饰领域产生的PVC 废料就可达6500t,如此低效率的回收会造成环境压力的不断增大、生产材料的浪费以及经济价值上的损失,相关再利用技术的开发已迫在眉睫。
热塑性复合材料在汽车外饰件上的具体应用分析
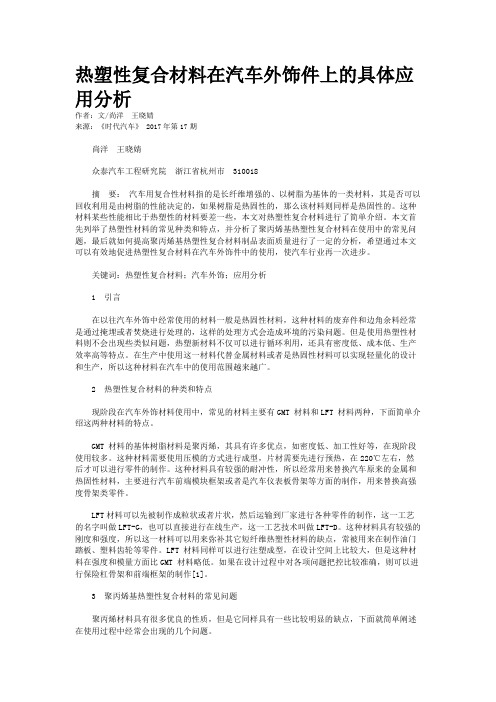
热塑性复合材料在汽车外饰件上的具体应用分析作者:文/尚洋王晓婧来源:《时代汽车》 2017年第17期尚洋王晓婧众泰汽车工程研究院浙江省杭州市310018摘要:汽车用复合性材料指的是长纤维增强的、以树脂为基体的一类材料,其是否可以回收利用是由树脂的性能决定的,如果树脂是热固性的,那么该材料则同样是热固性的。
这种材料某些性能相比于热塑性的材料要差一些,本文对热塑性复合材料进行了简单介绍。
本文首先列举了热塑性材料的常见种类和特点,并分析了聚丙烯基热塑性复合材料在使用中的常见问题,最后就如何提高聚丙烯基热塑性复合材料制品表面质量进行了一定的分析,希望通过本文可以有效地促进热塑性复合材料在汽车外饰件中的使用,使汽车行业再一次进步。
关键词:热塑性复合材料;汽车外饰;应用分析1 引言在以往汽车外饰中经常使用的材料一般是热固性材料,这种材料的废弃件和边角余料经常是通过掩埋或者焚烧进行处理的,这样的处理方式会造成环境的污染问题。
但是使用热塑性材料则不会出现些类似问题,热塑新材料不仅可以进行循环利用,还具有密度低、成本低、生产效率高等特点。
在生产中使用这一材料代替金属材料或者是热固性材料可以实现轻量化的设计和生产,所以这种材料在汽车中的使用范围越来越广。
2 热塑性复合材料的种类和特点现阶段在汽车外饰材料使用中,常见的材料主要有GMT 材料和LFT 材料两种,下面简单介绍这两种材料的特点。
GMT 材料的基体树脂材料是聚丙烯,其具有许多优点,如密度低、加工性好等,在现阶段使用较多。
这种材料需要使用压模的方式进行成型,片材需要先进行预热,在220℃左右,然后才可以进行零件的制作。
这种材料具有较强的耐冲性,所以经常用来替换汽车原来的金属和热固性材料,主要进行汽车前端模块框架或者是汽车仪表板骨架等方面的制作,用来替换高强度骨架类零件。
LFT材料可以先被制作成粒状或者片状,然后运输到厂家进行各种零件的制作,这一工艺的名字叫做LFT-G,也可以直接进行在线生产,这一工艺技术叫做LFT-D。
TPO工艺技术
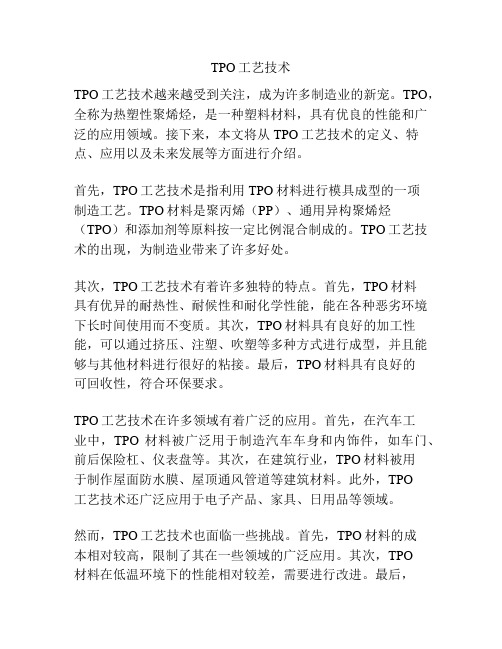
TPO工艺技术TPO工艺技术越来越受到关注,成为许多制造业的新宠。
TPO,全称为热塑性聚烯烃,是一种塑料材料,具有优良的性能和广泛的应用领域。
接下来,本文将从TPO工艺技术的定义、特点、应用以及未来发展等方面进行介绍。
首先,TPO工艺技术是指利用TPO材料进行模具成型的一项制造工艺。
TPO材料是聚丙烯(PP)、通用异构聚烯烃(TPO)和添加剂等原料按一定比例混合制成的。
TPO工艺技术的出现,为制造业带来了许多好处。
其次,TPO工艺技术有着许多独特的特点。
首先,TPO材料具有优异的耐热性、耐候性和耐化学性能,能在各种恶劣环境下长时间使用而不变质。
其次,TPO材料具有良好的加工性能,可以通过挤压、注塑、吹塑等多种方式进行成型,并且能够与其他材料进行很好的粘接。
最后,TPO材料具有良好的可回收性,符合环保要求。
TPO工艺技术在许多领域有着广泛的应用。
首先,在汽车工业中,TPO材料被广泛用于制造汽车车身和内饰件,如车门、前后保险杠、仪表盘等。
其次,在建筑行业,TPO材料被用于制作屋面防水膜、屋顶通风管道等建筑材料。
此外,TPO工艺技术还广泛应用于电子产品、家具、日用品等领域。
然而,TPO工艺技术也面临一些挑战。
首先,TPO材料的成本相对较高,限制了其在一些领域的广泛应用。
其次,TPO材料在低温环境下的性能相对较差,需要进行改进。
最后,TPO工艺技术的成熟度较低,还需要进一步研究和改进。
未来,TPO工艺技术将继续发展壮大。
首先,随着技术的进步和成本的下降,TPO材料将更加普及,并在更多领域得到应用。
其次,TPO工艺技术将进一步完善,提高产品质量和生产效率。
最后,TPO工艺技术还将与其他工艺技术相结合,形成更加复合和多功能的制造方式。
总之,TPO工艺技术是一项具有广阔前景的制造工艺。
它不仅具有优异的性能和广泛的应用领域,而且还能为制造业带来许多好处。
随着技术的进步和发展,相信TPO工艺技术将会在未来取得更大的成功与突破。
- 1、下载文档前请自行甄别文档内容的完整性,平台不提供额外的编辑、内容补充、找答案等附加服务。
- 2、"仅部分预览"的文档,不可在线预览部分如存在完整性等问题,可反馈申请退款(可完整预览的文档不适用该条件!)。
- 3、如文档侵犯您的权益,请联系客服反馈,我们会尽快为您处理(人工客服工作时间:9:00-18:30)。
汽车内饰热塑性聚烯烃弹性体(TPO)搪塑表皮性能及工艺研究关键词:汽车内饰表皮;搪塑TPO;搪塑PVC;绿色环保为解决汽车内饰搪塑PVC 表皮在抗老化、耐低温、环保等方面的缺陷,介绍了一种新型的搪塑TPO 表皮,通过对比分析搪塑TPO 表皮和搪塑PVC 表皮的性能及其成型工艺特点,搪塑TPO 表皮具有密度小、低气味、低VOC、耐低温、耐老化等优异的特性,也需要更长的凝胶和塑化时间。
在轻量化和绿色环保的趋势下,搪塑TPO 表皮将在汽车内饰制造领域得到更加广泛的应用。
搪塑成型工艺最开始是为聚氯乙烯(PVC)类材料设计开发的,其广泛地应用于汽车内饰领域,可以生产出纹理和结构复杂的零件(如仪表板、门护板等零件)。
但PVC 在抗老化、耐低温等方面存在缺陷。
TPO 作为一种新型的热塑性聚烯烃弹性体材料可用搪塑工艺成型。
TPO 具有密度小、低气味、低VOC、耐低温、耐老化等优异的特性,可以满足汽车内饰复杂设计、轻量化以及绿色环保的要求。
01汽车内部装饰表皮成型工艺车内部零件(仪表板/门护板等)装饰表皮成型工艺主要有真空吸塑(阳摸和阴模)、聚氨酯喷涂(PU Spray)和搪塑(Slush molding)等。
搪塑具有设计自由度高、制品美观、手感舒适、无内应力、材料成本低等优点,目前在欧美车系中应用比较普遍。
日、韩系车型仪表板/门护板以TPO 真空吸塑为主,聚氨酯喷涂工艺由于成本高,只在部分高端车型上有应用。
各种表皮成型工艺的特点如表1 所示。
表1 汽车内饰表皮成型工艺对比项目阳摸吸塑阴模吸塑PU喷涂PVC搪塑设计自由度复杂纹理低中等高高尖角低中等高高标识/刻字低中等高高成型过程效率高中等中等低模具成本低中等中等高模具寿命高高高低成型材料技术难度低低高中等成本低低高中等总成本低中等高中等02搪塑原理搪塑工艺是对模具加热,将用于制造表皮的粉末状材料与受热的模具型腔面接触塑化、烧结等, 最终得到与模具型腔形状及纹理一致的表皮成型过程[1]。
搪塑过程主要分如下几个步骤(图1)。
对带皮纹的搪塑模具进行加热;加热后的模具与装有粉末材料的粉料箱合膜;c.旋转或者边旋转边加热模具,粉料箱中的材料落入模具内表面受热后凝胶化并形成塑料膜;模具与粉料箱分开;加热模具,使材料进一步塑化均匀;f.冷却模具;取出搪塑表皮。
图1 搪塑工艺流程搪塑工艺的优势在于整个加工过程都在一个无应力作用的摸具中,搪塑粉受热在自身重力和模具的旋转作用下均匀地熔融覆盖在模具内表面上[2]。
模具的设计形状不受限制,适合复杂的三维设计并可以保证稳定的表面纹理,从而使汽车内饰在美观性和舒适度上比其他软质内饰材料更有优势。
03搪塑TPO 材料与一般成型工艺相比,搪塑对原材料的流动性能、力学性能、热稳定性能以及熔融性能等方面都有严格要求。
传统的搪塑工艺均采用聚氯乙烯(PVC)粉末材料,其具有良好的复型能力并且成本相对低廉,在汽车内饰上应用非常广泛。
但是PVC 材料普遍存在耐光老化、耐热老化、耐低温性能以及耐胺性能差,并且其气味重、VOC 高、增塑剂易迁移且材料不可回收,行业内一直在积极寻找更加优良的替代材料方案,其中热塑性聚烯烃弹性体(TPO)材料就是其中之一。
主要对搪塑PVC 表皮和搪塑 TPO 表皮的材料性能以及工艺特点进行分析。
TPO(聚烯烃类热塑性弹性体)由橡胶和聚烯烃混合而成,它既具有橡胶材料的特性,又具有热塑性树脂的性能,是 100%可以回收的热塑性弹性体。
TPO 是仅次于苯乙烯类热塑性弹性体(TPS)的第二大类 TPE(热塑性弹性体)材料,广泛应用于电线电缆、家用电器、汽车制造业、医疗等领域。
TPO 材料具有优异的耐热性、耐光性和耐寒性,并且其密度低、气味小、VOC 含量低,在汽车行业应用比较普遍。
TPO 在汽车装饰表皮中以真空吸塑成型工艺为主,搪塑 TPO 才刚刚起步。
2008 年北美,搪塑 TPO 第一次被用于Saab 9-7X 仪表板,该零件相对于搪塑 PVC 减重 20%,且挥发性有机化合物(VOC)和雾化的性能更好。
目前国内吉利汽车已开始进行搪塑TPO 样件试制,通用、福特和神龙汽车也对其进行了材料验证。
TPO 搪塑粉的制造程序如图2 所示[3]。
PVC 搪塑粉的微观结构类似于球形,而 TPO 搪塑粉的微观结构不太规则(图3),因此TPO 粉末的流动性没有PVC 粉末好,其成型性也较差、脱模困难。
但经过不断改进,TPO 搪塑表皮外观已经可以和 PVC搪塑表皮相媲美。
图2 TPO 搪塑粉生产流程(a)搪塑PVC粉(b)搪塑TPO粉图3 微观示意04搪塑TPO 表皮的性能汽车内饰用覆盖材料不仅要求质量轻、美观精致、手感舒适,并且对安全性能(低硬度、低脆性),环保性能(无毒、低气味),使用性能(耐热性、耐寒性、抗渗透、光稳定性、抗划痕、抗胺)都有较高的要求[4]。
PVC 材料已经应用多年,原材料来源相对广泛,价格相对低廉。
TPO 是一种新型的热塑性聚烯烃弹性体材料,在国外汽车制造中已有少量应用。
这里选用了颜色、纹理厚度相同的恩坦华搪塑TPO 表皮和三菱化学搪塑PVC 表皮进行部分材料性能对比。
如表 2 所示,TPO 在轻量化、可回收、低温韧性、雾化方面的性能优于PVC。
表2 搪塑TPO 表皮和搪塑PVC 表皮性能对比表材料物性搪塑TPO搪塑PVC密度/g·cm^-30.9 1.2邵氏A硬度6871雾化(100 ℃/3 h)雾化指数99%雾化指数97.1%可回收性可回收不可回收玻璃化转变温度/℃-34-27近几年第三方调研数据显示,“车内有令人不愉悦的气味”问题排名持续第一。
因车内气味问题造成的车辆召回事件也时有发生,车内环境品质已成为影响消费者购车的主要因素之一。
气味等级按大众标准分为 6 级(1 级为无气味/觉察不到;2 级为强度较弱/用力嗅才能觉察到;3 级为中等强度/气味分明;4 级为高强度/气味突出;5 级为很高的强度/气味很重;6 级为难以忍受/不得不拿开)。
将 20 cm3 的搪塑PVC 表皮和 TPO 表皮样品分别放入密封的玻璃瓶中在烘箱内加热至 80 ℃, 保温 2 h 后放在恒湿恒温间 1 h 后用于气味实验。
两者的试验结果表3 所示,TPO 表皮的气味明显优于PVC 表皮。
表3 搪塑TPO 表皮和搪塑PVC 表皮气味等级对比表样品名称气味等级不可接受率搪塑PVC 3.5级20%搪塑TPO3.0级0%挥发性有机化合物(VOC)随着我国汽车保有量的急剧攀升以及消费者健康意识的不断增强,车内空气质量正越来越多地被全社会关注。
尤其是环保部决定将国标GB/T 27630《乘用车内空气质量评价指南》修订为强制标准后, 消费者的绿色环保意识和维权意识空前提升。
利用热解吸/气相色谱法/质谱测定法联合测定搪塑PVC 、TPO 表皮材料释放出的VOC 含量结果如表4 所示, TPO 表皮的苯系物和TVOC 含量低于PVC 表皮,因此搪塑TPO 表皮在汽车内饰上使用更加环保。
表4 搪塑TPO 表皮和搪塑PVC 表皮VOC 对比表mg/kgVO C 物质样件甲醛乙醛丙烯醛苯甲苯乙苯二甲苯苯乙烯TVO C (C166)~C搪塑PVC 0.04---0.060.20.2-63搪塑TPO0.02-------28热老化将搪塑 TPO 表皮和 PVC 表皮放入烘箱中进行120 ℃/21 天的热老化试验,分别测试老化前后的断裂强度 、断 裂伸长率以及玻璃化转变温度(Tg )。
图 4 显示了搪塑 TPO 表皮和 PVC 表皮经过热老化后断裂强度和断裂伸长率的变化情况;图5 为 2 种材料的玻璃化转变温度变化情况。
PVC 在老化过程中大分子链会发生脱氯化氢(HCL )反应,分子主链上会产生不稳定的不饱和键,同时部分增塑剂会迁移到材料表面并挥发掉,所以 PVC 表皮老化后明显变脆,断裂强度和伸长率均出现了明显降低。
120 ℃/21 天热老化后的搪塑 TPO 和PVC 表皮外观如图 6 所示,TPO 表皮外观保持较好,但 PVC 表皮边缘有明显翘曲。
汽车在暴晒的情况下,车内温度可高达80 ℃,仪表板的温度可高达120℃,因此搪塑TPO 表皮耐高温性能更优异。
图4 热老化后的断裂强度和伸长率的变化率气味性光老化将搪塑PVC 表皮和TPO 表皮暴露在ATLAS司生产的氙弧灯(CI 3000)的光照及热辐射下300 h,通过模拟自然气候和日光照射等实验条件来测试材料的耐光老化性能,结果如表5 所示。
PVC 本身易发生光/热降解且伴随颜色变化,这是因为PVC 分子链受激发后产生链式脱HCL 反应,且脱出的HCL具有催化效果,会加速脱去更多的HCl,在主链上形成多烯序列-(C=C)n-,当n 达到8 时,就会形成发色基团(吸收可见光中的蓝光,样品会显黄),因此TPO 表皮的耐光老化性能比PVC 表皮更优异。
图5 玻璃化转变温度随热老化天数的变化图6 120 ℃老化三周后的搪塑TPO 和PVC 表皮外观表6 搪塑TPO表皮和搪塑PVC表皮磨擦色牢度性能对比/级样品名称灰度卡评级搪塑PVC3/4级搪塑TPO4/5级摩擦色牢度为评估搪塑 TPO 表皮的摩擦色牢度性能,采用CROCKMETER 摩擦色牢度仪、用干燥和浸润有化学介质的标准白布摩擦样件表面,并参照灰度卡对标准白布(沾色)和表皮样件(褪色)进行评级,实验结果如表 6 所示,搪塑 TPO 表皮耐乙醇性能不及搪塑PVC 表皮,但也在可接受范围。
05搪塑TPO 表皮的成型搪塑 TPO 表皮与搪塑 PVC 表皮成型工艺类似,可以共用成型设备,但是由于TPO 材料具有流动性较差,加工温度区间较窄,熔体粘度随温度变化较大等缺点,搪塑TPO 表皮成型难度较大,搪塑工艺参数也与PVC 有所不同,具体如下。
表2 搪塑TPO 表皮和搪塑PVC 表皮性能对比表搪塑PVC搪塑TPO褪色沾色褪色沾色干态4/54/54/54/5水4/554/55肥皂水4/554/55稀释50%乙醇4/554/54/5预加热- 模温,搪塑 TPO 需要更高的模具温度,模具温度比搪塑PVC 高20 ℃左右,TPO 的塑化温度在230~250 ℃。
模具温度太高会导致表皮烤焦,温度太低搪塑粉没完全转化为熔化的薄膜,表皮会出现小孔。
成型和旋转,由于 TPO 材料密度低,同时 TPO 粉料熔体流动性比PVC 差,所以搪塑TPO 模具的转速要高于搪塑PVC,否则无法得到厚度均匀的搪塑表皮,参考转速为 16 r/min。
具体转速设定需要根据设备及零件结构进行调整,如果转速太快粉末的流动会比较混乱,表皮上会出现波浪状图案,还可能粉末自身出现粘结,在角落里堆积。
如果转速太慢,粉末不能及时落到粉盒里,造成加热时间过长,粉末形成凝块,造成制品厚度不均等缺陷。