PCB碱性蚀刻液循环再生系统计划书(福建三江源环保)精品PPT课件
蚀刻废液回用
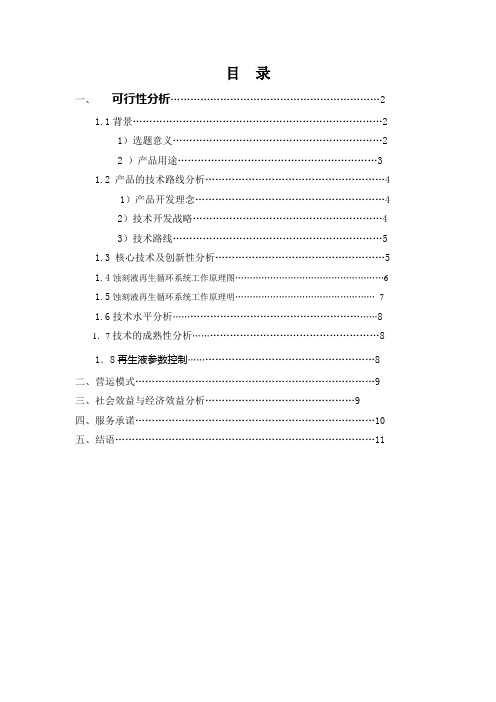
目录一、可行性分析 (2)1.1背景 (2)1)选题意义 (2)2 )产品用途 (3)1.2 产品的技术路线分析 (4)1)产品开发理念 (4)2)技术开发战略 (4)3)技术路线 (5)1.3 核心技术及创新性分析 (5)1.4蚀刻液再生循环系统工作原理图 (6)1.5蚀刻液再生循环系统工作原理明 (7)1.6技术水平分析 (8)1.7技术的成熟性分析 (8)1.8再生液参数控制 (8)二、营运模式 (9)三、社会效益与经济效益分析 (9)四、服务承诺 (10)五、结语 (11)《铜蚀刻液再生循环系统》项目建议书一、可行性分析1.1 背景1)选题意义印制电路板(PCB)行业是电子工业、信息产业和家电行业的基础,近20年来,作为重污染行业之一的PCB行业纷纷向中国转移,使得中国的PCB行业近几年一直保持高于10%的年增长速度。
目前全国约有各种规模的PCB企业近3000家,年产量达到2亿平方米以上,每年消耗精铜在10万吨以上,产出的蚀刻废液中总铜量在5万吨以上,对我国环境尤其是PCB厂周边地区的水资源环境构成了严重威胁和危害。
蚀刻生产线是PCB生产中消耗药水量较大的工序,也是产生废液(即危险废物——废蚀刻液,按国家环保总局的废物分类命名)和废水(即一次洗涤废水和二次洗涤废水)最大的工序。
一般而言,每生产一平方米正常厚度(18μm)的双面板消耗蚀刻液约为2—3升,并出废蚀刻液2—3升、一次洗涤废水5—10升、二次洗涤废水8——12升。
目前的做法是定时或不定时地从蚀刻槽排出部分铜含量很高的母液——废蚀刻液,同时向其中添加新的蚀刻液。
由于蚀刻液的最佳蚀刻铜离子浓度在100—140克/升,而废液外排时则希望铜离子浓度越高越好(常在150——160克/升),以尽可能提高蚀刻液利用率,降低溶液总的使用量。
因此,不论是采用人工间歇排放工艺还是比重控制的连续排放工艺,实际生产中蚀刻液并未处于其最佳技术状态。
从经济成本上说,目前的做法对PCB企业不利,一方面需要花费大量的钱购买蚀刻子液,而外排的废蚀刻液交给有废水处理能力的企业无偿或有偿处理后达标排放,增加了PCB企业的运菅成本和环保压力。
蚀刻废液回用
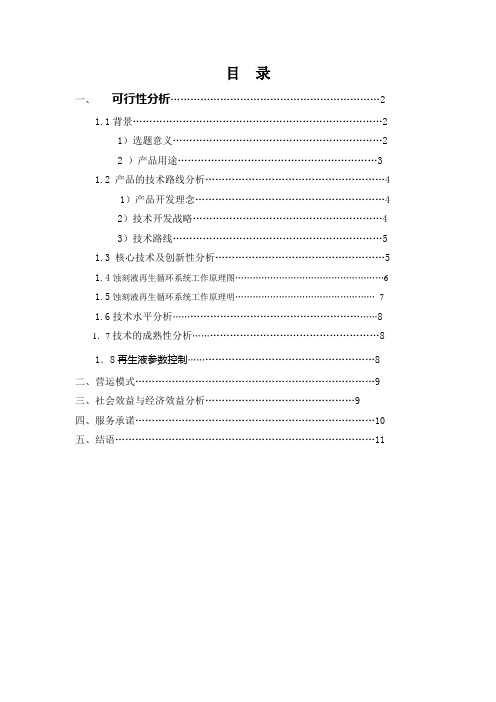
目录一、可行性分析 (2)1.1背景 (2)1)选题意义 (2)2 )产品用途 (3)1.2 产品的技术路线分析 (4)1)产品开发理念 (4)2)技术开发战略 (4)3)技术路线 (5)1.3 核心技术及创新性分析 (5)1.4蚀刻液再生循环系统工作原理图 (6)1.5蚀刻液再生循环系统工作原理明 (7)1.6技术水平分析 (8)1.7技术的成熟性分析 (8)1.8再生液参数控制 (8)二、营运模式 (9)三、社会效益与经济效益分析 (9)四、服务承诺 (10)五、结语 (11)《铜蚀刻液再生循环系统》项目建议书一、可行性分析1.1 背景1)选题意义印制电路板(PCB)行业是电子工业、信息产业和家电行业的基础,近20年来,作为重污染行业之一的PCB行业纷纷向中国转移,使得中国的PCB行业近几年一直保持高于10%的年增长速度。
目前全国约有各种规模的PCB企业近3000家,年产量达到2亿平方米以上,每年消耗精铜在10万吨以上,产出的蚀刻废液中总铜量在5万吨以上,对我国环境尤其是PCB厂周边地区的水资源环境构成了严重威胁和危害。
蚀刻生产线是PCB生产中消耗药水量较大的工序,也是产生废液(即危险废物——废蚀刻液,按国家环保总局的废物分类命名)和废水(即一次洗涤废水和二次洗涤废水)最大的工序。
一般而言,每生产一平方米正常厚度(18μm)的双面板消耗蚀刻液约为2—3升,并出废蚀刻液2—3升、一次洗涤废水5—10升、二次洗涤废水8——12升。
目前的做法是定时或不定时地从蚀刻槽排出部分铜含量很高的母液——废蚀刻液,同时向其中添加新的蚀刻液。
由于蚀刻液的最佳蚀刻铜离子浓度在100—140克/升,而废液外排时则希望铜离子浓度越高越好(常在150——160克/升),以尽可能提高蚀刻液利用率,降低溶液总的使用量。
因此,不论是采用人工间歇排放工艺还是比重控制的连续排放工艺,实际生产中蚀刻液并未处于其最佳技术状态。
从经济成本上说,目前的做法对PCB企业不利,一方面需要花费大量的钱购买蚀刻子液,而外排的废蚀刻液交给有废水处理能力的企业无偿或有偿处理后达标排放,增加了PCB企业的运菅成本和环保压力。
碱性蚀刻废液再生新方法研
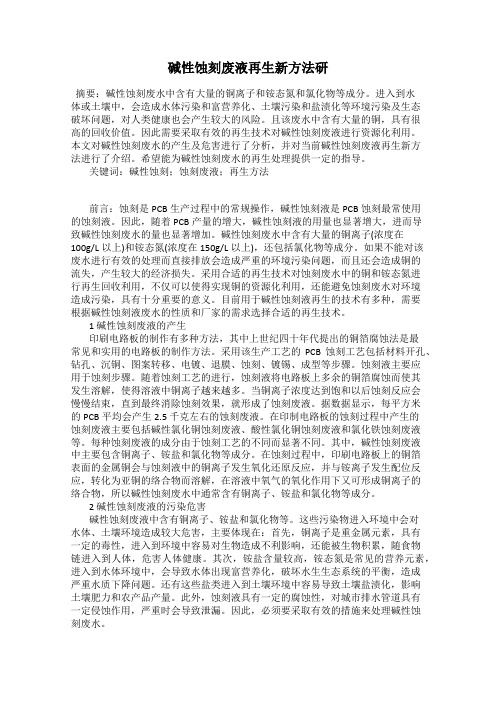
碱性蚀刻废液再生新方法研摘要:碱性蚀刻废水中含有大量的铜离子和铵态氮和氯化物等成分。
进入到水体或土壤中,会造成水体污染和富营养化、土壤污染和盐渍化等环境污染及生态破坏问题,对人类健康也会产生较大的风险。
且该废水中含有大量的铜,具有很高的回收价值。
因此需要采取有效的再生技术对碱性蚀刻废液进行资源化利用。
本文对碱性蚀刻废水的产生及危害进行了分析,并对当前碱性蚀刻废液再生新方法进行了介绍。
希望能为碱性蚀刻废水的再生处理提供一定的指导。
关键词:碱性蚀刻;蚀刻废液;再生方法前言:蚀刻是PCB生产过程中的常规操作,碱性蚀刻液是PCB蚀刻最常使用的蚀刻液。
因此,随着PCB产量的增大,碱性蚀刻液的用量也显著增大,进而导致碱性蚀刻废水的量也显著增加。
碱性蚀刻废水中含有大量的铜离子(浓度在100g/L以上)和铵态氮(浓度在150g/L以上),还包括氯化物等成分。
如果不能对该废水进行有效的处理而直接排放会造成严重的环境污染问题,而且还会造成铜的流失,产生较大的经济损失。
采用合适的再生技术对蚀刻废水中的铜和铵态氮进行再生回收利用,不仅可以使得实现铜的资源化利用,还能避免蚀刻废水对环境造成污染,具有十分重要的意义。
目前用于碱性蚀刻液再生的技术有多种,需要根据碱性蚀刻液废水的性质和厂家的需求选择合适的再生技术。
1 碱性蚀刻废液的产生印刷电路板的制作有多种方法,其中上世纪四十年代提出的铜箔腐蚀法是最常见和实用的电路板的制作方法。
采用该生产工艺的PCB蚀刻工艺包括材料开孔、钻孔、沉铜、图案转移、电镀、退膜、蚀刻、镀锡、成型等步骤。
蚀刻液主要应用于蚀刻步骤。
随着蚀刻工艺的进行,蚀刻液将电路板上多余的铜箔腐蚀而使其发生溶解,使得溶液中铜离子越来越多。
当铜离子浓度达到饱和以后蚀刻反应会慢慢结束,直到最终消除蚀刻效果,就形成了蚀刻废液。
据数据显示,每平方米的PCB平均会产生2.5 千克左右的蚀刻废液。
在印制电路板的蚀刻过程中产生的蚀刻废液主要包括碱性氯化铜蚀刻废液、酸性氯化铜蚀刻废液和氯化铁蚀刻废液等。
碱性蚀刻液循环再生系统

碱性蚀刻液循环再生系统
一、技术简介
碱性蚀刻液循环再生系统是专门针对PCB印制线路板厂生产中产生的碱性蚀刻废液而设计的,采用先进的封闭式自体循环和平行式无损分离技术(CSC-PLS)进行金属铜的分离和蚀刻液的回用,经严格有效的工艺过程,实现了溶液的长期循环再生和100%铜回收率的目标,同时将生产运行成本控制到最低。
该系统与蚀刻机在线闭环连接,自动循环运作。
二、设备说明
1、工艺流程
蚀刻机中溢流出的碱性蚀刻废液进入母液罐,再用泵送入电解槽。
调整主机内铜离子浓度、氯离子浓度和碱度至规定标准,然后通电电解。
取出产品电解铜,将溶液泵至再生子液罐,并检测溶液各离子浓度、pH值,根据检测结果调整各成分含量,调整完毕再次检测,合格后泵入子液罐中待PCB厂家使用。
三、环保指标
◆该系统采用封闭式自体循环和无损分离技术(CSC-PLS)实现了废液的100%回用
◆在整个过程中无固体废弃物、废液、废气产生
◆完全符合国家清洁生产、节能减排的环保要求
四、特点及优势
◆本系统采用PLS平行式无损分离技术,整个过程无需使用任何萃取剂、添加剂,真正实现了对废蚀刻液的无损分离,保证了蚀刻液回用的质量。
◆本系统采用CSC封闭式自体循环技术对废蚀刻液进行循环再生,整个过程既不带入其他外来物质,也没有产生有害物质,更不会破坏溶液成分,再生蚀刻液性能可以与新购子液相媲美,特别适用于高精度PCB 板制作。
◆该系统稳定性强,设备操作简便,便于维护。
采用一站式闭环控制系统,使设备运行更加可靠,运行成本为同行业最低。
碱性蚀刻液再生循环处理系统介绍
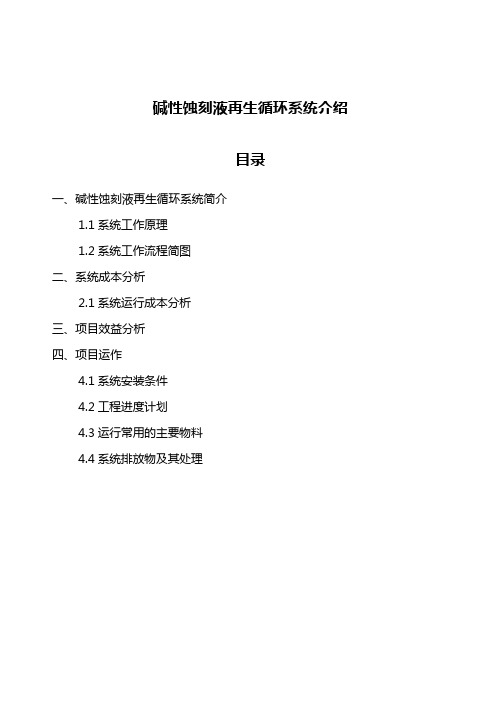
碱性蚀刻液再生循环系统介绍目录一、碱性蚀刻液再生循环系统简介1.1系统工作原理1.2系统工作流程简图二、系统成本分析2.1系统运行成本分析三、项目效益分析四、项目运作4.1系统安装条件4.2工程进度计划4.3运行常用的主要物料4.4系统排放物及其处理一、碱性蚀刻液再生循环系统简介1.1系统工作原理本系统采用多级萃取-反萃及电解再生工艺组合,可实现碱性蚀刻液完全回用零排放,是将碱性蚀刻废液提铜处理和再生利用进行组合的系统设备,可根据需要调整再生液的品质,完全确保PCB企业蚀刻工序产品质量的稳定。
该系统主要由以下部分组成:铜分离系统、铜提取系统、存储及调配系统。
1)铜分离系统:是将废蚀刻液中的铜离子通过铜吸附剂从废液中无损分离吸取铜离子,并将铜离子转移到铜提取系统,释放铜离子后的吸铜剂再回到此系统循环工作。
2)铜提取系统:吸铜剂中的铜离子释放到此系统中,通过电解提取高纯度产品铜。
3)存储及调配系统:系统将已降低铜含量的蚀刻液通过组份调节,使Cu2+、Cl-、PH 值及相关工艺元素达至生产所需要求,待生产所用。
整个系统工作时无排放封闭式循环运行。
系统工作时,只需在碱性蚀刻设备的溢流排出口接一管道,直接将废液引入再生循环设备中,经过系统处理后,再通过自动添加系统循环回到蚀刻工序,整个系统无排放封闭式循环运行,系统设备与生产线对接时,产线不需停机。
1.2系统工作流程简图碱性蚀刻液在线循环技术工艺原理图本项目所用的碱性蚀刻液再生循环系统,已通过市场实际使用认可,可实现PCB碱性蚀刻废液零排放,达到清洁生产的要求:1)碱性蚀刻废液全部转变为循环再生使用的蚀刻新液及金属铜板。
2)由于实现碱性蚀刻废液的零排放,大量原有处理工艺浪费的化工原料被全部循环再生使用,综合处理成本更低,效益大幅提升,更利于污染物总体排放量的控制。
二、系统成本分析2.1系统运行成本分析(废液处理量100吨/月)生产物料成本明细表(元/吨铜)项目名称吨铜耗量价格运营支出/吨铜1 萃取剂16L 220元/L 3520元2 硫酸(98%)100kg 1.6元/ kg 160元3 电费3500度0.7元/度2450元4 水10m35元/ m350元5 液氨0.2吨5500元/吨1100元6 蚀刻盐0.2吨2000元/吨400元7 添加剂20L 15元/L 300元8 阳极片0.33片6000元/片1980元9 阴极片(铜片)5片100元/片(抵后)500元9 设备维护100元10 人工工资3人4500元/人1350元吨铜总成本11910元/吨三、项目效益分析铜价假设为45000元/吨计算(实际价格参照当期上海有色金属交易网报价),以每月100吨废液(含铜10%质量比)为例,对系统作经济效益分析:1)月产铜量:100吨×10%=10吨。
PCB碱性蚀刻液的资源回收及高氨氮废水的处理、应用
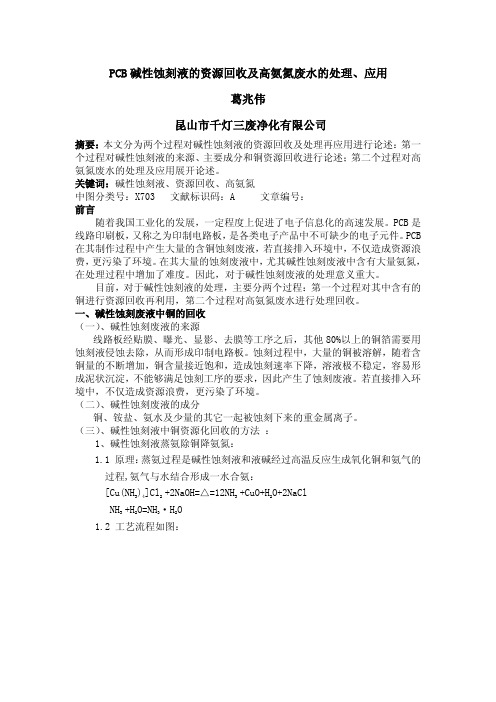
液销往PCB线路板厂,重新回到蚀刻生产线。 4、碱性蚀刻液再生的意义: 综上,本文提出的碱性蚀刻液再生的方法,不仅把碱性蚀刻废液中含有的铜
进行了资源回收,而且能够使全部废液再生,整个过程无废水排放;再生过程中 只需添加氨水和碳酸氢铵的添加剂来补充期间消耗的铵根,生产的碱性蚀刻液又 回归PCB线路板厂,达到了资源回收以及循环经济。 三、结论
综上所述,通过碱性蚀刻液蒸氨或酸碱中和生产铜产品,得到氧化铜、硫 酸铜或碱式氯化铜等产品,进行铜产品的资源回收。而分离铜后的高氨氮废水, 通过三效蒸发浓缩,得到氯化铵产品进行销售,馏出水通过RO膜后生产去离子水, 回用于生产,一方面减少了废水的排放,另一方面节约了水资源。
1.蒸发浓缩: 1.1 碱性蚀刻液通过一系列物理、化学反应后,得到高氨氮废水。 1.2 蒸发浓缩原理: 1.2.1 蒸发器降膜结构: 采用降膜结构蒸发器流程如下,溶液进入蒸发器顶部的进料室,靠分布器将 溶液平均分配到各传热管,并在管内壁形成连续向下流动的液膜。溶液受热蒸发, 蒸发出来的二次蒸汽沿管子中心与管壁液膜同方向向下流动,随后流入蒸发器下 部的分离室,蒸汽与物料在此分离。物料进入泵吸入口,蒸汽进入分离器进一步 除去挟带的液滴。第一效经过分离后的蒸汽作为第二效的加热蒸汽使用,第二效 经过分离后的蒸汽作为第三效的加热蒸汽使用,第三效的二次蒸汽去冷凝器。因 为二次蒸汽得到充分利用,故三效蒸发器的耗汽量为单效的三分之一。溶液流向 与蒸汽相反,首先进入第三效,顺次进入第二效,第一效,浓缩液从第一效排出。 1.2.2 蒸发器升膜结构: 采用升膜结构蒸发器流程如下,高氨氮溶液通过板式换热器时被馏出水进行 预热后进入一效蒸发器,进入一效蒸发器的加热蒸汽加热由提升泵从板换预热器 抽到一效蒸发器的物料,加热蒸汽冷凝成冷凝水进入冷凝水罐,物料经过加热产 生二次蒸汽,二次蒸汽将物料带到第一效分离器,经过分离器分离成热物料和二
PCB碱性蚀刻液的资源回收及高氨氮废水的处理、应用
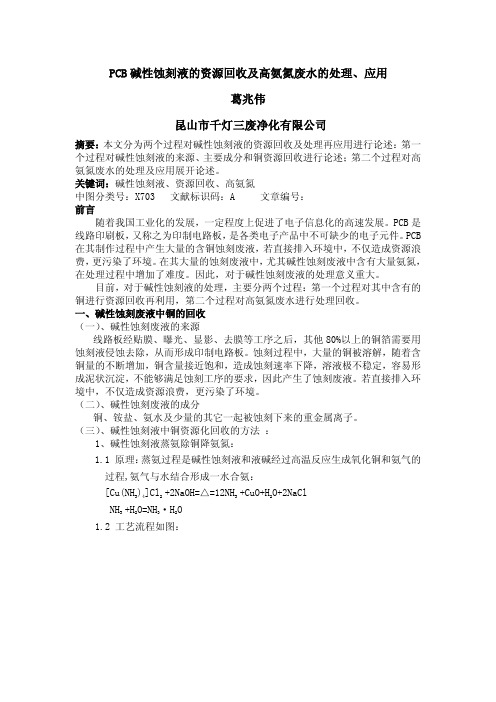
CuCl2+[Cu(NH3)4]Cl2→CuCl2●3Cu(OH)2●n H2O↓+NH4Cl 随着酸性蚀刻液与碱性蚀刻液的缓慢加入,慢慢析出碱式氯化铜晶体,通过 离心、洗涤的碱式氯化铜产品。 3.2 工艺流程图如下:
目前,对于碱性蚀刻液的处理,主要分两个过程:第一个过程对其中含有的 铜进行资源回收再利用,第二个过程对高氨氮废水进行处理回收。 一、碱性蚀刻废液中铜的回收 (一)、碱性蚀刻废液的来源
线路板经贴膜、曝光、显影、去膜等工序之后,其他 80%以上的铜箔需要用 蚀刻液侵蚀去除,从而形成印制电路板。蚀刻过程中,大量的铜被溶解,随着含 铜量的不断增加,铜含量接近饱和,造成蚀刻速率下降,溶液极不稳定,容易形 成泥状沉淀,不能够满足蚀刻工序的要求,因此产生了蚀刻废液。若直接排入环 境中,不仅造成资源浪费,更污染了环境。 (二)、碱性蚀刻废液的成分
该工艺环保但成本相对较高。 2、酸碱中和生产硫酸铜:
2.1 原理:酸性蚀刻液与碱性蚀刻液混合,发生中和反应,生产Cu(OH)Cl 沉淀,加入98%硫酸酸化后冷却结晶,得到硫酸铜:
CuCl2+[Cu(NH3)4]Cl2→Cu(OH)Cl↓+NH4Cl 反应过程中产生的氯氧化铜浆料,经过打浆、浓硫酸酸化就得到了硫酸铜饱 和溶液。饱和溶液经过冷却降温后,经过离心、洗涤得到五水硫酸铜产品。 2.2工艺流程如图:
次蒸汽。二次蒸汽通入第二效蒸发器加热由 一效分离器进入第二效蒸发器的物料,二次蒸汽冷凝成冷凝水进入冷凝水罐,物 料经过加热产生二次蒸汽,二次蒸汽将物料带到第二效分离器,经过分离器分离 成二次蒸汽和物料。二次蒸汽进入第三效蒸发器加热由强制循环泵从第二效分离 器抽到第三效蒸发器的物料,二次蒸汽冷凝成冷凝水进入冷凝水罐,物料经过加 热产生二次蒸汽,二次蒸汽将物料带到三效分离器,经过分离器分离成二次蒸汽 和物料。物料排入结晶釜进行冷却结晶,二次蒸汽进入冷凝器冷凝成冷凝水进入 冷凝水罐。
PCB蚀刻、土壤修复、废水处理
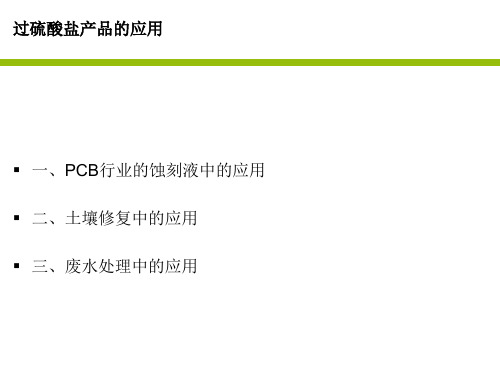
稳定,Cu2+ 浓度过低时,微蚀速率低,Cu2+ 浓度过高,微蚀速 率不易控制。(文中数据均来自文献)
4、过硫酸盐-硫酸体系蚀刻工艺
(3)单过硫酸氢钾蚀刻速率影响因素: 温度:温度升高,蚀刻速率上升,过高的温度可能会导
致KHS05分解,
硫酸浓度:硫酸参与反应,起主要作用
大
80~116g/L
25g/L
NH4Cl NH3・H2O
NaClO3、 H2O2、稳定剂、硫
H2O2、O2
酸
Na2S2O8
/ / 1%~5% / 50~150g/L 28g/L
KHSO5、H2SO4
三、蚀刻液处理工艺比较
四、蚀刻液比较
▪ 1.碱性蚀刻液: 氨是碱性蚀刻液的主要组分之一,起着配位体作用,以稳
2、酸性CuCl2蚀刻工艺
Cu2Cl2+4HCl+O2=4CuCl+H2O 随着反应的进行,Cu2+浓度下降,Cu+浓度上升,蚀刻能力 下降,需要再生蚀刻液,使Cu+转变为Cu2+,常用方式是通 过添加氧化剂(NaClO3等)或者通入O2使蚀刻液再生。
2、酸性CuCl2蚀刻工艺
(2)工艺特点: 蚀刻剂以氯化铜(CuCl2・H2O)为基础,加入HCl和其他可 溶性氯化物配制,适用于丝网漏印印料、干膜、金和锡— 镍合金为抗蚀层的印制板的生产。
1、碱性CuCl2蚀刻工艺
蚀刻最佳工艺条件: Cu2+=100 g/L,Cl-=120 g/L,pH=8.5, T=50 ℃,静态蚀刻速率可达8.76 μm/min。
2、酸性CuCl2蚀刻工艺
(1)化学反应机理: 蚀刻过程中的化学反应:
碱性蚀刻液循环再生系统

套
项
36
钛板组件
1050×660mm
组
37
阴极片组件
1065×714mm
组
3
40
抽风管道工程 废气处理塔组件
项 2440×1380×1200 组
41
电气及管道工程
项
42
电控组件
1200×800×400 组
43
电控系统
配电组件
800×600×400
组
44
50
储存设备
电气工程 大型存储系统
项
PT-10000L
套
51
中型存储系统
PT-6000L
套
1 1
1
1
32000
1
1
1
1
28000
1
1
1
1
1
31000
1
1
1
1
5
115
5
5 102000
4
10 4 1 5 1 1
60
300000
55
11000
1
1 12000
1
1 1
1
23000
1
4
57000
2
以客为尊、实现9双913赢!
五、设备清单、造价(100 吨/月废液处理规模)
序号 成品名称
1
2
铜
3
分
解
4
系
统
5
6
7
半成品名称
规格
单位 单套数量 金额
废液中转缸组件
1490×600×650 组
1
3500
再生中转缸组件
1810×1105×650 组
PCB碱性蚀刻液循环再生系统计划书(福建三江源环保)
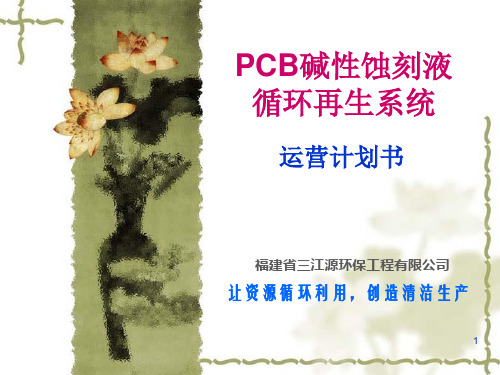
5、贵公司配合完全的工作项目
1)废液处理系统占地面积约:60平方 米,由贵公司完成建设; 2)处理系统总电功率为70KW,供电 装好总关,380V三相五线制进入现场; 3)流量10-30L/m自来水由贵公司提 供到现场; 4)蚀刻线废液收集至处理现场管 线设计施工由贵公司完成。
10
6、社会效益
12910元/吨成本
根据上述分析,月实际效益为:20万-12910*4=14.8万元。原变卖废液按3000/吨,购买 子夜1200元/吨计算,贵司以35吨废液计算原效益*1800元/吨=6.3万,现合作按照甲方7: 乙方3的比例分配效益,甲方现增加4.06万元/月。剩余30%作为乙方设备及技术人员投入 摊提费用。 甲方按照该系统设备后,将给贵司在原卖废液效益的基础上每年增加4.08万*12月=48.72 万的收入,以设备使用8年计算,8年共产生效益近389.76万。
3
1.2、项目原则
客户意志 该项目旨在为PCB企业解决面临的具体环境保护问题,因此项目的出发 点和最终目标都服务于PCB企业的意志,项目一切服务以是否符合PCB 企业长远利益为出发点。 共同工作 本项目一经确立,项目运作过程中双方应本着团结合作的前提,建立共 同工作的平台,共同推动项目的运行,我司负责系统提供运行,PCB企 业负责场地提供,共同建立良好的工作关系; 信息互动 项目合作双方应定时联系和沟通,与项目有关和有用的信息应予以开放, 保证信息的及时性和有效性,使项目得以顺利进行; 质量保证 我司的三级质量控制体系能够保证项目的质量符合客户的需求(项目承 接时的胜任评估、项目安装的过程严格控制、项目运行的首板确认)。 上述原则保证了我司以专业的环保技术能力,贴近客户实际的解决方案 设计,以专业的职业道德、专业精神和服务品质;赢得客户信赖和长期 发展!
4-PCB碱性蚀刻液
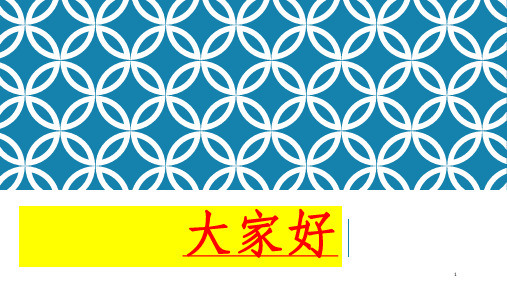
影响蚀刻速率的因素
4.温度的影响 蚀刻速率与温度有很大关系,蚀刻速率随着温度的
升高而加快。蚀刻液温度低于40℃,蚀刻速率很慢,而 蚀刻速率过慢会增大侧蚀量,影响蚀刻质量。温度高 于60℃,蚀刻速率明显增大。但NH3的挥发量也大大增 加,导致污染环境并使蚀刻液中化学组份比例失调。 故一般应控制在45℃~55℃为宜。
10
影响蚀刻速率的因素
3.溶液PH值的影响 蚀刻液的PH值应保持在8.0~8.8之间。当PH值降到8.0
以下时,一方面是对金属抗蚀层不利。另一方面,蚀刻液 中的铜不能被完全络合成铜氨络离子,溶液要出现沉淀, 并在槽底形成泥状沉淀。这些泥状沉淀能在加热器上结成 硬皮,可能损坏加热器,还会堵塞泵和喷嘴,给蚀刻造成 困难,如果溶液PH值过高,蚀刻液中氨过饱和,游离氨释 放到大气中,导致环境污染。另一方面,溶液的PH值增大 也会增大侧蚀的程度,而影响蚀刻的精度。
大家好
1
培训课题:PCB碱性蚀刻液 讲 师: 培训时间:
2
蚀刻
印制电路板(PCB)加工的典型工艺采用“图 形电镀法”。即先在板子外层需保留的铜箔部分上 (是电路的图形部分)预镀一层铅锡抗蚀层,然后 用化学方式将其余的铜箔腐蚀掉,称为蚀刻。
PCB蚀刻分为碱性和酸性两种,一为盐酸双氧 水体系(酸性);二为氯化铵氨水体系(碱性)。
注:1加仑(美制)=3.785升 1盎司=28.35克 1盎司/加仑 =28.35/3.785=7.5G/1
9
影响蚀刻速率的因素
2.氯化铵含量的影响 通过蚀刻再生的化学反应可以看出:[Cu(NH3)2]1+的再
生需要有过量的NH3和NH4Cl存在。如果溶液中缺乏 NH4Cl,而使大量的[Cu(NH3)2]1+得不到再生,蚀刻速率就 会降低,以至失去蚀刻能力。所以,氯化铵的含量对蚀 刻速率影响很大。随着蚀刻的进行,要不断补加氯化铵。 但是,溶液中Cl-含量过高会引起抗蚀层被浸蚀。一般蚀 刻液中NH4Cl含量在180g/l左右。
线路板蚀刻液循环回收系统

线路板蚀刻液循环回收系统一、概述IT产业的印制线路板(PCB)行业是一个对环境污染性较大的行业,他在蚀刻生产工艺过程中会产生大量的失效蚀刻废液,该废液中富含铜(135~165g/L)、氨及氯化铵。
传统处理方法是把失效蚀刻液给回收公司生产硫酸铜,其中大量含铵液体得不到有效利用,造成资源浪费,特别对线路板厂没有一点效益。
为此我司引进国外先进技术及采用专业物料,针对"蚀刻生产工序"专门设计制造本"系统"。
本"系统"采用先进的溶剂萃取电解技术,对废液进行PH值、络合剂及蚀刻液添加剂的浓度进行调整,使其重新恢复蚀刻功能。
对蚀刻工序产出的液体废物(废蚀刻液、一级洗涤水、二级洗涤水)进行有效处理并回收回用,帮助企业达到清洁生产之要求。
本"系统"与蚀刻机连接后自动循环工作,使蚀刻工序成为既达到清洁生产的要求又大大降低成本并获得巨大的经济效益和环保效益,可为企业实现,降耗、环保、获益的可持续发展的目标。
碱性[蚀刻液回收再生系统]设备采用"萃取分离-电沉积铜"工艺。
"萃取分离"是将废蚀刻液中的铜离子分离出来,使废蚀刻液获得再生,再生蚀刻液经调整参数后,返回蚀刻机循环使用。
"电沉积铜"是将萃取分离出来的铜离子电沉积成高纯度电解铜。
碱性[蚀刻液回收再生系统]设备是一套高新环保型、全封闭式系统,无废水、废气及废物排放。
该系统与蚀刻机相互连接后,自动循环运作,进行蚀刻液和氨洗水的回收及再生工作,蚀刻效果稳定;它的性能优越,使用寿命长,能为贵公司创造丰厚的经济效益。
其主要功能和特点表现如下:(1)、将废蚀刻液进行再生,经再生后的蚀刻液可以循环使用;(2)、将废蚀刻液和氨洗水中的铜离子进行回收,还原成高纯度(含铜量99.95%)以上的电解铜,铜回收率100%;(3)、该设备操作维护简单,在安装调试过程中不影响生产,安装调试完毕即可投入使用。
- 1、下载文档前请自行甄别文档内容的完整性,平台不提供额外的编辑、内容补充、找答案等附加服务。
- 2、"仅部分预览"的文档,不可在线预览部分如存在完整性等问题,可反馈申请退款(可完整预览的文档不适用该条件!)。
- 3、如文档侵犯您的权益,请联系客服反馈,我们会尽快为您处理(人工客服工作时间:9:00-18:30)。
点和最终目标都服务于PCB企业的意志,项目一切服务以是否符合PCB 企业长远利益为出发点。 ❖ 共同工作 ❖ 本项目一经确立,项目运作过程中双方应本着团结合作的前提,建立共 同工作的平台,共同推动项目的运行,我司负责系统提供运行,PCB企 业负责场地提供,共同建立良好的工作关系; ❖ 信息互动 ❖ 项目合作双方应定时联系和沟通,与项目有关和有用的信息应予以开放, 保证信息的及时性和有效性,使项目得以顺利进行; ❖ 质量保证 ❖ 我司的三级质量控制体系能够保证项目的质量符合客户的需求(项目承 接时的胜任评估、项目安装的过程严格控制、项目运行的首板确认)。 ❖ 上述原则保证了我司以专业的环保技术能力,贴近客户实际的解决方案 设计,以专业的职业道德、专业精神和服务品质进入电积液,释放出铜以后成为贫铜萃取剂,恢复萃取功 能,经棉芯过滤、炭芯过滤后又回用于蚀刻液的萃取操作,如此形成萃取剂的闭路循环。
❖ (4)氨洗水的闭路循环
❖ 把电路板厂蚀刻工序后段每天需更换排入废水池的氨洗水,引入到多级萃取后段体系中,
一是可以洗涤萃取后的油相,通过洗涤可以把油相夹带的微量Cl-离子除掉,二是氨洗水
4
2、碱性蚀刻循环再生工艺原理
❖ 蚀刻线上的蚀铜液随着蚀刻过程的进行,铜含量逐渐饱和,蚀刻速度变慢,溶液极不稳定, 易形成泥状沉淀,不能满足蚀刻工序要求,此时蚀刻液成为废液而被排放,同时补充低铜 含量的新蚀铜液。该项目采用萃取—反萃—电解—膜处理—组份调节对碱性蚀刻废液进行 再生处理,其处理方法为以下五个点:
❖ 酸性设备工艺流程图:
6
3、碱性循环再生效益分析
❖ 按照贵司月产能2万平米计算约产铜4吨,依据上海有色金属长江现货铜价当天均价计算,当铜价5万元/ 吨 时,每月产铜效益为20万(计算不含税,不计算卖铜折扣) 循环再生设备运作成本如下表:
中的铜离子通过流量-流程控制与萃取剂发生萃取反应而转移到油相中,使铜离子从15g/L
降低到1g/L,降低铜离子后的氨洗水经过中途缸静置、过滤后返回蚀刻线用于线路板的氨
水洗涤。如此形成了氨洗水的循环使用,实现了氨洗水减排达90%以上。
5
❖ (5)油相洗水的闭路 循环
❖ 萃取后的油相呈碱性 并含有微量氨,而反 萃后的油相呈酸性会 携带微量酸,通过在 工艺过程中引入两道 酸碱洗水把油相中的 氨氮和酸根除掉,并 且巧妙地利用两道洗 水的酸碱性质,把两 道洗水循环使用,使 它们在循环的过程中 发生酸碱中和反应, 提高洗涤效果,减少 了系统的硫酸和液氨 用量,两道洗水循环 使用从而形成了洗水 的闭路循环。
❖ (2)电解液的闭路循环
❖ 富铜油相的萃取剂用硫酸铜电积后的液体(简称电积后液)多级反萃,油水分离后,富铜 油相萃取剂中的铜进入电积后液,使之成为电积新液进入电积槽,电积后产出标准阴极铜 和电积后液,电积后液经棉芯过滤、炭芯过滤后又回用于反萃,如此形成硫酸铜电解液的 闭路循环。
❖ (3)萃取剂的闭路循环
❖ (1)蚀刻液的闭路循环
❖ 使用萃取剂将排出的含铜量高的蚀刻液(称为蚀刻废液)中的铜部分萃取进入萃取剂成为 富铜油相,油水分离后,水相即萃取铜后的蚀刻废液经过棉芯过滤、炭芯过滤和膜处理后, 只需补充少量氨水、氯化铵等,调整恢复蚀刻功能后,又可作为蚀刻新液(称为再生蚀刻 液)使用于蚀刻线,形成蚀刻液的闭路循环。
PCB碱性蚀刻液 循环再生系统
运营计划书
福建省三江源环保工程有限公司
让资源循环利用,创造清洁生产
1
目录
1、项目背景及原则 2、碱性循环再生工艺原理 3、碱性循环再生工程效益分析 4、贵公司配合之工作项目 5、服务承诺 6、社会效益
2
1.1、项目背景
❖ 近20年来,中国的PCB行业一直保持10-00%的年增长速度,目前有多种规模的PCB企业 3500多家,月产量达到1.2亿平方米,消耗精铜6万吨/月以上,产出的铜蚀刻废液中总铜 量在5万吨/月以上,对社会尤其是PCB厂周边地区的水资源和土壤造成了严重污染。
❖ 铜是一种存在于土壤及人畜体内的重金属元素,土壤中含量一般在0.2ppm左右,过量的铜 会与人畜体内的酶发生沉淀/络合反应,发生酶中毒而丧失生理功能。自然界中的铜通过水 体、植物等转移至人畜体内,使人畜体内的微量元素平衡遭到破坏,导致重金属在体内的 不正常积累,产生致病变性、致癌性等结果。
❖ 中国的工业废水排放标准中铜的监控指标为0.5ppm,饮用水标准为0.03ppm,欧美的相关 标准则更加严厉。美国国家环保局(USA-EPA)指出饮用水中的铜须采取特殊的处理技术 (TreatTechnology)进行处理,如SWT(源水处理,SourceWaterTreatment)和CC (腐蚀控制,Corrosioncontr01)等。由于废铜蚀刻液中含铜为几十至上百克/升,且含有 大量其它的有机及无机致病变性化合物,因此,国家环保总局将PCB废铜蚀刻液(废蚀铜 液)定位为危险液体废物(HazardousWaste),规定就地处理,禁止越境转移。
❖ 末端污染治理毕竟是无奈之策,更非环保工作之目的。探索铜蚀刻过程的清洁生产技术, 使铜蚀刻废液消除在生产过程中,实现在线循环再生,以彻底杜绝污染源及其污染扩散, 实现真正意义上的源头治理,既是环境保护部门强制执法的第一选择,也是PCB行业降低 生产成本,走可持续发展之路的必然选择。
3
1.2、项目原则
❖ 尽管如此,当前中国大陆在处理废铜刻液方面存在的“属地经营、分散运输、集中处理” 的杀鸡取卵局面己是不争的事实。仅广东省境内,处理废蚀刻液的合法不合法的厂家均采 取简单的中和沉淀方法回收硫酸铜的中间产品,而排放的废水中含铜量高达数克/升,其它 无机及有机物更无视其存在,即使是一些较大型的处理厂,其外排水中铜浓度也常高于 1ppm,而氨氮用有机氰化物更无法达标。除此之外,周边地区的政府及民众对运输废铜蚀 刻液过程中产生的跑冒滴漏更是忧心忡忡。据统计,运输损失达3-5%,其危害可想而知。