清洁验证计算实例
清洁验证检验方法验证.
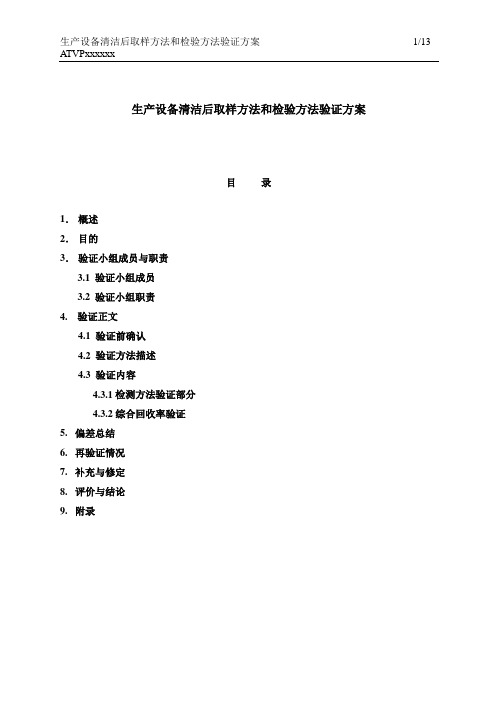
生产设备清洁后取样方法和检验方法验证方案目录1.概述2.目的3.验证小组成员与职责3.1验证小组成员3.2验证小组职责4. 验证正文4.1 验证前确认4.2 验证方法描述4.3 验证内容4.3.1检测方法验证部分4.3.2综合回收率验证5.偏差总结6.再验证情况7.补充与修定8.评价与结论9.附录1.概述生产过程中所用的生产设备均可能有残留物遗留,为了最大程度的避免由于上一批次生产产品的残留影响下一批次或其他品种,故必须对生产所用的设备进行清洁。
清洁后要对该清洗方法进行取样检测残留量。
一般通常的取样方法为棉签擦拭法和淋洗法。
2.目的本验证方案的目的是考察清洗验证涉及取样过程和所用检测方法的过程,是对人员取样操作、残留物转移、测试过程的考察,考察项目最低定量限、线性、综合回收率等。
3. 验证小组成员与职责3.1验证小组成员组长:xxx组员:xxx、xxx3.2验证小组职责组长:质量副总经理xxx,负责批准验证方案和验证报告。
组员:xxx,参与验证方案的制定,对验证操作过程监督检查,收集验证资料和数据,参与起草验证方案和验证报告。
组员:xxx,负责参与验证方案的制定,对所取样品进行化验,收集数据并报告结果,审核验证报告。
组员:xxx,负责审核验证方案,审核清洁验证方案和报告,协助验证方案的实施,并审核验证报告。
4. 验证正文4.1验证前确认棉花/棉签材质:棉签紫外分光光度计编号:校验有效期□接受□不接受天平编号:校验有效期□接受□不接受批号:4.2 检测方法描述4.2.1检测过程结构中含有很强的紫外吸收官能团,如双键的苯环等,故可采用紫外分光光度法。
1cm比色皿,在合适的最大的吸收波长处,以甲醇为空白,测定样品溶液的吸收度。
根据测得的吸收度来计算样品残留的量。
4.2.2贮备液的配制取对照品约10mg,精密称定,置于200ml容量瓶中,用甲醇溶解并稀释至刻度,混匀,得贮备液(50μg/ml)。
4.2.3计算测定时同时进行对照品的测定,根据朗伯比尔定律,按下列公式计算:A样C样=×C对A对A:分别为样品和贮备液的吸收度C:分别为样品和贮备液的溶液浓度4.3 验证内容4.3.1检测方法验证部分为了保证清洗验证和日常清洗结果的可靠性,故对本方案采用的紫外分析方法考察了最大吸收波长确定、最低检测限/定量限、线性和范围、精密度、回收率。
清洁验证(白)
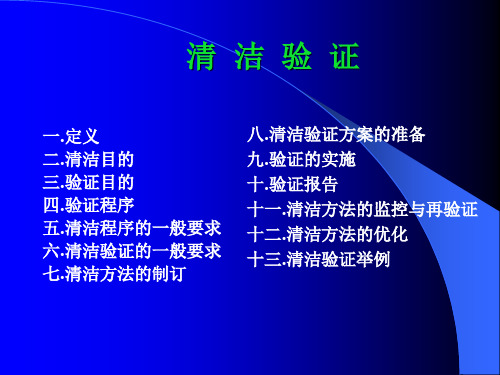
ICH在“残留溶剂指南”中将溶剂分
为3个级别,并明确列表。
八、清洁验证方案的准备(5)
微生物污染控制标准:
以单位体积的菌落数计,一般小于
25CUF/ml
八、清洁验证方案的准备(6)
取样与检验方法: 擦拭法 对最终清洗液取样 空白品生产 直接进行下一品种生产,检查残余物 外观检查 有机溶媒提取 厂房设施表面及环境空气取样
十三、发酵罐清洗清洁验证举例
可接受的限度范围 以10ppm为限量的计算(洗液法)
最大允许残留浓度=(罐工作体积/最终冲洗液体积)×0.01mg/ml 最大允许残留量=最终冲洗液体积×最大允许残留浓度 =罐工作体积×0.01mg/ml
以活性物残留浓度不超过原浓度的0.001为限 量的计算
清洗液终浓度=(罐工作体积/最终冲洗液体积)×发酵液浓度 ×0.001
五. 清洁程序的一般要求
Байду номын сангаас
清洁作用的机理 设施、设备清洁的原则 清洁剂的选择 清洁级别的划分 清洗的方法和步骤 清洗的检查验收
五. 清洁程序的一般要求(1)
清洁作用的机理: 机械作用、溶解、去污、化学反
应
五. 清洁程序的一般要求(2)
设施、设备清洁的原则: 新设备使用前 设备检修前后 连续使用一段时间后 物料出现质量问题或受到污染时 更换产品时 静置超过一定时间后,在重新使用前
清洗的表面微生物验证
可接受标准=(罐工作体积/最终冲洗液体积)×25CFU/ml
验证实施应严格按照批准的方案进 行。关键在于清洁规程的执行和数据 的采集,即取样、化验、写验证报告。
十、验证报告
内容:验证方案、设备一览表、 清洁参数、清洁规程的执行情况描 述、检验结果及其评价、偏差说明、 验证总结
-清洁验证(五篇模版)

-清洁验证(五篇模版)第一篇:-清洁验证********注射液********(设备名称)清洗验证方案验证(/代替验证)编号:YZ-**-**上海XXXXXXX公司二○XXX年**月**日一、概述根据GMP要求,每次更换品种要认真按清洁规程对设备、容器进行清洁和消毒。
生产设备清洁是指从设备表面(尤其是直接接触药品的内表面及各部件)去除可见及不可见物质的过程,这些物质包括活性成分、辅料、清洁剂、润滑剂、微生物及环境污染物等。
***(设备)是****(产品或剂型)生产的必备设备,位于本厂车间****(工序)的通用设备。
为评价该设备清洁规程的效果,需对其清洗过程进行验证。
内容说明:内容应该包括验证设备的用途、设备放置场所、本验证的目的用途,仅需简要介绍即可。
二、验证目的***(设备名称)清洗验证是采用化学分析和微生物检测方法来检查设备按清洁规程清洁后,设备上残留的污染物量是否符合规定的限度标准,证明本设备清洁规程的可行和可靠,从而消除了换品种设备清洗不彻底造成残留物对下一个生产药品污染的发生,有效地保证药品质量。
通过该验证试验,评价本公司****(药品或剂型)****(工艺)按清洁规程****进行清洁后的清洁效果能稳定达到预定要求。
三、验证范围1.设备:****(设备),位于*****房间。
内容应该包括验证设备的名称、型号、放置场所、在产品生产工艺中的用途 2.待验证药品品名:****(药品)内容应该包括验证产品的药品名称及其选择依据。
四、验证所需具备的条件1、验证所需文件清洁程序SOP No.JDJS-内容说明:包括本验证过程中需要参考的文字资料(主要包括现有的生产操作、分析操作等有关工作中的SOP等)。
2、验证所需的仪器设备内容说明:包括本验证过程中采样、分析测试需要使用的仪器设备。
3、所需的其他物件取样工具取样溶剂五、验证要求与内容在生产****(药品名称)后按清洁规程SOP *****实施清洁。
清洁验证合格限度计算

复方氨基酸注射液生产清洁验证残留限度推算以10 ppm为标准计算单位面积的残留量。
假设残留物均匀分布在设备内表面。
计算过程10 ppm =10 μg/ml ≅ 10 mg/kg某产品日常生产最小批量:2500L ≅ 2500kg 每批产品生产接触总面积S= 20m2,(配制系统 19 m2和灌封机1 m2)每批总残留量(产品中所有氨基酸组分残留到下批产品中的总量):=10 mg/kg x 2500 kg=25000 mg单位面积残留量限度:=25000 mg/20m2=1250 mg/m2=12.5 mg/100cm2取安全因子F=10,最后的残留限度=1.25 mg/100cm2氯雷他定片剂生产清洁验证残留限度推算以最低日治疗剂量的1/1000为标准计算单位面积的残留量。
假设残留物均匀分布在设备内表面。
最小批量:10kg最低日治疗剂量(MTDD)=每天最少给药片数x含量/片(mg)=1片x10mg/片=10mg每天最大服用量 (LDSD)=每天最多给药片数x重量/片(mg)=1片x87mg/片=87mg相关设备内表面积9制粒机:8000cm29烘干机:50000cm29整粒机:1000cm29V形终混机:10000cm29压片机:1000cm2设备总表面积:70000cm2计算过程产品残留允许的最低限度= MTDD (mg) x 1/1000 x 1/LDSD(mg) = 10x10-3(mg)/87(mg)换算成每公斤B产品中A产品残留量=10x10-3x106(mg)/87(kg)=104(mg)/87(kg)下批最小批量为10(kg),则活性物质总残留量=104(mg)/87(kg)*10(kg)=105/87(mg)因生产设备总面积为70000(cm2),则单位面积残留限度L =105/87(mg)/70000(cm2)=1.64mg/100cm2。
清洁残留限度原理和计算公式解析

清洁残留限度原理和计算公式解析清洁验证在制药生产过程中起着重要作用, 其是防止药品污染和交叉污染的重要控制措施, 目的是确保共线生产产品之间不会产生交叉污染, 影响产品正常药理学作用。
01残留的举例要讲述药物残留,我想先以一个例子作为代入:芝麻炒饭我们都做过炒饭,假设炒饭需要加芝麻,我们把黑芝麻粒看作是炒锅的残留物,当我们加入米饭进行翻炒时,我们假设炒饭结束后,黑芝麻粒在炒饭操作的过程中被均匀分散到炒饭中。
这时我们需要将炒饭等量分给几份给顾客,但是这几个顾客都不太喜欢炒饭中有太多的芝麻,比如一碗米饭(假设是200g)不能有超过2g的芝麻粒,那么在下一次炒饭时,我们就需要根据顾客的数量以及米饭的数量,确定我一开始应该放多少g的芝麻才不会引起顾客的不适。
药物的残留限度也和以上举的例子是一样的道理,只是芝麻粒转变成了药物残留,炒锅转变成了生产设备,米饭转变成了拟生产的产品,顾客转变成了用药对象。
02药物残留原理和意义要想了解药物残留限度的计算公式,我们先了解药物在生产过程中残留的方式,以及其所产生的实际意义,可以帮助我们更好的理解计算公式和应用。
对于清洁验证中的残留限度,一般主要针对的是共用设备的直接接触设备内表面的活性药物残留。
1、A生产后残留于设备内表面所表达的是上一生产产品(A产品)生产结束后的活性药物残留,默认均匀的分布(考虑到清洁验证最差条件,实际以最难清洁部位,最大残留量的位置计)千生产过程中物料所接触的设备内表面。
2、A的所有残留全部被带入B中然后在下—产品(B产品)生产时,物料在接触与A产品共用的设备内表面,将A产品的API残留全部(实际可能不全部带入,但清洁验证按最差情况考虑)带入B产品的物料(按1批计)中,此时也是默认均匀的分散在B产品的物料中。
3、被带入B中的残留均匀分散通过生产成型均匀分布在每一个单位剂量的B产品中。
4、患者服用B时吸入A患者在服用B产品时,会将残留千B产品的A产品活性药物也同步吸收,如果A的活性残留量较大,B 产品的单位剂量中所残留的A产品活性残留也就越高。
清洁验证方案

清洁验证方案清洁验证是确保产品或设备达到一定卫生标准的过程。
在某些行业,如食品加工、医疗设备等,清洁验证是非常重要的。
下面是一个清洁验证方案的示例。
1. 确定清洁指标:首先,需要确定清洁的标准和指标。
这可以包括微生物水平、残留化学物质的含量等。
根据不同的行业和产品,确定适当的指标。
2. 制定清洁程序:制定一个适当的清洁程序。
这包括使用适当的清洁剂、清洁工具和方法。
确保清洁程序能够彻底清除污染物,并达到指定的清洁指标。
3. 设计清洁验证试验:根据产品或设备的特性,设计适当的清洁验证试验。
试验应该包括适当的样本采集和测试方法。
确保试验能够准确地衡量清洁程度。
4. 进行清洁验证试验:根据设计的试验方案,进行清洁验证试验。
确保试验的过程严格按照设计的方案进行。
采集样品,并使用适当的方法进行测试。
5. 分析试验结果:分析试验结果,根据指定的清洁指标来评估清洁程度。
如果试验结果满足指标要求,那么产品或设备就通过了清洁验证。
如果试验结果不满足指标要求,则需要重新考虑清洁程序和方法。
6. 记录和报告:记录清洁验证试验的结果,并形成报告。
报告应包括试验方法、结果和评估。
这些记录和报告可以作为追溯和证明清洁验证过程的文件。
7. 定期进行清洁验证:清洁验证不是一次性的过程。
产品或设备应定期进行清洁验证,以确保其持续满足卫生标准。
制定一个适当的计划,以便定期进行清洁验证。
清洁验证是确保产品或设备达到卫生标准的重要步骤。
通过制定适当的清洁程序和进行清洁验证试验,可以确保产品或设备的卫生效果。
这不仅有助于保护消费者的健康,还有助于提高产品质量和信誉。
因此,清洁验证是必不可少的过程。
清洁验证最全计算公式截止到2020年

ISPE 指南RISK-mapp (第1版2010年) ADE (mg/天)=NOAEL (mg/kg/天)×BW (kg )UFc (综合不确定因子)×MF (修正因子)×pk (药代动力学调节因子)EMA 指南(2014年)PDE (mg/天)=NOAEL (mg/kg/天)×BW (kg )F1(物种间推断因子)×F2(个体间差异因子)×F3(短期重复剂量毒性研究的因子)×F4(毒性如致癌致畸致毒情况下可能试用的因子)×F5(未建立无效水平应用的可变因子)ISPE 指南RISK-mapp (第2版2017年)PDE 或ADE (mg/天)=POD (mg/kg/天)×BW (kg )AFc (综合调整因子)×MF (修正因子)×pk (药代动力学调节因子)ASTM 组织E3219部HBEL 推导(2020年) ADE (mg/天)=POD (mg/kg/天)×BW (kg )Ft (综合调整因子)×PK-AF (累积因子)×α(接触途径的生物利用度)说明:POD 为人某途径给药最低剂量,且为成人则BW 不纳入。
◆ PK-AF 计算◆ A:适用于研究的给药时间表是间歇性的,或者研究的时间太短而无法达到稳态浓度,如果临床文档中未提供1、PK-AF=11-e-0.693/t 1/2*t :(e 自然对数,t 给药时间间隔;t 1/2为药物消除半衰期;药代动力学房室模型评估)2、PK-AF=1.44*t 1/2t3、凯尔方程假设一阶动力学,并提供一个修正因子来反映人类的代谢率,生物蓄积和正常的排泄机制4、还可以通过使用规定的剂量间隔(以天为单位)每日平均剂量来计算PK-AF 。
例如,如果每周一次给药,则PK-AF 为7 B 、 如果PoD 给药间隔达到稳态浓度,则通常不需要PK-AF ◆ α(PK-ABS )计算1、α=FHBEL /FPoDFPoD =研究中使用的给药途径的生物利用度分数(如口服0.2FHBEL =建立HBEL 的给药方式的生物利用度分数.(如IV 静脉为1.0),则α为5 2、如果已知人类口服生物利用度,则可以使用生物利用度范围的平均值。
清洁验证方案模板

双氯芬酸钠精烘包清洁验证方案方案编号:方案制定方案审核方案批准验证小组人员名单目录1.设备清单----------------------------------------------2.验证目的-------------------------------------------------3.验证时间-------------------------------------------------4.验证所需文件列表-----------------------------------------5.人员培训情况---------------------------------------------6.清洁验证部位的确定---------------------------------------7.清洁程序-------------------------------------------------8.取样方法----------------------------------------------9.检测方法---------------------------------------------10.接受标准--------------------------------------------11.偏差及变更处理--------------------------------------12.再验证----------------------------------------------13.验证结果分析与评价----------------------------------14.附件------------------------------------------------1.设备清单2.验证目的验证×××设备、×××设备、×××设备、×××设备按照其批准的清洁方法进行清洁后,能够有效地除去产品残留,达到预先确定的限度,从而达到对下批产品无影响。
原料药生产清洁验证取样方法回收率试验
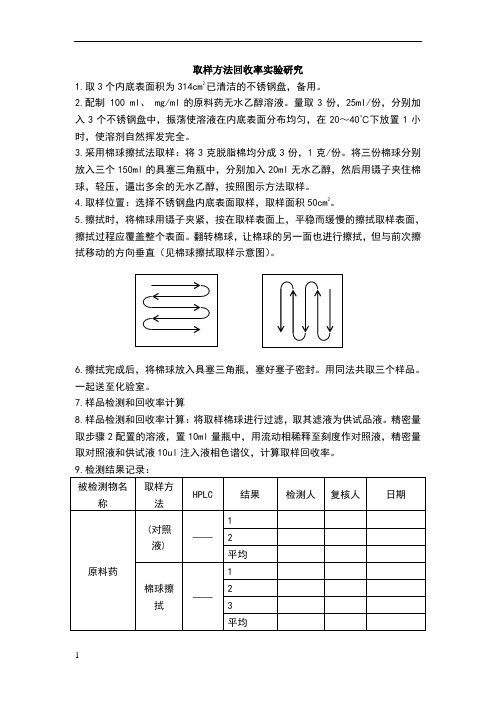
取样方法回收率实验研究1.取3个内底表面积为314cm 2已清洁的不锈钢盘,备用。
2.配制 100 ml 、 mg/ml 的原料药无水乙醇溶液。
量取3份,25ml/份,分别加入3个不锈钢盘中,振荡使溶液在内底表面分布均匀,在20~40℃下放置1小时,使溶剂自然挥发完全。
3.采用棉球擦拭法取样:将3克脱脂棉均分成3份,1克/份。
将三份棉球分别放入三个150ml 的具塞三角瓶中,分别加入20ml 无水乙醇,然后用镊子夹住棉球,轻压,逼出多余的无水乙醇,按照图示方法取样。
4.取样位置:选择不锈钢盘内底表面取样,取样面积50cm 2。
5.擦拭时,将棉球用镊子夹紧,按在取样表面上,平稳而缓慢的擦拭取样表面,擦拭过程应覆盖整个表面。
翻转棉球,让棉球的另一面也进行擦拭,但与前次擦拭移动的方向垂直(见棉球擦拭取样示意图)。
6.擦拭完成后,将棉球放入具塞三角瓶,塞好塞子密封。
用同法共取三个样品。
一起送至化验室。
7.样品检测和回收率计算8.样品检测和回收率计算:将取样棉球进行过滤,取其滤液为供试品液。
精密量取步骤2配置的溶液,置10ml 量瓶中,用流动相稀释至刻度作对照液,精密量取对照液和供试液10ul 注入液相色谱仪,计算取样回收率。
HPLC 检测的样品浓度=20⨯⨯⨯对对样稀释倍数A C A =对对样A C A ⨯50cm 2涂布量=ml ×25ml/314cm 2×50cm 2=10mg 50cm 2取样量=HPLC 检测的样品浓度×20ml公式:回收率=50cm 2取样量/50cm 2涂布量X100%=A 样/A 对×100% 结果计算:回收率=评价人: 日期:。
清洁验证限度计算及方法学验证

药物研发完成小试研究以后,进入预中试或者中试生产阶段,这一阶段通常需要在药厂完成,并遵守GMP关于设备的使用和清洁要求,清洁符合标准的基本原则是证明清洁方法能够去除污染物或将污染降低至可接受的水平。
当单品种单独生产线时,只要目视洁净就可以,当多产品共线生产时,则需要考虑上一品种在下一品种中的残留,因为这些残留可能产生副反应或者毒副作用。
所以在进行清洁验证前要计算允许残留限度(即检验清洁是否合格的标准),有三个比较常用的计算残留的方法,分别是基于毒理的限度、基于浓度的10ppm的限度和基于最低日治疗剂量的千分之一的限度。
1、基于毒理的限度标准2、基于浓度的10ppm的限度标准3、基于最低日治疗剂量的千分之一的限度标准在计算清洁限度的时候需要注意所讨论产品的日标准治疗剂量(有效成分)和下一产品的日标准治疗剂量(制剂)的区别,例如某制剂规格2ml:200mg,日治疗剂量20mg/kg,成年标准体重50kg,那么日标准治疗剂量(有效成分)为20mg/kg×50kg=1000mg,日标准治疗剂量(制剂)为1000mg÷200mg×2ml=10g。
清洁限度确定以后,进行清洁方法验证,可根据《化学药物质量控制分析方法验证技术指导原则》和《中国药典2020年版》9101 分析方法验证指导原则等制定验证内容,验证指标主要包括专属性、检测限、定量限、线性与范围、仪器精密度、重复性、中间精密度、准确度、溶液稳定性和耐用性。
1.溶液配制:1.1空白溶液:水1.2空白棉签溶液:取2个棉签放入具塞试管中,精密加入水10ml,密封,超声10分钟,取超声后溶液过滤即得。
1.3对照品溶液:精密称取xxxx对照品xxmg,置100ml量瓶中,加水溶解并稀释至刻度,摇匀,作为擦拭限度对照品溶液。
1.4供试品溶液:精密称取xxxx(含量约为100%)约xxmg,置于100ml量瓶中,加水溶解并稀释至刻度,摇匀,在10*10cm的区域均匀涂布0.5ml,待溶剂挥干后,用2个棉签擦拭,每个棉签分别先横向蛇形擦拭,再翻转棉签纵向蛇形擦拭,之后将2根擦拭棉签放入具塞试管中,精密加入水10ml,密封,超声10分钟,取超声后溶液过滤即得。
洁净车间清验证方案 -(清洁+消毒验证+表格)

LOGOXXX 医疗器械有限公司XXX Medical Devices Inc.洁净车间清验证方案目录一. 验证目的二. 验证范围三. 验证职责四. 清洁流程五. 验证内容六. 验证方案七. 验证结论附件实验记录一、验证目的验证洁净车间按照操作规程中的方法,进行必要的清洁和消毒后。
能有效的控制微生物污染水平,防止微生物在生产环境中污染及交叉污染产品,保证产品质量。
对车间清洁消毒方法可行性和可靠性进行确认对车间清洁消毒周期进行确认二、验证范围本方案适用公司车间洁净区域清洁实际效果的评价。
三、验证职责1 管理者代表1.1 负责验证方案的审核。
1.2 负责验证的协调工作,以保证本验证方案规定项目的顺利实施。
1.3 负责验证数据及结果的审核2 质量部2.1 负责取样。
2.2 负责样品检验及检验数据的填写。
2.3 负责验证过程审核和各项验证、操作记录及数据整理。
3 生产车间3.1 负责编制《洁净室管理规程》、《工服清洁操作规程》文件。
3.2 负责对本方案措施的实施。
3.3 负责各项验证、操作记录及数据的填写。
四清洁流程4.1 车间主要设施清洁标准4.1.1 参照标准4.1.2 清洁要求设备、工作台面、容器等用75%的酒精或3%过氧化氢浸润的抹布进行擦拭,如表面有很多杂质或料屑则先用吸尘器除去后,再进行擦拭和清洁。
早晚各清洁一次,如发现异常根据实际情况适时增加频次。
4.2 洁净服清洗标准4.2.1 清洗条件a) 空调净化系统已运行30分钟以上后,b) 使全自动洗衣机c) 国内知名品牌洗衣液4.2.2 清洗周期a) 已清洗但未发放使用的洁净服,有效期为清洗时日算起的第七天。
b) 已清洗且已发放使用的洁净服,其有效期为发放时日算起的48小时内。
但不得超过该洁净服的清洗有效期。
4.3 清洁效果要求五、验证内容5.1 验证时机a) 在按照《工服清洁操作规程》、《洁净室管理规程》完成清洗清洁工作后;b) 在洁净服达到规定的有效期。
清洁验证方案

目的:通过对颗粒剂生产设备清洁效果的验证,证实各设备按其清洁操作规程操作能够有效地除去残留物,达到预先规定的限度,从而达到对下批产品无影响。
适用范围:适用生产车间(一)生产设备的清洁方法和储存有效期的确定。
制定依据:依据《中国药典(2010年版)》、《药品生产质量管理规范(2010年修订)》、《药品生产验证指南(2003年版)》、设备相应清洁规程操作文件,制订本验证方案。
内容:1. 验证组织及职责1.1验证组织见《验证总规划》,由清洁验证小组执行本验证方案。
1.2职责2. 概述2.1根据GMP要求,在每次更换品种、批号或生产工序完成后,要认真按清洁规程,对设备、容器、生产场地进行清洁,以避免造成不同批号或不同品种产品之间的污染和交叉污染,有效地保证药品质量。
2.2设备清洁在制药生产中有特殊地位,生产设备的清洗是指从设备表面去除可见及不可见物质的过程。
这些物质包括活性成分及其衍生物、辅料、清洁剂、环境污染物质、水冲洗残留物及设备运行过程中释放出的异物。
为正确评估清洗程度的效果,需定期对直接接触药品的设备进行清洁验证。
3. 颗粒剂生产设备3.1颗粒剂生产设备清单3.2本次验证设备的主要材质为304不锈钢。
3.3本次验证设备及与产品接触面积4. 验证周期为了验证清洁方法的稳定性和可靠性,三批生产后,分别进行清洁验证。
5. 清洁验证准备工作5.1进行生产设备清洁验证前,所有与清洁验证有关的仪器、设备应进行过校验或确认。
仪表、计量器具等应校验合格,仪器、设备等应建立相应的操作、维护保养规程,对清洁验证的样品应建立相应的检验操作规程。
本次清洁验证中所使用设备的确认情况及QC检验过程中所使用的仪器、设备、仪表、计量器具等确认或校验情况见附表。
5.2设备清洁规程及文件编号5.3清洁介质及用品清洁介质:饮用水、纯化水、压缩空气、75%乙醇清洁用品:清洁布、一次性清洁布5.4清洁方式及取样部位5.4.1清洁方式:生产设备的清洁方式为手工清洁方式,由操作工持清洁工具,按预定的要求清洗设备,根据目测确定清洁的程序,直至清洁完成。
清洁验证及其残留限度计算培训 (N)

取样点选取原则
• 靠近产品的地方 • 与产品直接接触的表面 • 与产品直接接触的物品周转的表面 • 气流流型 • 活动频繁的地方 • 其它
取样点应包括各类最难清洁部位。
企业应根据其生产设备和产 品的实际情况 制订科学合
清洁验证项目及允许限度
活性残留物允许限度
理的能实现并通过适当的方 法检验的限度标准
一般治疗性药品 常用此标准进行计算
• 毒性
强致敏性、高活性药品
计算公式一、基于浓度限度
R
其中 R1----单位面积上残留物A允许限度,mg/cm2 L1----下批产品B中含上批产品A活性物质的残留物浓度限度 10mg/kg
1
SBS L S SF
1
SBS kg mg S SF
/ 10
制剂/原料
SBS---下批产品B的最小批量 ,kg
即设备中总残留物量参照ich和fda指南新原料药中的杂质原料药中单个未知杂质如最低日治疗剂量的11000最小批产量01分析方法客观能达到的能力如浓度限度百万分之十10106法检验的限度标准理的能实现并通过适当的方品的实际情况制订科学合企业应根据其生产设备和产生物活性的限度清洁验证项目及允许限度活性残留物允许限度zzzzg毒性一般治疗性药品常用此标准进行计算最低日治疗剂量mtdd的11000通常用淋洗水样进行测定但淋洗水样应当经过适当循环回流较高适用于水溶性较好的产品比较容易清洁检测方法灵敏度比采用残留物浓度限度10mgkg即10ppm的限度标准清洁验证项目及允许限度标准适用zzzzg先生产a产品再生产b产品s上批产品a与下批产品b共用设备累计接触面积cm2sf安全系数一般取1000sbs下批产品b的最小批量kgl1下批产品b中含上批产品a活性物质的残留物浓度限度10mgkg单位面积上残留物a允许限度mgcm2r1其中制剂原料sbskgmg10sbs计算公式一基于浓度限度zzzzg先生产a产品再生产b产品s上批产品与下批产品共用设备累计接触面积cm2maco代表产品a能进入到产品b中而不致引起风险的最大量mgsf安全系数取1000sbs下批产品的最小批量kgdabmin的106数每公斤b中含有a的百万之毫克数l2下批产品中含上批产品活性物质的残留物浓度限度mgkg单位面积上残留物允许限度mgcm2r2制剂其中ldsdsf10macosbsmtddsbs计算公式二基于日治疗剂量的11000zzzzg先生产a产品再生产b产品sf安全系数取10002000一个经验常数70一个成年人的平均体重kgld50动物的半致死量证明动物如小鼠和给药途径如静注口服很重要gkgldsdtddnext在设备中生产产品的最大日剂量mgnoela产品的无作用剂量未观察到作用的剂量g人sbsb产品的最小批量kgs上批产品与下批产品共用设备累计接触面积cm2maco代表产品a能进入到产品b中而不致引起风险的最大量mg制剂单位面积上残留物允许限度mgcm2r3ldsdsf2000tddsfnextmbsnoelmacosbskgkgld其中计算公式三基于毒性zzzzg擦拭回收率验证时取最小值进行擦拭用供试液浓度的计算取最小值r1r2r3比较比较zzzzg不应超过初始溶剂的05原料车间清洁验证项目及允许限度残留三类溶剂的限度zzzzg30201510
精益清洁验证案例分析

Buffer CIP返回 Vessel 缓冲罐
CIP SUPPLY CIP供应
Product Vessel 产品罐
Product Vessel 产品罐
CIP RETURN CIP返回
8
Cleaning Overview (Continued) 清洁概述(续)
Typically 6 cleaning Phases: 典型的6个清洁阶段:
Buffer Vessel 缓冲罐
Product Vessel 产品罐
Product Vessel 产品罐
7
Example of CIP circuit: 2) Schematic for cleaning CIP管路示例: 2)清洁图
CIP RETURN
CIP SUPPLY
CIP供应
CIP SUPPLY CIP供应
16
CV Approach (continued) : Family approach – worst cases清洁验证方法(续):族方法–最坏情况
The worst case selection is based on sound scientific rational: 最坏情况选择基于良好的科学原理: »MIX systems and worst case media or buffer => most concentrated and highest risk with repect to cross-contamination »MIX系统与最坏情况的培养基或缓冲 =>交叉污染方面最浓的与最高风险 »FF Buffer vessel => because of its position within manufacturing train (and risk of a theorethical impurity to end up in the final product bulk) »FF缓冲罐=>因为其位置在制造序列中(以及理论杂质直 到最终原料药中风险)
清洁验证方案

胶囊剂生产设备清洁再验证方案1、验证概述及目的:根据GMP要求,在生产结束后,要对生产设备及操作间进行彻底清洁,以避免造成不同批号或不同品种产品之间的污染和交叉污染,根据各设备的构造、操作、清洁及维修保养操作规程及产品成分在水中的溶解性进行风险分析,选出最差情况的产品;为了验证清洁方法的可靠性及稳定性,对所选的最差情况的产品进行3次清洁验证,每批产品生产结束后,对所有在生产过程中使用的设备及容器具进行清洁,清洁后对设备的物理外观、检测化学残留及微生物残留,要求应低于设定残留限度要求,更好的保证产品质量。
2.验证范围:适用于固体制剂车间所有的胶囊剂生产线设备的清洁验证。
相关设备见下表:3.职责3.1验证小组:3.1.1负责验证方案的制定并实施验证活动。
3.1.2负责验证工作的组织与协调。
3.1.3负责收集、整理清洁验证数据。
3.1.4负责编制验证报告,进行数据汇总、分析、结果评价,得出验证结论。
3.2.质量保证部:3.2.1负责验证管理的日常工作。
3.2.2负责起草验证方案和报告。
3.2.3负责组织和协调验证活动。
3.2.4负责验证过程中的监控及取样。
3.2.5负责拟定检测项目及验证周期。
3.2.6负责收集、整理清洁验证数据,编制验证报告和结果评价。
3.2.7负责发放验证证书。
3.2.8负责管理验证文件并归档保存。
3.3生产部:3.3.1负责审核验证方案和报告。
3.3.2负责验证过程中设备的清洁。
3.3.3负责清洁剂、消毒剂的配制和使用。
3.3.4协助进行设备的维修保养。
3.4工程部:3.4.1负责仪器、仪表、量具的校准。
3.4.2负责设备的维修保养。
3.4.3负责验证方案和报告的审核。
3.5质量控制部:3.5.1负责验证过程中样品的检测,并根据检验结果出具检验报告。
3.5.2负责验证方案和报告的审核。
3.5.3负责检验仪器设备的维护保养。
3.6验证时间:年月日至年月日4.风险评估:4.1经风险管理领导小组人员共同对直接接触物料及药品的生产设备进行了清洁程序风险评估,对存在的质量风险提出了处理措施,具体见《验证总计划》;4.2由于上一产品对下一产品的污染并不是均匀的分布在整个设备的接触面上,选择设备的最差区域,这些区域在清洁难度和残留水平方面代表对清洁规程的最大挑战,因此清洁验证的活性成分的取样计划的确定必须先进行风险分析,具体见《验证总计划》。
清洁验证方案

清洁验证方案KFG300D抗生素瓶螺杆分装机清洁验证方案2011年10月验证方案的起草与审批部门人员职责粉针剂车间李海龙负责验证方案组织与实施粉针剂车间黄仁春负责验证方案的拟定、验证报告的起草设备部霍育生负责验证所需仪器、设备的正常运行QA部宋新莉负责验证过程中的监控和取样QC部张华负责验证过程中环境和样品的检测部门起草人日期审核签名日期验证委员会进行审阅会签批准人批准日期方案实施日期:目录1. 验证概述 (4)2. 验证目的 (5)3. 风险评估 (5)4. 验证标准 (16)5. 验证范围 (16)6. 验证周期 (17)7. 验证职责 (17)8. 验证实施的前提条件 (18)9. 验证方案的起草与审批 (19)10. 验证时间安排 (19)11. 验证 (20)11.1本次验证具体措施及检测项目 (20)11.2 取样工具: (21)11.3 取样溶剂 (21)11.4 检验仪器 (21)11.5 取样和检验方法 (21)11.6 取样位置 (25)11.7 验证具体实施方法及可接受标准 (29)(1)清洁效果验证 (29)(2)确定设备存放时间 (30)11.8 取样计划 (32)12 偏差处理 (43)13 风险的接收与评审 (43)14 验证结果评审和结论 (44)15.方案修改记录 (46)16.附件 (47)1. 验证概述本公司粉针剂车间生产设备KFG300D抗生素瓶螺杆分装机,主要用于新产品注射用头孢米诺钠的分装生产, 该设备主要结构、清洁方法及其所有接触药品零部件具体面积见附件。
为了确保后续产品中没有带入超过接受标准的污染物,避免产品的交叉污染,须对KFG300D 抗生素瓶螺杆分装机生产后的清洁进行验证,测定验证对象清洗程度,并对设备清洁最终效果作出评价。
确保药品生产开始前设备表面的清洁程度符合要求。
设备清洁:是擦拭清洁设备本身、拆洗设备关键零部件和擦洗相关容器具等,其中主要是设备关键零部件的清洗,其清洁后随时用随时传进,不用时就传出清洁灭菌。
CIP清洁验证方案设计设计

附件5:水样检验汇总报告
附件1
领用记录
领用日期
名称
用途
领用量
领用人
复核人
附件2
CIP操作记录
日期
工艺用水
冲洗时间
NaoH
投料量
NaoH
溶液温度
碱洗时间
工艺用水
冲洗时间
H3PO4
投料量
H3PO4
溶液温度
酸洗时间
工艺用水
冲洗时间
热工艺用水
冲洗温度
持续时间
操作人
附件3
感官、理化检验原始记录
可判定CIP清洁验证效果符合要求。
4.5.7验证结果评定及结论:
验证小组根据CIP清洁验证的情况,做出相应评定及结论。
4.5.8再验证周期
CIP操作程序做重大修改时,须再验证。
5验证进度安排
年月日-年月日对CIP清洁进行验证
6附件:
附件1:领用记录
附件2:CIP操作记录
附件3:感官、理化检验原始记录
4.5.3.2取样步骤
4.5.3.2.1先放流3-5分钟;
4.5.3.2.2用广口瓶取充填机排放口水,冲洗瓶内2次,装取所需量,密封。
4.5.4检测项目、标准及方法
4.5.4.1检测项目:感官、理化和微生物
4.5.4.2检测标准:
4.5.4.2.1感官标准:无色透明液体、无臭、无味、无肉眼可见物
4.5.4.2.2理化标准:pH、电导率与原水比较,pH的波动范围在±0.1内,电导率的波动范围在±0.1μs.cm-1内,金康贝特活力源口服液残留液<10ppm(以牛磺酸在630nm吸光度<0.006判定)
4.3.8开启蒸汽阀,把氢氧化钠、工艺用水、磷酸加热至50℃。
某车间清洁验证评估报告示例

某车间 文件编号: 版本: 页码: 1 of 26
某车间清洁验证评估报告示例
User
用户
Location
位置
Project NO.
某制剂车间
项目编号
Document NO.
文件编号
Revision
版本
01
某车间清洁验证评估报告示例
某车间 文件编号: 版本: 页码: 2 of 26
某车间 文件编号: 版本: 页码: 4 of 26
目
1. 2. 3. 4. 5. 6. 7. 8. 9.
录
概述 ................................................................................................................................................. 5 评估目的及范围 ............................................................................................................................... 5 评估原因及评估依据........................................................................................................................ 5 评估人员 .......................................................................................................................................... 5 培训 ................................................................................................................................................. 6 生产设备及产品简介........................................................................................................................ 6 清洁程序 .......................................................................................................................................... 7 评估原则 .......................................................................................................................................... 8 取样方法及选择原理...................................................................................................................... 10