鼎隆机械LED高低压贴片灯带挤出生产线
TENON中空生产线操作规程

4.3在板压线控制柜区域按下“电源”的“ON”按钮,5秒左右进入电脑控制操作页面,输入密码,并设置“板压压合延时”项目中的“压合时间”(一般为4秒)。
4.4按下“自动”的“ON”按钮,开启压合线设备,并进入待机状态。
4.5将“压合”按钮调至“自动”。
4.6根据订单要求,调整好铝条框的限位挡块(一般为6mm)。
4.7在清洗机控制柜区,将“工作方式”调至“自动”,再按“自动ON”按钮;如果工作方式为选择“手动”,则需依次按下风机ON—毛刷ON(如生产LOW-E,则需旋转中间旋钮以调节毛刷转速)—水泵ON—灯ON。
4.8将“输送玻璃”调至“进”,按下“输送ON”
4.9根据玻璃大小调节“速度”旋钮,以清洗出来的玻璃烘干效果为准来调节。
编制审核批准
有限公司
文件编号
0
版次
0
页次
0
文件名称
TENON中空生产线操作规程
生效日期
0
5.3玻璃进入板压区5秒后,开始进行压合,压合时间4秒钟后,玻璃自动会被输送到下片区。成后的关机步骤:先在板压线控制柜区域按下“自动”的“OFF”按钮—在清洗机控制柜区域按下“自动”的“OFF”按钮—按下“电源”的“OFF”按钮—按下“照明”的“OFF”
8.应急异常处理
遇到紧急情况,按下紧急开关,并卸下玻璃,尔后查找原因,并予以解决。
编制审核批准
按钮—关断水源,放干水箱的脏水—关断气压—切断电箱总电源。
6.维护保养
6.1工作完毕后,将清洗机毛刷辊道等清洗一遍,并将机舱打开通风,防止其生锈。
6.2定期清洗风机滤网。
6.3定期给辊道、链条和轴承注润滑油。
6.4定期排放油水分离器的积水。
YL-335B介绍

项目一了解Y L-335B自动生产线实训考核装备亚龙Y L-335B型自动生产线实训考核装备由安装在铝合金导轨式实训台上的供料单元、加工单元、装配单元、输送单元和分拣单元5个单元组成。
其外观如图1-1所示。
图1-1Y L-335B外观图其中,每一工作单元都可自成一个独立的系统,同时也都是一个机电一体化的系统。
各个单元的执行机构基本上以气动执行机构为主,但输送单元的机械手装置整体运动则采取步进电机驱动、精密定位的位置控制,该驱动系统具有长行程、多定位点的特点,是一个典型的一维位置控制系统。
分拣单元的传送带驱动则采用了通用变频器驱动三相异步电动机的交流传动装置。
位置控制和变频器技术是现代工业企业应用最为广泛的电气控制技术。
在Y L-335B设备上应用了多种类型的传感器,分别用于判断物体的运动位置、物体通过的状态、物体的颜色及材质等。
传感器技术是机电一体化技术中的关键技术之一,是现代工业实现高度自动化的前提之一。
在控制方面,Y L-335B采用了基于R S485串行通信的P L C网络控制方案,即每一工作单元由一台P L C承担其控制任务,各P L C之间通过R S485串行通讯实现互连的分布式控制方式。
用户可根据需要选择不同厂家的P L C及其所支持的R S485通信模式,组建成一个小型的P L C网络。
小型P L C网络以其结构简单,价格低廉的特点在小型自自动生产线仍然有着广泛的应用,在现代工业网络通信中仍占据相当的份额。
另一方面,掌握基于R S485串行通信的P L C网络技术,将为进一步学习现场总线技术、工业以太网技术等打下了良好的基础。
1.2Y L-335B的基本功能Y L-335B各工作单元在实训台上的分布如图1-2的俯视图所示。
图1-2Y L-335B俯视图各个单元的基本功能如下:1、供料单元的基本功能:供料单元是Y L-335B中的起始单元,在整个系统中,起着向系统中的其他单元提供原料的作用。
铜排连续挤压生产线的工艺流程

铜排连续挤压生产线的工艺流程下载温馨提示:该文档是我店铺精心编制而成,希望大家下载以后,能够帮助大家解决实际的问题。
文档下载后可定制随意修改,请根据实际需要进行相应的调整和使用,谢谢!Download Tip: This document has been carefully written by the editor. I hope that after you download, they can help you solve practical problems. After downloading, the document can be customized and modified. Please adjust and use it according to actual needs. Thank you!铜排连续挤压生产线的工艺流程:①原料准备:选用符合规格要求的铜杆,进行表面清洁处理,去除油污和氧化层,确保材料质量。
②加热:将清理干净的铜杆送入连续加热炉中,采用感应或电阻加热方式均匀加热至适宜的塑性加工温度,一般在600°C~900°C之间。
③铸坯成型:加热后的铜杆通过连续铸造机,高压下高速挤出,形成初步形状的铜坯,此步骤可调整铜坯的截面尺寸和形状。
④挤压成型:铜坯随即进入挤压机,通过精密设计的模具,在强大压力作用下连续挤压变形,形成所需的铜排截面形状,如矩形、槽型等。
⑤冷却与拉伸:挤压出的铜排立即进行水冷或空气冷却,以固定其形状并提高机械性能。
随后,可能根据需要进行拉伸处理,改善内部晶粒结构,提升导电性和机械强度。
⑥矫直与切割:冷却后的铜排通过矫直机消除弯曲,保证直线度,然后根据指定长度由自动切割机切割成段。
⑦质量检验:对切割好的铜排进行尺寸、表面质量及电性能检测,确保产品符合相关标准和客户要求。
⑧包装与入库:合格的铜排经过防氧化处理后,进行打包密封,最后入库或直接发往客户。
SMT自动化生产线方案

SMT自动化生产线方案引言概述:SMT(表面贴装技术)自动化生产线方案是一种高效、精确的电子组装解决方案,它在电子创造业中得到了广泛应用。
本文将介绍SMT自动化生产线方案的五个主要方面,包括设备选型、生产流程、质量控制、人机交互以及未来发展趋势。
正文内容:1. 设备选型1.1 设备类型:选用适合生产需求的贴装机、回流炉、自动输送设备等。
1.2 设备性能:考虑设备的速度、准确性、稳定性等指标,以满足高质量的生产要求。
1.3 设备配置:根据产品特性和生产规模,选择合适的设备配置方案,如单线、双线或者多线生产。
2. 生产流程2.1 材料准备:确保原材料的质量和数量满足生产需求。
2.2 贴装过程:包括自动上料、贴装、焊接等步骤,保证高效、准确的组装。
2.3 检测与调试:通过自动检测设备对产品进行质量检测和调试,确保产品质量。
2.4 包装与出货:将组装好的产品进行包装,并进行出货准备。
3. 质量控制3.1 质量检测:使用自动光学检测设备对贴装过程中的错误进行实时检测和纠正。
3.2 过程监控:通过数据采集和分析,实时监控生产过程,及时发现和解决问题。
3.3 质量管理:建立完善的质量管理体系,包括质量标准、检验流程、异常处理等。
4. 人机交互4.1 操作界面:设计直观、易用的操作界面,提高操作人员的工作效率。
4.2 报警与提示:设置合理的报警和提示机制,及时提醒操作人员处理异常情况。
4.3 数据分析与反馈:通过数据分析和报表生成,为管理层提供决策参考。
5. 未来发展趋势5.1 智能化:引入人工智能技术,实现自动化程度更高的生产线。
5.2 灵便性:提高设备的灵便性,适应多品种、小批量生产的需求。
5.3 网络化:实现设备之间的信息共享和远程监控,提高生产效率和管理水平。
总结:综上所述,SMT自动化生产线方案是电子创造业中一种高效、精确的电子组装解决方案。
通过合理的设备选型、优化的生产流程、严格的质量控制、人机交互的改进以及未来发展趋势的把握,可以提高生产效率、降低成本、提升产品质量,为电子创造企业带来更大的竞争优势。
led灯带生产工艺

led灯带生产工艺LED灯带的生产工艺主要包括以下几个步骤:材料准备、PCB制作、贴片、封装、测试和包装。
第一步是材料准备。
根据产品设计要求,准备LED芯片、PCB板、电阻、电容、电感等器件以及胶水、导线等辅助材料。
第二步是PCB制作。
将选购的FR4基板进行切割,然后在表面涂覆阻焊油墨,通过曝光和蚀刻的工艺,在基板上形成电路的导线和焊盘。
之后,通过孔铜、骨架、镀金等工艺制作完整的PCB板。
第三步是贴片。
使用自动化贴片机将SMT元件精确地贴附在PCB板上。
贴片机先将PCB板定位,然后通过吸嘴将元件从料盘上吸取,并精确地放置在PCB板的焊盘上。
贴附完成后,通过热风炉进行焊接,将元件固定在PCB板上。
第四步是封装。
将贴片完成的PCB板放入封装机中,通过自动化设备将LED芯片、电阻、电容等元件进行固定和封装。
封装方式可以选择胶滴封装或者封装模具,具体方法根据产品设计要求和生产规模而定。
第五步是测试。
将封装完成的LED灯带连接上测试设备,对其进行亮度、电压、电流、色温等参数的测试。
通过测试,筛选出合格品和不合格品。
不合格品可以选择修复或者淘汰。
第六步是包装。
将合格品的LED灯带进行整理、清洁和包装。
常见的包装方式有塑料袋包装、纸盒包装和真空包装等。
包装完成后,进行产品标识和质量检查,然后入库待发货。
综上所述,LED灯带的生产工艺经过材料准备、PCB制作、贴片、封装、测试和包装等步骤,通过自动化设备的使用,能够高效地完成LED灯带的生产,并确保产品的质量和稳定性。
挤出生产线

挤出生产线挤出生产线是一种常见的生产方法,它在许多工业领域中被广泛使用。
这种生产线的特点是将原材料或半成品输送到不同的工作站,然后经过一系列加工和组装过程,最终生产出成品。
挤出生产线具有高效、快速和稳定的特点,能够满足大批量生产的需求。
首先,挤出生产线的工作原理是通过输送带或其他方式将原材料或半成品传送到不同的工作站。
每个工作站都负责完成特定的加工或组装任务。
这种方式可以使生产过程流程化,减少人为操作错误的可能性,提高生产效率。
其次,挤出生产线配备了各种先进的设备和技术,可以实现自动化操作。
例如,自动挤出机可以将熔化的塑料或金属推送到模具中,并根据需要进行成型。
这种自动化生产方式可以大大减少人力投入,提高生产效率和产品质量。
此外,挤出生产线还可以根据不同的生产需求进行灵活调整。
例如,可以根据产品的不同规格和尺寸,更换不同的模具和工作台,从而生产出不同类型的产品。
这种灵活性可以使生产线更加适应市场需求的变化,提高企业的竞争力。
当然,挤出生产线也存在一些挑战和局限性。
首先,该生产线需要大量的设备和技术投入,对企业来说具有一定的成本压力。
其次,由于生产过程中的机械运作和自动化操作,对维护和故障排除的技术要求较高,需要专业人员进行维护和管理。
在应用挤出生产线时,企业应充分考虑产品的市场需求和生产规模。
如果需求量较大且比较稳定,挤出生产线是一个较为适合的选择。
然而,如果需求量较小或经常有变化,可能需要考虑其他生产方式,以提高生产的灵活性和效率。
总的来说,挤出生产线在现代工业生产中发挥着重要的作用。
通过提高生产效率、降低成本和提高产品质量,它能够帮助企业增强竞争力,满足市场需求。
在未来,随着科学技术的不断进步和工业制造的发展,挤出生产线有望进一步发展和应用,为各行业的生产带来更多的便利和机遇。
电线电缆挤压加工

电线电缆挤压加工是一种工业生产生活中常用的技术。
其作用就是通过机械压力将电线电缆中的导体与导体之间的绝缘层连接起来,来达到固定、传输电信号的目的。
作为电线电缆加工行业的一种重要工艺,已经在现代化生产制造中得到了广泛应用。
的原理是利用机械压力将电线电缆连接器、插座等零部件的端子压接到电线电缆的导体上,以确保连接的牢固性和可靠性。
从理论上来说,只要将连接部位贴合并受足够的压力,就能够实现电路的顺畅传输。
但实践上却不是那么简单的,它还需要结合人工智慧与电线电缆挤压设备的灵活性共同发挥作用。
主要依靠挤压设备完成。
目前市场上使用的电线电缆挤压设备常见有三种类型:手动挤压设备、强制挤压设备和自动挤压设备。
其中手动挤压设备虽然价格低廉,但是操作的工艺比较简单,需要的工人技能一般,输出的效果也没有保证。
强制挤压设备本身带有储能机构,以增大挤压力度和效率,同时减小人工操作的范畴,其成本较高。
自动挤压设备与强制挤压设备类似,但其自带电脑芯片,能够根据设定的规定,自动进行电线电缆挤压操作,输出的效率与产品牢固度均有保证,但价格则十分昂贵。
操作比较繁琐,有时会需要多人来完成。
如果工人的技能不足或操作不当,那么就可能引发不良后果,导致产品品质下降。
此外,在挤压加工过程中,机器的压力需要调整,如果不能达到适当的压力,就不能确保电路的通畅,从而影响产品的使用效果。
因此,时,技术人员需要保持良好的注意力和技术水平,才能保证产品的品质和生产效率。
在现代生产中有着不可忽视的作用。
在工业生产制造中,已经被广泛应用。
例如汽车、电子、航空航天、铁路等各个领域都需要使用技术。
特别是在电子通讯、精密测量等领域,电线电缆的链接需要具有极高的可靠性。
这就要求不断推进技术创新,提高生产效率和质量水平。
总之,是一个技术性较高的工艺过程。
虽说并不是一项艰巨的工作,但要求从业人员具备扎实的专业技能和经验,在操作和管理中时刻保持高度的警惕性。
而技术的不断创新和提升,则对于现代生产制造来说是非常支持和必不可少的。
尼龙护套电线挤出生产线工艺技术特点

D、在尼龙6的挤制前,应清除挤出机中螺杆与螺筒内杂质,如塑化不完善的塑料或其焦烧颗粒。有时,将干净的塑料如PVC绝缘料、尼龙加人料筒,并启动挤出机,借助于螺杆旋转用干净塑料顶出杂质,这过程我们俗称为“开机前的打料”,但是应注意 如设备加装旁通装置BYPASS的,开机前打料可将螺杆里的料通过旁通装置流出 如设备没有加装旁通装置,打料时一定要先打PVC绝缘料,再打尼龙料,否则先打尼龙料,尼龙会倒流到模芯,而模芯的温度约为160-180℃,尼龙6就会在模芯外壁冷凝为不均匀的凝固物,造成绝缘偏心。
2 绝缘和护套分别进行挤出的模具选择。
①绝缘挤出的挤压式模具通常按常规选取模具 见图2 。模具结构尺寸的选择如下
模芯孔径=导线外径+0.1+0.15mm
模芯承线长度= 4 - 5 mm
模套孔径=绝缘外径+0.05mm
模套承线长度=2-4mm
②尼龙护套挤出的挤管式模具
若使尼龙挤出的拉伸比小,则模芯和模套的间隙要小,出胶量和生产线速度就小,生产效率低 若拉伸比过大将发生料流的圆锥形拉破、撕裂和表面粗糙等缺陷,所以应合理选择拉伸比S=5-7。拉伸比计算公式为
我司即从2002年伊始即开始了尼龙电线挤出机的研发制造,至目前为止,已有数十台此类机器的制造经验,比较典型的即为03年重庆鸽牌80+40双层共挤尼龙线挤出生产线,04年印度RRCABLE公司之70+40双层共挤尼龙线挤出生产线,05年青岛电缆60+40尼龙护套及汽车线共挤生产线、05年重庆鸽牌80+40双层共挤尼龙线挤出生产线左右向共二条,05年马来西亚万泰之90+40双层共挤尼龙线挤出生产线。以上机器现均在客户工厂完好地使用,且所做产品完全达到客户各项技术要求。同时,通过与这些客户长期的合作,我司已掌握了全套的尼龙电线挤出生产线的完全生产工艺。目前所获得的尼龙双层共挤技术(一个机头一次挤出)、尼龙印字等多项工艺技术均属行业独创。正因如此,目前该产品已成我公司一主打优势产品,订货不断。
408 灯壳冲压自动生产线用下料机械手设计

摘 要本文简要的介绍了下料机械手的概念,机械手的组成和分类,机械手的自由度和坐 标形式以及液压驱动技术的特点,PLC控制的特点以及国内外机械手的发展状况。
本文对机械手的总体方案进行设计,根据设计要求,确定机械手为圆柱坐标形式并 且具有四个自由度,以及机械手的技术参数如手臂伸缩行程 500mm、手臂升降行程 100mm,同时确定了机械手的手部结构为夹钳式结构,设计了手腕、手臂和基座结构, 绘制了机械手液压系统原理图,通过对液压系统工况图进行研究,提高了图纸的质量和 绘图的效率。
采用 PLC 点位控制对机械手进行控制,选取了合适的 PLC 型号,根据设计要求选用 的 PLC 型 FX2N-48M,根据机械手的工况流程图,制定了 PLC 控制方案,分配 I/O 接线 口,绘制PLC外部接线图以及梯形图。
关键词:机械手,液压驱动,PLC控制ABSTRACTThis paper introduces the concept, composition, classification, degree of freedom, coordinate form of the manipulator, and the feature of hydraulic drive technology, as well as PLC control. It also introduces the development of the manipulator in our country and foreign country.This paper designs the manipulator’s whole precept, according to the design requirements, forming the manipulator’s cylindrical coordinate and four degrees of freedom, and its technical parameters as the arm telescopic stroke is 500mm,the arm lifting stroke is 100mm, at the same time, the manipulator hand structure is determined for clamp type, the manipulator’s wrist, arm, and base structure, drawing the manipulator hydraulic system diagram. Researching hydraulic system diagram, improve the quality and efficiency of drawing.Control manipulator by PLC position control, select a suitable PLC type, According to the design requirements, using FX2N48M according to the manipulator working flow diagram, setting PLC control precept, assign I/O connect port, drawing the exterior connect diagram of PLC.Key words: manipulator, hydraulic, PLC control目录1 绪论 (1)1.1 选题背景及意义 (1)1.2 国内外研究现状和趋势 (1)1.3 设计原则 (3)1.4 机械手的总体研究方案 (3)1.5 本章小结 (4)2 机械手机械部分的设计和计算 (5)2.1 手部的设计和计算 (5)2.2 手腕的设计和计算 (9)2.3 手臂的设计和计算 (11)2.4 本章小结 (18)3.液压系统设计 (19)3.1 液压系统的组成 (19)3.2 液压系统的优缺点 (19)3.3 制定液压系统的基本方案 (20)3.4 液压缸的结构设计 (20)3.5 液压元件的选型 (21)3.6 液压系统性能验算 (23)3.7 液压控制原理及过程 (24)3.8 油缸泄露问题与密封装置 (25)3.9 管路布置 (25)3.10 本章小结 (26)4 PLC 控制系统设计 (27)4.1 PLC的功能和应用 (27)4.2 常用的位置检测元件 (28)4.3 PLC控制系统的设计 (28)4.4 本章小结 (31)5 结论 (32)参考文献 (33)致谢 (34)1 绪论灯壳冲压自动生产线视为冲制汽车、拖拉机外装式大灯和防雾灯的灯壳而设计的。
12型/小时六工位转台式负压造型生产线

作者简介 : 张俊峰( 9 1 ) 男 , 17 一 , 高级工程 师 , 总工程师 , 主要 从事铸造机
械的研究与开发
中国铸造装 备与技术 42 1 C F l I / 0 1 VT
4 7
装 备 技 术 E up n e h oo y q ime t c n l T g
行解箱 。两条线轮流浇注给冷却 留出了足够 的时间。
期;
单条生产线运行总功率 :50 W; 10 k
压缩 空 气 消耗 :m / ; 83 h
压缩 空气 压力 :.~ .MP ; 05 06 a
单条线冷却水循环量 :5 m/ 。 10 3 h
3 设备 组成 及工 艺流 程
整条生产线 由造型单元 、 浇注冷却单元 、 下芯单元
摘要 : 负压造型生产 线( 该 亦称 V法造型 ) 主要用于生产工程机械用履 带板 , 生产线不仅包括传统 的造 型单 元、 浇注 、 冷却单元及砂处理单元 , 而且为提高生产效率 , 增加 了下芯单元。 关键 词 : 负压造 型 ; 法造 型 v
中图分类号: G 4 . : T 2 9 9 文献标识码 : ; B 文章编号: 6 9 5 ( 0 ) 4 3 10 — 682 儿 0— 0
造型单 元 工艺 流 程 : 造 型线 为六 工 位转 台造 型 , 该
六工位分别是覆膜工位 、 喷涂工位 、 扣箱工位 、 烘干工
位 、 砂振 实工 位 、 模 工位 。三对 模板 对 称分 布 在转 加 起
台六个工位上 , 同时工作。随着转 台转动一周 , 单个模 板依据覆膜 、 喷涂 、 设置冷铁及浇 冒口、 扣箱 、 烘干 、 加 砂、 振实、 覆背膜、 起模翻箱等工序连续进行操作 , 完成 上下砂箱的造型。 起模机械手分别对上箱 、 下箱进行起 模, 下箱翻转后 由 1 号造型转运车运至下芯单元下芯 , 然后在 2 号造 型转运小车上等待 与修好型的上箱合 箱 , 箱后 转运 至浇 注线 。 合 32 浇 注单元 及 工艺 流程 .
全套生产线简介QS-5180C
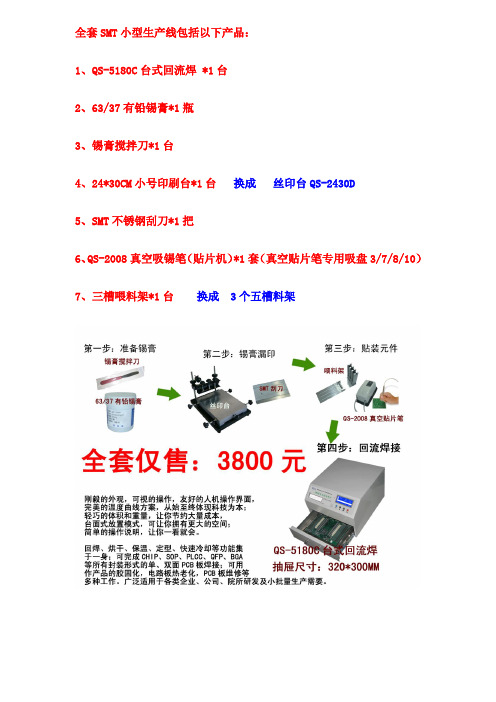
全套SMT小型生产线包括以下产品:1、QS-5180C台式回流焊 *1台2、63/37有铅锡膏*1瓶3、锡膏搅拌刀*1台4、24*30CM小号印刷台*1台换成丝印台QS-2430D5、SMT不锈钢刮刀*1把6、QS-2008真空吸锡笔(贴片机)*1套(真空贴片笔专用吸盘3/7/8/10)7、三槽喂料架*1台换成 3个五槽料架QS-5180C无铅抽屉式回流焊主要技术参数1、输入电源:AC220V/(AC110V定购)2、工作频率:50~60Hz3、输入最大功率:1650W4、红外线辐射加微热风混和加热方式5、抽屉面积:320x300mm6、外型尺寸:418x372x250mm7、操作系统:QS-5180C中英文双语操作系统8、工作模式:自动回焊模式、可调恒温维修模式9、温度曲线段:预热段、加热段、焊接段、保温段、冷却段共五段10、预热段温度设置范围和时间:70~150℃、时间:0~5min11、加热段温度设置范围和时间:预热段温度~220℃、时间:0~5min12、焊接段温度设置范围和时间:加热段温度~280℃、时间:0~30s13、保温段温度设置范围和时间:焊接段温度-(0~50℃)QS-5180C回流焊是最新开发的一种用于在电子产品,维修的SMT工艺的便捷式的回焊设备。
该产品采用远红外线加热元件和感温元件。
通过微电脑的精密控制,使回流焊的温控曲线完全符合SMT生产工艺的回焊要求,“温度曲线”精密可调,可满足不同材料参数的焊膏要求。
可通过“设置”功能使设备具有回焊,维修烘干等多种功能。
整机共有两套运行参数可以选择,分别是“回焊”和“维修”。
“回焊”是针对焊接电路板元件而设计的,运行的整个过程有加热,保温,(设定的焊接)温度和降温;“维修”是针对对拆卸电路板元件\、而设计的,运行的过程中有加热和保温,与“回焊”相比就少了个降温过程。
活全压机操作指引

350
70
6
195
5
7
195
30
8
180
15
9
160
10
抽真空
保持
释放
第1段
0分钟
第7段15分钟
第8段
15分钟
7.2 PTN2(使用于2116×2、2116×4(RC:50%以下)、2116×2+1080×2、结构)最高排12层;
段数
温度(℃)
时间(min)
压力(psi)
时间(min)
1
130
2
段数
温度(℃)
时间(min)
压力(psi)
时间(min)
1
130
5
100
20
2
140
15
3
150
10
250
30
4
160
10
5
170
10
6
180
10
380
65
7
195
10
8
195
45
9
180
10
200
20
10
150
10
抽真空
保持
释放
第1段
0分钟
每7段10分钟
第9段
10分钟
7.7 PTN7(使用于六至十层高TG结构)最高排8层;
4.5.3自动压合中定期检查压力、温度、真空是否符合设定值。
4.5.4热压完成后,压机按自动程序,释放真空。开门及热盘下降,则完成压板程序。
4.6压力计算方式
每段设定压力(psi)×板面积(in²)×每层件数÷2.2
实际压力(kg/cm²)=
挤出生产线

挤出生产线挤出生产线是一种流程化的制造工艺,通常用于生产塑料产品。
挤出生产线的工艺流程简单,但却可以生产出高质量、精确尺寸的产品。
本篇文章将会介绍挤出生产线的工艺流程和一些常见的应用。
一、挤出生产线的工艺流程挤出生产线是通过将一个高温、高压的塑料熔体通过一个模具挤出,然后将其冷却成型。
以下是挤出生产线的主要工艺流程:1. 塑料颗粒熔化首先,塑料颗粒被放入挤出机中,并通过加热、混合和压缩将其熔化。
这一步通常需要使用高温和高压,以使塑料颗粒达到流动状态。
2. 熔体挤出熔化后的塑料通过挤出机中的螺杆和筒体经过挤压,然后被挤出到一个具有所需形状的模具中。
此时,模具通常被加热以保持熔体的流动性。
3. 冷却和固化一旦塑料从模具挤出,它会迅速冷却下来并固化成所需形状。
通常在挤出生产线中,会使用水或空气来冷却模具和塑料。
4. 活动切割或定长切割完成冷却和固化后的塑料是一条连续的膜或管状物,需要被切割成特定的长度或大小。
这一步通常由一台切割机器来完成。
5. 转运和包装最后,被切割成特定尺寸的产品被转移到包装区域,并用包装材料包装以便保护和运输。
二、挤出生产线的应用挤出生产线是非常流程化的制造工艺,可以适用于许多应用领域。
以下是挤出生产线的几个常见应用:1. 包装挤出生产线通常用于生产各种类型的包装材料,如塑料袋、保鲜膜、泡沫箱等。
这些材料通常需要具有一定的柔韧性和耐用性,以保护所包装的物品。
2. 建筑挤出生产线经常用于生产建筑材料,如PVC管道、墙壁板、屋顶板等。
由于其高强度、抗腐蚀性和耐用性,它们被广泛应用于住宅和商业建筑。
3. 汽车制造挤出生产线还可以用于生产汽车零部件。
例如,塑料车门板、汽车排气管和车顶都可以通过挤出生产线来制造。
4. 医疗器械挤出生产线的应用还可以扩展到医疗器械制造领域。
医疗管道、输液器和零部件等可以通过挤出生产线来生产。
结论挤出生产线是一种高效、流程化的生产工艺,可以用于生产各种类型的塑料制品。
LED软灯带硅胶挤出生产线P2

LED硅胶共挤灯带是一款硅胶材质全包裹灯带,是硅胶和灯带同时通过挤出机一起挤出的,相对于环氧胶灌封灯带,PU胶灌封灯带,液态硅胶灌封灯带而言此系列灯带具有以下显著特点:
现场生产线实图
1、色温飘移更小,能够保证封胶后与原始色温相差不大并色温
一致性很好。
2、本产品为外方内弧镂空的设计,胶与灯珠剥离,有效解决色
差问题,发光角度更好,以及修补比较容易。
3、由于灯带一次压出出型,堵头通过模压与挤出灯带融为一体,其具有优异的防水性,不被水浸蚀,长期水中亮灯不脱离
4、本产品为硅胶与灯带共挤,通过模具成型,一次可以挤出上千米,挤出尺寸更标准,效率高。
5、本产品为加热固化型,所以深度固化时间短,出货速度快。
6、具有优异的透光率和折射率,能够最大限度降低的光源的光衰。
7、具有优异的耐候性能,能保证灯条在较宽的温度范围内
(-40~220℃)以及水底等特殊环境中正常使用,从而使得灯条使用地域几乎无限制。
8、耐酸碱盐更好,在弱酸弱碱弱盐情况下,灯带外观无变化,正常使用。
9、具有超强的抗紫外线能力,能够保证灯带长时间在户外使用。
10、优异的硅胶强度,使得在特殊环境中,灯带的抗破环能力高。
11、封胶原材料环保等级更高,本产品的胶体为食品级硅胶。
12、灯板与胶体粘合性非常好,致使灯带外观更亮丽。
13、挤出工艺解决非常规尺寸灯带封胶成型难等相关问题,一次性挤出,按客人要求规格裁剪。
14、通过模具成型可以满足客人对灯带的任何设计需求(尺寸,形状,颜色等)
15、适用产品:高低压软灯带、双色霓虹管、光学灯带、硅胶套管等。
- 1、下载文档前请自行甄别文档内容的完整性,平台不提供额外的编辑、内容补充、找答案等附加服务。
- 2、"仅部分预览"的文档,不可在线预览部分如存在完整性等问题,可反馈申请退款(可完整预览的文档不适用该条件!)。
- 3、如文档侵犯您的权益,请联系客服反馈,我们会尽快为您处理(人工客服工作时间:9:00-18:30)。
鼎隆LED高低压贴片灯带挤出生产线
一.LED高低压灯带挤出设备
1.挤出技术介绍
利用挤出主机色特定形状的螺杆,机筒中旋转,将由料斗中送来的胶料向前挤压,使胶料均匀熔融,通过机头和不同形状的模具,使胶料料挤压成连续性的所需要的各种形状的塑料层,挤包在灯带上。
2.LED灯带挤出分类
2.1按挤出原理来区分,可分为PVC/PU软灯带挤出设备(热挤出)和硅胶软灯带挤出设备(冷挤出)
2.2按挤出材质的颜色分,可分为PVC/PU软灯带单色挤出设备、硅胶软灯带单色挤出设备、PVC/PU软灯带双色共挤设备、硅胶软灯带双色共挤设备.
2.3 LED硅胶套管挤出机组
3.设备的用途
适用于单/双色LED灯带、LED彩虹管、LED柔性霓虹灯带、各种高低压贴片软灯带、灯串的外包PVC、PU、硅胶等胶料挤出成型。
技术参数+威信3 5 4 2 6 3 3 1 2
二.挤出灯带的特点
相对于环氧胶灌封灯带,PU胶灌封灯带,液态硅胶灌封灯带而言此系列灯带具有以下显著特点:
a. 色温飘移更小,能够保证封胶后与原始色温相差不大并色温一致性很好。
b. 本产品为外方内弧镂空的设计,胶与灯珠剥离,有效解决色差问题,发光角度更
好,以及修补比较容易。
c. 由于灯带一次压出出型,堵头通过模压与挤出灯带融为一体,其具有优异的防水
性,不被水浸蚀,长期水中亮灯不脱离
d. 本产品为胶料与灯带共挤,通过模具成型,一次可以挤出上千米,挤出尺寸更标
准,效率高。
e. 本产品有专用固化装置,所以深度固化时间短,出货速度快。
f. 具有优异的透光率和折射率,能够最大限度降低的光源的光衰。
g. 硅胶灯带具有优异的耐候性能,能保证灯条在较宽的温度范围内(-40~220℃)
以及水底等特殊环境中正常使用,从而使得灯条使用地域几乎无限制。
h. 优异的硅胶强度,使得在特殊环境中,灯带的抗破环能力高。
i. 灯板与胶体粘合性非常好,致使灯带外观更亮丽。
j. 挤出工艺解决非常规尺寸灯带封胶成型难等相关问题,一次性挤出,按客人要求规格裁剪。
k. 通过模具成型可以满足客人对灯带的任何设计需求(尺寸,形状,颜色等)。