AI电容焊点爆锡,气孔问题处理
激光焊接过程中气孔产生的原因及预防气孔产生的方法

激光焊接过程中气孔产生的原因及预防气孔产生的方法气孔是激光焊接过程中常见的焊接缺陷之一,对焊接质量和强度有直接影响。
以下是关于激光焊接中气孔产生的原因以及预防气孔产生的方法的详细描述:1. 气体污染:激光焊接过程中,如果焊接区域周围存在大量的气体,例如空气中的氧气、水蒸气等,这些气体会被激光能量激发,形成气泡或气孔。
首先要确保焊接区域周围的气体洁净。
2. 金属材料表面含气:金属材料的表面可能存在一定的气体含量,尤其是会被吸附的气体,如氧、氮等。
在焊接过程中,这些气体会被加热并释放出来,形成气孔。
为了预防气孔产生,需要对金属材料进行预处理,如去除表面气体、氧化皮等。
3. 焊接材料中含有挥发性元素:有些焊接材料中含有挥发性元素,如镁、锌等。
这些元素在激光焊接过程中会挥发,并形成气泡或气孔。
为了预防气孔产生,可以选择低挥发性的焊接材料。
4. 激光功率过大:激光焊接过程中,如果激光功率过大,会导致焊接区域瞬间升温过高,形成蒸汽,进而形成气孔。
要合理控制激光功率,尽量避免过高的温度。
5. 极性不当:激光焊接中,电极和焊接工件的极性选择不当也会导致气孔产生。
正确选择和调整电极和工件的极性可以有效地减少气孔的产生。
6. 引热区不足:激光焊接时,引热区的大小直接影响了焊接过程中金属材料的液态区域大小。
如果引热区不足,金属材料无法充分熔化,容易形成气孔。
要根据焊接材料的性质和要求,合理调整引热区的大小。
7. 激光焊接速度过快:焊接速度过快会导致焊缝区域的金属无法完全熔化和扩散,从而形成气孔。
在焊接过程中,应根据具体情况适度降低焊接速度,保证金属熔池的稳定性。
8. 过高的焊接压力:焊接压力过高会导致焊接区域的金属材料被排压,并使金属熔池内的气体无法自由扩散和排除,从而形成气孔。
在激光焊接过程中,需要合适地选择和调整焊接压力。
9. 不适当的气体保护:激光焊接中常用的气体保护有惰性气体,如氩气、氦气等,以及活性气体,如氧气、二氧化碳等。
焊接气孔产生的原因及措施
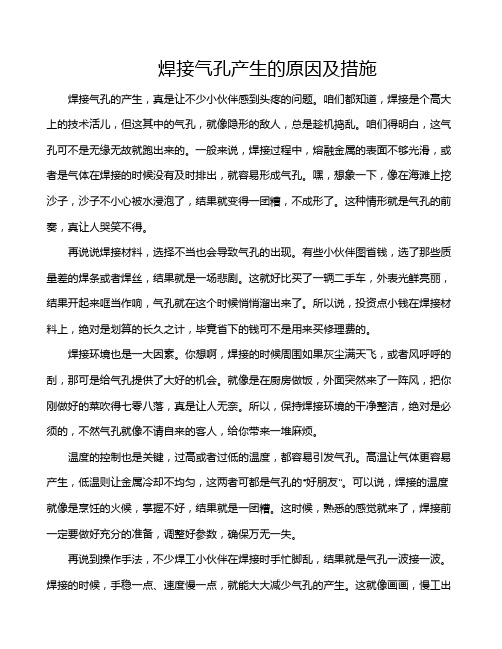
焊接气孔产生的原因及措施焊接气孔的产生,真是让不少小伙伴感到头疼的问题。
咱们都知道,焊接是个高大上的技术活儿,但这其中的气孔,就像隐形的敌人,总是趁机捣乱。
咱们得明白,这气孔可不是无缘无故就跑出来的。
一般来说,焊接过程中,熔融金属的表面不够光滑,或者是气体在焊接的时候没有及时排出,就容易形成气孔。
嘿,想象一下,像在海滩上挖沙子,沙子不小心被水浸泡了,结果就变得一团糟,不成形了。
这种情形就是气孔的前奏,真让人哭笑不得。
再说说焊接材料,选择不当也会导致气孔的出现。
有些小伙伴图省钱,选了那些质量差的焊条或者焊丝,结果就是一场悲剧。
这就好比买了一辆二手车,外表光鲜亮丽,结果开起来哐当作响,气孔就在这个时候悄悄溜出来了。
所以说,投资点小钱在焊接材料上,绝对是划算的长久之计,毕竟省下的钱可不是用来买修理费的。
焊接环境也是一大因素。
你想啊,焊接的时候周围如果灰尘满天飞,或者风呼呼的刮,那可是给气孔提供了大好的机会。
就像是在厨房做饭,外面突然来了一阵风,把你刚做好的菜吹得七零八落,真是让人无奈。
所以,保持焊接环境的干净整洁,绝对是必须的,不然气孔就像不请自来的客人,给你带来一堆麻烦。
温度的控制也是关键,过高或者过低的温度,都容易引发气孔。
高温让气体更容易产生,低温则让金属冷却不均匀,这两者可都是气孔的“好朋友”。
可以说,焊接的温度就像是烹饪的火候,掌握不好,结果就是一团糟。
这时候,熟悉的感觉就来了,焊接前一定要做好充分的准备,调整好参数,确保万无一失。
再说到操作手法,不少焊工小伙伴在焊接时手忙脚乱,结果就是气孔一波接一波。
焊接的时候,手稳一点、速度慢一点,就能大大减少气孔的产生。
这就像画画,慢工出细活,不急于求成,才能画出美丽的图画。
再加上多加练习,熟能生巧,等到水平提升了,气孔自然就会减少。
万一出现气孔,也别慌,解决办法还是有的。
最直接的方法,就是对焊缝进行打磨和清理,把气孔处的金属去掉,重新焊接。
虽然听起来麻烦,但这就是焊接的一部分嘛。
焊接气孔产生的原因及解决方法
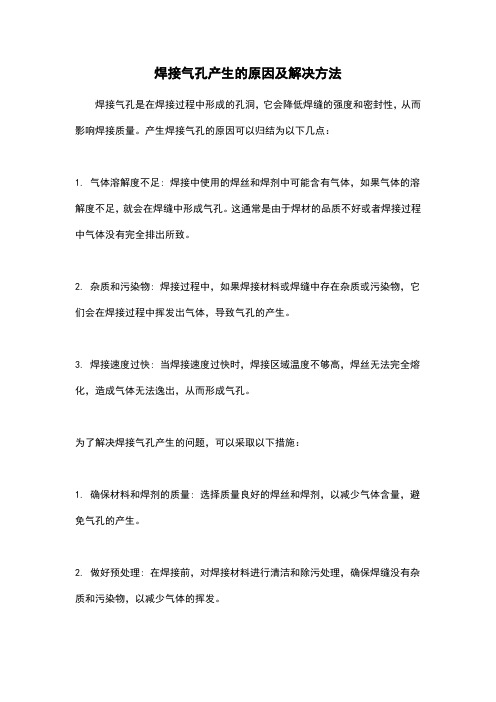
焊接气孔产生的原因及解决方法
焊接气孔是在焊接过程中形成的孔洞,它会降低焊缝的强度和密封性,从而影响焊接质量。
产生焊接气孔的原因可以归结为以下几点:
1. 气体溶解度不足: 焊接中使用的焊丝和焊剂中可能含有气体,如果气体的溶解度不足,就会在焊缝中形成气孔。
这通常是由于焊材的品质不好或者焊接过程中气体没有完全排出所致。
2. 杂质和污染物: 焊接过程中,如果焊接材料或焊缝中存在杂质或污染物,它们会在焊接过程中挥发出气体,导致气孔的产生。
3. 焊接速度过快: 当焊接速度过快时,焊接区域温度不够高,焊丝无法完全熔化,造成气体无法逸出,从而形成气孔。
为了解决焊接气孔产生的问题,可以采取以下措施:
1. 确保材料和焊剂的质量: 选择质量良好的焊丝和焊剂,以减少气体含量,避免气孔的产生。
2. 做好预处理: 在焊接前,对焊接材料进行清洁和除污处理,确保焊缝没有杂质和污染物,以减少气体的挥发。
3. 控制焊接速度: 确保焊接速度适中,使焊接区域的温度能够达到熔化焊丝的温度,避免气体无法逸出。
4. 确保焊接环境: 在焊接过程中,保持焊接环境的干燥和无风状态,以减少气体的挥发和吸入。
5. 使用合适的焊接技术: 选择适当的焊接技术,如氩弧焊等,可以减少气孔的产生。
总之,焊接气孔的产生是由于气体溶解度不足、杂质和污染物以及焊接速度过快等原因所致。
要解决焊接气孔问题,需要从材料和焊接环境的质量控制、预处理、控制焊接速度以及选择合适的焊接技术等方面着手。
炸锡的原因和处理方法

炸锡的原因和处理方法
炸锡,又称爆锡,是指在焊接过程中,焊点出现锡珠四射或者锡块飞溅的现象。
出现炸锡现象的原因可能有以下几种:
- 环境问题:由于空气中存在水份,特别是在春天雨季或潮湿的环境中,焊锡丝或线路板可能会因保管不周而受潮,表面附着有水份,进行焊锡作业时就会引发炸锡。
- 焊锡丝加工问题:在生产焊锡丝过程中,经过拉丝机时,焊锡丝如有裂缝,拉丝油可能会随裂缝渗入其中,这也会引发焊接作业时炸锡现象的发生。
- 烙铁头温度过高:不同的焊锡丝中助焊剂的含量成分也不尽相同,过高的温度会使助焊剂变得异常活跃,从而引发炸锡。
为了避免炸锡现象,可以采取以下措施:
- 加强保管措施,防止受潮现象,控制温度和湿度,干燥的仓储或作业环境。
- 在焊锡丝生产工艺时,加强巡检和管控,避免有裂缝的焊锡丝进入拉丝环节,如有发现应剪掉有裂缝的部位以作废处理。
- 加强半成品和成品抽检力度。
- 如果遇潮湿或连下大雨天气的环境下,在焊接作业前,请将需焊接的板材烘干,以去除板材焊盘表面来自空气中的水份。
焊接气孔产生原因及处理方法

焊接气孔产生原因及处理方法随着时代的发展,现代工业对焊接技术的工艺要求也越来越高,而焊接气孔产生的不良影响成为大多数焊接作业者的关注和急需解决的问题,本文就常见气孔形成的原因及一些处理措施进行论述。
标签:气孔;形成因素;防治措施焊接是在工程施工中广泛应用的一项专业技术,实践性较强。
在平常的焊接作业中,钢构的仰焊、管道的定位焊和管道的横焊出现气孔的机率与平焊、立焊相比要多。
在实际施工中,管道的定位焊和横焊由于焊接的位置空间比较狭小、盲区较多,焊接过程中的操作会受到限制,以致于无法观察熔池的形态,因此出现气孔的可能性会大大增加。
本文结合作者的实践和理论经验,浅谈气孔形成的因素和处理措施。
一、气孔的定义和类形(一)定义气孔就是在焊接时,熔池中的气泡在凝固时未能逸出而残留下来形成的空穴。
(二)分类按气孔产生的部位不同,可分为表面气孔和内部气孔。
按气孔的分布状况,分为单个气孔、疏散气孔、均布气孔、密集气孔和链接气孔。
按气孔的形态,分为球形气孔、条形气孔、针状气孔等。
按气体成分,分为氢气孔、氮气孔、氧气孔、一氧化碳气孔等。
二、气孔形成的因素一般施工条件中常见的气孔形成必然与气体有联系,气孔的实质是:在金属凝固期间没有及时浮出熔池而残留在金属中的气泡。
焊接金属中的气体主要有氢、氧、一氧化碳、二氧化碳、硫化氢等多种气体。
这些气体可能来源于母材、焊丝、焊材、保护气体、大气等,不同的焊接母材所选用的焊接材料、焊接方法、焊接环境都会起到不同的作用,根据不同的焊接作业条件,从以下几个方面分析影响气孔形成的因素。
(一)母材在工程施工中不同的施工工艺要求用不同的焊接母材,这就需要焊接作业者有更高的技能要求,焊缝的处理、焊缝的清理是焊接作业中的一项重要环节,因为母材表面往往都会有水分、油、漆、锈等物质,这些物质会导致形成焊接气孔。
要通过机械处理、钢丝刷处理、化学处理的办法清理母材表面,处理后的母材要恢复原有的金属色泽。
(二)焊材焊材是焊缝填充的主要来源,也是对焊缝影响较大的因素之一。
铝合金MIG焊气孔成因及消除措施

铝合金MIG焊气孔成因及消除措施原创 2015-06-08 彭勇军1. 概述铝合金MIG焊时,焊缝容易产生气孔,这由于焊丝是以细小熔滴形式通过弧柱进入熔池,由于弧柱温度高,且熔滴比表面积大,有利于熔敷金属吸收氢;同时,MIG焊时的熔池熔化母材的深度较大,由于铝合金金属的密度小,冷却速度快,不利于熔池中的气泡逸出,导致焊缝产生气孔。
从焊接生产来分析,导致焊缝产生气孔主要有焊接现场湿度的控制;焊接区的水分、脏物和氧化膜;焊接保护气体的纯度;焊丝表面是否受潮和氧化;焊接设备的影响;焊工的操作技能等。
为查找现场焊缝产生气孔的原因,我们通过焊接性试验及采取相应的检验方法来验证解决措施的有效性。
2. 现场情况及原因分析(1)现场的湿度控制现场采用大型空调进行整体除湿和控温。
现场湿度在45%~60%内,符合铝合金焊接生产湿度控制要求。
由于下午工作结束后,大型空调会自动关闭,到了次日上班时间再启动。
这样,造成在非工作时间段,现场的盘状焊丝的外表层受潮。
(2)焊丝?首先,焊丝储存库房面积45~50m2,高3.2~3.5m,库房空间偏大,且靠窗户部位与其他房间能够形成少量的空气对流。
库房内有一台含水箱除湿机,除湿机降湿形成的水仍然存在于库房中。
这样,造成库房内的焊丝除湿效果有限。
其次,现场使用的盘状焊丝有三家品牌。
三家焊丝焊接出来的焊缝都存在气孔超标的情况。
由于铝合金焊丝易受大气条件的影响,焊丝在海运和陆地的物流过程中,存在包装破损的可能。
包装破损将导致盘状焊丝被受潮和氧化。
从盘状铝合金焊丝生产之日算起,铝合金焊丝在外包装不破损的情况下,存储时限有一年和两年的之分。
焊丝超过期限后,焊丝在使用前应全面检查:即焊丝是否吸潮或氧化应通过焊接性试验来检测焊缝气孔是否超标,确认超过期限能否用于焊接生产。
存储时限为一年的焊丝,其内包装材料为透明的塑料薄膜;存储时限为两年的焊丝,其内包装材料为铝制压膜。
由于三家品牌焊丝为透明的塑料薄膜包装,存储时限不足一个月时间就将到期,不能完全排除焊丝导致气孔产生这一因素。
焊锡问题点解决方案

锡焊工程的不良原因分析及改善对策(一)1.短路(SHORT)焊接设计不当,可由圆型焊垫改为椭圆形。
加大点与点之间的距离。
零件方向设计不当,如S0IC的脚如与锡波平行,便易短路,修改零件方向,使其与锡波垂直.自动插件弯脚所致,由于PCB规定线脚的长度在2mm以下(无短路危险时)及担心弯脚角度太大时零件会掉,故因此造成短路,需将焊点离开线路2mm以上.基板孔太大.钖与孔中穿透至基板的上侧而造成短路,故需缩小孔径至下影响零件装插的程度。
自动插件时,残留的零件脚太长,需限制在2mm以下.锡炉温度太低。
钖无法迅速滴回锡槽,需调高锅炉温度.轴送带速度太慢,锡无法快速滴回,需调快轴送带速度.板面的可焊性不佳,将板面清洁。
基板中玻璃材料溢出,在焊接前检查板面是否有玻璃物突出.阻焊膜失效,检查适当的阻焊膜和使用方式.板面污染,将板面清洁。
2.针孔及气孔(PINHOLES AND BLOwHOLES)外表上,针孔及气孔的不同在于针孔的直径较小,现于表面.可看到底部。
针孔及气孔都表现为焊点中有气泡.只是尚未变大王表层,大部分都发生在基板底郎,当底部的气泡完全扩散爆开前已冷凝时,即形成了针孔或气孔。
形成的原因如下:基板或零件的线脚上沾有有机污染物.此类污染材料来自自动插件面,零件存放及贮存不良因素。
用普通的溶剂即可轻易的去除此类污染物,但遇sILICOK0II类似含有SILICON的产品则较困难。
如发现问题的造成是因为SILICON OIL,则须考虑改变润滑油或脱膜剂的来源。
基板含有电铍溶液和,类似材料所产生之水气,如果基板使用较廉价的材料,则有可能吸入此类水气,焊锡时产生足够的热,将溶液气化而造成气孔装配前将基板在烤箱中烘烤,可以改善此间题。
基板储存太多或包装不当,吸收附近环境的水氟,故装配前需先烘烤。
助焊剂活性不够,助焊剂润湿不良.也会造成针孔及氧孔.助焊剂槽中含有水份,需定期更换助焊剂。
助焊剂水份过多,也是造成针孔及气孔的原因,应更换助焊剂.发泡及空压机压缩中含有过多的水份,需加装滤水器,并定期排水.预热温度过低,无法蒸发水氟或溶剂,基板一旦进入锡炉,瞬间与高温接解,而产生爆裂,故需调高预热温度.3.吃锡不良(POOR WETTING)现象为线路板的表面有部分未沾到锡,原因为:表面附有油脂、杂质氧化等,可以溶解洗净。
电容器的常见故障处理方法与技术

电容 器 油 、 二 烷 基苯 、 丙基 联 苯 、 芳 基 异 烷 十 异 二 苯 甲基硅 油 ; 按照 电容 器 固体 电介 质可 分为 : 电 全 容器 纸 电介质 、 聚丙 烯 薄 膜 介 质 、 、 膜 复合 全 纸 薄
容器 、 串联 电容器 、 电热 电容 器 、 均压 电容 器 、 波 滤
电容器 、 脉冲电容器 、 标准电容器等 8 个系列。不 同类 型 的电力 电容器 具 有不 同的用途 。 并 联 电容 器 与负 荷 或 者 供 电设 备 并 联 运 行 ,
施, 正确掌握 电容器各种常见故障相应的处理方法和注意事项。可以延长电容器的使 用寿命 , 减 少运行 中 出现 故 障的机 会 , 保证 电力 系统 正 常 的运行 。 关键 词 : 电容 器 ; 故 障 ; 运行 ; 处 理 ; 检修 ; 防 火措施 中图分类 号 : M 3 . 文献 标识 码 : T 5 14 B 文章编 号 : 6 4 15 ( 0 0 0 - 6 - 1 7 —7 7 2 1 )40 1 4 0 0
r t fc pa i ra d a s r r lo e ai n o o rs se . a e o a ct n s u e no ma p r t fp we y t m o o K e wo d c p ct r a l; o r to y r s: a a i ;f u t pea in;te t n ;ma n e n e;fr r v n o a u e o r ame t i tna c i e p e e t n me i s rs
焊接气孔产生原因及防治措施

焊接气孔产生原因及防治措施一、表面气孔1、现象焊接过程中,熔池中的气体未完全溢出熔池(一部分溢出),而熔池已经凝固,在焊缝表面形成孔洞。
2、原因分析⑴焊接过程中由于防风措施不严格,熔池混入气体;⑵焊接材料没有经过烘培或烘培不符合要求,焊丝清理不干净,在焊接过程中自身产生气体进入熔池;⑶熔池温度低,凝固时间短;⑷焊件清理不干净,杂质在焊接高温时产生气体进入熔池;⑸电弧过长,氩弧焊时保护气体流量过大或过小,保护效果不好等。
3、防治措施⑴母材、焊丝按照要求清理干净。
⑵焊条按照要求烘培。
⑶防风措施严格,无穿堂风等。
⑷选用合适的焊接线能量参数,焊接速度不能过快,电弧不能过长,正确掌握起弧、运条、息弧等操作要领。
⑸氩弧焊时保护气流流量合适,氩气纯度符合要求。
4、治理措施⑴焊接材料、母材打磨清理等严格按照规定执行;⑵加强焊工练习,提高操作水平和操作经验;⑶对有表面气孔的焊缝,机械打磨清除缺陷,必要时进行补焊。
二、内部气孔1、现象在焊缝中出现的单个、条状或群体气孔,是焊缝内部最常见的缺陷。
2、原因分析根本原因是焊接过程中,焊接本身产生的气体或外部气体进入熔池,在熔池凝固前没有来得及溢出熔池而残留在焊缝中。
3、防治措施预防措施主要从减少焊缝中气体的数量和加强气体从熔池中的溢出两方面考虑,主要有以下几点:⑴焊条要求进行烘培,装在保温筒内,随用随取;⑵焊丝清理干净,无油污等杂质;⑶焊件周围10~15㎜范围内清理干净,直至发出金属光泽;⑷注意周围焊接施工环境,搭设防风设施,管子焊接无穿堂风;⑸氩弧焊时,氩气纯度不低于99.95%,氩气流量合适;⑹尽量采用短弧焊接,减少气体进入熔池的机会;⑺焊工操作手法合理,焊条、焊枪角度合适;⑻焊接线能量合适,焊接速度不能过快;⑼按照工艺要求进行焊件预热。
4、治理措施⑴严格按照预防措施执行;⑵加强焊工练习,提高操作水平和责任心;⑶对在探伤过程中发现的超标气孔,采取挖补措施。
三、夹渣1、现象焊接过程中药皮等杂质夹杂在熔池中,熔池凝固后形成的焊缝中的夹杂物。
常见焊接缺陷产生原因及处理办法
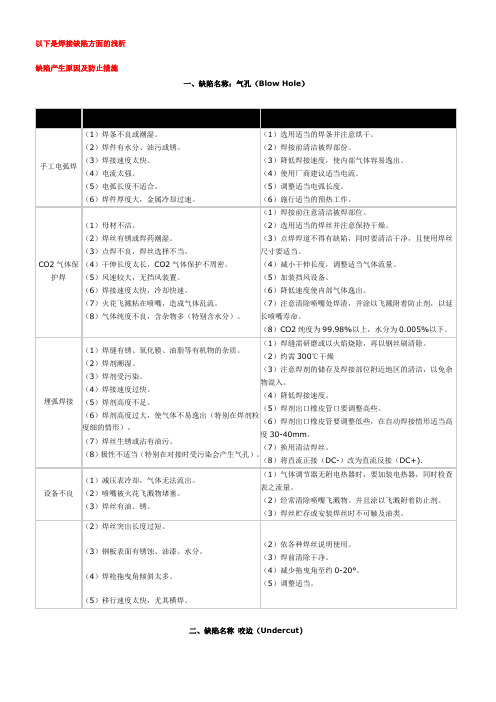
(2)提高电弧长度。
(3)焊丝不可离交点太远。
火花飞溅过多
(1)焊条不良。
(2)电弧太长。
(3)电流太高或太低。
(4)电弧电压太高或太低。
(5)焊丝突出过长。
(6)焊枪倾斜过度,拖曳角太大。
(7)焊丝过度吸湿。
(8)焊机情况不良。
(1)采用干燥合适之焊条。
(2)使用较短之电弧。
CO2气体
电弧焊
(1)母材倾斜(下坡)使焊渣超前。
(2)前一道焊接后,焊渣未清洁干净。
(3)电流过小,速度慢,焊着量多。
(4)用前进法焊接,开槽内焊渣超前甚多。
(1)尽可能将焊件放置水平位置。
(2)注意每道焊道之清洁。
(3)增加电流和焊速,使焊渣容易浮起。
(4)提高焊接速度
埋弧
焊接
(1)焊接方向朝母材倾斜方向,因此焊渣流动超前。
(3)多层焊接时,第一层焊道过小。
(4)焊接顺序不当,产生拘束力过强。
(5)焊丝潮湿,氢气侵入焊道。
(6)套板密接不良,形成高低不平,致应力集中。
(7)因第一层焊接量过多,冷却缓慢(不锈钢,铝合金等)。
(1)注意适当开槽角度与电流的配合,必要时要加大开槽角度。
(2)采用含碳量低的焊条。
(3)第一道焊着金属须充分能抵抗收缩应力。
(4)焊丝伸出长度太短。
(5)电压太高,电弧太长。
(6)电流太大。
(7)焊接速度太快。
(1)·电弧偏向一方置一地线。
·正对偏向一方焊接。
·采用短电弧。
·改正磁场使趋均一。
·改用交流电焊
(2)调整接地线位置。
(3)减小焊枪拖曳角。
(4)增长焊丝伸出长度。
焊缝气孔的处理方法

焊缝气孔的处理方法焊缝气孔是焊接过程中经常出现的一种焊接缺陷,它对焊接接头的强度和密封性能会产生负面影响。
因此,及时有效地处理焊缝气孔是保证焊接质量的关键。
焊缝气孔产生的原因主要有两方面,一方面是由焊接材料内部的气体排放所造成的,另一方面是由焊接过程中不良的保护气体环境所致。
因此,处理焊缝气孔的方法也可以从这两个方面来考虑。
首先,针对焊接材料内部的气体排放问题,可以从以下几个方面进行处理。
1.选择合适的焊接材料:合理选择焊接材料可以减少气孔的产生。
对于易产生气孔的焊接材料,可以选择低气含量的焊丝或焊条,以减少气体的排放。
2.控制焊接材料的含水量:焊接材料的含水量过高也会导致气孔的产生。
在进行焊接前,应确保焊接材料的含水量在合理范围内,以减少气孔的形成。
3.预热和干燥焊接材料:对于一些特殊材料,需要在焊接前进行预热和干燥处理,以减少气体的排放。
这样可以有效地降低气孔的产生率。
其次,针对焊接过程中的保护气体环境问题,可以从以下几个方面进行处理。
1.选择合适的保护气体:选择合适的保护气体是减少气孔产生的重要措施。
对于一些易产生气孔的焊接材料,可以选择直流极性焊接方式和高纯度的保护气体,以减少气孔的形成。
2.控制焊接环境的湿度和温度:焊接环境的湿度和温度过高会导致气孔的产生。
因此,在进行焊接时,应控制好环境的湿度和温度,以减少气孔的生成。
3.合理控制焊接电流和电压:合理调节焊接电流和电压也是减少气孔产生的重要方法。
通过调节电流和电压的大小,可以控制好焊接过程中的热量分布,从而减少气孔的产生。
4.增加焊接速度:增加焊接速度可以减少焊缝中气体的进入,从而减少气孔的形成。
但是要注意控制好焊接速度,避免焊接过快导致质量下降。
在实际焊接过程中,以上方法可以根据实际情况进行综合应用。
焊接前的材料选择和预处理对于减少气孔的产生非常重要,焊接过程中的保护气体和环境控制也需要进行有效的调节。
此外,焊工的操作技术和经验也是影响焊缝气孔形成的关键因素。
焊接气孔产生的原因和防范措施
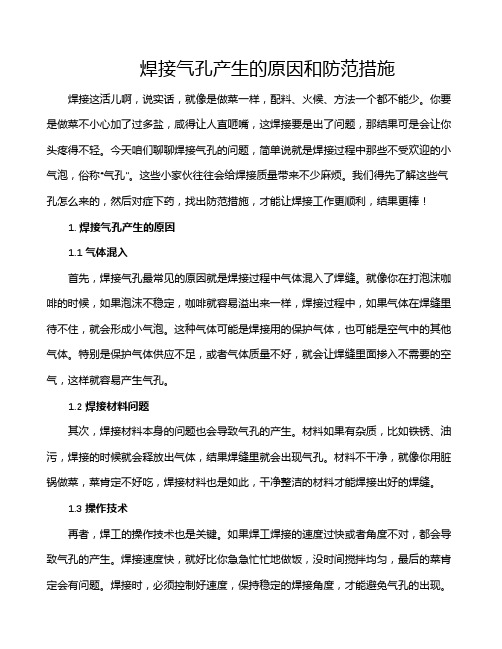
焊接气孔产生的原因和防范措施焊接这活儿啊,说实话,就像是做菜一样,配料、火候、方法一个都不能少。
你要是做菜不小心加了过多盐,咸得让人直咂嘴,这焊接要是出了问题,那结果可是会让你头疼得不轻。
今天咱们聊聊焊接气孔的问题,简单说就是焊接过程中那些不受欢迎的小气泡,俗称“气孔”。
这些小家伙往往会给焊接质量带来不少麻烦。
我们得先了解这些气孔怎么来的,然后对症下药,找出防范措施,才能让焊接工作更顺利,结果更棒!1. 焊接气孔产生的原因1.1 气体混入首先,焊接气孔最常见的原因就是焊接过程中气体混入了焊缝。
就像你在打泡沫咖啡的时候,如果泡沫不稳定,咖啡就容易溢出来一样,焊接过程中,如果气体在焊缝里待不住,就会形成小气泡。
这种气体可能是焊接用的保护气体,也可能是空气中的其他气体。
特别是保护气体供应不足,或者气体质量不好,就会让焊缝里面掺入不需要的空气,这样就容易产生气孔。
1.2 焊接材料问题其次,焊接材料本身的问题也会导致气孔的产生。
材料如果有杂质,比如铁锈、油污,焊接的时候就会释放出气体,结果焊缝里就会出现气孔。
材料不干净,就像你用脏锅做菜,菜肯定不好吃,焊接材料也是如此,干净整洁的材料才能焊接出好的焊缝。
1.3 操作技术再者,焊工的操作技术也是关键。
如果焊工焊接的速度过快或者角度不对,都会导致气孔的产生。
焊接速度快,就好比你急急忙忙地做饭,没时间搅拌均匀,最后的菜肯定会有问题。
焊接时,必须控制好速度,保持稳定的焊接角度,才能避免气孔的出现。
1.4 温度控制不当最后,温度控制也很重要。
焊接的时候,如果温度过高或过低,都可能导致气孔的产生。
温度过高就像把牛奶煮得过热,容易产生很多泡沫,温度过低则会让焊缝的熔合不完全,气体难以逸出,最终也会形成气孔。
2. 如何防范焊接气孔2.1 保障气体供应首先,确保焊接用的气体质量合格,供应稳定。
就像你做菜时要用新鲜的食材一样,焊接用的气体也要确保纯净。
如果气体供应不足,容易出现问题。
避免电焊渣引发的气孔问题的实用方法
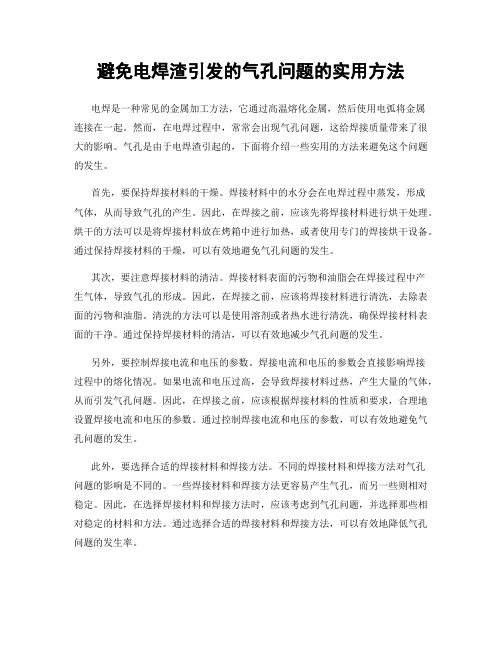
避免电焊渣引发的气孔问题的实用方法电焊是一种常见的金属加工方法,它通过高温熔化金属,然后使用电弧将金属连接在一起。
然而,在电焊过程中,常常会出现气孔问题,这给焊接质量带来了很大的影响。
气孔是由于电焊渣引起的,下面将介绍一些实用的方法来避免这个问题的发生。
首先,要保持焊接材料的干燥。
焊接材料中的水分会在电焊过程中蒸发,形成气体,从而导致气孔的产生。
因此,在焊接之前,应该先将焊接材料进行烘干处理。
烘干的方法可以是将焊接材料放在烤箱中进行加热,或者使用专门的焊接烘干设备。
通过保持焊接材料的干燥,可以有效地避免气孔问题的发生。
其次,要注意焊接材料的清洁。
焊接材料表面的污物和油脂会在焊接过程中产生气体,导致气孔的形成。
因此,在焊接之前,应该将焊接材料进行清洗,去除表面的污物和油脂。
清洗的方法可以是使用溶剂或者热水进行清洗,确保焊接材料表面的干净。
通过保持焊接材料的清洁,可以有效地减少气孔问题的发生。
另外,要控制焊接电流和电压的参数。
焊接电流和电压的参数会直接影响焊接过程中的熔化情况。
如果电流和电压过高,会导致焊接材料过热,产生大量的气体,从而引发气孔问题。
因此,在焊接之前,应该根据焊接材料的性质和要求,合理地设置焊接电流和电压的参数。
通过控制焊接电流和电压的参数,可以有效地避免气孔问题的发生。
此外,要选择合适的焊接材料和焊接方法。
不同的焊接材料和焊接方法对气孔问题的影响是不同的。
一些焊接材料和焊接方法更容易产生气孔,而另一些则相对稳定。
因此,在选择焊接材料和焊接方法时,应该考虑到气孔问题,并选择那些相对稳定的材料和方法。
通过选择合适的焊接材料和焊接方法,可以有效地降低气孔问题的发生率。
最后,要注意焊接设备的维护和保养。
焊接设备的维护和保养对焊接质量的影响是很大的。
如果焊接设备不正常工作,会导致焊接电流和电压的波动,从而引发气孔问题。
因此,应该定期对焊接设备进行检查和维护,确保其正常工作。
通过注意焊接设备的维护和保养,可以有效地避免气孔问题的发生。
通孔上锡的气泡-概述说明以及解释
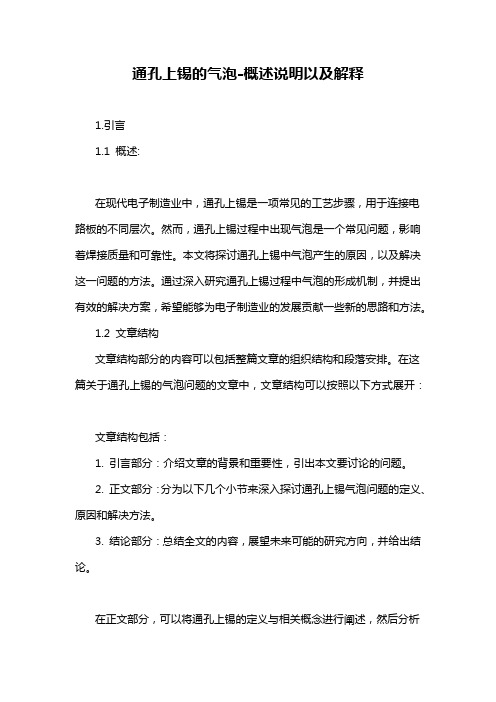
通孔上锡的气泡-概述说明以及解释1.引言1.1 概述:在现代电子制造业中,通孔上锡是一项常见的工艺步骤,用于连接电路板的不同层次。
然而,通孔上锡过程中出现气泡是一个常见问题,影响着焊接质量和可靠性。
本文将探讨通孔上锡中气泡产生的原因,以及解决这一问题的方法。
通过深入研究通孔上锡过程中气泡的形成机制,并提出有效的解决方案,希望能够为电子制造业的发展贡献一些新的思路和方法。
1.2 文章结构文章结构部分的内容可以包括整篇文章的组织结构和段落安排。
在这篇关于通孔上锡的气泡问题的文章中,文章结构可以按照以下方式展开:文章结构包括:1. 引言部分:介绍文章的背景和重要性,引出本文要讨论的问题。
2. 正文部分:分为以下几个小节来深入探讨通孔上锡气泡问题的定义、原因和解决方法。
3. 结论部分:总结全文的内容,展望未来可能的研究方向,并给出结论。
在正文部分,可以将通孔上锡的定义与相关概念进行阐述,然后分析引起气泡问题的原因,最后提出有效的解决方法。
通过这种组织结构,读者可以逐步了解通孔上锡气泡问题的相关知识,并掌握解决这一问题的方法。
整篇文章的结构应该紧凑明了,逻辑清晰,引人入胜,这样读者可以更好地理解文章内容,加深对该问题的认识。
1.3 目的通孔上锡的气泡问题是电子制造过程中常见的质量缺陷之一,它会影响焊接质量和产品可靠性。
因此,本文的目的是探讨通孔上锡气泡问题的根本原因,并提出相应的解决方法,以帮助电子制造行业更好地解决这一难题,提高焊接质量和产品可靠性。
同时,通过研究通孔上锡气泡问题,也可以为未来研究提供一定的借鉴和启示,推动电子制造技术的进步和发展。
2.正文2.1 通孔上锡的定义通孔上锡是指在PCB(Printed Circuit Board,印制电路板)制造过程中,通过在通孔内部涂覆焊膏,并经过加热处理使其融化,以实现通孔内部的焊接。
通孔上锡是一种常见的焊接方法,可以有效地连接电路板上的不同层次的电路。
LGA器件焊点缺陷分析及解决措施

doi: 10.14176/j.issn.l001-3474.2021.01.011LGA 器件焊点缺陷分析及解决措施王文龙,陈帅,谭小鹏(中国电子科技集团公司第二十研究所,陕西西安710068 )摘 要:针对LGA 器件回流焊后常见的空洞和锡珠等缺陷,对其产生的原因进行了分析。
通过对LGA 器件采 用预上锡回流工艺和印制板钢网LGA 器件处一字架桥开口的方式,使回流焊过程中焊膏的挥发气体加速逸出。
通过对比试验,找到合适的预上锡钢网尺寸,解决了LGA 器件焊接中常见的空洞大的缺陷问题。
关键词:LGA ;空洞;锡珠;预上锡中图分类号:TN60文献标识码:A 文章编号:1001-3474 (2021) 01-0038-04Analysis and Solution of Solder Joint Defects for LGA DevicesWANG Wenlong, CHEN Shuai, TAN Xiaopeng(The 20th Research Institute of CETC, Xi 'an 710068, China )Abstract: The causes of defects such as voids and solder beading after reflow soldering of LGA devices are analyzed. Through the pre tinning reflow process and the way of bridging the opening at the LGA devices of PCB steel mesh, the escape of volatile gas during reflow soldering process is improved. Through the comparative test, the appropriate size of pre tinning mesh is found, and the defects such as large voids in LGA soldering are solved.Keywords: LGA; voids; solder beading; pre tinningDocument Code: A Article ID: 1001 -3474 (2021)01 -0038-04LGA (Land Grid Array,平面网格阵列封装) 属于面阵列封装形式。
AI电容焊点爆锡气孔问题处理
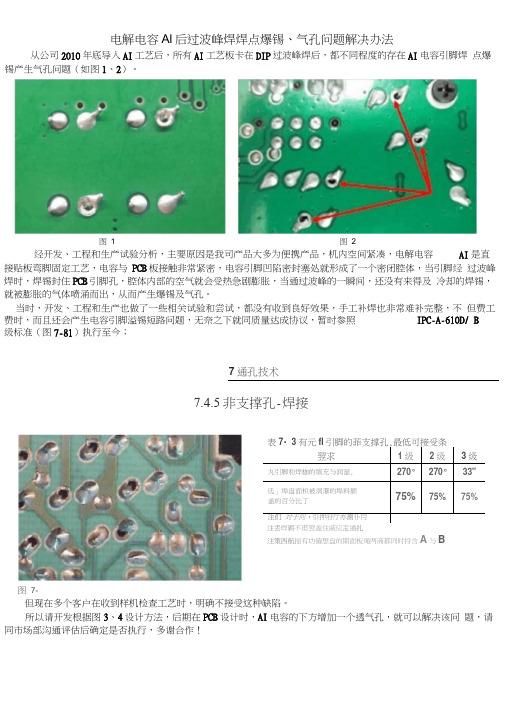
电解电容Al 后过波峰焊焊点爆锡、气孔问题解决办法
经开发、工程和生产试验分析,主要原因是我司产品大多为便携产品,机内空间紧凑,电解电容 AI 是直 接贴板弯脚固定工艺,电容与 PCB 板接触非常紧密,电容引脚凹陷密封塞处就形成了一个密闭腔体,当引脚经 过波峰焊时,焊锡封住PCB 引脚孔,腔体内部的空气就会受热急剧膨胀,当通过波峰的一瞬间,还没有来得及 冷却的焊锡,就被膨胀的气体喷涌而出,从而产生爆锡及气孔。
当时,开发、工程和生产也做了一些相关试验和尝试,都没有收到良好效果,手工补焊也非常难补完整,不 但费工费时,而且还会产生电容引脚溢锡短路问题,无奈之下就同质量达成协议,暂时参照 IPC-A-610D/ B 级标准(图7-81)执行至今;
7通孔技术
7.4.5非支撑孔-焊接
但现在多个客户在收到样机检查工艺时,明确不接受这种缺陷。
所以请开发根据图3、4设计方法,后期在PCB 设计时,AI 电容的下方增加一个透气孔,就可以解决该问 题,请同市场部沟通评估后确定是否执行,多谢合作! 翌求
1级 2级 3级 丸引脚和焊枷的填充与润湿,
270° 270° 33" 氐」埠盘面枳被润瀑的埠料额
盖的百分比丁
75% 75% 75% 注们 対于冋・引押府厅亦测仆冃
从公司2010年底导入AI 工艺后,所有AI 工艺板卡在DIP 过波峰焊后,都不同程度的存在AI 电容引脚焊 点爆锡产生气孔问题(如图1、2)。
图 1 图 2
图 7-
81 表7・3有元fl 引脚的菲支撑孔,最低可接受条
注丢焊羁不甫翌盖住威应盂通扎
注策西航揺有功確想盘的期面板绳两商都同时捋含A 与B
图3
图4。
PWBA 焊点锡洞的成因与改善

PWBA焊点锡洞的成因与改善【摘要】焊点锡洞是PWBA组装过程中的主要缺陷之一,大面积锡洞的存在会严重影响产品的使用性能及可靠性。
本文以三个比较典型的实际案例为分析对象,采用金相切片分析技术,分析了锡洞的形成原因和形成机理。
分析结果表明:PWB PTH (Plated Through Hole) 破孔是导致焊点锡洞形成的直接原因,而破孔则归因于PWB钻孔质量差、化学铜不良以及抗蚀刻金属阻剂保护不良。
同时,本文亦提出了相应的改善对策,如改善钻孔质量、优化化学铜工艺等,可有效降低后续生产中锡洞的产生机率,提高产品的使用寿命。
【关键词】PTH、锡洞、破孔、钻孔、化学铜、金属阻剂■作者:刘燕芳、潘启智 中达电子(江苏)有限公司物性失效分析实验室1. 引言波峰焊接可实现PWB与电子元件之间的电气连接,是目前PWBA的主要组装工艺之一,具有省时、省能、对PWB以及元件伤害小等优点。
然而在实际生产作业中,尤其是步入无铅时代后,不可避免地会出现焊接不良相关问题,如焊点剥离[1]、漏焊、虚焊、锡洞、锡珠以及锡桥等,从而影响产品的可靠性或整机功能。
其中焊点锡洞是PWBA组装制程中的主要缺陷之ㄧ,大面积锡洞的存在会严重影响产品的使用性能及可靠性。
焊点锡洞的形成原因有很多,如PTH破孔、PTH 孔壁氧化、元器件的可焊性不良、焊接温度曲线设计不良以及助焊剂活性不足等。
本文以比较典型的且实际发生机率相对较高的三个锡洞案例为分析对象,探讨锡洞的形成原因及机理,提出解决问题的改善方法,防患于未然,对实际生产具有积极的指导意义。
2. 分析內容本文研究三个锡洞案例,编号分别为Void1、Void2及Void3。
先对锡洞位置进行外观观察,然后再对其进行金相切片分析。
2.1外观观察先用实体显微镜对分析位置进行外观观察,观察结果如图1~图3所示,插件引脚经波焊炉后,焊点表面均存在大小不等的锡洞。
图1 Void1外观图片图2 Void2外观图片图3 Void3外观图片2.2金相切片分析使用精密切割机分别切下三个分析样品,分别用丙烯酸树脂镶埋,然后在研磨抛光机上研磨至焊点内部空洞位置,随后对样品进行自动抛光,最后用金相显微镜观察焊点内部微观结构。
印刷电路板焊锡常见问题及解决方案

印刷电路板焊锡常见问题及解决方案印刷电路板的焊锡作业永远有不良焊点的问题存在,而这种问题曾出不穷,似乎永远都会有新问题出现应接不暇,因此我们整理出一些规,可做为找出问题所在依据。
PCB板上的问题常是由焊锡作业中造成的,但在确定是焊锡作业造成问题以前,应先考虑其他各种因故,再考虑焊锡作业,焊锡作业之间题大多出在材料的变化及操作条件改变,我们整理出下列最常见的问题焊点,如锡尖、不沾锡、锡点过大、绿漆上有锡丝、白班、锡孔等。
1、沾锡不良*这种情况是不可接受的缺点,在焊点上只有部分沾锡,如果是在裸铜面上焊接,可看到某些完全不同的现象,很容易分辨出来。
分析其产生原因及改善方式如下:*外界的污染物如油、脂、臘等,此类污染物通常可用溶剂清洗。
些类污染物有时是在印刷助焊剂时沾上的,可用打磨方式支除,但必须非常小心,不可残留打磨粉末在表面。
*Silicon Oil通常用于脱模及润滑之用,常会在PCB板及零件脚上发现,而SiliconOil等要非常小心,如使用SiliconOiL当作抗氧化油,亦常会发生问题因为SiliconOil会蒸发SiliconOil 会蒸发,沾露在PCB板上而造成沾锡不良。
*严重氧化,通常是由于宁存状况不佳或PCB板制程上有问题,发生严重氧化后,助焊剂是无法去除的,因些出现沾锡不良。
氧化轻微两次焊锡可解决此问题。
*涂敷焊剂方式不正确,造成原因为发泡气压不稳定或不足,致使*泡沫高度不稳或不均匀而使PCB板部份无法涂敷上助焊剂。
焊锡时间不足或温度不够,会造成沾锡不良,因为熔锡需要足够的温度及时间于元件脚和PCB接触,才能形成良好的焊点。
2、局部粘锡不良些种现象与粘锡不良相似,不同的是局部粘锡不良的情况,不会露铜面,只有薄薄的一会焊锡无法形成饱满的焊点,其形成原因于粘锡不良相似。
两次焊锡出许无法改善些状况,必须用焊锡剥除剂除去焊锡,重新清洁表面再做焊锡。
电镀时污染未清理干净,亦会产生局部沾锡不良,此类问题,宜送回PCB板厂家重新处理。
焊接机器人出现气孔的排查方法及解决措施
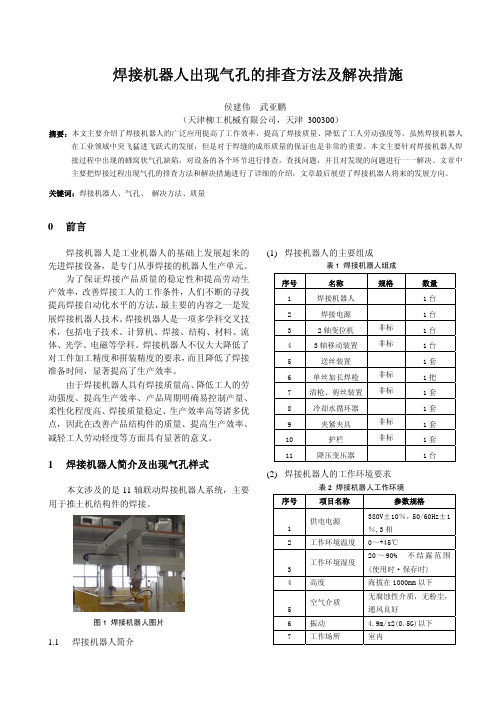
11 部不合理
焊接姿势合适
枪 体 的 干 身 长 选择合适的干身长度(20mm),
12
度不合理
保证气体保护良好
工 件 表 面 不 清 增强工件表面的清洁处理,保证
13 洁
工件表面的清洁度
图 4 气塞第二次更换
图 5 保护套第一次更换
图 6 保护套第二次更换
4 整改后的效果及注意事项
4.1 焊缝效果 整改后焊接的焊缝,表面光滑,成形均匀一
9 枪体送丝管是否通畅
枪体送丝管不通畅,熔池 稳定
10 气塞是否适用
气塞不合适保护效果较 差
焊接程序出现气孔的部位是 编程的角度及姿势不合
11 合理
适,保护效果较差
12 干伸长度是否合理
伸长度不合适保护效果 差
13 工件是否清洁
工件表面不清洁容易出 气孔
3 解决措施
表 5 列举了各个排查项存在的问题和解决办
焊缝周围存在油污水分和铁锈22出现气孔的排查方法针对焊接机器人出现蜂窝状气孔的问题对设备的各个部位及焊接的全部过程进行排查最终能找到问题的原因所在具体的排查内容见表排查内容序号排查的内容影响的事项焊枪是否良好是否有漏气气问题影响保护气气压保护气体的气压是否合适压力的偏高偏低都可能熔池保护出现不稳量的气路是否破损气压不足气体纯度是否达到了要求气体不纯保护效果较差气体流量是否合适不能出现大或过小的现象气体流量过大或过小对护效果都差气体是否有紊流的现象紊流保护效果较差焊接环境气流是否过大焊接环境气流大侵入熔池产生气孔保护套的直径过大或过小保护套过大或过小保护果较差枪体送丝管是否通畅枪体送丝管不通畅熔池稳定10气塞是否适用气塞不合适保护效果较11焊接程序出现气孔的部位是合理编程的角度及姿势不合适保护效果较差12干伸长度是否合理伸长度不合适保护效果13工件是否清洁工件表面不清洁容易出气孔列举了各个排查项存在的问题和解决办法
银焊料 气孔

银焊料气孔
银焊料在焊接过程中,如果操作不当或者原料中含有杂质,可能会产生气孔。
气孔的存在会影响焊接接头的质量和性能,可能导致焊缝强度降低、耐腐蚀性下降等问题。
银焊料产生气孔的主要原因如下:
1.焊接过程中,焊接区域受到加热,使得周围的空气中的气体溶解在焊缝中。
随着冷却过程的进行,这些气体无法逸出,从而形成气孔。
2.银焊料中含有的杂质,如铜、镍、铅等,在焊接过程中易产生气体,进而形成气孔。
3.焊接速度过快或焊接温度过高,使焊缝来不及充分填充,也可能导致气孔的产生。
为了减少银焊料焊接过程中的气孔,可以采取以下措施:
1.严格控制焊接参数,如焊接电流、电压、焊接速度等,以保证焊接过程的稳定性。
2.采用适当的焊接方法,如气体保护焊、真空焊等,减少焊接区域受到空气中气体的影响。
3.确保焊接材料的纯度,减少杂质对焊接过程的影响。
4.在焊接前,对焊接区域进行充分清理,去除油污、氧化物等,以降低气孔的产生。
5.适当延长焊接过程中的保温时间,使焊缝充分填充,减少气孔的产生。
- 1、下载文档前请自行甄别文档内容的完整性,平台不提供额外的编辑、内容补充、找答案等附加服务。
- 2、"仅部分预览"的文档,不可在线预览部分如存在完整性等问题,可反馈申请退款(可完整预览的文档不适用该条件!)。
- 3、如文档侵犯您的权益,请联系客服反馈,我们会尽快为您处理(人工客服工作时间:9:00-18:30)。
精心整理电解电容AI后过波峰焊焊点爆锡、气孔问题解决办法
从公司2010年底导入AI工艺后,所有AI工艺板卡在DIP过波峰焊后,都不同程度的存在AI电容引脚焊点爆锡产生气孔问题(如图1、2)。
图1图2
经开发、工程和生产试验分析,主要原因是我司产品大多为便携产品,机内空间紧凑,电解电容AI是直接贴板弯脚固定工艺,电容与PCB板接触非常紧密,电容引脚凹陷密封塞处就形成了一个密闭腔体,当引脚经过波峰焊时,焊锡封住PCB引脚孔,腔体内部的空气就会受热急剧膨胀,当通过波峰的一瞬间,还没有来得及冷却的焊锡,就被膨胀的气体喷涌而出,从而产生爆锡及气孔。
当时,开发、工程和生产也做了一些相关试验和尝试,都没有收到良好效果,手工补焊也非常难补完整,不但费工费时,而且还会产生电容引脚溢锡短路问题,无奈之下就同质量达成协议,暂时参照IPC-A-610D/7.4.5B级标准(图7-81)执行至今;
但现在多个客户在收到样机检查工艺时,明确不接受这种缺陷。
所以请开发根据图3、4设计方法,后期在PCB设计时,AI电容的下方增加一个透气孔,就可以解决该问题,请同市场部沟通评估后确定是否执行,多谢合作!
图3
图4。